Italiana
International Journal of the Italian Association for Metallurgy
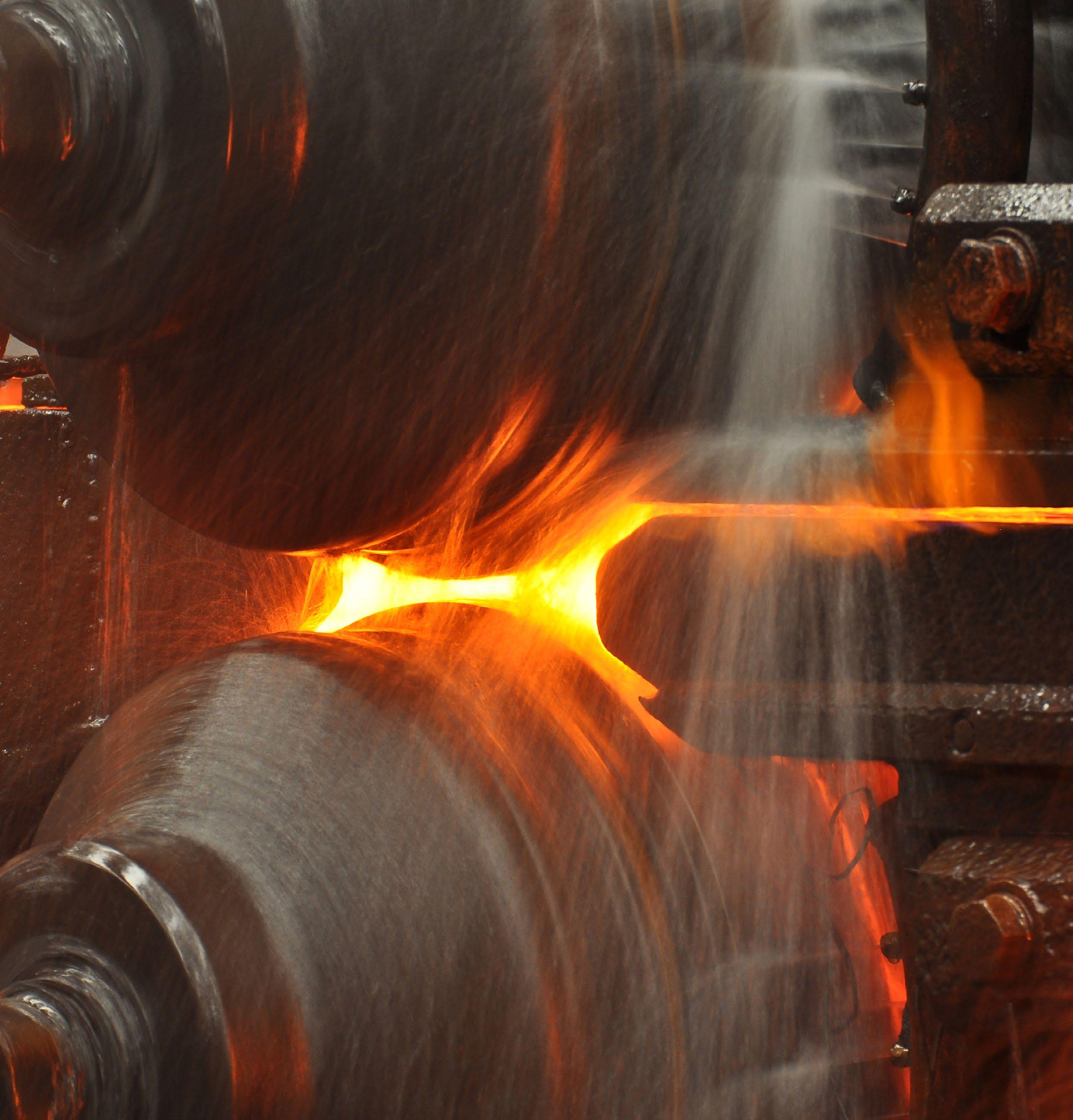
n.05 maggio 2023
Organo ufficiale dell’Associazione Italiana di Metallurgia.
Rivista fondata nel 1909
La Metallurgia Italiana
International Journal of the Italian Association for Metallurgy
Organo ufficiale dell’Associazione Italiana di Metallurgia. HouseorganofAIMItalianAssociationforMetallurgy. Rivista fondata nel 1909
Direttore responsabile/Chiefeditor: Mario Cusolito
Direttore vicario/Deputydirector: Gianangelo Camona
Comitato scientifico/Editorialpanel:
Marco Actis Grande, Silvia Barella, Paola Bassani, Christian Bernhard, Massimiliano Bestetti, Wolfgang Bleck, Franco Bonollo, Irene Calliari, Mariano Enrique Castrodeza, Emanuela Cerri, Vlatislav Deev, Andrea Di Schino, Donato Firrao, Bernd Kleimt, Carlo Mapelli, Denis Jean Mithieux, Roberto Montanari, Marco Ormellese, Mariapia Pedeferri, Massimo Pellizzari, Barbara Previtali, Evgeny S. Prusov, Dario Ripamonti, Dieter Senk
Segreteria di redazione/Editorialsecretary: Marta Verderi
Comitato di redazione/Editorialcommittee: Federica Bassani, Gianangelo Camona, Mario Cusolito, Carlo Mapelli, Federico Mazzolari, Marta Verderi, Silvano Panza
Direzione e redazione/Editorialandexecutiveoffice: AIM - Via F. Turati 8 - 20121 Milano tel. 02 76 02 11 32 - fax 02 76 02 05 51 met@aimnet.it - www.aimnet.it
Reg. Trib. Milano n. 499 del 18/9/1948. Sped. in abb. Post. - D.L.353/2003 (conv. L. 27/02/2004 n. 46) art. 1, comma 1, DCB UD
Immagine in copertina: Shutterstock
Gestione editoriale e pubblicità Publisher and marketing office: siderweb spa sb Via Don Milani, 5 - 25020 Flero (BS) tel. 030 25 400 06 - fax 030 25 400 41 commerciale@siderweb.com - www.siderweb.com

La riproduzione degli articoli e delle illustrazioni è permessa solo citando la fonte e previa autorizzazione della Direzione della rivista. Reproduction in whole or in part of articles and images is permitted only upon receipt of required permission and provided that the source is cited.
siderweb spa sb è iscritta al Roc con il num. 26116
i ce
Memorie scientifiche / Scientific papers
Laminazione / Rolling
A fully integrated roll deflection and strip buckling model for calculating strip flatness
S. Kiakidis, N. Mandagi, C. Hol .......................................................................................................................... pag.09
Numerical simulation of dynamic recrystallization behavior of 316L stainless steel under flexible rolling state
C. Liu, S. Liang, Y. Peng, S. Guo, R. Li, S. Barella, A. Gruttadauria, S. Bazri, M. Belfi, C. Mapelli .......................... pag.15
Quantitative evaluation of relative sliding between billets and rolls in hot rolling
B. Tian, S. Kleber, C. Turk, S. Tolliner, S. Schneller, P. Markiewicz .................................................................... pag.24
Correlation of digital twin and roller surface sensor results for AZ31 alloy twin roll casting process
S. Kwiecień, M. Weiner, M. Schmidtchen, M. Ullmann, U. Prahl, L. Hamm, W-G. Drossel . pag.29
Attualità industriale / Industry news
Finite Element Modeling evaluation of a void closure criterion using a multi-scale approach during hot rolling
edited by: C. Pondaven, B. Erzar, A. Spadaccini, M. Grion.............................................................................................. pag.36
Automated groove pass predesign of asymmetrical profiles
edited by: M. Stirl, C. Renzing, M. Weiner, M. Schmidtchen, U. Prahl............................................................................ pag.42
Sophisticated and advanced plant and process technologies in steel and nonferrous rolling mill
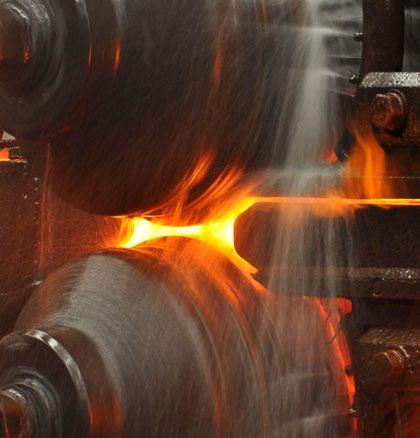
edited by: M. Degner, M. Breuer, A. Sprock, C. Hassel, O. Jepsen, M. Quoika, A. Bregante........................................ pag.47
Le aziende di AIM/AIM's companies
ORI Martin, il filo rosso dell’innovazione, della qualità e della sostenibilità “dal Maglio all’ Internet of Things”
U. De Miranda, M. Zanforlin ................................................................................................... pag.54
Scenari
Acciaio e metalli: dinamiche, cicli e tendende di mercato
A. Fornasini pag.60
Atti e notizie / AIM news
i
Verbale della Settantanovesima Assemblea Ordinaria dei Soci AIM pag.65
Relazione del Consiglio Direttivo anno: 2022 pag.66
Relazione del Tesoriere 2022 pag.68
Bilancio culturale 2022 pag.73
Relazione del Collegio dei Revisori sul Bilancio al 31 dicembre 2022 pag.78
Stato patrimoniale 2022 pag.80
Rendiconto gestionale pag.82
Budget per l'anno 2023 ........................................................................................................ pag.83
Eventi AIM / AIM events ...................................................................................................... pag.84
Comitati tecnici / Study groups
pag.88
pag.86 Normativa / Standards
ROLLING-12
Il Centro di Studio AIM - LPM Lavorazione Plastiche dei Metalli, che ho l’onore di presiedere dal 2014, nel tempo si è concentrato, tra le altre attività, nello studio e nell’approfondimento di numerosi processi produttivi tipicamente espressione del settore, con particolare riferimento ai procedimenti di laminazione, trafilatura, estrusione, forgiatura, fucinatura e stampaggio.
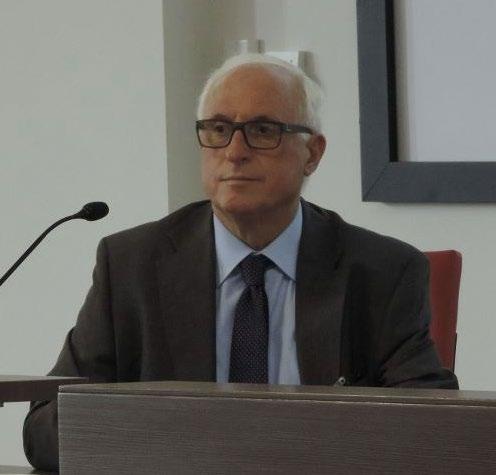
Si pensi che già dal finire dell’epoca del bronzo e l’inizio di quella del ferro (intorno al 700 a.C.) alcune popolazioni indo-germaniche, come i Nori ed i Celti, svilupparono la cultura dell’estrazione dei metalli e del ferro e, conseguentemente, anche le conoscenze sulla fusione delle stesse con la relativa formazione di spugne metalliche; analogamente, esaminarono i primi processi delle
ROLLING-12
The AIM - LPM Centro di Studio Lavorazione Plastiche dei Metalli (AIM - LPM Metal Plastic Processing Study Centre), which I have been chairing since 2014, has over time concentrated, among other activities, on the study and in-depth study of numerous production processes that are typical of the sector, with particular reference to the processes of rolling, drawing, extrusion, forging and stamping.
Consider that as early as the end of the Bronze Age and the beginning of the Iron Age (around 700 a.C.), some Indo-Germanic peoples, such as the Noris and Celts, developed the culture of metal and iron extraction and, consequently, also the knowledge of how to melt them with the consequent formation of metal
"La deformazione plastica dei metalli è l’essenza tecnica e tecnologica che regola i processi di laminazione e richiede l’assoluta conoscenza dei fenomeni metallurgici della deformazione."Guido Capoferri Presidente del Centro Studio AIM Lavorazione Plastiche Metalli
“The plastic deformation of metals is the technical andtechnologicalessence thatgovernsrolling processes and requires absoluteknowledgeofthe metallurgicalphenomenaof deformation.”
successive lavorazioni a caldo e a freddo.
Si può quindi comprendere come il più ampio tema della deformazione plastica dei metalli sia, di fatto, studiato e applicato dalla nascita della metallurgia, impegnando da sempre la mente e il lavoro degli addetti a questa materia.
È noto a tutti che i processi di lavorazioni plastiche, in particolare la laminazione dell’acciaio, mirano ad ottenere l’allungamento di un prodotto come conseguenza di una riduzione (generalmente come cambiamento di forma) imposta alla sezione trasversale tramite rulli.
Come sopra menzionato l’azione di riduzione viene contrastata dalla resistenza del materiale a farsi deformare.
Ancora è noto, che l’allargamento del prodotto durante la laminazione specie per spessori elevati, limita l’allungamento che crea problematiche di laminazione.
Pertanto, abbiamo dedicato spazio alla pura deformazione plastica a caldo e freddo dei metalli, che è e rimane l’essenza vera e pragmatica della laminazione e delle altre lavorazioni metallurgiche deformanti sopra menzionate.
In tempi non lontani, il dott. Nino Goldoni di Cofermet ebbe modo - nel suo libro “Lavorazioni per Deformazione Plastica a Caldo e a Freddo”, edito da AMI - Associazione Meccanica Italiana nel 1968 - di affrontare ulteriormente il tema (cfr. lezione 8):
“La deformazione a caldo e a freddo dei metalli non segue leggi rigorosamente applicabili e riproducibili, in quanto avviene sotto l’influenza di diverse grandezze fisiche che si combinano in azioni non esprimibili con
sponges; similarly, they examined the first processes of subsequent hot and cold working.
It can therefore be understood how the broader topic of plastic deformation of metals has, in fact, been studied and applied since the birth of metallurgy, engaging the minds and work of those working in this field since time immemorial.
It is well known that plastic machining processes, in particular steel rolling, aim to obtain elongation of a product as a result of a reduction (generally as a change of shape) imposed on the cross-section by rollers.
As mentioned above, the reduction action is counteracted by the material's resistance to being deformed.
Again, it is known that the widening of the product during rolling, especially for high thicknesses, limits the elongation that creates rolling problems.
Therefore, in the remaining part mentioned below, we have devoted space to the pure hot and cold plastic deformation of metals, which is and remains the true and pragmatic essence of rolling and the other deforming metallurgical processes mentioned above.
In times not so long ago, Dr. Nino Goldoni of Cofermet had the opportunity - in his book 'Hot and Cold Plastic Deformation Processing', published by AMIAssociazione Meccanica Italiana in 1968 – to further address the issue (see lecture 8):
"The hot and cold deformation of metals does not follow rigorouslyapplicableandreproduciblelaws,asitoccurs under the influence of different physical quantities that combine in actions that cannot be expressed with a
una azione rigorosamente matematica. Quindi, in altri termini, la deformazione a freddo e a caldo dei materiali metallici non può essere definita una disciplina nel senso scientifico, bensì una applicazione sperimentale che segue le leggi che variano di volta in volta in funzione di molti parametri non sempre tutti prevedibili”
rigorouslymathematicalaction.Inotherwords,thecold and hot deformation of metallic materials cannot be defined as a discipline in the scientific sense, but rather as an experimental application that follows laws that vary from time to time depending on many parameters that are not always all predictable".
Dal 1968 al 2023, dopo 55 anni, è innegabile che vi sia stato un reale cambiamento rispetto a questa qualificata enunciazione, grazie allo sviluppo di modelli di simulazione, alla crescente applicazione della automazione industriale basata su idonei algoritmi ed alla estesa applicazione di sensori e misuratori, con l’emergente presenza della Intelligenza Artificiale.
Tali sviluppi sono in grado di di migliorare ulteriormente la performance delle persone e degli impianti.
Si pensi per esempio, nel campo dell’automazione industriale, alle macchine piegatrici idrauliche o meccaniche per lamiere, dotate di un sistema di gestione in grado di riconoscere le caratteristiche meccaniche delle lamiere e, di conseguenza, in grado di generare un ciclo di lavoro personalizzato e puntuale per ogni tipo di acciaio che compone la lamiera in piegatura, ottenendo un risultato qualitativamente eccellente e sicuro.
Sono altresì evidenti, parallelamente, le odierne capacità (e, per certi versi, le complessità) dei sistemi di programmazione digitale delle fasi di produzione, in grado di gestire una moltitudine di dati e processi con velocità e precisione.
Le conoscenze nel campo delle deformazioni plastiche dei metalli, sia a caldo che a freddo, sono cresciute enormemente. Tralasciando gli elementi primari per la produzione dei manufatti primari in metallo, quali lingotti, bramme, billette, le successive fasi di trasformazione del prodotto, con lavorazioni a caldo e a freddo, implicano processi di deformazione plastica.
La conoscenza di tali processi, delle caratteristiche di
From 1968 to 2023, after 55 years, it is undeniable that there has been a real change to this qualified statement, thanks to the development of simulation models, the growing application of industrial automation based on suitable algorithms and the extensive application of sensors and meters, with the emerging presence of Artificial Intelligence
These developments are able to further perform the action of people and plants.
One thinks, for example, with respect to industrial automation, of hydraulic or mechanical sheet-metal bendingmachines,equippedwithamanagementsystem capable of recognizing the mechanical characteristics of the sheets to be bent and, consequently, similarly capable of generating a customized and punctual work cycle for each type of steel that makes up the sheet being bent, achieving a qualitatively excellent and safe result.
Also evident, in parallel, are the capabilities (and, to some extent, the complexities) of today's general digital programming systems of the production phases, capable of managing a multitude of data and processes with speed and precision.
Knowledge in the field of plastic deformation of metals, both hot and cold, has grown enormously. Leaving aside the primary elements for the production of primary metal artefacts, such as ingots, slabs, billets, the subsequentproducttransformationstages,withhotand cold working, involve plastic deformation processes.
Knowledge of these processes, of the deformability characteristics of various metals, the application of
deformabilità dei vari metalli, l’applicazione di adeguati strumenti tecnici, la conoscenza e competenza del personale tecnico addetto, sono fattori essenziali per ottenere risultati competitivi.
Ne consegue che lo scambio costante di informazioni tra i vari attori coinvolti nei processi produttivi - dalle figure inserite nelle fasi produttive a quelle di coordinamento e servizio, dai progettisti ai costruttori di macchine dedicate al processo di deformazione – è di assoluta rilevanza; come sarebbe possibile, altrimenti, ricavare dalla trafilatura a freddo di un tondino di 10 millimetri un ago per iniezioni? Ecco (anche) l’importanza della comunicazione tecnica (e non) tra le varie figure coinvolte nel processo.
In quest’ottica auspico che nel mondo scolastico vengano trasmesse, tramite un rinnovato slancio di concreto nozionismo tecnico, anche le conoscenze di base della deformazione dei metalli a caldo e freddo, con un approccio pragmatico e funzionale alle successive necessità.
“Conoscere”, attraverso l’insegnamento, è per certi aspetti fondamentale per comprendere tutto quello che quotidianamente ognuno di noi vede e utilizza; sarebbe davvero importante far apprezzare le basi del nostro settore, anche per avvicinare finalmente i giovani al mondo (tecnico) del lavoro nel tentativo di compensare, solo parzialmente, quella sinergia scuola-lavoro purtroppo ancora carente.
appropriate technical tools, and the knowledge and expertise of the technical personnel involved, are essential factors in achieving competitive results.
It follows that the constant exchange of information between the various players involved in the production process - from those involved in the production phases to those of co-ordination and service, from the designers to the manufacturers of machines dedicated to the deformation process - is of absolute importance; how else would it be possible to make an injection needle from the cold drawing of a 10 millimeters rod? Hence (also) the importance of technical (and other) communication between the various figures involved in the process.
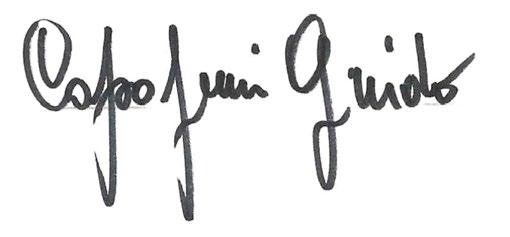
With this in mind, my hope is that in the scholastic world,througharenewedimpetusofconcretetechnical notionism, the basic knowledge of hot and cold metal deformation will also be transmitted, with a pragmatic and functional approach to subsequent needs.
"Knowing', through teaching, is in some respects fundamental to understanding everything that each of us sees and uses on a daily basis. It would be really important to make people appreciate the basics of our sector, also to finally bring young people closer to the (technical) world of work in an attempt to compensate, unfortunately only partially, for the school-work synergy that is sorely lacking today.
MILANO 27-30 MAY 2024
AIM and Federacciai proudly announce that the 22nd International Forgemasters Meeting will be held in Italy in 2024.
Save the date! IFM 2024 will be in Milan on 27-30 May 2024.
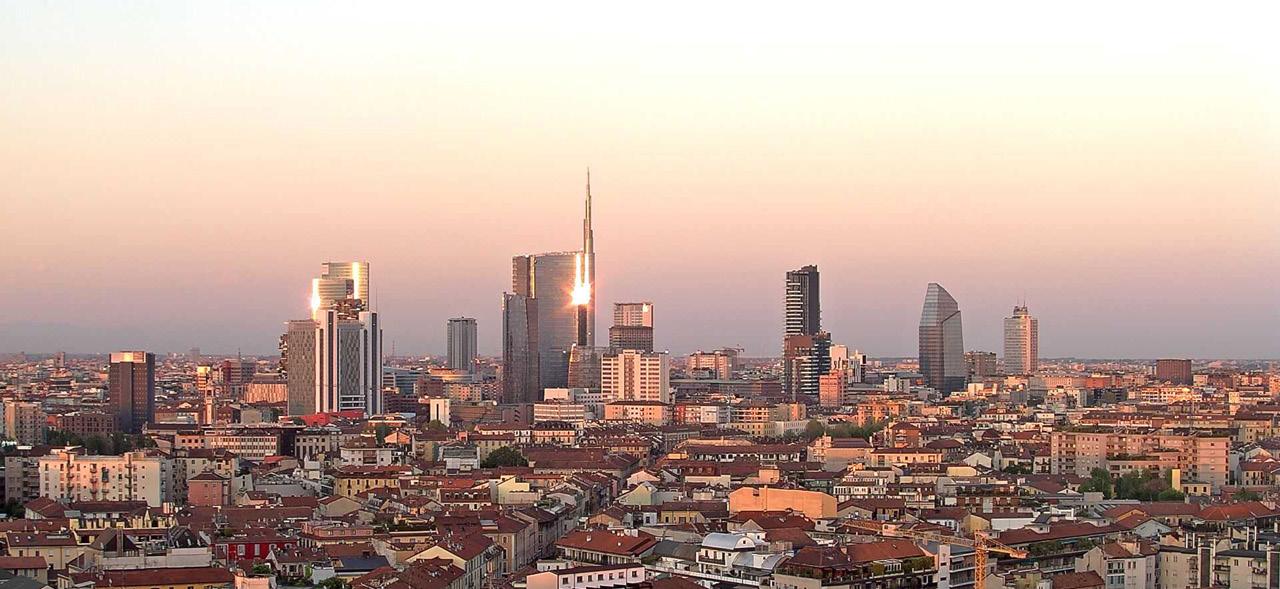
All involved in and interested in the area of open die forging and ring rolling are warmly invited to attend.
At IFM 2024 the most important and current issues affecting the sector will be discussed. Experts in the fields of greatest interest will be attending and addressing such issues.
IFM is a unique forum to meet researchers, skilled technicians and decision makers; in other words IFM 2024 is an unmissable event for the forging industry!
Topics
- Developments in the Global Heavy Forging Industry
- Power Generation Green Energy, such as Hydrogen Production, Coal Chemical Industry and Wind Power etc.
- Power Generation Nuclear (SMR, Fusion etc.)
- Other Product Developments in the Offshore Oil and Gas, Rolls, Power Generation, Aircraft, Aerospace, Shipbuilding and Heavy Machinery
- Decarbonisation in the Forging Industry including energy storage and environment. Use of hydrogen as fuel
- Green steel production
- Advances in Steelmaking, Forging, Heat Treatment and Machining
- Special Steels Development for forged components
- Simulation including equipment, processes and Industry 4.0
- Quality Management including Quality Control, Non- Destructive Testing and on-line measurement
Call for Papers
Prospective authors wishing to present papers are invited to submit a tentative title and an abstract of about 400 words (in English), specifying a maximum of two topics for each proposal.
The abstract should provide sufficient information for a fair assessment and include the title of the paper, the author’s names and contact details (address, telephone number and e-mail address). The name of the presenting author should be underlined. A poster session might be organized as well.
Abstracts should be either submitted online at www.ifm2024.org or by email to aim@aimnet.it.
Deadlines
Submission of abstracts: 30 June 2023
Information on acceptance: 13 October 2023
Submission of full papers and speakers registration: 15 December 2023
Organising secretariat
A fully integrated roll deflection and strip buckling model for calculating strip flatness
S. Kiakidis, N. Mandagi, C. HolStrip flatness is an important quality aspect of cold rolled strip. In a tandem cold mill, latent strip flatness errors depend on many factors, such as work roll profiles, rolling forces, bending forces, and thermal expansion, in a complicated interaction. If latent flatness errors manifest themselves, they may lead to centre buckles, wavy edges, quarter buckles or other flatness defects. Excessive strip buckling may even cause operational problems in the mill such as pinches and work roll damage, resulting in downtime and high roll repairing costs. In this paper a fully integrated roll deflection and strip buckling numerical model is presented. The model comprises a strip rolling model, a roll stack deflection model, a roll flattening model and finally a strip buckling model. The roll stack deflection model contains the work roll and backup roll profiles and the main deformation aspects of the rolls: bending, Poisson effect and flattening. This allows us to calculate the non-uniform thickness reduction over the strip width. Non-uniformity of the thickness reduction translates into flatness errors, and these are input to the buckling model to evaluate when these flatness errors become manifest. The model is illustrated for a practical case study of a 4-high tandem rolling mill.
KEYWORDS: ROLLING, MODELS, STRIP FLATNESS, SHAPE, NUMERICAL
METHODS
INTRODUCTION
The quality of the steel strip depends on both its material and geometrical properties. Inhomogeneities in strip thickness across the width direction (profile) lead to longitudinal internal stresses (shape). Flatness issues arise when shape manifests itself due to insufficient strip geometrical stiffness (buckling). Flatness can be studied as an elastic buckling problem, to not only get the critical buckling limit Pcr (imposed load multiplied by the 1st eigenvalue), but also the way the strip will buckle (eigenvector). Note that the magnitude of the buckled shape cannot be obtained by the elastic buckling analysis. The latter would require highly complex post-buckling analysis.
Strip flatness is an important quality aspect of cold rolled strip. Flatness errors depend on many factors, such as work roll profiles, rolling forces, bending forces, and thermal expansion. The interaction of all these components lead to inhomogeneous reduction across the strip width. At excessive internal stresses, the transversal cross-
section of the strip has regions where the normal stresses may alternate between positive (tension) and negative (compression) values. Depending on the distribution of the regions under tension/compression, different forms of buckled geometries may appear. Most typical flatness errors include centre buckles, wavy edges and quarter buckles.
Excessive strip buckling may even cause operational problems in the mill such as pinches. These pinches can cause work roll damage, resulting in downtime and high roll repairing costs. In this paper a fully integrated roll deflection and strip buckling model is presented, together with a case study of a 4-high mill. In [1] strip deformation models and buckling models have been coupled but based on a finite element approach. In this work the models are based on finite differences, which are typically faster to compute and therefore more suited to use for fast analysing tools.
The outline of the paper is as follows. First the roll stack deflection model and buckling model will be explained briefly. Then validation of important buckling modes is presented, followed by a practical example from a 4-high rolling mill.
ROLL STACK DEFLECTION MODEL
The roll stack model is a segmented model dividing the rolls into discs. The model is similar to the ones described in e.g. [2]. Inputs are the roll geometry including the roll profiles, the total roll force, and the bending forces. The
output is the deformed roll gap profile and strip shape at the entry and exit. This strip shape is used in the buckling model.
All constitutive equations are written out for each segment and then are linearised around the current working point. The linearised set of equations is a matrix equation Mx=l where matrix M contains the coefficients of the system of equations, vector x contains the unknowns, and vector l contains the constant terms. Solving this matrix equation gives a new working point, linearise again etc. until the difference in subsequent solutions becomes benign.
An example of a coefficient matrix M and its corresponding unknown vector x for a symmetric 4-high mill is shown in Fig. 1. Submatrices MWR and MBUR correspond to the work roll and back-up roll, respectively. These matrices describe the deformation of the rolls (e.g. curvaturebending relation, moment balance, force balance, and Poisson effect). Submatrix MWR-BUR describes the flattening relation on the interfaces between work roll and back-up roll. Submatrix MRG describes the relation between the roll force distribution, the strip and the deformation of the work rolls in the roll gap. Submatrices xWR and xBUR contain the unknowns: curvature (∂2ν⁄∂x2), gradient (∂ν⁄∂x), deflection (ν), moment (M), shear force (D), normal force (F) and line load (q). Sub-vector xStrip contains the unknowns: strip profile, strip shape, and entry tension.

BUCKLING MODEL
The buckling model is a finite difference model based
on the Kirchhoff’s thin plate bending theory, see [3]. The governing equation in Cartesian coordinates is given by
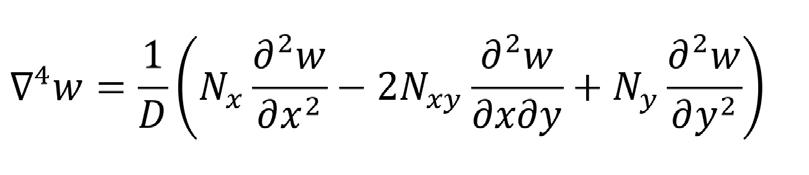
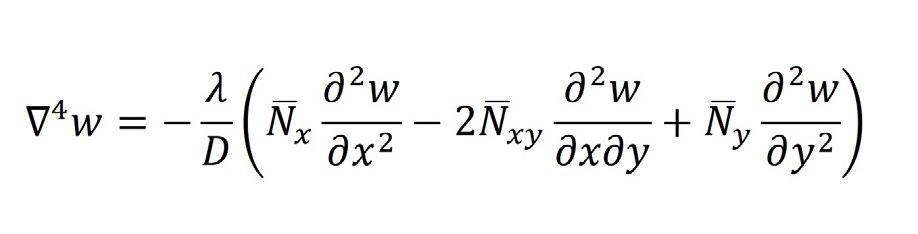
where ∇4 is the bi-Laplacian operator, w is the deflection, D is the flexural rigidity given by D=(Eh3)⁄12/(1-ν2), E is the Young’s modulus, ν is the Poisson ratio and h is the strip thickness. x is the coordinate in the width direction and y is the coordinate in the rolling direction. The inplane specific forces N x, N y, and N xy can be found from the solution of the plane stress problem for the given geometry (rectangular plate), in-plane external loadings (line tension), and internal stresses (shape).
The buckling limit is obtained by transforming the above problem into an eigenvalue problem. Here, a multiplication factor λ is introduced such that , where and are the reference value of the loads. Substituting these into (1) results into an alternative form of the governing equation:
The solution of the above problem requires two boundary conditions to be satisfied at each side of the strip:
• clamped
• simply supported and
• free edge
In combination with a finite difference method, (2) can be written as for i=1,...,n where n is the size of the matrices A and B.
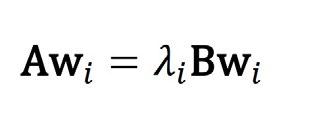


The matrix equation shown in (3) is known as the generalized eigenvalue problem. Here, λi are the eigenvalues and wi are the corresponding eigenvectors. The 1st eigenvalue and its eigenvector are used to determine the critical buckling limit, P cr, and the way the strip will buckle, respectively.
ELASTIC BUCKLING CALCULATIONS VALIDATION Simulations settings
The aim of this chapter is to evaluate the accuracy of integrated model in predicting different buckling modes for strips under residual stresses. The validation is done at various strip buckling cases in two ways:
• against the paper by Fischer [4], where buckling
analysis of cold rolled strip is studied without coupling to a rolling model. These are cases 1-6, see Fig. 2 for the numbering,
• against the commercial finite elements software (ANSYS, 2020 R2), cases 7-13.
All 13 simulations share the same strip width, thickness, and elasticity properties. At the first 6 cases the strip length is chosen to be 4 times the wavelength as reported by Fischer. The reason for using a precise multiple is that exact results are then obtained as if a strip of infinite length is used. At the rest of the cases, the chosen strip length is four times the strip width, sufficiently long not to affect the results. The short edges of the strip are either simply supported (cases 1-12) or clamped (case 13).
The side edges are free. The mesh in both the integrated model and in ANSYS consist of 100 and 200 elements in the width and rolling direction, respectively. The coordinate system is such that x is in the strip width direction and y in the length (rolling) direction.
There are various ways to mathematically describe the distribution of the residual stresses along the strip width direction. Fischer’s paper uses both the cosine and the polynomial description (cases 1-6), whereas at cases 8-13 the W-polynomials were used. A schematic of the input residual stress per case is illustrated in Fig. 2 (left part). The red/green colour represent the areas under compression/tension.
Simulations results
The most important result of the elastic buckling analysis is the 1st eigenvalue (and eigenvector) because it is connected to the critical buckling load. Focusing on centre buckles (cases 1-6 & 8), the critical load difference between the developed model and Fischer’s work is very
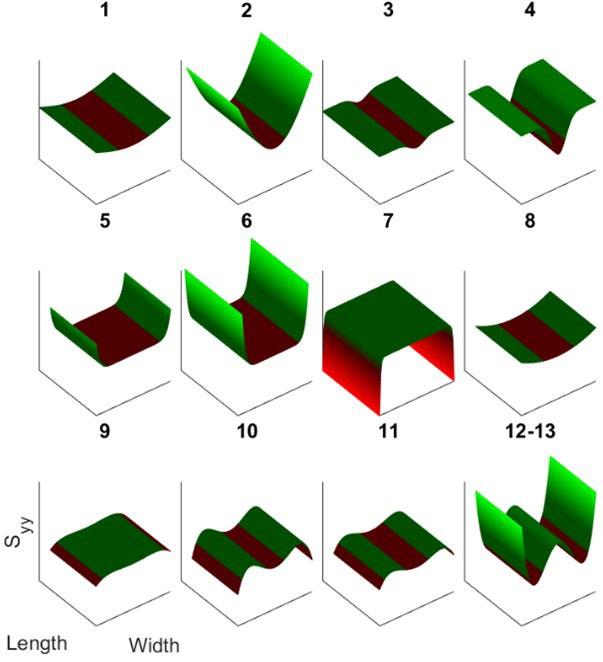
small for the first 5 cases, i.e. <0.4%. In the 6th and 8th case the deviation is 3.3% and 1.0%, respectively, and it may be attributed to mesh size difference. Nevertheless, the results are satisfactory for buckling prediction in the rolling process, since an uncertainty of about 3% in calculating critical buckling loads is acceptable, in view of other uncertainties when calculating the process conditions in rolling mills. The wavy edges cases (7, 9-11) and the quarter buckles ones (12-13), exhibit an eigenvalue error of less than 1.5% between the developed model and ANSYS. Concerning the eigenvectors, the long wavelength (case 9) is simulated with remarkable accuracy. However, when the wavelength is shorter (cases 7,10,11), minor deviations between the buckling model and the FEA eigenvectors were observed, with a maximum error in wavelength of 2.8%. The same also holds for the quarter buckles, which both have short wavelength.
As stated in the previous paragraph, the integrated model exhibits eigenvector results similar to Fisher and ANSYS. In principle, a structural component prone to buckling will follow the equilibrium path of the 1st buckling mode, being the lowest one. However, in most of the investigated
cases in this report, the first 2 eigenvalues are very close to each other (<1% difference). This has an impact on the analysis. Small changes at the mesh or at the distribution of the residual stresses may lead the solution to follow the path of a higher buckling mode. These modes are
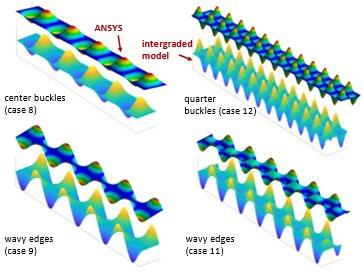
very similar, and in most cases symmetric to each other. The eigenvalue calculation is more sensitive to numerical errors, if the first few eigenvectors are almost in the same direction of the vector space.
In conclusion, the integrated model is deemed capable of modelling the elastic buckling of strip under residual stresses. Being a finite difference model, it outperforms ANSYS in calculation speed and can thus be used for both on/off-line calculations.

