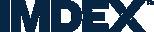
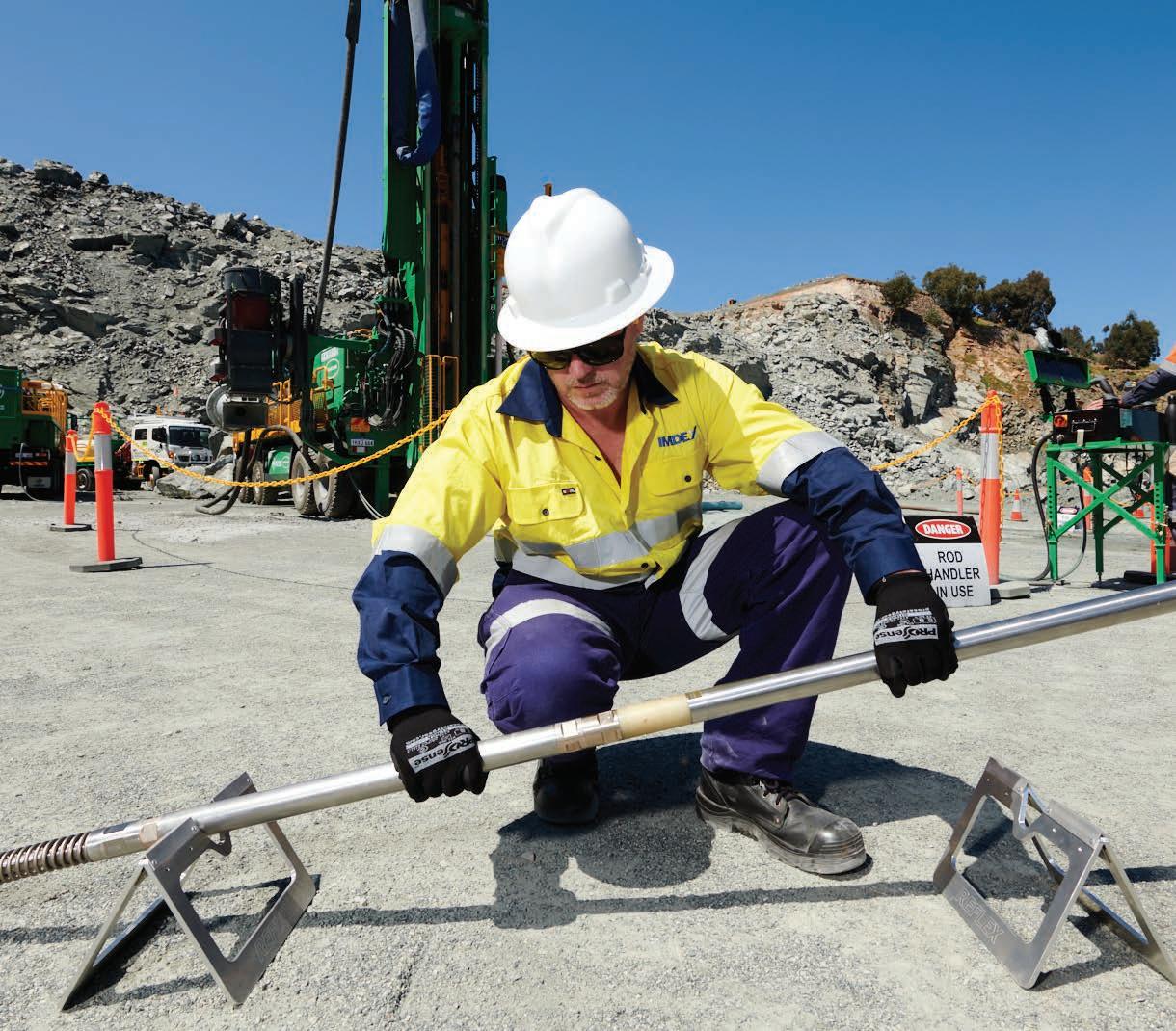
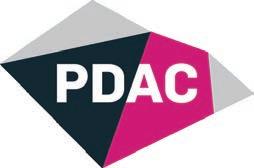
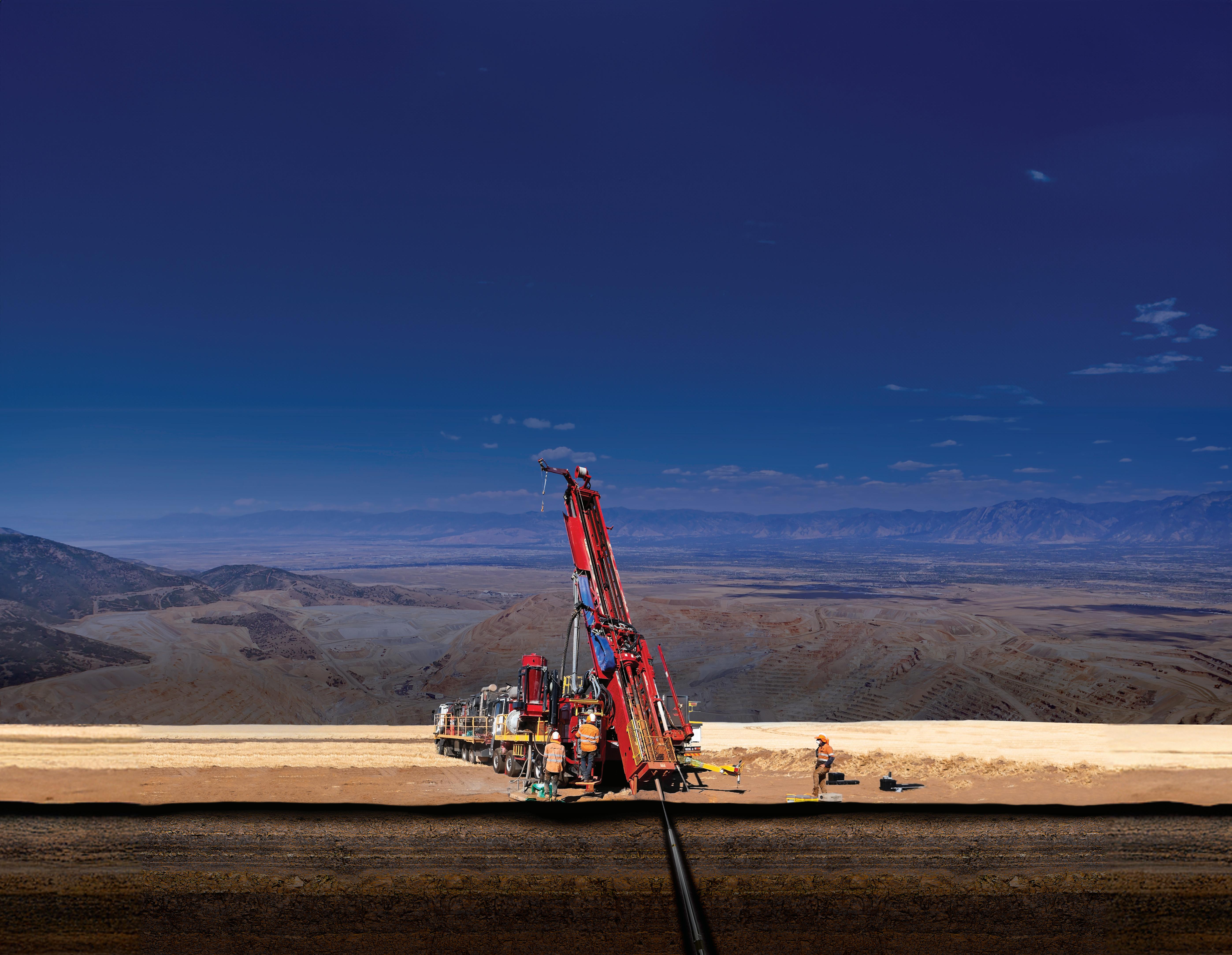
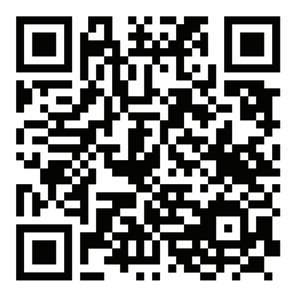
Exclusive interview with Stephen Dann, Director of PT.
From exploration to extraction: Drilling optimization, rock knowledge & software solutions backed by over 600 years of collective geoscience expertise
18 Face the toughest conditions with Christensen 160 Smart
Winter drilling in Maine: A story from the old days by Mike Junkins, Senior Drill Operator
24 PDAC 2025
26 Discoveries 2025 Mining Conference: Exploration, innovation and development
/EXPLORATION & MINING GEOLOGY
29 Q&A from the experts: In conversation with Dr James Siddorn, Corporate Consultant (Structural Geology) at SRK Consulting
34 Structural geology: A key element for optimization in mining exploration by César Rubín, SPT Engineer Geologist
38 The Ertsberg copper skarn deposit: A geologic and mining story like no other by Michael Thomsen, Chairman at North American Strategic Minerals Inc.
42 Shallow oxide gold formation: The role of redox reactions and groundwater by Dr Jim Yaxley, Owner of Grasstree Resources
46 New era in mineral exploration with machine learning by Somdutta Ghosh, Master in Geology at University of Calcutta
/EXPLORATION DRILLING CATALOG
50 Drilling services
51 Drilling equipment & accessories
55 Survey equipment
55 Miscellaneous
Dr James Siddorn Corporate Consultant (Structural Geology) at SRK Consulting
Stephen Dann Director of PT. Promincon Indonesia
March 2025
Cover photo IMDEX
Issue 30
ISSN 2367-847X
Not for resale. Subscribe: coringmagazine.com/subscribe
Contact Us
Coring Media Ltd.
57A Okolovrasten pat street, r.d. Manastirski Livadi, Triaditsa region, 1404 Sofia, Bulgaria
Phone +359 87 811 5710
Email editorial@coringmagazine.com Website coringmagazine.com
Publisher Coring Media
Executive Officer & Editor in Chief
Martina Samarova
Editor Maksim M. Mayer
Section Editor – Exploration & Mining Geology
Dr Brett Davis
Digital Marketing Manager
Elena Dorfman
Assistant Editor Adelina Fendrina
Graphic Design Cog Graphics
Want to contribute to Coring Magazine? Get in touch with us at: editorial@coringmagazine.com
Coring Magazine is an international quarterly title covering the exploration core drilling industry. Published in print and digital formats, Coring has a rapidly growing readership that includes diamond drilling contractors, drilling manufacturers and suppliers, service companies, mineral exploration companies and departments, geologists, and many others involved in exploration core drilling.
Launched in late 2015, Coring aims to provide a fresh perspective on the sector by sourcing authentic, informed and quality commentary direct from those working in the field.
With regular interviews, insightful company profiles, detailed product reviews, field-practice tips and illustrated case studies of the world’s most unique diamond drilling and mineral exploration projects, Coring provides a platform for learning about the industry’s exciting developments.
Stephen found his start in the industry in an unusual wayhe was working at a newspaper when a friend of his got a job on an exploration drill rig. It sounded like an adventure and it took him from a hands-on driller to a general manager of multinational companies. Across his career, he has managed drilling businesses in Australia, Thailand and Laos, before settling into his current role as a Director of PT. Promincon in Indonesia in 2024. Stephen has extensive experience in Asia and an understanding of the industry from the ground up, which he credits with teaching him the importance of forward planning and time management. Now he is in charge of PT. Promincon that owns a fleet of 23 heli-portable and three underground rigs and provides diamond coring and geotechnical work to its clients.
Grigor Topev: It’s a pleasure to have you as our guest interviewee at Coring Magazine! What led you to choose diamond drilling as your career path?
Stephen Dann: I was working in a totally unrelated field – at a newspaper –when a mate of mine got a job on an exploration drill rig. It sounded like an adventure, so I thought I would give it a go. Getting a start wasn’t easy but continual badgering of the late John Emerson finally got me a start on April Fool’s Day 1981.
GT: Could you share some insights into your early years in the industry?
