Wipak strengthens gravure division and supports sustainability pledge with BOBST oneECG
Wipak strengthens gravure division and supports sustainability pledge with BOBST oneECG

Analysis of Dot Gain
Produced by Interactions of Flexo Plate and Anilox Roll Screen

Labelexpo Europe
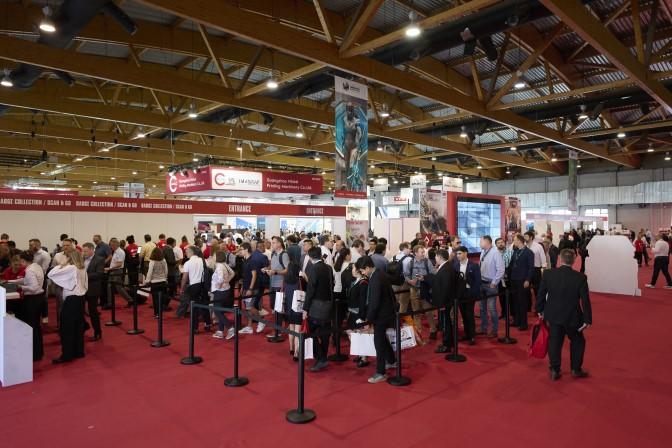
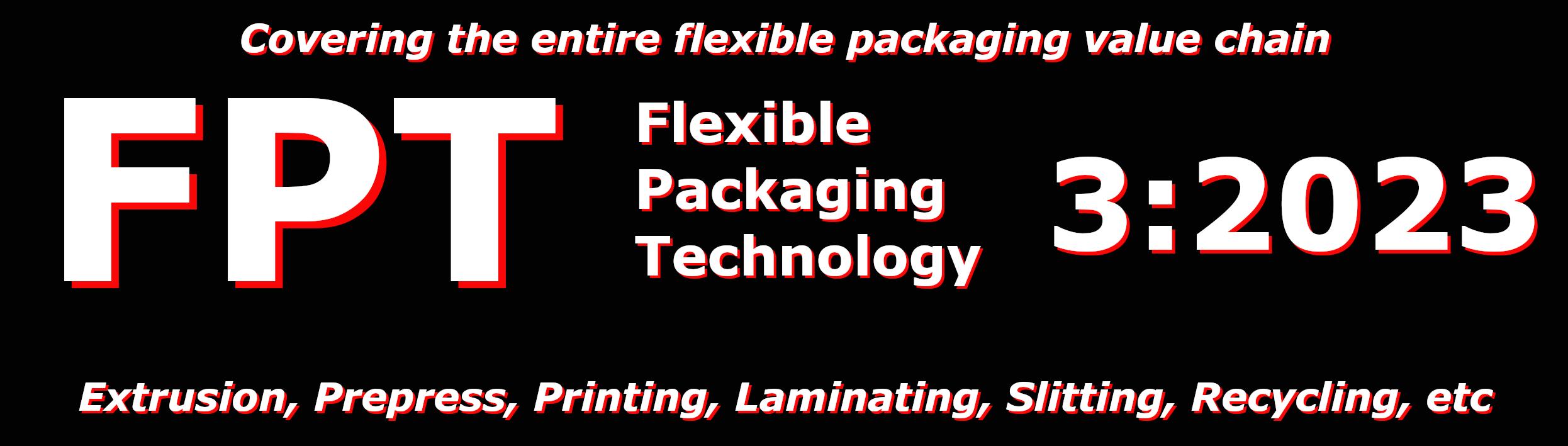
2023 showcases vibrant industry
The EREMA Group drives a new era in plastics recycling

Understanding the performance of sustainable consumer goods packaging
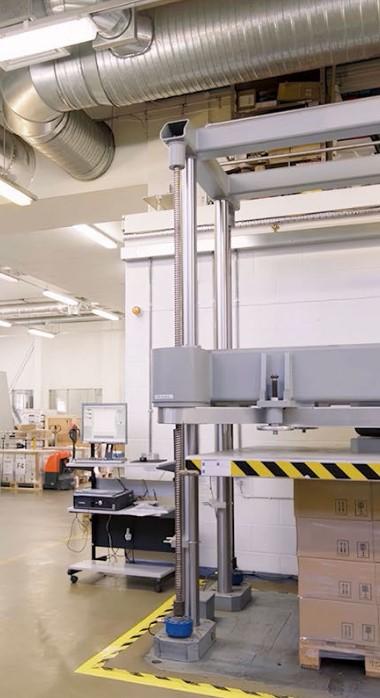
Flexography prints on non-absorbent as well as absorbent substrates using liquid ink. With developments in photopolymer plate and anilox roll manufacturing technology, we can print half tone with screen frequencies exceeding 150 LPI (Lines per Inch) where the print quality can be comparable with offset printing results.

The first edition of Labelexpo Europe since 2019 has closed on a high note, with a total of 637 exhibitors taking part in the show, which took place between 11-14 September at Brussels Expo in Belgium.
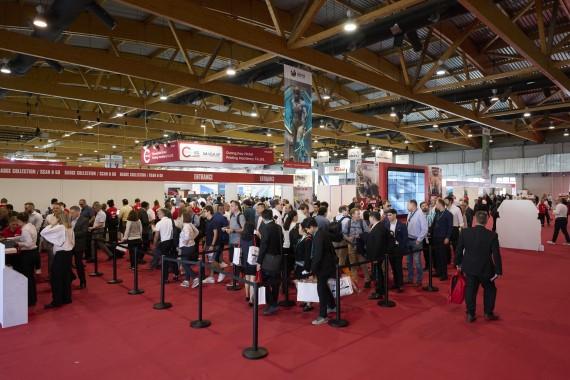
In recent years, the world has witnessed a shift in demand for more sustainable packaging designs, particularly for consumer goods packaging. Legislation – particularly variations on a plastic tax – has driven this change in the packaging industry.
Driven by its vision to become the most sustainable company in the flexible packaging sector, Wipak Walsrode, together with BOBST, has set out to take its gravure printing division to a new level with BOBST’s oneECG technology. The company is thus continuing its long-standing partnership with BOBST.
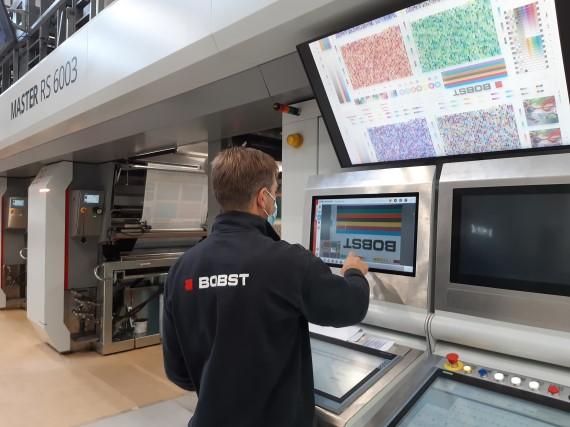
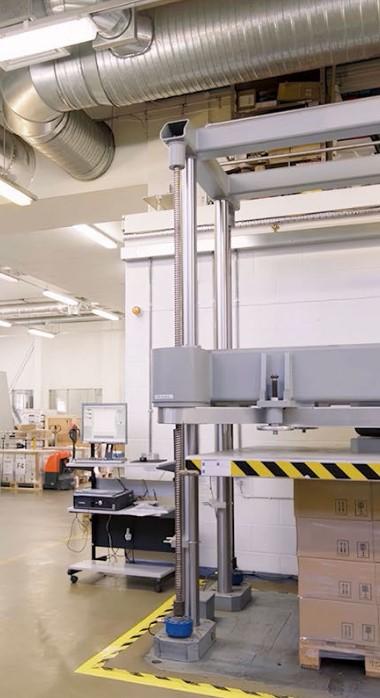

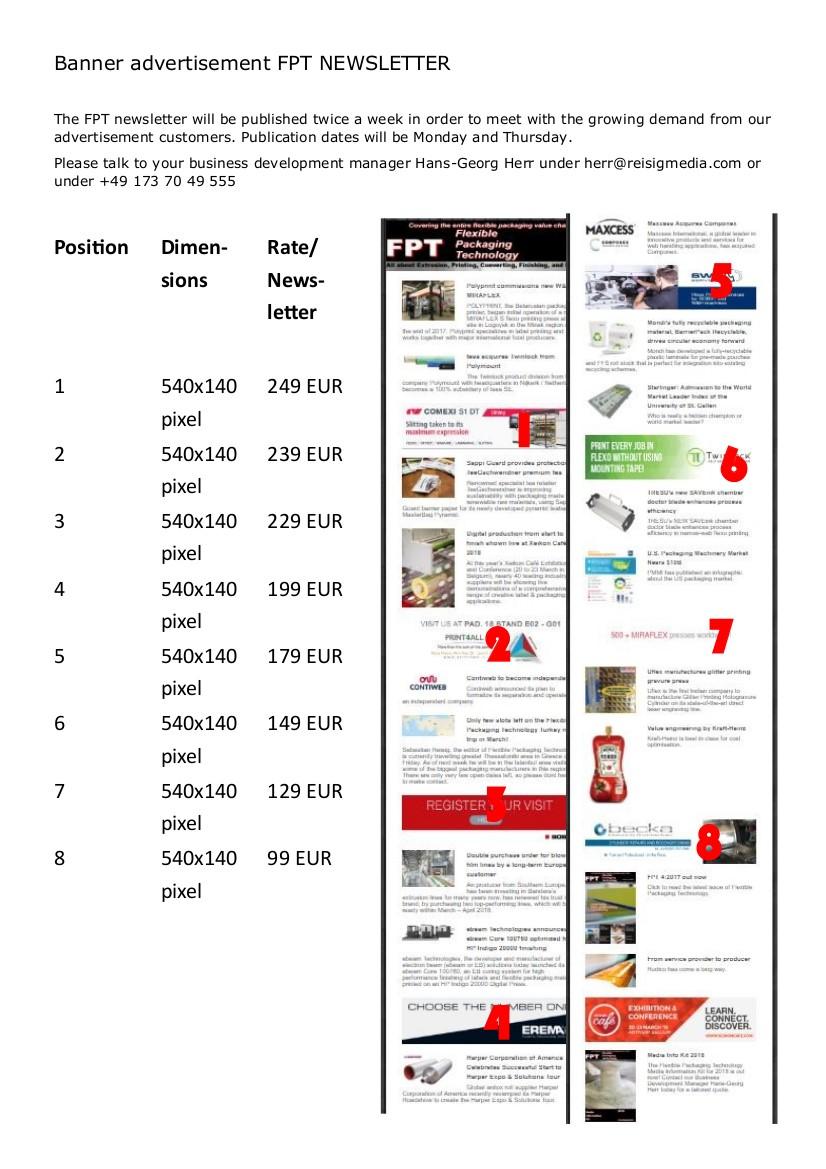
Analysis of Dot Gain Produced by Interactionsof Flexographic Plate and Anilox Roll Screen Frequencies
Flexography prints on non-absorbent as well as absorbent substrates using liquid ink. With developments in photopolymer plate and anilox roll manufacturing technology, we can print half tone with screen frequencies exceeding 150 LPI (Lines per Inch) where the print quality can be comparable with offset printing results. This has helped flexographic printer to reproduce the blackand- white, single colour tone and full colour graphic original, satisfying the printing and packaging needs of many customers. But unlike other printing technologies in flexographic printing screen frequency of plate i.e. image carrier and engraving line frequency of anilox roll collectively affect the smoothness and uniformity of reproduced half tone image. Furthermore, the LPI of the screen used in plate making also adds to variation in tonal reproduction. In the presented work 3 line frequencies expressed in CPI (Cells per Inch) of anilox roll and 5 screen frequency of image carrier are selected and their effect on print characteristics is studied using the plot of theoretical dot area against apparent dot area. Given the sizable capital investment involved in manufacturing of anilox roll, this work is directed at finding the optimum combination of screen frequency and line frequency required to achieve tonal balance.
