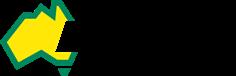
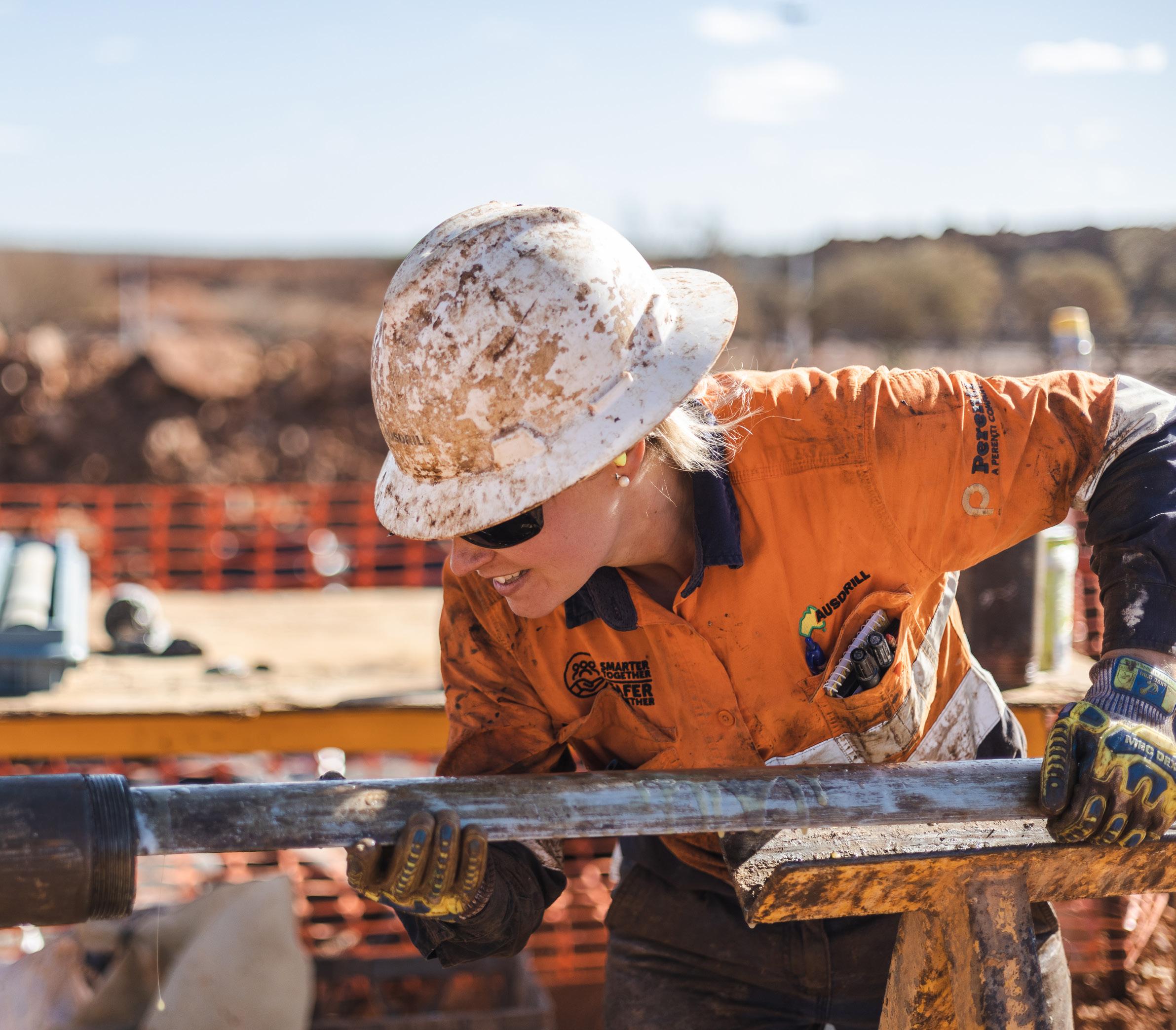
Newly Improved Surveying Capabilities:
Next-generation Axis engineering to enable High Speed Vertical Continuous
Surveying from Vertical to Horizontal
Re-engineered for improved Azimuth accuracy & repeatability
Further optimisation of sensors & software for high-latitude North-Seek stability
Ausdrill: 37 years of innovation in safety, sustainability, and productivity by Mary Jane Rowan, Marketing & Communications Specialist at Ausdrill
REVIEW
20 BlastGyro®: Born in the oilfield, matured underground by Dag Billger, Owner & Business Manager and Duncan McLeod, Owner & Product Manager at Inertial Sensing
26 Exploring the future of Snow Lake with Rodren Drilling by Derek Anderson, Health & Safety Manager and Denis Desrosiers, General Manager at Rodren Drilling /TECHNICAL ARTICLE
28 Exploration rigs and electronic controls by Peter Kuusimaa, Owner of Comet Tech
/EXPLORATION & MINING GEOLOGY
33 Q&A from the experts: In conversation with Dr Sally Goodman VP Generative Exploration at Newmont Corporation
38 The dilemma of geological control for underground ore development by Steve Rose, Principal Mining Geologist at Rose Mining Geology Consultants
42 Unveiling hidden treasures: The fascinating process of gemstone and mineral specimen exploration and exploitation in Pakistan by Noor Ullah, Business Owner at Gandhara Gemstones
46 The big history of mining in Serbia and the bigger challenges of today by Dragan Dragić, Exploration Manager at Konstantin Resources
Drilling services
Drilling equipment & accessories
Survey equipment 58 Miscellaneous
Viktor Tokle
Founderof Devico
Derek Anderson, Health & Safety Manager
Denis Desrosiers, General Manager at Rodren Drilling
Mary Jane Rowan Marketing & Communications Specialist at Ausdrill
Dag Billger, Owner & Business Manager
Duncan McLeod, Owner & Product Manager at Inertial Sensing One AB
Peter Kuusimaa
Owner of Comet TechDr Sally Goodman
VP Generative Exploration at Newmont CorporationCORING MAGAZINE
May 2024
Cover photo Ausdrill Issue 27
ISSN 2367-847X
Not for resale. Subscribe: coringmagazine.com /subscribe
Contact Us
Coring Media Ltd.
57A Okolovrasten pat street, r.d. Manastirski Livadi, Triaditsa region, 1404 Sofia, Bulgaria
Phone +359 87 811 5710
Email editorial@coringmagazine.com Website coringmagazine.com
Steve Rose Principal Mining Geologist at Rose Mining Geology Consultants
Noor Ullah
Business Owner at Gandhara Gemstones
Publisher Coring Media
Executive Officer & Editor in Chief Martina Samarova
Editor
Maksim M. Mayer
Section Editor – Exploration & Mining Geology
Dr Brett Davis
Digital Marketing Manager Elena Dorfman
Assistant Editor Nevena Lyubenova
Graphic Design Cog Graphics
Dragan Dragić
Exploration Manager at Konstantin Resources
Coring Magazine is an international quarterly title covering the exploration core drilling industry. Published in print and digital formats, Coring has a rapidly growing readership that includes diamond drilling contractors, drilling manufacturers and suppliers, service companies, mineral exploration companies and departments, geologists, and many others involved in exploration core drilling.
Launched in late 2015, Coring aims to provide a fresh perspective on the sector by sourcing authentic, informed and quality commentary direct from those working in the field.
With regular interviews, insightful company profiles, detailed product reviews, field-practice tips and illustrated case studies of the world’s most unique diamond drilling and mineral exploration projects, Coring provides a platform for learning about the industry’s exciting developments.
Exploration & Geoscience
We believe efficient data collection and smart analytics are key in unlocking ore body insights, leading to better decisions.
With a stronger than ever offering and reinforced expert team, we can help you achieve this. From the initial hole in the ground, to the empowering data on your screen, we can accelerate exploration. United. Inspired.
Viktor Tokle began his career at the research institute SINTEF after getting a mechanical engineering degree from Trondheim Technical College. His work took him to numerous construction sites and mines across Europe. It was during a rock mechanics assignment in 1986 that Viktor got the idea for a steerable drill. He took a leap of faith, and in 1988, he started Devico and forever changed exploration drilling.
Viktor knew accurate borehole steering is only possible with accurate borehole surveys and efficiently planned drill programs. So, four years later, in 1992, he launched the DeviSoft directional drill planning software and in 1995, the DeviTool, the first electronic survey tool in the industry to stay onboard during drilling.
In the years since then, Devico has become the number one global provider of directional drilling services in mineral exploration. The group has 21 companies in 15 countries and about 200 employees.
Grigor Topev: Viktor, it’s been a while. Having started my career at Devico, I hold some wonderful memories, so it’s a true pleasure to have you here for this interview. Let’s start by telling us more about your employment with the industrial research foundation SINTEF and how the foundation helped shape your career.
Viktor Tokle: Thank you, Grigor, I also have many good memories from that time. After completing my mechanical engineering studies at Trondheim Technical College, I was employed as a field engineer at SINTEF. There, I worked with rock mechanics and mine measurements, carrying out assignments across Europe. I worked in a research environment and had the opportunity to intern in various departments at the institute. I also gained experience with measurement techniques, including measuring rock stresses with strain gauges. This technology later proved to be applicable in DeviFlex. The assignments were numerous and varied, allowing room for creativity and problem-solving. It was during the rock mechanics assignments that I got the idea for the steerable drill. It was also during these assignments that I was exposed to rock dust, which would later limit my physical capacity and lead to a slightly early winding down of my active career. I hereby urge everyone in the industry to take HSE seriously; nothing is more important than health.
GT: You developed a system for directional core drilling, which later became DeviDrill. How did you come up with the idea? Was it initially intended for mining and tunnelling, considering Norway’s significant oil and gas industry?
VT: Part of my job involved measuring borehole deviations around the country, both for tunnel construction and mining. I quickly realized that there is a need to control boreholes as they often ended up far from where they were planned. In one instance, the drill ended up 500 m (1640 ft) away from where it should have been after 700 m (2297 ft) of drilling. The idea came after we made a drill in connection with rock mechanics that was supposed to bore completely straight. By tilting the drill bit and using a gripping system, we could steer the drill wherever we wanted. We tested various mechanical gripping systems but settled on using pressure differential in the drilling fluid to design a gripping system. This turned out to be the key to creating a functional drill. The principle of pressure differential has been present in all variations of the drill, from Stepdrill to Slidingdrill and finally to the wireline version.
body allowed the outer body to slide forward during drilling. DeviDrill also included a mud pulse tool called DeviGuide that sent a pressure pulse as soon as the drill came out of orientation.
GT: What’s the story behind Devico? How did you decide to establish the company, and who were your partners?
VT: After we patented the principle, SINTEF wanted the idea to be sold to a larger company or alternatively for me to start my own company. After pondering for a few days, I decided to start Devico, which stands for Deviation Control. SINTEF became a 30% shareholder and also donated measuring instruments so that borehole measurement activities could contribute financially to the company. At that time, there were film-based multi- and single-shot instruments. After a couple of years of operation, the Trondheim company Teeness joined as a shareholder.
Around the same time, Reflex launched the Maxibor measuring instrument. The development had cost too much, and the founder was out of funds. I believed this was a good match and recommended Teeness to acquire Reflex. The plan was for Devico to develop directional drills and Reflex to develop measuring instruments. We were too early, and it didn’t turn out to be a good match at that time. After a few years, we bought ourselves out and continued on our own. Reflex and the founder Claes Erikson also ended up going on their own and eventually ended up in IMDEX. Now, almost 30 years later, both companies are once again united, so we believe the time is right now.
‘When we started on our own, we also began developing our own instruments - IR orientation instrument, mud pulse orientation, Devitool EMS, Deviflex and later gyro instruments.’
When we started on our own, we also began developing our own instruments - IR orientation instrument, mud pulse orientation, Devitool EMS, Deviflex and later gyro instruments. One of the first projects after the Teeness period was in Hong Kong. It turned out to be a good market for us as the authorities eventually required all tunnels and underground work to be surveyed using the Devico method. We have had continuous assignments there since then.
GT: I presume you were in the field for DeviDrill’s first field tests. Can you share some stories from these times?
GT: It would be really interesting if you could tell us more about these first directional drills and how they worked.
VT: The very first version was called the Vic drill and had a rubber packer and a powerful spring that pushed the outer body forward after every 20 cm (7.9 in) of drilling.
The next version was the Stepdrill where we removed the spring and used a locking piston to push the outer body forward.
After a while, we ended up with the sliding DeviDrill where we could drill continuously without stop. Installing sharp knives on the packer
VT: The very first tests were done while I was still at SINTEF, where we drilled 20 m (66 ft) through a rock hammer and bent the hole 3 degrees. Considering the idea was to create a domestic market, I couldn’t have chosen a worse time to start Devico. Almost all mines in Norway were closed in the late 1980s, and I had to look for other markets and applications. Sweden had an active mining industry, and we were well-received there, getting jobs in both nuclear power and mining. The first commercial project was in the Viscaria mine in Kiruna, a project that lasted a couple of years and proved the technology’s validity. This was in the early pioneering days, and inventory and logistics were not as developed, so there were many long and rushed car trips over the 1100 km (684 mi) to Trondheim to repair or pick up spare parts. In the absence of a domestic mining market, we opened a market for the survey of underwater tunnels. I believe Devico has been involved in every recent Norwegian fjord crossing. We also demonstrated to
↑ Viktor holding a photo of himself with the very first DeviDrill
the Trondheim municipality tour capability to drill accurate pilot holes for gravity sewer pipelines, leading to a series of similar projects in several Norwegian cities.
