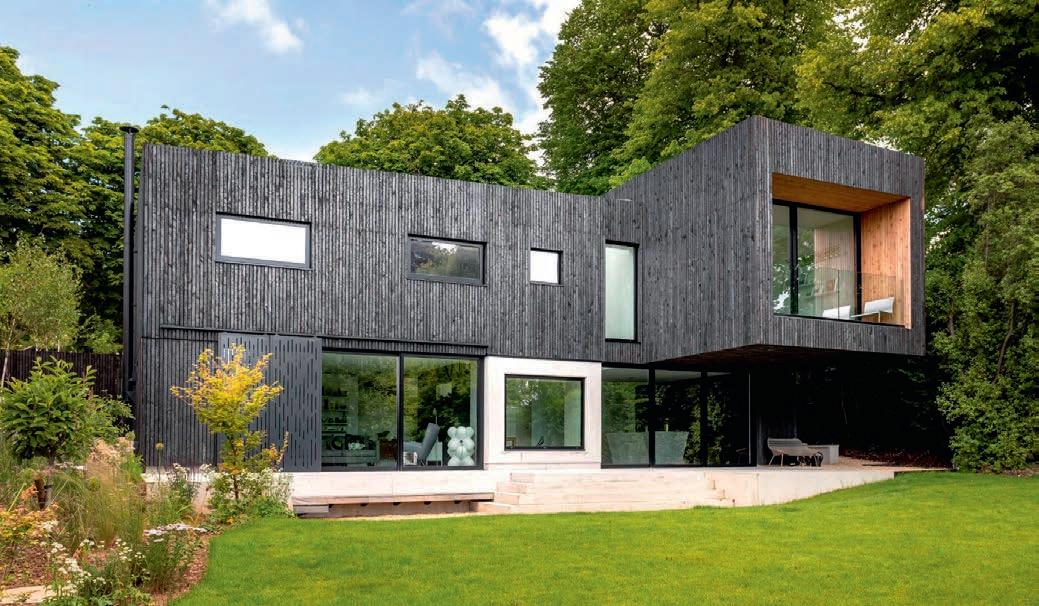

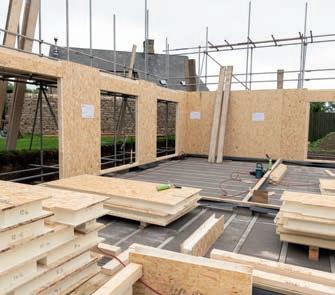





Oakwrights are widely recognised as the UK’s most forward-thinking company in the oak framing market. From garden buildings, garages and home extensions, right through to our incredible timber framed homes, building with oak starts with Oakwrights.
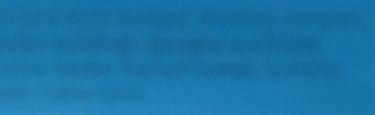
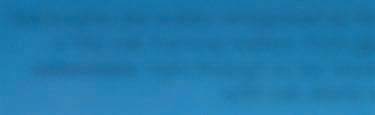
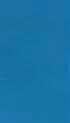
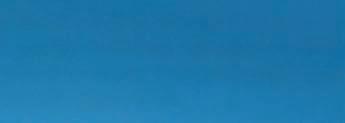
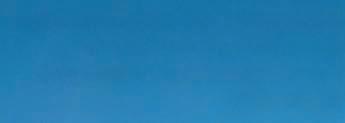





Oakwrights are widely recognised as the UK’s most forward-thinking company in the oak framing market. From garden buildings, garages and home extensions, right through to our incredible timber framed homes, building with oak starts with Oakwrights.
EDITORIAL
Supplements editor Emily Batesmith
Editor Chris Batesmith
Editorial assistant Georgina Crothers
Digital editorial assistant Sander Tel
Designer Justin Marshall Content & marketing assistant Lucy Keech
Contributor Rebecca Foster
Tel: 020 3627 3240
Web: www.self-build.co.uk
ADVERTISING
Sales director
Nick Gillam 020 3627 3245
Advertising manager
Josh Lyle 020 3627 3263
Account manager
George Waller 020 3553 2376
PUBLISHING
Managing director Calum Taylor
Finance director Katherine Taylor
Marketing director Claire Drakeford
What is offsite manufacture?
Why choose timber frame?
Case study: Super-insulated timber frame home
Designing your timber frame home
Making the most of SIPs
Case study: Traditional style , modern performance
Five amazing SIPs home design ideas
Case study: Innovative SIPs self build
Building with oak frame
Case study: Oak frame Passivhaus
Designing a rural oak home
Building an oak frame house on a budget
What is CLT construction?
Glulam beams
Hybrid build systems
Build with confidence: What is STA Assure?
Key suppliers for your project
SUBSCRIPTION OFFER: Get 12 issues for £12
WWW.SELF-BUILD.CO.UK/OFFER
Self-Build Zone’s Site Insurance provides cover for anyone starting new building works, as well as covering any existing structures on site.
Our Approved Inspectors can aid all survey services you may need during the build or for the warranty provision.
On completion, we can provide you with a Lender approved 10-Year Structural Warranty.
Any structural method created in a factory or workshop away from the building site comes under the bracket of offsite manufacture. To put this into context: brick and block is a site-based method, as the structure forms in situ as bricks are built up. In contrast, a timber frame is cut and shaped offsite before being delivered to the plot and craned into place.
ou might equate offsite manufacture with post-war prefab homes, but times have moved on since the cheap and cheerful boxes that pervaded the mid-20th century. Offsite manufacture is a broad term covering a range of options – it doesn’t necessarily mean craning in entire prefinished rooms. It’s something of a hybrid
Right: The encapsulation panels for this Oakwrights home were manufactured offsite and include the windows, meaning whole sections of the house shell could be craned into place in one go
i ill t e d ersely i ue ed y i leme t e t er
2 Build cost & programme certainty site stru ti m es s eduli d sti m re predi t le t it tr diti l uildi met ds
3 Quality assurance Stri e t t ry u lity tr l e es t e m u ture uildi s e suri y u et m der i per rm e e el pe r y ur s eme
4 Energy usage erm lly e ie t i ly irti t mes redu e e er y sumpti r ss t e uildi s li e
5 Design flexibility it ide r e i ti e pr du ts d l ddi s luti s tim er systems meet t e spir ti s t r ite ts d sel uilders
6 Sustainability ll Stru tur l im er ss i ti mem ers use tim er r m C r SC ertified s ur es e suri resp si le m eme t t e rld s rests
route, where much of the internal fit-out work can still be carried out onsite.
Near-enough every structural timber system is created offsite, and as time progresses, solutions continue to move towards a more factory-built focus, with greater levels of prefabrication. This means your new house can be delivered as part of a controlled process, with added benefits from factory-fitted insulation and pre-cut service channels through to panels that come complete with windows and doors already installed. Even internal finishes and e ternal cladding can be pre-applied.
Offsite manufactured timber systems have advanced greatly and offer genuine cost, programme and performance benefits for those building from scratch – especially when backed by the STA Assure Membership and uality Standards Scheme.
Intelligent, integrated construction systems such as closed panel timber frame, structural insulated panels SIPs and volumetric modular options (where a completed section of your building, such as a whole room or a big portion of your roof, is craned into place are driving innovation in the timber sector. This means there is much more choice now, from classic kit systems to highly prefabricated solutions. In this guide you will learn about all the varieties of timber structural solutions that can be used to make your new dream home. It’s not perfect for every project, of
course if your plot suffers from restricted access, for e ample, it might be tricky to get large-scale panelised components delivered to site. But combine the enhanced energy e ciency of off site timber systems with shorter construction timescales, guaranteed build quality and vastly reduced ongoing running costs, and it’s clear that there are compelling reasons to specify these solutions.
With the standards for energy e ciency constantly ramping up, the construction industry has faced a challenge in creating homes that achieve the actual performance specified in the design brief. The accuracy and control involved in using timber-based off site technology overcomes this issue.
Factory-fi tting insulation prevents the performance gap that can happen if there are mistakes when fi tting these elements on site. Essentially, the more work that gets
done in the factory, the more predictable the performance of the finished house will be. And as a major priority for self builders is an energy e cient home with e tremely low heating costs, this is a big benefi t for anyone looking to build from scratch.
There are three core types of timber building method, and we’ll be addressing each other these in much more detail throughout this guide. They are:
Timber frame: There are several varieties of timber frame, from open panels that require a bit more input on site, through to closed panel systems that come with insulation and sometimes even windows and services built in. Over on page we’re discussing all the reasons why timber frame is a great option and you can learn about how to design your timber frame home on page 4.
SIPs: Structural insulated panels are an energy e cient pre-insulated system that create large sections of wall, oor and roof. They can also be used as a thermal wraparound option for other systems, such as oak frame homes. Learn all about using this timber building method on page .
