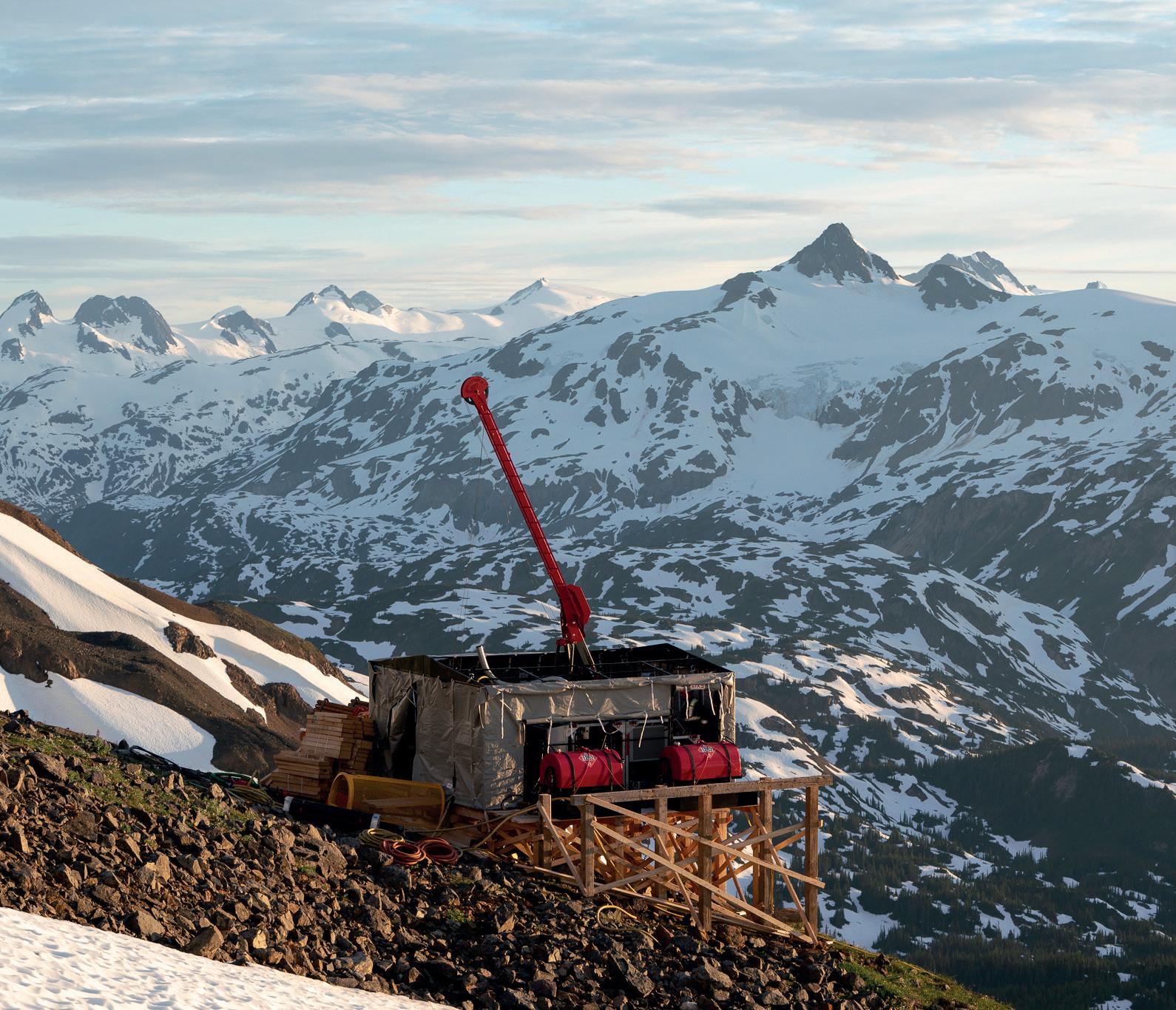
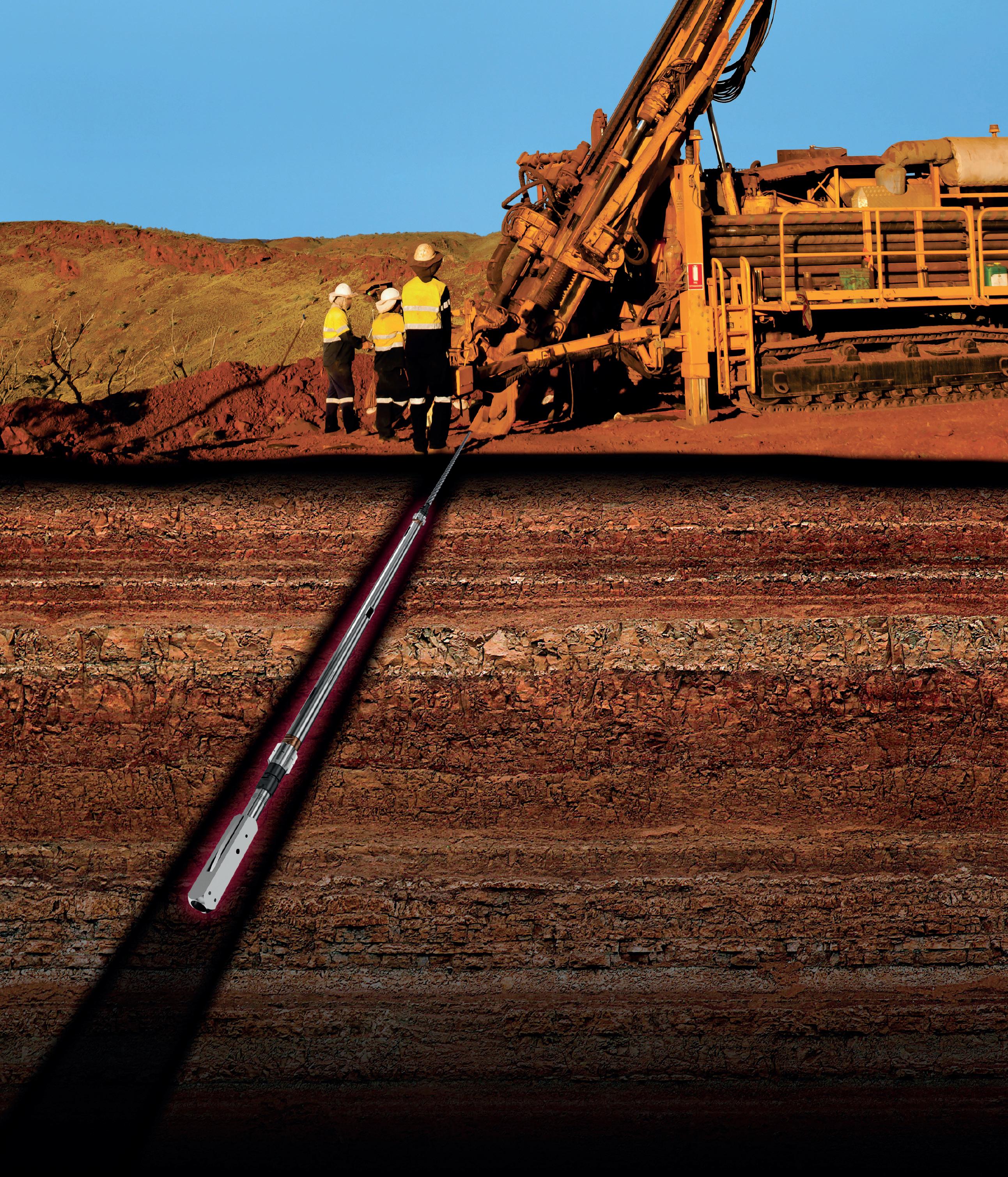
6 Exclusive interview with Dave Harper President, CEO and Director at Geodrill
12 RockDrill: Experts in drilling Rock Drill: Expertos en perforación by Herbert Vilcapoma Lopez, CEO & Executive Director at Rock Drill Group / CEO & Director Ejecutivo at Rock Drill Group
24 Harris Drilling: Safety is our core by Garth Patterson, Director of U.S. Operations at Harris Exploration Drilling
26 A blitz drill venture deep into Namibia’s Kaokoland by Kirsten Günzel, Manager at Günzel Drilling
30 The importance of instrument calibration: Part II by Dag Billger, Owner & Business Manager and Duncan McLeod, Owner & Product Manager at Inertial Sensing One AB
35 Q&A from the experts In conversation with Greg Hall, Principal at Golden Phoenix International Consulting Pty Ltd
40 Will AI take geologists jobs? Discussion on whether AI is a threat or a boon to humanity by Nick Tate, Specialist Consultant Mapper of Geology, Alteration and Mineralization Systems
20 Scratch testing applications with Boart Longyear by Jon Peterson, Product Manager –Diamond Products at Boart Longyear
44 The importance of groundwater in mining and how drillers and hydrogeologists work together to achieve the best results by Mariajose Romero-Segura, Freelance Project Hydrogeologist and Technical Translator
48 Vektore’s new AR tool brings speed, accuracy, precision and universal reading of structures to the core shack by R.N. Monteiro, P.Geo., M.Sc., FSEG, Ph.D., President and Chief Structural Geologist at Vektore Exploration Consulting Corp.
52 The future of Geoscience education and the National Exploration Undercover School (NExUS) by Richard Lilly, Program Leader at the University of Adelaide
DRILLING CATALOG
54 Drilling services
55 Drilling equipment & accessories
61 Survey equipment
62 Miscellaneous
R.N.
CORING MAGAZINE
August 2023
Cover photo
Multi-Power Products
Drill site: Helm Diamond Drilling, Canadian Golden Tringle
Issue 24
ISSN 2367-847X
Not for resale. Subscribe: coringmagazine.com/subscribe
Contact Us
Coring Media Ltd.
119B D. Petkov Str., Sofia 1309, Bulgaria
Phone +359 87 811 5710
Email editorial@coringmagazine.com Website coringmagazine.com
Publisher Coring Media
Founder Grigor Topev Executive Officer & Editor in Chief Martina Samarova
Editor Maksim M. Mayer
Section Editor – Exploration & Mining Geology Dr Brett Davis
Digital Marketing Manager Elena Dorfman
Graphic Design Cog Graphics
Coring Magazine is an international quarterly title covering the exploration core drilling industry. Published in print and digital formats, Coring has a rapidly growing readership that includes diamond drilling contractors, drilling manufacturers and suppliers, service companies, mineral exploration companies and departments, geologists, and many others involved in exploration core drilling.
Launched in late 2015, Coring aims to provide a fresh perspective on the sector by sourcing authentic, informed and quality commentary direct from those working in the field. With regular interviews, insightful company profiles, detailed product reviews, field-practice tips and illustrated case studies of the world’s most unique diamond drilling and mineral exploration projects, Coring provides a platform for learning about the industry’s exciting developments.
Open the box and GO. The GoGyro is fully integrated and designed specifically for simple, easy everyday use.
Configure your GoGyro as you need it for your surveys without unnecessary extra running gear. Simply add the needed fitting to run as:
• Core retriever
• Wireline
• Centralizers
Minimize downtime & Maximize efficiency. Simply GO Survey!
Fully integrated with SurveySafe for fast, convenient and secure online survey data management.
Dave Harper is the President, Chief Executive Officer and Director of Geodrill. With over 35 years of experience in the drilling industry, 30 of those years in management and 28in West Africa, he is passionate about the future of drilling on the continent.
Dave’s goal to establish a leading international drilling company, based in Ghana, has been achieved and the company has expanded its operations into seven countries and two continents, namely: Ghana, Burkina Faso, Cote d’Ivoire, Mali in West Arica; Egypt in North Africa; and Peru and Chile in South America.
Integrating ESG principles into the company’s vision from day one, Geodrill has built a strong legacy of CSR projects in Africa.
Grigor Topev: Dave, thanks for taking the time for this interview. How did you start Geodrill? What was your first drill rig and project?
Dave Harper: Growing up in Melbourne, my parents had everything in place for me to excel academically. To their dismay, as a young rebellious teenager I decided that a life of adventure was more fitting and headed to Coober Pedy (an opal mining town in South Australia) where I stumbled upon a job as a fuel pump attendant. The customer with the most impressive car and passengers, filling up from one holiday to the next, turned out to be a local legend and driller: Lenny Butts, and my inspiration to pursue drilling.
When the chance to join as a drilling offsider came up, with the condition being to pack up and be ready by the next day, I thought back to Lenny and just went for it. In a stark contrast to the lifestyle Lenny the driller had portrayed, there I was travelling deeper into the outback, some five days in the back of a pickup truck with a dog, my backpack and AUD 50 to my name; no turning back.
Day One of my drilling career, no fault of my own, I hear ‘GET OUT OF THE WAY’, with barely time to take two steps, a big sheeve block hits the ground exactly where I was standing; it would have killed me for sure! HSE standards have clearly come a long way from when I started, and thankfully so. Moving on to a more professional drilling company in Kalgoorlie, I worked my way up and was part of their expansion to West Africa and was transferred to Ghana. Thanks to a mate, Chris Bonwick (Bonza) at Resolute Mining, I was given more opportunities to go my own way in Ghana, and in 1998, with a single rig - Geodrill was born.
GT: What was the industry like back then?
DH: It certainly favored the bold, brave and adventurous.
GT: Geodrill started in Ghana. Where is Geodrill operating or active?
DH: Geodrill principally operates in Mali, Cote d’Ivoire and Egypt in Africa. Our subsidiary, Recon Drilling, is active in LATAM, operating in Chile and Peru at present.
GT: Let’s talk a little bit about the team at Geodrill. How many people work in the company? What’s their background?
DH: Currently 1500. Most joined with low skills and have worked their way up through training, promotion, etc. Our retention is high. We still have some of the original team that joined us 25 years ago.
GT: Are Geodrill’s employees local or expats? Tell us more about the training and HSE campaigns.
DH: Mostly local. We recognized early on that to be successful, we needed to develop skills that would lead to career opportunities (not just jobs) for our local workforce, which has proven very successful. Today only a small percentage of our workforce is expat.
