Improvement in Daily Environmental
Improvement in Daily Environmental
Footprint for Flexo Platemaking Available to Anyone
Footprint for Flexo Platemaking Available to Anyone
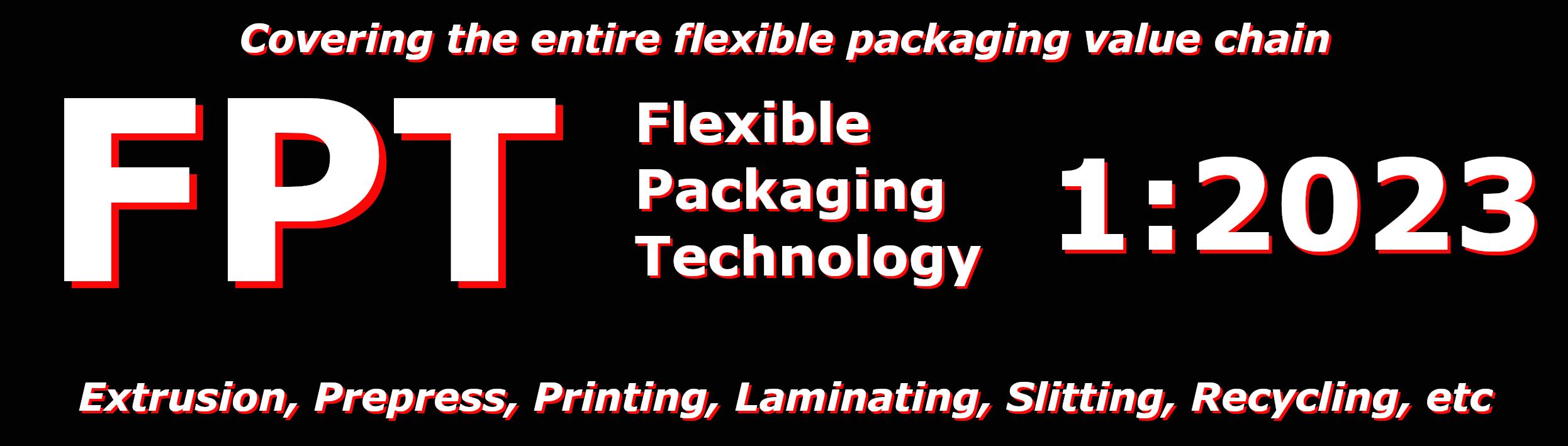
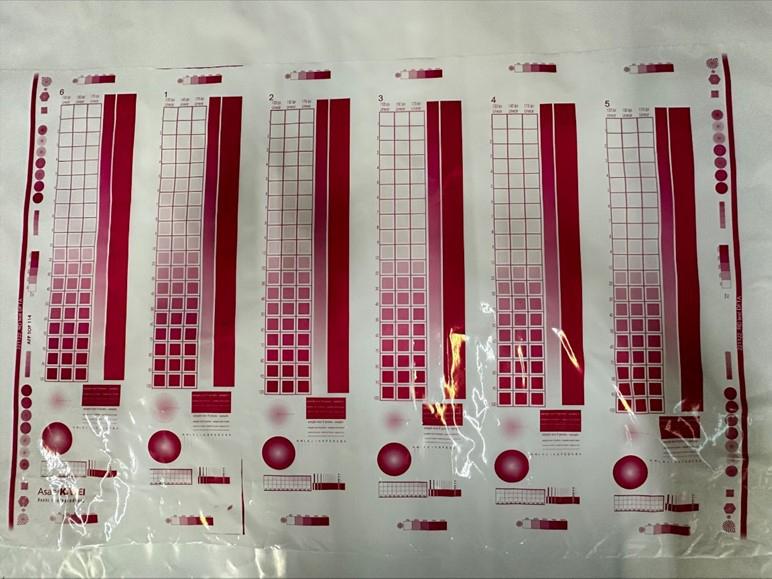
Current European regulatory trends and food contact testing requirements
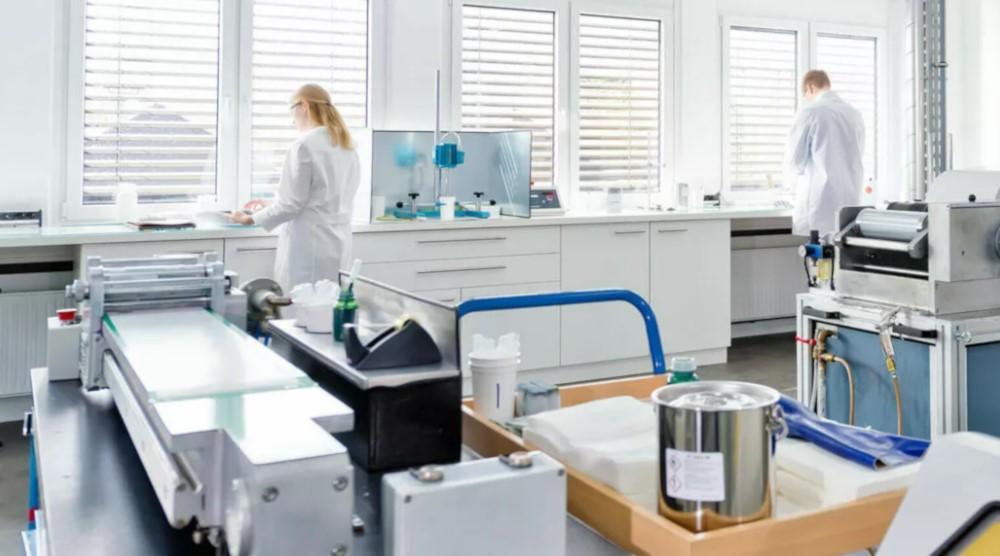
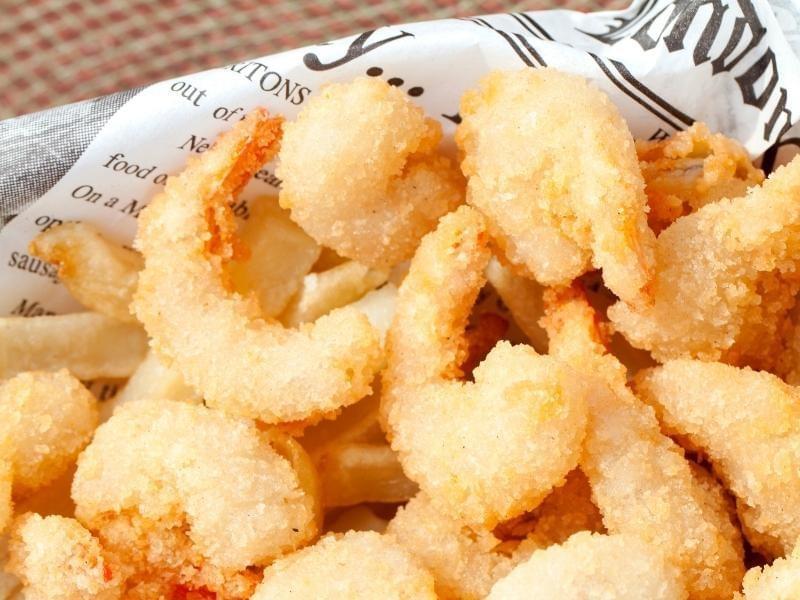
Digital color communication in printing processes
ICE Europe 2023: Exhibition’s success with record numbers of prepandemic times
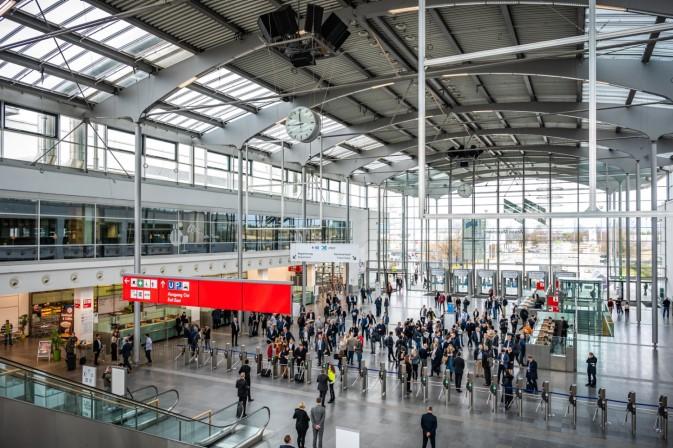
Dörken has started to produce technical building membranes on SML lamination lines
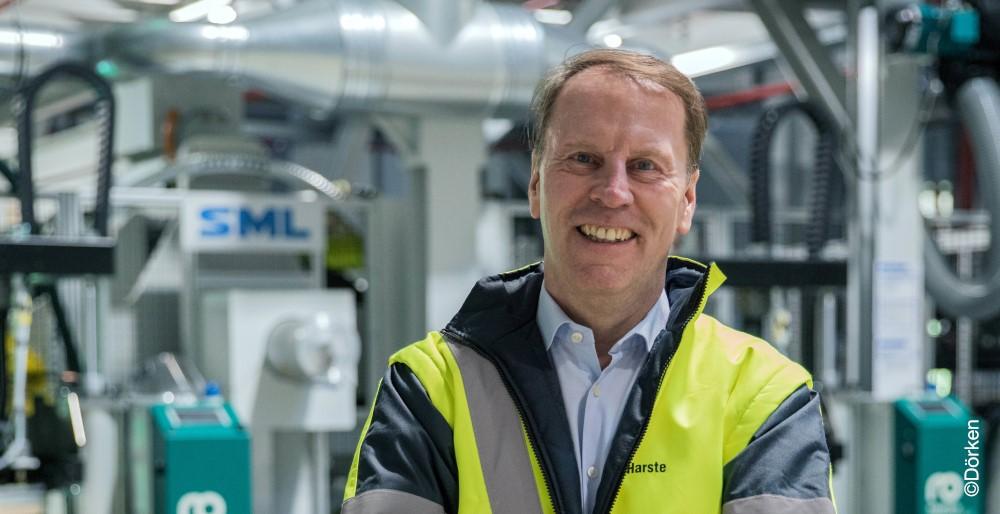
“
No Greenwashing” and “Environmental Sustainability” are the most echoed buzzwords reflecting brand owners’ key challenges in the packaging industry according to Gabriela Bertoni dos Santos, Henkel, 7th Packaging and Converting Innovation Forum, Munich, September 1st, 2022.
In the last 20 years, the EU regulator has made significant changes to European food contact requirements. This has been in-part driven by public perception as well as by technical developments from research laboratories.
Last week, the 13th International Converting Exhibition ended after three days of flourishing business. From 14 - 16 March, a total of 4,850 trade visitors from 64 countries came to Munich to discover the latest machinery, systems, materials, and accessories, which is a more than 30 % increase in visitor numbers compared to the previous event.
