

Vacuum Metallising of Flexible Colour
Vacuum Metallising of Flexible Colour
Shi ing Films without using inks, pigments or flakes
Shi ing Films without using inks, pigments or flakes
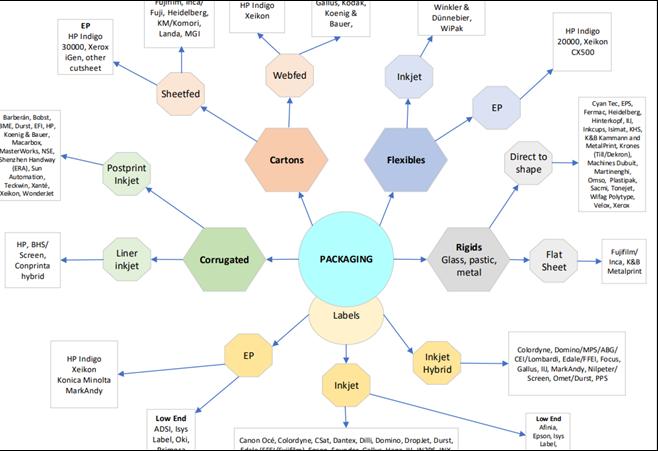
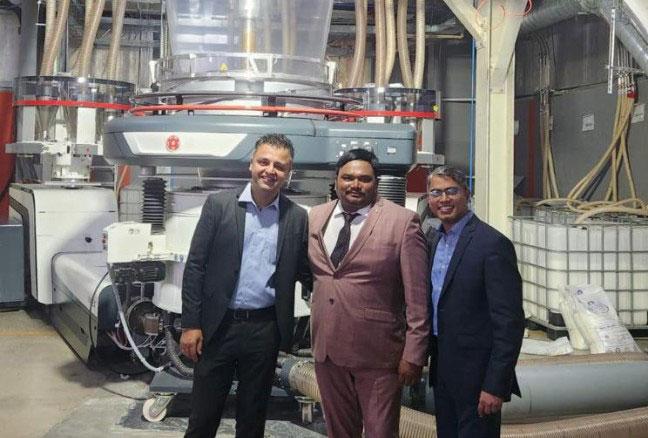
Digi za on of Packaging
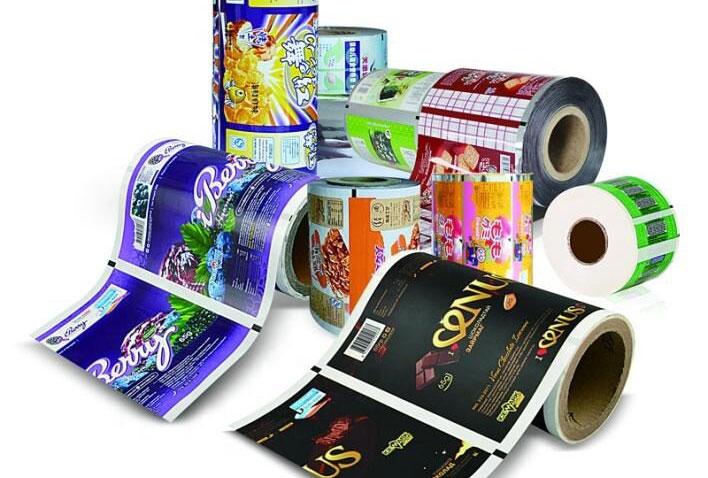
Packaging Laminate Market is Expected to Reach a High Valua on of USD 9,694.9 Million
Lorven Group Boosts Produc on with VAREX II: New
Benchmark
Vetaphone coronaequipment favoured by Amcor Flexibles
Colour shift effect is produced in nature by different mechanism including pigments, light absorption and interference as well as by a mechanism called photonic crystals. In industrial applications various methods have been employed to reproduce such effect. These methods rely on physical, chemical, and mechanical principles. This includes optical absorption, interference, micro-structuring and scattering.
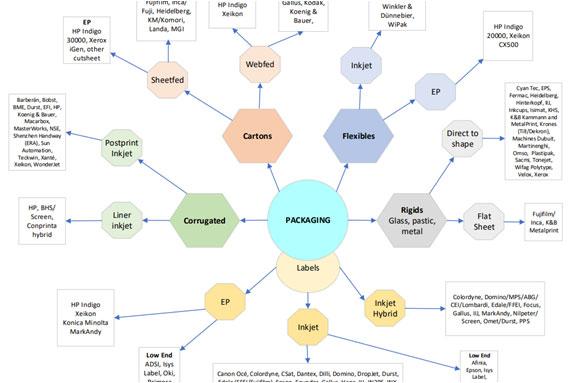
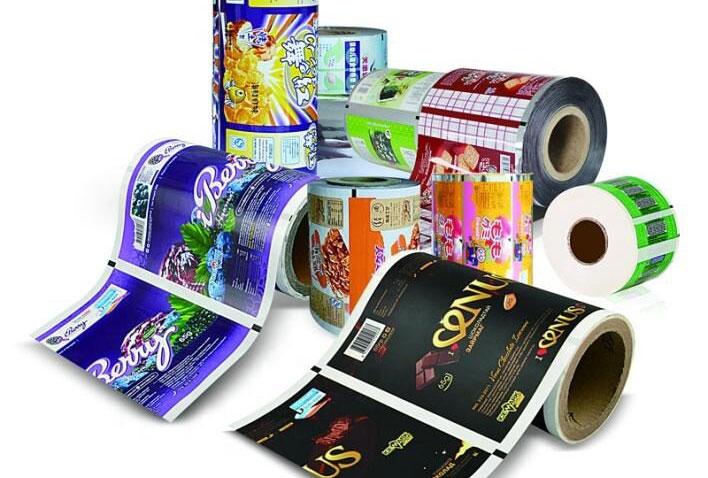
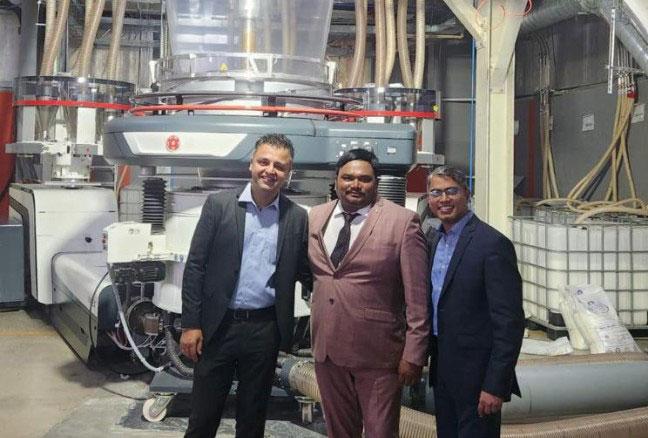
At last. drupa is back, with less than a year to go the anticipation is building. Trying to work out what the theme of the show will be tricky, after eight years and the impact of COVID. The drivers of sustainability, automation and workflow as the world continues to digitise dominate most print and packaging operations.
The global packaging laminates market is set for significant growth, with sales expected to rise from USD 6,336.3 million in 2024 to an impressive USD 9,694.9 million by 2034, reflecting a compound annual growth rate (CAGR) of 4.3% over the forecast period. This follows a strong market performance in 2023 when packaging laminate revenue reached USD 6,118.4 million.
At W&H, innovation is at the heart of everything we do. Our mission is to develop cutting-edge solutions that empower our customers to achieve new heights of efficiency and quality. The recent installation of our VAREX ll blown film extrusion machine at Lorven Group exemplifies our commitment to this mission, delivering an impressive output of over 900 Kg/hr and setting new benchmarks in the industry.
