
41 minute read
tEchNology
Automation in sanitaryware production: anthropomorphic robot-assisted casting Automazione nel sanitaryware: il colaggio asservito da robot antropomorfi
Sacmi Sanitaryware (Imola, Italy)
Advertisement
Quality, repeatability and operator efficiency are the three main advantages of total automation, a solution that Sacmi has continued to develop ever since it installed the first anthropomorphic robots in casting cells Over the course of its history, Sacmi has built and put into operation more than 6,000 moulds and 570 casting machines for the ceramic sanitaryware industry. A pioneer in the use of anthropomorphic robots in casting cells since the 1990s, the company has driven the development of the sector and now supplies more than 90% of its plants equipped with robots or ready for future implementation. One of these advanced systems is the AVI cell for high-pressure casting of complex WC bowls with stick-on rims. First launched onto the market five years ago, more than 30 of these machines have been installed in various countries around the world. As in the case of all latest-generation Sacmi machines, the distinctive feature of the AVI is the complete elimination of hydraulics due to the use of pneumatic mould clamping with special air cushions. Proportional mould clamping control during all phases of the casting cycle improves process sustainability and ensures perfect product quality. The AVI cell is highly innovative in terms of automation and offers the perfect combination of quality, process repeatability and workplace health and safety. In this solution every single stage is performed by a robot, from sticking through to deQualità, ripetibilità, qualificazione del lavoro. Tre vantaggi dell’automazione totale che vede Sacmi protagonista sin dalle prime installazioni di robot antropomorfi all’interno delle celle di colaggio. Nel corso della sua storia, Sacmi ha realizzato e messo in funzione oltre 6.000 stampi e 570 macchine di colaggio per ceramica sanitaria. In prima linea, già dagli anni Novanta, nell’utilizzo di robot antropomorfi in asservimento alle celle di colaggio, l’azienda ha accompagnato l’evoluzione del settore che oggi vede oltre il 90% delle forniture di nuovi impianti equipaggiati con robot o predisposti per future implementazioni. Tra queste l’AVI per il colaggio in alta pressione di vasi complessi a brida incollata. Lanciata sul mercato cinque anni fa, conta già oltre 30 installazioni in diversi Paesi del mondo. Segno distintivo dell’AVI, così come di tutte le macchine Sacmi di ultima generazione, è la completa eliminazione dell’idraulica, resa possibile grazie al serraggio pneumatico degli stampi realizzato tramite cuscini ad aria. Risultato, una maggiore sostenibilità del processo che si coniuga alla perfetta qualità del prodotto grazie al controllo proporzionale del serraggio degli stampi in tutte le fasi del ciclo di colaggio. Estremamente innovativa sotto il profilo dell’automazione, la cella AVI porta all’estremo i concetti di qualità, ripetibilità del processo, salubrità dell’ambiente di lavoro. In questa soluzione ogni singola fase, dall’incollaggio alla sformatura fino al carico del carro, viene gestita da robot.

moulding and car loading. While maintaining the same configuration, the AVI can manage the most varied types of pieces. In addition to WC bowls with stick-on rims, it can also produce the modern rimless WCs and even the highly complex one-piece and shell-engine models, a technology whereby the internal functional part of the WC (engine) and the external section (shell) and the rim are made in separate moulds. At the same time, Sacmi guarantees compatibility with existing moulds already used by customers on machines such as the single-mould AVM and the multi-mould AVE. Quality and functionality in the production of articles requiring up to 12 mould parts are assured by the perfectly repeatable robotic movements and the single gluing line on the external surface of the WC bowl, which guarantees an optimal aesthetic result. As is now standard practice, a pre-dryer is installed in the cell to drastically reduce the time required for the piece to harden sufficiently for loading onto the dryer cars, which are moved manually or - increasingly - by means of laser-guided vehicles (LGVs). Thanks to the use of automatic casting machines combined with anthropomorphic robots, a pre-dryer and automatic car loading, the entire process can be fully controlled and the production operations systematically reproduced, minimising the external variables capable of causing errors and generating rejects. Nella stessa configurazione, AVI può gestire le più svariate tipologie di articoli, oltre ai vasi a brida incollata, i moderni WC rimless sino ai più complessi one-piece e motore-carena (una tecnologia, quest’ultima, che prevede la realizzazione su stampi separati della parte interna funzionale, il motore, quindi della parte esterna estetica, la carena, e della brida), mentre è sempre garantita la compatibilità con stampi preesistenti, già utilizzati dai clienti nelle consolidate soluzioni monostampo AVM e multistampo AVE. Qualità e funzionalità sono sempre garantite nella realizzazione di articoli che richiedono fino a 12 parti stampo, grazie a movimentazioni robotizzate perfettamente ripetibili ed alla singola linea di incollaggio sulla superficie esterna del vaso, che ne garantisce la migliore forma estetica. In linea con una consolidata tendenza del mercato, all’interno della cella viene installato un pre-essiccatoio che riduce drasticamente il tempo necessario per garantire un consolidamento del pezzo sufficiente a consentirne il carico sui carri dell’essiccatoio, movimentati manualmente o, sempre più spesso, tramite veicoli laserguidati (LGV). Macchine di colaggio automatiche abbinate a robot antropomorfo, pre-essiccatoio e carico automatico del carro permettono di controllare tutto il processo e di riprodurre sistematicamente le operazioni per la realizzazione dei prodotti, riducendo il più possibile le variabili esterne che sono causa di errori e quindi di aumento degli scarti di processo.

ALV cell ~ Cella ALV

The level of automation achieved in these cells means that the robots can also be assigned many of the finishing operations (including sponging of the outside, siphon and under rim area), which also minimises the need for manual operations during these stages. The AVI is equipped with the rapid mould change-over system (it takes well under an hour to complete compared to the several hours required with traditional systems), making it the ideal solution for handling complex production mixes and small batches while fully eliminating the more heavy-duty and low-value operator tasks.
The Sacmi ALV solution for the production of washbasins, especially countertop washbasins, differs in terms of aesthetics and functionality but was developed in accordance with the same concepts of automation and total quality. Designed to handle up to 6 casting modules with a single robot (which can also be tasked with the automatic finishing operations and car loading), the ALV cell is uniquely versatile thanks to the possibility of rotating the mould from 0 to 90° during each stage of the cycle. Independent control of the work cycle for each single module means that different products can be made at the same time, even with different bodies. After casting, the robot handles the part of the mould holding the piece and performs demoulding onto a support ready for the finishing operations. For certain types of articles, this completely eliminates the need for supports and for operator intervention in manual finishing operations, thereby simplifying factory logistics and reducing the footprint. Advanced tracking functions, such as adding a barcode to the piece, make it possible to implement advanced MES (order scheduling) functions, monitoring and preventative maintenance with a small number of operators and optimised flow control. These operations can be controlled by customers completely independently, although a Sacmi technician is always available to provide remote assistance and help customers resolve any production stoppages. ✕ Il livello di automazione raggiunto in queste celle permette di assegnare al robot anche gran parte delle operazioni di rifinitura (comprese spugnature esterne, del sifone e sotto la brida), riducendo al minimo, anche in queste fasi, la necessità di interventi manuali. Equipaggiata con sistema di cambio rapido dello stampo – poche decine di minuti a fronte delle diverse ore necessarie con sistemi tradizionali –, AVI rappresenta la soluzione per la gestione di mix produttivi complessi e lotti ristretti, anche in questo caso, eliminando totalmente le operazioni faticose e a basso valore aggiunto
Differente per estetica e funzionamento, ma sviluppata nella stessa logica di automazione e qualità totale, è la soluzione Sacmi ALV per la produzione di lavabi ed in particolare lavabi d’arredo. Progettata per gestire sino a 6 moduli di colaggio tramite un singolo robot (a cui possono essere assegnate anche le operazioni di finitura automatica e carico su carro), la cella ALV offre una versatilità unica nel suo genere, grazie alla possibilità di ruotare lo stampo da 0 a 90° durante ogni singola fase del ciclo. La gestione indipendente del ciclo di lavoro di ogni singolo modulo consente inoltre di realizzare in parallelo prodotti diversi, anche utilizzando impasti differenti. Dopo le operazioni di colaggio, è il robot che si occupa di movimentare la parte di stampo che trattiene il pezzo per poi realizzare la sformatura su un supporto (dove avverranno le operazioni di finitura) o anche, per alcune tipologie di articoli, eliminando totalmente la necessità di supporti e la presenza dell’operatore per le operazioni di finitura manuale, con una semplificazione ulteriore della logistica di fabbrica e la riduzione del footprint. Avanzate funzioni di tracking – come l’inserimento del codice a barre nel pezzo – consentono di implementare, con pochi operatori e una gestione ottimizzata dei flussi, avanzate funzioni MES (schedulazione ordini), monitoraggio e manutenzione preventiva, che può essere gestita dalle aziende clienti in maniera totalmente autonoma, mentre un tecnico Sacmi è a disposizione per intervenire in teleassistenza e guidare l’operatore nella risoluzione di eventuali fermi produttivi. ✕
Migliorare il processo di controllo qualità sulla piastrella ceramica
System Ceramics (Fiorano Modenese, Italy)
Quality control is a delicate and vitally important step in the ceramic tile production process and can be performed at various points along the line using a variety of different technologies. For example Creavision, the vision and self-regulation system for digital printing, improves the quality and efficiency of tile printing prior to firing and ensures considerable savings in terms of resources and raw materials. Inspections are of course also needed after firing to verify not just the structural integrity of the product but also the print quality, the colour tones and the graphic designs in general. The Qualitron vision system from System Ceramics is specially designed for this stage of the production process and brings significant benefits.
