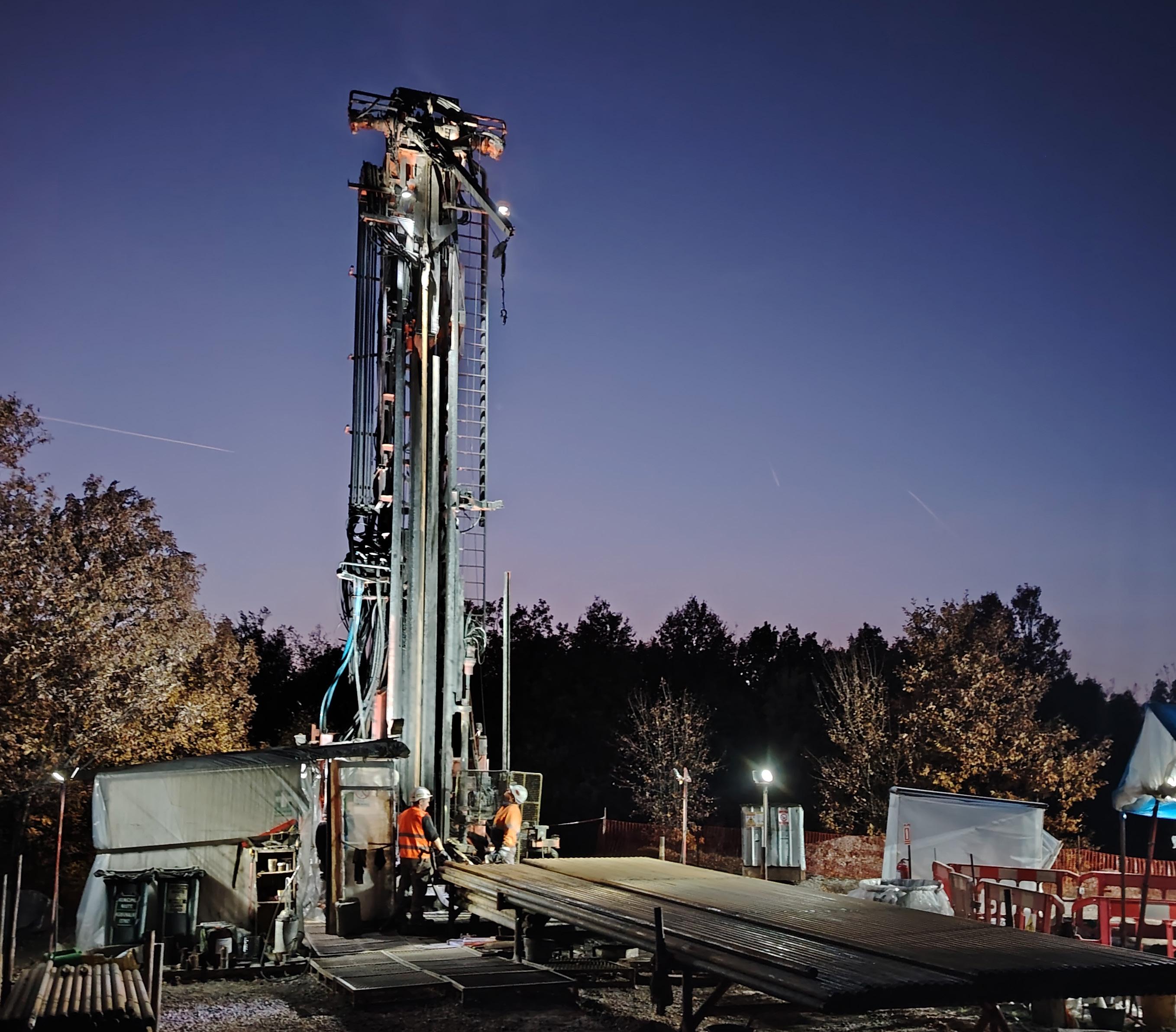
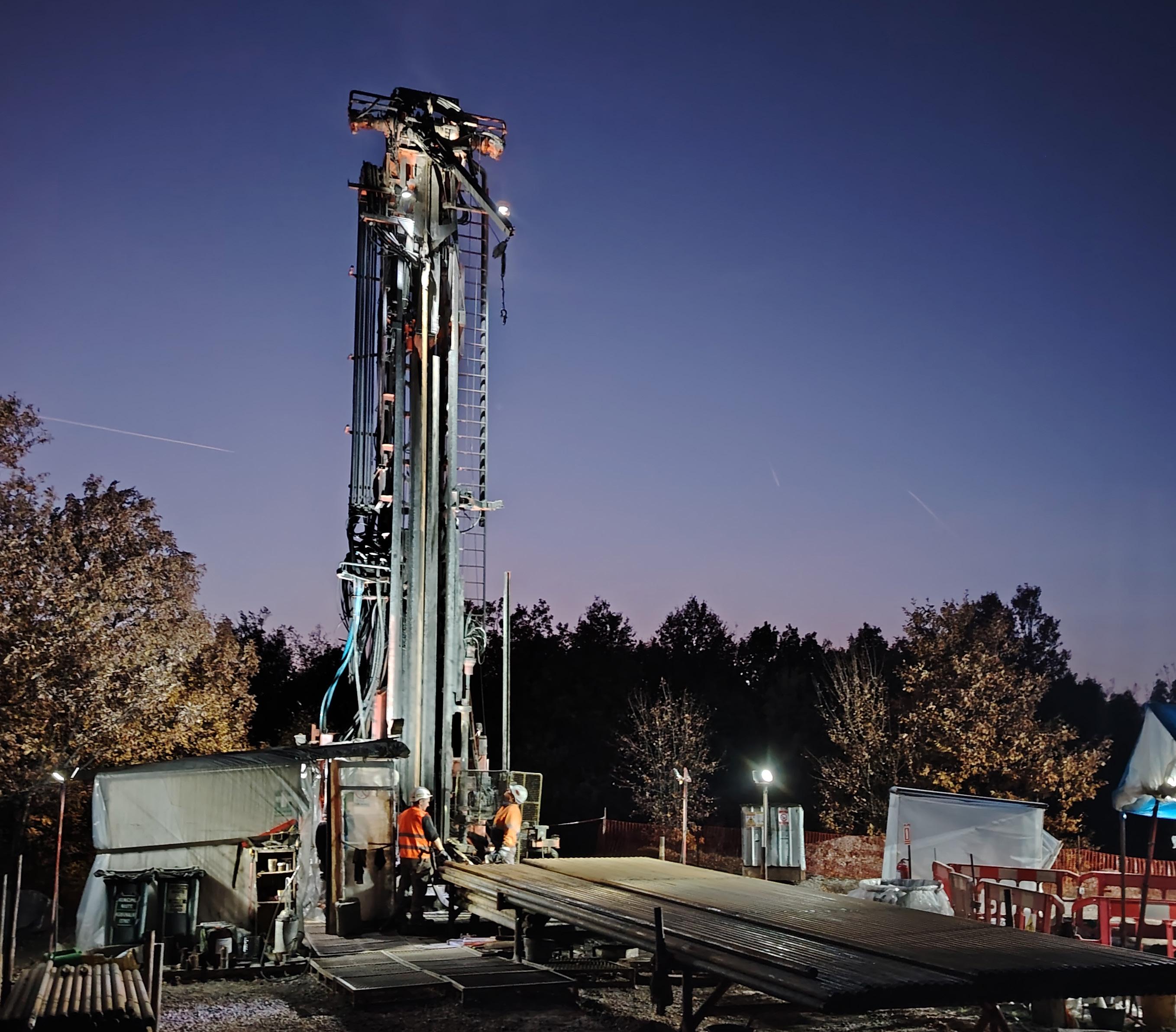
AXIS CONNECT™
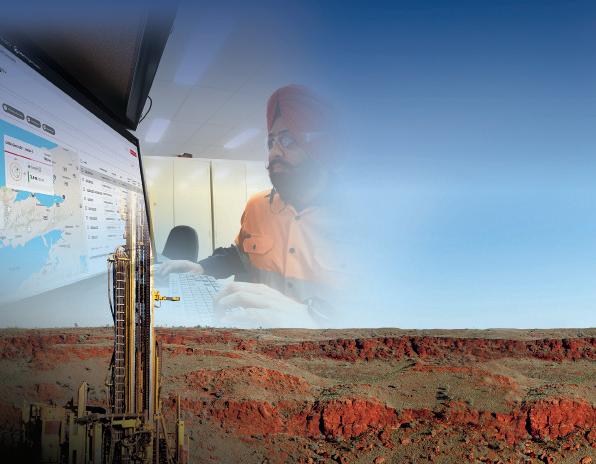

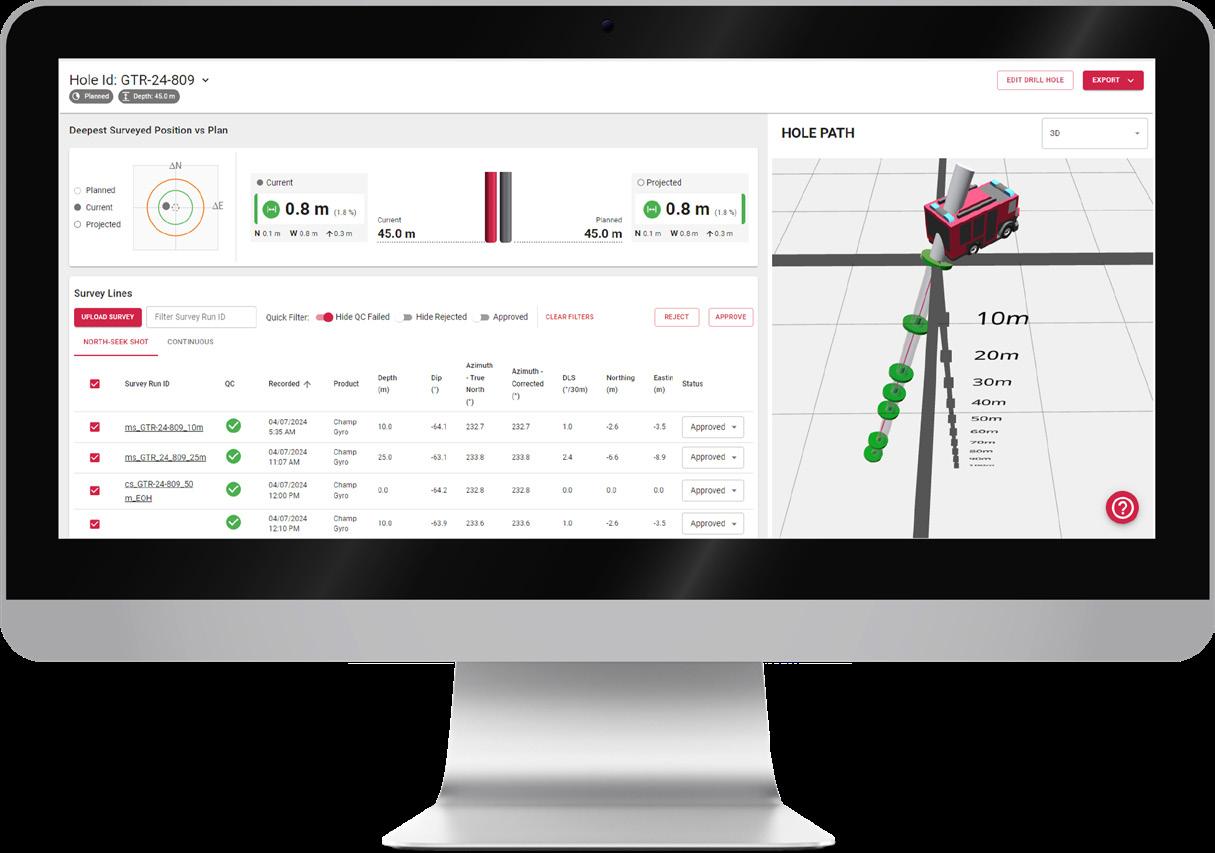
SIMPLE, RELIABLE, EFFECIENT SURVEY MANAGEMENT
AXIS Connect™ enables you to:
Reduce operating costs
Integrate workflows to enhance productivity
AXIS Connect™ is an open, secure and integrated survey management tool, where survey tools connect to the cloud, drillers connect with geologists, and measurements connect with reporting and geological modelling.
The platform simplifies drilling operations, minimising disruptions while ensuring accurate and efficient data collection in the field.
To learn more about AXIS Connect™ and how it can support your operations today, please contact your local representative, or scan the QR code
Enhance orebody knowledge
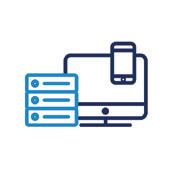
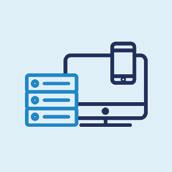
Connect survey to geological models
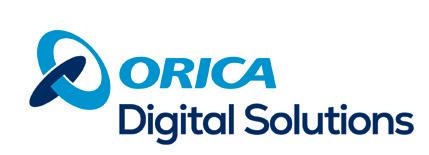
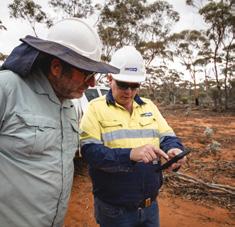
26 AXIS Connect™ improves the accuracy and reliability of directional survey data by Darren Palmer, Senior Product Manager - Orebody Intelligence at Orica Digital Solutions
29 Q&A from the experts: In conversation with François Robert, Independent Consultant at FR Geo-consult
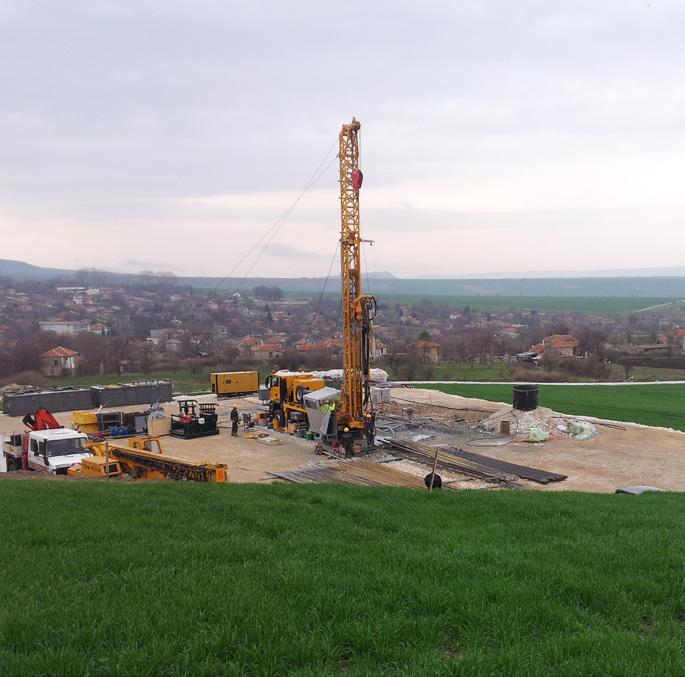
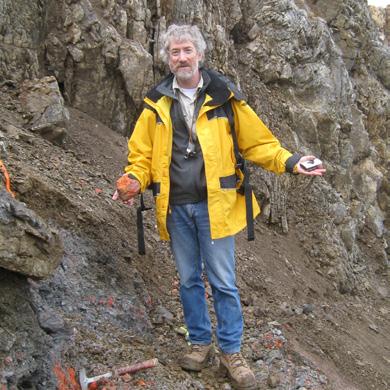
34 How to fail in mineral exploration but do it successfully by Carl Brauhart, Principal Consultant at Camp Oven Exploration
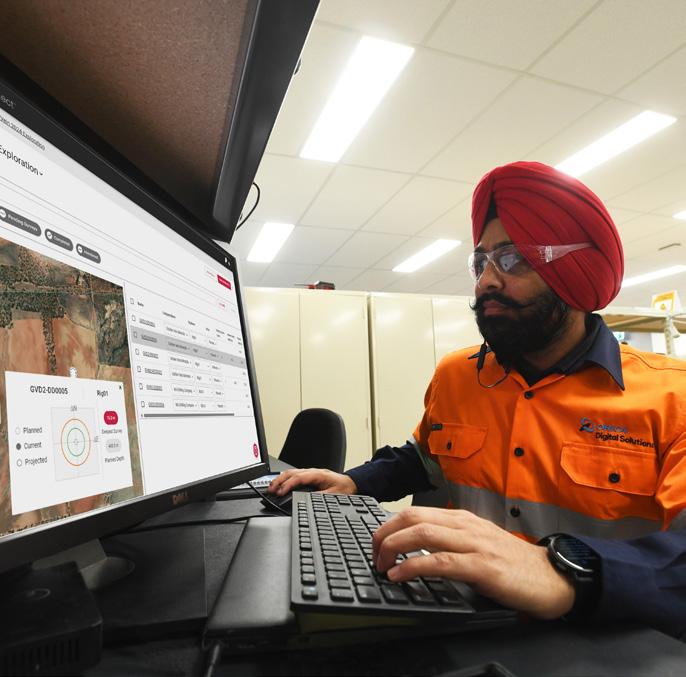
38 Preparation of diamond core for geotechnical logging: The dos and don’ts by Lyndell Juggernaut, Engineering Geologist at MineGeoTech 42 Drilling data quality –more than just samples by James Lally, Principal Consultant at Mining Associates

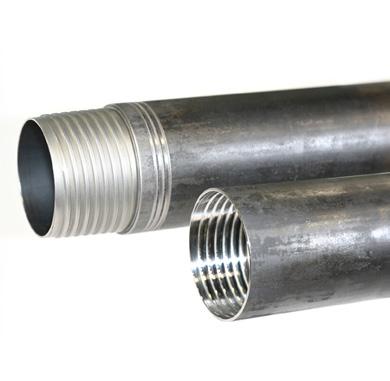

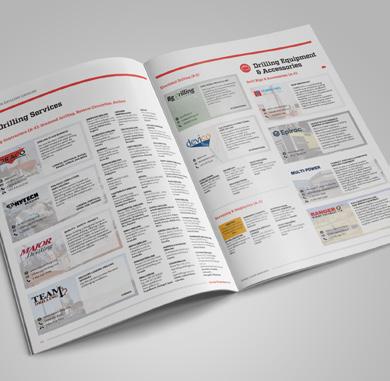
Authors in this issue

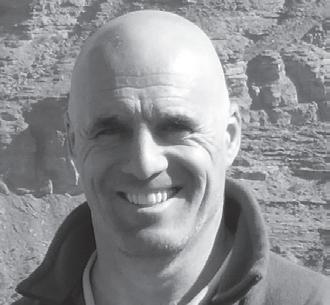
Carl Brauhart
Principal Consultant at Camp Oven Exploration
Tim Topham
Managing Director at Topdrill
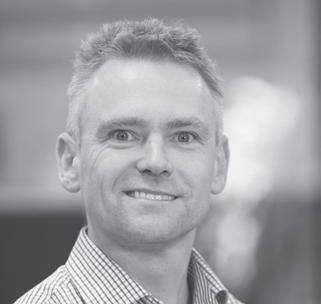
Darren Palmer
Senior Product Manager - Orebody Intelligence at Orica Digital Solutions

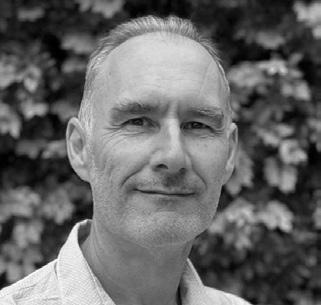
CORING MAGAZINE
December 2024
Cover photo GEOPS
Issue 29
ISSN 2367-847X
Not for resale. Subscribe: coringmagazine.com/subscribe
Contact Us
Coring Media Ltd.
57A Okolovrasten pat street, r.d. Manastirski Livadi, Triaditsa region, 1404 Sofia, Bulgaria
Phone +359 87 811 5710
Email editorial@coringmagazine.com Website coringmagazine.com
James Lally
Principal Consultant at Mining Associates
Sayers Marketing Manager at Di-Corp
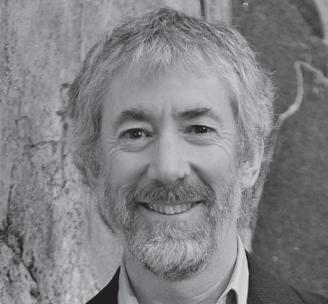
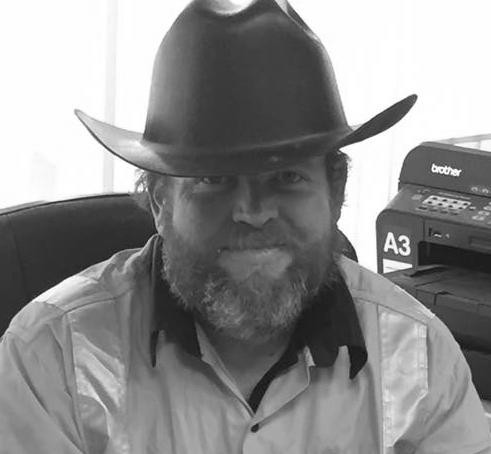
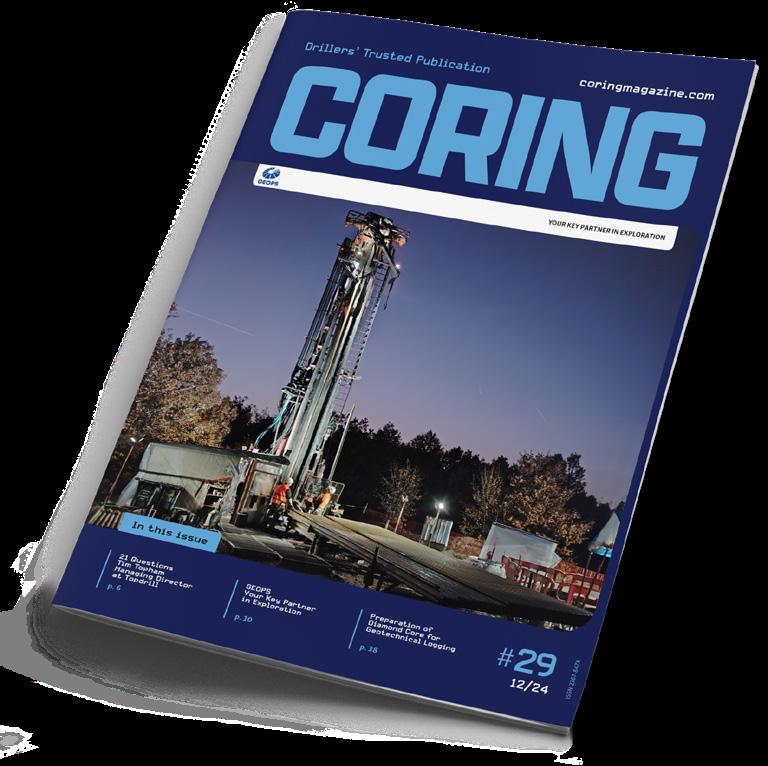
Publisher Coring Media
Executive Officer & Editor in Chief
Martina Samarova
Editor Maksim M. Mayer
Engineering Geologist at MineGeoTech
Section Editor – Exploration & Mining Geology
Dr Brett Davis
Digital Marketing Manager
Elena Dorfman
Assistant Editor Nevena Lyubenova
Graphic Design Cog Graphics
Want to contribute to Coring Magazine? Get in touch with us at: martina@coringmagazine.com
Coring Magazine is an international quarterly title covering the exploration core drilling industry. Published in print and digital formats, Coring has a rapidly growing readership that includes diamond drilling contractors, drilling manufacturers and suppliers, service companies, mineral exploration companies and departments, geologists, and many others involved in exploration core drilling.