SD: The job was as a water truck driver/offsider on a Longyear 44 situated around 200 km (124 mi) west of Coober Pedy (South Australia) in the Great Victoria Desert. Our water supply was from a bore on the Commonwealth Hill sheep station around 120 km (75 mi) away. There were no roads, just tracks across the sand dunes, pushed in for us by a contractor, and it was about a 10-hour return trip for a 2000 gal (7571 l) load of water. We had a three-man crew with two old caravans with no heating or air conditioning and temperatures would range from over 40°C (104°F) in the summer to 0°C (32°F) or below in the winter.
GT: Can you tell us more about your professional journey and the drilling companies you have worked with over the years?
SD: I spent my first 15 years with Western Mining Corporation Exploration (WMC) where I advanced through the ranks from Multipurpose Driller to Supervisor, before joining Boart Longyear in 1996. I then had 12 great years with the company going from Manager Special Projects to managing drilling businesses in Australia, Indonesia, Thailand and Laos.
Since then, I have worked for a couple of smaller companies, then at BHP overseeing up to three different drilling contractors before joining Asiadrill (Indonesia) in 2012 for six years. From there I returned to Kalgoorlie Australia for a brief period with Ausdrill, then back to Indonesia with Global
Drilling (Indodrill). I had a couple of years off thanks to COVID-19 and semi-retirement before heading back to Indonesia for my current role with PT. Promincon Indonesia (PMC).
GT: From your extensive field experience, what would you say is the most valuable skill you’ve learned?
SD: From the early days when drilling logistics in the desert were difficult, I learned that forward planning and time management were a crucial part of a smooth operation. Foreseeing issues that may arise and having a Plan B in place, just in case, made the workday easier and more productive.
GT: You have worked in multiple countries. Was there a particular location that left a lasting impression on you?
SD: I have been fortunate throughout my career to work with and have the support of some fantastic people, many of whom are still great mates to this day. Running Thailand and Laos for Boart Longyear whilst based in the beautiful city of Chiang Mai would have to be one of the highlights.
GT: Which country posed the toughest working conditions, and why?
SD: Every country comes with its own unique issues, whether it is the logistics of distance working in the remote parts of Australia, or the weather in the tropics. Trying to explain to an accountant in Salt Lake City why the rigs had been shut down for five days in Laos because we had had 12 in (30 cm) of rain in an afternoon, or to the Global Safety Manager why the accident report said ‘a ghost pushed me, and I fell off the walkway’ was sometimes a challenge.
GT: Could you share a challenging drilling-related issue you’ve successfully overcome and thus, it has become a life lesson for you?
same rules. PMC achieved seven years LTI-free in September 2024 at PTAR’s Martabe Site.
GT: Do you have a favorite type of drilling and why?
SD: Being a diamond driller from the start, I guess, it is my favorite, although in exploration we predominantly used multipurpose rigs, so you had to know how to drill RC, aircore, etc. as well.
GT: What are your thoughts on directional drilling?
SD: It’s a specialized skill that I did not have a lot to do with in my time as a driller, using mainly Hall-Rowe and casing wedges when required. Being able to hit a target the size of a car at 2000 m (6562 ft) deep or more using different barrel configurations, drilling speeds and downhole motors is an impressive feat. This presents significant cost savings to the client when drilling multiple branches off a parent hole.
‘Creating a proper Safety Culture from the beginning is critical in running a safe operation. When everyone is working to the same standards, it ensures new employees know exactly what is expected of them.’
SD: Being sent to a job in northern Queensland that had been having multiple issues with ground conditions, lost core and production made me look at a completely different way of diamond coring than what I had been used to. I think this instilled in me that sometimes you need to think out of the box and to not be focused on what you have always believed is the ‘right way’ of doing things.
GT: In your opinion, what is the most effective and practical tool for ensuring drill site safety?
SD: Creating a proper Safety Culture from the beginning is critical in running a safe operation. When everyone is working to the same standards, it ensures new employees know exactly what is expected of them. Leading by example is critical for this to work, be it the Helper, Driller, Supervisor or Senior Management, everyone works to the
GT: We’d love to hear more about PMC’s story.
SD: PMC was originally founded in 2011 and provides diamond coring and geotechnical work to our clients. Nowadays, PMC owns a fleet of 23 man-/heli-portable rigs with capabilities ranging from 200 to over 1200 m (656 to 3937 ft), as well as three underground rigs.
PMC’s biggest and longest running contract has been for PT Agincourt’s Martabe Gold Mine in North Sumatra. Since 2013, PMC has drilled around 700 000 m (2 296 588 ft), with the busiest year being 2021 when we had up to 15 rigs operating and we drilled 117 000 m (383 858 ft). The majority of the work is heli-portabe. PMC also supplies rigs for numerous geotechnical drilling projects.
GT: What are your goals for PMC for the next years?
SD: Whilst it may sound a bit cliché, providing job stability for our workforce and positive returns for our owners in what is a very demanding market are the key goals.
GT: As the market is relatively foreign to our readers, they would love to learn what are the unique characteristics of the Indonesian diamond drilling market.
SD: As it is an archipelago of islands, Indonesia presents numerous issues in regard to mobilizing equipment and supporting jobs logistically. A single job may require transport by truck, ferry and helicopter to get supplies to the site and can take from days to weeks. Dealing with mountainous terrains, local communities, wet season weather, including floods and landslides, as well as navigating local labor regulations, local governments and environmental issues, etc. can make for fun times!
GT: Which are the biggest players offering diamond drilling in Indonesia?
SD: Over my 27 years of involvement in Indonesia the market has changed significantly both on the Client and Contractor sides. In the early days, the Clients were the big Australian, American and Canadian explorers, such as Normandy, Newcrest, Newmont, BHP, Rio Tinto, etc. The drilling companies were predominantly owned or run (or both) by expats. Boart Longyear was a significant player along with Pontil (now Major Drilling) as well as other contractors, such as Maxidrill, Indodrill, and BMP, all being run and owned by expats.
Now, some of the main mining companies have withdrawn from Indonesia, while others have sold out their interests to local companies, and few of the big players remain. Local Indonesian drilling companies have advanced significantly in terms of size, quality of equipment, safety standards, etc., and are now far more competitive holding a large portion of the work. So, I think it will become harder and harder for foreign-/expat-run companies to compete against the ever-evolving Indonesian companies.
GT: What is your opinion of this ongoing trend of consolidation within the Australian market in particular?
SD: Consolidation seems to be somewhat cyclical like the drilling business itself.
Larger companies buy up small well-run companies, but more often than not those small companies reappear under a different name with the same management. I believe there will always be a place for the smaller well-managed companies and I have a great deal of respect for those willing enough to take on the challenge.
GT: Being the Director of PMC, what are your daily responsibilities? Which of them do you find the hardest? Why?
SD: Keeping the company running smoothly on a day-to-day basis in a safe, cost-effective manner is my prime responsibility. Dealing with local entities, who have a different perception of how to do business, is probably the hardest thing to deal with. Agreements can become long drawn-out negotiations which quite often result in nothing after a lot of effort.
GT: How often do you visit your crews in the field and, being an executive, what are the issues you must tackle?
SD: I make a point of getting to site almost every month. Being from a drilling background, I enjoy going to the rigs, although the mountainous terrain is getting harder to climb. It’s important to see how we are progressing and what issues the site is dealing with. I also use this time to meet with the Client and get their perspective on how things are going.
GT: What are the qualities that in your view make a great leader of a drilling company?
SD: My opinion is that understanding the industry you are in from the ground up provides you with a solid basis to be a good leader. Having the knowledge of what people are going through out in the field makes it far easier to make decisions in relation to the operations.
GT: Is there something you think you still have to learn or improve?
SD: I don’t think we should ever stop learning and seeking new ways and new ideas. Technology in our industry has advanced significantly during my time and you need to stay in touch with the latest developments, even if they are not directly applicable to the environment you operate in.
GT: What qualities do you look for in a driller, and do you have any advice for young people looking to succeed in the industry?
SD: The willingness to learn and adapt is a key attribute along with being a team player. A good sense of humor also certainly helps at times!
This industry is not easy, although the advancements in working and living conditions have certainly improved over the years. Spending long periods away from family and friends, missing birthdays, weddings, anniversaries and funerals is all part of the job, and you need to be able to be resilient to this. If you work hard, the opportunities and rewards are there for advancement and to travel the world with your skills, if you so desire.
GT: Lastly, outside of the drilling industry, what are some of your personal interests or hobbies?
SD: When at home, I am a keen gardener looking after our couple of acres of fruit and nut trees and harvesting what the birds, kangaroos and rabbits haven’t already eaten. For relaxation (?), I play golf which is a great time to catch up with mates, have a few beers, and solve the problems of the world. C
SPT is unveiling something BIG at PDAC 2025. Join us at the presentation event.
Can’t make it? See you at Booth #441 Limited seats Reserve yours
From exploration to extraction: Drilling optimization, rock knowledge and software solutions backed by over 600 years of collective geoscience expertise
IMDEX is a leading global mining-tech company uniquely positioned to enable resource companies to sustainably find, define, and mine orebodies with precision, at speed and safely.
Beginning in 1980 as Pilbara Gold NL before a name change to IMDEX in 1985, by the late 1990s, the company had established itself as a key player in the global mining services market.
The company has grown organically and through key acquisitions and today has an unrivaled global footprint, operating in all major mining jurisdictions around the world.
With 496 patents, 261 trademarks and more than 600 collective years of geoscience knowledge, IMDEX is a company rich in expertise and capability, which have been harnessed during many significant moments over its long history.
In 1990, IMDEX technology was used to align underground construction undertakings started in France and England as part of the ambitious Channel Tunnel project.
In 2010, IMDEX mud motors and survey instruments were used along with consultation from some of the company’s directional drilling experts to help locate the 33 Chilean miners trapped after an underground mine collapse.
In the 2000s, IMDEX strategically acquired several companies to complement its technological capabilities, with the 2020s bringing a sustained period of expansion through acquisition.
In 2020, IMDEX bought AusSpec, the industry leader in automated mineralogy, and its unique, cloud-based aiSIRIS technology.
aiSIRIS complements IMDEX’s existing in-field GeoAnalysis solution and integrates with IMDEX ioGAS™ exploratory data analysis software application to provide further interpretation and analysis. IMDEX has continued to develop and refine the aiSIRIS technology, releasing aiSWYFT in 2023.
In 2021, IMDEX acquired California-based DataCloud’s MinePortal software, a purchase that significantly enhanced IMDEX’s data visualization and analysis capabilities and built on its real-time orebody
knowledge technology. MinePortal is a next-generation, cloud-connected orebody knowledge technology which interprets and models geological data to enable real-time 3D visualization.
The acquisition continued the evolution of IMDEX with its focus on technology to deliver real benefits for clients throughout the mining value chain. IMDEX Managing Director and Chief Executive Officer Paul House said at the time that the purchase was in line with IMDEX’s strategy to move into the production end of the mining value chain.
A strategic stake in image analysis company Datarock followed in 2021. Datarock’s cloud-based platform applies Artificial Intelligence and Machine Learning to automate the extraction of geological and geotechnical information from core imagery, videos, and point clouds.
In 2023 IMDEX took a strategic stake in drilling analytics market leader Krux, which collects and analyzes exploration and production drilling data in near real-time.
That same year saw the most significant acquisition in IMDEX’s history, buying Devico, a leading provider of advanced sensors and the
global leader in directional drilling technologies. The acquisition of the Norwegian-based company reinforced IMDEX’s market-leading position in mining technology and delivered increased market penetration and growth particularly in Europe and South America.
But growth through acquisition and collaboration is only part of IMDEX’s strategy. The company has a rich history of research and development, allocating around 8% of revenue to R&D every year in all market conditions.
A disciplined stage-gate development process and R&D targeted on existing and emerging technologies has enabled IMDEX to maintain market leadership and win market share as the company continues to outperform industry growth.
The company’s integrated solutions operate in three broad pillars, with the combined results delivering benefits throughout the mining value chain.
A suite of products that enhance drilling productivity and performance, while improving safety and reducing impact on the environment. These include:
• Drilling fluids and equipment;
• Solids removal units;
• Rig alignment technologies;
• Directional drilling technologies and services.