❱ What is Qualitron?
Qualitron is a vision system for detecting the colour tone of ceramic surfaces. It captures the image using a series of latest-generation cameras coupled with sophisticated lighting systems and performs detailed analysis of the graphic design in order to identify any structural or colour defects. Qualitron’s software was developed entirely by the System Ceramics Software Engineering team and recently underwent a major upgrade that has significantly improved its performance. It is an advanced computer vision system that uses an automated procedure to recognise and self-learn ceramic surface defects and communicate them to the subsequent technologies along the line. This guarantees accurate, rapid and consistent product classification based on objective data and considerably reduces or even eliminates the quantity of non-conforming firstchoice product released on the market. Il delicato processo di controllo qualità all’interno dell’articolata linea di produzione della ceramica piana industriale rappresenta un passaggio cruciale. Può avvenire in più punti della linea e con differenti tecnologie a supporto. Ad esempio, Creavision, il sistema di visione e autoregolazione per la stampa digitale, interviene sulla qualità ed efficienza della stampa della piastrella prima del suo passaggio in forno, garantendo anche un considerevole risparmio di risorse e materie prime. Ovviamente, è importante disporre di step di controllo anche dopo la fase di cottura per verificare non solo l’integrità strutturale del prodotto, ma anche la qualità della stampa, delle tonalità cromatiche e la correttezza grafica in generale. Una delle tecnologie di System Ceramics in questo ambito è Qualitron un sistema di visione capace di garantire una serie di vantaggi.
❱ Cos’è Qualitron?
Qualitron è il sistema di visio-
❱ What defects does Qualitron detect?
The three cameras (2 greyscale and 1 colour) coupled with LED lighting and latest-generation infrared vision technologies ensure an extremely high level of precision in focusing on tile defects. Qualitron can be installed on any ceramic production line and is capable of detecting decoration defects (tone, bands or lines from digital printing, pitting or spots) and structural imperfections on any individne per il rilevamento del tono della superficie ceramica. Grazie ai sofisticati sistemi di illuminazione, cattura l’immagine con un’accurata rete di telecamere di ultima generazione e garantisce una verifica dettagliata del design, identificando eventuali difetti di struttura o tono della grafica. Il software di Qualitron, completamente sviluppato dal team di Software Engineering in System Ceramics, è stato recentemente potenziato con un upgrade significativo che ne migliora sensibilmente le prestazioni. Si tratta di un avanzato sistema informatico di Computer Vision che, attraverso una procedura automatizzata, permette di riconoscere, auto-apprendere e comunicare alle tecnologie successive sulla linea i difetti della superficie ceramica. Ciò garantisce una classificazione del prodotto accurata, rapida e coerente sulla base di dati oggettivi, riducendo sensibilmente (o addirittura azzerando) la quantità di prodotto non conforme in prima scelta da immettere sul mercato.

❱ Quali difetti rileva Qualitron?
Le 3 telecamere, 2 in scala di grigio e 1 a colori, supportate da impianti di illuminazione a LED e tecnologie di visione a infrarossi di ultima generazione assicurano estrema precisione nella focalizzazione delle anomalie della piastrella. Implementabile su qualsiasi linea di produzione ceramica, Qualitron può individuare difetti di decorazione (tono, bande o ri-
ual piece, such as imperfect glaze application. Once the irregularities have been detected, Qualitron completes the classification procedure extremely rapidly so as to maintain a smooth production process, even on lines operating at speeds of up to 200 pieces per minute.
❱ No risk of error with Creasync
As already mentioned, Qualitron’s software was recently updated to expand its potential and increase the range of activities it can perform. A driver of innovation that further improves the qualities of Qualitron, the updated software ensures that Creasync’s functions are fully integrated. Creasync allows Qualitron to check that the surfaces are defect free by comparing the graphic representation of the tile created by Qualitron itself directly with the source graphic file used for decoration of the tiles or slabs. Creasync is also an exclusive System Ceramics technology, patented and developed in-house by the software engineering teams. It is a highly innovative solution that eliminates all risk of classification errors. Thanks to Creasync, the comparison with the source file guarantees a high level of precision in detecting defects, correctly balancing the colour tone and checking every single graphic detail. The machine is able to process a very large quantity of information and can therefore guarantee a consistently high quality finished product. With Creasync it is no longer necessary to create graphic design samples using physical pieces, an operation that frequently involves the risk of setting imprecise values and of having to carry out numerous machine set-ups before achieving the desired result. The production process is more efficient for the following reasons: • the operator does not have to use physical pieces for analysis and set-up of the quality control process with Qualitron; • Creasync enables Qualitron to recognise the graphic designs and check that they are correct even if the tiles enter the machine in a 180° rotated position; • if the tiles are produced by cutting large slabs into sub-sizes, the system is able to independently determine which portion of the graphic design is displayed on the tile; • in the case of multi-face production, even in totally random mode, the machine is able to detect the correct position of the design; • use of the original graphic design makes the process rapid and precise.
❱ A Prime Ready technology
Qualitron is a Prime Ready technology that integrates seamlessly with Industry 4.0 software. Qualitron’s software can be used to archive, extract and consult production data in real time, thereby improving performance and finished product quality. The data extracted by Qualitron and made available to the user provide a high level of detail for each single product. For each product, the system communicates not only data relating to defects but also the process images used for the analysis. This information is crucial for subsequent production evaluations. Just think for example how important it is to have the complete image of a slab in the database subsequent to production. 5 ghe da stampa digitale, puntinature o macchie), ma anche imperfezione strutturali su ogni singolo pezzo, come ad esempio una errata applicazione dello smalto. Identificate le irregolarità, Qualitron esegue poi la classificazione con una rapidità tale da mantenere fluido il processo di produzione, anche su linee molto veloci da 200 pezzi al minuto.
