Italiana La Metallurgia
International Journal of the Italian Association for Metallurgy
n. 02 febbraio 2024
Organo ufficiale dell’Associazione Italiana di Metallurgia. Rivista fondata nel 1909
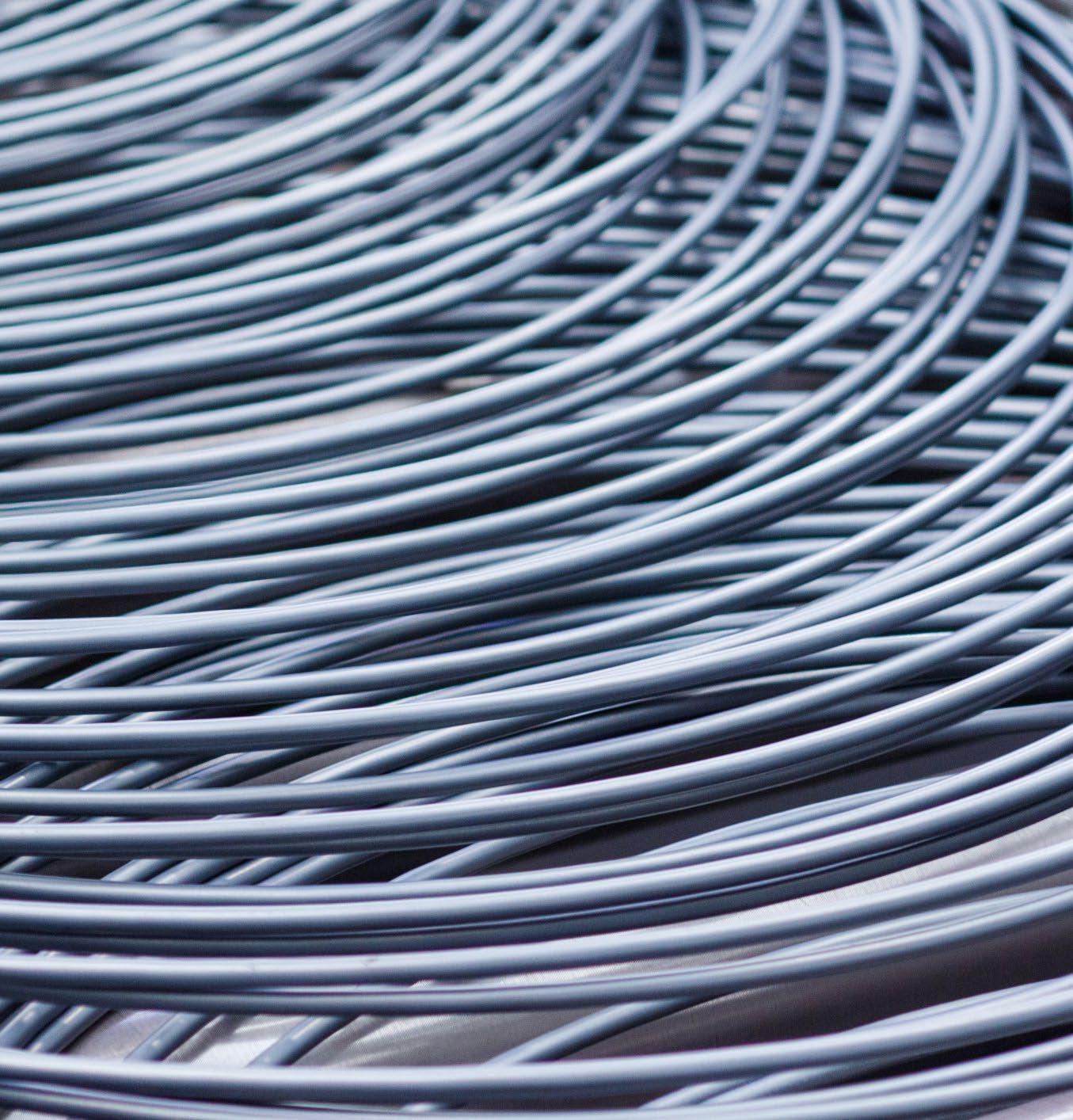
International Journal of the Italian Association for Metallurgy
n. 02 febbraio 2024
Organo ufficiale dell’Associazione Italiana di Metallurgia. Rivista fondata nel 1909
International Journal of the Italian Association for Metallurgy
Organo ufficiale dell’Associazione Italiana di Metallurgia. HouseorganofAIMItalianAssociationforMetallurgy. Rivista fondata nel 1909
Direttore responsabile/Chiefeditor: Mario Cusolito
Direttore vicario/Deputydirector: Gianangelo Camona
Comitato scientifico/Editorialpanel: Marco Actis Grande, Silvia Barella, Paola Bassani, Christian Bernhard, Massimiliano Bestetti, Wolfgang Bleck, Franco Bonollo, Irene Calliari, Mariano Enrique Castrodeza, Emanuela Cerri, Vlatislav Deev, Andrea Di Schino, Donato Firrao, Bernd Kleimt, Carlo Mapelli, Denis Jean Mithieux, Roberto Montanari, Marco Ormellese, Mariapia Pedeferri, Massimo Pellizzari, Barbara Previtali, Evgeny S. Prusov, Dario Ripamonti, Dieter Senk
Segreteria di redazione/Editorialsecretary: Marta Verderi
Comitato di redazione/Editorialcommittee: Federica Bassani, Gianangelo Camona, Mario Cusolito, Carlo Mapelli, Federico Mazzolari, Marta Verderi, Silvano Panza
Direzione e redazione/Editorialandexecutiveoffice: AIM - Via F. Turati 8 - 20121 Milano tel. 02 76 02 11 32 - fax 02 76 02 05 51 met@aimnet.it - www.aimnet.it
Reg. Trib. Milano n. 499 del 18/9/1948. Sped. in abb. Post. - D.L.353/2003 (conv. L. 27/02/2004 n. 46) art. 1, comma 1, DCB UD
Immagine in copertina: Spire di vergella di acciaio speciale su tappeto LCC® Fonte: Andrea Taurino SMS group S.p.A.
Gestione editoriale e pubblicità Publisher and marketing office: siderweb spa sb Via Don Milani, 5 - 25020 Flero (BS) tel. 030 25 400 06 - fax 030 25 400 41 commerciale@siderweb.com - www.siderweb.com
La riproduzione degli articoli e delle illustrazioni è permessa solo citando la fonte e previa autorizzazione della Direzione della rivista. Reproduction in whole or in part of articles and images is permitted only upon receipt of required permission and provided that the source is cited.
siderweb spa sb è iscritta al Roc con il num. 26116
n.02 febbraio 2024
Anno 115 - ISSN 0026-0843
Editoriale / Editorial
A cura di Ing. Ettore Anelli ................................................................................................................................
Memorie scientifiche / Scientific papers
Acciai Alto Resistenziali / High Strenght Steels
On the discussion of the classification of High-Strength cold-Resistant steels
M. Polyakova, O. Kupriyanova ........................................................................................................................... pag.08
Prediction of end-point RH refining furnace based on improved whale optimization algorithm and stochastic configuration network
C. Shi, P. Sun, T. Zhou, B. Wang, Y. Wang, L. Zhang . pag.18
Attualità industriale / Industry news
Flessibilità, qualità e tolleranze: i risultati dopo quattro anni di attività nel laminatoio di Caleotto
a cura di: L. Angelini, N. Bolognani, A. Parimbelli, A. Taurino, F. Coppola, F. Paternoster ....................................... pag.32
Flexibility, quality and tolerances: results after four years of activity in the Caleotto rolling mill
edited by: L. Angelini, N. Bolognani, A. Parimbelli, A. Taurino, F. Coppola, F. Paternoster ....................................... pag.42
Physical modelling of additives dissolution features in the bath of an induction furnace crucible
edited by: M. Lavr, G. Tetiana, K. Ganna, K. Andrii, K. Tetiana pag.52
Scenari
Acciaio e metalli: dinamiche, cicli e tendende di mercato
A. Fornasini pag.62
Atti e notizie / AIM news
Eventi AIM / AIM events pag.70
Comitati tecnici / Study groups pag.72
Normativa / Standards pag.75
AIM and Federacciai proudly announce that the 22nd International Forgemasters Meeting will be held in Italy in 2024.
All involved in and interested in the area of open die forging and ring rolling are warmly invited to attend.
IFM is a unique forum to meet researchers, skilled technicians and decision makers; in other words IFM 2024 is an unmissable event for the forging industry!
Over 140 oral and poster papers will define the latest developments in open die forging and ring rolling over 3 days of presentations. Full information on programme, planned planned tours and registration are available at www.ifm2024.org
Four technical visits are scheduled in the morning of May 30th:
. FOMAS in Osnago, Lecco - Italy
FORGE MONCHIERI in Cividate Camuno, Brescia - Italy
IRE-OMBA in Bergamo, Italy
. OFAR in Canneto Sull’Oglio, Mantova - Italy
In order to be considered for one of the proposed plant tours, delegates should apply early and must receive an approval to participate by the Organizing Secretariat.
Via Filippo Turati 8 - Milan - Italy
t. +39 0276021132 or +39 0276397770 aim@aimnet.it - www.aimnet.it
“"L'industria continua a sviluppare nuovi tipi di acciaio e concetti di design innovativi per rispondere alle sfide legate al miglioramento delle prestazioni dei componenti, con riduzione della massa, incremento dell'efficienza produttiva, aumento della sicurezza e diminuzione dell’impatto ambientale. "
“Theindustrycontinuesto developnewsteelgrades andinnovativedesign concepts to meet the challengesofimproving component performance with mass reduction, increased production efficiency,improvedsafety, and lower environmental impact.”
Ettore Anelli Senior metallurgist, consultant, coordinator of R&D projects
L'acciaio è utilizzato in molti settori industriali grazie alle sue proprietà e al suo costo, basso rispetto ad altre leghe. È un materiale dominante a livello globale ed è un motore fondamentale dell'economia mondiale. In questo contesto, si inseriscono gli acciai alto-resistenziali (HSS) che svolgono oggi un ruolo essenziale in molte applicazioni ingegneristiche, grazie alla loro eccellente combinazione di proprietà, quali la resistenza a fatica e all’usura, la tenacità alla frattura, la saldabilità, ecc.. Nel caso di applicazioni complesse, gli HSS spesso costituiscono l'unica soluzione.
Inoltre, l'aumento della domanda da parte dei settori strutturale, energetico, automobilistico e petrolifero ha favorito la crescita dei prodotti HSS. Pertanto, i produttori sono costantemente alla ricerca di miglioramenti in termini di resistenza meccanica, pur mantenendo una buona tenacità e saldabilità dell’acciaio. Questo obiettivo può essere raggiunto attraverso diverse vie: aggiunta di microleganti, trattamenti termici avanzati (ad esem-
Steel is used in many industries due to its properties and low cost compared to other alloys. It is a globally dominant material and a key driver of the world economy.
In this context, the high-strength steels (HSS) play an essential role in many engineering applications due to their excellent combination of properties, such as fatigue and wear resistance, fracture toughness, weldability, etc. In the case of complex applications, HSS are often the only solution.
Moreover, the increase in demand from the structural, energy, automotive and oil sectors has encouraged the growth of HSS products. Manufacturers are constantly looking for ways to improve strength while maintaining good impact toughness and weldability of steel.
This aim can be achieved through several routes: micro-alloying, advanced heat treatments (e.g., intercritical quenching, bainitic quenching, quenching and partitioning, etc.), high additions of Mn and
pio, tempra intercritica, tempra bainitica, quenching e partitioning, ecc.), elevate aggiunte di Mn e Al, processi termo-meccanici. Pertanto, la conoscenza delle relazioni tra composizione dell’acciaio, condizioni di processo, caratteristiche microstrutturali e le proprietà risulta fondamentale per sviluppare componenti sicuri e durevoli.
Queste tematiche son state discusse nel recente workshop internazionale sugli High Strength Steels (HSS2023), organizzato da AIM a Bergamo dal 26 al 27 ottobre 2023, presso il Distretto dell’Innovazione del Kilometro Rosso.
Il workshop è la continuazione di una serie di conferenze di successo. La prima Conferenza internazionale sugli "Acciai super-altoresistenziali" fu organizzata da AIM e Centro Sviluppo Materiali (CSM) nel 2005 a Roma. Poi seguita dalla Conferenza su "Nuovi sviluppi sulla metallurgia e sulle applicazioni degli acciai ad alta resistenza", tenutasi dal 26 al 28 maggio 2008, a Buenos Aires, organizzata da Ternium, Tenaris e Asociación Argentina de Materiales (co-sponsor AIM, TMS e ABM) e dalla seconda Conferenza internazionale sugli "Acciai ad alta resistenza", organizzata da AIM a Peschiera del Garda dal 17 al 20 ottobre 2010.
Con questo evento si è proseguito il percorso di collaborazione tra industria e università sul tema degli HSS. La manifestazione ha raccolto un buon numero di contributi scientifici di ottima qualità e i 50 partecipanti provenienti da Italia, Francia, Spagna, Germania, Austria, Svizzera, Polonia, Russia e India, hanno animato il confronto sulle sfide che l’industria è chiamata ad affrontare nel campo degli HSS.
Essendo la situazione sanitaria tornata alla normalità, la partecipazione è avvenuta in presenza, elemento fondamentale per promuovere scambi e contatti tra gli esperti e i giovani dottorandi, ricercatori e ingegneri.
I lavori presentati hanno riguardato varie tipologie di prodotti HSS (piani, lunghi e tubolari), le condizioni di processo necessarie per sviluppare microstrutture sia bifasiche (ferrite + martensite), sia bainitiche che martensitiche, i processi da adottare, sia tradizionali che
Al, and thermo-mechanical processes. Therefore, the knowledge of the relationships between steel composition, process conditions, microstructural characteristics, and properties is critical for developing safe and durable components.
These topics were discussed at the recent international workshoponHighStrengthSteels(HSS2023),organized by AIM in Bergamo, Italy, October 26-27, 2023, at the Kilometro Rosso Innovation District.
The workshop is the continuation of a successful series of conferences. The first International Conference on "Super-High-Strength Steels" was organized by AIM and Centro Sviluppo Materiali (CSM) in 2005 in Rome. Then followed by the Conference on "New Developments on the Metallurgy and Applications of High Strength Steels," held May 26-28, 2008, in Buenos Aires, organized by Ternium, Tenaris and Asociación Argentina de Materiales (co-sponsors AIM, TMS and ABM) and the second International Conference on "High Strength Steels," organized by AIM in Peschiera del Garda, October 17-20, 2010.
This event continued the collaboration between industry and academia on HSS. The workshop gathered a good number of scientific contributions of excellent quality, and the 50 participants from Italy, France, Spain, Germany, Austria, Switzerland, Poland, Russia and India, brought the discussion on the challenges facing industry in the field of HSS.
As the health situation has returned to normal, participation was by presence, a key element in promoting exchanges and contacts between experts and young PhD students, researchers and engineers. The papers presented covered various types of HSS products (flat, long and tubular), the process conditions neededtodevelopbothdualphase(ferrite+martensite), bainitic and martensitic microstructures, the processes to be adopted, both conventional and through additive manufacturing, and the weldability of new products.
In the case of oil & gas transportation pipes, the economic benefits of using HSS steels (grade X80
mediante manifattura additiva, la saldabilità dei nuovi prodotti.
Nel caso dei tubi per il trasporto di oil & gas, si sono valutati i benefici economici legati all’impiego di acciai HSS (grado X80 invece di X65), considerando oltre ai costi di produzione dei tubi, anche quelli di fabbricazione ed installazione della condotta.
Lo sviluppo e la messa a punto degli HSS, passa necessariamente attraverso lo studio dell’effetto di nuovi trattamenti termici e della composizione dell’acciaio sulle cinetiche di recovery di prodotti deformati a freddo, oppure richiede approfondimenti sull’influenza delle condizioni di austenitizzazione, raffreddamento (tempra) e rinvenimento sulla formazione, stabilità e decomposizione dell’austenite.
L’applicazione di tecniche di simulazione virtuale e la combinazione di varie metodologie d’indagine, tra cui quelle di microscopia elettronica (SEM, EBSD e TEM), diffrazione a raggi X (XRD), tomografia a sonda atomica (APT) e nano-durezze, si sono rilevate utili per la comprensione di alcuni comportamenti dei materiali e per la messa a punto delle condizioni di processo ottimali.
L’evento HSS2023 ha favorito la dialettica tra mondo accademico ed industriale, con uno scambio di informazioni ed idee, sia sui meccanismi che è possibile sfruttare per migliorare le combinazioni di proprietà richieste agli acciai HSS sia sugli strumenti tecnologici disponibili per il loro sviluppo.
I vari interventi hanno evidenziato che per la ricerca e lo sviluppo in questo campo serve personale sempre più qualificato ed aggiornato, che abbia capacità di visione, competenze e solide basi di conoscenza per affrontare la complessità dei fenomeni.
In questo numero della rivista, sono pubblicati alcuni lavori presentati all’evento, che mettono in evidenza la continua ricerca di soluzioni tecnologiche innovative per lo sviluppo dei prodotti HSS.
In particolare, un articolo riassume i criteri di classificazione degli acciai alto-resistenziali per impieghi alle basse temperature, in condizioni estreme (elevati carichi statici e dinamici, usura, ecc.).
instead of X65) were evaluated, considering not only the costs of pipe production but also those of pipeline fabrication and installation.
The development and fine-tuning of HSS, necessarily goes through the study of the effect of new heat treatments and steel compositions on the recovery kinetics of cold deformed products, or requires insights into the influence of austenitizing, cooling (quenching) and tempering conditions on austenite formation, stability and decomposition.
The application of virtual simulation techniques and the combination of various investigation methodologies, including those of electron microscopy (SEM, EBSD and TEM), X-ray diffraction (XRD), atomic probe tomography (APT) and nano-indentations, have been important in understanding certain material behaviors and in fine-tuning the optimal process conditions.
The HSS2023 workshop fostered a dialectic between academia and industry, with an exchange of information andideas,bothonthemechanismsthatcanbeexploited to improve the combinations of properties and on the technological tools available for their development.
The various speeches outlined that research and development in this field require increasingly qualified and up-to-date personnel with vision, skills and solid knowledge bases to deal with the complexity of the phenomena.
Some of the works presented at the workshop, which highlight the ongoing search for innovative technological solutions for the development of HSS products, are published in this issue of the journal.
In particular, a paper summarizes the classification criteria for HSS for low temperature applications, under extreme conditions (high static and dynamic loads, wear, etc.).
M. Polyakova, O. Kupriyanova
Low-temperature technologies are increasingly used in various industries. Cold-resistant materials have gained particular popularity in the field of building machines working at low temperatures. The need for a special approach when choosing cold-resistant materials and their variety used in the production of machines, equipment, and constructions, which operate under extreme conditions (low temperatures, dynamic/static loads and (or) intense wear), created a necessity to systematize them according to a complex of mechanical properties. Despite the fact that a wide variety of products is manufactured from new cold-resistant materials, neither the scientific literature nor the regulatory documentation provide a common unified classification, which covers a wide range of categories. The article considers and summarizes various criteria used to classify cold-resistant materials, as well as preferred classification features, determines numerical ranges of constituent properties. The article points out a classification system of structural steels according to strength, cold resistance, weldability, and hardness. This article presents comprehensive systematization of scientific data of new structural cold-resistant steels for various leading industries of strength class up to 1550 MPa with corresponding characteristics of ductility and cold resistance. The use of the proposed classification of structural steels and different alloys makes it possible to select material of a certain strength class depending on operational loads of structural elements, machines, and equipment in the conditions of low temperatures, and also to predict their reliability depending on interval of low-temperature operating threshold.
KEYWORDS:
The phenomenon of cold fracture, i.e. brittle failure associated with the impact of low temperatures, was first widely discussed in connection with the rapid construction of railways at the end of the XIX century [1]. Special attention was paid to the issues of reliability, safe operation, and durability of low-temperature systems in the second half of the 1990s, because of sharply tightened the requirements for low-temperature productions, which was widely reflected in scientific research [2]. Today, this problem has become especially important due to the intensive development of the northern territories [35]. The efficiency of equipment and transport is greatly impaired in these areas in winter [6].
An analysis of the efficiency of motor-transport services in areas of harsh climate has shown that the service life of vehicles is reduced by half compared to temperate climate, and accidents and breakdowns associated with climatic conditions incapacitate up to 25% of vehicles. It was shown in scientific research [7] that the failure rate of drilling rigs in winter increases by more than 2 times compared to the summer period. The modern development of innovative
M. Polyakova,
O. Kupriyanova
Department of Materials Processing, Nosov Magnitogorsk State Technical University, Russia
m.polyakova@magtu.ru olganikitenko@list.ru
technologies of refrigeration equipment is aimed at increasing the service life and capacity of equipment, reliability, and safety of its operation, increasing automation and robotization of production.
The urgency of low-temperature equipment is explained by the fact that low-temperature technologies are increasingly used in various industries, new processes and devices, which operate in the low-temperature range and appear annually. These are high-tech defense industries, in particular rocket and aerospace, high-energy physics, industries related to the processing, purification and liquefaction of various gases, food, medical industry, etc. [8]. The successful development of oil, gas, petrochemical, oil refining, energetic, machine-engineering, and other industries require the creation of materials that ensure high performance during the entire planned life of their operation under the influence of high pressures, corrosive environment, and temperature changes in a wide range [9].
From the standpoint of materials science, the creation of new low-temperature structural materials is an important task, ensuring high reliability and safety of structures and elements of mechanical engineering under extremely harsh operating conditions [10]. A wide range of products made of new low-temperature materials manufactured in different countries has created the need for their unified identification and classification.
