VALMET: The future of the bioindustry
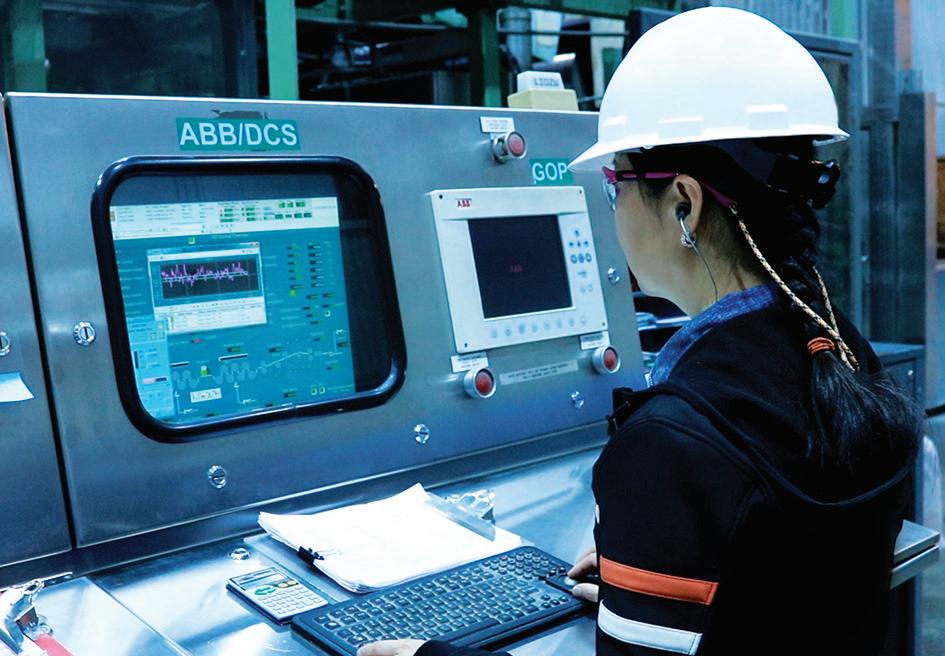

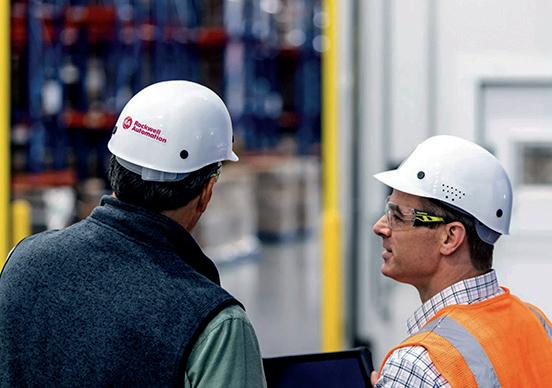
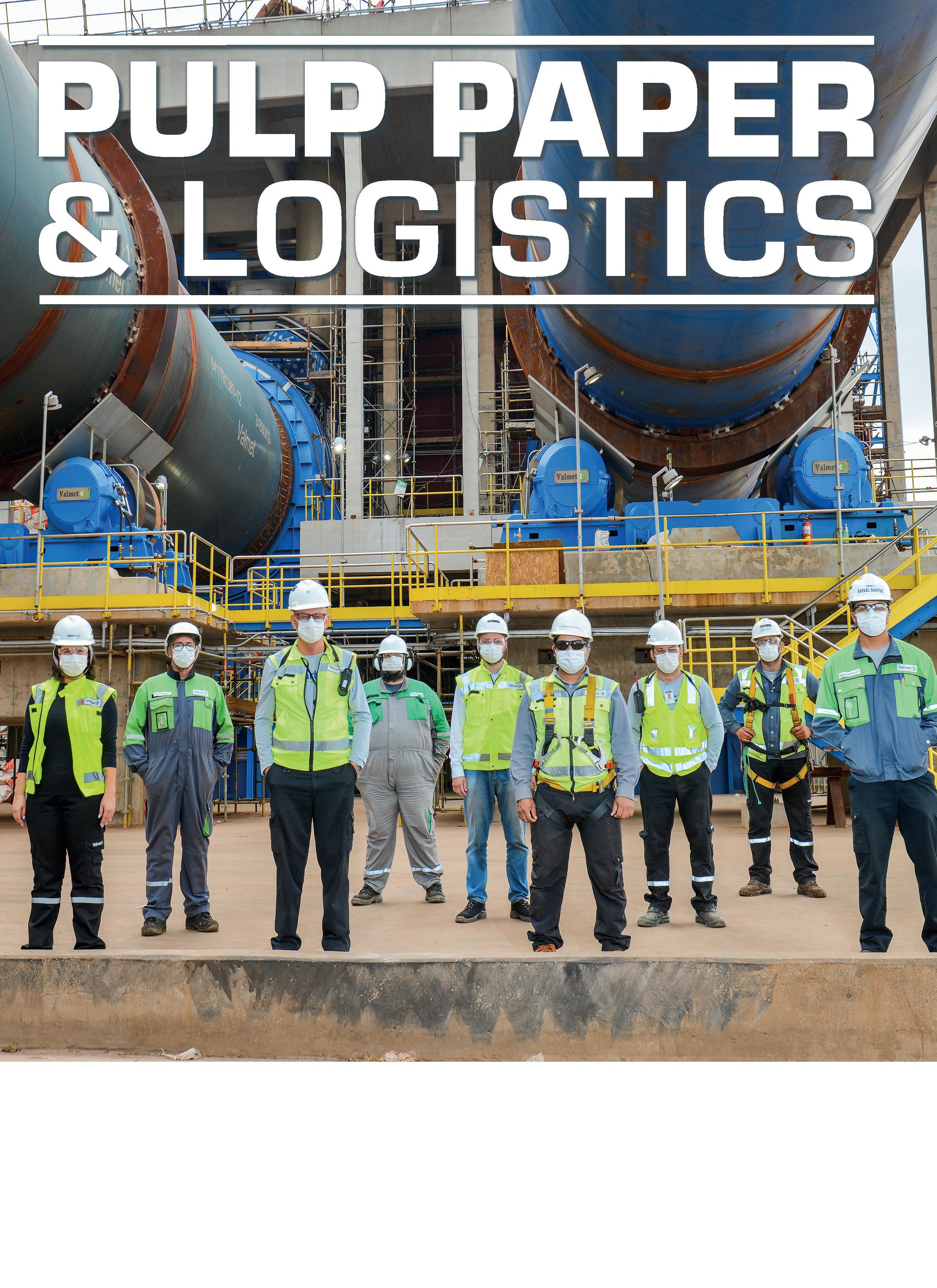
100 percent carbon neutral production for all our pulp by 2030. We believe that technology plays a key role in mitigating climate change and global warming in the transition to a carbon neutral
We have estimated that around 95 percent our value chain's environmental impact is caused when our customers use our technologies over their entire life cycles. In our climate program − Forward to a carbon neutral future − we have set ambitious targets to enable 100 percent carbon neutral production for all our pulp and paper customers and to improve the energy efficiency of our current offering by 20 percent by 2030.
Already today we offer an extensive range of solutions for reducing CO2 emissions and other environmental impacts.
Explore how on www.valmet.com/climateprogram
Welcome to the first issue of Pulp Paper & Logistics for 2023. With energy costs showing no sign of easing, pulp and paper mills are turning more to technology to help reduce power consumption and improve productivity.
While new technologies are helping to monitor energy consumption, it is data acquisition and analysis that has the greatest potential to highlight how items such as pumps or valves are not running at optimum levels or are mismatched to the production process.
Management and optimisation systems are being increasingly integrated and embedded deeper into a mill’s processes and equipment. Monitoring is of course not limited to just production processes but extends to areas such as environmental emissions – both direct and indirect –and managing the targets set by higher authorities.
As an industry, the long-term aim is to create a circular closed-loop system. This starts with the efficient use of water through to the recovery of paper and board at recycling centres for feeding back into pulp production. There is then the next area of importance which includes waste water recovery and re-use, and production waste recovery for conversion into alternate revenue streams or even bioproducts and sources of energy.
These are all areas that readers of Pulp Paper & Logistics have highlighted as the editorial topics they want covered. So for the March-April issue we will be inviting contributions about steam generation, mill management and software technology plus the optimisation of processes and production.
Submissions for the March issue should be with us ideally no later than 10 March. Vince Maynard, publisher
Vol. 13 Issue No. 76, January/February 2023
ISSN 2045-8622 (PRINT)
PUBLISHER & EDITORIAL DIRECTOR
Vince Maynard
Tralee, Hillcrest Road, Edenbridge, Kent, TN8 6JS, UK
Tel: +44 (0) 1732 505724
Mobile: +44 (0) 7747 002286
Email: pulppaperlogistics@virginmedia.com
CONSULTANT EDITOR
David Young
Tel: +44 (0) 1737 551687
Mobile: +44 (0) 7785 796826
EDITOR
John Nutting
Email: johnnutting47@gmail.com
REGIONAL REPRESENTATIVE
Einar Johansson
Tel: +46 8 540 255 15
Mobile: 0046 70 234 80 85
Email: einar.lennart@gmail.com
PRODUCTION
Anthony Wiffen
ASTAC Business Publishing Ltd
Tel: +44 (0) 1460 261011
Mobile: +44 (0) 7557 280 769
Email: anton_print_1@mac.com
PRINTER
Brown Knight and Truscott
Tunbridge Wells, Kent, TN2 3BW
United Kingdom
Tel: +44 (0)1892 511678
Apaper mill in France is pioneering the use of hydrogen-fuelled power as part of a collaborative research project to exploit the benefits of renewable energy.
The Smurfit Kappa paper mill at Saillat is the first in the world to introduce an integrated hydrogen gas turbine demonstrator.
The first stage of the project is being masterminded by the Hyflexpower consortium, a collaboration across a number of industries, academic bodies and research institutes, including Engie Solutions, Siemens Energy, Centrax, Arttic, the German Aerospace Center (DLR), and four European universities.
The hydrogen pilot was successfully trialled in November 2022 with a mix of 30 per cent hydrogen and 70 per cent natural gas. The aim of the Hyflexpower project is to demonstrate that renewable energy can be converted to hydrogen and serve as a flexible means of storing energy which can then be used to power an industrial turbine.
The project officially marks the implementation of the world’s first industrial-scale P2X-to-power demonstrator with an advanced hydrogen-fuelled turbine. In 2023, trials will continue to increase the proportion of hydrogen up to 100 per cent.
Sustainability chief at Smurfit Kappa Garrett Quinn commented: “We are focused on reducing our emissions with the best available technology today, but equally this announcement demonstrates how we are focused on looking
beyond 2030 and trialling new technology, such as hydrogen, today. This project will allow us and our partners to understand the technical feasibility of using hydrogen with a lot of our existing energy infrastructure. This is an exciting project for us, and industry in general, as we progress on our journey towards net zero.”