GT: Devico launched the wireline version of the DeviDrill in 2001. What are the main differences compared to the original version? How much time did the product development take?
VT: There wasn’t much difference between the original DeviDrill and the wireline version. The principles of the pressure differential-based gripping system, orientation, and offset of the drill bit were the same. It was mainly standard wireline technology attached to a standard DeviDrill, with some adjustments, especially around the thrust bearing and orientation of the drill.
As for how long this took, it’s a relative question. We continuously work on improvements. It’s more of an ongoing process with constant improvements in design, functionality, material choices, etc.
GT: Bearing in mind that Devico opened a new niche, what was its impact on the drilling industry?
VT: It took a long time to convince a conservative industry. Perhaps we started a bit from the wrong end by trying to convince drilling companies and equipment suppliers. They didn’t save anything on reduced meters drilled by so-called branching drilling, nor were the suppliers of drill bits particularly enthusiastic. When we shifted more towards end-users, we were met with more interest, but there was still a lot of skepticism. Now, clients are reporting big savings,
DCD (directional core drilling) has become an accepted technology and is part of geologists’ planning for drilling new deposits.
GT: Can you tell us some unknown facts and stories about Devico?
VT: In connection with the buyout of Devico from Teeness, there was an unpleasant conflict. The owners had agreed with a potential buyer, but the deal required me to be part of it and to move away from Trondheim. I had no desire to move, which led the buyer to withdraw. I was dismissed for disloyal behavior, which was a very unpleasant experience. However, the conflict was resolved when, with the help of good friends, I bought back the company.
GT: What were the most significant moments in the company’s history?
VT: One of the most significant moments was when we got in touch with Bob Dowdell in the Ontario Hydro environment in Canada. They have been patient and supportive during periods when things might not have gone smoothly. They also secured major projects in Boston, New York, Taiwan, and Mexico in addition to the projects in Canada.
Another significant moment I remember was meeting Tokishiro Tani from the Japanese Nikko Exploration at a cabin in Rindal. Nikko offered to contribute to the further development of DeviDrill, which also brought funding from Innovation Norway and external investors. This gave us the financial muscle to enhance DeviDrill and the business model.
GT: Devico is not only successful in directional core drilling (DCD) but also in the realm of downhole surveying tools. Is there one surveying product/development you are proudest of?
VT: There are several measurement instruments I am proud of, perhaps Deviflex ranks high on the list. The first prototype was developed while I was still at SINTEF.
Otherwise, it’s the gyro instruments that we have developed and are among the most advanced and accurate available. I am incredibly fascinated by how the development team has brought this product to life. They are all experts within their field and they work well together. The gyro has become a better product than I had envisioned. For example, ADE (Automatic Depth Estimation), which allows measurement without a wire counter, was something I had not imagined when the project started. This is something the development team has seen along the way and developed as a separate service.
The entire infrastructure and business model around DCD and instruments make great strides when DeviDrill, Gyro, and Cloud work so well together. The end customer now has progress and borehole data almost in real-time through our cloud solution.
GT: Devico as a company has given so much know-how to the industry; several companies, such as BG Drilling Solutions and Aziwell, have begun from Devico. Was this a disappointment or a testament to Devico’s impact on the industry?
VT: Looking back, I feel a sense of pride knowing that the ideas and business model I developed have led to several spin-off companies and generated numerous jobs. I have to admit, though, that initially it was disappointing. We were mostly concerned that copies and imitations would come from outside, and perhaps we were a bit naive towards the risk that employees represented.
GT: Following up on your last comment, I’m interested to hear your thoughts on the Aziwell’s case.
VT: I will not say much about what I think and feel about the Aziwell case, other than to refer to the Court of Appeals’ conclusion that Aziwell unlawfully used the sum of experiences and knowledge (trade secret) that underpins the development and improvements of the Devidrill. For this Aziwell was fined 5 million Norwegian Kroner, but inexplicably to us was allowed to continue using the drill. We appealed the verdict to the Supreme Court but it was rejected.
GT: By my count, there are more than 80 Bulgarian engineers working in the field of directional drilling. That’s substantial. Why do you think they are a good fit?
VT: The Bulgarian field engineers turned out to fit well into our organization. They are reliable, hardworking and very pleasant. Some came directly from university, others with a bit of drilling experience. This mix of experience and education has proven to be a success factor.
GT: Devico’s sale to IMDEX was one of the biggest shifts in our industry. It must have been a difficult decision, so if I may ask, how did you come to it, and were there other options?
VT: Initially, the plan was to own Devico forever. Things have changed along the way, and we realized that Devico had become large and complex. There were subsidiaries all over the world and over 200 employees. We felt that it was time for new owners with more financial muscle. We saw plenty of opportunities to bring out more products, but we didn’t have the capacity. A larger owner could unlock this potential.
Moreover, there was the danger that others could now sell the technology since Aziwell could freely use it after paying the fine they were imposed. We also considered going public, but that wouldn’t solve these issues.
GT: I have heard that IMDEX was not among the initial bidders. Is that true, and who was the main bidder?
VT: There were several bidders, both industrial and private equity funds.
It is true that IMDEX entered the second round after they heard rumors that Devico was for sale. Initially, we had no desire to sell to a competitor and both the management and I did not see IMDEX as a good match. After IMDEX CEO Paul House had some initial discussions with Erlend Olsø (CEO) we became aware of IMDEX’ interest and the potential compatibility. The management team looked into this for a short but hectic period of time, and it was suddenly obvious to all. The vision from 1988 to become the world leader in directional core drilling, borehole deviation measurement, and associated software is now completed.
After giving it some thought, when IMDEX entered the scene, our choice was easy. Reflex and Devico together will become a powerhouse in the industry, something Teenees hoped for 30 years too early.
GT: Do you expect Devico to go through serious changes or restructuring after the acquisition?
VT: IMDEX, which is publicly traded, runs the company in a more professional manner than we did as owners. There has probably been a bit of a different everyday life for the employees with new routines for reporting, budget processes, approvals, etc. Decisions could be taken on a lower level under our management, so it will take some time to get used to this new management style.
So, yes, there has already been a lot of restructuring, it seems to be working fine and most people seem to be satisfied.
GT: What do you think the future holds for surveying equipment and directional drilling?
VT: I think the market will continue to grow as we saw with electronic multishot instruments in the 1990s and with gyro instruments in the 2000s. Equipment will become more user-friendly, more accurate, and we will see further developments in cloud solutions. Deposits are getting deeper and deeper, and the need for DCD will increase in the years to come.
GT: What was the toughest business lesson you have learned?
VT: One of the most important lessons is that you must build the business step by step; it always takes longer time than you think when you start. If you don’t have perseverance and an unwavering belief in what you’re doing, it becomes exhausting. From when we started Devico until we could take dividends, it took almost 20 years. If we hadn’t built the business step by step and made money along the way, we would never have succeeded.
In addition, I would say that I have tried to be honest and fair to both employees and customers all the way. I believe that has paid off in the long run and has given me many friends whom I greatly appreciate.
GT: Viktor, your story is really inspiring and full of valuable input! It was indeed a pleasure to have you featured in our magazine. Thank you! I have one final question. Are you planning to completely retire from entrepreneurship? If not, what are your plans?
VT: I have a few shares in IMDEX, and I will for sure follow them closely, and I am also a discussion partner for the development department. Devico has been a big part of my life, and I wish them all the success in the future. I think it’s an exciting topic and look forward to seeing which way the industry goes forward. Beyond that, I work together with my family investing in new startups in the Trondheim region. We already have many exciting technology companies in the portfolio. C
Editorial note:
The original statements by Viktor Tokle about the legal dispute between Devico and Aziwell raised concerns from the latter and have been revised by the author at the request of the publisher.
Made from 4140 USA Steel
• 3m barrel consists of 2 interchangeable pieces for rotation when front end wears
• Only Core Barrel with fully machined outer diameter
• About 15% heavier for long-lasting durability
Deep Milled Spiral Channels
• Deep milled spiral channels reduce water pressure by 15-20%
• Reduced chance of getting stuck due to absence of flat sides
• Minimal vibration from continuous spiral grooves
• Improved bit lifespan by 10-15% with better flushing and hole cleaning
• Facilitates in-hole pump action for clearing cuttings
Customer Experience
• Achieved 3-4 times more meterage than competitors
• Achieves substantial less deviation than any competitor.
• Option to add stabilizer ring for inner tube stabilization
• Can be used for both 1.5m & 3m by changing reamer length
• Easy shipping in 2m box
• High client satisfaction, evidenced by reorders
Available in N, H, P, 1.5m & 3m Configurations
Ausdrill was founded in 1987 by Goldfield’s legend and pioneer of the Australian drilling industry, Ron Sayers, who started the company with one second-hand rig at the Super Pit, where Ausdrill remains in action 37 years later. Partnering with Golden Shamrock in 1991, Ausdrill expanded throughout Australia and broke into the African market. Within five years, the one-person operation with a few contractors had grown to 225 employees in Australia and 80 in Africa. In 1994, Ausdrill was worth AUD 11 million and listed on the Australian Stock Exchange.
By 1996, Ausdrill had acquired assets from other exploration and drilling companies and entered the specialized lake drilling market. Then, with Eltin, Ausdrill created African Mining Services, diversifying into a broader mining offering. Ausdrill Northwest was formed in 2003, and in 2007, Ausdrill established Drill Rigs Australia as a manufacturer and maintenance service provider for drill rigs and drilling support equipment. The same year, Ausdrill entered a 50/50 joint venture with underground mining company Barminco, which led to the creation of African Underground Mining Services.
Over the years, Ausdrill Group continued to acquire and sell mining-related businesses, culminating with the 100% purchase of Barminco in 2018, transforming the company into one of Australia’s largest mining services companies. In 2019, the Ausdrill Group rebranded as Perenti, while the brand Ausdrill remained with the surface division where it all began 32 years prior.
Today, Ausdrill is a part of the Perenti Drilling Services Division, along with DDH1 Drilling, Ranger Drilling, Strike Drilling and Swick Mining Services, which were recently acquired by Perenti. Together, they form Australia’s largest drilling service provider. Ausdrill’s 590 employees continue to provide exploration drilling, production drilling, blasting services, and geotechnical services to mining majors and junior explorers across Australia.
Ausdrill’s exploration services offer clients assurance through dynamic scalability, reliable operations, and stringent quality control. Exploration rigs include diamond drill rigs with deep hole directional capability to 2000 m+ (6562 ft), RC drilling rigs capable of vertical and angled holes to 500 m+ (1640 ft), and air core drilling, which can be truck or track-mounted. Ausdrill’s cutting-edge hands-free technology and advanced autonomous pathways have positioned them as an industry leader, and with their ‘hands-off steel’ approach, Ausdrill has taken safety standards to new heights in the field.
In October 2023, Ausdrill acquired the Explorac RC30 Smart, a joint development project with Epiroc. This project has resulted in a rig, featuring fully automated rod handling, high-speed operation, process monitoring, remote control, and a range of other improvements. These advancements not only make the job faster, safer, and more efficient but also reflect Ausdrill’s commitment to delivering top-quality equipment.
The Explorac RC30 Smart rig improves operating performance and safety and has also been designed to support future scaling of rig features and functionality. As a result, Ausdrill can easily upgrade the equipment when new automation features become available, keeping pace with industry changes and getting the highest possible return on their investment throughout the drill rig’s life.
More recently, the AustEx X1550TH, a fully integrated electric over hydraulic diamond drill rig operated by a wireless remote, was dispatched by Ausdrill to a client in the Pilbara. The AustEx X1550TH surpasses all other rigs in terms of safety, with a cage barrier protecting ↑ Ausdrill exploration site
the platform. Any access to the platform isolates all rig and sloop functions, creating a zero-energy workspace for the driller’s offsiders to perform tasks. To further strengthen safety, the Freedom Loader sloops have also been modified to use a virtual exclusion zone barrier, utilizing cameras with human recognition capabilities that immobilize functions to the sloop before any personnel can access a live work area.
The AustEx X1550TH is not just about safety; it’s also about efficiency. The drill rig handles rods and inner tubes with ease, even delivering the inner tube to the processing racks. Manual intervention is minimal; only changing the overshot and processing the innertube’s core requires it. Hole collaring and casing are performed hands-free, with the pusher sub seamlessly integrated into the drill spindle.
With Cortex’s advanced rig control system, the AustEx X1550TH takes remote monitoring and control to a whole new level. Operations and maintenance workers can monitor all drill rig data points live from anywhere in the world. This data can be stored for further analysis, helping to optimize the drilling process and maximize productivity.
