#cartiflex
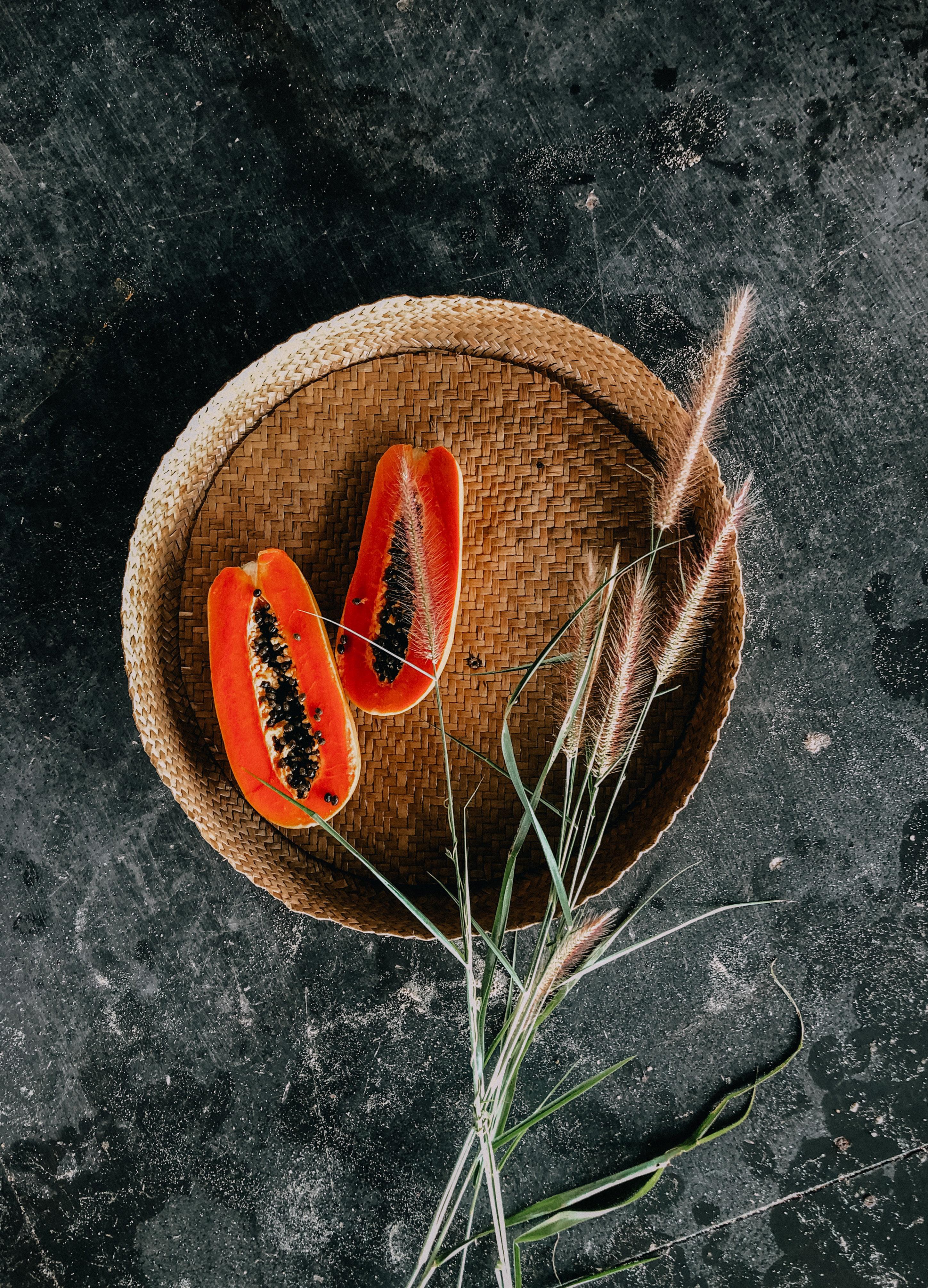
Ofrecemos la digitalización más avanzada para una alta calidad, alta productividad al coste de adquisición más bajo.
Flexo, inkjet o Todo-en-Uno – ahora puedes optimizar por completo tu planta de producción con BOBST.
“No hay nada de malo en esperar lo mejor, siempre y cuando estés preparado para lo peor”
Stephen Edwin King, más conocido como Stephen King y ocasionalmente por su seudónimo Richard Bachman, es un escritor estadounidense de novelas de terror, ficción sobrenatural, misterio, ciencia ficción y literatura fantástica. Sus libros han vendido más de 350 millones de copias y en su mayoría han sido adaptados al cine y a la televisión. Ha publicado 61 novelas (siete de ellas, bajo el seudónimo Richard Bachman) y siete libros de no ficción. Ha escrito, además, alrededor de doscientos relatos y novelas cortas, la mayoría de los cuales han sido recogidos en once colecciones.
Desdeñado por críticos y académicos literarios por ser considerado un autor «comercial», su obra ha generado mayor atención desde la década de 1990, aunque algunos de estos círculos continúan rechazando sus libros. Es criticado regularmente por su estilo presuntamente "no literario" y por la excesiva extensión de algunas de sus novelas. Por el contrario, su sentido de la narración, sus personajes animados y coloridos y su capacidad para jugar con los temores de los lectores han sido objeto de elogios. Si bien en la mayoría de sus historias utiliza el recurso del terror, también aborda de manera regular temáticas como la infancia, el racismo y la guerra, brindando un retrato social muy realista de los Estados Unidos.
Dar precios y vender no es lo mismo. Dando simplemente un presupuesto como respuesta a una solicitud de un cliente se está centrando el tema hacia una sensibilidad con respecto al precio. Existen dos caminos cuando un cliente solicita un precio: presupuestar o vender.
Presupuestar es algo rápido y fácil. Resulta gratificante casi al momento. Tanto si el cliente pide un presupuesto como si el vendedor lo ofrece, el vendedor tiene la sensación de haber completado su obligación en el momento que entrega el presupuesto. En otras palabras, la petición del cliente en cuanto a obtener un precio ha sido respondida. Después, el vendedor acepta una posición paciente, esperando que el cliente decida en qué dirección se va a mover y dejando que el cliente revise el presupuesto y haga preguntas. El vendedor ha creado un estado de “esperanza” y “espera”.
Presupuestar o cotizar es simplemente jugar con números. Puede ser que genere ventas pero lo que va a generar después no es predecible. Los vendedores que van haciendo un número elevado de presupuestos obtendrán, con seguridad, algunas
ventas. La diferencia entre presupuestar y vender, no obstante, es que los resultados de presupuestar no son repetibles, es decir, que el vendedor no va a tener los mismos resultados de ventas en los mismos clientes ni en las mismas situaciones de ventas, una y otra vez.
Vender significa ir aprendiendo las necesidades del cliente y saber por qué las tiene y, entonces, relacionar esas necesidades con las posibilidades de la empresa de servicios gráficos. Si las necesidades y las soluciones coinciden, los temas del presupuesto y el precio van a parar a una posición inferior en la escala de prioridades.
Se debe enfocar el tema hacia los resultados que el cliente desea obtener. El hecho de esperar sin tener una estrategia ni una dirección clara no es parte de la acción de ventas. El verdadero camino hacia una venta se esta-
blece a partir del conocimiento del cliente, antes de dar un precio y antes de empezar a tratar sobre los detalles específicos del proyecto.
El objetivo final de la venta es llenar las máquinas de imprimir: para ello, se precisa llegar a un estado mutuo de entendimiento y de confianza de manera que el cliente quiere comprar, incluso antes de tratar sobre los aspectos específicos de un trabajo o un proyecto individual. La venta crea resultados repetitivos con los que se puede contar hacia el futuro.
La entrega de presupuestos y la venta tienen tres elementos básicos, cada uno de los cuales puede dar resultados enteramente diferentes.
Los tres elementos del presupuesto o cotización
1. Obtener la petición del cliente
2. Entrega del precio
1. Obtener la petición del cliente Éste es el objetivo principal diario de muchos vendedores, con la finalidad de que se pueda, al final, preparar y dar un presupuesto. Conlleva un falso sentido de seguridad y de cumplimiento. Por otra parte, precisa poca experiencia de ventas, poco conocimiento de las necesidades o expectativas del cliente y puede ser llevado a cabo por cualquiera, incluso desde la propia empresa de servicios gráficos.
Tanto si se recibe por e-mail, por teléfono o directamente del cliente en forma personal, la solicitud o consulta, en sí misma, únicamente es una posibilidad de venta. Realmente es la respuesta que dé ese vendedor frente a ese acercamiento del cliente lo que puede establecer la diferencia entre presupuestar y vender.
El hecho de obtener una consulta o petición de precio por parte de un cliente es un paso elemental, que con demasiada frecuencia se interpreta como una gran consecución. El verdadero progreso se realiza cuando ese contacto lleva a un cierto compromiso de comprar por parte del cliente y no cuando, simplemente, lleva a la preparación de un presupuesto. Ni siquiera una vez entregado el presupuesto se puede considerar que el vendedor ha cumplido con su tarea.
2. Entrega del precio
Muchos vendedores consideran que la entrega de un presupuesto ya es un paso automático hacia la creación de una relación sólida con el cliente. No lo es. La preparación y entrega de un presupuesto es una actividad empresarial, es la comunicación de un valor y no tiene, necesariamente, una relación directa proporcional con la venta, ya que los clientes dan un valor importante al seguimiento, la entrega, la relación con el vendedor y el aseguramiento de que se está cumpliendo con sus necesidades y expectativas.
El hecho de dar un precio reduce la acción del vendedor a una rutina, no le da ninguna razón al cliente a considerar a la empresa que oferta o a su vendedor en ningún otro factor que no sea el precio y el vendedor se queda en una posición que supone tan sólo “esperar”.
Se debe enfocar el tema hacia los resultados que el cliente desea obtener. El hecho de esperar sin tener una estrategia ni una dirección clara no es parte de la acción de ventas. El verdadero camino hacia una venta se establece a partir del conocimiento del cliente, antes de dar un precio y antes de empezar a tratar sobre los detalles específicos del proyecto
3. Esperar su decisión
Esto es lo que hacen muchos vendedores después de haber dado un precio y es, por tanto, una pérdida de energía y de oportunidad. La esperanza no es una herramienta de ventas ni un objetivo ni un avance positivo. La esperanza se genera cuando el hecho de dar un precio es puramente un sustituto de la verdadera venta, cuando el vendedor no sabe nada del cliente más que una lista de especificaciones de impresión que se utilizan para crear un presupuesto y, con ello, el vendedor no puede evaluar los resultados que puede tener el servicio que ofrece su empresa en cuanto a cumplir con las necesidades y expectativas de ese cliente. Desgraciadamente, no es a base de “esperanza” como se van obteniendo ventas.
Lo peor que puede suceder cuando un vendedor se dedica a pasar presupuestos más que a vender es que
obtenga el trabajo. Sus acciones y su comportamiento quedan entonces reforzados con ese resultado positivo; en cambio, esos resultados no suponen repetición en situaciones futuras.
La entrega de un presupuesto es algo pasivo, mientras que la venta es algo activo. El presupuesto es una consecuencia de la petición del cliente que es quién a puesto la iniciativa. La recepción de un presupuesto no le da al cliente ninguna razón por la cual haya de comprar de una forma habitual. El vendedor que basa su actividad en la presentación de presupuestos como aspecto base en su proceso de venta está adoptando un papel pasivo y sumiso frente al cliente.
Los tres elementos de la venta
1. Determinar las necesidades del cliente
2. Ofrecer una solución a esas necesidades
3. Dar un precio
1. Determinar las necesidades del cliente
El cliente tiene una necesidad que precisa una solución. La pregunta del cliente frente al vendedor es: “¿Puede usted entender mi necesidad y me puede explicar cómo su empresa me dará una solución?”.
La primera prioridad del vendedor para poder vender en un entorno en el que “el precio no cuente” consiste en definir y entender las necesidades del cliente. Sin conocer este aspecto no
existe venta, tan sólo se trata de pasar un presupuesto. Una petición de precio por parte de un cliente es siempre algo precipitado provocado por una necesidad, ante la cual ese cliente está buscando una solución y pretende encontrarla por sí mismo.
El primer reto del vendedor consiste en descubrir qué hay detrás de esa petición de un precio y conocer las verdaderas necesidades del cliente. Para ello, se pueden plantear las siguientes preguntas:
- ¿Qué es lo que le ha movido a plantear este trabajo?
La intención de esta pregunta, aparte de mostrar interés personal en lo que el cliente está llevando a cabo, es saber lo que hay detrás del trabajo. ¿Qué información se puede obtener, desde el punto de vista del objetivo de la impresión, para descubrir o confirmar la dirección hacia la que se mueve el cliente y poder presentar, quizás, una alternativa que mejore los resultados esperados?
La forma de seguir profundizando en el tema puede ser una pregunta como ésta: ¿Me puede detallar más este aspecto…? Cuanto más pueda aprender el vendedor, más armas tendrá para desplazar a un competidor y sentirse más fuerte en la posición privilegiada frente al cliente.
- ¿Qué es lo que le gustaría que tuviera como resultado este trabajo?
El objetivo del vendedor con esta pregunta es el de poder ofrecer algo que el cliente no esté obteniendo de la competencia (no porque no lo pueda proveer, sino porque no sabe que le podría interesar) de manera que se puedan descubrir aspectos a los que da importancia el cliente y que no tienen nada que ver con el precio.
La forma de seguir adelante con este tema es con una pregunta, como por ejemplo: ¿Puede ser un poco más específico sobre la forma en que va a ser utilizado este trabajo impreso? Se seguirá recibiendo información adicional que el vendedor puede usar para reforzar los resultados que podrán ser ofrecidos por la empresa de servicios gráficos.
- ¿Ha intentado anteriormente llevar a cabo acciones de este tipo con un impreso?
Vale la pena saber lo que funcionó anteriormente y lo que fracasó y, en consecuencia, aquello que se está
Las soluciones, especialmente las soluciones diferentes a las que conoce el cliente, facilitarán que esa empresa de servicios gráficos se diferencie de la competencia y se pueda tener un diálogo más profundo y más abierto por parte del cliente que lleve a una relación más continuada
cambiando en esta ocasión. Los clientes siempre acostumbran a estar abiertos a sugerencias que puedan mejorar los resultados, lo cual precisa, por parte del vendedor, conocer lo que ha sucedido anteriormente.
La forma de seguir con este tema es plantear una pregunta tal como: ¿Cómo se sintió usted con esos resultados anteriores? El hecho de saber su reacción permite plantear un tema tal como, por ejemplo: Si yo le pudiera ayudar a crear un proceso que esta vez le resultara satisfactorio, ¿me consideraría usted como preferente en su lista de empresas de servicios gráficos con las que trabaja?
El conocimiento y la interpretación de las respuestas del cliente es lo que puede llevar a ofrecer una buena solución. Las soluciones, especialmente las soluciones diferentes a las que conoce el cliente, facilitarán que esa empresa de servicios gráficos se diferencie de la competencia y se pueda tener un diálogo más profundo y más abierto por parte del cliente que lleve a una relación más continuada.
Es importante no suponer nunca las que pueden ser las respuestas del cliente. Si se deben entender clara -
mente las necesidades conviene pedir clarificaciones a cualquier respuesta que presente la más pequeña duda.
2. Ofrecer una solución a esas necesidades
En esto es lo que consiste realmente la acción de ventas. En ese momento es cuando el cliente determinará si el vendedor es preferido o no. La segunda prioridad del vendedor, después de determinar las necesidades del cliente, es buscar y definir de qué manera las posibilidades de la planta de impresión pueden aportar una solución a esas necesidades y poder entonces describir y mostrar al cliente, en forma clara y resumida, en qué consiste esa solución.
Vender es aportar soluciones, un proceso a largo plazo que debe sustituir la rápida y peligrosa respuesta de dar tan sólo un precio. La venta tiene lugar antes de entregar el presupuesto. El vendedor que espera a iniciar la venta hasta después de haber cotizado el precio se pone en una posición de tener que “defender el precio”, área en la que las conversaciones normalmente se centran en cómo obtener un precio más bajo o todo lo que puede obtenerse de más por ese mismo precio.
Las “soluciones” que no se conectan bien con las necesidades del cliente, tales como aquellas que presenta el vendedor haciendo supuestos, tendrán un efecto opuesto. El cliente perderá interés debido a que el vendedor demuestra no entender la situación. El vendedor puede bajar un precio y prácticamente regalar el trabajo y, en cambio, el cliente no quedará motivado para comprar lo que ese vendedor presenta.
El trabajo del vendedor consiste en traducir las necesidades del cliente en resultados que puede ofrecer la planta de impresión y presentarlas como soluciones. Por ejemplo:
- Un cliente que está preocupado
sobre la forma de hacer corresponder el color entre el material impreso y el de su producto (especialmente en productos relativos al ramo de la alimentación, los tejidos y la madera) puede estar interesado en conocer detalles sobre los procesos de pruebas. Ésta puede ser la solución temporal o parte de ella que quizás el cliente está buscando.
- El servicio de tipo personal, de tipo práctico, puede ser la solución para otro cliente. El cliente puede desear que exista una persona de contacto o representante de servicio al cliente que esté siempre “a mano” durante todo el proceso, especialmente si ese cliente sugirió tener una falta de confianza sobre lo que puede suceder durante el proceso de producción o ya expresó disconformidades respecto a experiencias anteriores con ese o con otro suministrador de servicios gráficos durante otro proyecto.
- Un cliente que está preocupado por el plazo de entrega, por la rapidez en la producción y porque debe distribuir sus materiales en un tiempo corto, puede estar abierto a nuevos desarrollos
tales como las pruebas en pantalla o a través de Internet, lo cual elimina no solamente horas, sino a veces días en el proceso de preimpresión. La solución podría estar entonces en preparar una reunión entre el jefe de preimpresión y el cliente.
- La distribución, la entrega final de muestras o el seguimiento una vez terminado el trabajo (incluso temas relativos a la facturación y a los procedimientos de contabilidad) son aspectos comunes sobre los que, muchas veces, los clientes consideran que no se están cumpliendo sus necesidades o expectativas. Si el cliente expresó alguno de estos tipos de preocupaciones, se debería entonces centrar la acción en esos aspectos para tratarlos adecuadamente.