The project was inspired by the European Commission’s ‘Hydrogen Strategy for a ClimateNeutral Europe’ report, which outlines the essential role that hydrogen will play within the European Green Deal carbon neutrality and energy transition initiative.
Commenting on the completion of the initial testing, Gaël Carayon, director of subsidiaries at Engie Solutions, said: “Ambitious
projects like this one require taking partnerships to the next level and being united in a joint mission to make decarbonisation a reality. Hydrogen will play a crucial role in the interaction between renewables and electricity storage and generation. Engie Solutions is proud to participate in this unique project.”
Bertrand Muguet, mill manager at Smurfit Kappa Saillat, added:
“We are delighted that the initial testing phase of the project was completed successfully at our Saillat paper mill. Smurfit Kappa is proud to be collaborating with our partners on this project which tests new technologies that we believe will form part of our net zero delivery.”
Global director of Hyflexpower at Siemens Energy is Dr Ertan Yilmaz,
who said: “With the Hyflexpower project we are showcasing that carbon-neutral and reliable power supply is possible – even for energy-intensive industries. Hydrogen-ready turbines will play a decisive role in climate-neutral energy, so it is very exciting to be looking forward to the next phase of testing.”
The project, first announced in 2020, is funded by the EC with two-thirds of the €15.2 million investment coming from the EU’s Horizon 2020 Framework Programme for Research and Innovation. The next trials for the project will be carried out in the spring of 2023.
More information from www. hyflexpower.eu
●Smurfit Kappa has won eight WorldStar 2023 Awards.
Mondi has expanded its range of medium, high and very high barrier paper-based packaging to offer more sustainable options to its customers.
The packaging manufacturer now offers a full range of FunctionalBarrier Papers. By applying different barrier technologies, such as extrusion coatings, aqueous coatings and other very high barriers, this range of paper-based packaging can be used for a variety of applications.
The medium barrier version, designed for industrial, eCommerce and personal care packaging, offers high sealability and medium water vapour protection, while the high barrier functional paper offers a medium
oxygen and water vapour barrier, as well as a high grease and mineral oil barrier for frozen foods and chocolates.
The very-high-barrier version, for consumer food products such as coffee, cereals and confectionery, provides excellent product
protection from water vapour and oxygen and ensures a long shelf life. All are produced in-house as renewable alternatives to plastic laminates and multi-material aluminium-based packaging.
Thomas Ott, chief executive of flexible packaging at Mondi,
Sylvamo, the US-based global producer of uncoated paper, has completed its acquisition of the Nymölla paper mill in Sweden from Stora Enso.
The deal, valued at about €150 million, adds two pulp lines and two paper machines with yearly capacity for about 485,000 tonnes of woodfree uncoated office papers to Sylvamo’s portfolio. The mill generates 85 per cent of its energy needs from carbon-neutral, renewable biomass residuals.
Based in Memphis, Tennessee, Sylvamo has annual sales of
about US$3.5 billion. It has two mills in North America, in New York State and South Carolina, three mills in South America, in Mato Grosso do Sul, Mogi Guaço and São Paulo, and one each in France, Poland and Sweden.
Stora Enso said last year that the Nymölla deal was part of its plan to divest four of its five paper mills to concentrate on renewable products in packaging, building and biomaterials. That plan has changed with Stora Enso now saying that it will not divest its
Anjala mill. But it has agreed to sell its Hylte paper mill to Sweden Timber, a sawmill and planing company, for about €18m.
The transaction does not affect Stora Enso’s Packaging Solutions division’s formed fibre and biocomposite operations located at the Hylte site.
The Anjala paper mill and the retained Langerbrugge paper mill in Belgium were integrated into Packaging Materials division at the beginning of 2023. At the Langerbrugge site, a feasibility study for a potential conversion
said: “We live by our approach of using paper where possible, plastic when useful and our range of FunctionalBarrier Paper is a perfect example of this. This is in line with our Mondi Action Plan 2030 commitment to make all our packaging solutions reusable, recyclable and compostable.”
Mondi won eight awards in five categories at this year’s WorldStar Global Packaging Awards.
The company has also started production of kraft paper bags at its new €16 million greenfield plant in Morocco, which can produce 100 million items a year. Mondi’s total capacity in West Africa is now more than 500 million bags a year. The Morocco plant is Mondi’s fourth site in West Africa (in addition to two plants in Morocco and one in Ivory Coast).
In a multi-million investment, Stora Enso is strengthening its focus on unbleached kraft pulp (UKP) and fluff pulp to support growing demand for non-bleached packaging and hygiene products. By increasing the share of UKP in its portfolio, Stora Enso is continuing a strategy to develop more specialised Nordic pulp grades while optimising its share in standard market pulp.
At Stora Enso’s Enocell mill in Finland, €38 million is being invested to enable the mill –currently with yearly capacity for 630,000 tonnes of softwood and hardwood pulp – to flexibly produce UKP and Nordic bleached softwood kraft (NBSK) pulp.
By using less bleaching chemicals, the carbon footprint per tonne of UKP will be more than 20 per cent lower than the equivalent amount of bleached pulp produced at the Enocell site. The investment is expected to be completed during the final quarter of 2024.
The second investment, of €42 million, is being made at Stora
Enso’s Skutskär mill in Sweden to reinforce the company’s position in Europe as the leading fluff pulp producer. Capacity for fluff, softwood and hardwood pulps is currently 545,000 tonnes a year. With the upgrades made at the mill, Stora Enso will be able to meet rising demand for specific roll sizes, improve safety, and grow fluff pulp production. The investment is expected to be completed during the second quarter of 2024.
“Through optimising our pulp portfolio, we advance the more
specialised pulp offering, while also improving production and sustainability performance. This will allow us to meet the rapidly growing demand for using unbleached and less bleached pulp in packaging and hygiene applications,” says Johanna Hagelberg, executive vice president of the biomaterials division at Stora Enso.
●Stora Enso’s sales for 2022 were 14.9 per cent up year on year at €11.68 billion, while net profit was up 21.2 per cent at €1.54bn. In the final quarter of 2022, the sales
Stora Enso was due in January to complete the acquisition of Netherlands-based De Jong Packaging Group following its approval by the EU Commission in December 2022.
Valued at €1.02 billion, the acquisition is expected to increase Stora Enso’s market share in renewable packaging in
Europe, as De Jong is one of the largest producers of corrugated packaging in the Benelux countries.
With the acquisition, Stora Enso’s Packaging Solutions division has increased its corrugated packaging capacity two-and-a-half times to more than 2 billion sqm a year.
When the acquisition was announced last year, Stora Enso’s chief executive Annica Bresky said: “In line with our strategy, we are investing in growing our market share in renewable and circular packaging solutions. De Jong Packaging has a solid presence in the corrugated packaging sector
growth was slower, increasing by 5.3 per cent year on year at €2.86bn. Net profit in the quarter was down 5.3 per cent at €584m.
Chief executive Annica Bresky commented: “After what has been an exceptional year in many ways, I am proud that we have delivered against our financial guidance for 2022 despite a disruptive, highly inflationary, and challenging environment.
“We have completed significant strategic projects, while making good progress to invest in strategic assets and innovation for growth in renewable packaging, sustainable building solutions and biomaterials innovations.
“Our performance in 2022 demonstrates the strength of our leading market positions and our ability to be proactive and agile in making necessary adjustments for a new reality both short and long term.”
Compared to 2022, margins are expected to be squeezed by increasing costs, particularly in relation to energy, wood, chemicals and logistics, said the company in its outlook for 2023.
and an impressive customer base. Acquiring their operations supports our future strategic direction to advance renewable packaging solutions within Europe.”
De Jong Packaging Group has 17 sites in the Netherlands, Belgium, Germany and the UK, and employs about 1,300 people.
The pulp and paper industries play a key role in the transition and transformation towards a fossil-fuel free circular bioeconomy. By developing circular operations to eliminate unused side streams, and creating new value-added bio-based products, it can be the global leader in zero emissions and zero waste industrial processes.
CircleToZero brings together the continuous development and improvement of existing ANDRITZ technology solutions to achieve this leadership position with clear environmental and financial benefits.
Our shared journey towards zero emissions and zero waste has already started.
Ivana Amorim Dias has won the Blue Sky Young Researchers and Innovation Award 2022-2023, which is promoted in Brazil by the International Council for Forest and Paper Associations (ICFPA) and locally coordinated by Indústria Brasileira de Árvores (Ibá).
A graduate in forestry engineering from the Federal University of Recôncavo da Bahia, and a master and doctoral student from the Federal University of Paraná, the researcher won the award for a project under the guidance of Professor Pedro Henrique Gonzalez de Cademartori, in partnership with Suzano. The objective was to develop sustainable processes to make
products with high added value, such as transforming wood residues by burning, and generating bio-oil with high
application potential.
Commenting on her award, Dias said: “Participating in the award was significant for my
career. In addition to bringing the research to greater visibility, it was important for me, as a woman, and I believe that for all other women that we have competence and deserve this space.”
First awarded in 2016, the Blue Sky Young Researchers and Innovation Award invites proposals from researchers aged up to 30 with innovative ideas that expand the contribution of the forest-based sector in the low-carbon economy, targeting industrial operations and forestry, as well as the supply chain. The most recent theme, ‘Building a low carbon economy with forests and forest products positive for the climate’, attracted 14 candidates from around the world.
Swedish premium paperboard maker Holmen Iggesund and Yangi, a pioneer in dry forming technology, have agreed to explore opportunities offered by bio-based and renewable packaging for the cosmetics and beauty industry.
The collaboration will focus on replacing rigid plastics with alternative renewable materials for packaging such as refills, inserts, testers, and other types of applications within the segment. Holmen Iggesund will supply fibrebased material and guarantee its high quality.
Hein van den Reek, director of Future Packaging at Holmen Iggesund, said: “There’s a real sense of urgency to make packaging ever more sustainable and purposeful, and at Holmen
Iggesund we see the benefits of working with others to solve challenges faster.
“The collaboration is aimed at helping beauty and cosmetics brands deliver what their customers are demanding –sustainable packaging. Holmen Iggesund is always interested in the latest ideas and potential new opportunities for purposeful packaging solutions, such as our Conic concept, launched in 2021.”
Yangi will make available its dry-forming technology and commit additional R&D resources to further develop current and future ideas for packaging producers and brands.
“Delivering sustainable solutions that eliminate fossil fuels and reduce the carbon footprint of a brand’s packaging
can make or break brand loyalty,” said Anna Altner, founder of Yangi. “Our dry forming technology offers a unique possibility to move into more resource- and cost-efficient renewable and recyclable packaging. The collaboration enables a stronger offer connecting the packaging value chain from raw material to
final packaging.”
The collaboration was initiated and will be facilitated by FutureLab & Partners, a ‘tech accelerator’ company that enables the shift from non-renewable materials to renewables through collaborative development projects with cosmetics and beauty brands.
Smurfit Kappa is planning to reduce the environmental impact of its Sanguesa paper mill in Spain with the use of solar energy generated by an array adjacent to the facility.
