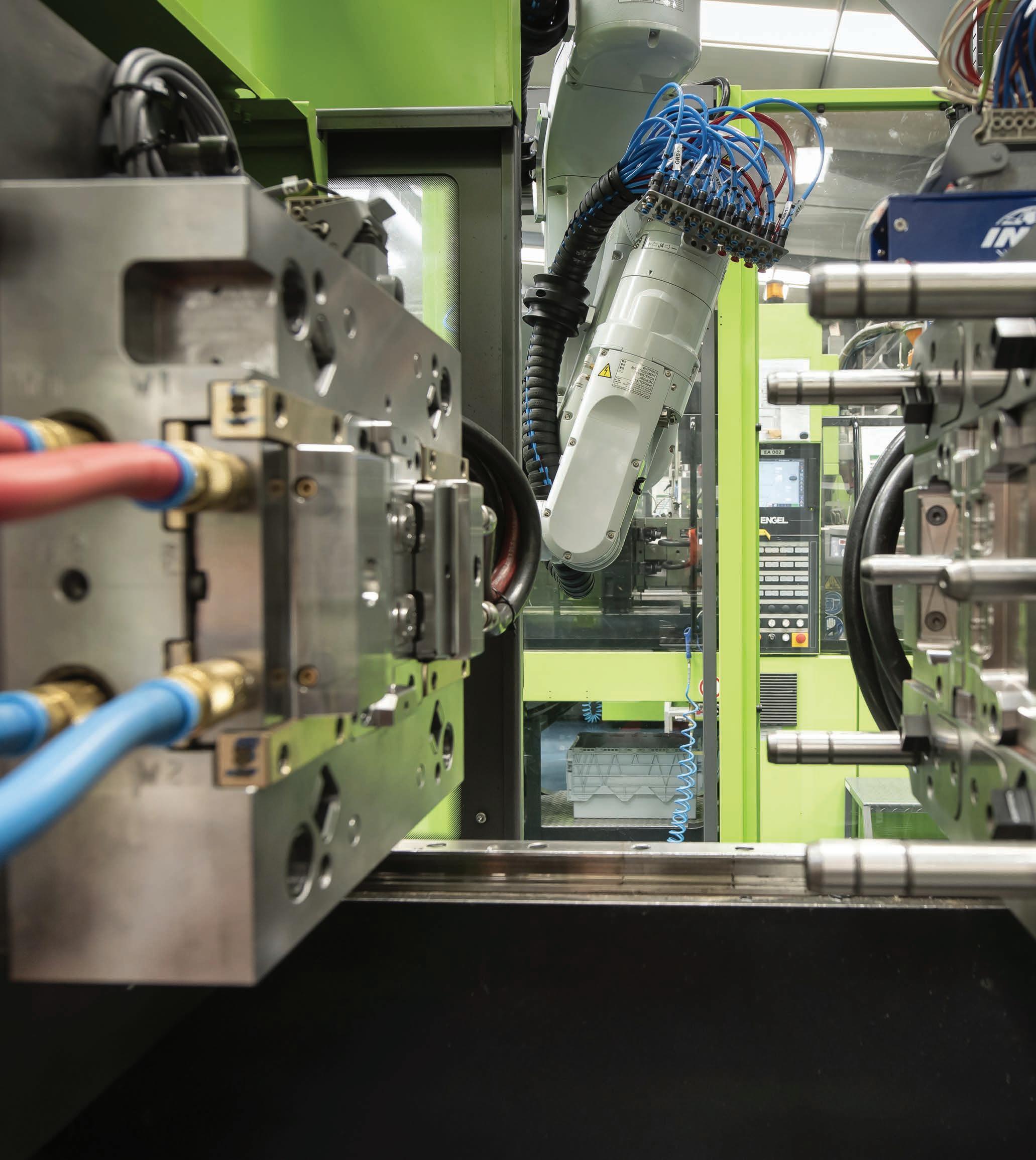




A NOVA GEOPOLÍTICA INDUSTRIAL
IMPORTÂNCIA DA GESTÃO E OTIMIZAÇÃO ENERGÉTICA NAS EMPRESAS
Com a nova mangueira ondulada de PTFE com malha metálica, HASCO oferece uma gama inovadora de mangueiras de sistema de refrigeração para aplicações exigentes em relação à segurança no trabalho e nos processos, temperatura, flexibilidade e longa duração.
▪ Altamente flexível, resistente à torção e não dobrável
▪ Marcação inequívoca das linhas de fluxo de entrada e saída e pontes de temperatura
▪ Elevada elasticidade e resistência à tração
▪ Aplicável nos sectores da tecnologia médica e na indústria alimentar
Encomenda
O QUE AS EMPRESAS CONCEBEM DE FORMA SINGULAR E INOVADORA
TECNOLOGIA
EQUIPAMENTOS . PROCESSOS . CONHECIMENTO
ECONOMIA .
Editorial
Notícias CEFAMOL
Notícias dos Associados
A Indústria à Lupa
Outras notícias
Testes são a chave para a excelência do fabrico do molde
Testes permitem aferir qualidade e eficiência da injeção do plástico
Qualidade e eficiência dos ensaios requerem especialização e experiência
A relevância do canal quente nos testes de moldes
Estudo de propriedades mecânicas de materiais plásticos em ciclos sucessivos de injeção e reciclagem
Controlo e monitorização remoto em tempo real de máquina de injeção com recurso a machine learning
DFM (Design for Manufacturing) – conceber eficiência e produtividade para desenvolver o negócio
Acertos de brilho e ajustes finais nos moldes com vista à otimização do aspeto das peças plásticas
Elementos móveis de longo curso - uma nova abordagem
A nova geopolítica industrial
Processos - se existem, porque não os cumprimos?
Importância da gestão e otimização energética nas empresas
ESG e o sector dos moldes e plásticos: um caminho para a sustentabilidade
CIRCVET promove formação em economia circular na indústria de plásticos
A obrigação de quantificar (e reduzir) as emissões de carbono
Indústria 5.0: integração humana e tecnológica em prol da sustentabilidade
Moldar o futuro: a liderança invisível
FICHA TÉCNICA
PROPRIEDADE CEFAMOL - Associação Nacional da Indústria de Moldes • CONTRIBUINTE 500330212 • SEDE DO EDITOR, REDAÇÃO E ADMINISTRAÇÃO Centro Empresarial da Marinha Grande - Rua de Portugal, Lt. 18 - Fração A / 2430-028 MARINHA GRANDE - PORTUGAL / T: 244 575 150 / F: 244 575 159 / E: revista_omolde@cefamol.pt / www.cefamol.pt • FUNDADOR Fernando Pedro • DIRETOR Manuel Oliveira • CONSELHO EDITORIAL António Rato, Eduardo Pedro, Luís Abreu e Sousa, Manuel Oliveira, Maria Arminda • TEXTOS Ana Pires, António Baptista, Armando Bastos, Artur Ferraz, Carlos Ribeiro, Carolina Feliciana Machado, Carolina Neves, Diana Dias, Eduardo Oliveira, Emanuel Silva, Gilberto Martins, J. Paulo Davim, Helena Silva, Maxime Daniel, Miguel Nuno Silva, Nuno Martinho, Raúl Souto, Rita Diniz, Rita Marques, Rui Rocha, Sílvia Cruz, Tânia Mendes, Vítor Ferreira • PUBLICIDADE Rui Joaquim • PRODUÇÃO GRÁFICA Colorestúdio – Artes Gráficas, Lda / Zona Industrial Casal da Azeiteira, Pav. 3 - Quintas do Sirol - 2420-345 St.ª Eufémia - Leiria / T: 244 813 685 / E: colorestudio.lda@gmail.com • PERIODICIDADE Trimestral • TIRAGEM 500 exemplares • DEPÓSITO LEGAL 22499/88 • REGISTO ERC 113 153 • Nº ISSN 1647-6557 • Estatuto Editorial encontra-se disponível em www.cefamol.pt
ANUNCIANTES S3D 2 / Simulflow 5 / HPS 7 / Cadsolid 9, 51 / Fuchs 13 / Newserve 17 / DNC Técnica 19 / Open Mind 23 / SB Molde27 / Universal Afir 29 / Projeto de Promoção Internacional 33 / Balzers 35 / Hrsflow 37 / Sigmasoft 39 / Isicom 41, 63 / Norelem 43 / FerrolMarinha 45 / RTC 47 / Ramada 49 / Cheto 53 / Eurocumsa 55 / Schunk 57 / Arburg 61 / TTO 65 / Grandesoft 71 / Fluxoterm 73 / Inovatools 75 / Hasco capa interior / Mafepre contracapa interior / Tebis contracapa
A Indústria Portuguesa de Moldes é um dos sectores mais dinâmicos e internacionalizados da economia nacional, com uma sólida reputação construída ao longo de décadas. Contudo, à medida que o cenário global se torna cada vez mais competitivo e incerto, torna-se imperativo que as empresas adotem estratégias robustas que garantam o seu crescimento e sustentabilidade. A diversificação de mercados, tanto na vertente geográfica quanto sectorial, surge, atualmente, como um elemento crucial para alcançar estes objetivos, mas para o efeito, é vital desenvolver uma estratégia consistente que permita identificar novos nichos, clientes que estejam a desenvolver produtos inovadores e que complementem a oferta “mais tradicional” em que o sector já atua.
Embora a Europa continue (e continuará) a ser um mercado crucial para as exportações nacionais, as suas previsões de crescimento são moderadas, o que coloca uma pressão adicional sobre as empresas que dependem fortemente desta região, o que, no caso do nosso sector representa cerca de 80% do destino dos moldes produzidos. Ao nível sectorial, a situação não é diferente, representando a indústria automóvel, aproximadamente 75% da nossa produção. No entanto, a questão que se coloca é: e há alternativas?
Não é uma resposta simples, até porque dificilmente conseguiremos, no imediato, ou até no curto prazo, inverter o atual paradigma, especialmente na indústria automóvel, onde a sua própria evolução originará, certamente, novas oportunidades para as nossas empresas. No entanto, não podemos deixar de, paulatinamente, estudar, analisar e contactar com mercados que se encontram em expansão e com áreas industriais emergentes.
Se pretendemos fazer este caminho temos de ser proativos e ir conhecer o que está a acontecer, contactar com os agentes de mudança, os novos players, e definir como posicionar as nossas empresas nestas novas cadeias de valor. Não podemos esperar que a mudança seja feita apenas com os clientes tradicionais, com quem lidamos e que nos vão trazendo novos produtos (e desafios). Sem dúvida que os devemos manter e preservar pois eles serão sempre a base de suporte do nosso crescimento, mas tal não nos deve impedir de fazer o nosso próprio caminho na procura de novas oportunidades.
Reduzir a dependência dos mercados e clientes tradicionais torna-se, portanto, uma prioridade estratégica. Há que conhecer e acompanhar o que está a acontecer nas regiões com maior potencial de crescimento, como é o caso da Ásia, da América do Norte (que contempla dois dos três maiores importadores de moldes a nível mundial) ou até mesmo do Norte de África, e perceber como tal poderá influenciar a nossa atividade (presente e futura) ou mesmo como as empresas se poderão posicionar para captar novas oportunidades de negócio. Mercados em expansão têm demonstrado um crescimento robusto e uma procura crescente por produtos manufaturados que requerem moldes de maior precisão e fiabilidade, podendo, em certa medida, compensar algum declínio de outros mais maduros
Manuel Oliveira Secretário-geral da CEFAMOL
Para além da diversificação geográfica, a indústria de moldes deve também procurar diferenciar as suas bases de clientes. Tradicionalmente, a indústria automóvel tem sido o maior consumidor de moldes produzidos em Portugal. No entanto, a dependência excessiva deste sector apresenta riscos significativos, especialmente numa época em que atravessa transformações profundas derivadas da transição para veículos elétricos ou das incertezas económicas globais.
A diversificação sectorial permite às empresas de moldes expandir a sua oferta para indústrias emergentes e em crescimento, como as de dispositivos médicos, embalagem, eletrónica, e até mesmo a indústria aeroespacial. Uma área particularmente promissora é o sector de defesa e segurança, que tem vindo a ganhar relevância no contexto internacional. O desenvolvimento de novos produtos e tecnologias nesta área, como equipamentos de proteção, componentes de aeronaves e veículos militares ou dispositivos de segurança, exigem moldes de precisão e alta qualidade, podendo criar uma oportunidade relevante para o sector.
É crucial que as empresas sejam dinâmicas na prospeção de novos clientes e na identificação de nichos de mercado em ascensão. Será essencial um investimento em ações de prospeção internacional. Visitar e participar em feiras ou missões internacionais dedicadas, desenvolver parcerias estratégicas e explorar redes de negócios globais são algumas das atividades que podem abrir portas a novos nichos de mercado.
Ao identificar novas tendências em desenvolvimento, especialmente em sectores emergentes, as empresas podem antecipar necessidades dos clientes e oferecer soluções que complementem e expandam a sua oferta. Este enfoque na prospeção permite às empresas estar na vanguarda da inovação e estabelecer parcerias estratégicas que sustentem a sua competitividade a longo prazo. Em paralelo, a diversificação estimula a inovação, uma vez que a exposição a diferentes mercados e sectores incentiva o I&D e a introdução de novas tecnologias, processos ou materiais. A capacidade de adaptação e a flexibilidade permitem que as empresas se diferenciem pela inovação, pela capacidade de resposta e pela customização de produtos, fatores críticos no cenário competitivo global.
Ao diversificarem mercados, as empresas não só protegem o seu negócio de choques externos, como também se posicionam como agentes de mudança, capazes de oferecer soluções inovadoras e personalizadas a uma ampla gama de clientes. Tal será, sem dúvida, um pilar fundamental para a sustentabilidade e diferenciação do nosso sector.
Ao expandir geograficamente e explorando novas áreas industriais, as empresas fortalecem a sua resiliência, estimulam a geração de novas soluções e posicionam-se para um crescimento sustentável. Num mundo cada vez mais incerto e competitivo, esta diversificação não é apenas uma opção, mas uma necessidade estratégica para assegurar o futuro da indústria de moldes em Portugal.
Virtualização e simulação estiveram em debate em mais uma sessão do Fórum TECH-i9, organizada pela CEFAMOL, que reuniu cerca de três dezenas de profissionais da indústria, no Centro Empresarial da Marinha Grande. Estas tecnologias, defenderam os intervenientes na ação, são essenciais para acrescentar qualidade ao molde, evitando correções e perdas de tempo.
“Fazer análises na fase de projeto e conceção da ferramenta moldante é vital para evitar correções e perdas de tempo posteriores no processo”, defendeu João Caseiro, representante do CENTIMFE, responsável pela contextualização ao tema ‘Virtualização e Simulação na Conceção do Molde’.
João Caseiro definiu a virtualização como um processo que transforma algo em digital, utilizando ferramentas digitais para atividades específicas, especialmente na indústria dos plásticos, salientando que a simulação numérica se baseia em equações matemáticas, e que é crucial que o utilizador compreenda o que o software está a fazer. Enfatizou também o facto de o sucesso da simulação depender de um conhecimento integrado entre o operador e a máquina.
Ao longo da sua exposição, o responsável exemplificou as diversas simulações utilizadas na indústria, incluindo a simulação reológica, a análise estrutural, a dinâmica de fluidos computacional e a dinâmica molecular, esta última menos divulgada e, na sua ótica, menos utilizada.
Destacando que a simulação deve ser aplicada desde a fase de conceção até à produção da peça, defendeu que a importância das análises como forma de acrescentar valor e rapidez ao processo de fabrico do molde. A simulação numérica, exemplificou, “gera conhecimento que permite explorar designs, prever defeitos em fases iniciais do projeto, resultando em menos iterações de teste e correção”.
Chamou ainda a atenção para os desafios que estas tecnologias também apresentam, como “a necessidade de formação, o investimento em software e hardware, a complexidade das geometrias, a calibração dos modelos e os tempos de cálculo”. Deixou ainda uma advertência, sublinhando que “é preciso conhecer o que estamos a fazer, entender as simulações e saber quais decisões estamos a tomar”.
Já na fase de debate do tema, o moderador Artur Mateus (Universidade de Coimbra) questionou os oradores – Teresa Neves, da Simulflow; e Marco Ruivo, da Sigmasoft, entre outras questões, sobre a fiabilidade da simulação.
Teresa Neves começou por traçar um quadro sobre a evolução da simulação na indústria, revelando ser pioneira em Portugal no uso destas ferramentas. No seu entender, nos últimos 40 anos, houve uma “evolução enorme dos softwares”, embora ainda existam limitações. É da opinião de que “a utilização destas ferramentas é fundamental para assegurar a qualidade do fabrico do molde”, defendendo que a sua aplicação é cada vez mais valorizada na indústria dos plásticos.
Alertou, contudo, que “simulação e realidade são sempre diferentes”, mas isso não deve desincentivar o uso dessas ferramentas. Para que se retire proveito, alertou, é fundamental que o utilizador tenha experiência e conhecimento. “Quem manuseia esta ferramenta deve ser alguém com um conhecimento profundo do processo de fabrico, e não um recém-formado”, advertiu.
Já Marco Ruivo contou que, pela sua experiência na indústria de moldes, “normalmente, cada problema complexo tem uma solução simples: no entanto, a indústria demonstra resistência em avançar para soluções que não conhece”. “No passado, quando os desenhos eram feitos à mão, havia uma maior abertura para investimentos em tecnologias emergentes. Hoje, a cautela predomina”, salientou, considerando que a adesão do sector à simulação “tem sido mais lenta do que seria necessário, o que resulta em práticas ainda bastante empíricas”.
Marco Ruivo considerou ainda que a fiabilidade da simulação pode ser melhorada com formação adequada, exemplificando com a metodologia aplicada pela sua empresa, e afirmando que “o investimento na solução só é rentabilizado quando toda uma equipa (e não apenas uma pessoa) é treinada para trabalhar com a simulação”.
Teresa Neves e Marco Ruivo foram unânimes no reconhecimento da falta de formação adequada para os jovens nesta área, destacando a necessidade de integrar mais estas tecnologias nas escolas. Teresa Neves enfatizou a importância de os alunos dominarem, não apenas a técnica de simulação, mas também
Teresa Neves | Simulflow
“Simulação ajuda a decidir com mais certeza, maior rapidez e menor risco de erros”
O facto de o nosso tecido empresarial ser constituído por micro e pequenas empresas acaba por criar algumas limitações. Apesar de, na generalidade dos casos, as empresas perceberem bem a relação custo-benefício destas soluções, elas implicam fazer investimento, não só em tecnologia, mas também em recursos humanos, para utilizarem a ferramenta de forma a retirar partido dela. São questões que levam as empresas a ponderar. Por essa razão, no nosso caso desenvolvemos dois tipos de solução para a indústria: temos duas empresas – uma que pode executar o serviço que as empresas necessitam e a outra que faz a representação do software. A simulação representa benefícios enormes uma vez que pode ajudar a prevenir os problemas. Além disso, as empresas aprendem mais sobre o seu processo e, por essa via, acabam por dar um melhor serviço aos seus clientes, decidindo com mais certeza, maior rapidez e menor risco de erros.
saberem interpretar os seus resultados. Por seu turno, Marco Ruivo sugeriu que iniciativas como a promoção de visitas a centros de aprendizagem especializados no estrangeiro, como na Alemanha, podem ajudar a preparar melhor os jovens para o mercado.
Marco Ruivo | Sigmasoft
“Um software de simulação é imprescindível para ajudar a antever os problemas”
Há muitas empresas que ainda não trabalham com a simulação por que estão à espera de que os clientes lhes deem essa informação; estão acomodadas. Mas há todo um conjunto de vantagens associadas à simulação que estão a colocar de lado. Por exemplo, a redução de custos na produção. É que se o produto tem problemas ao longo da cadeia de produção, isso acarreta perdas de tempo e de dinheiro, obrigando o molde a manutenções que, com a simulação, poderiam ser evitadas. Logo, estas tecnologias permitem aumentar a produtividade das empresas. A redução dos custos de produção é hoje essencial para a vitalidade e o futuro das empresas. E se conseguimos ser mais efetivos a fazer a produção da ferramenta, ou da peça de plástico, temos de aproveitar. Um software de simulação é imprescindível para ajudar a antever os problemas de A a Z, ou seja, desde a conceção ao final do processo de fabrico.
‘Gestão da Produção na Indústria de Moldes’ foi a segunda sessão do Fórum TECH-i9 e atraiu cerca de meia centena de profissionais da indústria, unânimes em considerar que a gestão da produção é essencial para assegurar a competitividade do sector. Foi defendida também a necessidade de consolidar a aposta na inovação nas práticas de gestão.
Irene Ferreira, da Stream Consulting, foi perentória no início da sessão que debateu o tema da Gestão da Produção: “para que tenham futuro, as empresas têm de conseguir fazer mais, melhor e com menos”. Este é, no seu entender, o grande desafio que se coloca. E a resposta, considera, é uma eficaz gestão da produção.
Destacando que, no atual contexto de concorrência aguerrida, especialmente com os preços significativamente mais baixos na Ásia, a adição de valor é crítica para a indústria, por isso, enfatizou que a gestão da produção é, sobretudo, “uma questão de sobrevivência”, uma vez que permite às empresas otimizar preços e tempos de resposta.
Irene Ferreira chamou a atenção para a pressão que os prazos e as condições de pagamento dos clientes exercem sobre as tesourarias das empresas, mencionando que, muitas vezes, os pagamentos acontecem, apenas, no final do projeto. A somar a esse desafio, realçou o facto de, em muitos casos, as empresas enfrentarem “o peso de retrabalho que pode chegar a mais de 20 %”, o que impõe a necessidade de uma gestão mais eficaz. “Temos de fazer melhor: não é uma opção, é uma obrigação”, enfatizou.
Explicando que a gestão eficaz é dificultada pelo facto de o sector se inserir na área da ‘engenharia por encomenda’, onde “cada peça produzida é única e diferente das demais”, considerou que isso dificulta sobremaneira a estimativa de tempos e prazos, uma vez que, de uma maneira geral, um molde não se repete. Além disso, adiantou, a necessidade de subcontratação torna as empresas dependentes dos prazos dos fornecedores, complicando ainda mais a gestão.
No seu entender, “muitas vezes, quem gere uma empresa tem conhecimento técnico, mas não tem tempo para se dedicar à gestão”, enquanto aqueles que se ocupam da gestão nem
sempre detêm o conhecimento técnico necessário. Por isso, embora algumas organizações tenham boas práticas de gestão e apostem em sistemas de gestão, “a digitalização impacta mais no controlo de atrasos e custos do que no planeamento”, sublinha. Para Irene Ferreira, a gestão deve focar-se em “fazer bem à primeira e fazer mais com menos”, sendo essencial um planeamento integrado e criterioso. “É fundamental melhorar o planeamento, em vez de estar, apenas, a acompanhar”, exortou, adiantando ser necessário também apostar em formação e sensibilização nesta área.
Já na fase de debate, que se seguiu à intervenção de Irene Ferreira, o moderador, Pedro Custódio (Politécnico de Leiria), trouxe à tona as notícias sobre a redução de estruturas em empresas do sector automóvel para aumentar a competitividade, observando que essa pressão se reflete também sobre os fornecedores, como os fabricantes de moldes e questionando como é que as empresas podem acrescentar valor e aumentar a qualidade enquanto baixam custos. Os oradores convidados para o debate, Manuel Novo, da Erofio, e Rui Ângelo, da GLN, expressaram as suas opiniões, perante uma plateia atenta e muito interventiva.
Manuel Novo argumentou a favor da especialização como uma forma de aumentar a qualidade, destacando que “as empresas não podem fazer de tudo”. Salientou ainda que os clientes exigem das empresas portuguesas padrões que não
são cobrados aos fornecedores asiáticos, indicando que “a competitividade não se pode resumir a fazer o molde mais rápido”. Tem de passar, também, pelas questões da qualidade e diferenciação.
Rui Ângelo abordou a inevitabilidade do mercado asiático, afirmando que as empresas precisam de aprender a trabalhar com essa realidade e lamentando que a indústria portuguesa tenha “perdido tempo”, ao não olhar para o futuro. Advoga que, em lugar de inventar, as empresas deveriam observar quem faz bem e procurar melhorar os seus processos.
O responsável destacou ainda que o caminho para o sucesso reside na colaboração, enfatizando que “as pessoas falam em cooperação, mas na realidade, muitas vezes, não a praticam”. Defendeu, também, a necessidade de um planeamento eficaz, que é frequentemente confundido com programação, e destacou a importância de preparar as pessoas para essas questões. “Precisamos de cativar as novas gerações e ser abertos à mudança”, disse.
O papel das pessoas nas organizações e, sobretudo, a questão da formação, acabaram por dominar os minutos finais da sessão, com uma interessante partilha de opiniões entre a plateia e os oradores, defendendo a necessidade de olhar as novas gerações e repensar os modelos formativos e profissionais, de forma a tornar a indústria mais atrativa.
Rui Ângelo | GLN
“É fundamental ter muita eficiência para ter competitividade”
A gestão da produção é uma questão fundamental, a base da nossa competitividade. No entanto, a indústria de moldes, pelo facto de não ter evoluído - principalmente ao nível da engenharia do processo – tem de acelerar a sua adaptação aos novos processos, à semelhança do que aconteceu, por exemplo, com indústria de plásticos. É fundamental ter muita eficiência para ter competitividade. Essa eficiência só se consegue se, por um lado, tivermos ferramentas disponíveis, e, por outro, adaptarmos as pessoas à sua utilização. Temos de encontrar o equilíbrio.
Manuel Novo |
Erofio
“As empresas têm de mudar se quiserem continuar competitivas”
A gestão da produção é uma questão essencial. Para ser produtiva, uma empresa tem de ter tudo muito bem definido: desde as tarefas que têm de ser executadas, a como é que devem ser (bem) feitas. Tudo o que diga respeito ao funcionamento da empresa tem de estar bem definido. As empresas têm de estar organizadas. É que para darmos a volta à situação e aumentar a produtividade, temos de conseguir fazer bem à primeira, da forma certa e o mais rapidamente possível. As empresas descuraram um pouco esta questão no passado recente porque estavam a dar resposta ao boom de trabalho que existiu. Havia margem para conseguir fazer as coisas sem grande planeamento e sem uma gestão de produção mais apertada. Mas a realidade mudou. E as empresas também têm de mudar se quiserem continuar competitivas e no mercado.
