Italiana
International Journal of the Italian Association for Metallurgy

n.06 giugno 2023
Organo ufficiale dell’Associazione Italiana di Metallurgia.
Rivista fondata nel 1909
La Metallurgia Italiana
International Journal of the Italian Association for Metallurgy
Organo ufficiale dell’Associazione Italiana di Metallurgia. HouseorganofAIMItalianAssociationforMetallurgy. Rivista fondata nel 1909
Direttore responsabile/Chiefeditor: Mario Cusolito
Direttore vicario/Deputydirector: Gianangelo Camona
Comitato scientifico/Editorialpanel:
Marco Actis Grande, Silvia Barella, Paola Bassani, Christian Bernhard, Massimiliano Bestetti, Wolfgang Bleck, Franco Bonollo, Irene Calliari, Mariano Enrique Castrodeza, Emanuela Cerri, Vlatislav Deev, Andrea Di Schino, Donato Firrao, Bernd Kleimt, Carlo Mapelli, Denis Jean Mithieux, Roberto Montanari, Marco Ormellese, Mariapia Pedeferri, Massimo Pellizzari, Barbara Previtali, Evgeny S. Prusov, Dario Ripamonti, Dieter Senk
Segreteria di redazione/Editorialsecretary: Marta Verderi
Comitato di redazione/Editorialcommittee: Federica Bassani, Gianangelo Camona, Mario Cusolito, Carlo Mapelli, Federico Mazzolari, Marta Verderi, Silvano Panza
Direzione e redazione/Editorialandexecutiveoffice: AIM - Via F. Turati 8 - 20121 Milano tel. 02 76 02 11 32 - fax 02 76 02 05 51 met@aimnet.it - www.aimnet.it
Reg. Trib. Milano n. 499 del 18/9/1948. Sped. in abb. Post. - D.L.353/2003 (conv. L. 27/02/2004 n. 46) art. 1, comma 1, DCB UD
Immagine in copertina: Shutterstock
Gestione editoriale e pubblicità Publisher and marketing office: siderweb spa sb Via Don Milani, 5 - 25020 Flero (BS) tel. 030 25 400 06 - fax 030 25 400 41 commerciale@siderweb.com - www.siderweb.com
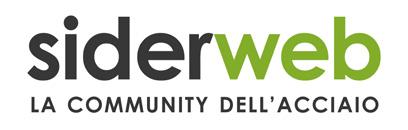
La riproduzione degli articoli e delle illustrazioni è permessa solo citando la fonte e previa autorizzazione della Direzione della rivista. Reproduction in whole or in part of articles and images is permitted only upon receipt of required permission and provided that the source is cited.
siderweb spa sb è iscritta al Roc con il num. 26116
i ce
Editoriale/Editorial
AcuradiGiovanniCaironi .pag.04
Memoriescientifiche/Scientificpapers Fonderia/Foundry
HeattreatmentoftheENAC-42100alloywithinindustrialfurnaces:theeffectof treatmentparametersonmechanicalproperties
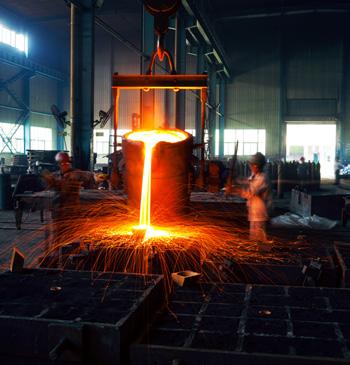
M.Merlin,E.Baroni,A.Fortini,C.Soffritti,F.Feggi......................................................................................pag.08
TrattamentotermicodellalegaENAC-42100all’internodiforniindustriali:effetto deiparametriditrattamentosulleproprietàmeccaniche
M.Merlin,E.Baroni,A.Fortini,C.Soffritti,F.Feggi......................................................................................pag.16
Attualitàindustriale/Industrynews
L’impiegodisoftwarededicatoall’analisieallaconvalidadeirequisiti prestazionalidelgettoinfunzionedeidifettidicolata
acuradi:X.Yang,R.S.Rawal,F.Biglietti...........................................................................................................................pag.25
Vacuumcap(VCAP)technologyforenhancedmaterialpropertiesinadvancedair castingapplications editedby:I.Vicario,M.Cagliero..........................................................................................................................................pag.37
Anewapproachonhydrogenpermeationforenamellinggradesteels editedby:C.M.Belardini,S.Corsinovi,R.Valentini,M.DeSanctis,B.D.Monelli,M.Leveaux......................pag.45
Migliorarel’efficienzaproduttivadiuncomponentehousingmotoriduttoredialta gamma acuradi:F.Lago,G.Scarpa..................................................................................................................................................pag.57
NuovemanichetroncoconicheCHEMEXperlariduzionedelvolumedi alimentazione acuradi:M.Pesci,L.Colombo...........................................................................................................................................pag.64
LeaziendediAIM/AIM'scompanies
IlcasoAsonext-Lasicurezzacomelevastrategicadisviluppo P.Artioli,L.Lancini...............................................................................................................................................................pag.74
Scenari
Il punto di vista di Assofond tramite le parole del suo Presidente Fabio Zanardi .................................................................................................................................................................................................. pag.77
Atti e notizie / AIM news
Piccola storia dello sviluppo tecnologico
E. Mosca......................................................................................................................................... pag.81
Eventi AIM / AIM events ...................................................................................................... pag.93
Comitati tecnici / Study groups pag.95
Normativa / Standards ....................... pag.97
"Thefoundrysectorhas playedandcontinuesto playanimportantroleinthe Italianproductionsystem bysupplyingcontracting companies with semifinished products that are increasinglyclosetotheir expectations in terms ofquantity,qualityand response time. "
Prof. Giovanni Caironi F.I.A.S. S.r.l. Presidente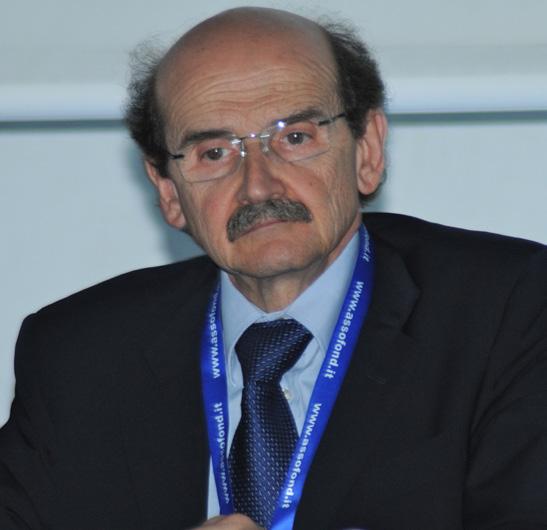
Parlare di Fonderia oggi potrebbe sembrare di fare riferimento a una attività obsoleta “vecchia”, ma se guardiamo alla produzione mondiale di getti di metalli ferrosi e non ferrosi vediamo che la produzione riferita al 2020 era di 105,56 milioni di tonnellate di getti suddivise in Ghisa 73,9 mln di t., Acciaio 10,3 mln di t., Leghe Non Ferrose 19,3 mln di t. con un calo rispetto al 2019 di circa il 3,8% associato alla epidemia del Covid-19.
Questo settore rappresenta ancora un’importante componente del mercato produttivo e di opportunità di lavoro per milioni di operatori a tutti i livelli.
L’Italia nel 2020 era posizionata al dodicesimo posto, con 1,55 mln di tonnellate nella classifica dei principali produttori di fusioni nel mondo, dove la Cina era al primo posto, con una produzione globale di circa 52 mln di t., che rappresenta circa il 49% del totale della pro-
Talking about Foundry today might seem to refer to an "old" obsolete activity, but if we look at the world production of ferrous and non-ferrous metal castings we see that the production referred to 2020 was 105.56 million tons of castings divided into Cast Iron 73.9 mln t., Steel 10.3 mln t., Non-Ferrous Alloys 19.3 mln t. with a decrease compared to 2019 of about 3.8% linked with the Covid-19 epidemic.
This sector still represents an important component of the production market and job opportunities for millions of operators at all levels.
Italy was ranked 12th in 2020, with 1.55 mln tonnes, in the ranking of the world's main castings producers, where China was in first place, with a global production of about 52 mln tonnes, representing about 49% of total production.
““Il settore della Fonderia ha svolto e continua a svolgere un ruolo importante nel sistema produttivo italiano fornendo alle imprese committenti semilavorati sempre più vicini alle loro aspettative in termini di quantità, di qualità e tempi di risposta alle loro esigenze.”del Centro di Studi AIM-Assofond per la Fonderia
duzione.
In Italia nel 2020 erano attive circa 1000 fonderie di metalli ferrosi e non ferrosi. Il comparto era costituito principalmente da piccole imprese con meno di 50 addetti che occupavano circa 24 mila addetti con una produzione di circa 1,9 mln di t. ed un fatturato di circa 7,4 milioni di euro; il comparto era posizionato al terzo posto in Europa, dietro Germania e Turchia. Nel 2021 il comparto delle fonderie di metalli non Ferrosi si è posizionato al primo posto in Europa per la produzione di questa famiglia di fusioni (Alluminio, Magnesio).
L’industria della fonderia permette una grande versatilità di progettazione nel realizzare componenti che trovano applicazione nell’industria automobilistica, meccanica varia, edilizia, aerospaziale, produzione dell’energia elettrica, nel design, nella nautica, nell’architettura, nell’arte e in molti altri settori realizzando particolari unici o in grande serie caratterizzati da pesi che possono variare da pochi grammi (Microfusi) a oltre 100 tonnellate.
Questo settore rappresenta ancora un’importante componente del mercato produttivo e di opportunità di lavoro per milioni di operatori a tutti i livelli.
Il settore della Fonderia ha svolto e continua a svolgere un ruolo importante nel sistema produttivo italiano, fornendo alle imprese committenti semilavorati sempre più vicini alle loro aspettative in termini di quantità, di qualità e tempi di risposta alle loro esigenze. Questo è stato possibile e lo è ancora per l’impegno delle fonderie a investire in innovazione tecnologica per rimanere competitivi con i principali partner europei ed ottenere una posizione di leadership in diversi settori e non solo di nicchia.
Anche la dimensione media delle fonderie italiane gioca
About 1,000 ferrous and non-ferrous metal foundries were active in Italy in 2020.
The sector consisted mainly of small enterprises with less than 50 workers employing about 24,000 people with a production of about 1.9 mln tonnes and a turnover of about EUR 7.4 mln ; the sector was ranked third in Europe, behind Germany and Turkey. In 2021, the non-ferrous metal foundry industry ranked first in Europe to produce this family of castings (Aluminium, Magnesium).
Thefoundryindustryallowsgreatdesignflexibilityinthe production of components that find application in the automotive industry, various mechanical engineering, construction, aerospace, power generation, design, boating, architecture, art and many other sectors by producing one-off or large series parts characterized by weights that can vary from a few grams (Microcastings) to over 100 tonnes.
This sector still represents an important component of the production market and job opportunities for millions of operators at all levels.
The foundry sector has played and continues to play an important role in the Italian production system, supplyingclientcompanieswithsemi-finishedproducts that are increasingly closer to their expectations in terms of quantity, quality, and response times to their needs. This has been possible and is still possible due to the commitment of foundries to invest in technological innovation to remain competitive with their main European partners and obtain a leadership position in various sectors, not just niche ones.
The average size of Italian foundries also plays a key role
un ruolo fondamentale rendendole più rapide ad adattarsi all’evolvere delle situazioni esterne.
Il ciclo di produzione della fonderia, sia di Metalli Ferrosi sia di Metalli Non Ferrosi, permette di realizzare una economia circolare utilizzando come materie prime materiali provenienti dal recupero e dal riciclo di rottami metallici e getti che al termine della loro vita di esercizio possono venire riutilizzati totalmente e reimmessi nel ciclo produttivo per realizzare nuovi prodotti. In questo modo si ottiene una valorizzazione degli scarti contribuendo in modo effettivo al processo di de-carbonizzazione dell’economia, contenendo l’impatto ambientale nella filiera di una economia a basse emissioni.
Il processo di fonderia permette ai progettisti di scegliere la lega più adatta all’impiego con la contemporanea possibilità di ridurre i pesi dei particolari da realizzare. Questa riduzione di peso si traduce anche in un risparmio di CO2 emessa, migliorando l’impatto ambientale.
Il futuro passaggio all’auto elettrica porterà inevitabilmente alla scomparsa di alcuni particolari realizzati ora in ghisa o acciaio, ma si assisterà a una maggiore spinta verso leghe più performanti ed a un maggior utilizzo di leghe leggere.
In questo numero della rivista sono riportati alcuni articoli presentati al XXXVI Congresso Tecnico di Fonderia organizzato dal Centro Studi AIM-Assofond per la Fonderia che mettono in evidenza la continua ricerca di nuove soluzioni tecnologiche, continuando in una proficua collaborazione con le Università e Centri di ricerca italiani ed Esteri.
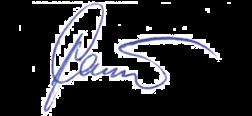
by making them quicker to adapt to changing external situations. The foundry's production cycle, both of Ferrous and Non-Ferrous Metals, makes it possible to achieve a circular economy by using as feedstock materials from the recovery and recycling of scrap metal and castings that, at the end of their service life, can be totally reused and re-introduced into the production cycle to make new products. In this way, waste is valorised, effectively contributing to the process of de-carbonisation of the economy, containing the environmental impact in the chain of a low-emission economy.
The foundry process allows designers to choose the most suitable alloy for use with the simultaneous possibility of reducing the weight of the parts to be manufactured.Thisweightreductionalsotranslatesinto asavinginCO2emissions,improvingtheenvironmental impact.
The future transition to the electric car will inevitably lead to the disappearance of some parts now made of cast iron or steel, but there will be a greater push towards higher-performance alloys and greater use of light alloys.
This issue of the magazine features some articles presented at the XXXVI Technical Foundry Congress organized by the AIM-Assofond Centre for Foundry Studies, which highlight the continuous search for new technological solutions, continuing a fruitful collaboration with Italian and foreign Universities and Research Centers.
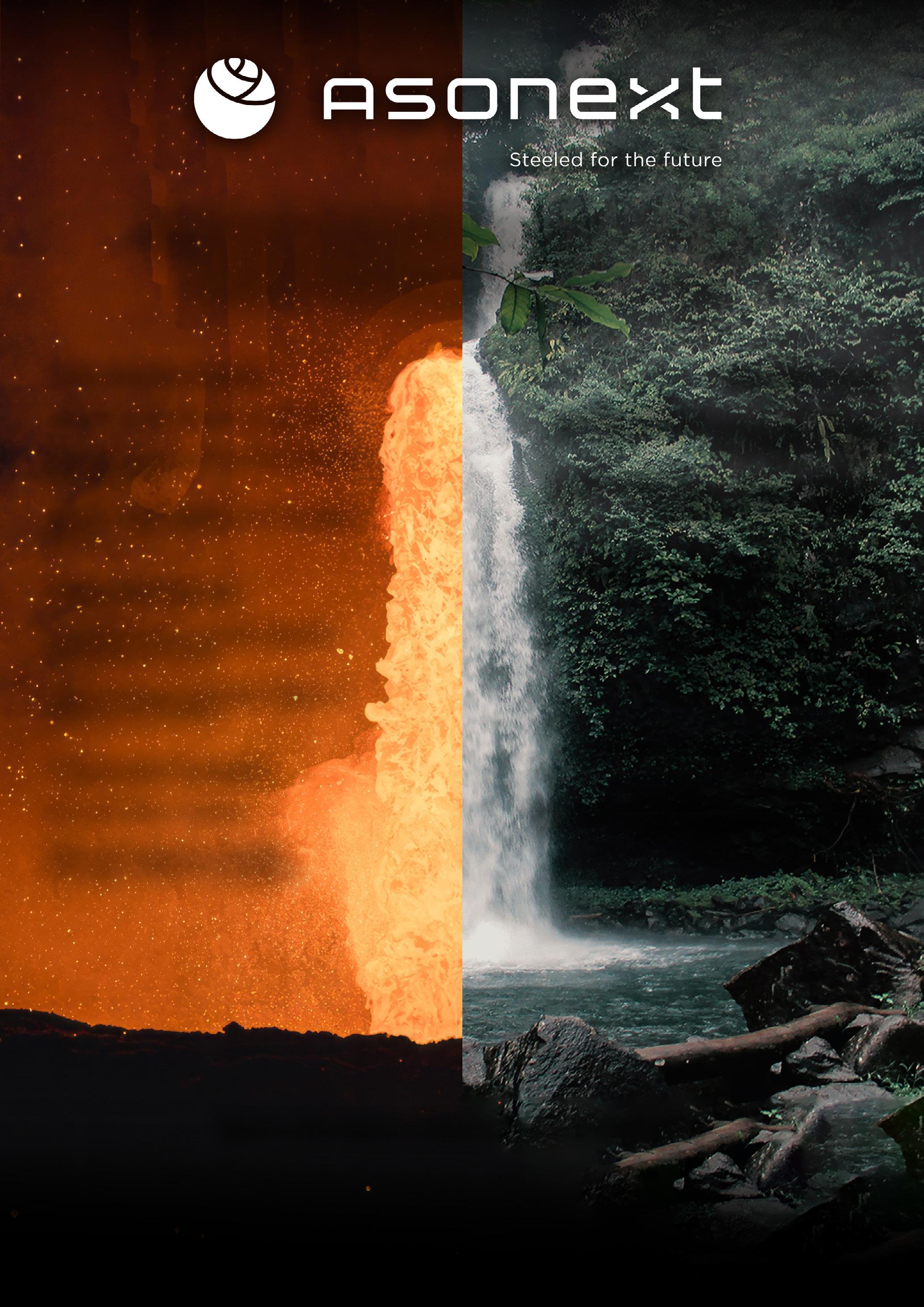
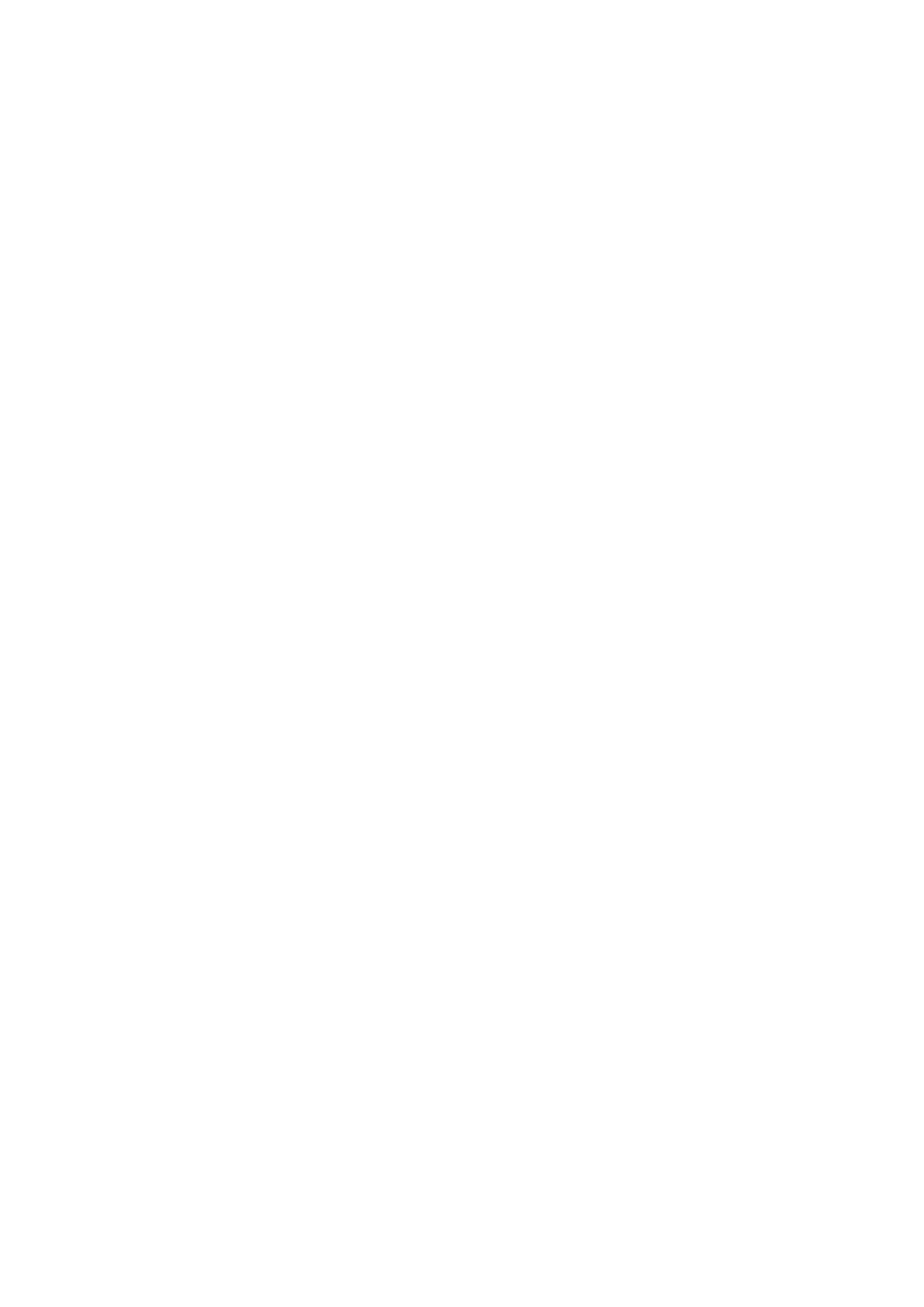
Heat treatment of the EN AC-42100 alloy within industrial furnaces: the effect of treatment parameters on mechanical properties
M. Merlin, E. Baroni, A. Fortini, C. Soffritti, F. FeggiWithin the aluminum foundry, the EN AC-42100 alloy is the most extensively employed for high-pressure or low-pressure casting processes due to its remarkable balance between castability and final properties of the castings. The mechanical properties of components intended for structural applications can be enhanced both by specific treatments applied to the melt and through heat treatments on the castings. The goal is to ensure an optimal combination of mechanical properties to meet the defined technical specifications for the end user. Hence, setting the proper heat treatment cycle for new components can be challenging and typically involves an iterative procedure to ascertain the optimal process parameters. Moreover, each furnace exhibits its own technical and operating characteristics resulting in variable outcomes when employing identical treatments across furnaces from different manufacturers. This paper presents the results of an experimental study performed in collaboration with the company HTT – Heat Treatment Torri to investigate the correlation between heat treatment parameters and the mechanical properties of experimental gravity castings treated in industrial furnaces. Specifically, in the first phase, the effect of different solution times was examined to identify the optimal solution time through tensile and hardness tests while keeping the aging parameters constant. Based on the results of such experiments, the second phase comprised a constant solution treatment and the analysis of combinations of aging times and temperatures to maximize both performance and productivity by the specified technical requirements defined by the customer.
KEYWORDS: EN AC-42100 ALUMINUM ALLOY, HEAT TREATMENT, MECHANICAL PROPERTIES, MICROSTRUCTURE
INTRODUCTION
Aluminum alloys have long played a crucial role in several engineering fields owing to their peculiar features, including specific mechanical strength, high thermal and electrical conductivity, good formability, and recycling properties [1]. The Al-Si alloys, in particular, are widely used in foundry processes due to their remarkable castability, reduced susceptibility to hot cracking, and the effective role of silicon in minimizing solidification shrinkage. Among these alloys, the hypoeutectic AlSi7Mg0.3 alloy is of great interest for foundry applications [2, 3]. It exhibits excellent mechanical and technological properties, crucial in the automotive sector, e.g. for the production of frames and suspensions through sand casting, shell casting, or low-pressure die casting (LPDC) techniques. To optimize the mechanical properties of castings
F.Feggi HTTHeatTreatmentTorriSrlproduced with this alloy is essential to conduct a thermal treatment sequence that involves solution heat treatment followed by artificial aging, known as the T6 heat treatment [4]. The initial phase of the treatment consists of a high-temperature solution stage, followed by rapid quenching in water, properly added with specific kinds of polymers, and thermostated between 60 °C and 70 °C. In the subsequent aging phase, the components are reheated to a predetermined temperature, significantly lower than the solution temperature, to achieve the formation of fine and dispersed intermetallic reinforcing phases. The aim of the solubilization treatment is to dissolve the majority of coarse intermetallic phases, particularly those containing Mg, which are formed during the early solidification stage [4]. This can be reached by maintaining the material above 500 °C for 4 to 8 hours [2]. Furthermore, both the duration and temperature of the solution treatment have been proven to directly influence the morphology of the eutectic Si in Al-Si alloys and, consequently, the final mechanical properties of the castings [5]. The quenching process, which occurs at the end of the solution stage, aims to cool the material as rapidly as possible to a temperature close to ambient temperature, to obtain an oversaturated solid solution [6-7]. The third and final phase of the T6 heat treatment is artificial aging, which involves heating the material for several hours, typically above 150 °C. Aging is intended to promote the formation of semi-coherent precipitates within the lattice of the primary α -Al phase, maximizing the mechanical properties through precipitation as the strengthening mechanism. To set up and optimize heat treatment parameters in both the solution and aging stages, necessary to gain the optimal compromise between the different required mechanical characteristics of castings, have been a matter of great scientific and industrial interest for many years. The solution temperature should be between 500 °C and 550 °C, whereas a higher temperature leads to better mechanical properties, but increases the risk of melting low-melting compounds at grain boundaries, thus compromising the material integrity. Furthermore, it is known that in the aging phase, time and temperature are interdependent in determining the optimal condition for matrix hardening: as the temperature increases, it has been observed that the peak of mechanical properties (yield and ultimate strength) can
be achieved with shorter holding times, but it is also true that when the same temperature increases, the peak becomes progressively smaller [8]. It should be highlighted that the above-reported findings and correlations result from experiments conducted in scaled-down furnaces, namely laboratory-scale furnaces, which neglect the scale effect of industrial furnaces and the influence of the thermal mass of sample baskets and potential heat losses. The present study, performed in collaboration with the company HTT - Heat Treatment Torri, aims to optimize the process parameters in the different stages of the T6 heat treatment in industrial-type furnaces. The research was carried out in two phases. Firstly, the influence of different solution times at a fixed temperature on the mechanical properties of an EN AC-42100 aluminum alloy was investigated, considering specific quenching and aging treatments. Once the ideal solution condition was determined, the second phase was focused on identifying the optimal parameters for the artificial aging treatment: different combinations of temperature and holding times were selected based on existing literature [8,9] and the expertise of the involved company. Finally, their impact on the mechanical and microstructural properties of the alloy was evaluated.
MATERIALS AND METHODS
The castings used for the study were made of EN AC42100 aluminum alloy by Fonderia S. Possidonio Srl (Modena, Italy) using a steel mold. The alloy was subjected to liquid treatments that involved the addition of Al5TiB1 grain refiners and Al-10%Sr master alloy rods. To ensure the compositional homogeneity, all samples were cast from the same ladle. The chemical composition of the alloy was determined using Optical Emission Spectroscopy (OES) technique. Table 1 presents the average and relative standard deviation of six measurements, as well as the reference chemical composition for the EN AC-42100 alloy according to UNI EN 1706 standard. The results highlight the correspondence between the investigated alloy and the specifications outlined by the standard. The Ti and Sr contents indicate the efficacy of refinement and modification treatments, respectively
The alloy was cast into a specific mold, as reported in Fig. 1, to obtain samples for the heat treatment investigation. From each of the castings a tensile test specimen was
machined to test the mechanical behavior resulting from the heat treatment route.
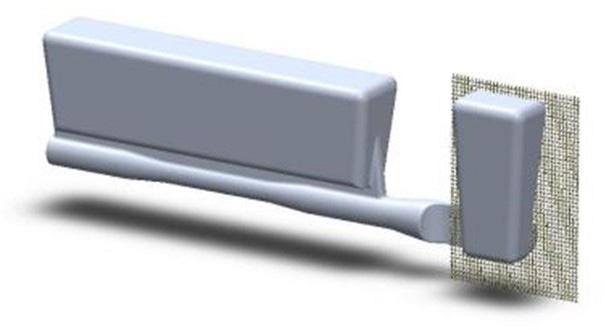
The heat treatments, carried out by the company HTTHeat Treatment Torri, were performed in various types of industrial furnaces with different configurations. For the solution treatment, a semi-continuous tunnel furnace consisting of four chambers, with the first chamber designated for pre-treatment and the last chamber used for quenching the sample basket in water at a temperature of 70 °C, was employed. Pneumatic movement between chambers was possible only when the entire furnace reached the set temperature and after the designated holding time. For the aging treatments, a batch-type furnace was employed and the temperature uniformity was checked inside the furnaces using thermocouples and a data acquisition and control system. The parameters for the heat treatments were selected based on the
company'sexperienceandliteraturestudiesthatutilized laboratory-scale furnaces. The experimental activity was divided into two steps, following the experimental plan summarized in Table 2.
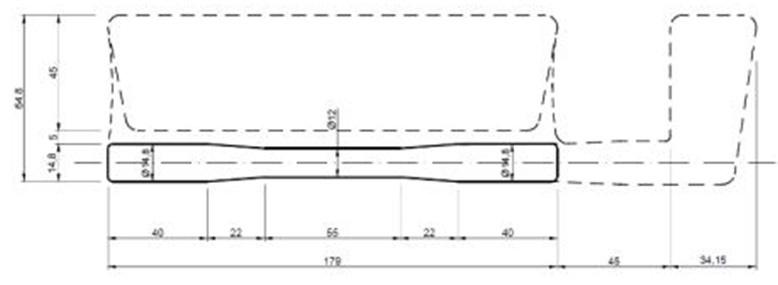
Tab.2 - Heat treatments sequence and parameters.
Step 1 was devoted to studying the influence of the solution treatment duration (120, 240 and 360 minutes) for a fixed temperature (535 °C). It followed standard aging at 160 °C for 300 minutes. Step 2 investigated the effect of different combinations of aging temperatures (135, 160 and 200 °C) and duration (120, 240 and 360 minutes) on samples previously solution treated according to the optimized parameters obtained from Step 1. For each condition, n° 5 castings were analyzed to ensure the statistical significance of the data, resulting in a total of n° 60 castings. To ensure tests that resembled realworld conditions, and to obtain reproducible heating and holding ramps, the baskets were also filled with scrap pieces. After solution quenching, the castings were extracted and stored at -18 °C to prevent natural aging; only once all the predetermined aging treatments were performed, tensile test specimens were machined from the castings to investigate the mechanical properties of the alloy under the different combinations of parameters. Tensile tests were conducted using a QUASAR 50 machine (Galdabini S.p.a., Cardano al Campo, Italy) with a load cell of 50 kN, in accordance with UNI EN ISO 6892-1. For the comparison of different treatment conditions, the ultimate tensile strength (UTS), yield strength (YS), and percentage elongation at fracture (Ef %) were considered. Brinell
hardness tests (HBW2.5/62.5) were also conducted using an Ernst AT130D hardness tester to get the variation in mechanical properties due to the performed treatments. Moreover, after Step 1, microstructural analysis was performed on three tensile test specimens, one for each investigated solution time. Samples were observed using a Leica DMi8 A metallographic optical microscope (Leica Microsystem, Wetzlar, Germany) equipped with LAS v4.13 image acquisition software.
RESULTS AND DISCUSSION
The average values of the tensile tests carried out on specimens drawn from castings treated according to the heat treatment parameters defined for Step 1 are summarized in Table 3. It can be observed that both UTS and YS increase with increasing solution time, although no significant variations are evident among the different conditions. In this regard, Zhang et al. [9] demonstrated that mechanical properties increased as a result of diffusion phenomena that occur within the first 30 minutes of solution treatment. As for Ef %, the highest value was obtained for 240 minutes of solution at 535 °C.
Table 4 shows the Brinell
test results obtained for the investigated solution times of Step 1. As seen, and considering the standard deviations, hardness did not
vary significantly with increasing solution time, despite showingaslightlyincreasingtrendastensileproperties.
Following the tensile tests, a microstructural examination was conducted. Figure 2 displays the representative optical micrographs of the different solution conditions.The
microstructure consists of α-Al dendrites and a eutectic structure; the Si phase appears correctly modified. A low amount of Fe-based intermetallic phases was detected.
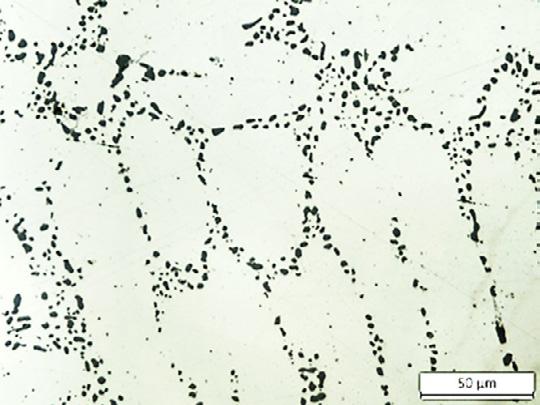
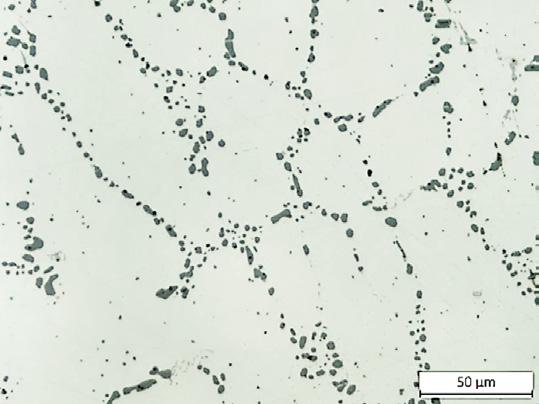
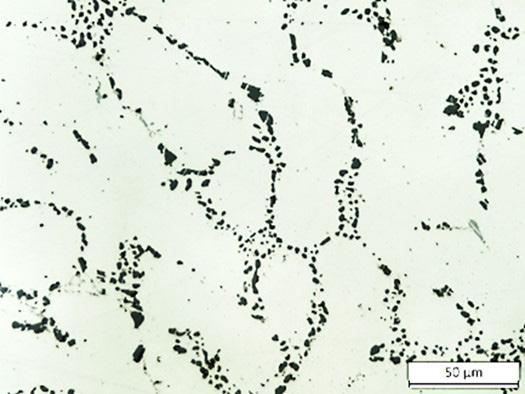
Based on the results from the mechanical and microstructural characterization of Step 1, the solution treatment at 535 °C for 240 minutes provided the best mechanical properties. Considering that this solution treatment guarantees a favorable performance-tocost ratio for the company compared to other longer treatment times, it was adopted as the solution treatment for subsequent investigations. Hence, Step 2 focused on investigating the influence of different combinations of aging times and temperatures while keeping the solution
treatment parameters constant (535 °C for 240 minutes). Table 5 presents the average values and corresponding standard deviations of UTS, YS, and Ef % for the investigated aging parameters.
Tab.5 - Tensile test results for the investigated aging temperatures and times (Step 2).
Figure3summarizesthetensiletestresultsofStep2:it can be seen that at lower temperatures (135 °C and 160 °C), the best mechanical properties (UTS and YS) are reached for longer aging times; nevertheless, for aging performed at 135 °C, the minimum targeted values of 290 MPa for UTS and 210 MPa for YS are not reached. In
contrast, for the highest aging temperature (200 °C), the best mechanical properties were achieved with shorter aging durations (120 minutes). This trend is supported by existing literature studies [8]. For all the performed treatments, the 4 % threshold value for Ef % was overcome.
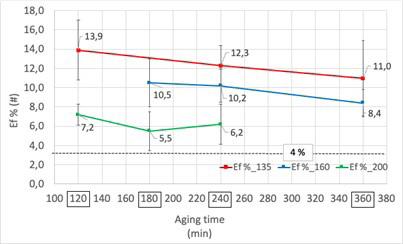
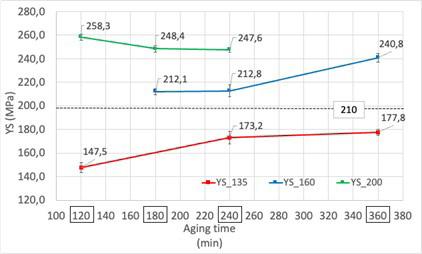
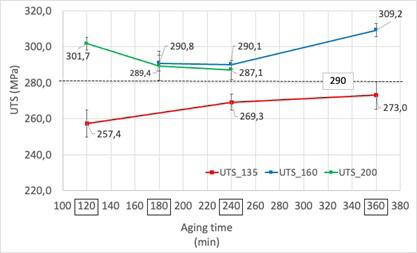
Table 6 summarizes the Brinell hardness test results for the investigated aging conditions of Step 2. The same valuesarealsodisplayedinFig.4:thehighestvaluescorrespond to the 200 °C for 120 minutes and 160°C for 360
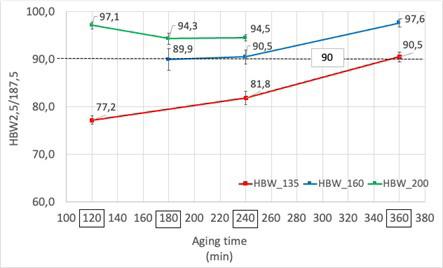
minutes conditions. Considering the standard deviations of the results, only the latter condition and all the aging performed at 200 °C are able to overcome the threshold value of 90 HBW2.5/62.5.
CONCLUSIONS
This study focused on analyzing the T6 heat treatment parameters performed in industrial furnaces to optimize the mechanical properties of the EN AC-42100 alloy. In the first step of the study, different holding times of a solution treatment performed at 535 °C were investigated to achieve the best compromise between mechanical properties and treatment times at the end of a subsequent aging treatment carried out at 160 °C for 300 minutes. In the second step, the influence of different combinations of aging times and temperatures on the mechanical properties was analyzed, while keeping as constant the solution conditions defined as optimal in the first step. Based on the experimental evidence, the following observations can be made:
• In the first step, solution duration affects the mechanical properties: UTS and YS increased with the solution time, despite the increment was not so remarkable, in particular
passing from 240 minutes to 360 minutes of holding time. Ef % showed the highest value for the specimens treated with a solution time of 240 minutes, suggesting that a longer time is unnecessary and not cost-effective;
• Hardness values did not vary significantly with increasing solution duration, although there was a slight increasing trendintheaveragevalues.Thestandarddeviationsindicated relatively low variability in hardness;
•Microstructuralanalysisconductedinsamplessubjected, in the first step, to different holding times, revealed the typical microstructural features of an hypoeutectic EN AC-42100 alloy whose melt is accurately modified. A low amount of Fe-based intermetallics was detected, so confirming the significant role of the combination of both solutionandagingparametersintheevolutionofmechanical properties;
• As for aging, at lower temperatures (135 °C and 160 °C), the highest mechanical properties (UTS and YS) were reached for longer aging times. Nevertheless, all the aging treatments performed at 135 °C were not able to overcome the threshold values of 210 MPa and 290 MPa for YS and UTS, respectively. Considering the standard deviations of the results, among the aging treatments carried out at 160 °C only the holding time of 360 minutes was able to
guarantee suitable mechanical properties. In contrast, for higher temperatures (200 °C), the highest mechanical properties were achieved with the shortest aging duration.
ACKNOWLEDGEMENTS
TheauthorswishtothankEng.DavideGramignaforhiseffective contribution to the experimental investigation.
REFERENCES
[1] Kaufman J. G., Introduction to aluminum alloys and tempers, ASM International, Materials Park, 2000, p. 87.
[2] Stroh J., Sediako D., Hanes T., Anderson K., Monroe A., The effect of heat treatment on the microstructure and tensile properties on an HPDC marine transimission, Metals 11, 517, 2021, 1-17.
[3] Fortini, A., Lattanzi, L., Merlin, M. et al. Comprehensive Evaluation of Modification Level Assessment in Sr-Modified Aluminium Alloys. International Journla of Metalcasting 12, 697–711, 2018.
[4] Ibrahim M. F., Elgallad E. M., Valtierra S., Doty H. W., Samuel F. H., Metallurgical parameters controlling the eutectic silicon characteristics in Be-treated Al-Si-Mg alloys, Materials 9, 78, 2016, 1-17.
[5] Li R. X., Li R. D., Zhao Y. H., Li C. X., Sun X. F., Guan H. R., Hu Z. Q., Effect of heat treatment on eutectic silicon morphology and mechanical properties of Al-Si-Cu-Mg cast alloys, Transactions of Nonferrous Metals Society of China 14, 2004,496-500.
[6] Apelian D., Shivkumar S., Sigworth G., Fundamental aspects of heat treatment of cast Al-Si-Mg alloys, AFS Trans. 97, 1989, 727–742.
[7] Roy E. L., Castings, 9th Ed, ASM International: Materials Park, OH, USA, 1992, vol. 15, pp. 743-769.
[8] Chen R., Xu Q., Guo H., Xia Z., Wu Q., Liu B., Correlation of solidification microstructure refining scale, Mg composition and heat treatment conditions with mechanical properties in Al-7Si-Mg cast aluminum alloys, Materials Science and Engineering: A, vol. 685, 2017, pp. 391-402.
[9] Zhang D. L., Zheng L. H., StJohn D. H., Effect of a short solution treatment time on microstructure and chemical properties of modified Al-7wt.%Si-0.3wt.%Mg alloy, Journal of Light Metal, 2002, 27-36.
Trattamento termico della lega
EN AC-42100 all’interno di forni
industriali: effetto dei parametri di trattamento sulle proprietà meccaniche
M. Merlin, E. Baroni, A. Fortini, C. Soffritti, F. FeggiIn fonderia, la lega di alluminio EN AC-42100 è quella maggiormente utilizzata per i processi di colata in conchiglia o bassa pressione in virtù dell’ottimo compromesso tra colabilità e proprietà finali dei getti. Le proprietà meccaniche di getti per impiego strutturale possono essere ottimizzate sia attraverso specifici trattamenti della lega liquida preliminari alle fasi di colata sia tramite trattamenti termici eseguiti sui getti a valle del processo stesso di colata. L’obiettivo ultimo è poter garantire al cliente finale la combinazione ottimale di proprietà meccaniche definita sulla base di specifiche tecniche. La progettazione del ciclo di trattamento termico per nuovi componenti può presentare delle criticità ed in genere richiede una procedura iterativa per la definizione dei corretti parametri di processo. Inoltre, ogni forno ha caratteristiche tecniche e strutturali proprie, per cui eseguire lo stesso trattamento su forni di produttori differenti può fornire risultati significativamente diversi. In questa memoria sono presentati i risultati di uno studio sperimentale condotto in collaborazione con l’Azienda HTT – Heat Treatment Torri avente lo scopo di investigare la correlazione tra parametri di trattamento termico e proprietà meccaniche di getti sperimentali prodotti per gravità in conchiglia e successivamente trattati in forni industriali. In particolare, in una prima fase è stato studiato l’effetto della variazione dei tempi di solubilizzazione a parità di paramentri di invecchiamento, individuando tramite prove meccaniche di trazione e durezza un tempo ideale di solubilizzazione. Nella fase successiva, mantenendo costante il tempo di solubilizzazione precedentemente individuato, sono state studiate diverse combinazioni di tempi e temperature di invecchiamento allo scopo di massimizzare sia le prestazioni sia la produttività in base a specifiche tecniche richieste a capitolato.
PAROLE CHIAVE: LEGA DI ALLUMINIO EN AC-42100, TRATTAMENTO TERMICO, PROPRIETÀ MECCANICHE, MICROSTRUTTURA
INTRODUZIONE
Le leghe di alluminio rivestono da sempre un ruolo fondamentale in svariati settori dell’industria grazie ad una serie di vantaggi che le contraddistinguono come la resistenza meccanica specifica, le elevate conduttività termica ed elettrica, la buona formabilità e la propensione al riciclo [1]. Le leghe del sistema Al-Si si prestano egregiamente ad essere utilizzate nei processi di fonderia grazie alla loro eccellente fluidità, alla ridotta tendenza alla formazione di cricche a caldo e all’azione efficace del Si nella riduzione dei ritiri in fase di solidificazione. Tra di esse, la lega ipoeutettica AlSi7Mg0.3 è una di quelle di maggior interesse nell’ambito della fonderia [2,3]. Si tratta di una lega in grado di offrire buone caratteristiche meccaniche e tecnologiche e trova largo impiego nel
F.FeggiHTTHeatTreatmentTorriSrl
settore automotive, principalmente per la realizzazione di telai e sospensioni con processi in sabbia, in conchiglia o in bassa pressione (LPDC). Al fine di ottimizzare le proprietà meccaniche dei getti prodotti con tale lega, risulta quasi sempre necessaria l’esecuzione di una sequenza di operazioni termiche che prevedono tempra di soluzione e successivo invecchiamento artificiale, nel complesso note come trattamento termico T6 [4]. La prima fase del trattamento consiste infatti in una solubilizzazione ad alta temperatura seguita da un rapido raffreddamento in acqua opportunamente additivata e termostata tra i 60 e i 70 °C. Nella successiva fase di invecchiamento i pezzi solubilizzati vengono nuovamente riscaldati a una temperatura fissata, sensibilmente inferiore a quella di solubilizzazione, in modo da ottenere la precipitazione fine e dispersa delle fasi intermetalliche rinforzanti. Lo scopo del trattamento di solubilizzazione è quello di mandare in soluzione solida la maggior parte delle fasi intermetalliche grossolane, specialmente quelle contenti Mg, generatesi in fase di prima solidificazione [4]. Ciò è reso possibile solo grazie al mantenimento del materiale per tempi mediamente compresi tra le 4 e le 8 h ad una temperatura superiore ai 500 °C [2]. Durata e temperatura di solubilizzazione, secondo studi di letteratura, risultano avere inoltre un’influenza diretta sulla morfologia del Si eutettico delle leghe Al-Si e di conseguenza sulle proprietà meccaniche finali dei getti [5]. La tempra, ovvero il raffreddamento che viene eseguito al termine della permanenza alla temperatura di solubilizzazione, è la fase in cui ci si pone l’obiettivo di raffreddare il materiale quanto più rapidamente possibile fino a temperatura prossima a quella ambiente al fine di ottenere una soluzione solida sovrassatura [6-7]. La terza ed ultima fase di trattamento termico T6 è quella di invecchiamento eseguito artificialmente riscaldando il materiale per alcune ore generalmente oltre i 150 °C. La finalità dell’invecchiamento è quella di ottenere precipitati semi-coerenti con il reticolo della fase primaria α -Al, in modo da massimizzare le proprietà meccaniche sfruttando la precipitazione come meccanismo di rinforzo.
La gestione e l’ottimizzazione dei parametri di trattamento termico nelle fasi di solubilizzazione ed invecchiamento, al fine di ottenere l’ottimale compromesso tra le varie caratteristiche meccaniche richieste sui getti, da molti anni risulta essere questione di grande interesse scientifico ed
industriale. La temperatura di solubilizzazione, ad esempio, deve essere compresa tra i 500 ed i 550 °C: maggiore è la temperatura, maggiore è la possibilità di ottenere proprietà meccaniche migliori, ma anche quella di favorire la fusione di composti basso fondenti a bordo grano compromettendo di conseguenza l’integrità del materiale. È noto, inoltre, che anche nella fase di invecchiamento, tempo e temperatura non sono tra loro interdipendenti al fine della determinazione della condizione ottimale di indurimento della matrice. Difatti, all’aumentare della temperatura si è visto come il punto di massimo delle proprietà meccaniche (carico a snervamento e a rottura) sia raggiungibile per tempi di mantenimento inferiori, ma è altresì vero che ad uno stesso aumento corrisponde un picco di entità via via minore [8]. Tali evidenze e correlazioni, che si riscontrano in letteratura, sono tuttavia frutto di sperimentazioni condotte all’interno di forni in scala dimensionale ridotta rispetto a quelli industriali, ovvero in forni da laboratorio, trascurando così l’effetto scala dei forni industriali così come l’incidenza della massa termica delle ceste di campioni e delle eventuali dispersioni. Il presente lavoro, frutto di una collaborazione con l’Azienda HTT – Heat Treatment Torri, si pone l’obiettivo di ottimizzare i parametri di processo nelle diverse fasi del trattamento termico T6 in forni di tipo industriale. La ricerca è stata condotta prevedendo due fasi, ovvero si è dapprima indagata l’influenza di diversi tempi di solubilizzazione a parità di temperatura sulle proprietà meccaniche di una lega di alluminio EN AC-42100, sottoposta a trattamenti di tempra e invecchiamento a parametri fissati. Una volta determinata la condizione di solubilizzazione ideale come risultato della prima fase, la seconda fase ha previsto l’individuazione dei parametri ottimali per l’esecuzione del trattamento di invecchiamento artificiale. Le diverse combinazioni di temperatura e tempo di mantenimento sono state scelte sulla base di lavori presenti in letteratura [8,9] e dell’esperienza della Azienda, ed è stata poi valutata la loro influenza sulle proprietà meccaniche e microstrutturali della lega oggetto di studio.
MATERIALI E METODI
I getti impiegati per lo studio sono stati realizzati in lega di alluminio EN AC-42100 dalla Fonderia S. Possidonio Srl (MO) per colata in conchiglia, utilizzando uno stampo in
acciaio. La lega liquida è stata sottoposta a trattamenti di affinazione e modifica mediante aggiunta rispettivamente di vergelle in lega Al5TiB1 e bacchette in lega madre Al10%Sr. Per garantire conformità e omogeneità di composizione chimica, tutti i campioni sono stati colati dalla medesima siviera. La composizione chimica della lega è stata determinata mediante spettrometria ad emissione ottica (OES). La media e la relativa deviazione standard di n° 5
misurazioni, oltre che la composizione chimica di riferimento per la lega EN AC-42100 secondo normativa UNI EN 1706, sono riportate in Tabella 1.
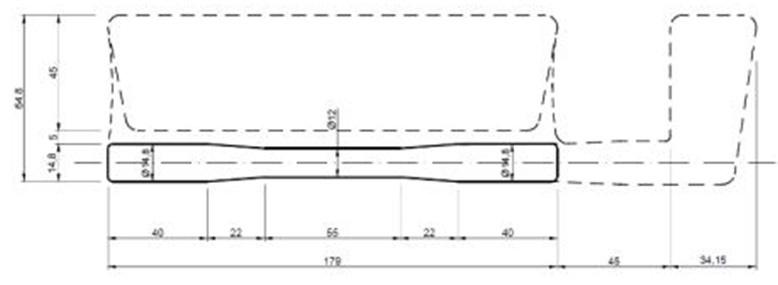
I risultati evidenziano l’ottima corrispondenza tra la composizione chimica della lega in esame e quanto previstodanormativa.ItenoridiTiediSrsonoindice dell’avvenuta esecuzione dei trattamenti, rispettivamente, di affinazione e di modifica. Con la lega così trattata sono stati colati dei getti in conchiglia, la cui geometria a
titolo esemplificativo è riportata in Figura 1 sotto forma di rappresentazione bidimensionale e tridimensione. Da ciascuno dei getti prodotti, a valle dei diversi trattamenti termici messi a punto per lo studio, è stato successivamente ricavato un provino di trazione per lavorazione meccanica.
I trattamenti termici sono stati eseguiti dall’Azienda HTT – Heat Treatment Torri in forni industriali di diversa natura e conformazione. Per condurre i trattamenti di solubilizzazione è stato utilizzato un forno a tunnel semi-continuo costituito da n. 4 camere, di cui la prima di pretrattamento e l’ultima in cui avviene la tempra della
cesta contenente i campioni in acqua alla temperatura di 70 °C. La movimentazione da una camera all’altra è pneumatica ed è possibile solo qualora la temperatura in tutto il forno raggiunga il valore impostato e dopo il tempo di permanenza previsto. Per l’esecuzione dei trattamenti di invecchiamento è stato invece utilizzato un classico
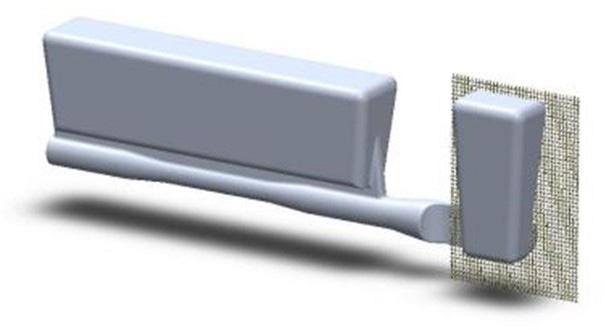
forno di tipo batch. Al fine di garantire la corretta esecuzionedeitrattamenti,medianteimpiegoditermocoppie e di un sistema di acquisizione e controllo sono state previsteedeseguiteverifichediuniformitàditemperatura all’interno dei forni. I parametri di trattamento termico
utilizzati sono stati scelti sulla base dell’esperienza della Azienda e di lavori di letteratura basati su sperimentazioni eseguite con forni da laboratorio. Si è pertanto proceduto suddividendo l’attività sperimentale in due fasi, secondo il piano sperimentale riassunto in Tabella 2.
In una prima fase (Fase 1) è stata indagata l’influenza della durata del trattamento di solubilizzazione (120 min, 240 min e 360 min) a parità di temperatura (535 °C) per poi eseguire un invecchiamento standard a 160 °C per 300 min. Nella seconda fase (Fase 2) è stato invece valutato l’effetto di diverse combinazioni di durata e temperatura di invecchiamento (n. 9 in totale) su provini solubilizzati secondo i parametri ottimizzati nella Fase 1. Per ciascuna condizione indagata sono stati analizzati n. 5 getti al fine di garantire la significatività del dato, per un totale di n. 60 getti. Per garantire che le prove fossero quanto più conformi possibile alla realtà, le ceste in cui sono stati trattati i getti sono state riempite con pezzi di scarto fino ad ottenere una quantità di materiale tale da riprodurre una normale carica di un forno di trattamento ed eseguire rampe di riscaldamento e mantenimenti con una certa regolarità e riproducibilità. Dopo la tempra di soluzione delle diverse ceste, i getti sono stati estratti e conservati
alla temperatura di -18 °C per non incorrere in fenomeni di invecchiamento naturale prima dell’esecuzione dei trattamenti di invecchiamento artificiale. Una volta eseguiti tutti i trattamenti prefissati, dai getti sono ricavati per lavorazione meccanica i provini di trazione utilizzati per indagare le proprietà meccaniche della lega trattata secondo le diverse combinazioni di parametri. Le prove di trazione sono state eseguite mediante macchina QUASAR 50 (Galdabini S.p.a., Cardano al Campo (VA), Italia) con cella di carico pari a 50 kN e rispondente alla normativa UNI EN ISO 6892-1. Per il confronto tra le diverse condizioni di trattamento sono stati considerati il carico di rottura (Rm), il carico di snervamento (Rp0.2) e l’allungamento percentuale a rottura (A%). Sono state inoltre effettuate prove di durezza Brinell (HBW2.5/62.5), mediante durometro Ernst AT130D, al fine di ottenere una ulteriore conferma sperimentale della variazione delle proprietà meccaniche in relazione ai trattamenti eseguiti.
Un controllo della microstruttura è stato infine effettuato a valle della Fase 1 dell’indagine sperimentale. Sono stati sezionati n. 3 campioni di trazione per ciascuna dei tre tempi di solubilizzazione indagati ed i saggi estratti sono stati inglobati a caldo in resina fenolica. Dopo opportuna preparativa metallografica i saggi sono stati osservati mediante microcopio ottico metallografico Leica DMi8 A (Leica Microsystem, Wetzlar, Germania), dotato di
software di acquisizione di immagine LAS v4.13.
RISULTATI E DISCUSSIONE
I risultati delle prove di trazione, eseguite sui provini a valle dei trattamenti termici previsti dalla Fase 1, sono mostrati in Tabella 3; in particolare, sono riportati i valori medi e relative deviazione standard di Rm, Rp0.2 e A%.
Dai risultati ottenuti è possibile notare come Rm e Rp0.2 aumentino all’aumentare del tempo di solubilizzazione pur senza mostrare variazioni particolarmente importanti tra una condizione e l’altra. Una possibile spiegazione di questo fenomeno può essere trovata in studi di letteratura. È stato infatti dimostrato da Zhang et al. [9] che l’incremento delle proprietà meccaniche della lega si ottiene in seguito ai fenomeni di diffusione nella lega
che avvengono nei primi 30 min di solubilizzazione. Per quanto riguarda l’allungamento percentuale a rottura, è possibilenotarecomeilvalorepiùaltosiastatoottenuto neiproviniditrazionericavatidagettisolubilizzatiper 240 min. In Tabella 4 sono invece riportati i risultati delle provedidurezzaBrinellHBW2,5/62,5eseguitesuglistessicampioni.
Tenendo conto delle deviazioni standard, è stato possibile constatare che anche la durezza non è variata in maniera considerevole all’aumentare della durata del trattamento di solubilizzazione, pur mostrando in analogia alle caratteristiche meccaniche un trend crescente dei valori medi al crescere del tempo di solubilizzazione. Avalledelleproveditrazione,sièprocedutoinoltrecon unaanalisi della microstruttura. InFigura 2 si riportano le micrografie, ottenute a microscopio ottico ad un ingran-
dimento di 500x, rappresentative delle diverse condizioni di solubilizzazione. La microstruttura consiste in tutti i casi di dendriti di α-Al e di una struttura eutettica in cui il Si appare correttamente modificato. È stato rilevato un contenuto relativamente basso di intermetallici a base Fe.
Fig.2 - Micrografie rappresentative delle diverse condizioni di solubilizzazione a 535 °C e a) 120 min, b) 240 min e c) 360 min.
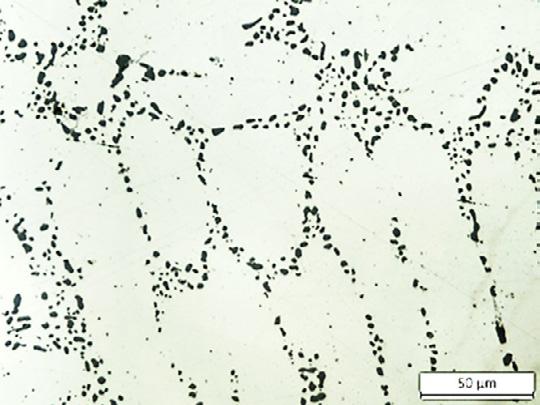
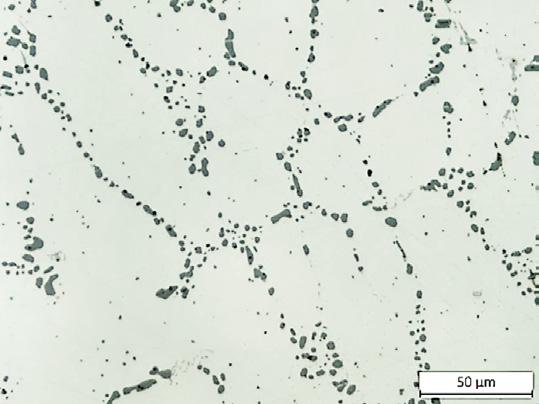
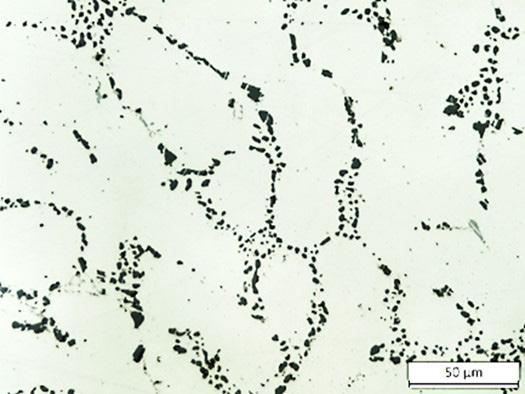
Sulla base dei risultati ottenuti dalla caratterizzazione meccanica e microstrutturale in Fase 1, si è deciso di optare per il trattamento di solubilizzazione a 535 °C per 240 min come il migliore per le proprietà meccaniche garantite e per il rapporto prestazioni/prezzo più conveniente per la Azienda rispetto a tempi più lunghi di trattamento. Pertanto, in Fase 2 è stata indagata l’influenza sulle
proprietà meccaniche di diverse combinazioni di tempi e temperature di trattamento di invecchiamento, a parità di trattamento di solubilizzazione (535 °C per 240 min). In Tabella 5 sono riportati i valori medi e relative deviazioni standard di Rm, Rp0.2 e A% al variare dei parametri di invecchiamento.
Tab.5 - Prove di trazione: valori di carico di rottura, carico di snervamento e allungamento a rottura per diversi tempi e temperature di invecchiamento (Fase 2).
Alfinedifacilitareletturaecomprensionedeidati,ivalori di Rm, Rp0.2 e A% sono stati rappresentati anche graficamenteinFigura3.Èpossibilenotareche,perlepiùbasse temperature di trattamento (135 °C e 160 °C), le migliori proprietà meccaniche (Rm e Rp0.2) sono state raggiunte per i tempi più lunghi di trattamento; nonostante ciò, per tutti gli invecchiamenti condotti a 135 °C i valori soglia di 210 MPa e 290 MPa, rispettivamente per Rp0.2 e Rm,
non sono stati raggiunti. Al contrario, per la temperatura più alta di trattamento (200 °C), le migliori caratteristiche meccanichesonostateraggiunteperiltempopiùbrevedi mantenimento (120 min). Questo andamento è supportato della letteratura più recente [8]. È importante evidenziare che, per tutti i trattamenti eseguiti, il valore di sogliadiA%parial4%èstatogarantito.
In Tabella 6 sono riportati i valori di durezza Brinell dei campionianalizzatinellediversecondizioniditrattamento di invecchiamento. Gli stessi valori di durezza sono diagrammati anche in Figura 4 ed è possibile constatare che i valori più elevati della durezza sono stati raggiunti
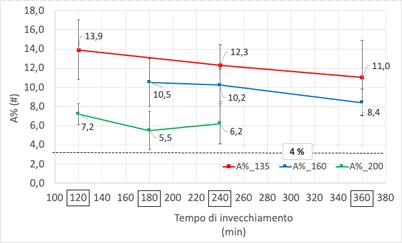
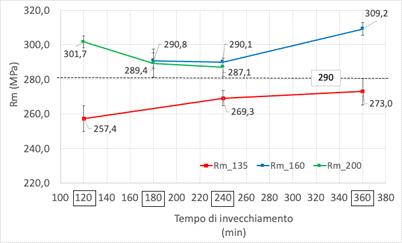
per le combinazioni 200 °C per 120 min e 160°C per 360 min. Considerando i valori di deviazione standard dei risultati, solo quest’ultima condizione e per tutti gli invecchiamenti condotti a 200 °C è stato possibile superare ilvaloresogliadi90HBW2.5/62.5.