With an investment of €6 million, 12,000 solar panels will be installed with the capability to generate more than 10 GWh of power year that will reduce the current external electricity consumption and dependency by 7 per cent. Carbon dioxide equivalent emissions at the mill will be cut by more than 3,200 tons a year, and provide significant cost savings.
The solar energy project is the latest for Smurfit Kappa which has launched similar initiatives in other plants in Spain, Colombia and Mexico to generate
sustainable energy.
The mill at Sanguesa is one of Smurfit Kappa’s key facilities, producing light MG kraft paper, which is widely used across industrial and consumer markets in products such as grocery bags
and wrapping paper. Commenting on the project, Reinhard Reiter, chief executive of Smurfit Kappa’s Virgin Fibre Cluster, said: “This investment to harness another renewable source of energy is testament
Metsä Group has been awarded as Finland’s most start-upfriendly company for a second year. The award, presented by the entrepreneurship community Tribe Tampere, is granted in recognition of the exceptional actions of large industrial corporations in collaboration with the start-up sector.
“We are once again extremely grateful and proud that our determined contribution has led to this recognition,” says Erik Kolehmainen, VP of corporate venturing at Metsä Spring, the innovation arm of Metsä Group. “Our involvement goes beyond
simply investing capital in promising start-ups. Through our strategic collaboration, start-ups benefit from access to Metsä Group’s industrial assets and knowledge to facilitate R&D and innovation, advancing the forestbased bioeconomy.”
The Finland-based forestry
group received particular praise for the openness of its collaborations, and the involvement of the top management, signifying clear strategic importance of collaborating with the start-up ecosystem.
Through Metsä Spring, the group invests in promising technologies that can improve the business ecosystem and bring value to the forestry and woodbased sectors.
Wood and bio-based innovations have recently been gathering momentum, says Metsä. According to Facts and
to Smurfit Kappa’s commitment to sustainability and our desire to make real environmental change at a practical level. Through collaboration and hard work, together we can make every aspect of our operations as sustainable as possible in our journey towards net zero.”
Pedro Mendarozketa, general manager of the Sanguesa mill, added: “We are delighted to officially announce the solar panel investment at our paper mill in Sanguesa. The solar panels will enable us to generate sustainable energy, reduce our overall external energy consumption and reduce our carbon dioxide emissions. We look forward to officially unveiling the solar panels later this year.”
Installation of the solar panels is expected to be completed by the end of this summer.
Factors, the global bio-based materials market was worth around US$21 billion in 2021 and is expected to grow to about $82bn by 2028.
Metsä Spring’s portfolio companies include start-ups such as Innomost, which offers cosmetics producers biodegradable and renewable ingredients derived from Finnish birch. Metsä Group’s internal demonstration projects include Kuura – an environmentallyresponsible textile fibre produced from softwood pulp, and Muoto, an alternative for plastic packaging.
The latest versions of USbased Sonoco’s rigid paper containers are due to be shown at the Packaging Innovations & Empack show being held at the NEC in the UK from 15-16 February.
Mondi has completed its acquisition of the Duino mill near Trieste in Italy from the Burgo Group.
Around €200 million is to be invested by Mondi in converting the existing lightweight coated mechanical paper machine at the mill into a high-quality, cost-competitive recycled containerboard machine with an annual capacity of around 420,000 tonnes.
Close to two important export harbours, the mill is said to be ideally located to source paper for recycling, supply Mondi’s corrugated solutions plants in Central Europe and Turkey as
well as to serve the growing local Italian market. The converted machine is expected to start-up in 2025.
“We are excited to welcome Duino mill to the Mondi Group and the opportunity this provides to grow our packaging business. We are committed to the longterm future of the mill and recognise its important role in the community and contribution to the local economy,” says Markus Gärtner, chief executive of Mondi Corrugated Packaging.
The €40 million deal to buy the mill was announced in August 2022.
Technology group Valmet is holding its next Customer Days over three days from 29-31 March at the Tivoli Hotel & Congress Center in Copenhagen, Denmark
Valmet’s Customer Days, held bi-annually, bring together pulp, paper, and energy producers from all around the world. This year’s theme is ‘Forward to a carbon neutral future’.
Subjects under discussion will involve case studies with global customers that have improved their business to ensure future
success and to reach their sustainability targets; Valmet’s offering to reduce CO2 emissions and other environmental impacts; a demonstration on what moving towards autonomous operations means in practice, demonstrations of tools such as simulators, digital twins and self-service analytics can empower mill or plant personnel to perform at their best; and the opportunity to meet colleagues and Valmet experts from around the world.
Along with the paper manufacturer’s EnviroCan and Greencan cylindrical packs, Sonoco’s Gravy paper-board drum, which received the Supply Chain Solution of the Year Award at the 2022 UK Packaging Awards, will be on show.
The EnviroCan (part of Sonoco’s EnviroSense range) with a paperboard end is made with recycled and recyclable paper fibres. The paperboard body is made of at least 95 per cent fibres with a minimum of 60 per cent recycled content and features a highly-effective oxygen and moisture barrier layer, which assures food safety and preserves shelf-life.
The wide variety of closures
available for this range –including the latest paper lids for 73mm-diameter paper cans and sprinkler options – will also be showcased.
Greencan is a pack made of 92-98 per cent paperboard, with a wide range of barrier properties. It is available in range of shapes and sizes – from round, square or rectangular; to oval, oblong or triangular – and provides a recyclable, mono-material pack, with robust barrier properties.
Philip Brown, interim North Europe sales director at Sonoco Consumer Products Europe, comments: “After the success of previous years, we’re delighted to return to Packing Innovations again in 2023. We never stop innovating to improve both the performance and the sustainability of our solutions, so we were delighted to see one of our latest innovations recognised with a UK Packaging Award last year.”
Anew regional operations centre has been set up by ABB for North America, to bring technology expertise closer to its customers.
An initial $1 million investment in the Mexico Technology and Engineering Center (MXTEC) in Merida, Yucatan, will increase ABB’s engineering capacity by a quarter and supports state government aims to develop the location – a community of technology and cyber security companies – develop as a technology and cyber security cluster.
The increase in capacity will also include projects involving the
commissioning of Ability System 800xA distributed control systems at customer sites. Further skills for supply chain, project management and sales support may be added in the future.
“Our aims for the Mexico Technology and Engineering Center are to grow our engineering competencies and capacity to deliver projects with local resources in the same time zones as Mexico, the US and Canada, but also become part of a technology-focused community in Merida where people can stay for a long time and grow their careers,” said Michel Blondeau, operations manager for North America at ABB.
The 2023 Paper Industry Gold Awards, which celebrate and recognise the achievements of the UK’s paper-based industries, will be presented during a ceremony held on Wednesday 22 March at the House of Commons Terrace in London.
The awards are backed by the Confederation of Paper Industries (CPI), in partnership with the Paper Gold Medal Association (PGMA), and are sponsored by the chairman of the APPG for the packaging manufacturing industry, Mark Pawsey MP.
This event follows the success of the inaugural awards in 2022 hosted in the House of Lords. The ceremony had more than 100
International Paper (IP) has agreed to sell its half share in Ilim SA, the holding company for its Russian Ilim joint venture, to its partners for US$484 million.
The deal indicates that Ilim, with headquarters in St Petersburg, has an enterprise value of $3.5 billion.
Memphis, Tennessee-based IP first considered pulling out of the business on 11 March 2022 following Russia’s attacks on Ukraine. About a week earlier at IP’s investor conference, chief executive Mark Sutton alluded to the possibility of exiting from Russia.
The joint-venture partnership
was created in 2007 with an investment of $650m from IP.
Ilim is Russia’s largest forest products company, operating three large pulp and paper mills with capacity for 3.6 million tons
a year, and two corrugated box plants. IP’s partner was Russian oligarch Zakhar Smushkin. Chief executive was Ksenia Sosnina.
The Ilim mills are located at Koryazhma in the Arkhangelsk
attendees from throughout the industry along with numerous Members of Parliament.
The awards, which were launched last December, comprise the same six categories as last year, covering recycling, ‘net zero’, sustainable innovation, skills, community engagement and health and safety.
The Paper Gold Medal will also be awarded at the ceremony, recognising an outstanding, lifelong contribution to this industry.
The deadline for entries this year is Friday 10 February. More information from Holly Whitbread at hwhitbread@paper.org.uk or by phone at 01793 889612.
Oblast, Bratsk and Ust-Ilimsk in the Irkutsk Oblast, Kommunar in the Leningrad Oblast, and Dmitrov in the Moscow Oblast.
Most recent investment in the JV was in 2019 with what was expected to be the world’s largest and fastest kraftliner machine installed at the UstIlimsk mill. The Voith-installed line would have capacity for 600,000 tons of kraftliner a year, and included two BlueLine refining lines, one XcelLine system, drive components and a training package.
IP operates mills in North America, Latin America, North Africa and Europe with sales in 2021 of $19.4 billion.
At a recent trade event, a number of industry experts discussed with Rockwell Automation the impact of increasing automation, digitalisation and data analytics in paper making. PPL reports
The pulp and paper industry and its many manufacturers have experienced more ups and downs than a roller coaster in recent decades due to fluctuating demands for different types of paper and the evolving technologies for producing them.
“I’ve had five different owners over 30 years, but somehow kept the same phone number. Early in my career, life was good and we built new equipment. Then came the downturn, and we had to focus even more on reliability to minimise costs,” said Greg Drewiske, PE, manager of engineering and capital at Billerud Americas, which produces coated papers in central Wisconsin. “Now, the mills that are still open have a lot of obsolete, proprietary equipment, and the need to incorporate more automation is even greater.”
Tom Shope, vice president of digital transformation solutions at Endress+Hauser, added, “There’s fewer staff, so it helps to have more intelligence in devices. However, the question now is: how to use all the data they’re generating? For example, how we can turn it into maintenance workorders and get them to skid builders or suppliers.”
Drewiske, Shope and other co-panelists explored how the pulp and paper industry is able to optimise and transform with an assist from automation
“We need devices to fill in for experts that have retired, but those devices need to first establish performance baselines before they can look for anomalies,” says Dan Timmers, solutions consultant for machine design, information and analytics at Rockwell Automation
and digitalisation at last year’s Automation Fair 2022 in Chicago.
The panelists reported that more detailed, targeted and distributed data can greatly enable pulp and paper processes if it quickly reaches decision-makers who can make the best use of it.
“At the 8am meeting, operators and managers want to know why their process was lost last night, and this usually means pulling up Excel spreadsheets and cross-correlating them,” said Dan Timmers, solutions consultant for machine design, information and analytics at Rockwell Automation.
“Now, more information is getting processed at the edge –such as signatures of flows on a
day-to-day basis – and getting it to the cloud, which has the potential of giving us the equivalent of Google Maps for process control. This is especially important because the old guys that could walk by equipment and tell that something was wrong from the vibrations are retiring. Because this tribal knowledge is vanishing, we need controls that can tell us what the 4-20 mA signals can’t, and that transition is coming.”
Timmers cautioned that, even if information can be shown on a dashboard, it can’t be just blind data points, and requires components and software that are smart enough to immediately put it in useful context.