Alberto Moura | Grupo Vangest “A gestão da produção é essencial para ter competitividade”
Penso que a gestão da produção está a decorrer a ritmos diferentes na indústria. As empresas integradas em grupos maiores, por exemplo, têm outra capacidade e outra forma de olhar para a questão que, para elas é um ‘must be done’. Contudo, há outras empresas – sobretudo as de menor dimensão – que ainda estão numa fase do ‘eu sempre fiz assim e pronto’. E são essas empresas que têm de dar a volta e começar a pensar de outra maneira. A gestão da produção é essencial para ter competitividade. É que os custos de produção estão a subir e é preciso encontrar soluções para ter uma atividade rentável. Não há outra forma: é uma questão de sobrevivência. Já as microempresas, para alcançarem esse patamar, necessitam que o sector trabalhe em cooperação. É fundamental que consigamos fazer isso: juntar-nos e trabalhar em conjunto. Se isso não acontecer, temo que muitas empresas não consigam sobreviver.
Nos dias 4 e 5 de setembro, a CEFAMOL acolheu a visita da divisão da área de moldes e tooling da SWISSMEM, associação suíça que, no seu global, representa mais de mil empresas dos sectores de engenharia, metalomecânica e elétrica.
Esta missão inversa teve como objetivo fortalecer os laços entre os dois países e explorar oportunidades de colaboração.
Durante a visita, a comitiva suíça teve oportunidade de contactar e visitar várias empresas de moldes na região da Marinha Grande, nomeadamente, Planimolde, Ribermold, SET, SRFAM, Tecnifreza e VL Moldes
Os representantes suíços manifestaram-se agradados com o nível tecnológico, a experiência e o know-how das empresas portuguesas, o que reforçou a confiança e o potencial para futuras parcerias.
Esta visita foi facilitada pelas relações estabelecidas entre as duas Associações no âmbito da ISTMA (International Special Tooling and Machining Association), que desempenha um papel crucial na promoção de interações e colaborações internacionais para o setor de moldes português.
A CEFAMOL liderou uma missão empresarial à Finlândia, entre os dias 9 e 13 de setembro, com o objetivo de promover as competências nacionais e identificar oportunidades de negócio e cooperação entre os dois países no sector dos moldes.
A visita integra o projeto de promoção internacional Engineering & Tooling from Portugal, que procura apoiar a expansão da presença dos moldes portugueses em termos geográficos, numa perspetiva de diversificação da oferta nacional.
De acordo com Manuel Oliveira, secretário-geral da CEFAMOL, a Finlândia assume-se como um mercado que se enquadra nesta estratégia, uma vez que se trata de uma economia aberta e altamente desenvolvida, com sectores industriais dinâmicos, incluindo áreas médica, engenharia, eletrónica ou biotecnologia.
A missão contou com a participação das empresas Imoplastic, Moliporex, Socem, TCC Moldes e VL Moldes, as quais realizaram, apresentações, encontros B2B e visitas a empresas locais. O
programa foi dinamizado e apoiado pela Teknologiateollisuus - Technology Industries of Finland, entidade que, tal como a CEFAMOL, também integra a ISTMA.
Esta missão surge na sequência de ações anteriores que promoveram o mercado da Finlândia, como o webinar Unboxing Markets, realizado em junho deste ano, e a visita da Technology Industries of Finland a Portugal realizada em setembro de 2022.
Tratando-se de um mercado que atualmente apresenta um reduzido impacto nas exportações nacionais, o mesmo apresenta nichos e áreas de intervenção que se podem revelar como oportunidades para as empresas nacionais. Manuel Oliveira revela que a deslocação a este país se saldou pela positiva, ficando na expectativa que num futuro próximo se possam concretizar algumas colaborações com empresas locais.
O mercado irlandês, reconhecido pela sua pujante indústria de dispositivos médicos, apresenta-se como uma oportunidade para a diversificação da oferta nacional e a entrada em novas cadeias de fornecimento para as empresas de moldes portuguesas. Foi neste contexto que a CEFAMOL organizou, entre os dias 23 e 27 de setembro, uma missão empresarial à Irlanda, no âmbito do seu projeto de promoção internacional Engineering & Tooling from Portugal, com o objetivo de destacar naquele mercado as competências da indústria nacional e explorar novas oportunidades de negócio e cooperação.
A missão contou com a participação das empresas AKA Moldes, Imoplastic, MD Group, Moliporex, Planimolde, Tecnifreza, UEpro e VL Moldes, para além do CENTIMFE e Pool-net.
Com o apoio do cluster irlandês ATIM (Advanced Technologies In Manufacturing) e da delegação da AICEP na Irlanda, foram organizados encontros estratégicos, apresentações e visitas a empresas locais, com destaque para aquelas ligadas à produção de peças e componentes para a indústria médica.
Manuel Oliveira, secretário-geral da CEFAMOL, salientou que o objetivo da missão foi "contactar diretamente com empresas locais (algumas delas multinacionais representadas naquele país), conhecer o contexto industrial irlandês e identificar oportunidades concretas para a indústria nacional". Destacou, ainda, a recetividade positiva com que as empresas portuguesas foram acolhidas, o que resultou em contactos promissores e, em alguns dos casos, reforçou as relações com parceiros já estabelecidos.
Durante a missão, as empresas portuguesas tiveram a oportunidade de participar e visitar a feira Medical Technology Ireland, realizada em Galway, nos dias 25 e 26 de setembro, evento que reúne os principais fornecedores da indústria médica, incluindo grandes multinacionais. "A feira enquadrou um ambiente propício ao desenvolvimento de novos e interessantes contactos e à consolidação de relações comerciais, especialmente com empresas da Irlanda, mas também do Reino Unido e Alemanha que estiveram presentes", explicou Manuel Oliveira. Embora o mercado irlandês apresente um potencial de crescimento, principalmente na vertente dos moldes técnicos de pequena e média dimensão, Manuel Oliveira sublinha que "a indústria médica é altamente exigente, requerendo uma abordagem especializada e persistente, de forma a possibilitar a entrada neste mercado competitivo". No seu entender, as empresas portuguesas que pretendem explorar este segmento “devem demonstrar experiência e competência no sector médico”, uma vez que o domínio da linguagem e dos procedimentos específicos “é fundamental para o sucesso”.
Esta missão surge na sequência de uma anterior deslocação ao mercado irlandês e de uma visita a Portugal do cluster ATIM durante a última Semana de Moldes, o que reforça a crescente ligação entre as indústrias de ambos os países. As empresas nacionais saíram da Irlanda com novas perspetivas e contactos com potencial, bem como com a expectativa de desenvolverem oportunidades de negócio futuras.
A 11.ª edição do programa Leiria-In, criado pela Fórum Estudante e Politécnico de Leiria, reuniu meia centena de jovens alunos que participam em diversas atividades nas cidades de Leiria e Marinha Grande, com destaque para visitas a diversas empresas da região, entre as quais, muitas do sector de moldes. Contando com a parceria das associações empresariais CEFAMOL e NERLEI, e as Câmaras Municipais de Leiria e Marinha Grande, esta edição contou com 50 estudantes de Portugal Continental e do Arquipélago dos Açores. A maioria foi surpreendida pela tecnologia e inovação que caracterizam a indústria de moldes.
Manhã cedo e cinco jovens acabados de sair de um autocarro da atividade Leiria-IN concentravam-se à porta do Grupo TJ Moldes, uma das várias empresas do sector aderentes a esta iniciativa. Nos primeiros minutos, revelaram não conhecer a região na qual estavam a iniciar o segundo de um conjunto de cinco dias de programa. Rapidamente, foi também fácil de entender que nunca tinham estado numa empresa de moldes.
David Bandeira, 16 anos, de Lisboa; Rodrigo Quitério, 17 anos, de São Miguel – Açores; Diogo Canejo, 15 anos, de Lisboa; Ana Alves, 17 anos, do Porto; e Martim Dias, 16 anos, de Beja, percorreram os vários pavilhões da empresa, num circuito que lhes permitiu compreender o processo de fabrico do molde: desde a área comercial que negoceia os projetos, à da injeção onde são feitos os testes, passando por toda a zona de fabrico.
No final, duas questões ressaltavam da opinião dos jovens visitantes: a diversidade de tecnologias que observaram e a
quantidade e dimensão das máquinas usadas nos processos de produção.
Contando que “não tinha noção de que esta indústria existia em Portugal”, Rodrigo Quitério considerou que a visita “foi interessante”, ao ter possibilitado o contacto com “novas realidades e tecnologias”. É que, salienta, os seus planos de futuro até podem passar pela indústria. “A minha ideia é seguir engenharia eletrotécnica e esta área dos moldes acaba por se encaixar um bocadinho nisso”, explica, adiantando que “este pode bem ser um emprego para o futuro”.
David Bandeira tem outros planos para o futuro. Este deverá passar pela área do desporto. No entanto, não esconde o fascínio pelas tecnologias. E a comprová-lo esteve a quantidade de questões que foi colocando ao longo da visita à empresa.
Diogo Canejo juntou-se ao Leiria-IN por considerar que “estas novas experiências ajudam-me a crescer enquanto pessoa e, ao contactar com estas novas áreas, vou sempre acrescentando mais informação e isso vai ajudar no meu futuro”. Apesar de ainda não ter escolhida a área profissional, tem, contudo, duas certezas: o seu caminho não será a indústria e, possivelmente, Luxemburgo ou Suíça serão os países onde pretende viver a partir de adulto.
Ana Alves e Martim Dias partilham da opinião dos colegas em relação à indústria de moldes. Ana gostaria de seguir na área da engenharia química e Martim em informática ou multimédia. Até visitarem a empresa TJ, a indústria de moldes não surgia como possibilidade de carreira. No final, manifestaram-se “impressionados” com o desenvolvimento tecnológico, não descartando essa possibilidade.
DESPERTAR
Gonçalo Gil, da Fórum Estudante, considera que, ao longo da sua primeira década, este programa conseguiu “despertar em muitos dos jovens participantes o interesse e até o gosto pela indústria”, sector que muitos desconheciam antes de participarem. "Ao longo dos anos, sabemos que alguns alunos ficam a estudar em Leiria e, posteriormente, a trabalhar na região. Presumimos que isso se deve ao facto de terem visto o potencial que a região tem, desde a qualidade de vida até à empregabilidade", explica Gonçalo Gil que, na sessão de receção aos jovens, os aconselhou a “aproveitarem as oportunidades, tal como fizeram os participantes em anteriores edições do Leiria-In”.
Já Manuel Oliveira, secretário-geral da CEFAMOL, congratulouse com o facto de, mais uma vez, um grande grupo de jovens ter optado por trocar uma semana de férias por uma semana
de conhecimento. "Têm a oportunidade de visitar empresas de referência e conhecer as várias ofertas formativas do Politécnico de Leiria", acentuou.
Henrique Carvalho, da NERLEI, explicou que a associação que representa colabora de forma integrada e estruturada com a indústria e o Politécnico de Leiria. "A nossa missão é ajudar as empresas a serem mais competitivas, apostando fortemente, por exemplo, na formação e workshops. Esta é uma associação multissetorial cujo trabalho contribui para o desenvolvimento da região", referiu.
Catarina Morgado, da Câmara Municipal da Marinha Grande, e Pedro Cordeiro, da Câmara Municipal de Leiria, deram as boasvindas aos jovens nos respetivos concelhos. Ambos destacaram o empenho da organização em tornar esta uma experiência inesquecível. "Leiria é uma cidade integradora que gosta de acolher as pessoas e é também um exemplo de inovação, com as suas empresas e o Politécnico de Leiria," acrescentou Pedro Cordeiro, considerando que esta iniciativa serve como “uma excelente ponte entre os desejos dos jovens e o que os espera no mundo profissional”.
O programa Leiria-In dá a conhecer a indústria de moldes, mas também permite a visita a empresas das áreas da cerâmica, robótica ou automóvel. O programa inclui workshops, visitas a empresas com tecnologia de ponta e diversas experiências inovadoras. Além disso, a cada edição os jovens têm a oportunidade de conhecer diferentes cursos do Ensino Superior ligados à tecnologia e ao sector industrial. O programa também garante momentos de lazer e interação com a comunidade.
Temos tempos difíceis. A indústria automóvel europeia está a desmontar-se a si própria, a insegurança relativamente ao futuro congelou os investimentos e a posição fragilizada da Europa fica cada vez mais evidente.
O sector de moldes não é uma exceção, até pior: posicionado no fim da “cadeia alimentar” sofre de forma multiplicada.
Coloca-se a questão: o que ainda está estável?
A resposta é simples: a importância das nossas equipas!
Mais do que nunca, será a força dos nossos recursos humanos e, sobretudo, a interação entre eles que vai decidir como vamos passar esta crise e assegurar o nosso futuro.
Na nossa qualidade de consultora reforçamos o nosso lema, “acreditamos na força humana, na comunicação assertiva e na definição perfeita de processos” com a criação de um novo serviço – a KOPPacademy. Atendemos, por um lado, ao requisito repetido de vários clientes de integrar a formação no nosso leque de serviços e, por outro, queremos dar justiça ao nosso foco principal: a capacitação de pessoas.
Temos a convicção de que uma formação sólida e sustentável tem de partir da estratégia empresarial e, desta forma, tem de ser fruto de um processo que poucas empresas praticam: a gestão de competências. Por este motivo colocamo-nos à disposição de trazer uma nova visão, holística e inovadora, ao tecido empresarial industrial. A integração vertical da gestão de competências, desde a identificação de valências-chave para o negócio atual e futuro, ao diagnóstico de gaps de conhecimento e até ao planeamento e realização de uma formação acertada e customizada garante o impacto positivo em toda a organização.
A cultura da empresa agradece.
A digitalização da produção tem transformado a indústria metalomecânica, trazendo novas oportunidades. Para mostrar como as tecnologias podem alavancar a produtividade das empresas do setor, a Tebis marcará presença na ExpoMetal 2024, de 7 a 9 de novembro, na Exposalão da Batalha.
Este evento é uma plataforma privilegiada para explorar as tendências que transformam a indústria metalomecânica, incluindo também as exposições i4.0 Expo, sobre a Indústria 4.0, Automação e Robótica, e a 3D Additive Expo, de Impressão 3D e Fabrico Aditivo. “Vamos apresentar as mais recentes inovações em tecnologia CAD/CAM e MES, e focar nas estratégias de otimização dos processos que têm impacto direto na produtividade e competitividade”, afirma Gonçalo Carmo, Diretor Técnico da Tebis.
Um dos destaques serão as demonstrações de soluções que respondem aos desafios do mercado. Os visitantes irão ver como a tecnologia de simulação permite otimizar a produção, antes de iniciar a fabricação. “Iremos tornar evidente o
potencial dos gémeos digitais e da automatização através dos templates CAD e CAM, e o seu impacto na eficiência, qualidade e segurança”.
A Tebis irá focar as estratégias de torneamento, fresagem, laser e trimming, mostrando como é possível reduzir tempos de ciclo, minimizar erros e maximizar a eficiência produtiva.
Para empresas que enfrentam desafios crescentes, como a falta de mão-de-obra qualificada e prazos cada vez mais curtos, a adoção de soluções digitais é um passo essencial para garantir a sustentabilidade e crescimento. A digitalização, aliada a uma gestão eficiente dos processos através do sistema MES ProLeiS, permitirá às empresas manterem-se competitivas num mercado global em constante mudança.
A entrada da feira é gratuita, mas requer a inscrição prévia com o código 624. “Convidamos todas as empresas a visitaremnos. Será um prazer tentar apoiar as empresas a transformar desafios em oportunidades”, conclui Gonçalo Carmo.
Num mercado cada vez mais competitivo, estar à frente nas tecnologias de produção não é apenas uma vantagem, mas uma necessidade. Este será um palco perfeito para moldar o futuro da indústria.
Fundada no ano 2000, a CR Moulds, com sede na Marinha Grande, é hoje uma das empresas de referência na indústria de moldes. Ao longo das últimas duas décadas, a empresa tem-se afirmado pela sua aposta em inovação tecnológica, automação e internacionalização, consolidando-se em mercados de grande exigência, como o automóvel ou a eletrónica. A história da CR Moulds caracteriza-se por uma evolução contínua e pelo seu compromisso de encontrar as melhores soluções para alguns dos desafios globais, como a falta de mão-de-obra especializada e a competitividade do mercado europeu.
Desde a sua fundação, em 2000, que a CR Moulds tem protagonizado um processo de evolução contínua, sendo, atualmente, uma das referências no sector do fabrico de moldes em Portugal. Localizada na Marinha Grande, com uma equipa de 40 colaboradores, iniciou a sua atividade como uma empresa de consultoria focada no mercado alemão. Oferecia, então, serviços de intermediação e acompanhamento de projetos de moldes para clientes internacionais. Contudo, rapidamente cresceu e expandiu a sua ação.
Em 2004, com a criação de um gabinete próprio para o desenvolvimento de projetos e estudos de reologia, a empresa começou a dar os primeiros passos rumo ao fabrico dos seus próprios moldes. Um dos passos significativos do processo de crescimento aconteceu em 2006, quando o aumento do volume de trabalho levou à necessidade de internacionalizar o processo produtivo, impulsionando a entrada em novos mercados, como a Suíça e a Chéquia.
A estratégia de crescimento da CR Moulds foi, desde sempre, pautada pela inovação tecnológica e pela busca da excelência. Condições que contribuíram para a consolidação da imagem e notoriedade da empresa. Entre 2013 e 2015, através de um projeto SI Inovação, impulsionou o departamento de qualidade e metrologia, além de obter certificações ISO 9001 e ISO 14001, fundamentais para fortalecer a sua posição no mercado internacional. Este período marcou também o início da expansão global da CR Moulds, que, atualmente, atua em mercados como a Alemanha, Roménia, a Eslováquia, Israel, Marrocos, Tunísia e África do Sul. A nível sectorial, destacam-se o automóvel e eletrónica, mas também aplicações domésticas e eletrodomésticos e a indústria médica.
Um outro momento crucial para o desenvolvimento da empresa foi o projeto submetido e desenvolvido com o apoio do programa PORTUGAL 2020, que trouxe consigo a automatização
dos processos produtivos e o reforço das ferramentas de planeamento e controlo de custos. Este importante passo de modernização permitiu à CR Moulds otimizar a sua produção e, ao mesmo tempo, aumentar a sua presença e competitividade no cenário global. Recentemente, entre 2022 e 2023, a empresa investiu no aumento do seu parque de máquinas, ampliando ainda mais a sua capacidade produtiva.
Marcando a sua história por passos seguros e consistentes a CR Moulds foi, ano após ano, ultrapassando os mais exigentes desafios. E, de acordo com o CEO, Joaquim Rodrigues, a empresa olha, hoje, com alguma apreensão para a realidade do sector. As principais preocupações da empresa, assinala, passam também pela “escassez de mão de obra especializada, a falta de interesse por parte dos clientes no mercado europeu - por falta de competitividade a nível de preços - e a instabilidade e incerteza nas diversas indústrias, principalmente o automóvel”.
Como principais desafios, enfatiza a necessidade de “tornar a indústria de moldes como carreira apelativa para chamar a atenção das novas gerações e a procura de novos mercados a nível sectorial e geográfico”.
A sua visão mantém-se focada, por um lado, na “inovação” e, por outro, “no desenvolvimento de competências”, considerando que as pessoas são o maior bem das empresas. "Precisamos de continuar a desenvolver as competências dos nossos colaboradores, criando uma equipa de sucesso que esteja preparada para enfrentar os desafios do futuro", afirma. Neste sentido, a formação de equipas multidisciplinares e o foco na automatização e controlo de qualidade são, no seu entender, pilares fundamentais da estratégia de crescimento da empresa.
A CR Moulds, conta ainda, tem procurado fortalecer a sua presença internacional através da participação em feiras, encontros bilaterais e visitas regulares aos clientes. A empresa valoriza também o estabelecimento de parcerias sólidas, com o objetivo de criar soluções cada vez mais inovadoras e personalizadas para as necessidades dos seus clientes.
Joaquim Rodrigues salienta ainda que a aposta no futuro “passa pela combinação entre tecnologia de ponta e uma equipa altamente qualificada e comprometida com a inovação”. Ao dotar-se das melhores ferramentas para enfrentar os desafios do mercado global, a CR Moulds mantém-se fiel à sua missão de entregar soluções de excelência, cumprindo aquelas que são as suas prioridades: “ser autónomos, ter comprometimento profissional, inovação, comunicação, foco nos resultados e gestão de crises”.
A SM3D, criada em 2001, integra o Grupo Gespro, destacando-se pela sua aposta contínua na qualidade e inovação. Especializada na produção de peças em grafite para diversas indústrias, com especial destaque para a de moldes, a empresa tem pautado a sua história numa trajetória de crescimento sustentado, apostando no crescimento da sua ação no mercado internacional, sempre com foco na excelência dos seus produtos e serviços.
Em 2001 nascia a SM3D, sendo parte de um projeto de expansão do Grupo Gespro. A criação da empresa coincidiu com um período de grande complexidade económica, num momento em que a indústria mundial enfrentava desafios inesperados, devido, sobretudo, aos atentados de 11 de setembro, nos Estados Unidos. Joel Rodrigues, fundador e administrador do grupo, recorda que a empresa “nasceu numa altura difícil, mas rapidamente encontrou o seu espaço no mercado”, prestando serviços de engenharia, programação e maquinação de elétrodos em grafite.
Para isso, adianta o responsável, contribuiu de forma decisiva a ação da primeira empresa do grupo – a PRO3D - criada com o objetivo de prestar apoio técnico às empresas de moldes da região de Leiria e Marinha Grande, nas áreas do design, da conceção de produto e, mais tarde, CAD/CAM/CAE. Após os primeiros anos de atividade, nos quais este gabinete se constituía
como uma mais-valia para os fabricantes de moldes, uma vez que permitia complementar – com grande rigor e qualidade – o trabalho dos seus quadros na área do projeto, a PRO3D passou a desenvolver o seu trabalho, quase exclusivamente, para o grupo Gespro, contribuindo para o crescimento e afirmação da SM3D. Fruto desta estratégia sustentada, a empresa conseguiu crescer e afirmar-se como uma referência na produção de peças em grafite.
Em 2004, um investimento significativo permitiu à SM3D modernizar o seu parque de máquinas, com a introdução de equipamentos HSM de motores lineares, 3 e 5 eixos da marca DMG MORI, um passo decisivo na automatização do processo produtivo. A mudança para novas instalações na zona da Barosa, em 2007, foi outro ponto crucial no desenvolvimento.
Após anos de luta e inovação – num período em que a automatização dava, ainda, passos muito incipientes -, em 2008 a SM3D atingiu um marco importante com a duplicação dos equipamentos existentes, consolidando a sua capacidade de produção. Nos finais de 2011, nasceu a primeira célula completamente automatizada, incluindo uma CMM, podendo produzir e controlar de forma automática peças em grafite até 1450 mm, que permitiu aumentar a produção de peças de grafite para a indústria de moldes, aeronáutica e espacial.
Com o aumento do número de clientes e o desenvolvimento de novas soluções, em 2014, a empresa transferiu-se para instalações que asseguravam maior capacidade produtiva, em Albergaria, na Marinha Grande, onde estabeleceu a maior célula de produção de peças em grafite da Península Ibérica.
Hoje, a SM3D distingue-se pela sua capacidade multifacetada e versátil. Com dez centros de maquinação CNC 3 e 5 eixos, serrotes de precisão, retificadoras e fresadoras convencionais, produzindo assim semanalmente mais de duas mil peças de grafite para diversas indústrias, incluindo a automóvel, biomédica, aeroespacial e eletrónica. O grupo Gespro dispõe ainda de três máquinas de erosão para peças até 20 toneladas, com uma equipa de trabalho constituída por 23 pessoas. A empresa é a única em Portugal a oferecer uma solução integrada e de elevada qualidade, desde a conceção, desenvolvimento e produção de peças em grafite certificado, da marca Toyo Tanso, da qual é representante desde 2018, até a erosão e controlo dimensional de peças em grafite e outras produzidas no grupo.
Para tal, contribuiu de forma decisiva a criação, no seio do grupo, da empresa Spark, dedicada à comercialização de matérias-primas certificadas, em especial o grafite Toyo Tanso. Esta aposta no controlo de toda a cadeia produtiva reforça o compromisso com a qualidade, permitindo à SM3D garantir produtos de excelência para os seus clientes, dos quais mais de 50 % estão fora de Portugal.
Apesar das adversidades resultantes da pandemia de Covid-19, a SM3D conseguiu superar os desafios e continua a olhar para o futuro com ambição. Joel Rodrigues sublinha que, num contexto de incerteza, a empresa “está a adaptar-se, a reinventar-se e a procurar novos mercados”, mas sem perder de vista a indústria de moldes, onde, salienta, “a conjuntura é hoje muito complexa”.
O empresário também destaca a importância de atrair novos talentos para a indústria, agradecendo a todos aqueles que têm permanecido nos quadros das empresas do grupo, sem os quais não teria sido possível chegar onde está ao longo destes 27 anos. Menciona ainda a possibilidade de criar programas de formação internos e reforça a necessidade de colaboração entre as empresas do setor.
Com uma visão clara de que o futuro passa pela inovação e pela excelência, a SM3D está determinada a continuar a oferecer produtos e serviços de excelência, adaptando-se às exigências de um mercado global em constante mudança.
A partir deste ano letivo, as empresas vão assegurar, integralmente, as propinas aos alunos do curso de Engenharia de Polímeros da Universidade do Minho. A medida insere-se num protocolo estabelecido com a indústria que pretende atrair mais jovens para esta área, dando resposta a uma necessidade sentida pelas empresas dos sectores de moldes e plásticos. Miguel Nóbrega, diretor do curso de Engenharia de Polímeros, manifesta-se otimista em relação ao sucesso da medida.
O curso de Engenharia de Polímeros acaba de celebrar um protocolo com a indústria. Quais os pontos importantes deste protocolo?
Este protocolo é uma iniciativa-piloto e tem aspetos muito interessantes, preconizando uma parceria forte entre o aluno e a empresa, que se vai materializar no facto de o aluno ter, na empresa associada, um tutor, ou seja, alguém que o vai acompanhar, que vai motivá-lo, que vai tentar perceber como é que está a decorrer a formação, que o vai orientar na procura de conhecimento em áreas que são importantes para a empresa, entre outros aspetos. Ou seja, o protocolo vai proporcionar a criação de um contexto de formação muito particular - que não existe em mais nenhum curso no país – e que nos vai permitir ter melhores profissionais: mais bem formados, muito mais orientados para aquilo que são as necessidades da indústria e com vantagens para todos os envolvidos, desde as empresas aos alunos. Este protocolo prevê que no final de cada ano de formação, o aluno passe entre duas semanas a um mês de estágio na empresa à qual está associado.