CONCLUSIONI
Il presente studio ha riguardato l’analisi dei parametri di trattamento termico T6 effettuato in forni industriali al fine di ottimizzare le proprietà meccaniche della lega EN AC42100. In particolare, nella prima fase di lavoro sono state eseguite solubilizzazioni a 535 °C per differenti tempi di mantenimento al fine di individuare il miglior compromesso tra proprietà meccaniche e tempi di trattamento a valle di un invecchiamento artificiale condotto a 160 °C per 300 min. Una seconda fase ha invece riguardato l’influenza sulle proprietà meccaniche di diverse combinazioni di tempi e temperature di trattamento di invecchiamento, assumendo come condizione di solubilizzazione quella individuata come ottimale nella precedente prima fase. A partire dalle evidenze sperimentali è stato possibile constatare che:
• Nella prima fase, la durata del trattamento di solubilizzazione ha avuto un effetto sulle caratteristiche meccaniche. Rm e Rp0.2 hanno mostrato un incremento all’aumentare della durata del trattamento di solubilizzazione, nonostante tale crescita non sia stata particolarmente significativa soprattutto passando dai 240 min ai 360 min di trattamento. L’allungamento percentuale a rottura ha raggiunto il valore massimo per un mantenimento a 535 °C pari a 240 min. Alla luce di tali risultati, si può pertanto ritenere che un tempo di solubilizzazione superiore ai 240 min si dimostra non necessario ed economicamente non vantaggioso per l’Azienda.
• Altrettanto, la durezza Brinell non sembra essere influenzata in modo significativo dalla durata del trattamento di solubilizzazione, sebbene si sia constatato un leggero trend positivo nei valori medi.

• Le analisi microstrutturali, condotte in Fase 1 sui campioni sottoposti a differenti tempi di solubilizzazione, hanno messo in evidenza le tipiche caratteristiche microstrutturali di una lega ipoeutettica EN AC-42100 correttamente modificata. La presenza di intermetallici a base Fe si è dimostrata molto limitata, confermando il ruolo significativo della combinazione dei parametri di solubilizzazione ed invecchiamento sull’evoluzione delle proprietà meccaniche.
• Con specifico riferimento all’invecchiamento, è stato possibile constatare come per temperature di trattamento inferiori (135 °C e 160 °C) le più elevate proprietà meccaniche siano state ottenute per i tempi più elevati di permanenza all’interno del forno. Ciononostante, tutti i trattamenti di invecchiamento condotti a 135 °C non sono stati in grado di far superare i valori di soglia di Rp02 e Rm, posti rispettivamente pari a 210 MPa e 290 MPa. Considerando i valori di deviazione standard, tra tutti i trattamenti condotti a 160 °C solo un tempo di mantenimento pari a 360 min è stato in grado di garantire proprietà meccaniche adeguate. Al contrario, per temperature maggiori (200 °C), il punto di massimo delle caratteristiche meccaniche è stato raggiunto per la durata più breve del trattamento.
RINGRAZIAMENTI
Gli autori ringraziano l’Ing. Davide Gramigna per il fattivo contributo nello svolgimento delle attività sperimentali.
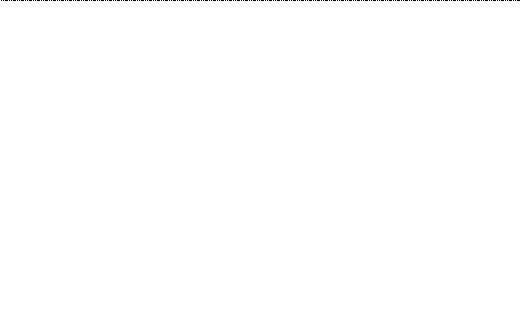
BIBLIOGRAFIA
[1] Kaufman J. G., Introduction to aluminum alloys and tempers, ASM International, Materials Park, 2000, p. 87.
[2] Stroh J., Sediako D., Hanes T., Anderson K., Monroe A., The effect of heat treatment on the microstructure and tensile properties on an HPDC marine transimission, Metals 11, 517, 2021, 1-17.
[3] Fortini, A., Lattanzi, L., Merlin, M. et al. Comprehensive Evaluation of Modification Level Assessment in Sr-Modified Aluminium Alloys. International Journla of Metalcasting 12, 697–711, 2018.
[4] Ibrahim M. F., Elgallad E. M., Valtierra S., Doty H. W., Samuel F. H., Metallurgical parameters controlling the eutectic silicon characteristics in Be-treated Al-Si-Mg alloys, Materials 9, 78, 2016, 1-17.
[5] Li R. X., Li R. D., Zhao Y. H., Li C. X., Sun X. F., Guan H. R., Hu Z. Q., Effect of heat treatment on eutectic silicon morphology and mechanical properties of Al-Si-Cu-Mg cast alloys, Transactions of Nonferrous Metals Society of China 14, 2004,496-500.
[6] Apelian D., Shivkumar S., Sigworth G., Fundamental aspects of heat treatment of cast Al-Si-Mg alloys, AFS Trans. 97, 1989, 727–742.
[7] Roy E. L., Castings, 9th Ed, ASM International: Materials Park, OH, USA, 1992, vol. 15, pp. 743-769.
[8] Chen R., Xu Q., Guo H., Xia Z., Wu Q., Liu B., Correlation of solidification microstructure refining scale, Mg composition and heat treatment conditions with mechanical properties in Al-7Si-Mg cast aluminum alloys, Materials Science and Engineering: A, vol. 685, 2017, pp. 391-402.
[9] Zhang D. L., Zheng L. H., StJohn D. H., Effect of a short solution treatment time on microstructure and chemical properties of modified Al-7wt.%Si-0.3wt.%Mg alloy, Journal of Light Metal, 2002, 27-36.
TORNA ALL'INDICE >
L’impiego di software dedicato all’analisi e alla convalida dei requisiti prestazionali del getto in funzione dei difetti di colata
a cura di: X. Yang, R. S. Rawal, F. BigliettiA seguito degli ultimi sviluppi tecnologici, la simulazione numerica e le tecnologie digitali stanno portando sempre maggiori vantaggi per i getti ottenuti per fusione, sia per il disegno delle colate e del sistema di alimentazione, che per la simulazione di flusso, termica, di stress e di microstruttura; questo porta benefici permettendo una migliore qualità dei getti e una riduzione dei costi.
L’impiego dell’Alluminio e le sue leghe si dimostra sempre più essere una valida alternativa a ghisa e acciaio, e nel settore automotive la produzione di getti per pressocolata è ampiamente diffuso. In questi anni, oltre alle applicazioni principali relative ai getti per basamenti e testate dei propulsori si sta avendo un progressivo aumento per le applicazioni riguardanti telaio, carrozzerie e componenti strutturali in genere.
Come risaputo ogni tipologia di metallo e/o lega metallica presenta i propri vantaggi e svantaggi e il fattore decisivo per un determinato impiego è la risposta che esso dà in termini di soddisfazione dei requisiti di progetto.
Riferendosi alla produzione di getti fusi, tipicamente, le disomogeneità nel metallo fuso dovute a porosità o inclusioni non sono considerate direttamente nella progettazione della parte, e vengono utilizzati fattori di sicurezza che spesso risultano essere critici, oltre ad influenzare la determinazione della massa del getto.
Un corretto approccio ingegneristico nella progettazione e nello sviluppo deve consistere nel considerare gli effetti delle diverse difettosità sulle prestazioni di servizio dei componenti fusi, tenendo ben presente che in funzione delle dimensioni e peso del getto, la conoscenza della posizione, della quantità e dell'effetto di esse sulla resistenza e sul comportamento alla fatica risulta essere più critica che mai.
Una soluzione software che permette di tener conto delle difettosità del materiale valutando le reali capacità prestazionali del getto oggi è di grande importanza per i progettisti. C3P Engineering Software mette oggi a disposizione il Cast Designer Performance come strumento avanzato di simulazione sviluppato appositamente per questo tipo di studio.
INTRODUZIONE
Il più alto volume di componenti utilizzato dalle case automobilistiche sono le parti in alluminio pressofuso. L’uso di questa tecnica si è ampliata negli anni anche alla produzione dei blocchi motore, includendo principalmente parti come testate dei cilindri, telaio e componenti del gruppo propulsore.
I requisiti molto elevati richiesti per le parti impiegate nel settore automotive, come durata della superficie, resistenza del materiale, ecc., vedono infatti l’impiego della lega di alluminio pressofuso preferita alla produzione in ghisa, grazie alle proprietà e caratteristiche metalliche che essa assume. La bassa densità dell'alluminio, ad esempio, conferisce una maggiore mobilità rispetto alla ghisa, fattore molto utile in spazi più piccoli. L’alluminio non arruggi-
Dipartimento Ricerca e Sviluppo, C3P Engineering Software International
yxj@c3p-group.com
raj@c3p-group.com
fbiglietti@c3p-group.com
nisce, per cui l’uso di una sua lega resiste alla corrosione in maniera molto più efficace, costituendo notevole vantaggio per l’impiego delle parti in ambienti difficili. Inoltre, l'alluminio è più facilmente riciclabile, rispetto alla ghisa. L'alluminio ha anche un'elevata conduttività termica ed elettrica che gli consente di raffreddarsi rapidamente dopo la sollecitazione termica a cui è sottoposto. Getti di alluminio vengono utilizzati comunque anche in diverse tipologie di parti, con varie applicazioni, come ad esempio componenti ingegnerizzati strutturali.
Per contro, uno dei principali inconvenienti dell’alluminio è che esso non è resistente come la ghisa ma comunque bisogna sempre tener presente che l’impiego di un metallo e delle sue leghe rispetto ad un altro, in un determinato impiego, presenterà sempre vantaggi e svantaggi il cui fattore decisivo per la scelta è sempre legato al comportamento e alle prestazioni di esso, in risposta alle condizioni di esercizio a cui è sottoposto.
METODOLOGIA
Tipicamente, le disomogeneità nel metallo fuso dovute a porosità o inclusioni non sono considerate direttamente nella progettazione della parte. Per sopperire ad eventuali deficienze di resistenza della parte sottoposta a lavoro, vengono utilizzati dei fattori di sicurezza che spesso portano ad avere progetti non ottimizzati per quantità di materiale impiegato. Il giusto approccio ingegneristico nella progettazione e nello sviluppo consiste nel considerare gli effetti della porosità sulle prestazioni di servizio dei componenti ottenuti per fusione. Man mano che i getti di ferro o acciaio diventano più leggeri e con sezioni più sottili, la conoscenza della posizione, della quantità e dell'effetto della porosità sulla resistenza e sul comportamento alla fatica è più critica che mai.
Nel caso dei getti, viene fatto ogni sforzo per produrre una parte solida e priva di porosità. Tuttavia, la porosità può ancora essere presente in una zona che non è critica o che non può essere eliminata senza costi irragionevoli, rendendo la parte tecnicamente complicata da colare. La microporosità può non comportare una perdita rilevabile di rigidezza, una concentrazione di sollecitazione localizzata o una ridistribuzione delle sollecitazioni, ma può influire notevolmente sulla duttilità e sulla resistenza alla fatica. Quando questa informazione viene combinata con la modellazione del processo di colata che prevede la posizione, la quantità e le caratteristiche dimensionali della micro e macro-porosità, ne emerge un processo di progettazione integrato
che consente ai progettisti di simulare i possibili effetti del processo di produzione del getto sulle prestazioni della parte nelle condizioni di esercizio reali. Ne consegue che tale processo di progettazione guiderà e migliorerà anche i criteri di verifica e controllo della parte stessa. Quando si utilizza come materiale di fusione non più la ghisa ma l’alluminio e si passa da un processo di colata per gravità alla pressofusione ad alta pressione, anche la porosità da gas e gli stress residui assumono maggiore importanza se si vuole tener conto dei difetti sulle prestazioni della parte finale. In questo caso i seguenti difetti di fabbricazione devono essere quindi considerati:
1) Porosità da ritiro del processo di colata
2) Porosità da gas del processo di colata, in particolare per la pressofusione ad alta pressione
3) Sollecitazione residua del processo di colata
In Cast-Designer è stato sviluppato un nuovo modulo strutturale chiamato Cast-Designer Performance (CDPE) per eseguire l'analisi delle prestazioni dei getti.
CDPE è un solutore FEM per modelli 3D sottoposti a carichi meccanici e termici. Un framework implicito viene impiegato per risolvere le equazioni globali non lineari dell'equilibrio ai nodi con un approccio incrementale-iterativo.
MODELLAZIONE E ANALISI
Flusso di lavoro CDPE
CDPE è un motore di analisi basato sulla tecnologia degli elementi finiti e completamente integrato nell'ambiente utente Cast-Designer. I file di input CDPE hanno una struttura straordinariamente semplice e di facile comprensione e sono direttamente generati dai modelli mesh prodotti da Cast-Designer o altri generatori di mesh.
Un flusso di lavoro semplificato prevede queste attività:
1) Generazione della mesh
2) Definizione dei dati del materiale, delle proprietà del modello, dei carichi/temperature ai nodi, dei carichi degli elementi (stress residui), delle condizioni al contorno, degli spostamenti e di altri parametri di controllo.
3) Esecuzione del solutore CDPE.
4) Controllo del risultato della simulazione per mezzo del post-processor.
Sollecitazione residua nel processo di colata
La colata è un processo in cui si manifestano sollecitazioni di ordine inferiore rispetto ad un processo di stampaggio, forgiatura e saldatura, ma a volte anche la sollecitazione
residua gioca un ruolo importante. Il solutore CDPE può accettare la deformazione residua e la sollecitazione come pre-deformazione e pre-tensione, quindi può importare direttamente il risultato della simulazione Cast-Designer standard. È possibile la selezione di uno fra gli step di calcolo per estrarne il risultato dello stress a cui può anche essere applicato un fattore per determinare eventuali condizioni speciali. Inoltre, la temperatura non uniforme della parte fusa può essere mappata direttamente anche sul modello CDPE.
Porosità nel processo di colata
Il risultato della porosità da gas (aria intrappolata) presente nel getto può avere una grossa influenza sulla tensione di trazione finale e sull’allungamento, e costituisce un fattore chiave per la determinazione delle effettive prestazioni finali del pezzo. Da parte delle industrie è sempre più ampia la richiesta di considerare l’effetto dell’accoppiamento dei difetti di porosità da gas e da ritiro nell’analisi delle prestazioni finali di una parte ottenuta per fusione.
Il flusso di lavoro dell’accoppiamento di porosità comprende i seguenti passaggi:
1) Attivare l'opzione 'includi il risultato porosità da gas e il risultato porosità da ritiro.
2) Selezione del file Cast-Designer che include il risultato della porosità da gas e da ritiro.
3) Definizione dell'oggetto nel modello di simulazione originale e nel modello CDPE; il nome della parte deve essere lo stesso. Poiché si studiano soltanto le proprietà della parte finale del getto, il sistema di gating, l'overflow e altri componenti inutilizzati possono essere separati da altri oggetti nella simulazione iniziale di Cast-Designer. Inoltre, poiché si utilizza la tecnologia di mappatura, gli elementi mesh del modello di simulazione del flusso termico e quelli del CDPE possono essere diversi, ma il sistema di coordinate deve essere lo stesso.
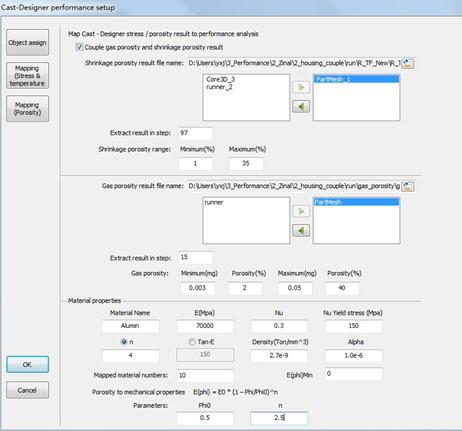
4) Definire lo step nel quale rilevare il risultato della porosità. Quello predefinito è l'ultimo step della simulazione iniziale.
5) Definire il valore minimo e massimo della porosità da ritiro. Se il risultato della porosità da ritiro è inferiore alla porosità da ritiro minima, verrà impostato a zero; se invece il valore è maggiore della porosità da ritiro massima definita, verrà impostato al valore massimo. Questo può rendere una simulazione CDPE più robusta.
Per la porosità da gas, il processo operativo è simile, ma bisogna convertire la dimensione della porosità da gas allo stesso livello standard della porosità da ritiro. Quindi considerare la presenza di entrambe le porosità. Per l'elemento con diverso livello di porosità (comprendendo sia la porosità da ritiro che la porosità da gas), in CDPE vengono assegnate diverse proprietà del materiale. Per quanto riguarda Il principale parametro che tiene conto della presenza di porosità per valutare le proprietà del materiale è il modulo di Young. La seguente formula viene utilizzata in CDPE
Dove E0 è il modulo di Young originale, φ è la porosità, φ 0 e n sono i parametri del materiale. È stato validato che, per acciaio e alluminio, φ 0 può essere impostato su un valore pari a 0,5 mentre n può essere impostato su un valore pari a 2,5. L'utente può definire i numeri di materiale corrispondenti a porosità di diverso livello, ad esempio 10 materiali. A seconda della distribuzione della porosità del modello, si suggerisce di usare da 10 a 20 materiali.
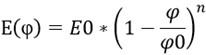
Risultati e discussione
A titolo di esempio e di discussione del tema in esame viene riportato di seguito uno studio affrontato nel settore automobilistico che riguarda un impianto frenante, e, nello specifico, il telaio di montaggio superiore del freno. Essendo quest’ultimo uno dei componenti chiave del sistema frenante, richiede un'alta qualità di fusione per assicurare prestazioni elevate. La figura 2 riporta il modello CAD 3D di un
telaio a montaggio superiore del sistema frenante automobilistico, originariamente progettato e prodotto mediante un processo di colata a gravità il cui materiale è ghisa. Tale materiale e processo esiste da molti anni ed è ampiamente utilizzato nell'industria automotive.
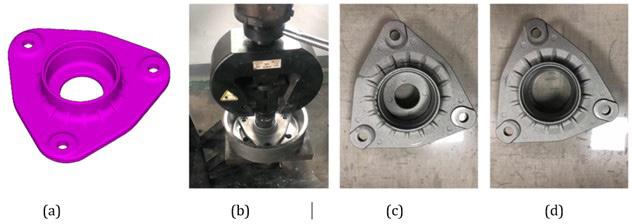
La Figura 2 (b) riporta il processo di test delle prestazioni. Un punzone si abbassa con una determinata forza per un dato tempo e se la parte non presenta conseguente rottura, allora soddisfa i requisiti di prestazione. Per questa parte, la forza minima richiesta è di 36KN, ma considerata la fatica della parte nell’impiego automobilistico, viene sempre utilizzato un fattore di sicurezza da 1,5 a 2. Per ridurre il peso della parte e migliorare la velocità di produzione, si suggerisce l’alluminio come materiale da impiegare e di passare dal processo di colata in sabbia a quello di pressofusione ad alta pressione. Si devono mantenere gli stessi requisiti di prestazione.
Tuttavia, nella reale condizione industriale, tale cambiamento non risulta così semplice. Dopo aver cambiato il materiale e il processo di colata si è sottoposto il pezzo ottenuto al test di qualità, riscontrando una riduzione del rapporto di resa dal 99% (ghisa) al 70% (alluminio), risultato ovviamente non accettabile. La Figura 2 (c) e (d) mostra il danneggiamento della parte e la frattura nella parte in alluminio. Il problema si è dimostrato essere abbastanza stabile e si è così proceduto ad affrontare la causa del problema e trovare una soluzione.
Modello di simulazione numerica del test di prestazione Come risaputo vengono da anni utilizzati software di simulazione numerica per il test delle prestazioni i cui risultati però non tengono conto della presenza dei difetti di colata che, come discusso in precedenza, svolgono invece un ruolo importante per la determinazione del reale comportamento della parte soggetta a sollecitazioni.
In questo documento, il CDPE è stato utilizzato per la simulazione della performance.
In Figura 3 viene mostrato in (a) la condizione al contorno del modello di simulazione CDPE; in (b) il risultato della simulazione rappresentante lo spostamento e in (c) il risul-
tato della simulazione rappresentante la forza di contatto. I parametri di simulazione di base del modello sono quelli di seguito.
Tipo di Analisi
Solver
Resistenza a rottura
Cast-Designer Performance (CDPE)
Tipo di Solver Implicito
Tipo di Elementi Esaedri
Materiale Gisa o Alluminio
Processo di colata per gravità e simulazione
Per tener conto dei difetti del processo di colata, vi è bisogno di informazioni dettagliate sul processo stesso, la simulazione numerica è anche il modo migliore per farlo. A tal scopo viene utilizzato il software di simulazione Cast-Designer. Il processo di fabbricazione di origine è relativo a colata di ghisa in sabbia con materiale di colata GGG40. La temperatura di colata è di 1370 gradi ed il tempo di riempimento inferiore a 30 sec. Come da esperienza pratica non è necessario aggiunger materozze a questa parte. Il sistema di colata è progettato con l’ausilio del Cad 3D incluso in Cast-Designer. La Figura 4 mostra il processo di colata in dettaglio per la parte in ghisa include sia il riempimento che la solidificazione: (a)-(d) riporta il processo
di riempimento; (e)-(f) riporta i punti caldi del processo di solidificazione. Il contorno di varie colorazioni da (a) a (d) indica il range di temperatura.

