La Metallurgia
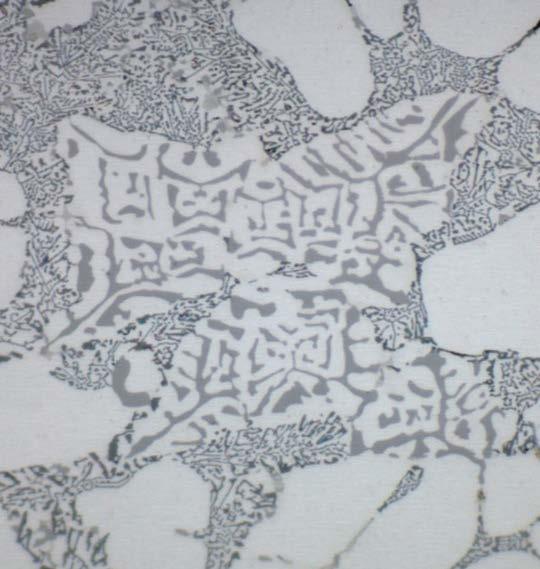
International Journal of the Italian Association for Metallurgy
n.04 aprile 2023
Organo ufficiale dell’Associazione Italiana di Metallurgia.
Rivista fondata nel 1909
International Journal of the Italian Association for Metallurgy
Organo ufficiale dell’Associazione Italiana di Metallurgia. HouseorganofAIMItalianAssociationforMetallurgy. Rivista fondata nel 1909
Direttore responsabile/Chiefeditor: Mario Cusolito
Direttore vicario/Deputydirector: Gianangelo Camona
Comitato scientifico/Editorialpanel:
Marco Actis Grande, Silvia Barella, Paola Bassani, Christian Bernhard, Massimiliano Bestetti, Wolfgang Bleck, Franco Bonollo, Irene Calliari, Mariano Enrique Castrodeza, Emanuela Cerri, Vlatislav Deev, Andrea Di Schino, Donato Firrao, Bernd Kleimt, Carlo Mapelli, Denis Jean Mithieux, Roberto Montanari, Marco Ormellese, Mariapia Pedeferri, Massimo Pellizzari, Barbara Previtali, Evgeny S. Prusov, Dario Ripamonti, Dieter Senk
Segreteria di redazione/Editorialsecretary: Marta Verderi
Comitato di redazione/Editorialcommittee: Federica Bassani, Gianangelo Camona, Mario Cusolito, Carlo Mapelli, Federico Mazzolari, Marta Verderi, Silvano Panza
Direzione e redazione/Editorialandexecutiveoffice: AIM - Via F. Turati 8 - 20121 Milano tel. 02 76 02 11 32 - fax 02 76 02 05 51 met@aimnet.it - www.aimnet.it
Reg. Trib. Milano n. 499 del 18/9/1948. Sped. in abb. Post. - D.L.353/2003 (conv. L. 27/02/2004 n. 46) art. 1, comma 1, DCB UD
Immagine in copertina: Composto intermetallico ricco in ferro in una lega secondaria di alluminio Fonte: Giulio Timelli
Gestione editoriale e pubblicità Publisher and marketing office: siderweb spa sb
Via Don Milani, 5 - 25020 Flero (BS) tel. 030 25 400 06 - fax 030 25 400 41 commerciale@siderweb.com - www.siderweb.com
La riproduzione degli articoli e delle illustrazioni è permessa solo citando la fonte e previa autorizzazione della Direzione della rivista. Reproduction in whole or in part of articles and images is permitted only upon receipt of required permission and provided that the source is cited.
siderweb spa sb è iscritta al Roc con il num. 26116
n.04 aprile 2023
Anno 114 - ISSN 0026-0843
Memoriescientifiche/Scientificpapers
Legheleggere/LightAlloys
EffettodiNaCl,KCleNa3AlF6nelprocessodirefiningdelleleghedialluminio
V.Milani,S.Capuzzi,G.Timelli .pag.07
CrescitadiLDHsullalegaAZ31perapplicazioniinortopedia
M.Ceccarelli,C.deCrescenzo,R.Montanari,R.Narducci,M.Richetta,A.Varone.........................................pag.17
ProduzioneecaratterizzazionedirivestimentiPEOconproprietàotocatalitiche contenentipolveridiTiO2darifiuto
L.Pezzato,E.Colusso,P.Cerchier,A.G.Settimi,A.Martucci,M.Dabalà,K.Brunelli........................................pag.26
Characterization of the Solidification Path and Microstructure of AlSi7Cu3Mg0.3 Alloy with Gd Content
O. Gursoy, G. Scampone . pag.34
Influenza delle caratteristiche dello strato nanoporoso di allumina sul comportamento tribologico della lega di alluminio EN AW-6082 trattata secondo un innovativo processo di ossidazione anodica
E. Baroni, A. Fortini, C. Soffritti, M. Merlin, G. L. Garagnani . pag.41
Addition of aluminum anodizing waste in different kinds of friction material formulations
Jayashree, G. Straffelini................................................................................................................................. pag.53
Attualità industriale / Industry news
Progettazione e utilizzo di un sistema sensorizzato a supporto del processo produttivo di pressocolata a cura di: A. De Mori, G. Scarpa............................................................................................... pag.65
ProduzionediPlatinoMalleabile:daiprimiprocessidisinterizzazionesupolverialle odiernetecnichedifusione acuradi:I.Ciabatti,C.Zambardi..........................................................................................................................................pag.76
Le aziende di AIM/AIM's companies Economia circolare
cura di: F. Mazzolari, P. F. Pepi - Arvedi ........................................................................................................................... pag.85
Atti e notizie / AIM news
Si può parlare di metalli leggeri e di leghe leggere a proposito del magnesio e delle sue leghe (densità pari al 25% di quella dell’acciaio); dell’alluminio e delle sue leghe (35%); del titanio e delle sue leghe (60%). È evidente come proprio la leggerezza abbia svolto, e svolga tutt’oggi, un ruolo chiave per lo sviluppo applicativo di magnesio, alluminio e titanio e delle loro leghe. Il fatto che le leghe leggere siano state tradizionalmente associate all’industria aeronautica e aerospaziale ha di fatto oscurato la loro crescente importanza come materiali ingegneristici. Ad esempio, l’alluminio è oggi il secondo metallo più utilizzato e si prevede che nei prossimi due decenni la sua produzione aumenti ad una velocità superiore a qualsiasi altro materiale utilizzato per applicazioni strutturali. In virtù della loro leggerezza, si continuano ad avere importanti applicazioni nei settori più svariati, ad esempio, dei trasporti, dell’elettronica e dell’imballaggio. Nel
We can talk about light metals and light alloys in terms of magnesium and its alloys (25% density of that of steel); aluminum and its alloys (35%); titanium and its alloys (60%). It is evident that lightness has played, and still plays, a key role in the application development of magnesium,aluminumandtitaniumandtheiralloys.The fact that light alloys have traditionally been associated with the aviation and aerospace industry has effectively obscured their growing importance as engineering materials. For example, aluminum is now the second most used metal, and its production is expected to increase at a faster rate than any other material used for structural applications in the next two decades. By virtue of its lightness, there continue to be important applications in a wide range of sectors, for example, transportation, electronics and packaging. In the automotive field, the development of new magnesium alloys has enabled an improvement in the
"Ricerca e innovazione nell’ambito delle leghe leggere non si sono certo arrestate ma stanno progredendo con la crescente formazione di reti di ricerca collaborative nazionali e internazionali."Prof. Giulio Timelli Università di Padova - DTG, Vicenza
“Research and innovation inthefieldoflightalloys havecertainlynotcome to a standstill but are progressingwiththe increasingformationof national and international collaborative research networks.”
campo automobilistico, lo sviluppo di nuove leghe di magnesio ha permesso un miglioramento della processabilità di tali materiali e un’ottimizzazione della progettazione, mentre l’alluminio garantisce un minor peso dei veicoli e conseguentemente una riduzione di emissione di gas inquinanti. Dall’altro lato, il settore aeronautico e spaziale si avvale delle caratteristiche chimico-fisiche e meccaniche del titanio e delle sue leghe per la realizzazione di motori e parti strutturali dei velivoli. Ad oggi, le leghe leggere risultano forza motrice di uno sviluppo che non ha eguali in termini di volumi produttivi. Nel 2022, si annoverano nel mondo circa 1 Mt di magnesio, 69 Mt di alluminio e 260.000 t di titanio utilizzati nei più svariati campi applicativi. Nonostante questi risultati consolidati, ricerca e innovazione nell’ambito delle leghe leggere non si sono certo arrestate, come testimoniano le memorie raccolte in questo numero della rivista, ma, al contrario, stanno progredendo con la crescente formazione di reti di ricerca collaborative nazionali e internazionali.
processability of these materials and optimized design, while aluminum ensures a lower vehicle weight and consequently reduced emissions of pollutant gases. On the other hand, the aeronautical and space sector takes advantage of the chemical-physical and mechanical properties of titanium and its alloys to make engines and structural parts of aircraft. To date, light alloys prove to be the driving force behind a development that is unparalleled in terms of production volumes. In 2022, there are approximately 1 Mt of magnesium, 69 Mt of aluminum and 260,000 t of titanium used in a wide variety of application fields worldwide. Despite these consolidatedresults,researchandinnovationinthefield of light alloys have certainly not come to a standstill, as evidenced by the papers collected in this issue of the magazine, but, on the contrary, are progressing with the increasing formation of national and international collaborative research networks.
GENOvA - ITALY
may 2023
CONFERENCE VENUE
Genova sits in a prime location, which encompasses the waterfront, centre and port. The city has always been a place of exchange, gatherings, trade and invention, and it is among the most musical Italian cities in terms of the number of musicians and singer-songwriters born and bred there. It offers an endless array of gastronomic specialities, imitated all around the world.
EXHIBITION & SPONSORSHIP
It is now possible to register to the event!
Organised by
in cooperation with
COMITATO ITALIANO DEI COSTRUTTORI DI FORNI INDUSTRIALI FEDERATA
Per massimizzare l’efficienza nell’utilizzo dei flussi salini durante la fusione del rottame di alluminio è necessario un corretto bilanciamento dei sali impiegati. Questo studio indaga preliminarmente l’influenza di diverse concentrazioni di NaCl, KCl e Na3AlF6 sulle caratteristiche chimico-fisiche dei flussi utilizzati nel processo di refining delle leghe di alluminio. Sono state analizzate la temperatura di fusione e la viscosità del flusso salino, nonché la capacità di dissolvere l’ossido di alluminio, a diverse concentrazioni di NaCl, KCl e Na3AlF6. Si è, inoltre, analizzato il tempo di dissoluzione del flusso salino in acqua dolce. I risultati hanno evidenziato come la temperatura di fusione dei sali diminuisca, mentre la viscosità aumenti al crescere del tenore di criolite nel flusso salino. La capacità di dissoluzione dell’ossido è favorita dall’aggiunta di Na3AlF6, anche a basse concentrazioni e ridotti tempi di trattamento. La dissoluzione dell’ossido consente all’alluminio liquido intrappolato nel rottame di essere liberato venendo così inglobato nel bagno fuso e aumentando la resa del processo. Di contro, la dissoluzione del flusso salino in acqua è ridotta dall'aggiunta di criolite.
Le operazioni di riciclo costituiscono un aspetto fondamentale nell'industria globale dell'alluminio poiché offrono grandi vantaggi rispetto alla produzione di Al primario in termini di costi di produzione [1], consumi energetici [2] ed emissioni di gas serra [3]. Si riduce, inoltre, l'esaurimento di materie prime dal sottosuolo, e questo è un fattore chiave considerando come l'alluminio sia un materiale competitivo in diversi settori e il suo consumo e utilizzo sia ancora in aumento [4].
Le rifusioni del rottame tramite forni rotativi e a riverbero risultano le tecnologie maggiormente utilizzate nella produzione dell’alluminio secondario; queste tecniche risultano utili laddove nella carica sia presente un elevato contenuto di rottame non-metallico [5]. Tali forni consentono un'elevata produttività [6], mentre i forni a crogiolo ed elettrici sono più adatti a volumi produttivi inferiori e a un livello di qualità del rottame superiore [5,7].
La scelta di un adeguato design del forno non è sufficiente per fondere rottami di bassa qualità. Nella carica di rottame si rende necessaria l'aggiunta di composti
chimici chiamati flussi salini, o più comunemente sali. Questi composti sono generalmente cloruri di sodio e potassio. Possono essere utilizzate diverse miscele di questi sali. Tuttavia, una miscela equimolare di NaCl-KCl consente un punto di fusione più basso perché si sviluppa una reazione eutettica a circa 665 °C [8]. Lo scopo del flusso è di proteggere il bagno dall'ossidazione perché il bagno di Al fuso forma rapidamente uno strato di ossido sulla superficie esposta ad un'atmosfera contenente ossigeno [9]; quindi, il flusso salino deve essere allo stato liquido durante la fusione del rottame. Inoltre, una diminuzione della temperatura di fusione significherebbe una riduzione dei consumi energetici e del tempo di trattamento del rottame.
Sebbene una miscela NaCl-KCl prevenga i fenomeni ossidativi, l'aggiunta di altri sali potrebbe aumentare il recupero di metallo. Il flusso raccoglie gli ossidi presenti nel rottame formando così una scoria dove vengono intrappolate gocce di Al metallico [10]. La capacità del sale di favorire la coalescenza di queste gocce diventa una caratteristica importante per determinare il recupero di alluminio. Una goccia di diametro maggiore, risultante dalla coalescenza di goccioline più piccole, aumenta la probabilità di passare dalla scoria nel metallo fuso. In primo luogo, il flusso salino deve rimuovere lo strato di ossido che ricopre le gocce di Al per consentire la coalescenza tra loro. Wang e Brochu [11] hanno dimostrato che il metallo all'interno dello strato di ossido tende ad assumere una forma sferica quando fonde. La differente espansione volumetrica tra il metallo fuso e l'ossido crea piccole crepe nello strato di ossido, ma ciò non è sufficiente per rilasciare l'alluminio liquido contenuto all’interno dell’ossido. Si è pensato che vari sali aggiunti alla miscela NaCl-KCl aumentino lo stripping dell'ossido e di conseguenza la coalescenza delle gocce. Tutti i risultati disponibili in letteratura concordano sul fatto che i fluoruri possono portare a questo specifico obiettivo [12-15]; in particolare, il fluoruro di sodio (NaF), il fluoruro di potassio (KF) e la criolite (Na3AlF6) offrono ottimi risultati secondo Roy e Sahai [16] e Friesen et al. [17].
Il modo in cui agiscono i fluoruri non è noto completamente e vengono proposti vari meccanismi. Peterson [18] ha considerato la solubilità dell'allumina nel sale fuso; Jordan et al. [19] e Storchai et al. [20] hanno
proposto un comportamento elettrochimico in base al quale l'alluminio agirebbe come un anodo, l'ossido fungerebbe da catodo e il flusso salino da elettrolita. La tensione all’interfaccia tra il metallo e il flusso salino viene spesso proposta come principale criticità. Ridurre al minimo tale tensione aumenta l'affinità tra il metallo e il sale, e facilita la rimozione dello strato di ossido [21]. Tenorio ed Espinosa [22] hanno suggerito che lo stripping dello strato di ossido di Al per mezzo del flusso salino avvenga secondo un meccanismo simile a un processo di corrosione a caldo.
Una volta che il metallo fuso viene rilasciato dallo strato di ossido, le gocce di Al devono poi potersi muovere per coalescere. La viscosità è la proprietà della scoria che controlla principalmente tali movimenti. Aumentandone la viscosità, il movimento delle gocce risulterebbe più difficoltoso. Sia il sale che l'ossido influiscono sulle proprietà finali della scoria. È stato dimostrato da Tenorio et al. [23] che l'aggiunta di NaF e KF diminuisce la viscosità della miscela equimolare di NaCl e KCl da 1.2·10-3 Pa·s (1.2 cP) a 0.4·10 -3 Pa·s (0.4 cP). Un incremento della viscosità della scoria è stato osservato da Xiao et al. [24] durante l’aggiunta di componenti non-metalliche nel sale. La viscosità è maggiore di 1000 cP se il contenuto di componenti non-metalliche è superiore al 10%.
Infine, le scorie solide ottenute dal processo di recycling dell’alluminio sono un rifiuto pericoloso e prendono il nome di massi salini o “salt cakes”. Due sono le possibilità di gestione dei massi salini: la separazione dei componenti presenti nelle scorie per un eventuale recupero, o lo stoccaggio in discariche speciali. A causa delle limitazioni legislative e in un’ottica di sostenibilità ed economia circolare, lo smaltimento dei massi salini sarà sempre più limitato o vietato nel prossimo futuro [25]. Il recupero dei massi salini prevede la separazione dei sali dalla massa non-metallica tramite la dissoluzione dei sali stessi in acqua. Perciò, la capacità dei flussi di dissolversi è un fattore chiave per ridurre il consumo di acqua e di tempo.
In questo lavoro sono state studiate alcune proprietà chimico-fisiche di miscele formate da NaCl-KCl-Na3AlF6.
In particolare, sono state studiate la temperatura di fusione, la viscosità, la capacità di dissoluzione dell’ossido di Al e la tendenza alla lisciviazione nel tempo dei flussi salini. Sono stati, inoltre, considerati gli effetti della temperatura e del tempo di mantenimento sulla viscosità
e sulla dissoluzione dell'ossido.
Le indagini sono state svolte su flussi salini composti da una miscela di NaCl-KCl-Na3AlF6 a diverse concentrazioni, come illustrato in Tabella 1. La concentrazione di Na 3AlF6 è stata variata nel range 0÷20 %pond., mentre il rapporto
NaCl / KCl è rimasto costante. Sono state utilizzate diverse tecniche per studiare le principali proprietà chimicofisiche del sale. Nel dettaglio, l'analisi termica è stata eseguita per indagare la cristallizzazione dei sali, mentre è stato scelto il metodo del body falling per misurarne la viscosità. È stata, inoltre, studiata la dissoluzione dell'allumina nei sali e di questi poi in acqua.
Tab.1 - Composizione chimica dei diversi flussi salini analizzati (%pond) / Chemical composition of the salt fluxes investigated (wt.%)
L'analisi termica è stata eseguita per valutare le temperature di fusione dei diversi flussi salini. Il sale è stato fuso in un forno a muffola a 900 ± 3 °C e versato in una tazza cilindrica di acciaio, il cui diametro e altezza erano rispettivamente di 30 e 50 mm. Prima di colare il sale, la tazza è stata preriscaldata a 800 ± 3 °C per raggiungere una velocità di raffreddamento inferiore a 1 °C/s.
Durante la cristallizzazione del sale, sono state misurate le curve di raffreddamento tramite l’ausilio di una termocoppia di tipo K (Chromel–Alumel) posta al centro della tazza, e i dati sono stati raccolti utilizzando un sistema di acquisizione, con una frequenza di campionamento di 0.5 s-1. Durante gli esperimenti, la termocoppia è stata protetta tramite un tubetto in acciaio AISI 304 in modo
da consentirne l'utilizzo in tutte le prove. La derivata prima è stata, quindi, calcolata per ciascuna coppia di valori di temperatura e tempo. L’analisi delle curve di raffreddamento e delle rispettive derivate hanno permesso di determinare le temperature di nucleazione (Tnuc), minima (Tmin) e di crescita (TG) per i diversi flussi salini. Sono state, inoltre, determinate la temperatura di nucleazione eutettica (Teut) e la temperatura di solidus (Tsolidus) dei diversi sali.
I test di viscosità sono stati eseguiti mediante il metodo del body falling [26] basato sulla legge di Stokes. La viscosità di un fluido è correlata alla velocità di una sfera lasciata cadere all’interno del fluido stesso tramite l'equazione:
dove η è la viscosità, rs e ρ s sono rispettivamente il raggio e la densità della sfera, ρ f è la densità del fluido, g è l'accelerazione di gravità e vs è la velocità di caduta. Si è assunto che durante la prova agisca solamente la forza di gravità, mentre l'espansione termica del sale è stata considerata tramite l’ausilio dell’equazione [27]:
dove d s è il diametro della sfera e D è il diametro del tubo. Bacon [27] ha affermato che l’eq. (2) è valida solo quando il rapporto tra i diametri ds/D è inferiore o uguale a 0.1.
In questo lavoro, sono state utilizzate sfere di nitruro di silicio con un diametro pari a 3 mm, mentre il flusso salino ha agito come fluido contenuto all’interno di un tubo al quarzo con diametro interno di 30 mm e posto all'interno di un forno a muffola. Le prove sono state eseguite a 790 ± 3 °C e 810 ± 3 °C. Il sistema è stato calibrato rispetto ai dati presenti in letteratura e riferiti al flusso salino 95NaCl–5KCl testato a 810 °C [28], ed è stato trovato un fattore di correzione pari a 0.102.
DISSOLUZIONE DELL’OSSIDO DI ALLUMINIO
Una sfera di allumina del diametro di 6 mm è stata posta
all'interno di un crogiolo ceramico insieme a 30 g di flusso salino variato in base alle condizioni sperimentali. Gli esperimenti sono stati eseguiti in un forno a muffola impostato a 810 ± 3 °C. Per ciascun sale sono stati considerati vari tempi di mantenimento, i.e. 10, 30, 40 e 60 minuti. La sfera di allumina è stata estratta dal sale, una volta cristallizzato, sciogliendo il sale stesso in acqua. Ciascuna sfera è stata pesata prima e dopo l'esperimento e la dissoluzione dell'ossido è stata stimata come riduzione di peso della sfera di allumina secondo:
dove wis e wfs sono il peso iniziale e finale della sfera di allumina. Ciascun esperimento è stato ripetuto almeno cinque volte utilizzando ogni volta una nuova sfera.
Dissoluzione del flusso salino
La dissoluzione del sale in acqua è stata studiata in funzione del tempo di permanenza in acqua a temperatura ambiente. Un crogiolo di porcellana riempito con 10 g di flusso salino è stato mantenuto all'interno di un forno a muffola impostato a 810 ± 3 °C per 10 minuti e quindi rimosso per raffreddare in aria calma. Il sale così cristallizzato è stato immerso in un contenitore contenente 0.9 dm 3 di acqua distillata e ivi mantenuto per diversi tempi: 10, 30, 60 e 120
minuti. Il materiale è stato quindi riscaldato a 100 ± 1 °C per rimuovere l'acqua in eccesso. La dissoluzione salina è stata valutata come variazione di peso prima e dopo trattamento in acqua.
Analisi termica
L'aggiunta di criolite influisce sulla cristallizzazione del flusso salino, come mostrato in Figura 1. Il tempo necessario per raffreddare il campione da 830 °C a 660 °C aumenta da 470 s per il Flusso 1 (95NaCl-5KCl) fino a 700 s se alla miscela viene aggiunto il 20% in peso di criolite (Flusso 4).
La Tabella 2 riassume le temperature caratteristiche di cristallizzazione dei diversi sali. La temperatura di nucleazione della miscela 95NaCl-5KCl è in accordo con quanto presente in letteratura [29]. Le temperature caratteristiche del sistema ternario NaCl-KCl-Na3AlF6 differiscono marcatamente da quanto si può evincere
dall’analisi del diagramma di fase del sistema binario NaCl-Na3AlF6 [30].
La temperatura di liquidus è un fattore chiave dal punto di vista industriale; una riduzione di questa temperatura implica una riduzione dei consumi energetici e dei relativi costi.
Tab.2 - Temperature caratteristiche di cristallizzazione dei diversi flussi salini analizzati / Chemical composition of the salt fluxes investigated (wt.%)
In letteratura, la determinazione della viscosità dei sali per alcuni sistemi binari è stata eseguita utilizzando codici di calcolo basati sulla dinamica molecolare [31]. Applicare tale metodo nei sistemi ternari è dispendioso a causa della complessità computazionale. Perciò, misurare sperimentalmente la viscosità dei flussi salini ternari risulta più conveniente.
Un esempio di prove di body falling eseguite a 810 °C
utilizzando i flussi 1 (95NaCl-5KCl) e 3 (85.5NaCl-4.5KCl10Na3AlF6) è illustrato in Figura 2. La velocità di caduta della sfera diminuisce quando si aggiunge criolite; di conseguenza, il tempo necessario per passare dal limite superiore al limite inferiore, aumenta da 0.34 s a 0.38 s. Una variazione di 0.01 s nel tempo di caduta all'interno delle condizioni sperimentali significa una variazione di viscosità pari a 0.176·10-3 Pa·s (0.176 cP).
La Figura 3 mostra la variazione della viscosità del flusso salino in funzione del contenuto di criolite a 790 °C e 810 °C, rispettivamente. Si può concludere che l'incremento del tenore di criolite nel sale fuso ne aumenti la viscosità che, al contrario, diminuisce all’aumentare della temperatura.
La viscosità del sistema ternario NaCl-KCl-Na3AlF6 è stata poco approfondita in letteratura. Al contrario, l’effetto della criolite sulla viscosità del sale NaCl è stato ampiamente studiato e sono stati trovati andamenti simili a quelle presentati in questo lavoro. Janz e Tomkins [32] hanno studiato la viscosità a 1000 °C del sistema NaCl-Na3AlF6 con un tenore di criolite nel range 6÷71%pond. La viscosità del flusso salino aumenta progressivamente al crescere del tenore di criolite da valori di 0.74·10-3 Pa·s (0.74 cP) a 2.12·10-3 Pa·s (2.12 cP). La stessa tipologia di sale binario è stata studiata da Votava e Matiasovsky [33] usando un pendolo di torsione nell'intervallo di temperatura compreso tra 850 °C e 1050 °C. In questo intervallo termico, la viscosità aumentava al crescere della concentrazione di criolite.
Roy et al. [34] hanno eseguito degli esperimenti sulla densità e viscosità di una miscela equimolare di NaCl-KCl con aggiunte di criolite comprese tra 0 e 2%. Sia la densità che la viscosità aumentavano al crescere del tenore di crioli-
te. Dai risultati sperimentali di questo lavoro, l’aggiunta di criolite produce, nel peggiore dei casi, un aumento della viscosità di 1.5·10-3 Pa·s (1.5 cP) rispetto alla miscela 95-NaCl-5KCl.
Secondo Xiao et al. [24], con un tenore di componenti non-metalliche inferiore al 10% in peso, si raggiunge un incremento della viscosità dieci volte superiore. Perciò l'effetto negativo della criolite sulla viscosità è mascherato da un contributo più significativo fornito dalla componente non-metallica, sempre presente nei flussi salini durante la rifusione del rottame.
La Figura 4 mostra il tempo calcolato di caduta di una goccia di alluminio attraverso i flussi salini analizzati in funzione del raggio della goccia stessa. Il tempo è stato calcolato utilizzando l'eq. (1) e considerando un'altezza di caduta di 100 mm alle due diverse temperature. Si nota una differenza significativa solo con raggi della goccia inferiori a 2 mm anche se il tempo di caduta è, in entrambi i casi, inferiore a 3 secondi.
Fig.4 - Evoluzione del tempo di caduta attraverso il sale fuso di una goccia di Al, lasciata cadere da un’altezza di 100 mm, in funzione del raggio e della temperatura di (a) 790 °C e (b) 810 °C / Evolution of the time needed by an Al drop to fall for 10 cm in the tested salts as function on its radius at (a) 790 °C and (b) 810 °C
La Figura 5 mostra la curva di dissoluzione dell'ossido di alluminio al variare dei flussi salini analizzati. Nell’intervallo temporale studiato, non è stato rilevato alcun effetto di dissoluzione dell’ossido da parte del sale 95NaCl-5KCl, mentre, incrementando progressivamente la concentrazione di criolite, la dissoluzione dell’allumina aumenta ad ogni intervallo temporale analizzato. L’effetto di dissoluzione appare maggiormente evidente nei primi 30 minuti di mantenimento all’interno dei sali, mentre l’andamento sembra stabilizzarsi negli ultimi 30 minuti.
Gli andamenti ottenuti in questo lavoro sono in accordo con quanto trovato nello studio di Tenorio et al. [23] dove è stata studiata la dissoluzione dell’allumina in funzione delle aggiunte di fluoruri, quali NaF, CaF2 e KF. I fluoruri sono qui citati in ordine di efficacia. La leggera differenza in termini assoluti dei valori ottenuti da Tenorio et al. [23] rispetto a quelli presentati in questo studio è da attribuirsi alle diverse tecniche utilizzate. Rimane, comunque, evidente come la dissoluzione dell'allumina aumenti per aggiunte progressive dei fluoruri analizzati.
La Figura 6 mostra la dissoluzione dei diversi sali analizzati in acqua. L'efficienza della lisciviazione dell'acqua si riduce aumentando progressivamente il contenuto di criolite nel flusso salino. Più del 90% del campione di 95NaCl-5KCl è stato dissolto in acqua dopo due ore di trattamento; men-
tre la massa del campione si è ridotta a meno del 20% quando la concentrazione di criolite è del 20%. Questi risultati sono correlabili alla diversa solubilità in acqua dei sali; ad esempio, la solubilità di NaCl e Na3AlF6 è rispettivamente 358 g/l e 0.4 g/l.
In questo lavoro sono state studiate alcune proprietà chimico-fisiche di miscele saline formate da NaCl-KCl-Na3AlF6. Da questo lavoro, si possono trarre le seguenti conclusioni:
• L'incremento progressivo di criolite nel sistema salino NaCl-KCl-Na3AlF6 provoca una diminuzione della temperatura di fusione e un cambiamento significativo della cristallizzazione del sale.
• L'aggiunta di criolite produce un incremento della viscosità del sale fuso, mentre aumentando la temperatura la viscosità diminuisce.
• Un flusso salino di 95NaCl-5KCl non è in grado di dissolvere l’ossido di alluminio nei range temporali studiati in questo lavoro; al contrario, l’aggiunta di criolite facilita la disgregazione dell’ossido.
• La velocità di dissoluzione dell’ossido di alluminio è maggiore nelle fasi iniziali di trattamento, mentre si riduce con il tempo.
• La dissoluzione del flusso salino in acqua è ridotta dall'aggiunta di criolite.
[1] Logozar K, Radonjic G, Bastic M. Resour Conserv Recycl. 2006;49:49-67.
[2] Blomberg J, Söderholm P. Resour Conserv Recycl. 2009;53:455-463.
[3] Sevigné-Itoiza E, Gasola C.M, Rieradevalla J, Gabarrella X. J Clean Prod. 2015;105:253-262.
[4] Capuzzi S, Timelli G. Metals, 2018;8:249
[5] Capuzzi S, Timelli G, Capra L, Romano L. Int J Sust Eng. 2019;12:38-46
[6] Newman P. Mater Sci Forum. 2010;630:103-110.
[7] Whiteley B.E.P. Mater Sci Forum. 2011;693:73-79.
[8] Crepeau P.N, Fenyes M.L, Jeanneret L.J. Mod Cast. 1992;82:28-30.
[9] Wang Y, Li Hu-Tian, Fan Z. Trans Indian Inst Met. 2012;65:653-661.
[10] Tsakiridis P.E. J Hazard Mater. 2012;217-218:1-10.
[11] Wang Z, Brochu L. Alcan 1993.
[12] Besson S, Pichat A, Xolin E, Chartrand P, Friedrich B. In European Metallurgical Conference 2011. (Dusseldorf, 2011), 1-16.
[13] Van Linden J.H.L, Stewart D.L. In Light Metals 1988, Ed. Paul G. Campell Tms: The Minerals, Metals & Materials Society. 1988;173-181.
[14] Capuzzi S, Kvithyld A, Timelli G, Nordmark A, Gumbmann E, Engh T.A. J Sust Metal. 2018;4:343-358
[15] Kim Ye-Si, Yoon Eui-Pak, Kim Ki-Tae, Jung Woon-Jae, Jo Duk-Ho. J Korea Foundry Soc. 2000;20:39-45.
[16] Roy R.R, Sahai Y. Mater Trans. 1997;38:995-1003.
[17] Friesen K.J, Utigard T.A, Dupuis C, Martin L.P. In Lights Metals 1997, Ed. Reidar Huglen Tms: The Minerals, Metals & Materials Society. 1997.
[18] Peterson R.D. In Second International Symposium-Recycling Of Metals And Engineered Materials, Ed. Jan H.L. Van Linden, Donald L. Stewart Jr And Sahai Yogeshwar Tms: The Minerals, Metals & Materials Society. 1990;69-84.
[19] Jordan M.F, Milner D.R. J Inst Metals. 1956;85:33-40.
[20] Storchai E.I, Baranov N.S. Chem Petrol Eng. 1976;12:252-255.
[21] Ye J, Sahai Y. Mater Trans. 1996;37:1479-1485.
[22] Tenorio J.A.S, Espinosa D.C.R. J Light Met. 2002;2:89-93.
[23] Tenorio J.A.S, Espinosa D.C.R, Carboni M.C. J Light Met. 2001;1:195-198.
[24] Xiao Y, Reuter M.A, Boin U. J Environ Sci Heal A. 2005;40:1861-1875.
[25] Gil A, Korili S.A. In Environmental Management, Ed. Santosh Sarkar Intech: Rijeka, Croatia, 2010.
[26] Leblanc G.E, Secco R.A, Kostic M. In The Measurement, Instrumentation, And Sensors: Handbook, Ed. John G. Webster Springer Science & Business Media. 1999;30:1-23.
[27] Bacon L.R. J Frank Inst. 1936;221:251-273.
[28] Janz G.J, Tomkins R.P.T, Allen C.B, Downey J.R. Jr, Gardner J.L, Krebs U, Singer S.K. J Phys Chem Ref Data. 1975;4:871-1178.
[29] Coleman D.S, Lacy P.D.A. Mat Res Bull. 1967;2:935-938.
[30] Madhavan T.P, Matiasovsky K, Danek V. Chemické Zvesti. 1970;25.
[31] Ciccotti G, Jacucci G, Mcdonald I.R. Phys Rev A. 1976;13.
[32] Janz G.J, Tomkins R.P.T. J Phys Chem Ref Data. 1983;12:591-813.
[33] Votava I, Matiasovsky K. Chem Pap. 1973;27:582-587.
[34] Roy R.R, Ye J, Sahai Y. Mater Trans. 1997;38:566-570.