❱ Nessun margine d’errore con Creasync
Come accennato, il software di Qualitron è stato perfezionato di recente grazie a un upgrade che ne ha ampliato le potenzialità e incrementato le attività che può svolgere. Un vettore di innovazione che rende indiscutibili i pregi di Qualitron. Il software aggiornato permette che le funzionalità di Creasync siano completamente integrate. Creasync consente a Qualitron di appuntare che la superficie non presenti difetti, mettendo in relazione l’acquisizione grafica della piastrella eseguita dal Qualitron direttamente con il file grafico sorgente utilizzato per la decorazione delle piastrelle o delle lastre. Anche Creasync è una tecnologia esclusiva di System Ceramics, brevettata e sviluppata internamente dai team di software engineering. Si tratta di un’evoluzione inedita, che non lascia spazio ad errori di classificazione. Grazie a Creasync, infatti, il confronto con il file sorgente garantisce un’elevata precisione nella rilevazione dei difetti, nella corretta equalizzazione del tono o nella verifica di ogni minimo dettaglio grafico. La quantità di informazioni che la macchina è in grado di processare è molto ampia e può quindi garantire una qualità del prodotto finito essere sempre molto elevata. Con Creasync non è più necessario realizzare campionature della grafica con pezzi fisici, attività che spesso comporta il rischio di impostare valori imprecisi e di eseguire numerosi setup della macchina prima di raggiungere il risultato desiderato. In sostanza, il processo di produzione è più efficiente in quanto: • l’operatore non deve utilizzare pezzi fisici per l’analisi e l’impostazione della fase di controllo qualità con Qualitron; • qualora i pezzi dovessero entrare in macchina in posizione ruotata di 180°, grazie a Creasync, Qualitron riesce comunque a riconoscere la grafica e a verificarne la correttezza; • in caso di produzione di piastrelle attraverso tagli in sottoformati da grandi lastre, il sistema è in grado di capire in totale autonomia quale porzione della grafica è riportata sulla piastrella; • in caso di produzione a molte facce, anche in modalità totalmente random, la macchina è in grado di rilevare la corretta posizione della grafica; • l’utilizzo della grafica nativa rende il processo rapido e preciso.
❱ Una tecnologia Prime Ready
Qualitron è una tecnologia Prime Ready, che si integra perfettamente con i software di industria 4.0. Il software di Qualitron permette di archiviare, estrarre e consultare anche in tempo reale i dati relativi alla produzione, per migliorarne da un lato le performance, dall’altro la qualità finale del prodotto. I dati estratti da Qualitron e resi disponibili forniscono un livello di dettaglio al singolo pezzo prodotto. Per ogni pezzo vengono comunicati non solo i dati rilevati sulle difettologie, ma anche le immagini di processo utilizzate per l’analisi. Queste informazioni sono cruciali per le valutazioni successive inerenti la produzione. Si pensi ad esempio all’importanza dell’avere a database l’immagine completa di una lastra successivamente alla produzione. 5

Focus on safety in ceramic product handling Focus “Sicurezza” nella movimentazione di ceramica
Stefano Lugli, ACIMAC (Italy), Ernesto Cappelletti, Quadra (Italy)
Automated guided vehicles (AGVs) are being used in an increasingly wide range of applications, from logistics warehouses to manufacturing companies and ports. The functions of these vehicles are evolving rapidly and now include, for example, robotic arms capable of automatically picking up and depositing transported products. One of the most important characteristics of automated guided vehicles is their ability to operate in spaces where people are present, so the safety aspects of these machines are paramount. Interactions between the vehicles and other machines or product storage locations also have significant implications in terms of safety. Manufacturers and users of AGVs therefore need technical standards that provide guidance on the design of the vehicles and their control systems, as well as on how to manage their interactions with the environment in which they are intended to operate and the machines they will interface with. Two international standards on this subject were recently published: • UNI EN ISO 3691-4:2020 “Industrial trucks – Safety requirements and verification – Part 4: Driverless industrial trucks and their systems”, which contains requirements for the design and manufacture of trucks and for the preparation of the operating and load transfer zones; • UNI EN 1175:2020 “Safety of industrial trucks. Electrical/ electronic requirements”, which deals with the electrical systems installed on industrial trucks, including AGVs.
UNI EN ISO 3691-4:2020, in particular, is a long-awaited standard for the ceramic sector. It deals with a machine that is designed to automatically handle heavy and bulky goods such as tile storage boxes and therefore raises inevitable issues in terms of operator safety. This is particularly critical because the flexibility and high level of automation typical of a ceramic production line means that the operating spaces cannot be enclosed by fixed perimeter barriers, resulting in the simultaneous presence or proximity of humans and machines. The standard EN ISO 3691-4:2020 provides guidance on the safety measures that must be adopted on trucks to enable them to operate safely (Chapter 4), including devices for detecting persons in their path. It provides detailed descriptions of the following rules, amongst others: I carrelli a guida automatica (o AGV) vengono impiegati con sempre maggiore frequenza in svariati campi, dai magazzini logistici alle aziende manifatturiere, fino ai porti. Le funzioni di questi veicoli si stanno evolvendo rapidamente, fino a comprendere, ad esempio, bracci robotizzati in grado di prelevare e depositare automaticamente i prodotti trasportati. Una caratteristica fondamentale dei carrelli a guida automatica è la capacità di muoversi in spazi in cui sono presenti persone, pertanto gli aspetti relativi alla sicurezza di queste macchine sono critici; anche l’interazione dei carrelli con altre macchine o con le locazioni di immagazzinamento dei prodotti ha risvolti di sicurezza tutt’altro che semplici. Per i fabbricanti e gli utilizzatori di AGV è quindi essenziale disporre di norme tecniche che diano indicazioni sulla progettazione dei carrelli e dei relativi sistemi di controllo, ma anche su come gestire la loro interazione con l’ambiente nel quale sono destinati a spostarsi e con le macchine con le quali si devono interfacciare. Su questo argomento sono state recentemente pubblicate due norme internazionali: • la UNI EN ISO 3691-4:2020
“Carrelli industriali – Requisiti di sicurezza e verifiche – Parte 4: Carrelli industriali senza guidatore a bordo e loro sistemi”, che contiene requisi-
ti sulla progettazione e fabbricazione dei carrelli e sulla preparazione delle zone operative e di trasferimento del carico; • la UNI EN 1175:2020 “Sicurezza dei carrelli industriali –
Requisiti elettrici/elettronici”, che si occupa degli impianti elettrici dei carrelli industriali, compresi gli AGV.
La UNI EN ISO 3691-4:2020, in particolare, è una norma da tempo attesa anche dal settore ceramico. Essa infatti regolamenta un’attrezzatura che, movimentando automaticamente merci pesanti e ingombranti quali i box di stoccaggio delle piastrelle, presenta inevitabili aspetti in termini di sicurezza per gli operatori; questo soprattutto perché la flessibilità e l’automazione spinta di una linea di produzione ceramica richiedono spazi non confinati da barriere perimetrali fisse, e quindi la contemporanea presenza o vicinanza di uomini e macchine. La norma UNI EN ISO 3691-4:2020 fornisce indicazioni sulle misure di sicurezza che devono essere presenti sui carrelli per permetterne un funzionamento sicuro (Capitolo 4), compresi i dispositivi per l’individuazione di persone sul percorso. Vengono analiticamente descritte, tra le altre, le regole da rispettare per: • la conformità dei Dispositivi di protezione elettrosensibili (ESPE), impiegati anche per il rilevamento delle persone;
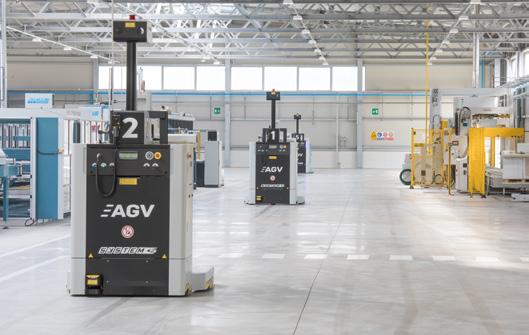
• conformity of Electro-Sensitive Protective Equipment (ESPE), which is also used for detecting persons; • avoiding automatic restart of the vehicle; • protecting lower limbs from contact with the vehicle; • conformity of the braking systems; • speed control; • load handling; • truck stability; • identification of the Performance Levels relating to safety functions. The section on information for use (Chapter 6) provides detailed information on warning signals and devices and safety signs (signs and written warnings), as well as extensive guidance on drafting the instruction handbook. A key part of the standard defines the requirements for the preparation of operating areas, including signs and floor markings, perimeter protection, sensitive equipment to protect truck access openings, and minimum spaces for the transit of persons. Information is also provided on load transfer zones and operations, which are particularly critical as these stages involve physical interaction between the truck and other machines or product storage locations.