Flexography’s application area label, flexible and rigid package printing and industrial printing application areas. Flexography as a print-
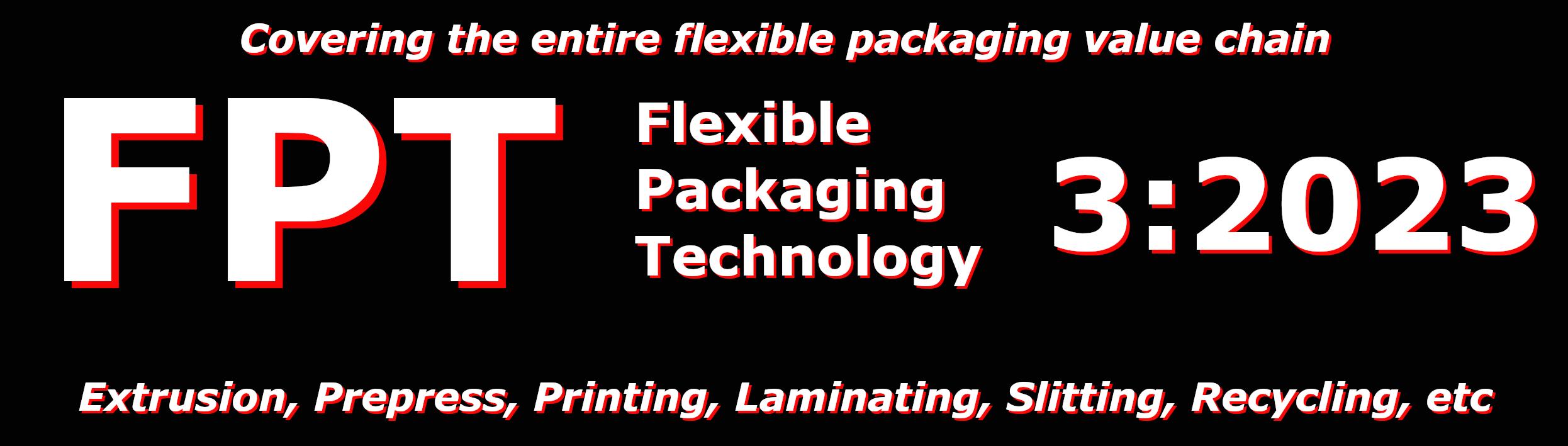
ing technology reproduces colour in line and half-tone form. It is capable of producing half tone print at screen frequency i.e. LPI (Lines
per Inch) of 150 and above [1]. It represents 75% of the $440 billion printed packaging market. 92% of its global volume is packaging,
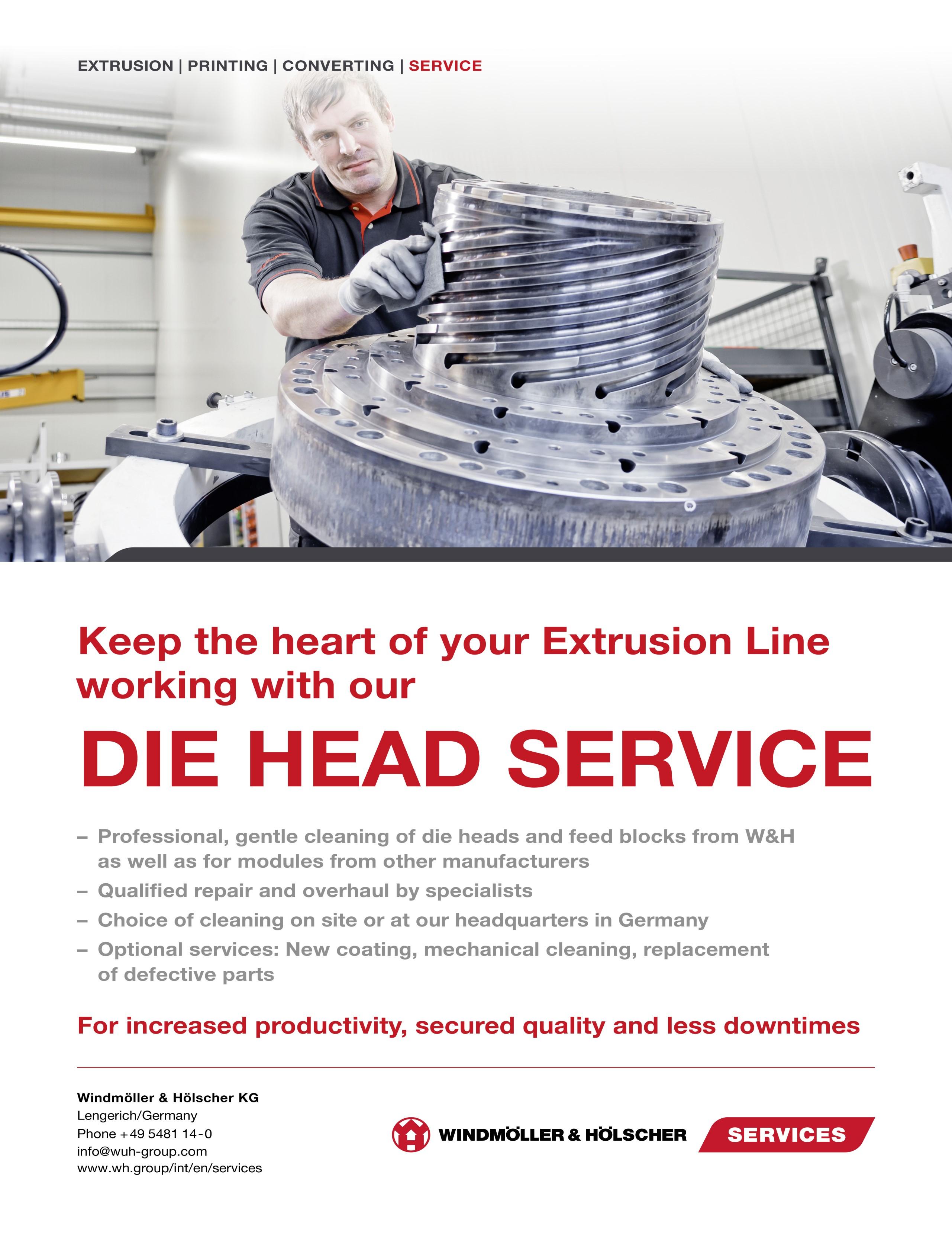
h 8% divided among pharmaceutical,security printing, printed electronics and similar markets[2].