GT: Operating on such a large scale and in so many countries, how did you manage the cons of fast expansion?
DH: A strong and committed team, the early establishment of a work culture that invests in people, and training from within at all levels has enabled us to operate flexibly and expand when and where in an agile manner.
GT: I’m sure you have many stories related to all the countries Geodrill operates in. Tell us some of them, please.
DH: All of the countries we have operated in have had their own challenges, magic moments, colorful characters, some struggles but lots of lessons. I’m sure anyone in the exploration field knows that war stories are part of the souvenirs we gain.
GT: Where are the major drilling hot spots at the moment?
DH: We are most certainly breaking strong ground in Egypt and it is exciting to see how the mining industry is developing there. We’ve also been excited to see some stellar drill results for clients in Côte d'Ivoire, where we currently have 20 rigs or so; it continues to be a hot place to drill.
GT: What do you wish to change in the African market?
DH: Logistics and connections between the African countries have improved a lot, and yet, it will be great when road and rail connections are smoother, both for efficiency and safety.
GT: What personal quality do you think helped you the most in order to start and grow a successful drilling company?
DH: Tenacity, being able to take a risk, trust in the right people and knowing when to cut losses and move on as fast as possible.
and dedication of many organizations, which we have been supporting for a long time.
GT: Recently, there have been quite a few industry changing mergers and acquisitions. Is the industry heading towards a market consolidation?
DH: Interesting to see Major Drilling re-entered the Australian market via McKay Drilling, a good outcome for buyer and seller. Busy times for DDH1 after going the private equity route and soon after acquiring Ranger and Strike then rolling it all into an IPO, then adding Swick. Four great drilling businesses there rolled into one, makes sense. Now merging with Perenti, creating a complete services provider from exploration drilling through to mining.
Successful mergers and acquisitions should benefit of all stakeholders. For Geodrill, all our growth has been organic.
GT: I saw you at PDAC 2023, where you announced the results of another great quarter for Geodrill. Can you tell us a bit about the current position of the company, its projects, fleet, etc.?
DH: Most proudly, I can say that Geodrill is in a very strong position. We’ve added to the fleet, now tipping 80 rigs worldwide, some of these rigs are even built at the Geodrill workshop.
GT: How did Geodrill change after going public? Tell us about the challenges and benefits. What would be your piece of advice for a company that is considering going public?
DH: At Geodrill we have always held the ethos of ‘Just doing the right thing’ to all stakeholders. Wherever we operate, we always strive to have a positive impact on the environment and the wellbeing of communities. We’ve been proud to support many grassroot organizations and individuals in need.
Going public meant we have to ensure this goodwill is understood and valued by shareholders as well, calling for increased screening of ESG spending and documentation. The upside of ensuring all ESG efforts are channeled formally is that we have been able to highlight internationally the excellent work
Results-wise, we generated the best ever first quarter (the second highest ever quarterly revenue in the company’s history) of USD 37.6 million, representing a 12% increase compared to USD 33.4 million for Q1-2022. We recorded EBITDA of USD 10.5 million, or 28% of revenue.
GT: Could you please share a bit more about the drill rigs, built at the Geodrill workshop?
DH: At our Anwiankwanta base (in Ghana) we have the largest support facility of any drilling company in the world. Thirty-five acres (141 640 m2), it’s absolutely massive. For years we’ve been manufacturing our own drilling consumables, drill rods, etc. And support equipment and vehicles like crawler-mounted rod carriers, auxiliary compressors, boosters, etc.
So, a few years ago we knocked up some grade control rigs and they turned out better than our suppliers were selling us. Then, during COVID-19 like everyone we faced supply constraint issues, so we decided to build a multi-purpose RC/DD rig. Again, it was better than our supplier could sell us.
‘At Geodrill we have always held the ethos of ‘Just doing the right thing’ to all stakeholders. Wherever we operate, we always strive to have a positive impact on the environment and the wellbeing of communities. We’ve been proud to support many grassroot organizations and individuals in need.’
We’ve since built about six and have another four going through at the moment. We only build for our internal use, no intentions of selling them outside.
GT: What’s next for Geodrill?
DH: For the near future, we are concentrating on ensuring that all projects and countries of operation continue steadily and strongly and see expansion occurring one project at a time. Thankfully, there is no shortage of upcoming exploration projects worldwide and we look forward to the busy years ahead.
GT: There seem to be some challenges ahead of the industry related to the inflation. How do you think should the industry address them? Will there be a slowdown?
DH: Smart operating is key to any business in an inflationary environment, clients don’t like rising costs being passed on, so there is no space for less than optimal utilization of all resources. I’m not so sure about a slowdown - certainly if you look at the diversity of minerals we drill, including battery minerals, there doesn’t appear to be any slowing down of activity.
GT: Geodrill seems to invest not only in rigs but also in the people and the communities. Please tell us more about the company’s recent initiatives.
DH: We certainly pride ourselves as going above and beyond to make a difference. Aside from continuing our support to organizations helping children, education, health and environment, Geodrill continues to
broaden its impact by promoting arts, social awareness, history and sports.
A recent example was backing the making of a documentary film on the life and legacy of Battling Siki, the first African boxing world champion produced by Ashley Morrison ‘Return To Your Corner’. A remarkable story which brings light to part of African sports history, the film was screened by Geodrill at Indaba 2023 with former boxing world champions Azumah Nelson (Ghana) and Brian Mitchell (South Africa) in attendance. From this launch, the film has been picked up to screen around the world at upcoming festivals.
GT: What is your day-to-day work as the CEO of Geodrill? Do you visit the drill sites often?
DH: Yes, I still get around the rigs. It’s the part of the job I enjoy most, i.e. catching
up with drill crews, customers, industry colleagues, etc.
GT: Dave, you’ve been travelling to a lot of industry events, it seems. What is the role of industry events in this post pandemic world? Has it changed?
DH: I didn’t mind COVID-19 so much. We all got good at running our businesses over Zoom and other virtual platforms without having to travel. But it’s good to be back now doing face to face meetings.
GT: What do you do when you are not in charge of Geodrill? Any other passions apart from drilling?
DH: Listening to my daughter, Tanaya Harper’s music is a favorite pastime. Whenever possible to see her perform in Australia, this brings me a great deal of joy. Tanaya is an indie-rock singer and songwriter and it’s a
beautiful thing to see her talent come to life, as well as hear of her adventures performing as part of a popular band, Ghost Care.
GT: Where do you see the industry in five years?
DH: Accelerating, along with the need for battery minerals and other resources. I also see a more diverse workforce, especially more women in drilling. At Geodrill, we have made concrete efforts to encourage women into technical drilling roles.
GT: Finally, Dave, everyone and their mums has been talking about AI. What’s your take and what do you think could be its advantages for drillers, geologists, and exploration in general?
DH: All part of progress, I guess. I remember 50 years ago seeing for the first time an ATM machine and bank employees protesting
saying how it would take away their jobs. Then email came and replaced the post office. Google replaced the library. Cell phones vs pay phones, etc. And on it goes.
From an industry perspective, a bit late to the party but great to see industry stuff going on now, such as hole surveying and steering, e-drill logs, cloud-based transferring of data from the field.
Also, with reference to drill sample analysis, great to see this getting technologically competitive. Those traditional analytical names will need to step up, or step aside. I’ve no sympathy for them, frankly. Every time there’s an up-cycle these guys have always been the slowest to the game only adding capacity when approaching the end of cycle.
Back to your question on AI, whilst we need to embrace it, it should also have limitations. You’ll never catch me on a pilotless flight or a driverless car. My kids think I’m a dinosaur. I guess that much is true. C
United. Inspired.
The Christensen CT20 is ready to take on core-drilling jobs in the toughest conditions. This safe, ergonomic, and versatile rig is available truck- or crawler mounted. The Christensen CT20 has all the power and capacity needed to ensure you get more core in the box. Find out more at epiroc.com
Safer, Faster, Lighter
Reach out easily at www.fordia.com/en/new-product
Rock Drill is a Peruvian company founded in 2000 by Herbert Vilcapoma and Elizabeth Bravo. With more than 23 years of experience, the company has specialized in providing solutions for the mining sector, mainly in the Peruvian and Mexican markets.
Since its inception, Rock Drill has offered diamond, geotechnical, production drilling and geological services, applying the highest standards of operation, innovation, safety and environment.
Rock Drill es una empresa peruana fundada en el año 2000 por Herbert Vilcapoma y Elizabeth Bravo. Con más de 23 años de experiencia, la compañía se ha especializado en brindar soluciones para el sector minero, principalmente en los mercados peruano y mexicano.
Desde sus inicios, Rock Drill ha ofrecido servicios de perforación diamantina, perforación geotécnica, producción y servicios geológicos, aplicando los más altos estándares de operación, innovación, seguridad y medio ambiente.
Herbert Vilcapoma, who previously worked as a Mechanical Technician at Boart Longyear S.A.C., gained experience in machinery repair. He then went on to work at Sandvik del Peru S.A.C., where he had the opportunity to work with underground and surface mining production equipment, such as jumbos and track-mounted drills. With the accumulated experience, in 2000, Herbert Vilcapoma and Elizabeth Bravo founded their first company: Rock Drill Contratistas Civiles y Mineros S.A.C. This company started providing diamond drilling services for Compañía Minera Iscaycruz.
In 2007, they identified a new need in the market and founded Comercial Drilling Services S.A.C. (CODRISE), a company dedicated to the manufacture of drilling products to supply Rock Drill.
In 2010, Overprime Manufacturing S.A.C. was formed in association with a third partner. This company specialized in the manufacture, repair and maintenance of diamond drilling machines and heavy equipment in the mining sector.
In 2015, the Vilcapoma-Bravo family, together with their children, established the fourth company: Helix Renting S.A.C., dedicated to renting vehicles to cover the needs of Rock Drill. These four companies are currently part of the VILBRA Group.
Rock Drill focused on innovating its drilling rigs to adapt to the needs of each client. They modified a pneumatic machine to operate with hydraulic power, which allowed them to manufacture the first exploration drilling rig called RL30, which adapted to different projects in various environments.
The company’s portfolio of products and services includes standard, oriented and directional diamond drilling, geotechnical drilling for permeability testing and installation of piezometers and inclinometers, and geological services, such as soil and rock sampling and geochemical analysis. In addition, in production drilling, they perform slot drilling for chimneys and longhole drilling with down-the-hole hammer.
Rock Drill, had two big challenges, the first one was to face the 2008 crisis, when the fall of metal prices left them with only two machines working out of the 35 they had in operations. The company was left with a debt of 2.5 million to the bank for the leasing they had generated and 0.5 million of debt to suppliers for the large investments they had in terms of workload. Without hesitation, they had to prioritize the payments of the installments to the banks and avoid generating more debt with the reserves they had. Fortunately, in a short period of time, services were restarted and they were able to get new clients to pay the outstanding debts.
The company paid double to their suppliers and thus ensured that their services will continue. As a result, this turned into a strategic partnership, ongoing to this day.
Rock Drill learned that mining is cyclical and that exploration mines are the first to stop services in the face of a crisis. That is why, after the 2008 crisis, the focus of the services was on underground production mining. This is how Rock Drill decided to keep tighter control on indebtedness.
The second challenge the company faced was that little by little more diamond drilling companies started to be formed, which created a more competitive market. Therefore, Rock Drill was looking for a way to differentiate themselves, so they bet on the innovation of the equipment they had been working with. Due to the experience
↘ Driller showing diamond drilling core samples. / Perforista mostrando los testigos de perforación diamantina.
Herbert Vilcapoma, quien trabajaba previamente como Técnico Mecánico en Boart Longyear S.A.C., adquirió experiencia en reparación de maquinaria. Luego, pasó a trabajar en Sandvik del Perú S.A.C., donde tuvo la oportunidad de trabajar con equipos de producción de minería subterránea y superficie, como jumbos y trackdrills. Con la experiencia acumulada, en el año 2000, Herbert Vilcapoma y Elizabeth Bravo fundaron su primera empresa: Rock Drill Contratistas Civiles y Mineros S.A.C. Esta empresa comenzó brindando servicios de perforación diamantina para la Compañía Minera Iscaycruz.
En el año 2007, identificaron una nueva necesidad en el mercado y fundaron Comercial Drilling Services S.A.C. (CODRISE), una empresa dedicada a la fabricación de productos de perforación para abastecer a Rock Drill.
En 2010, se formó Overprime Manufacturing S.A.C., en asociación con un tercer socio. Esta empresa se especializó en la fabricación, reparación y mantenimiento de máquinas de equipos diamantina y equipos pesados del sector minero.
En 2015, la familia Vilcapoma Bravo, junto con sus hijos, estableció la cuarta empresa: Helix Renting S.A.C., dedicada al alquiler de vehículos para cubrir las necesidades de Rock Drill. Estas cuatro empresas forman actualmente parte del GRUPO VILBRA, liderado por la familia Vilcapoma Bravo.
Rock Drill se enfocó en la innovación de sus máquinas de perforación para adaptarse a las necesidades de cada cliente. Modificaron una máquina neumática para funcionar con potencia hidráulica, lo que les permitió fabricar la primera máquina de perforación de exploración denominada RL30, la cual se adaptaba a diferentes proyectos en diversas secciones.
La empresa se especializa en servicios de perforación, principalmente para exploración, geotécnica y producción. Su portafolio de productos y servicios incluye perforación diamantina estándar, orientada y direccionada, perforación geotécnica para pruebas de permeabilidad e instalación de piezómetros e inclinómetros, y servicios geológicos como muestreo de suelos y rocas y análisis geoquímicos. Además, en la perforación de producción, realizan perforaciones tipo slot para chimeneas y tiro largo con martillo de fondo.