As a result of advances in digitalization, a lot has changed in the packaging and printing industry in recent years. How digital color communication in printing processes compares to the conventional process of ink formulation was tested by SAUERESSIG
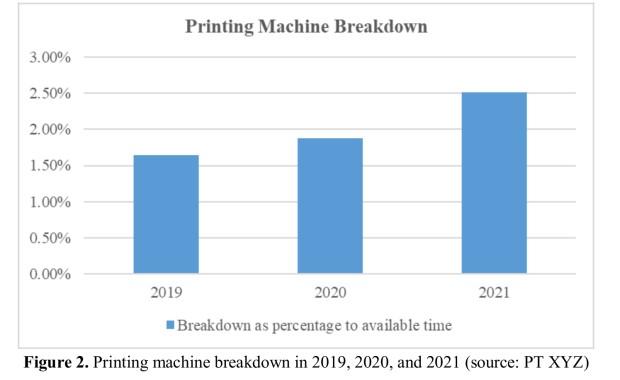
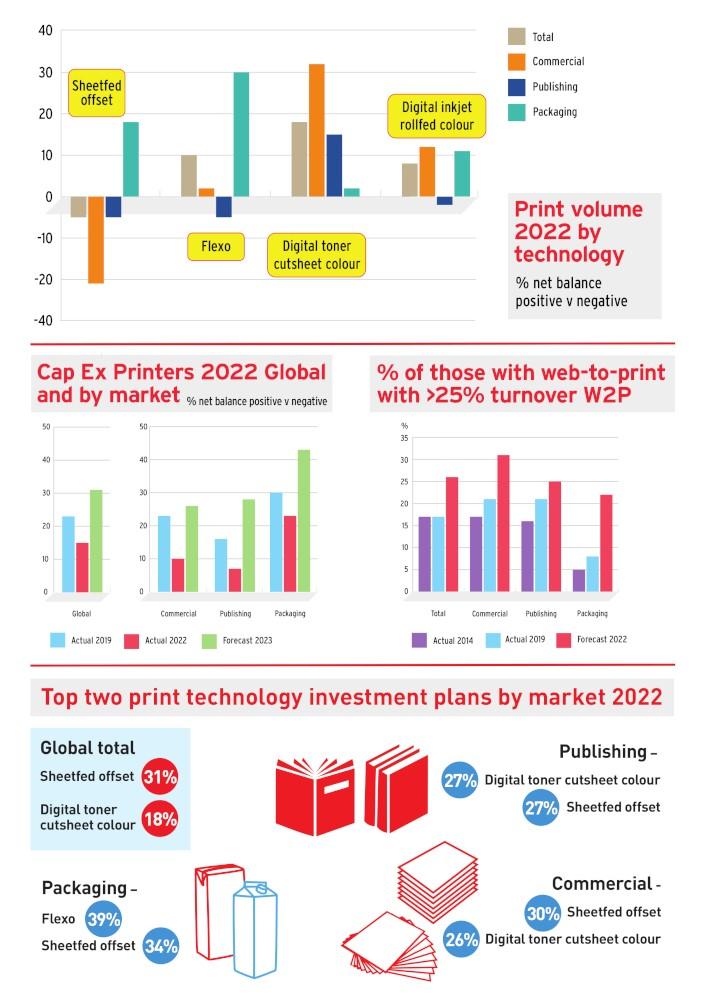
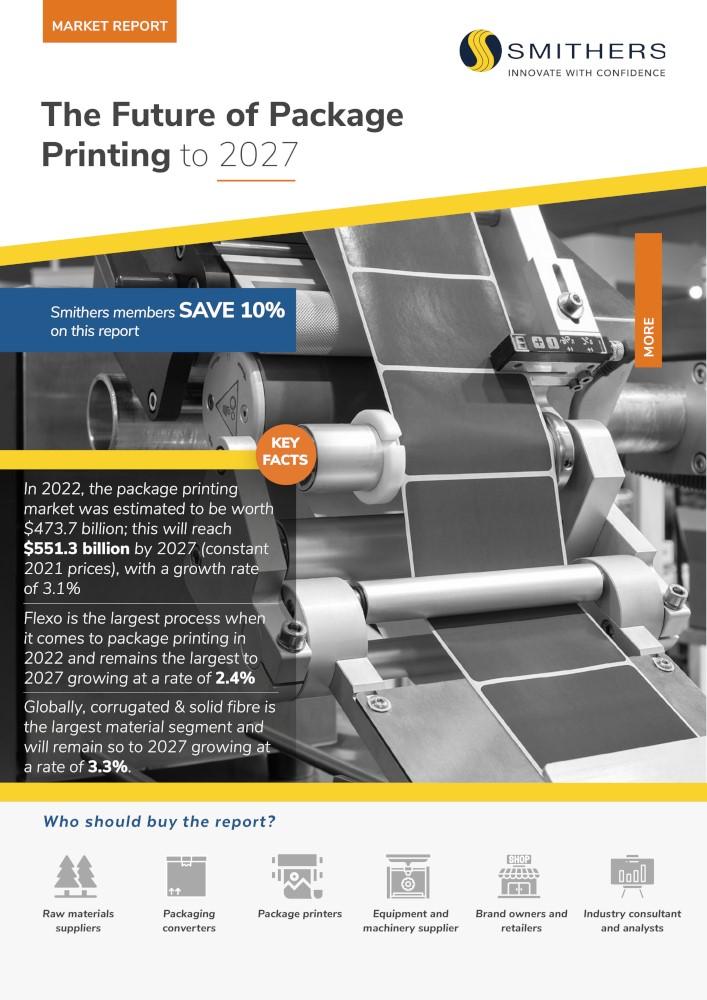
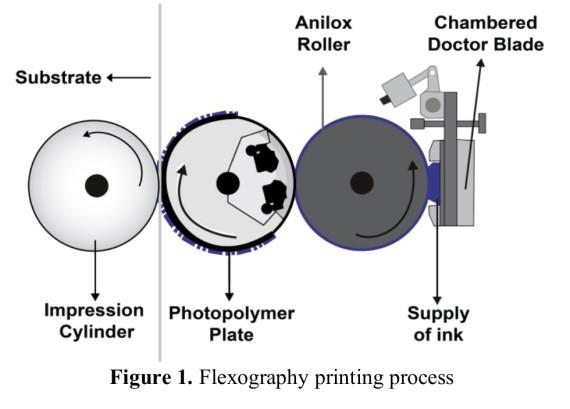
In the past few months, the German company, Dörken, has put two new production lines from SML into operation. Highly permeable roof and facade membranes are manufactured as part of the company’s product portfolio. In addition to innovative properties, a large number of the new composite films are making a statement due to their particularly resource-saving and efficient manufacturing processes.
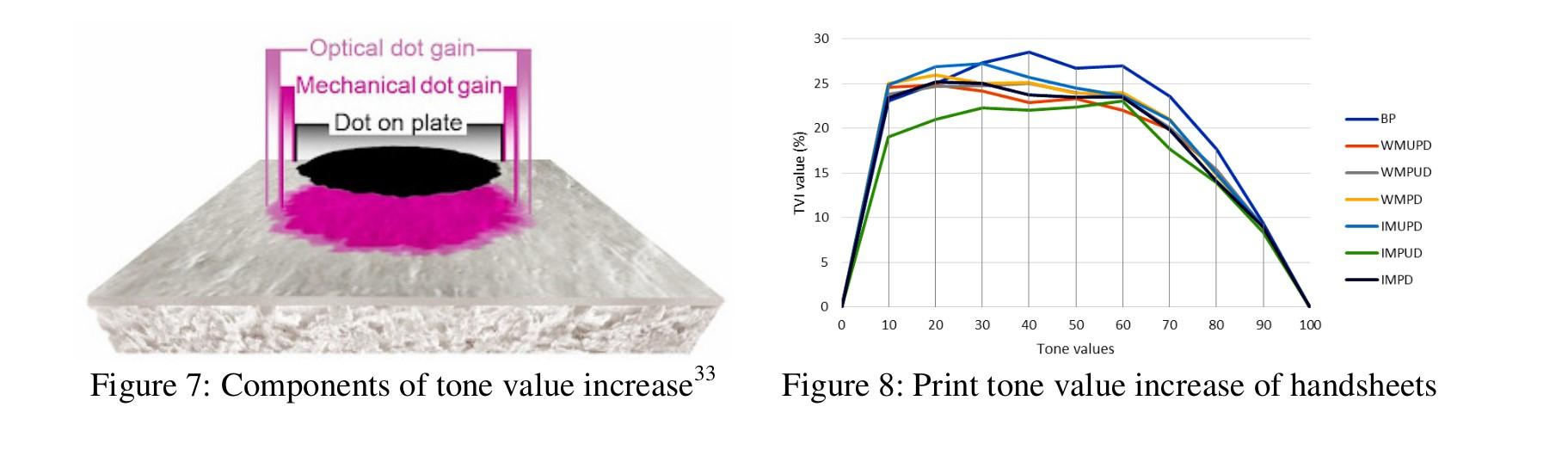
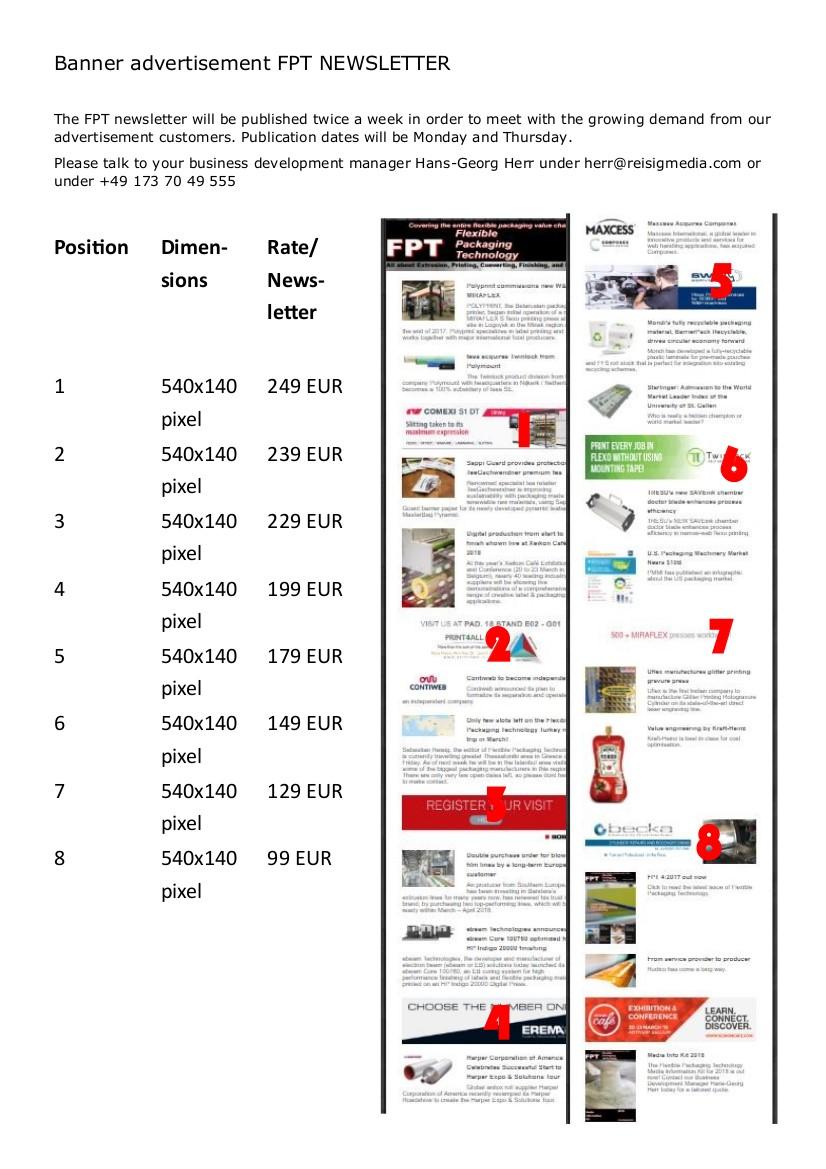
Improvement in Daily Environmental Footprint for Flexo Platemaking Available to Anyone
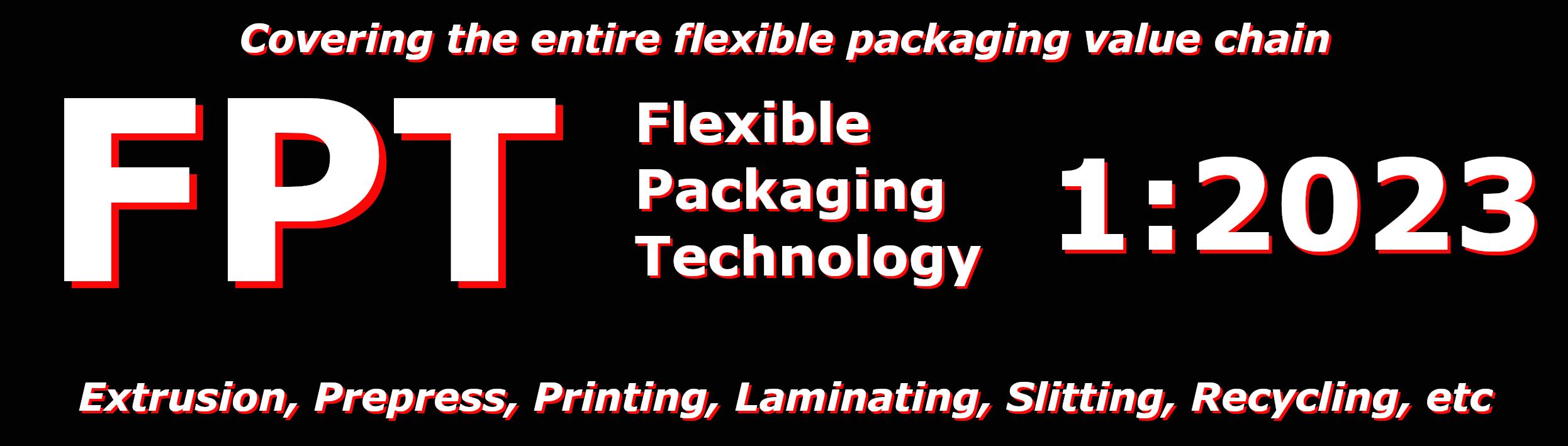
“No Greenwashing” and “Environmental Sustainability” are the most echoed buzzwords reflecting brand owners’ key challenges in the packaging industry according to Gabriela Bertoni dos Santos, Henkel, 7th Packaging and Converting Innovation Forum, Munich, September 1st, 2022.