In flexography ink transfer and print quality is controlled by an anilox roll that transfers ink to half tone image on a flexographic image carrier i.e., plate. The anilox roll has a helical row of tiny cells engraved at regular spacing and angle. The fineness of an anilox roll is defined by a number of engravedcellsperlinear inch often called line frequency expressed in CPI. Therefore, the regular geometrical patterns of half tone image screen frequency in question and the anilox roll of identified line frequency interact with each other and decides the ultimate half tone print quality of half tone and process colour flexographic printing [3]. The screen frequencies employed in a label, flexible and rigid package printing and industrial printing applica-
tionsare55,65,70,85, 100, 120, 133, and 150 with increasing screen frequency officering smoothened print. The line frequencies of anilox roll available range between 250 and 1200 [3]-[4]. The flexographic printers follow the industry standard that the line frequency of anilox roll should be at least 3- 4 times that of printing plate screen frequency so that 3% half tone dot can be printed. Even in some situations printers maintainthisratioat45. With this yardstick printer for a screen frequency of 70 LPI can select an anilox roll line frequency between 280 and 550 CPI [5]. Of course, the print requirement of the smallest halt tone dot area demands a finer anilox roll but still, the printer has a choice of anilox line frequencies. Therefore printer is required to keep an inventory of anilox roll with multiple line frequency for the intended screen frequency. The anilox roll
being the costliest part of the flexographic printing unit; for small and medium scale printers this requirement adds to the procurement and carrying cost of the anilox roll inventory. This general situation prevails in the label, flexible and rigid packageprintingandindustrial printing application areas of flexography. The use of reduced anilox inventory has other advantages like the benefit of independence on the supplier for providing specific type roll, less lead time in case of breakdown, less storage space required to maintain inventory, no more downtime in changing the anilox roll at the time of change in product or application, improved productivity, reduction in consumption of cleaning solvents used during each changeover and reduced operating cost. The tiny cells are engraved at 300, 450, 600, and 900 angles to the axis of the metallic anilox roll. The hexago-
nal cell geometry engraved at 600 increases the resolution of the anilox roll and is widely used in flexographic printing. The ink storage capacity of an anilox roll is expressed inBCM(BillionCubicMicron) per square inch of engraved surface. Typical values of anilox roll ink volume range from 9-4 BCM for heavy lines and solids to 2.8 to 0.9 for process colour printing [5]. Higher volume translates to higher solid ink density, more colour or a heavier coating thickness. Lower volumes apply thinner ink films directly associated with higher print quality and process efficiency. The higher the line frequency of the anilox roll the lower its ink volume and vice versa. Multiple choicesofaniloxrollline frequencies for a given half tone print resolution i.e., screen frequency can result in the use of anilox roll with too low or too high line frequencies and limits print quality in half tone printing. The printing

troubles arising on account of the use of anilox roll with too low line frequency are bleeding-smudging, blocking, bridging, ink build up on edges of the
image, halo effect or squeezed edges on the half tone dot moiré effect, High color strength. On the other side too high line frequency results in a
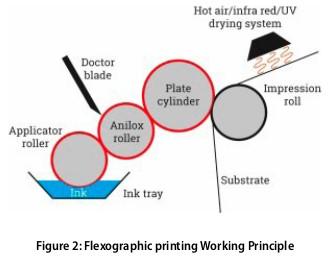
transfer of lower ink volume ghosting effect low colour strength [6]. It is also observed that the higher line screen anilox rollers tend to become more clogged more and lose their advantage of introducing higher LPI counts if not cleaned properly [7]. The proposed work involves identifying an aniloxrolllinefrequency that is capable of half toneprintingatdifferent screen frequencies leading to a reduction in inventory of anilox rolls with varying line frequencies. Half tone printing performance in term of characteristics curves is compared for variation at identified anilox roll. The anilox roll line frequency showing overlapping or close characteristics curves with reduced dot gain can be preferred over others. This systematic approach eliminates the reliance on industry standard of selecting anilox roll line frequency with 4- 5 multiple of screen frequency and the need of
maintaining inventory of multiple anilox line frequencies. At present, the selection of anilox rolls during half tone printing for various applications is governed by industry standard recommendations given by technical services of anilox roll manufacturers. Such recommendations presented in terms of the range ofmultiplying factors to get anilox roll line frequency from a given screen frequency are observed to take place from 3 to 5.5. The approach of plotting characteristics curves, a useful element in describing half tone print performance, has been
used in identifying common screen angles for multiple screen frequencies involved in half tone screen printing. This approach provided a tool to reduce secondary moiré problems in printing [8]. The characteristics curve is largely used in colour control during lithographicoffsetprintingin process optimization and identification of significant variables. Also, the effects of laser engraving settings on etch depth of polymer clichés was carried out for different screen frequency and screen angles to studypadprintingquality [9]. But the applica-
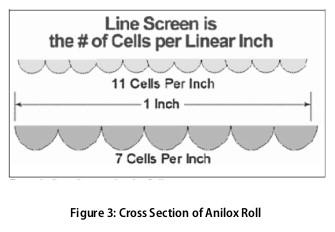
tion of such a subjective approach in identifying an anilox rolls line frequency that can accommodate has not been suggested by authors and anilox roll manufacturers.
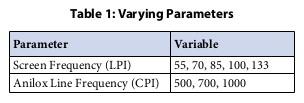
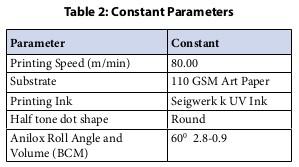
2. FLEXOGRAPHIC PRINTING TECHNOLOGY
The printing unit of the flexographic press and principle is shown in figure 1 and 2. The flexographic press is a roll-to -roll, direct rotary technology using wrongreading flexible relief image carriers called plate.Theinkingsystem of the flexographic printing unit consists of an ink fountain and an anilox roll. The anilox roll has a pattern introduced by engraving on its surface to hold and transfer ink to the substrate in question. The structure of the anilox roll surface is shown in figure 2. Anilox roll is a mild steel cylinder with a finely engraved chromium or ceramic surfaceandisdippedinthe ink reservoir. During
inking the excess ink is scraped off the surface of the anilox troll by a metallic doctor blade [9]. The resolution of anilox engraving is expressedin cells per linear inch i.e. CPI. The ink from anilox is received by the relief parts, that is, image areas of the plate and finally transferred onto the sub-
strate producing print. Flexographic printing technology uses liquid ink with a viscosity range of 50-500 mPas and offers an ink film thickness of 10-15 microns [10]. The remaining paper is structured to discuss the materials, parameters and required trials run in section 3, results and dis-

cussion is considered in section 4. Identified conclusions are communicatedinsection5.
3. MATERIALS AND PARAMETERS
The experimental set up includes varying and constant parameters as statedintables1and2.

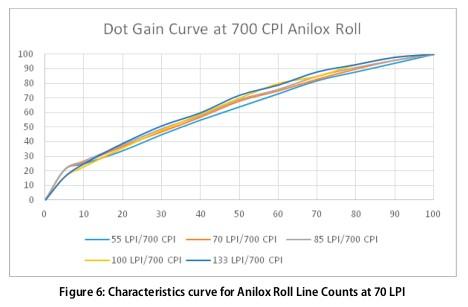
The experimental model chosen covers a total of 15 trials. The printing was carried out on a narrow web flexographic printing machine. Fifty sheets were printed for each trial with strict control keeping over constant parameters. The response variable identifiedis thedot area of each gradation expressed in percentage. The test image identified for printing 15 trials as designed above has combined five half tone grey scales of five screen frequencies and three anilox roll engraving frequencies as shown in table 1. The grayscale helpsfacilitate the measurement of the dot area of each tone gradation from each trial print using an elecwww.packagingnewsletter.com
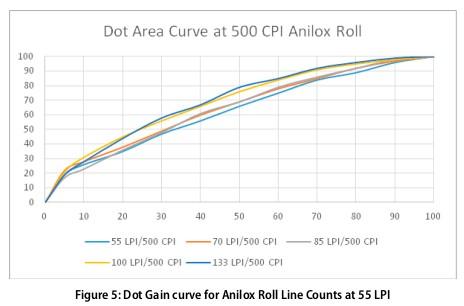
tronic densitometer. The test image as used in the trials is shown in figure 3. During the measurement of percentage dot area five random prints of each trial were selected as samples wherein each sheet i. e. sample involved dot area measurement of 180 half tone steps. A round dot shape is typically used to counter the possibility of high dot gain [11]. The parameters shown in table 2 are process variables capable of affecting print quality and are held constant to get characteristics curve plots giving performance relationship between screen and anilox roll line frequency. The substrates have different ink absorption rates and give different ink film thicknesses. UV (Ultraviolet) inks have high colour strength with workable viscosity as that of water- and solvent-based inks [12]. Dot area measurement is carried out with a SpectroEye photodensitometer with www.packagingnewsletter.com
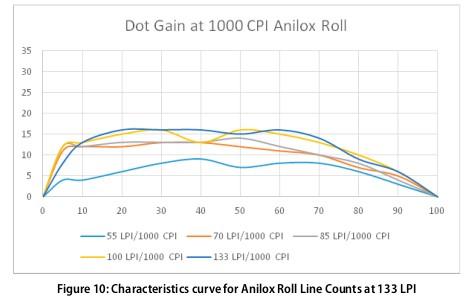
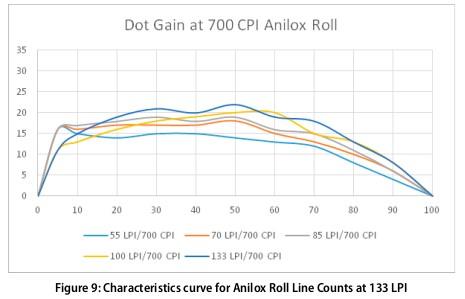
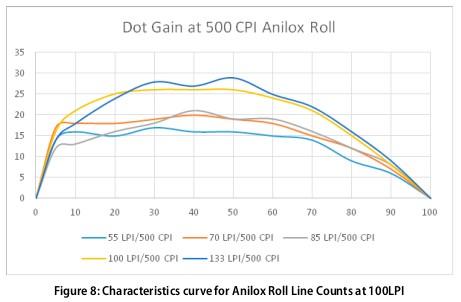
D50 illuminant, 100 observer angle, density standard T, and 45:0 measuring geometry setting. 100 observer angle was preferred to 20 for a wider area of view in the blue-green region of the spectrum. A standard calibration andoperatingprocedure isfollowedduringmeasurement. All measurementsyielded150readings as data to be processed for getting informationaboutdotgain.