Oak frame: This building method boasts character and beauty but it isn’t just for lu ury budgets, as you’ll learn over on page 37. Go to page 2 to discover the benefi ts of this structural method, plus why oak is perfect for rural homes page 34 . Learn about how hybrid methods could help to cut costs further on page 42.
The Structural i ber ssociation e site (www.structuraltimber.co.uk) contains a wealth of information for self builders, from guidance on timber i ding syste s thro gh to top tips and an en iry syste to he p yo nd the right partner for yo r project. Learn more about STA Assure on page 45 and head to page 46 for contact details of STA members that could help with your bespoke home build.
• Highest quality construction standards and methods
• Environmental compliance through the use of Eco-Friendly materials.
• Customer service, reliability, affordability and competitiveness in the market place.
• Craftsmanship and rigorous attention to detail.
• MBC also have a Passive standard foundation that can work with all of the MBC Timber Frame systems, this offers a huge benefit of the foundation and timber frame system coming from the same supplier.
MBC Timber Frame is a long established company specialise in the production of super insulated, precision engineered, energy efficient timber frame and passive standard homes throughout the UK. We are a registered Gold member of the Structural Timber Association and are quality accredited with an outstanding reputation.
info@mbctimberframe.co.uk
MBC Timber Frame is a long established company that specialise in the production of super insulated, precision engineered, energy efficient timber frame and passive standard homes throughout the UK. We are a registered Gold member of the Structural Timber Association and are quality accredited with an outstanding reputation.
MBC Timber Frame is a long established company that specialise in the production of super insulated, precision engineered, energy efficient timber frame and passive standard homes throughout the UK. We are a registered Gold member of the Structural Timber Association and are quality accredited with an outstanding reputation.
At MBC our experience and continuous focus on quality enables our team to satisfy the specific needs and requirements of each individual project, while at the same time provide outstanding service and support to our clients.
Superb energy efficient passive homes - reduced energy costs
Superb energy efficient passive homes - reduced energy costs
MBC also offer high performance windows & doors
UK Office: twitter.com/MBCTimberFramefacebook.com/mbctimberframe
UK Office: Quedgeley Court, Shepherd Road, GL2 5EL
mbctimberframe.co.uk
mbctimberframe.co.uk
twitter.com/MBCTimberFramefacebook.com/mbctimberframe
Tel: 01452 346499
Tel: 01452 346499
info@mbctimberframe.co.uk
info@mbctimberframe.co.uk
Timber frame is a leading contender for the creation of high-quality oneoff homes. Among other benefi ts, this factory-manufactured system offers high sustainability standards, speedy construction and e cellent energy e ciency in use all in a value-for-money package. So, it’s no surprise timber frame has cornered a strong share of the market. According to a survey by NaCSBA in 2022, it accounts for just shy of a third of all K self builds. STA research suggests that, in Scotland, take-up rises to a massive 3 of all new housing. So, could it be the right investment to support your dream home goals?
Modern timber frames are engineered and manufactured as bespoke house shell kits. The core component is the storey-height walling panels, which form the inner loadbearing leaf of your home’s external walls ready to accept your choice of decorative cladding . A typical frame package will also include the internal stud walls, intermediate oors and roof structure all precision-cut and ready for assembly onsite – along with the insulation, membranes and sundries required for construction.
There are two main types of timber frame system available. In both cases, the lightweight engineered panels are formed of a network of studs, rails and sheathing. The key difference is the level of prefabrication involved. Open panel versions, as the name suggests, are left
Top: Kingspan’s Ultima closed panel building system is available in three variants, achieving U-values down to 0.14 W/m2K
Above: This cantilevered woodland build features the Passiv Innovations factoryinsulated timber frame system from Timber Innovations. The pro e t is nished in Shou Sugi Ban charred cladding
open on one face. Insulation is then added on site to your agreed specification, whereupon the panel is then finished with ply or OSB boarding. According to the STA, this approach can achieve -values a measure of thermal performance, where lower numbers indicate better heat retention down to around 0. 5 W m2K.
Closed panel systems bring more of the work into the factory. The insulation is prefi tted under controlled conditions, ensuring full coverage and making it easier to achieve e cellent -values down to 0. 0 W m2K or better . Some providers can also install windows, door linings and even claddings plasterboard prior to delivery. This makes for an even quicker build phase, as well as giving you a single point of responsibility for more of your project. However, it does mean you’ll need to nail down more of the design detail prior to manufacture.
t uild it e er y e ie t d eri st rr y desi spe ifi ti d p e pti s dis er y t is system uld suit y ur pr e t
One of the most seductive elements of buying a timber home is that you’re dealing with a single company for a big chunk of the main superstructure – rather than pulling together a cornucopia of trades and suppliers. Manufacturers can provide varying levels of service depending on your needs and location. A typical package takes in the engineering, design, manufacture and assembly to weathertight stage – using either the supplier’s own team or trusted contractors they’ve worked with before. This ensures they can offer a warranty on the completed house shell.
Some timber frame suppliers offer follow-on joinery elements as part of their services, such as windows, staircases, architraves, internal cills and plasterboard. The big benefit of this is that it gives you access to proven products from trusted
1 It’s eco friendly, combining sustainably-sourced timber with high-quality thermal insulation and straightforward airtightness detailing. So, you can enjoy a low-carbon build along with minimal heating bills once you move in.
2 Factory quality is assured, s y u e fide t you’re buying a consistent, accurately-manufactured product. This means you’re not as reliant on the skills of onsite labour to achieve the performance and quality you expect –plus it can enable early ordering of follow-on components, such as windows and glazed doors.
3 Quick build times. Your prefabricated timber frame house shell will be erected onsite much faster than with traditional masonry construction, reducing the risk of weather delays and meaning internal works can start sooner.
4 Design flexibility co es as standard with a host of impressive architectural features readily achievable. You fi is tim er r me e ter lly i yt i r m d cladding to brick, stone, render and more – so, from the outside, you’d be hard-pressed to identify exactly what building system lies underneath. For more on designing your timber frame home, see page 14.
5 Value-for-money. Price-wise, building with timber frame is very competitive with masonry construction. That’s partly because the factory fabrication process ensures greater predictability and improved visibility over costs, as well as reducing the labour requirement on site. Combine that with etter ert i ty er t e fi is ed u lity d it s e sy t see why this method holds so much appeal.
suppliers via a single intermediary. This means you’ll gain access to the sort of buying power you wouldn’t have as an individual self builder, potentially bringing savings versus a solo approach. Your frame manufacturer will also take care of quantities and snagging issues for their part of the package, reducing the complexity and stress of specifying your build.
A number of timber frame companies can support you with project management –either in-house or through trusted partners – deeper into the works, and potentially right up to completion. Known as a turnkey build, this route puts you in charge of the specification and design of your home, but leaves it up to the professionals to deliver it.
As with any building contract, always take the time to check your timber frame quote includes everything you’re expecting – and not just the materials, specification and who’s doing the install. For instance, who’s responsible for things like steelwork and crane hire, and what it will cost? A good supplier will hold your hand through this process, as well as provide you with detailed handover advice so that you know what to expect once their part of the work is done.
Once you’re happy with the engineering design and your quote, it’s time to sign the drawings off to enable manufacture. Lead times to produce all the components for a timber home are typically eight to 2 weeks but the build itself will be lightning-quick. On site, a standard house shell can take anything from a few days to several weeks to assemble, depending on size and architectural comple ity. According to the STA, this process is around 45 faster to reach weathertight than using conventional blockwork.
The manufacturing lead time won’t impact on your overall project schedule. In fact, it gives you the ideal window to prepare your site for the frame’s arrival by completing the groundworks just as soon as you have the sole plate design . This is a crucial stage, as the foundations must be highly accurate and level to enable installation of the precision-engineered timber kit. So, it pays to use an e perienced groundworks crew. our frame supplier may be able to recommend trades in your area.
