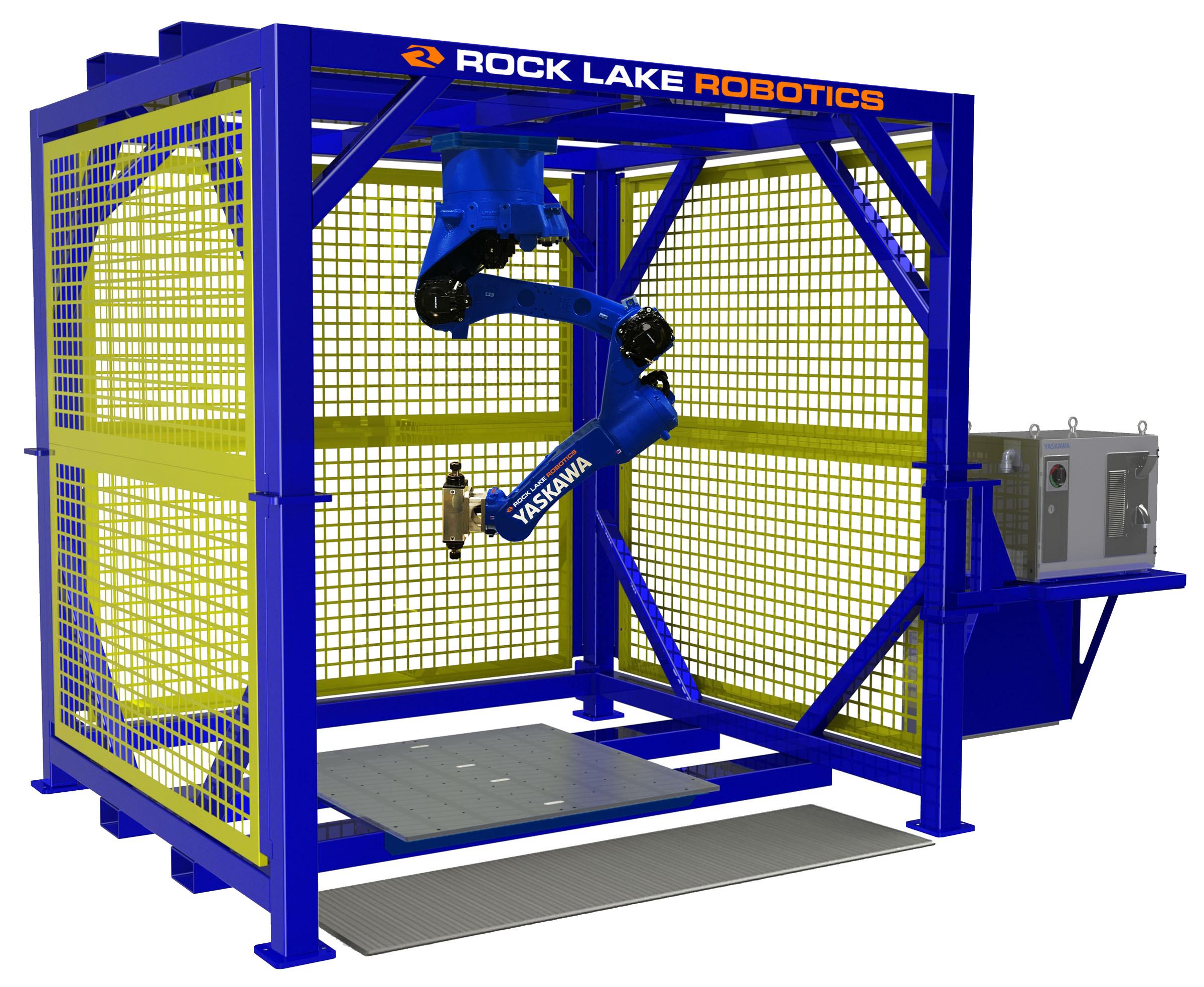
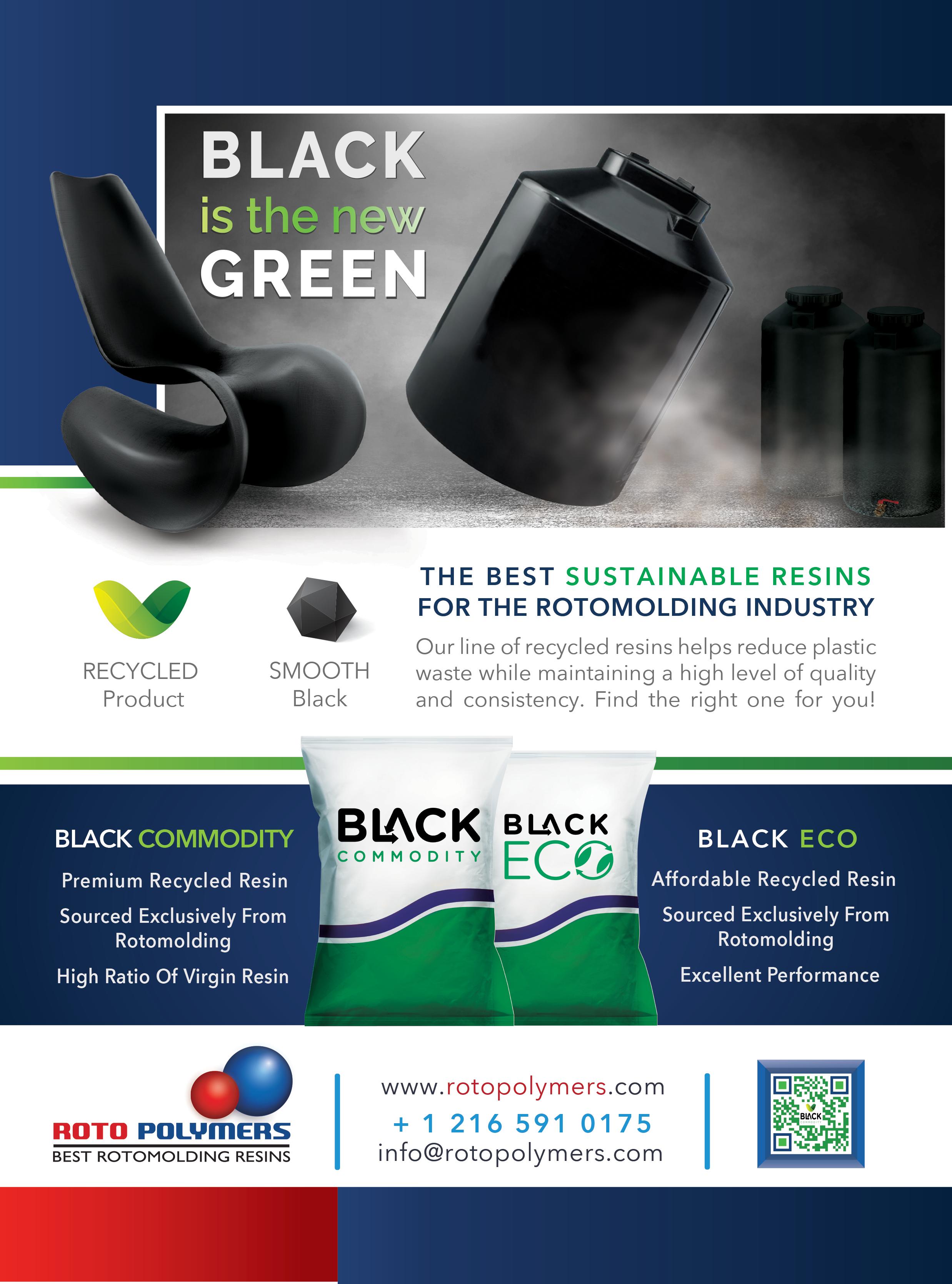
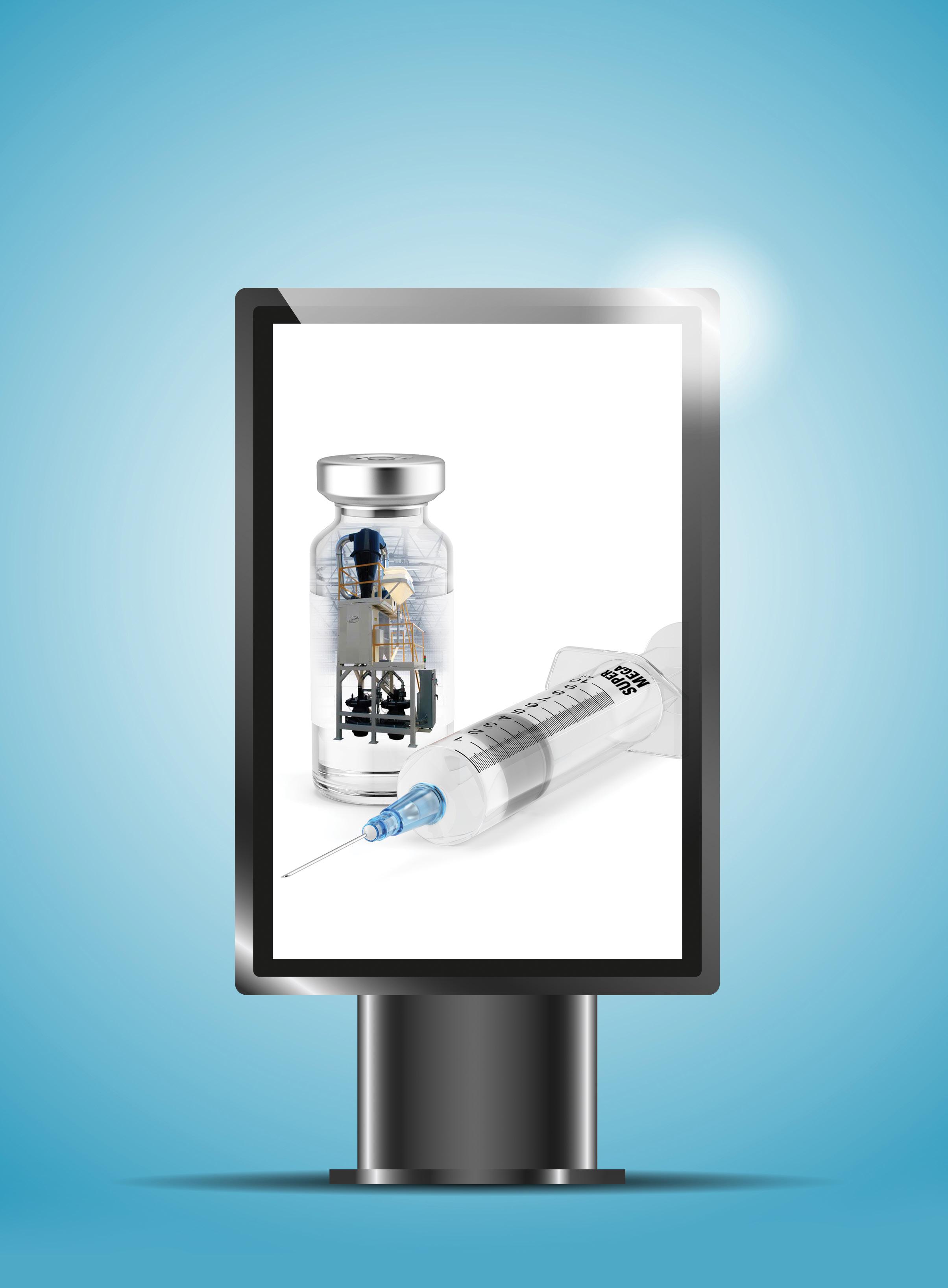
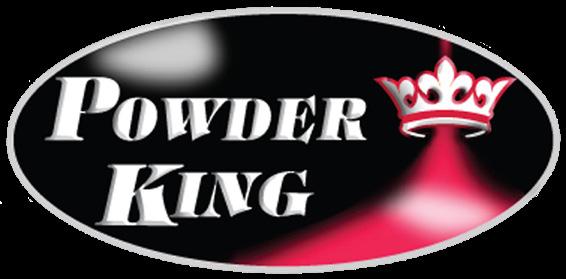
26
Jennifer Gibson-Hebert, JSJ Productions, Inc. A growing and employee-owned company.
31
Meese Düsseldorf
The most international trade fair of the global plastics and rubber industries.
34
A. Michael Gellman, Fiscal Strategies “4” Nonprofits A call to action to spur change.
40
Michelle Rose, ARMA CEO
A back to basics, in-person conference with an exceptional business program and opportunities for connections.
52
Dr. J Carlos Caro, PhD Polymer Chemistry, GRAFE Polymer Solutions
The benefits of using micropellets.
Industry is flooded with information addressing the hot topic of a circular economy. The simple definition is a model of production and consumption, which involves sharing, leasing, reusing, repairing, refurbishing, and recycling existing materials and products if possible. In this way, the life cycle of products is extended. In practice, it implies reducing waste to a minimum. There is a lot of mention about a circular economy inside this issue.
Restorative and regenerative by design, a circular economy means materials constantly flow around a closed-loop system, rather than being used once and then discarded. In the case of plastics, this means simultaneously keeping the value of plastics in the economy, without leakage into the natural environment. We take materials from the Earth, make products from them, and eventually throw them away as waste – the process is linear. In a circular economy, by contrast, we stop waste from being produced in the first place.
In a circular economy, manufacturers design products to be reusable. For example, electrical devices are designed in such a way that they are easier to repair. Products and raw materials are also reused as much as possible. For example, by recycling plastic into pellets for making new plastic products.
This is underpinned by a transition to renewable energy and materials. A circular economy decouples economic activity from the consumption of finite resources. It is a resilient system that is good for businesses, people, and the environment. The circular economy is a systems solution framework that tackles global challenges like climate change, biodiversity loss, waste, and pollution.
Experts say this is how we will manage resources for the future, how we will make and use products, and what we will do with the materials afterward. Only then can we create a thriving circular economy that can benefit everyone within the limits of our planet.
One only must ask: What will it take to transform our throwaway economy into one where waste is eliminated, resources are circulated, and nature is regenerated? The circular economy gives us the tools to tackle climate change and biodiversity loss while addressing important social needs. It gives us the power to grow prosperity, jobs, and resilience while cutting greenhouse gas emissions, waste, and pollution.
We are so pleased to present an inside look at how Scott Seljan, Seljan Company, has engaged in a fast-growing employeeowned robotics manufacturing company, Rock Lake Robotics. His inspiring journey began due to a need for labor in his own rotomoulding company. Read all about the ideology behind this exciting USA innovative manufacturing story.
I also think you will enjoy reading noted economist Michael Gellman’s article on how inflation affects planning, budgets, and operating reserves, but more importantly perceptions. He says to “get out in from of inflation, we need to turn inflation-driven negative feelings into a positive driver for innovative planning and a wake-up call to action”.
Michelle Rose, ARMA CEO, contributes a great review of the 2022 ARMA Conference held recently in Melbourne, Australia. This was the first time ARMA has met in person in three years due to Covid. Their backto-basics programming along with great business and social opportunities drove a very successful conference. Ronny Ervik reports on the 2022 Nordic ARM Conference held earlier this year in Copenhagen. The focus of this conference was the circular economy, automation, and innovations.
Susan Gibson Publisher & EditorI hope you enjoy the issue!
In the case of plastics, this means simultaneously keeping the value of plastics in the economy, without leakage into the natural environment.