4. RESULT AND DISCUSSION
150 gradations from 15 trials printed with offset press used for measurement of the response variable that is dot area percentage from individual grey scale wedge for all combinations of screen frequencies (LPI) and anilox screen rulings (CPI). the percentage dot area values were calculated. The observed dot area and absolute dot gain values are tabulated for anilox rolls of 500, 700 and 1000 lines per inch with screen frequencies of
55,70,85,100and133
LPI in appendices 1 and 2 respectively. Graphs are plotted with data tabulated in appendices 1 and 2. Figures 5, 6 and7showthepercentage dot area curves, which is the tonal curves of the prints at various screen frequencies for the anilox roll line frequencies of 500, 700 and 1000 lines per inch. In these graphs xand y- axes are represented by theoretical dot area (%) and observed area on print (%) respectively. Similarly,figures8,9and10 show the absolute dot gaincurvesataniloxroll line frequencies of 500, 700 and 1000 lines per inch. In these graphs xand y- axes are represented by theoretical dot area (%) and calculated absolute dot gain respectively Figures 5 to 10 show that at the same anilox frequency, theabsolutedotgainincreases with screen ruling (LPI). Therefore, in these trials screen, the ruling of 133 LPI is showing the maximum
whereas the 55 LPI is the minimum dot gain. Also, absolute dot gain decreases with increasing anilox frequency if the screen ruling is held constant.Thisbehaviour is observed with print i.e. screen frequencies 55, 70, 85, 100 and 133. Also, figures 5 to 10 suggest that the absolute dot gain is not varying much for 70, 85, 100 and 133 LPI for anilox frequencies as corresponding plots in figures 8, 9 and 10 show that except 55 LPI screen curves of70, 85, 100 and 133 LPI appear comparatively closer at higher anilox frequency that is 100 CPI. At 500 CPI the behaviour of dot gain curves plotted for 50,70,85,100and133 LPI are different, in this case, they are clearly distinct. In the case of anilox frequency 700 CPI the dot gain curves plotted for 50, 70, 85, 100 and 133 LPI appear to be a little closer. The AniloxLineFrequencyto Screen Ruling ratio for 55, 0, 85, 100 and 133 screen rulings and 500,
www.packagingnewsletter.com
700 and 1000 CPI is shown in table 3 below. As compared to table 1 of ISO 12647-6:2020 instead of the tone values on the printing form the value on the printed sheet are measured for 55,70,85,100and133 LPI and the dot gain values are observed to be +/- 2 and +/- 3 for ruling up to 120 LPI and above 120 LPI respectively. Furthermore, measurement condition is kept uniform and measured tone values are considered for results and discussion. As per ISO 12647-6:2020 recommendation. No measurement of tone values on the printing plateiscarriedout.
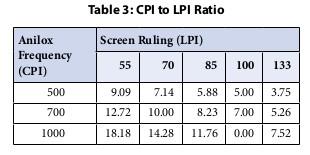
5. CONCLUSION
It can be concluded from these trials that in flexographic halftone printing the dot gain increases with increasing screen frequency and decreasing anilox roll line frequency. The anilox frequency is responded to clearly by the lower and higher screen rulings. Hence,
selecting one anilox roll line frequency for multiple screen frequencies thatoptimizesthattonal loss in half tone printing remains the best alternative for the flexographic printer. The dot gain curves at a given anilox frequency show the same pattern that a higher CPI:LPI ration produces the minimum dot gain and vice versa, but these ratios offer many distinct values and suggest irregular deviation amongthe dot gain curves. Also, the extreme LPIs behave differently but the middle three LPIs offer comparable performance in terms of dot gain as compared to the lowest and the highest LPIs that any printer handle. Though the se-
lection of an anilox roll having a higher CPI count is always useful, the economy is also one of the important factor. Industrial houses associated with the manufacturing of anilox roll have proposed different anilox roll frequency-toLPIratioforflexographic printers which varies between 4 and 6 instead of one anilox engraving frequency for the printer. Besides this significant variation in anilox frequency variation; the flexographic printers also have to consider the customer requirement of minimum reproducible dot percentage on print. A flexographic printer is, therefore, required to keep cell opening smaller than the minimum
reproducible plate dot, and such a situation will demand more finer anilox roll. In identifying an anilox roll that matches with the plate LPI printer may invariablyendupusingtoofiner an anilox roll. Such instances can increase the possibility of an inventory which is more than required and blocking of funds. This experiment has helped flexographic printer to optimize both engraving frequency and reproducibleLPI.
6. FUTURE SCOPE
The CPI:LPI ratio as a guide to select the anilox roll for a screen frequency in question is actually a recommended value and every printer selects an anilox roll as per the economy he can afford to keep customer requirements in mind. There cannot be the best CPI:LPI ratio in flexographic printing insteadthereisarangeof anilox roll frequencies that printer can select from. Anotherissue that printer can face in flex-
ography is the secondaryortertiarymoirebecause of an anilox roll patterned surface. Besides flexography, screen printing also shows problems of secondary and tertiary moire because of pattern of screen mesh. This more problem can occur with both singlecolor half tone and process colour printing. This work can be extended to design an experiment to optimize screen angle for half tone printing in flexography that involve the use of multiple anilox roll and screen frequencies.
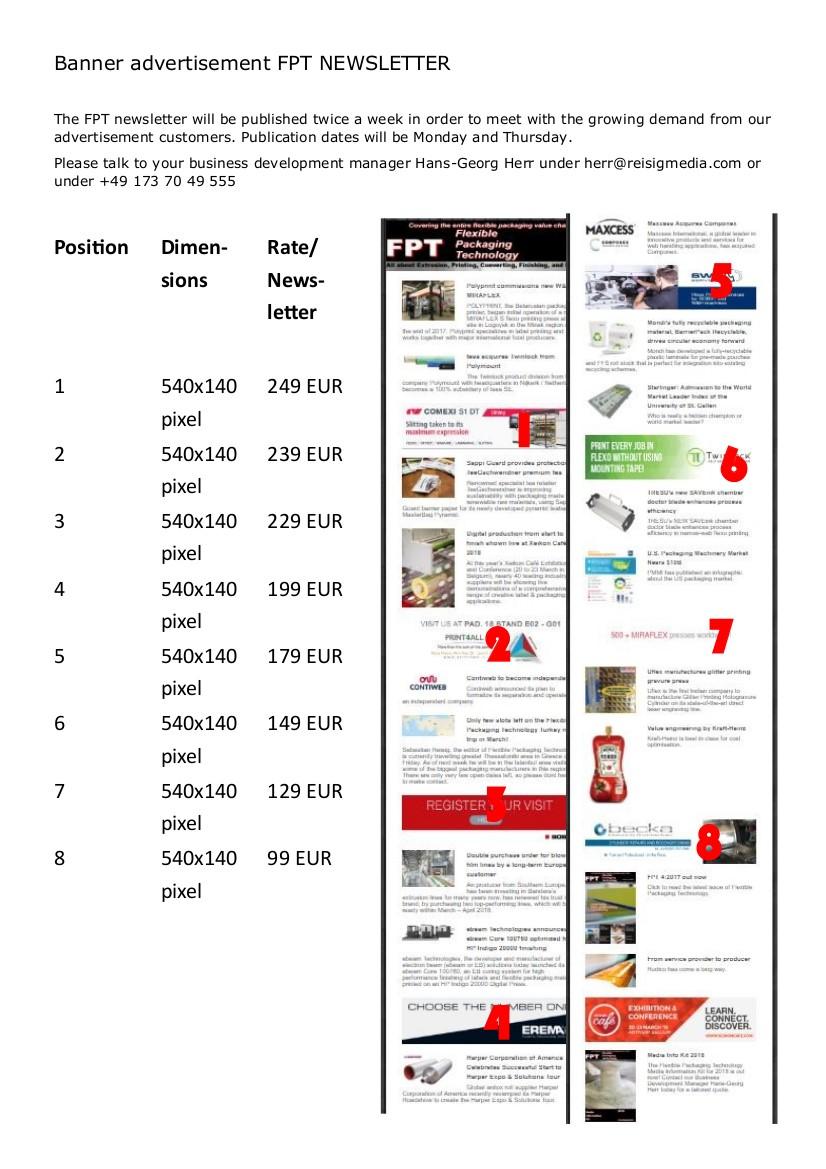
In recent years, the world has witnessed a shift in demand for more sustainable packaging designs, particularly for consumer goods. Legislation, particularly variations on a plastic tax – has driven this change in the packaging industry. This article examines the concept of a plastic tax for consumer goods packaging, challenges, and how you can ensure sustainable packaging performs as required throughout complex supply chains.
