SUSTAINABILITY REPORT 2022
LEADING THE CHARGE FOR SUSTAINABLE WASTE COLLECTION
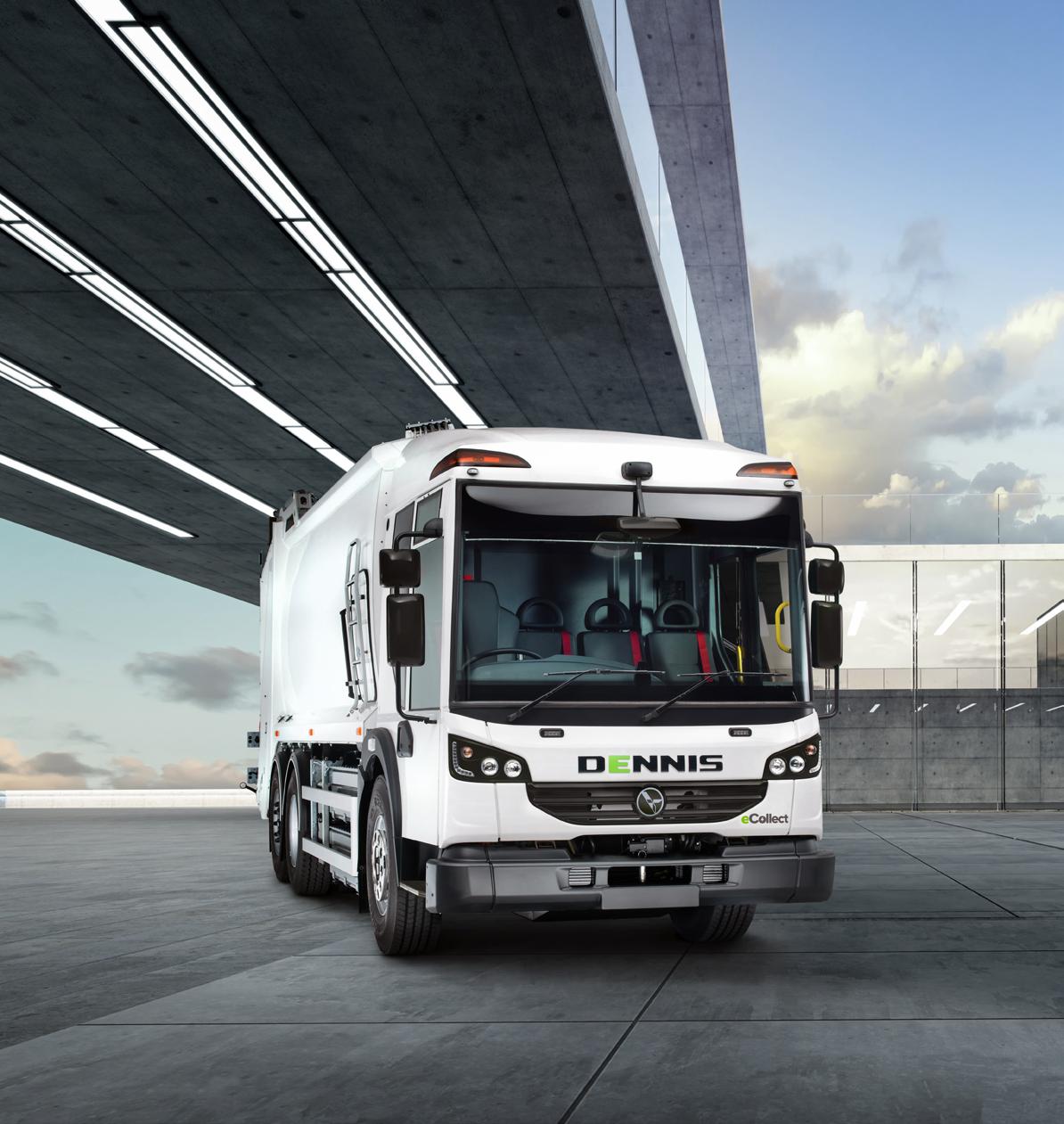
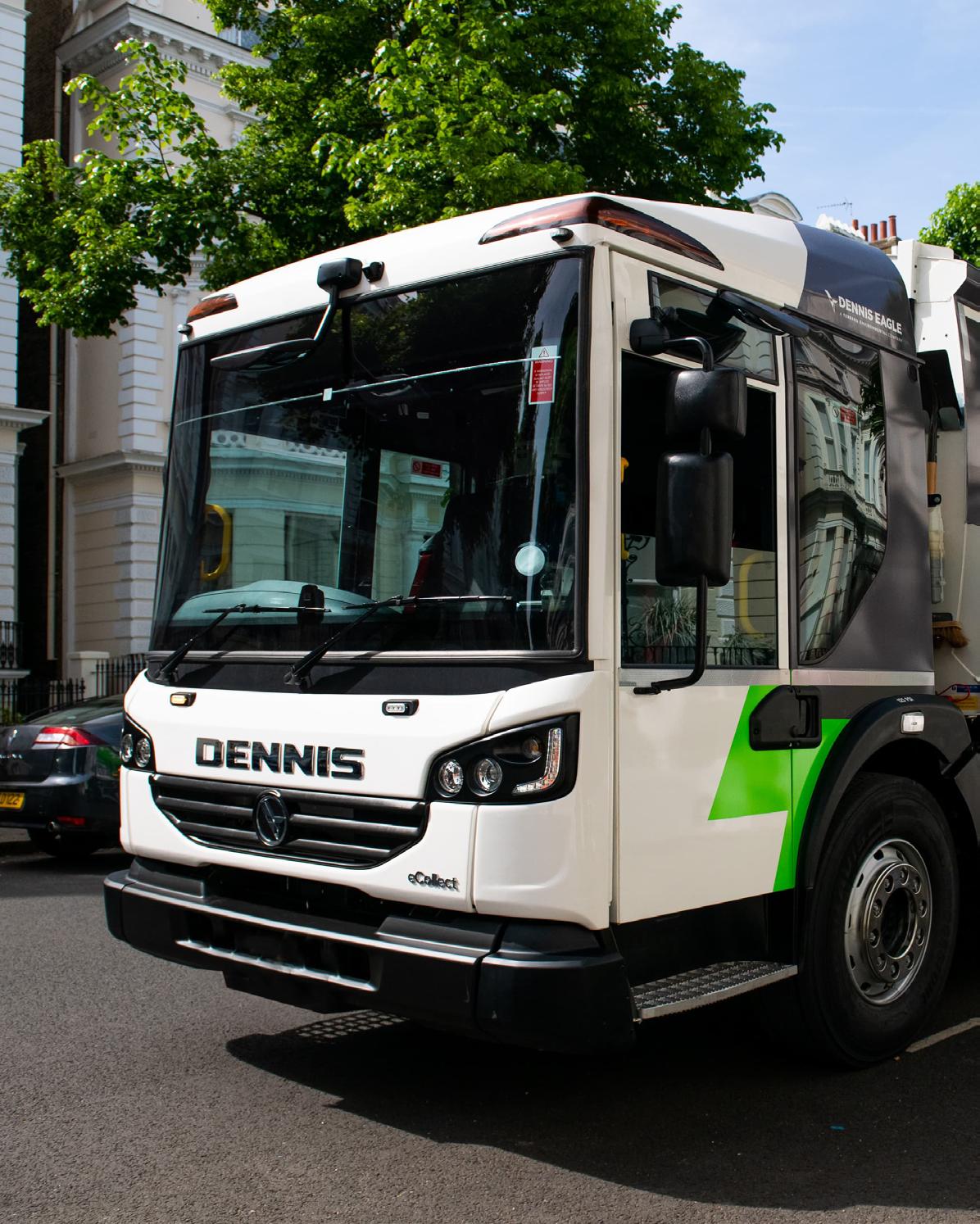
We aim to become a genuinely carbon-neutral company by 2035 and reach net zero before 2050, in line with government targets.
• ‘Carbon-neutral’ means balancing our total carbon emissions by capturing or offsetting them.
• ‘Net Zero Carbon’ means making no carbon emissions in the first place by running entirely on renewable energy and using no fossil fuels.
To achieve this, we will constantly strive to reduce waste and emissions in everything we do, from sourcing materials and supply chains, to manufacturing and delivery. And we will balance our reduced emissions with certified carbon offsetting schemes based in the UK.
By working with our stakeholders, we can provide a sustainable and enhanced environment for the communities in which we operate and influence.
Dennis Eagle has mapped the route to a fully sustainable future where our people, our processes and our vehicles operate safely with full efficiency and environmental responsibility.
Perhaps because of the industry we work in and the ethos of our customers, sustainability has always been a part of what we do. But these new reports give those principles a formal basis, alongside financial reporting. In fact, the two are intertwined and often dependent on each other.
Our customers do not just judge us on the quality and cost-effectiveness of our products and services. Our environmental credentials and social responsibility already help them make procurement decisions.
Going forward, the sustainability of our operations will inevitably become increasingly important to our commercial success.
This first report sets out to produce a benchmark against which the sustainability of different parts of our business can be assessed in future.
In these yearly reports, however, aspects of our operations will have been accurately and reliably measured and reported in line with recommended standards. And our results will be compared with those published by our competitors.