“This capability is immensely useful. Some applications can
predict motor failures two or three months ahead of time,” he said. “We need devices to fill in for experts that have retired, but those devices need to first establish performance baselines before they can look for anomalies.”
To gain the benefits of added automation and more digitalised data, some wrinkles must inevitably be smoothed out. Drewiske reported that Billerud’s mill installed a single-loop distributed control system (DCS) about 10 years ago, which included HART-enabled devices that pointed out new details when they were connected.
“It turned out that 30 per cent of our instruments had issues we didn’t know about before, such as valves sticking,” said Drewiske. “We also implemented controlloop, performance-monitoring software to identify tuning issues. In our drying section, we took current feedback, and relayed them to FactoryTalk Historian software.”
Shope added: “IT is taking over some of these areas, but the question remains: how do we get 30 years of plant-floor experience into just three years of staff training?” Because IT is getting more closely involved with production issues, Timmers advised users to designate a leader and cross-functional team to handle IT’s presence in the process space, such as deciding on a policy for configuring switches.
“We have to educate our IT guys,” said Drewiske. “Previously, if we couldn’t get email for threeto-five seconds, not many people would notice. However, if we lose
control of our paper process for three-to-five seconds, a lot of people would notice.”
Tooting automation’s horn Drewiske reported that increasing automation, digitalisation and data analytics in paper making is also important for meeting enterprise requirements and achieving corporate goals.
“It’s pretty simple to meet basic production and product priorities,” he said. “However, it’s harder to also stay ahead of technical obsolescence, as well as address what a company wants to do as it goes from being familyowned to hedge fund-owned to internationally owned.”
Drewskie explained that plant-floor personnel tend to fix equipment and systems and not make a big deal about it, but this can result in other parts of the organisation not being aware of OT’s importance or what it requires.
“Equipment becomes obsolete,
and parts can’t even be found on eBay, and then we have to negotiate. I always say the best time to negotiate is at 2am after 10 hours of downtime,” said Drewiske. “In any case, we have to make clear what our processes and equipment need to maintain availability and uptime, and hopefully invest in a phased approach.”
Unfortunately, another hurdle
to securing investment in pulp and paper is the fact that operations issues and the cost of fixing them typically overshadow maintenance concerns and advocating for them, according to Drewiske.
“We measure overall efficiency and target speed and quality, but when we’re looking at lost time, dealing with operating problems outweighs maintenance, and makes it hard to justify investing in it,” he explained. “If a company is looking at a multi-million-dollar project, they usually want a 30 per cent return on investment, and it would take maintenance far too long to reach that ROI and justify that investment.”
Drewiske added that automation and digitalisation take operations, maintenance and other data sources out of their formerly separate silos, making them easier to pull together.
“We don’t look at these reports as much as we should, but we have a corporate reliability initiative to focus on developing systems that can integrate our data sources. I think integrating them is going to get easier in the future, once we get over the hump of bringing them all together.”
Organisations throughout the pulp and paper sector sit at the forefront of addressing the Dual Challenge –meeting increasing demand from a growing population but in a sustainable way.
On the one hand, availability, performance and quality are essential for the profitable production of pulp and paper mills. On the other, the need for cost-effective and sustainable production continues to be a priority for businesses across the sector.
Every pulp or paper mill today is certainly fully focused on the need to increase production. It is a common challenge for firms. Since the pandemic triggered increased demand for pulp and paper products such as toilet paper and paper towels, producers throughout the industry have been under increased pressure to be more agile. Improved reliability, safety, and sustainability are the other key strategic initiatives pulp and paper companies are pursuing to ensure they have the capacity to operate at maximum potential.
While pulp and paper manufacturers could potentially revamp their equipment to operate at a higher capacity, taking this approach would require a huge investment of time and money. Instead, forwardlooking companies are investing in technology and embarking on digitalisation journeys to improve efficiencies of their people, processes and equipment. Historically, pulp and paper mills have focused primarily on leveraging digital technologies to look at four essential impact areas.
● Raw materials control: Plants must closely monitor the quality of incoming raw materials, such as the wood that will go into the digester. With different grades of wood (hard and soft) and varying specifications within each grade, this is a key area for managing costs
● Process and quality control: Minimising off-grade production and maximising efficiency
is essential to maintaining a competitive stance in this industry
● Process monitoring: Mills must continually assess their performance, compare themselves against other facilities and measure progress toward their goals. In some cases, it’s valuable to benchmark against competitors with a goal to boost competitive advantage
● Monetary control: Operators need to pinpoint high-cost areas, establish cost breakdowns, and identify the monetary basis for consideration of alternative proposals for production processes.
Today, there are a range of digital technologies available that can bring pulp and paper mills significant benefits across all these areas. In terms of process monitoring, predictive and prescriptive maintenance has a key role to play in improving the reliability and availability of
physical assets while minimising risks and managing costs. Prescriptive analytics can give back time to production across the pulp and paper industries, extend equipment life, and safeguard people, equipment, and the environment.
The story of Veracel Celulose, a Brazil-based agro-industrial company that produces an average of more than a million tons of pulp each year, is a case in point. Veracel turned to the Aspen Mtell, a prescriptive maintenance offering from AspenTech, to keep maintenance costs under control, increase availability and run assets with greater confidence in order to achieve higher throughput.
Using both process and mechanical data, Aspen Mtell successfully detected impending failures up to 59 days in advance, providing financial benefit and reducing wastage through the avoidance of production losses. Early warnings enabled better maintenance planning, reduced
Operating pulp and paper mills for both productivity and sustainability is a challenge. Pratibha Pillalamarri* explains how to make it happen
maintenance costs and increased output to meet market demand.
Today’s pulp and paper facilities must effectively manage their fibre losses, waste discharge and emissions. While Predictive Analytics can help when it comes to this key impact area rapidly emerging across the pulp and paper industry – there is a need here for a more multifaceted approach.
These industries are after all significant emitters. According to the International Energy Agency (IEA), the pulp and paper sector was responsible for about 190 million tonnes of carbon dioxide emissions in 2021, about 2 per cent of all emissions from industry and a historic high.
As production is projected to continue increasing, the emissions intensity of paper production must decline significantly to get on track with the Net Zero Emissions by 2050 scenario, which sees emissions intensity fall by about 4 per cent annually between 2021 and 2030. This will require considerable effort, as emissions intensity has been roughly flat since 2018. From leveraging
The Veracel Celulose mill in Brazil, which produces more than a million tons of pulp each year, used Aspen Mtell, a prescriptive maintenance offering from AspenTech, to keep maintenance costs under control, increase availability and run assets with more confidence
alternate or renewable sources of energy to deploying innovative technologies that improve process efficiency, there are multiple steps that manufacturers can take to reduce emissions.
While prescriptive maintenance solutions can help reduce the incidence of equipment breakdowns and the associated environmental impacts, decarbonisation, and the technology that supports it, will be key to efforts here.
We are seeing a growing number of plans in place worldwide that are designed to help decarbonise the sector. Japan, for instance, released a decarbonisation plan for its pulp and paper industry in early 2022, including new decarbonisation targets and steps for achieving them.
Digital technologies will certainly have a crucial role to play in this context. Examples of recent innovations that are delivering results today in the pulp and paper sectors include systemslevel risk-modelling technology that ranks the most practical and economically feasible options for carbon reduction, capture, storage and re-use.
More generally, the latest carbon capture, utilisation and storage (CCUS) tools are likely to play a critical role, having significant relevance across many assetintensive industries including the pulp and paper sector. These industries need closedloop systems for recycling their waste streams through carbon
sequestration. That’s why we are seeing a rapid expansion of carbon capture projects worldwide, many driven by significant government investment.
Other technology solutions and industries play into this focus on CCUS. Process simulation software already has a strong track record of helping companies reduce emissions. This same software is even more crucial in CCUS, enabling organisations to improve carbon capture and storage. Approaching the pursuit of effective solutions below ground, industry leaders are using subsurface geophysical and geological modelling software to quickly determine the best reservoir targets for reliable, longterm carbon storage.
Digital grid management software is another effective solution, optimising the use of distributed energy sources. Separately, these digital solution areas impact CCS and CCU projects; combined in a more holistic, collaborative approach, the possibilities are even greater. The powerful combination of breakthroughs in process simulation, subsurface geophysical and geological modelling, AI-powered hybrid modelling, AI-powered prescriptive maintenance, process optimisation software and digital grid management can deliver results at scale –both economically and at an accelerated pace to meet the requirements of industrial carbon mitigation.
Moving forward, the pulp and paper industries will be focused on continuing to digitalise to meet the demands of the dual challenge and drive-up performance levels. In managing this challenge, tools
that support digitalisation from prescriptive maintenance to CCUS solutions will certainly be key as this article has shown. But technology can only part of the way towards solving the problems of the pulp and paper sector. A collaborative and problem-solving mindset will be equally key. For firms to reach their net zero targets, innovation in the approach to digitalisation and the adoption of the latest solutions need to advance quickly. Leading companies like Lighthouse and Frontrunner need to work towards optimising both the strategy and the technologies that support it. After all, regardless of where companies are in their net zero journey, it is important that they adopt an innovative, problemsolving mindset and are prepared to partner with peers and other technology leaders with the expertise to help meet the Dual Challenge and achieve critical sustainability goals while driving operational excellence.
*Pratibha Pillalamarri is Senior Product Marketing Manager at AspenTech. More information from AspenTech.com
Based in Bedford, Massachusetts, and with 30 sites worldwide, Aspen Technology is a software leader that helps industries meet the dual challenge of using resources to support a growing global population in a profitable and sustainable manner. AspenTech addresses complex environments where it is critical to optimise the asset design, operation and maintenance lifecycle.
Bracell’s new mill at Lençóis Paulista in Brazil brings together the most modern and innovative technologies to achieve the highest levels of sustainability in the pulp production process.
This project considerably diversifies and expands Bracell’s
Project Star is one of the largest private investments in Brazil in the last 20 years, and it has made Bracell the largest producer of dissolving pulp in the world. The mill runs without any fossil fuels and can produce up to three million tonnes of kraft pulp per year, report Ana Luiza Branco and Livia Bianco. Photography byThiago Filla
production of kraft pulp, increasing it from 250,000 tonnes per year to 1.5 million tonnes per year of dissolving pulp, or up to three million
tonnes per year of kraft pulp.
The mill has two flexible lines designed primarily to produce dissolving pulp using the latest production technologies,
without the use of fossil fuels. The plant will be self-sufficient in energy production, and the surplus will be used to supply the National Interconnected
System with clean, high-quality electricity.
After two years of extensive work, the mill started-up in
September 2021. Valmet was one of the project’s main partners and delivered the evaporation plant, which has a capacity of 3,500 tonnes of evaporated water per hour; the recausticising plant, which has a capacity of 31,000 cubic metres of white liquor per day; two lime kilns, which use biogas as fuel with a production
capacity of 1,200 tonnes per day; two biomass dryers; and two biomass gasification plants each with a capacity of 87 thermal megawatts.
