

BUILT TO CONNECT
Sustainable Innovation
As a decades-long leader in asphalt plant innovation, Astec has introduced numerous products contributing to sustainability. From the Double Barrel® dryer/mixer introduced in 1988 to the debut of the high RAP Double Barrel XHR in 2016. In addition to these industry-changing products, Astec also leads in sustainability with our warm mix system, the V-PAC stack temperature control system, low emission burners, and blue smoke systems.
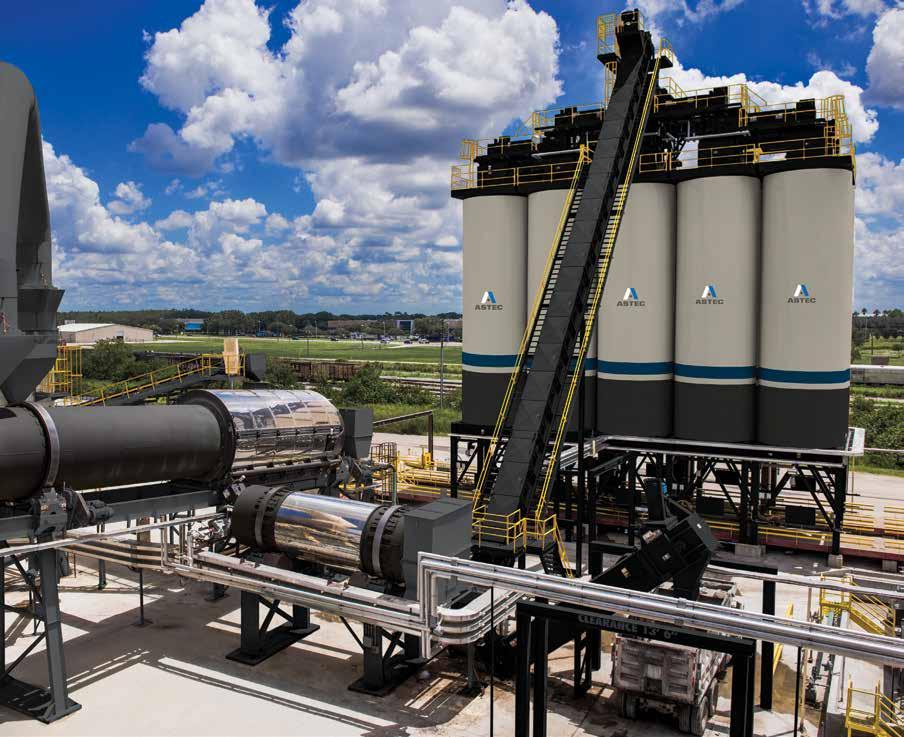
Astec is well-equipped to carry our culture of innovation into the future. Our dedication to sustainability includes new product development teams and an on-staff product manager for sustainability.
COME VISIT BOOTH C30235
MARCH 14-18, 2023 • LAS VEGAS, NV
Reach out to learn more about how we can help you meet your asphalt plant sustainability goals.

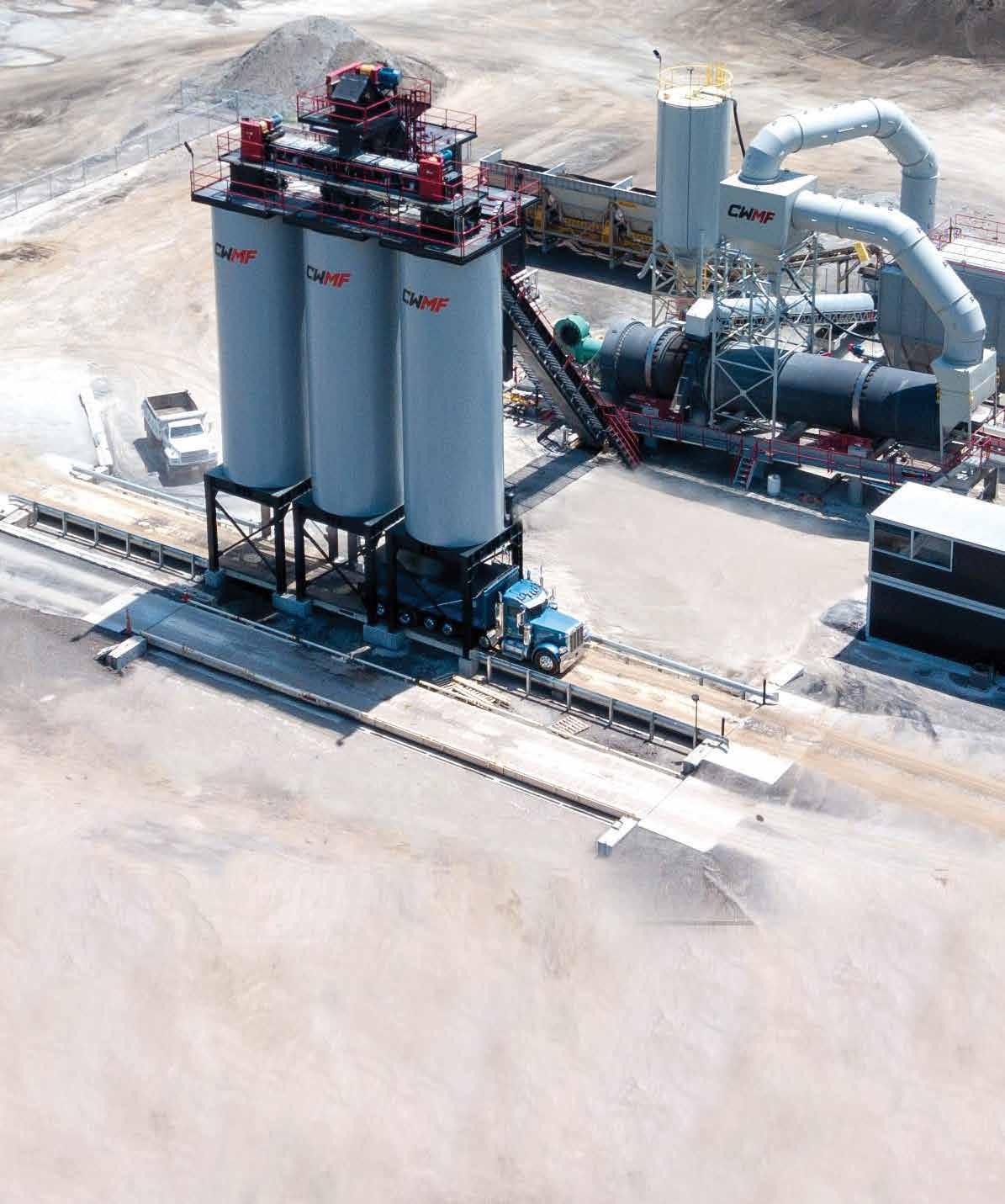
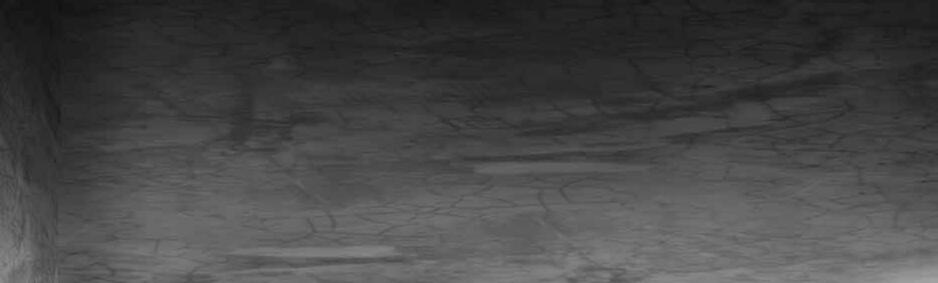
At Gencor, we’ve led the industry with the most fuel-efficient, environmentally clean and lowest-maintenance design available to the hot mix industry. From the award winning Ultraplant® to the Green Machine, our record is unrivaled in innovative design. That’s the kind of leadership you’ve come to expect from Gencor.
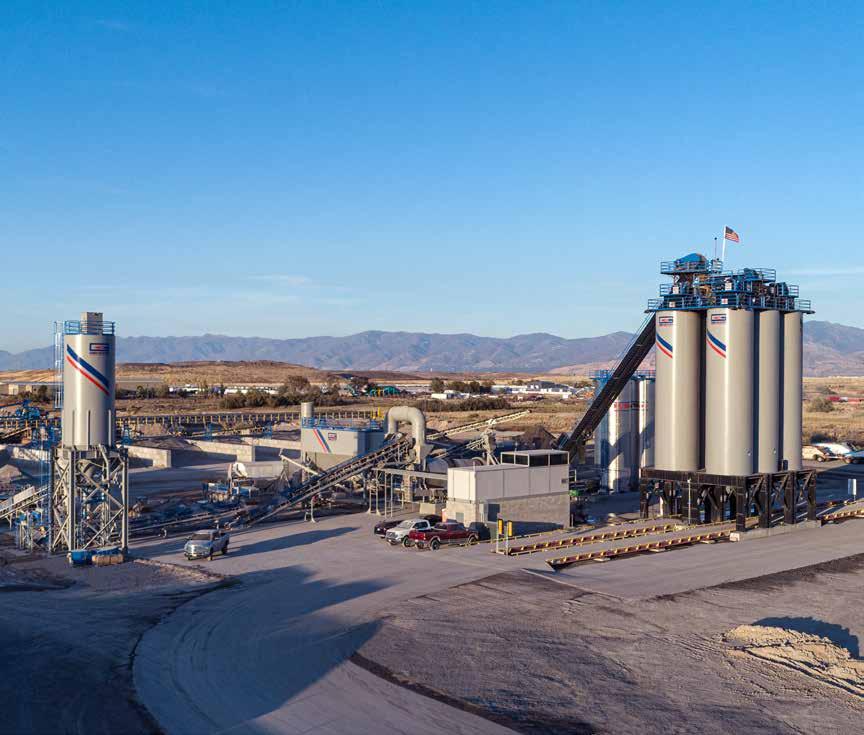
The Trusted Choice!
Call 407-290-6000 or visit www.gencor.com

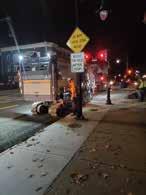
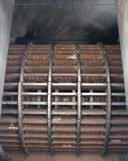
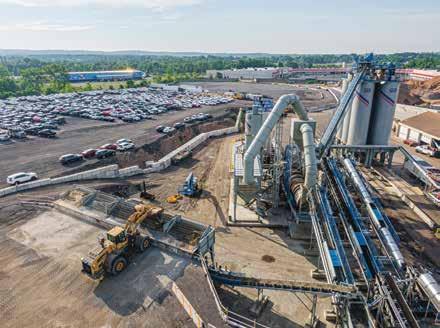
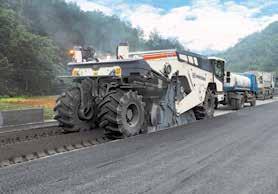
Signal Your Recycling Virtue
Back in June 2022, the National Asphalt Pavement Association (NAPA) released a 34-page document titled “GHG Emissions Inventory for Asphalt Mix Production in the United States: Current Industry Practices and Opportunities to Reduce Future Emissions.” Within this report, authors Joseph Shacat, J. Richard Willis and Ben Ciavola shared data that confirms the asphalt pavement production industry within the United States had cradle-to-gate greenhouse gas (GHG) emissions representing a mere 0.3% of the total U.S. GHGs during the year 2019, which is the year of our industry’s highest production of the years studied.


What I’m drawing your attention to is this: During our most productive year of the study, the year representing the most mix we made, we were responsible for 0.3% of the total GHGs in the entire country. That means other industries were causing the other 99.7%.
If you’ve been reading my notes since 1998, you know what I’m about to write next. I’m about to suggest “the government” go after some of those big emitters and leave the 0.3% alone.
But, to beat a dead horse, why not put some more filters on some more equipment and capture some more droplets of smaller microns and spend some more money on some more research to find some more ways to lower the asphalt industry’s numbers some more? I mean, we can print as much research money as we need, right? The government will hand us a grant to study this stuff at this point. Let’s go for it.
Part of me wonders if I could become a multi-millionaire by inventing a stapler that will affix money to the clouds in such a way that it attracts GHGs upward, pulls them through the money’s paper, traps them on the moon’s side of the money’s surface, and keeps the emissions there like a fancy, research-funded net of Earth-saving awesomeness. Anyone who would like to contribute to the development of my Climate Change Stapler (CCS) can have their company logo printed directly on the money and will receive five free tweets to signal your virtue when the money-net is deployed.
To be serious, you can do more than put your logo on a website’s call to help our environment, and as a member of the asphalt industry, you probably already are doing more. I’m not sure how many times we have to say it, but asphalt is the top recycled product. What might be new to shout from the rooftops is a set of impressive stats gleaned by NAPA, in partnership with the Federal Highway Administration (FHWA), through the annual recycled materials and warm-mix usage survey and posted on the association’s website.
We, as an industry, recycled 87 million tons of RAP into new mixes in 2020, which spared about 2.3 million metric tons of CO2 equivalent from the atmosphere. While I see no problem with the responsible and safe movement of virgin asphalt binder for our industry’s use, there is a loudly shrieking minority that thinks we have more rare-earth minerals than fossil fuels right now. And that screaming group should be pleased to know our industry replaced 24 million barrels of virgin asphalt binder with recycled binder from RAP and RAS in 2020. That not only saves costs for the end user, but it also sends a message to the people gluing their hands to pricy paintings in fancy museums. Think of the animals to be saved from the glue/cartilage factories if we let those folks know we’re reducing virgin asphalt binder use in favor of recycled material.
Stay Safe, Sandy Lender
February 2023 • Vol. 16 No. 5
602 W. Morrison, Box 6a Fayette, MO 65248 (573) 823-6297 • www.theasphaltpro.com
GROUP PUBLISHER
Chris Harrison chris@ theasphaltpro.com
PUBLISHER
Sally Shoemaker sally@theasphaltpro.com (573) 823-6297
EDITOR
Sandy Lender sandy@theasphaltpro.com (239) 272-8613

DIGITAL EDITOR
Sarah Redohl sarah@theasphaltpro.com (573) 355-9775
MEDIA SALES
Cara Owings
cara@theasphaltpro.com (660) 537-0778
ART DIRECTOR
Kristin Branscom
BUSINESS MANAGER
Susan Campbell (660) 728-5007
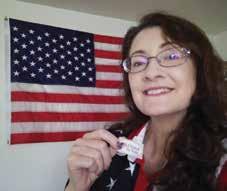
AsphaltPro is published 11 times per year.
Writers expressing views in AsphaltPro Magazine or on the AsphaltPro website are professionals with sound, professional advice. Views expressed herein are not necessarily the same as the views of AsphaltPro, thus producers/contractors are still encouraged to use best practices when implementing new advice.
SUBSCRIPTION POLICY: Individual subscriptions are available without charge in the United Sates, Canada and Mexico to qualified individuals.
One year subscription to non-qualifying Individuals: United States $90, Canada and Mexico $125.00. For the international digital edition, visit theasphaltpro.com/subscribe/
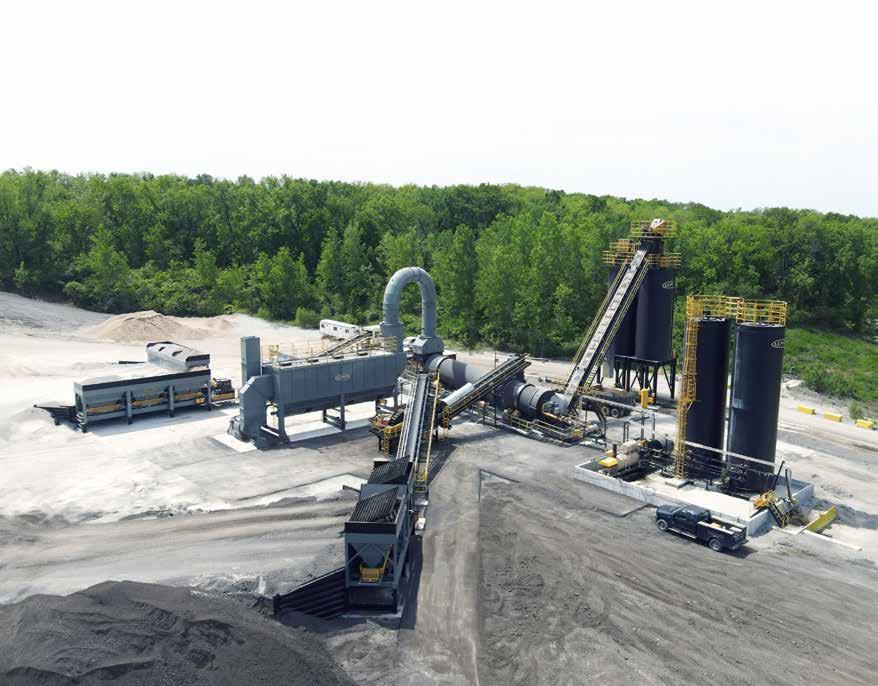