When a major global packaging group like Amcor chooses Vetaphone surface treatment equipment for its flexible packaging plant in Belgium, it’s a massive testimonial to the quality and reliability of the Danish manufacturer’s technology. 4 12 16 20 22

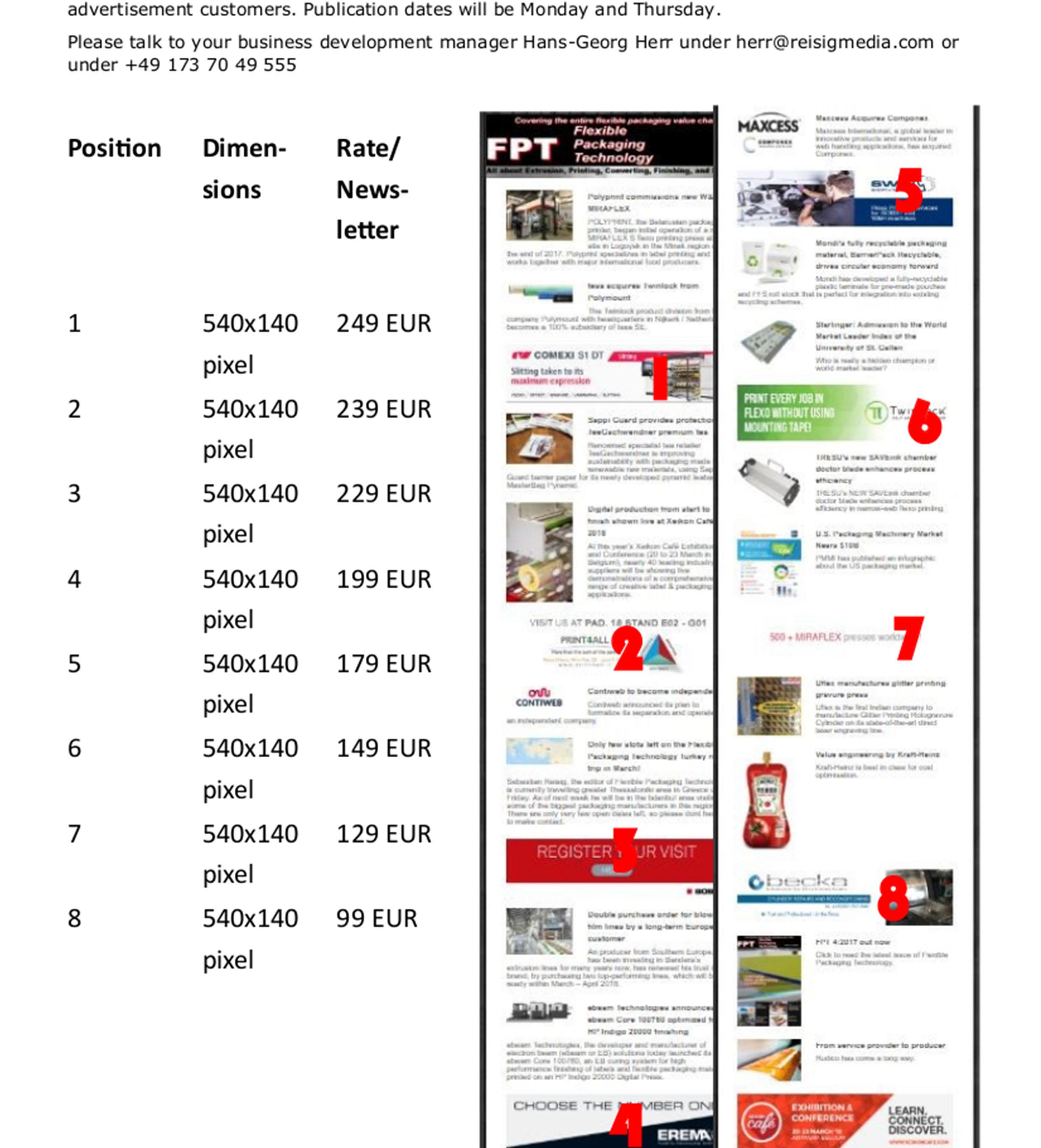

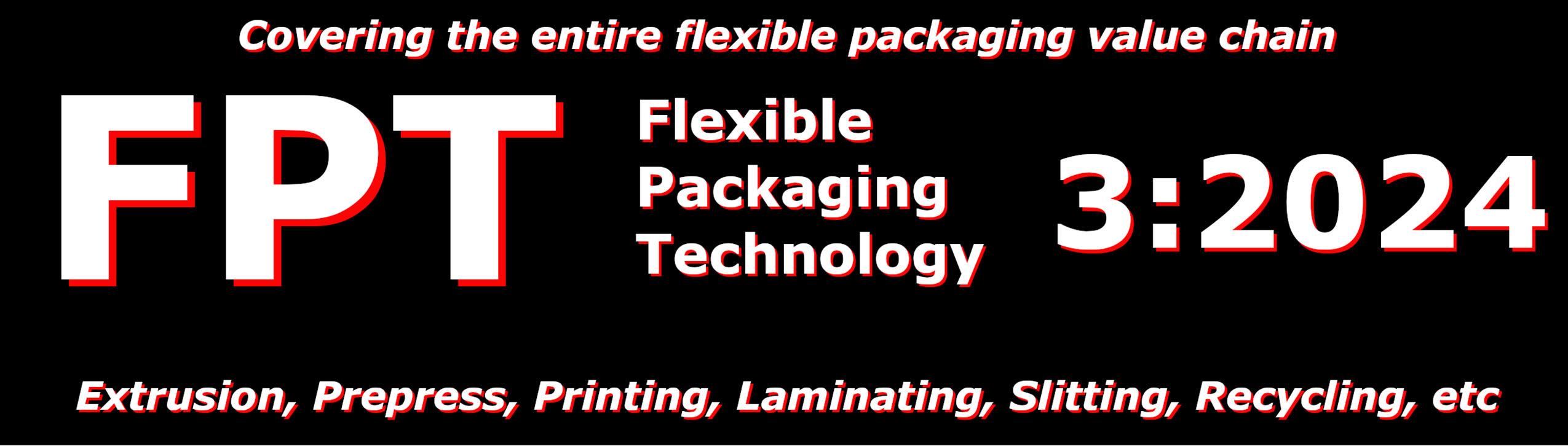
Vacuum Metallising of Flexible Colour Shifting Films without using inks, pigments or flakes
Colour shift effect is produced in nature by different mechanism including pigments, light absorption and interference as well as by a mechanism called photonic crystals. In industrial applications various methods have been employed to reproduce such effect. These methods rely on physical, chemical, and mechanical principles. This includes optical absorption, interference, micro-structuring and scattering.
Idvac ltd, a UK innovative vacuum R&D specialist, has recently developed a vacuum metallising process of flexible colour shifting films without the use of structural embossing, inks, flakes or pigments. The process exhibits an aesthetically appealing colour shifting effect from red to green depending on the angle of viewing. This process is cost effective and can be used for many applications.
The Colours with brilliant lustres found in nature have long attracted the scientific interest. Such colours can be observed in flowers, pearl, jewel, butterflies, peacock tail, beetles and fishes. Natural colour lustres are caused by different mechanisms including pigments, light absorption and interference as well as by a mechanism called nano-structuring. To reproduce such colours in the laboratory scientists have used various physical, chemical, and mechanical principles including optical absorption, interference, plasmonic micro-structuring and scattering.
Plasmonic nanostructures systems (Figure 1) are generally containing nanostructured metallic components allowing for the exploitation of surface plasmon resonances to capture, concentrate, and propagate optical energy. This produces coloration which originates from the variation
www.packagingnewsletter.com
at a length scale structure comparable to the optical wavelength.
On the other hand, vacuum web metallizing technique has been employed to reproduce such coloured lustres for commercial use. This technique is a powerful and flexible tool that has so far been used successfully to metallize flexible films and papers with aluminium for packaging applications. It is also used to reproduce structural colours by metallizing holographic embossed films with aluminium or high refractive index material. Vacuum web metallizing offers faster and cost effective method for producing colour lustres as compared to other processes which have been carried out using slow and time consuming physical or chemical processes.
Vacuum web metallizing can provide a manufacturing opportunity to increase production throughput of iridescent or colour shifting prod-
ucts at high speeds and low cost. However, this approach is mainly used for decorative and some security applications. This article will outline the basic principles of thin film optical interference for the production of colour lustres and will discuss the physics of iridescent colour shifting effect.
The Physical Principles of Thin Film Interference
Interference effects occur when two optical waves constructively or destructively combine after reflecting from two parallel surfaces. If the optical path of the two surfaces is a multiple of exactly one full wavelength, the two waves will constructively interfere and there will be a strong reflection at that wavelength.
On the other hand, if the phase of the reflected wave differs by onehalf wavelength or an odd multiple of one-half wavelength, then the
www.packagingnewsletter.comwww.packagingnewsletter.com

reflected waves will be completely out of phase. Consequently, a destructive interference will occur at that wavelength. In the latter case, the reflected wave will be low, and therefore a maximum in transmission. The phase of the two waves depends on the thickness and refractive index of the media separating the two surfaces, the wavelength of the light and the angle at which light strikes the surfaces.
The simple form of thin film interference consist of three layer stack; opaque metal layer coated with a transparent dielectric layer then a semi- transparent layer on the top (Figure. 2). When a monochromatic beam of light is incident upon the first semi-transparent layer, its amplitude will split or divided by partial reflection. The reflected wave will propagate towards the observer whilst the second transmitted beam will travel an opti-
cal path length of 2ndcosØr, where n is the refractive index of the transparent material; d is the thickness of the
transparent material; Ør is the angle of refraction. The transmitted beam will then be reflected from the metal
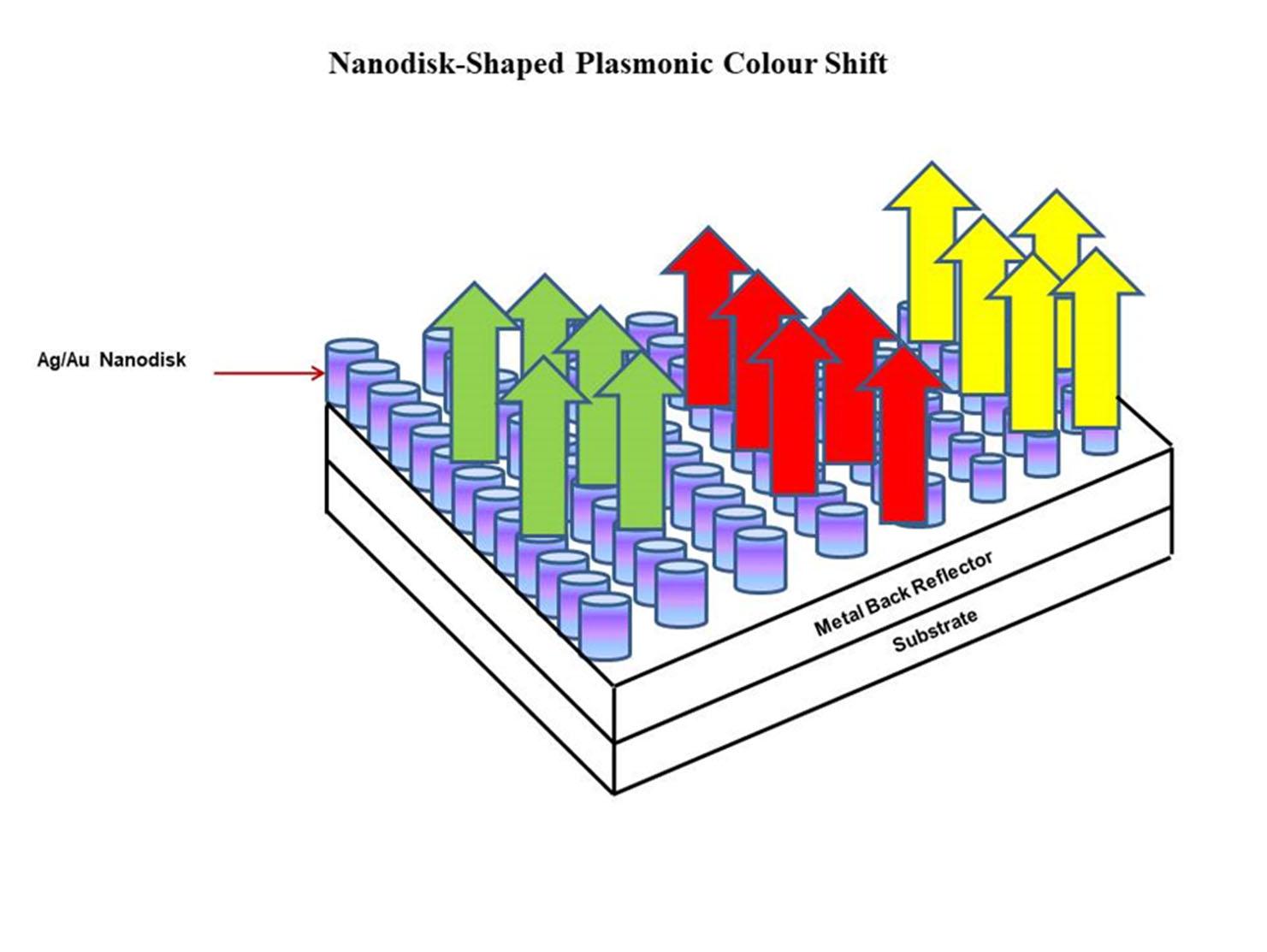

www.packagingnewsletter.com
opaque layer and propagate towards the observer. If the two reflected light (or partial amplitudes) exit the stack with the same phase then they constructively interfere, thus enhancing the reflectivity of the stack at that wavelength. In this case, the path difference between all corresponding points on the two wave fronts must equal some integer multiple, p, of the incident wavelength.