Competition of this nature will lead to innovation and progress. Thankfully, this desire to find new solutions, better products, improved systems, greater efficiency … it's already in our DNA.
Now, under the spotlight of these reports, this will drive us to become increasingly sustainable.
The reasons businesses need to focus on sustainability, as outlined on page 12, do not make comfortable reading. These are serious issues and there is no doubt the world faces major challenges. But all is not doom and gloom. Our industry is used to facing challenges and succeeding.
At Dennis Eagle, our connection with science and engineering is immensely strong. We turn to these resources every day for answers and we find them.
And I am confident that this is where, once again, we will find the solutions we are looking for.
Zero landfill and zero waste may seem a long way off at the moment. But so too did zero emissions, until recently. This report and those that follow it, are crucial steps in helping us tackle these challenges.
For many years, businesses have published information on their financial performance in an annual report. Now Dennis Eagle, like many others, will also begin publishing information on our sustainability.
Most people understand that the environment and sustainability go hand-in-hand. The Environmental, Social and Governance (ESG) approach, however, are the cornerstones of sustainability. But how Social and Governance issues have an impact is not always as clear.
The United Nations spells it out when it says doing business in ways that benefit society and protect people will benefit the business itself.
So, it is important to manage the impact this business has on our stakeholders, such as employees, suppliers, customers and local communities. In turn, how any of these groups feel about us, interact with us and talk about us has an impact on this business.
Similarly, good governance is based on economic, social and environmental improvements which all promote sustainability and improve a company’s relationship with its stakeholders.
It is important to this business and all our stakeholders that we commit to improve all three strands of sustainability.
I’m greatly encouraged that our customers have a similar determination to succeed.
The scientific consensus is that, in order to limit global warming to 1.5°C by the end of the century, we must halve annual greenhouse gas emissions by 2030. By the start of 2021, 80% of UK local authorities had climate action plans in place so they could lead by example and play their part in achieving this.
Their plans vary according to their operational circumstances but there are common themes. Among them, the transition to zero-emissions waste and recycling fleets is prominent.
The timescales different councils and private operators have set themselves depend on a range of practical issues which they have clearly considered carefully. Reassuringly, their targets reflect the urgency of the situation; they are ambitious.
Our approach is loud and clear; ambitious targets require customer-focused solutions.
I hope this outlines our commitment to sustainability as the best way forward.
This first report will set a benchmark against which our progress can be assessed. It will highlight aspects of our business which we need to improve,alongside others where we can learn from success.
This division manufactures specialist vehicles for logistics functions, such as loading and movements in ports, airports and freight terminals.
Provides a diverse range of efficient, eco-technology solutions for the waste management and recycling industry.
The Royal Terberg Group is a family-owned business based in the Netherlands that operates worldwide and produces specialised transport vehicles and equipment.
This division fits additional axles and specialist ePTO systems to forestry, construction and municipal vehicles, helping them carry heavier loads, be more sustainable and operate on poor surfaces.
Kinglifter truck-mounted forklift trucks help make deliveries more efficient where conventional forklift trucks cannot be used.
We are part of Terberg Environmental which has established companies in the UK, Spain, Germany, Portugal, Belgium, France, the Netherlands, Poland, United Arab Emirates and the United States and Canada. It also has an extensive and growing network of distributors worldwide.
Dennis Eagle manufactures more than 1,000 vehicles-a-year for UK local authorities and private sector contractors. In addition, we have a continually expanding customer base in continental Europe, Scandinavia, Australia and the USA.
The Royal Terberg Group’s solutions are designed to be the most sustainable, efficient, safe and futureproof solutions that our customers require. Our ethos is well established:
• We develop products, processes and technologies that contribute to the well-being of human needs while respecting natural resources.
• We have a responsibility for the environmental impact of our operations, so we take the effect of our activities on our planet into account.
• We focus on energy consumption, a cleaner (working) environment, sustainable use of raw materials, sustainable technological developments, social policy and our relationship with regions where we provide solutions.
With this in mind, Dennis Eagle aims to help increase our customers’ efficiency, achieve business growth and make both ours and our customers’ operations more sustainable through innovation.
Dennis Eagle is part of Terberg Environmental –a division of the Royal Terberg Group which is a family-owned business employing more than 3,000 people worldwide with a turnover in excess of €1bn.
“ Terberg is a family business providing best-in-class solutions worldwide in the special vehicle market, enabling businesses and the public sector to transport goods efficiently, safely and sustainably.”
Godfried Terberg
Terberg Chairman of the Board of Directors
Our bodies, chassis and bin lifts are available as individual components or as complete refuse collection vehicles (RCVs). We design and build them to be highly efficient, reliable, safe, durable and cost-effective. Each of these parameters contributes towards the sustainability of the product. We also offer a wide range of aftermarket services to support our products and our customers.
Our main production facilities in the UK are at our HQ in Warwick where our RCVs are made and support teams based. Our cabs are produced in Blackpool.
A division of Dennis Eagle – Terberg Matec UK –produces specialist recycling vehicles (SRVs) in Worksop while Terberg bin lifts are assembled in Warrington.
We operate in markets around the world. In the USA we have a new and purpose-built manufacturing facility in Summerville, South Carolina assembling the ProView chassis for the North American market. Sales and customer support are provided through local dealerships.
Vehicles and products for other global markets are exported from the UK. Sales and customer support are once again provided by dealers.
We also run a network of 10 Dennis Eagle regional Service Centres across the UK to provide local support to our customers. Another network of mobile Field Service Engineers supports customer’s operations across the UK. And when providing a full repair and maintenance contract for a customer, we operate from local workshops and depots specifically for them.
Dennis Eagle is focused solely on the waste management industry. Our specialist knowledge and experience in this sector are unrivalled. This enables us to design and manufacture a range of products to cover every operational need.
Manufacturing Sites
Service Centres
Contract Centres Dealers
Northern Ireland
Republic of Ireland
Blackpool
Manchester Isle of Man Warrington
Aldridge
Warwick
Leeds
Coundon Worksop
Witham
Human activity has caused the Earth’s temperature to rise by 1.1°C since 1880, leading to the climate crisis.
The consequences of this unsustainable approach include the loss of nature and biodiversity, increasingly extreme and destructive weather, rising sea levels and pollution of land, sea and air. Air pollution alone causes 7 million premature deaths globally every year.
To combat this, the United Nations has set targets to decarbonise our economies. Individual countries have formed plans and introduced legislation to achieve this as well as to recycle and to protect and restore the natural environment.
The UK Government has set a target for our economy to be ‘carbon net zero’ by 2050.
Businesses and other organisations are changing the way they work to lower emissions and reduce waste. Consumers are also being encouraged to modify their behaviour and change their lifestyles.
Local authorities – our customers – have set targets too, including decarbonising fleets and producing zero emissions. Private operators have similar goals. To achieve this, they all need to fully understand the sustainability of the products and services they purchase.
Consequently, as a supplier, we need to set out our stall to ensure the sustainability of our business activities are fully transparent to our customers. And we need our suppliers to provide the same transparency for us.
In short, every person, organisation and country is being given the responsibility for helping to save the planet.
We’re using renewable resources faster than we can replace them –it would take 1.6 Earths to replenish them.
World Wildlife Fund
Non-renewable resources are running out. Without new reserves, oil and gas will run out by the middle of this century.
Octopus Energy
NASA’s Earth Observatory
This first report will set a benchmark against which our progress can be assessed. It will highlight aspects of our business which we need to improve, alongside others where we can learn from success.
The focus of the report is on three areas recognised as being at the heart of sustainability: Environmental, Social and Governance (ESG). Businesses and other organisations around the world are being urged to follow a similar framework.
• The Environmental aspect encompasses the human impact on our planet, from climate change to water management.
• The Social aspect considers our impact on each other and how we can improve the well-being of individuals and societies. It includes issues ranging from promoting race and gender diversity to increasing customer satisfaction and employee engagement.
• Governance covers every topic from what is morally right and fair to what is safe and legal. Among them are issues as diverse as board composition, data security, management structure, pay scales and anti-corruption practices.
In this first report, covering 2021–22, we are reporting on what are known as Scope 1 and Scope 2 emissions. These are different sources of greenhouse gas emissions that are categorised by the widely used global accounting tool, the Greenhouse Gas Protocol. We are also working on reporting Scope 3 emissions and will include them in our future reports.
Just as our stakeholders will be able to assess our
sustainability, it is vital that we do the same. This is how we will drive improvement in all these areas.
And this is not only crucial to reaching our sustainability goals but also our commercial goals.
Of course, environmental responsibility is not an isolated issue. It goes hand-in-hand with social responsibility too. This means taking a similarly responsible approach to the well-being of our staff, the communities we live in, the customers and suppliers we work with and society as a whole.
With that in mind, this report also outlines our activities relating to those other aspects of our business.
Finally, as this first report is about setting a benchmark, we need an appropriate starting point. 2021 is the period we’ve chosen. By the start of that year, we had overcome most of the issues faced during the pandemic when activities were by no means normal.
The start of a project like this, in a business of our size and scope, is challenging. Inevitably, there are inconsistencies, such as areas in which we need to harmonise reporting and measuring processes.