Calculate the Cost of Occupational Injuries & Illnesses
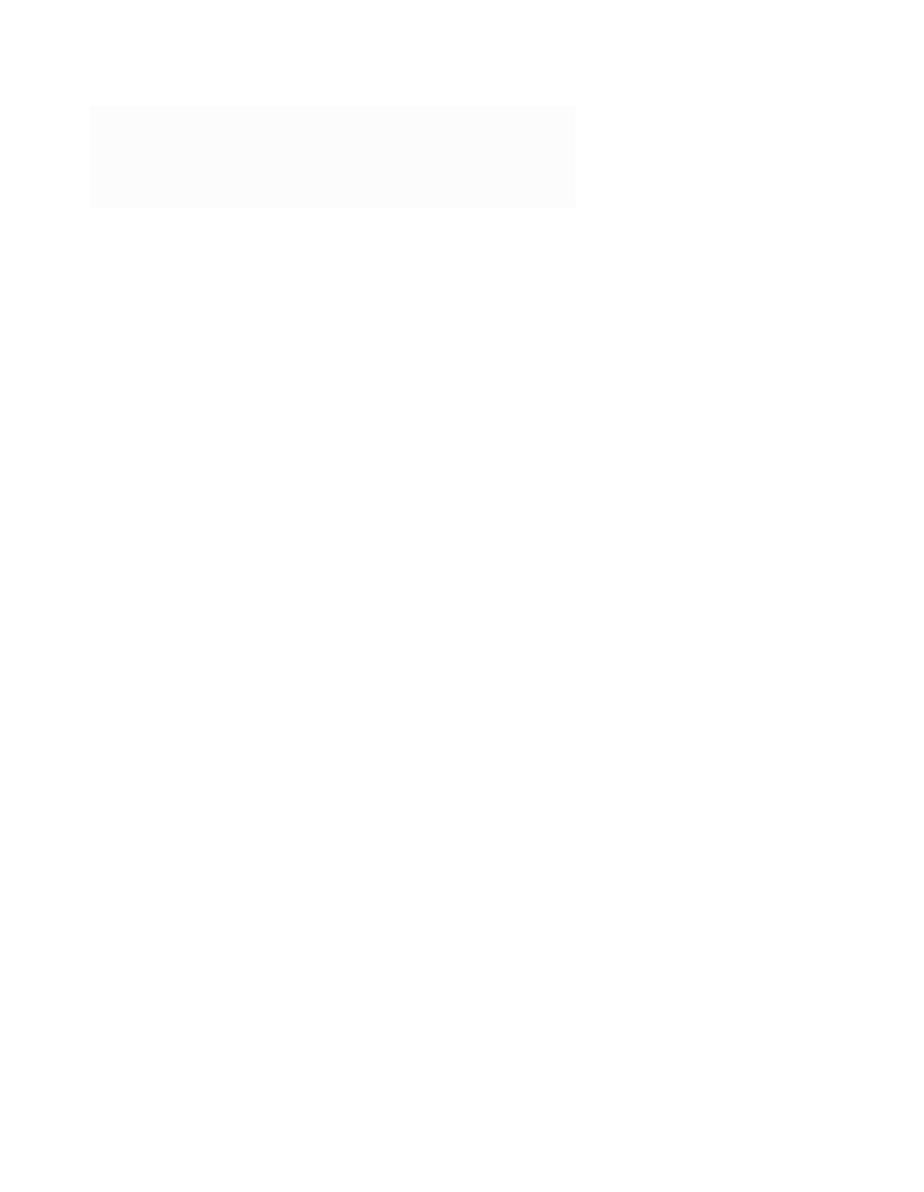
From increased productivity to simply being the right thing to do, there are many reasons to prioritize safety on the paving train or at the asphalt plant. But reducing workplace injury and illness is also a matter of profitability.
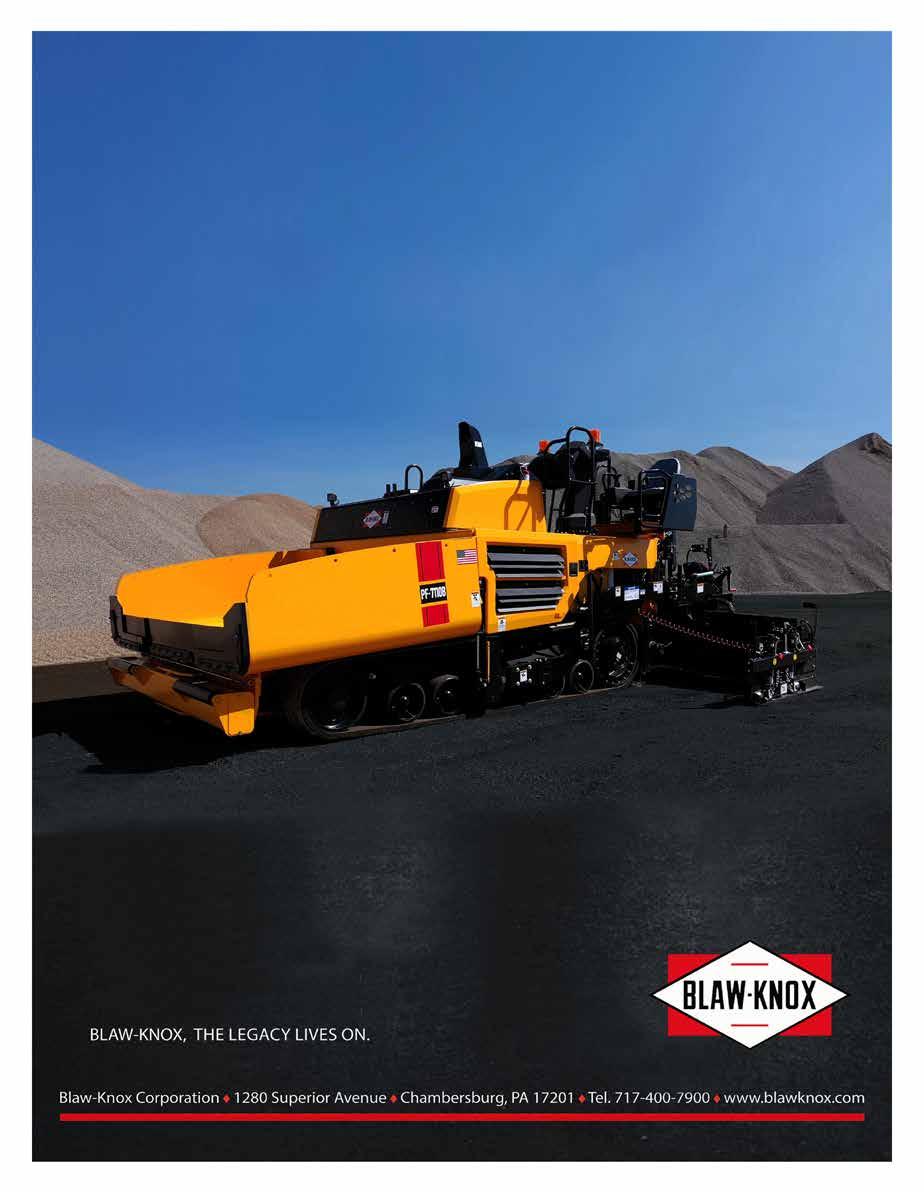
The Occupational Safety and Health Administration (OSHA) aims to make it easy for companies to estimate the cost of workplace injuries with its Safety Pays online calculator. This includes both direct and indirect costs, as well as the estimated sales a company might need to make to recover these costs.
According to OSHA, Safety Pays does not set a new standard or regulation, creates no new legal obligations, and information entered into the tools or calculated by the tools is not captured by OSHA. “[The tool] is intended to help raise employers’ awareness of the impact of occupational injuries and illnesses on profitability,” the Administration writes. More privacy information is available in the Department of Labor’s Privacy and Security Statement.
How Does the Safety Pays Calculator Work?
Employers can use the Safety Pays tool in several ways, depending on the information they have available, though OSHA says the tool will be most useful if the user has a recent record of their company’s workplace safety performance. For example, if you fill out OSHA Form 300A, you can enter the rate/100 of injury and illness cases per year. If that information is unavailable, the user can either enter the number of injury and illness cases per year or use the industry average for businesses in their North American Industry Classification System (NAICS) code.
Then, the user inputs how many of these cases included days away from work, work restriction or job transfer, either the rate/100 from OSHA Form 300A, the number of lost-time cases per year, or the industry average based on NAICS code.
Employers can further customize the data they input with their profit margin, type of workers’ compensation insurance, deductible amount, actual workers’ compensation costs per year, and actual indirect costs per injury. Then, Safety Pays will calculate both direct and indirect costs of workplace injuries and illnesses.
For users who don’t have company-specific data available, the tool can still be useful to learn about a company’s potential burden based on the likelihood of an injury occurring in your industry for a company of your size and to explore the potential costs of a typical injury in your industry.
For example, a company with 100 employees in the construction industry has an expected annual cost of $197,000 ($110,000 indirect costs and $87,000 workers’ compensation claims/direct costs). Top performers in the construction industry experience annual costs of $22,000 in direct and indirect costs.
According to OSHA, indirect costs are often inversely related to the seriousness of the injury. “The less serious the injury the higher the ratio of indirect costs to direct costs,” the Administration says. “While they may account for the majority of the true costs of an accident, indirect costs are usually uninsured and therefore, unrecoverable.”
Indirect costs might range from wages paid to injured workers for absences not covered by workers' compensation and training costs for a replacement worker to administrative time spent on that injury or even repair of damaged materials or machinery, to name only a few. The estimated indirect costs do not include potential OSHA fines, third-party liability and legal costs, worker pain and suffering, and/or the cost of related bad publicity.
What is OSHA’s Individual Injury Estimator?
Within OSHA’s Safety Pays toolkit is a second calculator that can be used to estimate how much a specific injury could cost a business and its impact on a company’s profitability.
To use the individual injury estimator, the user chooses an injury type from a drop-down menu of 40 injuries or enters their workers’ compensation costs, the company’s profit margin and the number of instances of that injury.
From that information, the tool uses the average direct and indirect costs of a given injury or illness, along with the company’s profit margin and an indirect cost multiplier, to project the total costs of the injury as well as the amount of sales a company would need to cover those costs.
For example, a single burn injury for a company with a profit margin of 3% results in a direct cost of $47,192, an indirect cost of $51,911, and requires an additional $3.3 million in total sales (given the 3% profit margin). An instance of hearing loss (occupational disease or cumulative injury) has a direct cost of $18,828, an indirect cost of $20,710, and requires $1.3 million in total additional sales.
“This tool can support you in fulfilling your responsibility to your workers’ safety and health,” OSHA writes. “You can also use the Safety Pays tool to explore the value of implementing workplace safety and health practices that keep your employees safe while lowering costs due to work-related injuries and illnesses.”
Safety Pays uses data on workplace injury costs compiled by the National Council on Compensation Insurance Inc. (NCCI), which manages the nation’s largest database of workers compensation insurance information. Indirect cost estimates are from the Business Roundtable publication, Improving Construction Safety Performance. For additional information on how the calculators work, see Background of the Cost Estimates available within each calculator.
ADDITIONAL RESOURCES
OSHA also highlights two additional tools to help calculate injury costs. This includes the Center for Construction Research and Training (CPWR) online ROI Calculator (www.safecalc.org), which allows contractors to input cost data to estimate their potential return on investment from implementing a safer work practice, material or tool. There’s also the ASSE Business of Safety Committee works, which aims to show how safety, health and environment investments can impact an organization’s profitability.
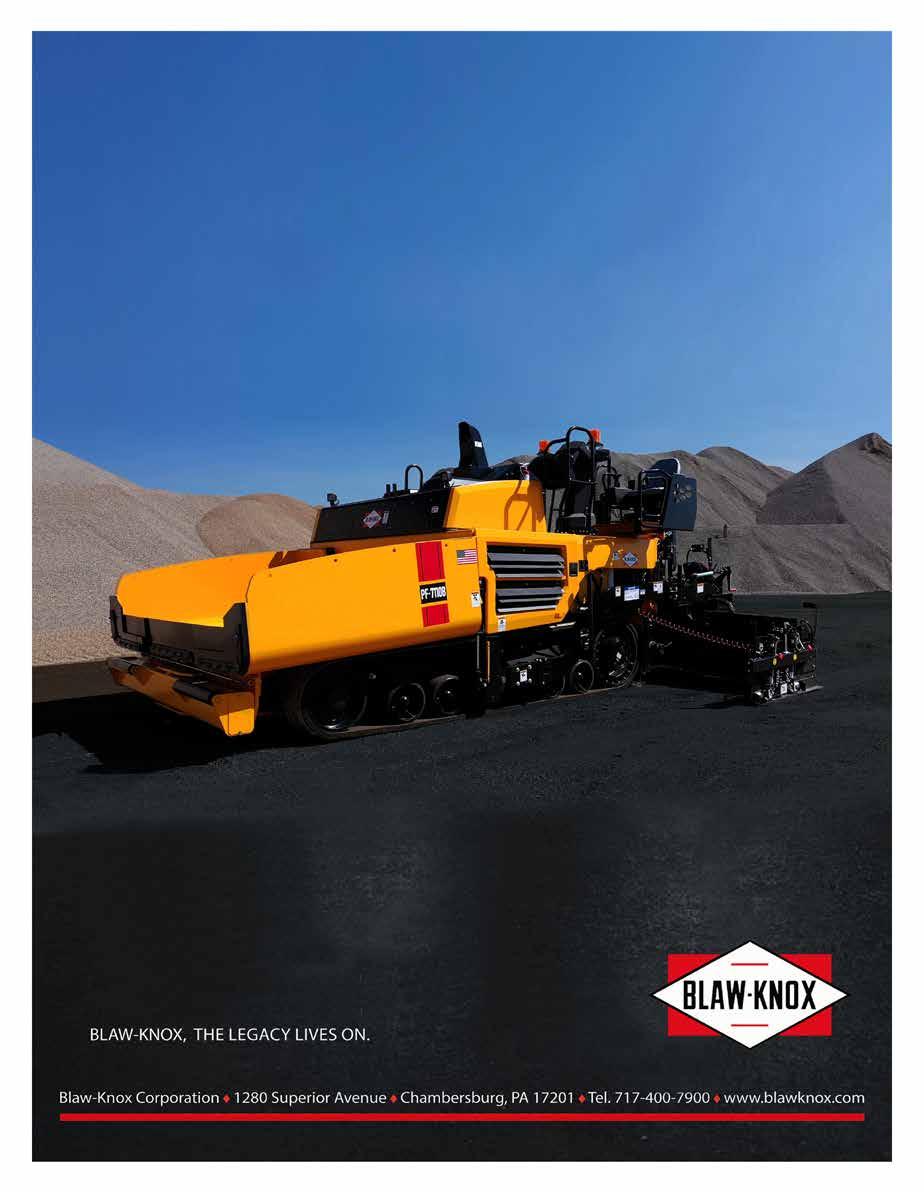
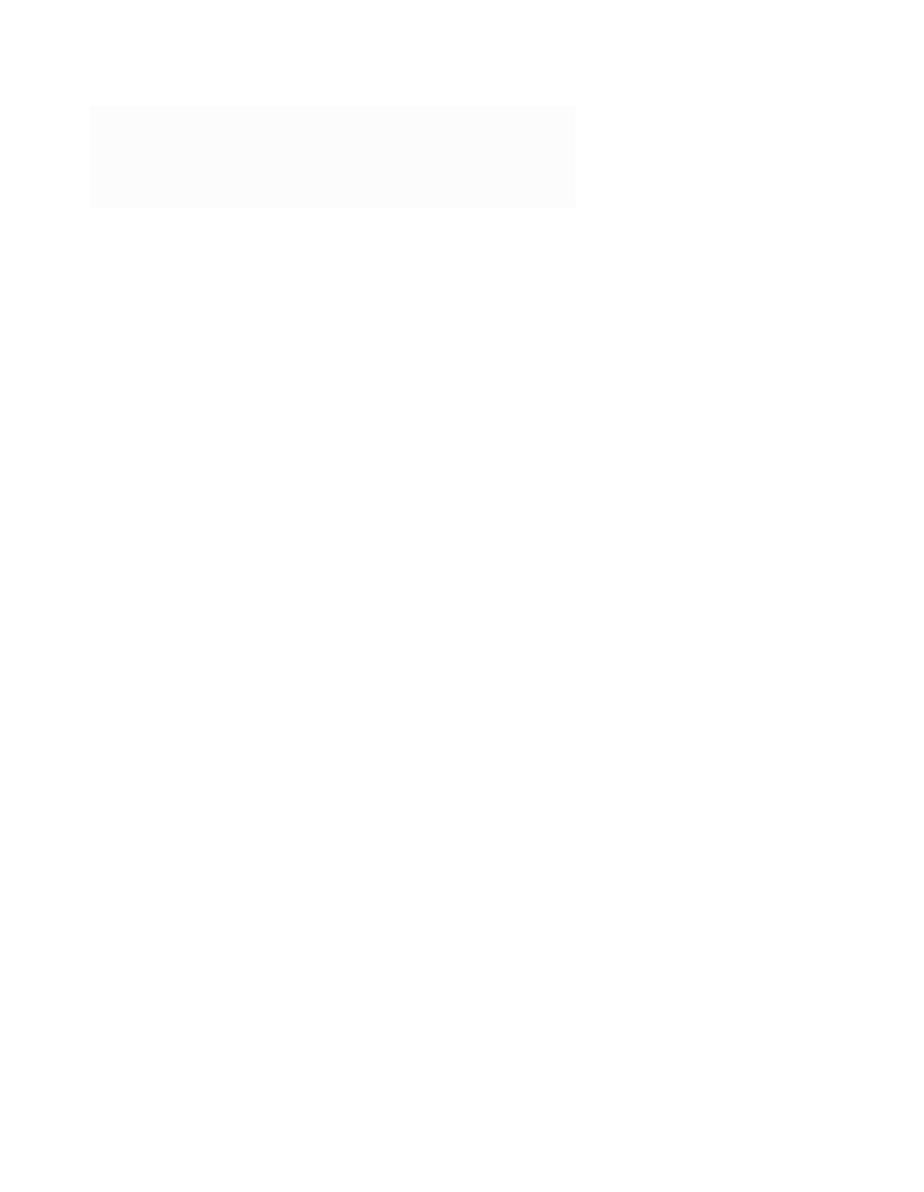
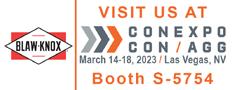
Which TAWG is Your Best Fit?
BY SANDY LENDERWe each have strengths and skills to employ in the mission to help colleagues in the construction industry with mental health wellness and suicide prevention. I’ll begin this article by inviting you to attend any and all of the sessions on this topic during next month’s CONEXPO-CON/AGG and IFPE event in Las Vegas. For example, I, along with fellow speakers Aaron Witt and Dave Lersch, will participate in the panel discussion “Constructing a Culture of Suicide Prevention” moderated by Michelle Walker, co-founder of the Construction Industry Alliance for Suicide Prevention (CIASP), on Thursday, March 16, in the west hall room 216218 at 10:45 a.m. This session is only one of many during the week that will help safety directors, managers and industry workers gather ideas to take back to their companies to save lives.
Direct link to the panel discussion: https://directory.conexpoconagg.com/8_0/sessions/ session-details.cfm?scheduleid=138
CONEXPO-CON/AGG isn’t the only resource for such education.
The Center for Construction Research and Training (CPWR) hosted a two-day workshop in Washington, DC, Aug. 1-2, 2022, with funding from the National Institute for Occupational Safety and Health (NIOSH) and subsequently produced a white paper titled “CPWR Workshop on Combating Suicide and Overdose Fatalities Among Construction Workers” to summarize the workshop and its resulting working groups. The white paper is available online for safety directors to peruse.
An item I found of immediate value from the CPWR paper was the four topic area work groups (TAWGs) developed during the workshop. They are as follows:
• Education and Training;
• Changing Culture and Ending Stigma;
• Peer Support; and
• Workplace Injury and Stress Prevention.
Each TAWG is summarized in the white paper, offering ideas, questions, topics and resources that work group members will continue to use and discuss in future meetings, but which also present good foundations for discussions in safety meetings around the industry.
Also in the white paper, the authors share from the workshop’s first day Brent Booker’s anecdote of negotiating a contract wherein two parties agreed “to fund a provision of mental health care on job sites.” Booker is the secretary-treasurer of North America’s Building Trades Unions (NABTU) and “he suggested using this model [of partnering to provide mental health care on job sites] moving forward, so the unions and employers can increasingly leverage their shared interests to include similar protections in future contracts.” This concept could be a topic of conversation for both prime and subcontractors in your upcoming workflows.
The information contained within the white paper is a summary of not only the activities held during the two-day workshop but is also a resource for ideas shared those days. Companies and safety
directors can review the white paper and mine it for information, discussion topics and ideas.
Direct link to the white paper: https://www.cpwr.com/ wp-content/uploads/RR-CPWR_Workshop_2022_ Suicide_Overdose.pdf
No matter how you choose to use the resources now popping up via online courses and with in-person training opportunities, the good news is these resources are occurring more frequently. The construction industry is working among a variety of groups to bring awareness, training, support and ultimately prevention of the tragedy of suicide among our colleagues. I encourage you to follow and work with whichever group you feel comfortable aligning with to be a part of restoring hope and saving lives.
CHALLENGE OF THE DAY
Near the end of the first day of the workshop in DC, the group participated in an exercise in which everyone was asked: “I’d like to collaborate with others on/about [blank] in an effort to combat suicide and overdose fatalities among construction workers.”
Such an exercise gives people the opportunity to think of individual skill sets, strengths and areas in which they’d be comfortable participating. As the editor of a construction magazine, I don’t have the same skill set or strengths as the paver operator who performs seasonal work or the CFO who manages multiple facilities’ balance sheets. I have different lived experiences from the lute artist and H.R. director and quality control consultant and so on.
Each one of us can do something different to assist in the mission of bringing awareness to the tragedy of suicide in our industry or ending the stigma surrounding opioid abuse in our industry or finding a way to support our colleagues or reducing workplace injuries and stress to reduce the need for pain medications and so on. Each one of us has a different comfort level with the topic area work groups (TAWGs) assembled during the CPWR workshop.
Which of the TAWGs would you be able to assist with? Or is there a different facet of the mental health wellness paradigm you would more comfortable being a part of? I encourage you to visit with your safety director to see how your company can be involved in helping save lives across the industry. I challenge you to write down your answer to the workshop’s question of where you’d like to collaborate to combat suicide and overdose fatalities among construction workers.
If you personally are seeking help, reach out.
Members of our industry are allies in the mission for better mental health wellness. The new national hotline for mental health help is 988.
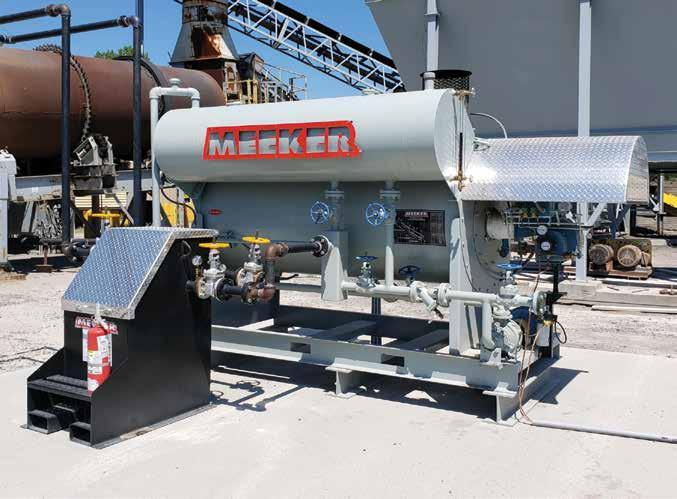
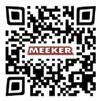
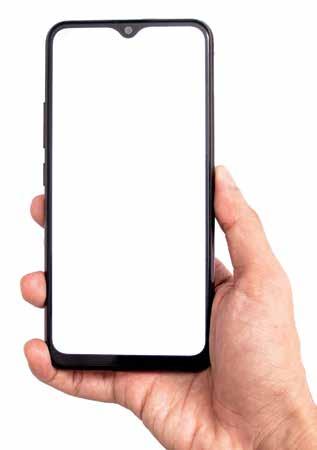




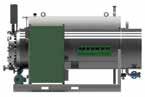
New Teeth Cut Through Pavement Maintenance
FROM ASPHALTPRO STAFF
The team from Wirtgen Group, a John Deere Company, with U.S. headquarters in Antioch, Tennessee, has released its new Generation Z2 round-shank picks—or milling teeth for those of us in the United States. These cutting tools will be on display in the manufacturer’s booth S2050 at CONEXPO-CON/AGG next month, but here’s some more information about them now to augment the Recycling theme of our February edition.
The Wirtgen team reminded readers that the demands on cutting tools for environmentally friendly cold recycling and efficient soil stabilization are varied, but they include:
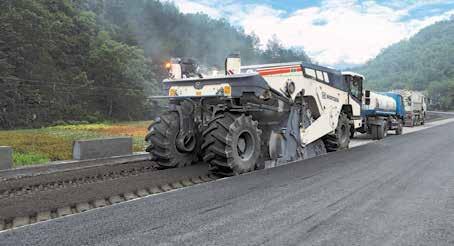
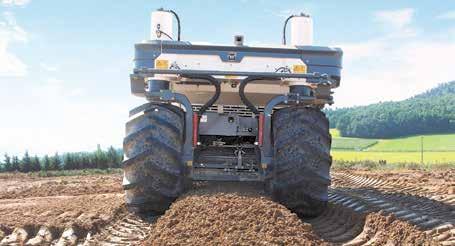
• high cutting performance,
• resistance to extreme impacts and
• maximum resistance to wear.
To address those important characteristics, the research and development department optimized the Wirtgen Generation Z2 cutting tools and presented them to industry at BAUMA 2022. Here are some stats and facts from a more recent press release.
The wear plate with the grooved profile—seen in the illustration on this page—is designed to increase efficiency. The newly developed wear plate with a special grooved profile is intended to improve centring and optimize rotation behaviour. This is to ensure that the carbide tip is always ready to cut and give best possible carbide use.
In addition, the grooved profile reduces lengthwise wear of the round-shank pick holder and extends service life by up to 25%, according to the manufacturer.

To assure consistently secure seating of the “tooth” in the pick holder bore, the Generation Z² roundshank picks feature the TwinStop clamping sleeve from Wirtgen. The optimised carbide composition with a higher proportion of cobalt guarantees additional resistance to even the highest impact forces, according to the manufacturer.
The Wirtgen team sees high savings potential for users as it continues to develop innovative cutting technologies. By integrating the technology between machines and high-performance cutting tools, contractors can realize optimized efficiency in everyday working scenarios. The use of the new Generation Z2 round-shank picks further increases operational reliability, according to the manufacturer, which results in higher machine use rates, higher productivity, lower operating costs and greater efficiency.

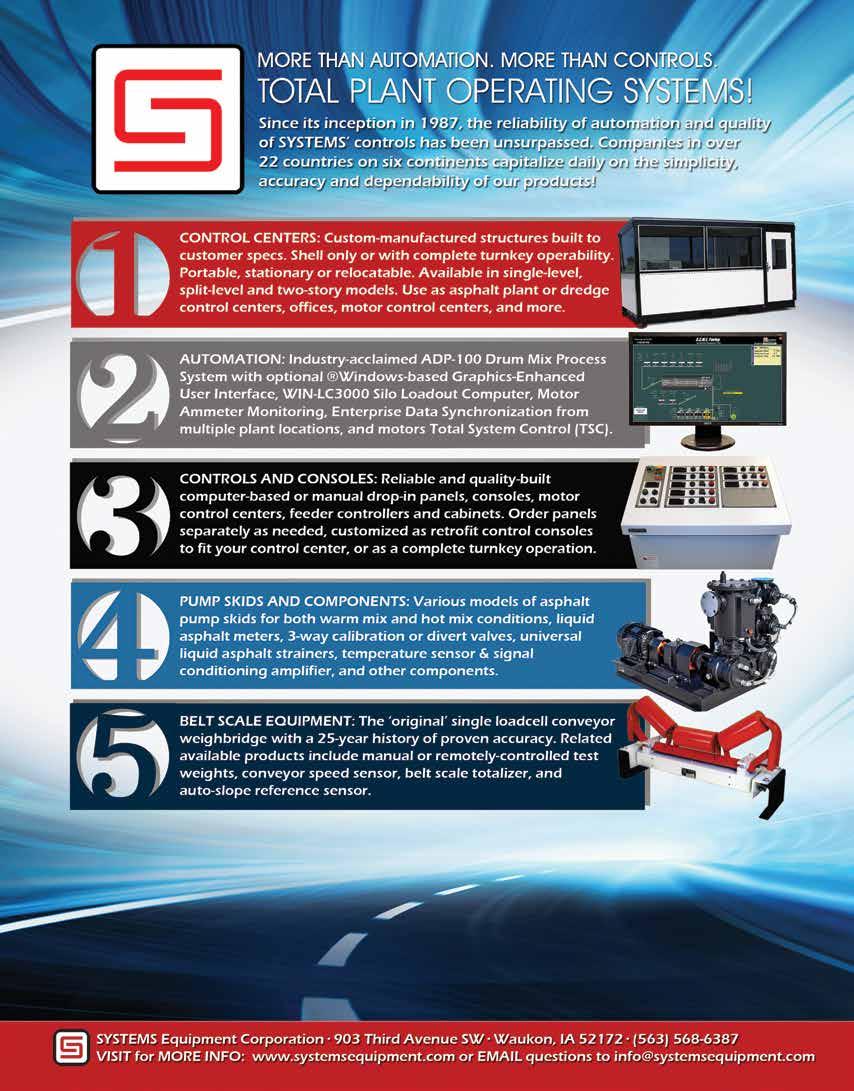
THE POWER

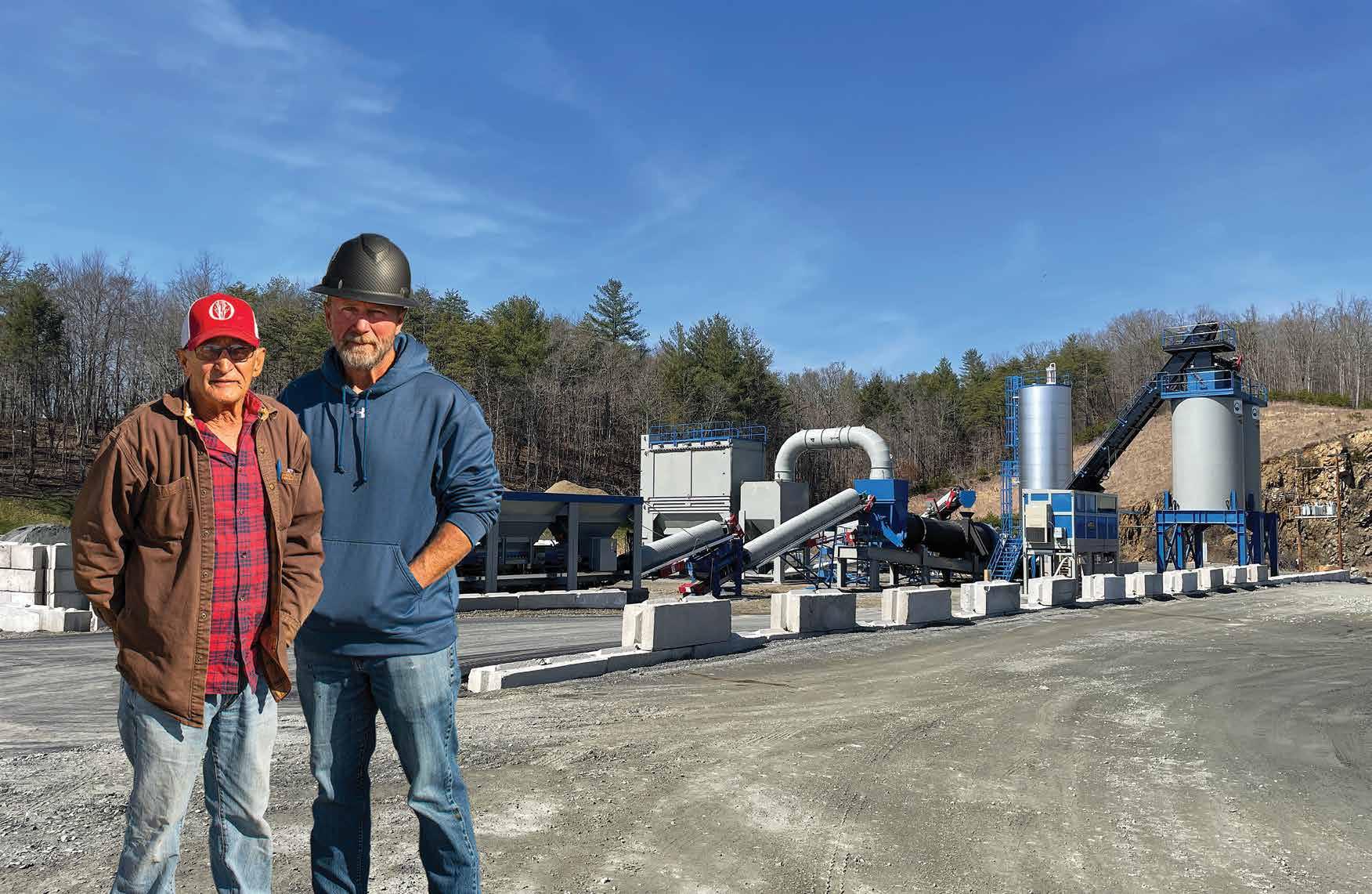
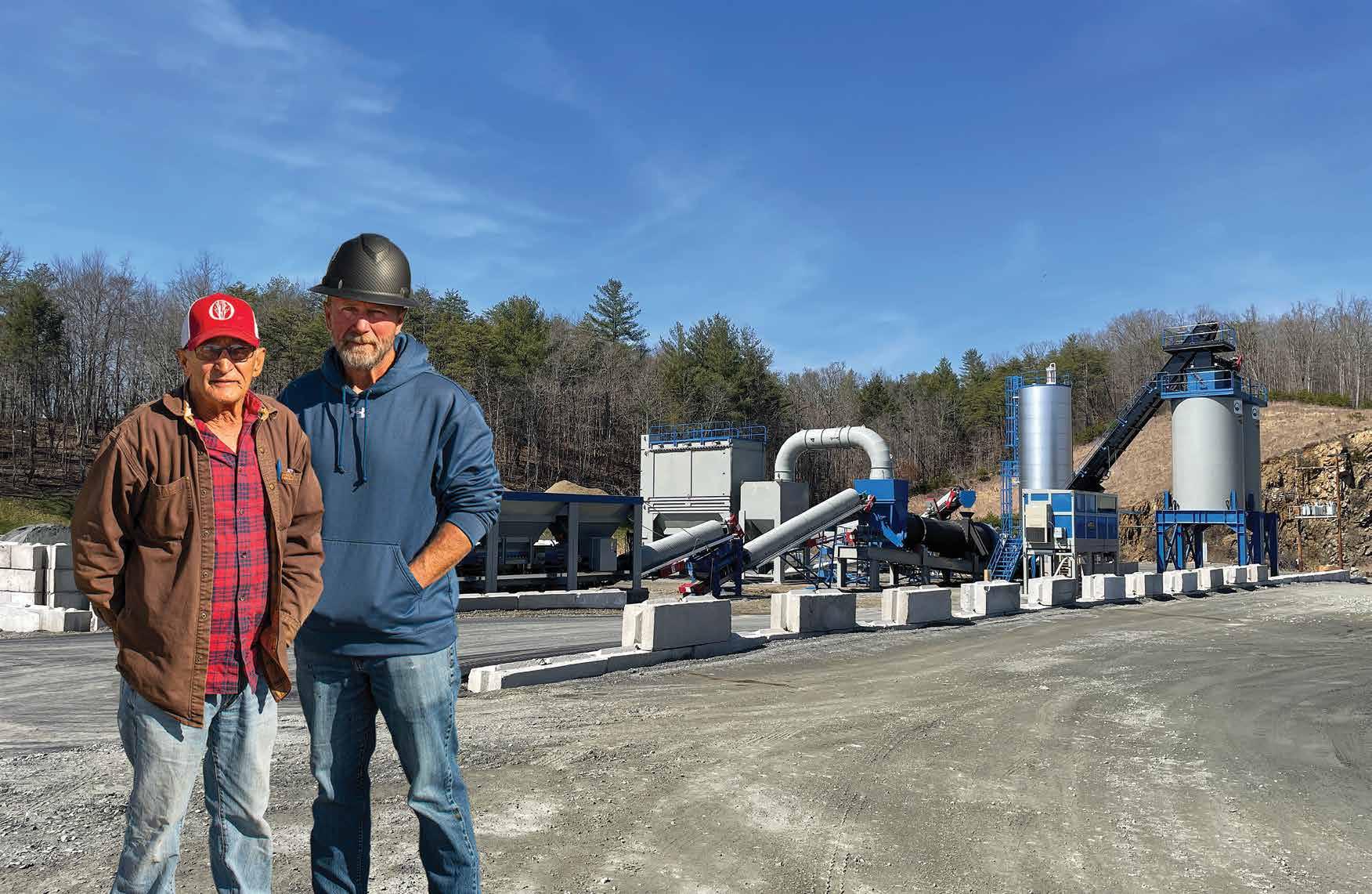
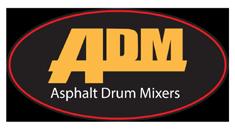
Here’s What to do When Half the Trucks Cancel
BY SANDY LENDERYour asphalt paving crew has on site all the necessary equipment to pave the final 1.5-inch (compacted) lift of a section of residential subdivision roadway. The superintendent has requested 300 tons of mix from the plant, which is 45 minutes from the job. This amount of mix will be sufficient for the day and will give the crew enough time to complete the job for the pavement marking subcontractor scheduled later in the day, and to load up to move to tomorrow’s project. The six haul trucks the super has ordered for the day each hold 20 tons.
Keep in mind, a 45-minute drive from the plant follows an indeterminate load-out time in the yard. Dumping time at the paver depends upon paving speed, size of the hopper or insert, and whether the crew is building a starter pad or flare during that round—remember that performing handwork of any nature tends to slow the operation and might leave a truck sitting on the sidelines while it waits its turn to charge the hopper. Cleanout time after dumping should be quick and not
add many minutes to the truck’s round-trip time, but traffic’s impact will fluctuate depending on the time of day and the route the driver selects—for example, does he know to avoid the local elementary school drop-off and bus traffic?
Here’s where our project management dilemma comes in.
When all crewmembers arrive at the jobsite and have the morning toolbox talk, the foreman receives a text message from dispatch saying three of the six trucks have cancelled.
We all know you can’t start and stop the paver waiting on trucks throughout the day without the risk of dips and bumps in the mat. We also know there are variables such as catch basins, utility covers, flares, stubs, intersections and so on to have as time-eaters in the back of your mind, so what’s the savvy foreman to do? A handful of industry consultants weighed in to share ideas for handling this mini crisis without compromising quality.

This component makes it possible for you to never have to second - guess how much material is in your A.C. tanks or hotmix silos. The Accu-Level continuously monitors tank levels aler ting the operator when an overfill is approaching.
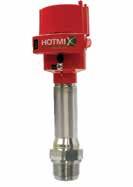
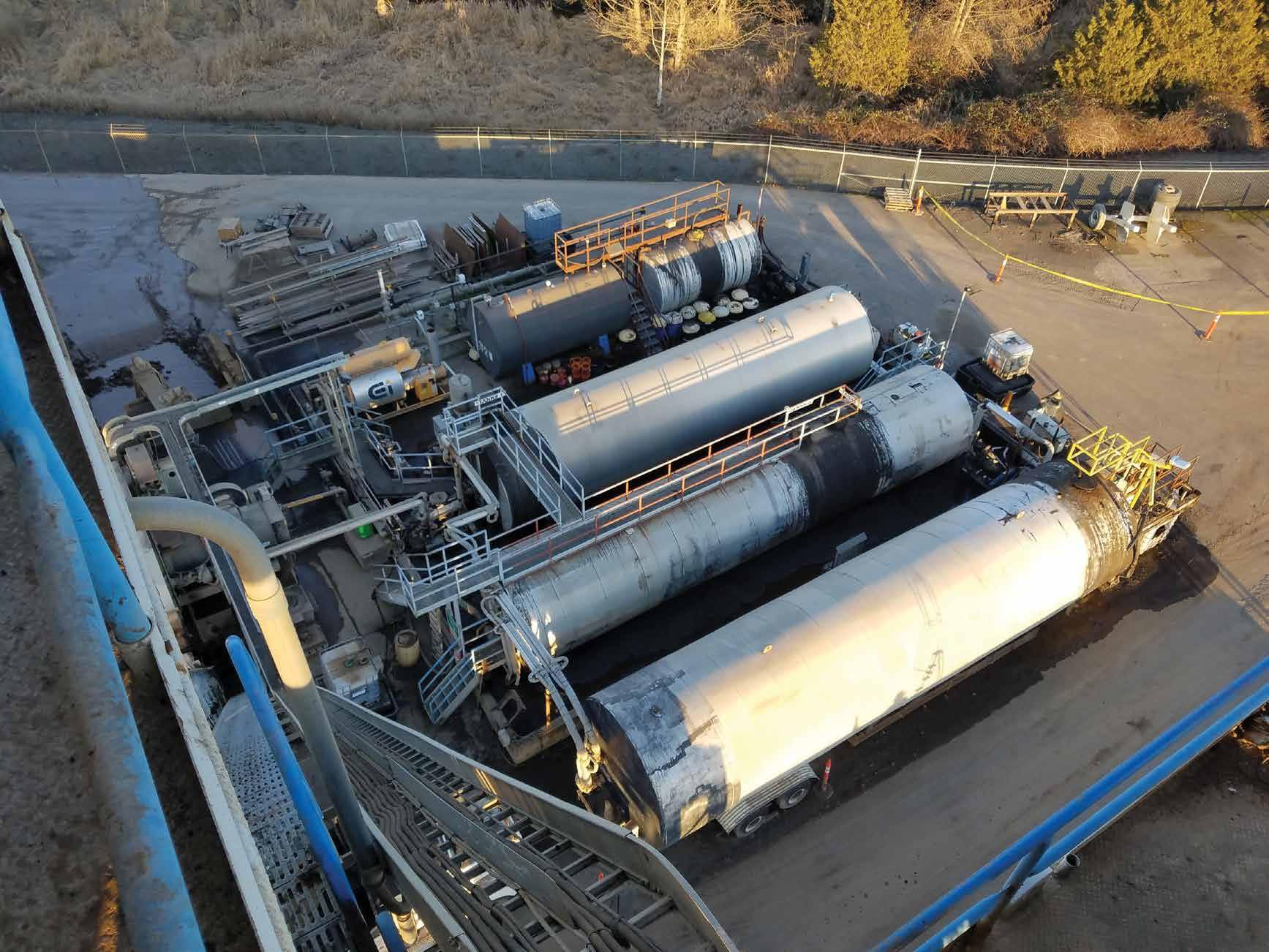
The app allows you to monitor specific operations of your plant. While using it, you can: observe tank and silo levels in real-time, keep track of temperatures, monitor hot oil heater vitals, receive error alerts, allow team access, and more. Completely mobile-friendly, the app can be operated on a computer, tablet or any smart phone.

This system allows you to monitor and regulate all of your A.C. tanks. Users can set individual tank high/low parameters for level and temperature to initiate a pump shutdown and prevent tank overflows. In addition, you can operate A.C. tank supply, return, and fill valves with the push of a button from the control room, tank farm or any smart phone.
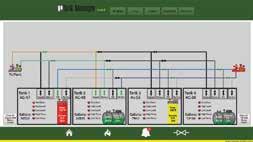
He shared: “For this situation, the mix temperature and cooling come into consideration. Tarping loads and using an MTV would be beneficial to keep the mix as hot as possible. Maybe also communicating with the plant to maximize mix temperatures. Depending on the temperature outside and the equipment being used, the first loads may be able to fill the MTV and sit for a moment for the trucks to start on their approximately 90-minute round trip back to the plant. With only 60 tons at a time and 1.5-inch compacted thickness, they would be paving about 500 feet for each round of three trucks. For a 90-minute pace, that is paving about 5 feet per minute. The crew is limited by how fast they can receive material. Even if they pave slower, the overall time onsite will be the same.”
Schaefer pointed out a great way for the paving crew to maximize the spacing of waiting on trucks.
“Ideally, since this is a residential street there would be stopping points for intersections or handwork areas. If the crew could pave up to these areas and wait for trucks, it would improve smoothness. If this was a highway pavement, hopefully they would have trucks on standby for this situation.”
Bryce Wuori of Wuori Consulting, Bismarck, North Dakota, shared: “As the paving super in this situation the first thing I would do is try to find more trucks to complete the paving as scheduled. Slowing the paver down to accommodate the material being delivered to the project is a good way to control quality as long as the weather conditions are in favor. Obviously, on top lift we want to eliminate joints and surface defections and build a high-quality road so trying to keep the project on schedule with the addition of trucks would be my first suggestion. Then if that fails, we slow the paver down and keep things moving at a pace that still allows quality and does not disrupt the schedule of the project more than we can already control.”
Wuori stressed the importance of pleasing the client here.
“Since this is in a residential neighborhood one of the biggest things I would try to do as the paving super is build a high-quality road that is aesthetically pleasing to the taxpayers/homeowners while using the equipment and trucks we have. It might end up being a longer day of paving to get the job done but this kind of thing happens almost every day in the field.”
PAVING CONSULTANTS YOU CAN COUNT ON
In alphabetical order by last name, here are the three consultants who offered commentary for the scenario in this article.
John Ball III
Top Quality Paving & Training
(603) 493-1458
tqpaving@yahoo.com • https://tqpaving.com
Nicholas Schaefer, PE
Surface Systems and Instruments Inc.
(415) 595-5302
nschaefer@smoothroad.com • smoothroad.com
Bryce Wuori
Wuori Consulting LLC
(701) 426-7873
Bryce.w.wuori@gmail.com
John Ball, the proprietor of Top Quality Paving & Training, based in Manchester, New Hampshire, has been on the job when the news came down that haul trucks weren’t showing up for the day. To stay on task, they solved the problem by looking for replacement trucks. “One option is to look for other trucks,” Ball said. “You need to ask how important is this job compared to another coming out of the plant because you might be able to scavenge three trucks from that other job to make this project happen today.”
He shared that a larger company will have more wiggle room than a smaller one. “At Pike, we had 24 paving crews. Whenever we had a situation where a couple trucks didn’t show up, I could call over to another super and say, ‘Hey, Jody, can you spare me three trucks for the day?’ A company with only one crew out paving might be tempted to call on someone they know who drives a truck. If you’re going to hire an independent driver, make sure they have all the insurance and properly maintained trucks for hauling asphalt.”
Once again, pre-planning comes into play. You’ll want to revamp the original plan at this point. If you can’t get all the trucks you need for the job, Ball said you have to plan where you’ll stop at the end of the workshift. “I’m not going to finish the job with half the trucks, unless I go more hours. Then you have to factor in overtime and might have to set up lighting. It depends on how crucial the job is, but if you can cancel and do the whole job all at once another day, that’s the best thing to do. I’d rather do it all at once than do part today, stopping near the end of the workshift with 200 tons delivered, and find out we can’t get back to finish tomorrow or the next day.”
Guessing the multitude of variables for this situation isn’t easy.
Not all residential paving contractors will have deployed an MTV with the paving crew, but they should all have a skid steer on the job. Employing a skid steer to move material for handwork, tight spaces, starter pad builds, flares and the like, the crew can trim some minutes off the time a haul truck driver spends waiting his turn to charge the hopper.
Not all haul truck drivers will be excited to double the number of trips they were scheduled or expected to perform for a day. Not all workers will be able to extend their workday beyond their scheduled shift. But if the paving foreman can show his flexibility and good attitude by working up a solution for his crew, they can still get a quality pavement for the client. There are ways to optimize the crew’s efficiency even if they must work with fewer trucks or if the paving speed is slowed, but keep in mind, the roller operator(s) must match the paving speed. He’s not bringing the breakdown roller onto the mat until the first pass is ready. If you’re moving too slowly, you could see cut marks and quality shortcuts in the rolling pattern. Keep an eye on this stage of the operation, too.
WEB EXTRA
You probably dealt with a similar situation in 2022 and have good ideas for handling it. We welcome you to share your ideas with one another. This issue mails Jan. 20, and we’ll post this article to our facebook page for discussion Jan. 30. Check the AsphaltPro Magazine facebook page on that date!
INNOVATION EAGLE
There’s always something new at Eagle Crusher. Eagle Crusher consistently leads the industry in new product innovations and 2023 will be no exception. Join us at CONEXPO-CON/AGG, and see our newest equipment and technologies on display, including the UltraMax®1600X-OC Portable Impactor Plant and the 8x20 Screen Plant with Integrated Feed Conveyor and Blending Gates.
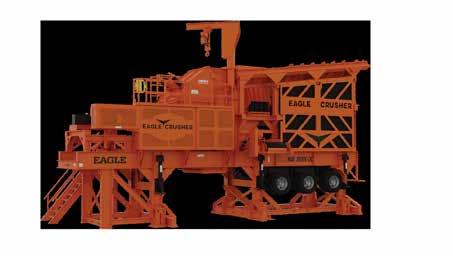
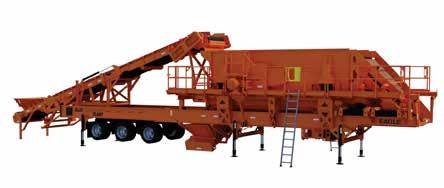

Learn about the many plant options for asphalt producers from our expert personnel in the booth. Outstanding plant options include onsite RAP systems for crushing and precise screening, allowing product consistency with a minimum of white rock and a minimum of fines. Also available are highly portable plant options for larger-sized jobs with high volumes of material at- or near-spec, allowing most to be removed before crushing to increase overall production and reduce wear.

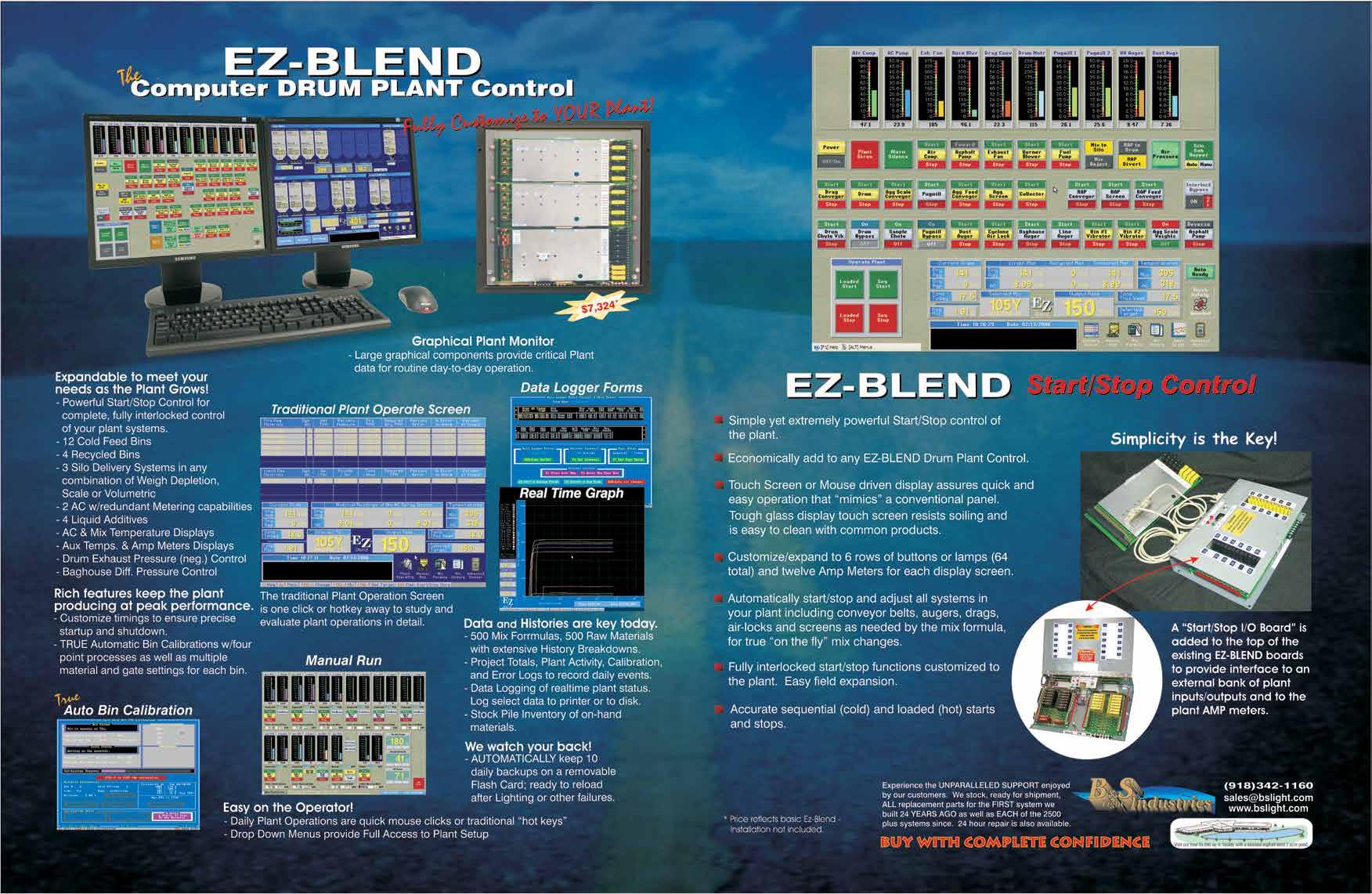
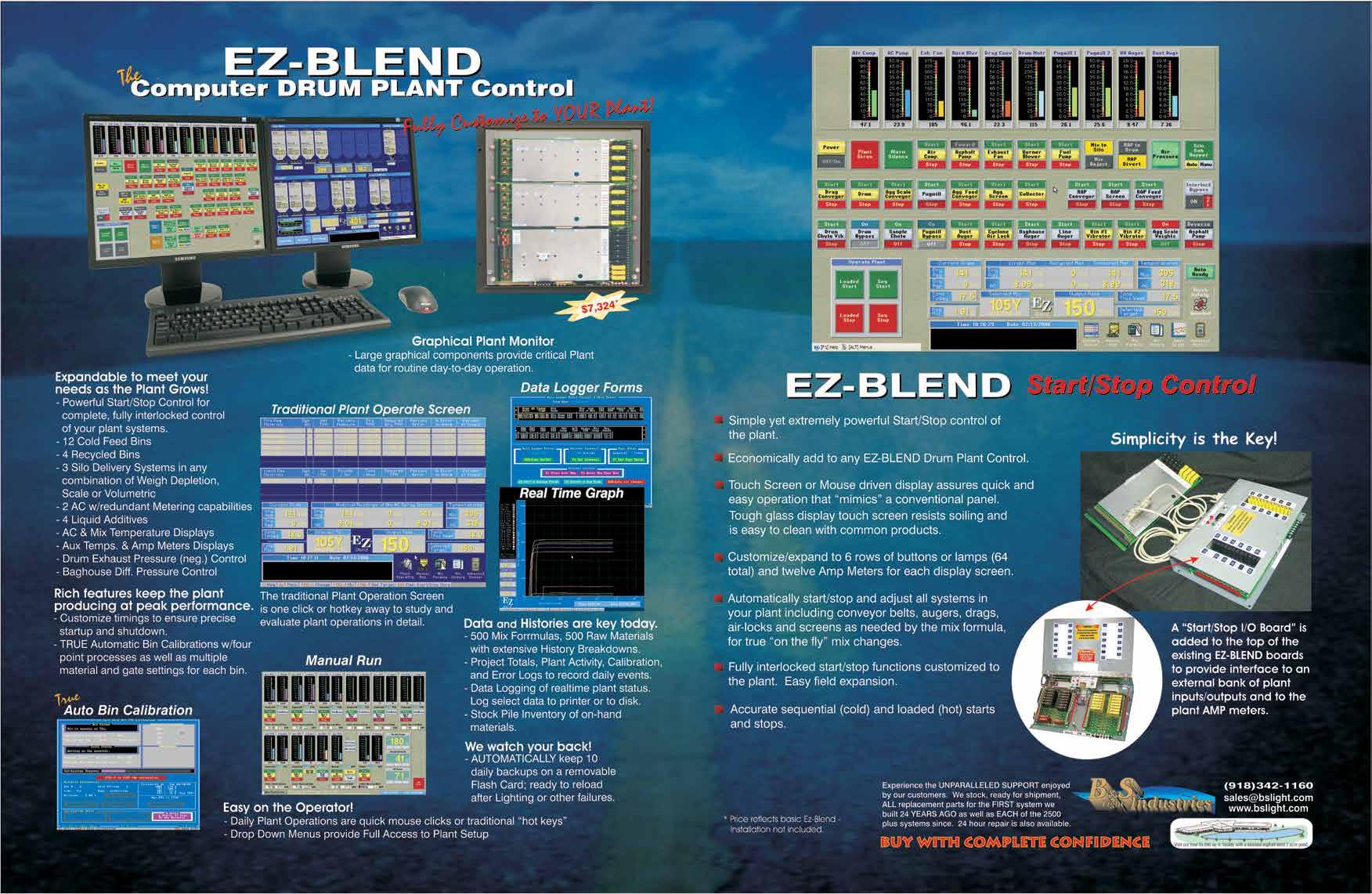
NEW YORK CITY TESTS MACREBUR PRODUCTION
Recycled plastic waste uses temps of 330 degrees on Staten Island
BY ASPHALTPRO STAFFEditor’s Note: All stats and figures are courtesy of Rutgers Center for Advanced Infrastructure and Transportation via MacRebur’s “August 2022 NYCDOT Trial Road MacRebur MR8” document.
SStaten Island became home to roads surfaced with recycled waste plastic mix design at the end of August 2022, offering a chance at recycled production for the team of the New York City Department of Transportation (NYC DOT); MacRebur, Lockerbie, Scotland; and City Asphalt LLC, Staten Island. Here’s what the team executed.
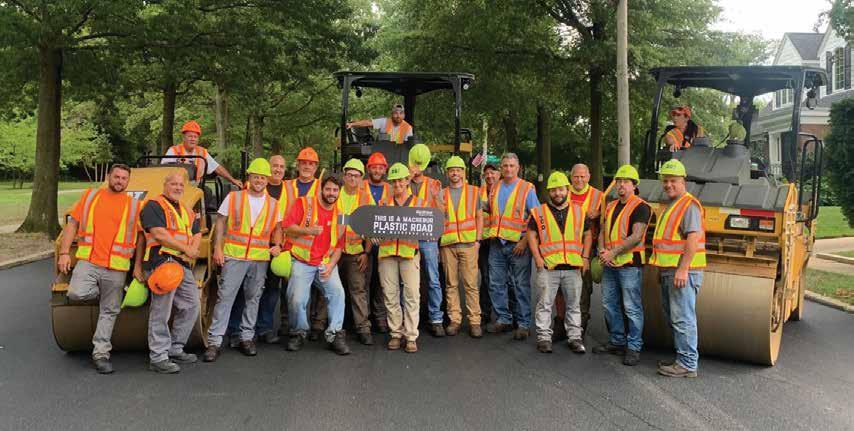
NYC DOT looked at four dosage rates of MacRebur MR8 product into asphalt mix with 40% recycled asphalt pavement (RAP) from City Asphalt’s fractionated stockpiles. The foundation mix had a nominal maximum aggregate size of 12.5 mm and PG64S-22 binder. The dosage rates tested were 0, 6, 10 and 12% by weight of virgin binder and 0, 3.8, 5.5 and 6.5% by weight of total binder. The MacRebur MR8 product was added by fiber feeder at the RAP collar of City
Asphalt’s Gencor Drum Mix Ultraplant, rated at 400 tons per hour, which was put into service March 2020 on Staten Island.
Plant production in late August 2022 was around 250 TPH to produce 2,200 tons of HMA, 1,800 tons of which contained 10,395 pounds of MacRebur MR8. The production temperature for the control mix was around 315°F. The production temperature ranged from around 320 to 330°F for the mixes dosed with recycled plastic waste. The mixes were allowed a 2-hour silo storage time and saw a 40- to 60-minute haul time. The two pavements are located on Rice Avenue and Royal Oak Road.
The team reported the amount of recycled waste plastic used was 10,395 pounds and the amount of virgin asphalt cement binder reduced, by weight, was also 10,395 pounds, which would suggest a 1:1 ratio. The team also reported the carbon savings as 7,331 kilograms of carbon dioxide equivalent (CO2e).
Testing took place Aug. 29, Aug. 30, Aug. 31 and Sept. 1, with dosages of MacRebur MR8 at 0, 6%, 10% and 12% respectively. The actual percent passing are listed for each of the sieves with the targets and limits for the job mix formula (JMF) listed to the right of the actuals. Table courtesy of MacRebur
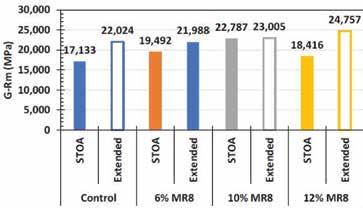
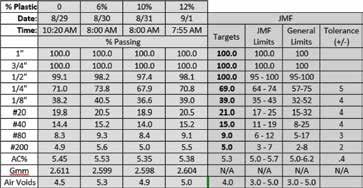
One of the graphs available from Rutgers and NYC DOT shows fatigue cracking results for the control and the different dosage rates of the recycled waste plastic. Additional graphs with more cracking performance data are available from MacRebur. Reach out to their marketing group via charlotte.dixon@pacecomms.co.uk and let them know you saw this request for data in AsphaltPro Magazine.
A spokesperson for MacRebur told AsphaltPro that the team at City Asphalt was able to run at its usual temperatures. “There were no changes to their production process or the paving process,” the spokesperson shared. “The initial results showed that our product met all the required QC measures and specifications with City Asphalt and NYC DOT.”
Matthew Cruz, general manager at City Asphalt, stated, “When NYC DOT advised us of the trial using waste plastic in asphalt, we were initially reluctant as we hadn’t had much experience with the introduction of new products into our new Gencor plant.

“However, as we researched the product and had the opportunity to discuss with other asphalt plant operators, our reluctance turned to curiosity and excitement. The opportunity to address a major environmental concern seemed too good to be true.”
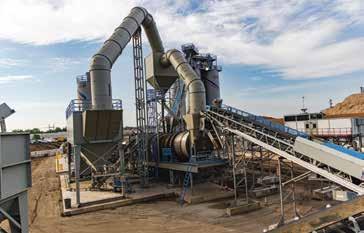
HIT GOAL
The stated goal of NYC DOT was to “not worsen” the existing pavement performance by adding the recycled waste plastic product. To ensure they hit their goal, they tested in the lab and the field. See the
table and graph included with this article for examples of data gathered so far. The trial sections will now be tested and monitored to measure performance against traditional asphalt by Thomas Bennert, Ph.D., at Rutgers University.
The agency also looked to improving environmental sustainability. While the NYC DOT is reported to produce and lay 1.1 million tons of asphalt each year, it is also reported as one of the United States’ leaders in using RAP, typically putting 40% RAP in its mixes. Now the project in Staten Island has diverted the equivalent weight of 214,534 single-use plastic bottles from landfill, according to the team at MacRebur.
“Having worked with the team at NYC DOT for just over a year, it’s refreshing to see such enthusiasm about new technology and products for use in asphalt,” Roddy McEwen said. He’s the international business officer at MacRebur. “Whilst trial sections such as these typically take up to three years from start to finish, we have worked together to begin trials within just four months—with a long-term goal of utilizing local waste for local roads.”
“We are excited to partner with MacRebur on this promising pilot and look forward to monitoring how its asphalt mix performs in New York City weather,” NYC DOT Commissioner Ydanis Rodriguez said.
For more information, visit www.macrebur.com/us.
HARTFORD PAVING CORP
HARTFORD PAVING CORP RESTORES ORIGINAL
NEIGHBORHOOD CHARM
RESTORES ORIGINAL NEIGHBORHOOD CHARM
BY SARAH REDOHLFFederal Hill is a historic neighborhood in Providence, Rhode Island, largely settled by Italian Americans in the late 1800s and early 1900s. Today, the district is known as the “Little Italy” of Rhode Island and is home to many restaurants, shops and markets that reflect the history of the area.
“Federal Hill is a very historic part of Providence where Italian families immigrated and lived together like they did in Little Italy in New York or The Hill in St. Louis,” said Anthony Corsinetti Jr., co-owner of Hartford Paving, Johnston, Rhode Island . “It’s more diverse now, but Italian restaurants and Italian culture is still the main vibe of the neighborhood, especially on Atwells Avenue.”
Atwells Avenue is the heart of the district. When Rhode Island Energy (RI Energy) needed to tear up the avenue in order to replace underground utilities servicing the area, the energy provider looked to
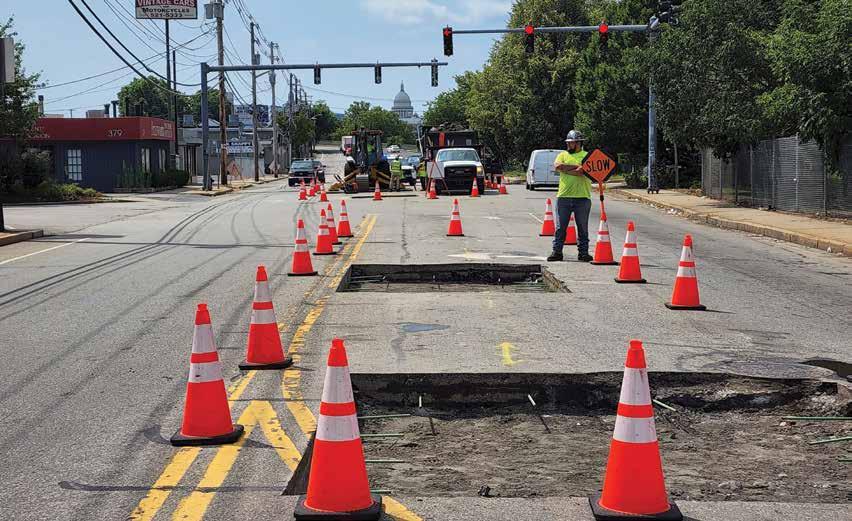
Hartford Paving to restore the street while retaining the old charm of the iconic avenue.
“Like any old city in the northeast, there are a lot of old neighborhoods in need of an infrastructure upgrade,” Corsinetti said. “Atwells Avenue needed to be torn up so the utility companies could replace the antiquated utility systems beneath the street.”
Hartford Paving began work on the $6 million project for RI Energy in March 2021 and finished the ninth and final phase of the project in November 2022. The avenue was a patchwork of materials—asphalt roads, concrete crosswalks and brick intersections—that together create the particular aesthetic of Atwells Avenue. One that Hartford Paving wanted to maintain.
Corsinetti explained the different utility crews left considerable patchwork on the avenue in 2019 and 2020. "It was our job to put it back together again,” Corsinetti said. “What we tried to do is keep the old look of the Italian neighborhood, but do so in a modern way.”
ALL IN THE FAMILY
Hartford Paving was founded in 1974 by Corsinetti’s father, Anthony Corsinetti Sr., and his business partner, Rocco Ciolfi, as a parking lot and driveway paving company. In 2000, Corsinetti Sr. bought out his partner. Then, in 2002, Anthony Corsinetti Jr. and his brother, Chris Corsinetti, took over the business when their father passed away.
In the following two decades, the brothers grew the business into a paving and site contracting company focused on paving municipal roads, parking lots, and patching (including utility patching and infrared patching).
The Corsinetti brothers also own a retail wholesale masonry yard. Today, the company employs 54 people across its divisions and has seven crews, paving more than 60,000 tons of asphalt in 2022.
Although the company has grown and changed over the years, some things have not—including many of Hartford Paving’s best customers.
“We’ve maintained working relationships with many of our customers over the years,” Corsinetti said. “We strive to do quality work for them, on time or early, and to make sure our customers get everything they ask for and more. That’s what keeps them coming back as repeat customers.”
One of the company’s most loyal customers is RI Energy. Hartford Paving won its first contract with the energy supplier back in 1982 when it was operating as Providence Gas. “We’ve had their business ever since,” Corsinetti said. “We can facilitate all their needs from large paving projects to patching.”
RI Energy delivers electricity and/or natural gas to more than 770,000 customers throughout Rhode Island.
RESTORE TO SERVICE
Asphalt paving made up the majority of Hartford Paving’s RI Energy project on Atwells Avenue.
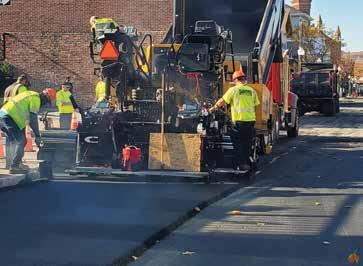
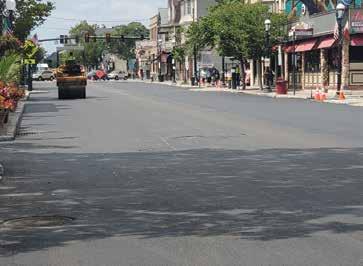
To start, subcontractor Dan Amorello Services, Inc., milled up 3 inches of the existing asphalt before Hartford’s crews placed 1.5 inches of base course and 1.5 inches of surface course with its Cat 1055 and 555 pavers equipped with Trimble 3D machine control. The mix used was a Rhode Island State approved 9.5mm mix supplied by Bevilacqua Asphalt, carried by Hartford’s own haul trucks.
Hartford relies on B2W software for estimating and cost tracking. “That’s been very helpful with our estimators and project managers to make sure we maintain the costs we bid and help us bid for future projects because we can catch mistakes and make sure not to make them again,” Corsinetti said.
At the end of 2021, Hartford’s crews finished paving the 3,000 tons of asphalt the job required and wrapped up its work on the concrete crosswalks. In 2022, it placed brick through four large intersections along the avenue.
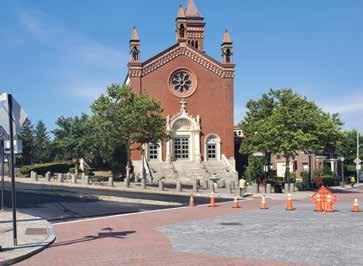
“Everything, from the pavers and brick to the asphalt paving came out quality,” Corsinetti said. “Other contractors in the state actually complimented us on the outcome of the project.”
Despite the variety of pavement types involved in the project, Corsinetti said the most challenging aspect of the project was minimizing impact to local businesses.
“This project came on the heels of the Covid-19 shutdown that had already really hurt these local businesses,” Corsinetti said. “Knowing how much those businesses had already suffered, we didn’t want to affect them anymore than we absolutely had to so it was important that we try to be as unobtrusive as possible.”
To do so, Hartford Paving tried to keep traffic flowing. “We set up 24 hour detours and one way travel as approved through the City of Providence Traffic Engineering to keep traffic flowing through the area at all times,” Corsinetti said. Once one side of the road was done and had reached the right temperature, they moved traffic to that side and started work on the other side. “We tried to do the same with the concrete pavers, which was a bit harder since it required more handwork.”
The brick intersections were removed by conventional means with a mini excavator and by hand as needed.
Corsinetti said Hartford’s project managers also did a great job giving businesses notice, working with local associations, keeping stakeholders informed and making it clear to motorists that local businesses were still open through the use of signs and message boards.
“We did our best not to disturb the local businesses there,” Corsinetti said. “But I still think they were glad to be rid of us when all was said and done.”
“Progress was needed up there and [the local business owners] knew it,” Corsinetti said. “They understood we were sympathetic to their plight, so they were sympathetic to ours.”
FROM STRUGGLE TO SUCCESS
Hartford Paving, like many contracting companies, understands firsthand the difficulty of surviving economic hardship.
“We struggled during the Great Recession, and my brother and I had to wear a lot of different hats to get us through that time,” Corsinetti said, including estimating jobs, performing sales, laboring and running equipment as needed to complete jobs in a timely manner.
They hired a consultant to help guide their business to the next level and learned the best way forward was to hire the right people for the right jobs. “We hired quality people for the field and the office and were able to delegate our vision to them, and that vision was of a company that gave its customers whatever they ask for and more.”
Corsinetti remembers conversations with the consultant about how price wouldn’t always be an issue on their bids. “When they told me that, I didn’t believe them,” he said. At the time, there was a lack of work and the company was being underbid on jobs while it was simultaneously attempting to grow its business. “Now, I can admit that I was wrong. We followed the mold they formed for us and took our company to where we are now, where we are still a profitable company even in difficult times.”
Corsinetti doesn’t yet know what the 2023 paving season will hold for the company, but he’s glad to have a team of employees he can rely on, a solid reputation for his company, and a book of repeat customers. “I think we’ll be plenty busy in our niche for the next couple of years,” he said. “But having contracts like the one we have with RI Energy gives us something to rely on.”
FIND & RETAIN EMPLOYEES
Although finding the right people for the right job was key to Hartford Paving’s success, Corsinetti said finding quality people is not always easy.
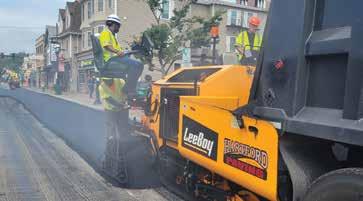
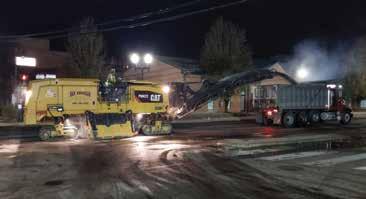
“We’re facing the same problems finding employees that everyone is nationwide,” Corsinetti said. “We’re trying to stay ahead of the curve, recruiting from tech schools in the area and making sure we are a teaching company where they can learn in the field. We still have consultants working with us on a monthly basis to train everyone on the best practices of paving. It’s important to teach the next generation who want to work with their hands, who don’t want to go to college, how to become leaders in this industry, how to become foremen, project managers, etc. We love promoting from within.”
Corsinetti said employee retention is very important to the success of the company, adding that the company’s great benefits package helps with retention. “We offer a 401K with 4% match, health insurance, biannual bonuses and profit sharing with employees,” he said.
The company also holds an annual employee appreciation day where it brings a variety of food trucks to the yard and the employees’ families are invited to join them for an afternoon of fun.
“We do our best to maintain good relationships with our employees,” Corsinetti said. “I get out in the field as much as I can, try to get to know the employees, ask how their kids are. Just knowing that we care about our employees’ lives goes a long way.”
“We’ve been a family business from the beginning,” Corsinetti said. “My brother and I treat everyone like family, from our employees to our customers. If you work for us or with us, you’re part of our family.”
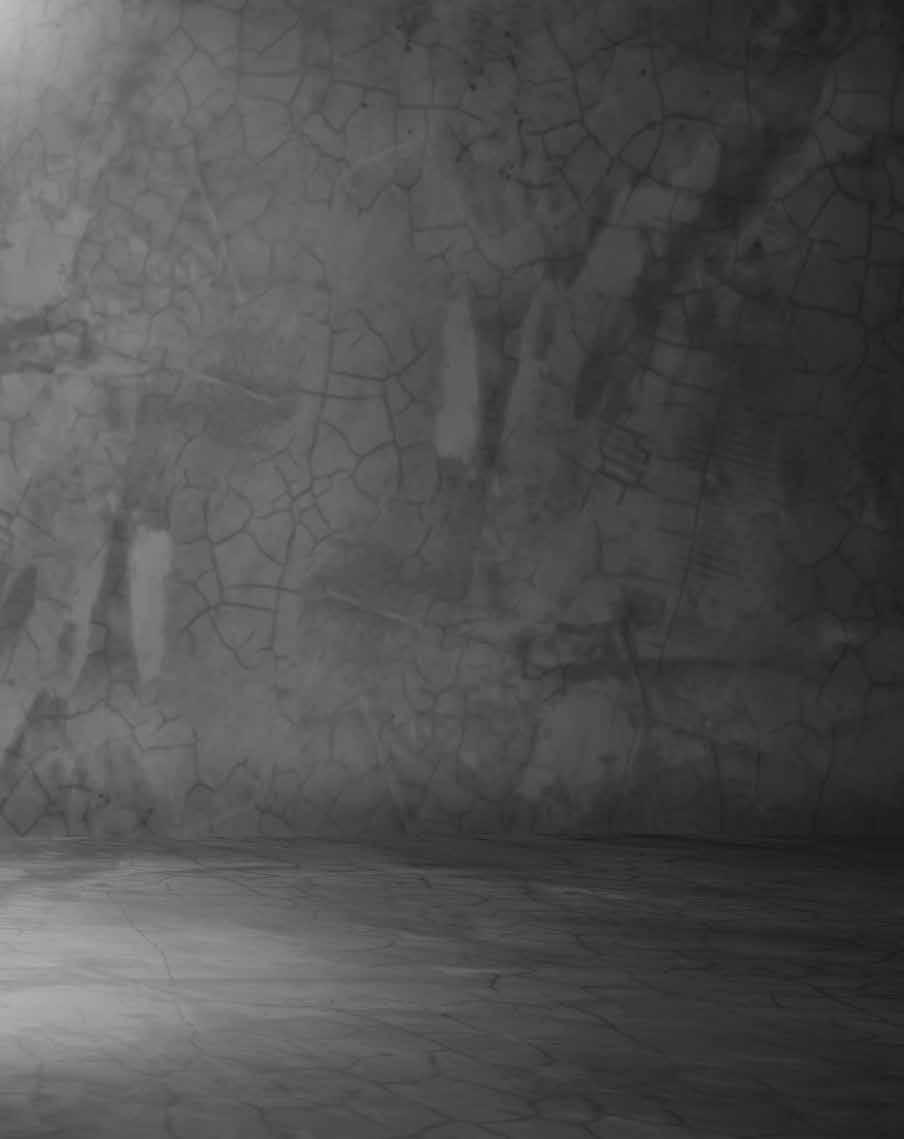
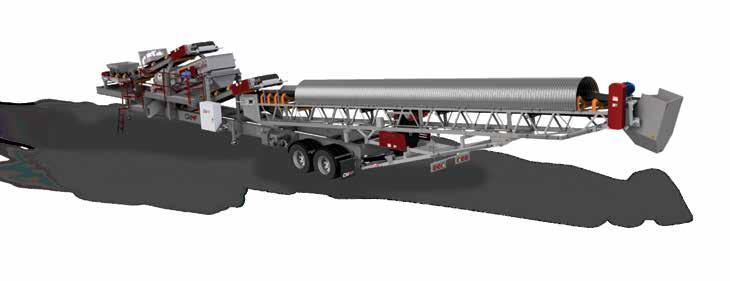
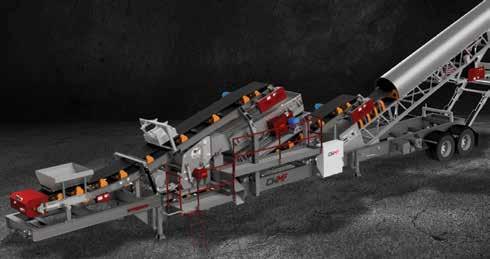
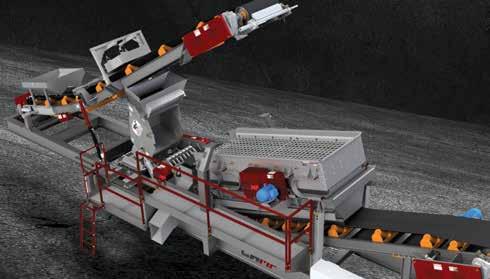
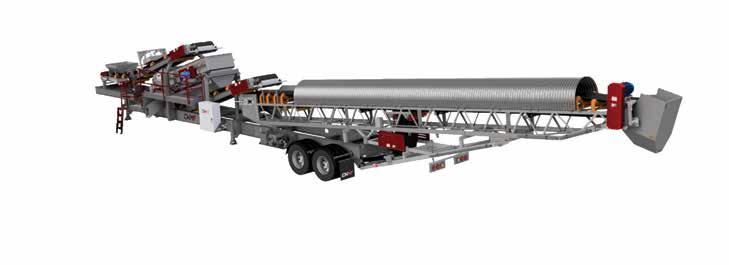
DUSTROL COMPLETES HIR FOR BUTLER COUNTY
BButler County, Iowa, is moving toward hot in-place recycling (HIR) to leave a legacy of restored rural roads benefiting taxpayers, agriculture and light industry. To this end, in early summer 2022, just west of Cedar Falls, subcontractor Dustrol Inc., used the method on the surface of County Road T47 (Sinclair Ave.) from Iowa 57 north 12 miles to Iowa 3.
BUTLER COUNTY’S CHALLENGE
Like many Iowa counties, Butler County is square in shape. It’s bisected by one state trunk highway north/south, and another east/ west. “The secondary road system branches off them, to all communities, generally on a three-mile grid,” said John Riherd, P.E., P.L.S., Butler County engineer.
The county is responsible for approximately 400 lane miles of secondary roads, including drainage structures and bridges. Unpaved (gravel) roads total another 1,600 lane miles. “We have one section of Portland cement concrete that’s 1,100 feet long, otherwise everything else is asphalt,” said Tom Hoodjer, PLS, assistant engineer.
Other than funding, the county engineers say fighting cracks in pavement is their biggest challenge. “Keeping the surface crack-free so it drains well is most important,” Riherd said. “Cracks will kill your road more than anything else. One of the first things we do is fill

the cracks. We try to either fill or eliminate the cracks so water’s not getting into the base and we’re holding that surface together.”
HERITAGE OF ENGINEERS
That the county roads aren’t plagued with potholes isn’t just a testament to staff keeping cracks filled, but to preceding civil engineers who knew how to build long-lived roads.
“The one thing we don’t generally have is a lot of potholes,” Hoodjer said. “The engineers before us spent a lot of time working on that base. The road system in Iowa was developed over time, and they had the foresight to make sure that they had constructed a good base before they paved it. They knew what they were looking to do.
“Also, another good thing for us is the availability of good limestone rock,” he added. “There have been quarries in all parts of the county and we still have most of them.” Indeed, one of Butler’s townships is named Shell Rock.
A typical road cross section in Butler is 6 inches of rolled, or compacted, stone, topped with 3/4-inch of seal coats, and later, 2 inches of hot-mix asphalt (HMA). Eight to 10 years later another inch or two of HMA would be placed and there would be 3 to 5 inches of asphalt on top of the base course.
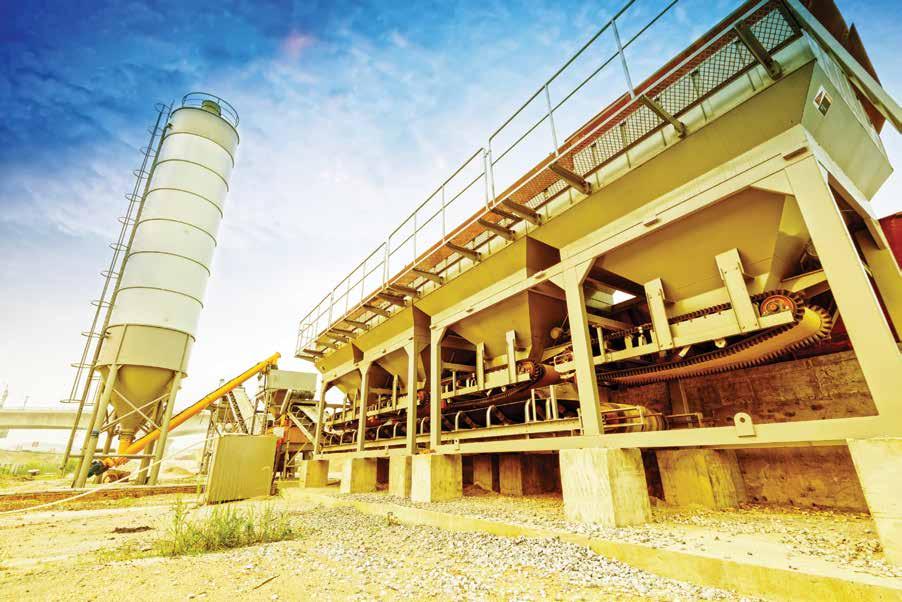
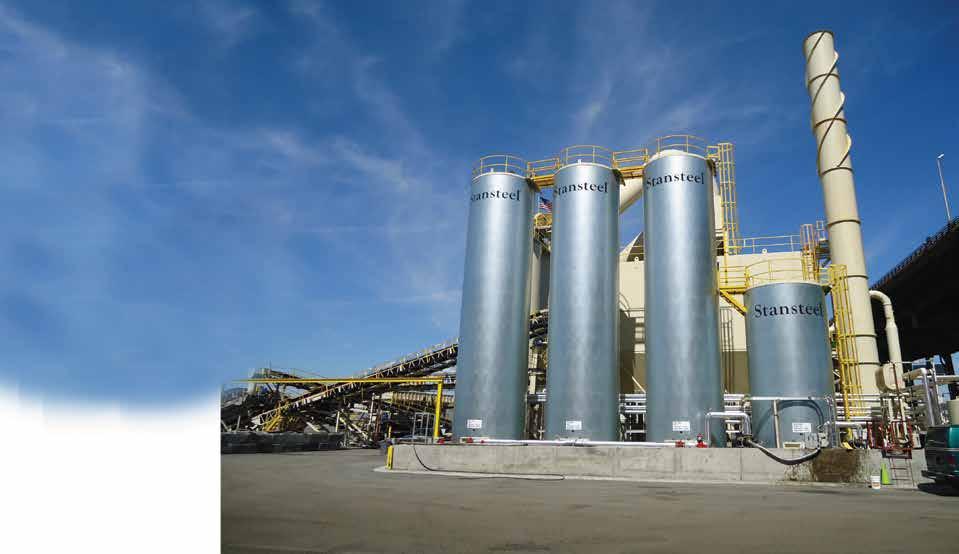
“Around the early- to mid-1990s we began doing a lot of cold in-place recycling [CIR] in the county,” Hoodjer said. “At that point most asphalt pavement had 5 to 6 inches of asphalt and bituminous seal coat. At this time approximately 90% of the county roads have been cold in-place recycled.”
MOVE TO HOT IN-PLACE
Over the years the layers of cold in-place recycled (CIR) asphalt rose higher and higher, and Butler County began to look at alternatives such as HIR.
Riherd said 2021 saw the county’s first trial of HIR. “We had a cold in-place program but started to get to a point where we asked, how much is too much cold-recycled pavement? We had some roads which were cold in-place-recycled in the 90s, and hit ’em again, cold in-place-recycling the either 2- or 3-inch cap that was on that, and into the old cold-recycle. At that point we were getting to 6, 7 inches of a cold- recycled mix, and then a 3-inch cap of asphalt on top. We didn’t know if that was really a good thing to continue to build these pavements up.”
Staff also began to see the function of the cold-recycled layer in a different light.
“We saw that cold recycle as a stress relief layer, a crack prevention layer, not necessarily a load-carrying layer,” Hoodjer said. “And we became concerned about having too much of the ‘softer’ mix in the middle of this pavement. We saw industry promoting hot in-place and thought that would be a good way to deal with that.
“That is, we’re planning to leave that CIR layer alone, essentially, but work with that 3-inch cap because that’s where the wear is. The cold inplace layer still is doing its job under there, but now we’re seeing some cracking in that cap. That’s what we saw with Sinclair Ave.”
Due perhaps to loads of stone headed to a different project on Sinclair Ave. from a local quarry, rutting began to appear shortly after it was resurfaced. “We felt it saw a lot of abuse in its first year or two of life and rutted because of that,” Riherd said. “We like to restore the cross-section before we in-place recycle, so we milled a nominal 3/4-inch to 1-inch to create a cross-slope again, and to generate RAP for a new cap and give the recyclers a good chance for a uniform surface.”
On Sinclair Ave., cores taken earlier were analyzed by consultant Road Science, a division of Arkema, which came up with the recycle mix design. The surface was recycled with HIR to a depth of 2 inches. This included preparing the surface by milling, softening the surface via uniform heating, and mixing with a rejuvenating agent, and spreading, leveling, and compacting the mixture for surfacing.
The rejuvenating agent was composed of a polymer modified asphalt emulsion, containing 3% styrene-butadiene solution polymer.
The final recycled course was compacted by a Hamm double-drum HD+ 140i high-frequency roller in breakdown position, followed by a Hamm double-drum HD+ 140i VO finish roller in oscillation mode, compacted to minimum 95% density.
The prime contractor, Heartland Asphalt Inc., of Mason City, Iowa, would then place a 3-inch HMA friction course in two 1.5inch lifts.
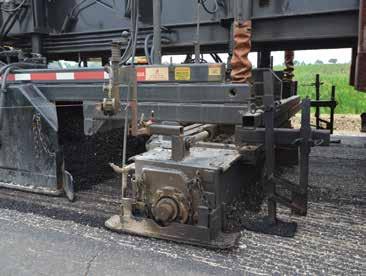
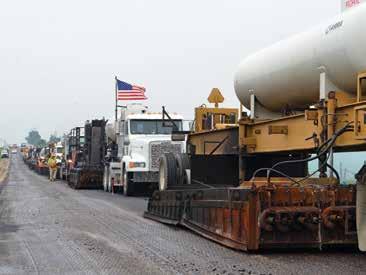
UNIQUE HIR SYSTEM
Dustrol’s eight-unit HIR train has four units pulled by tractor cabs, and four pushed by the heater mill units. “Each of the eight heaters and heater mills have an operator, who does not drive the truck, but operates the equipment,” said Ron Wilson, vice president for Dustrol.
Dustrol’s MARS process, which stands for Mobile Asphalt Recycling System, is the contractor’s current method of hot in-place recycling asphalt 2 inches or more. The process begins with one custom-made, propane-fueled preheater. The next heater in the train is equipped with grade-controlled milling drums, which windrow the top 1/2 to 3/4 inch of softened material. The milling heads are capable of cutting 16 feet wide.
Tunnel heaters follow, heating the underlying pavement while maintaining the temperature of the windrow in the tunnel. The surface again is milled and heated by up to three more milling heaters alternating with tunnel heaters, depending on material and depth. The last milling heater in the process has an oil metering system that injects and mixes the rejuvenating agent into the milled asphalt and aggregate.
“We don’t have a direct flame going down to heat,” Wilson said. “Instead, the flames heat fire brick within the unit’s ‘oven.’ It helps us retain heat and is better than insulation only. It’s a gentle heat above 200 degrees F that is not very long on the surface, as we are trying to go 20, 30 or 40 fpm; we are not exposing it deeply to very hot temperatures.”
This protects the recycled material from premature aging caused by excessive production temperatures. “Yet, there is a degree of
Lift Your Operations Out of the Stone Age

Apex Scale Ticketing Software combined with simple site automation technology gets your trucks in and out in record time.
With Apex You Can:
• Eliminate gaps in communication between dispatch and back office
• Simplify quote-to-cash processes by integrating with ERP
• Reduce time at plant by streamlining and automating your processes
• Reduce errors throughout your entire order cycle with digital tickets
• Capture complete visibility to make more accurate decisions, quicker
• Support business growth with one reliable, scalable, and maintainable system
burning some of the volatiles out,” Wilson said. “That’s why we are replacing them with a quality rejuvenator and polymer modifier at the end of the process.”
The rejuvenating agent is added just ahead of the paver, chemically reacting with the material. Finally, after adding and mixing the rejuvenating agent, the windrow of material is picked up with a conventional windrow elevator, modified by Dustrol. The paving of the recycled material is done with a conventional electronic grade control/electric screed paver, in Butler County, using Dustrol’s Bomag Cedarapids CR662RM rubber-tracked paver.
The material is compacted using conventional rollers. The road can be opened to traffic after a cool-off period similar to an asphalt paving operation, typically within an hour after the process is complete.
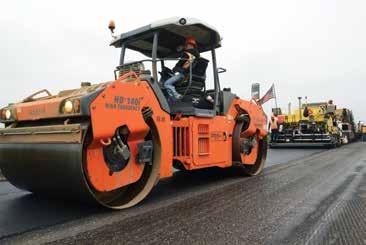
“Our equipment can go from 13 to 16 feet wide,” said Donn Johnson, consultant for Dustrol. “In this application we are working 12 feet wide. It’s originally a 22-foot roadway and they’ve added a foot to either side, which is recycled in-place, so we will wind up with a beautiful 24-foot pavement after processing.”
“We make all our own equipment, the heaters, of course,” Wilson said. “The pavers and rollers are conventional. We modified the windrow elevator because we can’t really find a windrow elevator we like well enough, so we extended it upward, so it dumps in the paver a little differently. We tend to modify just about everything, but the heaters, heater-tractors, milling drums, even the scarification equipment is all built by us. We manufacture for ourselves and do our own construction.”
The preheater/heater-miller/heater-scarifying/tunnel heater system allows Dustrol to reduce project costs and improve project timeliness. “We do everything on-site,” Johnson said. “We don’t haul materials off for mixing or processing. This speeds up timelines and reduces our fuel consumption, in turn providing lower-cost maintenance for removing cracks, ruts and low areas on existing surfaces, as well as offering environmental advantages like much lower fugitive dust emissions during reconstruction.”
Traffic delays are minimal as the process is fast at 20 to 40 fpm, allowing the contractor to repair 2 to 4 lane-miles per day.
“Dustrol can complete the HIR process as either a single-lift or multiple-lift rejuvenation,” Wilson said. “In the single-lift method, scarifiers loosen the heated material to a depth of up to 1 inch. The multiple-lift operation allows for the rejuvenation to go to 2 inches or more using milling heads to loosen the material.” Both processes allow surfacing to be placed the same day, or up to weeks later if necessary.
DESTRUCTIVE LOADINGS
On Butler County roads, passenger cars don’t provide the kind of destructive loading that causes pavements to deteriorate, nor do most agricultural hauls of hay or harvested products if they are distributed over the proper number of axles, Butler County’s Riherd said. But large-scale cattle and hog confinement operations generate hauls of manure that are taken to fields as fertilizer and are very heavy.
“The hauls of manure are pretty hard on our roads,” he said. “Additionally, recent legislative action has permitted the allowable axle weights to increase, which will undoubtedly cause our roads to wear much faster than they do with today’s axle weights.”
“One of the biggest variables in our system is pavement age,” said Butler County’s Riherd. “Nearly every road in the county has the same base, and it has the same weather and same traffic. So, a lot of what we do is age-based. We don’t have a formal pavement management program; instead, we have a starting point in which we know which roads are of a certain age. We will drive them and see what the crack count is, and how the ride is.”
The pavement condition then is measured, but without a great deal of variance among pavements. “We don’t have a red spot on the map for bad conditions, or orange or green or whatever the color is. Instead, most roads have the same characteristics regarding pavement condition index. We stay aware of their condition as we have a reasonable assumption that we’re going to have this many dollars to spend in the next five years. We ask, ‘where will we spend this money?’”
A main source of revenue for Butler County’s rural roads is the Iowa Farm-to-Market road account. “That’s a road use tax funding coming from the state fuel tax and vehicle registration fees,” Riherd said. “It’s a formula based on your area, your number of road miles, and it’s distributed throughout the state. Another source would be federal aid on a portion of our system, that is programmed through our region. But most of the time our farm-to-market account is what we use.” The county’s annual secondary road budget is around $8 million to $9 million.
Riherd said none of this would be possible without the confidence and support of the county’s board of supervisors.
“We have a very supportive board of supervisors who are the elected leadership of the county, and they’re ultimately responsible to the taxpayers,” he said. “They’re the ones who determine the tax levies in the county and recycling is important to them because it makes the best use of our tax dollars.
“And that’s what we’re attempting to do here as well, make the best use of our tax dollars, building a good road that will last many years,” he added. “What might be a small maintenance project is more of an investment in a high-quality road that the supervisors can be proud of.”
Edited from editorial content provided by Dustrol Inc. This article previously appeared in Pavement Preservation Journal. Used with permission
“WHAT MIGHT BE A SMALL MAINTENANCE PROJECT IS MORE OF AN INVESTMENT IN A HIGHQUALITY ROAD THAT THE SUPERVISORS CAN BE PROUD OF.”—JOHN RIHERD
From innovative designs to Caterpillar dealer service and support, Weiler is paving the way to success for contractors across North America. Weiler material transfer vehicles, commercial pavers, road wideners, windrow elevators, compactors, soil stabilizer, rock drills, grader, screeds and tack distributors are engineered with proven features to increase productivity while reducing operating costs. Weiler equipment is sold and serviced exclusively at Caterpillar dealers throughout North America, providing unmatched support with factory trained technicians and readily available parts to keep your operation up and running.
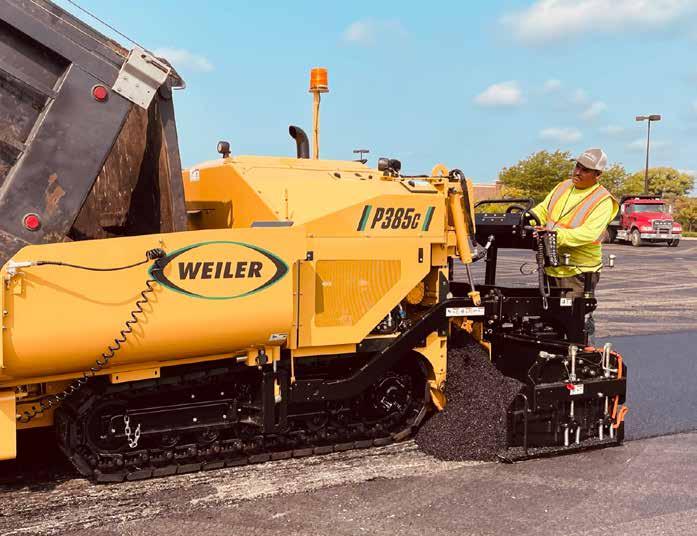
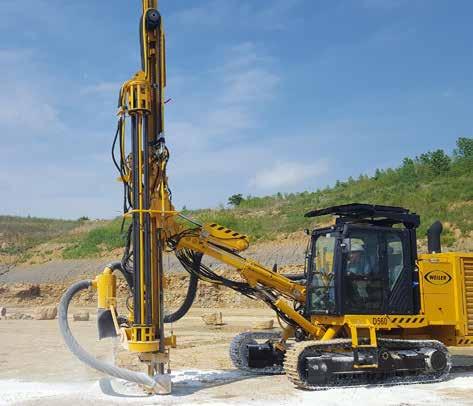
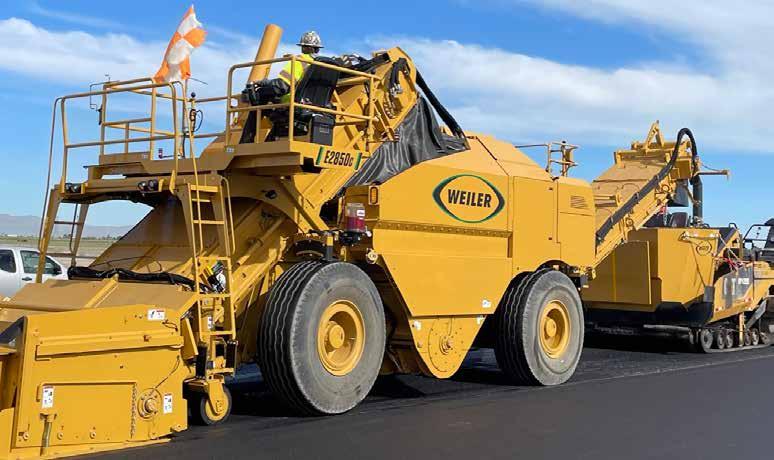
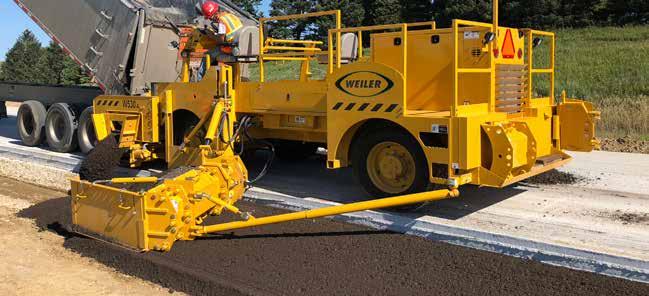
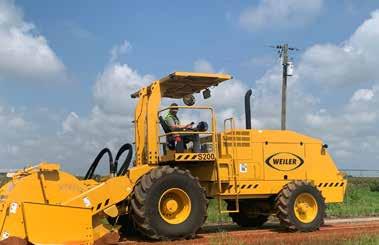
weilerproducts.com
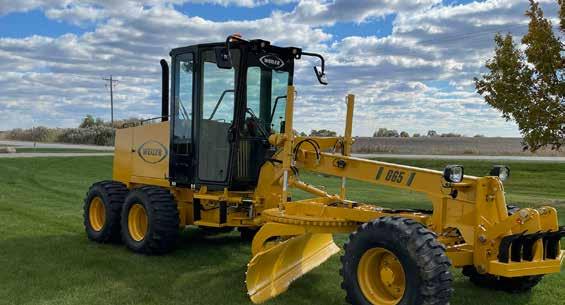
WOMEN OF ASPHALT
Meet Superior Construction’s WIC Initiative
FROM SUPERIOR CONSTRUCTION
Apilot program from Superior Construction, a family-owned infrastructure contractor headquartered in Jacksonville, Florida, launched November 2022 to support, empower and advance women in the construction industry. The internal pilot program is intended to identify motivated women in the construction industry and offer them essential tools for their personal and professional development. Superior Women in Construction, an initiative designed in collaboration with certified executive and team coach Dale Beaman, PCC, MPH, will help cultivate an inclusive culture that aligns with Superior’s mission, vision and values. Identifying and developing diverse internal talent is good for morale and good for business. Research shows a direct link between the diversity of a company’s leadership and its business performance, as well as profitability. The Superior Women in Construction initiative marries both these principles and has the full support of company leaders.
Superior Construction is an American family-owned and operated infrastructure contractor dedicated to providing innovative solutions with industry experts and leaders. First established in 1923 as the J Largura Company, the now fourth-generation family business evolved into Superior Construction by 1938. Learn more at superiorconstruction.com and follow Superior on LinkedIn.
“We want to be intentional in making Superior among the best places to work while building future leaders,” Superior’s CEO Nick
Largura said. “To do that, we must remove the barriers women have faced in their effort to advance in an industry where they’re chronically underrepresented and where few hold middle manager or executive roles. As the industry continues to evolve, we must empower women in order to advance construction. This program aims to do both.”
In developing the initiative, company executives selected 12 rising women leaders to partake in the pilot program. With their feedback, Superior identified key ways to foster an environment that supports diverse leaders.
The pilot program officially launched Nov. 2, 2022, and will include the following components:
• A supportive forum to learn, grow and share experiences with their colleagues;
• Monthly group coaching on customized leadership topics;
• Individual career coaching sessions to personalize professional development;
• A mentor program to tap the knowledge and experience of seasoned Superior leaders;
• Opportunities to learn about other parts of the business through peers and mentors;
• Interaction with executive leaders that increases visibility of participants’ talents and skills; and
• Completion of a collective team project centered around creating value for Superior.
Beaman shared that cultural shifts don’t happen overnight. “It takes industry leaders like Superior and programs like Superior Women in Construction to affect industry-wide change.”
Superior Construction’s leaders hope the Superior Women in Construction initiative will become an industry standard and transform mentees into mentors who can continue to advocate for other women in construction.

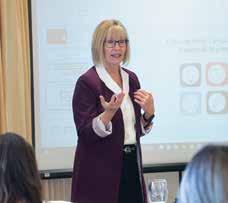
MIX MASTERS
BEST
Why do asphalt producers turn to Ammann when investing in batch and continuous plants? The plants’ advanced technology drives ownership and operating costs lower – and profits higher. In addition, Ammann’s unique approach to heating and mixing yields higher-quality asphalt than conventional methods.
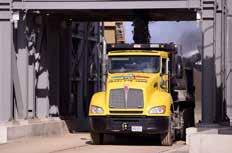
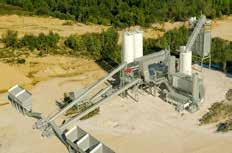
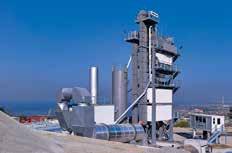
Ammann has you covered with:
• Advanced heating and mixing systems
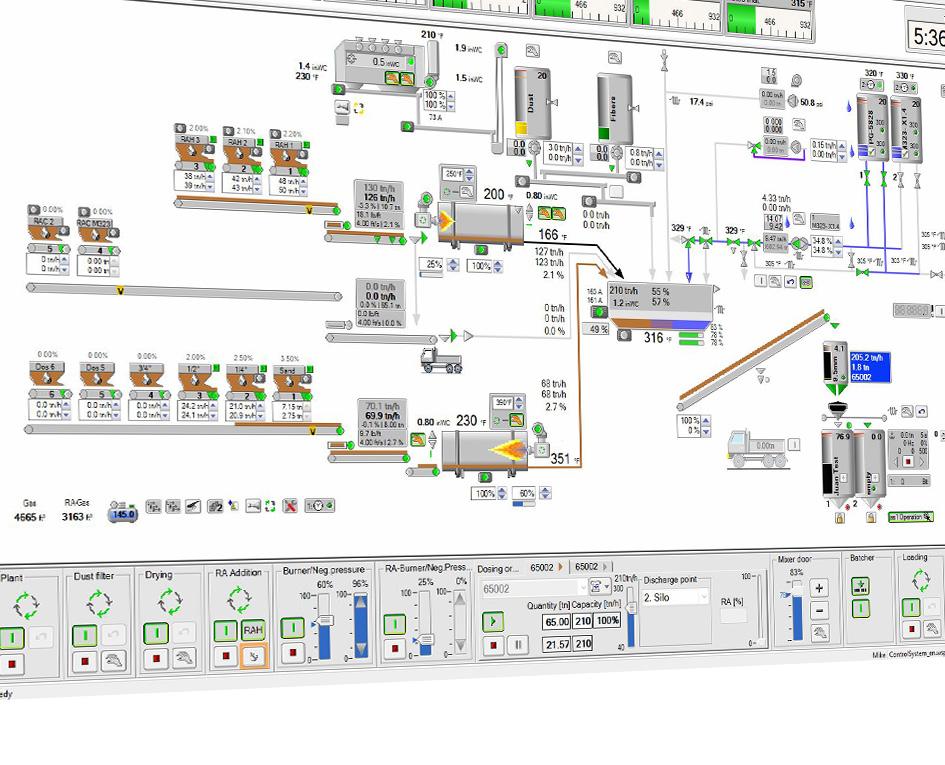
• Intuitive operation
• Outstanding productivity
• Remarkable reliability and durability
• Exceptional training and service support after the sale
INTERNATIONAL SNAPSHOT
NGE Monitors Emissions
FROM HIBOONGE, an independent French civil engineering company, will be reducing the carbon footprint of its construction worksites using a Hiboo-developed functionality to collect and display the CO2 equivalent (CO2e) emissions generated by the fuel consumption of its plant and machinery.
This is the first time that any major construction company will have tested this tool developed out of the Hiboo single, multi-manufacturer, seamless data platform. It will enable NGE to collect 100% of the data transmitted by its plant and machinery worldwide, which is more than 2,600 separate pieces of machinery, including 1,500 items of production plant.
With the “Solar Impulse Efficiency Solution” label, awarded by the Solar Impulse Foundation, Hiboo’s technology in data management and analysis is used to reduce the carbon footprint of the industrial sector.
NGE management has asked all its equipment suppliers worldwide (manufacturers, dealerships, rental companies, etc.) to give Hiboo access to the data generated by all the plant and machinery in its fleet.
“You can’t improve something until you measure it,” said Thierry Robert, the chief plant & machinery officer at NGE Group.
“So, we’ve been committed for several years now to a very realistic and real-world approach to this issue. The ability to measure the actual CO2 emissions for all the plant and machinery we operate is a major step forward, because it gives us the opportunity to work on real-life scenarios that will eventually benefit all our worksites. It also aligns our actions directly with the expectations of our customers, who want to see concrete evidence of our environmental footprint reductions. This partnership with Hiboo is an integral part of the NGE strategy to reduce GHG emissions by 4% year-on-year.”
Hiboo is a French specialist in equipment-generated data processing, and will provide NGE with data covering the full range of key operating indicators (usage, engine idling rate, fuel used, faults, etc.) re-
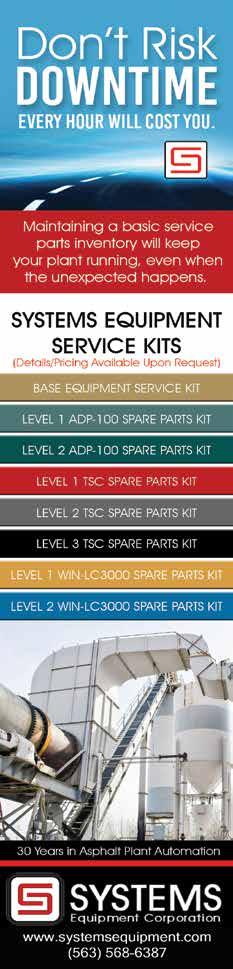
quired to optimize productivity worksite by worksite and region by region.
Already ahead of the industry curve in terms of collecting and measuring data on engine idling hours (see sidebar online) using the Hiboo platform, NGE is now taking its commitment to a new level. Another important development is that BM Rent and ENCO have become the first national rental companies to support this innovation in fleet management by providing access to the data generated by plant and machinery rented to NGE.
From now on, Hiboo will be able to measure the actual CO2 emissions of its production plant and machinery fleet in real time on the basis of parameters including equipment category, geographic area and/or worksite, instead of conducting retrospective assessments based on fuel costs.
The goal for NGE is to pinpoint its most emissive production worksites so that it can prioritize them as the focus for its initiatives. The experience gained will then be used to generate feedback and share best practices.
The new system will also enable fuel savings to be measured for each piece of machinery, as well as assessing the progress made by drivers and operators as a result of eco-driving training provided by the company.
As part of continuing to drive innovation in CO2 emissions reduction, NGE also intends to fit some of the tires used on its plant and machinery with telemetry systems developed by GCS, which specializes in tires for civil engineering applications. The data generated will be processed and analyzed by Hiboo. Ensuring that tires are used in accordance with recommended pressures and temperatures extends their life, at the same time as reducing fuel consumption, and therefore CO2 emissions.
“Construction companies hold a wealth of key data that can be used in creating a plan for carbon reduction in their equipment,” said Hiboo CEO Clément Bénard. “Our task is to enable access and use of this data in order to help customers like NGE in their environmental strategy. Because of its technology, Hiboo has been helping NGE with its environmental strategy for several years. Measuring the CO2 emissions of construction sites is a key step in de-carbonizing the construction industry.”
For more information, visit nge.fr or hiboo.io.
It takes a road to get there.


CLOSE TO OUR CUSTOMERS
And a world of experience to build that road. As the global leader in road construction and minerals processing technology, we‘ve seen just about everything there is to see. In every climate, every condition, every twist, turn and terrain. And we put that world of experience in your hands, so you can sustainably build North America’s infrastructure today, for future generations.
wirtgen-group.com

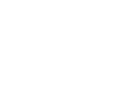

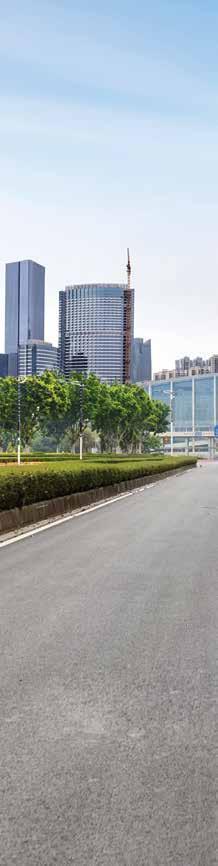
Update Your Plant for Spring Startup
BY ASPHALTPRO STAFFThis month’s production-related product gallery focuses on the asphalt plant and production of asphalt pavement mixes. To produce hot-mix asphalt (HMA) and warm-mix asphalt (WMA) most efficiently today, an owner must take more than dollars into account. You’re also looking at the environmental impact of the operation. While you’re taking the winter season to perform routine and annual maintenance, use the ideas on the next few pages to plan upgrades and enhancements for your most efficient and sustainable operation at season startup and beyond.
The original equipment manufacturers (OEMs), service providers and consultants who provided information for this department are listed in alphabetical order. For easier connecting, look up this department on www.TheAsphatPro.com where those entities who are advertising partners—thus supporters of your industry—will have live links directly to their websites for you to click. When calling for more information, make sure you let folks know you saw them in AsphaltPro Magazine.
ADM
The EX Series asphalt plants from Asphalt Drum Mixers (ADM) are designed to meet production capacity demands from 120 to 425 TPH under strict environmental regulations. The EX Series’ single-drum counterflow system uses the latest in innovative technology, resulting in the longest aggregates drying and mixing times in the industry, according to the manufacturer. The EX Series comes in portable, skid-mounted and relocatable versions designed to meet all federal and state specifications to ensure consistent, quality asphalt.
The EX Series’ unique single-drum counterflow technology system uses separate drying and mixing zones to achieve the optimum heat transfer and fuel efficiency. EX plants are capable of processing high percentages of recycled asphalt pavement (RAP), producing hot mix containing up to 50 percent recycled material, according to the manufacturer. Visit ADM in their booth S5467 at CONEXPO-CON-AGG to learn more.
For more information, call (260) 637-5729 or visit https://www.admasphaltplants.com/ ex-series/.
AHERN INDUSTRIES
With over 40 years of experience in the asphalt plant industry, Ahern Industries specializes in asphalt plant disassembly, relocation, complete fabrication and season startup.
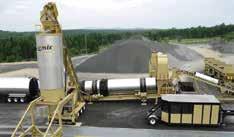
For more information, call (210) 240-8395 or visit www.ahernindustries.com.
ficiently burn oil, natural gas or propane. Its compact flame makes it compatible with virtually all drum designs without complicated adjustments. Rapidly swirling high energy air is the key to its combustion. The swirling air and flame are created by the fixed internal spin vanes and the patented castellated nose, ring and nozzle design. True to its name, the Whisper Jet burner is designed and equipped to reduce burner noise.
Its nominal maximum aggregate drying capacity, at 5% moisture content, is rated at 140 TPH for the WJ-35 up to 600 TPH for the WJ-150. There are six models to choose from, ranging in integral blower horsepower from 40 to 150. Visit Astec in their booth C30235 at CONEXPO-CON/AGG to learn more.
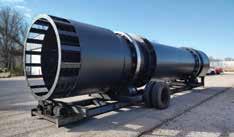
For more information, visit https://www. astecindustries.com/products/details/whisperjet-burner
B&S LIGHT
ALMIX
At the center of each customizable UF Series asphalt plant from ALmix, you’ll find the UF Series drum mixer. These are counterflow drum mixers that include a bolt-in flight layout, that when coupled with VFD-controlled rotational speed are designed to allow for maximum drying and mixing efficiency, lower stack temperature and reduced fuel consumption. The UF Series drums are available in a variety of sizes, with countless features and options. Visit ALmix in their booth S6816 at CONEXPO-CON/AGG to learn more.
For more information, call (260) 672-3004 or visit https://almix.com/the-uf-series.
ASTEC
The Astec Whisper Jet® burner is designed with patented technology to cleanly and ef-
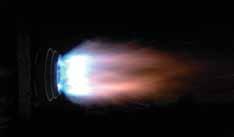
B&S Light Industries offers the EZ-Loader silo/truck loadout system for virtually unlimited capacity for tickets, customers, trucks, materials and more. Operators view, modify and/or reprint any previous ticket(s) as needed from logical, well organized and intuitive menu screens, according to the manufacturer.
While the operator manual—including scale manuals with illustrations—is contained in the “help” file for viewing or printing, B&S offers support to customers and stocks—ready for shipment—all replacement parts for the first system the company built nearly three decades ago as well as each of the 2,500+ systems since. Simulation for training is extensive and realistic, according to the manufacturer.
The system offers automatic daily backup of current plant data to inexpensive, removable flash disk. The operator can achieve
2.7M Square Feet of Exhibits
130,000 Attendees
1,800 Exhibitors
150 Education Sessions
REGISTER at conexpoconagg.com
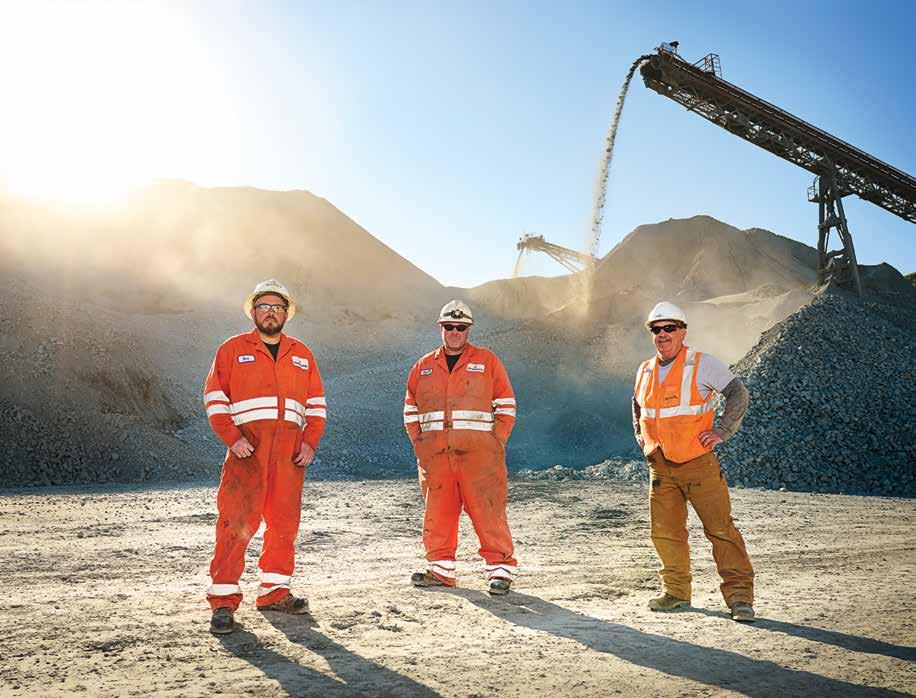
Save 20% with promo code SHOW20
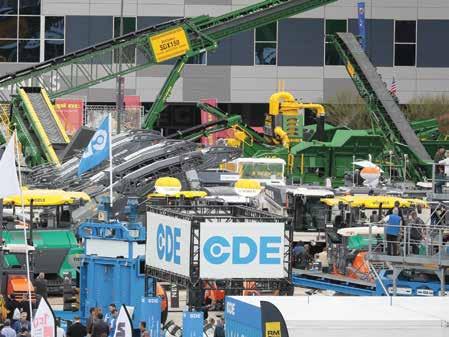
“CONEXPO-CON/AGG SHOWS US THE FUTURE OF OUR INDUSTRY, WITH INNOVATION, EQUIPMENT AND IDEAS YOU CAN’T FIND ANYWHERE ELSE.”
— GRANITEROCK, AROMAS, CA
continuous real time data synchronization of multiple office computers and plants, numerous file transfer protocols to interface with most popular accounting packages, and have TCP/IP communication.
For more information, contact (918) 3421160 or sales@bslight.com.
safety, with other days devoted to mix quality, production, and electro-mechanical, depending on the track you sign up for.
These courses run through March 17, with in-person information during the Rocky Mountain Asphalt Conference and Equipment Show (RMACES) in Denver Feb. 7-8, at booth 505.
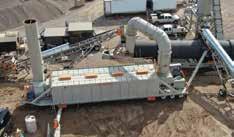
For more information, contact (952) 9396000 or visit www.clarencerichard.com.
COMMAND ALKON
Command Alkon offers the Apex Scale Ticketing Software to eliminate gaps in communication between dispatch and the back office, to reduce truck time at the plant, and to offer complete visibility. Combine Apex with simple site automation technology to get trucks in and out of the plant efficiently. Visit with Command Alkon and attend one of their live demonstrations in their booth N12315 at CONEXPO-CON/AGG to learn more.
For more information, visit commandalkon. com/getapex.
BROCK
BROCK is pleased to announce Lance Clark as its new regional sales manager – Southwest. He takes over the states previously covered by Sales Representative Phil Hoffman who will be helping Clark as he transitions into the area. Clark’s territory includes the states of Texas, Oklahoma, Arkansas, Louisiana, Mississippi and Alabama. In his role he will be responsible for providing outstanding customer service while selling BROCK equipment, parts and on-site construction services in the territory.
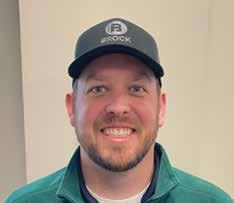
Clark has over 16 years of successful engineering and sales experience in the hot-mix asphalt (HMA) equipment industry. He came to BROCK in 2021 after several years with Astec Industries to help develop the BROCK line-up of quality hot oil heaters and liquid asphalt storage tanks.
For more information, contact (423) 4769900 or visit www.brock.llc
CLARENCE RICHARD
The Clarence Richard Company offers more than hot-mix asphalt (HMA) components and service. The Plant Operation Workshop, taught in person and via intensive online courses, is designed to teach plant and production personnel improved safety, mix quality and production techniques as well as tips for improving operating costs. Weeklong courses include an entire day devoted to
CONVEYOR COMPONENTS
The Model CT, manufactured by Conveyor Components Company, is comprised of a control unit and tilt probe, which senses the presence or absence of material. The control unit is enclosed in a rugged cast aluminum housing with external red and green LED status indicator lights and surface mount printed circuit boards. Weatherproof, dust-ignition proof and explosion proof models are available. Optional black epoxy powder coating is available for corrosive environments.
The Model CT is commonly used when other controls won’t work due to bin vibration, or actual bin walls aren’t available for mounting other controls. Typical applications include level detection in hoppers, silos, stackers, crushers and conveyor transfer points.
The CT tilt probes are available as a standard 9-inch tilt probe or a compact 6-inch tilt probe and have 25 feet of electrical cable. Stainless steel probe housings are available as an option. Float ball and paddle accessories are also available for fine-grain materials.
For more information, contact (800) 2333233 or visit the Conveyor Components website.
CWMF
CWMF, Waite Park, Minnesota, now offers a fines metering system for its portable Dust-Eater® baghouses, allowing producers better control of fines and reducing set-up time. As mix designs evolve, controlling dust
is imperative to producing a quality product that will meet specifications. This device is designed to consolidate a remotely located dust pod and additional augers. It works when baghouse fines are first conveyed to the discharge auger on the baghouse. The discharge auger has a drop-out point where the dust will be stored in a small pod. This pod will have a rotary vane feeder attached, which will meter the amount of fines returned to the drum. If you are producing more fines than you are returning, the auger will bypass the dust pod, discharging them to a wet auger. At this point, water will blend with the fines, and it can be rejected.
For more information, contact sales@ cwmfcorp.com.
EAGLE CRUSHER
The team from Eagle Crusher, Galion, Ohio, offers the RapiDeploy® 1000, which includes the features of the original RapiDeploy 500®, plus the Eagle Crusher UltraMax 15 impactor. The RapiDeploy 1000 is designed to crush, screen, separate and stockpile—all in one pull. Look for the new UltraMax 1600XOC portable impactor plant and the 8x20 screen plant with integrated feed conveyor and blending gates at Eagle Crusher’s booth C30949 at CONEXPO-CON/AGG.
For more information, contact (800) 25-EAGLE or visit www.EagleCrusher.com.
GENCOR
The heart of the Gencor Ultraplant® is built around the unique, patented, counterflow Ultradrum® technology. The Gencor Ultra II® burner is extended well inside the dryer for maximum efficiency and contact with the wet aggregates and uses compressed air to atomize each droplet of fuel for optimum fuel efficiency.
The isolated mixing section of the Ultradrum is located behind the burner so there is no chance of liquid asphalt encountering the burner flame. This means there is no oxidation of the asphalt, no degradation of the mix and no asphalt vapors entering the ex-
haust gas stream. Vapors generated in the mixing section are pulled through the burner by a patented volatile reclaim system and consumed as fuel.
Recycle is added to the isolated mixing zone through a wide collar behind the burner flame. Gencor’s fines return system is designed to provide simple metering and easy transportability. The optional Ultradrum insulation package substantially reduces thermal heat loss by reducing fuel usage as much as 7%.
Standard features include:

• Patented adjustable 5-way veiling flights;
• Patented combustion T-flights;
• Sweeping material inlet flights for even drum loading;
• Self-cleaning RAP inlet to allow up to 50% RAP;
• Large drum diameter to reduce air velocity and dust carry-out;
• Friction driven trunnion rolls for lower noise, maintenance and energy; and
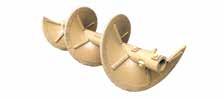
• Positive volatile reclaim system to capture and destroy hydrocarbons.
For more information, contact (407) 2906000 or visit www.gencor.com.
HOMESTEAD VALVE
Homestead Valve division of Olson Technologies Inc. offers a full line of hot-jacketed, 2-way shutoff and 3-way diverter valves to meet flow requirements, including those made of cast iron (to 450°F), of ductile iron (to 650°F) and with high temperature seals. Actuator types include pneumatic, electric, open-close and modulating.
For more information, contact (610) 7701100 or sales@homesteadvalve.com.
KENCO
Kenco Engineering Inc. offers innovative products for the aggregates, road building and biomass industries to protect your investment in your production equipment. Within the past couple of years, the engineers have innovated new concepts, including one originally designed for the vertical construction industry: the foundation drilling auger protection concept from Kenco is designed to reduce downtime at the asphalt plant and at the paver by retaining auger diameter. Kenco’s unique tungsten carbide impregnated (TCI) process protects auger flights from abrasive wear. Crushed tungsten carbide (TC) is im-
Kenco’s unique tungsten carbide impregnated (TCI) process protects auger flights from abrasive wear.
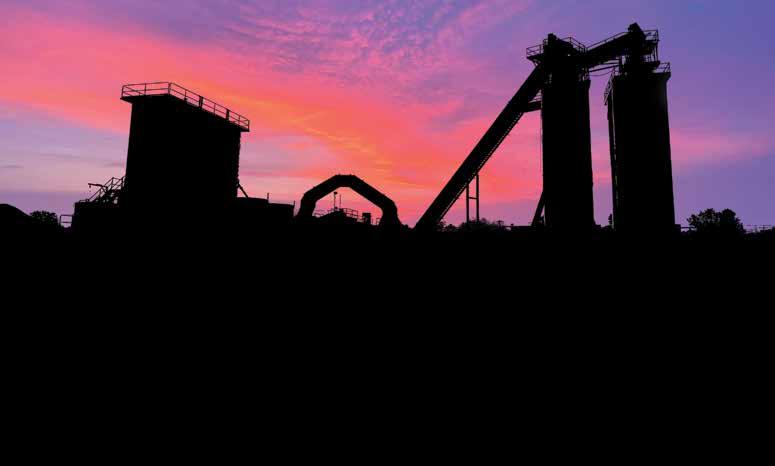
pregnated into the flight edges (and outer faces, if desired) by melting the flight metal to a depth between 0.25 and 0.375 inches and dropping crushed TC particles into the molten puddle. After cooling, the TC is solidified deep into the parent metal.
TC wear strips featuring the Kenco TCI process can be welded to flight edges and any other drill tooling that needs extra protection. It’s not an overlay or spray-on. The TC becomes a part of the steel. Kenco crushes and sizes the TC raw material in-house to maintain quality. TC has a hardness exceeding 90 Rockwell A.
For more information, contact (916) 7828494 or visit www.kencoengineering.com.
Are you exploring NAPA’s climate challenge, but unsure of your navigation? We can help you take at least one step forward — by replacing your tank heaters, hot oil heaters, fuel oil preheaters, and distributor truck heaters with our zero-emission, 100% efficient, Lo-Density® drywell-style electric heat. Check out our new operating cost calculator
MEEKER
Meeker Equipment designed the Patriot hot oil heater for both reliability and efficiency. The 2-pass helical heater absorbs BTU energy out of the burner flame, which directly correlates to low stack temperatures. Using Meeker’s SABER STACK option drops stack temperatures even lower, sometimes as much as 100°F, according to the manufacturer.
All heaters come with a programmable logic controller (PLC). Once the heater starts up, the PLC tracks such things as:
• the hours the burner ran (some states require you to report this);
• number of times the burner cycles (for trouble shooting);
• stack limits;
• temperature limits; and
• flow limits, to name a few.
The removable expansion tank is mounted off center of the heater to allow it to keep cool. The tank comes with a magnetic shutoff switch and a visual expansion tank level indicator.
The heater uses a high flow SIHI centrifugal pump with mechanical seals for 12-foot per second flow through the coil. This turbulent flow through the heater keeps the oil from degrading.
The burner is a Webster JB1 burner, which features an adjustable combustion head assembly, allowing for unmatched fuel to air mixing, smooth lights-offs and quiet operation. The modulating burner operation creates a wide turn down ratio, allowing the burner to fire only at its demand. In other words, if less heat is required, then the burner fires only to that output.
All heaters from the OEM are prewired, pre-fired and pressure-tested before shipping. The OEM states that it normally has the heaters in stock for quick delivery. Visit Meeker at booth C32553 at CONEXPO-CON/AGG to learn more.
For more information, contact (888) 3330323 or visit www.meekerequipment.com.
MEYER LAB
The family owned and operator Meyer Lab offers specially formulated temporary and semi-permanent release agents and coatings, drag slat cleaners, and extraction solvents designed to work on all asphalt mix designs, including all performance-grade mix designs such as PG76-22. These are state-approved and NTPEP-listed products formulated and made in the United States with custom-built dispensing systems. Meyer is a full-service supplier with more than 75 service representatives and numerous warehouses located throughout the United States.
For more information, contact (800) 5807677 or sales@meyerlab.com.
ed, the Vulcan Burner opens completely to allow for easy access.
Vulcan burners come equipped with two safety switches in case of overheating or separation while in operation. The 75-horsepower motor is designed to move the same amount of air as other burners with larger motors, which offers energy efficiency and cost savings. The fan intake is sound-insulated for quieter operation. The flame shaper can be adjusted while the burner is in operation.
For more information, contact (866) 6471782 or visit www.reliableasphalt.com.
STANSTEEL
PUGMILL SYSTEMS
Pugmill Systems designs and manufactures custom mixing solutions for the asphalt (and other) industries. The company builds stationary pugmills from 5 to 2,000 TPH capacities with coordinated feeder systems and site-specific plant arrangements. The team also builds portable pugmills with capacities from 5 to 1,500 TPH and options like asphalt pump plus meter, water pump meter, silo systems, feed hoppers, conveyors and the like. Their pugmill mixers include timed and untimed with models from 5 to 2,000 TPH customized to the customer’s needs.
For more information, contact (931) 3880626 or visit pugmillsystems.com.
RELIABLE
Reliable Asphalt Products offers the Vulcan burner. Vulcan burners are total air burners with a single motor and a coaxial blower, which provides a near-linear fan curve. They can be run on multiple fuels, simultaneously if required. There are optional blower mount configurations, and they can be converted from long to short nose.
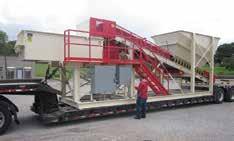
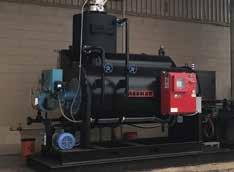
Vulcan Burners are designed to be low maintenance—the direct driven fan has no belts or pulleys. When maintenance is need-
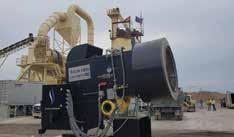
The Tank Manager System™ from Stansteel®, Louisville, Kentucky, allows plant operators and superintendents to monitor and regulate all their AC tanks and hot mix silos. Users can set individual tank high/low parameters for level and temperature to initiate a pump shutdown, thus preventing tank overflows. In addition, users can operate AC tank supply, return and fill valves with the push of a button. The Tank Manager System also allows users to send emails and texts to specific individuals notifying them during alarm events—such as “low hot oil temperature”— that action needs to be taken. The system is designed to be operated on a computer or any

smart phone. Essentially, the Tank Manager System gives you the control to run your business while it runs your tanks:
• Preventing tank spills and overfills;
• Avoiding AC waste and contamination;
• Offering remote control of all valves and pumps;
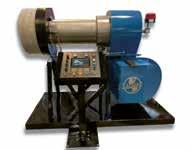

• Knowing silo and tank levels 24/7 from anywhere; and
• Offering new non-contact accu-level technology.
For more information, contact (800) 8260223 or visit https://stansteel.com/tankmanager/.
SYSTEMS EQUIPMENT
Systems Equipment Corp offers The Peacekeeper drum mix process computer, which is an ADP-100 asphalt blending system with optional Windows-based graphics-enhanced user interface. The Peacekeeper system is designed to offer improved proportioning accuracy of aggregates and additives according to prescribed mix formulas while it measures and controls liquid asphalt mass flow rate so blends are accurately interlocked to the measured aggregate.
For more information, contact (563) 5686387 or visit www.systemsequipment.com.
TARMAC
Tarmac International Inc. launched the 30NOx burner with PLC controller in 2022. The burner features two fuel valves—a primary in the back and a secondary in the center. “We pre-mix the fuel and air early,” President Ron Heap said. The burner uses early mixing of fuel and air along with internal gas recirculation to reduce NOx down to 30 PPM. This 30 PPM NOx is a level that Tarmac’s customers are experiencing in the USA.
The new burner controller allows for improved fuel and air valve positioning (parallel positioning) with both manual and auto control. An Allen Bradley PLC with 10-inch touch screen controls the burner and interlocks. Manual operators are included for backup control should the PLC fail. There is a “dashboard” where management can see burner production, fuel per ton, position of the fuel and air valves, position of the ID fan, negative pressure of the burner faceplate. Over-the-phone service is available with the
technician seeing the parameters of the burner controller.
For more information, contact (816) 2200700 or visit www.tarmacinc.com.
WEM
WEM Automation offers replacement controls for all makes and models of asphalt batch and drum plants, including silo loadout and data analytics. The company’s 24/7 service and support assists with easy-to-use, configurable automation and control systems, according to the manufacturer.
For more information, contact (262) 7822340 or visit www.WEMAutomation.com.
Leica Geosystems 3D Milling Keeps Yield on Track
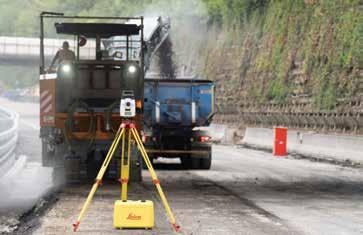
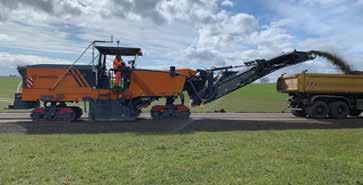
3D solutions for paving are nothing new to Leica Geosystems, part of Hexagon, headquartered in Heerbrugg, Switzerland. In 1999, the company launched its 3D stringless solutions for concrete and asphalt paving and in 2006 introduced its first 3D milling solutions.
But, in the past few years, Leica Geosystems has taken several steps to raise the bar on its 3D milling solutions. In 2018, it launched its third generation profile milling solution within Leica Geosystems’ MC1 iCON pave and also its differential milling solution iCON site milling pilot.
According to Juergen Seemann, Business Development Manager Road and Compaction at Leica Geosystems, machine control technology can help prevent over-milling and subsequent over-paving, thereby helping to reduce the carbon footprint of road construction.
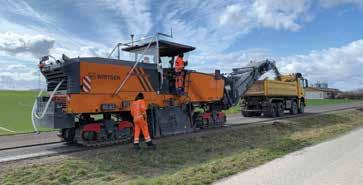
“Both methods also provide bottom line higher accuracy on the milled surface, avoiding copy effects and thereby preparing a better ground for the following placement process,” Seemann said. “Our contractors aren’t just looking into the milling process but the entire road renovation process. When the milling is done right, the asphalt paving job will be easier and higher quality.”
For example, on a recent project in Switzerland, a contractor was milling asphalt placed on a concrete bridge. “It was very important that they didn’t cut too deep because they could damage the concrete foundation of the bridge and that would result in very costly rework,” Seemann said. The contractor used ground penetrating radar from Hexagon to measure the thickness of the asphalt pavement and used this information to create a profile of the existing surface and the design surface for use with Leica Geosystems’ differential milling solution. “It’s not always the big jobs that most benefit from 3D milling solutions,” Seemann said. “3D technology can be just as important on smaller jobs like this one.”
HOW LEICA GEOSYSTEMS’
3D MILLING SOLUTIONS WORK
Leica Geosystems’ iCON site milling pilot is a differential milling solution where the contractor uses two files—one of the current surface, one of the design surface—and Leica Geosystems’ software calculates the difference between the top surface and the target to determine how much material to mill off that exact location. According to Seemann, Leica Geosystems’ differential milling solution works with just a GNSS receiver mounted on the machine because the system uses only the machine’s x and y coordinates.
Leica Geosystems’ MC1 iCON pave features a profile milling solution, which requires a prism to be mounted on the milling machine and tracked by total stations placed on the road to be milled. The total station automatically measures the position and height of the machine down to its milling bits in millimeter accuracy and the system compares that to the digital reference model. Any deviations are then sent to the machine controller for correction. “Both systems use 3D technology and offer similar results, but the concept is different,” Seemann said.
“It isn’t a matter of one solution versus the other,” he added. “Together, they offer a complete portfolio of 3D milling solutions our customers can choose from based on their requirements.”
Leica Geosystems’ differential milling solution works with just a GNSS receiver mounted on the machine because the system uses only the machine’s x and y coordinates.
Leica Geosystems’ differential solution offers manual mode on any brand of milling machine and automatic mode on Wirtgen machines equipped with 3D kits.
Leica Geosystems’ MC1 iCON pave features a profile milling solution, which requires a prism to be mounted on the milling machine and tracked by total stations placed on the road to be milled.
DIFFERENTIAL OR PROFILE?
Seemann said there are a number of factors to consider when choosing which solution is right for a particular contractor. For example, contractors performing a variety of activities may already have Leica Geosystems’ MC1 platform in their ecosystem, which offers machine control solutions for equipment ranging from excavators, soil rollers, graders to loaders. So, it might make more sense to opt for Leica Geosystems’ profile milling solution.
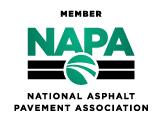
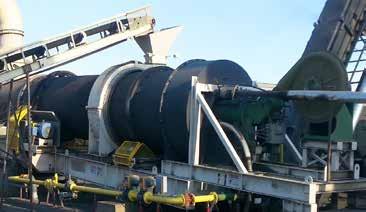
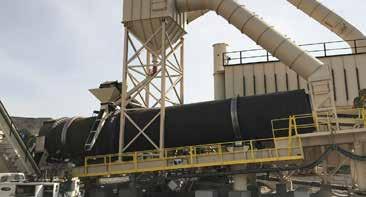
“They’d have the experience and partly the hardware to make it easier to adapt this technology to milling,” Seemann said, adding that the use of total stations makes this solution a bit more complex. “The user who positions the total station has to have a certain knowledge and understanding of surveying topics, so this solution is more complex than just having a GNSS receiver mounted on your machine.”
“For milling contractors who want to use 3D technology but don’t have a lot of experience, Leica Geosystems’ iCON site milling pilot might be an easier way to step into this type of technology,” Seemann said. “It doesn’t provide all the features we have in MC1, but is a good entry solution.”
Seemann recommends profile milling for complex projects such as race tracks, jobs with slope correction and other projects that require millimeter precision. But for jobs where there may be several milling machines working at once, the need for one total station for each machine makes the process even more complex. “In this case, differential milling would be simpler to use because it only requires the GNSS on top of each machine.”
Seemann said the key difference—apart from the different concept—is that total stations achieve a level of precision not possible with GNSS, but added that Leica Geosystems’ differential milling solution can also be used with total stations. “This is a great feature for jobs in areas that don’t have a GNSS signal, like a tunnel or in a downtown area with a lot of tall buildings,” Seeman said. “That gives contractors using that system more flexibility.”
Another difference between the two solutions is the functionality to Leica Geosystems’ ConX cloud platform. Both 3D milling solutions offer data sharing and reference file storage features, but ConX offers additional features such as remote support and storage of surface log data taken in profile milling.
At Bauma 2022, Leica Geosystems showed its new Safety Awareness Solution. “If an employee comes too close to the danger zone of a machine, our system will give a warning to the operator via the control panel on the machine,” Seemann said. “This solution is integrated into our MC1 platform, it does not need another panel, and the data is stored in ConX for later analysis.”
The Leica Geosystems’ MC1 profile milling solution is available on all main machine brands, including Wirtgen, Bomag, Roadtec and XCMG. The differential solution offers manual mode on any brand of milling machine and automatic mode on Wirtgen machines equipped with 3D kits. With manual mode, the operator sees how deep to cut at any given point and must input this data into the machine themselves, whereas the data is automatically transferred to the machine controller with automatic mode.
Leica Geosystems continues to expand 3D solution support to more OEM (original equipment manufacturer) partners. “We believe customers shall make their choice about their preferred 3D technology provider regardless of which machine brand they want to use,” Seemann said.
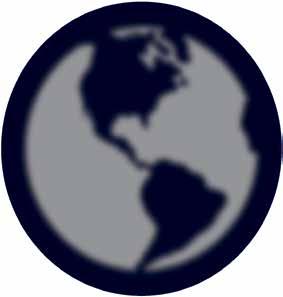

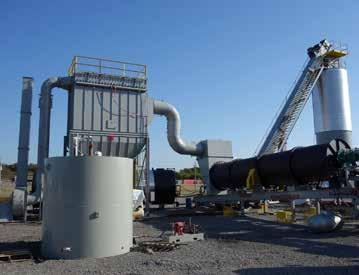
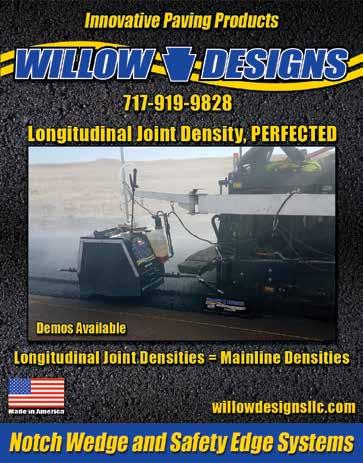
GREAT PEOPLE. GREAT WORK.
Specially formulated temporary and semi-permanent release agents and coatings, drag slat cleaners, and extraction solvents. Designed to work on all asphalt mix designs, including on all PG grade asphalt mix designs such as PG-76-22 and 70-22.
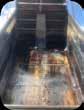
Our asphalt release agents are state DOT-approved and NTPEP tested and listed.

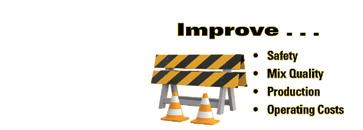

All our proprietary asphalt products and equipment are proudly formulated and manufactured in the United States

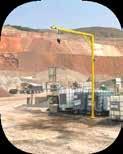
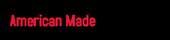
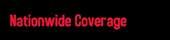
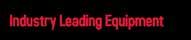
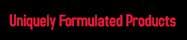
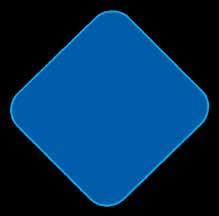
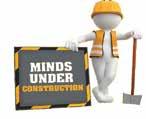
PLANT OPERATION WORKSHOP
We custom build our dispensing systems to meet each customers unique needs
DENVER – FEBRUARY 09 – 11, 2023
ZOOM – FEBRUARY 13 - MAR 17, 2023

Meyer is a full-service supplier with more than 75 service reps and numerous warehouses located across the United States We can serve any customer, anywhere and anytime

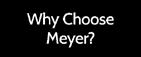
com
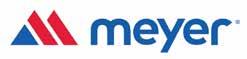
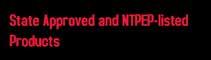
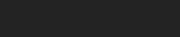
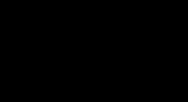
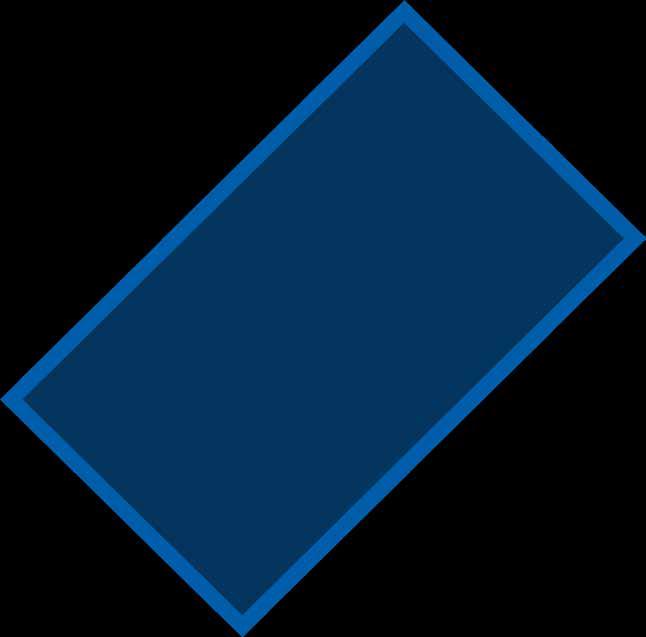
AD INDEX
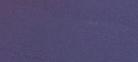
AsphaltPro’s advertiser index is designed for you to have quick access to the manufacturers that can get you the information you need to run your business efficiently. Please support the advertisers that support this magazine and tell them you saw them in AsphaltPro magazine.
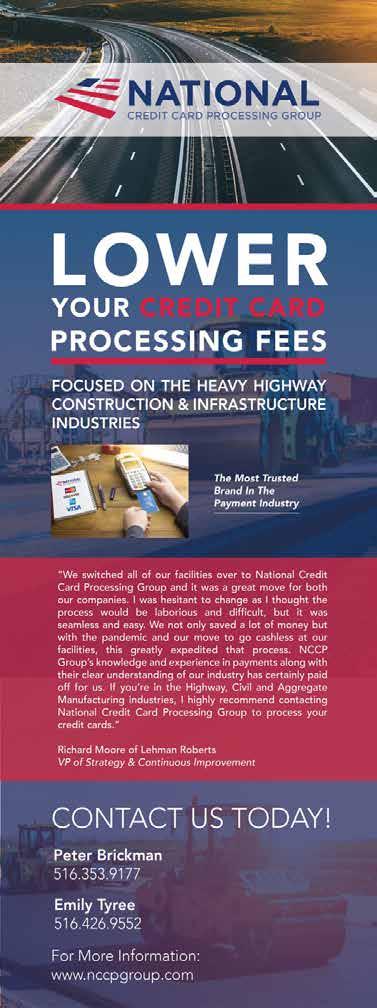
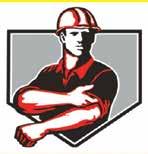
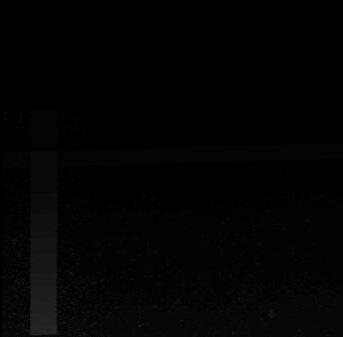
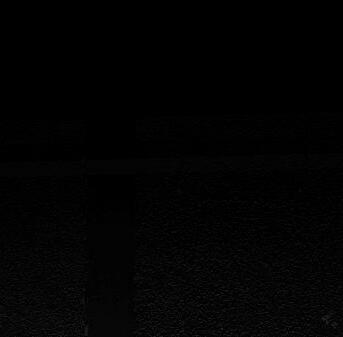

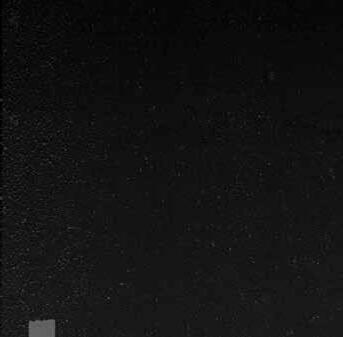
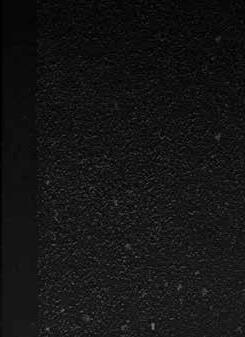

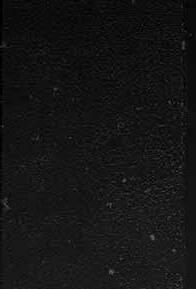
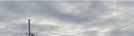

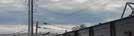



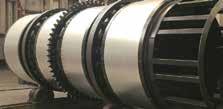
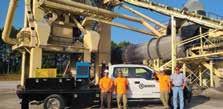

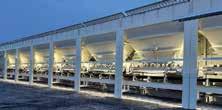
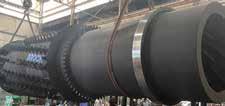
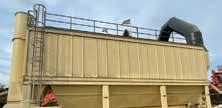
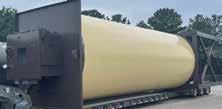
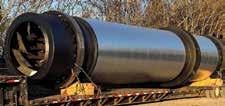
Hydrogen ICE Equipment
BY ASPHALTPRO STAFFIf you’re watching electric off-highway vehicle (EOHV) development, then the hydrogen internal combustion engine (ICE) should be on your radar screen as well. According to new research from Interact Analysis—a market intelligence authority for global supply chain automation from the technology used to automate factory production, through inventory storage and distribution channels, to the transportation of the finished goods—a qualitative report released November 2022 suggests hydrogen ICE vehicle shipments will hit 400,000 by 2040. That’s total vehicles including on-road and off-highway, construction and agricultural, according to Jamie Fox, a principal analyst at Interact Analysis.
“The number of registered H2 ICE vehicles is forecast to grow to 58,000 in 2030,” Fox shared in a Jan. 5 press release. “Covering all on road and off-road vehicles (including trains, agricultural equipment, trucks and passenger cars), this figure is set to see significant growth post 2030, with uptake of H2 ICE technology projected to soar to more than 400,000 shipments by 2040.”
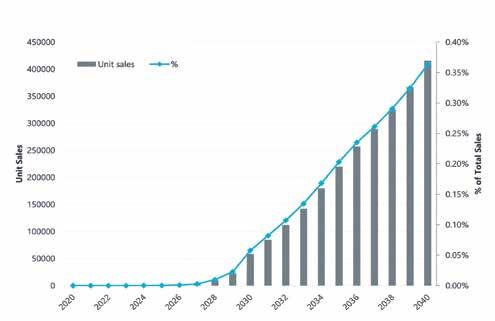
Fox shared with AsphaltPro that several factors will slow the construction equipment sector’s adoption of this technology. “Excavators, lift and loaders could see some adoption but the percentage of the market will be very low to 2030, under 1%, because diesel machines are less expensive and well known with less infrastructure difficulty. H2 ICE can be used where there are regulations for construction in city centres, or where a company wants to try a small number of vehicles without fossil fuels to prepare for the long term, zero fossil future, or in order to showcase its green image.
“We do not see hydrogen being larger than battery electric vehicles but there are niches with opportunities, for example where the machine has to work 15-20 hours a day, which is difficult for battery electric vehicles.”
The key takeaways from the “Hydrogen ICE Market and Technology Assessment” report include how hydrogen ICE will develop as a solution in different applications; what impact regional hydrogen production plans will have; who the main suppliers of hydrogen ICE technologies are; which OEMs are developing hydrogen ICE-powered vehicles; and how the cost compares with other low- and zero-carbon solutions.
Let’s look at that last point: cost comparison.
When you change a machine’s engine, you also change the components supporting that engine, thus increasing costs.
Interact Analysis explained, “Hydrogen ICE vehicles require a series of minor changes compared with traditional ICE vehicles, including different spark plugs and other changes to materials. On their own, individual changes do not present too much of a challenge, but in combination the total cost of manufacturing the vehicle soars. In addition to this, adding greater complexity increases the potential risks once the vehicle is in mass production. Hydrogen ICE vehicles are most attractive to those companies who are most climate aware, or where battery electric alternatives are either unavailable for a particular vehicle or not fit for purpose. Without either of these catalysts for adoption, uptake of hydrogen ICE vehicles is likely to remain low in the short term. Off-road vehicles are perhaps best suited to this technology since battery electric and fuel cell alternatives face greater infrastructure challenges in off-road environments.”
Interact Analysis offered this statement comparing the H2 with other engines: “The total cost of a hydrogen engine is only slightly higher than that of a diesel engine. On average, for a class 8, 40-tonne truck, a hydrogen tank would cost around $76,000, a figure far in excess of the price of a diesel equivalent.
“However, the unit price of an H2 vehicle is still less than a FCEV alternative. Therefore, because the average cost of fuel per mile for H2 vehicles is higher than for FCEV and BEV vehicles, H2 technology is best suited to applications with low mileage/hours per day. Interact Analysis predicts that the cost of hydrogen will reduce significantly over time and, if it continues to fall at pace, it could become more competitive across a wider range of applications in the future. Although maintenance costs for H2 vehicles will be similar to those of other vehicles, fuel costs for hydrogen vehicles mean the TCO will be worse than for diesel and battery electric alternatives. Therefore, H2 vehicle application is likely to be limited to applications or regions where diesel has been legislated against or where BEV alternatives are not available.”
Infrastructure remains a key stumbling block for non-diesel alternatives.
“Due to unfavorable TCO and high fuel costs, H2 ICE vehicles are unlikely to become the market leader. Despite the many environmental benefits to the use of hydrogen vehicles, for mass adoption to occur the refueling infrastructure required must be developed and customer payback improved. We are still seeing many limitations to refueling infrastructure for battery electric vehicles so it is unlikely that we will see a significant amount of change in the H2 infrastructure for many years.”
BUILT TO CONNECT
Efficiency and Productivity
Designed with safety and operator comfort in mind, the SB-3000 Shuttle Buggy ® material transfer vehicle features adaptive cruise control, bright LED lighting, four-wheel steering for easy transport and ground-level maintenance access for added convenience. Operators can rely on clear sightlines and the ground operator is safely protected inside the structure of the machine. The Roadtec SB-3000 is the perfect blend of traditional craftsmanship and modern technology.
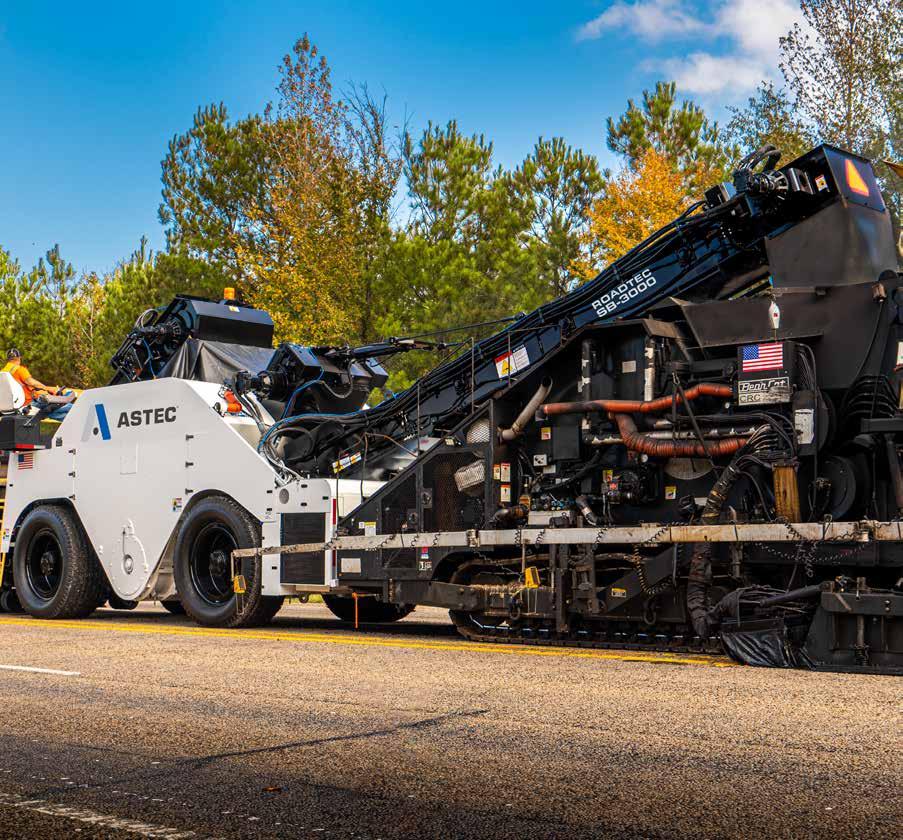
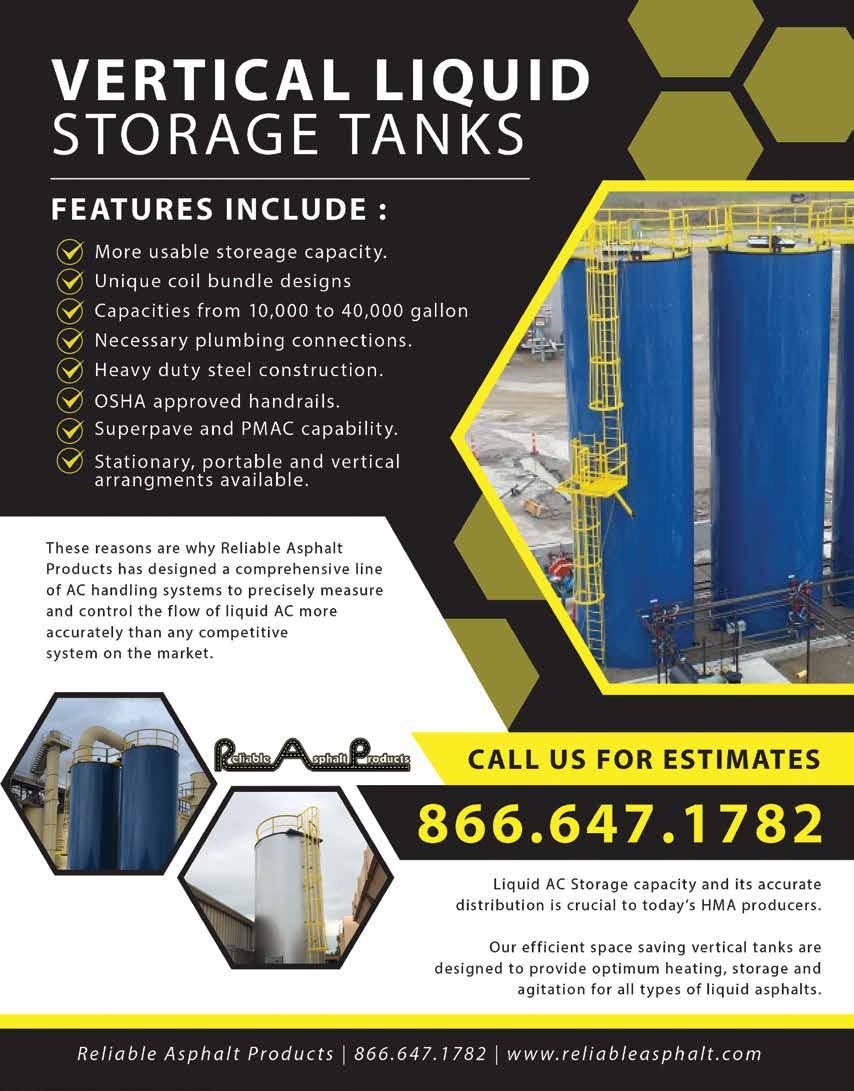