It can be seen from Figure 2 that if the reflective phase shift is the same then the condition of constructive interference is
mλ= 2 nd cosß. If the path difference between the two wavelengths is equal to an odd multiple of half wavelength ( i.e. χ= [(m+½)λ], then they will destructively interfere. This will reduce reflectance at that wavelength. For high quality iridescent reflection the constructive and destructive interfer-
ence should be optimised to achieve high degree of luminosity and spectral selectivity. Also, the peak reflective wavelength, i.e. the colour of the stack should changes as the observer changes the viewing angle. This will produce a clear colour shift or interference when the optical stack is tilted by certain degree.
The types of dielectric materials utilized to fabricate interference films depend on the application. In general, such dielectrics are nonconductive materials having
a specific low or high refractive index. Materials such as zinc sulphide (n=2.6), Titanium oxide (n=2.7), or Aluminium oxide (n=1.76), Silicon oxide (n=1.54) and sodium aluminium fluoride ( Cryolite) have been used. However, some of these materials are hygroscopic and must be insulated from the environment by a protective coating. In addition, the zinc and Cryolite salts suffer from temperature instability, which further reduces their performance, even though
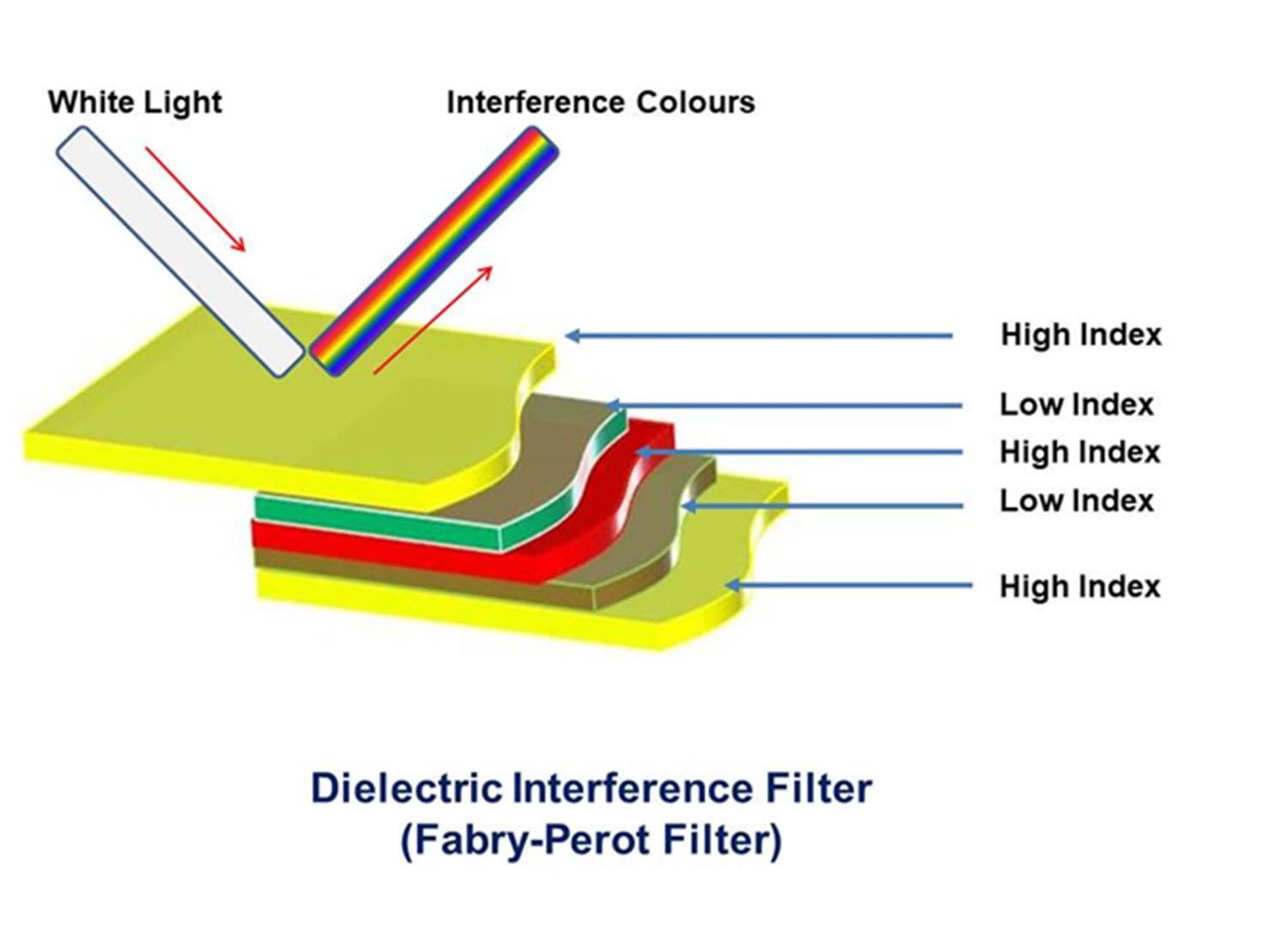
they are simple and relatively cheap to manufacture. After deposition of the dielectric salt layers, a final layer of silicon oxide or a protective polymeric coat are applied on top of the multi-layered stack for protection.
In other optical interference designs, alternating high and low refractive index values are applied on substrates such as flexible films. The critical element of this design is the interface between two dielectric materials of differing refractive index (one much higher than the other), which is responsible for partially reflecting incident light forward and backward through the filter and producing the interference effect that results in wavelength selection. Reflected and transmitted wavelength values are determined by the thickness and refractive index of the interspersed dielectric layers. Even though the thin coatings themselves are transparent,
light waves reflected and transmitted by the dielectric materials interfere to produce brilliant iridescent colours that appear to be emanating from the film surface.
Colour Shifting by Fabry-Perot Structure
Optical coatings consisting of one or more films of dielectric or metallic materials are widely used in applications ranging from mirrors to eyeglasses and interference filters. Many conventional dielectric coatings rely on Fabry–Perot
type interference, involving multiple optical stacks of transparent layers with thicknesses of the order of the wavelength to achieve functionalities such as anti-reflection, highreflection and interference. The Fabry-Perot interferometer was designed in the late 1800s by Charles Fabry and Alfred Perot. The Fabry–Pérot interferometer is an optical cavity resonator made from two parallel reflecting surfaces. It only transmits light of its resonant frequency (Figure 3).