Ausdrill is recognized as a top-tier provider of drill and blast services. With over 35 years of drilling experience and the use of advanced technology, Ausdrill is capable of addressing the specific needs of its clients while ensuring the protection of the ore body, minimizing dilution, and optimizing the mine-to-mill process. The company has a wide range of drilling capabilities, including probe drilling for voids, drilling at heights, hard-to-reach drilling, and extensive blasting capabilities for both civil and mining projects.
Ausdrill’s commitment to innovation is a cornerstone of its success. The company has a long history of designing and building custom rigs in-house, such as the iconic Rock Commander, a constant symbol of progress and innovation in the mining industry. The Rock Commander was recently upgraded with the introduction of the One Touch Drilling feature, marking a pivotal moment in Ausdrill’s drilling operations and streamlining the entire drilling process with a single touch of a button. One Touch not only optimizes the drilling process for efficiency and precision but also enhances safety by reducing the need for manual intervention and reduces wear and tear, extending the life of components and saving time and money.
The Rock Commander has also been upgraded with advanced features like a training cabin, Trimble Groundworks High Precision GPS, Starlink for remote access to electrical diagnostics, and the latest PLC air control. These additional features enhance the machine’s performance, ensuring precision, safety and efficiency in every drilling operation.
Ausdrill has extensive expertise in blasting with a strong emphasis on ensuring safety. They are adept at working in challenging locations, including those near town sites, powerlines, and gas pipelines and have developed controlled blasting techniques that effectively limit noise, vibration, air overpressure, and dust, ensuring minimal disruption to
the surroundings. Along with extensive blasting knowledge and experience, Ausdrill also offers a range of bulk-licensed products and mobile mixing units, which complement and reinforce the dependability of their blasting services. These additional resources enable them to deliver exceptional blasting solutions while maintaining the highest safety and efficiency standards.
Ausdrill recognizes the pivotal role of grade control programs in mine planning and design, adopting a collaborative approach to ensure their clients achieve the mine’s optimum operational capability. What sets Ausdrill apart is its ability to design and build its own purpose-built rigs, a testament to its commitment to delivering the highest-quality samples and the most reliable service.
Ausdrill’s custom-built auto-sampling drill rig is at the forefront of technology, providing specialized grade control. The autonomous sampling feature is enabled by integrating the Ray-Trac RFID sampling system, which provides clients with a trackable chain of custody, allowing for programmed, executed, and tracked sampling. Their grade control rig also features the Trimble DPS900 high-precision survey guidance system, eliminating the need for drill hole survey markout and pick-up. The Trimble and Ray Trac features facilitate data interface with clients’ software, improving transparency, accuracy, and productivity.
The auto-sampler rig designed by Ausdrill offers notable efficiency improvements and safety enhancements. Its autonomous feature allows operators to avoid exposure to high levels of dust, noise, and hazardous materials typically associated with traditional RC drilling. Moreover, the rig can now be operated 24 hours a day, 365 days a year, so operators previously limited to day shifts can now work around the clock.
The geotechnical team at Ausdrill places great emphasis on workplace safety to ensure that client operations are both productive and safe. Services include technical access drilling, cable bolting, rock bolting, and self-drilling anchors. A team of IRATA-qualified rope access experts can perform manual and hydro scaling operations, drape meshing, catch fences, and safety barriers. Other services offered include shotcreting and fibercrete services, prism and monitoring installations, depressurization drilling, dewatering installation and repairs.
With a large fleet of geotechnical plants and equipment, Ausdrill’s extensive experience is further enhanced by detailed information collected daily in the field. This adds value through informed service delivery, prediction of potential issues, and identification of efficiencies.
The geotechnical team at Ausdrill offers its services to various sectors, such as infrastructure, civil works, construction, and rail. Additionally, Ausdrill invests heavily in designing, building, researching, and developing semi-autonomous and remote geotechnical alternatives, like the virtual reality and rock scaling robotic system HALO (High Access Localized Operations). These alternatives remove safety risks, efficiently address geotechnical project needs, and offer seamless and integrated data collection experienced across other industry equipment.
↑ AustEx X1550TH drill rig
Ausdrill is an OEM in its own right and continues to manufacture and evolve the Rock Commander product line while supporting operational projects across the Drill and Blast, and Exploration divisions. With over 70 years of combined experience, Ausdrill employs experienced drill fitters, electricians, hydraulic specialists, boilermakers, and component rebuild mechanics. They are capable of rebuilding and refurbishing rigs within 10-16 weeks, and their offsite support provides first-class operational service to their project teams. Ausdrill also has dedicated specialist mechanical and design engineers. Additionally, they have an award-winning apprenticeship development program that currently employs 17 apprentices both on-site and in their Canning Vale workshop.
The KCGM Super Pit, a monumental feat in Australia’s mining landscape, stands as one of Ausdrill’s most enduring and significant projects.
Beginning with the first award in 1989, it continues today, a testament to Ausdrill’s commitment and expertise.
The project employs approximately 115 employees and operates 13 long-reach Rock Commander drill rigs and two grade control GC600 drills, all owned and manufactured by Ausdrill’s in-house maintenance division. These machines have proven their worth in the KCGM project’s ever-evolving nature.
The long-reach Rock Commander was initially designed for KCGM operations for its effective void approach. It later developed into a more diverse drill, a multi-echelon approach that can drill three lines without tramming. The dual-cab Rock Commander, a two-seat operator training unit for hands-on training, was recently added to the KCGM operations and was followed by the successful launch of the one-touch Rock Commander, with a second one-touch machine scheduled for delivery in mid-2024. Ausdrill continues to develop and modify the Rock Commander to meet the industry’s evolving mining and operating nature.
Ausdrill supports having a locally based workforce and presence in Kalgoorlie, and all key management on site reside locally and are supported by the Ausdrill Kalgoorlie branch.
Ausdrill has been operating at the St Ives Gold Mine for more than 25 years. The mine is located on the 510 km² (197 mi2) salt pan known as Lake Lefroy, which is situated 57 km (35 mi) east of Kalgoorlie.
The primary output of the mine is gold, although some nearby regions produce nickel as well.
The conditions on the lake can be treacherous, with soft mud and clays upwards of two meters deep hidden below a two-inch layer of salt, which is very harsh on equipment. Other conditions include drilling in up to three feet of water with 40-50 km/h (25-31 mi/h) winds blowing across the lake. Drill sites can also be located one or two hours of tram ride from shore without any navigational landmarks, requiring the use of a GPS and compass.
Ausdrill uses tracked vehicles to traverse between the drill rig and the lake shore, as well as custom-built drill rigs with extra-wide tracks and high decks to distribute the rig’s weight across a large surface area, allowing the machines to navigate the lake surface without sinking. However, sometimes even that is not enough. Depending on feasibility and proximity to the shore, the client may opt to build causeways out of waste rock to the drill hole location. This allows Ausdrill to drive truck-mounted drill rigs with greater hole depth capabilities onto the lake surface.
Over the last 25 years, Ausdrill has drilled thousands of holes across the lake and surrounding bushlands using every drilling discipline, including Rab, Aircore, RC, and Diamond Drilling. At St Ives, Ausdrill has custom-built Lake RC (DRA RC 600), Aircore, and Diamond rigs that are mostly mounted on track bases. Ausdrill’s rigs can access areas where no standard drilling equipment would even be considered. At one point, Ausdrill built a hovercraft with a 60 m² (646 ft2) deck and mounted an RC 600 shramm on top to complete 180 m (591 ft) RC percussion hammer holes in some of the most inaccessible areas of the lake where if someone tried to walk on the surface, they would sink to waist level.
The deepest hole drilled by Ausdrill at St Ives was completed with an Austex 1550. The hole was drilled NQ² down to precisely 2001 m (6564.96 ft) and took approximately five weeks to complete. Some of the issues encountered were pockets of gas and shear zones that were intermittent throughout the hole.
Ausdrill’s commitment to its workforce is unwavering, as evidenced by its continued investment in its 590 employees. This year, the company is particularly proud to celebrate the tenure of its longest-serving employees, some of whom have been with the organization for an impressive 35 years. As Ausdrill honors its history, it also looks to the future with a progressive 50:50 leadership team led by female general manager Kym Low and a commitment to creating a safe and respectful workplace and achieving gender balance.
Joining the Perenti Drilling Services Division, alongside DDH1 Drilling, Swick Mining Services, Ranger Drilling, and Strike Drilling, marks an exciting new chapter for Ausdrill. As part of Australia’s largest drilling contractor, Ausdrill continues to focus on innovation in safety, sustainability, and productivity as it provides clients with quality equipment and services. C
For more information
Visit: ausdrill.com.au
Try CoreMatrix™ bits for enhanced bit life and faster penetration rates across every ground condition.
The new CoreMatrix line-up is delivering field results equal to or better than leading manufacturers. With 21 matrices and a comprehensive matrix selection chart to guide you, it’s easier that ever to find the perfect CoreMatrix bit for your drilling conditions. Available with three waterway configurations and several specialty options for Abrasive conditions, Extended life, and Free-cutting matrices.
Drilling is tough. Get rugged to the core with the all-new CoreMatrix bits from Di-Corp.
info@di-corp.com www.di-corp.com
DELIVER A SEISMIC SHIFT FOR MINING OPERATIONS.
The Swick GenII Mobile Diamond Drill Rig optimises resource extraction, reduces costly site moves and unearths mine asset value with proven 97% mechanical availability in the field.
↑ Figure 1 - Sweden
Of late, there has been increasing interest in surveying production blast holes using gyro survey technology. With the growing realization that even holes of only 20 m (66 ft) depth can deviate by a large degree, this interest is only natural. Blast hole surveying to determine the deviation was once the domain of inexpensive, yet inaccurate, mechanical lever systems. But the demand for improved productivity of a mine, and hence from blasting results, means that the precision given by a high-end gyro is increasingly sought after.
The BlastGyro® from Inertial Sensing is the original gyro solution tailor-made for the job. Although several other similar imitations have appeared in the recent years, it is only the original BlastGyro® that has a pedigree stretching back over a decade in the toughest of environments.
The BlastGyro® had its genesis in work that was done with the Swedish mining company LKAB in 2012, at the Kiruna mine in northern Sweden. An original isGyro survey instrument was attached to the hose of a charging truck, which was used to survey elevated holes in the mine prior to blasting (Figure 1). This proved invaluable in improving the quality and results of the blasting and the conclusions were presented in 2014 at a conference in Chile.1
At this point in time, gyro surveying of blast holes was not widespread. This was partly due to the benefits of precision surveying of blast holes not being widely appreciated at the time. But also, in part, because very lightweight survey gyros did not yet exist. The regular isGyro accomplished the job in situations where it could be mounted on an existing mechanical system, for instance, but it was not suitable for manual use.
By 2014, plans were underway to develop a new line of gyro for the oil & gas market, to survey inside the tubing of production gas holes. It is often necessary to re-survey gas wellbores already in production, but doing it with a conventional large gyro means days of work in removing tubing, surveying, and reinstating the hole. A slim gyro that could enter through a lubricator and fit inside the production tubing would save hundreds of hours of lost production time, labor and material. Thus was born the SlimGyro, and it entered service in Texas in 2015.
wound on a portable feeder reel, it could be comfortably used by a team of two, or even one with simple training.
With systems in operation in Australia and also making its way into Africa, by 2016 the SlimGyro was proving itself to be the go-to choice for operations demanding precision measurements of blast holes. The innate qualities of the SlimGyro lent themselves perfectly to the job, and to this day are unavailable in other systems:
• Low power consumption gives over 80 hours of operation before recharging is required. There is no need to worry about swapping batteries during a shift, or an entire day.
• Memory is practically unlimited. An entire blast ring (or more) can be surveyed in one pass, without pausing between holes for download.
• Oil-field grade precision.
• No limits on latitude, inclination or direction of the holes.
By 2018, the use of the SlimGyro in blasting had gained such acceptance that it was bundled in its own product package, the BlastGyro®. This greatly simplified the logistics of sales and administration, as the name suggests the purpose extremely well. The BlastGyro® had taken off, particularly in Africa, and it was appearing in diverse locales, such as Sweden, Central Asia and Spain (Figure 2).
One shining example is the unit sold to Rosh Pinah Zinc Corporation, then part of Trevali Corporation. In this instance, there was an extensive push to not only utilize the accurate survey results in themselves but to also integrate the data with the results of drone surveying provided by Hovermap from Emesent.² In the words of the mine:
‘[The BlastGyro®] has become an integral part of the survey office equipment and contributes immensely to our striving for a safe and productive environment when conducting a survey task.’
Gerhard Louw, Senior Mine Surveyor, Trevali RPZC
The potential application to blasting was quickly seized upon by Inertial Sensing distributor Simon Williams at GyroMax in Australia. At this time, the SlimGyro was still designed to be used with separate 26 mm (1.02 in) running gear, however, its light weight, slimness and ease of use meant it was entirely feasible to be used as a manual system. By attaching the gyro to a commonly available fiberglass rod,
‘[The BlastGyro®] has become an integral part of the survey office equipment and contributes immensely to our striving for a safe and productive environment when conducting a survey task.’ Gerhard Louw, Senior Mine Surveyor, Trevali RPZC.