Publisher & Editor
Susan D. Gibson President - JSJ Productions, Inc. susan@jsjproductionsinc.com
Technical Editor
Alvin Spence PhD MEng aspence@centroinc.com
Process Editor
Paul Nugent PhD MEng paul@paulnugent.com
Design Editor
Michael Paloian President - Integrated Design Systems, Inc. paloian@idsys.com
Global Contributing Editors
Celal Beysel Chairman - Floteks Plastik beysel@superonline.com
Martin Coles Matrix Polymers martin.coles@matrixpolymers.com
Adam Covington Ferry Industries acovington@ferryindustries.com
Mark Kearns Moulding Research Manager m.kearns@qub.ac.uk
Ravi Mehra Managing Director - Norstar International LLC maramehra@aol.com
Advertising and Art Production
Marketing/Advertising Director Jennifer Gibson Hebert Vice President, JSJ Productions, Inc. jennifer@jsjproductionsinc.com
Chief Art Director Anya Wilcox JSJ Productions, Inc. awilcox@designintersection.com
Circulation & Distribution Administration
Sheryl Bjorn JSJ Productions, Inc. sheryl@jsjproductionsinc.com -
Editing & Translations
Suzanne Ketron | Oliver Wandres | Sheryl Bjorn
Website & Online Technology
Jason Cooper JSJ Productions, Inc. jason@bound.by
RotoWorld ® is a JSJ Productions, Inc. Trade Publication JSJ Productions, Inc. 625 West Market Street, Salinas, CA 93901 Phone: (512) 894.4106; Fax (512) 858.0486 Email: rotoworldmag@rotoworldmag.com and Website: www.rotoworldmag.com
Subscriptions One-year subscription (six issues), print or digital, $60 US, $90 Canada/Mexico, $135 All Other Countries. To subscribe or to submit change of address information, call us at (512) 894.4106; fax us at (512) 858.0486; visit us online at www.rotoworldmag.com; or email us at sheryl@jsjproductionsinc.com. You may also write to RotoWorld ® Subscriptions, JSJ Productions, Inc., 625 West Market Street, Salinas, CA 93901
Advertising For information on advertising, please contact Advertising Director Jennifer Gibson Hebert, JSJ Productions, Inc. Email Jennifer Gibson at jennifer@jsjproductionsinc.com
Letters We welcome letters about our contents. Write Letters to the Editor, JSJ Productions, Inc., 625 West Market Street, Salinas, CA 93901 512.894.4106 phone 512.858.0486 fax, or Email susan@jsjproductionsinc.com.
Editorial Queries We consider unsolicited contributions. Send manuscript submissions as email attachment to Susan Gibson at susan@jsjproductionsinc.com.
JSJ Productions, Inc. bears no responsibility for claim or factual data represented in contributed articles.
Postmaster Send changes of address to RotoWorld®, JSJ Productions, Inc., 625 West Market Street, Salinas, CA 93901
RotoWorld® is a JSJ Productions, Inc. independently owned, bi-monthly trade magazine for the international rotational molding and plastics design industries. JSJ Productions, Inc. owns all copyrights on articles published herein unless ownership is otherwise stated. Reproduction of this magazine, in whole or in part, without the express written permission of the publisher is not permitted.
Alvin Spence is Vice President Engineering at Centro, Inc., North Liberty, Iowa. He provides leadership for Centro’s product development team and quality resources. Alvin received his Bachelor’s degree in Mechanical & Industrial Engineering and PhD from Queen’s University Belfast. aspence@centroinc.com
Paul is a consultant who travels extensively across six continents assisting clients in many roles from training to expert witnessing. He received his Eng. degree in Aeronautical Engineering and Ph.D. in Mechanical Engineering from Queen’s University of Belfast. Paul developed the Rotolog system, the first complete computer simulation (RotoSim), and authored a book entitled Rotational Molding: A Practical Guide paul@paulnugent.com
Celal is Chairman of Floteks Plastik, the pioneer and innovative leader of the rotational molding industry in Turkey and a Global Contributing Editor for RotoWorld® magazine. Being an ARM member for more than 20 years, he has made many presentations at ARM meetings in various countries. He is also active in business and political organizations in his country. Celal has authored numerous articles published in various newspapers and magazines about politics, plastics, rotomolding, and innovation. beysel@superonline.com
Michael is President of Integrated Design Systems, Inc., Great Neck, New York. Over the past 25 years, Mike has developed a broad range of plastic products utilizing various processing methods including rotational molding. Mike’s B.S. degree in Plastics Engineering and Masters in Industrial Design, combined with his extensive experience, has formed the basis for his branded and unique insights into the field of plastics part design. paloian@idsys.com
Martin Coles, CEO of Matrix Polymers co-founded the business 30 years ago and is the company’s largest shareholder. Shortly after graduating from London University, he began his career in the plastics industry working for a major Italian petrochemical and soon became passionate about the unique world of rotomoulding. Matrix Polymers are experts in rotomoulding materials and have become a global supplier with compounding and grinding plants in the UK, Poland, Australia, New Zealand, and Malaysia. The company sells more than $150 million of rotomoulding materials each year and has 230 employees. martin.coles@matrixpolymers.com
Adam Covington is President of Ferry Industries, Inc. in Akron, Ohio U.S.A. Covington has been with Ferry Industries for over 11 years, advanced through the manufacturing, engineering, sales, and service positions within the company and was appointed President in 2019. Adam strives to find solutions for customer’s needs and advance machine technology for the rotomolding industry. He is a graduate of Ohio University’s Russ College of Engineering and Technology with a Bachelor’s degree in Industrial Technology. acovington@ferryindustries.com
Mark Kearns is the Rotational Moulding Research Manager of the Polymer Processing Research Centre at Queen’s University of Belfast. He is a Chartered Chemical Engineer with a M. Phil Degree in Rotational Moulding. Mark manages rotational moulding research and development projects for companies across Europe, Australasia, and North America. M.Kearns@qub.ac.uk
Rob Miller is Owner/President, Wittmann Battenfeld Canada Inc. Rotoload. Rob started in the plastics pneumatic conveying industry in 1986. He has spent his entire career developing, engineering, and designing all types of catalog, standard, and custom pneumatic conveying systems for the plastics industry. He started in the rotational molding industry in 2013, has enjoyed learning the idiosyncrasies of the industry and market, and most of all meeting the people and building relationships for the future. Rob.Miller@wittmann-group.ca
Ravi Mehra has been associated with the rotational molding industry since the early 1970’s. He is a Past President of ARM – Association of Rotational Molders, and has been inducted into the ARM Hall of Fame. He is the Founding Chairman of StAR – the rotational moulding Trade Association of India. He was the Chairman of ARMO – Affiliation of Rotational Moulding Organizations from 2012 to 2014. Ravi consults internationally with companies in the rotational moulding arena to help their global strategy, facilitate technology tie-ups, and business alliances. maramehra@aol.com
Ian Hansen has over 30 years of experience in the rotational moulding industry and has presented to conferences around the world on the subject of quality, safety, and tank design standards. Rotomoulders around the globe have problems from time to time. Rota Consult delivers production solutions so rotomoulders can improve productivity and profitability, without wasting more of their valuable time. ianhansenconsult@gmail.com, www.ianhansenconsult.com
Jim is the General Manager of PSI Brand, the permanent graphics for plastics division of their family business, Polymer Systems International in New Zealand. Starting out as an engineer and rotomoulding operator, the past 20 years has involved leading a team, developing graphic systems to service global brands, and assisting rotomoulders decorate their plastic products to deliver long-lasting brand experiences. jim@psibrand.com
Jennifer Gibson is Vice-President and partner of JSJ Productions, Inc. with offices in Austin, Texas and Monterey County, California.
Jennifer serves as the Executive Director for the Culligan Dealers Association of North America and Publisher/Editor of Connection magazine, which is dedicated to the Independent Culligan Dealers of North America. In addition, Jennifer oversees marketing and advertising for RotoWorld ® magazine, the only magazine dedicated to the worldwide Rotational Molding Industry and Plastic Design Industry. Jennifer also collaborates on independent production/ marketing/event/fundraising projects for various clients worldwide.
Jennifer holds a BS and Masters degree in Macro Administrative Social Work/Fundraising for Non-profits, and following graduate school; she worked as a lobbyist/fundraiser on behalf of disadvantaged youth throughout the state of Indiana. Jennifer began working for JSJ Productions, Inc. in 2000 and became a partner in 2007. She has extensive experience in lobbying, event planning, project production, board management, association leadership, marketing, advertising, publishing, and online digital media.
Jennifer is a member of the ASAE (Association Society of Account Executives) and active and several non-profit charities geared towards autism awareness and education.
Dr. Herrero is the CEO and lead designer of products and services at The Chalfont Project Ltd, an international firm of organizational architects. He is also the Managing Partner of Viral Change Global LLP, which specializes in the application of organizational change. Dr. Herrero is a psychiatrist by background who, after medical practice and academia, spent many years in hands-on leadership positions in global companies. He is an international speaker on organizational challenges, has received the Grand Davos Award in a World Communication Forum, and is an accomplished TEDx speaker.
With a Degree in Hotel Management and a background in event organisation, Michelle started with the ARMA almost 15 years ago, in the role of Deputy Executive Officer. During her career so far, Michelle has organised conferences and study tours all over the world and gained extensive experience in membership management, stakeholder engagement, and administrative services, as well as business and project management. Due to her commitment, hard work, and wide range of expertise, as well as the value of her current industry relationships, Michelle was selected for the role of CEO starting January 2021.
Michael Gellman is an independent fiscal and financial strategist for nonprofit organizations and a founding principal partner for Fiscal Strategies “4” Nonprofits, LLC where the primary focus is helping legacy organizations and new organizations build and achieve a sustainable and financially healthy future. Gellman was a former 20-year Shareholder for Rubino & Company, Chartered, CPA’s and Consultants. He has more than 35 years’ experience in nonprofit fiscal, financial and accounting systems working as a chief financial, fiscal and management consultant where he has focused on specialized management and advisory services for trade and professional associations, public charities and endowment-based foundations. Gellman has also developed comprehensive budget and projection-based systems in support of senior management and organizational leadership.
Despite the significant challenges of the past few years, the rotational moulding market has continued to thrive – contributing to the continued rapid growth of Matrix Polymers and our parent company, Revolve Group.
The specialist rotomoulding raw material supplier launched a new regional website earlier this year and now has a shiny new product brochure to complement. It reflects the group’s local approach, providing our customers with the most relevant experience possible and showcasing our global product portfolio.
Customers worldwide can now browse the wide range of products and services offered, quickly and easily, no matter where they are. The new brochure is easy to navigate, interactive, and smartphone friendly, making it even easier to find the information you need.
CEO of Matrix Polymers, Martin Coles, commented: “We will continue to invest heavily in our manufacturing facilities and additional production capacity, whilst continually reviewing and improving our communication channels with our customers.”
For more information, go to www.matrixpolymers.com
• Anti-scratch additive for PP & TPO formulations boost reuse potential of plastics used in consumer applications
• Extend service life of agricultural mulch films with new light stabiliser solution
• Novel bio-based lubrication and nucleation additive for polyesters in E&E and transportation sectors
MUTTENZ, SWITZERLAND — K 2022 visitors looked forward to new Clariant additive solutions to progress more sustainable plastics and reduce resource use. New developments give applications greater resilience to support longer use and reuse on the path to circularity. Plus, solve production challenges while achieving better efficiency and a lower carbon footprint during compounding and processing.
“By extending a product’s service life and by boosting reuse potential, the plastics industry can contribute positively towards reducing wasteful consumption and increase circularity in key segments. Adopting ways to reduce material waste and energy use in production brings further sustainability advantages and improves product carbon footprint. With these new additives, including renewable-based solutions, in our portfolios, we’re excited to offer plastic processors and value chains more support to collaborate and further innovate together,” comments Martin John, Head of Advanced Surface Solutions at Clariant.
New anti-scratch additive to extend the service life of consumer goods
Surface aesthetics play a crucial role in the perceived quality of consumer goods. Clariant’s new renewable raw material-based anti-scratch additive for polypropylene (PP) and thermoplastic olefins (TPO) formulations – Licowax® AS 100 TP – enables molded plastic goods across a wide range of consumer applications to maintain their original look and feel for longer. This offers significant potential to extend service life and improve properties’ retention and parts’ reuse.
The new additive helps to prevent scratches and mars on the surface of goods during handling, transportation, and end-use. This is particularly beneficial for otherwise scuffprone applications such as interior automotive parts like dashboards and door panels, household appliance casings, cosmetics packaging, and lightweight luggage.
New light stabilizer supports more sustainable agricultural films
Mulch films perform an important role in optimizing crop growing conditions, by protecting both crops and soil from contamination and from the loss of moisture and nutrients
Clariant launches new additives at K 2022 to support plastics sustainable evolution
“With these new additives, including renewable-based solutions, in our portfolios, we’re excited to offer plastic processors and value chains more support to collaborate and further innovate together.”
— Martin John, Head of Advanced Surface Solutions at Clariant
that could jeopardize yields. New AddWorks® AGC 970, Clariant’s latest light stabilizer solution for polyethylene agricultural films, offers the mulch segment a step up in product durability. Addition of the additive enables converters to extend the service life of their products, by increasing UV resistance and resistance to high levels of agrochemicals. The granular additive can be dosed directly during conversion which supports more tailored use.
Benefit from a unique combination of lubrication and nucleation in engineering plastics for greater efficiency in compounding and processing. Compared to more conventional products, new biobased Licocare® RBW 560 TP Vita can withstand higher processing temperatures thanks to excellent thermal stability and low volatility and works more effectively at low dosage. It also has outstanding color stability. The combined benefits make it particularly attractive to formulators of polyester compounds for use in the E&E or transportation industries.
The new additive promotes easier mold release which improves the surface quality. Productivity-wise, it also means fewer polyester parts get stuck in the mold and therefore less molding downtime.
The risk of short shots and rejects is reduced too. It is possible to produce more parts per machine hour due to faster cycle times driven by shorter cooling cycles. As a result, energy consumption is reduced.
Licocare RBW 560 TP Vita is the latest extension to Clariant’s Licocare range of high-performing additives based on renewable, non-food-competing feedstock. They are derived from crude rice bran wax, a by-product from the production of rice bran oil. Vita designated products use real renewable content of at least 98% Renewable Carbon Index (RCI), thus offering the advantage of a lower carbon footprint compared to state-of-the-art alternatives.
Clariant has applied for FDA food contact approval for its entire range of Licocare RBW additives. This will open up their use by plastics compounders and masterbatch producers in an even wider range of plastics applications.
Clariant’s additive products and solutions offer exciting opportunities for the plastics industry to strengthen the links between efficiency and sustainability, safety, performance, value, and low carbon footprint.
For more information on these featured new additives, as well as Clariant’s wider support to meet sustainability and circular economy challenges, visit www.clariant.com/K-2022.