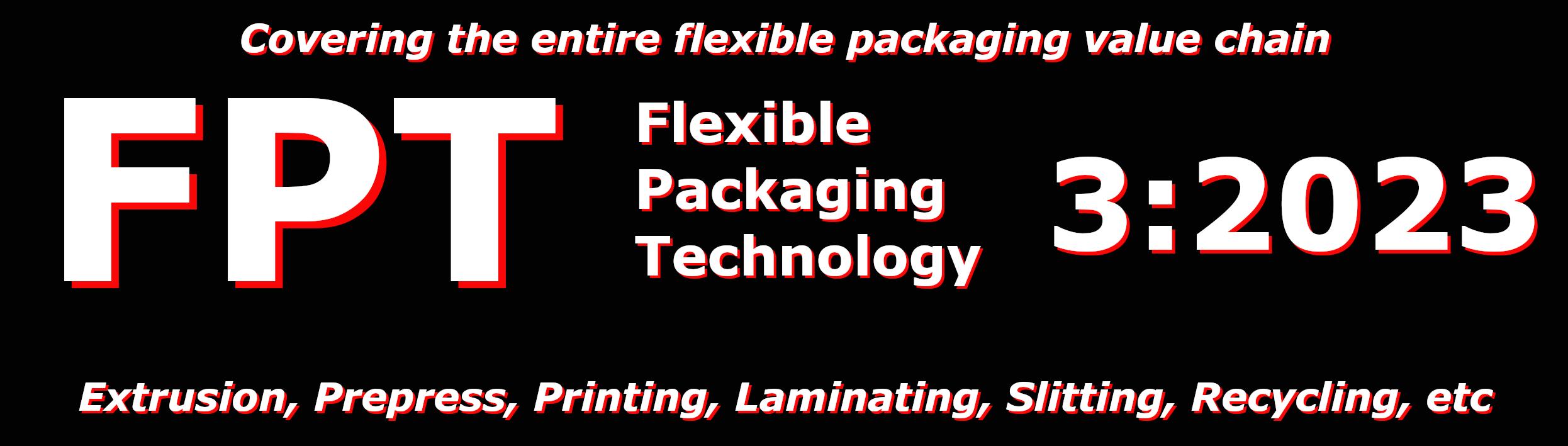
What is the plastic tax? The plastic tax is an initiative designed to create economic incentives for businesses and consumers to reduce their reliance on singleuse plastics. It encourages manufacturers and brandownerstoexplore alternative packaging materials for their products. In the UK for example, you will have to pay the Plastic Packaging Tax if you have manufactured or importedplasticpackaging components which contain less than 30% recycled plastic. Fines are
introduced per-tonne of packaging. This especially impacts medium to large-sized, fastmoving consumer goods (FMCG) companies, where fines can quickly amount to significantpenalties.
Challenges for consumer goods Theintroduction of a plastic tax drives manufacturers and brand owners to investigate redesigning packs with new material compositions, using non-virgin plastics and other alternative materials. This includes void fill and other pro-
tective layers to avoid having to pay fines.Not only is redesigning packaging a costly process in itself; it also brings about many unknowns around pack performance, quality, functionality and durability. There are concerns that should a pack not be able to cope with the rigours of the supply chains in which it will need to function, then there is severe risk to the integrity of the product and an increased likelihood that the product would not be saleable in a re-
tail environment.
Manufacturers want to ensure that any redesigns have been validated and performance levels are known before new packaging designs enter the supply chain.
Different transit routes require different considerations to packaging When a team develops new packaging and utilises alternative materials, particular consideration must be made to the challenges the pack will face throughout its service life. For example, a premium consumeritemsuch as a new mobile phone will likely be shipped around the globe on shipping containers
which can vary dramatically in temperature and humidity throughout a single journey. Once the pack reaches land, it will likely travel via lorry by roads which can vary in quality. The pack will need to be able to endure vibration and harsh braking loads. Following this the pack would have to cope with the associated drops and impactsthatcan occur during manual handling when unloading items at their end-destination. This journey alone poses many risks to a pack. Other supply routes can be even more demanding for a pack, such as air freight with pressure and temperature fluctuations, so
it is important to have confidence in its capabilities before entering the supplychain.
How Smithers can help Smithers offers comprehensive packaging design support, leveraging years of expertise to help clients createandevaluate new packaging solutions. Through using advanced equipment to simulatevariousconditions and realworld scenarios, their team assists in ensuring that new pack designs can withstand the challenges of the entire supply chain, providing assurance of their suitability and reliability in their intended applications.
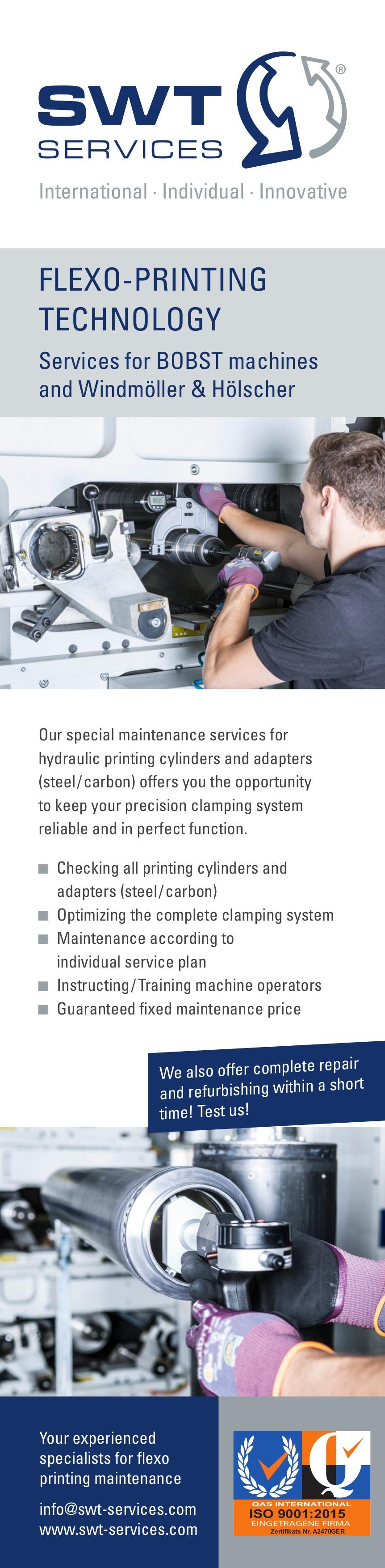
Labelexpo Europe 2023 showcases vibrant industry
The first edition of Labelexpo Europe since 2019 has closed on a high note, with a total of 637 exhibitors taking part in the show, which took place between 11-14 September at Brussels Expo in Belgium.
Spreadacrossninehalls and covering 36,588 sqm of floor place, this year’s show featured over 250 product launchesfocusedparticularly on flexible packaging, digitization and automation.
The unprecedented heatwave in Brussels did not deter 35,889 visitors from 138 countries attending the fourday show. Countries such as Germany, France and Italy were especially well represented, with large visitordelegations.
Equipment manufacturers announced multiple
sales across the four days and an exhibitor rebook rate of 96% was reported for Labelexpo Europe2025.
Demonstrating how Labelexpo Europe is evolving into a package printing show, digital printing of paper-based flexible packaging materials was evident on the show floor, with paper-based packaging printed by Xeikon on the new TX-500 Titon toner press and SCREEN on the Truepress Pac520P –seen for the first time at a Labelexpo. HP launched the 200k mid-web digital press,
successor to the hugely successful HP Indigo 20000. The company also ran a ‘digital pouch factory’ ecosystem demonstrating pouch manufacture and finishing of other unsupportedfilmsincludingshrink sleevelabels.
Flexo made a major comeback at this show, with Nilpeter, Lombardi and BOBST demonstrati ng printing of flexible packaging and unsupported label film materials on 26in/670mm mid-web UV flexo press lines on the show floor. OMET made the show debut of its KFlex modular flexo platform
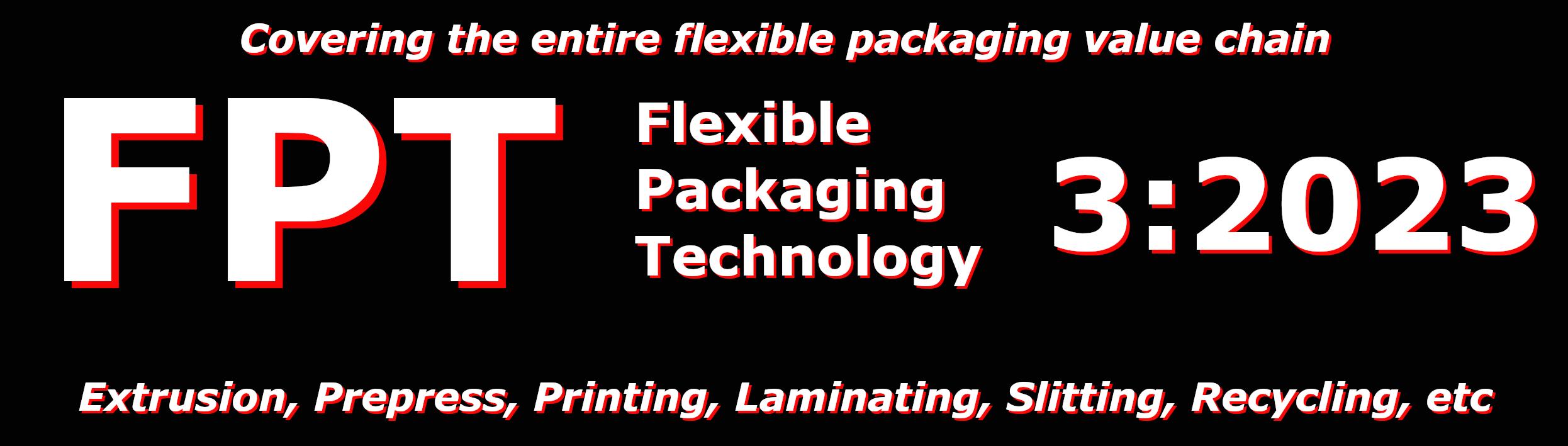
and Mark Andy launched the Pro Series flexo press, upgradable to a hybrid machine.