However, development did not stop there. The system has had a major overhaul to make it fully integrated, removing the separate running gear and reducing the diameter to 25 mm (0.98 in) and the weight to under 3 kg (6.61 lb), without compromising on the system accuracy or other characteristics. An added benefit of the fully integrated BlastGyro® is that Bluetooth radio communications are directly available without removing an instrument from a pressure barrel.
The software was updated to incorporate blast plans, allowing the operator to define entire survey campaigns from the office and they were then available on the survey computer. The BlastGyro® surveyor then simply selects the appropriate hole in turn, removing the need to enter survey information on-site. This greatly reduces sources of mis-
takes in naming and data entry and speeds up surveying.
The BlastGyro® also directly integrates with the SurveySafe™ cloud service, enabling quick and secure transfer of data and QA/QC information between relevant parties once the survey computer picks up an internet connection.
A downhole survey instrument must have a suitable length to measure the tangent of the hole, but not be so long as to be heavy
and unwieldy; or impossible to get into the hole in the first place! Instruments under 1 m (3.28 ft) in length cannot measure borehole angles accurately, while those approaching 2 m (6.56 ft) are too cumbersome for a blast hole. The BlastGyro® comes in at under 1.5 m (4.92 ft), making it ideal for the job.
The 25 mm (0.98 in) BlastGyro® is the only truly slim gyro available for the job, while similar systems come in at 30 mm (1.18 in) or more.
The BlastGyro® is not dependent on downhole north-finding technology which has important directional limitations.³ It is therefore usable without loss of accuracy at any
latitude on Earth, in holes of any inclination, in any direction and without the need to wait for north-finding shots.
High precision calibration in temperature and alignment means that the results are reliable, run after run. While the goal is to measure the true deviation of blast holes, it is evident that other systems can give a systematic overestimate of how much the drilling has veered from true. It is debatable which is the worse problem: simply assuming a hole is straight, or unknowingly using excessively bent incorrect surveys! The BlastGyro® measures true, as proven in its birth in the deep gas holes of Texas.
Surveying of production blast holes, both underground and in open pits, has come a long way in the last few years. While there are now a number of imitation systems available on the market, only the BlastGyro® combines the necessary elements of true slim design, light weight, long-lasting battery, virtually unlimited survey time, ease of use and proven oil field accuracy. The BlastGyro® began as the only package suitable for everyday manual use in blast holes, but it has consistently remained at the head of the pack as others have imitated it. Of course, it does not stop here, new refinements and innovations are under development. C
References
1. ‘Methodology for up-hole drilling accuracy measurements at Kiruna SLC mine’. Wimmer, Nordqvist & Billger. 3rd International Symposium on Block and Sublevel Caving (pp. 625-637). Santiago, Chile: Universidad de Chile. Jan 1, 2014
2. ‘SlimGyro and Drone Technology – The integration of SlimGyro and drone technology at Rosh Pinah’, Gerhard Louw, Tech*Carnival-23, South Africa. May 2023.
3. ‘Similarities between magnetic and north-finding survey tools’, McLeod and Billger, Coring Magazine, Issue 9, 2019.
For more information Visit: inertialsensing.com
As the temperatures began to drop outside in December, the heat was on in the Rodren Drilling (Rodren) shop as the team was in its final stage of preparation and planning for an extensive eight-drill winter program in Snow Lake, MB, Canada, for our good colleagues at Hudbay Minerals. Ensuring a great plan is in place for a project of this magnitude can be crucial in the overall success of the program, and with a highly skilled and experienced team of individuals working side by side, it was a plan for success right from the start.
With the drill fleet (for this program), which included six EF-75 Discovery, one EF-100 Discovery, and one brand new Duralite 1800N, Rodren’s team was ready to tackle the eight-drill winter program up in Snow Lake, Manitoba. The seven EF Discovery drills are all drilling the Lalor mine expansion area at depths of 1200-2088 m (3937–6850 ft) all of which were skid/landbased drills. The Duralite 1800N, which drilled the winter as a skid drill and was converted to a fly drill in late March, is working in the Cook Lake area at depths from 400–1800 m (1312–5906 ft). The EF-75s have a drilling capacity of 2160 m (7087 ft) of N-size drill rod while the Duralite can drill up to 1800 m (5905 ft) N-size and the EF-100 –3000 m (9843 ft) in N-size, allowing Rodren to offer a wide variety of services based on clients’ needs whether it be location, site access or depth.
With the intention to extend the life expectancy of the Snow Lake Mine beyond 2038, this year was the kick-off to the largest-ever Snow Lake exploration program in the company’s history. Rodren’s team aims to provide a high-quality core product to Hudbay Minerals (Hudbay) at a high rate of production while maintaining a positive and safe work environment. In turn, with the core product provided by Rodren and the guidance of Hudbay’s exploration team, both parties aim at intersecting appropriate copper/gold veins/bodies in order to expand the mine’s imprint of operations and overall longevity. With abnormally warm temperatures through December, the winter roads were still being built and weren’t suitable for hauling heavy equipment. This was the first obstacle pushing the start of drilling to the later than anticipated January 8th 2024 when we were able to pull the first drill onto its pad and start setting up. We then spent two weeks working with winter road builders and Hudbay personnel in getting the remaining seven drills online and coring. With the length of the drill season dependent on Mother Nature, keeping the winter roads well maintained and in safe condition was imperative to our overall success.
Our team managed to drill a total of 23 600 m (77 428 ft) at the Lalor area, which was targeted for 24 000 m (78 740 ft) and another 7298 m (23 944 ft) at Cook Lake, which was targeted for 4800 m (15 748 ft) by mid-April. A grand total of 30 898 m (101 371 ft) was drilled out of a targeted 28 800 m (94 488 ft) in the span of three months.
With all eight drills up and running, Rodren had 40 employees on site and another 20 on the roster for shift-change. In order to keep the drill fleet’s down/repair time to a minimum, Rodren had a mechanic on site for the majority of the project to work with and support the drill crews. The company had their management team not only readily available, but they were on site regularly to help reinforce a positive work environment, quality assurance and safe work environment. With daily interaction and weekly Teams meetings between Hudbay and Rodren, we were able to maintain open communication and navigate any questions or concerns as they arose. This open chain of communication also allowed us to proactively plan and prepare for upcoming project tasks.
In what began as the 13th consecutive year of drilling operations for Rodren at Hudbay, both parties are now preparing to transition into a summer drilling program that will involve a smaller fleet to be comprised of a combination of heli-portable drill packages and land-based skid drills. Over the course of this 13-year relationship, Rodren takes pride and satisfaction in working hand in hand with Hudbay on building not only a safe and productive work environment but an overall positive future for all workers involved.
Rodren in conjunction with Hudbay remain committed to our continual growth and development of all aspects of business from communication, safety, quality assurance, production and the list goes on. We at Rodren Drilling remain vigilant in exploring the future of Snow Lake from the core and up.
Hudbay Minerals (TSX, NYSE: HBM) is a copper-focused mining company with three long-life operations and a world-class pipeline of copper growth projects in tier-one mining-friendly jurisdictions of Canada, Peru and the U.S.
Hudbay’s operating portfolio includes the Constancia mine in Cusco (Peru), the Snow Lake operations in Manitoba (Canada) and the Copper Mountain mine in British Columbia (Canada). Copper is the primary metal produced by the company, which is complemented by meaningful gold production.
Hudbay’s growth pipeline includes the Copper World project in Arizona, the Mason project in Nevada (both in the U.S), the Llaguen project in La Libertad (Peru) and several expansion and exploration opportunities near its existing operations.
The value Hudbay creates and the impact it has is embodied in its purpose statement: ‘We care about our people, our communities and our planet. Hudbay provides the metals the world needs. We work sustainably, transform lives and create better futures for communities.’ Hudbay’s mission is to create sustainable value and strong returns by leveraging its core strengths in community relations, focused exploration, mine development and efficient operations. C
I have decided to write this article since electric control in drilling rigs and particularly in exploration rigs is often regarded as unreliable and too complicated. However, more manufacturers already have electrical control options as well as HMI (humanmachine interface = display) in their fleets to give more accurate information of the drilling process and parameters, as well as the option to log drilling parameters on the go.
Then why do electronics have such a bad reputation amongst drillers and drilling companies? I can name a couple of things from my experience, and I am sure you can think of a few more. Before, the biggest issue was to find components that are protected against the elements, since usually exploration rigs won’t have a driller’s cabin or any other safe place where they could be placed. Programmable logic controllers (PLCs), for example, which are meant for factory automation, need to operate in an air-conditioned enclosure. With water, grease, temperature fluctuations, etc. being a constant part of drilling, a PLC won’t last very long in a rig. Since it is mandatory for the components to have a good enough IP rating, they tolerate extremely high and in some cases low temperatures as well vibration. The second issue is troubleshooting. If something does not work, you only need a spanner to crack the hose and see if that practical actuator or valve gets oil from the system. In electrical systems, particularly in CAN bus ones, troubleshooting can be more difficult depending on how the system is designed. Not to mention that you need at least a good quality multimeter and basic knowledge of the system itself to troubleshoot. The old maxim that electricity is blue, and it hurts isn’t enough anymore.
I have been fortunate to be part of the change in the drilling industry from the early 2000s when I was working as a young design engineer and I got to clearly see the benefits of electrics and CAN. I have also seen firsthand some issues they have caused. I have prepared three examples (see Examples 1-3) from a practical point of view of
different kinds of controls without getting too deep into the topic.
These examples are manually/direct-controlled mobile valve, pilot hydraulic-controlled mobile valve and electrically controlled hydraulic mobile valve. It is also good to remember that hydraulic pressure generates a force which is moving the spool in both hydraulic- and electric-controlled valves, excluding valves meant for lower flow rates.
Examples 2 and 3 increase the flexibility to locate controls to an ideal place for the operator without moving the main valve and large amount of hosing with it. Example 3 is especially more flexible since valve is controlled by electrical joystick, so no hoses or any type of hydraulic valves are close to the operator. This type of system is very convenient to use and safer than the other two, as there is no possibility of a high-pressure oil injection, there is less noise and less heat. So why do we need CAN bus systems if electrical control is just as convenient and safe? I believe the following systems (see examples 4 and 5) are the best example to show the benefits of CAN bus. Let’s say we have four-spool mobile control valve, which has two PWM (pulse width modulation) controlled solenoids per each spool. So, we need a total of 8 wires from the spool to the control unit, which supplies control signal to the solenoids. The same control unit is also connected to joysticks which are normally either hall sensor or potentiometer type. Usually, the control unit is located close to the joysticks because the signal they supply is more sensitive to interference and its level is lower than the control signal to coils. In that type of system, we already have 8 individual wires which can be damaged. Not to mention that the wires must be big enough to be able to transmit control current, so we are talking about a rather large bundle. Also, the more valves you need to control, the more wires you will need.
If instead of ‘normal’ PWM coils, we use coils with CAN receivers in directional control valves, here’s how the system would work (see Example 5). We have CAN bus system, so we only need two CAN wires between the control unit and coils. Those wires are only transmitting low level voltage signal between the control units, which means that wires don’t need to have a large cross section. Instead of eight possible points of malfunction, in this system we only have two. If for example we have 20 valves, the benefits of this kind of system are undeniable compared to the previous system with only one control unit. Admittedly, we still need oper-
ating voltage and ground to every coil, but still, the number of needed wires is lower compared to the system from the previous example.
Now that we have established the benefits of the system where control signals can be multiplexed between control units, like CAN bus, let’s think about the other benefits of the electrical control system. For example, we have a cage around the mast, which protects the driller from rotating parts and there is a door in the cage (see Example 6). If the cage’s door is open, the rotary head can’t be activated or can be rotated at a really slow speed.
Let’s now use the systems from the previous examples: direct/manual-controlled hydraulic, hydraulic pilot control and electrical
control. In direct/manual-controlled systems we need to direct the rotation oil flow from the control valve first to a valve in the cage which then would allow oil flow to rotate the head motors in case the cage is closed. In this kind of system, hoses must be big enough to minimize flow losses and should also be able to withstand the maximum system pressure. The valve which senses if the door is closed or open must be as large for the same reason and it will need a lot of force to operate due to its sheer size. This kind of system is not only difficult to make but also increases loses in the system because of the long hose runs.
In a hydraulic pilot-operated systems (see Example 7), stopping or slowing the rotation can be done in two ways. We could use a system similar to the one described above
↑ Example 5 - CAN bus system with multiple valves ↑ Example 4 - Electric controls with multiple valvesor place the valving in a pilot circuit. When the valving is placed in a pilot circuit, there are the following benefits: the sensing valve for the cage door does not need to be large, it does not need to withstand the maximum operating pressure of the hydraulic system and it can be activated with less force. Also, it is more convenient for the driller to operate a hydraulic joystick compared to a
direct-operated valve. However, if we instead have one or several valves which can rotation interlock, the system becomes more complex, and more hosing is needed. Also, long pilot lines sometimes result in delay in control and the system becomes awkward to operate.