ROTTERDAM, NETHERLANDS — LyondellBasell and Shakti Plastic Industries, India’s largest plastic scrap recycler and waste collection company, have signed a Memorandum of Understanding (MoU) to form a joint venture to build and operate a fully-automated, mechanical recycling plant in India. The plant is intended to process rigid packaging post-consumer waste and produce 50.000 tonnes of recycled polyethylene (PE) and polypropylene (PP) per year, equivalent to the single-use plastic waste produced by 12.5 million citizens. It is envisaged that the new facility will become the largest mechanical recycling plant in India and is estimated to start at the end of 2024. LyondellBasell will market the recycled products produced by this joint venture adding volume to its Circulen Recover range of existing PE and PP materials to help meet the increasing demand by converters and brand owners in India for recycled polymer materials.
“The proposed joint venture will allow us to address the issue of plastic waste in the second most populated country in the world and expand our circular polymer product offering to India,” says Yvonne van der Laan, LyondellBasell Executive Vice President, Circular and
Low Carbon Solutions. “Combining our respective expertise with Shakti Plastic Industries will create an innovative system that can be scaled as the circular economy grows.”
Once established, the joint venture will leverage each partner’s strengths. With the development of a recycling infrastructure in India, Shakti Plastic Industries will provide structure and formality to the waste collection process to secure materials to be used at the new venture. LyondellBasell will apply its long-standing leadership in innovative plastic production technology, vast experience in product development, and strong knowledge of the polymer markets in India.
“The circular economy will increasingly develop into a critical part of the plastic value chain in India, requiring solutions across the value chain to develop a sustainable world of plastic recycling,” says Rahul V. Podaar, managing director of Shakti Plastic Industries. “As we move towards becoming a value player in the circular economy, we will continue to seek opportunities for future growth. Together with LyondellBasell, we will be on the forefront in India taking significant steps to recycle rigid plastic waste which supports the government initiative to reuse recycled plastic applications.”
» ROTOLOAD™ is the ONLY solution to ALL of your powder resin handling needs.
» ROTOLOAD™ is the ONLY comprehensive line of powder resin conveying and weighing equipment, specifically designed to meet the demands of the Rotational Molding Industry.
» ROTOLOAD™ uses vacuum to load your material, hold it above your process machine, and dispense, quickly and accurately. In addition it is the ONLY solution to the question of how to reduce under and overweight parts, mess, downtime and resin loss.
CALGARY, ALBERTA, CANADA — NOVA Chemicals Corporation (“NOVA Chemicals”), a leading producer of polyethylene resins, announced the launch of its new, mechanically recycled polyethylene resin: EX-PCR-NC4. Incorporating this product allows converters and brand owners to meet their sustainability goals, without compromising package performance in applications such as shrink, e-commerce, heavy-duty sacks, and protective packaging.
EX-PCR-NC4 contains 100 percent post-consumer recycled polyethylene (rPE) and offers highly versatile design flexibility making it an ideal solution to lower the carbon footprint of packaging and address climate change. NOVA Chemicals’ rPE is sourced from a distribution center flexible film, which includes a blend of back-of-store stretch and front-of-store consumer drop off. Source materials are processed with state-of-the-art technology resulting in a low odor, consistent, and stable product. NOVA Chemicals’ proven technical expertise can help guide customers to incorporate rPE and maintain the necessary level of performance while also creating recyclable flexible packaging that remains in the
PE stream through a design for recycling approach.
“Through customer trials and applications development at our Center for Performance Applications in Calgary, we have successfully incorporated our new rPE resin in various end-use formats,” said Anna Rajkovic, NOVA Chemicals Circular Economy Market Manager.
Commercial quantities of EX-PCR-NC4 are available today. “Our new rPE product line is the definition of a win-win. It provides converters and brand owners with a more sustainable packaging solution without compromising overall quality or strength. And, by utilizing rPE, we’re diverting plastic waste from landfills while also enabling a fully recyclable new product: a true demonstration of circularity,” said Alan Schrob, NOVA Chemicals Mechanical Recycling Director. “We aim to deliver commercial quantities of consistent high-quality rPE products to meet the needs of our customers and the desires of the brand owners and consumers. NOVA Chemicals continues to demonstrate leadership in providing sustainable polyethylene solutions, and we look forward to additional growth in this space.”
Rotoworld Magazin Issue 4/2022 AZ: 177,8x122,276 + 3mm Coated FOGRA39 PDF/X-1a:2003 hd-kunststoffe.com
MALMO, SWEEDEN — Perstorp is aligning with the new industry standard for product carbon footprint (PCF), developed by the industrial initiative Together for Sustainability. Perstorp can already provide product carbon footprint values for about 85% of its products (based on sales volume) and is continuously adding more products.
The focus on product carbon footprint is strongly increasing, in line with the emerging emphasis on reducing CO2 emissions and sharing carbon footprint at a product level. Swedish-based sustainable solutions provider Perstorp currently has product carbon footprint values for more than 80 products, which corresponds to about 85% of the sold volume. These values are updated annually, based on production plant-specific conditions. All the PCF values for Perstorp’s Pro-Environment products, contributing to the sustainable transformation of value chains by substituting fossil feedstock with renewable and recycled, are ISCC PLUS certified.
Carbon footprint data is central for companies working towards CO2 emission reduction targets, and for making informed decisions by comparing the footprint of different products. To enable companies further down the value chains including brand owners to make carbon footprint calculations of their individual products, it is crucial that the chemical industry can provide this data for their products, which in turn are raw materials used in thousands of end products.
“Transparently sharing this type of information with our customers is an important part of being a sustainable solutions
provider and serving value chain needs,” says Anna Berggren, VP Sustainability at Perstorp. “Product carbon footprint is an important way of providing value with our Pro-Environment products; it shows how they reduce CO2 emissions by substituting fossil feedstock with renewable or recycled alternatives, which gives an effect on all downstream parties and products in the value chain. We have products already today that are climate positive up to our gate when including biogenic CO2 uptake, and we will continuously reduce the carbon footprint of all our products along our reduction roadmaps towards reaching our Science-Based emission reduction targets in 2030.”
As part of the joint initiative Together for Sustainability, companies from the global chemical industry have agreed on a global guideline for calculating product carbon footprints. Perstorp was one of several companies who evaluated and tested the new methodology during spring 2022. Perstorp has been calculating and sharing product carbon footprint values with customers for many years but has now also developed a digital tool that makes it easy and accessible to share the values with customers.
Together for Sustainability is an industry-leading initiative driven by chemical procurement specialists. Each member is dedicated to building sustainable chemical supply chains, regulatory requirements, and responding to the needs and expectations of society.
For more information contact Perstorp, Perstorp Holding AB, Neptunigatan 1, SE-211 20 Malmö Sweden, +46 435 380 00, perstorp@perstorp.com, www.perstorp.com, @perstorpgroup
is a family-owned injection moulding company established in 1994 with the aim to supply quality injection moulded components to the rotational moulding industry, primarily the rotationally moulded tank market.
Over the last 28 years, through constant product development and innovation, we have expanded our range and now offer one of the most extensive product ranges for rotationally moulded tanks on the market. Our products are covered by over 10 patents and registered designs and are distributed to over 15 countries worldwide.
In addition to our own products, we offer product development and custom injection moulding services to customers. With the aid of CAD software (SolidWorks and MasterCam), 3D prototyping facilities, and a full in-house toolroom we can help bring our customers’ ideas to life.
Now on our second generation of family management, with key management roles being filled by non-family members. We are continually expanding into new markets and new locations all the while striving to enhance the overall customer experience.
For more information, go to https://rotoquip.co.za/2022/10/18/ roto-quip-who-we-are/
Perstorp makes product carbon footprint values available for 85% of its sales volume
Roto Quip, who we are…
BATANG-INDONESIA — As the largest economy in Southeast Asia, Indonesia is home to a rapidly growing urban population that is navigating pressing challenges surrounding sanitation and water supply. As the country’s water resources and infrastructure have continued to be put under pressure during the pandemic, the Indonesian government has introduced initiatives such as The National Rural Water Supply and Sanitation Project (PAMSIMAS) to provide millions with water and sanitation facilities.
In alignment with Indonesia’s sustainable development efforts, Orbia’s Building and Infrastructure business, Wavin, announced the opening of its new production plant in Batang, Indonesia to provide its expanding customer base in Indonesia and the Asia Pacific region with sustainable sanitation and water management solutions.
Said Sameer S. Bharadwaj, CEO of Orbia, “In Indonesia, 33.4 million people lack access to clean drinking water, and 99.7 million lack access to safely managed sanitation. We are solving this challenge by manufacturing Wavin UPVC and Wavin PPRbased pipes and fittings that deliver clean water and sanitation safety, cost-effectively and cleanly.” Continued Bharadwaj, “This
investment brings our business’ innovative water management solutions to a high-need market. It is a decisive step on our journey to advance life around the world.”
The Wavin production plant in new Grand Batang City will be built on a 20-hectare (49 acre) greenfield plot. When operational, the factory will employ approximately 200 people in production roles with room for further expansion in the coming years. Beyond manufacturing Wavin UPVC pipe and fittings, the space can accommodate the production of resilient city and energy-efficient building products like Wavin’s low-noise drainage systems and rainwater and stormwater management systems.
“We are very pleased to announce the opening of this new location,” said Maarten Roef, President of Orbia Building and Infrastructure (Wavin). “It allows us to further expand our solution offerings while bringing jobs and economic activity locally. With Wavin’s technology, innovation capabilities, and existing customer base, we are focusing on bringing more plumbers, engineers, contractors, installers, and municipal leaders complete solution systems for both above and below-ground water management and resilient urban development.”
The Solid Waste Infrastructure for Recycling grant program is a new grant program authorized by the Save Our Seas 2.0 Act and initially funded through the Infrastructure Investment and Jobs Act. The Infrastructure Investment and Jobs Act, also referred to as the Bipartisan Infrastructure Law, provides $275 million for Solid Waste Infrastructure for Recycling grants authorized by the Save Our Seas 2.0 Act. This is allocated as $55 million per year from Fiscal Years 2022 to 2026 to remain available until expended. EPA was provided an additional $2.5 million in the Fiscal Year 2022 funding to implement the program.
The Solid Waste Infrastructure for Recycling program provides grants for strategies to improve post-consumer materials management and infrastructure; support improvements to local post-consumer materials management and recycling programs; and assist local waste management authorities in making improvements to local waste management systems.
The entities eligible to apply for Solid Waste Infrastructure for Recycling grants are as follows:
• U.S. States and political subdivisions of states
• Puerto Rico, Virgin Islands, Guam, American Samoa, Commonwealth of Northern Mariana Islands
• District of Columbia
• Federally recognized tribal governments
• Former tribal reservations in Oklahoma (as determined by the Secretary of the Interior)
• Alaskan Native Villages as defined in Public Law 92-203
• Intertribal Consortia consistent with the requirements in Title 40 of the Code of Federal Regulations, Section 35.504(a)
EPA was interested in your needs and concerns to inform the development of the Solid Waste Infrastructure for Recycling grant program. EPA hosted a series of feedback sessions and issued a request for information to seek input on needed improvements to solid waste management systems (e.g., waste reduction, collection, sorting, processing, and end-markets for reuse and recycling). This input informed the Agency’s efforts to develop effective grant programs to improve solid waste prevention, management, and recycling infrastructure across the nation.
EPA accepted comments on through the docket on Regulations. The comment period was open until July 25, 2022. EPA anticipates the requests for applications will be released this fall. Prepare for grant applications now, before the Notice of Funding Opportunities is posted.
Provide input or submit questions about this program to SWIFR@epa.gov. Contact Us to ask a question, provide feedback, or report a problem.
Ferris State University Proud to Partner, Champion a ‘Once-in-a-Century’ Local
BELFAST, NORTHERN IRELAND — Queen’s has launched a new funding stream for academic staff interested in developing research links in Canada and the United States. The Research Mobility Fund was created by the North America Strategy Group and is being delivered in partnership with Research and Enterprise.
This exciting new funding opportunity represents one of many new initiatives being developed through the second phase of the University’s North America Strategy. First launched in 2018, the strategy spans three pillars – Research, Reputation & Education – and seeks to enhance the University’s success in engaging worldleading scholars, students, and institutions.
Professor Richard English, Chair of the North America Strategy Group, said: “The work of many colleagues has in recent years transformed the University’s relationship with the USA and Canada, and it has been very exciting to see that research and educational work develop so well. The Research Mobility Fund
offers another opportunity for QUB academics to develop and consolidate their research and partnerships. It will be excellent to see the important work that emerges as a result.”
The North America Strategy will provide funding for two Research Mobility calls. The first call opened in Spring of 2022 and, after a competitive review process, eight colleagues from across the University have received support to travel to North America in the academic year 2022-23.
The COVID-19 pandemic and other global events have forced companies to assess their fundamental operations. Chief among the considerations of U.S. companies in 2022 is how potentially relocating manufacturing can mitigate the risks of unstable international trade and supply chain management.
The COVID-19 pandemic affected 98% of global supply chains. Industries that invested significantly in offshoring to reduce costs saw dramatic risk increase, according to an article in The New York Times. Thus, U.S. executives are looking to “reshoring,” or the repatriation of industrial production and manufacturing to U.S. soil, as an attractive opportunity.
While relocating manufacturing may not be the “lowest cost” option, it may be the “best cost” option when weighed against supply chain resiliency and sustainability. According to the Kearney 2021 Reshoring Index, the primary reasons U.S. companies consider reshoring include labor cost, labor availability, delivery times, logistics costs, and reduced carbon footprint.
The common belief is that manufacturing jobs left the United States long ago for more cost-effective offshore labor. Recently, though, offshore manufacturing in countries like China has experienced wage inflation. Whereas, the Pew Research Center estimates the relative cost of U.S. labor has remained flat for over a decade. Reshoring could mitigate these costs and offer better service delivery, product quality, and brand perception.
The Kearney 2021 Reshoring Index found that 92% of the CEOs surveyed stated positive sentiments toward reshoring. Additionally, 79% of executives with manufacturing operations in China have already moved part of their operations to the United States or plan to do so in the next three years.
Reshoring efforts have occurred across many industrial sectors. Bloomberg highlights that the construction of new U.S. manufacturing facilities has increased by 116% over the past year and aluminum and steel manufacturers are building new plants across the Southeast. Semiconductor chip factories in New York have opened, according to a Vox article, to help alleviate supply chain disruption in the automotive and electronic industries. To meet further demand in the electronics industry, semiconductor companies have announced new facilities in the Midwest that are projected to support tens of thousands of long-term jobs.
Major U.S. retailers reportedly have vowed to spend hundreds
of billions of dollars over the next 10 years on domestically created goods. Finally, billion-dollar federal and state support aimed at encouraging domestic manufacturing underscores the impact that this trend will have on our economy.
Completely relocating manufacturing to the United States is not the only possibility — “near-shoring” or moving part of a company’s supply chain to the nearby countries of Mexico, Canada, or some countries in Central America are possible prospects for future investments. The Kearney Reshoring Index found that nearly 70% of the surveyed CEOs stated that they are evaluating near-shoring, have near-shored, or will near-shore to these regions.
Companies planning to move home or near home should consider several possible challenges. Manufacturers may face a shortage of supplies and skilled workers in their new locales. If a company cannot readily secure raw materials in the new location, importation costs of these materials may reduce profit margins. Moreover, some have pointed out that access to skilled domestic technicians may hinder relocation efforts unless a plan is in place to train new workers. Companies creating a transition plan should also think about tax implications, employment matters, real estate issues, and transportation availability.