Cold resistance steels are among the most advanced
materials in the field of new developments, technological innovations that ensure maximum operational safety of different constructions. These steels can be used at temperatures of the climatic cold ranging from 60℃ to 70℃ below zero and at liquefaction temperatures of gases such as nitrogen, hydrogen, helium, i.e., 196-269℃ below zero. However, the analysis of scientific and technical literature has shown that the issue of the classification of coldresistant materials as well as steels of the machine-building and mining industries remains open, so far neither the scientific literature nor the regulatory documentation contains a generally accepted classification. Nowadays, there are many criteria for the classification of cold-resistant materials. Let us take a closer look at each criterion and classification features.
According to the scientific researches it is established that cold-resistant materials can be classified according to the following criteria: chemical composition, cold resistance, weldability, strength and hardness.
Classification of materials by chemical composition
Cold-resistant materials, depending on their chemical composition, are divided into the following main groups, as it is shown in Figure 1.
Fig.1 - Classification of cold-resistant materials by chemical composition.
Steels with BCC lattice are mainly used in the conditions of the climatic cold. The temperature limit of their application is limited by the cold breaking threshold, which varies
from 0 to -60°C depending on the quality of steel and its structure. Austenitic steels with FCC lattice retain high ductility and viscosity at a temperature of -196°C [11, 12].
The transition of austenite to martensite at low temperatures is undesirable: stresses arise, there is a tendency to brittle failure. The stability of austenite is provided by an increase in the content of austenite-forming elements over 15%. The disadvantage of austenitic steels is low yield strength. Along with alloyed steel C1.2-Cr18-Ni10-Ti, stronger chrome-manganese steels (C0.3-Cr13-Al-Mn19) and special dispersion-hardening steels (C1.0-Cr11-Ni23-Ti3Mo-B, C1.0-Cr11-Ni20-Ti3-B) are used.
Welded low-alloyed steels C0.9-Mn2-Si, C1.4-Mn2-Al-V, etc. are used for large constructions [13]. In addition to low-carbon steels, medium-carbon improved and spring steels (C0.45, C0.40-Cr, C0.65-Mn, C0.60-Si2-Al) are used. Their minimum operating temperature is -50℃. Nickelplated steels have better cold resistance; C0.12-Cr-Ni3-Al and C0.18-Cr2-Ni4-Mo-Al steels are used at a temperature of -196°C after thermal improvement. Martensitic-aging steels (C0.3-Cr11-Ni8-Mo2-V, C0.3-Cr9Co14-Ni6-Mo3-Cu, C0.4-Cr14-Co13-Ni4-Mo3-Ti-W, C0.5Cr12-Ni7-Co6-Mo4-Nb, etc.) are used for the manufacture of parts for refrigerating machines (bearings, rollers, valves, etc.) when increased strength and high hardness are necessary.
Aluminum and its alloys which have no cold-breaking threshold, remain viscous within the temperature range of -253℃ to -269℃. Fracture toughness does not practically decrease. Due to the large thermal expansion (significant thermal conductivity) of aluminum, significant thermal stresses are inevitable when structural elements are rigidly fixed in them. To reduce thermal stresses, deformation compensators are used or individual parts of the structure (for example, the necks of cryostats) are made of materials with lower thermal conductivity, for example, austenitic steels or plastics. At low temperatures (from -253℃ to -269℃), aluminum and thermally non-hardened welded alloys Al-Mn, Al-Mg2, Al-Mg5 are most commonly used. Thermally hardened alloys such as Al-Cu-Mn, Al-Cu-Mg, as well as foundry alloys are used for non-welded products operating at temperatures up to -253℃
Copper and its alloys are ductile and do not have a coldbreaking threshold. In addition, their fracture toughness increases in the process of cooling. They are used for pipe structures, fasteners, welded housings operating at temperatures up to -269℃. Due to the higher cost compared to aluminum, copper and its alloys are increasingly being replaced by aluminum alloys.
Titanium and its alloys are not embrittled at temperatures
from -196℃ to -269℃ and because of the high specific strength are used in aerospace technologies. Technically pure titanium and its single-phase alloys Ti-Al5, Ti-Al4 are widely used. They are ductile, easy to weld, and no heat treatment of the joints is required after welding. Stronger, but less ductile, Ti-Al3 and Ti-Al6 alloys with two-phase structure are used at temperatures up to -196℃. These alloys are harder to weld than single-phase ones, and annealing is required for their welded joints.
Non-metallic cold-resistant materials have lower strength and toughness compared to metals. They are used for the manufacture of thermal insulation, as well as individual parts and structural elements. Foamed polystyrene or polyurethane is used for thermal insulation. Foamed polystyrene and polyurethane are characterized by low thermal conductivity. Plastics filled with glass fiber (polyamides, polycarbonates) are used for parts and structural elements, and fluoroplast (up to -269℃) and rubber (up to -70℃) are used for movable seals.
Classification of steels and alloys by cold resistance
Normative documentation defines the recommended temperature range for each type of material used in coldresistant structures, pressure vessels, pipelines, and other refrigeration and cryogenic equipment. The minimum operating temperature is determined by the temperature of the viscous-brittle transition, at which the viscosity drops sharply.
According to the definition, cold resistance is the ability of materials, elements, structures and their joint elements to resist brittle failure at low ambient temperatures; brittle failure is destruction (destruction of the integrity of the material) which occurs without visible plastic deformations. In scientific research on cold resistance, metal materials used at low temperatures are conventionally divided into four main groups (Figure 2):
- the first group consists of metals and alloys, which mechanical properties allow them to be used at temperatures up to -60°C, i.e. at low climatic temperatures, for the manufacture of products which can be exploited in northern regions. This group includes high-quality carbon and low-alloyed steels of ferritic and perlite classes with BCC lattice.
- the second group includes alloys that retain viscosity and ductility when cooled to -100℃. These are steels with 0.20.3% C, additionally alloyed with Ni, Cr, Ti, Mo. This group includes, for example, low-carbon ferritic steels with 2-5%
Ni, used at temperatures of from -60℃ to -123℃. - the third group includes alloys capable to withstand temperatures up to -196 ℃ (the boiling point of liquid nitrogen) without the deterioration of their properties.
This includes steels of the type C1.2-Cr18-Ni10-Ti, C0.1Ni9-Al, most alloys based on Al, Ti, Cu, which do not show tendency to brittle fracture. For unloaded structures steels of grades C1.0-Cr14-Mn14-Ni4-Ti, C0.3-Cr13-Al-Mn19, C0.7-Cr21-Mn7-Al-Ni5 are used.
- the fourth group includes alloys operating at temperatures below -196℃. Materials used in space technology, hydrogen production and consumption, and experimental physics belong to this group. Only high-alloy corrosionresistant steels such as C0.3-Cr20-Ni16-Al-Mn6, C1.0Cr11-Ni23-Ti3-Mo-B, some bronzes, nickel, aluminum alloys alloyed with magnesium, and titanium alloys are suitable for operation at such temperatures.
Fig.2 - Classification of metals and alloys by cold resistance.
However, the analysis showed that the intervals for the athan those in the classification given above [14]. For example, Table 1 shows examples of temperature ranges for the use of structural materials.
Tab.1 - Temperature intervals for application of structural metals and alloys.
Material
The boundary temperature of reliable operation of the material, °С without additional treatment after improving the cold resistance Steels
Nickel steel alloys:
with 6 % Ni
with 9 % Ni
martensitic-aging steels
C0.3-Cr9-Co14-Ni6-Mo3-Ti
Austenitic steels:
chrome-manganese steel
C0.3-Cr13-Al-Mn19
chrome-nikel steel
C1.2-Cr18-Ni10-Ti
It is shown that low-temperature materials can be used at -20℃, and at -40℃. Thus, in addition to the numerical low-temperature classification features, along with the requirement of guaranteed strength, the following groups should be added according to the requirements for guaranteed brittle fracture resistance (cold resistance):
- I group: metals and alloys without guaranteed cold resistance;
- II group: metals and alloys with guaranteed cold resistance for metal constructions operating under normal temperature conditions (specified temperature up to -20°C);
- III group: metals and alloys with guaranteed cold resistance for metal constructions operating under reduced temperature conditions (specified temperature below -20 °C, but up to -40°C);
- IV group: metals and alloys with guaranteed cold resistance, but for constructions operating at a specified temperature below -40℃, but up to -60 ℃. This indicator is regulated by the impact strength at temperatures below or at a temperature of 20℃ after mechanical aging.
Classification of cold-resistant steels and alloys by weldability
Weldability is one of the most important technological properties. Weldability is the property of a metal to form a joint in the process of welding that meets the requirements for the design and operation of the product [15 - 19]. Welding is widely used in the production of northern designs and sealed cryogenic equipment [20 - 22]. The general classification of steels by weldability is given in Table 2.
Tab.2 - General classification of cold-resistant steels and alloys according to their weldability.
Weldability Equivalent carbon content, Ceqv*, %
Technological parameters Steels and Non-ferrous metals and alloys grades
preheating aeat treatment after welding alloyed steels non-ferrous metals and alloys prior attendant
good ≤0,25 - - -
C0.9-Mn2, C0.9-Mn2-Cu-Тi, C0.9-Mn2-Тi, C1.0-Mn2, C1.4-Mn2, C1.0Cr-Mn-Si-Ni-Cu, C0.15-CrSi-Ni-Cu, C0.2-Cr-Mn-Si-Al Al, Al-Mg1, Al-Mg2, Al-Mg3, Cu, Cu-Al9-Fe3, Cu-Be2,Cu-Cr1, Ti, Ti-Al
Scientific papers - High Strenght Steels
satisfactory 0,25-0,35 necessary -
limited 0,35-0,45 necessary necessary
C0.2-Cr-Ni3-Al, C0.2-Cr-Ni, C0.2-Cr-Mn-Si-Аl, C0.3-Cr, C0.3-Cr-Мo, C0.2-Cr2-Ni4-МoАl, C0.12-Cr-Ni2, C0.12-Cr-Ni3-Аl
C0.40-Cr-Mo-V-Al, C0.40Cr-Ni, C0.30-Cr-Mn-Si, C0.30-Cr-Mn-Si-Аl, C0.35-Cr-Mo, C0.20-Cr2-Ni4-Mo-Al
Cu-Sn3-Zn12-Pb5, Cu-Sn5-Zn5-Pb5, Cu-Sn8-Zn4, Cu-Sn10-Zn2, Cu58-Zn40-Mn2, Cu63-Zn34-Pb3, Cu62-Zn37-Sn1, Al-Si6, Al-Si8, Ti-Al4, Ti-Al5
Al-Cu-Mg, Ti-Al-Mo, Ti-Al-Mo-Cr-Fe-Si, Ti-Al-Mo-Zr-Si, Ti-Al-Mo-V
poor >0,45 necessary necessary necessary
C0.45-Cr-Ni3-Мo-V-Аl, C0.12Cr18-Ni10-Тi, C0.50-Cr-Ni, C0.6-Cr-Si,
Cu-Al5, Cu-Al7, Cu-Sn3-Zn7-Pb5-Ni1, Cu-Sn4-Zn7-Pb5, Cu-Sn10-Pb10, Cu59-Zn-Pb1-Fe-P-Sb-Bi, Al-Cu-Mn
C eqv * (equivalent carbon content) - the quantitative characteristic of weldability is determined by the formula: , C carbon content, %; Mn, Cr, Mo, V, Ni, Cu alloying elements content, %.
According to the weldability steels are divided into four groups:
- the first group is easily weldable; - the second group is satisfactorily weldable; - the third group is limitedly weldable; - the fourth group is poorly weldable.
The first group includes steels and alloys, which can be welded using conventional technology, i.e. without heating before welding and in the process of welding and without subsequent heat treatment. However, the use of heat treatment to relieve internal stresses is possible (for steels with carbon equivalent Ceqv ≤ 0.25%) [23].
The second group mainly includes steels and alloys, which do not form cracks in the process of welding under normal production conditions. The same group includes alloys that need preheating to 100-150℃, as well as preliminary and subsequent heat treatment (0.25 < Ceqv< 0.35%) in order to prevent the formation of cracks.
The third group includes steels and alloys that are susceptible to cracking under normal welding conditions. When welding, they are subjected to preliminary heat treatment and heated to temperature of 200-250°C. In addition, most of the steels included in this group are processed after welding (0.35 < Ceqv < 0.45%).
The fourth group includes steels and alloys that are the
most difficult to weld and are susceptible to the formation of hot and cold cracks. These steels are limitedly weldable, so they are welded with mandatory preliminary heat treatment, heated to 250-300 ℃ in the process of welding and subsequent heat treatment (Ceqv > 0.45%). But even these measures do not always prevent defects in the welds. The welding quality is low, and the strength of the welded joints is also low.
The weldability of various steels, and, in particular, the weldability of cold-resistant steels, depends on meeting the following conditions [24, 25].
1. Obtaining a welded joint, without any defects and, above all, without cold and hot cracks.
2. Obtaining a welded joint with a level of strength, ductility and viscosity that ensures proper performance under the required operating conditions.
3. The necessity to apply special technological measures in the process of welding (heating, regulation of linear energy, etc.) to meet conditions 1 and 2.
4. The necessity of heat treatment after welding of coldresistant steels has its own characteristics related to the composition of the welded steels, their structural condition before welding.
Meeting the conditions given above will ensure a workable welding joint.
In addition to the criteria of cold resistance and weldability, the indicators of strength, hardness, and ductility also serve as the basis to choose a material. It is known that with a decrease in temperature, the strength properties of steel increase, and the viscosity and ductility decrease. Therefore, when choosing a material suitable for these conditions, the following criteria should be considered: strength at maximum operating temperature; viscosity and ductility at minimum temperature. In addition, the strength properties of each grade of steel vary greatly depending on the content of elements in the range of composition, inhomogeneity of the ingot and rolling conditions [26, 27]. The desire to make more complete use of the real strength of rolled products in structures leads to the selective separation of the entire set of metal products of this brand into separate strength groups, differing in guaranteed values of yield strength, temporary tensile strength, and guaranteed hardness at manufacturing process [28]. As practice shows, steel has been and remains the most popular material in construction, engineering, mining, and other leading industries [29-31]. This classification is necessary to systematize the entire variety of cold-resistant steels, since the classification used today is incomplete and ambiguous.
According to national standards of the Russian Federation, each grade of steel is divided into several groups due to the level of yield strength, and the guaranteed values of yield strength and tensile strength are 10-40 MPa higher for the second group than for the first group. Usually, the first strength class corresponds to rolled carbon steel of ordinary quality in a hot-rolled state, the second strength class corresponds to rolled low-alloy steel in a hot-rolled or normalized state, the third strength class corresponds to rolled low-alloy steel, in a thermally improved state. However, it is also possible to obtain rolled products of the second and third classes by thermal and thermomechanical hardening or controlled rolling [32]. It should be noted that steels with yield strength less than 265 MPa are not used as cold-resistant steels due to low strength characteristics. Today, steels with yield strength more than 800 MPa have found their wide application in various industries and are used as structural high-strength
cold-resistant steels. They are often called wear-resistant steels in scientific literature, but additional requirements are imposed on these classes, along with cold resistance and strength, not in terms of wear resistance, but in terms of guaranteed hardness [33-37].
Thus, a review and analysis of the scientific and technical literature showed that cold-resistant steels are assessed and classified according to a variety of criteria. The existing classifications of steels take into account only one criterion, and the comprehensive classification of coldresistant materials (by cold resistance and mechanical properties) is only available for shipbuilding steels, and little attention (or not at all attention) is paid to highstrength cold-resistant steels for machine-building and mining complexes, which is very important and relevant for today. In this regard, this paper proposes to classify high-strength cold-resistant steels of machine-building and mining complexes into 5 strength groups: normal, high and higher, similar to shipbuilding steels. Also it is proposed to add 2 additional groups to this classification: very high strength steel (σ s from 800 to 1200 MPa) and ultra-high strength steel (σ s from 1250 to 1550 MPa) with corresponding indicators of cold resistance and hardness (Table 3). The strength group number should be assigned to the steel in accordance with the values of the yield strength, for example: if σ s is 590 MPa, steel strength class is 590 and category III should be assigned to the this steel (high strength); if σ s is 1250 MPa, steel strength class is 1250 and category V should be assigned to this steel (ultra-high strength steel).
Tab.3 - Classification of structural steels according to strength, cold resistance, and hardness.
The "+" sign means that the definition of indicators depending on the category is made before a set of statistical data. The "-" sign means that the indicator is not regulated.
The paper reviewed and summarized various criteria used for the classification of cold-resistant materials, established preferred classification features, and clarified the numerical intervals of the constituent properties. The classification system of structural steels according to strength, cold resistance, and hardness was developed. The proposed criteria, unified and expanded classification of cold-resistant alloys are considered to be complex indicators of the reliability of structural elements of mining, engineering, construction, and other leading industries.
The use of the proposed classification of structural alloys
makes it possible to justify the choice of design solutions and manufacturing technologies of making structures for various industries, to choose a material of a certain strength class depending on operational loads and temperatures, to predict the life of the structure depending on the interval of the low-temperature threshold of operation, and to collect the new scientific data on low-temperature structural materials.
[1] R. Lewis, U. Olofsson. Wheel-Rail Interface Handbook, 1st ed.; Woodhead Publishing Limited: Cambridge, UK, 2009.
[2] O. Hajizad, A. Kumar, Z. Li, R.H. Petrov, J. Sietsma, R. Dollevoet. Influence of Microstructure on Mechanical Properties of Bainitic Steels in Railway Applications. Metals, 2019, 9, 778.
[3] I.V. Gorynin. Structural materials are an important element of the reliability and environmental safety of the Arctic infrastructure. Arctic: ecology and economics 2015. Vol. 3, no 19, pp. 82-87. (In Russian)
[4] E.I. Khlusova, O.V. Sych. Creation of cold-resistant structural materials for the Arctic. History, experience, modern state. Innovations 2018. Vol. 11, no 241, pp. 85-92. (In Russian)
[5] V.R. Kuz'min, A.M. Ishkov. Forecasting the cold resistance of structures and the operability of equipment at Sever. M.: Mashinostroenie, 1996. (In Russian)
[6] I.S. Filatov, A.M. Ishkov, I.N. Cherskii. Problems of improving the quality and reliability of materials and equipment for cold climate conditions. Yakutsk: Center of scientific and technical information, 1987. (In Russian)
[7] A.K. Andreev, B.S. Ermakov. Materials for low-temperature equipment. S-Petersburg: University ITMO, 2016. (In Russian)
[8] Yu.P. Solntsev, B.S. Ermakov, O.I. Sleptsov. Materials for low and cryogenic temperatures. S-Petersburg: Khimizdat, 2008. (In Russian)
[9] B.S. Ermakov. Resource and repair of steel structures of low-temperature and food equipment. S-Petersburg: SPbGUNiPT, 2011. (In Russ.)
[10] A.I. Rudskoi, S.G. Parshin. Advanced Trends in Metallurgy and Weldability of High-Strength Cold-Resistant and Cryogenic Steels. Metals 2021, 11, 1891.
[11] J.-K. Ren, Q.-Y. Chen, J. Chen, Z.-Y. Liu. Role of vanadium additions on tensile and cryogenic-temperature charpy impact properties in hot-rolled high-Mn austenitic steels. Materials Science and Engineering A 2021, 811, 141063
[12] 12 B. Kim, S.G. Lee, D.W. Kim, Y.H. Jo, J. Bae, S.S. Sohn, S. Lee. Effects of Ni and Cu addition on cryogenic-temperature tensile and Charpy impact properties in austenitic 22Mn-0.45C–1Al steels. Journal of Alloys and Compounds 2020, 815, 152407 .
[13] C. Li, K. Li, J. Dong, J. Wang, Z. Shao. Mechanical behaviour and microstructure of Fe-20/27Mn–4Al-0.3C low magnetic steel at room and cryogenic temperatures. Materials Science and Engineering A 2021, 809, 140998.
[14] P.P. Poletskov, A.S. Kuznetsova, D.Yu. Alekseev, Analysis of world-class developments in the production of hot-rolled high-strength cold-resistant steel sheet products with a yield strength of ≥ 600 N/mm2. Vestnik of Nosov Magnitogorsk State Technical University 2020. Vol. 18, no 4, pp. 32-38. (In Russian)
[15] L.M. Roncery, S. Weber, W. Theisen. Welding of twinning-induced plasticity steels. Scripta Materialia 2012, 66, 997–1001.
[16] A.B. Pereira, R.O. Santos, B.S. Carvalho, M.C. Butuc, G. Vincze, L.P. Moreira. The Evaluation of Laser Weldability of the ThirdGeneration Advanced High Strength Steel. Metals 2019, 9, 1051.
[17] J. Verma, R.V. Taiwade. Effect of welding processes and conditions on the microstructure, mechanical properties and corrosion resistance of duplex stainless steel weldments - A review. Journal of Manufacturing Processes 2017, 25, 134–152.
[18] C.K.H. Martin-Root. Laser Welding of Complex Phase and Dual Phase Advanced High Strength Steels - The Effects That Welding Has on Microstructure and Formability. Ph.D. Thesis, University of Waterloo, Waterloo, ON, Canada, 2020.
[19] M. Rozanski, M. Morawiec, A. Grajcar, S. Stano. Modified Twin-Spot Laser Welding of Complex Phase Steel. Archive of Metal Materials 2016, Vol. 61, pp. 1999–2008.
[20] V.I. Gorynin, M.I. Olenin. Ways to Improve the Cold Resistance of Steel and Welded Joints; CRISM Prometey: St. Petersburg, Russia, 2017. (In Russian)
[21] C. Wang, X. Lin, L. Wang, S. Zhang, W. Huang. Cryogenic mechanical properties of 316L stainless steel fabricated by selective laser melting. Materials Science and Engineering A 2021, 815, 141317.
[22] M. Morawiec, A. Grajcar. Metallurgical aspects of weldability of multiphase steels for automotive industry. Applied Engineering Letters 2017, Vol. 2, pp. 38–42.