Jade Grace, Managing Director, Labelexpo Global Series said:
“We’ve just delivered Labelexpo Europe 2023 after a four-year break and what a show it has been! The feedback we have received from visitors and exhibitors alike has consistently shown the high quality of leads, enquiries and contacts made at the show, with an incredible numberofsalessecured on the exhibition floor. We have also secured a rebook rate of 96% for Labelexpo Europe 2025, which bodes well for our firstshowinBarcelona."
Continued Grace: “I would like to thank all
our exhibitors for your partnership and commitment in supporting the diverse and exciting industry of labels and package printing, together with us. Thank you to all who visited from 138 countries, and to our association and mediapartners.”
“
Ithasbeenthehardest show yet forus to deliver,butthemostrewarding. We are looking forward to the next chapter in 2025 where we willbebringingLabelexpo Europe to its new home at the Fira in Barcelona, with many plans to stimulate growth and collaboration in the industry.”
Echoing this sentiment, Jules Lejeune,Managing Director, FINAT said:
“
FINAT was once again proud to be the lead as-
sociation partner of Labelexpo Europe this year. In spite of the heat at the beginning of the show, there was a vibrant mood and general state of pleasure especially among the overseas visitors to reconnect with the global label community after suchalongabsence."
“For us, Labelexpo is always an excellent opportunity to meet with members, potential members and other interested parties and to engage in conversations about our current and future programmes, and to recruit members and enlist volunteers for our working groups and taskforces. This year, we featured our efforts to facilitate value chain collaboration on sustainability such as
CELAB-Europe, UV FoodSafe and Product Carbon Footprint, and to act as spokesperson of the label industry towards European legislatorsandstakeholders.”
Continued, Lejeune: “WewillmisstheAtomium and the World Expo 1958 building as the background images for many selfies taken during the show, but we are convinced that the Fira and its Olympic Montjuich will be a worthy replacement in 2025.”
Noam Zilbershtain, VP & General Manager of HP Indigo & Scitex said: “It’s through trade shows like Labelexpo, industry leaders have the opportunity to connect, network and discuss the trends driving our industry, such as digital innovation and sustainability. I love being in the thick of it all connecting with our customers and partners."
“This year, we were thrilled to have the op-
portunity to showcase the leading LEPx-based HP Indigo V12 and HP Indigo 200K digital presses for the first time in Europe. This was also a key moment for us to showcase the HP Indigo First mindset and how it can deliver flexibility at speed for converters.”
Continued, Zilbershtain: “It was also a pleasure speaking with peers within the print industry, discussing how we are committed to making bold moves that push innovation boundaries and deliver value for customers. The label Industry is now poised to become the first fully digital industry, and it is through digital print solutionswewilltransform businessesglobally.”
Steve Flannery, SVP & GM Materials Group EMENA, Avery Dennison said: "We were thrilled to be back at Labelexpo for the first time since the pandemic and connect together. Our booth was buzzing with conversations around a
linerless future, the benefits of EcoDesign, digital innovations and so much more. Thanks for an amazing turnout!"
Robert Rae, Managing Director of Sales, GEW said: “It was fantastic to return to Labelexpo Europe for the first time since 2019. The exhibition was exceptional for GEW, with a record number of visitors to our stand, and a very healthy order book to show for it. We displayed our full product range but UV LED was top of the agenda for mostofourvisitors."
“Our air-cooled AeroLED UV curing system was the subject of particular interest, and our ability to demonstrate this technology in action, live on OEM presses at the show, meant that we could clearlydemonstrate the huge energy and cost savings that printers can expect with a switch to UV LED. We measuredandpublished our energy consumption live, and were able to
repeatedly demonstrate a 77% saving when compared to conventional UV arc technology."
“To see Malcolm Rae, my father and GEW’s founder, being honoured at the Label Industry Global Awards made it the perfect end to the Brusselsera.”
Other major show features for Labelexpo Europe 2023 included the Automation Arena which drew in large crowds to every one of its ten live demonstrations. Visitors witnessed a fully automated workflow from file creation to turret rewind with automated inspection and MIS integration, without any manual intervention. The participants included CERM, Esko, Xeikon, KURZ, Grafotronic and Fedrigo niSelf-Adhesive.
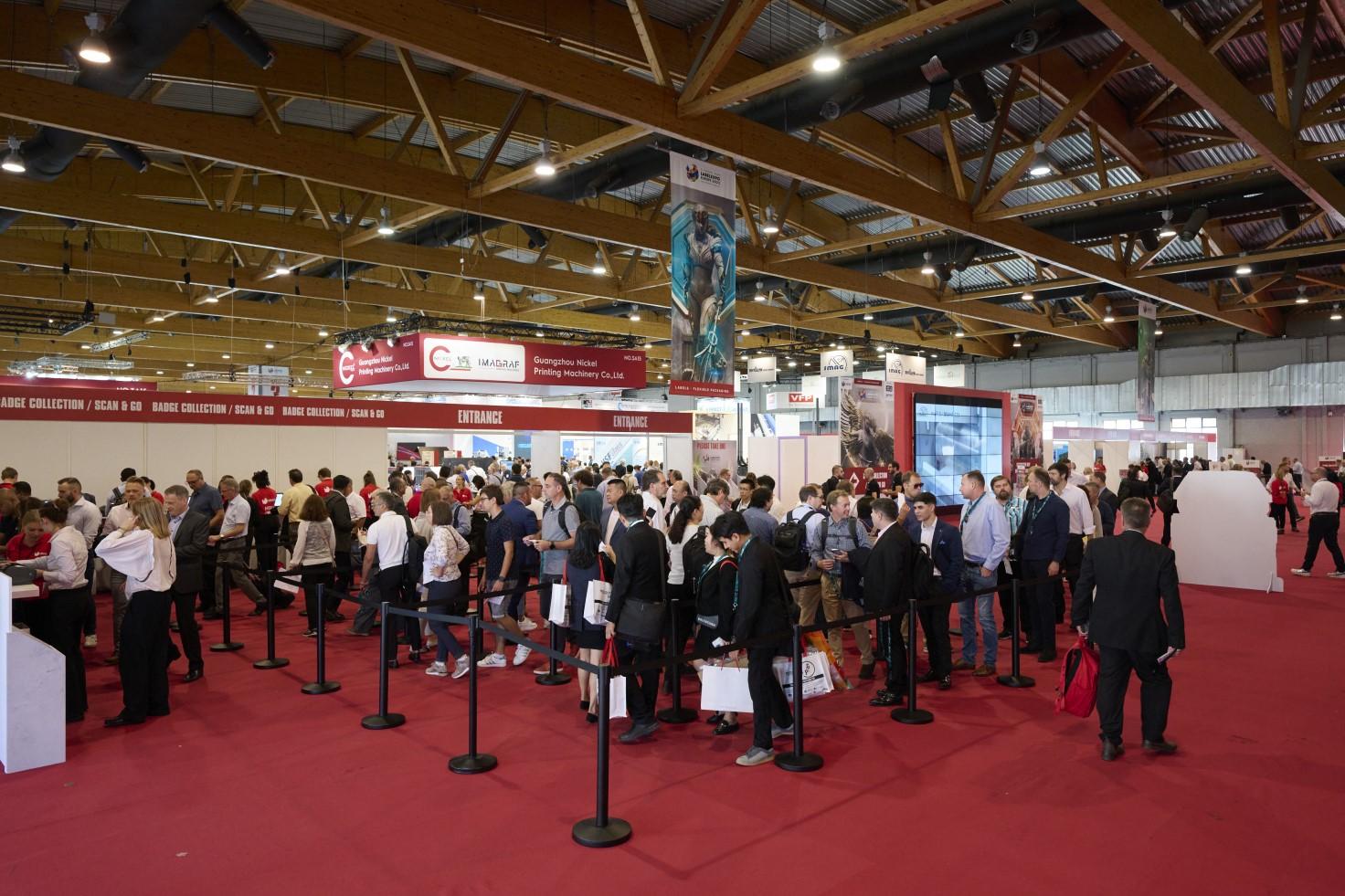
Another key show feature was the Flex Pack Trail, where visitors could deep dive into digital and conventional press technologies, flex
pack material constructions, coating, laminating, ink and curing requirements, in-line and near-line decoration options, QC and migration testing.
Also well received was Flexo’s Future – ECG, a series of presentations on Expanded Color Gamut (ECG) printing led by Dr Kai Lankinen. This was supported by guided tours across the showfloor.
A joint presentation by Graphimecc and Avery Dennison on setting up a track and trace operation was also well attended.
aging and sustainable labels.
Pierre Dogliani, R&D innovation manager, NW Europe, Flint Group, who spoke at the sustainable labels and packaging master class said: "Engaging in this educational platform has been a truly enriching experience, and it's been very inspiring to observe the immense enthusiasm among participants when exploring the realm of sustainable inks and coatings. I believe these insights offered attendees a broader and more informed perspective on sustainability in the labelindustry."
Two expert Academy classes covered the hot topics of flexible pack-
The EREMA Group drives a new era in plastics recycling
Q: How does the EREMA Group see the future?