If using electrics, the simplest solution would be to use a proximity switch, a relay and a solenoid valve (see Example 8). By doing so, long hose runs can be replaced by a proximity switch and wiring, which controls the interlock valve. Options for component location are many, but I believe that everyone agrees that running two core cable is in most cases easier than hydraulic hoses and takes up less space. Also, if one solenoid valve is close to another, the valves system has minimal delay. Again, thinking of a more complex system with multiple functions which can interlock rotation, this one will become complex and difficult to troubleshoot due to the many interlocks. But if instead of using relays with proximity switches, we had a PLC where all proximity switches are connected – which can be more expensive, however – there are undeniable benefits. Some of them: the system is more reliable as PLC does not have mechanical contacts as relays do, the status of proximity switches can be monitored, so cable breakage can be detected, more complex interlocking can be done via the PLC software and its characteristics can be easily altered without doing any phys-
ical changes to the system. When the system has an HMI, the operator gets real time information of different interlock statuses and whole system diagnostics.
I hope this article was able to point out some benefits of using electrics in drilling rigs. However, the most important thing to consider when deciding between hydraulic and electric controls is the level of technical expertise of the people who will maintain the systems and equipment available. Even the most advanced PLC-controlled system is useless if no one knows how to fix it or has any troubleshooting equipment when a problem arises. C
Peter Kuusimaa is a Finnish mechanical engineer who has been working with and designing hydraulic and control systems for drilling rigs for over 20 years and in different continents. He is currently based and works in Australia. He has been part of many major drilling companies, nowadays he works as a consultant and a freelancer. You can find Peter at Comet-Tech Pty Ltd, on www.comet-tech.com.au or at comet-tech@bigpond.com
In this issue:
Q&A from the experts
In conversation with Dr Sally Goodman VP Generative Exploration at Newmont Corporation
The dilemma of geological control for underground ore development by Steve Rose, Principal Mining Geologist at Rose Mining Geology Consultants
Unveiling hidden treasures
The fascinating process of gemstone and mineral specimen exploration and exploitation in Pakistan
Noor Ullah, Business Owner at Gandhara Gemstones
The big history of mining in Serbia and the bigger challenges of today by Dragan Dragić, Exploration Manager at Konstantin Resources
Brett Davis: Firstly, thanks for giving Coring the opportunity to interview you, Sally. I was really keen to capture you for an interview, given your international profile in the mining and exploration industry, plus your expertise in my field of interest, structural geology. I’ll start with my standard lead-in question – what got you interested in a career in geology?
Sally Goodman: Like many young people, I was fascinated by dinosaurs – in my case triggered by a Ladybird Book called Our Land in the Making. We spent many summer holidays on the Northumbrian coast (UK), and I had quite the collection of big chunks of limestone with very small fossils which I collected, as well as assorted mineral specimens I spent my pocket money on. But I never thought of geology as a profession – I was actually planning to study languages at university – until my mum suggested turning my geological hobby into a career. At sixteen, I went to talk to the local university about what a geologist does – and was sold on the idea of lots of travel, not being chained to a desk, and every day being different. And that’s pretty much how things have turned out.
Sally Goodman is Head, Global Discovery for Newmont, spearheading the drive to discovery across the company’s global portfolio of early-stage exploration projects. Newmont is the world’s leading gold company and a producer of copper, silver, zinc and lead. The company was founded in 1921 and has been publicly traded since 1925. With its head office in Denver, Colorado, Newmont has a world-class portfolio of assets in Africa, Australia, Latin America & Caribbean, North America, and Papua New Guinea.
Before joining Newmont, Sally was Chief Geoscientist with Atlantic Gold, following five years with Goldcorp in a variety of corporate technical positions. Prior to that, she traveled globally as a consultant in structural geology with SRK Consulting, after holding various lecturing and research posts in universities in Canada and the UK. She has a PhD in Economic Geology and an MSc in Mineral Exploration from the Royal School of Mines, London (UK), and a BSc in Geological Sciences from Leeds University (UK). Sally is currently Chair of the Board of the Mineral Deposits Research Unit, University of British Columbia, and was the Society of Economic Geologists’ Thayer-Lindsay Lecturer in 2023.
BD: Coring is a drilling magazine, and we like to keep to our roots. So, I’ll ask you a multi-faceted drilling-related question - do you do much work with oriented core? Do you have any horror stories with regard to core orientation? And do you work with other structure orientation methods pertaining to drilling?
SG: Oriented core – that’s a charged subject! Good orientation data is priceless; bad orientation data is worse than none at all. I have a few horror stories – probably the worst was a gold deposit that had amassed a huge database of orientation data - but when I plotted it up, it didn’t seem to make much sense. So I did some field checking – a large glaciated surface a few hundred meters from the core shed had a very strong E-W foliation; the oriented core data suggested the foliation was N-S. A few more spot checks showed that much, but not all, of the data was 90ᵒ out in strike. As there was no way of knowing
what data was correctly oriented, I threw the whole dataset out, much to the dismay of the clients!
I’ve used Televiewer data extensively – it provides a more reliable dataset, but the structures that are significant from a mineralization point of view can be lost in the sheer quantity of measurements that are churned out. It’s vitally important to check the data back against the drill core to validate your interpretation.
BD: Very few people can boast the high-level roles you have now and have occupied historically. I also note that there are not many women in mining and/or exploration who have achieved this. Why do you think this is, and are things changing?
SG: That’s an easy one. It’s difficult and it’s a constant battle to get your voice heard, and not be relegated to making coffee and taking notes, which are important field skills, but
hardly limited to one gender. The workplace is changing slowly, but it is still difficult to balance a mining or exploration career with family life, so we lose many women who choose to step away from the industry in their late 20s or 30s, and then find it difficult to get back. At the age when I had young children, I was in academia and consultancy, where I was able to make my own schedule to a certain degree –working my schedule around schooldays, holidays, birthdays… I made my time commitment very clear: I would only go to site for two weeks at a time, and after a site visit, I would need several weeks at home before the next trip. This boundary never caused any issues with clients; it just became part of the way we worked together, but it’s not always easy to build family time into a career.
BD: Leading on from the previous question, I note that forums such as LinkedIn are showing more and more posts directed at women in mining and exploration. What do you see as the main impediments to women pursuing careers in mining and exploration and do you have any broad advice for helping women advance in these industries in a positive way?
SG: The industry has to become more flexible. There tends to be an ‘all or nothing’ thinking, where women who no longer want to spend long periods of time at exploration camps or at site, tend to be sidelined. The pandemic taught us that we can do good work remotely, and we need to build on that and apply technology where we can allow women the flexibility to work from home. Of course, that doesn’t just apply to women. There are plenty of geologists who can’t – or would prefer not to – spend extended periods at site. If we want to attract the next generation of mining professionals, the industry has to adapt. As for advice, I suggest asking for work arrangements that suit your lifestyle. I found that if I asked for flexibility, it was often possible to
arrange. Male colleagues or clients weren’t intentionally arranging things to make my life difficult. They just hadn’t thought of factoring in flexibility, as they had never needed it themselves. Once I asked, they were (usually) happy to comply.
BD: Who have been some of the positive influences in your career?
SG: I’m not going to name names here, as I’d be sure to forget someone and upset them. However, I would say that the mentors who have made the most difference to me during my university career and while working, are those who presented me with a challenge. They then just let me get on with it, with a bit of gentle steering where needed. I don’t do so well with micromanagers!
BD: Given the current multi-commodity mineral boom, are you doing a lot of work outside of the commodities and deposit styles you have traditionally worked on?
SG: As a consultant, I worked on a wide range of commodities and deposit types. For the last ten years, it’s mainly been gold and now gold-copper deposits. What is changing is becoming wise to the possibility that a project may have by-products that fall into that ‘critical metals’ bucket. Where previously they were simply a nuisance, there’s now recognition that we need to understand the deportment of the entire metal suites, rather than just the major payable metals. It’s a new way of thinking about deposit types that previously may not have been attractive targets – it challenges some old paradigms.
BD: You worked for the international consultancy SRK earlier in your career. What were some of the highlights and lessons you learned from the consulting game?
SG: Highlights would have to be the places I worked and the people I had the opportunity to meet. There’s nothing like wandering around a vineyard in Portugal, or the steppes of Kazakhstan, or the high Andes with a bunch of like-minded individuals, debating the geology on the rocks and enjoying the local hospitality.
The main lesson I learned is to listen first and speak afterward. You can (and should) read up about a deposit before heading to site, but it’s the people on the ground who live, eat and breathe the deposit every day who have made the key observations – whether they realize it or not. Sometimes, published descriptions leave out critical factors because they don’t fit the narrative, and there’s a wealth of knowledge at site that simply never makes it into the literature or technical reports. Many times, a seemingly random fact or enigmatic outcrop has proved to be the key that unlocks the whole system.
The other thing I learned is to keep asking: ‘How do you know that?’ to filter out the accepted wisdom that has been passed down through generations of geologists – the sort of myth that may have no basis in fact.
BD: I have to ask – political instability/insecurity aside, what part of the world do you think is highly prospective for finding new world-class orebodies?
SG: Well, every year at PDAC I pick up one of those brochures about the mineral wealth of Afghanistan. I’ll just leave that here.
BD: Is there a particular mineralization style or deposit type that interests you, and why?
SG: Really anything where you have to unravel the geological history to understand the geometry of the deposit, and to be able to predict where you might find the next big one. No two deposits are ever the
same, but when you throw in a few phases of deformation, and maybe some metamorphism along with the alteration and mineralization, it really becomes challenging – and it’s the intellectual challenge that keeps it fresh. This is also why machine learning only gets us so far in exploration – the recipe is never exactly the same from one deposit to the next.
BD: Leading on from the previous question - everyone has a handful of deposits that have left a mark on them, be it because of the amazing geology, the hideous conditions, the people they worked with, etc. Which deposits do you hold dear and which ones really were difficult to work on?
SG: My first job as a consultant was to produce an updated interpretation of the reprocessed geophysics of the Thompson Nickel Belt for Inco – marrying the accepted wisdom with the aeromag data. That sounded fairly straightforward until I got to the site, and the orebodies looked nothing like my preconception of an ‘orthomagmatic’ nickel deposit, and the existing map interpretation and the structural story didn’t match. Getting that sorted out was equal parts terrifying and exhilarating, which pretty much sums up life as a consultant, actually. More recently, I’ve had a love/hate relationship with Peñasquito in Mexico, where we’re mining two breccia pipes that fired off the shoulder of a buried intrusive body. Everything about the deposit geology is complex, and the next discovery is likely to be under tens of meters of cover – but again, that’s what makes it interesting. It was immensely satisfying to produce a 3D model of the deposit in Leapfrog – months of work and probably the most time I’ve spent on a single model, but very rewarding.
I’ve been lucky to work with some great people throughout my career – there aren’t many that I wouldn’t want to work with again. And apart from the occasional deprivations of life in camp, you know, cold showers, bad coffee, biting bugs of various types, I can’t think of anything I’d describe as hideous. The worst field experience was probably the combination of food poisoning and the first night at altitude at Antamina in Peru when I really questioned my life choices, but even that experience was worth it in the long run for the opportunity to work on a worldclass ore deposit.
BD: Where do you see the most exciting technological developments being
made in mineral exploration and mining going forward?
SG: The ability to truly map in 3D, driven by increasing availability and decreasing price of lidar units integrated into mapping tablets. We are already using these systems both in open pit and underground mines for detailed mapping and have also utilized a system to do detailed outcrop mapping of vein geometries. Having the ability to map structure where we can’t lay hands on the rock, and to have a permanent record is going to be huge – once we have a generation that grew up with electronics and doesn’t default to paper and pencil when the going gets tough. These technological advancements are going to help our geological models and grade control and have significant potential to improve geotechnical mapping and modeling. And it’s one version of the truth, no more having mine geos and geotechnical staff producing two separate maps and models. And if we add in drone capability and spectral mapping, the possibilities are endless…
BD: Do you think that there are any mineral exploration strategies or technologies that are under-employed, but could make a big difference to an exploration campaign if people used them more?
SG: I’d like to see us be more agile in getting from drill core to model and feeding that information back into the drill program in real-time. It slows us down so much to conduct a drill program, then wait for the assay results, and then model the deposit up, and then plan the next program. Of course, this is a particular problem with gold exploration where the appearance (or otherwise) of gold in drill core is not always a good indicator of overall grade, and geochemical proxies can be misleading. Scanning technologies are taking us in the right direction, but I’m jealous of the downhole tools the petroleum industry uses, allowing to interpret geology while drilling. Imagine how much more efficient we would be if we could do something similar. I think sometimes we accept the status quo too much, as it’s ‘the way we’ve always done it’ rather than setting stretch goals.
BD: We hear all about the advances and benefits of technologies, such as 3D modeling, geochemical analysis, and utilization of drones. Have you noted any negative impacts to effective exploration and mining because of these e.g. less people out kicking rocks?
