SUSTAINABILITY 2020 - 2021 REPORT
























































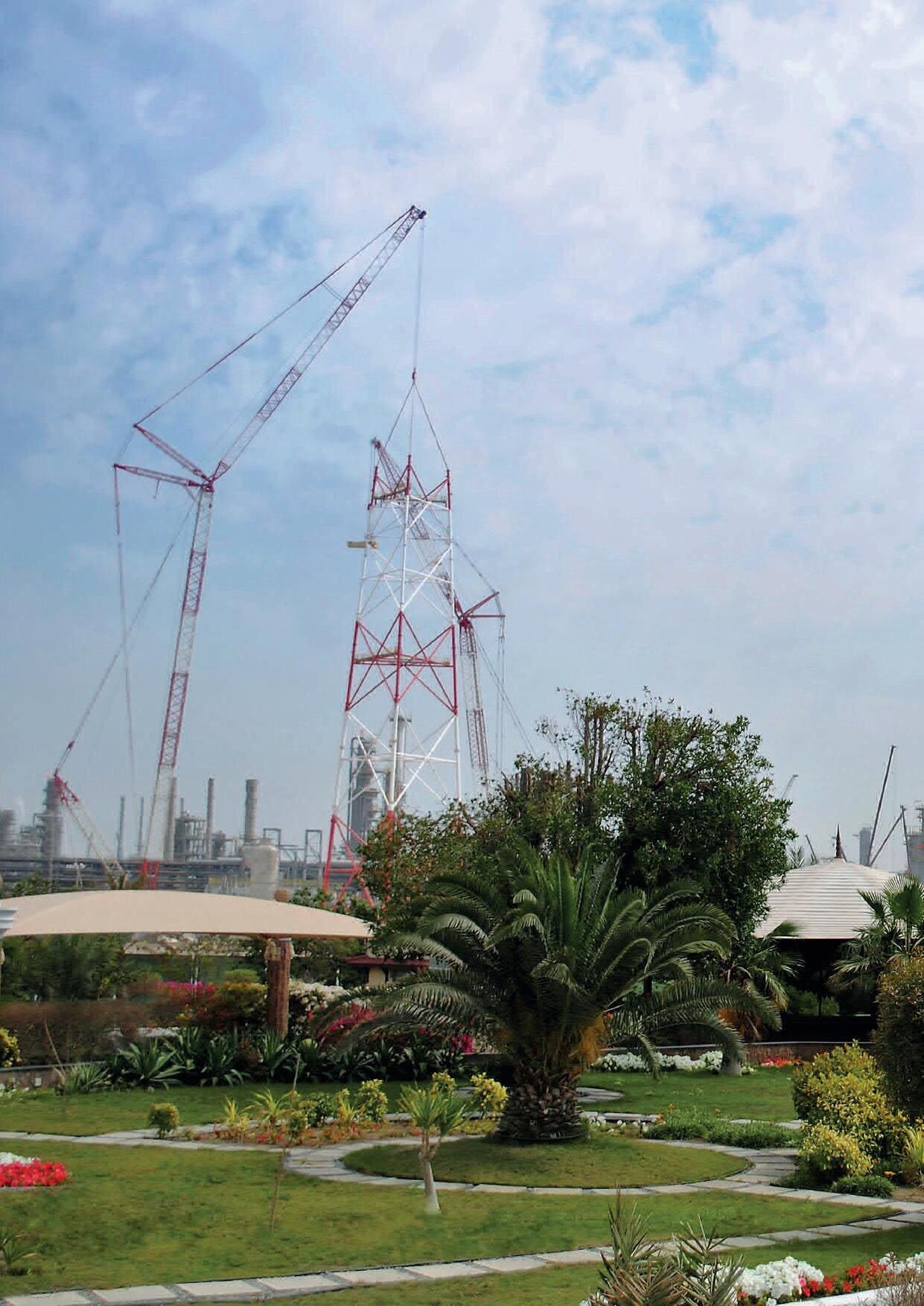
His Royal Highness Prince Salman bin Hamad Al Khalifa
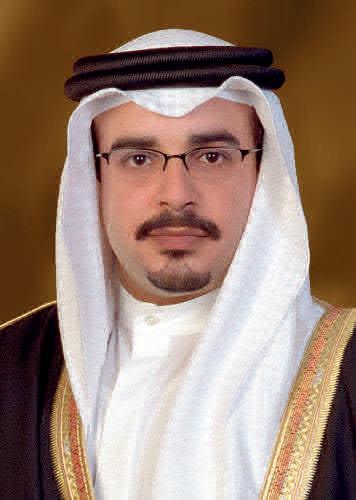
Crown Prince, Deputy Supreme Commander, and Prime Minister of the Kingdom of Bahrain
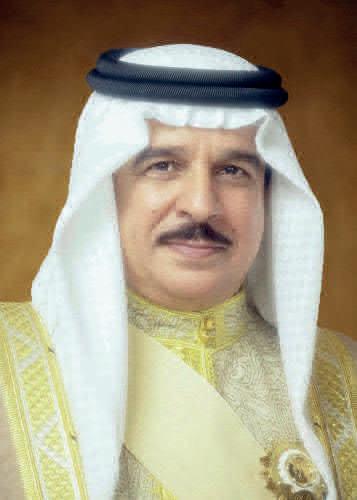
His Majesty King Hamad bin Isa Al Khalifa
King of the Kingdom of Bahrain
His Royal Highness Prince Salman bin Hamad Al Khalifa
Crown Prince, Deputy Supreme Commander, and Prime Minister of the Kingdom of Bahrain
His Majesty King Hamad bin Isa Al Khalifa
King of the Kingdom of Bahrain
To achieve success we require individual self-discipline and perseverance in the face of volatility. The pandemic has taught us how each individual is responsible for the outcomes of our future, for the resilience of our economy, the continuity of businesses and the health of our families. Sustainability requires everyone to play their part in ensuring a safe and reliable future for the next generation to meet their economic, societal and environmental needs. The Kingdom emerges from the pandemic with bountiful experiences and lessons learned to build upon and progress towards a sustainable Bahrain for everyone.
The Kingdom of Bahrain’s Economic Vision 2030 is designed to balance the many conflicting needs of sustainability, fairness and competitiveness. At its heart is a shared goal of building a better life for every Bahraini. By achieving this vision, we have aligned the aspirations of our future generations with sustainable development. Bapco’s contribution to the Economic Vision is measured by alignment with the 17 Sustainable Development Goals (SDGs) issued by the United Nations in 2017, which encompass technological advancement, environmental stewardship, economic progress and societal welfare. Collectively, these goals are reflected in this report as “Bapco of Tomorrow”, highlighting the vision and strategy of Bapco that will support the Kingdom’s journey towards sustainability.
I am inspired by the youth of Bahrain as I see them overcome many challenges with optimism and energy. Our capability to respond to adversity is enhanced by access to the best education, affording the opportunity to invest in the strengths of the next generation. Giving back to the Kingdom with passion is a key to our success.
Bapco’s contribution to education is long-established, taking students from many educational establishments and training them for a career that benefits the Kingdom and helps with their professional development.
Throughout our Kingdom’s history there have been significant transformation opportunities that accelerate economic development and invest in our communities. The Bapco Modernisation Program (BMP) is one such opportunity. During my recent visit to BMP, I remarked on the contribution being made by both men and women to BMP that is driving the economic growth of the Kingdom. Bapco has continued to diversify its workforce, with several high-profile appointments of women to the Executive Management during 2020-21. The project’s economic legacy will be powerful, but perhaps more importantly BMP is building the capability of Bahrainis to operate world-class technologies.
Sustainability is, above all, a measure of hope and second chances for the youth of Bahrain who will shape the future of the Kingdom. We are bound through the fabric of our great nation to a common future, and it is everybody’s responsibility to give back to the Kingdom when success is achieved. Bapco is allowing the next generation to achieve their own successes and is therefore making a fundamentally important contribution to the sustainability of the Kingdom of Bahrain. This report highlights our stories that tell of a very positive future for us all.
His Highness Shaikh Nasser bin Hamad Al Khalifa nogaholding Chairman Kingdom of Bahrain“ We are bound through the fabric of our country to a common future and it is everybody’s responsibility to give back to the Kingdom when success is achieved
I am honoured to be appointed as the Chairman of the Board of Directors for Bapco, and to provide our 2020-21 Sustainability Report foreword.
Bapco has a rich heritage from over 90 years as the Arabian Gulf’s oldest operator and is one of the largest employers in the Kingdom of Bahrain. We have always placed great emphasis on ensuring the wellbeing and safety of our employees and protection of the environment, whilst at the same time providing our employees with continuous education to create a highly skilled workforce. This human capital is a significant asset and competitive advantage to the Kingdom of Bahrain, and one in which Bapco continues to invest heavily.
Our pioneering multi-billion dollar BMP is the largest capital investment in our company’s history and our main priority is the safe, reliable and timely completion of the project to the benefit of the Kingdom of Bahrain. BMP is especially important as it further aligns the company with the Bahrain Economic Vision 2030 and the ongoing work of our shareholder nogaholding in defining the energy road map for the Kingdom of Bahrain. The variety of ongoing initiatives within Bapco are linked to the 17 United Nations Sustainable Development Goals focusing on technological advancement, environmental stewardship, economic progress and societal welfare. BMP provides significant new job opportunities to the youth of Bahrain, building our human capital.
BMP also establishes Bahrain as one of a handful of countries worldwide to be using the latest LC Fining Chevron Lummus Global (CLG) licensed technology, which reduces waste and energy consumption and increases the value generated from production.
The vision is to further develop Bapco as one of the leading world-class companies in the petroleum refining sector. This forms part of a wider national goal of sustainable value creation in the Kingdom’s oil and gas sector and to achieve the ambitions under the wise leadership of His Majesty King Hamad bin Isa Al Khalifa, and His Royal Highness Prince Salman bin Hamad Al Khalifa, Crown Prince, Deputy Supreme Commander, and Prime Minister.
This mandate has been given to us by His Highness Shaikh Nasser bin Hamad Al Khalifa, His Majesty the King’s Representative for Humanitarian Work and Youth Affairs and the Chairman of the Board of Directors of The Oil and Gas Holding Company (nogaholding), and one which I, my fellow Board Directors and Dr. Abdulrahman Jawahery, Chief Executive Officer of Bapco and the Executive Management, are committed to delivering.
With the full support of the Board of Directors, the management and employees I am confident that we will work together to realise this bold ambition, to improve our operating model and deliver breakthrough value built on the safe, reliable, timely and successful completion of BMP; integration of the Kingdom’s SDGs; and higher standards of ethics and integrity - all delivered with Bapco’s passion to excel and innovate.
His Excellency Abdulla Jehad Al Zain Bapco Chairman Kingdom of Bahrain“ BMP establishes Bahrain as one of a handful of operators worldwide to be using advanced LC Fining technology
Welcome to Bapco’s 2020-21 Sustainability Report, which is being published to the Global Reporting Initiative’s (GRI) Comprehensive Level, reflecting even greater coverage and transparency on what we are reporting to you.
The theme of this report is “Bapco of Tomorrow”, meaning Bapco’s transformation journey to be more competitive, profitable and environmentally friendly. The journey will enable Bapco to serve the industry’s demands and Bahrain Economic Vision 2030.
Achieving our transformation requires a clear mission and vision. Our mission is to create value for our shareholders, customers and employees, which we will achieve by operating as a dynamic and empowering national energy company that can compete globally. Our role as the Executive Management is to translate the vision of leadership and the mission of the Board, under the chairmanship of H.E. Mr Abdulla Jehad Al Zain, into a sustainable reality.
Our sustainability report draws attention to two very different and equally important facets of our business. Firstly, the technological; BMP construction is now well progressed and will deliver to the Kingdom world-class technologies only currently operated at a handful of locations across the world. Secondly, the human capital; Bapco is only able to operate these new technologies by recruiting and training the very best talent across the Kingdom. One facet cannot exist without the other.
Since our last sustainability report was published, great strides have been made on BMP, consolidating Bapco’s contribution to the Kingdom of Bahrain for the decades ahead. At the end of the 2020-21 reporting period BMP construction was 79% complete and we continue to have over 15,000 workers onsite involved in the construction activities. Bapco is rightly proud of its exemplary personal and process safety record for BMP with some remarkable statistics that demonstrate our commitment to environment, health and safety, for example working over 3 years on the BMP project without a Lost Time Injury (LTI) and accruing over 49 million safe project hours.
What is even more remarkable about BMP is that construction as well as operation of our base business continued throughout the COVID-19 pandemic. This difficult period represented one of the greatest challenges faced by Bapco in living memory. Whilst many organisations were able to shift their operations from office-based to remote work, we were faced with the daunting prospect of having to sustain 24-hour operation of our Refinery. For our staff in operational positions there was no option for work to be conducted remotely, shift work had to continue throughout the pandemic in a manner safe for Bapco personnel and sustainable for the company. Managing BMP construction schedules with its sizeable workforce was an additional complication. Numerous initiatives were implemented, and educational programmes were rolled out, to enable work at site to continue uninterrupted, whilst keeping all employees, contractors and workers safe. Innovative techniques were also implemented to carry out detailed engineering work in various
“ The theme of this report is “Bapco of Tomorrow”, meaning Bapco’s transformation journey to be more competitive, profitable and environmentally friendly
operating centres around the world, which redefined many engineering processes that may continue in the new world post-pandemic. The ability to innovate and respond in a timely manner has been a key component to our success.
The fact that we not only continued operating throughout the pandemic but did so without significant business interruption to either the base business or BMP is a truly remarkable achievement. We are very proud to have such a dedicated and talented workforce who made many personal sacrifices to ensure business continuity.
Our transformation journey requires us to change how Bapco is organised and to recruit the best talent to lead the organisation. A range of transformation projects are currently being implemented from across the organization including finance, IT, human resources, procurement and others. All of these transformational initiatives are aligned to prepare the “Bapco of Tomorrow”, and ensure that our business is safe, reliable, sustainable and competitive for decades to come.
Bapco has always recognised the important role that women bring to the business. During 2020-21 there were several new appointments to the Executive Management as well as other senior roles across Bapco that were made to women. We have celebrated these appointments by including profiles of nine of the most senior women at Bapco in this report.
We have additionally provided other profiles from across our business to highlight the talent that can be found at all career stages across all Departments. The profiles include both male and female employees, the latter accepted within the cohorts of trainees by Bapco for some years. Several of the profiles are from those who joined through the Bapco International Scholarship programme, which support the students during their further education. Some of the profiles are also from those who have attained senior positions within their disciplines. Their experience is invaluable in assuring continuity of operations within the business. What is common across all the included profiles is the sense of belonging and pride of being part of the Bapco family.
Our links to the community remain as strong as ever, with many initiatives taken each year by Bapco employees for the benefit of the community. INJAZ Bahrain, a non-governmental organisation empowering the next generation of Bahrainis, continues to be a very popular programme with many volunteers across the company. BMP has additionally afforded Bapco the opportunity to undertake major social and environmental initiatives such as the rehabilitation of Eker Garden and sponsorship of Shaikh Ebrahim bin Mohammed Al Khalifa Centre for Culture and Research celebrating its 20th anniversary. Bapco also has a long-term aspiration to expand mangrove plantations around the Kingdom. We have a Mangrove Nursery within the Refinery and have now established several plantation sites across the Kingdom of Bahrain with the guidance of the Supreme Council for Environment (SCE). This will also contribute to the Bahrain National Target to combat Climate Change announced at the COP26 held in Glasgow, UK during October-November 2021.
Our commitment to sustainability across all facets of our business is further demonstrated by our membership of the UN Global Compact and commitment to the ten principles that underpin a sustainable approach to conducting business. Bapco anticipates building these principles into its various transformation programmes that will be completed in future years.
We are grateful for the continuous guidance and wise leadership of His Majesty King Hamad bin Isa Al Khalifa, and His Royal Highness Prince Salman bin Hamad Al Khalifa, Crown Prince, Deputy Supreme Commander, and Prime Minister. Coupled with the direction provided by the Chairman of nogaholding, His Highness Shaikh Nasser bin Hamad Al Khalifa, and guidance of the Chairman of the Bapco Board of Directors, H.E. Mr Abdulla Jehad Al Zain, we are confident that we are building a sustainable and competitive company for the future: “Bapco of Tomorrow”
Thank you for taking the time to read this report and we look forward to sharing our sustainability journey with you.
The Bahrain Petroleum Company Kingdom of Bahrain
Wholly owned by the Government of the Kingdom of Bahrain, the Bahrain Petroleum Company B.S.C. (Closed), referred to in this report as Bapco, is primarily engaged in petroleum refining, storage, production and export of petroleum products.
Bapco was established in 1929 by the Standard Oil Company of California. In 1932, Bahrain was the first country to discover oil in the Arabian Peninsula. Bapco started exporting crude oil in 1934 and refining in 1936, with an initial capacity of 10,000 barrels of oil per day (BPD). Some 90 years later our refining capacity is 267,000 BPD. With the commissioning of Bapco Modernization Programme (BMP), our refining capacity will have increased 42% to 380,000 BPD.
The company continues to shape the modern Kingdom of Bahrain through its many economic, social, and environmental initiatives in line with our Vision, Mission and Purpose, some of which are described in this report. These initiatives directly support sustainable development as defined by the United Nations Sustainable Development Goals and the Ten Principles of the United Nations Global Compact.
The company’s core business is the production of high-quality refined petroleum products. The company owns a Refinery, storage facilities for 14 Million barrels (MMbbl) of crude oil and products, a Local Marketing Terminal and a Wharf for the export of petroleum products.
About one-sixth of our refined crude oil originates from the Bahrain Field, with the remainder being pumped from Saudi Arabia by pipeline. About 90% of Bapco’s refined products are exported. Our customers are regional, predominantly Gulf Cooperation Council (GCC) countries that account for almost half of export destinations, followed by the Far East, with the balance to Europe, Africa, South East Asia, and the Indian subcontinent.
Project sanctioned and feasibility study completed
Refinery Master Plan renamed to Bapco Modernisation Program
Project Front-End Engineering Design completed
Project Front-End Engineering Design commenced
Refinery Master Plan study completed
Technology selection process commenced
Environmental approval received from the Supreme Council for Environment
Environmental Screening (EA-2) Form submitted to Supreme Council for Environment
Engineering, Procurement and Construction contract (EPC) signed with Joint venture consortium consisting of TechnipFMC (Italy/USA), Técnicas Reunidas (Spain) and Samsung Engineering (South Korea) - TTSJV
90% detailed engineering (major works) completed
Foundation stone laying ceremony
This report describes how we at Bapco are supporting the Kingdom of Bahrain’s sustainable development objectives, described in the Bahrain Economic Vision 2030. Our report has been prepared in accordance with the GRI Standards Comprehensive option
Sustainability means achieving an environmental, economic and social status quo that meets the needs of future generations without compromising the needs of current generations. The concept of sustainable development was originally proposed in 1987 by the United Nations World Commission on Environment and Development. Since then, the concept has expanded to encompass a range of economic, environmental, technical and social objectives that collectively represent sustainable development.
Sustainability reports are issued by all major global corporations, including the oil industry, to help others understand their commitment to sustainable development. A sustainability report transparently reports an organisation’s financial, social and environmental risks and obligations, and provides opportunities for others to understand these obligations.
Bapco makes a very substantial contribution to sustainable development through technological innovation, investment in our workforce education and training, and our economic productivity. We are delighted to be documenting some of these contributions in this latest sustainability report.
The GRI Standards are internationally recognised as a leading framework for public sustainability reporting, allowing organisations to demonstrate how they contribute to national and international SDGs. The GRI standards are used by over 10,000 companies internationally as their framework for sustainability reporting.
The GRI Standards help companies identify material topics with the most significant impacts and influence on their stakeholders, in addition to reporting on general contextual information about the organisation, its reporting practices, and its approach to how material topics are being managed.
The GRI standards are regularly updated with the last major revision - the launch of the revised Universal Standards - occurring in 2021. This report uses GRI as its reporting basis and has been fully updated against the latest standards as of 2021.
GRI Disclosure numbers are provided throughout the report in the format Disclosure number, Disclosure title. The icon is used to emphasise each Disclosure number. Where Disclosures are for a Management Approach then the title is given as the same. The same Management Approach may be applicable to several disclosures, in which case all applicable Disclosure numbers are listed. Refer to page 155 for the GRI Content Index and complete list of Disclosures, year and version.
“
Bapco makes a very substantial contribution to sustainable development through technological innovation, investment in our workforce and our economic productivity
Our Commitment
Bapco’s transformation journey has a common theme of sustainability. Speaking at the 26th United Nations Climate Change Conference of the Parties (COP26), His Royal Highness Prince Salman bin Hamad Al Khalifa, Crown Prince, Deputy Supreme Commander, and Prime Minister pledged to cut the Kingdom’s emissions by 30 per cent by 2035. The Kingdom further aims to reach Net Zero by 2060.
Under the umbrella of its parent company, nogaholding, Bapco will have a leading role to play in the aspirations of the Kingdom through the many projects already underway and those that have yet to start. For example, Bapco’s commitment to increase solar energy generation through the Bapco Distributed Solar Energy Pilot Project (BDSEPP) and enhance blue carbon sinks through the transplanting of mangroves in coastal areas, supporting the Kingdom of Bahrain’s objective to quadruple mangrove coverage.
All of Bapco’s sustainable development initiatives can be linked to the 17 SDGs, through the GRI. This section provides a list of GRI disclosures for each SDG and a short summary of some of Bapco’s initiatives that relate to the SDGs.
Bapco supports the SDGs. Bapco’s sustainable development initiatives can be linked to the 17 SDGs through the GRI. The table overleaf provides a list of GRI disclosures for each SDG and a short summary of some of Bapco’s initiatives that relate to the SDGs. Refer to the content index at the back of the report to find the page number where each disclosure is reported.
Bapco commits to the United National Global Compact (UNGC) Bapco has written to the United Nations to give its commitment to adopt the Ten Principles of the United National Global Compact. The Principles provide a valuable framework that will guide the various transformation programmes described in this report and due for completion in future years.
The significant size of the BMP project provides both short and long term opportunities for the local labour market and local supply chain. BMP will create new skilled positions filled from positions advertised locally within the Kingdom.
Separately from the very significant contribution made by Bapco to the local economy, Bapco makes special provision for providing to the community during particular times of the year. During the holy month of Ramadan, Bapco provides all operators with meals during Iftar and arranges food distribution campaigns to the community.
All Bapco employees have access to the Refinery clinic and free treatment at Awali hospital. Bapco supports community wellbeing awareness via campaigns and events, for example the Family Day which was held in January 2020 at the Bahrain International Circuit and attended by more than 37,000 people. Each month a specific health campaign is run on various topics such as breast and prostate cancer awareness.
Bapco established the Oil and Gas Academy in 2017 which provides the company with the best skilled workforce necessary for the future. Along with the support provided to the employees and students, Bapco employees participate in the INJAZ programme, lecturing to students on science and engineering.
Bapco believes in equal opportunities irrespective of gender - refer to this report’s special topic on Senior Women. Bapco has many women holding senior appointments across Bapco including that of Acting Deputy Chief Executive - Corporate Support.
Bapco has invested in the latest technologies to minimise water abstraction required for refining. Bapco’s Waste Water Treatment Plant and Sewage Treatment Plant (STP) uses state-of-the art advanced Membrane Bioreactor Technology for water and effluent treatment.
Bapco has established an Energy Group and an Energy Committee that focus on energy conservation throughout the Refinery, leading to projects and initiatives focusing on energy reduction and efficiency improvement using the latest technologies and means of monitoring. Bapco additionally operates a 5 MWp solar energy facility.
Bapco continues to provide new opportunities through the BMP expansion, creating one of the most technologically advanced Refineries in the world. CLG, NAPCON, and Bapco have opened the LC-FINING Center of Excellence in Bapco’s Oil and Gas Academy. The Academy also plays a leading role in training for existing employees throughout their career at Bapco.