Best-in-class solutions that originate critical data on the four elements of rock knowledge: location, grade, mineralogy, and texture. IMDEX’s comprehensive offering maintains a focus on high-quality data and optimized workflows, whilst providing customers a range of choices suited to their specific challenges, environments, and data requirements. Solutions include:
• Downhole gyro technologies and purpose-built running gear;
• Core orientation tools;
• Gamma logging sensors;
• Structural measurement.
Secure cloud platform and market-leading geoscience analytical software that enables real-time decisions to be made further upstream. The technology includes:
• Cloud-based data management and validation platform, integrated with rock knowledge sensors;
• Advanced reporting software;
• Geoscience analytics software;
• Interpretive mineralogy software;
• 3D visualization software;
• Drilling analytics software.
As IMDEX’s advanced technology and geoscience expertise continue to evolve, customers benefit from real-time insights into the drilling process and deeper understanding of orebodies. Likewise, productivity gains become increasingly valuable as the cost of drilling increases, and as the demand to address some of society’s most urgent challenges intensifies.
There is an imperative for resource companies to replenish diminishing reserves and to deliver the critical minerals needed for the energy transition.
Future discoveries are likely to be at greater depths, and have greater geological complexity, meaning that the cost of conventional exploration will further increase, unless significant improvements in productivity, safety and environmental compliance can be found.
Faced with these challenges, an increasing number of companies are turning to directional drilling, seeking the advantages of being able to hit more targets with less drilling, at optimal angles for a better orebody understanding.
Directional drilling is expanding globally, particularly into Africa, the United States, and Australia, and IMDEX’s DeviDrill services continue to be at the forefront.
Based on the wireline core drilling technology used in exploration drilling, DeviDrill is a directional core barrel that drills the hole in a curve whilst collecting a 3 m (10 ft) core sample.
The ability to steer the borehole enables multiple targets to be hit from one single mother hole, significantly reducing the number of drill pads and overall drilled meters required. As a result, water consumption and associated carbon emissions are reduced, whilst the achievable degree of accuracy leads to fewer abandoned holes, further reducing environmental impact.
For exploration sites like Sakatti in Finland (Anglo American), DeviDrill directional core drilling services have enabled the execution of accurate diamond drilling programs in deep and complex deposits in environmentally sensitive areas.
‘The successful drilling program (2022-2023) enabled us to achieve a constant 25 m (82 ft) drilling pattern in certain key areas of the deposit with the required 5 m (16 ft) target precision (up to 800 m/2625 ft depth), which would have not been possible by any other practical means.’ said Janne Siikaluoma, Anglo American Principal Geology and Resource Estimator.
IMDEX’s structural geology offering recently reached new heights with the release of ground-breaking digital core orientation system ACTx, premium gyro solution OMNIx38, and developments to LOGRx (formerly IQ-Logger) structural measurement device.
Together with HUB-IQ, the combination delivers repeatable and auditable conversion of alpha/beta angles based on drillhole trajectory. Smooth integration into ioGAS enables in-depth analysis, incorporating assay and other geoscience data to ensure structural geology interpretations are efficient and error-free.
ACTx is the first digital core orientation system to offer resource companies and geologists auditable data seamlessly transferred into a secure digital platform. Multiple quality assurance flags collected during the core orientation process help determine confidence ratings for drill runs where the orientation lines do not match, resulting in enhanced drill program management and geotechnical planning.
In addition, the thoughtfully engineered design and workflow improve core marking at the drill rig, thus increasing the number of attempted and successful core orientations.
LOGRx is an innovative, handheld digital device that significantly enhances both the speed and accuracy of capturing the orientation of structural features in diamond core. Its ability to easily transfer structural measurements digitally creates a dependable audit trail.
The built-in data-verification capability, utilizing stereonet projections, guarantees the accuracy and reliability of measurements. This real-time verification ensures that informed decisions can be made as data is collected, making geological assessments more efficient and dependable.
The OMNIx line of products, including OMNIxBOLT, is the newest generation of survey tools, using north-seeking gyros to measure borehole deviation in applications ranging from exploration to production. OMNIx42 is a fast and accurate north-seeking gyro with extensive field-proven reliability and Bluetooth transfer. The solution is available in a range of lightweight running gear configurations defined for all standard, reverse circulation and diamond drilling applications,
↑ ACTx digital core orientation system at an underground drill site in Western Australia
including surveying whilst pulling core, orientation and near-horizontal to horizontal pump-in applications.
OMNIx38 is a premium, north-seeking and all-attitude continuous gyro, delivering the highest performance accuracy ratings in downhole navigation. It reduces uncertainties associated with survey measurements to provide geologists with critical borehole information they can trust, in a small form factor that caters to the driller and operator. Its ability to run continuously in vertical drillholes offers significant productivity benefits in this application. A recent analysis conducted at a site in South Africa found the drilling contractor saved two days of rig time and their associated costs when surveying one B-size vertical drillhole over 1000 m (3281 ft) deep.
Production hole deviation is known to be a contributor to poor fragmentation, dilution, bridging and ore loss, which can cost the mining industry millions of dollars in lost production every year.
IMDEX developed OMNIxBOLT to assist in the prevention of these issues by enabling resource companies to accurately measure and analyze blast hole deviation at any time to make informed decisions prior to blasting. The system is fast, easy to use and accurate, and overcomes the challenge of needing multiple operators and an IT or elevating work platform to perform uphole surveys. To further
improve ore recovery in the production process, IMDEX’s Borehole Stabiliser drilling additive is specifically designed to tackle some of the ground challenges faced in air drilling applications.
A product of extensive in-house research and development, BLASTDOG is a multi-sensor downhole data-acquisition, analysis and visualization system that combines automation and machine learning with a data-driven approach to target higher ore recovery and better blast outcomes. It delivers rapid, reliable, and precise geoscientific and physical data and analytics from RC holes and blastholes, for better mine planning and blasting.
Data and knowledge derived from BLASTDOG can be visualized with HUB-IQ or in 3D within MinePortal without the need for exporting/importing. No other technology has the capacity to produce the same information and provide as large an impact on downstream processes, including enhancing productivity and improving sustainability. The data has the potential to be used to develop programs which could improve:
• Safety;
• Mine planning;
• Blast design;
• Fragmentation of the rock;
↑ LOGRx structural measurement device
• Air-blast and dust;
• Material assignment after the blast.
The long-term industry fundamentals remain compelling. There is, however, significant need to replace diminishing reserves. Demand for battery metals is increasing the supply-demand imbalance while reserves are becoming deeper and more complex to find. Building new mines to counter resource depletion emerged for the first time in EY’s annual assessment of risks and opportunities in the mining sector. Innovation and the technology it delivers provides exploration and mining companies with ways to tackle some of the issues surrounding resource depletion, as well as assisting in the drive for improved sustainability and the need to deal with a lack of skilled labor.
The supply shortfall for gold and copper, which represents about 75% of global exploration activity, is predicted to result in substantial demand in the medium to longer term. Similarly, demand for other battery metals is expected to intensify in the medium term due to increasing decarbonization targets. This supply shortfall has resulted in higher commodity prices, particularly gold.
IMDEX has a unique competitive position to address the increasing demand for productivity and greater orebody knowledge. The company maintains its clear objective of outperforming industry growth through technology leadership together with integrated offerings and the delivery of end-to-end solutions. New growth is pursued via its Digital and IMDEX Mining Technologies business units, where building geoscience analytics, AI and computer visualization capabilities will provide unparalleled orebody knowledge while leveraging its core capabilities in the mining production market. C
IMDEX will be showcasing its comprehensive technology offering at PDAC 2025: Booth 323.
WE ARE SWICK.
Hard rock mining’s heavyweight - innovating, manufacturing and delivering end-to-end excellence in drilling and underground diamond coring. A partnership with us is an investment in safety and versatility improvements in diamond drilling like no other.
INDUSTRY-LEADING DIAMOND DRILL RIGS MATCHED BY A TEAM DETERMINED TO ALWAYS PERFORM BETTER THAN THE DAY BEFORE? THAT’S EXCELLENCE UNEARTHED. THAT’S SWICK.
DRILL INTO THE POSSIBILITIES.
When the COVID-19 pandemic was raging, Epiroc’s team of engineers had the idea to create a truly heliportable surface drill rig that can tackle the toughest, coldest, and remotest parts of Canada, while offering unparalleled smart and safety features. Long and sometimes heated discussions between experienced engineers and drillers followed, until Christensen 160 Smart was introduced during PDAC 2024.
Size and weight become a problem when drilling in the most remote parts of Canada. Christensen 160 Smart has been meticulously designed by engineers and drilling experts and assembled in Canada. Its
primary goal is to provide the most modern technologies and safety features for drilling programs in extreme conditions. The rig can be easily transported on a truck bed and can be set up on a variety of platforms. It has a small enough footprint to be put in a reasonably small shack, which makes heating less problematic.
To facilitate that, Christensen 160 Smart can be split into seven lightweight units. Each of them weighs no more than 1120 kg (2468 lb) and comes fitted with sturdy lifting points to reduce the number of trips between distant locations.
Once in the field, Christensen 160 Smart can be assembled within one shift or less, depending on ground conditions and the setup, so drillers can focus on what they do best.
Christensen 160 Smart features the Cummins QSB 4.5 diesel engine. It generates 149 kW (200 hp) at 2200 rpm, while maintaining maximum fuel efficiency. This engine was selected as it has the highest ‘Power Density’ available in the market for an engine of this size. Comparable engines of this power class are much larger and by nature much heavier. This engine also meets or exceeds Tier IV stage V certifications that will accommodate many markets. In summary, the Cummins QSB 4.5 diesel engine, and Christensen 160 Smart by extension, has a high power level for a small ‘footprint’ and meets environmental standards in many countries.
With this much power, the rig can achieve depths of up to 2363 m (7753 ft) in B-size, 1751 m (5745 ft) with N-size, or 1023 m (3356 ft) in H-size. Epiroc also offers an optional P-size rotation unit of the Christensen 160 Smart, further enhancing their product offering to meet the demands of this segment of the surface market. Additionally, the hydraulic system can handle temperatures down to -25°C (-13°F). Epiroc also offers an optional Arctic Kit, which ensures that the rig can provide samples even in the worst of winters.
In the Canadian wilderness, hours away from the base, serious injury can be fatal, so advanced safety was essential for Christensen 160 Smart. The rig features the proven and well-liked by drillers Epiroc Smart Control System (RCS) with automated functions. These functions improve productivity and can dramatically increase the life of consumables.
In addition, data from each hole is logged by the RCS and can be exported into Exploration Manager. This software presents users with the ability to analyze data, find improvements and optimize drilling performance. With the help of the automated functions of the RCS, rods are extracted by head (pull-by-head), providing improved safety and reliability. Essentially, the most dangerous operations are handsfree, and Christensen 160 Smart is quite adept at manipulating the rods, so only one driller and an assistant need to be on-site.
Controls are only part of safety. Christensen 160 Smart also has interlocks on important functions, such as the guard and the rotation unit, complying fully with the European EN 16228 Engineering Standard.
Even the best equipment, such as the Christensen 160 Smart rig, needs to be serviced regularly to make sure it sustains peak efficiency. An Epiroc service solution guarantees maximum availability of parts and performance throughout the lifetime of equipment.
Epiroc’s core focus is on safety, productivity and reliability. By combining genuine parts and an Epiroc service through their certified technicians, the company safeguards productivity — wherever the drill, even in the deepest Canadian wilderness.
The team at 518 Drilling is used to seeing a lot of technology being deployed to the mineral exploration industry. Yet the drilling rigs to date have not advanced as quickly in comparison to other drilling applications in aspects such as data collection, automation, driller-operated gyro tools, as well as Starlink Wi-Fi on all of drilling equipment.