MH: In the past business year 2022/23 alone, the extruders supplied by the companies within the EREMA Group deliver an additional 1.6 million tonnes of recycling capacity. Our vision is that by 2030 the circular economy in plastics is a reality. That is why the recyclingindustry needs to continue developing and evolving. This will require new technologies and innovations to set positive signs for the future, even in the current challenging times for our custom-
ers.
The whole industry is working on solutions, including a reduction in the use of raw materials, plastic packaging that is designed for recycling, traceability standards for packaging, more efficient collection and sorting processes, and innovative technical solutions for higher recyclate quality. As a result, people in the value chain are gaining an ever better overall understanding of the market. This is accelerating the developmentstowardsmorerecycling and a better circulareconomy.Withour group of companies, we would like to play a
central role in this, actively shaping the future as a real driver in the new era of plastics recycling.
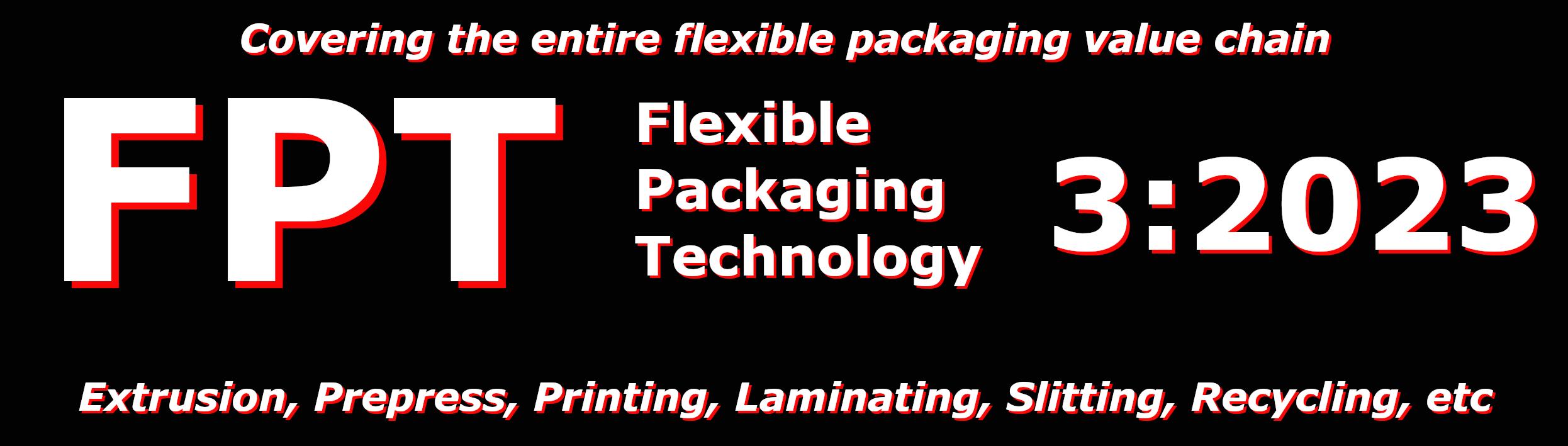
Q: What do you mean specifically when you talk about driving a new era of plastics recycling?
MH: Circular economy and plastics recycling are key topics in politics, day-to-day life and business. Only once the circular economy has been properly implemented will it be possible to fully utilise all the positive properties of plastics. And that is what the EREMA Group has been striving for
since it was founded 40 yearsago.
In recent years, we have become a pioneer in recycling technologies, and we have worked very hard to bring together stakeholders in the plastics industry for discussion and interaction. At the EREMA Group we have also broadened our product portfolio for our customers. We are well integratedintonetworks and can rely on longterm partnerships and research cooperations. This means that we are able to understand even better what it is that our customers need. At the same time, however,itisessentialthatwe take the entire value chainintoconsideration. We need to include the whole picture to create better recycling technologies and optimum solutions for our customers.

Q: What does that involve?
MH: We will continue to expand our group of
companies. Our next goal is to further increase the extent of addedvaluewitha clear focus on the polyolefin sectorandtosetfurther industry benchmarks. To get from waste material to recycled pellets, potential new raw materials need to go through several different recycling processes. The processes range from sorting, shredding, washing and drying to extrusion including filtration and compounding as well as odour optimisation. The challenge lies precisely in the optimum fine-tuning of all the individual recycling steps - especial-
ly when high quality recyclate and consistent stability as well as energy efficiency are to be achieved.Withourcompany KEYCYCLE GmbH, wealreadyofferturnkey solutions for the entire recycling process including sorting, washing and extrusion. We see the next step as an important stepping stone in perfectly matching the washing process and the recycling extruder. This will enable us to offer all-in-one packages that are custom-built to meet the requirements of the market and the needs ofourcustomers.
Wipak strengthens gravure division and supports sustainability pledge with BOBST oneECG
Driven by its vision to become the most sustainable company in the flexible packaging sector, Wipak Walsrode, together with BOBST, has set out to take its gravure printing division to a new level with BOBST’s oneECG technology. The Lower Saxony company is thus continuing its longstanding partnership with BOBST.
The multiple benefits of Extended Color Gamut (ECG) printing will support Wipak’s sustainability commitment to reduce its carbon emissions to zero by 2025. With oneECG from BOBST – the most developed technology for printing with seven standardized colors in gravure – the company will be able to counter massive price pressure more effectively and enable brand owners and retailers to achieve shorter product launch times, all while main-
taining high and consistent quality throughouttheentireprintrun. Make gravure printing competitive again with oneECG
In combination, BOBST’s expertise in gravure printing and its oneECG technology are crucial for the industry and offer a variety of advantages. For Wipak, it was particularly important to make better use of its gravure press by being able to reduce ink consumption by 30%, setup waste by
50%, and work with fewer printing cylinders on press. All of which allow the company to deliver its products to customers faster. Flexibility, speed, and delivery reliability with ever smaller runs and frequently changing designs are among the most important demands from customers. With ECG, these key requirements can be met, while at the same time lowering manufacturing costs, and reducing environmentalimpact.
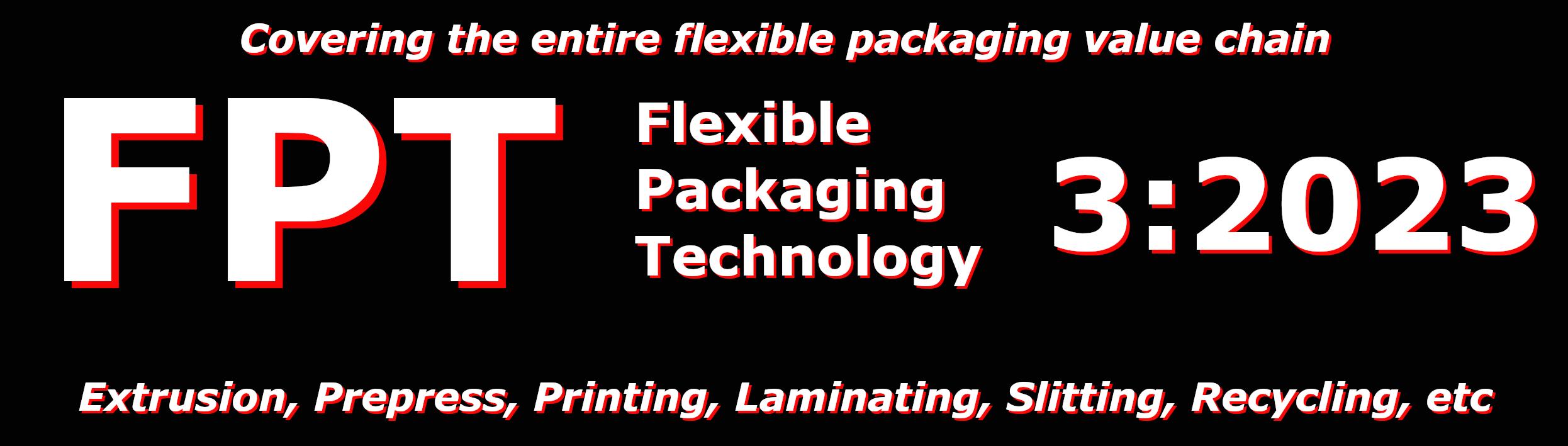
Thanks to the standardization by oneECG, machine downtimes are significantly reduced, as color changes are no longer necessary with every print job. In addition, almost all color matching processes take place in pre-press before the job goes to print. The result is higher color stability and long-term color consistency even over the longest runs, as well as accurate repeatability, regardless of whether repeat jobs are printed on the same printing press or on a different press running oneECG technology.