WORK ROLL BENDING AND STRIP SHAPE
Strip shape is strongly affected by the work roll bending forces, BFWR. Excessive roll stack bending leads to larger thickness reduction (equivalent to strip elongation at plane strain) at either strip centre (BFWR>0) or edges (BFWR<0). The strip being a single entity, adjacent regions with different reductions will restrict the variations in elongation. This will generate internal stresses (strip shape) in the rolling direction.
In this paragraph the integrated model is used at a casestudy of the work roll bending force effect on strip shape. A 4-high tandem mill with typical roll diameters has been used. The strip is 2000 mm wide. The entry/exit line tension usually prevents strip shape issues to manifest themselves in the line. Therefore, significant positive/ negative bending force was used to generate sufficient internal longitudinal compressive stresses to overcome the tensile line tension. The resulting longitudinal stresses together with corresponding buckled strip are shown in Fig. 3. The strip runs in the figure from left to right, as indicated by the arrow. The colour of the strip indicates the longitudinal stress, with blue being compressive and yellow tensile and green in-between. Note that the amplitude of the buckles is exaggerated at the graph. On the left, centre buckles arise due to positive bending, whereas on the right wavy edges are demonstrated for negative bending.
CONCLUSIONS
The presented model combines roll stack deflection and buckling analysis to predict latent and manifest shape errors during rolling. It links the most common process parameters directly with the buckling analysis results, providing an intuitive simulation tool. The elastic buckling validation shows that errors are below 3.3% and
2.8% for the critical loads and wavelengths, respectively. The application section demonstrates that the buckling model is capable of predicting both critical buckling limit and modes that are characteristic for rolling.
REFERENCES
[1] A. Sami, R. Nakhoul, H. Zahrouni, P. Montmitonnet and N. Legrand, “Applications of advanced models to prediction of flatness defects in cold rolling of thin strips,” in 15th International Conference on "Advances in Materials and Processing TechnologiesAMPT 2012, Wollongong, 2012.
[2] S.-H. Kim, G.-H. Lee, S.-J. Song and B.-M. Lee, “Study on the improved accuracy of strip profile using numerical formula model,” Journal of Mechanical Science and Technology, vol. 25, no. 8, pp. 2101-2109, 2011.
[3] E. Ventsel and T. Krauthammer, Thin Plates and Shells, Marcel Dekker, 2001.
[4] F. D. Fisher, F. G. Rammerstorfer and N. Friedl, “Residual Stress-Induced Center Wave Buckling of Rolled Strip Metal,” ASMA, vol. 70, pp. 84-90, 2003.
Numerical simulation of dynamic recrystallization behavior of 316L stainless steel under flexible rolling state
C. Liu, S. Liang, Y. Peng, S. Guo, R. Li, S. Barella, A. Gruttadauria, S. Bazri, M. Belfi, C. MapelliWith the rapid development of continuous rolling technology, the rigid connection of production equipmenttechniques often results in roll wear and frequent shutdowns for roll replacement, which restricts the development of its technical advantages. In this paper, ASTM-316L is used as the experimental steel, based on the numerical simulation technology to carry out the numerical simulation and process optimization research of online roll changing of flexible rolling, comprehensive material high-temperature plastic flow behavior, coupling recrystallization kinetic model embedded in Deform-3D software, to establish a multi-field coupled collaborative control model of online roll changing of flexible rolling, simulating the impact of online roll change on the strip DRX behavior. The results show that the reduction rate of the online roll change, the roll exit speed, the roll input speed, and the deformation temperature have essential effects on the microstructure uniformity of the strip along the thickness direction. Smaller reduction rate, faster roll exit speed, slower roll input speed, and lower deformation temperature are all beneficial to reduce the gradient of DRX volume fraction in the core and surface of the strip and avoid stress concentration and instability. The roll diameter has little effect on the DRX volume fraction gradient at the core and surface of the strip. Therefore, it is necessary to control the online roll changing process of flexible rolling according to the actual rolling process, considering the load of the rolling mill and the mass of the rolls. The research on the recrystallization behavior of online roll changing in this paper can provide a theoretical basis for designing and optimizing the microstructure control of flexible rolling.
KEYWORDS: FLEXIBLE ROLLING, ONLINE ROLL CHANGE, DYNAMIC RECRYSTALLIZATION, NUMERICAL SIMULATION
INTRODUCTION
With the development of traditional rolling in the direction of short process and near-net shape, high-efficiency continuous rolling technology has been increasingly applied in recent years [1-3]. Due to the long rolling kilometers in the continuous rolling process, this leads to serious roll wear. When the roll is worn, it needs to stop rolling to replace the roll, which affects the product yield and production efficiency. For this reason, some researchers have put forward the concept of flexible rolling, which realizes continuous rolling through online roll change, and fully releases the equipment unit’s process potential [4,5]. Dynamic recrystallization behavior during rolling plays an important role in optimizing rolling mill load and improving the organizational properties of the product [6-8]. In recent years, many scholars have conducted research in this area. Wang et al. investigated the dynamic and static recrystallization behavior of 15V38 alloy bar rolling process, constructed a dynamic model
based on physical simulation and embedded it into the simulation system, simulated the effect of deformation volume and distortion temperature on recrystallization behavior during steady-state rolling of the bar, and obtained that the dynamic recrystallization volume fraction increased with increasing distortion temperature [9,10]. Duan et al. studied the dynamic recrystallization behavior of 34CrNiMo6 high-strength steel under uniaxial compression based on physical and numerical simulations and showed that the recrystallization behavior of the experimental steel under uniaxial compression could be accurately predicted by embedding the established recrystallization model into the simulation system [11]. Dong et al. constructed recrystallization models based on physical simulations and embedded them in simulation software to simulate subdynamic and static recrystallization behavior under various deformation conditions. The results show that accurate construction of simulation model boundary conditions is a prerequisite for obtaining good prediction results [1214]. Gu simulated the dynamic recrystallization behavior of 38MnVS6 steel during compression. The results show that the non-uniformity of dynamic recrystallization is related to the machining state of the workpiece and that the dynamic recrystallization volume fraction decreases with increasing deformation temperature and decreasing strain rate. The experimental results agree with the simulation results and can be used to predict the dynamic recrystallization behavior of 38MnVS6 steel during compression [15]. Although there has been some research into the numerical simulation of dynamic recrystallization, these studies have all been based on a stable rolling condition, that is, the roll gap does not change. However, there is a process of roll exit and input in the online roll change of flexible rolling. During this process, the key process parameters of DRX change drastically, heat transfer occurs between the strip and the surrounding environment and the roll, and both the volume work generated by the plastic deformation of the strip and the frictional heat generated by the friction of the roll will cause the temperature of the strip to increase, the lifting of the roll makes the deformation of the strip in the rolling direction change continuously, and the material flow behavior changes accordingly. Compared with traditional rolling, online roll change of flexible rolling is a more complex and highly nonlinear irreversible change process. Therefore, the study of the mapping relationship between the variation of DRX and the heat deformation process parameters is the theoretical basis for regulating
of the recrystallization behavior of flexible rolling online roll change. In this paper, Deform-3D simulation is used to simulate the effects of reduction rate, roll exit speed, roll input speed, deformation temperature, and roll diameter on DRX under the online roll change state of experimental steel flexible rolling to provide theoretical support for forecasting and optimizing the strip flexible rolling online roll change forming process.
MATERIALS AND METHODS
Experimental details
In this paper, ASTM-316L hot-rolled strip steel is selected to simulate the flexible rolling process. Before constructing the simulation model, it is necessary to obtain the hightemperature flow behavior of the material and establish the dynamic recrystallization dynamics model of the experimental steel. The material flow behavior analysis and dynamic recrystallization dynamics model have been given in the author's previous article [16]. The established model was embedded into the Deform simulation software to simulate the dynamic recrystallization behavior of the flexible rolled strip.
Simulation details
The established DRX kinetic model was embedded into DEFORM-3D software to simulate the DRX behavior of the hot rolling process of strip. During the online roll changing process of flexible rolling, the stress state of the strip under the action of external forces such as tension, rolling force, and friction is complex. In the process of high-temperature plastic deformation, the strip is subjected to the interaction of deformation temperature, strain, and strain rate, resulting in dramatic changes in the internal microstructure of the material. Therefore, it is necessary to establish an accurate finite element model to reveal the variation regulation of the strain field during the online roll change of flexible rolling, the high-temperature plastic flow behavior of metal materials, and the DRX situation. Considering the accuracy and efficiency of the model calculation, the following assumptions are made in this paper in the establishment of the geometric model of online roll change for flexible rolling:
(1) As the rolling process studied in this paper is a symmetrical rolling process, the upper and lower rolls have the same diameter and rotational speed and are arranged symmetrically. In order to reduce the number of meshes to improve the efficiency of the model calculation,
Scientific papers - Rolling
a 1/4 geometric model of online roll changing for flexible rolling of strips was established with the transverse and longitudinal center planes of the strips as the symmetrical planes.
(2) In actual production, the elastic deformation of the roll is smaller than the plastic deformation of the strip, and the rigidity and stability are higher, so the roll is set as a rigid body in the simulation model.
(3) Flexible rolling can be arranged in two modes of "5+1" and "5-1", and the online roll change process of flexible rolling is completed through coordination and adaptation between different stands. In order to improve the efficiency of simulation analysis and calculation and simulate the production and operation process of the strip wedge region after the roll is lifted, a two-stand arrangement is used to establish a simulation model of online roll change
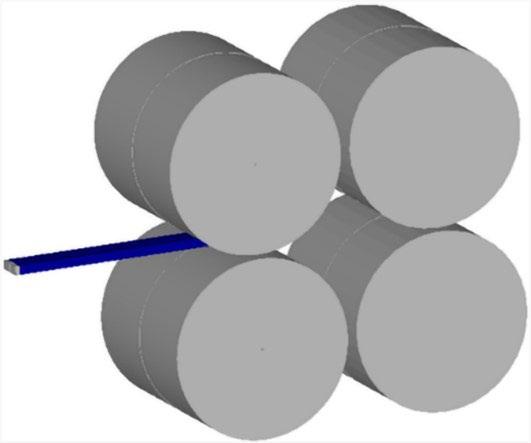
of flexible rolling, which simulates the geometric shape and microstructure variation law of the strip after the roll of the previous stand is lifted.
Based on the above assumptions, the geometric model of online roll changing for flexible strip rolling is established, as shown in Fig. 1. The mesh cell type is hexahedral, the material is the experimental steel selected in this paper, and the relevant theoretical model is imported to simulate the microstructure evolution of experimental steel during online roll change of flexible rolling. The relevant process parameters of the finite element model are based on the existing rolling mill in the laboratory, as shown in Table 1. After the simulation is completed, the results are extracted for the surface and core of the wedge region of the strip along the rolling direction.
RESULTS AND DISCUSSION Effects of deformation degree on DRX behavior
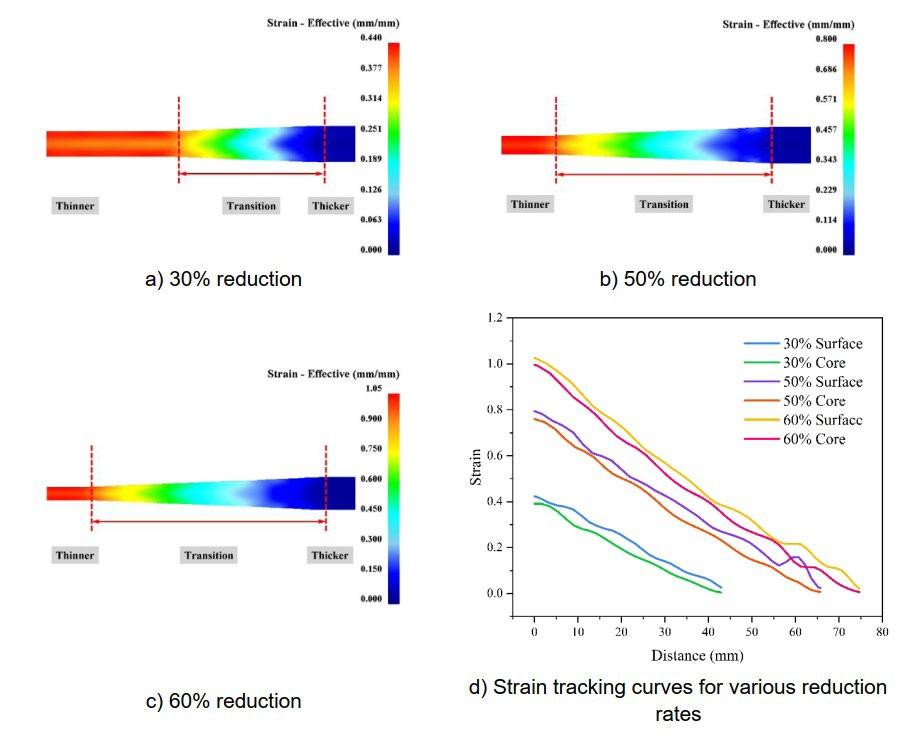
In actual production, the roll diameter, contact friction coefficient, and strip thickness cannot be changed by active adjustment, while the roll reduction rate can be adjusted according to the production schedule during the rolling process, which leads to the effect of the roll uplift and exit from rolling on the plastic deformation of the strip under various reduction ratios.
Fig. 2 a), b), and c) are the nephogram of the strain distribution in the thickness direction of the rolling strip when
the rolls are lifted and withdrawn at various reduction rates. The wedge-shaped transition region is extended with the increase of the reduction rate, and the strip is non-uniformly deformed along the thickness direction. Fig. 2 d) shows the tracking curves of the core and surface strains of the strips at various reduction rates when the rolls are lifted and withdrawn from the rolling process. With the increase of the reduction rate, the deformation gradually penetrates into the core of the strip, and the maximum strain appears in the near-surface area of the strip.
Fig. 3 a), b), and c) are the nephogram of the DRX distribution in the thickness direction of the strip after the rolls with various reduction rates are raised and withdrawn from rolling. The volume fraction of DRX is different at various reduction rates, and the DRX distribution characteristics are the same as the strain distribution nephogram. The volume fraction of DRX at the core of the strip increases significantly after the roll is lifted and withdrawn from rolling under the high reduction ratio, indicating that the DRX behavior of the core of the strip is promoted under the high reduction ratio. Fig. 3 d) shows the DRX tracking curves for the core and surface of the strips at various reduction rates when the rolls are raised and withdrawn from the rolling process. As
the reduction rate increases, the volume fraction gradient of the recrystallization of the core and surface increases, increasing the non-uniform distribution of grain size in the thickness direction of the strip, bringing a negative impact on the mechanical properties of the strip such as strength and plasticity. Therefore, it is preferable to transition from the high reduction rate mode to the low reduction rate mode during the online roll changing process of flexible rolling, which is conducive to the uniform transition of the deformation in the strip thickness direction and can reduce the DRX volume fraction gradient in the thickness direction of the strip. It is beneficial to the uniform distribution of the structure, and it can also reduce the load of the rolling mill.
Effects of roll exit speed on DRX behavior
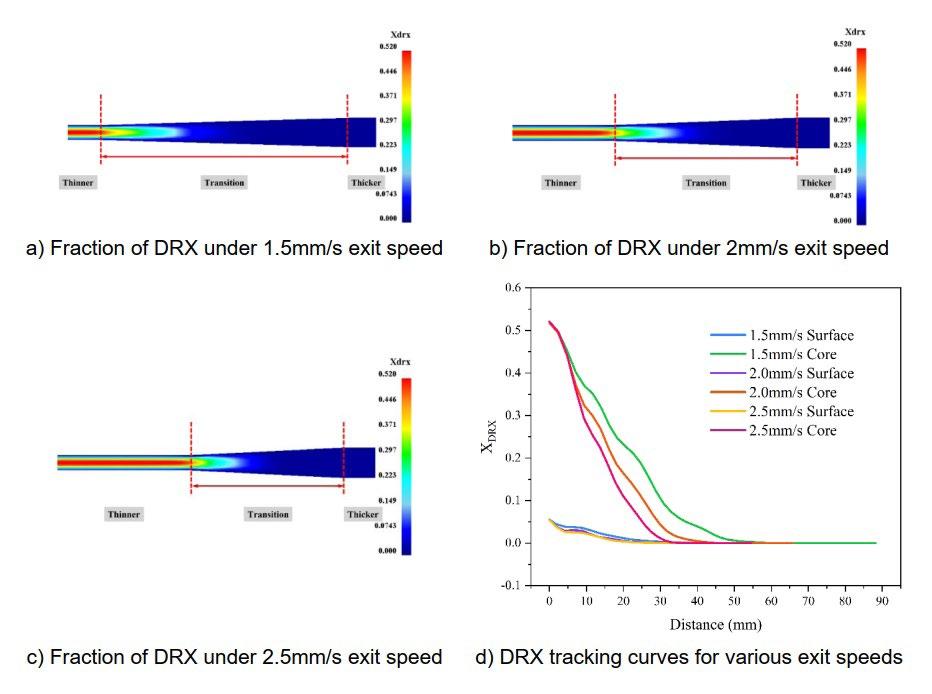
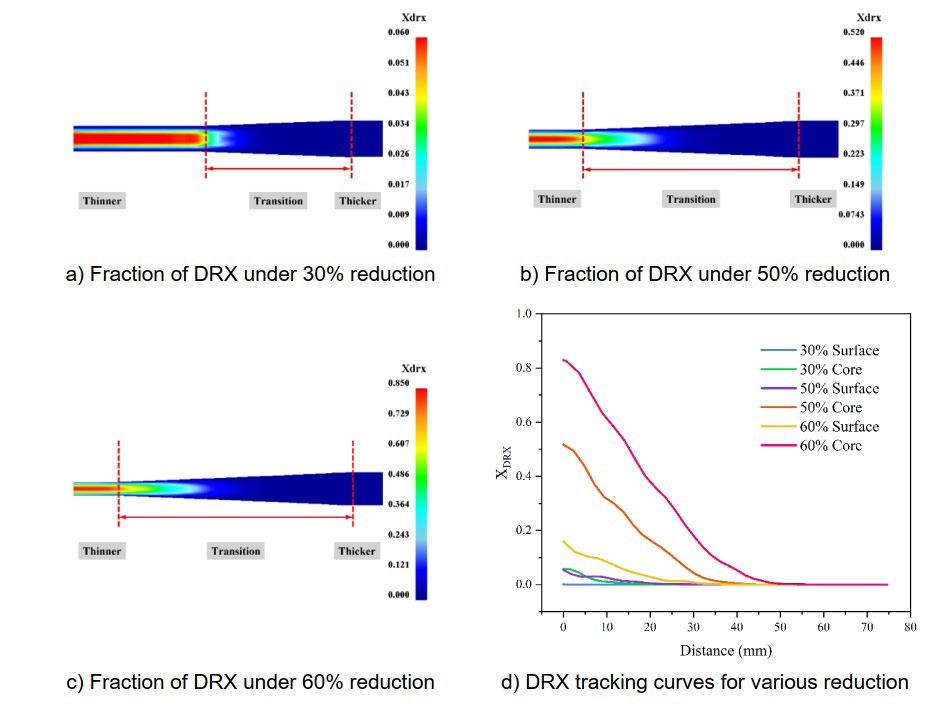
Fig. 4 a), b), and c) are the cloud diagram of DRX distribution in the strip thickness direction with various roll exit speeds (the upper roller raised speed, the lower roller lowered speed). When the roll exit speed is slow, the separation between the roll and the strip takes a long time to complete, resulting in a longer wedge transition region of the strip, and the strip has adequate time for the DRX process. The lower roll exit speed can also enhance the deformation of the strip surface, which increases the DRX degree of the strip surface to a certain extent. Fig. 4 d) shows the DRX tracking curves for the core and surface of the strip at various roll exit speeds.
When the roll exit speed is slow, the gradient of DRX volume fraction on the core and surface in the thickness transition region changes significantly. When the roll exit speed is fast, the rapid withdrawal of the roll makes the roll and the strip quickly separate, and the wedge-shaped transition region is formed quickly, which suppresses the DRX volume fraction gradient on the core and surface in the thickness direction. To avoid stress concentration and instability during the online roll change of flexible rolling, it is preferable to perform online roll change of flexible rolling at a faster roll exit speed.
Effects of roll input speed on DRX behavior
Fig. 5 a), b), and c) are the cloud diagram of DRX distribution in the thickness direction of the strip at various roll input speeds (the upper roller lowered speed, the lower roller raised speed). When the roll input speed is faster, the wedge-shaped transition region of the strip along the rolling direction is shorter. Fig. 5 d) is the DRX tracking curve of the strip core and surface at various roll input
speeds, which is opposite to the roll exit speed. When the roll input speed is fast, the roll and the strip contact quickly and reach the target position in a short time, forming a wedge-shaped transition region quickly, which increases the DRX volume fraction gradient on the core and surface in the thickness direction of the strip. Therefore, it is preferable that the online roll change of the flexible rolling is carried out in the mode of slower roll input speed.
Effects of deformation temperature on DRX behavior
Fig. 6 a), b), and c) are the cloud diagram of DRX distribution in the thickness direction of the strip at various deformation temperatures. The volume fraction of DRX increases with the increase of the deformation temperature during the online roll change process of flexible rolling.
From Fig. 6 d) DRX tracking curves of the core and surface of the rolled strip after the roll lifts at different deformation temperatures, it can be clearly seen that with the increase in deformation temperature, the DRX volume fraction on the strip surface increases significantly, and the DRX volume fraction gradient of the strip core and surface keeps increasing. For example, at the deformation temperature of 950°C, the volume fraction of DRX at the core and surface of the strip is 13.2% and 0% respectively, when the deformation temperature is increased from 950°C to
1150°C, the volume fraction of DRX increases to 91.2% and 29.1% respectively. This is due to the enhanced fluidity with increasing deformation temperature, which promotes DRX behavior. In addition, at higher deformation temperatures, the recrystallization region in the transition region is extended, the strip has a larger recrystallization gradient along the rolling direction, and the strip will have higher requirements for the high-temperature resistance of the flexible rolling online roll change equipment at higher deformation temperatures. In order to ensure the smooth transition of the strip during the roller raise and exit of the rolling process of flexible rolling, and green and low-carbon production, the online roll-changing of flexible rolling is preferably carried out in the mode of lower deformation temperature.
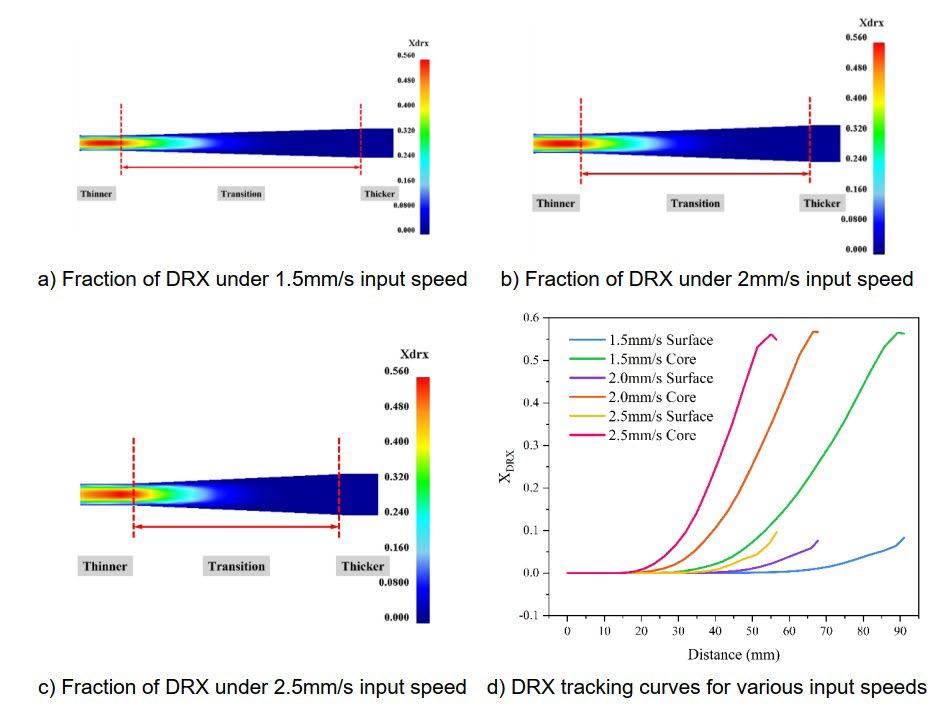
Effects of roll diameter on DRX behavior
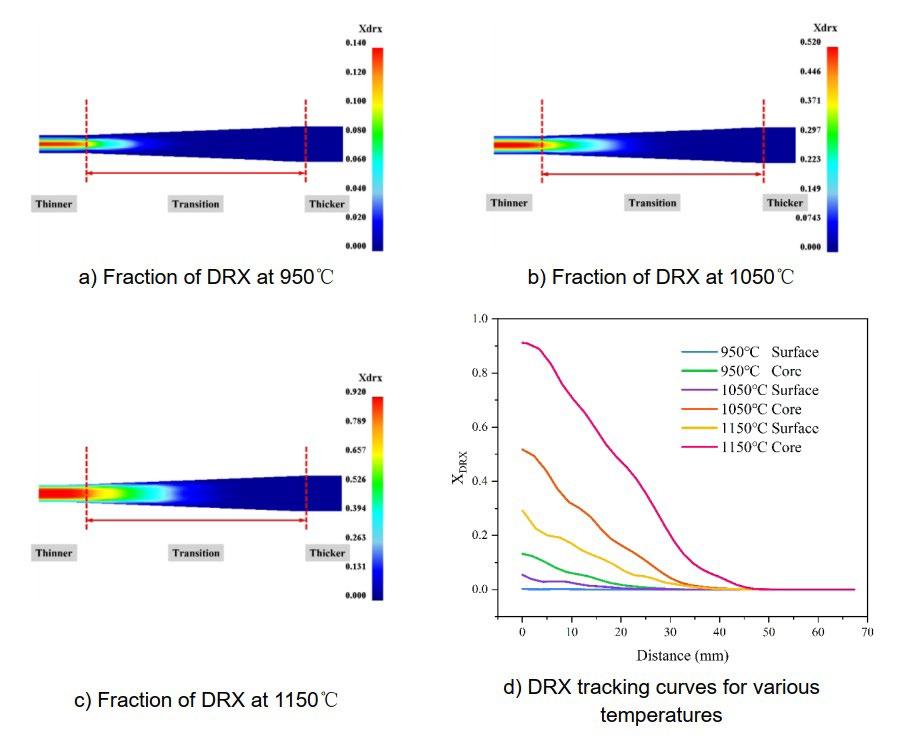
Fig. 7 a), b), c), and d) are the DRX distribution cloud diagram and the DRX tracking curve of the core and surface in the thickness direction of the strip after the rolls with various diameters are raised and withdrawn from rolling. It can be seen that as the diameter of the roll increases, the length of the wedge transition region changes little, and the change of the DRX volume fraction gradient on the strip core and surface is not apparent. The volume
fraction of DRX near the strip surface decreases slightly after the roll with a larger diameter is raised and withdrawn from rolling, and the effect of roll diameter on the DRX volume fraction gradient is not as pronounced as the reduction rate, roll exit speed, roll input speed and deformation temperature. Therefore, it is necessary to control the online roll change process of flexible rolling according to the actual rolling process, considering the load of the rolling mill and the mass of the rolls.
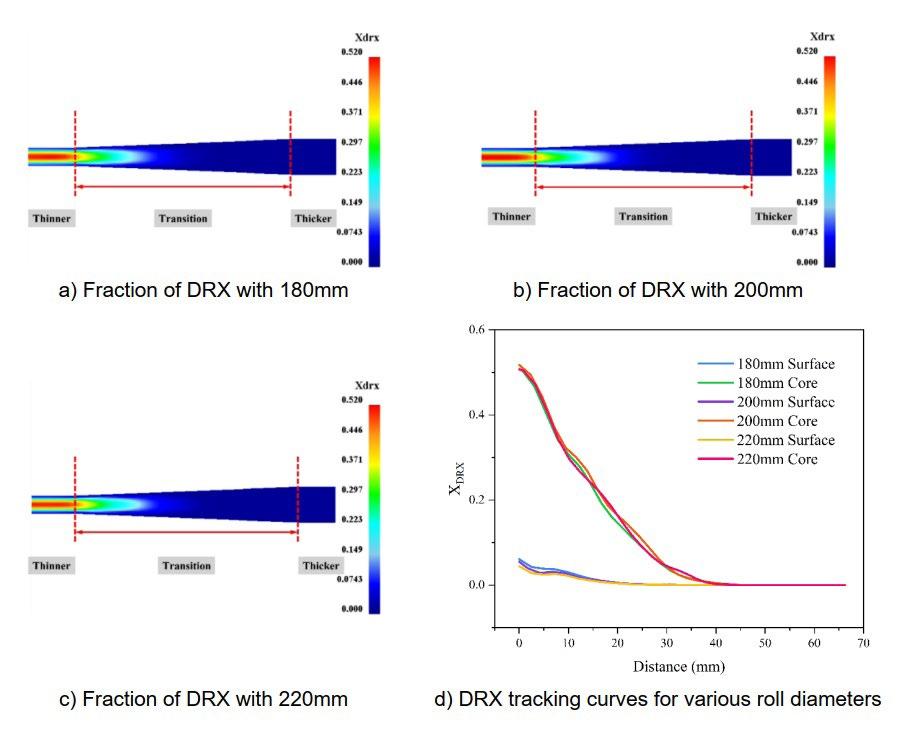
CONCLUSIONS
Based on the simulation, this paper studies the dynamic recrystallization behavior of online roll-changing in flexible strip rolling, and analyzes the effects of reduction rate, roll exit speed, roll input speed, deformation temperature, and roll diameter on the strip microstructure field. The main conclusions are as follows: The low reduction rate mode is beneficial in reducing the gradient of the recrystallization volume fraction at the core and surface of the strip in the transition region. When the roll exit speed is fast, the rapid withdrawal of the roll makes the roll and the strip quickly separate and quickly form a wedge-shaped transition region, which suppresses the DRX volume fraction gradient on the core and surface in the thickness direction of the strip. When the roll input speed is fast, the roll and the strip contact quickly and reach the target position in a short time, forming a wedge-shaped transition region quickly, which increases the DRX volume fraction gradient on the core and surface in the thickness direction of the strip. Higher deformation temperatures increase material fluidity and promote DRX
REFERENCES
behavior, with a higher gradient in DRX volume fraction at the core and surface of the strip in the transition region. As the diameter of the roll increases, the length of the wedge transition region changes little, and the change of the DRX volume fraction gradient on the strip core and surface is not obvious. The effect of roll diameter on the DRX volume fraction gradient is not as pronounced as the reduction rate, roll exit speed, roll input speed, and deformation temperature.
ACKNOWLEDGMENTS
This work was supported by Regional Joint Funds of the National Natural Science Foundation of China (Grant No. U20A20289); Innovative Research Groups Project of the Natural Science Foundation of Hebei Province (Grant No. E2021203011); Central Guidance on Local Science and Technology Development Funding Project (Grant No. 206Z1601G).
[1] B. Linzer, A. Jungbauer, Arvedi ESP for high-quality hot-strip production at Rizhao Steel, Materials Science Forum, Trans Tech Publ, 2016, pp. 207-214.
[2] R. Venturini, A. Bianchi, M. Andraghetti, C. Guarnaschelli, M. Cesile, P. Di Nunzio, Metallurgical design and production of AHSS grades DP800 and CP800 ISP and ESP thin slab technology at Acciaieria Arvedi in Cremona, Italy, La Metallurgia Italiana (2020) 43.
[3] W. Peng, X. Chen, L. Zhang, X. Li, J. Sun, D. Zhang, Finite element analysis of temperature uniformity in transverse induction heating process in ESP rolling, The International Journal of Advanced Manufacturing Technology 115(11) (2021) 3423-3439.
[4] C. Liu, C. Mapelli, Y. Peng, S. Barella, S. Liang, A. Gruttadauria, M. Belfi, Dynamic Recrystallization Behavior of Low-Carbon Steel during the Flexible Rolling Process: Modeling and Characterization, steel research international 2100490.
[5] C. Liu, Y. Peng, S. Barella, C. Mapelli, S. Liang, Characterization of dynamic recrystallization behavior of low carbon steel under flexible rolling process, Materials Today Communications 29 (2021) 102777.
[6] J. Zhang, Y. Yi, S. Huang, X. Mao, H. He, J. Tang, W. Guo, F. Dong, Dynamic recrystallization mechanisms of 2195 aluminum alloy during medium/high temperature compression deformation, Materials Science and Engineering: A 804 (2021) 140650.
[7] C. Zhang, C. Wang, R. Guo, G. Zhao, L. Chen, W. Sun, X. Wang, Investigation of dynamic recrystallization and modeling of microstructure evolution of an Al-Mg-Si aluminum alloy during high-temperature deformation, Journal of Alloys and Compounds 773 (2019) 59-70.
[8] F. Siciliano, S.F. Rodrigues, C. Aranas Jr, J.J. Jonas, The dynamic transformation of ferrite above AE3 and the consequences on hot rolling of steels, Tecnologia em Metalurgia, Materiais e Mineração 17(2) (2020) 90-95.
[9] X. Wang, K. Chandrashekhara, S.N. Lekakh, D.C. Van Aken, R.J. O'Malley, Modeling and Simulation of Dynamic Recrystallization Behavior in Alloyed Steel 15V38 during Hot Rolling, steel research international 90(4) (2019) 1700565.
[10] X. Wang, K. Chandrashekhara, M.F. Buchely, S. Lekakh, D.C. Van Aken, R.J. O’Malley, G.W. Ridenour, E. Scheid, Experiment and simulation of static softening behavior of alloyed steel during round bar hot rolling, Journal of Manufacturing Processes 52 (2020) 281-288.
[11] X.W. Duan, J.J. Liu, B. Gong, P. Li, J.S. Liu, Experimental Study and Numerical Simulation of Dynamic Recrystallization Behavior of a High-Strength Steel, Metals, and Materials International 27(5) (2021) 1044-1059.
[12] D. Dong, F. Chen, Z. Cui, Investigation on metadynamic recrystallization behavior in SA508-Ш steel during hot deformation, Journal of Manufacturing Processes 29 (2017) 18-28.
Scientific papers - Rolling
[13] H. Jiang, L. Yang, J. Dong, M. Zhang, Z. Yao, The recrystallization model and microstructure prediction of alloy 690 during hot deformation, Materials & Design 104 (2016) 162-173.
[14] W. Shen, C. Zhang, L. Zhang, Q. Xu, Y. Cui, Y. Xu, A modified Avrami equation for kinetics of static recrystallization of Nb-V microalloyed steel: Experiments and numerical simulation, Vacuum 150 (2018) 116-123.
[15] S.D. Gu, L.W. Zhang, J.H. Ruan, P.Z. Zhou, Y. Zhen, Constitutive modeling of dynamic recrystallization behavior and processing map of 38MnVS6 non-quenched steel, Journal of Materials Engineering and Performance 23(3) (2014) 1062-1068.
[16] C. Liu, S. Barella, Y. Peng, J. Sun, S. Guo, S. Liang, A. Gruttadauria, C. Mapelli, Dynamic recrystallization behavior under steady and transient mutation deformation state, Materials Science and Engineering: A 843 (2022) 143138. TORNA
Quantitative evaluation of relative sliding between billets and rolls in hot rolling
In rolling process relative sliding happens due to the different velocities between billets and work rolls. The sliding affects the roll wear, the tribological characteristics and the failure of rolls. Quantitative evaluations of the relative sliding are essential to the failure analysis and damage prediction of rolls.
The velocity and the distance of the relative sliding are investigated with finite element simulation and evaluated at different billet sizes, reduction ratios, frictions, rolling temperatures and velocities, and compared between flat and caliber rolling. The velocity and the distance are increased with increasing the billet size, the reduction ratio and the rolling speed, and reduced with increasing the friction coefficient and the temperature inhomogeneity on the cross section of billets. The influence of the caliber rolling on the relative sliding is significant as the width of billets beyond that of the caliber.
KEYWORDS: SLIDING, VELOCITY, DISTANCE, HOT ROLLING, FINITE ELEMENT SIMULATION
INTRODUCTION
Relative movement between workpieces and tools takes place in most cases of metal manufactures and productions. This movement results in tool wear and contributes to tribological characteristics at the contact surface [1,2]. In rolling process workpieces are moved by frictions with work rolls. Due to plastic deformation, the movement of materials at the contact surface cannot be exactly the same as the rotation of rolls. The speed is different between workpieces and rolls except on the neutral point line. Relative sliding always takes place in the rolling process. Roll wear and failures are complicatedly originated and influenced by the relative sliding, roll forces, surface conditions, frictions, lubrications and so on. Evaluations and analysis of these interactive factors can provide crucial information to reduce roll wear and to prevent the unexpected failures of rolls. The relative sliding is one of the key influencing factors concerning deterioration of work rolls [3,4].
Quantitative evaluations of the relative sliding are important not only to improve the performance of
work rolls, but also to optimize rolling schedules. With applications of finite element method (FEM), the influences of the billet size, the reduction ratio, the friction coefficient, the rolling temperature and speed on the velocity and the distance of the relative sliding are investigated and compared between the flat and caliber rolling.
METHOD
Finite element simulation with a one quarter and non-
isothermal model has been carried out for hot rolling using the software DEFORM™ 3D. The rectangular or the quadratic (Q) cross section of billets has a size ranging from 206 to 440 mm. The initial temperature difference between the surface and the center on the cross section is noted as Td, as defined in Fig.1a. The flat roll has a diameter of 778 or 950 mm. The caliber roll has a box shape with a width of 251 mm at the top and a diameter of 778 mm. Both rolls rotate at a constant initial temperature and angle velocity.
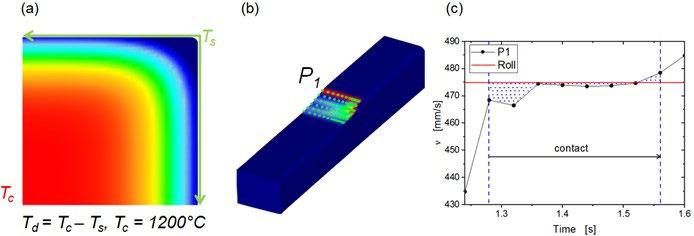
To evaluate the relative sliding, the mean value of the velocity and the total distance of the sliding in the contact region are employed. The relative sliding
velocity (∆v) is defined as the mean difference in the velocity at the contact node between the billet and the roll, as shown in Fig.1b and 1c.
vi is the velocity at the contact node, vR the velocity of the roll, N the number of the contact nodes. The relative sliding distance (∆s) is the area of the velocity difference