Launched in late 2015, Coring aims to provide a fresh perspective on the sector by sourcing authentic, informed and quality commentary direct from those working in the field.
With regular interviews, insightful company profiles, detailed product reviews, field-practice tips and illustrated case studies of the world’s most unique diamond drilling and mineral exploration projects, Coring provides a platform for learning about the industry’s exciting developments.
Lyndell Juggernaut
François Robert Independent Consultant at FR Geo-consult
Andy
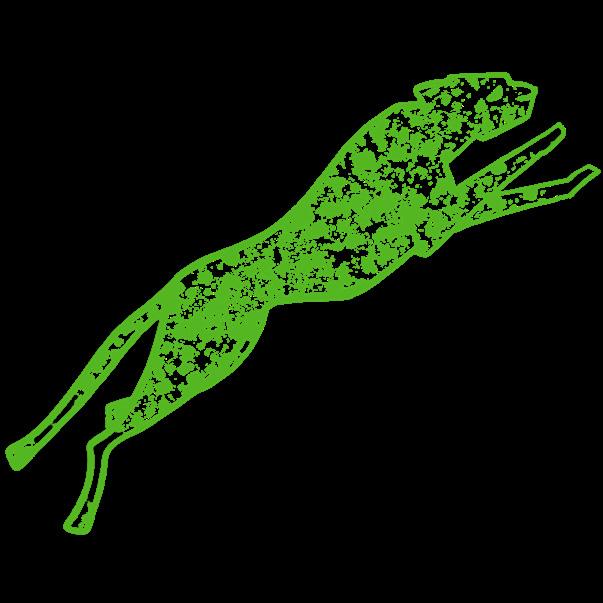
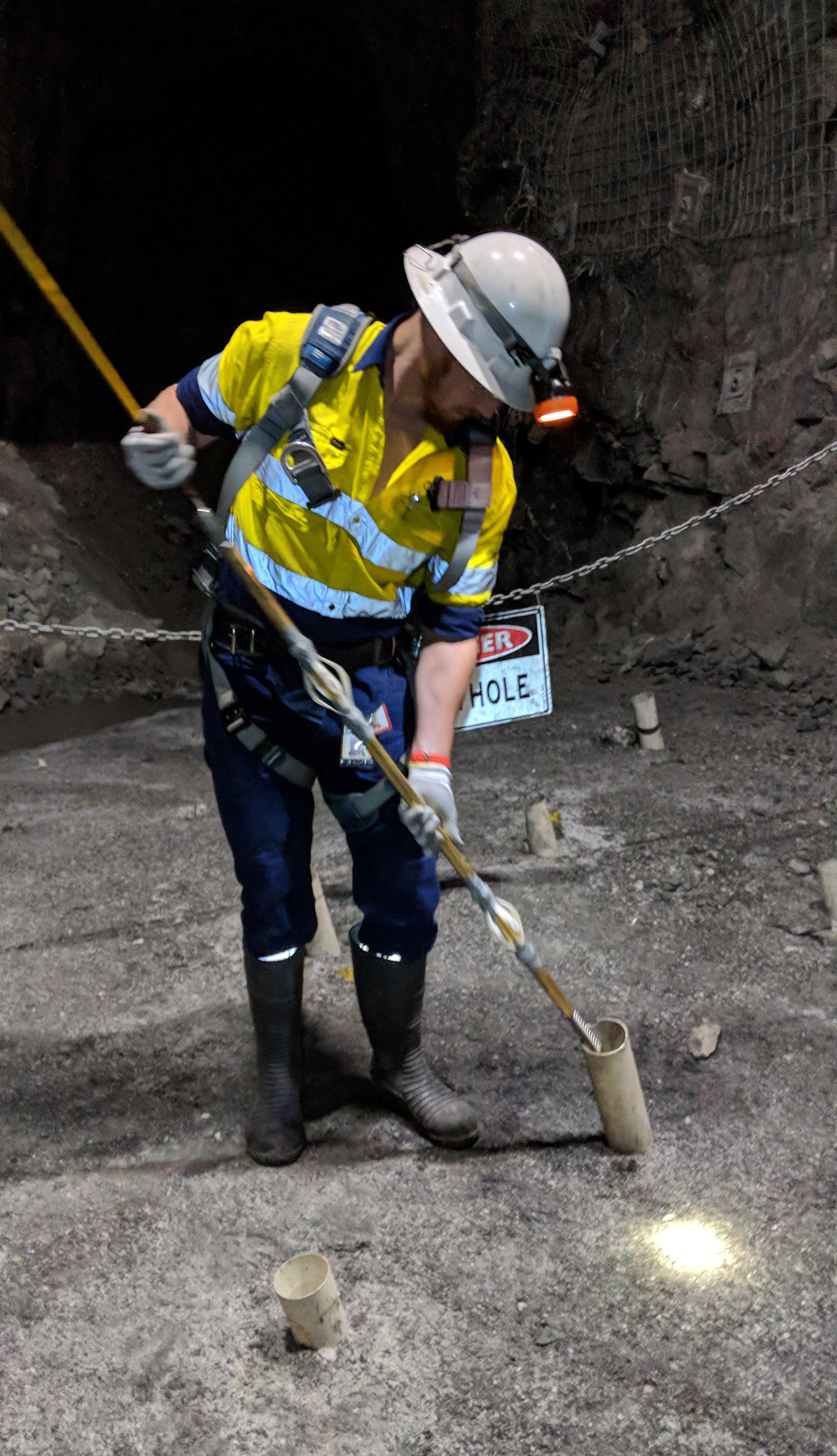
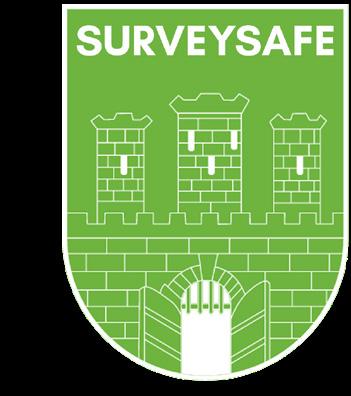

TIM TOPHAM
Managing Director at Topdrill
Tim Topham moved to Australia from New Zealand with a degree in agricultural science and the dream of owning a farm. Eventually, he found himself at a drill rig, and just a couple of years later, in 2006, he started Todrill.
The 2008 financial crisis decimated the Australian market. Work dried up, and Tim had to figure out how to make ends meet.
The same year, he bought his first brand-new rig, and in the following, as the industry was grappling with the effects of the crisis, Topdrill was only growing.
Tim admits that success wasn't a smooth ride, but today, he is the Managing Director of the company in charge of 425 people, a fleet of 32 rigs, and projects across Western Australia and the Northern Territories. Over the years, Tim has also won numerous awards, became part of the coveted cohort of 40 Under 40 for 2019, joined the board of ADIA in 2022, and developed the Toplytics software before AI was the talk of town.
questions
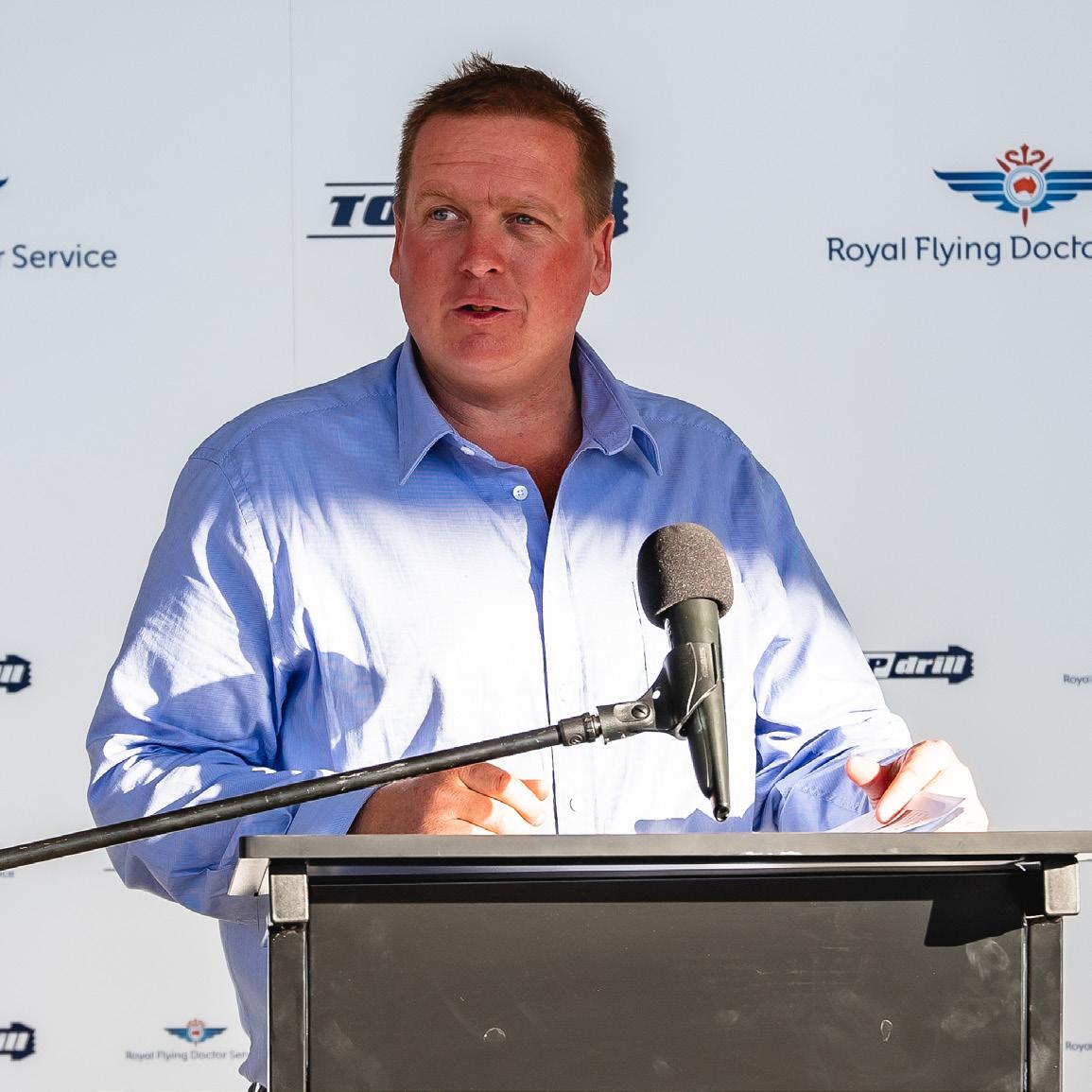
Grigor Topev: Hi Tim! It’s an honor to have you as Coring’s interviewee! First, tell us as much as you can about your early years and how did you get involved in the drilling industry?
Tim Topham: I moved to Kalgoorlie, Western Australia from New Zealand straight after I graduated university, with a dream of making enough money one day to be able to buy a farm. The Goldfields was booming at the time, and I had heard that drilling was a great career pathway to earning a great income, and there was plenty of drilling, jobs and mining activity around Kalgoorlie.
GT: How did you decide to start Topdrill?
TT: If you ask my parents, I have always had an entrepreneurial streak with many business ideas in my high school days. Then in 2006, I saw an opportunity in the market to get closer to my dream farm and purchased my first drill rig. The demand for mining services was huge at the time in the Goldfields.
GT: What were the toughest moments for you, trying to establish a brand-new company on the Australian drilling market?
TT: Starting any business comes with immense challenges, and most of your learnings happen from failing first. Resilience is a must! Two years into founding Topdrill, the Great Financial Crysis hit. Work dried up overnight and my brother also exited the business at the same time, returning to New Zealand. I was on my own to run the business and had to quickly figure out how to make ends meet. These moments taught me so many lessons about determination, innovation and my ability to pivot.
GT: Please tell us about the most important milestones in the company’s development throughout the years.
TT: Purchasing my first brand new drill rig in 2008 was definitely a milestone. Bringing hands free rod handling to diamond rigs in WA, winning the 40 under 40 Awards, Best Large Business sticks in my mind, and developing a product before AI was a word on everyone’s mind – Toplytics.
We developed Toplytics three years ago – this software has transformed our performance and safety compliance.
This year, Topdrill achieved the goal of raising AUD 1 million for the Royal Flying Doctor Service and Full Circle Therapies which was an absolute milestone and achievement by the team.
Today, we are a well-oiled high-performing team focused on quality drilling, backed up by the best gear and people in the drilling industry.
GT: Please tell our readers about Topdrill today.
TT: Today, Topdrill is one of the largest private founder-led drilling companies in Australia. We offer RC, DD and water well drilling services. We currently have 32 drill rigs in our fleet (19 Schramm 685 rigs, 13 Sandvik D880 rigs and one T130 rig).
Our team is 425 members strong with rigs drilling across both Western Australia and the Northern Territory. Projects primarily include gold, lithium and iron ore markets.
Below are the drilling statistics for FY24.
RC DRILLING:
• Total meters drilled: 642 198 m (2 106 949 ft);
• Number of holes drilled: 3733;
• Deepest hole: 648.2 m (2126.64 ft).
DD DRILLING:
• Total meters drilled: 215 156 m (to be exact: 215 155.5 m/ 705 890.75 ft);
• Number of holes drilled: 906;
• Deepest hole: 1170 m (3839 ft).
GT: Which are the company’s most remarkable projects?
TT: The most remarkable projects include:
• Sandfire Resources DeGrussa Copper find
also have a new discovery of gold in the Pilbara region of Western Australia. Lithium is a focus currently and is a mineral that has not been prospected in Western Australia. Western Australia is lucky enough to be endowed with some of the best spodumene deposits in the world!
GT: What’s the competition like and is there anything on the Australian market that should change?
TT: We are currently experiencing a downturn in rig utilization in the Australian market. That means Topdrill has to continuously strive to enhance our efficiency and competitiveness to maintain our strong position as market leaders. That brings its own set of challenges, particularly with the added pressure of inflation.
Our team at Topdrill remains committed and focused on overcoming these obstacles by our focus on innovation, drilling quality and continued excellence in customer satisfaction.
GT: What do you think gives Topdrill an edge over the competition?
‘Topdrill has a reputation of a performance culture, underpinned by safety and integrity, we are driven and focused on our vision to be market leaders.’
• De Grey Mining Hemi Gold discovery (13 m ounce deposit)
• Spartan Resources Gold discovery
• Capricorn Metals Gold discovery
• Northern Star Resources Gold discovery
GT: Many of our readers are not Australian, how would you describe the Australian drilling market to them? In your view, what makes it different compared to other regions like Canada, Latin America, or Africa?
TT: Ground water in the Goldfields region is eight times saltier than the ocean. We also operate in temperatures above 45°C (113°F). And some of our projects are 4300 km (2672 mi) away from home base!
GT: Which are the ‘hottest’ drilling spots in Australia right now?
TT: The Goldfields region in Western Australia continues to be a hot drilling spot with some of the largest gold deposits in the world. We
TT: Topdrill has a reputation of a performance culture, underpinned by safety and integrity, we are driven and focused on our vision to be market leaders.
Topdrill is unique from competitors as for the past four years we have invested heavily into our in-house data and analytics, developing Toplytics for our clients to view key drilling performance, safety and compliance data in real time – no matter their location.
GT: Personally, what would you like to see change or evolve within Topdrill in the next 10 years?
TT: In ten years, our Topdrill Drill School will continue to produce the best graduates in the country, and our teams will be renowned for their performance and capability.
As AI and technology develops, Topdrill will take advantage of autonomous methodologies to achieve safer operations and even more drilling productivity.
Topdrill is also investigating electrification and alternate fuels such as hydrogen to power drill rigs. We also continue to focus on ESG initiatives throughout the business.
GT: Have you worked in other countries, and do you have any future plans in that regard?
TT: Topdrill has plans to further expand its global footprint and is currently in talks with stakeholders to investigate opportunities to take our expertise and service offering into jurisdictions where we see we can add value.
GT: What is the most effective and practical tool for good drill site safety?
TT: Good quality equipment, training and awareness and a robust, ongoing Verification of Competencies process for our team.
GT: What qualities do you look for in a new employee?
TT: Qualities include:
• Technical expertise;
• A team player with good communication skills;
• Growth mindset and a clear willingness to learn;
• Can-do attitude;
• Demonstrates practical and adaptable attributes.
GT: Finally, what do you like to do in your free time? Any hobbies outside the drilling world?