Una solución práctica y efectiva podría ser una corta reunión entre el cliente y el representante de la empresa de servicios gráficos que se responsabilice de cada una de esas operaciones. Este paso en sí mismo, en el cual el cliente y la empresa, a nivel de producción, se encuentran cara a cara, establece mucha diferencia en la forma
de trabajar y la manera de entender los productos.
3. Dar un precio
El precio no es nada más que un valor en dinero del coste para llegar a la solución que necesita el cliente. El hecho de dar un precio es el resultado natural del proceso de venta pero no es el centro alrededor del cual se establece ese proceso. Es, simplemente, el intercambio de valor entre lo que está dando la empresa de servicios gráficos y lo que está recibiendo el cliente en cuanto a funcionalidad. Al vender, es totalmente posible obtener una venta, o llegar a un punto suficiente de compromiso por parte del cliente, antes de haber dado el precio. Pero las decisiones no se toman solamente en base al precio.
Los compradores sitúan primero, como prioridad, sus necesidades y expectativas específicas. Cuando se cumplen estos aspectos la decisión de a quién se compra se tomará antes de recibir el presupuesto.
Más información en www.rccsa.net
Creo que todos recordamos las famosas letras JDF (Job Definition File), ¿te acuerdas?. Hace unos pocos años atrás se habló mucho y mucho de ellas, este artículo no trata sobre lo que ha conseguido, de si continua su desarrollo o si por el contrario ha sido una leyenda urbana, sobre ello “el JDF” hablaré en otro articulo. Pero si que me da pie para escribir este con el que quiero que aprendas cómo ha evolucionado todo, sobre todo en el ámbito de la postimpresión para pequeñas cantidades y/o en tamaños de pequeño formato impreso en máquinas digitales.
Como ya sabrás, en los últimos años, la demanda de la impresión ha cambiado mucho, no voy a descubrirte nada al decirte que la cantidad de impresos se ha visto reducida drásticamente, cómo es lógico muchas de estas impresiones se realizan mediante la impresión digital en pequeño formato. Pero una cosa es la impresión y otra el proceso de postimpresión que se requiere para cada una de ellas.
Si te paras a pensar, cuanto mayor es el número de pedidos que realizamos, la necesidad de que estos se automaticen es mayor, la impresión digital no tiene mucho misterio, cada máquina permite imprimir x cantidad de copias en función del tipo de material y por supuesto de la capacidad de impresión de cada máquina. El proble-
ma viene cuando se tienen que finalizar esos impresos, bien por el tema de plegados, encuadernación, guillotina, etc.
Si pensamos en la postimpresión tradicional el funcionamiento es diferente, realizamos la preparación de la/s máquina/s para procesar cientos o miles de hojas que tienen que realizar corte, encuadernación, plegado, etc., podemos estar 5/10 minutos preparando el programa y/o ajustes de la máquina sin que eso conlleve una merma significativa en la productividad de la empresa.
Pero, la postimpresión que se realiza de las impresiones digitales es muy distinta, cada trabajo que realizamos
puede tener unas características diferentes: medidas, acabados, tipo de plegado, etc. Es una de las ventajas e inconvenientes existentes, es por ello que si tenemos que preparar la/s máquina/s de postimpresión sin ningún tipo de automatización sería una locura y lo único que conseguiríamos es un enorme culo de botella donde perderíamos productividad. Podemos pensar que la preparación de una de estas máquinas es de unos 5 minutos (no es mucho), pero, ¿que ocurre si tenemos 20 trabajos con medidas diferentes?, sencillo multiplica 5*20 y verás la cantidad de tiempo que se pierde, y, ahora continúa multiplicando por más trabajos y días de producción, al final el resultado es alarmante, de ahí que sea del todo necesario su automatización.
Debido a esta necesidad, la mayoría de fabricantes que fabrican máquinas de postimpresión para impresos digitales han buscando soluciones que fueran sencillas de implementar, aunque el JDF continúa siendo el estándar para integrar la automatización global, su implementación no es sencilla, por eso han desarrollado nuevos sistemas que permitieran algo similar al JDF pero que a su vez, su puesta en marcha, funcionamiento y conectividad fueran sencillos de realizar. Consiguiendo de esta forma que la mayoría de empresas puedan implementar la automatización de estos dispositivos sin tener que realizar grandes inversiones en JDF.
Es posible que pienses “Dani”, todo esto esta muy bien, pero, ¿qué opciones de automatización existen?. La verdad es que existen varias de ellas, y, cómo leerás las hay para todas las necesidades:
Memoria Manual: Igual que antiguamente, cada una de estas maquinas permite almacenar una serie de programas manualmente, en ellos normalmente solemos almacenar los ajustes de los tipos de trabajos más repetitivos. No nos engañemos, esto no es automatización, este es el sistema con el que hemos trabajado siempre.
Códigos QR: En la actualidad, la mayoría de las máquinas de Postimpresión, permiten guardar diferentes programas con ajustes ya preestablecidos y asignarles un código. Este código se puede poner mediante código QR en cada hoja de impresión, para que de esta forma el lector de la máquina lea el código de cada hoja de impresión para utilizar en cada una de ellas el programa indicado en el código QR. Aquí ya tenemos un avance importante, el problema es que trabajamos con medidas estáticas.
QR Inteligentes: En un nivel de automatización superior es la utilización de códigos QR inteligentes, dónde aquí ya no solamente indicaremos en el QR el número de programa a utilizar, sino que además indicaremos las medidas a utilizar, estas medidas pueden ser variables, la máquina se ajustará según los datos introducidos o requeridos en el código QR.
Vinculación de diferentes dispositivos: Cómo es lógico el sistema más avanzado es el que no solamente permite automatizar una máquina, sino con el que podemos automatizar varias de ellas mediante una integración total. Para ello existen soluciones en las que damos de alta nuestros dispositivos de postimpresión con las capacidades de cada uno de ellos. En este caso al crear la imposición que se crea un JDF con toda la información, posteriormente se divide y envía a cada máquina por separado. Esto sería la Automatización total.
¿Quién controla todo esto?
Inicialmente se podría pensar que esto lo gestiona el ERP o Programa de Gestión mediante JDF, pero, cómo te he comentado la implementación del JDF no es una tarea sencilla para la mayoría de empresas, entonces, ¿quién lo controla?. Muy sencillo, el software de imposición es el encargado de ello. Ten en cuenta que es el que sabe las medidas, los cortes, tipo de plegado, etc. Al conocer toda esta información es el que se encarga según el tipo de trabajo de añadir los códigos necesarios para los dispositivos de postimpresión. Perfecto, ¿a esto le podemos llamar Imposición
4.0?, si y no, un sistema de Imposición
4.0 es mucho más que esto, pero si que tiene una parte en la que se utiliza la conexión con otros sistemas mediante la inserción automática de códigos QR con datos fijos o variables según el tipo de imposición realizada, además de mucha más información.
Todas, en el mercado actual en el que vivimos y sobre todo en el de la postimpresión para impresos digitales tener o no tenerlos automatizados es una gran diferencia. Cómo has leído no son sistemas caros o complejos de implementar, existen varias opciones y formas para ponerlos en marcha sin que ello suponga unos altos conocimientos técnicos o una gran inversión.
Está claro que todo lo que sea automatizar conlleva una mejora sustancial en la producción, tanto por productividad cómo por seguridad en los trabajos realizados. Como has leído existen diferentes formas para conseguirlo, unas más automáticas que las otras, es posible comenzar por algo sencillo para paulatinamente ir aumentando el grado de automatización. Ten en cuenta que hoy en día la mayoría de maquinas de postimpresión permiten su conectividad y automatización, sería ilógico no aprovecharnos de ello y comenzar su implementación. Los fabricantes han desarrollado diferentes formas para conseguirlo y la verdad es que creo que lo han conseguido. Es cierto que cinco minutos de preparación manual no es mucho, pero ya has visto que la suma de muchos minutos es la diferencia entre ser productivo y rentable o no. ¿qué opinas?, ¿aun piensas que 5 minutos no es mucho o estás en el lado de la automatización?
En el pasado artículo hablé de forma genérica de la impresión con una paleta de colores fija. He recibido bastantes preguntas y comentarios al respecto así que he decidido recopilar las respuestas y compartirlas con el resto de lectores, para todos aquellos a los que le pueda interesar.
Como recordatorio, definimos la impresión en paleta fija de colores como una solución que nos permite disponer de unos colores concretos en nuestro sistema de impresión y mantenerlos para el máximo número de trabajos.
De esta simple definición me llegaron varios comentarios:
- Si estos sistemas no pueden sustituir el 100% de la carta Pantone, esto se convierte en una utopía y no sabemos verle la rentabilidad.
Ciertamente, comentamos que no es posible sustituir el 100% de la carta Pantone.
Hemos de tener en cuenta el sistema de impresión que utilizamos, el tipo de tintas y la lineatura a la que trabajamos, esto determina la cantidad de colores que finalmente podremos llegar a sustituir, y como decíamos, no llegaremos probablemente ni a un 90%. Esto es debido a varios factores:
- Como decíamos, según las tintas que usemos y el sistema de impresión
nos encontraremos con Pantone que no vamos a poder reproducir, puesto que su conversión no nos dará un valor de Delta E inferior a 3, por lo que, la diferencia tonal será demasiado elevada para cumplir los estándares establecidos.
- Por otro lado, hay otros Pantone que al ser convertidos a diferentes tintas van a necesitar tramarse y, aunque el Delta E esté dentro de los parámetros aceptados, según sea la lineatura a la que trabajemos podemos ver el efecto de la trama. Este efecto visual que no va a ser lo deseado por el cliente, por lo que no deberíamos usarlo.
Sabiendo esto nos hemos de seguir preguntando si puede ser viable y rentable una solución de este tipo y para ello deberíamos preguntarnos qué configuración tenemos en nuestro taller:
Si tenemos mas de un equipo de impresión, podemos destinar uno de ellos a mantener esta paleta fija de colores para los trabajos que sí sean compatibles, y en el resto de máquinas de impresión seguir trabajando como hasta
ahora, con cambio de colores.
Si calculamos el coste en cambio de trabajo que tienen nuestros equipos actuales y el número de cambios que realizamos, sacaremos rápidamente números favorables para esta implementación en un solo equipo de impresión.
Si no tenemos mas que un equipo de impresión, deberemos realizar un estudio de número de trabajos que sean viables de convertir y de cómo tenemos estructurado el sistema de planificación.
Si podemos trabajar con una buena planificación de trabajos y reunir aquellos que cumplan estas características, nos ahorraremos gran parte de los cambios de trabajo, y para los que no, será un cambio mas.
Tengamos en cuenta que, aunque el porcentaje del estudio sobre el número de trabajos que podríamos realizar en esta tecnología sea bajo, hemos de ver el coste de estos pocos cambios de trabajos que nos ahorramos, y si esto nos compensa incluir este tipo de tec-
nologías, que, como dije en el anterior artículo, no sólo nos reportan ahorro de costes, sino que nos aportan un salto tecnológico para nuestros clientes, que ya demandan de estas tecnologías. Por otro lado, nos preguntabais:
¿Qué ocurre si mi equipo de impresión sólo tiene 6 cuerpos?
Para implementar estos sistemas la mejor opción siempre es tener una máquina de 7 colores, para poder añadirle a la cuatricromía, los tres colores complementarios que ayudan a ampliar al máximo la gama tonal y representar el máximo número de tintas planas.
Dicho esto, ¿qué ocurre si sólo tengo equipos de 6 cuerpos?
Raramente los trabajos necesitaran de los 3 colores complementarios, pero, al fin y al cabo, casi todos los trabajos necesitan de alguno de estos tres. Esto convierte el proyecto de manera que pasamos a tener 3 combinaciones diferentes, en vez de una sola. Las combinaciones de tintas que podremos crear serán las siguientes:
- CMYK GV (Verde y Violeta)
- CMYK GO (Verde y Naranja)
- CMYK VO (Violeta y Naranja)
Si tenemos una buena planificación de trabajos podremos cambiar únicamente uno de los colores cuando sea necesario.
Con ello el número de cambios de trabajo se verá disminuido drásticamente y el ahorro asegurado.
Pero, como decía anteriormente, siempre hemos de realizar primero un estudio de los trabajos que tenemos para ver la rentabilidad del proyecto.
¿Cuáles son las tintas idóneas para trabajar con estas tecnologías?
Si lo que pretendemos es estandarizar al máximo nuestra producción, no tiene sentido que usemos tintas especiales para los colores de cuatricromía, por lo que yo os recomendaría seguir usando las mismas tintas que usáis en la actualidad.
Para los 3 colores complementarios, coloquialmente hablamos de Verde (Green), Violeta o Azul (Violet)y Naranja (Orange). Especificar qué colores concretos vamos a usar depende del siste-
ma de impresión con el que estemos trabajando y el tipo de tintas a usar, por lo que según si trabajamos en Offset, Flexografía o huecograbado y según sean las tintas: grasas, UV, solventes, base agua…, la definición de los colores puede ser diferente.
En los procesos de implementación se definen estos colores de forma conjunta entre el especialista y la imprenta de forma que se halle la mejor solución para el sistema en cuestión y para la configuración general de toda la imprenta.
Hay colores de marca que pueden hacer decantar algún color por un color específico debido al volumen de impresión de un cliente en concreto, usando este Pantone o tinta especial como uno de los colores complementarios.
En el próximo artículo os contaré de forma mas detallada el proceso de implementación que se realiza para que pueda entenderse la forma de trabajar en la producción diaria.
Como en el anterior escrito, os animo a que me lancéis las dudas y preguntas que os surjan para poder aclararos al máximo estos conceptos.
Asahi Photoproducts, pionera en el desarrollo de planchas de fotopolímero flexográficas, informó de su exitosa participación en SinoFlex, la plataforma comercial líder en Asia que se enfoca en embalajes flexibles.
En la feria, que se celebró en Shanghái del 14 al 16 de julio, Asahi presentó su nueva plancha flexográfica lavable en agua AWP™ CleanFlat FlatTop lista para usar con tecnología CleanPrint, y mostró su gama completa de planchas CleanPrint, explicando a Los asistentes vieron cómo estas planchas no solo ofrecen impresión flexográfica en armonía con el medio ambiente, sino que también brindan una calidad mejorada y una eficacia general del equipo (OEE). Las planchas Asahi CleanPrint están disponibles para una amplia gama de aplicaciones y sustratos y han sido desarrolladas específicamente por nuestros ingenieros químicos para transferir la tinta restante al sustrato impreso, lo que reduce las paradas de prensa para la limpieza de planchas y ofrece una calidad uniforme excepcional durante todo el ciclo.
“Estamos muy contentos con la cálida recepción de los asistentes a nuestra línea de planchas CleanPrint, especialmente la plancha FlatTop lavable con agua AWP™ CleanFlat que hizo su debut mundial en la feria”, dijo Ryo Ichihashi, (Gerente de ASEM China). “En toda Asia, las operaciones de impresión flexográfica buscan procesos de producción de planchas más sostenibles a medida que se concentra en reducir su huella de carbono. La línea de placas CleanPrint de Asahi cumple todos los requisitos en este sentido".
La plancha Asahi AWP™ CleanFlat FlatTop con tecnología CleanPrint se utiliza fuera de la caja sin necesidad de
un flujo de trabajo o equipo especial. Las planchas CleanFlat son compatibles con los flujos de trabajo estándar, incluidos los tubos de luz de banco UV, los sistemas de exposición UV LED o FULL HD, así como las modernas tecnologías de detección de microcélulas para garantizar el más alto nivel de calidad y consistencia en toda la tirada de impresión.
Otras planchas Asahi CleanPrint que se exhibieron en la feria incluyeron:
- AWP ™ -DEW, ideal para aplicaciones flexográficas de la más alta calidad, incluidos envases y etiquetas flexibles. Diseñado para alejarse del procesamiento de planchas a base de solventes de lavado de COV, ofreciendo una alternativa más limpia a la industria flexográfica.
- AFP ™ BFTK, una solución de planchas FlatTop de lavado con disolvente de alta calidad con la mejor consistencia de imprenta de su clase. Estas planchas ofrecen una mejor disposición de la tinta en sustratos de etiquetas, papel y película de embalaje flexible de banda ancha en combinación con patrones de tramado sólidos y mantienen los puntos destacados con una calidad perfecta.
- AFP ™ Leggero, planchas súper blandas diseñadas específicamente para imprimir con una presión mínima al tocar las cajas de transporte de cartón ondulado, lo que proporciona un mínimo de lavado y una buena cobertura de tinta para obtener la máxima calidad al tiempo que elimina el aplasta-
miento de la tabla para proteger mejor los productos empaquetados.
- AFP ™ -TOP, una plancha flexográfica digital dura de primera calidad que ofrece una amplia gama de colores y tonos suaves que se desvanecen hasta cero. La presión de impresión al tacto facilita la calidad de impresión repetible y menos paradas de la prensa de limpieza. Compatible con tecnologías de tramado de alta definición y patrones de microcélulas.
- AFP ™ -TSP, el plato perfecto para tintas pegajosas y para productos como el envasado de alimentos para mascotas. Es la solución de plancha perfecta para la mayoría de las fórmulas de tinta pegajosa, lo que permite menos paradas de limpieza de la prensa y una calidad de impresión constante.
- AFP ™ -APC / TPC son planchas digitales y analógicas desarrolladas para el mercado de la impresión de señalización y visualización de cartón ondulado de alta calidad, donde la calidad de la imagen es importante. En cartulina revestida de doble ranura, la plancha ofrece con su tecnología CleanPrint un rendimiento de impresión de imagen excepcional con un mínimo de marcación de ranura de ganancia de punto.
"Los visitantes de nuestro stand se alegraron de ver cuán extensa es la línea CleanPrint de Asahi", agregó Ryo Ichihashi, (Gerente de ASEM China), "con las planchas CleanPrint ahora disponibles para casi cualquier aplicación flexográfica".
Con más de 35 años de experiencia en la industria gráfica, Chemence Graphics, empresa líder en soluciones de preimpresión flexográfica, fue pionero en el mercado español años atrás con la instalación de un CTP KODAK FLEXCEL NX Wide 4260. Ahora ha decidido agrandar el formato de la laminadora e instalar un sistema KODAK FLEXCEL NX Wide 5080 también de Miraclon, en sus instalaciones de Amposta, España. El nuevo equipo les va a permitir "fabricar clichés para el mercado del cartón ondulado, de la más alta calidad, de gran tamaño, sin necesidad de realizar empalmes, ahorrando mermas y optimizando la producción", explica Jorge Rubio, Gerente de Chemence Graphics.
