Multi-country study setting new benchmark for detail and understanding of plastic packaging in European waste streams
Multi-country study setting new benchmark for detail and understanding of plastic packaging in European waste streams
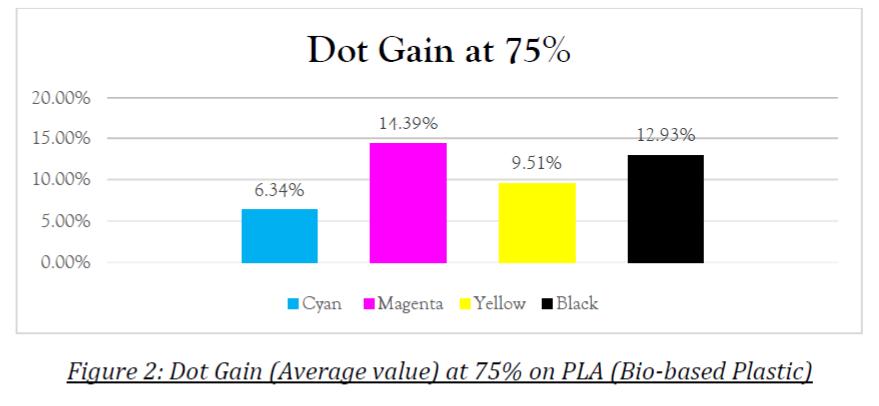
Study of Printability of Bio-based Plastic in Gravure Process
New study on the climate relevance of packaging: 94% less CO2 achievable by 2045
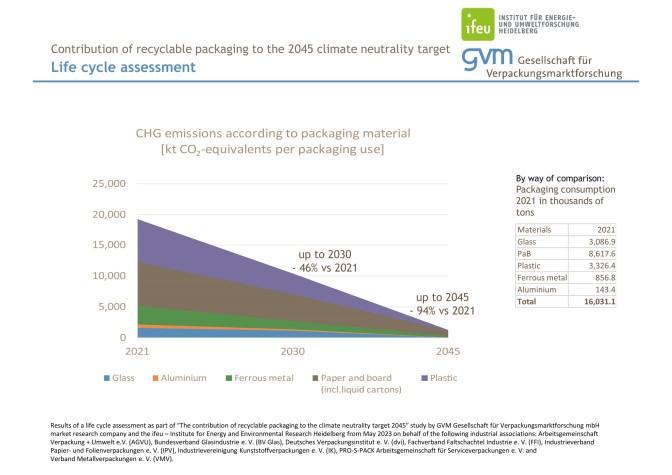
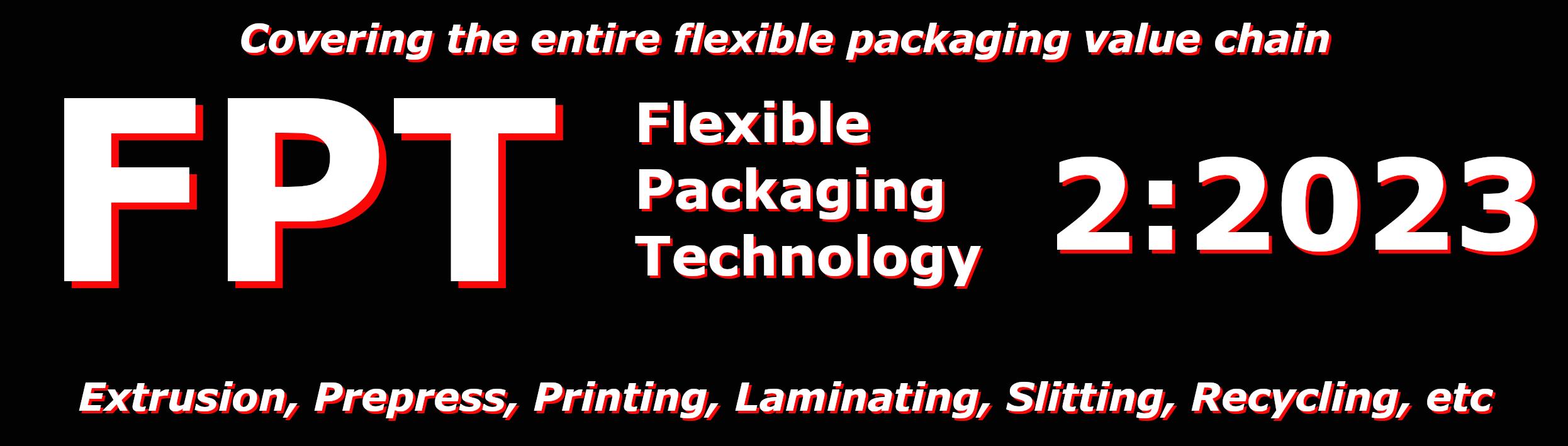
European Packaging Producers embrace the Circular Economy but few
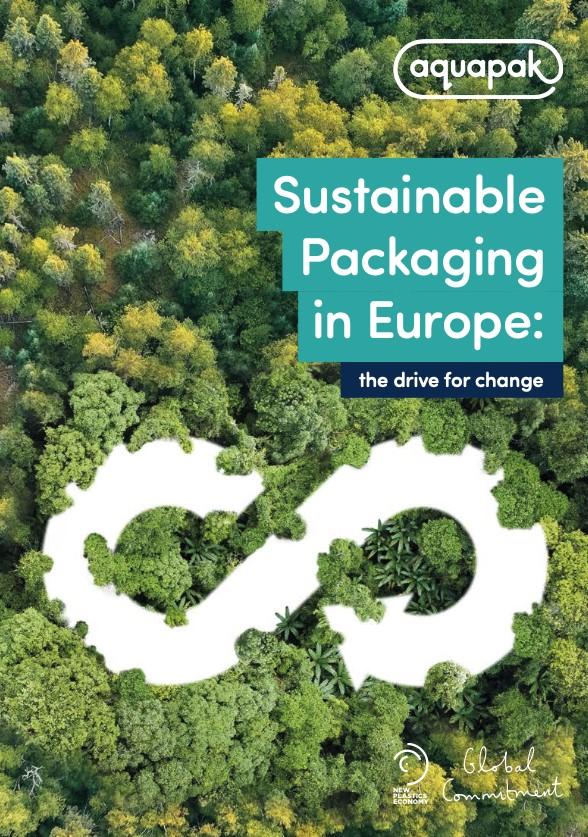
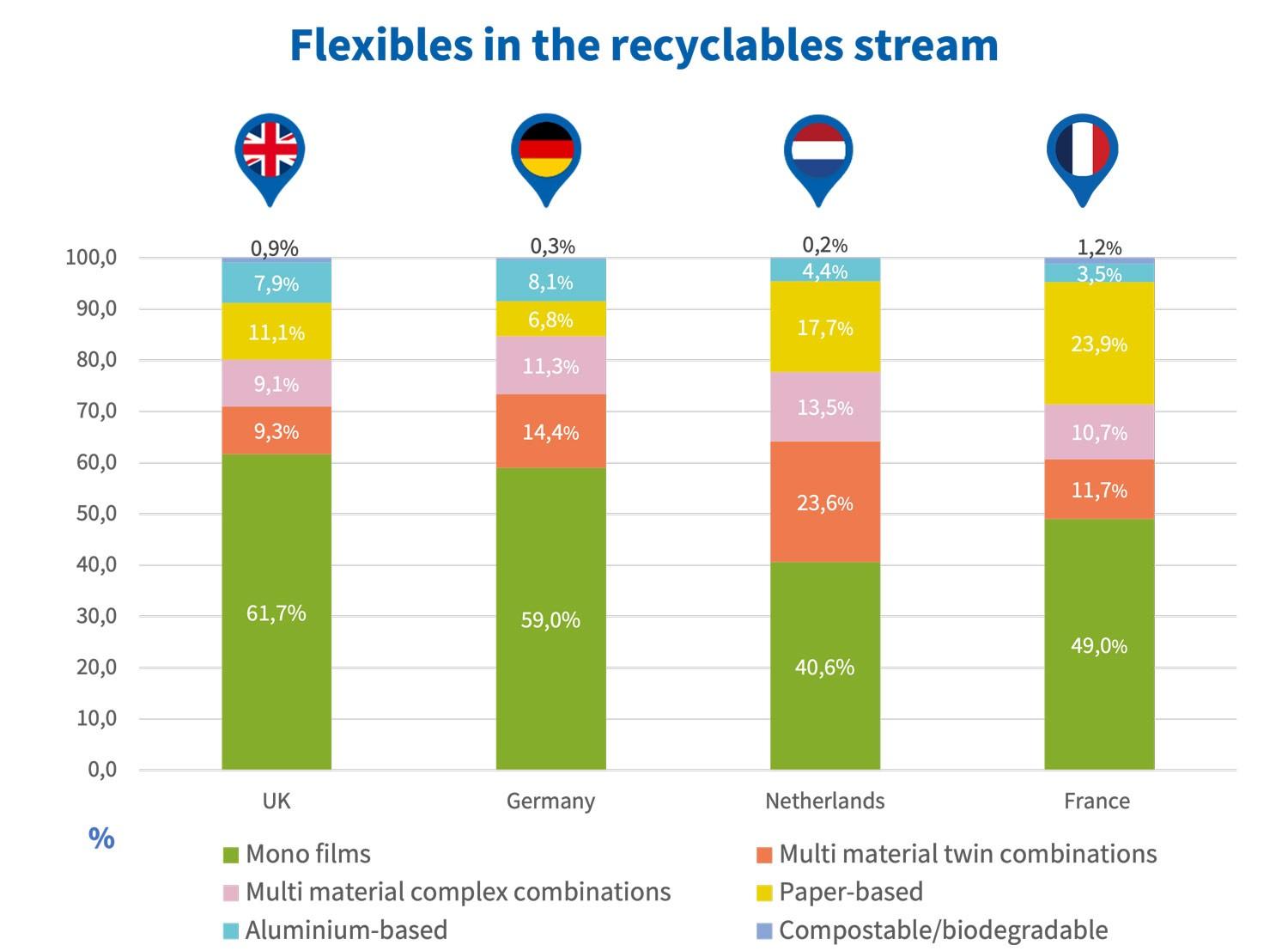
Dörken has started to produce technical building membranes on SML lamination lines

Printability is function of different printing technical parameters which describes whether the printing on any media can be made at par with printing standards. In this modern era bio-based plastic have emerged as new alternative for replacing conventional plastic to protect Mother Earth as usages of printing plastic is very common in our day to day life.
A recent study by the GVM Gesellschaft für Verpackungsmarktforschung market research company and ifeu – Institute for Energy and Environmental Research Heidelberg gGmbH, commissioned by eight industry associations, shows that the greenhouse gas emissions associated with packaging in the German market could be reduced by 94 per cent by 2045.
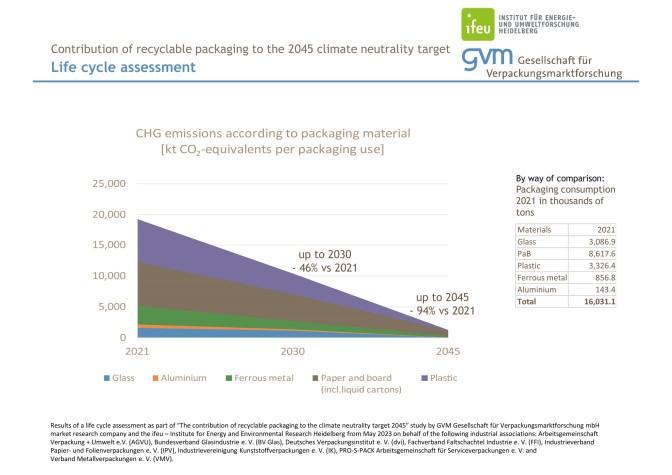
New research commissioned by material technologies business, Aquapak, with sustainable packaging producers and users in the UK, Italy and Germany1, shows that European packaging businesses are committed to the circular economy, but few are acting ahead of legislation.