[23] J. Chen, Z.-Y. Liu. The combination of strength and cryogenic impact toughness in low carbon 5Mn–5Ni steel. Journal of Alloys and Compounds 2020, 837, 155484.
[24] H. Wang, L. Meng, Q. Luo, C. Sun, G. Li, X. Wan. Superior cryogenic toughness of high-Mn austenitic steel by welding thermal cycles: The role of grain boundary evolution. Materials Science and Engineering A 2020, Vol. 788, 139573.
[25] J.C. Lippold, D.J. Kotecki. Welding Metallurgy and Weldability of Stainless Steels, 1st ed.; Wiley: Hoboken, NJ, USA, 2005
[26] A. Kalhor, M. Soleimani, H. Mirzadeh, V. Uthaisangsuk. A review of recent progress in mechanical and corrosion properties of dual phase steels. Archive of Civil Mechanical Engineering 2020, Vol. 20, 85.
[27] T. Nanda, V. Singh, V. Singh, A. Chakraborty, S. Sharma. Third generation of advanced high-strength steels: Processing routes and properties. Proceedings of the Institution of Mechanical Engineerings, Part L: Journal of Materials: Design and Applications 2016, Vol. 233, pp. 209–238.
[28] H.L. Groth, J. Pilhagen, R. Vishnu, J.Y. Jonsson. Use of duplex stainless steels at low temperatures. A new way to present toughnesstemperature-thickness data. In Proceedings of the Fifth International Experts Seminar on Stainless Steel in Structures, London, UK, 18–19 September 2017; pp. 1–8.
[29] N. Fonstein. Advanced High Strength Sheet Steels; Springer: Berlin/Heidelberg, Germany, 2015; pp. 193–195.
[30] M.Y. Demeri. Advanced High-Strength Steels. Science, Technology, and Applications; ASM International: Materials Park, OH, USA,
2013.
[31] D. Raabe, B. Sun, A.K. Da Silva, B. Gault, H.-W. Yen, K. Sedighiani, P.T. Sukumar, I.R.S. Filho, S. Katnagallu, E. Jägle, et al. Current Challenges and Opportunities in Microstructure-Related Properties of Advanced High-Strength Steels. Metals Materials Translations A 2020, Vol. 51, pp. 5517–5586.
[32] B. Hwang, C. Gil Lee, S.-J. Kim. Low-Temperature Toughening Mechanism in Thermomechanically Processed High-Strength LowAlloy Steels. Metals Materials Translations A 2011, Vol. 42, pp. 717–728.
[33] V.N. Nikitin, S.I. Kiselev, T.N. Popova, V.M. Maslyuk, V.Yu Kolesnikov. New high-strength welded wear-resistant steel with a temporary resistance of at least 1050 N/mm2. Metallurg. 2005. Vol. 1. pp.36-37. (In Russ.).
[34] M.V. Chukin, P.P. Poletskov, M.S. Gushchina, A.S. Kuznetsova, O.A. Nikitenko, D.Yu. Alekseev. Development of import-substituting technology for the production of sheet metal from high-strength structural steel of the northern version. Proizvodstvo prokata. 2019. Vol. 4. pp. 5-11. (In Russian).
[35] P.P. Poletskov, K. Khakimullin, D.G. Nabatchikov, M.S. Gushchina, D.Yu. Alekseev, A.S. Kuznetsova. The purpose and the application of ultralow temperature resistant nanostructured rolled steel. Vestnik of Nosov Magnitogorsk State Technical University. 2017, Vol. 15, no. 2, pp. 85–88.. (In Russian).
[36] P.P. Poletskov, A.S. Kuznetsova, O.A. Nikitenko, D.Yu. Alekseev. The study of influence of heat treatment procedures on structure and properties of the new high-strength steel with increased cold resistance. CIS Iron and Steel Review. 2020, Vol. 20. pp. 50–54.
[37] Introducing the new generation Hardox® wear plate.
[38] http://wardesteelandmetals.com/upload/files/Partners/SSAB/Classifies/Hardox/Datasheet/SSAB_Hardox_400.pdf.
AIM is pleased to announce the 5th International Conference on Thermal Process Modeling and Simulation (TPMS-5) and the 4th Mediterranean Conference on Heat Treatment and Surface Engineering (MCHTSE 2024).
The two IFHTSE Conferences will be held together in Lecce - Italy, on 17-19 April 2024.
The two conferences aim at providing a forum within which engineers, scientists, researchers and production managers can review and discuss fundamentals, new challenges, recent progress and emerging topics in the fields of advanced heat treatment and surface engineering technology.
C. Shi, P. Sun, T. Zhou, B. Wang, Y. Wang, L. Zhang
A model for predicting the end-point temperature and end-point carbon content of RH refining steel based on an improved whale optimization algorithm and a stochastic configuration network (LWOA-SCN) is proposed to solve the existing problem of inaccurate detection of the steel composition in the ladle during the steelmaking process. The algorithm has an implicit layer structure that can be generated adaptively based on the training effect and has the ability of strong generalization performance, simple structure, fast convergence, high accuracy, and jumping out of local optimum. Firstly, the LWOA-SCN algorithm is used to construct the prediction model. Secondly, the model was tested against RBF, GA-BP, and PSO-SVM models, and the results showed that the LWOA-SCN model had the highest predicted effect. Finally, the LWOA-SCN model was tested in industrial production applications, and the results showed that the hit rate is 90.6%, 95.6%; 93.7%, 94.3% for refining end-point temperature and end-point carbon content error within ±5°C, ±10°C; and ±0.005%, ±0.01%, respectively. which can well meet the practical needs of a steel mill. The model provides theoretical guidance and production guidance for studying the control of refining end-point temperature and end-point carbon content.
KEYWORDS: RH REFINING, STOCHASTIC CONFIGURATION NETWORK, LEVY FLIGHT ALGORITHM, IMPROVED WHALE OPTIMIZATION ALGORITHM, END-POINT TEMPERATURE AND END-POINT CARBON CONTENT PREDICTION MODEL
With the increasingly fierce competition of steel mills, the quality of products is more and more valued by enterprises, and the fluctuation of end-point carbon content and end-point temperature in steelmaking has a great influence on the adjustment of process parameters and the performance of final products. The high superheat of the continuous casting molten steel temperature and the deviation of the molten steel temperature drop from the target value can have a direct impact on the product quality. The results show that the equiaxed crystallinity of molten steel decreases with the increase of superheat, and the shrinkage, porosity, segregation, and crack are closely related to the superheat, thus reducing the competitiveness of the product. According to the production process, the average RH refining process time in a steel mill is about 40 min. reducing a temperature measurement, smelting efficiency can be increased by
School of Electrical and Automation Engineering, Liaoning Institute of Science and Technology, China - Liaoning Provincial Engineering Research Center of Robotic Drive and Control, China.
Peng Sun, Baoshuai Wang, Yikun Wang, Lei Zhang
School of Electrical and Automation Engineering, Liaoning Institute of Science and Technology, China
Tian Zhou
Benxi Beiying Steel (Group) Co. Benxi, China.
scy9090@126.com.
10%[1]. Therefore, it is necessary to reduce the number of manual temperature measurements in the refining process to reduce the smelting time, reduce energy consumption, and control production costs.
More and more attention has been paid to the role of refining, and RH vacuum refining technology has become a widely used technology in various mills. It mainly has the following metallurgical functions: dehydrogenation, decarburization, deoxidation, desulfurization, precise control of molten steel composition and temperature, inclusion control, and removal. The varieties suitable for smelting are greatly increased, and it has become indispensable refining equipment for smelting highgrade pipelines, ultra-low carbon steel, silicon steel, and other high value-added steels. The precision of endpoint temperature and end-point carbon content control of refining determines whether the steel quality meets the standard. The traditional process mainly adopts the combination of mechanism analysis and empirical control. It mainly analyzes the change of molten steel temperature through the influence of ladle thermal state and other factors on molten steel temperature based on heat transfer theory[2-5]. However, the main drawback of this method is that the temperature and carbon content change of molten steel in the ladle is affected by many factors in the actual production process, and they are in a strong coupling and strong nonlinear relationship, so it is difficult to consider comprehensively, which leads to the phenomenon that the traditional mechanism analysis method will have complex prediction process, slow control speed and unguaranteed prediction accuracy[6-10].
To achieve the precise requirement of end-point temperature and end-point carbon content control, intelligent control methods tried by domestic and foreign researchers are attempted to control the end-point temperature and end-point carbon content[11-13]. With previous research on the subject, the study of refining models based on intelligent algorithms has become a hot issue in automated steelmaking. Many scholars have carried out in-depth research on the prediction and control of the refining end-point temperature and end-point carbon content by using methods such as neural networks, fuzzy logic systems, and so on, and achieved certain research results. Whereas there are still some shortcomings in the prediction accuracy and end-point hit rate, because the influence factors are not comprehensive enough, the algorithm is easy to fall into a local minimum, poor
training ability of small samples, and low computational efficiency[14-17]. To address the aforementioned issues, this work develops prediction model employing the LWOASCN algorithm for controlling end-point temperature and end-point carbon content in the RH refining production process for an actual 210 t ladle in a steel mill. By comparing this model with RBF, GA-BP, and PSO-SVM prediction models, a study of the model accuracy is carried out to verify the superiority of the proposed model, which provides a theoretical basis for the problem of optimal control of end-point temperature and end-point carbon content in the actual production of a steel mill.
The subject belongs to the latest application in the field of metallurgical intelligent control, combining metallurgical technology with predictive technology in a favorable way. It is another new milestone in the development of metallurgical technology, breaking the deficiencies of the end-point temperature and end-point carbon content control in the traditional process and transforming what might otherwise be produced as a substandard product into a qualified product by pre-adjusting the process parameters online. It reduces the scrap rate and reduces production costs at the same time.
RH refining process is a method of vacuum circulation degassing. After forming a closed container inside the vacuum tank, turn on the vacuum pump, and the vacuum is formed above the molten steel. Under atmospheric pressure, the molten steel is pressed into the vacuum tank, so that the molten steel enters from the riser and flows out from the downcomer to complete the degassing and decarburization of the molten steel.
The experiment process is carried out by the actual production RH refining process in a steel mill. The RH refining process is shown in Fig 1. After the ladle reaches the RH refining process position, the ladle is started to enter the station for temperature measurement, and then blow argon with a large flow rate. While the ladle is vacuumed, a certain amount of alloy is added. According to the process requirements. The vacuum is stopped, and the temperature is measured after 15 min. Then, the vacuum is continued for the ladle, and the alloy is added to reduce the argon blowing rate until it is stopped. Finally, the ladle temperature is measured once more, the end-point temperature of the RH refining process. During the whole refining process, the temperature of
molten steel is measured by a thermocouple at the early, middle, and late stages of the experiment. In order to improve the accuracy of the temperature of molten steel, it is measured by the average value of multi-point temperature measurement (5-point temperature measurement is used during the experiment) and the insertion depth is 210 mm
(the distance is longer than the height of slag surface above the molten steel, so as it can yield accurate measurement of the steel temperature). Finally, the measured temperature is displayed on the monitor. The RH refining process structure and temperature measurement point position are shown in Fig 2.
During the industrial trials online data of 210 t ladle refining were collected. The different liquidus temperatures of different steel grades were taken into account in the data collection process, which resulted in the different refining end-point temperature and end-point carbon content
required by the process. Therefore, the same steel grade was used as the research object (the most representative low carbon steel SPCC was used as the research object in this experiment), a total of 2000 furnace times.
BASED ON LWOA-SCN
Sample data processing
In this paper, the error data and noise data are removed according to the Laida criterion to obtain the online detection data of 2000 groups of steel. of which 75% (1500 groups) are taken as the training sets; 25% (500 groups) are taken as the test sets, and the correlation analysis is carried out using SPSS to obtain the correlation coefficients of each factor, and several factors with small correlation coefficients are excluded. The corresponding data table is shown in Table 1. Finally, 7 parameters, including the
start temperature of refining, the tonnage of molten steel, refining time, alloy addition amount, the amount of slag added, the thickness of slag, and the ladle age, are obtained as the input factors of the model. The correlation between the factors is shown in table 1.
Due to the large and complex nature of the raw data, large forecasting errors caused by order of magnitude differences in the different dimensions of the data are eliminated. Therefore, it is necessary to normalize the input and output of the established model by mapping the input and output data to the [0,1] interval data normalization using the following equation.
where:
min (xi), the minimum value of the model input or output raw data; max (xi), the maximum value of the model input or output raw data; (xi), the raw data of the model input or output.
Improved whale optimization algorithm
Compared with other optimization algorithms, the WOA algorithm has a faster operation speed, simple adjustment parameters, and a certain ability to jump out of the local optimum. However, since the algorithm itself only uses a random system for exploration, and the excessive dependence on random limits the search speed of the WOA algorithm, the convergence speed and convergence accuracy of the WOA algorithm are further accelerated. In addition, due to the limitation of coefficient vector B, the WOA algorithm will lose the ability to jump out of the local optimum when the number of iterations reaches half of the
maximum set number of iterations. Therefore, the WOA algorithm has a certain risk of falling into the local optimum, resulting in inaccurate prediction results of the algorithm. To solve the above defects of the WOA algorithm, Levy flight is used to improve the WOA algorithm. The improved algorithm has a faster convergence speed and higher convergence accuracy and has a better ability to jump out of the local optimum. Levy flight is a search based on Levy distribution, which is a random way of smallrange search and large-range jump. Established using the following mathematical model for the predatory strategy of humpback whales:
where:
t, the current number of iterations; B and M, coefficient vectors.
The WOA algorithm is used to solve the optimization problem for SCN. The whale optimization strategy is
shown in Equation (5). The WOA algorithm is iterated iteratively to find the final solution.
where:
l, constant; update the magnitude of the distance; H, vector of coefficients;
X*(t), the position vector of the current optimal solution; X(t), the current position vector of the humpback whales; Xrand(t), the random position vector of the whale population;
τp, the distance between the whale population and the prey; a, the variable that decreases from 2 to 0;
ε, describes the shape of the spiral motion; m, a random vector in the interval [–1, 1]; n, probability variable.
In the established model process, the industrial trial data are quickly used and normalized. Then the input variables are determined, and 7 input variables are optimized by the LWOA algorithm. The search range of variables is [–1, 1], the number of populations is 30, and the number of iterations is 500. The first iteration randomly generates 30 groups of initial solutions, calculates the fitness of each group of solutions, and saves the group of solutions with the smallest fitness as the current optimal solution to complete this iteration. When entering the next iteration, according to the whale optimization strategy, the positions of 30 solutions are updated, and a group of solutions with the smallest fitness is compared with the current optimal solution to save the group of solutions with smaller fitness. After 500 iterations, the group of
solutions with the smallest fitness is the global optimal solution, and then the optimization value of the input variable is obtained by inverse normalization processing, and the optimization process is completed.
Compared with the traditional machine learning model, the hidden layer structure of SCN can be generated adaptively based on the training effect, and it can start from a small network, then, new hidden nodes are added gradually with random parameters until the training precision of the network meets the termination condition, and the network has strong generalization performance. The basic structure diagram of the SCN is shown in Fig 3.
Fig.3 - The basic structure diagram of the SCN.
The specific steps for SCN are as follows:
Step 1: Given the objective function f: RM→RK, after the L-1 addition of the node, the output of the current network is:
Residuals for the current network:
If the residual ‖eL-1‖ does not meet the expected tolerance range, a new hidden node is added (a set of w L, βL,and bL) such that the approximation function is:
Step 2: when adding a new hidden node, the input weight vector wL and deviation vector βL are generated randomly.
Where a pair of randomly generated wL, βL satisfy the following inequalities:
where:
Step 3: Calculate the output weights.
Step 4: Calculate whether the error eL is smaller than the pre-given error criterion: if it is satisfied, the SCN model training is completed, otherwise, continue to add intermediate layer nodes according to step 2 until the error criterion is satisfied.
If the specified error tolerance is not reached, the model will generate new hidden layer nodes under the constraint and satisfy the trend of decreasing deviation as the number of nodes increases, finally achieving
The model outputs the weights according to the updated model as follows:
where:
When the number of training samples is small, the L2 norm penalty term is introduced into the objective function of the model to avoid over-fitting of the SCN and to improve
the generalization performance of the network. The objective function of SCN is improved as follows: (17)
where:
C, the penalty weight coefficient of the model. The least squares output weight is defined as:
The penalty parameter C of SCN is optimized by the LWOA algorithm. The relational flow chart of the LWOA optimized SCN is obtained as shown in Fig 4. Firstly, the actual production data are extracted and normalized, then the parameters of the SCN are optimized by the LWOA, and then the regression model is trained and tested with the optimal solution. Finally, the prediction model of end-point carbon content and end-point temperature is obtained by inverse normalization of the regression production data.
Fig.4 - The process of LWOA optimized SCN.
Through the above steps, the forecasting effect of the end-point carbon content and end-point temperature prediction model of the LWOA-SCN is finally obtained and compared with the actual value, as shown in Fig 5 and Fig 6.
Fig.5 - The predicted effect of end-point carbon content.
Fig.6 - The predicted effect of end-point temperature.
COMPARISON OF THE MODEL AND RESULT ANALYSIS
To examine the prediction effectiveness of the LWOASCN algorithm relative to the typical algorithm, four algorithms (RBF, GA-BP, PSO-SVM, and LWOA-SCN) are used to build the corresponding models for comparison. SSR/SST and SSE/SST are used to judge the fitting effect of the models, where the closer the SSR/SST value is to 1, the closer the oscillation between the model prediction
and the practical value is to the same degree; the smaller the SSE/SST value is, the better the fit between the model prediction and the practical value is. The MAE, RMSE, and Relative error are used to evaluate the prediction accuracy of the model, and the HR (hit rate) is used to examine the degree to which the model met the standard. The predicted values of the four algorithms are compared with the actual production data, and the results are shown in Fig 7 and Fig 8.
Fig.7 - Comparison of end-point carbon content results.
Fig.8 - Comparison of end-point temperature results.
As can be seen from Fig 7 and Fig 8, the deviations from the actual production data of the four models are in the order of small to large: LWOA-SCN, PSO-SVM, GA-BP, and RBF. According to the evaluation indexes of the four models in Table 2, it can be seen that among the end-point carbon content prediction models, the RMSE and MAE of the LWOA-SCN model are smaller than the
other three algorithms, and the SSR/ SST is closer to 1, and the oscillation between predicted and true values is closer; the SSE/SST value is the lowest, and the model obtained the best fit. Finally, the LWOA-SCN model has the smallest RMSE and MAE compared to the other three algorithms, and SSR/SST is closer to 1, SSE/SST is also the lowest, and the best fit obtained by the model.
Tab.2 - Comparison of the regression effects of the four models.
End-point temperature model
To investigate the prediction accuracy of these models, this paper uses relative error as the error indicator to analyze the models. The smaller the value of relative error indicates the higher the prediction accuracy of the models. The calculation formula is Equation (21), and the relative error of LWOA-SCN, PSO-SVM, GA-BP, and RBF models are shown in Fig 9 and Fig 10.
Fig.9 - Comparisons of relative error of end-point carbon content models.
Fig.10 - Comparison of relative error of end-point temperature models.
From Fig 9 and Fig 10, it can be seen that the relative error of LWOA-SCN is the smallest among the four algorithms for both the end-point carbon content model and the endpoint temperature model. The LWOA-SCN prediction model outperforms the other models.
To investigate the degree of compliance of the model, the HR (hit rate) performance index is used for the analysis. In the analysis of the prediction model, the prediction results are considered as hits when the end-point carbon content and end-point temperature satisfy Equation (22), and
the corresponding hit rate calculation formula is shown in Equation (23). From Table 3, the LWOA-SCN model has the highest hit rate under the same conditions, thus
indicating that the prediction accuracy of this method is better than other algorithms.
where:
CS, the measured results of the model; C y, results of model forecast; k, Hit accuracy.
In summary, according to the actual production data of a steel mill, through the comparison of RMSE, MAE, SSE/ SST, SSR/SST, Relative error, and HR, the prediction performance evaluation index of the LWOA-SCN prediction model is the best, and the end-point hit rate is higher, indicating that the LWOA-SCN algorithm has
(22)
(23)
higher approximation accuracy. It is verified that the LWOA-SCN prediction model has higher prediction performance. The model can be used to guide the actual production.
To verify the practical application of the established LWOA-SCN prediction model, the model is applied to a steel mill for actual production tests. Fig 11, and Fig 12 show the predicted data for 300 furnace times with the model applied. The hit rate is 90.6%, 95.6%; 93.7%, 94.3% for refining end-point temperature and end-point
carbon content error within ±5°C, ±10°C; and ±0.005%, ±0.01%, respectively.
Fig.11 - Comparison of predicted and practical values of end-point carbon content model in the application.
Fig.12 - Comparison of predicted and practical values of the end-point temperature model in the application.
In this paper, we propose a prediction model for RH refining end-point temperature and end-point carbon content based on LWOA-SCN, which has the advantages of fast convergence and high accuracy. The main conclusions are as follows:
(1) The prediction model of end-point temperature and end-point carbon content of RH refining based on the LWOA-SCN algorithm overcomes the shortcomings of traditional modeling's slow convergence speed and low convergence precision and improves the model's generalization ability and accuracy.
(2) The predicted data for 300 furnace times with the model applied. The hit rate is 90.6%, 95.6%; 93.7%, 94.3% for refining end-point temperature and carbon content error within ±5°C, ±10°C; and ±0.005%, ±0.01%, respectively. (3) It is validated by the comparison of four forecasting models. The results show that the LWOA-SCN model has the smallest MAE, RMSE, and Relative error, thus verifying that the LWOA-SCN prediction model has good generalization ability. The model provides theoretical and production guidance for studying the control of refining end-point temperature and carbon content.