È chiaro che il processo di riempimento risulta abbastanza stabile, senza alcun rischio di grandi turbolenze e intrappolamento di gas, inoltre la distribuzione della temperatura è ragionevole per cui la porosità del gas del processo di riempimento risulta piuttosto limitata. Il risultato della solidificazione mostra che l'ultima regione solida si trova nella parte centrale del getto prossima all’anello, per cui in tale regione possono esistere porosità da ritiro o microporosità. Considerando l'espansione del materiale GGG durante la solidificazione, anche la porosità da ritiro finale è molto ridotta. Le foto a raggi X hanno confermato questo risultato della simulazione. Eseguendo poi anche la simulazione dello stress di tale processo si riscontra che lo stress residuo risulta molto piccolo nella parte finale. Verrà poi utilizzato il risultato della simulazione di cui sopra per la simulazione delle prestazioni della parte nella fase successiva.
Processo e simulazione di pressofusione ad alta pressione
Per migliorare la velocità di produzione e la manutenzione, per ottenere uno standard di qualità più consistente e una buona qualità della superficie, il nuovo processo
di produzione introdotto, come citato e proposto all’inizio, è la pressofusione ad alta pressione (HPDC), con uno stampo a due impronte. La figura 5 mostra i dettagli del processo di riempimento. Anche in questo caso il sistema di colata è stato progettato con il sistema Cad 3d integrato in Cast-Designer. Dalla simulazione ne risulta in generale che il sistema di iniezione è abbastanza efficace, il processo di riempimento è equilibrato e il sistema di overflow valido. Si è riscontrato altresì un problema all’attacco di colata che viene riempito alla fine dal metallo liquido, e questo può comportare in tale regione il rischio di intrappolamento di gas.
Dopo la simulazione, utilizzando gli strumenti dedicati all’analisi di intrappolamento dei gas, possiamo avere la distribuzione finale della porosità del gas e della porosità da ritiro a seguito della solidificazione. La Figura 5 mostra entrambi i risultati di porosità. Dal risultato della porosità del gas, abbiamo scoperto che la massa di gas bloccata vicino all’attacco di colata risulta maggiore che in altre regioni, quindi costituisce un rischio per la formazione e la crescita di fratture. La porosità da ritiro è risultata essere abbastanza simile al processo di colata a gravità. Ciò dipende principalmente dalla forma geometrica della parte

fusa. Anche in questo caso viene eseguita la simulazione per l’identificazione degli stress relativi a tale processo di pressofusione ad alta pressione e anche lo stress residuo
rilevato risulta essere piccolo nella parte finale. Il risultato di questa simulazione verrà usato nella fase successiva per la simulazione delle prestazioni del getto.
Simulazione CDPE: influenza dei difetti di colata
Con i risultati della simulazione relativi ai due processi di produzione visti, possiamo iniziare ora la simulazione delle prestazioni della parte per mezzo di Cast-Designer Performance (CDPE).
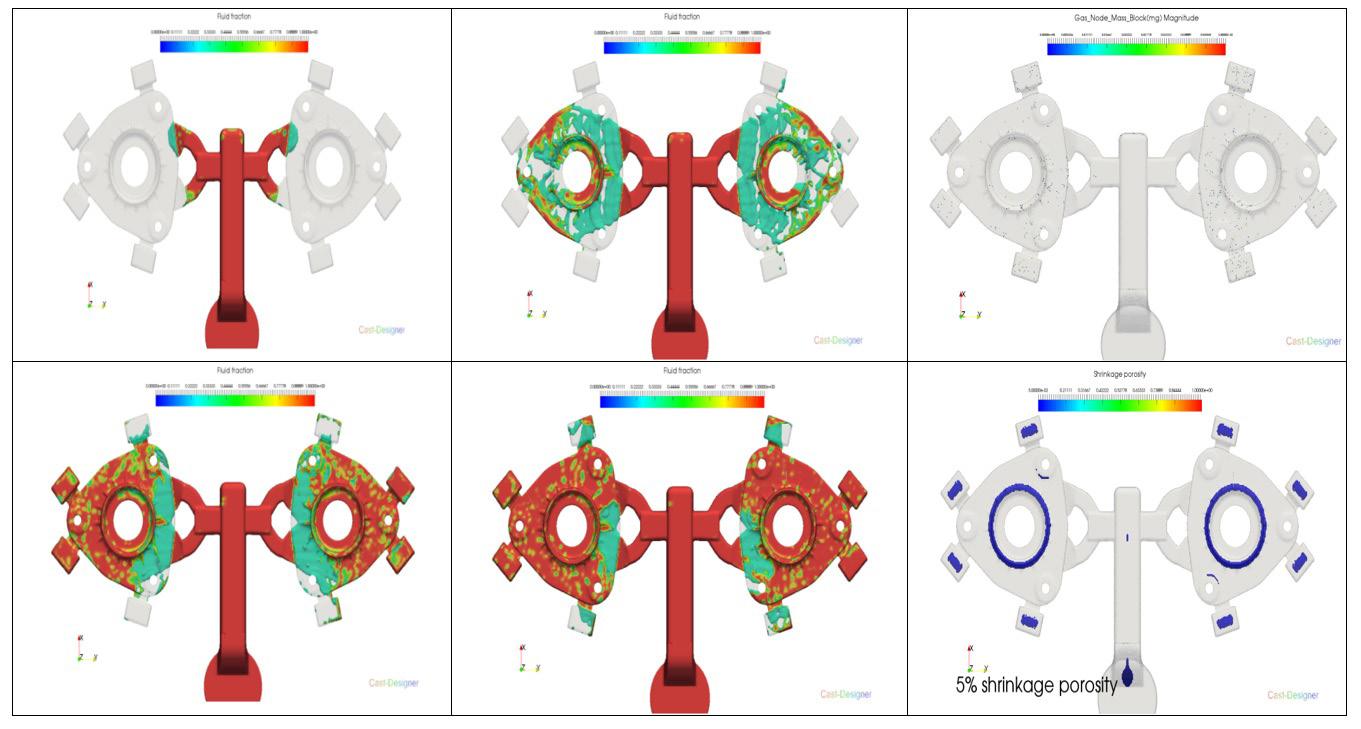
Cast-Designer Performance (CDPE), completamente integrato nell'ambiente utente Cast-Designer, è un software di progettazione basato su modelli che usa un’interfaccia intuitiva. L'utente deve solo seguire le linee guida del processo passo dopo passo, quindi completare l'impostazione del modello. È molto potente e flessibile e di facile utilizzo. Osserviamo che a differenza dei tradizionali software FEM che in generale richiedono tempi lunghi di
apprendimento, con CDPE bastano invece poche ore. L'utente può utilizzare in CDPE lo stesso modello mesh utilizzato per la simulazione di colata; il tempo necessario per creare lamesh è molto ridotto e il processo avviene in maniera completamente automatica. L'analisi dei risultati di CDPE è come qualsiasi altro software di analisi strutturale e viene effettuata all’interno dello stesso post-processor di Cast-Designer. Inoltre, CDPE supporta modelli di grandi dimensioni e la sua capacità di calcolo in parallelo consente di ridurre notevolmente i tempi di elaborazione.
La Figura 6 mostra il risultato della simulazione di CDPE, in cui la forza del punzone di prova ricordiamo essere di 36KN (come Figura 2). In figura 6 A ed A' sono relativi alla parte in ghisa ricavata dalla colata in sabbia, mentre B e B', C e C' sono relativi alla parte in alluminio realizzata mediante pressofusione ad alta pressione. In particolare, B e B' non includono i difetti di colata mentre C e C' considerano lo stress residuo e l’effetto della porosità. Il Damage
Crack Criteria (DCC) può essere utilizzato per valutare la sicurezza della parte fusa in differenza di forza applicata. Il DCC è stato calcolato con la formula riportata di seguito. Come sappiamo, la massima sollecitazione di taglio in un punto del materiale sarà uguale alla metà della differenza tra la massima e minima sollecitazione principale, per cui si scrive la seguente equazione.
Si determina il valore dello sforzo di taglio corrispondente al limite di snervamento del materiale. In caso di tensione semplice, lo stress sarà presente solo in una direzione e quindi al limite elastico le sollecitazioni principali saranno σ t, 0 e 0.
Valore dello sforzo di taglio corrispondente al limite di snervamento del materiale = (1/2) x σ t Scriviamo di seguito la condizione limite di crisi
Se impostiamo lo snervamento del materiale come σ y, avremo la seguente formula
Nella formula, se K>= 1, allora si verificherà la crisi se K<1, il materiale sarà sicuro. Si può considerare anche il fattore di sicurezza, ad esempio pari al 30%, quindi se il valore è maggiore di 0,7, allora

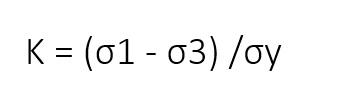
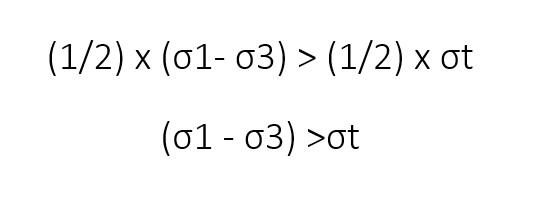
dobbiamo considerare il rischio di frattura. Nelle immagini seguenti, il contorno è la K ottenuta come discusso sopra. Questo si può definire come DCC (Damage Crack Criteria).
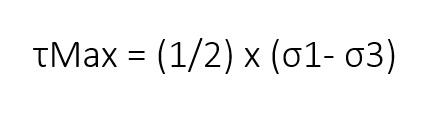
Per i test delle prestazioni, con una forza applicata di 36 KN, anche se impostiamo il 30% come fattore di sicurezza, tutti e tre i casi A, B e C sono abbastanza sicuri. Osserviamo però che la forza di resistenza del caso B è più debole di quella di A mentre nel caso C risulta essere più debole di quella del caso B. Dal caso B/B' e dal caso C/C', possiamo scoprire che i difetti produzione del getto giocano un ruolo importante nelle prestazioni della parte finale. Nelle condizioni di lavoro reali, sono sempre presenti fenomeni di fatica e di sovraccarico, quindi dobbiamo anche aumentare la forza di test per la verifica delle prestazioni. Per questa parte, viene sempre applicato il doppio della
forza di progetto secondo l'esperienza industriale, per cui usiamo un carico di 70KN per verificare le prestazioni. La figura 7 mostra il risultato della simulazione di una forza applicata di 70 KN, tutte le altre condizioni e i criteri di analisi restano gli stessi di cui sopra. In queste condizioni, la parte in ghisa è risultata ancora sufficientemente sicura ma la parte in alluminio subisce già un danneggiamento (la regione rossa in B, B', C e C'), soprattutto per il caso C. La regione danneggiata risulta intorno all'anello interno (B e C) e attorno all'anello esterno (B' e C').
Il risultato della simulazione ha avuto un ottimo accordo con il risultato effettivo del test. La Figura 8 (a) mostra i dettagli della frattura della parte reale e (b) è il risultato della simulazione CDPE. Portando a confronto solo la parte di prova effettiva con B' nella Figura 7, si scopre che è simile ma non esattamente uguale, specialmente per la direzione di crescita della frattura. Quindi risulta chiaro che i difetti del processo produttivo devono essere considerati opportunamente per avere un risultato di simulazione virtuale più accurato del getto finale.
Un altro aspetto molto interessante è il seguente: nella Figura 8 (b), quando si è confrontata la cricca del test reale e la distribuzione della massa di gas bloccata del processo HPDC Figura 8 (c) abbiamo rilevato che la direzione di crescita della frattura seguiva quasi quella dal gas bloccato.
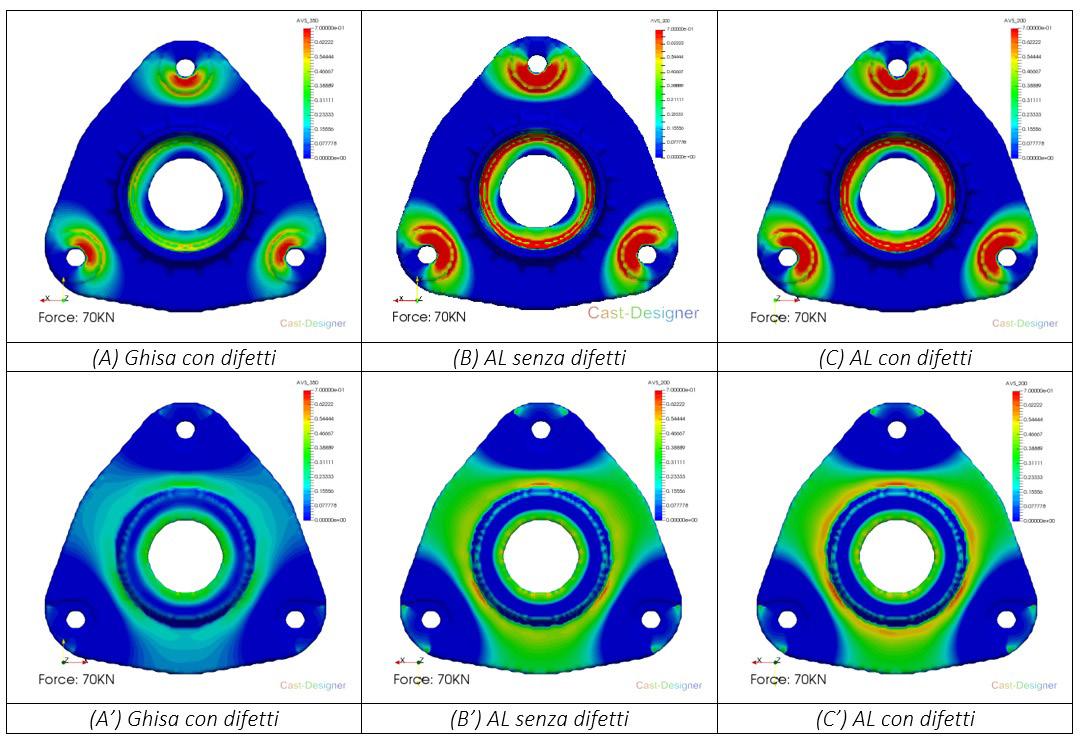
In considerazione di quanto sopra, se ne trae che è possibile sostituire il materiale della parte passando dalla ghisa all’alluminio, ma la resistenza alle sollecitazioni viene ridotta e il rischio di frattura aumenta. Questo cambiamento del processo di produzione riduce quindi la resistenza dal 99% al 70%. Per migliorare la produzione, proviamo ad apportare alcune modifiche al design della parte.
Nuovo piano di progettazione
Poiché eventuali modifiche geometriche della parte sono spesso legate a vincoli di progetto come, ad esempio, mantenere tutte le caratteristiche della funzione e nessuna possibilità di intervenire anche sull’assieme che contiene il componente, questo tipo di modifica deve essere effettuata sulla base di una comunicazione completa con il cliente. Per il telaio di montaggio superiore, come studio
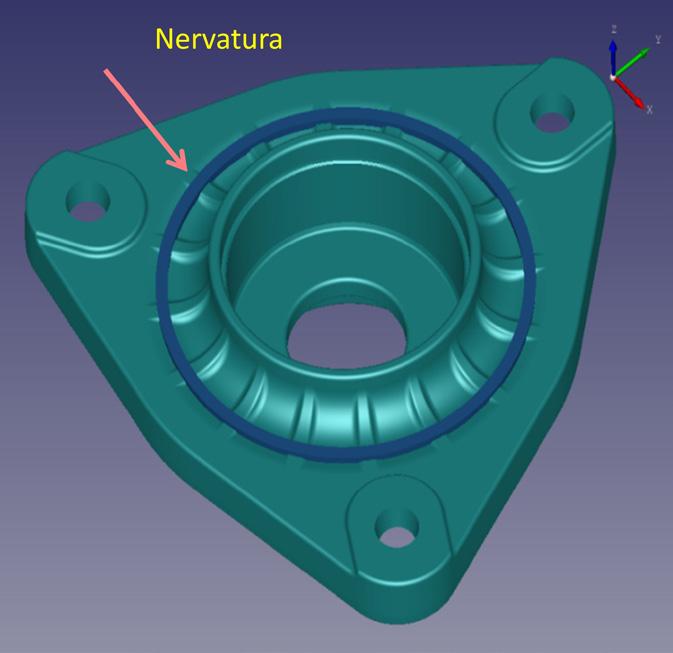
di dettaglio e discussione, proviamo ad aggiungere una nervatura ad anello attorno al cilindro esterno della superficie superiore per migliorare la rigidità della parte. Questa modifica non porta alcuna influenza sul requisito della funzione e sull'assemblaggio (Figura 9). Poiché questo è il concetto di progettazione iniziale, eseguiamo l'analisi della struttura in CDPE in modo semplice senza considerare i difetti di colata in questa fase. Ma come il risultato della Figura 7, possiamo avere un'idea di base sugli effetti delle difettologie causate dal processo di produzione.
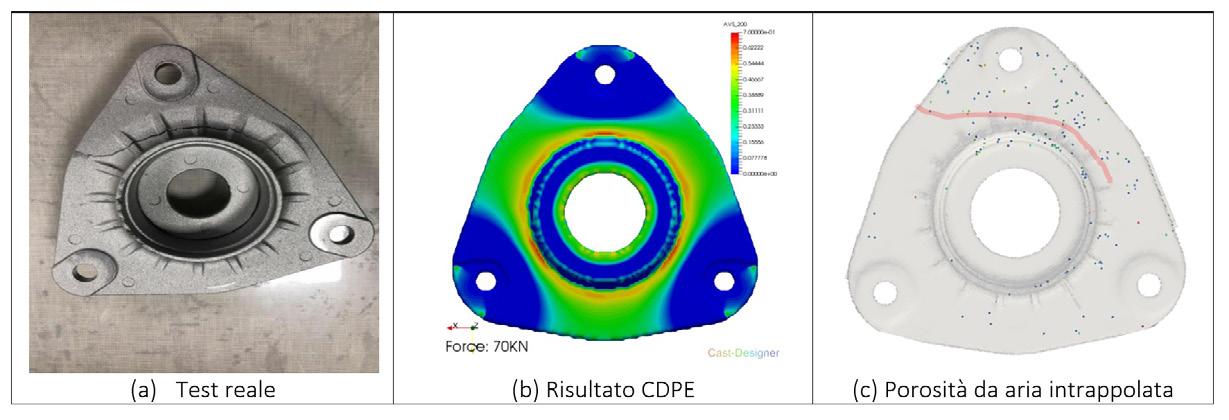
Dalla Figura 10, si riscontra che il nuovo piano di progettazione può migliorare i criteri di danno e modificare la distribuzione DCC (A1 vs. B1, A2 vs. B2), anche la distribuzione della deformazione totale presenta una differenza minore (A3 vs. B3). Tale nervatura aggiunta all'anello migliora la rigidità della parte originale specialmente per la regione della frattura, elevando così le prestazioni come risposta alle sollecitazioni. Un'altra questione fondamentale per migliorare la resistenza al danno è aumentare lo snervamento del materiale, perché lo snervamento dell'alluminio dato era solo 200 MPa ma nel materiale di ghisa era superiore a 300 MPa. La regolazione della composizione chimica può aiutare in questo. In conclusione: l'azienda approva il piano di modifica della geometria e migliora la composizione della lega del materiale, in tal modo il rapporto di resistenza è aumentato con successo al 96%. Il risultato del getto ottenuto risulta quindi abbastanza simile a quello di materiale in ghisa, ma il tasso di produzione è 20 volte superiore rispetto alla colata in sabbia.
CONCLUSIONI
Il modulo software di analisi delle prestazioni Cast-Designer è uno strumento utile per valutare le prestazioni di un getto, e ben si integra con il solutore termico, di flusso e di sollecitazione di Cast-Designer. CDPE può gestire dati materiali molto complessi includendo l'influenza della
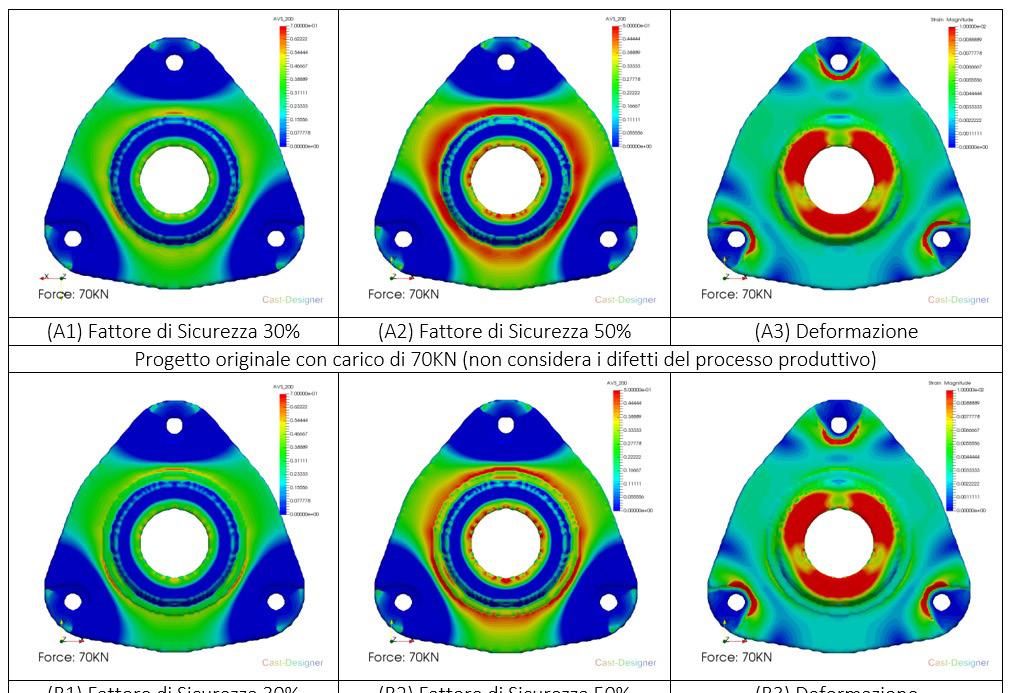
porosità da ritiro e della porosità da gas, nonché lo stress residuo. Tali difetti dovuti al processo di fabbricazione possono avere un grande impatto sulle prestazioni finali. Il sistema Cast-Designer diventa una soluzione completa per l'intero processo produttivo del getto. Tutti i dati possono essere utilizzati per gestire la progettazione, la valutazione e l’ingegnerizzazione del getto.
RINGRAZIAMENTI
Si desidera ringraziare il Sig. Ma Mingtuan e il Sig. Gong Hongtao del CSSC No. 12 Research Institute, Cina per il loro contributo al test degli esperimenti e alla convalida del modello.
BIBLIOGRAFIA
[1] A.A. Luo, “Magnesium casting technology for structure applications,” Journal of Magnesium and Alloys, vol. 1, pp. 2–22, 2013.
[2] K.K.S. Thong, B.H. Hu, X.P. Nui and I. Pinwill, “Cavity pressure measurements and process monitoring for magnesium die casting of a thin-wall-hand-phone component to improve quality,” J. Mater. Process. Tech., vol. 127, pp. 238–241, 2002.
[3] Piyanut Meethum, Chakrit Suvanjumrat, “Evaluate of Chill Vent Performance for High Pressure Die-Casting Production and Simulation of Motorcycle Fuel Caps”, MATEC Web of Conferences 95, 07025 (2017) DOI: 10.1051/matecconf/2017950, ICMME 2016
[4] P. Meethum, C. Suvanjumrat, “Porosities Comparison between Production and Simulation in Motorcycle Fuel Caps of Aluminum High Pressure Die Casting”, World Academy of Science, Engineering and Technology International Journal of Mechanical and Mechatronics Engineering Vol:9, No:3, 2015
[5] RICHARD A. HARDIN, CHRISTOPH BECKERMANN,“Prediction of the Fatigue Life of Cast Steel Containing Shrinkage Porosity”, The Minerals, Metals & Materials Society and ASM International 2009, VOLUME 40A, MARCH 2009—581
[6] P. Kavya Aahalda, P. Alen Thomas, Jayanth Ivvala, SaiKiran Neela “Optimal feeder design of Oldham’s coupling by using Casting simulation Technology”, INTERNATIONAL JOURNAL OF SCIENTIFIC PROGRESS AND RESEARCH (IJSPR) ISSN: 2349-4689, Volume-19, Number - 01, 2016
[7] Rajesh Rajkolhe, J. G. Khan, “Defects, Causes and Their Remedies in Casting Process: A Review”, IJRAT, Vol.2, No.3, page no.379, March 2014
[8] M. Jagdishwar, “Casting Feeder Design Optimization Based on Feied Path and Temperature Analysis”,Technical papers, E- Foundry, IIT-B, June 2012
[9] Rabindra Behera , Kayal.S , Sutradhar.G , “Solidification behavior and detection of Hotspots in Aluminium Alloy castings: Computer Aided Analysis and experimental validation”, INTERNATIONAL JOURNAL OF APPLIED ENGINEERING RESEARCH, DINDIGUL Volume 1, No 4,abstract,2011.
Vacuum cap (VCAP) technology for enhanced material properties in advanced air casting applications
edited by: I. Vicario, M. CaglieroAir melting processes can suffer from limited control of alloy cleanliness composition. Oxygen and nitrogen levels change from heat to heat, and the current practice to decrease them is to add virgin material because deoxidation with only aluminum could cause non-metallic inclusions. Low vapor pressure tramp elements like Pb, Bi, Zn, etc. are reduced via dilution. The reduction of carbon is also a metallurgical challenge in air melts. VCAP furnaces are a hybrid of air induction and vacuum refining capability. Once the main charge is melted in air, a vacuum cap is applied that can produce a significant degassing effect for reduced casting defects, removal of tramp elements and decarburization.
Our results from research and production units will show improved mechanical properties and better microcleanliness. We present the main features of the VCAP technology as a recommended technique to obtain enhanced material properties and a more reliable air casting process.
INTRODUCTION
Air induction melting technology is a very common and extensive manufacturing method used all over the world, which enables producing complex castings on many different types of alloys. However, performance requirements on alloys are becoming more stringent for end users in industries such as aerospace, medical, power generation, oil and gas, specialty automotive and trucks. These requirements include few if any defects and better mechanical properties. However, these properties are difficult to attain using standard air-melting techniques.[1]
In this point, VCAP technology becomes a great solution to face all these challenges because of the advantages unique to the vacuum induction melting process, such as excellent control over the entire alloy chemistry, not only the desired alloy composition but also the beneficial trace elements and harmful impurities. Additionally, the reproducibility of precise composition control from heat-to-heat is exceptional and results in a remarkable
consistency of material properties at high levels.
VCAP technology, shown in Figure 1, is a hybrid process that combines the techniques from air melting and vacuum induction melting ones (VIM). It is essentially an
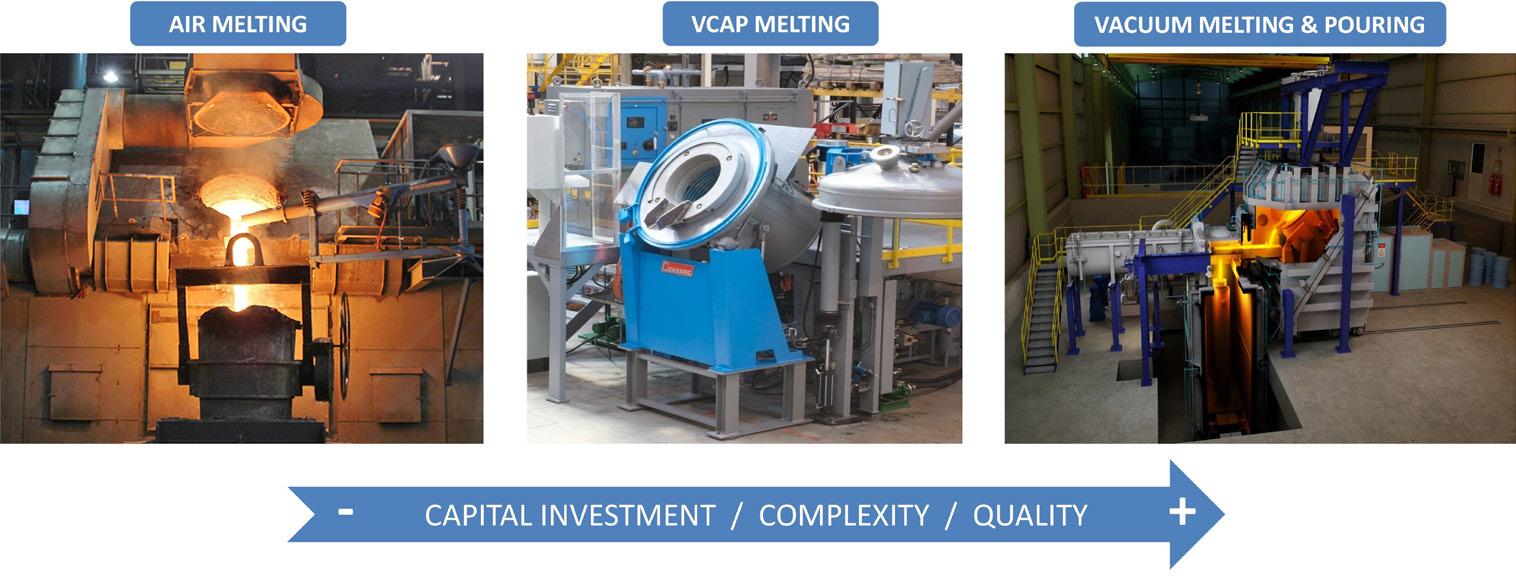
air melting furnace that includes a cap that can be placed on the top of the induction melting coil enabling vacuum degassing cycles once the alloy is fully melted in air.
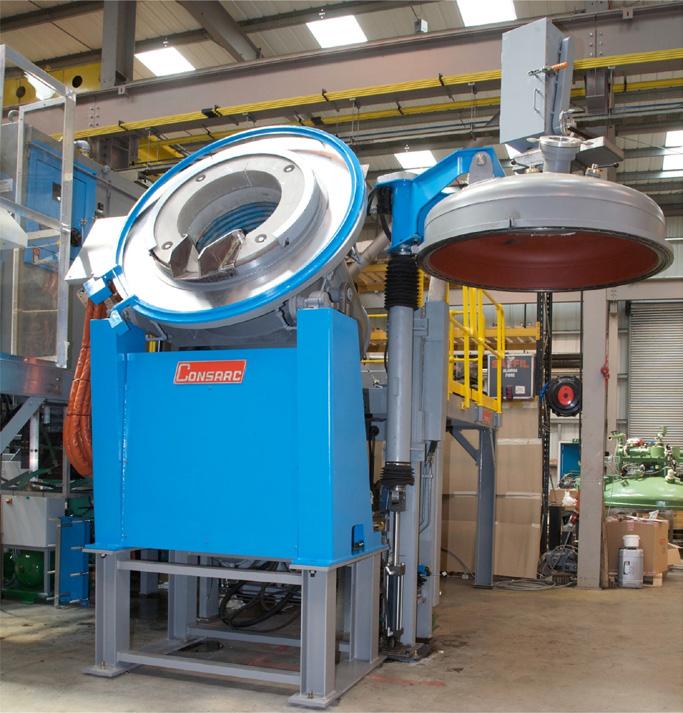
Figure 2 explains the basics about VCAP technology showing on the left hand-side an air melting furnace, on the right-hand side a vacuum induction melting furnace, and finally, the VCAP furnace in the middle, shown as a hybrid technology between the other two technologies. There is an arrow indicating that capital investment, complexity and quality of the material produced increases as you progress from left to right.
The position and application of the main specialty melting processes for High Performance Alloys (HPA) is best illustrated in a flow diagram. Figure 3 shows the principal production methods for wrought and cast premium quality intermediate products.
The primary melting products become the feedstock for subsequent secondary melting processes to produce the intermediate and final product forms for thermomechanical processing, powder consolidation work or investment casting.
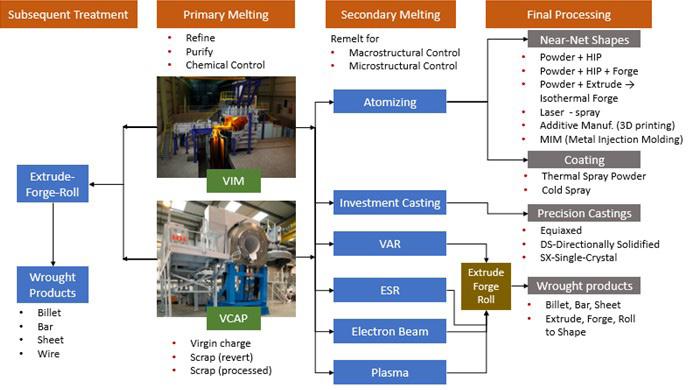
VCAP main highlights
VCAP technology includes the following main highlights that make it an advantageous option compared to air melting technology:
• It is available in a wide size range from 50kg to 20,000kg:
o This allows customers to choose furnaces sized for small pour weights or research purposes, and also for large pour weights.
• Vacuum levels ranged from 100mbar to 0.01mbar:
o This means pressure levels from low vacuum range close to atmospheric pressure, with or without argon partial pressure, to quite high vacuum levels.
o More precise chemistry control of the alloy.
o Vacuum levels highly depend on the C and O composition and following decarburization reaction.
• Argon partial pressure atmosphere melting also available.
• Argon/nitrogen porous plug systems are available for additional agitation inside the melt and then, promote good mixing, degassing and overall metallurgical reactions.
• Can be used to process almost all metals:
o It is available to melt and mix of selected raw materials / revert.
o Many different material types such as stainless steels including duplex and super duplex, austenitic stainless steels, carbon steels, nickelmolybdenum-chrome alloys, high speed tool steels, iron-nickel-chrome heat resistant alloys, iron-cobalt-chrome heat-resistant alloys, nickel superalloys, nickel copper alloys, nickel-cobalt alloys, pure copper, etc.
• Some different metallurgical processes may be achieved:
o Reduction of hydrogen, oxygen and nitrogen (vacuum degassing).
o Reduction of low vapour pressure tramp elements like Pb, Cd, Bi, Zn.
o Deoxidation using combination of vacuum and C-O reaction.
o Decarburization - intensified C-O reaction at low pressure enabling excellent decarburization for extra low carbon levels (improvement of alloy
workability/machinability).
o Desulphurisation (limited) – Use of reducing slags and / or powder injection in air or controlled atmosphere
• Better micro-cleanliness due to strong carbon deoxidation and smaller residual inclusions, and subsequent:
o Increase of the fluidity of the metal, which improves filling of the mold.
o Significant improvement of mechanical properties.
o Improvement of technological characteristics like hot workability, weldability and machinability.
o Significantly reduced scatter in product properties and characteristics, so less rejections.
MAIN APPLICATIONS
Overall, VCAP technology focuses on high-quality foundry applications that do not require complete vacuum melting, but where air melting does not produce good quality castings.
Here are some examples of VCAP specific applications:
• Investment Casting Foundries: higher-end air melt business.
• Nickel and super alloy melters: lower grade alloys not requiring VIM.
• Steel foundries.
• Steelmakers.
• Stainless steel melters: where VCAP shows better decarburization levels compared to AOD, and with much smaller size.
• Non-ferrous applications:
o Copper.
o Aluminium.
• Metal powder production plants.
• Others.
The following list summarizes some specific examples of materials processed by VCAP technology:
• Stainless steels including duplex and super duplex: ASTM Gr4A, Gr5A, Gr6A, EN 1.4517, 2507,
• Austenitic stainless steels: AISI 304.
• Carbon steels.
• Nickel-Molybdenum-Chrome alloys: Hastelloy B/C, Alloy 59.
• High speed tool steels: 1.3243.
• Iron-Nickel-Chrome heat resistant alloys: ASTM A297, ASTM A351/CF3/CF8 and its variations, EN 10283 GX4CrNi13-4.
• Iron-Cobalt-Chrome heat-resistant alloys: UmCo50.
• Nickel superalloys: Alloy 625, Hastelloy C22.
• Nickel steels: A352LC3.
• Nickel Copper alloys: Monel 500.
• Nickel-Cobalt alloys: MARAGING 350
• High purity Copper.
PROCESS STEPS
Essentially, VCAP process has 3 big steps that will be detailed below (also shown in the figure 4 below):
• Atmosphere charging (cap OFF step)
This is with the chamber open to atmosphere
1. The alloy is charged inside the melting furnace.
2. Once the alloy is charged, the power is switched on and melting starts.
3. When the alloy is fully melted, a first temperature reading is taken by using a hand immersion thermocouple.
• Cap ON step
Induction power remains still on.
4. The cap is moved into position over the furnace.
5. Once the cap is in position, evacuation of the chamber starts.
6. Once the target vacuum level is reached, flow of bottom porous plug is activated.
7. Additional charges are made as required through an auxiliary chamber.
8. Temperature is measured under vacuum (through an auxiliary chamber too), and melting power adjusted accordingly.
9. Sample is taken to check the chemistry.
10. Additions are done based on the chemistry obtained. Additional sampling for chemistry may be performed if necessary.
11. Once the desired final values are obtained, the melting chamber is backfilled using gas (air, argon, nitrogen) as required.
• Pouring/Tapping
12. The cap is removed again after the chamber is vented.
13. The final pouring is done. Eventually, there might be some final temperature measurements just before pouring to adjust the induction melting power.
*Melting might also be done under vacuum **Pouring may be done with cap ON in specific VCAP furnaces.
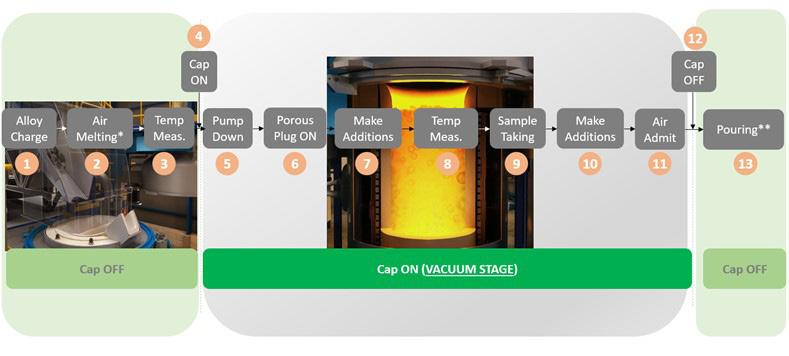
Case study at Brno University of Technology
The following cases studies are within the partnership with Brno University of Technology. The VCAP furnace installed at Brno University is an 80kg melt size Consarc VCAP furnace as seen in figure 5. The experiments are usually performed together with experimental calculations of activities based on the chemical composition and comparison of the results of the measured activities. It also approaches the evaluation of the microstructure or mechanical properties. For the
department of Foundry Engineering at Brno University of Technology, students participate in research as part of their diploma thesis in order to gain practical experience in conducting and evaluating experiments. [4], [5]. The following table presents some examples of the benefits obtained from the VCAP technology tests. It includes different experiences with different alloys, and with different metallurgical objectives for each one of them:
In case study number 1 described above, done with 1.3243 tool steel, were carried out some industrial trials using the VCAP furnace to compare air-melted parts vs. VCAP melted castings. The intention was to obtain a better understanding of gas-related casting defects such as pinholes, nitrides, oxides, and gas porosity. To a certain degree, gas levels can be controlled in air melting using deoxidation agents such as aluminium.
However, this can cause different issues like non-metallic inclusions. Consequently, a vacuum treatment can be applied but can add significant costs to the entire process. Therefore, a vacuum treatment was tried and validated against a traditional air melt process. For trial purposes, a 1.3243 tool steel was chosen due to its sensitivity for gas solubility. [3]
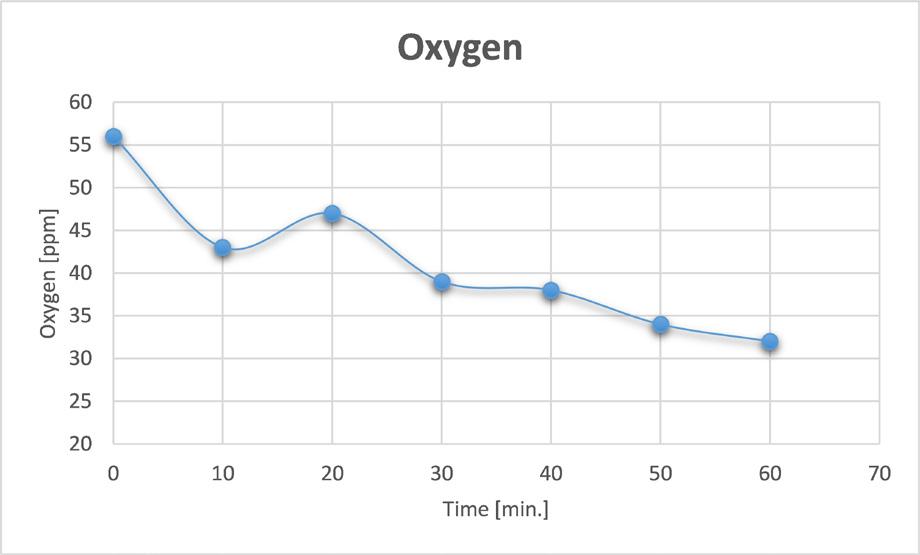
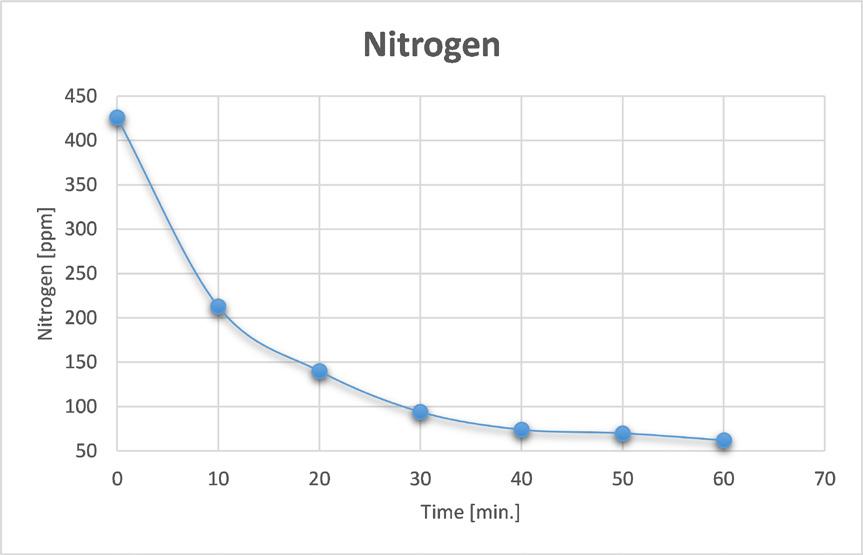