As a result, while the company operates in many different markets around the world, this first report is largely focused on our core UK operations. Where facts and figures have a different basis, we will flag this up and explain how they are derived to ensure full transparency. Other parts of our operations will come into line with our core business in the very near future so that they can be included in subsequent reports.
We recognise the urgent need to protect the environment by minimising our impact on it. This not only encompasses our operational activities but also the products and services we provide and the materials and supply chains we develop.
We understand the importance of ensuring employees are treated with dignity, respect and equality. This requires us to constantly encourage employee engagement, ensure we are always mindful of their wellbeing and actively promote greater diversity.
We commit to finding customer-focused solutions to enable the end-users of our products and services to meet their sustainability goals. Our activities are determined by their needs and we can only understand what they are through constant engagement.
All our business activities must adhere to the law and to regulations and directives relating to our industry. We recognise that only by total compliance can we protect the health, safety and well-being of the people and the environment in all our different communities.
The sustainability of our business is based on four principles which we have developed and implemented to underpin all Dennis Eagle activities.
We listen to our customers and tailor our product development to them.
We always aim to recognise and seize opportunities presented by our markets.
We have an ability to adapt and survive when circumstances change.
Aim for the best of the best, without quality there is no basis for our work.
We will accept change and allow ourselves to be challenged, do not be afraid of the impossible.
Make sure you are always a reliable business partner who keeps to agreements, verbal and written.
As a family business, we want to act responsibly towards our planet, now and in the future. We want to hand over a healthy family business to the next generation.
Dennis Eagle plays a critical role within the industry by providing efficient and cost-effective solutions for the collection and transportation of waste and recycling materials from domestic and commercial sources. Our customers are both local authorities and private operators.
In the last two decades there has been a determined effort to increase recycling. In the UK, the complexities of devolution have led to different strategies in different constituent countries. However, legislation has made landfill increasingly expensive and provided targets for recycling. This has led to a significant increase in the proportion of material recycled.
In addition, new uses for recycled materials have led to the introduction of more waste streams such as food waste. The different scale and nature of these materials can require different containment, handling and frequency of collection.
Vehicles have had to be developed to cope efficiently with these changing needs and provide the flexibility that different operators require for operations to be costeffective.
Further developments come thick and fast. Dedicated weekly food collections are being introduced throughout England next year and Deposit Return Schemes (DRS) will come first to Scotland in 2023 and the rest of the UK shortly afterwards.
But with innovation at the heart of our business, we have been able to work closely with customers and lead the way forwards to meet their changing needs.
Local authorities are responsible for collecting houseshold waste and recycling in the UK and – if requested –commercial waste.
Under constant public scrutiny, they are keen to behave responsibly. Many have made great strides in reducing emissions to combat climate change and continue to lead by example. A key aspect of this is the decarbonisation of their fleets.
In anticipation of this, Dennis Eagle assessed the different zero-emissions options and in 2010 began developing all-electric RCVs. Our first – a genuine zeroemissions alternative to our best-selling diesel RCV – went into production in 2020. The eCollect is now widespread in the UK, growing in popularity and helping operators demonstrate the numerous benefits of EVs.
UK local authorities are also responsible for ensuring air quality standards are met. The issue was brought sharply into focus when, in 2020, a coroner recorded air
The waste and recycling industry is at the sharp end of the sustainability goals of the UK and other territories around the world.
pollution as a factor in the death of a child in London.
All our vehicles are built to the highest specification and meet the latest European emissions standard – Euro 6. Diesel technology has improved significantly in recent years and pollution from modern engines is much lower, which will help reduce air pollution. But consultation with our customers on this issue led us to develop our second eCollect model, a smaller 4x2 version with a five-tonne payload.
Vehicles of this size are needed in urban areas characterised by restricted access in narrow, cluttered streets. These same locations often suffer most from air pollution.
As well as being cost-effective over the course of their lifetime, our electric vehicles address other environmental issues too, such as the noise traditionally associated with waste collection vehicles.
Other innovations continue to be implemented in different markets. Improving operational safety has been an industry focus for many years and Dennis Eagle, once again, led the way.
In the 1990s, we were the first to introduce the lowentry cab to our industry. This not only made it easier and safer for crews to get in and out – as they do numerous times each day – but also gave drivers a lower seating position from which they were more connected with other
road users. Its panoramic windows won many accolades for the improved safety they delivered.
In 2016 the Elite cab was among 40 vehicles independently assessed for Transport for London and it was found to provide the best Direct Vision for Drivers of any truck on the UK’s roads. This has since been improved in the Elite+ cab launched in 2022.
The introduction of a similar low-entry walk-through cab with panoramic windows has also enabled our ProView vehicle to make major inroads in the North American market since 2021.
Almost every aspect of waste collection has also been vastly improved by the introduction of telematics solutions to the industry. Our system, DE-Connect, was developed specifically for this industry, as opposed to others which were developed with freight and other truck operations in mind.
It has enabled operators to optimise routes, analyse and improve driving standards, reduce emissions, streamline service and maintenance, reduce fraudulent insurance claims, protect drivers and crews and improve customer satisfaction.
Our record of innovation is second to none in this industry. And through constant dialogue with our customers and continued investment in R&D, we remain committed to driving it forward.
This report summarises our energy usage, associated emissions, energy efficiency actions and energy performance under the government policy Streamlined Energy & Carbon Reporting (SECR). This is in accordance with the Companies (Directors’ Report) and Limited Liability Partnerships (Energy and Carbon Report) Regulations 2018.
Dennis Eagle Ltd is a UK incorporated business. Under
Scope
Dennis Eagle Ltd’s Scope 1 direct emissions (combustion of natural gas and transportation fuels) for this year of reporting are 3,577.23tCO²e, resulting from the direct combustion of 16,693,419 kWh of fuel. This represents a carbon increase of 15.14% from last year.
Scope 2 indirect emissions (purchased electricity) for this year of reporting are 922.88 tCO²e, resulting from the consumption of 4,346,440 kWh of electricity purchased
the SECR legislation we are mandated to include energy consumption, emissions, intensity metrics and all energy efficiency improvements implemented in our most recent financial year.
An organisational boundary has been applied for the purposes of the reporting. 8% of consumption data used for SECR has been required to be estimated to achieve 100% data coverage.
and consumed in day-to-day business operations. This represents a carbon reduction of 1.32% from the previous year.
Our operations have an intensity metric of 0.09 tCO²e/kWh per m² and 4.91 tCO²e/kWh per Full Time Equivalent (FTE) for this reporting year.
This represents an increase in operational carbon intensity of 9.42% from our previous reporting year.
All Dennis Eagle Ltd’s electricity and gas invoices have been entered into a fully managed energy database up to 31st December 2021, and data quality checks have been carried out for data completeness and accuracy. All transport information has also been entered into the energy database up to 31st December 2021.
There were a number of instances, equating to 8% of the total reported consumption, where it was necessary to calculate some estimated consumption to achieve 100% data coverage. Methodology of these estimation techniques is detailed in the appendix.
The following figures show the consumption and associated emissions for our operations in this reporting year, with figures from the previous reporting period included for comparison. Scope 1 consumption and emissions relate to direct
combustion of natural gas, and fuels utilised for transportation operations, such as company vehicle fleets. Scope 2 consumption and emissions relate to indirect emissions relating to the consumption of purchased electricity in day-to-day business operations.
The total consumption (kWh) figures for reportable energy supplies are as follows:
The total emission (tCO²e) figures for reportable energy supplies are as follows. Conversion factors utilised in these calculations are detailed in the appendix:
Intensity metric’s of tCO²e per m² and tCO²e per FTE have been applied for our annual total emissions. The methodology of the intensity metric calculations are detailed in the appendix, and results of this analysis is as follows:
efficiency.
Measures ongoing and undertaken through 2021:
Warwick
• Installation of a new roof, insulation and skylights in Unit 1.
• The additional natural light into the building has reduced the lighting demand.
• New energy efficient burners have been installed in the Beta 2 paint shop, Unit 1.
• Timers have been installed on the compressors in Unit 3, restricting usage to periods of demand.
• New control panels & timers have been installed for the extraction systems in Fabrication & Paint, minimising energy waste.
Blackpool
• An energy efficient boiler has been installed in the paint shop mixing room.
Terberg – Warrington
• Installation of lighting occupancy sensors in office areas.
Measures prioritised for implementation in 2022:
• Understand carbon emissions and develop and implement plan to mitigate emissions with Inspired PLC
• Sourcing of green energy, wherever possible for all sites
• Review energy usage and implement a turn off when not in use policy. Utilise controllers with timer sensors wherever possible
• Review diesel usage – both bulk tank (where applicable) and business vehicles
We are committed to year-on-year improvements in our operational energy
As such, a register of energy efficiency measures available to us has been compiled, with a view to implementing these measures in the next five years.
This report has been prepared by Net Zero Compliance (a division of Inspired Energy PLC) for Dennis Eagle Ltd by means of interpreting the Companies (Directors’ Report) and Limited Liability Partnerships (Energy and Carbon Report) Regulations 2018 as they apply to information supplied by Dennis Eagle Ltd and its energy suppliers.
Dennis Eagle Ltd’s registered CEO and CFO are ultimately responsible for complying with the Regulations.