ACKNOWLEDGMENTS
This research was supported by the basic scientific research fund projects of the Educational Department of Liaoning Province in 2023(JYTMS20231800); the Liaoning Institute of Science and Technology doctoral research initiation fund project in 2023(2307B04) and the natural science fund program projects of the Department of Science & Technology of Liaoning Province in 2022(2022BS-297).
[1] Z.C. Xin, J.S. Zhang, J. Zheng, Y. Jin, Q. Liu. A hybrid modeling method based on expert control and deep neural network for temperature prediction of molten steel in LF[J]. ISIJ international 62(3) (2022)532-541.
[2] Y.D. Zhang. Research of temperature prediction model in the process of RH refining process[D]. Taiyuan university of science and technology (2016).
[3] D.f. He, F. He, A.J. Xu, N.Y. Tian. Online molten steel temperature control in steelmaking and continuous casting process[J]. Journal of Engineering Science: S1(2014)200-206.
[4] N. Kikuchi. Development and prospects of refining techniques in steelmaking process. ISIJ International 60.12(2020)2731-2744.
[5] Y.N. Wang, Y.P. Bao, H. Cui, B. Chen, C.X. Ji, Final temperature prediction model of molten steel in RH-TOP refining process for IF steel production[J]. Journal of Iron and Steel Research, International 19(3) (2012)1-5.
[6] C. Gao, M.G. Shen, X.P. Liu, L.D Wang, M. Chen. End-point Prediction of BOF Steelmaking Based on KNNWTSVR and LWOA[J]. Transactions of the Indian Institute of Metals, 2019, 72: 257-270.
[7] J.P. Yang, J.S. Zhang, W.D. Guo. S. Gao, Q. Liu, End-point temperature preset of molten steel in the final refining unit based on an integration of deep neural network and multi-process operation simulation[J]. ISIJ International 61(7) (2021)2100-2110.
[8] Z.C. Xin, J.S. Zhang, J.G. Zhang, Z. Jin, J. Yu, Q. Liu, Predicting Temperature of Molten Steel in LF-Refining Process Using IF–ZCA–DNN Model[J]. Metallurgical and Materials Transactions B, 54(3) (2023)1181-1194.
[9] H.X. Tian, Z.Z. Mao, An ensemble ELM based on modified AdaBoost. RT algorithm for predicting the temperature of molten steel in ladle furnace[J]. IEEE Transactions on Automation Science and Engineering 7(1) (2009)73-80.
[10] K. Feng, A.J. Xu, D.F. He, H.B. Wang, Prediction of RH refining process molten steel endpoint temperature based on integrated case reasoning method[J]. Journal of Engineering Science 40(S1) (2018)161-167.
[11] K. Feng, D.F. He, A.J. Xu, H.B. Wang, End Temperature Prediction of Molten Steel in LF Based on CBR-BBN[J]. Steel Research International 87(1) (2015)79–86.
[12] W. Lv, Z.Z. Mao, P. Yuan. Ladle Furnace Steel Temperature Prediction Model Based on Partial Linear Regularization Networks with Sparse Representation[J]. Steel Research International 83(3) (2013)288-296.
[13] F. He, A.J. Xu, H.B. Wang, D.F. He, N.Y. Tian, End Temperature Prediction of Molten Steel in LF Based on CBR[J]. Steel Research International 83(11) (2012)1079-1086.
[14] F. Yuan, A.J. Xu, M.Q. Gu, Development of an improved CBR model for predicting steel temperature in ladle furnace refining[J]. International Journal of Minerals, Metallurgy and Materials 28(2021)1321-1331.
[15] L.Z. Yang, B. Li, Y.F. Guo, S. Wang, B.T. Xue, S.Y. Hu, Influence Factor Analysis and Prediction Model of End-Point Carbon Content Based on Artificial Neural Network in Electric Arc Furnace Steelmaking Process[J]. Coatings 12(10) (2022)1508.
[16] L.M. Liu, P. Li, M.X. Chu, C. Gao. End-point prediction of 260 tons basic oxygen furnace (BOF) steelmaking based on WNPSVR and WOA[J]. Journal of Intelligent & Fuzzy Systems 41(2) (2021)2923-2937.
[17] C.Y. Shi, X.X. Yin, R. Chen, R.X. Zhong, P. Sun, B.S. Wang, S.Y. Guo, S.D. Li, Z.C. Ma, Prediction of end-point LF refining furnace based on wavelet transform based weighted optimized twin support vector machine algorithm[J]. Metallurgical Research & Technology 120(1) (2023)1.
a cura di: L. Angelini, N. Bolognani, A. Parimbelli, A. Taurino, F. Coppola, F. Paternoster
In questi ultimi anni il mercato dell’acciaio è cambiato sostanzialmente, diventando nell’immediato molto variabile, sia come quantità prodotta sia come richieste. Nonostante ci sia da parte dei produttori la volontà di ridurre i sempre più crescenti costi di produzione, c’è stato un certo interesse ed un risveglio nelle richieste di produzione di acciaio in quasi tutti i settori, dal cemento armato a quello ad uso automobilistico. Il mercato chiede flessibilità e la capacità di adattarsi alle condizioni quotidiane, salvaguardando la marginalità. Ovviamente anche il gruppo Feralpi, impegnato sempre di più nell'ambito dell’acciaio sostenibile, “Green Steel”, non è rimasto di certo alla finestra, attivandosi e puntando, anche con lo stabilimento di Caleotto, a sviluppare al meglio la produzione di vergella in acciai di alta qualità, e anche a garantire ai clienti finali i più elevati standard in termini di prodotti, processi, servizi e assistenza.
Dopo i primi ottimi risultati ottenuti già nel 2019 con l’utilizzo del calibratore a 4-passi MEERdrive®PLUS assieme alle ultime tecnologie sviluppate da SMS group S.p.A., agli inizi del 2023 sono state laminate diverse classi di acciaio nei diametri 4.5 mm e 5.0 mm in vergella, ottenendo risultati sorprendenti, confermati anche dagli utilizzatori finali. Come sono stati prodotti? Che cosa è stato ottenuto dopo quattro anni di lavoro? Lo scopriremo in dettaglio in questo articolo.
PAROLE CHIAVE: MEERDRIVE®PLUS, BLOCCO CALIBRATORE, ORRR (CALIBRATURA OVALE-TONDOTONDO-TONDO), CALIBRATURA A CALATA UNICA, VERGELLA 4.5 MM
INTRODUZIONE
Tecnicamente la parola qualità indica “l’insieme delle caratteristiche che determinano la rispondenza di un prodotto alla funzione per la quale è utilizzato”: il certificato, inteso come garanzia di qualità, è l’attestazione di fabbricazione accurata di un prodotto”.
Con queste premesse Caleotto, attivo nel mondo della laminazione dal 1896, è uno dei pionieri e tra i leader nel mercato italiano per la produzione di vergella di alta qualità. Dal 2020 fa parte del gruppo Feralpi, fondato nel 1968, uno dei principali produttori di acciaio in Europa, specializzato nella produzione di acciaio da costruzione e per applicazioni speciali.
L’obiettivo di Caleotto - come l'azienda sta dimostrando già da diversi anni - è sviluppare al meglio la produzione di vergella in acciai di alta qualità, garantendo ai clienti finali i più elevati standard in termini di prodotti, processi, servizi e assistenza.
La strada per entrare in nuove nicchie di mercato in pre-
Lorenzo Angelini, Nicola Bolognani, Andrea Parimbelli Arlenico S.p.A., Lecco
Andrea Taurino, Fabio Coppola, Francesco Paternoster SMS group S.p.A., Tarcento
cedenza inesplorate ed elevare sempre di più la qualità dei prodotti vergella era già stata tracciata da quando è entrato in funzione il blocco calibratore/finitore a 4-passi MEERdrive®PLUS in grado di rispondere al 100% alle esigenze di mercato di Caleotto.
Il blocco calibratore MEERdrive®PLUS, adottando la tecnologia di azionamento a motore singolo per ogni passo, è la tecnologia migliore sul mercato per la produzione di vergella di qualità, e contribuisce a ridurre notevolmente i costi operativi in termini di inventario degli anelli di
laminazione, tempi di cambio e manutenzione. Il MEERdrive®PLUS offre una solida opportunità di produrre una vergella eccezionale in termini di tolleranze dimensionali e qualità superficiale, ma non solo questa singola macchina fa il "lavoro giusto". È un connubio di tecnologie che consente il controllo costante delle dimensioni e delle temperature prima e dopo il blocco finitore, garantendo nuove opportunità a Caleotto, anche in termini di consolidamento della propria posizione nel mercato.
EQUIPAGGIAMENTI E PROCESSI – LA PLANIMETRIA DELL’IMPIANTO
Il laminatoio di Caleotto è stato profondamente rinnovato da SMS group con l’introduzione delle più moderne tecnologie, in particolare il blocco finitore/calibratore
MEERdrive®PLUS in grado di garantire le migliori tolleranze dimensionali e la linea di raffreddamento ed equalizzazione (con tecnologia multi-loop) per laminazione termomeccanica.
Fig.1 - Planimetria per la laminazione della vergella con inserita anche la linea di produzione bordioni.
La tecnologia multi-loop, con diversi possibili percorsi di raffreddamento, a seconda del tipo di acciaio e della dimensione del prodotto finito, aumenta la flessibilità produttiva e migliora il fattore di utilizzo del laminatoio. Nello stabilimento di Caleotto la laminazione termomeccanica, con temperature finali al di sotto degli 800°C, può essere utilizzata per tondi superiori a 13.0 mm, mentre la laminazione a bassa temperatura per tondi di gamma inferiore. L’elevato raffreddamento consente di ottenere microstrutture molto fini, con notevoli vantaggi per gli utilizza-
tori finali. Nello specifico il concetto “multi-loop” presenta una serie di vantaggi operativi. Tutta la manutenzione programmata del blocco pre-finitore può essere eseguita mentre il blocco viene bypassato, utilizzando il percorso alternativo, riducendo così i tempi di fermo macchina. Il blocco pre-finitore viene utilizzato solo quando strettamente necessario, e per molti diametri viene bypassato. Ciò consente di effettuare i cambi di prodotto con minori vincoli di tempo, e garantisce che le impostazioni possano essere controllate con precisione, minimizzando i problemi derivanti dai cambi produzione
Utilizzando il solo blocco calibratore MEERdrive®PLUS, per prodotti superiori a 13.0 mm, si riducono i costi energetici, in quanto il blocco pre-finitore è spento. Si prolunga anche l’efficienza del sistema di lubrificazione, poiché vi sono meno possibilità di contaminazione con l’acqua di raffreddamento.
L'utilizzo di un'unica calata di laminazione nel treno intermedio consente un drastico risparmio in termini di tempi di cambio e costi di cilindri di laminazione e guide. La capacità del laminatoio di Caleotto di laminare a temperature più basse con temperatura della barra completamente equalizzata genera ulteriori risparmi sui costi, riducendo l’incidenza dei trattamenti termici a valle. Durante la laminazione degli acciai stampati a freddo, ad esempio, il miglioramento della microstruttura dovuta alla laminazione termomeccanica consente l'eliminazione della ricottura di addolcimento per alcuni tipi di acciaio al boro-manganese e una sostanziale riduzione della ricottura di addolcimento (fino al 50% in meno) per gli acciai al cromo, cromo-boro e cromo-molibdeno. Il blocco calibratore MEERdrive®PLUS, con la sua unica tecnologia mul-
ti drive (un motore per passo di laminazione) consente il controllo assoluto delle velocità fra i vari passaggi, riducendo al minimo la tensione sulla barra e garantendo le migliori tolleranze oggi ottenibili su un treno vergella.
MEERdrive®PLUS: OTTIMIZZAZIONE DELLE
CALIBRATURE
Al tempo dell’installazione del MEERdrive®PLUS la calibratura era già stata pensata per i prodotti in vergella con diametro inferiore a 5.5 mm. Il layout dell’impianto è infatti ottimale per la produzione di prodotti di piccolo diametro e dunque a produttività limitata, grazie alle prime quattro gabbie sbozzatrici svincolate dal resto del treno e alle diverse dimensioni di billette disponibili.
Le prime prove sono state svolte nel mese di giugno del 2022, e si sono concentrate sulla produzione della vergella con diametro di 5.0 mm laminata alla velocità di 100 m/s. Gli ottimi risultati ottenuti in termini di tolleranze dimensionali e caratteristiche meccaniche del prodotto finito hanno convinto a proseguire le prove sul diametro 4.5 mm che si sono svolte nel mese di gennaio 2023 impostando la velocità di test a 90 m/s. In futuro si prevede di raggiungere e superare i 100 m/s per entrambi i diametri con convogliamenti dedicati. Attualmente la massima velocità operativa della linea vergella è di 120 m/s per il tondo da 5.5 mm.
In entrambe le campagne sono state testate diverse classi di acciaio normalmente prodotte da Caleotto. La prova relativa al 4.5 mm ha confermato gli ottimi risultati già ottenuti col diametro 5.0 mm.
Tab.1 - Alcuni acciai e denominazioni dei prodotti laminati per le prove sulla vergella.
C7D 1.0313 EN 16120-2 Basso carbonio
CAL055 C56D2 1.1220 EN 16120-4 Medio carbonio CAL072 C72D2 1.1242 Alto carbonio per trafilatura CAL082 C82D2 1.1262
CAL04F C4C 1.0303 EN 10263-2 Basso carbonio
3Si1 1.4341 En 14331-21 Filo saldante
Gli innegabili vantaggi della tecnologia MEERdrive®PLUS sono di seguito riassunti in:
• Perfetta adattabilità alle diverse gamme dimensionali delle prese provenienti dal blocco pre-finitore o dal treno posizionato a monte (calibratura a calata unica suddivisa per famiglie di prodotto);
• Possibilità di laminazione a bassa temperatura (750°C) su tutte le classi d’acciaio per cui è applicabile questa tipologia di processo, nella gamma dimensionale di Ø 4.5÷28 mm;
• Possibilità di utilizzare e regolare le riduzioni in maniera ottimale per ogni singolo prodotto;
• Massima flessibilità nella gestione dei tiri inter-gabbia
e velocità anelli;
• Possibilità di utilizzare anelli di diametri diversi sui singoli passi (tecnologia multi-drive).
È stato quindi semplice ottenere le strette tolleranze dimensionali richieste da Caleotto (±0.05 mm – ovalità 60%), sfruttando la calata esistente del blocco pre-finitore a 10 passi localizzato a monte, grazie anche all’accurato studio delle calibrature eseguito col nuovo programma di simulazione e calcolo SMS-SIMPRO 4.0.
È stata utilizzata la classica calibratura del MEERdrive®PLUS ovale-tondo-falso tondo-tondo, dove i primi due passi lavorano a riduzioni più alte, preparando una presa per i successivi due passi, atti ad ottenere un prodotto "calibrato" con basse riduzioni. La stabilità del processo e l’ottenimento delle migliori tolleranze dimensionali sono
garantiti dalla distanza estremamente ridotta fra gli ultimi due passi e dalla ottimale gestione dei tiri inter-gabbia.
Fig.3 - SMS-SIMPRO 4.0 Software di simulazione della calibratura per le prove del tondo 4.5 mm e 5.0 mm in vergella
Caleotto produce acciaio a basso, medio e alto tenore di carbonio per tutte le applicazioni, per stampaggio a freddo, acciaio per la produzione di funi, catene, molle, acciaio al boro, filo per la saldatura ed altri, anche con processo di laminazione termomeccanico. Il recente potenziamento dell'impianto è stato studiato per ottenere prodotti di qualità superiore, in termini di tolleranze dimensionali e di microstrutture fini migliorate grazie alla laminazione di finitura a bassa temperatura, ottenendo tutti i relativi benefici sulla granulometria finale e omogeneità della microstruttura. I recenti diametri 5.0 e 4.5 mm, sono di fatto la vergella più piccola mai prodotta su un blocco finitore/ calibratore SMS group e consentono a Caleotto di produrre la vergella più sottile in Europa. Questo prodotto
può essere utilizzato per molte applicazioni, sia quando è richiesta elevata duttilità per trafilatura profonda, tipica della produzione di funi, sia quando è richiesta elevata plasticità, per la produzione di componenti stampati a freddo. Il tondo da 4.5 mm è più sottile del 33% rispetto allo standard da 5.5 mm e consente una drastica riduzione di molti processi successivi, come la trafilatura e la ricottura. I vantaggi che ne risultano per gli utilizzatori finali sono particolarmente evidenti nella produzione di filo trafilato di piccolo diametro per funi ad alte prestazioni e per il filo di medie dimensioni utilizzato per lo stampaggio e laminazione a freddo. A titolo di esempio lo schema seguente illustra il processo standard per produrre fili sottili, partendo dal diametro del prodotto standard 5.5 mm.
L'utilizzo di un diametro iniziale più piccolo produce notevoli vantaggi, come l'eliminazione di una delle fasi del processo di patentamento, o di una o più fasi della trafilatura. Un altro vantaggio che ne deriva è la microstruttura finale, che risulta più fine ed omogenea, dovuta al migliore effetto di raffreddamento delle spire sul tappeto, con la conseguente riduzione della spaziatura delle lamelle perlitiche. La successiva trafila diventa più affidabile e fluida; si riduce la frequenza di rottura del filo e conseguenti
interruzioni del processo. Caleotto ha in programma di effettuare un'analisi approfondita, insieme agli utilizzatori finali, per valutare con precisione i vantaggi economici di questo prodotto, in funzione dell’applicazione finale, che include oltre alle funi e fili per pneumatici, anche fili per saldatura, molle per uso automobilistico e altre molle meccaniche, fili da laminare a freddo per ottenere piccoli piatti e altri prodotti sagomati.
- Vergella 5.5 mm, 5.0 mm e 4.5 mm prodotte sul blocco calibratore MEERdrive®PLUS .
CONTROLLO E GESTIONE DELLA LINEA DI RAFFREDDAMENTO
Nelle prime prove di laminazione la linea di raffreddamento è stata adattata alle diverse qualità di acciaio, in particolare per quanto riguarda la temperatura di formazione
delle spire sul tappeto. Il grafico seguente riproduce l’andamento della temperatura relativa ad un acciaio ad alto tenore di carbonio, con una temperatura finale compresa tra gli 800 °C – 900 °C.
Fig.6 - Diagramma di temperature e raffreddamento di un acciaio ad alto contenuto di carbonio.
A valle del blocco pre-finitore il materiale viene leggermente raffreddato per alimentare il blocco finitore/calibratore MEERdrive®PLUS ad una opportuna temperatura, e viene infine successivamente raffreddato per avere una ottimale formazione delle spire.
Per gli acciai ad alto contenuto di carbonio, il tempo di raffreddamento sul tappeto spire viene accuratamente regolato per ottenere una struttura perlitica fine, con la quantità minore possibile di ferrite proeutettoide e perlite a lamelle grossolane, fasi che riducono la duttilità e la trafilabilità.
Per ottenere una struttura perlitica fine, è necessario raffreddare il materiale, portandolo dalla temperatura di av-
volgimento a quella di inizio trasformazione, processo che deve essere eseguito in breve tempo, mantenendo il materiale a temperatura costante per un determinato intervallo di tempo necessario a completare la trasformazione. Il raffreddamento delle spire con diametro 4.5 mm sul tappeto a rulli è regolato in modo tale da avere la trasformazione di fase dopo circa 12-15 secondi, come analogamente eseguito per prodotti di piccolo diametro (5.5 mm) destinati alla trafilatura. Il grafico seguente mostra il profilo indicativo della temperatura, misurato lungo il tappeto di raffreddamento spire, per il grado C82D.
Per altre qualità, ad esempio acciaio a basso tenore di carbonio o debolmente legati, il gradiente di raffreddamento sul tappeto di raffreddamento a rulli è molto lento; perché lo scopo è quello di ottenere una struttura ferritica di bassa durezza, che serve alla successiva laminazione a freddo o allo stampaggio. Lo stesso trattamento viene applicato anche agli acciai destinati alla produzione del filo saldante, per i quali l'obiettivo è avere una struttura completamente ferritico-perlitica, senza alcuna traccia di martensite.
LA VELOCITÀ DI LAMINAZIONE PER I DIAMETRI PICCOLI
È noto che la vergella di piccolo diametro, laminata ad altissima velocità, richiede essere convogliata e guidata in modo estremamente preciso, per evitare vibrazioni e possibili incagli lungo la linea di laminazione. La configurazione della linea di processo, in termini di diametro degli ele-
menti raffreddanti e dei vari convogliamenti utilizzata per le prime prove con il tondo da 4.5 mm, era originariamente la stessa progettata per il tondo da 5.5 mm. In realtà il tondo da 4.5 mm è molto più piccolo e meno rigido e richiederebbe guide e convogliamenti dedicati. Con questa configurazione si è raggiunta una velocità di laminazione stabile di 90 m/s, velocità limite per un prodotto così piccolo. D’altra parte la vergella da 4.5 mm ha un intrinseco limite produttivo, dovuto alla sezione ridotta, ed è necessario poter raggiungere la velocità limite massima che possa coniugare elevata produttività con stabilità di processo. Il grafico seguente mostra il livello di produzione ottenibile con una linea standard e con una linea ottimizzata per un tondo da 4.5 mm. Utilizzando una linea di convogliamento con un diametro dedicato, quindi più piccolo, si può aumentare la velocità di finitura fino a 105 m/s, aumentando la produttività del 18%.
Fig.8 - Potenzialità dei nuovi elementi raffreddanti dedicati.
Le bobine di vergella prodotte durante i test sono state inviate ad alcuni clienti di Caleotto, per valutare la qualità generale del prodotto e i possibili vantaggi derivanti dalla riduzione del diametro. Nella tabella seguente sono elencate le marche di acciaio e le principali caratteristiche mec-
caniche e microstrutturali ottenute durante le varie prove. I valori di decarburazione, la difettosità superficiale e le caratteristiche meccaniche sono in linea con la produzione corrente dell’impianto e conformi con i principali standard qualitativi. Le caratteristiche microstrutturali sono risultate conformi alle richieste dei clienti.