The following picture shows an example of the internal casting defect:
As a conclusion from the tests done, it was noticed that the VCAP melt shows a significantly lower gas level compared to an air melted alloy. Additionally, no significant loss of alloying elements was observed during VCAP melting. The microstructure is currently being examined and shows promising first results; however, no data can
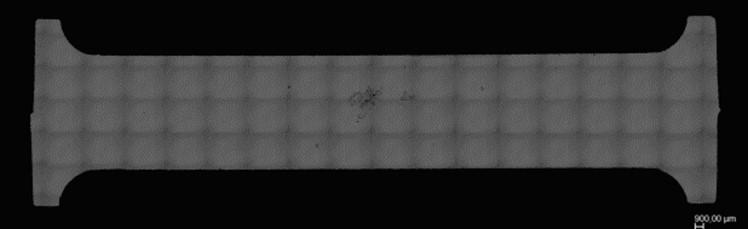
be published yet. [3]
Case studies from production sites
The following cases studies summarize the tests done at production sites:
The following picture shows a real tapping stage from a VCAP furnace in a production site:
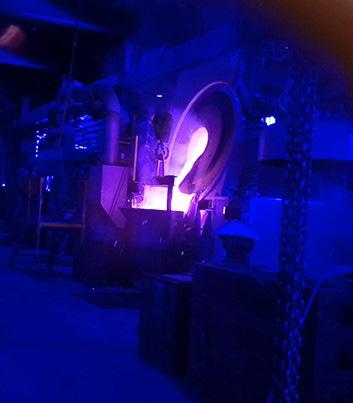
FINAL CONCLUSIONS
VCAP technology is a hybrid technology between existing air melting and vacuum melting technologies. It combines the simplicity of air melting process and benefits from vacuum melting, such as reduction of deleterious gases like Hydrogen, Oxygen (by deoxidation) and Nitrogen, low vapour pressure tramp elements like Pb, Cd, Bi, Zn.
Moreover, VCAP process can also perform decarburization and desulphurisation reactions to reduce Carbon and Sulphur respectively.
As a result of the benefits of VCAP technology, foundries can achieve process improvements and significantly reduce scatter in product properties and characteristics, so a more consistent casting process and less rejections on cast parts. This is because VCAP enables better chemical control of the alloys casted, better micro-cleanliness, clear improvement of mechanical and foundry properties, and an improvement of technological characteristics, like hot workability, weldability and machinability.
CROSS REFERENCES
[1] Carpenter Technology: outlines how high-tech melting creates high-performance metal alloys
[2]. Evaluation of technological properties of high-alloyed chromium-nickel steels. Myška Martin. Brno University of Technology.
[3]. VCAP tests done at Brno University with 1.3243 tool steel alloy.
[4]. Šenberger, J. A V. Pernica. Contribution to Deoxidation of Austenitic Steels in a Vacuum Induction Furnace with carbon. Archives of Foundry Engineering. 2015, 15(2), 105-109. ISSN 2299-2944. Dostupné z: doi:10.1515/afe-2015-0048.
[5]. Záděra, A., M. Dulava, V. Pernica A V. Kaňa. Oxygen Activity in Melts of Fe-C-Cr-Ni Based Alloys. Archives of Foundry Engineering. 2016, 16(4), 181-186. ISSN 2299-2944. Dostupné z: doi:10.1515/afe-2016-0106.
[6]. J.W. Pridgeon et al., in Superalloys Source Book, American Society for Metals, 1984, p 201–217
TORNA ALL'INDICE >
Anewapproachon hydrogenpermeationfor enamellinggradesteels
editedby:C.M.Belardini,S.Corsinovi,R.Valentini,M.DeSanctis,B.D.Monelli,M.LeveauxHydrogen diffusivity is strongly affected by the presence of traps, which are defects of the metal matrix that offer a location for hydrogen atoms with a lower energy state than regular interstitial lattice sites. The study of hydrogen diffusion is relevant for multiple different reasons, according to the specific application that is considered. In the context of enamelling grade steels, hydrogen is the cause of the defect known as fishscaling, or the detachment of enamel pieces from the metal surface. Study of hydrogen trapping and diffusion is part of the process of understanding fishscaling, since for many materials, a strong link was found between high diffusivity and fishscaling susceptibility. This study is performed with the use of hydrogen permeation tests, but the interpretation of permeation data is not straightforward because of the trapping effect. In this paper, temperature programmed desorption tests were performed on enamelling grade interstitial free steels to provide an initial understanding of the type of traps expected. Then hydrogen permeation tests were performed to further characterize the trapping parameters of the materials. Common methods to estimate the apparent diffusivity were compared, and the experimental curves were reconstructed using McNabb and Foster’s trapping and diffusion model. Finally, a simple method is proposed that may lead to simple empiric formulae to estimate trapping parameters from permeation tests for specific families of materials, possibly overcoming the issues inherent in employing the common and simplified apparent diffusivity approach.
INTRODUCTION
Enamelling steel products are commonly used for domestic and sanitary appliances or in architecture. Enamelling steels have excellent resistance to typical conditions expected for their applications (corrosion protection, resistance to thermal shock and fire, abrasives...) and generally good formability. They comply with hygiene and food safety requirements and allow for a vast range of surface aesthetics [1, 2]. Enamel is applied on the steel in one or more layers and bonded to it by one or more firing rounds in controlled high-temperature conditions. During the firing processes, excessive humidity may cause hydrogen entry into the specimen. Hydrogen, being the smallest atom, can easily enter into the metal matrix and diffuse even at room temperature. If excessive hydrogen enters the material a defect known as fishscaling can occur, which is an irregular detachment of enamel from the surface. Therefore, to assess the fishscaling resistance of enamelling steels, the knowledge of the diffusive proper-
C.M. Belardini, R. Valentini, M. De Sanctis, B.D. Monelli Università di Pisa carlomaria.belardini@phd.unipi.itS.
CorsinoviLetomec s.r.l.
M.
LevauxArcelorMittal
ties of hydrogen in said steels is a fundamental step [3, 4, 5].
Hydrogen occupies interstitial sites in the metal matrix, and thermally activated random jumps cause its diffusion along the hydrogen concentration gradient. To study hydrogen diffusion, hydrogen permeation tests are the most direct experimental technique available [6, 7, 8]. During the test, hydrogen is generated on one side of a metal membrane, and a hydrogen detector on the other side is used to measure hydrogen flux. The diffusion of hydrogen in steels is far from straightforward. Since the work of Darken and Smith [9], it is well known that hydrogen trapping in the metal matrix strongly influences its diffusion. Trapping is a phenomenon involving "irregular" sites characterized by stronger hydrogen binding energies in comparison with normal interstitial lattice sites, wherein a hydrogen atom spends a longer average time before eventually jumping out again. The existence of trapping sites makes the interpretation of hydrogen permeation data more difficult since more complicated models are required to understand the diffusion behaviour of hydrogen [10, 11].
This work is focused on understanding trapping and diffusion properties from hydrogen permeation data. Temperature programmed desorption tests are preliminarily performed to establish the type of traps present. Hydrogen permeation tests are subsequently performed and analyzed using different methods critically.
MATERIAL AND METHODS
Enamelling Al-killed IF steels (designation DC06EK according to EN 10027-1 [12]) samples from six different coils, provided by ArcelorMittal, were analyzed in this work: A,B,C,D,E, and F. The typical chemical composition of ArcelorMittal commercial IF enamelling grade steel of this kind is C<50ppm, N<50ppm, S>0.015%, P>0.015%, Mn>0.25%, Si>0.01, 0.05%<Ti<0.1%. The samples were all L = 0.8 mm thick. Metallographic analysis was performed with an optical microscope (Leica DMI3000 M) after Nital 3% etching. Figure 1 shows the ferritic microstructure of the material. Those materials, nominally equal, come from different plants and may have been subjected to different production cycles, thus may exhibit different trapping properties.
TEMPERATURE PROGRAMMED DESORBTION TEST
Temperature Programmed Desorption (TPD) tests were performed on small samples (about 6 g) of the material. The samples were prepared with scotch brite grit and cleaned with ethanol and distilled water. The samples were thereafter weighted and their surface area
was measured. Cathodic electrochemical hydrogen charging was performed by putting the samples in a 0.9M CH3COONa, 0.9M CH3COOH, 3.0 % w/w NaCl, 0.3% w/w NH4SCN solution and imposing a 10 mA/cm2 current density for 60 min. During this process, hydrogen is reduced on the sample surface. Part of this hydrogen
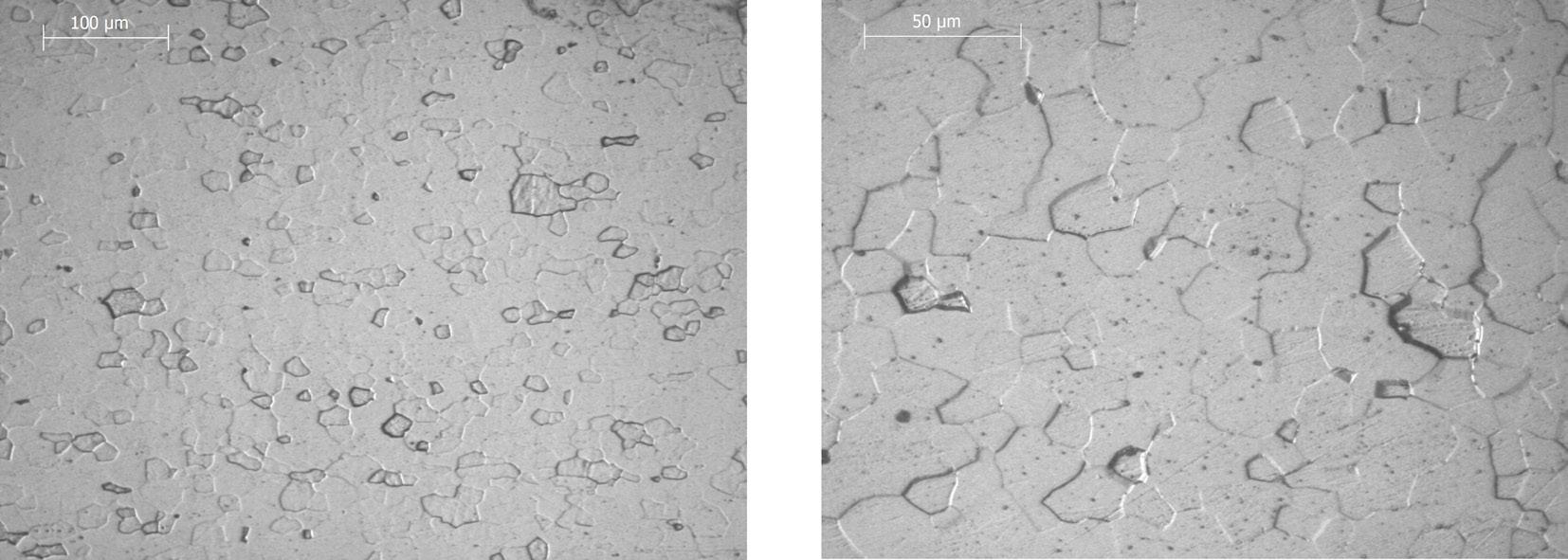
enters the specimen and part combines into hydrogen gas and escapes in the environment. For this material, as confirmed by subsequent permeation tests, 60 minutes charging is enough to assume a homogeneous hydrogen concentration is reached in the sample. After its removal, the specimen was cleaned with distilled water and dried with a cold blow drier. The time required for those operations was always less than 2 minutes. The sample was subsequently inserted into the commercial Helios 3 apparatus [13] in order to perform the TPD test, which entails imposing a linear temperature vs time profile and measuring the escaped hydrogen during the process. Helios 3 employs a solid-state sensor with a controlled airflow for this purpose. The starting temperature of the oven was 50 °C. Samples from coils A, B and C were tested at four different heating rates: 1, 2.5, 5 and 7.5 °C/min. Samples from coils E-G were only tested at 5 °C/min.
HYDROGEN PERMEATION TEST
Hydrogen permeation tests were performed on the studied materials. The samples were prepared with scotch brite grit, cleaned with ethanol and distilled water, and dried with a blow drier. The specimens were subsequently
mounted on the commercial Helios 2 apparatus [13]. One side of the specimen was submerged in the hydrogen charging solution (0.9M CH3COONa, 0.9M CH3COOH, 3.0 % w/w NaCl, 0.3% w/w NH4SCN) and a cathodic current density of 10 mA/cm2 was imposed. The solution and current density were the same of the TPD tests. The other side of the specimen was attached to a hydrogen gas solid-state sensor to measure the hydrogen flux. This apparatus provides a simple and fast setup, suitable for industrial settings. The tests were performed at around 30 °C ambient temperature.
The models most widely employed to rationalize hydrogen diffusion and trapping are McNabb and Fosters' [10], and Oriani's [11] models. McNabb and Foster's model assumes that hydrogen atoms that occupy regular lattice interstitial locations (with concentration C), in addition to their diffusion due to concentration gradient with coefficient D, interact with a certain concentration of traps N, which can be filled. The dynamic of the trap occupancy rate n is governed by the frequency parameters k and p, linked to trapping and detrapping energies.
Oriani's model, by assuming that the local trapped population is always in equilibrium with local lattice hydrogen, is a simplification of the above equations,
which ultimately results in a Fick-type law with a diffusion coefficient that depends upon hydrogen concentration:
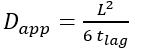
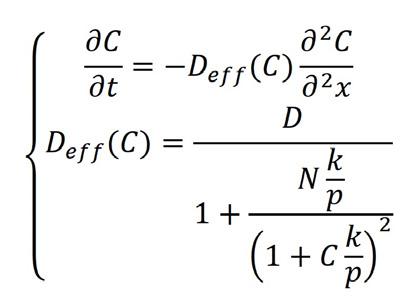
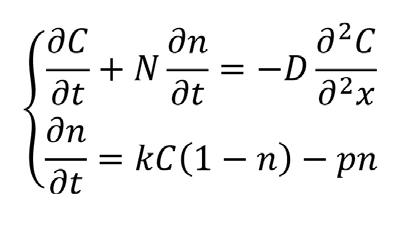
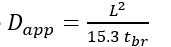
Both models show how the apparent diffusivity Dapp exhibited by the material with hydrogen traps has to be, in general, a function of trap saturation. For this reason, during the same permeation test, the Dapp may very well change as the hydrogen concentration in the specimen
raises up to equilibrium. Various methods have been proposed in order to estimate the D app value from permeation data:
• Breakthrough time
• Time lag method
•
63% method
• Fourier fit
• Laplace fit
The breakthrough time tbr method estimates the diffusivity from the linear rising transient of the permeation curve: the linear fit of that part of the curve is found and the value tbr is taken to be the time of the intercept on the time axis of that fit. The time lag method tlag focuses on a sort of delay to the steady-state conditions. First, ∫Jdt is plotted against time, then the linear steady-state region is extrapolated to its intercept on the time axis, where the value tlag is found. Arguably, the simplest method is the t63 method, where the data of virtually one single point of the normalized permeation curve is directly used in the calculation: t63 is the time corresponding to =63%. The method stems from observations of Devanathan and Stachursky who observed that value tlag could be easily estimated by looking for t63, a claim that is not true in general, since trapping can strongly change the shape of the curve [8, 14].
The main drawback, jointly shared among each of the common interpretation methods, is their link to Fick's diffusion law. In fact, each method looks for the "closest" Fick permeation curve and claims its diffusivity value


to be representative of that of the tested material. Each method essentially proposes a different definition of "closeness", by focusing on different areas of the curve or approximation methods. The same applies to the Fourier or Laplace method, here not considered [14].
Finally, permeation data can also be studied by estimating the parameters of McNabb and Foster's diffusion model. For this purpose, we employed a matlab script solving McNabb and Foster's equations (Eq. 3) with constant concentration boundary conditions. The specimen was assumed to be sufficiently thin, allowing us to solve McNabb and Foster's PDEs using one spatial dimension. For its solution, both Matlab's pdepe routine and a custom backward time-centered space implicit finite difference scheme can be used. The non-linear problem was solved with an iterative approach. Both methods provided the same results for the range of parameters used in this work.
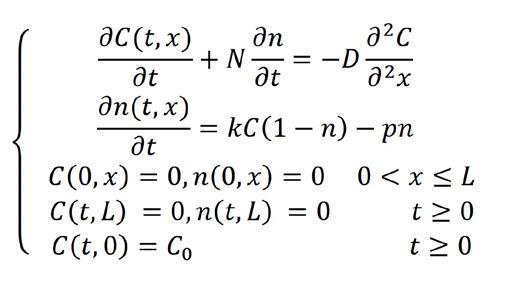
Given a tentative set of parameters, the prediction error can be calculated by taking the square error between predicted and experimental flux for each time step. Matlab's function fminsearch was then used to find the parameters of McNabb and Foster's model better fitting the experimental data.
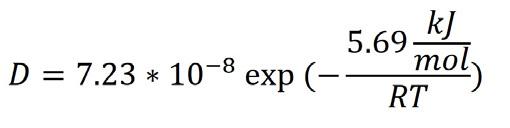
The hydrogen concentration on the inlet surface was assumed to be equal to , and the parameter D was calculated using:

Where T is the measured absolute temperature during the test, and R is the real gas constant. The specimen thickness was L=0.8 mm and parameters k, p and N were calculated from the optimisation procedure.
RESULTS
Temperature Programmed Desorbtion Test
(Eq.3) (Eq.4)
Figure 2 shows the results for coils A, B and C. Curves corresponding to faster heating mostly show a higher
peak height located at higher temperatures, as expected. In some cases, incoherent results were found, such as a higher peak flux or peak temperature with a lower heating speed. This is evidence of some experimental error, possibly due to the handling time between charging and the desorption test, or due to microcracking on some
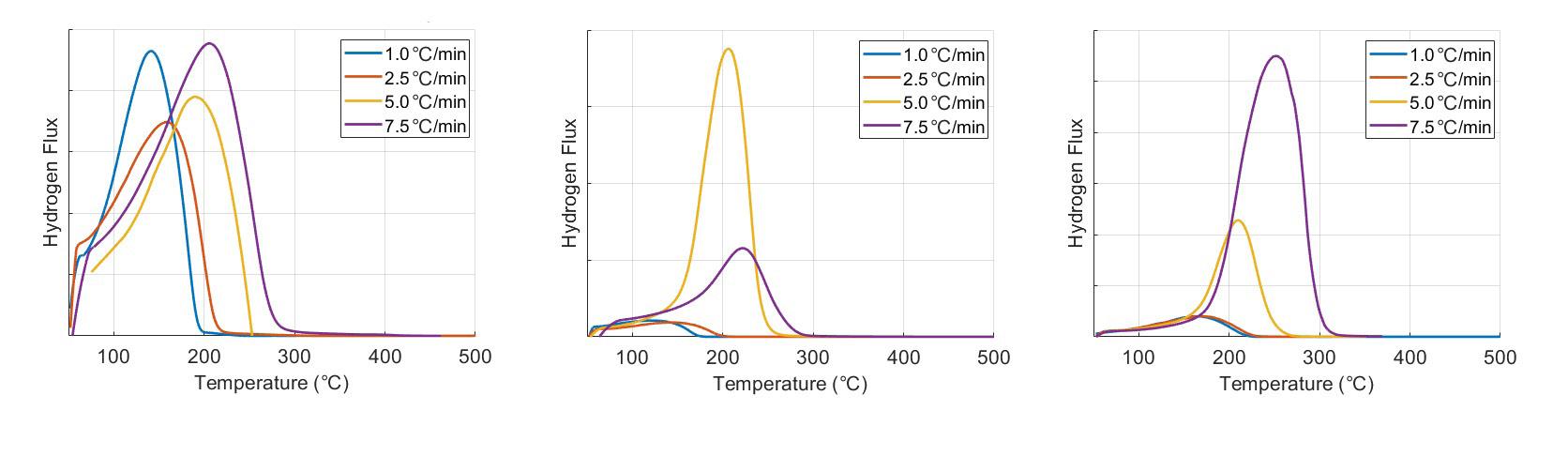
specimens. Therefore, TPD data has to be used carefully and only as guidance for further analysis.
What can be ascertained from the test results is that only low to medium energy trap types were detected for each specimen: no high-temperature peak was ever detected.
where E a is the detrapping activation energy and TP is the temperature at which a desorption peak is measured. To identify partially superimposed peaks, gaussian deconvolution is usually employed. With the obtained data, a single-peak deconvolution seems to better fit most curves, but the results are not reliable enough to draw
definite conclusions. Figure 3 shows the results of this calculation.

TPD results from coils E-F, here not shown in full for brevity's sake, are similar to results from coils A-C and show no high-temperature peak.
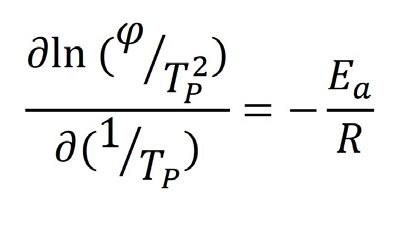
Hydrogen Permeation Test
Figure 4 shows the results from Hydrogen permeation tests for each coil. Figure 5 graphically shows the different methods used to estimate the diffusivities from permeation data for coil A: the breakthrough method, the time lag method, and the t63 method. Table 1 shows
the calculated values for D app for each coil. The significant difference among the results obtained from different methods is a telltale sign of the influence of trapping on the transport of hydrogen, and of the general unsuitability of those methods.
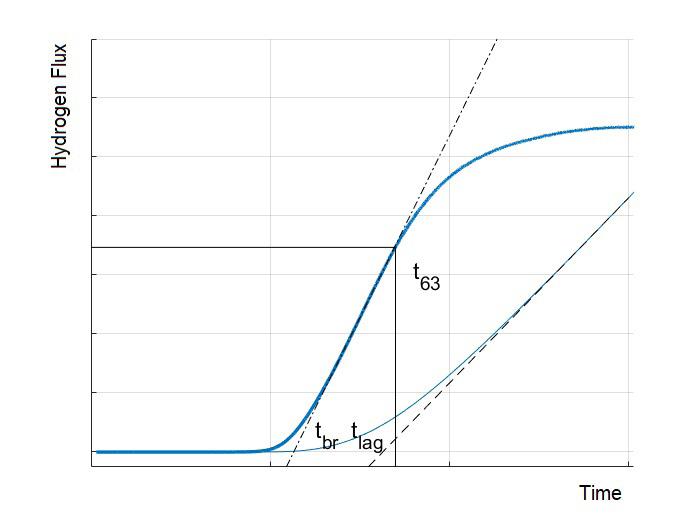
Tab.1 - Estimation of diffusion and trapping parameters from permeation tests, various Dapp are measured in m2/s, the trap binding energy Eb is kJ/mol and traps density N is mol/m3
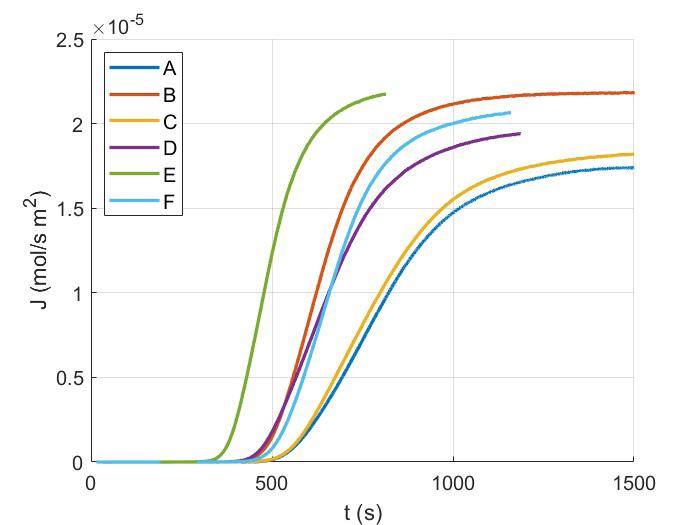
Possibly the most thorough method to elaborate permeation data is the comparison with predictions using McNabb and Foster's model. Figure 6 shows the comparison between simulated and experimental curves. The curve reconstruction is almost perfect, and the

obtained energy values are coherent among each material. The trap binding energy represents a value that is a bit higher than what is reported for dislocation traps (20 to 30 kJ/mol) in the literature.
DISCUSSION
Data from TPD tests clearly show that only a single type of trap, or at least multiple traps with similar binding energy levels, is activated in the employed charging conditions. The energy estimation is not reliable due to the significant data scatter, but the peak temperatures are clearly compatible with weak traps such as dislocations and grain boundaries.
Permeation tests show how specimens from nominally identical coils can have different properties. The estimation of Dapp, performed using three different methods commonly found in the literature shows how trapping has influenced the permeation curves due to
significant differences, mainly between the breakthrough method and the similar time lag and t63 methods. To overcome this problem, McNabb and Foster's equations were solved to find a set of parameters able to reproduce the behaviour of the whole permeation curve. The results show comparable values of trap energy, but the results are higher than those obtained by TPD.
As proposed by Fallahmohammadi et al. [17], one could estimate D app employing the t63 method but varying the target value of ,thus providing a simple estimation of the apparent diffusivity at different points of the transient curve. For this purpose, the transient solution of a 1D permeation problem for a Fick material is employed:
The solution of this problem is commonly expressed in terms of normalized flux and normalized time (the expressions in [14]
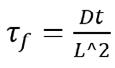


have two printing mistakes, [18] can be used to compare the results):

With the use of those expressions, the function , that is the normalized time at which Fick's permeation curve reaches the desired normalized flux, can be calculated.
Conversely, for each experimental point , only a single solution of Eqs. 6 that intersects the point can be found, and its diffusion coefficient can be calculated by equating : (Eq.9)
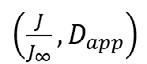

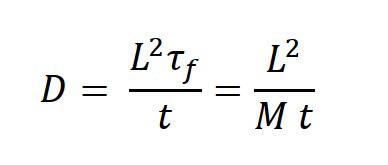
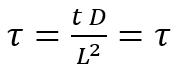

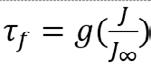
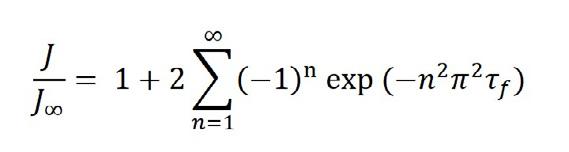

where M is tf-1, thus providing us with an estimation of Dapp by using the selected experimental point.
Fig.7 - Permeation curves (a) and apparent diffusivity vs normalized flux curves according to Eq. 9 (b) for a sample material with and without trapping. The diffusivity of the trap-less material is Dfick, equal to D63 for the material with traps.
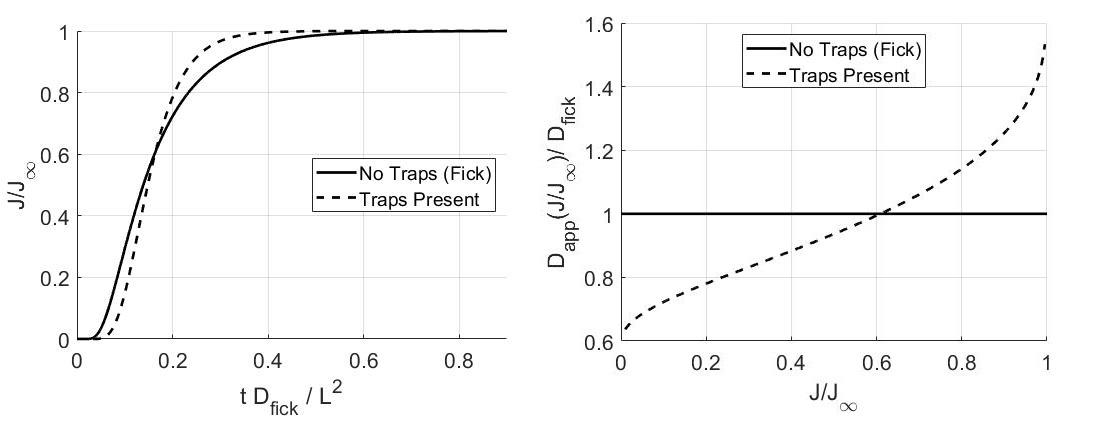
With this procedure, the whole permeation curve can be mapped on a new graph: Figure 7 (a) shows a characteristic permeation curve for a material with no traps and diffusion coefficient Dfick, and one of a material following McNabb and Fosters's model, chosen so that D63%=Dfick. Figure 7 (b) shows the Dapp calculated with the described procedure for both curves. For the Fick curve, the calculated diffusion coefficient is obviously constant on the whole range. On the other hand, the calculation for the material with trapping shows that
D app increases during the permeation, as trap occupancy increases.
Figure 8 (a) shows the procedure applied to permeation data from coil A. This figure highlights that the breakthrough method reflects the diffusivity at about 10% flux, and the time lag method reflects the diffusivity at a slightly later stage than the t63 method. Due to different trap occupancies at those stages, the Dapp values are significantly different. As a consequence, a Dapp measurement that relies upon the first part of the curve
appears to be less adequate to differentiate materials by their permeation properties. The same trend applied to the other coils.
Figure 8 (b) shows the same procedure applied to each permeation curve. Clearly, the curves which exhibited a faster diffusion are placed above, but it can also be observed that they show a higher slope. This can be intuitively explained by using the expression for Deff (Eq. 2). In that framework, Deff increases with increasing C as traps are saturated and thus stop influencing the diffusive behaviour, but the speed of this change is affected by trap density and the energy parameter k/p. With increasing N or decreasing k/p, Deff grows more slowly since more or weaker traps are harder to saturate. Trapping parameters
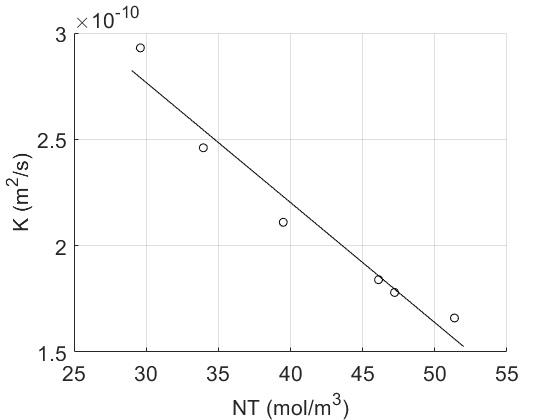
could therefore be estimated from the characteristics of this new curve. For this purpose, and to make a step towards simplicity and industrial use, only a limited set of points are used: = 1, 10, 30, 40, 63, 80, and 90 %, the same points highlighted in [17].


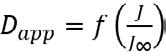
Since D app shows a reasonably linear behaviour for each curve, these points are used to fit a line: Dapp =D0+K , where D0 and K are the fitted parameters. Both trap density and trap binding energy have an influence on D0 and on K but given the, expected, low variability of the calculated values of Ea, N is the parameter that mainly influences D0 and K. Figure 9 shows the graph of K vs N: the points show a strong linear correlation.
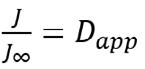

CONCLUSION
In this work, coils of DC06EK interstitial free steels were studied. Temperature programmed desorbtion tests were performed on hydrogen-charged specimens. Data from those tests showed a single desorption peak for each iteration and material, showing no influence of high-energy trapping. Hydrogen permeation tests were performed. The parameters of McNabb and Foster's diffusion and trapping model that best fitted the experimental data were found, allowing for an estimation of trapping energy and trap density for each material. Results showed a reasonably similar trap energy among all tests, with trap density being the main variable parameter. Commonly used methods to estimate diffusivity from permeation data were used, and their inadequacy was shown. To further explain where their inadequacy lies, the apparent diffusivity at
each point of the permeation curve was calculated using the solution of a Fick permeation problem. Results showed that the breakthrough and the time lag methods provide the apparent diffusivity of the permeation data at around 10% and slightly above 63% respectively. Finally, the apparent diffusivity at 1, 10, 30, 40, 63, 80, and 90 % was used to fit a line. The slope of this line was correlated very precisely with trap density for this set of materials, suggesting that, given a sufficiently well-defined applicability range, empiric formulae could be found for specific steel classes or steel designations in order to estimate trap density from this data. Additionally, preliminary numerical investigations show that combined use of the height and slope of the D app line could help estimate both trap energy and trap density. Further study with a larger sample size is necessary.
BIBLIOGRAPHY
Steel for Enamelling and Enamelled Steel - User Manual, ArcelorMittal.
G. H. Spencer-Strong, “Some examples of the functional use of porcelain enamel and ceramic coatings for Steel,” Symposium on Porcelain Enamels and Ceramic Coatings as Engineering Materials, 1954.
M. A. Collins, Atlas of enamel defects, Institute of Vitreous Enamellers, 1995.
W. W. Higgins and W. A. Deringer, “Investigation of fish-scale phenomena,” Journal of the American Ceramic Society, vol. 24, p. 383–392, 1941.
Pemco Enamel manual, Pemco International, 2008.
Ente Nazionale Italiano di Unificazione, “UNI EN 10209:2013.,” Cold rolled low carbon steel flat products for vitreous enamellingTechnical delivery conditions, 1998.
Ente Nazionale Italiano di Unificazione, “UNI 11734:2018,” Determining fish-scale susceptibility of enameling steel, 2018.
M. A. V. Devanathan and Z. Stachurski, “The adsorption and diffusion of electrolytic hydrogen in Palladium,” Proceedings of the Royal Society of London. Series A. Mathematical and Physical Sciences, vol. 270, p. 90–102, 1962.




L. S. Darken and R. P. Smith, “Behavior of Hydrogen in Steel During and After Immersion in Acid,” Corrosion, vol. 5, p. 1–16, 1949.
A. McNabb and P. K. Foster, “A New Analysis of the diffusion of hydrogen in iron and ferritic steels,” Trans. of the metallic Soc., vol. 227, p. 618–627, 1963.