With regard to the Italian ceramic industry, the sector’s trade associations and trade unions have in the past conducted numerous reviews of the safety of AGVs and LGVs (laser-guided vehicles). One example is the document published in 2014 by Acimac, Confindustria Ceramica, the Emilia Romagna Regional Health Service and the trade unions CGIL, Femca CISL and UILTEC. This document provides useful guidance on the design of AGVs - with a particular focus on the working environment, on vehicle-machine coordination and on parking - and can be used effectively in conjunction with the new international standards. It has the merit of clarifying several important aspects of the systems present in ceramic factories, for example: when the assembly is to be CE marked; how to manage modifications to the system, again in relation to CE marking; how to safely design the layouts of the box and loading unit (LU) parking areas and how to safely interface the handling system with the other machines in the production cycle (loading/unloading machines, palletisers, sorting lines); it also provides technical details on entry points to confined and controlled areas. 5 • evitare la ripartenza automatica del veicolo; • proteggere gli arti inferiori da contatti con il veicolo; • la conformità dei sistemi di frenatura; • il controllo della velocità; • la manipolazione del carico; • la stabilità del carrello; • l’individuazione dei Performances Level correlati alle funzioni di sicurezza. Molto dettagliata è anche la parte relativa alle informazioni per l’uso (Capitolo 6), quali i segnali e i dispositivi di allarme e la segnaletica (cartelli e avvertenze scritte). Il Capitolo 6 è anche particolarmente ricco di indicazioni su come strutturare il manuale d’uso della macchina. Una parte fondamentale della norma è poi quella che definisce i requisiti per la preparazione delle zone operative, tra cui cartelli e segnaletica orizzontale a terra, protezioni perimetrali, dispositivi sensibili per proteggere le aperture per l’accesso dei carrelli, spazi minimi per il passaggio delle persone. Sono poi riportate informazioni sulle zone e sulle operazioni di trasferimento del carico, particolarmente critiche essendo necessario in queste fasi un’interazione fisica tra il carrello e altre macchine o con postazioni di immagazzinamento dei prodotti. la sicurezza correlata agli AGV e agli LGV (veicoli a guida laser) era già stato oggetto in passato di numerosi approfondimenti da parte delle associazioni di categoria del settore, congiuntamente alle organizzazioni sindacali. Si ricorda ad esempio, il documento pubblicato nel 2014 da Acimac, Confindustria Ceramica, Servizio Sanitario Regionale Emilia Romagna e dai sindacati CGIL, Femca CISL, UILTEC. Tale documento fornisce utili indicazioni sulla progettazione degli AGV - con particolare focalizzazione sull’ambiente di lavoro, sul coordinamento tra veicolo e macchine e sui parcheggi - e può essere efficacemente utilizzato in congiunzione con le nuove norme internazionali. Il suo pregio è di chiarire alcuni aspetti importanti dei sistemi presenti negli stabilimenti ceramici, ad esempio: quando l’insieme è da marcarsi CE; come gestire le modifiche di impianto, sempre in funzione della marcatura CE; o ancora, come progettare in sicurezza i layout dei parcheggi di box e unità di carico (UDC) e come inter-facciare in sicurezza il sistema di movimentazione con le altre macchine del ciclo produttivo (macchine di carico/scarico, pallettizzatori, linee di scelta); esso fornisce inoltre approfondimenti tecnici relativi all’attraversamento di varchi per l’accesso a zone confinate e controllate. 5


Sacmi
Solutions that combine high productivity with flexibility in handling small batches and different sizes are now an essential market requirement, a need that Sacmi has met by offering major innovations in end-of-line management, from finishing through to sorting. These solutions have been developed in keeping with principles of digital plant management for a ready-to-use ceramic production process and maketo-order management of production flows. These sorting line innovations are focused on the goal of optimising flow management to cope with highly diversified production mixes. With Ekosort Dinamica, Sacmi ensures more agile and flexible control of manufacturing queues thanks to independent software-guided control of the picker/feed carriages moving inside the carousel. As the product size varies, the machine automatically adapts the number of carriages to ensure safe and efficient product pick-up (a single carriage for standard sizes up to 60x60 cm, up to 4 carriages for larger slabs). The machine is highly configurable according to customer requirements and operates at maximum speed with medium-small sizes (up to 130 pieces per minute with 20x20 cm and 30x30 cm tiles) while maintaining outstanding performance across all sizes. One of the most important opportunities offered by the solution is the possibility of fully integrating the squaring, finishing and sorting stages in order to gain advantages in terms of optimised logistics, shorter production lead times and a smaller footprint. A global partner from project through to product, Sacmi works with customers to identify the best solutions to their needs using digital simulations and other technology. Digital twin models allow for fast, precise assessment of the best line configuration according to the number and variety of product codes and the manufacturing practices adopted by individual customers. This, together with the interconnection with the Sacmi HERE supervisor, creates an authentic virtual twin of the plant that is not only useful in the design phase but can also operate in the field, providing valuable information on performance, monitoring and control of OEE (Overall Equipment Effectiveness) and total operating costs. Sacmi’s range of end-of-line solutions includes a series of integrated downstream systems for packaging, storage, quality control and warehouse intralogistics that use laser-guided vehicles and robotised pickers. This range meets the needs of modern ceramic factories facing a steady reduction in minimum production batch size, a significant increase in numbers of product codes and in general a need for dynamic order management both upstream and downstream of post-processing.

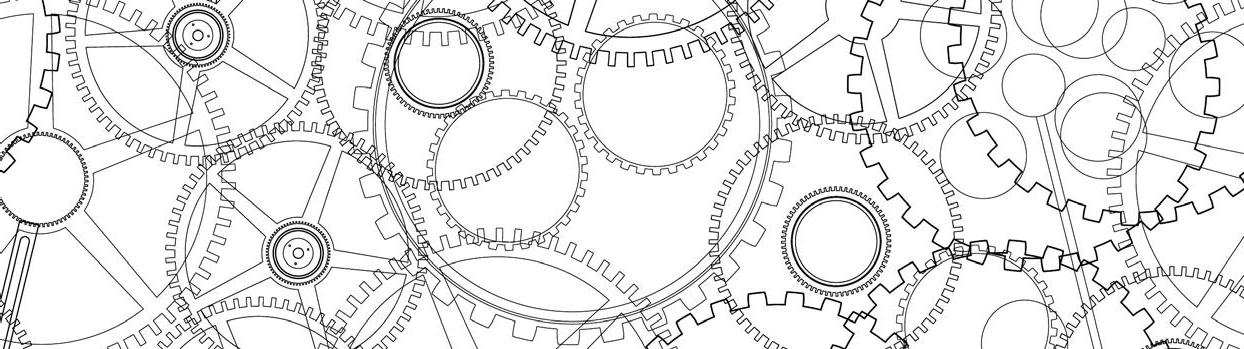
Disporre di soluzioni altamente produttive ma anche e soprattutto flessibili nella gestione di lotti ristretti e formati differenti è oggi un must del mercato, cui Sacmi risponde con importanti innovazioni nella gestione del fine linea, dalla finitura alla scelta. Tali soluzioni sono sviluppate in una logica di governo digitale dell’impianto, per una ceramica ready-to-use e una gestione make-to-order dei flussi produttivi. Ottimizzare la gestione dei flussi in presenza di mix produttivi diversificati è alla base delle innovazioni proposte sulle linee di scelta. Con Ekosort Dinamica, Sacmi consente una gestione più agile e flessibile delle code di produzione, grazie al governo indipendente, guidato da software, dei carrelli di presa e trasporto che si muovono all’interno della giostra. Al variare del formato, infatti, la macchina adatta automaticamente il numero di carrelli necessari per garantire una presa sicura e performante sul prodotto (un singolo carrello per i formati standard, fino al 60x60, sino a 4 per le lastre più grandi). Altamente configurabile in base alle esigenze del cliente, la macchina restituisce il massimo delle velocità sui formati medio-piccoli (sino a 130 pezzi al minuto sul 20x20 e 30x30 cm) e migliori prestazioni su tutti i formati. Tra le opportunità, la possibilità di realizzare l’integrazione totale delle fasi di squadratura, finitura e scelta, con vantaggi in termini di ottimizzazione logistica, lead time di produzione, riduzione del footprint. Partner globale dal progetto al prodotto, Sacmi affianca i clienti nell’individuazione della migliore soluzione anche sfruttando i vantaggi delle simulazioni digitali. Grazie ai modelli digital twin, è infatti possibile ottenere una valutazione puntuale, rapida e precisa, sulla migliore configurazione della linea, in base al numero ed alla varietà di codici prodotto ed alle prassi produttive consolidate in uso presso ogni singolo cliente. Il risultato, anche grazie all’interconnessione con il supervisore HERE Sacmi, è un vero e proprio gemello virtuale dell’impianto, utile non solo in fase progettuale, ma in grado di operare sul campo, restituendo preziose indicazioni sulle performance, monitoraggio e controllo dell’OEE (Overall Equipment Effecctiveness) e dei costi totali di esercizio. L’offerta Sacmi per il fine linea si completa, a valle, con sistemi integrati per il confezionamento, lo stoccaggio, il controllo qualità, l’intralogistica di magazzino tramite veicoli laserguidati e soluzioni di picking robotizzato. Una proposta, anche in questo caso, coerente con le esigenze di una fabbrica ceramica moderna, che vede una progressiva riduzione dei lotti minimi in produzione, un aumento importante dei codici prodotto e, più in generale, la necessità di una gestione dinamica degli ordini sia a monte sia a valle delle ri-lavorazioni.