SG: With all the technology available, it’s sometimes easy to forget we are targeting a
geological concept, rather than an anomaly, and it’s really important to get into the field and understand what we’re dealing with. We need to build the geological understanding into the target concept, then all results are meaningful, even the negative ones. If the target is just an anomaly, drilling the red spots, then the results are digital – yes, we hit something, or no we didn’t. If we have a target concept, then it’s a learning experience and we can modify the strategy as we go. All of these examples might sound obvious, but there is the temptation to shortcut the process and simply go from collection of data (of whatever type) to drilling, without taking the time to develop the geological concept. This is where experienced staff has an important role to play in reviewing the program and continuing to keep abreast of the results as they come in, to ensure the team is learning and adapting as they go.
BD: What is your opinion of the geological skillsets, experience, and knowledge of geologists today, especially those who are newly graduated?
SG: That is a loaded question! Many of the basic skills that were drummed into us, I’m thinking crystallography and mineralogy in particular, have gone by the wayside in favor of more multidisciplinary courses. I’d comment that new graduates have a broader view of geology’s links to other earth sciences – climate, environment, ocean science –than we did. The one essential skill we seem to be losing is geological mapping, the ability to read the landscape and know where you are (without GPS coordinates) and draw a cross-section on the fly. A good geological map is a 4D interpretation of the subsurface, not just a representation of surface distribution of rock units. It drives me crazy to see a surface ‘map’ with no topographical information. If we’re interested in bedrock geology, the map should be top-of-bedrock, without large areas of here-be-dragons cover.
BD: Has there been any single satisfying moment in your career that rates above all the others?
SG: For me, the experience that rates the most satisfying, is always the latest one. Right now we are finally drilling a very exciting prospect that has never been drilled before. It will take a while to understand the scale of what we have, but initial results look promising.
BD: I’ll ask a question on the flipside to the previous one. Many of us have interfaced with less than savory individuals
or experienced toxic workplaces. Has there been any incident or incidents that really disappointed you?
SG: It’s really disappointing that discrimination still exists within the mining industry. Things have improved since I was a student and was told I’d never get a job in the field but should be happy to work in a lab. However, many mine sites and exploration camps are still built around the assumption of a male workforce. And there is still toxic behavior from off-color ‘jokes’ to outright physical assault. At least, throughout the industry and at Newmont, we are now talking about it, and making concerted efforts to listen to the staff’s concerns and taking practical steps. Sometimes, it can be the simple things that make a big impact, like making sure walkways are well lit, or the layout of shower blocks, but changing the culture isn’t easy. And gender-based harassment is only one aspect of bullying. As an industry, we still have a long way to go. However, if we don’t change, we’ll find new generations will vote with their feet, and find a more pleasant work environment elsewhere.
BD: In addition to your professional role, you also manage to find time to compile and deliver an impressive volume of public geology-focused presentations. What is Sally Goodman’s secret to time management?
SG: Where possible, I try to align the work demands to fit my mindset on any given day. Some days are good for sifting through budget spreadsheets and finding the error that messes up the totals; other days are good for getting the team together and brainstorming targeting strategies; and I also enjoy days for writing reports and presentation texts, or time to find a coffee shop with a good internet connection and catch up on recent publications. I have a number of scheduled calls with colleagues across the globe, but in the flex time between, I try and fit the work to my current mood. There’s nothing more frustrating than sitting in front of a screen and struggling to move something forward when there’s no inspiration.
Of course, an adrenaline-fueled panic due to impending deadlines also focuses the mind.
BD: What have you learned from field practice and your job experience that is not taught at university?
SG: I’m lucky in that I did a Masters in Mineral Exploration, so gained at least a rudimentary understanding of mineral exploration methods, which is an educational gap that some students have coming straight from their undergraduate degree into the mining industry. But on the non-technical front, a couple of things that spring to mind that are not taught at university are integration of information and deposit economics, in its broadest sense. University courses tend to divide knowledge into subjects, and then divide the subjects into bite-sized chunks. In contrast, value is really derived from pulling the strands of knowledge together. I realize courses have to be passed individually for credits, and it is difficult to plan integrated courses which might require different prerequisites, but this is a really important skill in exploration. As for deposit economics, it is key to have at least some idea of how big a certain deposit type needs to be, to be economically viable. An understanding of what drives value in exploration is important, even for junior exploration colleagues. In fact, I’m in support of junior staff knowing as much about their company as possible; they are the future SVPs, after all.
BD: If you had abundant financial funding, is there a fundamentally annoying geology question you’d like to solve or a topic you’d like to work on?
SG: Currently, I’m spending a significant amount of time thinking about how we develop process models for exploration, rather than relying on deposit models. Deposit models have been useful in teaching, or as a descriptive shortcut, but can be limiting in generating exploration concepts. I believe we are missing the point of the mineral systems approach to exploration when we talk about a mineral system for orogenic gold deposits, for example. If we look at a mineral system from the bottom up, from fundamental mantle processes to what ultimately happens in the upper crust, it should be agnostic of outcome. The same mineral systems may result in different deposit types, in different locations and at different times. But to think in those terms we need process models, either conceptual or numerical. I know there are a few groups looking at this in a piecemeal fashion, and it would take a lot of brainpower and computing power to build a whole-earth model based on mineral systems principles, but it could fundamentally change how we approach exploration. And if climate scientists can build models with complex inter-
dependencies, which are used as a basis for global future planning, I think it’s feasible for mineral exploration too – but that’s where abundant funding is required.
BD: Do you think that geological societies such as the Society of Economic Geology have adapted with the times in terms of being useful entities for their members? Or are there basic things that such societies should be providing and/ or promoting?
SG: My view is that many geological societies are adapting, some faster than others. There has been a change over the last few years, with many of the learned societies making a more intentional attempt at representing the interests of all their membership, whether by ensuring more diverse boards, planning meetings in different locations, encouraging global reach of student groups, etc. The newsletters have also improved, and there is more relevant information being shared on social media, which is where many people now find their news. However, I have to think there’s a better format than the traditional paper for dissemination of research; journals used to make sense, but is it still the case? We’ve developed an internal ‘geoscience learning platform’ which is a website where topics are presented as text, images, videos – with voiceover and multilingual transcript – and linked, so the user can select a single part of the topic or drill down into the detail as needed. Maybe it’s time to take a similar approach to the dissemination of research?
BD: Any concluding comments or words of wisdom from an industry leader?
SG: I have found that people are fascinated by the earth, whether it’s the child in the rock shop more interested in crystallography than chakras, from the hikers in the bar who’ve picked up a big lump of quartz, to the photographer at the beach waiting for the sun to hit the sea cliff at the right angle. But very few people have had the opportunity to study earth sciences, and as a result, there’s a lot of ignorance when it comes to earth history and earth resources. If we want acceptance of the mining industry, we must be ambassadors whenever we get the chance to share our stories and our enthusiasm. Who have you spoken to today? C
For more information
Reach out to Sally via LinkedIn
From the beginning of underground mining, it has been the practice to develop ore drives along the mineralized structure with decisions on the direction of that development made by the miner (pre-19th Century; see Agricola, 1556), the engineer or the surveyor (19th Century). Once mining geology became a profession (Mckinstry, 1948), this decision has become the responsibility of the geologist.
My first job as an underground mine geologist (and it’s usually the domain of the junior geos on the team) was to go underground each day to map the new headings and provide a call on which direction to drill the next cut. There was a certain thrill in being put on the spot each day and being the only one on the team with the intimate knowledge of the orebody and that ‘special’ insight to give the development crew the instruction. Mostly, of course, the development crew already knew where to go, and we were just playing along in the geologist-miner charade. Usually, this resulted in zigzag drives following a surprisingly straight lode.
In narrow-lode mines, where a mineralized structure has a defined hangingwall (e.g., narrow vein gold deposits such as Norseman or Kundana in Western Australia), the usual arrangement is:
• Development round is bogged out. The heading is barred down and supported.
• The mine geologist maps the face, takes samples across the face.
• Mine geologist measures the position of the face from the last survey peg.
• Mine geologist then sprays an arrow or some other instruction on the backs or the face for the direction of the next round (see Figures 1 and 2).
• Back in the office, the mine geologist completes the face map and shares it with the production team.
The benefits of having ore drive development under geological control are:
• Reduction in sample drill meters to define the lode. Only enough drilling is needed to justify the decision to carry out the development.
• Reduction in drill cuddy requirements.
• The decision to develop can be made earlier; and
• Minimizes delays in the developing turn-outs from the crosscuts, and then the ore drives.
The pitfalls:
• The development drive becomes part of the resource definition/ grade control process. It is serving as both an access for sampling and mapping, and also as the platform for subsequent stoping.
• There is a tension between the need to develop the vein as perfectly as possible for geological sampling and mapping, and the need to have economically useful ore coming out of the development (on narrow vein mines, development can be 40-50% or even more of the production source), and the need to have the development drive in the right place to allow effective stoping (Figure 3).
• Making the wrong call and following a promising splay (Figure 4). For a couple of cuts the face grade is high, but then peters out, so need to restart development on what is now recognized as the main lode. The splay development can cause problems for subsequent stoping, due to an increase in drive width.
• Making the wrong call and chasing a splay that leads to unplanned breakthrough in a neighboring drive; and
• Delays in the development drive schedule due to:
» Mining extra meters in order to follow a splay;
↑ Figure 1 - Example of face painted up, with the blue arrow showing the direction for the next cut» Extending the development drive because still in ore;
» Needing to slash out the side of the drive to expose the vein; and
» Putting the development on hold while waiting on assays because unsure if the face is still in ore.
Analysis was carried out from level plans from five different narrow lode gold mines. All mines were developed in the last 15 years. Four of the mines were developed with conventional jumbo drill rigs, with the mining method planned to be longhole open stoping, and one was developed using airlegs, with the planned mining method to be a variant on shrink-stoping. Four mines are in Australia, and one is in Asia. Measurements were taken of ore drive development length, and simply the length of any errors during that development. In this simple first run no account was taken for apparent mistakes like ore drives not pushed to natural extent, as these situations could be due to planning or scheduling constraints rather than problems when developing. A summary of the measurements is shown in Table 1. The total measurements are 9462 m (31 042 ft), of which an additional 741 m (2431 ft) was developed, this is an average error of 8%, but on individual drives, the highest was 46%.
A simple approach has been used: ‘Is it an economically better strategy to reduce drilling costs by carrying out ore development under geological control?’
Assumptions
• Development cost per meter: AUD 7500
• Existing drilling is already to 25 m (82 ft) spacing. Halving this spacing to 12.5 m (41 ft) would reduce uncertainty in interpretation and grade estimation.
• The average length of infill drill hole is 75 m (246 ft)
• Drilling cost per meter: AUD 150. From this
• Cost of development errors: AUD 5.6 million
• Cost to infill drill: AUD 4.2 million
Where ore drives are developed for the purpose of stoping, it is recommended that the priorities should be:
• Design and mine the drive for stable and effective stoping;
• Have the drive under survey control;
• Geologists interpret a mineralization model that is the basis for mine design, and then carry out mapping and face checks to confirm the interpretation;
Development of ore drives in narrow-lode underground mines is often carried out under geological control, as a means of reducing infill drilling costs and to maximize the grade of the development ore. There is a tension inherent in this strategy where the ore drive is then to be used as the platform for stoping.
Analysis of nearly 9500 m (31 168 ft) of ore drive development plans from five different gold mines shows that on average this can lead to 8% more meters of development being carried out. On individual drives, however, the extra development can be as high as 46%. On a simple cost comparison between the value of the extra development meters and the cost of infill drilling there is clear support for carrying out the infill drilling to reduce drive development meters.
• If there are significant differences between the mineralization interpretation and what is being mapped in the drive, then update the interpretation and issue a new survey instruction. C
• Mckinstry, H. E. (1948). Mining Geology.
• Agricola, G. (1556). De Re Metallica.
more information Contact Steve on LinkedIn
2.5sm
Ability to manoeuvre on steep terrain
• 280 HP (209 kW) or 350 HP (261 kW) w. high altitude kit
• 50,000 lb (222.4 kN) pull back capacity
• Caterpillar 320 tracks
• Optional isolated climate-controlled cabin
• Drill rig depth capacity: 2,908 m (N) 1,972 m (H) 1,303 m (P)
Discover our new product
a
and
Pakistan, a land with a vast history and diverse landscapes, has long been a treasure trove of precious gemstones waiting to be discovered. The process of exploring these hidden riches is a meticulous and intriguing journey that combines geological expertise, cutting-edge technology, and the spirit of adventure. In this article, we will briefly delve into the intricate and mesmerizing process of exploring for gemstones in Pakistan.
Pakistan is home to a variety of precious and semi-precious gemstones, including rubies, sapphires, emeralds, and topaz, which are found in a variety of geological settings, including metamorphic rocks, igneous rocks, and sedimentary rocks. In addition to an impressive array of gemstones, the deposits yielding the gems are also host to world-class mineral specimens, many of which adorn high-end mineral collections and museum displays.