518 Drilling is a small company with a small team, but Epiroc has consistently provided it with access to new tooling to increase drilling efficiency downhole. Epiroc has stood the test of time within the industry,
and the leaders of 518 Drilling knew that it will be there to fulfill their needs as they grow their fleet with both surface and underground drilling applications. So when Epiroc first presented the opportunity to be a leader in adopting the new Christensen 160 Smart that can be integrated into this push to advance exploration drilling technology, 518 Drilling saw a futuristic vision of how this new technology will change the way their drillers view their daily tasks. It was an easy decision for 518 Drilling to take on the test.
Christensen 160 Smart offers several functions that the drillers from 518 Drilling haven’t seen on any other drills in their fleet. Automatic rod pulling, tube retrieval, as well as tube pumping, allowed their drillers to have some mental rest and also have time to complete training and mentorship to their assistants. This will have long-term positive effects for all the crews working at the company, as Christensen 160 Smart saved the drillers from sitting white-knuckled on the controls, performing routine functions that this technology can repeat safely and consistently as necessary to complete rod pulls and retrieve core samples, etc.
For 518 Drilling the long-term goal is to change the way drillers do their work and eliminate operator error and potential injury due to repetitive tasks, and Christensen 160 Smart will accelerate this process tremendously. C
For more information Visit: epiroc.com
Challenge accepted.
Setting the standard, with 99% hole completion.
With a focus on dependability, Hy-Tech Drilling is the long-term partner you can trust to ensure safe and seamless execution, giving you peace of mind.
‘The fact that it is a modular design, easily dismantled and then flown, or alternately transported in any number of ways, further allows it to be easily mounted in a drill shack, or a platform in a remote drilling location, or adapted to any number of challenging drilling applications.’
by Mike Junkins, Senior Drill Operator
‘Drilling was tough work, but there was nothing like the feeling of finishing a hole and retrieving the tools.’
Drilling for minerals in northern Maine during winter in the 80s was no easy task. Snow was chest-deep in places, and temperatures stayed well below zero. We had three rigs in operation—two Longyear 44s and one 38—running double 12-hour shifts. There was no leaving the Bean supply pumps unattended, so shift changes happened right at the drill site.
Frozen water lines had been a recurring issue, but with crews on-site around the clock, we caught and dealt with problems before they got out of hand. Trying to fit hoses together while the pump was running was brutal—water sprayed everywhere, freezing instantly on our hands and faces.
We had the rigs set up so the B- and N-size tubes could be dumped inside, where a woodstove burned cherry red. Beech and birch made for hot-burning fuel, and we kept a stockpile of stove wood outside the rig. The day-shift helper would take the Muskeg up and yard a couple of logs down to the rig in the daylight. The Homelite chainsaw made short work of bucking them into stove-length logs. At night, the helper split and stacked the wood, keeping the stove full so we could work in some semblance of warmth.
The foreman, Ramone, was a burly, gritty old-timer who had seen it all. He ran an old Cat D-6 dozer. The ancient type with a gas pop motor to start the diesel. Getting that beast running took three arms and four hands to work the levers just right.
Ramone kept the roads cleared after every snowfall and bulldozed new accessways as we moved from site to site. The two Longyear 44s were drilling deep—1500 to 2500 ft (457 to 762 m)—while the 38
worked shorter 500 to 700 ft (152 to 213 m) intercept holes, moving every three to five days on average.
We pumped water from a pond about half a mile from the drilling sites. During the day, Ramone kept an eye on the pump. At night, the helpers would swing by to check the water temperature coming out of the main sump hose. As long as it stayed between 37 and 42°F (3 to 6°C), we were in good shape.
Four 100-pound propane cylinders, connected in series, kept the coil torch running. Those tanks lasted about two and a half to three days. The warmed water from the main pump fed into a communal sump, supplying all three rigs with drilling fluid. If the main pump went down or the lines started freezing, we were all on the scene in minutes—water was the heartbeat of any drilling program. Without it, we weren’t pulling any core.
We were drilling near Mount Chase, just north of Patten, Maine. The company had purchased a house in Patten to serve as our quarters. One of the local helpers arranged for his mother to cook for us, and the company paid her for the service. Needless to say, I didn’t lose any weight—she was a fantastic cook. She also packed our sack lunches and filled our thermoses with coffee before each crew change.
At the drill, we kept tin foil on hand so we could heat our sandwiches on the wood stove. The drive to the site was about 12 mi (19 km) up Route 11 on pavement, then another 10 mi (16 km) into the bush on a logging road to the laydown area. There, we had a small container stocked with tools, a welder, a torch set, and spare parts. We all knew how to weld, use torches, and handle most of the repairs that came up.
Drillers are true jack-of-all-trades—whether fabricating a fix to keep the rig running or replacing hydraulic lines, every day was a learning experience.
Drilling was tough work, but there was nothing like the feeling of finishing a hole and retrieving the tools. We had our share of light moments too. Green helpers were always initiated with a wild goose chase for some nonexistent tool. We’d send them off looking for muffler bearings, axle straighteners, elbow grease, or the infamous ‘head slaps’ (not usual nowadays).
The best was when a driller sent a helper to the foreman asking for a set of ‘hard head slaps’—making sure they weren’t the soft ones. The wise old foreman would play along, giving the helper a solid whack on each side of the head before asking, ‘Hard enough?’. It was all in good fun, and any bruised pride was quickly smoothed over with a cold beer at the house later on. It was a rite of passage that turned us into comrades.
During the day, the foreman would grab a helper who could be spared for a few hours to haul rods, barrels of diesel fuel, core boxes, and other essential supplies to each rig site. They also hauled out the full core boxes so the geologist could access them and transport them back to the logging shed in town. Since pickups couldn’t reach the rigs from the laydown yard, we had to navigate snow-filled trails littered with stumps and boulders.
Drilling in these wintry bush conditions was doubly tough. Tripping pipe in a blinding snowstorm was just part of the job. The weather was
a constant battle, but we adapted. The Muskeg was an invaluable tool on these jobs—its wide tracks and cargo areas on both sides made it our go-to vehicle for winter drill operations.
For moving rigs from site to site, we relied on a Timberjack skidder. Maneuvering the drill through dense woods required finesse—using the winch to work around trees and boulders took skill, patience, and a feel for the terrain. But that was the job, and we did whatever it took to keep those drills running.
After our ten-day hitch, we’d head home for four days. The night shift didn’t work on the final night, and the day shift shut down drilling operations around 2:00 p.m. At that point, we had to thoroughly drain the pumps and water lines. To make sure we could find them easily after a snowfall, we hung the water lines on tree limbs before heading out. When we returned the following Monday, we switched shifts—the previous day crew became the night shift, and the night crew took over days. It was the fairest way to keep things balanced.
Looking back now, I wonder how we managed to work through the relentless cold and deep snow. At 71, I doubt I could handle that kind of strain anymore. But I’m grateful—for the experiences, the friendships, and the memories of those rugged days in the Maine wilderness. C
Get in touch with Mike on LinkedIn
The annual PDAC ConventionThe World’s Premier Mineral Exploration & Mining Convention - will take place from March 2-5 2025 in Toronto, Canada. The award-winning PDAC Convention is widely considered the ‘Super Bowl’ of the mineral exploration and mining community and is the leading event for people, companies and organizations connected to mineral exploration.
The convention brings together up to 30 000 attendees from over 135 countries for its educational programming, networking events, business opportunities and fun. Since it began in 1932, the convention has grown in size, stature and influence. Today, it is the event of choice for the world’s mineral industry, hosting more than 1100 exhibitors and 700 presenters.
by PDAC’s team
This includes the Northern Ontario Mining Showcase (NOMS) – the largest pavilion at PDAC – featuring over 110 exhibitors and interactive displays showcasing innovative products and services to help plan, build, maintain and rehabilitate projects around the world!
The Core Shack will provide a unique venue for companies to display their core samples. Attendees can get up close to new or ongoing projects that are generating exciting drill results. The latest discoveries from all corners of the Earth will be featured along with maps, charts and technical information.
Visitors will be welcome to discuss investment potential with more than 440 junior mining companies, mid-sized producers, major mining companies, financial institutions and prospectors to discover new business opportunities.
The Prospectors Tent is the door to the heart of the industry. Self-employed prospectors will be there to discuss their maps, samples and claim results.
The SMC brings together geoscience students and industry professionals to highlight innovative student research on projects essential for the successful evolution of the modern mining industry. Students (BSc, MSc, PhD) working on projects linked to mineral deposits including mapping, mineralogy, geochemistry, geophysics, environmental and hydrogeology will have the opportunity to share their research with an audience of academics and industry professionals.
Spread over both the North and South Buildings of the Metro Toronto Convention Centre (MTCC), PDAC 2025 will showcase another full slate of exhibitors from across the globe and plenty of opportunities to learn, network and celebrate.
Visit over 1100 exhibitors showcasing the world’s leading technologies, products and services, and meet government representatives from across the globe.
An initiative aimed at showcasing work of talented artists from Indigenous communities. C
For more information
Visit: pdac.ca/convention
Don’t miss the world’s premier mineral exploration and mining convention
2-5 5
PROSPECTORS & DEVELOPERS ASSOCIATION OF CANADA
Up to 30,0 00 attendees 700+ hours of programming
1,100+ exhibitors Delegates from 130+ countries
Meet investors & senior executives Unrivaled networking
pdac.ca/convention | Toronto, Canada
The 2025 edition of the Discoveries Mining Conference will take place between April 8-10 at the prestigious Mazatlán International Center in the vibrant coastal city of Mazatlán, Sinaloa, Mexico.
Organized by Mexico Mining Center, the annual event has earned its reputation as one of the foremost technical conferences for the mining industry in Latin America with its focus on exploration, innovation and development. This 11th edition will continue a tradition of excellence and dedication to contributing to the responsible and efficient development of Mexico’s mineral resources.
Every year the conference attracts key players from the mining sector, including upper-level mining professionals, investors and industry experts from around the world. With over 2000 international attendees expected this year, including representatives from more than 85 mining companies, the event offers unparalleled networking opportunities to do business and acquire knowledge.
In the exhibition area, leading suppliers and contractors will showcase cutting-edge technologies that are transforming the mining industry at every stage of development, from exploration through production.
With over 50 speakers participating, the conference will feature presentations covering topics ranging from the latest geological discoveries, new technologies applied to mining and exploration, social, legal and political issues affecting the industry, as well as the challenges and obstacles that were faced and overcome on the way to production.
One of the networking highlights of the Discoveries Conference is the Core Shack. It is a meeting place for geologists, mining executives and
investors to gather and examine rock samples, drill core and technical information from some of Mexico’s most important mining projects.
The conference offers ample opportunities to network with key players in the Mexican mining industry, learn about new discoveries and disruptive technology, as well as find great business and investment opportunities in one of the world’s most important mining jurisdictions.
Participating companies have the chance to increase their exposure and awareness and reinforce their position as leaders in the mining community. C
For more information Visit: discoveriesconference.com
Specifically designed to meet the needs of today’s modern driller, S-Maxx™ drill rods’ unique dual start thread and anti-jamming features will help drillers reach greater depths and achieve new limits not possible with any other rod on the market.
a wireline coring rod that delivers max rod life, max joint strength, max depth capacity, and max efficiency.
In this Issue:
Q&A from the experts
In conversation with Dr James Siddorn, Corporate Consultant (Structural Geology) at SRK Consulting
The Ertsberg copper skarn deposit: A geologic and mining story like no other by Michael Thomsen, Chairman at North American Strategic Minerals Inc.
Shallow oxide gold formation: The role of redox reactions and groundwater by Dr Jim Yaxley, Owner of Grasstree Resource
New era in mineral exploration with machine learning by Somdutta Ghosh, Master in Geology at University of Calcutta
Dr James Siddorn Corporate Consultant (Structural Geology) at SRK Consulting
Brett Davis: Firstly, thanks for giving Coring the opportunity to interview you, James. I know you do a lot of interviews, but this one will obviously be the most interesting you’ve done! Very few people in the mining and exploration consulting world are as high-profile as you. Coupled with your academic publication history and role as a practice leader with SRK Consulting (Canada), I can understand why the demand for your services outstrips your time to undertake all the client requests you get. So, given that you’ve worked across the spheres of academia, mining, exploration, and business development, can you tell us what interested you in a career in geology?