TT: I enjoy off-roading with my family in and around the Goldfields region. We also spend some time on the white sandy beaches of Esperance, located on the south-west coast of Western Australia. C
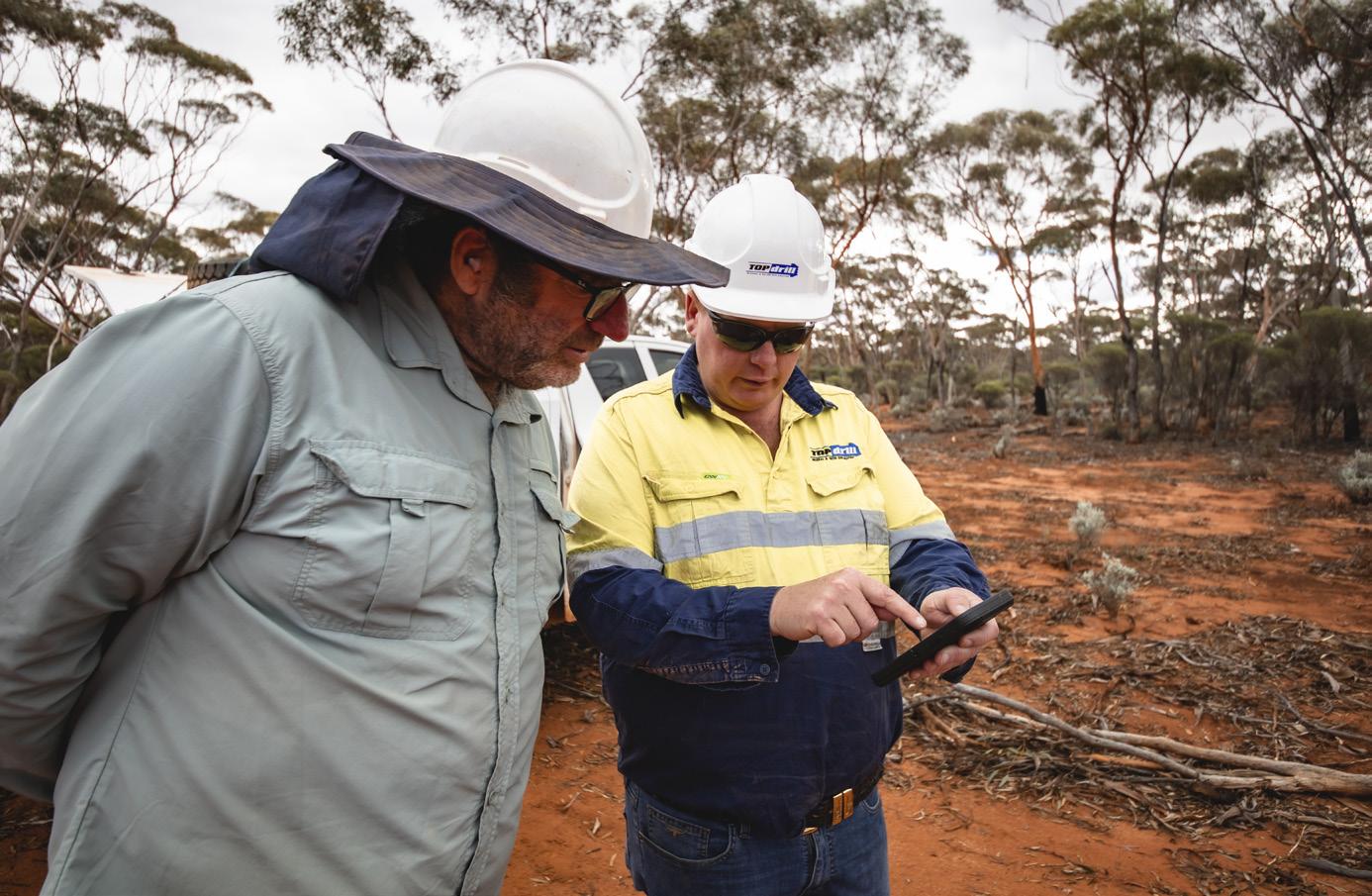
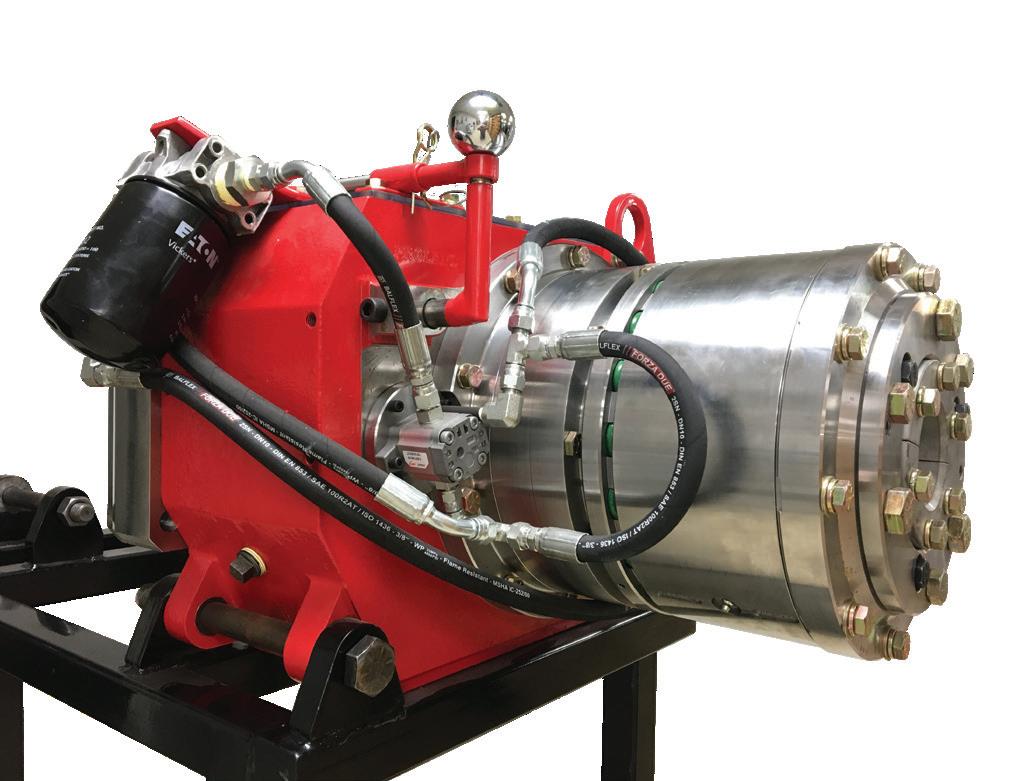
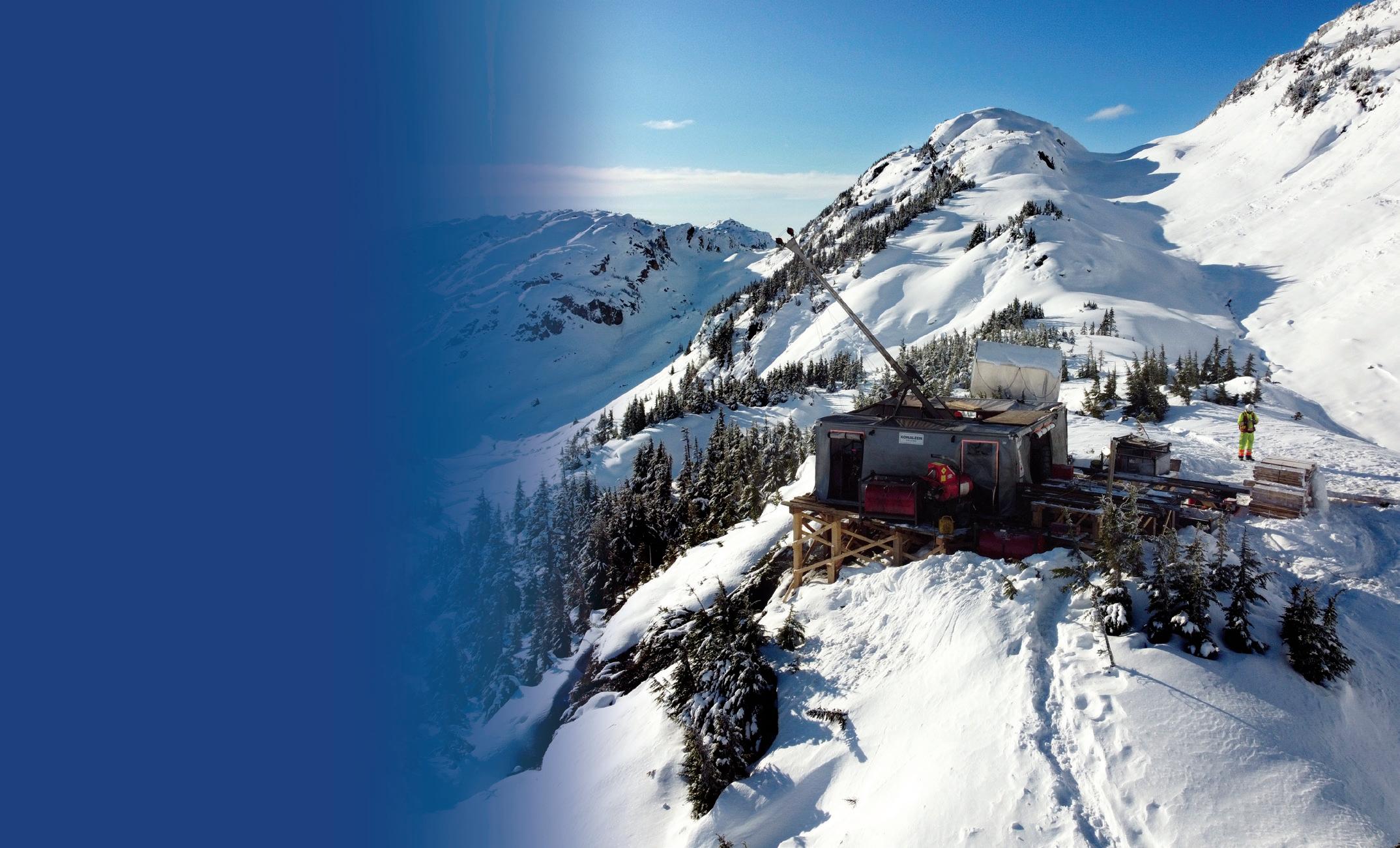
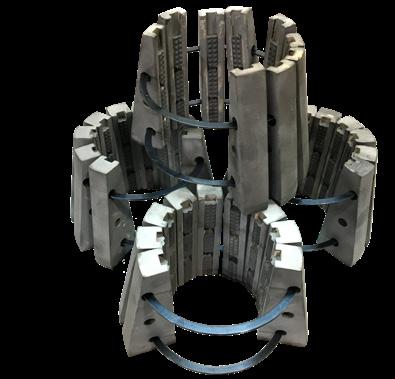
Konaleen Drilling Golden Triangle, BC
↑ Tim Topham (on the right) in the field
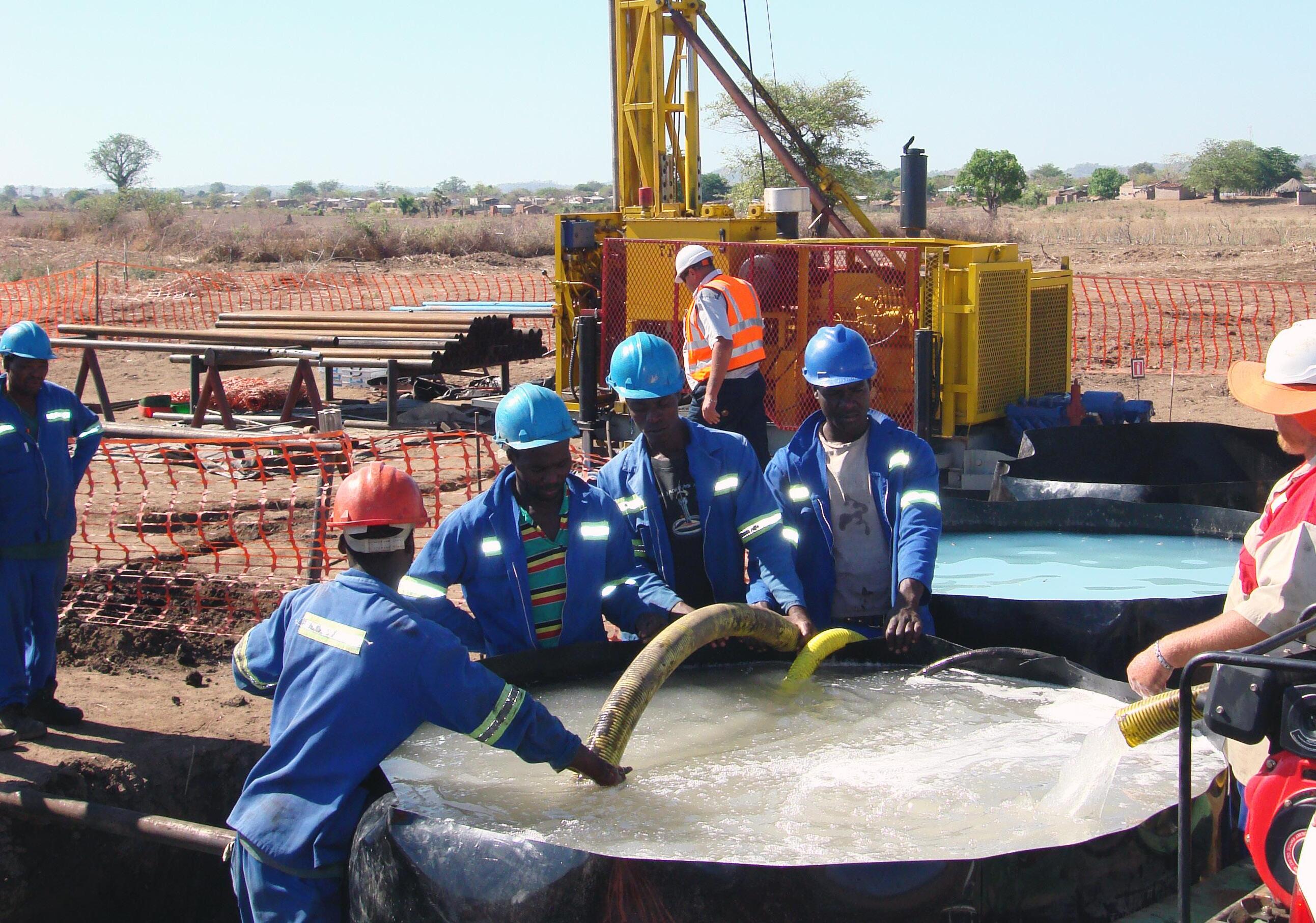
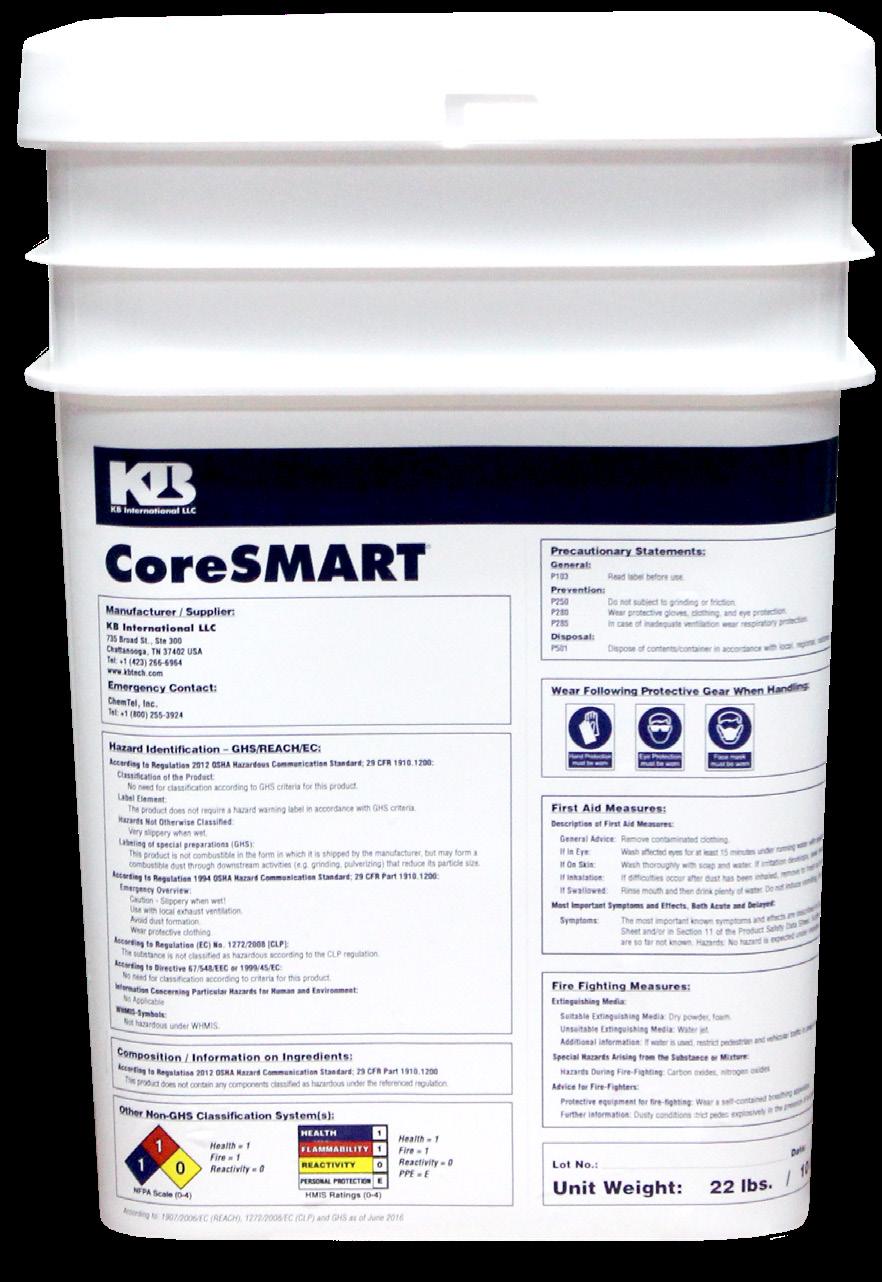
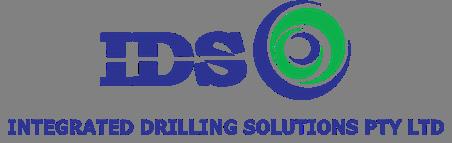
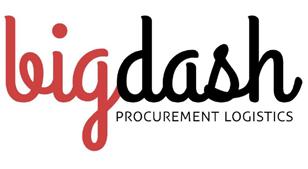
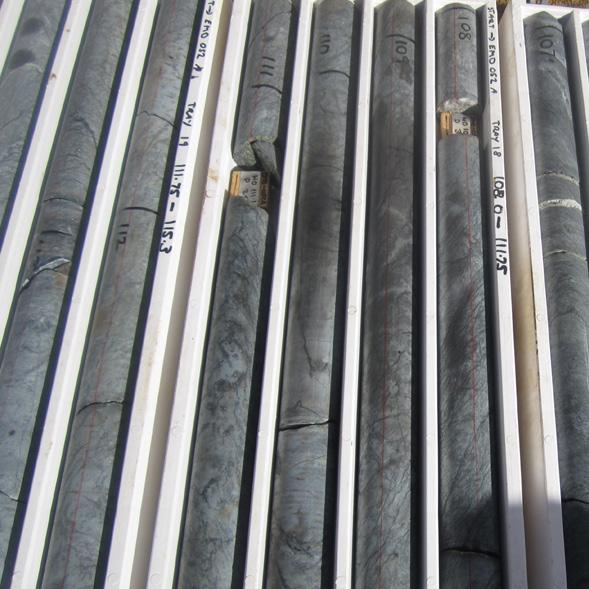
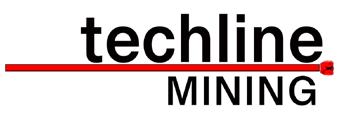
GEOPS
Your key partner in exploration
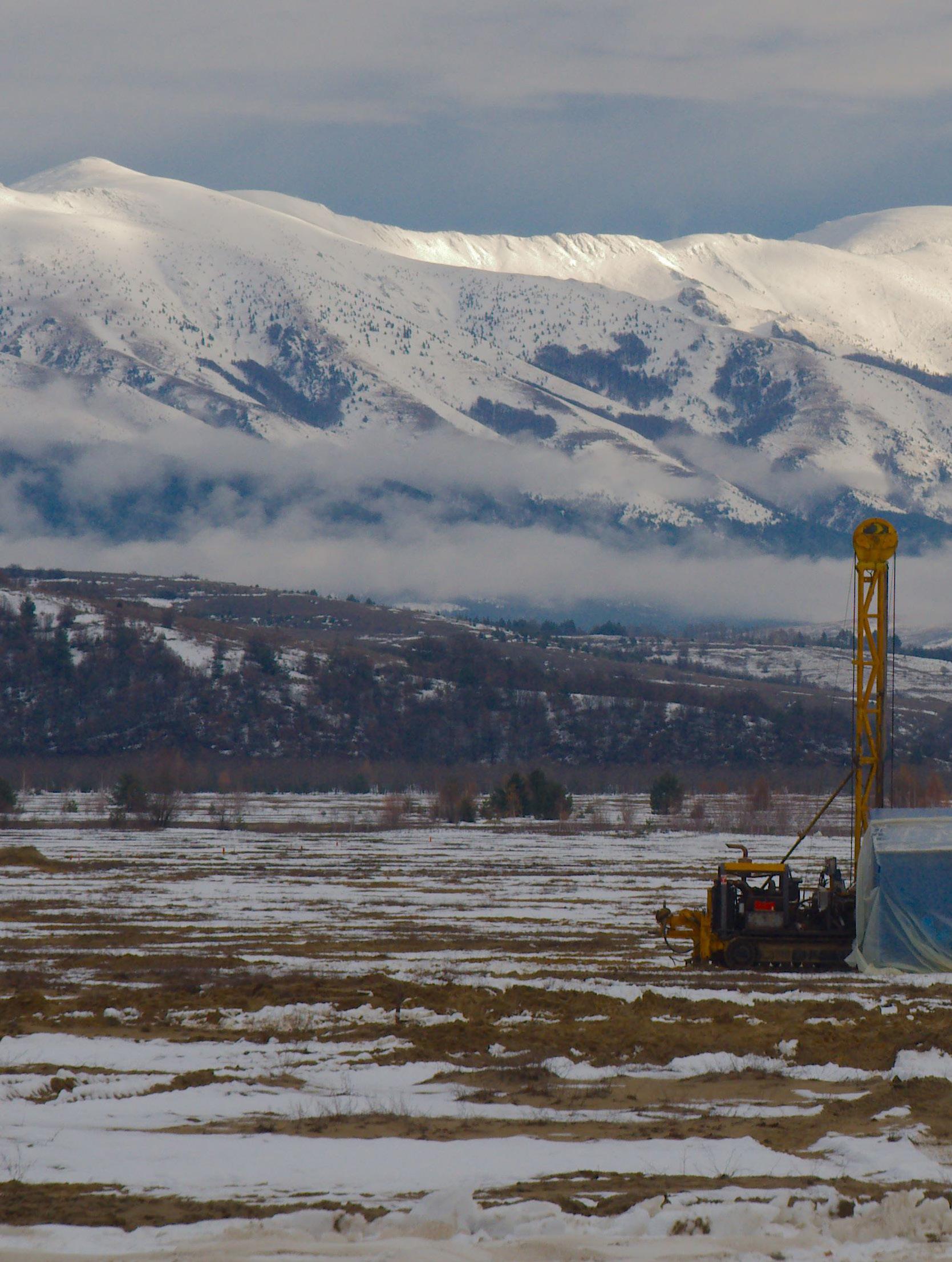
GEOPS was founded in 2004 by Vasil Andreev - a drilling engineer with over 35 years of experience in the field. In 2024, the company celebrates a 20-year anniversary.
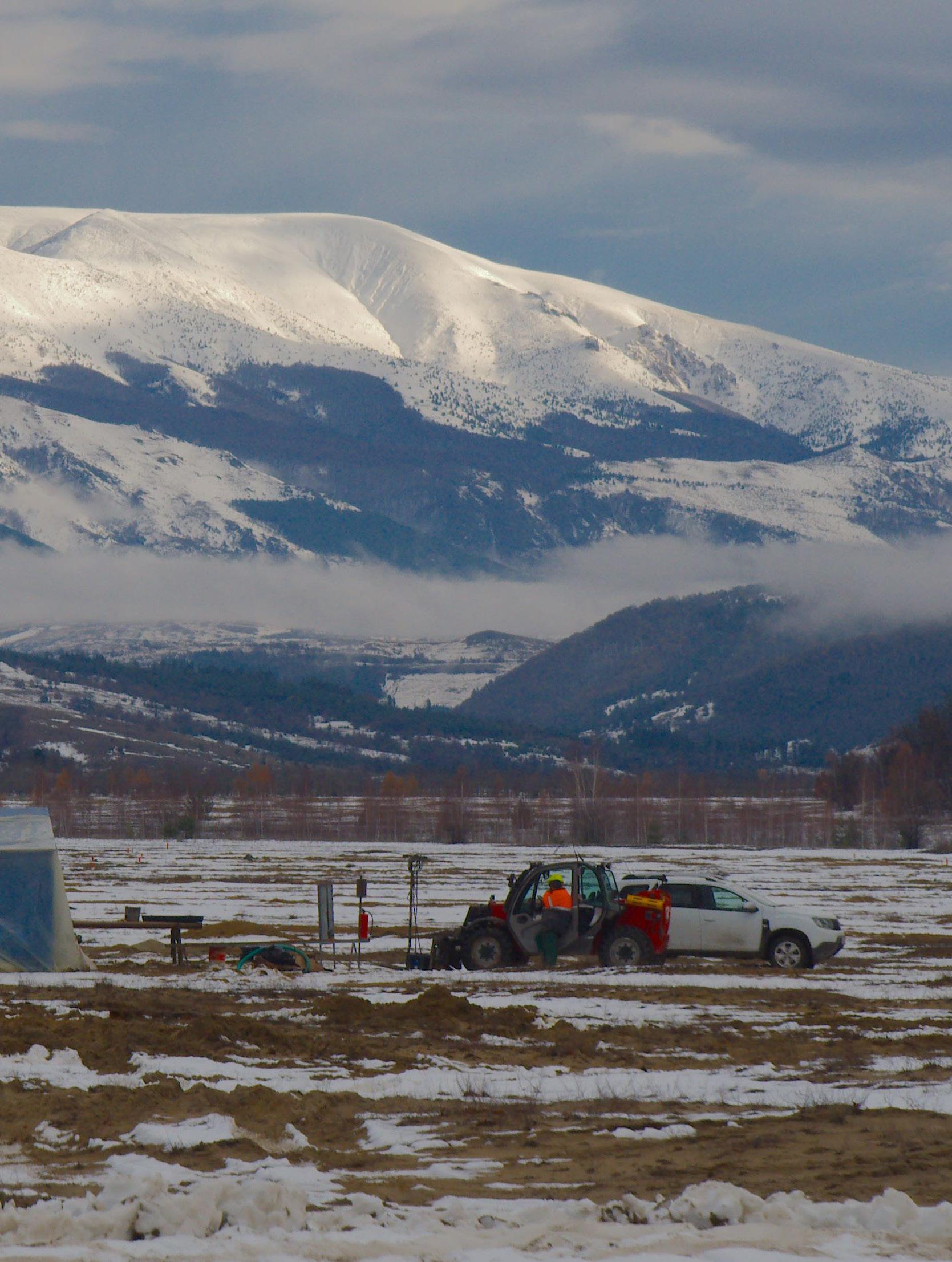
Mine tail drilling, Bulgaria
After 20 years of dynamic development, GEOPS has become one of the largest providers of mineral exploration drilling services in Eastern and Central Europe. The company has 45 drilling rigs, with capacities ranging from 5 to 90 tonnes of pull pack, covering the entire range of drilling services required for mining from greenfield to blackfield.
By continually investing in personnel, equipment and new technologies, while maintaining the highest standards in safety and environmental performance, GEOPS is the preferred drilling contractor for the region’s largest companies, such as Rio Tinto, Free Port, Zijin Mining, Dundee Precious Metals and many others.
Twenty years of dedication
From the idea and conception, through the growth and strengthening, until the strong market position, GEOPS’ major customers have been supporting the company. The exceptional requirements for safe work, environmental protection and quality of work gave the company the best standards and practices and trained the company’s staff. Continuously expanding knowledge and skills made GEOPS the partner of choice.
GEOPS understands its responsibilities in the two-way relationship with customers and the current market conditions and strives to cover them impeccably.
Mr Andreev is thankful to all of the company’s clients and employees for being a part of GEOPS’ history, present and future.
Operations
GEOPS’ headquarters are based near Plovdiv, Bulgaria. The company also operates through established subsidiaries in six other countries. While its main operations are in Europe - mainly in the Balkans and Central Europe - GEOPS has also successfully completed large-scale projects in Tunisia and Kazakhstan. The company has drilled millions of meters since its establishment.