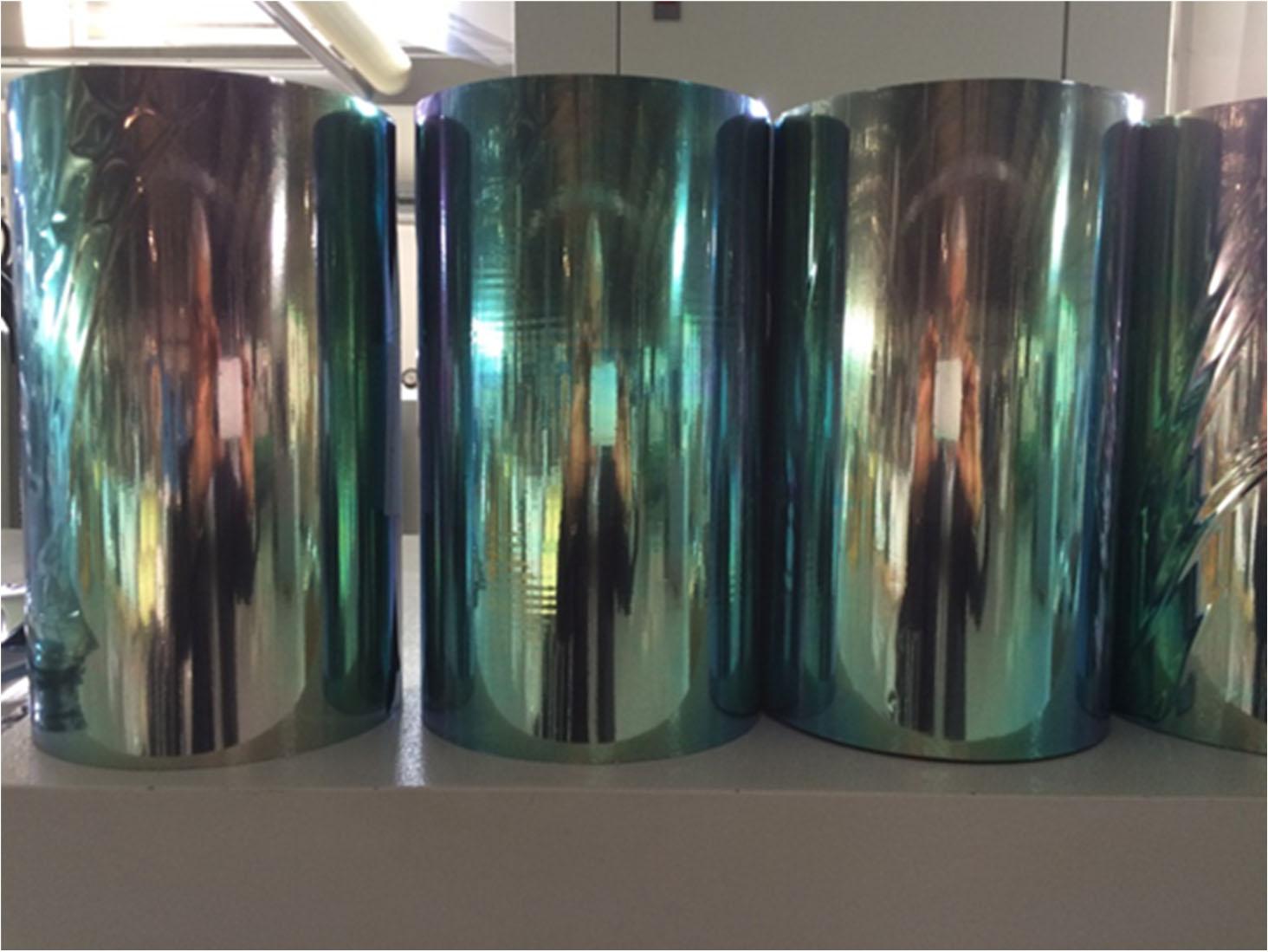
Opaque, inorganic based colour shifting Fabry-Perot structures have been used for many years and have excellent colour shifting effects. Typically, structures of this type are made by depositing upon a substrate, a reflector layer, followed by a dielectric layer followed by an absorbing layer. Such products appear highly reflective from one side due to the presence of a reflector layer and appear highly reflective with a colour that changes in an angle dependent manner when viewed from the opposite side due to the Fabry-Perot structure. Iridescent Flakes used in paints and inks can be obtained from symmetric Fabry-Perot structures of the type Absorber/Dielectric/ Reflector/Dielectric/ Absorber, where two single Fabry-Perot structures share same reflector, by stripping off the deposited layers in the form of Flakes from the substrate , and subsequently dying the
Flakes. Such Flakes can be made opaque or transparent and are used to make colour shifting paints and inks.
Idvac ltd Recent Colour Shifting Effect
Idvac Ltd. has recently developed a colour shifting effect on flexible film without the use of structural embossing, inks or pigments. This process is based on Fabry-Perot optical principles for quick colour switch. It is a combination of vacuum metallizing process and low index polymeric coating. The process exhibit an
aesthetically appealing colour shift effect from red to green depending on the angle of viewing. (Figure 4).
The metallization process is carried out at fast film line speed and can be done inside a standard vacuum web metallizer without the need of any additional parts or modification. This effect can be combined with holographic micro- embossing images to add extra security element to a hologram. It can also be used for security threads and decorative packaging in-
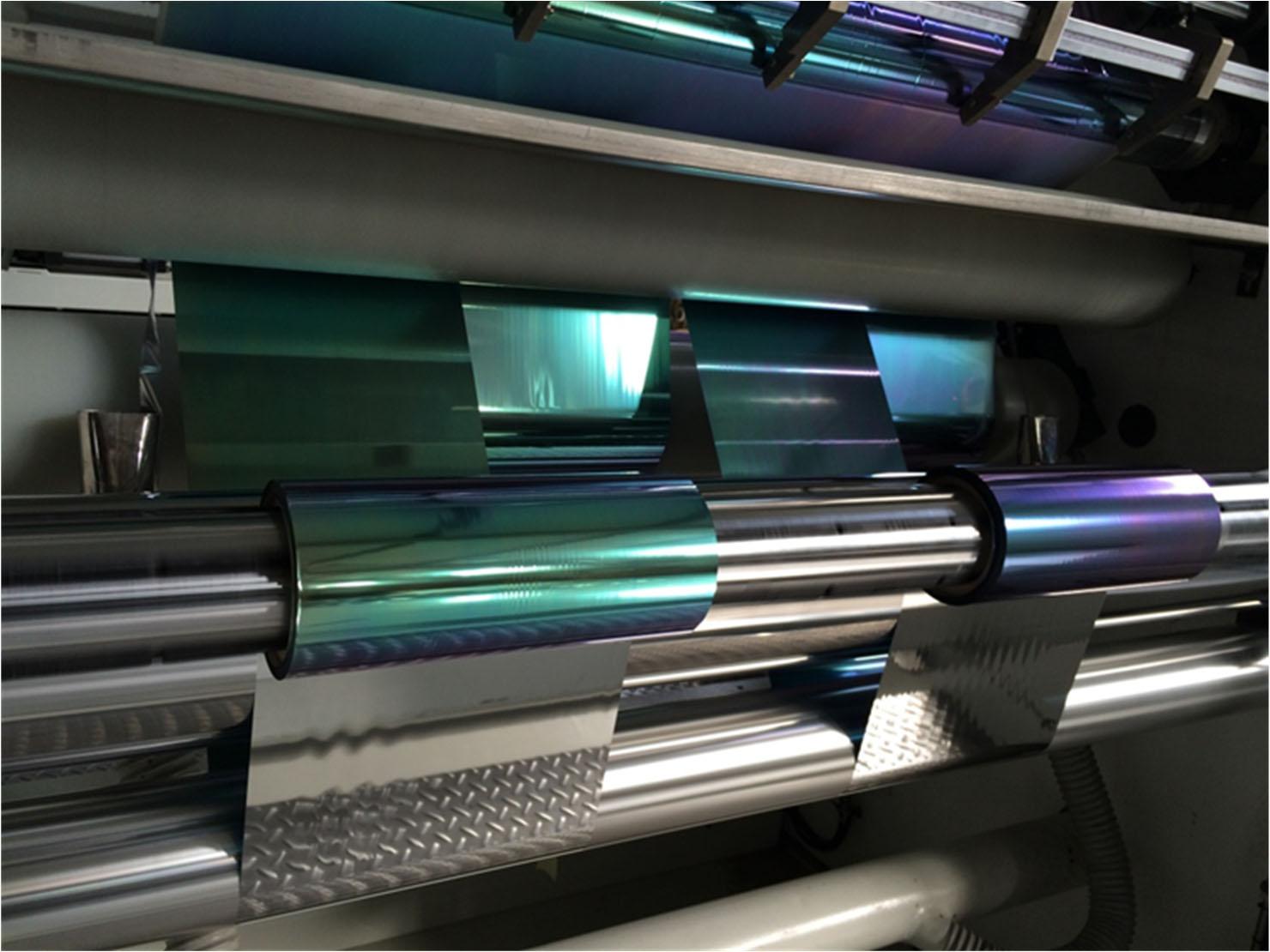
cluding pharmaceutical to add visual appeal to packed products. This colour shift effect can also be printed on films to produce texts, logos and patterns with a quick colour switching between red and green (Figure 5&6).
Conclusion
There are various processes that can be employed to produce iridescent or colour shift-
ing effect. The selected process depends on the final application and market.
However, the employment of Fabry-Perot principles, which consists of multi-layered optical stack, allows the tuning of the reflected colours according to applications and requirements. This provides good spectral selectivity performance over particular wavelengths to
give flexible films unique features such as selective see-through (transparency) with colour shifting effect or selective visible reflected (opaque) colour shifting effect. The product can be used in many applications including packaging, pharmaceutical and security.