"Las planchas de mayor tamaño nos ofrecen flexibilidad a la hora de combinar trabajos, lo que nos permite ser más agiles y reducir la merma producida, gracias al formato máximo de plancha de 1.270 x 2.032 mm. Utilizamos la plancha KODAK FLEXCEL NXC que permite obtener mejor cubrición de tinta en impresiones de tintas planas, y una buena transición en degradados. De este modo ayudamos al impresor de cartón ondulado a minimizar el efecto de las ondas de material, permitiendo trabajar con menos presión entre la plancha y el soporte", comenta Rubio.
Para el Gerente de Chemence estaba claro que Miraclon iba a ser la empresa elegida para realizar esta mejora en la empresa. "Chemence Graphics Spain tiene un gran parque de maquinaria para producir todo tipo de clichés, y es verdad que en los últimos años el sector en general ha avanzado mucho en calidad, tanto en plancha como en maquinaria y software, pero la tecnología Flexcel de Miraclon todavía está un paso por delante a nivel de calidad, y nosotros hemos querido seguir apostando por ofrecer la más alta calidad posible".
Con la instalación del sistema Kodak FLEXCEL NX Wide 5080 Chemence ha mejorado no sólo en calidad y en flexibilidad de formato, sino que también ha incrementado su capacidad de producción aproximadamente un 40%, asegura Rubio, así que se muestra satisfecho con la inversión realizada. "Llevamos muchos años trabajando con el sistema FLEXCEL NX y estamos plenamente
convencidos de su calidad y resultados. Tanto nosotros como nuestros clientes que utilizan esta solución estamos totalmente satisfechos. Y aunque todavía es
pronto para valorar el impacto del nuevo equipo, ya que la instalación es reciente, no tenemos dudas de que la calidad que ofrece el sistema FLEXCEL
NX, junto con nuestra experiencia con la tecnología NX nos ponen en la vanguardia de la calidad en España".
La reproducción fina de las imágenes, el contraste de impresión y las altas densidades de impresión aportadas por el sistema FLEXCEL NX permiten a Chemence competir en trabajos que tradicionalmente quedaban fuera de las capacidades de la flexografía, de modo que los clientes finales pueden aprovechar la flexibilidad y la rentabilidad de la flexografía y la calidad que normalmente esperarían del offset, el huecograbado o la impresión digital. Además, las planchas Flexcel NX proporcionan eficiencias de impresión como unos tiempos de preparación más breves, menores residuos y mayor vida útil de la plancha.
DIGICAP NX Patterning y Tecnología de Filmación KODAK SQUARESPOT de Miraclon
La texturización de la superficie de la plancha mediante el Kodak DIGICAP NX Patterning, que forma parte del Sistema FLEXCEL NX, garantiza mayores densidades, una gama de colores más amplia y mejoras en el aprovechamiento de planchas combinadas, lo que abre la oportunidad de reducir el número de planchas requeridas para cada trabajo. Rubio comenta al respecto que "la posibilidad de utilizar DIGICAP NX Patterning nos ha permitido mejorar la transferencia de tinta sobre distintos soportes y por lo tanto conseguir mayores densidades, así como ampliar el gamut de color. También realizar los planteamientos de diseños con menos colores, resolvien-
Chemence Graphics Spain tiene un gran parque de maquinaria para producir todo tipo de clichés, y es verdad que en los últimos años el sector en general ha avanzado mucho en calidad, tanto en plancha como en maquinaria y software, pero la tecnología Flexcel de Miraclon todavía está un paso por delante a nivel de calidad, y nosotros hemos querido seguir apostando por ofrecer la más alta calidad posible
do en algunos casos los trabajos con un número menor de tintas".
Chemence Graphics Spain también utiliza la tecnología de filmación
KODAK SQUAREspot para proporcionar una calidad, productividad y uniformidad excepcionales que para Jorge Rubio son incuestionables. "Esta tecnología nos da la posibilidad de trabajar con una resolución de grabación muy alta, nos permite grabar consistentemente porcentajes mínimos por debajo del 1%, consiguiendo así un gran resultado en diseños con altas luces. También nos facilita mantener nuestro proceso con mayor estabilidad, y comercialmente estas prestaciones, nos permiten aplicar mejoras en los distintos mercados que servimos". "Miraclon es, desde hace muchos
años, un proveedor clave para Chemence Graphics Spain. Cooperamos en varios proyectos y ofrecemos una solución diferenciada y nos apoyan en nuestro objetivo de ofrecer la mayor calidad y el mejor servicio. Respecto a la calidad, estamos haciendo pruebas con tramas alternativas con las que estamos obteniendo resultados extraordinarios. En cuanto al nivel de servicio, la nueva planta de producción y un renovado equipo en Madrid nos acerca a nuestros clientes de la zona centro y nos permite cubrir los estándares de servicio más exigentes. Actualmente, servimos directamente tanto en Cataluña, como en Levante, y ahora también en Madrid", concluye el Gerente de Chemence Graphics, Jorge Rubio.
Chemence Graphics
Chemence Graphics surgió a partir de la adquisición de varias compañías de preimpresión reconocidas en el sector europeo de la flexografía. Todas estas compañías contaban con una gran riqueza de conocimientos y una amplia experiencia construida a lo largo de muchos años, suministrando soluciones a medida para la cambiante industria gráfica y con un compromiso importante a nivel de medio ambiente y de Normas de Calidad. Actualmente Chemence Graphics dispone en Europa de 4 sedes repartidas entre España y Francia y un total de 150 empleados permitiendo ofrecer a su cliente una gestión global y optimizada de su packaging.
"Nuestro trabajo es principalmente la fabricación de todo tipo de clichés para flexografía, con particular énfasis en impresiones de alta calidad y enfocándonos en el valor añadido que ofrece nuestro equipo experto en preimpresión. Además, Chemence Graphics Spain es de los pocos proveedores que cuenta también con una división fabricante de troqueles para cartón ondulado", precisa Jorge Rubio.
"Desde nuestra implantación en España, a finales de 2014, estamos comprometidos con una mejora continua y progresiva y el mercado va reconociendo nuestro buen trabajo. Nos hemos convertido en un proveedor total, esto es, ofrecemos la gama más amplia de calidades de cliché y producción local", concluye Rubio.
Esko ha lanzado una novedad mundial en la producción conectada de packaging, sacando el máximo rendimiento a las prestaciones de la Impresión de Datos Variables (VDP) segura tanto en términos de velocidad como de escala para una nueva colaboración con Scantrust y la empresa pionera en packaging ePac Flexible Packaging®. Esko Automation Engine se halla en el centro de la operación, con su innovadora tecnología de VDP, que permite imprimir códigos QR seguros y serializados a gran escala, impulsando el potencial de la VDP para el nuevo servicio de packaging conectado y productos conectados, ePacConnect™.
“La Impresión de Datos Variables puede llevar el papel del packaging a un nivel totalmente nuevo”, ha comentado Paul Land, Product Manager de Esko. “Haciendo posible la localización, serialización, personalización y trazabilidad, los avances en la automatización hacen que ahora se pueda aprovechar aún más la tecnología para transformar el entorno de la preimpresión”.
Utilizando la nube para un acceso global 24/7 a los datos y nuevas prestaciones de escalabilidad, Automation Engine permite a ePac delimitar el potencial de la VDP para una organización, sin inconvenientes.
“Conectando el módulo de VDP de Automation Engine con Scantrust, hemos creado una estructura de códigos que facilita el uso por parte de los convertidores”, ha señalado Paul. “Esta implementación no es solo la primera de su tipo, sino que también hace posible prestaciones que antes era difícil lograr”.
Como todos los envases flexibles de ePacConnect™ incluyen un código QR Scantrust, todas las bolsas se convierten en un acceso a Internet. El código único incluido en el envase, que es más pequeño que un sello postal, activa el conjunto de productos conectados y herramientas de packaging conectadas de Scantrust. Las funciones accesibles van desde herramientas para implicar al consumidor hasta funciones activas para proteger la marca y evitar falsificaciones, que funcionan mediante el escaneo de un código QR seguro del envase.
“Scantrust proporciona a todos y cada uno de los productos físicos un identificador digital único, lo que añade complejidad para la preimpresión y la producción” ha comentado Peter Kostur, director de Ventas y Colaboraciones de Scantrust. “Nuestra plataforma puede proporcionar protección contra las falsificaciones y mejorar
Como todos los envases flexibles de ePacConnect™ incluyen un código QR Scantrust, todas las bolsas se convierten en un acceso a Internet.
la trazabilidad en la cadena de suministro, ya que se puede localizar cualquier etiqueta, bolsa o botella, incluso cuando esté en manos del consumidor”, ha añadido. “Las marcas utilizan dicha tecnología de interfaz digital para conectar con los consumidores, integrarse con plataformas de fidelidad y herramientas de gestión de relaciones con el cliente, y también para operaciones internas de la cadena de suministro”. Al incentivar a los clientes para que interaccionen con los productos, no solo se puede mejorar considerablemente la relación y la confianza entre la marca y el consumidor, sino que también se puede ayudar obteniendo de forma colaborativa datos de la cadena de suministro para realizar mejoras estratégicas adicionales.
“La elaboración de un packaging conectado consta de tres elementos”, ha añadido Peter. “Hay un código QR variable, un entorno móvil que posibilita las interacciones de los clientes y una plataforma que permite al cliente gestionar los códigos y el contenido de los productos y extraer los datos. No obstante, cada proyecto empieza con un pregunta por parte de la marca: ¿cómo obtenemos los datos variables de nuestro producto?”
Con Automation Engine, integrar los requisitos de la VDP es tan sencillo como hacer unos pocos clics. “Ahora,
es sencillo integrar los requisitos de la VDP en el proceso”, ha señalado Paul Land. “El proceso puede tener lugar incluso en la nube, para una mayor flexibilidad de cara a la impresión de un trabajo desde cualquier lugar”.
“Normalmente, una vez introducidos los detalles del pedido, la información pasa por Automation Engine, que actúa como la plataforma de enlace entre todos los sistemas”, ha añadido. “Recopila y recupera la información de los datos variables, determinando las cantidades y parámetros del trabajo. Por ejemplo, con una cantidad de 100.000 registros, amplía los archivos y los elementos variables para imprimir y, a continuación, amplía automáticamente el archivo de muestra a las cantidades necesarias (cada una con su código QR único) y las prepara para pro-
ducción. Gracias a la automatización, un proceso que solía llevar horas o incluso días, ahora se completa en tan solo unos minutos”.
Ryan Kiley, director de Desarrollo comercial de ePac Flexible Packaging®, ha comentado que la capacidad de producir VDP a gran escala independientemente del volumen de la tirada ha marcado la diferencia. “La escala es el momento de la verdad”, ha señalado. “La escala es lo que podemos lograr trabajando juntos”. Ahora, con un solo clic, un cliente puede convertir su packaging en una plataforma interactiva que proporciona la implicación del cliente, la prueba de la procedencia y la protección de la marca y, a la par, reduce puntos de contacto en la preimpresión y la producción.
“Con la automatización de la VDP,
podemos acelerar nuestro crecimiento, ya que añadimos plantas, personal, sistemas, idiomas, monedas, sustratos, estructuras y otras tecnologías”, ha comentado Ryan. “Y el hecho de que Automation Engine se base en la nube supone que tengamos el control total de nuestra producción: nuestros equipos pueden acceder a los archivos desde cualquier lugar y a cualquier hora para un funcionamiento 24/7, podemos ampliar o reducir la producción para satisfacer la demanda y podemos derivar la producción a cualquier planta del mundo”.
“Por consiguiente, nuestro servicio ePacConnect™ ha logrado un packaging flexible y personalizado con funciones de packaging conectado con un coste anticipado mínimo o cero, requisitos de pedido mínimo inferiores y una configuración técnica mínima”.
Flint Group anuncia que ha firmado un acuerdo definitivo para vender su división XSYS (“XSYS”), que se especializa en el desarrollo y suministro de planchas de impresión, manguitos y adaptadores, y equipos de preimpresión para la industria del embalaje, a una filial de Lone Star Funds, una firma global de capital privado ("Lone Star"). La transacción permanece sujeta a las condiciones de cierre habituales, incluidas las aprobaciones regulatorias.
Los términos de la transacción no fueron revelados
Tras el cierre, el equipo de gestión de XSYS estará dirigido por Antoine Fady como director ejecutivo, Dagmar Schmidt como director de operaciones y Martin Sauer como director financiero. Steve Dryden sucederá al Sr. Fady como director ejecutivo de Flint Group.
"La separación que anunciamos representa el siguiente paso lógico para Flint Group y XSYS", dijo Fady. “Permitirá además que el negocio XSYS avance como el mejor proveedor independiente de soluciones completas para las industrias de preimpresión flexográfica y tipográfica, con soluciones a medida desarrolladas para cada segmento de mercado y tipo de cliente. Esperamos trabajar con Lone Star, cuya experiencia y trayectoria serán de gran beneficio a medida que avanzamos XSYS en esta próxima fase”.
"Con esta transacción, crearemos dos equipos de gestión dedicados con un mayor enfoque estratégico y operativo", dijo Steve Dryden, direc-
tor ejecutivo recientemente elegido de Flint Group. “Flint Group se posiciona para seguir invirtiendo en los segmentos en crecimiento estructural de papel y cartón, envases flexibles y etiquetas, a los que se les da servicio con nuestros consumibles de impresión digital y convencional. Esta exitosa estrategia, centrada en la innovación de productos y servicios, permite a Flint crecer con los clientes que valoran nuestra propuesta de color ayudándoles a estandarizar y reducir sus costos”.
"Esperamos trabajar con XSYS, un proveedor global líder de soluciones de impresión", dijo Donald Quintin, presidente de Lone Star Opportunity
Funds. “Reconocemos no solo la resistencia del negocio XSYS y la diversidad de sus ofertas, sino también sus perspectivas de crecimiento. Apreciamos el valor que XSYS ofrece a sus numerosos clientes y tenemos una gran confianza en el compromiso del equipo de gestión de aprovechar el potencial de XSYS en los años venideros".
Goldman Sachs Bank Europe SE y J.P. Morgan actuaron como asesores financieros y Freshfields Bruckhaus Deringer LLP actuó como asesor legal de Flint Group. Lone Star fue asesorado por Perella Weinberg Partners y Weil, Gotshal & Manges.
Michael se incorpora a Esko con más de 25 años de experiencia en estrategia empresarial y desarrollo de la experiencia del cliente en los sectores del software, los servicios financieros y las telecomunicaciones, y se encargará de la organización de servicios de software de los proveedores de envases en la región EMEA. Sus funciones incluyen la gestión del despliegue de software, la formación, el soporte remoto, el soporte electrónico, los servicios de soluciones y las operaciones de éxito del cliente.
Eddy Fadel, vicepresidente de Esko EMEA, ha comentado al respecto: “La estrategia de Esko es garantizar que el cliente esté en el centro de todo lo que hacemos. Michael aporta unas habilidades extraordinarias a nuestra organización que nos garantizan poder maximizar las oportunidades de nuestros clientes para digitalizar, automatizar y conectar para el éxito del negocio.
“Con su nombramiento, queremos
crear un enfoque sin fisuras en toda la empresa, con el apoyo de una cultura de empoderamiento y propiedad, lo que significa que nuestros equipos tengan al cliente en mente en todo momento".
De su designación, Michael ha dicho: “Creo que el factor crítico para impulsar el éxito de los clientes consiste en dar prioridad en todo momento a las personas, tanto a
nuestros compañeros como a los clientes. Es obvio que las personas felices y motivadas prestan un mejor servicio, lo que se traduce en clientes satisfechos. Tenemos grandes soluciones de productos y servicios en Esko y estoy encantado de liderar la misión de ofrecer un nuevo nivel de experiencia del cliente y de éxito para todos.”
Obtener la máxima calidad en impresión flexográfica: Eso es realmente artístico. Con DuploFLEX® está en la posición adecuada. Porque DuploFLEX® es la cinta para aquellos que realmente se preocupan por la calidad. Lohmann no solo aporta la cinta óptima, sino también el mejor asesoramiento. Especialmente cuando las cosas se complican, nuestros FLEXperts ponen a su disposición toda su experiencia y le ofrecerán soluciones que son dignas de su obra de arte.
Lohmann Spain, S.A.
C/ Miquel Torello i Pagés 38
Polígono Industrial El Pla
08750 Molins de Rei (Barcelona)
Teléfono: +34 93 666 71 01
graphics@lohmann-tapes.com
www.lohmann-flexperts.com
BOBST y sus socios anuncian un verdadero hito en su trabajo pionero de reemplazar estructuras de envase multicapa de alta barrera no reciclables por alternativas monocapa diseñadas para ser recicladas.
El lanzamiento de una nueva generación de 'héroes' BOBST representa un hito importante en la misión de diseñar soluciones de vanguardia que utilizan una nueva generación de polímeros.
Después de lanzar varias muestras diferentes de bolsas standup monocapa (MDO PE, BOPE, BOPP y CPP) en K 2019, los socios mantuvieron su considerable inversión e intensa investigación para seguir avanzando en el cumplimiento de todos los requisitos de la industria en cuanto a procesabilidad, barrera, seguridad y calidad óptica.
“Encontrar alternativas sostenibles a los plásticos no reciclables es uno de los retos más importantes de nuestro tiempo,” explicó Nick Copeland, Director de I+D en BOBST. “Es particularmente difícil para los envases flexibles como los de uso alimentario, en los que la protección de alta barrera contra el oxígeno y el agua que previene el deterioro es actualmente obtenida por envases multicapa de diferentes materiales que no se pueden reciclar. Esta nueva generación de estructuras monocapa de alta barrera nos acerca a soluciones completamente reciclables que reemplazarán los envases que no lo son.”
“Brückner está convencido de que el futuro seguirá perteneciendo a los plásticos siempre que se usen y reutilicen de forma sostenible,” dijo Helmut Huber, Director de Operaciones de Ventas y Proyectos en Brückner Maschinenbau GmbH & Co. KG.