Often, however, communities in the United States are eager to support relocating or expanding manufacturing by improving infrastructure, job credit, and outright grants. For example, Missouri offers incentive programs to eligible companies for financing public or private infrastructure on capital improvement projects. Similarly, unions supporting U.S.-based companies may prove to be supportive of moves that bring more stability to the workforce.
Rather than wait for circumstances to return to “normal,” companies instead can work to evolve their businesses to become even more agile and resilient in our “new normal.” They should consider taking advantage of the government or other programs that might support reshoring. Jackson Lewis attorneys can help manufacturers navigate the benefits and difficulties of reshoring and provide consultation services to make an effective plan. (Legal Clerk Kennedy E. Dickson contributed to this article.)
“Relocating manufacturing can mitigate the risks of unstable international trade and supply chain management.”
In an earlier “At Issue” article, I had flagged up my concerns about our industry’s dependence on gas, particularly in light of the recent NZ Gas Ban (NZ Gas Ban – a Wake-up Call for All Rotomoulders?).
With several countries proposing to ban any new installations of gas infrastructure, I saw this as a longterm problem.
I had no idea that only a few months later, rotomoulders in many parts of the world would pay a heavy price for their gas dependence. Some would have justifiable concerns about getting enough gas to run their factories.
We are experiencing an unprecedented energy crisis. The situation is particularly acute and worrisome here in Europe. Supplies from Russia have been drastically cut due to sanctions on Russia and Russia’s insistence on being paid in Russian Rubles.
Before the war in Ukraine, Germany received over 60% of its gas from Russia, as did many other western and southern European countries.
It is a real concern in Europe that if we get a particularly cold winter, the gas will run out and industry will suffer. Every government will prioritize the supply of heating, lighting, and cooking to domestic users, and everything else will be secondary and possibly rationed.
As a result, the rotomoulding industry faces a real threat in the coming weeks. Will gas supplies be sufficient to heat our industry’s ovens, and will moulders be able to pass on these significantly higher costs to their customers?
I saw a rotomoulder in the UK last week who said the cost of gas had more than tripled.
As gas becomes an increasingly global commodity, rotomoulders are not immune to cost increases, especially due to the surge in LNG that makes gas transportable around the globe.
The good news is that the current energy crisis should give our industry the extra motivation and impetus to become more energy
efficient and explore alternative energy sources.
Rotomoulding is a very energy-inefficient process (5-8% of energy is converted into making the mould), and we need to do better. Molders are increasingly interested in investigating technologies such as direct heating moulds (such as AMS Robomould and Persico’s SMART) and asking machine manufacturers like Reinhardt for information on conventional machines that run on renewable electricity rather than gas.
There are lots of other things moulders can do to reduce their energy usage, like improving oven seals to reduce heat loss, optimise the loading of arms, use materials requiring lower PIAT, using more efficient burners and finding ways to reuse exhaust heat.
As a result of this crisis, our industry should use this as an opportunity to become more innovative, and to move away from our dependency on gas. This will enable us to create a sustainable future that is much more energy efficient.
I recently had the honor of interviewing Scott Seljan, President/CEO of Seljan Company to discuss Seljan division Rock Lake Robotics, an employee-owned company located in Lake Mills, WI. After a long discussion, I was so impressed with this USA innovative manufacturing story, a growing company with so much potential and owned by employees. I asked for an interview to learn more about the company, its story, and the ideology behind being a company-owned business. I wanted to understand their successful journey. It is so exciting to share this story with our readers. Not only will you be inspired by the company, but I also think you will be super impressed with learning more about Scott Seljan’s drive, compassion, variety of gifts and talents, and how he gives to his companies and the world.
Per RockLake Robotics website: www.rocklakerobotics.com
Rock Lake Robotics is a division of Seljan Company, focusing on helping plastic manufacturing companies improve production, efficiency, and safety. With over 25 years in machine design and automation, Rock Lake Robotics can help with your most challenging integration needs. Experience in assembly, advanced fastening, fluid dispensing, and packaging as well as robotic cells.
Industries served include Rotational Molding – Blow Molding – Vacuum Forming – Injection Molding.
Rock Lake Robotics uses the latest engineering tools. Utilizing SolidWorks 3D design software, we can provide our customers with a complete design of their project, Mechanical Engineering, and Design · Electrical Engineering and Design. Controls and Robot Programming · Complete Project Management.
Q – Gibson Hebert: How would you best describe Rock Lake Robotics?
A – Seljan: We are a Robot Integrator for rotomolders. We understand the process.
Q – Gibson Hebert: What is the company structure, i.e., independent, a division of, corporately held?
A – Seljan: Rock Lake Robotics is an employee-owned LLC that is closely associated with Seljan Company. The 11 owners (so far) of Rock Lake Robotics are employees that have worked for Seljan Company for 20 years or more or managers at Seljan Company that fill key roles for Rock Lake Robotics.
Q – Gibson Hebert: Provide a background of the company, how, why, and when it came to be, and how it has grown and developed over the time of its existence (include any strategic/important stages of development for the company).
A – Seljan: In 2016, as Seljan Company was renewing our worker’s compensation insurance, the agency notified us that they were raising our premium. At that meeting, I learned we had eight very similar injuries in a 120-day period. All the injuries were caused by scraping parting lines on one of Seljan’s proprietary products. None were serious, mostly stitches.
I called a staff meeting and told the group we are going to buy our first robot. One of our VPs, Scott Woerpel, and I set up appointments with 3 different local integrators. We kept hearing the same thing, “It was going to take far too long to get a machine and entirely too much money to build.” None of the integrators were really listening to us, and a large part of the problem was they did not understand rotomolding. Therefore, I decided to go in a different direction and looked to find the right person to get us started in the business. The man we hired to help us had over 20 years in the industry and did a great job getting us set up with designs, pricing models, and the best suppliers. It helped that Seljan Company was Rock Lake Robotics’ first customer! Since Seljan installed that first robot
cell, we have had NO injuries. Our scrap ratio on that part is as close to zero as it will ever need to be. In addition, quality has been as good as the scrap ratio.
Q – Gibson Hebert: What is the company’s value proposition? Core Values? Strengths?
A – Seljan: Being teamed up with Seljan’s metal fab department and tool room is the key strength. We design, build, and test-run everything including the fixtures under the same roof as Rock Lake Robotics. Seljan’s metal department is very complete. Having this partnership eliminates a large layer of profit taking as we don’t have to go to outside companies to build everything we assemble.
We have a long history as Seljan Company as we started in the rotomolding industry in the early 1980s building fabricated tools for over 25 different rotomolders around the US. Seljan Company bought its first Ferry 220 in 2000.
Q - Gibson Hebert: What do you consider to be unique about this business – what sets it apart from others in the market?
A – Seljan: All the people that work for Rock Lake Robotics know rotomolding and they know it from hands-on experience. We can try things that other companies would never try. First - drilling, sawing, and routing, which we found was the easy part. We believed we could come up with a solution to spin-weld fittings on rotomolded parts. We saw the robot as being a superior way to flame parts. Scraping parting lines is another process we have developed successfully. We are currently working out a tool changer for our standard system with the goal of completely finishing a part with just one handling. The tool changer is expected to be fully tested late this year. What we are doing is applying robotic technology to our specific industry at a much lower cost than any of the mainstream integrators.
Q – Gibson Hebert: Can you tell us more about being an employee-owned company?
A – Seljan: When Rock Lake Robotics started, it was the perfect vehicle to give back to the people that built Seljan Company. When an employee hits the 20-year mark they get free shares in Rock Lake Robotics. The catch is they must work to build it. If we have a robot cell that needs to ship Monday, the owners will be working all weekend if that is what it takes. The payoff is that they all get annual dividend checks and when they retire at age 65, they take their shares with them and will receive those dividends as a very good retirement supplement. We have 2 more people that will be joining the Rock Lake Robotics ownership group this December.
Q – Gibson Hebert: How many employees and plant locations does Rock Lake Robotics have?
A – Seljan: Rock Lake Robotics currently has 11 employees and one location – 100 South CP Avenue, Lake Mills, Wisconsin.
Q – Gibson Hebert: What is the management structure?
A – Seljan: I am the managing partner. Scott Woerpel is the V.P.; and Eric Seaman is the Operations Manager. Eric oversees day-today operations of the company.
Q – Gibson Hebert: What are the trending growth sectors for robotics products throughout the world?
A. Seljan: We are specifically working with rotomolders at this time. We see a bright future for Rock Lake Robotics. Seljan Company shares the same problems as every other rotomolder so our focus for at least the next few years is to stay with what we really do well. Robots are the clear solution for labor shortages.
Q – Gibson Hebert: How does Rotomolding fit in? How does the process serve the company?
A – Seljan: Our customers report back to us that they are seeing solutions to difficult problems. Robots don’t take time off; they
make better quality parts that they can sell all the time. And we can take dangerous and expensive risks to operate hand tools like routers, saws, and grinders out of the hands of humans. Compressed air is not inexpensive to create. Every year since Seljan Company installed our first robot cell, our lost time injury rate has dropped dramatically. Since COVID, we have grown Seljan Company’s rotomolding division by over 20% and we are doing it without having any additional employees.
Seljan Company has 4 robotic cells now, and when resin prices started to increase the importance of reducing scrap and increasing quality and productivity became obvious.
Q – Gibson Hebert: What concerns you the most …. what keeps you awake at night?
A – Seljan: Potential supply chain issues. Our strength has been staying loyal to the vendors for the safety devices and most importantly the robot and controls. To date, our two main vendors have been flawless. Yaskawa is a world-class robot manufacturer and all these years later, they have been perfect on all marks. They make every delivery date on time, and we have not had any warranty claims on over twenty robotic cells that Rock Lake Robotics has sold.
Q – Gibson Hebert: What are some of the greatest challenges that your business faces?
A – Seljan: Internally, it is training more technicians to assemble and program robots. Externally, it is educating customers to design new rotomolded parts to work better with robotic technology. We can install vision systems on our robotic cells, but those add a lot of cost. Designing parts to work with robots is the best value for our customers. Keeping it simple is our motto.
Q – Gibson Hebert: What are your hopes for the future?
A – Seljan: That more rotomolders find the benefits and success that Seljan Company has experienced. Since Seljan started using robots in our secondary operations, our success is measurable, and we know we will only get better. The biggest change Seljan Company has seen is that we can now easily finish more parts in a 24-hour day than we can mold.
Q – Gibson Hebert: Does the company have strategic partnerships with suppliers/vendors that are core to the company’s success? If so, whom and why?
A – Seljan: Definitely it’s Yaskawa. We entered a distributor relationship on day one. It’s a relationship that has been excellent. They continue to innovate their products and offer the best school for training we thought possible. Several of the owners of Rock Lake Robotics have gone to the school and they all can do the basic operations of a robotic cell.
Q – Gibson Hebert: Scott, explain more about your direct affiliation with Rock Lake Robotics?
A – Seljan: I am the Managing partner. I oversee finances and consult with the design team on new systems. I am also a part of the advertising and tradeshow decision process.
Q – Gibson Hebert: What is your background, education, and experience?
A – Seljan: After coming out of the US Army in 1975, I started with Seljan Company, which was only in the metals business, as a punch press operator. From there, I took a 5-year Tool & Die Maker apprenticeship and went to Madison Area Technical College to learn to engineer. After 10 years in the shop and really learning the business, it was time to grow the company. I traded in my toolmaker career and went into sales and tool design. I worked in that position until my father passed away in 1998. That same year, I became President of the company. After a few years, it became clear that metal stamping was losing ground to Chinese companies. In 2000, we bought our first Ferry rotational molding machine. We were in a 30,000-square-foot building at the time. We added our second Ferry in 2002 and it quickly became apparent we were going to need more space. We leased an old factory down the street and relocated the metals shop. We added another Ferry and after a few years our parking lot got too small. In 2012, we purchased the building we now call home. This building is 502,000 square feet sitting on a 45-acre lot. Since then, our metals division has come back strong. We have added injection molding, blow molding, roll forming, powder coating, and laser cutting and now have a press capacity of up to 750 tons. The strange part of this process to this day is that I remember looking at this building when it was empty and it seemed absolutely enormous! Today, it is completely filled. We have added several proprietary product lines to complement our custom molding operations.
Q – Gibson Hebert: What led you to become involved in the robotics industry?
A – Seljan: It was the need to improve safety foremost. But as the production teams began to embrace rather than fear the robot everyone got excited about it! The goal of working smarter rather than harder is being achieved.
Q – Gibson Hebert: What industry and professional affiliations do you have? Why?
A – Seljan: First off, by default, I am a member of ARM (Association of Rotational Molding.) Ken Bather is our VP of Plastics and is quite involved. I am a member of ESGR, it’s a group that works between employers and active National Guard and Army Reserve units. Being an Army veteran, I know firsthand the training men and women receive in the military are skills that any business would find valuable. Locally, I belong to the Lake Mills Chamber of Commerce and the Main Street Program. Years ago, I was a member of the State of Wisconsin Apprenticeship Advisory Board. The mission was to keep apprenticeship training in line with current manufacturing trends and technology. We are also
involved with PPAI and ASI, which are groups that oversee the sales and marketing of promotional products.
Q – Gibson Hebert: How would you describe your leadership style?
A – Seljan: I have had the pleasure of working with so many very talented and dedicated people over the years. I have been a hands-off manager since I started. When someone asks me for an opinion, I will take the time to give my honest assessment. My philosophy has been to hire good people, treat them fairly, and with respect. I let them do their jobs.
Q – Gibson-Hebert: What would you say is your primary passion in business, and in life?
A – Seljan: I have always enjoyed adding new processes, taking on new challenges, and turning them into something profitable. Even after nearly 50 years on the job, it’s still fun. Back in the 90s when we started to grow the business, we hired new engineers. They really didn’t need me that involved anymore so I learned HTML and designed our company’s first website. I still do that today. I build and maintain all the websites that we have. Everything from coding to designing the graphics.
Personally, I play guitar. I started when I was nine and have never stopped. I played in rock bands, sat in with just about every genre of music, and finally found I really preferred jazz. A few years ago, I had the music highlight of my life. I played on stage with Grammy award-winning guitar player Eric Johnson (Cliffs of Dover). Along with that, I have a passion for sports cars. The list is too long for this article. Last on the list is working outdoors. My wife and I live on a 20-acre heavily wooded country parcel. Together, my wife and I are a team and maintain all the land. These days the tractor gets a lot more seat time than the sports cars!
For more info go to www.rocklakerobotics.com
Innovation driver for the global plastics and rubber industry —Many concrete solutions, machinery, and products for the transformation to a circular economy.
The joy of the plastics and rubber industry to finally be able to exchange ideas in person on a global level again after three years was characterized the K 2022 trade fair in Düsseldorf, Germany. The 3,037 exhibitors reported extremely good leads and a marked willingness of the trade visitors to invest, promising new customer relationships, and numerous business deals – some of them spontaneous.
“K in Düsseldorf has once again fulfilled the highest expectations. It continues to be the most international, complete, and innovative trade fair of the global plastics and rubber industry,” said Erhard Wienkamp, Managing Director of Messe Düsseldorf. “The trade fair has impressively demonstrated just how valuable face-to-face networking, chance meetings, and physical brand and product experiences are. We are very satisfied to see that K 2022 succeeded in sending out strong signals as an innovation driver of the industry and that our exhibitors did business with a high number of international customers with strong decision-making authority.”