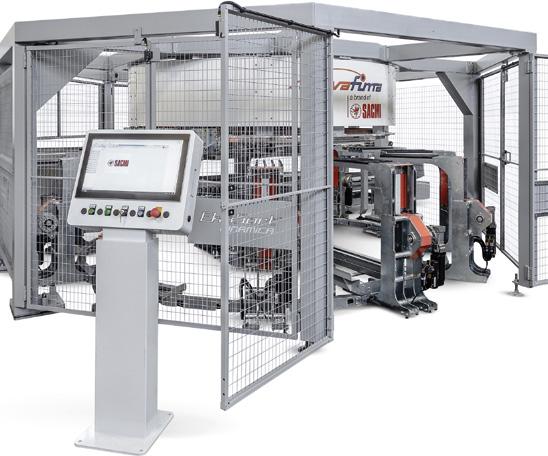

Robatech
With its automatic filling system for granular adhesives, Robatech is focusing in particular on workplace safety. The RobaFeed 3 automatic feeder with GlueFill tank gives operators greater protection from burns while increasing line efficiency and reducing costs. Protecting employees means determining the root causes of accidents and minimising the risk of injuries. Robatech is committed to creating a safe and healthy protective workplace for operators involved in the adhesive application process and consequently to saving costs. The RobaFeed 3 automatic filling system with GlueFill granulate container makes an important contribution by protecting workers during the filling of hot melt systems, maximising productivity and ensuring a problem-free production process. Although a preventive occupational health and safety strategy has a certain cost, at the same time it can save large sums of money in the event of accidents and production stoppages due to workers on sick leave. Robatech sees health and safety of adhesive application system operators as one of its most important corporate values because the way in which these devices are used has a big impact on employee safety. In particular, filling a hot melt adhesive system involves a certain degree of risk as the tank systems can reach temperatures of up to 200°C. When opening the tank for filling, the operator is at risk of burns due to splashes or contact with molten adhesive. These risks can be avoided by using an automatic filling system. In addition to the moral obligation to protect personnel from injury, there are also legal requirements to ensure the safety of machinery, as well as valid economic reasons to prevent accidents. A safe company is an efficient company because it avoids downtimes and saves costs. Hanspeter Huber, Industry Manager at Robatech, comments: “Safety must be considered across all usage phases of a system from the planning stage onwards. So working with Robatech’s adhesive application systems should meet all safety requirements in keeping with the principle that people always come first.” Robatech, headquartered in Muri/AG in Switzerland, is a world-leading provider of adhesive application systems for a variety of industrial sectors. Its service and technology portfolio for green adhesive applications includes hot melt adhesive and cold glue as well as polyurethane solutions. Robatech has a presence in more than 70 countries and since 1975 has delivered high-quality controls, application heads and dosing systems, all of which are unmatched in terms of their speed, precision and reliability.
Con il sistema di riempimento automatico per adesivi in granuli, Robatech si focalizza sulla sicurezza in azienda. Il caricatore automatico RobaFeed 3 con serbatoio GlueFill offre agli operatori una maggiore protezione da possibili ustioni, aumentando inoltre l’efficienza della linea e riducendo i costi. Proteggere gli operatori significa individuare le cause degli infortuni e ridurre al minimo il rischio di lesioni. Robatech si impegna a creare un ambiente di lavoro protetto e sicuro per gli operatori addetti al processo di applicazione di adesivo, conseguendo contemporaneamente un risparmio sui costi. Il sistema di riempimento automatico RobaFeed 3 con serbatoio GlueFill svolge una funzione fondamentale: garantisce maggiore protezione durante il caricamento di adesivi in granuli dei fusori che lavorano a temperature elevate e massimizza la produttività del sistema, assicurando così un processo di produzione senza inconvenienti. L’antinfortunistica preventiva, la salvaguardia della salute e la sicurezza nel luogo di lavoro comportano solitamente dei costi, ma consentono di evitare le ingenti spese che possono derivare da infortuni e interruzioni del ciclo produttivo dovute a congedi per malattia. La salvaguardia della sicurezza e della salute degli operatori che operano su sistemi di incollaggio è uno dei valori aziendali primari di Robatech, poiché il modo di gestire questi dispositivi influisce pesantemente sulla sicurezza dei dipendenti. In particolare, introdurre l’adesivo in un sistema di incollaggio a caldo comporta un certo grado di rischio, dato che i serbatoi raggiungono temperature che possono arrivare fino a 200°C. All’apertura del serbatoio per riempirlo, è possibile tra l’altro procurarsi ustioni dovute a schizzi di adesivo o contatti con adesivo già fuso. Un sistema di riempimento automatico permette di prevenire questi rischi. A prescindere dall’obbligo morale di salvaguardare gli operatori da possibili lesioni, la legge obbliga a garantire la sicurezza dei macchinari. Inoltre, vi sono valide ragioni di carattere economico in materia. Infatti, solo un’azienda sicura è un’azienda efficiente, perché in questo modo non si verificano interruzioni del ciclo produttivo attuando così un risparmio sui costi. Hanspeter Huber, Industry Manager di Robatech afferma: “La sicurezza deve essere presa in considerazione fin dall’inizio della fase di programmazione di un sistema e per tutte le fasi dell’utilizzo. Lavorare con i sistemi di applicazione adesivo di Robatech significa pertanto soddisfare tutti i requisiti in materia di sicurezza, perché al centro deve sempre esserci questo principio: le persone contano” Il gruppo Robatech, con sede principale in Svizzera a Muri / AG, è fornitore leader mondiale di sistemi di applicazione di adesivo per numerosi settori. L’offerta di prodotti e dell’assistenza per applicazioni “green” comprende soluzioni per adesivi a caldo, a freddo e poliuretanici. Robatech è presente in oltre 70 paesi e dal 1975 fornisce programmatori, pistole applicatrici e sistemi di dosaggio di qualità che non conoscono rivali per velocità, precisione e affidabilità.