between the contact node and the roll, summed for all contact nodes in the contact region (Fig.1c for one contact node P1). ∆s can be calculated as:
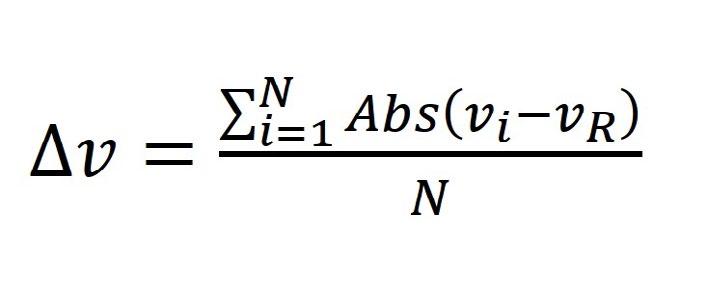
(1) (2)
M is the number of the contact lines, k the number of the contact nodes (k>1) on each contact line, ∆t the time step in the simulation. The reduction ratio is calculated with
∆H/H0=(H0-H1)/H0. H0 and H1 are the billet height before and after rolling, respectively.
RESULTS
The relative sliding velocity (∆v) and the distance (∆s) increase with increasing the billet height, as shown in Fig.2a and 2b respectively. At the same height, ∆v does
not change, while ∆s increases slightly with increasing the billet width. The variations in ∆v and ∆s depend significantly on the reduction in the billet height, but not on the billet width.
∆v and ∆s increase with increasing the reduction ratio (∆H/H0), as shown in Fig.3a and 3b, respectively. The
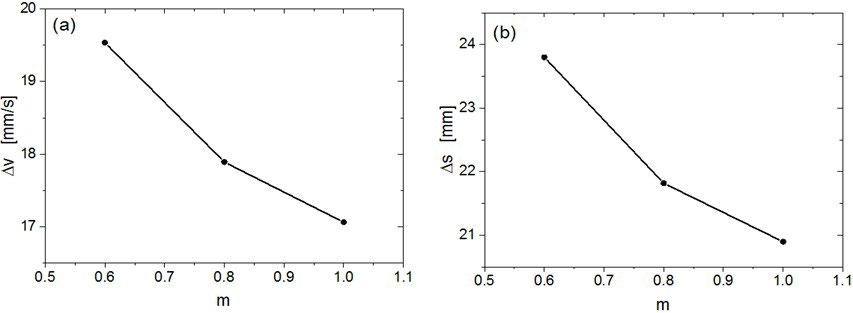
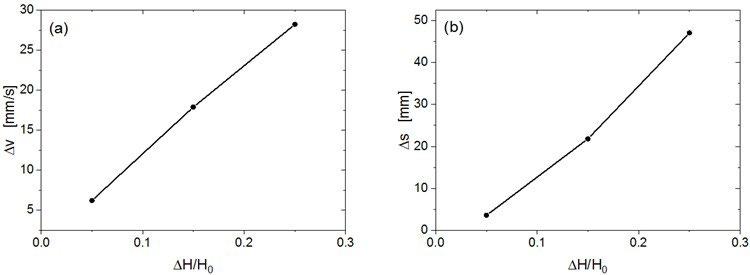
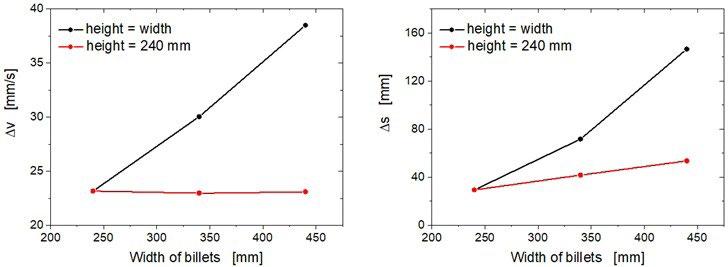
increases of ∆v and ∆s with ∆H/H0 are nearly linear.
The effect of the friction coefficient (m) on ∆v and ∆s is shown in Fig.4. Both ∆v and ∆s decrease with increasing m. As compared to those with the size or the reduction
ratio, the variations in ∆v and ∆s with m are merely within 15% and are more significant as m is smaller than 0.80.
Scientific papers - Rolling
The influences of Td (Fig.1a) on ∆v and ∆s are shown in Fig.5. ∆v and ∆s decrease with increasing Td. The relative sliding velocity and the distance are increased with
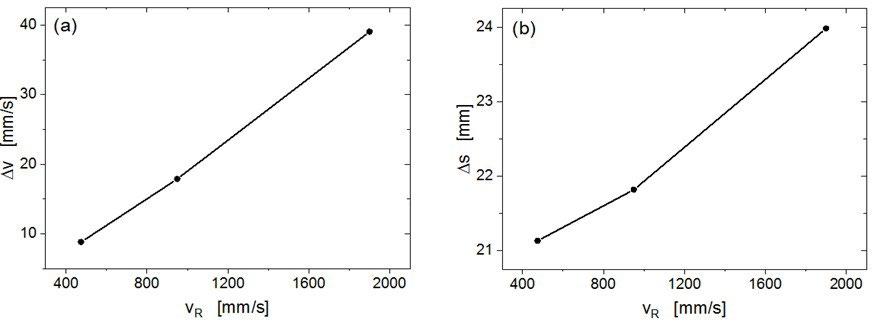
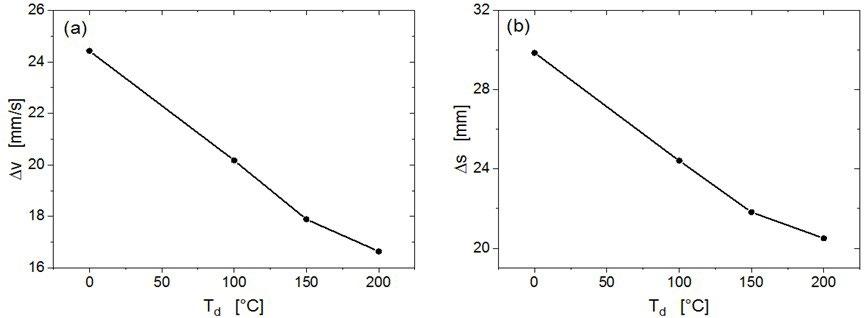
a homogeneous temperature distribution on the cross section of billets. The variations in ∆v and ∆s with Td are approximately 50% as the Td is within 200°C.
Fig.6 shows the ∆v and ∆s increasing with increasing the roll speeds (vR). The increase in ∆v with vR is significant
and nearly linear. In a contrast, the increase in ∆s is below 13.5%.
∆v and ∆s at the different billet widths but the same billet height are shown in Fig.7. The caliber rolling is similar to the flat one as the billet width (206 mm) is much smaller than that of the caliber (251 mm). For the flat rolling ∆v and ∆s increase slightly with increasing the billet width. For the caliber rolling, ∆v decreases slightly as the billet width equals to that of the caliber. The remarkable increases in ∆v and ∆s appear as the billet width is beyond the width of the caliber.
DISCUSSION
The relative sliding between rolls and workpieces is a
well known phenomenon in rolling process. It affects not only the deterioration of work rolls, but also the surface qualities of the rolling products. Nevertheless, the quantitative measurements of the relative sliding have been proved to be difficult [5].
Finite element method (FEM) has been widely used in the simulation of rolling processes. The relative sliding can be quantitatively evaluated with the help of FE simulation. The advantages are that the complicated influencing factors under harsh working conditions can be excluded or simplified, and the time- and
cost-consuming experiments or measurements are avoidable. However, the quantities in FEM depend on the settings in the simulation models, for example, the size and the shape of the elements. The parameters in the relative sliding are comparable merely with the same selective settings in the simulations. The accuracy of the evaluation can be improved by employing fine meshes, while, a compromise has to be made between
the precision of the results and the consumed CPU time. The present investigation of the relative sliding with FEM paves a way to quantify the influencing factors like the geometric settings and the working conditions in the hot rolling. This method has a great potential in developing damage models, predicting roll wear and optimizing rolling schedules.
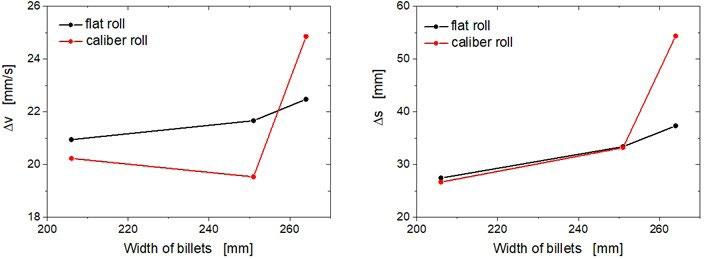
CONCLUSION
The relative sliding velocity and the distance are dominantly increased with increasing the billet height and the reduction ratio. Their variations with the temperature difference on the cross section of billets are moderate. The relative sliding velocity but not the sliding distance is sensitive to the rolling speed. The influence of
REFERENCES
the friction coefficient on the velocity and the distance is not remarkable.
As compared to the flat one, the effect of the caliber rolling on the relative sliding velocity and distance gets to be significant when the billet width is over the width of the caliber.
[1] Zhang S, Hodgson PD, Cardew-Hallb MJ, Kalyanasundaram S. A finite element simulation of micro-mechanical frictional behaviour in metal forming. J Mater Proc Technol. 2003;134:81–91.
[2] Wang Z, Nakamura T, Dohda K, Obika T. FEM analysis of contact mechanism in press-forming of lubricant pre-coated steel sheet. J Mater Proc Technol. 2003;140:514–19.
[3] Kramer P, Groche P. Defect detection in thread rolling processes – Experimental study and numerical investigation of driving parameters. Inter J Machine Tools and Manufacture. 2018;129:27–36.
[4] Ma B, Tieu AK, Lu C, Jiang Z. A finite-element simulation of asperity flattening in metal forming. J Mater Proc Technol. 2002;130131:450–55.
[5] Kim HH, Kim SJ, Yoon SM, Choi YJ, Lee MC. Sliding mode control with sliding perturbation observer-based strategy for reducing scratch formation in hot rolling process. Appl. Sci. 2021;11:5526. https://doi.org/10.3390/app11125526.
Correlation of digital twin and roller surface sensor results for az31 alloy twin roll casting process
S. Kwiecień, M. Weiner, M. Schmidtchen, M. Ullmann, U. Prahl, L. Hamm, W-G. DrosselDue to the growing interest in lightweight construction in the automotive and aerospace industries, among others, continuous twin roll casting (TRC) of lightweight metals is constantly expanding. This is due to the cost-effectiveness of the process, as it combines several steps in the production of metal sheets. Due to the nature of the process, the parameters in the rolling gap, such as for example pressure and temperature, are unknown, which significantly affects the ability to understand the phenomena occurring in the rolling gap and thus in the material during rolling. In this work, a key development for a live analysis of the TRC parameters in the rolling gap by means of inline sensors will be presented. Therefore, at IMF Freiberg, a special rolling gap sensor was mounted in the surface of the TRC roller, consisting of a piezoelectric pressure sensor and two thermocouples measuring the temperature at two different heights, in the same measuring plane. This combined sensor data offers access to the roll surface temperature and the pressure in the rolling gap to be monitored live during the TRC process. The measurements were further supported using a digital twin in the form of a layer model by Weiner et al.. The model used in this work is an extension to the viscous part of the layered model proposed by Schmidtchen and Kawalla, based on the classical elementary theory of plasticity, which aimed to model the nonuniform deformation behaviour during flat rolling. This resulted in a new model, which combines the liquid (as viscous) and solid (as elastic-plastic) regions for each layer in a combined approach. Calculations in this tool are performed offline and the computational time is in the order of seconds, what is multiple shorter than comparable finite element method simulations. Experimental results have been obtained allowing a direct correlation between the shape of the pressure curve and the temperature evolution and the length of the fully solidified (and thus compressed) part in the rolling gap zone (deformation length – LD), which directly correlates with the effective total equivalent stress. By using the sensor and layer model, it is possible to adapt a digital twin that can be used for on-line estimation of the final strip parameters obtained in the TRC process.
KEYWORDS: TWIN ROLL CASTING, ROLLING, LAYER MODEL, DIGITAL TWIN, SENSOR
INTRODUCTION
The aim of the research was to create a digital twin that will operate online in real time during the TRC trial, by using data from the rolling plant measurement system together with data from a combined pressure and temperature sensor in the rolling gap. In this way it will be able to calculate in a very short time the final parameters of the currently rolled strip, allowing manual control of the process to achieve the desired microstructure. So far, in this work an offline digital twin has been developed and an innovative sensor concept for pressure and temperature measurement in the rolling gap has been implemented and adjusted. So far, the experimental study with pressure and
S. Kwiecień, M. Weiner, M. Schmidtchen, M. Ullmann, U. Prahl
IMF - Institute for Metal Forming, Technical University of Freiberg, Germany
szymon.kwiecien@imf.tu-freiberg.de
temperature sensor has been carried out on the wrought alloy Mg AZ31 (1-3). In addition, first trials have been carried out with ZAX210 (4) alloy at IMF to further extend the study to other magnesium alloys at a later stage. As a solidification start point is not yet measurable, the solid part and thus the forming length of rolling gap can be identified, which can be further aided by a digital twin. Due to the nature of the TRC, current control of the processes occurring in the rolling gap is difficult due to bad physical accessibility and due to the high temperatures. For this purpose, a sensor concept consisting of a pressure sensor and two thermocouples placed under the surface of the roller was developed. It provides data on the temperature distribution changes in the roller at different rotational speeds and on pressure variation with the selected parameters. The data from the sensor and the TRC plant measurement system were used as input parameters
for the digital twin, which is the layered model presented by Schmidtchen, extended with a viscous layer [6]. When the measured and calculated results were compared, they were found to be similar, confirming the effectiveness of the layered model.
SENSOR USED IN RESEARCH
An important part of the initial research was to develop a sensor concept that can operate at high temperatures, up to approx. 600 °C. finally, it was decided on a sensor with a piezoelectric layer (5), which can be mounted in very small mounting space and is suitable for incorporation into a roller surface. As this sensor is only able to measure pressure, so it was also decided to put two thermocouples in one measuring line, measuring temperature at two different heights.
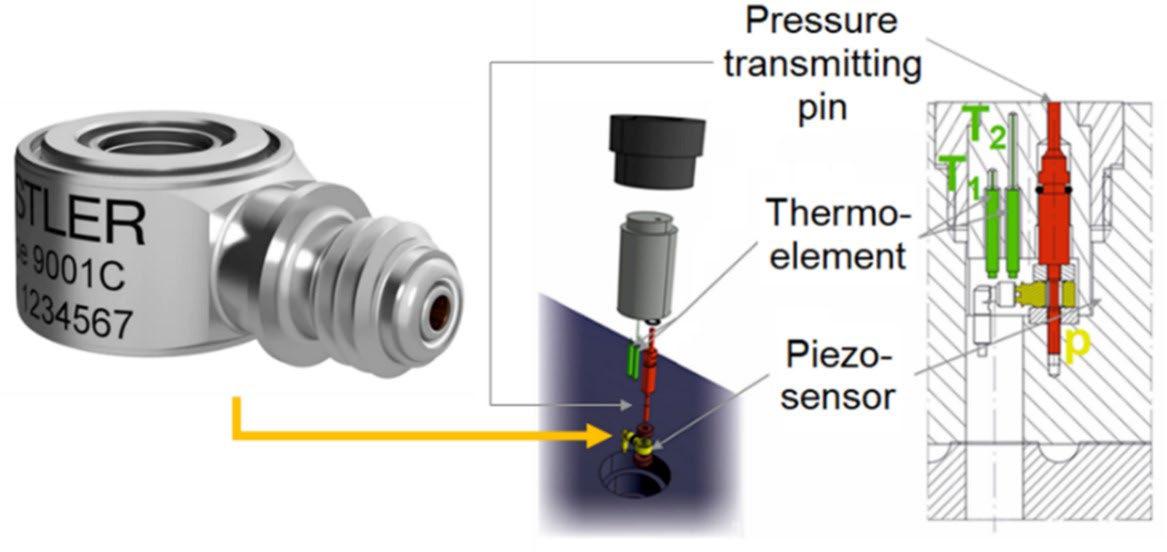
As presented in figure 1, Kistler 9001C sensor was used for pressure measurement, which measures forces in the Z direction. Unfortunately, the use of long sensor wires was unavoidable for this measurement system. If a small amount of charge is applied to the sensor through a long wire with sufficient capacity and insulation resistance, the measurement signal at the end of the wire will be very low, so an additional signal amplifier was installed. However, the biggest advantage of this sensor is that it can be placed under rough conditions. Signal wires were routed through an additional cooling channel inside the roller. The pin (red in Figure 1) is guided to the surface of the roller and measures the pressure over a small area. In addition, two thermocouples placed at different heights (green in Figure 1) were mounted to observe the heat flow in the roller surface. In order to mount the whole sensor, a hole was
drilled from the outside, which connects to the cooling channels. Sensor signals are detected on the roller and transmitted wirelessly to the system. In the rotating roller, energy is supplied by a battery that allows for 12 hours of operation.
ANALYSIS OF THE RESULTS OF THE TRC PROCESS AND THE DIGITAL TWIN
The most important recent development of Layer Model is the extension of the classical elementary elastic-plastic theory to the viscous model (6-7). Two main regions can be distinguished (Figure 2 left side): the red region is the viscous region where the material is melted and formed as a viscous fluid according to Newton's law. Different shades of red indicate the viscous states – from dark to light they are liquid and mushy, while the blue part is the fully solidified, elastic-plastic model. In the layered model of the TRC process, the material is divided into individual layers parallel to the rolling direction, which are subject to local solidification conditions, strength development, and solid deformation. The partial approach consists of a viscoplastic design core for the liquid and mushy region and an isotropic-elastic-plastic design core for the solidified region. The solution is the same as in classical elementary theory, except that models are created individually for each layer.