“Dentro de la economía circular, las incuestionables ventajas del plástico se pueden combinar perfectamente con los objetivos de sostenibilidad de una sociedad moderna. En cuanto a la discusión sobre los objetivos de reciclaje
Después de lanzar varias muestras diferentes de bolsas standup monocapa (MDO PE, BOPE, BOPP y CPP) en K 2019, los socios mantuvieron su considerable inversión e intensa investigación para seguir avanzando en el cumplimiento de todos los requisitos de la industria en cuanto a procesabilidad, barrera, seguridad y calidad óptica.
del plástico, vemos claramente el auge de los envases monocapa.”
La ‘Generation 2.0’ de BOBST incluye:
- Nuevas bolsas laminadas de polipropileno de alta barrera, impresas en huecograbado y reciclables, con opción de una barrera metalizada AluBond o transparente AlOx (óxido de aluminio) y adhesivo y/o acabado sin disolventes.
- La primera flexografía UV combinada con chorro de tinta digital sobre bolsas laminadas de polipropileno con metalización AluBond y propiedades de barrera, usando adhesivo sin disolventes para una bolsa monocapa diseñada para el reciclaje.
- La impresión flexográfica UV de baja migración de las bolsas de polietileno laminado de baja densidad que aporta barrera con la metalización AluBond.
- La impresión flexográfica CI a base de agua en bolsas laminadas de MDOPE con metalización AluBond, con adhe-
sivo de barrera ultra alta sin disolventes. Cada socio del proyecto ha desempeñado un papel esencial en el desarrollo y la industrialización de una serie de nuevas soluciones de material monocapa.
- Dow es el principal proveedor mundial de resinas de polietileno (PE) y representa el primer paso de la cadena de producción de muestras Generation 2.0.
- Brückner Maschinenbau es líder del mercado en líneas de extrusión y estirado de film biaxial (BO). Con los recursos en I+D de Brückner, se han podido conseguir buenas prestaciones de los films BO en cuanto a propiedades de barrera y procesabilidad.
- Hosokawa Alpine es líder mundial del sector de la Extrusión Soplado y experto en tecnología MDO (orientación de dirección de la máquina), un componente fundamental para fabricar compuestos monocapa de polietileno de altas prestaciones.
- Elba desarrolla y fabrica máquinas automáticas para hacer bolsas a alta velocidad. La empresa convierte las
bobinas acabadas en bolsas.
- Sun Chemical, líder mundial en tintas, recubrimientos, pigmentos y materiales avanzados, aporta los adhesivos barrera de oxígeno sostenibles y sin disolventes usados en el programa.
- Michelman desarrolla y fabrica los productos químicos especiales y sostenibles utilizados en la impresión digital y en los envases alimentarios; ha aportado el acabado barrera a base de agua usado en parte del proyecto.
- Indopoly fabrica una amplia gama de films de polipropileno de orientación biaxial (BOPP) para la industria del envase flexible; aportó un film BOPP con una lámina especial para una de las bolsas.
- UFlex es la mayor empresa india de envases flexibles y de films orientados (BOPET & BOPP); aportó el film BOPP utilizado en algunas pruebas.
"La reciclabilidad supone un grado más de complejidad a la hora de diseñar un envase eficaz y eficiente. Creemos sinceramente que esta colaboración con
toda la cadena de valor es la forma no sólo más rápida sino la única de acelerar el paso del mercado hacia objetivos de sostenibilidad ambiciosos,” expuso Jaroslaw Jelinek, Director mundial de marketing de tecnologías de PE en Dow Packaging & Specialty Plastics. “Estamos encantados de formar parte de este proyecto creativo e innovador y de aportar soluciones de última generación al mercado.
y a ayudar a la industria del envase flexible a ser más sostenible,” comentó Nicolas Bétin, Director de estrategia de producto para EMEA, Director de tintas y materiales
& Líder Empresarial de Sostenibilidad Global. “Una estrecha colaboración entre varios de los implicados en la cadena de valor, compartiendo conocimientos y competencias, puede llevar a resultados tangibles susceptibles de ser introducidos eficazmente en el mercado. Precisamente, es el caso de esta cooperación”.
“Sun Chemical se compromete a contribuir a una economía más circular
“Es una asociación de empresas de mentalidad similar, todas decididas a diseñar unas alternativas sostenibles a los envases flexibles no reciclables,” comentó Nick Copeland. “Los Centros de Competencia BOBST sirven para probar la viabilidad de los materiales en cuanto a sus propiedades barrera, su impresión y laminación, y asegurar su idoneidad en todo el proceso de producción. Estamos felices de contribuir a este importante hito.”
“Encontrar alternativas sostenibles a los plásticos no reciclables es uno de los retos más importantes de nuestro tiempo,” explicó Nick Copeland, Director de I+D en BOBST
Ovelar, compañía de referencia en fabricación de sleeves en España, acaba de obtener la certificación BRCGS Packaging, para envases y materiales de envasado, continuando así con su compromiso de mejora continua de calidad, garantizado a través de los certificados ISO 9001:2015, ISO 14001:2015, FSC®, PEFC y Empresa Familiarmente Responsable logrados anteriormente.
La empresa está certificada como una organización comprometida con la seguridad y afianza así su compromiso por la calidad y la seguridad de sus productos.
Se trata de la certificación de mayor prestigio en el sector y establece un modelo de gestión y un protocolo de buenas prácticas, con el fin de asegurar que el producto cumple con todos los requerimientos de seguridad, calidad y legalidad exigibles. Este es un requisito indispensable para la homologación de muchos de los clientes de Ovelar en la fabricación y la comercialización de sleeves y etiquetas envolventes, que ofrece claramente una ventaja competitiva en el mercado: velar por la inocuidad alimentaria.
Además, la certificación en BRCGS Packaging, para envases y materiales de envasado, permite tener documentado, implantado, evidenciado y avala-
do un plan contra el fraude alimentario, un plan food defense y uno cultura de la organización, además de garantizar su cumplimiento con las normativas, reglamentos y requisitos exigidos.
BRCGS Packaging es la certificación de mayor prestigio en el sector y de reconocimiento internacional
Asimismo, y de acuerdo con esta norma de reconocimiento internacional, Ovelar puede ofrecer a sus clientes la
trazabilidad en un espacio muy breve de tiempo para facilitar así la identificación, movimiento y localización de un producto.
La certificación BRCGS Packaging dará, sin duda, un impulso importante a la empresa fabricante de sleeves y favorecerá una comunicación protocolizada, operativa y organizada para las cadenas de distribución, consumidores e intermediarios. En definitiva, esto conducirá a Ovelar a optar a un mejor posicionamiento para la venta de sus productos en el sector alimentario, detergencia, lácteo, farmacéutico y cosmético del mercado nacional e internacional.
Comexi, empresa especializada en la industria de la impresión y conversión del envase flexible, donde es un referente mundial, entra en la última fase de construcción de sus renovados centros tecnológicos (CTec) de Girona y Miami. La compañía ha invertido un millón de euros en la remodelación de los dos centros con el objetivo de ofrecer mejores servicios a sus clientes, en un claro ejemplo de su apuesta por la proximidad, innovación y sostenibilidad en todo el mundo.
Los nuevos Demo Center, con un equipo de 18 personas, abrirán sus puertas en el último trimestre del 2021 y mostrarán las herramientas más avanzadas en la digitalización de los procesos y workflows de trabajo para printing y converting.
La empresa, que está presente en más de 100 países de los cinco continentes, cuenta con centros de producción propios en Girona y Brasil y oficinas comerciales en Estados Unidos y Rusia. En el último trimestre del 2021 entrarán en funcionamiento los dos nuevos CTec diseñados bajo los parámetros de sostenibilidad y consumo energético que distinguen a Comexi desde hace tiempo.
El Centro Tecnológico Manel Xifra Boada, Comexi CTec, de Girona está integrado en el centro de producción de la marca y cuenta con un espacio polivalente de 2500 metros cuadrados destinados a la innovación y desarrollo de proyectos I+D, formación, consultoría, demostraciones y laboratorio industrial. Contará con 9 máquinas de última generación, una zona de preimpresión
pionera donde colaboran empresas líderes del sector como ESKO, DuPont y Asahi, además de un espacio para el grabado de planchas offset. El CTec de Girona será un espacio de referencia a nivel internacional, no sólo por su espacio y polivalencia, sino porque será el reflejo del proyecto corporativo de sostenibilidad e industria 4.0 marcados como unos de los objetivos principales de la empresa.
También en octubre, pero en Miami (Florida), el CTec de Comexi North America iniciará su actividad con la instalación de una laminadora y una cortadora, a las que seguirá una CI flexo el próximo año. Este centro respira la misma filosofía que el CTec de Girona y supone un paso más no solo en la expansión norteamericana de la compañía, sino también en la proximidad y
el desarrollo de soluciones a medida de forma ágil para clientes norteamericanos. El centro tecnológico, que consta de 1000 metros cuadrados, se convertirá en un espacio polivalente único para la formación, la investigación y la demostración industrial, que lo situarán como el referente del envase flexible en el mercado norteamericano.
La presencia en Estados Unidos de Comexi se verá reforzada no solo con esta gran instalación de CTec, sino también con nuevas oficinas y un almacén de repuestos y una inversión logística de más de un millón de dólares estadounidenses.
En palabras de Albert López, Manager Global del centro tecnológico, “nuestros CTec de Girona y Miami son la respuesta natural a una necesidad latente en el mercado, así como un
ejemplo de la importancia que tiene la innovación en nuestro sector desde hace mucho tiempo. Gracias a los renovados centros tecnológicos ofrecemos la mejor solución a medida para su negocio a nuestros clientes de todo el mundo, respondiendo de esta manera a la confianza que depositan en nosotros”.
Comexi CTec inició sus actividades en junio de 2010 en Girona con un curso Advanced de flexo para clientes de Oriente Medio. El centro tecnológico nació con el mismo objetivo que mantiene hoy en día, transferir conocimiento a los clientes de Comexi. Desde el inicio, Comexi CTec ofrece asesoramiento de diferentes tipos y tecnologías, y formación presencial, personalizada en casa del cliente, y online. Con el transcurso del tiempo ha incorpora-
La presencia en Estados Unidos de Comexi se verá reforzada no solo con esta gran instalación de CTec, sino también con nuevas oficinas y un almacén de repuestos y una inversión logística de más de un millón de dólares estadounidenses
do también el soporte a cliente a nivel de pruebas industriales, R + D y el soporte a la innovación.
El nuevo Centro Tecnológico de Comexi mostrará las herramientas más avanzadas en la digitalización de los
procesos y workflows de trabajos para printing y converting. Una de estas herramientas es Comexi Cloud, una plataforma digital que aporta soluciones a los clientes para mejorar el rendimiento de su planta mediante el análisis de datos de producción en tiempo real, lo que les permite construir y desarrollar fábricas inteligentes. Comexi Cloud ha reinventado la forma en que los impresores y los convertidores gestionan todos los procesos, ya que es la plataforma en línea más completa del mercado para visualizar, compilar, analizar y almacenar todos los datos.
Los CTec de Girona y Miami cuentan con una plantilla de 18 miembros que se encargan de la ejecución de los diferentes servicios del centro tecnológico, así como del desarrollo de estos nuevos espacios.
Comexi, especialista en soluciones para la industria de la impresión y conversión del envase flexible, ha celebrado un nuevo éxito tras la adquisición de una cortadora de torreta compacta S2 DT por parte de una empresa de Guatemala. Con esta operación, la compañía catalana alcanza las 150 ventas de cortadoras de la familia S2 DT, situando de esta manera en el mercado más de 350 máquinas de doble torreta (contando también las ventas de la familia S1 DT).
“La cortadora compacta S2 DT ha significado una revolución en el sector del envase flexible. Con la creciente presión en costes y el incremento de la necesidad de soluciones cada vez más eficientes y productivas, la Comexi S2 DT ofrece una relación rendimiento/coste inigualable”, explica Raúl El-Fakdi, director de la unidad de negocio de Corte de Comexi, que añade que “la apuesta de la empresa por soluciones que garantizan la calidad, a la vez que se alinean con las necesidades de nuestros clientes, no podía dar otro resultado que un posicionamiento líder en tecnología que el mercado ha respaldado, una vez más, con la creciente cifra de ventas”. La cortadora Comexi S2 DT se vende principalmente en los mercados europeo (40%) y americano (40%).
Fiable y robusta, la Comexi S2 DT es una máquina de última generación creada para ofrecer una alta productividad gracias a sus rápidas rampas de aceleración y desaceleración, a la vez que una elevada flexibilidad. Cuenta con un control de tensión único entre
Fiable y robusta, ofrece una alta productividad gracias a sus rápidas rampas de aceleración, con un control de tensión único entre las cortadoras de esta gama.
las cortadoras de esta gama y ofrece una alta versatilidad en rango de materiales, pudiendo trabajar con PE de bajo micraje y transpirable, así como con aluminio y papel. El manejo de la Comexi S2 DT es extremadamente fácil e intuitivo gracias al enorme trabajo que se ha realizado para
ofrecer una interfaz intuitiva, cómoda y ágil. Esta cortadora, equipada con un sistema de torretas para agilizar los cambios de trabajo, es especialmente útil para las compañías que necesitan producir gran cantidad de bobinas. Con esta cortadora, la calidad y la cantidad no son incompatibles.
SP GROUP, empresa española especializada en la fabricación de envases flexibles, rígidos y termoformables de vacío, sigue avanzando hacia su objetivo final, ser certificada como empresa RESIDUO CERO en 2025. Para ello ha puesto en marcha, desde hace tres años, distintos proyectos e iniciativas como son el Proyecto “Merma 0”, el proyecto “Pallets sostenibles”, o el proyecto de I+D+i que trabaja sobre la línea ECO en la que se engloban los nuevos materiales reciclables como el recién lanzado PP HB ECO, cuya reciclabilidad ha sido recientemente certificada por el Instituto alemán CYCLOS-HTP, especializado en la clasificación, evaluación y certificación del reciclado de envases alimentarios.
En primer lugar, el Proyecto “MERMA 0” que persigue reducir el residuo sobrante de la fabricación de la línea de coextrusión multicapa (PA/PE), a través de su reintroducción en el proceso de fabricación. Desde hace algunos años, la planta de Espiel (Córdoba), cuenta con dos equipos de extrusión en línea que han ido evolucionando, hasta conseguir que hoy en día se pueda recuperar casi la totalidad de las mermas que se producen durante el proceso de fabricación. Estas mermas provienen, tanto de bobinas intermedias, como de los refilos que se van incorporando en línea, y que no afectan ni a la producción ni al material final. Desde que arrancó este proyecto en 2018, se han conseguido reutilizar hasta un 80% de las mermas, y el objetivo para finales de 2021 es el de logar el 100%, algo que parece posible teniendo en cuenta que en el primer trimestre
de este año se estaban reutilizando el 95% de las mermas generadas en las distintas coextrusiones de PA/PE. Estos datos son significativos si se tiene en cuenta que en SP GROUP se generan más de 350 toneladas de merma. Además, la empresa está realizando estudios para ver la viabilidad de otras coextrusiones multicapa (PA/PP o PA/barrera/PA/PE), ya que generan un gran volumen de desperdicio plástico virgen que podría formar parte de proceso de reciclaje circular, sin que afecte a su producción y evitando que acaben en el vertedero.
Por otro lado, y en aras de lograr su objetivo de certificación como empresa RESIDUO CERO, la empresa ha adquirido recientemente, para su fábrica de Villarrubia (Córdoba), una novedosa máquina con la que fabrican sus propios pallets de plástico a partir de los residuos que generan, y que además son
óptimos para el transporte de distintos tipos de cargas. De esta manera reducen, reciclan y reutilizan sus residuos internos, especialmente los procedentes de las bobinas, lo que supone un paso más en su compromiso con la sostenibilidad y el respeto al medio ambiente.
Aunque aún está en fase inicial, el objetivo es que esta máquina sea capaz de incorporar unas 600 toneladas de plástico al año, lo que supondría la reutilización del 30% de los residuos generados durante 2021 y dejar de emitir a la atmósfera 18,3 toneladas de CO2 provenientes de la compra de pallets. La idea es que estos pallets de plástico sean utilizados de forma interna, tanto en la planta de Villarrubia como en la de Espiel (Córdoba), sustituyendo a los más de 40.000 pallets de madera que se utilizan anualmente en ambas fábricas. Los pallets de plástico pueden ser triturados de nuevo, y así
reincorporarse al proceso de extrusión. Sin olvidar que, al disminuir los residuos con destino vertedero disminuyen también las tasas reguladas por la Ley de residuos, y se produce un importante ahorro a nivel general.
Por último, un paso más hacia la sostenibilidad ha sido la certificación del nuevo PP HB ECO por parte del Instituto CYCLOS-HTP, recibiendo una puntuación AA las bolsas con o zin zipper, lo que significa que el 90% del envase puede reciclarse, ya que está compuesto casi en su totalidad por polipropileno. Y en cuanto a las bolsas PP HB ECO con tapón babyfood, han logrado una puntuación AAA, dando un 96% de reciclabilidad al envase. Estas pruebas de clasificación se llevan a cabo en países como Alemania, Austria, Francia, Italia, Países Bajos o Noruega, que disponen de estructuras de recogida y reciclaje, por lo que es de esperar que pronto se implanten en el resto de los países de la Unión Europea.
Se destaca que el nuevo PP HB ECO es un complejo en base a polipropileno con propiedades alta barrera y esterlizable, que permite reemplazar a estructuras no reciclables como son las lámi-
nas de aluminio, recubrimientos metálicos o estructuras multimateriales. Una estructura monomaterial que logra un 90% de reciclabilidad, pero que al mismo tiempo soporta tratamientos térmicos como la esterilización, pasteurización, llenado en caliente y microondas. Gracias a estos tratamientos, se prolonga la vida útil de los alimentos, por lo que también se ayuda a reducir el desperdicio alimentario.
Todos estos avances demuestran
que desde SP GROUP se están dando los pasos necesarios para lograr una certificación como empresa RESIDUO CERO en los próximos años. De tal forma que además de desarrollar soluciones reales acordes a las necesidades del mercado y los consumidores finales, se toman medidas de carácter interno para favorecer y logar la máxima reciclabilidad en sus propias fábricas. En materia de sostenibilidad, todo suma.
Desde 2018, todo el proceso de fabricación en la sede central de Doneck en Luxemburgo es climáticamente neutro. Esto lo confirma la huella de carbono certificada.