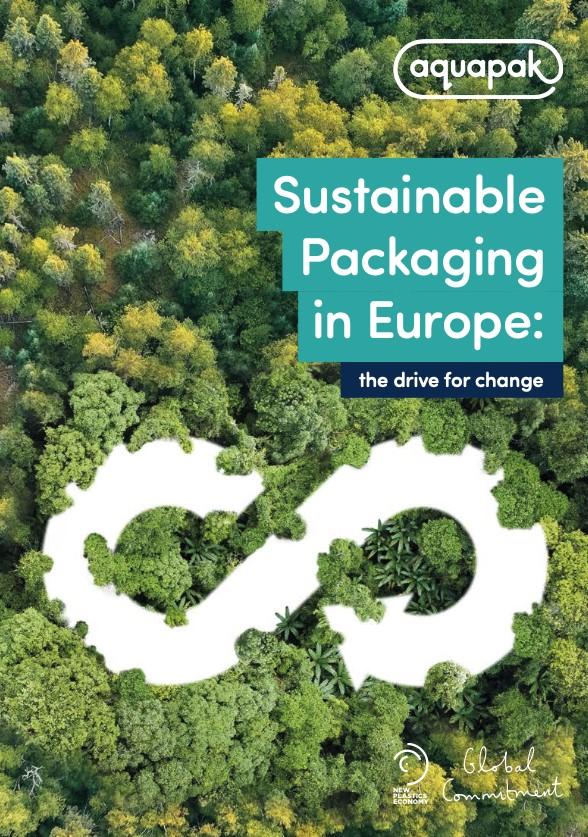
CEFLEX and partners are conducting a multi-country compositional analysis to research the type and amount of flexible packaging and rigid plastic packaging in the post-consumer waste stream. The research is providing valuable data to understand the collection, sorting and recycling infrastructure needed in each country.
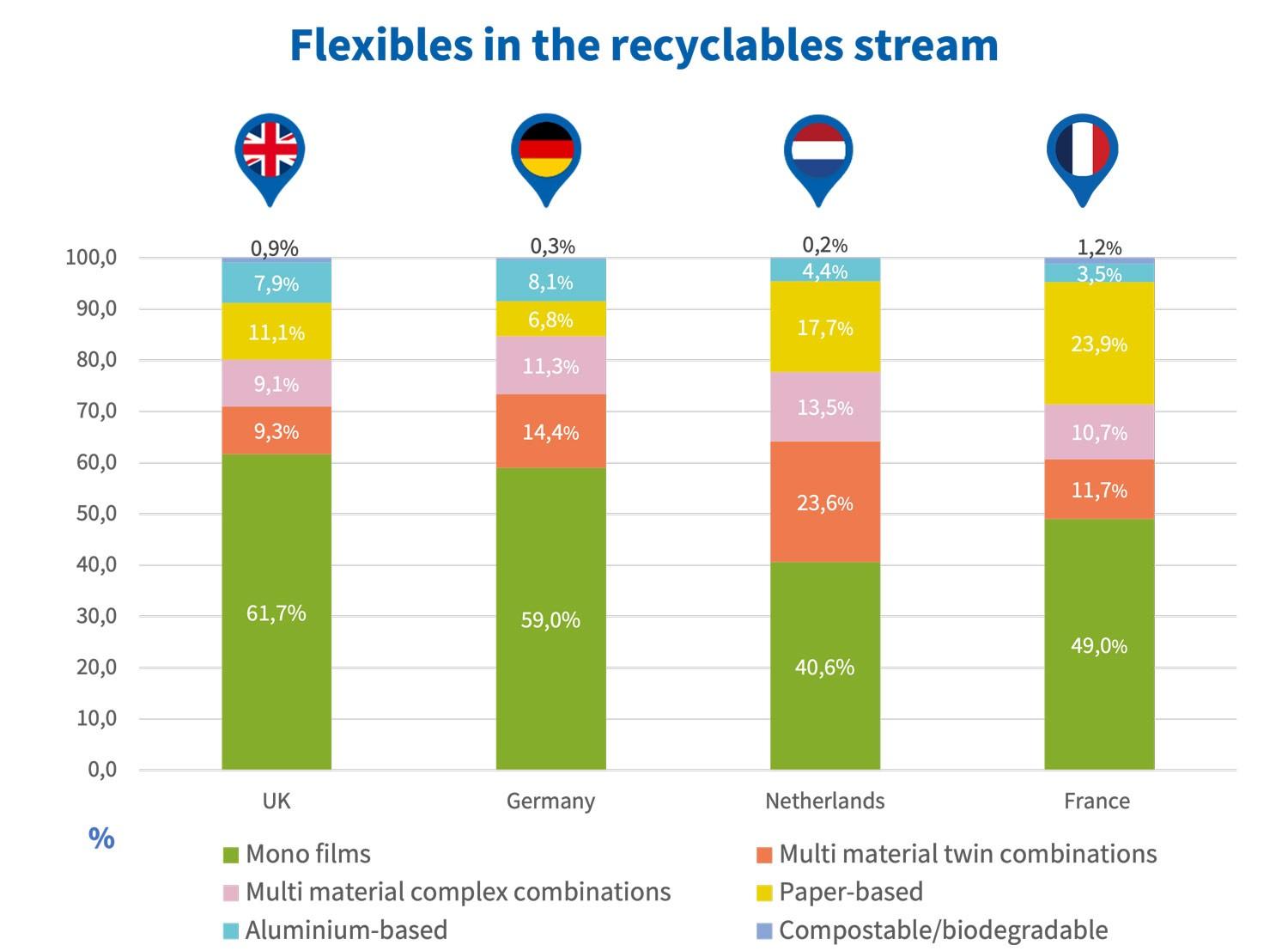
Investments in capacity are just the tip of the iceberg for Minipak as it showcases quality and competitiveness in the flexible packaging industry

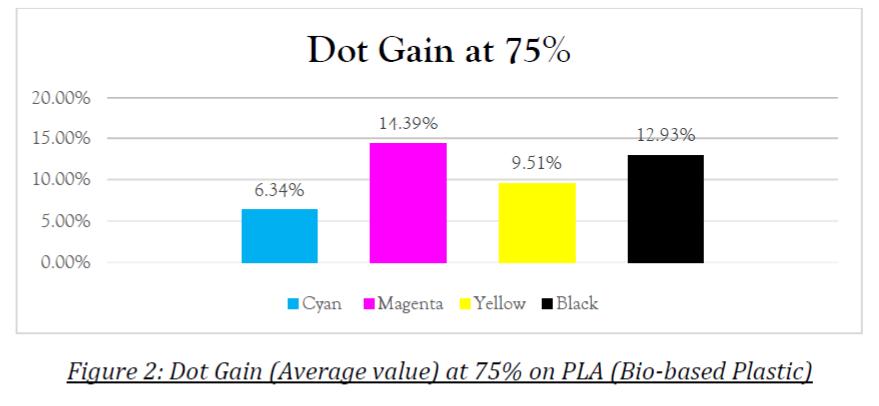
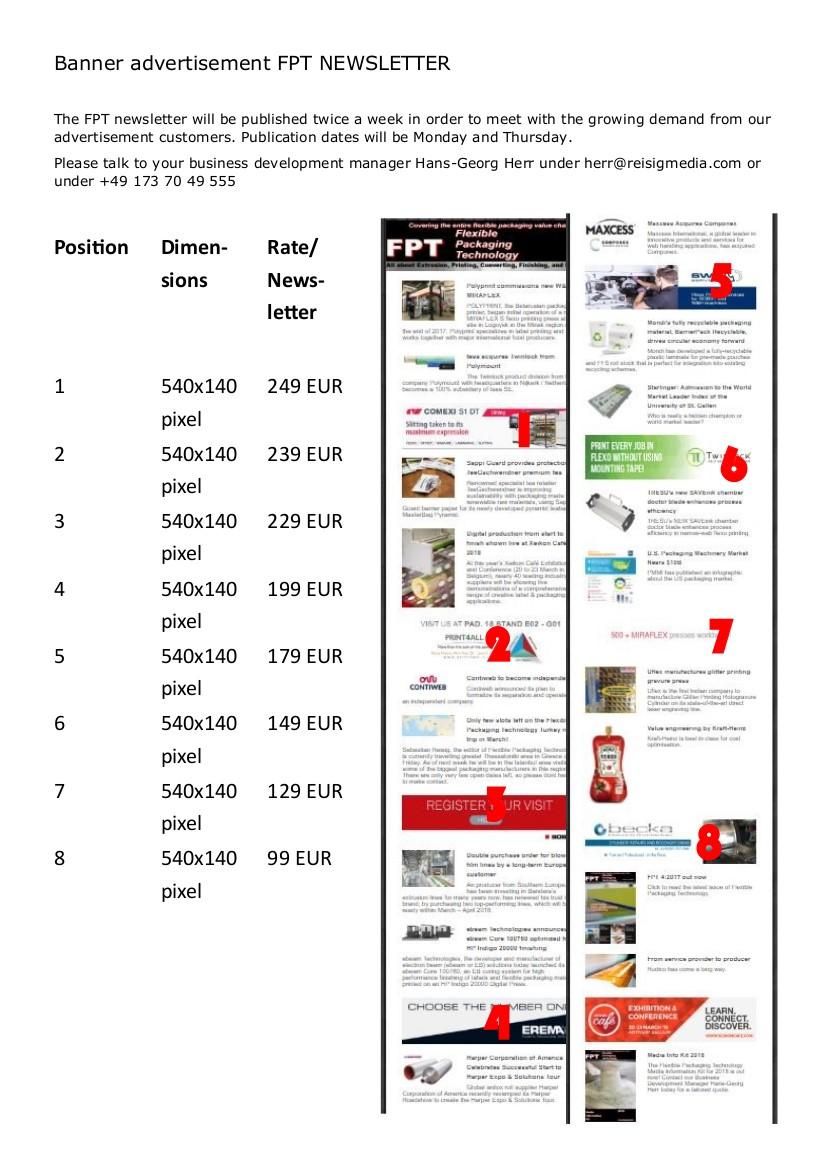
Study of Printability of Bio-based Plastic in Gravure Process
Printability is function of different printing technical parameters which describes whether the printing on any media can be made at par with printing standards. In this modern era bio-based plastic have emerged as new alternative for replacing conventional plastic to protect Mother Earth as usages of printing plastic is very common in our day to day life. In this domain Gravure printing is known for good printability with high speed production. But compatibility of bio-based plastic with gravure printing is still a major concern. Hence to study printability aspects on bio-plastic is an attempt to make for exploration of mutual compatibility of media and printing process which will prove a boon in upcoming future by replacing conventional plastic.
By Pankaj Kumar, Prof. Ambrish Pandey, Prof. Rajendrakumar AnayathOverInthiseraofglobalization and evergrowing demand for convenience in all walks of life, polymer family offers a wide range of plastic films includes new generation environmentally friendly substrates for various printing and packaging applications. Plastics: Withtheadventofplas-
tic material and growth of industrializations leads to printing on plastic materials to cater the need of evergrowing demand of packaging especially flexible packaging. Printing on plastics was one of the most challenging jobs in last centuryforprinters.