Due to the complexity of the problem, most simulations currently used for this purpose are based on the finite element method. However, the finite element method, compared to the layer model, requires too much computational time to generate larger variants of data, especially for nonlinear problems, due to the large number of iterations. For highly nonlinear problems, the computation time of FE calculations range from several hours to several days, which definitely prevents the FEM
from being a fast digital twin. The Freiberger layer model, on the other hand, requires an order of magnitude less computational time for conventional rolling processes by taking approx. 300 seconds when computing for five layers. The most important input parameters for the layer model include the number of layers, liquid metal temperature, rolling gap height, roll radius, roll speed, and roll temperature. Within the current model formulation, all these data are kept constant. In addition, parameters such as friction values, initial material deformation, and fluid pressure must be determined. The material data of the AZ31 material was used as the thermo-mechanical properties. With these inputs, the layered model can provide data such as the deformation length (LD), but also temperature and pressure distribution as well as rolling force and torque.
ANALYSIS OF THE RESULTS OF THE TRC PROCESS AND THE DIGITAL TWIN
Figure 3 shows the results for the piezosensor and the two thermocouples for the entire length in the rolling direction for three exemplarily TRC speeds. It can be seen that with increasing TRC speed the temperature measurements close to the roll surface (Temperature 2) and for the pressure decrease. This is due to the fact that at higher TRC speeds the solidification front moves towards the
exit of the rolling gap, so that the deformation time and thus the deformation length LD is lower. In contrast, the thermocouple further away from the roll surface recorded higher temperatures as the TRC speed increased, due to the interior of the roll was getting hotter because of less time in between two material contacts.
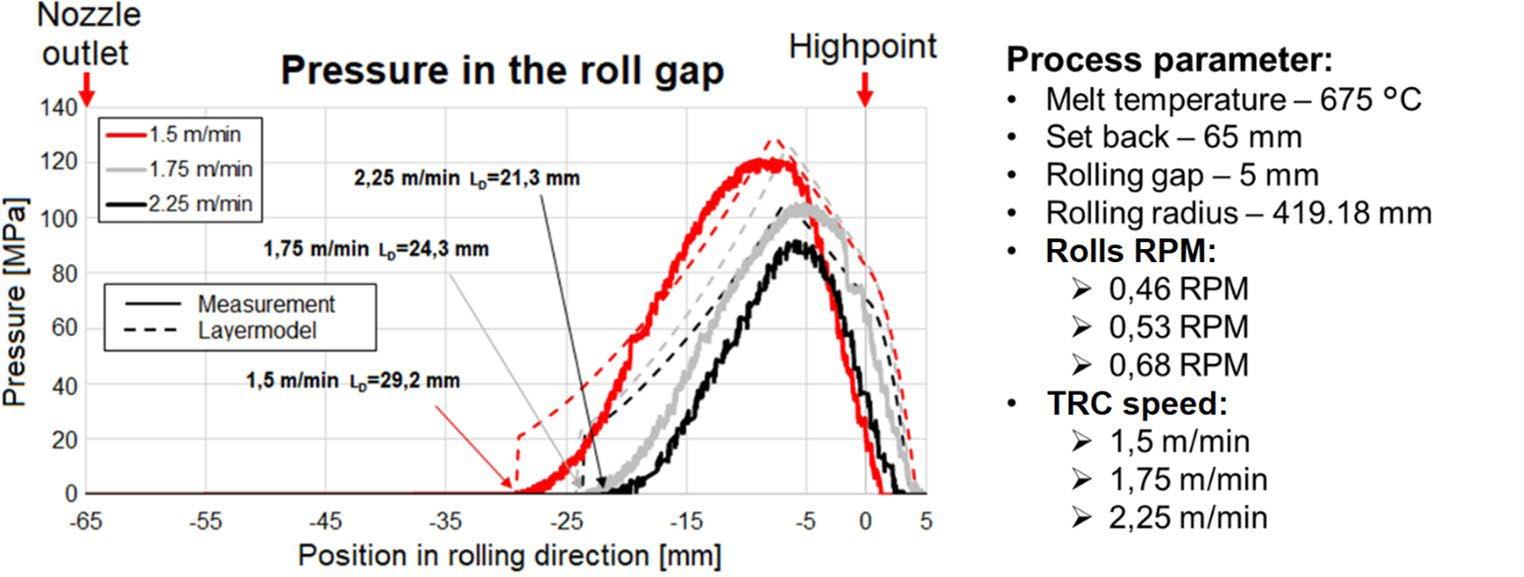
Figure 4 shows the results for pressure obtained from the layered model using only the mentioned initial parameters compared with measured data. It can be seen that the pressure spike starts immediately, it is due to the fact that once the liquid is in contact with the roller surface, rapid heat transfer occurs and the liquid is cooled to a temperature where plastic deformation is possible. At higher rotational speed and thus increasing TRC speed, the fluid is transported a greater distance into the gap before it
reaches a temperature sufficient to solidify and to initiate deformation. As the liquid temperature decreases, the LD increases, causing the solidification front to move toward the nozzle. It is shown that the shift of the solidification front can be observed by measuring the pressure near the roller surface. Additionally, this confirms that the layered model as well as the new combined sensor yield reasonable results.
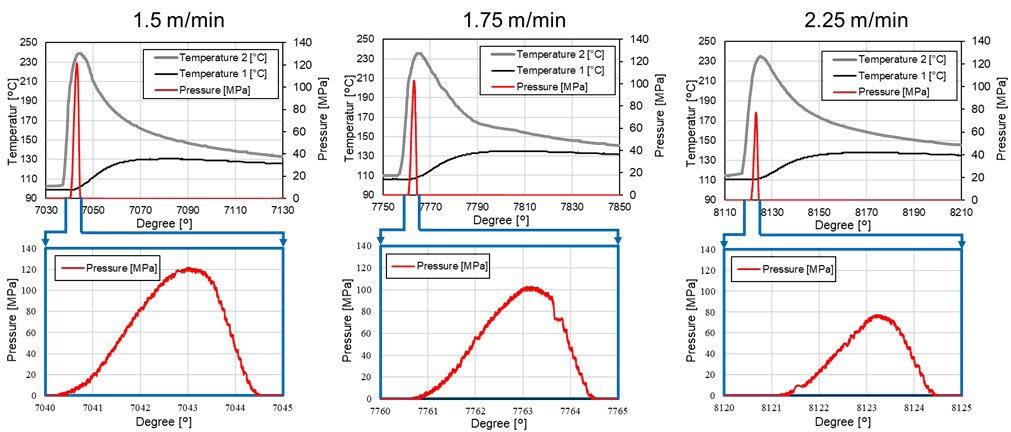
For all three rolling velocities, microstructure observations and tensile tests were carried out in three directions relative to the rolling direction (0, 45 and 90 °). Grain height and length were also measured as part of the microscopic analysis. Figure 5 shows the relationship between tensile strength and average grain size in length and height as a function of LD. It can be seen that the grains increasingly deform as the TRC speed decreases, which correlates with the stress increase inversely proportional to the TRC speed. In addition, texture studies have shown that AZ31 exhibits an increasing basic texture with decreasing TRC speed, which is a result of the forming conditions with an increase in deformation length and which is undesirable at further stages of forming.
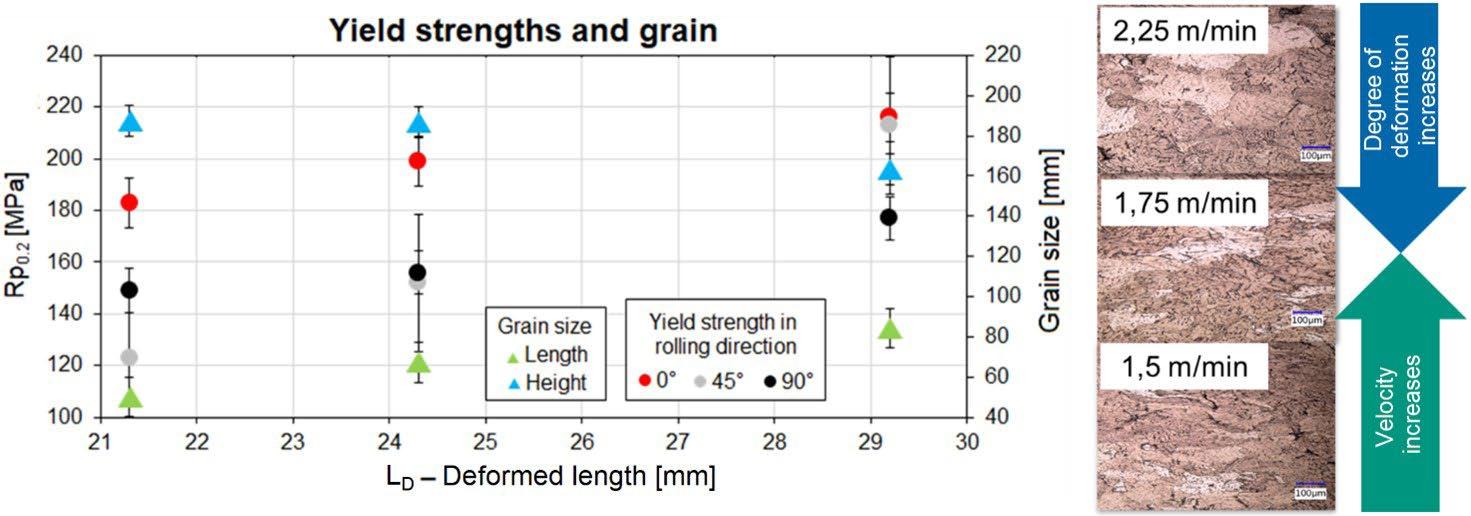
Depending on the degree of solidification, the maximum deformation length can be obtained at a TRC speed of 1.5 m/min. At high speeds, at the highest point of the rolling gap, the core material is still liquid and its solidification structure resembles that of the casting process, so dendritic structures are much more common.
Looking at the results of the tensile test, it can be seen that the highest material strengths were obtained at a speed of 1.5 m/min, for 0° orientation in the rolling direction. This can be seen when comparing it to the results for 90°, where the yield strength is lower.
CONCLUSION
A successful TRC process using a sensor to record pressure and temperature in the rolling gap, aided by an offline digital twin in the form of a layered model, allowed for a deeper understanding of the mechanisms occurring
during the process and in the material itself. The results obtained from the sensor were compared with the values measured by the rolling plant measurement system. It was found that the pressure varies in proportion to the torque and rolling force and inversely proportional to the linear TRC speed, which agrees with the reasonable process relationships. In parallel, a simulation was performed using the data collected by the measurement system as input parameters. By analyzing the results, it was confirmed that the starting point of the deformation length LD moves towards the nozzle as the rolling velocities decreases. On the other hand, as LD increases, the pressure in the rolling gap increases because the deformation starts earlier. This is caused by the distance at which the first contact between the liquid and the roll surface occurs, as well as by the exposure time of the rolls to the cooling system and the environment. The sample obtained at 1.5 m/min showed the best properties.
REFERENCES
[1] Wells M., Hadadzadeh A.: Twin Roll Casting (TRC) of Magnesium Alloys – Opportunities and Challenges. Materials Science Forum. 2014; 781-786:527-533.
[2] Javaid A., Czerwinski F.: Progress in twin roll casting of magnesium alloys: A review. Journal of Magnesium and Alloys 9. 2021; 362–391.
[3] Kurz G., Bohlen J., Letzig D., Kainer K.-U.: Influence of Process Parameters on Twin Roll Cast Strip of the Alloy AZ31. Materials Science Forum. 2013; 765:205-209.
[4] Kittner K., Ullmann M., Henseler T., Prahl U., Kawalla R.: Dynamic recrystallization behaviour of twin roll cast ZAX210 strips during hot deformation. 28th International Conference on Metallurgy and Materials. 2019 May 22-24; Brno, Czech Republic; 1528-1534
[5] Horsky J., Jonsson N.G., Gade D.: Advanced roll gap sensors for enhanced hot and cold rolling processes. Final report, Brussels: European Commission. 2016.
[6] Weiner M., Schmidtchen M., Prahl U.: Extension of the Freiberg Layer Model by Means of Solidification for Roll Casting. Advanced Engineering Materials. 2022.
[7] Weiner M., Schmidtchen M., Prahl U.: Extension of the Freiberg Layer Model by Means of Elastic–Plastic Material Behavior. Steel Research International. 2021
HIGH STRENGTH STEELS
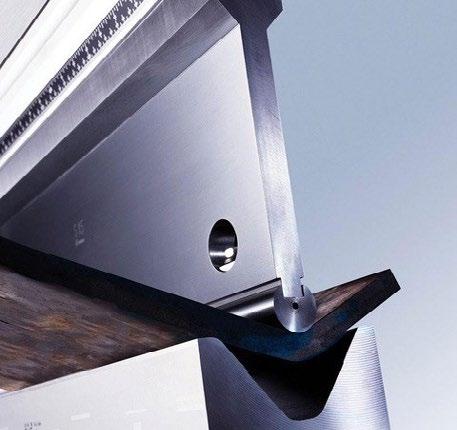
Bergamo . Italy, 26-27 October 2023
Increasing demand from the structural, energy, vehicles applications as well as oil & gas sector has boosted the rapid growth of the market for High Strength Steels. Steel manufacturers are constantly seeking the possibility of increasing strength, maintaining good toughness and weldability. Such a goal can be achieved by several routes: micro-alloying, advanced thermal treatment (i.e. intercritical quenching, bainitic quenching, quench and partitioning procedure etc.), high alligation by Mn and Al, thermo-mechanical processing. The scope of the workshop is to bring together the international community to highlight state-of-theart research and development of such steel grades.
MAIN TOPICS
Both fundamental and applied aspects will be covered concerning:
- Alloying design - HSLA steels
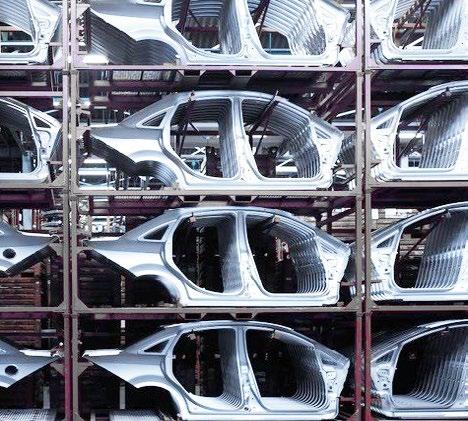
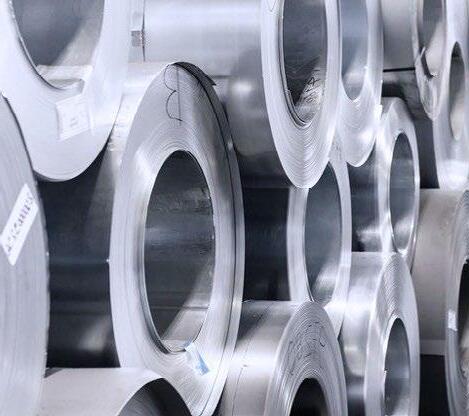
- Advanced heat treatment - Thermo-mechanical processing
- AHSS
The workshop will be performed through presentations both invited and selected on the basis of the submitted abstracts. The event will be a suitable meeting place for those involved in research, development and applications of HSS, interested to share recent advances on metallurgical design, set-up of production routes, paying attention to surface and inner quality, properties of HSS products. The deadline for abstract submission is June 30 in order to fulfil the selection for the final program.
WORKSHOP CHAIRPERSON
Ettore Anelli – Franchini Acciai
ORGANISING COMMITTEE (to be completed)
Silvia Barella – Politecnico di Milano
Federica Bassani – Associazione Italiana di Metallurgia
Manuele Dabalà – Università di Padova
Carlos Garcia-Mateo - CENIM-CSIC
CALL FOR PAPERS
Carlo Mapelli – Politecnico di Milano
Marina Polyakova - Nosov Magnitogorsk University
Ilchat Sabirov – Arcelormittal
The deadline for abstract submission is June 30 in order to fulfil the selection for the final program. Prospective speakers wishing to present are invited to submit a tentative title and an abstract of about 400 words (in English) to the Organising Secretariat (met@aimnet.it). The abstract should provide sufficient information for a fair assessment. To submit the abstract, fill in the form on the Workshop website at http://www.aimnet.it.
ORGANISING SECRETARIAT
Finite element modeling evaluation of a void closure criterion using a multi-scale approach during hot rolling
edited by: C. Pondaven, B. Erzar, A. Spadaccini, M. GrionThe hot rolling of long products is a manufacturing process aiming to refine the microstructure and to guarantee the internal soundness of cast products by contributing to the healing of shrinkage porosity. The understanding of the mechanism involved in the latter phenomenon is necessary to improve the final mechanical properties of rolled products. The pore closure is strongly connected to the thermomechanical loading and to the morphology of the voids respecting to the loading direction. These multiple parameters involved make it thus difficult the application of predictive mean-field model to assess the closure state of voids during complex industrial forming routes. In this study, a multi-scale full-field approach using Representative Volume Element (RVE) is applied to study the evolution of an explicitly modeled spherical void during the rolling process. This multi-scale approach allows modeling the evolution of voids with dimensions representatives of shrinkage porosity. observed in blooms in an acceptable computation time. A Finite Element model of the studied rolling mill is firstly developed to extract the thermomechanical loadings during the rolling. The loadings of each rolling pass are then applied as boundary conditions of RVE containing a single pore. The evolution of dimensions of the explicitly modeled void is eventually compared with the value of a simple mean-field criterion to evaluate its capacity to predict the void closure capacity of the studied rolling route.
KEYWORDS: PORE CLOSURE, FINITE ELEMENT MODELING, MULTISCALE, HOT ROLLING, REPRESENTATIVE VOLUME ELEMENT, SHRINKAGE POROSITY
INTRODUCTION
The hot rolling of long products is a forming process aiming to reach simultaneously the needed dimensions of rolled products while refining the microstructure and reducing the internal defects generated during the casting. This improvement of internal soundness is interesting to guarantee the fatigue performance and the mechanical properties of the parts manufactured from rolled products.
The current study is focused on the closure of shrinkage porosity generated during the casting of steel. This phenomenon is strongly connected to the thermomechanical loadings applied to the voids during the forming operations. In fact, the impact of high effective strain level was identified by Lee et al. [1] as a factor promoting the void closure. The stress state applied during the forming process also has an impact on void
Corentin Pondaven, Benjamin Erzar
ABS Centre Métallurgique, France
Andrea Spadaccini, Matteo Grion
Acciaierie Bertoli Safau (ABS), Italy
closure. The lower the negative triaxiality ratio depicting a compressive state is, the faster is the void closure as identified by Saby et al. [2]. The closure kinetics is also in relation with the initial dimensions and orientations of the cavity regarding the loading orientations as identified by Chen and Lin [4]. The authors therefore defined a void
shape factor to describe the void geometry and study its impact on void evolution. This defined shape factor is presented in equation (1), where Si is the shape factor in the i direction of loading (x, y or z), Dx, Dy and D z are respectively the projected dimensions of the pore in the x, y and z direction.
To evaluate the capacity of void closure of a forming process, Tanaka et al. [5] proposed the hydrostatic integration defined in equation (2) as an indicator of void closu-
re. In this equation, Tx is the triaxiality defined by the ratio of the mean stress over the equivalent stress and ε eq is the equivalent strain.
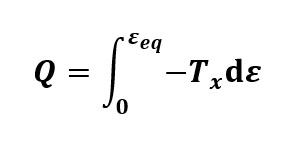

Using this indicator, Kakimoto et al. [3] defined a threshold value of Q ≥ 0.21 to observe the complete closure of porosity during a single pass process. Concerning multi-pass processes, a threshold of 0.85 is proposed by Kukuryk [6] to observe the closure with an alternation of forming direction. This difference of thresholds highlights the limitations of this kind of criterion that must be linked with the specificity of the studied metal forming route. More advanced criterion integrates void aspect ratio and dimensions to predict the final evolution of the voids as the Cicaporo criterion proposed by Saby et al. [7]. This criterion is, however, not able to model the pore evolution on forming processes including several directions of loading.
To overcome these limitations, simulations with explicitly modeled void can be performed to study their closure during the forming process. The difference of scale between the formed products, with initial cross section about one meter, and the internal pores, with initial dimensions about ten millimeters, imposes to perform this type of simulation using scale transition with Representative Volume Elements (RVE) using the thermomechanical loading of the full-scale process as boundary conditions.
In the present study, the closure behavior of a single spherical void with an initial diameter of 10 mm located
in the center of a bloom section is studied using a fullfield approach in simulations. The pore evolution of the explicitly modeled pore is studied during a rolling sequence performed on the Rotoforgia mill of ABS in Italy. The sequence is composed of eight rolling pass presenting alternating direction of forming to reduce an initial round bloom with a diameter of 750 mm to a round section of approximately 440 mm. The results of the fullfield simulations are then faced with the observed Q value of each pass to evaluate the capacity of this criterion to estimate the pore closure during the selected rolling sequence.
METHODS
All the simulations presented in the current study are done using the Forge NxT 3.2 software developed by Transvalor. The steel studied is a 35CrMo4 steel modeled by a Hensel-Spittel law.
The studied rolling sequence is firstly modeled using a full-scale 3D simulation model. The thermomechanical loadings experienced by the center of the bloom are then extracted from the full-scale model using a sensor. They are then applied as boundary conditions on RVE containing a single pore to model the evolution of the cavity during each rolling pass explicitly. The temperature is imposed overall the RVE to follow the temperature loss observed on the full-scale model. The mechanical
loadings are reproduced using the boundary conditions definition described by Li et al. [8]. It means that in the first hand, the displacements are imposed in the transverse direction of rolling, y and z direction, corresponding to the direction of rolling loads. The stress is, on the other hand,
imposed on the face perpendicular to the longitudinal rolling direction x, the direction of the bar elongation. The initial RVE containing a single spherical pore is presented in Fig. 1 with a schematic representation of the boundary conditions used in simulations.

The RVE dimensions are initially of 40x40x40 mm3 to obtain RVE dimensions of at least three times larger than the pore dimensions in all directions as defined by Saby et al. [2]. After each pass, the volume and the projected dimensions of the void are extracted. The pore evolution is thus evaluated by the calculation of the ratio of its current volume over its initial volume. The geometry is then integrated into a new RVE with parallelepiped shape suited to the new dimensions of the void to apply the loadings of the following pass.
The full-field model provides thus information on the thermomechanical fields and allows the evaluation of post process criteria such as Q whereas simulations with RVE provide the explicit evolution of the void.
RESULTS AND DISCUSSION
Void evolution results
The evolution of the volume ratio of the single pore during the rolling sequence is presented in Fig. 2. The volume ratio evolution is depicted using disk marks and is showing an advanced closure of the void after the fifth pass of rolling.
Concerning the evolution per pass depicted using the bar diagram, one can notice the effect of the change of the loading direction, materialized by the dashed lines on the Fig. 2, by the observations on void volume ratio per pass higher than one for the third pass which follow a loading direction modification.

Void evolution associated with the hydrostatic integration
The void volume ratio per pass obtained using the RVE simulation is plotted in Fig. 3 with the corresponding Q amplitude observed per rolling pass on the full-scale model. On the global rolling sequence, one can note that the overall hydrostatic integration value is Q = 0.42 and especially Q = 0.26 after the fifth pass where the initial void
is presenting an advanced state of closure.
Concerning the Q amplitude and the void volume ratio per pass, high values of Q amplitude are observed for the pass P2, P4 and P5 which respective value of 0.08, 0.07 and 0.1. The corresponding void volume ratio are 0.4, 0.9 and 0.02. Other high Q values are observed for P6 and P7 with respective value of 0.09 and 0.07.
Fig.3 - Hydrostatic integration amplitude per pass during the rolling sequence and void volume evolution per pass
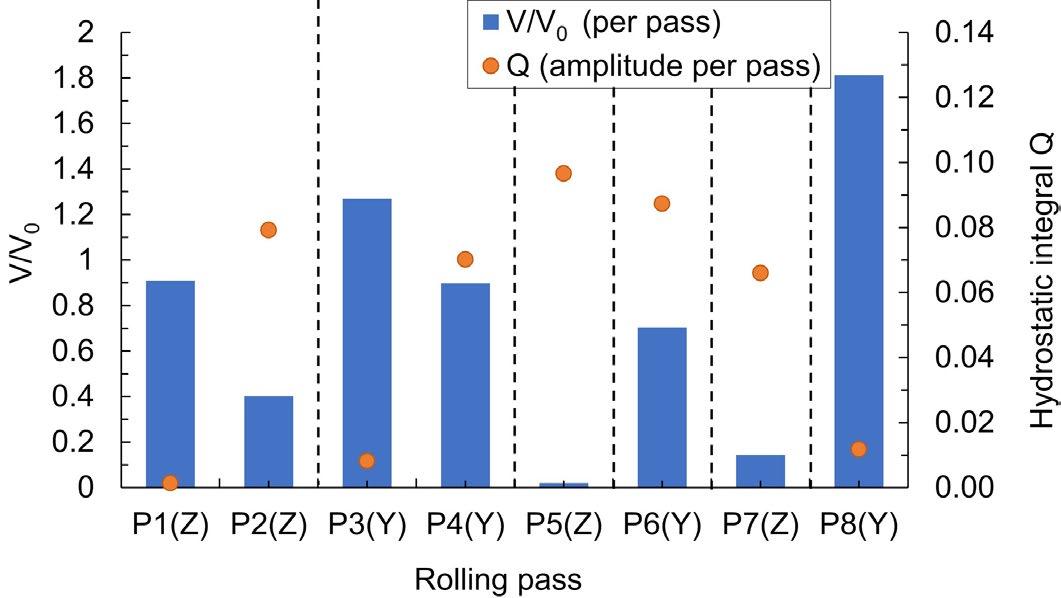
DISCUSSION
The results presented in Fig. 3 highlight the lack of correlation between high Q amplitude observed during a rolling pass and the corresponding void reduction ratio. This observation is especially significant for the second and the fourth pass of rolling which are presenting similar Q amplitudes and are performed after a rolling pass using the same loading direction.
Concerning this aspect, the analysis of the shape factors of the void given by the Fig. 4 a) could provide an explanation for these discrepancies. In fact, the shape factor of the pore in the loading direction is more favorable for the second pass with a value of 0.65 in comparison with the shape factor of 1.24 for the fourth pass which is depicting an elongated void in the forming direction. The stronger impact of the shape of the pore over the applied thermomechanical loading is also confirmed by the correlation diagram presented in Fig. 4 b). On this figure, the eighth pass is omitted given the advanced state of closure of the void after this pass which makes
the results non-interpretable given the residual cavity dimensions are approaching the meshing size. Regarding the other passes, a good correlation is observed between the volume reduction ratio per pass and the initial shape factor before each pass. The hydrostatic integration depicted by the areas of the disks is rather unrelated to the observed void volume reduction ratio per pass. This finding confirms the strong impact of the void shape on the closure phenomenon and confirms the interest of integrating these parameters in mean-field models.
This strong dependence to the shape factor is also highlighting that the analysis of void evolution by only regarding the Q value is insufficient for comparing two similar rolling routes in terms of porosity closure capacity especially for multi-pass processes. In fact, each modification of the loading (roll gaps, initial temperature gradient in blooms …) will affect the final shape of the void and thus its shape factor which will be modifying its closure behavior on the following passes for the same initial void. Analysis using the Q factor are therefore only appropriate for comparing two single pass processes using identical initial pores.
Eventually, the overall Q needed to obtain an advanced closure of the void during the selected rolling sequence using the VER approach, Q = 0.26 after the fifth pass, this value is way inferior of the threshold of 0.85 observed in the literature for multi-pass forming process. One can nevertheless note that this result is obtained with a simple spherical void and it may not totally represent the complexity of real pores closure with tortuosity. This observation still highlights the too conservative aspect of the threshold value of Q to evaluate the void closure. The application of this method needs in fact to identify a specific threshold for each studied forming routes with multiple initial void geometries. This use of this factor alone is thus not well suited for industrial applications because of its limited possibility of generalization.
SUMMARY
In the present paper, a methodology is described to explicitly model the evolution of shrinkage porosity during an industrial rolling pass using simulation. This methodology is then applied to evaluate the capacity of a simple mean-field indicator to evaluate the closure of a void and emphasize the limited information provided by the hydrostatic integration during multistage forming process even for comparing rolling routes with minor modifications.
This study highlights the interest of the method to validate mean-field criteria in a context of an industrial forming process. As a perspective, this kind of approach could be considered to analyze the evolution of real pore geometries from microtomography to integrate the tortuosity aspects of the defects and improve the understanding of the pore closure phenomenon during the rolling of long products.
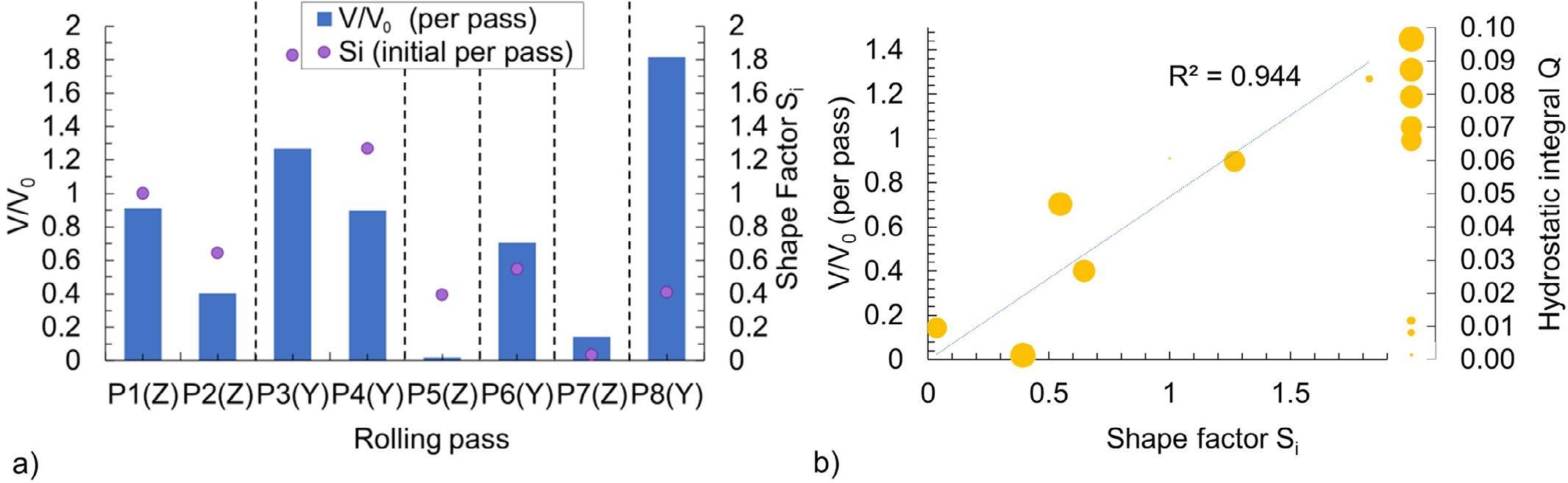
REFERENCES
[1] Lee YS, Lee SU, Van Tyne CJ, Joo BD, Moon YH. Internal void closure during the forging of large cast ingots using a simulation approach. J Mater Process Technol 2011;211:1136–45. https://doi.org/10.1016/j.jmatprotec.2011.01.017.
[2] Saby M, Bernacki M, Roux E, Bouchard P-O. Three-dimensional analysis of real void closure at the meso-scale during hot metal forming processes. Comput Mater Sci 2013;77:194–201. https://doi.org/10.1016/j.commatsci.2013.05.002
[3] Kakimoto H, Arikawa T, Takahashi Y, Tanaka T, Imaida Y. Development of forging process design to close internal voids. J Mater Process Technol 2010;210:415–22. https://doi.org/10.1016/j.jmatprotec.2009.09.022.
[4] Chen M-S, Lin YC. Numerical simulation and experimental verification of void evolution inside large forgings during hot working. Int J Plast 2013;49:53–70. https://doi.org/10.1016/j.ijplas.2013.02.017
[5] Tanaka M, Ono S, Tsuneno M. Factors contributing to crushing of voids during forging. J Jpn Soc Technol Plast 1986;27:927–34.
[6] Kukuryk M. Experimental and FEM analysis of void closure in the hot cogging process of tool steel. Metals 2019;9. https://doi. org/10.3390/met9050538
[7] Saby M, Bouchard P-O, Bernacki M. A geometry-dependent model for void closure in hot metal forming. Finite Elem Anal Des 2015;105:63–78. https://doi.org/10.1016/j.finel.2015.07.003.
[8] Li X, Liebsch C, Hirt G, Lohmar J. Modelling of void healing in hot rolling due to recrystallization. Prod Eng 2020;14:43–52. https://doi. org/10.1007/s11740-019-00938-8
Automated groove pass (pre-)design and optimisation of symmetrical and asymmetrical wires and profiles
edited by: M. Stirl, C. Renzing, M. Weiner, M. Schmidtchen, U. PrahlTo understand the material flow and behaviour during the production of shaped wires different simulation approaches like the finite element method or the pillar theory [1-2] are available, the latter ones enables optimisation routines due to high accuracy and geometric flexibility at low computing speeds. Semi-automated optimisation programmes of the groove pass can only map the forward calculation process - the upstream backward design with an initial pass sequence is carried out using empirical manufacturing rules [3-5]. A numerical description of the groove contour is necessary and complicated due to the high number of degrees of freedom of the groove geometry. Within this work, model approaches for automated groove pass (pre-)design and optimisation are demonstrated. Based on rolling tests carried out in breakdown passes as well as selected asymmetrical shaped profiles, correlations have been investigated to obtain an automatic backward calculation and groove pass predesign. Mathematical design guidelines as well as different target intervals of relevant degrees of freedom, e.g. coefficient of elongation, their distributions and geometric values of the respective profiles, are derived which are used as boundary conditions for subsequent optimisation procedures. The challenges which arise due to the asymmetry of the profile contour are presented and considered for shape profiles. The methodology is shown by breakdown passes as well as for Z-profiles, whereby the approach can be transferred to other profiles.
KEYWORDS: ROD ROLLING, SIMULATION, GROOVE PASS DESIGN, COLD ROLLING, GEOMETRY MODEL, PYROLL
INTRODUCTION
The production of profile rod and wire is carried out by hot and cold groove rolling. In contrast to flat rolling there are additional challenges in the design of pass schedules for profile rolling due to the more complex geometric conditions in the roll gap which can only be solved at great expense without simulations. The classical process of groove pass design and pass schedule of irregular profiles is shown in figure 1. It can divide into two major phases: backward design (calculating from final shape to starting shape) and forward calculation (from starting shape to final shape). The steps of forward calculation are mainly addressed in common simulation approaches and programs (e.g. FEM-programs, PyRolL, MPC) and always presuppose an existing groove shape drawing which results from the previous backward design. Depending on the shape of the profile, there are various empirical rules and approaches for groove pass design to create the backward design mostly given as optimal parameter ran-
ge. Examples for those approaches can be found for breakdown passes [7, 8, 9], angle profiles [10, 11], T-profiles [12, 13] or Z-profiles [14, 15]. Caused by the high individual effort needed to get the backward design (e.g. choice of initial values for degree of elongation, their distribution, groove types, geometric constrains) a direct integration of the backward design into the common simulation programs of groove rolling is challenging. Furthermore, due to numerical optimization calculations a complete numerical description of the shape contour is necessary which complements the design guidelines. Likewise, target intervals of relevant degrees of freedom, for example for the degree of elongation, their distributions as well as other
geometric quantities of the respective profiles, are necessary for an optimization calculation. Although there are some efforts to semi-automated groove pass design and mapping of these steps with computer-aided systems, these are limited to restricted, rigid groove types [3, 4]. Within this paper, some aspects for an automated backward design are presented on the example of breakdown passes and irregular profiles. A fast, parametric geometry model is developed and the backward design is based on the degrees of elongation regarding information on their value and distribution.
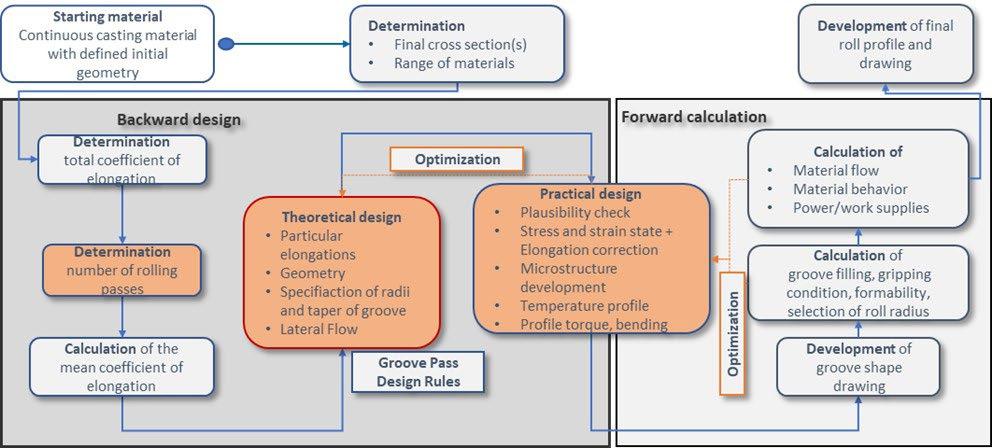
METHODOLOGY
In general, the backward design of groove rolling is characterized by some specifications noticed in figure 1. The final and starting geometry are crucial to know, moreover the material selection is needed as well as some basic information about the maximum possible degree of elongation λ , the distribution of λ over the rolling passes and the number of rolling passes. The backward design in general is strongly orientated on the degree of elongation, the total coefficient of elongation λ tot is defined by the initial and final cross-sectional areas or by the partial coefficient of elongations of the individual rolling passes.
(1)
With this information, the following basic steps can be down:
• Calculation of the end profile and their geometry, which is mostly given with its area and basic geometric sizes. A general profile contour with a parametrized geometry model is necessary.
• Calculation of the cross-sectional areas from the final profile back to the previous rolling passes due to knowledge of the λ n and their distribution.
• Determination of the intermediate profile contours up to the initial profile on the basis of experimental data.
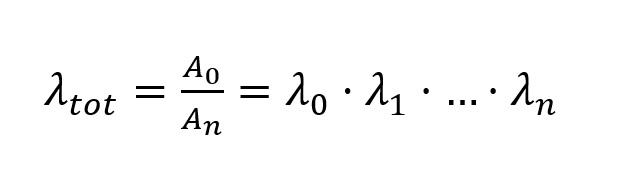
With the numerical depiction of these three steps an automated theoretical design is possible. Characteristic geometric parameters as well as requirements regarding the properties to be achieved are given as specifications for the profile to be produced. The results are an initial groove pass design and geometrical constraints due to the analysis of the experimental data. In addition, properties can already be specified here which, for example, are to be achieved by mandatory standard specifications. In the area of cold rolling this can be the strength, which is influenced by the material selection and the respective strain. These parameters can be used to calculate the strength.