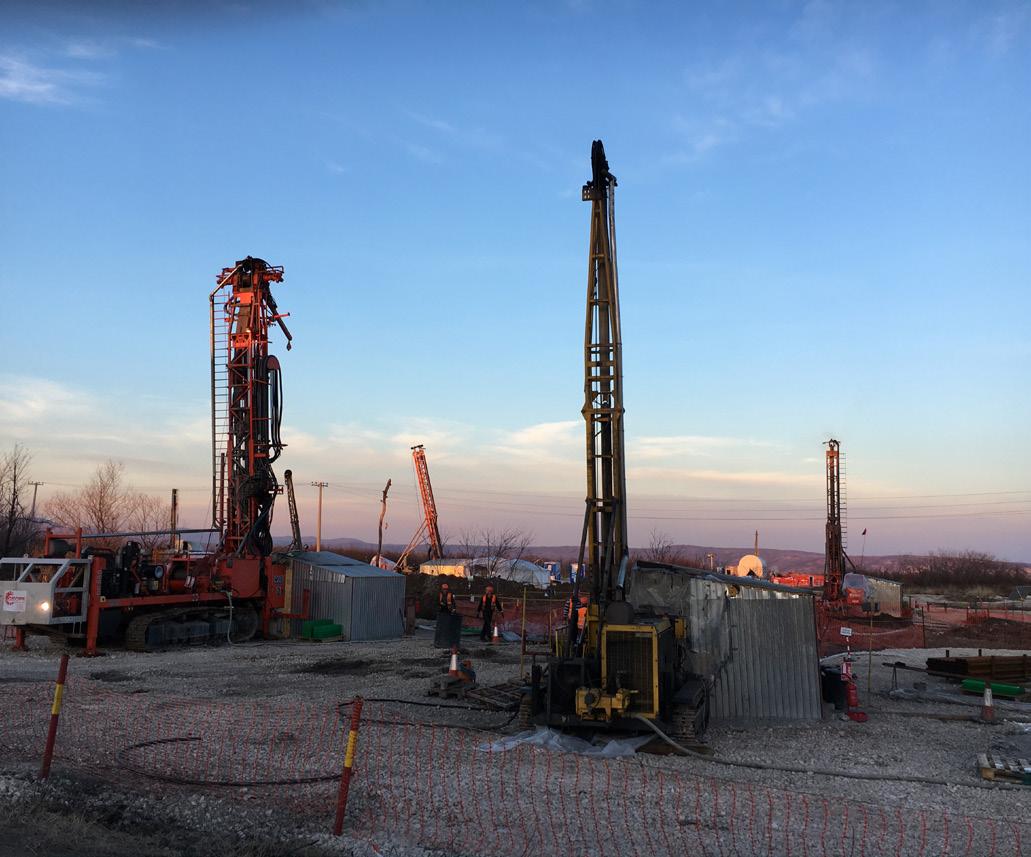
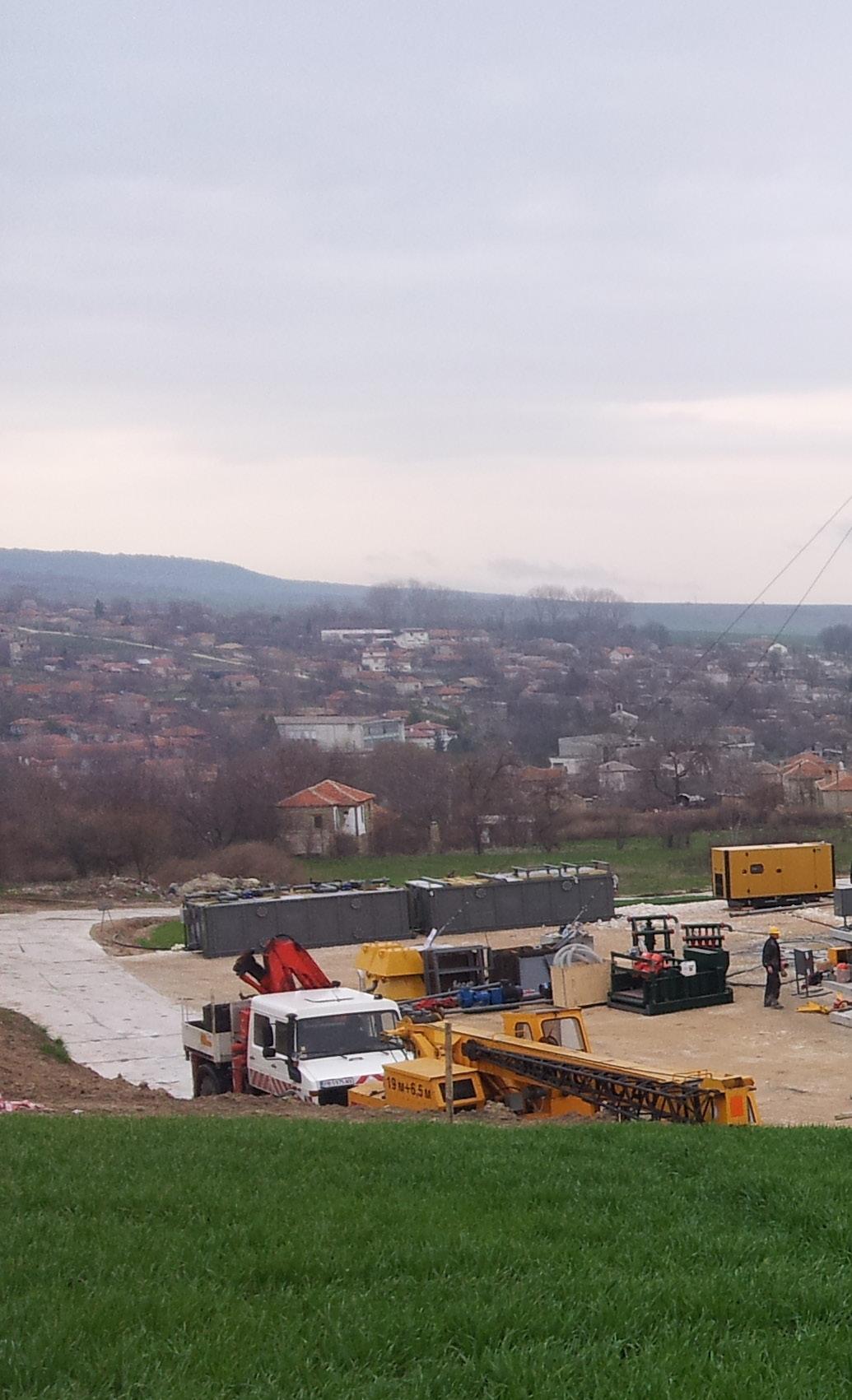
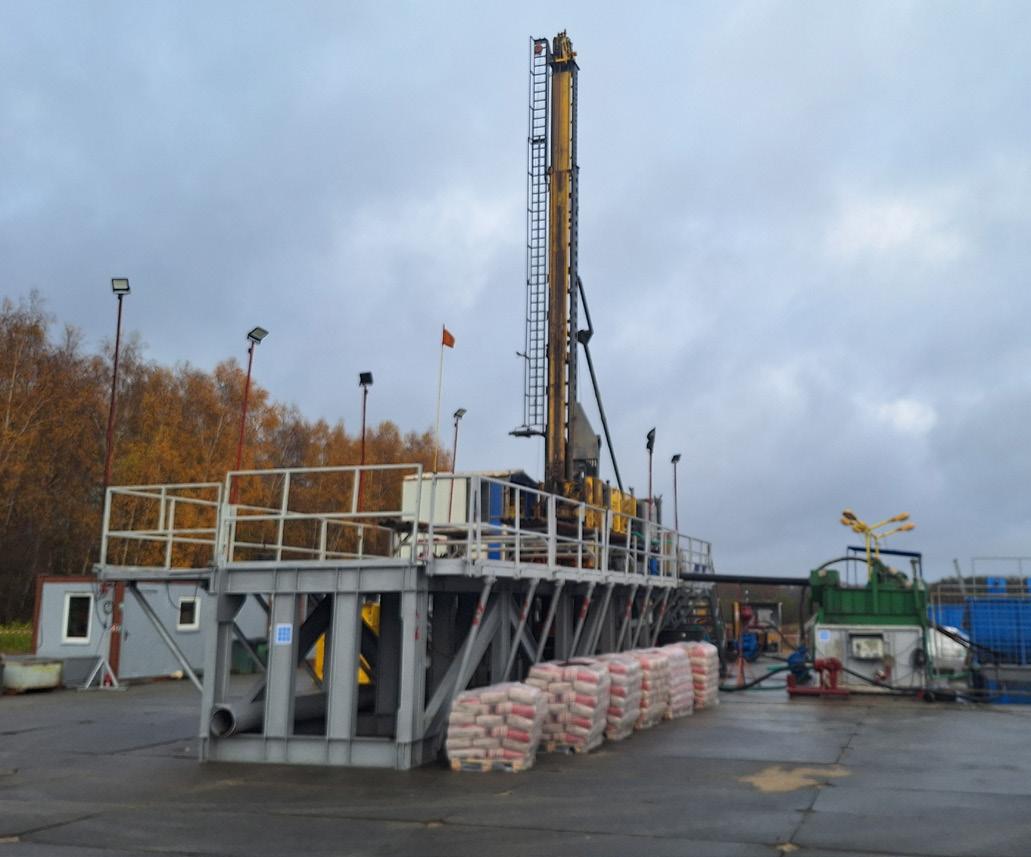
↑ Čukaru Peki, Serbia
↑ Milich, Poland
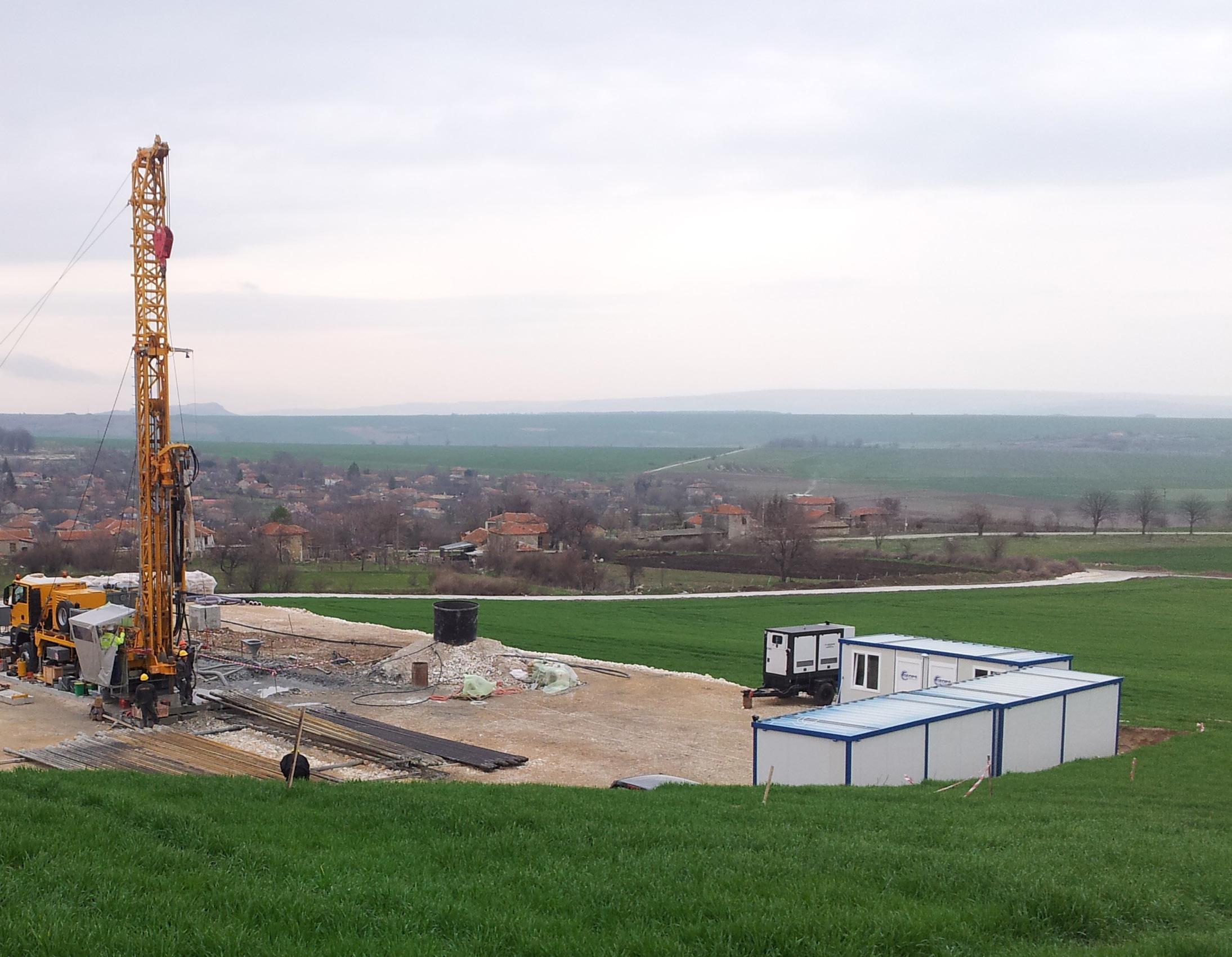
+ 2000 m (+6562 ft) drill hole, PQ3 final diameter, Bulgaria
Employees
The true backbone of any successful organization lies in its people. Currently, GEOPS has more than 430 employees. The company believes that placing employees at the center of organizational strategies is not just beneficial but essential for long-term success.
GEOPS employees have many years of experience and most of them have been working for the company for more than ten years. Exploration crews mobilize quickly and consistently deliver what exploration projects need: accurate drilling, quality samples and drilling programs executed on time.
Fleet
GEOPS has more than 45 drill rigs suitable for surface exploration drilling, underground and multipurpose. The company has been continuously developing its surface drilling infrastructure and currently, the surface fleet consists of over 35 rigs made by Sandvik and Epiroc that can drill down to 2500 m (8202 ft). The underground drill rig division consists of eight rigs, which are perfect for both exploration
and geotechnical tasks, for drilling deep holes, as the compact design of each rig makes it easy to maneuver. These underground rigs are equipped with a unique, versatile, and easy-to-use positioner for drilling in any direction.
GEOPS is also producing small portable drill rigs suitable for specific projects.
For multipurpose and geotechnical drilling, GEOPS’ multipurpose division is the finest. Powerful, extremely efficient and professionally handled, these machines are made for the most challenging tasks.
In addition, the fleet currently consists of a large variety of auxiliary equipment, such as a cementing unit, mud systems, BOP, high-pressure water pumps, generators, compressors, etc.
Projects
Copper shale exploration, Poland
Since 2012, GEOPS has been working on the exploration of Copper shale deposits in Poland for Amarante Investment and Miedzi Copper. The challenge here is that wireline diamond core drilling at depths
of up to 2500 m (8202 ft) is being carried out in conditions at risk of high-pressure oil and gas ingress (including hydrogen sulphide).
For the successful execution of the projects, GEOPS created a hybrid technology that combines the standard oil and gas drilling with wireline core drilling. For holes over 1500 m (4921 ft), the drillers use a Schramm TXD drilling rig with 90 tonnes of pullback capacity. For those up to 1500 m, they utilize an Epiroc CT 20 rig.
To implement this hybrid technology, a number of facilities have been designed, manufactured and certified at the GEOPS workshop including: a sub base for the Epiroc CT 20 which allows the installation of a full stack BOP under the machine and above the ground; a core winch with a stacker and a capacity of 3000 m (9843 ft) of with an 8 mm rope (0.32 in); a mud system, etc.
Over the years, GEOPS has completed hundreds of exploration holes on this project, thanks to its vast experience, engineering potential and production capacity, which have enabled the company to offer a suitable technical solution at a competitive price.
Directional drilling, Chelopech Gold Mine, Bulgaria
Since 2006, Dundee Precious Metals has been one of GEOPS’ most important customers. Over the years, the company has conducted
exploration, hydrogeological, geotechnical and operational drilling above and below ground.
In 2023, at the Chelopech Gold Mine, in Bulgaria, as part of a major exploration program that commenced in 2019, the company had to complete a multilateral directional drill hole and reached targets bypassing the existing underground mine. One of GEOPS’ most experienced teams on drill rig DE880-1 was charged with the task.
The mother hole started in P-size on inclination -75° and azimuth of 350° and after a long section of directional drilling, it ended with N-size at inclination -49° and azimuth of 2° at a total length of 2324.2 m (7625.33 ft). The daughter hole was started in H-size from 650 m (2133 ft) and after an additional section of directional drilling was completed, it was ended with N-size at -30° and azimuth of 15°. Its total length was exactly 1989 m (6525.59 ft).
This is probably one of the most difficult, most deviated and longest mineral exploration drillholes in the Balkans
Lithium exploration, Zinwald, Germany
In 2017, GEOPS began its first project on the territory of Germany, for Deutsche Lithium within the Zinnwald area laying the foundations for a successful business in the country.
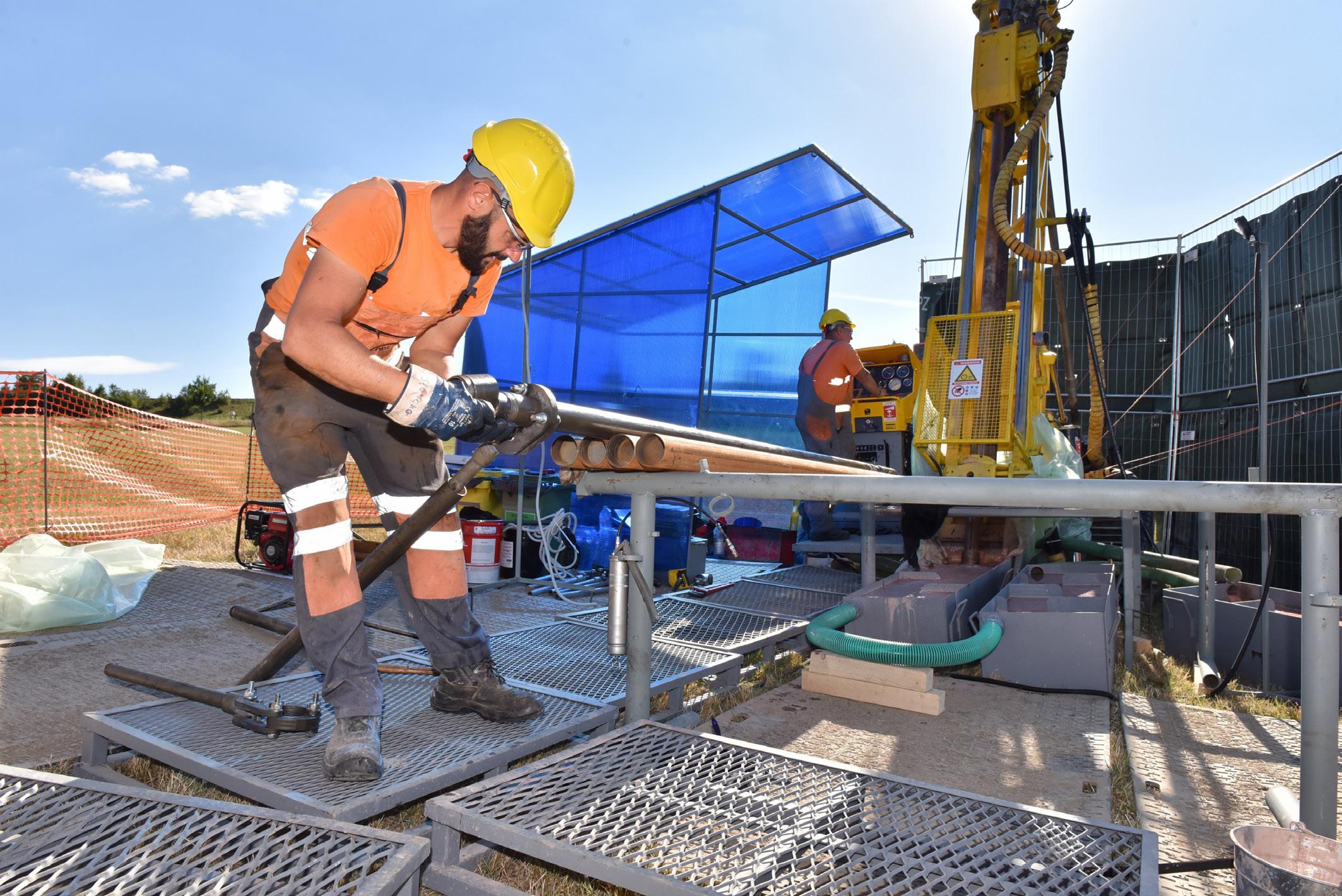
↑ Zinnwald, Germany
In 2022, GEOPS was contracted again for an expanded drilling program. Over the course of the project, which spanned between July 2022 and October 2023, GEOPS successfully drilled a total of 29 400 m (96 457 ft) with P-, H- and N-size diameters at depths ranging between 200 and 600 m (656-1969 ft). At certain stages, GEOPS operated with six drill rigs simultaneously and did not take a break during the tough winter conditions of this mountain region.
GEOPS coped very well with the project-specific challenges of operating in an environmentally protected but also populated area, where very often drilling had to be carried out only a few meters away from the nearest houses. The drilling crews set up mobile noise protection barriers on most of the drill sites, to avoid disturbing the peace within the village.
In addition, many of the sites were located on agricultural lands and protected grass meadows. Temporary access roads were built to protect the soil while moving the equipment and during the operations. GEOPS performed well on the client’s primary concern of drilling within a populated area, keeping social sentiment positive.
Helping Central Europe to develop the critical materials, alongside the Zinnwald Lithium project, GEOPS also executed successful exploration campaigns for the lithium project of European Lithium in Wolfsberg, Austria, the silver project near Freiberg for Saxony Silver and some other small projects.
Large-diameter core drilling
In August 2018, GEOPS was challenged to execute a large-core drilling program for a major mining company. This program was part of one of their long-term projects in the Balkans. The scope of work demanded one borehole at 444 mm (17.48 in) in diameter and 292 mm (11.5 in) of core to be conducted to a depth of 623 m (2044 ft).
No suitable equipment was found on the market, so GEOPS designed and produced something that would accomplish the goal.
The final result was a triple-tube conventional core barrel with an outer diameter of 444 mm that would collect 3 m (9.84 ft) of the 292 mm diameter core. When empty, the core barrel weighted 1500 kg (3307 lb) and when full, 1800 kg (3968 lb). A special drill bit design with diamond inserts was devised for the job.
Atlas Copco’s RD20IIIXC drill with a pull-back capacity of 50 tonnes was required to complete the job successfully. A special drilling mud system of 40 m3 was designed and provided by GEOPS, with two duplex mud pumps NB125 and two 220 kVA generators to supply the necessary power.
