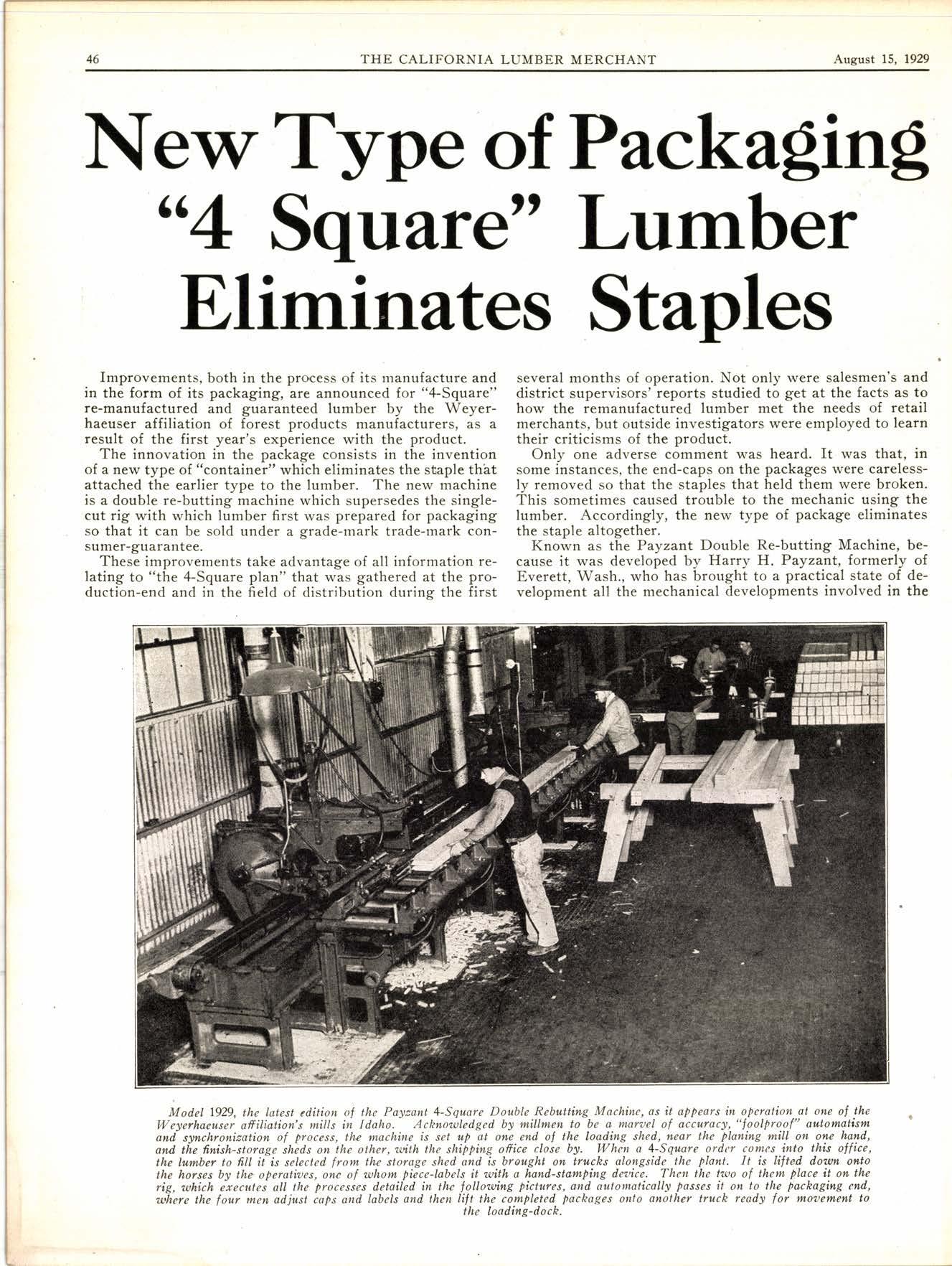
6 minute read
NewType of Packaging "4 Square" Lumber Elimitrates Staples
Improvements, both in the process of its manufacture and in the form of its packaging, are announced for "4-Square" re-manufactured and guaranteed lumber by the Weyerhaeuser affiliation of forest products manufacturers, as a result of the first year's experience with the product.