A total of 176,000 trade visitors from all continents traveled to
K 2022. At over 70%, the proportion of international attendees at K 2022 remained at a consistently high level.
Ulrich Reifenhäuser, Chairman of the K 2022 Exhibitor Advisory Board, is also very pleased about the show: “After hardly any trade fairs could take place worldwide also on a national level over the past three years, K 2022 was even more eagerly anticipated as the world’s No. 1 trade fair of the plastics and rubber industry and succeeded in providing fresh impetus in all sectors of our industry. The many, in part, unexpected concrete contract negotiations held at the trade fair speak for themselves!”
The current unpredictability and uncertainty of events make for a tense situation in the sector overall, but this did not dampen the exhibitors’ commitment and visitors’ interest, quite the opposite: “Especially now in turbulent times and where the plastics industry is undergoing a transformation towards the circular economy, K 2022 was the ideal place to jointly and actively chart the course for the future,” stated Ulrich Reifenhäuser.
The trade visitors were especially inspired by the wealth of new technology developments presented by raw materials producers, machinery manufacturers, and plastics processors for the realization of the circular economy, resource conservation, and climate protection. Ulrich Reifenhäuser commented: “It can be clearly felt that all companies have embraced the need to take on social responsibility and think about plastics in a sustainable way
from the beginning of the process chain. The variety of solutions, machinery, and products for transformation towards a circular economy presented at K 2022 was incredible.”
The trade visitors at this year’s K came from 157 nations. In addition to Germany, European countries strongly represented included the Netherlands, Italy, Turkey, France, Belgium, Poland, and Spain. With 42% of the visitors coming from overseas, the international reach of K was as strong as usual. While less visitors from the East Asian region were at K 2022 compared to three years ago due to the currently more difficult conditions in those countries because of quarantine regulations, many visitors from the U.S., Brazil, and India attended K 2022.
According to a survey, about two-thirds of all visitors were primarily interested in machinery and plant construction. 57% (5% more than at K 2019) were interested in raw and auxiliary materials, with recyclates and bioplastics being particularly popular. For 28%, semi-finished products and technical parts made of plastics and rubber were the main reason for coming to the show (multiple answers possible). Over 70% of all visitors were from top and middle management.
Visitors gave K 2022 top marks for the completeness of the ranges and the presentation of the entire supply chain. 98% of all professionals stated they had fully achieved the goals associated with their visit.
During the eight trade fair days, it became evident that this year’s K was right on target with its selection of hot topics: circular economy, climate protection, and digitalization. In terms of investment intentions, machinery and equipment for processing and recycling stood out at 43%. The focus was particularly on sustainability, but also on circular economy and energy/resource efficiency in production. Around 40% of decision-makers said they are dealing with the topic of decarbonization.
K 2022 again featured two U.S. Pavilions with 35 exhibitors, organized by Messe Düsseldorf North America (MDNA) and co-sponsored by PLASTICS, The Plastics Industry Association. Overall, 105 U.S. companies showcased their products at K.
The K specials, which also focused on the three hot topics, were also very well received. The official special show, ‘Plastics Shape the Future, addressed the economic, social, and ecological challenges and potential solutions around the K key themes during high-caliber discussions and lectures and was well
attended throughout. The Circular Economy Forum, where the VDMA (German Engineering Federation) and 13 of its member companies impressively demonstrated the importance of technology in the implementation of the circular economy in the plastics industry was also popular with the international audience.
Also, much discussed at this year’s K was the global production language, OPC UA. This standard allows the processing parameters of the machinery and equipment involved to be coordinated more precisely and in a more targeted manner. This, in turn, is considered an important prerequisite for optimized circular management. 40 companies from eight countries participated in an OPC UA demonstration project at the trade show.
At the Science Campus, both exhibitors and visitors were provided with a concentrated overview of scientific activities and findings in the plastics and rubber sector. Numerous universities,
institutes, and funding organizations offered opportunities for direct dialogue.
Many trainees and students took advantage of the Plastics Training Initiative’s (KAI) offer to get information about career opportunities in the plastics industry.
The next K will be held in Düsseldorf, Germany from October 8 – 15, 2025. For further information on visiting or exhibiting at K 2025, contact Messe Düsseldorf North America; Telephone: (312) 781-5180; E-mail: info@mdna.com; Visit www.k-online.com and www.mdna.com; Follow us on twitter at http://twitter.com/mdnachicago
For hotel and travel information, contact TTI Travel, Inc. at (866) 674-3476; Fax: (212) 674-3477; E-mail: info@ttitravel.net; www.ttitravel.net
With proper anticipation and planning, inflation can be a call to action to spur change and innovation and stimulate “out-of-the-box” thinking. Avoid inflation’s potential negative impact on operations and service capacity by responding with new thinking and moving away from old legacy programs and operating platforms.
Inflation has always been present at some level. When inflation is low, it lurks quietly in the corner of our minds. But when inflation is revving, the ringing in our ears will not go away. During periods of uncertainty and economic volatility, inflation tends to draw attention, often triggering regressive non-thinking reactions. Inflation needs to be treated as an economic reality to be confronted and a challenging obstacle to be solved, not as a call to action by itself.
Don’t wait for inflation to drive change. This only causes narrow reactive responses that will be too late to be truly impactful and game changing. Typical kneejerk responses include raising fees, scrambling to search for additional funding, and as a last resort, instituting general, across-the-board cost-cutting measures. These
can be somewhat effective in the short run, however, in the long run, delivery on the business organization’s value proposition will suffer.
Instead, we must learn to treat inflation as a constant but everchanging factor to consider. Anticipation and planning are the keys to getting ahead of inflation and responding to it in a way that helps to drive assertive positive change.
When it comes to inflation, human nature frequently has us in a denial mindset. During periods of low inflation, we adopted a mindset that subnormal inflation will continue forever. However, during periods of high inflation, we first try to ignore the consequences. We then shift to overreaction mode, especially when the bottom line turns ugly with large deficits.
From a financial perspective, incorporating inflation factors into strategic and tactical planning and related key financial assumptions below must be part of the anticipation process.
This will help temper the tendency to count on overly optimistic outcomes. It will also force us to confront raising costs and hopefully trigger different thought patterns and consideration of new pathways and options.
“The nest egg must continue to grow to ensure future financial health.” Anticipation cannot happen if inflation awareness levels are out of balance. Balancing our awareness of inflation is as much art as science. Finding the right balance can be elusive. Aim for the middle, keeping inflation on staff’s consciousness but not making it the main, and especially not the only, factor for consideration. When inflation is low, we must work to raise awareness levels to anticipate that inflation will eventually accelerate. During periods of changing and/or high inflation we must do the opposite, attempting to temper overreaction. However, it is never too early to encourage early consideration of new strategies and tactics.
Case in point: price sensitivity vs. perceived value. At some point, if your main strategy to stay ahead of inflation is to raise fees, the price compared to return on value proposition will turn negative quickly. Paying more for the same experience will not go over well.
My favorite “go-to” tactic for working through complex planning challenges is to develop a short list of “key assumptions” that focuses on strategic objectives and desired results. This approach helps to simplify messaging and fast-track consensus and approval by diminishing feelings of negativity and confusion.
Building consensus and confidence is the main pathway to breaking down the negative barriers in any planning process. Using an approach that emphasizes a small number of key assumptions will bring clarity to planning while keeping the focus on the big picture and desired results.
It is best to view key assumptions as a short list of the most significant strategic objectives and desired outcomes for a planning effort (building next year’s budget), an unexpected challenge (reacting to non-renewal of a large grant), or a new project (acquiring a new program).
For example, when developing a new budget, the short list of key assumptions could be:
• Increasing fees (last increase was 5 years ago).
• Expand service hours at a medical clinic (due to increasing demand and new funding commitments).
• Adding a new income center.
Strive to have at least three, but no more than five, key assumptions on the list. Less than three makes the list too narrow in scope, and more than five will cause the list to be too broad and hard to remember.
To get out in front of inflation, we need to turn inflation-driven negative feelings into positive drivers for innovative planning and a wake-up call to action.
I recently reached out to a few to a few business organizations and asked them how they are reacting to inflation. Some of their responses surprised me and affected my thinking. A few comments that changed my thinking the most included: “I am not going to let fear creep into inflation discussions”; “Inflation is not going to beat us”; and my favorite inspirational takeaway; “Let’s use inflation to end R&R” (rinse and repeat).
These reactions provided a clear tactical path forward. Business organizations must constantly innovate and evolve to deliver on a strong value proposition. They must use whatever means available to encourage new thinking and innovation. The pandemic triggered a call to action and change. Inflation can do the same. It’s not about adjusting to meet inflation; it’s about doing things differently. If current programs
Focusing on a short list of key assumptions has numerous benefits. First, this approach will help management and staff to frame and focus their internal planning. Management and staff must consider all elements of planning down to the smallest detail. However, a thoughtful list of key assumptions will help management and staff remember the big picture. When done well, key assumptions convey the urgency of the organization’s needs and the benefits of success. Minor details can be distracting and disheartening, causing momentum to be lost. Keeping the focus on key assumptions will remind staff of the essential goals and help them to find solutions to meet those goals.
Additionally, key assumptions will help with external messaging others involved with the organization’s planning efforts. Board members and owners can be easily distracted, feel uncertain or afraid of new efforts, and sometimes overwhelmed by the details of a project. Sticking to consistent messaging though the framework of key assumptions will enhance focus, allowing them to confidently monitor progress, make inquiries, and ultimately provide approval when necessary.
Using an annual budget building process as an example, key assumptions help management and staff to define significant strategic budget modifications and goals while providing key insights to consider for approving the budget.
“Balancing our awareness of inflation is as much art as science.”
and activities are succumbing to inflationary pressures, then reconfigure, reposition, and change methods. Do not just raise fees and look for quick cost-cutting solutions. Throw R&R out the window and embrace innovation and change. Fears of inflation and change are not options anymore.
Operating reserves and inflation have a special symbiotic relationship. For me, no operating reserve is ever large enough. Inflation presents another vivid illustration of the importance of building operating reserves. The nest egg must continue to grow to ensure future financial health. Inflation is just another compelling reason to stay the course: keep adding to operating reserves, budgeting for surpluses, and building financial security.
With proper anticipation and planning, inflation can be a call to action to spur change and innovation and stimulate “out-of-the-box” thinking. Avoid inflation’s potential negative impact on operations and service capacity and return on value proposition. Remember that innovative business organizations are not succumbing to inflation. Rather, they are responding with new thinking and moving away from old legacy programs and operating platforms.
Planning Tip – Begin the next year’s budget building process with a short survey of questions related to current year budget performance and expectations for the next budget year. Design one short set of survey questions to be answered by owners, management, and staff. Track the results anonymously for each group and designate an inclusive working group to compile and analyze the results. This process will yield important insights that will help set the key assumptions for next year’s budget.
The process of identifying key assumptions also provides a great opportunity to pencil out initial thoughts around a new project or challenge. Some of my best key assumption lists have come from sketching a few quick notes while waiting at an airport or in an Uber. It is very comforting and calming to sit back and focus on the big picture and temporarily forget the many small details.
Framing messages is essential for strong leadership. Frames provide people with a quick and easy way to process information. They are cognitive shortcuts we use to help make sense of complex information, enabling us to interpret the world around us and represent that world to others.
Through framing, complex phenomena can be organized into coherent, understandable concepts. The most striking examples of modern-day framing were the different viewpoints expressed by Donald Trump and Joe Biden about the same issues during their televised debates in 2020.
Dr. Leandro Herrero is an internationally recognized speaker, author, and change management consultant with a penetrating understanding of organizational issues. He writes a short Daily Thoughts blog about these issues. This article comprises key extracts from three daily blogs Dr. Herrero has written about the importance of leadership framing. Especially relevant are his comments on ‘Intention and outcome – framing the use of data or insights,’ below.
I put framing at the top of the list of ‘leadership tasks’ because the framing of messages is essential for strong leadership. One of those non-rocket sciences around us that we refuse to pay attention to. Yes, I think we in business organizations completely underestimate the power of (mental and behavioral) framing to trigger and sustain behaviors, emotions, ways of doing, etc. Framing of messages is especially essential for strong leadership communication.
For me, there are three aspects of framing that are very simple,
and perhaps because of this, we take them for granted, or simply dismiss them. These are my three:
1. Framing of behaviors so that they can be copied and scaled up
2. Framing of the overall narrative of the organization
3. Framing of the use of data or insights
Let’s start with the simplest components on the behavioral side. On the behavioral side there is plenty of repeated experimental data showing, for example, how being helped (e.g. to fix a computer problem) increases the level of collaboration by those people with the people who have helped them. Collaboration for completely new, different goals. So far you may think, big deal. But here is the trick. The group that has been helped will then increase their collaboration with any other group afterward, no matter what the subject of collaboration is, versus a controlled group that has not been helped. ‘Helping’ is copied and spreads. It frames the future.
Lots of studies as well on the difference between people in a group that receives a clear ‘thanks’ versus a control group that receives a neutral acknowledgment. Similarly, the thanked group behaves differently afterward on a few parameters that are not
directly connected with the previous reason for the thanks.
Studies on altruism in neighborhoods show similar patterns. Somebody starts, others copy, a critical mass is created, and many other houses in the neighborhood do the same. It becomes normal. No manual is required on how to be altruistic. No team, no committee.
The corollary is: start your mini-mini-behavioral revolution somewhere and persistently focus on a couple of very granular [specific, separate, readily identifiable] behaviors. You don’t have to explain much. Just do it. The more you explain why, the less power. Make it the norm. One-off shows don’t work. You will be framing the conversation and seeding behaviors that may even seem small or trivial. If you get used to the technique, you’ll see the benefits grow.
It’s not a particular behavior because it’s good (I am sure it is) but because you are framing what comes next.
Frame the overall narrative of the organization
In business organizations, we completely underestimate the power of (mental and behavioral) framing to trigger and sustain behaviors, emotions, ways of doing, etc.
What about the framing of the overall narrative of the organization? Well, here are some frames:
• Enhance shareholder value
• Solve health problems
• Improve the quality of life
• Transform the way the medicine works
• Enhance life
• Provide innovative medicines
• Discover new treatments
• Make drug treatment affordable
• Save lives
I have deliberately taken an example of a pharmaceutical company to make the point that:
1. All the above are theoretically compatible.
2. But the frames are different, what you do is different, your priorities are different, and the people you attract are different. All the frames are like roads taking you to different places.
It’s not a simple question of ‘language’. It’s a view of the world, a concept of the world; in fact, a ‘space in the world (my preferred frame) that is different. Use the excuse ‘it’s all the same at your peril. It’s not.
Using the same example of a pharma company, I personally would like to hear how many lives you save, how many people are treated, how many kids are vaccinated, for example, as opposed to, say, how many R&D plants you have and how many people worldwide you employ. But that is just me.
These frames are completely different: solving, creating, building, modifying, inventing, providing, reforming, reorganizing, etc. Choose your frame before the frame, by default, chooses you. Then you are stuck with it.