They must be satisfied that to the best of their knowledge all relevant information concerning Dennis Eagle Ltd’s organisation structure, properties, activities and energy supplies has been provided to Inspired Energy.
This includes details of any complex ownership structures (e.g. private equity funds, franchises for private finance initiatives) and generated on-site (including CHP), or supplied to/from a third party (i.e. not a licenced energy supplier or a landlord/tenant).
Our suppliers are highly valued by Dennis Eagle and our relationships are strong and mutually beneficial. The nature of our markets and our production regimes means that for many, we are a steady and reliable source of orders. This they value, as orders from other customers in different markets may be far more irregular.
During the pandemic, supply chains were severely tested but thanks to the strength of our relationships and the excellent support from suppliers, our factories were able to continue operating with only a short pause in production.
Against this backdrop, our approach to sustainability through our supply chains has been to commit to working with our existing and valued suppliers wherever possible for both the sake of efficiency and the further strengthening of our relationships. This has required additional engagement with them in two immediate aspects of our work:
• We need them to help us assess our Scope 3 emissions
• We need them to work with us to eliminate packaging waste.
In addition to these initial requirements, we also want to lead by example and encourage and help our suppliers to begin similar journeys towards Carbon Net Zero within their businesses.
We have worked hard to help suppliers understand both the needs and the benefits of reducing or eliminating different sorts of packaging waste. Here, we are typically dealing with wood (such as pallets and crates), cardboard, paper, various forms of plastic and shrink wrap.
Working with selected suppliers, we have been able to replace much of this packaging material with bespoke, stackable stillages. These are both returnable and re-usable.
This project was started in 2018 and savings on packaging up to the end of 2022 had reached 221,000kg. In the first year, the team targeted the lowest hanging fruit for the greatest impact and achieved savings of more than 89,000kg of waste. In the year ending December 31 2021, the waste packaging savings amounted to more than 37,800kg.
Much of this would have been incinerated or would have gone to landfill with the negative consequences of further carbon emissions and other air pollution and more non-biodegradable plastics introduced to the wider environment.
As well as reducing the packaging requirements, this project has also created more space on delivery vehicles which, in turn, has led to fewer delivery journey being
required. The net benefits of this have been a reduction in greenhouse gas emissions, consequent improvements in air quality, a reduction in road traffic volume and a reduction in working time for both Dennis Eagle and our suppliers.
While the initial cost of the bespoke, reusable stillages is significant, it is expected that there will also be significant long-term cost savings for both suppliers and Dennis Eagle.
Our Scope 3 emissions will be included in the second Sustainability report.
As well as working with existing suppliers to encourage their commitment to reaching Net Carbon Zero status, we are also updating guidelines for new suppliers.
Among these changes, we will ensure that, new suppliers are actively seeking voluntary Scope 3 Carbon Neutrality or engaged in Carbon Net Zero initiatives wherever possible. We will also ensure they are legally compliant with their Scope 1 and Scope 2 emissions declarations.
And we will encourage them to focus on Carbon Net Zero activities, such as replacing non-reusable packaging in favour of stillages, ensuring vehicle deliveries are as efficient as possible and seeking opportunities to reduce delivery mileages wherever possible.
Dennis Eagle adopts and operates within a broad range of standards, regulations, strategies, acts and guidelines, which amount to more than 200 in total covering the environment, health and safety, conformity of production, vehicle type approval (including all vehicle emission legislation) and all employment law requirements.
In addition, there are policies in place which surpass the basic requirement in the areas of pay (including real living wage accreditation), leave, holiday and pension contributions.
We aim for all our people managers to be appropriately trained in the areas of employment rights, employee relations, equality and modern slavery to better support their interaction with people.
Among the key compliances and standards we work to are:
This process ensures vehicles meet relevant environmental, safety and security standards before they ever reach the market.
All our new models are rigorously tested to ensure they are safe, efficient, durable and meet all environmental, safety and security standards required of them. They are all given WVTA before they go to the market.
These regulations also apply to RCV bodies. All our vehicles’ bodies are compliant with these regulations for both Great Britain and for Northern Ireland before they are placed into those markets.
This directive from the EU in 2006 ensures that all machinery is safe and standards harmonised across the EU. It still applies to machinery in the UK after Brexit and it applies to the bodies of RCVs.
In this heavy industry, producing specialist vehicles requires hands-on engineering. The safety of our processes and our products is paramount. Quality is critical. Compliance is essential.
All our vehicles’ bodies are designed and manufactured to be safe and are compliant with the European Machinery Directive.
A Certificate of Conformity is issued with every Terberg Matec UK bin lift. This is in line with UK Government guidelines relating to the Supply of Machinery (Safety) Regulations 2008.
It also complies with the UK directive on Electromagnetic Compatibility Regulations 2016 and the UK standards: BS EN 1501-1 + A1 (2015), BS EN1501-5 (2011), BS EN 60204-1 and BS EN ISO 13849-1/2.
As Dennis Eagle enters new markets around the world, we ensure all parts of our vehicles and fully compliant with the relevant regulations in those territories.
This is the international standard that assesses our environmental management systems. Dennis Eagle is fully certified to have achieved ISO: 14001 (Environmental) standards.
This international standard demonstrates our ability to consistently provide products and services that meet customer and regulatory requirements. Dennis Eagle is fully certified to have achieved ISO: 9001 (Quality) standards.
Dennis Eagle has been awarded the IiP Silver accreditation, one of the highest levels of accreditation within the Investors in People framework. For furthe information on Dennis Eagle's Investors in People profile turn to page 46.
While the company has always had an ongoing programme to meet this end, the effort and investment to achieve these goals has never been greater than it is now.
Recent and ongoing improvements in sustainability at our Warwick production facilities can be considered as follows:
A new transformer and low voltage board was fitted in 2022. It is far more efficient than its predecessor and it is estimated it will save 41,601kWh of electricity annually. Alongside the subsequent cost savings, this alone reduces our emissions by 9.6 tonnes of CO² per year.
New distribution boards throughout the site add to these savings thanks to lower energy usage and improved efficiency.
A new air conditioning control system has been installed to manage use in all office areas. It follows Government guidance on how to restrict its use and recommendations for maximum energy efficiency.
Across the entire company, LED lighting has been installed both internally and externally. This alone has reduced the energy need for lighting by 70%. A temperature issue in our paint booths meant we couldn’t initially install LED in them but this has been overcome and a trial in now under way. Emergency lighting has also been upgraded to a more energy efficient system.
A new roof has been fitted to Unit 1 at Warwick. This is better insulated for better temperature control and to reduce wasted energy. Speed doors have also been
The production process in any manufacturing business is at the heart of its sustainability. It is, of course, in Dennis Eagle’s direct interest to reduce energy consumption, improve processes, replace old equipment with more efficient equipment, improve the fabric of the buildings and the safety and wellbeing of staff.
installed in the factory. These allow much quicker entry and exit and so, once again, reduce heat loss from the buildings.
Meanwhile, in the Fabrication Shop, the extractor fans in the roof have been replaced with fans featuring more efficient motors to further reduce energy consumption in this workspace.
The factory units have also had Ecotile flooring fitted over the concrete floors that were previously worked on. This not only provides better temperature control but is also more comfortable for people to walk on.
Where feasible, our air tooling has been replaced by direct electric power which is more efficient than an electric compressor. Other compressors have had their timers and override changed to save more energy and a transducer has been fitted to the main compressors to
balance loading. The remaining air tool oilers have also been upgraded to reduce oil waste.
We have also carried out a full Argon Line replacement to reduce the risk of leakage and remove waste. And with similar goals, the ongoing Air Leak Repair project aims to eliminate leaks and the waste it entails.
New bulk tanks have been installed for diesel, hydraulic fluid, transmission fluid and Ad Blue. These include a filtration system to ensure vehicles going to our customers will always be delivered with totally clean fluids. And it minimises the risk of environmental pollution and waste.
There has also been a full upgrade of welding equipment for maximum safety and efficiency.
Our fork lift trucks have been fitted with telematics to monitor their efficiency. This has enabled a re-organisation of the fleet and a reduction in usage, leading to cost and emission savings.
The close working relationship with our facility at Blackpool, where our cabs are made, have meant many of the improvements at Warwick have also been implemented in Blackpool at the same time. Others have been based on their own initiatives and opportunities. Among them are the following:
A completely new roof over the factory has made a massive improvement to the heating with significant reduction in both carbon emissions and costs thanks to better heat retention.
Skylights in the new roof have also improved lighting. This, along with the fitting of LED lights throughout the factory and offices, have enhanced the workspace while reducing electricity usage.
Even more electricity has been saved by ensuring the new lights were controlled by both light sensors and movement sensors throughout the facility. This means that lights switch off when natural light levels are high enough and also when there is nobody in a particular area.
Water metering has reduced usage. Old piping, plumbing, fixtures, and fittings have been replaced with more efficient versions which have reduced consumption.
Speed door and emergency doors have also been replaced with more efficient doors. This has improved speed of movement and efficiency around the facilities as well as saving energy through better hear retention.
Ecotile flooring has also been installed in busy working areas. This not only provides better temperature control but is also more comfortable for people to walk on than the concrete floors they have covered.