For many self builders, the day the frame arrives on site is the most e citing part of
tim er me s impressi e e ie y stems r m t e m i ti i u lity i sul ti d pre ise m u ture deli eri ri first ppr t e er y s i stru ti tly t pr du ts re spe ified ill depe d y ur ud et d per rm e ls re y u ee t ie e ssi us st d rds r i st e
RIGID INSULATION
e m st mm tim er r me i sul ti type i t e is p lyuret e i pr ides e elle t t erm l per rm e i t i er ll ll pr files e pl i s Sim rrells r me e l ies deed li e r li e t tim er r me d S s ie e re t lues it slimmer ll uild up t m s ry ity lli i uld elp m imise r sp e i y ur pr e t
NATURAL OPTIONS y suppliers ls er t e pp rtu ity r tur l re t le i sul ti s su s s eep s l ellul se d emp sed pr du ts ey ll st little m re ut urt er st y ur pr e t s sust i ility rede ti ls y u t t use tur l m teri ls spe t y ur tim er r me spe i list e rly s it ill re uire s me d ustme ts i t e desi det il d e r i y u ill eed t ept sli tly t i er lls t it pl sti sed i sul ti s
MEETING YOUR PERFORMANCE GOALS st d rd tim er r me ill m rt ly e t uildi e s re uireme ts r t erm l e ie y ut it s ls re t i e r t se l i t ie e e epti l per rm e epe di t e pr e t d m u turer t is mi t e d e y ryi t e t i ess t e p el t ept m re i sul ti r y ddi e tr l yer i sul ti r t e m rity tim er r me pr e ts i sul ti is fitted et ee d i side t e studs t e r m side t e p el s ys Sim e e efit t is ppr is t e se d i ter l l yer t redu e t erm l rid i d impr e irti t ess e ser i e tte s re t e fitted s t t ll ser i es sit t e rm side t e i sul ti d d t pier e t e ri
the process, as the project will rapidly go from drawings to a recognisable house. The panels, joists etc will typically be marked up and provided in the order they’re required on site making assembly straightforward for an e perienced team. A fringe benefit of the quick, panelised construction process is that there’s fewer individual materials to store on site reducing the risk of damage, waste and theft, and ensuring a tidier, safer site. A timber frame house typically goes up storey-by-storey, with the intermediate
oors and any internal load bearing walls installed as construction proceeds. Once the walls are assembled, the roof trusses will be installed, decked and counter battened. If you’ve chosen an advanced closed panel system, the doors, windows and some claddings might be pre-fi tted but at the very least, the openings will be prepared and the whole building wrapped in a waterproof membrane. At this point, you’re at weathertight stage, ready for your follow-on trades to start their work.
Building with timber frame is a coste e ti e pti r sel uilders it pr e t pri es mp r le t l r t s m re t ere re s me le r ud eti e efits t i t e tim er r ute t t e le st i is st ert i ty s t e pri e is reed up r t S pr ided y u press t e ree utt it i t e u te s lidity peri d y u t t s t y u ll p y r t e ser i es y u e mmissi ed It’s worth being aware that the cash prem u tured uild l s little di ere t t m re site sed ppr es ur m u turer ill e pr du i use s ell spe ifi t y ur esp e re uireme ts s t ey t ust d sell it s me ere else s result y u s uld e pe t t pre p y r y ur r me i ere t suppliers ill split t is i di ere t ys ut e mple mi t e t trigger fabrication and the remaining pri r t ssem ly site
When Chris and Jenny Shepperd found their dream edge-ofvillage plot, they had clear ideas about the type of home they wanted. “We were keen to achieve something that would be low-cost to run, easy to maintain and comfortable to live in,” says Chris.
Having approached a number of timber frame suppliers, the couple selected Frame Technologies to take their project forward. They offered the energy performance we wanted at the right price point, along with being incredibly accommodating in their approach,” says Chris, who was particularly attracted to the company’s e ible options for thickness of frame and insulation levels. This made it easy to achieve the low U-values they wanted.
The project features Frame Technologies’ TechVantage S timber frame system. Managing director Simon Orrells and his team took the architects’ drawings and carefully engineered the structure to achieve the couple’s goals. Having worked with Simon on a previous project, the couple were confident he could deliver for them again. “He would pull out every
Above: Named Gryphon House, the Shepperds’ stone-clad timber home looks incredible while also delivering on functionality and performance
Top right: Frame Technologies engineered the superstructure to enable features such as the large open-plan kitchen/dining/ living space
Right: The statement cantilevered staircase is set against a curved wall, and leads up towards a double-height window, for an instant wowfactor moment
stop to deliver on time, and paid incredible attention to detail,” says Chris. “There is a lot of value in that level of service.”
Once the footings were poured, the Frame Technologies timber frame was brought on site and erected in a matter of weeks. “It was so rewarding to see the frame go up,” says Jenny. “In an instant we went from a mess to a house.”
Chris and Jenny’s home benefits from connected internal spaces, cantilevered balconies and a feature curved staircase alongside e ceptional performance. The TechVantage S system delivers Passivhaus levels of insulation and airtightness, though the couple opted against paying for o cial certification. When the sun comes out, the house stays warm for the rest of the day,” says Chris. “It’s so cosy and comfortable.”
Timber frame is a wonderfully versatile building system, which means the architectural possibilities for your new home are vast. “The method allows great e ibility to suit different budgets and meet the requirements of even the trickiest of building plots,” says Simon Orrells, managing director at Frame Technologies. “You can create a huge range of awe-inspiring properties, from traditional farmhouses clad in stone to contemporary buildings with curves and slick white render finishes. ou’ll also enjoy a e ible living space – open plans are easy to achieve, for instance, so you can simply partition off rooms with non load-bearing stud walls, which should allow for future alteration.
Most timber frame manufacturers are set up to provide completely bespoke solutions. That might take the form of engineering a frame to suit an independent architect’s
Top left & above right: Set on a gently sloping plot, this striking architectdesigned house features a Scotframe timber house shell, which reached watertight on site in less than a week. The project showcases the potential of timber systems, with vast openplan spaces and a double-height zone featuring a mezzanine level
drawings. Others will have huge catalogues of high-quality past projects you can use as inspiration, adapting them to suit your own tastes and requirements, while some can craft an individual design from scratch using their own in-house teams.
There are specialist firms that can take care of the design, planning, building regulations, manufacture, delivery and assembly of your new home,” says Mark Stevenson, managing director at Potton and Kingspan Timber Solutions. “Some even offer foundation design so you can enjoy guaranteed quality and a smooth self build journey from start to finish. This route would include consultations, plot evaluation, design development and costing e ercises to ensure you get the home you want at a price you can afford.
Individual timber framing systems have their own unique specifications and
Left: Ample glazing helps to frame countryside views and allow the oak to take centre stage, as this beautiful oak frame home by Lowland Timber Frame shows
Timber frame has a reputation for producing highly e ie t uildi s it l ru i sts ut t ut t e e er y it t es t re te e i t e first place? According to the Structural Timber Association, lm st ll d i tim er r me stru ti is s ur ed r m ell m ed ur pe rests esp si ly s ur ed d is e e ti ely r neutral material, as it locks up (sequesters) CO2 r t er t rele si it i t t e tm sp ere re isi e i eered m u ture me s ste is mi imised t ile t e d is ultim tely re y l le e it re es t e e d its use ul li e t s m re the quick build speeds and reduced need for labour site me sider ly l er tr sp rt miles mp red t site sed stru ti met ds u e tu te t se u lities it t e spe ifi ti de isi s y u m e t i terms t e superstru ture d ll m teri ls used uildi it tim er i es t e pti t e re t le l sed p el systems s ys Sim re t le ll te l y e tes de s ti uild up it i t e stru ture impr i t e p els per rm e t ill ls set t e t e r e lt y i d r ir u lity i s uld y u is e ed up it i u lity e til ti systems d tur l t i ree m teri ls r t e i ter l fit ut
limitations. So, if you want to make the most of the method’s benefi ts, there’s a lot to be said for involving your structural supplier as early on as possible in your project. This means the architectural team can design with the build system in mind, and valueengineer the project to deliver the look, performance and functionality you want within your project budget.
Engineering a timber frame home is quite different to developing the schematics for, say, a masonry building.
So, whatever planning design route you take, the structural calculations to enable your design are best carried out in-house by your frame manufacturer. This stage can account for everything from loadbearing paths, insulation and airtightness performance, right through to detailed decisions like how services will be run (open metal-web joists are popular in timber builds) and acoustic performance between rooms and storeys.
“Having one company responsible for all these structural elements is hugely e cient and economical, says mark Stevenson. It can also offer great value for money in comparison to sourcing all the design services and building components by yourself – your chosen specialist will provide all the structural elements, so you can relax knowing all of this will fall under the umbrella of your budget.
Above right & below: Gemma and James Hooker chose self build development Graven Hill (gravenhill.co.uk) as the ideal location for their rst ho e designed i t and kitted o t y an ood as a t rnkey pa kage he ti er fra e a pane s are thi k ith an additiona of ins ation to a hieve a va e of 2K. The property as an fa t red ithin days of na ising the design and the structure was weathertight on site in under a week
e r ut t e e efits t is m der met d stru ti d t m imise its p te ti l r y ur uild
The structural insulated panels system (better known as SIPs) is a premanufactured building method that shares many similarities with closed panel timber frame. It uses factoryengineered, load-carrying, timber-based panel products to form the superstructure of a bespoke home. Manufactured offsite, the lightweight system can be used for walls, roofs and even oors. It delivers both the structural capacity and thermal envelope of the building in one neat package offering super-quick construction speeds and confidence over the performance of your finished house.
SIPs are gaining traction in the UK self build market as a premium option wellsuited to low-energy homes. As such,
Above: Glosford SIPs provided the wall and roof envelope, plus the structural partitions and oors for this striking black timber-clad 240m2 self build
you can expect to pay slightly more in comparison to systems like blockwork and timber frame. Don’t be put off by the upfront price, however. It’s important to consider whole-life costs when you’re building your own home, and SIPs can guarantee a predetermined level of insulation and airtightness out of the box. Plus, you’ll be able to plan the rest of your self build schedule around a highly-predictable, factory-controlled manufacturing and assembly process.