By choosing the 444 mm drilling diameter, the team could switch from mud rotary to core drilling without involving any additional operations, like casing and reaming. This way, the core could be extracted at any desired interval of mineralization and that was very valuable

↑ Bor, Serbia
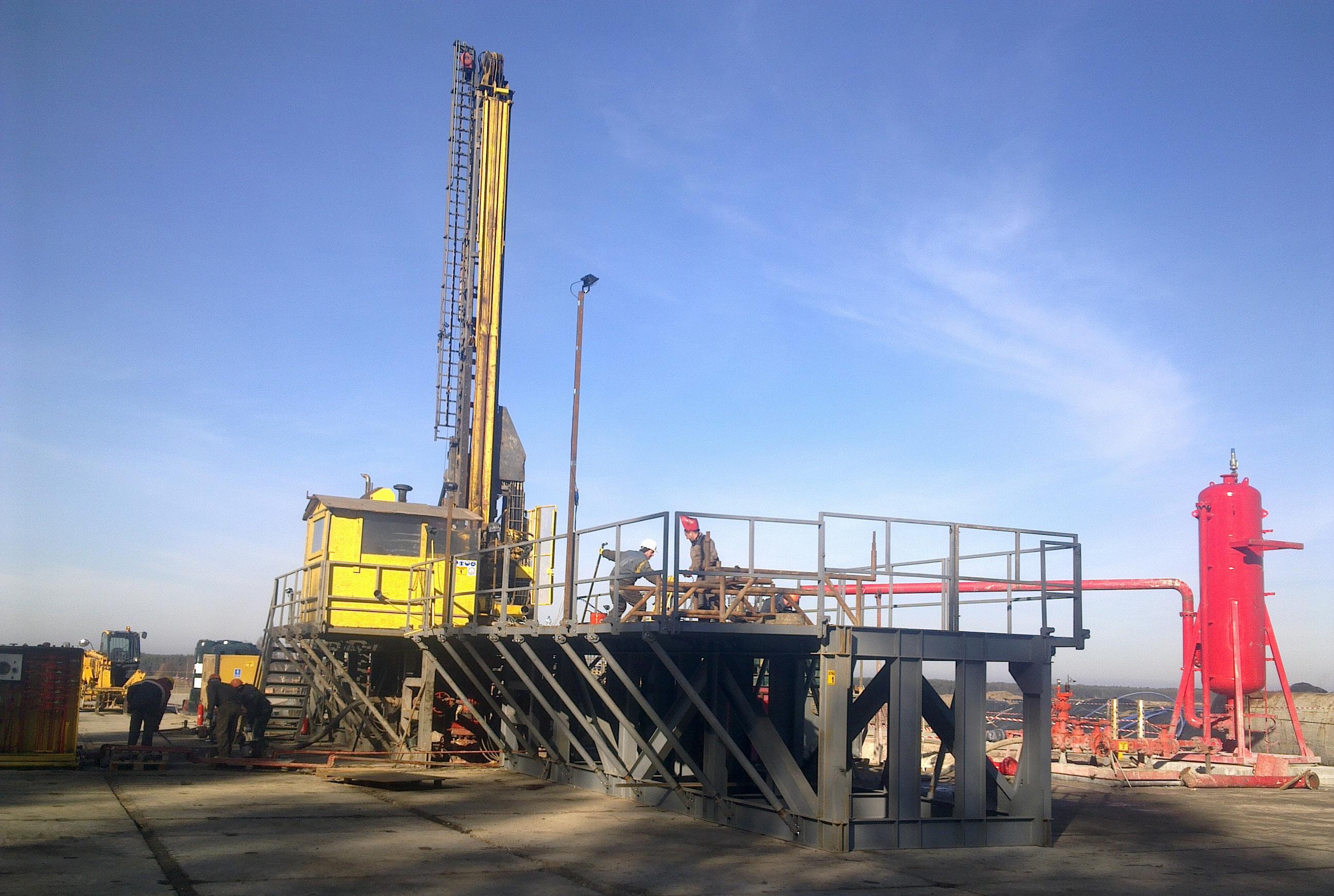
and cost-efficient for the client. To cover the overburden a 473.07 mm (18.63 in) casing was installed to a depth of 50 m (164 ft).
The first series of large-diameter conventional drilling started at 293 m (961 ft) and was finished off by the geologists to a depth of 335 m (1099 ft). From 335 to 480 m (1099 to 1575 ft) mud rotary drilling was used with the same 444 mm diameter drill bit and then from 480 m coring was begun again until the end of the hole at 623 m (2044 ft). A total length of 185 m (607 ft) core with a volume of 12.4 m3 was recovered, weighing approximately 37 tonnes.
The mud rotary drilling was as fast as usual, and the production from the section of coring was around 12 and 6 m (39 and 20 ft), at shallower and deeper sections respectively. Core recovery of more than 95% was achieved. At the depth of 600 m (1969 ft), the core breaking force reached 28 tonnes (pull-out).
The biggest challenges faced by the company were using a prototype on-site and achieving a high percentage of core recovery. Despite such obstacles and the particular geology, complicated even for wireline drilling, all goals were met.
Drilling was carried out in accordance with the requirements and safety standards of the client and with zero incidents.
Looking into the future
GEOPS continuously invests its resources to develop and implement new technologies. The company is working particularly hard to equip all its drill rigs with a mud-recirculating system and hands-free pipe handlers. GEOPS is also exploring new geographical markets and forming strategic partnerships to increase its global presence and client base. C
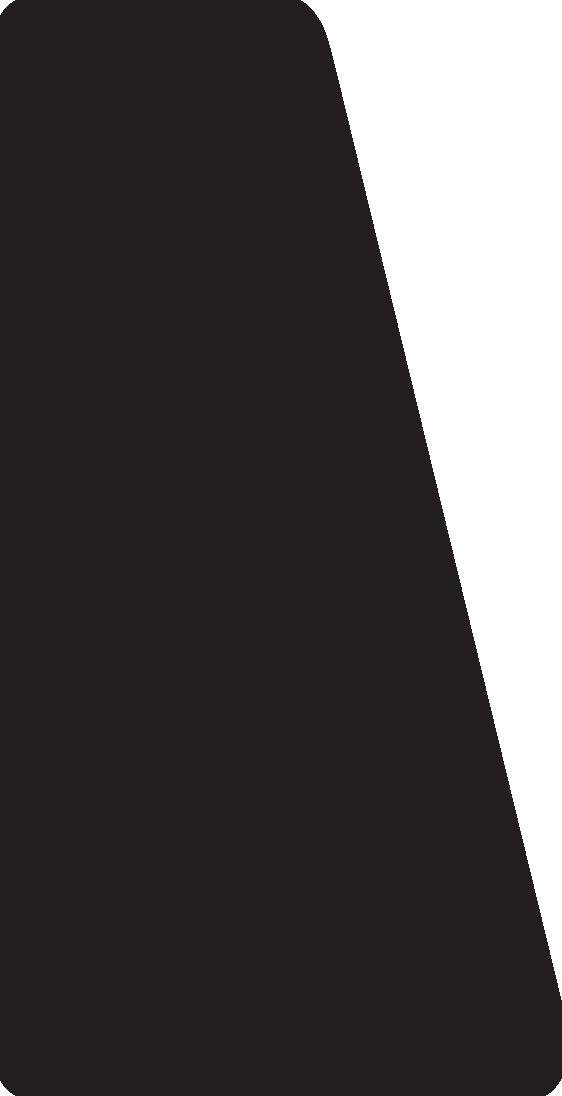
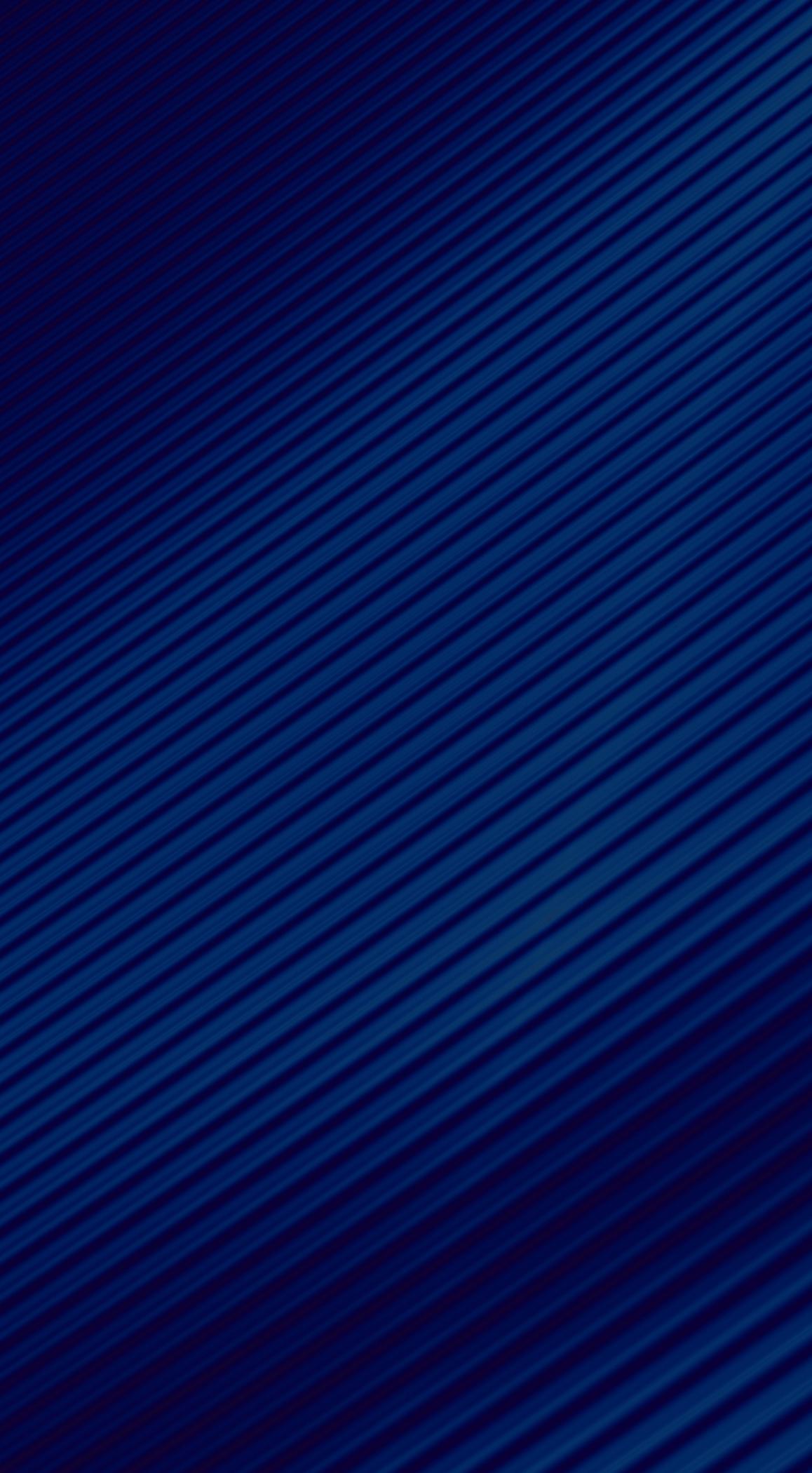
↑ GEOPS’ drill site
An environmentally safe DSPA (Dry Suspended Polyacrylamide) designed to maximum performance and core recovery in sands and gravels:
Provides a drilling fluid capable of stabilizing and maximizing the encapsulation of core recovery in the most di cult sand and gravel conditions.
Reduces the need of casing in most unconsolidated formations.
Builds a matrix tying shifting sands and gravels together thus stabilizing the borehole and maximizing core recovery.
Lubricates down hole motors and eliminates magnetization of drill rods.
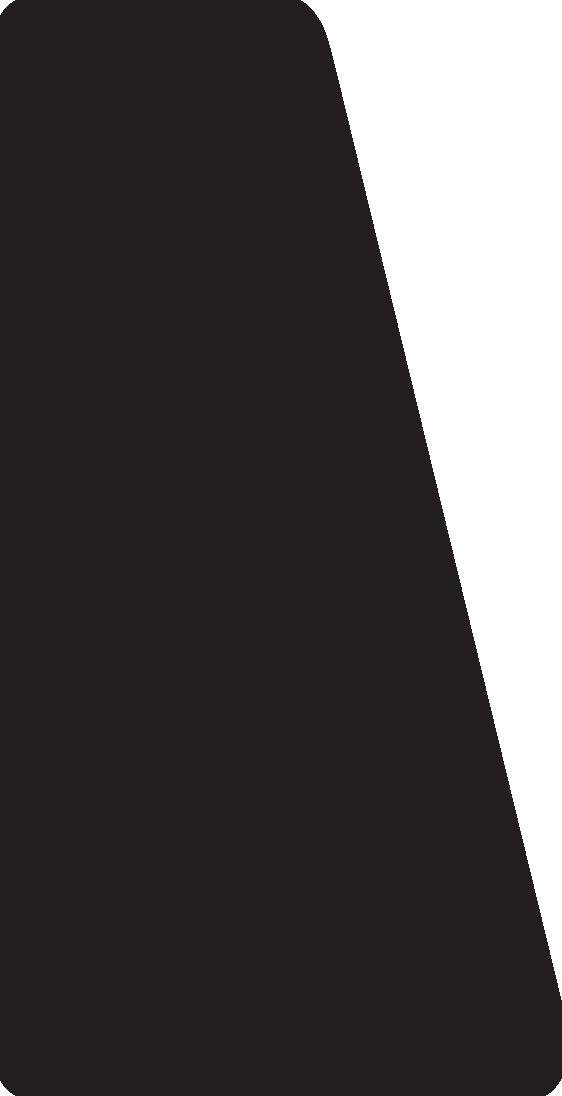
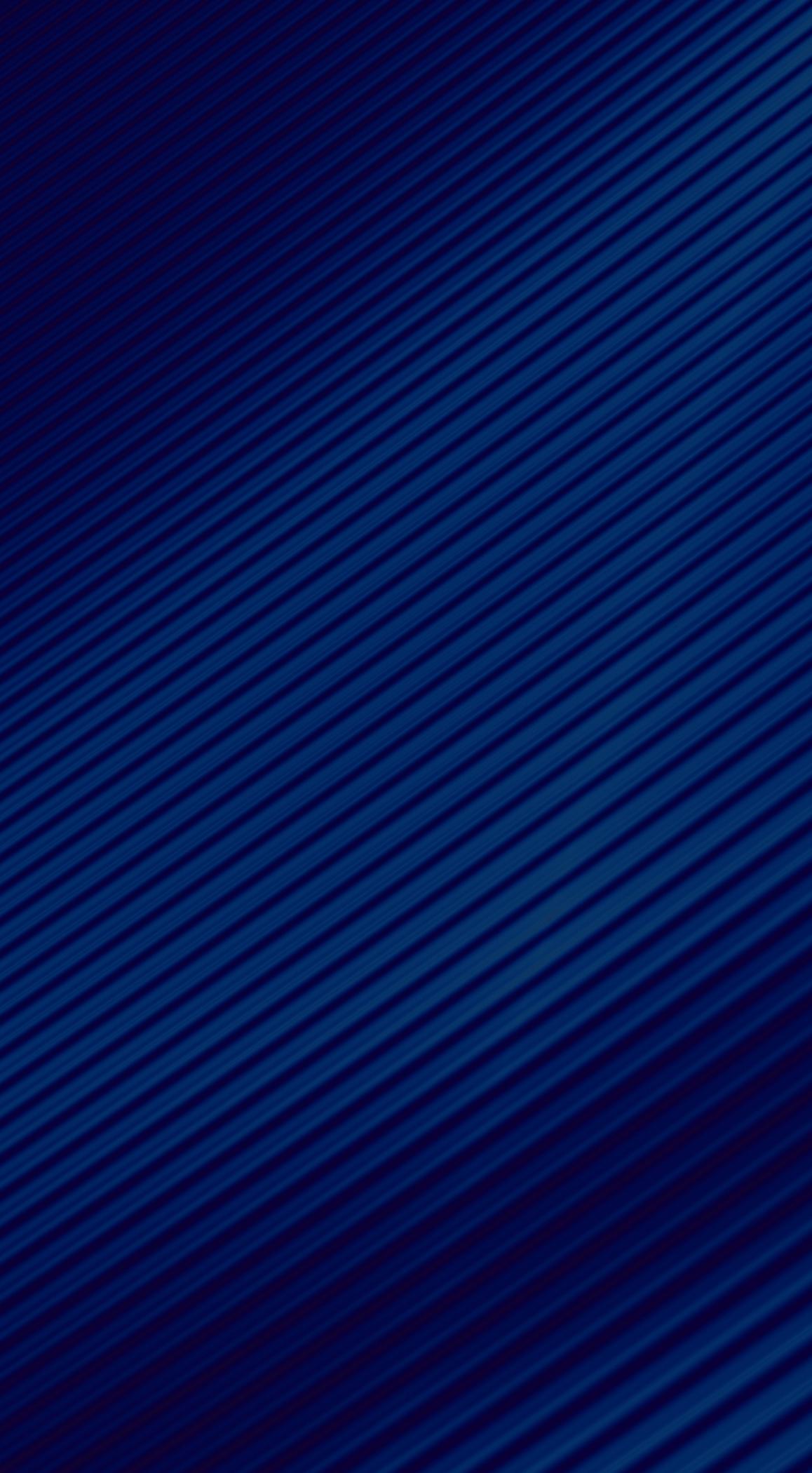
SAN D-XPRESS
Core Recovery in Sands & Gravels
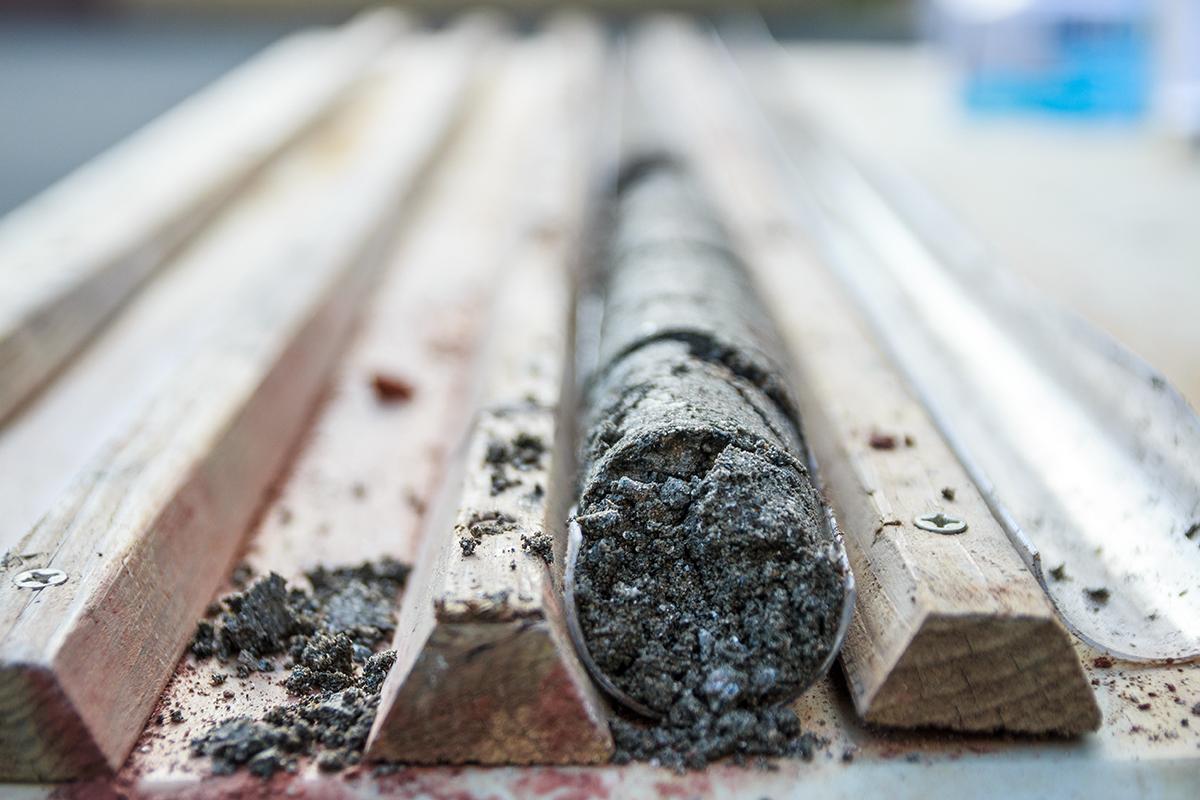
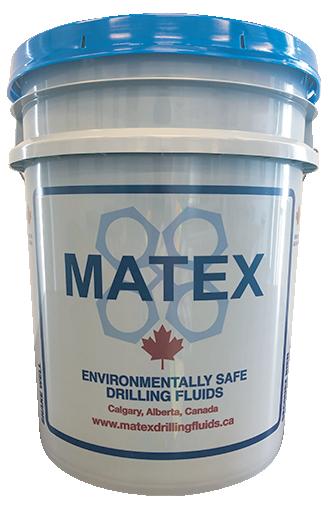
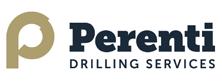
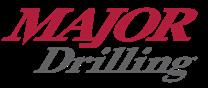
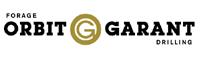

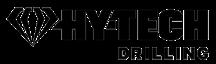
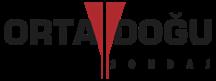
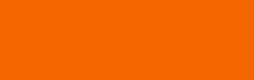
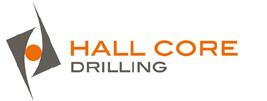
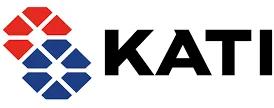
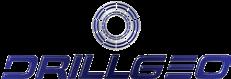
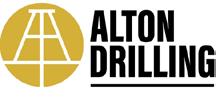

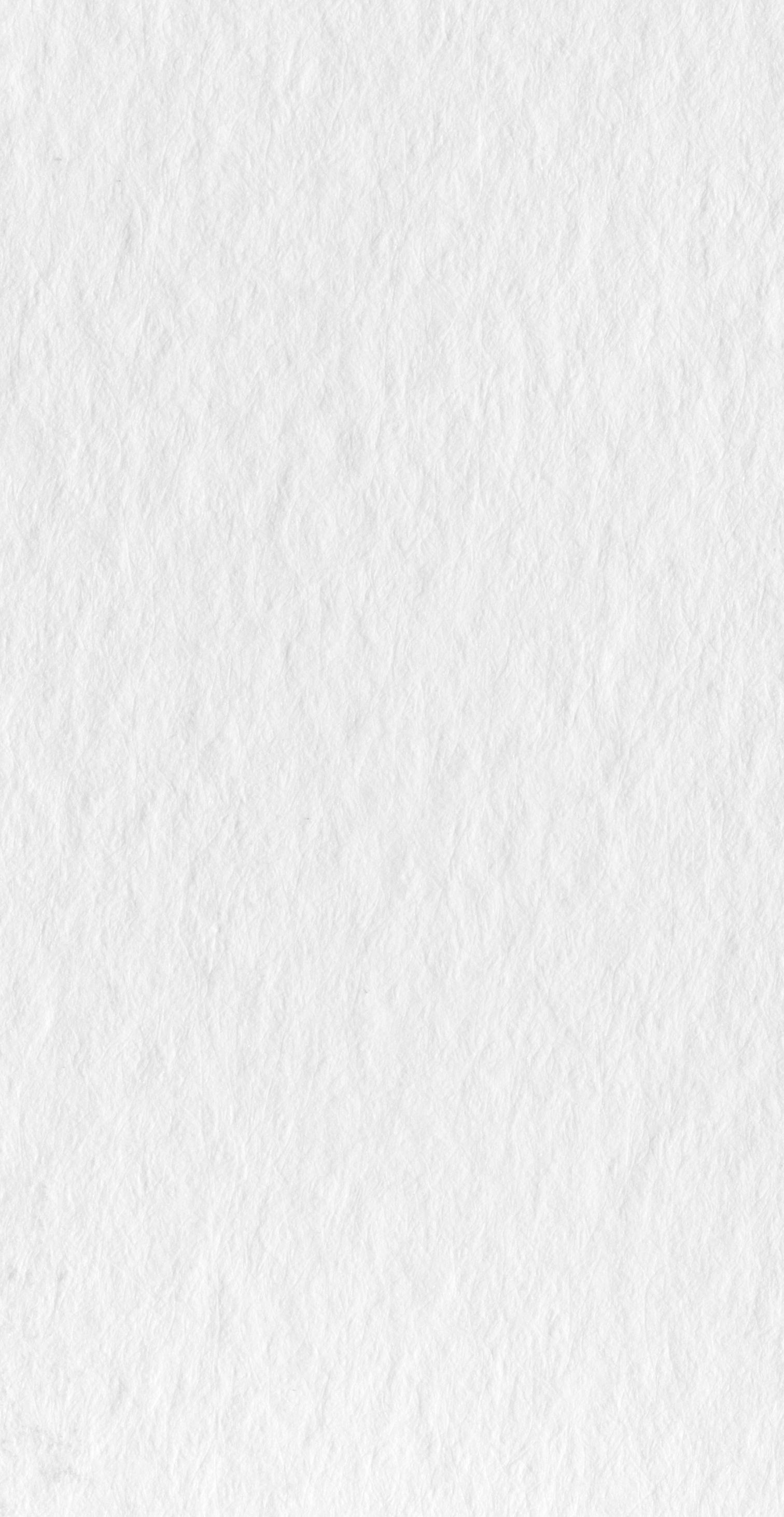

by Coring Magazine’s team
Disclaimer
Coring Magazine is proud to present the new statistics of ‘Top mineral exploration drilling contractors for 2023’. Companies are classified by the number of meters achieved only through diamond drilling. These results were provided and confirmed by the companies themselves and have been rounded to whole numbers, where needed. The statistics present results for calendar 2023, as at the time of publication (December 2024), complete data for 2024 was not available.