Reforça a ligação entre a indústria e a academia?
Tem havido uma proximidade grande com a indústria e isso tem sido notório ao longo dos anos. Mas acreditamos que vai consolidar-se com esta recente ação que inauguramos este ano, sobretudo pelo carácter inovador: pela primeira vez, a indústria oferece-se para suportar integralmente as propinas dos alunos na engenharia de polímeros. Esta é a componente mais visível deste recente protocolo de colaboração estabelecido e esperamos que seja também uma chamada de atenção para a sociedade e que as pessoas comecem a questionar-se sobre as razões que levam as empresas a investir, desta forma, na formação dos jovens. E se o faz é porque esta é uma área com futuro, que precisa de mais profissionais. Há outros cursos no país que têm situações semelhantes, mas penso que nenhum deles conseguiu chegar a este nível de ligação com a indústria que é a certeza de que todos os alunos que entrarem no curso vão ter as propinas financiadas pela indústria.
Como é que nasceu o curso de Engenharia de Polímeros?
O curso foi criado em 1978 e, naturalmente, foi sofrendo inúmeras alterações desde então. O curso surgiu como resposta a um desafio da indústria de materiais plásticos que, então, estava a ser confrontada com um novo desafio que se prendia com o surgimento de novos materiais. Lançou um repto às universidades em Portugal para que se criasse um curso que permitisse formar pessoas com conhecimento na área e, na altura, foi a Universidade do Minho que que pegou neste desafio. Havia poucas pessoas com conhecimentos na área e houve, inclusivamente, pessoas que foram doutorarse fora do país para adquirir o conhecimento necessário. Foi a partir daí que deram origem ao departamento. Desde então, a Universidade do Minho tem vindo a alimentar o curso. Inicialmente, havia apenas a licenciatura, mas foram criados alguns mestrados de especialização. A partir da década de 2000, o curso foi reestruturado e passou a ser um mestrado integrado de cinco anos, conferindo o grau de mestre. Mais recentemente e também por reestruturação dos cursos, este voltou a ser dividido numa licenciatura de três anos e um mestrado de dois anos. A nível de doutoramento, nesta área, temos, por exemplo, Ciência de Energia com Compósitos e, futuramente, prevemos avançar para o Fabrico Digital Direto. Estes estão, de alguma forma, associados a esta área, uma vez que têm uma forte componente nos materiais plásticos.
Qual tem sido a adesão dos alunos a este curso, ao longo do tempo?
Tem havido fases distintas. A adesão já foi maior, mas também já foi menor. Tem vindo a crescer. Mas, a exemplo de outras engenharias, a adesão não é a que desejaríamos, naturalmente.
No caso do vosso curso, a que se deverá essa baixa procura?
Acredito que tenha a ver, essencialmente, com o desconhecimento daquilo que é esta área e da necessidade efetiva destes profissionais por parte das empresas. As pessoas desconhecem esta realidade. Depois, mais recentemente, penso que estamos a assistir a uma reação daquilo que tem sido a forma como a opinião pública, de uma maneira muito genérica, está a tratar a questão dos materiais plásticos. São conhecidos como ‘os vilões ambientais’. E isso está muito relacionado com a perceção que as pessoas têm e que está errada porque os materiais plásticos não vão ser abandonados; vão continuar a ser utilizados. As pessoas acreditam que esta indústria vai deixar de existir, por isso pensam que não vale a pena formarem-se numa área que vai ‘morrer’.
Mas isso não vai acontecer…
Como é óbvio, isto é totalmente errado. Os plásticos são muito mais do que aquilo que é veiculado. A imagem que se transmite tem origem, de uma maneira geral, nas notícias negativas; ou seja, que destacam alguns aspetos negativos dos materiais plásticos. As pessoas criam essa imagem de que vamos passar a viver, daqui a algum tempo, sem materiais plásticos. Mas basta olharem em volta para perceber que isso não é possível e nem é viável. Muito pelo contrário: há vários estudos que demonstram que os materiais plásticos são muito mais amigos do ambiente do que os materiais alternativos.
E como têm procurado alterar essa imagem junto da sociedade?
O departamento de Engenharia de Polímeros da Universidade do Minho tem procurado divulgar e mostrar o trabalho que faz. Temos um impacto significativo naquilo que é a investigação
na área dos plásticos, também. Para além disso, e igualmente importante, é a associação que temos com a indústria. Somos um departamento que é um parceiro da indústria, através, por exemplo, do Polo de Inovação em Engenharia de Polímeros que é uma iniciativa conjunta da universidade com as empresas.
De que forma é concretizada esta associação à comunidade?
Desenvolvemos várias ações anualmente, como dezenas de palestras em escolas ou a receção de alunos e professores do ensino secundário. Nas últimas quatro edições do Dia Aberto fomos, até, obrigados a alargar para dois dias, tentando divulgar aquilo que é a nossa atividade. E procuramos demonstrar que esta é uma área tecnologicamente prática. Para além disto, destaco este recente protocolo estabelecido com a indústria que irá, também, ser um apoio enorme para as famílias dos estudantes, ao permitir reduzir substancialmente os custos. Esperamos que esta medida possa atrair mais alunos, mas também mais empresas, de forma a crescer e ganhar dinâmica nos próximos anos.
Os alunos ficam obrigados, por este protocolo, a permanecer ligados às empresas após o curso?
O protocolo não estipula isso: não há essa obrigatoriedade. Os alunos podem, naturalmente, optar por aquilo que desejem para o seu futuro. Mas acredito que o mais natural é que venha a ser criado um vínculo laboral com a empresa a que o aluno está associado. Gostaria de salientar que, neste ponto, terá um papel fulcral a figura do tutor responsável pela orientação do aluno.
Esse tutor é designado por cada uma das empresas…?
Sim. E as empresas têm a noção da importância desta figura. Este é, até, um fator totalmente diferenciador relativamente àquilo que já alguma vez foi feito, em termos de ensino, e as empresas estão conscientes disto. E por isso estão dispostas a fazer também este investimento – o papel e o tempo que este tutor dedica ao aluno é um investimento acrescido para a empresa. Mas, no final, acreditamos – e as empresas também –que se traduzirá em vantagens.
O presidente da Production Technologies Association of South Africa (PtSA), Tapiwa Samanga, deslocou-se a Portugal para visitar a indústria de moldes nacional e conhecer a sua envolvente e identificar oportunidades de colaboração entre empresas e entidades sectoriais dos dois países. Durante a visita, conheceu algumas empresas do sector, bem como o centro tecnológico (Centimfe) e o centro de formação (Cenfim).
Manifestando-se “impressionado com a organização e a cooperação da indústria de moldes em Portugal”, Tapiwa Samanga destacou o papel crucial da CEFAMOL na união e coordenação das empresas. "Sendo eu presidente de uma associação empresarial do sector não poderia deixar de evidenciar o papel da CEFAMOL em Portugal”, salientou, considerando que “os moldes estão incrivelmente implantados aqui e os fabricantes, que se conhecem há muitos anos, conseguem ser amigos e competir nos negócios”. No seu entender, isso resulta de “uma forte visão e coordenação, na qual as pessoas competem, mas também conseguem trabalhar em conjunto”. Algo que considera “incrível" e que, no seu entender, “só é possível através do papel de uma associação muito dinâmica”.
O presidente da associação sul-africana elogiou também os esforços conjuntos das várias entidades de apoio ao sector, como o Centimfe e o Cenfim, que desenvolvem programas direcionados para a indústria. "Fiquei impressionado com a quantidade de projetos e iniciativas que a associação desenvolve e coordena, com o suporte das restantes entidades; em conjunto, desenvolvem programas direcionados e pensados para o sector", afirmou.
Em relação às oportunidades que o seu país tem para os moldes portugueses, mencionou que “África está em grande transformação, com um mercado em crescimento e cheio de potencial”.
"Durante muito tempo, estivemos muito fechados, mas isso está a mudar. O mercado tem muito potencial de crescimento e isso nota-se nos mais diversos sectores, desde os eletrodomésticos ao automóvel, entre outros. Isto representa uma grande oportunidade para todos”, enfatizou, acentuando a importância de Portugal reconhecer estas oportunidades e de as empresas portuguesas darem passos no sentido de explorar tais mercados, procurando parceiros estratégicos localmente. "É preciso que as empresas deem passos no sentido de encontrar soluções para trabalhar neste mercado", rematou.
Foi a sua primeira deslocação a Portugal. Antes desta visita, que imagem tinha dos fabricantes de moldes portugueses?
Foi a minha primeira visita a Portugal. Tinha muita curiosidade. E questionava-me: ‘afinal, como é que estas empresas conseguiram tornar-se, praticamente, os mais importantes fabricantes do sector na Europa?’. Por isso, quis conhecer para perceber o que fizeram, como é que começaram, mas, sobretudo, como é que conseguem trabalhar e crescer em cooperação. E isto é para mim importante, uma vez que sendo eu o CEO da PtSA [associação congénere da CEFAMOL na África do Sul], também queria perceber qual o papel da associação nestas questões e na afirmação deste sector.
A que conclusões chegou no final da visita?
Fiquei bastante impressionado.
O que o impressionou mais?
O que percebi é que uma área (geográfica) bastante pequena consegue reunir o essencial a esta indústria: para onde quer que vamos, para onde quer que nos viremos, ao lado de uma empresa de moldes há outra empresa. A indústria de moldes está incrivelmente implantada aqui. As empresas têm raízes, tradição e uma história imensa. As pessoas que estão neste sector conhecem-se há muito tempo e muitos deles até são amigos, mas conseguem desenvolver os seus negócios, cooperando e competindo. Ora, para se conseguir isto, percebi que é fundamental ter uma associação forte – como têm. Só isso é que permite a existência de uma forte área coordenada, na qual as pessoas competem, mas também conseguem trabalhar em conjunto e, dessa forma, catapultar os seus negócios. E isto é incrível.
Quais os principais atributos que reconheceu na CEFAMOL?
A CEFAMOL tem um papel muito importante nisto tudo, mas sobretudo na forma como consegue que as empresas se juntem e trabalhem em conjunto. A associação tornou-se o ponto de encontro, o ponto nuclear de todas estas empresas que integram a associação. Mas tem um papel muito importante também no desenvolvimento de projetos e ações que beneficiam as empresas. Fiquei bastante impressionado com a quantidade de projetos e iniciativas que a CEFAMOL desenvolve e coordena. Mas também com outras entidades que apoiam o sector e que tive oportunidade de visitar: o Centimfe e o Cenfim. Em conjunto, estes organismos desenvolvem programas direcionados e pensados para a indústria.
Na sua opinião, que oportunidades existem para os fabricantes portugueses na África do Sul?
Eu diria que há imensas oportunidades. Com o passar dos anos, na África do Sul, fomos perdendo a capacidade de produzir moldes. O que procuramos e necessitamos hoje são empresas que fabriquem moldes e que possam instalar-se na África do Sul, que possam desenvolver-se em conjunto com as empresas sul-africanas. Esta é uma grande oportunidade. Depois há outra questão, não menos importante: é que o mercado africano está em crescimento e o nosso país é, atualmente, o líder deste crescimento, no sector dos moldes e ferramentas. E noutros sectores também.
Qual o primeiro passo que as empresas deverão dar para entrar nesse mercado?
Se tiverem vontade de entrar no mercado africano, a África do Sul é um excelente ponto de partida. Convidamos as empresas portuguesas a ir conhecer o país, perceber o que podem fazer e que lhes é mais vantajoso – podem investir diretamente ou participar com outras empresas nativas, encontrando parceiros locais. Durante muito tempo, a África esteve muito fechada, mas isso está a mudar. O mercado está em grande ebulição, está em crescimento e tem muito potencial. E isso nota-se nos mais diversos sectores: eletrodomésticos, automóveis, entre outros. É preciso que as empresas deem o primeiro passo, no sentido de encontrar soluções para trabalhar este mercado.
TESTES SÃO A CHAVE PARA A EXCELÊNCIA DO FABRICO DO MOLDE
TESTES PERMITEM AFERIR QUALIDADE E EFICIÊNCIA DA INJEÇÃO DO PLÁSTICO
QUALIDADE E EFICIÊNCIA DOS ENSAIOS REQUEREM ESPECIALIZAÇÃO E EXPERIÊNCIA
A RELEVÂNCIA DO CANAL QUENTE NOS TESTES DE MOLDES
Helena Silva * * Revista MOLDE
No fabrico de moldes, a precisão e a qualidade são a chave para garantir o sucesso de qualquer projeto. Embora a tecnologia tenha avançado com simulações muito completas e sofisticadas, três empresas ouvidas pela revista MoldeTecnimoplás, Ribermold e Tecnijusta -, concordam que o ensaio físico continua a ser um fator crucial para assegurar a fiabilidade e a excelência dos moldes que produzem. O teste, enfatizam, é um passo imprescindível no processo de fabrico.
Apesar de a indústria dispor de ferramentas tecnologicamente avançadas, como simulações e análises, “nada substitui os testes reais” ao funcionamento do molde. Quem o defende é Hugo Carlos, da Tecnimoplás. No seu entender, as tecnologias de simulação são ferramentas essenciais, mas “não são suficientes” para aferir a eficiência que se pretende que o molde alcance. É que, salienta, apenas os ensaios constituem a forma mais fiel de "garantir a qualidade, o aspeto e o funcionamento do molde". A simulação, adianta, não consegue prever todos os resultados, como manchas ou imperfeições nas peças. Portanto, o ensaio físico é vital para assegurar a viabilidade do produto final.
Um dos desafios neste processo, acentua, é a variedade de novos materiais com os quais as empresas têm de lidar. Muitos, conta, chegam de fornecedores diferentes e requerem tempo para se compreender completamente o seu comportamento. "Os ensaios permitem-nos conhecer as características desses materiais e garantir que o molde cumpre as expectativas", defende.
A eficiência dos ensaios também tem impacto direto na competitividade da empresa. Hugo Carlos realça a importância de fazer bem à primeira. "Cada vez mais, o fabricante tem de acertar à primeira para conseguir ser competitivo", sublinha, voltando a enfatizar a importância dos testes também nesta questão. “Os testes são imprescindíveis para garantir a produção ininterrupta e identificar ajustes antes do envio dos moldes”, realça.
Outro ponto essencial abordado por Hugo Carlos é a relação estreita com os clientes durante o processo de ensaio. Em muitos casos, os clientes – e destaca, como exemplo, os originários dos Estados Unidos -, assistem ao ensaio e a sua presença, em muitos casos, agiliza a tomada de decisões rápidas. "Se houver uma questão, o cliente pode tomar uma decisão no local", explica. Para os clientes que não estão presentes, a Tecnimoplás assegura os ajustes necessários até o molde corresponder às expectativas desejadas, esclarece.
Além disso, a empresa assegura um serviço pós-venda, garantindo manutenção e acompanhamento contínuo. "Dependendo do tipo de problema, podemos necessitar de ajustes, e a maioria dos fabricantes oferece serviços pós-venda
para garantir o bom funcionamento", destaca, reforçando que os ensaios regulares são parte integrante deste processo de manutenção.
A Tecnimoplás, conta, decidiu estabelecer o seu próprio centro de ensaios de moldes há 16 anos, uma decisão que considera “estratégica”. A criação deste departamento ‘em casa’ permitiu maior rapidez e eficiência, especialmente por questões logísticas e de confidencialidade de projetos. "O nosso centro de ensaios é uma parte crucial da nossa operação", enfatiza, adiantando que isso também é valorizado pelos clientes no momento da tomada de decisão da entrega dos projetos.
/ / Hugo Carlos - Tecnimoplás
O responsável da empresa refere ainda outros desafios que a Tecnimoplás enfrenta no campo das novas tecnologias e materiais, especialmente quando não se justifica o investimento em equipamentos muito específicos. E nesses casos, acrescenta, justifica-se o recurso a empresas especializadas em ensaios. Nos restantes, a ligação e proximidade entre as equipas dentro da empresa afiguram-se como uma mais-valia para a aposta no centro interno de ensaios dos moldes.
Hugo Carlos considera ainda que o teste do molde não é apenas uma validação da sua qualidade, mas antes “uma aprendizagem contínua”. É que, sustenta, a experiência adquirida através dos ensaios que realiza permite à Tecnimoplás responder com rapidez e qualidade às exigências crescentes dos seus clientes.
RIBERMOLD: TESTES FORNECEM DADOS VALIOSOS PARA AJUDAR NOS FUTUROS PROJETOS
Alberto Ribeiro, fundador da Ribermold, sublinha o papel indispensável dos ensaios dos moldes para garantir a robustez mecânica e a qualidade final das peças produzidas. No seu ponto de vista, os ensaios não só revelam problemas, mas também oferecem dados valiosos que podem ser aplicados em futuros projetos, ajudando a evitar imprevistos e a otimizar o processo produtivo.
Os ensaios dos moldes, são essenciais para validar tanto a mecânica do molde como o resultado final: as peças que serão produzidas. Estes testes asseguram que o molde cumpre com os requisitos de produção e identificam áreas que possam necessitar de ajustes, acrescenta.
Além de detetar problemas, os ensaios proporcionam “uma importante aprendizagem, especialmente em relação a zonas mais frágeis, tratamentos de materiais e qualidade dos aços”. Alberto Ribeiro destaca que os dados recolhidos ao longo dos testes ‘históricos’ ajudam a prever melhor as contrações e empenos de certas peças, facilitando “a melhoria contínua dos processos”.
Um dos grandes desafios no ensaio de novos moldes é a variabilidade. "Mesmo pequenas variações nas espessuras, materiais e temperaturas podem resultar em surpresas durante os testes", refere. Estas surpresas, adianta, podem colocar pressão sobre a produção, uma vez que os ensaios são, geralmente, realizados muito próximo da data de entrega ao cliente, o que exige “respostas rápidas e soluções eficientes”.
Conta ainda que quando são detetados problemas nos ensaios, as correções variam. Podem ir desde pequenos ajustes no molde até a revisões significativas no projeto, o que pode implicar custos e prazos elevados. Salienta que, dependendo da gravidade do problema, a resolução pode acontecer no imediato ou, apenas, após a discussão das situações com o cliente.
A Ribermold, explica, realiza sempre ensaios, independentemente de o cliente assim o exigir, de forma a garantir o bom funcionamento dos moldes. Embora alguns clientes confiem na empresa e não exijam testes, a maioria prefere acompanhar de perto o processo. "Ter peças de validação após o ensaio permitenos assegurar uma maior confiança e comparações futuras, caso surjam dúvidas", acrescenta Alberto Ribeiro.
Os ensaios implicam custos, lembra, mas, na sua perspetiva, são uma parte essencial do processo e da garantia que a empresa oferece aos seus clientes. Estes custos são geralmente contabilizados no orçamento dos projetos, e os resultados obtidos, considera, “justificam plenamente o investimento, pois garantem um produto final de alta qualidade”.
Apesar de os ensaios gerarem sempre algum desperdício, como peças defeituosas e material que precisa de ser reciclado, enfatiza que a sua importância é muito superior a qualquer constrangimento. Os testes, adianta, ajudam a reduzir falhas em grande escala, o que, a longo prazo, contribui para uma produção mais eficiente e sustentável.
A reputação da empresa, acentua, está diretamente ligada à capacidade de garantir moldes sem falhas antes do envio ao cliente. "Zero erros é o objetivo de qualquer fabricante de moldes", frisa, adiantando que a realização de ensaios contribui para essa meta, proporcionando aos clientes “confiança” no produto final.
A possibilidade de realizar ensaios dentro da própria empresa é, na sua opinião, uma grande vantagem. "A autonomia para testar a qualquer momento, sem depender de terceiros, é uma maisvalia tanto para nós como para os nossos clientes", explica. Esta capacidade permite não apenas otimizar o tempo, como também garantir que os moldes estão prontos para produção contínua, minimizando riscos durante o processo.
Com décadas de experiência no fabrico de moldes, Alberto Ribeiro reflete sobre a evolução do papel dos ensaios ao longo dos anos. Antigamente, recorda, os testes eram principalmente para extrair plástico e verificar medidas. Hoje, no entanto, “os ensaios são utilizados para produzir peças funcionais e, muitas vezes, vendáveis”. E atualmente, sublinha, a responsabilidade de garantir que essas peças cumprem todas as especificações recai, em grande parte, sobre o fabricante do molde.
TECNIJUSTA: O TESTE AO MOLDE É ESSENCIAL PARA PERCEBER A REALIDADE
“As simulações indicam caminhos, mas não são a realidade. Não substituem o teste prático do molde, no qual variáveis como a temperatura, o comportamento dos materiais e as uniões moldantes podem impactar o desempenho final". É desta forma que Pedro Mateus, da Tecnijusta, justifica o papel, no seu entender “crucial”, que têm os ensaios, uma prática que considera essencial no fabrico de moldes. Acrescentando que as simulações computacionais oferecem uma previsão útil, adverte que, no entanto, “não conseguem refletir com precisão a realidade do funcionamento do molde”.
Um dos grandes desafios que afirma sentir é a adaptação aos novos materiais, como os biodegradáveis, que, sustenta, “ainda apresentam comportamentos imprevisíveis” em fases de teste. “Estamos a lidar com materiais inovadores, como compostos
com sementes de girassol ou madeira, entre outros, que exigem um conhecimento contínuo e uma abordagem experimental para compreender as suas características reais”, sublinha.
Na Tecnijusta, conta, os testes de moldes são geralmente divididos em duas fases: o teste inicial (T0), feito internamente pelos fabricantes, e um segundo teste (T1), que valida o molde para produção. “Nos moldes mais técnicos, realizamos ensaios em dois tempos, de forma a avaliar não só o processo de injeção, mas também a resistência mecânica do molde”, explica.
Um outro aspeto que sublinha é o facto de a empresa apostar fortemente na realização de testes dentro das suas próprias instalações. “A proximidade entre a equipa técnica e a área de testes permite uma comunicação mais eficaz e uma maior rapidez no processo", justifica. A empresa acredita que a capacidade de realizar testes internamente reduz custos e aumenta a eficiência, evitando despesas adicionais associadas ao aluguer de máquinas externas.
ACOMPANHAMENTO
Pedro Mateus realça ainda a importância de ter técnicos qualificados, bem como máquinas de qualidade para garantir um teste eficaz. “Um bom teste exige um bom molde, uma boa máquina e um técnico competente para interpretar os resultados. No final de cada teste, emitimos um relatório técnico detalhado com todos os parâmetros usados”, revela.
O envolvimento do cliente também é fundamental, no seu entender. Por isso, defende que os clientes devem assistir aos testes sempre que possível, para compreenderem melhor as condições do processo e as potenciais necessidades de ajustes. Além disso, salienta também a necessidade de uma colaboração estreita entre os fornecedores de sistemas, os fabricantes e os clientes e que esta se estabeleça logo nas fases iniciais do processo de fabrico.
“É crucial que os fornecedores estejam envolvidos o mais cedo possível para garantir que todos os componentes estejam alinhados, garantindo a qualidade final do produto", enfatiza Pedro Mateus, realçando que, por isso, mesmo quando os testes não são exigidos pelos clientes, a empresa os realiza como parte da sua política de assegurar a excelência dos moldes produzidos.
É através de ensaios rigorosos que se consegue assegurar que os moldes correspondem aos parâmetros exigidos, desde a funcionalidade até à resistência mecânica, minimizando o risco de falhas e otimizações dispendiosas. Empresas responsáveis pela injeção de plástico, como a Vipex, Plastimago e Eugster Frismag, destacam que os testes de moldes são cruciais para garantir a qualidade e a eficiência do processo produtivo, sublinhando que embora as ferramentas tecnológicas auxiliem no desenvolvimento, os testes reais continuam a ser insubstituíveis.
Gonçalo Duarte, da Eugster Frismag, destaca a importância dos testes no fabrico de moldes como meio imprescindível de aferir a qualidade e eficiência do processo produtivo, explicando como estas avaliações impactam a qualidade final dos produtos e são cruciais para identificar problemas que podem ser evitados.
No seu entender, os fabricantes de moldes devem realizar testes em várias fases do processo de fabrico, de forma a garantir a qualidade. Gonçalo Duarte sublinha que os ensaios incluem a avaliação do molde em operação, o processo de injeção e a análise das peças produzidas. "Estas avaliações permitem-nos identificar atempadamente as correções necessárias, garantindo que o processo avança sem comprometer a qualidade do produto final", refere.
Os testes fornecem parâmetros essenciais para a produção. As peças injetadas são analisadas através de relatórios dimensionais e submetidas a testes de montagem e funcionamento. "Estes ensaios permitem que as peças sejam corrigidas em conformidade e asseguram que estão de acordo com as especificações, garantindo a consistência e a qualidade do produto final", explica ainda o responsável.
Para Gonçalo Duarte, os ensaios evitam problemas críticos - como variações dimensionais, por exemplo -, que podem comprometer a montagem das peças. Além disso, possibilitam otimizar o ciclo de injeção, reduzindo desperdícios de material e tempo. "Identificam também falhas que afetam a consistência do produto e a durabilidade do molde, permitindo que estas sejam corrigidas, aumentando assim a eficiência do processo", afirma.
A Eugster Frismag não aceita moldes sem que tenham sido devidamente testados, esclarece, enfatizando, desta forma, a importância que assumem os testes. "As peças injetadas nos ensaios são essenciais para validar o funcionamento do molde, e só após essa verificação consideramos o molde pronto para transferência para as nossas instalações", acentua, reforçando que este processo “é fundamental” para garantir a continuidade do projeto com qualidade.
Embora a empresa não tenha um ‘teste final’ formal, os ensaios realizados, com exceção do primeiro, são considerados como potenciais validações finais, declara. Esta abordagem permite antecipar a produção assim que um ensaio é bem-sucedido, contribuindo para reduzir o tempo de entrada no mercado (time to market).
Por questões de disponibilidade, a Eugster Frismag nem sempre assiste presencialmente aos ensaios, mas Gonçalo Duarte afirma que a empresa confia na competência dos fornecedores. "Os nossos parceiros compreendem a importância dos testes para o sucesso do projeto e têm autonomia para os realizar conforme os nossos padrões de qualidade", salienta.
Os testes assumem uma importância crítica no processo do fabrico do molde, sendo a chave para garantir a funcionalidade. Assim o considera Tiago Febra, da Plastimago, empresa com mais de quatro décadas de experiência na injeção de plástico, afirmando que, apesar do avanço tecnológico, o teste final continua a ser essencial para validar a qualidade. No seu entender, os testes são fundamentais para garantir
que os parâmetros definidos pelo cliente são respeitados pelo fabricante do molde.