The project features state-ofthe-art technical, energy and environmental performance equipment. For black liquor evaporation, Valmet provided its Tubel technology in the concentrators and first evaporation effect. This technology is the most robust and reliable on the market, with liquor flow on the outside of the tubes to prevent clogging and maintain the plant’s very high availability. One hundred per cent of the lime kilns’ energy requirements is supplied by gas from the gasification of biomass, significantly reducing production costs and carbon dioxide emissions. This is the first biomass gasification lime kiln technology supplied to a South American pulp mill.
Fernando Scucuglia, pulp and energy director at Valmet South America explains: “Valmet has
combined its technical knowledge obtained from investments in R&D and the experience gained in similar projects implemented around the world for Bracell’s new mill. The lime kilns are operated completely with fuel obtained from biomass gasification. This is the first pulp mill in South America that will not use fossil fuels in this process. Our mission is to convert renewable resources into sustainable results, so I’m very happy to have delivered this key technology for Bracell.”
Another sustainable technology
This project has been a significant milestone in Bracell’s history. It’s much more than a pulp mill
Project
delivered by Valmet is the non-condensable gas (NCG) treatment system, which controls and minimises odours from the chemical pulping processes.
One of the global leaders in the production of speciality
pulp, Bracell has always based its operations on sustainable eucalyptus cultivation and stateof-the-art plants. The company has created around 10,000 jobs in the two states where it operates, including direct and permanent outsourced workers in industrial, forestry and logistics activities. Continuously investing in technology and research to offer
high quality products, Project Star is a pioneer in consolidating the company’s sustainable performance.
Alexandre Figueiredo, senior industrial manager at Bracell in São Paulo, says that the new mill is one of the largest and most sustainable pulp mills in the world.
“The project stands out for
its sustainable performance, with advanced technology that eliminates the use of fossil fuels and uses renewable raw materials to create biodegradable products. This project has been a significant milestone in Bracell’s history. It’s much more than a pulp mill – it’s the future of the bioindustry, the most modern and sustainable mill in the sector,” he says.
Improve your press section efficiency! SmartScan™ contactless sensor accurately measures paper web dryness after the press section 24 hours a day, 7 days a week. Using a proprietary microwave technology, it is developed to overcome the typical limits of the NIR (near-infrared) sensors. SmartScan™ is available both for fixed point positions or traversing web scan. To save hundred of thousands of Euros in energy costs, stop collecting samples, choose the safe accuracy of SmartScan™ technology.
To thrive and survive in today’s increasingly competitive and digital industry, smart investment decisions are needed. Lu Athnos* offers advice on how to make them
Digitalisation, Industry 4.0, Industrial Internet of Things: however you want to phrase it, we live in the digital age. But with the many challenges facing pulp and paper mills, not enough mills have been able to move with the times, and some continue to rely on ageing control systems. Legacy equipment and poor maintenance can result in motors and drives breaking more often, in turn creating one of the biggest challenges for papermakers –machine uptime performance – which impacts both profitability and productivity.
Those falling behind are simply doing the basics to keep operating rather than taking full advantage of modern digital systems to remain competitive. Mills need to invest and innovate to stay ahead. If not, it becomes a spiral of failure. Mills don’t invest, productivity decreases, revenues fall, and competitiveness suffers.
While investment is crucial, the reality is that it’s not always readily available. The good news is that it can be carried out in phases and does not have to mean a one-off upgrade at an extortionate cost.
Baby steps approach to mill modernisation
So, what to do? Where to spend?
What to prioritise? A mill’s to-do list is not empty of good ideas.
This depends on where your mill is in its digitalisation process and where you can achieve highest
return-on-investment (ROI). Every mill is different, and each has its own priorities based on the spec and volume of its output. However, there are some critical steps that are common to all mills looking to modernise and increase production.
Continuous, ongoing updates and improvements – taking small systematic steps, one at a time, all leading to the same end goal – will break down the complexity and risk of an infrastructure upgrade while enabling mills to test the success and ROI as they go.
To achieve optimum performance, managers must be relentless about constant, incremental updates, no matter
how small. It is critical to be able to see and measure results, yet a small number of mills still don’t even yet have basic online sensor measurements such as weight and moisture, for example. If you can’t measure quality, the consumption of raw materials such as fibre, chemicals and energy is often not optimum for the paper products produced, which affects your efficiency and productivity.
In one case, a central US mill had not invested in new technology for years but wanted to increase throughput by adding a new steambox. However, to handle the increase in available information and measure it more accurately, management realised it would have to upgrade to a newer Quality Control System (QCS). This obsolescence conflict could have been avoided if the mill had
kept up with equipment advances through regular upgrades. Examples such as this abound. It is important to understand that the improvements that can be realised are not restricted to any one part of a mill’s processes. From wet end to roll handling, there are numerous opportunities, as shown by the following case histories.
● In Sweden, Holmen Paper Braviken provided an example of how an optimisation project can help to reduce downtime and improve runnability. Operational disruptions were affecting the availability of the mill’s RM3 winder, which produces jumbo rolls of printing papers weighing up to 50 tonnes. The mill opted for ABB’s automation and electrical system, upgrading to ABB Ability System 800xA, which
included control and operation of the winder, as well as Winder Performance Optimization, which monitors key performance indicators (KPIs), identifies improvement opportunities and enables the dynamic adjustment of speed to meet capacity for each roll set. This integrated solution drove better runnability, reduced downtime, easier troubleshooting, and increased productivity.
● In Asia, a major paper mill running a complex operation with 13 paper machines needed to maintain high production while being able to correctly predict service costs and constantly improve process performance. They turned to ABB’s remote monitoring and predictive analysis technologies. This helped the mill harness the tremendous amount of data to address production, quality and cost issues – one step at a time – and reduce both the time needed to complete
bump tests by 70 per cent and the overall loop tuning effort by 75 per cent. This contributed to increased production, lower chemical costs, accelerated grade changing, fewer sheet breaks, reduced unplanned downtime and machine direction ash variability.
● In Sweden, a tissue mill had planned to install the newest technology on its PM8 measurement platform. On its other paper machines ABB scanners were installed in the 1990s. However, some of the sensor material was radioactive which, as well as degrading over time, also presented safety issues. It was decided to install the ABB High Performance Infrared Weight and Moisture single sensor (HPIR-FW), which replaced two separate weight and moisture units, making for easier maintenance and improved reliability while also removing a source of radiation from the mill.
Buying an expensive new home and not taking care of it properly will inevitably lead to costly repairs. As can be seen by the aforementioned case histories, it is the same with a mill’s process control operations. Ongoing maintenance and upkeep are essential, or the benefits of any modern system will be lost.
Too many mills run to failure or adopt an ‘if it isn’t broke, don’t fix it’ mentality. Then, it is not a matter of ‘if’, but ‘when’ equipment will fail. If required maintenance is ignored for too long, damage becomes irreparable.
This was particularly relevant during the pandemic, a challenging time for mill operations that were focused on surviving rather than thriving and had to keep mills running in difficult conditions, while running on empty themselves. It’s not
surprising that under such intense pressure, certain disciplines became of a lesser priority. That said, now is the time to restore the discipline of regular, physical inspection and remind ourselves of the importance of the basic, daily maintenance that is so critical to mills.
There are recommended proactive processes, such as Reliability Centered Maintenance (RCM), which takes advantage of a variety of maintenance strategies to optimise all assets in a facility and ensure the most efficient running of a mill. RCM finds the right approach for the right piece of equipment by analysing the criticality of your assets, identifying and prioritising failure modes, and then implementing maintenance planning, asset condition monitoring, predictive and preventive maintenance strategies to avoid equipment failure. This not only reduces maintenance hours and costs
but will also decrease unplanned (emergency) repairs.
The increasing sophistication and capability of technology means that reams of data become available to operators. So how do you avoid the risk of getting lost in this flood of information?
While the industry is increasingly embracing digitalisation –particularly in terms of an enhanced ability to collect data – knowing how best to utilise it is key. Effective data management requires having a strategy and reliable methods to access, integrate, cleanse, govern, store and model: to prepare data for analytics so that it adds value. Data can only be effective when it is validated. A mill needs to know from the outset what it wants from its control system and accept the veracity of the data it receives.
ABB offers digital services that monitor and set thresholds for performance data variability. If operations go outside the threshold, it triggers an alarm so action can be taken thus preventing failures. And if additional support is needed for troubleshooting, remote connection coupled with data monitoring gives experts the tools to immediately start diagnosing – something that became even more critical when Covid restricted site visits.
Measure, analyse and act – and automate: this is how advanced control systems help a mill optimise operations.
With the vast amount of data comes the need to train operators to be able to read and use it
Big investments need to be backed up with data acquisition and management but with that comes the need to train operators to be able to read and use it properly. Humans will not be replaced by artificial intelligence (AI), but they will be replaced by other humans who can use AI
properly. Humans will not be replaced by artificial intelligence (AI), but they will be replaced by other humans who can use AI.
The ‘silver tsunami’ is a reality. A lot of papermaking knowledge has been lost in recent years through retirement, with an evident knowledge gap between generations, and paper makers are faced with competition for talent from the other process industries.
However, this is offset by the opportunity that the rise of digitalisation and inclusion of gaming elements in future automation systems designed to harness the talents of Generation Z brings, particularly in the way it is creating new opportunities for the engineers of tomorrow. Most of the new generation of operators entering the workforce don’t yet fully understand the paper making processes but this should not prohibit any mill or system from reaching its potential. The young ‘Nintendo’ generation – sometimes referred to as ‘button
pushers’ – is agile and attracted to new technology systems and knows how to leverage them to become better paper makers. Success relies on a combination of paper making process training and understanding and embracing digital systems, so it is critical for mills to continue to bridge the generation gap and increase understanding on both sides of the aisle. Our industry is at the dawn of a new era. It is well placed to shift our recognition of skills and adopt a digital-first approach that will be essential in competing with other industries. We have a unique opportunity to cross-train and combine the best of both worlds; embracing the new, technologically-savvy generation of engineers while maximising and augmenting the skills of process experts who have been serving the industry for years. If we are to raise our profile as an attractive sector in which to build a career, we need to work together to strike the balance between sharing the established
knowledge we already have and training up the next generation of talent.
The benefits of investing in and maintaining a modern control system go far beyond a few more tons out of the door. As the mill examples cited have shown, along with improved production comes enhanced and consistent quality, a safer work environment as well as reduced energy and raw material consumption. Operating efficiency increases and critically, improved competitiveness results in a healthier bottom line.
ABB firmly believes that the future of the pulp and paper industry is sustainable – both environmentally and commercially – but to succeed mills need to keep moving the needle forward with a phased approach that also maximises data and talent at hand.
*Lu Athnos is Regional Sales Manager at ABB Pulp & Paper
An updated QCS Automation Software Maintenance (ASM) program has been launched by ABB that allows evolution to the latest versions. It also provides continuous improvements between versions through access to regular software updates, thereby helping pulp, paper, packaging and tissue mills to maximise their system investment.