Need of Environmentally friendly plastics for Printing and Packaging: Plastics are not inherently bad in nature but they are bad for environmentastheyarenot environment friendly because plastic materials are not degradable. So, there is great need arises for the development of degradable
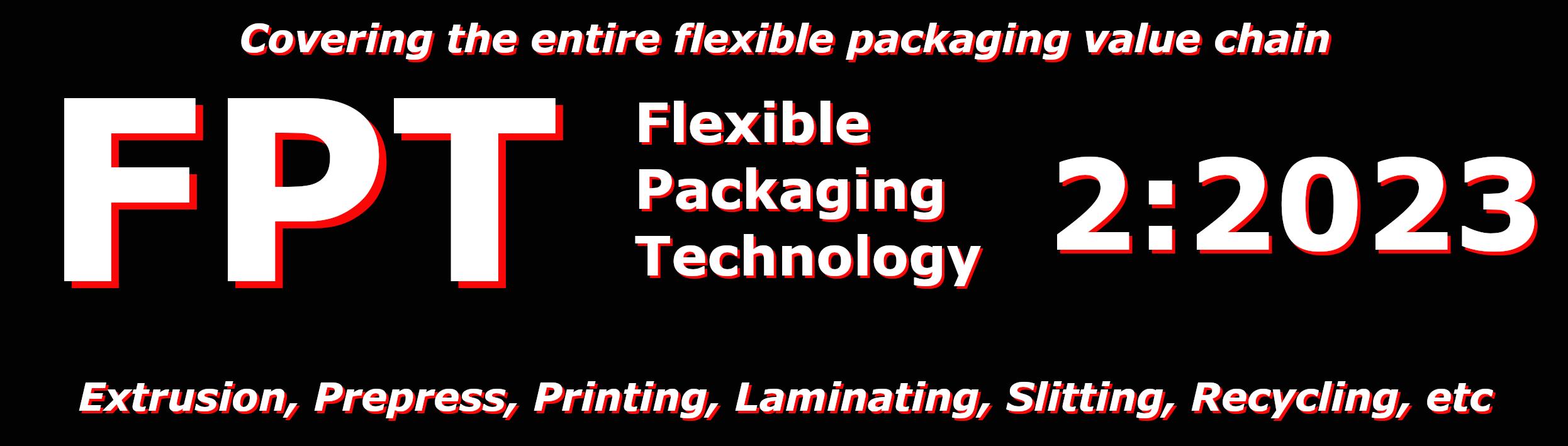
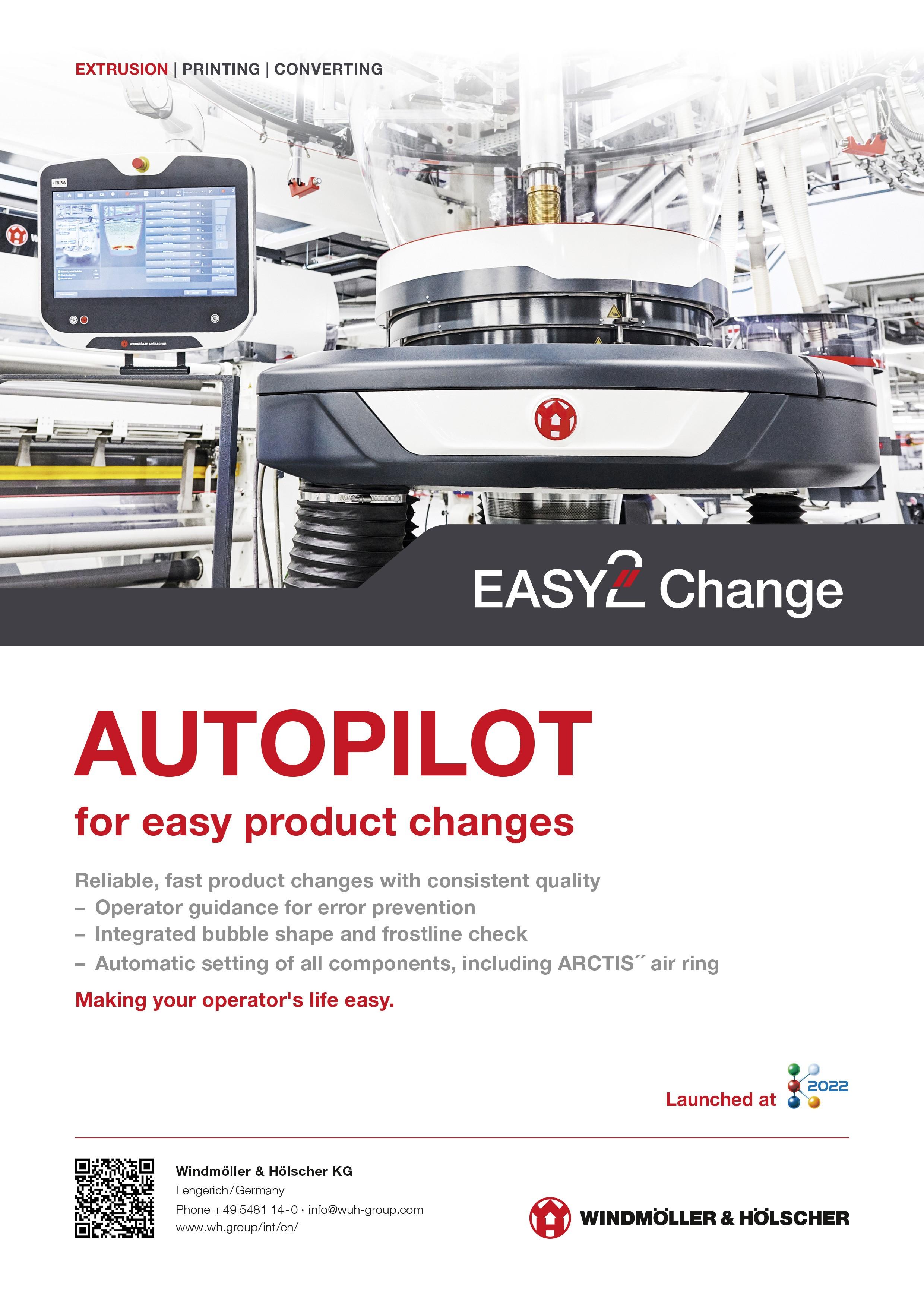
strates/ materials for printing & packaging applications. Recently some fossil/ bio-based plastic has been reported by the researchers which can be shaped suitably for application as substrates for printing for packaging applications. Sustainability and biodegradability are the biggest strengths of bio-plastics and hence, they have been readily accepted even in applications where they are marginally or sometimes expensive than conventional plastics. Bio-plastics have an excellent potential to be used for printing & packaging applications, due to ability to their degradability. Printing on Plastics: Printing is considered as one
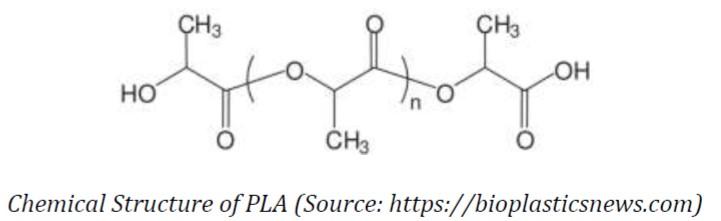
among greatest invention of mankind. It has touched almost every life after its invention either in form of printed product or in form for packages. There are various processes of printing, categorically divided into impact and non-impact process printing suitable for printing on different substrates for different applications. Different printing process has their own applications, advantages and limitations and is suitable for printing on different set of materials. Printing on plastics usually comes underflexibleprintingin which Gravure Printing Process and Flexography Printing Process areleadingprintingprocessesinthisfield.
Gravure Printing Process: Gravure Printing Process is high-speed, high-quality printing process primarily used for printing on plastics for packaging applications and comes under flexible printing. Gravure process is suitable to produce consistent and very high-quality printing even on thin films and low-grade substrates. Gravure process has many advantages, but it has some operational difficultiesduetospecialrequirements on machine during printing, for substrates having tendency to elongate during printing under pressure. Printability: Printability refers to the suitability of substrate for reproduction of good quality
text, picture and pattern in single as well as in multi-color. So, Printability is the ability of substrate to take print, itissum total ofvarious factors affecting quality and quantity during print production. It is an important factor affecting selection of materials (Printing Substrate, Inks, Auxiliary arrangements and Special requirements) for print productions. Several factors play important role to decide printability of a substrate, which are surface characteristics like thickness, porosity, smoothness, color & whiteness and surface coating apart from that compatibility of substrate with printing process is also very important. Various printing attributes are measured for getting objective views for printability of selected materials either for selection or to determination for print production. There are various print properties elements are available for measure-
ment and incorporation for better and specific print production, however following are the necessary print attributes which should be followed for determination of Solid Ink Density (SID), Dot Gain and Hueerror.
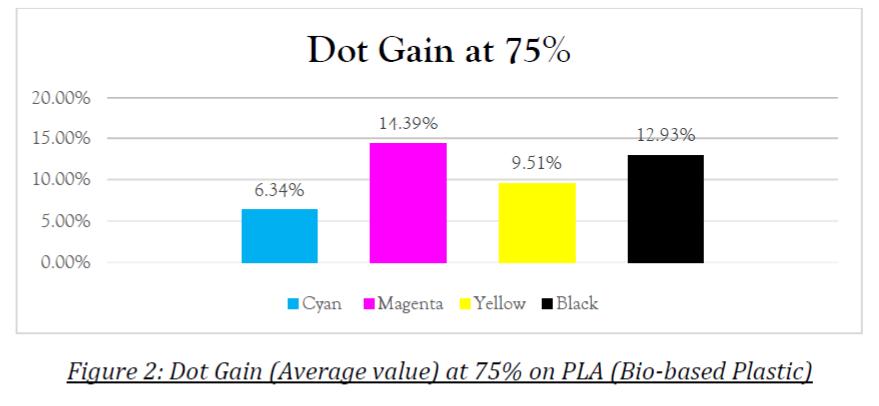
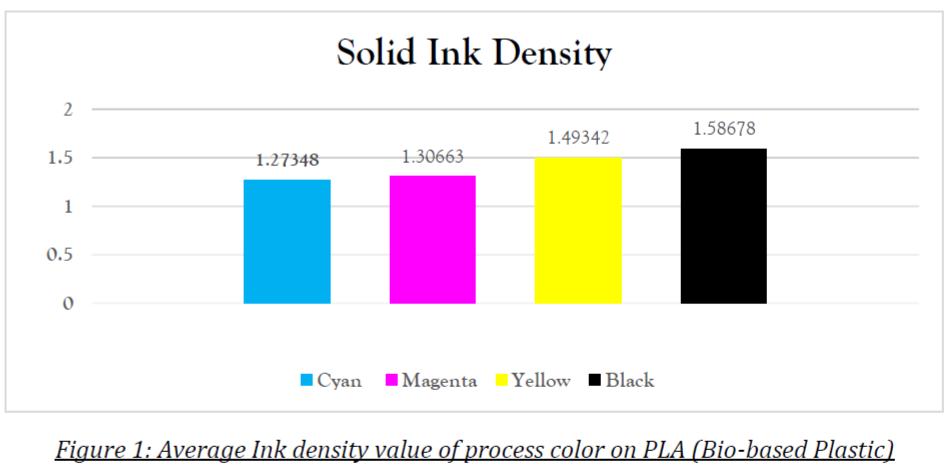
ResearchObjective
The key objective of the study is to analyses printability of bio-based plastic gravure printing process.