Actualmente, la compensación climática para llegar a la neutralidad se lleva a cabo fomentando la energía eólica limpia en Ovalle, Chile. En años anteriores, hubo otros dos proyectos: un proyecto de protección forestal en Brasil y un programa de reducción de emisiones en Perú. Así lo confirma a Doneck el especialista en protección del clima Climate Partner en su certificado.
Además, Doneck protege de forma activa y exhaustiva el medio ambiente: p. ej., evitando y reduciendo los residuos (p. ej., plásticos), empleando reutilizables en lugar de desechables, electromovilidad, así como electricidad de origen hidroeléctrico (desde 2011) y gas verde (desde 2018) y más. Doneck optimiza conti-
nuamente su estrategia de sostenibilidad con el lema «We think green».
HYDRO-X Green Line Premium, el nuevo sistema de series al agua de hubergroup Print Solutions, ofrece más sostenibilidad y flexibilidad a los impresores y fabricantes de embalajes. Con este artículo los clientes pueden elegir los componentes de la cartera que necesiten sus productos exactamente, gracias al sistema de elementos combinables. Todos los componentes han obtenido la certificación Cradle to Cradle Certified® Bronze, permitiendo así que los embalajes sean sostenibles y coloridos al mismo tiempo.
El objetivo de hubergroup en el desarrollo de HYDRO-X Green Line Premium era obtener una amplia gama de colores y un extenso campo de aplicación combinados con la sostenibilidad. "Para nosotros era importante desarrollar algo más que un producto sostenible en base al agua. Queríamos elaborar todo nuestro surtido de forma sostenible y ofrecer a los clientes la posibilidad de elegir con flexibilidad los componentes que mejor se adapten a sus embalajes", explica el Dr. Christian Schirrmacher, Global Project Manager Water Based Inks de hubergroup, sobre los fundamentos del nuevo sistema de elementos combinables. Puesto que todos los concentrados, las mezclas y los aditivos de color se combinan entre sí y pueden combinarse libremente, HYDRO-X Green Line Premium ofrece una gran variedad de aplicacio-
nes en el ámbito de la impresión flexográfica y el huecograbado, desde los embalajes flexibles de papel, aluminio o láminas de plástico hasta el papel ondulado o las cajas plegables.
hubergroup ha colaborado con el Cradle to Cradle Products Innovation Institute para investigar y mejorar desde un enfoque global los efectos de todos los componentes del sistema de mezcla de colores sobre el medio ambiente. El Instituto se ha comprometido a impulsar la innovación para una economía circular y concede la certificación basada en su Cradle to Cradle Certified Product Standard, que abarca criterios exhaustivos en materia de salud de los materiales, reutilización de materiales, gestión de energías renovables y carbono, administración del agua y justicia social. Todos los componentes del sistema de mezcla de
pintura HYDRO-X Green Line Premium recibieron la certificación Cradle to Cradle Certified Bronze.
"Con la evaluación externa queremos ofrecer a nuestros clientes transparencia y seguridad sobre el impacto medioambiental de nuestros colores. Sin embargo, también era importante para nosotros que la certificación no influyera en la utilización de nuestros productos. Los impresores que quieran utilizar los productos Cradle to Cradle Certified de nuestra familia HYDRO-X no tendrán que modificar sus procesos y podrán obtener un rendimiento y una capacidad de carga tan buenos como los que han tenido hasta ahora. Las marcas pueden utilizar los mismos diseños y formatos de embalaje como hasta ahora, pero de forma más sostenible", afirma el Dr. Christian Schirrmacher.
Nord Technique Etiquetage (NTE), una empresa familiar de los alrededores de Lille, con 35 años de experiencia en la fabricación de etiquetas, se ha convertido en la primera empresa que instala una impresora digital de etiquetas BOBST en Francia, la Mouvent LB702-UV.
Es la segunda inversión en una máquina BOBST que hace la empresa, después de haber comprado una impresora flexográfica en línea BOBST M4 en 2016. La inversión en impresión digital responde a la creciente demanda de tiradas cortas y medias.
Ahora, según Thibault Duponchel, el director general de NTE, la empresa está “perfectamente situada” para asumir cualquier combinación de trabajos que se le demande.
“Desde que tenemos la Mouvent LB702-UV, hemos optimizado totalmente la planta de producción y somos capaces de ofrecer la mejor tecnología en todos los trabajos,” declaró. “Usamos la impresora flexo para las tiradas muy largas y la Mouvent para el resto. Está claro que con una máquina ultrarrápida como esta, la impresión digital ya no es solamente para tiradas cortas. Es la herramienta perfecta para tiradas cortas y medias, y ahora estoy pasando todos los trabajos de varios miles de metros lineales a digital.”
Con su alta productividad y calidad, esta impresora de etiquetas digital puede abarcar casi todo
La Mouvent LB702-UV puede abarcar el 90% de todos los trabajos de etiquetado en tiradas de hasta 8.000 metros lineales (26.000 pies lineales) de manera rentable, con un rendimiento de hasta 200.000 m2 al mes y una velocidad de impresión de hasta 100 m/min. Es vital que no comprometamos la calidad del resultado. La Mouvent LB702-UV ofrece una resolución de 1200 x 1200 dpi con líneas más finas, gradientes más suaves, imágenes más nítidas y colores más vibrantes.
La tecnología digital inkjet de Mouvent, diseñada por BOBST, permite producir
La tecnología digital inkjet de Mouvent, diseñada por BOBST, permite producir etiquetas de forma industrial sobre sustratos muy variados como papel o materiales adhesivos y flexibles, con un coste total de propiedad (TCO) incluso menor que los procesos tradicionales más rentables.
etiquetas de forma industrial sobre sustratos muy variados como papel o materiales adhesivos y flexibles, con un coste total de propiedad (TCO) incluso menor que los procesos tradicionales más rentables. La prensa vino con cuatro colores y una amplia gama de tonalidades. Pero fue la alta productividad de la impresora, comparada con otras prensas digitales, lo que llamó la atención del Sr Duponchel y de su equipo.
“La necesidad de producir etiquetas rápida y rentablemente está liderando el sector del etiquetado,” comentó. “Fue para ganar ese desafío que compramos nuestras primeras impresoras digitales ya en 2017. Sin embargo, no eran suficiente para responder rápida y rentablemente a la demanda de nues-
tros clientes. Necesitábamos una impresora digital de etiquetas para asumir no sólo la demanda de hoy, sino también las de mañana. Como ya teníamos una estrecha relación con BOBST, acudimos a nuestro partner planteando esta necesidad y fue cuando nos presentaron la Mouvent LB702UV. Ser capaces de ofrecer altas velocidades de impresión y una completa gama de colores a menor coste era exactamente le que necesitábamos.”
El Sr Duponchel contó que su empresa está produciendo a velocidades 8 veces más altas que la máquina digital anterior, reduciendo el TCO. Es más, NTE también ha reducido los desperdicios. “Estas ventajas nos permiten ofrecer un mejor servicio y producto a nuestros clientes,” dijo.
El paquete completo
El equipo de Nord Technique Etiquetage se quedó impresionado por la rapidez de la configuración y la facilidad de uso. La experiencia general del cliente desde el contacto inicial y la preparación del sitio hasta la entrega y la formación fue muy positiva. En diez días la máquina estaba instalada y toda la formación importante hecha, así que NTE pudo empezar a trabajar enseguida. El Sr Duponchel mandó al operario de la flexográfica a la nueva máquina digital. “Aprendió a manejarla muy pronto porque es muy cómoda y fácil de usar,” explicó.
El éxito de esta inversión marca el último capítulo de la gran relación de colaboración entre BOBST y NTE, que ha aprovechado el excelente servicio, el soporte técnico y el mantenimiento que le brinda BOBST. Ahora, el Sr Duponchel sabe que su empresa está mucho mejor preparada para el futuro y es un gran defensor de la impresión digital inkjet de etiquetas.
“La impresión digital va a jugar un papel cada vez mayor en el sector de las etiquetas y, a medida que evolucione la industria, nos capacitará para cambiar al mismo ritmo,” continuó. “Nos hemos dado cuenta de que con BOBST, NTE ha tomado el camino de un brillante futuro en la producción de etiquetas. Sentimos que ahora nuestra empresa es más grande.”
Ser la primera empresa que instala una impresora digital de etiquetas
A medida que los fabricantes de marcas demandan cada vez más todo tipo de etiquetas impresas offset altamente creativas e informativas, los impresores de etiquetas están recurriendo a Koenig & Bauer para obtener las velocidades de impresión más rápidas, excelente calidad de impresión y unos paquetes de sustratos probados para ofrecer unas etiquetas llamativas y consistentes con la marca para sus clientes.
La nueva prensa Rapida 106 X ofrece las 20.000 páginas por hora más rápidas, una productividad excepcional y una calidad de impresión excelente para la producción de etiquetas.
"Con la creciente demanda de etiquetas, estamos acelerando nuestro papel de liderazgo en este mercado tan importante", dice Chris Travis, director de tecnología de Koenig & Bauer. "Este mercado es uno de nuestros pilares principales junto con el comercial y el envasado, y estamos profundamente comprometidos con el desarrollo de las últimas innovaciones específicamente para cada segmento del mercado".
Si bien se prevé que la demanda de etiquetas en los EE.UU. aumente un 3,3% anual a 20.600 millones de dólares en 2025, Koenig & Bauer está experimentando un "crecimiento significativo", especialmente aquí en América del Norte y en todo el mundo. ¿Qué es lo que atrae a los impresores de etiquetas líderes para invertir en Koenig & Bauer? Travis dice que, abrumadoramente, se debe a la tecnología superior de la empresa lo que ha convencido a los impresores de etiquetas en realizar la transición a Koenig & Bauer. “Nuestras prensas producen etiquetas a 20.000 p / h a diferencia de cualquier otra prensa
del mercado”, dice. "Tenemos clientes de etiquetas que rompen récords de producción con nuestras prensas".
Lo que distingue a Koenig & Bauer es su proceso completo único desde la entrada del sustrato hasta la salida del etiquetado. Esto comienza con el lanzamiento de la Rapida 106 X de nuevo diseño, una alta velocidad de 20.000 pph. La prensa, que tiene un atractivo cuerpo negro y gris con paneles laterales de vidrio iluminado, ofrece la mayor productividad y una producción y eficiencia optimizadas para los productores de etiquetas. Sus populares innovaciones de Koenig & Bauer, como DriveTronic SIS, un sistema único de colocación lateral libre que permite un registro preciso de los sustratos más delgados a la máxima velocidad, que forma parte del importante paquete de viaje de hojas de etiquetas, QualiTronic PDFCheck, un sistema de inspección de imágenes en línea que compara cada hoja impresa con los datos PDF de la preimpresión, y QualiTronic ColorControl, un sistema de control de
Lo que distingue a Koenig & Bauer es su proceso completo único desde la entrada del sustrato hasta la salida del etiquetado. Esto comienza con el lanzamiento de la Rapida 106 X de nuevo diseño, una alta velocidad de 20.000 pph. La prensa, que tiene un atractivo cuerpo negro y gris con paneles laterales de vidrio iluminado, ofrece la mayor productividad y una producción y eficiencia optimizadas para los productores de etiquetas
color en línea que mide cada hoja, son extremadamente importantes para la producción de etiquetas, en la que cada
etiqueta debe ser coherente e incluir información pertinente específica.
“Todas nuestras impresoras de etiquetas tienen sus prensas Rapida equipadas con nuestros sistemas superiores de control de calidad y color”, dice Travis. “Las marcas son muy conscientes de que sus etiquetas deben tener el mismo aspecto en el estante de la tienda. La consistencia es la clave y nuestras rotativas Rapida lo cumplen”.
Travis dice que el equipo de Koenig & Bauer es significativamente más productivo debido a la trayectoria de la etiqueta a través de la prensa y su entrega a la troqueladora rotativa. Sus ingenieros han desarrollado un sistema más productivo para producir más etiquetas gracias a este rápido sistema. A diferencia de las impresoras comerciales o de embalaje, los fabricantes de etiquetas requieren sustratos específicos y Koenig & Bauer ha desarrollado una serie de paquetes de sustrato desarrollados para la producción de etiquetas sofisticadas. Estos incluyen peso ligero, plástico y papel, según el tipo de etiqueta que se vaya a producir.
El crecimiento dinámico de las etiquetas en molde es otro segmento importante para Koenig & Bauer. “La impresión de etiquetas en molde se produce en plástico delgado, de hasta 50 micrones, y presenta su propio conjunto de desafíos. Debido a nuestro concepto único de desplazamiento de la hoja, desde el rollo a la hoja hasta la entrega, que es exclusivo de Koenig & Bauer, podemos imprimir etiquetas en molde de manera eficiente y exitosa a las velocidades de producción más altas”, dice Travis. “También somos líderes en el mercado de secado LED-UV, lo que impacta significativamente en el mercado de etiquetas IML, si la etiqueta permite el curado energético. Dado que este tipo de etiqueta se imprime en sustratos tan delgados, puede ser propenso a deformarse cuando se somete al proceso de secado. LED-UV no emite calor, por lo que proporciona un mejor control sobre el proceso de producción, permite un mejor registro y proporciona una mayor calidad al tiempo que aborda la necesidad de tiempos de secado más rápidos y la capacidad de ejecutar una
pila completa en la entrega".
Koenig & Bauer ha puesto tanto énfasis en el mercado de las etiquetas que ha dedicado un área individual conocida como Label Center además de su nuevo Customer Experience Center en Alemania. Los visitantes pueden presenciar todo el proceso de producción de etiquetas en la nueva Rapida 106 X de siete colores con laca hasta la nueva troqueladora rotativa CutPRO X. Esta nueva máquina está equipada con el alimentador DriveTronic, SIS (Sensoric Infeed System), sistema de guía de hojas de etiquetas y entrega AirTronic y proporciona una rápida automatización para los cambios de trabajo y un concepto de operación intuitivo.
“Nuestros clientes norteamericanos de etiquetas en molde Koenig & Bauer están cosechando las recompensas y disfrutando de los enormes beneficios de su flujo de trabajo completo de etiquetas que se lleva a cabo en la Rapida 106 X y CutPRO X 106 con una mejora de hasta un 50% en la producción desde el rollo hasta el hoja, imprimir, cortar, rayar y tapar”, dice Travis.
Adaptándose a las preferencias cambiantes de los clientes, el fabricante de equipos de acabado, AB Graphic International (ABG) ha lanzado la próxima evolución de su popular máquina de corte por láser digital DigiLase 4.0. Tras un número récord de pedidos de esta máquina en 2020, los últimos refinamientos incluyen nuevas opciones de piezas individuales y velocidades más rápidas, que, cuando se combinan con su tecnología de corte por láser de última generación, hacen que DigiLase 4.0 sea incomparable en cuanto a garantía de uniformidad y resultados precisos.
La adición de opciones de piezas individuales será de interés para las empresas de impresión que buscan brindar a sus clientes capacidades de marketing mejoradas. El láser cortará la forma de cada pegatina, proporcionando un corte desde el material frontal, a través del sustrato, hasta el revestimiento. Cuando la banda se retira del área del láser, las pegatinas se colocan en el sistema transportador y los desechos se rebobinan. Luego, las pegatinas van a un transportador de clasificación donde se pueden empaquetar en lotes de la cantidad preestablecida deseada.
Con el nuevo software diseñado por el equipo de ABG Digilase que permite una mayor velocidad desde su único cabezal láser, el DigiLase 4.0 actualizado, reduce aún más los tiempos de
entrega. Al combinar la última tecnología de flujo de trabajo con el escaneo de códigos de barras, que permite el cambio automático de los trabajos, DigiLase 4.0 ahora puede ofrecer una flexibilidad completa en una amplia gama de aplicaciones de impresión y aplicación, incluidas las opciones de rollo a rollo, hoja y, más recientemente, piezas individuales. El diseño modular de la máquina es totalmente compatible con el módulo DigiJet de ABG para embellecimiento digital, lo que significa que es posible imprimir y enviar el mismo día junto con la tecnología láser DigiLase. Esta velocidad y flexibilidad garantizan una clara ventaja competitiva. Como beneficio adicional, ABG proporciona todo el código de software y el servicio, sin la participación de terceros, lo que convierte al fabricante en la
fuente directa de contacto para todas las consultas.
El lanzamiento de las nuevas funciones para DigiLase 4.0 representa un cambio radical en la producción directa de etiquetas y adhesivos", dijo Floriana Montella, gerente de producto de DigiLase en ABG. "La inclusión de opciones de piezas individuales y una mayor velocidad da a las empresas de impresión unas mayores capacidades en un momento en el que la mayoría busca mejorar su producción".
Dadas las circunstancias actuales, si los clientes prefieren no visitar ferias comerciales o salas de exposición para ver DigiLase 4.0 de ABG en acción, la empresa puede organizar demostraciones remotas personalizadas utilizando los archivos y materiales impresos del cliente.
En el ámbito de las etiquetas, Sappi, como especialista en soluciones basadas en el papel, no solo convence por su calidad y variedad, sino que también apuesta por un servicio al cliente óptimo en cuanto a producción y fiabilidad de entrega. Desde hace poco, la empresa también ha comenzado a producir papeles para etiquetas en su planta de Gratkorn, ampliando así su capacidad en este sector.
Ampliación de la cartera con una alta seguridad de suministro:
- Parade Label Pro 80 y 90 g/m² para el etiquetado con cola húmeda
- Parade Label SG 77, 78, 80 g/m² para autoadhesión
Sappi también ha comenzado recientemente a producir papeles para etiquetas en su moderna fábrica de Gratkorn, en Austria, una de las mayores fábricas de papel de Europa. Esta ampliación de la oferta permitirá a Sappi satisfacer mejor la demanda de los clientes de papeles base para etiquetas autoadhesivas y de cola húmeda y no húmeda y seguir el ritmo de crecimiento del mercado. Con más de 400 años de experiencia en la producción de papel, la planta de Gratkorn es conocida por sus papeles finos multicapa de alta calidad para aplicaciones gráficas. Como hasta
ahora los papeles para etiquetas en Europa solo se producían en Alfeld (Alemania) y Carmignano (Italia), además de en Estados Unidos en la planta de Somerset, Gratkorn pasa a suponer una ampliación ideal de la oferta. Las modernas instalaciones de producción, desde las máquinas de papel hasta los equipos de encolado, y los muchos años de experiencia en la producción de papeles estucados son los mejores requisitos para obtener productos de primera calidad. La capacidad disponible se está ampliando de manera gradual para incluir la producción de papeles para etiquetas Parade junto con los grados gráficos existentes. Esto significa que se dispone de un volumen suficiente para abastecer de forma fiable a los clientes, incluso en el caso de grandes necesidades.