We treat narratives as aesthetic statements, not as triggers of behaviors. For me, ‘building’ always wins. I am genetically unable to get up in the morning to ‘reform’ or to ‘increase shareholder value. Yet, these may be serious needs for many. I respect that. But don’t wake me up.
Intention and outcome – framing the use of data or insights – framing of these messages is essential for strong leadership
My third framing comment is about the purposeful use of data or insights. The mode I use is very simple. I have encapsulated it into a meme: ‘intention and outcome’.
Data is data. What you do with it, however, requires an intention (why you are saying what you are saying) and an outcome (what you are trying to trigger). Let’s say that 35% of employees do X:
• ‘Only 35% of employees do X’ has one clear ‘intention and outcome’: we are not doing very well; we need to step up our efforts.
• ‘35% of employees already do X’ means we are advancing, this is good news, would you not join that crowd? In both cases the facts are the same: 35% of employees do X.
The strength of the ‘intention and outcome’ is even greater if you abandon the numbers in favor of:
• ‘Just about a third of employees do X.’
• ‘Already a third of employees do X.’
It’s astonishing how, by and large, corporate language ignores the true power of the nudging frame and uses ‘cold numbers’ leaving the receiver complete freedom in interpretation.
I don’t buy the usual charge of ‘manipulation’ that is occasionally attributed to my ‘intention and outcome’ model. As a business leader or social change agent, for example, I am not neutral. If I am in a hospital and want to boost the ‘wash your hands’ behavior, I do care about what the data is going to trigger.
If I started from a very low baseline of people doing it, ‘already a third of health care workers wash their hands, intends to signal progress. Even better if it’s followed by, ‘Join them – we need to get to at least half by next month’.
If I started from a baseline of people dismissing the call to action or simply assuming (wrongly) that this is common practice, ‘only a third of health care workers wash their hands, means not really, it’s not the norm; we have a long way to go, don’t be complacent. Along all those scenarios, the facts have not changed.
From internal/corporate communications to ‘change programs’ of some sort, framing exercising and testing should be mandatory. Also, framing messages is essential for strong leadership. And, by the way, you can dress it up with a lot of elegant Cognitive Sciences theory behind it to sound scientific. Or you could just ask yourself ‘intention and outcome’ next to any statement.
Is it great to be back! It is hard to believe it has been over 3 years since the Australasian industry last came together in person, in Brisbane in 2019. The landscape and ARMA looked a little different then, and we have all come a long way. At the beginning of 2022, the ARMA Board was uncertain if this would be the year
to do a conference, and in March decided to jump in and take a chance. From the get-go, we were a little late with the organisation and had to move quickly.
The first step was to engage a new conference manager. As most of you would know, I had been running the Rotomould
“Just wanted to say congratulations on a terrific conference, good to see climate message being pushed so aggressively, looking forward to next year already.”
“The flow of speakers and how the topics all related to each other, was very well organised. Congratulations!”
“While it doesn’t directly affect me in my role, the emphasis on recycling, clean sweep, and environmental concerns was welcome and I believe very timely and proactive.”
“The number of attendees made the conference very special. Overall, I thought that the conference was very well executed. Qenos dinner was a highlight.”
conferences for almost 20 years, and it was time to relinquish some control and put it into the hands of someone that was equally capable. Karly Gniel was appointed as our Conference Manager, and what an outstanding job she did.
We agreed to take the conference back to basics, an exceptional business program that flowed, and opportunities for connections within the industry, by way of social events and interactive informative sessions.
Sunday kicked off in the Trade Exhibition with the Matrix Polymers Coffee Lounge and Keep Cups before we moved into the opening session and Rotomould 2022 was officially opened by Trudi Duncan, ARMA President. I then stepped up to the podium for the first time in person as CEO and replied to a very full room of what ARMA has been working on and where we are heading.
Then came the time for our keynote, Rob Edwards. For perspective, Rob had been booked back in 2019 to present at the 2020 conference and we had to reschedule multiple times. I had forgotten what exactly his presentation was going to be other than he is known as the “The Health Presenter”. I must admit I was quite concerned when one of the first slides was a picture of a man on a toilet and the words “how many times a day do you poop”. Rob covered the major health issues that are affecting men and women in this day and the small changes you can make to counteract things, with usable takeaways. Although I was unsure at the start, the feedback was exceptional. It was timely and informative and many points from his presentation were carried throughout the entire conference. Usually with jokes about fruit intake being in the form of wine! We then moved back to the exhibition for “welcome back drinks with the ARMA Board”. Sunday finished with the Price Plastics Welcome Dinner and included light entertainment and roving food.
3 key initiatives attendees learned and intend to implement: “Operation Clean sweep - Go early, Maintenance check - from Ian’s talk 100% recyclable stickers on appropriate products.”
“Operation clean sweep, closing the circle on products supplied offering a recycling feature in the business, mental health, and team development.”
“Getting clean sweep ready. Research into electrification, or other low-emission moulding. Improving customer experiences.”
“Look at Mental Health with my team in more detail and focus even deeper on my data analysis - to make better decisions. Interested in new materials.”
“Work on staff culture. Continue to work with ARMA environmental. Network more with the roto industry to keep up to date with trends & insights.”
Monday was a full day of plenary sessions with Vision Plastics Environment Sessions to start. VPlas shared the steps they are taking towards a sustainable future, and this was followed by Helen Millicer from One Planet Consulting presenting what major changes are coming for plastics. There was a lot of discussion after her presentation as she provided hard-hitting facts about recycling, offsets, circularity, and climate change. Blaise Costabir from GMI Zarhak India then talked about ethical decisions small and medium businesses should consider.
Following morning tea, the sessions were a little more technical with Ian Hansen of Rotaconsult providing his moulders guide to machine maintenance, a lively Philip Adetunji of Qenos talking about cracking failures, and Aaron Lederhose from the PARTEC training institute imparting his knowledge on sensors and automation.
The Rotomachinery Group Lunch was held in the Trade Exhibition and enjoyed by all.
After lunch, Martin Coles of Matrix Polymers informed the industry of the investment they are making in Australia and New Zealand for the future and then Bill Spenceley stepped up to provide advice with hints and tips on recruitment and retention, another timely presentation.
One of the most well-rated presentations was by Larissa LloydWard discussing the ethics and economics of dealing with mental health in the workplace, something that the majority of attendees felt more equipped to return to work with her suggested actions. Jim Crawshaw had the difficult task of backing this presentation up with advice on how to improve the customer experience, something he did very well.
As delegates sat down after the coffee break, their tables were now equipped with a variety of beer and RotoLoad glasses for an interactive beer tasting and presentation by Rob Miller on how RotoLoad can with material handling.
We were also lucky to have Peter Bury from Chemistry Australia assist by finishing the day talking about Operation Clean Sweep, something we are working hard on as an industry.
It was a big day, and everyone was ready to relax and enjoy the Qenos Conference Dinner and have a laugh with the comedic entertainment. The Icon of Rotomoulding Award was presented to Graeme Hall and the establishment of the ARMA 20+ years of Membership with the following companies recognized and awarded with plaques.
Barron & Rawson
Bushmans Group ChemTrend Australia Devan Plastics Duraplas Industries Ferry Industries Global Rotomoulding Gough Plastics Gyro Plastics Indac Limited KK Kingston Matrix Polymers PFG Group
Plastic Rotational Moulding Company Plastimac Polyworld Price Plastics
Qenos Rimco Rotadyne Rudplas Rotomoulders
RX Plastics
STP Rotomachinery
Viscount Rotational Moulding Weida Integrated Industries West Coast Poly
Tuesday was the final day and Aaron Bellette of Global Rotomoulding had the difficult task of waking everyone up with how to use data to make informed business decisions, followed by a Rotomachinery Group presentation on their growth and development in the South Pacific. Tim & Jessica Leed then stepped up to talk about moving factories and software management, followed up by Tony Mercieca presenting on the ChemTrend mould surface technology.
The last sessions of the day were from Rising Sun Rotomoulding on aesthetic mould design and Garth Galloway on the concept, design testing and release of complex products with international customers.
With over 120 attendees across the 3 days, delegates were gifted with a Micropellets Australia cooler bag filled with goodies from Austworld and PSI Brand. Name badges were provided by ChemTrend Australia and an honourable mention to Rising Sun Rotomolding Machinery and Wuxi Yisong Rotomolding Technology Co., Ltd for their support from across the ocean.
I would like to finish with words from the attendees when asked what they enjoyed most about Rotomould 2022.
“Networking with old friends.”
“Networking and health presentation. Dinner discussions with people at my table.”
“As always, it’s the networking and discussing issues firsthand with other moulders and supplier representatives.”
“Interaction with new people discussing ideas etc. and I came away with some new contacts and insights.”
“It was fantastic to see everyone again. Good location that was able to cater to all our needs. The food was beautifully presented. There was plenty enough space for everyone in the exhibition area. Well organized.”
“Great to be back, lots of new faces, and the vibe continued to be a forum for our industry to openly discuss the issues and see what solutions are out there.”
Queenstown will be held in June and dates will soon be announced.Thank you to all Rotomould 2022 Conference sponsors DESIGN
Rotational molding has historically been applied to molding tanks and containers because of its inherent ability to mold hollow water-tight shapes. Tanks and containers still represent the majority market share for this versatile plastic molding process. However innovative molders and designers have realized the benefits of this process. They have creatively applied it to hundreds of other applications, expanding its popularity as a highly desirable molding process. Today, the rotational molding process has been specified for molding products ranging from playground slides and farm equipment to medical devices. Some of these applications were initially specified for this process while others have been converted from another manufacturing process to rotational molding. What are the most important parameters one must consider when deciding if rotational molding can effectively replace another material and manufacturing process?
Cost – The unit cost has always motivated OEMs to consider switching from one manufacturing process to another. Production cost is typically based on materials and labor. However, there are other cost-related considerations to also consider such as investment, shipping costs, and part count. The rotational molding process requires an upfront investment in molds. This initial cost is typically amortized over time such as one year or several parts. Therefore, tooling investment should be included in any cost comparison. The rotational molding process is ideally suited to molding lightweight, large hollow parts. Parts such as these are typically costly to transport since their bulk density is so low. Designers should therefore consider packing density as an important factor when designing parts. Packing density can be increased by nesting or designing parts to be shipped as knock-down. On-site assembly should be weighed against parts consolidation and part count.
Investment – Designers should estimate tooling costs during the very early stages of any conversion project. Tooling costs can be estimated quickly by CAD modeling a basic overall size and shape of the product which can be distributed to a few mold makers for ballpark pricing. Molders need to understand features that could complicate the mold such as undercuts, tolerances, and intricate features.
Performance – Product performance is another important reason OEMs convert from one process and material to another. Improving performance can be attained by changing materials or design. Material-related properties might include improved corrosion resistance, impact strength, or molded-in color. Design improvements might include consolidating parts, reducing weight, or extending product life.
Productivity – Molders and designers must consider productivity another important parameter when converting from one process to rotational molding. Processes such as injection molding are highly efficient versus sheet metal fabrication which may require a high labor content for complex parts. Although rotational molding has effectively competed with both of these processes, complex sheet metal parts are easier to convert versus injection molding. Processes with high labor content are easier to convert. These include hand-laid fiberglass, sheet metal, casting, fabricated weldments, wood, and thermoforming.
Quality – Rotational molding part quality varies depending on the molder, tooling, equipment, and process control. Part quality and consistency are critical factors to consider during a conversion assessment. Designers should emphasize details such as parting lines, tolerances, and surface finish in any comparison assessment. Rotational molding may be the ideal process or may not be suitable, depending on the application.
Aesthetics and Appearance – The last and very significant consideration is appearance. Many products have been converted to rotational molding because of aesthetics. Rotational molding allows designers to cost-effectively replicate almost any shape they can imagine. This single benefit has popularized this process into unending markets ranging from recreational products to high-end furniture. The horizons have proven to be endless.
I hope this brief editorial has enlightened and inspired you to pursue new markets for this process. The future looks bright for rotational molding as long as designers and molders use their imagination. I welcome your comments. Please feel free to contact me at paloian@idsys.com.
The mission of the Association of Rotational Molders is to promote, educate, and inspire the rotomolding industry. For more information, visit ARM’s website at www.rotomolding.org or contact the Association at 630-942-6589 or info@rotomolding.org.
As you read this, we have wrapped up our annual meeting in Atlanta. I sincerely hope you were able to attend. It was packed full of great content pertinent to current and future opportunities. If you were not able to attend, we usually have a few presentations from the meeting delivered as webinars in the following months. Check your ARM email newsletter for our upcoming schedule of presentations.
As we approach the holiday season, I realize another year is coming to an end. I wonder how time always flies by so quickly and take a moment to reflect on the state of ARM and the Rotomolding Industry of Rotational Molding.
From my perspective: Our Industry is Thriving
• Most molders are busy
• Growth continues
• Materials and supplies appear to have stabilized
• New projects/applications are on the rise
• New technology is being developed and embraced
• General consensus is optimistic
ARM is Thriving
• Financials are strong
• Membership is up
• Participation levels are high
• Innovation continues
• Value to the membership continues to grow
• Engagement with designers and educators is on the rise
I will continue to lead ARM to promote, educate, and inspire the Rotomolding Industry through 2023. Our next scheduled program is the ARM Executive Forum in Carlsbad, California from March 20-22.
Let’s all maintain this positive energy!
Matt Bushman
2022 President, Association of Rotational Molding President, Plasticraft Corporation
“One of the main benefits of attending is the efficiency of the meeting process.”
Q: How do I establish the correct molding conditions for nylon, compared to my usual grade of polyethylene?
Dr. Nick: “Nylon” is a generic term, commonly used to identify a family of polymers known as polyamides. These polymers exhibit different physical properties to polyethylene, most notable of which are:
• Increased stiffness, hardness, and temperature stability
• Improved paintability
• Significantly better barrier properties to hydrocarbons (e.g., gasoline)
• Reduced cold impact strength and increased brittleness
There are many different versions of polyamide (PA) offered for sale. In North America, the main options available as rotomoldable powders are PA6 and PA11. In Europe, PA12 is more readily available than PA11. When I sold these products, many years ago, I used to joke that the numbers referred to their price relative to PE; significantly increased cost is something you’ll notice immediately! In reality, the numbers designate differences in molecular structure.
You will also see polyamides with two trailing numbers (e.g., polyamide 6,6), but these are not generally suitable for rotomolding.
Over the years, I’ve tried to rotomold a number of non-PE polymers, with success and failure in roughly equal measure. My common experience is that polyethylene is much more tolerant to process variations than most other polymers.
Setting up your process to mold nylon involves a similar set of principles to polyethylene. Most importantly, you need to establish the molding window for the product.
The “molding window” or “processing window” has traditionally been defined as the set of process conditions where the material is neither under-cured nor over-cured.
Polyethylene has the big advantage for rotomolding that this window can be relatively wide, especially when compared to other materials. In practice, rotomolders can get away with molding at conditions representing a degree of under- to a degree of overcure. In my experience many molders do this, even if they are not aware of it!
The simplest way of establishing a set of processing conditions (in terms of oven temperature and cook time, for a conventional machine) is to use a device that can measure Internal Air Temperature. If you’re new to this, ARM ran a webinar recently on choosing and using these devices.