gmm gRoup
Thanks to its recent acquisitions and the expertise built up over more than 40 years of experience and partnerships with the best international brands, the GMM Group, a Global Industrial Partner for key industrial sectors, is committed to continuously studying innovative services and strategic solutions capable of supporting its customers in the ongoing process of improving logistics and production efficiency. In particular, GMM Industrial Components, the Group’s parent company responsible for distributing high quality components and technical spare parts, constantly invests expertise and resources in the study of cutting-edge solutions for industry with a view to optimising logistics and supply costs through a combination of competitiveness and efficiency. Recent changes in the market suggest that availability and speed, combined with optimal management of supply chain processes, are of paramount importance in fulfilling customers’ production requirements. To do this, the experts at GMM Industrial Components conduct an analysis of the efficiency of the various production processes and the corresponding component usage in order to draw up a detailed efficiency report. This enables them to offer a complete supply package tailored to the customer’s actual usage, thereby creating a functional warehouse containing key products. The result of this study is the GMM Solution, a tailor-made logistics package that involves drawing up a supply contract with the end customer to determine stock levels calculated according to actual usage. Stock is always available at the customer’s premises and can also be used as consignment inventory to boost and speed up the supply process. The advantages of this solution have been confirmed by leading companies in the ceramic and other sectors that are currently exploiting its potential and include: a significant reduction in costs through supplier base rationalisation; the possibility of setting a fixed price level for the entire duration of the contract; a rapid procurement service; standardisation of stocks and elimination of duplicate codes; evaluation and cleaning of inventories; creation of a production plant database; and above all a reduction in warehouse stock, thereby freeing up resources and working capital that can be reinvested in higher value-added activities and strategic processes. All of this, combined with the diversified solutions offered synergically by the GMM Group’s subsidiaries, ensures that customers’ production lines are up and running 24/7, thereby supporting end-users in the continuous process of production efficiency and avoiding costly unscheduled plant downtime in keeping with the GMM Group’s longstanding mission.
Il Gruppo Gmm, Global Industrial Partner per i principali settori industriali, grazie alle recenti acquisizioni e il know-how costruito in oltre 40 anni di esperienza e partnership con i migliori brand a livello globale, si dedica costantemente allo studio di servizi innovativi e soluzioni strategiche che possano sostenere i propri clienti nel continuo processo di miglioramento dell’efficienza logistica e produttiva. In particolar modo, Gmm Industrial Components, capofila del Gruppo che si occupa della distribuzione di componenti e ricambi tecnici di alta qualità, investe costantemente competenza e risorse per lo studio di soluzioni all’avanguardia per le industrie, in un’ottica di ottimizzazione dei costi logistici e di fornitura, con l’obbiettivo di coniugare competitività ed efficienza. I recenti riassetti del mercato suggeriscono come disponibilità e celerità, uniti ad una gestione ottimale dei processi di approvvigionamento della supply chain, risultano essere elementi di primaria importanza per soddisfare le esigenze produttive dei clienti. Per rispondere a tali necessità, Gmm Industrial Components propone tramite i propri esperti una analisi dell’efficienza dei vari processi produttivi con i relativi consumi di componentistica in modo da fornire un report dettagliato di efficientamento, con l’obiettivo di offrire un pacchetto di fornitura integrale valutato sulla base dei consumi effettivi del cliente, dunque la possibilità di generare un magazzino funzionale contenente i prodotti chiave. Il risultato di questo studio è il Gmm Solution, una soluzione logistica tailor made che prevede la stesura di un contratto di fornitura con il cliente finale che predisponga uno stock calibrato sugli effettivi consumi dello stesso, sempre disponibile presso le proprie sedi e con eventuale possibilità di attivazione di un consignment stock per potenziare ed accelerare il processo di approvvigionamento. I vantaggi di tale soluzione - confermati da importanti aziende ceramiche e fuori settore che ad oggi ne sfruttano le potenzialità – sono: la sensibile diminuzione dei costi dovuta alla razionalizzazione del parco fornitori; la possibilità di fissare una linea di prezzo fissa per l’intera durata del contratto; un celere servizio di approvvigionamento; la standardizzazione degli stock e l’eliminazione di codici doppi; la valutazione e pulizia degli inventari; la creazione di un database relativo agli impianti di produzione; e, soprattutto, la riduzione dello stock di magazzino con conseguente smobilizzo di risorse e capitale circolante che può essere reinvestito in attività e processi strategici a più alto valore aggiunto. Tutto questo, unito alle soluzioni diversificate offerte sinergicamente dalle consociate del Gruppo Gmm, garantise che le linee di produzione dei clienti siano continuamente in movimento 24/7, supportando gli end-user nel continuo processo di efficientamento produttivo evitando onerosi fermo impianti non programmati, da sempre mission del Gruppo Gmm.

eLLek automazioni
Over the last 30 years, process automation has had a big impact on all aspects of the ceramic industry, from plant operation to gains in productivity and from raw materials preparation processes through to packaging and logistics. One of the primary goals of industrial automation is to optimise the production process in terms of accuracy, precision, productivity and output consistency. This results in a significant improvement in performance as well as a major step forward in the way manufacturing companies operate. Automating processes by adopting new technologies and instrumentation (intelligent sensors and actuators, vision and control systems, supervision systems with application software for data processing, etc.) is now a prerequisite for companies of all sizes, often with the support of state incentives (in Italy for example, the Industry 4.0 Plan and the new National Transition Plan 4.0 approved in the 2021 Budget Law). Ellek Automazioni has gained extensive experience in the field of supervision systems and places its expertise at the service of the ceramic industry. Ellek Automazioni’s supervision systems are based on a screen from where the user can access the various areas in order to monitor production stages and events, view the alarm situation (in the event of faults or malfunctions), check stocks (raw materials, semi-finished and finished products), manage maintenance work, and acquire consumption and production data which are subsequently archived and available for several months. They systems compile statistics on plant usage and provide extensive reporting on the volumes produced and the raw materials, semi-finished products and components used. As well as facilitating production management, they are also capable of monitoring the movement of raw materials, ingredients and semi-finished and finished products, and consequently also tracking and tracing of a product or batch that is not to be sold or is to be withdrawn from the market. Ellek Automazioni supervision systems can be integrated with higher-level MES (Manufacturing Execution Systems) and company ERP (Enterprise Resource Planning) systems. The process automation sector is evolving constantly and is seeing major developments aimed at reducing production costs and ensuring the conformity and safety of finished products. Personnel responsible for operating and maintaining the lines must be specially trained in the use of increasingly complex systems. New-generation PLCs with high levels of reliability are being developed and will be able to replace older PLCs for limited costs. Field instrumentation is also evolving, and instruments for directly measuring certain physical and chemical characteristics of raw materials (moisture content of powders, density and viscosity) are now in daily use. Automation will soon be used to control all infrastructure, from incoming raw materials to the outgoing finished products. Examples include the various installations that have been completed or are still in progress aimed at integrating the process from the cutting line through to product packaging.