La ubicación de Gratkorn ofrece otra ventaja: la mayor capacidad de producción permitirá al líder en innovación Sappi seguir ampliando su cartera de papeles para etiquetas y abrir nuevos segmentos, lo que antes no era posible debido a la limitada capacidad de los centros anteriores. «En junio de este año, lanzaremos Parade Label Pro en pesos base de 80 y 90 g/m², después de haber completado con éxito los procesos de calificación internos y externos. Estamos muy satisfechos con los comentarios tan positivos que hemos recibido de nuestros socios de desarrollo —impresores europeos líderes, algunos de los cuales son actores globales— en relación con los resultados de impresión y la capacidad de ejecución.
Es el resultado de una estrecha colaboración durante la fase de desarrollo. Esperamos que el lanzamiento al mercado del producto Parade Label SG para la industria autoadhesiva se pro-
duzca a finales del verano de 2021. Junto con los papeles para etiquetas de nuestras fábricas de Carmignano, Alfeld y Somerset, ampliaremos de forma considerable nuestra posición en el
mercado. Hay previstas otras ampliaciones de la gama de productos», anuncia Michael Bethge, Sales Director Speciality Papers de Sappi.
Con más de 400 años de experiencia en la producción de papel, la planta de Gratkorn es conocida por sus papeles finos multicapa de alta calidad para aplicaciones gráficas
La fábrica integrada de Gratkorn es una de las mayores y más modernas de Europa. En 2014, la máquina de papel para grados revestidos se actualizó con la tecnología más avanzada. En 2015 se renovaron partes de la caldera recuperadora y se completó la planta de recuperación. Desde entonces, la zona circundante ha disfrutado de menos ruido y menos emisiones de SO2.
CVNE ha escogido a Epson como su partner tecnológico para avanzar en la personalización de sus productos. Gracias a la serie de impresoras Epson ColorWorks, la bodega puede personalizar las etiquetas de las botellas según los gustos de sus clientes. Este modelo permite la inyección de tinta a color y hace posible que CVNE pueda imprimir sus propias etiquetas en alta calidad con gran rapidez.
Los equipamientos Epson permiten personalizar al instante las etiquetas de las botellas como el cliente desee. Con esta personalización de sus productos, CVNE da un paso más en su transformación digital y cercanía con los clientes.
Concretamente, el modelo utilizado por CVNE es la ColorWorks C3500, que permite la personalización de sus botellas reserva, tanto para venta on-line, como para eventos y celebraciones. A través de esta solución se han cuadriplicado las ventas del producto en dos años y se ha ampliado el proyecto creando un “fotomatón” que permite al visitante de las bodegas fotografiarse para personalizar su propia botella. Se abre así un nuevo mercado de cliente final con un alto potencial que busca una suma de valor a la propia calidad del producto, además de mayor satisfacción y nuevas experiencias.
Asimismo, las impresoras ColorWorks destacan por su alta fiabilidad y facilidad de uso. Gracias a la tecnología en frío del cabezal piezoeléctrico Epson, no se requiere apenas mantenimiento por desgaste ni sustitución a lo largo de la vida de la impresora. Los cuatro cartuchos de color independientes permiten la impresión de cali-
dad en un amplio espectro de colores.
Xavier Aliaga, Head of Sales Business Systems de Epson Iberia, apunta que “nuestra misión es ayudar a transformar la industria del etiquetado para pasar del monocromo al color, ya que la incorporación de este último permite elevar la imagen de marca y atraer la atención del consumidor para incrementar la voluntad de adquisición del producto”. Además, concluye: “En los últimos años hemos visto crecer el catálogo de los fabricantes en cuanto a materiales autoadhesivos diseñados para el etiquetado. Esta amplia gama de materiales, combinada con el uso de las impresoras ColorWorks, permiten a todo tipo de empresas de cualquier sector beneficiarse del etiquetado a color “en casa”. El hecho de que se pueda hacer bajo demanda permite reducir costes totales de impresión y etiquetado por almacenamiento e inventario. De esta manera, se evita la obsolescencia (cambios de diseño o
normativos) y el desperdicio (por cantidades mínimas de fabricación o deterioro del material pasado un tiempo), contribuyendo a los objetivos de desarrollo sostenibles”.
Javier Moreno, Responsable de Comunicación de CVNE, afirma que “en CVNE siempre hemos apostado por el valor tradicional y por sumarle todo aquello innovador que nos permita seguir mejorando. Por eso mismo estos detalles nos ayudan a acercarnos al público cuidando la calidad y creando un producto más personalizado. Estamos muy contentos de haber sido y seguir siendo referencia en España y en todo el mundo. Sin pensar en una mejora continua, eso no sería posible”.
Epson, a través de su equipamiento tecnológico, sigue ofreciendo a las empresas un producto único. La tecnología Epson tiene como objetivo aumentar la productividad, reducir los tiempos de espera y liderar la transformación digital de las empresas.
Con la gama de productos FASSON® ponemos a tu disposición una amplia gama de materiales Premium y de especialidades que cubren el extenso abanico de aplicaciones en los diferentes segmentos de uso del autoadhesivo. Además, con su reconocido y patentado sistema de corte en diagonal Crack-Back® Plus, los productos FASSON® facilitan la retirada del soporte, la aplicación de la etiqueta y generan una exclusiva diferenciación al no existir en el mercado una solución parecida. Y ahora, distribuidos por Torraspapel Distribución.
https://fassonsheets.lecta.com www.torrasdistribucion.com
AIFEC, la Asociación ibérica de fabricantes de etiquetas en continuo, ha anunciado la primera empresa en obtener el Sello de Excelencia QAIFEC.
El Sello de Excelencia QAIFEC certifica el compromiso de la empresa con los requisitos establecidos en el reglamento normativo del referencial que es verificado y confirmado mediante una auditoría de una empresa de certificación independiente mediante un plan de progreso plurianual.
Adhesivos del Segura fundada en 1986, fabrica todo tipo de etiquetas adhesivas industriales y de promoción. Carlos Col, director de la División de etiquetas del Grupo Printeos al que pertenece Adhesivos del Segura, nos contó el porqué decidieron pasar la auditoría para obtener el sello “teníamos muchas ganas de mostrar quienes somos en materia de excelencia. Actualmente la exigencia que todos los segmentos le piden a una etiqueta autoadhesiva es muy elevada. En AS hemos ido creciendo en este sentido, ofreciendo niveles muy elevados de excelencia, y el sello ha sido una magnífica oportunidad para mostrar lo preparados que estamos. Nos permitirá mostrar a los clientes todo nuestro conocimiento y buenas practicas, lo mucho que nos importan, en definitiva. Mejoramos siempre para ellos y esto es una excelente forma de reconocimiento”.
El Sello de Excelencia QAIFEC certifica el compromiso de la empresa con los requisitos establecidos en el reglamento normativo del referencial que es verificado y confirmado mediante una auditoría de una empresa de certificación independiente mediante un plan de progreso plurianual. Para las empresas interesadas en como se realiza el proceso, Adhesivos del Segura nos explica como ellos se organizaron: “En resumen, podría decir que ha sido ágil y eficiente. Nuestro equipo de calidad en Murcia ha estado bien asesorado y guiado en todo momento por los auditores. No hemos tenido ninguna complicación y las dudas que han surgido se han resuelto de forma rápida y eficiente. También me gustaría añadir que, a pesar de ser un proceso de auditoría, el dossier de los criterios de obtención esta tan adaptado nuestra industria que resulta cómodo para los
intervinientes. El proceso de inscripción y registro es realmente sencillo, y además permite “reservar” fecha para la auditoria, adaptando así la agenda a las necesidades de la empresa”.
Los objetivos de obtener el Sello Excelencia QAIFEC es promocionar y poner en práctica el respeto de los valores comunes de AIFEC. Promover y promocionar asociados que deseen destacar su profesionalismo y saber hacer. Y apoyar a los asociados en un proceso de mejora continua. Adhesivos del Segura envían un mensaje a todas las empresas que están interesadas, pero todavía no han pasado la auditoría: “Porque es el único referencial especifico que les proyectará como un proveedor excelente en todos los segmentos de uso, además les permitirá mostrar su excelencia sin perjuicio alguno en relación al tamaño de la empresa. En según qué segmentos tenemos clientes de una
cierta envergadura que pueden tener algún prejuicio por comprar a un proveedor demasiado pequeño. Ser excelente no tiene nada que ver con la envergadura de la compañía, y por tanto estos perjuicios podrán verse eliminados con este reconocimiento.
También lo veo interesante porque les permitirá mostrar su situación más
allá de otros referenciales que solo consideran criterios de calidad, normativas, etc... El sello QAIFEC esta creado por y para fabricantes de etiquetas, y esta especificidad del sector permite que cualquier avance que hayas implementado en la empresa, sume de forma importante”.
Desde AIFEC felicitan a todo el equi-
po de Adhesivos del Segura por su trabajo y tiempo invertido. Invitamos a todas las empresas fabricantes de etiquetas a inscribirse para pasar la auditoria y reservar fechas antes de final de año. Recordamos que para cualquier información pueden meterse en la página web del Sello de Excelencia QAIFEC.
Desde el lanzamiento del sello de excelencia QAIFEC el pasado 30 de mayo, han tenido bastantes peticiones para poder presentarse a la auditoria con OCA Global y así poder obtener el certificado de excelencia QAIFEC como fabricante de etiquetas. Ya hay empresas confirmadas que están pasando los procesos y que pronto obtendrán el certificado que les da acceso al sello QAIFEC. De momento Adhesivos del Segura es la primera empresa en obtener el certificado.
Para ello solo tendrán que pasar los 8 criterios de cumplimiento para el proceso de certificación en los cuales se les analizará su nivel de competencia en estrategia y gestión, calidad, aspectos reglamentarios, responsabilidad medioambiental, gestión de riesgos, competencias RRHH, técnicas de conocimiento, automatización y digitalización.
AIFEC tiene como objetivo con el lanzamiento del sello el poder apoyar a sus asociados en un proceso de mejora continua, promover y promocionar los asociados que deseen destacar su profesionalismo y saber
hacer y poner en práctica el respeto de los valores comunes de AIFEC. Por eso invitan a todas las empresas del sector a tomar la decisión de presentarse para poder obtener el Sello QAIFEC.
Para la vuelta de verano tendran una lista de empresas que se están preparando y esperan para final de año que por lo menos 12 empresas ya tengan su Sello QAIFEC. Para saber como prepararse para la auditoria y obtención del sello, puede encontrar toda la información en la página web del sello Qaifec www. aifec.eu/qaifec
Siguiendo con su política de desarrollo de información del mercado, AIFEC publica los resultados de la encuesta de mercado del sector de etiquetas correspondiente al primer cuatrimestre del 2021.
Siendo la primera vez que se lanza esta encuesta, se ha conseguido una buena participación que supone un 40% de representatividad en términos de facturación y un 23% en número de empresas del sector.
En base a los mismos, el sector marca una tendencia de un 2,4% de incremento en 2021 respecto al mis-
mo cuatrimestre del año anterior. Para facilitar la lectura de los resultados por tamaño de empresa se ha dividido también entre empresas de más y de menos de 3 millones de facturación, observándose una tendencia alcista en las empresas pequeñas y medianas.
Todos los datos que aportan las
empresas para estos estudios son confidenciales a título individual y los únicos resultados que se muestran son los agregados del sector, siguiendo la normativa de competencia y de la LOPD y RGPD. AIFEC continuará con la monitorización del mercado en próximos cuatrimestres.
El sector de etiquetas marca una tendencia alcista en el primer cuatrimestre de 2021
Soest Medical Group (SMG) y Lohmann han llegado a un acuerdo mediante el cual SMG adquiere el negocio de cintas adhesivas reutilizables y el know-how de Lohmann a partir del 1 de septiembre de 2021. Esta adquisición comprende cintas adhesivas (DuploMED® VP6141 y DuploMED® 2806) destinadas al mercado de los paños quirúrgicos reutilizables y la base de clientes global de Lohmann para estas cintas.
Lohmann considera que esta adquisición se adapta a su estrategia corporativa y al reciente realineamiento de sus competencias clave y áreas de focalización.
“Si bien creemos que nuestra amplia propuesta de valor brinda a los clientes las soluciones que necesitan para ser competitivos, sabemos que esto solo se obtiene al poder utilizar nuestros recursos de la manera más eficiente y efectiva”, afirma el Dr. Jörg Pohlman, CEO de Lohmann.
“SMG se complace en fortalecer su marca Eurotape de productos adhesivos para el mercado de paños quirúrgicos reutilizables y estoy seguro de que los clientes se beneficiarán de esta transacción al tener un único punto de contacto para todos sus productos adhesivos médicos”, resu-
me Hans van der Meer, director ejecutivo de SMG. Además, esta adquisición encaja bien con la estrategia de SMG de centrarse en ciertos nichos de mercado en adhesivos médicos y reforzará la posición de SMG en el mercado general.
Ambas compañías esperan que la transición se lleve a cabo en el mes de septiembre de 2021 con el apoyo total de los profesionales tanto de Lohmann como de SMG y al contar con suministros suficientes que respalden las necesidades de los clientes.
La Gallus Labelmaster se entrega ahora con amplias funciones nuevas y optimizadas. El nuevo concepto operativo no solo garantiza una mayor comodidad para el operador de la máquina, sino también menos desperdicio en la producción diaria.
Máquina más corta, menos desperdicio
Gallus ahora puede ofrecer un sistema de máquina aún más compacto. La Gallus Labelmaster ahora tiene una longitud de máquina más corta, ya que la corona, la limpieza de la banda, el transporte y la tensión de la banda están integrados en las nuevas unidades de bobinado, lo que
significa que se puede guardar un módulo. El diseño compacto permite reducir los residuos gracias a una longitud de máquina hasta 3,30 metros más corta, lo que garantiza una huella ecológica mejorada en comparación con la versión anterior.
La “facilidad de uso para el opera-
dor”, es decir, el manejo simple e intuitivo de la Labelmaster por parte del operador de la máquina, siempre ha sido el foco del desarrollo posterior de la Gallus Labelmaster. A este respecto, las unidades de bobinado ahora no solo se pueden operar localmente directamente en el bobinado, sino que sus parámetros se pueden ver y ajustar de forma centralizada a través del panel táctil en la
interfaz hombre-máquina (HMI) del sistema de la máquina, en línea con el " facilidad de uso" concepto.
En este sentido, el proceso de carga del sustrato también se ha rediseñado y revisado por completo. Con un nuevo sistema de carro, es decir, un elevador móvil fuera de la imprenta, el sustrato se puede cargar y descargar fácilmente sin tocar el suelo. Ya no es necesario un elevador integrado y el operador puede usar el
carro de manera flexible según sea necesario, incluso en otras máquinas. El resultado es una carga simple y flexible del sustrato.
Nuevas funciones como configuración estándar
Otras características optimizadas, como la accesibilidad mejorada al pretratamiento de corona y los módulos de transporte de banda con
un sistema de cambio rápido para una limpieza rápida y sencilla, completan el desarrollo posterior de Gallus Labelmaster.
Más de 160 instalaciones de Gallus Labelmaster en todo el mundo hablan del éxito de este sistema de máquina flexible. La Labelmaster está ahora disponible con estas nuevas características, incluidas en parte en el paquete de serie o según los deseos y necesidades de la imprenta.
Desde los inicios de su historia, la empresa tirolesa Durst ha estado comprometida con la producción sostenible y el desarrollo de tecnologías que contribuyan a minimizar la huella ecológica, así como con el desarrollo de propuestas que garanticen la seguridad de las personas. Con base en este compromiso, en el mercado de la producción de etiquetas, fue el primer proveedor de soluciones de impresión digital inkjet en ofrecer tintas de baja migración, aptas para su aplicación en envases y embalajes primarios de alimentos.
Ahora, da un nuevo paso en esta dirección, auditando sus tintas Tau RSC a través del Greenguard Environmental Institute, organización independiente de la industria, que tiene como objetivo proteger la salud humana, mejorando la calidad del aire en interiores y reduciendo la exposición de las personas a productos químicos y otros contaminantes.
Los análisis realizados por el Greenguard Environmental Institute han demostrado que las tintas Tau RSC cumplen con los más exigentes estándares en términos de emisión de sustancias químicas, otorgándoles las certificaciones Greenguard y Greenguard Gold. La certificación GreenGuard sólo es obtenida por aquellos a productos que cumplen con los estándares más exigentes sobre emisiones de sustancias químicas del mundo, garantizando que el producto certificado es aceptable para el uso en ambientes de interior, que está libres de más de 360 compuestos orgánicos volátiles y que la emisión de otras sustancias químicas están por debajo de los límites establecidos. La certificación Greenguard Gold confirma los factores de seguridad que deben tenerse en cuenta para las personas más sensibles
(como niños y ancianos), y garantiza que el producto puede utilizarse en lugares como escuelas y hospitales. Debido a la elección de materias primas y a las tecnologías aplicadas en sus procesos, Durst ha demostrado estar en cumplimiento con los estándares de calidad, ISO 9001; medio ambiental, ISO 14001 y de salud ocupacional, OHSAS 18001. Además, la empresa está firmemente comprometida con el cumplimiento de los Objetivos de Desarrollo Sostenible (ODS) de la ONU en las dimensiones de salud y bienestar, agua limpia e innovación, poniendo a disposición de las empresas productoras de artes gráficas soluciones que ayuden a diri-
gir sus procesos hacia un enfoque de producción más ágil y sostenible.
Celmacch, la empresa italiana que ha sido el principal referente en la industria de la maquinaria para cartón ondulado, busca más que nunca alcanzar nuevos y ambiciosos objetivos estratégicos.
Después de superar el año de la pandemia con resultados alentadores, la compañía registró un récord histórico de ventas en el primer semestre de 2021, con una gran cartera para 2022.
Los clientes han apreciado y recompensado la confiabilidad de Celmacch y, como resultado, los resultados de ventas y los pedidos para 2022 han superado significativamente las expectativas.