With a limited amount of trial and error, you can link oven temperature and cook time to the achievement of a Peak Internal
Air Temperature (PIAT). Your material supplier should be able to guide you towards a suitable PIAT for the product they are supplying. You should also ask them to provide a suitable range of acceptable PIATs, because, in a normal industrial environment, it can be hard to hit an exact figure.
If you don’t have PIAT information, you need to establish a molding window yourself.
For PE, the boundaries of the window can be identified by impact testing, using the ARM Protocol. Remember that this involves conditioning test plaques at -40º before they are impacted.
Beyond the lower boundary of the window, the failure mode of plaques will be predominantly brittle. Beyond the upper boundary of the window, the failure mode of plaques will also be predominantly brittle. For well-formulated roto grades, the failure mode of plaques will be predominantly ductile (with <20% of failures being brittle) within the molding window. The picture below shows the differences between brittle failure (left) and ductile failure (right).
The transition from predominantly brittle to predominantly ductile will usually be quite marked (see below). In the graph, “BF%” means the percentage of failures that are brittle. In under-cooked and over-cooked conditions, BF% normally reaches 100%. So, the boundaries of the molding window are quite sharply defined.
I originally suggested this way of defining molding window in a paper presented to ARM in 1996 and, in the following years, almost all PE suppliers have adopted it.
For other polymers, this “PE approach” may not be as helpful. For example, nylons will not exhibit the same low temperature (i.e. -40º) impact behavior as polyethylene and failures are likely to all be brittle, whether inside or outside the molding window. If you substitute -40º conditioning for something less aggressive (e.g., Room Temperature conditioning), you may find that all failures are ductile. So, for non-PE polymers, the “PE approach” will need to be modified.
The lower boundary of the PE molding window coincides with the point where entrapped air bubbles (created as the powder particles sinter together) have mostly disappeared. Below this boundary, the bubbles act as stress concentrators and cause brittleness in the part.
For non-PE polymers, you can define the lower boundary of the molding window in the same way. Have the entrapped air bubbles disappeared?
In the early days, we cut shavings across the wall thickness of samples and examined them under a microscope. A much easier way is to track bubble presence and effect using a densitometer, which is a modified chemical scale and measures Part Density (aka “As Is” density). Phil Dodge, one of our industry’s original giants, introduced this concept in 2001. Densitometers are relatively lowcost pieces of equipment and can be used as a handy quality check.
In the graph below, you can see how the Part Density registers as significantly lower than the expected Material Density (in this case 0.935 g/cm3), because of the buoyancy effect of entrapped air bubbles.
the inside surface of the part degrades and forms a thin layer that will act as a crack propagator during impact.
You can see evidence of this degradation simply by comparing the outside (the “mold side”) surface of the part to the inside (“air side”) surface; the airside will normally start to yellow and will attain a glossy appearance. See below for a comparison of appearance of the mold side (left) and the airside (right). You will also notice an acrid smell.
Having established the lower boundary of the processing window, what about the upper boundary?
The upper boundary of the molding window is associated with the tendency of the material being molded to degrade. Polymer on
The attached paper describes some work I did with polymer scientists at Manchester Metropolitan University in the UK, that provided new insights into this effect. Using infra-red spectroscopy, we were able to link loss of impact with the sudden formation of degradation products such as aldehyde species (that’s mainly what you smell).
With PE, the degradation is thermo-oxidative; caused by a combination of heat and oxygen from air. In the case of heavily unsaturated polymers (e.g., the polybutadiene component of ABS), the material will degrade, even in an inert atmosphere (i.e., with no oxygen present).
Polyamides are hygroscopic polymers; nylon 6 is especially hygroscopic, but PA11 and PA12 also suffer from this property. This means that atmospheric water will chemically bind on to the polymer surface and this will catalyze (i.e., speed up) degradation.
So, for a non-PE polymer, your molding window is the gap between:
• the point at which bubbles disappear and
• the point at which the material starts to degrade
If you’re lucky, the gap will be wide enough to work with. Unfortunately, with some polymers (e.g., ABS), this gap is pretty much non-existent! My bottom line is as follows: Defining the molding window for PE is relatively easy. Other polymers will need to have their own definitions developed; preferably something that makes practical sense.
Train your employees, reduce scrap, connect with customers, learn from experts and peers. This is what comes with membership and the return on your investment is tremendous.
Complimentary Registration for the 2022 Annual Meeting
Provided for one employee for each new member company. This is your free entry to the world’s preeminent rotomolding meeting, held once every three years.
We review sales leads typically from companies seeking molders – and email them to our member companies. We actively advertise for leads on behalf of our members.
An 80+ page document calling out the highlights of nine company’s operator instructions. Also more than 700 documents and presentations from past Annual Meetings.
Immediate Free Access to more than 100+ on-demand webinars
Topics range from Determining Your True Cost to Proper Sampling Techniques. Twenty new titles were added in 2022.
Immediate Free Access to ARM’s classic training video library
Includes programs on curing, venting, and good manufacturing practices. All videos include Spanish subtitles.
These moderated teleconferences are conducted every six weeks (eight
per year) and allow you to troubleshoot your process and discuss HR issues with other molders, suppliers, and rotomolding experts.
The greatest ARM benefit: Informal learning at a coffee break could revolutionize your process or reduce your expenses by tens of thousands of dollars. We hear it from members again and again.
Awards and Awareness
Showcase your company in our online member directory and through awards including Safety Award, Product Competition, and more.
Discounted Registration to all ARM Meetings
Includes regional meetings, the in-depth Hands-On Rotomolding Workshop at Penn College, and our Executive Forum which will be held in Italy.
Rotolink
Our twice weekly e-newsletter shares important industry news.
The premier event for rotomolders, their suppliers, designers and educators. Programming includes professional and industry speakers, valuable networking, group workshops, and exhibition.
To apply for membership, please visit www.rotomolding.org
Starting up a new branding project requires good preparation. We would like to share the knowledge gained through the previous 20+ years of experience, so have prepared a shortlist of the 5 essential steps, outlined in the following sections.
In Section 1 – Product design and mold detail, we covered surface textures, product shape and thickness, brand positioning & purpose along with plastic types & molding processes.
Section 2 was about choosing graphic types such as the various graphic constructions, color options and UV stability, transparency and opacity, along with special features.
Vector graphics are digital art that is rendered by a computer using a mathematical formula, which means it is scalable without losing detail, i.e. staying sharp and crisp in appearance. Raster images, such as .jpg and .png, are made up of tiny pixels, making them resolution dependent, i.e. blurred and fuzzy edges on detail when enlarged, so not ideal for screen or digital printing processes.
Standard samples are readily available and are consider a ‘must’
In Sections 3 & 4 we cover graphic design specifications and what’s required for testing and validation to ensure success.
Good luck on your branding journey.
Resolution and halftones verses spot colour
Screen-print spot colour process typically supports up to 70 lines per inch (lpi) or 150 dots per inch (dpi) which is suited for colour half-tones such as drop-shadows, shading, and CMYK print colour process.
Digital print technology, on the other hand, features a greater resolution of up to 1200 dpi, providing photo-quality finish.
To ensure best quality print your supplier will request vector artwork supplied in file types such as .ai, .eps, .cdr, and .pdf.
PSI Brand team of artists are trained to work with any file types, however by supplying your artwork in the file types supported, will ensure detail is not lost during any artwork conversions.
before any production cycle. PSI Brand’s policy is ‘try-before-youbuy’ and supported by their ‘full refund or replacement guarantee’, which means there is little or no risk by the consumer. Custom samples are available at little cost, and strongly recommended for any prototype work.
Let us first ask the question, what is the cost of no branding? No brand = opportunity for lost sales.
There are many variables that influence the cost and can be summarized as following; 1. Graphic type, 2. Quantity required
3. Colours, and 4. Dimensions. To submit your specifics, please go to https://psibrand.com/quote/ to obtain no-obligation pricing within 24-hours.
Example Price: In-mold graphic, 1000 units, 3 colours, 100x50mm (4”x 2”) = USD $0.99 per unit.
Additional costs to consider where applicable include shipping, tools required, one-time setup costs, and any mold or adhesive cleaners.
Validation is based on alignment of you and your
customer’s expectations, along with what your supplier has promised.
Be sure to ask for customer sign-off based on the prototype and/or graphic proof supplied. Is this process repeatable, is your team on-board, do you need further samples to prove this real-time, and are all questions to consider before going to production.
We hope you found this guide to graphic artwork & design and testing & validation useful in maximising your branding opportunities. To see more on Sections 1 through to 5 in the complete design guide, please visit our website at www.psibrand. com/design-guide.
With the industrial introduction of the rotational moulding process in the early 1940s, technologies in the field of equipment and machine configurations have continued to evolve. However, the types of materials used have not changed significantly since the development of macromolecular chemistry (“monomer to polymer”) by Staudinger and Ziegler-Natta, when they discovered catalyst-induced polymerization of ethylene more than 70 years ago. Starting with plastisol (liquid PVC) as the standard material, today polyethylene (PE) in powder form is used 85-90% worldwide as the main material for rotational moulding.
The advantages for PE (powder) are obvious: grinding on conventional mills, fast availability, wide processing window, easy handling, wide defect tolerances, reusability, and high recyclability (among others). Despite constant price increases and shortages in the raw material market, PE remains by far one of the lowest cost and most versatile plastic compared to other thermoplastics. While there is a greater drive than ever to reduce energy and gas consumption, PE in itself does not place high demands on modern equipment (moulds, rotomoulding equipment, pulverizing or grinding techniques).
Over time, other plastics have become popular for niche rotomoulding applications, such as PP, Crosslinkable PE, PA6, PA11, PA12, and PC, but not to the same extent as polyethylene.
In the early 2000s, the technology and materials for industrial production of micropellets (particle size <1000 mm) by extrusion were first introduced, allowing them to be considered as an alternative to PE powders. Figure 1 shows the size difference between a normal lens granule of 4 mm diameter and micro pellets of Ø 500-700 µm (micrometers).
Since its foundation in 2012, HD Kunststoffe has set itself the goal of driving these developments forward and has specialized
in ensuring the supply of micropellets outside rotomoulding applications as well. Currently, micropellets with a particle size distribution of 500 to 800 (max.) micrometers are mainly used as an alternative or supplemental to powders in rotomoulding, but the same micropellets are also used in the powder coating industry where the nature or behaviour of powders during processing no longer brings the desired goal.
So, what are the benefits of using micropellets for rotomoulding companies during production and for rotomoulding end-users in the final product? Compared to powder, micropellets for rotomoulding requires a higher production effort, which is reflected in the manufacturing costs and thus in the price. On the other hand, micropellets can be produced in smaller quantity units using customer specific formulations at any time.
The challenge for micropellets is that PE powder is widely available and has been the material of choice for many applications. Therefore, it has been difficult for moulders to change from an acceptable functioning material, making it difficult for micropellets to be substituted. This resistance to change is likely because of a lack of knowledge or understanding about micropellets and their capabilities. However, if the mould geometries are complicated and not optimal for PE powders, or the scrap rates and thus the labour costs increase significantly due to incompletely filled moulds, micropellets will come into play as a serious alternative.
Another benefit of micropellets is that there is no risk of potential air dust explosions that exists with PE powdered materials. Micropellets do not have “fines” and therefore there is no dust or moulding defects relating to too many fine particles.
Toxicological concerns when grinding plastic granules into powders are increasingly part of a discussion among the occupational health and safety bodies responsible at EU level. Here, micropellets play a health protective role in improving the working air in the production environment (lack of dust), which objectively contributes to an improvement of the working climate and better motivation of the employees.
What other differences are there? Firstly, there are fundamental differences in the production process itself, which in turn has an impact on delivery times. Powders for rotomoulding are produced when a lenticular or cylindrical granulate is ground into powder by means of mills (disc or ball). Depending on the plastic, this grinding often takes place at ambient conditions (e.g. PE). However, some polymers require cold grinding (cryogenic pulverization) e.g. PP, PA6 or PC, which is more expensive and
time consuming than standard ambient grinding. The micropellet production is similar to a normal granulation of plastic pellets by extrusion, with the difference that a powerful melt pump and a micro perforated plate (hole size<1mm) connected to an underwater pelletizer are required. Extrusion can then be performed on any thermoplastic. Other differences between powder and micropellets for rotomoulding lie in the particle size distribution, dimensions, structure and surface. Figure 2 shows a microscope image of micropellets with the area scale (in yellow) of 1mm².
dry flow value of powder at 25-30 seconds. During rotation, the fast dry flow in the mould is noticeable in that the micropellets are distributed more easily and quickly within the most complex mould geometries. Due to the uniform shape, all edges and corners of the mould are filled with micropellets, which cannot always be achieved with powder due to bridging. Threads or corners in the end product can be better reproduced by the micropellets.
The powder for rotomoulding applications ranges uniformly between 100 and 500 (max.) µm, with a median d50 of 250-300 µm. The fine fraction below d50 melts most rapidly during the rotomoulding process during the oven cycle. In contrast, the distribution of the micropellets ranges from 500 to 800 µm with a d50 value of about 550 µm. As can be seen, the micropellets per se are already larger than the powder, but their overall distribution including all particles is narrower. The sieve analysis comparison between PA6 micropellets (Fig. 3) and a PA6 powder for rotomoulding (Fig. 4) illustrates this analysis.
Due to the constant improvement in extrusion technologies, there is a continuous optimization of micropellets production towards higher output. Since the beginning of 2010, the product range has expanded from PE alone to PP, and 10 years later to PC, PA6, TPU and EVA, among others. Many companies in the rotational moulding sector are taking advantage of the additional benefits of micropellets over traditional powder PE to reduce the number of defective products and increase profitability.
Dr. J Carlos Caro studied Chemistry at Leipzig University (Germany). He joined GRAFE in 2002 after obtaining a PhD in Polymer Chemistry at Technical University Dresden (Germany). He has been involved in the areas of research & development, project management, product development and sales for the GRAFE business units focusing on electrically conductive compounds and for HD Kunststoffe in the areas of Rotomoulding and powder coating.
GRAFE Polymer Solutions GmbH was founded in 1991 and offers thermoplastic masterbatches and compounds. With over 300 employees in the Blankenhain facility (Thuringia, Central Germany), they develop and manufacture products for the domestic and international markets.
In 2015 HD Kunststoffe GmbH was acquired and integrated into the GRAFE Group of companies to serve the market of the rotational moulding industry with thermoplastic compounds (micropellets and powders) and colour powders for dryblends.
A consequence of the uniformly narrow particle size distribution and the lenticular or spherical microgranule shape is the faster flowability (or dry flow measured according to ASTM D1895-96 and ISO R60) of about 12 seconds, compared to the
The mood in the room at the first Annual ARMA Conference, this year in Melbourne in September, reflected the growth and resilience of the Rotational Moulding industry these last few years. I was reminded many times over of how lucky we are as an association group to have so many ‘competitors’ in the room avidly listening, excited, and inspired to share with each other. Most memorable, the roomful of members receiving their recognition for 20 plus years of membership to ARMA and in addition, the great contribution of Graeme Hall to Rotational Moulding – a great friend, mentor, and colleague.