Cardboard and plastic waste has also been significantly reduced. Like Warwick, new and bespoke stillages are being introduced and plans to increasingly reuse packaging materials are being implemented.
An ongoing programme to reduce energy consumption of air lines has been introduced. Around 60% of power tools are now battery powered. These are not only more efficient but also quieter, improving the environment for staff to work in.
On-tip extraction systems are now used throughout the Fabrication Shop for welders. These are not only more cost-effective and energy efficient but also more flexible than other options. Their introduction coincided with the arrival of new, more efficient welding machines.
The Blackpool manufacturing facility now produces more than 1,000 units a year. Variety has increased too, with the new Elite+ cab going into full production in the last year and four new cabs for the North American market being introduced in the last three years.
Despite this increase in complexity and scale, Blackpool has reduced both the output time and the cab production time year-on-year for at least the last 10 years thanks to constantly improving efficiency.
Just as our headquarters and main manufacturing facility at Warwick has made great strides forward to improve our sustainability, so too have our other manufacturing centres.
The principle behind the eCollect was to provide a genuinely zero-emissions alternative to our best-selling RCV: the 26-tonne diesel-powered Elite chassis with a 19m³ Olympus body and Terberg OmniDEL lift.
This meant it had to be at least as efficient, safe and cost-effective over the course of its lifetime.
After extensive discussions with operators, we knew this was the vehicle our customers most wanted. We also understood that this configuration would be the easiest to test operationally, provide the most data for analysis and consequently, it presented the best base from which to develop other models.
As an OEM it was never our intention to rush to the market. Our products must always meet the exacting standards of our brand and to do so, require exhaustive testing. The eCollect was no exception.
We built five test vehicles that underwent more than 180 validation activities, driving more than 450,000km in the process – that is further than a journey to the Moon.
This not only took considerable time but also required significant investment, the likes of which most other specialist vehicle manufacturers would not engage in. Of course, it also initially added to the carbon footprint of both the eCollect and Dennis Eagle Ltd.
In the long term, however, it made the eCollect more efficient, more robust and more reliable. This has significantly improved the sustainability of the vehicle in comparison with eRCVs that have not undergone such rigerous tests.
The eCollect was the world’s first all-electric RCV produced by an original equipment manufacturer (OEM). It took 10 years to develop and the first were delivered to customers in late 2020.
By the end of 2022 – two years since the first customer order was fulfilled – almost 100 eCollects had gone into service with customers in the UK and Ireland. This accounts for more than half of all eRCVs working in the UK and Ireland at this time.
In the summer of 2022, the second iteration of the eCollect was made available to customers in the UK and Ireland: a 4x2 eCollect with five-tonne payload.
Again, this involved minimal changes from the 18-tonne diesel model and was essentially a smaller version of the original eCollect.
The configuration was, again, made in close consultation with our customers. Air quality was high among their priorities and they wanted a nimble eRCV with a smaller footprint that could operate efficiently on narrow, cluttered urban roads and back streets. These locations suffer from some of the poorest air quality in the UK.
We have also developed a bespoke repowered eCollect programme. In this, a conventional RCV operating on diesel is removed from service and all the diesel components are stripped out and replaced with the eCollect electrical drivetrain, battery packs and cab. The body, much of the chassis and often the lifts remain the same.
This is an efficient way of converting a significant asset that a customer needs to replace with an emissions-free vehicle quickly, cost-effectively and with full environmental sensitivity. The diesel parts are also recycled, either as quality used parts or in our DE Used Approved vehicles where possible.
A key aspect of all our products is that we fully support them. Our Aftermarket network is by far the largest in the UK with an unrivalled numeric and geographic spread and a reputation for industry-leading customer service.
The development of the revolutionary eCollect vehicle was mirrored by the development of our Aftermarket support for it.
Working with high voltage (HV) systems presented new challenges for the industry and required a new approach. When the Health and Safety Executive firmly placed the onus to develop best practices on each industry, as the forerunners in our industry, we took it upon ourselves to do so.
We developed a strict set of workshop rules and procedures and introduced appropriate safety equipment. And all staff and visitors to our premises where electric vehicles may be present either in construction, operation or repair and maintenance are now provided with safety instructions.
These guidelines remain freely available to customers, competitors and anyone else in our industry.
Meanwhile, our skilled engineers have been fully trained to provide expertise in the service, maintenance and repair of electric vehicles that few of our customers could provide.
In doing so, we have made sure this vital aspect of waste management operations presents no barrier to operators wishing to decarbonise their fleet.
And we have also remained true to our declaration that the eCollect will be at least as cost-effective as its diesel forebears.
Per week
Cost CO² emissions
Diesel £796.50 (fuel) 1.15 tonnes (biofuel) = 1.21 tonnes (mineral)
eCollect £432.00 (electricity) 0
Over 70 miles (112km) 240kWh electricity used Electricity price per kWh in pence = 0.36p* Electricity used = 240kWh
Over 70 miles (112km) 90 litres of fuel used Diesel bunker price per litre = £1.77*
Fuel used = 90 litres
The eCollect not only cuts CO² emissions but it also has much lower operating costs, as this example illustrates: Over a typical 70 mile (112km) collection round, the eCollect used an average of 240kWh of electricity. Over the same round, a similar diesel truck used an average 90 litres of fuel (achieving 3.5 miles per gallon). *While
Per year
Cost CO² emissions
Diesel £40,621 (fuel) 58.7 tonnes (biofuel) = 62 tonnes (mineral)
eCollect £22,032 (electricity) 0
Lifetime (7 years)
Cost CO² emissions
Diesel £284,350 (fuel) 411 tonnes (biofuel) = 433 tonnes (mineral)
eCollect £154,224 (electricity) 0
Diesel (average biofuel blend) 2.56kg CO² per litre
Diesel (100% mineral diesel) 2.70kg CO² per litre
TMUK moved into new premises in Warrington in April 2021 where it assembles bin lifts which are mounted on both Dennis Eagle bodies and other manufacturers’ RCVs too.
Its Omni range covers bin lifts for both domestic and commercial waste and includes electric bin lifts which can significantly reduce the environmental impact of hydraulic lifts due to the improved energy efficiency of electric motors.
A carefully designed study carried out with Terberg customers found vehicles with electric OmniDEL bin lifts used 9.7% less fuel than similar vehicles with hydraulic OmniDEL lifts covering the same rounds in similar conditions.
This equates to a potential fuel saving of 1400 litres of diesel per vehicle per year or a carbon saving of 3.5 tonnes for RCVs operating on the typical domestic rounds this lift is largely used for. Customers would benefit from the resulting operational cost savings too.
Other ways the Terberg electric bin lifts contribute towards improved sustainability include much quieter operation (<57dB) and significantly reduced running costs.
Just as TMUK has fully embraced both its customers’ needs and sustainability through its products, the organisation has also led the way within the company in implementing waste management principles to reduce wastage. And they have been remarkably successful.
At Warrington, sustainability has always been the buzz word, and this didn’t change when they moved locations. Fitting out the new offices with furniture made from recycled materials and continuing to embrace and expand upon the environmental possibilities of their new home.
In the workshop, all the lighting is LED to reduce electricity consumption and cut emissions and due to the great natural light, we are able to turn off the lighting completely on bright days. Around the site, every low-
occupancy room and office is fitted with P.I.R sensors to switch off lights when nobody is there to need them. We are taking the next step and investigating automating the switching using LUX levels, rather than P.I.R sensors.
Heating was made significantly more efficient by the installation of destratification fans in the roof. These react when the temperature in the roof space reaches a set point and switch on to redistribute the hot air that has accumulated there. The savings are currently being assessed but it is clear the system has led to a significant reduction in energy usage and costs.
TMUK has also installed an on-demand compressor to power tools which is much more energy efficient than the previous equipment. Furthermore, a reduction of the compressors maximum working pressure of just 1 bar has given a 10% energy saving in that piece of equipment.
When tooling is required, we always explore the merits of cordless versions over pneumatic as the running costs to charge batteries is significantly less than charging the compressor for a relatively short application.
Cardboard and single-use plastics have also come under scrutiny with initiatives to reduce both.
The company identified that almost half a tonne of plastic was used in packaging and 3500kg of cardboard waste was collected in 12 months so they invested in a cardboard shredder that would convert waste cardboard into both void fill and wrap.
Aside from being the right thing to do, there will be 25 fewer skip collections, significantly reducing CO² emissions annually along with negating the need for single use plastics, paying back the initial investment within 12 months.
Paper use in the offices was also targeted and each department was challenged with looking at their process’s and identifying potential reductions without compromise. Many documents were digitalised, and on-screen viewing was promoted rather than printing to view. In the two year period up until the end of 2022, collectively TMUK Warrington achieved an astonishing 47% reduction.
All purchases, large or small must have sustainability
Within the Dennis Eagle family, Terberg Matec UK (TMUK) and its range of bin lifts are not only market leaders in many areas but are also among our most successful products.
and energy efficiency as a minimum consideration and is equally as important as cost.
Waste Management is so much more than simply providing a means to remove waste from site. Waste streams need to be identified, segregated at source, measured and recycled at every opportunity. But Parts & Quality Manager Mick Bullock, soon realised that he needed to understand what was going on behind those numbers in order to make sense of them and use them to maintain and improve recycling levels.