Tab.2 -Risultati su acciai e denominazioni dei prodotti laminati per le prove sulla vergella.
C4C EN 10263-2
+ carbides C7D EN 16120-2
EN 16120-4
Note (*) Il valore di decarburazione non è significativo per acciaio a basso tenore di C (**) Billette colate a getto libero; i difetti superficiali non sono stati misurati
Ferrite + carbides
ACCIAIO A BASSO CONTENUTO DI CARBONIO - C4C
L’acciaio a basso carbonio C4C è destinato alla produzione di componenti poco sollecitati, ottenuti per stampaggio a freddo. Per questo tipo di lavorazione il prodotto viene innanzitutto sottoposto a trafilatura. Rispetto al tondo 5.5 la resistenza meccanica del 4.5 mm è inferiore e i passi di trafila necessari sono passati da 10 a 7. Il cliente non ha riscontrato nessuna anomalia nell’uso di questo prodotto; il vantaggio principale è costituito dalla diminuzione del 30% dei passi di trafilatura.
ACCIAIO A BASSO CONTENUTO DI CARBONIO – C7D
L’acciaio C7D è destinato alla produzione, tramite laminazione a freddo, di piattine sagomate. Per questo tipo di lavorazione il prodotto laminato viene sottoposto ad una serie di trattamenti:
1. Decapaggio acido, per eliminare la scaglia e ottenere una superficie perfettamente liscia
2. Trafilatura, per adeguare il diametro del laminato alla dimensione finale del prodotto
3. Laminazione a freddo
4. Confezionamento
Per le piattine di minori dimensioni la vergella di partenza deve avere un diametro inferiore a 5.5 mm, e quindi viene sottoposta ad una serie di lavorazioni (passaggi) in trafilatura. L’utilizzo di un diametro ridotto può permettere di ottenere una gamma di prodotti finiti senza questo passaggio, o con un numero di passaggi inferiore, con notevole risparmio economico.
Nemmeno il produttore di barre piatte laminate a freddo ha
incontrato difficoltà all’uso del nuovo prodotto. Resta da valutare se la produzione di diametri intermedi molto precisi, compresi fra 4.5 e 5.5 mm, possa completamente eliminare, per un certo gruppo di prodotti finiti, le operazioni di trafilatura.
0.56 –0.72%C
L'acciaio a medio e alto tenore di carbonio viene utilizzato principalmente per produrre vari componenti meccanici, mediamente o altamente sollecitati, come le molle.
Per questa applicazione, la vergella viene sottoposta a rimozione della scaglia superficiale e quindi trafilata al diametro corretto per il successivo avvolgimento. Questa operazione può avvenire solo se la plasticità residua del materiale, misurata come numero di torsioni prima della rottura, è rimasta sufficientemente elevata. Il vantaggio costituito dall’uso di un semilavorato di diametro inferiore è proprio la maggiore plasticità residua, dovuta ai minori passi di trafila, e conseguente minore incrudimento.
ACCIAIO AD ALTO TENORE DI CARBONIO, 0.82 – 0.84
Questo acciaio è usato principalmente per la produzione di funi ad alta resistenza.
Per questa applicazione, la vergella di partenza viene trafilata fino al raggiungimento di diametri molto sottili, processo chiamato trafila profonda. La massima riduzione dell’area per uno stadio di trafilatura senza necessità di un trattamento termico intermedio è fissata nel 92%, e quindi il minimo diametro ottenibile è funzione del diametro di partenza:
Fig.9 - Schemi di trafilatura profonda per vergella da 5.5 mm e 4.5 mm.
Il vantaggio che si ottiene partendo da un diametro inferiore è dato dalla diminuzione del numero di trattamenti termici intermedi.
Un ulteriore vantaggio è costituito dalla struttura perlitica più fine che il tondo 4.5 mm ha rispetto al 5.5 mm, dato dal-
la maggiore efficienza del trattamento di patentamento effettuato in linea sul tappeto di raffreddamento controllato. Il patentamento in linea è un processo di raffreddamento controllato delle spire che si compie fino ad una temperatura di 550 °C, seguito da un mantenimento isotermico
fino al completamento della trasformazione da austenite a perlite. La microstruttura finale è costituita da perlite finissima, non visibile al microscopio ottico. L’effetto risultante è un’elevata duttilità e trafilabilità per un processo senza interruzioni dovute a rottura del filo.
Caleotto è l’impianto siderurgico del gruppo Feralpi specializzato nella produzione di vergella di qualità, ottenuta da billette prodotte nella acciaieria di Calvisano. Grazie all’ammodernamento del laminatoio ad opera di SMS
Questi prodotti, applicabili ad un'ampia gamma di marche di acciaio, sono attualmente forniti da Caleotto ai numerosi clienti italiani tradizionalmente vocati alla trafilatura e allo stampaggio, e potenzialmente a clienti in tutta Europa. I nuovi diametri posizionano Caleotto tra i più innovativi produttori di acciaio di qualità per trafilatura. La vergella super sottile in alto carbonio può eliminare la necessità di ricottura intermedia del filo e ridurre il numero di passaggi si trafilatura. Ciò riduce i costi di produzione durante le lavorazioni finali. La vergella per componenti stampati è ge-
group S.p.A., l'impianto produce una estesa gamma dimensionale, che recentemente è stata ampliata con l’introduzione dei diametri piccoli, 5.0 e 4.5 mm. La vergella di piccolo diametro rende possibile realizzare riduzioni drastiche in molti processi secondari e i vantaggi che ne derivano per i clienti sono pienamente riconosciuti, in particolare nella produzione di filo trafilato sottile per funi ad alte prestazioni, e filo trafilato di spessore vario per molle, componenti stampati o laminati a freddo.
neralmente più plastica, non diventa fragile grazie ai minori passaggi di trafilatura e presenta una maggiore formabilità a freddo. Caleotto, grazie alle tecnologie fornite da SMS group S.p.A., è lieta di poter espandere la propria gamma dimensionale e offrire ai propri clienti la vergella più sottile prodotta in Europa. In futuro, la lunga collaborazione verrà consolidata con la messa in servizio della nuova linea bordioni per diametri grandi, prevista per il terzo quadrimestre del 2024.
edited by: L. Angelini, N. Bolognani, A. Parimbelli, A. Taurino, F. Coppola, F. Paternoster
In recent years the steel market has substantially changed, becoming highly variable in the short term, regarding both demand and quantity produced. Despite the manufacturers' willingness to reduce the ever-increasing production costs, there has been a certain interest as well as a revival in the demand for steel in almost all sectors, from reinforced concrete to the automotive steel.
The market demands flexibility and ability to adapt to everyday conditions while preserving marginality. Obviously, the Feralpi Group, which is increasingly engaged in the field of sustainable steel, i.e. “Green Steel”, has certainly not been waiting to see what happens next either: it has taken action and aimed, also with the Caleotto plant, at developing the production of wire rod from special steel to the best of their ability, and also to ensure the highest standards to the end customers in terms of products, processes, services and technical assistance.
After the first excellent results that were already obtained back in 2019 with the use of the four-stand MEERdrive® PLUS sizing block, along with the latest technologies developed by SMS group S.p.A., several steel grades were rolled in 4.5 mm and 5.0 mm wire rod products at the beginning of 2023, achieving surprising results, which were also confirmed by the end users. How were they produced? What has been achieved after four years of work? Let us take a closer look in this article.
KEYWORDS: MEERDRIVE®PLUS; SIZING BLOCK, ORRR (SIZING OVAL ROUND ROUND ROUND); SIZING WITH SINGLE FAMILY PASS DESIGN; 4.5 MM WIRE ROD
INTRODUCTION
From a technical point of view, the term quality means "a set of characteristics that determine a product’s compliance with the function for which it is intended": the certification, intended as a guarantee of quality, is an acknowledgement of the accurate manufacturing of a product".
Under these premises, Caleotto, active in the rolling field since 1896, is one of the front-runners and among the leaders in the Italian market for the production of highquality wire rod. Since 2020 Caleotto has been part of the Feralpi Group founded in 1968, and one of the leading steel producers in Europe, specializing in the production of construction steel and steel for special applications. As Caleotto has been demonstrating for many years now, the company has been aiming at producing wire rod from high-quality steels to the best of their ability, while ensuring end customers the highest standards in terms of products, processes, services and technical assistance.
Lorenzo Angelini, Nicola Bolognani, Andrea Parimbelli
Arlenico S.p.A., Lecco / Italy
Andrea Taurino, Fabio Coppola, Francesco Paternoster
SMS group S.p.A., Tarcento / Italy
The way to enter new, previously unexplored market niches and to further improve the quality of wire rod products had already been mapped out since the fourstand MEERdrive®PLUS sizing/finishing block, capable of meeting 100 percent of Caleotto's market requirements, went into operation.
By adopting the single drive technology for each stand, the MEERdrive®PLUS sizing block is the best technology on the market for the production of high-quality wire rod, and contributes to significantly reduce operating
costs in terms of roll rings inventory, changing times and maintenance. MEERdrive®PLUS offers a sound opportunity to produce an excellent wire rod in terms of dimensional tolerances and surface quality - but it is not only this single machine that does the "right job". It is a combination of technologies, allowing a constant control of dimensions and temperatures before and after the sizing block, which provides Caleotto with new opportunities, including consolidating its position on the market.
The Caleotto rolling mill has been heavily upgraded by SMS group with the introduction of the latest technologies, namely the MEERdrive®PLUS finishing/sizing block that
ensures the best dimensional tolerances and the cooling and equalizing line (with multi-loop technology) for thermo-mechanical rolling.
Fig.1 - Wire rod rolling plant layout including also the bar-in-coil production line.
The multi-loop technology, with several possible cooling paths, depending on steel type and finished product dimensions, increases production flexibility and improves the rolling mill utilization factor. In the Caleotto plant the thermo-mechanical rolling, with final temperatures
below 800°C, can be used for rounds exceeding a 13.0 mm diameter, while the low temperature rolling can be used for smaller diameters. The high cooling impact allows obtaining very fine microstructures, offering considerable advantages to end users. Specifically, the "multi-loop"
concept has a number of operational advantages. All the planned maintenance of the pre-finishing block can be performed while the block is bypassed, using an alternative path, thereby reducing the scheduled machine downtimes. The pre-finishing block is only used when strictly necessary, and is bypassed for several diameters. This allows product changes to be made with fewer time constraints and ensures that settings can be precision controlled, minimizing any problems arising from product changes.
By using the MEERdrive®PLUS sizing block alone, for products exceeding 13.0 mm, the energy costs are reduced, as the pre-finishing block is switched off. The efficiency of the lubrication system is also extended, as there is less chance of contamination with cooling water. The use of the single family rolling in the intermediate mill allows a drastic savings in terms of changing times and costs for rolls and guides.
The ability of the Caleotto rolling mill to roll at lower temperatures with fully equalized rod temperature generates further cost savings by reducing the incidence of downstream heat treatments. During the rolling of cold heading steels, for example, the improvement of the microstructure resulting from thermo-mechanical rolling makes it possible to eliminate soft-annealing for some types of boron manganese steels and to substantially reduce soft-annealing (up to 50 percent less) for chromium, chromium boron and chromium molybdenum steels. Thanks to its unique multi-drive technology (one motor per each rolling stand) the MEERdrive® PLUS sizing block allows absolute control of speeds between the
different pass sequences, minimizing bar tension and ensuring the best tolerances achievable nowadays on a wire rod mill.
At the time of the MEERdrive® PLUS installation, the pass scheme had already been designed for wire rod products with a diameter of less than 5.5 mm. Indeed, the plant layout is the optimal solution for producing smalldiameter products with limited productivity, thanks to the first four roughing stands being separated from the rest of the mill and the different billet sizes available.
The first trials were performed in June 2022, and focused on the production of 5.0 mm wire rod, rolled at a speed of 100 m/s. The excellent results obtained in terms of dimensional tolerances and mechanical characteristics of the finished product encouraged us to continue trials using the 4.5 mm diameter wire rod, which took place in January 2023, with a test speed of 90 m/s. In the future, we envisage reaching and exceeding 100 m/s for both diameters with dedicated conveyors. Currently, the maximum operating speed of the wire rod line is 120 m/s for 5.5 mm rounds.
Different steel grades that are usually produced by Caleotto were tested in both campaigns. The 4.5 mm trial confirmed the excellent results that had already been obtained with the 5.0 mm diameter.
Tab.1 - Some of the steels and rolled product designations used for the wire rod trials.
The undeniable advantages of the MEERdrive®PLUS technology are summarized below:
• Perfect adaptability to different dimensional ranges of the entry side passes from the upstream pre-finishing mill (single family pass design);
• Possibility of rolling at low temperature (750°C) on all steel grades for which this type of process is applicable, in the Ø 4.5 to 28 mm dimensional range;
• Possibility of optimal use and adjustment of reductions for each single product;
• Maximum flexibility in managing inter-stand tensions and roll ring speeds;
• Possibility of using roll rings with different diameters
on the single stands (multi-drive technology); As a result of the above advantages it has been easy to achieve the tight dimensional tolerances required by Caleotto (±0.05 mm – 60 % ovality), exploiting the existing single family pass design of the pre-finishing block with 10 stands positioned upstream, also thanks to the accurate sizing study performed with the new SMS-LPPS simulation and calculation program
The classical MEERdrive®PLUS oval-round-false_roundround sequence has been used, where the first two stands work at higher reductions, preparing an entry feeder pass for the next two stands to obtain a precise finished product with low reductions. The stability of the process and the achievement of the best dimensional tolerances are
ensured by the extremely small distance between the last two stands and the optimal management of inter-stand tensions.
- SMS-SIM PRO 4.0 software for round sizes for 4.5 mm and 5.0 mm wire rod.
Caleotto produces low, medium and high carbon steel for all applications, for cold heading, steel for the production of ropes, chains, springs, boron steel, welding wire and others, also using a thermo-mechanical rolling process. The latest plant upgrade was designed to achieve higher quality products in terms of dimensional tolerances and improved fine microstructures, thanks to low-temperature finish rolling, with all the related benefits on final grain size and microstructure homogeneity. The recent 5.0 and 4.5 mm diameters produced are, in fact, the smallest wire rod diameters ever produced on an SMS group finishing/ sizing block and allow Caleotto to produce the thinnest wire rod in Europe. This product can be used for many applications, both when high ductility is required for deep
drawing, which is typical of rope production, and when high plasticity is required, for the production of cold heading components. The 4.5 mm wire rod is 33 percent smaller than the standard 5.5 mm diameter round and allows a drastic reduction in many processes that follow, such as drawing and annealing. The resulting advantages for end-users are particularly clear in the production of small-diameter drawn wire for high-performance ropes and for medium-sized wire used for cold heading and cold rolling. As an example, the following diagram illustrates the standard process for producing thin wires, starting with the standard product diameter of 5.5 mm.
The use of a smaller initial diameter produces significant advantages, such as the elimination of one of the patenting process steps, or of one or more drawing steps. Another resulting advantage is the final microstructure, which is finer and more homogenous, due to the improved cooling effect of the coils on the cooling conveyor, leading to a reduction in pearlitic lamellar spacing. The subsequent drawing becomes more reliable and smooth; the frequency of wire breakage and consequent process
interruptions are reduced. Caleotto plans to carry out an in-depth analysis, together with end users, to precisely assess the economic benefits of this product, depending on the final application, which includes not only ropes and tyre bead wire, but also welding wires, automotive springs as well as other mechanical springs, wires used for cold rolling of small flats and other shaped products.
In the first rolling trials, the cooling line was adapted to the different steel grades, especially as regards the temperature at which the coils are formed on the cooling conveyor. The following chart shows the temperature curve for a high-carbon steel grade with a final temperature between 800°C and 900°C.
Fig.6 - Temperature and cooling chart for high-carbon steel.
Downstream, of the pre-finishing block the material is slightly cooled to feed the MEERdrive®PLUS finishing/sizing block at the correct temperature, and is finally cooled for optimal coil formation.
For high-carbon steels, the cooling time on the coil cooling conveyor is carefully adjusted to achieve a fine pearlitic structure, with as little proeutectoid ferrite and coarse lamellar pearlite as possible, phases that reduce ductility and drawability.
In order to obtain a fine pearlitic structure, the material must be cooled, from the coiling temperature to the
transformation start temperature - a process that must performed in a short time - while keeping the material at a constant temperature for the period of time required to complete the transformation.
Cooling of 4.5 mm diameter coils on the conveyor is adjusted so that the phase transformation occurs after about 12-15 seconds, as similarly performed for small diameter products (5.5 mm) intended for drawing. The following graph shows the indicative temperature profile, measured along the coil cooling conveyor, for the C82D steel grade.
For other grades, such as low carbon or low alloy steels, the cooling gradient on the cooling conveyor is very slow; since the aim is to obtain a low hardness ferritic structure, required for subsequent cold rolling or heading. The same treatment is also applied to welding wire rod production, the aim of which is to obtain a fully ferritic-perlitic structure, without any trace of martensite.
It is well known that small wire rod, rolled at very high speed, needs to be conveyed and guided very accurately, to avoid vibrations and possible cobblers along the rolling line. The configuration of the process line, in terms of the diameter of the cooling elements and the various conveyors used for the first trials with the 4.5 mm wire rod, was originally the same as that designed for the 5.5 mm round. The 4.5 mm wire rod is indeed much smaller and less rigid and
would require dedicated guides and conveyors. With this configuration, a 90 m/s steady rolling speed was achieved, i.e. the maximum speed for such a small product. On the other hand, the 4.5 mm wire rod has an inherent production limit due to its small cross-section; hence it is necessary to reach the maximum speed that can combine high productivity with process stability. The chart below shows the output level that can be achieved with a standard line and with a line optimized for 4.5 mm wire rods. By using a conveyor line with a dedicated diameter, therefore a smaller one, the finishing speed can be increased up to 105 m/s, boosting productivity by 18 percent.
Fig.8 - Potential of the new dedicated cooling elements.
The wire rod coils produced during the trials were sent to some of Caleotto's customers to assess the overall quality of the product and the possible benefits resulting from the reduction of diameter. The following table lists the steel grades and the main mechanical and microstructural characteristics obtained during the various trials.
Decardburization values, surface defects and the mechanical properties are in line with the current plant production and in accordance with the main quality standards. The microstructural characteristics were found to be compliant with customer requirements
Tab.2 -Results on steel grades and designations of the rolled products for the wire rod trials.
Notes:
(*) The decarburization value is not significant for low-C steel (**) Free cast billets; surface defects were not measured
The C4C low carbon steel is intended for the production of standard components, obtained by cold heading. For this type of processing, the product is first drawn. Compared to the 5.5 mm round, the mechanical strength of the 4.5 mm wire rod is lower, and the required drawing steps have decreased from 10 to 7. The customer has not reported any irregularity when using this product; the main advantage of which is the 30 percent reduction in drawing steps.
The C7D steel is intended for the production of cold rolled shaped flats. For this type of processing, the rolled product undergoes a series of treatments.
1. Acid pickling, to remove scale and achieve a perfectly smooth surface
2. Drawing, to reduce the diameter of the rolled product to the final product size
3. Cold rolling
4. Packaging
For smaller flats, the diameter of the starting wire rod must be less than 5.5 mm, followed by several phases of the drawing process (pass sequences). The use of a smaller diameter allows to obtain a range of finished products without undergoing this pass sequence, or with a lower number of passes, with significant cost savings. No problems in the use of the new product have been
reported by the manufacturer of cold rolled flat bars either. What remains to be evaluated is whether the production of very precise intermediate diameters, between 4.5 and 5.5 mm, can completely eliminate drawing operations for a certain group of finished products.
Medium and high carbon steel is mainly used to produce various medium or high-demanding mechanical components, such as springs.
For this application, the wire rod undergoes surface scale removal and is then drawn to the correct diameter for subsequent coiling. This operation can only be carried out if the residual plasticity of the material, measured as number of torsions before breakage, has remained sufficiently high. The advantage of using a semi-finished product with a smaller diameter is, in fact, the greater residual plasticity, due to the fewer drawing steps, and consequently less work hardening.
This steel is mainly used for the production of high-strength ropes.
For this application, the starting wire rod is drawn to very thin diameters, a process called deep drawing. The maximum area reduction for a drawing stage without intermediate heat treatment is set at 92 percent; therefore the minimum diameter obtainable depends on the starting diameter:
The advantage of starting from a smaller diameter is the reduced number of intermediate heat treatments required. A further advantage comes from the finer pearlitic structure of the 4.5 mm wire rod compared to that of the 5.5 mm round, due to the greater efficiency of the on-line patenting treatment on the controlled cooling conveyor. On-line patenting is a controlled cooling process of coils carried
out up to a temperature of 550°C, followed by isothermal maintenance until the transformation from austenite to pearlite is completed. The final microstructure consists of very fine perlite, which is not visible under an optical microscope. The resulting effect is high ductility and drawability for a process without downtimes due to wire breakage.