By Dieter Niederstadt, Technical Marketing Manager, Asahi PhotoproductsOver the last three to four years, the world’s environmental consciousness was raised by young activists marching on Fridays to draw attention to the need for reduction of greenhouse gases in all sectors of life. The task to improve, however, is not for one person or company alone, but for many to think within their areas of influence and expertise whether they can contribute positively towards this goal, and then take stepstodoso.
Although flexographic plates only represent a tiny fraction of the overall package environmental footprint impact, it should nevertheless be the goal of everyone using these plates not to simply accept the current status quo, but to constantly strive to push boundaries higher and higher, leveraging philosophies such as KAIZEN, a Japanese strategy where employees at all levels of a company work together proactively to achieve regular, incre-
mental improvements to the manufacturing process.
In flexo platemaking today, we find a variety of different platemaking technologies used in various markets. Some are less hazardous, such as Water-Wash or Thermal plate making, but the vast majority, representing approximately 70% of all flexographic operations, use hydrocarbon-based solvents to wash out their flexo plates. This not only requires a special-
ized production room environment, but it may alsocontributetoahazardous ambient working environment in the platemaking room if not handledwell.
Based on that data, we have looked at a large segment of solvent wash platemaking users in our industry to find ways to suggest how these operations can modify their platemaking process, helping them to take action to reduce their environmentalfootprint.
The magic trick and answer to improve the environmental footprint is: “Plate relief depth reduction.”
Lookingatflexible packaging, one of the largest segments of flexographic printing representing a global market share of approximately 25 to 30%, a standard plate relief depth of 0,6 mmwitha1,14mm(45 thou) plate gauge is being used. The relief depth, however, is changing region by re-
gion. Whereas Europe was more conservative in allowing a large margin of tolerance between the printing elementandthe base floor, on the South American continent printers have long used a plate relief depth of 1/3 of that standard plate thickness, with a plate relief depthofabout0,35mm being more commonly used in that hemisphere.
What are the advantages of reducing the plate relief depth and what are the limits of technical tolerance before the floor of the plate hits the substrate? A printing project was
set up to confirm the limits and highlight potentialimprovements.
A full platemaking and printing trial was arranged using different plate relief depths starting at 0,6 mm and going down to 0,1 mm for a 1,14 mm (45 thou) plate.
Platebackexposure:
Theplate backexposure time needs to be elongated to polymerize more plate material. For areliefdepthof0,6mm a UVA energy of approx.. 330 mJ is needed and for 0,3 mm an energyof1000mJ.
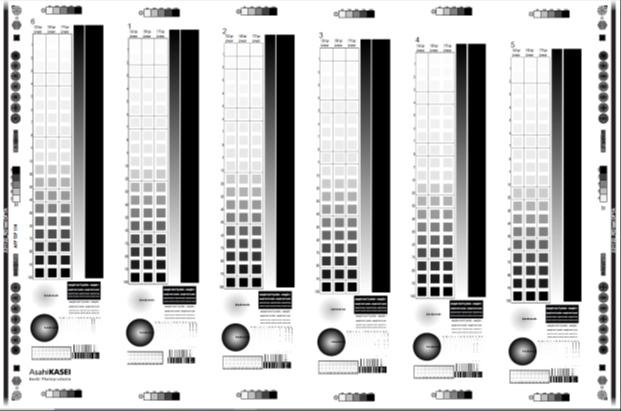
This back exposure time can be partially compensated by a reduction of the main exposure time as the plate is largelypolymerized.
Asanexample, forarelief depth of 0,3 mm, the back exposure time is elongated by approximatelyafactorofthree.
Plate washout time: InourGraphicArtsCenter, we use Ecowash 320 at 28°C and 3,3% polymersaturation.
Ecowash 320 is a lowVOC version of Ecowash and generally results in a slower washout speed compared to more aggressive washout solvents on the market. The industry uses a large variety of washout solvents, anditistherefore recommended that flexo platemaking operations check their individual conditions using their equipment, plate
and solvent specifications.
For a good plate washouttime, we alwayscalculate a safety margin of 0,2 mm and add that to the plate reliefdepth. Thissafetymargintakes account of the fluctuation of washout solvent quality and should be added. So, in our example of a relief depth target of 0,3 mm, we would look at a 0,5 mm washout relief depth with the safety margin

included. In that case, the washout time would be approximately 165 mm/min for a relief depth of 0,3 mm vs. 90 mm/min for a relief depth of 0,6 mm. The washout speed improvementwouldbe approximately 80% if we target a relief depth of 0,3mm.
In the above illustration, it is easy to see that a flexo plate with a relief depth of, for example, 0,3 mm is
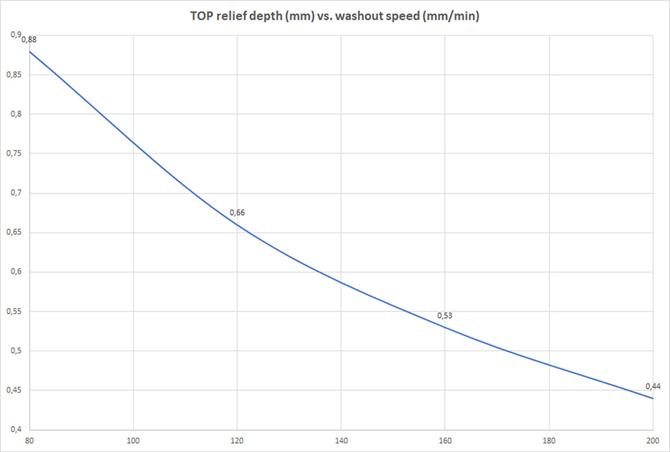
washed out with 50% less polymer waste in the washout solvent compared to a flexo plate with a relief depth of 0,6 mm. The standard solvent processor today replenishes solventonthebasisofpolymer content or viscosity of the washout solvent. Hence, a company which reduces the plate relief depth from 0,6 mm to 0,3 mm can wash two plates instead of one before solvent replenishing in the tank is required. This is a massive saving of 50% of solvent in your operations just by lowering the plate relief depth, and it is a big step towards operating with a bettercarbonfootprint.
The plate drying time depends on the length of time the plate has been in contact with the solvent. Hence, with a washout speed of 90 mm/min, a plate will be more swollen with solventsthanaplatewhich was washed out at much faster speed. Subsequently, if the
plate is submerged into solvent at amuch faster processing speed, the recovery time to nominal plate thickness in thedryerismuchquicker than for a plate that spends a longer time in thewashoutequipment.
In the example of a relief depth of 0,6 mm, theplatewashoutspeed wasadjustedto90mm/ min, giving a plate drying time of approximately 120 min. The washout speed of a plate washed with a relief depth of 0,3 was 165 mm/min, resulting in a plate drying time of approximately 75 min to recover back to nominal thickness. This also equates to an approxi-
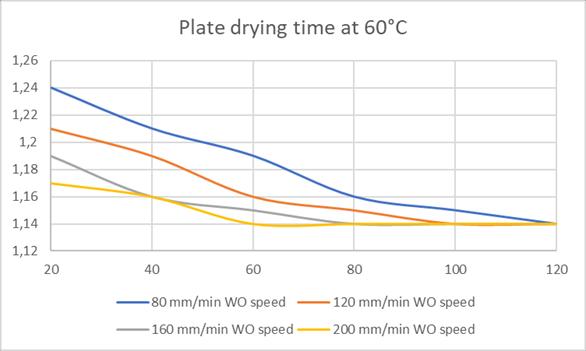
mate reduction in energy use by the dryer from 4,8 KW down to 3 KW per m² of plate materialused.
PrintingTest:
Despite all the solvent, time and energy savings, the biggest concern, of course, is whether the plate floor would print using a shallow plate relief depth.
In the example below, we worked at the DFTATZ facility of the Stuttgart University and printed the different relief depth plates with a setting of 70 microns extra pressure over Kiss Print. Anilox pressure
was 60 microns of extra pressure.
The numbers on the top of the print sample indicate the different relief depths of 0,6 mm on the left and 0,5 mm on theright.