To maximize the efficiency of the fluxes during the refining of the aluminium alloy scrap, a proper balance of the salts is required. This study preliminarily investigates the influence of different concentrations of NaCl, KCl and Na3AlF6 on the chemical and physical properties of the fluxes used during the refining process of the aluminium alloys. The melting temperature and the viscosity of the flux at different concentrations of NaCl, KCl and Na3AlF6 were analysed, as well as the ability to dissolve the aluminium oxide. Furthermore, the dissolution of the flux in water was investigated. The results showed how the melting temperature of the flux decreases, while the viscosity increases as the cryolite content increases. The attitude of dissolving the Al oxide is favoured by the addition of Na3AlF6, even at low concentrations and reduced time of treatment. The dissolution of the oxide allows the liquid aluminium entrapped in the scrap to be released and to return into the molten bath, thus increasing the yield of the refining process. On the contrary, the dissolution of the flux in water is reduced after the addition of cryolite.
KEYWORDS: FLUX, REFINING, SECONDARY ALUMINIUM, VISCOSITY, OXIDE DISSOLUTION, SUSTAINABILITY
Tra i materiali metallici biodegradabili la lega di Mg AZ31 è uno dei più studiati per le applicazioni biomediche. In ortopedia è di particolare interesse per impianti temporanei al fine di evitare un secondo intervento chirurgico per la rimozione. Oltre la biodegradabilità tra i vantaggi di AZ31 ci sono l’eccellente biocompatibilità, l’ottima capacità di osseointegrazione ed un valore del modulo elastico simile a quello dell’osso. Inoltre il Mg è essenziale per il metabolismo in tanti meccanismi biologici e gli ioni Mg2+, che si formano a seguito della sua degradazione, sono di aiuto per la guarigione e la crescita del tessuto. Infine la lega ha un basso contenuto di Al che, in alta concentrazione, potrebbe essere dannoso per il sistema nervoso e gli osteoblasti.
Come altre leghe di Mg AZ31 ha tuttavia lo svantaggio di degradarsi rapidamente in presenza di fluidi biologici per cui è necessario controllare la velocità di corrosione in relazione al processo di guarigione del tessuto osseo. I processi corrosivi possono comportare una riduzione delle proprietà meccaniche dell’impianto con conseguente compromissione della sua funzionalità.
La crescita di LDH (Layered Double Hydroxides) sulla superficie della lega AZ31 ha come scopo non solo quello di ritardare i processi corrosivi ma anche quello di incorporare farmaci che possano essere rilasciati in-situ dall’impianto con azione locale antinfiammatoria, analgesica e antimicrobica. Il materiale svolgerebbe così un ruolo attivo nella guarigione del tessuto osseo.
Questo lavoro riporta e discute i primi risultati di una campagna sperimentale volta ad individuare le condizioni ottimali per la crescita degli LDH sulla lega AZ31 finalizzata ad applicazioni in ortopedia.
PAROLE CHIAVE: LEGHE DI MAGNESIO, AZ31,
In campo biomedico le leghe di Mg sono materiali di grande interesse per impianti temporanei per la loro buona biocompatibilità, proprietà meccaniche e biodegradabilità. Per le applicazioni in ortopedia sono particolarmente importanti l’eccellente osteointegrazione ed il basso valore del modulo elastico, simile a quello dell’osso, che permette di evitare l’effetto negativo dello stress-shielding [1]. Inoltre, il Mg è essenziale per il metabolismo in numerosi meccanismi biologici, essendo un cofattore per tanti enzimi [2], ed infine gli ioni Mg2+ risultanti dalla sua degradazione aiutano la guarigione e la crescita dell’osso.
La richiesta di nuovi materiali per impianti ossei è in rapida crescita per l’aumento di fratture dovute a malattie, incidenti o invecchiamento, che spesso richiedono un
intervento chirurgico. Il problema è maggiormente sentito per le fratture costali, presenti nel 78% di tutti i traumi toraci (dati ISTAT) con una mortalità del 2%. Se la frattura di varie costole coinvolge più settori, in più del 30% dei casi si origina un flap toracico mobile e la mortalità sale al 20%. Fratture multiple, bilaterali e scomposte necessitano di essere trattate chirurgicamente [3]. Oggi i principali sistemi di osteosintentesi sono realizzati con placche e viti bicorticali di Ti, che non sono ottimali per il fissaggio delle costole [4]. Altri approcci basati sull’utilizzo di fili o graffe di Judet, si ancorano al bordo inferiore della costola e possono così danneggiare il nervo intercostale dando luogo a dolore permanente o tumore neurale [5]. Si possono anche usare placche a U, che si vanno a fissare sul bordo superiore della costola mediante viti. Tutte queste tecniche possono portare a serie complicazioni e in ogni caso gli impianti debbono essere poi rimossi con un secondo intervento chirurgico.
Un fissatore fatto con materiale biodegradabile rappresenta pertanto una valida alternativa per immobilizzare le costole durante l’osteosintesi [6] poichè la rimozione dell’impianto dopo la guarigione dell’osso non è più necessaria con significativi benefici per i pazienti e, in termini di costi, per il sistema sanitario nazionale.
Un inconveniente è la rapida degradazione delle leghe di Mg nell’ambiente biologico del corpo umano che porta alla perdita delle proprietà meccaniche con compromissione della funzionalità dell’impianto. In esperimenti con fluidi simulanti quelli del corpo umano le leghe di Mg mostrano bassa resistenza a fatica in presenza di corrosione [7] e allo stress corrosion cracking (SCC) [7-9]. Un ulteriore aspetto negativo risultante dalla corrosione rapida delle leghe di Mg è lo sviluppo di bolle di H e l’alcalinizzazione, che possono dar luogo anche alla necrosi dei tessuti. Al fine di superare tali inconvenienti la ricerca si è principalmente concentrata su due aspetti: (i) l’affinamento del grano per migliorare le proprietà meccaniche, (ii) la calibrazione della composizione di lega e lo studio di rivestimenti superficiali per migliorare la resistenza a corrosione.
Leghe di Mg nanocristalline sono state ottenute con lavorazioni criogeniche [6] oppure tramite processo ECAP [10-13]. Per quanto riguarda il secondo punto, una scelta mirata degli elementi di lega può portare ad un significa-
tivo miglioramento delle proprietà meccaniche e della resistenza a corrosione, tuttavia è necessario tener conto della loro potenziale tossicità [14] per cui lo sviluppo di nuove leghe comporta necessariamente prove specifiche in vitro e in vivo. Tra le leghe di Mg la AZ31 ha il vantaggio di avere un basso contenuto di Al (3 wt%), elemento che, in alta concentrazione, potrebbe essere dannoso al sistema nervoso e agli osteoblasti [15].
Tra i metodi anticorrosione, che sfruttano rivestimenti della superficie delle leghe di Mg, vanno ricordati l’ossidazione con microarco, il dip-coating e l’elettrodeposizione. Una descrizione di dettaglio e una discussione critica di queste e di altre tecniche di rivestimento si può trovare nel lavoro di Wu et al. [16].
In relazione alle fratture ossee debbono essere anche considerati problemi come infiammazione, dolore ed infezioni, che richiedono specifici trattamenti farmacologici. A tale riguardo leghe di Mg con la superficie idoneamente modificata per rilasciare farmaci con un’azione locale antiinfiammatoria, analgesica e antimicrobica potrebbero costituire un’eccellente soluzione, tuttavia molto poco è riportato in letteratura [17-20].
Nel campo delle nanotecnologie, è stato già dimostrato che gli LDH (Layered Double Hydroxides) possono ritardare i processi di corrosione del Mg [21-22]. Le loro potenziali applicazioni nel campo della medicina sono dovute alla buona biocompatibilità, biodegradabilità dipendente dal valore di pH, capacità di scambio anionico e la possibilità di farli crescere su varie superfici metalliche [23-24]. La struttura degli LDH è idonea ad incorporare farmaci, che possono essere rilasciati lentamente mediante scambio con anioni presenti nel corpo umano [25-26]. Questo lavoro riporta alcuni risultati preliminari di uno studio più generale finalizzato a realizzare un fissatore costale [27-28] in lega AZ31 biodegradabile con la superficie modificata mediante crescita di LDH ed incorporazione di farmaci. Lo scopo dell’attività svolta è stato quello di individuare le condizioni sperimentali migliori per la crescita degli LDH sulla lega AZ31.
Gli LDH sono nano-composti lamellari bidimensionali appartenenti alla classe delle argille anioniche (tipo idrotalcite). La loro struttura consiste in strati di idrossidi di me-
tallo carichi positivamente (tipo brucite), che incorporano metalli cationici di- e tri-valenti, circondati da ioni OH- ai vertici della disposizione ottaedrica e con gli atomi idrogeno diretti verso l’interno della regione interstrato, a formare appunto legami idrogeno (vedi schema in Fig. 1). Le regioni interstrato, a carica negativa, contengono anioni di compensazione e molecole di solvatazione.
La sostituzione di cationi metallici divalenti (M2+) con trivalenti (M3+) determina appunto la ripetizione delle lamelle positive intercalate da regioni a carica negativa, con formula stechiometrica (Eq.1)
dove “x” rappresenta il rapporto molare M2+/ M3+, variabile tra 0.20 e 0.40.
Le frazioni nell’interstrato (anioni, molecole d’acqua, specie organiche/inorganiche neutre o cariche) sono debolmente legate e possono essere: i) localizzate durante la crescita della struttura tridimensionale; ii) inserite tramite una sostituzione successiva (per scambi anionico e non-anionico).
Nanostrutture LDH (Zn, Al) sono già state cresciute da noi in passato su fogli di Al [29-30] mediante la tecnica di crescita del film in-situ. In tali casi è stata utilizzata una soluzione nutriente composta, in rapporto 1:1, di cloruro di Zn
(ZnCl2) e esametilenetetrammina (C6H12 N4) in concentrazione 5 mM, per la regolazione del pH. La temperatura del bagno in cui erano immersi i fogli di Al è stata mantenuta costante (80°C) e i tempi del trattamento variabili tra 6 e 24 ore. È stata anche preparata una serie di campioni intercalando anioni , invece che Cl-, usando come sale in soluzione Zn(NO3)2. In Fig. 2 sono riportate immagini SEM relative alla morfologia degli LDH ottenuti in questi esperimenti.
24 ore
Nell’ambito della ricerca a cui questo lavoro si riferisce, si è stabilito di adottare la stessa tecnica di crescita delle nanostrutture citata in precedenza, sostituendo ai fogli di Al, lamierini in lega AZ31. Lo scopo consiste nel modificare le proprietà superficiali della lega, ritardando, grazie al film di LDH, la corrosione del Mg come dimostrato in letteratura [23]. In futuro sarebbe inoltre possibile sfruttare le proprietà di intercalazione degli LDH stessi per sostituire, all’interno della zona inter-lamellare, farmaci antinfiammatori, antibiotici e antidolorifici.
Materiale ed esperimenti
I lamierini di lega AZ31 (Goodfellows) usati in questo lavoro avevano la seguente composizione nominale (in peso): Al 3.1, Zn 0.73, Mn 0.24, Si 0.02, Fe 0.005, Ca 0.001, Mg (resto).
Lo spettro di diffrazione dei raggi X mostrato in Fig. 3 è stato registrato usando la radiazione Cu-K α (lunghezza d’onda λ = 0,1508 nm), con passi 2 ϑ di 0.05° e tempo di conteggio di 5 s per passo.
Le intensità relative dei picchi di diffrazione sono state confrontate con quelle del Mg riportate nel database JCPDS-ICDD [31], file 35-821, corrispondenti al materiale avente grani con orientazione casuale. Da tale confronto risulta
che la lega ha una forte tessitura {002}, cioè i piani basali coincidono in larga misura con la superficie dei lamierini (Fig. 4).
Fig.4 - Rappresentazione schematica dell’orientazione dei grani rispetto alla superficie dei campioni. DL, DT e DN sono rispettivamente le direzioni di laminazione, trasversale e normale / Schematic representation of grains’ orientation with respect of the samples’ surface. DL, DT and DN are the rolling, transverse and normal directions respectively.
I campioni di lega AZ31 sono stati preliminarmente lavati in acqua distillata e sapone, poi immersi in una soluzione in acqua di NaOH 0.1 M per circa 1 minuto, ed infine sciacquati in acqua distillata ed etanolo per 10 minuti. Dopo un ulteriore lavaggio in acqua deionizzata, i campioni sono stati immersi in una soluzione nutriente composta di nitrato di
zinco esaidrato [Zn (NO3)2*6H2O], (5 mM) e urea (15 mM) in 150 mL di acqua distillata e tenuti a 90°C per 12 ore. Infine sono stati raffreddati nella soluzione nutriente, estratti dal reattore, sciacquati in acqua distillata ed etanolo ed asciugati in aria.
Lo stesso procedimento è stato adottato in altri esperimen-
ti dove si sono usati come sali nella soluzione nutriente, invece che nitrato di zinco esaidrato, nitrato di magnesio esaidrato [Mg (NO3)2*6H2O] e cloruro ferrico [FeCl3].
I campioni ottenuti sono stati poi studiati mediante osservazioni di microscopia elettronica in scansione (SEM) e diffrazione dei raggi X.
Dopo il trattamento eseguito con la soluzione nutriente composta di nitrato di zinco esaidrato e urea la superficie della lega AZ31 risulta essere coperta totalmente ed omogeneamente da strutture come quelle mostrate in Fig. 5 (ab). Mentre gli LDH cresciuti su Al (Fig. 2) mostravano una morfologia che ricorda i petali di un fiore in questo caso le strutture sono allungate e di tipo dendritico. La crescita ha
una direzione preferenziale (ramo primario) con rami secondari di diametro di circa 0.5 μ m.
In Fig. 5 (c) si vede la superficie della lega dopo il trattamento con nitrato di magnesio esaidrato: lo strato di LDH depositato è così sottile che sono evidenti irregolarità come le rigature da laminazione, inoltre qua e là sporadicamente si notano degli aggregati di di forma rotondeggiante che osservati a più alto ingrandimento (Fig. 5 d) risultano essere costituiti da fasci di lamelle molto sottili di spessore attorno a 10 nm. La bassa percentuale di Al (il metallo trivalente) al 3.1% in peso nella lega, fa sì che la reazione per la formazione dell’LDH con il catione bivalente Mg2+ sia di bassa entità, giustificando la debole copertura superficiale e la formazione di aggregati con distribuzione ad “isola” osservate al SEM.
Fig.5 - Strutture presenti sulla superficie della lega dopo il trattamento eseguito con la soluzione nutriente composta di nitrato di zinco esaidrato ed urea (a-b), nitrato di magnesio esaidrato (c-d) e cloruro ferrico (e-f) / Structures on the alloy surface after treatment performed with the nutrient solution, consisting of zinc nitrate hexahydrate and urea (a-b), magnesium nitrate hexahydrate (c-d) and ferric chloride (e-f).
La superficie della lega dopo il trattamento con cloruro ferrico non mostra (vedi Fig. 5 e-f) strutture con la morfologia tipica degli LDH. La via del ferro trivalente è stata intrapresa per evitare la presenza di Al nella formazione dell’LDH, proponendo un altro metallo con migliori proprietà di biocompatibilità rispetto a quest’ultimo. Probabilmente nelle condizioni di reazione, si forma dell’idrossido ferrico, come testimoniato dal fatto che la superfice stessa diventa rosso bruno ed insolubile in acqua. Lo sviluppo primario di questo idrossido sottrae il Fe3+ all’ambiente di reazione impedendone la reazione con il Mg della lega per la forma-
zione dell’LDH.
Fig. 6 mostra gli spettro di diffrazione dei raggi X della lega dopo il trattamento eseguito con la soluzione nutriente composta di nitrato di zinco esaidrato ed urea (a), nitrato di magnesio esaidrato (b) e cloruro ferrico (c). In (a) e (c) evidenti a basso angolo due picchi riferibili a LDH mentre in (b) si osservano solo i picchi del Mg a conferma di quanto osservato tramite SEM, cioè lo strato di LDH depositato è molto sottile e i corrispondenti picchi di diffrazione X sono così deboli da non essere rilevabili.
Fig.6 - Spettri di diffrazione dei raggi X della lega AZ31 dopo il trattamento eseguito con la soluzione nutriente composta di nitrato di zinco esaidrato ed urea (a), nitrato di magnesio esaidrato (b) e cloruro ferrico (c) / X-ray diffraction spectra of AZ31 alloy after treatment performed with the nutrient solution, consisting of zinc nitrate hexahydrate and urea (a), magnesium nitrate hexahydrate (b) and ferric chloride (c).
Sulla base di questo studio preliminare possiamo affermare che il trattamento con nitrato di zinco è il migliore tra quelli esaminati, producendo uno strato denso, compatto ed omogeneo di LDH sulla superficie della lega AZ31. In base ad un recente studio di letteratura [20], la presenza stessa di cationi Zn2+ garantisce una superiore attività antimicrobica nel momento del rilascio in soluzione. Questa
proprietà intrinseca del materiale in esame, può evitare il caricamento del preparato stesso con molecole ad attività antimicrobica come ad esempio le cefalosporine [32]. Questo “risparmio” di capacità di scambio ionico permette di aumentare la concentrazione di altre molecole, con differenti proprietà e target come ad esempio il Diclofenac uno dei più conosciuti ed usati farmaci antinfiammatori
non steroidei (FANS) [18]; la presenza poi dello ione nitrato come controione nello spazio interlamellare dell’LDH facilita lo scambio di queste molecole aventi grandi dimensioni.
In futuro, variando tempo e temperatura di reazione, verrà studiata l’influenza di questi due parametri sulla morfologia stessa del materiale in esame, trovando la combinazione più adatta agli scopi del lavoro, in base anche alla capacità di scambio ionico, di rilascio del farmaco e durabilità nelle condizioni.
Questo lavoro riporta i risultati preliminari di uno studio finalizzato a realizzare un fissatore costale in lega AZ31 biodegradabile con la superficie modificata mediante crescita di LDH per l’incorporazione di farmaci. I campioni sono stati preparati mediante immersione a 90°C per 12 ore in soluzioni nutrienti con sali diversi: 1. il nitrato di zinco esaidrato e urea; 2. nitrato di magnesio esaidrato;
3. cloruro ferrico. Sono stati quindi esaminati mediante diffrazione dei raggi X ed osservazioni SEM.
I risultati ottenuti mostrano che il trattamento con nitrato di zinco è in grado di produrre uno strato denso, compatto ed omogeneo di LDH a copertura della lega AZ31.
Il trattamento con nitrato di magnesio esaidrato da luogo ad una debole copertura superficiale con la formazione di aggregati distribuiti casualmente mentre con il cloruro ferrico non si osservano strutture con la morfologia tipica degli LDH.
Si conclude che il trattamento con nitrato di zinco è quello più idoneo a realizzare LDH sulla superficie della lega AZ31. Lo sviluppo futuro di questa ricerca sarà dedicato all’ottimizzazione dei parametri di processo trovando la combinazione tempo di immersione-temperatura del bagno più adatta al fine di ottenere i migliori risultati in termini di capacità di scambio ionico, rilascio dei farmaci e durabilità nelle condizioni.
[1] Tsakiris V, Tardei C, Clinischi Fm, Biodegradable Mg Alloys For Orthopedic Implants - A Review. J. Of Magnesium And Alloys 2021; 9:1884–1905.
[2] Hänzi Ac, Sologubenko As, Uggowitzer Pj, Design Strategy For New Biodegradable Mg-Y-Zn Alloys For Medical Applications. Int. J. Mater. Res. 2009; 100(8):1127–1136.
[3] Mineo Tc, Ambrogi V, Cristino B, Pompeo E, Pistolese C, Changing Indications For Thoracotomy In Blunt Chest Trauma After The Advent Of Videothoracoscopy. J. Trauma 1999; 47:1088–1091.
[4] Bemelman M, Poeze M, Blokhuis Tj, Leenen Lph, Historic Overview Of Treatment Techniques For Rib Fractures And Flail Chest. European Journal Of Trauma And Emergency Surgery: Official Publication Of The European Trauma Society 2010; 36:407–415.
[5] Wu Wm, Yang Y, Gao Zl, Zhao Tc, He Ww, Which Is Better To Multiple Rib Fractures, Surgical Treatment Or Conservative Treatment? Int. J. Clin. Exp. Med. 2015; 8(5):7930–7936.
[6] Ambrogi V, Ceccarelli M, Fixing Plate For Osteosynthesis Of Fractured Ribs, Patent Request N. 102019000005638, Italy, 12/4/2019
[7] Jafari S, Harandi Se, Singh Raman Rk, A Review Of Stress-Corrosion Cracking And Corrosion Fatigue Of Magnesium Alloys For Biodegradable Implant Applications. Jom (J. Occup. Med.) 2015; 67(5):1143–1153.
[8] Jafari S, Raman Rks, Davies Chj, Hofstetter J, Uggowitzer Pj, Leoffler Jf, Stress Corrosion Cracking And Corrosion Fatigue Characterisation Of Mgzn1ca0.3 (Zx10) In A Simulated Physiological Environment. J. Mech. Behav. Biomed. Mater. 2017; 65:634–643
[9] Jafari S, Raman Rks, Davies Chj, Stress Corrosion Cracking Of An Extruded Magnesium Alloy (Zk21) In A Simulated Body Fluid. Eng. Fract. Mech. 2018; 201:47–55.
[10] Peron M, Bertolini R, Ghiotti A, Torgersen J, Bruschi S, Berto F, Enhancement Of Stress Corrosion Cracking Of Az31 Magnesium Alloy In Simulated Body Fluid Thanks To Cryogenic Machining. J. Mech. Behav. Biomed. Mater. 2020; 101:103429.
[11] Linderov M, Vasilev E, Merson D, Markushev M, Vinogradov A, Corrosion Fatigue Of Fine Grain Mg-Zn-Zr And Mg-Y-Zn Alloys. Metals 2017; 8(1):20.
[12] Minarik P, Jablonska E, Kral R, Lipov J, Ruml T, Blawert C, Hadzima B, Chemlík F, Effect Of Equal Channel Angular Pressing On In Vitro Degradation Of Lae442 Magnesium Alloy. Mater. Sci. Eng. C. 2017; 73:736–742.
[13] Peron M, Skaret Pc, Fabrizi A, Varone A, Montanari R, Roven Hj, Ferro P, Berto F, Torgersen J, The Effect Of Equal Channel Angular Pressing On The Stress Corrosion Cracking Susceptibility Of Az31 Alloy In Simulated Body Fluid. J. Mech. Behav. Biomed. Mater. 2020; 106:103724.
[14] Razavi M, Fathi M, Savabi O, Boroni M, A Review Of Degradation Properties Of Mg Based Biodegradable Implants. Res. Rev. Mater. Sci. Chem. 2012; 1(1):15–58.
[15] Zhang S, Zhang X, Zhao C, Li J, Song Y, Xie C, Tao H, Zhang Y, He Y, Jiang Y, Bian Y, Research On An Mg-Zn Alloy As A Degradable Biomaterial. Acta Biomater. 2010; 6:626–640.
[16] Wu W, Wang Z, Zang S, Yu X, Yang H, Chang S, Research Progress On Surface Treatments Of Biodegradable Mg Alloys: A Review. Acs Omega 2020; 5:941−947.
[17] Ambrogi V, Fardella G, Grandolini G, Perioli L, Intercalation Compounds Of Hydrotalcite-Like Anionic Clays With Antiinflammatory Agents--I. Intercalation And In Vitro Release Of Ibuprofen. Int. J. Pharm. 2001; 220:23-32.
[18] Ambrogi V, Fardella G, Grandolini G, Perioli L, Tiralti Mc, Intercalation Compounds Of Hydrotalcite-Like Anionic Clays With Antiinflammatory Agents, Ii: Uptake Of Diclofenac For A Controlled Release Formulation. Aaps Pharm. Sci. Tech. 2002; 3:E26.
[19] Silion M, Hritcu D, Jaba Im, Tamba B, Ionescu D, Mungiu Oc, Popa Im., In Vitro And In Vivo Behavior Of Ketoprofen Intercalated Into Layered Double Hydroxides. J Mater Sci. Mater Med 2010; 21:3009–3018.
[20] Awassa J, Cornu D, Soule S, Carteret C, Ruby C, El-Kirat-Chatel S, Divalent Metal Release And Antimicrobial Effects Of Layered Double Hydroxides. Applied Clay Science 2022; 216:106369.
[21] Guo L, Zhang F, Lu Jc, Zeng Rc, Li Sq, Song L, Zeng Jm, A Comparison Of Corrosion Inhibition Of Magnesium Aluminum And Zinc Aluminum Vanadate Intercalated Layered Double Hydroxides On Magnesium Alloys. Front Mater Sci. 2018; 12:198–206.
[22] Yao Qs, Zhang F, Song L, Zeng Rc, Cui Ly, Li Sq, Wang Zl, Han Eh, Corrosion Resistance Of A Ceria/Polymethyltrimethoxysilane Modified Mg-Al-Layered Double Hydroxide On Az31 Magnesium Alloy. J Alloys Compd. 2018; 764:913–928.
[23] Cai Z, Bu X, Wang P, Ho Jc, Yang J, Wang X, Recent Advances In Layered Double Hydroxide Electrocatalysts For The Oxygen Evolution Reaction. J. Mater. Chem. A 2019; 7:5069–5089.
[24] Yan L, Gonca S, Zhu G, Zhang W, Chen X, Layered Double Hydroxide Nanostructures And Nanocomposites For Biomedical Applications. Mater. Chem. B 2019; 7:5583–5601.
[25] Costantino U, Ambrogi V, Nocchetti M, Perioli L, Hydrotalcite-Like Compounds: Versatile Layered Hosts Of Molecular Anions With Biological Activity. Microporous And Mesoporous Materials 2008; 107:149–160.
[26] Donnadio A, Bini M, Centracchio C, Mattarelli M, Caponi S, Ambrogi V, Pietrella D, Di Michele A, Viviani R, Nocchetti M, Bioinspired Reactive Interfaces Based On Layered Double Hydroxides-Zn Rich Hydroxyapatite With Antibacterial Activity. Acs Biomater. Sci. Eng. 2021; 7:1361−1373.
[27] Ramirez O, Torres-San-Miguel Cr, Ceccarelli M, Urriolagoitia-Calderon G, Experimental Characterization Of An Osteosynthesis Implant, T. Uhl (Ed.), Advances In Mechanism And Machine Science, Springer Nature Switzerland Ag 2019; 73:53–62.
[28] Arreguin Jl, Montanari R, Ceccarelli M, Ambrogi V, Richetta M, Torres-San-Miguel Cr, Varone A, Design Solutions From Material Selection For Rib Fixators. Materials Science Forum 2021; 1016:303–308.
[29] Richetta M, Digiamberardino L, Mattoccia A, Medaglia Pg, Montanari R, Pizzoferrato R, Scarpellini D, Varone A, Falconi C, Orsini A, Kaciulis S, Mezzi A, Soltani P, Surface Spectroscopy And Structural Analysis Of Nanostructured Multifunctional (Zn, Al) Layered Double Hydroxides. Surface And Interface Analysis 2016; 48:514–518.
[30] Richetta M, Ciotta E, Montanari R, Narducci R, Pizzoferrato R, Varone A, Effect Of Al Substrate Microstructure On Layered Double Hydroxide Morphology. J. Of Mater. Sciences 2019; 54:12437–12449.
[31] Jcpds-International Centre For Diffraction Data, Newtown Square, Pa 19073, Usa.
[32] Ryu S, Jung H, Oh Jm, Lee J, Choy J, Layered Double Hydroxide As Novel Antibacterial Drug Delivery System. Journal Of Physics And Chemistry Of Solids 2010; 71:685–688.
Among biodegradable metallic materials, AZ31 Mg alloy is one of the most studied for biomedical applications. In orthopedics it is of particular interest for temporary implants in order to avoid a subsequent surgical removal. In addition to the biodegradability, the advantages of AZ31 include excellent biocompatibility, excellent osseointegration and an elastic modulus value similar to the human bone one. Furthermore, Mg is essential for the metabolism in many biological mechanisms and the Mg2+ ions, which are produced as a result of its degradation, are useful to promote healing and tissue growth. Finally, the alloy contains a low amount of Al which, in high concentration, could be harmful for the nervous system and osteoblasts.
Like other Mg alloys, AZ31 has the disadvantage of quickly degradation in presence of biological fluids, therefore it is necessary controlling the corrosion rate in relation to bone tissue healing process. Corrosion processes can lead to a reduction of the implant’s mechanical properties, compromising its functionality.
The growth of LDH (Layered Double Hydroxides) on the surface of the AZ31 alloy is not only aimed to delay corrosion processes but also to incorporate medicines that can be released in-situ from the implant with local anti-inflammatory, analgesic, and antimicrobial action. The material would thus play an active role in the healing of bone tissue. This work reports and discusses the first results of an experimental campaign aimed at the identification of the optimal conditions for the LDH growth on the AZ31 alloy for applications in orthopedics.
KEYWORDS: MAGNESIUM ALLOYS, AZ31, BIODEGRADABLE MATERIALS, LDH (LAYERED DOUBLE HYDROXIDES)
Nel presente lavoro è stata studiata la possibilità di incorporazione all’interno di rivestimenti PEO di particelle di biossido di titanio TiO2, provenienti da un processo di riciclo di pannelli fotovoltaici dismessi. In particolare tali particelle costituiscono la principale carica del polimero costituente la parte posteriore dei pannelli e sono caratterizzate dal possedere proprietà fotocatalitiche. Le particelle sono state quindi aggiunte in diverse quantità all’elettrolita (una soluzione basica contente silicato di sodio) ed è stata studiata la loro incorporazione nel rivestimento PEO prodotto su di una lega di alluminio 1050 e la possibilità di conferire proprietà fotocatalitiche alla superficie dei campioni. I diversi campioni sono stati dapprima caratterizzati dal punto di vista microstrutturale mediante analisi al microscopio ottico e mediante SEM e XRD e dal punto di vista della resistenza a corrosione mediante prove potenzio-dinamiche. Le proprietà fotocatalitiche delle particelle e, successivamente, dei campioni sono state valutate, con uno spettrofotometro UVvisibile, misurando la degradazione di soluzioni acquose di blu di metilene con esposizione ad una lampada UV. Le particelle sono state inglobate con successo nel rivestimento e la loro presenza non altera le caratteristiche di resistenza a corrosione, che risultano migliorate rispetto al campione non rivestito. Le particelle, inizialmente composte da una miscela di rutilo e anatasio, risultano invece composte solo da rutilo dopo l’incorporazione, a causa delle temperature localmente molto elevate che si possono registrare durante il processo PEO. Nei campioni ottenuti con maggiore quantità di particelle di biossido di titanio (60 e 80 g/l) si osserva un significativo effetto fotocatalitico con una significativa riduzione del blu di metilene.
PAROLE CHIAVE: RIVESTIMENTI, PLASMA ELECTROLYTIC OXIDATION, BIOSSIDO DI TITANIO, PROPRIETÀ FOTOCATALITICHE
INTRODUZIONE
Il processo Plasma Electrolytic Oxidation (PEO) è un trattamento superficiale concettualmente simile al processo di anodizzazione convenzionale, ma nel quale vengono utilizzati elettroliti diversi (alcalino neutro-basico invece di acido) e voltaggi e correnti maggiori. (1,2). Alcune delle caratteristiche principali dei rivestimenti ottenuti mediante PEO sono l’elevata porosità dello strato più esterno e la possibilità di incorporare direttamente all’interno del rivestimento particelle disperse all’interno dell’elettrolita funzionalizzando quindi di conseguenza la superficie del metallo (3,4). In particolare, è possibile incorporare tali particelle mediante semplice aggiunta di queste all’elettrolita usato nel processo. (5). A seconda
della tipologia di particelle utilizzate è possibile conferire caratteristiche particolari al rivestimento e nel dettaglio alcuni autori hanno già riportato la possibilità di conferire proprietà fotocatalitiche alla superficie mediante l’aggiunta di biossido di titanio (6,7), le cui caratteristiche di fotocatalisi son ben note (8).
Obbiettivo del presente studio è analizzare la possibilità di inserire nel rivestimento PEO particelle di biossido di titanio provenienti dal processo di recupero di pannelli solari ed in particolare originariamente contenute come carica nel polimero costituente il retro del pannello. Questo in un’ottica di economia circolare e di recupero di materiale da rifiuto. Sono state quindi dapprima verificate le proprietà fotocatalitiche delle particelle e successivamente quelle dei rivestimenti a seguito dell’incorporazione di queste ultime durante il processo. Si è osservato come per elevati contenuti di particelle incorporate la superficie rivestita presenti delle proprietà fotocatalitiche anche se le temperature raggiunte durante il processo PEO portano alla trasformazione dell’anatasio in rutilo e quindi alla perdita di parte delle capacità di fotocatalisi.
Sono stati utilizzati come substrato per rivestimenti PEO campioni in lega di alluminio 1050. I campioni sono stati preventivamente lucidati con carte abrasive e paste diamantate e sgrassati tramite bagno a ultrasuoni in acetone per 10 minuti. L'elettrolita utilizzato è stata una soluzione acquosa 25 g /l di Na2SiO3 e 2.5 g/l di NaOH con l’aggiunta di varie quantità di particelle di biossido di titanio (0, 10, 20, 40, 60 e 80 g/L).
Le caratteristiche morfologiche e composizionali delle particelle, ottenute dal processo di riciclo di pannelli fotovoltaici dismessi, sono state valutate mediante analisi al microscopio elettronico a scansione (SEM) e XRD.
Il generatore di corrente continua impiegato per il rivestimento PEO è un alimentatore TDK Lambda in grado di erogare 2400W (315V, 8A). Durante il trattamento il campione ha lavorato come anodo mentre il catodo era costituito da una gabbia di acciaio al carbonio. I trattamenti sono stati eseguiti mantenendo costante la densità di corrente e lasciando il potenziale libero di variare. I trattamenti sono stati effettuati lavorando a 0.5 A/cm2 in corrente pulsata (con frequenza di 20 Hz e duty cycle 50% grazie ad un si-
stema di interruttori connesso al generatore). I campioni realizzati sono stati trattati per un tempo di 4 minuti. Dopo il trattamento, i campioni sono stati lavati con acqua deionizzata ed etanolo e asciugati con aria compressa. Le superfici dei vari campioni ottenuti sono state osservate mediate stereo microscopio Zeiss Stemi 2000-C. Sia le superfici che le sezioni trasversali sono state analizzate con un microscopio a scansione elettronica SEM Cambridge Stereoscan LEO 440, dotato di microanalisi Philips PV9800 EDS, al fine di valutare le caratteristiche morfologiche, lo spessore del rivestimento e la composizione elementare oltre che chiaramente la presenza o meno delle particelle. La composizione delle fasi costituenti il rivestimento è stata valutata mediante analisi di diffrazione raggi X (XRD) mediante diffrattometro Siemens D500 utilizzando come sorgente Cu (dimensione dello step 0.05°, conteggio 5 s) La resistenza alla corrosione del rivestimento è stata analizzata mediante prove potenzio dinamiche (PDP) a temperatura ambiente. I test sono stati eseguiti in una soluzione contenente 0.1 M Na2SO4 e 0.05 M NaCl, con un potenziostato AMEL 2549, utilizzando un elettrodo a calomelano come elettrodo di riferimento (SCE) e un elettrodo di platino come controelettrodo Per testare le proprietà di fotocatalisi si è utilizzato un test basato sulla degradazione di metilene blu (MB). I campioni sono stati immersi in 50 mL di soluzione acquosa di metilene blu (15 ppm), e successivamente irradiati con lampada UV (365 nm, LC5 Hamamatsu). I test sono stati condotti a diversi tempi di irradiazione, per un massimo di 60 minuti. Per ogni tempo è stata estratta un’aliquota di soluzione e e si è raccolto uno spettro di assorbimento con uno spettrofotometro UV-VIS nel range 350-850 nm (Jasko V570). Scegliendo una lunghezza d’onda convenzionale (corrispondente al picco di assorbimento caratteristico del MBa 664 nm), si è determinata la concentrazione del MB (C) mediante la legge di Lambert-Beer. I risultati dei vari campionamenti sono stati normalizzati rispetto alla concentrazione iniziale (C0) ed è stato ottenuto un andamento temporale correlato alla concentrazione di metilene blu.