Bapco has a strong track record for technological innovation. Bapco has an Innovation Centre to nurture new ideas suggested by employees, using initiatives such as the ‘Seed’ programme to recognise employees for their innovative ideas. Bapco additionally participates in community initiatives designed to encourage innovation, such as the Green School Award Scheme launched in 2005, aimed at local secondary schools to identify and pilot green ideas.
Bapco has specific policies designed to tackle inequality, implemented by a dedicated team who work with contractors to monitor any potential breaches in Bapco policy. Bapco has for several years inducted both men and women trainees into engineering disciplines. Bapco’s merit-based International Scholarship Programme provides financial support for students of all backgrounds to study at some of the best institutions worldwide.
Bapco has undertaken many recent initiatives to improve social and environmental capital within the Kingdom of Bahrain. Several are described in this report - for example the rehabilitation of Eker garden for the community.
305-01; 305-02; 305-03; 305-06; 305-07; 306-01; 306-02; 306-03; 306-04; 306-05; 417-01
BMP will contribute to an important reduction of energy use through its new technology. Additional initiatives are being taken by Bapco, such as the use of innovative software to optimise steam and power generation and the replacement of heaters with the latest energy efficient technologies.
7, 8 and 9
201-02; 302-01; 302-02; 302-03; 302-04; 302-05; 305-01; 305-02; 305-03; 305-04; 305-05
Bapco is committed to support the Bahrain National Target to combat Climate Change announced at COP26. Bapco has been reporting its Greenhouse Gas (GHG) emissions since 2014 and has implemented several initiatives to reduce those emissions, such as the hydrogen plant CO2 recovery project that saves 40,000 tonnes of CO2 emitted per year, the solar benches installed across Bahrain, our BDSEPP and the maintenance of green spaces such as Princess Sabeeka Park.
Bapco has been conducting regular marine assessments since 1981 around the Bapco Refinery and Sitra operating facilities to monitor marine ecosystems. Results have shown a steady improvement due to Bapco initiatives such as biological effluent treatment plant. Bapco’s efforts to plant mangroves will stabilise near-shore sediments and encourage ecosystem diversity.
Bapco closely follows the guidance provided by SCE on enhancements to the natural and built environments. The Princess Sabeeka Park in Awali and the Oasis initiative inside the Refinery are two of the many environmental projects implemented.
Bapco is proud to follow all applicable national and international regulations for fair process. Bapco has an established code of ethics that describes the behaviours expected from all employees, contractors and other third parties who work for Bapco.
Bapco conducts comprehensive social impact assessments for our major projects in accordance with applicable laws and regulations, with stakeholder engagement to facilitate community consultation. Bapco is a long-standing partner of INJAZ, with wide participation in the programme by Bapco employees to volunteer time for the benefit of the community.
H.H. Shaikh Khalifa Al Khalifa from Bapco’s BMP Health, Safety and Environment (HSE) function attended the 26th session of the Conference of the Parties (COP26) to the United Nations Framework Convention on Climate Change (UNFCCC). The two-week event held in October and November 2021 in Glasgow, United Kingdom, attracted over 30,000 visitors from 127 countries.
Bahrain’s delegation to the COP26 included representatives from the Oil and Gas Industry, nogaholding and SCE. The delegation participated in a number of sessions and meetings such as the Group 77 and China meetings, Arab Group meetings, the meetings on adaptation and mitigation of emissions and the discussions of Article 6 of the Paris Agreement on the integrity of carbon markets. The delegation also attended discussions on the future of hydrogen in the Middle East, and the benefits of nature-based solutions to achieve net-zero target.
Environmental experts at COP26 recommended a variety of solutions to climate change mitigation and adaptation that the Kingdom of Bahrain can implement, such as water resource management, renewable energy use and financial solutions to enhance diversification towards a more sustainable and less polluting economy. As part of the Kingdom’s plans to reach Net Zero by 2060, Bapco has constructed a 5MWp photovoltaic
solar energy installation within the Refinery, Awali and the University of Bahrain (the BDSEPP). Bapco has also enhanced blue carbon sinks through the transplanting of mangroves in coastal areas around Bahrain, in addition to the construction of a new mangrove nursery in Ras Sanad.
The photo opposite was taken at the COP26 Action Zone, shortly after His Royal Highness Prince Salman bin Hamad Al Khalifa, Crown Prince, Deputy Supreme Commander, and Prime Minister had announced Bahrain’s commitments to reach Net Zero by 2060. The Action Zone is a dynamic events space that can host a variety of events such as talk-shows, special launch events, competition winners announcements, games, interactive activities and digital demonstrations - all of which focus on concrete climate action and provide a voice to the audience.
“
Bahrain commits to reaching Net Zero by 2060, Bapco will be with the country on that journey
2,799 Employees
An increase from 2,521 - Page 27
74.6 MMBBL Products exported - Page 28
808 Suppliers
Majority local supply chain - Page 28
5 High priority topics
Materiality matrix - Page 45
Who we are, our markets and products, the associations that we hold to promote sustainable development and further information on how we report on our sustainability.
The Bahrain Petroleum Company B.S.C. (Closed), i.e. company shares are not offered to the public for investment.
GRI 102-02:
Bapco is primarily a merchant export refinery, engaged in the refining of crude oil within the Kingdom of Bahrain. The company’s main products are Liquefied Petroleum Gas (LPG), naphtha, gasoline, kerosene, aviation turbine fuel, ultra-low sulphur diesel, heavy lube oil, fuel oil and asphalt.
GRI 102-03: Location of headquarters
Awali, Kingdom of Bahrain.
GRI 102-04:
Ma’ameer (Refinery complex) and Sitra (Local Marketing Terminal, Sitra Tank Farm and Wharf), Awali (Headquarters and other central functions), West Riffa (BMP project offices), all within the Kingdom of Bahrain.
GRI 102-05: Ownership and legal form
Bapco is wholly owned by the Government of the Kingdom of Bahrain under the Oil and Gas Holding Company B.S.C. (Closed) (“nogaholding”).
GRI 102-06: Markets served
90% of our production is exported. Our customers are regional, predominantly GCC countries that account for almost half of export destinations, followed by the Far East, with the balance to Europe, Africa, South East Asia, and the Indian subcontinent.
During 2020-2021, the total number of employees within Bapco reached 2,799 divided between Operations, Awali Township support and the Awali hospital. During 2021, we exported a total of 74.6 MMBBL of our products and sold 1.65 MMBBL locally.
102-08:
The total number of employees has increased by around 11% since the 2018-19 reporting period, due to requirements related to BMP execution and post project operation. Refer to the table below. Bapco is committed to reaching 90% Bahrainisation within the next five years, post BMP.
During the reporting period no significant changes occurred within Bapco’s supply chain.
The number of employees who were members of a Trade Union in 2020 and 2021 was 904 (37.7%) and 1,058 (37.8%) respectively.
GRI
in the consolidated financial statements
Bapco has a subsidiary and joint venture within its financial statements. Bapco holds 42.5% of the share capital of Bahrain Gasoline Blending W.L.L., a company involved in trading and blending of gasoline fuels. In addition, Bapco owns 27.4% of the share capital of Bahrain Lube Base Oil company B.S.C. (Closed), which is a manufacturer of high quality Group III lube base oil products.
Bapco has integrated operations in production, refining and marketing. We operate a 267,000 BPD Refinery producing finished products for sale and distribution. Crude oil is imported from two sources. Locally produced crude oil from the Bahrain oil field is purchased from Tatweer Petroleum. Arab light crude oil is purchased from Saudi Aramco and transported to the Kingdom of Bahrain via the AB crude oil pipeline.
The raw materials used by our Refinery are crude oil, natural gas and a smaller quantity of other semi-finished raw materials used in the manufacture of our products, e.g. additives required for diesel and petrol sold at fuel service stations. Other semi-finished raw materials, i.e. materials that have already undergone some processing elsewhere, are purchased according to demand and include fuel oil cutter stock (lighter petroleum fractions used to adjust finished product specifications) and vacuum gas oil. Natural Gas from the Khuff Gas Reservoir, used in the operation of the Refinery, is purchased from Tatweer Petroleum.
In 2021, more than 74 MMBBL of products were exported, with middle distillates (kerosene plus diesel) accounting for about 56.9% of sales, followed by black oil products (fuel oil and asphalt) at 20.9%, naphtha at 19.1%, and base oil at 2.1%.
During the same period, Middle East countries (predominantly GCC) accounted for half of export destinations (53.1%), followed by the Far East (17.5%), with the balance to Africa (10.6%), Southeast Asia (5.9%), the Indian Subcontinent (4.9%), Europe (4.5%), South America (2.7%), and other countries (0.8%).
International diesel exports were all with an ultra-low sulphur content of 10 parts per million, consistent with the worldwide trend to promote environmental stewardship by adopting cleaner fuels. Bapco also sold diesel grades with more stringent distillation requirements at additional premiums.
Within the local market, the total volume of refined product sales amounted to 1.65 MMBBL in 2021, slightly up by approximately 5% year-on-year. Demand for most products were negatively affected by the ongoing pandemic, which resulted in a decrease in local consumption in all local sales except gasoline.
In 2021 the local market continued to favour the “fit for purpose” Jayyid gasoline grade (91 Research Octane Number - RON) over the higher octane Mumtaz (95 RON) gasoline. As a result, Jayyid gasoline accounted for almost half of the refined products sold domestically at 51.4% compared to 48.7% in 2020. Mumtaz gasoline accounted for 15.0% of the domestic sales versus 14.2% in 2020, while Super gasoline (98 RON), the premium gasoline grade, accounted for less than 1%. The remainder of local market sales were ultra-low sulphur diesel (22.5% in 2020 and 20.5% in 2021), LPG (8.1% in 2020 and 7.6% in 2021), kerosene (1.2% in 2020 and 1.0% in 2021), and Asphalt (2.7% in 2020 and 2.0% in 2021).
Bapco works with suppliers and contractors that share similar values. Our suppliers and contractors must pass a prequalification assessment to verify their commercial experience, organisation, financial stability and other management processes for quality, environment, and safety.
We strive to support an ethical and locally based supply chain that supports the Kingdom of Bahrain. During the reporting period there were a total of 808 active suppliers, of which 57% were local.
Bapco took the initiative in 2019 to produce its first sustainability report based on the GRI Standards. We have also recently written to the United Nations to give our commitment to adopt the Ten Principles of the United National Global Compact. The Principles provide a valuable framework that will guide the various transformation programmes described in this report and due for completion in future years (refer to our Introduction to this report).
Bapco is additionally certified and continues to maintain the certification to the following ISO standards:
• ISO 9001:2015 Quality Management, supporting our commitment to continuous improvement. (Certified since 1994);
• ISO 14001:2015 Environmental Management, supporting our commitment to environmental management (certified since 2008 to the previous version ISO14001:2004 and since 2017 to the current version);
• ISO 22301:2012 Business Continuity, ensuring our contingency planning and disaster recovery process follows recognised international best practice (certified since 2016); and
• ISO 45001:2018 Occupational Health and Safety, ensuring our occupational health and safety management is robust, and that it supports alignment with all other Bapco ISO standard certifications (certified since 2019). We have held equivalent OHSAS 18001 certification since 2003.
Bapco is an active member of several local, regional and international associations that promote sustainable development. We are pleased to have an active role in the following associations:
• Bahrain Health & Safety Society
• British Safety Council
• Campbell Institute
• Centre for Chemical Process Safety
• Energy Institute
• GCC Health and Safety Committee for Oil Refineries & Joint Ventures for Refinery Operating Companies (JVROC)
• Founding Member of Gulf Downstream Association (GDA)
• Gulf Petrochemicals and Chemicals Association (GPCA)
• Industrial Environmental Networking Committee
• INJAZ
• Board Member of Oil Spill Response Ltd (OSRL)
• Regional Clean Sea Organisation (RECSO), for which Bapco currently holds the Chairmanship
• Supreme Safety and Health Committee, Ministry of Labour and Social Development
• U.S. National Safety Council
• United Nations Global Compact (UNGC)
GRI 102-48: Restatements of information
Data reported under GRI 403-09 (Page 139) in the 2018-19 Sustainability Report have been revised in this report for consistency against the reported data for 2020-21.
The material topic “Diversity and Inclusion” listed in Bapco’s first sustainability report 2018-19 was changed to “Equal Opportunities” in this edition of the sustainability report, as it is more representative of the topic area. The topic-specific disclosures reported under the material topic “Contractor Management” were merged with “Human Rights”.
The reporting period is from January 2020 to December 2021.
Bapco issued its previous sustainability report for the reporting period 2018-19.
The reporting cycle is currently planned to be biennial.
Please send any comments or feedback on this report to:
Ahmed Khalil, Director HSE
Email: ahmed_khalil@bapco.net
Telephone: +973 1775 2970
This report has been prepared in accordance with the ‘Comprehensive’ reporting level as defined in the GRI Standards GRI 101 Foundation 2016.
Refer to the GRI Content Index at the back of this report for the year and version of General Disclosures and Topic Specific Disclosures used in this report.
We have commissioned an independent third party to provide assurance that this report meets the requirements of the GRI Standards. The report has been overseen by our Decision Review Board (DRB), chaired by the Acting Deputy Chief Executive and BMP Project Director, and comprising selected Bapco General Managers. The DRB has met regularly during report development to approve report content and the selection of material topics.
Our governance arrangements and highest governing bodies, our company strategy and how we set our strategy, and our approaches to the control of business risks.
Bapco is committed to the highest standards of corporate governance, which it believes are critical to maintaining stakeholder and shareholder confidence. Bapco applies high ethical standards to its operations to ensure that its governance structure complies with all laws and regulations that govern its business. Bapco’s corporate governance framework ensures that Bapco operates within the guidelines and practices of corporate governance as set out in the Corporate Governance Code 2018 and its Articles of Association.
nogaholding is Bapco’s sole shareholder. The oversight provided by nogaholding aims to create shareholder value through the successful management of governmental oil, gas and petrochemical assets. The Board of Directors comprises seven members, including the Chairman. The Board of Directors reports to the shareholder and sets the company’s vision and policies that shape organisational strategy.
In addition, there are three Board committees :
• The Bapco Board Audit and Risk Committee is responsible for oversight of the integrity and quality of financial reporting process, the effectiveness of Bapco’s risk management and internal controls, the review of Bapco’s legal and regulatory compliance and the performance and independence of Bapco’s auditors.
• The Bapco Board Executive Management is responsible for assisting the Board in its responsibilities for medium and long-term strategy, including any strategic initiatives.
• The Bapco Board Nomination, Remuneration and Governance Committee is responsible for assisting the Board on matters relating to nomination, compensation and remuneration of the Directors, senior executives, and general managers of Bapco, corporate governance matters and human resources (HR).
The listed Board Committees have been established as of 1 November 2021 following the appointment of the new Board of Directors, replacing the previous committees.
Bapco’s delegated authority cascades from the Board of Directors to the Executive Management, who are responsible for implementing the company vision set by the Board of Directors. Bapco has two Acting Deputy Chief Executives for Technical and Corporate Support to whom other General Managers report. Department Managers hold functional accountability across Bapco, each with a team of Superintendents with management responsibility.
GRI 102-20: Executive-level responsibility for economic, environmental, and social topics
The expectation of nogaholding is that Bapco provides a leading contribution to the Kingdom of Bahrain’s Economic Vision 2030, for example through the technical innovation and value creation of BMP. The Executive Management is responsible for aligning Bapco’s initiatives with the principles of sustainable development. Items related to sustainability are directly reported to Dr. Abdulrahman Jawahery, the Bapco CEO, who takes overall accountability for Bapco’s contribution to sustainable development.
GRI 102-21: Consulting stakeholders on economic, environmental, and social topics
Bapco has an extensive programme of stakeholder engagement to support its major initiatives - refer to 102-43, page 45. Interested third parties may otherwise contact senior members of Bapco via methods that include email, committee meetings and public or town hall meetings.
GRI 102-22: Composition of the highest governance body and its committees
Refer to infographic on pages 34 and 36.
GRI 102-23: Chair of the highest governance body
The highest governance body for Bapco is the Board of Directors. The Board Chairman is not an Executive Officer for Bapco and the Board comprises non-executive Directors.
GRI 102-24: Nominating and selecting the highest governance body
nogaholding, Bapco’s sole shareholder, is the highest governing authority for Bapco. The Bapco Board of Directors is appointed by nogaholding. Board members are typically appointed for a period of three years, renewable for subsequent periods as per Article 12 of Bapco’s Articles of Association. The Board is composed of individuals who have the competence and independence to provide stewardship of Bapco’s affairs. The Board approves Bapco’s corporate governance statement, which is reviewed annually.
GRI 102-25: Conflicts of interest
The Bapco Code of Conduct applies to both Directors and employees of Bapco, and is therefore equally applicable to the Board of Directors. All are expected to be familiar with the Code of Conduct and to uphold to the highest standard. The Code of Conduct is designed to help all those who work with Bapco make informed ethical decisions, and provide mechanisms to report unethical conduct. Conflict of Interest is articulated in Section 2 of the Bapco Code of Conduct, emphasising the importance of bringing suspected conflicts to the attention of an appropriate higher authority.
Purpose
Bringing energy to the world for the enduring prosperity of the Kingdom of Bahrain
Vision
To be recognised as a dynamic and empowering national energy company competing globally
Mission
To sustainably manage and operate an integrated energy business, leveraging best practices and creating value for shareholders, customers and employees
Enterprising
We are empowered and dynamic. This attitude and our business mentality enable us to innovate
Trusted
We are honest and respect others. By acting with integrity we garner trust internally and externally
Committed
We are determined and passionate. Personal accountability and teamwork produce the best results
H.E. Abdulla Jehad Al Zain, Chairman of the Board of Directors, regularly leads a review of Bapco’s vision and strategy, supported by the Executive Management. Bapco has a medium and long-term strategy derived from elements that include but are not limited to: the Kingdom of Bahrain’s commitments to the concept of Net Zero; the Economic Vision 2030; medium and long-term forecast demand for petroleum products; and anticipated technical innovation in refining.
The strategy is implemented by the Executive Management, who commission changes in strategic direction through organisational transformation programmes, each with defined objectives and identified accountable senior leader, and sets the Bapco mission statements. The alignment of Bapco’s mission, vision and values with this strategy are reviewed annually to confirm their adequacy to deliver company strategy. Dr. Abdulrahman Jawahery, the Bapco CEO, signs copies of mission, vision and values to indicate his approval for their communication to the wider Bapco workforce.
The Board of Directors are uniquely qualified in the functional areas of corporate finance, audit and risk management, refining technologies, major projects delivery, and human capital management. The Board of Directors additionally offers Bapco insights in business and risk management from their other non-executive oversight of organisations within the Kingdom of Bahrain. Mr. Mark Thomas, Deputy Chairman, is also Group CEO for nogaholding, Chairman of the Board of the Bahrain National Gas Company “Banagas” and Member of the Board of Tatweer Petroleum. Mr Yusuf Abdulla Mohammed Taqi is also a Member of the Board of Aluminium Bahrain (Alba).
Bapco’s three Board Committees report annually against their remit, in addition to their more regular reporting to the Board of Directors and their independent oversight of company governance arrangements. The performance of Dr. Abdulrahman Jawahery, the Bapco CEO, is reviewed annually by the Board of Directors.
Bapco has a DRB responsible for formal review of Bapco’s sustainability reporting. The DRB is chaired by Mr. Hafedh Al Qassab the Acting Deputy Chief Executive Technical and BMP Project Director and Chairman of the Environment, Health and Safety (EHS) Committee. The DRB seeks final approval from Dr. Abdulrahman Jawahery, the Bapco CEO. Bapco’s sustainability report includes performance statements from His Highness Shaikh Nasser bin Hamad Al Khalifa the nogaholding Chairman, H.E. Abdulla Jehad Al Zain, the Bapco Chairman and Bapco Executive Management.
We have a Code of Conduct for all employees, whom we expect to work to the highest ethical standards. Our Code of Conduct applies as well to all workers at the BMP site, it is supplied through induction, written instructions and regular/refresher training which help workers to understand and respect the cultural norms in Kingdom of Bahrain.
Bapco’s guiding principles are expected to be followed by all employees and business partners, they go above and beyond compliance with all laws and regulations of the Kingdom of Bahrain and we expect all business partners to adhere to. Our Code of Conduct provides detailed guidance to all employees on avoiding potential conflicts of interest. This includes:
• Conflict of financial or other interests, such as personal interests in organisations with which we have an existing business relationship;
• Political conflicts of interest, which may conflict with activities related to work in Bapco;
• Solicitation or fundraising, which could be perceived as coercive or be potentially unlawful;
• Misuse of position, separating personal interests from work;
• Guidance on gifts and hospitality arrangements in line with applicable laws and regulations and reflecting current international standards of good practice; and
• Management of confidential information to respect employee privacy and protect our assets.
The Code of Conduct is published in Arabic and English as both e-copy and hard copy. Employees are required to sign that they have read and understood the Code of Conduct with records kept by HR.
Employees can consult with their supervisor or line manager for additional advise and clarification on ethical behaviours presented in our Code of Conduct. We highly encourage and advise employees, in case of any doubt of breaching one of the principles of the Code of Conduct, to report immediately any concerns to HR.
Bapco’s internal control framework (the company’s business principles, policies, standards, guidelines and processes), has four objectives:
1. Ensure management, transactions and personal conduct comply with guidelines relating to corporate business conduct, as set out by the Bapco bodies responsible for corporate governance;
2. Ensure accounting, financial and management information provided to the bodies responsible for corporate governance in the company fairly reflects the financial position of Bapco;
3. Compliance with laws and regulations; and
4. Prevent or control business, legal and financial risks associated with company operation.
A ‘precautionary principle’ refers to the strategy for managing potential harm in the absence of extensive scientific knowledge. This concept applies equally to recent areas of risk (safety, financial, business and environment) and is widely considered within our risk management strategies, the strength of which have been validated by their application throughout the COVID-19 pandemic.
For the purposes of sustainability reporting, The GRI Standards only consider environmental harm within the context of this section, as introduced by United Nations Principle 15 of the ‘The Rio Declaration on Environment and Development’
Application of the ‘precautionary principle’ within our business considers four areas:
• Risk management processes;
• Environmental monitoring programs;
• Adoption of international best available technologies; and
• Crisis and emergency response.
We have clearly defined risk management processes for key business risks. Each risk is assigned a score that is regularly reviewed by our Senior Management to understand the portfolio of risks managed by the organisation. Bapco’s corporate risk matrix includes environmental risks associated with major incidents involving oil spills, release of hydrocarbons and other losses of containment.
We have a comprehensive environmental monitoring programme to verify compliance with the local laws and regulations of the Kingdom of Bahrain, e.g. for our air emissions and effluent discharges. The emissions limits stipulated by law are ‘precautionary’, with statutory limits reflecting the level of uncertainty in cause and effect attributed to a given type of emission. We work in close coordination with SCE, the environmental authority within the Kingdom of Bahrain, whose representatives routinely inspect our emissions and effluent monitoring procedures. All new units comply with applicable local environmental regulations as well as international lender standards; including International Finance Corporation (IFC) standards and World Bank guidelines.
We have adopted some of the international best available technologies for BMP, which will significantly increase the energy efficiency index of our refining operations and allow us to produce higher-value products for supply to our domestic and international customers. There is growing evidence of the harm caused by global warming. A precautionary approach to GHG emissions is therefore considered international best practice. We are reducing CO2 emissions per barrel of crude oil processed and improving energy efficiency, and hence increasing energy conservation as part of our sustainability journey.
We help the Kingdom gather data on the potential impacts associated with GHG emissions by publishing our emissions data in accordance with relevant international reporting guidelines.
We have further offset our GHG emissions by investing in renewable energy production through our BDSEPP and initiatives such as the community solar bench project.
Our Crisis and Emergency Response Plan (CERP), which is based on the internationally recognised Incident Command System (ICS), includes a comprehensive precautionary oil spill response capability to safeguard the environment in the event of an incident.
Bapco’s structured approach to its operations and processes facilitates rapid identification of internal and external emerging risks.