Para Tiago Febra, os testes são cruciais para validar o conceito e garantir que o produto é viável e ainda que a matéria-prima pode ser injetada, com êxito, nas máquinas especificadas. "Os testes confirmam que todos os critérios definidos foram seguidos e resultaram no produto desejado. Pela minha experiência, 99 % dos casos correm bem", afirma.
Apesar de todas as tecnologias hoje disponíveis, como os softwares de simulação, defende que estas não substituem a necessidade do teste final, pois “há fatores externos que não são controláveis” e que podem afetar o resultado. Um dos exemplos que usa é a matéria-prima. Esta, salienta, pode ser um fator decisivo no sucesso ou insucesso do fabrico. "Por vezes, deparamo-nos com lotes de matéria-prima que apresentam ligeiras alterações, condicionando o resultado final. Embora nós, ou outro cliente final, escolhamos e forneçamos a matéria-prima, esta nem sempre é compatível com os critérios de qualidade definidos", sublinha, adiantando que a solução, muitas vezes, passa por escolher outra matéria-prima ou rever os parâmetros do processo.
Os testes, considera ainda, permitem aferir três aspetos essenciais: a funcionalidade do molde, a qualidade dimensional e visual da peça, e a qualidade mecânica do molde. "É necessário encontrar um equilíbrio entre estes três fatores para garantir o sucesso do projeto", defende. Este equilíbrio nem sempre é alcançado num único teste, exigindo vários ensaios para avaliar as diferentes condições de funcionamento do molde, acrescenta.
PROVA DE FOGO
O teste final, conhecido como "run and rate", é descrito como a prova de fogo do molde. Este teste ocorre depois de uma série de ensaios prévios, nos quais são avaliados todos os parâmetros de qualidade e funcionamento. "Nesta fase, de uma maneira geral, o molde já funciona bem, mas ocasionalmente há necessidade de correções e o molde retorna ao fabricante para ajustes", explica.
Para Tiago Febra, a articulação entre todos os players envolvidos no processo de fabrico do molde é fundamental para chegar com sucesso ao final. "Desde a escolha da matéria-prima até à fase de montagem, é importante que todos estejam envolvidos. O técnico da injeção, por exemplo, acompanha os primeiros testes
e, se tudo correr bem, pode sair do processo, mas se surgirem problemas, continua a monitorizar o processo", explica. No caso da Plastimago, esclarece, o fabrico do molde é acompanhado de perto, desde o momento da conceção ao desenvolvimento, com controlo dos prazos e da qualidade.
Embora as simulações desempenhem um papel crucial no fabrico dos moldes, Tiago destaca que estas não substituem o teste real. "A simulação permite-nos prever problemas, mas não garante 100 % de certezas. O teste final é insubstituível, pois só ele avalia a qualidade do molde em condições reais", sublinha. Além disso, destaca o conhecimento humano como elemento essencial, especialmente no acompanhamento dos testes. É a experiência de quem acompanha o teste que, no seu entender, permite identificar rapidamente possíveis problemas.
Tiago Febra acredita que a inteligência artificial terá um papel crescente na indústria de moldes. Contudo, salienta, ainda não está implementada de forma significativa e isso deve-se, no seu entender, à complexidade técnica do processo de fabrico. "Nos próximos 5 a 10 anos, acredito que veremos grandes mudanças, com a inteligência artificial a apontar caminhos e a otimizar processos. No entanto, mesmo com a IA, será difícil substituir o teste final, pois a injeção não é uma ciência exata", considera.
FABRICO DO MOLDE
Para a Vipex, não há exceção à regra: "a Vipex não recebe moldes sem que os ensaios sejam realizados", afirma Carlos Santos, explicando que a empresa acompanha todos os testes para garantir que o molde funciona de acordo com o previsto e que todas as informações necessárias para uma produção eficiente estão disponíveis. É que, para Carlos Santos, o ensaio final é a única forma de validar se o molde está pronto para ser transferido para a Vipex, considerando, por isso, que os ensaios são uma etapa insubstituível no processo de fabrico. Na sua experiência, apesar de haver outros ensaios ao longo do processo, nenhum é tão crítico como o final, que pela sua duração e exigência garante a funcionalidade do molde e o cumprimento das especificações e objetivos definidos.
O ensaio final, sublinha, é o mais longo e rigoroso, de forma a assegurar que o molde, além de produzir a peça cumprindo com as respetivas especificações, suporta as condições de produção a que vai ser submetido de uma forma estável. "Nesta fase, o molde é avaliado o mais próximo possível dos parâmetros de produção estimados, permitindo uma visão aproximada do processo de injeção final e da sua eficiência", explica Carlos Santos.
A presença física durante os ensaios é fundamental, de acordo com Carlos Santos. "Apesar de podermos receber fotos e vídeos, os mesmos não substituem o acompanhamento presencial, são, no entanto, um complemento importante. Certos pormenores que vão para além das características principais registadas em imagens e nas cartas de parâmetros dos ensaios, só são detetados estando no local", esclarece. Este acompanhamento presencial permite identificar rapidamente possíveis problemas e encontrar soluções imediatas, que poderão ser um dado importante durante o ciclo de vida do molde. Além disso, a experiência e o conhecimento do processo produtivo das pessoas que acompanham os ensaios são fundamentais", enfatiza.
Reconhecendo que as ferramentas de simulação são uma enorme mais-valia para prever o comportamento dos moldes, o responsável sublinha que, contudo, não substituem o teste real. "As simulações ajudam a prever o comportamento da injeção e do produto final, mas só o ensaio final é que vai validar o molde, o seu funcionamento e se o produto cumpre com as especificações determinadas.
Um outro aspeto que acentua é a cooperação entre todos os intervenientes no processo produtivo. A Vipex, explica, valoriza a colaboração entre todos os envolvidos, desde os fabricantes de moldes até os fornecedores de matérias-primas e sistemas de injeção. "Nos moldes mais técnicos, é essencial que o fabricante, os fornecedores e o cliente estejam presentes nos ensaios. Isso permite encontrar soluções mais rápidas para os desafios que eventualmente possam surgir", afirma. A falta desta colaboração pode, no seu entender, comprometer a eficiência do projeto.
Carlos Santos destaca ainda o impacto dos novos materiais, especialmente aqueles com uma componente ecológica. "Há um interesse crescente por matérias-primas “verdes”, mas muitas vezes o seu processamento é mais difícil, e as diferenças entre lotes podem afetar a estabilidade do processo e/ou a qualidade final do produto", destaca, acrescentando que, por exemplo, a estabilidade das matérias-primas recicladas ou bio “ainda é um desafio”. Mostra-se convicto, no entanto, de que esta tendência atual, com particular destaque nas matérias-primas recicladas, terão uma presença muito importante no futuro desta indústria.
O responsável da empresa defende ainda que quanto mais cedo se iniciarem as parcerias com clientes e fabricantes, melhor será o resultado. "Se começarmos cedo, o projeto ainda está aberto a alterações, o que aumenta a eficiência para todas as partes envolvidas”, elucida. No entanto, adianta, “isso nem sempre acontece", o que lamenta. Dar voz a todos os especialistas, desde o fabrico do molde até à escolha dos materiais, seria benéfico para o processo, especialmente na indústria automóvel – principal cliente do sector dos moldes -, na qual, pensa, “haver pouca margem para sugestões”.
As empresas que se dedicam, exclusivamente, aos ensaios dos moldes asseguram um trabalho cuja qualidade é difícil de igualar por outras que o façam ocasionalmente. Mariteste, Teste e Wetest defendem que o teste final “é a prova de fogo” do processo de fabrico do molde, não havendo tecnologias que substituam esta fase. No entanto, sublinham que a eficiência dos ensaios requer especialização e experiência por parte de quem os faz.
A empresa Wetest, fundada em 2017, iniciou a sua atividade em 2018 por Nuno Gândara e Rita Calé, e começou por se especializar em ensaios de moldes e pequenas produções, principalmente para o sector automóvel. Com o tempo, e face às mudanças no mercado, a empresa expandiu o seu foco. Para tal contribuiu a aposta na certificação IATF 16949:2016 e ISO 9001, o que permitiu atrair clientes internacionais e aumentar significativamente o volume de negócios.
Hoje, a empresa, composta por seis colaboradores, destaca-se pela sua abordagem meticulosa aos ensaios de moldes. Antes de iniciar qualquer ensaio, conta Nuno Gândara, são analisadas as características do molde, desde a cinemática, como as suas dimensões até aos sistemas de canais quentes e valve gates (entre outros aspetos), garantindo que está adequado à máquina correta.
A escolha da matéria-prima, em 80 % dos casos, é responsabilidade do cliente, adianta ainda, explicando que a empresa aconselha os fabricantes de moldes em 20 % dos casos, garantindo que os materiais mais recentes são bem compreendidos, recorrendo às suas fichas técnicas. Quando surgem dúvidas, a Wetest recorre a testes adicionais para garantir que os parâmetros técnicos são cumpridos.
Nuno Gândara sublinha a importância de elementos como as barras de segurança e a parte elétrica dos moldes, destacando que a empresa “está preparada para adaptar e ajustar estas variáveis quando necessário”. Este cuidado é essencial, especialmente no primeiro teste, no qual, geralmente, apenas o fabricante do molde está presente. Nos ensaios seguintes, pode haver a presença do cliente final para garantir que as peças estão em conformidade com as especificações, salienta.
Após o ensaio, todas as peças passam por um controlo dimensional rigoroso, o que permite identificar eventuais problemas em cotas críticas. “Se o molde não cumprir os requisitos, é ajustado para garantir o sucesso nas futuras produções”, acrescenta.
Nuno Gândara destaca ainda que a evolução tecnológica é fundamental para assegurar a qualidade do serviço. Por isso, a Wetest mantém-se em atualização contante. Um dos exemplos que aponta é a implementação de um software próprio que automatizará a criação de relatórios finais diretamente a partir das máquinas, otimizando assim o processo, além de outros aspetos.
Os ensaios de moldes são essenciais para identificar problemas que podem surgir, como erros de projeto, rebarbas ou falhas nas dimensões das peças. Nuno Gândara destaca que, “mesmo com os avanços tecnológicos, os testes continuam a ser fundamentais para garantir a funcionalidade e a qualidade dos moldes”.
Além disso, realça o papel crítico do técnico de injeção, cuja formação, acentua, “leva anos”, e que deve deter um “profundo conhecimento sobre matérias-primas e moldes”. O técnico tem a responsabilidade de detetar pequenos detalhes que podem afetar o processo e garantir que os moldes funcionam corretamente, especialmente em sistemas robotizados. “Este nível de conhecimento e experiência é fundamental para a eficiência do ensaio”, enfatiza.
No que diz respeito aos centros de ensaio dos fabricantes de moldes, Nuno Gândara considera que a sua eficácia depende da forma como são utilizados. E concretiza: “se forem apenas para uso interno, podem ser vantajosos, mas, quando o objetivo é oferecer o serviço a terceiros, surgem desafios, nomeadamente no que toca à concorrência e ao sigilo industrial”.
Nuno Gândara defende ainda a importância da colaboração entre todos os intervenientes para garantir o sucesso nos ensaios. “A confiança no trabalho conjunto e a preparação adequada são elementos essenciais para que o processo do ensaio corra da
melhor forma possível”, afirma, considerando que, quanto mais a certeza em relação à qualidade do molde que vai a teste, maior a possibilidade de minimizar a pressão sobre os fabricantes e garantir a qualidade final do produto.
A empresa Teste, com quase 30 anos de atividade e mais de quatro décadas de experiência do seu fundador, Acácio Francisco, destaca a importância dos ensaios de moldes na indústria. Mais do que um simples processo técnico, considera Acácio Francisco, estes ensaios são “cruciais para garantir a qualidade do produto final, resultado de um esforço conjunto entre equipa técnica e cliente”.
Sublinhando que o ensaio de moldes “evoluiu significativamente ao longo das últimas décadas”, refere que, por exemplo, “se, há 50 anos, o processo era mais rudimentar e sem os avanços tecnológicos que hoje conhecemos, como o uso de termorreguladores que atingem temperaturas de 200°C, atualmente a tecnologia é indispensável”. Contudo, no seu entender, “não é suficiente”. E explica a razão: “não basta ter a tecnologia, é preciso ter conhecimento”. Ou seja, o técnico que faz o ensaio tem um papel preponderante no êxito deste processo.
“Como o próprio nome indica, o ensaio de moldes é muito mais do que injetar umas peças de plástico, saídas dentro de um bloco de aço que já foi trabalhado durante uns tempos”, enfatiza, considerando que o técnico que o faz tem de ter “conhecimentos à altura”; caso contrário “dificilmente a peça a moldar sairá conforme o que se exige”. É que, salienta, “temos de nos mentalizar que ensaiar um molde não é, nem nunca será, carregar num botão”.
O sucesso de um ensaio, esclarece, depende de um conjunto de operações meticulosas, como o ajuste da matéria-prima, as dimensões do molde ou os requisitos específicos do cliente, entre outros. “Exige preparação prévia, como garantir que a matéria-prima esteja desumidificada e que todos os parâmetros do cliente sejam seguidos à risca”, acentua.
O responsável chama ainda a atenção para um facto sobre o qual, defende, todos os fabricantes deviam refletir: “cada vez mais, os clientes têm enviado os seus técnicos para acompanhar os ensaios”. Isso, salienta, é sinónimo de uma preocupação crescente com a qualidade final do produto.
E essa qualidade só se consegue quando são chamados ao processo experiência e conhecimento. “A experiência e o conhecimento acumulado são fundamentais para o êxito do ensaio”, sintetiza, considerando que “se o técnico que realiza o ensaio não tiver o conhecimento adequado, dificilmente a peça sairá conforme o esperado".
Os fabricantes de moldes em Portugal têm, na opinião de Acácio Francisco, investido na qualidade. Por isso, reforça que uma grande parte dos moldes é bem-sucedida logo no primeiro ensaio. No entanto, adverte que “o sucesso da indústria depende da sua capacidade de adaptação às novas tecnologias e exigências do mercado global”.
Acácio Francisco sublinha ainda que a partilha de conhecimento, através de formações e seminários, e o trabalho em equipa, “são elementos-chave para manter a competitividade e qualidade na indústria dos moldes”, enfatizando a importância de se estar sempre aberto “a aprender e ensinar”.
MARITESTE: SÓ OS TESTES SÃO GARANTIA DE QUALIDADE E EFICIÊNCIA
Fundada em 2004 por Luís Cardoso, a Mariteste é uma empresa com 20 colaboradores, especializada em ensaios de moldes (e na produção). A sua principal atividade é a realização de ensaios para fabricantes de moldes, principalmente nas regiões de Leiria/ Marinha Grande e Oliveira de Azeméis, garantindo que os moldes estão em conformidade para uma produção eficiente.
Para Luís Cardoso, a preparação do molde “é essencial para garantir que os ensaios correm de forma adequada”. Um dos pontos críticos que destaca é a presença de barras de segurança, barras de transporte, olhais e anéis de centragem. Estes, no seu entender, “são elementos nem sempre considerados pelos fabricantes, mas que são fundamentais para o sucesso do ensaio”.
“Felizmente, a qualidade dos moldes tem melhorado significativamente nos últimos anos, com os fabricantes a demonstrar maior atenção a estes detalhes”, salienta, considerando que tais precauções têm um impacto enorme no resultado final, sobretudo no cumprimento de prazos que, atualmente, são cada vez mais espremidos.
Para Luís Cardoso, uma das grandes vantagens da Mariteste em comparação com os centros de ensaio dos próprios fabricantes de moldes é “a sua experiência e especialização”. A empresa, esclarece, possui uma variedade de máquinas adequadas a diferentes dimensões e condições de moldes, além de uma equipa altamente qualificada. É que, destaca, “o know-how técnico é fundamental para garantir que o teste seja bem-sucedido, algo que os fabricantes, apesar de possuírem maquinaria avançada, nem sempre conseguem assegurar”.
A Mariteste, conta, emite um relatório detalhado após cada ensaio, onde são descritos os parâmetros e condições de funcionamento do molde. Este relatório é fundamental para o cliente final, pois assegura que o molde está em condições de produzir peças de qualidade. “Apesar de, atualmente, os moldes raramente apresentarem falhas graves, é frequente que tenham de ser feitos alguns ajustes”, refere, salientando que, por isso, é essencial atestar o bom funcionamento, através de testes realizados de forma eficiente.
Luís Cardoso salienta ter notado, nos últimos anos, uma melhoria significativa na qualidade dos técnicos nas empresas de moldes. No entanto, destaca sentir uma lacuna de conhecimento técnico em alguns diretores de projeto, que, sublinha, “por vezes desconhecem os detalhes mais técnicos dos moldes”. Este conhecimento técnico é, no seu entender, “crucial para identificar problemas durante os ensaios, como fugas de gás ou falhas nos canais quentes, especialmente quando se utilizam materiais inovadores ou bi-materiais”.
Para garantir que o molde funciona com os novos materiais, a empresa consulta as fichas técnicas, ajustando os parâmetros necessários, como os de temperatura e tempo de injeção. Caso haja falta de informação, a equipa prepara-se adequadamente, garantindo que tudo corre conforme o esperado, adianta. O responsável sublinha ainda que, quanto mais cedo a empresa de testes for envolvida no processo, melhores serão os resultados. Em alguns casos, conta, “a empresa atua como consultora, ajudando os fabricantes de moldes a ajustar o processo de fabrico, embora essa função nem sempre seja devidamente valorizada”.
Outro ponto importante que destaca é a presença de responsáveis de projeto durante os testes. Estes, no seu entender, “são uma presença mais necessária, até, do que a do cliente final, que se preocupa sobretudo com a qualidade das peças”.
Apesar da evolução tecnológica e da utilização de softwares avançados de simulação, Luís Cardoso reforça que os testes ao molde são indispensáveis. "As simulações ajudam, mas não são suficientes para prever tudo. O teste é a prova de fogo do molde", afirma. O processo permite detetar pequenos ajustes que garantem a funcionalidade do molde.
No final, o desempenho futuro do molde, como a quantidade de peças a produzir, depende das condições de produção do cliente, mas o teste realizado pela empresa, enfatiza Luís Cardoso, oferece uma previsão clara da performance esperada, garantindo um produto final de qualidade.
Um passo crucial na produção de peças de qualidade. É desta forma que os fornecedores de sistemas classificam os ensaios dos moldes, que consideram o garante de que o produto final cumpre as especificações técnicas e de qualidade esperadas. Empresas como a Gecim, Oerlikon e YUDO partilham a visão de que o sucesso destes testes depende não apenas da preparação técnica, mas também da colaboração entre os fabricantes de moldes e os fornecedores de sistemas de injeção. Este sistema, que regula o fluxo de material para o molde, é visto como um elemento essencial para otimizar o processo e evitar desperdícios, especialmente no fabrico de peças complexas.
Carlos Galo, representante da YUDO, partilha a sua visão sobre a importância dos ensaios no processo de fabrico de moldes, enfatizando que este é “o momento crucial de validação do produto final”. Na sua perspetiva, o sucesso do projeto depende não só do ensaio, mas também de uma preparação cuidadosa e de uma colaboração eficiente entre todos os envolvidos.
Este "teste final" ao trabalho realizado é também, no seu entender, o momento de validação das expectativas do cliente
em relação ao produto final. "O projeto inicia-se com a expectativa do cliente relativamente ao produto final e, a partir desse molde, o produto em polímero deve ter as propriedades e características desejadas", sustenta. Até ao momento do teste, o funcionamento do molde é baseado em teorias que precisam de ser confirmadas através do ensaio.
Uma etapa que classifica como essencial para garantir o sucesso do teste é a preparação. Carlos Galo divide o processo em quatro variáveis críticas:
Em primeiro lugar, o molde: e este tem de "estar pronto a montar na máquina, com toda a cinemática apta e testada, e com os circuitos de refrigeração e fugas de gases preliminares em funcionamento", destaca, defendendo que, atualmente e na prática, “a nova geração de afinadores tem mostrado mais rigor no cumprimento das especificações”, algo que considera “um reflexo positivo da sua formação”.
Em segundo, a máquina de injeção: “a escolha da máquina é fundamental e deve ser feita com base nas características da máquina que será usada na produção real”, salienta, destacando que “fatores como a capacidade de injeção, a força de fecho e até a marca influenciam diretamente o resultado do ensaio”.
Em terceiro, elenca a matéria-prima: "É importante que seja igual à que será usada pelo cliente final, ou tenha as mesmas características", sublinha, enfatizando a necessidade de “garantir a compatibilidade total da matéria-prima” para evitar surpresas durante o ensaio.
Em quarto lugar, destaca o canal quente (quando aplicável): “este desempenha um papel importante no sucesso do teste. Todas as ligações elétricas e sistemas de refrigeração devem ser cuidadosamente verificados para assegurar o bom funcionamento durante o processo de injeção”, acentua.
Para Carlos Galo, um ensaio bem-sucedido passa por “seguir rigorosamente todos os procedimentos técnicos”. Isso inclui a análise da ficha técnica do material a ser injetado, a definição das temperaturas corretas para o molde e para o material fundido, e a observação dos alertas indicados na ficha técnica. Após um período de operação, é crucial verificar a qualidade das amostras e a estabilidade do processo, assegurando que o molde funcione de forma consistente e dentro dos parâmetros estabelecidos.
Outro detalhe importante que menciona é a necessidade de limpar o canal quente no final do ensaio, seguindo sempre as recomendações da ficha técnica. "A limpeza é essencial para garantir o bom funcionamento do sistema e evitar problemas em testes subsequentes", afirma.
Destacando que a YUDO está, cada vez mais, envolvida nos ensaios, especialmente quando o sistema ou a matéria-prima apresentam maior complexidade, considera isso um aspeto muito relevante. "Assistimos a alguns ensaios, normalmente aqueles em que a complexidade do sistema ou do material exige uma atenção especial", explica.
No seu entender, a realização destes ensaios nas instalações do fabricante de moldes traz vantagens ao processo, considerando, por isso, positiva a aposta de algumas empresas em criar áreas de injeção internas. "A equipa que trabalhou no molde está toda reunida, e isso facilita a aprendizagem e a resolução de problemas durante o ensaio", destaca.
O momento do ensaio é, muitas vezes, vivido sob grande pressão, especialmente quando há atrasos e o cliente espera as peças. "Se o teste corre mal e o cliente está à espera, é um momento de grande stress", reconhece Carlos Galo, defendendo, por isso, que é preciso acautelar melhor o bom funcionamento do molde. Para isso, defende que “a articulação” entre todos os envolvidos
– empresas de injeção, fabricantes de moldes e fornecedores de canal quente – é fundamental para “garantir a qualidade do ensaio”. Conta que na YUDO, essa colaboração tem sido cada vez mais precoce, com a empresa a ser envolvida desde as fases iniciais do projeto. "Quanto mais cedo entrarmos no processo, melhor. Conseguimos fazer uma análise detalhada que ajuda a detetar falhas e melhorar o desempenho do molde".
Pedro Faria, diretor geral da Oerlikon, sublinha a importância dos testes no fabrico de moldes, destacando não só o seu papel na definição dos parâmetros ideais, mas também a necessidade de colaboração e inovação tecnológica. Com a transição para soluções sustentáveis e a implementação de novas tecnologias, conta que a Oerlikon aposta numa abordagem que privilegia a eficiência, a qualidade e a redução de desperdícios.
Num momento em que as práticas sustentáveis ocupam lugar de destaque, os ensaios tornam-se cada vez mais importantes para “garantir qualidade, eficiência e sustentabilidade” ao processo. "Os testes são cruciais para determinar os parâmetros ideais com base no polímero, na aplicação pretendida e no peso da peça", afirma Pedro Faria, acrescentando que, além disso, ajudam a garantir que “o sistema de câmara quente seja corretamente concebido, de acordo com as especificações do material”.
Com a transição para polímeros sustentáveis, especialmente em indústrias como a embalagem, cosméticos e tampas, os testes assumem uma importância redobrada, na sua opinião. "A mudança para alternativas ecológicas apresenta desafios e oportunidades, sendo essencial testar soluções especializadas para processar materiais de base biológica e PCR sem comprometer a qualidade estética ou funcional", salienta.
Um ponto que considera crucial é o papel dos dispositivos técnicos, como as unidades de controlo térmico e sistemas de condicionamento de moldes. "Estes equipamentos são essenciais para garantir um elevado desempenho e a repetibilidade do processo", explica. A qualidade da injeção não depende apenas da câmara quente e do molde, mas também destes dispositivos que ajudam a manter o controlo rigoroso do processo, acentua.
Para o sucesso do processo, destaca a relevância da colaboração entre os fornecedores de câmara quente e os fabricantes de moldes. Esta, enfatiza, é vital no sucesso do processo, destacando, por isso, a importância da comunicação antecipada em toda a cadeia de fornecimento: "A comunicação em relação às considerações de design melhora o desempenho da câmara quente e do molde, otimizando a geometria da peça", defende. "A troca detalhada de dados desde o início do projeto melhora significativamente o processo de fabrico e ajuda a evitar erros dispendiosos", adverte.
Com a introdução da Indústria 4.0, o processo produtivo evolui para um novo nível de eficiência, na sua perspetiva. Estas novas ferramentas, acrescenta, permitem a interligação de máquinas, reduzindo o desperdício e aumentando a produtividade. "Estas tecnologias são desenhadas para simular o enchimento de peças e otimizar os processos de arrefecimento", refere, a título de exemplo, adiantando que essas inovações oferecem ferramentas
avançadas que permitem um fluxo de trabalho mais eficiente e preciso. E isso, destaca, é algo que reflete a aposta, atualmente, dos clientes finais da indústria de moldes.
Para Pedro Faria, os testes também são essenciais para avaliar rapidamente o resultado final de uma peça, seja a nível estético ou funcional. Por isso, sustenta, "com as novas e desafiantes aplicações, é fundamental entender o comportamento do polímero e garantir que a peça cumpre os requisitos do cliente".
Outro benefício dos testes é a redução de ajustes frequentes no molde, evitando assim atrasos nos prazos de entrega. "Os testes ajudam a reduzir o desperdício de materiais, melhorando a eficiência global do projeto", afirma. Através de testes cuidadosos, é possível garantir um processo mais fluido e sem erros dispendiosos.
GECIM: TESTES CERTIFICAM QUE O MOLDE SATISFAZ A EXPECTATIVA DO CLIENTE
A Gecim leva quase três décadas de história, tornando-se uma referência na indústria de moldes. Para isso, contribui sobremaneira a vasta experiência de profissionais como Acácio Telmo. Com mais de 30 anos de experiência em ensaios de moldes, partilha a sua visão sobre a importância deste processo no fabrico de moldes, refletindo sobre as etapas essenciais, os desafios e a evolução da indústria.