Caleotto is a steel plant of the Feralpi Group that specialized in the production of high-quality wire rod, obtained from billets produced at the Calvisano steel plant. Thanks to the modernization of the rolling mill by SMS group S.p.A., the plant produces a vast dimensional range, which has recently been expanded to include small diameters, i.e. 5.0 mm and 4.5 mm. The small-diameter wire rod makes it
These new products, rolled in a wide range of steel grades, are currently supplied by Caleotto to the many Italian customers traditionally dedicated to wire drawing and cold heading, and potentially to customers throughout Europe. The new diameters allow Caleotto to be ranked among the most innovative producers of high-quality drawing steel. The super thin high-carbon wire rod can eliminate the need for intermediate wire annealing and reduce the number of drawing pass sequences, thereby reducing production costs during final processing. The wire rod for
possible to achieve drastic reductions in many secondary processes, and the resulting advantages for customers are fully acknowledged, especially in the production of thin drawn wire for high-performance ropes, and drawn wire of various diameters for springs, cold heading or rolled components.
cold heading components is generally more plastic, less brittle due to fewer drawing steps, and features greater cold formability. Thanks to the technologies provided by SMS group S.p.A., Caleotto is pleased to be able to expand its dimensional range and to offer its customers the thinnest wire rod produced in Europe. In the future, the long-standing collaboration will be consolidated thanks to the commissioning of the new large-diameter bar-in-coil line, scheduled for the third quarter of 2024.
edited by: Molchanov Lavr, Golub Tetiana, Kononenko Ganna, Koveria Andrii, Kimstach Tetiana
The technology of melting metals in an induction furnace allows the production of a wide range of alloyed steels to meetthedifferentneedsofsocietyandismoreenvironmentallyfriendlyasitproducesfeweremissions.Aspecialinterest for modern metallurgy isthe processes of alloying and deoxidizing, which occur directly in the induction furnace by introducing lump additives. In this work, the investigation of the process of melting of additives during induction melting has been studied in order to determine the optimal modes of introduction of deoxidizing and alloying additives into the melt, providing their maximum assimilation by the liquid metal. The study was carried out on the physical model simulating the crucible of a laboratory induction furnace equipped with a closed system of hydrodynamic circulation of liquid. The results demonstrate that the most rational place for the introduction of ferroalloys into the inductionfurnacecrucibleistheareaofthemeltlocatedatadistanceof1/2radiusfromthecenterofthecrucible.There isalsoatendencyforthedissolutiontimetodecreaseasthedepthofintroductionintothemeltincreases.Considering that in practical industrial conditions, it is extremely difficult to organize the introduction of deoxidizing and alloying agentsintothevolumeofmetalmelt,thenecessityofholdingthemeltwhenintroducingferroalloyisreasonable.
KEYWORDS: INDUCTION FURNACE, ALLOY STEEL; FERROALLOY, DISSOLUTION TIME, STIRRING SPEED, PHYSICAL MODELLING
INTRODUCTION
The technology of melting metallic melts in an induction furnace has been known for over 100 years [1]. This enables to obtain both alloyed steel grades for the needs of mechanical engineering and special high-quality alloys, which is due to the high yield of obtaining molten steel (98-99%) and the ability to achieve and maintain the required composition in induction crucible melting [2]. In addition, the melting process in induction furnaces is more environmentally friendly, producing fewer vapors and smoke.
The alloying and refining processes carried out directly in the working chamber of the induction furnace through the addition of solid additives are of particular interest to modern metallurgy.
The analysis of the existing publications on the study of melting processes in an induction furnace mostly involves mathematical modelling of various aspects of this process. For instance, publications [3-7] provide a mathematical description of electromagnetic
Molchanov Lavr, Golub Tetiana, Kononenko Ganna
Z.I. Nekrasov Iron and Steel Institute, National Academy of Sciences of Ukraine, Ukraine
Koveria Andrii
Department of Chemistry, Dnipro University of Technology, Ukraine
Kimstach Tetiana
Nekrasov Iron and Steel Institute, National Academy of Sciences of Ukraine, 49107 Dnipro, Ukraine - Ukrainian State University of Science and Technologies, Dnipro, Ukraine
metall729321@gmail.com isinasu.golubts@gmail.com perlit@ua.fm
Koverya.a.s@nmu.one(Correspondingauthor) 1375tatyana@gmail.com
and thermodynamic phenomena. In works [8, 9], a computational mathematical analysis of the influence of turbulence on the processes in the induction furnace is conducted. A method for calculating the melting rate of the charge based on mathematical modelling is proposed in [10, 11]. By the use of a physical model, the present study aims to investigate the melting process of additives during induction melting to determine the optimal conditions for introducing refining and alloying agents into the melt, ensuring their maximum assimilation by the molten metal.
The research was conducted via methods of physical modelling based on the use of low temperature melting materials [12, 13]. It considered the features of molten metal movement in the crucible through the combined action of electromagnetic and gravitational stirring. A specially designed laboratory set-up was developed,
simulating the crucible of a laboratory-scale induction furnace with a capacity of 10 kg on a 1:1 scale (see Figure 1).
The experimental set-up consists of a transparent model of a 10 kg induction furnace crucible, a hydrodynamic circulation system (a pump with adjustable rotation speed and a system of branched pipes for the supply and discharge of liquid), a thermocouple to control the temperature of the liquid, a lighting system based on a solid-state light source with a brightness of 10000 lm, and a video recording system. The hydrodynamic fluid circulation system allowed the creation of hydrodynamic conditions inside the crucible model that corresponded to the real processes during the central lifting of the metal (along the vertical axis of the crucible). In this configuration, the design of the liquid inlet and outlet tubes ensured the formation of a complete circulation circuit directly within the crucible volume.
Fig.1 - Scheme of the experimental set-up for the simulation of hydrodynamic processes in the crucible of a 10 kg laboratory-scale induction furnace: 1 - transparent model of a 10 kg induction furnace crucible on a 1:1 scale; 2pump with adjustable rotation speed; 3 - distributor tank for organizing the hydrodynamic flow; 4 - solid-state light source; 5 - photo camera.
The assimilation process of the deoxidizer (alloying agent) is highly complex and can be roughly divided into dissolution, melting and distribution processes within the melt volume. Therefore, criteria of physical similarity were applied to maintain correspondence between the conditions of low-temperature modelling and those occurring during deoxidation and alloying in the 10 kg crucible of the laboratory furnace. In particular, thermal
similarity conditions were satisfied for the Nusselt number (Nu); it was necessary to maintain the Weber number (We) for dynamic similarity of fluid flows; for an accurate description of the stirring process, modified Euler (Eu), Reynolds (Re) and Froude (Fr) criteria were applied [14, 15]. The ratio of the density and melting temperatures of the molten metal and the alloying additive achieves compliance with these criteria. The average density and melting temperatures of deoxidizers and alloying additions
used in the production of alloyed steels were taken from the study reported in [16].
Considering the availability of the source materials and the specificities of performing low-temperature modelling, water was chosen as the substance to simulate liquid steel and ice coloured with a green food dye (15 ml water and 0.07 g dye) to simulate ferroalloys. The comparison of the main physical parameters of the substances in the real and the model systems is presented in Table 1.
Tab.1 -Basic physical parameters of substances in the model and real systems.
* - averaged data from [16].
Considering that the difference between the melting temperatures of ferroalloys and steel is about 50°C, and the temperature between ice and water is 25°C, the obtained indicators for this parameter should be reduced by 2 times. In addition, the density ratio of liquid steel to water, which is 7000/997 ~ 7, must be considered. Thus, the real-time
scale for modelling will be 3.5:1 (all processes in the model will occur approximately 3.5 times faster than in the real furnace).
To assess the speed of metal phase movement in the crucible of an induction furnace, the term stirring index (SI) is used [17], which can be calculated by the Eq. 1
kW is the power of the induction furnace, kW;
f – operating frequency, Hz;
D – diameter of the furnace crucible, m;
SG – specific density of liquid metal in the inductor, kg/m3;
ρ – resistivity of metal in the furnace crucible, μ Ω ·cm;
A is the area of the cross-section perpendicular to the vertical axis of the crucible, m2
Thus, according to the calculations based on formula (1), it has been determined that the stirring index in the crucible of the laboratory furnace will correspond to flow velocities in the transparent low-temperature model of the crucible at a liquid flow rate that pumped through the pump at 5.83·10-4 m3/s.
In order to determine the optimal position for introducing alloying agents and ferroalloys into the crucible of the induction furnace, a series of tests was planned with variations in the introduction place both radially and in height within the crucible. The experimental conditions included introducing materials onto the surface of the melt near the crucible wall, at a distance of 1/4, 1/2, and 3/4 radius from the crucible wall, and directly on the vertical axis of the crucible. To determine the optimal height for introducing ferroalloys, experiments were conducted with the forced immersion of the test sample on the bottom of the crucible, at 1/4, 1/2, and 3/4 of the crucible height from the bottom, and on the surface of the melt. Studies on the influence of the depth of ferroalloy introduction were based on the most effective variant of radial introduction into the crucible. The dissolution process in the simulation model was accompanied by video recording, allowing for the determination of the hydrodynamic conditions of the process (predominant trajectories of ferroalloy lump movement in the melt volume under the influence of hydrodynamic flows), the time of model ferroalloy lump dissolution, and the time of homogenization of the melt
model in the crucible.
Moreover, the influence of melt movement velocity in the induction furnace crucible on the efficiency of ferroalloy dissolution processes and melt homogenization in the crucible was investigated. This was based on the best introduction variant identified in the previous research stage. The research methods and monitored parameters were similar to those of the previous case.
Each experiment was repeated three times. In addition to visual observations of the ferroalloy fragment, the criteria for the complete dissolution of the fragment and the complete homogenization of the metal bath was the absence of a gradient in the intensity of the liquid color (determined based on the video recording).
Determination of the rational place for introducing the ferroalloy/deoxidizer by the radius of the induction furnace crucible and its height. In the first stage, the efficiency of dissolving a fragment of ferroalloy in the melt in the middle of the crucible of an induction furnace was investigated. In particular, consider the behaviour of a piece of ice imitating a ferroalloy at different places of its introduction into the model. Figure 2 shows characteristic trajectories of the movement of the ice piece and its dissolution, for example, when introduced near the wall (A), at a distance of 1/2 the radius (B) and in the centre of the model (C). The images for a distance of 3/4 of the radius were similar to those for 1/2 of the radius and at 1/4 of the radius were similar to those obtained when introduced near the wall, so that they are not shown.
According to the data presented in Fig. 2, it can be concluded that the optimum radial position for introduction into the induction furnace crucible is a distance greater than 1/2 of the radius from the crucible wall. In cases where it is less than 1/4, the ferroalloy is “forced” to the wall by flows or holding it on the surface, which increases the time for the melt to absorb the ferroalloy and creates conditions for significant oxidation of its constituents by atmospheric oxygen. When ferroalloys are introduced into the specified area (more than 1/2 of the radius), they are captured by the liquid phase flows and introduced into the melt volume. This leads to rapid dissolution of the ferroalloy fragment in
the melt volume, preventing oxidation of its constituents by atmospheric oxygen. Centre introduction reduces the dissolution rate of the ferroalloy fragment, possibly due to upward flows at the centre of the model, which slows down its capture by the volume.
To evaluate quantitatively the effectiveness of different radial positions for introducing ferroalloys into the induction furnace crucible, a dependence of the time of dissolution of the ferroalloy fragments and the time of homogenization of the liquid phase on the insertion distance from the wall was built using averaged data (Fig. 3).
y = 0,001x 2 -
Distance from the crucible wall to the centre, %
Dissolution time of a ferroalloy fragment, s; The time of homogenisation of the liquid phase, s
Dissolution time of a ferroalloy fragment, s; The time of homogenisation of the liquid phase, s
Fig.3 - Dependence of the dissolution time of the ferroalloy fragment and homogenization of the liquid phase on the place of ferroalloy introduction, obtained from the results of low-temperature modelling based on averaged experimental data.
From the data it can be concluded that there is an optimum radial place for introducing ferroalloys into the crucible, which is at a distance from the wall of 1/2 of the crucible radius. In this case, the processes of dissolution and redistribution in the liquid phase are coordinated by the organization of the hydrodynamic flows in such a way that they keep the ferroalloy fragment in the volume of the liquid phase. When the ferroalloy fragment is introduced closer to the crucible wall, melting occurs at the surface of the liquid phase, and redistribution in the melt volume is significantly difficult because of the presence of a stagnant zone.
The results of determining the hydrodynamic characteristics (dominant trajectories) of the interaction of the ferroalloy fragment with the liquid metal under different conditions of depth and radial distance of introduction into the crucible of the induction furnace are presented in Fig. 4.
Fig.4 - Images of the interaction of the ferroalloy fragment with liquid metal for different introduction conditions along the height of the crucible of an induction furnace at a distance of 1/2 radius at the same time from the start of introduction – 1.5 s: a – introduction to the surface of the melt; b – introduction at 1/4 of the crucible height from the melt surface; c – introduction at 1/2 of the crucible height from the melt surface; d – introduction at 3/4 of the crucible height from the melt surface; e – introduction to the crucible bottom.
From the data presented in Figure 4, it can be concluded that in all cases, the dissolution of the ferroalloy fragment takes place in the melt volume, which positively affects its efficiency in being assimilated by the metallic phase. For a quantitative assessment of the trend identified, a graphical dependence of the time of dissolution of a ferroalloy fragment and homogenization of the liquid phase was built on the depth of introduction of a ferroalloy fragment into the melt (Fig. 5).
According to the data presented in Figure 5, there is a trend
confirming the increase in the efficiency of the deoxidation and alloying processes with an increase in the depth of material introduction into the melt. This can be explained by more intensive stirring in the melt volume and, consequently, an increase in the efficiency of the element redistribution process throughout the melt volume. Based on the experimental studies carried out, this is confirmed by a significant decrease in the bath homogenization time with an increase in the depth of introduction, with a slight influence of the dissolution time of the ferroalloy fragment.
y = 4,959e-0,01x
R² = 0,948
y = -0,012x + 5,2 R² = 0,75
Distance from the crucible top to the bottom, %
Dissolution time of a ferroalloy fragment, s; The time of homogenisation of the liquid phase, s
Fig.5 - Dependence of the dissolution time of ferroalloy fragments and liquid phase homogenization on the place of ferroalloy introduction as a function of model height, obtained from the results of low-temperature modelling based on averaged experimental data.
Determination of the influence of the melt stirring speed on the bath homogenization rate. The next research stage was to determine the influence of the melt stirring speed in the induction furnace crucible on the alloy and ferroalloy dissolution processes using identical ice fragments introduced at the same place in the model. The results
of the quantitative assessment are illustrated in Figure 6. The data show that an increase of 40-50% in the stirring speed reduces the dissolution and homogenization time by almost 2 times. This effect is associated with increased efficiency of the mass exchange processes in the metal bath due to forced convection.
y = 59,66e-0,07x
R² = 0,978
y = 38,37e-0,05x
R² = 0,902
Stirring speed of the liquid phase in the crucible, l/min
Dissolution time of a ferroalloy fragment, s; The time of homogenisation of the liquid phase, s
Fig.6 - Dependence of the dissolution time of ferroalloy fragments and liquid phase homogenization on the stirring speed of the liquid melt in the volume of the induction furnace crucible.
Summarizing the results on the low-temperature modelling of the processes of interaction of ferroalloys with the liquid bath of an induction furnace by the example of the interaction of colored ice and water, it should be noted that the most rational place for the introduction of ferroalloys into the crucible of an induction furnace is the area of the melt located at a distance of 1/2 radius from the centre of the crucible. In this case, due to the characteristics of the hydrodynamic flows that formed in the furnace crucible, there is an effect of keeping the ferroalloy fragment within the volume of the metal melt throughout the complete dissolution process.
Regarding the depth at which the ferroalloy is introduced into the melt volume, the observed tendency is the dissolution time to decrease when the depth of the ferroalloy as introduced into the melt increases. However, in the production conditions, it is very difficult to obtain
the introduction of deoxidizers and alloying agents into the volume of the metal melt, so their introduction is carried out on the surface of the melt.
Thus, according to the results of the conducted lowtemperature modelling, it was established that when introducing a hemispherical ferroalloy fragment with a diameter of 20 mm at a distance of 1/2 of the radius of the induction furnace crucible, the time of complete dissolution is 5 s that in terms of the actual process in the furnace will be 5·7/2 = 17.5 s. The data obtained correspond to the results of studies on the dissolution of ferromanganese fragments of different fractions in a metal melt [10], which indicates the consistency of the data obtained with production conditions. It should be noted that deoxidation processes are significantly influenced by the processes of oxygen redistribution and removal from the melt of the products of their interaction with deoxidizing and alloying elements
[18]. Based on this, the required holding time of the metal in the crucible of the laboratory induction furnace with a capacity of 10 kg is at least 5 minutes, and for production conditions (crucible capacity up to 150 kg), it is 10-15 minutes.
Considering the features of the affinity of alloying elements for oxygen (Fig. 7) and the essential for guaranteed removal of non-metallic inclusions formed in the melt, the following scheme of deoxidation and alloying is proposed.
The first stage is the introduction of aluminium or silicon into the melt for deep deoxidation. Afterward, the introduction of elements with low affinity for oxygen (nickel, copper, tungsten, and molybdenum). Further, at the next stage is manganese and chromium. Then is carbon (during deoxidation, gaseous products are formed, which additionally remove non-metallic inclusions from the melt). The last stage is the introduction of rare earth materials for the final modification of the structure of both the finished steel and non-metallic inclusions.
Based on the results obtained from the low-temperature modelling of the interactions between ferroalloys and the molten bath of an induction furnace, exemplified by the interaction of colored ice fragments with water, it should be concluded that the most rational place for the introduction of ferroalloys into the crucible of an induction furnace is the area of the molten bath located at a distance of 1/2 the radius from the centre of the crucible, with better results being obtained by avoiding the central area. At the same time, due to the features of hydrodynamic flows formed in the furnace crucible, the effect of holding a ferroalloy fragment in the volume of the metal melt during the time of complete dissolution is observed. Concerning the depth of introduction of the ferroalloy
into the volume of the crucible, there is a tendency for the dissolution time to decrease with increasing depth of introduction into the melt. However, in real production conditions, it is very difficult to obtain the introduction of deoxidizers and alloying agents into the volume of the molten metal; therefore, their addition is carried out on the surface of the melt. Consequently, there is a reason for holding the melt when introducing a ferroalloy.
[1] Ketul M Patel. An overview of applications of induction heating. International Journal of Electrical Engineering & Technology, 2019, 10 (2), 81-85. ISSN Online: 0976-6553
[2] D.F. Cherniega, V.S. Bogushevskiy, Yu.Ya. Gotvianskiy Basics of metallurgical production of metals and alloys. 2006. 503 (in Russian).
[3] V. Bojarevics, R.A. Harding, M. Wickins. Experimental and numerical study of the cold crucible melting process. Proceeding of the Third International Conference on CFD in the Minerals and Process Industries, CSIRO, Melbourne, Australia 10-12 December 2003, 599-606.
[4] J.H. Songa, B.T. Mina, An electromagnetic and thermal analysis of a cold crucible melting, International Communications in Heat and Mass Transfer. 2005, 32, 1325-1336. https://doi.org/10.1016/j.icheatmasstransfer.2005.07.015
[5] S. Spitans, A. Jakovics, E. Baake, B. Nacke. Numerical modelling of free surface dynamics of conductive melt in the induction crucible furnace. Magnetohydrodynamics, 2010, 46, 317-328. https://doi.org/10.22364/mhd.46.4.12
[6] S. Spitans, A. Jakovics, E. Baake, B. Nacke, Numerical modelling of free surface dynamics of melt in an alternate electromagnetic field. Magnetohydrodynamics. 2011, 47(4), 461-473.
[7] P. Bulinskij, J. Smolka, S. Golak, R. Przylucki. Coupled numerical model of metal melting in an induction furnace: sensitivity analysis and validation of model. Przeglad elektrotechniczny, 2016, 1(3), 51-54. https://doi.org/ 10.15199/48.2016.03.11
[8] K. Adler, R. Schwarze, V Galindo, Numerical modelling of the evaporation process of an electromagnetically stirred copper melt, Proceedings of the FLUENT CFD Forum 2005, Bad Nauheim, Germany, 2005.
[9] P. Bulinskij, J. Smolka, S. Golak, R. Przylucki, L. Blacha, R. Bialecki, M. Palacz, G. Siwiac. Effect of turbulence modelling in numerical analysis of melting process in an induction furnace. Archives of Metallurgy and Materials, 2015, 60(3), 1575-1579. https://doi. org/10.1515/amm-2015-0275
[10] I.V. Portnova, I.M. Yachikov. Modeling the dissolution process of ferromanganese with forced stirring of a liquid bath. Theory and technology of metallurgical production, 2016, 1, 34-38. (in Russian)
[11] Onigbajumo Adetunji, Seidu Saliu Ojo, Akinlabi Oyetunji, Newton Itua.Melting Time Prediction Model for Induction Furnace Melting Using Specific Thermal Consumption from Material Charge Approach. J. of Minerals and Materials Characterization and Eng., 2021, 19. https://doi.org/10.4236/jmmce.2021.91005
[12] F. Gonçalves, M. Ribeiro, R. Correa, R. Silva, B. Braga, B. Maia, R. Tavares, D. Carvalho, J. Schenk. Measurements methodologies for basic oxygen furnace cold modeling. Journal of Materials Research and Technology. 2021, 13, 834-856. https://doi.org/10.1016/j. jmrt.2021.04.050
[13] T. Golub, L. Molchanov, A. Koveria, L. Kieush. Study on a two-phase low-temperature model of the features of metal tapping in basic oxygen furnace. Acta Metallurgica Slovaca. 2022, 28 (3), 151-156. https://doi.org/10.36547/ams.28.3.1566
[14] A. A. Durmagambetov, Leyla S. Fazilova. Navier-Stokes Equations—Millennium Prize Problems. Natural Science. Scientific Research an Academic Publisher. 2015, 7 (2), 88-99. https://doi.org/10.4236/ns.2015.72010
[15] Nord-Eddine and Sad Chemloul. Dimensional Analysis and Similarity in Fluid Mechanics. 1st Edition. Wiley-ISTE, 2020.240.
[16] G. Kucher, V.I Olshanskiy, I.I. Filipov, I.I. Kucher. Directory of ferroalloy maker. 2000, 288. (in Russian)
[17] Mixing metal in crucible induction furnaces (in Russian) https://on-v.com.ua/novosti/ttexnologii-i-nauka/peremeshivanie-metallav-tigelnyx-indukcionnyh-pechax/
[18] G. Kniupel. Deoxidation and vacuum treatment of steel: Chapter I. 1973. 426.