Negli ultimi trent’anni l’automazione di processo ha avuto un forte impatto in tutto il settore ceramico, dalla conduzione degli impianti all’incremento di produttività, dai processi di preparazione materie prime, al confezionamento, alla logistica. Tra gli obiettivi primari dell’automazione industriale c’è quello di ottimizzare il processo produttivo con innumerevoli benefici sull’accuratezza, la precisione, la produttività e l’uniformità degli output. In sintesi, un deciso incremento di prestazioni, ma an-
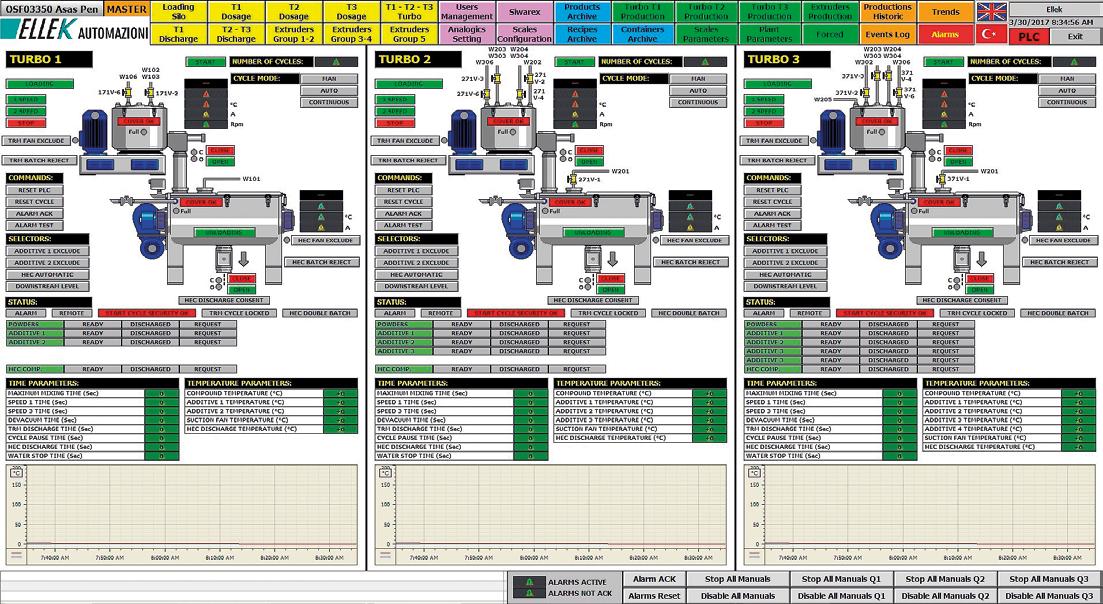
che un cambio di passo nel modo di lavorare delle aziende manifatturiere. Automatizzare i processi dotandosi di nuove tecnologie e strumentazioni (sensori e attuatori intelligenti, sistemi di visione e controllo, sistemi di supervisione con software applicativo per l’elaborazione dati, ecc …) è un passaggio ormai obbligato per le imprese di qualunque dimensione, spesso supportate anche da incentivi pubblici (vedi, in Italia, i Piano Industria 4.0 e il nuovo Piano Nazionale Transizione 4.0 approvato nella Legge di Bilancio 2021). Nell’ambito dei sistemi di supervisione, Ellek Automazioni ha sviluppato un profondo know-how che mette a disposizione dell’industria ceramica. I sistemi di supervisione di Ellek Automazioni si basano su una schermata da cui si accede alle varie aree per monitorare fasi ed eventi in produzione, visualizzare la situazione degli allarmi (in caso di guasti o malfunzionamenti), controllare le giacenze (materie prime, semilavorati, prodotti finiti), gestire gli interventi di manutenzione, acquisire i dati sui consumi e sulle produzioni effettuate archiviandoli e rendendoli quindi disponibili per diversi mesi. Elaborano statistiche sull’utilizzo degli impianti e forniscono un’ampia reportistica sui volumi prodotti e sulle materie prime, i semilavorati e i componenti