Começar por sublinhar que, apesar de algumas empresasclientes optarem por realizar os testes de moldes nas suas próprias instalações, essa prática nem sempre resulta como esperado. “Há clientes que prescindem de fazer os testes cá e preferem fazer lá, mas muitas vezes isso não corre bem”, destaca, lembrando que este tipo de ensaio é fundamental para garantir que o molde cumpre todas as suas funcionalidades antes de ser entregue ao cliente.
No fabrico de moldes, o ensaio desempenha, de facto, um papel fundamental, na sua perspetiva.
Acácio Telmo destaca a sua importância para validar várias funcionalidades críticas do molde, como a estrutura física, o funcionamento da mecânica, o equilíbrio térmico e o enchimento. “Certificamos que o resultado está dentro do objetivo produtivo solicitado pelo cliente”, explica, acrescentando que a verificação dos sistemas de controlo de temperatura e a conformidade do produto final com as especificações são igualmente cruciais.
A complexidade do molde e a experiência do fabricante determinam o número de ensaios necessários. Um processo mais detalhado e bem conduzido resulta numa maior garantia de sucesso na produção final, defende. E é categórico ao afirmar que “a preparação para o ensaio é um fator determinante para o seu sucesso”.
Entre os aspetos mais críticos, sublinha “a escolha correta da máquina de injeção, o conhecimento profundo do projeto do molde, e a consideração das especificações da matéria-prima a utilizar, como as temperaturas de processamento e tempos de secagem”. “Muitos fabricantes já fazem um estudo adequado antes do teste”, salienta.
Um teste bem preparado, na sua opinião, reflete-se na qualidade do produto final e na imagem que o fabricante projeta para os seus clientes.
Um dos pontos que faz questão de acentuar é a importância da limpeza adequada dos equipamentos, particularmente das unidades de injeção. E explica que, muitas vezes, resíduos de testes anteriores podem comprometer os resultados. “Há uma grande resistência em usar materiais específicos de limpeza, mas uma unidade de injeção bem limpa resulta em testes mais curtos, melhores resultados e menos surpresas”, adverte.
Além disso, chama também a atenção para a necessidade de uma manutenção rigorosa dos canais de refrigeração e circuitos hidráulicos, para evitar problemas como contaminação e falhas na refrigeração, que podem prejudicar o processo.
Acácio Telmo entende também que a evolução dos materiais, especialmente na indústria automóvel, onde novos compostos substituem metais, exige uma constante atualização. Por isso, defende que todos os envolvidos no processo de fabrico e ensaio de moldes devem investir em formação contínua. “Precisamos de estar abertos a aprender e a ensinar”, diz, sublinhando que o conhecimento dos novos materiais e tecnologias é essencial para manter a competitividade. Para isso, sugere que as empresas promovam ações de formação e seminários, nos quais possam “trocar experiências e aprender em conjunto”.
A formação contínua, defende, “é um pilar para o progresso da indústria e para a criação de soluções inovadoras que satisfaçam as necessidades dos clientes”. “Estamos num sector cada vez mais competitivo e globalizado, onde o sucesso depende da capacidade de adaptação e inovação”, sublinha.
O QUE AS EMPRESAS CONCEBEM DE FORMA SINGULAR E INOVADORA
ESTUDO DE PROPRIEDADES MECÂNICAS DE MATERIAIS PLÁSTICOS EM CICLOS SUCESSIVOS DE INJEÇÃO E RECICLAGEM
CONTROLO E MONITORIZAÇÃO REMOTO EM TEMPO REAL DE MÁQUINA DE INJEÇÃO COM RECURSO A MACHINE LEARNING
Maxime Daniel *, Gilberto Martins **, António Baptista ** * Universidade de Rennes; ** CENTIMFE
O plástico desempenha atualmente um papel fulcral na vida humana. É utilizado diariamente em praticamente todos os produtos que nos rodeiam, em lazer ou trabalho, na saúde ou deslocações, na alimentação ou bens de consumo e é, por isso, o material de eleição de múltiplas aplicações em diversos setores industriais. No entanto, a utilização generalizada dos materiais plásticos levou a uma elevada procura de matérias-primas exploradas na natureza e a danos consideráveis no ambiente e na perda da biodiversidade. Por outro lado, o descarte dos plásticos em final de vida conduziu a uma acumulação massiva de resíduos, considerada por todos como um enorme desperdício a nível económico, já que envolveu custos de produção, energéticos e de transporte, um enorme impacto ambiental visual e a contaminação de cursos hídricos e do subsolo.
Os plásticos podem ser divididos em três grandes grupos: a) plásticos de grande consumo, em que se encontram embalagens, sacos que todos nós utilizamos no dia a dia; b) termoplásticos de engenharia, em que as aplicações podem ir desde a escova de dentes ao tablier do automóvel; e c) plásticos para aplicações especiais capazes de resistir a ambientes considerados perigosos.
Os plásticos estão a ser utilizados também como meio de substituição de componentes e aplicações até agora produzidas com recurso a metais. A maior dificuldade para a reciclagem e reutilização dos plásticos é a garantia de não contaminação com outros plásticos ou contaminantes, constituindo a separação e preparação os aspetos mais relevantes.
Diversas questões podem ser colocadas neste processo. i) O que fazer aos produtos plásticos em fim de vida?; ii) Podem ser reutilizados noutras aplicações e produtos?; iii) A libertação de microplásticos pode ser minimizada?; iv) A cadeia de tratamento de resíduos plásticos fecha o ciclo de reciclagem?; v) Todos os plásticos podem ser reciclados?
Todas estas questões obrigaram os governos a legislar sobre a implementação de soluções sustentáveis, nomeadamente, mas não só, relativamente às aplicações nos setores da embalagem e do automóvel. Destaca-se aqui o facto de a UE ter introduzido vários regulamentos e diretivas que exigem a utilização e incorporação de materiais reciclados nos produtos de vários setores. Estas incluem o Plano de Ação para a Economia Circular, que estabelece metas ambiciosas para a reciclagem e a utilização de conteúdos reciclados nos produtos. Além disso, a Diretiva Plásticos de Utilização Única (Diretiva (UE) 2019/904) e a Diretiva Embalagens e Resíduos de Embalagens (94/62/CE e 2004/12/CE) enfatizam a importância da incorporação de materiais reciclados para reduzir a dependência de recursos virgens. O Plano de Ação para a Economia Circular visa aumentar a taxa de reciclagem de plásticos e exige que certos produtos contenham uma percentagem mínima de conteúdo reciclado. Por exemplo, as garrafas de plástico deverão ter pelo menos 25 % de plástico reciclado até 2025, aumentando para 30 % até 2030. Espera-se que estes regulamentos impulsionem uma procura significativa de materiais reciclados e promovam a inovação e desenvolvimento de novas tecnologias de reciclagem. A reutilização e a reciclagem de plásticos para produzir matéria-prima de bens de consumo, são respostas promissoras, mas levantam-se muitas questões e dúvidas sobre a qualidade e o desempenho dos produtos com eles produzidos, em comparação com os produzidos a partir de materiais virgens.
O CENTIMFE, Centro Tecnológico da Indústria de Moldes Ferramentas Especiais e Plásticos, está integrado no cluster Engineering & Tooling a acompanhar os desenvolvimentos na indústria de plásticos e as dificuldades associadas, e a utilizar os seus recursos em atividades que promovem a criação de conhecimento e a transferência de tecnologia para a indústria. Desta forma, pretende implementar soluções de sustentabilidade numa perspetiva de redução e otimização de consumo de energia e de circularidade dos materiais plásticos nas perspetivas de reutilização e reciclagem dos materiais. O CENTIMFE tem-se associado à indústria no desenvolvimento de projetos de I&DT em copromoção, com o objetivo de encontrar soluções para os desafios na área dos materiais plásticos como, por exemplo, o projeto mobilizador S4PLAST – Sustainable Plastics Advanced Solutions. Deste projeto resultaram guias para a área do desenvolvimento e conceção de produto em plástico, novos materiais plásticos compostos e sustentáveis e sistemas multiprocesso para montagem, controlo e embalagem de peças totalmente digitalizados.
Por outro lado, o CENTIMFE aposta na criação de conhecimento na tecnologia de injeção e na área da circularidade dos materiais plásticos, bem como na transferência de tecnologia para a indústria através de ações de formação e de inovação. Neste âmbito, investiu em novos equipamentos de injeção e equipamentos auxiliares e estabeleceu parcerias com diversas entidades para a realização de testes e ensaios complementares aos materiais plásticos injetados, das quais se destacam o CDRSP e o Politécnico de Leiria. Adicionalmente, o CENTIMFE tem em curso parcerias com universidades estrangeiras que se dedicam ao estudo dos materiais plásticos e compósitos, como a Universidade de Rennes e a Universidade de Bordéus.
O presente documento apresenta alguns dos resultados do trabalho realizado por um aluno da Universidade de Rennes e pelos técnicos do CENTIMFE, cujo principal objetivo foi avaliar e compreender o impacto nas propriedades mecânicas dos materiais plásticos quando submetidos a processos sucessivos de reciclagem. Foi investigada a evolução da resistência à tração e flexão de provetes injetados com seis materiais plásticos submetidos a sete ciclos de reciclagem sucessivos.
Para esta investigação foram selecionados materiais plásticos virgens e reciclados. Os parâmetros de moldação por injeção foram ajustados para cada composição de material para produzir amostras de qualidade e isentas de defeitos. Os ensaios de tração e flexão são essenciais para compreender o impacto dos ciclos de reciclagem nas propriedades e no desempenho mecânico dos materiais plásticos. Para este estudo foram analisados parâmetros considerados relevantes pela literatura científica, a resistência à tração, resistência à flexão, alongamento à rotura, módulo de cisalhamento e módulo de Young
Ao examinar o efeito da reciclagem nas propriedades mecânicas dos plásticos, esta investigação visa fornecer uma melhor compreensão das vantagens e desvantagens associadas à utilização de materiais reciclados. Os resultados alcançados podem ajudar as empresas a tomar decisões informadas sobre a incorporação de plásticos reciclados nos seus produtos, contribuindo assim para reduzir o consumo de recursos naturais e o impacto ambiental, mantendo os padrões de alta qualidade e funcionalidade. Foi selecionada uma variedade de materiais termoplásticos como materiais de partida para esta investigação, cada um com propriedades mecânicas distintas e com diferente potencial de reciclagem.
• Polipropileno (PP) no estado regranulado a partir de tampas de embalagem de detergente.
• Polietileno (PE) no estado virgem.
• Policarbonato (PC) no estado regranulado.
• Acrilonitrilo Butadieno Estireno (ABS) no estado regranulado.
• Poliamida (PA) no estado reciclado e obtido a partir de redes de pesca.
• Poliuretano (TPU) no estado reciclado.
Para a injeção dos provetes foram considerados os parâmetros fornecidos pelos fabricantes para cada material em estado virgem. No caso da PA (redes pesca) e PP (tampas de detergentes) foram utilizados como base os parâmetros típicos para esta família de material, procedendo-se depois a um estudo inicial de otimização para aferir os melhores parâmetros de processo. Foram reunidos os valores iniciais indicados pelos fornecedores de materiais para propriedades como a resistência à tração, o alongamento e o módulo de Young. Para cada um dos materiais foram analisadas as recomendações de secagem e desumidificação para o processamento nas melhores condições operacionais, evitar defeitos e assegurar repetibilidade das condições iniciais.
Os provetes foram injetados com recurso aos equipamentos disponíveis no CENTIMFE: a) Máquina de injeção 30 Ton e; ii) Molde com cavidade moldante para provetes produzida com base na norma ISO 294. O processo de injeção dos seis materiais plásticos selecionados foi repetido até perfazer os sete ciclos de injeção e regranulação. De cada ciclo de injeção e após estabilização do processo foram recolhidos dez provetes.
Uma vez produzidos os provetes, estes foram enviados para testes de tração e flexão nos laboratórios do Politécnico de Leiria,
onde foram caracterizadas as suas propriedades mecânicas, nomeadamente, a resistência máxima à tração e flexão, o seu módulo de elasticidade e cisalhamento e outras propriedades.
Nesta pequena série de testes verificou-se que a resistência máxima para os diferentes materiais não se modifica acentuadamente, apesar dos sete ciclos de reciclagem. Também a resistência máxima à flexão para os diferentes materiais não sofre muitas alterações apesar dos sete ciclos de reciclagem, como se observa no gráfico seguinte.
De salientar que os materiais foram injetados e reciclados per se, a incorporação de material virgem não foi o foco deste estudo. Os resultados deste estudo são promissores e demonstram que há potencial de reutilização dos materiais testados. Podese verificar que propriedades como a resistência à flexão e módulo de flexão tiveram variações residuais nos diversos testes realizados para cada ciclo de injeção. A variação das propriedades, nomeadamente a flexão, deve ser tomada em consideração em cada caso, de modo a ponderar eventuais condicionantes de uso.
Os resultados deste estudo contribuirão para o desenvolvimento de trabalhos futuros na mesma linha de investigação, bem como para os esforços contínuos para desenvolver materiais plásticos sustentáveis e de elevado desempenho, atendendo às crescentes exigências técnicas, funcionais e de sustentabilidade na indústria moderna. A investigação futura poderá debruçar-se sobre formas de compor os materiais, a partir de reciclados, para incorporarem propriedades específicas a cada aplicação.
Como conclusão, considera-se que este trabalho deu um pequeno contributo no longo caminho a percorrer na área da sustentabilidade e para atingir a meta da neutralidade carbónica em 2050.
Eduardo Oliveira, Carlos Ribeiro, Emanuel Silva, Sílvia Cruz, Diana Dias, Rita Marques PIEP
O processo de moldação por injeção é amplamente utilizado na produção de peças plásticas de elevada qualidade e precisão, especialmente em grandes volumes, devido ao seu baixo custo. No entanto, fatores como a globalização, as exigências crescentes e a concorrência aceleraram a inovação na indústria. O principal desafio é garantir a produção de peças com um bom acabamento superficial, estabilidade dimensional e sem defeitos. Atualmente, a correção de defeitos é realizada por tentativa e erro, ajustando manualmente os parâmetros ou, ainda, utilizando a simulação numérica com o objetivo de acelerar a redefinição das condições de processo.
O projeto europeu InnoVatIve processing Technologies for biobased foAmed thermopLastics (VITAL) visa o desenvolvimento de soluções de processamento inovadoras para componentes à base de termoplásticos bio-based dotados com estruturas microcelulares, contendo tanto agentes expansores como termoplásticos bio-based em substituição de base fóssil. Especificamente no pacote de trabalho Foam Injection Moulding (FIM), com o objetivo de melhorar a eficiência e reduzir desperdícios, encontra-se em curso o desenvolvimento de métodos automáticos para correção de defeitos. Através de uma monitorização eficaz de variáveis críticas, tais como, por exemplo, temperatura e pressão, aliada ao controlo em tempo real, é pretendida a garantia de qualidade, eficiência e repetibilidade da produção, reduzindo simultaneamente as taxas de rejeição e custos.
No que concerne à automação e digitalização do processo, a abordagem aplicada na implementação de sistemas ciber-físicos CPS (Cyber-Physical System), integram processos físicos e digitais por meio de algoritmos, comunicação e controlo através da rede. Estas tecnologias são cruciais para a quarta revolução industrial, comummente denominada Indústria 4.0 [1].
Os requisitos de aumento de produtividade, flexibilidade e redução de defeitos nos processos de produção refletem o conceito de Indústria 4.0. Os modelos de referência como o
IIRA (Industrial Internet Reference Architecture) [2] e o RAMI 4.0 (Industrie Reference Architecture Model 4.0) [3], apresentados na Figura 1, demonstram uma abordagem estruturada para os desafios industriais existentes de forma estruturada.
No IIRA, os domínios funcionais e as funções transversais tratam a forma como o sistema funciona, enquanto as características do sistema enfatizam o quão bem este funciona. A intenção no RAMI é padronizar a comunicação entre várias fontes de dados, analisar e encaminhar as informações para os destinatários correspondentes.
A Indústria 4.0 na área de desenvolvimento e produção possibilita a seleção do tipo de comunicação das camadas 1 a 4, incluindo a possibilidade de utilizar redes sensíveis ao tempo (TSN) e 5G. Nas camadas 5 a 7, a Indústria 4.0 padroniza a comunicação entre a produção e a gestão empresarial ou nuvem, por meio de protocolos como OPC-UA (Open Platform Communications Unified Architecture) e MQTT (Message Queuing Telemetry Transport), conforme ilustrado na Figura 2.
/ / Figura 2: Interoperabilidade da camada de comunicação. [4]
Para alcançar essas metas, torna-se essencial a implementação de sistemas focados em interoperabilidade. Estes sistemas são baseados na Internet das Coisas Industrial IIoT (Industrial Internet of Things), que possibilita o acesso a dispositivos ciberfísicos capazes de integrar novas tecnologias. Os sistemas IIoT englobam dispositivos capazes de conectar a internet, identificarse na rede e comunicar com outros dispositivos, garantindo a interoperabilidade do processo e a monitorização eficiente. Desta forma, os equipamentos de produção podem ser facilmente monitorizados, operados e controlados.
Para aplicações IIoT [5], o fluxo de dados transmitidos de sistemas de tecnologia operacional OT (Operational Technology) para sistemas de tecnologia da informação IT (Information
Technology), requer uma latência mínima ou inexistente entre dispositivos conectados em ambas as redes, para que os operadores possam tomar decisões com base em dados de tempo real.
No entanto, segundo o autor [6], a adoção da IIoT, aumenta o volume total de dados gerados, transformando a forma como os dados industriais são tratados. Assim, dado o elevado fluxo de informação, torna-se crucial a utilização de abordagens eficazes de análise de dados, sendo a utilização de sistemas de gestão de base de dados particularmente relevante. Existem muitos tipos de base de dados disponíveis como, por exemplo, MySQL, PostgreSQL, Apache Cassandra e MongoDB.
Para automatizar e digitalizar o processo de moldação por injeção, foi desenvolvido um sistema, apresentado na Figura 3, para a aquisição e gravação de dados recolhidos da unidade de injeção da máquina Ferromatik Elektra 110 ton. Esta máquina encontrase equipada com um módulo de interface OPC-UA via rede Ethernet para a interoperabilidade de informações sobre cada moldação. Aqui é importante sublinhar que alguns dados não se encontravam disponíveis na interface OPC-UA da máquina
e, por isso, foi necessário utilizar outro dispositivo de aquisição de dados com uma interface MQTT. Posteriormente, através da plataforma Node-RED, procedeu-se à integração deste conjunto de dados numa base de dados MySql e procedeu-se ao desenvolvimento de um sistema de monitorização remoto para controlar o processo em tempo real.
Paralelamente, foi desenvolvido outro sistema capaz de adquirir e gravar informações recolhidas do interior do molde de injeção (Figura 4). Este molde encontra-se equipado com sensores Kistler (2 ou 4 sensores), permitindo, assim, a medição instantânea da pressão e da temperatura. Aqui foi utilizado um dispositivo de aquisição de dados (DAQ) com a interface MQTT, para recolher dados de temperatura e pressão, com intuito de se obter dados sobre a viscosidade do material na cavidade moldante. Tal como no sistema anterior, a partir da plataforma Node-RED procedeuse à integração de todas as informações na base de dados MySql, tendo sido obtida a monitorização remota para controlar o processo em tempo real.
O cálculo dos valores de viscosidade foi realizado com base no trabalho conduzido por Sykutera et al. [7]. Assim, a partir dos valores instantâneos de pressão e temperatura, adquiridos através dos sensores integrados na ferramenta moldante, a viscosidade aparente foi calculada através da equação (1).
Na equação, ηi representa a viscosidade aparente, Δp a variação na pressão entre os sensores, Δt é a variação na temperatura entre os sensores, H é a espessura da cavidade e Li é a distância entre os sensores de pressão e temperatura na cavidade do molde.
Com a caracterização da qualidade das peças, a criação de um modelo preditivo de inteligência artificial com recurso a Machine Learning (ML) permite efetuar as correções do processo de forma autónoma, minimizando peças rejeitadas. Este trabalho encontra-se a ser desenvolvido no âmbito do projeto VITAL, com apoio do Horizon Europe Framework Programme (HORIZON) (Call: TWIN GREEN AND DIGITAL TRANSITION 2021; ID: HORIZON-CL4-2021-TWIN-TRANSITION-01-05: Manufacturing technologies for bio-based materials) e no âmbito do Projeto POLARISE - PRR - Investimento RE-C05-i02: Missão Interface – CT.
Trabalho realizado no âmbito do Projeto POLARISE – Innovation in Polymer Engineering for a Circular and Digital Environment – apresentado ao abrigo da Medida RE-C05-i02 – Missão Interface, cofinanciado pelo PRR – Plano de Recuperação e Resiliência pela União Europeia.
[1] K. Wan, Jiafu Cai*, Hu Zhou, “Industrie 4 . 0 : Enabling Technologies,” in International Conference on Intelligent Computing and Internet of Things (IC1T), 2015, pp. 135–140, doi: 10.1109/ICAIOT.2015.7111555.
[2] S.-W. Lin et al., “The Industrial Internet of Things Reference Architecture,” Industrial Internet Consortium, 2019.
[3] M. Hankel and B. Rexroth, “The Reference Architectural Model Industrie 4.0 (RAMI 4.0).” ZEI, 2015, doi: 10.1200/JCO.2005.01.016.
[4] S.-W. Lin et al., “Architecture Alignment and Interoperability,” IIC:WHT:IN3:V1.0:PB:20171205, 2017.
[5] A. Veneri, G., Capasso, Hands-On Industrial Internet of Things. Packt Publishing, 2018.
[6] D. Mourtzis, E. Vlachou, and N. Milas, “Industrial Big Data as a Result of IoT Adoption in Manufacturing,” Procedia CIRP, vol. 55, pp. 290–295, 2016, doi: 10.1016/j.procir.2016.07.038.
[7] Sykutera, D., Czyżewski, P. & Szewczykowski, P. The microcellular structure of injection molded thick-walled parts as observed by in-line monitoring. Materials 13, 1–22 (2020).
EQUIPAMENTOS . PROCESSOS . CONHECIMENTO
DFM (DESIGN FOR MANUFACTURING) – CONCEBER EFICIÊNCIA E PRODUTIVIDADE PARA DESENVOLVER O NEGÓCIO
ACERTOS DE BRILHO E AJUSTES FINAIS NOS MOLDES COM VISTA À OTIMIZAÇÃO DO ASPETO DAS PEÇAS PLÁSTICAS
ELEMENTOS MÓVEIS DE LONGO CURSO
UMA NOVA ABORDAGEM
Armando Bastos * * Consultor Sénior
Num sector industrial como o da indústria de moldes, onde a precisão, a qualidade e a produtividade são cruciais para as empresas garantirem o crescimento próprio e dos clientes através da excelência dos produtos que concebem e comercializam, temos identificado ao longo do tempo uma necessidade crescente de integração das soluções técnicas com os requisitos de excelência operacional nas cadeias de valor do cliente final. As especificações utilizadas na conceção dos moldes deverão imperativamente integrar os requisitos operacionais definidos pelos clientes como necessários para a eficiente gestão operacional do molde e dos processos produtivos. Tendo em conta que a decisão de outorga do projeto se baseia fundamentalmente em critérios económicos, técnicos e de prazo, a diferenciação no mercado tem obrigatoriamente de passar pela fiabilidade e facilidade de operacionalidade do molde.
Esta evolução do paradigma prevalente terá de ser acompanhada por uma crescente coordenação e integração dos departamentos internos envolvidos e do cliente no processo de gestão de projetos. Para a indústria de moldes, em que a redução de prazos de entrega e dos respetivos custos de conceção e produção é critica para a sua evolução, a integração e sincronização dos processos internos conduzem a uma eficiência acrescida em utilização dos tempos e dos recursos necessários. Sabemos que atrasos recorrentes ao longo da produção e a necessidade de um número elevado de ensaios estão diretamente associados à perda de eficiência, o que pode resultar num dano irreparável: a perda de confiança dos clientes.
O ensaio de um molde é uma etapa crítica no desenvolvimento de qualquer projeto dependente da indústria de moldes. Este tem como objetivo verificar se o molde dá resposta às
especificações técnicas e de qualidade requeridas pelo cliente, antes que a produção em série seja iniciada. No entanto, quando os ensaios se tornam frequentes e demorados, o cliente poderá subentender que existem problemas subjacentes, como falhas no design, imprecisões na fabricação ou insuficiência na análise de viabilidade técnica. Esses fatores não apenas atrasam o cronograma de entrega, como também geram custos adicionais, tanto para a empresa que o produz, como para o cliente.
Além disso, a repetição de ensaios pode ser vista como um sinal de que o processo de desenvolvimento não foi bem conduzido desde o início, o que gera insegurança em relação ao produto final.
A integração facilita a comunicação e informação atempada e acelera o processo de tomada de decisão à medida que o projeto avança e novos desafios se apresentam. A reputação da empresa que desenha e constrói moldes e o seu crescimento radicam no respeito dos prazos e custos acordados e na quase inexistente variabilidade dimensional e de qualidade do produto resultantes do processo de moldação o que, na perspetiva do cliente, se traduz em eficiência dos processos produtivos e controlo eficaz de custos.
A adoção de tecnologias avançadas de simulação e prototipagem permite reduzir significativamente a necessidade de ensaios físicos, além de permitir ajustes e correções antes mesmo que o molde seja fabricado. Além disso, a formação contínua das equipas e a melhoria na comunicação entre os departamentos envolvidos no desenvolvimento, são fundamentais para garantir que todos os aspetos técnicos e de qualidade sejam atendidos desde o início. Torna-se assim importante refletir sobre o impacto de pequenos atrasos, que somados e repetidos continuadamente, tornam-se um círculo vicioso.