Stefan Bruns, Process & Quality Manager Converting and Project Manager ECG at Wipak Walsrode, explained, “oneECG from BOBST offers us the great advantage that we can work with fewer – completely standardized printing inks – and therefore significantly shorten the time when our machines are not producing. This in turn
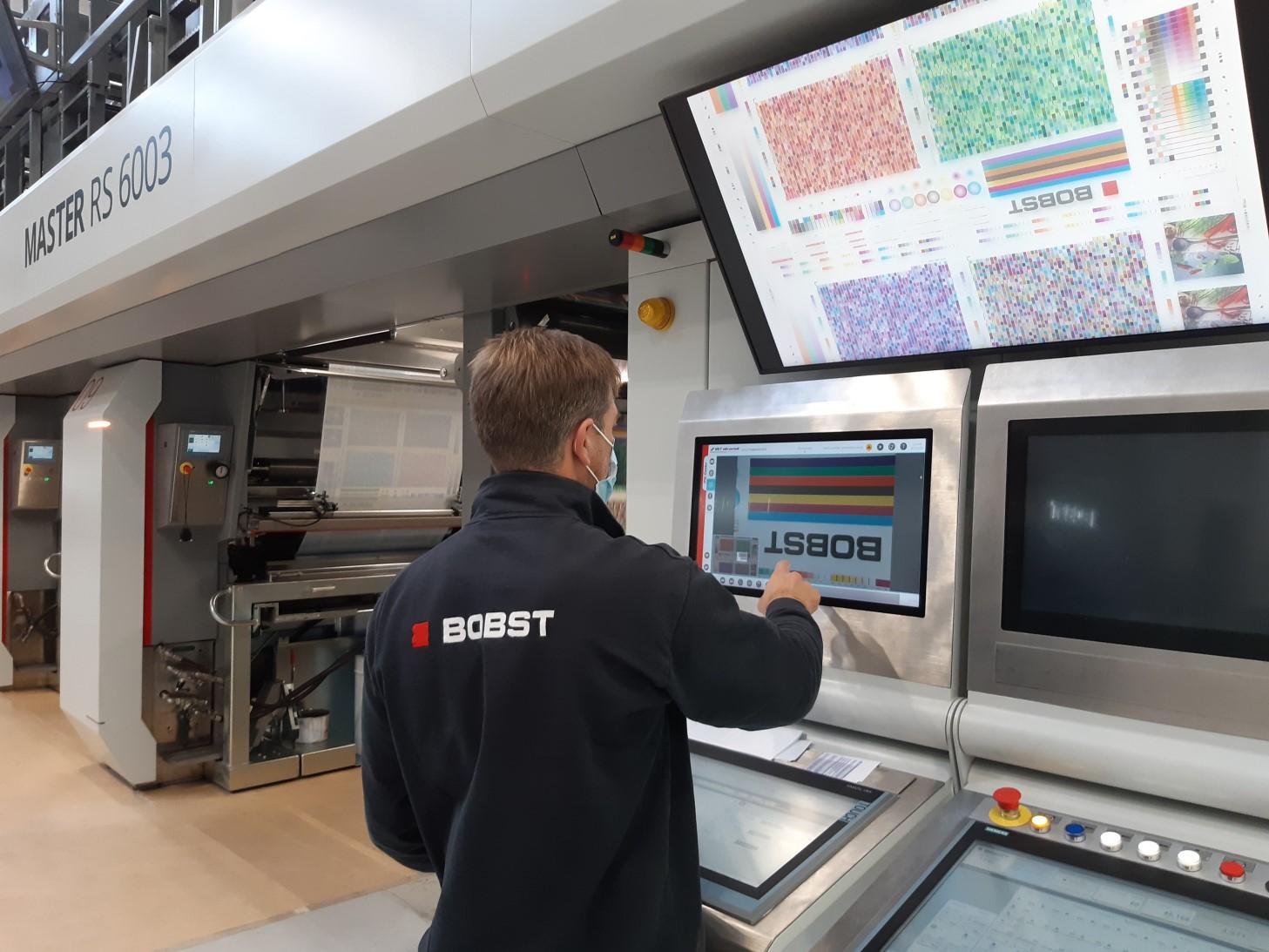
leads to significantly higher productivity. In a very competitive market where there is currently extremely intense pressure on prices, we have to increase our efficiency in gravure printing in order to compete sustainably with flexo printing.BOBSToneECG technology is the solution for us to this and many more challenges ingravure.”
Many advances have been made in flexographic printing over the past decade, including significant improvements in print quality, greater control over the
entire production process, the ability to profitably print smaller runs, and reductions in waste during set-up and production changeovers. As a result, many brand owners and retailers have recognized the opportunity to save costs by switching from gravure to flexographic printing. With oneECG from BOBST, gravure printing technology can stand up to this development and shine with its outstanding print quality for both small and medium-sized as wellaslargeprintruns.
Bruns said, “Gravure printing has a great chance of becoming ‘sexy’ again after being pushed back by other printing processes for a long time. At Wipak we call printing in the ECG color space ‘GCP –Green Choice Printing’. This Green Choice is embedded in our sustainability strategy as a very important building block in overcoming the challenge for the plastic packagingindustry.”
Partnerships built on mutual trust and support
BOBST’s oneECG is built on major advances in printing and pre-press technology. These enable more precise control of processes and allow packaging manufacturers to work within significantly tighter tolerances.
The oneECG solution for gravure printing was developed by BOBST in close collaboration with industrypartners.Itisa complete system with color management soft-
ware from Esko, color measurement technology from X-rite, printing cylinder engraving from ICR SpA, and process inks from, among others, Sun Chemical and Siegwerk. It is available on BOBST gravure presses either on new machine installations or as a retrofit option. In both cases, BOBST and partners work closely with printers to exploit the full potential of this technology.
“With its decades of practical experience and the entire know-how of the former Italian machine manufacturers (e.g., Schiavi, Cerutti) that are now part of the company, BOBST is the gravure printingspecialist par excellence,” says Mr. Bruns. “Our longstanding cooperation with BOBST is invaluable for Wipak, but it also offers our customers enormous advantages. Theyappreciatethefirst -class print quality and the cost advantage due tothesometimessignificant reduction in print-
ing cylinder costs that we can offer them thanks to oneECG. The successful realization of the oneECG project in gravure printing is not only based on the right technology, but also on trust and support at all levels.”
The close partnership with BOBST, which dates back more than 20 years, was also evident in 2022 when Wipak supported the Swiss company to win the Golden Cylinder Award for technical innovation from the GAA (Gravure AIMCAL Alliance). Wipak’s glowing testimonial was instrumental in BOBST winning the trophy for ‘Advanced Register Control for Precision Printing and ECG in Gravure’ – a prestigious accolade thatrepresentsthe14th Golden Cylinder for BOBST in the history of theseawards.
Wipak Walsrode is currently developing a oneECG future strategy together with its customers in the branded
goods industry and retail. “In our view, oneECG from BOBST represents an enormous opportunity to make gravure printing in the Central European market for flexible packaging more attractive again – with the highest print quality across the entire run, higher efficiency, and resourcesaving production while at the same time reducing costs for all parties involved, because fewer printing cylinders are needed,” said Bruns, summarizing the currentposition.
Wipak Walsrode GmbH & Co. KG is part of the Wipak Group, a global supplier of packaging solutions and services for the food industry as well as for medical devices and pharmaceutical products. The group of companies, headquartered in Finland, employs more than 1,800 people at 11 production sites throughout Europe and Asia as well as in sales offices in 18 countries. Sustainability isoneofthecorevalues of the group, which achieved carbon neutrality in its operations at the end of 2022 by
minimizing its CO2 emissions in accordance with GHG Protocol Scope 1 and 2 and offsetting the remaining emissions.
Further information on the oneECG project at Wipak Walsrode will be available later in 2023 when the company takes part in an event dedicated to innovation in gravure printing at BOBST’s Competence Center in San Giorgio Monferrato,Italy.
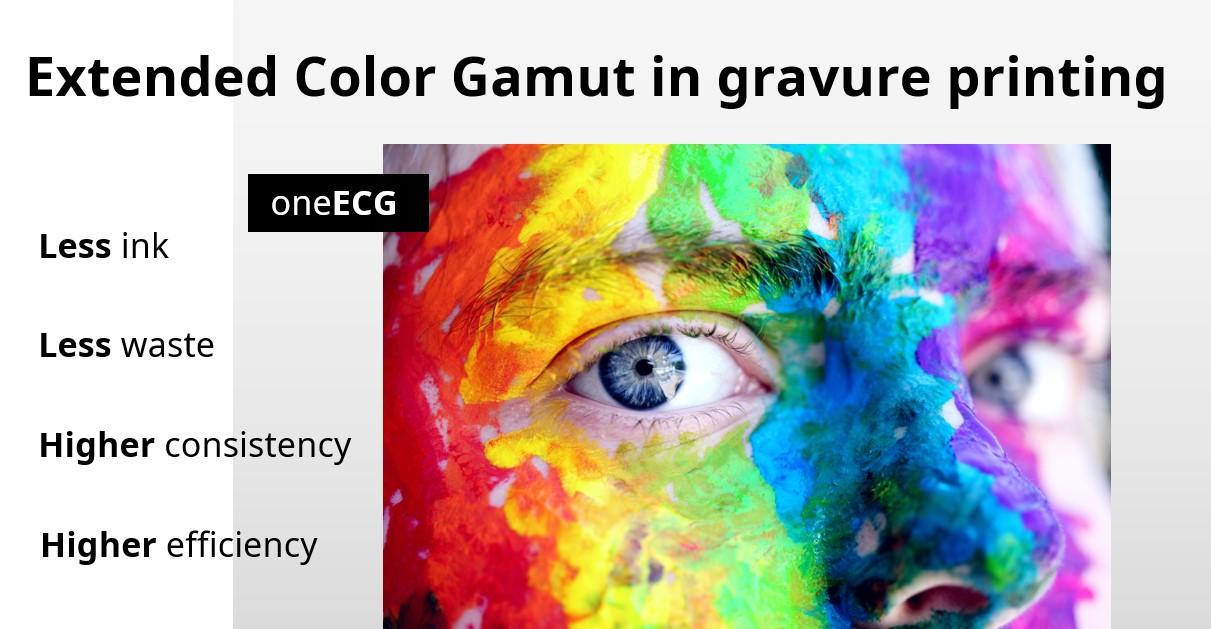