Le particelle, come si può osservare dall'osservazione SEM in Fig.1, sono risultate caratterizzate da dimensioni
sub-micrometriche e forma sferica. L'analisi XRD effettuata sulle particelle (Fig.2) evidenzia la presenza di biossido di titanio sia in forma di Rutilo che di Anatasio ma sono
presenti anche altri composti come solfato di bario, silicio e ossido di silicio, come prevedibile a causa del fatto che il le particelle vengono recuperate dai rifiuti fotovoltaici.
Una prima ispezione visiva dei campioni, riportata in Fig.3, evidenzia che le particelle di biossido di titanio producono la formazione di zone nere sulla superficie del campio-
ne, rispetto a quella prodotta senza l'aggiunta di particelle (Fig.3a). La quantità di zone nere aumenta con l'aumento del contenuto di particelle.
con rivestimento PEO: 0 g/L di particelle (a), 5 g/L (b); 10 g/L (c); 20 g/L (d); 40 g/L (e); 60 g/L (f); 80 g/L (g) / Images of the samples with the different PEO treatments: 0 g/L of particles (a), 5 g/L (b); 10 g/L (c); 20 g/L (d); 40 g/L (e); 60 g/L (f); 80 g/L (g).
In Fig.4 si trovano riportate le osservazioni effettuate lungo la sezione del rivestimento per i vari campioni. Si può innanzi tutto osservare come la presenza delle particelle non modifichi la morfologia del rivestimento che rimane poroso e con una buona adesione rispetto a substrato (cfr Fig.4a del campione ottenuto senza particelle con le altre). Si può altresì osservare come le particelle vengano effettivamente incorporate all’interno del rivestimento mediante un meccanismo parzialmente reattivo che le porta a ri-solidificare all’interno del rivestimento stesso. Infatti dalle immagini ottenute con elettroni retrodiffusi si osserva come le zone ricche in TiO2, più chiare rispetto alle altre ed evidenziate da circoletti rossi nelle immagini, aumentino all’aumentare del contenuto delle particelle. L’avvenuta incorporazione delle particelle è dimostrata anche dalle analisi XRD riportate in Fig.5 (campione 0 g/L di particelle) e Fig.6 (campione 80 g/L di particelle). Comparando i due spettri si può infatti osservare come nel campione ottenuto con 80 g/L di particelle siano chiaramente osservabili i picchi del Ru-
tilo, oltre che quelli dell’allumina (dal rivestimento PEO) e dell’alluminio (dal substrato). Nela campione ottenuto senza particelle i picchi del rutilo non sono visibili. Confrontando lo spettro di Fig.6 con quello relativo alle sole particelle riportato in Fig.2 si può osservare come a seguito dell’incorporazione non sia più visibile la forma cristallina dell’anatasio, che invece era presente nelle particelle. Infatti nel rivestimento PEO risulta visibile solo il Rutilo. Ciò è dovuto al fatto che le alte temperature raggiunte durante il trattamento PEO (anche se solo localmente e per la breve durata delle scariche) provocano la trasformazione dell’anatasio in rutilo. Tale trasformazione infatti generalmente avviene a temperature attorno ai 900°C/1000°C (9), decisamente inferiori a quelle localmente raggiungibili durante il processo di formazione delle scariche del PEO (1800 °C circa (10)). Tale trasformazione non risulta favorevole per l’ottenimento di superfici con caratteristiche fotocatalitiche in quanto l’effetto fotocatalitico dell’anatasio è maggiore rispetto a quello del rutilo.
Sono state anche effettuate analisi della resistenza a corrosione dei rivestimenti ottenuti ed i risultati sono riportati in Fig.7. Si può innanzi tutto osservare come tutti i campioni rivestiti presentino una resistenza a corrosione superiore rispetto al campione non rivestito in quanto a seguito del trattamento si osserva un deciso calo nella corrente di corrosione e quindi nella velocità di corrosione. Non si osserva invece un andamento definito relativo all’influenza delle particelle, infatti tutti i campioni trattati con la presenza di particelle di biossido di titanio presentano un comportamento tra loro simile e simile a quello del campione trattato PEO senza particelle. Ciò si può collegare al fatto che, come osservato dalle immagini al SEM, la presenza delle particelle non porta a grandi va-
riazioni microstrutturali o morfologiche nel rivestimento, non comportando quindi sostanziali variazioni nel comportamento a corrosione.
In Fig.8 si possono osservare i risultati comparati dei test sulla soluzione di blu di metilene, eseguiti con la sola lampada UV, un campione trattato con PEO senza particelle, e dei campioni trattati con PEO e varie quantità di TiO2. La riduzione di assorbimento nel tempo della soluzione, e quindi la riduzione di concentrazione del pigmento, è rilevante anche al netto di altri fenomeni non correlati con la fotocatalisi. Fra il campione senza biossido di titanio e quelli ottenuti con l’aggiunta di 80 e 60 g/L si nota una riduzione di quasi il 10% dopo 60 minuti, per cui l’effetto
non può essere imputato solo all’assorbimento della tinta nelle porosità; né alla sola presenza della luce UV. Si può quindi affermare che, nonostante la trasformazione dell’anatasio in rutilo, i campioni contenenti alte quantità di biossido di titanio (60 e 80 g/L) presentano una significativa attività fotocatalitica. Considerando che le particelle utilizzate risultano essere uno scarto del processo di riciclo dei pannelli fotovoltaici dismessi il risultato risulta comunque promettente per un possibile futuro utilizzo delle particelle stesse.
In conclusione è possibile riassumere i risultati ottenuti come segue:
- Le particelle di biossido di titanio vengono incorporate con successo all’interno di rivestimenti PEO su lega di alluminio 1050. L’incorporazione avviene mediante semplice aggiunta delle particelle all’elettrolita utilizzato durante il processo sfruttando la formazione di canali di scarica durante il processo PEO. L’incorporazione risulta parzialmente reattiva in quanto le particelle perdono la loro forma originaria e ri-solidificano nel rivestimento.
- La presenza delle particelle non porta a grandi variazioni microstrutturali al rivestimento che in ogni caso risulta ricco di porosità.
- L’incorporazione porta invece a significativi cambiamenti nella struttura cristallina delle particelle. Le particelle, inizialmente costituite da un a miscela di rutilo e anatasio, dopo incorporazione risultano costituite solo da rutilo a causa delle temperature localmente molto alte ottenute durante il processo PEO (anche se solo per lassi di tempo brevissimi)
- Tutti i campioni rivestiti presentano caratteristiche di resistenza a corrosione superiori a quelle del campione non rivestito. La presenza delle particelle non influenza la resistenza a corrosione in quanto il comportamento dei campioni ottenuti con le particelle risulta paragonabile a quello del campione senza particelle.
- Nonostante la sfavorevole trasformazione anatasio-rutilo che avviene durante l’incorporazione, la presenza delle particelle conferisce proprietà fotolitiche alla superficie dei campioni rivestiti. Tali caratteristiche aumentano all’aumentare del contenuto di particelle e risultano massime nei campioni ottenuti con 60 e 80 g/L di particelle nell’elettrolita. Per tali campioni si osserva una capacità di ridurre il blu di metilene dopo 60 minuti attorno al 10%.
- L’utilizzo delle particelle di biossido di titanio recuperate dal riciclo di pannelli fotovoltaici dismessi come additivo per la produzione di rivestimenti PEO con proprietà fotocatalitiche risulta quindi una promettente applicazione in un’idea di economia circolare.
[1] Yerokhin AL, Lyubimov V V., Ashitkov R V. Phase formation in ceramic coatings during plasma electrolytic oxidation of aluminium alloys. Ceram Int. 1998;24(1):1–6.
[2] MATYKINA E, ARRABAL R, MOHEDANO M, MINGO B, GONZALEZ J, PARDO A, et al. Recent advances in energy efficient PEO processing of aluminium alloys. Trans Nonferrous Met Soc China (English Ed [Internet]. 2017;27(7):1439–54. Available from: http:// dx.doi.org/10.1016/S1003-6326(17)60166-3
[3] Pezzato L, Lorenzetti L, Tonelli L, Bragaggia G, Dabalà M, Martini C, et al. Effect of SiC and borosilicate glass particles on the corrosion and tribological behavior of AZ91D magnesium alloy after PEO process. Surf Coatings Technol. 2021;428(August).
[4] Lu X, Mohedano M, Blawert C, Matykina E, Arrabal R, Kainer KU, et al. Plasma electrolytic oxidation coatings with particle additions – A review. Surf Coatings Technol [Internet]. 2016;307:1165–82. Available from: http://dx.doi.org/10.1016/j.surfcoat.2016.08.055
[5] Cerchier P, Pezzato L, Moschin E, Coelho LB, Olivier MGM, Moro I, et al. Antifouling properties of different Plasma Electrolytic Oxidation coatings on 7075 aluminium alloy. Int Biodeterior Biodegrad [Internet]. 2018;133(June):70–8. Available from: https://doi. org/10.1016/j.ibiod.2018.06.005
[6] Lu X, Schieda M, Blawert C, Kainer KU, Zheludkevich ML. Formation of photocatalytic plasma electrolytic oxidation coatings on magnesium alloy by incorporation of TiO2 particles. Surf Coatings Technol [Internet]. 2016;307:287–91. Available from: http://dx.doi. org/10.1016/j.surfcoat.2016.09.006
[7] Tadić N, Stojadinović S, Radić N, Grbić B, Vasilić R. Characterization and photocatalytic properties of tungsten doped TiO2 coatings on aluminum obtained by plasma electrolytic oxidation. Surf Coatings Technol. 2016;305:192–9.
[8] Nuño M, Ball RJ, Bowen CR. Photocatalytic Properties of Commercially Available TiO2 Powders for Pollution Control. In: Cao W, editor. Semiconductor Photocatalysis [Internet]. Rijeka: IntechOpen; 2016. Available from: https://doi.org/10.5772/62894
[9] Gouma PI, Mills MJ. Anatase-to-Rutile Transformation in Titania Powders. J Am Ceram Soc. 2001;84(3):619–22.
[10] Lee KM, Lee BU, Yoon S Il, Lee ES, Yoo B, Shin DH. Evaluation of plasma temperature during plasma oxidation processing of AZ91 Mg alloy through analysis of the melting behavior of incorporated particles. Electrochim Acta [Internet]. 2012;67:6–11. Available from: http://dx.doi.org/10.1016/j.electacta.2012.01.053
In this work, the possibility of incorporating TiO2 titanium dioxide particles, derived from recycling process of photovoltaic panels, into PEO coatings was investigated. These particles constitute the main filler of the polymer constituting the rear part of the panels and are characterized by possessing photocatalytic properties. The particles were added in different quantities to the electrolyte (a basic solution containing sodium silicate). The incorporation into the PEO coating, produced on an aluminium alloy 1050, and the possibility of conferring photocatalytic properties to the surface of the samples were studied. The different samples were first characterized by optical microscope analysis and by SEM and XRD and, from the point of view of corrosion resistance by means of potentio-dynamic tests. The photocatalytic properties of the particles and, subsequently, of the samples were evaluated by measuring, with a UV-visible spectrophotometer, the degradation of aqueous solutions of methylene blue with exposure to a UV lamp. The particles have been successfully incorporated into the coating and their presence does not alter the corrosion properties, which are improved compared to the uncoated sample. The particles, initially composed of a mixture of rutile and anatase, are instead composed only of rutile after incorporation, due to the locally very high temperatures that can occur during the PEO process. In the samples obtained with higher quantities of titanium dioxide particles (60 and 80 g / l) a significant photocatalytic effect is observed with a significant reduction of methylene blue.
KEYWORDS: COATINGS, PLASMA ELECTROLYTIC OXIDATION TITANIUM DIOXIDE, PHOTOCATALYTIC PROPERTIES
Al-Si-Cu alloys are widely used in the power train production, such as engine block and cylinder head. Since the service temperature of those parts is higher than 200°C, a thermally stable microstructure is essential. Gd has a potential to form secondary phases which may retard the coarsening behaviour in microstructure. In this study, the effect of Gd addition on the solidification path and microstructural evolution of AlSi7Cu3Mg0.3 alloy was investigated. Thermal analyses and microstructural investigation techniques were performed to evaluate the changes associated with Gd content. The results show that although Gd is ineffective on grain refinement, it can refine the eutectic Si crystals. The addition of Gd leads to the formation of GdAl2Si2 and Gd3Al2Si3Cu2 phases, which may improve the thermal stability of the alloy at high temperatures.
KEYWORDS: AL-SI ALLOY, SOLIDIFICATION, GADOLINIUM, HIGH TEMPERATURE, THERMAL STABILITY
Since light weighting is one of the most effective method to decrease the fuel consumption and CO2 emission, the importance of aluminium alloys in automotive and aerospace industry is gradually increasing. Al-Si alloys are widely used in automotive industry, especially for the power train production, such as engine block, cylinder head, etc. Advanced mechanical properties are directly related to the microstructure of the alloys, and they can be enhanced by preliminary molten metal treatments and the addition of some alloying elements. The mechanical performances of Al-Si alloys can be significantly improved by alloying with Cu and Mg. However, Cu- and Mg-rich phases can only be effective at temperatures below 200°C, due to the dissolution and coarsening phenomena that occur at higher temperatures and reduce the mechanical performance of the alloy [1].
To improve the high-temperature mechanical properties of Al–Si alloys, it is necessary to induce the formation of thermally stable and coarsening resistant precipitates in the microstructure.
Rakhmonov et al. [2] reviewed the effect of adding transition elements on the high-temperature behavior
Ozen
Gursoy, Giulia Scampone University of Padova, Department of Management and Engineering yozen.gyursoy@phd.unipd.it;giulia.scampone@phd.unipd.it
of Al-Si alloys. These elements, such as Zr, V, Ti, lead to the formation of fine and homogenously distributed precipitates, which are more coarsening resistant and thermally stable than the traditional secondary Mg2Si and Al2Cu precipitates. The addition of rare earth (RE) has also a beneficial impact on the high-temperature tensile properties of Al-Si alloys. Stroh et al. [3] reported that the precipitation of AlSiRE and Al20Ti2RE intermetallics in REmodified A356 alloy allows a significant increase of the yield and tensile strength at 250 °C and 300 °C. Among rare earth elements, Gadolinium (Gd) has low diffusivity and solid solubility in α -Al [4], and it can positively influence the mechanical performance of Al alloys at high service temperatures by forming thermally stable secondary phases. Previous studies show that the addition of Gd refines α -Al grains and modifies eutectic Si crystals [5,6]. Despite those studies, the effect of Gd addition on Al-Si alloys for high temperature performance has not been investigated in detail. To compensate this lack of knowledge, the present work aims to characterize the effect of Gd content on the solidification path and the microstructure of AlSi7Cu3Mg0.3 alloy.
Primary AlSi7Mg0.3 alloy in the form of commercial ingots was melted by using SiC crucible in an electrical resistance furnace at 750°C. The melt was then alloyed with commercially pure Cu wires to achieve the desired content of 3 wt. % in AlSi7Cu3Mg0.3 alloy. AlGd5 waffle-shaped master alloy was added, when necessary, to increase the concentration of Gd. The chemical compositions of the experimental alloys were measured by optical emission spectrometry (OES) and presented in Table 1. Some other elements, such as Ca, Cr, P, Zr, Bi, Pb, Sb and Sn, are present in an amount of less than 0.005 wt. % and these elements are not reported in Table 1. After the additions, the molten metal was held at 750°C for 45 minutes to ensure the complete dissolution of the master alloy [7]. The melt was then carefully skimmed, stirred and poured into a boron nitride-coated truncated conical steel cup (lower diameter 45 mm, upper diameter 70 mm, height 60 mm, and a uniform wall thickness of 1 mm). The cup was preheated at 550 °C. No degassing was performed in the experimental work.
*If present, Sr and Na were below the lower detection limit (<1ppm) of OES.
Computer aided two-thermocouple thermal analysis and differential scanning calorimetry (DSC) were performed to characterize the solidification path of the experimental alloys.
For the two-thermocouple thermal analyses method, K-type thermocouples (ø1 mm) were fixed at the lid of the cup, and they were located along the central axis and adjacent to the wall of the cup. They were covered with tight stainless-steel tubes and inserted into the melt at a depth of 30 mm below the surface of the lid. The temperature and time data were collected with a sampling rate of 0.1 s-1 and an accuracy of 0.1 °C using a high-speed data acquisition system. The thermal analyses sample was
then allowed to cool in air with a cooling rate of 0.2 °C/s. To determine the characteristic temperatures of the primary α -Al phase and Al–Si eutectic reaction, the cooling curves and the corresponding derivative curves (cooling rate) were plotted for each alloy. The nucleation temperature of Regular-Al (TN, Al), the minimum temperature of α- Al (Tmin, Al), the growth temperature of α -Al (TG, Al), the recalescence undercooling of α -Al (ΔTR, Al), the eutectic nucleation temperature (TN, eu), the minimum eutectic temperature (Tmin, eu), the eutectic growth temperature (TG, eu), the recalescence undercooling of eutectic (ΔTR, eu) and the nucleation temperature of Cu-rich phases (TN, Al-Cu) were analyzed to estimate the efficiency of grain
refinement and eutectic modification.
The DSC analysis was carried out at a scan rate of 1°C/ min for cooling conditions on cylindrical-shaped discs weighing about 35 mg and extracted from the samples used for the analysis of the chemical composition.
For the macro- and microstructural investigation, the samples were sectioned longitudinally in half and the region close to the tip of the central thermocouple was analyzed. Optical microscope (OM) and Scanning electron microscopy (SEM) equipped with energy dispersive spectrometer (EDS) were used to characterize the evolution of the microstructure and the type and morphology of the phases precipitated during the solidification. A total of at least 200 secondary dendrite arms and 2000 eutectic silicon particles were measured for each sample in OM with image analyzer for the investigation of secondary dendrite arm spacing (SDAS) and eutectic structure, respectively.
To quantitatively analyze the grain size, the polished samples were etched in the concentrated Keller’s reagent (7.5 ml HNO3, 2.5 ml HF, 5 ml HCl and 35 ml H2O). The grain size of the samples was then measured by using the intercept method (ASTM standard E112-12).
The cooling curves and the corresponding cooling rates obtained from the thermal analysis of the experimental
alloys are shown in Figure 1. Table 2 presents a summary of the characteristic temperatures that were determined by analyzing the cooling curves and the cooling rates of the experimental alloys.
The precipitation of α -Al, Al-Si eutectic and Cu-rich phases can be easily identified in the cooling curve and cooling rate of the AlSi7Cu3Mg0.3 alloy (Figure 1a). No significant change in the precipitation of α -Al is observed after the addition of Gd, while the undercooling of Al-Si eutectic reaction in the cooling curve of AlSi7Cu3Mg0.3Gd increases (Figure 1b).
The regions of the cooling rate associated with the precipitation of eutectic Si and Cu-rich phases in Gdcontaining alloy show sharper and higher peaks due to the slower release of latent heat compared to the Gd-free alloy. Indeed, the addition of Gd depresses the characteristic temperatures of Al-Si eutectic reaction, and it increases the recalescence undercooling of eutectic. However, the Gd content is ineffective on the recalescence undercooling of α -Al (Table 2). No peaks associated with the precipitation of Gd-rich phases were detected in thermal analyses, most likely due to unfavorable cooling rate and low number of Gd-rich phases in AlSi7CuMg0.3Gd alloy (Figure1b).
Tab.2 - Characteristic temperatures from thermal analysis of experimental alloys in (°C).
DSC analyses were carried out for the experimental alloys and the cooling curves are shown in Figure 2. The cooling DSC curve of AlSi7Cu3Mg0.3 alloy exhibits the same phase reactions detected by thermal analysis, whereas DSC
curve of AlSi7Cu3Mg0.3Gd alloy reveals two additional peaks (Figure 2). It is believed that those peaks are related to the precipitation of Gd-rich phases.
Figure 3 shows the macrostructures of the experimental alloys. The AlSi7Cu3Mg0.3 alloy exhibits coarse α -Al grain, most likely due to the low cooling rate of the
sample (Figure 3a). After the addition of Gd, no refinement is observed in the macrostructure of AlSi7Cu3Mg0.3Gd alloy (Figure 3b).
The microstructures of AlSi7Cu3Mg0.3 and AlSi7Cu3Mg0.3Gd alloys are displayed in Figure 4. Both microstructures exhibit α -Al matrix, Al-Si eutectic, θ -Al2Cu and Q-Al5Si6Cu2Mg8. Additionally, Gd-rich phases
appear in the AlSi7Cu3Mg0.3Gd alloy, as indicated by arrows in Figure 4b.
The AlSi7Cu3Mg0.3 alloy shows coarse, flake-like eutectic Si crystals (Figure 4a), while the eutectic structure is refined
after the addition of Gd (Figure 4b). It is well known that Sr and Na are widely used as eutectic modifiers, which lead to the formation of finer eutectic Si particles [8]. However, in the present work, these elements are not present in the chemical composition of the alloys, as reported in Table
1. Therefore, the refinement of eutectic Si can be fully attributed to the addition of Gd, which is consistent with the results reported by Shi et al. [5].
Figure 5 shows the quantitative investigations on the evolution of the macro- and microstructure of the experimental alloys. According to the quantitative analysis reported in Figure 5a, the grain size decreased from 1.3 ± 0.06 to 1.2 ± 0.08 mm after the addition of Gd. It can be noted that Gd is inefficient on grain refinement of α -Al grains. Similar results were found for secondary dendrite arm spacing (SDAS) analyses. The average SDAS value in the AlSi7Cu3Mg0.3 alloy is 74.0 ± 9.9 µ m, while
in the AlSi7Cu3Mg0.3Gd alloy it is 72.1 ± 10.2 µ m (Figure 5a). Although Gd addition has been reported to refine α -Al phase in Al-Si alloys, no significant change in grain size or SDAS were observed after Gd addition. This can be related to the large mismatch in structure and lattice parameters between α -Al (FFC, a= 0.4049 nm) and Al3Gd (HCP, a= 0.3634 nm, b= 0.5781 nm).
Figure 5b shows the variation of the morphological parameters of Si eutectic particles after the addition of Gd. In the AlSi7Cu3Mg0.3Gd alloy, the eutectic Si particles are refined, indeed the equivalent diameter of Si decreases from 16.1 ± 10.3 µ m to 8.3 ± 3.8 µ m. It is well known that AlP compounds play an important role in the precipitation of eutectic Si. They segregate at the dendrite/liquid interface and act as sites for the nucleation of eutectic Si during the growth of α -Al dendrite [8]. When Gd is added into the melt, it poisons AlP compounds by forming GdAl2Si2, and AlP can no longer react with the Si in the melt. During the solidification process, the liquid front of the eutectic cells is enriched of Gd, resulting in the refinement of the eutectic Si particles.
Figure 6 shows the SEM micrograph of the AlSi7Cu3Mg0.3Gd alloy. Eutectic Si crystals, θ -Al2Cu and Q-Al5Si6Cu2Mg8 and two different Gd-rich phases
were detected in the interdendritic region, and those phases were confirmed by EDS spot analyses. GdAl2Si2 were observed in a blocky shape and surrounded by Gd3Al2Si3Cu2, while it can also precipitate independently. Almost all Gd-rich phases tend to segregate into the interdendritic region during solidification due to the low solid solubility of Gd in α -Al matrix. It can be assumed that the pre-eutectic peak detected in the DSC curve of the Gd-containing alloy (Figure 2) is related to the precipitation of GdAl2Si2 while the post-eutectic peak corresponds to the precipitation of Gd 3Al2Si3Cu2 phase. However, there is lack of information on Gd3Al2Si3Cu2 phase in the database of many solidification calculation software. Therefore, further investigation must be carried out to characterize in the detail the formation of Gd-rich compounds and to understand if these phases may have a beneficial effect on the thermal stability of the alloy at high service temperatures.
In this work, the effect of Gd content on the solidification path and the microstructure of AlSi7Cu3Mg0.3 alloy was investigated. The following conclusions can be drawn:
• The addition of Gd results in a refinement of eutectic Si particles while it has no effect on the size of α -Al grains.
• During the solidification of AlSi7Cu3Mg0.3 alloy, two different Gd-rich phases precipitate at pre- and posteutectic temperatures. These phases are: GdAl 2Si2 and Gd3Al2Si3Cu2.
• Gd-rich phases may have beneficial effect on high temperature mechanical properties, therefore further investigations should be carried out on this topic.
The work was developed with the financial support of Fondazione Cassa di Risparmio di Padova e Rovigo (CariPaRo), Padova (2019).
The authors would like to thank Prof. Giulio Timelli for his invaluable feedback and support.
[1] Javidani M, Larouche D. Application of cast Al–Si alloys in internal combustion engine components. Int Mater Rev. 2014; 59:132-158.
[2] Rakhmonov J, Timelli G, Bonollo F. The Effect of Transition Elements on High-Temperature Mechanical Properties of Al–Si Foundry Alloys–A Review. Adv Eng Mat. 2016, 18:1096-1105.
[3] Stroh J, Sediako D, Weiss D. The Effect of Rare Earth Mischmetal on the High Temperature Tensile Properties of an A356 Aluminum Alloy. Light Metals 2021. The Minerals, Metals & Materials Series, Springer, Cham. 2021, 184–191.
[4] Mondolfo L F, Aluminum alloys: structure and properties, Elsevier. 1979.
[5] Shi Z, Wang Q, Shi Y, Zhao G, Zhang R. Microstructure and mechanical properties of Gd-modified A356 aluminum alloys. J Rare Earths. 2015, 33:1004-1009.
[6] Liu W, Xiao W, Xu C, Liu M, Ma C. Synergistic effects of Gd and Zr on grain refinement and eutectic Si modification of Al-Si cast alloy. Mater Sci Eng A. 2017, 693:93-100.
[7] Gursoy O, Timelli, G. The effect of the holding time on the microstructure of Gd-containing AlSi7Mg alloys. In Light Metals 2022. The Minerals, Metals & Materials Series, Springer, Cham. 2022, 779-784.
[8] Gursoy O, Timelli,G. Lanthanides: a focused review of eutectic modification in hypoeutectic Al–Si alloys. J Mater Res Technol. 2020, 9:8652-8666.
Il presente lavoro riguarda la caratterizzazione tribologica di una lega di alluminio da deformazione plastica EN AW6082 trattata secondo un innovativo processo di ossidazione anodica in cui i nanopori dello strato di ossido anodico sono stati sigillati con ioni Ag+ (tecnologia G.H.A.®). I test tribologici, eseguiti in condizioni non lubrificate, sono stati condotti in configurazione ball-on-disk (normativa ASTM G99). Il disco, realizzato nella lega di alluminio scelta, è stato trattato G.H.A.® e sottoposto ad un processo di fissaggio a caldo con ioni Ag+. I pin sferici, utilizzati come antagonista e anch’essi realizzati in lega EN AW-6082, sono stati trattati secondo processo G.H.A.® ma utilizzando n. 3 diverse condizioni sia di ossidazione anodica sia di sigillatura a caldo finale. Campioni trattati secondo un tradizionale processo di ossidazione anodica sono stati considerati come riferimento per il confronto delle proprietà tribologiche. In una prima fase dell’attività si è valutato l’effetto di una lucidatura meccanica sul comportamento tribologico in test condotti secondo le condizioni previste dalla normativa ASTM G99. Successivamente, le prove tribologiche hanno previsto due differenti velocità lineari pari a 0.05 e 0.10 m/s ed un carico di 5 N per confrontare coefficienti di attrito (COF) e tassi di usura specifici (WR). Sono state eseguite tre repliche per tutte le differenti condizioni considerate. I risultati hanno consentito di mettere in evidenza una sostanziale dipendenza del COF e della durabilità superficiale dalla velocità di strisciamento per i diversi accoppiamenti studiati.
PAROLE CHIAVE: LEGA DI ALLUMINIO, OSSIDAZIONE ANODICA, USURA, BALL-ON-DISK, MICROSTRUTTURA
Le leghe di alluminio stanno assumendo un ruolo progressivamente sempre più importante in svariati settori grazie ad una serie di vantaggi che le contraddistinguono come la resistenza meccanica specifica, le elevate conduttività termica ed elettrica, la buona formabilità e la propensione al riciclo [1]. Le principali limitazioni al loro utilizzo sono rappresentate da scarsa resistenza a fenomeni di corrosione intensa e all’usura. Una delle soluzioni più comuni e in grado di garantire un miglioramento netto di queste ultime caratteristiche, è senza dubbio quella dei trattamenti di ossidazione anodica grazie ai quali viene promossa, a partire dall’immersione del componente in un bagno elettrolitico dalla composizio-
ne chimica opportunamente definita, la formazione di uno strato di ossido anodico [2,3]. Tale strato, formato principalmente da α -allumina ( α -Al2O3) amorfa, è caratterizzato da un primo strato barriera, a diretto contatto con il metallo base, e da uno strato nanoporoso più esterno [4,5]. Diversi studi presenti in letteratura hanno consentito di mettere in evidenza come la morfologia e le proprietà meccaniche dello strato nanoporoso siano notevolmente influenzate dai parametri di processo, in modo particolare la composizione chimica dell’elettrolita utilizzato oltre che la differenza di potenziale e la densità di corrente del circuito elettrico alla base della cella elettrolitica [6-8]. La naturale propensione della struttura nanoporosa a fungere da naturale riserva di lubrificante ha permesso di mettere in luce come il rilascio del lubrificante nel corso delle prove di usura sia in grado di migliorare significativamente il comportamento tribologico delle leghe così trattate [9]. In quest’ottica, risulta di particolare interesse scientifico un trattamento noto come Golden Hard Anodizing (G.H.A.®), caratterizzato da un particolare procedimento di sigillatura per cui, grazie all'aggiunta di sali di argento contestualmente al processo di sigillatura a caldo, si promuove la sigillatura dello strato nanoporoso mediante ioni Ag+. In questo modo, le superfici trattate beneficiano dell’effetto combinato autolubrificante ed antibatterico degli stessi ioni Ag+, anche se sino ad oggi sono pochi i documenti presenti in letteratura in cui si è investigato nel dettaglio la resistenza ad attrito e usura di tali rivestimenti [3,10,11]. L’influenza delle caratteristiche geometriche dello strato nanoporoso sul comportamento tribologico di leghe di alluminio anodizzate è stata indagata in prove di usura con carichi inferiori a 1 N, mostrando come un aumento del carico implichi una diminuzione del COF per via della formazione di un tribolayer sulla superficie di contatto [12]. Guezmil et al. [13] hanno infine indagato il comportamento tribologico di strati anodizzati a diverse combinazioni di carichi di bassa entità e velocità di strisciamento, utilizzando acciaio 100Cr6 come controparte. Ciò che in letteratura è al momento difficile trovare è un’analisi dell’influenza della velocità di strisciamento per carichi normali di media entità (5-10 N) e su campioni in lega di alluminio anodizzata accoppiata con controparte della medesima natura.
Lo scopo del presente studio è pertanto l’indagine dell’influenza della velocità di strisciamento sul comportamento tribologico di lega di alluminio EN AW-6082, anodizzata utilizzando n. 3 trattamenti G.H.A.® caratterizzati da differenti parametri di processo di anodizzazione ed n. 1 ossidazione anodica convenzionale, accoppiati ad una controparte costituita dalla stessa lega base e trattata secondo il medesimo processo. In particolare, il duplice obiettivo è quello di valutare in una prima fase l’influenza di una lucidatura antecedente il trattamento di ossidazione anodica e mettere successivamente in evidenza eventuali differenze in termini di andamento del coefficiente di attrito (COF) nel tempo e poter confrontare i tassi di usura specifici (WR).
L’analisi del comportamento tribologico ha previsto l’impiego della lega di alluminio da deformazione plastica EN AW-6082, sottoposta a trattamento di ossidazione anodica. Nello specifico, pin a testa sferica di diametro pari a 10 mm sono stati sottoposti a n. 4 diversi trattamenti di ossidazione anodica. Alcuni pin sono stati sottoposti al processo brevettato con il nome di Golden Hard Anodizing (G.H.A.®) e diversificati per parametri di processo non rivelabili in quanto coperti da vincolo di riservatezza, ma che si differenziano per spessore finale dello strato di ossido anodico e per la eventuale sigillatura finale. Nel corso del presente lavoro tali trattamenti verranno denominati con le sigle G1, G2 e G3. Infine, un quarto classico trattamento di ossidazione anodica (OA) è stato considerato come riferimento per poter confrontare il comportamento tribologico dei diversi trattamenti innovativi considerati. Contestualmente, dischi aventi diametro pari a 75 mm e spessore pari a 3 mm, realizzati nella medesima lega di alluminio EN AW-6082, sono stati trattati secondo un processo G.H.A.® secondo gli stessi parametri di processo dei pin G1. Al fine di valutare un’eventuale influenza di operazioni preliminari di pulizia del substrato in lega di alluminio, parte dei dischi sono stati sottoposti ad una preliminare procedura di lucidatura meccanica delle superfici, che sono state poi successivamente anodizzate. I dischi lucidati e non lucidati verranno rispettivamente identificati dalle sigle G1_L e G1_NL. La caratterizzazione
preliminare dei trattamenti eseguiti ha previsto la valutazione di durezza, spessore e rugosità superficiale degli strati anodici realizzati sui componenti utilizzati per la campagna sperimentale. Microdurezze e spessori degli strati anodici sono stati determinati sulla base di misurazioni effettuate sulla sezione trasversale dei componenti a valle delle usuali operazioni di preparativa metallografica. Le prove di microdurezza sono state effettuate mediante micro-durometro Vickers Future-Tech FM-110 (Future-Tech Corp., Kawasaki, Giappone) utilizzando un carico di 10 g. Per ciascuno strato anodizzato analizzato, i valori di microdurezza e di spessore sono stati calcolati come media su n. 10 misurazioni. Mediante microscopio ottico metallografico Leica DMi8 A (Leica Microsystem, Wetzlar, Germania), dotato di software di acquisizione di immagine LAS v4.13, si sono determinati gli spessori dei diversi strati di ossido anodico. Infine, mediante profilometro 3D ottico a non contatto Talysurf CCI-Lite (Taylor Hobson, Leicester, UK) è stata inoltre valutata la rugosità di tutti i componenti coinvolti nella campagna sperimentale tribologica.