“La estrategia que adoptamos - dice el director general de Celmacch, Luca Celotti” se basa en un proceso de mayor industrialización de la empresa, estructuración de los distintos departamentos y crecimiento de los recursos internos”.
Las líneas de productos Chroma Print (impresoras flexográficas de alta definición) y Chroma Cut (troqueladoras rotativas HBL) se han mejorado a fondo desde el punto de vista del proyecto y ahora están siendo elegidas por los principales actores del mercado que ahora representan a clientes leales. La nueva aspiradora y apiladora también se ha añadido recientemente a la lista de máquinas de Celmacch.
Los clientes han apreciado y recompensado la confiabilidad de Celmacch y, como resultado, los resultados de ventas y los pedidos para 2022 han superado significativamente las expectativas.
Junto con las inversiones en varias tecnologías nuevas, la empresa está reorganizando los recursos internos con la introducción de nuevos roles clave. “Involucrar y valorar los recursos internos y los contratistas - continúa Luca Celotti - introducir nuevas personas con experiencia que sean capaces
de aportar nuevas ideas y perspectivas, contribuye a un crecimiento positivo y bien estructurado de la empresa”.
La estructura organizativa también se ha visto reforzada con la introducción de un Director de Operaciones, con una sólida y dilatada experiencia en la
industria del cartón, que garantizará una mayor eficiencia e industrialización en todos los departamentos.
Un departamento de servicio dedicado, con almacén propio y técnicos de asistencia e intervenciones postventa, garantiza una respuesta rápida y eficaz
a las necesidades del cliente. Esto representa el resultado de la filosofía de "orientación al cliente" de Celmacch.
La eficiencia de la organización se ha mejorado también gracias a un restyling de la instalación, con una reciente ampliación de oficinas y de las áreas de producción, nuevas grúas puente para optimizar y agilizar el montaje, un almacén automático Modula, la implementación de la solución SAP ERP para supervisar y gestionar mejor las diferentes fases del proceso de la empresa y, finalmente, una gestión de la cadena de suministro basada en una esbelta producción justo a tiempo.
Se ha prestado especial atención a la selección de nuevos proveedores, que trabajarán codo con codo con los existentes, todos ellos con sede en Europa y capaces de producir componentes de alta calidad.
2022 será un año muy importante para Celmacch, con una cartera de pedidos de aproximadamente 30 millones de euros: la compañía, que se ha ganado la confianza de algunos de los principales actores del mercado, está orgullosa y honrada por estos resultados. Además, 2022 verá a Celmacch ocupada en la finalización de un nuevo proyecto importante: la impresora Chroma Print 2 caras HBL que podrá imprimir en ambas caras del cartón. La combinación de un módulo de impresión inferior con uno de impresión superior brindará a los clientes la oportunidad de imprimir hojas tanto en el interior como en el exterior. Esto beneficiará especialmente al sector del comercio electrónico, que actualmente se encuentra en una fase de rápida expansión.
En conclusión, Celmacch ha definido
2022 será un año muy importante para Celmacch, con una cartera de pedidos de aproximadamente 30 millones de euros: la compañía, que se ha ganado la confianza de algunos de los principales actores del mercado, está orgullosa y honrada por estos resultados alabrent.com
y puesto en marcha una estrategia detallada que combina recursos humanos, tecnología de vanguardia, proyectos innovadores e inversiones clave, todo lo cual impulsará un crecimiento sólido y continuo de la empresa.
Jackson Paper Manufacturing Co., un proveedor líder de cartón ondulado de EEUU., está ampliando sus operaciones con el lanzamiento de servicios de impresión digital con la prensa digital HP PageWide C500 de grado industrial, a medida que amplía su gama de productos ondulados sostenibles.
La nueva prensa HP PageWide C500 operará en Sustainable Printing, un nuevo brazo de impresión digital de Jackson Paper, ubicado en Georgia, donde se instalará la unidad este verano. Con sede en Carolina del Norte, Jackson produce y suministra fabricantes de cajas de cartón corrugado medio a corrugado 100% reciclables en todo Estados Unidos a través de Jackson Corrugated and Sustainable Corrugated Company.
Sustainable Printing operará como una impresora comercial mayorista para la impresión digital a pedido de cajas de cartón corrugado de calidad litográfica para que sus clientes de láminas se beneficien de una entrega rápida y pedidos de tamaños variables. La nueva producción de rotativas HP PageWide C500 permitirá a Jackson
Papers acceder al creciente mercado de envases de alta calidad para aplicaciones de comercio electrónico, listas para estantes y de alimentos y farmacéuticas.
“La compra de HP PageWide C500 amplía nuestra oferta de sostenibilidad a nuestros clientes y al mercado con una impresión digital más sostenible y de alta calidad. Como experto en cartón corrugado y proveedor para la industria de la impresión gráfica, agregar servicios para tableros gráficos impresos posicionará de manera única a Sustainable Printing para ofrecer un producto de alta calidad excepcional junto con un tiempo de comercialización revolucionario”, dijo Thomas Barker, vicepresidente ejecutivo.
La HP PageWide C500, basada en la tecnología HP Thermal Inkjet, propor-
La HP PageWide C500, basada en la tecnología HP Thermal Inkjet, proporciona calidad de impresión offset para una amplia gama de aplicaciones de presentación y embalaje corrugado en hojas recubiertas y no recubiertas, brindando texto y códigos de barras nítidos, transiciones de tonos suaves y colores vivos, de baja a alta volúmenes de hojas
ciona calidad de impresión offset para una amplia gama de aplicaciones de presentación y embalaje corrugado en hojas recubiertas y no recubiertas, brindando texto y códigos de barras níti-
La HP PageWide C500, basada en la tecnología HP Thermal Inkjet, proporciona calidad de impresión offset para una amplia gama de aplicaciones de presentación y embalaje corrugado en hojas recubiertas y no recubiertas, brindando texto y códigos de barras nítidos, transiciones de tonos suaves y colores vivos, de baja a alta volúmenes de hojas.
dos, transiciones de tonos suaves y colores vivos, de baja a alta volúmenes de hojas. Diseñada para producir impresiones de alta calidad en entornos de producción exigentes, la prensa imprime a 246 pies lineales / min con la máxima calidad de impresión con una resolución de 1200 npi utilizando un millón de boquillas.
Según Barker, las verdaderas tintas a base de agua de HP también permiten
a la empresa avanzar en su posición de sostenibilidad en los mercados objetivo de alimentos, así como en las categorías de salud y belleza.
Las verdaderas tintas a base de agua HP C500 se pueden utilizar para imprimir las aplicaciones más sensibles de cajas de cartón ondulado, incluso para productos alimenticios y agrícolas que entran en contacto directo con el interior de la caja. Las tintas HP pue-
den cumplir con estrictos requisitos de seguridad alimentaria, como USDA FDA 21 CFR, directrices de Nestlé, Swiss Ordinance y EuPIA.
Jackson Paper es una empresa familiar que se esfuerza por proporcionar láminas corrugadas del más alto valor manteniendo los costos bajos, optimizando la eficiencia y siendo extremadamente receptivo a las necesidades de los clientes.
Menasha Packaging, empresa subsidiaria de Menasha Corporation y el mayor proveedor independiente y minorista de la industria de envases y expositores, amplía sus capacidades de impresión con una Barberan Jetmaster 2.0. La Jetmaster 2.0 es la nueva generación en impresión digital single-pass con alta resolución y una velocidad impresionante.
La nueva Barberán Jetmaster 2.0 se emplazará en las instalaciones de Menasha, en Hartford, Wisconsin, es el modelo de 1840 mm de ancho, equipado con 6 colores y ofrece una reproducción de color precisa y consistente.
Con sede en Wisconsin, un legado de 172 años de experiencia en embalaje y un gran compromiso con el éxito de sus clientes, MenashaPackaging ofrece productos de alta calidad gráfica en rápidos plazos de entrega. Bajo estas premisas, Menasha Packaging confía en la nueva Jetmaster 2.0 de Barberan, capaz de imprimir gráficos extraordinarios a alta velocidad sobre cartón corrugado, con alta definición en textos, códigos QR, y con colores vívidos y naturales.
La nueva Barberán Jetmaster 2.0 se emplazará en las instalaciones de Menasha, en Hartford, Wisconsin, es el modelo de 1840 mm de ancho, equipado con 6 colores y ofrece una reproducción de color precisa y consistente. Las impresoras Jetmaster de Barberán están preparadas para obtener la certificación de color G7 de Idealliance. Además, incorpora el sistema de inspección MasterVision diseñado para el ajuste automático de alineación, tonalidad e inspección de imágenes.
"Estamos entusiasmados con la instalación de esta impresora digital, que es una de las impresoras single-pass más eficientes del mundo", dijo Mike Riegsecker, presidente de Menasha Packaging Company. "No solo vamos a satisfacer la necesidad de nuestros clientes de gráficos excelentes, sino que también esta impresora reduce el desperdicio general de funcionamiento y utiliza menos agua que otras impresoras. Es una gran inversión ambientalmente sostenible y se alinea con la prioridad de Menasha de proporcionar soluciones de embalaje sin precedentes en apoyo de un futuro sostenible".
"Contar con un cliente como Menasha es muy emocionante para Barberán. Es uno de los mayores proveedores de envases gráficos en América del Norte y ganarse su confianza es un testimonio no solo de la calidad de la impresora, sino de todo nuestro equipo", dijo Garrett Bradley, presidente de Barberan US. "Estamos ansiosos por expandir los límites de lo
Menasha Packaging con más de 50 instalaciones en América del Norte, Menasha Packaging diseña, imprime y produce embalaje, expositores y material de comercialización personalizados, y proporciona servicios de empaquetado y cadena de suministro
que las personas consideran elegible para la impresión digital. Nuestra impresora 2.0 funciona a casi el doble de la velocidad de cualquier otra impresora en el mercado y con mayor resolución que nos permite lograr mejores resultados en fuentes de letra pequeñas y códigos de barras, así como con los sólidos. Gracias a Menasha por su confianza y la oportunidad. Les deseamos un gran éxito en el futuro".
La Jetmaster 2.0 cuenta con los últimos avances tecnológicos y de software diseñados por Barberan para el mercado del cartón ondulado, amplía las posibilidades de impresión con mayor personalización y garantiza a los clientes un rápido acceso al mercado con productos de alta calidad, que potenciarán su imagen de marca.
Con una amplia experiencia de más de 35 años, RTS ha desarrollado una plataforma de aplicaciones vertical y de última generación específica para las empresas del sector.
Global Business Application Suite es una plataforma con ERP Core específica para fábricas de transformación de cartón, onduladores e integrados, que crece de forma gradual y armoniosa con su empresa. Con una funcionalidad completa para los procesos de producción, logística y fuerza de ventas, se destaca por una experiencia de usuario simple e intuitiva, garantía de continuidad del negocio e inteligencia de datos en tiempo real, con Dashboard y KPIs para el análisis estadístico.
Global Business Application Suite es la solución ideal para empresas dispuestas a enfocarse en la innovación.
Grupo Saica, empresa líder en la fabricación de papel reciclado para cartón ondulado, invertirá más de 700 millones de euros en su proyecto de expansión en Estados Unidos. El objetivo, enmarcado en la estrategia “Saica 2025” que la compañía comunicó a principios de junio, es crecer en cartón ondulado construyendo nuevas plantas o adquiriendo fabricas existentes en el mercado norteamericano, lo que permitiría poner en marcha también una nueva fábrica de papel y aprovechar la ventaja competitiva que tendrá el Grupo con la introducción de gramajes ligeros en el país.
Grupo Saica planea invertir más de 700 millones de euros en su proyecto de expansión en Estados Unidos para crecer en cartón ondulado, lo que permitiría poner en marcha también una nueva fábrica de papel.
La primera planta comenzó a construirse en septiembre de 2020 y la compañía estima su plena operatividad a principios de 2022. La nueva fábrica producirá envases de cartón ondulado en un edificio de aproximadamente 30.000 metros cuadrados, que también incluye un almacén de bobinas de cartón ondulado, con zonas de fabricación, producción y conversión en las que imprimir y plegar las cajas de embalaje. En el edificio también se incluirán diferentes salas técnicas y oficinas, siendo un emplazamiento con espacio para futuras incorporaciones y ampliaciones de actividad.
De acuerdo con Ramón Alejandro, presidente del Grupo Saica, la andadu-
ra en Estados Unidos “no ha sido un camino fácil, pero estamos convencidos que los papeles reciclados de bajo gramaje, en los que somos especialistas y referentes a nivel mundial, pueden aportar un producto diferenciador al mercado estadounidense, reduciendo la huella medioambiental y creando empleo estable y de calidad”.
El condado de Hamilton, en Ohio, ha sido el lugar escogido del Grupo para la primera fábrica en Estados Unidos. Hamilton tiene un amplio historial como zona industrial y se ha convertido en un área de grandes oportunidades para los fabricantes de cartón ondulado.
Los principales ejes del proyecto se basan en los amplios conocimientos de
Ramón Alejandro, presidente del Grupo: “Podemos aportar un producto diferenciador al mercado estadounidense”
la compañía sobre la producción de papel reciclado de bajo gramaje, que aportarán valor añadido al mercado local; la alta densidad de fabricación en el medio Oeste, con un elevado consumo de cajas de cartón; y el interés creciente de Saica por entrar en el mercado estadounidense.
Fundada en 1977, Paprinsa opera en el negocio de aglomerado de revestimiento blanco reciclado (WLC). En la actualidad, es el segundo productor de cartón reciclado de España y el octavo fabricante de cartón de Europa. La empresa tiene tanto su sede como molino en Mollerussa, a tan solo 130 km de Barcelona y a menos de una hora de la planta de RDM Barcelona Cartonboard.
RDM Group anuncia el cierre de la adquisición por parte de su filial RDM Barcelona Cartonboard S.A.U. del 100% del capital social de cuatro sociedades constituidas en España. El acuerdo preliminar ya publicado el 30 de septiembre de 2020 cubre la adquisición de uno de los principales actores europeos de la industria de tableros de partículas recubiertos, Papelera del Principado SA (“Paprinsa”), y tres empresas más pequeñas que operan en negocios contiguos con sede en el mismo sitio: Fergerdell SL, Cogeneraciò del Pla, S.A. y Ondupacart, S.A. Los 15 vendedores, titulares de las participaciones en las sociedades adquiridas, incluyen tanto personas jurídicas como personas físicas.
La planta tiene un ancho de corte de 4,8 metros, lo que la convertirá en la planta más amplia de RDM Group, ya que es una de las papeleras más grandes de este sector en Europa. Al explotar aún más este tamaño, RDM Group puede contar con un aumento potencial en la capacidad de producción de la fábrica de las actuales 140.000 toneladas al año a más de 200.000 toneladas al año, en línea con las otras plan-
tas principales que hoy forman parte del Grupo. La planta tiene una plantilla total de unos 140 empleados.
El precio provisional para la adquisición de las cuatro empresas se basa en un Valor Empresarial total de 30,4 millones de euros, calculado sobre el EBITDA1 informado para 2020 de 5,1 millones de euros y sobre una Deuda Financiera Neta1 de 18,9 millones de euros al 31 de diciembre de 2020.
Al cierre de la operación se abonó un importe inicial de 5,9 millones de euros, calculado teniendo en cuenta un NFP de 21,1 millones de euros a 31 de agosto de 2020 y un valor de empresa de 27 millones de euros, que corresponde al nivel mínimo del rango de VE originalmente identificado de € 27 - € 33 millones. El precio estará sujeto a los ajustes previstos en los acuerdos, con base en el NFP, el capital de trabajo y el EBITDA general de las cuatro empresas objetivo a la fecha de vigencia de la transacción al 1 de julio de 2021.
Michele Bianchi, CEO de RDM Group, afirmó: “La adquisición de Paprinsa confirma claramente nuestro posicionamiento competitivo como la empresa líder en
el sur de Europa en el segmento de cartón reciclado, como parte de una clara estrategia a largo plazo y apalancando una sólida posición financiera”.
Sobre la base de un EBITDA1 informado de 5,1 millones de euros para 2020, el Grupo RDM espera alcanzar un aumento del EBITDA de entre 3 y 5 millones de euros durante el proceso de integración de los próximos tres años. Estos beneficios se conseguirán principalmente gracias al incremento de la producción debido a la plena utilización de la capacidad productiva de Paprinsa, las sinergias con la planta de Barcelona y la revisión de determinados contratos de aprovisionamiento.
En virtud de los acuerdos alcanzados con los vendedores, Reno De Medici S.p.A. se ha comprometido a ser garante de la filial RDM Barcelona Cartonboard S.A.U. para todas las obligaciones derivadas de los contratos de adquisición suscritos por este último.
EY y Osborne Clarke actuaron como asesores financieros y legales de Reno De Medici S.p.A., mientras que Gasso Capital Market actuó como asesor financiero de los Vendedores.
Smurfit Kappa ha anunciado el acuerdo de adquisición de Verzuolo por 360 millones de euros, una fábrica de papel de cartón reciclado de última generación con una capacidad de 600.000 toneladas al año. Está situada cerca del puerto de Savona, en el noroeste de Italia, por lo que cuenta además con una ubicación estratégica que permite a la compañía atender tanto a las regiones del sur de Europa, entre ellas España y Portugal, como a otros importantes mercados para su negocio, brindándoles un servicio de primer nivel.
Ignacio Sevillano, CEO de la División de Cartón Ondulado de Smurfit Kappa España | Portugal | Marruecos, asegura que “la adquisición de Verzuolo nos permite ofrecer una seguridad adicional a nuestros clientes en el suministro de embalajes en base papel para que reciban sus soluciones de packaging a tiempo y con la misma calidad de siempre. Además, refuerza nuestro exclusivo modelo operativo integrado y fomenta nuestra apuesta por la sostenibilidad a través del desarrollo de embalaje ecológico de cartón ondulado, cada vez más demandado”.
La adquisición de esta planta aportará a Smurfit Kappa importantes beneficios sinérgicos, incluidas la optimización técnica y de producción y una mayor integración del cartón. Su compra en efectivo se financiará
con los recursos existentes del Grupo y se espera que culmine a lo largo del cuarto trimestre del año, según las condiciones habituales de cierre, incluida la aprobación reglamentaria.