PERDAS DE EFICIÊNCIA: UM CÍRCULO
As perdas de eficiência podem ser observadas em diversas áreas, sendo as mais impactantes:
1. Aumento de custos operacionais: cada ensaio adicional requer recursos materiais, humanos e tempo. À medida que os testes se multiplicam, os custos operacionais aumentam exponencialmente. Isso inclui o uso de matérias-primas, energia, e a alocação de pessoal técnico qualificado, que poderia estar dedicado a outros projetos. Além disso, a necessidade de refazer ensaios ou prolongar os já planeados gera custos imprevistos, que pressionam as margens de lucro;
2. Desperdício de tempo: o tempo é um dos recursos mais valiosos em qualquer indústria. Atrasos nos ensaios resultam em cronogramas de produção comprometidos, levando a uma cadeia de atrasos subsequentes que afetam todo o fluxo produtivo. Quanto mais tempo se leva para concluir os ensaios, maior o impacto na entrega final do produto, o que pode resultar em penalidades contratuais ou na necessidade de renegociar prazos, prejudicando a imagem da empresa;
3. Subutilização de equipamentos: equipamentos que deveriam estar a operar em projetos subsequentes ficam inativos ou são subutilizados devido à extensão dos ensaios. A subutilização não apenas reduz o retorno sobre o investimento em
máquinas, como também diminui a capacidade produtiva da empresa, limitando a sua capacidade de dar resposta a novos pedidos e aumentando do tempo de inatividade;
4. Impacto na moral e produtividade da equipa: repetidos atrasos e a necessidade de múltiplos ensaios podem ter um efeito desmoralizador sobre as equipas, principalmente de engenharia e produção. A pressão para corrigir falhas, muitas vezes sob prazos apertados, pode levar a um aumento de erros e à diminuição da produtividade geral. Além disso, a repetição de ensaios pode gerar frustração entre os colaboradores, que podem sentir que os seus esforços não foram de todo eficazes;
5. Redução da capacidade de inovação: quando recursos significativos são consumidos em ensaios prolongados e repetitivos, a capacidade da empresa de investir em inovação e em novos projetos é reduzida. Em vez de se focar no desenvolvimento de novos produtos ou na melhoria dos processos existentes, a empresa vê-se obrigada a alocar recursos para resolver problemas imediatos. Isso compromete a competitividade a longo prazo e pode levar à estagnação no mercado.
A confiança dos clientes é fundamental para a sustentabilidade de qualquer negócio, especialmente em indústrias onde a relação fornecedor-cliente é frequentemente baseada em contratos de longo prazo e em projetos de alta complexidade. As perdas de eficiência internas de uma empresa, afetam essa confiança de várias formas:
1. Comprometimento dos prazos de entrega: os clientes confiam nos fornecedores para cumprir prazos rigorosos. Quando os prazos são constantemente alterados devido a ensaios demorados, os clientes começam a questionar a confiabilidade do fornecedor. Essa desconfiança pode levar à procura de novos fornecedores, o que representa uma perda significativa de receita para a empresa fornecedora;
2. Perceção de falta de competência técnica: o cliente pode interpretar a necessidade de múltiplos ensaios como uma indicação de que o fornecedor não possui o conhecimento técnico necessário ou que há falhas graves no processo de design e fabricação. Isso afeta negativamente a reputação da empresa, tornando-a menos competitiva no mercado;
3. Custos adicionais para o cliente: atrasos e ensaios prolongados podem resultar em custos adicionais para o cliente, como a necessidade de modificar cronogramas de produção, reorganizar linhas de montagem ou até mesmo adiar o lançamento de novos produtos. Esses custos indiretos aumentam a insatisfação do cliente e podem prejudicar a relação comercial a longo prazo;
4. Dificuldade em estabelecer parcerias futuras: a confiança abalada torna mais difícil a renovação de contratos e o estabelecimento de novas parcerias. Clientes insatisfeitos podem-se tornar defensores de concorrentes, utilizando as suas experiências negativas como argumento para justificar a troca de fornecedor. Isso não só reduz a base de clientes existente, mas também torna mais difícil atrair novos clientes.
FATORES INTERNOS QUE LEVAM AOS ATRASOS
Apesar de todos os esforços para garantir que os moldes sejam entregues a tempo, várias razões podem contribuir para os atrasos:
• Complexidade do design do molde: moldes complexos, especialmente aqueles com geometrias intrincadas ou múltiplas cavidades, podem exigir mais tempo de desenvolvimento e ajustes. Erros de design ou a necessidade de modificações durante a fase de produção podem facilmente prolongar os prazos previstos;
• Problemas visíveis na produção: a fabricação de moldes envolve o uso de tecnologias avançadas. Contudo falhas em equipamentos, erros de design ou programação, ou dificuldades na obtenção de precisão dimensional podem atrasar a produção. Além disso, a necessidade de retrabalho devido a não conformidades ou defeitos descobertos até e durante o ensaio do molde também pode ser um fator;
• Paragens não planeadas, tendencialmente não visíveis:
1. a falta de fluxo contínuo na comunicação entre departamentos;
2. a falta de informação para realizar atividades de valor acrescentado à primeira;
3. a falta de automatismos simples, para tarefas repetitivas;
4. a falta de planeamento e abastecimento de materiais e consumíveis quando efetivamente necessários;
5. o incorrer em atividades que exigem movimento ou transporte por parte dos colaboradores, que assim se tornam atividades sem valor acrescentado;
6. o consumo de tempo díspar na montagem de um molde, para elementos semelhantes e o retrabalho necessário para finalizar a operação;
Todas estas microparagens, todo este somatório de pequenas frações de tempo que são possíveis de observar diariamente, ao longo da cadeia de valor, são desperdício recorrente de recursos, custo desnecessário.
Sem a medição dos mesmos e sem a aplicação de uma metodologia de análise VA/NVA, passo a passo, que todos na organização entendam, são mais difíceis de eliminar, porque continuam invisíveis.
IMPACTO NA PRODUTIVIDADE
Se observarmos estas perdas de perto, conseguimos observar a quebra. Real, mas invisível, de produtividade na empresa, que pode se traduz em:
1. Paragens da produção: o principal impacto de atrasos torna-se visível na paralisação parcial ou total da produção. A inatividade de equipamentos e colaboradores, afeta negativamente a produtividade geral da empresa;
2. Replaneamento: quando os ensaios atrasam ou são recorrentes, torna-se necessário replanear as suas operações para minimizar impactos na produção. O que pode envolver a reorganização dos equipamentos para outros produtos, o que, tendencialmente, gera ineficiências e reduz a produtividade em outras áreas da empresa;
3. Pressão para compensar o tempo perdido: uma vez com o molde finalmente aprovado, a empresa pode ver-se sob pressão para compensar o tempo perdido. Isso pode resultar em sobrecarga de trabalho, horas-extra para os funcionários e maior desgaste das máquinas, o que pode comprometer a produtividade a longo prazo devido a manutenção inesperada ou falhas mecânicas;
4. Impacto no ciclo de desenvolvimento de novos produtos: em sectores em que a inovação e o tempo de lançamento no mercado são cruciais, atrasos nos ensaios dos moldes podem retardar o desenvolvimento de novos produtos. Isso pode resultar na perda de janelas de oportunidade no mercado, permitindo que concorrentes lancem produtos similares mais rapidamente.
Com a produção parada, a empresa ainda incorrerá custos de inatividade, como custos fixos, salários, energia e manutenção de equipamentos, sem a correspondente geração de receitas. Esses custos de inatividade acumulam-se e impactam diretamente a margem de lucro e, consequentemente, a sustentabilidade da empresa;
Para compensar os atrasos, as empresas podem recorrer em horas-extra ou na contratação temporária de mão-de-obra ou até mesmo a terceirização de partes da produção, aumentando os custos operacionais
Em muitos casos, os atrasos nos ensaios dos moldes podem resultar em multas e penalidades. O que impacta negativamente o fluxo de caixa da empresa.
Se os ensaios são apressados para cumprir prazos, há um maior risco de falhas não detetadas no molde, que podem resultar em produção de peças defeituosas, aumentando o retrabalho e o desperdício. Tendo assim um forte impacto nos custos de produção.
Ficando assim afetada a imagem e relação com clientes: A longo prazo, a confiabilidade da empresa pode ser questionada, levando a uma perda de contratos ou a exigência de descontos para manter clientes satisfeitos. Manter uma boa relação com clientes pode, em casos extremos, exigir compensações financeiras, aumentando ainda mais os custos.
Os atrasos nos ensaios dos moldes de injeção de plástico afetam diretamente a produtividade e os custos de uma empresa, gerando uma cadeia de consequências que pode comprometer a eficiência operacional e a lucro estimado. Para minimizar esses impactos, é essencial que as empresas invistam em planeamento rigoroso, monitorização contínuo dos seus processos e na comunicação eficaz com todos os envolvidos nos projetos. Ao antecipar possíveis problemas e adotar uma abordagem proativa, as empresas podem mitigar os efeitos negativos e manter sua competitividade no mercado.
Para reverter esse cenário, as empresas da indústria de moldes precisam adotar uma abordagem proativa em relação à eficiência dos seus processos. Isso inclui o investimento em tecnologias avançadas, a otimização dos fluxos de trabalho e o desenvolvimento contínuo das competências das equipas.
A excelência operacional e a confiança do cliente estão intrinsecamente ligadas.
Empresas que conseguem manter processos ágeis, reduzir prazos como consequência de fluxo de processos desenhados para a eficiência estão condenadas aumentam a rentabilidade e a consolidação e crescimento do seu mercado porque dessa forma reforçaram a confiança dos seus clientes.
Portanto, é essencial que os fabricantes de moldes implementem práticas eficazes de gestão de projetos, comunicação clara com os clientes e iniciativas que garantam o cumprimento dos requerimentos dos clientes e dos compromissos assumidos deixando para trás as ações de sistemáticas de resolução de atrasos. Desta forma deixarão reagir como reflexo de uma crise para passarem a pilotar o presente e a definir o seu futuro.
Existem diversas empresas na indústria de moldes, que ao contar com o apoio de consultorias de processos, conseguiram mudar radicalmente o paradigma melhorando simultaneamente a sua eficiência e a competitividade num mercado exigente.
A implementação das melhores práticas é o desafio.
O resultado é o caminho virtuoso da melhoria, em equipa.
Raúl Souto * * General Manager - MOLD-TECH PORTUGAL
Com o aumento da exigência por parte dos clientes finais no que se refere ao aspeto das peças plásticas, os ajustes no brilho da textura e outros ajustes na fase final da texturização de moldes tornam-se cada vez mais indispensáveis, gerando algumas vezes questões sobre a definição de responsabilidades sobre quem deve suportar os custos destas operações, ensaios adicionais, desmontagens e montagens dos moldes, transportes, entre outras.
Na resposta a essa questão há que considerar o seguinte:
1. Quando texturizamos um molde com texturas do tipo das que mais se usam na indústria automóvel, estamos a introduzir-lhe uma alteração de enormes proporções que inevitavelmente vai alterar o seu comportamento em produção.
• O coeficiente de atrito das superfícies texturizadas aumenta exponencialmente.
• O plástico passa a fluir de forma diferente no processo de injeção e é imperativo ajustar parâmetros de injeção para mitigar fenómenos indesejáveis, que só aparecem com a texturização do molde. Por exemplo, se houver ondulações na superfície da peça plástica moldada pelo macho, antes da texturização do molde a peça não gripa no lado da cavidade, mas depois da texturização do molde gripa de certeza, devido aos movimentos de contração do plástico antes da abertura do molde e às diferenças de espessura da própria peça, provocadas pelas ondulações no macho.
2. Na fase de projeto e na fase de acabamento dos moldes, tem de se ter sempre em consideração que vai haver movimentos da peça plástica dentro do molde, antes da abertura do mesmo, devido à contração do plástico. De um modo geral, antes da abertura do molde, a periferia das peças desloca-se sempre no sentido do centro, nalguns casos milímetros.
Há que ter presente que a periferia das peças plásticas, ao deslocar-se para o centro das mesmas antes da abertura do molde, tem de passar de uma área de menor folga no molde (menor espessura na peça plástica) para uma área de maior folga (maior espessura), senão gripa inevitavelmente, seja qual for o ângulo de saída que aí exista.
Muitas vezes isto não é tido em consideração e os moldes voltam ao texturizador para eliminar raspados quando o problema não deveria ser resolvido do lado da textura, mas sim do lado do macho.
Isto é apenas um exemplo.
3. Relativamente ao brilho, nenhum texturizador pode garantir que se vai conseguir um determinado valor de brilho nas peças plásticas produzidas no primeiro ensaio do molde com textura, porque o brilho de uma peça plástica depende de muitos fatores, sendo que a maioria deles está fora do controlo do texturizador. São eles os seguintes por ordem de importância:
• Natureza do material plástico;
• Corante e sua percentagem;
• Parâmetros de injeção (temperaturas, velocidade de injeção, pressões de compactação, tempo de ciclo, etc.);
• Forma e profundidade da textura;
• Microrrugosidade da textura;
• Geometria do molde e da peça plástica;
• Fugas de gases do molde ou falta delas;
• Sistema de injeção;
• Máquina de injeção;
• Outros.
De todos estes fatores, o único que o texturizador pode controlar e alterar é a microrrugosidade da textura, já que a sua forma e profundidade são definidas por um padrão aprovado pelo cliente e, se as alterarmos, a textura poderá ser rejeitada.
É por isso que ninguém pode garantir um valor de brilho na textura das peças plásticas antes de:
• se fazerem os primeiros ensaios do molde texturizado;
• se estabelecerem os parâmetros definitivos de injeção;
• verificar os resultados obtidos com estes parâmetros para, a partir destes resultados, se fazerem os ajustes de brilho necessários no aço.
Os texturizadores razoavelmente equipados têm todas as condições para poderem garantir valores de brilho da textura no aço, mas não podem garantir valores brilho da textura nas peças plásticas, porque estes são influenciados por fatores que não controlamos.
O problema é que os nossos clientes também não nos sabem dizer qual é o nível de brilho que necessitam no molde, para poderem produzir peças plásticas com o brilho dentro da especificação recebida do cliente deles.
Após o primeiro ensaio de um molde com textura e a correta definição dos parâmetros de injeção, para se respeitarem as tolerâncias dimensionais, é o momento certo para medir o nível de brilho obtido e ajustar a microrrugosidade da textura, de forma a garantir um brilho das peças plásticas conforme a especificação do cliente final. Esse é o trabalho que o texturizador pode fazer, mas apenas nesta altura.
O mesmo se passa em relação aos gripados. Porém, se se voltarem a alterar os parâmetros de injeção ou as percentagens de corante
ou mesmo o material plástico, voltamos a perder o nível de brilho.
Com tolerâncias de brilho tão apertadas como as que agora são exigidas (até há cinco anos, o normal era +/- 0,5, e agora rondam +/- 0,2) acontece, muitas vezes, apenas trocar um molde de máquina de injeção e já ser suficiente para as peças plásticas começarem a sair com brilho fora de especificação.
O acima exposto ajuda a compreender que não é realista pensar que se pode texturizar um molde com as texturas que hoje se utilizam na indústria automóvel e obter peças plásticas com o nível de qualidade exigido por essa indústria, logo no primeiro ensaio com textura, dispensando intervenções adicionais.
Nas discussões em que participamos com os construtores automóvel e com os seus fornecedores, defendemos sempre, em função da nossa experiência, que para otimizar o aspeto de uma peça plástica até aos níveis que hoje são exigidos, devemos considerar, em média, duas intervenções na textura do molde e dois ensaios do mesmo, após a sua texturização. Se, nalguns casos, uma intervenção após o primeiro ensaio do molde texturizado é suficiente, nas geometrias mais complexas duas intervenções podem não o ser.
Este facto é normalmente aceite por toda a gente, incluindo as compras das OEM, e considerado nos orçamentos que os Tier 1 passam às OEM para o desenvolvimento das ferramentas.
Acontece algumas vezes que depois de se afinarem os brilhos e depois de se obterem peças boas, o molde segue para o cliente que, quando lá chega, reclama, pois as peças estão a sair com o brilho fora de especificação e, algumas vezes, até com gripados.
Isto pode acontecer por vários motivos:
• O cliente pode não estar a usar os mesmos parâmetros de injeção;
• A máquina de injeção pode ter características muito diferentes daquelas em que o molde foi testado anteriormente;
• Pode haver diferença no material plástico ou na percentagem de corante que está a ser utilizado.
Às vezes, é preciso uma nova intervenção no molde para que volte a produzir peças dentro de especificação nestas novas condições. Contudo, o custo desta nova intervenção deve ser interpretado como um custo de início de produção serie (custo de industrialização da peça plástica, ou seja, custo de otimização de processo) e suportado pelo cliente que vai fazer a produção. Não faz sentido considera-lo como um custo de desenvolvimento, construção e fornecimento do molde.
Quando um fabricante de moldes vende ao seu cliente um molde texturizado, deve ter em consideração o que acima se diz.
O molde provavelmente tem de ir várias vezes ao texturizador, tem de ser desmontado, montado e testado várias vezes.
Quando o cliente do fabricante de moldes decide pagar a textura ao texturizador, é justo que o fabricante do molde reclame ao seu cliente o pagamento da sua participação nesta operação, que são as desmontagens e montagens do molde, os testes, os transportes do molde entre o fabricante dos moldes e o texturizador e o envio de peças plásticas ao cliente, se aplicável.
Creio ser este o entendimento correto deste negócio.
Espero não ter sido demasiado pesado e que estas considerações passam esclarecer e ajudar todos os envolvidos nestes negócios.
Rui Rocha * * Eurocumsa
É com alguma frequência que nos deparamos com artigos que apresentam cavidades relativamente profundas, o que representa um desfio que, não sendo difícil de superar, obriga a alguma ginástica e a muitos inconvenientes.
Se um elemento móvel com curso até 50 mm é uma situação de fácil resolução, a partir deste limite a situação começa a complicar, agravando-se à medida que este limite vai aumentando.
A primeira opção (e a mais convencional) será a utilização de guias inclinadas em que as inclinações utilizadas variam entre os 8 e os 16 graus. Para cursos mais longos, a guia terá de ser mais comprida que o normal sendo que quanto maior for a sua inclinação maior será o risco de partir durante a produção. Esta opção tem a vantagem de ser totalmente mecânica, mas apresenta várias dificuldades que poderão inviabilizar a aplicação. As guias mais compridas, principalmente as de menor diâmetro,
tendem a fletir em demasia e a sua rotura representa um risco real. Adicionalmente, obriga a guias fora de standard com custos e prazos de entrega acrescidos em que, muitas das vezes, as mesmas saem fora dos limites do próprio molde ou “invadem” zonas pouco desejáveis.
Descartando esta possibilidade, a segunda opção é normalmente a aplicação de um cilindro hidráulico para realizar o movimento. Além do investimento que poderá significar, esta solução traz normalmente dois grandes inconvenientes:
1.º - A utilização de um circuito hidráulico;
2.º - O incremento significativo das dimensões do molde.
É sabido que o injetador evita, sempre que possível, a utilização de circuitos hidráulicos devido a problemas de contaminação da zona moldante e chão-de-fábrica. Adicionalmente, aumentamos
o tempo de ciclo e complicamos a sinemática do molde no momento de colocar o molde a trabalhar.
Relativamente às dimensões, tendo em conta que os cilindros são, na maioria dos casos, aplicados na face do molde, vamos ter um corpo “estranho” a sobressair do molde. Quanto maior o curso, maior o inconveniente e, no limite, pode ser necessário desmontar o cilindro hidráulico para o molde poder passar entre as colunas da máquina. O manuseamento do molde também perde bastante, já que são frequentes os acidentes devido a toques com este “corpo estranho” em que a solução pode passar pela aplicação de proteções bastantes volumosas.
Com base nesta problemática, a nossa equipa de desenvolvimento começou a trabalhar numa nova abordagem que pudesse solucionar parte ou mesmo todos estes problemas.
Com base na nossa tecnologia de cremalheiras (rack system), fomos capazes de encontrar uma solução capaz de realizar movimentos de 50 a 150 mm de forma relativamente fácil e totalmente mecânica.
Ao substituir a guia inclinada por uma cremalheira perpendicular à linha de junta, conseguimos reduzir a sua dimensão e dar maior robustez.
Graças aos seus dentes a 45 graus, obtemos uma relação de 1/1 em que o comprimento da “guia” é igual ao curso a realizar, ou seja, para 150 mm de curso, precisamos de uma haste de 150 mm que irá trabalhar na perpendicular.
No entanto, esta guia “cremalheira” não esta aplicada no lado cavidade, mas sim na bucha junto ao elemento móvel sem nunca perder o contacto com o mesmo. Desta forma, após executar o movimento, bloqueamos o elemento móvel mantendo a sua posição, atuando assim como retensor. Para garantir este bloqueio, recorremos a um outro sistema com provas já dadas do nosso sistema de dupla extração.
Desta combinação resulta a possibilidade de movimentar qualquer elemento móvel de forma segura, absolutamente mecânica e sem aumentar as dimensões do molde.
Aplicado na lateral do elemento móvel de forma simples, ou em duplicado (1x em cada lateral do movimento), permite ainda inclinações no movimento de +25 a -25 graus com enorme facilidade.
Nesta inovadora solução tentamos ser o mais universal possível, pelo que o sistema pode ser aplicado a qualquer movimento convencional, mesmo em moldes já existentes com alterações mínimas.
Está, assim, desmistificado mais um dos dogmas do projeto de moldes.
ECONOMIA . MERCADOS . ESTATÍSTICAS
A NOVA GEOPOLÍTICA INDUSTRIAL
PROCESSOS - SE EXISTEM, PORQUE NÃO OS CUMPRIMOS?
Vítor Ferreira *
* Diretor Executivo da Startup de Leiria e docente do Politécnico de Leiria
No chamado Sul Global (termo que se refere aos países em desenvolvimento, principalmente na América Latina, África e Ásia, destacando as diferenças económicas, políticas e sociais em relação ao Norte Global), podemos encontrar cidades modernas, cosmopolitas, sejam elas Lima, Nairobi, São Paulo, Banguecoque ou Santiago. Estas cidades são em muito semelhantes a outras capitais mundiais, mas um olhar mais atento aos carros, telemóveis ou eletrodomésticos à nossa volta quando as visitamos poderão quebrar a familiaridade com o contexto europeu.
Marcas chinesas como a Chery, a BYD e a Great Wall têm uma quota de mercado muito relevante (e crescente), oferecendo veículos que combinam tecnologia avançada com preços acessíveis, mesmo que as marcas coreanas e japonesas continuem a ter forte popularidade. Já as marcas europeias e americanas estão cada vez menos presentes – com os esperados
impactos indiretos na indústria nacional e, em particular, na indústria de Leiria. Esta ofensiva reflete-se não apenas nos carros, mas também na proliferação de smartphones chineses na região, liderada por gigantes como a Xiaomi, a Huawei (proibida no ocidente, mas com imensa expressão no sul global) e a Oppo, que oferecem dispositivos de alta qualidade a preços competitivos.
Durante décadas, o Ocidente reinou no comércio global, impulsionado por multinacionais dos EUA, Europa e Japão. No entanto, essa hegemonia é hoje desafiada pelas empresas chinesas, que estão a expandir as suas operações para além das fronteiras nacionais e a penetrar nos mercados emergentes do Sul Global, a uma velocidade surpreendente – quer produzindo (a China expandiu as suas cadeias de valor, com o investimento direto a triplicar para 160 mil milhões de dólares em 2023, contruindo fábricas de Marrocos à Malásia), quer vendendo (as vendas das empresas chinesas ultrapassaram, no Sul Global,
os 800 mil milhões de dólares, superando as vendas dessas empresas nos países desenvolvidos).
Este avanço chinês não é acidental, mas sim o resultado de políticas bem orquestradas. À medida que os países ricos ergueram barreiras comerciais para proteger as suas indústrias, a China intensificou as suas relações com o Sul Global. Este movimento aproxima os países em desenvolvimento da China, enquanto o Ocidente se isola cada vez mais. O Ocidente, outrora o defensor mais fervoroso da globalização, agora recua, enquanto a China avança – a história diz-nos que raramente o protecionismo cego é uma boa política económica. Esta mudança traz oportunidades e desafios para todos os envolvidos, mas uma coisa é certa, o mundo não está a parar, e aqueles que melhor se adaptarem a esta nova realidade serão os que colherão os frutos no futuro.
As transformações geopolíticas e comerciais mencionadas anteriormente têm impactos profundos e diretos nas cadeias de valor globais, especialmente nas indústrias localizadas em países como Portugal. Com a ascensão das empresas chinesas no Sul Global, a competição nos mercados de automóveis, eletrónicos e outros bens de consumo está a intensificar-se, com implicações para a indústria de moldes e de desenvolvimento de produto em Portugal.
O avanço das empresas chinesas, que agora estão fortemente presentes em mercados emergentes, está a alterar as dinâmicas das cadeias de valor. Estas empresas não só dominam a produção e a venda de produtos finais, mas também estão a investir pesadamente em tecnologia de fabricação e desenvolvimento de novos produtos, áreas em que Portugal tradicionalmente desempenhou um papel crucial. Note-se que a questão passou de competir com fornecedores chineses na cadeia de valor dos players tradicionais para a substituição dos próprios players tradicionais (no fundo novos líderes das redes empresariais estão a emergir).
Os fabricantes portugueses de moldes enfrentam uma pressão crescente para se adaptarem a este novo cenário competitivo. Por um lado, existe uma oportunidade de colaboração com estas empresas emergentes, fornecendo moldes e soluções de alta precisão para suportar a expansão das marcas chinesas no mercado global. Por outro lado, a concorrência direta de fabricantes chineses, que muitas vezes operam com custos significativamente mais baixos, pode ameaçar as margens de lucro e a sustentabilidade das empresas portuguesas, especialmente se estas não conseguirem inovar e agregar valor
aos seus produtos – sobretudo num contexto em que os próprios clientes tradicionais começam a definhar.
O sector automóvel é um dos maiores consumidores de moldes de alta precisão, e as mudanças na geopolítica comercial global estão a ter efeitos profundos neste mercado. Com as marcas chinesas a expandirem-se rapidamente em mercados como a América Latina, África e Sudeste Asiático, a procura por moldes específicos para novos modelos de automóveis muda (como já havia acontecido com a emergência dos novos players e fabricantes de carros elétricos). As empresas portuguesas de moldes, que tradicionalmente forneciam grandes fabricantes europeus e americanos, estão agora a ver uma redução nas encomendas destes clientes, à medida que as suas quotas de mercado diminuem no Sul Global. Em contrapartida, há uma oportunidade de se reposicionarem como fornecedores estratégicos para as marcas chinesas em expansão. Para tal, será necessário que as empresas portuguesas invistam em inovação, desenvolvam capacidades de produção mais flexíveis e se adaptem às especificidades dos novos mercados e produtos. Isso inclui, por exemplo, a capacidade de produzir moldes para veículos elétricos, que estão a ganhar popularidade rapidamente, e para componentes que utilizam novos materiais mais leves e sustentáveis.
O protecionismo crescente no Ocidente, combinado com a expansão das empresas chinesas no Sul Global, significa que as cadeias de abastecimento se tornam mais fragmentadas e regionalizadas. As empresas portuguesas terão de explorar novas parcerias e mercados fora da sua zona de conforto tradicional. Além disso, será crucial que estas empresas invistam em tecnologia de ponta como fabricação digital, automação avançada e inteligência artificial, para aumentar a sua competitividade.