Le prove di usura sono state condotte in configurazione ball-on-disk mediante tribometro TR-20 LE (Ducom Instruments, Bengaluru, India). In una prima fase i test tribologici sono stati condotti seguendo le condizioni previste nella normativa di riferimento ASTM G99: distanza di strisciamento complessiva pari a 1000 m, velocità di strisciamento di 0.1 m/s, carico normale applicato pari a 10 N. Si è poi proceduto con l’esecuzione di prove tribologiche a
carico del disco trattato in grado di garantire una maggiore resistenza all’usura in modalità reciprocating con due diverse frequenze di inversione del moto, al fine di generare velocità di strisciamento lineari rispettivamente pari a 0.05 e 0.1 m/s. I test tribologici sono inoltre stati effettuati ad un carico normale costante pari a 5 N e regolando la durata di prova in modo da garantire la percorrenza in tutte le prove effettuate di una distanza pari a 100 m. Per ogni condizione testata sono state effettuate n. 3 repliche. Mediante il software WinDucom associato al tribometro utilizzato è stato possibile monitorare e registrare l’andamento del COF in tempo reale nel corso delle diverse prove. Per quanto riguarda l’usura dei pin utilizzati, si è calcolato il volume asportato a partire dall’estensione della traccia di usura, valutata a sua volta mediante stereomicroscopio Leica MZ6 (Leica Microsystem, Wetzlar, Germania) ad un ingrandimento di 20x ed elaborando le immagini mediante software Leica Application Suite (LAS). Ottenute le immagini allo stereomicroscopio, mediante il software di elaborazione di immagine LAS sono stati misurati i due diametri perpendicolari della traccia di usura a carico dei pin sferici. Calcolata la superficie media della traccia, si è poi calcolato il volume della calotta sferica asportata per ognuno dei pin studiati. Per le grandezze relative all’usura dei dischi, invece, si è proceduto con la valutazione dell’area trasversale delle varie piste di usura mediante profilometro ottico 3-D a non contatto, misurandola in 3 diverse zone della pista di usura. Conseguentemente, il WR è stato calcolato sia per i pin sferici sia per i dischi mediante la formula riportata in Eq. 1:
in cui V è il volume asportato (per il pin sferico è la calotta sferica asportata con superficie determinata analizzando le immagini catturate mediante stereomicroscopio, per i dischi è dato dal prodotto della sezione trasversale della pista di usura e l’estensione della pista di usura), P il carico normale applicato ed L la lunghezza totale di strisciamento per ogni test di usura.
La caratterizzazione preliminare dei trattamenti eseguita a monte delle prove tribologiche sui dischi e sui pin ha consentito di determinare gli spessori e la microdurezza dei diversi strati anodizzati, oltre che i valori di rugosità Ra e Rz di pin e dischi utilizzati. In Fig.1 sono riportate le micrografie ottiche ottenute ad un ingrandimento di 200x dei diversi ossidi anodici realizzati ed utilizzate per la misura del loro spessore. È possibile osservare come
lo spessore vari in funzione dei diversi processi anodizzati nonostante, a livello macroscopico, non si evidenzino differenze sostanziali tra i diversi ossidi anodici. Nella loro sezione trasversale è possibile osservare gli intermetallici a base di Si e Mg che vengono inglobati nell’ossido dalla
lega substrato, mentre l’Ag+ non è visibile a causa delle sue ridotte dimensioni su scala ionica.
In Fig.2 sono raccolte le ricostruzioni tridimensionali delle superfici analizzate per ricavarne i valori di rugosità Ra ed Rz, indicative della topografia degli ossidi anodici ottenuti. Sfruttando la scala cromatica offerta dalla legenda è possibile constatare come i campioni G2 e G3 siano quelli contraddistinti da una maggiore irregolarità delle superfici se confrontati con i pin sferici G1 e OA. Analogamente per
i dischi studiati, il campione G1_L sottoposto a preventiva operazione di lucidatura risulta essere quello con una topografia maggiormente omogenea. La determinazione computazionale dei parametri di rugosità Ra e Rz ha consentito di avere riscontro numerico della topografia superficiale dei campioni.
Fig.2 - Immagini tridimensionali delle superfici di pin e dischi trattati: a) G1, b) G2, c) G3, d) OA, e) G1_L e f) G1_NL. / Tridimensional images of the treated surfaces of pins and disks: a) G1, b) G2, c) G3, d) OA, e) G1_L e f) G1_NL.
I dati acquisiti relativi alle rugosità Ra e Rz, allo spessore e alla durezza degli strati anodizzati sono raccolti in Tab. 1.
Tab.1 - Valori di rugosità Ra e Rz, spessore e microdurezza degli strati anodici considerati. / Roughness Ra and Rz, thickness and microhardness values for the different anodized layers.
Sulla base dei risultati riportati in Tab. 1 è possibile constatare come i trattamenti G1, G2 e G3 eseguiti sui pin presentino durezze comparabili a quelle del trattamento G1_L eseguito sul disco, a differenza del trattamento OA contraddistinto da una minor durezza. Gli spessori dei
trattamenti eseguiti sui pin sono piuttosto simili ma alquanto diversi rispetto a quello ottenuto sul disco. Pur non presentando alcuna differenza sostanziale in termini di durezza, è possibile osservare come la lucidatura meccanica eseguita sul campione G1_L abbia favorito la
crescita di uno strato di ossido anodico più spesso e caratterizzato da una rugosità finale inferiore rispetto all’omologo campione G1_NL. Differenza confermata anche dal valore della rugosità Rz che risulta ben quattro volte superiore per i dischi G1_NL.
In Fig. 3 sono riportate le curve rappresentative dell’andamento del COF per ciascun accoppiamento tra i pin G1 e i dischi G1_L e G1_NL. Le frecce colorate presenti nel diagramma indicano il termine dello stadio stazionario caratteristico dello sfregamento tra strati anodizzati. Il grafico consente di mettere in evidenza come nel caso dell’accoppiamento G1-G1_L il primo stato stazionario del COF, corrispondente allo sfregamento tra le due superfici anodizzate, fosse di durata maggiore al caso di
contatto G1-G1_NL (rispettivamente la transizione nel valore di COF è visibile dopo circa 370 m e 120 m). In tale finestra le operazioni di lucidatura non hanno influenzato il comportamento tribologico in termini di COF: nel caso di contatto G1-G1_L il COF è risultato essere pari a 0.55 ± 0.01, mentre per il contatto G1-G1_NL pari a 0.57 ± 0.01. Dopo le transizioni indicate dalle frecce colorate, è possibile individuare due ulteriori stadi stazionari: un primo che termina dopo circa 800 m sia per G1_L sia per G1_NL relativo all’accoppiamento tra disco rivestito e substrato dei pin a testa sferica; un ulteriore stadio stazionario (da 900 m in poi) determinato dallo sfregamento tra i substrati scoperti dall’usura completa degli strati anodizzati.
Data la maggiore resistenza all’usura mostrata nel primo stadio di strisciamento stazionario, si è scelto il disco G1_L come controparte per la seconda parte dell’indagine sperimentale. In Fig. 4 sono riportate le curve rappresentative dell’andamento del COF per ciascun accoppiamento studiato nella seconda fase dell’attività, rispettivamente nel caso di velocità di strisciamento pari a 0.05 m/s (Fig. 4a) e 0.10 m/s (Fig. 4b), nelle condizioni di prova indagate. A velocità più elevate, il COF di tutti gli accoppiamenti in-
dagati risulta essere inferiore rispetto ai medesimi accoppiamenti a velocità inferiori (0.05 m/s).
Fig.4 - Andamento del COF nel corso delle prove di usura per le due diverse velocità di strisciamento considerate:
a) 0.05 m/s e b) 0.10 m/s. / COF variation during wear tests conducted at two different sliding speeds: a) 0.05 m/s and b) 0.10 m/s.
In Tab. 2 sono invece raccolti i valori del COF stazionario per ciascun tipo di campione nelle diverse configurazioni di prova. È possibile notare come il COF cambi in modo sostanziale al variare della velocità di strisciamento. Per velocità più basse, il COF supera lo 0.60 per tutte le condizioni ad eccezione del trattamento G1 caratterizzato dal valore più basso del COF e pari a 0.58 ± 0.01. Il trattamento OA è invece risultato essere quello caratterizzato dalla più elevata variabilità con una deviazione standard pari a
0.03. Per velocità più elevate, il COF risulta essere inferiore di oltre un punto decimale per ogni condizione studiata e presenta il suo valore minimo nel caso del trattamento G3, pur con una deviazione standard superiore alle altre condizioni.
Tab.2 - Valori del COF stazionario per ciascuna condizione indagata. / Steady-state COF values for all the analyzed conditions.
Al termine delle prove di usura si è proceduto con il calcolo del WR per ciascuna condizione, sia per il disco sia per i diversi pin. In Fig. 5 è riportata, a scopo esemplificativo, una delle immagini ottenute ad un ingrandimento di 20x mediante stereomicroscopio, attraverso cui è stata
determinata l’estensione delle piste di usura e successivamente calcolato il volume di materiale asportato dal pin sferico e di conseguenza il WR.
Nella successiva Fig. 6 è rappresentata una ricostruzione tridimensionale delle piste di usura a carico dei dischi G1_L ed uno dei profili estratti per la determinazione dell’area trasversale delle stesse tracce. Mediante tale
strumento è stato difatti possibile calcolare il volume di materiale asportato dai dischi ed il tasso di usura WR.
the quantitative evaluation of the wear track’s transversal area.
Dal grafico a barre riportato in Fig. 7 è possibile notare come nel caso di velocità di strisciamento basse (0.05 m/s) il WR si mantenga contenuto per tutti i trattamenti indagati. All’aumentare della velocità di strisciamento (0.10 m/s), i WR aumentano e in particolare sono le condizioni G3 e OA ad essere più gravose, sia ai danni del pin sia, soprattutto, del disco. Risulta inoltre interessante sottolineare come la condizione di ossidazione anodica tradizio-
nale OA sia quella caratterizzata dalle maggiori deviazioni standard, sia a carico dei pin sia del disco utilizzato come controparte.
Il presente studio ha riguardato l’indagine tribologica di n. 3 varianti del trattamento G.H.A.® (G1, G2, G3) e di un trattamento classico di ossidazione anodica (OA) considerando l’effetto di due diverse velocità di strisciamento al fine di determinare in quali condizioni operative i diversi strati anodici possano garantire il migliore comportamento a usura se accoppiati con una controparte trattata con un processo G.H.A. ® (G1_L). A partire dalle evidenze sperimentali è stato possibile osservare che:
• La procedura di lucidatura effettuata sui campioni G1_L ha determinato, a parità di condizioni di trattamento, una crescita più rapida dello strato di ossido anodico (visto lo spessore finale maggiore rispetto ai campioni G1_NL) ed un’inferiore rugosità Ra e Rz. La durezza non è risultata essere influenzata dalla lucidatura, visti i valori analoghi presentati dai campioni G1_L e G1_NL.
• Nelle prove tribologiche in condizioni previste dalla normativa ASTM G99 è stato possibile mettere in evidenza come i trattamenti G1_L e G1_NL, accoppiati con pin sferico sottoposto ad analogo trattamento G1, presentino il medesimo COF. La differenza sostanziale risiede nella durata del regime stazionario di sfregamento reciproco: nel caso di contatto G1-G1_L il COF pari a 0.55 ± 0.01 e si
è mantenuto costante per circa 370 m; per il contatto G1G1_NL un COF di 0.57 ± 0.01 è risultato essere costante solamente nei primi 120 m. Si è pertanto deciso di proseguire l’indagine tribologica utilizzando come disco antagonista il campione G1_L.
• Il trattamento G1 è risultato essere quello in grado di garantire il valore inferiore del COF pari a 0.58 ± 0.01 senza compromettere l’integrità dello strato anodizzato. I valori del COF delle prove eseguite a 0.10 m/s non sono indicativi dell’accoppiamento tra le diverse combinazioni di ossidi anodici.
• All’aumentare della velocità di strisciamento, sono i pin trattati secondo i processi G3 e OA a soffrire maggiormente, manifestando valori del WR di diversi ordini di grandezza più elevati rispetto alle velocità inferiori. LInoltre i valori del WR dei processi G3 e OA manifestano deviazioni standard più elevate.
Ulteriori indagini sono in corso per comprendere l’effetto degli ioni di argento che sigillano lo strato di ossido anodico nei trattamenti G.H.A.® nel corso delle prove tribologiche ed il modo in cui lo stesso argento influisca sulle proprietà ad usura del rivestimento.
Gli autori desiderano ringraziare l’azienda G.H.A.® Europe S.r.l. di Zola Predosa (BO) per aver fornito il materiale studiato nel presente lavoro ed in particolare il Prof. Franco Cicerchia e l’Ing. Costantino Cicerchia per il costante supporto tecnico.
[1] Kaufman J. G., Introduction to aluminum alloys and tempers, ASM International, Materials Park, 2000, p. 87.
[2] Bensalah W., Feki M., De-Petris Wery M., Ayedi H. F., Chemical dissolution resistance of anodic oxide layers formed on aluminum, Transaction of Nonferrous Metals Society of China 21, 2011, 1673-1679.
[3] Soffritti C., Fortini A., Nastruzzi A., Sola R., Merlin M., Garagnani G. L., Dry sliding behavior of an aluminum alloy after innovative hard anodizing treatments, Materials 14, 3281, 2021, 1-19.
[4] Keller F., Hunter M. S., Robinson D. L., Structural features of oxide coatings on aluminum, Journal of Electrochemical Society 100, 1953, 411-419.
[5] Takahashi H., Chiba M., Role of anodic oxide films in the corrosion of aluminum and its alloys, Corrosion Reviews 36(1), 2018, 35-54.
[6] Sulka G. D., Parkola K. G., Anodizing potential influence on well-ordered nanostructures formed by anodisation of aluminum in sulphuric acid, Thin Solid Films 515, 2006, 338-345.
[7] Bensalah W., Elleuch K., Feki M. De-Petris Wery M., Ayedi H. F., Optimization of anodic layer properties on aluminum in mixed oxalic/sulphuric acid bath using statistical experimental methods, Surface & Coatings Technologies 201, 2007, 7855-7864.
[8] Aerts T., Dimogerontakis T. H., De Graeve I., Fransaer J., Terryn H., Influence of the anodizing temperature on the porosity and the mechanical properties of the porous anodic oxide film, Surface & Coatings Technologies 201, 2007, 7310-7317.
[9] Lee G.-S., Choi J. H., Choi Y. C., Bu S. D., Lee Y.-Z., Tribological effects of pores on an anodized Al alloy surface as lubricant reservoir, Current Applied Physics 11, 2011, S182-S186.
[10] Santecchia E., Cabibbo M., Hamouda A. M. S., Mushavarati F., Popelka A., Spigarelli S., Dry sliding tribological properties of a hard anodized AA6082 aluminum alloy, Metals 10(2), 2020, 1-15.
[11] Nastruzzi A., Cicerchia F., Fortini A., Nastruzzi C., Gold hard anodized (GHA) materials with antimicrobial surface properties: mechanical, tribological and microbiological characterization, Emergent Materials 4, 2021, 249-263.
[12] Kim H.-S., Kim D.-H., Lee W., Cho S. J., Hahn J.-H., Ahn H.-S., Tribological properties of nanoporous anodic aluminum oxide layer, Surface & Coatings Technologies 205, 2010, 1431-1437.
[13] Guezmil M., Bensalah W., Khalladi A., Elleuch K., De-Petris Wery M., Ayedi H. F., Effect of test parameters on the friction behaviour of anodized aluminium alloy, International Scholarly Research Notices 2014, 2014, 1-9.
The present work concerns the tribological characterization of an EN AW-6082 wrought aluminum alloy treated according to an innovative anodic oxidation process in which the nanoporous anodic oxide layer was sealed with Ag + ions (G.H.A.® technology). The tribological tests in dry conditions were conducted in ball-on-disk configuration (standard ASTM G99): the disc, made of the selected aluminum alloy, was treated with G.H.A.® and subjected to the standard process of hot fixing with Ag+ ions. Spherical-headed pins, used as counterpart material and made of the same aluminum alloy, were treated with G.H.A.® using n. 3 different conditions of anodic oxidation and final heat sealing. Samples treated with a traditional hard anodizing treatment were also taken in account to compare the wear properties of the different surfaces. Firstly, the influence of a preliminary polishing procedure before anodizing treatment on the anodic oxide characteristics was evaluated together with the tribological behavior in wear tests complying ASTM G99 standard. In the second part of the work, tribological tests were conducted at linear speeds equal to 0.05 and 0.10 m/s and a load of 5 N to compare the coefficient of friction (COF) and specific wear rates (WR). All wear tests were performed in triplicate. The results allowed to highlight a substantial dependence of the COF and of the surface duration on the sliding speed for the couplings examined.
co-organised by
On behalf of the Organizing Committee, we are pleased to invite you to the 17th International Conference on Semi Solid Processing of Alloys and Composites (S2P2023), which will be held from September 6th to 8th, 2023 in Brescia, Italy. The 17th S2P International Conference focuses on the advancement in fundamental knowledge and development of materials and industrial processes for semi-solid manufacturing of high-performance metal components. This conference will continue a successful series of conferences on semi-solid processing of alloys and composites started in 1990.
The Conference is devoted to all aspects of semi-solid processing of metals alloys and composites with emphasis on basic research, engineering application as well as market aspects. Results of engineering research and experience as well as scientific issues are relevant for the conference. The Preliminary programme overview is now available on the Conference website!
AIM – Associazione Italiana di Metallurgia
Tel: +39 0276021132 or 0276397770
E-mail: met@aimnet.it
The study focuses on the characterization of aluminum anodizing waste (AAW) in different friction material formulations. AAW was observed to have a dominant presence of hydroxide, sulfate hydrate, and a fraction of alumina. After heat treatment at 400°C for 4.5 hours, the AAW also constituted of AlOx, obtained from the conversion of hydroxides. The AAW was included in two kinds of friction material compositions – a basic composition (BC) with few constituents, and a commercial composition (CFM), wherein, the AAW was added at 12, 24, and 32 wt.% of variation, and subjected to friction, wear, and emission analysis. The tests were conducted on a pin on disc testing equipment, in mild conditions and at room temperature. The analysis with BC revealed the mild abrasive nature of the AAW, along with acceptable friction, wear, and emission characteristics. With the CFM, the permissible CoF, pin and disc wear, and desirable emission characteristics were observed with 12 wt.% addition of AAW. Higher AAW content led to the degradation of wear and emission characteristics of the CFM specimens. Through this preliminary investigation, the possibility of the recycling/utilization of AAW in friction materials was explored, paving the path for further exploration and feasibility analysis of the inclusion of AAW in braking applications.
KEYWORDS: ALUMINUM, ANODIZING, RECYCLING, INDUSTRIAL WASTE, FRICTION MATERIAL, EMISSIONS, FRICTION, WEAR
The generation of manufacturing by-products or wastes leads to major disposal issues and results in environmental imbalance [1]. Amongst the various aluminum wastes generated (like red mud, salt cakes, dross, and slags [1]), aluminum anodizing waste (AAW) is perhaps one of the most underutilized products [1]–[4]. In their comprehensive review study, Souza et al. [5] have stated that the majority of AAW constitutes ≈ 80 wt.% of water, along with aluminum hydroxide, calcium/ sodium, and aluminum sulfates. Due to similar properties irrespective of the origin, the Al-rich AAW can be utilized as an alternative raw material to produce other materials. A new promising option is to utilize these wastes in friction material compositions. In fact, some studies on the addition of different types of industrial wastes have established precedence for the implementation of other industrial waste alternatives in friction material formulation.
The constituents in a typical friction material can be
classified as binders, fillers, reinforcements, and friction modifiers [6]–[8]. Abrasives help in the removal of the pyrolyzed film formed on the counterface surface and impart frictional stability to a wear system. A few examples of abrasives are zirconia, silica, silicon carbide, quartz, alumina, and zirconium silicate [9]–[11] Tomášek et al. [12], Sugözü et al. [13], and Öztürk et al. [10] have shown that the presence of alumina in a non-metallic friction material composition removed negative wear rate and helped elevate and stabilize friction coefficient magnitude. Fan et al. [14] and Boz et al. [15] explained that in semi-metallic friction material, the presence of alumina led to a higher friction coefficient, efficient friction coefficient recovery, and the friction traces were more stable when compared to the wear system without the presence of alumina. Keeping this in mind, the first part of the current study provides the characterization of AAW, with a detailed and step-by-step analysis of the determination of the appropriate heating cycle and required particle size before adding the AAW in different kinds of friction material formulations. The second part of the study is focused on the friction, emission, and wear behavior of two kinds of friction material formulations with varying AAW content. The first friction material composition was formulated inhouse, with only the essential constituents, to highlight the role of the AAW, concerning the friction, wear, and emission characteristics. Considering from the literature, after appropriate heat treatment, the composition of AAW should be like alumina [5]; an ingredient in friction materials that acts as an abrasive. Therefore, two basic formulations were proposed - the first containing AAW,
and an alternative to the composition which replaced AAW with alumina particles. Subsequently, a second composition was selected to have a practical application/ approach. A highly optimized friction material formulation, currently being utilized in automotive braking applications was employed with AAW additions at 12, 24, and 32 wt.%. These preliminary tests were mainly aimed at determining the possibility of using AAW in properly developed formulations, without altering its core composition. The tests were carried out using a pin on disc (PoD) apparatus to understand the role of the AAW additions on the wear mechanisms, with the awareness that specific dynamometric bench tests must be carried out in future developments of the research.
The aluminum anodizing waste (AAW) was provided by Ossicolor SRL, Trento, Italy. The AAW was a dull grey and clumped together. Additionally, the clumps had considerable moisture content in them (close to 75%), originating from the anodizing process. The first type of friction material composition, in which the AAW was added, was termed ‘basic composition’ (BC). The BC was developed in-house with the least possible constituents to effectively demonstrate the characteristics of any additives added to the mix. It is assumed that the AAW is like alumina and therefore would behave like an abrasive. On this basis, alumina particles were utilized as abrasives in the reference BC and were later replaced by AAW in the formulation under study. Table 1 shows the composition.
The second friction material composition was an extensively tested and highly optimized commercially employed formulation, containing over 20 ingredients, which are maintained confidential. This composition is termed ‘CFM’ in this study (Commercial Friction Material).
A few of the main constituents and their functions are shown in Table 2 [16]. Four different CFM compositions were tested with varying AAW content; the first was virgin CFM (no AAW addition), followed by 12, 24, and 32 wt.% of AAW in the CFM composition.
Tab.2 - Main constituents of the commercial formulation with their respective function in (wt.%) [16] / Costituenti principali del materiale d’attrito commerciale con la loro funzione tribologica.
Both friction materials with their respective variations in AAW content were tested in the form of pins. The pins were produced in-house through a standardized procedure [16]. For the sample production with BC, except for the steel wool, the other corresponding constituents listed in Table 1 were measured carefully and mixed in a TURBULA® mixer for 60 mins. After the first round of mixing, the steel wool was then added to the mixture and again mixed for an additional 10 mins. The separate addition and limited time for mixing steel wool ensured that the fibers wouldn’t clump together or form agglomerates. On the other hand, with the CFM, no second step in mixing was employed and the mixture with corresponding AAW content was mixed for a continuous 60 mins. The pins were obtained using the hot-pressing technique. The required quantity of powders was ‘tap-pressed’ in a cylindrical mold made of tool steel and subjected to hot pressing in a BUEHLER® hot mounting press. The production conditions were a compaction pressure of 100 MPa, temperature of 150°C, and holding time of 10 mins. The process was followed by a post-curing method, wherein, the specimens were heated for 4 hours at 200°C in a muffle furnace. The pins were paired with a pearlitic grey cast iron counterface for subsequent wear testing and analysis. The counterface was tested in the form of discs of diameter 60 mm and thickness of 6 mm.
The pins and discs were subjected to dry sliding tests on a pin on disc (PoD) testing apparatus (Ducom Instruments, India). The pins had an average height and diameter of 10 mm. Before the beginning of all tests, the discs were polished thoroughly with a SiC 180 grit abrasive paper and cleaned repeatedly with acetone to remove any dirt, scales, oil, or impurities. Each trial used a fresh new disc. All tests were conducted at room temperature. The
testing conditions for all trials were a contact pressure of 1 MPa (79N), and a constant sliding velocity of 1.51 m /s (for a wear track of 48 mm, which amounted to 600 rpm). The testing conditions were chosen to replicate mild braking conditions [17], [18]. Furthermore, mild braking conditions were also employed to observe the characteristics and properties of the deposited secondary contact plateaus, which could have been difficult (with respect to the extension of the secondary contact plateaus) if a ‘severe’ testing condition was employed. Four trials for each testing condition with varying compositions of AAW in CFM and BC were conducted to obtain repeatability in the results.
Fig. 1 presents the setup of the PoD testing equipment with the particle collection apparatus attachment. The air from the lab (A) was taken in using a fan (B), which was circulated in a High-Efficiency Particulate Air (HEPA) filter (C) to remove dust particles and impurities, leading to the introduction of clean air inside the PoD chamber (D). The air velocity was kept at 11.5 m/s, the magnitude determined from a previous investigation [19]. Before starting any trials, the air cleanliness was always monitored and maintained below 1 #/cm3 .
To obtain the particle number concentration, a TSI® (TSI Incorporated, Shoreview, USA) Optical Particle Sizer Spectrometer (OPS, model 3330) was attached to the enclosed chamber of the PoD testing equipment at site F in Fig. 1. The OPS could measure the total particle number concentration in the size range from 0.3 μ m to 10 μ m, divided into 16 channels, and with a sampling frequency of 1 Hz [19]. The OPS could record and measure particle concentration up to 3000 particles/cm3, operating with a self-controlled sampling flow rate of 1 l/min.
For both friction material compositions, to obtain proper contact/conformance between the pin and the disc surface, a ‘bedding step’ was performed for a duration of 30 mins. Following the bedding step, the actual testing duration was 90 continuous minutes to establish desirable conditions for the attainment of a proper friction layer. The instantaneous magnitude of friction coefficient
(CoF) and total particle concentration during the PoD and emission tests were obtained directly from the software connected to the PoD and the OPS equipment respectively. On the other hand, the specific wear coefficient (pin wear) was calculated by weighing the pins before and after each test, using an analytical balance with a precision of 10-4 g, and the following equation:
(eq.1)
Where:
V: wear volume loss; F: load applied; d: sliding distance (~8150 m). The disc wear analysis were obtained through a stylus profilometer, acquired perpendicular to the wear track from a transverse profile. The worn surfaces of the pins and discs and the morphologies of the AAW particles were obtained through SEM (JEOL IT300, JEOL, Japan), attached with Energy Dispersive X-ray Spectroscopy (EDXS; Bruker, USA) system. Further, the AAW particles were also subjected to Thermogravimetric Analysis (TGA, STA 409 PC Luxx®, Germany), X-ray Diffraction (XRD, Italstructures IPD3000 powder diffractometer with an Inel CPS120 detector, Italy), and Fourier Transform Infrared Spectroscopy (FT-IR, Varian Excalibur series 4100, USA) analyses to determine their thermal stability, phase constituents, and composition respectively. The TGA analysis was
conducted in the air until 1000°C. From the TGA analysis, the high moisture content in the as received AAW was observed. From the XRD analysis, the AAW was observed to be highly amorphous in nature, thereby, not providing the exact phases [5].
The as-received AAW contains considerable moisture content. Hence, with this high moisture content, the addition of as-received AAW in friction material formulations was not feasible and required heat treatment. Hence, in this study, the as-received AAW was subjected to heat treatment at 400°C for 4.5 hours to remove all the moisture content and potentially convert the Al hydroxide into AlOx as suggested in Ref. 5. After the heat treatment, an apparent change in color was observed; from dark grey to light orange, signifying a change in the constituent
phase of the AAW [5].
To understand the morphology of the AAW, the heattreated powder was subjected to SEM and point EDXS analysis. Fig. 2 (a) represents the low magnification SEM image. Two distinctive shapes can be observed – wellrounded ones and flat-faced sharp-edged. The sharp
edges and flat faces could be attributed to the crushing of the AAW clumps and then to their brittleness. The EDXS analysis showed that the particles mainly contain Al (43%) and O (45%), and constituents like Ca and Sn that can be considered minor constituents.
Next, to select the best particle size, the heat-treated AAW was sieved to two particle sizes - <180 µ m and <90 µ m. Both particle size samples were added separately to the CFM composition and mixed for 1 hour. It was observed that the mixture containing <180 µ m particles did not mix well with the CFM and would settle at the bottom of the mixing bottle. On the other hand, the mixture containing <90 µ m had undergone uniform mixing with no settlement at the bottom. Hence, for the friction and emission analysis, AAW heat-treated at 400°C for 4.5 hours and sieved to <90 µ m were added to the BC and CFM (at 12, 24, and 32 wt.%) compositions.
A slight decrease in the density of the produced materials is observed with the replacement of alumina by AAW. Nevertheless, the pin density for both BC pins (with
alumina and AAW) is high, in the range of 2.26-2.5 g/cm3 .
With the CFM, a steady decrease in the pin density was observed with the increase in the AAW content. The CFM has a density of 2.26 g/cm3, and the least density was seen for CFM with 32 wt.% AAW addition, which was close to 1.87 g/cm3 .
Table 3 compares the steady state CoF, average (steady state) particle concentration, and pin and disc wear of BC with alumina and AAW. With respect to BC containing AAW, we see similar CoF and pin wear, and a slight decrease in average (steady state) particle concentration when compared to the alumina containing BC. On the other hand, the disc wear for BC AAW is lower than BC alumina, even if in both cases, the wear can be classified as ‘very mild’.
Table 4 shows the steady state coefficients of friction (CoF) magnitudes of CFM and with AAW additions. The CoF magnitude is observed to slightly increase with the addition of 12 and 24 wt.% of AAW. On the other hand, a significant increase of steady state CoF is observed at 32% of AAW addition. For the average (steady state) particle concentration, the magnitude steadily increases with an increase in the AAW content. In the case of pin wear, like
the average particle concentration, a steady increase in pin wear is observed with an increase in AAW content. All the pin wear magnitude is categorized in the ‘mild to severe’ wear regime (wear above 2x10-14 m2/N and below 10-13 m2/N). A broadly similar trend was observed with the disc wear. In particular, the disc wear for 24 and 32% of AAW addition in CFM are similar to each other
Tab.4 - Friction, wear, and emission characteristics of BC containing alumina and AAW. / Attrito, usura ed emissioni delle formulazioni BC contenenti allumina e AAWW.
Fig. 3 shows the worn pin surfaces of BC alumina and BC AAW. It is widely known that the primary contact plateaus like steel fibers assist in and compact the wear debris produced during sliding, which is known as the secondary plateaus. In Fig. 3 (a), the surface is covered by bright white regions shown by red dots. They are steel fibers. Additionally, the presence of compacted and well-spread
light grey regions can be observed. These regions are the secondary plateaus. From the EDXS analysis, we can see that these regions are made of Fe and O (overlap of Fe and O maps), inferring Fe oxides [6], [18]. The observations with the BC pin containing AAW (Fig. 4 (b)) are similar to the BC pin containing alumina (Fig. 3 (a)), in terms of the primary and secondary plateau characteristics.
To ascertain the composition, point EDXS analyses were conducted on six different sites on the secondary plateaus for both BC compositions. The results are shown in Table 5. The primary constituent of the secondary plateaus is
Fe oxides. The Fe oxide is accompanied by other minor constituents like Al, Ba, Sn, Mg, and Ca. It should be noted that the Fe content in BC AAW is slightly lesser than the Fe content in the secondary plateaus of BC alumina.
Fig. 4 shows the worn CFM pin surface. Like the observation with the BC samples, the worn surface constitutes bright regions (steel fibers), smooth and well-compacted light grey regions (secondary plateaus), and black regions
(graphite). The secondary plateaus are not only deposited in the vicinity of the primary plateaus but are also present throughout the worn surface. The secondary plateaus are made of Fe oxides [16].
Tab.5 - Point/object analysis of the secondary plateaus deposited on the worn BC pin surface with alumina and AAW. / Analisi puntuale mediante EDXS dei plateaux secondari presenti sulle superfici di usura dei materiali BC.
Similar to Table 5, Table 6 compiles the point EDXS analysis of secondary plateaus on CFM specimens. Like the secondary plateaus of the BC, the presence of Fe and O suggests Fe oxides, as known from previous studies [10], [17]. Additionally, the presence of Al is observed to naturally increase with the increase in AAW content. The secondary plateaus constitute other minor constituents like Zn, Si, Sn, and Mg.
To further understand the extension of the presence of Al particles on the secondary plateaus of BC and CFM with their respective AAW additions, a basic estimation of the
area was conducted on the worn surfaces using the ImageJ open-source software with reference to the EDXS maps of Al. The obtained data are shown in Table 7. In the case of BC, the Al coverage for BC Alumina and BC AAW are quite similar. For CFM, an obvious increase in the Al coverage is seen with the increase in the AAW content. The Al coverage increases from 11% (CFM) to 40% (32% AAW).
As an example, Fig. 5 shows the worn disc profiles paired with BC containing alumina and AAW. In the case of BC alumina, Fig. 5 (a), deep grooves/scratches can be easily observed in the direction of sliding. On the other hand,
for the BC AAW, Fig. 5 (b), though the surface presents scratches, they are not as deep or severe as the ones observed with BC alumina.
For CFM and with AAW variations, the worn surface
characteristics were similar to Fig. 5. However, the intensity of scratches/abrasions on the disc surface was observed to increase with the AAW content.
Tab.6 - Point/object analysis of the secondary plateaus deposited on the worn CFM pin surface with varying AAW content. / Analisi puntuale mediante EDXS dei plateaux secondari presenti sulle superfici di usura dei materiali CFM.