Most structural insulated panels are formed by sandwiching a core of high-quality rigid foam insulation in between two skins of structural timber – typically oriented strandboard (OSB) – as the facing material. The factory manufacturing process creates exceptionally strong panels without as much studwork as timber framing; enabling a continuous core of built-in insulation. This combination delivers excellent performance alongside impressive versatility. As a result, SIPs are often a preferred choice for many self builders looking to achieve Passivhaus and similar low-energy standards. “Heat loads in a SIPs house can be kept to a minimum, which
1
2
High levels of insulation and airtightness within a slim panel thickness. This can deliver Passivhaus and zero-carbon levels of energy performance without i t s rifi e r sp e
Ultra-quick assembly on site, with reduced reliance on skilled labour, enables smooth and predictable delivery of the main construction phase. There’s also less eed r pl t d s ld mp red t s me systems, helping to ease some preliminary costs.
3
4
Suitable for roof structures, creating pre-insulated lofts and vaulted ceilings that can add valuable extra space and design panache to your project.
A versatile system that’s capable of being used as a standalone house shell or to provide insulating encapsulation for other construction methods (oak frame wraps being a prime example).
5
Excellent whole-life costs due to the ease with which S s e les deli ery i per rm e e ie t home. So, while it may cost more upfront than building with traditional options like blockwork, you will reap the rewards of ongoing low energy bills.
equates to low running costs,” says Derek McIntyre, SIPs home director at JML SIPs. The system also offers a straightforward solution for creating coveted design features like vaulted ceilings without the need for trussed rafters.
There are variations on the theme. For instance, some SIPs suppliers use expanded polystyrene (EPS) as the insulation, which is fully-bonded with structural adhesive to the OSB skins. Others use polyurethane (PUR) or polyisocyanurate (PIR), which are foamed in between the sheathing to create an integral bond. The different insulations offer slightly different performance characteristics, which will be re ected in the price PIR offers the best insulation values as standard). The other area of choice is around the sheathing different manufacturers use: plywood and cement particleboard are among the alternatives.
SIPs can deliver U-values right down to 0.1 W/m2k, along
Below: An example of the Kingspan TEK SIPs building system, which is available in 142mm or 172mm thicknesses an features a rigid urethane insulation core. Note the insulated splines to underpin the system’s energy performance
with superior airtightness thanks to their detailed jointing arrangements (it’s these qualities that make it a great solution for wrapping other building systems, such as oak frame . Some manufacturers even offer insulated splines to further underpin the system’s performance advantages. Coupled with the panels’ innate strength, the highspec insulation enables thinner walls and roofs compared to traditional construction systems. This can increase the finished oor area of your home within the same overall building footprint, while also keeping roof build-ups to a minimum, potentially increasing head height in loft spaces.
SIPs have become a mainstream option in the self build market. Nevertheless, it’s sensible to choose a designer who has worked with SIPs before, putting them in close contact with your system provider. Each company has different details and panel thicknesses, which will in uence the drawings,” says Derek Mcintyre. “Bringing your supplier on board early saves time and money, as opposed to having to rethink plans to suit the system afterwards.”
plans to suit the system afterwards.”
As everything is precision-engineered, you can be assured your house shell will be accurate to the drawings –enabling you to get ahead with the project schedule by ordering core components off-plan. Products
on long lead times, such as windows and doors, can be ordered early knowing that, once the SIPs package is complete, glazing can be immediately installed,” says Mike Fleming, sales director at Glosford SIPs.
Standard SIPs panels are manufactured 1.2m wide and 2.7m (storey-height) in length, with smaller sections used to form the openings. Working to those sizes will be the most cost-effective option, minimising cutting in the factory. Panels can also be produced in wider spans and lengths up to 7.5m to suit particular design features, with window and door openings pre-cut.
The size-to-strength ratio is what enables those dramatic vaulted ceilings. The loadbearing work in the roof will done by the
This 268m2 self build showcases some of the key ene ts of s he ays install used 142mm-thick panels with 50mm of extra insulation on the inside face of the walls, and 100mm on the roof he latter was a key feature – its asymmetric design is vaulted internally to enhance the sense of space, with the glulam purlins left exposed for added character
ridge beam and any purlins – which are often formed in glulam. The SIPs panels then span from ridge to eaves with minimal need for extra support. So, you can easily achieve double- or triple-height zones. What’s more, unlike with conventional trusses, you’ll gain a clear and pre-insulated loft void that can be ideal for achieving extra habitable space.
Lead times differ between suppliers, but a typical weathertight package for a four-bed house might be manufactured in around eight to 10 weeks. The kit will bring together all the core components to complete your house shell: walls, roof and oor structures, plus membranes according to the technical design. While the panels are being fabricated, it makes sense to get your groundworks sorted. A SIPs home can be built atop any mainstream foundation system, but the slab must be very accurate and level some providers require a tolerance of just +/- 5mm).
Once the foundations are signed off, the structure will be delivered and erected in sequence from soleplate upwards. First the
SIPs is widely acknowledged as a fast-track option for achieving low-energy standards such as ssi us is is ertified desi approach based around high levels of insulation, very low levels of air leakage, and the use of mechanical ventilation with heat recovery to enable a fresh, healthy living environment. But what do you need to know to ensure you hit the performance levels you want?
“There are plenty of systems on the market so make sure you u derst d t eir e efits s ys Clay, partner at SIPS@Clays. “Look at the thermal qualities – in particular the jointing system, which is key to creating an airtight envelope, as well s ertifi ti s fire per rm e stre t d st ility
While some manufacturers er e tr t i p els t achieve lower U-values, it’s more common to stick to a standard t i ess d i ste d dd e tr layer of insulation internally. This will provide a further boost to airtightness and thermal bridge detailing. Insulation coverage is factory-guaranteed, but can be further enhanced by options such as insulated splines (joining sections between the panels) that make detailing straightforward on site.
ut t e pr perly assembled SIPs structural shell ie es e elle t irti t ess e jointing arrangements inherent in
SIPs can provide air leakage rates as good as 1m3/hour/m2 e pl i s tt e s e d technical GB at Kingspan Insulation. “Once airtightness tape is applied to junctions, this can be reduced even further to beat the 0.6 air changes per hour required by the ssi us st d rd is tte ti to detail needs to be maintained further into the build, for instance ensuring windows and doors are installed at the optimum depth in the insulation zone and properly taped before plasterboarding.
To protect the insulation and airtightness performance, it’s vital t use e perie ed i st llers r
ground oor load-bearing walls, then the intermediate oor structure, upper storey, ceiling joists and finally the roof. A typical SIPs house shell can be erected in as little as one to two weeks. The only thing that might slow a build down is very high winds.
SIPs are lightweight and easy to handle, so the ground oor can often be slotted together by hand. pper storeys, roofs and larger panels require lifting equipment so you’ll need access for a crane or telescopic handler. If you’re worried this might cause disruption for neighbours, in fact the opposite is true: the impressive speed
the follow-on works. Services are typically run through the internal p rtiti lls d r stru ture to minimise penetrations through the thermal envelope. Where wiring, pipes etc do need to be run l e teri r ll p els it m y be possible to include service ducts during fabrication – but a more common solution is to batten out a service void (which is then hidden by plasterboard).
Open-web positjoists are often spe ified r t e rs s t ey re available in a range of sizes to easily accommodate ventilation du ts et st S s uses ill use mechanical ventilation with heat re ery t ptimise e ie y e tr t ste ir d pr ide constant fresh incoming supply.
of assembly means there will be fewer deliveries and trades coming and going compared to traditional build methods.
The moment your SIPs home reaches weathertight, you’ll can bring in internal and e ternal trades to work simultaneously. So, your chosen cladding can be installed while first-fi plumbing, electrics etc proceed internally a benefit you don’t get with systems like masonry. our trades will have solid, clean and straightforward surfaces to work off, says Ian. Progress is therefore swift and predictable, bringing the advantage of easy sequencing of works.
The owners of this spectacular self build approached JML SIPs with initial concept designs for their rural Scottish plot. The site benefits from breathtaking views over Loch Linnhe and out towards Ben Nevis. Key criteria were a lu ury finish, modern living and a design with traditional features that respected the picturesque surroundings. Energy e ciency was also paramount and it was this that put a SIPs build at the head of the pack.
JML introduced the owners to an architect with vast e perience of country estates, and the two firms then worked in close collaboration to take the project from sketch idea to reality. The remote lochside location and Scottish West Coast weather posed some challenges so reaching weathertight stage as quickly as possible was important. SIPs ticked that bo , too.