Dados recentes mostram que o investimento em tecnologia na indústria de moldes em Portugal cresceu cerca de 5 % ao ano, mas isso pode não ser suficiente num ambiente de rápida evolução tecnológica global. A colaboração com instituições de I&D e a formação contínua dos trabalhadores serão também fatores-chave para manter a relevância e competitividade da indústria de moldes em Portugal. Ao mesmo tempo, políticas governamentais que incentivem a inovação e o investimento em novas tecnologias serão essenciais para apoiar esta transição.
A nova geopolítica comercial está a reconfigurar as cadeias de valor globais, e a indústria de moldes em Portugal deve posicionar-se estrategicamente para aproveitar as oportunidades e mitigar os desafios. Adaptação, inovação, dimensão e colaboração serão os
Miguel Nuno Silva * * Consultor Internacional em Supply Chain, Procurement & Logística
Duas coisas poderão ter ocorrido para parar nesta página e iniciar a leitura deste artigo – coincidência (o famoso “calhou” português) ou, porventura, se leu e/ou se recorda do primeiro artigo, com este mesmo tema, redigido na edição anterior.
Antes de mais, obrigado(s). À CEFAMOL, por dar continuidade à minha colaboração nesta revista, o que muito me honra e a todos os que direta ou indiretamente entraram em contacto comigo aquando do artigo anterior.
Esperando que o (normal) período de férias tenha sido retemperador de energia(s), vontade(s) e tenha insuflado o nosso/vosso “querer ser e fazer melhor”, estou aqui para vos falar da segunda vertente da minha contribuição neste espaço editorial – processos
Se no primeiro artigo vos falei de pessoas, este segundo – e esta é, só pode ser a ordem das coisas… – tem que ver com regras. Quem (pessoalmente) me conhece, diz que sou disciplinado, metódico, em suma, (muito) organizado. Todos os amigos, colegas e profissionais - o «os», pela segunda vez neste artigo, é e será sempre com a inclusão de todos os géneros – com quem tive privilégio de partilhar conhecimento e experiências, sabem, decerto, que respondo que tal não é verdade, ou seja, que não sou organizado; apenas não deixo que me desorganizem.
Os processos (a sua definição, desenho e estruturação) são vitais para a arquitetura de base de qualquer organização. Os processos têm de ser e estar escritos. Que processos? Os inerentes aos principais fluxos da organização e, por isso, transversais a todas as áreas ou departamentos.
o conhecimento (ou acesso) aos procedimentos (não existe por exemplo uma rede de intranet para consulta) fazendo com que, por exemplo, em empresas de alta rotatividade laboral os novos colaboradores façam o que veem fazer. É preciso, pois, uma reciclagem permanente que leve a questionar os procedimentos (…que não são para cristalizar!) e a proceder à sua revisão;
• Pressão de sobrevivência – não é novidade (penso eu) a pressão de tesouraria a que muitas organizações estão sujeitas – devida a fatores internos, externos e/ou conjunturais – e, por isso, por vezes a decisão é uma tomada de escolha entre ‘pular os procedimentos’ e ‘fazer entrar dinheiro na empresa’;
• «O nacional porreirismo» – não queremos estar mal com ninguém e ‘o patrão manda’. Somos assim; é cultural. Será que pode(mos) fazer algo? Nem me atrevo a ir mais longe, apenas a mencionar a frase de um general francês, que um dia se referiu sobre a nossa pátria «… é um povo difícil de entender – por um lado não se governa; por outro não se deixa governar…».
• A Fábula do Pedro e do Lobo – a melhor forma de perceber a importância dos processos e dos procedimentos é, infelizmente, quando o erro ocorre e por vezes, a sua gravidade é impactante. O que acontece nesses momentos, querem mesmo que descreva?
Sobre esta minha formulação (que sinceramente espero que discordem e não se revejam…) gostaria de ser cáustico dizendo que felizmente estamos em Portugal, pois em certos países uma situação das acima descritas teriam severos dissabores a quem optasse por essa conduta.
Definidos que estejam, são detalhadamente explicitados em procedimentos que, claramente, definem as etapas de suporte / execução e atribuem responsabilidades. O SGQ (Sistema de Gestão de Qualidade) é o suporte para este efeito, assente na grande maioria das organizações a nível mundial na norma ISO. (…) Quanto a este tema, os países nórdicos têm um entendimento distinto, assente na premissa de que a «qualidade» não deve ser exigida e menos ainda imposta, pois é o atributo linear e tácito que definirá a própria subsistência da empresa e que, na sua inexistência, será rapidamente detetado pelo mercado (…).
Do meu percurso profissional retenho empresas desorganizadas com excelentes procedimentos e, em contraponto, entidades muitas vezes sem procedimento escritos, mas com boa organização operacional.
Porque é que isto acontece? Reconhecendo que não tenho as qualidades do Luís de Matos em matérias de magia e adivinhação, penso que estão em causa cinco pontos fundamentais:
• O fazer antes do fazer bem – a pressão de, em muitas ocasiões, o «entregar», o «faturar» estar acima de tudo, ou seja, é permitido por isso ‘furar’ os procedimentos;
• Falta de comunicação – em muitas organizações nem todos têm
Palavra de ânimo. Sim claro! Nem tudo são rosas, mas também, nem tudo são espinhos. Espera-se dos novos gestores melhoria da gestão geral. E o que é gestão? Gestão é a soma de planeamento e previsão. Se todos, ao nível do nosso desempenho pessoal, pudéssemos melhorar a esses dois níveis, muitos dos fatores que referi seriam mitigados o que, por isso, faria com que diretamente a empresa deixasse de incorrer em custos de «não qualidade» e, desse modo, aumentasse diretamente os seus proveitos.
Fica a provocação: “Não será o facilitismo a antecâmara do oportunismo?” (dixit Victor Hugo).
Como ficaria se eu (ou alguém) falasse consigo e lhe dissesse que é um “oportunista” (…fique descansado, não vou fazer isso!) isto é, passando diariamente por cima dos procedimentos sem os denunciar e colaborando, por essa omissão, na continuidade do… fazer antes do fazer bem?
Não se chateiem, mas, por favor, melhorem a todos os níveis o vosso planeamento e previsão.
Segundo de quatro pilares – PROCESSOS! (done).
NOTA: Sugestões, análises críticas e/ou comentários são (serão sempre) bemvindos pois são o meu boost para, a cada dia, fazer (e ser) mais e melhor –miguelnunosilva@gmail.com
IMPORTÂNCIA DA GESTÃO E OTIMIZAÇÃO ENERGÉTICA NAS EMPRESAS
ESG E O SECTOR DOS MOLDES E PLÁSTICOS: UM CAMINHO PARA A SUSTENTABILIDADE
CIRCVET PROMOVE FORMAÇÃO EM ECONOMIA CIRCULAR NA INDÚSTRIA DE PLÁSTICOS
A OBRIGAÇÃO DE QUANTIFICAR (E REDUZIR) AS EMISSÕES DE CARBONO
Nuno Martinho* , Rita Diniz * * Gestores da Área de Energia – STREAM
Num contexto global marcado pela crescente preocupação com as alterações climáticas e a necessidade urgente de reduzir as emissões de carbono, a eficiência energética emerge como um pilar fundamental para a sustentabilidade e competitividade das empresas. A otimização do uso de energia não só contribui para a diminuição dos custos operacionais, mas também se encontra alinhada com os objetivos de descarbonização estabelecidos a nível nacional, europeu e mundial.
O Acordo de Paris, estabelecido em 2015 durante a COP21, é um marco global na luta contra as alterações climáticas. O seu objetivo central é limitar o aumento da temperatura média global e empregar esforços para limitar o aumento da temperatura a 1,5°C acima dos níveis pré-industriais durante este século,
incentivando os países a alcançarem, o mais rápido possível, um equilíbrio entre as emissões emitidas e as removidas da atmosfera na segunda metade deste século. Este objetivo implica atingir a denominada neutralidade carbónica até 2050.
A eficiência energética é um pilar central nas estratégias para alcançar os objetivos estabelecidos no Acordo de Paris, pois contribui diretamente para a redução das emissões de Gases de Efeito de Estufa (GEE), limitando o aumento da temperatura global através da redução do consumo de energia, bem como diminuindo a dependência de combustíveis fósseis. Neste contexto, estabeleceu-se que cada país deverá apresentar as suas próprias metas de redução de emissões, conhecidas como Contribuições Determinadas Nacionalmente (NDC), metas estas que devem ser revistas e reforçadas a cada cinco anos, criando um mecanismo de "ambição crescente". De acordo com
os relatórios do Painel Intergovernamental sobre Mudanças Climáticas (IPCC), as emissões globais de GEE durante a última década (2010-2019) foram maiores do que em qualquer outro período da história humana, atingindo 59 ± 6,6 GtCO2-eq em 2019. Embora a taxa média anual de crescimento das emissões tenha sido mais baixa na última década (1,3 %) em comparação com a década anterior (2,1 % entre 2000-2009), a quantidade total de emissões ainda cresceu consideravelmente, com um aumento médio anual de 9,1 GtCO2-eq em relação à década anterior e continuam ainda a crescer nos setores da indústria, edifícios e transportes, impulsionadas por um aumento na procura global de produtos e serviços.
De facto, o consumo de energia primária (energia obtida diretamente da natureza, incluindo fontes como petróleo, carvão, gás natural e fontes renováveis como solar, eólica, hidroelétrica e biomassa) tem evoluído significativamente, apresentando valores inferiores a 10.000 TWh por ano, no início do século XIX e passando, em apenas cerca de 200 anos, a valores superiores a 160.000 TWh por ano em 2022 – Figura 1.
Quando analisadas as proporções de energia primária de origem fóssil e de origem renovável, verifica-se que a ponderação desta última tem vindo a aumentar de forma significativa nas últimas décadas – Figura 2. Saliente-se que, apenas nestas cerca de duas últimas décadas, o consumo de energia aumentou 46 %! No entanto, talvez ao contrário do que possa ser a perceção mais comum, a proporção de fontes de energia renovável atualmente produzida representa ainda uma fração muito baixa – 17 % do total - relativamente às de origem fóssil – Tabela 1.
Se tivermos em consideração o potencial de energia disponível anualmente nas diferentes fontes de energia – Figura 3, facilmente se percebe a importância da aposta, da necessidade e da imperativa estratégia de investimento em fontes de energia renovável – Figura 3.
Numa análise simples dos dados constantes na Figura 3, facilmente se conclui que:
- A quantidade de energia solar que atinge a terra em 7 horas é mais do que a energia necessária para alimentar o mundo durante um ano;
- A energia eólica disponível num ano daria para alimentar o mundo durante cerca de 4 anos;
- As reservas (soma) das fontes de energia primária de origem fóssil, considerando a potência média anual de consumo de 16 TW, darão para cerca de mais 100 anos, considerando apenas o consumo atual.
Estes valores, por si só, devem justificar e estimular os desenvolvimentos e investimentos a realizar na utilização e transformação de fontes de energia primária de origem renovável, em detrimento, gradual, da utilização de fontes de energia de origem fóssil.
A energia secundária, resultante da transformação da energia primária, é exemplificada principalmente pela eletricidade e combustíveis refinados como gasolina e diesel, além de biocombustíveis como etanol e biodiesel.
O conceito do laser, baseado na teoria da "Amplificação de Luz por Emissão Estimulada de Radiação" proposta por Albert Einstein em 1917, apenas foi concretizado, por Theodore Maiman,
/ / Figura 3. Potencial de fontes de energia primária. (https://www.ucdavis.edu/climate/definitions/how-is-solar-power-generated)
em 1960. Todo este período entre 1917 e 1960 foi marcado por pesquisas significativas, frequentemente financiadas, em alguns casos fortemente financiadas para “alguém andar a brincar com a luz” (como cheguei a ler em textos antigos) por agências governamentais como a DARPA (Defense Advanced Research Projects Agency dos EUA), num contexto de Guerra Fria, sem uma aplicação imediata prevista. Hoje, é inquestionável a utilidade do laser e as evoluções tecnológicas, aos mais diversos níveis, que o mesmo permitiu e permite, desde aplicações da área industrial, passando pela medicina e, até mesmo, lúdicas.
Ainda que apresentados de forma muito resumida, a necessidade e os efeitos de descarbonização, bem como os dados de energia disponível atrás apresentados, deverão justificar, por si só, a necessidade de utilização de energias renováveis, não obstante os desenvolvimentos e respetivos investimentos que isto possa representar.
Quando comparado com o laser, tanto a energia solar quanto a eólica onshore, já passaram por fases semelhantes de incerteza inicial e dependência de incentivos financeiros, estatais ou outros. Hoje representam já formas mais rápidas e viáveis (se não diretamente comparadas apenas pelo correspondente custo do kWh) de energia renovável, com infraestruturas e tecnologias já maduras e amplamente adotadas globalmente. No entanto, o desenvolvimento e a adoção deste tipo de fontes de energia renovável, as mais abundantes, com potencial também tecnologicamente já bastante conhecido de se transformarem numa das fontes de energia secundária por excelência – a eletricidade, requer ainda investimento, ou mesmo apoios, nomeadamente se quisermos ter uma “perspetiva laser” para o que poderão e deverão representar no futuro próximo.
É, mais recentemente, um significativo exemplo desta aposta o conjunto de investimentos e incentivos que têm vindo a ser dados a todos os desenvolvimentos e incentivos à produção e utilização de hidrogénio verde, nomeadamente se produzido através de fontes de energia renovável, que se apresenta como uma das potenciais e mais significativa fonte de energia do futuro próximo. Sem estratégias e apostas de investimento nesta fonte de energia, não estaríamos já no patamar de evolução da sua produção, com o objetivo de que, no futuro próximo, o "custo nivelado de hidrogénio", apesar de ainda longe do custo equivalente de combustíveis de origem fóssil, venha também a tornar-se competitivo e alternativo quando comparado com estes.
As necessidades de mitigar as alterações climáticas, a par com as imposições normativas e legislativas, num mundo cada vez mais consciente da necessidade de sustentabilidade, conforme atrás referido, tornam a gestão eficiente da energia num pilar essencial para a competitividade e sustentabilidade das indústrias. A implementação de Sistemas de Gestão de Energia (SGE), mais ou menos complexos, de acordo com, entre outros, a dimensão e o setor das respetivas empresas, surge como ferramenta estratégica que permite às empresas, não apenas monitorizar e controlar o consumo energético, mas também integrar fontes de energia renovável, aproveitando os incentivos disponibilizados por governos e mesmo organismos internacionais. Na atualidade, a definição da estratégia energética de uma empresa, além dos importantes procedimentos técnicos que devem estar na base da definição desta estratégia, devem também considerar as políticas e estratégias mais abrangentes de descarbonização, que podem ter implicações diretas na colocação dos próprios produtos das empresas no mercado, no seu financiamento e no procurement feito à empresa/seleção de fornecedores. Atente-se, nos últimos anos, ao conceito de ESG (Environmental, Social, and Governance) que ganhou destaque como uma estrutura essencial para a avaliação e gestão da sustentabilidade nas empresas. Apesar de ainda em número reduzido, nomeadamente quando se trata de PME, existem já exemplos de sucesso pela implementação de Sistemas de Gestão de Energia baseados na norma ISO 50001 – incluindo empresas da área dos moldes e dos plásticos da região de Leiria. Através da monitorização em tempo real e da otimização dos processos de produção, estão a conseguir reduzir o consumo energético e as respetivas taxas de emissão de carbono nos últimos dois anos.
INDUSTRIAIS – “O CAMINHO FAZ-SE CAMINHANDO”
A otimização de energia nos processos industriais envolve a análise detalhada das operações para identificar ineficiências e implementar melhorias que reduzam o consumo energético sem comprometer a produtividade ou a qualidade.
A implementação de sistemas de gestão de energia nas empresas deverá envolver e/ou aprofundar a realização dos seguintes passos:
• Monitorizar em tempo real: acompanhar o consumo de energia em todas as etapas do processo de produção, identificando picos de consumo e áreas de desperdício;
• Análise preditiva: utilizar dados históricos e modelos preditivos para antecipar necessidades energéticas futuras, ajustando os processos de forma proativa;
• Automatização de processos: integrar sistemas automatizados que ajustem parâmetros operacionais para otimizar o uso de energia, como temperaturas, tempos de ciclo de produção, entre outros;
• Manutenção preventiva: identificar e corrigir falhas nos equipamentos que podem levar a um aumento do consumo energético, antes que se tornem problemas graves;
• Relatórios e compliance: gerar relatórios detalhados que facilitam a conformidade com as regulamentações ambientais e a comunicação dos esforços de sustentabilidade aos stakeholders.
O Gabinete Europeu para a Investigação sobre Transformação Industrial e Emissões publicou um conjunto de documentos que abordam a melhoria da eficiência energética em instalações industriais, fornecendo orientações genéricas sobre como abordar, avaliar, implementar e lidar com questões relacionadas com a eficiência energética, juntamente com os correspondentes procedimentos de licenciamento e supervisão (https://eippcb.jrc.ec.europa.eu/index.php/reference/energyefficiency).
Empresas que implementam estes sistemas, não apenas melhoram a sua eficiência energética, mas também fortalecem a sua posição no mercado global, onde a sustentabilidade é cada vez mais valorizada pelos clientes e parceiros de negócios.
Além disso, o apoio governamental e os incentivos para a modernização industrial e a adoção de tecnologias verdes facilitam a transição para sistemas de gestão e otimização de energia. Investir em gestão de energia pode resultar numa redução substancial dos custos energéticos, aumento da competitividade e cumprimento das metas de descarbonização, contribuindo para um futuro mais sustentável.
Desenvolver e implementar uma estratégia de gestão de energia nas empresas é, hoje, também um requisito fundamental para o sucesso. A gestão eficiente da energia é uma componente vital para a sustentabilidade e competitividade das indústrias contemporâneas. Os Sistemas de Gestão de Energia (SGE) oferecem uma abordagem estruturada para monitorizar, analisar e otimizar o consumo energético, enquanto facilitam a integração de fontes de energia renovável. A nossa experiência de estudo e implementação prática de SGE em empresas de diversos setores, resultante de análise técnica e estratégica realizada com as empresas, revela que a adoção de SGE, aliada com a vigilância dos incentivos disponíveis para energias renováveis, pode transformar a maneira como as indústrias operam, promovendo a eficiência, reduzindo custos e contribuindo para a descarbonização. O compromisso com a sustentabilidade não é, nem deve ser, apenas uma 'marca ideológica', de panfleto ou publicidade. As empresas bem posicionadas para liderar esta transição perceberão que a eficiência energética e a utilização de energias renováveis são, não apenas viáveis, mas também estratégicas para o sucesso a médio e longo prazo.
Carolina Neves * * Inovação Empresarial – CENTIMFE
ESG é a sigla de Environmental, Social e Governance (Ambiental, Social e Governança), e refere-se a um conjunto de critérios utilizados para avaliar a sustentabilidade e o impacto ético de uma empresa ou de um negócio. Estes critérios são divididos em três categorias principais: impacto ambiental, responsabilidade social e práticas de governança.
A adoção do ESG tem vindo a crescer de forma significativa, impulsionada pela necessidade de equilibrar os retornos financeiros com os impactos ambientais e sociais das atividades empresariais.
O conceito de ESG emergiu no início dos anos 2000 como a evolução das práticas de responsabilidade social corporativa, ganhando destaque com a publicação dos Princípios para o Investimento Responsável (PRI) pela ONU, em 2006. Estes princípios incentivaram investidores a integrarem fatores ambientais, sociais e de governança nas suas decisões de investimento, destacando a importância de práticas empresariais sustentáveis.
A partir de 2015, com a adoção dos Objetivos de Desenvolvimento Sustentável (ODS) e o Acordo de Paris sobre as alterações climáticas, o ESG tornou-se central na estratégia das empresas e nos critérios de investimento. Regulamentações como a Diretiva de Relato Não Financeiro (2014/95/UE) da União Europeia, que entrou em vigor em 2018, começaram a exigir que grandes empresas divulgassem informações sobre o modelo de monitorização e gestão dos impactos ambientais, sociais e de governança.
Nos últimos anos, as diretivas ESG têm sido reforçadas, especialmente com a proposta da nova Diretiva de Relato de Sustentabilidade Corporativa (CSRD) da UE, que entrou em vigor no início deste ano. Esta normativa europeia desencadeou o aumento da valorização por investidores e financiadores, que atualmente procuram empresas comprometidas com a sustentabilidade e a responsabilidade social. Esta
procura desencadeou o aumento das exigências do relato de sustentabilidade e ESG, tornando-os mais detalhados e acessíveis a um leque mais vasto de empresas, passando a ser um fator decisivo para o crescimento, inovação e competitividade das empresas.
Ultimamente, a indústria de moldes e plásticos tem-se mostrado cada vez mais consciente da importância de integrar a sustentabilidade nos seus modelos de negócio. Esta integração é essencial não só para responder às exigências de um mercado cada vez mais orientado para a sustentabilidade, mas também para garantir a viabilidade a longo prazo das empresas do sector.
E BENEFÍCIOS DA IMPLEMENTAÇÃO DE ESG NA INDÚSTRIA DE MOLDES E PLÁSTICOS
Para implementar o ESG de forma eficaz é essencial começar por capacitar uma equipa responsável, permitindo a tomada de decisões informadas e responsáveis. Em seguida, deve-se identificar e avaliar os impactos mais relevantes na empresa, evidenciando a dupla materialidade, que considera tanto os efeitos financeiros como os impactos ambientais e sociais. Este estudo é crucial, pois fortalece a transparência e a confiança com os stakeholders, além de promover a resiliência e competitividade da empresa a longo prazo.
Após isso, é necessário estabelecer metas ESG ambiciosas, mensuráveis e alinhadas com a estratégia empresarial. A transparência é fundamental, e o relatório de sustentabilidade deve divulgar os resultados e impactos das atividades da empresa, permitindo a comparação com metas anteriores e a definição de novos objetivos. Divulgar os resultados de forma clara e padronizada melhora a competitividade e atrai investidores.
A implementação de princípios ESG traz diversas oportunidades para o sector dos moldes e plásticos. Por exemplo, a adoção de práticas mais sustentáveis pode resultar numa redução significativa de custos através da otimização de recursos e melhoria da eficiência operacional. Além disso, a busca por soluções mais sustentáveis pode impulsionar a inovação, especialmente na utilização de novos materiais recicláveis ou biodegradáveis, na adoção de processos de lean manufacturing e no desenvolvimento de novos produtos e soluções.
O ESG não beneficia apenas as empresas, mas também os stakeholders e a sociedade em geral. Práticas que minimizam o impacto ambiental, como a redução da poluição e o uso eficiente de recursos, permitem que as empresas operem de forma mais sustentável. Paralelamente, ao promover a responsabilidade social e a boa governança, as empresas melhoram a sua reputação, tornando-se mais atrativas para investidores que valorizam a segurança e a responsabilidade a longo prazo.
A adoção de práticas ESG é particularmente relevante na indústria de moldes e plásticos, tradicionalmente associada a impactos ambientais negativos. A crescente pressão para reduzir as emissões de carbono e o desperdício está a levar a mudanças significativas no sector. Empresas que implementam práticas ecológicas, como o uso de materiais reciclados e a inovação tecnológica, não só contribuem para um ambiente mais limpo, como também se destacam num mercado cada vez mais voltado para a sustentabilidade.
No campo social, a indústria está a focar-se na melhoria das condições de trabalho e na promoção da igualdade e inclusão. Estas iniciativas beneficiam não só os colaboradores, mas também reforçam a responsabilidade social das empresas perante as comunidades onde operam.
Em termos de governança, a transparência e o cumprimento das normas são fundamentais para garantir a confiança dos investidores e do público. Empresas que implementam boas práticas de governança tendem a ser mais resilientes e adaptáveis às mudanças regulatórias e de mercado.
RELATÓRIOS DE SUSTENTABILIDADE E APOIO À IMPLEMENTAÇÃO DE PRÁTICAS ESG
Os relatórios de sustentabilidade são instrumentos essenciais para a comunicação das práticas ESG. Estes relatórios permitem que as empresas divulguem de forma detalhada o seu desempenho em relação aos três pilares do ESG, fornecendo informações cruciais para investidores, clientes, reguladores e
outros stakeholders. A utilização de frameworks como o ESRS, GRI, SASB ou TCFD ajuda a estruturar estes relatórios de forma padronizada e comparável, facilitando a avaliação do compromisso das empresas com práticas sustentáveis e contribuindo para um desenvolvimento económico mais equilibrado e justo.
A integração de ESG nos relatórios de sustentabilidade é, portanto, essencial para a transparência corporativa e para uma tomada de decisões informada por parte dos diversos stakeholders.
O futuro do ESG na indústria de moldes e plásticos é promissor, mas também apresenta desafios significativos. As empresas que adotarem estas práticas de forma célere estarão mais bem preparadas para prosperar num ambiente cada vez mais competitivo e consciente. Embora os investimentos e mudanças necessárias possam ser desafiantes, os benefícios a longo prazo para o planeta e a sociedade são inegáveis, tornando o ESG uma estratégia essencial para o sucesso futuro. A adoção de práticas ESG representa uma oportunidade única para as empresas do sector de moldes e plásticos se posicionarem na vanguarda da sustentabilidade, garantindo não só o seu crescimento, mas também contribuindo para um futuro mais equilibrado e justo para todos.
O CENTIMFE tem uma equipa ao dispor do sector para a implementação de práticas ESG e apoio à elaboração dos relatórios de sustentabilidade, de acordo com as diferentes normativas de referência. Procura-se, assim, não apenas garantir que as empresas cumpram os requisitos ESG, mas também melhorar a sua sustentabilidade e competitividade no mercado.
Inicie o caminho para a sustentabilidade, com o nosso apoio, contacte-nos: inovação@centimfe.com
• Eccles, R. G., Ioannou, I., & Serafeim, G. (2014). The Impact of Corporate Sustainability on Organizational Processes and Performance. Management Science, 60(11), 2835-2857.
• United Nations. (2006). Principles for Responsible Investment. Disponível em: https://www.unpri.org/
• União Europeia. (2014). Diretiva 2014/95/UE do Parlamento Europeu e do Conselho. Jornal Oficial da União Europeia.