Other companies qualify but are not listed here for reasons beyond our control. We did our best to contact and include as many diamond drilling contractors as possible. However, many did not respond to our invitations; others were omitted per their request. Everyone is invited to get in touch and submit their numbers as long as their results equal or exceed 50 000 diamond drilling meters per annum.
Coring Magazine cannot be held liable for any errors or inconsistencies presented in this report.
Market analysis
On the back of the past two record-breaking years, results in 2023 are noticeably tamer. This is caused by reduced exploration activity in light of increased costs of financing, sticky inflation, slowing prices of commodities and lack of capital raisings in the exploration sector. Worldwide capital raisings have been subdued since November 2022, which coincides with a lack of drill meters in 2023.
According to S&P Global data, in 2023, the approximate number of completed exploration drillholes decreased by 23% to 53 582 vs 70 008 in 2022. Projects were estimated to be 1515, which is around 15% less than the year prior’s 1751.
The results for 2023 of only the companies participating in Coring’s drilling statistics paint a more complicated picture. While indeed there is an average decrease in the meterage achieved, it is much smaller at around 5%. Some of the participating companies did report significant drops, others single-digit reductions, while several have improved on their results from 2022. This is likely driven by interest in the type of commodity drilled, as well as the regions where companies operate. Looking at early estimates, 2024 should bring higher results than 2023 and possibly even surpass 2022.
Financial results from 2023 are similarly complex. Some of the contractors have achieved increases both in revenue and profits. Yet, the tremendous double-digit raises reported in 2022 are few, and some companies have notched slight decreases. Reports commonly highlight the second half of the year as weaker than the first. As in the previous years, 2023 was marked by significant mergers and company changes both amongst contractors and equipment manufacturers.
There has been a slight increase in the total number of drill rigs owned by the participating companies; less than 5%, driven by several that have made large investments in expanding their fleets. Almost all contractors have made enhancements to safety and efficiency. Reported rig utilization rates remain high at over 70%.
In Focus: Company results
Boart Longyear takes the leading spot with 2 471 792 m (8 109 554 ft) achieved through diamond drilling. This is a reduction of a little over 1% from 2022. The company’s total drill fleet is 609. Late in 2023, it was announced that Boart Longyear would become a private company, and the process was completed in 2024.
Perenti Drilling Services takes the second spot and has achieved 2 325 746 m (7 630 400 ft) through diamond drilling in 2023; an increase of almost 10%. Perenti Drilling Services was formed through an industry-reshaping merger between Perenti and DDH1, and now includes the drilling brands DDH1, Swick, Ausdrill, Ranger and Strike. Collectively these 5 brands now have over 300 drill rigs, with ~200 of the fleet operating in the diamond drilling space.
Major Drilling achieved 2 100 979 m (6 892 976 ft) through diamond drilling in 2023. This is a decrease of around 10% in comparison to 2022. RC drilling results were 956 515 m (3 138 173 ft), also a slight decrease. The company’s drill fleet grew slightly to 604 rigs, of which 483 are used for diamond drilling. In November 2024, Major Drilling announced the acquisition of Explomin Perforaciones, another participant in the statistics, to expand its presence in Central and South America and reshape the drilling industry yet again.
Orbit Garant Drilling is another company with growth in results. The company achieved 1 452 230 m (4 764 534 ft) in 2023, which is more than a 5% increase over the year prior.
In 2023, Foraco International reported 962 665 m (3 158 350 ft) achieved through surface and underground diamond drilling. Further 161 410 m (529 560 ft) were completed in RC. Both results represent a decrease of around 5% from 2022. According to their annual report, the number of rigs in the company’s fleet has remained unchanged at 302. Foraco’s financial results for FY2023 (ended in Dec. 2023) have improved on average 20%, with another highlight being a sustained decade-long trend of decreases in LTI and injury frequency rates.
Canadian Hy-Tech Drilling has achieved 574 464 m (1 884 724 ft) with diamond drilling. This is a slight decrease from 2022, however the company’s fleet has continued to grow, reaching 82 (from 69).
Forages Rouillier Drilling, another Canadian company, reported 570 530 m (1 871 818 ft) achieved with diamond drilling. While this is a decrease in comparison to 2022, the company has provided early estimations for 2024 in the range of 600 000 m (1 968 504 ft).
Explomin Perforaciones, one of the largest companies in Latin America, which will be part of Major Drilling, achieved 533 417 m (1 750 055 ft) through diamond drilling in 2023. These results may signify around 10% decrease from 2022, however the company has reported working on more projects - 41, 37 of which diamond drilling (DD) vs 30 (26 DD) in 2022. Explomin’s fleet consists of 67 rigs (65 DD) and it has also reported an increase in drilled meterage and number of projects in 2024.
The results of Geodrill along with their South American subsidiary Recon Drilling for 2023 for diamond drilling sit at 348 544 m (1 143 517 ft). The company has performed significantly more RC drilling - 875 288 m (2 871 680 ft). Both numbers are <10% lower than in 2022, however the company is expecting to deliver record meterage drilled in 2024, along with record earnings. In addition, the estimations for diamond drilling results suggest a growth of close to 30%.
Capital Drilling achieved 218 884 m (718 123 ft) through diamond drilling and 276 270 m (906 398 ft) by RC in 2023. Of note, the company has reported 4 133 455 m (13 561 204 m) achieved through other types of drilling. In terms of drill rigs, Capital has reported significant
growth in the size of its fleet for 2023 – 92 vs 57 in 2022, the majority of which used for other types of drilling.
Turkish contractor and manufacturer Ortadoğu Drilling reported an increase of over 10% in the number of drilled meters through diamond drilling to 217 644 m (714 055 ft) in 2023. The fleet of in-house manufactured drill rigs has increased to 40, compared to 35 in 2022. Ortadoğu had 35 projects in 2023, primarily in the Eurasian region.
Arctic Drilling Company, based in Finland, completed 202 900 m (665 682 ft) of diamond and further 30 300 m (99 410 ft) of RC drilling in 2023.
GEOPS, covered in the In Focus article of this issue, has reached 197 673 m (648 534 ft) through diamond drilling. The company has achieved <10% higher results than in 2022.
Canadian contractor Team Drilling reported a diamond drilling result of 189 500 m (621 719 ft), achieved in 2023, and 210 000 m (688 976 ft) in 2022.
South African contractor Hall Core Drilling has once again reported growth in its diamond drilling activities. The company achieved 170 392 m (559 029 ft), primarily from the expansion of operations at the Limpopo mine. This represents an increase of over 5% from 2022. Hall Core has the same number of diamond drill rigs as in 2022 – 35, with 5 of these rigs now being underground, marking an important milestone as it is Hall Core’s first underground project.
Australian Topdrill reported achieving 154 697 m (507 536 ft) from diamond drilling in calendar 2023 and 130 504 m (428 162 ft) in 2022.
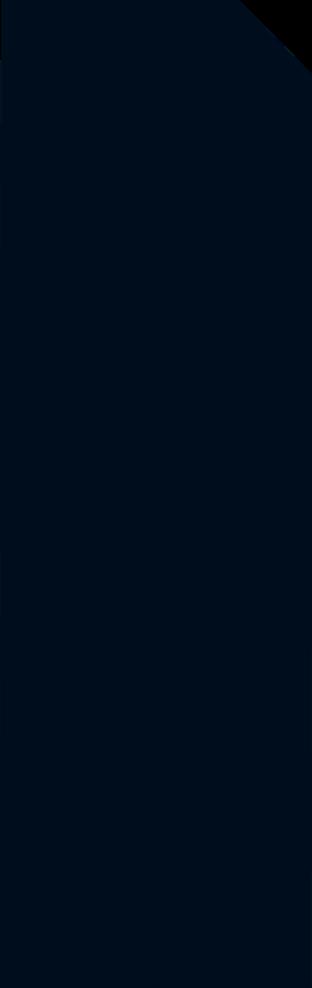
2024 marks a tremendous increase to the company’s diamond drilling results, reaching 225 821 m (740 882 ft), driven by new projects.
A new participant in the statistics, Finnish company KATI Oy, has achieved 143 000 m (469 160 ft) through diamond drilling in 2023 and 146 000 m (479 002 ft) in 2022.
Brazilian contractor DrillGeo also disclosed more than a 10% increase in its diamond drilling results for 2023. The company achieved 139 036 m (456 155 ft) and a further 10 160 m (33 333 ft) through RC drilling, also a modest increase from 2022. Nonfinal results for 2024 suggest a tremendous 25% growth in DD operations and a 50% increase for RC drilling.
Alton Drilling, New Zealand’s largest drilling contractor reported 90 703 (297 582 ft) diamond drilled meters and 31 864 m (104 541 ft) achieved through other types of drilling for 2023. The company had a total of 21 rigs drilling across the country for the year 2023, they have seen substantial growth and currently have 24 rigs of their 40 rig fleet in operation.
A first-time participant in these annual statistics and a key-player in the Mexican market of diamond drilling services - Maza Drilling, announced 78 700 m (258 202 ft) in 2023 and 121 783 m (399 551 ft) in 2022. Its results for 2024 are 88 060 m (288 909 ft).
Coring Magazine extends its congratulations to all companies for their outstanding results and expresses gratitude for their support in compiling these statistics! C
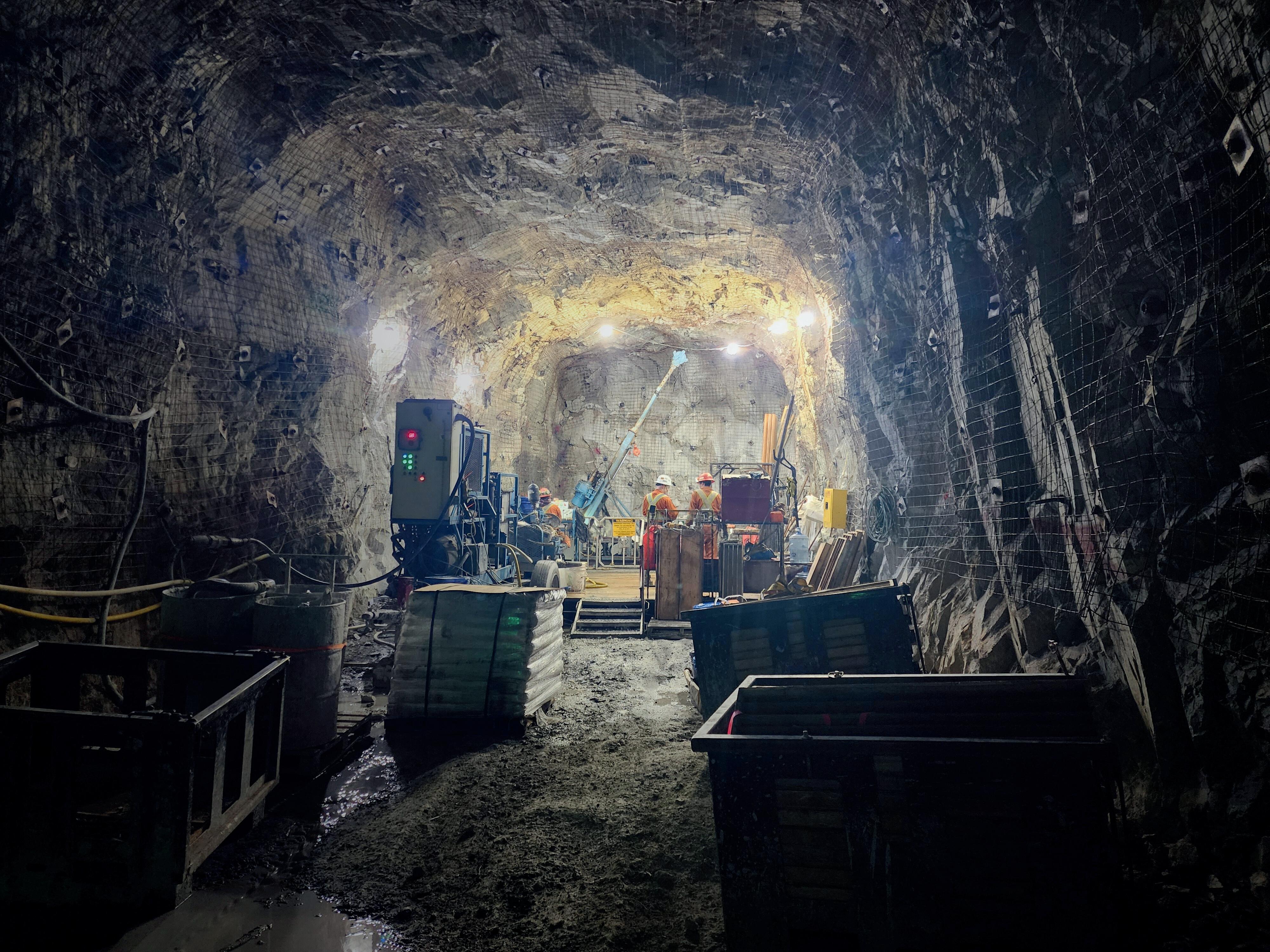
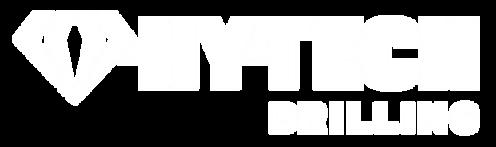
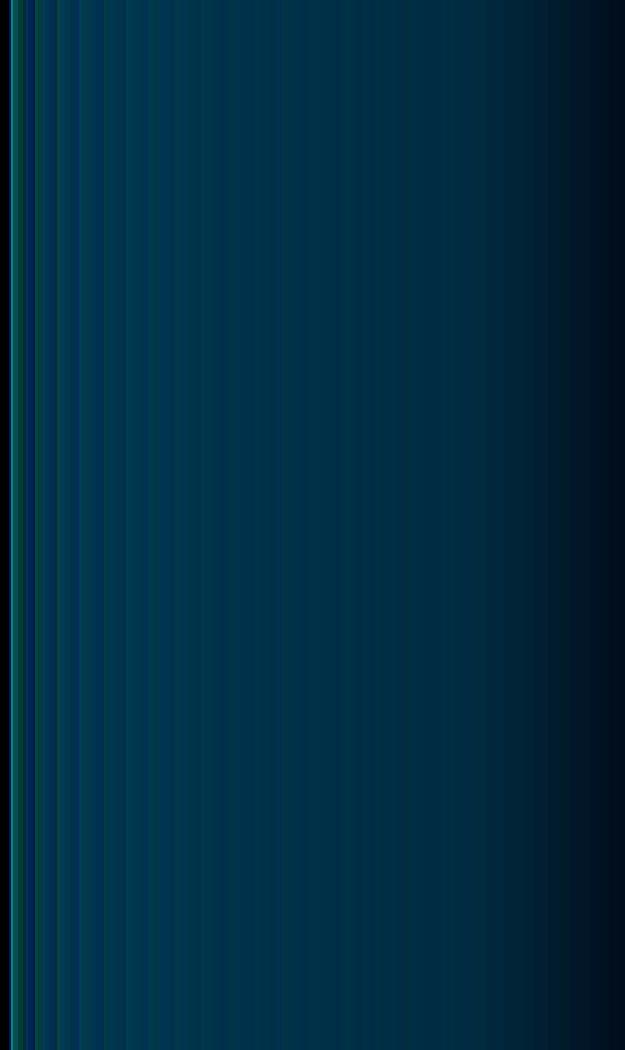
Di-Corp launches the next generation of drill rod
by Andy Sayers, Marketing Manager at Di-Corp
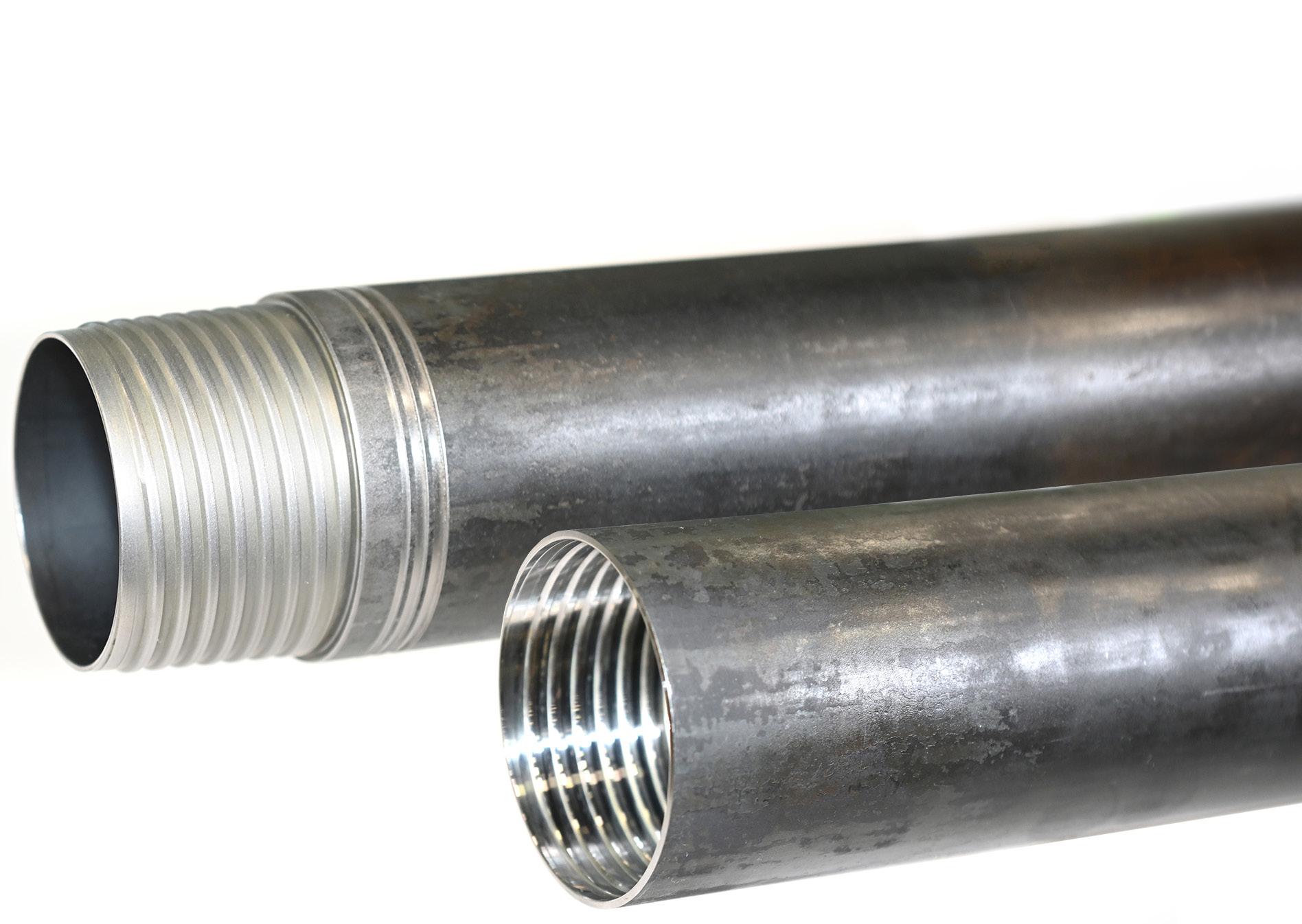
↑ S-Maxx’s patented ‘S’-shaped dual start thread gives it a more even load distribution, allowing the S-Maxx to spread stress throughout the entire length of the thread and provide greater durability
Drilling nowadays involves challenges previous generations rarely faced, if ever. From deeper, harder-to-access deposits to operational challenges with automated rod handlers to tighter margins from a more competitive and volatile global mineral exploration market, today’s driller needs efficient solutions to difficult situations.
It’s for these reasons that Di-Corp created the next generation wireline drill rods: S-Maxx™. Specifically designed to meet the needs of today’s modern driller, S-Maxx drill rods’ unique dual start thread and anti-jamming features will help drillers reach greater depths and achieve new limits.
Why S-Maxx?
The S-Maxx name comes from two parts: a patented ‘S’ shaped interlocked profile thread and the ‘maximum’ performance delivered by the rod. The dual start S thread delivers more surface area and contact than previous thread forms, resulting in faster make and breaks and the highest torsional and tensile strength in the market.
The ingenuity of the S-Maxx comes from the S-shaped thread. The S-shaped curvature of the load flank creates a self-locking thread profile resistant to bulging while the large corner radiuses improve
The new S thread and anti-jamming features are machined onto Drillers Edge tubing, undergoing the same manufacturing processes that have given Di-Corp rods a global reputation for durability. The result is a coring rod that delivers max rod life, max joint strength, max depth capacity, and max efficiency.