COAL,
Bardolino . Italy . 16-18 October 2024
AIM is glad to announce the 9th European Coke and Ironmaking Congress (ECIC) to be held in Bardolino, Italy, on 16-18 October 2024.
ECIC 2024 will focus on the newest technologies in coke making, sintering, pelletizing, pyrolizing the biomasses and ironmaking (blast furnaces, direct reduction and carbon-based smelting processes).
The 2025 goal of carbon neutrality and the related intensive efforts of the steel industry will significantly affect the technologies for iron ore reduction. In this perspective, the shortage of iron ores matching the requirement for direct reduction by gas and for melting in electric arc furnace makes important proposal of new technologies and devices that can ensure the carbon neutrality even for the coal based routes. This Congress will focus on technologies that can achieve such a goal improving the efficiency of the existing process, applying the devices that avoid a net emission of green house gases and to point out new routes based on exploitation of biomasses whose net emission is intrinsically neutral.
The 9th ECIC will address both fundamental research work and evaluation and plant operational results and plant construction. The Congress will bring together a wide range of experts, coming from plant operation, plant suppliers, universities and research institutes, who share expertise in:
. Cokemaking
Production of Biocoal/biochar
. Industry 4.0 in ironmaking
. Sintering, pelletising, briquette production
Direct reduction and Smelting reduction
. Blast furnace ironmaking
Blast Furnace muds
. CCS/CCUS (Carbon Capture, Use and Storage)
. Impact of Carbon Border Adjustment Mechanism (CBAM)
H2 and Syngas exploitation
The event will provide a forum for best practise and state-of-the-art technology, new developments, new ideas and research results.
CONGRESS CHAIRMEN
Prof. Carlo Mapelli - Politecnico di Milano, Italy
SUBMISSION OF PAPERS AND DEADLINE
Prof. Johannes Schenk - Montanuniversität Leoben, Austria
All paper proposals must be submitted online, at www.aimnet.it/ecic, by 28 March 2024.
All abstracts will be refereed by the scientific international experts. In the case of too many submissions, abstracts of equal quality will be accepted on a first come, first serve basis. To submit an abstract, please proceed as follows:
1. Write your abstract (max. 300 words).
2. Submit your abstract online at: www.aimnet.it/ecic > Call for Papers section (please fill out all fields).
3. Papers must be submitted in English.
ORGANIZING SECRETARIAT
Via Filippo Turati 8 - 20121 Milano MI - Italy
tel. +39 02 76021132
aim@aimnet.it . www.aimnet.it
Acciaio e metalli: dinamiche, cicli e tendenza di mercato
Rubrica trimestrale a cura di Achille Fornasini
Ha insegnato all’Università Bocconi di Milano, all’Università di Venezia e all’Università di Brescia, dove è responsabile del Laboratorio per lo studio delle Dinamiche dei Sistemi e dei Mercati finanziari. Coordina l’osservatorio congiunturale di Confindustria Brescia e di ANIMA Confindustria. Partner di Sidewerb, da vent’anni cura rubriche dedicate ai mercati siderurgici e metallurgici. È autore di libri e centinaia di saggi, editoriali e articoli su temi economico-finanziari.
Il 2024 si è aperto con l’escalation degli attacchi portati dagli yemeniti Houthi al traffico marittimo in transito nello Stretto di Bab al-Mandab verso il canale di Suez. Con la conseguenza che le più importanti compagnie di shipping preferiscono tuttora la rotta più sicura, ma molto più
lunga, e dunque più costosa, che doppia il Capo di Buona Speranza per accedere all’oceano Atlantico e al Mediterraneo. Le ricadute più immediate sono la dilatazione dei tempi necessari per collegare l’Asia all’Europa, e viceversa, e il conseguente forte aumento dei costi di trasporto.
Fig.1 - Le dinamiche dei noli mercantili.
Gli effetti dell’allargamento della tensione nello scacchiere medio-orientale sono illustrati nella figura 1: come si può osservare, il World Container Index, che sintetizza i costi di noleggio per il trasporto marittimo di container di misura standard sulle principali rotte mondiali rilevati dall’agenzia Drewry, nel periodo che va dall’inizio delle ostilità yemenite alla fine di gennaio segna un +195,4%, che sulle rotte Shanghai-Rotterdam, decisiva per le catene di fornitura europee, e Shanghai-Genova, che ci riguarda più da vicino, lievitano ri-
spettivamente a +396,4% e a +373,6%. Si tratta di aumenti straordinari, ma il confronto con quanto accadde ai noli marittimi tra il 2020 e il 2021 rischia di alimentare attese fuorvianti: a differenza di quel periodo, infatti, in questa fase l’economia è in deciso rallentamento e la capacità complessiva di stiva da allora è letteralmente esplosa. Una overcapacity destinata a pesare anche in concomitanza di ulteriori tensioni geopolitiche. Non è dunque un caso che, a metà febbraio, l’indice generale evidenzi già un ripiegamento (-4,5%) che intercetta i cali lungo le
Steel and metals: market dynamics, cycles and trends
rotte dirette in Europa, a differenza dei costi per la tratta Shanghai-New York, che si mantengono invece al rialzo: +145,6%. Cionondimeno, pur considerando lo storno in corso, non si può escludere che tali aumenti possano ostacolare il calo dell’inflazione, orientando le banche centrali a ritardare i tanto attesi tagli ai tassi d’interesse. La complicazione del passaggio dal Mar Rosso introduce peraltro un ulteriore elemento di destabilizzazione che si innesta tra le determinanti dei prezzi delle materie prime agenti in questa complicata fase storica: mentre le tensioni geopolitiche e il peggioramento della logistica navale sospingono al loro aumento, la debolezza del ciclo economico mondiale e gli alti tassi d’interesse reali zavorrano le quotazioni. Una situazione, insomma,
dominata dall’incertezza che genera dinamiche di mercato scarsamente direzionali, la cui volatilità si accentua solo in occasione di recrudescenze belliche e in funzione delle altalenanti aspettative riguardanti le decisioni delle banche centrali. Alla luce di tali condizioni di contesto, e tenuto conto della frenata della crescita mondiale certificata anche dalle più recenti stime del Fondo Monetario Internazionale, nel primo semestre 2024 la domanda di commodity appare destinata a mantenersi debole. Valutiamone dunque le conseguenze sui mercati siderurgici e metallurgici.
Fig.2 - Gli elementi basilari del ciclo integrale dell’acciaio.
La figura 2 illustra gli andamenti dei prezzi medi settimanali in dollari/tonnellata del minerale di ferro (scala di destra) e del carbone metallurgico (scala di sinistra).
Come si può osservare, in apertura del 2024 le quotazioni del minerale segnano il loro top nella prima settimana di gennaio, estendendo a +41,2% la performance dai minimi di maggio dello scorso anno, per poi flettere nelle settimane successive (-10,6%).
I prezzi del carbone metallurgico ne seguono l’orientamento, flettendo dai massimi di novembre (-6,3%) per puntare verso i minimi di ottobre. Nell’immediato futuro non si prefigurano radicali cambiamenti alla situazione corrente dei due mercati.
La dinamica del valore “core” della carica d’altoforno, ovvero limitata ai soli contributi ponderati dei due elementi basilari del ciclo integrale dell’acciaio, ne intercetta la
duplice inclinazione ribassista, esprimendo da inizio 2024 un cedimento (-8,1%) che sintetizza la debolezza della domanda corrente. La ghisa grezza (basic pig iron) si mantiene invece al rialzo da inizio novembre 2023 (+21,3%), muovendosi dunque in un’anomala controtendenza, che è probabile possa correggersi a breve.
In una prospettiva di medio-lungo termine, com’è ormai noto, i mercati del minerale di ferro e del coke risentiranno della progressiva contrazione delle produzioni da altoforno e della contestuale maggior crescita dei processi produttivi meno inquinanti tipici dell’elettrosiderurgia. Senza drastici tagli dell’offerta la minor domanda dei due elementi basilari non potrà dunque che portare a ribassi dei prezzi: la realizzazione di una tale prospettiva, tuttavia, richiederà qualche anno.
Acciaio e metalli: dinamiche, cicli e tendenza di mercato
Fig.3 -I mercati internazionali dei coils.
A supporto dell’analisi delle produzioni a ciclo integrale soccorre la figura 3, comprendente le curve di prezzo in dollari/tonnellata dei coils a caldo per le rese FOB Shanghai, FOB Black Sea e CIF Houston. Se il benchmark europeo segue quello asiatico che funge tradizionalmente da driver, i valori nordamericani appaiono più volatili: nell’ultimo trimestre 2023, più in particolare, si è registrato un rialzo sostenuto dal calo temporaneo dell’offerta acuito da scioperi che hanno generato un prolungamento dei tempi di consegna. La fase corrente vede le
tre curve indebolirsi nell’ambito di ampi corridoi laterali compresi tra i massimi registrati nel mese di marzo 2023 e i minimi fissati nell’ultimo quadrimestre 2022. L’andamento scarsamente direzionale causato da una domanda asfittica e da un’offerta più che sufficiente a farvi fronte, appare destinato a proseguire anche nel primo semestre 2024 malgrado la maggior durata delle spedizioni di semilavorati asiatici dirette verso l’Europa: un aspetto che, per il momento, sfavorisce i fornitori indiani e cinesi a vantaggio di quelli turchi.
Fig.4 -Il mercato nazionale dei prodotti piani.
A livello nazionale gli andamenti dei prezzi rilevati settimanalmente da Siderweb in euro/tonnellata dei principali prodotti piani sono sintetizzati nella figura 4: le quattro curve altamente concordanti si muovono in ascesa a iniziare dal mese di ottobre 2023, accelerando nel mese di gennaio, quando gli analoghi riferimenti internazionali tendono invece a muoversi lateralmente: +24,1% i coils, +21,5% le lamiere nere, +18,8% le lamiere zincate, +9,5%
Steel and metals: market dynamics, cycles and trends
le lamiere da treno. La debole domanda proveniente dai settori degli elettrodomestici e dell’Automotive si avverte peraltro sulle dinamiche correnti, innescando fasi correttive, che infatti già stanno prendendo corpo: -0,6% le lamiere zincate, -1,3% le lamiere da treno a metà febbraio. Nei prossimi mesi si profila dunque la continuazio-
ne delle tendenze moderatamente rialziste nell’ambito dell’ampio corridoio compreso tra i livelli massimi di marzo e i livelli minimi ottobre dello scorso anno.
Fig.5 -Le quotazioni dei rottami ferrosi.
Poiché la carica del forno elettrico è costituita principalmente dal rottame ferroso, il suo andamento costituisce un attendibilissimo termometro dello stato dell’elettrosiderurgia. Si osservi al riguardo la figura 5 dedicata alle evoluzioni in euro/tonnellata del rottame CFR Turkey e della media delle quotazioni di varie tipologie di rottame (frantumato, da demolizioni, torniture e lamierino) rilevate da Siderweb a livello nazionale: le quotazioni internazionali archiviano il rialzo avviatosi a fine luglio nella seconda metà di dicembre 2023 (+23,8%). Alla defi-
nizione del top segue un movimento oscillatorio laterale compreso tra i massimi e minimi di dicembre. La media dei prezzi nazionali si mantiene invece al rialzo dall’ottobre dello scorso anno fino a metà febbraio (+18,4%). Sebbene le tensioni in Medio Oriente abbiano introdotto elementi di incertezza sui mercati internazionali del rottame ferroso, si profila la persistenza dell’evoluzione blandamente rialzista corrente diretta verso i massimi registrati nel mese di marzo 2023.
Fig.6 -Il mercato nazionale dei prodotti lunghi.
Riguardo alle tipiche produzioni a forno elettrico, si consideri la figura 6, che illustra le dinamiche dei prezzi medi settimanali in euro/tonnellata dei principali prodotti lunghi rilevati da Siderweb: si noti come gli ampi ribassi che hanno caratterizzato buona parte del 2023 a carico di tutte le produzioni si siano esauriti nell’ultimo trimestre dello scorso anno, quando ha preso corpo una serie di blandi recuperi, taluni dei quali sono proseguiti anche nel primo scorcio del 2024: +18% il tondo, +21% la vergella da rete, +19,4% la vergella da trafila, +4,7% i
Acciaio e metalli: dinamiche, cicli e tendenza di mercato
laminati mercantili, +4,2% le travi. Tra gennaio e febbraio, peraltro, gli squilibri di mercato generati dall’eccesso di offerta hanno contribuito al progressivo indebolimento dei prezzi di tutti i prodotti lunghi: -2,8% il tondo, -1,3% la vergella da rete, -1,6% la vergella da trafila, -0,8% i laminati mercantili, -2% le travi. Sintomi di una fiacchezza dinamica, che appare destinata a proseguire anche nei prossimi mesi.
Fig.7 - I metalli non ferrosi quotati al London Metal Exchange.
In questo contesto si consideri la figura 7, che rappresenta l’andamento della media delle quotazioni medie settimanali dei prezzi in dollari/tonnellata dei principali metalli non ferrosi quotati al London Metal Exchange (scala di destra) e la contestuale evoluzione del complesso delle loro scorte (stock) detenute presso i magazzini ufficiali dello stesso mercato (scala di sinistra). Come si può osservare, dopo gli eccessi rialzisti e ribassisti del 2022, l’intero 2023 della media dei sei metalli - alluminio, rame, nickel, zinco, piombo e stagno - è stato connotato da un sistematico declino esauritosi a inizio dicembre (-28,7%). Nel medesimo arco temporale, inoltre, l’entità delle giacenze medie è incrementata complessivamente del 70% a conferma di una domanda particolarmente debole. Nel primo scorcio del 2024 si nota invece un leggero calo delle giacenze (-5%), che non sembra peraltro sostenere, per il momento, alcun
significativo recupero del mercato.
Le prospettive di più ampio respiro dei metalli non ferrosi sono legate all’evoluzione congiunturale: mentre nel breve termine si prefigura la persistenza delle dinamiche stazionarie dei prezzi, il miglioramento delle condizioni finanziarie utili alla formazione di scorte potrebbe favorire l’avvio di tendenze rialziste più decise.
Fig.8 - I prezzi delle principali ferroleghe.
Per l’analisi dei tipici elementi di colata inox si consideri la figura 8: come si può osservare, i prezzi del Nickel si mantengono al ribasso dal mese di dicembre 2022 a metà febbraio 2024 (-48,1%), portandosi al di sotto dei minimi del 2021. Dal mese di luglio 2023, inoltre, gli stock di nickel sono in sistematica risalita: fenomeno che zavorra i prezzi nel quadro di una depressione destinata a proseguire fatti salvi i rimbalzi motivati da acquisti occasionali. Le quotazioni del Ferro-Cromo si sono fortemente ridimensionate dopo gli eccessi rialzisti concomitanti allo scoppio del conflitto russo-ucraino: -60,5% dai massimi
di giugno 2022 ai minimi di dicembre 2023. In quest’ultimo periodo si segnala una modesta ripresa (+3,9%), che segna l’esaurimento del trend ribassista e l’avvio di una fase stazionaria. Dopo il tracollo (-59,6%) seguito ai picchi anomali del 2023 per i timori di una carenza di offerta, i prezzi del Ferro-Molibdeno si risollevano in novembre (+19%) per poi consolidarsi: una prospettiva destinata a consolidarsi in questo primo semestre.
- L’evoluzione dei prezzi delle lamiere inox.
Le dinamiche dei prezzi degli elementi basilari e del rottame ferroso spiegano in larga misura gli andamenti delle quotazioni delle lamiere inox riferite alle tipologie di acciaio AISI (American Iron & Steel Institute) specificate nella figura 9. La causa principale delle ampie flessioni dei prezzi risiede nella lentezza con la quale si sono esaurite le scorte cumulatesi durante il periodo più euforico, quando le imprese trasformatrici ritenevano che la domanda sarebbe proseguita malgrado i prezzi record. L’eventuale ripresa del mercato dei piani inox, che attualmente vede i prezzi delle diverse categorie AISI muoversi nell’ambito di stretti corridoi laterali compresi tra i minimi di luglio e i massimi di ottobre 2023, anche in questo caso è legata al cambiamento delle politiche monetarie in senso espansivo. Fino a quando non si manifesterà una sensibile riduzione dei tassi d’interesse,
le tendenze dei prezzi si manterranno in deriva laterale sostenute da acquisti di natura tattica motivati dal fabbisogno stringente e dai rallentamenti produttivi. In definitiva, si profila un 2024 preda di crescenti tensioni geopolitiche, commerciali e finanziarie, che accompagneranno la complicata riarticolazione delle catene globali del valore e di fornitura, deprimendo la produzione industriale e la domanda di materie prime. Continueremo dunque a monitorare la situazione dei mercati metallurgici e siderurgici, valutandone l’evoluzione trimestre dopo trimestre.
La mia rubrica proseguirà anche nel 2024, mantenendo la medesima cadenza temporale - febbraio, maggio, luglio-agosto, dicembre - per aggiornare di volta in volta l’attualità e le immediate prospettive dei mercati metallurgici e siderurgici in continuità con l’ultimo intervento proposto lo scorso anno (Dicembre 2023; pagg. 69-76). Per le domande e i sempre graditi confronti: achille.fornasini@unibs.it
CONVEGNI
MCHTSE-4 & TPMS-5 - 4th Mediterranean Conference on Heat Treatment and Surface Engineering + 5th International Conference on Thermal Process Modeling and Simulation – Lecce, 17-19 aprile 2024
IFM 2024 - INTERNATIONAL FORGEMASTERS MEETING – Milano, 27-30 maggio 2024
ESOMAT 2024 - 12th European Symposium on Martensitic Transformations – Lecco, 26-30 agosto 2024
40° CONVEGNO NAZIONALE AIM – Napoli, 11-13 settembre 2024
ECIC 2024 - 9TH EUROPEAN COKE AND IRONMAKING CONGRESS – Peschiera del Garda, 16-18 ottobre 2024
International Meeting on CIRCULAR METALLURGY - Raw Materials, By-products & Recycling – Bergamo (Italy), 28-29 November 2024
CORSI E GIORNATE DI STUDIO
Corso modulare CORROSIONE – 14-15-29 febbraio, 1-14-15 marzo 2024
Corso FORGIATORI – Brescia, 6-7 marzo, Mairano BS c/o Franchini Acciai, 13 marzo, Mantova c/o Belleli Energy CPE, 14 marzo 2024
Webinar NORMATIVA NEL CAMPO DEI TRATTAMENTI TERMICI - 15 marzo 2024
Giornata di Studio EVOLUZIONE DEGLI ACCIAI NELLA STORIA DELL’AUTOMOBILE – Ferrara, 22 marzo 2024
Corso IGIENE DELLE LEGHE DA FONDERIA – Rovigo c/o TMB, 17-18 aprile 2024
Corso modulare TRATTAMENTI TERMICI – Milano, 8-9-15-16 maggio, Avigliana TO c/o Motivexlab, 22-23 maggio, Campogalliano MO c/o Tec Eurolab, 5-6 giugno 2024
Corso itinerante METALLURGIA FUORI FORNO – maggio-giugno
Giornata di Studio SBM – Smart Bean Manufacturing: NUOVO LAMINATOIO PER TRAVI – San Zeno sul Naviglio c/o Duferco, 7 giugno 2024
Corso PROVE MECCANICHE - Miano, 12-13-19-20 giugno 2024
Giornata di Studio FUTURO SOSTENIBILE E COMPETITIVO DELLA METALLURGIA DELLE POLVERI – 13 giugno
Corso MICROSCOPIA ELETTRONICA IN SCANSIONE - Milano, 18-19 giugno 2024
Corso RIVESTIMENTI – II MODULO: RIVESTIMENTI SPESSI – Milano, 19-20 giugno
METALLURGY SUMMER SCHOOL ON ADDITIVE METALLURGY – Bertinoro, giugno-luglio 2024
Corso METALLURGIA PER NON METALLURGISTI – Milano, 15-16-22-23-29-30 ottobre 2024
Giornata di Studio MICROSCOPIA ELETTRONICA APPLICATA ALLA FAILURE ANALYSIS – Milano, 6 novembre
Giornata di Studio RAGGI X – Milano, 3 dicembre 2024
FaReTra (Fair Remote Training) - FORMAZIONE E AGGIORNAMENTO A DISTANZA
Modalità Asincrona (registrazioni)
Giornata di Studio STATO DI SERVIZIO DEGLI IMPIANTI, CON PARTICOLARE ATTENZIONE ALLA METALLURGIA E AGLI ESAMI UTILIZZATI
Giornata di Studio LA NORMATIVA: GLI ACCIAI E I TRATTAMENTI TERMICI NELL'INDUSTRIA AUTOMOTIVE
Corso PROVE NON DISTRUTTIVE
Giornata di Studio TRATTAMENTI SUPERFICIALI DELL’ALLUMINIO A SCOPO DECORATIVO E PROTETTIVO
Corso Modulare METALLOGRAFIA – I MODULO, II MODULO “METALLI NON FERROSI”
Corso modulare FONDERIA PER NON FONDITORI
Corso DIFETTOLOGIA NEI GETTI PRESSOCOLATI: METALLIZZAZIONI
Corso ADDITIVE METALLURGY
Corso METALLURGIA PER NON METALLURGISTI
Giornata di Studio PRESSOCOLATA DELLE LEGHE DI ZINCO
Giornata di Studio LA SFIDA DELLA NEUTRALITÀ CARBONICA
Corso modulare TRATTAMENTI TERMICI
Corso modulare I REFRATTARI SIDERURGICI E LE LORO APPLICAZIONI
Corso GLI ACCIAI INOSSIDABILI 11ª edizione
Corso FAILURE ANALYSIS 11a edizione
L’elenco completo delle iniziative è disponibile sul sito: www.aimnet.it
(*) In caso non sia possibile svolgere la manifestazione in presenza, la stessa verrà erogata a distanza in modalità webinar
www.aimnet.it
MATERIALI PER L’ENERGIA (ME) (riunione del 18 gennaio 2024)
Consuntivo di attività svolte
• GdS “Nucleare: prospettive e criticità”: la manifestazione si è svolta il 12 ottobre presso la prestigiosa Aula Magna del Rettorato del Politecnico di Milano. L’iniziativa ha avuto un notevole successo ed ha riscosso molto interesse, sia per quanto riguarda gli interventi più istituzionali che per quelli tecnici (ENEA, Ansaldo Energia ecc.). Negli interventi è stata rimarcata la possibilità di far rinascere il nucleare in Italia partendo dalle industrie manufatturiere, i costruttori, che posseggono ancora il know how su questo tipo di impianti. I presenti concordano sul fatto che è necessario ricostruire il sottofondo culturale indispensabile alla realizzazione e all’esercizio di impianti nucleari anche di nuova generazione, per i quali è essenziale lavorare in sicurezza: per il nucleare esistono numerose norme (es. ASME e RCC-M) da cui non è possibile prescindere. Il presidente Gavelli sottolinea inoltre la difficoltà nel trovare le sedi per gli impianti nuovi, così come va ancora definito tutto il processo di decommissioning di quanto esistente. Dai questionari compilati da circa la metà dei partecipanti si ricava un giudizio complessivamente positivo con punteggi di buono/ottimo; numerosi gli argomenti per cui è stato chiesto un approfondimento in eventi successivi.