Tab.7 - Area estimation of Al coverage in the secondary plateaus, obtained from the EDXS maps (from ImageJ analysis software). / Estensione delle zone di Al nei plateaux secondari, ottenuta dalla mappe EDXS (usando il software ImageJ).
The AAW analyzed in this study was received without any pre-treatment, resulting in high moisture content due to the aluminum anodizing process. During the heat treatment at 400°C for 4.5 hours, a change in the color characteristics of the AAW was observed – from dull grey to light orange, signifying phase change. [5]. In a previous investigation, it has been also shown that the as received powder is amorphous and the heat treatment induces a partial conversion of aluminum hydroxide into AlOx [22]. The addition of powder with size <90 µ m resulted in uniform mixing of the AAW in the CFM and BC composition. Nevertheless, the addition of smaller AAW particles led to its subsequent large volume addition in the mix, resulting in a reduction of the pin density. This explains the lowering density with an increase in the AAW content in CFM composition in Table 5. When compared to the BC composition, the CFM composition inherently has low density, which is further reduced at high AAW additions (especially at 32 wt.%).
The tests with the basic composition (BC) were intended to understand the AAW characteristics from the friction, wear, and emission studies. As observed, the AAW constituted of Al-oxide and hence was perceived as abrasive and compared to a BC composition containing conventional alumina in it. Kim et al. [20] investigated the role of different abrasives and the CoF was in the order of silicon carbide> zircon > quartz > magnesia. Fan et al. [14] investigated the role of alumina particles and when comparing the CoFs, it was inferred that the abrasion properties of alumina particles were intermediate [12]. The tests with the BC enforced this observation, showing that the AAW behaves as an abrasive, as it had similar friction and wear behavior when compared to the BC alumina specimens. However,
the abrasive nature and characteristics of AAW were milder than conventional alumina. The AAW were found in the secondary plateaus, which led to the counterface abrasion. This is validated by the softer scratches on the counterface surface, leading to lower Fe presence in the secondary plateaus on the worn BC AAW surface and lower disc wear. As mentioned, the wear of the BC friction material was mild, and that of the counterface disc was very mild. Therefore, it is expected that the emissions of airborne particles are low as well. From previous observations [19], [21], it was shown that the particle concentration below 500 #/cm3 is considered to be a low value. In the case of BC with AAW, the particle concentration was well below 500 #/cm3, showing desirable emission characteristics, along with permissible CoF, and pin and disc wear.
As previously mentioned, the CFM utilized in this study is a highly optimized friction material composition. Due to its efficient combination of constituents, any change in its composition would immediately affect its wear and emission characteristics. Since it is already known from the BC tests that the AAW is a mild abrasive, it is then expected that any variation in the CFM properties would directly be attributed to the AAW addition. As a matter of fact, an increase in CoF is observed with an increase in AAW content. To better clarify this point, Fig. 6 represents the relationship between the average CoF with the Al area coverage on the worn pin surfaces of the CFM specimens. It can be seen that as the Al area coverage increases, so does the average CoF. Essentially, the Al particles enter the secondary plateaus and act as an abrasive, thereby, increasing the CoF. The abrasive character of AAW was further enforced with high disc wear at elevated AAW content.
Straffelini and Gialanella [21], and Nogueira et al. [19] have presented a concrete proportional relationship between the average CoF and average particle concentration of a wear system. Similar observations were also recorded in this study. For the CFM specimens, an increase in
CoF observed an increase in emissions. Hence, the 32% addition of AAW observed the highest emissions (with the highest CoF) and the 12% AAW addition had comparatively low emissions (with the lowest CoF) in all AAW containing CFM specimens, as seen in Fig. 7.
As the AAW is a mild abrasive, at 12 wt.% addition in CFM, lower wear, optimum CoF, and permissible average particle concentration were observed. The CFM composition already constitutes abrasives and with the addition of 12 wt.% of AAW, the wear and emission characteristics of the CFM were not changed significantly. Hence, the 12 wt.% addition of CFM is the ideal addition, compared to the higher AAW addition which varied the CFM characteristics drastically.
Through the initial analysis conducted on the one-ofa-kind addition of aluminum anodizing waste (AAW) in different friction material formulations, the positive effects of the addition of AAW were observed, the addition being limited to 12 wt. %. The future work of this study will be focused on specific dynamometric testing to appropriately establish the behavior of the friction materials at effective braking conditions. After a comprehensive analysis and conducting a feasibility check, a modified version of CFM could be produced, wherein, an abrasive fraction could be removed and replaced by AAW, while still maintaining its highly optimized composition and well-balanced wear and emission characteristics.
In a novel attempt to effectively recycle aluminum anodizing waste (AAW), this study focuses on the feasibility
of its utilization in friction material compositions.
• The as-received AAW was characterized to understand its thermal stability and composition. The FT-IR analysis revealed that the hydroxide and sulfate hydrate curves shrunk with an increase in temperature. Additionally, all the samples at different temperature treatments recorded the presence of alumina. As the as-received AAW had a high moisture content, the AAW was subjected to heat treatment at 400°C for 4.5 hours, as the temperature was apt to convert hydroxide into AlOx, which was witnessed by the change in the AAW color from light grey to orange, and by SEM analysis. Further, the particle size was maintained at <90 µ m for homogeneous distribution of the AAW in the friction material composition.
• The wear and emission analysis were conducted by adding the heat-treated and sieved AAW to the basic composition (BC) and commercial friction material (CFM) composition. With the BC, the AAW was compared with conventional alumina. The CoF and pin wear were similar. The emissions were slightly reduced, and the disc wear was significantly lower when compared to BC alumina. These observations highlighted the role of AAW as a mild abrasive, further validated by the low presence of Fe in the secondary plateaus.
• With the CFM, the higher the AAW content, the higher the CoF, pin and disc wear, and emissions. Essentially, the AAW enters the secondary plateaus and causes abrasive wear on the counterface, resulting in an increase in disc wear. The higher CoF is attributed to the abrasive action of the AAW, which in turn, resulted in higher emissions at elevated AAW content.
• The addition of 12 wt.% of AAW in CFM produced comparable CoF, pin wear, and emissions to virgin CFM. Along with the already present abrasives in the CFM composition, the 12 wt.% addition of AAW
worked extremely well without altering the CFM properties significantly. Hence, through this analysis of the suitability of the addition of AAW in friction material formulation, the feasibility of the waste addition was clearly observed.
The authors would like to thank Dr. Roberto Masciocchi of Ossicolor SRL., Trento, Italy, for providing the raw material and for the helpful discussions.
[1] A. Erdoğan, M. S. Gök, V. Koç, and A. Günen, “Friction and wear behavior of epoxy composite filled with industrial wastes,” Journal of Cleaner Production, vol. 237, Nov. 2019, doi: 10.1016/j.jclepro.2019.07.063.
[2] L. F. Xavier and P. Suresh, “Wear Behavior of Aluminium Metal Matrix Composite Prepared from Industrial Waste,” Scientific World Journal, vol. 2016, 2016, doi: 10.1155/2016/6538345.
[3] R. Galindo, I. Padilla, O. Rodríguez, R. Sánchez-Hernández, S. López-Andrés, and A. López-Delgado, “Characterization of Solid Wastes from Aluminum Tertiary Sector: The Current State of Spanish Industry,” Journal of Minerals and Materials Characterization and Engineering, vol. 03, no. 02, pp. 55–64, 2015, doi: 10.4236/jmmce.2015.32008.
[4] H. Kumar, R. Prasad, P. Kumar, S. P. Tewari, and J. K. Singh, “Mechanical and tribological characterization of industrial wastes reinforced aluminum alloy composites fabricated via friction stir processing,” Journal of Alloys and Compounds, vol. 831, Aug. 2020, doi: 10.1016/j.jallcom.2020.154832.
[5] M. T. Souza, L. Simão, O. R. K. Montedo, F. Raupp Pereira, and A. P. N. de Oliveira, “Aluminum anodizing waste and its uses: An overview of potential applications and market opportunities,” Waste Management, vol. 84. Elsevier Ltd, pp. 286–301, Feb. 01, 2019. doi: 10.1016/j.wasman.2018.12.003.
[6] M. Leonardi, C. Menapace, V. Matějka, S. Gialanella, and G. Straffelini, “Pin-on-disc investigation on copper-free friction materials dry sliding against cast iron,” Tribology International, vol. 119, no. October 2017, pp. 73–81, 2018, doi: 10.1016/j.triboint.2017.10.037.
[7] J. Kukutschová et al., “Wear performance and wear debris of semimetallic automotive brake materials,” Wear, vol. 268, no. 1, pp 86–93, 2010, doi: 10.1016/j.wear.2009.06.039.
[8] G. Straffelini and L. Maines, “The relationship between wear of semimetallic friction materials and pearlitic cast iron in dry sliding,” Wear, vol. 307, no. 1–2, pp. 75–80, 2013, doi: 10.1016/j.wear.2013.08.020.
[9] B. Pérez and J. Echeberria, “Influence of abrasives and graphite on processing and properties of sintered metallic friction materials,” Heliyon, vol. 5, no. 8, 2019, doi: 10.1016/j.heliyon.2019.e02311.
[10] B. Öztürk, S. Ö. Ztürk, and A. A. Adigüzel, “Effect of type and relative amount of solid lubricants and abrasives on the tribological properties of brake friction materials,” Tribology Transactions, vol. 56, no. 3, pp. 428–441, 2013, doi: 10.1080/10402004.2012.758333.
[11] V. Tomášek, G. Kratošová, R. Yun, Y. Fan, and Y. Lu, “Effects of alumina in nonmetallic brake friction materials on friction performance,” Journal of Materials Science, vol. 44, no. 1, pp. 266–273, 2009, doi: 10.1007/s10853-008-3041-z.
[12] V. Tomášek, G. Kratošová, R. Yun, Y. Fan, and Y. Lu, “Effects of alumina in nonmetallic brake friction materials on friction performance,” Journal of Materials Science, vol. 44, no. 1, pp. 266–273, Jan. 2009, doi: 10.1007/s10853-008-3041-z.
[13] B. Sugözü, B. Dağhan, and A. Akdemir, “Effect of the size on the friction characteristics of brake friction materials: a case study with Al2O3,” Industrial Lubrication and Tribology, vol. 70, no. 6, pp. 1020–1024, Aug. 2018, doi: 10.1108/ILT-02-2017-0035.
[14] Y. Fan, V. Matějka, G. Kratošová, and Y. Lu, “Role of al2o3 in semi-metallic friction materials and its effects on friction and wear performance,” Tribology Transactions, vol. 51, no. 6, pp. 771–778, 2008, doi: 10.1080/10402000802011760.
[15] M. Boz and A. Kurt, “The effect of Al2O3 on the friction performance of automotive brake friction materials,” Tribology International, vol. 40, no. 7, pp. 1161–1169, 2007, doi: 10.1016/j.triboint.2006.12.004.
[16] V. Matějka, M. Leonardi, P. Praus, G. Straffelini, and S. Gialanella, “The Role of Graphitic Carbon Nitride in the Formulation of CopperFree Friction Composites Designed for Automotive Brake Pads,” Metals (Basel), vol. 12, no. 1, p. 123, Jan. 2022, doi: 10.3390/ met12010123.
[17] M. Leonardi, M. Alemani, G. Straffelini, and S. Gialanella, “A pin-on-disc study on the dry sliding behavior of a Cu-free friction material containing different types of natural graphite,” Wear, vol. 442–443, no. November 2019, p. 203157, 2020, doi: 10.1016/j. wear.2019.203157.
[18] C. Menapace, M. Leonardi, V. Matějka, S. Gialanella, and G. Straffelini, “Dry sliding behavior and friction layer formation in copper-free barite containing friction materials,” Wear, vol. 398–399, no. July 2017, pp. 191–200, 2018, doi: 10.1016/j.wear.2017.12.008.
[19] A. P. G. Nogueira, D. Carlevaris, C. Menapace, and G. Straffelini, “Tribological and emission behavior of novel friction materials,” Atmosphere (Basel), vol. 11, no. 10, 2020, doi: 10.3390/atmos11101050.
[20] S. S. Kim, H. J. Hwang, M. W. Shin, and H. Jang, “Friction and vibration of automotive brake pads containing different abrasive particles,” Wear, vol. 271, no. 7–8, pp. 1194–1202, 2011, doi: 10.1016/j.wear.2011.05.037.
[21] G. Straffelini and S. Gialanella, “Airborne particulate matter from brake systems: An assessment of the relevant tribological formation mechanisms,” Wear, vol. 478–479, no. January, 2021, doi: 10.1016/j.wear.2021.203883.
[22] P. Jahashree and G. Straffelini, “The influence of the addition of aluminum anodizing waste on the friction and emission behavior of different kinds of friction material formulations”, Tribology International, vol. 173, 2022, doi: 10.1016/j.triboint.2022.107676.
Lo studio si concentra sulla caratterizzazione e l'utilizzo di scarti di anodizzazione dell'alluminio (AAW) nella formulazione dei materiali di attrito. Gli scarti hanno un contenuto dominante di idrossido e solfato di alluminio. Dopo trattamento termico a 400°C per 4.5 ore, l'AAW è costituito anche da AlO x, ottenuto dalla conversione degli idrossidi. L'AAW è stato quindi aggiunto in due tipi di composizioni di materiali di attrito: una composizione di base (BC) con pochi costituenti e una composizione commerciale (CFM), in cui l'AAW è stato aggiunto al 12, 24 e 32% in peso. I materiali prodotti sono stati quindi sottoposti a prove di strisciamento a secco, con l’obiettivo di studiarne il comportamento triboilogico durante frenata automobilistica in condizioni moderate. I test sono stati condotti su un'apparecchiatura “perno contro disco” (PoD), in condizioni di test moderate, a temperatura ambiente, misurando il coefficiente di attrito, l’usura dei campioni e dei dischi e le emissioni in ambiente di polveri sottili. Lo studio della composizione base ha rivelato la natura leggermente abrasiva dell'AAW, insieme a caratteristiche accettabili di attrito, usura ed emissione. Questo risultato è stato sostanzialmente confermato nelle prove con la composizione commerciale. In questo caso è stata anche studiato il limite massimo di possibile aggiunta delle polveri AAW, senza degradare le prestazioni tribologiche. Un'aggiunta del 12% in peso di AAW si è rivelata ottimale. In questa indagine preliminare, è stata esplorata la possibilità del riciclaggio/utilizzo dell'AAW in materiali d’attrito, aprendo la strada a ulteriori analisi di fattibilità dell'inclusione dell'AAW nei sistemi di frenata.
PAROLE CHIAVE: ALLUMINIO, ANODIZZAZIONE, RICICLAGGIO, RIFIUTI INDUSTRIALI, MATERIALE DI ATTRITO, EMISSIONI, ATTRITO, USURA
TORNA ALL'INDICE >
Il principale processo produttivo utilizzato per la produzione di componenti automotive è il processo di pressocolata. La ragione è legata alla sua economicità, a causa di un'alta frequenza produttiva e alla precisione dei componenti stampati. D'altra parte, le velocità particolarmente elevate, che regolano il processo, influenzano le dinamiche produttive interferendo notevolmente sulla qualità delle parti realizzate.
Avere il controllo del processo, conoscendone i punti di instabilità può essere un notevole vantaggio per gestire la stabilità qualitativa delle parti stampate.
L’attività che verrà illustrata, sviluppata nell'ambito del progetto SMARTI 4.0, presenta i risultati di uno studio condotto nell’ambito del controllo di processo.
L'obiettivo è progettare e definire un sistema di controllo basato sulle informazioni fornite da appositi sensori per garantire la stabilità di processo e di conseguenza la qualità dei componenti pressofusi.
Il dimostratore utilizzato è una CCU, un sistema di ricarica di bordo per pacchi batteria in veicoli ibridi ed elettrici puri.
La pressofusione (HPDC) è un processo versatile e altamente produttivo per la produzione di parti metalliche complesse. Tale processo forza il metallo fuso ad alta pressione in stampi di acciaio fino a quando il metallo non si solidifica completamente, grazie all’utilizzo di una specifica macchina. I parametri che governano il processo processo sono interdipendenti e in conflitto tra loro in modo complicato; l'ottimizzazione della combinazione delle impostazioni di processo richiede molto tempo. Nella letteratura esistente, si possono trovare alcune linee guida di correlazione ai comuni difetti di colata e i parametri che governano il processo [1,2]. Tuttavia, non ci sono standard per selezionare la migliore soluzione in base a leghe, processo, metodo e design; infatti, la qualità della colata dipende da molti parametri difficili da controllare, specie se si influenzano reciprocamente [3]. Il processo può essere monitorato e controllato attraverso l'introduzione e il posizionamento più idoneo di una rete di sensori. I sensori hanno lo scopo di monitorare temperature, pressioni, deformazioni geometriche e parametri di processo. I dati raccolti dai sensori possono essere correlati non solo alle variazioni dei parametri ma
anche all'esito qualitativo del pezzo prodotto. Non tutto il sistema macchina-stampo ha la stessa sensibilità alla variazione dei parametri di processo. Infatti, alcune zone possono essere molto sensibili alle variazioni del processo, mentre altre non ne risentono affatto.
L’utilizzo di sistemi virtuali aiuta ad individuare le zone più sensibili e i parametri più pervasivi. Attraverso simulazioni di Autonomous Engineering è possibile definire un piano di test virtuale automatizzato per perseguire diversi obiettivi di qualità e di costo contemporaneamente.
Questo contributo presenta, con il supporto di avanzati sistemi virtuali, un lavoro volto a individuare il numero giusto e le posizioni più idonee di un certo numero di sensori. Vi è inoltre la possibilità di valutare la correlazione tra i segnali dei sensori, le variabili di processo e la qualità della colata. L'attività sviluppata si basa su un vero e proprio campionamento virtuale attraverso il quale i parametri di processo vengono variati sulla base di un Design of Experiments (DOE).
Nell'ambito del progetto di ricerca SMARTI 4.0 – Smart Manufacturing for an Automotive TIer 4.0 – il lavoro sviluppato ha visto la collaborazione tra Meccanica Cainelli ed Enginsoft. Il lavoro è strutturato in tre parti principali:
• Il posizionamento di termocoppie virtuali nello stampo per monitorare la variazione termica dell'utensile e della lega durante il processo;
• La definizione delle variabili di processo;
• La definizione di DoE
La definizione delle posizioni delle termocoppie è il risultato dello studio tra la fonderia (Meccanica Cainelli), il produttore di stampi (Tomos) e il fornitore MAGMASOFT® (Enginsoft). Poiché il dimostratore industriale scelto, una CCU per auto ibride ed elettriche, era già in produzione, la valutazione della posizione (Fig. 1) si è basata su molteplici aspetti: posizioni dei canali di raffreddamento, posizioni dei perni di espulsione e progettazione dello stampo.
L'impostazione del modello virtuale prevede l’utilizzo dei parametri di processo derivanti dalla produzione, considerando in particolare:
• i parametri che controllano la curva di iniezione (v1, v2 e punto di commutazione)
• i circuiti di termoregolazione, il mezzo termoregolante con la sua portata e temperatura di esercizio (Fig. 2)
• tutti i tempi che scandiscono il ciclo produttivo partendo dall’inizio dell’iniezione, passando alla fase di solidificazione per concludere alla fase di apertura delle parti stampanti, tenendo in considerazione i tempi di lubrifica, di soffiatura e la fase di chiusura finale
Inoltre per tenere in considerazione il raggiungimento della condizione di regime termico sono stati simulati 10 cicli produttivi.
La progettazione degli esperimenti è uno strumento di raccolta e analisi dei dati che consente di manipolare più fattori di input (variabili), determinandone l'effetto su un output desiderato (obiettivi).
Questa pianificazione di esperimenti, permette di analizzare, una volta eseguita, le correlazioni e interazioni che esistono fra le variabili e gli obiettivi comprendendo meglio i fenomeni che governano il processo e la qualità dei componenti prodotti
In questo lavoro le variabili scelte sono state le seguenti variabili:
• La curva di iniezione, in particolare il punto di commutazione e la velocità del pistone della seconda
fase;
• Temperatura iniziale della lega;
• Tempo di spruzzatura;
• Intensificazione della pressione di terza fase
Per la definizione del DOE sono stati utilizzati due algoritmi statistici:
• Fattoriale Ridotto: utilizzato per identificare tutti i design estremi. Tale algoritmo permette di identificare tutti i design creati dalla combinazione dei valori min e max di ogni variabile
• Sobol: algoritmo utilizzato per ottenere design equidistanti tra loro all’interno del confine n-dimensionale identificato con il metodo precedente.
• Applicando questi due algoritmi è stata ottenuta una distribuzione variabile omogenea e simmetrica basata su 5 variabili, per un totale di 312 disegni (vedi Fig. 3).
Per tenere sotto controllo la qualità del getto sono stati presi in considerazione 4 obiettivi:
• Avoid Misrun: che controlla la temperatura della lega durante la fase di riempimento ed evidenzia i valori minimi raggiunti. Permette l'identificazione di giunti freddi o getti incompleti
• Pressione dell'aria (AP): questo criterio fornisce informazioni sull'aria intrappolata nel getto durante la fase di riempimento
• AirMass (AP_Mass): indica la massa d'aria intrappolata nel getto durante il riempimento
• Porosità (Por): criterio che da riscontro sulla porosità da ritiro generata durante la solidificazione.
L'analisi dei risultati è condotta utilizzando diagrammi che
permettono la correlazione tra Variabili-Obiettivi-Termocoppie. Per la visualizzazione dei risultati sono stati utilizzati due tipi di grafici:
• Matrice di correlazione: mette in correlazione variabili e obiettivi e sensori fornendo un valore di correlazione percentuale (0 nessuna correlazione, 1 piena correlazione)
• Coordinate parallele: sistema utilizzato per visualizzare spazi n-dimensionali e analizzare dati multivariati. Per mostrare un insieme di punti in uno spazio a n dimensioni, vengono disegnate n linee parallele, solitamente verticali e poste a uguale distanza l'una dall'altra. Un punto nello spazio n-dimensionale è rappresentato come una linea spezzata con i vertici sugli assi paralleli.
La prima analisi eseguita ha permesso di analizzare le correlazioni tra variabili e obiettivi. I risultati ottenuti (Fig 4) hanno evidenziato:
• Una forte correlazione diretta tra velocità di seconda fase (v2) e i risultati dell'aria intrappolata (cioè AP = AirPressure e AP_Mass = Massa d'aria intrappolata)
• Una correlazione indiretta tra la posizione del punto di commutazione (cioè il punto in cui lo stantuffo passa dalla prima alla seconda fase) e la temperatura minima della lega durante il riempimento
• Una correlazione diretta tra la porosità da ritiro e la pressione di compattazione di terza fase
Il confronto tra Variabili e Termocoppie è stato effettuato analizzando i valori minimi e massimi registrati dalle termocoppie (Fig. 5 e Fig. 6).
L’analisi svolta ha evidenziato una fortissima correlazione fra la temperatura iniziale della lega e i valori registrati dalle termocoppie. Tale comportamento è risultato sovrastare e coprire completamente l’effetto di tutte le altre variabili.
È stato, quindi, necessario isolare la temperatura iniziale raccogliendo tutti i design con la stessa temperatura iniziale della lega in sottofamiglie.
La temperatura iniziale è stata quindi scelta pari a Ti=640°C, valore utilizzato durante la produzione dalla fonderia.
La nuova matrice di correlazione (vedi Fig. 7) mostra chiare correlazioni tra le restanti variabili e gli obiettivi in particolare in termini di:
• Effetto della velocità di seconda fase (V2) sull'aria intrappolata (AP e AP_Mass)
• Effetto della posizione del punto di commutazione sulla temperatura della lega durante la fase di riempimento (AvoidMisrun)
• Tempo di lubrifica ed intensificazione della pressione sulla porosità da ritiro.
Buone correlazioni tra variabili fluidodinamiche (v2 e switch) e termocoppie sono state mostrate anche dalle Ma-
trici di Correlazione tra Variabili e Termocoppie (Fig. 8 e Fig.
Lo scopo del lavoro è identificare quali fra i sensori posizionati risulti essere efficiente e ben correlato a variabili e obiettivi, al fine di ridurne il numero, il costo e avendo la certezza dell’efficacia delle informazioni fornite. Inoltre
lo studio permette di identificate gli effetti dei parametri di processo sulla qualità dei pezzi prodotti fornendo l’opportunità di creare un sistema di monitoraggio che in tempo reale fornisce indicazioni sull’andamento del processo reale,
Una prima analisi ha messo a confronto le termocoppie 1 e 2 evidenziando un comportamento, nel rilevare le temperature, pressochè identico. Va inoltre considerato che l’estrema vicinanza della termocoppia 1 al pistone, la sottopone a forti pressioni con il rischio di essere danneggiata. Pertanto, poiché TC01 e TC02 sono comparabili, TC01
può essere evitata. Dall'osservazione delle posizioni delle altre termocoppie (Fig. 10), si può notare che TC03-TC05 e TC04-TC08 sono molto vicine tra loro. Quindi, ci si può aspettare un comportamento molto simile.
Per quanto riguarda le termocoppie TC03 e TC05, il diagramma che le mette in correlazione con Variabili (Fig. 11) e Obiettivi (Fig. 12) mostra che i due sensori hanno un comportamento simile; ciò è confermato anche dalle Co-
ordinate Paralleli (Fig. 13 – 14) che mostrano che al diminuire della temperatura dei sensori si ha una progressiva riduzione dei difetti.
Una conclusione simile si può trarre anche per le termocoppie TC04 e TC08; poiché mostrano quasi lo stesso comportamento (Fig. 15 – 18).
L'analisi condotta mostra una buona correlazione tra termocoppie, variabili e obiettivi. Mostra che la modifica dei parametri di processo può influenzare chiaramente il risultato e la qualità della colata. Per quanto riguarda il numero di termocoppie da utilizzare nello stampo, il risultato è che non sono necessarie tre termocoppie, ovvero
TC01, TC04 e TC05, quindi possono essere evitate. Le informazioni così ottenute sono state implementate sulle attrezzature reali fornendo un compelato monitoraggio del sistema e permettendo il controllo della produzione.
Questo lavoro è stato sviluppato nell'ambito del progetto
SMARTI 4.0. Gli autori desiderano ringraziare tutti i part-
ner coinvolti nel suo sviluppo: Meccanica Cainelli, Enginosft, Tomos, Fisep e New Olef.
[1] ] W. G. Walkington, Die Casting Defects – Troubleshooting Guide, NADCA (2003) Arlington Heights, Illinois.
[2] J. Campbell, The 10 Rules of Good Castings, in: Complete Casting Handbook, second ed. (2015) pp. 535-638.
[3] E. Battaglia, F. Bonollo, G. Timelli, E. Fiorese and G. Kral, Correlation between process, microstructure and properties in high pressure die casting Aluminum-Silicon alloys, Adv. in Mat. Proc. Tech. (2016) 111-124.
[4] A. E. Kopper, Knowledge Creation via Data Analytics in a High Pressure Die Casting Operation, PhD Thesis WPI University (2020).
[5] UNI EN 1706, Aluminium and aluminium alloys – casting – chemical composition and mechanical properties, Brussels: European Committee for Standardization (2010).
a cura di: I. Ciabatti, C. Zambardi
La produzione di platino malleabile su larga scala costituisce una delle sfide più importanti registrate nel campo della metallurgia, i cui progressi si sono protratti per più di due secoli. In questo contributo vengono ripercorse le tappe più rappresentative a partire dalle prime attività precolombiane fino ai recenti sviluppi industriali.
CHIAVE: PLATINO,
I più antichi manufatti di platino rinvenuti sono costituiti, per lo più, da dei cimeli di oreficeria realizzati dai nativi americani in età precolombiana, i quali venivano ottenuti mediante un complesso trattamento di sinterizzazione [1]. Nello specifico, la procedura prevedeva un pretrattamento di agglomerazione secondo il quale veniva addizionato platino in forma di granelli su un bagno di metallo fuso relativamente bassofondente come l’oro [2].1 Non subendo direttamente il processo di fusione, nel semilavorato ottenuto, i granelli di platino si presentavano quindi dispersi in segregazione di fase dal resto della massa. La miscela solida così ricavata veniva sottoposta all’azione di una fiamma il cui calore era concentrato mediante l’utilizzo di una cerbottana al fine di indurre una parziale permeazione del metallo bassofondente all’interno dei grani di platino. Attraverso ripetuti cicli di lavorazione, l’alternanza di questo trattamento a quello della forgiatura permetteva di ottenere una lega metallica omogenea. È difficile, in questa fase del nostro sviluppo tecnologico, apprezzare pienamente la grande ingegnosità degli artigiani che svilupparono questa tecnica in un periodo storico in cui si sapeva ben poco di ciò che costituisce l’attuale conoscenza della materia e, nello specifico, dei metalli.
I primi tentativi di fusione e le certezze della metallurgia delle polveri
L’introduzione del platino in Europa e il suo successivo riconoscimento come nuovo elemento, avvenuto nel 1750
1 È importante sottolineare che, non essendo sottoposto a processi di affinazione, il platino utilizzato era svilito dalla presenza di altri metalli contaminanti ed il suo titolo, molto variabile, difficilmente superava il 90 %.
per opera di William Brownrigg [3], accese l’interesse della comunità scientifica per la sua caratterizzazione. Le ricerche intraprese nel XVIII secolo furono incentrate sia su aspetti prettamente chimici (e.g. reattività con altre sostanze) nonché sullo studio delle proprietà fisiche sebbene in forma tendenzialmente qualitativa. Date le sue caratteristiche di refrattarietà, la fusione del platino divenne una delle sfide di maggior interesse scientifico favorendo un forte impulso nell’evoluzione delle tecniche metallurgiche. Infatti, fino alla seconda metà del XVIII secolo, le fornaci erano in grado di raggiungere temperature poco superiori a 1400 °C rendendo impossibile la fusione del platino la quale avviene a 1769 °C [2]. Come conseguenza, gli unici metodi per produrre platino malleabile, inizialmente, si concretizzarono mediante l’applicazione di processi termomeccanici di sinterizzazione. Pioniere di questi trattamenti fu Pierre Francois Chabaneau, chimico francese trasferitosi in Spagna, il quale nel 1786 fu in grado di produrre platino malleabile portando all’incandescenza una polvere finemente suddivisa del suddetto metallo. Nonostante l’immenso impatto industriale che ebbe il trattamento2, la qualità del prodotto ottenuto era estremamente variabile. Infatti, nonostante Chabaneau fosse in grado di rimuovere la maggior parte delle impurità del platino, il metallo fucinato mostrava comportamenti incoerenti presentandosi a volte in forma duttile e malleabile, mentre altre con caratteristiche di fragilità. Queste incongruenze non erano tanto dovute alla contaminazione degli altri platinoidi, ancora sconosciuti, quanto alle condizioni di pressatura della polvere di platino. Infatti, la consistenza fragile dei prodotti era spesso frutto di lavorazioni condotte in carenza di ossigeno per cui la silice occlusa all’interno della polvere di platino si riduceva a silicio elementare inducendone lo svilimento.3
Gli iniziali approcci alla metallurgia del platino invece, si incentrarono sulla produzione di alcune sue leghe le cui temperature di fusione erano tecnicamente raggiungibili. I primi riferimenti alla composizione di queste leghe compaiono fugacemente nel rapporto del naturalista Josè Cele-
stino Mutis nel quale si sottolinea l’importanza di utilizzare leghe Pt-Cu al fine di evitare il rilascio di verderame [4]. Il primo a fondere platino impuro fu probabilmente Henrik Theophil Scheffer nel 1751 mediante alligazione con arsenico. Infatti, come si deduce dal diagramma di equilibro Pt-As (figura 1), è sufficiente un contributo di circa 5 % di arsenico per ridurre le temperature di fusione ad un valore tecnicamente accessibile utilizzando le fornaci di quel tempo [5]. Fu proprio utilizzando leghe Pt-As che il maestro orafo parigino Marc-Etienne Janety fu in grado di produrre platino malleabile rimuovendo arsenico mediante una procedura di “ricottura” in muffola che mantenne segreta per molti anni [6].
Per quanto concerne la fusione del “solo platino” uno dei primi tentativi, quasi riusciti, avvenne nel 1758 per opera di Pierre Macquer il quale, insieme al suo assistente Antoine Baumé, espose il metallo all’azione dei raggi solari concentrati mediante una lente focale [7]. Il macchinario fu in grado di fondere il ferro, traguardo che non fu invece possibile raggiungere nel caso del platino. Infatti, solo alcuni parti del provino posto al trattamento manifestarono dei segni di incipiente fusione attraverso la formazione di particelle arrotondate a seguito del locale eccesso di impurità che ne abbassavano il punto di fusione. In maniera analoga, nel 1774 un grande vetro focale del raggio di 1,2 m fu allestito su una carrozza e portato nel Jardin de l’Infante a Parigi (figura 2). Ancora una volta il dispositivo fu in grado di fondere molti materiali refrattari, ma non il platino [8].
Il cambiamento di passo verso la fusione del platino mediante utilizzo di una fornace avvenne con la scoperta dell’ossigeno e della sua produzione mediante decomposizione termica di ossidi. Se è vero che vi è ancora qualche controversia sul fatto che Antoine Lavoisier abbia scoperto la “nuova aria” in modo indipendente da Joseph Priestley4 non vi è invece dubbio che il chimico francese fu l’unico che, all’atto pratico, credette fermamente nel suo utilizzo per incrementare le prestazioni fusorie delle fornaci5. Nel 1782 Lavoisier riuscì per la prima volta a sciogliere una pic-
2 Vista l’unicità della tecnica, il re di Spagna ordinò che la procedura non venisse divulgata ed in effetti rimase segreta per circa 150 anni fino a quando, solo nel 1914, un opuscolo scritto nel 1862 arrivò nelle mani di Louis Quennessen, capo della raffineria parigina.
3 Il silicio ridotto in situ crea una lega eutettica a 830 °C che avanza lungo i bordi del grano cristallino.
4 Nel suo articolo sulla fusione del platino, Lavoisier allude infatti a malincuore alla priorità di Priestley: “…quest’aria, che M. Priestley scoprì più o meno nello stesso periodo di me, e credo anche prima di me …”.