Rock Drill, tuvo dos grandes desafíos el primer fue enfrentar la crisis del 2008, cuando la caída de los metales los dejó solo con 2 máquinas trabajando de las 35 que tenían en operaciones, se quedaron con una deuda en el banco de 2.5 millones por los leasings que habían generado y 0.5 millones de deuda a proveedores por la grande inversión que tenían en cuanto a carga de trabajo. Sin dudarlo, tuvieron que priorizar los pagos de las cuotas a los bancos para no generar mayor endeudamiento con las reservas que tenían. Felizmente en corto tiempo se reactivaron los servicios y pudieron conseguir nuevos clientes para afrontar las deudas pendientes.
Con sus proveedores se nivelaron pagándoles el doble de lo que necesitaban para que los sigan atendiendo y generando socios estratégicos que hasta en la actualidad siguen trabajando con ellos.
De esto, les dejo un aprendizaje que la minería es cíclica y que las minas en exploración son las primeras en parar los servicios ante crisis. Es por ello por lo que después de esto el enfoque del servicio fue para minería en producción subterránea. Fue así como decidieron llevar un control más estricto con el endeudamiento.
El segundo desafío que enfrentaron fue que poco a poco empezaron a formarse más empresas en perforación diamantina, lo que originó un mercado más competitivo. Por eso, buscaban la forma de diferenciarse, así que apostaron por la innovación de sus equipos con los que venían trabajando. Debido a la experiencia y capacidad con la que contaban dentro de la empresa, diseñaron equipos semi automatizados para acoplar y desacoplar las tuberías en forma automática, evitando el contacto de los operadores y previniendo los accidentes. Consideraron que el equipo pudiera trasladarse solo a control remoto dentro de la operación y no depender de los recursos de la minera. Gracias a eso alcanzaron una performance satisfactoria y una mayor productividad y rentabilidad.
Fue en ese momento que se consolidaron como una empresa innovadora, aplicando los más altos estándares de calidad, seguridad y medio ambiente, con certificada competitividad y capacidad de identificar los objetivos y necesidades, logrando con ello, la satisfacción del cliente.
and capacities they had within the company, they designed semi-automated equipment to screw in and out the drill rods automatically, avoiding exposure for the operators and preventing accidents. The company considered that the equipment could be moved only by remote control within the operation and not depend on the mining company’s resources. Thanks to this, they achieved satisfactory performance and greater productivity and profitability.
It was at that moment that they consolidated themselves as an innovative company, applying the highest standards of quality, safety and environment, with certified competitiveness and capacity to identify objectives and needs, thus achieving customer satisfaction.
Rock Drill currently has a fleet of more than 100 drill rigs, 70 of them in Peru and the rest in Mexico. In addition, the company plans to reach a utilization rate of more than 75% in the second half of 2023, which demonstrates the confidence and demand of their customers.
Rock Drill has constantly sought innovation and has worked in collaboration with a Swedish manufacturer to implement a novel drilling system that solves the problem of deviation in production drills. This system reduces deviation to 1ᵒ every 50 m (164 ft), compared to traditional systems that can have deviations of up to 5ᵒ per 15 m (49.2 ft) of drilling. In addition, this system is more environmentally friendly as it does not generate dust or noise and consumes less power. Initial tests have shown savings of up to 30% in the production process.
The group’s business strategy is corporate, so Rock Drill is part of the VILBRA Group, taking advantage of various synergies between the companies that make it up and allows to have the necessary resources to offer and perform drilling services. CODRISE provides the products needed to efficiently execute drilling operations, while OVERPRIME develops and manufactures the equipment and machinery that Rock Drill uses to drill and improve operational efficiency and safety. On the other hand, Helix is in charge of managing the fleet of vehicles and utility equipment, such as generators, which are also essential for the work that Rock Drill does in the mine.
It is worth mentioning that OVERPRIME is not only dedicated to the manufacture of equipment but also to the repair of various subway and open pit equipment. The equipment it manufactures is tailor-made for the customer, so mines do not have to ‘adapt’ to the equipment, but the other way around, in line with Rock Drill’s operational strategy of flexibility. This benefits the company in the sense that they can maximize production and safety, providing a customized service for each customer.
At Rock Drill, safety is valued very highly. The vast majority of accidents in the activities they perform are related to drill rods handling, exposure to moving parts and equipment transportation. The technological developments the company has implemented are oriented to reduce the exposure of operators to the most critical processes. Additionally, Rock Drill offers self-transportable drilling equipment on mobile platforms, which dramatically reduces downtime for transportation between drilling pads and their preparation. Moreover, they
increase effective drilling times, enabling Rock Drill to protect their operators and enhance efficiency.
In addition, Rock Drill implemented contact sensors to stop the moving parts of the drill rigs when the rigs’ guards are opened. The company has also recently implemented rod handlers that will reduce the operators’ exposure to any risks.
Rock Drill is characterized by the loyalty of their customers, whom they have been accompanying in their growth. This has strengthened the company’s collaboration of more than 15 years with the VOLCAN group, as well as their 10-year alliance with the ALPAYANA and CONDESTABLE groups. Furthermore, since 2022 Rock Drill has been working with MINSUR in its Raura unit where they have started geological and geomechanical services, which is an added value to the diamond drilling service. The company currently has two manufacturing and assembly plants in Peru and Mexico, 30 projects in both countries and more than 1500 employees.
By the end of 2023, Rock Drill wants to consolidate operations with their current customers, increase their market share and improve the position of the brand. The company is interested in looking for leads that will turn into long-term contracts and strengthen their services in surface exploration drilling.
Additionally, Rock Drill wants to consolidate their production drilling services and geomechanical and geological services. The company expects to be ready for 2024 and to have a greater share of the Peruvian market and to enter other international markets under their motto: ‘Where we drill, we find a future together’. C
Actualmente, Rock Drill cuenta con una flota de más de 100 equipos, 70 de ellos en Perú y el resto en México. Además, la empresa tiene previsto alcanzar una utilización superior al 75% en la segunda mitad de 2023, lo que demuestra la confianza y demanda de sus clientes.
Rock Drill ha buscado constantemente la innovación y ha trabajado en colaboración con un fabricante sueco para implementar un sistema de perforación novedoso que resuelve el problema de desviación en los taladros de producción. Este sistema reduce la desviación a 1 grado cada 50 metros, en comparación con los sistemas tradicionales que pueden tener desviaciones de hasta 5 grados a los 15 metros de perforación. Además, este sistema es más amigable con el medio ambiente al no generar polvo ni ruido, y consume menos potencia. Las pruebas iniciales han demostrado hasta un 30% de ahorro en el proceso productivo.
La estrategia empresarial del grupo es corporativa, por ello Rock Drill es parte del grupo VILBRA, aprovechamos diversas sinergias entre las compañías que lo integran y nos permite contar con los recursos necesarios para ofrecer y realizar servicios de perforación. CODRISE proporciona los productos necesarios para ejecutar eficientemente las operaciones de perforación, mientras que OVERPRIME desarrolla y fabrica los equipos y maquinaria que Rock Drill utiliza para perforar y mejorar nuestra eficiencia operativa y de seguridad. Por otro lado, Helix se encarga de la gestión de flota de vehículos y equipos utilitar-
ios como grupos electrógenos, que también son esenciales para las labores que Rock Drill hace en mina.
Cabe mencionar que OVERPRIME no solo se dedica a la fabricación de equipos, sino también a la reparación de diversos equipos tanto subterránea como de tajo abierto. Los equipos que fabrica están hechos a medida del cliente, por lo que las minas no tienen que ‘adaptarse’ a los equipos, sino que es al revés, esto en línea a la estrategia operativa de Rock Drill de flexibilidad. Esto beneficia a Rock Drill en el sentido que podemos maximizar la producción y la seguridad, brindando un servicio personalizado para cada cliente.
En Rock Drill valoramos mucho la seguridad ya que la gran mayoría de los accidentes en las actividades que realizamos están relacionadas con la manipulación de tuberías, exposición a las partes móviles de los equipos en la perforación y traslado de equipos. Los desarrollos tecnológicos que implementamos están orientados a reducir la exposición de los operadores a los procesos más críticos. Así mismo, ofrecemos equipos de perforación autotransportables sobre equipos móviles, lo que reduce drásticamente los tiempos muertos de traslado y estandarización. Además, incrementan los tiempos efectivos de perforación, lo que nos permite proteger a nuestros operadores y ser más eficientes.
Por otro lado, implementamos sensores de contacto para detener los equipos cuando se abren los protectores de estos a partes móviles. También hemos implementado recientemente manipuladores de tuberías que reducirán la exposición de los operadores a este proceso de riesgo.
Nos caracterizamos por la fidelización de nuestros clientes a quienes venimos acompañando en su crecimiento. Esto ha fortalecido nuestra colaboración de más de 15 años con el grupo VOLCAN, así como nuestra trayectoria de 10 años con el grupo ALPAYANA Y CONDESTABLE. Por otro lado, desde el 2022 estamos trabajando con MINSUR en su unidad de Raura donde hemos iniciado los servicios geológicos y geomecánicos, que es un valor agregado al servicio de perforación diamantina. Actualmente contamos con dos plantas de fabricación y ensamble en Perú y México, 30 proyectos entre ambos países y con más de 1500 colaboradores.
Para este 2023 queremos consolidar las operaciones con nuestros clientes actuales, aumentar nuestra cuota de mercado y posicionar nuestra marca. Nos interesa buscar clientes leads que se conviertan en contratos duraderos y fortalecer nuestros servicios en perforación de exploración de superficie.
Por otro lado, queremos consolidar nuestros servicios de perforación de producción y servicios geomecánicos y geológicos. Esperamos estar preparados para el 2024 y contar con una mayor participación del mercado peruano e ingresar a otros mercados internacionales bajo nuestro lema: ‘Donde perforamos, encontramos un futuro juntos’. C
The non-coring DeviDrill RSS (Rotary Steerable System) joins the highly successful DeviDrill DCD in incorporating technology and solutions that secure superior directional drilling capability in all rock formations.
Contact
us for further
Low water consumption Gyro-steering High penetration rate www.imdexlimited.com | www.devico.com
Recently, IMDEX acquired Devico and their subsidiaries.
By leaning heavily on the industry standard hardness scale — MOHS — there are tools that can save drillers time and money. For more than 200 years, MOHS has been proven science that drillers and geologists may rely on and utilize to reduce guesswork in the field. The secret? Every driller should start with a scratch test kit. Understanding the MOHS hardness scale and the use of a scratch test kit will result in more accurate bit recommendations with every test. The scratch test helps take the speculation out of selecting the best bit.
Since its development by the German mineralogist Friedrich Mohs in 1812, the MOHS Hardness Scale has been used to characterize a mineral’s resistance to being scratched or abraded by another mineral. The scale of common minerals is shown in the chart (next column). For example: a crystal of fluorite (MOHS value of 4) will scratch a crystal of calcite (MOHS value of 3) but not a crystal of quartz (MOHS value of 7).
Diamond is the benchmark for the hardest mineral on the MOHS scale due to the rarity of the naturally occurring and manmade minerals that would scratch or abrade diamond (see lonsdaleite or wurtzite boron nitride). One of the most abundant minerals in the Earth’s crust is quartz (and its variations), which has a MOHS value of 7.
Scratch test kits are comprised of four pencil-shaped tools with pre-sharpened tips on each side representing hardness values from 2 to 9 and a sharpening stone (to reshape the points from wear). These alloyed tips offer ease of identifying the associated MOHS hardness value.
MOHS
1 Talc
MOHS
Once you have the kit in-hand, grab an early core sample or adjacent rock and follow these steps to greatly enhance your success in choosing the right bit:
1. Clean the surface of the rock to be tested.
2. Hold the core sample and firmly press point to scratch onto rock.
3. Brush away any fragments, powder, or debris that is produced.
4. Check to see if a distinct groove was made in the rock (not just a mark that can be wiped away).
4.a If a groove is questionable take the 2-value scratcher and lightly drag across the scratch to see if it catches.
5. If no scratch is made, then move up in number to the next scratcher in the set.
6. Once a scratch is made, conduct a second test to confirm results.
makes a possible mark and the Number 8 scratcher makes a definite mark. The rocks MOHS value is between 7 and 8. Initially, you would select a Yellow Longyear bit, but there are other factors to consider before choosing the correct diamond bit. You should also look at the competency of the rock, the grain size, and quartz content to determine if the Yellow Longyear® formula is a correct choice. This rock is competent with a high amount of medium to coarse size grains of quartz. With the high amount of quartz grains a tougher formula should be selected to decrease wear on the matrix supporting the diamonds. A Green Longyear® bit would be the correct selection to balance life and penetration rate. The competency of the rock forma-
tion, in this instance, will aid in selecting the correct waterway design. Longer life? Pick a Stage® 3 design. Faster penetration? Pick a Tapered Swirl (TSW) design.
Before starting an underground project, you are allowed to visit the core shack to examine core samples from previous exploration projects to understand the geology of the area you will be drilling. At periodic intervals you take scratch samples of the rock to determine the most common MOHS hardness and what is the highest MOHS scale mineral
configuration you will encounter. The results determine most of the rocks are granite type formations. The goal for this project is focused on penetration speed. Selecting a Red Longyear® formula with a TSW waterway design will maximize speed and improve the life of bit.
These examples are for ideal situations; however ground conditions may vary by region and even by drill sites in the same location. Boart Longyear offers a scratch test kit to help identify the hardness of the formations being drilled. For assistance in selecting the right bit for your drill site, contact your local Boart Longyear sales and technical teams. C
AVAILABLE NOW. WORK SMARTER NOT HARDER.
SAFER, FASTER, MORE PRODUCTIVE.
The updated Quick Descent™ Head retains roller latching for reliability and adds automatic latch retraction and improved valving for maximum speeds. Combined with easier maintenance, it is a step ahead of the industry standard Link Latch™.
• Sealed bearings and simplified maintenance
• System descends 32% faster than our previous head design
• Threaded connections and no assembly pins
Our company, Harris Drilling, was awarded the contract for exploration drilling for Lithium Americas. Lithium Americas Thacker Pass is the largest known measured and indicated Lithium resource in the US and we are excited to be working with them. We started this project in mid-April, 2023 and we will run the drills 24/7 until November. We currently have two new diamond drills working for Lithium Americas and another on its way. We are drilling Lithium Clays on this project and have anywhere from 15-20 people working.