R. A. Oriani, “The diffusion and trapping of hydrogen in steel,” Acta metallurgica, vol. 18, p. 147–157, 1970.
Comité Européen de Normalisation, “EN 10027-1:2016,” Designation systems for steels - Part 1: Steel Names, 2016.
R. Valentini, Method for Permeation Hydrogen Measurements, European Patent EP2912452B1, 2012.
A. Turnbull, M. S. de Santa Maria and N. D. Thomas, “The effect of H2S concentration and pH on hydrogen permeation in AISI 410 stainless steel in 5% NaCl,” Corrosion Science, vol. 29, pp. 89-104, 1989.
H. E. Kissinger, “Reaction kinetics in differential thermal analysis,” Analytical chemistry, vol. 29, p. 1702–1706, 1957.
W. Y. Choo and J. Y. Lee, “Thermal analysis of trapped hydrogen in pure iron,” Metallurgical Transactions A, vol. 13, p. 135–140, 1982.
E. Fallahmohammadi, F. Bolzoni and L. Lazzari, “Measurement of lattice and apparent diffusion coefficient of hydrogen in X65 and F22 pipeline steels,” International Journal of Hydrogen Energy, vol. 38, pp. 2531-2543, 2013.
J. Crank, The mathematics of diffusion, Oxford university press, 1979.
nuovo
allo studio
Gli acciai interstitial free da smaltatura sono comunemente utilizzati in molte applicazioni industriali per la loro resistenza a molti agenti ambientali (corrosivi, abrasivi…), perciò trovano svariate applicazioni, tra le quali il settore degli elettrodomestici oppure in componenti per l’architettura. Uno dei tipici difetti di fabbricazione che possono ritrovarsi in questa famiglia di materiali è il cd. fishscaling, cioè il distacco di parte dello smalto dalla superfice del componente a seguito del processo di smaltatura. Il fishscaling è dovuto all’idrogeno atomico che, penetrato all’interno del materiale durante le varie fasi del processo produttivo, diffonde verso lo smalto il quale, essendo sostanzialmente impermeabile all’idrogeno, determina un punto di accumulo di idrogeno nella interfaccia metallo-smalto. L’idrogeno, se eccessivamente accumulato, determina alla fine una separazione tra i due materiali. Risulta chiaro come la comprensione del fenomeno diffusivo dell’idrogeno nell’acciaio sia un componente fondamentale per la comprensione del fishscaling. Ma il processo diffusivo dell’idrogeno negli acciai è complicato dalla presenza delle trappole, che sono siti (come bordi di grano, interfacce con precipitati, microvuoti o dislocazioni) in cui l’idrogeno si trova in uno stato energetico inferiore ai siti interstiziali regolari; perciò, tenderà a permanervi un tempo sensibilmente più lungo rispetto al tempo medio di salto tra gli stessi siti interstiziali regolari. Un modello matematico che permette di comprendere il fenomeno è il modello di McNabb e Foster, che prevede che l’idrogeno “libero”, oltre che diffondere nello spazio seguendo la legge di Fick, possa dinamicamente diventare idrogeno “intrappolato” e viceversa. In questo lavoro, sei campioni da lotti diversi sono stati preliminarmente studiati con la tecnica del desorbimento a temperatura programmata (TPD), per cui a seguito di un caricamento elettrochimico di idrogeno, al provino viene imposta una rampa lineare di temperatura mentre un sensore rileva l’idrogeno che esce dal provino. Questa prova permette di avere una prima caratterizzazione della quantità e tipologia di trappole presenti nel materiale e una stima della loro energia di legame. Successivamente sono state svolte delle prove di permeazione: l’idrogeno generato per via elettrochimica su una superfice del provino tende ad attraversarne lo spessore e viene quindi rilevato da un sensore posto sull’altra superfice. L’andamento temporale del flusso di idrogeno misurato permette quindi di ottenere una caratterizzazione del comportamento diffusivo dell’idrogeno nel provino studiato. In letteratura esistono numerosi metodi utilizzati per stimare una “diffusività apparente” a partire dalle prove di permeazione, metodi che rappresentano un tentativo di condensare in un solo parametro un fenomeno che necessariamente richiede più informazioni per essere caratterizzato, allo scopo di fornire in modo semplice e ripetibile un singolo parametro di riferimento per, ad esempio, la definizione di condizioni contrattuali e parametri per il controllo qualità. Tutti questi metodi si basano alla fine sull’individuazione della diffusività del materiale privo di trappole che determinerebbe la curva di permeazione “più vicina” a quella sperimentale. La differenza sta nel modo in cui questo “più vicina” viene operazionalizzato. In questo articolo sono stati considerati il metodo del breakthrough, del time lag e del t_63. Quest’ultimo consiste nel ricercare il tempo dall’inizio della prova, appunto t_63, in cui il flusso misurato abbia raggiunto il 63% del flusso a regime. Per ottenere un modello che riesca a ricostruire al meglio la reale curva sperimentale, abbiamo fatto uso del modello di McNabb e Foster, che ci ha permesso di ottenere una stima della densità delle trappole e della loro energia per i vari provini. I risultati (evidenziati in Tabella 1) mostrano come l’energia delle trappole ottenuta sia omogenea per tutti i materiali, come atteso essendo tutti nominalmente uguali, ma la densità delle trappole risulti diversa, determinando quindi la misurata differenza nelle diffusività apparenti. La rielaborazione del metodo del t_63, proposta da Fallahmohammadi et al, permette di ottenere una stima della diffusività apparente a partire, in generale, da ogni valore percentuale di flusso rispetto al flusso a regime, ed è stato qua inizialmente impiegato per evidenziare l’effetto delle trappole. La Figura 8 mostra come la presenza di trappole de-
Un
approccio
della permeazione dell’idrogeno in acciai da smaltatura
termini un progressivo aumento della diffusività apparente mentre il flusso misurato aumenta. Questo procedimento è stato applicato a tutte le prove svolte, ed è stato osservato come le curve che mostravano una diffusione più veloce mostravano anche una maggiore differenza tra la diffusività apparente ottenuta da bassi valori di flusso rispetto a quelli ottenuti da valori più alti. Questo effetto, giustificabile partendo da uno studio effettuato da Oriani, può essere usato per offrire un metodo alternativo per la stima della densità di trappole a partire dalle prove di permeazione, utilizzando comunque una procedura semplice e ripetibile: cioè una relazione tra la variazione della diffusività apparente con il progressivo aumento di flusso misurato, valida chiaramente solo all’interno della ristretta cerchia di materiali considerati. Con la quantità limitata di prove effettuate per questo lavoro una relazione lineare sembra adeguata a tale scopo, come mostrato in Figura 9.
Migliorare l’efficienza produttiva di un componente housing motoriduttore di alta gamma
a cura di: F. Lago, G. ScarpaINTRODUZIONE
Lo sviluppo di sistemi produttivi ad alta efficienza che consentano di minimizzare i costi di produzione, migliorare la produttività e la qualità del prodotto è uno dei temi centrali nella visione dell’Industry 4.0 e dello smart manufacturing. L’elevata efficienza produttiva permette, infatti, alle imprese di ottenere un buon livello di competitività nel mercato raggiungendo un miglioramento delle performance differenziandosi così dai paesi a basso costo. Diventa, quindi, fondamentale la realizzazione di prodotti di alta qualità conseguendo al tempo stesso una riduzione degli scarti anche in ottica di sostenibilità ambientale ed efficienza energetica.
Il processo produttivo di pressocolata caratterizzato da cadenze produttive elevate è sicuramente uno di quelli in cui un’alta efficienza gioca un ruolo strategico. Un contributo fondamentale alla realizzazione di processi produttivi efficienti è dato dall’implementazione di piattaforme di monitoraggio intelligente che hanno il compito di identificare eventuali anomalie dei parametri di processo grazie a dei segnali provenienti da dei sensori posizionati nello stampo i quali verranno correlati ai livelli di difettologia individuati per lo specifico processo indagato. Le soglie di accettabilità del pezzo prodotto guideranno l’utente nella determinazione dei range ottimali di lavoro dei parametri di processo e ogni eventuale deviazione significativa di quest’ultimi attiverà un processo di allerta. Lo studio descritto nel presente articolo illustrerà come la simulazione numerica di processo oltre a svolgere un ruolo fondamentale nell’ottimizzazione della progettazione stampo e del processo diventa dunque un valido supporto per la definizione della posizione della sensoristica nello stampo e l’individuazione delle variabili di processo significative, aspetti che stanno alla base dello sviluppo di tali
piattaforme di monitoraggio intelligente. Tale studio si colloca all’interno del progetto di ricerca PREMANI (MANIFATTURA PREDITTIVA): progettazione, sviluppo e implementazione soluzioni di Digital Manufacturing per la previsione della Qualità e la Manutenzione Intelligente, finanziato nell’ambito del POR FESR VENETO
2014-2020 Azione 1.1.4 “Bando per il sostegno a progetti di Ricerca e Sviluppo sviluppati dai Distretti Industriali e dalle Reti Innovative Regionali”
Il progetto intende sviluppare tecniche che possano af-
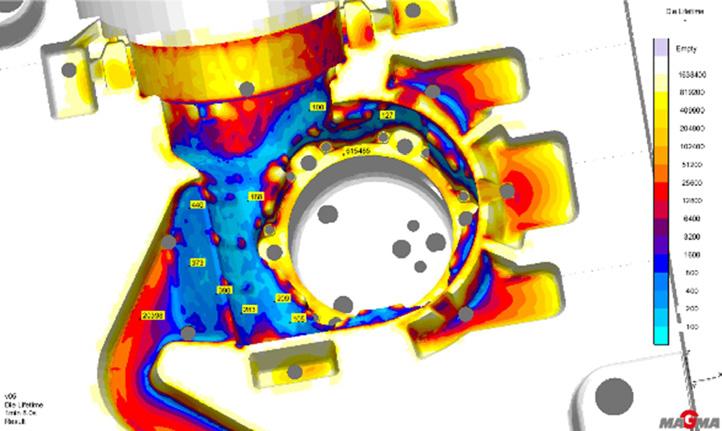
frontare il tema della predizione delle caratteristiche di funzionamento di macchine e impianti, coniugando l’analisi della qualità (del prodotto) con quello dell’efficienza (degli impianti), in un contesto che viene quindi descritto come Manifattura Predittiva.
Il CASO
Il componente oggetto di studio è la carcassa per l’alloggiamento del motoriduttore utilizzato per diverse applicazioni come le scale mobili (fig. 1).
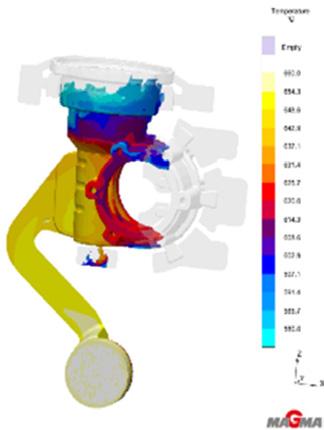
Tale particolare viene prodotto da RDS Moulding Technology con processo di pressocolata su stampo mono impronta con lega EN AB 44100 (AlSi12). Fin dalle prime fasi di produzione vengono rilevate delle non conformità sul componente che determinano lo scarto di una parte della produzione. Tali difettologie corrispondono a: giunti freddi nella parte alta del getto, inglobamenti d’aria nel mozzo centrale e nella parte alta
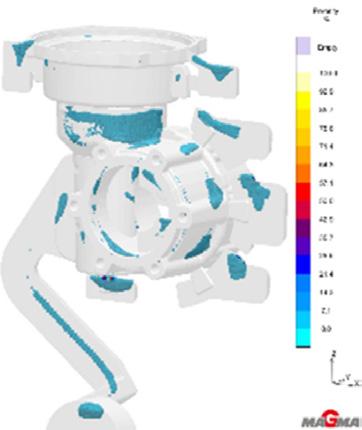
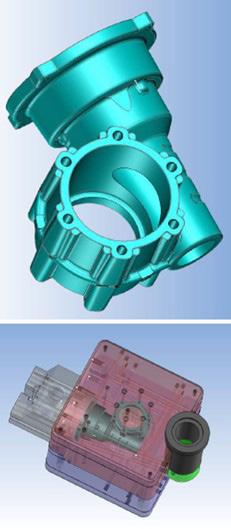
del componente, porosità da ritiro distribuite nel mozzo centrale e nella parte alta del corpo, erosione dello stampo nella zona frontale degli attacchi e infine crettature dello stampo dopo poche battute di produzione che determinano una breve vita dello stampo stesso. Una prima analisi del processo produttivo, svolta con MAGMASOFT, ha permesso di identificare le cause e di valutarne le azioni correttive (fig.2)
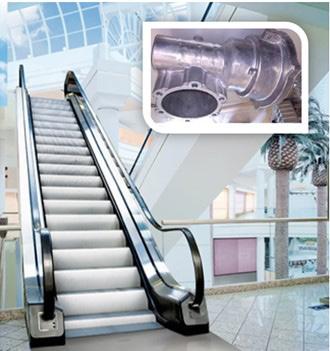
Distribuzione della temperatura durante il riempimento per la valutazione del rischio di giuntifreddi Criterio del porosity per la
valutazione di possibili porosita’ daritiro Criterio del die life per per la valutazione del rischi crettature nello stampo.
LA RIPROGETTAZIONE DELLO STAMPO
La fase di riprogettazione viene suddivisa in due step: Ottimizzazione fluidodinamica e Ottimizzazione termica
L’ottimizzazione fluidodinamica considera la riprogettazione del sistema di colata e di sfiato al fine di migliorare la qualità del componente in termini di aria inglobata, sottoraffreddamenti e massime velocità della lega all’interno dello stampo.
La fase di preparazione consiste nell’impostazione di geometrie parametriche del sistema di colata e di sfiato, alle quali sono attribuite specifiche variabili che il sistema

(MAGMA Optimizator) utilizza per identificare, autonomamente, la configurazione ottimale in grado di assolvere agli obiettivi di miglioramento qualitativo del componente sopra elencati.
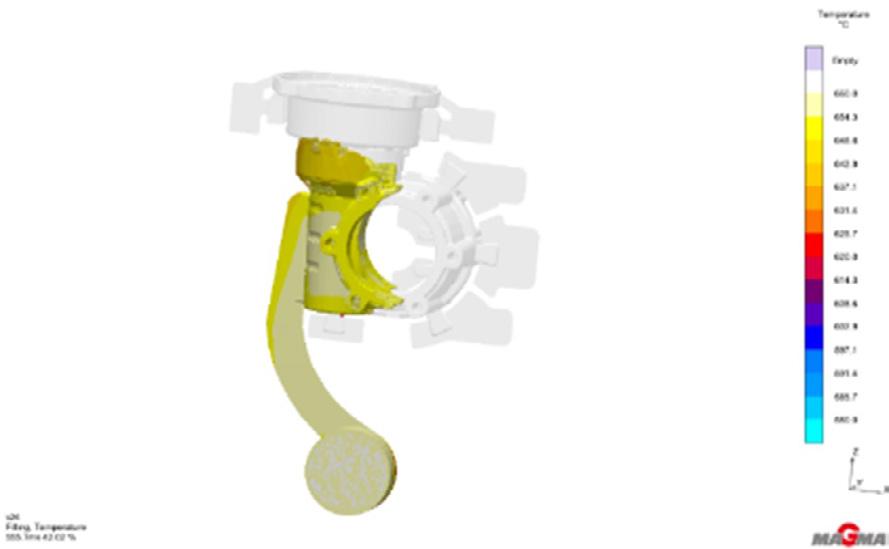
Graficamente è possibile quindi individuare, al termine dell’ottimizzazione, la geometria ottimale. Nel caso specifico il Design 18 rappresenta un ottimo compromesso tra il rischio di inglobamento d’aria nel getto e il rischio di abbassamenti di temperature durante il riempimento (fig.3) migliorando notevolmente la qualità del componente (fig.4 – fig.5).
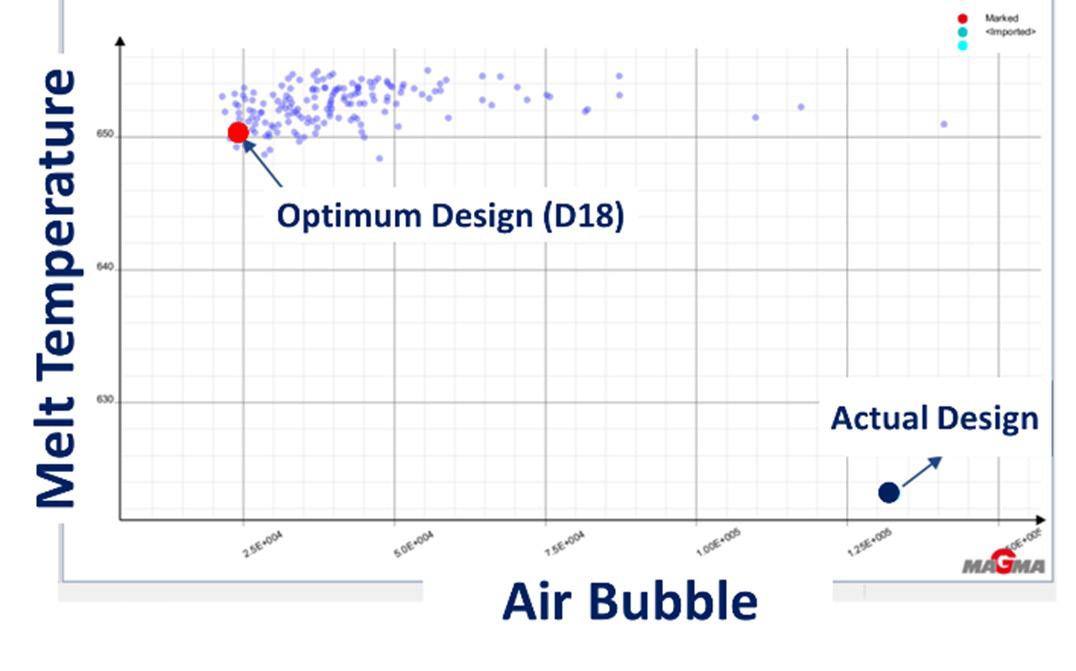
Actual Design Optimum Design
L’ ottimizzazione termica si pone di ricercare la configurazione ottimale dei circuiti di termoregolazione e i parametri che li governano (tipo, temperatura e portata del mezzo termoregolante).
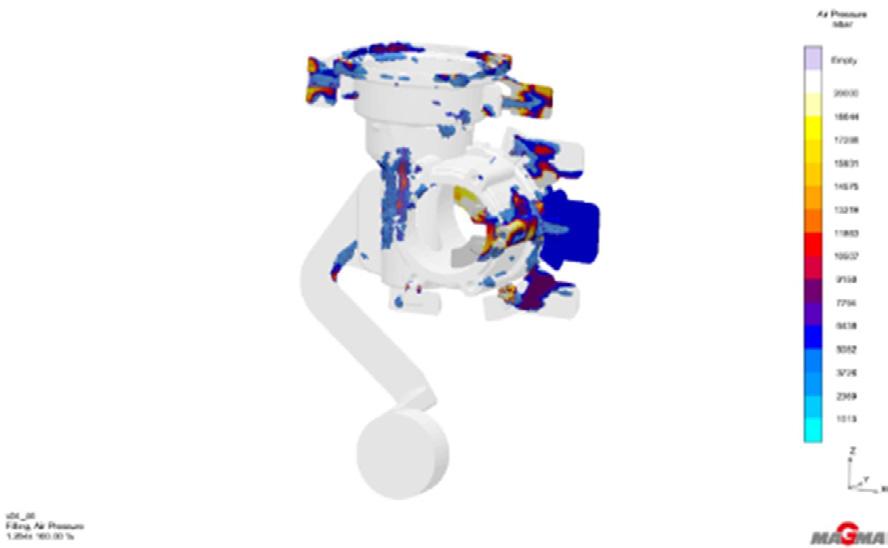
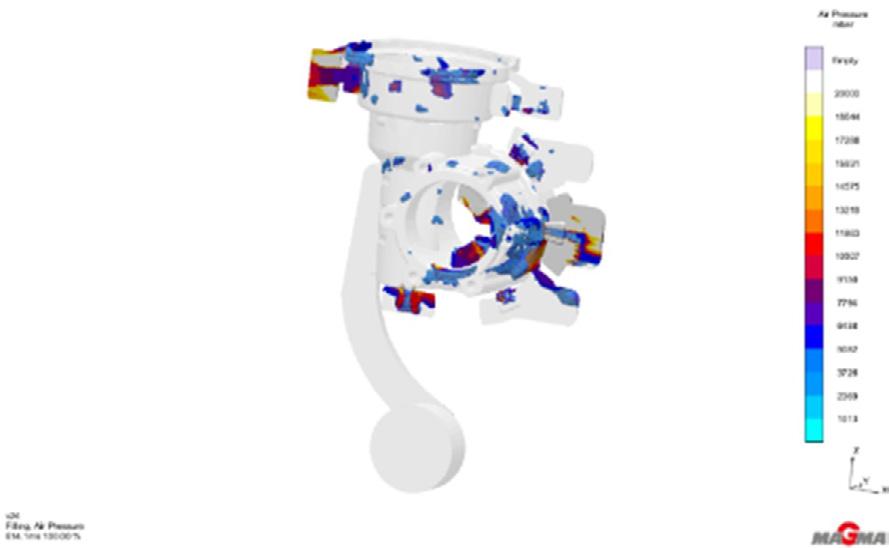
Gli obiettivi in questo caso risultano contrastanti tra loro, infatti, si ricerca da un lato, la massima riduzione delle zone a rischio di porosità da ritiro nel getto e dall’altro nella massima riduzione dello shock termico nella superficie dello stampo con lo scopo di ridurre le problematiche di insorgenza di cricche da fatica termica. Analogamente a quanto fatto nell’ottimizzazione fluidodi-

namica, vengono introdotte le variabili che governano le geometrie dei circuiti e i parametri di termoregolazione, permettendo a MAGMA Optimizator di individuare autonomamente il design ottimo che assolva agli obiettivi sopra indicati.
L’analisi dei risultati rileva il design ottimo n°136, che migliora significativamente la vita a fatica delle parti stampanti con una buona riduzione delle porosità da ritiro (fig.6 – fig.7).
Actual Design Optimum Design
DOE VIRTUALE PER LO STUDIO DELLA DIFETTOLOGIA
DEL GETTO E DELLO STAMPO
Ultimata la riprogettazione dello stampo viene calcolato un DOE (Design of Experiment) virtuale di 300 Design allo scopo di valutare la correlazione tra parametri di processo
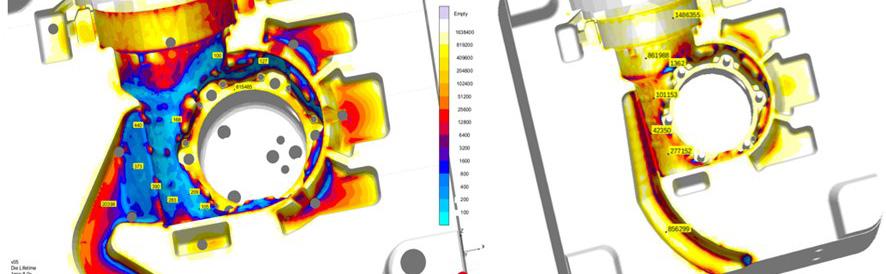
- difetti nel getto.
Dallo studio è emerso che le variabili sensibili sono: la velocità di seconda fase del pistone, il punto di commutazione tra la velocità di prima e seconda fase e la temperatura di colata (fig.8).
Unitamente all’analisi sul componente viene indagato anche l’impatto dei parametri di processo sulla vita a fatica termica degli stampi evidenziando che anche nel caso peggiore il numero di battute a cui lo stampo dovrebbe cominciare a deteriorarsi è circa 17 volte più alto rispetto alla configurazione di partenza in cui le prime crettature
iniziavano a svilupparsi dopo 10000 cicli.
La produzione con lo stampo riprogettato è stata eseguita (fig.9) controllando i parametri di processo grazie al sistema di monitoraggio Smart ProdACTIVE, sistema che monitora la stabilità del processo garantendo la qualità del componente e la vita delle parti stampanti.
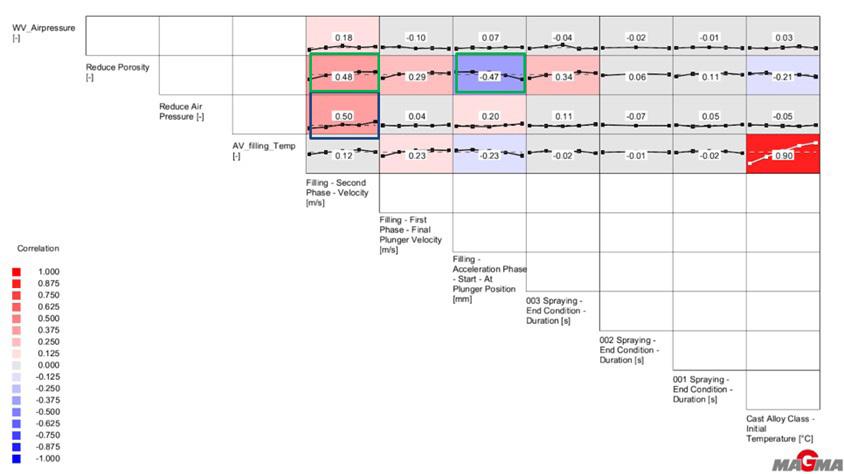
L’installazione di appositi sensori sugli stampi e sulla macchina (fig.10) permette di mantenere sotto controllo il processo produttivo identificando istantaneamente l’e-
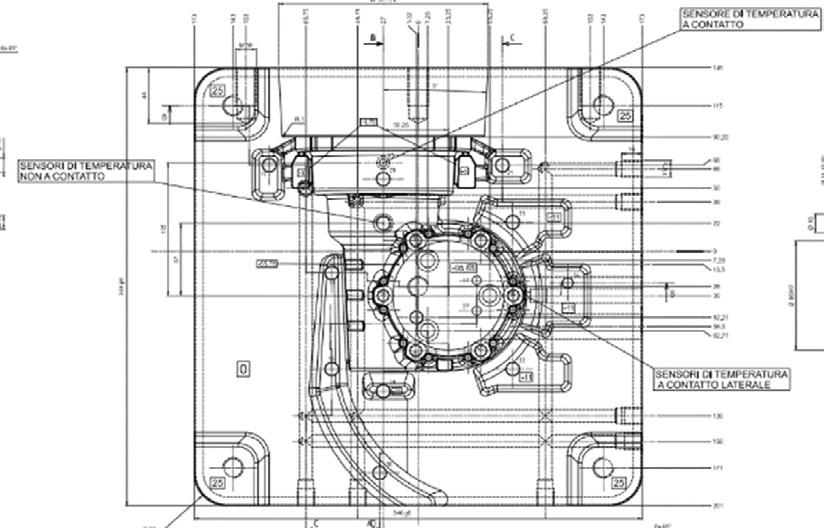
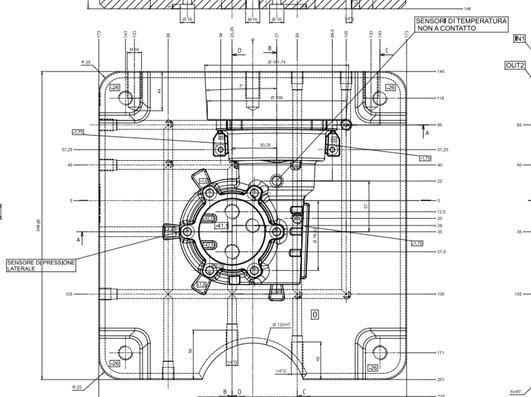
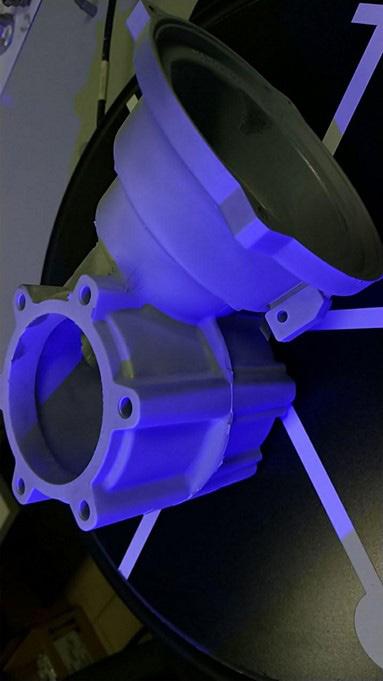
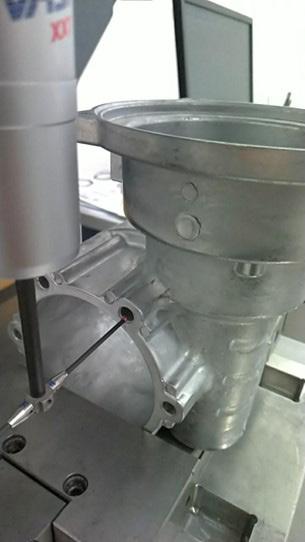
Questo sistema permette di monitorare la stabilità del processo (fig.11) garantendo la qualità del componente e la vita delle parti stampanti.

CONCLUSIONI
L’ottimizzazione virtuale dello stampo attraverso la simulazione numerica si dimostra ancora una volta fondamentale nella realizzazione di prodotti di qualità sempre più elevata.
La necessità’ però di coniugare la qualità del prodotto con un elevata efficienza produttiva del processo per migliorare la competitività rispetto ai paesi a basso costo rende necessario sviluppare delle piattaforme di monitoraggio intelligente che hanno il compito di identificare eventuali anomalie dei parametri di processo in real-time individuando i getti potenzialmente scarti senza alcun

controllo qualitativo e consentendo all’operatore a bordo macchina di intervenire tempestivamente.
I progetti di ricerca forniscono un contributo sempre più importante a sostegno dell’innovazione verso nuove frontiere come nel Progetto descritto.
RINGRAZIAMENTI
Si ringrazia il Consorzio SPRING, capofila del progetto GAP, e tutti i partner del progetto con particolare riferimento al Dipartimento di Tecnica e Gestione dei Sistemi Industriali (DTG) dell’Università di Padova e le aziende RDS Moulding Technology e Unilab.
BIBLIOGRAFIA
[1] N. Gramegna, M. Bucci, S. Poles, “Optimization of casting parameters for aluminum alloy suspension arm using new MAGMAfrontier module”, 10th Int. MAGMASOFT Users’ Meeting, 2002
[2] Alluminio e sue leghe: Classificazioni e trattamenti termici. Elio Gianotti. Trattamenti Termici Ferioli & Gianotti (Torino)
[3] F. Bonollo, N. Gramegna, S. Odorizzi: “La pressocolata delle leghe di alluminio: simulazione numerica del processo”, Edimet (1999)
[4] F. Bonollo, S. Odorizzi: “Numerical simulation of Foundry Processes”, SGEditoriali 2001
[5] E. Gariboldi, F. Bonollo, P.Parona: “Manuale della difettologia nei getti pressocolati – Handbook of defect in high pressure diecasting”, Associazione Italiana di Metallurgia, 2010
Nuove maniche troncoconiche CHEMEX per la riduzione del volume di alimentazione
a cura di: M. Pesci, L. ColomboGli attuali scenari mondiali, che hanno causato aumenti di costo delle materie prime, spingono la fonderia moderna alla sempre più attenta riduzione di metallo colato e la conseguente ottimizzazione dei sistemi di alimentazione. Non solo, l’importante aspetto ambientale legato al consumo di energia sarà il motore della ricerca tecnica dei prossimi anni, portando sempre di più la fonderia alla ricerca di soluzioni audaci, al fine di minimizzare il consumo di risorse, passando anche attraverso l’aumento spinto delle rese placca.
Con l’obiettivo di aiutare le fonderie in questo compito, CHEMEX ha messo a punto innovativi sistemi di alimentazione in grado di sostituire le classiche tecnologie di maniche troncoconiche. Questa nuova tecnologia di maniche troncoconiche T-type è ora diventata attuale; poiché il nuovo design, combinato alle ricette esotermiche esenti fluoro di CHEMEX, permette di ridurre il metallo di alimentazione a parità di modulo termico, garantendo comunque tutti i vantaggi di assenza di degenerazione grafitica, massima resistenza meccanica in formatura e precisione dimensionale. In questo studio si vuole mettere in evidenza come le maniche esotermiche troncoconiche di nuova concezione permettano di ridurre fortemente il volume di alimentazione, pur mantenendo la stessa richiesta di modulo termico necessaria al progettista dell’ufficio tecnico per garantire la sanità delle fusioni.
Con questo lavoro è stato possibile verificare la massimizzazione dell’efficienza di alimentazione attraverso la valutazione dei risultati in applicazioni reali in alcune fonderie, dove è stata osservata un’ottimizzazione del sistema di alimentazione fino ad una riduzione del 60% di metallo della materozza, con il conseguente risparmio energetico nonché di costi dell’intero progetto.
INTRODUZIONE
Molto spesso la redditività di una fonderia dipende dall’avere una buona resa placca e scarti ridotti. Per raggiungere questo obiettivo, è necessario utilizzare un buon programma di progettazione e simulazione, in grado di calcolare valori di modulo termico precisi, per progettare correttamente il sistema di alimentazione. Infatti, l’utilizzo della sola esperienza passata spesso porta alla definizione di alimentatori molto più grandi del necessario; questo sovradimensionamento abbatte drasticamente la resa placca aumentando i costi di fusione e rilavorazione associati [1].
L’aspetto di massimizzare le rese placca è sempre stato un aspetto importante in fonderia, ma visti gli attuali scenari globali con le conseguenti ripercussioni su costi energetici e materie prime, il tema è diventato ancor più
matteo.pesci@ha-italia.com
luca.colombo@ha-italia.com
centrale e non più trascurabile. Nei prossimi paragrafi si tratteranno brevemente gli aspetti energetici e di materie prime del contesto attuale che spingono le fonderie moderne alla ricerca di soluzioni di ottimizzazione sempre più estrema.
La scelta degli alimentatori per getti Durante il raffreddamento e la solidificazione, il volume del materiale si riduce (Fig. 1). Dalla temperatura di colata alla temperatura ambiente si incontrano tre ritiri differenti:
1.Ritiro liquido: durante il raffreddamento tra la temperatura di colata e quella di inizio solidificazione (TL);
2.Ritiro in fase di solidificazione: durante il
raffreddamento tra la TL e fine solidificazione (TS);
3.Ritiro in fase solida: durante il raffreddamento in fase solida tra TS e temperatura ambiente (ritiro prettamente lineare).
Il ritiro in fase di raffreddamento liquido e di solidificazione si compensa attraverso l’uso di materozze, cioè dei serbatoi di materiale liquido che vengono collegate alla cavità e consentono, se ben dimensionati, di fornire materiale liquido all’interno della cavità per compensare il ritiro durante la fase di solidificazione. Il materiale all’interno della materozza deve rimanere liquido per un tempo maggiore di quello del getto così da raffreddarsi dopo il getto stesso.
Fig.1 -Variazione di volume in funzione della temperatura per due ghise differenti (1 e 2). Il liquido inizialmente si contrae nella prima fase di raffreddamento (a), quindi si espande per merito della crescita grafitica (b). Verso la fine della solidificazione, l’ultimo liquido rimasto solidifica con contrazione (c) [2].
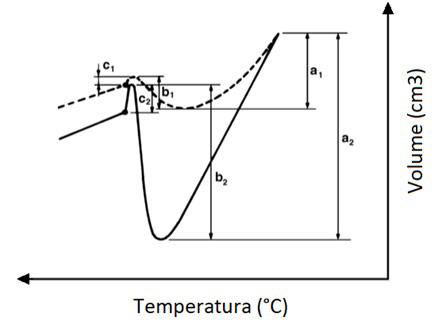
Naturalmente il primo passo per ottenere una buona alimentazione è mantenere una buona qualità del metallo [1]: raggiungere un buono stato nucleativo, ottenere le
forme di grafite desiderate ed evitare la formazione di carburi (Fig. 2).
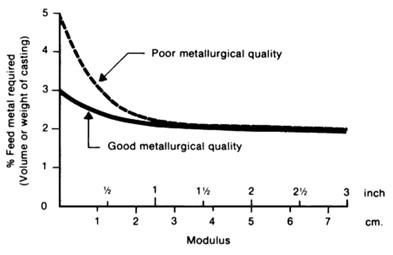
Anche un buon mezzo di formatura è necessario per garantire la migliore alimentazione possibile. Infatti, una buona resistenza della forma aiuterà a contenere la pressione generata dall’espansione della grafite, riducendo così al minimo le dimensioni della materozza [1]. La temperatura di colata è solitamente piuttosto critica, non solo per assicurare il riempimento di tutte le sezioni di colata, ma anche per far funzionare bene il sistema di alimentazione. La quantità di ritiro liquido iniziale diminuisce con la diminuzione della temperatura di colata. Va ricordato che gli alimentatori di grande diametro, specialmente con grandi superfici superiori (come una forma a cupola) di solito non cedono perfettamente metallo; infatti, potrebbero non iniziare a cedere il metallo liquido necessario a compensare la contrazione liquida, quando la temperatura scende al di sotto di un livello critico [1]. In generale, la definizione del sistema di alimentazione procedere per i seguenti punti [2]:
1. Calcolo del modulo termico critico del getto;
2. Determinazione del modulo termico di alimentazione (Mfeeder=Mcasting∙1.2);
3. Calcolo del peso di alimentazione (funzione della resa dell’alimentatore);
4. Definizione del numero di alimentatori;
5. Definizione del collo dell’alimentatore.
Infine, ricordiamo che l’applicazione di manicotti esotermici, mantenendo più a lungo il metallo liquido, permette di aumentare fortemente le rese placca grazie alla loro efficienza termica fino a raggiungere volumi di metallo
liquido ceduto maggiori del 50%.
Materie prime ed energia: un nuovo volano per ottimizzare le rese placca
Nel 2021 l’economia mondiale ha fatto segnare una rapida e significativa ripresa. Ripresa che è stata bloccata dal repentino rialzo dei prezzi delle materie prime, come i metalli, e di quelli dell’energia elettrica e del gas [3]. Livelli di prezzo impazziti che difficilmente potranno ridursi a breve, considerando la guerra in atto tra Russia e Ucraina.
Risulta quindi ancor più fondamentale applicare tutti gli sforzi possibili anche in fase di progettazione dei getti, al fine di contenere gli sprechi energetici ed il consumo di materie prime.
Effetto Materie Prime
Il caro materie prime ha segnato un durissimo contraccolpo sui costi di approvvigionamento di tutti i fattori produttivi. Solo nel 2021 gli incrementi sono stati intorno al +60% per le ghise in pani e i rottami di acciaio e dal +50% al +110% per le varie tipologie di ferroleghe [4].
Dall’analisi dei dati più recenti, confrontando i prezzi delle materie prime nell’anno 2020 e nel 2022, è possibile notare variazioni anche a tre cifre percentuali (Tab. 1).
Portando ad un’immediata ripercussione sulla produzione del metallo liquido ed i successivi trattamenti di elaborazione ed affinazione.
Tab.1 - Variazione % 2022 vs 2020 (gen-giu) delle materie prime ferrose e materiali atti alla trasformazione (fonte dati: ASSOFOND – Assemblea nazionale 29.06.2022).
Materia Prima
Effetto Energia
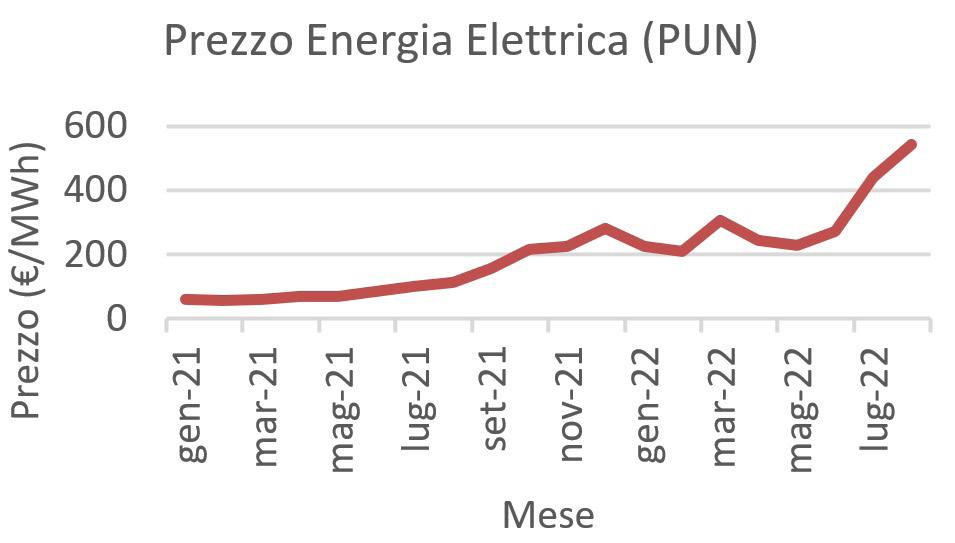
I temi energetici hanno registrato negli ultimi mesi una crescente attenzione in relazione alle forti tensioni sui prezzi di energia elettrica e gas che si sono registrate. Impennate che hanno costretto molte fonderie a sospendere la produzione, anticipando e/o prorogando i fermi impianti [5].
Un quadro che oggi, in relazione a una situazione geopolitica di tensione che coinvolge i paesi tradizionalmente esportatori di gas naturale, vede l’Europa in generale e il nostro paese in particolare, vivere una profonda crisi energetica. Crisi ulteriormente aggravata da componenti speculative che incidono, a vario titolo, negli incrementi di prezzo dell’energia elettrica [5].
Il quadro fin qui descritto rende ancora più rilevante il tema dell’energia e della sua razionalizzazione per le fon-
derie, chiamate a mettere in campo tutto quanto possibile per contenere i consumi energetici. Ricordando soprattutto che i reparti più energivori riguardano la fusione del metallo e la formatura, reparti che assorbono cir-ca l’80% dei consumi delle attività principali [5].
Analizzando l’andamento del Prezzo Unico Nazionale della borsa elettrica (PUN) da gennaio 2021, si può notare come a partire dal 2021 e ancor di più ad inizio 2022, il prezzo dell’energia elettrica ha raggiunto livelli eccezionalmente alti (Fig. 3). Con l’inizio delle ostilità fra Russia e Ucraina (24 febbraio 2022) i prezzi hanno ripreso ad aumentare repentinamente [3]. L’energia elettrica ha visto una corsa senza sosta a partire da maggio, dopo aver fatto segnare un primo picco preoccupante a marzo, fino ad arrivare ad un prezzo medio in agosto di 543 €/MWh.
Per quanto riguarda il gas naturale, tutti gli indici di mercato mostrano una crescita repentina già a fine 2021, che si è

In conclusione, l’impennata dei prezzi energetici ha portato ad un fortissimo incremento dei costi per le fonderie italiane. Costi che resteranno probabilmente elevati anche nei prossimi anni, ma che soprattutto per il 2022 si stanno rivelando insostenibili; rischiando di abbattere la competitività interna nei confronti dei concorrenti internazionali [3].
Parte sperimentale
Questo progetto si basa sulla valutazione sperimentale di diversi casi studio realizzati in produzione in due fonderie italiane: Arizzi Fonderie S. Giorgio e Ironcastings. Nello specifico, le innovative maniche troncoconiche CHEMEX T-type (Fig. 5), prodotte con ricette esenti fluoro e legante cold-box ecologico, sono state confrontate con le tradizionali troncoconiche di diversi produttori.
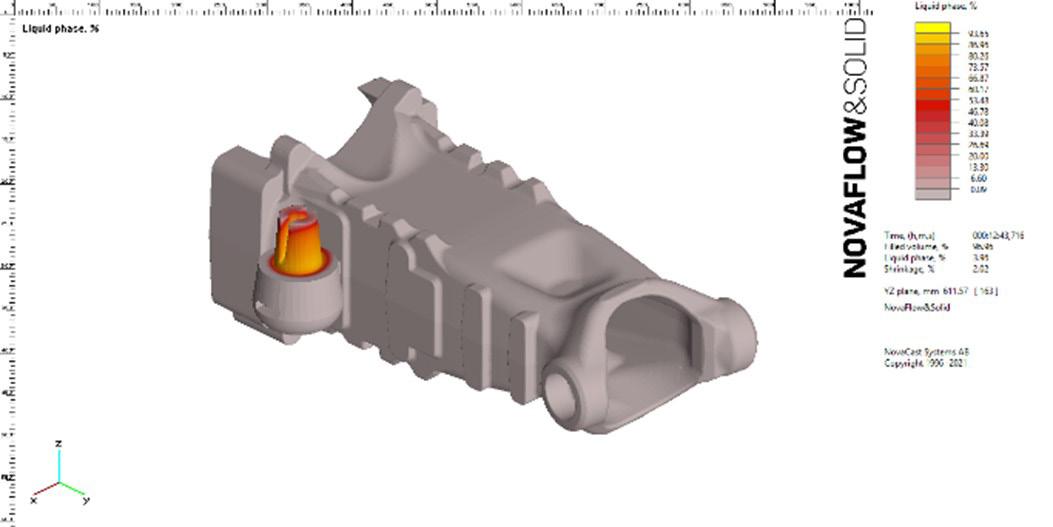
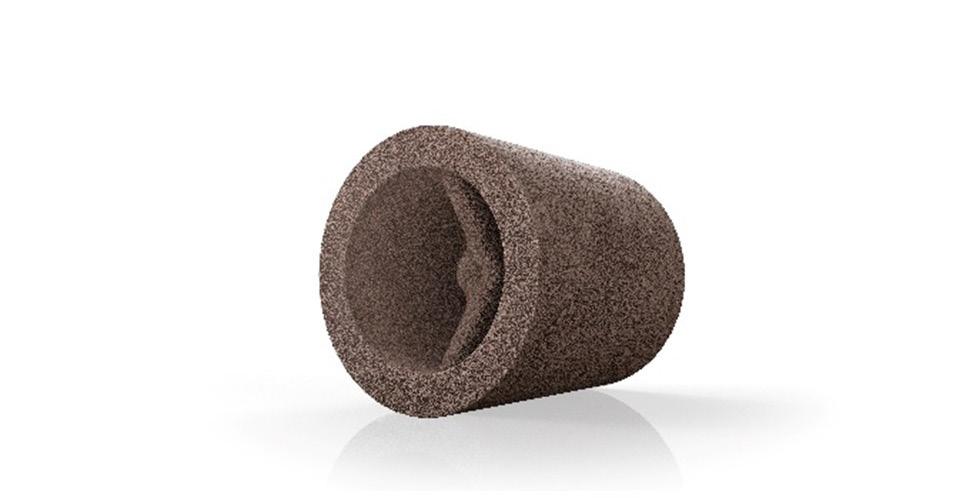
In tutti i casi, prima di realizzare il campionamento reale in produzione, è stato verificato il comportamento del
Entrambe le fonderie hanno monitorato il proprio processo fusorio tramite l’utilizzo di software di analisi termica, seguendo i propri parametri di processo definiti nelle schede di produzione per ciascun caso studio.
Tutti i getti e le materozze, oggetto delle varie prove sperimentali, sono state sezionate dopo pulitura.
Case Study Arizzi Fonderie
Il progetto ha previsto lo studio di diverse soluzioni. Nello specifico la fonderia ha studiato due casi differenti con due diverse soluzioni di alimentazione. Nel primo caso studio, la progettazione prevedeva la
presenza di dieci getti in staffa, ogni coppia alimentata con una manica troncoconica di tipo 6/9 (Fig. 7). Per la prova tecnologica è stato deciso di sostituire ogni classica manica troncoconiche 6/9 con una CHEMEX EK 50/80 T (Tab. 2).
Nel secondo caso studio, la progettazione prevedeva la presenza di dieci getti in staffa, alimentatati con una serie di alimentatori esotermici, tra cui quattro maniche troncoconiche: due di tipo 6/9 e due di tipo 10/13. Per la
prova tecnologica è stato scelto di sostituire le due 10/13 con maniche CHEMEX EK 80/140 T (Tab. 2).
Tutti dati tecnici delle diverse comparazioni sono riportati in Tab. 2.
Tutte le prove sono state condotte seguendo gli standard di processo definiti dalla fonderia.
Case Study Ironcastings
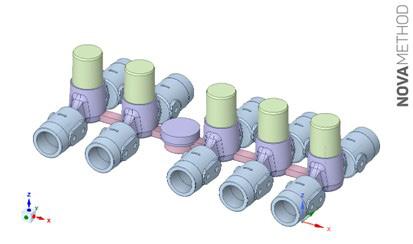
In questo caso studio, la progettazione prevedeva la presenza di due getti in staffa, ciascuno alimentato con una serie di alimentatori esotermici, tra cui tre maniche troncoconiche: due di tipo 7/10 e una di tipo 6/9. Per la prova
tecnologica è stato scelto di sostituire una delle due 7/10 con una manica CHEMEX EK 60/90 T (Tab. 3). In parallelo nella stessa staffa, il secondo getto è rimasto con la configurazione tradizionale per un confronto diret-to.
Tutte le prove sono state condotte seguendo gli standard di processo definiti dalla fonderia.
Risultati
Nei prossimi paragrafi sono riassunti i risultati salienti ottenuti nelle varie prove industriali di confronto tra le maniche troncoconiche di concezione tradizionale e le maniche troncoconiche CHEMEX T-type realizzate con miscele esenti fluoro e legante cold-box ecologico.
Case Study Arizzi Fonderie
La sezionatura dei pezzi ha evidenziata l’assenza di porosità e la corretta alimentazione. Dunque, nel primo caso a parità di integrità, con la manica CHEMEX EK 50/80 T è stato possibile un risparmio di 73cm3 di metallo liquido per ciascuna manica sostituita (Tab.4). Dunque, con un potenziale di riduzione di 2,65kg per ciascuna staffa (Fig. 8).
Nel caso dell’alimentatore con modulo maggiore è stato possibile un risparmio di 406cm3 di metallo liquido per
ciascuna manica sostituita (Tab. 4). Dunque, con un potenziale di riduzione di 5,84 kg per ciascuna staffa.
Case Study Ironcastings