APPLICATION ON BREAKDOWN PASSES
The design of breakdown passes has been addressed due to the use of regular and simple complicated groove forms and the symmetry that prevails with them by various authors [3, 4, 7, 12]. In addition to basic design guidelines,
e.g. for the choice of individual groove geometries and the degrees of stretching as well as their distribution over the rolling passes, investigations are known. Furthermore, there are various simulation programs that allow an automated design of a backward calibration. The CARD program from Körmer [4] is worth mentioning. Moreover, several authors [15-17] developed parametrized geometry models for breakdown passes. The profile contour in this model is achieved by the interrelationships of the geometric sub-elements and is based on the free variables bkn, bd, bd , d,
. Furthermore, various boundary conditions are given, which apply to these parameters as a result of achieving geometrically meaningful solutions. The advantage compared to a simple representation, e.g. by splines, is that individual limit values are clearly defined, which leads to variants that make sense from a rolling technology point of view.
APPLICATION ON Z-PROFILES
Z-profiles are complicated irregular profiles which are mainly used in rope production [18]. The rolling process is based on a round wire, which is cold formed into the final shape by groove rolling or drawing rolls. The groove pass design of Krautmacher [13] is generally used as a basis which allows production in four passes on the basis of empirical rolling tests. An industrial data set was generated in order to obtain a general geometry model for the profile contour and knowledge about the coefficient of elongation and its distribution over
the rolling passes. The characteristic values of the head width K, the waist width N, the foot width F as well as the outer radius R1 and the profile height H specified by DIN EN 10264 were examined. For the final profile contour, the centre of the coordinate system is determined by R1, which marks the centre of the final rope. In addition, characteristic measures for the intermediate profiles with profile heights h1 to h6 were investigated which were used for backward calculation from the final contour to the previous rolling passes. The point of view for that former passes varies from the final profile. The profile
height h is the sum of h1 and h6 and takes the maximum dimensions of the profile together with the profile breath b. Through nine arcs and three straight lines and their transition points a clear definition of the end profile can be made. Geometric constraints are to be defined at the transition points P01 to P13 in order to obtain geometrically reasonable solutions. Furthermore, boundary conditions result from the circle and straight line equations. These are used to create linear equation systems to get the x and y coordinates of the finale contour. This results in nonlinear systems of equations which are solved by applying appropriate optimization algorithm. Due to the circular equations there are multiple solutions when solving the systems of linear equations. In order to determine the correct solution in each case, the relative position of the coordinates to already known ones is considered. As an example, the value of the x-coordinate of P05 must be between
(a)
the value of P03 and P01 (fig. 3). The y-coordinate has to be lower than the y-coordinate of P03 and greater than R1-2 Rn. These boundary conditions are used by an algorithm to determine the right solution of the circular equations.

In order to be able to calculate back to the previous cross-sectional areas, the coefficient of elongation of the individual partial areas are required. The total coefficient of elongation is calculated with equation 1 and determined using the rolling trails. The largest average coefficient of elongation in the first rolling pass with is 0.8, which is typical for shape profiles and reasonable due to the mass distribution with respect to the final shape to be achieved. These tendencies of distribution of coefficient of elongation can also be seen in other profile shapes. The extreme values can initially be seen as boundary conditions of the coefficient of elongation for an optimization procedure.
Fig.3 - a) generic geometric values of Z-Profiles for final and intermediate passes, b) contour of the final pass of Z-profile with geometric elements (dark blue: arcs, light blue: lines) and transition points (Pxx) and middle points of arcs (Mxx), c) pass schedule of Z-profiles oriented by Krautmacher [13].
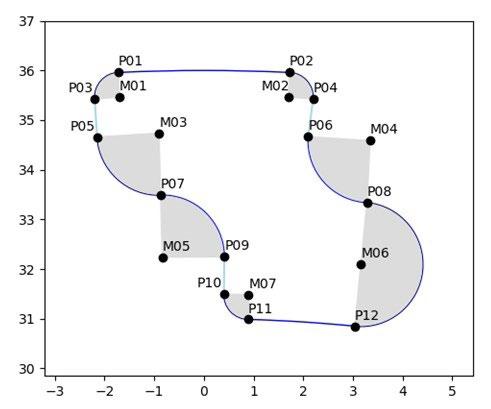
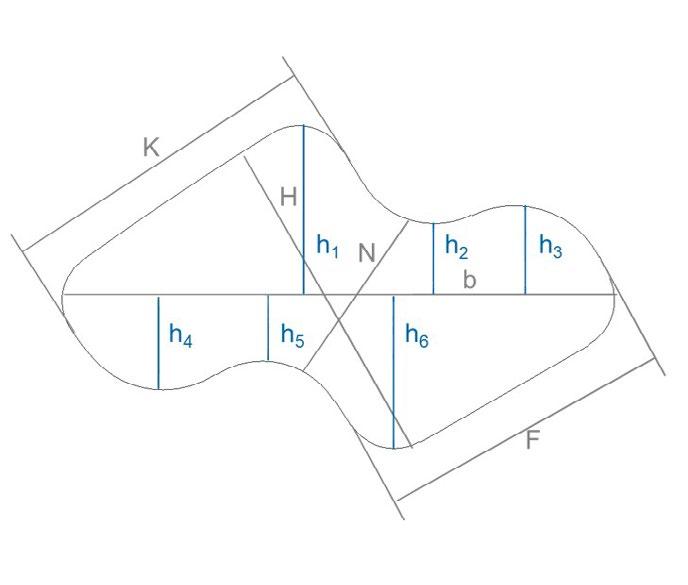
To obtain equivalent initial values for the other passes, the geometric quantities h1 to h6 estimate as a function of the final cross sectional-area, so that an estimate of the geometric quantities can be made for the respective determined profile area on the basis of the coefficient of elongation. Correlations could be established with regard to the geometric description of the profile contours as a function of the profile sizes by measuring the data set.
The initial round is described exclusively by the dimensions b and h, the first rolling pass requires only h1 and h6 as additional support points. h2 to h4 are mainly relevant for describing the construction at the tail which start to occur from the 2nd rolling pass. h2 and h5 become smaller with increasing number of passes since the web is formed out more and more. These correlation coefficients can be used to obtain a solution for backward design.

CONCLUSION AND OUTLOOK
Groove pass design of asymmetrical profile correlations with respect to the geometric design as well as the coefficient of elongation distributions are to be recognized for the necessary steps of the backward design. These can be made usable via sufficiently large test data sets and serve as a necessity to enable a complete numerical optimisation of existing groove passes with respect to material flow and material side criteria. For this purpose, a groove pass pre-design is requisite which is based on a parametric general geometry model for the respective profile shape as well as knowledge about the characteristics of the coefficient of elongation and their distribution over the rolling passes. A corresponding procedure for the design of the pass schedule has been carried out on the basis of the
design of Z-profiles. A transfer to other profile shapes can be realized with corresponding data sets. The theoretical prediction can then be used as starting solutions for further forward calculation simulations in order to optimize various process- and material-related properties. An implementation of the geometric profile generation as well as the steps of the backward design is for example possible in the PyRolL project. This can further be used for optimization procedures which require fast models for different process and material criteria such as material flow, microstructure or mechanical properties. The further development of such models, specific solution algorithms and the extension of the methodology, presented here to other profile shapes, will be addressed by future work.
REFERENCES
[1] M. Schmidtchen, F. Hoffmann, U. Prahl: Development of Fast Simulation Tools with Higher Modelling Depth for Improved Description of Local Material Flow, Stress State and Microstructure in Breakdown and Shaping Grooves, Kalibreur, 80 (27–40), 2020.
[2] M. Schmidtchen, U. Prahl: Status of developments in (fast simulation assisted) groove pass design for asymmetric profiles, Kalibreur, 81 (15–32), 2021.
[3] P. J. Mauk: Rechnergestütztes Kalibrieren, Diss., RWTH Aachen, 1983.
[4] A. Körmer: Modellierung von Streckkaliberreihen, Diss., TU Bergakademie Freiberg, 1987.
[5] H. Wehage: Beitrag zur rechnergestützten Erarbeitung von Projekten und Technologien für kontinuierliche Feinstahl- und Drahtstraßen, Diss., TU Bergakademie Freiberg, 1990.
[6] https://github.com/pyroll-project
[7] Z. Wusatowski. Grundlagen des Walzens. Leipzig: VEB Deutscher Verlag für Grundstoffindustrie, 1963.
[8] A. E. Lendl. “Rolled Bars - Part II - Application of Spread Calculation to Pass Design”. In: Iron and Steel 21.14 (1948), pp. 601–604. ISSN: 0021-1532.
[9] W. K. Smirnov, V. A. Schilov, and J. W. Inatovic. Kalibrierung von Walzen: Lehrbuch für Studierende der Metallurgie an Hochschulen. kyr. Moskau: Teplotechnik, 2010.
[10] B. P. Bachtinov and M. M. Schternov. “Kalibrierung von Walzen”. kyr. In: Metallurgisdat (1953).
[11] I. W. Litowtschenko, B. B. Biomidow, and W. A. Kurdjumowa. “Kalibrowka walkow sortowick stanow (Walzenkalibrierung von Sortenstahl)”. kyr. In: Metallurgisdat (1963).
[12] H. Neumann. Kalibrieren von Walzen. 2nd ed. Leipzig: VEB Deutscher Verlag für Grundstoffindustrie, 1975.
[13] H. Krautmacher. “Das Kaltwalzen und Ziehen von hochfesten profilierten Seildrähten”. In: Neue Hütte 76.17 (1956), pp. 1085–1099.
[14] M. Schmidtchen and U. Prahl. “Status of developments in (fast simulation assisted) groove pass design for asymmetric profiles”. In: Der Kalibreur 81 (2021), pp. 15–32. issn: 0022-796X.
[15] B. Huang, K. Xing, K. Huang, und H. Lan, „Development of a geometric modelling strategy for roll pass optimal design“, Robot. Comput.-Integr. Manuf., Bd. 30, S. 622–628, 2014.
[16] J. Betshammer, „Improved Billet Shape Modeling in Optimization of the Hot Rod and Wire Rolling Process“, candthesis, Linköpings university, 2006.
[17] K. Huang, B. Huang, L. Fu, und K. Abhary, „Towards Energy Efficient Shape Rolling: Roll Pass Optimal Design and Case Studies“, Chin. J. Mech. Eng., Bd. 32, Nr. 1, S. 1–11, 2019.
[18] R. Aschauer. “Verfahren zum Herstellen d¨unner Profildr¨ahte”. In: Draht-Welt 66.12 (1980), pp. 496–498.
Sophisticated and advanced plant and process technologies in steel and nonferrous rolling mills
edited by: M. Degner, M. Breuer, A. Sprock, C. Hassel, O. Jepsen, M. Quoika, A. BreganteKey factors in the effective operation of rolling mills, now and over recent years in particular, are yield, economy, and sustainability. This applies not only to the erection of new rolling plants but also to the modernization and modification of existing mills. By illustrating some examples of projects completed by SMS group GmbH in the past few years, this paper demonstrates the highly advanced tools used to ensure a smooth ramp up that take sustainability and resource efficiency into consideration while minimizing the CAPEX and OPEX. Nowadays, such tools include methods of process and plant documentation, such as Thoroughgoing Quality Control as well as the latest measuring and control techniques and knowledge regarding material and deformation behaviors. The transfer of experience and knowledge between the customer and seller is essential for solving the tremendous challenges posed by these tasks.
KEYWORDS: MEASURING AND CONTROL TECHNIQUES, STEEL ROLLING MILL, NON FERROUS ROLLING, THOROUGHGOING QUALITY CONTROL, CAPEX AND OPEX FIGURES, EDUCATION
INTRODUCTION
The current economic situation in the steel producing industry is characterized by high overcapacity worldwide. One major reason for this is steel overcapacity in China and the lower demand for steel in sectors such as shipbuilding, thermal power plants, infrastructure, and the automotive industry [1]. There were two exceptional growth periods, one after the Second World War and one described as the Chinese steel boom starting in the late 1990s. However, the higher volume of exports compared to imports, especially in China, led to a downturn, Fig. 1. Looking at the market in detail, the side effects of this are obvious: a return to economic growth during the COVID-19 pandemic. Today in 2022, the Ukraine war in Europe and the Taiwan crisis in Asia are fragmenting the world with rapid increases in food and gas prices, among other things.
Although rolling technology has been around for a long time, there is always good reason for updating the machinery and equipment, either due to new concepts, such as quality improvements (stability, thickness, tolerances etc.), or the constant demand for cost and energy efficiency, or developments in IT technology, e.g. Industry 4.0. This paper highlights some examples of best practice in former and current SMS group activities based on research and documentation. The rules given can be transferred to non-ferrous products and mills.
PREDICTIVE PROCESS CONTROL
In the past, several digital twins of the rolling process were developed by SMS group GmbH [2]. In terms of hot rolling, important models include
• Furnace model DFC (Dynamic Furnace Control): Heating the slabs, calculating the temperature increase to ensure a uniform temperature
• Rolling mill model X-Pact® Pass Schedule Calculation

(PSC): Predicting roll forces, speeds, times, and setup for the mill actuators, adaptation cycles etc.
• Cooling section model CSC (Cooling Section Control): Calculating water volumes, making adjustments to ensure the required coiling temperatures
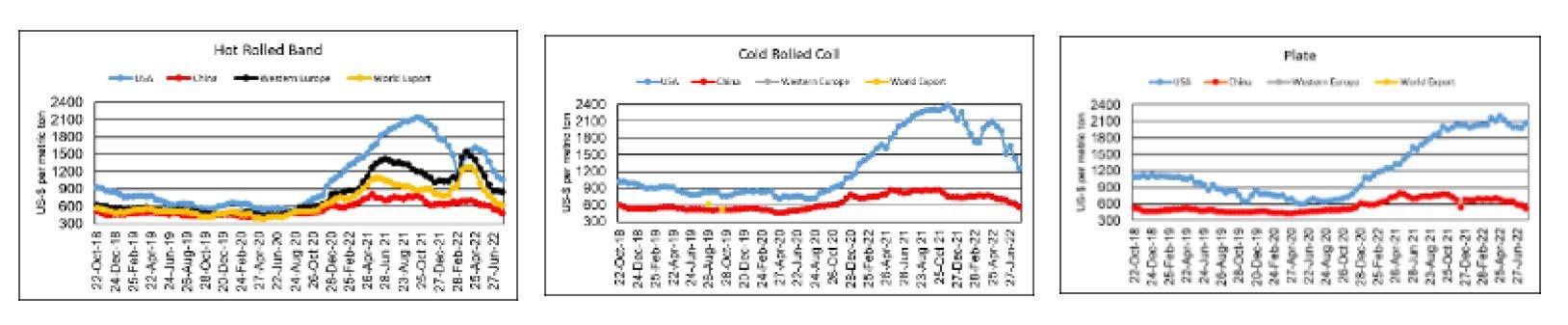
The task of these models – located on level 2 – was primarily to predict and set up the mill actuators, roll forces and torques, speeds, cooling water volumes etc. based on physical laws and measurements, such as temperatures, in order to achieve the requisite process targets including thickness, profile, and final rolling and coiling temperatures. These models were equipped with adaptation routines to recalculate the observed process conditions as closely as possible. Together with technological control systems – located in Level 1 – the process can be controlled effectively and precisely, Fig 2, [2].
With this knowledge of all the process conditions, material science models were added, Fig. 3:
• Furnace model: calculation of the segregation of alloying elements
• Rolling mill model PSC: calculation of grain sizes, recrystallization, and work hardening (micro alloyed
steel), grain size development during rolling, phase transformation
• Cooling section model CSC: phase transformation, specific heats, phase composition, mechanical properties such as yield and tensile strength of final strip
The task of predictive process control is to retain the mechanical properties of the strip by changing the process.
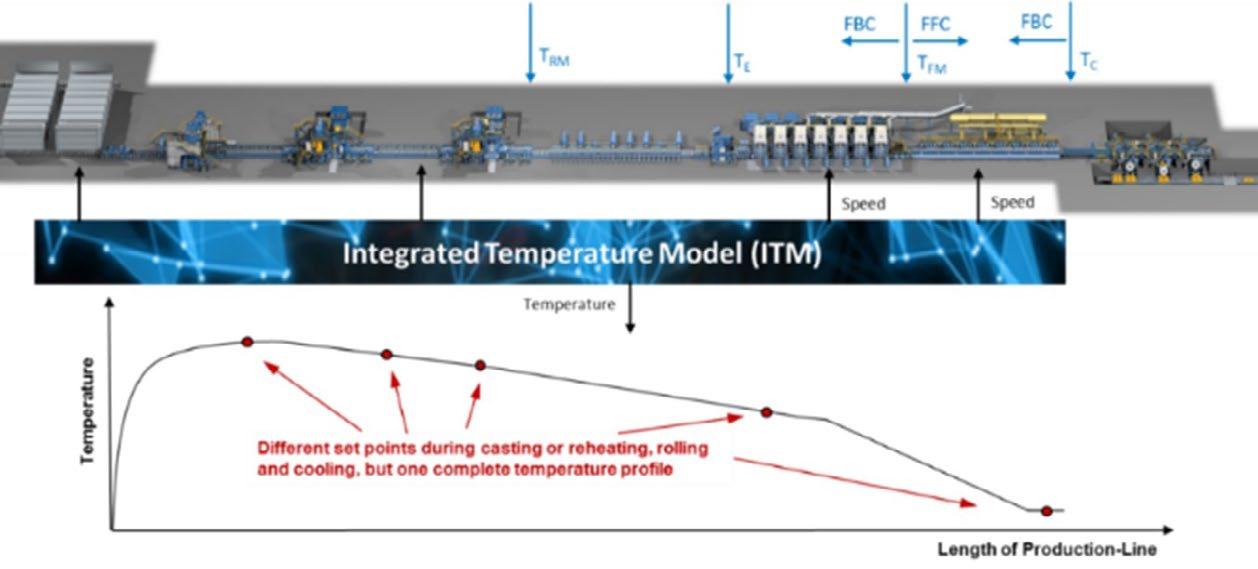
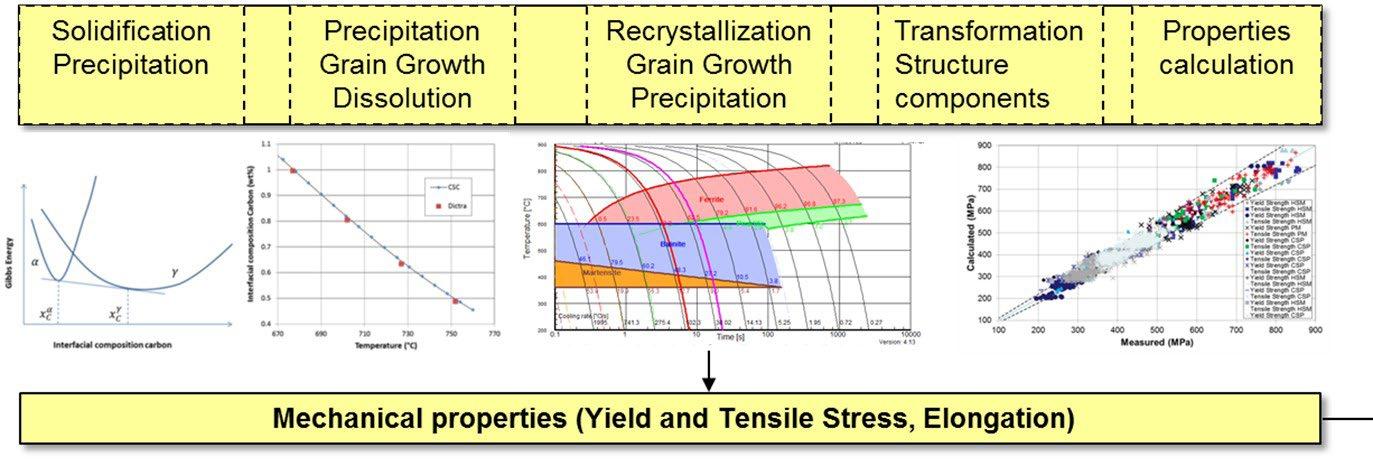
The first step in developing this was to exchange important data between the different models using traditional communication methods. Each digital twin received the necessary data from the other model.
For example, the performance of the cooling line is directly linked to the final rolling speed and the final rolling temperature of the strip. Direct communication between PSC and CSC models provides these speed-temperature data and enables the correct setup of the cooling line, Fig. 4 left. The controller of the cooling line is disburdened and has only needs to react on small process disturbances.
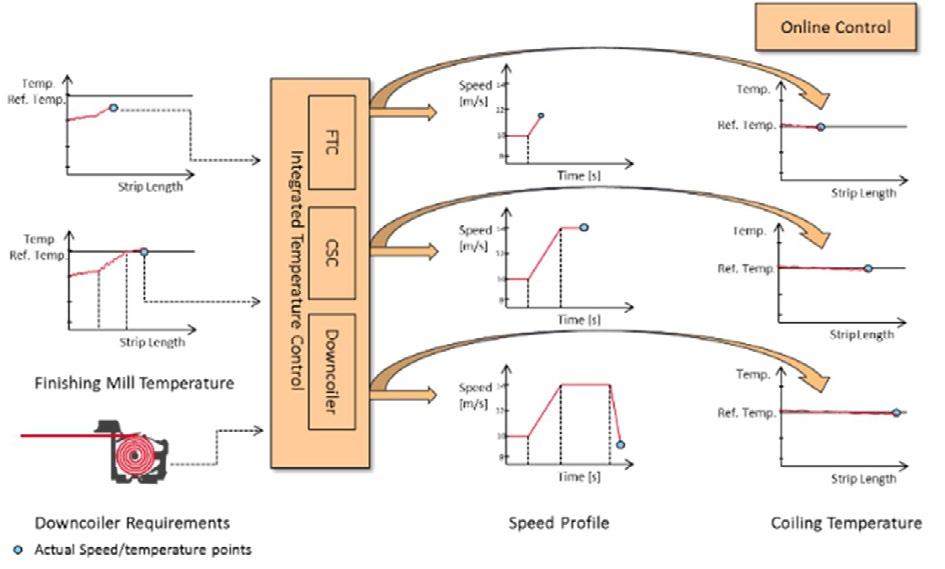
The second step is to establish a new optimization process covering the individual digital twins, Fig. 4 right. The goal of the system is to achieve the required mechanical properties of the strip:
- Based on an established process
- Actual changes to the process are fed back to the models and recalculated
- Changes to mechanical properties are evaluated
- Models modify the process conditions to evaluate the impact of each process step
- Predictive process control collects these data and corrects the process step(s).
- This is repeated until the target mechanical properties are achieved
- A new setup is generated for the process with modified targets for the individual process values
These changes in the process conditions also bring about changes in the process control targets. The cooling rate or final coiling temperature may differ from the original process design. A system of providing feedback to the Quality Execution System QES must be established in order to transfer the new rule parameters, Fig. 5.
The ITM “optimizer” is designed to work out recommendations for process changes. It is an assistance system for our customers to ensure product quality and increase yield. Other objectives are conceivable:
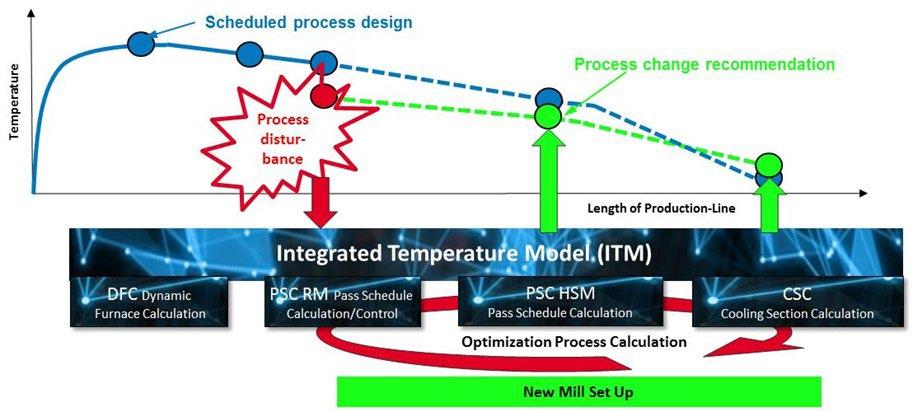
- Production capacity maximization
- Low energy consumption
- Low water consumption
- Reduction in costs for chemical composition
- Resource savings in total
An application is reported in [3].
CUTTING EDGE TECHNOLOGY FOR HSM – STRIP STEERING CONTROL
The stability of the hot strip mill rolling process remains a major topic when it comes to processing thin and hard materials. Strip steering problems, especially at the end of rolling, and tail-out are a primary source of unscheduled down times in a hot strip mill. The main focus of the new X-Roll® Guide system is to improve mill stability and strip quality. An overview of SMS group developments in recent
years with regard to equipment and control strategies is given below, Fig. 6 left [4]. The new side guiding system in the entry area of the finishing mill is introduced and explained with examples of operating practice. The system provides reproducible conditions for the threading process as well as during rolling. Steering control directly benefits the availability of the mill. New developments in roll alignment control strategies based on the roll force and mill stand entry guide force measurement [4] have improved steering control performance.
Additionally, a camera-based measuring system is introduced that generates direct process feedback on the strip position. Together with the roll alignment control, it provides the necessary control parameters for adjusting the roll gap and guiding the strip in a correctly centered position through the mill. In the area of the down coiler, the coiling stability and quality, including the optimal coil shape, is controlled with the side guides and, in the case of high-strength material in particular, with the hydraulically-driven chute roll [4].
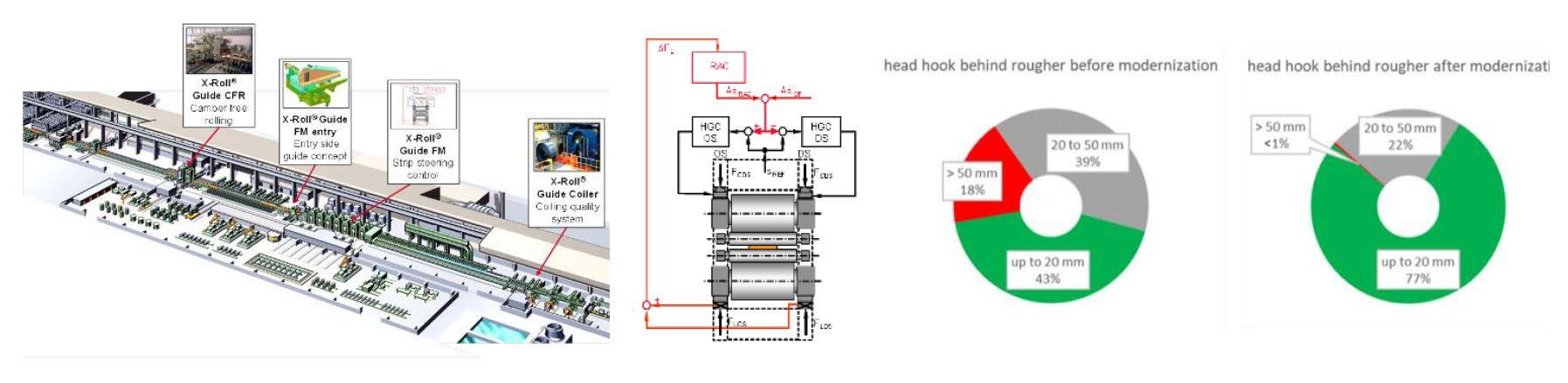
The new X-Roll® Guide system is the next step in digitalization aimed at achieving a fully automatic rolling process. It comprises SMS group’s holistic approach to improving hot strip mill rolling stability in all relevant stages of the process.
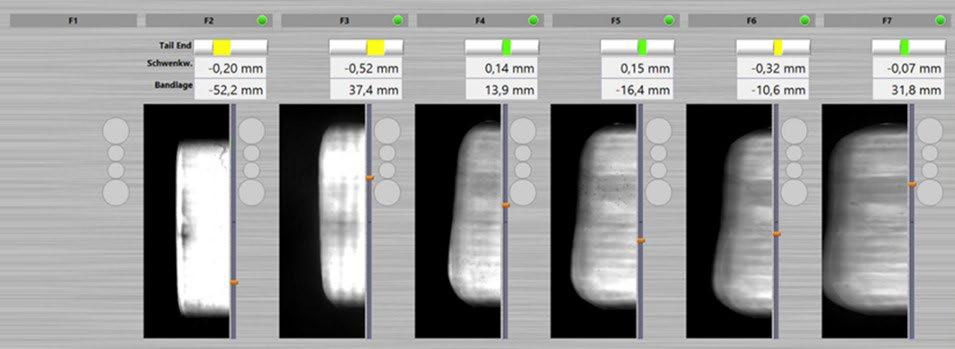
Different systems for controlling the strip steering developed by SMS group GmbH are highlighted [4, 5].

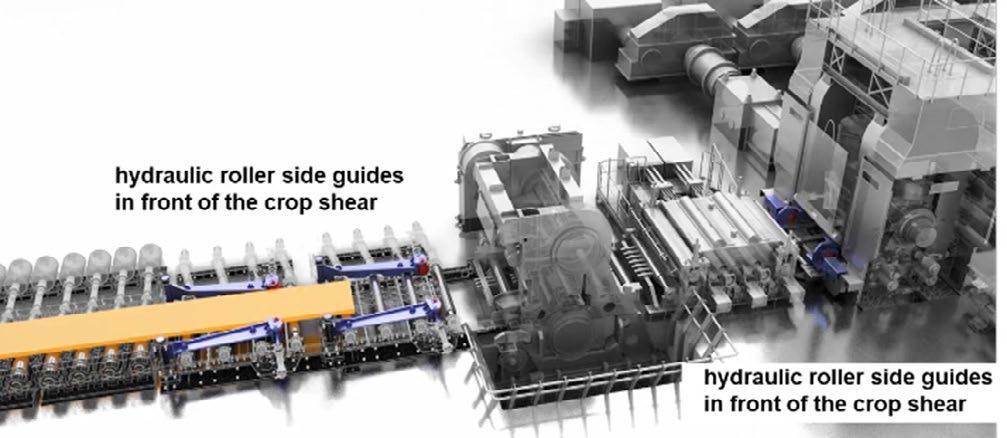
- Roughing mill: X-Roll® Guide Camber Free Rolling CFR
for rolling perfect transfer bar shapes and for reducing wedges, Fig. 6 center and Fig. 6 right
- Finishing mill entry: X-Roll® Guide FM entry; stabilizing the threading and fillet rolling process, Fig. 7
- Finishing mill area: X-Roll® Guide FM; stable threading and tail-out, reduction in torn strips and work roll damage, Fig. 8
- Down coiler area: X-Roll® Guide Coiler; straight coils with minimal telescopicity
All performance modules combine reliable mechanical actuators, sensors and automation systems with adequate control loops and tracking. These mechatronic systems are controlled and adapted with corresponding measuring devices. They can be added to an existing rolling plant as a whole unit or in packages. Each module has its own advantages and helps to increase a hot strip mill’s rolling stability and yield. The selection of the technology packages depends on preconditions like the
product mix, mill condition, or the automation standard used. Such systems also have to show an adequate return on investment. In a hot strip mill, the investment can be justified simply by the amount of torn strips, downgraded material, and the resulting work for roll changes, unscheduled down times, and roll grinding. Additional rolling time can be used to boost production capacity. The higher the volume of thin-gauge hot strip and hard material produced, the greater the benefits of the systems.
FUTURE ACTIVITIES AND CONCLUSIONS
The sophisticated hot rolling models developed in the last decades also include the development of microstructure models during rolling of the strip. Predictive process control is becoming a reality. Disturbances during the rolling process can be compensated to achieve the target strip properties or to change the target values. This avoid downgrades or additional property testing in the future. With the modules for strip steering, the operational performance of a hot strip mill can be gradually improved. Cobbles and torn strip ends can be reduced, and the coil
REFERENCES
quality and yield can be optimized. The combination of rigid and reliable equipment coupled with automation solutions creates a system that represents a huge leap forward in process control and safe rolling conditions. These systems will be developed further to meet the demanding requirements of future steel and non-ferrous products [1,6]. The next steps to be taken relate to performance optimization and connection coupling to level 3 systems, to allow fast responses in production planning and order change management.
[1] Buchmayr, B.( ), Montanuniversität Leoben, A-8700 Leoben, Austria; Degner, M., SMS group GmbH, Germany; Palkowski, H., TU Clausthal, Germany: Future challenges in the steel industry and consequences for rolling plant technologies, Proceedings ESTAD 2017, p. 61.