Manifestazioni in corso di organizzazione
• La GdS “Stesura specifiche dei materiali” (coordinatore Pinciroli), confermata per il 25 gennaio a Milano, ha già un numero considerevole di iscritti: c’è soddisfazione per la forte partecipazione dal settore industriale, a conferma che l’argomento è di interesse. Il programma prevede interventi per una visione a 360° della tematica: si parte dalla normativa vigente fino ad arrivare alla certificazione, passando dalla presentazione di casistiche ed esperienze reali e pratiche.
Iniziative future
• Nella scorsa riunione del CT era stata proposta una giornata dal possibile titolo: “Materiali e tecnologie per impianti a ciclo combinato di nuova generazione”. Si discute sull’impostazione da dare alla giornata: diversi argomenti potrebbero essere sviluppati nel corso di un evento di questo tipo, che dovrebbe comunque focalizzarsi sui requisiti richiesti ai materiali per i cicli combinati e allo stesso tempo presentare l’evoluzione che stanno avendo questi impianti. Le grandi aziende da coinvolgere potranno mostrare gli aspetti ingegneristici legati a questi impianti, estrapolando la discussione da siti e casi reali in modo da non incorrere in problemi di riservatezza.
(riunione del 20 dicembre 2023)
Notizie dal Comitato
• Il presidente Morgano ricapitola l’andamento della situazione delle manifestazioni del comitato nel 2023, che si sono svolte in linea con le previsioni eccezion fatta per la giornata di Pisa. Sottolinea ancora una volta l’importanza della partecipazione in presenza alle riunioni del CT: l’incontro fisico migliora il confronto interpersonale ed allarga la rete di conoscenze. Occorre anche studiare strategie per incrementare la presenza del pubblico alle giornate di studio e in genere alle manifestazioni organizzate dal comitato. È fondamentale coinvolgere il personale delle grosse aziende facendo conoscere le opportunità e i vantaggi derivanti dalla frequenza ai nostri eventi.
• Ospite della riunione odierna è il Prof. Mattia Merlin, dell’Università di Ferrara, che si occupa di metallografia e trattamenti termici. Merlin si presenta al CT che approva il suo ingresso.
Consuntivo di attività svolte
• La GdS “Stato dell’arte ed evoluzione dei processi termici e meccanici“, in programma a Pisa a novembre 2023, è stata rinviata al 2024. Nei prossimi incontri si decideranno data e location.
• La GdS “Diffrattometria a raggi X applicata ai trattamenti termochimici ed alla pallinatura controllata” – coordinatore Morgano – si è svolta il 17 novembre 2023 ad Agrate Conturbia. Ottima organizzazione, location di eccellenza, ampia partecipazione (una cinquantina di persone) e temi molto interessanti ed accattivanti. La visita ai laboratori ed i test eseguiti in presenza sono stati molto apprezzati.
• La GdS “Il Mondo Industrial - aspetti metallurgici e metodologie di controllo” si è svolta presso CNH Industrial Village a Torino il 6 dicembre 2023 – coordinatrice Ecclesia. La manifestazione ha suscitato l’interesse dei partecipanti, con una proficua discussione finale. L’interesse si è confermato con la cospicua richiesta di contatti anche successivamente alla giornata di studio. Location, logistica e catering hanno riscontrato feedback positivi.
Manifestazioni in corso di organizzazione
• Il tradizionale Corso Modulare Trattamenti Termici è giunto alla sua XIX edizione. Il comitato di coordinamento (Vicario, Petta, Cusolito, Gelfi e Firrao) ha definito tutti i dettagli. Vicario presenta il programma e le date, definendo argomenti e location. Il corso è stato diviso in sei moduli, con molte innovazioni rispetto al passato. Cinque delle sette giornate saranno gestite in presenza o in streaming, mentre le due che comportano una visita ai laboratori Motivexlab (Avigliana – TO) e Tec Eurolab (Campogalliano – MO) saranno esclusivamente in presenza. Le date sono distribuite tra 8 maggio e il 6 giugno 2024, e la locandina sarà lanciata in gennaio.
• Il seminario sulla normativa, alla sua terza edizione, si svolgerà in una mezza giornata a fine febbraio in streaming per fare il punto sulla situazione e la applicazione delle norme.
Iniziative future
• Merlin comunica che è in programma una manifestazione presso l’Università di Ferrara sull’evoluzione degli acciai nel mondo automotive, con particolare focus su carrozzeria, tecniche di giunzione, prevenzione della corrosione, migrazione verso l’elettrico. Merlin propone al CT TTM di partecipare: sarebbe la terza GdS a Ferrara organizzata con AIM. Si discute del possibile coinvolgimento di altri CT insieme al CT Storia della Metallurgia, principale promotore dell’iniziativa. Possibile periodo: fine marzo, inizio aprile 2024.
• La GdS per stampatori e forgiatori, tradizionalmente organizzata con Confindustria Canavese, sarà discussa nei prossimi incontri. Si prevede di pianificarla per la prima metà del 2024.
(riunione 17 gennaio 2024)
Consuntivo di attività svolte
• Il Presidente Loconsolo comunica che la GdS “Riparazioni tramite saldatura”, che si è svolta a Milano il 22 novembre 2023, è andata bene, vista anche la buona partecipazione. Il coordinatore Rossetti conferma quanto detto e sottolinea le numerose domande pervenute durante ed alla fine della GdS.
Iniziative future
• L’organizzazione della GdS su “Sostenibilità ambientale nel campo delle costruzioni civili” è a buon punto. Sono stati individuati quasi tutti i relatori e a breve dovrebbero arrivare le ultime risposte. Questa giornata potrebbe essere programmata entro l’autunno 2024.
• GdS sul mercato dei metalli: i coordinatori Debernardi, Oreglia e Varalda studieranno una possibile linea di programma. Entro la primavera dovrebbero riuscire a raccogliere una documentazione sufficiente a fare da ossatura per una GdS.
• Il presidente Loconsolo informa che è stata diffusa una bozza della normativa europea sui metalli a contatto con l’acqua potabile. Uno dei temi più critici è quello del Pb negli ottoni: la soglia ammessa sarà di 5 g/l, un valore molto basso che tiene conto che il Pb è un elemento bio-accumulabile e quindi potrebbe creare problemi alla salute sul lungo periodo. I test di cessione dimostrano che con le quantità di Pb aggiunte alle leghe attualmente impiegate questo limite non può essere rispettato. Per l’importanza e l’impatto che questa normativa avrà sul mercato dei metalli, specialmente in alcuni settori, il Presidente ritiene che sarà possibile ed auspicabile organizzare una GdS entro l’autunno 2024.
• Si discute della possibilità di organizzare una GdS legata alla saldatura delle leghe speciali. Se ne discuterà nelle prossime riunioni.
(riunione del 18 dicembre 2023)
Iniziative future
• GdS “Refrattari per la fonderia”: la giornata si svolgerà in modalità telematica. Il contributo dei vari fornitori sarà fondamentale: il presidente Caironi chiede a loro la disponibilità a produrre delle memorie sui vari materiali refrattari disponibili, sulla loro messa in opera e sulla conduzione dei forni. Il presidente invita inoltre i membri della commissione a predisporre un elenco degli argomenti che vorrebbero trattare ed un possibile programma, in seguito al quale i membri del comitato potranno contattare i vari fornitori di materiali refrattari per invitarli a partecipare.
• Corso “Fonderia per non fonditori” – moduli successivi al primo: sulla base dell’iniziativa di Zanardi Fonderie, che ha dato vita alla Zanardy Academy in collaborazione con l’Università di Padova, il Presidente e i membri del CT Fonderia auspicano che anche in AIM si possa inserire, nel corso “Fonderia per non fonditori”, uno specifico modulo sulle fonderie di ghisa, e in particolare una panoramica sulle tipologie di ghisa e le loro diverse applicazioni. Per la prossima riunione ciascuno potrà predisporre un elenco degli argomenti da trattare ed un possibile programma.
• Corso sui materiali refrattari: il presidente condivide la proposta del comitato di organizzare in via prioritaria la giornata studio sui materiali refrattari usati in fonderia e in base al successo della esperienza, valutare la necessità di sviluppare un corso esteso.
• Pillole di fonderia su “Conduzione dei forni ad induzione”: anche in questo caso il Presidente chiede ai membri di predisporre un elenco di argomenti da trattare ed un possibile programma, in base al quale si possano poi contattare i vari fornitori di forni per chiedere la disponibilità a partecipare al corso, a presentare memorie e predisporre anche filmati sull’utilizzo dei forni.
• Pillole di fonderia su “Il processo di scorifica delle leghe ferrose”: Il Presidente segnala che il Professor Carlo Mapelli si è reso disponibile a realizzare un corso dedicato alle fonderie sulla base dell’esperienza maturata nel corso sulla scorifica in siderurgia, e suggerisce che il corso comprenda, tra i vari argomenti, una classificazione delle scorie basata sulla loro composizione chimica e le tecniche di scorifica stesse.
• XXXVII Congresso di fonderia – sessioni tecniche: la prossima edizione del Congresso si terrà sia in presenza che online, ma la sessione plenaria sarà solo in presenza, per ripristinare la natura conviviale dell’evento. Assofond si occuperà dell’individuazione della sede. Le altre giornate saranno invece tenute in modalità digitale in modo da assicurare il maggior numero di partecipanti.
(riunione del 19 gennaio 2024)
Manifestazioni in corso di organizzazione
• Corso base di Corrosione: il corso, coordinato da Balbo e Bellezze, si svolgerà su quattro moduli dal 24 gennaio al 15 marzo 2024, per un totale di otto giornate in presenza. Il programma elaborato appare buono, sebbene al momento gli iscritti non siano molti. Il presidente Bolzoni passa in rassegna il programma e Bassani aggiorna sullo stato delle iscrizioni ai vari moduli e fornisce le informazioni logistiche dell’organizzazione.
Manifestazioni future
• GdS sull’interazione dei vari materiali con l’idrogeno: la manifestazione su questo tema attuale, sulla traccia di quella organizzata nel 2022, si potrebbe svolgere a fine 2024 o inizio 2025. I coordinatori saranno Bolzoni, Gavelli e Cabrini, la quale ipotizza che l’iniziativa si possa svolgere a livello internazionale. Si discuteranno i dettagli nelle prossime riunioni.
Norme pubblicate e progetti in inchiesta (aggiornamento 31 gennaio 2024)
Norme UNSIDER pubblicate da UNI nel mese di gennaio 2024
UNI EN 10305-3:2024
Tubi di acciaio per impieghi di precisione - Condizioni tecniche di fornitura - Parte 3: Tubi saldati calibrati a freddo
UNI EN ISO 23062:2024
Sicurezza del macchinario - Requisiti di sicurezza le macchine per fonderia e per la preparazione delle forme e delle anime e per le attrezzature ad esse associate
UNI EN ISO 13520:2024
Determinazione del contenuto di ferrite nei getti prodotti in acciaio inossidabile austenitico
UNI EN 1092-2:2024
Flange e loro giunzioni - Flange circolari per tubazioni, valvole, raccordi e accessori designate mediante PN - Parte 2: Flange di ghisa
UNI CEN/TS 17991:2024
Verifica statistica dei fattori parziali per costruzioni secondo l'Eurocodice EN 1993-1-1 Allegato E
UNI EN 10088-3:2024
Acciai inossidabili - Parte 3: Condizioni tecniche di fornitura dei semilavorati, barre, vergella, filo, profilati e prodotti trasformati a freddo di acciaio resistente alla corrosione per impieghi generali
UNI EN ISO 8062-3:2024
Specifiche geometriche dei prodotti (GPS) - Tolleranze dimensionali e ge-
ometriche dei pezzi ottenuti da fusione - Parte 3: Tolleranze dimensionali e geometriche generali e sovrametalli di lavorazione dei getti utilizzando tolleranze + o - per indicate dimensioni
UNI EN 10359:2024
Profili saldati al laser (Tailored Blanks)Condizioni tecniche di fornitura
UNI EN 10088-1:2024
Acciai inossidabili - Parte 1: Lista degli acciai inossidabili
UNI EN 10278:2024
Dimensioni e tolleranze dei prodotti finiti a freddo di acciaio inossidabile ed altri acciai speciali
UNI EN 10264-3:2024
Filo di acciaio e relativi prodotti - Filo di acciaio per funi - Parte 3: Fili tondi e sagomati di acciaio non legato per applicazioni speciali
Norme UNSIDER ritirate con sostituzione da UNI nel mese di gennaio 2024
UNI EN ISO 13520:2019
Determinazione del contenuto di ferrite nei getti prodotti in acciaio inossidabile austenitico
UNI EN 710:2010
Sicurezza del macchinario - Requisiti di sicurezza per gli impianti e le macchine per fonderia, per gli impianti per la preparazione delle forme e delle anime e per gli impianti ad essi associati
UNI EN 1092-2:1999
Flange e loro giunzioni - Flange circolari per tubazioni, valvole, raccordi e accessori designate mediante PN - Flange di ghisa
UNI EN 10305-5:2016
Tubi di acciaio per impieghi di precisione
- Condizioni tecniche di fornitura - Parte 5: Tubi saldati calibrati a freddo di sezione quadrata e rettangolare
UNI EN 10088-1:2014
Acciai inossidabili - Parte 1: Lista degli acciai inossidabili
UNI EN 10305-3:2016
Tubi di acciaio per impieghi di precisione
- Condizioni tecniche di fornitura - Parte 3: Tubi saldati calibrati a freddo
UNI EN 10264-3:2012
Filo di acciaio e relativi prodotti - Filo di acciaio per funi - Parte 3: Fili tondi e sagomati di acciaio non legato per applicazioni speciali
UNI EN ISO 8062-3:2009
Specifiche geometriche dei prodotti (GPS) - Tolleranze dimensionali e geometriche dei pezzi ottenuti da fusione - Parte 3: Tolleranze dimensionali e geometriche generali e sovrametalli di lavorazione dei getti
UNI EN 10359:2016
Profili saldati al laser (Tailored Blanks)Condizioni tecniche di fornitura
UNI EN 10088-3:2014
Acciai inossidabili - Parte 3: Condizioni tecniche di fornitura dei semilavorati, barre, vergella, filo, profilati e prodotti trasformati a freddo di acciaio resistente alla corrosione per impieghi generali
UNI EN 10278:2002
Dimensioni e tolleranze dei prodotti di acciaio finiti a freddo
Norme UNSIDER pubblicate da CEN e ISO nel mese di gennaio 2024
EN ISO 19901-3:2024
Oil and gas industries including lower carbon energy - Specific requirements for offshore structures - Part 3: Topsides structure (ISO 19901-3:2024)
ISO 19901-3:2024
Oil and gas industries including lower carbon energy — Specific requirements for offshore structures — Part 3: Topsides structure
ISO 16904-2:2024
Installation and equipment for liquefied natural gas — Design and testing of marine transfer systems — Part 2: Design and testing of transfer hoses
ISO/TR 15263:2024
Measurement uncertainties in mechanical tests on metallic materials — The evaluation of uncertainties in tensile testing
ISO 10544:2024
Cold-reduced steel wire for the reinforcement of concrete and the manufacture of welded fabric
ISO 6338-1:2024
Calculations of greenhouse gas (GHG) emissions throughout the liquefied natural gas (LNG) chain — Part 1: General
Progetti UNSIDER messi allo studio dal CEN (Stage 10.99) – febbraio 2024
prEN 10219-1 rev
Cold formed welded steel structural hollow sections - Part 1: Technical delivery conditions
prEN 10210-1 rev
Hot finished steel structural hollow sections - Part 1: Technical delivery conditions
EN ISO 683-3:2022/prA1
Heat-treatable steels, alloy steels and free-cutting steels ” Part 3: Case-hardening steels ” Amendment 1
Progetti UNSIDER in inchiesta prEN e ISO/DIS – febbraio 2024
prEN – progetti di norma europei
prEN ISO 19901-5
Petroleum and natural gas industries
- Specific requirements for offshore structures - Part 3: Topsides structure (ISO/DIS 19901-3:2022)
ISO/DIS – progetti di norma internazionali
ISO/DIS 22504
Oil and gas industries including lower carbon energy — Pipeline transportation systems — Onshore and offshore pipelines pig traps design requirements
ISO/DIS 20182
Refractory test-piece preparation — Gunning refractory panels by the pneumatic-nozzle mixing type guns
ISO/DIS 16468
Investment castings (steel, nickel alloys and cobalt alloys) — General technical requirements
ISO/DIS 10855-3
Offshore containers and associated lifting sets — Part 3: Periodic inspection, examination and testing
ISO/DIS 10427-1
Oil and gas industries including lower carbon energy — Equipment for well cementing — Part 1: Casing bow-spring centralizers
ISO/DIS 8353
Steel sheet, zinc-aluminium-magnesium alloy-coated by the continuous hot-dip process, of commercial, drawing and structural qualities
ISO/DIS 4991
Steel castings for pressure purposes
Progetti UNSIDER al voto FprEN e ISO/FDIS – febbraio 2024
FprEN – progetti di norma europei
FprEN ISO 10113
Metallic materials - Sheet and stripDetermination of plastic strain ratio (ISO/ FDIS 10113:2019)
ISO/FDIS – progetti di norma internazionali
ISO/FDIS 24476
Steel — Determination of oxygen — Infrared absorption method after fusion under inert gas (Routine method)
ISO/FDIS 9042
Steels — Point counting method for statistically estimating the volume fraction of a constituent with a point grid
ISO/PRF 8371
(il progetto ha superato due inchieste DIS ed è attualmente in fase di Proofing da parte della segreteria- Pubblicazione come ISO 8371 entro il 2024-03-01)
Iron ores for blast furnace feedstocks — Determination of the decrepitation index
AIM è lieta di annunciare la 40a edizione del proprio Convegno Nazionale che si terrà dall’11 al 13 settembre 2024 a Napoli.
Il Convegno Nazionale AIM è un appuntamento irrinunciabile per le Aziende ed i ricercatori che, a vario titolo, sono coinvolti nell’utilizzo e lo studio dei metalli. L’obiettivo dell’iniziativa è fare il punto su materiali, prodotti, processi e tecnologie nei vari settori produttivi e proporre attività innovative. A completamento delle sessioni tecniche, sarà organizzato uno spazio espositivo in cui le aziende dei diversi settori rappresentati nel Convegno potranno far conoscere i loro prodotti e le ultime novità.
La bellissima città di Napoli sarà la sede ideale per ospitare il Convegno, che non solo è un’occasione unica di confronto e di aggiornamento professionale, ma anche un’imperdibile opportunità di incontro, di scambio di idee e di esperienze tra vecchi e nuovi amici.
Organizzato da
Sponsorizzato da PRESENTAZIONE DI MEMORIE
Gli interessati a presentare memorie scientifiche (sia per le sessioni orali che per la sessione poster) dovranno inviare entro le deadline indicate sul sito dell’evento, il titolo della memoria, i nomi degli autori e la loro affiliazione ed un sommario di circa 300 parole. Ci sono due modi per sottoporre le proposte di memorie: - compilando il form online presente sul sito dell’evento: www.aimnet.it/nazionaleaim - inviando titolo, autori con affiliazioni, recapiti del relatore e sommario) a: info@aimnet.it
Una selezione degli atti del Convegno verrà pubblicata su La Metallurgia Italiana - International Journal of the Italian Association for Metallurgy. Gli interessati a sottoporre il proprio lavoro per l’eventuale pubblicazione su La Metallurgia Italiana sono invitati a: - segnalarlo in fase di invio della proposta di memoria (se inviata online, usare il campo note) - rispettare le deadline e le istruzioni per la preparazione della memoria, che verranno inviate con la notifica d’accettazione
Spazio aziende e sponsorizzazione
È previsto uno spazio per l’esposizione di apparecchiature, per la presentazione dei servizi e per la distribuzione di materiale promozionale. Le numerose proposte ideate per le aziende sono disponibili online sul sito dell’evento. Per maggiori informazioni e adesioni contattare la Segreteria organizzativa.
SEGRETERIA
ORGANIZZATIVA
Via Filippo Turati 8
20121 Milano
t. +39 0276397770
t. +39 0276021132
info@aimnet.it www.aimnet.it/nazionaleaim