Tony Smurfit, CEO del Grupo Smurfit Kappa, ha asegurado que “en Smurfit Kappa recibimos con los brazos abiertos a todos los profesionales altamente cualificados de Verzuolo, que nos ayudarán a seguir reforzando nuestro liderazgo mundial en el sector del embalaje a base de papel. Creemos que esta adquisición supone un avance más tanto para la compañía como para nuestros clientes y todos los accionistas. El Grupo cuenta con una habilidad demostrada para identificar, adquirir, integrar y optimizar actividades complementarias. Además, esta adquisición es también una muestra de la agilidad inherente
de nuestro enfoque para movilizar capital con rapidez y eficacia”.
Por su parte, Saverio Mayer, CEO de Smurfit Kappa Europa, ha añadido que “desde Smurfit Kappa Europa nos complace anunciar este acuerdo para adquirir Verzuolo. Una operación que llevamos valorando desde hace tiempo y que demuestra nuestro compromiso con este importante mercado para el Grupo, lo que nos permitirá complementar a la perfección las importantes inversiones que estamos haciendo en nuestras instalaciones de cartón ondulado en el continente”.
La planta, propiedad de Burgo Group, cuenta con una máquina PM9 instalada en 2002 y convertida en 2019 en una máquina para cartón reciclado con capacidad de 600.000 toneladas.
AFCO arranca el curso con nuevas propuestas de formación digital dirigidas a los socios, con el objetivo de continuar potenciando la mejora de la productividad profesional de los trabajadores que componen el sector.
El programa de formación de AFCO se imparte de la mano del Instituto del Cartón Ondulado y el centro educativo Tajamar e incluye diferentes áreas de conocimiento vinculadas a la producción del cartón ondulado.
La primera de las propuestas formativas es una Masterclass sobre Performance Packaging”, que se celebrará los días 6 y 7 de octubre en horario de 16:00 h a 18:00 h. Se trata de un curso online enfocado al análisis del comportamiento estructural de los papeles y del cartón ondulado, cuyo objetivo es formar a los profesionales del sector en la optimización y reducción de las materias primas empleadas en la fabricación del embalaje.
El día 15 de octubre arrancará la
segunda edición del programa especializado de troqueladora rotativa que tendrá una duración de cuatro meses y abordará el proceso de troquelado rotativo, impresión y plegado de planchas de cartón para la obtención del embalaje, así como la resolución de los problemas cotidianos en la fabricación y la mejora de la calidad del embalaje.
El curso especializado en sistemas de impresión comenzará el 20 de octubre y dotará al alumnado de conocimiento de cada una de las partes de la maquinaria que componen el sistema de impresión de una plancha de cartón ondulado, tipos de impresión, clichés, sistemas de regulación de tintas, además de adquirir las destrezas necesa-
rias para el control de máquina.
Para aquellos que deseen profundizar en los componentes de la maquinaria que compone el proceso de ranurado, impresión, plegado y pegado de planchas de cartón para la obtención del embalaje (la Flexo Folder Gluer/Casemaker), el 25 de octubre se inicia el programa especializado casemaker, que tendrá una duración de dos semanas.
Durante el mes de noviembre empezarán dos cursos: el programa avanzado de onduladora y el programa especializado en formación técnica sectorial, que ayudarán a profundizar en el conocimiento de la máquina onduladora y de los procesos relativos a la fabricación y transformación del cartón ondulado.
una nueva papelera de cartón reciclado con capacidad de 600.000 toneladas que ofrecerá una seguridad adicional en el suministro de embalajes
Explórelo con Heidelberg y MK Masterwork. Como el mayor proveedor mundial de máquinas para la impresión de embalajes, le ofrecemos la cartera de productos más amplia del sector. Con total seguridad, MK Masterwork es el único proveedor en el que todas sus máquinas poseen certificación GS. heidelberg.com/es
la estrategia de ACTEGA en materia de sostenibilidad así como los requisitos técnicos, comerciales y normativos de los revestimientos de
Este artículo de preguntas y respuestas analiza cómo la sostenibilidad está transformando el mundo que nos rodea y, más concretamente, los mercados en los que operamos. Es indiscutible: marcas y consumidores exigen soluciones de envasado medioambientalmente responsables, y están poniendo a la industria del envasado bajo una presión tremenda para que trabajen de una manera más sostenible.
¿Qué significa la sostenibilidad para vosotros?
Ben: La sostenibilidad es un concepto que llevo oyendo desde que trabajo en este sector. Lleva 15 años siendo una tendencia al alza, pero la buena noticia es que ahora ha dado un paso más: hoy día, sin duda, se ha convertido en un requisito y una expectativa fundamental en el mercado.
Como desarrolladores y actores en este sector, para ACTEGA también implica una gran transformación. Y para nosotros resulta muy importante entender con exactitud qué es lo que nos ha llevado hasta aquí. Entender por qué es importante la sostenibilidad - y qué estamos haciendo para concretarla - nos ayuda a perfilar nuestras decisiones actuales y futuras.
¿Cuál es el impacto en las empresas de este paso hacia la sostenibilidad?
Ben: Antes, la sostenibilidad surgía como resultado de las preferencias de los consumidores, y esto sigue siendo así hoy día. Sin embargo, ahora las marcas ponen en valor también las prácticas sostenibles, y no solo como una manera de satisfacer al consumidor. Estas marcas entienden la responsabilidad que tienen de cara al planeta,
y son conscientes de que es un requisito fundamental para la viabilidad y la rentabilidad a largo plazo de su negocio. La sostenibilidad ya no es una tendencia de nicho, sino un concepto que las empresas han asumido con seriedad y que ellas mismas están potenciando, especialmente en el sector de los envases.
Un buen ejemplo de ello es la nueva «economía del plástico», un proyecto multinacional de cientos de marcas diferentes que han dado un paso adelante y han asumido voluntariamente algunos compromisos valientes en torno a la sostenibilidad. Se han fijado unos objetivos muy ambiciosos y, al hacerlo, están impulsando la sostenibilidad en toda la cadena de suministro, especialmente en lo que respecta a los envases.
Además, si analizamos las afirmaciones que hacen estas marcas, vemos que hablan de compromisos de gran
calado, valientes y transparentes. Compromisos que van más allá del envasado y que establecen un marco de referencia para otras empresas, como la nuestra. En este contexto, ahora vemos cómo algunas de las empresas más importantes del mundo incorporan a su ADN y a sus estrategias diarias estos mismos objetivos en materia de sostenibilidad.
¿Qué pasos están dando estas empresas hacia la sostenibilidad?
Markus: Las grandes marcas globales han puesta en marcha muchas iniciativas para reducir su impacto en el medio ambiente; en concreto, una de las más destacadas es la tendencia a utilizar más alternativas de papel en los envases. Otra tendencia destacada es la evolución hacia revestimientos de barrera más sostenibles, una tendencia que seguirá al alza y que acabará representando el grueso del mercado de los envases, ya que estos recubrimientos a base de agua ofrecen una solución eficaz, económica y verdaderamente sostenible para la industria de la impresión y el envasado. A medida que las empresas sigan asumiendo estos compromisos con la sostenibilidad, se verán obligadas, en última ins-
tancia, a trabajar con nuevas estrategias sostenibles y, paralelamente, a alejarse poco a poco de los productos y técnicas tradicionales que ya no serán adecuados para su propósito.
¿Qué implicaciones tiene todo esto para el mercado de los revestimientos de barrera en los envases?
Markus: Bueno, implicaciones hay muchas. Pero un cambio en profundidad en el sector que tendría una repercusión extraordinariamente positiva en términos medioambientales sería la sustitución de los laminados de polietileno plástico (PE). Actualmente es el material más utilizado en el campo de los recubrimientos de barrera, y por una buena razón: está consolidado en la cadena de suministro y ofrece un gran rendimiento funcional. Sin embargo, no es un material reciclable, y por eso suele acabar en los vertederos o en los mares. Debemos encontrar materiales de sustitución que sean adecuados y sostenibles.
¿Qué otros obstáculos podemos encontrar?
Ben: A la hora de estudiar nuevas soluciones, una de las mayores dificultades la encontramos en un ámbito normativo caracterizado por su complejidad y sus constantes modificaciones. Los materiales de cartón mencionados anteriormente ya tienen un perfil normativo consolidado, lo que significa que es más fácil poner un parche para resolver estos problemas en lugar de crear nuevos productos - algo que hay que hacer sí o sí. Sin embargo, para ver un avance real y potenciar un cambio en profundidad, las empresas tendrán que enfrentarse a la complejidad de las leyes, políticas y reglamentos.
En los Estados Unidos, por ejemplo, la normativa puede ser distinta según la zona o incluso según el municipio, lo que complica enormemente este proceso. ACTEGA cuenta en estos momentos con un equipo global de expertos en materia normativa que se encargan cada día de abordar estas cuestiones. De todos modos, aunque ACTEGA sea un proveedor global, esto no deja de suponer un reto mayúsculo.
Markus: Con la nueva directiva sobre plásticos de un solo uso, la Unión Europea pretende reducir el impacto
negativo que algunos productos plásticos generan en el medio ambiente y la salud humana. Este es un ejemplo de la importancia de esta cuestión en el mundo de hoy día. A diferencia de los productos empleados habitualmente en la industria del envasado, los revestimientos de barrera de ACTEGA son a base de agua, y eso permite reciclar los sustratos de una manera sencilla y generalizada empleando prácticas estándar.
¿Cuáles son las dificultades que plantea la aplicación de revestimientos de barrera?
Ben: Un aspecto que siempre hay que tener en cuenta es la posibilidad de que se produzca migración de tinta en el exterior del envase. Otro elemento que preocupa a la industria es que estas tintas podrían llegar al sustrato del envase, y pasar después al producto de consumo. Además, a medida que utilizamos cada vez más papeles reciclados, es habitual encontrar más impurezas dentro del sustrato, lo que dificulta aún más la reutilización de los materiales y la protección del producto contra las impurezas. Hay que resolver esta cuestión.
¿Qué está haciendo ACTEGA para acometer esta transformación y qué creéis que deparará el futuro?
Markus: Estamos colaborando con otras empresas con el fin de crear soluciones óptimas para el sector y amplificar su repercusión. Abordamos esta cuestión tratando de comprender en profundidad todo lo relacionado con la sostenibilidad y definiendo sus ejes fundamentales, y ahí se incluyen también otros aspectos importantes para el éxito de cualquier solución de producto.
Ben: Básicamente, nuestros esfuerzos pasan por contribuir positivamente incorporando soluciones sostenibles. Para lograrlo, estamos desarrollando nuevas cadenas de suministro capaces de hacer realidad estas tecnologías y productos, trabajando con las marcas, los proveedores de materias primas y las agencias reguladoras. Esperamos que este enfoque centrado en los socios, combinado con la tecnología y los conocimientos más avanzados disponibles hoy en día, contribuyan a construir un mañana mejor.
Pascual, empresa líder de alimentación y bebidas en España, en colaboración con el Grupo Saica, referente europeo en la producción de papel reciclado para cartón ondulado, producción de embalajes y el desarrollo de soluciones circulares para el aprovechamiento de residuos, ha conseguido desarrollar con éxito tres modelos de circularidad de residuos: reintroducción de los desechos de papel y cartón en nuevas formas de packaging sostenible; recuperación del polietileno de baja densidad para darle una segunda vida en forma de film de agrupación; así como la valoración energética de los residuos para producir electricidad y vapor.
¿Cómo recuperamos el papel y el cartón en Pascual?
En el primer modelo de circularidad, relativo al reciclaje y a la reintroducción de los residuos de papel y cartón, el Grupo Saica consiguió recuperar 574 toneladas de papel y cartón de Pascual en 2020. Estas toneladas se reciclan y transforman en bobinas de papel reciclado de alta calidad. Posteriormente, se ha utilizado para fabricar alrededor de 5,2 millones de cajas nuevas, que vuelven a los lineales en forma de nuevos embalajes con productos Pascual.
En el segundo modelo, Saica ha recuperado 59 toneladas de polietileno de baja densidad transparente para darle una segunda vida. Este material plástico se transforma en granza reciclada de alta calidad que puede ser utilizada en múltiples productos. En concreto, parte se ha destinado a la fabricación equivalente de 271.000 m 2 de film de agrupación, que se ha usado para el embalaje de productos Pascual.
Además, la utilización de este recurso reciclado, en vez de virgen, consigue reducir la huella de carbono de la materia prima en un 73% y el consumo de agua, durante la fabricación del mismo, en un 78%. En el caso de Pascual,
La empresa de alimentación y bebidas trabaja tres modelos de circularidad: reciclado de papel y cartón, recuperación del polietileno de baja densidad y valorización energética.
se utiliza un 50% de granza reciclada y un 50% de granza virgen para el embalaje de los productos de la compañía.
Por otro lado, Pascual, bajo su política de Residuo Cero a Vertedero, y con la ayuda del Grupo Saica, valorizó energéticamente 33 toneladas de plástico no reciclable a lo largo del año, generando así 68.227 kWh, energía eléctrica equivalente al consumo de 21 hogares en España para todo un año.
Estas buenas prácticas, basadas en
el desarrollo de tres modelos de circularidad de residuos, forman parte de los objetivos medioambientales de Pascual, que buscan minimizar el impacto de sus actividades, favoreciendo la economía circular.
El Grupo Saica tiene como objetivo, igualmente, seguir avanzando en el camino hacia una economía cada vez más circular. Estas iniciativas se enmarcan dentro de los Objetivos de Desarrollo Sostenible (ODS) de las Naciones Unidas y, en concreto, en los ODS 12 (producción y consumo responsable), 13 (acción por el clima) y 17 (alianzas para lograr los objetivos).
Pascual, empresa familiar con un conjunto de valores consolidado y diferenciador, referente en el sector de la alimentación, inició su andadura en 1969 en Aranda de Duero, Burgos, para implantarse en poco tiempo en toda España y exportar hoy a 67 países. Con una gama de más de 200 productos, 6 plantas, 27 delegaciones a través de su empresa de distribución Qualianza y más de 2.200 empleados, su principal actividad es la preparación, envasado, distribución y venta, entre otros, de lácteos y derivados con la marca Pascual, aguas minerales Bezoya, bebidas vegetales Vivesoy, Bifrutas, y Mocay ‘Maestros del café’.
Hispack, el salón de packaging, proceso y logística referente en España que organiza Fira de Barcelona, se celebrará del 24 al 27 de mayo de 2022. Las nuevas fechas, refrendadas por el sector, son más favorables para asegurar una mayor presencia de visitantes internacionales, una de las principales demandas de las empresas exportadoras, y reunir una atractiva oferta que reactive el negocio y la innovación de múltiples sectores a través del envase y embalaje.
Esta mañana el Comité Organizador de Hispack –donde están representadas las firmas líderes, entidades y asociaciones profesionales de la industria española del packaging–, ha acordado que el evento tenga lugar el próximo mes de mayo con el fin de poder celebrarlo en una coyuntura más normalizada en cuanto a movilidad internacional y una mejor situación económica y social.
De este modo, Hispack gana solidez y un encaje óptimo en el calendario de grandes citas europeas especializadas en packaging, después de la alteración de la actividad ferial que ha supuesto la pandemia. Así, la feria española será de las primeras del sector en celebrarse presencialmente, contribuyendo al impulso del mercado y de las exportaciones, a las oportunidades comerciales, y a la recuperación económica que se prevé más consolidada para entonces. Tras esta edición, Hispack tendrá lugar de nuevo en 2024 y retomará a partir de entonces su periodicidad trienal.
El presidente del Comité Organizador de Hispack, Jordi Bernabeu, ha destacado “la importancia para el sector de celebrar la feria en una coyuntura que garantice una edición fuerte a nivel internacional para que su eficacia y alcance como plataforma comercial suponga un verdadero revulsivo en la actividad de las empresas participantes tras este periodo tan complejo”.
En la misma línea, el director de Hispack, Xavier Pascual, ha subrayado: “Con el cambio de fechas buscamos reafirmar el papel referente de Hispack dentro y fuera de nuestro país a la hora de proyectar la potencia, la innovación y la transversalidad de la industria española del packaging y atraer la mejor demanda”.
El próximo año Hispack reunirá una extensa oferta expositiva de maquinaria, materiales, tecnología, procesos, logística, y soluciones para la fabricación de todo tipo de etiquetas, envases y embalajes, así como elementos de Publicidad
en el Lugar de Venta. También incluirá jornadas, encuentros de negocios y otras actividades, que incidirán en la sostenibilidad, la digitalización y la innovación como los ejes que marcan la evolución del packaging, elemento necesario en la fabricación, distribución y comercialización de cualquier producto.
Mientras, y como viene siendo habitual, Hispack continuará manteniendo un estrecho contacto con el sector dinamizando y promoviendo –en colaboración con entidades, empresas y asociaciones–, espacios de relación que propicien el conocimiento y el networking entre profesionales vinculados a la industria del packaging.
En la pasada edición de Hispack, celebrada en 2018, participaron 843 expositores directos que representaron más de 1.400 marcas, procedentes de 24 países. La edición de este año estaba prevista para el próximo mes de octubre junto a Alimentaria Foodtech, que tendrá lugar en septiembre de 2023.
Edición #7
N E T W OR K IN G
D E MOSTR A CIO NE S
W OR K S H O P S
C ON FE RENCI A S
E VE N TO H ÍBRID O
Consigue tu acreditación gratuita registrándote en www.salon-cprint.es con el código P-ALCPM22
Vuelve el evento líder del sector de la impresión, la comunicación visual y la personalización
O S
HEMO S
E CHAD O
D E
M EN O S
salon-cprint.es
Con todas las medidas de control sanitario para garantizar tu seguridad
Suministradores de maquinaria para la producción de etiquetas:
Offset Semirotativo ∞ Flexo ∞ Estampación Serigrafía ∞ Acabados para Digital Rebobinadoras / Inspeccionadoras Extracción Desperdicios
Camisas de flexografía, huecograbado y laminación, Anilox, cerámicos, planchas de barniz, portaclichés, limpiadores
918 859 577 ventas@boettcher-systems.com
Lohmann Spain S.A. c/Miquel Torelló i Pagés, 38 P.I. El Pla 08750 Molins de Rei (Barcelona) /Spain www.lohmann-tapes.com
Lohmann Spain S.A.
c/Miquel Torelló i Pagés, 38 P.I. El Pla 08750 Molins de Rei (Barcelona) /Spain www.lohmann-tapes.com