The process of gemstone exploration, exploitation, processing, and commercialization begins in mines that are typically remote and subject to seasonal mining periods since they are in the series of mountain ranges collectively comprising the Himalayas. The miners are as tough as the country that yields the gemstones, working in some of the most inhospitable geological environments in the world. The rewards, however, for anyone who has the privilege of owning or viewing these specimens, make it worthwhile.
Pakistan is known for its rich deposits of various gemstones, and there are several mines across the country where these precious and semi-precious stones are extracted. Some notable gemstone mines include:
• Mogok Mine
Location: Gilgit-Baltistan
Gemstones: rubies, pink topaz, aquamarine, tourmaline, quartz
• Shigar Valley Mines
Location: Skardu, Gilgit-Baltistan
Gemstones: aquamarine, topaz, emerald, quartz
• Swat Valley Mines
Location: Swat, Khyber Pakhtunkhwa
Gemstones: emerald, malakite, pink topaz, tourmaline, quartz
• Kala Dhaka (Kohistan) Mines
Location: Kohistan, Khyber Pakhtunkhwa
Gemstones: peridot, aquamarine, tourmaline, quartz
• Khyber Agency Mines
Location: Khyber Agency, Khyber Pakhtunkhwa
Gemstones: period, tourmaline, quartz
• Chumar Bakhoor Mines
Location: Hunza Valley, Gilgit-Baltistan
Gemstones: aquamarine, topaz, quartz
Photos of some of the highly sought-after, collectible mineral specimens are shown throughout the article.
The discovery of gem-bearing areas variously involves the use of satellite imagery, geological maps, and on-site fieldwork to pinpoint regions of interest. Geological maps and remote imagery (e.g. satellite imagery showing alteration and host-rock signatures) are employed initially to identify regions with potentially favorable geology. Next, a review of the local geology is undertaken, including literature reviews, identification of known mines and liaisons with local geologists and prospectors. The next step becomes logistically more challenging because it requires on-ground geological investigation. Commonly, access is poor, and the terrain is brutal, and cultural sensitivities/awareness need to be employed. Steep valleys, near-vertical cliffs, lack of roads, threats of landslides, dealing with different communities, large rivers, seasonal influences, lack of communication, etc., all make the process challenging. These factors have to be combined with the process of identifying misinformation, where people will deliberately give mines different names or locations to throw competitors off the scent!
Regardless of the difficulties, once promising sites with the correct host-rocks are located, the exploration process transitions to sampling, including drilling and diamond coring. Portable drill rigs, commonly known as man-portable or backpack drill rigs, are carried to sites by people or animals rather than being transported by trucks. These rigs are commonly used in remote and challenging terrains where larger truck-mounted rigs cannot access. Getting even the portable drill rigs into exploration areas in the mountainous regions can still pose challenges. The difficult terrain, lack of proper roads, and altitude can make transportation a logistical hurdle. In some cases, the equipment may need to be disassembled and carried in sections to reach the desired exploration site.
The collected samples are analyzed both for gemstones (direct indication) and/or associated minerals and alteration (indirect association). These samples undergo thorough laboratory testing, including mineralogical and chemical analyses, to confirm the type and quality of gemstones present. The exploration process doesn’t stop there. It evolves into a delicate balance of environmental consciousness and sustainable practices. Mining operations, if deemed viable, are conducted with strict adherence to environmental regulations to cause minimal ecological impact.
Once a promising volume of mineralized rock has been defined, the process of tunnel planning is undertaken. Eventually the zone of rock containing the mineralized pockets will be intersected. It is then an intricate process of extracting the host-rock, much of which will be the correct composition for hosting gemstones but will not be mineralized. Generally, the gemstones occur in preferentially mineralized volumes within larger zones of poorly mineralized to unmineralized rock. The
voids are best described as vugs geologically but tend to be referred to as ‘pockets’ in the mineral and gemstone collecting world.
The exact locations of the pockets within the lesser mineralized rock are unknown, so the process of exploitation can be time-consuming as the host-zone is progressively removed. If too little care is taken, e.g. by trying to mine too aggressively, priceless specimens can be damaged. Unfortunately, untold numbers of specimens have been destroyed in the past. And there can be a lot of Pakistan between the destroyed pocket and the next one, meaning it is in the best interests of everyone involved to proceed with care. As such, a combination of geological mapping and careful excavation is employed to provide the highest rates of success for the discovery and extraction of the minerals in these pockets.
The pockets that host the gemstones are the product of a complex interplay of geological processes. These pockets may result from the dissolution of minerals, opening of voids in conjunction with other processes such as, faulting and volcanic activity, complex fluid/crystallization fractionation processes, fluid mixing, evolution and overprinting of mineral species as new fluids have entered the pockets, etc. The result is an array of different precious and semiprecious mineral species that is unparalleled globally. As such, ongoing interaction between geologists and miners (who are commonly very geologically-savvy) is very important.
Miners employ a combination of traditional methods and modern techniques to locate and extract gemstone pockets. An overview of the general mining process is given below, followed by details of the extraction process. General mining involves the following steps:
Once a potential site is identified, miners may use drilling equipment to extract core samples to assess the quality and quantity of gem-
↑ Some magnificent aquamarine crystals growing from the roof of a quart- and feldspar-lined vug. The helmet in the bottom-right of the photo gives an idea of scale.
stone deposits in the area. Drilling ahead of the blasting allows miners to gather information about the geological structure and the presence of gemstone pockets.
After identifying a promising area, miners begin tunneling using techniques such as drilling and blasting. As the tunnels progress, miners may use handheld tools to carefully extract and inspect the rock for signs of gemstones, a process requiring skill and experience. The choice of blasting technique depends on the type of rock and the proximity to valuable gemstone deposits. Miners commonly use ‘softer’ blasting techniques or controlled blasting when they are closer to known gemstone pockets.
This helps minimize the risk of damaging or fracturing the gemstones during extraction. Soft packing materials such as foam or cloth blankets may be used to protect the extracted gemstones from damage during the extraction process.
Pakistani miners commonly employ hydraulic and electric drills, which have multiple drilling bits for different rock-types. The diamond saw is not the best option for mining in the mountains. The biggest issue is that heavy machinery, including diamond saws, can have a significant impact on the environment. In regions with delicate ecosystems, as is the case with certain areas in Pakistan, the environmental consequences of large-scale mining operations need to be carefully considered. Furthermore, diamond saws are expensive to purchase and maintain. Such initial investment in such equipment can be prohibitive, especially for small-scale miners in Pakistan. Otherwise, chisels allow miners to have more precision and control when extracting gemstones. This is crucial when dealing with valuable and delicate materials, as it reduces the risk of damaging the gemstone during extraction.
Throughout the mining process, surveying is crucial. Miners use instruments, such as theodolites and laser range finders to map the tunnels accurately. Surveying helps in understanding the orientation of the tunnels, ensuring safety, and providing valuable data on the location of gemstone pockets.
As gemstone pockets are exposed, miners often resort to manual extraction methods. Hand sorting allows for careful examination of each gemstone, ensuring it is not damaged during the extraction process.
It’s important to note that the specific methods used can vary based on the type of gemstone, geological conditions, and the scale of mining operations. Sustainable and ethical mining practices are increasingly emphasized to minimize environmental impact and promote the well-being of local communities.
The minerals that are extracted fall into two broad categories – specimens for processing for the jewelry trade, and specimens that are retained in their natural state for display in mineral collections. The remoteness of the gemstone areas, and the apparently primitive conditions, have unfortunately led to a perception of the miners being unskilled. This is unfounded and couldn’t be further from the truth, as
↑ Pakistan is famous for aquamarine, one of the most desirable, blue forms of beryl. Aquamarine specimens from the mines in Pakistan grace the best mineral collections in the world and command extremely high prices. The specimen I am holding was sold to me by a private collector about a year ago. It was acquired from Shigar Valley, Skardu District, Gilgit-Baltistan Province, and weighs more than 1 kg (2.2 lb) with no repairs and no damage.
the miners take great care and pride in their job. One only has to see the fragile, delicately crystalline morphologies of the specimens that have arrived in mineral collections all over the world to appreciate the great care with which they extract the gemstones and mineral specimens.
Once extracted, gemstones are typically cleaned and sorted. Special care is taken to wrap them in materials that prevent scratch-
ing or damage during transportation. Gemstones may be individually wrapped in soft materials like tissue paper or cloth and then placed in secure containers or padded boxes. For higher-value gemstones, additional precautions such as custom packaging with shock-absorbing materials may be taken. Transportation methods can vary depending on the scale of the operation. Larger mining operations may use secure courier services or transport gemstones to cutting and trading centers for further processing and distribution.
In the case of minerals for jewelry, the gem-laden rocks go to processing centers equipped with state-of-the-art machinery. There the stones undergo a series of meticulous steps. First, they are cleaned to remove any impurities accumulated during extraction. Next, expert gem cutters carefully examine each stone to determine the optimal cut that will enhance its natural beauty. This step is crucial, as the cut plays a significant role in the gem’s brilliance and overall appeal.
In a significant development for Pakistan’s gemstone industry, a notable collection of precious stones has found its way into the hands of local jewelry manufacturers. This strategic acquisition not only represents a key milestone in the gemstone trade but also underscores the growing influence of Pakistani artisans on the global jewelry mar ket. The jewelry crafted from these gems will serve as ambassadors, representing the craftsmanship, culture, and sophistication of Pakistani artisans on the world stage. As these gems take their place in the hands of skilled artisans, they become the building blocks of masterpieces that will shine with the essence of Pakistan’s gemstone legacy.
Major Drilling is one of the world’s largest drilling services companies primarily serving the mining industry. We maintain field operations and offices in Canada, the United States, Mexico, South America, Asia, Africa and Australia.
info@majordrilling.com
Recently, I’ve participated at the 13th International Conference titled ‘Mineral Resources in Serbia - Sustainable Growth Through Responsible Mining’ as a panelist in the discussion ‘Challenges and Issues in Mineral Exploration’.
In a preparation for this event, I have asked myself, ‘What is the rate of big discoveries in Serbia and how long will take someone to discover a minable economic deposit and put it in production, as well what would be the challenges and issues?’.
Geology is a fundamental science and economic geology plays a significant role. Mining is a fundamental industry for any society and country. The Serbian Geology Society dates to 1891 and it is one of the first in Europe and the world. Teaching of geology has been ongoing since 1880 with the establishment of the Department of Mineralogy and Geology at the Great School in Belgrade, the ancestor of Belgrade University.
In the period from 1880 to the present day, Serbia and the world as a whole went through rough times and many changes in the government, society, technology, etc. Those changes affected mining as a whole as well.
But let’s start from the beginning where the history of mining in Serbia goes back to the Neolithic Vinča culture. This culture was one of the first to introduce metal and mining in human history, with archaeological evidence preserved at Rudna Glava, approx. 10 km (6.2 mi) southeast from Majdanpek mine (that has tremendous history by itself) in Eastern Serbia. This area preserves what is considered
as one of the first copper mines and smelters in Europe, dating back to the period 7000–5500 BC. Some other Vinča culture mining and smelting localities in Serbia include: Belovode near Kučevo in Eastern Serbia; Pločnik near Prokuplje in Southern Serbia; Avala near the capital Belgrade.
As time went by, human civilization changed, and we entered the Roman period in present day Serbia. Romans continued developing mining and left the evidence at the fortress Kraku Lu Jordan, a smelting complex at Brodica village in Eastern Serbia.
The next stage of this constant change was Medieval Serbia where mining played a significant role. In 1254, Serbian King Uroš introduced the Saxon miners, who brought know-how and played a major role in the development of medieval mining at several sites, including: Brskovo, in present-day Montenegro, at the time largest silver mine; Rudnik (active Pb-Zn mine) in central Serbia; Trepča and Novo Brdo, located in Kosovo. The Law on Mines, or the ‘Novo Brdo Code’, of Despot Stefan Lazarević from 1412 precisely determined the working conditions in the mines, starting with the obligation of the owner to constantly maintain the mine, through determining the length of permitted interruption of work in certain parts of the mine, to standardizing the dimensions of mining tools and accessories.
The only period in Serbian history where mining was relatively subdued was when the Medieval Serbian kingdom was overtaken by the Ottoman Empire. As the rise of Habsburg Monarchy and subsequent the Austro-Hungarian Empire began after the signing the
‘Peace of Požarevac’ in 1718 between Austria and Venice on one side and the Ottoman Empire, mining in present-day Serbia restarted.
Serbia regained autonomy within the Ottoman Empire and regained its independence and freedom in 1867 when the last Ottomans left, while at the Berlin Congress in 1878, Serbia received international recognition. This new chapter is characterized by the establishment of the first mining state institution in 1838. Prince Miloš issued the Mining Law, which regulated work and management in the mines of Serbia. In 1865, the Ministry of Education decided to send twenty young men to study at European universities, which indicated that the state of Serbia invested in mining. Since 1919, mining is regulated by the Ministry of Forests and Mines, and after the Second World War, an independent Ministry of Mining was established, represented by the present-day Ministry of Mining and Energy.