Take your drilling to the Maxx
‘Today’s driller is dealing with a more competitive and volatile global mineral exploration market’, says Di-Corp’s Manufacturing Technology Manager Chris Van Schaayk. ‘When margins are tight, efficiency is key. With S-Maxx, you gain efficiency by preventing cross-threading – resulting in faster trips back in the hole and getting back to putting core in the box. You gain efficiency from more durable rods, resulting in reduced downtime, and smoother shifts at the rig. Who wants drama at
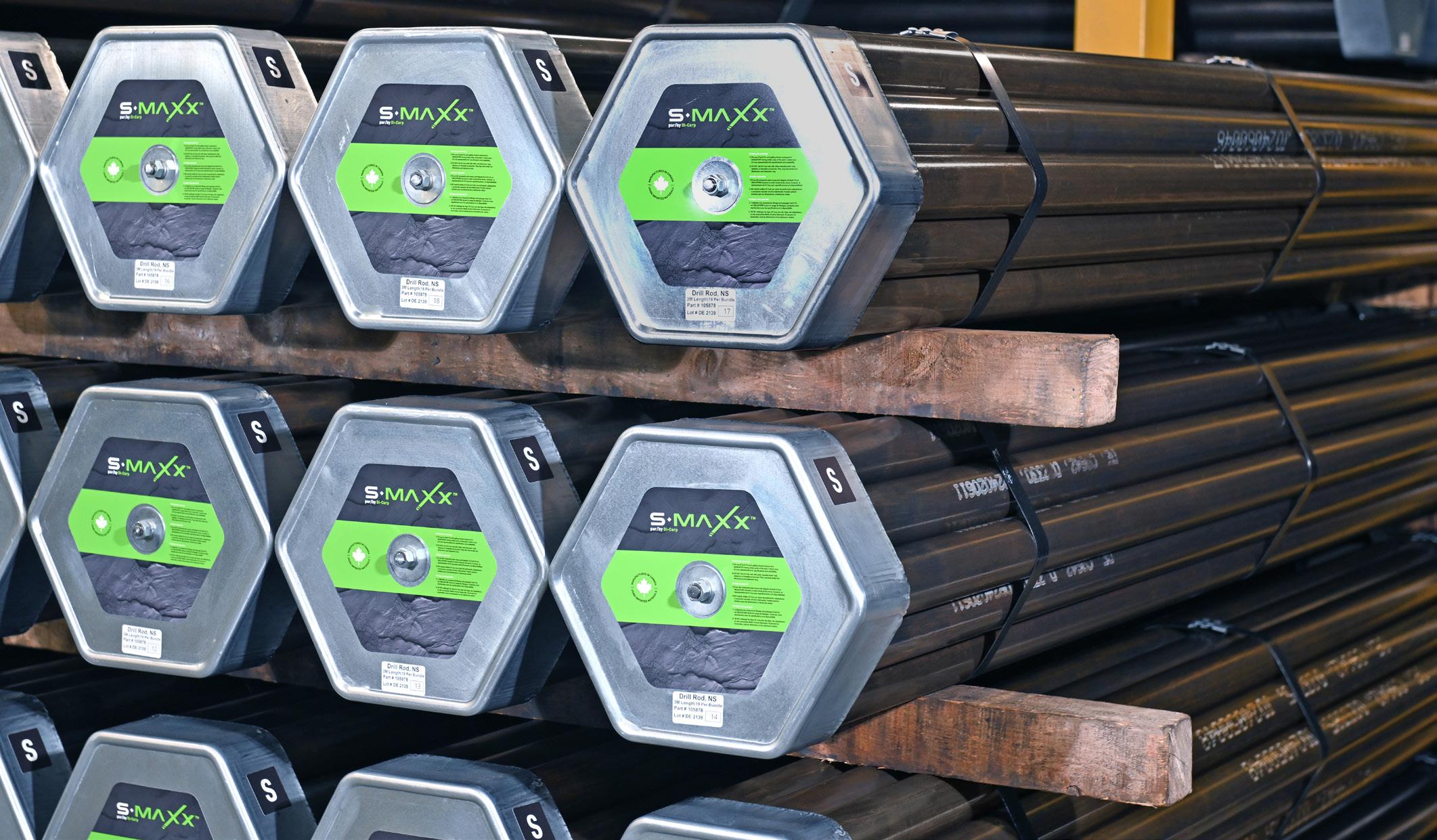
↑ Di-Corp spent years designing, researching, developing, improving, and testing the S-Maxx to ensure it was ready to meet the needs of modern drilling
fatigue cycling by eliminating areas of high stress concentration, improving the cycle life of the joint.
The dual start thread gives a finer thread pitch allowing for more threads to be engaged without sacrificing make-up speed. This provides a more even load distribution along the length of the thread, improving performance when compared to traditional designs. An additional patented anti-jam feature prevents cross-threading and jamming to ensure quick and easy make up and allows the driller to remain out of harm’s way.
the drill site? By investing slightly more on drilling rods, you gain lower cost per meter drilled throughout the project.’
In independent, third-party lab tests, the S-Maxx proved to be greater than +20% stronger in tension to failure testing and greater than to 35% stronger in torsion to failure testing than the most popular thread forms available in the market today.
In addition to the benefits provided to standard drilling operations, the S-Maxx is an ideal rod for conditions, such as automated rod handling, deep hole drilling, and directional drilling.
Automated rod handling has become the standard for drilling. S-Maxx is ideal for that as its dual start thread and anti-jamming features prevent cross threading and improve safety as a result. This means your automated rod handler can make the connection right the first time, every time, saving a lot of time and effort for the drilling operation.
In deep hole drilling and demanding conditions, the S-Maxx’s unmatched torsional and tensile strength allow the rod to make deeper depths than existing rods – with a recommended max depth of 4300 m (14 107 ft) when using the N-size lite wall version of the rod, which exceeds the maximum depth rating of any other rod on the market.
When it comes to deep hole drilling, efficiency is king. The greater the depth, the more time becomes a factor when changing out the rod string or dealing with rod failures. Seconds become minutes and minutes become hours the longer the drill string becomes.
S-Maxx’s dual start thread prevents cross-threading, allowing for faster make and breaks with anti-jamming features that virtually
eliminate jamming. This helps you assemble, break, and reassemble the rod string faster each time, with a more durable rod that is less likely to need replacing in the first place. Spend less time tripping in and out and more time hitting your target.
For directional drilling, the unique profile of the S-Maxx thread reduces stress risers in the connection, reducing joint fatiguing during deviated drilling. Because there are no sharp corners on the thread, there are fewer pressure points for microcracks to develop. Instead, the pressure is spread throughout all threads of the joint. With each part of the thread sharing the load, the S-Maxx can withstand greater pressure when deviating than can other thread forms.
Drilling has changed – drillers need drill rods that change to meet these challenges. S-Maxx by Di-Corp are next generation drill rods specifically designed for modern drilling challenges.
Di-Corp is a registered trade name of Diversity Technologies Corp. C
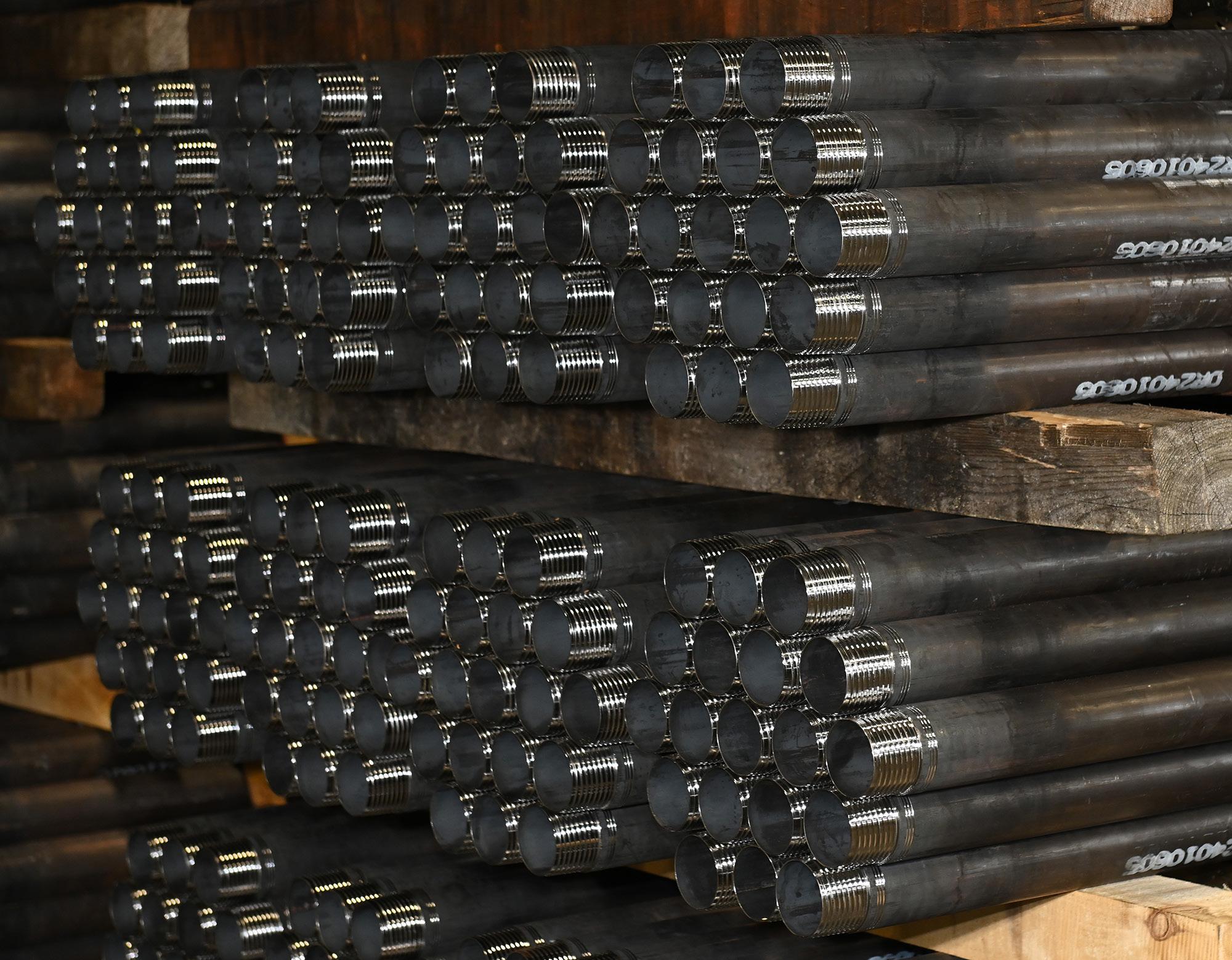
↑ The S-Maxx wireline coring rod is available in B- and N-sizes in both parallel and lite wall tubing. H-size will be available by the end of 2024.
↑ A typical representation of how preload stress sits in a single start thread using heat mapping. Stresses within the connection typically concentrate near the final full wrap of the pin thread (shown on the right side of the model).
↑ How S-Maxx distributes the preload further down the entire length of the thread, much more readily than a single start thread.
For more information
Visit: di-corp.com
e-mail: info@di-corp.com or call: 1 800 661 2792
The Next Generation of Drill Rod
Specifically designed to meet the needs of today’s modern driller, S-Maxx™ drill rods’ unique dual start thread and anti-jamming features will help drillers reach greater depths and achieve new limits not possible with any other rod on the market.
Discover a wireline coring rod that delivers max rod life, max joint strength, max depth capacity, and max efficiency. Di-Corp is a registered trade name of Diversity Technologies Corp.
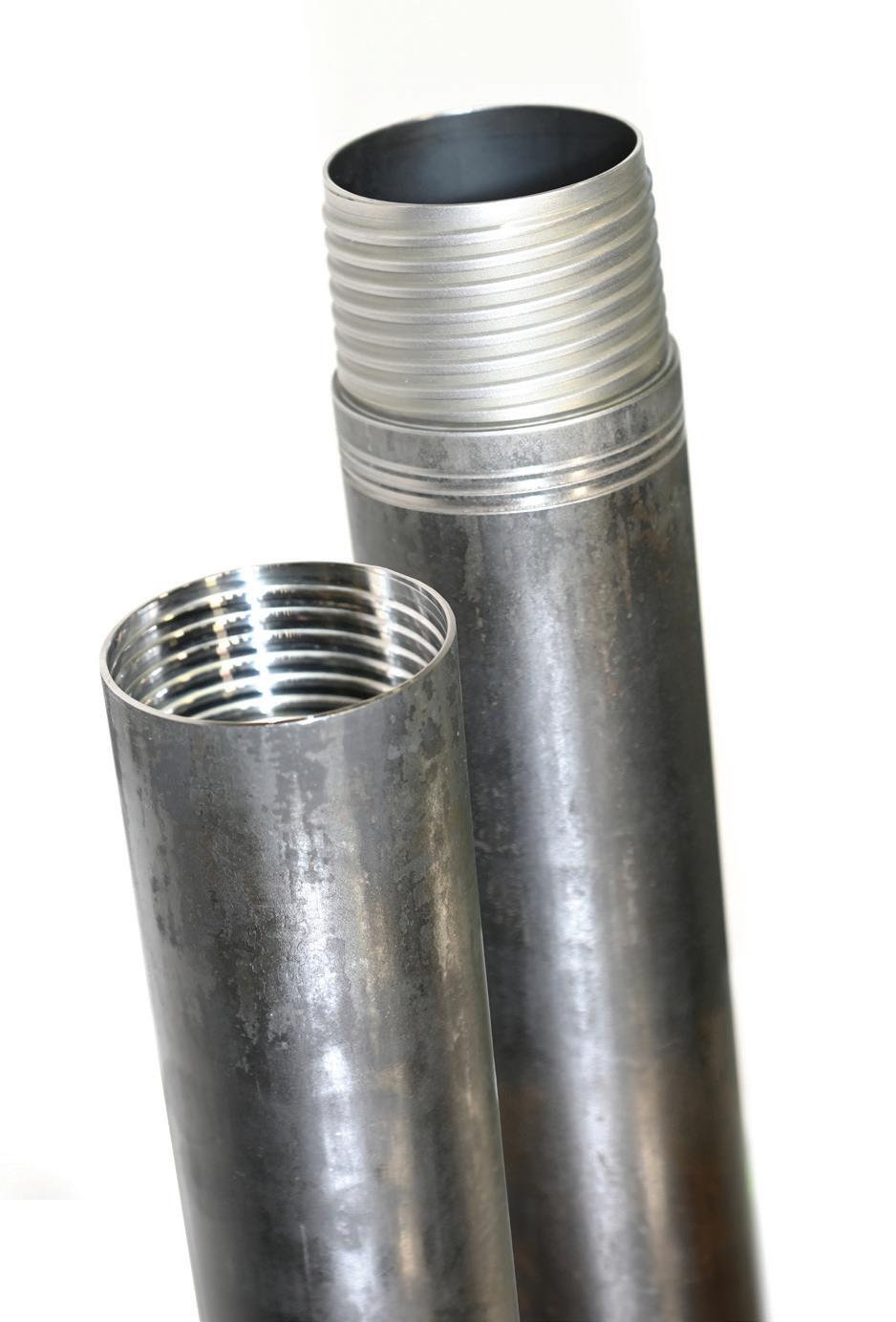
AXIS Connect™ improves the accuracy and reliability of directional survey data
by Darren Palmer, Senior Product Manager - Orebody Intelligence at Orica Digital Solutions
As holes get deeper and more complex, so do directional surveys, and the need for timely decision-making increases. Orica Digital Solutions AXIS Connect™ solution brings all surveys for a hole into one place with the ability to view them all, relative to each other, in an intuitive 3D viewer. This enables reliable interpretation of an accurate hole path from the surveys, rapid digestion of new information, easy identification of misallocated or incorrect surveys, and immediate feedback on the location of the hole, relative to the plan.
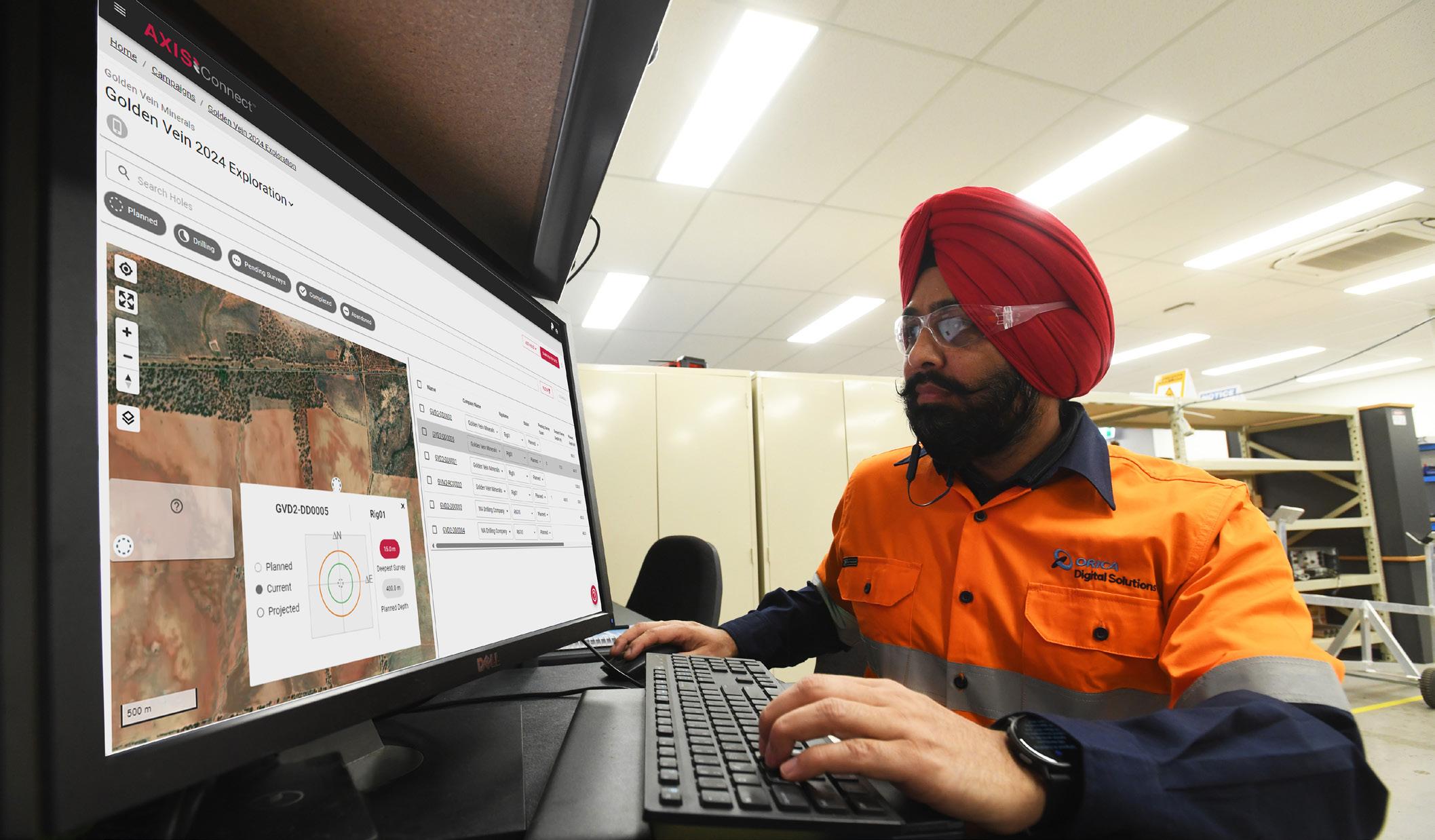
Early adopters of AXIS Connect™ have greatly appreciated the ease of setup, intuitive workflow and design, and speed with which they can complete their work. Our early adopters have averaged less than 5 minutes from when a survey was received by AXIS Connect™, to when it was approved and sent onward for geological modelling and analysis. That’s fast.
Flexibility and minimal disruptions to drilling while ensuring accurate data collection
AXIS Connect™ works seamlessly with our Champ™ software that controls our downhole tools. Geologists can set up drilling campaigns in AXIS Connect™ that involve more than one drilling company, assigning holes to different companies and different rigs without leaving the campaign.
For the driller on the rig, time surveying is time not drilling. Minimizing the time to set up and acquire a survey with a list of relevant hole names to choose from, and then simple, reliable export of a completed survey to AXIS Connect™ means teams can get back to drilling knowing high-quality data has been acquired, and successfully delivered. Furthermore, if information is not available in AXIS Connect™, the driller can still send a survey and remain confident that their data has been transmitted, and operations can progress.
Native integration with Axis hardware provides a seamless experience for managing directional surveys. Flexibility to use other hardware provides drillers with choice and the capability to acquire data using their desired systems, whilst still delivering data to the preferred platform for their customers.
Faster decisions and reduced costs per meter drilled
AXIS Connect™ enables faster decisions and reduced costs per meter drilled. As an example, a deep diamond drillhole may require an Overshot North survey using a Champ™ Navigator Gyro every third barrel pull, giving daily updates on drillhole directional progress. With AXIS Connect™, you can see quickly and clearly the progress of the hole, as well as how far from the plan the hole may finish. Choosing to re-direct a hole early can significantly reduce the cost of remedial steps. Additionally, in some cases drillers are held accountable for delivering holes within a tolerance to a planned location. AXIS Connect™ lets drillers assess how their holes are performing to make on the fly adjustments to improve the end product they deliver to their customers, eliminating re-drills.
Strategic partnerships to enhance drilling workflow and data analysis
Critically maintaining a reliable system record of hole names and directional surveys is made simple and easy with AXIS Connect™. When working with our key partners, geologists and drillers can maintain a single list of holes in one place, and maintain a traceable link to original data. For example, users of AXIS Connect™ can create a link to CorePlan and import a hole list directly from their project. Once surveys are available they can then be exported directly back
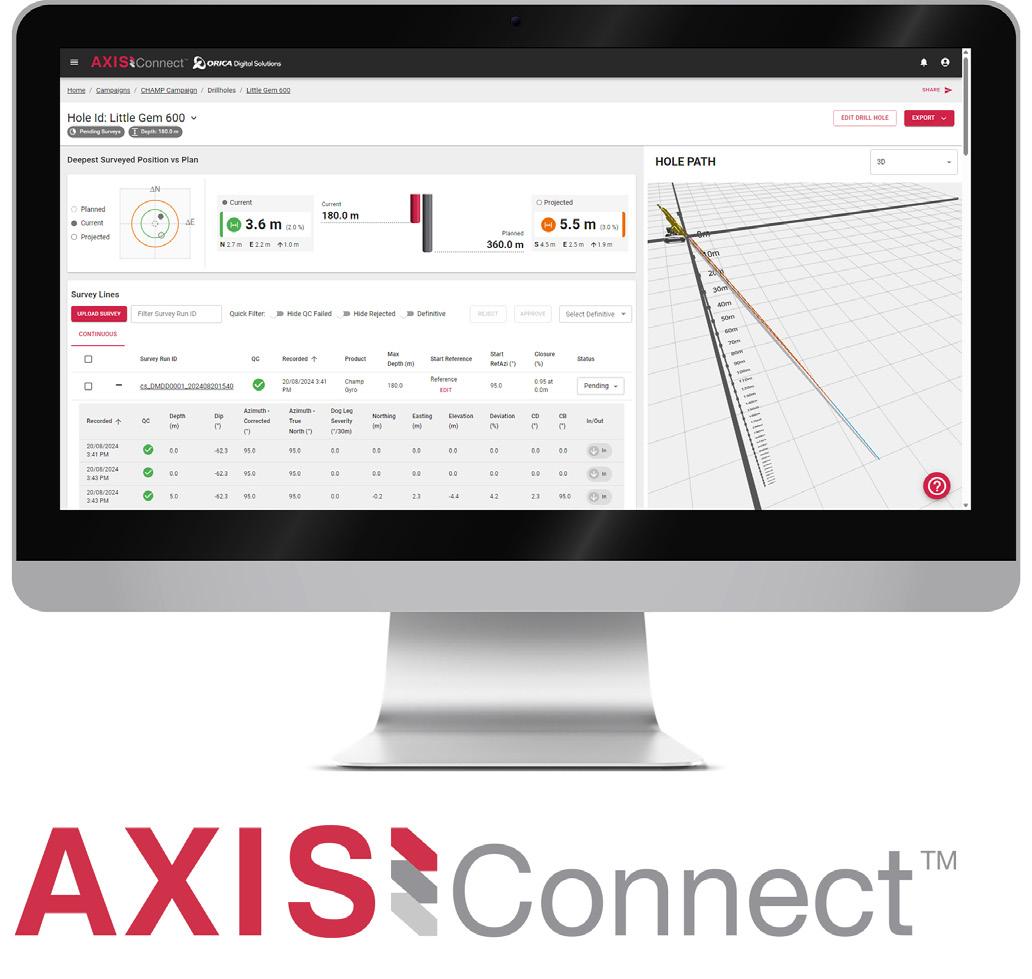
↑ Simple, reliable and efficent survey management for geologists and drillers
to CorePlan, eliminating any chance of data loss, miss assignment or incorrect matching. All of this can be done as part of a streamlined workflow minimizing time spent on administrative tasks and maximizing time spent drilling or doing real geology.