[2] Breuer, M. SMS group GmbH, Germany; Sprock, A., SMS group GmbH, Germany; Peretic, M., SMS group Inc. USA: Predictive Process Control – the next step to quality assurance. Report AISTECH 2019.
[3] Grybel, K., SMS group GmbH, Germany; Hassel, C. SMS group GmbH, Germany; Pronold, K. SMS group GmbH, Germany; Dickel, D., SMS group GmbH, Germany: Integrated Temperature Model for CSP® Nexus Plants for Superior Hot Strip Production. Report AISTECH 2022.
[4] Jepsen, O., SMS group GmbH, Germany¸ Mengel, C, SMS group GmbH, Germany¸ Breuer, M., SMS group GmbH, Germany: Cutting edge technology – Strip steering control. Report AISTECH 2022.
[5] Olaf Jepsen, Adolf Müller, Joachim Immekus, EP1896200B1, Process and device for intentionally influencing the geometry of roughed-down strips in a roughing-down stand
[6] F. Gorgels, O.N. Jepsen, P. Siemann, SMS group, Italy: X-Shape Hot - Flatness Measurement in hot rolling mills. 12th International ROLLING Conference – Trieste (Italy), 26-28 October 2022.
D acco aldo premio
L’AIM è lieta di indire il bando per l’edizione 2023 del prestigioso Premio Aldo Daccò, con l’obiettivo di stimolare i tecnici del settore e contribuire allo sviluppo e al progresso delle tecniche di fonderia e di solidificazione con memorie e studi originali.
L’Associazione invita tutti gli interessati a concorrere al Premio “Aldo Daccò” 2023, inviando a mezzo email il testo di memorie inerenti le tematiche fonderia e solidificazione, unitamente al curriculum vitae dell’autore concorrente, entro il 30 novembre 2023
Saranno presi in considerazione e valutati i lavori riguardanti le varie tematiche di fonderia e di solidificazione, sia nel campo delle leghe ferrose che in quello delle leghe e dei metalli non ferrosi.
Il premio, pari a Euro 5000 lordi, è offerto dalla Fondazione Aldo e Cele Daccò, istituita dalla signora Cele Daccò, recentemente scomparsa, per onorare la memoria del marito Aldo Daccò, uno dei soci fondatori dell’AIM e suo encomiabile Presidente per molti anni.
Le memorie verranno esaminate da una Commissione giudicatrice designata dal Consiglio Direttivo, il cui giudizio sarà insindacabile.
Nel giudicare, la Commissione terrà conto, in particolar modo, dell’originalità del lavoro e dell’argomento in relazione alla reale applicabilità dei risultati. Non sono ammesse candidature da chi abbia già ottenuto riconoscimenti, anche per lavori diversi, dalla Fondazione Aldo e Cele Daccò.
Le memorie premiate e quelle considerate meritevoli di segnalazione, potranno essere pubblicate sulla rivista La Metallurgia Italiana.
Il Premio verrà conferito in occasione dell’Assemblea dei Soci AIM, che si terrà a Milano nella primavera del 2024. La cerimonia di premiazione con la consegna della medaglia avrà luogo in occasione del 40° Convegno Nazionale AIM.
ORI Martin, il filo rosso dell’innovazione, della qualità e della sostenibilità
Dagli approfondimenti dell’archivio fotografico Pedrali
“Se la siderurgia del periodo precedente la Prima guerra mondiale è dunque caratterizzata dall’im¬piego del coke, negli anni del conflitto avrebbe preso piede una nuova tecnologia, quella del forno elettrico, che nel Bresciano conobbe le sperimentazioni decisive avviate a Darfo da Ernesto Stassano. Le potenzialità dell’impiego dell’energia elettrica nell’industria siderurgica, soprattutto nella realtà locale, venivano lucidamente sottolineate da Arnaldo Gnaga in occasione dell’Esposizione Provinciale del 1904: «poiché sembra quasi impossibile che noi possiamo per deficienza di combustibile competere economicamente con altri forni esteri che producono da 1.000 a 1.550 quintali di ghisa ogni 24 ore, il procedimento del forno elettrico rappresenta, nelle nostre condizioni, un trovato di altissima importanza economica. Esso ci permetterebbe di vincere la concorrenza nella qualità non potendo competere nella quantità; e però io mi auguro che il processo Stassano od altro consimile ci conceda presto di usufruire delle immense forze elettriche, che tuttora ci restano inoperose, non meno che dei minerali metallici, nostro ingente ma infruttifero
capitale».
A questo augurio, che forse sottovalutava l’impiego di rottame che il forno elettrico avrebbe indotto, si aggiungeva la speranza che il forno elettrico potesse assicurare la produzione di “acciai finissimi” o “speciali”, sempre più richiesti dall’industria meccanica e che «si ottengono ora – riferisce sempre Gnaga – per varie e costose trasformazioni delle ghise migliori, mentre il forno elettrico li può fornire con una sola fusione».”
È in questo contesto storico in cui prende vita il filo rosso conduttore che attraversa e unisce tutta la lunga, complessa affascinante vicenda industriale della Ori Martin attraverso quasi un secolo di storia. Una storia che può essere ricondotta l’acronimo ESG, sempre più conosciuto anche fuori dal mondo della finanza e della “sostenibilità”: Environmental (ambiente), Social, e Governance, si tratta di tre dimensioni fondamentali per verificare, misurare, controllare e sostenere l’impegno in termini di sostenibilità di una impresa o di una organizzazione. Dimensioni che ORI Martin fece sue con decenni di anticipo grazie ad una visione etica e lungimirante.
Un filo rosso che si dipana con due
nodi di partenza, distanziati tre decenni. Il primo, agli inizi del Novecento, è la nascita dell’azienda meccanica che assumerà poi il nome di Officine Riunite Italiane. Il secondo, a metà degli anni Trenta, è l’avvio dell’attività produttiva della Ferretti & Martin. Dall’intreccio di queste due realtà aziendali deriva infatti, attraverso un processo di crescita e trasformazione durato oltre mezzo secolo e tuttora aperto, l’attuale complesso industriale di S. Bartolomeo nella zona a nord di Brescia. Riavvolgendo il nastro tutto parte da un distinto ingegnere arrivato a Brescia dal Belgio, Oger Martin nato nel 1890 a Filot (Liegi). Nel 1911 arriva a Brescia come “esploratore” di nuovi mercati per una azienda armiera belga. Dopo vari successi professionali decide di avviare una attività in pro-
“Dal Maglio all ‘Internet of Things”Uggero De Miranda, Maurizio Zanforlin ORI Martin U. De Miranda, M. Zanforlin
AIM's companies - Le aziende di AIM
prio.
Prende corpo così, nel 1933, un’impresa congiunta la Ferretti & Martin dalle dimensioni inizialmente ridotte, due magli ad acqua, una quindicina di operai, sufficienti ad animare una significativa produzione di attrezzi agricoli, ricavati lavorando il ferro recuperato dal taglio di rotaie in disuso. Tre anni dopo, nel 1936 il raddoppio degli impianti con l’acquisto di un maglio con forno a nafta. Al maglio si affianca un primo piccolo laminatoio per trasformare il materiale preparato dal maglio. Durante la Seconda guerra mondiale il laminatoio viene smon-
tato e messo al sicuro e la produzione prosegue con zappe, picconi e badili, nella classica tradizione dei magli bresciani.
Nel 45, con la fine della guerra, inizia la ripresa economica e la rinascita sociale del paese, l’ampia disponibilità in quantità rilevanti e a basso costo, di materiali come rotaie, linee tramviarie, ordigni bellici, “code di porco” dei reticolati. Questa disponibilità di materia prima, genera la rincorsa a dotarsi di tecnologia per la trasformazione in prodotti commerciali.
Nel 46 parte un laminatoio a tre gabbie per lavorare il materiale preparato
dal maglio partendo da recuperi vari (rotaie, ordigni bellici, travi, …), nasce il tondo da cemento armato che diventerà il filone d’oro della siderurgia bresciana, trasformando la provincia di Brescia in un fenomeno internazionale noto come “The Bresciani”. Nel 1950 in ORI Martin si installa il primo forno elettrico da tre tonnellate, da cui si ricavano lingottini tondi da 25-30kg. Nel 1956 si installa un nuovo forno da 12 tonnellate e un nuovo impianto di laminazione con forno di riscaldo a metano.
Il nuovo laminatoio era costituito da sette gabbie con “serpentaggio” del filo, operazione che veniva eseguita a mano dagli operai detti “serpentatori”. Nel 1961 arriva il terzo forno elettrico nei nuovi capannoni; si tratta di un forno elettrico da 35 tonnellate della TiBB (Tecnomasio Italia Brown
Boveri), il più grande e moderno forno prodotto in Italia in quel periodo. Nel 1962 le Officine Riunite Italiane (O.R.I.) società per azioni, diventano “O.R.I. Martin (Officine Riunite Italiane, acciaieria e ferriera di Brescia) S.p.A. in ricordo del fondatore mancato nel 1961.

A partire dagli anni Sessanta ORI Martin diversifica la sua produzione affiancando al tondo da cemento armato, la produzione di vergella di qualità in rotoli.
Nel 1965 compare negli stabilimenti di San Bartolomeo a Brescia la prima colata continua con lingottiera curva.
In quel periodo anche un’altra società lombarda del settore, la “Riva” nata nel 1954 a Caronno Pertusella (Va), sperimenta la colata continua. Ma pur accumunate dalla capacità di guardare oltre il contingente e di scommettere su una innovazione tutta da verificare, ORI Martin S.p.A. e Riva si differenziano nella scelta dei progettisti e costruttori a cui affidarsi e ne
tempi e nelle modalità di utilizzo dei nuovi impianti. Mentre Riva sceglie come fornitrice la Danieli di Buttrio (Ud) che ha iniziato la propria attività a Brescia per poi migrare in Friuli. ORI Martin S.p.A. punta sulla società svizzere Concast di Zurigo. Inoltre, mentre nell’avvio sperimentale degli impianti la Riva anticipa di un anno la ORI Martin, la prima colata avviene a
Caronno nel giugno 1964 e nel settembre 1965 la prima colata a S. Bartolomeo; l’azienda bresciana anticipa quella varesina nella messa a regime e quindi nell’utilizzo totale dei nuovi impianti.
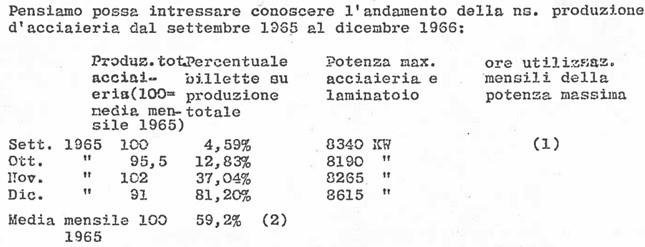
Da “un anno di esercizio della colata continua alla O.R.I. Martin S.p.A.”:
Nel giro di pochi anni sono 18 le società siderurgiche, per lo più bresciane, che imitano la ORI Martin. Tra le diciotto i colossi “Falk” e “Italsider”. Ma il magico “filo rosso” dell’innovazione, oltre agli impianti produttivi tocca anche la qualità del prodotto colato e per garantire livelli qualitativi sempre più elevati, ORI Martin è la prima a dotarsi di uno spettrometro in grado di analizzare venti elementi. Un “filo rosso” che ha portato ORI Martin ad essere un faro per il settore siderurgico italiano, creando il fenomeno delle “mini acciaierie” bresciane.
Gli anni Settanta sono caratterizzati
da una importante crisi siderurgica europea che influenza le strategie aziendali della società di San Bartolomeo, portando verso la sempre maggiore produzione di vergella di qualità entrando di fatto nel mercato automobilistico con acciai per bulloneria e molle per ammortizzatori. È un periodo caratterizzato anche da forti tensioni sociali e anche nei rapporti con le maestranze, ORI Martin è stata antesignana proponendo e firmando accordi basati su temi di fondo come l’ambiente di lavoro, l’ambiente circostante la fabbrica, l’aumento dei livelli occupazionali attraverso investimenti oculati, la
creazione di servizi collettivi come la mensa e i trasporti per i dipendenti, (otto pullman a disposizione dei dipendenti per il tragitto dalla stazione a San Bartolomeo).
Temi antesignani delle moderne ESG, ossia Environmental, Social e Governance e si riferiscono ai tre fattori chiave per misurare la sostenibilità e l'impatto etico di un investimento in un'azienda.
Con la crescita industriale cresce anche la città che si sviluppa attorno al polo produttivo di San Bartolomeo, è quindi necessario trovare nuovi equilibri tra la realtà industriale e i nuclei urbani. Nel 1971 ORI Martin installa
un filtro a maniche, impianto innovativo e molto più efficace, rispetto ai normali impianti ad abbattimento ad umido che rappresentavano lo stato dell’arte. Anche la gestione dell’acqua di raffreddamento degli impianti diventa fonte di innovazione, si passa infatti a sistemi di riciclo, riducendo il consumo di oltre il 90%.
Nel periodo 85-86 si evidenziano le criticità legate all’impatto ambientale connesse all’inquinamento acustico e atmosferico. ORI Martin risponde con l’utilizzo della “Dog House”, un sistema innovativo della società Danieli che serve ad “ingabbiare” il forno elettrico attraverso una struttura isolante e mobile che serve ad isolare la macchina fusoria in una scatola chiusa durante le fasi di fusione e che si apre durante la carica del rottame con le ceste. Ma non è solo l’area del forno fusorio ad essere oggetto di importanti modifiche, in acciaieria si spengono due dei tre forni fusori ed uno viene trasformato in forno di affinazione “LF” (Ladle Fournace), iniziando a parlare di affinazione fuori forno, concetto determinate per garantire la produzione di acciai di elevata qualità, una visione decisamente innovativa per l’epoca. Tra la fine del 1985 e l’inizio del 1986 iniziano le prove del nuovo laminatoio “vergella” Danieli specifico per produrre acciai di qualità sempre maggiore, Un impianto che caratterizzerà la svolta della ORI Martin S.p.a. verso il mercato degli acciai di qualità per il mercato nazionale ed estero.
Il concetto di qualità e la ricerca di nuovi prodotti e mercati porta anche alla diversificazione e verticalizzazione, Nel 1987 compaiono i primi
due forni di ricottura per vergella da impiegare soprattutto nel settore automobilistico. Nello stesso anno, in colata continua compare la torretta “gira siviere”, altra importante pietra miliare per la siderurgia degli acciai di qualità, in grado di migliorare la sicurezza operativa, la qualità e la quantità di acciaio colato. Ormai si tratta di acciai colati al 100% a getto protetto, per quegli anni una garanzia del livello tecnologico e qualitativo raggiunto dal know-How aziendale. Nel 1989 il forno TIBB viene sostituito con un nuovo forno “EBT” della società Danieli della capacità di 75 tonnellate, Il nuovo forno rappresenta una innovazione nel sistema di spillaggio della colata, rispetto allo stato dell’arte che prevedeva lo spillaggio con canale nel tradizionale forno a becco.
Con il nuovo forno, si sperimenta anche un nuovo sistema di iniezione dell’ossigeno con lancia supersonica dalla porta, e nuovi bracci porta corrente, sempre in collaborazione con Danieli. Lance supersoniche e bracci porta corrente di questo tipo saranno poi una presenza costante in tutti i progetti di innovazione delle acciaiere elettriche nel mondo. Nello stesso periodo anche la colata continua subisce un profondo cambiamento sia nell’ottica di migliorare la qualità del prodotto, che di aumento della produttività che della sicurezza degli operatori. ORI Martin sceglie di togliere tutti gli operatori dal piano di colata ed effettuare tutte le operazioni di gestione e controllo del processo di colaggio da un pulpito in cabina di controllo, una soluzione decisamente innovativa per l’epoca, anticipando la gestione da remoto
(ancora in epoca pressoché analogica), generando un salto quantico nella sicurezza e qualità del lavoro degli operatori di colata.
Nel 1993 si diversifica ulteriormente la produzione del laminatoio, inserendo una linea “barre” per la produzione di barre di acciai di qualità, prevalentemente bulloneria e molle, sempre per il settore automotiv nel mercato europeo in concorrenza con i grandi gruppi siderurgici soprattutto tedeschi (Usinor, Tyssen, Krupp). Anche sul piano ambientale ORI Martin S.p.a. si pone in evidenza: nel 1994 ORI Martin anticipa le scadenze previste dalla Regione Lombardia, in termini di emissioni e rumore, ampliando l’impianto fumi, eliminando la “Dog House” e sostituendola con una “Elephant House” ossia la costruzione di un cappotto isolante su tutto il capannone del forno fusorio. Sempre il forno fusorio, nel 1998, è oggetto di una importante innovazione che diventerà un punto di riferimento e attenzione per la siderurgia internazionale. In collaborazione con la società tenova di Milano. Viene sviluppato il progetto di un forno a carica continua “Consteel®”, è il primo forno in Europa. Si tratta di un forno, pensato dall’italo americano Jhon Wallomy, che riduce i consumi di energia elettrica sfruttando il preriscaldo del rottame e migliora la qualità dell’acciaio colato. Il tutto garantendo un impatto sonoro decisamente inferiore rispetto ai tradizionali forni con carica a ceste.
Il 2010 è un altro anno di profondi cambiamenti impiantistici, viene implementata una nuova colata continua Danieli da 10 m di raggio in grado di colare billette quadre
dalla sezione 140 mm alla sezione 200 mm, utilizzando tecnologie innovative per migliorare sicurezza operativa e qualità del prodotto. Nel 2012, sempre nel solco del filo rosso dell’innovazione, il reparto acciaieria si dota di un innovativo impianto di degasaggio e stazione di raspatura; in collaborazione con la società Concast si studia e progetta un impianto di degasaggio, primo in Europa, funzionante con sole pompe meccaniche, in sostituzione dei più complessi impianti a vapore. L’introduzione delle pratiche di degasaggio contribuisce ad ampliare considerevolmente la gamma di acciai prodotti migliorandone la qualità.
Tra il 2011 e il 2015 ORI Martin S.p.a. si appoggia ai progetti di ricerca europei per sviluppare un importante progetto ambientale, una sinergia tra industria e città. Nel 2015, grazie ad un progetto di ricerca finanziato dalla comunità europea, entra in funzione l’impianto “iRecovery®”. È un progetto complesso, primo in Italia, sviluppato in collaborazione tra le società ORI Martin, Tenova, Turboden e A2a la municipalizzata di Brescia e Milano. L’impianto progettato dalla società tenova recupera il calore dei fumi primari del forno fusorio, trasformandolo in vapore che nel periodo invernale viene ceduto alla linea del teleriscaldamento della città di Brescia gestito da A2a, nel periodo estivo, il vapore viene deviato verso una turbina ORC progettata e costruita da Turboden (società bresciana) per la produzione di energia elettrica destinata all’autoconsumo. Sempre nell’ottica di ridurre ‘impatto ambientale, nel 2019, grazie ad un
progetto Europeo “Life”, ORI Martin e la società Turboden sviluppano un progetto per l’inserimento di una pompa di calore in grado di valorizzare i “waste Heat” del forno fusorio, incrementandone la temperatura attraverso una pompa di calore innovativa, la prima nel mondo per dimensioni, Questo calore “valorizzato” viene poi veicolato verso il circuito cittadino per incrementare la quota di calore che l’acciaieria fornisce alla città contribuendo a ridurre l’inquinamento legato alla produzione di energia termica. L’impianto è stato avviato nell’inverno del 2023. Ma le innovazioni non riguardano solo l’ambito ambientale e impiantistico, sempre nel 2019 ORI Martin S.p.a. in partenariato con la società tenova e con il supporto del Cluster Fabbrica Intelligente di regione Lombardia, propone al MISE un progetto di ricerca per la digitalizzazione del settore siderurgico. Il progetto viene approvato ed entra di diritto nel gruppo dei quattro progetti Lighthouse che il MISE vorrebbe come dimostrativi del “saper fare” italiano. Il gruppo delle società Lighthouse è composto da: Tenova-ORI Martin, Ansaldo Energia, ABB, Hitachi Rail.
Il progetto Lighthouse “Acciaio_4.0” ORI Martin Tenova che si conclude nel giugno 2023 ha come obiettivo di creare una Cyber Physical Factory che, grazie all’utilizzo delle tecnologie abilitanti di Industria 4.0, permetta l’integrazione verticale, orizzontale e trasversale dell’intero processo produttivo dell’acciaio, rendendolo più efficiente, flessibile e sostenibile: questo è l’obiettivo di “Acciaio_4.0”, uno dei quattro Lighthouse Plant
selezionati dal Cluster Fabbrica Intelligente per conto del MISE.
Il progetto prevede un piano di Ricerca e di Sviluppo Industriale con lo scopo di realizzare la best practice dell’industria siderurgica italiana, primo esempio di applicazione massiccia delle tecnologie abilitanti più innovative della Quarta Rivoluzione Industriale.
ORI Martin si propone come “system integrator” di innovazioni, sviluppate da tenova, nel sito produttivo di Brescia che ambisce a diventare un di smart factory nel settore siderurgico, non solo in Italia. Si tratta di un progetto trasversale che ha toccato tecnologie ed ambiti di ricerca decisamente diversi tra loro, ma complementari; si va dalla raccolta e gestione dei dati, all’inserimento di robot, alla manutenzione predittiva e preventiva, all’utilizzo di algoritmi di intelligenza artificiale per la classificazione del rottame e la gestione dei flussi di acciaio in acciaieria, al miglioramento della sicurezza delle persone, allo sviluppo di algoritmi per la gestione delle informazioni di processo per definire LCA dinamici del prodotto.
Grazie al continuo svolgersi del “filo rosso” dell’innovazione e del miglioramento, ORI Martin S.p.a. assume sempre più importanza nel mercato europeo dell’acciaio di qualità e al fine di consolidare la sua presenza verticalizza la produzione acquisendo società di trasformazione e verticalizzazione del prodotto, entrano quindi nel gruppo società come Sapes, Trafileria Lariana, Novacciai. Oggi ORI Martin è un gruppo di dieci aziende con oltre 940 dipendenti
AIM's companies - Le aziende di AIM
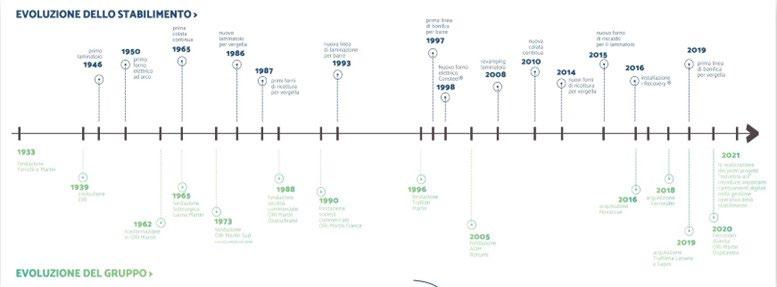
ed è una presenza di riferimento nel mercato europeo degli acciai di qualità
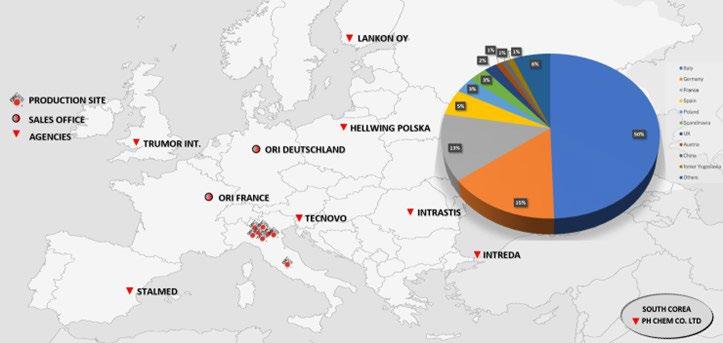
Acciaio e metalli: dinamiche, cicli e tendenze di mercato
Rubrica trimestrale a cura di Achille FornasiniHa insegnato all’Università Bocconi di Milano, all’Università di Venezia e all’Università di Brescia, dove è responsabile del Laboratorio per lo studio delle Dinamiche dei Sistemi e dei Mercati finanziari. Coordina l’osservatorio congiunturale di Confindustria Brescia e di ANIMA Confindustria. Partner di Sidewerb, da vent’anni cura rubriche dedicate ai mercati siderurgici e metallurgici. È autore di libri e centinaia di saggi, editoriali e articoli su temi economico-finanziari.
Dopo il primo contributo pubblicato nel numero di febbraio de La Metallurgia Italiana (pagg. 91-94), con questa rubrica torniamo ad occuparci degli andamenti dei prezzi siderurgici ribadendo la convinzione che essi rappresentino, nel loro divenire temporale, l’effetto delle decisioni e delle aspettative di tutti coloro che partecipano ai mercati anche se non ufficialmente regolamentati. Rispettando l’impegno preso con i lettori, questo secondo appuntamento è dedicato alle evoluzioni delle quotazioni delle materie prime, dei semilavorati e dei prodotti finiti tipici delle produzioni di acciaio a forno elettrico. Peraltro, prima di entrare in questo specifico approfondimento, delineiamo le condizioni di contesto nel frattempo maturate.
Il contesto generale
Nel primo quadrimestre è proseguito il rallentamento economico globale, che trova conferma nelle stime del Fondo Monetario Internazionale e dell’Ocse: nel 2023 si prospetta una crescita globale intorno al 3%, inferiore alla media annuale degli ultimi due decenni. Una condizione fondamentalmente orientata dalla Cina, che rappresenta uno dei principali consumatori di metalli di base e minerale di ferro, nonché il più grande produttore mondiale di acciaio. E’ proprio nel gigante asiatico che si origina la frenata dell’economia che a sua volta sta contribuendo a ridurre la domanda nei settori metallurgico e siderurgico per effetto delle politiche zero-Covid che hanno bloccato intere aree di attività, tra le quali i
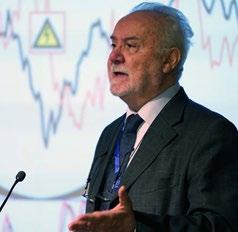
cruciali settori infrastrutturale e immobiliare. Malgrado il deterioramento delle relazioni con gli Stati Uniti, la ripresa del Dragone susseguente ai recenti lockdown si sta svolgendo a un ritmo molto rapido con un'accelerazione alimentata soprattutto dalla domanda e dalla spesa interna. La vera svolta potrà peraltro arrivare con la fine delle politiche monetarie restrittive e con il miglioramento della situazione geopolitica. A livello europeo si sono ridimensionate le tensioni sui mercati energetici grazie all’inverno mite, a riserve adeguate e all’ottimizzazione dell'uso del gas nelle sue diverse forme. Resta la tensione esercitata dalla persistenza del conflitto russo-ucraino nella speranza di uno sbocco verso una risoluzione negoziata che ponga fine alle ostilità militari e limiti i rischi di una nuova escalation. In questo quadro le quotazioni delle materie prime hanno continuato a scendere.
La produzione di acciaio a forno elettrico
La nostra analisi inizia valutando l’evoluzione storica più recente del rottame ferroso, ovvero la “materia prima seconda”, com’è ufficialmente definita, proveniente da sfridi di lavorazione dell’industria siderurgica oppure da materiali ferrosi derivanti da demolizioni o da altri scarti industriali. Il recupero e la rifusione di questi materiali costituisce la base di ogni processo produttivo siderurgico imperniato su impianti a forno elettrico: il rottame e le ferroleghe prescelte formano infatti la carica solida in funzione della tipologia target di acciaio, che diviene oggetto di fusione grazie all’arco elettrico formato dagli
Steel and metals: market dynamics, cycles and trends
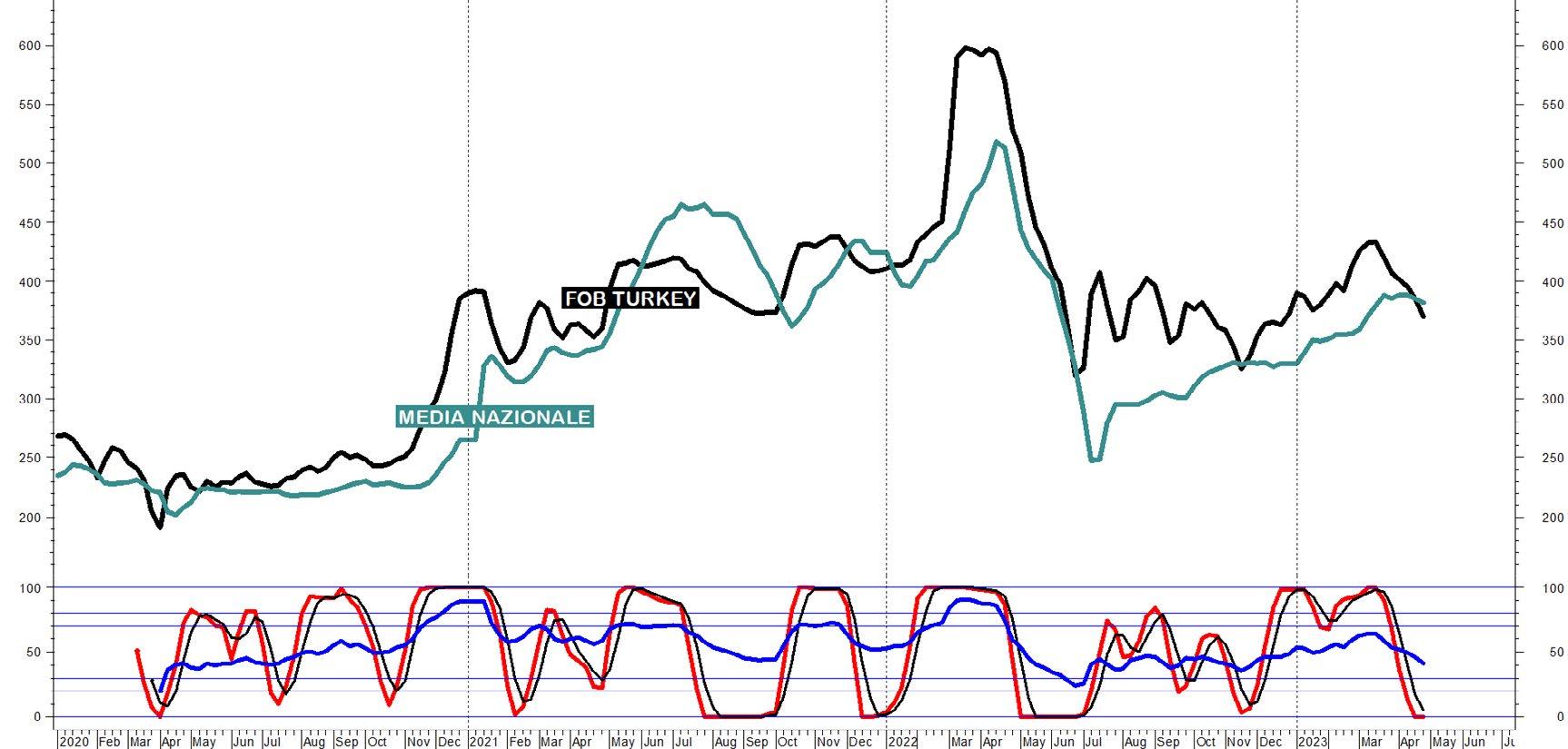
elettrodi calati in sua prossimità. Ciò premesso, si osservi la figura 1, che illustra gli andamenti medi settimanali in euro/tonnellata dei prezzi del rottame ferroso FOB Turkey e della media dei prezzi delle quattro principali categorie di rottame rilevate da Siderweb a livello nazionale: lamierino, torniture, frantumato e da demolizioni. Come accaduto per tutti i mercati, anche quello del rottame di origine turca accelera al ribasso durante l’intero primo trimestre 2020, proseguendo nel trend declinante già avviatosi nel biennio precedente. Registrato il suo minimo, la dinamica si volge decisamente al rialzo per effetto della corsa agli acquisti scatenatasi dopo la prima fase pandemica: +104,3% dai livelli registrati nell’ultima settimana di marzo. Nel 2021 l’ascesa rallenta consolidandosi attraverso ampie ondate, che archiviano l’anno a +5%. E’ nel 2022 che la volatilità riprende ad accendersi: complici la fase prebellica e l’avvio del conflitto russo-ucraino, i timori di una crisi dell’offerta innesca infatti un’impennata delle quotazioni che si esaurisce nella terza settimana di marzo (+46,2%). Svanite le paure, i prezzi crollano toccando il fondo a fine giugno (-46,5%). Iniziano quindi a svilupparsi estese oscillazioni laterali, che fermano il declino e fissano la performance dello
scorso anno a -4,2%. Il 2023 si apre in deciso rialzo, che però si esaurisce agli inizi di marzo (+15,8%), quando prende corpo un deciso movimento ribassista (-14,6%), che riporta i valori sui livelli d’inizio anno con una performance quadrimestrale a -0,8%.
L’andamento della media dei rottami nazionali segue, con il consolidato ritardo temporale di due settimane, le evoluzioni del benchmark turco. Chiuso il 2020 a +12,5%, i prezzi risalgono rapidamente, toccando il top a fine luglio (+75,7%) per poi stornare e recuperare fino a chiudere il 2021 a +60,3%. Il 2022 inizia con il balzo dei prezzi provocato dallo scoppio dell’evento bellico (+22,3%), che si esaurisce a metà aprile. Segue la repentina caduta che termina nella prima settimana di luglio (-52,2%), quando la media dei prezzi risale velocemente in controtendenza rispetto alla contestuale dinamica del rottame turco. Un rialzo che prosegue fino alla terza settimana di marzo (+56,7%) quando la dinamica tende dapprima ad assestarsi e quindi a flettere (-1,7%) in scia al contestuale indebolimento del riferimento europeo. Gli indicatori posti a piè di grafico lasciano presagire il proseguimento della fase ribassista di entrambi i movimenti per l’intero primo semestre.
- I prezzi del rottame ferroso. Il tondo per cemento armato
Le due scosse di terremoto che hanno colpito la Turchia e la Siria il 6 febbraio 2023 hanno contribuito ad alterare i mercati europei dell’acciaio. In Turchia, come nel nostro Paese, è infatti insediata una siderurgia imperniata prevalentemente sul forno elettrico per la produzione di
semilavorati lunghi. E’ dunque presumibile che gli effetti del drammatico evento possano determinare il prossimo avvio di un intenso programma di ricostruzione degli edifici e delle infrastrutture danneggiati dal sisma con conseguenti ricadute sulle importazioni turche di billette e rottame, che eserciterebbero pressioni crescenti
Acciaio e metalli: dinamiche, cicli e tendenza di mercato
sui prezzi europei. Si profila d’altra parte la contrazione dell’export turco di tondo per cemento armato, di laminati mercantili e di vergella destinati alla ricostruzione interna: una temporanea opportunità commerciale, dunque, per le acciaierie italiane ed europee.
Si consideri al riguardo la figura 2, che illustra le dinamiche dei prezzi medi settimanali in euro/tonnellata del tondo per cemento armato rilevati in Turchia e a livello nazionale da Siderweb. Si noti l’alta concordanza che contraddistingue le due curve fino a tutto il primo trimestre 2022 con i prezzi turchi che anticipano regolarmente i movimenti nazionali. Seguendo coerentemente le evoluzioni del rottame ferroso (figura 1), i prezzi del tondo turco chiudono il 2020 a +28,8% e il 2021 a +16,7% per poi accelerare fino agli inizi di aprile 2022 sull’onda della pressione provocata dalla guerra in Ucraina (+43,9%). Nello stesso arco temporale i prezzi nazionali registrano
+27,2% (2020), +42,6% (2021) per puntare infine al top del 2023 (+50,4%). Nel secondo trimestre dello scorso anno i prezzi del tondo turco e nazionale si ridimensionano, archiviando il 2022 con performance rispettivamente a +2,8% e a +2,3%. Un’evidente controtendenza delle due curve caratterizza il primo trimestre del 2023: mentre i prezzi turchi si volgono al rialzo fino a metà marzo (+11,5%) per poi flettere (-11,8%), nello stesso periodo le quotazioni nazionali proseguono al ribasso (-12%) per poi reagire ed assestarsi a fine quadrimestre (+4,6%). Una situazione di mercato che ben interpreta la condizione di indefinitezza tendenziale dei mercati conseguente alla fase di stagnazione economica che stiamo attraversando. Gli indicatori di breve periodo prefigurano, come nel caso del rottame, il proseguimento delle correnti derive declinanti.
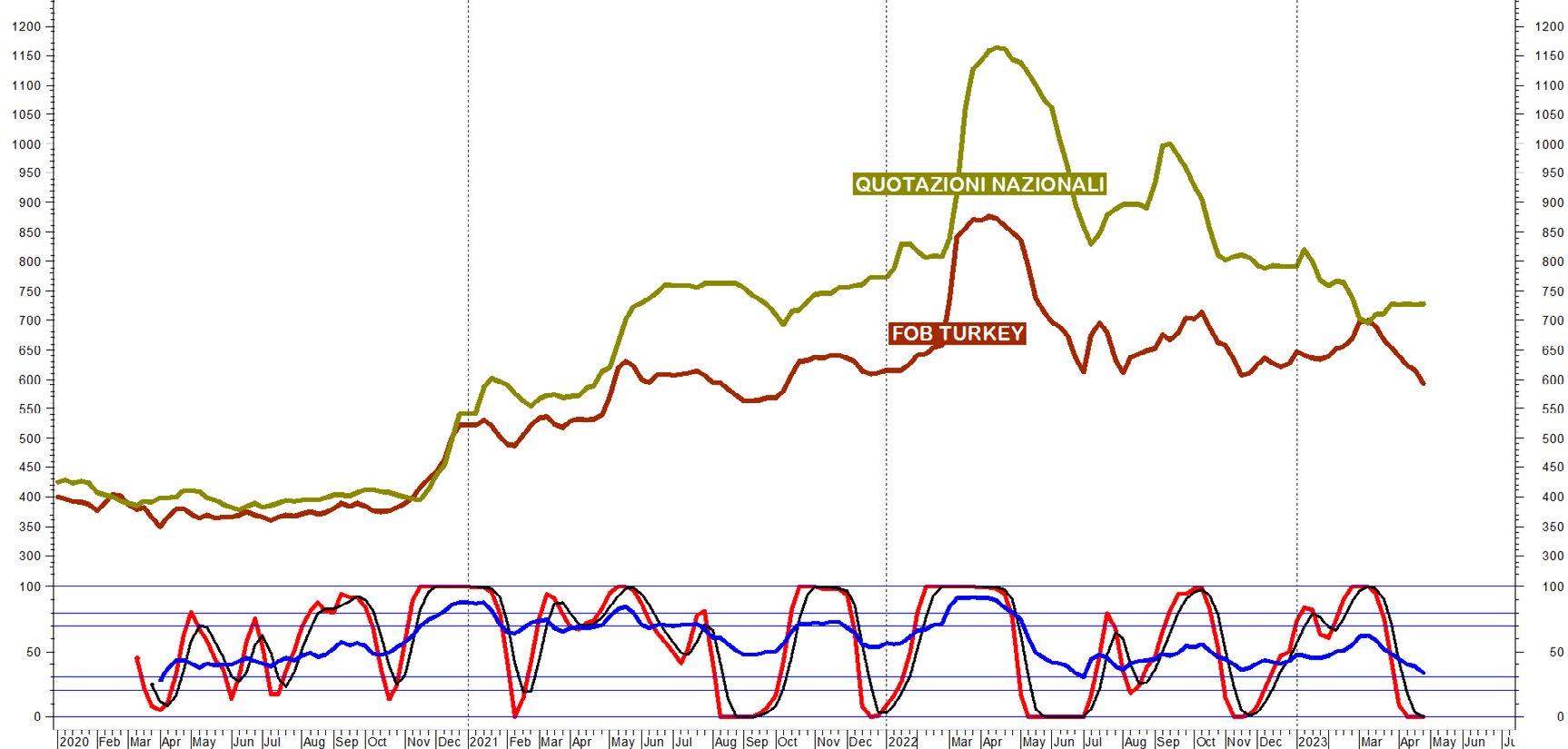
Altri prodotti lunghi Completiamo l’analisi osservando gli andamenti dei prezzi delle principali produzioni da forno elettrico rilevati settimanalmente in euro/tonnellata a livello nazionale da Siderweb (figura 3). Pur nel quadro di dinamiche altamente concordanti e di analoghe performance sintetizzate in tabella, che riassume il triennio 2020-2022, nel primo terzo del 2023 possiamo distinguere le differenti
modalità evolutive della coppia di vergelle rispetto alle dinamiche di travi e laminati mercantili. Mentre le vergelle tendono ad assestarsi lateralmente, confermandosi per l’intero primo quadrimestre sugli stessi valori d’inizio anno, le travi e i laminati mercantili estendono ulteriormente le rispettive flessioni dai massimi fissati a metà aprile 2022: -34,4% le prime, -30,4% i secondi.
Steel and metals: market dynamics, cycles and trends
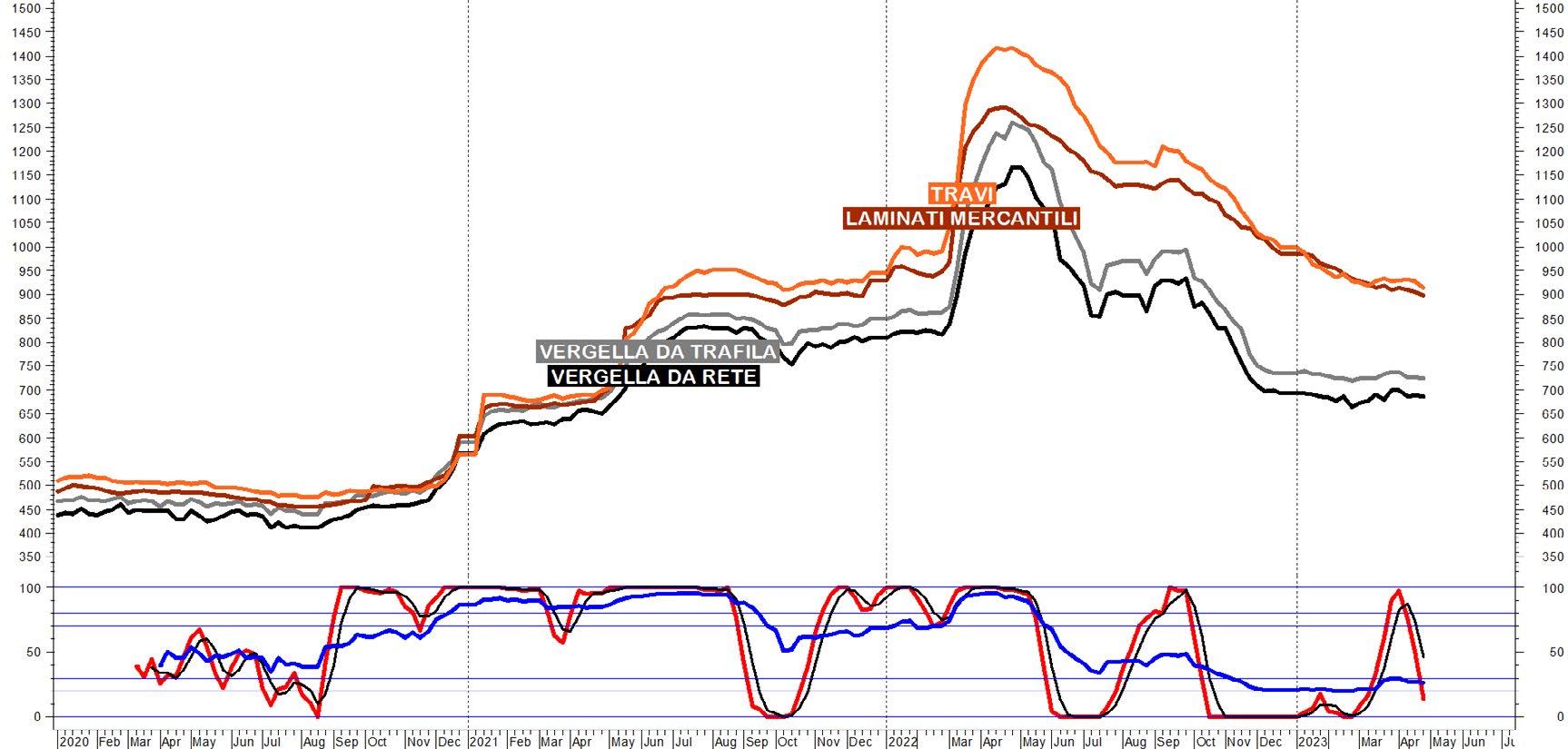
L’analisi degli indicatori tecnici posti a piè di grafico conferma la condizione di generale consolidamento dei prezzi, che profila la continuazione della corrente fase stazionaria e poco volatile per l’intero primo semestre.
Passando a considerazioni più generali e di lungo periodo, il futuro potrebbe riservare significativi squilibri tra domanda e offerta di rottame ferroso come conseguenza della progressiva diminuzione delle disponibilità di materiali originata dai Paesi sviluppati, tradizionalmente esportatori netti: una condizione che trova solo parziale
compensazione nella produzione di preridotto, destinata a sopperire la crescente indisponibilità di rottame di qualità. Un disequilibrio che rischia di aggravarsi se la Cina decidesse di accelerare il processo di decarbonizzazione attraverso il passaggio dall’inquinante altoforno al forno elettrico: per il nostro Paese, già impegnato nella transizione ecologica del settore siderurgico, ciò implicherebbe maggiori difficoltà nel reperimento di rottame con ovvie ripercussioni sul livello dei prezzi a carico dell’intera filiera.
Nei prossimi appuntamenti di questa rubrica indagheremo i mercati dei metalli non ferrosi (luglio/agosto), per sintetizzare infine l’annata e delineare le possibili linee di sviluppo delle tre filiere per l’anno successivo (novembre/ dicembre). Per domande e confronti: achille.fornasini@unibs.it
The Bright World of Metals