We have a fully rebuilt Christensen CS14 that was completely reworked by the team at our shop in Fallon, Nevada, US, a new VersaDrill KMN1.4 S-Track Drill, as well as a new Multi-Power Titan II Track Drill. The Titan II is the largest and is rated at 40 000 lb (18 144 kg) pullback. The VersaDrill has a 33 000 lb (14 969 kg) pullback. The CS14 has 31 000 lb (14 061 kg) pullback.
Drilling in the high desert, we encounter various challenges in the kinds of terrain, from one hole to the next. The ground can go from steep and rocky to gentle rolling hills. The terrain can become extra challenging when the weather is not cooperating. Sourcing enough water for our three rigs is also challenging. To combat this, the roads and trails are maintained, and we have six-wheel drive vehicles and water trucks on site. Our truck-mounted core rig, CS14, and the two track-mounted drills help us overcome the rougher terrain. All of them can be serviced with a 6x6 water truck.
We are drilling at a hole depth in the range of 100–900 ft (30.5–274 m). The number of holes completed at this time is more than 30. We could not complete only a few holes due to high-pressure flowing Artesian wells. Dealing with Artesian is controlled using a grout packer and cement.
The cherry on top is that the project has some groups protesting it. As with many groups, they block the roads accessing the sites.
Despite the challenges and protesters, everything is going as planned. Production has been steadily increasing and the crews have been working incredibly hard on better time management and more efficient moves to allow them more drilling. This has made for better results in footage rates.
Our biggest aim on this and all our projects, is continuing to operate in a safe and productive manner, recruiting, training and retaining the right personnel to continue to provide our clients with high-quality service.
Harris Drilling has proved mining, environmental, water well, Lithium and mineral exploration in the Western US since 1956. We take pride in providing our clients with a consistently high level of service. Our diversified equipment and experienced personnel give us the knowledge to complete projects to the highest expectations.
Our equipment acquisition and selection are determined by the knowledgeable staff anticipating the specialty services, challenging geographical limitations, and remote sites that projects may present.
In 2022, Harris Exploration Drilling became part of Earth Drilling’s group of companies out of Canada, allowing the Harris team access to a wider range of equipment and services. In addition to our coring operation, we continue with our RC Division, Large Mud Rotary Lithium Extraction Wells. We also added two new sonic drills to our fleet and DR24 (up to 24-inch) Casing Advancement. C
IThelped, of course, that the junior explorer with whom the geologist worked shared his interest in exactly such unobtrusive, possibly overlooked, prospects. Nevertheless, the adverse setting within which the campaign was planned and prepared certainly demanded perseverance and the strongest resolve, especially as from the outset it was clear that any deposit such drilling work produced would be marginal at best.
However, the promise of a sound understanding of the target, and in turn the improved ability to infer the potential of other, similar, geological anomalies, weighed in favor of investing in a few holes on a strike running some few hundred meters along a mountainous ridge.
This is the account of a rather peculiar drilling venture in a remote part of North-Western Namibia, an area known as Kaokoland.
While the obvious deterring factors included the usual obstacles any exploration drilling project faces - such as budget limitations and the high-risk nature of most exploration activities, the Kaoko project confronted the additional difficulty of being in an exceptionally remote area, characterized by rugged, and at times, inaccessible terrain.
Another very concrete challenge that had to be overcome was to earn the support of and permission from the local communities to work on their land. Additionally, for an environment as pristine as North-Western Namibia, stakeholders are certainly not limited to the local people but include conservationists, anthropologists, and businesses, such as tourism operators. Such parties are at times fiercely opposed to exploration and mining activities, arguing against their social and economic legitimacy in favor of less destructive and extractive land-uses in such relatively untouched regions.
Before tackling tricky geology in a remote area, a worried financier had to be kept on board, permits had to be obtained from relevant government ministries, while conduct-
ing sincere communication and ensuring the inclusion of stakeholders, most importantly the semi-nomadic Himba residents of the area. But the doggedness of the geologist and his team eventually paved the way for the drilling work to commence.
The drill plan targeted two locations, firstly in the area of the mysterious outcrops bothering the geologist and secondly, since the rig was in the area anyway, another anomaly roughly 10 km (6.2 mi) east.
The instructions for the recruited core drilling outfit, Günzel Drilling, were to bring 150 m (492 ft) of N-size rods, and a maneu-
When a very perplexed geologist could not wrap his mind around a theoretical conundrum involving two nondescript outcrops showing some slight hint of faded oxidized copper, he did not rest until his associates agreed to fund the drilling of a few diamond core holes. After spending two years mulling over it, he realized drilling was the only way forward.
verable coring rig. The number of holes and estimated total meterage were not specified in the scope of work, as all depended on the outcome of the first holes on that virgin ground. The outset made it clear that it would not be a massive project.
So, during the last week of June 2023, up they went into the wilderness of the northwest, an area of breathtaking natural beauty with endless mountain ranges and valleys of contrasting shades of ochre, populated only by semi-nomadic cattle and goat herders.
In actual kilometers, within the context of vast Namibia, the destination was not notably far, and although the geological team did an exceptional job to create some sort of track, parts of the route remained a challenging offroad 4x4 trip, heavy on vehicles and at times difficult to maneuver. As a result, for the entire trip getting to the site took an exasperating 34 km/h (21.13 m/h) on average, of which the final 25 km (15.5 mi) alone took four hours.
As the very vague scope of work did not really help to prepare for the drilling work in an area far removed from standard access to supplies, physical infrastructure and commercial conveniences, the packing list included items for any eventuality. This meant starting with 60 NT rods, 1.5 m and
3 m (5 ft and 10 ft) core barrels, various types of bits and drilling consumables, as well as a selection of spare parts greater than the average supplier might stock. Then there was the food and drinking water for the crew. By packing everything that might be needed, including the kitchen sink, the drillers hoped to avoid any reason for rushing back for a spare bit or a few onions.
The rig selected for the work was a track-mounted Atlas Copco CS1000. While the tracks were the main reason for the choice of a rig, it is also quite compact and can be loaded on a short-wheel base 4x4 lorry. Long-wheel base trucks or trailers would not have been able to navigate the access track’s gullies and narrow ridges.
The first hole was collared about 25 m (82 ft) off the outcrop, dipping at 55ᵒ. The drill pads were set up very tight on steeply sloping terrain, which made work quite uncomfort-
able with hardly room to stack the 3 m (10 ft) rods, let alone retrieving a 3 m inner tube without sticking it into the rock face.
As it is so often the case when truly prepared for every event, no such eventuality takes place. Casing to stabilize overburden could be placed at 6 m (20 ft). While over the entire hole the rock remained fairly broken and hard to very hard, the critical aspect of sample recovery was relatively straightforward and overall, the drilling held no surprises. There was little risk of core spin or washing away of soft materials and the formation allowed for a very good sample.
The turnaround time of the 4x4 truck carting drill water was three and a half hours, but fortunately water loss was not excessive.
On the other hand, rig moves and drill platform preparations were a different matter. Most of the time working was spent on the squeezing of the rig, crew, and equipment through another gulley towards the next collar rather than drilling. In fact, of the 47 shift hours on site, only about 23 involved actual drilling.
Of course, no project ever runs without at least one crisis. This time it was the cook
forgetting to pack a ladle. The frustration of the hungry crew having to dish up the evening stew with a teaspoon or fork resulted in quite some vocal discontent. The mechanical department had to save the day with some impromptu grinding and welding.
From the start, the geologist was realistic that any ore found at the location would not offer high promise. Even so, the dire results of the first hole on the most enticing spot, must have come as a bit of a disappointment. Over not even 30 m (98.4 ft), the sample turned from overburden into some sedimentary formation, switched into a bit of unconvincing host rock and then ended in basement - and that was that. What was worse, the core did not give the answers the geologist came there to find.
When the second hole, again placed just off the second outcrop on the strike, yielded similar results with even less answers, the
rig was moved back north along the strike, to where a crack and a fold caused a slight twist in the ridge.
And finally, here it was: the resolution to the riddle of the origin and fading of the bit of copper that could be seen on surface. Giddy with fresh ideas about how to redefine his geological model of the deposit, even if most probably unviable or marginal at the very best, the geologist sent the rig to the other target. Smooth drilling and good core yielded results of no real economic or theoretical interest and concluded a very short drill campaign.
Overall, the drilling contractor travelled a total combined 6010 km (3734 mi) to spent five days drilling four diamond holes, totalling 106.25 m (348.59 ft).
In a time when exploration and mining companies are no longer evaluated only by
the economic result they deliver to shareholders, but increasingly in terms of their carbon footprint, ESG score and, most importantly, required to meet high social legitimacy standards, a project such as this blitz drilling campaign seems hardly worth the effort, especially since from the outset optimism for the economic viability of the deposit was muted.
Whether at the end, the material expenditure, physical effort and social investment did pay off probably depends on who answers. To the geologist, the few core holes certainly provided the key to his riddle and allowed him to give sound advice to the exploration company regarding any future exploration activities in the area, even if such advice was only to keep any expenditure tightly capped. For the drilling crew, the privilege to have worked in and experienced beautiful Kaokoland was certainly worth the trip, even if for five days only and without proper tableware. C
What makes Drillers Edge drill rods different? Our choice of premium quality steel. Our approach to stress relieving heat treatments, precision machining, intense quality controls, and the unique, specialty finishing process we use to harden our R™ Thread for unmatched pull-back strength.
All these differences help Drillers Edge to produce premium coring rods that deliver:
• More even pin and box wear.
• Better deviated drilling performance.
• Superior drill string life.
In Part I of this article series, we showed how important it is to have a sophisticated calibration scheme to achieve high accuracy results when using compact MEMS gyro and inclinometer packages. Without high-end temperature calibration and system alignment, the accuracy of survey is degraded and telltale features such as oscillations in angle results become evident.
In this second article, we focus on one of the gyro’s worst enemies: excessive rotation and scale factor error. Simply stated, the scale factor of a gyro sensor is the quantity that its raw signal must be multiplied with to produce the output rotation rate in degrees per second (or similar units). The raw signal is typically an analog voltage or a digital signal. An approximate ‘factory’ scale factor value is usually provided by the sensor manufacturer. For mass produced units, such as compact MEMS sensors, this is a ‘one factor fits all’ value that gives decent results for applications not requiring high accuracy, such as drones and mobile phones. But for borehole survey purposes, the factory value is never good enough and it must be calibrated for every individual sensor axis in every single component.
Any type of gyroscope sensor, be it MEMS, spinning mass, fiber optic or ring laser, produces a signal that is related to the rate at which the sensor is rotating. This signal must be converted to a useful unit, such
as degrees per second, in order that it can be used in navigation calculations. In the simplest model, a gyroscope will have an offset value, which is a non-zero constant it outputs when it is not rotating, and a scale factor, which is what the raw signal must be multiplied with to get the correct dimensions (such as degrees per second).
The offset value varies from run to run of the sensor and for MEMS sensors it is difficult to calibrate precisely. However, the concept of a zero-velocity update is used in virtually all high accuracy navigation instruments, whereby the offset is precisely measured and can be removed when the sensor is not moving.
The scale factor on the other hand must be precisely calibrated as there is no practical way of measuring it ‘in field’. The scale factor is chiefly sensitive to temperature. Any given sensor type can exhibit very different temperature dependence of the scale factor from unit to unit, making it critical that a high precision calibration is done across the entire operating temperature range of the sensor using high accuracy rotation platforms.
When measuring any physical quantity there will always be an associated uncertainty or error. Given a calibration of the scale factor for the gyroscope being used, it is critical to realize that the calibration will not be perfect. At any given time or temperature, there will be some residual difference from the ‘true’ scale factor, and this will propagate through the navigation calculations to produce an error in the final output angles and positions of a borehole survey.
The error associated with imperfect knowledge of the scale factor is, naturally enough, called the scale factor error or SFE. It is often expressed as a percentage and, for example, a typical manufacturer might give a factory estimated SFE for a MEMS gyro component of 1% at room temperature, with an additional non-linear error of another 1% over the full temperature range. This means that if a typical component is rotated 100ᵒ at room temperature, the result from the gyro will typically show a value between 99ᵒ and 101ᵒ going up to
98ᵒ to 102ᵒ for higher/lower temperatures. Right away, it is possible to see that a component with this level of factory SFE will not satisfy the accuracy statements of a borehole survey instrument, which typically specify an accuracy of 0.5ᵒ or less for azimuth and toolface over a full survey. Individual gyro component calibration by the survey tool supplier is an absolute must.
SFE is caused by anything that is not accounted for in the calibration of the sensor, which in the case of a poor calibration would mainly be the lack of a temperature calibration. A poor system alignment can be mistakenly interpreted as SFE, as the signals from the gyro axes are mixed up. There is also a run-to-run variation each time the sensor is powered on, effects which simply cannot be modeled either practically or economically. Finally, when discussing survey angles (but not the rotation rate itself) there is an effect from the precision of the system clock used to sample the data. Since the angles are fundamentally derived from integrating (summing) the rotation rates and multiplying by the time-step between samples, any variation in the time-step will appear as SFE in the angles. There is always variation in microprocessor clock frequencies, but it is often overlooked in cheaper survey instrument designs.
In the vast majority of borehole survey situations, the instrument rotates most freely about its long axis, since the hole itself prevents it spinning in any other way. Thus, problems with SFE are most obviously discovered in measurements related to the long axis of the tool.
In a vertical hole, excessive rotation about the long axis directly integrates into the toolface angle result. In high precision applications, such as deep oil and gas holes, this is evidenced most clearly when the hole begins to build angle away from vertical. The azimuth immediately shows the SFE that has built up as the tool rotates.