Materials and Methodology
To study and analysis of printability of bio-based plastics on Gravure processfollowing stepsare followed:
Preparation of Test Chart: Suitable test chart was prepared by incorporating various elementstocheckprintability, run-ability and readability of printed samples.
ii. Printing Processes: Gravure printing pro-
cess was selected for thisstudyunder standard press room condition.
iii. Machine: Printing on Gravure proofing machine was done for selectedsubstrate.
iv. Selection of Substrate: Selection of substrate was limited to PLA(Bio- based)forthis study.
v. Selection of Printing
Inks: Solvent based Gravureprintinginkwas usedforthis study.
vi. Colorimetric Measuring instrument: X-rite, Exact spectrophotometer was used for capturingofdata.
vii. Gravure Cylinder Preparation: Gravure cylinder was prepared using Laser engraving on HelioKlischograph smartK5.
Selected substrate PLA (Bio-Based) was printed on gravure proof machine with suitable process inks in standard press room conditions maintaining all printing
parameters. Prints were selected for study onequalregiontocheck the consistency and accuracy of printing parameters for checking printability.
DataAnalysis
To study printability aspects of bio-based plastic using gravure process numerous printing parameters were taken into consideration. Theseareasfollow:
Ink Density: Ink density value (Avg. Value) for all process color i.e. Cyan, Magenta, Yellow and Black is presented in figure 1. During observation it was found that cyan color demonstrated minimum ink density value while black color demonstrated highest ink density value followed by yellow color.
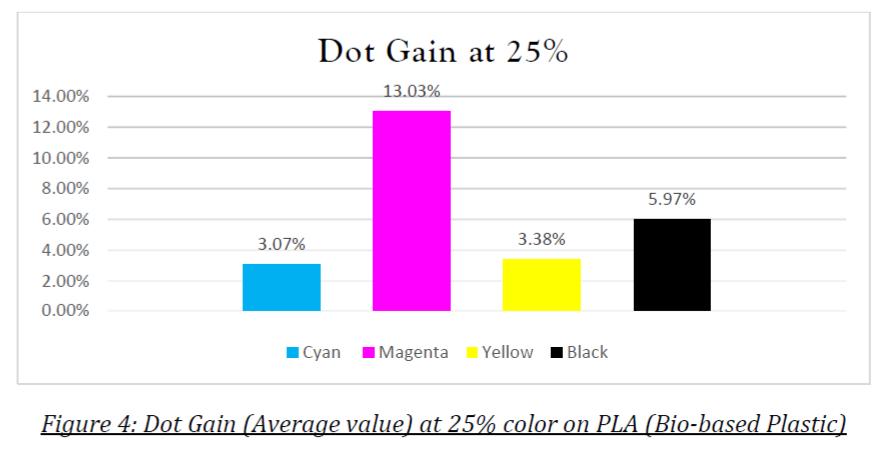
ii. Dot Gain: Value of dot gain for process col-
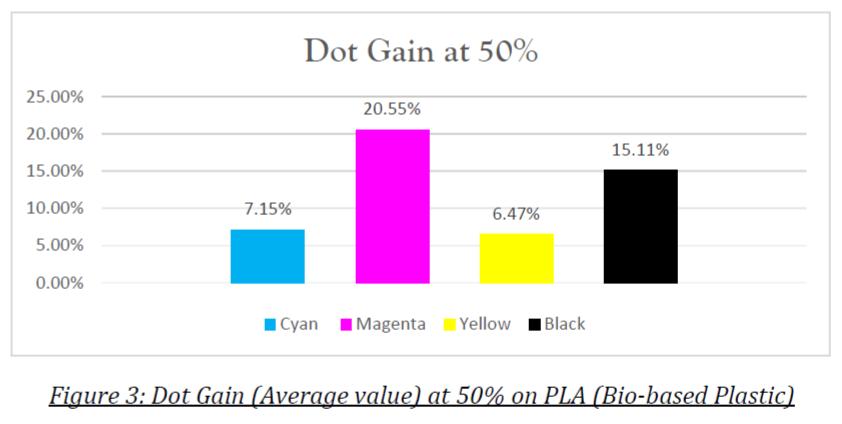
or at different level i.e. 75%,50%and 25%on bio-plastici.e.PLAusing gravure process is showninfigure2,3and 4 as below. a. Dot Gainat75%:It wasobserved that magenta color demonstrated highest dot gain followed by black color on selected substrate, while lowest dot gain was observed for cyan color.
b. Dot Gain at 50%: In case of 50% dot gain, it was observed that on magenta color demonstrated highest dot gain followed by black color, while yellow color exhibited lowest dot gain on PLA bio-based plastic.
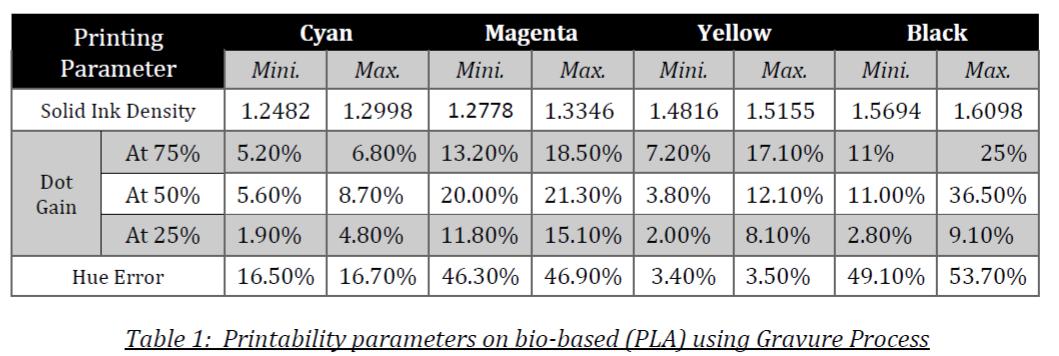
c. Dot Gain at 25%: While observing dot
gain at 25%, it was observed that magenta color demonstrated highest dot gain followedbyblackcolor,cyan color dot gain was lowest on PLA bio-based plastic. Hue Error: The average hue error for all process color i.e. Cyan, Magenta, Yellow and Black is depicted in figure 5. It was found that yellow color exhibited minimum hue error value while black color exhibited highest hue error
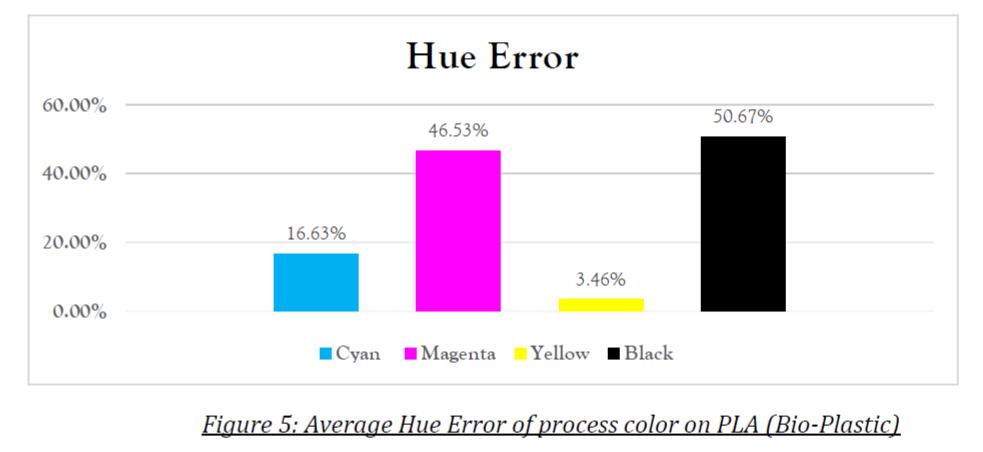
followed by magenta color.
Results and Discussion
Inordertostudyprintability aspects on biobased plastic using gravure process numerous parameters were taken into consideration. Collected information while study for various printing parameters is summarizedasbelow:
Conclusion
Analysis of data reflects thatmostoftheprinting
parameters are very closetostandard value. It was observed that Solid Ink Density (SID) of all process color were in the range even PLA (Bio-based) has acceptabilityofhigherinkdensity which in turn leads to better ink density and colorimetric values. Dot gain was measured at 75%, 50% and 25% for all process color, it is found that dot gain was in acceptable range of 5 to 15 percent for printing along with solid ink density and other printing parameters. Hue error was also observedinrangeforCyan andYellow.
References
1. Kapoor, S. G., & Wu, S. M. (1979). Predicting printability of gravure and embossed papers by time series analysis. Journal of Physics D: Applied Physics, 12(12), 2005.
2. Borude P., Tora S., Sharma S., (2016), Effect of Substrate Topography on Print Qualit y in Gravure Press, InternationalJournalofInno-
vative Research in Science, Engineer ing and Technology, Vol. 5, Issue 6, June 2016, ISSN (Online): 2319-8753, ISSN (Print ): 23476710.
3. Lewis K., Simon E., (2016) Bioplastics Simplified: Attributes of Biobased and Biodegr adable Plastics, SPI: The Plastics Industry Trade Association, plasticindustry.org, Feb2016.
4. Chung S. & 5 more, (2015), US Patient 9579878 B1 – Gravure Printing System and m ethods of using the same, for Industrial TechnologyResearchInstituteon30/10/20 15.
5. Arikan E. B., Ozsoy H. D., (2014) Time to Bioplastics, Akademic Platform, ISEM2014 Adiyaman–Turkey.
6. Chen Y. J., (2014), Bioplastics and their role in achieving global sustainability, Journa l of Chemical and Pharmaceutical Research, Bejing, 2014, S (1):
226-231, ISSN: 09757384.
7. Pathak S., Sneha CLR, Mathew B. B., and Bioplastics: Its timeline Based Scenario & Ch allenges, Journal of Polymer and biopolymer Physics Chemistry, 2014, Vo. -2, No.-4, 84 -90, DOI: 10.12691/ jpbjc-2-4-5.
8. Joshi A. V., Bandyopadhyay S., (2013), Comparative Study of Printability Analysis on PVC Cast and Pet-G Films, International Journal of Advanced Research in Engineerin g and Technology (IJARET), Volume 4, Issue 4, May- June 2013, pp. 208-221, ISSN 09 76-6480 (Print), ISSN 0976-6499(Online).
9. Pandey A., Poonia A., Nishant, (2012), Study of Print Quality on different Substrates i n Gravure Printing, International Journal of Engineering Research and Development.
10. Pandey A., Kumar P., Singh V., (2010), Application of Bioplastics
in Bulk Packaging: A revolutionary and sustainable approach, Bulk Pack 2010, Hyderabad, India.
11. World Bank Group, (2007), Environmental, Health, and safety Guidelines for Printin g, by International Finance Corporation, 30/04/2007.
12. Lv X., Liu C., Wu Y., Ipsen H., (2010), Variation of Gravure printing Characteristic Cur ve, in Proceeding of the 17th World Conference on Packaging in Scientific Research, i n 2010
ISSN:978-1-935068-36 -5
13. Wu Y. J., (2008), The Effect of Substrate Properties on Print Attributes for Gravure P rinting – From Proof to Press, Western Michigan University,June - 2008.
14. Kuruppali Z., (2011), Green Plastics: An emerging alternative for petroleum-based Pl astics? Proceedings of the 2011, IAJC-ASEE International Confer-
ence, ISBN 978-1-60 643-379-9.
15. Kirwan, M. J., Plant, S., & Strawbridge, J. W. (2011). Plastics in food packaging. Food and beverage packaging technology,157-212.