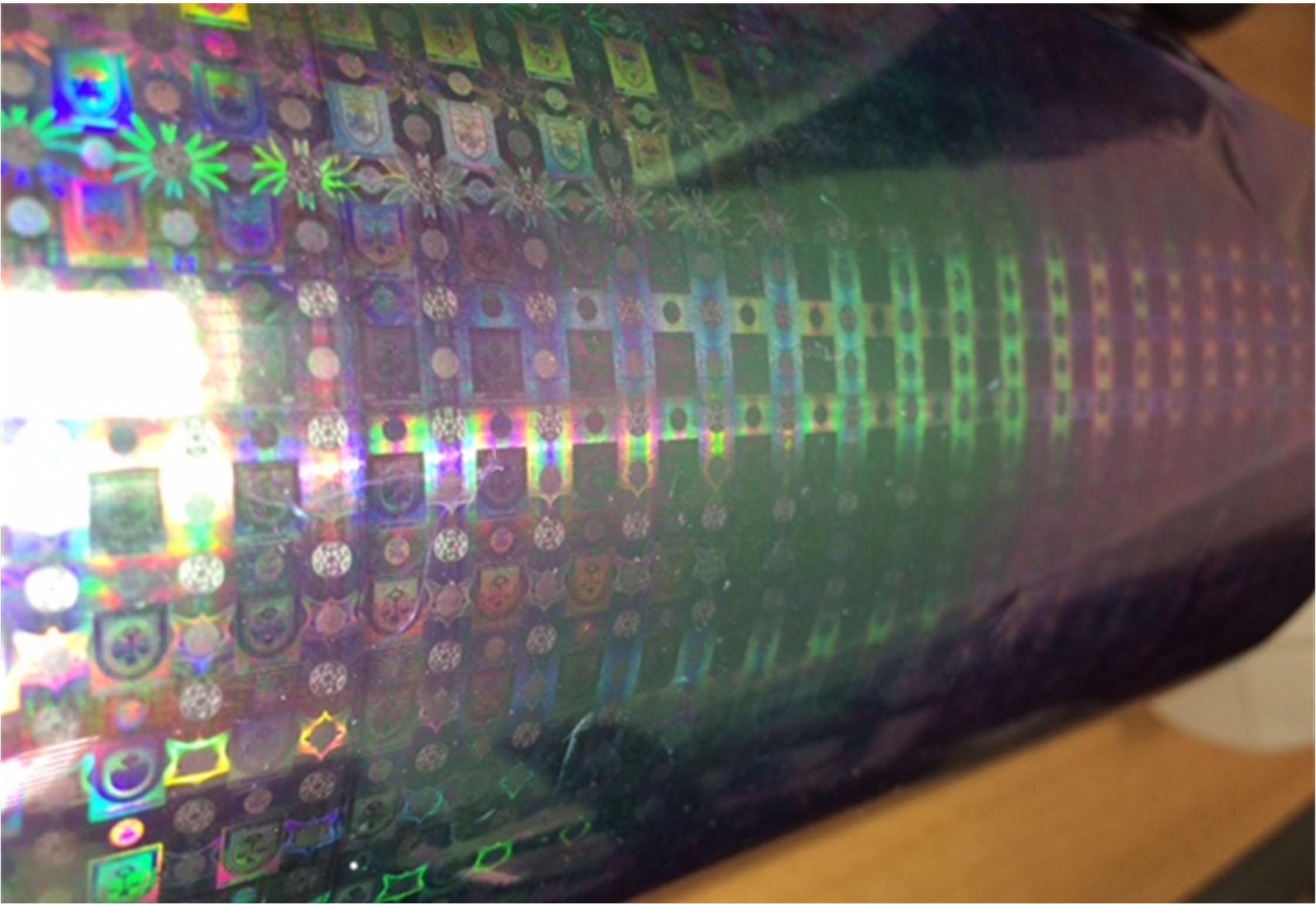
www.packagingnewwww.packagingnewsletter.com



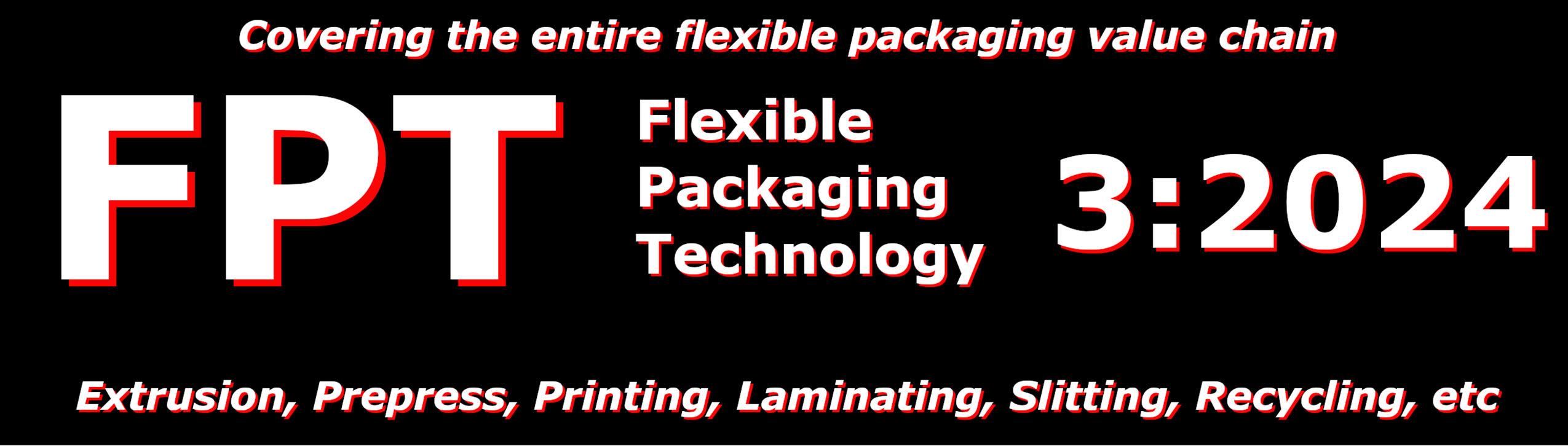
Digitization of Packaging
At last. drupa is back, with less than a year to go the anticipation is building. Trying to work out what the theme of the show will be tricky, after eight years and the impact of COVID.
The drivers of sustainability, automation and workflow as the world continues to digitise dominate most print and packaging operations. Recruiting and retaining skilled staff is increasingly difficult for many businesses as baby boomers retire and the younger digital native generations demand a different approach to their working life.
by Dr Sean Smyth – Analyst & Consultant, Smithers
The Digital print developments will be centre stage across all graphics, industrial and packaging and there will be further announcements this year at drupa. Digital packaging offers many opportunities for commercial printers looking to move into new sectors as many traditional print applications continue to decline. The same dynamic is en-
couraging more equipment suppliers to offer digital printing systems for labels, corrugated, cartons, flexible packaging, rigid plastics, glass and metal packaging.
The figures show how the suppliers of digital print equipment for labels and packaging has developed since this technology map was first produced in 2019. There has been a
steady stream of new entrants, from established analogue print equipment suppliers and new providers leveraging their digital print expertise.
Image 1 and 2 Digital printing systems for packaging and labels in 2019, and in 2023 (right)
On top of these there are digital overprint
www.packagingnewsletter.com
systems and sophisticated bespoke integrations, some operating as a part of manufacturing and filling lines. While there has been consolidation in the supply side it is striking that there have been few exits from the sector, the high number of players now competing in the wide range of packaging applications, offering new capabilities and functionalities, with steadily increasing productivity and lower costs.
Well, the good news for us print techies is this diagram will get even more crowded this year. Smithers tracks the developments in this sector, publishing reports and running conferences on digitally printed packaging. The European, American and
Asian events bring together hundreds of brands, retailers, packer/fillers, converters, agencies and designers together with equipment, substrate and ink/toner suppliers, with workflow and logistics companies also involved. These are excellent forums and over the years the discussion moved from technology issues into tangible benefits and improved business processes from adopting digital printing, and increasingly digital finishing. Today quality, reliability and productivity are no longer issues for inkjet and electrophotography packaging presses. At drupa there will be sheetfed inkjet machines offering the equivalent of process colour sheetfed litho at
speeds of 11,000 B1 sheets per hour, while web presses offer speeds in excess of 400m per minute up to 2.8m wide. These are mainstream alternatives to litho, flexo and gravure alternatives.
The printhead and press manufacturers are developing methods to eliminate inkjet artefacts, compensating for nozzle outs and deviations in real time that extend the life of the heads and machine uptime. Inkjet will be the real winner, with faster machines being shown, particularly in flexible packaging. Ink technology is improving, with UV and water-based inks being employed for specific applications. There will be more highly pigmented formulations helping reduce the

www.packagingnewsletter.com
inkfilm thickness while lowering the total cost of ownership further boosting the share of digital print.
It is not just printing. Some vendors will show single pass, highly automated systems to print and finish corrugated boxes, cartons and flexibles in a single pass. The enabler is the combination of digital print with digital finishing. These will feature automated control systems that drive the press, measure and check the print then track through finishing which may be coating, laminating, cutting, creasing, folding and gluing, together with a wide variety of embellishments. The digital front end controllers are becoming increasingly powerful, automating and driving the digital print unit while at the same time measuring and controlling quality and then to set and drive the finishing technology. This approach helps replaces the traditional skills of
press minders and finishing journeymen operators – important as skilled labour resources become scarcer.
While new digital presses are the shiny and sexy headline grabbers, even more important is the enabling workflow software. The only way of making money from a digital press is to produce saleable output and powerful workflow is vital to prepare the artwork files and keep the print queue well stocked. This can be a barrier for packaging converters entering the sector as many do not have the necessary prepress and data handling skills. drupa will see many companies providing solutions, in-
tegrating with management information systems to automate the administration needed to handle many short run jobs. Workflow will become increasingly collaborative, with new designs produced and approved, then loaded into job queues for automated colour management and imposition with no manual involvement at the converter. The MIS is linked, ordering substrates and planning the production on printer and finishing to meet the customer requirements and optimise capacity at the converter.
Digital workflow can be daunting for packaging converters used to handle a few large jobs but
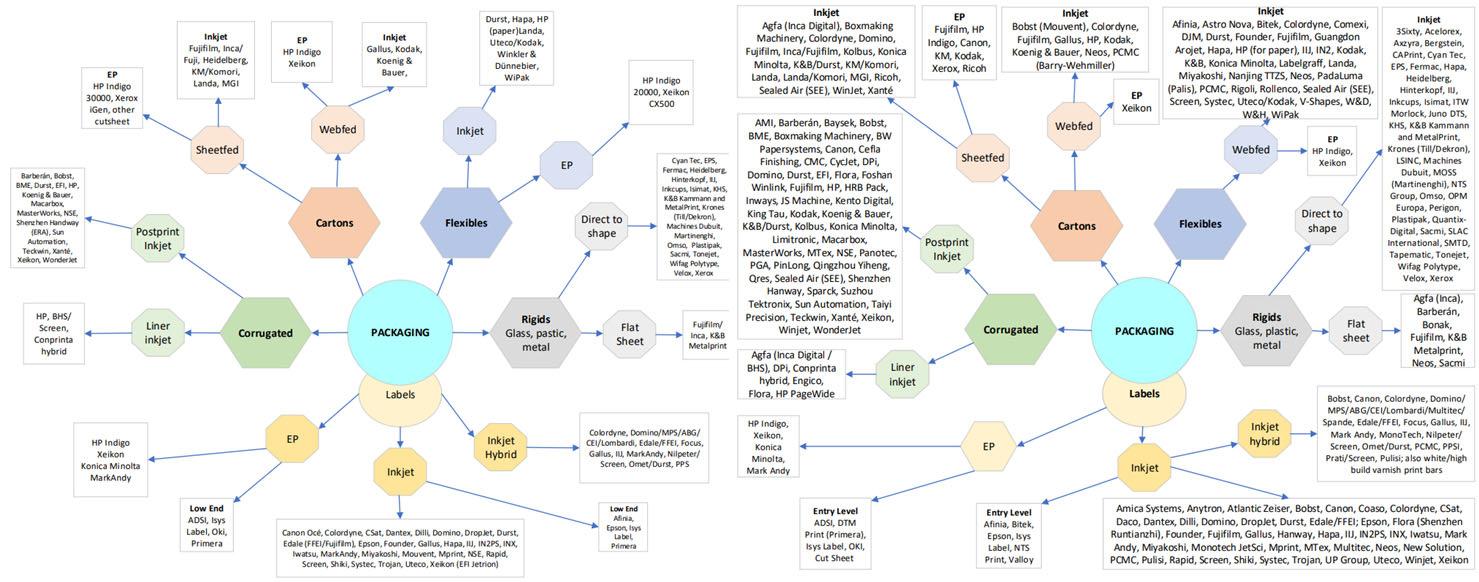
Image 1 and 2
Digital printing systems for packaging and labels in 2019, and in 2023 (right)
www.packagingnewsletter.com
it is the way of the world. Companies can explore solutions at drupa to simplify supply chains that will be key to future success supplying packaging and labels. The market leaders offer a broad variety of creative software. They will show new methods to automate the repetitive processes involved with packaging design, approvals and prepress taking time and cost out of the process. Other players will offer specific solutions for integration and to optimise colour management, imposition and providing variable data capability.