James Siddorn: Thanks for inviting me to be interviewed, I know we tried to do this a few years ago so it’s great to finally make this happen.
I got interested in geology through my enjoyment of physical geography in high school. I was then lucky to be able to study an A-level in Geology at a different high school to mine (in the same town) with a fantastic teacher, Colin Bagshaw. At first, I was not sure about this new subject, being at
James is a Corporate Consultant (Structural Geology) with SRK Consulting based in Toronto, Canada. He has been lucky to build a career of over 20 years with SRK, working with some excellent geologists and engineers worldwide. Originally from the Midlands in England (Burton-on-Trent - a beer town), James emigrated to Canada in 1996 following his BSc (Geology) at Durham University and then working in Newcastle, England. He did his MSc and PhD at the University of Toronto, which paved the way for his career focused on the structural geology of ore deposits (he says that he still does what he did for his PhD at work). His work currently is divided between South America, Europe, and the Middle East.
a different school, but from our first field trip for a day to look at Devonian sandstones in Derbyshire (UK) I was hooked.
The teacher was then amazed at how I went from a mediocre student to one of the best in the class. From that point I was sure to go to university to study Geology, something alien in my family as they didn’t normally go to university. So I studied Geology at Durham University in the northeast of England. A fantastic Geology department and I was able to work with two excellent structural geologists, Bob Holdsworth and Donny Hutton.
BD: You’ve worked in a lot of countries and on a lot of continents. Are there any skills or mindsets that have helped you in your roles in these places? And what are a few of the pros and cons of interfacing with people in other countries?
JS: I think I am currently up to 42 countries that I have worked in or stayed in (i.e. not just flown through), which I count as not bad but not super high. I come from a working-class
background in my family, so I like to treat everyone equally and listen to everyone equally. I am also always interested in learning about different cultures, life in other countries. For all of that listening and learning are always important.
The big pro is always learning something new about a place you do not know, especially as we are lucky to visit countries and locations people don’t normally go to. The big con is dealing with people who think they are more important than others, especially in hierarchical societies.
BD: Apart from me, who have been some of the positive influences in your career (just on the off chance there are others)?
JS: Of course, you Brett. Well, you know there are a few of us in our consulting practices that get on well because of our personalities but also because we think similarly about structural geology problems. I have been lucky to have had the opportunity to work with some great people, some for a long time, and with others just briefly.
One that was always important to me was Bob Hauser, Head of Technical Services at the Con Mine (Canada). Bob taught me so much about working within the mine, to always think critically and to pose the right question. He always had time to talk, and I always appreciated my time with Bob.
BD: Where would you say the focus of most of your work is? Is it on a particular commodity or a deposit type? Given the current multi-commodity mineral boom, are you doing a lot of work outside of the commodities and deposit styles you have traditionally worked on?
JS: As you know, I started off with a focus on orogenic gold deposits through my PhD and much of my early consulting work. Then throughout my career at SRK, I have been involved with lots of deposit types and terranes around the world.
This started with work in the Sudbury basin on magmatic nickel (I have been lucky to
work on most mines and deposits in Sudbury). Afterward, I was off to South America and Mexico working on epithermal and porphyry deposits, with a little orogenic gold thrown in there.
Then off to Spain and Portugal to start working on all of the deposits in the Iberian Pyrite Belt, well trying to, I think I am up to six deposits now. Now a lot of my work is between orogenic gold and VMS deposits, from Iberia through Eastern Europe, Turkey, Saudi Arabia, and Egypt. I have been lucky to work on all the orogenic and epithermal gold mines in Saudi Arabia, so I am building a comprehensive understanding of gold in Egypt and Saudi Arabia.
BD: I know you do a lot of geotechnical work. Has this been an obvious extension to your skills as a structural geologist, or was it a new field for you that required acquiring fundamentally different skills?
JS: One of the great things about structural geology is that it is adaptable to different deposits, or different stakeholders. I got involved in geotechnical work because I like working around underground mines and when I started with SRK, I was able to work with some great geotechnical engineers.
Structural geology has come a long way, practically in understanding important problems like fault properties and failure mechanisms. Yet, there’s one difference in seismically active underground mines, and that’s time. Normally, as geologists we look at finite geology, finite strain and so on - things that occurred millions or billions of years ago, but when dealing with seismicity today you must look in 4D, examining how it is changing as a mine advances. This is a complex problem.
BD: As a widely traveled geologist, what part of the world do you think is highly prospective for finding new world-class orebodies? I’m interested to hear this regarding geological attributes irrespec-
tive of the no-go zones associated with impediments such as environmental concerns and geopolitical/security risks.
JS: I always think South America is so prospective. There are still discoveries, particularly in gold and within the Andes, where there are so many new places that are relatively untouched. A good example of this is the exploration success of Filo Sur (Lundin) in Argentina, in an area previously only accessible by donkey. But I must admit I am biased towards the countries and jurisdictions I know!
BD: Is there a particular mineralization style or deposit type that interests you, and why?
JS: I really enjoy working on VMS deposits right now. One, because I am learning a lot, two, because structural geology is often poorly done in these deposits, and three, you can make a big impact in terms of exploration strategy.
BD: Leading on from the previous question - everyone has a handful of deposits that have left a mark on them, be it because of the amazing geology, the hideous conditions, the people they worked with, etc. Which deposits do you hold dear, and which ones really were difficult to work on?
JS: I hold a series of deposits dear in the Iberian Pyrite Belt, from Aguas Tenidas to Magdalena to Cobre Las Cruces. I really enjoyed working on these mines. It’s amazing geology in this part of the world, combined with great food and drinks.
BD: I know you are very passionate about mentoring and that you were awarded the Past Presidents Memorial Medal by the
Canadian Institute of Mining, Metallurgy and Petroleum, in recognition of your efforts to teach and inspire young members of the mining industry. Can you provide your perspective on what inspires you to do this and why you think it is important?
JS: I guess, I like helping people in the same way people in my career helped me. I remember great conversations with Jim Franklin when I was involved with the Geological Survey of Canada during my PhD, for example. It’s always great to learn from younger people too, I have a philosophy that we should always build teams of people smarter than us.
BD: Leading on from the previous question, what is your opinion of the geological skillsets, experience, and knowledge of geologists today, especially new graduates?
JS: To be honest, I don’t get to interact with many newly-graduated geologists now. Though, I am impressed by the computing and programming skills of younger geologists. When combined with good field geology skills, it is an awesome combination.
I often get surprised by the technical skills of geologists overseas. I have been lucky to work with some great Somali and Pakistani geos in the field recently. They are passionate about learning and hard working in the field.
BD: Applied structural geology is core to your career and you run a lot of applied structural geology courses. Have you found the content and focus of these courses has changed during Subsurface exploration requires
JS: I have always been an advocate for 3D geological modeling since I built my first 3D model using AutoCAD 2000 (yes, a few years ago).
I pushed the limits of Leapfrog when it was first released building kimberlite stratigraphic models using domain boundaries, long before the software had any geology modeling capability. For sure, our early courses had paper-based problems, and now with a small enough group we can run exercises and problems in 3D on a computer. After nearly 20 years of teaching courses, I can honestly say the material always improves, especially with so many case studies from different deposits.
The key that remains the same is that the course needs to teach and empower geologists to do structural geology, to give everyone the confidence and knowledge to use structural geology daily.
BD: Coring is also a drilling magazine, and we like to keep to our roots. So, I’ll ask you a drilling-related question. Do you do much work with oriented core? Do you have any horror stories with core orientation?
JS: As you know, Brett, oriented core is still a challenge for many companies, even with the new tools and QA-QC methods that are available. Many people get frustrated with core orientation. I remember one advanced gold exploration project where the project manager refused to use oriented core, even though the deposit was vein-hosted and totally blind under a lake. He thought it was too complicated to understand the quality issues. After 15 minutes of showing them the issues using their own core, he was sold, once he understood that the solutions were so practical.
People need to understand that doing oriented core is a mechanical problem, ensuring all the steps from the drill to the measurement are done well.
BD: Has there been any single satisfying moment in your career that rates above all the others?
JS: The day I received my PhD is a moment I will not forget. As I mentioned earlier, it is not normal for people in my family to go to university and I was lucky to do so, but then to earn my MSc and PhD is even more amazing. That, combined with the fact that I started consulting (independent at first and then with SRK) during my PhD and many people did not think I would finish, makes it more special… It took my PhD supervisor telling
me that he was moving continents to put the fear of God into me to finish. Thanks Sandy!
BD: I’ll ask a question on the flipside to the previous one. Many of us have interfaced with less than savory individuals or experienced toxic workplaces. Has there been any incident or incidents that really disappointed you?
JS: That’s a good question, but I have to say I have been lucky that I have not had many situations like this. A huge number of clients I work with have become good friends, in fact, it’s a philosophy of mine that if we are working together closely, then we automatically are friends. It’s a great way to work.
More than toxic workplaces, I have been in mines where people are working extremely
‘People need to understand that doing oriented core is a mechanical problem , ensuring all the steps from the drill to the measurement are done well.’
hard in poor conditions for probably low pay. This is always a good reminder of how lucky we are and how little we need in life.
BD: One topic we commonly talk about but rarely put into print is that of the health hazards of working in different countries and environments. Has your health ever been particularly challenged and, if so, what happened?
JS: Great question and wow yes, some underground environments can be tough. I keep myself physically fit not only because I enjoy it, but it does also help with work. I have worked many times at above 5000 m (16 404 ft) in the Andes and luckily, I do not have issues at altitude, normally with the Peruvians or Chileans on site being amazed.
Also, I am rarely in an area for more than a couple of weeks, so you can live with most conditions. But looking back, I have worked from -56°C (-69°F) in the north of Canada up to 50°C plus (122°F) in Saudi Arabia. It’s amazing what the human body can adapt to.
BD: You are one of the rare breeds of geologists who works in the industry but manages to maintain a publishing career. What inspires you to publish and how do you overcome the challenges, such as finding the time? I know this detracts from your time in your workshop where you make those amazing woodwork projects I’ve been privileged to see.
JS: I like to write, but I have to say, I don’t have a great and extensive publishing career. It does take time and focus to do so. Finding the time requires I commit and carve it out because I am always first to try and fit in another site visit to help a client I know well. So I must tell myself to not say ‘YES’ to everything.
I would like to write a few papers, especially synthesis works on ore controls in the areas I know well, but I need to sketch out the content and then sit down and read recent publications.
Oh, and I love building things with my hands, though I must admit, I am still a novice woodworker. I hope to build a workshop this year so I can start to practice and learn more.
BD: Are you undertaking any active research now?
JS: I am working on a method to integrate multiple drillhole datasets to build a ‘fault’ probability classification. I have the concept, and I am working on this with two other team members that have a background in machine learning. Let me explain a little. When building 3D fault interpretations, we often use a variety of drillhole datasets, which could include logged faults, RQD %, alteration, recovery, etc. We analyze these datasets individually, turning them on and off in 3D to look for structural trends. I want to build a method that automatically evaluates drillhole intervals for the potential that a fault exists, building a fault probability. So, if a given interval has a low RQD %, clay alteration, and poor recovery, but without a logged fault by the geologist, it would be highlighted. This would enable the geologist to work first from one integrated dataset, and then if needed, look at the individual data.
BD: What have you learned from field practice and your job experience that is not taught at university? Will you be incorporating these insights into a set of memoirs?
JS: No, no memoirs please, I am not that special. I really like to impart to people the methods and ability to think in 3D, especially in the field. It is a challenging skill for many, even with the software we have now. Just look at the Shepard and Metzler 3D problems, get good at those, and then you can train yourself to think in 3D.
BD: If you had abundant financial funding, is there a fundamentally annoying geology question you’d like to solve or a topic you’d like to work on?
JS: Umm, these are all great questions. Here’s a great one. The time scale of tectonic and
sedimentary events in major orogenic gold districts is still a problem. In many districts, the timing of burial and metamorphism, then flysch sediment deposition (at surface), and then burial again in time for gold deposition results in the concept that these districts are underground burial, rapid exhumation, and rapid burial again (the concept of ‘vertical tectonics’). Examining this within some of the major Archean and Proterozoic gold districts would solve a question that no one seems to want to tackle.