The innovation in the package consists in the invention of a new type of "container" which eliminates the staple that attached the earlier type to the lumber. The new machine is a double re-butting machine which supersedeS the singlecut rig with which lumber first was prepared for packaging so that it can be sold under a grade-mark trade-mark consumer-guarantee.
These improvements take advantage of all information relating to "the 4-Square plan" that was gathered at the production-end and in the field of distribution during the first several months of operation. Not only were salesmen's and district supervisors'reports studied to get at the facts as to how the remanufactured lumber met the needs of retail merchants, but outside investigators were employed to learn their criticisms of the product.
Only one adverse comment was heard. It was that, in some instances, the end-caps on the packages were carelessly removed so that the staples that held them were broken. This sometimes caused trouble to the mechanic using the lumber. Accordingly, the new type of package eliminates the staple altogether.
Known as the Payzant Double Re-butting Machine, because it was developed by Harry H. Payzant formerly of Everett, Wash., who has brought to a practical state of development all the mechanical clevelopments involved in the
Modet 1929, the latest edition ol the Payzant 4-Square Double Rebutting Machine,os it appears in operation at one of the Weyerhaeuser afriliation's mills in ld.aho. Achnowledged by millmen to be a marael of accurac!, "tooliroof" automatism ,,.JE".qvw.rt and slmchroniaation of process, thc machine is set up at one end of the loading shed,,,near the planing mill on 9rye h911d' and tite finish-storaee sheds on the other, with the shi\line oftice close by. lilhen a 4-Square ord.'r comcs into this otfice finish-storage shipping order otfice, the lumber to fill it is selected, from the storage shed and is brought on trucks alongside the plant. It is lilta.d dozan onto the horses by the operatiaes, one of zlhom piice-labels it laitk a hand-stamping deztice. Then the two of them place it or the rip. zahich irecu.tes all the lrocesses detailed in thc lollowing pictures, and outomotically passes i't on to the packaging cnd, selected. br processes the tollowing i'tzahere the f our men adjust caps and labels and then lilt the completed pachoges onto another truck ready f or movement to the loading-dock.
4-Square program, the new machine presents the following advantages over the earlier rig:
1. Rapidity of production. It puts the re-manufacturing and pa,ckaging operation on a volume-basis consistent with the. increasing demand for the packaged line among progressive lumber merchants. At the end of trvo rveeks' operation, the initial installation rvas clipping out a complete packag'e every 10 seconds-r,vith a green crew.
2. Still greater precision. The detaili of the machine, that will be described presently, show how this equipment depends upon the human element in its operation even less than the earlier type, so that the rnaximum of mechanical precaution is exercised to make the lumber exact in length and perfect in finish.
3. Pr'otection of the product. This principle rvas strong- ly established in the first 4-SQUARE machines, but is fuither reinfor,ced in the present equipment so that it is virtually impossible for any defect to occur in any piece of packaged lumber during the rebutting, packaging and loadlng processes.
experience with the plan justify investment and permanent machinery. improved
In the most general terms the machine may be described as a long iron bench with a sawhead at each end, both motivated from a single control so as to re-butt both extremities of a small pile of boards simultaneously. Only two men are required to run it. Lumber is brought alongside it on trucks, is lifted dorvn onto a pair of horses, and there is p_iece-labeled with a small manual stamping implement by the second man. Both operatives togettrer arrange th-e boards in_ piles of the number contained in a single palkage, and lift them onto the machine. Then the marr at the control-end presses a light lever which makes an electric contact that sets the several suoceeding operations in process.