16. Emblem, A. 1. (2012). Plastics propertiesforpackagingmaterials. In Packaging Technology (pp. 287309). Woodhead Publishing.
New study on the climate relevance of packaging: 94% less CO2 achievable by 2045
A recent study by the GVM Gesellschaft für Verpackungsmarktforschung market research company and ifeu – Institute for Energy and Environmental Research Heidelberg gGmbH, commissioned by eight industry associations, shows that the greenhouse gas emissions associated with packaging in the German market could be reduced by 94 per cent by 2045. The study predicts that packaging consumption in Germany will have peaked in 2021 and continue to decline in the future. On top of this, the use of recycled materials and recycling proportions will both increase.
The study entitled “The contribution of recyclable packaging to the 2045 climate neutrality target” was produced in May 2023 to mark the 9thDayofPackagingon 15 June 2023. It explores the contribution that recyclable packaging can make across all materials with a view to the German 2045 climate neutrality target and predicts the development of relevant factors such as recycling
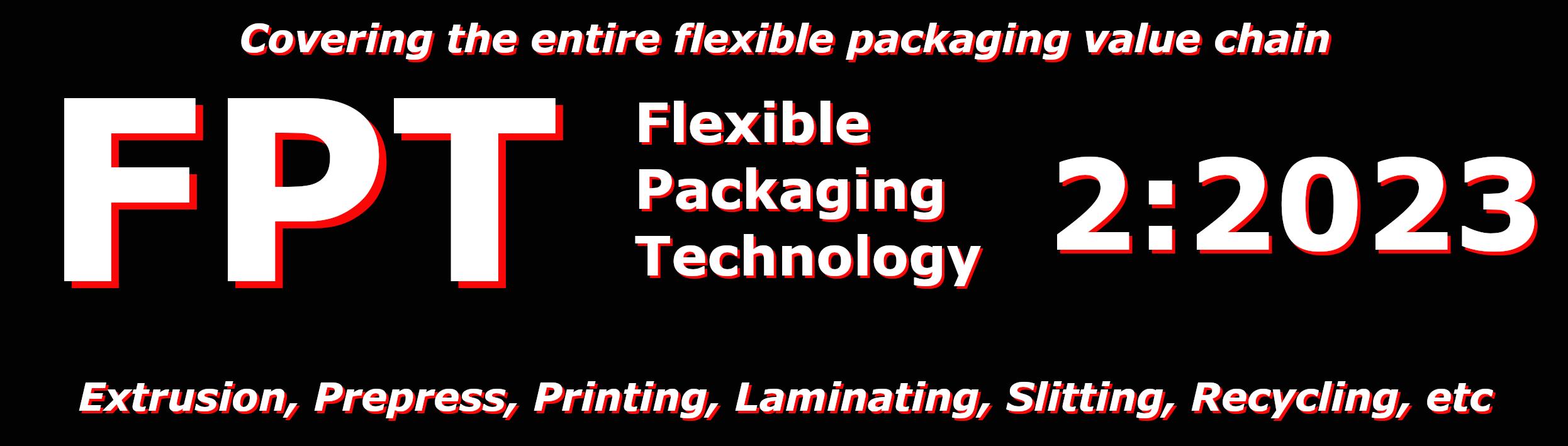
ratios, recyclate use, packaging optimisation and packaging volumes. The life cycle stages of raw material production, packagingmaterial production, distribution as well as disposal and recycling were balanced out to reflect typical Germanconditions. The study’s reference year is 2021. The situation in 2030 and 2045 was modelled. The study takes into ac-
count governmental or European control interventions that are already committed. Specific regulations either inplanningorexpected, such as the new European Packaging and Packaging Waste Regulation(PPWR), have not been included in the forecasts though. However, the study indicatesthatthetrajectory is similar due to fundamental ambitions that are also found in the
PPWR’s catalogue of measures. The results of the study were announced by GVM and ifeu at a press conferenceinBerlin.Thecommissioning associations are happy to provide the report to interested parties. Greenhouse gas emissions on a continuous decline “The results of the life cycle assessment show that greenhousegasemissionsassociated with packaging volumes are steadily decreasing, with a 94 per cent reduction achievable by 2045. This corresponds to a savingof 18,025 kt CO2 equivalents,” says Benedikt Kauertz, Head of the Industry and ProductsDepartmentatifeu.
“39.3 percentage points of the savings are attributable to factors
from the “Packaging market and circular economy” field of action. These include, for example, lighter packaging, reusable packaging, packagingsaving consumer behaviour, increasing use of recycled materials and, last but certainly not least, the greatly improved recycling of packaging. The remaining 54.4 percentage points come from the “Climate andenergy transition and process optimisation” fieldofaction.
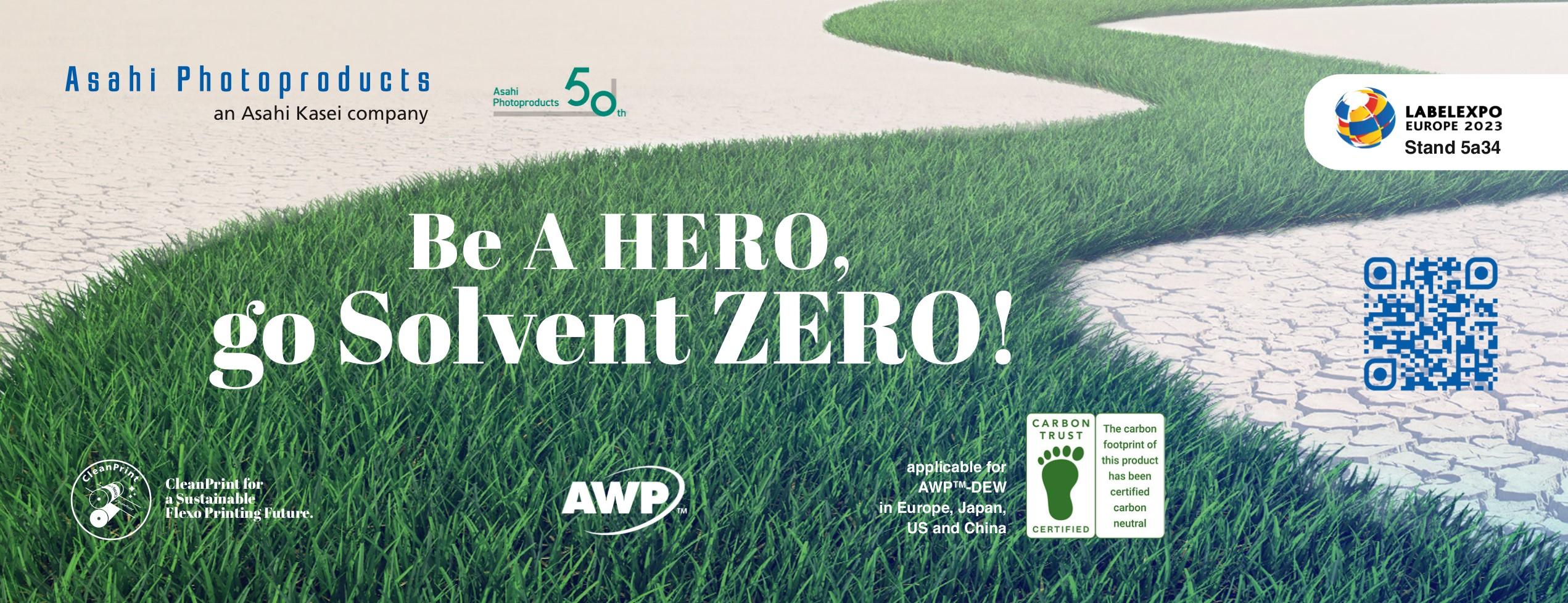
“The key points here are,forexample,decarbonisation of industrial production processes, green energy sources and energy savings in production and transport,” says Kurt Schüler, Managing Partner of GVM. Use of
packaging has peaked The study predicts that packaging consumption will have peaked in 2021 and continue to decline in the coming years. While packaging consumption (excluding wood) was still 16 million tonnes in 2021, the study calculates that it will drop to 14 million tonnes by 2030 and to 11.7 million tonnes by 2045. “This equates to a 13 per cent saving by 2030 and a 27 per cent saving by 2045,” says Kurt Schüler. Evaluation of the results The study was commissioned by the following industrial associations: Arbeitsgemeinschaft Verpackung + Umwelt e.V. (AGVU) (Packaging + Environment Working Group), Bundesverband Glasindustrie e. V. (BV Glas)
(Federal Association of the Glass Industry), Deutsches
Verpackungsinstitut e.
V. (dvi) (German Packaging Institute), Fachverband Faltschachtel
Industrie e. V. (FFI) (FoldingCartonIndustry Association), Industrieverband Papier und Folienverpackungen e.
V. (IPV) (Paper and Film Packaging Industry Association), Industrie vereinigung Kun-
ststoffverpackungen e.
V. (IK) (Plastics Packaging Industry Association), PROSPACK Arbeitsgemeinschaft für Serviceverpackungen e.
V. (Working Group for Service Packaging) and Verband
Metallverpackungen e.