Bapco’s corporate risk management process is aligned to ISO 31000:2018 and certified to ISO 22301:2012. Bapco has an established framework for business resilience management implemented throughout the company. Significant risks with potential business impact are captured in Bapco’s Corporate Risk Register. As of the date of publication of this report there are 26 identified risks within four categories (strategic, operational, compliance and financial), comprising:
• One Strategic Risk;
• Twenty Operational Risks;
• Four Compliance Risks; and
• One Financial Risk.
The risks cover a wide category of internal and external risks representing aspects of Bapco’s activities that include safety, health and environment, reputation, cyber security, marketing, material availability, market volatility, human competency, and recruitment and retention. Bapco regularly evaluates these risks to ensure the effectiveness of the risk controls, to ensure effective reporting, and to ensure effective engagement in their control. Initial risk assessment is conducted with subject matter experts (SME) by workshop to identify each risk and its risk controls. Following the initial workshops there are three stages of verification and approval of the assessment. Initial review is by the General Manager of the respective area; then by the Business Resilience Management Committee; and finally by the Audit, Finance and Risk Committee. An annual review of the Corporate Risk Register is conducted to incorporate any updates.
The COVID-19 pandemic was an existential business risk during the reporting period. The potential impact of the pandemic on Bapco was effectively controlled by a Crisis Management Team (CMT). The CMT was multi-disciplinary and was therefore able to quickly build response strategies to emerging risks. Refer to the Special Topic on Bapco’s response to the COVID-19 pandemic on page 70.
An indirect consequence of the pandemic was the market volatility for petroleum products. Bapco was able to mitigate this impact through cost optimisation and, where necessary, temporarily reducing production output. The new technologies incorporated into BMP will provide Bapco with opportunities to sell an improved product slate with greater energy and production efficiency.
Bapco maintains a Corporate Risk Register that documents all significant business risks to which Bapco is exposed. The risks represent those encountered across economic, environmental and social domains both within the Kingdom of Bahrain and within the wider economic region. The types of risk included on the Corporate Risk Register align with Bapco’s potential high-level economic, environmental and social impacts on sustainable development. Successful management of Bapco’s business risks therefore also positively impacts on Bapco’s contribution to sustainable development.
The Board of Directors is ultimately accountable for Bapco’s enterprise risk, business continuity and other control frameworks established for Bapco. Management of Bapco’s Corporate Risk Register is delegated to the Executive Management. Bapco has independent Committees at both Board and Executive Management level designed to strengthen governance processes.
Bapco’s Corporate Risk Register is a key input for Bapco’s strategy. Whilst the Executive Management has responsibility for management of business risks, it is the Board who holds ultimate accountability for oversight of Bapco’s risk management processes. Each of Bapco’s three Board Committees has a specific input to risk oversight dependent on their charter and each Board member provides functional advice relevant to their domain expertise.
Topic review occurred regularly throughout the reporting period (with meetings conducted remotely via web conferencing when necessary). Bapco’s Board of Directors typically meets four times a year. The various Board Committees meet more regularly. Bapco holds Annual General Meetings and invites the Ministry of Industry and Commerce to attend. Topics of importance relevant to economic, environmental and social topics include Bapco’s response to COVID-19, changes in global demand for petroleum products, and workforce training for the anticipated commissioning of BMP.
Bapco has three independent formal means of reporting critical concerns to its government shareholder. Firstly, the Executive Management is responsible for communicating critical concerns to Bapco’s Board of Directors. Secondly, Bapco has strong independent governance processes that provide assurance of Bapco’s activities (refer to 102-18) and that may independently raise and communicate critical concerns to the Board of Directors. Thirdly, Bapco conducts external audits where there is a statutory requirement. The external auditors report their audit opinion to the shareholders independently of the Executive Management and Board Committees.
102-34:
As a Closed company, the exact nature and total number of Bapco’s critical concerns are not published. However, Dr. Abdulrahman Jawahery, the Bapco CEO and former Chief Executives have presented on several critical concerns to the Bapco workforce during the reporting period. These include Bapco’s response to pandemic and changes in market conditions encountered during the reporting period.
GRI 102-35: Remuneration policies
As a Closed company, Bapco does not report on its remuneration policies for its highest governance body. Refer to 102-18 for details of how Bapco assures remuneration.
GRI 102-36:
All new graduates joining the company are assigned an Individual Development Plan (IDP) with performance metrics as part of their training programme. Annual performance appraisals evaluate individual performance and are used to guidance changes to remuneration. The HR business processes used to set remuneration are as expected fully aligned with the Kingdom of Bahrain’s labour laws.
GRI 102-37: Stakeholders’ involvement in remuneration
Bapco’s Board of Directors sets the company strategy that is used by the Executive Management to determine employee compensation. Dr. Abdulrahman Jawahery, the Bapco CEO has actively sought to make appointments reflective of Bapco’s sustainability strategy - for example the continued appointment of women to senior positions within Bapco described in this report.
GRI 102-38: Annual total compensation ratio
As a Closed company, Bapco does not report on its compensation ratios.
GRI 102-39: Percentage increase in annual total compensation ratio
As a Closed company, Bapco does not report on its compensation ratios.
Diversity and Inclusion is an important component of sustainable development, with the expectation that a sustainable society is one in which the contribution made by all genders is valued equally.
Bapco is proud of its track record in providing equal opportunities for all, employing the best talent irrespective of gender. The company makes great efforts to increase the number of women it employs, and has undertaken steps to leverage the critical role of women and increase their visibility within its organisation. The current reporting period is no exception, with several senior appointments made to women, including to the Executive. Refer to the separate section on Equal Opportunities to understand more about our demographics and the diversity of our workforce.
Profiles of senior women working in Bapco have been included throughout this report to celebrate Bapco’s commitment to the important role of women. The women selected are qualified in a variety of disciplines including engineering, HR, law and finance. All represent the high calibre of our employees.
Bapco celebrates Bahrain Women’s Day on the 1st of December of each year. Under the wise leadership of Her Royal Highness Princess Sabeeka bint Ibrahim Al Khalifa, the themes in 2020 and 2021 were Bahraini Women in the Diplomatic Field and Bahraini Women in National Development respectively.
We are very pleased to be able to include these profiles in our sustainability report and hope that you enjoy finding out more about some of those who work for Bapco.
How we assure report quality, how we identify our stakeholders and the material topics important to them, and the changes in our material topics that have occurred since our last report was published.
Topic boundaries describe how far an organisation is responsible for its impacts. ‘Impact’ can be defined as a change or effect attributed to, and caused by, the company’s operations. There may be both positive and negative dimensions to an impact.
Each material topic included in this report includes a description of:
• Where the impacts occur;
• Organisational involvement with the impacts, e.g. whether we have caused or contributed to the impacts or are directly linked to those impacts through our activities; and
• Any specific limitations concerning the topic boundary, e.g. procurement decisions that may restrict supply chains.
Recognised international good practice is used to define boundaries where appropriate, e.g. the calculation of GHG emissions in accordance with relevant international guidelines from the Intergovernmental Panel on Climate Change (IPCC).
GRI101 describes five principles governing report quality, which collectively ensure that the information provided is both reasonable and appropriate. These principles have been achieved through the involvement of SMEs providing information from across the organisation, and rigorous review by the DRB. Each report quality principle is considered in more detail below.
Report accuracy has been achieved by describing how data have been calculated. Raw (measured) data have been used wherever possible and in the majority of disclosures; where an estimate is used this is indicated in the supporting description. If there is a margin of error in the data provided, then this is also described.
Report balance has been achieved by presenting information factually and without unreasonable exclusion. Trends comparing data with the previous sustainability report have been included where relevant.
Report clarity has been achieved through clear descriptions of technical terms used in the report supported by a glossary. The report complies with corporate branding guidelines, which are designed for clear communication of information to stakeholders and other third parties.
Report comparability has been achieved by carefully following GRI guidelines on how data should be presented within each disclosure.
Report reliability has been achieved by careful independent review of the information presented. Much of the information reported here is already made available to third parties who may have undertaken separate verification of that information.
Report timeliness has been achieved by retrieving the latest available data and, where this is not available, providing a full explanation within the disclosure.
Bapco has identified its stakeholders and key sustainability concerns. Bapco scored the identified sustainability topics for their potential stakeholder impact (as determined from documented stakeholder opinion) and impact on Bapco. The materiality matrix generated for our previous sustainability report was reviewed against the new scores and updated to reflect changes in impact.
The revised matrix was presented to the DRB, who provided further feedback on the relative positions of each sustainability topic presented in the matrix. On approval of the materiality matrix, a table of reportable disclosures was developed, considering the reporting level and the availability of data.
Stakeholder inclusiveness was ensured throughout this process by early involvement of stakeholders, who provided insight into known stakeholder concerns. Extensive stakeholder engagement conducted for BMP has provided a clear picture of the opinions of a wide range of stakeholders on sustainability issues. Additionally, stakeholder groups internal to Bapco were identified and open invitations were issued to those groups. The stakeholders were invited to bring other Bapco personnel to the workshops to avoid unconscious bias within the initially identified issues. Stakeholder workshops were held, and topic scores were modified according to the feedback.
Sustainability context was ensured by review of key regional sustainability concerns. Topics have been reviewed to confirm that the context for each item is understood and can be related to the topic-specific disclosures required by GRI. The relevance of each topic area to sustainability is further described in each section within this report to communicate its importance to the reader.
Topic materiality was determined from the ranked topic areas and development of the materiality matrix. Internal stakeholder workshops were convened to verify the relative positions and importance of each topic area.
Completeness was ensured by commissioning an independent consultant to assist with the development of this report; the consultant reviewed the available data provided by us for each topic-specific disclosure, identified any gaps in the data and noted these as exceptions in the completed report.
Review previous topic scoring.
Identify changes in Bapco impact on stakeholders.
Stakeholder workshops to score topics (using a 1-5 scale).
Present completed materiality matrix to Bapco stakeholders.
Update scores based on feedback.
Presentation of results to DRB for approval.
Final selection of sustainability topics to include in this report.
Bapco identified sustainability topic areas representing the range of concerns identified by regional peers, our internal and external stakeholders and the downstream oil and gas sector. Topic areas were assigned to environment, people, society or business continuity categories and scored using the methodology described under GRI 102-46 to determine the relative importance of each topic to us and our stakeholders.
All topics shown on the chart are regarded as material topics for the purposes of reporting. Five areas were identified as highest priority to Bapco and its stakeholders, i.e. the top right hand quadrant of the materiality matrix.
Health, safety and wellbeing
Value generation and distribution
Emergency preparedness
Asset integrity & security
Learning and Development
Occupational health and safety, promotion of worker health, work-related injuries and illness
Contribution to the Bahrain economy and including indirect economic impact
Community emergency planning, crisis management and community engagement
Process safety, asset integrity management and operational excellence
Worker education and career professional development
Since the previous reporting period three topics have been assessed as of increased importance to both Bapco and our stakeholders. These are:
• Emergency Preparedness and Response, given the very significant and sustained response to the global pandemic that has allowed the Refinery to continue operating;
• Responsible Supply Chain Management, recognising the critical role of the supply chain in delivering BMP and Bapco’s commensurately strong commitment to contractor management; and
• Learning and Development, recognising the investment in workforce competence ahead of BMP commissioning.
Scores assigned to other topics were also revised but the changes were less significant.
Bapco has identified its key stakeholder groups:
• Government and regulatory authorities
• Financiers and insurers
• Suppliers and contractors
• Customers (both local and international)
• Non-Governmental Organisations (NGO) and academia
• Local communities
• Local industries
• Employees
We define stakeholders as entities or individuals that can be affected by our activities, products, or services; or whose actions can affect our strategies or objectives. Our key stakeholder groups have been
identified from the extensive list of parties that we interact with, in line with implementing our company management systems. We have also undertaken a comprehensive stakeholder engagement exercise supporting BMP to identify project-specific stakeholders. The feedback received from external stakeholders was used to determine selection of the relevant sustainability topics presented in this report.
We recognise that open and transparent engagement with all stakeholders is key to understanding the materiality of different sustainability topics. We aim to build long-term relationships with stakeholders that impact, or are impacted by, our projects and activities. Through BMP we have taken this a step further by actively and regularly engaging with those who might be directly affected by our operations. We achieve this by:
• Disclosing relevant project information;
• Providing opportunities for stakeholder consultation;
• Creating opportunities for stakeholder feedback through varied media, e.g. written correspondence or social media platforms; and
• Reviewing the effectiveness of stakeholder dialogue.
We have applied similar principles to the internal stakeholder consultation completed in support of this report, which included:
• Refreshing training courses on sustainability and the GRI Standards were held virtually in August and September 2021 for Bapco employees, and managers;
• Consultation workshops, which included a presentation on the methodology used to determine the materiality matrix and topic materiality; and
• Sharing of draft outputs from the workshops for comments, and incorporating feedback into the revised matrix.
GRI 102-44: Key topics and concerns raised
Stakeholder Group
Engagement mechanisms
• Formal review of company strategy and plan with third parties, including reporting on the outputs of internal governance activities where appropriate
• Regular coordination meetings
Government and Regulatory Authorities
• Direct meetings and consultation with regards to compliance and planning of new projects
• Bapco website, emails and letters
• Conferences, forums and workshops
• Events and other outreach campaigns regularly coordinated with relevant government authorities
• Written communication through letters and emails
Financiers and insurers
Suppliers and contractors
Non-Governmental Organisations and academia
• Site visits and inspections when possible due to the COVID-19 pandemic
• Formal joint venture arrangements for projects
• Virtual meetings with suppliers, as mandated in relevant procurement management procedures
• Audits and other formal feedback mechanisms on contractor performance
• Established supplier agreements
• Formal feedback from vendors and suppliers
• Joint research projects and Memoranda of Understanding, including collaboration with Ph.D. students to develop innovative solutions
• Direct meetings, company events and campaigns
• Focus group meetings with local community representatives, specifically for BMP, including special interest groups such as the elderly and the disabled
• Emails, telephone calls and social media (including WhatsApp and Instagram)
Local communities
• Visual material presentation, e.g. billboards
• Media outreach through TV and Radio
• Targeted campaigns
• Regional meetings including regular established networking committee meetings held virtually
Local industries
Customers
• Conferences held virtually in 2020 and resumed back to normal , forums and workshops
• Meetings when possible and regional sector meetings
• Daily communications, including emails and telephone calls
• Customer feedback
• Forums and events which run throughout the year
• Regular meetings at all levels of the organisation
Employees
• Communication using a variety of media, including the Bapco intranet portal, the large electronic screen placed at the Refinery main entrance, desktop screensavers, departmental posters, and various Company electronic notifications and information boards
Stakeholder Group
Government and Regulatory
Authorities
Key Topics
• Compliance with governmental policies and regulations
• Maintenance of good financial performance
• High operational efficiency for product import and export
• Meeting Environment, Health and Safety (EHS) performance and expectations
• Sponsoring various projects as part of the Company’s Corporate Social Responsibility serving the wider public/community
• Compliance with all standards and requirements as applicable (including international finance corporation and World Bank environmental and social guidelines)
Financiers and insurers
• Compliance audits and site visits
• Secure external financing/loans (specifically with regards to BMP) and ability to pay back loans
• Financial, environmental and social performance
• Prompt payment of contractual commitments
• Potential social impacts from contractors’ labourer accommodation (specifically for BMP)
Suppliers and contractors
• Legal compliance, including EHS and the Ministry of Labour and Social Development regulations
• Provision of medical surveillance of workers
• Use of social media to promulgate information
• Importance of prioritising local employment
Non-Governmental Organisations and academia
• Active involvement in the community, including the construction and refurbishment of services such as public parks and infrastructure (specifically applicable for BMP)
• Research opportunities and knowledge sharing
• Technical training programs for Bahraini youth
• Environmental monitoring, including air emissions and water effluent, to safeguard public health and protect marine life and fisheries, and effective management of hazardous and non-hazardous waste
Local communities
• Future employment opportunities, especially for graduates and women
• Sponsoring various programs as part of community outreach
• EHS awareness programs
• Traffic management, specifically that associated with the Refinery expansion activities
• Optimising services to meet multiple companies’ needs
Local industries
• Emergency preparedness and mutual aid
• Local employment opportunities
• Uninterrupted supply of finished products
• Availability of the Bapco Wharf for product supply
Customers
• Prompt and efficient services
• Legal compliance with EHS requirements
• A productive and supportive work environment
• Robust non-discrimination policy
• Competitive employee benefits
• Efficient HR services
Employees
• Attractive professional development opportunities
• Employee wellbeing programme and routine medical check ups
• Provision of medical facilities, including a fully equipped hospital in Awali
• Consultation on company plans and initiatives
Our people are Bapco’s most valuable asset, safely operating our world-class Refinery and providing for the succession of our future leaders.
We are very pleased to provide a cross-section of employee profiles in this sustainability report, representing the many technical disciplines and career stages at Bapco. The profiles include both male and female engineers, the latter accepted within the cohorts of trainees by Bapco for some years.
Several of the profiles are from those who joined through the Bapco International Scholarship Programme, which supports the students during their further education. On successful completion of their degree the best candidates are invited to return to work for Bapco. Irrespective of whether the candidates joined Bapco from school or following a higher degree, the selection progress is rigorous and competitive. The profiles represent some of the best and brightest that we are proud to have working at Bapco.
Some of the profiles are also from those who have attained senior positions within their disciplines. Their experience is invaluable in assuring continuity of operations within Bapco, and they are called on to act as trainers and mentors to more junior colleagues.
What is common from all the included profiles is the sense of belonging and pride of being part of the Bapco family. We hope that you enjoy reading these profiles as much as we have enjoyed documenting life at Bapco.
Included in this section - Page 52
Protecting the environment - Page 66
Safeguarding our business - Page 70
Included in this section - Page 67
Afaf Zainalabedin has had a long career in corporate finance within the Kingdom of Bahrain prior to joining Bapco.
Originally a graduate in Accounting from the University of Bahrain, Afaf was the first Bahraini woman to attain Chartered Accountant Status from the Association of Certified Chartered Accountants, England and Wales. Afaf subsequently joined Ernst & Young where she spent her formative years. Afaf progressed rapidly, obtaining regular promotions until she reached Manager level at their Bahrain office. Afaf comments that the international travel and exposure to different industries was a rewarding facet of her audit work. During her career at Ernst & Young, Afaf was responsible for creating two standards relating to Islamic Banking, also representing Ernst & Young and the Accounting and Auditing Organisation for Islamic Financial Institutions at various seminars.
Afaf then moved to Arcapita Bank B.S.C (Closed), initially as a Principal responsible for handling the accounts of offshore investment structures, and then Financial Controller, responsible for oversight of financial records and reporting to the Central Bank of Bahrain. Afaf completed her career at Arcapita as Head of Internal Audit, a Director-level position with responsibility for financial audit of different legal entities as well as Arcapita’s Head Office.
After leaving Arcapita, Afaf’s career move into the oil and gas sector occurred when she joined nogaholding, the Oil and Gas Holding Company of the Kingdom of Bahrain. Afaf is proud of being the first woman to achieve the role of General Manager Finance and Administration in the oil and gas sector in the Kingdom of Bahrain. During this time Afaf was actively involved in the financial aspects of various investment projects and represented nogaholding on financial subcommittees.
During the same period Bapco recognised that it was entering a period of transformation within the industry, and therefore set out to make several senior appointments to lead the transformative processes. Afaf joined Bapco In January 2021, holding the position of Chief Financial Officer for the company. The appointment includes responsibility for Bapco’s Finance, IT and Procurement divisions, as well as a requirement to head the Enterprise Resource Planning (ERP) transformation programme. Afaf reports to the Executive Management and the Board on the financial results of Bapco’s operations. Afaf additionally acts as a Board member to the BAC JET Fuel Company W.L.L, a joint venture between nogaholding and Bahrain Airport Company.
Afaf’s recent appointment as Acting Deputy Chief Executive - Corporate Support was the first time that this position was considered for a female. The appointment was celebrated by the Dr. Abdulrahman Jawahery, the Bapco CEO in an open letter to the President of the Supreme Council for Women (SCW), where Dr Jawahery commented on the potential of Bahraini women to achieve the most senior positions. Dr Jawahery further stressed that Bapco believes in equal opportunities and appoints the right candidate irrespective of gender.
Outside of her work at Bapco, Afaf likes to contribute to the community through charity work with special needs children. In her spare time Afaf enjoys art, classical music, baking and outdoor sports.
Afaf commented that the sense of belonging and loyalty to Bapco are very striking amongst her colleagues. However there is also recognition that Bapco is changing to meet future needs of the Kingdom and that this is a very exciting time to be working at Bapco.
“
There is recognition that Bapco is changing to meet future needs of the Kingdom, this is a very exciting time to be working at Bapco
Afshan Parveen Akhtar is currently the Chief Legal Counsel and Board Secretary for Bapco.
Afshan was born and raised in London, attending the London School of Economics and Political Science where she graduated with a Bachelor of Laws (LL.B.), subsequently completing a postgraduate Legal Practice Course at the University of Law, London.
On graduating Afshan joined Clifford Chance, one of the prestigious ‘magic circle’ London law firms, where she worked in the General Banking and Finance Team. Eventually progressing to Senior Associate, Afshan’s responsibilities were in global acquisition financing where she was seconded to leading investment banks and other listed corporates.
After spending eight formative years at Clifford Chance, Afshan moved to Bahrain where she joined Aluminium Bahrain (Alba) to manage their Legal and Corporate Affairs Department. Afshan reported directly to the Chairman of the Board of Directors, with responsibility for legal advice and support to the business. During Afshan’s tenure at Alba she was credited with building a high-performing legal function that went on to be short-listed as Legal Team of the Year, Middle East, by Corporate Counsel Middle East and Legal Week.
Afshan subsequently returned to the banking sector to join ABC Bank as a Senior Group Counsel. Afshan was responsible for providing legal advisory services to the bank’s management, whose operations spanned Middle East, North Africa, Europe, the Americas and Asia. Afshan provided advice on a range of legal documentation for banking transactions, corporate banking, structured finance, retail and digital banking, and Islamic banking.
From her time at ABC Bank to present, Afshan has also served on the Board of the Middle East and North Africa Chapter of the Associated of Corporate Counsel, which is a non-profit organisation provided education and training services to its membership of 45,000 lawyers in 85 countries around the world.
Following her tenure at ABC Bank, Afshan was delighted to join Bapco as Chief Legal Counsel and Board Secretary. Afshan now advises the Board of Directors and management across the breadth of the business.
Of the several areas of significant transformation now taking place within Bapco, Afshan leads the transformation of the legal function to build legal capability in-house and codify legal best legal practice. Afshan observes that the oil and gas industry is entering a period of rapid change as the sustainability agenda is developed by the sector. Afshan is proud to be able to use her experience of other sectors - especially corporate finance - to support Bapco in this journey.
Afshan holds several awards, including General Counsel for the year (2013) by Corporate Counsel Middle East General Counsel Power List Middle East (2013, 2015 and 2016) and has subsequently participated in the judging panel for the profession’s regional legal awards.
Afshan comments that Bapco is very much a national treasure of the Kingdom of Bahrain and that there is demonstrable pride amongst all those who work within the large community of Bapco.
Legal Counsel
“Bapco is very much a national treasure of the Kingdom of
Afshan leads on transformation of Bapco’s legal function
Sherifa Al Doseri is the Manager of the CEO’s Office, where she oversees the activity within the office and assists in following up on the directives and implementation of strategies and plans. Dr. Abdulrahman Jawahery, the Bapco CEO commented on Sherifa’s appointment that ‘... Sherifa is a resourceful person and can be relied on by everyone in the Executive Team to handle issues with confidentiality and efficiency’.
Sherifa holds a Bachelors degree in International Relations and Affairs from the American University Sharjah United Arab Emirates, a Bahrain Institute of Banking and Finance Level 7 Human Resources Advanced Diploma and a Leadership Diploma from the University of Westminster, UK.
Sherifa started her career as a Research Assistant, then Executive Assistant to the Vice Chancellor at the University. Sherifa joined Bapco in 2009 as a Senior Recruitment Officer and pursued a career at Bapco in Human Resources, holding appointments in different functions from manpower selection to recruitment and administration. Sherifa was promoted to HR Business Partner for the BMP, moving to the project team in 2019 to support in her new role.
The COVID-19 pandemic created particular challenges for both Bapco and BMP - described elsewhere in this report. BMP, unlike the base business, has a high proportion of contractors who are foreign nationals. Those who were previously free to leave and enter the country were now prohibited from travelling, risking significant project delay. Sherifa was responsible for liaising with the contractors based in other countries to try and determine how to minimise the ensuing disruption. In some cases, Bapco obtained special dispensation for travel once the appropriate COVID-19 test regimes were put in place. Sherifa also initiated virtual weekly ‘toolbox’ meetings to raise awareness of the
impact of the COVID-19 pandemic on project planning.
Sherifa’s second important role during this time was acting as liaison between Bapco and the Ministry of Health. The restrictions imposed by Bapco - for example the requirement for home-working - had to follow those imposed by government and therefore change in accordance with the latest Ministry of Health guidance. As an active member of the COVID-19 CMT, Sherifa was responsible for interpreting Ministry of Health requirements so that they could be applied properly to BMP.
Sherifa also supported the campaign to vaccinate the BMP workforce, coordinating with Awali hospital and other Bapco departments. Vaccination was critical for BMP’s contractor workforce where there was greatest potential for transmission. Sherifa was responsible for encouraging uptake of the vaccines amongst all those eligible.
Sherifa comments that she is proud to be associated with Bapco and regards every day as a learning opportunity. Sherifa sees the company culture as fast-paced with an aspiration for transformation.
Sherifa’s appointment as Manager of the CEO office is just one of the many examples highlighted in this report of Bapco’s commitment to sustainable development; in this case through the recruitment of the best talent irrespective of gender and a contribution to a fairer society.
“Sherifa sees the company culture as fast-paced with an aspiration
Governance and ethics refer to the systems, rules, practices, and processes by which we ensure the interests of our business stakeholders are in balance.
We have a Code of Conduct that describes the company policies that employees must adhere to.
We have a dedicated internal audit team that uses procedures based on the requirement of the “Standards for the Professional Practice of Internal Auditing” and the “Code of Professional Ethics of the Institute of Internal Auditors”. Internal audit processes verify the effectiveness of risk management, control and governance processes. The internal audit team reports functionally to the Audit and Finance Committee of the Board of Directors and administratively to Dr. Abdulrahman Jawahery, the Bapco CEO.
Business Continuity, ISO 22301, is verified by the Integrated Management System audit team, who check the activities of the internal auditors, the latter responsible for their contribution to Business Continuity. The audit team is responsible for the annual review of the Business Continuity Management process.
Risks related to corruption are within Bapco’s audit protocol for their evaluation of operational activities. All of Bapco’s operational activities are assessed for this risk.
GRI 205-02: Communication and training about anti-corruption policies and procedures
Bapco’s employees adhere to Bapco’s Code of Conduct. Induction training is completed for all employees on the Code of Conduct. All employees receive a copy of booklet as part of the onboarding process.
GRI 205-03: Confirmed incidents of corruption and actions taken
There have been no confirmed incidents of corruption during the current reporting period.
GRI 206-01: Legal actions for anti-competitive behaviour, antitrust and monopoly practices
There have been no reported incidents of the above legal actions during the current reporting period.
GRI 307-01: Environmental compliance
Bapco did not have any reported breaches of environmental compliance during the current reporting period. Bapco is certified to ISO14001:2015.
GRI 419-01: Non-compliance with laws and regulations in the social and economic area
There have been no incidents of non-compliance during the current reporting period.
This topic assures legal compliance with relevant legislation governing product quality standards. It includes the mechanisms by which EHS-related standards are addressed across the product life cycle.
Ongoing review of conformity to product requirements ensures that customer requirements for supply of products to agreed specifications are met in a timely and efficient manner.
Bapco has defined mutually acceptable processes for communicating effectively and efficiently with its customers and other interested parties. The processes ensure adequate understanding of the needs and expectations of its interested parties, and for translation into requirements for the organisation. These processes include identification and review of relevant information, and are required to actively involve customers and other interested parties.
Examples of relevant process information include:
• Requirements of the customer or other interested parties;
• Market research;
• Contract requirements;
• Competitor analysis; and
• Statutory or regulatory requirements.
Bapco requires its management to have full understanding of customer requirements, or other interested party, before initiating any action to comply. This understanding and its impact should be mutually acceptable to the participants.
The potentially hazardous nature of our hydrocarbon products requires strict adherence to the relevant national laws and international guidelines on safe production, storage, local distribution and export. We test for product quality at our onsite Refinery Laboratory to ensure that our products meet the required customer specifications and comply with applicable regulations.
We issue a Safety Data Sheet (SDS) for all our international products conforming to the European Commission Regulation (EC) No. 1907/2006 for the Registration, Evaluation, Authorisation and Restriction of Chemicals (REACH), Annex II.
We maintain a comprehensive suite of standards governing product quality and safety which include:
• Risk assessment and hazard identification;
• Evaluation of product environmental impact;
• Occupational health and safety;
• Safety signs and signals and chemical classification and labelling;
• Medical surveillance for occupationally exposed workers; and
• Individual safety standards for hazardous compounds, such as for hydrogen sulphide (H²S).
Where applicable, our company standards use the United Nations Globally Harmonised System for the Classification, Labelling and Packaging of Chemicals (Amendments to Secondary Legislation) Regulations 2015.
GRI 416-02: Incidents of health and safety non-compliance
There were no non-compliances with regulations and voluntary codes during the reporting period.
GRI 417-01: Requirements for product and service information and labelling
All Bapco products that are considered hazardous under national and international laws are subject to labelling using SDS, detailing the composition, safety measures, handling and storage, physical and chemical properties, stability and reactivity characteristics, toxicological and ecological properties, disposal considerations, transportation and other regulatory information.
GRI 417-02: Incidents of non-compliance concerning product and service information and labelling
There have been no recorded incidents of non-compliance during the reporting period.
GRI 417-03: Incidents of non-compliance concerning marketing communications
There have been no recorded incidents of non-compliance during the reporting period.
GRI 418-01: Substantiated complaints concerning breaches of customer privacy and losses of customer data
There have been no recorded incidents during the reporting period.
We provide systematic and rigorous control of EHS across the life cycle of our products.
Life cycle of our products by activity
Life cycle activity Description
Bapco produces various hydrocarbon products from the refining of crude oil. New products are selected based on market demand but with careful consideration of the environmental, and health and safety impacts associated with their production and use.
Product concept
This includes evaluation of product environmental impact associated with refining activities during normal, abnormal and emergency situations and identification of control measures to prevent or mitigate identified impacts. It would not be possible to obtain the relevant licences to supply our products without the rigorous environment, occupational health and safety and process safety management systems which are implemented by Bapco.
Research
Certification
Once the required product specifications have been agreed with customers, developed products are not subject to additional research and development.
Additional product certification is not required. However, Bapco is certified to ISO 9001:2015, ISO 14001:2015, ISO 22301:2012 and ISO 45001:2018.
Production
Refining activities are tightly controlled through the identification of Fire, Lightning, Explosion, and Act of God risks and the associated safety critical elements that mitigate loss of containment or other accident scenarios. Our process safety management system helps mitigate loss of containment events that can lead to employee injury, environmental damage or asset damage.
Our ISO 45001 Occupational Health and Safety Management System is used to prevent or mitigate hazards leading to employee harm.
Marketing & distribution
Disposal & recycling
Our product EHS risks are communicated to our customers through SDS conforming to the requirements of Annex II of the Registration, Evaluation, Authorisation and Restriction of Chemicals (REACH) Regulations.
Our SDS include relevant information on safe disposal and recycling, where applicable.
Noor Ahmadi is a Chemical Engineer by training and currently works in the Planning and Economics Department within the Bapco Marketing Division.
Noor originally graduated from Northeastern University, located in Boston USA, with a BEng in Chemical Engineering. Noor joined Bapco in 2019 and recalls how pleased she was to find an opening for employment at such a prestigious employer.
Like many graduate engineers, Noor was slightly unsure of what a career at Bapco might entail. Assigned to the Marketing Division, Noor recalls the excellent mentorship that she received in areas such as Refinery optimization, supply logistics and market dynamics. Noor discovered a strong interest in planning and economics that has been formative in her career to-date.
Noor currently works with a diverse group of chemical engineers, traders, sales managers and strategists who together predict the future for Bapco’s products and services. Noor comments ‘Bapco’s career opportunities are both welcoming and empowering’, and is delighted to have found such an interesting area to work in for her future career.
Fatema Shukri joined Bapco in 2018 and currently works in the Maintenance Services Department.
Prior to joining Bapco, Fatema had studied Mechanical Engineering at the University of Bahrain, where she graduated with a BSc in 2016. Fatema is continuing her education at present by studying for a Masters in Business Administration at the University of Strathclyde, Scotland.
Fatema’s responsibilities focus on evaluating the root causes of failure of rotating equipment (e.g. pumps, compressors, etc.) and creating action plans. Fatema recalls her pride at supporting Bapco on shut-downs as she was supervising overhaul activities on major machines such as recycle gas compressors, steam turbines and hydrogen makeup compressors.
Fatema was recognised in 2021 by Dr. Abdulrahman Jawahery, the Bapco CEO as a High Performance Employee. She was also privileged to meet His Highness Shaikh Nasser Bin Hamad Al Khalifa, Chairman nogaholding, during his visit to Bapco.
Fatema comments that she sees her position as one of the hundreds of Bapco employees contributing to the economy of the Kingdom of Bahrain and is very proud of what she has achieved.
Emergency preparedness and response refers to our ability to effectively mitigate potential consequences of an incident to people (community and employees), the environment and company assets and reputation, and enables an efficient resumption of normal operations.
The CERP delivers an Incident Management System (IMS) based on the incident command system framework that is widely used worldwide. ICS is a standardised all-hazards incident management concept that incorporates a set of proven organisational and management structure, terminology, processes and procedures. The CERP incorporates guidance issued by various organisations such as the International Petroleum Industry Environmental Conservation Association (IPIECA) and Oil and Gas Producers Joint Industry Project (2014), to learn from previous incidents and improve our emergency response plans.
The purpose of the CERP is to:
• Describe the expectations, scope and content of Bapco’s IMS;
• Provide guidance to Bapco Emergency Response Teams, Incident Management Team (IMT), Crisis Management Team and those supporting them for the response to, and control of an emergency, incident or crisis associated with Bapco facilities or personnel;
• Explain the response organisational structure, its functions and the roles and responsibilities of key personnel;
• Define response team notification and activation procedures; and
• Describe the planning processes for, and implementation of, emergency, incident and crisis management.
CERP has a scalable response depending on incident type and severity, comprising:
• Level 1: On Scene Commander and Emergency Response Teams
‘Operational Response’;
• Level 2: IMT ‘Tactical Response’; and
• Level 3: CMT ‘Strategic Response’.
The three response levels are designed to ensure a standardised approach to CERP between organisations. They have the capability of expanding, contracting or substituting expertise within the response organisation to match the complexities and demands of single, multiple or complex incidents.
A key component of our ‘All-Hazards’ approach to incident management is to provide an effective organisation with the necessary functionality and connectivity to deal with any potential emergency that endangers people, the environment, company assets or business reputation. It is a commitment made in the best interests of Bapco employees, customers, shareholders and the wider society.
Bapco conducts building and industrial fire drills to prepare for incidents. Our building fire drills check preparedness of employees to respond in the event of an alarm. Our industrial fire drills are carried out in process units within the Refinery, Sitra Tank Farm, Marketing Terminal and Wharf. The drills are used to test firefighting equipment and the capabilities of fire teams to cope with the varied scenarios that might be encountered within Bapco facilities.
The OSCP incorporates tiered preparedness and response in accordance with international best practice, consistent with the 1990 International Convention on Oil Pollution Preparedness, Response and Cooperation. The tiered approach based on ICS offers structure to oil spill response arrangements. The OSCP supplies our Oil Spill Response Team with the response strategies required during an oil spill response.
For small (Tier 1) spills we have a dedicated oil spill response team and an oil spill response equipment warehouse located at the Refinery and Wharf, which contains specialised oil spill clean-up equipment, such as absorbent pads, booms, skimmers, etc. For larger (Tier 2 and Tier 3) spills, we are members of OSRL, the largest international industry funded cooperative for effective response to oil spills. Bapco is also a founding member of RECSO, established in 1972 with the concept of mutual aid. RECSO is one of the oldest environmental cooperatives in the world and its members include all the major oil companies in the GCC.
The IMT uses the ICS for the command, control and coordination of the emergency response to an oil spill. ICS has been widely adopted and is recommended by IPIECA guidelines.
We maintain preparedness for oil spills through an extensive training program, including both operational and strategic elements involving practical deployments and table top exercises. Our personnel also receive internationally recognised training, such as the International Maritime Organisation accredited Oil Preparedness, Response and Co-operation Levels 1, 2 and 3 training courses.
Even with the restrictions created by the COVID-19 pandemic, a number of practical exercises were conducted during the reporting period.
In 2020, we conducted three oil spill exercises in collaboration with OSRL, which were used to test different equipment types and techniques for their use. These included:
• Fast water booming to test our response inland waterway oil spills;
• Vessel-based dispersant simulation, a practice dispersant application to understand the challenges associated with response during COVID-19 pandemic and to increase responders level of competency; and
• Offshore boom to practice deploying offshore oil spill equipment.
In 2021, we identified a minimum set of training requirements for CERP’s IMT to ensure their full preparedness to effectively respond to any emergency. Training using the new requirements was held across all our departments.
The RECSO Table Top Exercise Clean Gulf-1 was successfully conducted on 2nd November 2021. The exercise was coordinated by Abu Dhabi National Oil Company (ADNOC) and Dubai Petroleum Establishment (DPE). Other RECSO Members which participated included Kuwait Oil Company (KOC), Wafra Joint Operations (WJO), Petroleum Development Oman (PDO), Al Khafji Joint Operations (KJO) and Saudi Aramco. Representatives from the Marine Emergency Mutual Aid Centre (MEMAC) also participated.
We have also conducted two successful CERP exercises that tested Bapco’s response capabilities at a national level. With the COVID-19 restrictions faced at the time of the exercises, a hybrid system was established with a number of participants in the Bapco Command Center, and others attended remotely or worked from their offices, supporting the team through various means of communication to ensure CERP’s IMT effectively functioned and met the required objectives.
Radhi has nearly 40 years’ service to Bapco. After joining Bapco in 1982 as an electrical trainee, Radhi moved to instrumentation where he conducted more than 20 theoretical and practical courses.
In 1985 he moved to the Fire and Safety Department, where he had the opportunity to complete training around the world with other fire safety schools including Williams Firefighting School in Texas and the Yorkshire Fire Service in the UK. Radhi has also visited numerous other countries including Spain, Oman and Hungary to maintain his expertise in the field of Industrial Firefighting.
Currently Radhi leads the induction activities for new firefighters at Bapco’s Fire School. Radhi comments, ‘at Bapco you live and work with family like you do at home’.
Abdulla Khalid is currently an Associate Shift Supervisor in the Oil Processing Department.
Abdulla graduated from the University of Leeds in 2017 with a Masters in Chemical Engineering. Abdulla joined Bapco at the beginning of 2018, initially as an Area Outside Operator. His IDP target career position is to become a Shift Supervisor after five years. This demanding career development requires candidates to successfully complete an accelerated programme that traditionally has taken much longer to complete. Bapco has promoted selected candidates with degree qualifications onto the IDP in recognition of their aptitude.
Abdulla joined BMP at the end of 2021 where his work responsibilities have been across both current and newly constructed process units that are being commissioned as part of BMP. Abdulla participated in the shutdown that occurred during Summer 2020, commenting that the work conditions and COVID-19 restrictions at that time were very challenging. Abdulla was proud of his contribution.
Abdulla describes Bapco as ‘very supportive’ and he is grateful for all the support that he has received from the early days of his education to his current position.
Abdulla Khalid Associate Shift SupervisorAsset integrity concerns prevention of equipment failure leading to hazardous events. The purpose of Asset Integrity is to prevent plant and equipment failure and safeguard asset availability. Asset Integrity supports sustainable development by reducing the risk of harm to personnel and the environment and has been identified as one of Bapco’s most important material topics.
The asset integrity management framework is documented in Bapco’s Mechanical Integrity Programme Overview Standard, which describes the programme scope and departmental responsibilities. We have a risk-based inspection standard for fixed assets, which provides Bapco-wide guidelines to ensure that the risk-based inspection processes are conducted consistently to the required standard. The basic premise of risk-based inspection is to prioritise assets whose failure leads to highest risk of loss of containment events.
Bapco has further specific standards for various sub-disciplines requiring asset integrity processes. These include standards for equipment scheduling and inspection, maintenance workflows for workshop activities, repair of relief valves and rotating equipment, and the provision of equipment and tools.
We conduct two types of maintenance for asset integrity:
• Preventive maintenance is conducted at a predetermined interval to address age related failures. Preventive maintenance includes lubrication, inspection of wearing parts and identification of damaged or poorly adjusted components. Repair work that is identified as being necessary during preventative maintenance can range from adjustment to complete overhaul of an asset that will normally be carried out within our workshops.
• Predictive maintenance is the application of measurement or testing techniques designed to detect likely future failures, to allow planned repairs before equipment failure. This provides information on the current condition of one item equipment or system to allow the timing and extent of preventive or corrective maintenance to be decided. We select predictive maintenance intervals based on engineering analysis of the probability of failure on-demand and likely time to failure.
Bapco undertakes regular active monitoring of maintenance activities to confirm performance standards, with any deviation from the standard rectified by actions assigned to relevant staff. Internal audits periodically monitor this process against the agreed risk based inspection and maintenance schedule.
Bapco has defined KPIs for monitoring the effectiveness of its asset integrity program. KPI targets are reviewed periodically. The KPIs include the monitoring of safety device failures, mean time between failure of rotating equipment (pumps, compressors, etc.) and losses of containment. Each KPI has an annualised target and overall objective to achieve the required performance.
Bapco’s process safety metrics are based on accepted global industry practice such as American Petroleum Institute (API) 754 ‘Process Safety Performance Indicators for the Refining and Petrochemical Industries’. API proposes a range of indicators for loss of containment, generally designated as Tier 1 to Tier 4, with Tiers 1 and 2 representing the most severe indicators. The GRI G4 Standard requires Bapco to report the number of Tier 1 and Tier 2 process safety events that occurred during the reporting period. These are given in the table below.
The COVID-19 pandemic represented one of the greatest challenges faced by Bapco in living memory. Whilst many organisations were able to shift their operations from office-based to remote work, Bapco was faced with the daunting prospect of having to sustain 24-hour operation of its Refinery. For the many staff in operational positions there was no option for work to be conducted remotely, shift work had to continue throughout the pandemic in a manner safe for Bapco personnel and sustainable for the company. Bapco additionally needed to undertake shutdown activities (i.e. stopping and making safe a process unit ready for maintenance) during what would later be recorded as the peak of the pandemic. Managing BMP construction schedules with the attendant workforce of several thousand contractors was a further complication.
The success of Bapco’s response to the pandemic was credited to the formation of a multi-disciplinary team with broad functional expertise in HSE. Medical practitioners from Awali Hospital worked alongside personnel from Departmental HSE teams to incorporate COVID-19 control measures into risk assessments for critical operational activities. The HSE teams, experienced in the audit of control measures, were able to quickly adapt their verification activities to include the new control measures. Toolbox talks - the regular onsite safety briefings that provide rapid dissemination of safety-related information - were adapted to include COVID-19 control measures. The focus of visits to contractor accommodation was similarly changed to consider applicable COVID-19 precautions.
Bapco not only continued operating throughout the pandemic but did so without significant business interruption to either the base business or BMP. This Special Topic describes some of the challenges faced by Bapco and how, at the peak of the pandemic, Bapco was sustained by the dedication and hard work of all personnel, who each played a role in Bapco’s response to the pandemic.
Activities and initiatives taken by Bapco’s COVID-19 response team to ensure employee and contractor safety
• 24/7 Hotline for all COVID-19 related inquiries
• Providing free accommodation and special medical care for infected individuals
• Daily updates provided to all medical personnel
• Daily call to all employees who had tested positive, to monitor physical and mental wellbeing
• Regular visits to departments to ensure that all employees are adhering to all precautionary measures
• Design and supply all posters related to the pandemic
• Hand wash training to all departments
• Rapid Antigen Test (RAT) training to all employees
• Conducting random testing
• Development and testing of Business Continuity Plans for critical areas of operation
• Creation of a COVID-19 dashboard to monitor workforce availability and any operational impacts
• Development of response procedures for COVID-19 cases and training of personnel on those procedures
• Conducting Town Halls meetings and supplementary communications throughout the pandemic to raise awareness and establish COVID-19 controls
• Reassessment of all Bapco day to day activities to incorporate any COVID-19 precautions
• Encouragement of all staff and contractors to receive COVID-19 vaccinations at the designated Bapco medical facilities
• Providing and monitoring digital thermometers at all gates
• More than 18000 cloth masks distributed
• Wearing and discarding masks procedure development
• Weekly medical visit to the Refinery canteen and Bapco Club
• Regular visits to the main operation control rooms
• Regular banner presentations at all gates
• Screen savers, updated regularly
Examples of a poster designed by the Health Promotion UnitThe outbreak of COVID-19 was declared a Public Health Emergency by the World Health Organisation on 30 January 2020. During that period Bapco health professionals had started briefing personnel on the signs and symptoms of COVID-19, and the precautions that could be taken to limit infection. Bahrain’s first COVID-19 infection was reported the following month, with the National Medical Taskforce under the guidance of His Royal Highness Prince Salman bin Hamad Al Khalifa, Crown Prince, Deputy Supreme Commander, and Prime Minister of the Kingdom of Bahrain, which started meeting and issuing directives from mid-February 2020. The Bapco CMT for COVID-19 commenced the first meeting on 26th of February 2020. The Bapco CMT and nogaholding CMT under the guidance of the National Medical Taskforce followed the “Test – Isolate – Track” process during the pandemic.
With the declaration of a pandemic by the World Health Organisation on 11 March 2020 and with rising numbers of COVID-19 infections reported in the Kingdom (mirroring that occurring across the region), the Bapco CMT coordinated response strategies and provided direction to ensure that the National Medical Taskforce directives were implemented, going above and beyond the minimum required response to create the safest possible working environment.
access by other non-critical personnel. Isolation rooms were established across Bapco for those exhibiting symptoms, and regular exercises conducted to raise awareness and evaluate the response of personnel when faced with a colleague who potentially had contracted COVID-19. The CMT adopted Business Continuity Plan (BCP) Escalation Levels that were aligned with the tiered restrictions introduced by the government. Escalations Levels from Stage 0 to Stage 4 set out the manpower requirements and priorities in the event that sufficient personnel were not available to continue normal operations.
Bapco enacted dozens of separate precautions to minimise the spread of COVID-19 between personnel who had to continue working across the organisation. The canteen was rearranged to maintain a 2m safe separation distance. All recreation areas were closed, including the Bapco Club and tennis courts, swimming pool and tennis courts at Awali. Physical meetings were stopped with use of Microsoft Teams mandated and smoking area capacity was reduced to 2 people to ensure safe distance. Food provision was intensively monitored and those involved treated as a critical workforce in a similar manner to others involved in Refinery operations. Thousands of cloth masks were issued. Continuous monitoring of the base business and BMP contractor camps was instigated early in the pandemic by Bapco. The camp was subject to regular auditing and the results were shared with the HSE Committee.
The CMT met twice a week during the initial stages of the pandemic. Under the direction of the Executive Management, the CMT included representatives from Awali Hospital, HR, HSE, Corporate Communications, IT Department and the Business Resilience team. The CMT facilitated the rapid sharing of information between diverse business functions who each had a critical role to play in Bapco’s response. Data on current numbers of infections, numbers of hospitalised cases and numbers of those recovered were shared daily by the CMT.
The CMT developed a strategy to isolate and contain identified cases of COVID-19 by individual process unit, allowing other units to continue operating without impact. Within each process unit critical workforce were identified - for example operations control room personnel. The critical workforce were subject to additional controls, such as restricting
Bapco Information Technology functions faced significant challenges in maintaining the connectivity of personnel who had previously conducted work through in-person meeting and office attendance. Bapco had taken the early decision to allow flexible home-working for the majority of office-based staff, significantly reducing the number of personnel who had to commute to Bapco’s sites. Whilst these facilities were in place prior to the pandemic, the move to home working for some employees greatly accelerated the need for remote connectivity. The Department responded by introducing a 24 hour service to assist personnel with any issues that might stop them from completing their work.
Isolation rooms were setup across the Refinery in case of needBapco has two permanently-staffed medical facilities: the Refinery Clinic and the Awali Hospital. The latter has 25 beds, two wards, two operating theatres, a maternity unit, day procedure rooms and a pharmacy. The medical staff include physiotherapists and a dietician. Bapco’s medical facilities were the focal point for Bapco’s response to the pandemic, leading on the clinic measures implemented by Bapco as information on COVID-19 was received.
At the onset of the pandemic, accurate tests to detect whether a patient had contracted COVID-19 were not available. Accurate testing was critical for Bapco to identify personnel infected with COVID-19, to prevent those exhibited no or mild symptoms from inadvertently infecting others. Bapco made an early and significant investment in technology for processing polymerase chain reaction (PCR) tests, considered the ‘gold standard’ for accuracy. Bapco purchased technology that could process batches of tests to obtain a result in 20 minutes. The tests supplemented the rapid antigen mass testing for those working at the Refinery. Testing was supplemented by temperature monitors installed at significant entry points to Bapco’s facilities - including the hospital entrance.
It is a measure of how successful these restrictions were that the hospital continued to operate with no reduced operational capability throughout the pandemic.
Bapco was an early recipient of the vaccines made available by the government in 2021. Bapco provided vaccinations on-site for both Bapco personnel and their family. Vaccine uptake was encouraged by webinars hosted by the Health Promotion Unit and attended by all Bapco personnel. At the time of this report more than 90% of Bapco personnel have been vaccinated with at least two doses and that proportion continues to rise, with the majority having received booster doses also.
With increasing knowledge of COVID-19, its symptoms and the approaches used to reduce the risk of transmission, Bapco undertook a comprehensive information campaign to raise awareness. The campaign oversaw the dissemination of information throughout the pandemic in multiple formats.
The Awali hospital enacted strict restrictions to isolate both staff and patients. The influenza centre (a separate building attached to the main hospital complex) was used to screen those with COVID-19 symptoms rather than allowing them access to the hospital. The Al Dar facility a few minutes away from the hospital was converted into an isolation centre where food and medical services were provided. Bapco also provided generous financial support for employees who needed to self-isolate in one of the 20 approved hotels. Some staff who commuted daily to work at the hospital - for example Janitors - were moved to Bapco accommodation and isolated from their families to eliminate a route of infection from the community.
Posters were a principle means of raising awareness and were produced in several languages. Screensavers were another means of disseminating information. Pamphlets were produced - also in multiple languages - for the health education of personnel.
Bapco took several important initiatives to safeguard the wellbeing of the workforce and reduce the risk of cross-infection. Personnel who experienced symptoms were encouraged to stay at home, a period of absence that was not counted as sick or annual leave. A hotline was put in place to support personnel, operated jointly by HR and Bapco’s Health Promotion Unit, and a mental health support system was developed with the support of a psychologist to promote well-being.
As the levels of COVID-19 infections peaked and then subsided, Bapco personnel have returned to work in line with government regulations. Bapco has implemented a return to work strategy required for all personnel before accessing Bapco premises, including a lateral flow antigen test for the first five days after returning. Additional testing has also been required prior to attending some essential in-person meetings. Other restrictions such as social distancing and the requirement to wear masks have remained in place through 2021.
Bapco has emerged from the pandemic stronger and with renewed confidence that it has the organisational resilience to cope with previously unforeseen challenges - a Better Normal.
9th Marine Survey
40 years of research - Page 92
Improved visual amenity - Page 98
2,672 tonnes
Waste diverted in 2021 - Page 96
2,075 TJ
Fuel gas reduction in 2021 - Page 82
Huda Yusuf currently leads Bapco’s Internal Audit Department, responsible for implementing audit process in line with international best practice. Huda’s professional qualifications include several certifications and Charterships from US and UK Associations.
Huda graduated from the University College of Bahrain with a Bachelors in Accounting and Finance. From there she joined KPMG Fakhro Bahrain, a partnership delivering national audit and accounting services within the Kingdom of Bahrain. During her career at KPMG Fakhro Bahrain, Huda was responsible for audits of leading Bahraini companies and became a local ambassador for KPMG’s Global Mobility Programme, advising local talent on the opportunities of cross-border assignments. Huda finished as a Deputy Manager at KPMG Fakhro Bahrain.
Huda then moved to London to work for KPMG as a Manager and External Auditor, responsible for a wide range of client assignments and staff management duties. During her career at KPMG Huda mentored and managed more than 100 colleagues in the UK and overseas. Huda also participated in the selection of KPMG joiners from their school leavers programme and used her career experience to provide counselling on education, career and their professional choices.
After a successful period with KPMG, Huda returned to KPMG Fakhro Bahrain before moving on to GFH Financial Group, a leading financial group who offer Islamic investment banking services within the region. This represented a change in career for Huda as she became an Internal Auditor - Senior Manager. Her new responsibilities included managing some of their largest audit programmes exceeding USD 1 billion of USA-based investments across nine states; conducting site inspection visits; and reviewing asset management process. Huda succeeding in improving GFH’s internal audit programme through efficiency increases in early detection of fraud and errors.
Huda joined Bapco in 2021 after some 14 years of experience in Internal and External Auditing to head the Internal Audit Department. Huda was delighted and honoured with the appointment as it was the first time a female had been appointed to this position. The Department reports directly to the CEO and Bapco’s Board Committee.
Huda’s responsibilities also include leading the restructuring of the internal audit department to align with international standards. This transformation has been initiated in response to the needs of BMP and comprises three pillars of enabling technology, audit methodology and governance.
Huda comments that on joining she immediately recognised the strong feeling of belonging and family at Bapco. This collegiate spirit is especially noticeable across Departments as many within Bapco have moved several times within their career and retain those links to friends and colleagues.
Huda feels privileged to have joined Bapco and believes that the hiring of senior women at Bapco will be just the first of many milestones.
Huda Yusuf Manager, Internal Audit
“ The hiring of senior women at Bapco will be just the first of many milestones
Ahlam Ebrahim Mohammed leads the Corporation Communications Department (CCD), which is responsible for maintaining Bapco’s brand image both internally and externally.
Ahlam joined Bapco in 1998 after completing an Advanced Diploma in Business Administration from the Bahrain Training Institute. Ahlam’s first four years were spent as an Assistant within the Translation Department. Ahlam was subsequently promoted to Editor of Bapco’s Arabic Publications, a position that she held for 10 years.
During her tenure as Editor, Ahlam completed several English courses, allowing her to develop bilingual language skills and therefore to oversee translation tasks within Bapco.
In 2007 Ahlam graduated with a Bachelors of Arts in Mass Communication (Public Relations and Advertising) from the University of Bahrain. The degree course provided Ahlam with experience of digital media, public relations and advertising, radio and television and print media - all used by Bapco to communicate with its stakeholders.
Ahlam commented that, during this time, CCD only had five employees but grew steadily to 12 to manage the increasingly diverse methods of mass communication used by Bapco - for example social media. Ahlam was recognised early by Bapco as an employee with leadership potential, with Ahlam attending the Institute of Leadership and Management to complete a Certificate Level 2 in Team Leading. Following award of the certificate, Ahlam was promoted to Superintendent for Corporate Publications where she was responsible for Bapco’s Annual Report, the weekly newsletter and other key corporate publications. Ahlam comments that some of her highlights during this time include organisation of high-profile events such as BMP Inauguration and the AB Pipeline Ceremony.
Whilst a Superintendent, Ahlam completed several further postgraduate courses including the Chevron Future Leaders Track Training, a course from the International School of Communication Scotland, and her Certificate Level 3 in Principles of Leadership and Management from the Institute of Leadership and Management.
In September 2021, Ahlam was assigned to lead the activities of CCD as Acting Manager, with accountability for the Department. Her day to day responsibilities include oversight of team performance, supervising events and publications, supporting Bapco sponsored events and Bapco’s Corporate Social Responsibility initiatives.
Ahlam comments that Bapco has supported her career and education ever since she first joined - one indicator of the company’s commitment to women. Ahlam notes that Bapco is supporting women to work in different professional disciplines and is very proud to be part of this organisation.
Ahlam has been closely involved in the successful publication of Bapco’s sustainability reports, providing images and carefully reviewing content against Bapco’s communication strategy. It is important to be able to recognise the profile of a senior Bapco employee who has contributed so much to this report.
“Bapco has supported my career and education ever since I first joined
Energy and Climate Change refers to global warming attributed to the consumption of fossil fuels. Bapco continually improves its energy efficiency through technical upgrade of our facilities and optimising the way in which those facilities are operated. Some of these initiatives are outlined in this section.
Our Energy Conservation Policy aims to reduce overall energy consumption to conserve natural resources. Bapco has established an Energy Committee with dedicated Energy Champions to focus on energy conservation through monitoring energy use, raising awareness and implementing energy efficient programs. We use solar energy to offset our consumption of fossil fuels. Solar energy generated onsite by us supplies our Waste Water Treatment Plant (WWTP) and the buildings in the Awali township.
It is our responsibility to:
• Develop energy management programs with the objective of improving energy efficiency;
• Emphasise energy conservation as a factor in the design of new facilities and during operation of all assets; and
• Encourage employee awareness of energy consumption within the home and workplace.
To improve our energy efficiency we:
• Operate existing facilities efficiently until such time that there is an economic justification for capital investment to reduce the energy consumption;
• Adopt initiatives that reduce the environmental impact of energy production within the Kingdom of Bahrain;
• Participate in various committees at the national level focused on energy conservation and development of renewable energy to meet Bahrain’s national target of 5% Renewable Energy by 2025 and 10% by 2035;
• Develop and coordinate energy conservation and optimisation strategies within the company;
• Use innovative and efficient technologies that are economically justifiable; and
• Ensure that all employees are aware of the importance of energy conservation through focused campaigns and programs.
To fulfil our responsibilities under the Energy Policy, Bapco established an Energy Group, as part of the Technical Services Department, and an Energy Committee which is formed by a multidisciplinary team with members from diverse departments.
The energy group and the committee focus on energy conservation throughout the Refinery via projects and initiatives focusing on energy reduction, efficiency improvement, raising awareness throughout energy campaigns and importing new technologies like energy monitoring software. 40 Energy Champions working directly with day-to-day field activities to promote and enhance energy conservation culture.
Our energy conservation awareness is not just limited within the company, but also extended to our community. We participate in safety weeks targeted to the public, as well as visiting schools and giving presentations on energy conservation.
Bapco is potentially impacted by climate change both through the physical risks for our industrial processes and the changing regulatory conditions under which we operate.
Climate change increases the potential physical risks of operation. Weather extremes are generally acknowledged to be more severe and occur more commonly. This requires us to consider the impact of potentially severe weather on both the design of our process units and the training of personnel who may encounter more extreme weather. Operational constraints such as wind loading are routinely considered within the design and operation of our facilities. We have invested in augmented reality training for personnel who have to work exposed to weather conditions, for example those working at height. Work would additionally not be undertaken if environmental conditions were unsafe.
Climate change also leads to increased ambient sea water temperature. Bapco requires water as the cooling medium to the various Refinery units, for utilities requiring a supply of water, and to make up (or replace) water lost during evaporative cooling. Refer to 303-03 under Our Environment. Both seawater and groundwater are used by Bapco in our refining activities. Climate change places greater demand on cooling processes, as greater volumes of water are required for heat transfer or during evaporative cooling. We have comprehensively redesigned our cooling water processes to support BMP and have considered projected seawater temperature rises within our design criteria. These considerations include the return water temperature to ensure that we will continue to meet the statutory requirements for water discharge set by SCE.
The world economy is fundamentally shifting in its view of fossil fuel consumption as nations seek to limit the impacts of climate change. Bapco, as a producer of petrochemical products, will inevitably be impacted with these changes. This is why we are initiating several transformation programmes now to better align Bapco to meet the future challenges. BMP is our medium-term response to changing economic need, improving both our product slate (i.e. the range and commercial value of our petroleum products) and the energy efficiency with which these products can be produced - thereby also helping reduce our impact on climate change.
Bapco’s facilities require fuel gas and electricity to function. Bapco has the capacity to generate both types of energy onsite, with the balance purchased from third party energy supplies. Refer to the table below for our data trends. The engineering basis for power consumption is thermal for fuel gas and electrical for electrical power.
The fuel gas flowrates are converted into thermal energy equivalents using the calculated Lower Heating Value of the fuel gas. Gas flaring (except for purge and pilot gas) is not included in the total fuel consumption.
For the current reporting period, data covering the energy consumption outside the organisation is not available.
Bapco calculates energy intensity using the proprietary Solomon Energy Intensity Index®, and therefore cannot publish these data.
This Disclosure concerns the reduction in energy requirements of sold products and services and therefore does not apply to Bapco.
Throughout the year 2020 and 2021, Bapco has taken several initiatives to reduce its energy consumption that include:
• Shutting down some crude and secondary unites instead of running at turndown due to low market demand;
• Optimising Sulphur recovery unit Incinerator by reducing the stack Temperature;
• Optimising of excess oxygen at process heaters;
• Optimising steam to Booster ejector;
• Optimising stripping steam;
• Optimising cooling by shutdown overhead fan coolers;
• Implementing the daily recommendation of the Energy real time Optimizer “Visual MESA”; and
• Maximising utility of the Hydrogen Makeup Compressor using HydroCOM “step-less load management system”.
The output of these initiatives are reflected by the data reported in the table below.
Mohammed Ghassan has worked at Bapco since 2016 in the Engineering Department as an Environmental Specialist, attached to the BMP team.
Mohammed graduated with a BEng in Mechanical Engineering from Manchester Metropolitan University and an MSc in Environmental Engineering from Newcastle University.
Since joining Bapco, Mohammed has been involved in a range of interesting projects including remediation of pitch ponds and environmental compliance of onsite construction activities. Involvement with BMP has afforded Mohammed with valuable experience of a major Refinery expansion programme and the many activities designed to minimise its environmental impact.
Mohammed comments that there is ‘nowhere better on the island’ than working at Bapco, a company that in his opinion provides the opportunity for all to express the views to come to the best collective decision on environmental matters.
In his spare time, Mohammed Ghassan is an accomplished author, having published the “Laymans Guide to Climate Change”, an explanatory guide that aims to educate on the basis for understanding climate change.
Mohammed’s guide breaks down the issue of climate change in an accessible manner for all readers. The book teaches about the fundamental mechanisms that govern our climate, and discusses topics such as whether recent increases are anthropogenic, why the climate change ‘debate’ exists and the role of climate treaties such as the Kyoto Protocol.
The book argues that we already possess the necessary technological tools to mitigate the worst of climate change, however it is the political and economic framework encouraging uptake of these technologies that historically has been missing. National initiatives such as the Kingdom of Bahrain’s Economic Vision 2030 are now providing that vital framework for action.
Air emissions refers to the release of gases into the atmosphere that occur as the result of our activities. Through our energy efficiency initiatives and renewable energy generation we aim to reduce our greenhouse gas emissions, therefore lower our impact on global warming.
We closely monitor all Refinery emissions for regulatory compliance and to understand our total environmental footprint
We prepare an annual GHG inventory report to determine our carbon footprint. Our Refinery includes many important energy saving technologies that help to further reduce our GHG emissions. We have improved the energy efficiency of our Refinery heaters, replacing three old heaters with a single higher efficiency heater at a cost of US$26.5 million. Our Low Sulphur Fuel Oil complex captures up to 200 tonnes per day of CO2, from the No. 1 Hydrogen Plant waste gases, and routes it to a plant operated and owned by a third party for reuse. Our solar project, with solar installations in use across our sites, makes a significant contribution to renewable energy and is the first of its type in Bahrain. We also contribute to carbon emissions offset through our Mangrove Nursery and planting project, and by maintaining the Princess Sabeeka Park at Awali.
Bapco has been recording its Scope 1 and Scope 2 GHG emissions since 2014 to support the compilation of the Bapco annual GHG inventory report. Scope 1 emissions refers to direct emissions from assets owned by or controlled by the company, such as process units and company vehicles. The methodology used to prepare the Scope 1 and 2 GHG emission data is based on the 2006 IPCC guidelines, the IPCC inventory software (version 2.691, January 2020), IPIECA petroleum industry guidelines for reporting greenhouse gas emissions (2011) and the API compendium of greenhouse gas emissions methodologies for the oil and natural gas industry.
Scope 2 GHG emissions refer to indirect emissions from energy consumption that are a consequence of asset activities, but which occur at companies outside of the organisational boundary, e.g. emissions attributed to electricity imported for operation of the Refinery and other facilities.
Scope 3 GHG emissions refer to all other indirect emissions that result from a company’s activities that are not Scope 2 emissions (e.g. contracted transport). Bapco currently does not report on Scope 3 emissions but will keep under review for future reports.
Bapco estimates its emissions intensity in tonnes of CO2 equivalent (CO2e) per unit of Utilised Distillation Equivalent Capacity (UEDC), the latter a standardised measure of Refinery throughput.
Bapco’s initiatives for energy reduction listed under 302-04 will be the main driver for GHG emissions reduction. Bapco has additionally improved the performance of several Refinery units, giving the following calculated reductions:
• 7,000 tonnes of CO2/year by improving the performance of the fired heaters;
• 26,000 tonnes of CO2/year by replacing 5 crude distillation unit and 3 older low efficiency fired heaters with a single high efficiency heater; and
• 40,000 tonnes of CO2/year by recovering the CO2 from the hydrogen plant and re-routing the gas for use by a third party.
In addition, Bapco’s community projects have had an positive impact on the GHG emissions reduction:
• 2,504 tonnes CO2/year calculated from Princess Sabeeka Park;
• 7.7 tonnes CO2/year from the Eker garden rehabilitation; and
• 3000 tonnes CO2/year from the 5MWp BDSEPP
Since 2020, Bapco has recharged or replaced all refrigeration and air conditioning equipment containing R-12, substituting with refrigerants that have a low ozone depletion potential (R-22) or no ozone depletion potential (R-410a and R-407C).
Emissions of ODS (metric tonnes of CFC-11)
GRI 305-07: Nitrogen oxides (NOx), sulphur oxides (SOx), and other significant air emissions
Unit shutdowns during 2020 led to a temporary increase in our SOx emissions, recorded in the table below. During the 2021 reporting period there were no shutdowns impacting SOx emissions, which therefore returned to levels similar to previous years.
SO x and NO x quantities are estimated from heater duties and assume excess oxygen. Empirical formulas are used in calculation.
Refer to the graph below for the normalised quantity of SOx and NO x emissions per total crude throughput.
Haya Darwish is an environmental engineer by training and a Bapco International Scholarship Student. Those accepted onto the scholarship programme are supported by Bapco during their further education and return to work for Bapco following their degree.
Haya attended the University of Colorado, Boulder and graduated in 2017 with a Bachelors in Environmental Engineering and a Minor in Geology. Haya also holds ISO 14001:2015 Lead Implementor and NEBOSH qualifications. Haya’s successful application as a Scholarship Student meant that she was able to return each summer recess for work at Bapco, gaining valuable experience and insight into her future career.
Haya started working full time for Bapco in 2018 in the HSE Department as an Associate Environmental Engineer, participating in a four year development programme that has provided Haya with a comprehensive grounding in the many areas of environmental engineering relevant to Bapco.
Haya has been involved in several technical and social projects, including environmental compliance monitoring and reporting, remediation planning, and multiple HSE community awareness activities such as the Green School Awards as well as volunteering for INJAZ. Haya is proud to be have been part of the team that developed Bapco’s first Sustainability Report and is now closely involved in producing subsequent reports.
Haya comments that Bapco is a supportive, welcoming and flexible working environment where your potential is recognised.
Hussain Al Oraibi works in the Power and Utilities Department at Bapco and has held many technical positions throughout his 25 year career.
Hussain joined Bapco in 1997 with a Diploma in Electrical Engineering from the College of Engineering, University of Bahrain. Hussain’s initial appointment was Area Outside Operator, and after some years experience was promoted to a Head Operator Position. During this period he played an important role in many projects, for example Bapco’s Steam Turbine Replacement Project completed in 2012. Hussain has held a Shift Supervisor Position where he was responsible for more than 25 operators and trainees.
The following year Hussain was picked for the Bapco Future Leader Track Training course, a milestone in Hussain’s career as it recognised his leadership and management abilities.
In 2014 Hussain was again promoted on the next step of his career to Specialist Electrical Distribution. Bapco encouraged Hussain to pursue Further Education and qualify as an electrical engineer. Hussain studied for a BEng in Electrical Engineering, graduating in 2018.
Hussain’s technical expertise has been in demand and he has travelled internationally to support BMP, visiting Korea and Rome.
Hussain comments that he enjoys working in operations and feels fortunate to have had career with such a supportive employer.
Water Withdrawal and Consumption refers to the quantity of and sources of the water used in our operations.
GRI 103-01,
We use water as a coolant throughput for Refinery processes to achieve the desired temperature for process operations. We monitor the return water temperature to meet the statutory requirements for water discharge. We try to minimise our groundwater abstraction, limiting its use to the Refinery cooling towers make-up where seawater would otherwise potentially cause corrosion.
GRI 303-03: Water withdrawal
The GRI Standards define ‘fresh water’ as water with Total Dissolved Solids (TDS) of less than 1,000 mg/l. Other sources of water with TDS greater than 1,000 mg/l are referred to by the GRI Standards as ‘other water’.
Groundwater is referred to as ‘well water’, which is supplied to the Refinery cooling towers as make-up water. The withdrawal flowrate is calculated based on the approximate circulation rates, considering evaporation and windage losses within the cooling towers. No changes have occurred for the estimated cooling tower circulation rates, therefore the calculated reported numbers are constant from 2018 to 2021.
Sea water withdrawal rates are based on the pump capacities in the High Lift Pump House, which supplies sea water as the cooling medium to the various Refinery units and also as feed to the desalination units in the Utilities Plant.
GRI 303-05: Water consumption
Groundwater consumption is assumed to be equal to the groundwater withdrawal due to the absence of flowmeters. As indicated in disclosure 303-03, the calculation is based on the approximate circulation rates, considering evaporation and windage losses within the cooling towers.
Sea water is fed to the desalination units and a reverse osmosis plant to produce flash evaporated distillate, which serves as boiler feed water to the steam generators/boilers and as feed to the Drinking Water Plant. The data is based on the daily and monthly average flowmeter readings.
Effluent Management refers to the methods that we use to dispose of our liquid effluent produced from our processes. The water we use may become contaminated as it passes through our processes. Through the correct treatment and disposal of our waste water we can prevent pollution of our environment.
Bapco has developed company standards for its effluent management that comply with Ministerial Order No. 3 of 2021 with respect to Environmental Standards (Air and Water). The existing Refinery discharges comprise cooling water, process waste water, site drainage and domestic type effluent (from offices). Bapco uses a state-of-the-art advanced membrane bioreactor technology for the treatment of its effluent, combining membrane ultra-filtration of solids with biological waste water treatment. The technology is recognised internationally as offering superior energy efficiency compared to other biological waste treatment processes. The membrane bioreactor technology is used within our WWTP and Sewage Treatment Plant (STP).
The WWTP is a 19,108 m3 per day facility for treating process waste water to meet discharge limits prescribed by the SCE. Process effluents and drainage water that may contain oil or other contaminants are routed, through a dedicated oily water sewer network, to a primary treatment system comprising oily water separation and induced air flotation. The effluent then passes through the WWTP that uses membrane bioreactor technology, which in turn reduces the organic loading and nitrogen content and removes the dissolved contaminants from the process effluents before discharge to sea via the main outfall.
The STP is a 1,000 m3 per day facility for treating effluent from offices and accommodation blocks. The STP uses dissolved air flotation, the membrane bioreactor biological treatment and a sludge treatment system before discharge to the sea via the main outfall.
Treated effluent is returned to the sea via the discharge flume in compliance with discharge limits as prescribed by the SCE. Cooling water and ‘reject water’ from the desalination plants is returned to the sea at a controlled temperature and salinity that does not exceed the parameters set by SCE.
Groundwater discharge volume is calculated based on the approximate circulation rates, considering evaporation and windage losses within the cooling towers. Seawater discharge volume is calculated by deducting the sea water consumption volume from the withdrawal.
We have been conducting regular marine assessments around the Bapco Refinery and Sitra operating facilities since 1981, using the same well known international experts who work for the World Maritime University, International Maritime Organisation and the Lund University in Sweden. The same stations have been visited measuring the same parameters, providing a unique insight into anthropogenic impact for 40 years. The survey is one of the longest running of its type in the region and followed the same protocol as in previous studies (1981, 1987, 1992, 1997, 2002, 2007, 2011 and 2015) to continue to provide consistent data to observe long term trends. The different variables measured supported analysis of long term ecosystem health.
The 9th marine assessment was carried out in 2021 as part of our commitment to the monitoring, preservation and improvement of our marine environment, providing some of the most comprehensive data of its type in Bahrain. The surveyed area covered the coastal waters outside the industrialized northeastern coast of Bahrain. Samples were collected from south of Askar along the coast towards the north and included parts of the reef area towards the east, along Sitra island and the jetty used by Bapco.
The survey has confirmed the continuing impact of land reclamation and other industrial activities on ecosystem diversity. However, for some important pollutants the concentrations in collected samples continue to decrease - for example petroleum hydrocarbons where an improvement is noted in the sample data compared to data from two decades previously. Pollutant levels from samples taken in waters outside the Refinery are not significantly different from those found in the larger survey area, or indeed compared to other areas in the Gulf near industrial areas.
“
The same stations have been visited measuring the same parameters, providing a unique insight into anthropogenic impact over 40 years
Waste management refers to the methods we use to correctly dispose of our waste. Sustainable waste management involves not only reducing and reusing our waste products, but also ensuring appropriate waste re-use, recycling, treatment and disposal.
Our management approach prioritises waste elimination, minimisation and re-use followed by recycling, treatment and safe final disposal. Our Hazardous Waste Management Facility (HWMF) was completed in 2006 and was built to US Environmental Protection Agency standards at a cost of US$5.2 million. The HWMF includes a Class 1 Hazardous Waste Landfill with a capacity of 68,000 m3 and a Stabilisation Unit for stabilising leaded legacy waste. The facility is currently being operated by a specialised third-party contractor. This project uses best available technology for the treatment of hazardous waste and significantly improves our ability to recycle this difficult-to-treat waste class, reducing our reliance on disposal of waste that cannot be recycled. We classify the waste generated from our activities into four categories:
• Hazardous waste;
• Non-hazardous industrial waste;
• Domestic and municipal waste; and
• Medical waste.
We have adopted a waste management strategy based on Crittenden (1995) and the UK Environmental Protection Agency (2008), which suggests a hierarchy of waste management: the highest priority will be source reduction, followed by recycling, then treatment and the lowest priority will be waste disposal. All our new projects follow the waste management hierarchy and are supported by a waste management plan. Where relevant and as required by the SCE, we conduct Environmental Impact Assessments for new major projects, to evaluate waste elimination/ reduction options in accordance with our ‘Standard for Environmental Assessment of Engineered Projects’.
We continuously monitor the amount of waste generated by our existing operations and identify opportunities for further waste minimisation. All approved waste reduction proposals are considered within our EMS ISO 14001 program.
Bapco signed a Memorandum of Understanding (MOU) in January 2015 with the Arabian Gulf University (AGU) to provide support and funding for research projects as part of the company’s Corporate Social Responsibility (CSR) endeavours.
Under this MOU, an agreement was signed between Bapco and AGU in October 2018 to fund and support a research project for the treatment of Refining waste oily sludge using bioremediation.
Preliminary work with AGU was carried out in November 2016 where different oily sludge samples were collected from Bapco Refinery. These samples were analysed by AGU and showed the potential of microbial cultures to treat refining oily sludge. However, further optimisation of the bioprocess conditions was necessary. We therefore commissioned further research that started in October 2018 to optimise the conditions for bioremediation of waste oily sludge.
This research study will help Bapco to identify potential environmentally friendly and cost-effective solutions for the treatment of waste oily sludge using bioremediation. The research is part of a broader programme of local academic collaboration supported by Bapco. The study was completed in July 2021 and concluded that the biotreatment of oily sludge can be achieved in the future, taking into account the required conditions to attain the desired bioremediation results.
Refer to disclosures 306-04 and 306-05 for further information on disposal methods. Over the last 3 years, the quantity of hazardous waste generated has increased for reasons associated with BMP excavation, periodic disposal of WWTP membranes, and tank cleaning that generated oily waste during shutdown.
In February 2017, we launched our Waste Segregation and Recycling Programme using colour coded bins for plastics, metal cans and paper/ cardboard collection. Colour coded cages and recycling boxes are used within the Refinery, Sitra Tank Farm, Marketing Terminal and Wharf. The programme has also been rolled out throughout our Awali offices and Township and BMP offices. Small office paper bins have been purchased and distributed in offices for the collection of paper only. In July 2021, steel recycling boxes were also distributed to offices in Awali including Awali Hospital, which increased the total of deployed bins from 186 to 232. This programme has helped conserve resources and reduce the amount of waste going to landfill on daily basis. Waste diverted from disposal is ultimately less likely to pollute the natural environment. In addition to reduction of greenhouse gases and pollution resulting from sending such waste to landfill, other benefits of this programme include conservation of resources and cost savings.
A total of 185 tonnes of recyclable materials have been collected since the launching of the programme in February 2017. Corresponding savings to date are estimated to be approximately US$10,945 on disposal costs, 170 tonnes of CO2 equivalent and a saving of 4,078 trees. The initiative supports sustainable development through reducing energy and resource use. The programme has helped to challenge existing behaviours around waste segregation and disposal. We believe achieving this change in behaviour is beneficial within the wider community where recycling has not previously taken place.
Waste treatment is the next priority and is carried out to minimise the impact on the receiving environment. We follow SCE regulations to decide on the most appropriate treatment methods and we ensure that the treated waste passes relevant acceptance criteria before disposal. We are also exploring options for oily sludge treatment from our facility which included a trial conducted by a third-party approved recycler in July 2021, to remove additional sludge in 2022.
Waste disposal is our least preferred option. All wastes generated at Bapco intended for disposal are collected, transported, and disposed of in accordance with relevant regulations. Domestic and municipal wastes are stored in waste skips and collected by a third-party contractor for disposal to Askar Municipal Landfill site. Medical waste generated from the Refinery Clinic and Awali Hospital is collected by a third-party contractor for off-site incineration as a final disposal route.
Hazardous waste directed to disposal are incinerated at an external facility or sent to Bapco landfill at the HWMF
“Waste diverted from disposal is ultimately less likely to pollute the natural environment
Project Description
We are enhancing the green spaces across our facilities in a project referred to as Refinery Beautification, with the objective of creating a healthier work environment for employees.
A significant project component is the landscaping of the Refinery entrance, with replanting of the North gate roundabout and the addition of several palms.
Within the Refinery Bapco has started a pilot project to determine the best types of tree for planting. We are selecting trees that require minimal watering, large green foliage for improved visual amenity and are evergreen to prolong this amenity throughout the year.
Bapco has extended the planting at various locations close to Refinery and Awali offices to provide green spaces adjacent to paths. Seating space is provided via benches located in these areas.
“
We are selecting trees that require minimal watering, large green foliage for improved visual amenity and are evergreen to prolong this amenity throughout the year
Biodiversity concerns the health of plants, animals and the ecosystems of which they are a part. Maintenance of the health of an ecosystem is a component of sustainable development, which underpins economic development and prosperity, and helps develop locally distinctive and sustainable communities.
We thoroughly assess the impact of our projects to evaluate any biodiversity impact. For instance, prior to the start of BMP two assessments were conducted on biodiversity: an Environmental and Social Impact Assessment (ESIA) that focused on the broader potential environmental impact of BMP, and a Critical Habitats Assessment (CHA) which focused specifically on the potential impact of BMP on the biodiversity of the surrounding areas and identified appropriate mitigation measures. In addition, and specifically for BMP, a Biodiversity Strategy Document and Biodiversity Action Plan were produced to ensure the prevention of any adverse impacts on biodiversity that might result from the construction work.
GRI 304-01: Operational sites owned, leased, managed in, or adjacent to, protected areas and areas of high biodiversity value outside protected areas
In 2021 Bapco conducted an ecological baseline study of the Arad Bay lagoon. This baseline study will serve to understand improvements in ecological habitats after Bapco’s efforts in transplanting mangroves in the area. Subsequently, Bapco transplanted 772 mangrove seedlings cultivated at Bapco’s Mangrove Nursery at the Refinery to different areas within Arad Bay. Once the mangrove stands reach maturity, another ecological study will be conducted to assess the changes to the local habitat. Not only will this study serve Bapco but will provide insight to suitable environments for mangrove transplantation, which aligns with the national plan to quadruple mangrove coverage and reach net-zero by 2060.
GRI 304-02: Significant impacts of activities, products, and services on biodiversity
With the development of BMP came the requirement to construct a new pipe bridge crossing the Ma’ameer Channel, a protected seawater canal to the East of Bapco’s Refinery, connecting Tubli Bay to the sea South of Bapco’s Refinery. Removal of some 30 mature mangrove trees was a requirement to construct the new pipe bridge crossing. The Ma’ameer Channel is frequented by migratory birds during the winter breeding season in Bahrain. Bapco has pledged to offset the removal of these mangroves and recreate a similar habitat in nearby Ras Sanad Mangrove Reserve in Tubli Bay as well as Arad Bay Reserve in Muharraq.
The marine ecosystem South of Bapco has seen degradation over the past 40 years. Our marine assessment studies which have been ongoing for 40 years indicate that lead and other petrochemical pollutants used in our refining process and which might contributed to this impact, have decreased significantly. Coral and sea grass loss continues due to the increasing land reclamation and dredging activities outside Bapco’s direct control. Bapco, however, is an active stakeholder in elevated governmental discussions and continues to raise sustainable, sciencebased alternatives in discussions of major projects.
Refining activities can have indirect impacts on biodiversity such as acid rain and exposure to hazardous air pollutants, however, there is no data which attribute this to Bapco activities. Bapco ensures to comply with all relevant air quality and effluent regulations and industrial best practices and continues to put all necessary measures in place to ensure that the commitment of the protection of the environment is met in line with Bapco’s EHS Policy.
Flamingos are a regular visitor to the ChannelIn coordination with the SCE, Bapco is conducting regular clean-up activities along the shorelines of the Ras Sanad Mangrove Stands. Bapco is also engaged in restoring degraded mangrove stands within Ras Sanad by transplanting new mangrove seedlings grown in Bapco’s dedicated mangrove nursery.
Bapco conducted an Environmental Baseline Study in Arad Bay Reserve prior to commencement of its mangrove transplantation project in the same area. The study aims to assess the ecological baseline in Arad Bay, which will later enable the detection of changes potentially induced by the mangrove transplanting process through examining specific indicator taxa and standard biodiversity indices. The results of this study shall be incorporated in the long-term monitoring programs to assess the effects of the mangrove transplantation project on marine biodiversity.
Following the baseline study, Bapco undertook a major mangrove transplantation project in Arad Bay Reserve to offset mangrove loss due to the construction of the new BMP pipe bridge in Ma’ameer Channel. A total of 772 mangrove stands were transplanted in the Bay in August 2021, and Bapco actively monitors the health of these stands on a weekly basis. The baseline monitoring programme is expected to continue for the next 15 years.
In recent governmental decisions to widen the Ma’ameer Channel, Bapco successfully lobbied to place mitigation measures which ensure construction activities have minimal effect on mature mangrove stands which were planted by Bapco in the past. The mangrove stands are in an intertidal zone close to Bapco’s Outfall area and frequented by sea birds. The widening activities of the Channel will now include culvert pipes to ensure hydrodynamic flow surrounding the intertidal zone and reduce the risk of habitat degradation.
In coordination with the SCE, Bapco is conducting regular clean-up activities along the high level security fence installed at Ma’ameer Channel. The clean up activities started in January 2021 and have been continuing since then. The clean-up includes the removal of excess algae, debris, general waste and any other material which is accumulates along the fence and potentially obstruct the flow of water through the channel. Bapco additionally participates in clean-up activities for the area that are organised by third parties, such as RECSO. These activities align with BMP stakeholder engagement efforts to ensure that the surrounded communities, including the Ma’ameer area, can live in a clean environment with a good quality of life.
GRI 304-04: IUCN Red List species and national conservation list species with habitats in areas affected by operations
We have classified the IUCN red list species and national conservation list species with habitats in areas affected by our operations under two level of extinction risk: near threatened and least concern. Refer to the below table which lists all species by level of threat.
Bar-tailed Godwit
Eurasian Curlew
Least concern : Water bird species
Great Cormorant
Western Reef Heron
Great White Egret
Grey Heron
Greater Flamingo
Black-winged Stilt
Common Ringed Plover
Kentish Plover
Lesser Sand Plover
Greater Sand Plover
Pacific Golden Plover
Grey Plover
Little Stint
Temminck’s Stint
Dunlin
Broad-billed Sandpiper
Curlew Sandpiper
Whimbrel
Spotted Redshank
Common Redshank
Marsh Sandpiper
Common Greenshank
Terek Sandpiper
Common Sandpiper
Ruddy Turnstone
Black-headed Gull
Slender-billed Gull
Lesser Black-backed Gull
Yellow-legged Gull
Caspian Tern
Lesser Crested Tern
White-cheeked Tern
Saunders’s Tern
Least concern: Non-water bird species
House Sparrow
White-eared Bulbul
Crested Lark
Collared Dove
Common Myna
House Crow
Collared Pratincole
Bee-eater
Barn Swallow
Common Kestrel
Cattle Egret
Yellow Wagtail
“Bapco undertook a major mangrove transplantation project in the Arad Bay Reserve
Species of wading bird at Arad Bay, where Bapco has supported the planting of mangroves
Sponsored 2020-21 - Page 118
Cultural contributions - Page 127
New 2021 suppliers - Page 125
Included in this section - Page 129
Bapco’s Health Promotion Unit provided extensive support to the employees and the community during the pandemic
Haifa Almarzooq is currently the Acting Manager for the Operational Excellent Department, within the Engineering Division. Haifa holds a Bachelor in Computer Science with Minor in Statistics, from Kuwait University, in which she graduated with Distinction, and a Masters in Business Administration with Finance Concentration at the New York Institute of Technology, where again she graduated with Distinction.
Haifa recalls her family encouraging her to consider a career in medicine. However, during her formative years, Haifa had developed a strong interest in computers, which led to the eventual selection of her degree course and then a career at Bapco.
On joining Bapco, Haifa gained experience on major projects such as new steam turbo generator control systems and the A/B pipeline. Haifa was promoted to a Senior Control Systems Engineer and then Superintendent Systems Support for the Process Control and Instrumentation Department. Haifa commented that she streamlined more than 15 major contracts for automation system suppliers during her time in this role.
In 2014 Haifa moved to Risk and Reliability where she led Risk Management and Centralized Reliability Engineering. Haifa managed a team of engineers and represented her department on committees including that for EHS and Crisis and Emergency Procedure (CERP).
Since 2019 Haifa has been the Acting Manager for the Operational Excellence Department where she manages a team of 30 professionals from a wide range of academic disciplines. Haifa has rolled out Lean Six Sigma projects, executed improvements to Bapco’s Operational Dashboard and led on Process Safety Management strategy. Haifa is also chairing the GDA Operational Excellence Committee.
During her career Haifa has always actively supported fellow women engineers. Haifa is proud to have been the member of the very first committee established by SCW to draft the Bahrain report on Convention of Elimination of all forms of Discrimination Against Women. In 2017 Haifa chaired the Bahraini Female Engineer Forum in support of SCW, which was organised by the then National Authority of Oil and Gas. Haifa has also participated the Society of Petroleum Engineers (SPE) and Leadership Excellence for Women Awards (LEWAS) 2018 and 2019. In 2021 Haifa spoke at the European Society for Quality Research (ESQR) conference, where Bapco was a recipient of an ESQR Quality Achievement Award (image opposite).
Haifa has managed to combine a successful career with raising three children. Haifa comments that her long career at Bapco is due to the many varied and interesting roles available to women throughout the company, which has allowed Haifa to pursue her passion in many technical and professional areas. Haifa observes that nowadays there is more support for women in Bapco and that there are more opportunities open to women compared to when she graduated, and reflects that it is an exciting time for women in this industry.
Haifa
“ There is more support for women and more opportunities - an exciting time for women in this industry
Dana Ebrahim Bukhammas joined Bapco in July 2021 as the Chief HR Advisor at Bapco and was appointed as Manager - Human Resources in December 2021.
Dana originally studied a Bachelors in Business Management at the University of Bahrain, reflecting her early interest in human capital management. Throughout her career Dana has continued to study, completing an Executive Human Resource Programme from the University of York and most recently studying for a Masters in Business Administration at Ahliya University, Bahrain.
Dana started her career in corporate sales with MTC Vodafone, where she held the position of Team Leader. Dana comments that this was a demanding role with sales targets and an expectation to manage 24-hour operations. However, Dana’s journey towards her current role in HR started when she moved departments at MTC Vodafone to join their Recruitment and Selection unit. Dana started to focus on internal and external recruitment, management of organisational structure and various special projects as directed by senior management. Dana was promoted several times from Team Leader to Manager and eventually to Director, HR where Dana reported directly to MTC Vodafone’s CEO.
During her career at MTC Vodafone, Dana became involved in the national Zain Al Shabab youth talent development programme. Dana commented that the programme has enabled more than 2000 Bahraini youths to find a permanent job and hence has been a true highlight of her career.
Dana joined Bapco from MTC Vodafone with several responsibilities that include leadership of the Digital Transformation Strategy alongside accountability for Bapco’s Human Resource Department.
Dana collaborates with the Oil and Gas Academy to screen and recruit the young Bahrainis who have finished their initial training programme at the Academy.
Dana is certified in Management Learning Programmes from the Association for Talent Development, is a Certified Counsellor for the Power of Choice Theory and holds a Level 5 qualification with the Chartered Institute of Personnel and Development. Dana is currently studying Executive Coaching Level 7 from the Institute of Leadership and Management.
Dana is very proud to have the opportunity to work at Bapco with its high positive impact on the economy and community of Bahrain. Dana observes that those who work at Bapco exemplify ‘brand value’; personal investment in the company’s mission and values. Dana is exciting to be working at Bapco during a time when there is such significant investment in Bapco’s talented workforce to support its future growth.
“Those who work at Bapco exemplify ‘brand value’; personal investment in the company’s mission and values
We manage our community impacts through a variety of measures that include social impact assessment and local community development.
We continue to work closely with our community via our CSR programme that includes:
• Creation of job opportunities at all levels for Bahrainis;
• A structured training and development programme for all employees;
• Empowering women and promotion of senior job opportunities for women;
• An active wellbeing programme encompassing a range of public health issues;
• EHS community awareness programs through school and home visits;
• Close cooperation with non-governmental organisations to understand their needs; and
• Sponsorships for various events/programs relating to sustainability.
BMP, as an internationally funded project of national importance, closely monitors social issues and actively manages any emerging community impacts. We have a dedicated project team that includes a Social Performance Officer and Community Liaison Officers.
All our major projects are subject to social impact assessment. We publish the latest social, environment and cumulative impact assessments on our website.
As part of the BMP social impact assessment, we have developed a stakeholder engagement plan, which provides for events and activities to be shared via social media. Our plan complies with international financing performance standards on environmental and social responsibility.
We have a local community development programme that encompasses comprehensive job creation and training. We have continued to hire and train technicians and operators throughout the reporting period. We have adapted our teaching methods to a balance between virtual and in-class learning to avoid any interruption during the COVID-19 pandemic and to provide a pipeline of skilled employees for the new BMP process units.
We have put in a place a social grievance mechanism for BMP with an online form and communication channels for contacting Bapco that includes a ‘hotline’, e-mail address and provision for face-to-face meetings.
BMP creates potential negative impacts on local communities (refer to 102-44 Key topics and concerns raised, page 46). To mitigate, Bapco conducts a social impact assessment to identify any negative impacts
that might exist and to develop mitigation actions. Some example mitigation actions are described in the section below.
Bahrain is largely dependent on oil and gas for its national income. Bahrain has had a petroleum-based economy since 1937; the industry accounts for 11% of GDP and approximately 70% of government revenue. 10% of the oil is consumed locally and the rest is exported. Commissioning of BMP will significantly contribute to these future revenues and therefore the project can be considered to have a strong positive impact on reducing physical or economic isolation.
Bapco is encouraging women participation throughout our organisation. Bapco has a strategic goal for complying with the stated national plan of empowering women, led by Her Royal Highness Princess Sabeeka Bint Ibrahim Al-Khalifa and Supreme Council for Women.
One of the strategic visions of Bapco is to develop the local community. For example, building the capacity of the local individuals by providing scholarships for the internal employees and public individuals. The Oil & Gas Academy admits school graduates from both male and female genders and provides them with an oil and gas diploma that will allow them to work in Bapco. We additionally offer advanced technical courses to different stakeholders, including contractors and subcontractors.
We conduct various campaigns to provide for the needs of local communities, and support the local authorities to serve the community. Recently, Bapco has approved more than 10 projects to serve different public / community categories, and executed one project for the conversion of Eker Garden to be the first sustainable garden in the Capital Municipality. Bapco has additionally installed 30 Sustainable Solar Benches serving different areas of the Kingdom of Bahrain.
Bapco has written to the relevant authorities requesting confirmation that all dwellings within the BMP project area of influence have access to electricity and water, and coverage has been confirmed verbally by the Bahrain’s Electricity and Water Authority. Bapco has also conducted a socio-economic survey of surrounding communities impacted by the BMP project site, to provide baseline socio-economic data for Bapco to incorporate into its social impact assessment and stakeholder engagement plan.
We have created a welfare programme that contractors are required to adhere to, for the protection of workers rights. Contractors are required to provide all the necessary services and infrastructure for worker welfare, including sources of drinking water, and sanitary and washing facilities. They must provide induction training, including training on
worker rights, project policies and procedures and cultural awareness. We conduct regular inspections to ensure compliance.
Our facilities are located to the East of Bahrain on the Arabian Gulf coast, to the south of Sitra Island and approximately 10 km south of Manama. The Refinery first operated in 1936, and so there is a long history of Refinery operations across multiple generations that we are aware of when considering Refinery impact on the community.
Social organisation (i.e. the strength of relationships between individuals and communities) has also given great attention by Bapco. We have a CSR annual plan for our community events. For BMP, there is a dedicated team for welfare and social issues. This dedication and effort reflects the importance that the company places on these social issues.
We are proud of our continued compliance with the local regulations for the environment, culture and labour. Bapco has recently also achieved compliance with International Standards of World Bank. The integration between local and international standards has enabled us to pioneer best practices that minimise our community impacts across the Kingdom of Bahrain.
Some examples of our initiatives are given below.
Use of hazardous substances that impact the environment and human health in general, and specifically impact reproductive health. Refining operations use chemicals and catalysts. All undergo risk assessment prior to use in order to identify if there are any risks to the environment or human health. We maintain an EHS legal risks register to evaluate our compliance (refer to Compliance with Customer Standards and 417-01, page 61).
Volume and Type of pollution released. Bapco’s EHS policy includes a commitment to the protection of the environment. All external releases to the environment are monitored and reported as per local regulations.
Status as major employer in the local community. We are proud of our positive employment track record within the region. We are very pleased to contribute to Bahrainisation through providing local opportunities for training and academic scholarships.
Land conversion and resettlement. Bapco’s operations and related projects do not result in resettlement or land conversion. All our activities and projects are confined to existing company or government property.
Natural resource consumption. We invest heavily in reducing our natural resource consumption, for example our use of both extracted groundwater and sea water (refer to 303-03 page 89) and the use of solar power to supplement the use of conventional fuels (refer to 302-01 page 82).
“ We are bound to the Kingdom of Bahrain by our actions and have an obligation to manage those actions positively for the benefit of all
On the 4th of March, we organised our annual Green School Award for the academic year 2020-2021. The ceremony was held virtually due to the COVID-19 pandemic, and was attended by H.E. Shaikh Mohammed bin Khalifa bin Ahmed Al Khalifa, Minister of Oil, H.E. Dr. Majid bin Ali Al-Nuaimi, Minister of Education in the Kingdom of Bahrain, Bapco’s management, employees and the participants.
The Green School Award is an annual competition started by Bapco in 2005 in cooperation with Bahrain Ministry of Education. It is designed for Bahraini secondary school students with each school submitting a sustainability project, evaluated by committee from Bapco, Ministry of Education and the Supreme Council for Environment. The winning school and students receive a financial reward and also get to raise the Bapco Green School Award Flag in their school premises. The aim of this award scheme is to raise awareness of sustainability and environmental issues amongst young students.
We are proud to have organised this competition since 2005, as it enables each young generation to create innovative solutions for a better and sustainable future.
Al Estiqlal Secondary School for Girls won first place for their project entitled “Recycling of Waste Car Tires”
Recycling of rubber from used/damaged car tires by using to replace a small percentage of bitumen in asphalt mixture with it, in order to eliminate the disposal of waste tires to landfills and to improve the specifications and performance of the asphalt mixture.
Al Fatih Secondary School for Boys won second place for their project entitled “Green Classrooms”
Providing a healthy environment in classrooms and laboratories that contributes to improving the quality of education using modern technologies such as measurement of pollutants, live measurements of student’s body temperatures, and automatic ventilation when classrooms are occupied.
Al Noor Secondary School for girls won third place for their project entitled “Energy from Plants”
Producing electrical energy from plant roots, considered a renewable source of energy that is environmentally friendly, inexpensive, and easy to obtain.
Lujayn Al Sayoof joined Bapco in 2015 as a Process Engineer in the Technical Services Department Planning Section and was promoted in 2020 to a Senior Process Engineer. Lujayn is responsible for the optimisation and evaluation of the Refinery process units and provides technical support to Bapco Management and the Supply Chain Planning team.
Lujayn attended the University of Bahrain, where she graduated with a BEng in Chemical Engineering in 2015 Based on her academic performance, she received Bapco local scholarship when she was in her second year. She also earned her MSc in Chemical Engineering in 2021.
Lujayn is passionate about sharing her knowledge and experience, she volunteers to mentor and support students at the University of Bahrain, and she is a regular volunteer with Injaz in Bahrain. In 2019, Lujayn won the Rising Stars Middle East Award at the Middle East Refining Technologies Conference.
Lujayn comments that Bapco has provided her with support and encouragement throughout her education and career. This has helped her to enhance her confidence, develop presentation skills, lead initiatives and projects and provide training and mentoring.
Ammar Al Mutawa is currently a Shift Supervisor for the Fluid Catalytic Cracking Unit (FCCU) Section in the Oil Processing Department and is nearing completion of his IDP. Ammar expects to move to BMP by the end of the year. In preparation for his move to BMP Ammar has spent two months at the Madrid Operating Centre to understand BMP process technologies.
Ammar holds a degree in Chemical Engineering from the University of Bahrain, where he graduated in 2018 and subsequently joined Bapco. His initial position was as Area Outside Operator, responsible for field measurements, sampling and equipment isolation. Ammar then moved to Control Operator and after that Head Operator. The latter positions included responsibility for process optimisation to meet a given product specification, as well issuing of work permits for controlled activities such as ‘hot works’ - work that generates a source of ignition and is therefore carefully controlled using Process Safety Management processes.
Ammar was involved in the 55 day FCCU shutdown that occurred whilst COVID-19 restrictions were in place. At that time Ammar was a Head Operator and had responsibility for coordinating the safe work of his team. Ammar comments that the shutdown required long periods of hard work with significant responsibility, and he is very proud of his contribution.
Ammar has additionally been attending monthly coaching and mentoring sessions to further develop his skills and leadership capabilities.
Ammar comments that working at Bapco is like ‘working with your family’. Ammar describes Bapco as a Madrassa (school) with continuous learning for your career.
Value generation and distribution refers to initiatives undertaken by Bapco supporting the wider principles of sustainable development that are not directly related to our core business activities.
Bapco offers technical training, leadership and management development, personal effectiveness and workplace skills
Bapco is a significant contributor to Bahrain’s economic development, playing a central role in improving the quality of life and prosperity of the Kingdom of Bahrain.
We share our technical expertise for the benefit of the wider community through a range of activities and outreach initiatives. We run a biennial EHS Family Day that, in 2020, was attended by over 37,000 Bapco employees, contractors and their families and members of the public.
We make a substantial commitment to further education and student sponsorship, allowing Bahrainis to attend some of the top universities within the Kingdom of Bahrain and overseas.
We support our community in maintaining a healthy lifestyle by sponsoring a range of sports clubs and sporting events, promoted through our publications. Many of our clubs compete successfully at national level and have won numerous competition awards.
We undertake many community focused events throughout the year. We hold an annual beach cleanup in association with RECSO. We also hold numerous events designed to promote community wellbeing on a wide range of topics such as diabetes, heart disease, hand hygiene, and heat stress.
Bapco conducts several activities which result in an important positive impact on the community as well as the local economy. Bapco encourages employees to provide support for education by volunteering to education programme like INJAZ, and to give lectures to school and university students.
Bapco is proud to have established the Oil and Gas academy which trains and prepare highly skilled workforce. Bapco also provides scholarships to top students who would like to continue their education abroad. Refer to 203-02 on this page for further information.
BMP’s CSR group has completed several projects which had a positive impact on the community like the rehabilitation of Eker Garden and installing several solar power benches around the Kingdom. Refer to the BMP Social and Community Projects Special Topic, page 126.
Bapco sponsoring events and activities is also a way of giving back to the community - refer to 203-02 page 117.
The Learning and Development (L&D) Department has been offering apprenticeship programs since 1955. The modern Oil and Gas Academy within L&D was established in 2017 and continues to provide the industry with the a highly skilled workforce necessary for our future.
The L&D Department is a strategic business partner delivering value to the business and to society through its core values:
• Satisfying customers through its activities as a recognised centre of excellence for world class learning;
• Promoting a spirit of enterprise amongst our teams, which are committed to growth through learning and trusted by all stakeholders; and
• Empowering team members to create a dynamic performanceoriented environment to meet changing business needs.
The L&D team provides internal and external learning solutions addressing Bapco’s training needs and requirements. These encompass technical training, leadership and management development, personal effectiveness and workplace skills. Those learning solutions are either delivered in house by our SMEs team members or through partnership with external training providers.
The team provides training, support and guidance in mechanical, electrical engineering, instrumentation, project management, and EHS. The team also provides company-wide training support with technologically advanced training solutions across electronic, mobile, microlearning and innovative future virtual reality and augmented reality media.
In addition to providing L&D opportunities to Bapco’s employees, the L&D team offer a number of programs such as Graduate scholarship programs and Diploma programs in technical disciplines. Our Graduate Scholarship programme was introduced to meet the current and future manpower requirements for the company and the Kingdom of Bahrain. We not only sponsor students financially, but also maintain a close relationship with them throughout their studies to ensure they achieve their full potential.
The Innovation Centre, part of the L&D team, offers services to employees from all departments to help them build a culture of innovation and adopt new technologies, which will provide opportunities to develop innovative products.
L&D identifies the most talented employees and manages their career development journey by:
• Designing career paths across the various functions (individual contributor versus a people management career);
• Providing career guidance to employees on professional growth;
Total number of students enrolled in the Graduate Scholarship program
• Designing accelerated training and development programs;
• Supervising the career growth of identified individuals; and
• Delivering learning solutions/interventions for leadership and management capabilities improvement.
We additionally provide other scholarships for our employees and the children of Bapco employees. These scholarships assist students studying at Universities and Colleges in Bahrain and overseas. Total number of scholarships
Our industrial training programme offers high school and university students the opportunity to gain valuable work experience which forms part of their academic curriculum and is required in order to fulfil the requirement of a degree. The purpose of the programme is to support students to achieve desired qualifications and to help fulfil their career aspirations. We support students for the entire duration required by their institutions, a service that helps students gain valuable industrial insight as well as to prepare them for their eventual entry into the Kingdom of Bahrain’s job market.
Both 2020 and 2021 were challenging years, we offered virtual workshops to university students’ trainees who were required to undergo industrial training for their graduation. These workshops covered soft skills and technical learning outcomes.
During 2020 - 2021 we sponsored several events that occurred in the Kingdom of Bahrain. This includes the following:
• Environment Booth at Environment National Day
• Bahrain Football Association, Bahrain Maritime Sports Association, Media First for Bahrain First and Annual Report
• Crown Prince Volleyball Cup
• Sponsorship for Bahrain International Horse Race
• Sponsoring Bahraini Women Day Activities
• Sponsorship of the LEWAS 2021 Programme
• Sponsorship for 13th King Hamad Trophy Golf Championship
• Sponsoring with Partnership in the 2nd Mentorship Forum Middle East on November 11, 2021
• Sponsoring A Football Tournament which organise by Sanad Cultural & Sports Centre
• Sponsorship for Children & Mothers Welfare society event 10th January, 2021
Local content refers to our approach to investment in the Kingdom of Bahrain through local suppliers, as well as local hiring, which contributes to the broader socio-economic standing of the nation.
We are committed to supporting our local supply chain and, by doing so, helping to strengthen development of the local economy. Most suppliers to Bapco are local and we regularly monitor these data as part of our supplier social assessment procedures.
Our Procurement Department supports contracting services and materials supply, and maintains the Refinery inventory and warehousing services. Consequently, procurement activities play a major strategic role within the organisation. We are proud to treat all our suppliers with courtesy, honesty, and fairness, fostering good relations and a positive work culture.
We are strongly committed to equal opportunities, with all recruitment, promotions, and career development being based on merit. We actively monitor the proportion of senior managers hired from the local community.
Bapco is proud to offer remuneration that typically significantly exceeds the defined local minimum wage. An attractive benefits package is additionally offered to employees. Both salary and benefits are offered irrespective of gender. Bapco is proud of its compliance with and support of the Kingdom of Bahrain labour laws.
For the purpose of this disclosure against the GRI Standards, ‘local’ refers to any Bahraini nationals, ‘senior management’ refers to executives that are General Managers and above, and ‘significant locations of operation’ includes our national operations in their entirety.
We try to support the local supply chain wherever possible within our procurement decisions. In 2020, 56% of all suppliers were classified as local to Bapco, i.e. had their main business premises in Bahrain. In 2021 the proportion of local suppliers was similar at 57%.
The topic of ‘human rights’ is recognised internationally and typically includes political rights, reasonable social freedoms and the right to decent working conditions. An organisation can impact human rights directly through its own actions and operations, but also indirectly through its positive influence on suppliers and the local community.
We fully comply with the Bahrain Labour laws that protect the rights of employees from discrimination and prohibit child and forced labour.
Our Code of Conduct governs the standards of behaviour and mutual respect expected of all Bapco employees. Within Bapco, our robust management systems and continued innovation in health, safety and wellbeing ensure that all enjoy a positive and safe working environment.
We provide equal employment opportunities for those wishing to join us and particularly encourage women to seek advancement to senior positions within the company.
We have a documented grievance procedure, which provides a framework to facilitate resolution of any grievances raised by employees and ensures that complainants are free from restraint, interference, coercion or reprisal. Our BMP also has a dedicated grievance mechanism and communication channels for the public to communicate any feedback and concerns, which include a hotline, email address and an online grievance form.
We have not identified any operations or suppliers associated with Bapco where there is either a violation or significant risk that workers would not be able to exercise these rights.
Bapco works in close collaboration with the Ministry of Interior’s Guards Training School on matters of training and security requirements.
All our security personnel receive appropriate ‘human rights’ training in accordance with the laws of the Kingdom of Bahrain. Some training modules, such as vehicle stop-and-search procedures, and customer service, are specific to security personnel, with others, such as training in the Bapco Code of Conduct, being common training for all personnel. Security personnel are subject to professional development systems overseen by Bapco HR and used for other personnel.
Bapco makes specific provision for ensuring respectful interaction with personnel. For example, personnel searches are carried out by male or female security guards, as required by the gender of the personnel entering the facilities.
GRI 411-01: Incidents of violations involving rights of indigenous peoples
Bapco fully supports Bahrainisation, which concerns support to Bahraini talent irrespective of racial background. We have not recorded any incidents that violate the rights of indigenous people.
GRI 412-01: Operations that have been subject to human rights reviews or impact assessments
GRI
We monitor our contractor operations and have determined that none have a risk of child labour. Bapco fully complies with Bahrain labour laws and uses robust contracting procedures to protect migrant workers.
We monitor our contractor operations and have determined that none have a risk of forced or compulsory labour. Bapco fully complies with Bahrain labour laws and uses robust contracting procedures to protect migrant workers.
GRI 410-01: Security personnel trained in human rights policies or procedures
Bapco has professionally trained security personnel employed on a permanent basis. The personnel provide a range of security functions for their operating areas and facilities, including guarding of entrance points, personnel and vehicle searches, monitoring of security cameras, patrol of facility perimeter fencing and other facilities, and monitoring of personnel working on its sites.
Bapco is proud to fully comply with the Kingdom of Bahrain labour laws. We additionally take steps to screen our contractors for fair working practices. BMP has been subject to extensive human rights review to ensure equitable living and working conditions for the workforce.
GRI 412-02: Employee training on human rights policies or procedures
The specific number of hours of human rights training is not available because fundamental respect for human rights is embedded throughout all training conducted by Bapco.
GRI 412-03: Significant investment agreements and contracts that include human rights clauses or that underwent human rights screening
The Kingdom of Bahrain Labour Laws include implicit requirement that human rights are respected. We are proud that all of our investment agreements and contracts to comply with these laws.
Suppliers may need guidance and encouragement to implement suitable policies for managing their potential environmental and social impacts. Some suppliers may present higher risks concerning human rights, potential environmental harm or labour practices. In this case the organisation that they are contracting to can conduct due diligence to identify these suppliers and hence help mitigate the negative impacts within the supply chain.
Bapco uses a prequalification procedure to screen suppliers, ensuring compliance with established Bapco EHS procedures and all relevant laws. The scope of the procedure covers all requirements necessary for prequalification prior to admission onto the Approved Vendor List maintained by Bapco. The procedure includes questions on commercial experience, organisation, financial stability and other management processes for quality, environment, healthcare and safety. It is designed to complement Bapco’s Code of Conduct that includes guidance on expected working relationships between employers and suppliers. Suppliers are subject to audit by Bapco to ensure compliance with the prequalification criteria and other technical and commercial criteria as decided by Bapco. Appropriate support and advice is provided by Bapco to local suppliers wishing to be prequalified.
Refer to 414-01 for the proportion of new suppliers that were screened; this screening procedure also includes environmental assessment.
GRI 308-02: Negative environmental impacts in the supply chain and actions taken
During the reporting period 2020 -2021, there were no cases of contract termination caused by negative environmental impact.
GRI 414-01: New suppliers that were screened using social criteria
The graph below gives the number of new suppliers that were approved by year. Bapco screens 100% of its suppliers to determine local content. We additionally screen a small proportion of suppliers based on their business activities against environmental and occupational health and safety criteria (refer to figure below). In 2020, 18% of new approved suppliers were classified as ‘local’ to Bapco and the proportion increased to 73% in 2021.
GRI 414-02: Negative social impacts in the supply chain and actions taken
During the reporting period 2020 -2021, there were no cases of negative social impact identified for suppliers.
Total number of approved new suppliers and number of suppliers screened for environmental and occupational health and safety criteria for the years 2018-2021
BMP is Bapco’s biggest infrastructure project in the company’s history and one of the largest infrastructure projects within the region. BMP is approximately 80% complete at the end of the reporting period. Throughout the pandemic, the BMP social and welfare team maintained community engagement to mitigate any negative impacts that could have emerged during the construction phase, in line with precautionary measures.
We have completed several projects during the reporting period, where we worked closely with our community to provide them with financial and moral support during the pandemic, with several projects undertaken to improve the visual amenity of community facilities.
Installation and distribution of sustainable solar benches
Rehabilitation of Eker Garden
Bahrain Autism Society
A total of 30 solar benches were distributed in April 2021 across various locations covering Southern and Northern Governorates in Bahrain, including Sitra-Bridge Walkway, Isa-Town Walkway, Sheikh Khalifa Garden, Askar Coast, Prince Saud Al Faisal Walkway, Princess Sabeeka Park in Awali, as well as several schools and health centres entrances.
In November 2021, we completed the rehabilitation work to Eker Garden with solar lighting, waste segregation bins, and a dedicated play area for people with special needs.
The society was provided with around 75 sensory boxes for their members, as a vital part of their educational program.
• Ma’ameer channel beach clean-up campaign is a regular activity conducted by local societies, contractors, employees, and labour working near Ma’ameer channel. Bapco has now achieved 75 days of cleaning and has gathered around 70,000 Kg of waste.
Beach clean-up activities
• RECSO beach clean-up that was attended by 50 volunteers and took place near the Ma’ameer shoreline.
• We have sponsored several beach clean-ups activities in various locations of the Kingdom, for example for the protected mangrove area in Ras Sanad.
Sponsorship of Professional Fishermen Society
We have sponsored fishermen by providing them waste bags at different fishing ports as well as first aid kits and rescue diving suit. This initiative was in cooperation with Professional Fishermen Society that aimed to minimize marine pollution generated from fishing activities.
Around 20 events for internal and external stakeholders were held during 2020-2021, for example:
• World Environment Day, several events were held including an Instagram photo competition for ecosystems that had been restored (see best from each category at the top of the page).
Other stakeholder engagement activities
• COVID-19 Campaign: we have provided the surrounding villages societies with disinfectants, personal and house hygiene products along with awareness leaflets that includes guidance to combat the spread of this pandemic.
• 20 million Safe Project Hours: we have shared special communication video reports on different social platforms: Bahrain television, Instagram, You Tube briefing about BMP project and its 4 fundamentals (Safety, Quality, Project Benefits & Budget).
We have sponsored the publication of two books that will be distributed for Shaikh Ebrahim Bin Mohammed Al Khalifa Centre for Culture and Research’s 20th Anniversary celebration, scheduled for January 2022.
One of the two books that we sponsored for the 20th anniversary celebration of the Shaikh Ebrahim Bin Mohammed Al Khalifa Centre for Culture and Research
BMP’s worker welfare team monitors welfare standards, which we believe exceed associated international standards. They have increased the number of inspections; re-arranged the accommodation to provide acceptable social distancing; and introduced enhanced hygiene measures.
Campaigns and activities were carried to continue to raise awareness, for example:
• Summer campaign that was held at different work sites under the title of “Stay Hydrated” which included electronic awareness emails, along with distributing water bottles and juice. This campaign was conducted with the cooperation of Bapco Health Promotion Unit to promote awareness of health practices to avoid heat related illnesses.
• Mental health campaign, which was held at the BMP camp, where workers attended a mental health awareness lecture given by our camp clinic doctor followed by a movie related to World Mental Health Day.
• Celebrating “One Year Zero Harm” at the Ma’ameer Sleeper Way Project to award workers who achieved a one year injury-free work personal milestone.
The environmental monitoring has been conducted on regular basis since the commencement of BMP construction activities as per the requirements of the Project Construction Environmental and Social Monitoring Plan.
The environmental monitoring includes ambient air quality monitoring at four locations in construction areas by using continuous ambient air quality monitoring stations and ambient air quality monitoring at three locations in worker accommodations areas by using passive diffusion tubes. Vehicle exhaust emissions monitoring for Carbon Monoxide and Hydrocarbons is being carried out during the construction phase of BMP.
Nine new groundwater monitoring boreholes were installed around the BMP Greenfield Area at the start of construction activities and groundwater monitoring is being carried out as per the project Groundwater Monitoring Plan.
Noise monitoring is being conducted at five sensitive receptors identified in BMP’s ESIA surrounding the BMP construction activities and at various locations within the BMP project site during the construction activities.
Dewatering activities in different areas whilst the excavations and foundation works are being carried out during the construction works. Total Suspended Solids monitoring has also been conducted on weekly basis to ensure compliance with project permit requirements, as required by SCE.
Distributing water during the “Stay Hydrated” campaignSara finished school in 2019 and, having done well in her studies, was selected for the first group of women trainees to join the Oil and Gas Academy. During her studies, she has learned not only the technical skills required for her career but also is proud to have improved her English language skills.
Noor initially opted to study Biology at the University of Bahrain, but was spotted by Bapco as a potential high calibre student for the Oil and Gas Academy. Noor was delighted to accept the opportunity to work for Bapco and hopes to be a Senior Technician in the next five years.
Rawan is another candidate who did well at school and was proud to be selected by Bapco to attend the Oil and Gas Academy. Rawan is already developing an interest in Power and Utilities and hopes that her future career will lead to a role in this area.
All three trainees are immensely proud to be amongst the first female trainees at the Oil and Gas Academy. The trainees were excited to have access to some of the benefits made available to Bapco employees, which includes access to Princess Sabeeka Park, loan of a tablet for studying Bapco’s Learning Management System and a paid allowance. Bapco wishes them well on their future careers!
Ahmed joined the Oil and Gas Academy in 2018, commenting that he is proud to have been picked from over 500 applicants. Ahmed notes that the application procedure was rigorous, involving aptitude tests in science and fitness for work medical examinations. Ahmed is enjoying his years’ rotation and appreciates the opportunity to start his career at a young age.
Muataz graduated from Riffa High School with high grades and initially attended the University of Bahrain, before being selected to apply to Bapco. Muataz joined the Oil and Gas Academy on a Diploma Programme in Electrical Engineering. Muataz expects to graduate in 2022 and is currently a Trainee in the Maintenance Department.
Ismaeel is a graduate of the Nasser Vocational Training Centre who joined the Oil and Gas Academy in 2019. His current rotation is within the Machine Shop where he expects to spend three months learning the technical skills for refabrication of equipment being returned to service. Ismaeel appreciates the great responsibility of being a Trainee and is proud of his contribution to the economy of the Kingdom of Bahrain.
Noor Hasan, Trainee Sara Al Dakhil, Trainee Rawan Al Thawadi, Trainee Noor Hasan, Sara Al Dakhil and Rawan Al Thawadi (left to right in picture) are all currently trainees placed in the Maintenance Department and are all recent graduates of Bapco’s Oil and Gas Academy. Ismaeel Ahmed, Trainee Muataz Alhasan, Trainee Ahmed Alabad, Trainee Ismaeel Ahmed, Muataz Alhasan and Ahmed Alabad (left to right in picture) are all trainees who graduated from the Oil and Gas Academy and are currently on their one year rotation through different Bapco departments.308,714 hours
Training conducted - Page 142
12.4% new hires
Women hired in 2021 - Page 151
37,000 attendees
EHS Family Day - Page 138
Profiles in this section - Page 148
Abelin Ferrer is currently a Manager in the Corporate Strategy Department, where she works closely with the Executive Leadership of Bapco.
Abelin has had a long and varied career in the oil and gas industry. Abelin originally trained as a Chemical Engineer, graduating from Adamson University, Manila, Philippines. She started her career at Caltex Philippines in a variety of roles from technical to managerial. Her initial roles were in Technical Services and Refinery Planning where Abelin was eventually promoted to Section Head.
During that time, Abelin successfully completed a Masters in Management Technology from Dela Salle (Lipa) Graduate School, Philippines. Following her postgraduate studies, Abelin was appointed as a Manager at the Caltex Philippines Refinery Planning Department, subsequently holding several management appointments first in Caltex and then in the newly formed Chevron Texaco Philippines. Abelin concluded her career at Chevron Texaco as a Manager-Supply Operations in the Supply Optimisation Department.
Abelin joined Bapco from Chevron Texaco as a Superintendent in the then Technical Services Department Strategic Planning. Abelin’s role was to conduct feasibility studies and economic analysis of business opportunities, with recommendations being made to the company Executive. Abelin’s career continued to focus on business strategy, developing new methodologies for tracking and reporting key performance indicators and providing recommendations for cost optimisation.
With the formation of the Corporate Strategy Department, Abelin was selected to become the Department Manager, where she coordinates the department of the company’s long term downstream growth
strategy; securing the long-term business resilience of Bapco (Note. Since the 2020-21 reporting period, Abelin’s responsibilities have further changed to oversight of Bapco’s supply chain).
Abelin has received numerous awards and commendations throughout her career. These include being chosen as one of the Top Ten Outstanding Overseas Filipino Workers in the GCC, awarded to Abelin by His Excellency the Philippine Ambassador of Bahrain, and her nomination for LEWAS. Abelin has also been personally recognised by former Bapco Chief Executives and more recently by the Acting Deputy Chief Executive and BMP Project Director for her remarkable contributions to the company, and especially for empowerment of Bahraini women.
Abelin is proud to contribute to society through various community outreach initiatives. Abelin has volunteered for INJAZ, teaching young Bahrainis to prepare them for their future careers, and supports high school students at her high school in the Philippines. Abelin also extended assistance to various charity missions that help people cope with the effects of the COVID-19 pandemic.
Abelin believes that everyone deserves to share in the available opportunities to further their career; Abelin’s goal is to pass on her many years of experience to the younger engineers as a legacy of her career in the petroleum industry.
“Abelin’s goal is to pass on her many years of experience to the younger engineers as a legacy of her career in the petroleum industry
Jenan Al Askari is a corporate communications specialist whose current appointment is Head of Employee Engagement.
Originally schooled in Bahrain, Jenan opted to continue her degree studies in the UK at the University of Portsmouth, where she graduated with Honours in Communication Design in 2006. Jenan joined Bapco the same year as a Graphic Designer in the Public Relations Department, able to use her bilingual skills to design and create publications for Bapco.
During her time in Public Relations, she supported several high profile projects and events. These included the inauguration of the Lube Base Oil Project by the late Prime Minister His Royal Highness Prince Khalifa bin Salman Al-Khalifa, the opening of Princess Sabeeka Park in Awali by Her Royal Highness Princess Sabeeka bint Ebrahim Al-Khalifa and the Bahrain International Airshow.
Jenan’s experience was recognised with her next promotion to Corporate Communications Specialist, responsible for Bapco’s internal and external communications. Jenan comments that this was an exciting period of her career, liaising with local and international media wherever there was interest in Bapco’s activities. Her other responsibilities included stewardship of the Bapco Annual Report, management of the social media accounts, issuing of press releases and scripting and production of the Chief Executive’s monthly videos. In this role, Jenan was also involved in crisis communication and reputation management, a vital role to provide transparency to Bapco’s stakeholders.
In 2020, Jenan joined the Chairman and Chief Executive’s office as a Communications Strategy Specialist as part of the Corporate Strategy Team. Working with the leaders of strategic projects, Jenan assisted by building commitment between stakeholders to deliver the intended strategic outcome. Jenan contributed to the Chairman’s vision and
mission, facilitating progress towards key performance indicators. Jenan also supported the quarterly Strategic Planning Council meetings.
Since late 2021 Jenan has led the newly formed Employee Engagement Section, reporting directly to the CEO. Jenan comments that the Section represents the internal voice of the business during the transformation journey that Bapco is currently undertaking and communicates the CEO’s vision.
Throughout her career, Jenan has always believed that people are the most important asset of the business, and her goal has been to open lines of communication between the managers and the employees. Jenan is proud to be included in Bapco’s Sustainability Report, as it reflects Bapco’s very welcome focus on women empowerment.
“ I have always believed that people are the most important asset of the business
Health and Safety refers to the avoidance of harm that may be caused through exposure to uncontrolled releases of energy within process environments, or to toxic or asphyxiant atmospheres. Employee wellbeing refers to the maintenance of physical and mental health in areas such as nutrition, fitness, medical screening and work-life balance.
GRI 103-01, 103-02, 103-03, 403-01, 403-02, 403-03, 403-04, 403-05, 403-06, 403-07: Management approach
Health, Safety and Wellbeing collectively represent some of the fundamental rights of workers, and are widely monitored and recognised internationally. Prevention of harm and promotion of wellbeing requires concerted and sustained commitment to process safety, occupational health and safety, the supporting management systems and the monitoring of safety-related performance indicators, commensurate with an organisation’s size and activities. We have ten principles called Osool Bapco (Arabic for principles) that guide our behaviours.
We believe that EHS is integral to our business and we are committed to achieving continual improvement in our EHS performance. In the absence of relevant local rules and regulations, internationally accepted standards have been adopted as appropriate, e.g. our Process Safety Management framework for guiding safety-related activities across relevant departments and EHS Policy for achieving continual improvement in EHS performance.
Our hazard and risk identification programme applies to all our employees and contractors to ensure a safe working environment. All hazardous activities are evaluated by a competent person trained in our risk assessment processes. Contractor Safety Officers involved with the preparation of risk assessments for high risk work are trade tested by the HSE department and possess a recognised health and safety qualification, e.g. a National Examination Board in Occupational Safety and Health (NEBOSH) International General Certificate or equivalent. Having identified the hazards, we do everything reasonably practicable to protect people from harm. We follow relevant international standards
and industry association guidelines, which we adopt within our company standards. When creating controls or considering changes to existing controls, we follow a risk control hierarchy (each control may use more than one barrier):
• Elimination;
• Substitution;
• Engineering controls;
• Administrative controls and/or barriers and signs; and
• Personal protective equipment.
Bapco has established a comprehensive set of leading and lagging indicators for the monitoring of health, safety and wellbeing. We collect data on safety related incidents, sickness, absenteeism and occupational illnesses and use these to identify trends to senior management. In common with widely recognised good practice, if an incident occurs, e.g. a ‘near miss’, an incident with the potential to cause harm, a description of these events are shared in ‘toolbox talks’ to raise awareness. We hold Safety, Health, Environment and Quality (SHEQ) moments at the beginning of all meetings to include either of Environment, Health, Safety or Quality as an item within meeting agendas. We have qualified onsite health practitioners who provide background screening for aspects of employee health, such as diabetes and women’s health, with data incorporated into leading occupational health indicators, and a fully equipped hospital at Awali.
During 2020 we held our EHS Family Day under the patronage of HE Shaikh Mohamed bin Khalifa Al Khalifa, the Minister of Oil at the Bahrain International Circuit. More than 37,000 Bapco employees, contractors, members of the public and their families attended the event.
During the reporting period we have continued our safety and occupational health activities covering several themes:
• Behaviour Observation Obtains Safe Trends (BOOST);
• Slips, Trips and Fall;
• Hands Safety;
• Enhancement of Lock out Tag out process;
• Ergonomics; and
• Management of hazardous chemicals.
All employees and contractors are required to follow our occupational health and safety management system. The level of audit differs by worker status. In 2021, out of the 134 contractors employed, 30 are regarded as ‘core’ to the business. Audits, inspections and KPIs are completed for ‘core’ contractors only. However, we reconfirm our commitment to a safe working environment for all those working for Bapco, including those not regarded as ‘core’ contractors, and the strict enforcement of health and safety management across all our sites and operations. Our contractor EHS committee meets monthly to oversee these activities.
Bapco’s Incident Investigation and Reporting standard has three injury classifications as follows:
• Lost Time Injury (LTI): An injury arising from or in association with work which results in the injured person being absent from work on his/her next scheduled working day or shift;
• Non-LTI: An injury in which an employee sustains an injury in association with work which does not result in absence from work on the next scheduled working day or shift; and
• First Aid Injury (FAI): Any one-time treatment of minor injuries, which does not ordinarily require medical care. Follow up visits for checking or observation only do not change the FAI classification.
Injury rates for employees and contractors is the number of injuries per 200,000 employee-hours worked. The injury frequency rate is calculated according to ANSI Z16.4-1977 (American National Standards Institute for uniform record keeping of occupational injuries and illnesses) calculated as number of injuries multiplied by 200,000, divided by the number of employee hours worked.
One of our several safety campaigns - “Your Hands Matter”
The Kingdom of Bahrain has high ambient summer temperatures. During these months, we provide extensive onsite support and run campaigns and initiatives to prevent illnesses related to the hot conditions, such as our ‘Drink water... Stay Hydrated’ campaign. During 2020-2021 there were seven recordable incidents of heat stress.
Learning and development concerns the development of a skilled and capable workforce that meets the needs of Bapco’s existing and future operations. It also includes the development of employee lifetime skills and capabilities. Learning and development is measured through performance and career development reviews to provide clear feedback on career performance.
Our L&D Department offers a wide range of internal and external training programs to Bapco’s employees. We report on a yearly basis the total number of employees trained, the total number of training programs and the total learning hours. We continue to add new training programs that will help the personnel and support the professional development of our employees. We have created the ‘Seed’ program, under which employees who propose an innovative idea receive a recognition award if their idea is adopted.
During 2020-2021 average hours per year per employee was:
• General training was 20 hours;
• BMP-related training was 200 hours; and
• Familiarization training was 1,127 hours
GRI
As part of the HR transformation program, Bapco has implemented a Goal and Performance Management System, a process that helps management and the individual employee to plan, manage, document, and evaluate their performance. One of the key elements of the system is the Structured Development Plan, which is a ‘smart’ goal statement aligned with the Department and company objectives. Bapco has also developed an IDP for all fresh graduates joining Bapco that builds an understanding of our operations into the personal and professional skills needed for their career at Bapco.
GRI 404-03: Percentage of employees receiving regular performance and career development reviews
As part of the new goal and performance management system, all Bapco employees receive a yearly performance review at the end of year. The total number of employees on active career development programmes in 2020 and 2021 is 134, of which 19% are female and 81% are male.
Our L&D Department is the hub of our L&D activities. Organisational change is a constant, however for Bapco the current pace of change is especially rapid. BMP and its eventual integration into our base business requires a substantial programme of training to equip our personnel with the skills to operate new technologies. The various transformation programmes currently underway across Bapco also require special attention to be paid to career development, vocational skills and succession planning. These exceptional activities place additional importance on the role of L&D to ensure that the workforce is continually rejuvenated, both by engaging existing personnel in continuous learning and supplying a pipeline of new personnel. Refer to our materiality assessment (Page 44) that shows L&D to be an area of highest importance to both Bapco and our stakeholders.
Bapco has physical training facilities hosted at the Oil & Gas Academy, Awali, used as the central point of contact for Bapco’s trainees. To deliver our training we have increasingly turned to the latest technologies to facilitate knowledge transfer, informed by the psychology of learning. Techniques such spaced repetition that use a variety of different learning techniques to improve knowledge retention. Mixed and augmented reality learning is used by Bapco to simulate real objects - especially important for our Area Outside Operators who need to learn safely how to work with complex equipment. Virtual reality is used by Bapco to allow operators to experience hazardous activities such as working at height from the controlled safety of our training facilities. This special topic provides an insight into some of our L&D activities currently used by us to invest in our most important asset - our people.
LC Fining is the CLG licensed technology for the ebullated bed resid hydrocracking process (RHCU) that will be the largest process unit in BMP and the main profit centre post commissioning. The Oil and Gas Academy has developed a state of the art training center including the LC Fining Operator Training Simulator. Due to the complexity of the LC Fining process, in-depth simulator training is required in a safe distraction free environment so that operators can practice addressing abnormal operating conditions and emergency operating procedures. The Generic RHCU simulator model is based on the initial design of a single reactor train configuration and includes highly complex catalyst section which is not typically simulated in other RHCU facilities around the world.
Bapco uses a wide range of digital tools to supplement traditional in-classroom learning techniques. The tools provide several benefits. They align learning style to individual need that is superior to a ‘one size fits all’ approach provided by traditional methods and they also provide safer and more cost-effective methods of learning where the work environment is potentially hazardous. Bapco has used computer-based training for some years but now supplement with micro-learning (short refresher courses delivered by App) as one approach to spaced repetition. Virtual and augmented reality bring the environment to the learner in a safe and realistic manner; research shows that skills are improved faster through experiential learning, which can include repeated exposure to stressful scenarios.
Our vocational training provides a structured training programme for the induction of school leavers and graduates into Bapco. Our vocational training is designed to meet Bapco’s departmental needs for highly trained individuals who are immediately useful to the teams operating and maintaining the Refinery. Different learning paths are assigned depending on initial experience levels, with training initially conducted at the Oil and Gas Academy before later rotations through the Departments. Bapco also offers Industrial Training to expose young talent from a wide range of academic backgrounds to work in the Oil and Gas Industry. Students gain valuable industrial insight to help them in prepare for their eventual entry into the Kingdom’s job market - an important facet of sustainable development.
We make a sustained commitment to careers at Bapco. As the workforce steadily ages, those that retire must be replaced by cohorts of skilled employees. We conduct workforce planning to determine future demand and determine the succession plan by discipline, mapping required competencies to each job role. Training programmes are matched to the competencies to support the succession plan. We are especially proud of our experience pool represented by our senior employees (refer to some of the profiles in this report). The contribution made to so-called ‘twilight careers’ through coaching and mentoring is invaluable to reinforce knowledge transfer to more junior cohorts.
Equal opportunities refers to the diversity demographic of our employees. When an organisation actively promotes equal opportunities at work it generates significant benefits for both the organisation and its workforce.
For us, equal opportunities mean embracing differences and promoting an inclusive organisation that values the diversity of our employees, customers, suppliers and community partners.
We are strongly committed to equal opportunities. We do not discriminate for recruitment and selection, career development, promotion, or fair remuneration.
We believe in the promotion and development of women in the workplace. During 2020-2021 we recruited over 70 women to various areas of the organisation. We have also promoted 10 women to senior level positions.
Algeria
Australia
Austria
Bahrain
Bulgaria
Canada
Colombia
Egypt
France
Germany
India
Indonesia
Ireland
Italy
Kazakhstan
Korea, Republic of
Myanmar
Netherlands
New Zealand
Nigerian
Pakistan
Peru
Philippines
Poland
Portugal
Romania
Bapco does not publish these data. However, Bapco is proud to confirm that the level of salary and benefits are determined irrespective of gender making Bapco an attractive employer, evidenced by the number of senior women appointments throughout the company.
We attach great importance to respect and tolerance for all religions and their practice. We see mutual trust, tolerance and understanding as the basis of harmonious and peaceful relationships. Any hindering by employees of the practice of religion as provided by law (Article 22 of the Constitution of Bahrain) is not tolerated.
Our approach to diversity and equal opportunity is formalised and defined within our Code of Conduct. We fully comply with all the laws and regulations of the Kingdom of Bahrain with respect to equal opportunities. As of 2021 there were 39 nationalities employed by Bapco.
Saudi Arabia
Serbian
Serbians
Singapore
South Africa
South Korea
Spain
Sri Lanka
Turkey
United Kingdom
United States
Venezuela
Yemen
During 2020-2021, there were no cases of discrimination. Bapco fully complies with Article 39 of Bahrain’s Labour Law.
Bapco has selected “Gender”, “Age” and, “Region” as diversity categories. For each category, we have reported the total number of employees per job role which is represented by 5 categories:
• Executive - Represent Bapco’s governance body •
Fatema studied Chemical Engineering in Monash University, Melbourne Australia. After graduating in 2015, she joined Bapco working in the Hydrocracking group and the Crude Processing group. Fatema works on feasibility and optimisation studies, and is the cofounder of the Bahrain Chemical Engineers (BChemE), where she led youth initiatives in regional oil and gas conferences. She served as the President of the Bapco Toastmasters Club and is a key player in the Bapco Youth Leadership Programme and Speech Craft Program. Fatema is a keen sportswoman, ultra-distance runner and National Champion in road cycling. Fatema won the regional LEWAS Rising Star Award in 2020, the AIChE Shining Star Award in 2020 and the ME World Refining Association Rising Star Award in 2018.
Maha graduated from The University of Manchester, UK, with a Masters in Chemical Engineering in 2017. Since joining the Technical Services Department, Maha has gained experience in performance monitoring, troubleshooting, optimisation projects and Turnaround and Inspection activities with the Crude Processing, Sulphur Recovery and Diesel Hydrotreating groups. Maha is also an adjunct lecturer for final year Chemical Engineering students at the University of Bahrain, where she teaches about Process Integration and the Pinch Technology. She was also shortlisted for the LEWAS Rising Star Award in 2021. Maha is an avid participant of Injaz, Bapco Mentorship Program, where she received the title of Top 10 Mentors, and various educational webinars with the Society of Petroleum Engineers and Bahrain Chemical Engineers to support the youth progression and development.
Basel AlJeshi is currently an Associate Shutdown Engineer in the Shutdown and Major Maintenance Department within the Reliability and Maintenance Division. Basel joined Bapco in 2021 after graduating from the University of Birmingham where he studied Mechanical Engineering. Bapco supported Basel through the Scholarship Program, providing financial assistance for his studies and summer work experience whilst at university.
Basel is currently enrolled in an IDP with a target position of Shutdown Engineer at the end of the expected four year duration. Within his current position, Basel is learning to take on various responsibilities such as coordinating contractor work, weld inspections, and ensuring procedures are followed correctly with activities such as equipment hydrotesting (a check using water only that equipment can handled expected operating pressures). Basel has also participated in the Sour Water Stripper shutdown, including the planning stage leading up to it, a complex process that occurs up to two years ahead of a planned shutdown, which involves constructing detailed inventories of required equipment.
Basel has an interest in software development and has experience of several programming languages. Basel would like to contribute to automated system development in the future. Basel has already volunteered for INJAZ and hopes to teach ‘Coding with Scratch’ in the near future. Basel comments that Bapco has a very strong safety culture, evident from his earliest induction at the company. Basel also notes the availability of continuous learning as he is currently enrolled in courses with L&D on mechanical equipment.
Employee Relations refers to our approach to ensuring the wellbeing and happiness of our employees. Maintaining positive employee relations benefits the business through reduced turnover and hence the retention of more experienced employees.
A merit increase is awarded in recognition of performance and as an incentive for continued good future performance. The company’s goal management system evaluates each employee’s year-end performance and identifies how close they are to achieves their goals. This process determines the annual merit increase and proportion received of any bonus if awarded.
We provide different types of social allowances that supplement employee standard of living, and transportation allowances that support those employees without a company vehicle. We also provide employees with primary medical care within our hospital, which includes a dental clinic at Awali Hospital, and the Refinery Clinic.
Our Home Ownership Plan for employees with four consecutive years of service is designed to support those intending to purchase or build a home. A savings plan is also available for Bahraini employees with three consecutive months of service.
We believe in the recognition of our most outstanding employees. We host an annual ceremony under the patronage of His Majesty the King of Bahrain in which we honour those who have excelled.
Our employees are continuously supported in their professional growth through our on-the-job and off-the-job development opportunities. These development opportunities ensure our employees have a fulfilling career in line with their strengths and ambitions.
We also support the children of employees through our academic scholarships which are awarded annually.
GRI 401-01: New employee hires and employee turnover
GRI 401-02: Benefits provided to full-time employees that are not provided to temporary or part-time employees
GRI 401-03: Parental leave
All our employees are entitled to a parental leave regardless their position and gender. During 2020, 85 employees went on parental leave (15 maternity leave and 70 paternity leave). In 2021, the total number of employees who had a parental leave was 108 (16 maternity leave and 92 paternity leave).
For employees, notice periods vary by labour contract and consider the important operational needs that arise within the Refinery. We are respectful of employee needs and maintain open dialogue through meetings between labour unions and Bapco management. Union representation is included within EHS committees to provide a forum for discussion of all issues arising. Bapco has a robust management of change process in place that includes process, equipment, operational and organisational changes. All aspects and risks are assessed and communicated to relevant staff.
Acronym Abbreviation
ADNOC Abu Dhabi National Oil Company
AGU Arabian Gulf University
AIChE American Institute of Chemical Engineers
API American Petroleum Institute
Bapco Bahrain Petroleum Company B.S.C. (Closed)
BBL Barrel (42 US gallons or 159 litres)
BCP Business Continuity Plan
BDSEPP Bapco Distributed Solar Energy Pilot Project
BMP Bapco Modernisation Program
BOOST Behaviour Observation Obtains Safe Trends
BPD Barrels per Day
CEO Chief Executive Officer
CERP Crisis and Emergency Response Plan
CHA Critical Habitats Assessment
CLG Chevron Lummus Global
CMT Crisis Management Team
CO Carbon monoxide
COP26 26th session of the Conference of the Parties
CO2 Carbon dioxide
CSR Corporate Social Responsibility
DMA Disclosure Management Approach
DPE Dubai Petroleum Establishment
DRB Decision Review Board
EHS Environment, Health and Safety
EPC Engineering, Procurement and Construction
ESIA Environmental and Social Impact Assessment
ESQR European Society for Quality Research
FAI First Aid Injury
FCCU Fluid Catalytic Cracking Unit
GCC Gulf Cooperation Council
GDA Gulf Downstream Association
Gg Gigagram (1 Gg = 1 billion grams)
GHG Greenhouse Gas
GRI Global Reporting Initiative
H2S Hydrogen sulphide
H.E. His Excellency
H.H. His Highness
HR Human Resources
HSE Health, Safety and Environment
Acronym Abbreviation
HWMF Hazardous Waste Management Facility
ICS Incident Command System
IDP Individual Development Plan
IFC International Finance Corporation
IMS Incident Management System
IMT Incident Management Team
IPCC Intergovernmental Panel on Climate Change
IPIECA International Petroleum Industry Environmental Conservation Association
ISO International Standards Organisation
JVROC Joint Venture for Refinery Operating Companies
KOC Kuwait Oil Company
KJO Al Khafji Joint Operations
KPI Key Performance Indicators
L&D Learning and Development
LEWAS Leadership Excellence for Women Awards
LPG Liquefied Petroleum Gas
LTI Lost Time Injuries
MEMAC Marine Emergency Mutual Aid Centre
MOU Memorandum of Understanding
MMbbl Million barrels
MW Megawatt (1MW = 1000 kW)
MWp Megawatt Peak, a maximum power output
NEBOSH National Examination Board in Occupational Safety and Health
NGO Non-Governmental Organisation
NLTI Non-Lost Time Injury
NO2 Nitrogen dioxide
nogaholding Oil and Gas Holding Company B.S.C. (Closed)
NO x Nitrogen oxides
ODS Ozone Depleting Substances
OSCP Oil Spill Contingency Plan
OSRL Oil Spill Response Limited
PCR Polymerase Chain Reaction
PDO Petroleum Development Oman
PM10 Particulate matter with a diameter of 10 microns or less
RAT Rapid Antigen Test
REACH Registration, Evaluation, Authorisation and Restriction of Chemicals
Acronym Abbreviation
RECSO Regional Clean Sea Organisation
RHCU Residue Hydrocracking Unit
RON Research Octane Number
SCE Supreme Council for Environment
SCW Supreme Council for Women
SDGs Sustainable Development Goals
SDS Safety Data Sheet
SHEQ Safety, Health, Environment and Quality
SME Subject Matter Expert
STP Sewage Treatment Plant
TDS Total Dissolved Solids
UEDC Utilised Distillation Equivalent Capacity
UNFCCC United Nations Framework Convention on Climate Change
UNGC United National Global Compact
WJO Wafra Joint Operations
WWTP Waste Water Treatment Plant
This sustainability report has been prepared in accordance with the GRI Standards Comprehensive option. The GRI Content Index provides a reference to the publication year for each GRI Standard used and the location of each topic specific disclosure in the report.
Newer disclosures require a specific Management Approach, where this is the case the Content Index lists each Management Approach disclosure number. The remaining disclosures refer to ‘103-01 to 03 Management Approach’ for:
• 103-01: Explanation of the material topic and its Boundary;
• 103-02: The management approach and its components; and
• 103-03: Evaluation of the management approach.
Bapco is a wholly owned government entity and is therefore not subject to corporate tax payable to government.
Bapco’s main products are shipped by pipeline and tanker, and are not packaged. Some production processes use catalyst and small quantities of chemical additive. Bapco does not otherwise use significant quantities of material in the production and packaging of its primary products.