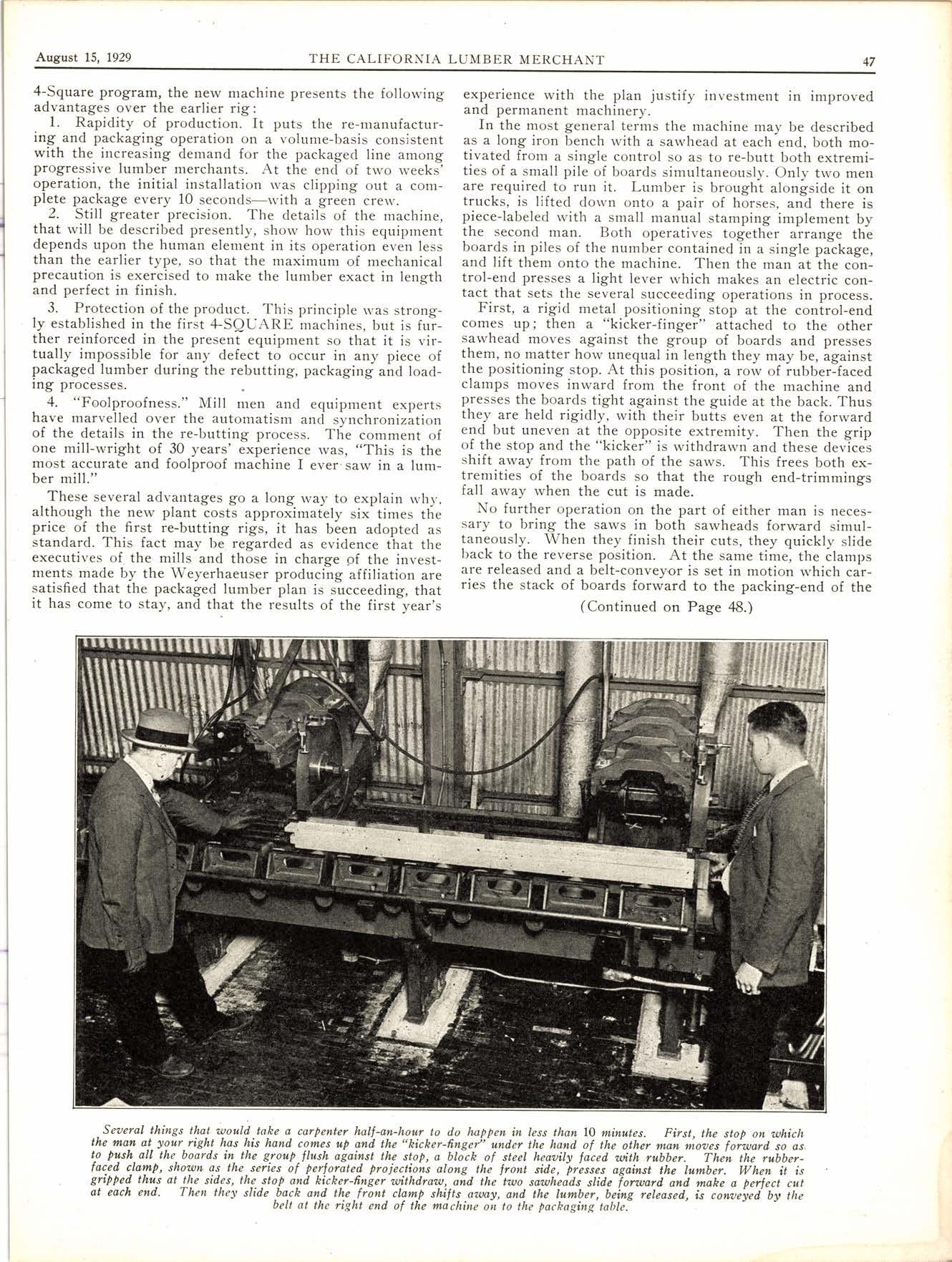
,
4. "Foolproofness." Mill men and equipment experts have marvelled over the automatism and synchronizition of the details in the re-butting process. The comment of one mill-wright of 30 years' &perience lvas, "This is the most accurate and foolproof machine I ever'saw in a lumber mill."