The new QCS ASM program means that when maintenance managers upgrade a system, they will benefit immediately and have continual access to the latest releases. Previously these ongoing, incremental enhancements were not easily accessible, leaving mill managers locked into the ‘status quo’ of the day-of-implementation
version of a specific system.
ABB’s newest lifecycle management program removes the complexity and cost of accessing new software releases
and features, corrections and enhancements between major system upgrades.
The new program also enables more cost-efficient, proactive system management by offering multiple program levels to align to different customers’ needs. The new Maintain Plus level opens first-time opportunities for customers with the latest version of QCS800xA to access the continuous software updates, new features, cyber security enhancements and patches within their current version. The Maintain & Evolve level caters to mills with earlier versions of the QCS800xA systems who need to upgrade. Both tiers include access to premium system documentation through myABB, ABB’s customer portal for managing their installed
A new chuck technology for the winding and unwinding operations of paper and board producers has been developed by Sonoco, the packaging manufacturer.
Called ViPer Chucks, the new technology is said to offer significant runnability improvements for paper and board reels in the most demanding winding operations, especially in centre drum winders and special unwinding stands such as sheeters and corrugators.
“To meet today’s challenges of paper and board manufacturers and to offer significant productivity improvements in a cost inflation environment, we developed a new generation of chucks exclusively with our
base, where licenses can be viewed and managed. Customers can also stay informed of any system updates through release notes published to ABB Library. Plus, both tiers include updates to any firmware-related devices within the QCS System, such as the Network Platform or the Actuator Control Center.
“The biggest differentiator of this enhanced program is the updated and tailored service support it offers customers,” says CarlMagnus Tjeder, global product manager for paper machine controls at ABB. “This is a major incentive for operators already on our latest version who can now get new features, delivered costeffectively by service teams rather than project teams, when they want them.”
cores in Europe.
“Our new chuck technology is a step change in paper and board winding and eliminates typical problems such as vibration, torque transmission issues and chew-out. We called this innovative technology ViPer Chucks in reference to the improved VIbration PERformance.”
Chuck cleaning is reduced, saving downtime. The chucks also provide better torque transmission for heavy reel weights. The result enables higher productivity due to fewer process interruptions along with an improvement on process safety.
The range of C-press screw presses offered by Andritz has been broadened to meet the dewatering needs of the wastewater or industrial treatment plants.
With its direct drive system and conical shaft with constant screw pitch, the C-Press screw press has now a feed capacity ranging from 1 to 95 cubic metres per hour, with an outlet capacity from 20 to 1,300 kg DS/hr.
In addition to a long lifecycle, the press also offers the advantages of easy operation, low maintenance, and – due to bi-sequential cleaning – 30 per cent less water consumption than comparable equipment. The C-press also complies with all regulations relating to safety, hygiene, and
environmental protection.
The C-Press offers simplified operation and processes free from contact with dewatered sludge, combined with low maintenance and energy consumption costs.
Andtritz product manager Nicolas Perrier says: “The screw dewatering technology is the best solution from low to high flow ranges, as it has an excellent performance in terms of cake
dewatering and filtrate quality. Furthermore, it has a very low noise level and an extremely low operating cost, as it operates at extremely low speeds. Due to these features, the C-Press has much lower energy consumption than other technologies and results in very low maintenance costs, leading to a very long life of the equipment.”
With a high-performance system, the C-Press maximises the basket’s open area, featuring high specific capacity and excellent capture rate, when compared to equivalent technologies. The screw speed is automatically adjusted, according to the input oscillation, ensuring a continuous flow with optimised performance in terms of drying and capture rate, even during the washing phases.
More sustainable paper manufacturing is being made possible with a range of offerings from Voith.
For example, a German graphic paper manufacturer reported that Voith’s SolarPress roll covers have enabled energy savings due to a 1.5 percentage point higher dry content after the press section.
Efficiency add-ons for press fabrics are another. In particular, +Peak technology, a speciallydeveloped elastomer material, optimises nip dewatering and increases the service life of a press fabric.
For one paper producer, +Peak resulted in higher dry content in the tandem press and reduced the average amount of steam by 11 per cent,
from 1.6 to 1.43 t/ton.
In addition to energy savings, significant water savings are also enabled. Typically, customers benefit from HydroSeal, the modern version of sealing strips for suction rolls. At a board mill in the USA, HydroSeal is said to have reduced water usage by 80 per cent and saved the paper maker more than $30,000 per year in
sealing strip lubrication.
“In addition to production that conserves resources as much as possible, it is important that the products themselves are also manufactured sustainably,” says Lidia Loskan, R&D project manager for sustainability at Voith Paper. Here, says Voith, it is important to be able to offer the same product properties as with
petroleum-based roll covers and fabrics.
Voith’s R&D team is also working on new possibilities with the help of life cycle analyses (LCAs). As an example, Dr Robert Hilbing, senior vice president of R&D FRS at Voith Paper, highlights the newly launched AiroGuide Tune Green roll cover.
This is certified according to the international DIN CERTCO standard for bio-based products, and is the first of its type available that offers the same performance as petroleum-based alternatives. The fibre composite roll cover is manufactured with bio-based raw materials and was specially developed for the wetend section. It also has improved corrosion properties and a long service life.
An optimised stock preparation portfolio for tissue production has been one successful result of Italian company Toscotec becoming a subsidiary of Voith two years ago.
Since then, more than 10 BlueLine stock preparation systems for the tissue sector have been ordered worldwide with some already in operation. Voith has delivered more than 70 machines, and many more are currently being processed.
“The cooperation between Voith and Toscotec has paid off for our customers right from the start,” says Steffen Bassmann, director of product management in Fiber Systems at Voith Paper. “I am impressed how well Toscotec and Voith harmonised in their cooperation from the very beginning. This is a real win-win situation with clear added value
for tissue producers worldwide.”
“Together, we can offer our customers the best possible technologies for the entire process chain,” adds Elisa Bertolucci, Fiber Systems engineering manager at Toscotec. “Our experts are always on hand to provide advice and support in achieving individual goals. Best-in-class technologies ensure highly efficient stock preparation and optimize resource efficiency.”
As a tissue systems provider, Toscotec draws on Voith’s stock preparation expertise. For optimised water and wastewater management, Voith and Toscotec also work together with Meri, another Voith subsidiary. Customers thus benefit from a full-line portfolio from one source. One system already successfully commissioned is at Vajda-Papír’s mill at Dunaföldvár in Hungary. Here, Toscotec’s Ahead 2.2L
machine has capacity for more than 80,000 tons per year running at up to 2,200 m/min. The turnkey delivery included the complete stock preparation system with equipment from the harmonised Voith-Toscotec portfolio.
These comprise IntensaMaXX, IntensaScreen, TwinFlo Refiner, a deflaker and a jointly-developed thick stock cleaner (IDH). A new HC pulper designed by Toscotec and based on Voith’s many years of pulping experience is also used. Furthermore, a new TT Hydromix was installed, which was jointly developed by Voith and Toscotec. The latter is said to have led to remarkable achievements on MD basis weight profile.
In addition to the stock preparation portfolio for tissue production, the cooperation extends to many other important areas such as paper machine components.
Another OnPerformance.
Lab (OPL) location has been opened by Voith, this time in Kunshan, China, to offer the comprehensive know-how and competencies of its experts worldwide as close to the customer as possible.
The opening expands the scope of the remote service centre, which offers data-based services such as data analysis, condition monitoring, smart monitoring and expert advice. From the OPL, the Voith team is available quickly and easily through remote support, regardless of whether short-term problems or long-term optimisation projects
are involved. OPL locations are already based in Heidenheim, Germany, and Tokyo, Japan. The opening of more regional offices is planned.
“Our new location in Kunshan is specifically geared toward our customers in the Chinese market who want to use automation and digitalisation even more profitably in their plants,” says Dr Dieter Wenninger, regional president of Products & Services Asia at Voith Paper.
“We also ensure more resourceefficient production so that customers can reliably achieve their sustainability goals. Voith supports both the installation
and commissioning of the digital applications as well as the subsequent monitoring and further process optimisation. As part of the global OPL network, the new site will also drive innovative projects and technologies for the Chinese market.”
All OPL services can be configured individually for each customer as a modular system. Together with OPL, paper producers define their targets and specific key performance indicators (KPIs), such as fibre consumption, basis weight and moisture stability as well as grade change times. Building on
continuous data analysis linked to data mining methods and artificial intelligence, targeted optimisation measures are then implemented.
“Voith customers have always and increasingly relied on our support and know-how when it comes to elevating their efficiency, production volume and availability,” says Ulrike Welp-Wallenmaier, senior manager for business development at Voith Paper. “OPL’s data-based remote services are an innovative way to profitably apply our knowledge for our customers and their individual challenges.”
UAE-based speciality tissue manufacturer
Star Paper Mill has signed an agreement with Khalifa Economic Zones Abu Dhabi - Kezad Group, the integrated trade, logistics, and industrial hub of Abu Dhabi, to build a facility to produce kraft paper jumbo reels.
The 50-year agreement will enable Star Paper to diversify its product range to serve a growing demand for biodegradable packaging papers in the UAE.
Star Paper Mill will collaborate with RC Paper Machines and expand its existing capacity with an investment of AED 200 million (€50.3m) in a 59,000 square metre site to produce recycled kraft paper jumbo reels that will be used to manufacture corrugated cartons and biodegradable bag papers out of recycled raw materials.
Hussain Adam Ali, chairman of Star Paper Mill commented: “In line with the vision of UAE leaders,
we in Star Paper Mill believe that to be successful and create longterm value in the future, being sustainable and adopting a circular system is vital. We are using this opportunity as a huge advantage for us to create products to achieve reduced carbon emissions and operate as a sustainable industry.
Star Paper Mill’s new facility will have installed capacity for 135,000 tonnes of recycled semi kraft liner, white top liner, testliner, fluting and bag paper, alongside areas for
storage and general use.
An additional 32,000 square metres is being reserved by Star Paper adjacent to the primary plot earmarked for the project to accommodate expected increase in demand. Together, the plots offer the project state-of-the-art primary infrastructure corridors alongside a natural gas pipeline network that would contribute to significant cost efficiency.
Star Paper says the project will apply the latest innovations
in processing waste generated from the facility, using an effluent treatment plant to recycle water and reuse it. The raw materials used, including OCC, NCC, NDLKC, and sack kraft waste, will be sourced locally in the UAE to reduce transport-related emissions.Established in 2019 at Industrial City in Abu Dhabi, Star Paper Mill Paper Industry used equipment from Italy’s Recard SpA to produce up to 40,000 tons per year of virgin tissue products.
Stora Enso has ordered a debarking line, a new biomass boiler, and an upgrade for the recausticising plant for its Oulu mill in Finland from Andritz. The project will help the paper maker achieve its sustainability goals.
The debarking line, equipped with digital Smart Wood Processing products, will have a capacity of about 270 cubic metres solid wood over-bark per hour.
The biomass power boiler will provide steam capacity of 216
per day and includes newgeneration equipment such as a LimeWhite-H filter to get the best quality and lowest effluent, along with a StiroX white liquor oxidiser.