“You’ve got to look beyond the numbers,” explained Mick.
“Recycling is about people, it relies on them to make the right choices. The numbers help but on their own, they can be misleading and by then sharing negative results, we risk the all-important buy in from our staff.
“For example, with the cardboard shredder in the spare parts department, our recycling rates will plummet as a result of reusing the commodity, so it is vitally important to factor in the gains.
“I recently noticed a sudden decline in our plastic recycling rate and a simple investigation identified that we had a temporary cleaner on board and I had not explained our recycling scheme to him, a simple fix but without tracking our waste management, the issue would have been overlooked.
“We have introduced waste streams for waste electrical and electronic equipment (WEEE) and batteries and actively encourage staff to bring items in from home because we can dispose of them properly. We don’t have to do it, but it helps, and they certainly use it.
“This kind of engagement between the people and the company helps everyone realise we are all in this together and what we’re trying to achieve is fundamental and is really what we’re all about.
“Other initiatives help both ourselves and the local community, which we are a part of. We have a local litter problem so, in National Litter-Picking Week, we joined other businesses in the area for a mass tidy up. Between us, we collected more than a tonne from a relatively short stretch of road.”
Other aspects of sustainability are in different stages of development at TMUK.
TMUK is currently implementing their environmental management system and aim to achieve ISO14001 accreditation in June 2023. This particular journey has enlightened and educated us as to where further improvements have been achievable.
Since the outbreak of the pandemic, as with the rest of the world, TMUK have conducted many business meetings and training courses using various online mediums and although there will always be a place for face-to-face contact in our industry, virtual meetings will remain the norm. We are developing our own training courses to present online. Along with the savings in time and expense, there is also a measurable carbon reduction for each trainee.
We are also engaging with our major suppliers to supply parts and equipment in re-useable returnable packaging. We already have these initiatives in place but our quest for continual improvement has identified further significant gains.
The introduction of remote access technology into our bin lifts allows us to diagnose defects and change certain parameters remotely rather than dispatching an engineer. Again, measurable carbon savings are captured and monitored in the quest for year-on-year improvements whilst utilising Terberg Connect.
TMUK currently have 15 field-based engineers and although fully electric vans are not yet a feasible option, hybrid versions will be evaluated in the near future.
The Terberg Matec UK manufacturing facility in Worksop, Nottinghamshire, produces a range of recycling vehicles covering all the main waste streams, collection regimes and operators’ needs.
Efficiency and reliability are both the hallmark of these products and also at the heart of their customers’ needs. So a sustainable approach to the entire operation is essential.
“We have customers coming and looking around the factory, seeing how the products they’ve ordered are made,” said Operations Manager Andrew Coulson.
“So it is essential, if we are to create the right impression, that we practice what we preach.”
With this in mind, the Worksop plant has, for several years, been working to reduce its carbon footprint and unit costs.
The use of gases for mild steel welding has been transformed in the last five years.
Gases were originally stored in cylinders and in a silo beside the building, a common set up in factories throughout the UK. But this is inefficient and significant amounts of gases are lost through leakage, while partempty cylinders were scattered around the factory.
This was replaced by a system of interchangeable gas banks from which the gas is piped into the building. The system is automated so that new banks are ordered and delivered before active ones run out. Two sets of banks are also used – one for mild steel and another for stainless steel.
The whole system has been run by a third party –Ayton Gas – since 2018. They ensure supply, delivery and maintenance as well as detailed reports and analysis of performance.
This system has drastically reduced the loss of gases through leakage. It has also reduced the carbon footprint of the operation by more than 100 tonnes of CO² in less than five years.
A new contract began in 2022 for the collection and recycling of waste from the factory.
The new system was put in place 10 months ago and
ensures better segregation of different waste streams in both the offices and factory. These are collected in different bins which are then emptied into larger containers for collection.
The installation of LED lighting in the entire factory in August 2018, heavily reducing our electricity usage each month since.
Plans have also been developed for solar panels to power the Worksop operation along with other options to reduce electrical consumption by improving efficiency. Similarly, plans to drastically reduce gas consumption have also been drawn up and are currently under consideration.
In addition, we are currently planning a system to use surplus waste heat from a neighbouring power generation plant to heat our workshops and offices. Further, the power plant makes use of carbon capture technology to yet further reduce their and our carbon footprint.
The extensive range of vehicles produced by Terberg Matec UK are all aimed at one cornerstone of sustainable life: recycling. Ultimately, we recycle for environmental reasons so the next, logical step is to ensure that our vehicles are as environmentally friendly as possible. And the first and biggest step towards that has been taken in the last year: the launch of the all-electric Kerbloader EV. This new vehicle is based on the tried and tested multi-stream recycling vehicle the Kerbloader, which has been the market-leader in this niche for several years as a diesel-powered truck.
It collects up to seven different waste streams and keeps them safely separate, just like the original Kerbloader, with overall payloads of around 3.2 tonnes.
It’s robust, easy to load, unload and discharge and it is safe. And the Kerbloader EV retains all the credentials of the original vehicle. These include:
• High grade stainless steel and composite GRP board making it corrosion-free.
• The automated plastic and can-press system and heavy-duty card-press significantly improves payload and efficiency.
• A noise-reducing system is fitted to the glass collection compartments.
• Glass is unloaded at the rear to reduce the risk of tyre-shredding.
• Discharge of materials is controlled from inside the cab which is both quicker and safer for the driver and crew.
• Stillages are removed with a fork-lift truck to avoid the ‘pushing-and-pulling injuries associated with manual handling.
• LED lighting illuminates the working area for safety and efficiency.
• LEDs in internal compartments help avoid crosscontamination.
• A colour HMI touchscreen in the cab provides the interface for the vehicle and diagnostics systems.
The result is a highly efficient and manoeuvrable onepass recycling vehicle.
The body has been engineered to create a carefully integrated interface with an electric chassis. Everything that was powered by the diesel engine now comes from zero-emissions electric battery power.
By producing no exhaust gases, the Kerbloader EV will not only help local authorities and other operators reduce their carbon footprint but also meet increasingly urgent air pollution targets.
The electric motor is also much quieter than the diesel engine. Reduced noise means collections can be made from sensitive locations at different times without causing disturbance. And better acceleration and torque can speed up collections to further increase operational efficiency.
The Kerbloader EV was extensively and successfully trialled in 2022. The first orders have since been received and the vehicles are currently being built.
The arrival of the Kerbloader EV means that as diesel engines are gradually phased out, the future of one-pass recycling is now assured. And it doesn’t end there.
The other recycling vehicles in Terberg Matec UK’s range include: the PBUV, the ORUS, the ABTL and the TopLoader. Between them, they cover all the main waste streams, collection regimes and operators’ needs in the UK. And plans to produce electric versions of them are already at an advanced stage.
Our goal has always been to provide the means to collect different waste streams as cleanly and efficiently as possible. Now that battery electric technology has come of age, we’re using it.
Everything we do is underpinned by our core values: Sustainability, Integrity, Flexibility, Quality, Innovation, Entrepreneurial Spirit and Customer Focus.
We recognise our people as our strongest asset.
Finding and nurturing new talent is at the heart of our commitment to providing local careers and to our future success.
Developing our people ensures that we continue to find innovative product solutions to support our customers and communities, whilst focusing on the environment and promoting sustainable, ethical business practices.
Our strategic people focus covers:
• Attracting the right people who reflect our local communities and have the right talent to support the business, both now and in the future.
• Retaining talent and increasing employee engagement.
• Creating and developing high performing individuals with a focus on succession planning.
• Supporting the health and well-being of our people.
At Dennis Eagle, we are passionate about creating long term, safe and rewarding careers for all employees. A naturally inclusive environment where our people can continuously develop and feel fulfilled.
Our age demographic is generally positive, with the company placing a high value on experience and creating the right conditions for retaining staff.
The waste management industry staffing, leadership and management lacks diversity across the board and is underrepresented of women and ethnically diverse people. We recognise that, while we have made some progress in recent years, Dennis Eagle still has a long way to go.
The challenge going forward, is for us to promote equality, tackle discrimination and foster positive relationships between diverse groups of people.
Our commitment is to take positive steps to be an inclusive organisation and to diversify our workforce.
In 2021, we started a programme of Equality, Diversity and Inclusion (EDI) training, starting with our management team and progressing to teams across the organisation. By the end of 2021, 150 employees had undergone this training and it has been rolled out for the rest of the workforce to be trained in 2022/2023.
We began to implement EDI audits in 2021 to help us understand the demographics and culture of our workforce and to identify factors that will specifically help us reach our goals. This soon highlighted the fundamental need to collect equal opportunities data.
It has also led to site accessibility improvements in 2021. We are currently preparing to join the Disability Confident scheme as a Committed employer.
We take on apprentices every year to support our future talent pipeline. Our partner colleges have been asked not to provide male-only shortlists and we have successfully welcomed female technical apprentices into the traditional male preserves of Aftermarket, Manufacturing and Engineering in the last five years as a result of this positive action.
We are also auditing the language we use in job adverts, profiles and job titles to ensure we are not using gender-biased phrases or words that may dissuade female candidates from applying for roles or promotions.
We have also implemented two flexible working policies: Flexitime and the Home Working Policy. These are, in part, intended to attract more female candidates.