BD: Do you think that geological societies, such as the Society of Economic Geology (SEG), have adapted with the times in terms of being useful entities for their members? Or are there basic things that such societies should be providing and/or promoting?
For more information
JS: I wish I was a little more involved in SEG, and I have dedicated a lot of time over the last 15 years to helping PDAC (including five years of fun as Convention Planning Chair). Key for any society is member engagement, ensuring that you are providing for their fundamental needs, be it scientific advancement or government advocacy. You must make sure the society is not self-serving and lives to its purpose.
BD: Finally, any concluding comments or words of wisdom from an industry veteran?
JS: To be honest, I don’t like to think that I am a veteran, but I guess I am not a youngster anymore. Only one thing to say to younger geos – go see more rocks…. Life is best in another country seeing new geology. C
A key element for optimization in mining exploration
by César Rubín, SPT Engineer Geologist
Each year, over USD 12 billion is invested in mining exploration worldwide. To maximize the return on this investment, geological interpretation through structural data is crucial for optimizing resources and minimizing risks in projects.
‘ Structural geology plays a crucial role not only in mining but also in geotechnical projects.’
Accurate and reliable data during exploration can prevent multimillion dollar losses in mining operations. It is estimated that proper geological investigation can reduce additional exploration costs by a factor of ten.
However, achieving this level of accuracy depends not only on the quantity of information collected, but also on the quality of its analysis and interpretation. The use of tools and methodologies that enable these elements to be properly identified, recorded and analyzed is therefore critical to strategic decision-making in the mining industry.
Structural geology plays a crucial role not only in mining but also in geotechnical projects. It provides key information on the orientation and configuration of geological structures, enabling the delineation of high mineralization zones and the continuity of deposits for mineral discoveries. Structural geology helps to understand the origin and development of a mineral deposit by identifying and mapping faults, joints and veins.
These structures often have irregular or deformed shapes, making them complex to analyze and display. This is a major challenge for geologists who analyze crustal deformation to understand the stresses acting on rocks and how they have altered the arrangement and orientation of rock layers.
A variety of tools and techniques are used to interpret mineral deposits and the resources they contain, including analysis of geophysical data processing, geological maps, detailed fieldwork and oriented core studies. These techniques provide valuable information during exploration campaigns.
In addition, structural geology not only optimizes resources by increasing the probability of success in exploration and exploitation but also plays a key role in engineering by assessing the stability of rock masses and slopes to prevent collapse and landslides, thereby improving the safety and efficiency of extractive activities.
When a potential mineral deposit is identified, exploration drilling becomes essential. Methods such as diamond drilling with core recovery provide direct structural data from extracted cores, making them the true value of mineral exploration. These cores, properly logged and sampled, contain critical structural information about discontinuities, veins, layers or vein systems - key aspects for constructing geological models and accurately determining the location of the mineralized body.
The orientation of these structures is recorded using tools, such as goniometers, templates and orientation frames (Rocket Launchers), to measure alpha (α), beta (β) and gamma (γ) angles. In addition, geological logging systematically and accurately documents rock characteristics at various depths.
This process includes the identification of features such as rock type, alteration, mineralization, structures and physical properties like density and magnetism. Codes, abbreviations, colors, numbers and symbols are used to facilitate data organization and analysis, allowing detailed deposit descriptions. The resulting information forms the basis for understanding lithology, generating key data for modeling and optimizing mining exploitation, and therefore makes structural data acquisition a priority during drilling.
These measurements are essential for analyzing and validating structural models and for determining the orientation (direction and dip) of geological structures. Accurate interpretation of these measurements contributes significantly to more effective exploration, strategic mine planning and engineering control of rock masses, slopes and dams.
However, measurement accuracy can be affected by variations in working conditions, operator experience and the need for constant recalibration of the system and devices used in the field. In addition, data acquisition and analysis challenges arise when structural controls are integrated with lithological, alteration and mineralogical information in complex geological or geotechnical scenarios.
Incomplete observations and the need to infer structural shapes from logged core fragments alone complicate the work of geologists, particularly in environments where precision is key to strategic decision-making.
Today, there are alternatives for more efficient core analysis, such as geological and geotechnical logging by oriented core scanning. These tools process data using reflectance spectroscopy, visual imaging and 3D laser profiling, among others, to provide mineralogical, geochemical and textural morphological mapping of the core.
However, most of these solutions require specialized hardware or constant access to external platforms. They also require additional software, accessories, machines or plug-ins, and significant processing time, which reduces accessibility in remote environments, making immediate implementation in exploration projects difficult, delaying results and increasing the likelihood of interpretation errors.
Although logging of diamond drill core follows a methodology, inconsistencies often arise during core logging and sampling, such as transcription errors, measurements errors in recovery data, wrong calculation of Rock Quality Designation (RQD), density and other parameters to mention some.
These inconsistencies often occur due to manual data entry, repeated digitization, incorrect application of formulae, missing intervals in data tables (e.g. Excel®), blank spaces due to insufficient information, not standardized abbreviations on logging sheets, even the absence of a proper logging protocol and sampling of the core.
Traditional mapping and manual representation techniques have significant limitations, especially when working with large volumes of data. Although digital tools have improved these processes, many still rely on manual data entry, which increases the likelihood of errors, resulting in less reliable geological models, especially when it comes
to structural data, which results in slower turnaround times and uncertain decision-making.
Manual structural logging is often a long process of data entry, highly influenced by human error. Lighting variability, seasonal changes and other external factors significantly affect the quality of structural observations, increasing the likelihood of inaccurate field and core data.
Another key issue is that interpretation of structural data can require a return to the core shack to recalculate or verify core samples and measurements made. Conducting these subsequent audits is made more challenging by the limited direct access to cores once they have been sampled and stored.
In addition, in many cases it is not possible to review original measurements for adjustment or validation because the core samples have been cut for geochemical analysis, leaving only segments or halfcore sections.
In a sector where interpretation can mean the loss or gain of millions of dollars, it is essential to have advanced tools that ensure that exploration projects are well executed and mining operations are carried out quickly, safely and sustainably. Most importantly, these tools must provide accurate, reliable and efficient information.
At this stage, a detailed understanding of the geological model with the great value of structural data can mean the difference between a successful project and a collection of costly mistakes. Modernizing logging and structural analysis processes - including automated calculations, instant stereographic plotting and visual measurement validation - is therefore essential.
The mining industry is constantly evolving towards developments that improve operational performance in many areas - not only in terms of production, environmental impact and safety but also in terms of providing companies with a competitive advantage by ensuring optimal and sustainable resource use.
Stockholm Precision Tools (SPT) has been developing high-precision tools for the mining industry for thirty years. With cutting-edge technology, SPT helps major companies ensure quality control, reduce costs and maintain precision standards in drilling projects worldwide.
From March 2 to 5, SPT will participate in PDAC, the largest mining and mineral exploration convention in Canada and one of the most important global industry events, bringing together key industry players to showcase StructMaster™, its latest innovation for oriented core structural logging that transforms geological analysis in mining.
This new digital solution facilitates the acquisition of structural information in the exploration phase and optimizes the results of mining operations. StructMaster™ is the next generation oriented core logging solution, designed to simplify data collection and reduce human error in real time from anywhere in the world.
At an exclusive event, geologists and industry experts will be able to witness the global launch of StructMaster™. With limited seating available, SPT invites all interested to reserve a seat for the presentation on March 2 at 3:00 p.m. in Room 204 - Level 200 of the North Building, Metro Convention Center – Introducing StructMaster™: The Next Generation in Oriented Core Logging.
This launch of oriented core logging expands SPT’s product catalog, which includes tools for rig alignment, directional surveying and core orientation, to take the accuracy of mining projects to the highest level. It demonstrates SPT’s commitment to data accuracy and reliability for more informed and strategic decision-making in mining exploration and development. C
↑ Figure 1 - Mineralized bedding replacement
by Michael Thomsen, Chairman at North American Strategic Minerals Inc.
Located in the Papua Province of Indonesia, the Ertsberg deposit lies within a mountainous region known for its rugged terrain and complex geological history.
It is positioned near the large Grasberg mine, making it part of a prolific mining district that yields substantial copper and precious metals. The geology of the immediate Ertsberg area is dominated by skarn deposits, a product of contact metamorphism where intruding magma interacts with carbonate rock, creating a mineral-rich environment through chemical replacement.
The Ertsberg deposit stands as a prime example of copper skarn mineralization and has contributed greatly to the geological understanding of such deposits. Its unique textures, for example the chal-
copyrite-replaced foraminifera and brecciated structures, make it a focal point of study for skarn formation processes and post-mineral structural modifications. Additionally, Ertsberg’s history illustrates the challenges and rewards of mineral exploration in remote and geologically complex regions.
For mining engineers, drillers and geologists, the Ertsberg deposit provides valuable lessons in resource estimation, mining design, and
the importance of recognizing geological processes. Its position in the mining world is emblematic of the resource potential that skarn systems hold, as well as the intricate geological processes that create such deposits.
The Ertsberg deposit has a vertical, ovoid structure, with approximately one-third of the orebody exposed above ground and the remaining two-thirds extending below ground level. Its vertical orientation in such a remote and rugged area adds to the deposit’s extraction complexity, necessitating innovative mining techniques. The mineralized zone is largely composed of chalcopyrite and magnetite, with unique textures and structural features resulting from various geological processes.
The Ertsberg deposit exemplifies a typical skarn replacement of the original silty carbonate host rock. During mineralization, fine-grained sediment bedding layers were massively and selectively replaced by primarily chalcopyrite and magnetite, resulting in detailed textural patterns. Below are some notable ore textures found in Ertsberg:
1. Replacement textures: In typical skarn deposits, primary host rock minerals are gradually replaced. Figure 1 from Ertsberg
demonstrates this process, where fine-grained sediment layers are intricately replaced by chalcopyrite and magnetite. This quiet, systematic replacement showcases the skarn’s mineralogical evolution, a defining feature of this copper-rich deposit.
2. Crackle breccia: Another distinctive feature is the presence of crackle breccias within the orebody. Figure 2 highlights a brecciated texture with angular fragments of chalcopyrite encased in an opaline silica cement. Crackle breccias form when post-mineralization structural forces fracture the orebody, creating angular fragments that are later cemented by secondary minerals. This texture provides valuable insights into the geological history of tectonic forces acting on the orebody post-mineralization.
3. Fossiliferous bedding and foraminifera: The host lithology of Ertsberg includes fossil-bearing layers with large foraminifera, particularly Discocyclina. During mineralization, these foraminifera were replaced by chalcopyrite and magnetite, resulting in elongated, wispy textures within a calcsilicate groundmass. This fossilized texture, visible in Figure 3, serves as an important marker of pre-existing biological activity within the host rock, overprinted and replaced by mineralization processes typical of skarn systems.
4. Shattered chalcopyrite zones: Ertsberg’s orebody also displays post-mineral shattering in certain zones. Figure 4 shows massive chalcopyrite fragmented by structural activity, likely due to tectonic stresses following mineral deposition. This texture is unique and provides evidence of the post-mineral deformation processes that have reshaped parts of the orebody.
5. Downstream cobble: Figure 5 is a fist-sized cobble found several kilometers downstream from the deposit, containing angular fragments of chalcopyrite, magnetite, and hematite embedded in a
siliceous matrix. This cobble offers a unique clue to the deposit’s presence upstream and the dispersal of its materials over time. Such cobbles serve as indicators of upstream mineralization, and in this case, offer a spectacular bit of evidence of what is outcropping upstream.
The Ertsberg deposit owes its formation to complex interactions between hydrothermal fluids and carbonate host rocks. As magma from deep within the Earth’s crust intruded into the sedimentary layers, high-temperature fluids rich in metals permeated through, chemically replacing the original rock with mineralized zones rich in copper and other metals. The chalcopyrite and magnetite present in Ertsberg are products of this process, typical in copper skarn deposits, where iron-rich minerals interact with sulfur and other metal-rich solutions, precipitating valuable ore minerals.