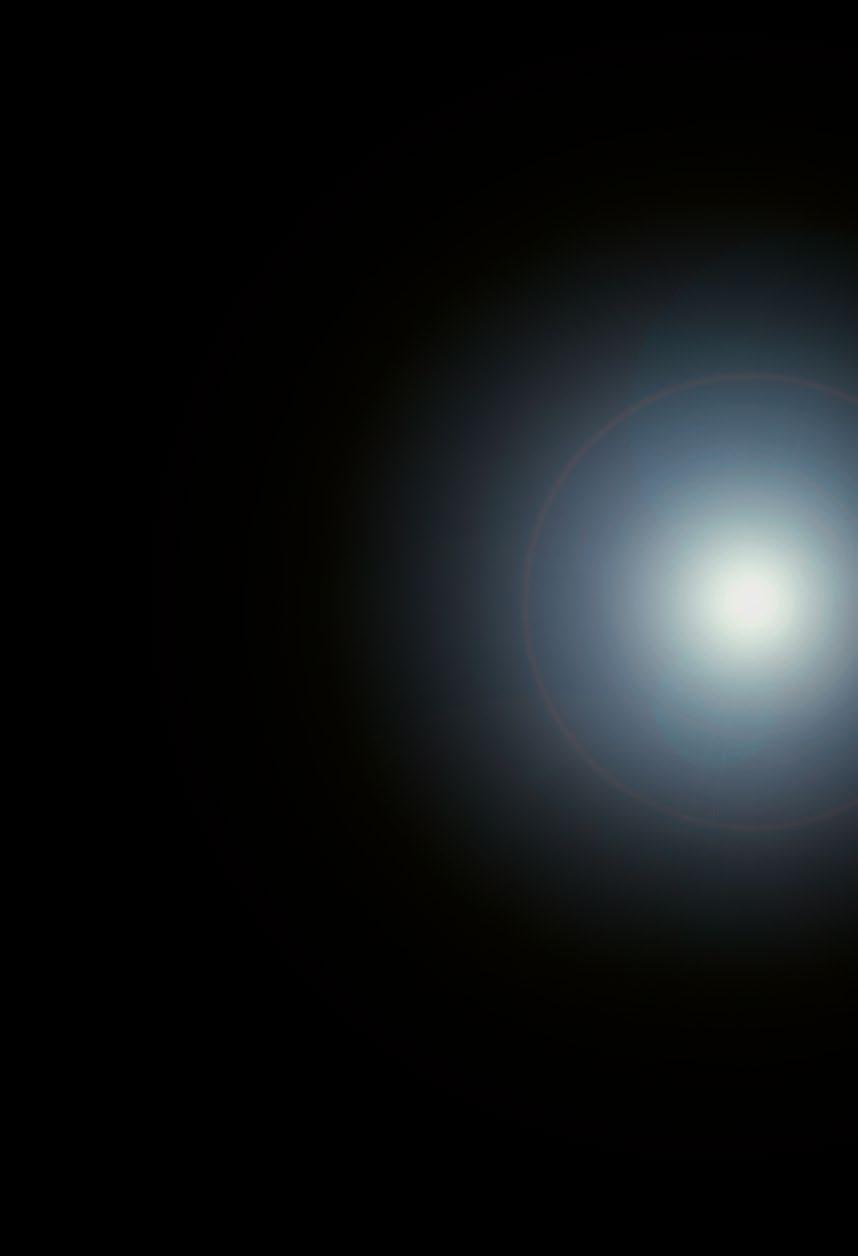
Evviva la metallurgia!
The Bright World of Metals è l’evento più importante per il settore della fonderia, dei processi termici, della produzione e della lavorazione dei metalli. Troverete tutte le nuove tecnologie per un’industria metallurgica sempre più sostenibile, di successo e soprattutto rispettosa dell’ambiente. Scoprirete nuovi percorsi di decarbonizzazione ed economia circolare con ecoMetals e ecoMetals Trails.
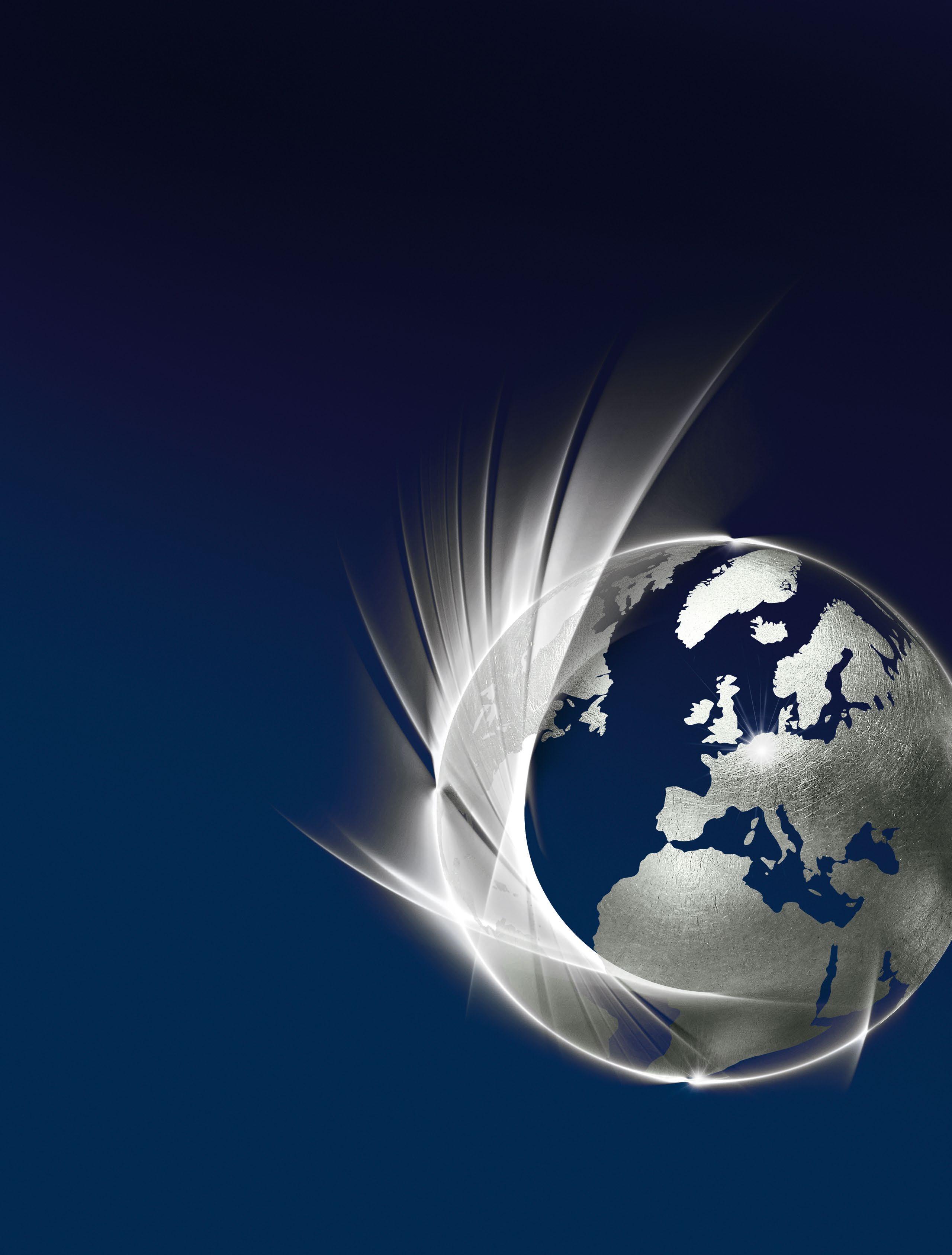
SINERGIA COMPOSTA: grazie al quartetto di fiere del metallo GIFA, METEC, THERMPROCESS e NEWCAST potrete arricchire il vostro know-how tecnologico!
Ci vediamo a Düsseldorf! www.tbwom.com
Verbale della Ottantesima Assemblea Ordinaria dei Soci AIM
La 80a Assemblea Ordinaria dei soci AIM ha avuto luogo venerdì 5 maggio 2023 alle ore 12.30 in seconda convocazione, dato che la prima era andata deserta. Sono presenti XX Soci (XX fisicamente e X rappresentati per delega).
Relazionano, oltre al Presidente, Silvano Panza, il Tesoriere, dr. Stefano Vittadini, e il Revisore dei conti, dr.ssa Arrigo Berenghi.
ORDINE DEL GIORNO:
1. Relazione del Consiglio Direttivo AIM
2. Relazione del Tesoriere
3. Relazione del Collegio dei Revisori dei Conti
4. Approvazione bilancio consuntivo 2022 e previsionale 2023
5. Varie ed eventuali
Il Presidente Panza comunica che l’Assemblea è stata convocata con avviso telematico ai Soci e, poiché si svolge in seconda convocazione, come previsto dallo Statuto, è valida qualunque sia il numero dei presenti.
Si passa quindi ad esaminare i punti all’Ordine del Giorno: circa il primo punto, il Presidente legge la relazione del Consiglio Direttivo relativa alle attività svolte nel 2022; il Tesoriere illustra in seguito la relazione sul bilancio 2022 ed il previsionale 2023; infine, il revisore dr. Berenghi, in rappresentanza del Collegio dei Revisori dei Conti, legge la relativa relazione sul bilancio 2022.
Dopo aver aperto e concluso la discussione, l’Assemblea approva all’unanimità il bilancio consuntivo 2022 e il bilancio previsionale 2023.
Il Presidente ringrazia e saluta i Soci convenuti.
L’Assemblea termina alle ore 13.30.
RELAZIONE DEL CONSIGLIO DIRETTIVO Anno: 2022
Cari Soci ed Amici, Vi ringrazio vivamente per la Vostra partecipazione all’Assemblea dei Soci, che si svolge in modalità ibrida.
Sono lieto di confermare che un anno eccezionalmente positivo sia in termini di partecipazione ai nostri numerosi eventi che di risultato economico.
Manifestazioni
Nel 2022 l’Associazione ha organizzato 30 manifestazioni, di cui:
- 9 Corsi di formazione ed aggiornamento;
- 16 Giornate di Studio;
- 2 Convegni nazionali, ovvero il 27° Convegno Nazionale Trattamenti Termici (Genova, 26-27 maggio) e il 39° Convegno Nazionale AIM (Padova, 21-23 settembre)
- 3 Convegni internazionali, ovvero il Convegno ESSC & DUPLEX dedicato a acciai inossidabili e acciai duplex (Bardolino, 15-17 giugno), la XII edizione del Convegno Rolling (Trieste, 26-28 ottobre) e la seconda edizione del workshop IWSQ dedicato alla qualità superficiale dei lingotti (Bergamo, 1-2 dicembre)
Le manifestazioni sopra indicate hanno raccolto complessivamente 2708 partecipanti, dei quali il 30% non soci ed il 10% studenti (soci junior).
Soci
Benemeriti 20
Sostenitori 80
Ordinari 1195
Senior 41
Junior 167
Si rileva un incremento rispetto al 2021, in particolare per benemeriti (+ 2), sostenitori (+ 6) e ordinari (+ 310).
Centri di Studio
Mi preme ringraziare tutti coloro che dedicano, con grande spirito associativo, tempo e risorse ad AIM, partecipando attivamente ai nostri Comitati Tecnici e organizzando con il supporto della Segreteria le numerose iniziative fulcro della nostra attività.
Ricordo che la partecipazione ai Comitati Tecnici è aperta a tutti i soci (a livello personale o aziendale) che desiderano mettere a fattor comune le proprie competenze e conoscenze, ricavandone in cambio importanti occasioni di confronto e crescita tecnico-scientifica.
Invito pertanto le aziende associate a designare propri tecnici per la partecipazione ai Comitati Tecnici AIM.
Attività editoriale
Si è provveduto alla ristampa di 100 copie del volume Corrosione e Protezione dei metalli (3° ed.) di Giuseppe Bianchi e Francesco Mazza e di 50 copie del volume Tecniche Sperimentali per la caratterizzazione dei materiali di Roberto Montanari.
E’ stato inoltre stampato un nuovo volume Diario di un corrosionista di Luciano Lazzari (500 copie).
Con il comitato di redazione ed in particolare il Direttore Mario Cusolito, abbiamo avviato un graduale processo di aggiornamento della nostra rivista La Metallurgia Italiana – International Journal of the Italian Association for Metallurgy, che continua ad essere edita da Siderweb: nuove rubriche, nuovi contenuti, nuove collaborazioni a partire dal numero di gennaio 2023.
Sostegno alla ricerca e alla didattica
Il Consiglio Direttivo AIM ha deciso di stanziare fondi per un ulteriore assegno di ricerca, proseguendo con l’attività di sostegno alla ricerca e all’insegnamento della Metallurgia.
Si sta inoltre lavorando con la famiglia Longaretti alla preparazione del bando per il premio intitolato alla memoria dell’ing. Carlo Longaretti.
Attività 2023
Il 2023 presenta un calendario molto ricco, con poco meno di 40 iniziative. Tuttavia riscontriamo rispetto al 2022 numeri di iscrizioni generalmente più bassi.
Con l’obiettivo di farci conoscere e promuovere al meglio le nostre iniziative, partecipiamo come espositori alle GNS dell’IIS e al Made In Steel; inoltre, abbiamo intensificato le collaborazioni con altri enti, in termini di patrocini e visibilità reciproca, oltre che di co-organizzazione di eventi.
Conclusioni
Esprimo grande soddisfazione per l’ottimo andamento culturale e economico dell’anno 2022, confermando la possibilità di finanziare un assegno di ricerca per il massimo valore storico pari a 25.000 €. La decisione dell’ateneo presso cui bandire l’assegno viene lasciata in capo al CoMet come per i precedenti. Informo inoltre con piacere che grazie al risultato economico eccezionalmente positivo, vi è anche la possibilità di destinare ulteriori risorse a favore di Istituti Tecnici, per sostenere e incentivare l’insegnamento della Metallurgia.
Rivolgo a tutti Voi un caloroso saluto e rinnovo il ringraziamento per la Vostra partecipazione.
RELAZIONE DEL TESORIERE SUL RENDICONTO DELL’ESERCIZIO 2022
Signori Soci,
Il presente bilancio assolve il fine di informare in merito all’attività posta in essere dalla Vostra Associazione nel conseguimento dello scopo istituzionale, esprimendo le modalità tramite le quali ha acquisito ed impiegato risorse, e di fornire, per mezzo di valori quantitativo – monetari, una rappresentazione chiara veritiera e corretta della situazione patrimoniale, finanziaria, e del risultato della gestione conseguito dall’Ente nell’intervallo temporale cui il bilancio si riferisce. Il presente bilancio è la sintesi delle istituite scritture contabili, volte alla sistematica rilevazione degli eventi che hanno interessato l’Associazione e che competono all’esercizio cui il bilancio si riferisce. Il bilancio si compone dello Stato Patrimoniale, del Rendiconto gestionale, della presente Relazione.
Il documento di Stato Patrimoniale esprime la complessiva situazione patrimoniale e finanziaria dell’Associazione alla data di chiusura dell’esercizio ed espone in termini comparativi i valori riferibili all’esercizio precedente.
Il documento di Rendiconto gestionale espone le modalità tramite le quali l’Ente ha acquisito ed impiegato risorse, evidenzia le componenti economiche positive e negative che competono all’esercizio e sintetizza il risultato di gestione conseguito. La forma prescelta è a sezioni contrapposte esponendo in termini comparativi i valori riferibili all’esercizio precedente, con separata specifica dei proventi e degli oneri in funzione della area gestionale di afferenza (attività tipica /istituzionale o attività accessoria/commerciale)
La presente relazione, facente funzione di nota integrativa, assolve lo scopo di fornire ulteriori informazioni sulle voci più significative, con criterio descrittivo ed analitico, ritenute utili ad una chiara comprensione delle evidenze riportate nei documenti di Stato Patrimoniale e Rendiconto gestionale ed a favorirne l’intelligibilità.
La redazione del bilancio è stata eseguita nel rispetto del generale principio di prudenza e nella prospettiva di continuazione dell’attività della Associazione; è stato inoltre applicato il principio della competenza economica. Lo Stato Patrimoniale e il Rendiconto gestionale sono redatti in unità di euro e la presente relazione contiene illustrazioni ai dati di bilancio in unità di euro.
Il bilancio che vado a illustrarVi rappresenta i dati consuntivi di un esercizio caratterizzato dal ritorno ai volumi pre-covid. Trascorso il biennio 2020-2021 cui avevamo assistito al significativo ridimensionamento all’attività convegnistica e formativa con conseguente impatto sui ricavi, il 2022 vede il dato dei ricavi addirittura superiore al dato 2019, trascinato dai ricavi per convegni e corsi che superano l’obiettivo di budget del 78%.
Il rendiconto che vado ad analizzare chiude con un avanzo di gestione pari ad Euro 283.378, dopo avere accantonato imposte correnti per Euro 35.440. L’esercizio precedente chiudeva con un avanzo di Euro 102.453.
Stato patrimoniale attivo
IMMOBILIZZAZIONI:
Le movimentazioni dell’esercizio sono le seguenti:
Le movimentazioni intervenute nell’esercizio sono interamente riconducibili all’accantonamento delle quote di ammortamento.
RIMANENZE:
Nel corso dell’esercizio, si è avuta la seguente movimentazione:
II criterio utilizzato per la valutazione delle rimanenze è quello del minore tra il costo unitario di acquisizione ed il valore di mercato.
CREDITI VERSO I CLIENTI:
Si tratta di crediti sia per quote di partecipazione a convegni che per acquisti di volumi e di atti dei convegni.
dell’esercizio sono stati effettuati accantonamenti al fondo rischi per euro 100,00; si è provveduto ad utilizzare il fondo medesimo a storno dei crediti comprovata inesigibilità, per euro 1.880;
TITOLI:
Il valore nominale dei titoli in portafoglio ammonta a euro 2.409.241; il valore è invariato rispetto a quello dell’esercizio precedente stante l’assenza di operazioni di investimento/disinvestimento. La quotazione di mercato dell’intero portafoglio al 31.12.2022 è pari ad € 2.332.569 (nel 2021 il dato si attestava a € 2.576.440) con una svalutazione media rispetto al valore di carico del 3,2%; in presenza di perdite di valore a carattere non durevole, l’Asso-
ciazione ha applicato la deroga prevista dal Decreto Legge 21 giugno 2022, n.73, articolo 45 comma 3-octies in base alla quale sono stati confermati i valori di iscrizione al 31 dicembre 2021 a fronte della destinazione a riserva di utili indisponibile del corrispondente valore delle svalutazioni non operate pari a € 76.672.
Nel dettaglio, le performances dei tre investitori che gestiscono il patrimonio dell’associazione sono le seguenti:
La situazione sopra rappresentata esprime il risultato globale della gestione del patrimonio mobiliare; a livello di pura rappresentazione contabile il risultato non compare nel bilancio che vi viene sottoposto che espone solamente i risultati conseguiti per cassa e quindi, precisamente, le
FONDO LIQUIDAZIONE:
La AIM ha in essere due polizze assicurative a garanzia delle indennità di cessazione del rapporto dei dipendenti in forza; a quella esistente fino al 2015 con INA si è assommata una stipulata con Cattolica, ove vengono versati i premi a partire dal 2016. Il saldo al 31.12.2022, pari a complessivi euro 152.405 (di cui 92.582 su Cattolica) risente di
RATEI ATTIVI:
plusvalenze realizzate da eventuali cessioni e l’ammontare delle cedole incassate.
Le cedole accreditate in conto sono passate da euro 3.006 a euro 4.135; non risultano plusvalenze né minusvalenza.
un utilizzo effettuato nel corso dell’esercizio a fronte di una liquidazione anticipata nonché dell’adeguamento annuale al fondo trattamento fine rapporto maturato a favore dei dipendenti (Euro 190.810), che verrà effettuato nel corrente 2023.
Accoglie i ricavi di competenza dell’anno in corso che avranno manifestazione finanziaria nel corso dell’esercizio successivo.
RISCONTRI ATTIVI:
Accoglie i costi di competenza degli anni successivi relativi a fatture contabilizzate nell’anno in corso.
Stato patrimoniale passivo
FONDO DI DOTAZIONE
E’ principalmente costituito da riserve costituite con il riporto a nuovo degli utili maturati nel passato per € 3.830.044, incrementatesi nel 2022 in virtù dell’accantonamento dell’avanzo 2021 (€ 102.453).
Giova menzionare nelle voci del patrimonio vincolato, il saldo dei fondi destinati a terzi costituito dai fondi borse di studio accantonati per € 50.000.
DEBITI VERSO ISTITUTI BANCARI
La partita in esame è sorta nel corso dell’esercizio 2016 in occasione dell’accensione del mutuo ipotecario contratto con il Banco Desio per complessivi Euro 800.000 della durata di 10 anni, per l’acquisto dell’ufficio di Milano. Il saldo al 31/12/2022 pari a Euro 131.141, è riconducibile al capitale residuo al netto delle rate pagate nell’esercizio per Euro 38.000 e del rimborso anticipato di capitale effettuato nel 2019 per Euro 300.000.
FORNITORI:
Il saldo esistente a fine esercizio è pari ad euro 25.862 comprensivo delle fatture da ricevere per 9.684. Nessuno dei debiti esistenti è scaduto.
DEBITI VERSO L’ERARIO E VERSO GLI ENTI PREVIDENZIALI:
Il debito si riferisce per Euro 27.840 agli importi dovuti per contributi e tributi relativi al mese di dicembre 2022 e già tutti versati nei termini di legge. La differenza pari a Euro 20.175 è riferibile allo stanziamento delle imposte correnti Ires e Irap.
ALTRI DEBITI:
La posta in questione pari a € 42.335, è principalmente rappresentata da incassi anticipati su quote di partecipazione di competenza del 2023.
RATEI PASSIVI:
Si tratta di costi imputati all’esercizio in corso che avranno manifestazione finanziaria nel corso dell’esercizio successivo.
Rendiconto gestionale
RICAVI:
Come accennato in sede di premessa l’esercizio 2022 registra un significativo incremento dei ricavi rispetto al dato 2021 (€ 684.325) registrando un dato complessivo pari a € 1.115.580, addirittura superiore al dato 2019 di € 812.713, che, come anticipato, supera sensibilmente le previsioni del budget.
In particolare nell’esercizio si sono svolte 31 manifestazioni di cui 25 in presenza, ciò ha determinato ricavi totali delle manifestazioni per euro 943.908, contro i 522.963 del 2021, i 116.737 del 2020 e i 535.795 del 2019
COSTI:
La dinamica sopra richiamata sul fronte dei ricavi ha consentito di assorbire i costi fissi che sono principalmente costituiti dal costo del personale che si attesta a complessivi € 302.326. Sono stati accantonati ammortamenti in misura ordinaria che impattano per € 38.933.
PROVENTI FINANZIARI:
Come già detto in commento alla gestione degli investimenti finanziari, la redditività espressa in bilancio è rappresentata dalle cedole incassate ed accreditate direttamente in conto corrente.
In bilancio non viene rappresentata la variazione di quotazione intervenuta nell’esercizio sul totale degli investimenti finanziari in forza della specifica deroga citata nella apposita sezione dell’attivo patrimoniale.
INFORMAZIONI SUI FATTI DI RILIEVO AVVENUTI DOPO LA CHIUSURA DELL'ESERCIZIO
Dopo la chiusura dell’esercizio non sono avvenuti fatti di rilievo da segnalare, i cui effetti possano impattare i saldi e le valutazioni testè dettagliate.
CONCLUSIONE:
La gestione economica dell’Associazione nell’anno 2022 chiude pertanto con un avanzo di Euro 283.378, dopo avere accantonato imposte correnti per Euro 35.440 In ottica di destinazione di detto avanzo, alla luce delle previsioni statutarie, l’ipotesi di stanziare una Riserva per l’erogazione di contributi per il sostegno ad iniziative di ricerca nell’ambito metallurgico risulta coerente con la struttura economica e finanziaria del bilancio consuntivo testè commentato nonché dei dati di budget per l’anno 2023, e sostenibile, in misura non eccedente il 16% dell’avanzo di gestione.
BILANCIO CULTURALE 2022 / CULTURAL BALANCE 2022
CONVEGNI
27° CONVEGNO NAZIONALE TRATTAMENTI TERMICI
Genova, 26-27 maggio 2022
Organizzato dall’AIM e dal CdS Trattamenti Termici e Metallografia
219 partecipanti
ESSC & DUPLEX - 11TH EUROPEAN STAINLESS STEEL CONFERENCE SCIENCE & MARKET & 8TH EUROPEAN
DUPLEX STAINLESS STEEL CONFERENCE & EXHIBITION
Bardolino (Verona), 15-17 giugno 2022
Organizzato dall’AIM e dal CdS Acciaieria
114 partecipanti
39° CONVEGNO NAZIONALE AIM
Padova, 21-23 settembre 2022
Organizzato dall’AIM
327 partecipanti
ROLLING-12 12TH INTERNATIONAL ROLLING CONFERENCE
Trieste, 26-28 ottobre 2022
Organizzato dall’AIM e dai CdS Acciaieria, Ambiente e Sicurezza, Forgiatori e Lavorazioni Plastiche dei Metalli
368 partecipanti
IWSQ 2022 – 2ND INTERNATIONAL WORKSHOP ON SURFACE QUALITY OF CONTINUOSLY CAST PRODUCTS
Bergamo, 1-2 dicembre 2022
Organizzato dall’AIM e dai CdS Acciaieria, Forgiatori e Lavorazioni Plastiche dei Metalli
131 partecipanti
CORSI
METALLURGIA PER NON METALLURGISTI Corso - 8-9-15-16-22-23-29-30 marzo - 5-6-12 aprile 2022 Webinar FaRe-
Tra - organizzato dall’AIM
145 partecipanti
ADDITIVE METALLURGY
Corso - 4-10-17-24 maggio 2022 Webinar FaReTra - organizzato dai CdS Metallurgia Fisica e scienza dei Materiali, Metalli Leggeri e Metallurgia delle Polveri e tecnologie additive
43 partecipanti
METALLOGRAFIA
Corso Modulare - Milano, 31 maggio, 7-8-9-14-15-28-29 giugno, 5 luglio 2022
METALLOGRAFIA – mod. NON FERROSI
Ferrara, 14-20-25 ottobre 2022
Ibrido - organizzato dal CdS Trattamenti Termici e Metallografia
73 partecipanti
MICROSCOPIA ELETTRONICA IN SCANSIONE PER METALLURGISTI-SEM (III Edizione)
Corso - Milano, 21 giugno 2022 - Lecco, 22 giugno 2022
Organizzato dal CdS Metallurgia Fisica e scienza dei Materiali
28 partecipanti
TRIBOLOGIA INDUSTRIALE
Corso - 22-23 giugno e Modena, 29-30 giugno 2022
Ibrido - organizzato dal CdS Rivestimenti e tribologia
35 partecipanti
FONDERIA PER NON FONDITORI
Corso modulare - 30 giugno, 1-7-8-12-13-14 luglio 2022 Webinar FaReTra - organizzato dal CdS Fonderia 57 partecipanti
SCUOLA DI METALLURGIA DELLE POLVERI
Imola c/o SACMI, 5-6 luglio 2022
Organizzata dal CdS Metallurgia delle Polveri e tecnologie additive 35 partecipanti
Metallurgy Summer School SURFACE ENGINEERING OF METALS
Bertinoro (FC), 24-27 luglio 2022
Organizzata dall’AIM e COMET 44 partecipanti
PROVE NON DISTRUTTIVE
Corso - Milano, 16-17 novembre 2022
Ibrido - organizzato dal CdS Controllo e Caratterizzazione Prodotti 26 partecipanti
GIORNATE DI STUDIO
IL RUOLO DEI MATERIALI NELL’ECONOMIA DELL’IDROGENO
Giornata di Studio - 27 gennaio 2022
Webinar FaReTra - organizzata dai CdS Corrosione, Metallurgia Fisica e scienza dei Materiali e Materiali per l’Energia 182 partecipanti
LE OPPORTUNITA’ REGIONALI PER LO SVILUPPO DI UN ECOSISTEMA CIRCOLARE NEL SETTORE METALLURGICO
Giornata di Studio - Milano c/o Regione Lombardia, 27 aprile 2022
Organizzata dal CdS Ambiente e Sicurezza 85 partecipanti
Giornata di Studio DIFETTOLOGIA NEI GETTI PRESSOCOLATI: METALLIZZAZIONI 3 maggio 2022
Webinar FaReTra - organizzata dal CdS Pressocolata 41 partecipanti
SVILUPPO TECNOLOGICO DEGLI IMPIANTI DI PRODUZIONE A CALDO DI VERGELLA DI ALTA QUALITÀ PER USI SPECIALI
Giornata di Studio - Lecco c/o Caleotto, 5 maggio 2022
Organizzata dal CdS Lavorazioni Plastiche dei Metalli 106 partecipanti
ALLUMINIO NELL’AUTOMOBILE: LA STORIA INCONTRA IL FUTURO
Giornata di Studio - Ferrara, 20 maggio 2022
Organizzata dal CdS Metalli Leggeri 51 partecipanti
GETTI PRESSOCOLATI PER APPLICAZIONI STRUTTURALI
Giornate di Studio - Brescia c/o Idra, 24 giugno e 29 giugno 2022
Organizzate dal CdS Pressocolata 64 partecipanti
LEGHE PER ALTA TEMPERATURA PRODOTTE CON TECNOLOGIE ADDITIVE
Giornata di Studio - Firenze (c/o Baker Hughes), 15 settembre 2022
Organizzata dal CdS Metallurgia delle Polveri e tecnologie additive 50 partecipanti
MICROSCOPIA ELETTRONICA APPLICATA ALLA FAILURE ANALYSIS
Giornata di Studio - Padova, 23 settembre 2022
Organizzata dal CdS Controllo e Caratterizzazione Prodotti 25 partecipanti
ANALISI INFORTUNI E NEAR MISS NEL SETTORE METALLURGICO
Giornata di Studio - Brescia, 28 settembre 2022
Organizzata dal CdS Ambiente e Sicurezza 117 partecipanti
ALLA SCOPERTA DEI PROCESSI TERMOCHIMICI DI CEMENTAZIONE E NITRURAZIONE CON UNO SGUARDO AL FUTURO
Giornata di Studio - Provaglio d’Iseo c/o Gefran, 6 ottobre 2022
Organizzata dal CdS Trattamenti Termici e Metallografia 57 partecipanti
EBSD: COME E PERCHE’
Giornata di Studio - Aosta c/o Cogne Acciai Speciali, 13 ottobre 2022
Organizzata dal CdS Metallurgia Fisica e scienza dei Materiali 48 partecipanti
LE GHISE STORICHE NELL’ARREDO URBANO: ARTE O INDUSTRIA?
Giornata di Studio - Longiano (FC), 21 ottobre 2022
Organizzata dal CdS Storia della Metallurgia 36 partecipanti
TRATTAMENTI SUPERFICIALI DELL’ALLUMINIO A SCOPO DECORATIVO E PROTETTIVO
Giornata di Studio - 10-11 novembre 2022
webinar FaReTra - organizzata dal CdS Metalli Leggeri 44 partecipanti
SFIDE TECNOLOGICHE NELLA MODIFICA SUPERFICIALE DI MANUFATTI ADDITIVE
Giornata di Studio - Milano, 25 novembre 2022
Organizzata dal CdS Rivestimenti e tribologia
27 partecipanti
DALLA SCELTA ALLA REALIZZAZIONE DI COMPONENTI TRATTATI TERMICAMENTE: COME EVITARE PROBLEMI
TECNICI E CONTRATTUALI?
Giornata di Studio - Brescia, 30 novembre 2022
Organizzata dal CdS Trattamenti Termici e Metallografia
57 partecipanti
SEMINARI
TRASMISSIONI NELL’AUTOMOTIVE: DAL GREZZO AL PROCESSO DI PALLINATURA
Seminario - Modugno (Bari) c/o Magna, 16-17 giugno 2022
Organizzato dal CdS Trattamenti Termici e Metallografia
73 partecipanti
VISITE DI STUDIO
Visita agli impianti c/o Caleotto Spa
Lecco, 5 maggio 2022
nell’ambito della GdS Sviluppo tecnologico degli impianti di produzione a caldo di vergella di alta qualità per usi speciali
Visita guidata c/o CAMERA ANECOICA DEL DE
Ferrara, 20 maggio 2022
nell’ambito della GdS Alluminio nell’automobile: la storia incontra il futuro
Visita in reparto c/o IDRA GROUP
Travagliato (Bs), 24 giugno 2022
nell’ambito della GdS Getti pressocolati per applicazioni strutturali
Visita e attività in laboratorio c/o POLITECNICO DI MILANO – Campus Bovisa
Milano, 5 luglio 2022
nell’ambito del Corso Metallografia
Visita agli impianti c/o SACMI Imola
Imola, 6 luglio 2022
nell’ambito della Scuola Metallurgia delle Polveri
Visita ai laboratori c/o BAKER HUGHES
Firenze, 15 settembre 2022
nell’ambito della GdS Leghe per alta temperatura prodotte con tecnologie additive
Visita agli impianti c/o Gefran
Provaglio d’Iseo, 6 ottobre 2022
nell’ambito della GdS Alla scoperta dei processi termochimici di cementazione e nitrurazione con uno sguardo al futuro
Visita ai laboratori c/o COGNE ACCIAI SPECIALI
Aosta, 13 ottobre 2022
nell’ambito della GdS EBSD: come e perché
Visita guidata al MIG, Museo Italiano della Ghisa
Longiano (Fc), 21 ottobre 2022
nell’ambito della GdS Le ghise storiche nell’arredo urbano: arte o industria?
Visita tecnica c/o ACCIAIERIE BERTOLI SAFAU
Pozzuolo Del Friuli (Ud), 28 ottobre 2022
nell’ambito del Convegno ROLLING-12
INIZIATIVE PATROCINATE E SOSTENUTE DA AIM
RIVESTIMENTI ANTICORROSIVI NELL’AMBIENTE INDUSTRIALE, NAVALE E OIL&GAS. METODI DI APPLICAZIONE, DEGRADO E COMPATIBILITÀ CON LA PROTEZIONE CATODICA
APCE – 21-22 aprile 2022
“E-MOBILITY: RIFERIMENTI, LINEE GUIDA E PROSPETTIVE PER ORIENTARSI IN UN CONTESTO…VUCA!” UPIVEB – 3 maggio 2022
IL MESE DELLA MANUTENZIONE
AIMAN – maggio 2022
METEF
EDIMET – giugno 2022
4TH EMECR - INTERNATIONAL CONFERENCE ON ENERGY AND MATERIAL EFFICIENCY AND CO2
ABM – 7-9 giugno 2022
SULLE VIE DELLA SOSTENIBILITÀ
UPIVEB – 24 giugno 2022
18TH EUROPEAN CONFERENCE ON APPLIED BEHAVIOR ANALYSIS (ABA)
AARBA – 8-9 luglio 2022
SOSTENIBILITÀ E AMBIENTE CARBON FOOTPRINT
UPIVEB – 15 settembre 2022
ARCHEOLOGIA MINERARIA: UN INCONTRO TRA LA STORIA DEL PIANETA E LA STORIA DELL'UOMO
Museo Civico Alpino TAZZETTI – 1 ottobre 2022
MAINTENANCE FORUM: MAINTENANCESTORIES HOMECOMING + MAINTENANCE DAYS
AIMAN – 5 ottobre 2022
CONFERENZA NAZIONALE AIPnD 2022
AIPnD – 19-21 ottobre 2022
BILANCI D’ACCIAIO 2022
SIDERWEB – ottobre-novembre-dicembre 2022
C’È MANUTENZIONE X TE!
AIMAN – 17-18 ottobre 2022
6° CONVEGNO MANUTENZIONE – EVOLUZIONE DEL PARADIGMA 4.0
AIMAN – 7-11 novembre 2022
XXX CONGRESSO NAZIONALE A.I.MAN.
AIMAN – 14-18 novembre 2022
CONVEGNO 4.0 E XXX CONGRESSO NAZIONALE A.I.MAN
AIMAN – 30 novembre 2022
GIORNATA DI STUDIO “PIETRO PEDEFERRI” - TERZA EDIZIONE CORROSIONE SOTTO SFORZO E INFRAGILIMENTO DA IDROGENO
PoliLaPP – 2 dicembre 2022
"SULLE VIE DELLA SOSTENIBILITÀ" - EVENTO N2 ECONOMIA CIRCOLARE
UPIVEB – 2 dicembre 2022
OXI2022 EUROPEAN OXIDE SCALE CONFERENCE - IOM3 CONFERENCE
IOM3 – 5-6 dicembre 2022
RELAZIONE DEL COLLEGIO DEI REVISORI SUL BILANCIO AL 31 DICEMBRE 2022
Signori Soci, il Bilancio di chiusura al 31 dicembre 2022 predisposto dal Vostro Consiglio Direttivo espone i seguenti dati (arrotondati all’unità di Euro):
Possiamo confermarVi che le singole voci dello Stato Patrimoniale e de Conto Economico concordano con le risultanze della contabilità, la cui regolare tenuta a sensi di legge, è stata da noi riscontrata nel corso dell’esercizio. I Revisori ricordano che l’Associazione, come per l’anno precedente, tiene separata contabilmente l’attività istituzionale dall’attività commerciale, al fine del corretto calcolo dell’IVA e delle imposte sul reddito Ires ed Irap. In particolare si da atto che:
- sono state rispettate le norme civilistiche circa la valutazione degli elementi dell’attivo, del passivo e del conto economico;
- le immobilizzazioni materiali ed immateriali sono state sistematicamente ammortizzate in relazione alla loro utilità sociale;
- le attività finanziarie che non costituiscono immobilizzazioni sono state valutate al costo non essendoci state perdite durevoli di valore; l’Associazione ha applicato la deroga prevista dal Decreto Legge 21 giugno 2022, n.73, articolo 45 comma 3-octies in base alla quale sono stati confermati i valori di iscrizione al 31 dicembre 2021 a fronte della destinazione a riserva di utili indisponibile del corrispondente valore delle svalutazioni non operate pari a Euro 76.672.
- i crediti sono valutati al valore presumibile di realizzo;
- le disponibilità liquide, depositi bancari e denaro e valori in cassa, sono espresse in base al valore numerario;
- i fondi rischi sono relativi al fondo svalutazione crediti;
- i ratei e risconti sono iscritti in bilancio nel rispetto della loro competenza temporale;
- il fondo trattamento di fine rapporto dei dipendenti risulta determinato in modo congruo e rappresenta quanto maturato a tale titolo a favore dei dipendenti al netto degli eventuali anticipi corrisposti. L’Associazione ha in essere due polizze assicurative a garanzia delle indennità di cessazione del rapporto dei dipendenti in forza.
- i debiti sono iscritti a bilancio al valore nominale.
I criteri di valutazione utilizzati nella formazione del bilancio chiuso al 31 dicembre 2022 non si discostano dai medesimi utilizzati per la formazione del bilancio del precedente esercizio.
La valutazione delle voci di bilancio è stata fatta ispirandosi a criteri generali di prudenza e competenza nella prospettiva della continuazione dell’attività.
Nel corso dell’esercizio abbiamo vigilato sull’osservanza della legge e dello statuto e sul rispetto dei principi di corretta amministrazione.
Diamo atto quanto segue:
- abbiamo partecipato all’Assemblea Ordinaria dei Soci ed alle riunioni del Consiglio Direttivo, tutte svolte nel rispetto delle norme statutarie e legislative che ne disciplinano il funzionamento;
- abbiamo ottenuto dal Consiglio Direttivo le informazioni sul generale andamento della gestione;
- abbiamo valutato e vigilato sull’adeguatezza del sistema organizzativo ed amministrativo/ contabile;
- abbiamo vigilato sull’impostazione generale data dal Consiglio Direttivo al bilancio chiuso al 31 dicembre 2022, verificandone la rispondenza ai fatti ed alle informazioni di cui abbiamo avuto conoscenza a seguito dell’espletamento dei nostri doveri e quindi non abbiamo osservazioni al riguardo.
In relazione alle informazioni sui fatti di rilievo avvenuti dopo la chiusura dell'esercizio, si segnala, come riportato nella Relazione del Tesoriere, che non sono avvenuti fatti di rilievo da segnalare i cui effetti possano impattare i saldi e le valutazioni del bilancio al 31 dicembre 2022.
Signori Associati, in considerazione di quanto sopra esposto, formuliamo il nostro assenso all’approvazione del bilancio in esame, nonché della proposta del Consiglio Direttivo in merito all’imputazione dell’avanzo di esercizio, pari ad Euro 283.378
IL COLLEGIO DEI REVISORI DEI CONTI Milano, 5 maggio 2023
Dott. Arrigo Berenghi
Dott. Maurizio Perugini
Dott.ssa Anna Giacovelli
STATO PATRIMONIALE 2022
A)
I-
III- ATTIVITA' FINANZIARIE NON IMMOBILIZZATE
RENDICONTO GESTIONALE
BUDGET PER L'ANNO 2023
Eventi AIM / AIM events
CONVEGNI
ECHT 2023 EUROPEAN CONFERENCE HEAT TREATMENT & SURFACE ENGINEERING – Genova, 29-31 maggio 2023
XV GIORNATE NAZIONALI CORROSIONE E PROTEZIONE - Torino, 5-7 luglio 2023 http://www.aimnet.it/gncorrosione/
S2P 2023 INTERNATIONAL CONFERENCE ON SEMISOLID PROCESSING OF ALLOYS AND COMPOSITES –Brescia, 6-8 settembre 2023 http://www.aimnet.it/s2p/
International Workshop on HIGH STRENGTH STEELS – Bergamo, 26-27 ottobre
International Meeting EAF: PRODUCTIVITY, ENERGY EFFICIENCY, RAW MATERIALS AND DECARBONIZATION – Bergamo, 30 novembre-1 dicembre
CORSI E GIORNATE DI STUDIO
Corso RIVESTIMENTI – I MODULO RIVESTIMENTI SOTTILI – Rivoli TO, 8-9 giugno
Corso itinerante MACCHINA FUSORIA – 7-21-22-28-29 giugno
Giornata di Studio SOSTENIBILITÀ IN TRATTAMENTO TERMICO – Veduggio con Colzano MB c/o A. Agrati Spa, 21 giugno
Giornata di Studio FATTORI DI INFLUENZA SULLA RESISTENZA A FATICA DEI MATERIALI METALLICI: ASPETTI TEORICI E CASI APPLICATIVI – Milano, 27 giugno
Giornata di Studio STATO DELL'ARTE ED EVOLUZIONE DEI PROCESSI TERMICI E MECCANICI – Pisa, 12 luglio
Giornata di Studio MATERIALI INNOVATIVI PER IL MONDO RACING – Milano, 4 settembre
Giornata di Studio PROCESSI POST STAMPA ADDITIVA: DAL DESIGN DEL CICLO DI PRODUZIONE AL MANUFATTO – Caravaggio BG c/o TAV, 19 settembre e Nembro BG c/o GFM, 20 settembre
Giornata di Studio MATERIALI METALLICI DA COSTRUZIONE E SOSTENIBILITÀ IN EDILIZIA – webinar, 21-22 settembre
Corso itinerante METALLURGIA SICURA – Lonato BS c/o Feralpi Siderurgica, Brescia c/o ORI Martin, Aosta c/o Cogne Acciai Speciali, 28 settembre e 5-12 ottobre
Giornata di Studio PREVENZIONE E RIDUZIONE DELLE DEFORMAZIONI IN SALDATURA – Genova, 28 settembre c/o Istituto Italiano di Saldatura
Giornata di Studio STATO DI SERVIZIO DEGLI IMPIANTI – ibrido, settembre
Giornata di Studio PALLINATURA E DIFFRATTOMETRIA RX – Agrate Conturbia (NO) c/o GNR, 12 ottobre
Giornata di Studio METALLO DURO – Pallanza VB, 12-13 ottobre
Corso ANALISI CHIMICHE – Milano, 18-19 ottobre
Giornata di Studio INNOVAZIONE DEI MATERIALI NELLA MOBILITA’ ELETTRICA – Bologna
Giornata di Studio CARATTERIZZAZIONE FUNZIONALE DI SUPERFICI MODIFICATE – novembre
Giornata di Studio IL MONDO INDUSTRIAL: ASPETTI METALLURGICI E METODOLOGIE DI CONTROLLO –Torino c/o CNH Industrial Village, novembre
FaReTra (Fair Remote Training) - FORMAZIONE E AGGIORNAMENTO A DISTANZA
Modalità Asincrona (registrazioni)
Giornata di Studio EMERGENZA COSTI ENERGETICI: CHE FARE IN FONDERIA?
Webinar FaReTra IL PRINCIPIO DI MATERIALITÀ NEL REPORTING DI SOSTENIBILITÀ
Giornata di Studio ASPETTI E GESTIONE DELLA NORMATIVA NEL CAMPO DEI TRATTAMENTI TERMICI
Corso PROVE NON DISTRUTTIVE
Giornata di Studio TRATTAMENTI SUPERFICIALI SU ALLUMINIO, A SCOPO DECORATIVO E PROTETTIVO
Corso Modulare METALLOGRAFIA – I MODULO, II MODULO “METALLI NON FERROSI”
Corso modulare FONDERIA PER NON FONDITORI
Corso TRIBOLOGIA INDUSTRIALE – I MODULO
Giornate di Studio GETTI PRESSOCOLATI PER APPLICAZIONI STRUTTURALI
Corso DIFETTOLOGIA NEI GETTI PRESSOCOLATI: METALLIZZAZIONI
Corso ADDITIVE METALLURGY
Corso METALLURGIA PER NON METALLURGISTI
Giornata di Studio PRESSOCOLATA IN ZAMA
Giornata di Studio LA SFIDA DELLA NEUTRALITÀ CARBONICA
Corso itinerante METALLURGIA SICURA
Corso modulare TRATTAMENTI TERMICI
Corso modulare I REFRATTARI E LE LORO APPLICAZIONI
Corso GLI ACCIAI INOSSIDABILI 11ª edizione
Corso FAILURE ANALYSIS 11a edizione
Giornata di Studio PERFORMANCE E DEGRADO DEI MATERIALI METALLICI UTILIZZATI IN CAMPO EOLICO: CAPIRE PER PREVENIRE
L’elenco completo delle iniziative è disponibile sul sito: www.aimnet.it
(*) In caso non sia possibile svolgere la manifestazione in presenza, la stessa verrà erogata a distanza in modalità webinar
Comitati tecnici / Study groups
CT ACCIAIERIA (A)
CT FORGIATURA (F) (riunione congiunta del 04 aprile 2023)
Notizie dal Comitato
Ubaldo Panzone entra a far parte del CT Forgiatura.
Manifestazioni in corso di organizzazione
• Lissignoli, coordinatore insieme a Saleri, segnala che le due GdS “Duplex e superduplex: filiera di produzione e networking (esperienze nella produzione, trasformazione ed utilizzo degli acciai inossidabili bifasici” previste a Erbusco (BS) per i giorni 18 e 19 maggio 2023 hanno raccolto finora oltre 70 partecipanti e si spera di arrivare a 100.
• Mapelli aggiorna sul “Corso itinerante Macchina fusoria”, previsto per giugno. Si stanno verificando le disponibilità delle varie aziende ospitanti con l’obiettivo di avere 4 o 5 visite. Si cercherà di integrare lezioni su stirrer, iniezione di polimeri e biochar. Si definiscono come possibili date: 7-8-21-22-28-29 giugno 2023.
Iniziative future
• Rampinini informa che la GdS “ITER experience for new DTT Enea Fusion Reactor”, ipotizzata in due giornate, non è realizzabile. La fusione non è ancora una tecnologia consolidata e si stanno costruendo impianti (sperimentali) di diversa tipologia per tentare di realizzare una reazione di fusione “conveniente”; la fissione invece si è evoluta fino ad arrivare ad un grado di sicurezza elevato e ora, con l’idea degli “Small nuclear reactor” potrebbe entrare nei progetti di transizione ecologica con costi decisamente inferiori alle attuali centrali.
• Rampinini, per le ragioni su esposte, ha proposto al comitato ristretto (di cui fa parte anche il CT Materiali per l’Energia) di dedicare una giornata al tema della fissione. Il programma potrebbe prevedere un accenno alla fusione e ai materiali che i progetti dedicati hanno gestito (in particolare il 316 LNH) coinvolgendo anche chi ha costruito i particolari e i produttori dei componenti finali. Si potrebbe quindi proseguire con interventi sulla fissione.
• Rampinini ricorda che in ottobre/novembre si svolgerà il Corso Forgiatori: è pronta una prima bozza che sarà controllata e diffusa a tutti i membri del CT per raccogliere disponibilità e commenti.
• Mapelli ricorda che si vorrebbe realizzare una Giornata dedicata al “Clean steel” inteso come progettazione e rimozione delle inclusioni non metalliche, trattando le tematiche di processo e qualità.
CENTRO RIVESTIMENTI E TRIBOLOGIA (R)
(riunione del 10 maggio 2023)
Manifestazioni in corso di organizzazione
• Corso “Rivestimenti” – 1° modulo “Film sottili”: la manifestazione è prevista a Rivoli (TO) l’8 e 9 giugno 2023 ospitata da Anton Paar Italia, che ha organizzato anche la cena sociale. Al momento le iscrizioni sono ancora poche, il presidente invita tutti a promuovere l’evento presso i propri contatti.
Iniziative future
• GdS sulla caratterizzazione delle superfici: viene ripercorsa la scaletta dell’edizione 2016 e si conferma l’intenzione di allargare l’argomento alla caratterizzazione delle superfici non limitandosi ai rivestimenti. Vengono definite in dettaglio le singole presentazioni, eliminandone alcune e accorpandone altre, per poterne introdurre di nuove. Il presidente predisporrà entro metà maggio un foglio condiviso da diffondere a tutti i membri del CT per raccogliere pareri e indicazioni. La giornata sarà fissata in novembre, con sede probabilmente presso un laboratorio in Veneto.
CT METALLI E TECNOLOGIE APPLICATIVE (MTA)
(riunione 10 maggio 2023)
Iniziative future
• GdS su “Sostenibilità ambientale nel campo delle costruzioni civili”: il Presidente Loconsolo contatterà CTA – Collegio dei Tecnici dell’Acciaio – per avere conferma degli interventi e degli argomenti trattati. Se non ci saranno problemi, la data del 22 e 23 giugno potrà
essere fissata, altrimenti si valuterà una seconda data.
• GdS sulla “Saldatura”: per ora si è avuta conferma per 2-3 relazioni. Alcuni altri interventi sono già definiti, e per altri ancora si sta definendo il tema e il possibile relatore. Il coordinatore Rossetti preparerà una bozza del programma per discuterne alla prossima riunione. La GdS dovrebbe essere programmata per fine 2023 o inizio 2024 con il titolo provvisorio: “Riparazioni tramite saldatura – Metallurgia e Tecniche Operative”
• GdS sui metalli impiegati nei motori elettrici: il coordinatore Morri ha inviato una scaletta che viene condivisa dal Presidente. A causa della indisponibilità di qualche relatore, occorre più tempo per concretizzare il programma e quindi la manifestazione si potrà tenere non prima di ottobre.
• Si discute ancora su una possibile GdS sul mercato dei metalli. Al momento non ci sono ancora gli argomenti per organizzare un evento, ma in gruppo organizzatore continuerà a raccogliere informazioni per essere pronti nel 2024.
Normativa / Standards
pubblicate e progetti in inchiesta (aggiornamento 28 marzo 2023)
Norme UNSIDER pubblicate da UNI nel mese di aprile 2023
CEN/TR 10261:2023
Iron and steel - European standards for the determination of chemical composition
EN ISO 13520:2023
Determination of ferrite content in austenitic stainless steel castings (ISO 13520:2023)
Progetti UNSIDER messi allo studio dal CEN (Stage 10.99) – maggio 2023
prEN ISO 19901-2
Petroleum and natural gas industries
— Specific requirements for offshore structures — Part 2: Seismic design procedures and criteria
prEN ISO 21809-3 rev
Oil and gas industries including lower carbon energy — External coatings for buried or submerged pipelines used in pipeline transportation systems — Part 3: Field joint coatings
prEN ISO 21809-5 rev
Petroleum and natural gas industries —
External coatings for buried or submerged pipelines used in pipeline transportation systems — Part 5: External concrete coatings
Progetti UNSIDER in inchiesta prEN e ISO/DIS – maggio 2023
prEN – progetti di norma europei
prEN ISO19901-5
Petroleum and natural gas industries
- Specific requirements for offshore structures - Part 3: Topsides structure (ISO/DIS 19901-3:2022)
ISO/DIS – progetti di norma internazionali
ISO/DIS 11772
Hot rolled longitudinally profiled steel plate
Progetti UNSIDER al voto FprEN e ISO/FDIS – maggio 2023
FprEN – progetti di norma europei
FprEN ISO 10113
Metallic materials - Sheet and stripDetermination of plastic strain ratio (ISO/ FDIS 10113:2019)
ISO/FDIS – progetti di norma internazionali
ISO/FDIS 22974
Petroleum and natural gas industry — Pipeline transportation systems — Pipeline integrity assessment specification
ISO/FDIS 204
Metallic materials — Uniaxial creep testing in tension — Method of test
Norme
giornate nazionali e protezione corrosione
La XV edizione delle Giornate Nazionali sulla Corrosione e Protezione si terrà in presenza a Torino nei giorni 5, 6 e 7 luglio 2023, presso il Politecnico di Torino.
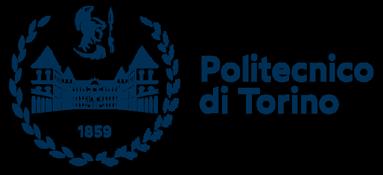
Le Giornate rappresentano l’evento di riferimento a livello nazionale per la discussione ed il confronto sulle questioni scientifiche, tecnologiche e produttive, nell’ambito della corrosione e protezione dei materiali. In particolare, il Convegno prevede la presentazione dei risultati raggiunti da vari gruppi di studio e da numerose aziende del settore.
aree tematiche principali
• Corrosione delle strutture metalliche esposte all’atmosfera