The order is part of Stora Ensoʼs project to convert a former paper machine at the Oulu mill into a high-volume consumer board production line.
will make operations more sustainable
China’s Asia Symbol (Guangdong) Paper has started up its first tissue making line supplied by Andritz at its Jiangmen City mill in Guangdong Province. The order included a stock preparation system with lowconsistency refiners, a PrimeLine W 2000 double-width tissue machine and an automation system.
The TM13 tissue machine runs at up to 1,900 m/min with a width of 5.65m and produces high quality tissue in the range of 11-42 gsm. It is equipped with a PrimePress XT Evo shoe press, a PrimeDry Steel Yankee and a steam-heated PrimeDry Hood.
To speed up the process of starting the line, Andritz and Asia Symbol’s team members collaborated
closely during its installation and commissioning. As a result, the first paper on reel was achieved 16
Tissue industry debut for Gayatrishakti is entering the tissue market and has ordered Ahead 1.8 tissue machine from Italy’s Toscotec for installing at its Vapi mill in Gujarat with startup planned for in 2024.
The Ahead 1.8 tissue machine has sheet trim width of 2.85m, an operating speed of 1,800 metres per minute, and a production capacity of more than 35,000 tons per year (tpy).
Shri G N Agarwal, managing director of Gayatrishakti Paper & Board, says, “We selected Toscotec because we wanted to invest in state-of-the-art tissue making technology. We value their solid experience in guiding and sharing their
expertise with newcomers in tissue. Gayatrishakti is a wellestablished board manufacturer in India and based on our strong background in paper and board, we understand the importance of choosing the right partner for this new market entry.”
The line features Toscotec’s drying configuration including an upgraded shoe press, a third-generation Steel Yankee Dryer and high-efficiency Hood. The order comprises key stock preparation and fibre recovery equipment, Toscotec’s patented Short Approach Flow System with Double Dilution for high energy efficiency, and two Optima 2200 slitter rewinders. The service package includes erection
supervision, commissioning, training programmes, YesConnect-Vision Augmented Reality on remote assistance system, and start-up support.
Gayatrishakti Tissue is a subsidiary of Gayatrishakti Paper & Board Ltd, a leading
days ahead of schedule.
Steven Hung Ching Lung, general manager of Asia Symbol, says: “With the new TM13 we enter the tissue business. It is essential for our expansion strategy to provide our customers with high-quality tissues that have minimum impact on the environment. We have a vast experience in the production of high-quality printing and writing papers. Now we want to achieve the same success with Andritz in the tissue market.”
Asia Symbol is a leading manufacturer of printing and writing paper in China. It is part of the RGE Group, a global player that focuses on sustainable pulp and paper production.
manufacturer of duplex packaging boards and kraft paper. Established in 1996, it has a head office in Mumbai and three manufacturing facilities with a combined installed capacity of 300,000 tpy in Vapi and Sarigam GIDC, Gujarat state, India.
Anew tissue machine installed for Turkey’s Essel Kâğıt just over a year ago by Toscotec has exceeded its guaranteed production by a large margin and surpassed bulk and softness parameters, reports the Italian equipment supplier.
The double-width Ahead 2.2L machine was commissioned as PM3 at Essel’s Osmaniye mill in October 2021. After start-up, Toscotec has been providing continuous support to finetune the plant and achieve best performance.
Essel Kâğit’s production coordinator Ahmet Temuroglu and maintenance manager Burak Ipek commented: “The target of our performance test was successfully accomplished with a production of 290.5 tons per
day on a 23 gsm towel grade at the speed of 1,810 metres per minute. We are now fully reaping the benefits of Toscotec’s firstin-class technology across our entire product range both for tissue quality and consumptions.”
Toscotec’s commissioning manager Andrea Rossi added: “The performance test confirmed the machine’s low energy usage we had been monitoring including at the speed of 2,000 m/min. The total energy
The Intertrade Hellas mill at Inofyta in Viotia, near Athens has started up a new tissue making line supplied by Italy’s A.Celli. The machine supplier said that the line produced its first jumbo roll on time and with the expected speed and product quality.
The line was developed to produce high-quality tissue from virgin fibre, taking into consideration Intertrade Hellas’ specific requests for layout and production capacity.
The project includes:
● A stock preparation line
● An Ideal Master 2000L tissue machine with web width of 5.6m, a design speed of 2,100 mpm and working speed of 2,000 metres per minute
● A forged Yankee Dryer, with diameter of 16ft and a width of 6.085m
● A 5.6m-wide three-ply E-Wind T200 slitter rewinder, with a speed of 1,800 metres per minute
● An R-Way automatic reel
handling system composed of conveyor belt, wrapper, upender and labeling system
A.Celli also provided its DCS process control system and an Industry 4.0-ready automation platform, developed to integrate the numerous systems implemented in the Intertrade Hellas’ plant
The tissue line is expected to reach a production capacity of 244 tpd (basis weight 20gsm) or 221 tpd (16 gsm).
Ioannis Delidimos, chief
consumption is well below the guaranteed figure. The cooperation with Essel’s team was extraordinary and they did a fantastic job in getting the machine ready to achieve its top efficiency.”
executive of Intertrade Hellas SA, commented: “The A.Celli Ideal Master 2000L combines high efficiency and superb tissue quality with minimum energy consumption. Over the last two years A.Celli has been proven a valuable partner in every stage of the process. We are indeed very happy with our decision: A.Celli fulfils the highest standards in tissue machines.”
Founded in 1992, Intertrade Hellas SA operates three mills in Acharnes and Metamorfosi.
Vietnam’s Xuan Mai Paper Co has ordered a PrimeLineCompact S1800 tissue machine from Andritz for its Ho Chi Minh City mill.
The PM2 tissue machine will be used to produce high-quality tissue grades made of either 100 per cent virgin or 100 per cent deinked pulp (DIP) with start-up scheduled for 2024.
With a width of 2.85 metres and a design speed of 1,800 metres per minute the PM2 will have a design capacity of 72 admt/d. The suction pressure roll will be covered with a polysoft
polyurethane cover for highperformance dewatering. The 16ft-diameter PrimeDry Steel Yankee will be combined with a steam-heated Combo hood
Two paper rewinders have been ordered from A.Celli Paper by China’s Xianhe Corporation for its mill at Shishou City plant, in Hubei province.
It will be Xianhe’s second E-Wind P100, the first of which was started up in 2017.
The E-Wind P100, with delivery and start up expected in the second half of 2023, will be used to process jumbo rolls of special paper with basis weights ranging from 30 to 180 gsm over a width of 3.96 metres, and at a design speed of 2,300 metres
per minute.
Xianhe also decided to equip the paper rewinders with automatic core gluing and dust removal systems.
Luo Zhirong, general manager of Xianhe New Material Co, says: “Hubei mill purchases production lines with the most advanced equipment on the market in order to establish the leadership of Xianhe products in the central China market.
We have decided to rely on the A.Celli rewinders on the basis of the three production lines for which we have cooperated in the past, so we are sure of the success of this new project.”
Xianhe Corporation operates three mills with 34 production lines making a range of special papers, pulp, paper products and corresponding chemical additives.
to provide efficient drying with energy savings.
Andritz will also deliver stock preparation and automation equipment, as well as process-,
fan- and multistage-pumps and auxiliaries.
Pham Van Dung, board member at Xuan Mai Paper, says: “Andritz ’s innovative tissue solutions offer both economic and ecological benefits. Professional service offers perfectly complement the technology. Since 2012, we have established a long-term cooperation that is built on mutual respect and trust. Our joint projects are in the areas of old corrugated containerboard lines, deinked pulp lines, and tissue production lines.”
The order follows the start-up of a similar line in 2020.
Chinese decorative paper producer Qifeng Group has ordered a sixth E-Wind P100 paper rewinder from Italy’s A.Celli Paper.
The rewinder will be used on Qifeng’s No 27 special paper line at its Guigang plant in the Guangxi Autonomous Region.
The machine, equipped with spool parking, automatic core gluing and a dust removal system, has been designed to process jumbo rolls of decorative paper with a diameter of 2.8 metres and a width of 3.86 metres at a design speed of 2,000 metres per minute.
“The collaboration between Qifeng Group and A.Celli began in 2009 with the supply of an AC842 rewinder. We are very honoured to have received the support of this important
partner for more than ten years. The establishment of a new production line in Guangxi is an important regional strategy of Qifeng Group and, thanks to it, we will achieve even higher achievements,” said Li Andong, general manager of Qifeng group, which was founded in 1976. Its main products are decorative base paper, wearresistant paper and nonwoven wallpaper base paper.
The world’s largest kraftliner machine has been started up by Voith at SCA’s Obbola mill in Sweden.
The machine has the capability to produce 725,000 tons of high-quality kraftliner per year. Compared to the line it replaced, the Voith machine increases SCA´s production capacity by 270,000 tons.
“Thanks to the excellent cooperation with Voith, the start-up of the most modern kraftliner machine took place ahead of schedule,” says Per Strand, project director at SCA commenting on the SEK 7.5bn project that started in 2019. “With this high-tech plant, we are setting new standards in the market. We are very pleased to have chosen Voith as our full-line supplier. The highly efficient solutions reduce our resource consumption and enable maximum productivity with the lowest overall production costs.”
Voith supplied the complete line, the basis of which is an XcelLine paper machine with a design speed of 1,400 metres per minute, a wire width of 10.2 metres that produces kraftliner with basis weights of between 100 and 200gsm.
Voith is also responsible for the automation of the line and all relevant auxiliary systems, from hall ventilation to roll transport, and together with Meri for a water and wastewater management system.
The XcelLine paper machine will be supplemented by a new BlueLine stock preparation
SCA’s mill at Obolla in Sweden, now home to the world’s largest kraftliner machine with capacity for 725,000 tons a year system, which is scheduled to replace the existing system next year. Voith has supported the SCA team throughout the start-up with a comprehensive training programme. In addition, SCA relies on a long-term service and efficiency partnership with Voith, resulting in maximum productivity from the line.
For the production of paper, SCA sources virgin fibre from its own forests which cover 2.6 million hectares, and are said to capture 10.5 per cent of Sweden’s total carbon dioxide emissions each year.
Furthermore, the new OCC plant is focusing on sustainable production. Voith’s BlueLine stock preparation plant is said to save up to 40 kWh per ton produced compared to conventional plants. The fresh water requirement is around 30 per cent lower than the previous production.
To ensure high production line
availability, SCA also ordered a spare and wear parts package from Voith and its subsidiary Meri.
“It was very good that we started the spare parts process so early,” says Per Asplund, project manager at SCA. “Everything went smoothly and efficiently. In addition, the good documentation from the technical teams helped us a lot. Now we have a perfectly matched package that also meets the highest standards in terms of safety.”
Europe’s largest forest owner, SCA operates a pulp mill at Östrand and two kraftliner mills at Obbola and Munksund, also having businesses in wood pellets, wind energy, liquid biofuels, wood products and logistics. Based at Sundsvall in Sweden, SCA has 4,000 employees and sales of about SEK18.8bn a year.