La sezionatura dei pezzi ha evidenziata l’assenza di porosità e la corretta alimentazione (Fig. 9). Dunque, a parità di integrità, con la manica CHEMEX EK 60/90 T è stato possibile un risparmio di 179cm3 di metallo liquido per ciascuna manica 7/10 sostituita (Tab. 5). Dunque, con un
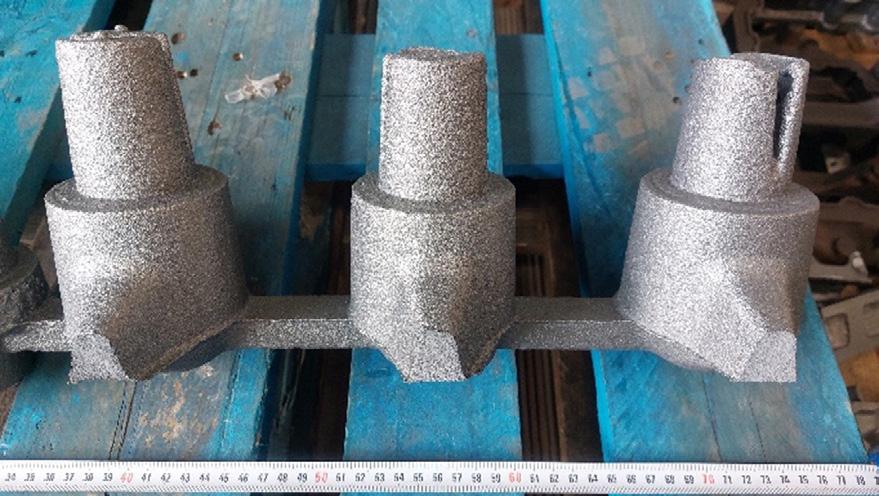
Conclusioni e prospettive
Gli attuali scenari mondiali, che hanno causato l’aumenti dei prezzi delle materie prime a partire dal 2021, nonché l’impennata dei costi energetici che stiamo vivendo in questo 2022, spingono la fonderia moderna alla sempre più attenta riduzione di metallo colato e la conseguente ottimizzazione dei sistemi di alimentazione. Non solo, l’importante aspetto ambientale legato al consumo di energia ed emissione di CO2 sarà il motore della ricerca tecnica dei prossimi anni, portando sempre di più la fonderia alla ricerca di soluzioni audaci, al fine di minimizzare il consumo di risorse, passando anche attraverso l’aumento spinto delle rese placca.
In questo studio è stato messo in evidenza come le maniche esotermiche CHEMEX troncoconiche T-type di nuova concezione, permettano di ridurre fortemente il volume di alimentazione, pur mantenendo la stessa richiesta di modulo termico necessaria al progettista per garantire la sanità delle fusioni.
Le prove condotte in entrambe le fonderie hanno dato risultati decisamente positivi. Le varie applicazioni indu-
striali hanno permesso di confermare l’elevata efficienza delle maniche troncoconiche CHEMEX T-type realizzate con miscele esenti fluoro e legante cold-box ecologico. Infatti, l’applicazione delle maniche T-type ha permesso un risparmio di volume di metallo liquido dal 41% al 60% rispetto alle tradizionali maniche troncoconiche, a pari condizione di modulo termico. Con questo lavoro è stato dunque possibile verificare la massimizzazione dell’efficienza di alimentazione, osservando un netto risparmio di metallo liquido colato; con il conseguente risparmio energetico nonché il risparmio di costi produttivi di ciascun caso studio.
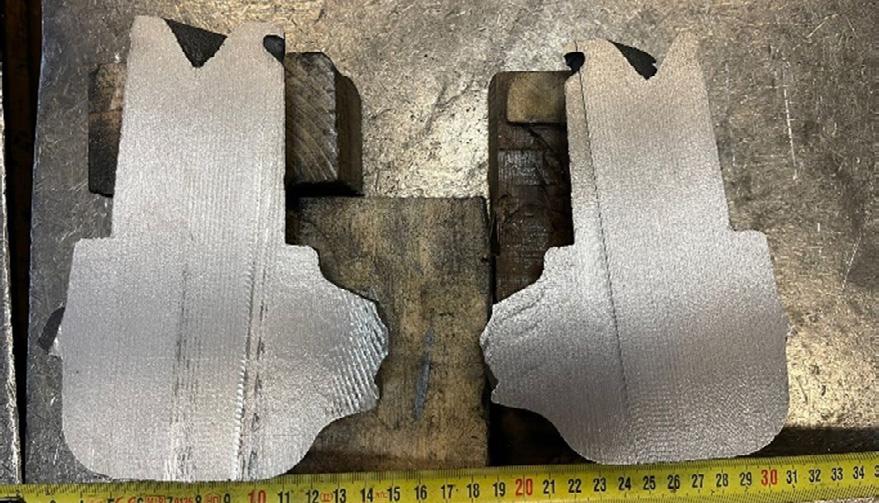
Ringraziamenti
Si ringraziano per la preziosa collaborazione e il fondamentale sostegno alla realizzazione dell’intero progetto, tutto il team dei tecnici delle fonderie protagoniste di questo lavoro: Ironcastings ed Arizzi Fonderie S. Giorgio. Nello specifico, un ringraziamento particolare ad Alberto Albertini per la fiducia e la stima reciproca, nonché a Gennaro Esposito per l’assistenza e la supervisione. Un
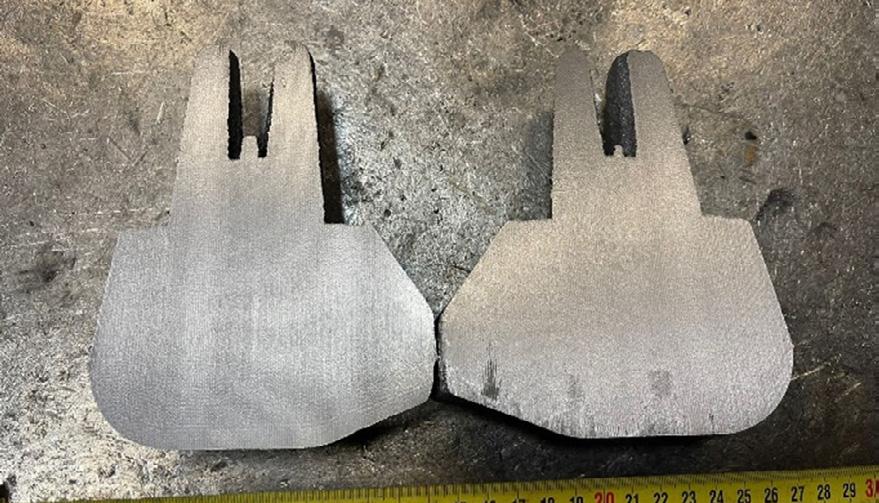
ringraziamento speciale va anche a Paolo Salvi e Simone Magli per la tenacia nella costante ricerca del miglioramento continuo.
BIBLIOGRAFIA
[1] J. D. Mullins, «Using bottle type risers to improve casting yield,» DIS Hot Topics #1, 2002.
[2] S. I. Karsay et al., Ductile Iron – The essentials of gating and risering system design, Rio Tinto Iron & Titanium Inc., 2000.
[3] O. Martinelli, «I costi delle materie prime energetiche continuano a salire senza freni,» In Fonderia, n. 2, pp. 36-41, 2022.
[4] M. Pisanu, «Rimbalzo del +19% nel 2021 per la produzione di getti ferrosi,» In Fonderia, n. 3, pp. 18-30, 2022.
[5] G. Corelli e M. Prando, «La struttura energetica delle fonderie: il quadro offerto dalle analisi delle diagnosi energetiche,» In Fonderia, n. 1, pp. 12-22, 2022.
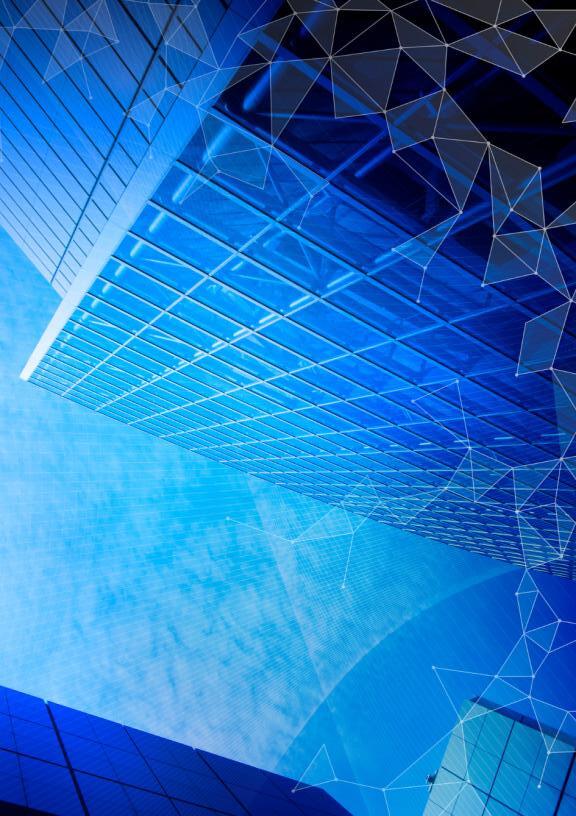
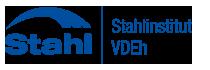

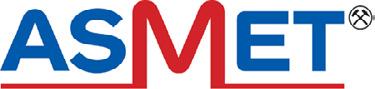
IlcasoAsonext
Lasicurezzacomelevastrategicadisviluppo:
Nel 2023 il gruppo Asonext presenta il suo primo Bilancio di Sostenibilità riferito al 2022, allo scopo di rendicontare i principali aspetti qualitativi e quantitativi della sua attività. “Nel solco di una consolidata propensione all’innovazione”, si dice nella lettera agli Stakeholder, “il futuro aziendale sarà sempre più legato allo sviluppo e all’integrazione della Corporate Social Responsibility e alle politiche ESG (Environment, Social & Governance), oggi fra gli strumenti strategici per realizzare una società più competitiva e coesa, nonché per modernizzare e rafforzare il modello sociale nazionale ed europeo. Ciò si tradurrà in una rinnovata politica aziendale che sempre di più permetterà di conciliare gli obiettivi economici con quelli sociali e ambientali del territorio di riferimento, in un’ottica basata sulla storica definizione di sviluppo sostenibile fornita nel 1987 dalla Commissione Bruntland: “uno sviluppo in grado di assicurare il soddisfacimento dei bisogni della generazione presente, senza compromettere la possibilità delle generazioni future di realizzare i propri”.
Nel proprio Piano Industriale e di Sostenibilità 2023-2025, inoltre, il gruppo ha indicato i cinque pilastri su cui si basa la crescita aziendale, già individuati nella Mission formulata nel 1990 dal Fondatore.
I cinque pilastri sono:
1. Formazione
2. Ricerca e innovazione
3. Sicurezza
4. Industria sostenibile
5. Digitalizzazione
Tra questi, il tema della Sicurezza è declinato negli obiettivi cardine del suo sviluppo quali:
• il miglioramento continuo dello standard di sicurezza delle persone
• la tecnologia al servizio della sicurezza
• l’aumento del livello di sicurezza informatica.
A partire dal 2020, dopo la scissione societaria che ha dato origine alla riorganizzazione del gruppo Aso e del ramo Acciai Speciali, oggi denominato Asonext, si è posta una nuova e più articolata attenzione ai temi della sicurezza in azienda, sia sul fronte del monitoraggio, delle misure da adottare e degli investimenti, che sui processi decisionali che portano alla loro realizzazione.
Nella convinzione che un modello di Governance di un’azienda che punti allo sviluppo e alla creazione di valore non possa che ancorarsi a dei principi etici e alla dimensione valoriale, Asonext si è data fra i suoi obiettivi strategici quello della centralità del capitale umano, che è destinatario di un’attenzione particolare anche per quanto attiene ai valori della salute e
dell’incolumità personale.
Va sottolineato, inoltre, che la pandemia da Covid-19 è stato un banco di prova importante e un forte stimolo per dimostrare quanto le aziende del gruppo fossero predisposte ad affrontare e superare anche quell’emergenza.
Negli anni più recenti, infatti, Asonext ha rivisto completamente la sua struttura interna e la sua organizzazione, ridistribuendo responsabilità decisionali in base al ruolo e alle competenze delle persone e graduandole in relazione alle materie da trattare e alle funzioni da presidiare.
Sono stati creati più team di lavoro che, mettendo a fattor comune capacità, informazioni e punti di vista, dopo aver elaborato una visione completa delle problematiche, individuano volta per volta le soluzioni
AIM's companies - Le aziende di AIM ottimali.
Come già evidenziato, il gruppo Asonext considera la sicurezza all’interno degli ambienti di lavoro come un pilastro fondamentale alla base di tutte le proprie attività. In quanto tale, tutte le decisioni strategiche intraprese dall’organizzazione sono integrate con le dinamiche legate alla salute e alla sicurezza dei lavoratori, diventando così parte indissolubile e inseparabile dei propri processi produttivi.
Il Sistema di Gestione per la Salute e la Sicurezza adottato da Asonext, certificato secondo la norma UNI ISO 45001, nasce con l’obiettivo di dotare l’intera organizzazione di uno strumento efficace in grado di implementare un processo iterativo basato sul concetto di PDCA (Plan-Do-Check-Act): •PLAN: identificare e valutare i rischi per la salute e la sicurezza sul lavoro connessi alle proprie attività produttive e, più in generale, i rischi e le opportunità in relazione al proprio contesto e agli obiettivi dichiarati; • DO: attuare i processi pianificati; • CHECK: determinare i controlli e i monitoraggi delle attività; • ACT: intraprendere azioni nell’ottica di un miglioramento continuo.
Sulla base di tale processo e del SDGs
8.8 dell’Agenda ONU 2030, che ha l’obiettivo di “proteggere i diritti del lavoro e promuovere un ambiente di lavoro sicuro e protetto per tutti i lavoratori, compresi i lavoratori migranti, in particolare donne migranti, e quelli in lavoro precario” nel 2021 è stato creato un gruppo di lavoro per affrontare le tematiche di salute e sicurezza dei lavoratori. Il gruppo di lavoro è formato dall’Amministratore Delegato in veste di Datore di lavoro, dal Direttore Operations per l’area Produzione, dal Responsabile dell’Ufficio
Tecnico e dai rappresentanti dell’Area HSE, cioè il Coordinatore HSE & Sustainability e l’RSPP.
I principali obiettivi del gruppo di lavoro sono:
• migliorare le condizioni di salute e sicurezza dei luoghi di lavoro
• contribuire a diffondere una maggiore consapevolezza nei lavoratori
• diminuire gli infortuni
• minimizzare i rischi
• ridurre gli impatti diretti e indiretti derivanti da eventuali infortuni.
Le funzioni tecniche del gruppo di lavoro si riuniscono settimanalmente, mentre il Datore di lavoro partecipa agli incontri con frequenza quindicinale.
I progetti di miglioramento elaborati dal gruppo di lavoro confluiscono nel “Piano di miglioramento di sicurezza e ambiente”.
Asonext ritiene indispensabile, al fine di perseguire con successo gli obiettivi prefissati per la salute e la sicurezza, che le attività debbano essere portate avanti da tutte le parti interessate, ognuna per quanto di sua competenza. In quest’ottica, diventa centrale la pianificazione e la predisposizione di attività e di strumenti orientati ad aumentare sempre più il grado di coinvolgimento di tutti i lavoratori, affinché tutto il personale interno ed esterno possa (e debba) apportare il proprio contributo. Asonext ha pertanto reso la partecipazione dei lavoratori il fulcro centrale del Sistema di Gestione adottato. Il coinvolgimento dei lavoratori viene garantito mediante una serie di misure, che passano dall’organizzazione di corsi di forma-
zione non obbligatori con l’obiettivo di sensibilizzare maggiormente il personale sulle tematiche di sicurezza, al coinvolgimento in momenti di confronto dedicati all’analisi degli eventi registrati o dalla programmazione di appositi “break formativi” sul campo, tenuti nei vari reparti produttivi. Tra gli strumenti adottati per facilitare la gestione di tutti gli aspetti inerenti alla sicurezza all’interno degli stabilimenti vi sono appositi software gestionali.
Asonext a partire dal 2017 ha introdotto nel Sistema di Gestione del gruppo un sistema informatico progettato appositamente per gestire la sicurezza a tutti i livelli aziendali, che va nella direzione di una sempre maggiore digitalizzazione dei processi produttivi e non, della raccolta dei dati e della comunicazione interna. L’adozione di un software consente, tra le altre cose, di gestire molti adempimenti obbligatori ma anche di allargare sistematicamente la raccolta di dati e costituisce un efficace database per elaborare statistiche e programmare tutte le attività.
Il software gestionale permette inoltre di raccogliere eventuali segnalazioni da parte dei lavoratori, i quali -attraverso i preposti/responsabili- possono comunicare all’Azienda near miss, situazioni pericolose o eventuali proposte di miglioramento.
Sulla base delle segnalazioni raccolte, di nuove esigenze produttive e di eventuali interventi di miglioramento, il gruppo di lavoro valuta il rischio connesso alle tematiche affrontate, definisce dei livelli di priorità in funzione del rischio e stabilisce delle linee progettuali per il miglioramento delle condizioni di sicurezza dei lavoratori.
In funzione degli interventi tecnico-gestionali da implementare, è stabilito un budget di spesa comprensivo di una stima dei tempi di realizzazione. Sul piano degli investimenti, (che vengono tenuti distinti dagli altri nel budget generale degli investimenti), è stato adottato il metodo del budget mobile su base biennale, che vede il Comitato Sicurezza impegnato a elaborare annualmente dal mese di ottobre un quadro dettagliato, per i due anni successivi, di tutte le opere capex che abbiano quale scopo principale il miglioramento delle condizioni di sicurezza dei lavoratori, suddivise per sito produttivo (acciaieria e forgia) e alle quali viene singolarmente attribuito un punteggio relativo all’urgenza e alla necessità di esecuzione da parte di
ciascuno dei tecnici componenti del Comitato.
Si può in questo modo stabilire una classifica di priorità dei diversi interventi e così procedere alla validazione definitiva della programmazione, condividendo con le altre funzioni interessate le informazioni (ai fini, ad esempio, delle gare di acquisto e degli stanziamenti necessari nel budget finanziario).
La pratica di questo metodo ha evidenziato che, distribuendo la responsabilità di portare avanti le azioni oggetto di decisione per competenze, si migliora il presidio delle aree di rischio e di rilevazione degli interventi necessari, realizzando allo stesso tempo la continuità della loro esecuzione, in
quanto le eventuali criticità vengono discusse e affrontate in tempi ristretti e portate subito a soluzione.
Negli ultimi anni l’attenzione verso la sicurezza deve essere puntata anche sugli asset tecnologici e digitali in quanto coinvolti nella protezione dei dati sensibili riferibili anche alle persone presenti in azienda o ai diversi portatori di interesse. Per questo scopo il gruppo ha già adottato i necessari accorgimenti per la sicurezza informatica e nel prossimo triennio intende completare, con risorse e progetti dedicati, le azioni rivolte all’aggiornamento del piano Cyber Security e la revisione del Recovery Plan.
Heat Treatment and Surface Engineering 4th Mediterranean Conference on
AIM is pleased to announce the 4th Mediterranean Conference on Heat Treatment and Surface Engineering (MCHTSE 2024) and the 5th International Conference on Thermal Process Modeling and Simulation (TPMS-5).
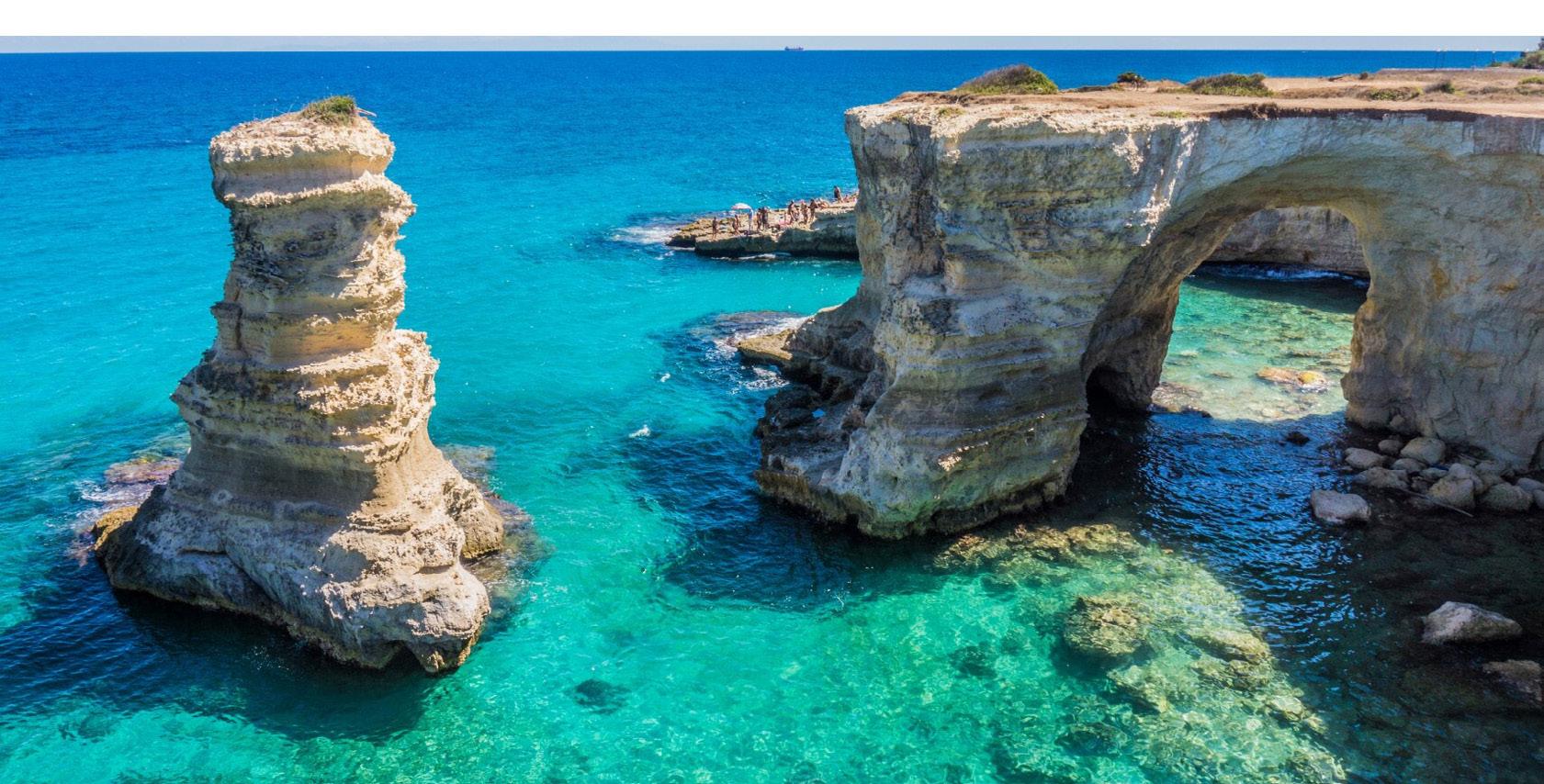
The two IFHTSE Conferences will be held together in Lecce - Italy, on 17-19 April 2024. The two conferences aim at providing a forum within which engineers, scientists, researchers and production managers can review and discuss fundamentals, new challenges, recent progress and emerging topics in the fields of advanced heat treatment and surface engineering technology.
IMPORTANT DATES
Abstracts Submission Deadline: October 31, 2023
Notification of acceptance: December 15, 2023
Preliminary program: January 31, 2024
Full Papers Submission Deadline: February 28, 2024
www.aimnet.it/mc-tmp.htm
Il punto di vista di Assofond tramite le parole del suo Presidente Fabio Zanardi
Il 2022 è stato un anno molto complesso per le fonderie italiane, caratterizzato da enormi incertezze e tensioni su diversi fronti.
L’invasione dell’Ucraina da parte della Russia ha bruscamente fatto emergere alcune criticità latenti e ne ha amplificato la portata: l’inflazione in accelerazione a fine 2021 è esplosa; agli ostacoli al funzionamento delle catene del valore si sono aggiunti il panico per l’approvvigionamento dei prodotti energetici e delle altre materie prime provenienti dalle zone del conflitto; la volatilità sui mercati delle commodity è stata rinfocolata dai fortissimi rialzi dei prezzi dell’energia e dalla immancabile componente speculativa; i problemi logistici si sono ulteriormente aggravati.
Nella prima parte dell’anno la produzione italiana di getti ha avuto una buona tenuta, sostenuta da una domanda globale dei settori utilizzatori tonica sia a livello nazionale sia internazionale, probabilmente spinta anche da approvvigionamenti dettati da timori di shortage di materiale e anche grazie a un trascinamento positivo dell’eccezionale rimbalzo del
2021 (produzione a +19% sul 2020 pandemico per le fonderie di metalli ferrosi e addirittura +34% per quelle di metalli non ferrosi).
A partire dai mesi estivi, i picchi di prezzo registrati dalle materie prime energetiche, che impattano fortemente sul settore delle fonderie, hanno costretto le imprese a utilizzare ogni leva disponibile per contenere i costi di produzione, incluse fermate produttive, rimodulazione dei turni e concentrazione dell’attività nei giorni o nelle fasce orarie giornaliere in cui il costo dell’energia era inferiore. Queste emergenze, cui si è aggiunto il cambio di intonazione delle politiche monetarie con l’aumento dei tassi di interesse e le conseguenti incertezze sui consumi e gli investimenti, hanno sgonfiato le prospettive di breve e medio termine dell’economia generale e frenato nell’ultima parte dell’anno il dinamismo della domanda interna e internazionale.
Il profilo di rallentamento, che ha toccato quasi tutti i principali settori di destinazione dei getti, è del resto in linea con la fase di normalizzazione della crescita mondiale e risente delle condizioni di domanda più

incerte determinate anche dello shortage di input intermedi, in particolare elettronici, che ha impattato soprattutto sul settore dell’automotive.
La produzione complessiva del settore si è dunque attestata, nel 2022, poco oltre il milione di tonnellate per i getti ferrosi (-0,7% rispetto al 2021) e a quota 820.000 tonnellate per quelli non ferrosi (-6,8% sul 2021). Dal punto di vista del fatturato, invece, l’effetto prezzi si è fatto sentire in modo importante, portando i ricavi complessivi a sfiorare i 7,5 miliardi di euro. L’incremento medio è stato del +32,6% rispetto al 2021 per le fonderie di metalli ferrosi e del +15,9% per quelle di metalli non ferrosi.
Nonostante le numerose difficoltà, questi dati ci dicono che le fonderie italiane sono riuscite ad affrontare efficacemente un anno imprevedibile. Un aiuto fondamentale, in particolare per quanto riguarda la gestione della crisi energetica, è arrivato dal lavoro di Assofond e delle altre associazioni che rappresentano i settori energivori, che sono riuscite a ottenere ascolto e comprensione da parte delle istituzioni e dell’opinione pubblica. Questo impegno ha portato a misure emergenziali concrete come il credito d’imposta per l’acquisto di energia elettrica e gas, che hanno sostenuto le forze produttive e che hanno permesso di contenere i danni. Altrettanto ha fatto il mercato, grazie a una domanda rimasta comunque tonica, nonostante il necessario adeguamento al rialzo dei listini, inevitabile per non trovarsi a lavorare in perdita.
Anche l’inizio del 2023 è stato positivo. Nei primi tre mesi dell’anno la variazione congiunturale della produzione (in tonnellate) si è attestata al +7,1% rispetto al quarto trimestre del 2022, mentre quella tendenziale, rispetto cioè allo stesso periodo del 2022, è cresciuta del +3,3%. Il fatturato, invece, ha fatto segnare una crescita congiunturale del +5,8% rispetto al trimestre precedente, che arriva al +7,7% se invece si confrontano i ricavi del periodo gennaiomarzo 2023 con quelli dello stesso trimestre dell'anno scorso.
Dal punto di vista delle aspettative di breve periodo, rileviamo invece una contrazione degli ordinativi. Non essendoci, almeno per il momento, prospettive di
recessione entro il 2023, il calo della domanda attuale è probabilmente imputabile a smaltimento scorte lungo la filiera, e ci auguriamo quindi di poter ritrovare una domanda più sostenuta a partire dal prossimo autunno. Lo scenario attuale, ad ogni modo, si conferma di forte volatilità, con tutti i rischi a essa connessi, come dimostrano l’andamento delle materie prime, di quelle ausiliarie e delle subforniture che ancora sono nel pieno del trend inflativo che abbiamo conosciuto nel 2022. D’altra parte, la “normalizzazione” dei costi energetici c’è, è vero, ma su livelli ancora molto elevati rispetto a quelli precedenti la crisi e con le misure eccezionali varate dal governo lo scorso anno che stanno andando a esaurirsi. Restano quindi forti incognite legate alla competitività strutturale delle fonderie italiane ed europee nel contesto globale, e la tenuta dell’economia europea con inflazione e tassi ai livelli attuali.
Se da un lato, dunque, le fonderie non possono far altro che affrontare giorno per giorno la volatilità dello scenario attuale, dall’altro non possono trascurare la visione di lungo periodo che, oggi più che mai, passa per la transizione ecologica, la vera e fondamentale sfida che abbiamo di fronte nei prossimi anni.
È cruciale, in questo senso, essere ben consapevoli che le fonderie rappresentano non un problema, ma piuttosto la soluzione al percorso di decarbonizzazione di gran parte dei settori industriali. Le nostre imprese sono, infatti, dei formidabili facilitatori della transizione, dato che solo con la nostra tecnologia è possibile realizzare componenti indispensabili per raggiungere gli obiettivi di sostenibilità fissati dall’Europa. Senza fonderie non ci sarebbero turbine eoliche, centrali idroelettriche, automobili sempre più leggere e dalle ridotte emissioni, e l’elenco potrebbe continuare a lungo. Il tutto – anche questo è bene non dimenticarlo – grazie a un processo produttivo energeticamente efficiente, che fa vasto uso di materiali provenienti dal riciclo e che rappresenta una tecnologia insostituibile per realizzare una vastissima gamma di prodotti, molti dei quali estremamente complessi.
Se da un lato quindi non dobbiamo temere questo trend che, anzi, potrebbe aprire nuove frontiere di mercato, dall’altro è necessario che i settori cosiddetti
“hard to abate” come quello delle fonderie possano beneficiare di una protezione comunitaria dalla concorrenza sleale di Paesi extra europei (nei quali le aziende possono operare su standard di sostenibilità molto meno stringenti dei nostri), nonché di sostegni agli investimenti e rimozione degli ostacoli autorizzativi per sviluppare progetti in energie rinnovabili che, troppo spesso, rendono ancora più accidentato un percorso già di per sé complesso.
Le fonderie italiane sono già all’avanguardia in fatto di decarbonizzazione del processo produttivo, e gli investimenti ambientali del settore che, come risulta dall’ultimo Rapporto di sostenibilità
Assofond, sfiorano in media il 20% del totale, stanno proseguendo a gran ritmo. Ora è essenziale che alle nostre imprese venga garantita la possibilità di giocare “ad armi pari” sia con i concorrenti extraeuropei, sia con quelli europei che possono beneficiare di condizioni più favorevoli in termini, ad esempio, di costi energetici.
Proprio su questo fronte Assofond sta impegnando e impegnerà nei prossimi anni una parte consistente delle sue risorse, sia in termini di sviluppo di strumenti operativi utili a misurare e migliorare la sostenibilità delle aziende, sia in termini di dialogo e confronto con i decisori pubblici chiamati a decidere del futuro industriale del nostro Paese. Una partita non semplice, ma che sono certo sapremo giocare ancora una volta al meglio.
giornate nazionali e protezione corrosione
Organizzate da
La XV edizione delle Giornate Nazionali sulla Corrosione e Protezione si terrà a Torino nei giorni 5, 6 e 7 luglio 2023, presso la sede del Politecnico di Torino. Le Giornate rappresentano l’evento di riferimento a livello nazionale per la discussione ed il confronto sulle questioni scientifiche, tecnologiche e produttive, nell’ambito della corrosione e protezione dei materiali.
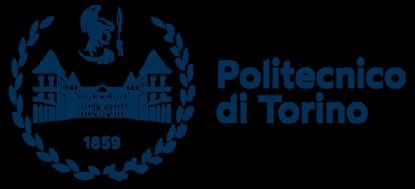
Il programma del Convegno e le modalità di iscrizione sono disponibili online sul sito www.aimnet.it/gncorrosione
sessioni tecniche
• Trattamenti superficiali e rivestimenti
• Degrado e rilascio biomateriali
• Tecniche di studio e controllo
• Protezione catodica
• Casi di studio
• Addditive manufacturing e alluminio
• Corrosione dei beni culturali
• Infragilimento da idrogeno
• Corrosione microbiologica
• Corrosione nel calcestruzzo
• Corrosione negli impianti industriali
Alle sessioni tecniche verranno affiancat da due Workshop organizzati da APCE - Associazione per la protezione dalle corrosioni elettrolitiche e da AMPP Italy Chapter. Al termine delle sessioni tecniche le Giornate Nazionali proseguiranno con un vasto ed esclusivo programma sociale che includerà tra gli altri l’Aperitivo di Bra, la Cena del Convegno e una visita guidata al museo Egizio di Torino.
coordinatrice delle giornate
in collaborazione con
segreteria organizzativa
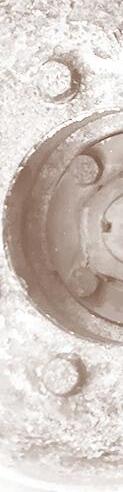
Via Filippo Turati 8 · 20121 Milano
t. +39 0276021132 +39 0276397770
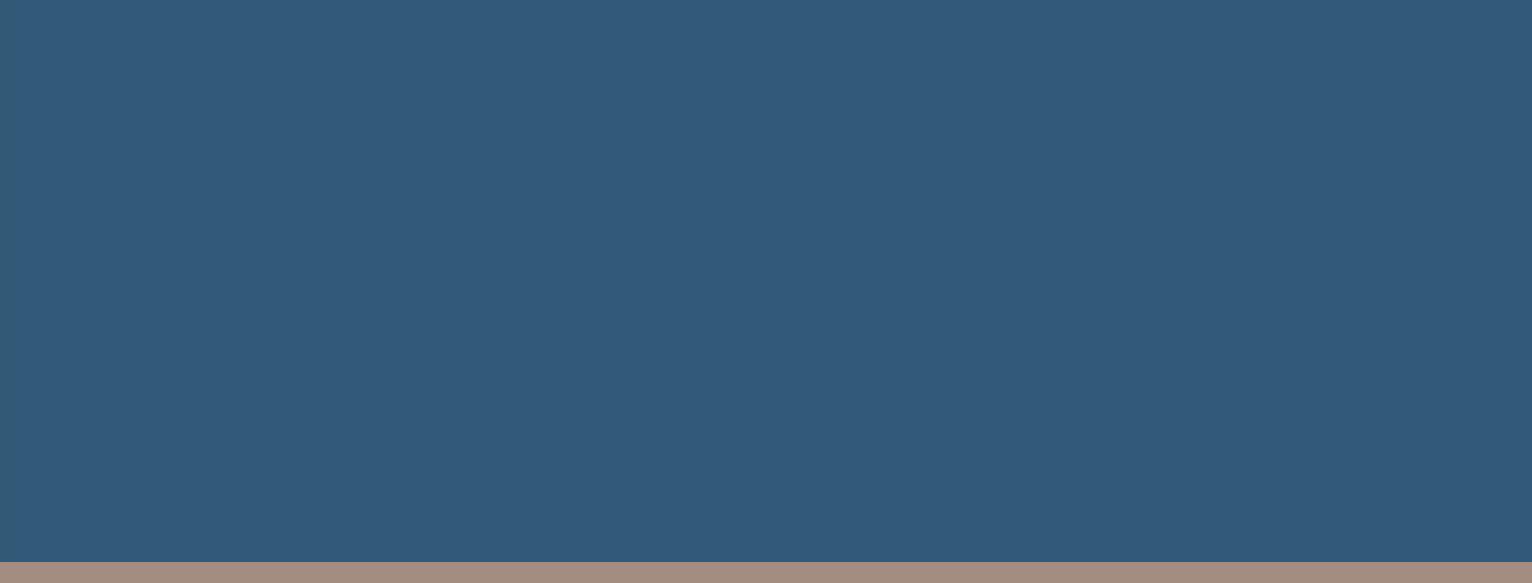
info@aimnet.it · www.aimnet.it
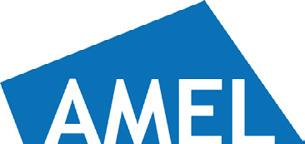
Sponsor del convegno