5 L’idea di poter utilizzare l’ossigeno per fondere il platino avvenne invece per opera del reverendo John Michell, come viene sottolineato da Priestley nel volume 1 della sua opera “Experiments and Observations on Different Kinds of Air”.
cola quantità di platino disposto su un pezzo di carbone alimentando la combustione con un flusso costante di ossigeno. L’esperimento suscitò immediatamente grandissimo scalpore nei circoli scientifici di Parigi [8]. Il rovesciamento dell'Impero spagnolo durante le guerre napoleoniche e i disordini della rivoluzione francese furono rispettivamente alla base del declino dell'industria spagnola del platino e dello scioglimento dei gruppi scientifici francesi. Non sorprende quindi come i successivi sviluppi per la produzione di platino malleabile siano stati compiuti principalmente in Inghilterra, dove la ricerca si incentrava sulla metallurgia delle polveri. La diffusione dei processi di sinterizzazione registrati nella prima metà del 1800 fu in buona parte dovuta alla messa a punto di un sistema di affinazione chimico, utilizzato nei suoi fondamenti tutt’oggi, che terminava con la formazione di una spugna metallica di bassa dimensione granulometrica e quindi ideale per subire il trattamento termomeccanico. La procedura di affinazione prevedeva la dissoluzione del platino mediante acqua regia a cui seguiva la precipitazione e calcinazione del sale esacloroplatinato di ammonio. Quest’ultimo trattamento pirometallurgico, portava alla formazione di una spugna la quale veniva successivamente pressata, prima a freddo poi alla temperatura di 800-1000 °C, ed infine fucinata a mano sopra un’incudine [9]. Gli sviluppi furono dominati dai contributi di Richard Knight, Thomas Cork e William Hyde Wollaston che condussero studi indipendenti. Si cominciò a prestare attenzione alla velocità e alla temperatura di riscaldamento del sale di platino, due parametri di esercizio fondamentali per il controllo della granulometria della spugna metallica nonché al lavaggio di quest’ultima per l’eliminazione del cloruro di ammonio residuo. Grazie ai loro contributi, la produzione del platino malleabile raggiunse la scala di una produzione industriale favorendone un grande successo commerciale.
Le prime fusioni di platino su larga scala
Parallelamente agli sviluppi sulla metallurgia delle polveri, dopo il successo di Lavoisier, il successivo progresso nella tecnica di fusione del platino avvenne nel 1801 per opera di Robert Hare mediante l’introduzione del cannel-
lo ossidrogeno [10]. L’idrogeno e l’ossigeno venivano immagazzinati in due recipienti fisicamente distinti, a causa della loro incongruenza in termini di sicurezza, per essere poi alimentati sotto pressione idrostatica e quindi accesi in corrispondenza di un orifizio comune (figura 3). Il miglioramento delle prestazioni di fusione risiedeva nell’utilizzo, per la prima volta, di un comburente in forma gassosa il quale permetteva un’intima miscelazione con l’ossigeno aumentandone la resa di combustione. Per la realizzazione dell’apparato e la successiva ottimizzazione Hare fu assistito da Joaquim Bishop, il quale ne intuì immediatamente la valenza industriale per cui, nel 1842, decise di metterlo in commercio fondando l’azienda J. Bishop & Co. Platinum Works mediante la quale, si specializzò nella fabbricazione di oggetti e strumenti in platino [11]. Ad ogni modo, nonostante fosse possibile raggiungere elevate temperature, largamente superiori a quella di fusione del platino6, il cannello di Hare risultava essere inadeguato per fusioni in cui erano coinvolte quantità di platino superiori al chilogrammo7 .
Nel 1856 Henri Sainte-Claire Deville e Jules Henri Debray furono in grado di fondere il platino utilizzando una fornace costituita da due blocchi di calce viva la quale oltre a manifestare buone proprietà refrattarie permetteva, sebbene parzialmente, di assorbire le impurità del metallo [12]. Ciascun blocco presentava una depressione speculare in maniera tale da formare una cavità a seguito della loro riunione (figura 4). Il platino veniva alloggiato all’interno di tale cavità su cui erano presenti due fori superiori per l’ingresso indipendente dell’ossigeno e del gas di carbone e un ultimo, laterale, per colare il metallo fuso [8]. Il metodo di Deville e Debray costituì la prima reale alternativa alla metallurgia delle polveri per la produzione di platino malleabile su scala industriale ma non riuscì mai a sostituirla completamente. Infatti la tecnica presentava molte carenze sia strutturali che per quanto concerne la qualità del prodotto ottenuto. In primo luogo, l’elevata usura dei blocchi di calce richiedeva una loro frequente sostituzione che, se mal programmata, portava alla loro rottura durante l’esercizio. Inoltre, l’impatto della fiamma sul metallo fuso favoriva indesiderati cali di lavorazione mentre la sua regolazione, tutt’altro
6 Mediante l’ausilio della medesima miscela Hare fu in grado di fondere elementi ancor più refrattari quali rodio e iridio le cui temperature di fusione sono rispettivamente di 1964 e 2446 °C.
7 Il cannello ossi-idrogeno e ossi-propano sono ancora in uso per i trattamenti su scala da banco [13].
che banale, influiva drammaticamente sulla qualità del prodotto. In particolare, fiamme troppo ossidanti inducevano la formazione di occlusioni di gas, mentre quelle riducenti incrementavano le contaminazioni di calcio e magnesio peggiorando le proprietà elettriche e meccaniche del metallo. Infine, rispetto ai tradizionali trattamenti di forgiatura, il metodo Deville e Debray risolveva solo in parte la necessità di garantire omogeneità di composizione nel caso della produzione di leghe platinifere la cui richiesta era in continua crescita date le importanti applicazioni.
L’ingresso dei forni ad induzione e le odierne sfide di produzione
La risoluzione di queste criticità si concretizzò nel 1920 con l’invenzione del forno elettrico ad induzione per opera di Edwin Fitch Northrup [14]. Nel primo prototipo messo in commercio dalla Ajax Electrothermic Corporation nel New Jersey, analogamente ai forni moderni, il metallo veniva posto all’interno di un crogiolo centrato sull’asse di una spirale di rame raffreddata ad acqua la quale trasportava corrente alternata. La resistenza elettrica all’induzione delle correnti secondarie sul metallo produce calore favorendo la fusione del metallo in tempi ridotti rispetto a quanto non avvenga con il tradizionale forno allestito con bruciatore. Inoltre, in caso di produzione di leghe, la tecnica si distinse subito per l’elevata efficienza di miscelazione degli elementi grazie alla vigorosa rotazione della massa fusa per effetto delle correnti elettromagnetiche. Per quanto concerne la fusione del platino, nel 1921 due tecnici della Johnson Matthey & Co. Limited si fecero inviare un forno Ajax-Northrup intuendone le grandi potenzialità che non furono deluse. Con l’introduzione in commercio del forno elettrico ad induzione in concomitanza allo sviluppo della qualità dei materiali refrattari dei crogioli (e.g. utilizzo della zirconia), la maggior parte della produzione di platino malleabile si orientò verso la sua fusione. Nonostante ciò, la metallurgia delle polveri non si estinse completamente poiché, nel caso in cui il processo di sinterizzazione veniva condotto a bassa temperatura, il platino ottenuto risultava essere più resistente alla ricristallizzazione dei grani [2].
La successiva evoluzione tecnologica dei forni fusori, come quello ad arco e a fascio di elettroni, si è concretiz-
zata ed implementata principalmente con lo studio di altri elementi ancor più refrattari del platino (e.g. iridio) spesso utilizzati in lega per la produzione di manufatti ad alto grado di inerzia chimica e termoresistenti. Ne sono un esempio i crogioli in lega Pt-Ir (figura 5), utilizzati in ambito di laboratorio, in cui l’aggiunta dell’iridio viene condotta allo scopo di affinare il grano cristallino e di aumentare l’inerzia chimica all’azione di acidi o sali corrosivi. Per fusioni massive (1-20 Kg) di solo platino, la fusione con forno ad induzione condotta all’aria e su crogiolo rimane la tecnologia di trattamento più diffusa. Infatti, la riluttanza del platino alla sua ossidazione unita al suo basso grado di svilimento, durante la fusione, per effetto del rilascio di elementi costituenti del crogiolo, riducono i vantaggi che contraddistinguono le implementazioni del forno ad induzione stesso quali, il sistema di colata in vuoto e quello a lievitazione magnetica. Ad ogni modo, nel caso della produzione di lingotti certificati, la fusione ad induzione ed il sistema in vuoto, pur non costituendo conditio sine qua non, viene spesso utilizzata al fine di standardizzare la produzione e ridurre al minimo la porosità della fase massiva. Oggi, l’integrità di un lingotto di platino (figura 6), viene stabilita attraverso i criteri di Good Delivery riconosciuti dall’associazione London Platinum & Palladium Market (LPPM) che fissano una serie di rigorose regole alle quali un raffinatore e il suo metallo prezioso devono conformarsi prima di essere ammessi alle negoziazioni [16, 17]. Recentemente l’azienda TCA S.p.A. [18] ha ottenuto tale riconoscimento [19] ed insieme a Chimet S.p.A. sono le uniche due aziende in Italia ad aver raggiunto questo traguardo. La prossima sfida nella produzione di lingotti di platino risiede nel passare da un sistema fusione-colata ad uno a tunnel come è già stato condotto con successo nel caso dell’oro e dell’argento. Ad ogni modo, il grande utilizzo del platino nel campo della catalisi, il quale domina circa il 50 % della domanda totale del mercato [20], impone una sua commercializzazione in forma di spugna. Questa diversificazione ha in parte ridotto gli stimoli per la concretizzazione di ulteriori migliorie nel settore. La recente possibilità di accreditamento Good Delivery per le sole spugne metalliche [21], similmente a quanto regolarizzato per la produzione dei lingotti, testimonia questo cambiamento di rotta fortemente voluto dalle raffinerie dei metalli preziosi.
da
e
per perlatrice automatica. Diffusione foto acconsentita da CIMI S.p.A. [15] / Left: platinum-iridium laboratory crucibles. Right: platinum-gold 95-5 crucibles and plates for automatic fusion machine. The photos publication is authorized by CIMI S.p.A. [15].
perfettamente conforme alle regole Good Delivery imposte dall’associazione London Platinum & Palladium Market (LPPM). Diffusione foto acconsentita da TCA S.p.A. [18] / Platinum ingot fully in line to the Good Delivery rules imposed by London Platinum & Palladium Market (LPPM). The photo publication is authorized by TCA S.p.A.
[1] Scott DA, et al. Ancient platinum technology in south America. Its uses by the Indians in pre-Hispanic times. Platinum Metals Rev., 1980, 24(4), 147-157.
[2] Chaston JC. The powder metallurgy of platinum. An historical account of its origins and growth. Platinum Metals Rev. 1980; 24(2): 7079.
[3] McDonald D. The first experiments on platinum. The life and work of Charles Wood. Platinum Metals Rev. 1965; 9(1): 20-25.
[4] Scheffer HT. Kungl. Vetensk. Akad. Handl. 1752; 13: 269-276.
[5] J. A. Pero-Sanza Elorz et al. Melting and sintering platinum in the 18th century: the secret of the Spanish. JOM. 1999; October: 9-13.
[6] J. A. Chaldecott. The bulk fusion of platinum. Early experiments by Lavoisier and Seguin. Platinum Metals Rev. 1970; 14(1): 24-28.
[7] L. B. Hunt. The first real melting of platinum. Lavoisier’s ultimate success with oxygen. Platinum Metals Rev. 1982; 26(2): 79-86.
[8] W. P. Griffith. Melting the platinum group metals. From Priestley, Lavoisier and their contemporaries to modern methods. Platinum Metals Rev. 2009; 53(4): 209-215.
[9] M. Taddia. Scienza e business nella storia dei metalli nobili: i segreti del dottor Wollaston sul platino e affini. La Chimica e l’Industria. 2018; 5: 28-33.
[10] D. McDonald. The history of the melting of platinum. Platinum Metals Rev. 1958; 2(2): 55-60.
[11] D. McDonald. The history of Matthey Bishop. Platinum Metals Rev. 1970; 14(4): 140-146.
[12] H. Sainte, Claire Deville, Ann. Chim. Phys., 1856, 46(3), 182.
[13] J. Wright. Final analysis. Melting the PGMs: the state of the art in welding platinum. Platinum Metals Rev. 2010; 54(4): 266-268.
[14] A. Muhlbauer, History of Induction Heating and Melting, Essen: Vulkan-Verlag GmbH, 2008.
[15] https://www.cimispa.it/
[16] https://www.lppm.com/
[17] T. Kendall. The London platinum and palladium market. Platinum Metals Rev. 2004; 48(1): 13-14.
[18] http://www.tcaspa.com/
[19] https://www.lanazione.it/arezzo/cronaca/tca-tra-le-30-aziende-top-al-mondo-il-palladio-e-la-nuova-frontiera-1.7891688I.
[20] Ciabatti et al. The role and the recovery of platinum-group metal catalysts in the pharmaceutical industry. Chimica Oggi-Chemistry Today. 2020; 38(6): 10-13.
[21] https://www.lppm.com/sponge-accreditation/
The large-scale production of malleable platinum represents one of the most important challenges in the metallurgical field, whose progresses lasted for more than two centuries. This article reports the main milestones from the first approach in pre-Columbian age to the recent industrial development.
KEYWORDS: PLATINUM, SINTERING, MELTING TEMPERATURE, INDUCTION FURNACE
METEC con la sua sezione dedicata alle tecnologie della forgiatura è l’evento globale per il futuro della produzione e la lavorazione climate-friendly del ferro grezzo, acciaio e dei metalli non ferrosi.
La presenza di eventi di alto profilo come la 6° edizione di European Steel Technology and Application Days (ESTAD) offrono, ai forum in programma sulle nuove tecnologie e applicazioni new green dell’acciaio, idee ed esempi pratici tra i più alti livelli professionali al mondo.
Benvenuti a Düsseldorf!
Italia, da sempre, il Settore tubi in metallo rappresenta un importante realtà industriale e commerciale sia in ambito nazionale che internazionale. Sul nostro territorio convivono parecchie industrie che fabbricano tubi in acciaio e in metalli non ferrosi. Queste aziende produttrici di tubi hanno una forte leadership sul mercato nazionale ed internazionale; la qualità dei loro prodotti è riconosciuta in tutto il mondo.
La valenza qualitativa dei diversi tubi prodotti a livello nazionale trascina un indotto notevole che riguarda Impiantistica, Siderurgia, Automotive, Oil&Gas, Termotecnica, ecc. Sono Settori che si sono imposti sul mercato sfruttando creatività e capacità di proporre prodotti di alta qualità.
Notevole è il settore nazionale di distribuzione di tubi in acciaio al carbonio costituito da una serie di aziende medio piccole che acquistano e vendono tubi in Italia, in Europa e nel resto nel mondo.
Con l’aumento della produzione mondiale di tubi in acciaio si è verificato anche un miglioramento delle tecnologie dei processi produttivi parallelamente ad una importante evoluzione delle normative.
Il Centro di Studio Lavorazioni Plastiche dei Metalli di AIM, attento a questo avanzamento produttivo e di mercato che si è verificato nelle aziende nazionali, ha organizzato una Giornata di Studio, in collaborazione con la Società Profiltubi SpA di Reggiolo (RE), azienda specializzata nella produzione di tubi elettrosaldati in Acciaio al Carbonio. Profiltubi SpA è una realtà consolidata nel mercato nazionale ed europeo dei tubi in acciaio saldati, con una vasta gamma di prodotti nelle dimensioni piccole e medie, ed offre al mercato una elevata qualità del prodotto ed un’eccellenza nel servizio.
Durante la Giornata di Studio saranno affrontati diversi aspetti tecnici e tecnologici del settore tubi, come le caratteristiche dei materiali, le tecnologie produttive e i sistemi di controllo qualità. E’ inoltre prevista una visita agli impianti di produzione dell’azienda ospitante.
L’evento è rivolto al mondo industriale e a quello universitario, ai tecnici della progettazione e costruzione di impianti meccanici, idraulici e siderurgici, agli addetti commerciali nell’ambito acquisto e vendite.
Si ringraziano vivamente Profiltubi SpA e O.M.V. SpA Officine Metallurgiche Ventura del Gruppo Profiltubi per la collaborazione.
Coordinatori:
Guido Capoferri
Presidente CdS AIM Lavorazioni Plastiche dei Metalli
Estore Donini
Vicepresidente CdS AIM Lavorazioni Plastiche dei Metalli
Giorgio Frigerio
Amministratore Delegato Profiltubi SpA
Roberto Cardinale
Direttore Commerciale Profiltubi SpA
Giornata di Studio organizzata in collaborazione con
BLU: RAL 5003 VERDE: RAL 6037
Via F. Turati, 8 20121 Milano Tel. +39 0276397770
e-mail: spedizioni@aimnet.it www.aimnet.it
Gli ultimi dati statistici rilevano che nel mondo siamo oramai 8 miliardi ed il modello di consumismo sviluppatosi negli ultimi tre decenni viene considerato da molti non più sostenibile. L’economia circolare diventa in questo contesto una necessità per preservare le risorse e continuare a godere di spazi vivibili. L’uomo è sicuramente l’abitante che occupa più spazio e condiziona in maniera spesso irreversibile i luoghi in cui vive. Rispetto al secolo scorso la popolazione è triplicata, le automobili non erano così diffuse e le città non erano pesantemente condizionate dalla intensa attività antropica come ai giorni nostri.
Dal canto suo il mondo della siderurgia conosce molto bene il significato e l’importanza del concetto di economia circolare e da qualche anno ha imparato ad affrontare ed ottimizzare i principali problemi legati ai propri cicli produttivi.
L’economia circolare è però un concetto molto più ampio che può essere definito come un modello di produzione (e di consumo) in cui il riutilizzo e il ciclo dei prodotti è fondamentale.
Secondo la definizione della Ellen MacArthur Foundation in tale economia i flussi di materiale sono di due tipi:
- quelli biologici, in grado di essere
reintegrati nella biosfera; - quelli tecnici, destinati ad essere rivalorizzati senza entrare nella biosfera.
L’obiettivo sostanziale è quello di diminuire i rifiuti estendendo il ciclo di vita dei prodotti e di riutilizzare il più possibile i materiali di cui sono composti, facendo in modo che i rifiuti di uno diventino risorse per l’altro. Questo rappresenta un rovesciamento del modello economico lineare dominante nel secolo scorso, che si basava sulle fasi di prelevare, produrre, usare e gettare (o mettere in discarica). Tale modello non è più sostenibile in quanto si basa sulla facile reperibilità di ingenti quantità di materiali e di energia a basso costo. La recente storia degli ultimi anni, dal primo lockdown alla guerra Russia Ucraina, ha dimostrato che non c’è solo un problema legato alla sostenibilità, ma anche alla disponibilità delle materie prime ed ai costi di trasporto, tema che abbraccia numerosi settori, dal siderurgico all’alimentare, dal farmaceutico al tecnologico.
Ecco che allora il principio di economia circolare offre soluzioni per far fronte non solo al riscaldamento globale ed alla crescita dei rifiuti, ma anche alla costante diminuzione delle risorse.
I primi interventi legislativi in mate-
ria di economia circolare in Italia si sono avuti con la L.n.166 del 19 agosto 2016, in ottemperanze ai programmi europei in tema di economia circolare a quel tempo orientati ad evitare lo spreco alimentare e farmaceutico. Successivamente il CDM il 5 marzo 2020 ha approvato gli schemi di decreto legislativo recanti attuazione delle disposizioni contenute nelle direttive UE risalenti al 2018, il cui obiettivo è l’aumento del riciclo limitando il conferimento in discarica al 10% dei rifiuti prodotti entro il 2035.
Nonostante i molteplici esempi di aziende nei vari settori, tra le quali il siderurgico, che hanno sviluppato con successo soluzioni circolari, i processi decisionali in materia di Economia circolare restano un argomento complesso soprattutto per la realtà delle piccole e medie aziende
che percepiscono queste strategie come qualcosa di difficilmente applicabile per una certa forma di inadeguatezza strutturale della loro organizzazione.
Acciaieria Arvedi è consapevole dell’importanza che riveste il recupero dei propri rifiuti e degli scarti di produzione per contribuire ad alleggerire l’impatto ambientale procurato dal ciclo produttivo.
La Certificazione carbon neutral da parte di RINA per lo scopo 1 e 2 del
GHG protocol consente all’Acciaieria di essere il primo produttore al mondo a produrre acciaio applicando criteri di sostenibilità.
L’azienda è giunta a questo risultato grazie ad un importante piano di decarbonizzazione dell’intera filiera lanciato nel 2018 a fronte di ingenti investimenti in tecnologie innovative, ricerca e sviluppo, e basando la propria produzione su ciclo produttivo da forno elettrico e rottame. La certificazione affianca altri impor-
tanti
Arvedi in ambito di sostenibilità quali l’approvazione della propria Dichiarazione Ambientale in accordo alla direttiva EMAS (Eco-Managent and Audit scheme)
Infine Acciaieria Arvedi è ZERO WASTE valorizzando il 98% dei propri rifiuti e sottoprodotti di lavorazione.
The EMC is the most important scientific-technological conference for non-ferrous metallurgists in Europe. It‘s a popular venue for experts from science, industry and public officials, and platform for knowledge transfer between stakeholders of all kind. Be there when the international community of non-ferrous metallurgists comes together to discuss contemporary challenges and trends of your industry!
Key Notes
gdmb.de/emc
Miguel Palacios, EVP General Metallurgy, Atlantic Copper S.L.U, Dr. Heiko Arnold, COO Custom Smelting & Products, Aurubis AG, Nils Voermann, Global Managing Director, Technology, Hatch Ltd, Prof. C. Hilgers, THINKTANK Industrial Resources Strategies, KIT, Sven Becker, Regional Chair BDEW in NRW und CEO Trianel GmbH
Regular Fee
EUR 1.186,00
GDMB Members
EUR 555,30
EUR 948,80 Chairs / Authors
* emc@gdmb.de * gdmb.de/emc * +49 5323 93790
ECHT 2023 EUROPEAN CONFERENCE HEAT TREATMENT & SURFACE ENGINEERING – Genova, 29-31 maggio 2023
XV GIORNATE NAZIONALI CORROSIONE E PROTEZIONE - Torino, 5-7 luglio 2023 http://www.aimnet.it/gncorrosione/
S2P 2023 INTERNATIONAL CONFERENCE ON SEMISOLID PROCESSING OF ALLOYS AND COMPOSITES –Brescia, 6-8 settembre 2023 http://www.aimnet.it/s2p/
International Workshop on HIGH STRENGTH STEELS – Bergamo, 26-27 ottobre
International Meeting EAF: PRODUCTIVITY, ENERGY EFFICIENCY, RAW MATERIALS AND DECARBONIZATION – Bergamo, 30 novembre-1 dicembre
Corso FAILURE ANALYSIS – ibrido, 16-17-23 maggio
Giornata di Studio DUPLEX E SUPERDUPLEX: FILIERA DI PRODUZIONE E NETWORKING – Erbusco BS, 18-19 maggio
Giornata di Studio I LAMINATI DI ALLUMINIO: APPLICAZIONI E INNOVAZIONI – c/o Laminazione sottile, 19 maggio
Giornata di Studio TUBI SALDATI E TUBI FORMA: INNOVAZIONE, SOSTENIBILITÀ E STRUMENTAZIONE –Reggiolo RE c/o Profiltubi, 26 maggio 2023
Giornata di Studio MATERIALI INNOVATIVI PER IL MONDO RACING – Milano, 31 maggio
Corso RIVESTIMENTI – I MODULO RIVESTIMENTI SOTTILI – Rivoli TO, 8-9 giugno
Giornata di Studio STATO DI SERVIZIO DEGLI IMPIANTI – ibrido, 15 giugno
Corso Itinerante MACCHINA FUSORIA – giugno
Giornata di Studio SOSTENIBILITÀ NELLA PRODUZIONE DI COMPONENTI MECCANICI – Veduggio LC c/o Agrati, 21 giugno
Giornata di Studio SOSTENIBILITÀ’ AMBIENTALE NEL CAMPO DELLE COSTRUZIONI CIVILI – webinar, 22-23 giugno
Giornata di Studio FATTORI DI INFLUENZA SULLA RESISTENZA A FATICA DEI MATERIALI METALLICI: ASPETTI TEORICI E CASI APPLICATIVI – Milano, 27 giugno
Giornata di Studio STATO DELL'ARTE ED EVOLUZIONE DEI PROCESSI TERMICI E MECCANICI – Pisa, 12 luglio
Giornata di Studio INNOVAZIONE NEI MATERIALI NELLA MOBILITA’ ELETTRICA – Bologna, 14 settembre
Corso itinerante METALLURGIA SICURA – Lonato BS c/o Feralpi Siderurgica, Brescia c/o ORI Martin, Aosta c/o Cogne Acciai Speciali, 28 settembre e 5-12 ottobre
Per ulteriori informazioni rivolgersi alla Segreteria AIM, e-mail: info@aimnet.it, oppure visitare il sito internet www.aimnet. it
Giornata di Studio PREVENZIONE E RIDUZIONE DELLE DEFORMAZIONI IN SALDATURA – Genova, 28 settembre c/o Istituto Italiano di Saldatura
Giornata di Studio METALLO DURO – Pallanza VB, 12-13 ottobre
Corso ANALISI CHIMICHE – Milano, 18-19 ottobre
Giornata di Studio IL MONDO INDUSTRIAL: ASPETTI METALLURGICI E METODOLOGIE DI CONTROLLO –Torino c/o CNH Industrial Village, ottobre
Giornata di Studio CARATTERIZZAZIONE FUNZIONALE DI SUPERFICI MODIFICATE - novembre
Giornata di Studio PALLINATURA E DIFFRATTOMETRIA RX – Agrate Conturbia (NO) c/o GNR, novembre
FaReTra (Fair Remote Training) - FORMAZIONE E AGGIORNAMENTO A DISTANZA
Modalità Asincrona (registrazioni)
Giornata di Studio EMERGENZA COSTI ENERGETICI: CHE FARE IN FONDERIA?
Webinar FaReTra IL PRINCIPIO DI MATERIALITÀ NEL REPORTING DI SOSTENIBILITÀ
Giornata di Studio ASPETTI E GESTIONE DELLA NORMATIVA NEL CAMPO DEI TRATTAMENTI TERMICI
Corso PROVE NON DISTRUTTIVE
Giornata di Studio TRATTAMENTI SUPERFICIALI SU ALLUMINIO, A SCOPO DECORATIVO E PROTETTIVO
Corso Modulare METALLOGRAFIA – I MODULO, II MODULO “METALLI NON FERROSI”
Corso modulare FONDERIA PER NON FONDITORI
Corso TRIBOLOGIA INDUSTRIALE – I MODULO
Giornate di Studio GETTI PRESSOCOLATI PER APPLICAZIONI STRUTTURALI
Corso DIFETTOLOGIA NEI GETTI PRESSOCOLATI: METALLIZZAZIONI
Corso ADDITIVE METALLURGY
Corso METALLURGIA PER NON METALLURGISTI
Giornata di Studio PRESSOCOLATA IN ZAMA
Giornata di Studio LA SFIDA DELLA NEUTRALITÀ CARBONICA
Corso itinerante METALLURGIA SICURA
Corso modulare TRATTAMENTI TERMICI
Corso modulare I REFRATTARI E LE LORO APPLICAZIONI
Corso GLI ACCIAI INOSSIDABILI 11ª edizione
Corso FAILURE ANALYSIS 11a edizione
Giornata di Studio PERFORMANCE E DEGRADO DEI MATERIALI METALLICI UTILIZZATI IN CAMPO EOLICO: CAPIRE PER PREVENIRE
L’elenco completo delle iniziative è disponibile sul sito: www.aimnet.it
(*) In caso non sia possibile svolgere la manifestazione in presenza, la stessa verrà erogata a distanza in modalità webinar
ibrida del 16 marzo 2023)
Notizie dal Comitato
• Alla riunione è presente Elisabetta Ruffino, del laboratorio meccanico MotivexLab – Automotive & Aerospace Test Express – di Avigliana (TO), a cui il presidente dà il benvenuto. Il Comitato approva il suo ingresso come membro effettivo.
Consuntivo di attività svolte
• Seminario online “Aspetti e gestione della normativa nel campo dei trattamenti termici” (9 febbraio 2023): l’incontro di mezza giornata è stato positivo, ma si può migliorare. I partecipanti avrebbero desiderato approfondire alcuni temi. I risultati che emergono dai questionari di soddisfazione dei partecipanti sono piuttosto discordanti, ma comunque utilizzabili come spunto di miglioramento per future manifestazioni.
• Corso “Metallurgia di base per i trattamenti termici”: il corso si sta completando proprio in questi giorni, con due giornate in presenza e due in diretta streaming. Tutti i docenti presenti in riunione sottolineano che le lezioni in presenza portano ad un maggiore e più approfondito dialogo con i partecipanti. Gli esiti della manifestazione saranno esaminati in dettaglio durante la prossima riunione del Comitato.
Manifestazioni in corso di organizzazione
• La GdS “Stato dell’arte ed evoluzione dei processi termici e meccanici” si svolgerà il 10 maggio 2023 presso l’Università di Pisa – coordinatore Enrico Morgano – vista la indisponibilità della proprietà Piaggio ad ospitare la manifestazione. È previsto un programma intenso e una tavola rotonda finale.
• GdS “Sostenibilità nella produzione di componenti meccanici” – coordinatrice Costanza Colombo – si svolgerà presso la Società Agrati di Veduggio (LC) in data 21 giugno 2023. Si stanno mettendo a punto i temi relativi a economia sostenibile, circolare, inquinamento, valutazione di impatto degli attuali impianti, possibili modifiche ecc. Sono previsti interventi tecnici in mattinata e poi visita allo stabilimento di Veduggio con particolare attenzione ai trattamenti termici. La locandina con il programma dettagliato sarà pronta in aprile.
• GdS “Il Mondo Industrial - aspetti metallurgici e metodologie di controllo”: dopo parecchi rinvii per motivi pandemici la GdS comincia a prendere forma. La manifestazione è prevista in autunno 2023, tra metà ottobre e inizio novembre. Si discute dei possibili argomenti da trattare, soprattutto per sottolineare la differenza tra il mondo “passengers” FIAT e quello “industrial” IVECO. Si approfondiscono anche gli aspetti logistici (disponibilità e costi della sala, catering ecc.).
• Seminario “Processi post-stampa additiva: dal design del ciclo di produzione al manufatto”: l’iniziativa di svolgerà in due giornate – 18 e 19 aprile salvo conferma – e sarà organizzato in collaborazione con il CT Metallurgia delle Polveri e Tecnologie Additive. Valentina Vicario è coordinatrice della manifestazione per parte del CT TTM. Sono previste visite alle aziende ospitanti.
Iniziative future
• Nella seconda metà di ottobre 2023 è prevista una GdS organizzata da GNR per trattare i temi di spettrometria e raggi X, con visita aziendale nel pomeriggio. I dettagli saranno definiti alla prossima riunione.
CT METALLI E TECNOLOGIE APPLICATIVE (MTA) (riunione 22 marzo 2023)
Iniziative future
• GdS “Sostenibilità ambientale nel campo delle costruzioni civili: il Presidente Loconsolo comunica che la scaletta finale è pronta: sono previsti nove interventi su sostenibilità in edilizia, salubrità e efficienza energetica, criteri ambientali minimi, ciclo di vita dei metalli, marcatura ed etichettatura dei prodotti, sicurezza sismica e contro gli incendi. La manifestazione è prevista per la seconda metà di giugno 2023. La partecipazione fornirà anche crediti formativi grazie al coinvolgimento di CTA – Collegio dei Tecnici dell’Acciaio.
• GdS sulla Saldatura: i membri del CT stanno contattando aziende e personaggi esterni in grado di partecipare a questa manifestazione portando la loro testimonianza. Si stanno aspettando le risposte per stilare il programma.
• GdS sui metalli impiegati nei motori elettrici: il coordinatore Morri ha preparato una scaletta quasi definiva che viene distribuita ai presenti. La manifestazione è prevista per il 14 o 15 settembre 2023 con il titolo (da confermare): “Innovazione nei materiali per la mobilità elettrica”.
(riunione del 7 marzo 2023)
Consuntivo di attività svolte
• GdS “Emergenza costi energetici: che fare in fonderia?”: la manifestazione si è svolta il 24 febbraio. Il coordinatore Parona ricorda che la GdS era nata a seguito delle preoccupazioni per l’escalation dei costi dell’energia e per fare il punto sulla possibilità da parte delle fonderie di sostenere tali costi. La presenza è stata piuttosto limitata, ma i contenuti sono risultati ricchi e utili. Vivo apprezzamento per la tavola rotonda finale con la presenza del dottor Angelo Ghidoni di Ghial.
Manifestazioni in corso di organizzazione
• Pillola di difettologia: “Giunzioni fredde”: il coordinatore Valente conferma questa mezza giornata in presenza come momento di networking. La data prevista è il 6 luglio 2023, nel pomeriggio, con tavola rotonda e aperitivo finale; la sede non è ancora definita. Verrà proposto un caso di studio relativo ad uno stampo, con una presentazione introduttiva microstrutturale e metallurgica della difettologia. La locandina sarà pronta per la prossima riunione.
Iniziative future
• Master “Progettazione Stampi”: AIM ha lanciato una indagine per definire/garantire la presenza di almeno 25 utenti per ogni modulo. I questionari raccolti sono stati esaminati durante la riunione. Si discute sulla possibilità di suddividere i moduli in presenza e quelli webinar. I coordinatori presenteranno alla prossima riunione un calendario preliminare di date e di moduli suddivisi, con inizio a ottobre 2023 e cadenza bisettimanale.
E TECNOLOGIE ADDITIVE (MP) (riunione del 9 marzo 2023)
Manifestazioni in corso di organizzazione
• GdS “Post-processing dei componenti realizzati in additive”: l’evento è organizzato con il CT Trattamenti Termici e Metallografia e si dovrebbe svolgere su due giornate, indicativamente il 18 e 19 aprile. Il coordinatore Stortiero presenta gli interventi previsti finora, da completare con altri per la seconda giornata, possibilmente più vicini al tema del post-processing. Si parlerà anche della produzione di polveri.
• Manifestazione sul Metallo duro, da tenere in lingua inglese il 12 e 13 ottobre 2023 a Pallanza presso l’hotel Majestic. Il coordinatore De Gaudenzi presenta gli interventi ed il programma che comprende undici relazioni nelle due mattinate, tra cui una memoria sulla storia del metallo duro e una sulla presenza di tungsteno in Italia; nel pomeriggio del primo giorno si visiteranno una miniera d’oro e una di scheelite vicino a Macugnaga, mentre il giorno dopo si visiteranno aziende del settore.
Iniziative future
• Rampin ritorna sulla possibilità di organizzare una GdS su press&sinter in tema automotive, chiedendo se altri CT stanno organizzando qualcosa di simile. Si discute anche della possibilità di limitare le presentazioni a mezza giornata online, oppure di riempire la giornata in presenza con una visita in azienda. Rampin conferma l’interesse su questo tema soprattutto nel passaggio da motore a combustione a motore elettrico.