Xianhe has ordered moisturising technology from Andritz for its two new paper making machines at its Shishou mill in Hubei province.
The machines will daily produce 300 tons of décor paper with a width of 3,860mm and at a speed of 1,000 metres per minute
With installation expected in the second half of 2023, the VIB MoistureTech moisture spray will be installed below the last cooling cylinder to increase the paper moisture up to 3.5 per cent with a 2-sigma value below 0.1 per cent.
VIB MoistureTech will also be
used for conditioning and curl control on laminated grades and silicone papers.
Södra Cell has ordered four PulpEye analysers for quality inspection online at its Swedish pulp mills at Mönsterås, Mörrum and Värö.
The three mills make Södra Cell a world-leading producer of market pulp, the bulk of its production consisting of bleached paper pulp, both long and short fibre. Textile pulp is also produced at the Mörrum pulp mill.
At the Mönsterås and Värö mills, two of the PulpEye analysers will also have samplers for measuring fibre dimensions
as well as coarseness and kinks. At Mörrum, two PulpEye units will be installed for measuring fibre dimensions as well as coarseness and kinks, plus one
module measuring fibre wall thickness based on the Canadian research institute FPInnovation’s patent.
“We have a unique system for
Final construction work is being carried out at UPM’s new pulp mill at Paso de los Toros in central Uruguay with the expectation that operations will start before the end of March.
The greenfield project, first announced in July 2019, will increase UPM’s capacity by
2.1 million tonnes a year of eucalyptus pulp in addition to the 3.7 million tonnes yearly produced by UPM at its four mills: Fray Bentos in Uruguay, and Kaukas, Kymi and Pietarsaari in Finland.
UPM says that the project work continues intensively and the
finalisation of the construction works is an important milestone in the project. Since the work started, more than 20,000 people have been involved in the various construction sites related to the investment, including the construction of the pulp mill, the pulp terminal in the port of
online classification of our pulps and here the analysis data from the PulpEye modules will provide important input,” says Annica Larsson Ahlstedt, head of product quality at Södra Cell.
“As a large producer of highquality paper pulps and dissolving pulp, it is important to use modern analytical technology to be able to manufacture pulp products of consistent and high quality for our customers.”
Södra Cell is also a significant producer and supplier of biofuels, green electricity, district heating and raw materials for biofuels.
Montevideo and the 11 housing areas around Paso de los Toros. The project now proceeds with the finalisation of the electrical, instrumental and automation works and commissioning. The auxiliary and power boilers have been commissioned. Water intake and water treatment process as well as the process air system are already in use. The recovery boiler testing has started and is advancing well, and commissioning is progressing in all process areas, says UPM.
UPM is one of the world’s leading producers of northern softwood, birch and eucalyptus pulp, supplying global customers in segments such as tissue, speciality, packaging and graphic papers, and board in the APAC region and Europe.
Sappi Europe has started upgrading and modernising the paper making lines at its Gratkorn mill in Austria. The mill is claimed to be Europe’s leading producer of coated woodfree paper on two machines, supporting Sappi Europe’s core commercial print business. The mill has benefited from a regular investment programme, including in recent years the upgrade of PM9 in 2019.
The current upgrade and modernisation project will focus on PM11, which will undergo extensive modernisation of automation and electrical equipment including drives, control systems, quality control
and inspection systems as well as upgrades to the coating profile and other areas.
Key components for the broke handling system on PM9 will be supplied by Andritz, high-consistency (HC) pulping, high-density (HD) cleaning and deflaking for processing the special type of broke.
Flavio Froehli, vice president of marketing & sales at Sappi Europe, says: “We are very pleased that we will also be able to produce wet-strength label paper at our Gratkorn mill in the future. This investment underscores our strategy to establish Sappi as the leader within the label sector, adding to the supply of value
adding products across our entire business.”
During the preparatory phase in December 2022 and the main period of work in January, production on PM11 was interrupted for a number of weeks. Some interruption will also occur on PM9 due to the need for a reorganisation of internal logistics. The Gratkorn mill yearly produces 950,000 tons of highquality, double- and triple-coated papers, used for premium quality publications worldwide, as well as one-side coated label papers. The mill also produces 250,000 tons per year of chlorine-free (TCF) bleached chemical pulp for its own consumption and it has an annual sheet finishing capacity of 875,000 tons.
Lipy Paper Mills in Bangladesh has ordered wastepaper processing systems for its mills in Changine, Modonpur, Kanchpur, Sonargaon.
Andritz will be supplying RCF (Recycled Fiber) systems, the first of their type to be used in the Asian country.
The two lines will have capacity to daily process 150 tons of local old corrugated containers and mixed office waste as raw material
for production of testliner, writing and printing paper.
Shahiar Hasan Khan, deputy managing director of Lipy Paper Mills says: “Andritz convinced us because of its energy-saving technology for screening and flotation and its focus on minimum fibre loss. In addition, with the Ultra High Dispersion we’ll be able to keep steam demand at a low level. All these topics are strategic development targets for an aspiring company like Lipy Paper Mills.”
● Two tissue machines were started up after rebuilds by Toscotec at mills in North and South America on the same day in November 2022. In both projects, the scope of the modifications was said to be extensive, covering the wet and the dry section of the two lines.
Toscotec project manager Andrea Paganucci commented: “One of the most challenging aspects on this large rebuild was the integration of Toscotec’s key components with the existing equipment. Creating an effective interface between different systems requires strong multistakeholder coordination. We are happy that the machine is now running efficiently as expected.”
● GrandBay Papeles Nacionales has ordered an Ahead 2.2 tissue line (PM5) from Toscotec for its Pereira mill in Colombia. It is Toscotec’s second project with GrandBay which is currently installing an Ahead 2.2L tissue line at GrandBay Papelera Internacional in Guatemala. The PM5 will have capacity for 40,000 tons a year when it starts up in 2024.
Cesar Solano, chief executive of GrandBay Group, says, “Continuing to grow with the market, satisfying the needs of the consumers with products of the best quality and accompanying the growth of our clients are guiding principles of our vision, which are supported by investment in the best technology.”
● The cooking, fibreline and evaporation plant at Andhra Paper’s Rajahmundry mill in India is to be rebuilt by Valmet with start-up planned for the first quarter of 2024.
“With this investment, we will be able to improve our cost competitiveness and profitability as well as increase production at our Rajahmundry mill. In line with Andhra Paper’s commitment to sustainable development, the processes will be based on the best available technology and the use of state-of-the-art equipment, such as Valmet TwinRoll press and Valmet Tube Evaporator effect with vent condenser,” says Nageswara Gadde, vice president of projects at Andhra Paper.
Andhra Paper’s mills at Rajahmundry and Kadiyam have combined production capacity of 240,000 tons per year.
Brazilian pulp producer Suzano has ordered a concentrated sulphuric acid plant from Andritz for its new Ribas do Rio Pardo mill in Brazil (see PPL NovDec 2022).
With start-up scheduled for the second half of 2024, the SulfoLoop plant will have the capacity to produce 153 tons of commercial grade (more than 97 per cent) sulphuric acid per day from the pulp mill’s concentrated
odorous gases and elemental sulphur, making the mill completely self-sufficient in sulphuric acid and recycling sulphur from waste streams. The plant will help to control the sodium and sulphur (Na/S) balance and the sulphidity of the pulp mill. Also, the resource-efficiency of the mill will be improved because less sulphate needs to be discharged.
With the retirement
Greg Wanta, senior vice president of International Paper’s North American Container business, the company has made a number of leadership changes.
Mark Sutton, chief executive of International Paper, paid tribute to Wanta: “I want to thank Greg for his 31 years of service and wish him well in his retirement.
Greg led the North American Container business since 2016 and his contributions to the company are foundational to our growth plans.”
The following leadership moves were made at the beginning of January:
Tom Hamic becomes commercial
Mary Lynn Ferguson-McHugh has joined the board of Smurfit Kappa Group (SKG), one of the world’s largest manufacturers of paper-based packaging products, with operations in Europe and the Americas.
A US citizen, Ferguson-McHugh retired from Procter & Gamble in 2021 after more than 35 years with the FMCG giant. She held a number of senior leadership positions there, including most recently roles as chief executive of Family Care (Paper Products) and
chief at North American Container.
Hamic joined the company in 1991 and most recently led significant commercial and financial improvements in the company’s Global Cellulose Fibers business.
Jay Royalty becomes senior vice president at Containerboard and Recycling, and retains interim responsibility for IP’s EMEA Packaging business. Jay also joined IP in 1991 and most recently served as senior vice president at EMEA Packaging.
P&G Ventures.
Ferguson-McHugh has also been a non-executive director of Molson Coors Beverage Company, the brewer and soft drinks producer, since 2015.
Chairman of SKG Irial Finan commented: “We are delighted to welcome Mary Lynn to the Board of Smurfit Kappa. Mary Lynn brings significant global operational experience and fast-moving consumer goods knowledge to SKG. Her insight and expertise will add greatly to the board.”
Brigitte O’Connor has joined Monadnock Paper Mills as its south east regional sales manager.
Based in Bennington, New Hampshire, and the oldest continuously operating paper mill in North America, Monadnock
Clay Ellis becomes senior vice president at Global Cellulose Fibers. Clay joined the company in 1992 and most recently served as senior vice president at Enterprise Operational Excellence.
“These moves reflect our leadership bench strength,” said Sutton. “Each of these business leaders have demonstrated strategic agility and drive in achieving industry-leading results.”
Two appointments have also been made to Sutton’s leadership team:
Aimee Gregg has been elected senior vice president at Supply Chain and Information Technology. Gregg joined the company in 2002 and most recently served as general manager at Containerboard and
Recycling.
Allison Magness has been elected senior vice president at Manufacturing and Environment, Health and Safety. Magness joined the company in 2000 and most recently served as vice president, South Area, North American Container.
“I’m excited about what’s next for our company with the diverse talent and perspective of our senior leaders guiding plans to Build a Better IP,” Sutton added.
paper industry, as operations director.
Buccieri has spent 36 years of his career with companies that include Solenis, Fontoura Wyeth, Sherwin Williams, Rhodia and Grupo Imerys.
manufactures
O’Connor has more than 25 years of experience in the industry with a strong background in graphic communications, paper, packaging and printing. Most recently, she was a senior account executive for Standard Press in Atlanta, Georgia.
Marcelo Buccieri has joined Contech Biodegradable Products, the Brazil-based speciality chemical supplier to the pulp and
“Our main objective is to ensure that Contech continues to be one of the main references in the Pulp and Paper segment and that it can increasingly contribute to sustainability, reducing the operating costs of the factories and increasing the productivity of the machines, a of the intrinsic characteristics in Contech’s DNA,” says Buccieri.
Evolving market demands require agility and efficiency for mills to deliver products on spec and on time. Trust ABB and our MES specifically designed for pulp and paper to help you deliver the best operational results. Our comprehensive and modular solution covers all the core MES functionalities across the value chain, helping you achieve new levels of operational efficiency.
Learn more: abb.com/pulpandpaper