These several advantages go a long way to explaip wlly, although the new plant costs approximately six times the price of the first re-butting rigs, it has been adopted as standard. This fact may be, regarded as evidence that the executives of the mills and those in charge pf the investments made by the Weyerhaeuser producing affiliation are satisfied that the packaged lumber plan is succeeding, that it has come to stay, and that the results of the first year's
First, a rigid metal positioning stop at the conirol-end comes up; then a "kicker-finger" attached to the other sawhead moves against the group of boards and presses them, no matter holv unequal in length they may be, igainst the positioning stop. At this position, a row of iubberlfaced clamps moves inward from the frontof the machine and presses the boards tight against the guide at the back. Thus they are held rigidly, with their butts even at the forward end but unevell at the opposite extremity. Then the grip of the stop and the "kicker" is withdrarvn and these dev'icei shift away from the path of the saws. This frees both extremities of the boards so that the rough end-trimmings fall away when the cut is made.
No further operation on the part of either man is necessary to bring the saws in both sawheads forward simultaneously. When they finish their cuts, they quickly slide back to the reverse position. At the same time, the ilamps are released and a belt-convey,or is set in motion which carries the sta,ck of boards forward to the packing-end of the
(Continued on Page 48.)
New Type of Packa$in$ "4 Squ are" Lumber Eliminates Staples
(Continued from Page 47) tig. After being brought to the right position for the men wIo apply the Jnd-caps, the lumber is moved transversely off the -rig p.op.t onto the supports on which the packaging is done.
-Eicept that it trims both ends of the package simultaneously ind that it is improved in all details, the new rebutting machine works on the same.principles as those upon which the first rigs worked. One big advance is in the con- according as the lumber is to be longer or shorter. Along the back of the machine is a tool-steel indexing plate. with a series of slots a foot apart-the distance between each pair being micrometrically exact. The machine cannot operate af all unless the movable sawhead is correctly set in the appropriate slot in the indexing plate. So lumber passing -through the machine is certain to be exact in length.
From this z,,iezu ol the control-end of the ntachine, lou cafl sec that, alter the hoards in'te-nded for cach lrachage orc placed in thc machine' thcre's just one 'shift '-of a light leaer artd' then tltc machine docs the r(st, crce l.rt lor the odjustme trt of caf s. trol. In last year's equipment. the saw was brought.dorv.n for the cut manually br by separate contact of an electric button. In the new ntachinery, this operation is entirely automatic.
Accuracy in the dinrensions of the product is assured by the fact that one of the two sawheads can be moved nearer or farther from the one at the control-end of the bench,
Hcre's h.ozu the new stapleless lumbcr pachage worhs. 'l-he ntoxable tray holds the cafs zuhich haae been la' belcd, fretiously in the stocleroom and o ltan of moistener. Here you see the !)oung rnan,'uho hos sl;pped the capbond around the boards, and a\Plied the gurnmed cambric to the top end, and forced that into place against the reaerse face of the top zwop-boord, now aP\lSring unothcr str;p ol the gummed cantbric to the bottom flonge of thc clf.
While the saws are of the sarhe type as those in the earlier rebutting rigs, there is one device in connection with them whi,ch has caused particular comment from those who have seen it. It is a trueing instrument on the casing of each saw, by which the set of the saw may be corrected immediately at any time that an operative observes even the slightest defect in the smoothness of the cut produced.

f.or Sale
For rale at a bargain, two thourand tonr strictly A. S. C. E. No. 1-6O pormd rel,aying railwith ansle bars, at a delivered price of $26.50 groer C. I. F. at Pacific portr.
In improving the package itself, Mr. Payzant started at the very bottom. He wrote new specifications for a special tlbre-board, that is light and extremely tough and strong. Caps of this material are fashioned differently from the first end-caps so as to cut down the time required f,or their adjustment to the lumber at the mill.

Afterthis adjustment, each end-cap is held in position by two strips of gummed cambric, one on the top and the other on the bottom wrap-board. A special adhesive is used and is moistened by a chemical mixture lvhi'ch makes it "set" quickly. As each end-cap is fixed on the package, it is clamped there by a pneumatic clamp which also was designed especially forthis use. By the time the clamp must be removed for another package, the carnbric is fast-