• Corrosione e protezione delle reti idriche interrate
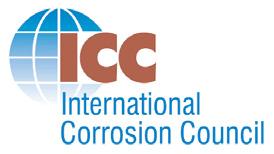
• Corrosione negli impianti industriali
• Protezione catodica: progettazione, collaudo, gestione e monitoraggio
• Comportamento a corrosione di leghe di titanio, nichel e acciai inossidabili
• Corrosione delle opere in calcestruzzo armato
• Corrosione dei beni culturali
• Corrosione negli impianti Oil & Gas
• Degrado e rilascio dei biomateriali metallici
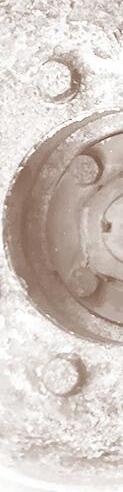
• Rivestimenti e trattamenti superficiali
• Inibitori di corrosione
• Impatto delle nuove tecnologie produttive sulla corrosione
• Tecniche di studio e monitoraggio della corrosione
• Meccanismi di corrosione
• Case histories
programma e iscrizioni
Il programma del Convegno, le quote e le modalità di iscrizione sono disponibili online sul sito www.aimnet.it/gncorrosione
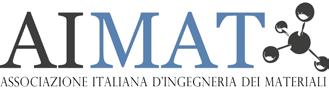
proposte per le aziende
Le aziende interessate ad uno spazio per l’esposizione di apparecchiature, la presentazione dei servizi e la distribuzione di materiale promozionale, possono aderire ad una delle proposte di sponsorizzazione dell’evento. Tutte le informazioni e la modulistica sono disponibili online sul sito dell’evento.
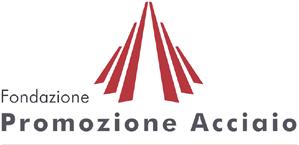
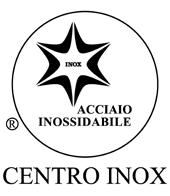
segreteria organizzativa
Via Filippo Turati 8 · 20121 Milano t. +39 0276021132 +39 0276397770 info@aimnet.it · www.aimnet.it