We are starting to advertise roles with home working options and flexible hours from the outset of employment to attract candidates who need to work flexibly around personal commitments.
Engineering and manufacturing have traditionally been a male dominated occupations and this is reflected at Dennis Eagle where only 12% of our workforce are female. We have more men in senior positions and women are underrepresented in many departments. This has led to a gender pay gap. More detail and the actions we are taking to address this issue can be found on our website.
We recognise that this traditional industry has been slow to promote equality, tackle discrimination and to foster positive relationships between diverse groups of people. However, we are committing to embedding EDI into our policies, processes, procedures, practices and people development.
The real Living Wage is the only UK wage rate that is voluntarily paid by over 10,000 UK businesses who believe their staff deserve a wage which meets every day needs, such as the weekly shop, or a surprise trip to the dentist. We are an Investors in People accredited company. During our last assessment in 2022, the following key strengths were highlighted:
• The provision and quality of learning and development, particularly the management development and apprenticeship programmes.
• Consistent performance management, a strong “family” culture, a great sense of empowerment, collaboration, and encouragement to progress through increased skills and responsibilities.
• A notable focus on continuous improvement and innovation in many parts of the business.
As a result of these strengths, Dennis Eagle Limited achieved Established or Advanced level in over half of the 27 themes in the revised Investors in People Standard. We reached IiP Gold standard in ‘Understanding people’s potential’ and ‘Supporting learning and development’.
77% believe we ‘manage performance well’.
76% of our workforce when surveyed stated that they have opportunities to learn at work. Management and employee feedback shows that performance is being consistently managed and employees feel listened to regarding their aspirations and development requirements. Managers also report being more focused on addressing skills gaps and on succession planning for their departments.
Our workforce is vital to our success and we aim to look after them with fair rewards, opportunities and working conditions.
“ The pride in the Company and your products was evident in every area.”
IiP Assessor
As part of a conscious effort to make Dennis Eagle an attractive place to work, we offer employees a wide range of discounts and services in addition to the core benefits. We recognise that to achieve our business aims we must ensure employees feel appreciated and rewarded for their contribution to the success of the company. These include:
• Medical cash plan
• Employee Assistance Programme
• Occupational Sick Pay
• Long service awards
• Bike to work scheme
• Discounted gym memberships
• Salary sacrifice pension
• 25 days holiday + statutory holidays
• Contributory pension scheme
• DIS insurance
• Discounts schemes
• Online health portal
• Free financial advice
• Free mortgage broker service
• Free elder care advice line
We have collective agreements in place in our Warwick, Blackpool and Worksop manufacturing facilities. Regular meetings every six weeks are held and our elected representatives are consulted on all appropriate areas concerning their employees.
All employees must follow the Business Code of Conduct shared across the Royal Terberg Group.
Dennis Eagle recognises that flexible working can be beneficial to both our employees and the organisation, improving work life balance and allowing the organisation to retain skilled employees. We offer part time, job share, flexitime and hybrid home working models across our organisation.
We revised our Performance Development Review (PDR) process which supports our Company core values and implemented it in 2021.
All employees are given at least one review each year to discuss their progress, development and aspirations. These are conducted one-to-one with their line manager.
We also launched our new Management Development Programme (MDP). Many managers have spent years learning about their technical area of expertise and may also have professional qualifications in this area. However, when it comes to the people management, many have been expected to just learn on the job. Yet this can be some of the most challenging work they do.
To help our managers achieve their short and long-term objectives, the MDP provides a progressive learning environment allowing them to develop their skills and the skills of their teams. These can be through both formal and informal learning methods.
Generally, recruitment has proved increasingly difficult in recent years, in line with other businesses in this sector.
Finding and nurturing new talent is a large part of our commitment to supporting careers in our local communities and is also vital to our future success as a company. Developing our people ensures that we continue to find innovative product solutions while focusing on the environment and our core commitment to sustainable and ethical business practices.
Our apprenticeship programmes offer an excellent opportunity to earn while you learn and to begin a long term, stable and exciting career supported with the latest recognised high level academic qualifications.
Since the new apprentice programmes launched in May 2017, we have recruited 62 apprentices in skill gap areas such as HGV mechanics, welders, electrical design engineers and auto electricians.
In 2019 we provided accredited training via St John’s Ambulance and Mental Health England for volunteer Mental Health First Aiders across the organisation.
We know that wellbeing is good for business and that healthy people are happier, more engaged and more productive.
Providing practical mental health skills and awareness training is key to creating a safe healthy workplace where the mental health and physical health of employees are valued equally.
Our mental health first aiders have been equipped with an in-depth understanding of mental health and factors that can affect wellbeing, including skills to enable them to spot triggers and signs of mental health issues.
They have the knowledge to help someone recover by guiding them to further support, whether self-help resources, internal support such as our Employee Assistance Programme, or external sources such as GPs and other recognised organisations.
We recognise that it can be difficult to balance the pressures of work with the needs of people’s home life, be they emotional, physical or financial.
Our employee assistance programme provides 24/7 support and guidance including:
• Face-to-face counselling sessions without any medical or company referral
• 24/7 confidential helpline
• Bereavement support
• Financial wellbeing support
• Legal information
• Online support
We offer all employees a fully funded cash plan so employees can simply claim back the costs of dental check-ups, fillings, eye tests, physiotherapy, scans, prescriptions and much more. This benefit has supported many employees to reduce NHS waiting times and to save costs during the last few years when medical interventions have been particularly challenging.
92%
22 fully qualified mental health first aiders across our organisation
In addition, 92% of our managers and leaders have attended Mental Health First Aid Champion training. This helps them spot signs and symptoms of common mental health issues, provide non-judgemental support and reassurance and guide employees to seek the professional support they may need to recover.
The welfare of all staff is vitally important in so many ways. We already have several support systems in place and are actively seeking to improve these.
We carry IOSH training for selected managers and supervisors every year, refreshing formal qualifications every five years. During 2021 we carried out 33 IOSH courses.
Dennis Eagle continually strives to deliver effective health and safety arrangements by subscribing to Managing for Health and Safety (HSG65) guidance for the Plan, Do, Check, Act approach.
This helps achieve a balance between the systems and behavioural aspects of management. It also treats health and safety management as an integral part of good management generally, rather than as a standalone system.
Dennis Eagle’s management team are appropriately qualified to provide Health and Safety guidance for the work their different teams do. A company Health and Safety Manager is responsible for the day-to-day management aspects of on-site work across our UK network. They are supported by a Safety and Compliance Manager in the Aftermarket Division.
We provide frequent health surveillance checks on all applicable employees.
We also provide specific Occupational Health Support for employees with medical conditions who required adjustments or who are phasing themselves back to work after a period of absence.
With our new NotifyIM Incident Reporting App, every employee can now report incidents and accidents in seconds. They can also assign and track actions, monitor through to resolution, share critical health and safety data securely, spot high-risk issues and constantly improve safety.
Over the last few years, incident trends have been fairly level across the business. Our Injury Frequency Rates are well below the industry standards in place.
However, the company fully understands the need to continue to raise H&S to the next level.
We currently have 110 first aiders across the UK which is 12% of our workforce. Refresher training is provided to all of them annually.
Axis is a web-based intranet platform that enables teams to work together, sharing documents and knowledge and collaborating on ideas and issues.
Company health and safety information is now available on Axis. Information hubs conveniently located in all Aftermarket sites, improving access to this valuable information.
An important part of achieving effective health and safety outcomes is having a strategy and making clear plans. Consequently, the Health and Safety Strategy Considerations for 2022 and 2023 has been set in motion.
Health and safety strategy considerations for 2022 & 2023 are focused on five Cs:
We offer work experience and work-placement opportunities to university, college and local school students at our different sites. These cover a range of different working roles and often multiple roles within a single placement.
We also partner local schools to support the Engineering Education Scheme (EES). This six-month
programme enables teams from schools and colleges to work with our staff on scientific, engineering and technology projects.
We take an active role in charity events in the various communities we operate in. These range in size and scope, from litter picking and clearing up fly-tipping
We recognise that we have a role to play in all the different communities we operate in across the UK, by both behaving responsibly and by giving back to them.
with other local businesses in Warrington to raising money for the annual Santa Dash for Myton Hospice in Leamington Spa.
Here, we were the main sponsors of the event and our team of volunteers (pictured) – human and canine –braved the wintery conditions to help the hospice raise £45,000 and smash its target.
We intend to step-up our fundraising activities and now have a designated member of staff to coordinate this.
Our anti-slavery policy reflects our commitment to helping stamp out modern slavery. We will only do business with organisations who fully comply with this policy or those taking verifiable steps towards compliance.
We only use specified, reputable employment agencies to source labour and always verify the practices of any new agency before accepting workers from them.
The Company always pays above the voluntary living wage or the legally authorised rates for apprentices in the UK and we hold voluntary living wage accreditation.
During 2021 we have recruited 102 people into employment.
102 people supported into employment across the UK by us during 2021
The cartoon character, based on a Dennis Eagle RCV, was created by author and designer Ash Sharma to engage children in the principles of recycling and environmental sustainability.