CT MATERIALI PER L’ENERGIA (ME) (riunione del 05 aprile 2023)
Notizie da Comitato
• Arianna Gotti lascia il CT e tutte le attività connesse, compreso il coordinamento del GdL Creep, a seguito del cambio di società di appartenenza. Continuerà a collaborare con AIM in altri CT. Gavelli la ringrazia per il lavoro svolto e le rivolge gli auguri per la nuova attività professionale. Si sta definendo la sua sostituzione in modo che non si verifichino discontinuità.
Consuntivo di attività svolte
• Corso Creep: entrambi i moduli del Corso hanno avuto un buon successo, anche di partecipazione. I questionari raccolti hanno regi-
strato un giudizio complessivo buono/ottimo, con apprezzamenti per la competenza e la chiarezza dei docenti e la possibilità di dialogo/interazione con i docenti grazie alle lezioni in presenza. Gli organizzatori valuteranno gli argomenti suggeriti per approfondimenti in modo da inserirli eventualmente nelle prossime edizioni.
Iniziative future
• Il presidente Gavelli aggiorna sul possibile evento dedicato alla fusione nucleare, che doveva tenersi in Francia a Cadarache presso il sito ITER in collaborazione con il CT Forgiatura. L’accesso a questo sito è possibile sono in pochi giorni durante l’anno, di solito di sabato e con lunghe liste di attesa. Viste queste difficoltà e soprattutto tenendo presente la missione del CT Materiali per l’energia, si decide di focalizzare l’impegno su una giornata più tecnica, che si rivolga principalmente alla fissione come tecnologia più vicina ad una applicazione reale a breve termine.
• Dopo l’annullamento della manifestazione di cui sopra, il coordinatore Ripamonti torna sulla GdS “Fissione nucleare”, partendo dalla scaletta che lui stesso aveva già predisposto. Viene fatta circolare una bozza aggiornata del programma previsto: ci sono ancora alcuni interventi da definire, tra cui uno sullo smaltimento dei contenitori e una presentazione che faccia cenno alla fusione come tecnologia in fase di studio. Il CT Forgiatura sarà coinvolto in una riunione a breve per definire tutti gli interventi. Si ipotizza una data tra ottobre e novembre 2023.
- Dimensional and geometrical tolerances for moulded parts - Part 3: General dimensional and geometrical tolerances and machining allowances for castings using ± tolerances for indicated dimensions (ISO 8062-3:2023)
Norme UNSIDER pubblicate da UNI nel mese di marzo 2023
UNI EN 10107:2023
Nastri e lamiere magnetici di acciaio a grani orientati forniti allo stato finito
UNI EN ISO 13704:2023
Industrie del petrolio, petrolchimiche e del gas naturale - Calcolo dello spessore dei tubi dei riscaldatori nelle raffinerie di petrolio
UNI EN 10248-1:2023
Palancole di acciaio laminate a caldoParte 1: Condizioni tecniche di fornitura
Norme UNSIDER ritirate da UNI nel mese di marzo 2023
UNI EN 10107:2014
Nastri e lamiere magnetici di acciaio a grani orientati forniti allo stato finito
UNI EN ISO 13704:2009
Industrie del petrolio, petrolchimiche e del gas naturale - Calcolo dello spessore dei tubi dei riscaldatori nelle raffinerie di petrolio
UNI EN 10248-1:1997
Palancole laminate a caldo di acciai non legati - Condizioni tecniche di fornitura.
Norme UNSIDER pubblicate da CEN e ISO nel mese di marzo 2023
EN ISO 8062-3:2023
Geometrical product specifications (GPS)
EN 10248-1:2023
Hot-rolled steel sheet piles - Part 1: Technical delivery conditions
ISO 13520:2023
Determination of ferrite content in austenitic stainless steel castings
ISO/TS 4689-1:2023
Iron ores — Determination of sulfur content — Part 1: Barium sulfate gravimetric method
Progetti UNSIDER messi allo studio dal CEN (Stage 10.99) – aprile 2023
prEN 17889
CEN/TS 17889, District heating pipes –Factory made flexible pipe systems with thermoplastic reinforced service pipes (TRSP)
prEN ISO 21068-4
Chemical analysis of raw materials and refractory products containing silicon carbide, silicon nitride, silicon oxynitride and sialon – Part 4: XRD methods
prEN ISO 3887 rev
Steels – Determination of the depth of decarburization
Progetti UNSIDER in inchiesta
prEN e ISO/DIS – aprile 2023
prEN – progetti di norma europei
prEN ISO19901-5
Petroleum and natural gas industries
- Specific requirements for offshore structures - Part 3: Topsides structure (ISO/DIS 19901-3:2022)
prEN 12560-1
Flanges and their joints - Dimensions of gaskets for Class-designated flangesPart 1: Non-metallic flat gaskets with or without inserts
prEN 1514-1
Flanges and their joints - Dimensions of gaskets for PN-designated flangesPart 1: Non-metallic flat gaskets with or without inserts
prEN 10248-2
Hot rolled steel sheet piles - Part 2: Tolerances on dimensions and shape
prEN 10249-2
Cold formed steel sheet piles - Part 2: Tolerances on dimensions and shape
prEN 10348
Steel for the reinforcement of concreteGalvanized reinforcing steel products
prEN 10080
Steel for the reinforcement of concreteWeldable reinforcing steel - General
prEN 10251
Magnetic materials - Methods of determination of the geometrical characteristics of electrical steel sheet and strip
EN 10217-1:2019/prA1
Welded steel tubes for pressure purposes
- Technical delivery conditions - Part 1: Electric welded and submerged arc welded non-alloy steel tubes with specified room temperature properties
Norme pubblicate e progetti in inchiesta (aggiornamento 30 marzo 2023)
ISO/DIS – progetti di norma internazionali
ISO/DIS 15544
Petroleum and natural gas industries — Offshore production installations — Requirements and guidelines for emergency response
ISO/DIS 9477
High strength cast steels for general engineering and structural purposes
ISO/DIS 4993
Steel and iron castings — Radiographic testing
ISO/DIS 4990
Steel castings — General technical delivery requirements
ISO/DIS 4179
Ductile iron pipes and fittings for pressure and non-pressure pipelines — Cement mortar lining
Progetti UNSIDER al voto FprEN e ISO/FDIS – aprile 2023
FprEN – progetti di norma europei
FprEN ISO 10113
Metallic materials - Sheet and stripDetermination of plastic strain ratio (ISO/ FDIS 10113:2019)
ISO/FDIS – progetti di norma internazionali
ISO/FDIS 22974
Petroleum and natural gas industry — Pipeline transportation systems — Pipeline integrity assessment specification
ISO/FDIS 6338
Method to calculate GHG emissions at LNG plant
ISO/FDIS 204
Metallic materials — Uniaxial creep testing in tension — Method of test
Enrico Mosca
stagno. Il bronzo, che darà poi il nome all’epoca caratterizzata da un suo diffuso impiego, non verrà usato solo per oggetti ornamentali e statuette votive ma servirà per tutta una serie di utensili, quali coltelli, scalpelli, punte, martelli e mazze, asce, e ancora per armi da caccia e da guerra.
Preistoria e antichità
Partendo dal neolitico, in cui l’uomo incomincia ad utilizzare oltre alla pietra altri materiali quali legno, osso ed argilla, quest’ultima capace di essere formata acquisendo strutture stabili e robuste dopo cottura, il progresso incomincia con la scoperta delle particolari proprietà dei metalli, resistenza e tenacità, decisamente appetibili rispetto a quelle dei materiali già in uso: la storia della metallurgia si può pertanto far risalire intorno al VII – VIII millennio AC, iniziando con le lavorazioni per martellatura, che saranno praticate su metalli reperibili allo stato nativo (rame, oro e occasionalmente, ferro meteorico); il loro uso incomincia in regioni come l’Asia occidentale, nelle quali si hanno giacimenti affioranti alla superficie; i primi oggetti lavorati dall’uomo sono però piuttosto piccoli, e destinati per lo più ad uso ornamentale; l’operazione di formatura sarà comunque limitata dalla incapacità di allontanare le impurezze rimaste dopo aver separato il metallo dal minerale che lo accompagnava.
La martellatura porta alla prima delle scoperte: i metalli induriscono durante questa operazione! Il fenomeno oggi è definito incrudimento, e comporta un utile incremento delle proprietà meccaniche, ma l’oggetto diventa fragile.
La seconda scoperta avviene intorno al 5000 AC, ed è quella della ricottura, cioè di un trattamento termico che permette ulteriori deformazioni sui metalli e che può essere ripetuto. In epoca posteriore troviamo la prima lavorazione a caldo, la forgiatura, cui segue l’applicazione della tecnica della giunzione a caldo di più pezzi metallici, in modo da ottenere oggetti di maggiori dimensioni.
Il ferro meteorico sarà utilizzato dagli egizi, intorno al 4000 AC.
Il passaggio dai forni a legna ai forni rudimentali per cuocere l’argilla comporta anche per la metallurgia un salto di qualità, in quanto questi nuovi impianti, grazie al tiraggio naturale dell’aria attraverso il fornello contenente il combustibile, sono capaci di raggiungere temperature più elevate, tali da permettere la riduzione di certi ossidi e carbonati, specie di quelli di rame: la presenza di questi minerali nel fornello (p. es. di malachite, che gli antichi artigiani potevano aver usato per smaltature decorative sui loro oggetti di ceramica) porta alla scoperta del processo di riduzione, e il rame che veniva trovarsi nelle ceneri era pronto per essere lavorato per martellatura. Dall’osservazione di questi fenomeni al riconoscimento dei minerali utili ad essere trasformati in metalli il passo è ancora piuttosto lungo: per ottenere per riduzione il piombo, l’argento, e più tardi anche lo stagno, sono necessari forni di cottura dell’argilla più efficienti, con l’adozione di schemi per favorire la circolazione dell’aria nella camera di combustione.
I primi processi di fonderia compaiono nella Mesopotamia, regione ricca di minerali adatti a queste primitive elaborazioni metallurgiche; la raffinazione mediante fusione viene sviluppata più tardi: nel 4000 AC si realizza la purificazione del rame mediante reazioni chimiche allo stato liquido e, nel millennio successivo, le tecniche raggiungono una certa maturità, in particolare nella Thailandia, culminando con la fabbricazione del bronzo (3600 AC) a partire dai minerali di rame e
Fusione e colata dei metalli sono effettuate usando crogioli e forme in pietra e in ceramica, ma i progressi, specie per quanto riguarda la qualità delle leghe, sono estremamente lenti, così come il miglioramento delle tecniche di formatura degli oggetti: il più antico getto conosciuto è una rana di bronzo, databile intorno al 3200 AC.
Il processo di formatura a cera persa compare in Egitto intorno al 2500 AC e viene impiegato soprattutto per gioielli e ornamenti vari; nel 1750 AC lo stagno compare come metallo a sé stante. Nel corso del secondo millennio AC è scoperto anche l’ottone, che diverrà poi importante sia in gioielleria, come imitazione dell’oro (Oricalco), sia dopo, come materia prima per la coniazione di monete, che compariranno intorno al 700 AC.
In metallurgia il perfezionamento delle conoscenze empiriche, ma comunque piuttosto complesse per il tipo di cultura allora esistente, determina il nascere di una nuova professione, quella di fabbro, altamente specializzata e tenuta in grande considerazione; le pratiche metallurgiche, spesso accompagnate da riti religiosi e magici, sono vincolate quasi sempre al segreto, data la loro importanza economica e politica. Poiché esse rappresentavano un’ovvia fonte di prosperità per le popolazioni che potevano approfittarne, possiamo comprendere perché le conoscenze tecnologiche ebbero una diffusione così lenta dai loro luoghi d’origine; il cammino è stato piuttosto lungo: dalle regioni intorno al Caspio e all’Armenia che disponevano di giacimenti minerari facilmente identificabili, le conoscenze si trasferirono tuttavia ai paesi vicini, Anatolia, Egitto e poi verso l’India, mentre nella direzione opposta si spostarono verso la Grecia e l’Italia, favorite anche dallo sviluppo del commercio. Nell’America del sud, non toccata da queste correnti di traffico, l’Età del bronzo si manifesterà solo intorno al 1000 DC!
In questo periodo avviene la scoperta del processo di coppellazione per estrarre l’argento dal piombo e per purificare sia l'argento che l'oro; è interessante notare come la produzione di gioielli favorisca le tecnologie ad essi collegate, quali stampaggio, brasatura, ribaditura, intarsio e lavorazione a sbalzo. Nuovi metalli sono introdotti nelle produzioni: oltre all’ottone anche piombo e zinco; oggetti e utensili acquistano maggiori dimensioni per il perfezionarsi delle tecniche di giunzione mediante forgiatura a caldo, e i processi metallurgici diventano più efficienti. Compaiono anche i primi metodi di analisi qualitativa (uso della pietra di paragone per saggiare la purezza dell’oro) ed anche quantitativa, per determinare il titolo dei metalli preziosi; l’arte orafa incomincia a utilizzare tecniche di nobilitazione dell’aspetto di oggetti di bronzo e argento mediante doratura con amalgama d’oro, grazie alla scoperta del mercurio nel 750 AC e della sua capacità di fare lega, p. es. con l’oro, e di essere liberato per semplice riscaldamento.
Il ferro, con le sue favorevoli proprietà meccaniche, in particolare la durezza, a parte qualche precedente esperienza degli egizi, giunge sulla scena mondiale più tardi, date le difficoltà di ottenerlo per riduzione del minerale; gli Ittiti perfezioneranno i forni, rendendoli
termicamente più efficienti (uso dei mantici per esaltare la combustione, 1800 AC) ma le temperature non saranno ancora sufficienti per ottenere la ghisa, mentre le aggiunte di fondenti, quali soda e calce, aiuteranno a purificare la massa metallica combinandosi con i minerali della ganga; è perfezionata intanto anche la tecnica di forgiatura dei masselli, con cui la massa spugnosa di ferro ridotto è trasformata in blocchi compatti, e le impurezze più grossolane sono eliminate con una prolungata azione di martellatura.
La temperatura necessaria per arrivare alla fusione del ferro è raggiunta solo tra il 1400 ed il 1300 AC dai fabbri indiani di Hyderabad, che sviluppano il processo per produrre il cosiddetto acciaio Wootz, miscelando minerale di ferro (magnetite) con carbone di legna in opportuna quantità: la massa era poi posta in un crogiolo sigillato, riscaldato esternamente nel forno su di un letto di carbone, la cui combustione era attivata da una energica corrente di aria; le reazioni esotermiche in un ambiente con efficiente isolamento termico permettevano di raggiungere lo scopo. Il processo di fusione e solidificazione era ripetuto più volte, realizzando così anche un’affinazione e pertanto al termine del ciclo si producevano dischi di ferro di notevole purezza, anche se di dimensioni limitate, con pesi dell’ordine del chilogrammo.
Il crollo dell’impero ittita intorno al 1200 AC favorì probabilmente la diffusione delle conoscenze, che furono portate dai fabbri costretti a emigrare, soprattutto verso l’Europa.
Intanto la siderurgia si sviluppa in Cina: risale al 600 AC la realizzazione di un tripode in ghisa del peso di 270 kg e una produzione corrente di oggetti in ghisa si ha intorno al 300 AC. Una successiva fondamentale scoperta avverrà circa due secoli dopo, col processo dell’affinazione della ghisa in acciaio, e conseguente possibilità di passare dai getti, piuttosto fragili, a prodotti forgiabili, con qualità superiori.
Il miglioramento delle proprietà del ferro è merito degli Etruschi (700 AC), che scoprono l’influenza del carbonio sulla struttura del ferro: si constatò che il prolungato riscaldamento ad alta temperatura in ambiente che oggi sappiamo essere carburante oltre che riducente, portava a ottenere un metallo con caratteristiche più favorevoli e soprattutto riproducibili in quanto a durezza e resistenza. Quando poi si notò che la durezza aumentava con la velocità di raffreddamento, si misero le basi del trattamento termico di tempra.
L’ultima raffinatezza, che permetteva di ottenere il massimo delle proprietà favorevoli. e cioè durezza accompagnata da tenacità, fu messa in pratica dai Romani (200 AC), che introdussero il trattamento di distensione (rinvenimento).
Mentre si viene sviluppando l’uso del ferro, anche il bronzo registra importanti progressi: sono elaborate leghe per impieghi specifici, come p. es. i bronzi al piombo per statue (p. es. i Bronzi di Riace risalgono al V secolo AC) e i bronzi ad alto tenore di stagno per specchi.
L’estendersi dei commerci e le campagne militari durante l’espansione della civiltà greca e poi di quella romana, contribuiscono in modo decisivo alla diffusione delle conoscenze tecnologiche lontano dai luoghi d’origine; tuttavia il principale contributo alla metallurgia dell’impero di Roma non è stato tanto quello dell’innovazione quanto quello dell’organizzazione: i migliori processi metallurgici
reperibili all’epoca furono impiegati ovunque, e questo contribuì a espandere le produzioni metallurgiche dalle centinaia di chilogrammi dell’epoca precedente alle decine di tonnellate.
Un'altra caratteristica di questo periodo è che le esperienze tecnologiche, come qualsiasi altro aspetto culturale, diventano oggetto di interesse e commento anche per il mondo letterario, con scritti di varia natura e finalità: nelle opere di molti scrittori greci e romani, da Omero a Lucrezio (De rerum natura) a Plinio il Vecchio (Naturalis Historia, in 37 volumi) si trovano cenni più o meno estesi o trattazioni sulle problematiche metallurgiche per cui, specie in tempi recenti, archeologi e tecnologi hanno sottoposto a confronto le informazioni contenute in questi testi con quelle rilevabili dai reperti dell’epoca, procedendo anche a verifiche sperimentali.
Occorre sottolineare che il contributo essenziale alle conoscenze di quale patrimonio tecnologico fosse in possesso dei nostri predecessori viene dagli esami metallografici e analitici dei reperti: a partire dalla composizione e dalla struttura dell’oggetto è possibile in una certa misura risalire al ciclo di fabbricazione praticato.
Medioevo
Il principale progresso tecnologico è nel campo della siderurgia per merito dei cinesi e dei giapponesi: tra il 600 e l’800 è acquisito il processo di produzione dell’acciaio a partire da ferro ottenuto per riduzione: questi è miscelato con ghisa e sottoposto a fusione, solidificazione e lavorazione a caldo; si giunge a comprendere l’importanza del tenore di carbonio (la cui influenza era già stata scoperta dagli etruschi) e pertanto, anche se in modo empirico, si cerca di controllarlo. Un ulteriore merito di questi tecnici è il perfezionamento dei forni, con l’invenzione dei forni a tino, progenitori in scala ridotta dei nostri attuali altiforni; in esso sono già presenti i principali accorgimenti atti a ottenere una produzione di acciaio di una certa consistenza: carica dall’alto di minerale, carbone e agenti scorificanti (calce) mentre dal basso, attraverso opportuni condotti (le odierne tubiere), si soffia aria con mantici azionati da salti d’acqua; ghisa e scorie sono poi spillate dal fondo. Si passa così da lingottini di qualche chilogrammo a lingotti e getti di peso molto più elevato, da avviare a successive lavorazioni.
Considerando il periodo successivo alla dominazione romana, il progresso metallurgico in Europa è ancora piuttosto lento, e sarà così per tutto il Medioevo; l’innovazione continua a essere basata su osservazioni casuali, poiché la maggior parte delle lavorazioni è organizzata in forma artigianale e le attività metallurgiche sono inquinate da pratiche in cui empirismo e magia hanno ancora una grossa rilevanza. La maggior parte delle lavorazioni di formatura è fatta manualmente: il fabbro faceva sollevare la massa battente, che poi era fatta ricadere per gravità, fornendo il colpo utile all’operazione di formatura, e questo modo di operare è rimasto in funzione fino a questa epoca; con l’uso di magli a leva comandati da salti d’acqua è infatti possibile forgiare barre e lamiere assai più agevolmente. Anche se la produzione dei metalli cresce, la loro introduzione in oggetti di uso comune è rallentata dal costo e dal fatto che le esigenze belliche sono sempre prevalenti sulle attività pacifiche: l’attenzione del metallurgista è rivolta soprattutto alle armi per l’offesa e la difesa, e ciò porta p. es. ad affinare le tecniche di fabbricazione delle
lame.
Una prima tecnica, già usata dai romani, consiste nella saldatura a pacchetto mediante martellatura di strisce di acciaio superficialmente decarburate per riscaldamento in ambiente ossidante e poi attorcigliate; si dà così origine a una struttura che, dopo tempra, presenta strati alternativamente duri e tenaci.
La seconda, che diede origine alle famose “spade di Damasco”, si originò probabilmente in India e fu adottata dagli arabi, che la diffusero successivamente in Europa, specie nella Spagna (armi di Toledo): essa consiste nel sottoporre a carburazione pezzetti di ferro miscelati con legno in crogioli chiusi riscaldati fino a formare ghisa liquida sulla superficie; estratti poi dal crogiolo e sottoposti ad accurata martellatura, questi sbozzati si saldano in una struttura stratificata, cui la tempra poteva conferire durezza per la trasformazione in martensite delle zone ricche di carbonio.
Una terza tecnica, praticata nell’Europa settentrionale, è basata sulla metallurgia delle polveri: consiste nel sinterizzare limatura di ferro, sbriciolare la spugna così ottenuta e infine sinterizzarla di nuovo in presenza di sostanze organiche (cessione di carbonio e azoto) con carbonitrurazione superficiale delle particelle di ferro; la forgiatura finale permetteva così di produrre lame con struttura molto fine e quindi con ottima tenacità e durezza. Per quanto riguarda le armature indossate dai cavalieri, agli inizi esse erano fatte con fili di ferro e solo verso la metà del 1200 furono assemblate con lamiere di ferro lavorato, rese snodabili da ingegnosi incastri meccanici; l’acciaio accoppiato a ferro in modo da aumentare la resistenza meccanica pur conservando la tenacità, fu usato assai più tardi.
In questo periodo sono da registrare eventi puntuali, che testimoniano sviluppi metallurgici locali; tra questi si possono citare:
• erezione della colonna di Dehli (7 metri di altezza, diametro alla base 420 mm, peso 5,44 t) prodotta saldando insieme per forgiatura blocchi di ferro Wootz praticamente puro (intorno al 400 DC)
• fusione in terra di calderoni e di campane per cattedrali (fonderie p. es. in Italia, Fiandre, intorno al 1200 DC)
• erezione di una colossale statua di Buddha a Kamakura, fusa in bronzo ad alto piombo in più sezioni: la sola testa pesa 140 t (intorno al 1200 DC)
• gli Incas usano una lega oro-argento per consolidare in lingottini polvere di platino con riscaldamento su carbonella, attizzando la fiamma con soffiaggio di aria
• compare il ferro forgiato catalano (1293, a partire da minerale ridotto in altoforno rudimentale)
• primo cannone fuso in bronzo a Gand (1313)
• avviamento della produzione di ghisa in altoforno rudimentale, (1350)
• il peltro è impiegato per coppe e tazze, (1350)
Verso la fine del Medioevo lo sviluppo delle tecniche metallurgiche comincia a essere documentato in raccolte specifiche d’informazioni scritte, che integrano la tradizione orale. Tra queste è da citare l’opera De Diversis Artibus, di Teofilo, prima metà del XII secolo, con descrizione dei principali procedimenti usati nella pratica dell’epoca.
Rinascimento
Questo periodo, che va dal secolo XIV al XVI, rappresenta una svolta nella storia della metallurgia, specie per l’Europa: alcune tappe di questo risveglio tecnologico sono l’introduzione del forno a tino (1440), che porta la nostra siderurgia al livello di quella orientale, l’uso di forni a riverbero di consistente capacità per l’elaborazione di metalli non ferrosi (impianti termicamente più efficienti e di maggiore produttività), l’impiego di nuove leghe, la purificazione dell’oro estraendo l’argento con acido nitrico, la produzione di cannoni fusi in bronzo (assedio di Costantinopoli, 1410) e poi in ghisa, la progressiva sostituzione dell’oro con l’argento nelle monete per motivi economici: questa problematica porta a perfezionare i processi di coppellazione per estrarre l’argento dal piombo, col quale è associato a livello di minerale e anche dal rame (l’argento passa in soluzione nel piombo fuso che si fa agire sul rame, e poi è separato da questo ultimo, ancora per coppellazione).
Agricola scopre l’antimonio.
In questo periodo si sviluppa anche la tecnica dell’attacco chimico selettivo a scopo decorativo, p. es. sulle armature dei cavalieri: bellissimi esempi si trovano nei nostri musei.
L’avvento del Rinascimento e lo sbocciare del fervore culturale che caratterizza questo periodo storico comporta fatti che sono forse più importanti che non i singoli sviluppi tecnologici.
Il primo è che le tecniche metallurgiche sono per la prima volta documentate in testi specifici scritti da tecnici e non più da letterati: l’invenzione della stampa, con l’introduzione dei caratteri mobili a base di una lega piombo antimonio (perfezionata da Gutemberg, 1447) favorisce la pubblicazione di due grandi opere, quella di Biringuccio da Siena, Pirotechnia, in 10 volumi, e quella di Agricola, De Re Metallica, che formalizzano così l’insieme delle conoscenze fino allora accumulate.
Il secondo è l’inizio di un processo d’integrazione tra le varie discipline tecniche: lo sviluppo della metallurgia è inscindibile dai progressi compiuti nei campi della fisica, della chimica e della meccanica (p. es. sono studiati i metodi di analisi per verificare l’efficacia dei processi di purificazione dei metalli); d’altro canto è proprio nel Rinascimento che compaiono figure come quella di Leonardo da Vinci, che con la sua presenza in ogni campo della scienza e dell’arte diventa emblematica da questo punto di vista.
Il terzo fatto, anch’esso molto significativo, è l’introduzione delle prime macchine idrauliche azionate da salti d’acqua: occorre tener presente che, ad eccezione dei processi di preparazione dei minerali (macinazione nei mulini) e della manovra dei mantici per il soffiaggio dell’aria nei forni, fino allora le lavorazioni dei metalli erano basate essenzialmente sulla forza muscolare dei fabbri e dei loro aiutanti. Con l’avvento delle macchine si costruiscono i primi magli per la forgiatura e poi i primi laminatoi: nel 1480 Leonardo da Vinci ci ha tramandato il progetto di una macchina per la laminazione del piombo utilizzato per fissare i vetri delle vetrate artistiche, e nel 1495 ha realizzato un laminatoio a due cilindri per la laminazione di lastre piane, utilizzabili quali semilavorati per monetazione. All’inizio si tratta di macchine rudimentali, ma ciò permette comunque di produrre in quantità e in modo più efficiente ed economico dei semilavorati da destinare anche a usi comuni.
L’attenzione dei tecnici e dei tecnologi comincia però ad essere attrirata dalle proprietà di nuovi materiali, anche non metallici; p. es. nel 1496 Cristoforo Colombo porta dall’America pezzi (palline) di gomma cruda. Nel 1500 in Francia è introdotto l’uso in fonderia di sabbie refrattarie. Epoca preindustriale (1600-1750)
Il coordinamento tra le varie discipline tecniche diventa uno strumento importantissimo per fornire spiegazioni sui fatti sperimentali osservati nei vari settori in cui si manifesta l’esperienza tecnologica dell’epoca, e tra questi anche in quello metallurgico: inizia lo studio delle proprietà fisico meccaniche dei metalli e l’influenza della composizione, s’impiegano metodi efficaci di analisi chimica per accertarla, la struttura dei metalli e delle leghe comincia a essere osservata al microscopio (nascita della metallografia con Henry Power, 1664) notando cricche, microcavità, inclusioni. Altro fatto importante è la nascita in questo periodo di una letteratura tecnica specifica sui processi metallurgici, con descrizione dei cicli produttivi e dei limiti dei loro parametri guida per ottenere migliori prestazioni. Per i processi metallurgici l’evento fondamentale è l’introduzione del coke (Darby, inizio del 1700), da usare come riducente al posto del carbone di legna: il carbon fossile era già noto da tempo e impiegato come combustibile, ma non era adatto a usi metallurgici, specie per il suo elevato tenore di zolfo; merito di Darby è quello di aver messo a punto il processo di distillazione del carbon fossile in ambiente riducente, ottenendo un materiale ideale per la carica dei forni, grazie alla resistenza meccanica, anche a caldo, alla relativa purezza e soprattutto al basso costo (facilità di preparazione in grandi quantità).
Tra l’altro Darby introduce in fonderia l’uso della staffatura (forme in sabbia in due metà, richiudenti la cavità in cui sarà colato il getto). Anche i forni fanno tesoro di sostanziali perfezionamenti, sia grazie all’uso di refrattari compatibili con i regimi termici praticati e con la composizione chimica della lega da affinare, sia dal punto di vista degli schemi costruttivi: dimensioni accresciute, disposizione e dimensionamento degli ambienti e dei condotti nei confronti dei processi che vi si praticano, introduzione delle ciminiere per migliorare il tiraggio e allontanare i fumi nocivi. A questo proposito è bene notare come si cominci a ricuperare lo zinco nei forni di affinazione del piombo: lo zinco che distilla e condensa sulle pareti relativamente fredde degli impianti è raccolto e usato per la produzione diretta dell’ottone sciogliendolo nel rame: in questo modo c’è un controllo più agevole della composizione della lega; verso la fine di questo periodo (Champion, 1738) è messo a punto anche il processo di affinazione dello zinco a partire dal minerale e, nel campo siderurgico, Reamur (1722) sviluppa il processo di produzione della ghisa malleabile a cuore bianco.
In fonderia è fusa (1733) la più grande campana del mondo, quella del Cremlino, pesante ben 200 t, che nella fase successiva alla distaffatura per un incidente (incendio supporto) subisce una frattura: si stacca un pezzo oltre 11 t.
Con le prove di trazione iniziano anche quelle per determinare le proprietà meccaniche dei materiali.
Nel campo delle lavorazioni dei metalli per deformazione plastica si
devono segnalare i progressi dei laminatoi: anche se usati prevalentemente per laminazione e cesoiatura dei metalli non ferrosi (lavorabili più agevolmente che non il ferro o l’acciaio); questi laminatoi, pur avendo una struttura con limitata rigidità meccanica ed essendo azionati da fonti di energia a basso rendimento (in questo periodo è disponibile solo l’energia fornita da macchine idrauliche), hanno già in sé in germe l’architettura dei moderni treni di laminazione, a due o tre cilindri sovrapposti.
Usi di nuovi materiali: nel 1615 il lattice di gomma è impiegato (Spagna) per impermeabilizzare pelli e tessuti.
Sviluppi collaterali riguardano altri aspetti del progresso tecnico; esempi:
• 1608: Lippershey brevetta un sistema ottico che permette di costruire il cannocchiale, poi il microscopio, (perfezionati da Galilei nel 1609 e negli anni successivi), e infine il telescopio a rifrazione; il telescopio a riflessione sarà costruito da Newton nel 1668
• Pascal (1642) realizza il primo esemplare di macchina da calcolo: la “pascalina”.
Fino al 1750 la Francia ha il primato per le invenzioni, che passerà poi al Regno Unito.
Dalla rivoluzione industriale a fine 800 – Le macchine utensili
La rivoluzione industriale inizia in Europa intorno al 1750, quando per la prima volta la produzione delle fabbriche supera in quantità quella artigiana e domestica; a questo contribuiscono sia la costruzione di macchine utensili capaci di lavorazioni specifiche, sia lo sviluppo delle motrici a vapore: l’invenzione di Newcomen del 1705 sarà perfezionata da Watt con l’introduzione del condensatore del vapore in uscita dal cilindro in cui scorre il pistone, dell’indicatore di pressione dello stantuffo e infine, 1763, col regolatore di velocità a forza centrifuga.
Con Le Blanc è sviluppato (ante 1800) il concetto di parti intercambiabili, applicato p. es. alla costruzione di pistole (North, 1799), e quindi avviene l’introduzione del concetto di tolleranza geometrica nelle lavorazioni meccaniche.
E’ del 1835 il brevetto del famoso revolver Colt.
A partire dal 1850, con l’avvento della seconda rivoluzione industriale, il primato delle invenzioni passerà agli Stati Uniti.
Lo sviluppo delle macchine utensili comincia con la costruzione dell’alesatrice (Wilkinson, 1775) e prosegue con la potente pressa idraulica di Bramah, il tornio per filettare viti di Maudslay (1790), la macchina per produzione di chiodi (Longstreth, 1809), il tornio con testata a ingranaggio posteriore e la pialla a bancale piano con guide (Roberts, 1817), la fresatrice (Whitney, 1818), la macchina automatica per dadi, la limatrice, il trapano con avanzamento meccanico automatico (Nasmith, rispettivamente nel 1829, 1836, 1840), il tornio automatico per perni (Howe, 1841), la piallatrice (Withworth, 1842), la sega a nastro (Perrin, 1853), il tornio a torretta verticale (Lawrence, Hove, Stone, 1855), il laminatoio a freddo degli acciai (Lauth, 1859), il maglio manovrato col vapore (Nasmyte, 1867), il freno ad aria compressa (Westinghouse, 1869), il calibro micrometrico (Brown e Sharpe, 1877), le rettificatrici universali (1880), il cambio di velocità (Norton, 1892), i torni automatici per la produzione viti (Spencer, 1895), i blocchetti di riscontro (Johnson, 1896), e infine torni
multimandrino, alesatrici verticali, piallatrici con inversione moto, fresatrici universali (ante 1900). Lo sviluppo delle macchine utensili ha un grosso impatto anche sui processi metallurgici: è possibile costruire particolari meccanici e componenti strutturali di altre macchine e di impianti, con i quali sono finalmente meccanizzate molte delle lavorazioni prima praticate manualmente, come preparazione e movimentazione dei materiali e dei prodotti, lavorazioni ai magli, alle forge e agli estrusori.
Il contributo maggiore allo sviluppo tecnologico viene dal progresso scientifico, che investe in particolare la chimica, la fisica e l’elettrochimica, permettendo tra l’altro di riconoscere e studiare i nuovi metalli che nel frattempo vengono isolati. Nasce la metallurgia fisica: con l’avvento della metallografia, dell’analisi termica e del perfezionamento dei metodi di analisi si comincia a interpretare i meccanismi con cui si originano le strutture, e come queste ultime condizionano le proprietà delle leghe più comuni.