• União Europeia. (2021). Proposal for a Corporate Sustainability Reporting Directive (CSRD). Disponível em: https://ec.europa.eu/
Tânia Mendes * * Inovação Empresarial (CENTIMFE)
O projeto CIRCVET - Materiais de formação prática em economia circular para as indústrias transformadoras de plásticos, um projeto Erasmus+ financiado pela Comissão Europeia, é uma iniciativa internacional centrada na promoção de práticas de economia circular (EC) na indústria de plásticos europeia.
O projeto é composto por 12 parceiros de toda a Europa. De Espanha, AIJU (Instituto Tecnológico de Producto Infantil y Ocio, Coordenador) e Universidad de las Palmas de Gran Canaria; da Lituânia, LINPRA Cluster (Lietuvos inzinerines pramones asociacija), VPM (Visagino technologijos ir verslo profesinio mokymo centras) e Aprc (Alytaus profesinio rengimo centras); da Alemanha, Kunststoff Institut Ludenscheid; de França, Polymeris and Infinitivity Design Lab; de Itália, Università di Trento, HIT (Fondazione Hub Innovazione Trentino) e Proplast Cluster; e de Portugal o CENTIMFE (Centro Tecnológico da Indústria de Moldes Ferramentas Especiais e Plásticos)
O projeto CIRCVET combina todas as competências e conhecimentos necessários para implementar o projeto e obter os melhores resultados:
- 5 parceiros (AIJU, CENTIMFE, PROPLAST, POLYMERIS, LINPRA) representam as PME do sector e 2 deles são também centros de investigação (CENTIMFE, PROPLAST) que apoiam simultaneamente a inovação;
- 5 parceiros (KIMW-Q, ULPGC, UNITRENTO, APRC, VPM) representam o setor da educação e formação, quer como universidades, quer como centros de formação profissional;
- 1 parceiro (IDL) tem as competências técnicas, conhecimentos e experiência para conceber e implementar os recursos TIC;
- 1 parceiro (HIT) representa a inovação nos modelos de negócio e o empreendedorismo, aspetos fundamentais para a transição para um modelo de economia circular.
O projeto já reuniu o interesse de um conjunto de entidades que estão dispostas a participar nas atividades e a implementar as formações desenvolvidas: Cluster MESAP, Cluster ATIM, Cassa Edile di Mutualità e Assistenza Interprovinciale del Veneto e Mancomunidad del Norte de Gran Canaria.
Os objetivos do projeto são:
• Desenvolver o programa de formação mais abrangente, gratuito e personalizado sobre economia circular na Europa, na área dos plásticos;
• Dar resposta às necessidades e desafios específicos enfrentados pelas empresas do setor dos plásticos;
• Promover a colaboração entre os vários stakeholders, incluindo universidades, centros de formação profissional, instituições de investigação, clusters e PME;
• Formar indivíduos com as competências «verdes» necessárias para contribuírem para uma sociedade mais sustentável e eficiente em termos de recursos.
Aspetos principais:
• Foco em formação prática adaptada às necessidades reais da indústria;
• Aliança entre stakeholders com experiência em diferentes áreas;
• Ênfase no desenvolvimento de competências "verdes" essenciais para um futuro sustentável.
ABORDADOS NO PROGRAMA DE FORMAÇÃO?
• Economia circular geral
• Conceção ecológica e avaliação do ciclo de vida (ACV)
• Competências digitais
• Reciclagem, Upcycling e Downcycling
• Processos de fabrico
• Utilizador e utilização
• Recuperação
• Empreendedorismo
Curso de Formação:
• Abordagem: Formação personalizada com base na avaliação das necessidades individuais;
• Etapas:
1. Definição personalizada do curso: foi criado um curso personalizado, combinando informação relevante e módulos de formação;
2. Entrega do curso: cada módulo é entregue como um MOOC (Massive Open Online Course), e o progresso do candidato é avaliado;
3. Variedade de formatos: uso de um mix de texto, imagens, vídeos, questionários e elementos interativos para envolver os alunos;
4. Interativo: incorpora atividades e avaliações para manter os alunos envolvidos e testar a sua compreensão;
5. Apoio multilingue: uma vez que o público-alvo será diversificado, os conteúdos são disponibilizados em várias línguas (além do inglês, todas as línguas dos parceiros: espanhol, português, francês, italiano, alemão e lituano);
6. Acompanhamento do progresso: permite aos utilizadores acompanhar o seu progresso e conclusão de diferentes módulos;
7. Construção de comunidades: inclui recursos como fóruns e painéis de discussão para promover a interação e o apoio aos alunos;
8. Certificação: os participantes que concluírem com sucesso cada módulo, recebem um certificado oficial e reconhecido.
2. COMO SE CANDIDATAR AO CURSO?
O curso de formação já foi testado por estudantes e trabalhadores de empresas, para avaliar as diferentes versões criadas para os diferentes grupos-alvo. Os níveis do curso de formação são o I-VET – VET (ensino e formação profissional), o I-VET-HE
(estudantes universitários) e o C-VET (formação profissional contínua para trabalhadores ativos).
Desenvolvendo um novo método de ensino e novas ferramentas de aprendizagem (MOOC), com materiais de formação e recursos de sala de aula. Estas ferramentas estarão disponíveis para professores e formadores ministrarem a formação de forma eficaz e implementarem um sistema de microcredenciais para reconhecer os conhecimentos e competências adquiridos.
A plataforma de e-learning, desenvolvida durante o projeto, oferece uma aprendizagem interativa e uma construção de comunidade entre profissionais e estudantes. Todo o material desenhado durante o projeto estará disponível para qualquer pessoa registada na plataforma a qualquer momento.
Por esta razão, a plataforma de e-learning oferece possibilidades de aprendizagem síncrona e assíncrona:
• Síncrono: inclui recursos como webinars, chats ao vivo e videoconferências para interação e discussão em tempo real;
• Assíncrono: oferece palestras pré-gravadas, materiais para download, fóruns de discussão e atividades individualizadas para uma aprendizagem flexível.
De um modo geral, o projeto CIRCVET tem potencial para melhorar significativamente as competências e o conhecimento dos profissionais da indústria dos plásticos, contribuindo para a sua inovação, resiliência e competitividade.
Os parceiros do CIRCVET pretendem envolver os stakeholders em todas as atividades do projeto seguindo as próximas etapas:
1) obtenção de interação e envolvimento de alguns atores-chave nos territórios dos parceiros envolvidos;
2) alargamento da rede de modo a incorporar intervenienteschave exteriores ao consórcio. Para chegar a esta rede, foram organizadas atividades específicas como questionários a empresas e alunos, boletins informativos de comunicação e divulgação, foram preparadas ações de disseminação e os parceiros participaram em eventos de promoção do projeto;
3) serão organizados workshops nos países e regiões participantes, com a colaboração e o apoio dos parceiros associados, para apresentar e demonstrar as atividades e os resultados do CIRCVET.
4) foram organizados workshops de pilotagem, ao nível dos parceiros, para discutir e analisar os materiais e recursos de formação, incluindo o curso, a sua viabilidade, aplicabilidade e replicabilidade nos seus próprios territórios e não só.
O projeto tem a duração de 36 meses e está agora a meio. No início do próximo ano terá início uma fase de validação dos conteúdos completos e definidos.
Ana Pires *
* Coordenadora da área de I&D (CENTIMFE)
A descarbonização é uma das principais estratégias globais para mitigar as mudanças climáticas, com o objetivo de reduzir as emissões de gases de efeito estufa (GEE) e, eventualmente, alcançar a neutralidade carbónica. A pressão sobre as empresas para se alinharem com as metas de descarbonização tem aumentado significativamente, resultando em maior ênfase na medição, divulgação, definição de metas, estratégias e ações relacionadas com a sustentabilidade e a redução de emissões.
Nesta era climática, o reporte das emissões de carbono realizado pelas empresas deve ser o mais rigoroso possível. Nos últimos anos tem ocorrido uma explosão de iniciativas que pretendem impulsionar a quantificação, o reporte e a definição de metas.
No que concerne à quantificação, é globalmente seguido o Greenhouse Gas Protocol (GHG Protocol). Esta norma fornece uma estrutura abrangente para quantificar emissões ao longo da cadeia de valor, divididas em três âmbitos (scope 1, 2 e 3). Este protocolo é essencial para que as empresas compreendam e contabilizem as suas emissões, permitindo-lhes definir estratégias eficazes de descarbonização.
REPORTE
Para reportar as emissões de carbono existem diversas plataformas que permitem divulgar as suas emissões de GEE, incluindo ainda outros pilares da sustentabilidade ambiental e social. Aqui são abordadas algumas plataformas de reporte.
A plataforma Global Reporting Initiative (GRI) é uma ferramenta que oferece um conjunto de normas que as empresas podem seguir para elaborar relatórios de sustentabilidade abrangentes e comparáveis. Estas normas cobrem diversos temas, incluindo emissões de carbono, gestão de resíduos, direitos humanos, práticas laborais, anticorrupção, entre outros. Ao adotar as normas do GRI, as empresas podem medir e gerir os seus impactos, bem como comunicar as suas ações e resultados para os seus stakeholders, incluindo investidores, clientes, reguladores e a sociedade em geral.
O CDP (anteriormente designado por Carbon Disclosure Project) é uma plataforma global de divulgação ambiental que permite às empresas medir e divulgar as suas emissões de GEE, bem como os seus impactos ambientais, riscos e oportunidades associados às alterações climáticas. A participação no CDP é voluntária, mas tem ganho uma importância crescente à medida que investidores, clientes e reguladores exigem maior transparência sobre as práticas ambientais das empresas. As informações divulgadas ao CDP são utilizadas para avaliar o desempenho ambiental das empresas e incentivar melhorias contínuas.
Outras iniciativas têm surgido mais recentemente, a nível nacional, como é o caso da SIBS ESG. Esta é uma plataforma direcionada para as práticas ambientais, sociais e de governança das empresas (ESG), onde estão diversos indicadores ambientais, incluindo os relacionados com as emissões de GEE. A plataforma SIBS ESG é uma solução digital desenvolvida pela SIBS, uma das principais empresas de serviços financeiros em Portugal, focada em oferecer às empresas e instituições ferramentas para a gestão e monitorização de práticas ESG. Esta plataforma permite que as organizações acompanhem o seu desempenho em termos de sustentabilidade, assegurando que as suas operações estejam alinhadas com os critérios ESG, que são cada vez mais valorizados por investidores, clientes e reguladores.
As empresas devem definir as suas metas de descarbonização com o máximo rigor, para que consigam contribuir de modo eficaz para a redução dos GEE na atmosfera. Para tal, surgiu a iniciativa Science Based Targets initiative (SBTi), que ajuda as empresas a definirem metas de redução de emissões de GEE baseadas na ciência climática, assegurando que estão alinhadas com os objetivos do Acordo de Paris, ou seja, limitar o aquecimento global a bem abaixo de 2°C e, preferencialmente, a 1,5°C. As metas definidas através da SBTi são verificadas e validadas pela iniciativa, proporcionando confiança aos stakeholders sobre o compromisso da empresa com a descarbonização.
A obrigação de quantificar pode não ser ainda uma realidade para todos os sectores, tipologias e dimensões das empresas. No entanto, começar este processo levará a uma transformação dentro das empresas, para que consigam manter-se atualizadas e capazes de responder às exigências do mercado. A formação é, sem dúvida, uma das ferramentas disponíveis para tal. O projeto Low Carbon, desenvolvido entre o Centimfe e a Cefamol e financiado pelo Plano de Recuperação e Resiliência (PRR), pretende desenvolver competências junto da indústria de moldes sobre o tema da descarbonização. Mais informações podem ser consultadas em lowcarbon.centimfe.com.
INDÚSTRIA 5.0: INTEGRAÇÃO HUMANA E TECNOLÓGICA EM PROL DA SUSTENTABILIDADE
MOLDAR O FUTURO: A LIDERANÇA INVISÍVEL
Carolina Feliciana Machado *, J. Paulo Davim **
* Professora Associada com Agregação - Escola de Economia e Gestão Universidade do Minho
** Professor Catedrático - Departamento de Engenharia Mecânica - Universidade de Aveiro
INTRODUÇÃO
A Indústria 5.0 surge como uma evolução natural da Indústria 4.0, indo muito além da automação e conetividade, para enfatizar a colaboração entre Homens e máquinas inteligentes. Enquanto a Indústria 4.0 trouxe a digitalização e a interconetividade através da Internet das Coisas (IoT), Big Data e inteligência artificial (IA), a Indústria 5.0 procura harmonizar a relação entre os trabalhadores e os robôs, promovendo um ambiente de trabalho onde a criatividade humana e a precisão das máquinas se complementam. Tendo presente a relevância que esta problemática assume na atualidade, o presente artigo de opinião procura, de um modo breve, reforçar o papel e a crescente interação que se faz sentir entre as três vertentes de suporte à indústria 5.0, como é o caso das pessoas, tecnologia e sustentabilidade.
Na Indústria 5.0, as pessoas assumem um papel central, onde a sinergia entre os seres humanos e as máquinas inteligentes é fundamental para o sucesso. As máquinas não substituem os trabalhadores, mas trabalham ao lado deles. A humanização do trabalho assume-se assim como um dos pilares da Indústria 5.0. Diferente da Indústria 4.0, que se focava predominantemente na automação, a Indústria 5.0 valoriza a colaboração entre os trabalhadores e robôs colaborativos, conhecidos como "cobots". Esses cobots são projetados para trabalhar ao lado dos trabalhadores, adaptando-se às suas necessidades e complementando as suas capacidades com precisão e eficiência. A criatividade, o pensamento crítico e a capacidade de resolução de problemas dos seres humanos são potencializadas pela IA e outras tecnologias avançadas, criando um ambiente de trabalho mais inovador e produtivo.
Além disso, a humanização do trabalho é uma prioridade, promovendo ambientes ergonómicos e seguros, que reduzem a fadiga e melhoram o bem-estar e a satisfação dos trabalhadores. A utilização de tecnologias vestíveis (wearables) para monitorizar a saúde e ajustar as condições de trabalho conforme necessário é um exemplo claro de como a Indústria 5.0 coloca as pessoas no centro do processo produtivo, garantindo não apenas a eficiência, mas também a qualidade de vida dos trabalhadores.
Na Indústria 5.0, as tecnologias desempenham um papel crucial ao facilitar a colaboração entre os seres humanos e as máquinas e ao impulsionar a eficiência e a inovação nos processos industriais. A integração de tecnologias avançadas como a inteligência artificial, robótica colaborativa, realidade aumentada (AR) e realidade virtual (VR) permite que os robôs não executem apenas tarefas repetitivas, mas também trabalhem em estreita colaboração com os seres humanos, adaptando-se às suas necessidades. A Internet das Coisas (IoT) continua a ser vital, interligando dispositivos e sistemas para recolher e analisar dados em tempo real, o que otimiza a tomada de decisões e melhora a manutenção preditiva. O Big Data, aliado à análise preditiva, possibilita a previsão de falhas e a maximização da eficiência operacional. Além disso, a AR e a VR são utilizadas para formação avançada e simulações precisas, preparando os trabalhadores para situações reais com maior eficácia. Assim, as tecnologias na Indústria 5.0 não só aumentam a produtividade, como também criam um ambiente de trabalho mais seguro, dinâmico e inovador.
A sustentabilidade é um pilar fundamental na Indústria 5.0, em que a inovação tecnológica é direcionada para práticas industriais mais ecológicas e responsáveis. A adoção de uma economia circular é central, promovendo a reutilização, reciclagem e redução de resíduos em todos os processos produtivos, minimizando o impacto ambiental. As tecnologias avançadas permitem rastrear materiais e produtos ao longo de seu ciclo de vida, garantindo transparência e responsabilidade ambiental. A eficiência energética é outra prioridade, com a integração de fontes de energia renovável, como a energia solar e a eólica, e o uso de sistemas inteligentes para monitorizar e otimizar o consumo de energia, reduzindo a pegada de carbono das operações industriais. Painéis solares, turbinas eólicas e outras tecnologias renováveis são integradas nas operações industriais para garantirem uma produção mais limpa e sustentável. Além disso, a pesquisa e desenvolvimento de materiais sustentáveis, através da biotecnologia e da nanotecnologia, resultam em produtos mais duradouros, mais eficientes e menos prejudiciais ao meio ambiente, assentes em processos de produção mais ecológicos. Daqui resulta que a Indústria 5.0 não procura apenas avanços tecnológicos, mas também se compromete com a criação de um futuro mais sustentável e equilibrado.
Conscientes da relevância que as problemáticas da Indústria 5.0 (com particular enfoque nas pessoas) e da atualização constante dos conhecimentos / competências, assumem na atualidade, os autores do presente artigo dinamizaram a
organização e publicação (entre outros) do livro Indústria 5.0: Pessoas, Tecnologia e Sustentabilidade, publicado pela Actual Editora com a chancela do grupo Almedina, o qual conta com um amplo conjunto de contributos proporcionados por diferentes professores / investigadores portugueses.
/ / Machado, C. e Davim, J. P. (Coords.) (2023). Indústria 5.0: Pessoas, Tecnologia e Sustentabilidade. Actual Editora / Grupo Almedina: Coimbra https://www.almedina.net/industria-50-pessoas-tecnologia-esustentabilidade-1696042898.html
Paralelamente a este livro, e também sob a chancela da mesma Editora, os autores deste artigo de opinião publicaram o livro Resiliência e Inteligência Emocional, o qual, perspetivando o paradigma de disrupção que a indústria 5.0 tem vindo a impulsionar na atualidade, aborda a problemática da Resiliência. Também considerada como um dos pilares fundamentais da Indústria 5.0, a Resiliência, tal como referido no prefácio deste livro, “(…) respeita à capacidade dos indivíduos lidarem com os problemas, adaptarem-se à mudança, ultrapassar obstáculos e/ ou resistir à pressão resultantes das mais diversas situações, ao mesmo tempo que procuram superar as adversidades.”
/ / Machado, C. e Davim, J. P. (Coords.) (2019). Resiliência e Inteligência Emocional. Actual Editora / Grupo Almedina: Coimbra https://www.almedina.net/resili-ncia-e-intelig-ncia-emocional-1564521487. html
Orientados para uma pluralidade de públicos – gestores, engenheiros, académicos, investigadores, bem como outros profissionais e público em geral -, com interesse nestas matérias, estes livros procuram dar um enfoque muito particular para a dinâmica subjacente à Indústria 5.0 na qual as pessoas e as máquinas interagem positivamente a fim de alcançarem um mundo mais resiliente e sustentável.
A Indústria 5.0 representa um novo paradigma na produção industrial, onde a tecnologia não apenas complementa, mas também enriquece o papel humano. A colaboração entre os seres humanos e as máquinas, impulsionada por tecnologias avançadas, cria um ambiente de trabalho mais seguro, eficiente e criativo. Ao mesmo tempo, a ênfase na sustentabilidade garante que o progresso industrial não se obtenha às custas do planeta. De todo o exposto resulta que a Indústria 5.0 não consiste, apenas, numa evolução tecnológica, mas, mais do que isso, num compromisso com um futuro mais resiliente, sustentável e humano.
1 - Machado, C. F. e Davim, J. P. (2024). Indústria 5.0: Uma Abordagem Centrada nas Pessoas. Revista Kéramica, maio/junho, pp. 4-6.
2 - Machado, C. F. e Davim, J. P. (2024). Indústria 5.0 – Pessoas, Tecnologia e Sustentabilidade. INGENIUM, II Série, Nº 184, abril/maio/junho 2024, pp. 44-46.
3 - Machado, C. e Davim, J. P. (Coords.) (2023). Indústria 5.0: Pessoas, Tecnologia e Sustentabilidade. Actual Editora / Grupo Almedina: Coimbra.
4 - Machado, C. e Davim, J. P. (Coords.) (2023). MBA para Gestores e Engenheiros. (2ª Edição, atualizada e alargada). Editora Sílabo: Lisboa.
5 - Machado, C. and Davim, J. P. (Eds.) (2023). Industry 5.0: Creative and Innovative Organizations. Springer: London, UK.
6 - Machado, C. and Davim, J. P. (Eds.) (2023). Management for Digital Transformation. Springer: Heidelberg, Germany.
7 - Machado, C. and Davim, J. P. (Eds.) (2023). Managerial Challenges of Industry 4.0. EDP Sciences: Les Ulis, France.
8 - Machado, C. and Davim, J. P. (Eds.) (2020). Industry 4.0: Challenges, Trends, and Solutions in Management and Engineering, Taylor and Francis Group/CRC Press: Boca Raton, USA.
9 - Machado, C. e Davim, J. P. (Coords.) (2019). Resiliência e Inteligência Emocional. Actual Editora / Grupo Almedina: Coimbra.
10 - Machado, C. e Davim, J. Paulo (Coords.) (2019). Organização e Políticas Empresariais. Actual Editora / Grupo Almedina: Coimbra.
Artur Ferraz *
* Consultor Internacional de Gestão de Pessoas
Setembro é um mês peculiar. É como se o ano tivesse uma pausa para refletir e nos convidasse a fazer o mesmo. Depois de um verão (ou do que tentámos que fosse um), voltamos ao trabalho, às rotinas, e àquele velho conhecido chamado “recomeço”. Setembro marca o início de uma nova fase, com projetos por desbravar e máquinas a roncar novamente. As chefias intermédias, tantas vezes esquecidas nas prioridades das organizações, voltam a moldar, bem ou mal, o futuro das empresas. A forma como vão atuar, as rotinas de trabalho que já desenvolvem vão ser novamente empregadas. Serão as melhores?
Vamos a um cenário comum. Uma empresa começa o mês de setembro com o pé no acelerador, pronta para correr em direção às metas do final do ano. Há pressa. As palavras de ordem são eficiência e entrega rápida. As equipas sentem o peso e os líderes intermédios, que muitas vezes não têm palco nem para uma breve apresentação, ficam encarregues de guiar o barco em águas turbulentas. A liderança intermédia, tão vital para a sustentação das operações diárias, torna-se o amortecedor entre a pressão dos resultados de curto prazo e a necessidade de dar espaço ao desenvolvimento contínuo das suas equipas. Esse amortecedor por vezes não atua da melhor forma, quando não desenvolvido ele próprio promove entropias desnecessárias.
E é aqui que entramos numa encruzilhada. Enquanto muitos gestores estão focados em atingir os números trimestrais, as abordagens de curto prazo ditam a vida nas empresas. Mas quem é que está a agir diariamente com os operacionais da empresa? É fácil esquecer que as lideranças intermédias são quem realmente promove ação, ou, em muitos casos, gera uma inércia terrível nas equipas. Portanto a chefia intermédia pode fazer com que as coisas aconteçam, ou, quando não tem as competências certas, pode ser o agente que não permite que as coisas progridam. Não é nada fácil perceber estes cenários sem sair do gabinete e perceber as dinâmicas internas de trabalho entre as pessoas. Quando a segunda situação é a realidade, precisamos de perceber que ações de curto prazo não resolvem os problemas, antes os alimentam e muitas vezes agravam.
E aqui está o problema: num ambiente onde as competências técnicas são cruciais e a precisão do trabalho é fundamental, há uma ironia gritante no facto de não aplicarmos a mesma lógica ao desenvolvimento das nossas pessoas. Se numa peça o erro de um milímetro pode ser fatal, o que dizer de uma liderança intermédia desajustada, incapaz de ouvir e de liderar com clareza? O erro pode não ser visível de imediato, mas quando o impacto se faz sentir, é como se estivéssemos a tentar enfiar uma peça quadrada num buraco redondo.
Os líderes intermédios precisam de tempo para se desenvolver, para afinar as suas competências, e para aprender a ouvir e perceber o meio onde estão – tanto as suas equipas como a estratégia da empresa. Não é apenas uma questão de produtividade, é uma questão de sustentabilidade a longo prazo. O desenvolvimento
contínuo destes líderes é o motor de inovação e estabilidade dentro das organizações. São eles que mantêm as equipas motivadas, que resolvem problemas com criatividade e que, no fim de contas, asseguram que a empresa não só responde às necessidades imediatas, mas que está preparada para o futuro.
Mas há algo que muitas vezes falta: a escuta ativa. Na correria para responder às metas de curto prazo, esquecemos a necessidade de ouvir. E quando não ouvimos, perdemos a oportunidade de compreender o que realmente se passa nas nossas operações. Um bom líder, é feito de detalhes. E tal como na criação de moldes, em que um pequeno ajuste pode melhorar todo o processo, na liderança o simples ato de ouvir pode ser o que transforma uma equipa média numa equipa de excelência.
Ouvir é o ponto de partida para qualquer tipo de desenvolvimento. Tal como Peter Senge recorda em "A Quinta Disciplina", as organizações que aprendem são aquelas que têm a capacidade de escutar, refletir e adaptar-se. E isto começa nas lideranças intermédias, que não só têm de gerir o presente, mas também de preparar as suas equipas para os desafios futuros. Se ignoramos essa necessidade, estamos apenas a alimentar uma mentalidade de curto prazo, em que o foco está em sobreviver à próxima meta, em vez de construir algo duradouro.
Afinal, o que seria da indústria se aplicássemos essa lógica de curto prazo ao fabrico de moldes? Se apenas procurássemos resultados rápidos, sem pensar nas implicações a longo prazo, as peças seriam frágeis, ineficazes, e a reputação desmoronaria tão rapidamente quanto a produção. O mesmo acontece com a liderança. Se não investimos no desenvolvimento contínuo dos nossos líderes, corremos o risco de criar equipas frágeis e desmotivadas, incapazes de enfrentar os desafios que o presente já nos está a colocar. Neste contexto de transições globais, a clareza com as pessoas promove um ambiente de tranquilidade, fundamental para os profissionais pensarem criativamente em soluções para a complexidade atual.
Então, enquanto recomeçamos, é tempo de refletir sobre como estamos a moldar o futuro das nossas equipas. Estamos a dar espaço para o crescimento e desenvolvimento dos nossos líderes intermédios? Estamos a ouvir as suas necessidades e a fornecer as ferramentas para que possam guiar as suas equipas com segurança e visão no longo prazo? Ou estamos apenas a correr atrás dos números, que sendo importantes, naturalmente, não podem ser os únicos elementos a ter em conta. Não podemos ignorar o impacto da liderança nas bases da empresa.
Tal como num bom molde, a liderança de sucesso é feita de ajustes contínuos, de precisão e de paciência. E assim como aprendemos a afinar as nossas máquinas e processos para criar as melhores peças, também devemos afinar as nossas lideranças, os tais elementos invisíveis, para moldar um futuro mais sólido e sustentável. Setembro pode ser o mês de recomeços, mas que seja também o mês em que ouvimos mais, investimos melhor e lideramos com a visão de quem sabe que o verdadeiro sucesso não se mede apenas no imediato.