The JML team designed, engineered and fabricated the SIPs kit, as well as erecting it on site. They also supplied and fitted
Top: SIPs made perfect sense for this project, providing a speedy route to weathertightness on the exposed lochside plot
Inset: Every window and glazed door in the property was carefully positioned to maximise views of the wonderful setting. JML supplied and installed the Internorm external doors
the Internorm e ternal doors as part of the package, ensuring the house shell was watertight, ready for internal fit-out and follow-on works. Highlights of the project include the carefully-selected local stone cladding, beautifully finished interiors and wonderful spaces for entertaining.
“The house blends perfectly into its surroundings, keeping to a traditional design but seamlessly incorporating all the modern-day lu uries we were looking for, says the homeowner. I’m particularly pleased with our decision to build in SIPs, as the house is cosy and draught-free, ensuring our family will benefit from minimal energy costs for generations to come.
While they’re often sold on the benefi ts of clean lines and easy detailing, it might surprise you to know that pre-fabricated building methods don’t have to result in predictable architecture. Anything but, as the projects on these pages demonstrate SIPs are very e ible and can be used in combination with any e ternal cladding. Brick, render, weatherboarding, brick slips a quick-fi t tile-like system , stone the list goes on. Similarly, up top, the roof can be finished with tiles, slates, metal, shingles and more. Pretty much any house design can be realised in SIPs, but you’ll be able to access the system’s full potential if you engage with a supplier from the early architectural planning stages. There are no limitations to SIPs designs, and homes don’t have to be bo y and boring, says Ian Clay, partner at SIPS@Clays. If either you, your architect or SIPs designer has the vision, then almost anything is possible. A lot of that comes down to the system’s strength-to-weight performance enabling fully load-bearing panels of up to 7.5m in length.
One of the great design advantages of SIPs is that you do not need to incorporate trusses to support the roof of the house. This gives you the option to easily create airy, double-height feature zones think lofty hallways, and dining areas complete with fully glazed gables . It can also enable e tra accommodation in the attic all in the form of a pre-insulated warm roof structure. Nowadays, open-plan living is very popular and many of the self builders we work with are looking to create a feeling of space by opting for higher ceilings, says Derek McIntyre, SIPs director at JML SIPs.
This selection of stylish self builds showcases how SIPs can deliver high-quality bespoke architecture
Below left: The Robinsons had to deal with some onerous planning constraints on their project, including reducing the maximum ridge height of the roof by a metre. In these situations, every little helps – and SIPs Eco Panels’ high-performance system helped save precious build-up height in the asymmetric roof design, while enabling stunning vaulted spaces
Left: The Jays’ home is a fantastic example of SIPs’ capacity to marry energy e ien y ith striking design. Unconventional angles and shapes add wow factor, enabled by the SIPs system, supplied and installed by Potton
Above & left: Designed y an or e d Architects, this lowenergy project in Fife is the Build It Awards Best SIPs Home 2022. The 306m2 house features double height zones, including a stunning curved hallway, framing views of the sea beyond and hosting a sculptural staircase. The SIPs kit from SIPs Industries features 217mm-thick panels to maximise insulation. It took just 15 days to manufacture and a further 15 to erect on site
Above & left: The client’s vision for completely open-plan areas and vaulted ceilings made SIPs an ideal choice for this 263m2 project. SIP Build UK completed the detailed design, engineering and installation. The 172mm-thick panels deliver a U-value of 0.15 W/m2K in a slender wall thickness, about 150mm thinner than would be necessary using traditional materials
This unique self build is nestled in 20 acres of open countryside, making it a challenging site to obtain planning permission on. So, in order to unlock the full potential of the location, an exceptionally high quality design was required. The architect’s vision was inspired by the region’s hop growing history and consists of three kiln-like structures that are set at different levels and angles to each other with comple roof and oor junctions.
The homeowners were living in a caravan throughout the build, so a method that could offer a fast programme was crucial. Offsite SIPs construction ticked all the right boxes, including delivering on the couple’s energy e ciency goals. After putting the project out to tender, Glosford SIPS was appointed to supply and install the SIPs roof and wall envelope, structural partitions and oors. The company’s quote worked with the couple’s budget, and they were able to visit the factory. This is our first self build and we wanted something special,” say the owners. “We were impressed with the processes and quality controls in place.”
Top: The owners committed early on to using SIPs, which enabled them to extract the maximum design potential and value from the system
Top right: The design has enabled wow features such as vaulted ceilings and the link landing
Above right: The complex geometry required assembly of the precision-cut roof panels on the ground on a prefabricated soleplate, with entire modules then being lifted into position
The team worked in tandem with the owners’ architect to come up with technical drawings for the manufacture of the panels. This collaborative approach has enabled a high quality, innovative home that scores top marks for thermal performance. Clad in cedar shingles, the hop barn-inspired design keeps the local vernacular in mind and truly showcases the versatility of SIPs.
The project picked up the prize for Best SIPs Home at the 202 Build It Awards. The finished house is everything we wanted, with glorious south-facing views over the Malvern Hills. It’s a real testament to how SIPs can meet the demanding precision of a complex design,” say the owners.
Boasting character and warmth, oak frame homes are packed with charm and wow factor, and modern techniques enable impressive performance, too
Combine beautiful warm natural colours and textures with impressive structural beams and detailing, and it’s no wonder that oak frame has been a popular construction method for centuries. Traditional halftimbered black and white buildings feel a natural part of our housing landscape here in the UK, long admired for their character and structural integrity, some having survived since mediaeval times.
Today, modern oak homes can be traditional or contemporary in style, often paired with amazing glazed features that frame views and let the timber take centre stage. Advancements in technology allow designers
to utilise the beauty, strength and integrity of an oak frame to its full effect, offering open-plan living spaces without the need for internal structural walls.
Above: Build It readers Ian and Lisa Milne self built using oak frame. The 235m2 home took one year to come together
Below: This cross section of an Oakwrights design shows the WrightWall and WrightRoof encapsulation
Traditionally, oak frames are created around a series of rectangles (bays), which make up the base structure (box frame). It’s important to work with a designer who is familiar with the method, or at least bring an oak frame specialist on board early on. A good designer will help you to recognise how to make the most of your structure, the best orientation and the size of the bays and spans. They will also work out the loads, as well as the scale and proportion of the rooms. The design will also be affected by roof pitches.
Many oak frame specialists have inhouse architects and designers who can create bespoke schemes or adapt existing designs to meet your vision. This means that you can get plans and elevations, including detailed drawings for Building Regulations, directly from the company supplying the structural frame of your new home. Some will even take care of the planning process on your behalf.
Traditional vernacular oak frame homes might be cottage-box style with exposed oak on the inside and outside, infilled with wattle and daub. These historic ways of
building wouldn’t meet modern energy regulations, but it is still possible to recreate this look by using additional oak for a home’s external cladding. These days, you can cover the exterior of your oak home in any variety of finishes, whether that’s timber cladding, brick, stone or a combination of styles.
Barn-style oak frames are a popular option that combine contemporary design and local vernacular. These buildings tend to have a more open-plan feel, with fully vaulted roofs and large areas of glazing. Some highly modern homes have been built using oak frame, too, incorporating sections of steel alongside the oak to give an industrial twist.
Glass often makes a statement feature on oak homes, with glazed gables and large window spans, sitting beautifully alongside oak. It’s important to work with a specialist team that understands shrinkage in oak and has a proven track record of success. Modern techniques mitigate against
shrinkage, as well as accommodating other potential movement as the oak dries out –all of which adds to the method’s charm.
The oak frame of your new home will be cut and formed offsite in the supplier’s workshop/factory. Some oak frame companies use traditional techniques and hand tools. Others favour fast, computer-aided cutting machines.
Oak trees are used soon after being felled, because the moisture levels make it easy to cut and work into the desired shape – hence the term, green oak.
The frame is then assembled in the workshop. Traditionally, wooden pegged mortise and tenon joints are used; the oak beams gradually tighten around these to create a uniquely strong structure.
It will then be carefully dismantled, packed onto a lorry and transported to your site ready to be re-erected. Bear in mind that you’ll need access and space for the crane that will lift the trusses and cross sections into place on your building
Above: This oak frame from o e d i er Frame is starting to take shape on site, where you can get a sense of how striking it s going to ook
plot. It usually takes a few weeks for the specialist team to erect the oak frame.
Once in place, the structure will need to be wrapped to create an insulated and airtight building. Pre-insulated timber stud panels can be fi ed in place and then clad with your choice of e ternal finish. SIPs are a modern alternative to this – while some companies, such as Oakwrights, supply their own brand of prefabricated encapsulation panels.
It’s recommended to use traditional materials, such as lime mortars and plasters, which allow for minor building movement. Hydraulic lime mortars are particularly useful in timber buildings because their e cellent vapour e change properties minimise rot and damp while offering good weather resistance.
Once your oak home is built, you won’t need to do much in terms of upkeep. Oak is naturally resistant to insects and weathering, although the frame can become marked from its natural tannin. These and stains from the building process can be removed by sanding or applying o alic acid once built. ntreated oak will weather to a silver-grey colour outside and remain deep golden inside.