Skarn deposits often exhibit zonation, with different minerals concentrated at varying distances from the intrusion. At Ertsberg, chalcopyrite and magnetite dominate the inner zones, while the presence of other skarn minerals (e.g. garnet and diopside) in surrounding areas suggests zoning reflective of temperature and chemical gradients.
This zonal distribution aids geologists in interpreting the fluid pathways and the thermal history of the deposit, enhancing the understanding of ore genesis within the deposit.
Ertsberg’s orebody shows clear signs of structural modification after mineral deposition. The presence of crackle breccias and shattered chalcopyrite zones speaks to significant post-mineral tectonic activity. These structural disruptions likely occurred during regional tectonic shifts, which fractured and re-cemented portions of the orebody, creating unique mineral textures. The opaline silica cement in crackle breccias further indicates secondary mineralization events that occurred after the primary copper and iron mineralization.
The Ertsberg deposit, a marvel of geological processes, offers insights into the formation and evolution of skarn-type copper mineralization. From its detailed replacement textures to post-mineral brecciation, Ertsberg encapsulates a rich history of geological activity. This deposit remains a significant case study for geologists and mining engineers, exemplifying the mineral wealth that skarn systems can yield and the complexity of their structural and mineralogical characteristics. For those involved in mining geology, understanding Ertsberg is essential, offering both inspiration and knowledge that is fundamental to the field. C
For more information Get in touch with Michael on LinkedIn
Made from 4140 USA Steel
• 3m barrel consists of 2 interchangeable pieces for rotation when front end wears
• Only Core Barrel with fully machined outer diameter
• About 15% heavier for long-lasting durability
Deep Milled Spiral Channels
• Deep milled spiral channels reduce water pressure by 15-20%
• Reduced chance of getting stuck due to absence of flat sides
• Minimal vibration from continuous spiral grooves
• Improved bit lifespan by 10-15% with better flushing and hole cleaning
• Facilitates in-hole pump action for clearing cuttings
Customer Experience
• Achieved 3-4 times more meterage than competitors
• Achieves substantial less deviation than any competitor
• Option to add stabilizer ring for inner tube stabilization
• Can be used for both 1.5m & 3m by changing reamer length
• Easy shipping in 2m box
• High client satisfaction, evidenced by reorders
Available in N, H, P, 1.5m & 3m Configurations
by Dr Jim Yaxley, Owner of Grasstree Resources
The beauty, rarity and unique properties of gold make it one of the most sought-after metals. One of the significant processes contributing to the genesis of gold nugget formation is the interplay of redox (reduction-oxidation) reactions driven by the ebb and flow of groundwaters in ancient surface systems. These reactions shape the mineralogy and availability of gold in unique geological settings.
Groundwater occurrence can be simplified by grouping into three aquifer categories: surficial, sedimentary, and fractured rock aquifers. Locally, groundwater provides most domestic and stock water requirements from small supplies of fresh to brackish groundwater sourced from colluvium, valley-fill alluvium, and laterite aquifers. Away from the drainage lines, low-yielding supplies can be sourced from colluvial hillslope wash, weathered bedrock and from fractures and shear zones within the bedrock. Bore yields from fractured rock aquifers are variable and water quality is mostly related to bedrock type, with fluctuations of water levels driving redox reactions below the surface often related to dissolved oxygen and the movement of ions as can be seen in Figure 1.
↑ Figure 3 - 59 oz (1.67 kg) nugget with manganese oxide coating
↑ Figure 4 - Gold formation within gossanous rock mass resulting from the oxidation of sulfides (images courtesy of Stephen Woods)
Australia is characterized by a rich geological history that includes the deposition of sediments in ancient palaeodrainage systems and lakes. These lakes provided an ideal environment for various geochemical processes to occur, particularly during periods of fluctuating water levels that drive redox reactions. The interaction between organic matter, minerals, and changing environmental conditions facilitated the growth of gold nuggets.
Large gold nuggets which have formed within a supergene alteration zone associated with hydrothermal mineralized deposits. These nuggets are intergrown with quartz and iron oxyhydroxide that have replaced sulfide minerals, and they can also be found along fractures in both quartz and the surrounding host rocks. The supergene in this case oxidation processes driven by groundwater interactions with rock (Figure 2), occur with the oscillation of reduction and oxidation driven by groundwaters. This process has been described in Craw et al. (2016) as involving clay alteration and oxidation extending up to tens of meters below the surface.
In sulfide deposits, the oxidation of pyrite and arsenopyrite produced temporary thiosulfate ligands that mobilized microparticulate gold previously encapsulated in sulfide minerals (Machesky et al., 1991).
Nugget morphology can vary markedly, ranging from large massive pieces (Figure 3) to those that display some crystalline structure, composed of anhedral grains, elongated gold plates, and intricate intergrowths of gold and iron oxyhydroxide. Their surfaces feature additional micron-scale overgrowths of microparticulate gold, gold plates, and gold crystals.
Redox, or reduction-oxidation reactions, are chemical processes involving the transfer of electrons between substances. In the context of shallow oxide gold formation, redox reactions play a pivotal role in mobilizing and precipitating gold from its primary sulfide sources. The cycling of redox states in sediments influences the solubility of gold-bearing minerals, affecting their concentration and localization. Oxidation of sulfides: The oxidation of sulfide minerals, often rich in gold, occurs when they are exposed to oxygen, particularly in shallow,
oxygenated (aerobic) waters. This can lead to the breakdown of sulfide minerals, releasing gold into the solution with subsequent deposition in the gossan (Figure 4). This process is pivotal in weathering environments, where oxidizing conditions prevail (see Boyle, 1979; Webster, 1984; and Mann, 1984).
Formation of gold complexes: As sulfides oxidize in the rock mass and become gossanous, gold may form complexes with various ligands, such as chloride or thiosulfate (Figure 5), which enhance its solubility in water and mobility. This solubility is affected by pH, temperature, and the presence of organic matter, which can act as stabilizing agents. The presence of organic matter can also play a crucial role, as it may contribute to the complexation of gold ions (Vasconcelos, 1991 and Kyle, 1991; Usher et al., 2009).
Precipitation and concentration: As conditions — such as changes in pH or redox potential — fluctuate, gold complexes can precipitate, often forming secondary gold minerals. This precipitation is more likely in environments with lower solubility, such as during dry periods when water table levels drop.
The interaction between groundwater and oxidizing conditions enhances the dissolution and subsequent reprecipitation of gold, creating nuggets characterized by distinctive textures and compositions (see Reith et al. 2007; 2010; 2012). Oxidizing groundwaters also play a critical role in the geochemical precipitation and gold formation within voids and fractures of the quartz (Figure 6) often accompanied by limonite (oxyhydroxide). As groundwater flows through reduced mineral-rich environments, it facilitates the breakdown of sulfide minerals, such as pyrite and arsenopyrite, releasing sulfuric acid and enhancing the acidity of the water. This acidic environment promotes the dissolution of gold and other metals releasing them, forming soluble thiosulfate complexes that can transport gold over considerable distances. The interplay between the oxidizing conditions and the reactive carbonaceous material creates a favorable setting for gold mobilization and concentration. As the groundwater continues to circulate and equilibrate, changes in pH and redox conditions lead to the precipitation of native gold in nearby structures, contributing to the formation of significant gold deposits within these quartz reefs.
↑ Figure 7 - This nugget is full of cavities and was quite ‘spongey’ due to the growth around alluvial sediments on a paleo lake shore in the Northern Territory
This intricate geochemical process underscores the importance of understanding groundwater chemistry in exploration.
Erosion subsequently transports these nuggets into sediments sometimes called placers, where they concentrate in placers located near the basal unconformity. Further recycling introduced gold into Pleistocene fluvial channels. During this process, gold dissolution and redeposition occur on the exterior surfaces of placer gold particles, resulting in the formation of plates and crystals with minimal change in mass.
Redox reactions drive the mobility of gold within shallow oxide zones, involving the transfer of electrons in the chemical environment, particularly the oxidation state of various minerals. The key processes include:
Gold complex formation: The released gold can form soluble complexes with inorganic ligands (e.g. chloride, thiosulfate) that enhance its mobility. This solubility is affected by pH, temperature, and the presence of organic matter, which can act as stabilizing agents (Vasconcelos and Kyle, 1991; Usher et al., 2009).
Precipitation mechanisms: As environmental conditions fluctuate—such as during periods of drying or changes in salinity— gold complexes may precipitate, leading to localized enrichment. This phenomenon is often observed in supergene environments, where weathering processes concentrate gold from underlying hydrothermal sources (Bowell et al., 1993; Hough et al., 2007; 2009).
Ancient water tables in northern Australia were dynamic ecosystems where the chemistry of the water influenced gold solubility and precipitation. Factors that contributed to gold remobilization and concentration include:
Evaporative processes: Seasonal evaporation can increase salinity, promoting the precipitation of gold as environmental conditions become less favorable for its solubility (Hough et al., 2007; 2009).
Biological mediators: Microbial activity can alter the local redox state, facilitating the oxidation of sulfide minerals and the subsequent release of gold. These biological processes are essential in understanding the gold dissolution pathways within these ecosystems (Reith et al., 2007; 2010; 2012).
Hydrological changes: Fluctuations in water levels and chemistry due to climatic changes impacted the concentration of gold in these ancient environments. As climate shifted towards more arid conditions, the cycling of water and sedimentation patterns further influenced gold distribution (Youngson and Craw, 1995). This can lead to formation of large nuggets, commonly with distinctive morphology (Figure 7). C
References
• Bowell, R.J., Gize, A.P. and Foster, R.P., 1993. The role of fulvic acid in the supergene migration of gold in tropical rain forest soils. Geochimica et Cosmochimica Acta, 57(17), pp.4179-4190.
• Boyle, R. W. (1979). The geochemistry of gold and its deposits. Geological Survey of Canada Bulletin, 280, 1-584.
• Craw, D., & Lilly, K. (2016). Gold nugget morphology and geochemical environments of nugget formation, southern New Zealand. Ore Geology Reviews, 79, 301-315.
• Hough, R. M., Noble, R. R. P., & Reich, M. (2007). Natural gold nanoparticles. Ore Geology Reviews, 42(1), 55-61.
• Hough, R. M., Noble, R. R. P., Hitchen, G. J., Hart, R., Reddy, S. M., Saunders, M., ... & Anand, R. (2009). Naturally occurring gold nanoparticles and nanoplates. Geology, 37(5), 443-446.
• Machesky, M. L., Andrade, W. O., & Rose, A. W. (1991). Interactions of gold (III) chloride and elemental gold with peat-derived humic substances. Chemical Geology, 102(1-4), 53-71.
• Reith, F., Lengke, M. F., Falconer, D., Craw, D., & Southam, G. (2010). The geomicrobiology of gold. The ISME Journal, 4(9), 1133-1147.
• Reith, F., Rogers, S. L., McPhail, D. C., & Webb, D. (2007). Biomineralization of gold: biofilms on bacterioform gold. Science, 313(5784), 233-236.
• Reith, F., Stewart, L., & Wakelin, S. A. (2012). Supergene gold transformation: Secondary and nano-particulate gold from southern New Zealand. Chemical Geology, 320-321, 32-45.
• Usher, A., McPhail, D. C., & Brugger, J. (2009). A spectrophotometric study of aqueous Au(III) halide–hydroxide complexes at 25–80°C. Geochimica et Cosmochimica Acta, 73(11), 3359-3380.
• Vasconcelos, P. M., & Kyle, J. R. (1991). Supergene geochemistry and crystal morphology of gold in a semiarid weathering environment: Application to gold exploration. Journal of Geochemical Exploration, 40(1-3), 115-132.
• Webster, J. G., & Mann, A. W. (1984). The influence of climate, geomorphology and primary geology on the supergene migration of gold and silver. Journal of Geochemical Exploration, 22(1-3), 21-42.
• Youngson, J. H., & Craw, D. (1995). Evolution of placer gold deposits during regional uplift, Central Otago, New Zealand. Economic Geology, 90(4), 731-745.