A metà del 18mo secolo i laminatoi cominciano a essere mossi da ruote idrauliche. Con l‘avvento della rivoluzione industriale cresce l’esigenza di disporre di grandi quantità di ferro e acciaio lavorati in modo da poter soddisfare la domanda di prodotti metallici, e quindi necessità di costruire macchine di maggiore potenza e con cicli più veloci: nascono così il maglio rapido a vapore già citato (la massa battente è sollevata dal pistone mosso dal vapore in un cilindro) e la pressa idraulica, anch’essa già citata, nella quale la forza è sviluppata da un liquido pressurizzato. L’introduzione della macchina a vapore permette anche la messa in opera di laminatoi (a due e tre cilindri sovrapposti) capaci di operare su quantità e formati di semilavorati fino allora non producibili.
La siderurgia, l’uso dei metalli oltre all’avvento di costruzioni metalliche sempre più imponenti e l’evoluzione tecnica in generale registra numerosi sviluppi: il progresso diventa incalzante!
Sono qui indicati alcuni eventi significativi
• trasporto su rotaia di materiali con carrelli a trazione animale (Outram, 1750)
• Diderot e D’Alembert pubblicano Encyclopédie des Arts et des Métiers (1751-1772)
• le rotaie in legno sono rimpiazzate da quelle in ghisa (Huntsmann, 1756)
• 1771: costruzione del “carro” di Cougnot, antenato dei veicoli semoventi, equipaggiato con un motore bicilindrico a vapore; la prima vettura munita di motore a combustione aria-idrogeno nascerà (de Rivaz) nel 1802, e la prima auto elettrica (Anderson) nel 1839
• viene costruito sul fiume Severn (Regno Unito) il primo ponte metallico; è realizzato in ghisa ed è lungo 30 m (The Ironbridge, 1779)
• avviamento della produzione di ferro a partire dalla ghisa col processo di puddellaggio: la ghisa è introdotta in un forno a riverbero, miscelata con ossido di ferro (come minerale o scaglie di laminazione) e fusa in fiamma ossidante; si ha violenta reazione esotermica del carbonio con l’ossigeno, favorita da un rimescolamento della massa liquida dall’esterno, con pale di ferro; al termine dell’operazione si ottiene una massa solida di ferro quasi puro, che si sottopone a forgiatura (Cort, 1784)
• illustrazione delle proprietà delle leghe più comuni (Achard, 1788)
• 1790: Talleyrand propone l’adozione di un sistema di pesi e misure basato su grandezze fisiche riproducibili e invariabili nel tempo;
nasce così il sistema metrico SI, oggi universalmente adottato
• avviamento della produzione di recipienti in lega platino-arsenico (la scoperta di questa lega fusibile nel 1781 è seguita dal suo uso nel 1790, in Francia)
• 1794: invenzione del cubilotto con rivestimento in metallo e con soffiaggio dell’aria realizzato con motore a vapore (Wilkinson); primo brevetto del cuscinetto a sfere (Vaughan)
• esperienze di Galvani e invenzione della pila (Volta, 1795)
• Bramah brevetta l’estrusione di tubi di piombo (1797), perfezionata poi da Burr (1820)
• va in produzione un laminatoio per lastre di rame (Revere, 1800)
• 1801: Lebon sperimenta l’illuminazione a gas nella sua casa; segue (1804) il brevetto di Winsor su questa tecnologia; essa sarà adottata per l’illuminazione stradale, p. es. a Parigi (1820)
• prima linea di tram a trazione animale su rotaia per trasporto pubblico (nel Galles, 1804)
• 1806: Jacquard costruisce un rivoluzionario telaio per la tessitura con cui i tessuti operati si producono grazie al sollevamento automatico dei fili dell’ordito con un sistema di cartoni forati, realizzando programmi di disegno ripetibili e modificabili a piacere
• preparazione del sodio metallico mediante elettrolisi (Davy, 1808)
• rilascio del brevetto dei barattoli di ferro stagnato (Durand, 1810)
• 1814: costruzione di una efficiente locomotiva a vapore, la Rocket di Stephenson; la prima a trainare un convoglio è stata quella costruita da Trevithick, 1804
• 1817: Drais inventa la “draisina”, antenata (in legno!) della bicicletta, mossa spingendo con i piedi; la trasmissione a catena tra ingranaggi mossi da pedali apparirà negli anni 1879-1885 (Lawson, Renold, Starley)
• nasce l’acciaio legato al nickel (Faraday, 1819)
• le rotaie in ghisa sono sostituite da quelle in ferro (Birkinshaw, 1820)
• per il riconoscimento dei minerali è proposta la prova di durezza mediante scalfittura (Mohs, 1822)
• introduzione delle alpacche, leghe rame-nickel-zinco (Frick, 1823)
• è adottato il preriscaldamento dell’aria da soffiare nei forni: aumento delle temperature di lavoro e risparmio di combustibile (Nelson, 1828)
• inizia la produzione di platino compatto per pressatura polvere e sinterizzazione (Wollanston, 1829, dopo che il metallo era stato sinterizzato ad alta temperatura in Russia, nel 1826)
• 1830: invenzione della macchina per cucire (Thimonnier); inizia la produzione via metallurgia delle polveri di monete di rame sinterizzate e poi coniate con un punzone (Osann)
• 1832: nasce l’alternatore, che avrà sviluppo pratico solo dopo la realizzazione del trasformatore; elaborazione del bronzo al nickel (Berry)
• 1834: Babbage progetta un calcolatore capace di elaborare formule algebriche complesse, in cui i dati sono da introdurre con schede perforate; realizzazione della cancellata in ghisa del Palazzo Reale di Torino su progetto del Palagi
• invenzione e costruzione del telegrafo elettrico (Morse, 1835)
• applicazione del processo di zincatura di lamiere di acciaio per immersione in zinco fuso (galvanizzazione) per aumentare la resistenza alla corrosione (1836)
• 1837: Hancock brevetta il processo di elaborazione delle mescole di elastomeri mediante cilindri controrotanti; con Daguerre nasce la fotografia
• 1839: scoperta del processo di vulcanizzazione degli elastomeri (Goodyear); uso dei metalli bianchi antifrizione (leghe di stagno con antimonio, rame e piombo) per cuscinetti a strisciamento (Babbit)
• comincia la produzione di funi di ferro (Roebling, 1841)
• 1843: varo del transatlantico Great Britain, costruito con lamiera di ferro; Hodkingson introduce la prova di resilienza sui metalli
• 1844: primo esperimento di illuminazione mediante lampade ad arco elettrico; sarà perfezionato poi da Jablochkov nel 1876
• avviamento della produzione di cannoni di acciaio fuso (Krupp, 1847)
• 1850: viene messo in funzione il cubilotto con fondo apribile; sono praticati rivestimenti galvanici (posateria argentata); sono messe in circolazione in Svizzera monete in alpacca; è sviluppato il processo ad alto rendimento per ricuperare l’argento dal piombo (Parkes)
• 1853: Barsanti e Matteucci brevettano il motore a combustione interna, perfezionato poi da Otto e Langen (1876, ciclo a 4 tempi), da Clerk (1879, ciclo a 2 tempi) e infine (1893) da Diesel (ciclo con accensione spontanea del carburante)
• si dimostra per la prima volta che l’alluminio è producibile via elettrolisi da sali fusi (Sainte-Claire Deville, 1854)
• invenzione della macchina per scrivere “cembalo scrivano” (Ravizza, 1855) che, opportunamente ingegnerizzata, andrà in produzione industriale (Remington, 1875);
• 1856: preparazione dei bronzi all’alluminio (Debray); disossidazione dell’acciaio con manganese in fase di affinazione (Mushet); realizzazione del laminatoio tipo trio per la laminazione degli acciai (Carslund); costruzione dei forni con rivestimento acido per convertire la ghisa a basso tenore di fosforo in acciaio (Bessemer, brevetto del 1855), e del forno a riverbero (Martin-Siemens)
• 1857: le rotaie in ferro sono sostituite da quelle in acciaio (Mushet); perfezionamento del sistema di preriscaldamento dell’aria per i forni (Cowper)
• posa del primo cavo telegrafico transatlantico (1857-58)
• 1860: Wöhler introduce la prova di fatica sui metalli; Pacinotti inventa il suo anello, con cui l’energia meccanica si trasforma in elettrica; in Belgio sono messe in circolazione monete in cupronickel
• brevetto della Xylonite, più nota poi come celluloide (Parkes, 1861, e poi Hyatt, 1870)
• le tecniche di esame al microscopio ottico cominciano a essere applicate allo studio sistematico della struttura dei metalli, in particolare degli acciai: nasce con Sorby la moderna metallografia (1863)
• 1865: prime teorie sull’indurimento di tempra degli acciai, spiegato con variazioni strutturali durante i trattamenti termici (Julien); sviluppo del processo di raffinazione del rame per via elettrolitica (Elkington)
• 1867: invenzione della dinamo, che mette a disposizione una sorgente di elettricità per le esigenze dell’industria (Siemens e Wheatstone); esce il brevetto del filo spinato (Smith)
• introduzione dei ventilatori per il soffiaggio dell’aria nei forni (Root, 1867 e Sturtevant, 1870)
• elaborazione dell’acciaio al tungsteno, antenato degli acciai rapidi (Mushet, 1868)
• pubblicazione della tavola periodica degli elementi (Mendeleiev, 1869)
• sono impiegati cuscinetti radenti ottenuti a partire da polvere di stagno miscelata con pece e poi pressata (Gwynn, 1870)
• 1871: Meucci e, separatamente, Bell brevettano il telefono
• 1873: Decauville perfeziona il sistema Corbin di ferrovia portatile a scartamento ridotto di semplice posa in opera, per trasporto materiali con vagoncini a due assi
• enunciazione della “regola delle fasi” in termodinamica (Gibbs, 1874)
• 1877: Edison brevetta il fonografo, sistema di registrazione e riproduzione del suono mediante solco inciso su di un rullo rotante, letto con un ago messo in vibrazione nel solco; sarà successivamente modificato da Berliner (1887, versione attualmente in uso), con solco inciso a spirale su disco piano rotante, letto sempre con ago a opportune velocità; sono introdotti gli acciai al cromo (Boussingalt e Brustlein); Thomas e Gilcrist brevettno il convertitore della ghisa ad alto tenore di fosforo in acciaio grazie al rivestimento in refrattario basico
• scoperta del processo nickel carbonile: l’azione dell’ossido di carbonio a opportuna temperatura e pressione su leghe contenenti nickel determina la formazione di Ni(CO)4 gassoso; questo è condensato, raccolto e decomposto per riscaldamento a temperatura superiore a quella della sua formazione, dando origine a polvere di nickel; dal residuo di nickel impuro, quale quello ottenibile per fusione, si possono così ricuperare metalli nobili e cobalto, che sono di solito presenti (Mond, 1880)
• !879-1880: sviluppo dell’illuminazione mediante lampade elettriche ad incandescenza (Edison e poi Swan)
• prima linea di tram elettrificata (Berlino, 1881)
• 1882: primi brevetti del trasformatore (Gaulard e Gibbs, traduzione in uso pratico dell’anello di induzione realizzato nel 1831 da Faraday)
• sviluppo degli acciai al manganese (Hadfield, 1882)
• 1884: Tilden ottiene il poliisoprene sintetico, praticamente identico come proprietà a quello presente nella gomma naturale; posa di una piramide di alluminio (al momento pregiatissimo) sul monumento a Washington
• 1885: costruzione del motore elettrico a campo rotante in corrente alternata (Ferraris); Goldschmidt scopre e utilizza la reazione della termite per produrre acciaio inossidabile ad alto cromo e basso carbonio; avviamento della produzione di tubi di acciaio senza saldatura per laminazione (processo Mannesmann); sviluppi dei forni elettrici a induzione (brevetto Colby)
• 1886: compare sul mercato il primo rasoio di sicurezza (Wilkinson); avviamento della produzione di alluminio a partire da allumina per elettrolisi in presenza di fondenti fluorati (Hall e Heroult); proposta di usare coni ceramici di diversa composizione, collassabili per riscaldamento a differenti temperature, per misura di temperature elevate (Seger)
• 1887: protesi dentali si realizzano col processo di fusione in cera persa (Philbrook); introduzione del forno fusorio a induzione con nucleo (Ferranti); processo di ricupero dell’oro per cianurazione (Mc Arthur e Forrest); analisi termica degli acciai con la determinazione dei punti caratteristici (Osmond); sviluppo della saldatura ad arco dell’acciaio (Bernados)
• 1888: brevetto dello pneumatico (Dunlop)
• viene costruita in acciaio la torre Eiffel, inaugurata in occasione dell’esposizione universale (1889); diventerà il simbolo di Parigi: è alta 320 m e pesa 7400 t
• primi brevetti sulle turbine a gas (intorno al 1890); le realizzazioni pratiche si avranno però negli anni Trenta del Novecento
• introduzione delle termocoppie Pt/Pt-Rh per la misura di temperature elevate (Le Chatelier, 1891)
• 1891-1901 sviluppi dell’invenzione della radio (Marconi, Tesla, Popov)
• 1892: invenzione del forno elettrico ad arco (Moissan, usato inizialmente per ottenere diamanti sintetici), che sarà poi largmente impiegato per la rifusione (riciclaggio) di rottami e scarti ferrosi e sarà poi perfezionato e curato nelle applicazioni da Sassano (1898); pubblicazione del primo libro di testo di metallurgia (Austen)
• 1894: i fratelli Lumiere brevettano il cinematografo; applicazione del processo di estrusione alle leghe di rame (Dick)
• illustrata la natura dell’austenite, una delle strutture dell’acciaio (Osmond, 1895)
• 1896: scoperta della radioattività (Becquerel); determinazione dello zolfo negli acciai (Schulte)
• 1878-1900: comincia la produzione di filamenti per lampade a incandescenza realizzati prima con carbone, poi con vari metalli refrattari – osmio (Auer von Welsbach), zirconio e tantalio, che sostituiscono l’osmio, e infine col tungsteno (processo Coolidge: riduzione di WO3 con idrogeno, pressatura, presinterizzazione a 1200°C, sinterizzazione a ≈ 3000°C)
• sviluppo del trattamento termico degli acciai rapidi (Taylor e White, 1898)
• 1899: viene inventato e costruito il primo forno elettrico ad arco diretto, per la fusione di acciai e leghe (Heroult)
• sviluppo degli acciai al silicio (Hadfield, 1899)
• viene tracciato il diagramma di stato ferro-carbonio: applicazione generale della regola delle fasi per determinare il comportamento della struttura delle leghe al variare della temperatura (Austen e Rozeboom, 1896-1900)
• 1900: la prova di durezza sui metalli entra nella pratica (Brinell); invenzione del processo di riscaldamento di pezzi di acciaio in presenza di polvere di zinco per realizzare un rivestimento resistente alla corrosione (sherardizzazione, Sherard Cowper –Coles); esce il brevetto del processo di colata in conchiglia a bassa pressione (Lake)
In questo periodo e, grazie anche alla interpretazione della tavola periodica degli elementi, sono scoperti ed isolati metalli non ancora noti, ma presenti in natura nei loro minerali: essi avranno una parte essenziale nella formulazione di nuove leghe, il cui uso oggi è ormai consacrato nella pratica quotidiana, con processi produttivi che, diventando sempre più efficienti, arrivano a offrirci prodotti di cui non possiamo fare a meno.
L’elenco include cobalto (Brandt, 1735), platino (Ulloa, 1748), nickel (Cronstedt, 1751), bismuto (Geoffrey, 1753), magnesio (Black, 1755, isolato da Bussy e Wöhler nel 1829), manganese (Scheele e Gahn, 1774), molibdeno (Scheele e Hyelm, 1778), tungsteno (Scheele, 1781, isolato da D’Ehluyar nel 1783), tellurio (Műller, 1782), stronzio
(Crawford, 1787), uranio e zirconio (Klaproth, 1789), titanio (Gregor, 1791), ittrio (Gadolin, 1794), berillio (Vauquelin, 1797, isolato da Bussy nel 1828), vanadio (Fernandez, 1801, isolato da Roscoe nel 1867), niobio (Hatchett, 1801), tantalio (Ekeberg, 1802), cerio (Berzelius e Hisinger), iridio e osmio (Tennant), palladio e rodio (Wollanston) nel 1803, potassio e sodio (Davy, 1807), bario, calcio (Davy) e boro (Gay Lussac) nel 1808, torio (Berzelius, 1815), cadmio (Strohmayer e Hermann), litio (Arfvedson), selenio (Berzelius) nel 1817, alluminio (Oerstedt, 1825), erbio e terbio (Mossander, 1843), cesio (Bunsen e Kirchhoff, 1860), rubidio (Bunsen e Kirchhoff) e tallio (Crookes) nel 1861, indio (Reich e Richter, 1863), gallio (Lecoq), scandio (Nilson), germanio (Winkler), protoattinio (Fajans) nel 1871, itterbio (Galissard, 1878), samario (Lecoq), tullio (Cleve) nel 1879, gadolinio (Galissard, 1880), praseodimio e neodimio (Auer, 1885), disprosio (Lecoq, 1886), polonio e radio (coniugi Curie, 1898), attinio (Debierne, 1899).
Verso la fine dell’Ottocento nascono le associazioni nazionali dei tecnici che si occupano di meccanica, di materiali non solo metallici, e che sono impegnati in attività ad esse collegate; tra queste risulta fondamentale quella normativa: è da citare la American Society for Testing Materials (ASTM), fondata nel 1898.
Novecento
Il progresso della metallurgia diventa incalzante non tanto per ulteriori nuove scoperte (che comunque completano il quadro delle conoscenze) quanto per il miglioramento del quadro di riferimento, in cui intervengono fattori non considerati prima e che diventeranno sempre più condizionanti, quali p. es. efficienza e rese, organizzazione della ricerca, costi, e poi ecologia, sicurezza, gestione, conservazione delle risorse.
Gli sviluppi sono rapidi e diversificati e non facili da analizzare nel dettaglio, come fatto nei precedenti periodi. I fattori che contribuiscono alla crescita sono le necessità dell’industria, le cui strutture produttive assumono dimensioni rilevanti, dovendo fronteggiare una concorrenza sempre più globalizzata, le esigenze di nuovi materiali e processi nell’aeronautica e nei trasporti in genere, la corsa agli armamenti e allo spazio, la lotta generalizzata contro la corrosione e l’usura. L’integrazione fra le varie discipline è altissima fra tutte quelle che possono concorrere al successo: scienza, tecnologia ed economia sono presenti in ogni fase e ogni nuova realizzazione è frutto di attività coordinate e sempre più dispendiose di esperti nelle varie branche.
L’età del ferro raggiunge la sua maturità: con l’assottigliamento delle risorse facilmente sfruttabili si intensifica la fase del riciclo degli scarti e la ritrasformazione dei materiali contenuti nei prodotti non più in uso; l’avvento di materiali innovativi, e cioè delle materie plastiche sintetiche e dei materiali ceramici (che possono sostituire vantaggiosamente e in molte applicazioni i metalli che avevano fino allora dominato la scena), rappresenta il completamento di quello che al momento era a disposizione.
Indicativamente, la prima metà del periodo raccoglie ancora tappe significative nel progresso tecnico; poi prevale un’attività di perfezionamento delle conoscenze e di adozione nella pratica di quanto elaborato in precedenza. Alcune di queste tappe sono indicate qui
di seguito.
• 1900: primo volo del dirigibile Zeppelin e, a Berlino, prima linea ferroviaria elettrificata
• invenzione della telescrivente (Morton e Krum, primi del Novecento)
• 1903: nasce l’aeronautica col volo dei fratelli Wright; la prova di resilienza Izod è normalizzata e nel 1906 lo sarà quella Charpy; sono introdotte le leghe di alluminio da bonifica, cui si aggiungeranno le leghe ferro-nickel-cromo (Guillet), il monel (Brown, 1906), le stelliti (Haynes, 1907), l’acciaio inossidabile ferritico ad alto cromo (Becket, 1907)
• 1904: con l’invenzione del diodo (Fleming) inizia lo sviluppo delle valvole termoioniche; esso proseguirà col triodo (De Forest, 1907), tetrodo (Schottky, 1919), pentodo (Tellegen, 1926) e, successivamente, coi tubi a vuoto multifunzione, divenuti di uso comune negli anni 40
• fonderia: esce il brevetto della macchina per presso colata (Doehler, 1905)
• 1906: Coolidge ottiene il brevetto sui fili di tungsteno per le lampade ad incandescenza
• sviluppo del trattamento termico di tempra di soluzione e invecchiamento nelle leghe di alluminio (Wilm, 1907)
• 1908: Ford mette sul mercato la sua auto, la Ford T, che sarà prodotta in 15 milioni di vetture fino al 1928
• è fondata la rivista “La Metallurgia Italiana” (1909)
• 1910: brevetto della resina fenolo-formaldeide, nota poi col nome di bakelite (Baekeland)
• nei laboratori diventa disponibile il microscopio metallografico (Reichert, 1911)
• 1912: introduzione dell’acciaio inossidabile austenitico (Maure e Strass); processo di produzione del polivinilcloruro – PVC (Katte); Sauveur pubblica Metallography and Heat Treatment of Iron and Steel
• Invenzione del Cellophane (Brandenberger, 1913)
• 1913: Bohr propone la struttura dell’atomo secondo il modello cosidetto quantico, in cui gli elettroni, particelle aventi carica negativa, ruotano attorno al nucleo in cui stanno i protoni, particelle con carica positiva, occupando regioni dello spazio definite come orbitali e caratterizzate da livelli differenziati di energia; questo a conclusione delle teorie sulla struttura, iniziate con Democrito (V secolo AC) e proseguite con Dalton (1808, atomi differenziabili dei diversi elementi, contraddistinti da una nuova simbologia), con Thomson (1897, postulata e dimostrata l’esistenza dell’elettrone), e infine con Rutherford (1911, modello planetario, con elettroni rotanti attorno al nucleo su orbite); il modello di Bohr sarà successivamente implementato da De Broglie, Heisenberg, Schroedinger, Pauli, infine, 1932, Chadwick dimostra l’esistenza del neutrone, particella come i protoni ma priva di carica elettrica, presente nel nucleo insieme con essi
• 1914: sono introdotte le prove di durezza Rockwell, di facile e rapida esecuzione
• i carburi metallici sinterizzati con legante cobalto sono elaborati a livello laboratorio (Lohmann e Voigtländer, e poi Schroeter, 1914); segue sviluppo industriale (1923-25) e infine brevetto (Widia, Krupp,
1926)
• il forno elettrico a induzione è impiegato per la fusione di metalli non ferrosi (1915)
• tra il 1900 e il 1924 sono prodotti materiali compositi sotto forma di contatti elettrici a base prevalentemente di polvere di tungsteno miscelata con polvere di rame o di argento pressata e sinterizzata, meno frequentemente con polvere di cobalto, ferro e nickel, e poi elettrodi, contrappesi, contenitori (p. es. per il radio, che è radioattivo)
• cuscinetti radenti sinterizzati in bronzo con grafite e impregnati con olio cominciano ad entrare nelle applicazioni meccaniche (Loeventhal, 1913, Gilson, 1921) e poi nell’auto (1927)
• 1916: sviluppo del forno elettrico a induzione senza nucleo (Northrup)
• 1918: invenzione della fusione centrifuga (Sensaud DeLavaud); la Krupp costruisce la “Grande Berta”, cannone con canna di diametro 38,1 cm e lunghezza 33,5 m, per l’assedio a Parigi, capace di sparare a una distanza di 122 km
• indagini strutturali sui materiali solidi con i raggi X (Debye-Scherrer e Hull, 1916-17), nuovi tubi proposti da Coolidge (1920) e applicazione del metodo al controllo qualità dei getti (1925)
• tra il 1900 e fine anni 20 uso di magneti permanenti e di nuclei di ferro per le radio prodotti via metallurgia delle polveri
• 1923: inizia la produzione di filtri metallici sinterizzati (Claus)
• sono introdotte le prove di durezza Vickers, adatte a molti materiali, anche non metallici (Sandland e Smith, 1924)
• sviluppo del cubilotto con aria preriscaldata (Griffin, 1925)
• 1926: Baird inventa la televisione, realizzata l’anno dopo da Fansworth
• sviluppo del forno a induzione ad alta frequenza (1927)
• 1928: Dirac postula l’esistenza dell’antimateria (particelle atomiche aventi cariche elettriche opposte a quelle che costituiscono la materia normale) cui seguono conferme sperimentali tra cui 1932 Alderson, antielettrone (positrone), Segre e Chamberlain, 1955, antiprotone, e 1959, antineutrone
• introduzione degli acciai indurenti per precipitazione (Kroll, 1929)
• 1930: la Avesta produce gli acciai inossidabili duplex; Bain e Davenport illustrano le trasformazioni dell’austenite negli acciai col raffreddamento; inizia l’impiego sistematico di atmosfere controllate nei trattamenti termici
• 1931: Ruska e Knoll costruiscono il prototipo del microscopio elettronico; Ragsdale inventa la saldatura elettrica a punti
• Anni 30: nasce la missilistica con gli studi di von Braun, culminati coi lanci delle V2 verso la fine della II Guerra Mondiale
• sintesi e produzione della poliammide - Nylon (Carothers, 1935)
• 1936: è sviluppato il primo modello fnzionante di radar (Bay)
• inizia la produzione di tubi al neon per illuminazione (General Electric, 1938, su brevetto Germer)
• progettato e costruito Z1 primo computer programmabile (Zuse, 1939); il primo computer commerciale, UNIVAC, sarà invece sviluppato negli USA nel 1951 (Eckert e Mauchly)
• produzione in Germania di corone di forzamento di ferro sinterizzato per proietti impregnate con paraffina in sostituzione di quelle in rame (II Guerra Mondiale)
• dal 1940 in avanti, introduzione nelle auto di componenti meccanici sinterizzati e degli elastomeri sintetici nelle gomme, in concorrenza con l’elastomero naturale
• 1941: brevetto del polietilentereftalato – PET (Whinfield e Dickson) e del poliestere - Terylene
• sintesi dei poliuretani (Hanford e Holmes, 1941)
• 1942: Fermi realizza con successo a Chicago la prima reazione nucleare a catena, che permetterà poi di costruire le centrali nucleari e gli ordigni atomici
• scoperta dell’effetto del magnesio sulla sferoidizzazione della grafite nelle ghise (1943)
• sviluppo della formatura a guscio dei getti (Croning, 1944)
• 1946: nasce l’Associazione Italiana di Metallurgia (AIM)
• realizzazione del transistor, che tenderà a sostituire i tubi a vuoto (Shockley, Bardeen, Bratain, 1947)
• sviluppo del convertitore LD (Linz-Donawitz) di affinazione della ghisa in acciaio mediante soffiaggio di ossigeno puro sulla superficie del metallo (Durrer, 1948)
• 1946-50: sviluppo delle resine epossidiche
• commercializzazione del politetrafluoroetilene – Teflon (USA, 1950)
• 1952: prima macchina utensile commerciale a controllo numerico (tornio - Cunningham e Alma Corporation)
• Anni 50: Canon in Giappone e HP nrgli USA avviano le esperienze con la stampa a getto d’inchiostro; inizia produzione e uso dei polietileni e Natta (1954) brevetta il polipropilene isotattico
• sviluppo del processo di affinazione AOD della ghisa in acciaio, in cui ossigeno e argon sono usati nel soffiaggio (Krivits, 1954), e poi VOD (decarburazione con ossigeno sotto vuoto)
• prima centrale nucleare, installata nel Regno Unito (1956)
• 1957: va in orbita Sputnik, il primo satellite nello spazio
• 1959: introduzione dei policarbonati (USA e Germania) e delle resine acetaliche (USA)
• Anni 50 e 60: componenti meccanici prodotti via metallurgia delle polveri con struttura compatta, componenti a base di superleghe, sbozzati di acciai per utensili, pezzi sinteroforgiati; avvento dei processi di pressatura isostatica a caldo (HIP) e a freddo (CIP)
• entra in servizio (1959) il rompighiaccio Lenin, prima nave a propulsione nucleare
• realizzazione del laser (Maiman, 1960)
• 1961: Yurij Gagarin, primo uomo in orbita nello spazio
• Anni 60: sviluppo dei processi di produzione di acciai speciali mediante rifusione di acciai prodotti al forno elettrico, tra cui ESR (rifusione sotto elettroscoria), EPSR (come ESR, in pressione di azoto), VAR (rifusione con forno ad arco sotto vuoto), VIM (rifusione a induzione sotto vuoto), e ancora produzione di acciai da utensili a partire da polveri
• 1962 compare sul mercato (Holonyak) il primo LED (Light Emitting Diode), inizialmente solo a luce rossa, e poi a diversi colori, grazie allo sviluppo di nuovi e molto più efficienti composti elettroluminescenti, culminati con quelli a luce bianca (ricerche di Nakamura, 1993-95), che sostituiranno progressivamente i sistemi di illuminazione oggi in uso
• invenzione del personal computer (Perotto, 1964)
• va in orbita geostazionaria Intelsat I, primo satellite commerciale per telecomunicazioni (Comsat, 1965)
• 1969: sbarco sulla Luna della missione Apollo 11 (Armstrong e Aldrin)
• Anni 70: componenti meccanici prodotti via stampaggio polveri a iniezione (MIM, Metal Injection Moulding); introduzione dei magneti permanenti ad altissimo prodotto di energia a base di terre rare (samario-cobalto e poi, 1983, neodimio-ferro-boro); sviluppo di materie plastiche di elevate prestazioni, tra cui p. es. polifenilensolfuri, fibre aramidiche,
• 1983 nasce la telefonia mobile (Cooper, Motorola) con il lancio commerciale del primo apparecchio rice trasmittente collegato alla rete telefonica fissa con modalità cellulare e nel 1992 la IBM progetta Simon, progenitore degli attuali smartphone, in cui compaiono alcune altre funzioni oltre a quelle di semplice telefono; esse saranno poi continuamente arricchite e ciò ne spiega la universale diffusione
• 1986: Hull brevetta la stereolitografia, che permetterà lo sviluppo dello stampaggio 3D, cioè la realizzazione di oggetti tridimensionali, di forma anche estremamente complessa, a partire da materiali in polvere, deposti con l’ausilio di un software ad hoc in una successione di strati trasversali, ciascuno consolidato sul posto ed ancorato a quello e formato in precedenza con l’azione di opportune sorgenti energetiche, p. es. laser
• Anni 80 e 90: diffusa applicazione degli strumenti CAD/CAM/CAE e dei metodi di modellazione e simulazione dei processi, grazie all’aumento della capacità di elaborazione dei computers; i dischi fonografici classisci sono in buona parte sostituiti prima da rigistrazioni su piste magnetiche (“musicassette”), e poi da sistemi ottici, nei quali la lettura delle incisioni è effettuata con laser (compact disc e poi DVD)
La tavola periodica degli elementi di Mendeleiev presenta ancora delle caselle vuote: prosegue pertanto in questo periodo l’attività d’isolamento di elementi in cui sono inclusi anche quelli transuranici, non esistenti in natura: europio (Demarçay, 1901), lutezio (Auer e Urbani, 1907), afnio (Coster e Hevesy, 1923), renio e tecnezio (Noddack e Berg, 1925), promezio (Law, Poll, Kurbatov, Quill, 1938), francio (Perey, 1939), astato (Carson, Ross, Segré), nettunio (MacMillan, Abelson), plutonio (Seaborg e altri) nel 1940, curio e americio (Seaborg, 1944), berkelio (Ghiorso, Seaborg, 1949), californio (Ghiorso, 1950), fermio ed einstenio (Ghiorso, 1952), mendelevio (Ghiorso, 1955), laurenzio (Ghiorso, 1961), nobelio (russi, 1966). Il Novecento si conclude con un bilancio certamente favorevole: abbiamo accumulato un complesso di esperienze nel mondo in cui operiamo: conosciamo le proprietà della materia a disposizione coi suoi pregi e le sue limitazioni, le leggi fisiche e chimiche che ne condizionano il comportamento, sappiamo gestire con buona efficienza i processi della sua trasformazione in oggetti di uso quotidiano, utilizziamo modi e strumenti atti a coordinare le attività, realzzando l’innovazione.
Dopo tanti lustri di rapido progresso, qual’è la situazione odierna?
C’e ancora abbastanza spszio per ulteriori sviluppi? La risposta è sicuramente positiva: le aspettative della collettività riguardo il soddisfacimento di esigenze anche solo latenti, originabili da invenzioni o eventi, sono la molla che spinge persone singole o gruppi di lavoro
a percorrere nuove strade.
Notizie storiche
R. F. Tylecote - A History of Metallurgy, 2nd ed., The Institute of materials, 1992
G.F. Bocchini – L’uomo e i metalli difficili, Napoli, 1978
G. Riccio – Un poco di storia della metallurgia, AIM
H.M. Cobb – Dictionary of Metals, ASM, 2012
UTET Grande Dizionario Enciclopedico, IV Ed.
Wikipedia
Organizzate
La XV edizione delle Giornate Nazionali sulla Corrosione e Protezione si terrà in presenza a Torino nei giorni 5, 6 e 7 luglio 2023, presso il Politecnico di Torino. Le Giornate rappresentano l’evento di riferimento a livello nazionale per la discussione ed il confronto sulle questioni scientifiche, tecnologiche e produttive, nell’ambito della corrosione e protezione dei materiali. In particolare, il Convegno prevede la presentazione dei risultati raggiunti da vari gruppi di studio e da numerose aziende del settore.
• Corrosione delle strutture metalliche esposte all’atmosfera
• Corrosione e protezione delle reti idriche interrate
• Corrosione negli impianti industriali
• Protezione catodica: progettazione, collaudo, gestione e monitoraggio
• Comportamento a corrosione di leghe di titanio, nichel e acciai inossidabili
• Corrosione delle opere in calcestruzzo armato
• Corrosione dei beni culturali
• Corrosione negli impianti Oil & Gas
• Degrado e rilascio dei biomateriali metallici
• Rivestimenti e trattamenti superficiali
• Inibitori di corrosione
• Impatto delle nuove tecnologie produttive sulla corrosione
• Tecniche di studio e monitoraggio della corrosione
• Meccanismi di corrosione
• Case histories
Il programma del Convegno, le quote e le modalità di iscrizione sono disponibili online sul sito www.aimnet.it/gncorrosione
Le aziende interessate ad uno spazio per l’esposizione di apparecchiature, la presentazione dei servizi e la distribuzione di materiale promozionale, possono aderire ad una delle proposte di sponsorizzazione dell’evento. Tutte le informazioni e la modulistica sono disponibili online sul sito dell’evento.
Via Filippo Turati 8 · 20121 Milano
t. +39 0276021132 +39 0276397770
info@aimnet.it · www.aimnet.it/gncorrosione