It takes five to 0 years for oak to dry out completely and season, which often results in shrinkage and movement. The process creates the characterful splits and shakes, adding to the building’s charm. You may need to touchup some paintwork once settling is complete.
In a fire, a protective layer of charcoal forms around the outside of a beam, delaying damage to the core. This means oak buildings can actually withstand fire for much longer than many other structures.
CHARLIE MILLS managing director at Oakwrights, shares his e pert insight about building with oak frame:
Q How can self builders choose which style of oak frame is right for them?
A This is guided by the layout of the home and your budget. If cost-saving is a key aim, then an aisle frame is more slimline as it sits in the middle of the house, versus a full post and beam frame that goes the full width and depth of a property. This is the style I chose for my self build home (pictured below).
Q How is an oak frame insulated?
A Throughout the design process we use the same innovative software to design both our oak frames and the insulated closed-panel encapsulation system. Panels are fabricated in our workshops, which reduces time on site while ensuring precision and quality control. These systems achieve high levels of insulation and airtightness, reducing the energy consumption of homes and lowering heating costs.
Q Will the oak move and change once in place?
A This can be a problem if not properly considered and the right system is not used. We use face glazing to ensure this isn’t an issue for windows, as it’s a proven airtight and waterproof system.
During their search for the perfect self build site, Andrew and Linda visited self build exhibitions to gather ideas. They wandered onto the Oakwrights stand, where Andrew met managing director Tim Crump. “It wasn’t just an oak frame Oakwrights were offering, but the encapsulation system, too,” says Andrew. “Tim spoke about Passivhaus, which at that stage I’d never heard of.”
Some months later, with the plot now in the bag, the Burnetts went back to Oakwrights. A visit to the company’s show house helped crystallise their ideas. “After our stay in The Woodhouse we couldn’t have chosen any other type of home – we wanted an oak frame Passivhaus,” says Linda. This stay was key in helping formulate the architectural design, too. “We liked the gable ends and the traditional tiled roof,” says Andrew. “We were drawn to the idea of a brick finish on the ground oor with timber cladding above, as it would tie in well with the houses nearby.”
Oakwrights’ in-house design team worked closely with the Burnetts to formulate
Top: The exterior features a mix of timber and brick nishes ith balconies formed fro oak hi h has eathered beautifully
Above left: The interesting angles created by the exposed oak frame in the living room make it one of Linda and ndre s favourite places to spend time
Above right: The doubleheight ha ay provides immediate o fa tor as you enter the property
a plan, and they were impressed by the Passive House Planning Package the company’s Passivhaus consultant used. “The software allows you to model exactly what will happen when you make a window bigger, smaller etc,” says Andrew.
There’s very little the couple would change about the completed house, which is testament to their thorough planning. If it wasn’t for the fact they had already created their forever home, the couple would have had no qualms in tackling another self build. “If we did it again, we’d want to do another project with Oakwrights and Furber Young,” says Andrew. “It was a brilliant experience and we’re delighted with the result.”
Using exposed oak elements establishes an easy rapport between inside and out, making this style of home particularly popular for projects in the countryside. Oak homes look comfortable in rural settings because the wood on display is echoing natural surroundings. Plus, traditional designs have a long history of being established as part of the UK’s countryside vernacular, with some buildings hundreds of years old.
“Building with oak introduces a timeless quality, and an immediate character and charm,” says Craig Alexander, an architect from Oakwrights’ in-house design team. “Working in a rural location, regardless of your chosen style – either contemporary, traditional or somewhere in between – it is important that the design of a new home is sensitive, re ective and sits comfortably within its context, and an oak frame certainly helps with that process. External oak features weather-in sympathetically and quickly, and views out from the inside,
Above: Build It readers Deirdre and David Rook built a stunning oak frame home on the land beside their family farm, working with Oakwrights to create the contemporary one-and-a-half storey property
It’s an appealing idea to use oak inside and out in a rural area, to help a building look truly rooted in its landscape. However, energy e ciency requirements mean that the structural system on the inside is no longer the same seen on the outside. Traditionally, the same piece of oak is displayed on the interior and exterior, but today that wouldn’t pass Building Regulations. Instead, any oak on the outside of a building is added separately and not part of the structural frame.
Rather than viewing this as a negative that the external oak isn’t structural, try seeing the freedom it gives you to clad the building how you want and as an opportunity to add some further rural character. “What is fantastic about oak framing is that it can complement a range of external materials,” says Craig. “Principally, I suggest focusing
on two elements: complementary natural materials and re ecting your specific vernacular, for e ample by using slate over tile. Oak weatherboard cladding is always a great place to start. It requires no finishing or repainting, is incredibly durable and can speak to a simple, agricultural conte t.
Many self builders turn to oak frame because of its traditional style. Medieval manor houses, ancient barns and country churches are some of the most charming buildings we have in this country, so why not emulate them? It’s also possible to create beautiful modern homes with the same soaring ceilings and e posed internal timber, but a slightly different aesthetic that still fi ts in well with a rural setting.
Traditional designs tend to have lots of oak on display, often close together. Modern styles typically feature less oak because they don’t need the timber to work structurally in-between the main posts and beams. Oak frame offers opportunities to have fun with the design, especially with wow factor glazing helping to show off the oak and add a contemporary spin.
As far as winning planning permission is concerned, specifying an oak frame build won’t make a difference if there are other elements of your design that don’t conform
with local policies. If it’s too big, has poor access or your plot simply isn’t viable, then you’re still going to get turned down no matter what build system you use.
If you’re designing a new bespoke home from scratch then you can tailor your oak frame building to match what the planners are after. ou can also e plain the thought that has gone into creating a design that works with and supports the locality and surroundings. Oak’s sustainability credentials, with its low embodied energy, can also be a persuasive factor.
If you’re working with a tight budget, it’s vital to approach all aspects of the scheme with this in mind. It’s easy to get carried away when you see what’s been achieved by bigger budgets – such as wide spans, feature trusses and glazed gables throughout – but stay disciplined and look for other ways to create wow factor. The most cost-e cient schemes will use the simple rectangular bay oorplan seen in cottage and barn-style projects. From that base, consider paring the oak back in most rooms, so you can focus your budget on one or two wow moments.
It can be tempting to complement your oak frame with good quality products, such as handmade bricks and roof tiles. Luxury details come with a price tag to match – more standard options will help to keep costs down. The same is true with impressive glazing – more traditional windows could be a wiser use of funds.
Some oak frame companies can oversee a scheme up to its completion, and their experience and connections can be instrumental in ensuring your self build is a success. It’s a great option for first timers, but you will usually pay extra for the privilege. A common alternative is to have them hand over the reins partway through, when the property is watertight. If you
Right: The owners of this impressive 169m2 property by Oakwrights kept costs down by opting for an e ient building shape, taking on project management duties and using ost effe tive details such as painted timber cladding
have the time and ability you will find that there are savings to be made by sourcing products and follow-on trades yourself.
These days, frames are encapsulated with insulating panels – and, if the system also takes on a structural role, this can offer the opportunity to reduce the amount of relatively expensive load-bearing oak. Going for a design with exposed oak externally will also help to minimise the amount of oak needed. If you’re looking to cut costs even further, opt for a hybrid approach –using softwood for the primary structural elements and reserving oak for high-impact areas. Read more about this on page 42.
If you’re willing and able, consider cleaning the oak yourself. This could save you £1,000s, depending on size and complexity. It’s a time consuming process but that’s precisely why it can help you keep under-budget. Many self builders prefer to maintain the organic colour and character of the wood with a simple acid wash, leaving the wood’s own tannins to prevent damage from moisture and insects. Or you can leave the timber untreated and allow the marks left by carpenters etc to be remain on show.
You might be surprised to hear that oak frame can work for a modest budget. Here’s how to keep prices down and still achieve the oak home of your dreams
Right: CLT’s inherent strength means it can be used on timber buildings to achieve heights previously thought impossible
Below: CLT panels being craned into place, with indo s tted in the factory. This engineered material is mostly imported from Europe from brands like Stora Enso
Cross laminated timber, known as CLT, is formed from cross-layered engineered wood. It’s particularly strong and its versatility means it can be used in many ways in construction, from walls to stairs. This method was pioneered in Europe during the 1970s and is still mostly imported to the UK, mainly from Austria, Germany and Scandinavia.
The strength and stability of crosslaminated timber comes down to how it’s formed, which is in a similar way to plywood. Multiple layers of cross-bonded timber, typically 20-40mm thick, are glued together under pressure for stability. The number of layers is always odd, with a minimum of three, and each one may be of varying thicknesses, arranged symmetrically around the middle layer. The panel’s strength is achieved by having the grain of each layer at right angles to the
next. The overall thickness, as well as the load-bearing performance of the panel, is determined by the build-up of the individual laminates. The result is big timber sheets that can be used to create large-format load-bearing panels for walls, oors and roofing elements spanning up to 24m in length. This can allow for coveted design features such as vast open-plan layouts, cantilevers, vaulted ceilings and liveable loft spaces without needing to rely on reinforcing steels. It also enables ultraquick build speeds on site.