The first half of the 20th Century is characterized with domestic and foreign investments in geology exploration and mining, leading to the major discoveries of world-class deposits including the Cu-Au mine in Bor in 1903 (Eastern Serbia), the Pb-Zn-Ag mine in 1930 in Trepča (Kosovo), and the Lece Pb-Zn-Au-Ag mine in 1931 (Southern Serbia). All three are still in production.
The second half of the 20th century, after the Second World War, was characterized by a Communism regime where all corporate and privately owned mines were nationalized. Great efforts were put in the revival of the production of existing mines, plus the opening of new ones. These include: the Lece Pb-Zn-Au-Ag in 1951, the Crnac Pb-Zn mine in 1968, the Blagodat Pb-Zn mine in 1964, the Rudnik Pb-Zn mine in 1952, the Veliki Majdan Pb-Zn-Ag mine in 1953, the Belo Brdo
Pb-Zn mine in 1970, the Majdanpek Cu-Au mine in 1961, and the Veliki Krivelj Cu-Au mine in 1979.
Since 2004, when the Serbian government allowed foreign investments in mineral exploration, significant discoveries have been made including: the Jadar Project with newly discovered mineral Jadarit - a sodium-lithium-borosilicate-hydroxide; Čukaru Peki HS-Porphyry CuAu deposit/mine; Timok Project Sediment-hosted Au; Kiseljak mine’s south extension; Yellow Creek Cu-Au porphyries; Tulare Project; the recently discovered Čoka Rakita Au skarn.
If we ruled out the Čoka Rakita Au skarn, because exploration is still ongoing, only Čukaru Peki has been put in production out of remaining deposits, commencing mining on 22nd October, 2021. The Čukaru Peki deposit was found in 2012 with the 10th deep drill hole, while exploration that led to the discovery was intensive in the period 2004 – 2012, although the Institute for Copper explored the area in 1980s. Development lasted from 2012-2021. This can be considered fast, as the whole process took only 17 years. For comparison, the last time a still-operating mine opened, in the Timok Region of Eastern Serbia, was the Veliki Krivelj Cu-Au porphyry in 1979, 42 years ago.
Other Projects are now on hold for various reasons, challenges and issues including environmental, social, technical, etc.
Exploration is a long-term, complex and multidisciplinary process that is directly dependent on investments. Present day explorers are facing challenges that include environmental impact and have to be prepared from day one, as environmental issues are often misused for political battles where companies along with geologists are collateral damage. Social challenges are more visible in the areas that are not historically mined, as introducing mining can be hard since people are
↑
zone of clay-sericite alteration at Degrmen Au-Cu porphyry prospect, Degrmen, Serbia
not coping well with the change of their lifestyles. Technical issues include grades, type of ore, and construction challenges in remote areas.
The most important challenge, however, comes before all the above-mentioned and that is to find the orebody that is economic and can be mined with all parties satisfied. As an illustration, prospection work on the project that I’ve worked on commenced in 1955, while the first drillhole was completed in 1969. A scout drilling program lasted for another year with 10 drillholes. The second campaign continued from 1977 to 1980 with 14 drillholes, and a third one was executed from 1984 – 1990 with 32 drillholes. To sum, this is 56 drillholes, totaling 11 282 m (37 014.44 ft) over 21 years.
The next stage of exploration at the Project commenced in 2007 with yet another four holes, 1001 m (3284.12 ft) in all. There was intense drilling over the period 2011-2014 with 119 drillholes for 54 150 m (177 657.48 ft) in all. Work in the period 2011-2014 resulted in an extension of the resource from 1988 and the discovery of a new orebody. In just three years, 4.8 times more drilling was done than in 21 years under the State-owned Geological Survey of Communist Yugoslavia.
So, why did the State geologists fail and what did we do differently to extend resources and discover new orebodies? Trust me, geologists that worked for the State Geological Survey on that project were smart and they used all the tools at their disposal to the best they could. What they lacked was support from the owner, in this case the State, as most likely the State did not want to take risks and maybe had a better idea of how to spend public money. Maybe. We learned from their work, and we collected any possible data we could, we developed models, we interpreted them, and we reinterpreted them. We shared our knowledge and ideas with a wide range of knowledgeable people, actively persuading our management to support our ideas based on facts collected on the ground. The company took all the risk, management bit the bullet and we drilled. Although this Project is not yet developed, knowledge about it significantly increased and one day someone will put the final piece into the puzzle.
It just explains how challenging explorations in general is, without all the other Project-specific considerations, as from the first drillhole in 1969 to the last one in 2014 there is a period of 45 years of hard work, risk taking and knowledge gaining.
In our present mining-social environment, with its evolving demand for metals and the need to address the energy transition, time is of the essence as we are all pressed by the market to deliver results as soon as possible. Part of this involves the use of high-end technology where emerging AI is the first choice. As a big believer in technology and its use, I’m also aware that its misuse is dangerous. Although AI can give you solutions, it is also based on a binary concept of yes/no, while geology is all about context, as no two deposits are the same. The development of great, informed geological models has helped in so many ways, but one cannot put a model in the deposit, we can only put a deposit in the model. Therefore, one needs to know one’s prospect to understand its unique features and to gain as many possible facts, and that is best done with boots on the ground. That is, critical knowledge of a particular prospect is essential.
Dragan is Exploration Manager at Konstantin Resources, Australian Company exploring in Serbia and consulting geologist with over 18 years of experience in geological explorations in Serbia, Eastern Europe and North America. During his career, he worked on various exploration projects for precious and base metals. He led a team of geologists working to define the Kiseljak copper and gold deposit and was one of the key figures in the discovery of the Yellow Creek deposit and the southern extension of the Kiseljak deposit. He also worked on other projects in the Lece Magmatic Complex, Timok Magmatic Complex and Surdulica Granodiorite Complex. He is a member of the Serbian Geological Society, Society of Economic Geologist, Mineralium Deposita. Dragan is licensed Euro Geologist no. license in 1546. C
For more information
Get in touch with Dragan Dragić on LinkedIn
Helicopter Portable Diamond Drill
1400 Meter NWL Depth Capacity
Cummins Power Unit 160 or 260 HP
‘P’ Size Rotation Unit & Clamp
Safety Package: Full Guarding, Multiple E-Stops, Interlock Rod Guard & Power Lock-Out
Available in Heli-Portable, Skid Shack Mounted and Track Carrier
Drilling Contractors (A-Z): Diamond Drilling, Reverse Circulation, AirCore
BRYSON DRILLING
Phone 306-323-2202 Fax 306-323-2203 info@brysondrilling.ca www.brysondrilling.ca Canada
CAPITAL DRILLING Phone +230 464 3250 info@capdrill.com www.capdrill.com East, North and West Africa
DDH1 DRILLING
Phone +61 08 9435 1700 admin@ddh1.com.au www.ddh1.com.au
Australia
DIAFOR Phone (819) 860-3957 info@diafor.ca www.diafor.ca Canada
info@oykatiab.com www.oykatiab.com
Finland
Australia
ATELIER VAL-D’OR
Phone (819) 824-3676 Fax (819) 824-2891 info@avddrills.com www.avddrills.com
WE ARE YOUR SONIC DRILLING PARTNER
Terra Sonic International knows what it takes for you to succeed. We are committed to making the world’s most productive and reliable SONIC Drill Rigs and SONIC Tooling while providing the best service and support in the industry. Experience the Terra Sonic Difference today. www.terrasonicinternational.com
sales@terrasonicinternational.com
+1 740.374.6608
+1 740.374.3618
BARKOM Phone 90-312 385 60 50 Fax 90-312 385 35 75 info@barkomas.com www.barkomas.com
Drill Rig Parts Cont.
PROLENC
Phone (250) 563-8899 Fax (250) 563-6704 khodgins@prolenc.com www.prolenc.com
BOART LONGYEAR
Phone 1-801-972-6430 Fax 1-801-977-3374 www.boartlongyear.com
DISCOVERY DRILL MANUFACTURER
Phone 1-506-542-9708 Fax 1-506-542-9709 info@discoverydrills.com www.discoverydrills.com
FORDIA POWERED BY EPIROC
Phone 514-336-9211 Fax 514-745-4125 info@fordia.com www.fordia.com
Specialized Machine Works (A-Z)
NORTH BAY MACHINING CENTRE
Phone (705) 472-9416
Fax (705) 472-2927
luc@nbmc.ca www.nbmc.ca
PROLENC
Phone (250) 563-8899
Fax (250) 563-6704 khodgins@prolenc.com www.prolenc.com
Diamond Products (A-Z)
www.boartlongyear.com marketing@boartlongyear.com
QUALITY AND EXPERTISE
DIATOOL is a young and dynamic company, founded in 2010. The company manufactures impregnated and set core bits, casing shoes, reaming shells, and geotechnical drilling bits. DIATOOL products are sold in North and South America, Australia, Asia, Africa, and Europe. DIATOOL Diamond Products are manufactured in a modern well-equipped plant, using the latest manufacturing technology. www.diatoolglobal.com anthonygraham6@gmail.com
DIAMANTINA CHRISTENSEN
Phone +562 2620 7808 christensen@christensen.cl diamantinachristensen.com
DIASET
Phone 1-800-663-5004 bits@diaset.com www.diaset.com
DIATOOL DIAMOND PRODUCTS Phone 852 2871 9028 diatool@163.com www.diatool@global.com
HOLE PRODUCTS
Phone (888) 465-1569
Fax (320) 631-0064 www.holeproducts.com
BOART LONGYEAR
Phone 1-801-972-6430
Fax 1-801-977-3374 www.boartlongyear.com
HOLE PRODUCTS
Phone 909-939-2581
Fax 909-891-0434 www.holeproducts.com
Drill Rods & Casings (A-Z)
BARKOM
Phone 90-312 385 60 50 Fax 90-312 385 35 75 info@barkomas.com www.barkomas.com
CORE TECH
Phone +51 983 856 666 info@coretech.com.pe www.coretech.com.pe
SINOCOREDRILL
Phone 86-510-82723272 Fax 86-510-82752846 sales@sinocoredrill.com www.sinocoredrill.com
FORDIA POWERED BY EPIROC
Phone 514-336-9211 Fax 514-745-4125 info@fordia.com www.fordia.com
WE ARE YOUR SONIC DRILLING PARTNER
Terra Sonic International knows what it takes for you to succeed. We are committed to making the world’s most productive and reliable SONIC Drill Rigs and SONIC Tooling while providing the best service and support in the industry. Experience the Terra Sonic Difference today. www.terrasonicinternational.com sales@terrasonicinternational.com
+1 740.374.6608
+1 740.374.3618
FORDIA POWERED BY EPIROC
Phone 514-336-9211 Fax 514-745-4125 info@fordia.com www.fordia.com
REFLEX
Phone 1-705-235-2169 Fax 1-705-235-2165 reflex@imdexlimited.com www.reflexnow.com
SONDA PARTS
Phone 55 – (31) 3391 3810 Fax 55 – (31) 3391 3810 comercial@sondaparts.com.br www.sondaparts.com.br/
sptab.com sales@sptab.com +34 952 17 99 18
ADVANCED DOWNHOLE SURVEY TOOLS FOR EXPLORATION AND BLASTING
SPT is your global partner for downhole survey technology. We manufacture advanced solutions for high precision downhole and blasthole survey data. Our commitment to quality and accuracy has made us an industry leader. Request a free demonstration today.
Wedges (A-Z) Drill Rods & Casings Cont.Drilling Fluids (A-Z)
AMC Phone 1-705-235-2169 www.amcmud.com
DI-CORP Phone +1 (705) 4727700 info@di-corp.com www.di-corp.com
Surveying & Geophysics (A-Z)
CORE TECH
Phone +51 983 856 666 info@coretech.com.pe www.coretech.com.pe Peru
DIGITAL SURVEYING Phone +27 18 788 6349 sales@digitalsurveying.co.za www.digitalsurveying. com.za Africa
Mudex Phone +61 (8) 9390 4620 info@mudex.com.au www.mudex.com.au
TRUST SOLUÇÕES
GEOLÓGICAS
Phone +55 62 992720023 contato@trustsg.com.br Brazil
Trays (A-Z)
CORE TECH
Phone +51 983 856 666 info@coretech.com.pe www.coretech.com.pe
DYNAMICS G-EX
Phone +61 7 54826649 sales@dynamicsgex. com.au www.dynamicsgex.com.au
Core Orientation (A-Z)
COREFINDER Phone +55 62 992720023 contato@corefinder.com.br www.corefinder.com.br
DEVICO AS Phone +47 72870101 devico@devico.com www.devico.com
PROSPECTORS
Phone +61 (02) 9839 3500 Fax +61 (02) 8824 5250 sales@prospectors.com.au
For more information regarding our catalog options and rates, get in touch at: editorial@coringmagazine.com
A special dry blend of polymers for drilling in sand, gravel & cobbles:
Reduces the need of casing in most unconsolidated formations.
E ectively stops shifting sands from collapsing into the bore hole.
Proven to increase productivity & profits.