All these packaging developments are ultimately driven by end customer expectations, or rather demands. In the increasingly connected world these demands and expectations are changing, with more engagement and interaction to improve the consumer experience of the brand. Digital printing allows brands to make content decisions
later in the supply chain, closer to the consumer that helps packaging offer additional valuable functions. These additional functions move packaging beyond the traditional containment and protection functions, with information and promotion. A unique digital print can be connected to the cyber world, opening new opportunities of logistical efficiency and greater consumer engagement.
drupa is the most important print show, because the exhibitors (and all the important ones will be there) show what they have, while using the event to showcase what they are working on to gain feedback. And digital packaging print (plus finishing) will very much be on the agenda. There will be more machines for labels; corrugated –post and preprint, replacements for litholam; for folding cartons; for flexible packaging; for metal and there will be direct-to-shape ma-
chines doing interesting things on cans, aerosols, plastic and glass. Established players will show improvements to quality, speed and formats, with new inks and toners broadening the types of packaging they can produce.
I am really looking forward to seeing the newcomers who have already announced developments that they will be showing off and I know of several potential developments sadly under NDA that I am not allowed to mention, which is the bane of a technology correspondent.
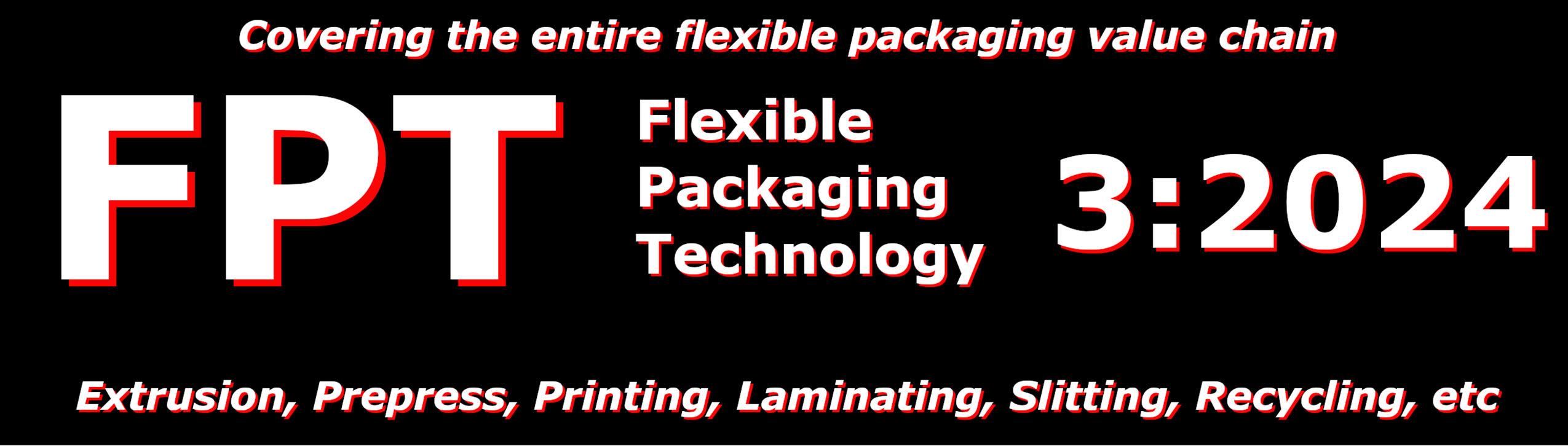
Packaging Laminate Market is Expected to Reach a High Valuation of USD 9,694.9 Million by 2034
The global packaging laminates market is set for significant growth, with sales expected to rise from USD 6,336.3 million in 2024 to an impressive USD 9,694.9 million by 2034, reflecting a compound annual growth rate (CAGR) of 4.3% over the forecast period. This follows a strong market performance in 2023 when packaging laminate revenue reached USD 6,118.4 million.
In 2024, the market is projected to exhibit a year-on-year growth of 3.6%, driven largely by increasing demand across multiple industries, particularly food and beverages. The food and beverage sector is anticipated to create a substantial incremental revenue opportunity of USD 1,199 million between 2024 and 2034, further bolstering the market’s expansion.
Plastic laminates are projected to dominate
the packaging laminates market in 2024, holding a remarkable 3/4th value share. This underscores the growing reliance on plasticbased packaging solutions across industries. Meanwhile, aluminum foil is expected to register a healthy 4.6% CAGR during the assessment period, showcasing the material’s increasing popularity in flexible packaging solutions.
See How Things Have Changed: Access the
Old Source for This Report!
Flexible laminate rolls and pouches within the 30 to 45-micron thickness range are set to capture 1/4th of the market share in terms of value. These laminates are expected to expand 1.4 times their current value over the evaluation period, reflecting the growing preference for lightweight, flexible packaging formats.
The packaging laminates market is projected to witness substantial growth opportunities over the next decade.
From 2024 to 2034, the market is expected to generate an incremental growth opportunity of USD 1,341 million and expand by 1.5 times its current market value. The food and beverage sector will remain a key
driver of this growth, with increasing demand for durable, protective, and flexible packaging solutions.
Key Takeaways from Market Study
The global packaging laminate market experienced a Compound Annual Growth Rate (CAGR) of 1.7% during the historical period.
Food industry holds a significant share in the demand for packaging laminates.
Canada is expected to generate USD 75.3 million in revenue and account for 22.5% market share by 2034.
The United Kingdom’s pharmaceutical industry has a turnover of USD 44.5 billion, supporting
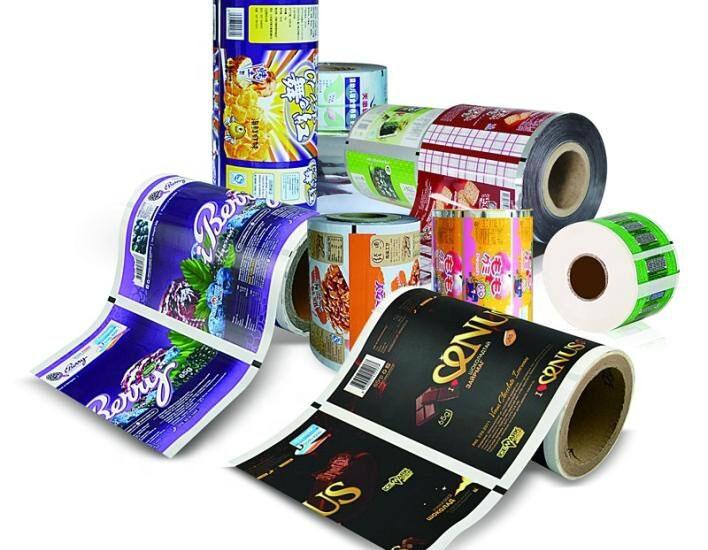
demand for specialized packaging laminates.
India, South Africa, and China are projected to exhibit high CAGRs of 7.2%, 5.5%, and 5.0% respectively through 2034.
The pouch segment of packaging is expected to grow at a CAGR of 3.8% through 2034, driven by convenience and sustainability trends.
By material, the plastic segment is set to witness a strong growth rate with a 4.3% CAGR from 2024 to 2034.
Competitive Landscape
Leading players in the market are developing and launching new products to woo more clients. They are integrating with different firms and expanding their geographical presence.
They are also collaborating and partnering with brands & stakeholders for new product
development. Recent activities and developments implemented by leading players in the market are:
In January 2024, UFlex, a Noida-based flexible packaging company, launched its latest coldform laminate with holographic effects for the pharmaceutical industry at the CPHI-PMEC India exhibition.
In November 2023, TIPA introduced its new home compostable laminate in the United States. The product can be used for snacks, bread, and spices packaging, as well as dry food packaging. It is also ideal for packaged protein gummies, fruits, and granola.
In August 2023, Amcor introduced AmFiber Performance Paper packaging in North America. The company aims to expand its AmFiber portfolio with this launch.