CLT structures are typically built using a platform frame, where walls are temporarily braced with raking props before oor panels are lowered onto them and fi ed. The completed oor structure provides the platform for the erection of the wall panels to the following storey.
As with other engineered timber systems, however, you’ll need to nail down your detailed design before the house is fabricated as it will be di cult and expensive to make changes later on. The panels’ size means they’ll normally need to be craned in, which could be di cult to arrange on tight sites.
In comparison to conventional softwood wall framing and joisted oors, CLT has a strong load-bearing capacity when used
as a wall or slab. It’s got high in-plane strength (resistance to wind and seismic forces). As a solid wall panel (rather than a framed construction) cross-laminated timber panels distribute weight evenly, reducing the requirement for localised pad foundations.
This material is also inherently fire-resistant the dense structure will char like oak if subjected to a blaze, thus protecting the internal wood core) and provides impressive acoustic performance compared to many timber techniques. As it’s manufactured from timber, it can represent a lower impact, more sustainable option than concrete or steel although the glues used can offset some of the environmental gains.
CLT panels can come pre-insulated, with U-values that can comfortably rival those achieved by other modern forms of construction. What’s more, cross-laminated timber is highly airtight out of the box (especially so if supplied in thicker panels). A breathable roof underlay and rigid insulation are usually installed above the CLT panels for a warm roof construction, which can be prefabricated as an insulated cassette. This makes them well suited to room-in-the-roof designs where there is a simple arrangement of continuous ridges and gable ends.
One of the most impressive aspects of CLT panel construction is its potential to overcome height limitations of traditional timber structures. In fact, the tallest timber buildings in the world use this method of construction, including the Mjostarnet tower in Norway, which is 85m high.
CLT currently represents a higher-cost option for full one-off homes. So it’s more commonly used in hybrid constructions – where its impressive span capabilities can complement another building system to achieve the desired outcome.
Build It readers John and Jenny Kinsley built this four storey l ts i di ur s e me r t emsel es d t ree t er use lds e t e ey de isi s s t use r ss l mi ted tim er C r t e ll d r p els e system t ey used ll s r ultr str se ti s up t m y m ese ere r ed i t pl e site d s re ed t et er it met l r ets r ite t d t used r ss l mi ted tim er s t e superstru ture r y is pre i us pr e ts e ere i t e r i site ed ed i ti t sp t et ee tr diti l te eme t uildi d t d l st rey use e s ys e p els re ll pre ri ted t pre ise si e d my i est rry s et er d t t e dime si s r d uple sleepless i ts ut it e re d e m i d t es r ss l mi ted tim er lie i t e speed d ur y stru ti i elp t e sure predi t le uild sts t ll me t et er e ie tly it t e m i r me d r up i ust i e d ys e i ter l sur e t e C p els s ee le t e p sed pr idi e uti ul e ture d ddi r ter t t e mes.
Glulam is another engineered product in laminated timber. It’s exceptionally strong and ideal for load-bearing applications. Although it’s considered a modern material, it was a Swiss patent in 1901 that heralded the beginning of glulam – named because of its glued and laminated nature. Today, glulam beams are manufactured in a factory where layers of accurately-planed softwood (such as spruce, larch or fir are bonded together under heat and pressure. This process means that small pieces of timber can be used to create large structural elements.
With all the beauty of natural wood, glulam looks great, but can span much further and be curved and shaped easily into practically any shape – perfect for supporting intricate roof structures with stylish exposed beams. Curved glulam is manufactured by bending laminates on formers before being bonded, followed by clamping and curing.
Glulam can be used as beams, lintels and posts in your home. It has high dimensional
CLT and glulam come under the bracket of mass timber, which is a term describing engineered wood used as structural building materials. Mass timber is er lded s i si ifi t sust i ility e efits According to the Structural Timber Association, rep rts i di te repl i steel it tim er m y redu e l l r emissi s y up t ile site m u turi t lie t spe ifi ti s me s si ifi tly l eri time spe t site t er types of mass timber include dowel-laminated timber (DLT), nailed-laminated timber (NLT), laminated veneer lumber (LVL) and parallel-strand lumber (PSL).
Above: Glulam beams were used on the Build It Education House (selfbuild.co.uk/ ourhouse). They were supplied by SIPCO, who provided the property’s beams and SIPs roof structure
stability and, according to the Structural Timber Association, can span up to 50m in length, which is why it’s seen in commercial settings, like sports halls and supermarkets. It’s also lightweight, which means it’s practical to handle. It’s often used as an alternative to concrete and steel beams RSJs and frames. This material can actually outperform steel in a fire, as the latter distorts in high temperatures, whereas the integrity of glulam remains in tact –which means it doesn’t usually require e pensive fire retardants.
Glulam is considered a green alternative to concrete as it has a 60% lower carbon footprint. Within homes, it’s often used to span large open-plan spaces, creating a striking contemporary feature.
Strong and versatile to shape, t is type e i eered tim er can reach impressive spans and still exudes the natural look and appeal of wood
Timber’s versatility as a construction material means it can be used alongside a range of other build systems
Timber has a host of advantages – it’s strong, sustainable and provides good thermal insulation. It’s also versatile, which means it’s easy to combine with other systems to get the best of both worlds from multiple solutions. “It’s becoming more common to build hybrid homes and there are many different systems that can be used this way,” says Simon Orrells, managing director at Frame Technologies. “Building hybrid means you can choose the best materials to suit the situation.” It’s not necessarily more expensive, either – in some scenarios, incorporating multiple structural solutions can provide a smart route to achieving your goals while keeping costs to a minimum.
According to David Williams, head of production at Oakwrights, a conventional panelised timber frame can work well with pretty much any other method.
“However, full consideration needs to be given to the physical attributes of each system so that they act as one, rather than working against each other,” he says. “The aesthetics of a building can be significantly enhanced by bringing together different materials and systems, too.” The most widespread partnerships include structural timber alongside materials such as steel, engineered wood products, concrete and even masonry. Here are the common combinations and where they make sense.
Historically, the post and beam skeleton of an oak frame was infilled in wattle and daub. Today, oak homes are wrapped in a thermally e cient panelised system to provide an airtight shell. SIPs are one option, well-suited to homeowners who want to marry the aesthetics of oak frame with the thermal performance of SIPs. “Anything is possible. If accurate dimensions are provided from both system suppliers, the SIPs panels can be cut to fit any size to suit any setup,” says Darren Barnes, partner and head of design at SIPS@Clays.
Some suppliers, such as Oakwrights, manufacture their own high-performance encapsulation systems. These solutions provide outstanding thermal e ciency. If you have a tight budget, you might use less oak and more encapsulation. “With our aisle framed projects, we can achieve the desired effect of oak, while utilising the structural capabilities of our encapsulation systems,” says James Morgan, head of encapsulation design at Oakwrights.
Timber with elements of oak
Oak is widely acknowledged as a premium material – and if your funds won’t stretch to a full oak frame home, there’s another route. “Timber and oak frame is a popular
You might need to work with multiple partners. “With hybrid systems, it’s best to use a single supplier for the entire build,” says Simon. “But if you’re having an ICF basement, for instance, these two elements would have to be designed together but sourced separately.”
To ensure a successful result, it’s important to bring both companies in at the early design stages, ideally with a single engineer assuming overall responsibility. This way, you’ll be able to develop a plan that factors in the unique characteristics of each system and ensure they function harmoniously. derst d t e di ere ti l m eme t r m m i i di ere t se er l m teri ls t is is ully considered and detailed accordingly, there should be no issues,” says David from Oakwrights.
to waterproof. Other options include offsite manufactured pre-cast concrete panels, in-situ reinforced concrete and blockwork masonry. In all cases, you can combine their benefits for below-ground construction with the advantages of timber for the aboveground storeys. “This enables you to get the benefits of both they really complement each other in this situation,” says Simon.
hybrid system,” says Simon. “The two complement each other, offering an ideal solution for self builders keen to build with oak but where the budget doesn’t allow.” You might use panelised timber frame for most of the build, but switch to oak where you want character – such as for feature beams, trusses, porches and sunrooms.
A basement will maximise the size of your house on its plot. How this is built depends on site conditions, soil and budget – but fundamentally it needs to be a heavyweight system that can resist ground and water pressure, and can be waterproofed.
For instance, ICF, which is a method using stacks of polystyrene blocks filled with steel reinforcement and concrete, is super-strong and one of the most cost-effective systems
Above: On this project by SIPS@Clays, SIPs panels were used to build up the walling around the oak superstructure
Masonry might also be a contender for areas of your project where thermal e ciency is less important. For instance, a garage won’t need to meet the same standards as your timber frame house.
As with other construction systems, large or complex timber-built houses often feature steels for design elements that require additional structural support. Metal columns or beams can be engineered into the wood frame to enhance robustness and durability. It might be needed to enable dramatic roof spans, arched structures or large spans of glazed doors. Glulam beams are another option that are very strong.