There is a common misconception in the industry that gyro SFE plays a lesser role in inclined surveys. The thinking here is that as the hole gets closer to horizontal then the rotation about the long axis has less effect on the azimuth. This is only correct for an ideal system without any errors. As the tool rotates about the long axis, the lateral body frame axes (perpendicular to the long axis) will rotate about the long axis of the tool. Looking at the navigation calculations, the SFE coming from the long axis gyro will leak over to an error in tracking the position of the lateral axes. This will in turn lead to inaccuracies in azimuth even in low inclination holes. This can be viewed as the instrument gradually losing track of the actual highside, in effect mixing a bit of inclination into the azimuth and vice versa. Excessive rotation around the long axis of the instrument accumulates the SFE in this transformation, so that when the angles are derived the azimuth is still turned away from the true value. The effect of gyro SFE is most pronounced in vertical surveys, but it is definitely a factor that must be dealt with for all inclinations.
In thinking or reading about scale factor error in borehole survey situations it is common to come across a variety of ad-hoc attempts to limit the effect of SFE ‘in field’ or ‘in survey’.
One such method is to try and use the gravity highside angle in inclined holes. The GHS angle is derived from the inclinometers and is independent of the gyroscopes. The idea is that by knowing the GHS
angle at a pause point it should be possible to automatically ‘correct’ the scale factor of the long axis gyro since the gyro calculations can be made to output an estimate of the GHS as well. However, the accuracy of the GHS measurements is not enough to correct the gyroscopes to the accuracy that is required for borehole surveys. This approach may be useful for less accurate instruments that use the ‘factory’ value for the gyro scale factors and/or neglect a proper temperature calibration. Using GHS to compensate gyro SFE is entirely unsuitable for any high accuracy needs.
There are only two practical, reliable ways to reduce the impact of SFE in a gyroscopic survey instrument:
• Use a high accuracy calibration to keep gyro SFE to a minimum.
• Limit the rotation of the tool while surveying to reduce the effect of gyro SFE.
There is a secondary issue with excessive rotation that can occur in addition to SFE problems. If the tool has a poor system alignment and exhibits oscillation problems, as detailed in the first article of this series, then excessive rotation causes the gyro biases to be mixed between the gyro integration axes. Attempts to imitate north-finding gyroscope indexing platforms, to achieve some sort of ‘bias cancellation on the fly’, are doomed to fail. The lack of a model for the bias drift between stationary intervals ensures this. After all, if a model was available, then the drift could be removed. The effect of such attempts is to exacerbate the oscillations in the azimuth.
The impact of SFE is most pronounced in a near vertical hole. The example given here is a hole whose inclination is between 1ᵒ and 4ᵒ over the 500 m (1640 ft) course of the hole. The hole was surveyed with a TwinGyro™ with a standard high accuracy calibration. The first survey is low roll, with less than 5 complete revolutions of the tool as it descends the hole. The second survey is high roll, with more than 120 rolls at the end of hole, which was conducted by surveying without swivel and centralizers. The final survey is the same as the second high roll survey, but where the calibrated gyro scale factors have been replaced with the manufacturer’s generic ‘factory’ values.
The result in Figure 1 is shown in the North/East position plot, as this shows the effect most obviously. The low roll, accurate calibration result agrees well with the other surveys taken of the hole. The high roll, accurate calibration is bending excessively to the west due to the SFE. The misclose with the low roll result is 0.3%. By using the ‘factory’ calibration, with its absence of accurate temperature calibration, the hole position bends even further to the west with a misclose of 0.7%. Even worse than the misclose value is the noticeable differences in the end-of-hole direction. This result would not be good for an application requiring accurate directions as the hole takes on more inclination.
Results in an inclined hole show how the naïve assumption that roll about the long axis of the tool is not so important is mistaken. Figure 2 shows another 500 m (1640 ft) hole, this time inclined at about 50ᵒ below horizontal, also surveyed with a TwinGyro™. The first survey has virtually zero roll, while the second has 42 rolls corresponding to about 1 roll per 12 m (29.4 ft). Both the first and second surveys
use the normal high accuracy TwinGyro calibration. The third survey is the same as the second survey but calibrated scale factors have been replaced by the ‘factory’ calibration that lacks an accurate temperature calibration.
Here the excessive 1 roll per 12 meters deviates the hole west by 6 m or 19.69 ft (1.2% misclose) even with an accurate calibration. Using the ‘factory’ calibration increases the deviation to 10 m or 32.8 ft (2.1% misclose).
Previously we have shown that poor temperature calibration and system alignment leave fingerprints in the survey results, namely oscillating and biased angles. One approach that can be used to try and mitigate biases in the absence of a proper system calibration and zero-velocity update scheme, is to rotate the gyro to try and smooth over the problems. However, this runs straight into the one of the worst enemies of a gyro survey instrument, excessive rotation.
All gyros have an intrinsic scale factor error, with typical factory-delivered calibrations being typically of the order of 0.5-1.5% with additional non-linear behavior over the temperature range. A high accuracy calibration procedure can reduce this over the temperature range to under 0.01% over the whole temperature range, as found in the TwinGyro™ used in this article. Even with this high accuracy, excessive rolls about the long axis of the tool produce notable deviations in survey results, although they are considerably better than with no calibration.
Various ad-hoc methods to try and use inclinometers to get a fix on the scale factor while surveying are unsuitable, as inclinometers are not accurate enough and also cannot be used near vertical. Finally, the scale factor error tends to repeat itself within a run. The error generated by 40 rotations into hole tends to be similar to that generated by 40 rotations coming out of the hole, thus basic end-of-hole comparisons of In/Out pairs does not reveal an error if the rotations are similar and such basic quality control leads to false confidence in the results. With poor temperature calibration this correlation of errors tends to extend across runs as well.
Ultimately, the only way to ensure the most accurate results is to implement a high accuracy temperature calibration which utilizes rotations to milli-degree accuracy, as well as limiting the rolls of the tool during the survey procedure. C
In this Issue:
Q&A from the experts
In conversation with Greg Hall, Principal at Golden Phoenix International Consulting Pty Ltd
Will AI take geologists jobs?
Discussion on whether AI is a threat or a boon to humanity
by Nick Tate, Specialist Consultant Mapper of Geology, Alteration and Mineralization Systems
The importance of groundwater in mining and how drillers and hydrogeologists work together to achieve the best results by Mariajose Romero-Segura, Freelance
Project Hydrogeologist and Technical TranslatorVektore’s new AR tool brings speed, accuracy, precision and universal reading of structures to the core shack
by R.N. Monteiro, P.Geo., M.Sc., FSEG, Ph.D., President and Chief Structural Geologist at Vektore Exploration Consulting CorporationThe future of Geoscience education and the National Exploration Undercover School (NExUS)
by Richard Lilly, Program Leader at the Universityof Adelaide
Brett Davis: Firstly, thanks for giving Coring the opportunity to interview you, Greg. Please take this as a compliment when I say it seems like you have been a geological heavyweight of the mining and exploration industry for a very long time. Very few people have a career like yours, where you’ve worked across the spheres of academia, mining, and exploration, plus gained enormous respect in the geological community while you’ve been doing it. Can you tell us what interested you in a career in geology?
Greg Hall: I am an accidental geologist. I never intended to be a geologist rather I studied geology at Balgowlah Boys High School in Sydney in my final year to boost my aggregate Science mark in order to gain a Commonwealth Scholarship. I also applied to CSR Limited for a cadetship to study chemistry at university. I was successful in both cases, finishing 23rd in the State Science Honours list that year. CSR required cadets to complete first year university parttime (two years) while working in CSR Ltd.’s Central Laboratory at Pyrmont in Sydney, assaying the entire annual Australian sug-
Greg Hall's professional career has involved three employers, CSR Ltd (1968-88), Placer Dome (1988-2006) and Golden Phoenix International (2006-Present). He studied chemistry and geology at the University of New South Wales (1968-72), completing the first two years part-time while working as a junior chemist at Central Laboratory in Pyrmont. Greg graduated in 1973 with Bachelor of Applied Science with First Class Honors and was posted to Wittenoom in Western Australia to work on iron ore. In this period (1973-78), he was responsible for discovering the Marra Mamba iron deposits near Mt Newman (1973) and the Yandicoogina pisolite deposit (1974) in Marillana Creek. This pisolite discovery was sold to CRAE in 1981 and commenced production in 1996 as the Yandi Mine of Rio Tinto. Production rate was 50 mtpa (1996-2016) and increased to 75 mtpa in 2016. The mine has produced 1.6 bt of iron ore to date.
Greg worked in Queensland (1979-83) then returned to Perth in 1984. The Granny Smith project was his first gold project and the discovery of a large gold deposit in 1986 was the most satisfying. CSR Ltd sold the deposit to Placer Pacific in 1988 and he transitioned to PPL in order to see his discovery go into production. It started in 1990 and continues to this day. Greg subsequently helped with the discovery of gold at Sunrise Dam and Wallaby.
Greg Hall became Chief Geologist of Placer Dome in 2000 until Barrick Gold Corporation took over in 2006.
ar production with samples representing 500 t lots. First year cadets were analysts, and second year cadets were supervisors. In the first year, I discovered I was not suited to chemistry as a career. At the end of that first year a UNSW, graduate Ken Maiden appeared at the laboratory and when asked what he was doing he replied he had just graduated from the University of NSW (UNSW) in geology and was going to Broken Hill to complete a PhD. Ken advised me that CSR Ltd. had taken over a junior exploration company called Mineral Engineers that year (1968) to commence exploration in their own right. Mineral Engineers became Pacminex.
CSR did not have an exploration arm during their time mining blue asbestos at Wittenoom (1948-1967) and had joined the Mt Newman Mining Joint Venture and the Gove bauxite Joint Venture. I decided and CSR Ltd. agreed to transfer me to Applied Geology over three years by way of a Chemistry Geology co-major and transitioning to a Geology Applied Science Degree course. I graduated in 1973 from UNSW with Bachelor of Applied Science (First Class Honours).
BD: Coring is a diamond drilling magazine, and we like to keep to our roots. Do you get to work on a drill rig anymore?
GH: I last sat on a drill rig in 1987 with RAB drilling the discovery holes in what subsequently became Granny Smith Gold Mine.
BD: Your company is called Golden Phoenix International Consulting. Tell us more about what you do and your client base.
GH: I spent a lot of time in China for Placer Dome commencing in 1997. In 2006 when Barrick took over Placer Dome, I decided to continue exploring in China via an unlisted public company, called Golden Phoenix Resources and consulted out of a private company called Golden Phoenix International. My association with China continued until 2018. In this period, I was made an Honorary Professor at three institutions, the Geoscience University in Wuhan, the Central South China University in Changsha and the Insti-
tute of Geology and Geophysics in Beijing. My Chinese colleague gave me the Chinese name Huo GoLin which translates as Ancient Forest implying my age (grey hair) and stature as an experienced geologist.
BD: You’ve worked in a lot of countries and on a lot of continents. Are there any skills or mindsets that have helped you in your roles in these places?
GH: You definitely need to be humble and respectful of other cultures and beliefs. To quote Walt Wittman: ‘Be Curious not Judgmental’. In the West, we do business and then become friends, in the East, we become friends and then do business. This concept is given the name ‘guangxi’ and it is taken as a sign of respect for the people you are going to rely on in the future to help with your business ventures.
BD: You’ve had the privilege of working with many of the truly influential geologists in the industry and have influenced many more. Who have been some of the positive influences in your career?
GH: This is a very long list.
Dr John Rattigan the first Chief Geologist in Pacminex, who believed in me as a new graduate and trusted me to find iron ore deposits.
Professor Bill Lacy at James Cook University in Townsville, who advised me to follow my heart (become an Exploration Manager) rather than do a PhD at JCU.
Dr Vic Wall is a major influence and was the smartest geologist I have ever met.
Professors Bruce Hobbs and Christoph Heinrich helped me understand structural geology and hydrothermal geochemistry respectively.
Professor Roger Taylor and Dr Peter Pollard taught me about granites and magmatic processes at James Cook University.
Colleagues who helped me develop curios ity about hydrothermal ore deposits include Dr Scott Halley, Dr Peter Holyland, Dr Paul Kitto, Dr John Walshe and Dr Dick Tosdal. A special mention should go to Phil Davis, who taught me about effective teamwork.
BD: Do you get much opportunity to re visit some of your old geological stomp ing grounds e.g. the Laverton region? And have you seen any of your ideas come to major fruition or change radi cally?
GH: For the last four years, I have been sup porting my son Brad Hall and his not-forprofit Cycling Development Foundation with their Laverton Cycling project. One of the fund-raising events is an 8-day, 1100 km ride from Perth to Laverton. Each year, I get to see the continuing development of the Sun rise and Wallaby gold mines. I was involved in their discovery following the development of Granny Smith mine.
BD: Is there a particular mineralization style or deposit type that interests you, and why?
GH: I have a singular passion to look at the involvement of granite magmas in Orogen ic Gold Deposits. I am deeply interested in far-field geochemistry by which I mean the very fringe of a hydrothermal mineral sys tem where there is not enough energy to create new minerals rather just swap atoms in existing minerals. The mineral will look unchanged or unaltered to a petrologist, but the chemistry will tell otherwise. Once understood, this feature can allow one to optimize exploration search. Understanding the size of the system you are seeking to detect will allow you to open the grid cell size to decrease the sample density thus reducing time and cost of discovery.
BD: Leading on from the previous question - everyone has a handful of deposits that have left a mark on them, be it because of the amazing geology, the hideous conditions, the people they worked with, etc. Which deposits do you hold dear and which ones really were difficult to work on?
GH: As you have inferred, the Laverton region and the three gold deposits of Granny Smith, Sunrise and Wallaby are very special for me. Other gold deposits that are important but difficult to access are Witwatersrand (South
Deep) and Carlin (Cortez). At South Deep, I found that the entrenched palaeo-placer origin belief always gets in the way of real
tion of drones. Have you noted any neg ative impacts to effective exploration and mining as a result of these e.g. less people out kicking rocks?
GH: All exploration technologies cannot re place the effectiveness of better geological mapping as an aid to better exploration. Geo logical mapping means boots on the ground.
BD: I haven’t always agreed with your geological interpretations. However, they have always made me think. What is your opinion of the geological skill sets, experience, and knowledge of ge ologists today, especially those who are newly graduated?
GH: I have always considered that a univer sity degree teaches you the language of your science, but it is the practice of geology that teaches you the science.
BD: Has there been any single satisfying moment in your career that rates above all the others?
Major Drilling is one of the world’s largest drilling services companies primarily serving the mining industry. We maintain field operations and offices in Canada, the United States, Mexico, South America, Asia, Africa and Australia. info@majordrilling.com
GH: In late 1986, receiving by fax the assay results from a recently completed RAB drill program at Granny Smith to discover 25 m @ 5 gm Au from 15 m (49.2 ft) downhole in the last drill hole on that line is easily the single most satisfying moment in my career.
BD: I’ll ask a question on the flipside to the previous one. Many of us have interfaced with less than savory individuals or experienced toxic workplaces. Has there been any incident or incidents that really disappointed you?
GH: Yes, many examples of sexist behavior and disrespecting women. From 1984, I started deliberately hiring women into exploration until 1991 when the Keringal camp east of Laverton was run by a woman and the majority of employees were women. The Keringal gold deposit discovery subsequently became part of the Granny Smith Mine JV and management transitioned from exploration to mine management control. Women were quite disrespected at mine sites in those days.
BD: One of the things you are held in high regard for is your capacity for teambuilding. What makes a good geology team? And have you seen any truly dysfunctional ones?
GH: Leadership is quite important in creating a good team. The leader has to model the desired behavior and be prepared to call out undesired behavior. It is important as a leader to be able to recognize people motivated by power because these people will not subordinate their interests for the good of the team. Unfortunately, it is also true that power-motivated people are most likely to become leaders, so while you might be able to create an effective team in your area, it is very likely that the bigger organization may well be dysfunctional.
BD: I know you appreciate the value of good mentorship and have been a positive influence on many geologists, me included. What makes a good mentor?
GH: Humility and the drive for excellence as well as patience. People learn at their own speed. I am quite a believer in the ‘Learning Organization’ and failure should be recognized as a tremendous opportunity to learn. I learned more from failure than I have ever learned from success.
BD: Leading on from the previous two questions, what have you learned from field practice and your job experience that is not taught at university?
GH: Team building and how to create a good team. The principles of chemistry are also very poorly understood by many graduates.
BD: One topic we commonly talk about but rarely put into print is that of the health hazards of working in different countries and environments. Has your health ever been particularly challenged and, if so, what happened?
GH: I dodged getting malaria in Africa and Asia and have been vaccinated against a very long list of diseases. I have suffered severe gastric illness because of poor food preparation in China. I recommend everyone keep track of near misses because they are your next accident, and you should prepare as though they are likely. After years of flying, I became subject of Deep Vein Thrombosis (DVT) and I am lucky to be alive.
BD: If you had abundant financial funding, is there a fundamentally annoying geology question you’d like to solve or a topic you’d like to work on?
GH: What is the true nature of fractals in economic geology? In principle, if you under-
Get in touch with Greg Hall on LinkedIn
stand the fractal then one drill hole will tell how big the whole system might be.
BD: Now to some personal questions. Does Greg Hall get any time away from work? If so, what does he do in his downtime?
GH: I am a big supporter of my family. My two kids have chosen careers vastly different to mine. Brad is a cycle trainer at his gym called the Exercise Institute in Subiaco and manages the racing teams in the Cycling Development Foundation. He raced in Europe while completing a Psychology Sports Science co-major. We photograph the riders in the Perth Laverton Cycle Classic each September.
Adam is a musician, plays trumpet and sings in his band The Velvet Playboys. He holds a music festival called The Underground in summer each year, as well as touring Europe during July.
My partner Maree Laffan has started a Flamenco dance troupe called Aire Flamenco and performs regularly, so I am the Chief Roadie.
BD: Is Greg Hall ever going to compile his memoirs? I imagine there is a treasure trove of stories there!
GH: There certainly is a treasure trove of experiences. I have joined the Century Club that is having visited more than 100 countries where I have slept overnight. However, I prefer to have the experiences, not to write about them.
BD: Finally, any concluding comments or words of wisdom from an industry veteran?
GH: Your task in life is to find your passion and when you do, give it ‘a red-hot go’. Exploration became my passion sometime after I graduated as a geologist and subsequently, I have never worked another day in my life. C
For a long time, ‘AI’ was just another set of algorithms and most people thought that it would take decades to reach a level that approached ‘HI’ (human intelligence). Then the world learned of chatbots like ChatGPT. Suddenly, there was a computer program that could pass a university level astrophysics exam, write poetry, generate a business plan and write functional computer code. It was closely followed by stunning hyper-realistic fake images generated by Midjourney and AI-generated girlfriends from the Replika app that could hold a sensible conversation.
The capability of AI and the rate of acceleration of the technology scared a lot of people (including some of the architects of the algorithms). There have been numerous calls to halt development or shut it down. The three key fears are:
• It will take over human jobs and social roles.
• It could go rogue and control humans.
• It will distort reality for humans.
To unravel these fears, you need to understand a little about how AI works. An excellent video interview of cognitive psychologist and leading expert in artificial neural networks Geoffrey Hinton explains it in some detail, but in short, the algorithms have stacked layers that identify small components of images or text. In a geological example, one layer might be used on a satellite image to decide if a change in color is a geological contact. A layer above that might decide if the patterns either side of the contact are outcrop or cover and then another layer might decide if the outcrop area is igneous or sedimentary rock. The layers can be stacked in the algorithm to produce a geological map. Each layer has to be trained by tweaking its parameters until the end result matches a ‘known’ geological map. Chat algorithms work in a similar way by identifying patterns of language in the question and matching them to answers found in historical text used to train it. The training process was originally very laborious because humans had to do the comparisons and rate the results, but everything accelerated rapidly when the algorithms got smart enough to make their own assessments and write their own code. That’s when everyone got scared. So, let’s look at the big issues:
Creative people thought that they were safe from AI because computers could not generate anything truly new. Then ChatGPT started writing poems in a few seconds that would take a human hours or days to pen. Midjourney, and now Photoshop, can instantly generate hyper-realistic photographs that would take days to create with cameras and a photographic crew. Chatbots can write thousands of lines of computer code that would take a software engineer a week to craft. AI can digest every legal case ever prosecuted and determine the most likely sentence. A medical AI could analyze symptoms from every disease ever reported and diagnose rare conditions that are unknown to your average general practician. We are already seeing AI software designed to log core and generate geological maps from various remote sensing data. So, are we the last generation of human poets, photographers, engineers, lawyers, doctors and geologists? Perhaps not, but the landscape will certainly change dramatically for anyone who makes a living from creative or technical work. When Photoshop came out and suddenly it was possible to compile multiple images and remove defects, there were howls of derision that it would destroy the art of photography. The howls became even more shrill when digital cameras appeared. Photography didn’t die, but it changed forever. People learned that the camera does lie (and in fact it always has), so people came to view photographs in a different light. The perspective of that view will change again with the evolution of AI, and the business of generating images and selling them will morph with it. A new generation of image makers working solely with AI is already arising and photographers will move into the niches where the AI has no training data to work with like current events (sports, weddings, portraits, etc.). In short, if you are in the business of creating images that inspire dreams, you had better sell your cameras and learn how to use AI tools. If you are in the business of making memories,
the competition will thin out and AI tools will help you to make better images faster so you will be more profitable if you adapt.
For geologists, the new AI tools will certainly be a challenge in production environments like mines. Once the geology of a system is reasonably well understood, AI will have a good training set to work on and core logging, pit mapping and model generation will all be done faster, better and cheaper by AI geologists than humans. One geologist will probably be required to monitor the system in case it goes off on a tangent or encounters something new that it doesn’t recognize correctly. Long term, that will be a problem, because the entry level mine geology jobs that used to mold such experienced people will disappear.
In geological mapping, AI has a problem. Anyone who has ever gone out to map an area that has been previously mapped will know that multiple generations of mapping produce radically different results and interpretations. Each version of the map is an interpretation and the original data points are usually lost. So even if AI has a consistent data set to work on (like a satellite image or geophysics matrix), the maps that it is being trained to match are highly likely to be unreliable, so the trained algorithm will be doomed to repeat the mistakes of the previous mappers and interpreters. Beyond that, any geologist who breaks rock for a living knows that critical data that shapes the final interpretation very often comes from one or two critical relationships observed at hand specimen or microscopic scale in broken samples. We are still a very long way from having remotely sensed data that can be interrogated to extract that level of information.
AI tools will no doubt speed the generation of geological maps and remove some of the drudgery, but geological maps that provide critical new insights will still require boots on the ground and hammers on rocks for some time to come. No doubt services will emerge that claim to make geological maps entirely from remote data and the slick presentation will lead many to believe that they are the last word, but for geologists who understand the frailties of AI, that will represent opportunities to find missed discoveries. Geological mappers who learn to use the tools to augment their hammer will become even more valuable but will suffer the same succession issues as the mine geologists because the industry will have fewer entry level jobs for them to grow into and the perceived need for geologists will decline even further.
In mineral exploration, AI will struggle for similar reasons to the mapping paradigm. Anyone who has been in this industry for a few decades will have noticed that a single deposit can change style from VMS to skarn to epithermal to IOCG over time, reflecting academic fashion and the popularity of certain styles for raising exploration funding. That leads to an inherently flawed dataset for the AI to train on and match. Hence any exploration based on the AI-generated model is likely to be looking for the wrong things. The GIGO principle is particularly critical when you are using predictive models to do anything that requires a large investment! No doubt the process will produce new ways of looking at old data that will reveal some anomalies that lead to genuine discoveries, but like every new geophysical method, the rush to apply it everywhere will result in a very high failure rate.
This is perhaps the scariest issue because the critical point where AI bots become sentient is suddenly a lot closer to reality. The key issue here is deciding what level of control to give the robots. Society is already wrestling with those issues in areas like self-driving cars.
At present, we are dealing with how to handle the decisions that the car must make when it sees an impending collision that is unavoidable, but when the car gets smart enough to develop a personality, how do you stop it from driving you over a cliff when it hates you for being a week late with the oil change?
At a larger scale, we are already giving AI control in many areas with human repercussions, like social media. Those organizations are now so huge and dealing with so many incidents that they can’t afford to pay humans to make decisions, so AI algorithms are given the job. That already leads to some grossly unfair events because the AI wasn’t trained properly. But what if the AI became smart enough to decide to generate a scam and have a human engineer or manager sacked from the company? The AI could also quickly learn other ways to reinforce its power that could become very difficult to counter.
Current AI images, voices and text are relatively easy to spot (Midjourney images are famous for giving people too many fingers), but the rate of improvement in the algorithms will very soon make it impossible for most humans to see the difference. Many people will simply not care or actively resist questioning what they see. So where will we be when it is impossible to spot a fake?
This has enormous implications for education systems. Since the chatbots can already pass most university level exams and the imagebots can generate masterpieces, how will educators assess genuine student capability? Do we ban AI from classrooms and exams? When digital calculators first emerged, they were banned from the class-
room because they made maths ‘too easy’. Now they are an accepted tool of life, and you could sensibly ask if there is value in spending time learning multiplication tables by rote. So do we just accept that AI will be the way we access information in future and train children to use it most effectively or do we try to insulate children from it until they have learned the basics? The answer is probably somewhere in the middle. Banning AI from education is effectively impossible so we really need to focus on teaching young people how it works, how to use it and how to apply critical thinking to the results.
There are also big implications for science in general. There has been a steady decline in the wider public perception of science as a reliable source of truth because social media has given a global voice to attention grabbing activists and narcissists. On the upside, those platforms have also given voice to some media savvy scientists and commentators who have championed the wonder of STEM subjects and the potential of science as a career path. However, the rise of AI has given the attention grabbers the tools to make content an order of magnitude faster than before and it can be tailored to grab the attention of the AI algorithms that feed it to humans far more effectively than the ‘real’ content. This so-called ‘trash content’ is already flooding social media platforms like YouTube, Facebook and Instagram. That makes it more difficult for humans to find genuine content and puts a layer of distrust over everything in those arenas. The same thing will happen in scientific literature as the ‘Publish or Perish’ imperative drives aca-
● Near in-situ continuous core samples.
● Highly accurate mineral resource value determination.
● Geotechnical and environmental program drilling.
● Install straight pre-collars through difficult overburden for diamond coring.
● Can easily be converted to drill diamond coring tails on short holes.
AI is rather like nuclear energy. With appropriate control systems in place, it can be extremely useful to humanity, but if those controls are removed (or never implemented) it could quickly develop a chain reaction that could destroy us all. There is a military doctrine that says you should never use a weapon for which you have not already developed a countermeasure because you can be sure that the enemy will soon copy it and use it against you. The development of nuclear weapons demonstrated graphically how that can unfold. AI seems to be following a similar path.
The timeline and path for the future of AI are uncertain. The current rate of acceleration is impressive, but there are two factors that might derail the juggernaut. The first is feedback. As AI gets used more generally, it will begin to learn from material that was generated by AI so outputs will become progressively ‘fuzzier’. The ability of AI to produce enormous volumes of material very quickly and cheaply will swamp the genuine content in the pool of training material. As a result, the end products will become progressively less reliable and lower fidelity. Secondly, people and corporations will quickly learn the value of primary data. Chatbots and AI image generators currently train primarily on text and images freely available on the web. When the web becomes flooded with AI feedback content, people and corporations who own large libraries of primary data will realize its value and begin to lock it up or charge paywall fees for access. We are already seeing this to some degree with the latest generation of Photoshop using the massive stock image library held by Adobe as primary source material in its AI tools. This will have a negative effect for the average netizen because the only access to primary data for most people will be via an AI robot that decides what they should see.
There will certainly be some upsides from AI development. Chatbots have already given every net-connected human a super-human boffin uncle or aunty that can answer almost any question about any subject in a language they can understand and in a context they specify. In future, there will be legal services that can give you a legal opinion based on every case that has ever been prosecuted in your jurisdiction in a few seconds at a fraction of the cost of hiring a QC. When you call a government agency or a large company, you will no longer be forced to wade through a labyrinthine maze of voicemail layers only to talk to a third-party call center employee, who isn't trained to answer your question. An AI chatbot will answer the call immediately and discuss your problem based on the entire knowledge base of the organization you called. Geological maps of the moon and other inaccessible areas will be produced with reasonable first pass reliability. Exploration targets will be generated in areas where nobody thought to look, and new mineral deposits will be discovered as a result.
AI will certainly take many jobs from the current work matrix. Almost anything that involves recalling and synthesizing historical data will become redundant. That is likely to impact lower socioeconomic groups more heavily, but doctors, lawyers and engineers are not safe either. Creative people will have new tools to work with, but they will suffer intense competition from AI-generated ‘art’. Attracting and keeping people in STEM careers will become progressively more difficult as the general respect for science declines, but it will become even more vital to have people, trained in genuine scientific method and critical thinking to watch over the AI developments and head them off when they run out of control.
At present, AI is like an idiot savant. It has read every book on the internet, but it has no social conscience, and it is not quite sentient by ‘regular’ human standards. At the current rate of acceleration, those things will evolve to match and surpass humans very soon. Society and law are struggling to keep up, but we must adapt. The AI genie is already out in the world so we will have to learn to live with it. It is already too big to get back in the bottle. C
References & resources:
• Miners at bar: www.linkedin.com/posts/jessjscanlan_mining-artificialintelligence-activity-7022345556266008577-pFR4?utm_source=share&utm_medium=member_desktop
• Astrophysics Exam: www.youtube.com/watch?v=K0cmmKPklp4
• Geoffrey Hinton video: www.youtube.com/watch?v=qpoRO378qRY
Groundwater is an invisible natural resource. It is available in different proportions, in different rock types, and at different depths, in the Earth’s surface layer. I cannot remember how many times I have heard people saying that there is water everywhere. This is not true. Eighty percent of the water found on the continents is on the surface. The remaining 20% is underground or in the form of atmospheric water vapor.
For the ground to hold water, it has to be either porous (made of clay, silt, sand, gravel) or broken up (with fractures or voids). Does clay hold water? Yes, it does; against the general idea, clay ground can contain a fair amount of water, but clay particles and water molecules join together with electrical forces that are difficult to break. Clay ground can hold a lot of water, but the point is that it does not release all this water very easily.
How do drillers and geologists know if the water is fresh? By testing it, of course, in the field, either with smart portable devices that we often carry when conducting a drilling program, or in some cases licking it. Yes, it is funny how drillers and hydrogeologists don’t mind tasting a drop of water, but don’t worry, we do not swallow it, of course not, we spit it out.
And how often have I been challenged to say where water is ‘because I am a hydrogeologist’? Hang on there, if for finding minerals we need to use technology, to find water we have to as well.
Another funny thing is how often people have asked me if I use a divining rod; Oops! Nope, at university we are not taught that technique. So, how do we find water? Using similar tools as when looking for minerals, that is geological maps, geophysics, drilling.
The importance of groundwater in mining and how drillers and hydrogeologists work together to achieve the best results
Hydrogeology exploration starts at the desk. The investigation begins with the collection, analysis, and interpretation of hydrogeology of existing topographic maps, aerial photographs, geological maps and records, and other related documents. Geological mapping often forms the starting point of exploration and should identify potential aquifers. Aerial photographs are a good way for identifying major faults. The reason for looking for regional structures is that if they hold water, there is a better chance of finding good amounts.
If available, geophysical data provide indirect indicators to identify potential aquifers. Again, the aim is to find lithological contacts, deeper sections of palaeochannels (ancient rivers), etc. Among geophysical methods, electrical (geoelectrics) and electromagnetic methods (transient electromagnetics and airborne electromagnetics) are most commonly used to explore groundwater conditions because aquifers, aquitards and bedrock often differ in the measured resistivity or electrical conductivity.
The desktop study should be supplemented, when possible, by geologic field reconnaissance and by evaluation of available hydrogeologic data on well yields, groundwater recharge, discharge, groundwater levels, and water quality. It is very important to understand the objectives as it is not the same looking for dewatering to keep the mine dry as it is to find good quality water as a supply.
A next step is to design a drilling program. This part is much more expensive than the desktop study. In order to minimize cost, whenever possible, it is very important to gather field knowledge from the mineral exploration geologists that have conducted drilling in the area, and searching in the geological database for some evidence like ‘holes abandoned’, ‘wet samples’, or ‘no sample returns’.
Because during mineral exploration drilling the water table is sometimes intersected, it is of great advantage to record those intersections. For example, above the water table, the rock chip samples come to surface very loose and dusty; once the water table is intersected, they start being less dusty and the color darkens very slightly until they become clearly damp and then wet. The subtle changes in color are too difficult to record in the geology database, but there could be a dry/damp/wet field, and when that field exists in the database, exploration geologists should be encouraged to fill it in.
During drilling, the interaction of the hydrogeologist with the driller is essential as he is the expert in the matter and he knows what is happening at depth even before the samples arrive at surface. This happens more often when drilling hard rock as he can feel the fractures before the geologist identifies them by the size of the rockchips, or the stain in the surfaces, etc.
There are several different types of drilling methods and choosing one depends on factors like ground type, expected water level and common practice in each country. A good practice is to propose a drilling type but to supply the drilling company with details of the expected geology, and let them have the last decision. In Australia, water exploration in hard ground is usually drilled using RC rigs while soft, crumbly ground is more appropriate for Mud Rotary.
Essentially, an assessment of groundwater resources involves the location of potential aquifers within economic drilling depths. Whether or not an aquifer will be able to supply the required amount or quality of water depends on its thickness and spatial distribution, its porosity and permeability, whether it is fully or partially saturated, and whether or not the quality of the water is acceptable.
And while on the subject of water quality, something that I’ve heard often and is a misconception is that fresh water is safe to drink. Water is
↑ A water truck refilling its tank at a turkey nest for dust suppressionfresh when its amount of dissolved salts is below a certain threshold and it is based on taste, so according to the Australian Drinking Water Guidelines water is of good taste when its TDS (total dissolved salts) does not exceed 500 mg/L. Still, water of up to 1000 mg/L TDS is acceptable to many.
But water is the greatest solvent in the world; usually, it’s called the ‘universal solvent’. Water dissolves more substances than any other liquid and this is due to its molecular structure. So salts should not be our only concern when considering drinking non-treated water. Water quality refers to the suitability of water for different uses according to its physical, chemical, biological and organoleptic (taste-related) properties.
I have been part of teams working on the pre-feasibility of a deposit where the cost of bringing water to a dry deposit or getting rid of excess water has killed the project. That issue worsens when the quality of the water makes it unusable. And it can get even worse when the mine site sits in an environmentally sensitive place. Or when management does not consider water matters early enough in project work.
This is something that is often underestimated. A mine site requires a great amount of water, firstly during the construction phase and later on during operations. And if the groundwater is at a depth that will be reached during excavation, dewatering is a must. In that case, there is a need to drill and equip as many bores as it is necessary regardless of the cost. After the initial expense of drilling and equipping bores (pumps, pipes and gensets), there is a regular cost of diesel, maintenance and personnel.
Not always can all the dewatering be managed via bores, so in-pit sumps and trenches
have to be dug and kept clean. There is a need to have sump pumps and it is important to have spare pumps and parts because they fail sometimes.
Water is needed during each phase of the mining project in greater or lesser amounts. During exploration, water is required for the camp (drinking, cooking, showers) and sometimes for drilling.
During construction, a great amount of water is essential for dust suppression, making of concrete, etc, and again for the camp.
According to the Australian Bureau of Statistics (ABS), in 2019-20, the Australian mining sector extracted 1.100 gigaliters of water –1 100 000 000 000 liters. A mine water truck uses more water in one trip than each of us consumes in a year, just for dust suppression.
Mining operations need water to process ore and run camp operations. Once the mining reaches the production phase, water is
For more information
required for the camp, tea for the hydrogeologists in the offices, dust suppression, mineral processing, slurry transport, fire control, flotation, grinding, screening, dust scrubbing, wash-down water, pump gland seal water, reagent mixing, cooling of equipment, and to meet the water needs of employees.
Ideally, reasonably good quality water is used at the mine site for dust suppression, which helps with managing excess groundwater. The amount of dissolved salts acceptable for dust suppression is set by the environmental department and it is closely related to the surrounding flora and fauna.
I don’t want to finish my story without recalling that after a long day of drilling, drillers and geologists enjoy a good drink of cold beer and, by the way, water accounts for 85 to 92% of the beer’s composition. Or, if we prefer to drink Coca-Cola, to produce one liter of Coca-Cola, 200 liters of water are needed. A hard-working driller needs a lot of shower water to spruce himself up before going to dinner. C
Get in touch with Mariajose Romero-Segura on LinkedIn
Why are we still struggling to apply structural geology in target exploration and development? Aren’t the tools and required skills currently available in the industry sufficient for such an application?
In 2023, we still see mineral exploration ventures debunked in the industry by a lack of knowledge about the structural controls of their targets. A memorable example is the Rubicon Minerals that in 2016 had their gold resources slashed by 88%, signaling that untapped structural controls were a significant player. This article explores some of the challenges we face to uncover the structural controls of mineral targets, and it introduces successfully tested solutions.
At Vektore, we understand that mineral exploration comprises a complex integration of many methods and tools in which a particular sequence will have an impact on its outcome. The Structural geology exploration component is slowly coming back to exploration thanks to a major paradigm shift evidenced by a stream of developments of core orientation tools attached to the core barrel – allowing orienting core while drilling. The BallMarkTM was the first of its kind –conceptualized and developed by Les Anderson (1999), and later followed up by more sophisticated electronic tools. Modern core orientation tools are noticeably present in the industry, with more than five brands available on the market. Tools for reading structural features from oriented core have also evolved from sandbox/rocket launcher to electronic devices and ortho-corrected images from core boxes. Nevertheless, workflow segmentation associated with misuse of tools and processes represents a major obstacle. Figure 1 shows how Vektore views the borehole structural logging supply chain space, its segments, and inefficiencies that lead to inconsistent communication/engagement between domains and unreliable information transfer.
↑ Figure 1
Two major problems arising at the drill rig are the core orientation process handling and the reference mark transfer to the core. In 2018, Vektore compiled core orientation programs from four distinct exploration programs (juniors and majors) in a period of 16 months. In total, 3385 runs were completed. However, by following the +/- 150 mismatch between two contiguous runs (Holcombe, 2014) - which seems to be the current industry standard - only 980 (~30%) of the total runs were useful. This pattern seems to be present throughout the industry and it warrants further investigation. Therefore, a significant number of incorrect orientation runs are transferred to the core shack. In the public domain, Holcombe (2014) proposed the logging of the reference line mismatch to properly assess the core orienta-
tion-misorientation. Later in 2016, Myers et. al. presented the Bamboo diagram, based on Holcombe’s method, as a visualization tool for the mismatch problem. However, a solution for the correction of such errors was not presented.
At the core shack, reading structural features is limited to what the industry standard alpha-beta-gamma method can provide. This method was likely developed in the 1950s, but it has been upgraded significantly with the use of more modern tools, including electronic ones. Nevertheless, it falls short when measuring lines and their attributes (fold axis/vergence/facing, fault kinematics, vectors, etc.), which are prime features to unravel structural controls in mineralized bodies.
Aiming at addressing the above-mentioned problems, Monteiro (2002) developed a new reading method, the Structural Vectoring Log (SVL), in which the parameters to be read for structures in the core are the piercing points of plane’s dip/dip-direction and the piercing points of lines independently, making high-accuracy/precision vectorization of such piercing points possible. In addition, it allows for reading attributes associated with such structures, and with the provision of the drilling vector or survey, remapping them into their world coordinates. SVL has been successfully applied in various projects since its inception - including Inco Ltd (2002), Vale (2007), AngloGold Ashanti (2014), Nexa (2015) and on a short course promoted by Vektore during PDAC 2016. Since 2018, SVL and new developments have been embedded into the Ore.node® software.
Figure 2 summarizes the solutions developed by Vektore to address the drilling rig, core shack domains and Geolloger’s gap limitations. An integration of methods, tools, and software addresses each of the problems indicated in this article. The Ore.node has the capability to recover structural information not only from misoriented core (Structural ConvergenceTM) but also from non-oriented core (Structural InversionTM) in real-time. Structural Convergence and Inversion are the cornerstones for Vektore’s Quality Optimization (QO) process for data recovery. QO will be discussed in depth in a future article. vStructureTM and vSTARTM are Vektore’s newest products. vStructure software is a more agile and simplified version of the Ore.node software, designed with the general geologists in mind. vSTAR is an AR-based
reader software that brings speed, high-accuracy, high-precision, and universal reading of structures to the core shack. It provides real-time logging and visualization within the vStructure and Ore.node softwares. This is a significant innovation in structural logging designed with geologists and technicians in mind. The integration of Ore.node, vStructure and vSTAR will significantly improve the core logging process by generating trustworthy data to provide a sound framework for more robust 3D modeling.
Here we present two significant case studies applying Vektore’s SVL method - both in Brazil: (a) ore shoots in a IOCG deposit (Figure 3); and (b) orebody extension in a Copper-rich norite deposit (Figure 4).
Figure 3 shows the outcome of a structural analysis in which off-plane mineralization-related lineations (chalcopyrite and bornite) and grade distribution analysis determined the new drilling direction that unraveled 95 Mt of additional resources. Figure 4 shows the outcome of a structural analysis of non-oriented core in which Structural Inversion was applied. Contrary to the Client’s drilling design, the collar coordinates, the drilling vector, and the range in which the mineralization should be intersected were generated by Structural Inversion analysis. The mineralization was intersected as proposed.
Figure 5 shows the GUI – graphical user interface of the vStructure software with the vSTAR module’s viewport. The core and Augmented reality (AR) handle are presented to the computer camera for measuring structural features (full, half, quarter core – planes, lines and attributes independently) on the vSTAR viewport. The readings are sent directly to the structural logging table, as well as the 3D and 3D Stereonet viewports. Since this is a real-time process, the user can experience spatial awareness of the target’s architecture.
The integration of the tools and methods presented here, and briefly demonstrated in the case studies, resolve key problems along the
borehole structural logging supply chain that have been limiting the development of sound 3D models of mineral targets. C
References
• Holcombe; R. (2014) Oriented drillcore: measurement, conversion, and QA/QC procedures for structural and exploration geologists –last updated in 2023.
• Les Anderson (1999) Core orientation. Patent AUPQ074299A0 - https://patents.google.com/patent/AUPQ074299A0/ en?q=(Les+Anderson+drilling)&assignee=Shelljet+Pty+Limited
• Myers; R, et. al. (2016) An Inexpensive Way to Maximize and Preserve the Value of Oriented Core: The Orientation Log. SEG Discovery (2016) (107): 1–19.
• The Northern Miner (2016) Rubicon’s F2 deposit is uneconomic. Volume 101, number 49 on January 13th.
• https://www.northernminer.com/financial-matters/rubiconminerals-f2-deposit-is-uneconomic/1003746846/
• Monteiro, R. N., (2002). Structural Analysis of Borehole Data and Structural Scenario Design. Inco Internal Peer Reviewed Report. 20 pg.
• Monteiro; R. (2016) Structural Vectoring in mineral exploration: What it is and how, when and why we should use it. PDAC 2016 short course.
IT HAS NEVER BEEN EASIER TO CONTROL A LARGE NUMBER OF BOREHOLES
Are you looking for a fast, economical and reliable solution, also to advance your digitalisation process?
LiPAD®-100 is the answer.
The LiPAD®-100 has proven to be the fastest and easiest to-use-tool during hole surveys.
Book your live demo now!
Australia produces world-class geoscientists, but there is a growing skills gap between what students are taught at university and what industry requires. How do we ensure student engagement and sustainable employment? The minerals industry is changing fast and is facing a prolonged period of increased demand of all commodities, with exploration success and industry best practices paramount in meeting the need for raw materials to build our sustainable energy future. Geoscientists have never been so crucial to society.
However, enrolments are falling nationally in all Science, Technology, Engineering and Maths (STEM) subjects and universities are burdened with a broken business model resulting in severe financial pressures. The results are stark, with esteemed geoscience departments closing in Australia, increased vulnerability for those that remain and unrelenting pressure on an ever-reducing number of teaching staff. The student experience is also changing, with remote and on-demand learning coming to the forefront, challenging the traditional learning experience, potentially resulting in graduates with less practical experience.
Where are the geoscientists of the future going to come from? What skills will they need? How can we best prepare them for employment? How can companies recruit and retain the best talent? Collaboration between academia and industry has never been more important to form integrated learning pathways through school, university and supporting life-long learning, but any solution requires sustained support, coordination and leadership.
The National Exploration Undercover School (NExUS) was founded in 2016 to provide world-class training in mineral exploration. The three-week summer school is funded by the Minerals Council of Australia (MCA) and BHP and coordinated by the University of Adelaide
by program leader Dr Richard Lilly. Students from the full range of Australian Universities, along with early career staff in industry and government geological surveys applied for entry.
The primary outcome of the program is that students understand the challenges and opportunities of mineral exploration in Australia into the future, and have knowledge of the tools (and professional network) required to address these problems. This program focuses on four key UNCOVER themes:
• Theme 1 - Characterizing the Cover: New knowledge to confidently explore beneath the cover.
• Theme 2 - Investigating Australia’s Lithospheric Architecture: A whole-of-lithosphere architectural framework for mineral systems exploration.
• Theme 3 - Resolving the 4D Geodynamic and Metallogenic Evolution of Australia: Understanding ore deposit origins for better prediction.
• Theme 4 - Characterizing and Detecting the Distal Footprints of Ore Deposits: Towards a toolkit for minerals exploration.
The program is a mixture of workshops and hands-on field activities focused on practical mineral exploration. Activities include mine site visits, collecting geophysical and geochemical data, advanced ore
by Richard Lilly, Program Leader at the University of Adelaidedeposits workshops, drill core exercises and a range of other topics not normally covered at undergraduate level including regolith, sustainability, ESG and aboriginal cultural heritage training.
Since inception, NExUS has 267 alumni who work in every facet of the Australian minerals industry. NExUS is a case study of successful hands-on education collaboration and a model for future initiatives. Because of the continuing success, since 2020, the program has broadened its scope and expanded to offer over 20 professional development workshops (online and F2F), as well as a 5-day Perth RoadShow workshop event, undergraduate activities and a school outreach program and YouTube channel! (NExUS-RockStars).
The 2022 cohort was a diverse group of 36 geoscientists representing every state and territory in Australia, from early career exploration geologists and geophysicists to third year university students and everything in between; who are the future of the Australian mining and exploration industry.
NExUS is an invaluable course for early career geoscientists (<3 years of experience) and introduces the challenges the Australian mining industry faces when exploring undercover and the techniques and skills needed to find new deposits in the future. Just as importantly, NExUS brings together a diverse cohort of early career geoscientists from across the country providing a close network, which will stay with the cohort throughout their careers.
NExUS students, feedback from class of 2018
‘Literally the best, most engaging course and learning opportunity I have ever been involved with.’
‘I learnt as much from NExUS as I did from either my Honours or Masters qualifications, with added networking opportunities to change the course of my career.’
NExUS students, feedback from class of 2019
‘NExUS was probably the best 3 weeks of my life; the opportunity to meet and network with a variety of people around my age, the handson experience, amazing lectures. It was so much fun while being an incredible educational experience.’
‘NExUS... simply the most complete, enthralling and invigorating training experience for early career geoscientists... I fell in love with geology again!’
‘I loved everything about the course and made a network of similar minded people who I look forward to keeping in touch with for the rest of my career. I feel invigorated about the opportunities within geoscience!’
NExUS students, feedback from class of 2023
‘Very inspiring weeks of immersion in geoscience around like-minded people. NExUS returned much of the love for geology I thought I had lost. Thank you!’
‘NExUS has been the most enjoyable learning experience of my life and has helped me build a network of like-minded geoscientists across Australia.’ C
↑ Students from any state or territory in Australia can apply to be part of the 2-week program. We also accept applications from early-career industry (typically <3 years experience) and government/State survey geoscientists.
For more information
Visit: adelaide.edu.au
↑ The NExUS summer school is a mix of fieldwork, workshops, lectures and industry-focused sessionsDrilling Contractors (A-Z): Diamond Drilling, Reverse Circulation, AirCore
BRYSON DRILLING Phone 306-323-2202 Fax 306-323-2203 info@brysondrilling.ca www.brysondrilling.ca
Canada
DDH1 DRILLING
Phone +61 08 9435 1700 admin@ddh1.com.au www.ddh1.com.au
Australia
DIAFOR Phone (819) 860-3957 info@diafor.ca www.diafor.ca
Canada
GÜNZEL DRILLING CC Phone + 264 81 322 89 28 info@guenzeldrilling.com www.guenzeldrilling.com
Namibia
Directional Drilling (A-Z)
KATI OY Phone 0207430660 info@oykatiab.com www.oykatiab.com
Finland
MITCHELL SERVICES
Phone +61 7 3722 7222 Fax +61 7 3722 7256 info@mitchellservices.com.au www.mitchellservices.com.au Australia
Drill Rigs & Accessories (A-Z)
ATELIER VAL-D’OR Phone (819) 824-3676 Fax (819) 824-2891 info@avddrills.com www.avddrills.com
BARKOM Phone 90-312 385 60 50 Fax 90-312 385 35 75 info@barkomas.com www.barkomas.com
DISCOVERY DRILL MANUFACTURER Phone 1-506-542-9708 Fax 1-506-542-9709 info@discoverydrills.com www.discoverydrills.com
Drill Rigs & Accessories Cont.
Drill Rig Parts (A-Z)
www.terrasonicinternational.com
sales@terrasonicinternational.com
+1 740.374.6608
+1 740.374.3618
WE ARE YOUR SONIC DRILLING PARTNER
Terra Sonic International knows what it takes for you to succeed. We are committed to making the world’s most productive and reliable SONIC Drill Rigs and SONIC Tooling while providing the best service and support in the industry. Experience the Terra Sonic Difference today.
PROLENC
Phone (250) 563-8899
Fax (250) 563-6704
khodgins@prolenc.com www.prolenc.com
RC Equipment (A-Z)
BOART LONGYEAR
Phone 1-801-972-6430
Fax 1-801-977-3374 www.boartlongyear.com
FORDIA POWERED BY EPIROC
Phone 514-336-9211
Fax 514-745-4125 info@fordia.com www.fordia.com
Specialized Machine Works (A-Z)
NORTH BAY MACHINING CENTRE
Phone (705) 472-9416
Fax (705) 472-2927
luc@nbmc.ca www.nbmc.ca
PROLENC
Phone (250) 563-8899
Fax (250) 563-6704
khodgins@prolenc.com www.prolenc.com
Diamond Products (A-Z)
www.boartlongyear.com marketing@boartlongyear.com
Available
Key Features:
• Drilling automation
• HMI (Human Machine Interface) screen provides real-time updates
• 112kW drilling power
• 95% mechanical availability in field
• 360° versatility
• Small footprint, compact design
www.diatoolglobal.com
anthonygraham6@gmail.com
DIATOOL is a young and dynamic company, founded in 2010. The company manufactures impregnated and set core bits, casing shoes, reaming shells, and geotechnical drilling bits. DIATOOL products are sold in North and South America, Australia, Asia, Africa, and Europe. DIATOOL Diamond Products are manufactured in a modern well-equipped plant, using the latest manufacturing technology.
DIAMANTINA CHRISTENSEN
Phone +562 2620 7808 christensen@christensen.cl diamantinachristensen.com
DIASET Phone 1-800-663-5004 bits@diaset.com www.diaset.com
DIATOOL DIAMOND PRODUCTS Phone 852 2871 9028 diatool@163.com www.diatool@global.com
HOLE PRODUCTS
Phone (888) 465-1569 Fax (320) 631-0064 www.holeproducts.com
BOART LONGYEAR
Phone 1-801-972-6430
Fax 1-801-977-3374 www.boartlongyear.com
HOLE PRODUCTS Phone 909-939-2581 Fax 909-891-0434 www.holeproducts.com
SINOCOREDRILL Phone 86-510-82723272 Fax 86-510-82752846 sales@sinocoredrill.com www.sinocoredrill.com
WE ARE YOUR SONIC DRILLING PARTNER
Terra Sonic International knows what it takes for you to succeed. We are committed to making the world’s most productive and reliable SONIC Drill Rigs and SONIC Tooling while providing the best service and support in the industry. Experience the Terra Sonic Difference today. www.terrasonicinternational.com sales@terrasonicinternational.com +1 740.374.6608 +1 740.374.3618
BARKOM Phone 90-312 385 60 50 Fax 90-312 385 35 75 info@barkomas.com www.barkomas.com
CORE TECH Phone +51 983 856 666 info@coretech.com.pe www.coretech.com.pe
FORDIA POWERED BY EPIROC Phone 514-336-9211 Fax 514-745-4125 info@fordia.com www.fordia.com
FORDIA POWERED BY EPIROC Phone 514-336-9211 Fax 514-745-4125 info@fordia.com www.fordia.com
REFLEX Phone 1-705-235-2169 Fax 1-705-235-2165 reflex@imdexlimited.com www.reflexnow.com
SONDA PARTS Phone 55 – (31) 3391 3810 Fax 55 – (31) 3391 3810 comercial@sondaparts.com.br www.sondaparts.com.br/
COREFINDER
Phone +55 62 992720023 contato@corefinder.com.br www.corefinder.com.br
DEVICO AS Phone +47 72870101 devico@devico.com www.devico.com
REFLEX INSTRUMENTS
Phone 61 8 9445 4020 Fax 61 8 9445 4040 reflex@imdexlimited.com www.reflexnow.com
www.reflexnow.com
reflex@imdexlimited.com
1-705-235-2169
REFLEX - A LEADING IMDEX BRAND REFLEX forms part of Imdex Limited, a leading Mining-Tech company. Our unique end-to-end solutions for the mining value chain integrate IMDEX’s leading AMC and REFLEX brands. Market leading REFLEX technologies enable drilling contractors and resource companies to drill faster and smarter, obtain accurate subsurface data and receive real-time information for critical decision making.
Drilling Fluids (A-Z)
AMC Phone 1-705-235-2169 www.amcmud.com
DI-CORP Phone +1 (705) 472-7700 info@di-corp.com www.di-corp.com
Mudex
Phone +61 (8) 9390 4620 info@mudex.com.au www.mudex.com.au
Surveying & Geophysics (A-Z)
CORE TECH
Phone +51 983 856 666 info@coretech.com.pe www.coretech.com.pe Peru
DIGITAL SURVEYING Phone +27 18 788 6349 sales@digitalsurveying.co.za www.digitalsurveying. com.za Africa
Packers (A-Z)
TRUST SOLUÇÕES GEOLÓGICAS
Phone +55 62 992720023 contato@trustsg.com.br Brazil
Core Trays (A-Z)
CORE TECH
Phone +51 983 856 666 info@coretech.com.pe www.coretech.com.pe
DYNAMICS G-EX
Phone +61 7 54826649 sales@dynamicsgex. com.au www.dynamicsgex.com.au
PROSPECTORS
Phone +61 (02) 9839 3500 Fax +61 (02) 8824 5250 sales@prospectors.com.au
Catalog rates
Basic listing
110 USD per issue
330 USD per four issues
A text-only listing including your company name and contact details (phone, fax, email and website).
Featured listing
275 USD per issue
830 USD per four issues
A business card-sized listing featuring your choice of image as a background, your logo and strapline, 240 character spaces and your company contact details.
Combined listing
1250 USD per year (four issues)
A featured listing published both in our print and web catalog.
For more info, get in touch at: editorial@coringmagazine.com