www.packagingnewsletter.com

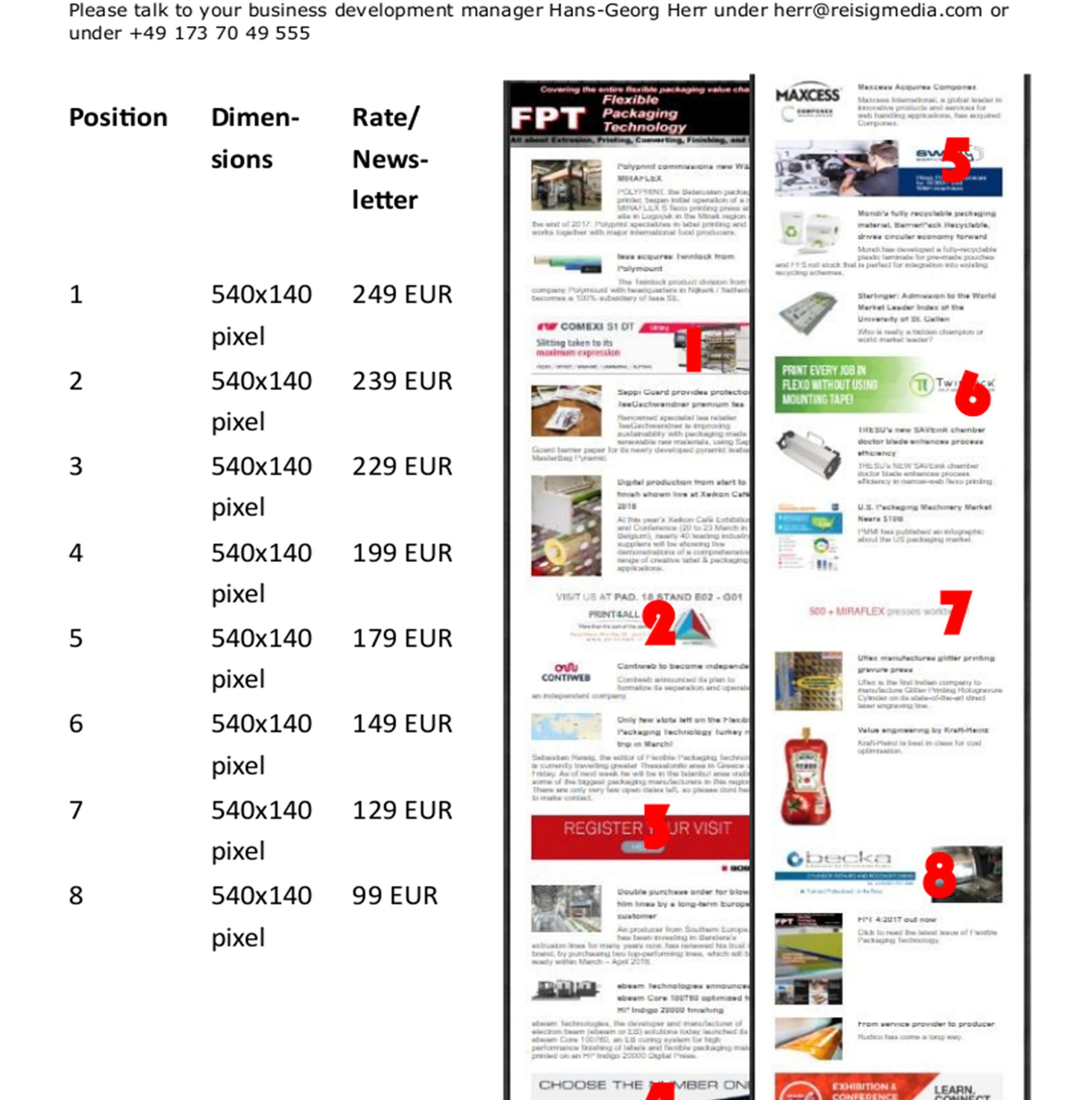

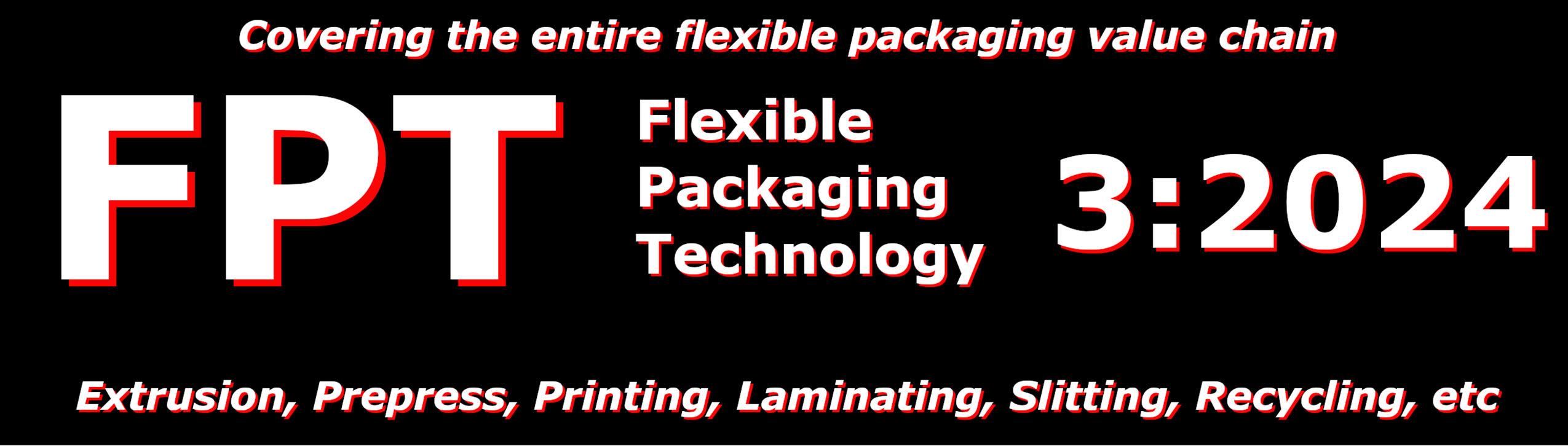
Lorven Group Boosts Production with VAREX II
At W&H, innovation is at the heart of everything we do. Our mission is to develop cutting-edge solutions that empower our customers to achieve new heights of efficiency and quality. The recent installation of our VAREX ll blown film extrusion machine at Lorven Group exemplifies our commitment to this mission, delivering an impressive output of over 900 Kg/hr and setting new benchmarks in the industry.
We take great pride in our partnership with Lorven Group, a company that shares our dedication to quality and excellence. Established in the early 1990s by Late Shri Devulapally Bhikshapati and transformed into a private limited company in 2010, Lorven Group has become a leader in comprehensive packaging solutions under the leadership of Chairman Mr. Devulapally Sunil Kumar, Chief Managing Director Devulapally Ni-
tesh Kumar, and Director Devulapally Kushal Kumar. With over 500 committed employees and state-of-the-art infrastructure, they continuously strive for perfection.
VAREX ll machine is designed to be a game-changer
This 3-layer high output blown film machine, measuring 2800mm in width, is capable of processing a variety of materials including LDPE, LLDPE, HDPE, and
mLLDPE. It produces films that are not only stiff and perfectly flat but also highly productive, thanks to our advanced die and extruder technology. By minimizing LDPE content, the VAREX ll offers significant cost savings, reinforcing our commitment to delivering value through innovation.
Equipped with a new high-pressure cooling system, the VAREX ll ensures improved output and profile tolerances. The fully automated
www.packagingnewsletter.com
winders provide precise tension control, reducing the need for manual adjustments and guaranteeing top-quality films with remarkable efficiency. This level of automation and precision reflects our dedication to engineering excellence and customercentric solutions.
"The VAREX ll embodies our commitment to engineering excellence tailored to meet diverse customer needs. Partnering with Lorven Group as they expand in the flexible packaging sector is truly inspiring."
Says Divyanshu Katiyar, Sales
Manager
at W&H
“Our experience with the VAREX ll has been outstanding. The installation was seamless, and the training provided by W&H's team was thorough and invaluable. Since integrating this state-of-the-art machine, we've noticed a significant increase in productivity and operational efficiency. The quality and performance have exceeded our ex-
pectations, confirming our decision to choose W&H.” Says Nitesh Kumar, MD at Lorven Group.