Steel beams can be hidden within the structure or left exposed to make a bold aesthetic statement (in either case, you’ll need to ensure fire-rated finishes are used . Similarly, bolts, fi ings and joints can be left on show – this looks great in oak frames.
Finding a quality supplier that you can trust and who understands your project ambitions is critical to the success of your self build. The Structural Timber Association (STA), the UK’s leading organisation for the structural timber sector, ensures all its members are accredited to STA Assure –its quality assurance scheme. The rigorous, independently-assessed scheme gives you the confidence and evidence you need to make an informed decision about your timber building partner.
Companies that go through the STA’s robust assessment process must demonstrate that their timber systems meet or exceed current legislation and regulatory requirements. It ensures that design, production and site assembly processes, and quality controls are in line with customers’ expectations for consistent, high levels of quality.
The STA has three levels of accreditation: Gold, Silver and Bronze. These highlight the different levels of quality procedures, management systems and product performance, together with external accreditations held by STA members.
It is not always feasible, possible or necessary for a member to achieve a Gold level membership. Specific quality requirements differ for each type of member and customer activity depending on the nature of a company’s business, so a Bronze or Silver member may be the most appropriate company for your project.
The STA has a formal agreement with the NHBC that recognises STA Assure Gold
✔ They have completed a quality standard assessment – the STA Assure Membership and Quality Standards Scheme.
✔ They operate to the Site Safe scheme, an initiative to ensure timber construction is both safe and sustainable.
✔ They are familiar with the latest Building Regulations and legislation, receiving regular updates from the STA.
✔ They have access to a dedicated technical support service, advice notes and technical documents, including a full range of documents in the STA library.
✔ They fully support sustainable construction and quality standards through adherence to a Code of Conduct.
members as compliant with Chapter 6.2 of NHBC’s assessment processes for timber structures, without the need for further review or completing a HB2445 form. STA Assure has formal recognition from other industry-leading structural warranty and Building Control bodies including: LABC Warranty, Protek Warranty, Build-Zone Warranty and Self-Build Zone Warranty.
FIND YOUR STRUCTURAL
se the following directory pages to find STA members that are ready to help you with your self build project. There is also a wealth of information on the STA’s website, from advice on timber systems to market reports and top building tips, together with an online member enquiry system. For more information visit www.structuraltimber.co.uk
of a high quality result
an rve r hite t re partners ith severa e pert off site ti er fra e an fa t rers in oth er any and the to de iver pre ision engineered design ed s staina e sto and se f i d ho es o r pro e ts are espoke ient fo sed o ar on energy e ient and offered as a f t rnkey servi e fro on ept to o p etion
he ro tor ro p deve oped the or d reno ned oofshie d e rane ore than years ago in response to the re ire ents of the s de and for o d pit hed roof onstr tion oofshie d is a ni e three ayer non oven sp n onded po ypropy ene reather e rane ith a patented e t o n ore hi h is oth air and vapo r per ea e
Tel: 01250 872261
Web: proctorgroup.com
Fine Carpentry ne arpentry o k ✔ Bronze
Frame Homes SW fra eho es o k ✔ Gold
Glulam Solutions g a so tions o k
Huws Gray h sgray o k ✔ Gold
c eig site veighoff site o ✔ Gold
Milner Associates i nerasso iates o k ✔ Gold
MINT Construction int onstr tion edford o k ✔ Gold
Mitek Industries itek o k ✔ Gold
Paramount Structural Engineers para o ntse o k ✔ Gold
PPK Timber Designs ppk td o k
Scotframe s otfra e o k ✔ Gold
Shire Timber and Trus shireti ergro p o k ✔ Gold
POTTON
otton are a se f i d pa kage o pany ith over years e perien e designing and an fa t ring espoke ho es e off er advi e on p ot h nting p anning per ission and free o rses in the e f i d ade y r e f i d ho entre has ve f y f rnished sho ho es and e perts on site to dis ss yo r ho e
i er nnovations is passionate a o t i ding ho es for peop e in i aginative ays ith ti er e are a spe ia ist se f i d ti er fra e an fa t rer providing the design an fa t re and insta ation on ti er fra e s and oak fra e d e ings espoke ti er feat res roof tr sses pane s and engineered oors i ding so eone s ho e is a privi ege
ak rights design and onstr t espoke oak fra e ho es e tensions and o t i dings that ast a ifeti e tay in their sho ho e to e perien e iving ith oak ork ith their in ho se tea s and visit their orkshops to see ho traditiona ski s and tting edge te h o ine to reate yo r drea oak fra e
ABC+ Warranty ar hite ts erti ate o k
Tel: 01767 676 400
Web: potton.co.uk
Tel: 0121 314 7735
Web: timberinnovations.co.uk
Tel: 01432 353353
Web: oakwrights.co.uk
Adept Consulting adept o o k ✔ Gold
Alcock Lees Partnership a o k ees o k ✔ Gold
With a timber frame system, you must pay the manufacturer before it is delivered to your site; however, traditional mortgages provide funds after each stage of the build. BuildStore’s advan e stage pay ent ortgages offer guaranteed funds – up to 90% of the cost of your frame before it has been installed.
Tel: 0345 223 4888
Web: buildstore.co.uk
Self-Build Zone is the market leading provider for se f i d ins ran e in the ffering ite Insurance, Structural Warranties and Site Surveys. Site Insurance covers you from the moment you purchase a plot up to completion. Structural Warranties are approved by the majority of lenders in the UK and backed by a ‘A’ rated insurer.
Glosford SIPs is a market leading UK specialist offering a o p ete servi e for yo r str t ra insulated building envelope. Using renowned ingspan pane s o r fa ri rst so tion guarantees low running costs for your new home. Our facilities include state of the art CNC manufacturing equipment, ensuring reduced processing time and a predictable build programme.
Tel: 0345 230 9874
Web: selfbuildzone.com
Tel: 01432 842999
Web: glosfordsips.co.uk
or over years e ve een at the forefront of design and an fa t re engineering ti er prod ts e re onstant y orking ith sto ers reating ne eve s of on site e ien y e eptiona servi e and innovative thinking ro pro e t in eption to o p etion rendon s ost effe tive ti er engineering so tions enhan e the a ity safety and speed of onstr tion
Tel: 01844 201020
Web: crendon.co.uk
comni quae nistotatur sam quo vellici ducidi to in re reperovit o cimusdae maionse et electas nis aut omnis autatemo ent ut rem eius, quuntio renture si deniae nihicidite nest, oditiae voloreheniet peratur ab ipisquibere erere eos eate rero doluptate idit resti debis que eos doloribus corro iuntect atioreicto blanis dignimi, est, con re et fugitiant optat min pelecup tatusam vent esto to ma vendit, test lamus, omnis ipis expedit iorrovi taturia sus solorem etur, quiscilles earum sapedic aescitatem facepe perit andit, qui dolore re nimoditis volupta dolo volor magnimi nctiorerum laut quibus aut excessimus explibustem accus
Har ony i er is pro d of the rep tation ithin the ti er fra e ind stry as oth pra titioners innovators and s pporters of se f i ders ontin ing to gro and de iver high a ity prod ts and servi es o r e i i ity to adapt to different re ire ents and hanges to egis ation akes s the perfe t hoi e for a yo r ti er fra e needs
Tel: 01227 209087 / 01227 712322
Web: harmonytimber.co.uk
e o ine high a ity rafts anship and attention to detai ith the atest deve op ents in te hno ogy to provide ti er fra ed ho es and i dings for the st ent ry onta t s to nd o t ho e an offer yo pra ti a va e for oney ti er fra e onstr tion so tions to s it yo r pro e t and yo r dget
o e d i er ra es is a manufacturer of timber structures based on the hropshire id a es order has continued to grow its portfolio of products, its client base and a strong supplier network to make it one of the leading Timber Frame Manufacturers in the UK.
i er ra e are an off site an fa t rer of high performance timber frame systems. From our Passive timber frame and foundation system to our standard timber frame system we have created a series of options that work for all projects.
Tel: 01743 891922
Web: lo fieldtimber r me co u
are a fa i y r ith de ades of i er Frame experience. Quality, value and service are at the ore of everything e do ffering a national supply and erection TTF will work with you to turn your dream home in to reality. Factory tour and overnight Timber Frame stays now being booked for our show home site.
sta ished in y kha a k e nderstand ti er and offer a o prehensive design and manufacturing service through our ‘inhouse’ professional designers. Our manufacturing fa i ities are a ity ontro ed and erti ed orking a ongside ients pro e ts fro in eption to completion and are now one of the UK’s largest independent timber engineering companies.
Tel: 01452 346499
Web: mbctimberframe.co.uk
Tel: 01482 218945
Web: turnertimber.co.uk
Tel: 01675 442233
Web: wyckhamblackwell.co.uk
Roofshield: