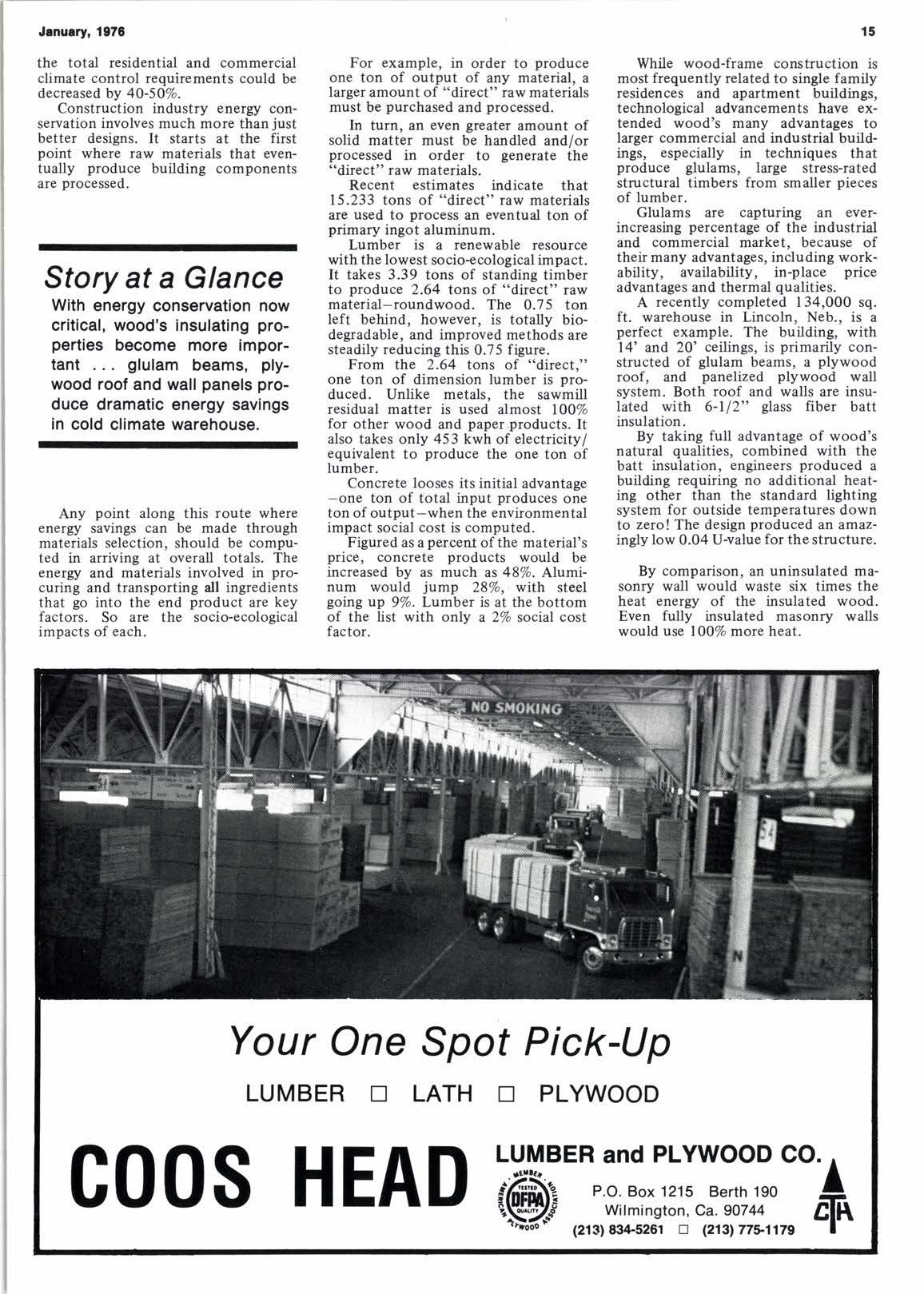
2 minute read
WOOD INSULATES:
structure, earns them plus ratings in energy conservation. And leading the pack is one of man's oldest and most reliable building materials-timber.
Because of its unique internal structure. wood is a natural insulator. Millions of tiny air cells, trapped within its fibers, make wood an excellent barrier against heat and cold.
With the expanding commitment to energy conservation, wood as a major structural material is receiving even greater attention at the same time that the forest products processing industry is undergoing a technological revolu- tion. Years of wood research is paying off as commercial industries put the results into practice.
Statistics from the American Society of Heating, Refrigerating and Air Conditioning Engineers (ASHRAE) show that, for equivalent thicknesses, wood is four times as efficient an insulator as concrete block, six times as efficient as brick, l5 times better than concrete or stone, tops steel 400 to l, and is 1,770 times as efficient as aluminum.
Through proper insulation and construction practices, it is estimated that
4 TIMES AS EFFICIENT AS CONCRETE BI.OCK
6 TIMES AS EFFICIENT AS BRICK the total residential and commercial climate control requirements could be decreased by 4O-5O7o.
Construction industry energy conservation involves much more than just better designs. It starts at the first point where raw materials that eventually produce building components are processed.
Story at a Glance
With energy conservation now critical, wood's insulating properties become more impor- tant... glulam beams, plywood roof and wall panels produce dramatic energy savings in cold climate warehouse.
Any point along this route where energy savings can be made through materials selection, should be computed in arriving at overall totals, The energy and materials involved in procuring and transporting all ingredients that go into the end product are key factors. So are the socio-ecological impacts of each.
For example, in order to produce one ton of output of any material, a larger amount of "direct" raw materials must be purchased and processed.
In turn, an even greater amount of solid matter must be handled and/or processed in order to generate the "direct" raw materials.
Recent estimates indicate that 15.233 tons of "direct" raw materials are used to process an eventual ton of primary ingot aluminum.
Lumber is a renewable resource with the lowest socio-ecological impact. It takes 3.39 tons of standing timber to produce 2.64 tons of "direct" raw material-roundwood. The 0.75 ton left behind, however, is totally biodegradable, and improved methods are steadily reducing this 0.75 figure.
From the 2.64 tons of "direct," one ton of dimension lumber is produced. Unlike metals, the sawmill residual matter is used almost 100% for other wood and paper,products. It also takes only 453 kwh of electricity/ equivalent to produce the one ton of lumber,
Concrete looses its initial advantage -one ton of total input produces one ton of output-when the environmental impact social cost is computed.
Figured as a percent of the material's price, concrete products would be increased by as much as 48Vo. Aluminum would jump 28%,' wil}l^ steel going up 97o. Lumber is at the bottom of the list with only a 2% social cost factor.
While wood-frame construction is most frequently related to single family residences and apartment buildings, technological advancements have extended wood's many advantages to larger commercial and industrial buildings, especially in techniques that produce glulams, large stress-rated structural timbers from smaller pieces of lumber.
Glulams are capturing an everincreasing percentage of the industrial and commercial market, because of their many advantages, including workability, availability, in-place price advantages and thermal qualities.
A recently completed 134,000 sq. ft. warehouse in Lincoln, Neb., is a perfect example. The building, with 14' and 20' ceilings, is primarily constructed of glulam beams, a plywood roof, and panelized plywood wall system. Both roof and walls are insulated with 6-ll2" glass fiber batt insulation.
By taking full advantage of wood's natural qualities, combined with the batt insulation, engineers produced a building requiring no additional heating other than the standard lighting system for outside temperatures down to zero! The design produced an amazingly low 0.04 U-value for the structure.
By comparison, an uninsulated masonry wall would waste six times the heat energy of the insulated wood. Even fully insulated masonry walls would use lOOTo more heat.