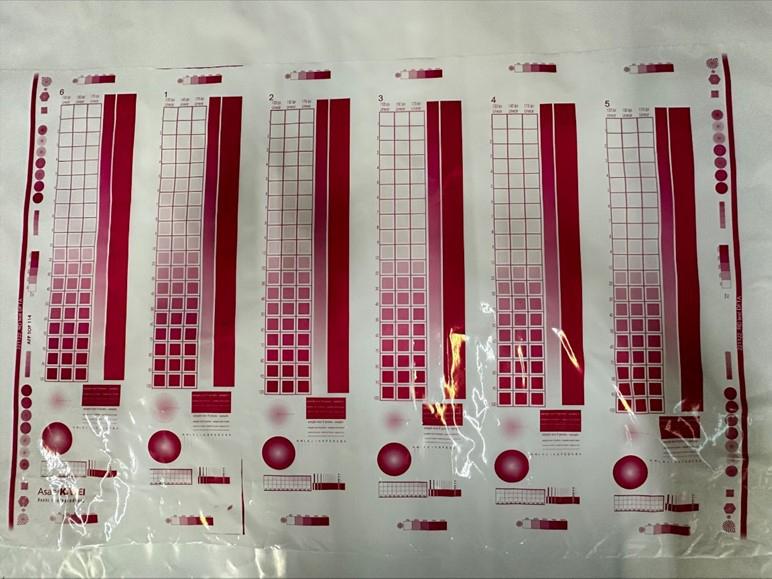
We compared the dot gaincurves betweenthe different plate relief depths and concluded that all curves are very similar and can be used without the need to make adjustments to printing curves. However, a small adjustment might be considered by the local repro on a case by case as we could not confirm the dot gain for longer run productionjobs.
In addition to the print dot gain curve, we also analyzed the highlight dot anchoring on the plate floor. As can easily be seen in the previous illustration repeated below, the dot anchoring is much more stable compared to the plate with higher relief depth, giving added rub resistance to the plate,
which is particularly useful for long runs. Hence, the plate quality isincreasedaswell.
To the surprise of the participants, while we thought that the 0,1 mm relief depth would be impossible to print, that was not the case. As can be seen in the red colour circle in the print sample above, there was a small area at the tail edge of the plate which actually printed from the plate floor, but the rest was fine.Forthatreason,we do not recommend using a plate relief depth of 0,1 mm. Going to the
next higher relief of 0,2 mm, it was confirmed that this relief depth poses no problem when printing,netherinterms of dot gain curve nor in terms of plate cleanliness. For customers who want to push flexo printing to the limit with modern machinery and high printing quality, this is certainly a relief depth to consider. For all other users, we would recommend the safer plate relief depth of 0,3 mm – 0,4 mm. This maintains enough tolerance to avoid any possible printing trouble, it considerably im-
proves plate quality and – most importantly –improves the environmental footprint of the platemakingproduction.
The message of this practical exercise is that anyone can make a significant contribution to the environmental footprint of platemaking in their company at a local level by taking these described actions while improving the overall quality and environmental footprint of flexographic printing as a whole. There is no need to wait; and flexographic printing will gain more recognition as the environmentally sustainable printing technologyofchoice.
The relief depth reduction may vary slightly depending on the washout solvent or plate materialused,butitwillalways show a significant impact of the ad-

vantages explained. The benefits of environmental improvements are primarily seen in the hydrocarbon washout solvent process, but this process can likewise be used in water-wash or other platemaking technologies too. Whether to use 0,2 mm, 0,3 mm or 0,4 mm, relief depth should be decided by each customer, but it is no longer reasonable for a relief depthof0,6 mm for 1,14 mm plates to be classified as a standard from a technical
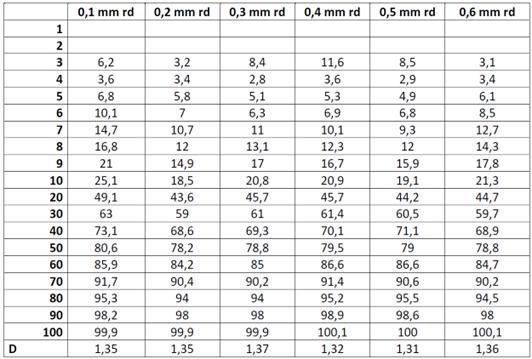
point of view. This is especially true today that, as we consider the changing environmental climate, we all examine our platemaking processes tomake as much of a contributionas possible to reduce our carbonfootprints.
Taking this approach over time, it dramatically adds up savings of washout solvent and reduction ofdryingenergy costs and plate production time. By extension, it reduces our industry
carbon footprints, improving our climate impact and opening the chance for anyone to participate.
www.packagingnewsletter.com

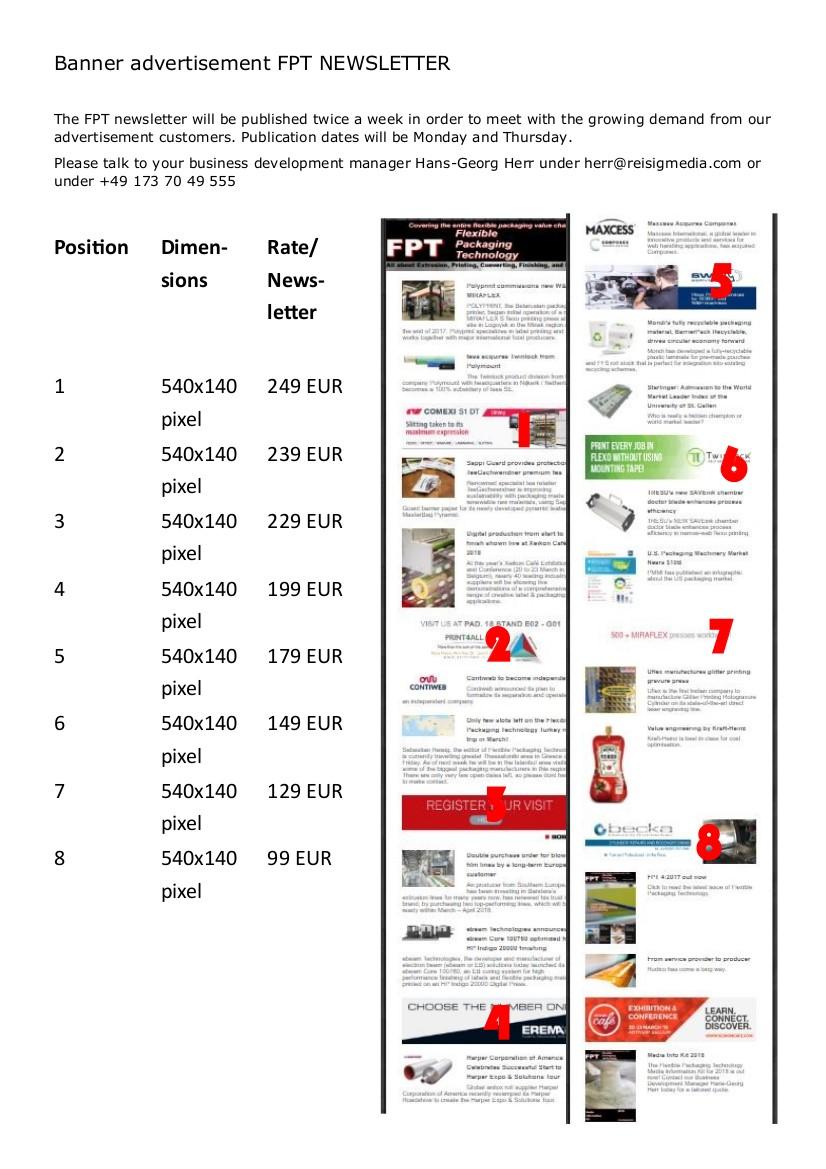
Current European regulatory trends and food contact testing requirements
In the last 20 years, the EU regulator has made significant changes to European food contact requirements. This has been in-part driven by public perception as well as by technical developments from research laboratories.
Recently we have seen a growing trend for taking a non-targeted approach to testing food contact materials. This is often referred to as non-intentionally added substance (NIAS) testing. NIAS are chemical compounds that are present in a material but have not been added for a technical reason during the production process. They arise from break-down products of food contact materials, impurities of starting materials, unwanted side-products and various contaminants from recycling
processes. Alongside NIAS, there is an increase in demand for the analysis of nonlisted substances (NLS) such as inks, coatings and adhesives. These substances are not subject to formal EU risk assessment, but may have regulation in place at a national level. In order to sell products across Europe, analysis of these substances would need to be performed as part of a package of due diligence. Finally, we are seeing a shift in focus towards studying ultralow levels of migration
– which means that higher resolution equipment and unique testing methods are requiredtoanalysethis.
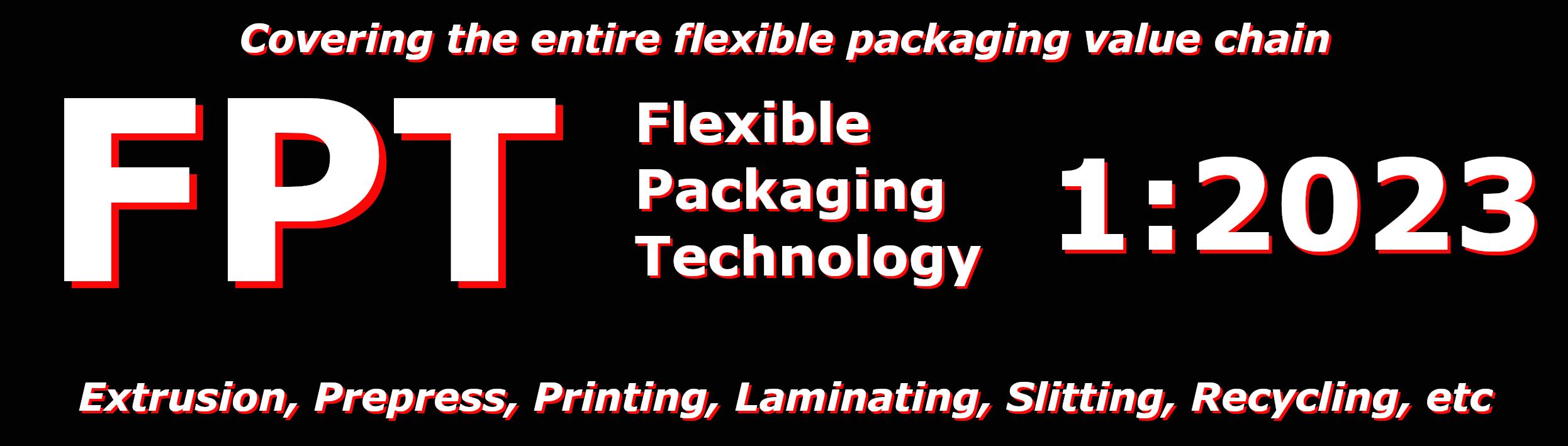
Upcoming changes to EUlegislation
In 2018, the European Commission launched a consultation process to re-evaluate their existing regulatory Framework for food contact safety detailed in EU Regulation 1935/2004. This drew on expertise from national authorities in Europe, food contact experts, industry leaders and non-
governmental organizations(NGOs).
There were three main root causes explaining the perceived weaknesses of the current regulatoryFramework:
• Insufficient resources are available for risk assessment, risk management and enforcement.
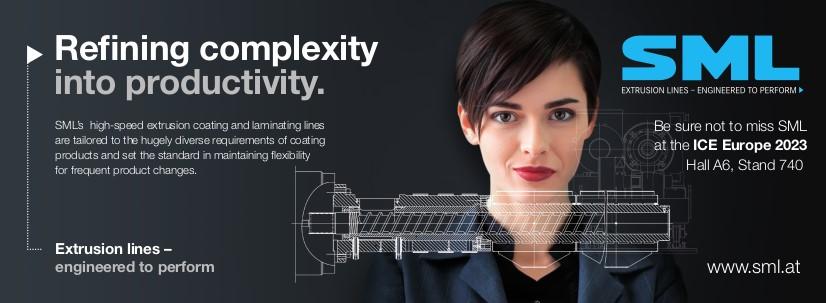
• An absence of consensus on the approach that should be followed to address any implementation gaps in the legislation.
• A lack of a regulatory mechanism to prioritizeactions.
The European Commission also identified that gaps remained for other food contact materials outside of plas-
tics,where no harmonized standards have been implemented. Five material groups are seenas apriority for futureregulation:
• Printinginks
• Paperandcardboard
• Silicones
• Varnishes and coatings
• Rubber Positive lists are already in place within some EU Member States for these materials and there is extensive knowledge on these substances within the industry. However, the report pointed out that there are at least 3400 substances used in these material classes which may need overarching formal risk assessment.
The European Commissionisconsidering:
• Shifting the emphasis onto the assessment of the final materials rather than focusing on the raw materials used to make food contact materials. We believe this will require wider adoption of the protocols developed for Nonintentionally added substances(NIAS).
• Adoption of a prioritized approach to risk assessment of food contact substances based around tiered riskclasses:
• Carcinogens, mutagens, substances harmful to reproduction and endocrine disruptors would
require the closestattention.
• Substances which may justify close attention based on assessment from other public authority assessments (e.g. REACH and nanoparticles), would also be prioritized.
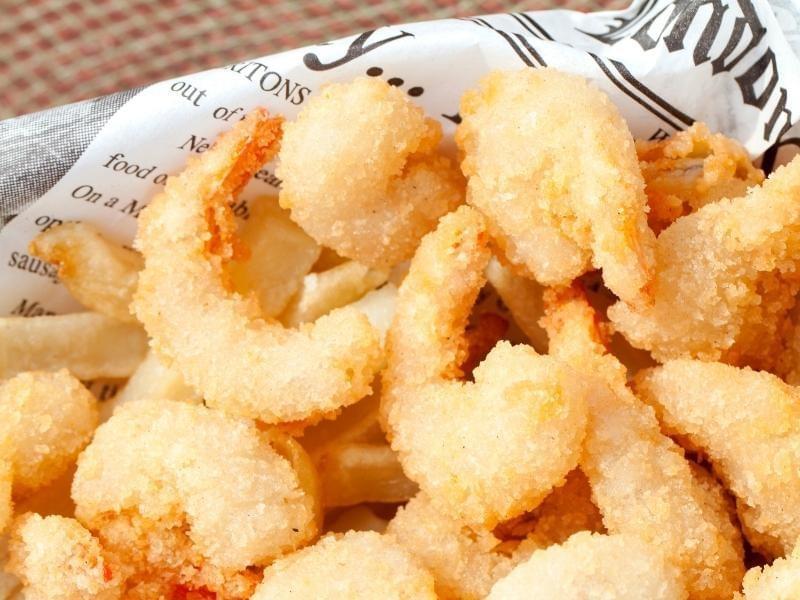
• More benign substances would be able to be self-assessed byindustry.
The European Commission currently aim to lay out more detailed proposals during 2022, withaview toestablishing new legislation in 2023.
NIAS and NLS testing to show compliance forprintinginks
NIAS require cuttingedge analysis to identify and measure their presence. This is especially true when using new or alternative packaging materials where the potential for unknowns is increased. As you can see above, printing inks in particular will likely
be coming under closer scrutiny with updated regulatory controls.
NIAS testing will be a crucial component for this. For example, when printing inks are manufactured, there can be degradation or reaction by-products forming –this would be classed as a NIAS. Because the substance is unknown at this point, a nontargeted approach with testing would be requiredtogainanunderstanding of what it is andassessforanyrisk.
The same logic also applies to high temperature food packaging. Printing inks could leach and react with other materials in the pack in a way that was not intended when the ink was manufactured. This requires NIAS testing, as the final ‘substance’ is not known until it is in place with the rest of the pack and heat applied. A similar approach is required for NLS. As these materials have not been formally risk-assessed, brand
owners will typically approach these with caution. Similarly to NIAS testing, analysis is performed to low migration levels to minimize risk and have confidence in the materials used. Frequent examples of NLS in printing inks include solventsanddefoamers.
How Smithers can support with NIAS testing
Smithers has over 30 years of experience helping clients comply with food contact legislation around the globe.Smithers supports clients looking to perform NIAS risk assessments on their packagingmaterialsbyutilizing high resolution testing equipment such as a GC -MS. This enables the identification of unknowns in packaging materials and shows compliance with Regulation EU No. 10/2011. This will also help with clients looking to meet any updated regulations in the near future.From regulatory guidance and consultancy through to
assist with your next project.
advanced analytical testing and training, our teamishere togive you confidence in your food contact materials and
ICE Europe 2023: Exhibition’s success built on quality whilst heading for record numbers of pre-pandemic times
Last week, the 13th International Converting Exhibition ended after three days of flourishing business. From 14 - 16 March, a total of 4,850 trade visitors from 64 countries came to Munich to discover the latest machinery, systems, materials, and accessories, which is a more than 30 % increase in visitor numbers compared to the previous event. Shaping the future of the converting industry, 338 exhibitors from 20 countries showcased their products and services on a net exhibition space of some 8,700 square metres at the world’s leading exhibition for the conversion of flexible, web-based materials, such as paper, film, foil and nonwovens. With the success of this year’s edition, the show organisers announced the next ICE Europe to take place from 12 - 14 March 2024.
In “We are delighted to see such a positive turnout and how this year’s exhibition matched the energy and enthusiasm of our shows before the pandemic! Both exhibitors and visitors were highly satisfied, whether meeting with existing contacts or establishing new business relations. This affirms our course
for the ICE Europe brand and makes us veryproudtobeable to provide the converting community with a regular key event – the only of its kind”, states Patrick Herman, Event Director of the Converting, Paper and Print Events,onbehalfofRX.
The majority of visitors camefromGermany, Italy, Austria, Switzer-
land, United Kingdom, Poland, Spain, Czech Republic, France and Turkey. The first results of the show analysis have also shown that the visitors mainly came from the following industry sectors: packaging, engineering, printing, plastics, paper, chemical, automotive, textiles/ nonwovens, electronics, pharma/
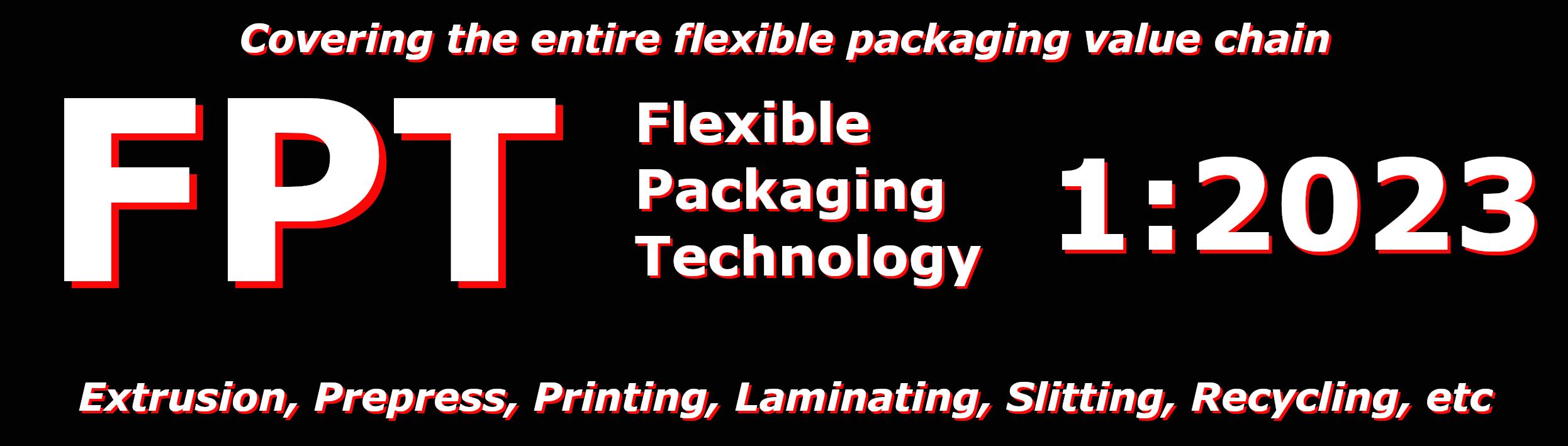
healthcare/ medical and others. They were primarily interested in coating/laminating,slitting/ rewinding, print technology, accessories and machine upgrades, control, test&measurement technology, finishing, drying/ curing, film extrusion, materials/ (semi) finished products and(pre)treatment.
The top exhibitor countries included Germany, Italy, Turkey, China, Great Britain, Spain, the
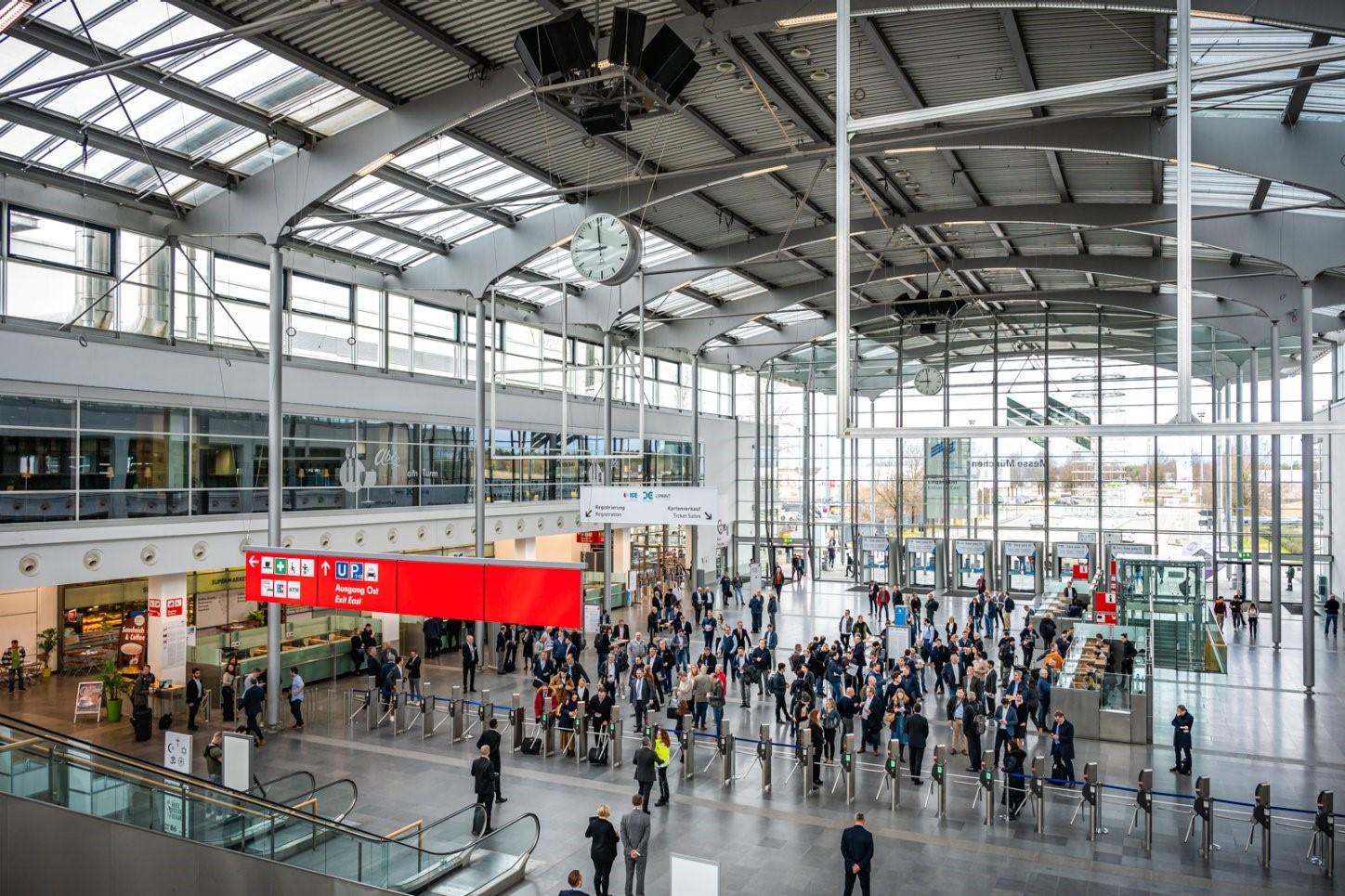
United States, Switzerland, France and the Netherlands. In addition to the strong line-up of leading brands, the prestigious ICE Awards took place on the first show day, honouring three exhibiting companies with the ICE Awards for their outstanding technological achievements.
ICE Awards 2023: Innovative exhibitors honoured with prestigiousawards
The award ceremony was hosted by RX, and for the very first time, in cooperation with C2 Magazines, where best practice, excellence, innovation and outstanding achievements of exhibitors were honoured with the ICE Awards, in the following categories: ‘Digital Converting Solutions’, ‘Sustainable ProductsandConverting Processes’, and ‘Efficient ProductionSolutions’.
Nicola Hamann, Managing Director of RX, in cooperation with Martin Hirschmann, Editor-inChief of C2 Magazines, presented the ICE Awards 2023 to three exhibiting companies on the first day of the show. The winners had previously been determined via a verified online voting. The competition received more than 30 entries from a wide spectrum of startups and leading brands, where over 2,500 con-
verting specialists submitted their casting vote to determine the winnersoftheindividual categories.
The company DIENES Werke für MaschinenteileGmbH&Co.KG.received 34% of all votes in the category ‘Digital Converting Solutions’ and won an ICE Award for its TEOC (“The End of Coincidences”), which combines DIENES’ digitalisation activities. Within this framework,
the recently launched TEOC Service Packages include a modular architecture with hardware and software features, which can be combined inaccordancetoindividualcustomers’ needs.
In the category ‘Sustainable Products and Converting Processes’, the company INOMETA GmbH received 38% of all votes and won the ICE Award for its heating roller, which has been designed to
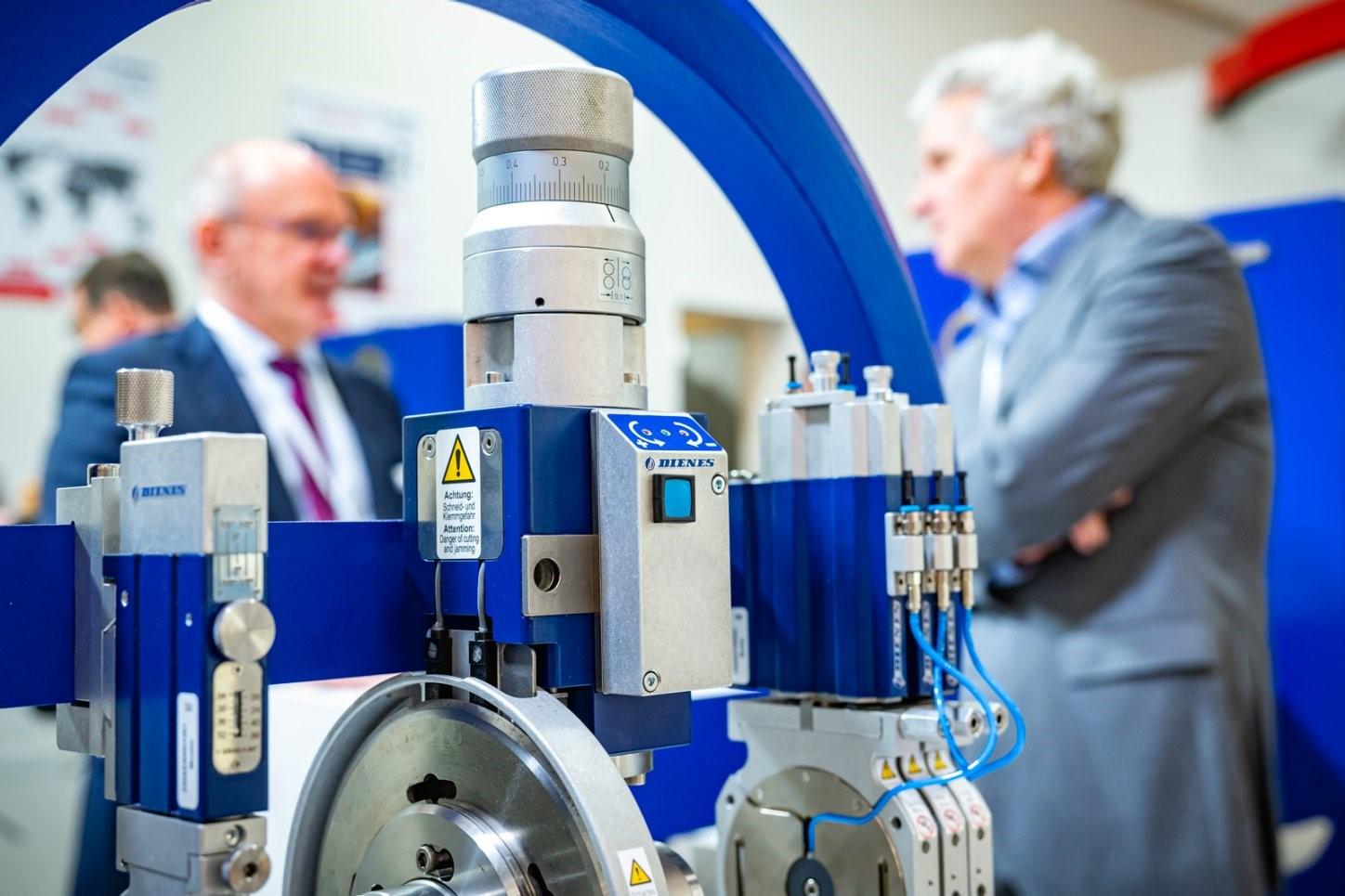
meet the needs and requirements for laminating foils and other substrates. It ensures a reliably constant and homogeneous surface temperature distribution, as this is the prerequisite for uniform webtempering.
With 29% of all votes, the company tesa SE won the ICE Award in the category ‘Efficient Production Solutions’ for its highly durable roller wrapping tape: the sili-
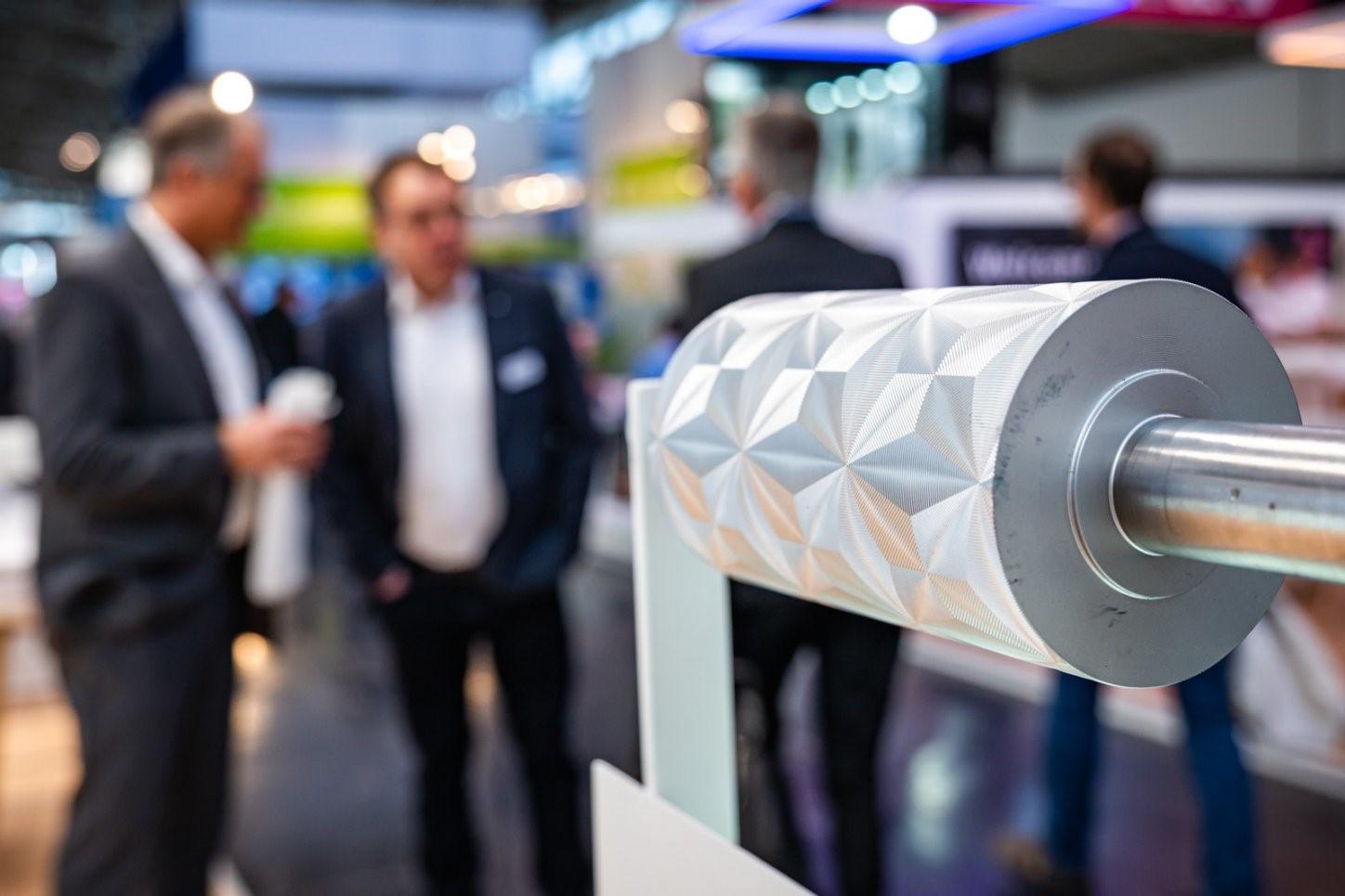
cone tape tesa Printer's Friend 4863 with an embossed surface. The product design ensures high resistance to wear and offers easy application and removal, even after a prolonged time period and exposure to hightemperatures.
Dates for the next shows
Existingandnewexhibitors have already expressed their interest in participating at the upcoming show edition in
2024. ICE Europe will take place from 12 - 14 March 2024 at the MunichTradeFairCentre.
In the ICE series of dedicated trade events for the converting industry,ICEChinawill be held from 11 - 13 October at the Shenzhen World Convention and Exhibition Centre. Early next year, RX will organise ICEC USA, from 9 - 11 January 2024, in Orlando, Florida.
Digital color communication in printing processes
As a result of advances in digitalization, a lot has changed in the packaging and printing industry in recent years. How digital color communication in printing processes compares to the conventional process of ink formulation was tested by SAUERESSIG in cooperation with the innovative packaging specialist ppg > flexofilm.
In The lasting impression of packaging, and, as a result, the outstanding placement of the product on the shelf in conjunction with a consistent brand identity are top priority for retail brands and experts from the packaging industry. The requirements placed on a balanced color concept, the achievement of color targets and a consistently high print quality are clearly defined. Until now, the process of color control has been associated
with an enormous expense of resources such as time, material, and energy. To ensure color fastness on packaging, physical mock-ups are produced, long set-up times are required at the press, test prints are run, and print approvals are made in person on site. But how could consequent savings of resources in printing processes and a continuous color communication based on digital processes look like? Which are the
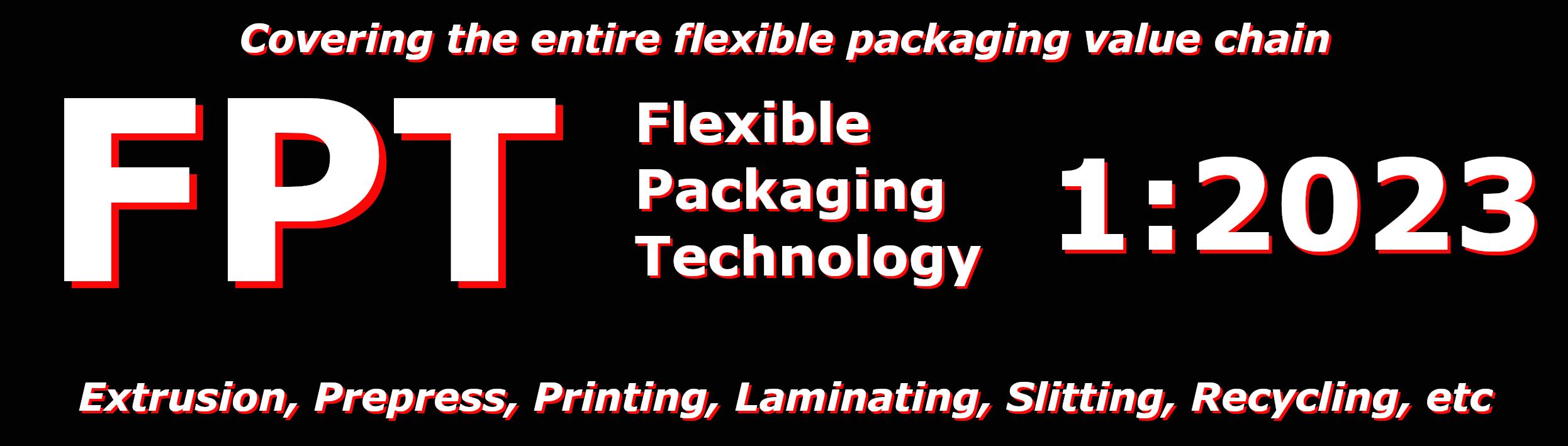
benefits as compared to conventionalmethods?
In conducting the case study in cooperation with ppg > flexofilm, the color technicians from c.INKTEC have tried out the benefits of the innovative process. Under production conditions, they tested the ink formulation and settings for the gravure printingprocessofflexible packaging on a Rotomec RS 4004 press. The conventional process of ink setting using purely visual methods was compared with the
new digital SAUERESSIG c.INKTEC workflow. Both processes were qualitatively compared and tested by spectrophotometric measurements. In order to enable a smooth and continuous digital color communication in printing processes from the beginning to the end of the process chain, the c.INKTEC workflow already integrates within the design to print process at an earlier stage. Ahead of the printing process, and by using
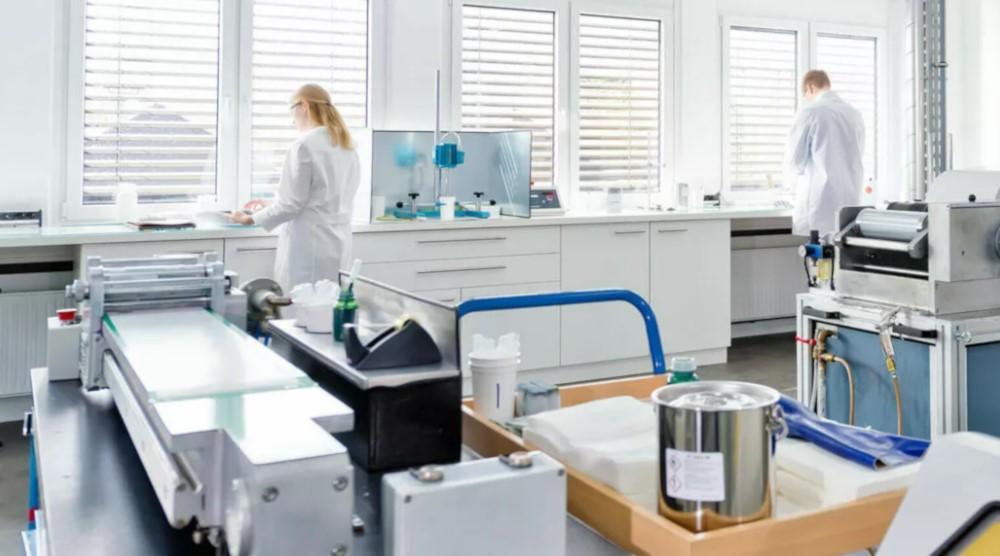
the ingenio laboratory printing machines, the c.INKTEC color technicians matched the ink to the required specifications for gravure printing and adapted it to the original substrate. By creating the ink formulation in the laboratory environment, the printing inks could be tested and validated in advance. The color separations could be used to adjust the repro data, in order to subsequently achieve the desired result on the productionmachinewithout
any additional effortful color control on site. The cloud-based software solution c.CLOUD, part of the SAUERESSIG e.GEN portfolio, also came into use. It centrally stores all the information on the colors that have been created aswellastherespective associated ink formulation – so that it can be reached anytime, anywhere in the world. Provided plug-ins allow the color specifications to be integrated directly intotheprocess.
The results of the study are promising. Ingo Büning, Senior Sales Manager of the SAUERESSIG Group, is convinced that color deviations of the production run to proof will soon be a thing of the past and states: “The analysis has shown that good preparatory work in color communication pays off. Costly and time-consuming corrections on the press can definitely be avoided.“ Savings of resources in printing processes can therefore be considered as one of the greatest benefits of this proceeding. Thanks tothe holistic approach, the process optimizations can also add benefit in follow-up projects.
c.CLOUD conveniently handles digital color communication between all stakeholders and provides complete transparency along the entiresupplychain.
But the possibilities of digitalization in printing processes are far from exhausted. The next big
step into the future is the development of virtual reality-supported processes that will enable business partners to move through the world of color regardless of time and place. “With these new possibilities, we will be able to enter a whole new dimension in the world of color in the near future, experience products virtually and interlock our processes evenmore closely,“ says Christian Groh, Business Unit Director
e.GEN, of the SAUERESSIGGroup.
On a sustainable path along a globalized value chain, SAUERESSIG is making a positive contributiontothetransformation to resourceconserving cycles – not only reshaping the way we work, but also the supply chain in the packaging and printing industry.
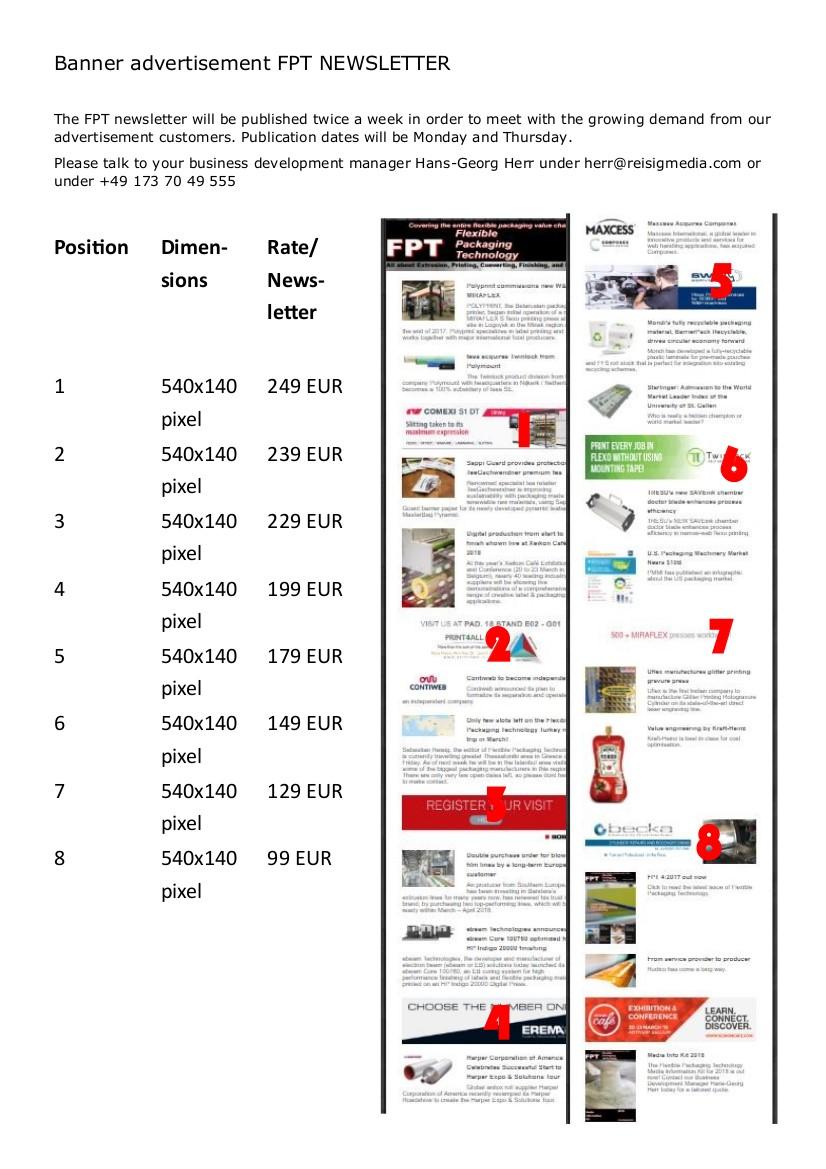
Dörken has started to produce innovative technical building membranes on SML lamination lines
In the past few months, the German company, Dörken, has put two new production lines from SML into operation. Highly permeable roof and facade membranes are manufactured as part of the company’s product portfolio. In addition to innovative properties, a large number of the new composite films are making a statement due to their particularly resourcesaving and efficient manufacturing processes. To a large extent, the products and production processes were developed in SML’s Technology Center - even before the lines were planned or installed at Dörken.