V. (VMV) (Metal PackagingAssociation).
Packaging + Environment Working Group (AGVU) The study sug-
gests that the packaging and recycling industry can make an important contribution to Germany’s climate neutrality. In particular, this look into the future shows how the circular economywill unleashits full effect in the coming decades – for example through increased use of recycled raw materials. (Carl Dominik Klepper, Chairman of the BoardAGVU)
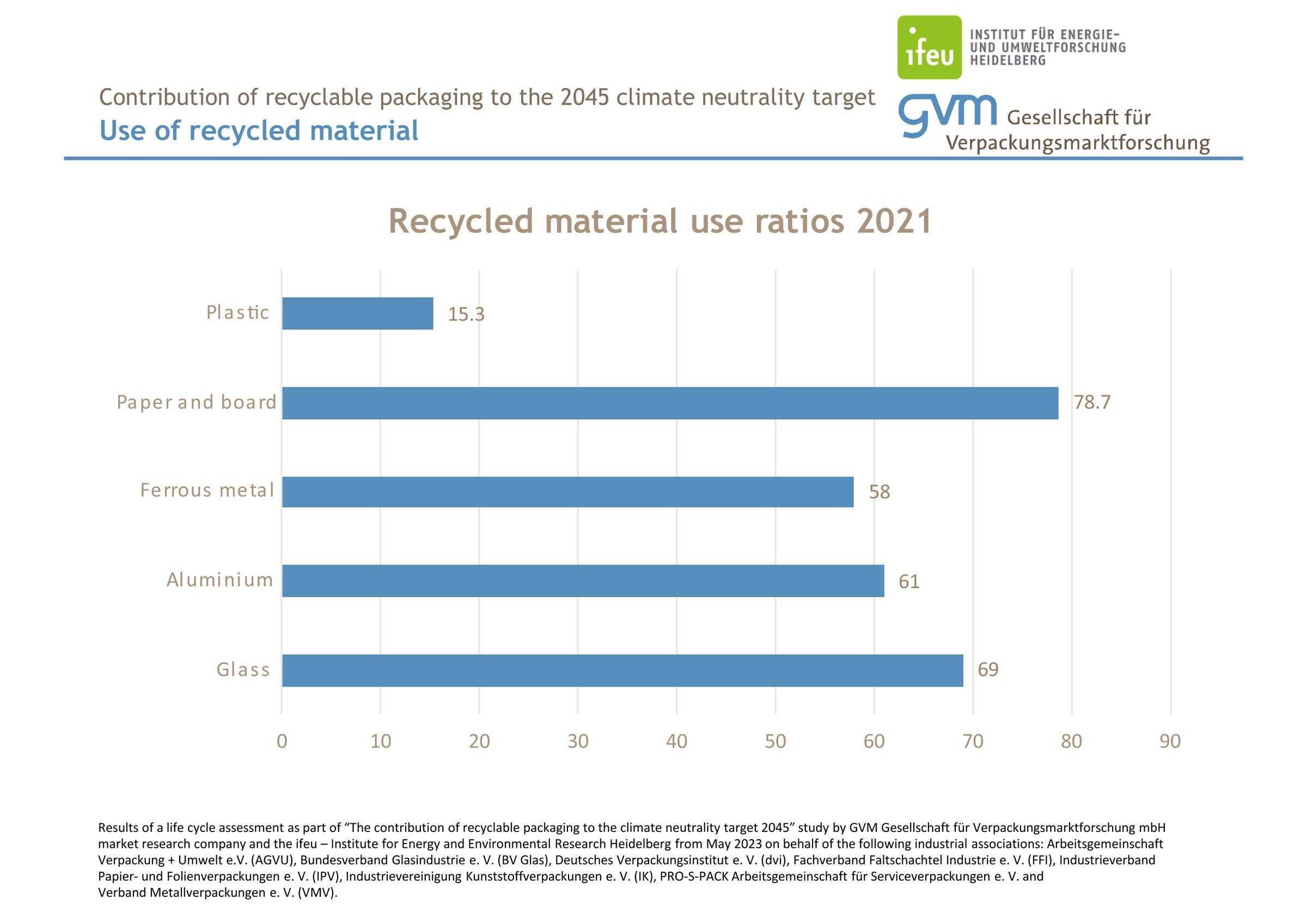
German Packaging Institute(dvi)Asasociety and as individuals, we consume and use many raw materials and products, meaning there is a correspondingly large amount of packaging. It is clear that packaging is a significant factor if we are to achieve the climate neutrality targets by 2045. This remains true even though packaging is already a climate protector due to
its product protection function. For example, food packaging only accounts for around 3 per cent of the climate footprintonaverage.97per cent is in the food itself – which is why the greatest damage to the climate occurs when a product is unused and goes bad. The study by GVM and ifeu shows what a key contribution packaging can make on Germany’s path to cli-
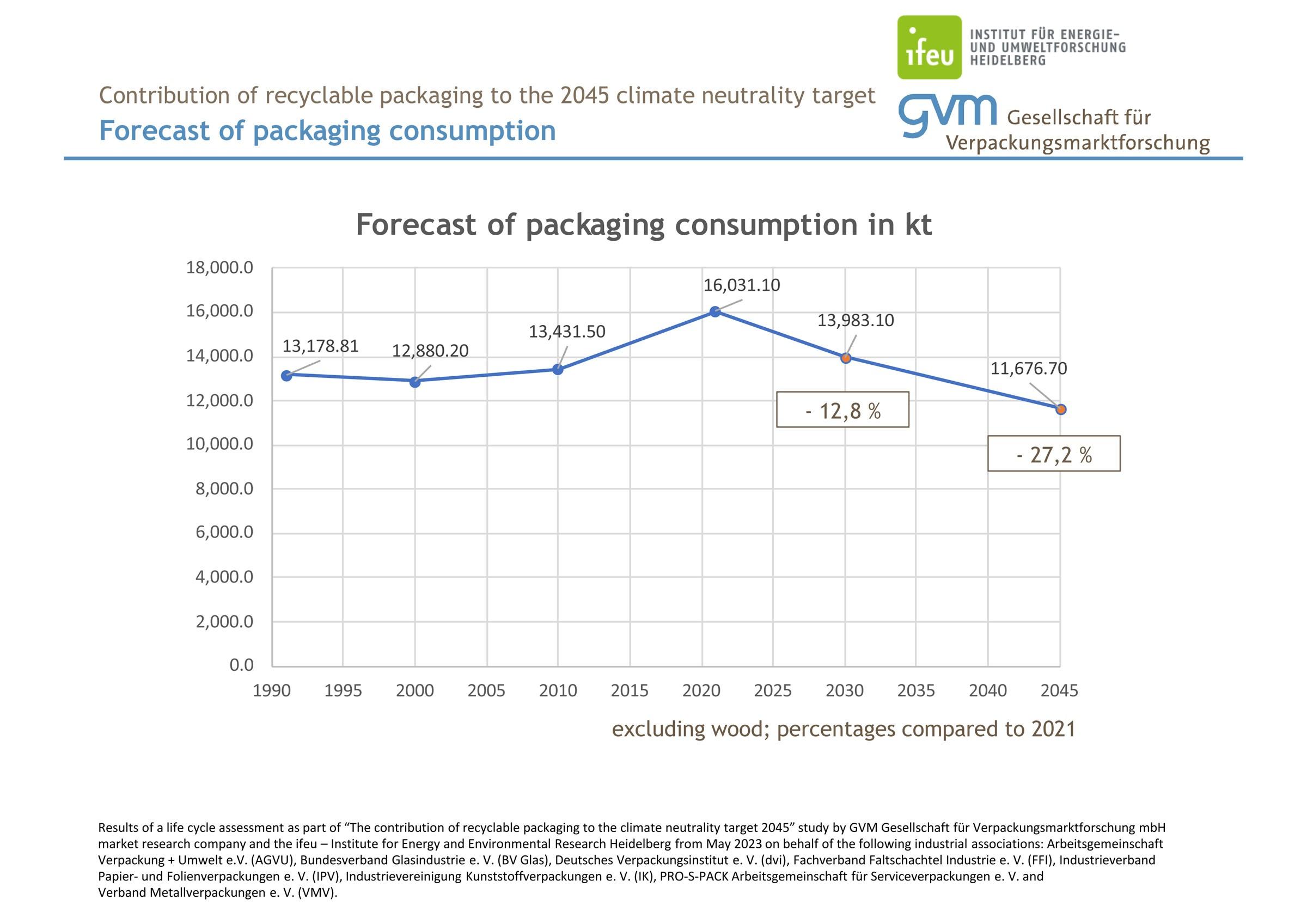
mate neutrality beyond 2045. A great deal is possible if everyone involved, from business and politics to consumers, makes their contribution and keeps recycling used packaging. (Kim
Cheng, Managing Directordvi)Plastics Packaging Industry Association e.V. (IK) For the first time, the study shows in hard figures the shared responsibility of politics,
industry and society in reducing greenhouse gases from packaging. As well as the essential energy turnaround, changed parameters close to the packaging itself can also open up significant potential. As far as plastic packaging is concerned, this also means a raw material turnaround no later than 2045. This means that in the future plasticswill notuseany fossiloilandthatrecycling, biomass and CO2 will provide the climate neutral raw materials.
(Mara Hancker, IK ManagingDirector)Industrial Association forPaperandFilmPackaging (IPV) Packaging thatbothsafelyprotects the packaged products, fulfils all other necessary functions and at the same time significantly reduces their associated greenhouse gas emissions is a daunting challenge. However, the study showsthatifallrelevant stakeholders work closely together, it can
be possible. As an industry,wearefacingup to these challenges. We are confident that we can find the right and sustainable solutions for flexible packaging made of paper and plastic.
(Karsten Hunger, IPV ManagingDirector)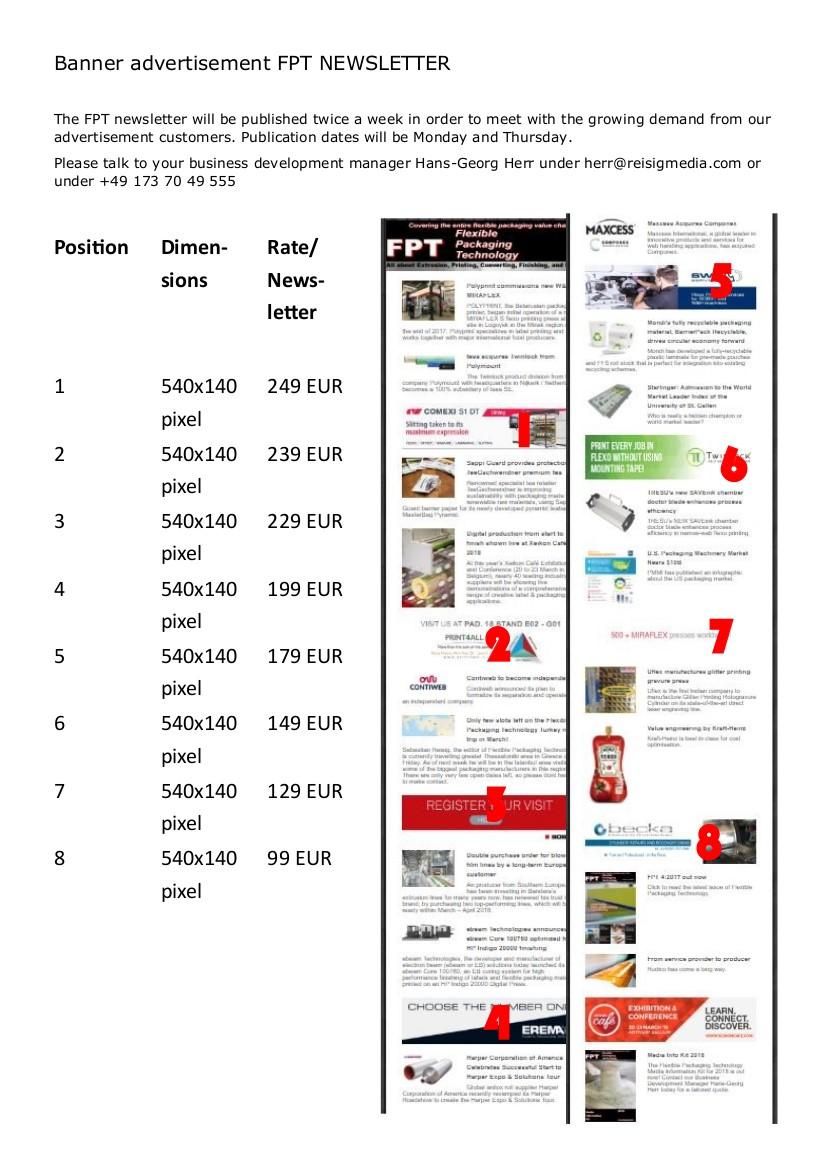
European Packaging Producers embrace the Circular Economy but few act ahead of Legislation
New research commissioned by material technologies business, Aquapak, with sustainable packaging producers and users in the UK, Italy and Germany1, shows that European packaging businesses are committed to the circular economy, but few are acting ahead of legislation.
The study shows that the majority of businesses (85%) have a circulareconomystrategy which involves reusing and recycling existing materials and productsaslongaspossible, with 21% saying they will be fully circular within three years. Almost a quarter (24%) have a three to fouryear time frame for achievingcircularityand a further 23%expect to meet this objective within four to five years. However, 11% said that they did not have such a strategy in
place and a further 5% didn’tknow.