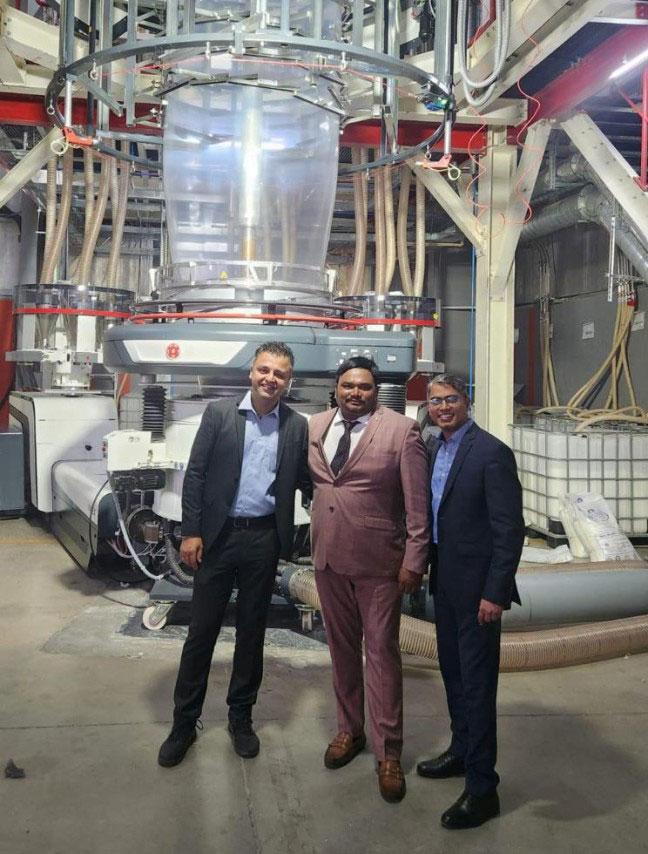
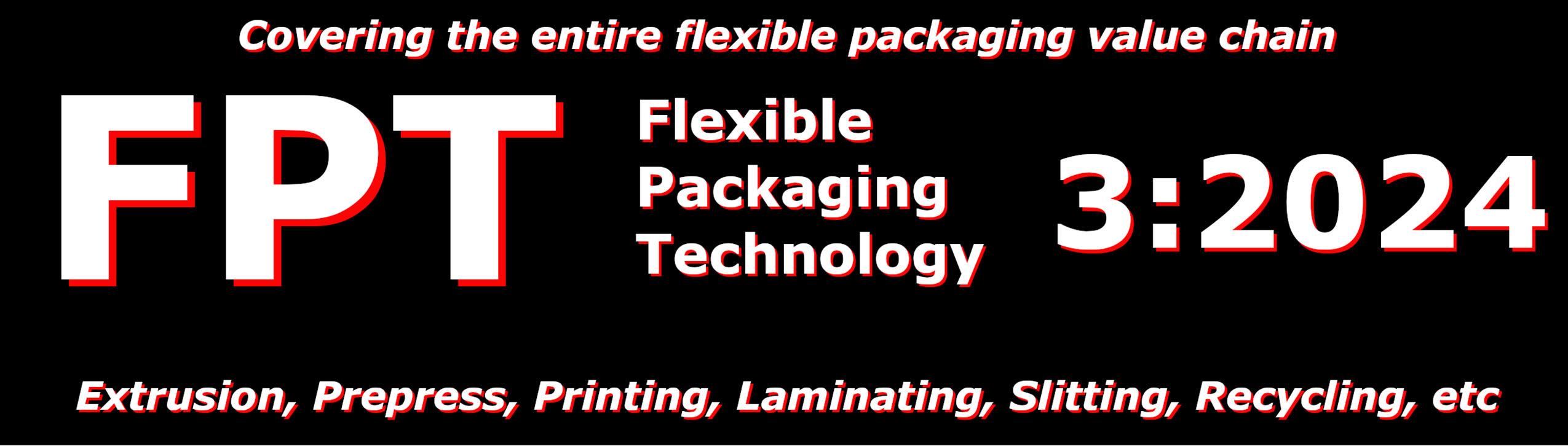
Vetaphone corona-equipment favoured by Amcor Flexibles
When a major global packaging group like Amcor chooses Vetaphone surface treatment equipment for its flexible packaging plant in Belgium, it’s a massive testimonial to the quality and reliability of the Danish manufacturer’s technology.
Amcor’s Gent production facility is a giant, housing gravure printing in up to nine colours, digital printing, solvent and waterbased coating, lamination, coextrusion, both cast and film up to nine layers, and Vision Systems for conversion and extrusion. It all began back in 1925 with the production of cellophane, which was the first plastic material used for food packaging. In 1950, the plant became the first to extrude in Europe, and by the 1960s Amcor Flexi-
bles was making strides in the pharmaceutical, films & packaging, and chemical sectors, with the establishment of a strong R&D culture.
Throughout the 1990s the Group expanded with numerous acquisitions including Danisco, A&R, Rexam, and Tobepal, with extruded volumes being consolidated at Gent and the UK plant in Ilkeston. 2008 brought a major €17m investment programme at Gent with four new extrusion lines and the construction of a new production hall, while
the acquisition of Alcan in 2010 saw conversion and extrusion separated at Gent and in 2019, with the addition of Bemis, the group became a major global leader in package print production.
Today, the Gent plant has a broad product range including peel and barrier packaging that serves all sectors. PE, PP, PA, and PETg are extruded in up to nine layers and on the converting side, gravure and digital printing combine with lamination, coating, and slit-
ting. Both extrusion and converting sectors are monitored by Vison Systems to assure quality.
It was into this production environment that Vetaphone set about selling its surface treatment technology, as Dirk Den Haese Sales Manager of Vetaphone Benelux explained:
“The challenge of working with a large and diverse group like Amcor is knowing where to start! But I knew that the company valued its reputation for quality very highly, and that the accuracy of much of the packaging it produced was critical, so there was clearly no room for any weak link
in the production chain.”
Beginning in 1990, Vetaphone has supplied a diverse range of corona technology to the Belgian plant that ranges from 1400 to 2300mm in web width and generators from 2 x 6kW for extrusion lines to 2 x 10kW for different lamination lines. For its food and pharmaceuti-
www.packagingnewsletter.com
cal work, Amcor is using exclusively Vetaphone VP2 ceramic rollers to ensure no contamination from the silicone sleeves, vulcanised and aluminium backing rollers. This has become a standard item for Amcor Flexibles in Gent, where the treaters have performed well, drawing praise for their low maintenance requirements and easy access, and reliable performance that provides the consistently even treatment essential for a quality end-product.
Speaking for Amcor, Andries Van Nieuwenhove, Plant General Manager at Amcor Flexibles Conversion Gent said: “It is key for us to have good partners who support us in our journey to be the reference supplier of specialty peelable and barrier laminates”
Amcor is very proud of its customer engagement that takes a bespoke approach to the challenges of modernday packaging. “From concept to prototype
and onto production and recycling, the company works hard at being innovative,” according to Commercial Director Johan Van Wesemael.
“Using our in-house pilot line and all the analytical assets and expertise we have gathered we can speed up developments and through real-world testing deliver validated solutions.”
Proof of this attention to detail is the number of international quality recognition awards held by Amcor, including ISO 9001, 14001, 45001, 50001, along with ISTA, Ecovadis, and BRC accreditations. They are, in fact, no more than one would expect from such a major player in the market, but are now the basic requirements for the food, pharma, and industrial sectors that Amcor supplies on a regular and global basis.
To put that size into perspective, Amcor employs 42,500 people across 220 locations in 43 countries – its pack-
aging products are used by more than 4000 brand owners – it holds 3700 patents, trademarks, and registered designs, spends over €100m on R&D each year, enjoying an annual sales turnover of US$14 billion. As Dirk Den Haese concluded:
“If Vetaphone technology is good enough for Amcor, by association it makes us a global leader too – and it’s something we are very proud of! I estimate we have now installed more than €1m’s worth of our technology at the Gent plant, making Amcor one of our largest customers in the Benelux region.”
www.packagingnewsletter.com

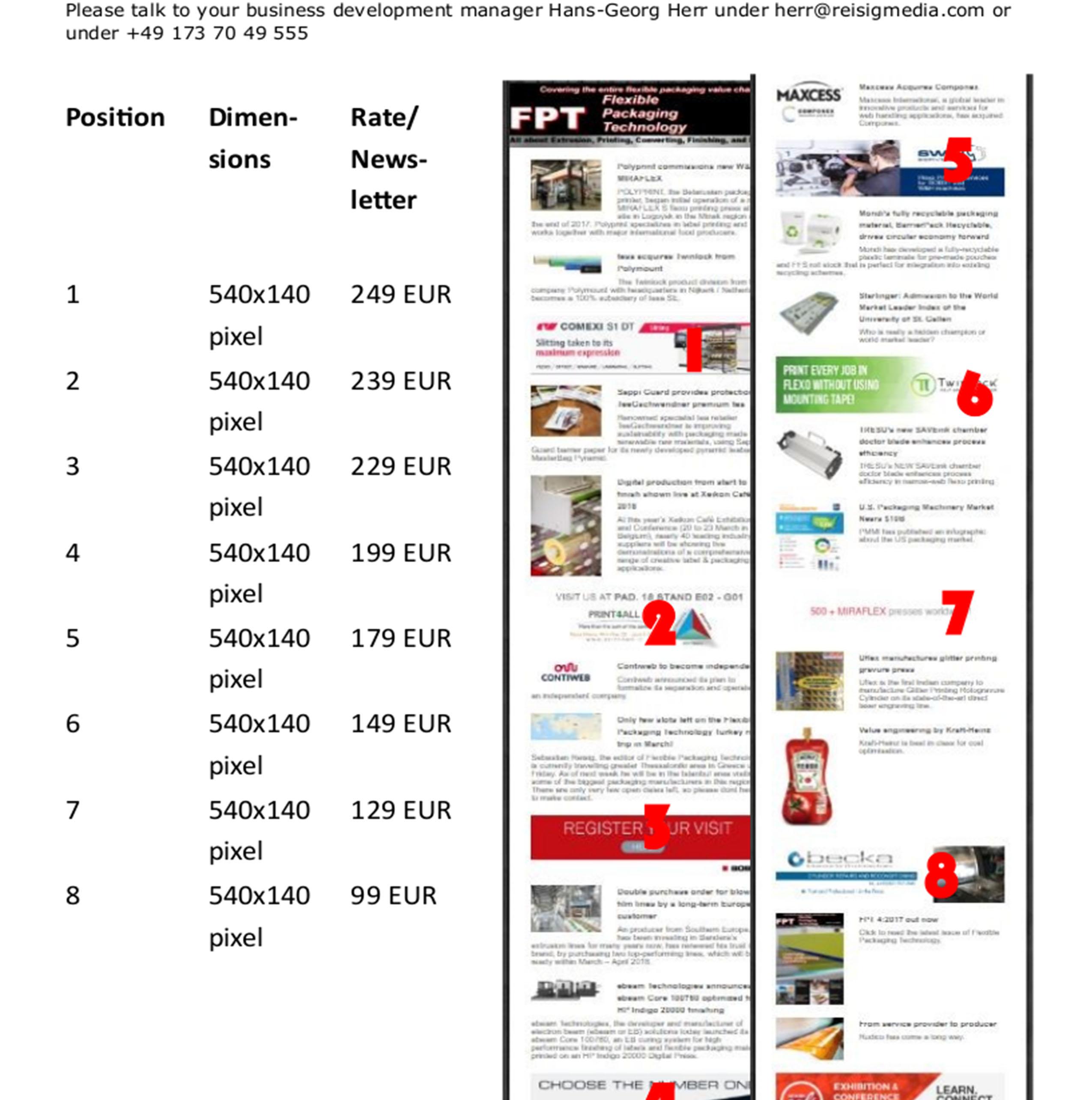