Piccola storia dello sviluppo tecnologico
Enrico MoscaPreistoria e antichità
Partendo dal neolitico, in cui l’uomo incomincia ad utilizzare oltre alla pietra altri materiali quali legno, osso ed argilla, quest’ultima capace di essere formata acquisendo strutture stabili e robuste dopo cottura, il progresso incomincia con la scoperta delle particolari proprietà dei metalli, resistenza e tenacità, decisamente appetibili rispetto a quelle dei materiali già in uso: la storia della metallurgia si può pertanto far risalire intorno al VII – VIII millennio AC, iniziando con le lavorazioni per martellatura, che saranno praticate su metalli reperibili allo stato nativo (rame, oro e occasionalmente, ferro meteorico); il loro uso incomincia in regioni come l’Asia occidentale, nelle quali si hanno giacimenti affioranti alla superficie; i primi oggetti lavorati dall’uomo sono però piuttosto piccoli, e destinati per lo più ad uso ornamentale; l’operazione di formatura sarà comunque limitata dalla incapacità di allontanare le impurezze rimaste dopo aver separato il metallo dal minerale che lo accompagnava.
La martellatura porta alla prima delle scoperte: i metalli induriscono durante questa operazione! Il fenomeno oggi è definito incrudimento, e comporta un utile incremento delle proprietà meccaniche, ma l’oggetto diventa fragile.
La seconda scoperta avviene intorno al 5000 AC, ed è quella della ricottura, cioè di un trattamento termico che permette ulteriori deformazioni sui metalli e che può essere ripetuto. In epoca posteriore troviamo la prima lavorazione a caldo, la forgiatura, cui segue l’applicazione della tecnica della giunzione a caldo di più pezzi metallici, in modo da ottenere oggetti di maggiori dimensioni. Il ferro meteorico sarà utilizzato dagli egizi, intorno al 4000 AC.
Il passaggio dai forni a legna ai forni rudimentali per cuocere l’argilla comporta anche per la metallurgia un salto di qualità, in quanto questi nuovi impianti, grazie al tiraggio naturale dell’aria attraverso il fornello contenente il combustibile, sono capaci di raggiungere temperature più elevate, tali da permettere la riduzione di certi ossidi e carbonati, specie di quelli di rame: la presenza di questi minerali nel fornello (p. es. di malachite, che gli antichi artigiani potevano aver usato per smaltature decorative sui loro oggetti di ceramica) porta alla scoperta del processo di riduzione, e il rame che veniva trovarsi nelle ceneri era pronto per essere lavorato per martellatura. Dall’osservazione di questi fenomeni al riconoscimento
dei minerali utili ad essere trasformati in metalli il passo è ancora piuttosto lungo: per ottenere per riduzione il piombo, l’argento, e più tardi anche lo stagno, sono necessari forni di cottura dell’argilla più efficienti, con l’adozione di schemi per favorire la circolazione dell’aria nella camera di combustione.
I primi processi di fonderia compaiono nella Mesopotamia, regione ricca di minerali adatti a queste primitive elaborazioni metallurgiche; la raffinazione mediante fusione viene sviluppata più tardi: nel 4000 AC si realizza la purificazione del rame mediante reazioni chimiche allo stato liquido e, nel millennio successivo, le tecniche raggiungono una certa maturità, in particolare nella Thailandia, culminando con la fabbricazione del bronzo (3600 AC) a partire dai minerali di rame e stagno. Il bronzo, che darà poi il nome all’epoca caratterizzata da un suo diffuso impiego, non verrà usato solo per oggetti ornamentali e statuette votive ma servirà per tutta una serie di utensili, quali coltelli, scalpelli, punte, martelli e mazze, asce, e ancora per armi da caccia e da guerra.
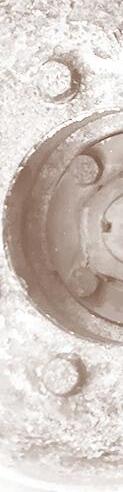
Fusione e colata dei metalli sono effettuate usando crogioli e forme in pietra e in ceramica, ma i progressi, specie per quanto riguarda la qualità delle leghe, sono estremamente lenti, così come il miglioramento delle tecniche di formatura degli oggetti: il più antico getto conosciuto è una rana di bronzo, databile intorno al 3200 AC.
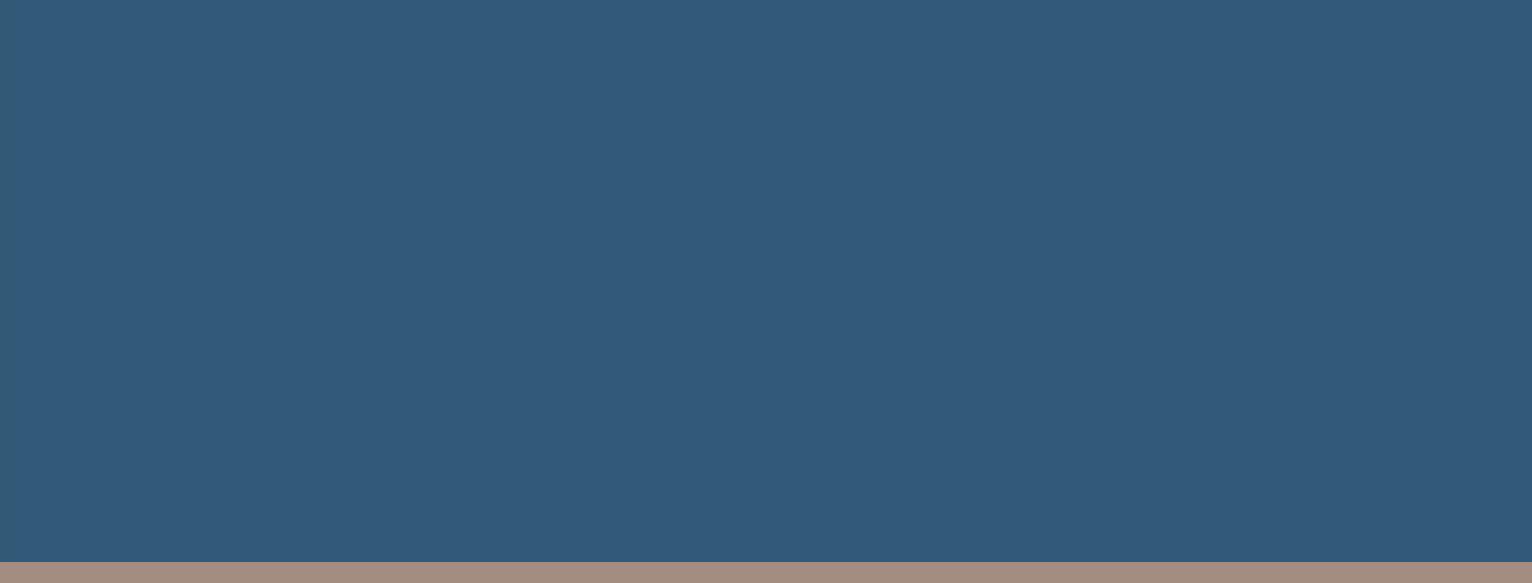
Il processo di formatura a cera persa compare in Egitto intorno al 2500 AC e viene impiegato soprattutto per gioielli e ornamenti vari; nel 1750 AC lo stagno compare come metallo a sé stante.
Nel corso del secondo millennio AC è scoperto anche l’ottone, che diverrà poi importante sia in gioielleria, come imitazione dell’oro (Oricalco), sia dopo, come materia prima per la coniazione di monete, che compariranno intorno al 700 AC.
In metallurgia il perfezionamento delle conoscenze empiriche, ma comunque piuttosto complesse per il tipo di cultura allora esistente, determina il nascere di una nuova professione, quella di fabbro, altamente specializzata e tenuta in grande considerazione; le pratiche metallurgiche, spesso accompagnate da riti religiosi e magici, sono vincolate quasi sempre al segreto, data la loro importanza economica e politica. Poiché esse rappresentavano un’ovvia fonte di prosperità per le popolazioni che potevano approfittarne, possiamo comprendere perché
le conoscenze tecnologiche ebbero una diffusione così lenta dai loro luoghi d’origine; il cammino è stato piuttosto lungo: dalle regioni intorno al Caspio e all’Armenia che disponevano di giacimenti minerari facilmente identificabili, le conoscenze si trasferirono tuttavia ai paesi vicini, Anatolia, Egitto e poi verso l’India, mentre nella direzione opposta si spostarono verso la Grecia e l’Italia, favorite anche dallo sviluppo del commercio. Nell’America del sud, non toccata da queste correnti di traffico, l’Età del bronzo si manifesterà solo intorno al 1000 DC!
In questo periodo avviene la scoperta del processo di coppellazione per estrarre l’argento dal piombo e per purificare sia l'argento che l'oro; è interessante notare come la produzione di gioielli favorisca le tecnologie ad essi collegate, quali stampaggio, brasatura, ribaditura, intarsio e lavorazione a sbalzo. Nuovi metalli sono introdotti nelle produzioni: oltre all’ottone anche piombo e zinco; oggetti e utensili acquistano maggiori dimensioni per il perfezionarsi delle tecniche di giunzione mediante forgiatura a caldo, e i processi metallurgici diventano più efficienti. Compaiono anche i primi metodi di analisi qualitativa (uso della pietra di paragone per saggiare la purezza dell’oro) ed anche quantitativa, per determinare il titolo dei metalli preziosi; l’arte orafa incomincia a utilizzare tecniche di nobilitazione dell’aspetto di oggetti di bronzo e argento mediante doratura con amalgama d’oro, grazie alla scoperta del mercurio nel 750 AC e della sua capacità di fare lega, p. es. con l’oro, e di essere liberato per semplice riscaldamento.
Il ferro, con le sue favorevoli proprietà meccaniche, in particolare la durezza, a parte qualche precedente esperienza degli egizi, giunge sulla scena mondiale più tardi, date le difficoltà di ottenerlo per riduzione del minerale; gli Ittiti perfezioneranno i forni, rendendoli termicamente più efficienti (uso dei mantici per esaltare la combustione, 1800 AC) ma le temperature non saranno ancora sufficienti per ottenere la ghisa, mentre le aggiunte di fondenti, quali soda e calce, aiuteranno a purificare la massa metallica combinandosi con i minerali della ganga; è perfezionata intanto anche la tecnica di forgiatura dei masselli, con cui la massa spugnosa di ferro ridotto è trasformata in blocchi compatti, e le impurezze più grossolane sono eliminate con una prolungata azione di martellatura.
La temperatura necessaria per arrivare alla fusione del ferro è raggiunta solo tra il 1400 ed il 1300 AC dai fabbri indiani di Hyderabad, che sviluppano il processo per produrre il cosiddetto acciaio Wootz, miscelando minerale di ferro (magnetite) con carbone di legna in opportuna quantità: la massa era poi posta in un crogiolo sigillato, riscaldato esternamente nel forno su di un letto di carbone, la cui combustione era attivata da una energica corrente di aria; le reazioni esotermiche in un ambiente con
efficiente isolamento termico permettevano di raggiungere lo scopo. Il processo di fusione e solidificazione era ripetuto più volte, realizzando così anche un’affinazione e pertanto al termine del ciclo si producevano dischi di ferro di notevole purezza, anche se di dimensioni limitate, con pesi dell’ordine del chilogrammo.
Il crollo dell’impero ittita intorno al 1200 AC favorì probabilmente la diffusione delle conoscenze, che furono portate dai fabbri costretti a emigrare, soprattutto verso l’Europa.
Intanto la siderurgia si sviluppa in Cina: risale al 600 AC la realizzazione di un tripode in ghisa del peso di 270 kg e una produzione corrente di oggetti in ghisa si ha intorno al 300 AC. Una successiva fondamentale scoperta avverrà circa due secoli dopo, col processo dell’affinazione della ghisa in acciaio, e conseguente possibilità di passare dai getti, piuttosto fragili, a prodotti forgiabili, con qualità superiori.
Il miglioramento delle proprietà del ferro è merito degli Etruschi (700 AC), che scoprono l’influenza del carbonio sulla struttura del ferro: si constatò che il prolungato riscaldamento ad alta temperatura in ambiente che oggi sappiamo essere carburante oltre che riducente, portava a ottenere un metallo con caratteristiche più favorevoli e soprattutto riproducibili in quanto a durezza e resistenza. Quando poi si notò che la durezza aumentava con la velocità di raffreddamento, si misero le basi del trattamento termico di tempra.
L’ultima raffinatezza, che permetteva di ottenere il massimo delle proprietà favorevoli. e cioè durezza accompagnata da tenacità, fu messa in pratica dai Romani (200 AC), che introdussero il trattamento di distensione (rinvenimento).
Mentre si viene sviluppando l’uso del ferro, anche il bronzo registra importanti progressi: sono elaborate leghe per impieghi specifici, come p. es. i bronzi al piombo per statue (p. es. i Bronzi di Riace risalgono al V secolo AC) e i bronzi ad alto tenore di stagno per specchi. L’estendersi dei commerci e le campagne militari durante l’espansione della civiltà greca e poi di quella romana, contribuiscono in modo decisivo alla diffusione delle conoscenze tecnologiche lontano dai luoghi d’origine; tuttavia il principale contributo alla metallurgia dell’impero di Roma non è stato tanto quello dell’innovazione quanto quello dell’organizzazione: i migliori processi metallurgici reperibili all’epoca furono impiegati ovunque, e questo contribuì a espandere le produzioni metallurgiche dalle centinaia di chilogrammi dell’epoca precedente alle decine di tonnellate.
Un'altra caratteristica di questo periodo è che le esperienze tecnologiche, come qualsiasi altro aspetto culturale, diventano oggetto di interesse e commento anche per il mondo letterario, con scritti di varia natura e finalità: nelle opere di molti scrittori greci e romani, da Omero
a Lucrezio (De rerum natura) a Plinio il Vecchio (Naturalis Historia, in 37 volumi) si trovano cenni più o meno estesi o trattazioni sulle problematiche metallurgiche per cui, specie in tempi recenti, archeologi e tecnologi hanno sottoposto a confronto le informazioni contenute in questi testi con quelle rilevabili dai reperti dell’epoca, procedendo anche a verifiche sperimentali. Occorre sottolineare che il contributo essenziale alle conoscenze di quale patrimonio tecnologico fosse in possesso dei nostri predecessori viene dagli esami metallografici e analitici dei reperti: a partire dalla composizione e dalla struttura dell’oggetto è possibile in una certa misura risalire al ciclo di fabbricazione praticato.
Medioevo
Il principale progresso tecnologico è nel campo della siderurgia per merito dei cinesi e dei giapponesi: tra il 600 e l’800 è acquisito il processo di produzione dell’acciaio a partire da ferro ottenuto per riduzione: questi è miscelato con ghisa e sottoposto a fusione, solidificazione e lavorazione a caldo; si giunge a comprendere l’importanza del tenore di carbonio (la cui influenza era già stata scoperta dagli etruschi) e pertanto, anche se in modo empirico, si cerca di controllarlo. Un ulteriore merito di questi tecnici è il perfezionamento dei forni, con l’invenzione dei forni a tino, progenitori in scala ridotta dei nostri attuali altiforni; in esso sono già presenti i principali accorgimenti atti a ottenere una produzione di acciaio di una certa consistenza: carica dall’alto di minerale, carbone e agenti scorificanti (calce) mentre dal basso, attraverso opportuni condotti (le odierne tubiere), si soffia aria con mantici azionati da salti d’acqua; ghisa e scorie sono poi spillate dal fondo. Si passa così da lingottini di qualche chilogrammo a lingotti e getti di peso molto più elevato, da avviare a successive lavorazioni. Considerando il periodo successivo alla dominazione romana, il progresso metallurgico in Europa è ancora piuttosto lento, e sarà così per tutto il Medioevo; l’innovazione continua a essere basata su osservazioni casuali, poiché la maggior parte delle lavorazioni è organizzata in forma artigianale e le attività metallurgiche sono inquinate da pratiche in cui empirismo e magia hanno ancora una grossa rilevanza. La maggior parte delle lavorazioni di formatura è fatta manualmente: il fabbro faceva sollevare la massa battente, che poi era fatta ricadere per gravità, fornendo il colpo utile all’operazione di formatura, e questo modo di operare è rimasto in funzione fino a questa epoca; con l’uso di magli a leva comandati da salti d’acqua è infatti possibile forgiare barre e lamiere assai più agevolmente.
Anche se la produzione dei metalli cresce, la loro introduzione in oggetti di uso comune è rallentata dal costo e dal fatto che le esigenze belliche sono sempre prevalenti sulle attività pacifiche: l’attenzione del metallurgista è
rivolta soprattutto alle armi per l’offesa e la difesa, e ciò porta p. es. ad affinare le tecniche di fabbricazione delle lame.
Una prima tecnica, già usata dai romani, consiste nella saldatura a pacchetto mediante martellatura di strisce di acciaio superficialmente decarburate per riscaldamento in ambiente ossidante e poi attorcigliate; si dà così origine a una struttura che, dopo tempra, presenta strati alternativamente duri e tenaci.
La seconda, che diede origine alle famose “spade di Damasco”, si originò probabilmente in India e fu adottata dagli arabi, che la diffusero successivamente in Europa, specie nella Spagna (armi di Toledo): essa consiste nel sottoporre a carburazione pezzetti di ferro miscelati con legno in crogioli chiusi riscaldati fino a formare ghisa liquida sulla superficie; estratti poi dal crogiolo e sottoposti ad accurata martellatura, questi sbozzati si saldano in una struttura stratificata, cui la tempra poteva conferire durezza per la trasformazione in martensite delle zone ricche di carbonio.
Una terza tecnica, praticata nell’Europa settentrionale, è basata sulla metallurgia delle polveri: consiste nel sinterizzare limatura di ferro, sbriciolare la spugna così ottenuta e infine sinterizzarla di nuovo in presenza di sostanze organiche (cessione di carbonio e azoto) con carbonitrurazione superficiale delle particelle di ferro; la forgiatura finale permetteva così di produrre lame con struttura molto fine e quindi con ottima tenacità e durezza. Per quanto riguarda le armature indossate dai cavalieri, agli inizi esse erano fatte con fili di ferro e solo verso la metà del 1200 furono assemblate con lamiere di ferro lavorato, rese snodabili da ingegnosi incastri meccanici; l’acciaio accoppiato a ferro in modo da aumentare la resistenza meccanica pur conservando la tenacità, fu usato assai più tardi.
In questo periodo sono da registrare eventi puntuali, che testimoniano sviluppi metallurgici locali; tra questi si possono citare:
• erezione della colonna di Dehli (7 metri di altezza, diametro alla base 420 mm, peso 5,44 t) prodotta saldando insieme per forgiatura blocchi di ferro Wootz praticamente puro (intorno al 400 DC)
• fusione in terra di calderoni e di campane per cattedrali (fonderie p. es. in Italia, Fiandre, intorno al 1200 DC)
• erezione di una colossale statua di Buddha a Kamakura, fusa in bronzo ad alto piombo in più sezioni: la sola testa pesa 140 t (intorno al 1200 DC)
• gli Incas usano una lega oro-argento per consolidare in lingottini polvere di platino con riscaldamento su carbonella, attizzando la fiamma con soffiaggio di aria
• compare il ferro forgiato catalano (1293, a partire da minerale ridotto in altoforno rudimentale)
• primo cannone fuso in bronzo a Gand (1313)
• avviamento della produzione di ghisa in altoforno rudi-
mentale, (1350)
• il peltro è impiegato per coppe e tazze, (1350)
Verso la fine del Medioevo lo sviluppo delle tecniche metallurgiche comincia a essere documentato in raccolte specifiche d’informazioni scritte, che integrano la tradizione orale. Tra queste è da citare l’opera De Diversis Artibus, di Teofilo, prima metà del XII secolo, con descrizione dei principali procedimenti usati nella pratica dell’epoca.
Rinascimento
Questo periodo, che va dal secolo XIV al XVI, rappresenta una svolta nella storia della metallurgia, specie per l’Europa: alcune tappe di questo risveglio tecnologico sono l’introduzione del forno a tino (1440), che porta la nostra siderurgia al livello di quella orientale, l’uso di forni a riverbero di consistente capacità per l’elaborazione di metalli non ferrosi (impianti termicamente più efficienti e di maggiore produttività), l’impiego di nuove leghe, la purificazione dell’oro estraendo l’argento con acido nitrico, la produzione di cannoni fusi in bronzo (assedio di Costantinopoli, 1410) e poi in ghisa, la progressiva sostituzione dell’oro con l’argento nelle monete per motivi economici: questa problematica porta a perfezionare i processi di coppellazione per estrarre l’argento dal piombo, col quale è associato a livello di minerale e anche dal rame (l’argento passa in soluzione nel piombo fuso che si fa agire sul rame, e poi è separato da questo ultimo, ancora per coppellazione).
Agricola scopre l’antimonio.
In questo periodo si sviluppa anche la tecnica dell’attacco chimico selettivo a scopo decorativo, p. es. sulle armature dei cavalieri: bellissimi esempi si trovano nei nostri musei.
L’avvento del Rinascimento e lo sbocciare del fervore culturale che caratterizza questo periodo storico comporta fatti che sono forse più importanti che non i singoli sviluppi tecnologici.
Il primo è che le tecniche metallurgiche sono per la prima volta documentate in testi specifici scritti da tecnici e non più da letterati: l’invenzione della stampa, con l’introduzione dei caratteri mobili a base di una lega piombo antimonio (perfezionata da Gutemberg, 1447) favorisce la pubblicazione di due grandi opere, quella di Biringuccio da Siena, Pirotechnia, in 10 volumi, e quella di Agricola, De Re Metallica, che formalizzano così l’insieme delle conoscenze fino allora accumulate.
Il secondo è l’inizio di un processo d’integrazione tra le varie discipline tecniche: lo sviluppo della metallurgia è inscindibile dai progressi compiuti nei campi della fisica, della chimica e della meccanica (p. es. sono studiati i metodi di analisi per verificare l’efficacia dei processi di purificazione dei metalli); d’altro canto è proprio nel
Rinascimento che compaiono figure come quella di Leonardo da Vinci, che con la sua presenza in ogni campo della scienza e dell’arte diventa emblematica da questo punto di vista.
Il terzo fatto, anch’esso molto significativo, è l’introduzione delle prime macchine idrauliche azionate da salti d’acqua: occorre tener presente che, ad eccezione dei processi di preparazione dei minerali (macinazione nei mulini) e della manovra dei mantici per il soffiaggio dell’aria nei forni, fino allora le lavorazioni dei metalli erano basate essenzialmente sulla forza muscolare dei fabbri e dei loro aiutanti. Con l’avvento delle macchine si costruiscono i primi magli per la forgiatura e poi i primi laminatoi: nel 1480 Leonardo da Vinci ci ha tramandato il progetto di una macchina per la laminazione del piombo utilizzato per fissare i vetri delle vetrate artistiche, e nel 1495 ha realizzato un laminatoio a due cilindri per la laminazione di lastre piane, utilizzabili quali semilavorati per monetazione. All’inizio si tratta di macchine rudimentali, ma ciò permette comunque di produrre in quantità e in modo più efficiente ed economico dei semilavorati da destinare anche a usi comuni.
L’attenzione dei tecnici e dei tecnologi comincia però ad essere attrirata dalle proprietà di nuovi materiali, anche non metallici; p. es. nel 1496 Cristoforo Colombo porta dall’America pezzi (palline) di gomma cruda. Nel 1500 in Francia è introdotto l’uso in fonderia di sabbie refrattarie.
Epoca preindustriale (1600-1750)
Il coordinamento tra le varie discipline tecniche diventa uno strumento importantissimo per fornire spiegazioni sui fatti sperimentali osservati nei vari settori in cui si manifesta l’esperienza tecnologica dell’epoca, e tra questi anche in quello metallurgico: inizia lo studio delle proprietà fisico meccaniche dei metalli e l’influenza della composizione, s’impiegano metodi efficaci di analisi chimica per accertarla, la struttura dei metalli e delle leghe comincia a essere osservata al microscopio (nascita della metallografia con Henry Power, 1664) notando cricche, microcavità, inclusioni. Altro fatto importante è la nascita in questo periodo di una letteratura tecnica specifica sui processi metallurgici, con descrizione dei cicli produttivi e dei limiti dei loro parametri guida per ottenere migliori prestazioni.
Per i processi metallurgici l’evento fondamentale è l’introduzione del coke (Darby, inizio del 1700), da usare come riducente al posto del carbone di legna: il carbon fossile era già noto da tempo e impiegato come combustibile, ma non era adatto a usi metallurgici, specie per il suo elevato tenore di zolfo; merito di Darby è quello di aver messo a punto il processo di distillazione del carbon fossile in ambiente riducente, ottenendo un materiale ideale per la carica dei forni, grazie alla resistenza mecca-
nica, anche a caldo, alla relativa purezza e soprattutto al basso costo (facilità di preparazione in grandi quantità). Tra l’altro Darby introduce in fonderia l’uso della staffatura (forme in sabbia in due metà, richiudenti la cavità in cui sarà colato il getto).
Anche i forni fanno tesoro di sostanziali perfezionamenti, sia grazie all’uso di refrattari compatibili con i regimi termici praticati e con la composizione chimica della lega da affinare, sia dal punto di vista degli schemi costruttivi: dimensioni accresciute, disposizione e dimensionamento degli ambienti e dei condotti nei confronti dei processi che vi si praticano, introduzione delle ciminiere per migliorare il tiraggio e allontanare i fumi nocivi. A questo proposito è bene notare come si cominci a ricuperare lo zinco nei forni di affinazione del piombo: lo zinco che distilla e condensa sulle pareti relativamente fredde degli impianti è raccolto e usato per la produzione diretta dell’ottone sciogliendolo nel rame: in questo modo c’è un controllo più agevole della composizione della lega; verso la fine di questo periodo (Champion, 1738) è messo a punto anche il processo di affinazione dello zinco a partire dal minerale e, nel campo siderurgico, Reamur (1722) sviluppa il processo di produzione della ghisa malleabile a cuore bianco.
In fonderia è fusa (1733) la più grande campana del mondo, quella del Cremlino, pesante ben 200 t, che nella fase successiva alla distaffatura per un incidente (incendio supporto) subisce una frattura: si stacca un pezzo oltre 11 t.
Con le prove di trazione iniziano anche quelle per determinare le proprietà meccaniche dei materiali. Nel campo delle lavorazioni dei metalli per deformazione plastica si devono segnalare i progressi dei laminatoi: anche se usati prevalentemente per laminazione e cesoiatura dei metalli non ferrosi (lavorabili più agevolmente che non il ferro o l’acciaio); questi laminatoi, pur avendo una struttura con limitata rigidità meccanica ed essendo azionati da fonti di energia a basso rendimento (in questo periodo è disponibile solo l’energia fornita da macchine idrauliche), hanno già in sé in germe l’architettura dei moderni treni di laminazione, a due o tre cilindri sovrapposti.
Usi di nuovi materiali: nel 1615 il lattice di gomma è impiegato (Spagna) per impermeabilizzare pelli e tessuti. Sviluppi collaterali riguardano altri aspetti del progresso tecnico; esempi:
• 1608: Lippershey brevetta un sistema ottico che permette di costruire il cannocchiale, poi il microscopio, (perfezionati da Galilei nel 1609 e negli anni successivi), e infine il telescopio a rifrazione; il telescopio a riflessione sarà costruito da Newton nel 1668
• Pascal (1642) realizza il primo esemplare di macchina da calcolo: la “pascalina”.
Fino al 1750 la Francia ha il primato per le invenzioni, che
passerà poi al Regno Unito.
Dalla rivoluzione industriale a fine 800 – Le macchine utensili
La rivoluzione industriale inizia in Europa intorno al 1750, quando per la prima volta la produzione delle fabbriche supera in quantità quella artigiana e domestica; a questo contribuiscono sia la costruzione di macchine utensili capaci di lavorazioni specifiche, sia lo sviluppo delle motrici a vapore: l’invenzione di Newcomen del 1705 sarà perfezionata da Watt con l’introduzione del condensatore del vapore in uscita dal cilindro in cui scorre il pistone, dell’indicatore di pressione dello stantuffo e infine, 1763, col regolatore di velocità a forza centrifuga.
Con Le Blanc è sviluppato (ante 1800) il concetto di parti intercambiabili, applicato p. es. alla costruzione di pistole (North, 1799), e quindi avviene l’introduzione del concetto di tolleranza geometrica nelle lavorazioni meccaniche. E’ del 1835 il brevetto del famoso revolver Colt.
A partire dal 1850, con l’avvento della seconda rivoluzione industriale, il primato delle invenzioni passerà agli Stati Uniti.
Lo sviluppo delle macchine utensili comincia con la costruzione dell’alesatrice (Wilkinson, 1775) e prosegue con la potente pressa idraulica di Bramah, il tornio per filettare viti di Maudslay (1790), la macchina per produzione di chiodi (Longstreth, 1809), il tornio con testata a ingranaggio posteriore e la pialla a bancale piano con guide (Roberts, 1817), la fresatrice (Whitney, 1818), la macchina automatica per dadi, la limatrice, il trapano con avanzamento meccanico automatico (Nasmith, rispettivamente nel 1829, 1836, 1840), il tornio automatico per perni (Howe, 1841), la piallatrice (Withworth, 1842), la sega a nastro (Perrin, 1853), il tornio a torretta verticale (Lawrence, Hove, Stone, 1855), il laminatoio a freddo degli acciai (Lauth, 1859), il maglio manovrato col vapore (Nasmyte, 1867), il freno ad aria compressa (Westinghouse, 1869), il calibro micrometrico (Brown e Sharpe, 1877), le rettificatrici universali (1880), il cambio di velocità (Norton, 1892), i torni automatici per la produzione viti (Spencer, 1895), i blocchetti di riscontro (Johnson, 1896), e infine torni multimandrino, alesatrici verticali, piallatrici con inversione moto, fresatrici universali (ante 1900). Lo sviluppo delle macchine utensili ha un grosso impatto anche sui processi metallurgici: è possibile costruire particolari meccanici e componenti strutturali di altre macchine e di impianti, con i quali sono finalmente meccanizzate molte delle lavorazioni prima praticate manualmente, come preparazione e movimentazione dei materiali e dei prodotti, lavorazioni ai magli, alle forge e agli estrusori.
Il contributo maggiore allo sviluppo tecnologico viene dal progresso scientifico, che investe in particolare la chimica, la fisica e l’elettrochimica, permettendo tra
l’altro di riconoscere e studiare i nuovi metalli che nel frattempo vengono isolati. Nasce la metallurgia fisica: con l’avvento della metallografia, dell’analisi termica e del perfezionamento dei metodi di analisi si comincia a interpretare i meccanismi con cui si originano le strutture, e come queste ultime condizionano le proprietà delle leghe più comuni.
A metà del 18mo secolo i laminatoi cominciano a essere mossi da ruote idrauliche. Con l‘avvento della rivoluzione industriale cresce l’esigenza di disporre di grandi quantità di ferro e acciaio lavorati in modo da poter soddisfare la domanda di prodotti metallici, e quindi necessità di costruire macchine di maggiore potenza e con cicli più veloci: nascono così il maglio rapido a vapore già citato (la massa battente è sollevata dal pistone mosso dal vapore in un cilindro) e la pressa idraulica, anch’essa già citata, nella quale la forza è sviluppata da un liquido pressurizzato. L’introduzione della macchina a vapore permette anche la messa in opera di laminatoi (a due e tre cilindri sovrapposti) capaci di operare su quantità e formati di semilavorati fino allora non producibili.
La siderurgia, l’uso dei metalli oltre all’avvento di costruzioni metalliche sempre più imponenti e l’evoluzione tecnica in generale registra numerosi sviluppi: il progresso diventa incalzante!
Sono qui indicati alcuni eventi significativi
• trasporto su rotaia di materiali con carrelli a trazione animale (Outram, 1750)
• Diderot e D’Alembert pubblicano Encyclopédie des Arts et des Métiers (1751-1772)
• le rotaie in legno sono rimpiazzate da quelle in ghisa (Huntsmann, 1756)
• 1771: costruzione del “carro” di Cougnot, antenato dei veicoli semoventi, equipaggiato con un motore bicilindrico a vapore; la prima vettura munita di motore a combustione aria-idrogeno nascerà (de Rivaz) nel 1802, e la prima auto elettrica (Anderson) nel 1839
• viene costruito sul fiume Severn (Regno Unito) il primo ponte metallico; è realizzato in ghisa ed è lungo 30 m (The Ironbridge, 1779)
• avviamento della produzione di ferro a partire dalla ghisa col processo di puddellaggio: la ghisa è introdotta in un forno a riverbero, miscelata con ossido di ferro (come minerale o scaglie di laminazione) e fusa in fiamma ossidante; si ha violenta reazione esotermica del carbonio con l’ossigeno, favorita da un rimescolamento della massa liquida dall’esterno, con pale di ferro; al termine dell’operazione si ottiene una massa solida di ferro quasi puro, che si sottopone a forgiatura (Cort, 1784)
• illustrazione delle proprietà delle leghe più comuni (Achard, 1788)
• 1790: Talleyrand propone l’adozione di un sistema di pesi e misure basato su grandezze fisiche riproducibili e invariabili nel tempo; nasce così il sistema metrico SI,
oggi universalmente adottato
• avviamento della produzione di recipienti in lega platino-arsenico (la scoperta di questa lega fusibile nel 1781 è seguita dal suo uso nel 1790, in Francia)
• 1794: invenzione del cubilotto con rivestimento in metallo e con soffiaggio dell’aria realizzato con motore a vapore (Wilkinson); primo brevetto del cuscinetto a sfere (Vaughan)
• esperienze di Galvani e invenzione della pila (Volta, 1795)
• Bramah brevetta l’estrusione di tubi di piombo (1797), perfezionata poi da Burr (1820)
• va in produzione un laminatoio per lastre di rame (Revere, 1800)
• 1801: Lebon sperimenta l’illuminazione a gas nella sua casa; segue (1804) il brevetto di Winsor su questa tecnologia; essa sarà adottata per l’illuminazione stradale, p. es. a Parigi (1820)
• prima linea di tram a trazione animale su rotaia per trasporto pubblico (nel Galles, 1804)
• 1806: Jacquard costruisce un rivoluzionario telaio per la tessitura con cui i tessuti operati si producono grazie al sollevamento automatico dei fili dell’ordito con un sistema di cartoni forati, realizzando programmi di disegno ripetibili e modificabili a piacere
• preparazione del sodio metallico mediante elettrolisi (Davy, 1808)
• rilascio del brevetto dei barattoli di ferro stagnato (Durand, 1810)
• 1814: costruzione di una efficiente locomotiva a vapore, la Rocket di Stephenson; la prima a trainare un convoglio è stata quella costruita da Trevithick, 1804
• 1817: Drais inventa la “draisina”, antenata (in legno!) della bicicletta, mossa spingendo con i piedi; la trasmissione a catena tra ingranaggi mossi da pedali apparirà negli anni 1879-1885 (Lawson, Renold, Starley)
• nasce l’acciaio legato al nickel (Faraday, 1819)
• le rotaie in ghisa sono sostituite da quelle in ferro (Birkinshaw, 1820)
• per il riconoscimento dei minerali è proposta la prova di durezza mediante scalfittura (Mohs, 1822)
• introduzione delle alpacche, leghe rame-nickel-zinco (Frick, 1823)
• è adottato il preriscaldamento dell’aria da soffiare nei forni: aumento delle temperature di lavoro e risparmio di combustibile (Nelson, 1828)
• inizia la produzione di platino compatto per pressatura polvere e sinterizzazione (Wollanston, 1829, dopo che il metallo era stato sinterizzato ad alta temperatura in Russia, nel 1826)
• 1830: invenzione della macchina per cucire (Thimonnier); inizia la produzione via metallurgia delle polveri di monete di rame sinterizzate e poi coniate con un punzone (Osann)
• 1832: nasce l’alternatore, che avrà sviluppo pratico solo dopo la realizzazione del trasformatore; elaborazione del bronzo al nickel (Berry)
• 1834: Babbage progetta un calcolatore capace di elaborare formule algebriche complesse, in cui i dati sono da introdurre con schede perforate; realizzazione della cancellata in ghisa del Palazzo Reale di Torino su progetto del Palagi
• invenzione e costruzione del telegrafo elettrico (Morse, 1835)
• applicazione del processo di zincatura di lamiere di acciaio per immersione in zinco fuso (galvanizzazione) per aumentare la resistenza alla corrosione (1836)
• 1837: Hancock brevetta il processo di elaborazione delle mescole di elastomeri mediante cilindri controrotanti; con Daguerre nasce la fotografia
• 1839: scoperta del processo di vulcanizzazione degli elastomeri (Goodyear); uso dei metalli bianchi antifrizione (leghe di stagno con antimonio, rame e piombo) per cuscinetti a strisciamento (Babbit)
• comincia la produzione di funi di ferro (Roebling, 1841)
• 1843: varo del transatlantico Great Britain, costruito con lamiera di ferro; Hodkingson introduce la prova di resilienza sui metalli
• 1844: primo esperimento di illuminazione mediante lampade ad arco elettrico; sarà perfezionato poi da Jablochkov nel 1876
• avviamento della produzione di cannoni di acciaio fuso (Krupp, 1847)
• 1850: viene messo in funzione il cubilotto con fondo apribile; sono praticati rivestimenti galvanici (posateria argentata); sono messe in circolazione in Svizzera monete in alpacca; è sviluppato il processo ad alto rendimento per ricuperare l’argento dal piombo (Parkes)
• 1853: Barsanti e Matteucci brevettano il motore a combustione interna, perfezionato poi da Otto e Langen (1876, ciclo a 4 tempi), da Clerk (1879, ciclo a 2 tempi) e infine (1893) da Diesel (ciclo con accensione spontanea del carburante)
• si dimostra per la prima volta che l’alluminio è producibile via elettrolisi da sali fusi (Sainte-Claire Deville, 1854)
• invenzione della macchina per scrivere “cembalo scrivano” (Ravizza, 1855) che, opportunamente ingegnerizzata, andrà in produzione industriale (Remington, 1875);
• 1856: preparazione dei bronzi all’alluminio (Debray); disossidazione dell’acciaio con manganese in fase di affinazione (Mushet); realizzazione del laminatoio tipo trio per la laminazione degli acciai (Carslund); costruzione dei forni con rivestimento acido per convertire la ghisa a basso tenore di fosforo in acciaio (Bessemer, brevetto del 1855), e del forno a riverbero (Martin-Siemens)
• 1857: le rotaie in ferro sono sostituite da quelle in acciaio (Mushet); perfezionamento del sistema di preriscaldamento dell’aria per i forni (Cowper)
• posa del primo cavo telegrafico transatlantico (1857-58)
• 1860: Wöhler introduce la prova di fatica sui metalli; Pacinotti inventa il suo anello, con cui l’energia meccanica si trasforma in elettrica; in Belgio sono messe in circolazione monete in cupronickel
• brevetto della Xylonite, più nota poi come celluloide (Parkes, 1861, e poi Hyatt, 1870)
• le tecniche di esame al microscopio ottico cominciano a essere applicate allo studio sistematico della struttura dei metalli, in particolare degli acciai: nasce con Sorby la moderna metallografia (1863)
• 1865: prime teorie sull’indurimento di tempra degli acciai, spiegato con variazioni strutturali durante i trattamenti termici (Julien); sviluppo del processo di raffinazione del rame per via elettrolitica (Elkington)
• 1867: invenzione della dinamo, che mette a disposizione una sorgente di elettricità per le esigenze dell’industria (Siemens e Wheatstone); esce il brevetto del filo spinato (Smith)
• introduzione dei ventilatori per il soffiaggio dell’aria nei forni (Root, 1867 e Sturtevant, 1870)
• elaborazione dell’acciaio al tungsteno, antenato degli acciai rapidi (Mushet, 1868)
• pubblicazione della tavola periodica degli elementi (Mendeleiev, 1869)
• sono impiegati cuscinetti radenti ottenuti a partire da polvere di stagno miscelata con pece e poi pressata (Gwynn, 1870)
• 1871: Meucci e, separatamente, Bell brevettano il telefono
• 1873: Decauville perfeziona il sistema Corbin di ferrovia portatile a scartamento ridotto di semplice posa in opera, per trasporto materiali con vagoncini a due assi
• enunciazione della “regola delle fasi” in termodinamica (Gibbs, 1874)
• 1877: Edison brevetta il fonografo, sistema di registrazione e riproduzione del suono mediante solco inciso su di un rullo rotante, letto con un ago messo in vibrazione nel solco; sarà successivamente modificato da Berliner (1887, versione attualmente in uso), con solco inciso a spirale su disco piano rotante, letto sempre con ago a opportune velocità; sono introdotti gli acciai al cromo (Boussingalt e Brustlein); Thomas e Gilcrist brevettno il convertitore della ghisa ad alto tenore di fosforo in acciaio grazie al rivestimento in refrattario basico
• scoperta del processo nickel carbonile: l’azione dell’ossido di carbonio a opportuna temperatura e pressione su leghe contenenti nickel determina la formazione di Ni(CO)4 gassoso; questo è condensato, raccolto e decomposto per riscaldamento a temperatura superiore a quella della sua formazione, dando origine a polvere di nickel; dal residuo di nickel impuro, quale quello ottenibile per fusione, si possono così ricuperare metalli nobili e cobalto, che sono di solito presenti (Mond, 1880)
• !879-1880: sviluppo dell’illuminazione mediante lampade elettriche ad incandescenza (Edison e poi Swan)
• prima linea di tram elettrificata (Berlino, 1881)
• 1882: primi brevetti del trasformatore (Gaulard e Gibbs, traduzione in uso pratico dell’anello di induzione realizzato nel 1831 da Faraday)
• sviluppo degli acciai al manganese (Hadfield, 1882)
• 1884: Tilden ottiene il poliisoprene sintetico, praticamente identico come proprietà a quello presente nella gomma naturale; posa di una piramide di alluminio (al momento pregiatissimo) sul monumento a Washington
• 1885: costruzione del motore elettrico a campo rotante in corrente alternata (Ferraris); Goldschmidt scopre e utilizza la reazione della termite per produrre acciaio inossidabile ad alto cromo e basso carbonio; avviamento della produzione di tubi di acciaio senza saldatura per laminazione (processo Mannesmann); sviluppi dei forni elettrici a induzione (brevetto Colby)
• 1886: compare sul mercato il primo rasoio di sicurezza (Wilkinson); avviamento della produzione di alluminio a partire da allumina per elettrolisi in presenza di fondenti fluorati (Hall e Heroult); proposta di usare coni ceramici di diversa composizione, collassabili per riscaldamento a differenti temperature, per misura di temperature elevate (Seger)
• 1887: protesi dentali si realizzano col processo di fusione in cera persa (Philbrook); introduzione del forno fusorio a induzione con nucleo (Ferranti); processo di ricupero dell’oro per cianurazione (Mc Arthur e Forrest); analisi termica degli acciai con la determinazione dei punti caratteristici (Osmond); sviluppo della saldatura ad arco dell’acciaio (Bernados)
• 1888: brevetto dello pneumatico (Dunlop)
• viene costruita in acciaio la torre Eiffel, inaugurata in occasione dell’esposizione universale (1889); diventerà il simbolo di Parigi: è alta 320 m e pesa 7400 t
• primi brevetti sulle turbine a gas (intorno al 1890); le realizzazioni pratiche si avranno però negli anni Trenta del Novecento
• introduzione delle termocoppie Pt/Pt-Rh per la misura di temperature elevate (Le Chatelier, 1891)
• 1891-1901 sviluppi dell’invenzione della radio (Marconi, Tesla, Popov)
• 1892: invenzione del forno elettrico ad arco (Moissan, usato inizialmente per ottenere diamanti sintetici), che sarà poi largmente impiegato per la rifusione (riciclaggio) di rottami e scarti ferrosi e sarà poi perfezionato e curato nelle applicazioni da Sassano (1898); pubblicazione del primo libro di testo di metallurgia (Austen)
• 1894: i fratelli Lumiere brevettano il cinematografo; applicazione del processo di estrusione alle leghe di rame (Dick)
• illustrata la natura dell’austenite, una delle strutture dell’acciaio (Osmond, 1895)
• 1896: scoperta della radioattività (Becquerel); determinazione dello zolfo negli acciai (Schulte)
• 1878-1900: comincia la produzione di filamenti per lampade a incandescenza realizzati prima con carbone, poi con vari metalli refrattari – osmio (Auer von Welsbach), zirconio e tantalio, che sostituiscono l’osmio, e infine col tungsteno (processo Coolidge: riduzione di WO3 con idrogeno, pressatura, presinterizzazione a 1200°C, sinterizzazione a ≈ 3000°C)
• sviluppo del trattamento termico degli acciai rapidi (Taylor e White, 1898)
• 1899: viene inventato e costruito il primo forno elettrico ad arco diretto, per la fusione di acciai e leghe (Heroult)
• sviluppo degli acciai al silicio (Hadfield, 1899)
• viene tracciato il diagramma di stato ferro-carbonio: applicazione generale della regola delle fasi per determinare il comportamento della struttura delle leghe al variare della temperatura (Austen e Rozeboom, 1896-1900)
• 1900: la prova di durezza sui metalli entra nella pratica (Brinell); invenzione del processo di riscaldamento di pezzi di acciaio in presenza di polvere di zinco per realizzare un rivestimento resistente alla corrosione (sherardizzazione, Sherard Cowper –Coles); esce il brevetto del processo di colata in conchiglia a bassa pressione (Lake) In questo periodo e, grazie anche alla interpretazione della tavola periodica degli elementi, sono scoperti ed isolati metalli non ancora noti, ma presenti in natura nei loro minerali: essi avranno una parte essenziale nella formulazione di nuove leghe, il cui uso oggi è ormai consacrato nella pratica quotidiana, con processi produttivi che, diventando sempre più efficienti, arrivano a offrirci prodotti di cui non possiamo fare a meno.
L’elenco include cobalto (Brandt, 1735), platino (Ulloa, 1748), nickel (Cronstedt, 1751), bismuto (Geoffrey, 1753), magnesio (Black, 1755, isolato da Bussy e Wöhler nel 1829), manganese (Scheele e Gahn, 1774), molibdeno (Scheele e Hyelm, 1778), tungsteno (Scheele, 1781, isolato da D’Ehluyar nel 1783), tellurio (Műller, 1782), stronzio (Crawford, 1787), uranio e zirconio (Klaproth, 1789), titanio (Gregor, 1791), ittrio (Gadolin, 1794), berillio (Vauquelin, 1797, isolato da Bussy nel 1828), vanadio (Fernandez, 1801, isolato da Roscoe nel 1867), niobio (Hatchett, 1801), tantalio (Ekeberg, 1802), cerio (Berzelius e Hisinger), iridio e osmio (Tennant), palladio e rodio (Wollanston) nel 1803, potassio e sodio (Davy, 1807), bario, calcio (Davy) e boro (Gay Lussac) nel 1808, torio (Berzelius, 1815), cadmio (Strohmayer e Hermann), litio (Arfvedson), selenio (Berzelius) nel 1817, alluminio (Oerstedt, 1825), erbio e terbio (Mossander, 1843), cesio (Bunsen e Kirchhoff, 1860), rubidio (Bunsen e Kirchhoff) e tallio (Crookes) nel 1861, indio (Reich e Richter, 1863), gallio (Lecoq), scandio (Nilson), germanio (Winkler), protoattinio (Fajans) nel 1871, itterbio (Galissard, 1878), samario (Lecoq), tullio (Cleve) nel 1879, gadolinio
(Galissard, 1880), praseodimio e neodimio (Auer, 1885), disprosio (Lecoq, 1886), polonio e radio (coniugi Curie, 1898), attinio (Debierne, 1899).
Verso la fine dell’Ottocento nascono le associazioni nazionali dei tecnici che si occupano di meccanica, di materiali non solo metallici, e che sono impegnati in attività ad esse collegate; tra queste risulta fondamentale quella normativa: è da citare la American Society for Testing Materials (ASTM), fondata nel 1898.
Novecento
Il progresso della metallurgia diventa incalzante non tanto per ulteriori nuove scoperte (che comunque completano il quadro delle conoscenze) quanto per il miglioramento del quadro di riferimento, in cui intervengono fattori non considerati prima e che diventeranno sempre più condizionanti, quali p. es. efficienza e rese, organizzazione della ricerca, costi, e poi ecologia, sicurezza, gestione, conservazione delle risorse.
Gli sviluppi sono rapidi e diversificati e non facili da analizzare nel dettaglio, come fatto nei precedenti periodi. I fattori che contribuiscono alla crescita sono le necessità dell’industria, le cui strutture produttive assumono dimensioni rilevanti, dovendo fronteggiare una concorrenza sempre più globalizzata, le esigenze di nuovi materiali e processi nell’aeronautica e nei trasporti in genere, la corsa agli armamenti e allo spazio, la lotta generalizzata contro la corrosione e l’usura. L’integrazione fra le varie discipline è altissima fra tutte quelle che possono concorrere al successo: scienza, tecnologia ed economia sono presenti in ogni fase e ogni nuova realizzazione è frutto di attività coordinate e sempre più dispendiose di esperti nelle varie branche.
L’età del ferro raggiunge la sua maturità: con l’assottigliamento delle risorse facilmente sfruttabili si intensifica la fase del riciclo degli scarti e la ritrasformazione dei materiali contenuti nei prodotti non più in uso; l’avvento di materiali innovativi, e cioè delle materie plastiche sintetiche e dei materiali ceramici (che possono sostituire vantaggiosamente e in molte applicazioni i metalli che avevano fino allora dominato la scena), rappresenta il completamento di quello che al momento era a disposizione.
Indicativamente, la prima metà del periodo raccoglie ancora tappe significative nel progresso tecnico; poi prevale un’attività di perfezionamento delle conoscenze e di adozione nella pratica di quanto elaborato in precedenza. Alcune di queste tappe sono indicate qui di seguito.
• 1900: primo volo del dirigibile Zeppelin e, a Berlino, prima linea ferroviaria elettrificata
• invenzione della telescrivente (Morton e Krum, primi del Novecento)
• 1903: nasce l’aeronautica col volo dei fratelli Wright; la prova di resilienza Izod è normalizzata e nel 1906 lo sarà
quella Charpy; sono introdotte le leghe di alluminio da bonifica, cui si aggiungeranno le leghe ferro-nickel-cromo (Guillet), il monel (Brown, 1906), le stelliti (Haynes, 1907), l’acciaio inossidabile ferritico ad alto cromo (Becket, 1907)
• 1904: con l’invenzione del diodo (Fleming) inizia lo sviluppo delle valvole termoioniche; esso proseguirà col triodo (De Forest, 1907), tetrodo (Schottky, 1919), pentodo (Tellegen, 1926) e, successivamente, coi tubi a vuoto multifunzione, divenuti di uso comune negli anni 40
• fonderia: esce il brevetto della macchina per presso colata (Doehler, 1905)
• 1906: Coolidge ottiene il brevetto sui fili di tungsteno per le lampade ad incandescenza
• sviluppo del trattamento termico di tempra di soluzione e invecchiamento nelle leghe di alluminio (Wilm, 1907)
• 1908: Ford mette sul mercato la sua auto, la Ford T, che sarà prodotta in 15 milioni di vetture fino al 1928
• è fondata la rivista “La Metallurgia Italiana” (1909)
• 1910: brevetto della resina fenolo-formaldeide, nota poi col nome di bakelite (Baekeland)
• nei laboratori diventa disponibile il microscopio metallografico (Reichert, 1911)
• 1912: introduzione dell’acciaio inossidabile austenitico (Maure e Strass); processo di produzione del polivinilcloruro – PVC (Katte); Sauveur pubblica Metallography and Heat Treatment of Iron and Steel
• Invenzione del Cellophane (Brandenberger, 1913)
• 1913: Bohr propone la struttura dell’atomo secondo il modello cosidetto quantico, in cui gli elettroni, particelle aventi carica negativa, ruotano attorno al nucleo in cui stanno i protoni, particelle con carica positiva, occupando regioni dello spazio definite come orbitali e caratterizzate da livelli differenziati di energia; questo a conclusione delle teorie sulla struttura, iniziate con Democrito (V secolo AC) e proseguite con Dalton (1808, atomi differenziabili dei diversi elementi, contraddistinti da una nuova simbologia), con Thomson (1897, postulata e dimostrata l’esistenza dell’elettrone), e infine con Rutherford (1911, modello planetario, con elettroni rotanti attorno al nucleo su orbite); il modello di Bohr sarà successivamente implementato da De Broglie, Heisenberg, Schroedinger, Pauli, infine, 1932, Chadwick dimostra l’esistenza del neutrone, particella come i protoni ma priva di carica elettrica, presente nel nucleo insieme con essi
• 1914: sono introdotte le prove di durezza Rockwell, di facile e rapida esecuzione
• i carburi metallici sinterizzati con legante cobalto sono elaborati a livello laboratorio (Lohmann e Voigtländer, e poi Schroeter, 1914); segue sviluppo industriale (192325) e infine brevetto (Widia, Krupp, 1926)
• il forno elettrico a induzione è impiegato per la fusione di metalli non ferrosi (1915)
• tra il 1900 e il 1924 sono prodotti materiali compositi sotto forma di contatti elettrici a base prevalentemente di polvere di tungsteno miscelata con polvere di rame o di argento pressata e sinterizzata, meno frequentemente con polvere di cobalto, ferro e nickel, e poi elettrodi, contrappesi, contenitori (p. es. per il radio, che è radioattivo)
• cuscinetti radenti sinterizzati in bronzo con grafite e impregnati con olio cominciano ad entrare nelle applicazioni meccaniche (Loeventhal, 1913, Gilson, 1921) e poi nell’auto (1927)
• 1916: sviluppo del forno elettrico a induzione senza nucleo (Northrup)
• 1918: invenzione della fusione centrifuga (Sensaud DeLavaud); la Krupp costruisce la “Grande Berta”, cannone con canna di diametro 38,1 cm e lunghezza 33,5 m, per l’assedio a Parigi, capace di sparare a una distanza di 122 km
• indagini strutturali sui materiali solidi con i raggi X (Debye-Scherrer e Hull, 1916-17), nuovi tubi proposti da Coolidge (1920) e applicazione del metodo al controllo qualità dei getti (1925)
• tra il 1900 e fine anni 20 uso di magneti permanenti e di nuclei di ferro per le radio prodotti via metallurgia delle polveri
• 1923: inizia la produzione di filtri metallici sinterizzati (Claus)
• sono introdotte le prove di durezza Vickers, adatte a molti materiali, anche non metallici (Sandland e Smith, 1924)
• sviluppo del cubilotto con aria preriscaldata (Griffin, 1925)
• 1926: Baird inventa la televisione, realizzata l’anno dopo da Fansworth
• sviluppo del forno a induzione ad alta frequenza (1927)
• 1928: Dirac postula l’esistenza dell’antimateria (particelle atomiche aventi cariche elettriche opposte a quelle che costituiscono la materia normale) cui seguono conferme sperimentali tra cui 1932 Alderson, antielettrone (positrone), Segre e Chamberlain, 1955, antiprotone, e 1959, antineutrone
• introduzione degli acciai indurenti per precipitazione (Kroll, 1929)
• 1930: la Avesta produce gli acciai inossidabili duplex; Bain e Davenport illustrano le trasformazioni dell’austenite negli acciai col raffreddamento; inizia l’impiego sistematico di atmosfere controllate nei trattamenti termici
• 1931: Ruska e Knoll costruiscono il prototipo del microscopio elettronico; Ragsdale inventa la saldatura elettrica a punti
• Anni 30: nasce la missilistica con gli studi di von Braun, culminati coi lanci delle V2 verso la fine della II Guerra Mondiale
• sintesi e produzione della poliammide - Nylon (Ca-
rothers, 1935)
• 1936: è sviluppato il primo modello fnzionante di radar (Bay)
• inizia la produzione di tubi al neon per illuminazione (General Electric, 1938, su brevetto Germer)
• progettato e costruito Z1 primo computer programmabile (Zuse, 1939); il primo computer commerciale, UNIVAC, sarà invece sviluppato negli USA nel 1951 (Eckert e Mauchly)
• produzione in Germania di corone di forzamento di ferro sinterizzato per proietti impregnate con paraffina in sostituzione di quelle in rame (II Guerra Mondiale)
• dal 1940 in avanti, introduzione nelle auto di componenti meccanici sinterizzati e degli elastomeri sintetici nelle gomme, in concorrenza con l’elastomero naturale
• 1941: brevetto del polietilentereftalato – PET (Whinfield e Dickson) e del poliestere - Terylene
• sintesi dei poliuretani (Hanford e Holmes, 1941)
• 1942: Fermi realizza con successo a Chicago la prima reazione nucleare a catena, che permetterà poi di costruire le centrali nucleari e gli ordigni atomici
• scoperta dell’effetto del magnesio sulla sferoidizzazione della grafite nelle ghise (1943)
• sviluppo della formatura a guscio dei getti (Croning, 1944)
• 1946: nasce l’Associazione Italiana di Metallurgia (AIM)
• realizzazione del transistor, che tenderà a sostituire i tubi a vuoto (Shockley, Bardeen, Bratain, 1947)
• sviluppo del convertitore LD (Linz-Donawitz) di affinazione della ghisa in acciaio mediante soffiaggio di ossigeno puro sulla superficie del metallo (Durrer, 1948)
• 1946-50: sviluppo delle resine epossidiche
• commercializzazione del politetrafluoroetilene – Teflon (USA, 1950)
• 1952: prima macchina utensile commerciale a controllo numerico (tornio - Cunningham e Alma Corporation)
• Anni 50: Canon in Giappone e HP nrgli USA avviano le esperienze con la stampa a getto d’inchiostro; inizia produzione e uso dei polietileni e Natta (1954) brevetta il polipropilene isotattico
• sviluppo del processo di affinazione AOD della ghisa in acciaio, in cui ossigeno e argon sono usati nel soffiaggio (Krivits, 1954), e poi VOD (decarburazione con ossigeno sotto vuoto)
• prima centrale nucleare, installata nel Regno Unito (1956)
• 1957: va in orbita Sputnik, il primo satellite nello spazio
• 1959: introduzione dei policarbonati (USA e Germania) e delle resine acetaliche (USA)
• Anni 50 e 60: componenti meccanici prodotti via metallurgia delle polveri con struttura compatta, componenti a base di superleghe, sbozzati di acciai per utensili, pezzi sinteroforgiati; avvento dei processi di pressatura isostatica a caldo (HIP) e a freddo (CIP)
• entra in servizio (1959) il rompighiaccio Lenin, prima nave a propulsione nucleare
• realizzazione del laser (Maiman, 1960)
• 1961: Yurij Gagarin, primo uomo in orbita nello spazio
• Anni 60: sviluppo dei processi di produzione di acciai speciali mediante rifusione di acciai prodotti al forno elettrico, tra cui ESR (rifusione sotto elettroscoria), EPSR (come ESR, in pressione di azoto), VAR (rifusione con forno ad arco sotto vuoto), VIM (rifusione a induzione sotto vuoto), e ancora produzione di acciai da utensili a partire da polveri
• 1962 compare sul mercato (Holonyak) il primo LED (Light Emitting Diode), inizialmente solo a luce rossa, e poi a diversi colori, grazie allo sviluppo di nuovi e molto più efficienti composti elettroluminescenti, culminati con quelli a luce bianca (ricerche di Nakamura, 1993-95), che sostituiranno progressivamente i sistemi di illuminazione oggi in uso
• invenzione del personal computer (Perotto, 1964)
• va in orbita geostazionaria Intelsat I, primo satellite commerciale per telecomunicazioni (Comsat, 1965)
• 1969: sbarco sulla Luna della missione Apollo 11 (Armstrong e Aldrin)
• Anni 70: componenti meccanici prodotti via stampaggio polveri a iniezione (MIM, Metal Injection Moulding); introduzione dei magneti permanenti ad altissimo prodotto di energia a base di terre rare (samario-cobalto e poi, 1983, neodimio-ferro-boro); sviluppo di materie plastiche di elevate prestazioni, tra cui p. es. polifenilensolfuri, fibre aramidiche,
• 1983 nasce la telefonia mobile (Cooper, Motorola) con il lancio commerciale del primo apparecchio rice trasmittente collegato alla rete telefonica fissa con modalità cellulare e nel 1992 la IBM progetta Simon, progenitore degli attuali smartphone, in cui compaiono alcune altre funzioni oltre a quelle di semplice telefono; esse saranno poi continuamente arricchite e ciò ne spiega la universale diffusione
• 1986: Hull brevetta la stereolitografia, che permetterà lo sviluppo dello stampaggio 3D, cioè la realizzazione di oggetti tridimensionali, di forma anche estremamente complessa, a partire da materiali in polvere, deposti con l’ausilio di un software ad hoc in una successione di strati trasversali, ciascuno consolidato sul posto ed ancorato a quello e formato in precedenza con l’azione di opportune sorgenti energetiche, p. es. laser
• Anni 80 e 90: diffusa applicazione degli strumenti CAD/ CAM/CAE e dei metodi di modellazione e simulazione dei processi, grazie all’aumento della capacità di elaborazione dei computers; i dischi fonografici classisci sono in buona parte sostituiti prima da rigistrazioni su piste magnetiche (“musicassette”), e poi da sistemi ottici, nei quali la lettura delle incisioni è effettuata con laser (compact disc e poi DVD)
La tavola periodica degli elementi di Mendeleiev presenta ancora delle caselle vuote: prosegue pertanto in questo periodo l’attività d’isolamento di elementi in cui sono inclusi anche quelli transuranici, non esistenti in natura: europio (Demarçay, 1901), lutezio (Auer e Urbani, 1907), afnio (Coster e Hevesy, 1923), renio e tecnezio (Noddack e Berg, 1925), promezio (Law, Poll, Kurbatov, Quill, 1938), francio (Perey, 1939), astato (Carson, Ross, Segré), nettunio (MacMillan, Abelson), plutonio (Seaborg e altri) nel 1940, curio e americio (Seaborg, 1944), berkelio (Ghiorso, Seaborg, 1949), californio (Ghiorso, 1950), fermio ed einstenio (Ghiorso, 1952), mendelevio (Ghiorso, 1955), laurenzio (Ghiorso, 1961), nobelio (russi, 1966). Il Novecento si conclude con un bilancio certamente favorevole: abbiamo accumulato un complesso di esperienze nel mondo in cui operiamo: conosciamo le proprietà della materia a disposizione coi suoi pregi e le sue limitazioni, le leggi fisiche e chimiche che ne condizionano il comportamento, sappiamo gestire con buona efficienza i processi della sua trasformazione in oggetti di uso quotidiano, utilizziamo modi e strumenti atti a coordinare le attività, realzzando l’innovazione.
Dopo tanti lustri di rapido progresso, qual’è la situazione odierna? C’e ancora abbastanza spszio per ulteriori sviluppi? La risposta è sicuramente positiva: le aspettative della collettività riguardo il soddisfacimento di esigenze anche solo latenti, originabili da invenzioni o eventi, sono la molla che spinge persone singole o gruppi di lavoro a percorrere nuove strade.
Notizie storiche
R. F. Tylecote - A History of Metallurgy, 2nd ed., The Institute of materials, 1992
G.F. Bocchini – L’uomo e i metalli difficili, Napoli, 1978
G. Riccio – Un poco di storia della metallurgia, AIM
H.M. Cobb – Dictionary of Metals, ASM, 2012 UTET Grande Dizionario Enciclopedico, IV Ed. Wikipedia
Increasing demand from the structural, energy, vehicles applications as well as oil & gas sector has boosted the rapid growth of the market for High Strength Steels. Steel manufacturers are constantly seeking the possibility of increasing strength, maintaining good toughness and weldability. Such a goal can be achieved by several routes: micro-alloying, advanced thermal treatment (i.e. intercritical quenching, bainitic quenching, quench and partitioning procedure etc.), high alligation by Mn and Al, thermo-mechanical processing. The scope of the workshop is to bring together the international community to highlight state-of-theart research and development of such steel grades.
MAIN TOPICS
Both fundamental and applied aspects will be covered concerning:
- Alloying design - HSLA steels
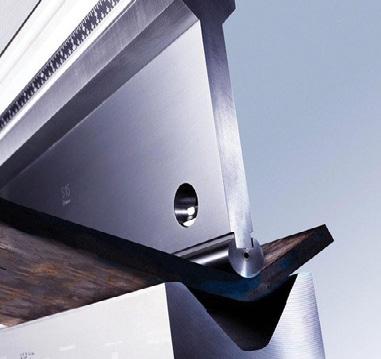
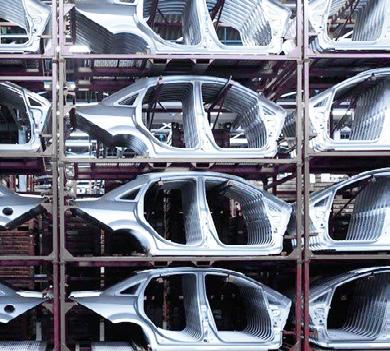
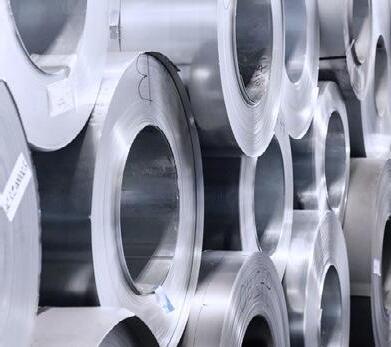
- Advanced heat treatment - Thermo-mechanical processing
- AHSS
The workshop will be performed through presentations both invited and selected on the basis of the submitted abstracts. The event will be a suitable meeting place for those involved in research, development and applications of HSS, interested to share recent advances on metallurgical design, set-up of production routes, paying attention to surface and inner quality, properties of HSS products. The deadline for abstract submission is July 14, 2023 in order to fulfil the selection for the final program.
WORKSHOP CHAIRPERSON
Ettore Anelli – Franchini Acciai
Ilchat Sabirov – IMDEA Materials Institute
ORGANISING COMMITTEE
Silvia Barella – Politecnico di Milano
Federica Bassani – AIM
Manuele Dabalà – Università di Padova
Andrea Di Schino - Università di Perugia
Carlos Garcia-Mateo - CENIM-CSIC
CALL FOR PAPERS & PROCEEDINGS
Carlo Mapelli – Politecnico di Milano
Roumen Petrov – University of Ghent
Marina Polyakova - Nosov Mgnitogorsk State Technical University
Dirk Ponge – Max Planck Institute
Prospective speakers wishing to present are invited to submit a tentative title and an abstract of about 400 words (in English) to: met@aimnet.it or online at: www.aimnet.it/hss23.htm by July 14, 2023
A special number of “La Metallurgia Italiana - International Journal of the Italian Association for Metallurgy” - which is covered in the Science Citation indexed by Clarivate Analytics, and in Scopus by Elsevier B.V - will collect the peer-reviewed submitted Workshop’s papers.
ORGANISING SECRETARIAT
Via F. Turati 8 - Milano t. +39027639770 | t. +390276021132 met@aimnet.it | www.aimnet.it/hss23.htm
Eventi AIM / AIM events
CONVEGNI
XV GIORNATE NAZIONALI CORROSIONE E PROTEZIONE - Torino, 5-7 luglio 2023 http://www.aimnet.it/gncorrosione/
S2P 2023 INTERNATIONAL CONFERENCE ON SEMISOLID PROCESSING OF ALLOYS AND COMPOSITES –Brescia, 6-8 settembre 2023 http://www.aimnet.it/s2p/
International Workshop on HIGH STRENGTH STEELS – Bergamo, 26-27 ottobre 2023
International Meeting EAF: PRODUCTIVITY, ENERGY EFFICIENCY, RAW MATERIALS AND DECARBONIZATION – Bergamo, 30 novembre-1 dicembre 2023
CORSI E GIORNATE DI STUDIO
Giornata di Studio STATO DELL'ARTE ED EVOLUZIONE DEI PROCESSI TERMICI E MECCANICI – Pisa, 12 luglio
Giornata di Studio MATERIALI INNOVATIVI PER IL MONDO RACING – Milano, 4 settembre
Giornata di Studio PROCESSI POST STAMPA ADDITIVA: DAL DESIGN DEL CICLO DI PRODUZIONE AL MANUFATTO – Caravaggio BG c/o TAV, 19 settembre e Nembro BG c/o GFM, 20 settembre
Giornata di Studio STATO DI SERVIZIO DEGLI IMPIANTI – Milano, 27 settembre
Corso itinerante METALLURGIA SICURA – 28 settembre e 5-12 ottobre
Giornata di Studio PREVENZIONE E RIDUZIONE DELLE DEFORMAZIONI IN SALDATURA – Genova, 28 settembre c/o Istituto Italiano di Saldatura
Giornata di Studio MATERIALI PER IL NUCLEARE (FISSIONE) – Milano, 10 ottobre
Giornata di Studio PALLINATURA E DIFFRATTOMETRIA RX – Agrate Conturbia (NO) c/o GNR, 12 ottobre
Giornata di Studio METALLO DURO – Pallanza VB, 12-13 ottobre
Giornata di Studio INNOVAZIONE DEI MATERIALI NELLA MOBILITA’ ELETTRICA – Bologna, 17 ottobre
Corso ANALISI CHIMICHE – Milano, 18-19 ottobre
Giornata di Studio CARATTERIZZAZIONE FUNZIONALE DI SUPERFICI MODIFICATE – Rovigo c/o Laboratorio
TESI, 15 novembre
Giornata di Studio RIPARAZIONI TRAMITE SALDATURA – Milano, 22 novembre
FaReTra (Fair Remote Training) - FORMAZIONE E AGGIORNAMENTO A DISTANZA
Modalità Asincrona (registrazioni)
Giornata di Studio EMERGENZA COSTI ENERGETICI: CHE FARE IN FONDERIA?
Webinar FaReTra IL PRINCIPIO DI MATERIALITÀ NEL REPORTING DI SOSTENIBILITÀ
Giornata di Studio ASPETTI E GESTIONE DELLA NORMATIVA NEL CAMPO DEI TRATTAMENTI TERMICI
Corso PROVE NON DISTRUTTIVE
Giornata di Studio TRATTAMENTI SUPERFICIALI SU ALLUMINIO, A SCOPO DECORATIVO E PROTETTIVO
Corso Modulare METALLOGRAFIA – I MODULO, II MODULO “METALLI NON FERROSI”
Corso modulare FONDERIA PER NON FONDITORI
Corso TRIBOLOGIA INDUSTRIALE – I MODULO
Giornate di Studio GETTI PRESSOCOLATI PER APPLICAZIONI STRUTTURALI
Corso DIFETTOLOGIA NEI GETTI PRESSOCOLATI: METALLIZZAZIONI
Corso ADDITIVE METALLURGY
Corso METALLURGIA PER NON METALLURGISTI
Giornata di Studio PRESSOCOLATA IN ZAMA
Giornata di Studio LA SFIDA DELLA NEUTRALITÀ CARBONICA
Corso itinerante METALLURGIA SICURA
Corso modulare TRATTAMENTI TERMICI
Corso modulare I REFRATTARI E LE LORO APPLICAZIONI
Corso GLI ACCIAI INOSSIDABILI 11ª edizione
Corso FAILURE ANALYSIS 11a edizione
Giornata di Studio PERFORMANCE E DEGRADO DEI MATERIALI METALLICI UTILIZZATI IN CAMPO EOLICO: CAPIRE PER PREVENIRE
L’elenco completo delle iniziative è disponibile sul sito: www.aimnet.it
(*) In caso non sia possibile svolgere la manifestazione in presenza, la stessa verrà erogata a distanza in modalità webinar
Comitati tecnici / Study groups
CT METALLURGIA FISICA E SCIENZA DEI MATERIALI (MFM) (riunione
del 01 marzo 2023)
Notizie dal Comitato
• La Presidente Bassani presenta la candidatura di Elena Colombini (Università di Modena e Reggio Emilia) a far parte del CT illustrandone il CV. I presenti valutano positivamente la candidatura all’unanimità, per cui Elena Colombini potrà partecipare ai lavori del CT a partire dalla prossima riunione.
Consuntivo di attività svolte
• La Presidente Bassani relaziona sulla GdS “I metalli e lo scambio termico: nuovi trend” organizzata con il CT “Materiali per l'Energia” e svoltasi il 24 gennaio a Milano presso il campus Bovisa del Politecnico. Si sono registrate circa 40 presenze, di cui molti dalle aziende. L’evento è stato caratterizzato da una proficua interazione tra partecipanti e relatori e da una buona partecipazione al sondaggio di gradimento (circa 20 questionari compilati).
• Alessandra Varone, coordinatrice della GdS “Tecniche sperimentali per la caratterizzazione dei materiali” – Vicenza, 23 febbraio 2023 –presenta un resoconto della manifestazione. Si sono contate 72 iscrizioni di cui molte da parte di aziende. I commenti sono stati positivi ma si attendono i questionari di gradimento.
Manifestazioni in corso di organizzazione
• Riccardo Donnini presenta la GdS “Fattori di influenza sulla resistenza a fatica delle leghe metalliche” che si terrà nell’ultima settimana di giugno presso la sede ICMATE del CNR a Milano. Viene presentato il programma e la lista provvisoria dei relatori in attesa della conferma da parte di alcuni di questi. Si valuta l’ordine degli interventi.
Iniziative future
• La Presidente Bassani propone di realizzare una GdS sulle orientazioni cristallografiche nei materiali metallici. Si ipotizza di affrontare la tematica in due parti, un’introduzione teorica seguita da esempi applicativi, considerando le informazioni che si possono ottenere sia mediante diffrazione di raggi X che tramite EBSD. Andrea Di Schino suggerisce di predisporre un tempo adeguato per la presentazione delle conoscenze di base sulle orientazioni cristallografiche prima di passare agli aspetti applicativi. Si valuta se svolgere la manifestazione su 1 o 2 giorni. Roberto Montanari avanza la sua candidatura ad organizzarla tra un anno circa. Il comitato si aggiorna alla prossima riunione.
• Per quanto riguarda il corso di Solidificazione, storicamente organizzato da Montanari, Paola Bassani propone di aggiornare alcuni dei contenuti. Si rimanda una discussione più approfondita alla prossima riunione del CT.
• Vedani e Casati propongono di organizzare un evento sui “Materiali per Motor Sport”. L’idea nasce dalla ristrutturazione della laurea magistrale in Ingegneria Meccanica del Politecnico di Milano e si pone come scopo la sensibilizzazione degli studenti circa l’importanza dei materiali. L’evento sarà focalizzato su leghe leggere, leghe per alte temperature, materiali in fibra di carbonio con un approccio orientato alle applicazioni. Viene proposta una bozza di programma con un’introduzione di stampo accademico seguita da interventi sulle applicazioni da parte delle aziende coinvolte. Bassani interviene suggerendo una strategia di comunicazione che ponga l’attenzione sui materiali.
CT METALLURGIA DELLE POLVERI E TECNOLOGIE ADDITIVE (MP)
(riunione del 23 maggio 2023)
Notizie dal Comitato
• L’ing. Bendotti e l’ing. Boccadoro hanno dato le dimissioni dal CT MP.
Manifestazioni in corso di organizzazione
• GdS “Post-processing dei componenti realizzati in additive” - organizzato con il CT Trattamenti Termici e Metallografia. Bassani condivide il programma ad oggi disponibile sul sito AIM e informa che si è reso necessario un posticipo a settembre perché il periodo inizialmente scelto (18-19 aprile) si è rivelato sovraffollato di altri eventi sul tema AM. Le nuove date, 19 e 20 settembre, sono state già comunicate ai relatori. Il programma verrà rilanciato non appena ridefinito, con la possibilità di aggiungere interventi riducendo il tempo dedicato alle visite aziendali.
• Manifestazione “Hard Metal century celebration & Workshop”: De Gaudenzi conferma che l’evento si terrà il 12 e 13 ottobre 2023 a Pallanza (Verbania-Lago Maggiore) presso l’Hotel Majestic. Il programma completo di titoli e interventi sarà presto disponibile. Bassani aggiunge che si è concordata la gratuità per i soci AIM (previa iscrizione da farsi tramite AIM il prima possibile per agevolare l’organizzazione logistica) e una quota ridotta per i non soci.
• Casati informa che il prossimo 4 settembre si terrà presso il campus Bovisa del Politecnico di Milano una GdS dedicata a “Materiali avanzati per il mondo racing” e presenta una bozza di programma che prevede 9 relazioni e la visita ai laboratori del Dipartimento di Meccanica.
Iniziative future
• GdS su “Press & Sinter in tema automotive”: ci sono perplessità circa la possibile organizzazione di questa manifestazione perché negli ultimi anni non ci sono stati particolari sviluppi innovativi nel settore: la GdS potrebbe risultare poco attraente. La discussione viene posticipata alla prossima riunione del CT.
Normativa / Standards
Progetti UNSIDER messi allo studio dal CEN (Stage 10.99) – giugno 2023
prEN ISO 16440 rev
Petroleum and natural gas industries
Norme UNSIDER pubblicate da CEN e ISO nel mese di maggio 2023
EN ISO 3785:2023
Metallic materials - Designation of test specimen axes in relation to product texture (ISO 3785:2023)
EN ISO 14556:2023
Metallic materials - Charpy V-notch pendulum impact test - Instrumented test method (ISO 14556:2023)
EN 10225-3:2019+A1:2023
Weldable structural steels for fixed offshore structures - Technical delivery conditions - Part 3: Hot finished hollow sections
EN 10359:2023
Laser welded tailored blanks - Technical delivery conditions
ISO 14556:2023
Metallic materials — Charpy V-notch pendulum impact test — Instrumented test method
ISO 9649:2023
Metallic materials — Wire — Reverse torsion test
ISO 6338:2023
Method to calculate GHG emissions at LNG plant
ISO 3785:2023
Metallic materials — Designation of test specimen axes in relation to product texture
— Pipeline transportation systems — Design, construction and maintenance of steel cased pipelines
Progetti UNSIDER in inchiesta prEN e ISO/DIS – giugno 2023
prEN – progetti di norma europei
prEN ISO19901-5
Petroleum and natural gas industries
- Specific requirements for offshore structures - Part 3: Topsides structure (ISO/DIS 19901-3:2022)
ISO/DIS – progetti di norma internazionali
ISO 13680:2020/DAmd 1
Petroleum and natural gas industries
— Corrosion-resistant alloy seamless tubular products for use as casing, tubing, coupling stock and accessory material — Technical delivery conditions — Amendment 1: Petroleum and natural gas industries — Corrosion-resistant alloy seamless products for use as casing, tubing, coupling stock and accessory material — Technical delivery conditions
ISO/DIS 11772
Hot rolled longitudinally profiled steel plate
ISO/DIS 6435
Stainless steel bars for the reinforcement of concrete
ISO/DIS 4954-1
Steels for cold heading and cold extruding — Part 1: Non-alloy and low alloy steels
ISO/DIS 4954-2
Steels for cold heading and cold extruding — Part 2: Stainless steels
Progetti UNSIDER al voto FprEN e ISO/FDIS – giugno 2023
FprEN – progetti di norma europei
FprEN ISO 10113
Metallic materials - Sheet and stripDetermination of plastic strain ratio (ISO/ FDIS 10113:2019)
ISO/FDIS – progetti di norma internazionali
ISO/DTS 19096
Metallic materials — Instrumented indentation test for hardness and materials parameters — Evaluation of stress change using indentation force differences
ISO/FDIS 6507-1
Metallic materials — Vickers hardness test — Part 1: Test method
ISO/FDIS 3887
Steels — Determination of the depth of decarburization
Norme pubblicate e progetti in inchiesta (aggiornamento 7 giugno 2023)
co-organised by
17TH INTERNATIONAL CONFERENCE ON SEMI SOLID PROCESSING OF ALLOYS AND COMPOSITES
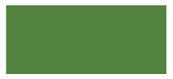
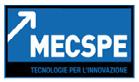
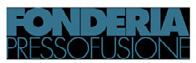