For more information
Get in touch with Jim on LinkedIn
by Somdutta Ghosh, Master in Geology at University of Calcutta
I have noticed that in every industry the main challenges are to reduce the cost and to ensure the value of time. The exploration and mining industry is no different and Machine Learning (ML) can be the best tool for this purpose. Nowadays, ML algorithms are performing by generating a bunch of code and can carry out thousands of people’s tasks. What are you thinking? The role of humans is going to be diminished?
Not at all, the real scenario is quite different. It is just a smart approach to use Artificial Intelligence (AI) and ML to increase the success rate because we are in the age of digital mining. As such, ML can be
used as a high-tech treasure hunter to find out our desirable minerals. The algorithms can typically give insight into hydrothermal mineral deposits much faster than the core sampling result can. I am not saying this is the replacement of manual fieldwork or laboratory work, but it can be the best way of doing some smart work to ensure the right direction.
ML is a sub-category of AI. Using this technique, we can solve complex problems even without being an expert in programming (Jooshaki et al., 2021). We can train the computer with the help of large available datasets and then ask it to make predictions when presented with new information.
ML can make predictions based on geological datasets and also perform data analysis. Examples include:
• It can help us visualize the pattern of datasets by generating figures and diagrams. Datasets can be geochemical data of an igneous complex, a core sampling dataset of an exploration or a geophysical seismic dataset.
• ML can train a model to create prospectivity maps before selecting a mining area, which can give us a better understanding of the presence of desirable minerals for a project.
• AI can analyze aerial photography and satellite imagery. It can assist with identifying the geological features, the alteration of mineralogies, and hydrothermal deposits.
• Risk assessment and environmental sustainability is the biggest concern nowadays. ML can help make decisions on dependable features and physical conditions.
• Missing values are a common headache for every sector. We also face problems with that in mining and exploration. ML fills the gap. We can handle it with deletion and imputation methods. Firstly, if there are a few missing values then we can go with the simple deletion method. Yet, when it comes to a major gap in the dataset, we use some common statistical methods like mean, median, or mode imputation. There are some other imputation methods in ML, such as K-Nearest Neighbors (KNN) imputation and other methods like model-based imputation.
The best part of ML is that it can study the data and find patterns in it that might be missed by humans.
Let’s say you already know where the minerals are and few treasures are buried. Now we can teach the computerized algorithms to discover the common spots that could contain our wanted minerals. This supervised model (Figure 1) is initially trained on known data (the training dataset), which
includes labeled data — data where each input is paired with a known output. After the model is validated, it can be used to predict or classify the unseen data (the testing dataset) based on what it has learned from the labeled data. There are many algorithms such as Random Forest (RF), KNN, Support Vector Machines (SVM), Artificial Neural Networking (ANN), and so on. Supervised learning techniques are used to classify the rock types based on mineralization patterns and geochemical data. In mineral processing, these models predict potential difficulties in mineral separation and identify the target mineral for extraction. SVM and RF have been used to recognize geological features and make classifications and predictions based on these characteristics. Additionally, KNN and ANN have been successfully applied to predict the ultimate tensile strength (UTS) of materials in exploration (Santos et al., 2009).
This one is a little bit mysterious. Because the algorithms have no previous experience, they try to find out on their own, which looks reliable. It can be just like one of your friends who always guides you without even having experience. That means it does not require labeled data like supervised learning. The clustering method and dimensionality reduction are the two major techniques for this type of ML. K-means clustering, agglomera-
tive clustering, and density-based clustering are used to group similar mining blocks, materials, or geological features based on some of their inherent properties like grade or mineral content. In material science, the clustering method has been used to classify nanoparticles, such as silver and platinum, according to their structural similarities and other properties. These can help enhance mining planning strategies. Additionally, unsupervised learning can be used to analyze satellite imagery for mineral exploration, which is advantageous for identifying potential deposits and making environmental assessments before digging.
By using these supervised and unsupervised algorithms, industries have recently made significant improvements in resource discovery, mining planning, sustainable operations, and cost optimization.
A January 2021 report from Northstar Gold Corp mentions the advancement of mining strategies in the exploration of the Miller Gold Property in Northeastern Ontario. They have found eight new gold spot discoveries by using the machine learning clustering method and 3D mapping technologies,
which were beyond their expectation. The discoveries were made by applying machine learning methodologies to data from previously known gold zones. After 2021, their fund increased by CAD 2.4 million and they started more drilling.
Rio Tinto is already using AI and data science to get better results. The company aims to modernize the mining industry and introduce digital technology. They employ predictive models that analyze geological data to predict new orebodies. The company also enhanced safety and reduced the risks for their exploration team by applying ML techniques to their reported data.
A September 2024 study from Datarock has mentioned some strategies with neural networks to enhance geological features in drill core photography. For geological core sample images, it is very common to have some artifacts, and sometimes it becomes very difficult to see the important features of the rocks. Using a Convolutional Neural Network (CNN) can help us. This methodology enhances the accuracy of the logging. By using this CNN deep learning method, detecting geological features like veins, fractures, grains, and similar textures has become easier.
So, there is no doubt that ML is considered a new technology in some mining industries. AI and ML are used globally to improve exploration and help companies discover precious metals in places that might have been overlooked. By mixing historical data with technology, we can reduce the exploration cost and make better estimations where to dig next.
ML is the green card for geologists to make a game-changing contribution to scientific work and industries as well. Now we can imagine the picture of a geologist without being out in the field with a hammer and collecting rock samples one by one. I think ML is not only about being dependent on technology, it is just getting smarter. Together, humans and ML are redefining exploration. The reasons why ML rocks (pardon the pun) include:
• Quick result: It can give us a result faster than manual digging.
• Accuracy: The accuracy depends on the data that the model has been trained on.
• Budget-friendly: It cuts down the cost of exploration by using datasets to predict the target area.
• Smart-learner: The more data we feed it, the smarter result it can give.
According to a report from Market.us, the global Al in mining market size is expected to reach around USD 7.2639 billion by 2033 from USD 939.1 million in 2023.
Now, some might think that ML is just like magic and that can fix everything, but it is not without flaws. In some cases, there is insufficient historical data, which makes training the ML model difficult. Another major issue arises when the model performs poorly when applied to real life problems. This could be the result of inaccurate or incomplete data used for training it, or not achieving the optimal balance between model complexity and its ability to generalize on new scenarios. We cannot imagine a tasty recipe without the availability of all ingredients needed and in appropriate quantities.
Looking ahead, in the future ML will have a promising role in the mining sector. On the other hand, we have already noted some challenges, including data quality and technological adaptations, which are under the supervision of computer scientists. We are proceeding in the right direction to become a part of a graceful future. In mineral exploration, ML is going to open a new pathway for discovering the mineral jackpot and helping solve the remaining mysteries of the hidden treasures of our mother Earth. C
• Jooshaki, M., Nad, A., & Michaux, S. (2021). A Systematic Review on the Application of Machine Learning in Exploiting Mineralogical Data in Mining and Mineral Industry. Minerals, 11(8), 816. https://doi.org/10.3390/min11080816
• Santos, I., Nieves, J., Penya, Y.K., Bringas, P.G. (2009). Optimising Machine-Learning-Based Fault Prediction in Foundry Production. In: Omatu, S., et al. Distributed Computing, Artificial Intelligence, Bioinformatics, Soft Computing, and Ambient Assisted Living. IWANN 2009. Lecture Notes in Computer Science, vol 5518. Springer, Berlin, Heidelberg. https://doi.org/10.1007/978-3-642-02481-8_80
For more information
Get in touch with Somdutta on LinkedIn
Environmentally safe drilling fluid systems and lubricants for diamond drilling, horizontal directional drilling, rotary and percussive drilling.
Downhole lubricants
Specialty polymers
Foams
Tool lubricants
Blast hole stabilizers
Thread compounds
All of our proprietary, vegetable oil-based products improve penetration rates and reduce drilling costs.
Drilling MADE EASIER
Drilling Contractors (A-Z): Diamond Drilling, Reverse Circulation, AirCore
Drilling Contractors (A-Z): Cont.
BRYSON DRILLING
Phone 306-323-2202
Fax 306-323-2203 info@brysondrilling.ca www.brysondrilling.ca Canada
CAPITAL DRILLING
Phone +230 464 3250 info@capdrill.com www.capdrill.com East, North and West Africa
DDH1 DRILLING
Phone +61 08 9435 1700 admin@ddh1.com.au www.ddh1.com.au Australia
DIAFOR
Phone (819) 860-3957 info@diafor.ca www.diafor.ca Canada
KATI OY
Phone 0207430660 info@oykatiab.com www.oykatiab.com Finland
MITCHELL SERVICES
Phone +61 7 3722 7222 Fax +61 7 3722 7256 info@mitchellservices.com.au www.mitchellservices.com.au Australia
ATELIER VAL-D’OR
Phone (819) 824-3676
Fax (819) 824-2891 info@avddrills.com www.avddrills.com
BARKOM
Phone 90-312 385 60 50 Fax 90-312 385 35 75 info@barkomas.com www.barkomas.com
PROLENC
Phone (250) 563-8899 Fax (250) 563-6704 khodgins@prolenc.com www.prolenc.com
BOART LONGYEAR
Phone 1-801-972-6430 Fax 1-801-977-3374 www.boartlongyear.com
DISCOVERY DRILL
MANUFACTURER
Phone 1-506-542-9708 Fax 1-506-542-9709 info@discoverydrills.com www.discoverydrills.com
NORTH BAY MACHINING CENTRE
Phone (705) 472-9416 Fax (705) 472-2927 luc@nbmc.ca www.nbmc.ca
PROLENC
Phone (250) 563-8899 Fax (250) 563-6704 khodgins@prolenc.com www.prolenc.com
www.diatoolglobal.com anthonygraham6@gmail.com
DIATOOL is a young and dynamic company, founded in 2010. The company manufactures impregnated and set core bits, casing shoes, reaming shells, and geotechnical drilling bits. DIATOOL products are sold in North and South America, Australia, Asia, Africa, and Europe. DIATOOL Diamond Products are manufactured in a modern well-equipped plant, using the latest manufacturing technology.
DIAMANTINA CHRISTENSEN
Phone +562 2620 7808 christensen@christensen.cl diamantinachristensen.com
DIASET Phone 1-800-663-5004 bits@diaset.com www.diaset.com
DIATOOL DIAMOND PRODUCTS Phone 852 2871 9028 diatool@163.com www.diatool@global.com
HOLE PRODUCTS Phone (888) 465-1569 Fax (320) 631-0064 www.holeproducts.com
Survey Tools Cont.
REFLEX
Phone 1-705-235-2169
Fax 1-705-235-2165 reflex@imdexlimited.com www.reflexnow.com
SONDA PARTS
Phone 55 – (31) 3391 3810 Fax 55 – (31) 3391 3810 comercial@sondaparts.com.br www.sondaparts.com.br/
AMC Phone 1-705-235-2169 www.amcmud.com
DI-CORP
Phone +1 (705) 4727700 info@di-corp.com www.di-corp.com
MUDEX Phone +61 (8) 9390 4620 info@mudex.com.au www.mudex.com.au
Fluids Cont.
COREFINDER Phone +55 62 992720023 contato@corefinder.com.br www.corefinder.com.br
CORE TECH Phone +51 983 856 666 info@coretech.com.pe www.coretech.com.pe
DYNAMICS G-EX Phone +61 7 54826649 sales@dynamicsgex.com.au www.dynamicsgex.com.au
Surveying & Geophysics (A-Z)
CORE TECH
Phone +51 983 856 666 info@coretech.com.pe www.coretech.com.pe Peru
DIGITAL SURVEYING
Phone +27 18 788 6349 sales@digitalsurveying.co.za www.digitalsurveying. com.za Africa
TRUST SOLUÇÕES
GEOLÓGICAS
Phone +55 62 992720023 contato@trustsg.com.br Brazil
United. Inspired.
Exploration & Geoscience
We believe efficient data collection and smart analytics are key in unlocking ore body insights, leading to better decisions.
With a stronger than ever offering and reinforced expert team, we can help you achieve this. From the initial hole in the ground, to the empowering data on your screen, we can accelerate exploration.