For most, the last few years have been filled with a full book of orders, plenty of positive outlooks, and a relatively well-oiled supply chain in the grand scheme of things. For some, emerging from the post-covid boom is a bit like a hangover after the party. Staff shortages advertised jobs taking longer to fill, skilled staff thin on the ground, gas shortages, energy price hikes, rising interest rates, the sliding Australian and New Zealand dollar, etc, all signs of a nervous economy. Despite this, as an industry, there certainly appears to have been considerable effort spent planning for “the next frontier” and time and money spent on R&D to see growth out the other side. If you
have been caught short in the momentum of the last 24 months, however, it is never too late to plan for change, and even a small amount of preparation will go a long way if your markets are starting to get tight.
To Michelle and the rest of the Board –Graeme, Chris, Ian, Grant, Anant, Karen, Mark, and Kate - the industry is very fortunate to have such a knowledgeable group of people working for the better of this association and our industry’s future. Your efforts do not go unnoticed. With our annual conference, continued work on the Tank Standard, submissions on the NZ Climate Commission Report, visits to members across Australia and New Zealand, In-Factory Training sessions, and a growing membership base and the working groups, good times were had, and our finances are in a healthy state with many highlights in the year to come.
It was a whirlwind start and a somewhat unusual term as President, but I feel very privileged to have been able to work with you all. Michelle’s work leaves me with great pride and a sense of confidence about the continued growth of our association and industry in this region and I look forward to connecting with you all again soon.
As I reflect on the last 12 months, it has thrown me with not only how quick the year has gone but also how busy it was. At the end of 2021, we were uncertain what the next year would bring as most of our regions were still in lockdown, but we kicked off 2022 with a bang and we were off, with unforeseen disruptions.
While the shipping and logistics delays were already underway, these were compounded by the rising costs of materials and energy, and then added in were staffing issues. Problems that were occurring not just in our part of the world but globally continue now. I am contacted several times a week by members needing staff and am helpless to assist, I have reached out to partner associations in other parts of the world to investigate sponsoring staff to find they are unwilling to ask their industries as no one wants to lose skilled staff. Some companies are now following the
path of obtaining government labour agreements just so they can man their machines.
And while this is all happening, there is still growth, with a lot of clients looking to bring their products back on shore as well as movement with company ownerships and parties looking to buy both here in Australia and New Zealand.
ARMA is also going through a stage of growth with the addition of Conference Manager Karly Gniel, who successfully stepped in to manage our first Rotomould Conference in 3 years. It was also my first opportunity to stand in front of you as CEO and to spend time talking to you in person again. Both Karly and I are already planning Rotomould 2023 in Queenstown and providing the opportunity to network again.
We also welcomed our next Icon of Industry for 2022 and a
huge congratulations to Graeme Hall for this achievement, it is most deserved. As well as this, we implemented the first of our annual Length of Membership Awards for companies that have supported ARMA for over 20 years. There were 28 honourees with the majority receiving their plaque at the conference.
It was an extremely frenzied year for me, with so much happening from webinars, to visiting factories and keeping on top of the everyday running of ARMA having just returned from a much-needed week off, it reminded me of how much we all need to take a breath, step back and reflect not only on where we have been but where we are heading.
The future direction of ARMA will soon be discussed in our strategic planning session by the ARMA Board
in December and I would like to take this opportunity to thank the Board for providing the support that was needed as volunteers this year.
I would also like to recognise Graeme Hall, who will be leaving the Board next month. You have provided us with exemplary leadership, and you will be missed. A final thanks to Trudi, the outgoing ARMA President. We were both new to our positions when we stepped up to lead ARMA, and I would like to personally thank you for your guidance and support over the last 2 years.
It’s exciting times and ARMA is poised to make the most of them as we step into a new year.
The Icons of Rotomoulding Award was implemented in 2016, and since then we have had 13 inductees. This year we received several nominations and the board reviews how each one meets the eligibility requirements and this year’s icon met most.
Graeme Hall of Viscount Rotational Moulding – PACT Group has made a significant invention or breakthrough along with the development of an outstanding product. He has provided a long and valuable service to the rotational moulding industry and ARMA, with a record of constructive, collaborative action within a range of government agencies and other groups.
Graeme has also dedicated his professional career to the rotational moulding industry both through an outstanding personal contribution and in helping to create growth through innovation. He has provided leadership in the industry through engagement with partners at the local, national, and international levels and left a positive legacy within the business they work for; and with ARMA.
Graeme has served within ARMA on various projects and sub-
committees, served on the Board for a few years rising to President and now as Past President. He has also been heavily involved in ARMO, the global affiliation, serving on the Board as the ARMA Representative.
Grant Palling from Matrix Polymers shared “Speaking as an ARMA Board member”. Graeme is the ultimate professional when it comes to representing PACT Group, ARMA, and the Rotational Moulding Industry. He is passionate about rotational moulding and about doing what’s right for ARMA members. We can always rely on Graeme’s words of wisdom and level head in a crisis. I’ve learned a lot from Graeme in my time in Rotomoulding and say congratulations on receiving this welldeserved Icon award. Thanks, mate.”
Ian Gough of Gough Plastics shared “Graeme is a mountain of knowledge, with a willingness to share and improve others. Working with him on the Board, he’s proven to be a wise man, with a cool head in many different situations.” That night Ann Rowland of Ferry Industries, our 2019 inductee, congratulated Graeme by video.
Copenhagen airport Kastrup was the perfect venue for the 12th Nordic ARM Conference for more than 110 attendees, including 25 exhibitors. The conference room, break-out rooms, restaurant, and beer tasting were all at the hotel. The conference was well attended from the ARMO board by 5 presidents from different affiliates.
As usual, the conference had a high technical level, and the Nordic moulders contributed well. Pekka Mustonen from Uponor presented how they successfully converted their rotational moulding machines burners from using propane to using natural gas. Christoffer Haarbye from Rotostøp presented how they managed to clean their moulds without damaging the mould surface by using laser technology. Dadi Valdimarsson from Sæplast and Rotovia shared their experience by using RFID labels from PSI together with Walter Bonazzi from PSI. Lars Haugli from Pioner Boats, explained about their new set-up buildings and their latest innovations.
The focus area for this conference was the circular economy, automatization, and innovations. Regarding circular economy
Conference 2022 (continued from page 56)
Christina Busk from the Danish Plastic Federation presented their amazing work they have made for product responsibility, Brede Mordal from Replast by Quantafuel presented new marking systems for rotomoulded products to ensure that they will be recycled as rotomoulded products, Ronny Ervik from Norner gave a presentation on the most important obstacles that need to handled when using recycled materials, Dr. Carlos Barreto from Norner presented an EU project were one of the results was how they managed to make rotomouldable PP from WEE waste and Ronny Ervik also presented a project run by Nordic Plastic Recycling (NPR) were NPR is now offering a recycled material from the end of life products, where mechanical properties are near to prime.
Regarding automatization, we got insightful information on how to increase productivity without increasing labour from Oliver Wandres from Maus, Matteo Cortesi from Persico, Johan Potargent from AMS Robomould, and Frank Harleman from Hengelo. The Nordic ARM is very grateful for the intensive innovations ongoing at the machine and mould manufacturer.
Regarding Innovations professor Marek Szostak from Poznan University presented their work of biobased polyethylene composites, Julie Philippron from P-Laser presented their latest laser technology used to clean moulds without damaging the mould surface, Katia Zoppetti from DRAM presented their always-growing portfolio of accessories, Angelique Brocatus from LyondellBasell presented their new high mfr polyethylene with amazing mechanical properties, Konstantia Asteriadou from
Lysis presented their new functional coatings and Magda Wolczynska and Dharana Jayawardane presented very interesting opportunities in hydrogen tanks.
The Nordic ARM workshops were very well attended. The enthusiasm and involvement were as always very good. Some of the workshops could have, if allowed, continued into the late hours.
This year the Nordic ARM invited a recognized micro-brewery to present remarkable design, excellent (tall) tales, and very good tastes. After the Nordic ARM dinner, the famous Nordic ARM quiz took place and this year’s winner was Kristoffer Fjeld Langrind from Pioner Boat.
The next Nordic ARM Academy will be in January / February 2023. The new thing will be that it will be held in Norway, in Norwegian for Norwegian moulder, in Sweden in Swedish for Swedish moulders, in Denmark in Danish for Danish moulders, and in Finland in English (with translator) for the other moulders.
Dadi Valdimarsson from Rotovia was elected as new board member for Nordic ARM.
The next Nordic ARM Conference will take place in January / February 2024 in Reykjavik, Iceland.
The BPF’s Annual Accident Survey helps to gather useful information to support the plastics industry in its quest for improved Health & Safety performance. This year’s report shows that the sector’s performance is improving after a challenging year in 2020. Key headlines:
• 95 accident returns, representing 16051 employees
• 0 fatal injuries to workers
• 13 major RIDDOR accidents reported – down from 18 the previous year
• Major RIDDOR accidents resulted in 484 lost days
• 1164 non-RIDDOR accidents were reported, resulting in 120 days lost
• 22 reportable diseases – down from 27 last year
The report not only shows the top 5 accident categories, but also the top accident categories by sector. This year’s report is available to download here – member log in required.
Members will have seen in the news that COVID-19 infections in the UK are rising and have topped more than one million, with a 14% rise in people testing positive - the biggest increase since the summer. BPF have received anecdotal reports that members are seeing this increase, and many are resuming some of the safe working practices.
Combined with warnings of an early “wave of flu” these challenges are likely to put members under enormous pressure to work safely in an already difficult period for the sector.
Additionally, there seem to be anecdotal reports suggesting that covid testing is less effective at detecting new variants and resulting in false negatives, therefore increasing the transmission rate. A
recent study looked at three rapid tests and found a modest decline in their sensitivity during the omicron wave versus delta. During omicron, the tests identified as few as 70% of symptomatic people infected with the virus, and only one test hit the WHO’s standard of 80% sensitivity among people with symptoms. The standard advice seems to be that despite having a negative result people should still repeat the test a few days later.
HSE no longer expects every business to consider COVID-19 in their risk assessment or to have specific measures in place, however, members are advised to monitor the HSE and Government websites and look out for BPF updates.
Association of Rotational Moulders Australasia Inc. Tel: +61 (0) 7 3812 1450 www.rotationalmoulding.com
CEO: Michelle Rose
Cheif Executive Officer: Michelle Rose michellerose@rotationalmoulding.com
Association of Rotational Moulders Southern Africa PO Box 6966
Birchleigh 1621 Gauteng, South Africa
Tel: +27 82 772 3769 Fax +27 12 541 1738
Chairman: Grant Heroldt info@armsa.co.za www.armsa.co.za
Association of Rotational Moulding (Central Europe) e.V. (ARM-CE)
MAUS GmbH - Rotationsgießformen Am Viehweg 9 - D-76229 Karlsruhe Amtsgericht Mannheim, HRB 103433 Tel.: +49 (0) 7 21 / 9 48 74 12 Fax: +49 (0) 7 21 / 9 48 74 44
Mr. Oliver Wandres, ARM-CE Chairman info@rotational-moulding.de www.rotational-moulding.de
British Plastics Federation Rotational Moulding Group 6 Bath Place Rivington Street London EC2A 3JE United Kingdom Tel: 020 7457 5000 Fax: 020 7457 5045
Chairman: Mr. Philip Maddox PhilipM@LeafieldEnv.com
IT-RO Italia Rotazionale
Katia Zoppetti Via E. Brigatti 12 20152 Milano (MI) Italy Tel: +039 348 7652560 www.it-ro.it
Society of Asian Rotomoulders (StAR) 40/145, Ground Floor, Chittaranjan Park New Delhi 110019
Tel: + 91-11-41630157 Fax: +91-11-41634952 Mob: + 91- 9810305356 sb.zaman@staraisa.org arnacz@satyam.net.in www.starasia.org
The Nordic Association of Rotational Moulders
Executive Board Chairman: Mr. Ronny Ervik ul. Zielona 8, 61-851 Poznan, Poland Tel: +48 607-126-004 Fax: +48 61-858-8611 info@rotomoulding-europe.org www.nordicarm.org
19 GRAFE Advanced Polymers GmbH
Waldecker Straße 21 99444 Blankenhain GERMANY +49 (36459) 45-287 mobile +49 151 16 34 20 44 manfred.fischer@grafe.com www.grafe.com
17 Diversified Mold & Castings
19800 Miles Road
Warrensville Hts., OH 44128-4118 USA 216.663.1814 | 888.642.1222 info@diversifiedmolds.com www.diversifiedmolds.com
64 ExxonMobil Chemical Co. PO Box 96126 West Springs Calgary, Alberta Canada, T3H 0L3 800.668.0177 kevin.c.jamieson@exxonmobil.com https://www.exxonmobilchemical.com /en/products-and-services/ polyethylene
5 Ferry Industries, Inc. 4445 Allen Road Stow, OH 44224-1093 USA 330.920.9200 sales@ferryindustries.com www.ferryindustries.com
51 JSJ Productions, Inc. 625 West Market St. Salinas, CA 93901 USA 512.894.4106 susan@jsjproductionsinc.com www.jsjproductionsinc.com
9, 21 Jerico Plastic Industries, Inc. 7970 Boneta Road Wadsworth, OH 44281 USA 330.334.5244 Minerva Plant: 330.868.4600 steve@jericoplastic.com www.jericoplastic.com
11 Matrix Polymers
The Priory Orchard Hill Little Billing Northhampton, NN9 9AG United Kingdom +44.1604.789100 sales@matrixpolymers.com www.matrixpolymers.com
7 OREX Rotomoulding SP. Z O.O. Cieszyriska 6, 43-520 CHYBIE Poland +48 32 440 83 15 magda.wantola@orex.pl www.orex-rotomoulding.com
15 PSI Brand 16 Thames Street Napier 4110 New Zealand +64 6-834 4808 sales@psibrand.com www.psibrand.com
23 Poliplast S.p.A. Via Carrali, 8 24020 Casnigo (BG) Italy +39.035.724145 info@poliplastspa.com www.poliplastspa.com
3 Powder King, LLC 41780 N. Vision Way Unit 120 Bldg. 2 Anthem, AZ 85086 USA 623.551.9897 sales@powder-king.com www.powder-king.com
37 Rock Lake Robotics 100 S. CP. Avenue Lake Mills, WI 53551 USA 920.648.3402 sales@rocklakerobotics.com www.rocklakerobotics.com
2 Roto Polymers 26210 Emery Road, Suite 202 Cleveland, OH 44128 USA 1.844.POLIMER (1.844.765.4637) info@rotopolymers.com www.rotopolymers.com
63 Rotomachinery Group
Via Crosa, 53 28065 Cerano (NO) Italy +39.0321.772021 polivinil@polivinil.com www.rotomachinerygroup.com
36 VMP, Inc. 24830 Avenue Tibbitts Valencia, CA 91355-3404 USA 888.4.VMP.INC 661.294.9934 info@vmpinc.com www.vmpinc.com
18 Wittmann Battenfeld Canada Inc. / ROTOLOADTM 35 Leek Crescent Richmond Hill, ON L4B 4C2, Canada 905.887.5355 Toll Free: 1.888.466.8266 info@wittmann-group.ca www.wittmann-group.ca
Your rotational molding capabilities begin with the quality and dependability of your polyethylene resin supply. Start your day with PE products and process innovations that help leading rotomolders bring their most complex designs to reality. Accomplish more with our reliable supply network, responsive sales support and expert technology team Learn more