With forthcoming legislation such as the revised European Commission’s Packaging and Packaging and Packaging Regulation (PPWR) as part of the Circular Economy package set to have a major impact on packaging and packaging design, the study also explored how this wasaffectingtherateof change in businesses as they seek to improve sustainability and circularity. Just 20% of businesses said they are acting ahead of leg-
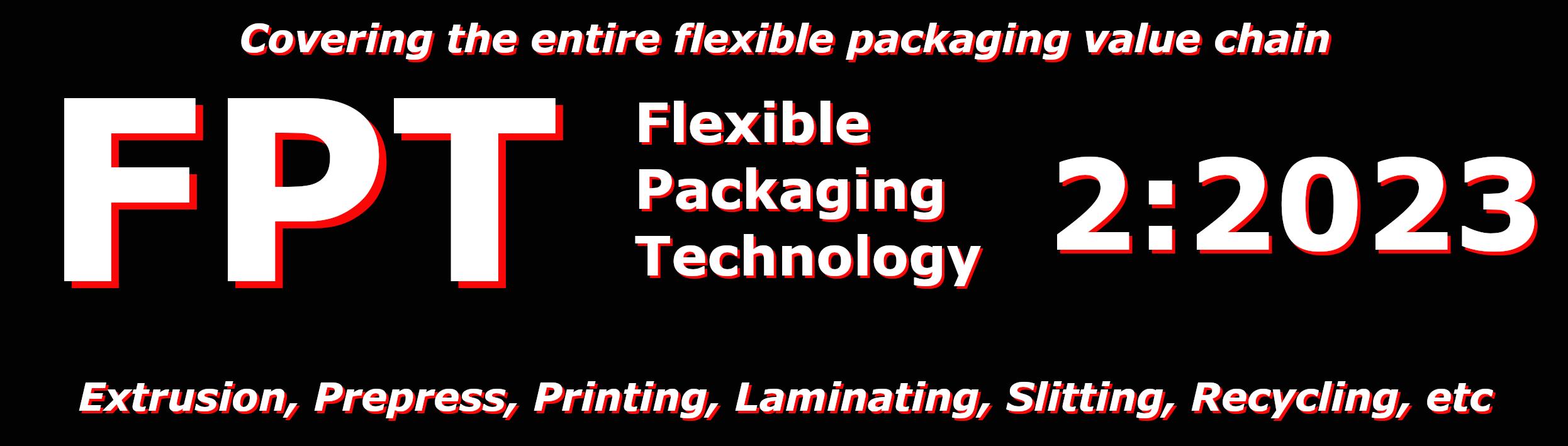
islation and 45% said they respond quickly to new rules when they are announced. However, 24% described their rate of change as ‘medium’ and 10% as ‘veryslow’.
Commenting on the findings, Mark Lapping, Chief Executive Officer, at Aquapak, said: “Our study shows that the European packaging producers is embracing the circular economy, with a focus on achieving full circularity. At Aquapak, we are supporting this goal by helping our customers
use the world’s resourcesmoreeffectively by reducing waste and increasing the reuse of valuable materials as part of the circular economy through new technologies which provide the functionality needed to protect products,whilstreducingthe impact on the environment.”
Aquapak has developed HydropolTM, a polymer based on PVOH, which can be successfully coated on to both paper and board, with proven gas and grease barrier properties, with additional functionality such as heat seal and increased paper sheet strengthcanalsobeimparted, making it suitable for a range of packaging uses suchas bags andpouches.
Aquapak has already proven that HydropolTM coated paper is 100% repulpable in standard pulping systems and can be fully recycled and it proven to give real improvement when set against
current regulations which allow the ‘recyclable’ label to be used if there is up to 15%unrecyclablematerial in the product. If littered HydropolTM is biodegradable, compostable, as well as be-
ing non-toxic and marine-safe.
To read the full report, visit Sustainable Packaging in Europe: The drive for change – aquapak
(aquapakpolymers.com)
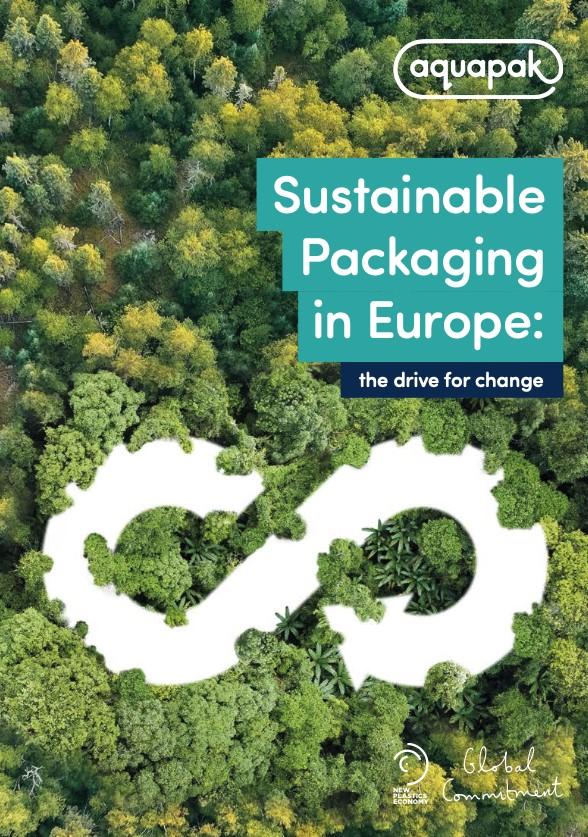
Multi-country study setting new benchmark for detail and understanding of plastic packaging in European waste streams
CEFLEX and partners are conducting a multi-country compositional analysis to research the type and amount of flexible packaging and rigid plastic packaging in the post-consumer waste stream. The research is providing valuable data to understand the collection, sorting and recycling infrastructure needed in each country.
Following indepth compositional analysis at sites in the UK and Germany, and now also The Netherlands and France, a multi-country study by CEFLEX, Resource Futures, and partners PCEP, Petcore Europe, Styrenics Circular Solutions and the Tubes Recycling Project managed by Stina Inc. continuestogatherinsights on the reality of today’s collected household packaging waste. The insights generated represent a vital step for-
ward towards a circular economy for packaging materials.
In addition to the extensive data gathered at each site, a first round of country-tocountry analysis is starting to be made. Across four countries (UK-Germany-The Netherlands-France), a total of 12.8 tonnes of residual waste and 4.9 tonnes of recyclables were sampled, sorted and analysed giving several levels of detaileddata.
CEFLEX will be focusing on key takeaways specific to flexible packaging and collaborating with its rigid plastics partners to explore insights across all formats.
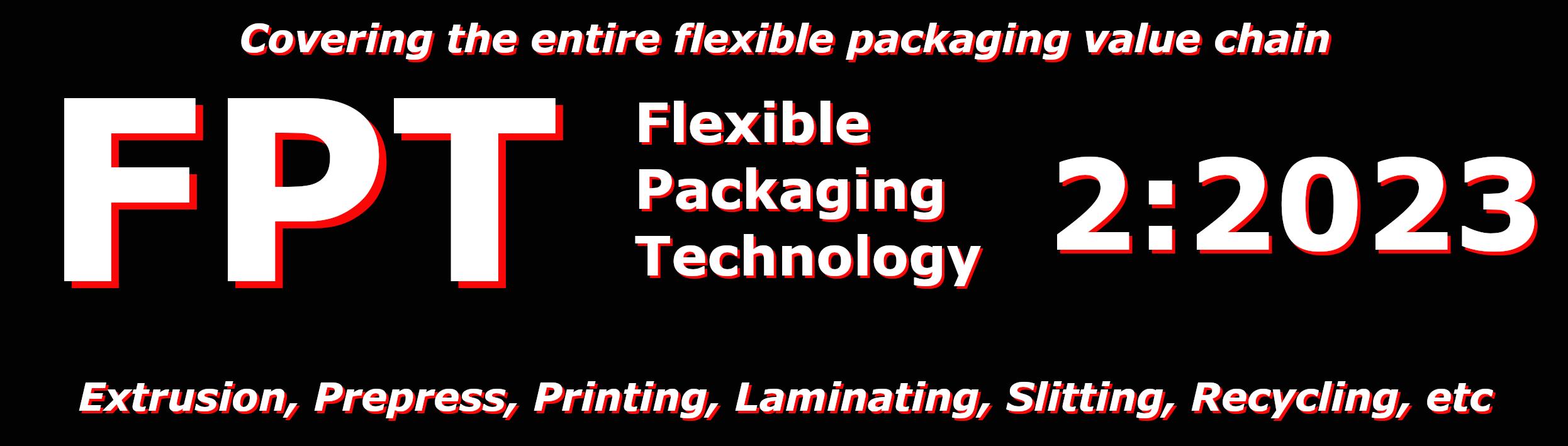
Separate collection and sorting can tap into lots of ready to recycle resources
Which waste stream flexible packaging is found in shows the impact of a wellestablished separate collectionsystemforre-
cyclables. For instance, flexibles are not widely separately collected for recycling in the UK, including by those local authorities where the research was conducted.Thisexplainsahigher percentage of flexible packaging found in the UK residual waste stream compared to Germany and the Netherlands
Headline percentage splits–excludingcarrier bags and bin liners – by weight of flexible packaging in separately collected recyclable and residual waste streams in four major European countries:


% (by weight) of flexiblepackagingin:
The study also found a significant amount of flexible packaging to be recyclable monopolyethylene (PE) and mono-polypropylene (PP) – between 40% and 60% of flexible packaging depending on the country and waste stream.
Thisencouragingfinding indicates significant quantities of recyclable flexible packaging are potentially available to be sorted and returned to the economy, with amounts expected to rise further as design changes increase the proportion of monomaterialpackaging.
Country by country insights
The composition by country – flexibles in the recyclable stream data shows variation in the proportions of the different types of flexiblepackagingstructures found in the separately collected recyclable wastestreamcountryto country. This reflects different collection schemes in terms of what materials are and aren’t separately collected,butalsodifferent consumer habits and markets in those countries.
In all countries studied the greatest proportion of flexible packaging found in the recyclable stream is monomaterials films, primarily mono-PE and monoPP. This is a positive
finding as these are the materials most easily recycled and CEFLEX’s preference for designing flexible packaging. There is a varying proportionofmulti-material structures country to country, with smaller amounts of paperbased, aluminium foilbased, biodegradable and compostable structures.