In When it comes to membranes forthe construction industry, Dörken is European market leader. In autumn 2022, the company opened a new production site in HagenVorhalle in North RhineWestphalia, where the two coextrusion coating and laminating lines from SML are now up and running. The tailormade plants are setting new standards in terms
of functionality, quality monitoring and the degree of automation involved.
Previous product development at SML’s TechnologyCenter
"The remarkable thing about this project is thatDörkendidnotcarry out substantial parts of the product development process at its own plants, but on an industrial scale FlexPack®
line located in our Technology Center," Dirk Beckendorff, Area Sales Manager at SML, explains. The product development process at SML took several years: Among other things, it included basic trials with the SML DoubleCoat process, test series with the most important products of Dörken’sportfolioandseveral test runs for the development and sam-
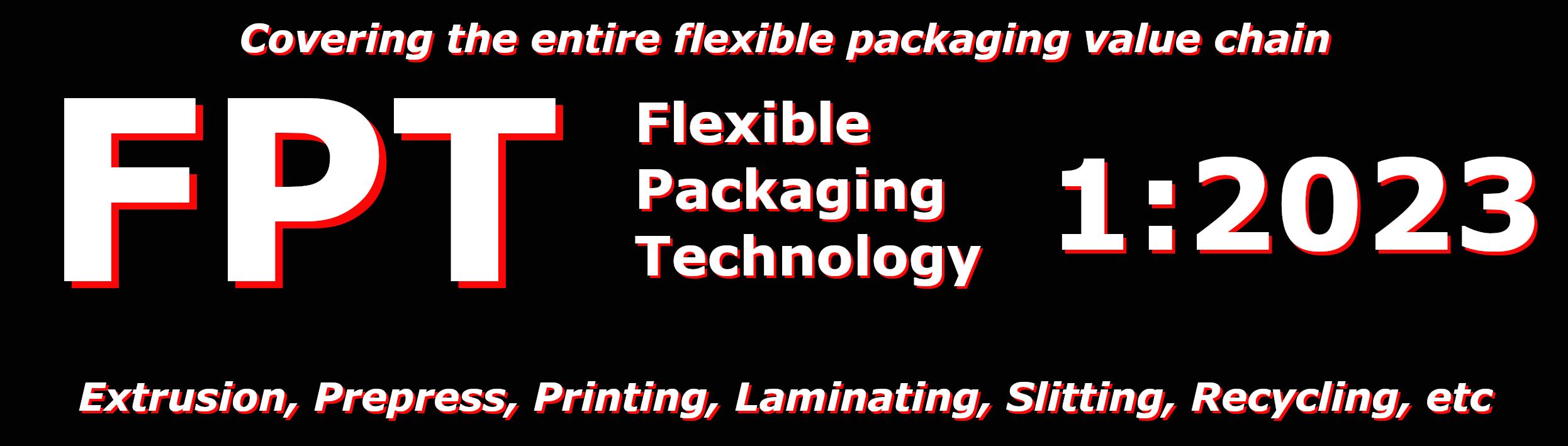
pling of new roofing membranes. Since it was possible to certify a number of products even before the lines were commissioned at Dörken, the over-all product development process was accelerated quite significantly. “It was important for us to benefit from the opportunity offered us by SML. In addition to confirming the known recipes and processes, we were able to use SML’s pilot plant for our innovations at a very early stage. In principle, we have actively integrated SML’s plant into our
Stage Gate process,” Christian Harste, CTO at Dörken, clarifies. Immediately after the installation of the two lines, Dörken was able to startregularproduction. New standards for products One of the two multipurpose coating and laminating lines at Dörken is equipped with SML's patented DoubleCoat technology. This technology enables a combined adhesive and extrusion coating process for the production of ultra-thin and highly breathable laminates. It
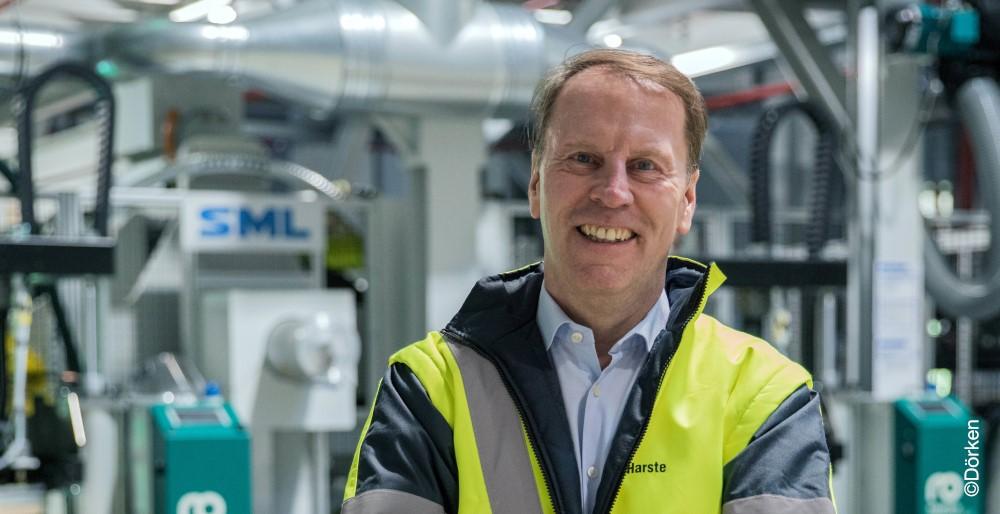
allows the manufacturing of a wide variety of technical composites for the construction industry, such as vapor barriers or waterproofing membranes.
The second production line is a combined line with two integrated adhesive roll coaters for the manufacturing of highly breathable roofing and facade membranes in one productionstep.
The thickness of the TPU membranes can be considerably reduced, compared to conventional products available
on the market. Thanks to the innovative system technology, significantly improved water vapor permeability values can be achieved, with, at the same time, excellent product properties with regard to longevity. “Our new underlay membranes are impressive with their proven durability and thus long-term protection. Extreme quality and long-term tests as well as special test procedures confirm their extraordinary resilience. With a high elasticity and integrated selfadhesive edges, this new generation of products is the perfect solutionforawidevarietyof applications. It enables ahigherenergyefficiency and a raised living comfort,” Dörken-CTO, ChristianHarste,states.
Intuitive operation –integrated inspection systems
A central element in both production lines is the SMILE control system developed by SML software application en-
gineers. This enables the highly intuitive operation of the lines, tailored to the respective production process and the associated functionalities. "Integrated inspection systems and our data management tool, BitWise, ensure the comprehensive monitoring of the entire process chain at both plants. The production parameters of each product can be completely traced," SML product manager, Johannes Danter, points out. This is an enormous help to Dörken when complying with the strictest quality standards,especiallyregarding the long-term product guarantees the marketdemands.
Modernisation with a significantincreasein efficiency
Thetwoproductionlines from SML allow a massive increase in efficiency because of their lower raw material consumption. Compared to the plant and process technology previously
available, the production of the new generationofhighlybreathable roofing and facade membranes takes place in just a single production step. In addition, the lines operate at a comparatively high production speed of up to 120 m/min. Along with considerable time savings, the waste generated during production is reducedtoaminimum.
The two new lines from SML replace several existing plants and give Dörken the opportunity to produce innovative membranes. They emphasize Dörken’s claim to manufacture as economically and resourceefficiently as possible –with greatly improved product properties achieved through furtherdevelopmentwork.
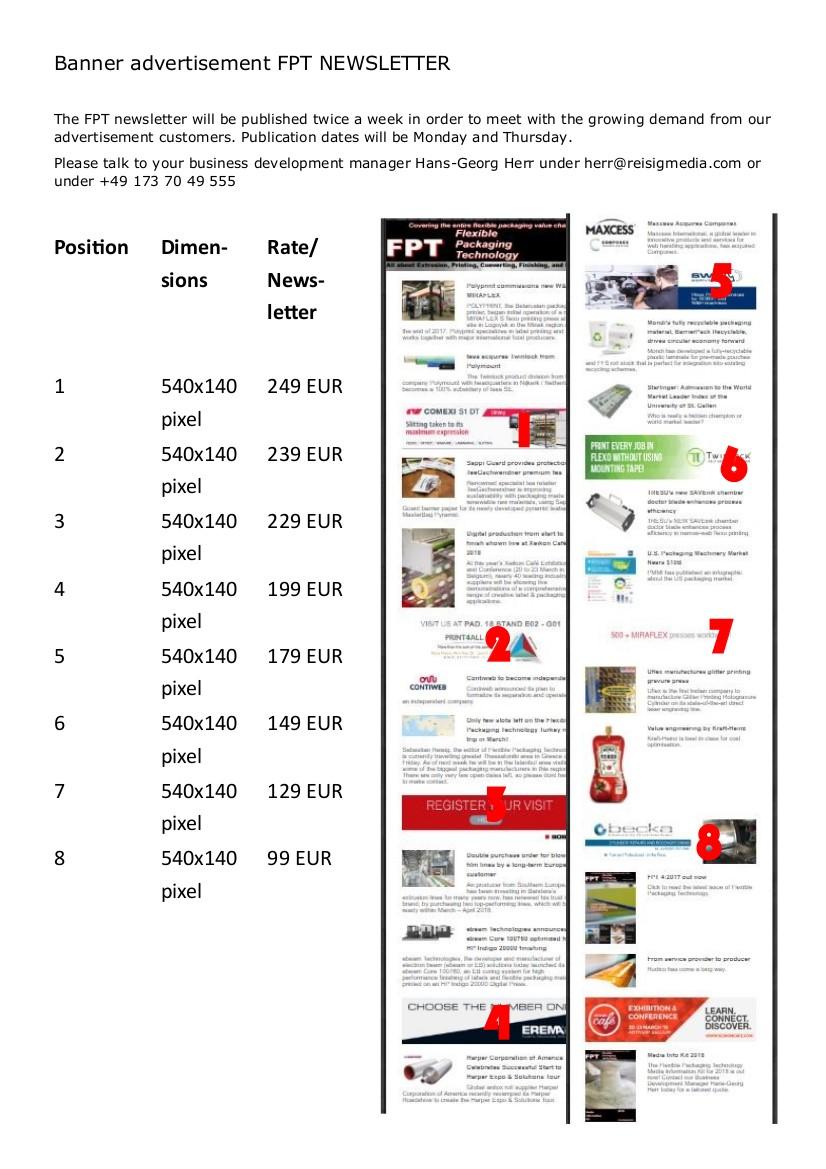