Dennis is delivered to primary schools in our customers’ communities, in the form of an engaging story book loaded with puzzles called Dennis to the Rescue! Recycling at Home
Inside, pupils learn about Wheelie Good and Wheelie Bad waste with the help of more cartoon characters. Jointhe-dot puzzles, crosswords, anagrams and word searches help children learn what they can put into recycling bins and what these things can be made into or how they can be reused. And Dennis shows them how all these activities help our planet and how important that is.
Win-win for Dennis
“The book itself is a great concept because Dennis is such an engaging character,” explained Dennis Eagle Marketing Manager Lee Rowland.
“He enables children to form a strong link between this lovable character and real life where they will see real Dennis dustcarts going down their streets collecting their recycling.
“And the educational experience doesn’t end there. Children take the book home and get their parents to help them and that gets them engaged too – including some of those who aren’t recycling at the moment.
“Just ask yourself: would you throw recycling into the waste bin if you knew your children were going to pull you up about it?”
the value-added propositions Dennis Eagle offers customers, one stands out as a serial winner: Dennis the Dustcart.
The books are produced by Ash’s company Skips Educational and co-branded with Dennis Eagle and sometimes the local authority. The lesson content is amended each time to fit in with a specific local authority’s approach recycling. Dennis can even get a livery to match the council’s colours.
And the idea has been so successful, it has developed even further. The books now spearhead a package which involves Dennis Eagle, Ash, local authorities and schools working together to deliver assemblies and lesson plans for teachers.
The Dennis Eagle mobile classroom – built from an old RCV that had reached the end of its natural working life –often visits the schools too.
The messages are simple so children can understand them but that means parents can too. And there are even notes pointing parents to the council’s website for full details of recycling in their area.
Dennis teaches them about everything, from the difference between ‘use by’ and ‘best before’ dates on food to the benefits of giving old toys to charity shops ... and it can be tailored to the specific needs of each local authority.
Teaching children about recycling and environmental responsibility is high of primary schools’ agendas. And with increasingly limited resources, demand for the total package continues to grow.
During the pandemic lockdowns, when children were not in schools, our partner Skips Educational Ltd created more Dennis the Dustcart colouring in pages. We sent a new page every week to customers and colleagues and asked parents to send the finished artwork to us. In return, we sent them Dennis Eagle goodies.
“It was small gesture but the response was terrific!” added Lee.
They also operate the telematics system DE-Connect which provides accurate and timely insights into the performance and needs of individual vehicles as well as fleet operations.
All these functions are based on efficiency.
Our Aftermarket teams aim to ensure vehicles are always available for their daily schedules and always safe, roadworthy and operationally efficient. To this end, we aim to minimise travelling times and distances of vehicles coming to our premises and get replacement parts delivered via our mobile engineers as quickly as possible.
In order to achieve this we have the biggest network of service centres in the UK industry, each well stocked with spare parts and the biggest network of Field Service Engineers. And our Repair and Maintenance contracts mean we have engineers permanently working fully fitted workshops on customers’ locations.
Our approach to repairing vehicles is also unique in the UK industry in that we routinely send our engineers to customers’ premises and to vehicles broken-down on the road in order to carry out repairs, rather than requiring the vehicles to come to us. This both saves time and reduces the carbon footprint of these operations.
Our staff are the best trained in the industry. In addition to the training and induction processes provided by the Dennis Eagle HR Team, all our staff receive specific training for their roles.
A detailed document created in early 2022 – Marginal Gains – described precisely what those roles entailed and set the standards expected in roles as diverse as Service Controllers, Workshop Administrators, Parts Advisors, Contract Engineers, Field Service Engineers and all managers.
Our teams around the UK look after our customers’ vehicles, providing the full range of scheduled services and maintenance as well as emergency repairs.
This enabled us to identify any further training needed while raising the standards of our customer service.
Our staff resource is also outstanding in its scale. We have over 60 service managers in the Aftermarket team and 61 Field Service Engineers – far more than anyone else in the UK industry. A key aspect of their work is visiting customers’ sites and building strong relationships.
Our network has 10 Dennis Eagle Service Centres across the UK and six other facilities offering support through dealership partners and manufacturing centres. The scale of the network reduces both time and distance between customers, vehicles, engineers and parts and minimises ‘vehicle-off-road’ time.
They are equipped with workshops, stores, admin, meeting and training facilities. Some are purpose built to modern building standards, others converted to meet the required standards.
Low-energy lighting and energy-efficient heating systems, fans and other fittings are the norm. A programme of modernisation in recent years has ensured our they are not only operating to the highest environmental standards available but that our Service Centres also provide a comfortable working environment for both staff and visitors.
Our workshops are fitted with modern efficient equipment which is well maintained and regularly serviced. Safety is our priority in all workshops and across our sites as a whole and our safe working practices often go beyond what is required by legislation.
The routine services we offer in our Service Centres includes preparing vehicles for MoTs. Here, we have an outstanding record of 98.9% first time pass rate in 2022.
Our parts system is set up for maximum efficiency in terms of time and movement. We have a Central Stores facility in the North-West England which stocks all parts for our vehicles.
Our Service Centres also carry most stock and our Field Service Engineers carry the most routinely needed parts with them.
All parts can be quickly and easily ordered through our Electronic Parts Catalogue (EPC) which includes diagrams specific for individual vehicles for quick, easy and certain identification. Customers with accounts are trained to use this facility, as are Dennis Eagle engineers.
Orders can be despatched immediately and delivered across the UK by our round-the-clock delivery service. Customers and Dennis Eagle engineers can also pick up parts in person from Central Stores and Service Centres if that is more convenient.
We have the highest levels of first-time selection for parts in our industry. Figures are routinely published. The average in 2022 was 96%.
96% 98.9%
98.9% first time MoT pass rate in our Service Centres in 2022.
An average of 96% of first time selection for parts in 2022.
We offer full Repair and Maintenance contracts for customers who wish to outsource this function. At the end of 2022, we had 25 such contracts on-going.
The scope of these varies but may involve us either identifying and renting suitable premises or working from customers’ existing workshops. In both cases, new, highly efficient tools and equipment is fitted to meet our exacting standards.
Existing staff are usually TUPEd to become Dennis Eagle staff and thoroughly trained to our requirements.
RCV fleets are then totally managed by our engineers. They are checked before they leave the depot in the morning and when they return. All vehicles must be fit and safe to work before they can be used.
Routine servicing, maintenance and most repairs are done on site. Staff routinely work on the vehicles until they are fit and safe for operations.
Service and maintenance of electric vehicles requires a unique approach. As the first Original Equipment Manufacturer (OEM) in our industry to introduce eRCVs, it fell to us to devise and implement rigorous safety regulations and best practices.
We have shared these with competitors and customers alike who wish to service and maintain eRCVs themselves.
Our approach is thorough. Training in safety around electric vehicles was provided to ALL Dennis Eagle staff across the UK and visitors to our premises are given clear safety briefings and shown awareness videos.
Only engineers trained in repairing electric vehicles can work on them in any capacity. eRCVs are routinely fenced off to keep unqualified staff away from them. Safety equipment for HV electrical systems is prominently displayed in workshops and staff trained to use it.
We offer full service, maintenance and repair services to all our eRCV customers at our premises. Every Service Centre has engineers trained to the highest standard to maintain them.
For commercial efficiency, slack time in our workshops is often filled with repairs and maintenance of third-party vehicles and equipment.
Some Service Centres take on specialist projects. Among them are repowering vehicles. This involves taking a customer’s existing diesel asset and converting it to an all-electric eCollect. Depending on the age and condition of the original vehicle, this can be cost-effective route to reducing emissions for some operators.
We also offer full refurbishment of suitable RCVs. Our experienced and trained staff provide detailed assessments of vehicles and costings for customers.
And we also provide an Approved Used service, buying back suitable vehicles and refurbishing them for resale. Suitable parts from all these vehicles are also refurbished and sold to customers as Approved Used.
All come with full warranty.
At the heart of our extensive operations is customer satisfaction and a culture of constant improvement has been developed among Aftermarket staff.
We need customer feedback to ensure this is happening and to identify opportunities for improvement. To this end, customers are all approached in a timely fashion for formal feedback and their responses are logged. Staff have monthly targets to achieve this. Answers are qualitative but while the responses are overwhelmingly positive, work is underway to analyse their patterns to identify areas in which we can improve.
Our staff and communities
Staff engagement is also crucial to our operation. The core elements of this are outlined in the HR section of this report but in addition to this, managers hold weekly meetings with their teams at which any issues can be raised and feedback garnered.
Our engagement goes beyond our immediate employees and customers and onto our suppliers and to the communities in which we have a presence. Local suppliers are used wherever possible to further benefit the local community. These typically include consumables and non-Dennis Eagle equipment.
With safety paramount in both ours and our customers’ operations, compliance and enforcement of compliance are essential. We take a strict and unyielding approach to this in all our workshops and depots: our vehicles can not go into operation unless they are totally compliant.
The emphasis we put on this and our culture of continuous improvement led us to create a dedicated role of Aftermarket Compliance Manager, a position we recruited for in summer 2021. Their sole role is to improve safety across all of our Aftermarket sites.
We have a similar approach to other legal aspects of our operations. A good example of this is data protection as our telematics system DE-Connect generates vast quantities of customers’ data. Data security is fundamentally important in all our dealings.