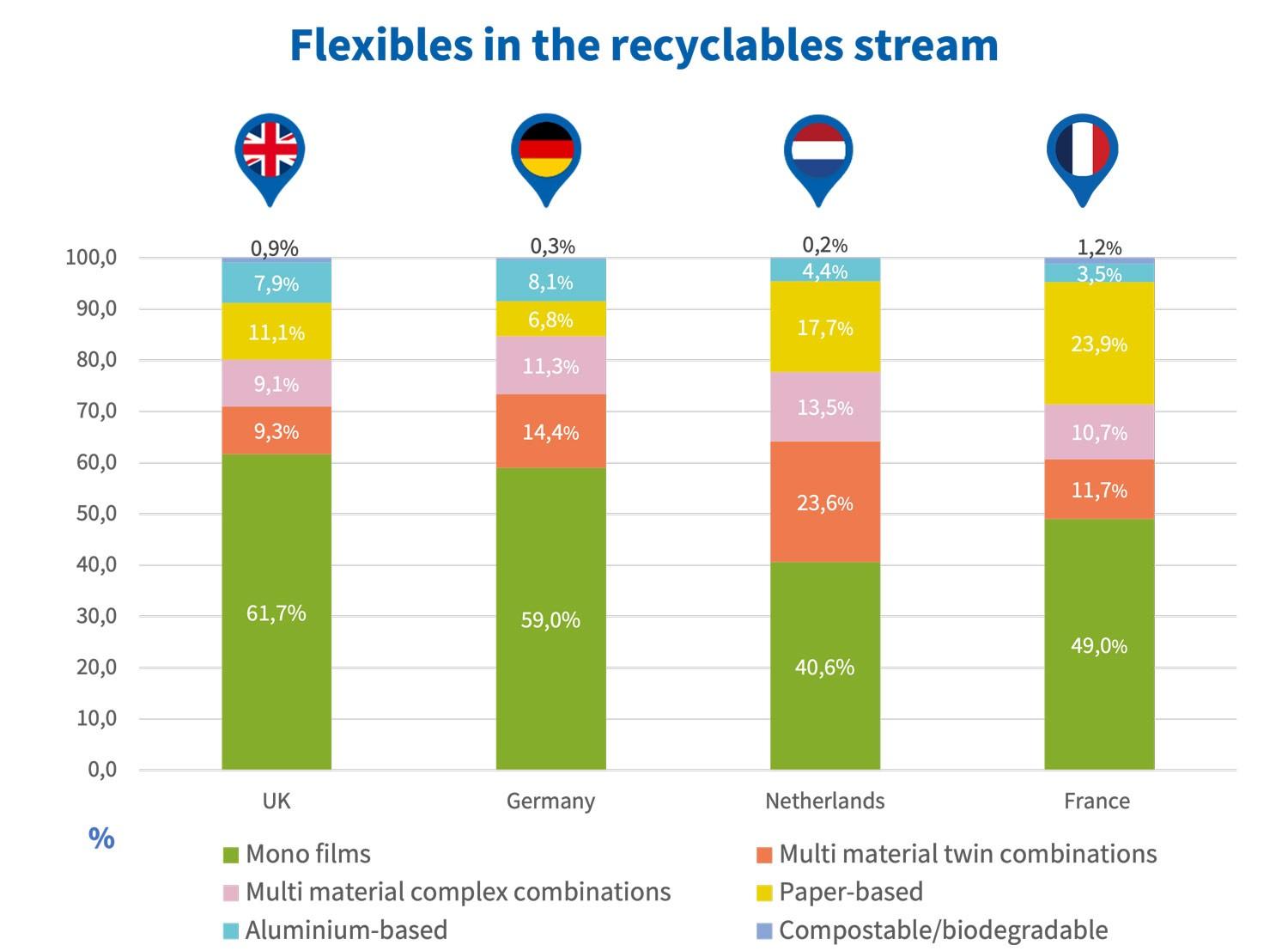
For rigid plastic packaging, categories most commonly found across all countries and both in the separately collected recyclables stream and the residual waste streamwerepolypropylene (PP) pots, tubs and trays; polyethylene terephthalate (PET) bottles and pots, tubs and trays; plus high density
PE (HDPE) bottles. There are relatively small amounts of other plastic packaging including tubes in the wastestreams.
Assessment and categorisation
All packaging was manually sorted, identified and categorised using a standard and consistent set of categories. Category descriptions were
simplified to support this process. ‘Multimaterial complex combinations’ included flexiblepackagingstructures such as those containing a combination of PET, Aluminium and PE for example, or structures with barriers materials or layers. ‘Multimaterial twin combinations’ included structures that contained PA and PE for instance, or mixedPOstructures’.
Assessment at each facility took place over five days, with 20 samples of 30-110kg recyclables and 20 samples of 140-180kg residual waste at locations in UK,Germany,TheNetherlands and France in 2020-2022. Samples were taken from different loads, locations and times, with the aim to reflect variety in households and socioeconomic factors. All samples were taken prior to the waste being sorted or processed. After identifying rigid plastic packaging, flexibles were separated by
material type and product area, with a handheld NIR used to identify multi-material plastic films. An extensive number of categories and data were developed with CEFLEX, its partners, brand owners and packaging technologists. This allowed for plastic film identification based on a product or brand; and a library of known samples built to support identification using a handheldNIRscanner.
Nextsteps
The four country study data has been extrapolated to a national scale, building our understanding of how much and what types of flexible packaging appears in the recyclable and residual waste streams in each country. This is vital to understand the collection, sorting and recycling infrastructure needed in each country and the implications for Extended Producer Responsibilityschemes.
With the compositional analysis study now achieving an important threshold of completing fieldwork in four countries,CEFLEXstakeholders and partners can look forward to further webinars sharing insights and expert analysis, plus an executive summary of findings during2023.
Investments in capacity are just the tip of the iceberg for Minipak as it showcases quality and competitiveness in the flexible packaging industry
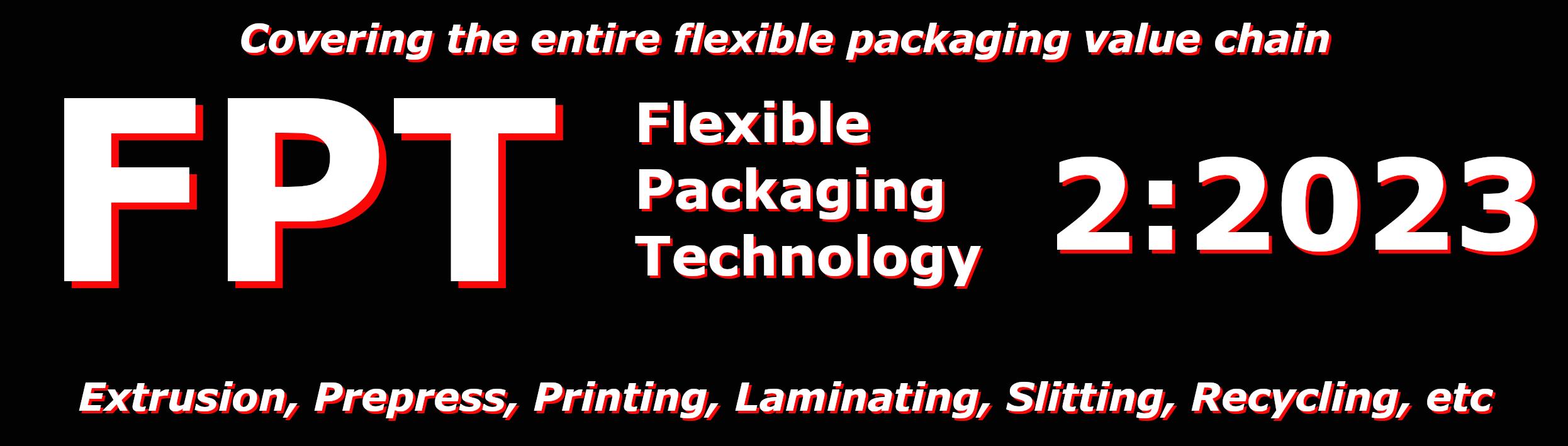
Founded in 1976, Minipak S.A.S. is one of the largest flexible materials manufacturers in Colombia, servicing the whole Americas with high quality flexible packaging. Minipak has seen significant growth over the years and currently has a turnover of more than USD 125 million, thanks to an outstanding investment strategy in its two plants in Colombia. There has also been a strong focus on ensuring its 800 employees have the best skillset to provide customers with the highest performing solutions.
Minipak began by providing the confectionery industry with high quality printed films. Since it was established, customers’ needs and challenges have always been front of mind to create a growth strategy that nowplacesMinipakasa leading player in the market. Over the years, the company’s approach and investments have enabled them to enter new markets, including chocolates,
snacks, food, pet food, personal care, and even industrial applications, with more sophisticated products.
“The investment level, which represents up to 15% of Minipak’s turnover, is targeted towards state-of-the-art equipment, the best technology available and reliable technical services to deliver an operation that is efficient and competitive,” says Humberto Portilla, vice-
president of production of Minipak. Continued investment has also enabled the business to broaden its geographic reach – today, it exportsmore than70% of what it produces to more than 35 countries aroundtheglobe.
As a company that strives for quality, it is no surprisethatMinipak has a long history with BOBST gravure technology. It first established a relationship with Ce-
rutti, which was acquired by BOBST in 2021, and then continued to invest its technology. Currently, the company counts 7 BOBST gravure presses among its assets and is about to install a brand newone.
Besides purchasing best -in-class equipment, Minipak also invests in maintainingitsassetsto ensure optimum performance at all times. Recently, the company invested in a Retrofit program to its 10-colour, inline lamination,
BOBSTRS6003HSgravure press. The result was an increase in output of 20% working at speeds up to 600 m/ min,greaterautomation and protection against unplanned downtime of the machine. “Being abletoconvertcoldseal applications at the maximum speed of conventional materials was a must for us, and the collaboration of BOBST and the Minipak team made it possible!” says Humberto.
However,theincreasein capacity was not
enough to meet the increase in demand, which led the company to consider investing in more capacity. The natural decision was to purchase a new 9colour BOBST MASTER RS6003gravurepress.
“Two main reasons explain our decision for BOBST machinery: Number one is the brand itself. BOBST brand resonates among the main large corporations as the ultimate technology in the industry, so when they are evaluating suppliers like

us for their packaged goods,theBOBSTbrand on the equipment nameplate is a plus. Second, from an internal perspective, is the reliability of the equipment and the repeatability of printing, which guarantees we deliver consistent quality time and again to our customers,” saysPortilla.
The recent investments not only support Minipak’s geographical expansion, but also provides the company with the quality and performance needed to delivermoreproducts,especially cold seal applications,tocustomers.
“Improving our capacity with a higher degree of technology, has been keyforustogainsignificant new businesses worldwide, mainly in more sophisticated products. The move towards cold-seal applications is a good example of that. We recently closed a deal with a leading global chocolate producer, which was only possible due to this
capability,” states the executive, mentioning some key differentiators as the colour consistency achieved by colour registration features, and tension control provided by the servo systems, which enables working on thinner and more complex materials.
“There are also significant logistics gains, allowing us to deliver faster. Considering an export to the US, currently our main market, we can deliver in five to six weeks. In some cases, we were able to deliver in less than two weeks!” he says. This is especiallyimportantina moment when companies are witnessing high pressure on the cost of working capital and interestrates.
Quality, sophistication and logistics gains are not the only advantages Minipak achieves. All these gains also translate into a more sustainable operation, as you can achieve more with the same re-
sources. “This is especially important considering we are servicing large global brands all over the world,” states Portilla.
“A well-established process, and relying on equipment that we can run faster, with the highest degree of quality and accuracy, saving us a lot of time and resources, ultimately translates into less waste, lower energy consumption, and resource optimization, making Minipak the supplier of choice when it comes to sustainability.”
Technology and processes are run by people, and that’s an additional strength of the company. Through the ‘CampusProject’, aneducational program created by Minipak for their employees, currently 250 people are studying towards a collegedegree,inareasincluding engineering, finance and logistics. The goal is to have all employees graduate in
about five years. “We are talking about industrial, mechanical, and chemical engineers, for instance. We want to service the market in the most proficient and skilledway.”
“I think that all those things, having the right people, the right equipment, the right technology, pumping in a lot of capital into R&D and having very competitive structure in terms of cost and lead times make us very optimistic about the future ahead of us,” concludes HumbertoPortilla.
Recently Minipak S.A.S., has joined the European Rotogravure Association (ERA), marking a new chapter in its longstanding journey as a key player in the international packaging industry.
Founded in 1976, Minipak has grown into a dominant packaging printer boasting an impressive array of 10 presses, divided equally between gravure and
flexographic methods. This latest partnership further solidifies the company’s foothold in theglobalmarket. The company has a formidable presence in the confectionary and cold seal packaging sector, exporting 70% of these products to over 35 countries worldwide. This strong global export network demonstrates the firm’s ability tomeetdiversecustomer demands while maintaining a robust supply chain across different continents.
JoiningtheERAwillprovide Minipak access to a larger network of industry professionals, cutting-edge research, and valuable insights into the latest industry trends and developments. This move will further enhance Minipak’s ability to deliver high-quality, innovative packaging solutions to itsexpansiveclientele.