utilizzati. Oltre ad agevolare la gestione della produzione, consentono anche il monitoraggio dei movimenti di materie prime, ingredienti, prodotti semilavorati e finiti, e quindi anche la tracciabilità e la rintracciabilità di un prodotto o lotto da non immettere o da ritirare dal mercato. I sistemi di supervisione Ellek Automazioni possono essere integrati con sistemi superiori MES (Manufacturing Execution System) e con l’ERP aziendale (Enterprise Resource Planning). Il settore dell’automazione di processo è in continua evoluzione. Sviluppi importanti andranno nella direzione di ridurre i costi di produzione e di assicurare conformità e sicurezza dei prodotti finiti. Il personale addetto alla conduzione e alla manutenzione delle linee dovrà essere preparato e addestrato per lavorare su impianti sempre più complessi. Si stanno sviluppando PLC di nuova generazione, con elevate prestazioni di affidabilità, ma anche in grado di sostituire PLC di generazioni precedenti a costi limitati. Anche la strumentazione in campo si sta evolvendo: sono ormai di utilizzo quotidiano strumenti per lettura diretta di alcune caratteristiche fisico-chimiche delle materie prime (umidità delle polveri, densità e viscosità). A breve, l’automazione governerà tutta l’infrastruttura, dall’ingresso delle materie prima all’uscita del prodotto finito. Ne sono un esempio le diverse realizzazioni, completate o ancora in corso, per l’integrazione del processo dalla linea di taglio al confezionamento del prodotto.

ISSN2039-8301
Search ‘Tile Edizioni’ and ‘MaterialiCasa’ economy news
interviews trends


27.9.2021 - 1.10.2021
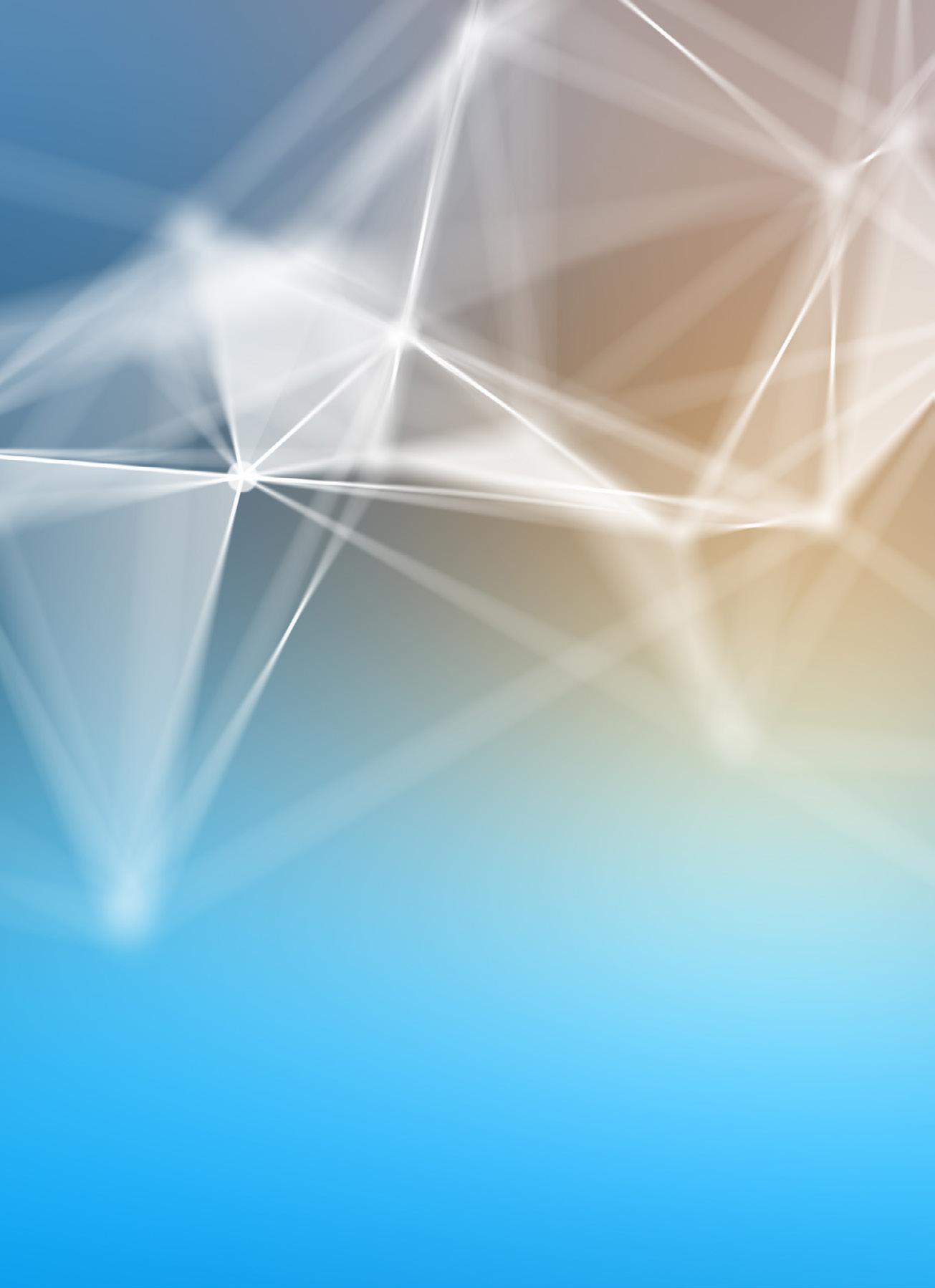
Rimini Exhibition Centre – Italy
tecnargilla.it
ORGANIZED BY IN COLLABORATION WITH WITH THE SUPPORT OF
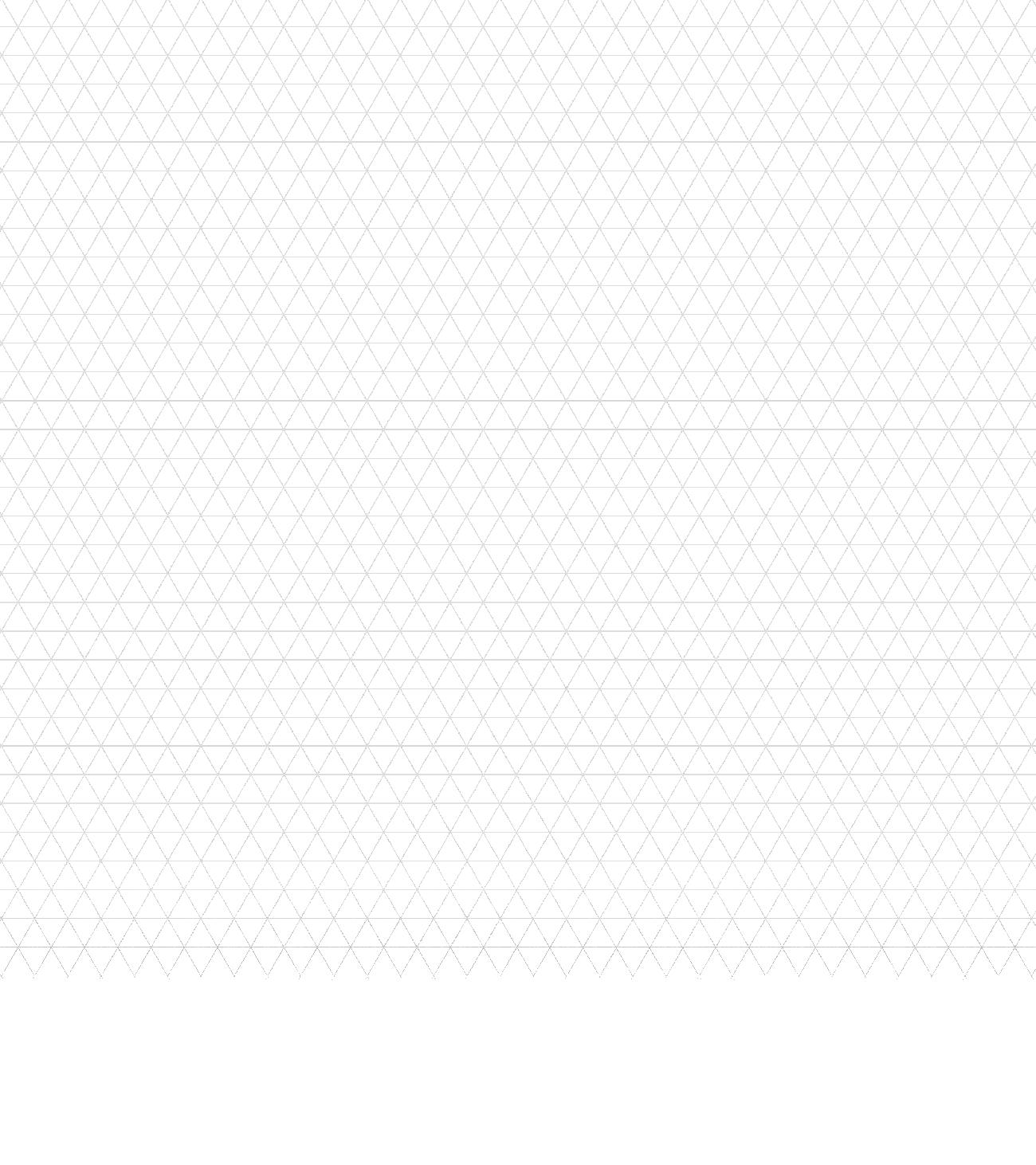
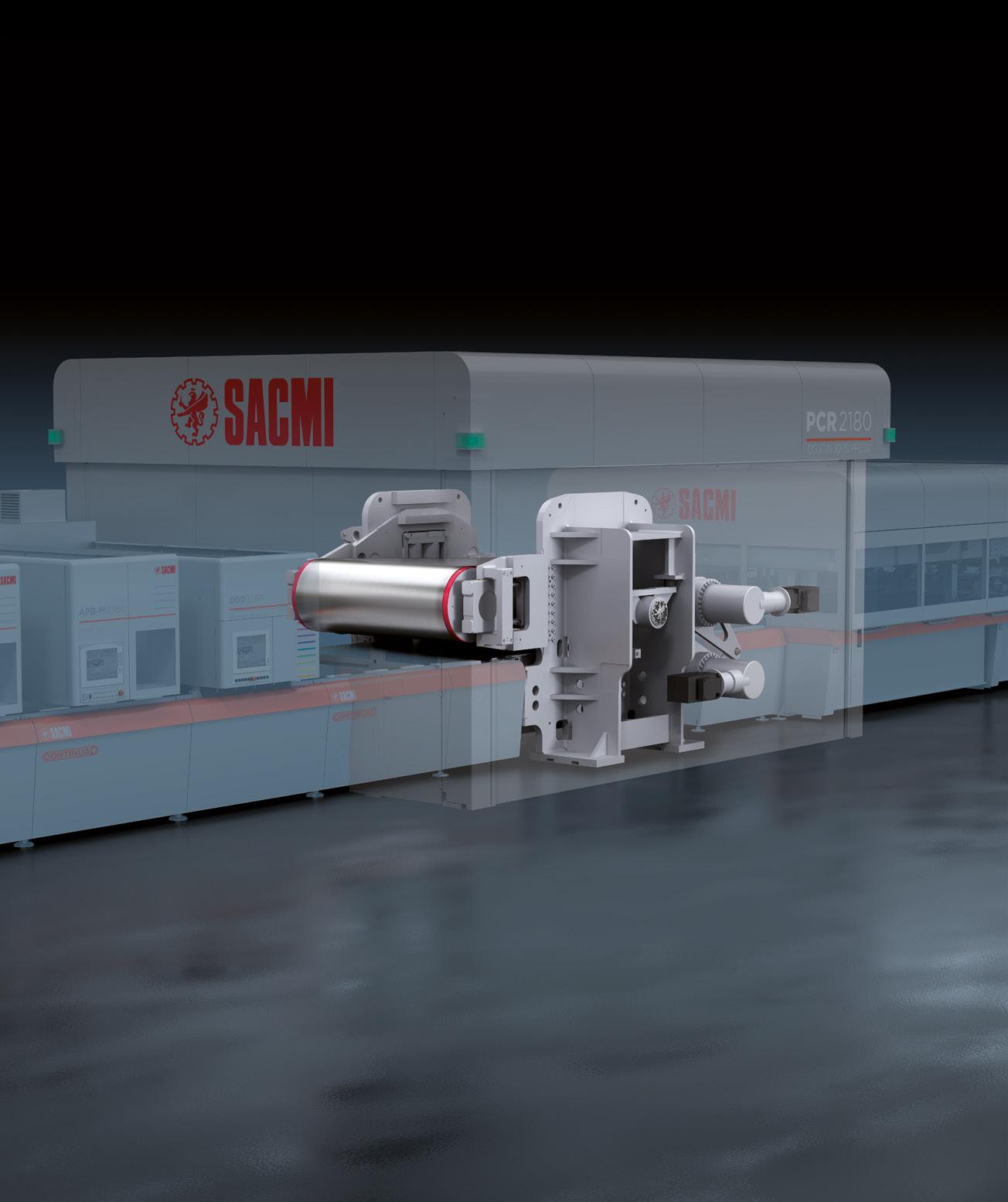
ENDLESS INNOVATION SINCE 1919