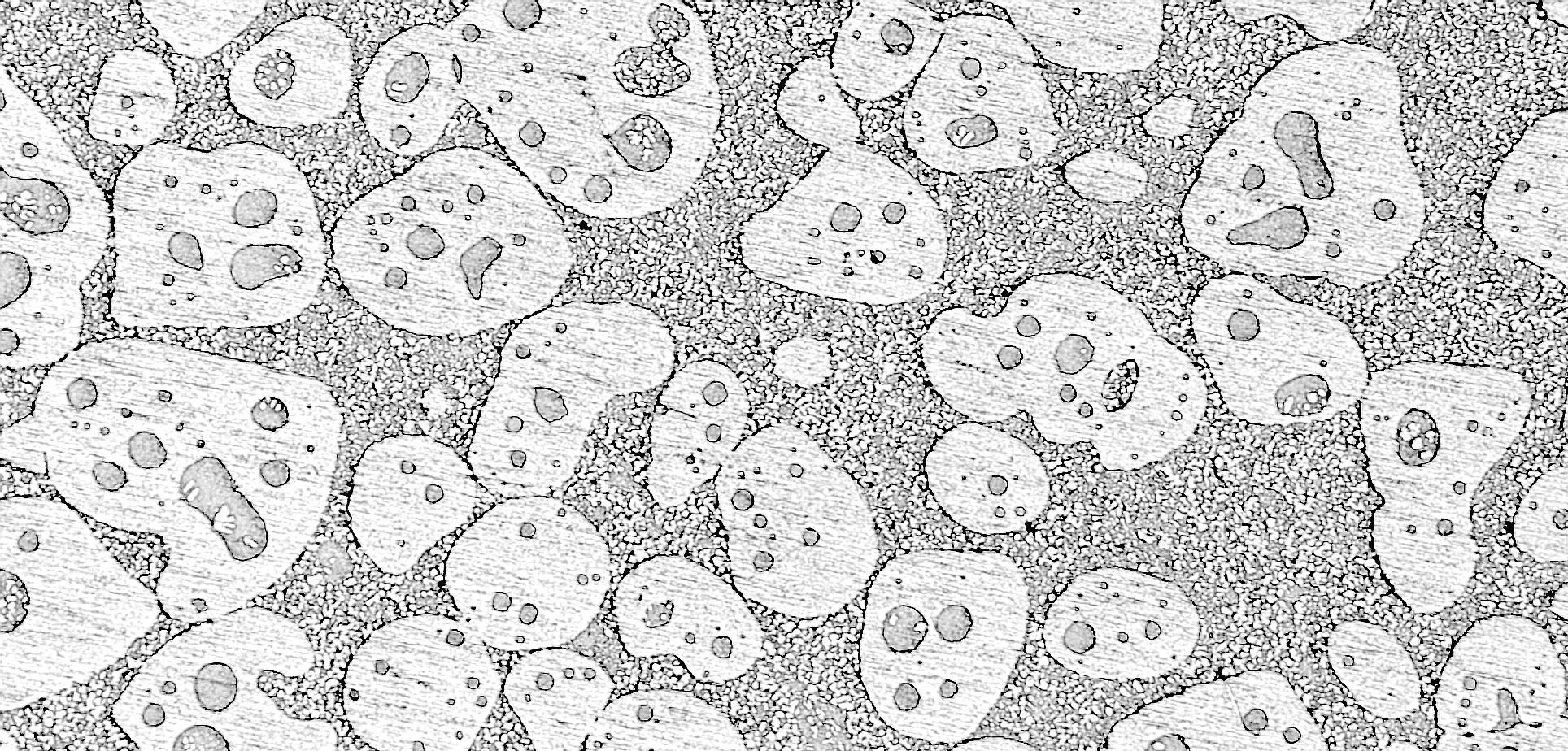
BRESCIA · ITALY, 6-8 SEPTEMBER 2023
On behalf of the Organizing Committee, we are pleased to invite you to the 17th International Conference on Semi Solid Processing of Alloys and Composites (S2P2023), which will be held from September 6th to 8th, 2023 in Brescia, Italy. The 17th S2P International Conference focuses on the advancement in fundamental knowledge and development of materials and industrial processes for semi-solid manufacturing of high-performance metal components. This conference will continue a successful series of conferences on semi-solid processing of alloys and composites started in 1990. The Conference is devoted to all aspects of semi-solid processing of metals alloys and composites with emphasis on basic research, engineering application as well as market aspects. Results of engineering research and experience as well as scientific issues are relevant for the conference.
REGISTER AND JOIN THE CONFERENCE HERE >> www.aimnet.it/s2p/
ORGANISING SECRETARIAT
Via Filippo Turati 8 20121 Milano Italy
Tel. +39 0276021132 or 0276397770
met@aimnet.it . www.aimnet.it/s2p/
SPONSORED BY
SUPPORTERS & MEDIA PARTNERS
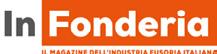