Supporting resource estimation, mine planning, and grade control from a drilling perspective
AXIS Connect™ provides a traceable path to see what survey was acquired with which tool and when, giving full confidence that the hole is where the model says it is. Moving into mine planning and grade control, efficiency and repeatability of the workflow are key and AXIS Connect™ delivers a simple, reliable and efficient workflow to ensure surveys acquired are delivered and completed. Drillers don’t need to wonder if the surveys are complete and received, they can see.
Further developments
Simple, reliable and efficient survey management accelerates drilling operations, and reduces the time from insight to decision making for geologists. Drilling professionals can continue to expect improvements in day-to-day processes as we deliver an integrated Axis application that can power all our downhole tools, connecting seamlessly with AXIS Connect™. Orica Digital Solutions is dedicated to delivering continuous improvements for drillers and geologists, now and into the future. C
Exploration Mining Geology
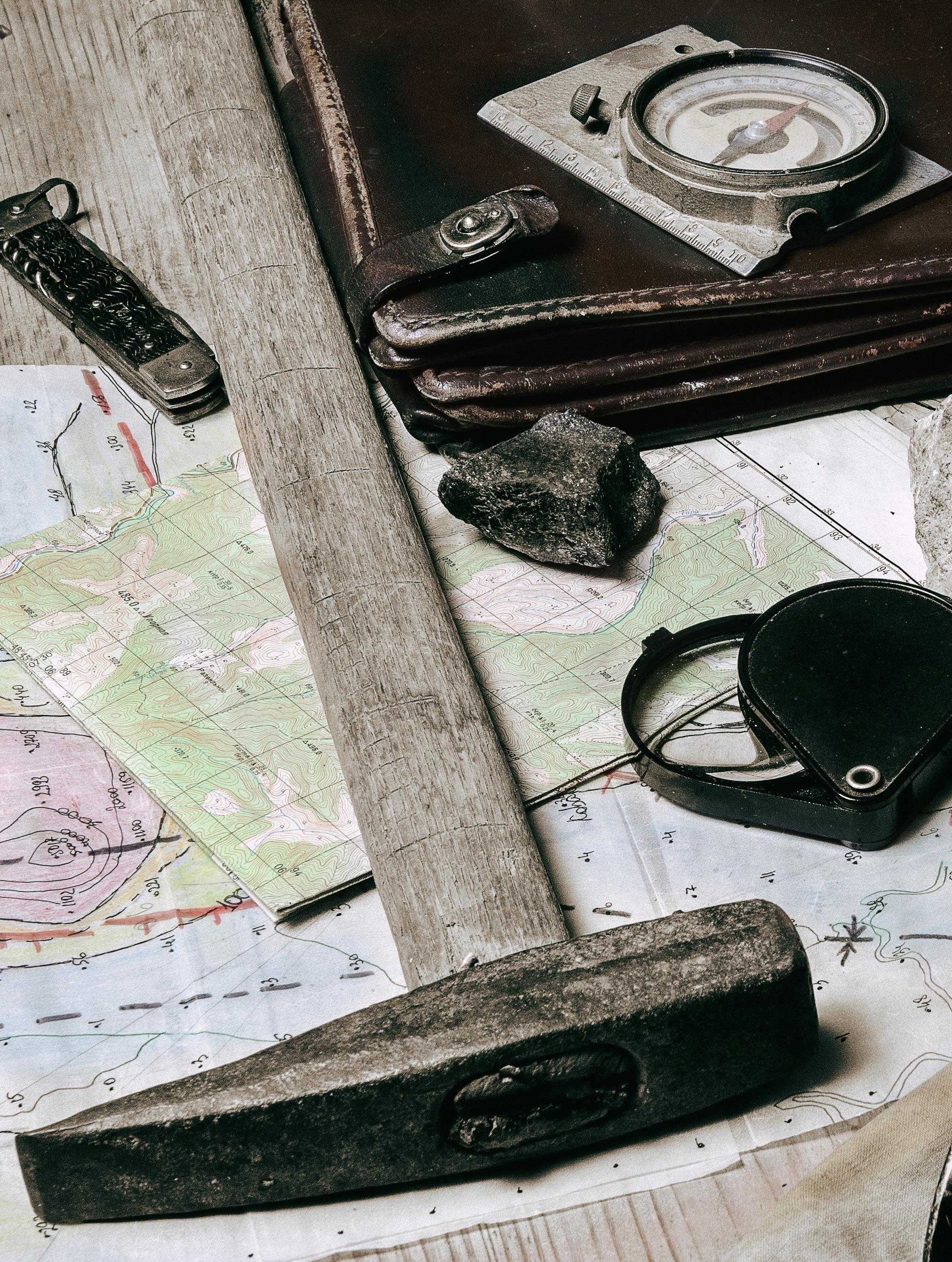
In this Issue:
Q&A from the experts
In conversation with François Robert Independent Consultant at FR Geo-consult
How to fail in mineral exploration but do it successfully by Carl Brauhart, Principal Consultant at Camp Oven Exploration
Preparation of diamond core for geotechnical logging: The dos and don’ts by Lyndell Juggernaut, Engineering Geologist at MineGeoTech
Drilling data quality - more than just samples by James Lally, Principal Consultant at Mining Associates
FROM THE EXPERTS
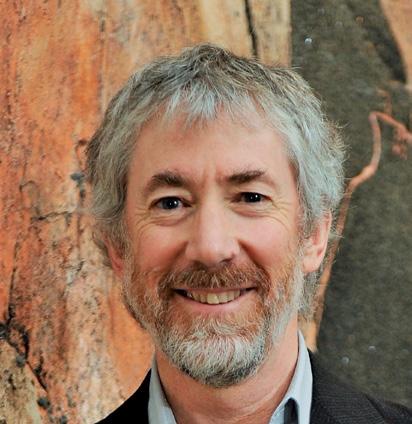
François Robert Independent Consultant at FR Geo-consult
Brett Davis: Firstly, thanks for giving Coring the opportunity to interview you, François. Please take this as a compliment when I say it seems like you have been a geological heavyweight of the mining and exploration industry for a very long time. Very few people have a career like yours, where you’ve worked across the spheres of mining and exploration, plus published highly regarded peer-reviewed papers, garnering enormous respect in the geological community while you’ve been doing it. Can you tell us what interested you in a career in geology?
François Robert: I have had my eyes on Earth sciences and geology very early on, but it’s hard to point to a specific turning moment or event. In 3rd year of high school, my dad brought me a kit from Bell Canada Laboratories on 'crystals and light' which really piqued my interest. This was about growing crystals and examining their effects on light through a fully functional cardboard polarizing microscope, which was my early introduction uniaxial and biaxial interference figures! In college, I took an optional geology course, which crystallized it for me (pun intended): the professor was very interesting and was organizing a few local field trips.
In conversation with François Robert
François cumulates over 40 years of worldwide experience in the geology and exploration of multiple types of gold deposits. He currently consults part-time in the Minerals Industry, following 22 years with the exploration team at Barrick Gold Corporation and 12 years with the Geological Survey of Canada. He holds a geological engineering degree and earned a PhD from Ecole Polytechnique, Montreal, Canada, on the Sigma gold-quartz vein deposit at Val d’Or in Abitibi. He has published numerous scientific papers and has been involved in several scientific organizations. He has also received multiple national and international awards for his contributions.
From then on, it was clear I wanted geology as a career, and I already had my eyes set on a PhD. The main attraction, as I saw it then, was a combination of doing science, working outdoors, and travelling.
BD: Coring is a drilling magazine, and we like to keep to our roots. Do you get to work much with the drilling side of the business anymore?
FR: In the type of consulting work I do, I don’t get involved with the logistics of drilling, core orientation or core scanning, nor with QA-QC protocols. However, every time I go to a mine or project, I make a point to spend as much time as possible looking at core. I am a keen user of data generated from drilling, from orientation measurements (after ensuring the quality of the data), to geochemistry. It is common that such data is collected but not fully leveraged by project geologists. In my work, I try to illustrate the use and full value of such datasets in constraining the local geometric architecture and in targeting.
BD: From stalking your LinkedIn profile, I note that you spent over 20 years with Barrick Gold Corporation. What inspired you to spend this amount of time with Barrick?
FR: There are two key factors explaining my 'longevity': the people I work with, and opportunities to learn and have impact. In my 22 years with Barrick Exploration, I had the privilege to work with some excellent geologists and managers. I only worked under two EVP-Exploration, Alex Davidson and Rob Krcmarov, both fantastic managers and well-known in the industry. They assembled strong, high-performing, and discovery-driven teams that were fun to work with. After my PhD, I decided to focus on gold because of the diversity of deposit types and geological environments in which it occurs: I thought it would be a good way to broaden my geological expertise. Well, Alex and Rob provided me with the opportunity to work all around the world, across a wide range of gold and copper deposits. In the process, I have also learned how exploration works and contributed to the development of a powerful set of exploration criteria. All this kept me very challenged and entertained. The work was intense and without any dull moment –just as I like it.
BD: Few people get the chance to chart the progress of a company over the time as you did with Barrick. So, another question to piggyback on the previous one: what were the most significant
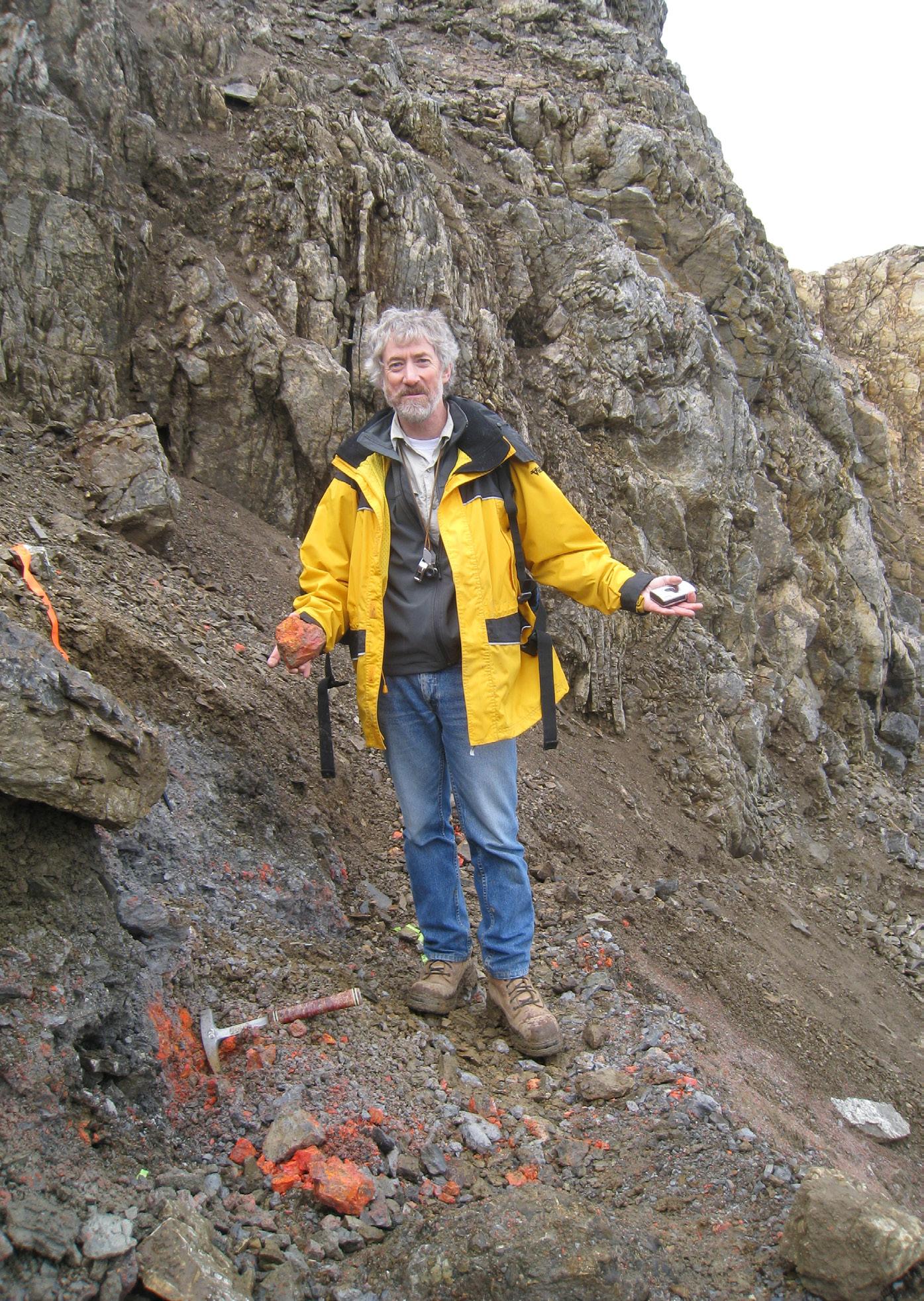
↑ Surprised to see this much realgar on outcrop in the early days of ATAC Resources discovery of Carlin-type mineralization in the Rakla belt, Yukon
changes you noted from a geological perspective during your time with the company?
FR: The most significant changes over these more than 20 years are certainly the increased pace of exploration and the ever-improving analytical, scanning, and modelling tools at our disposal. As a result of the increased pace, we now rarely take time to report on exploration or drilling programs and
think about the results and their significance. And similarly, we generate a ton of new data that are not always fully leveraged to maximize exploration success.
BD: You’ve worked in a lot of countries and on a lot of continents. Are there any skills or mindsets that have helped you in your roles in these places?
FR: Tough question. Your ability to connect with people and to work with them is critical. By this I mean adapting your level of language, trying to understand their challenges and how they work rather than radically imposing your views. This requires flexibility, patience, and humility on your part. Transparency and good humor also help. And stay away from politics as much as you can. These are good ways to earn respect from local teams. It also helps if you understand the local culture, which was one of my initial blind spots when I became Chief Geologist in South America after having that role in Australia.
BD: You’ve had the privilege of working with many of the truly influential geologists in the industry and have influenced many more. Apart from me, who have been some of the positive influences in your career?
FR: Many geologists mentored me, most of the time informally, and influenced my career so it’s difficult to single out just a few, but here we go. At the Geological Survey of Canada, colleagues such as Howard Poulsen and the late Jim Franklin helped shape my field-based approach to constrain the geological setting, architecture and controls of mineral deposits. I still work in the field with Howard, and I keep learning from him.
My encounter with Rick Sibson opened my eyes to the dynamics of faulting and the link with earthquake processes. It changed the way I think about gold-quartz vein arrays.
At Barrick, Alex Davidson (VP-Ex) and Jay Hodgson (Chief Geologist), who hired me, provided fantastic development opportunities through successive assignments to Goldstrike in Nevada, Western Australia, and South America, covering a wide range of deposit types and geological environments. Jay, as a creative and lateral thinker, taught me the value of empirical relationships in exploration and the importance of scale integration, from regional to local.
Rob Krcmarov, with whom I worked for many years, taught me the key drivers of the mining industry and their link with exploration strategies. He also guided me through the corporate world when I became global chief geologist.
As you can see, I was very fortunate to work with such individuals. Sorry, but you did not make the list!
BD: Is there a particular mineralization style or deposit type that interests you, and why?
FR: Gold deposits in greenstone belts, the socalled ‘orogenic’ gold deposits are my number one. Partly because this is where I started my career, but mostly because of their complexity and their diversity of attributes and structural history. Most are assigned to the orogenic basket, but are they all? I think not. There is no single model that explains 75% of what you see in these deposits, unlike the well-established epithermal, porphyry, or VMS deposits.
BD: Leading on from the previous question: everyone has a handful of deposits that have left a mark on them, be it because of the amazing geology, the hideous conditions, the people they worked with, etc. Which deposits do you hold dear, and which ones really were difficult to work on?
FR: The Sigma-Lamaque deposit in the Abitibi greenstone belt, where I did my PhD (on the Sigma portion), is at the top because it turned out to be such a classic gold-quartz
significant amount of time there for Barrick, the only certainty I have is that the deposit has been strained and metamorphosed: I still don’t understand what deposit type it is and probably never will!
Porgera, in Papua New Guinea, impressed me for both its unique size and vertical extent for an epithermal vein deposit, combined with its very challenging location.
BD: Given your international experience, where in the world would you go to make a truly significant mineral discovery? I’m particularly interested in your perspective on precious metal and base metal opportunities. And have there been any lost opportunities that you lament?
FR: I will partly avoid this question: I consult for several companies, and I need to maintain my neutrality with respect to where to go and where not to go! I will only say that, in addition to focusing on areas with high discovery potential, one needs to consider
BD: We hear all about the advances and benefits of technologies such as 3D modelling, geochemical analysis, and the utilization of drones. Have you noted any negative impacts to effective exploration and mining as a result of these e.g. less people out kicking rocks?
FR: One consequence of all this technological arsenal is that geologists spend more and more time at their computers at the expense of looking at the rocks. These technologies, and now AI, should be leveraged to improve our geological interpretations and help define ore controls and quality targets. But increasingly, it is as if their use and the generation of data have become the end game rather than the starting point for integration with geology and interpretation.
As indicated above, the increased pace of exploration limits the amount of time available for analysis and interpretation. We should never forget that field (or drill core) observations and mapping remain the
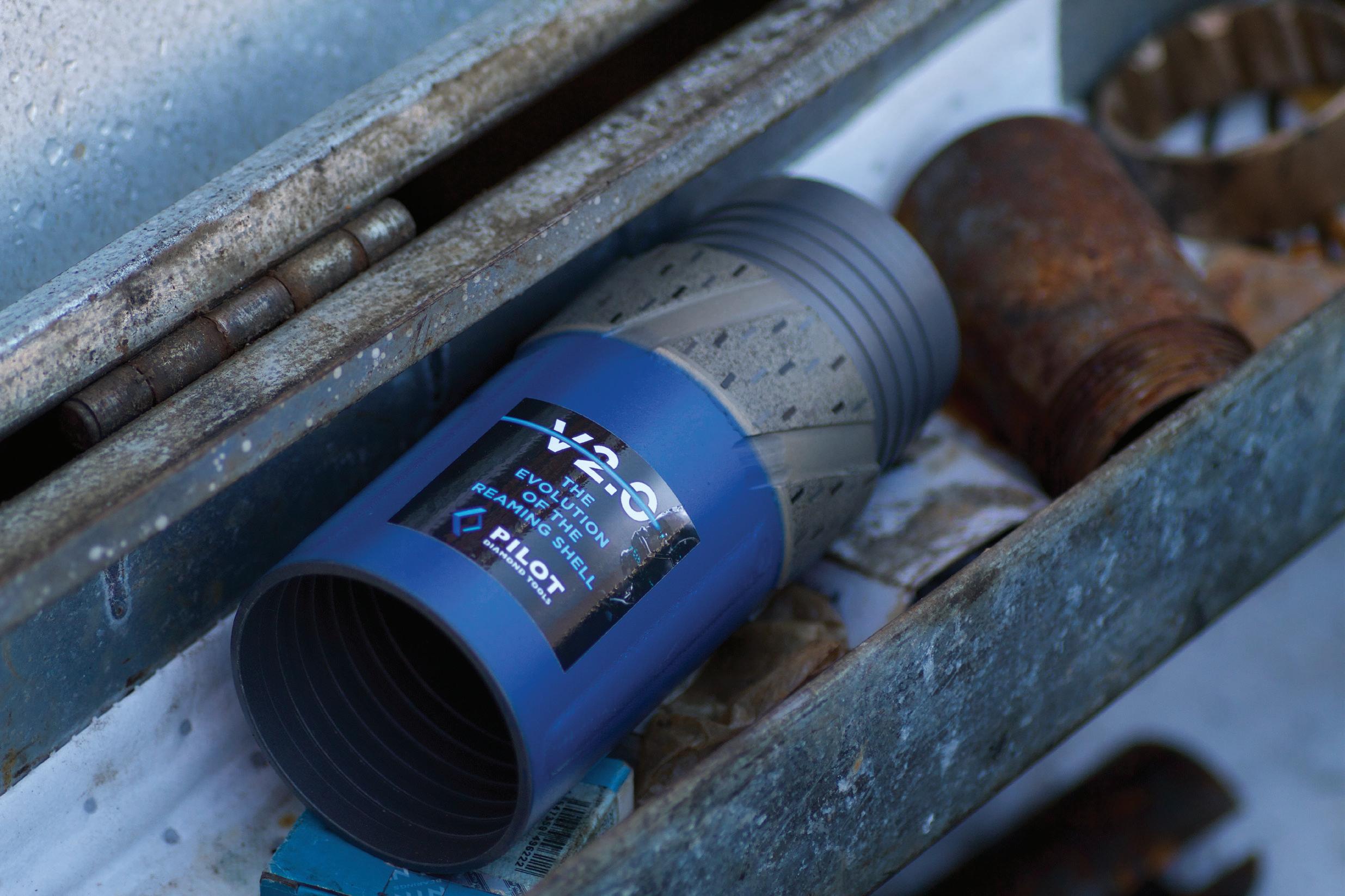
BD: What is your opinion of the geological skillsets, experience, and knowledge of geologists today, especially those who are newly graduated?
FR: Well, the business of exploration and mining has become increasingly complex, and this is reflected in the diversity of courses now included in undergraduate geology programs. This is appropriate but it dilutes the time dedicated to some basic disciplines and to field school. It is dangerous to generalize, but I find recent graduates to be well-versed in genetic models, analytical techniques (isotopes, fluid inclusions, etc.) and relevant software. But this comes at the expense of field skills: how many new graduates would be able to operate independently on an outcrop, extract relevant information and link with a property-scale map?
Interestingly, this is not a new problem, as illustrated by this quote from H. Smith, 1936 (in McKinstry, 1948, Mining Geology, p. 1): ‘Few recent college graduates seem to have had training in mapping methods known to be effective. The student is expected to acquire the needed skill somehow after graduation’. I also find that there is limited interest in going back to old geological reports prepared by geologists, who spent much time mapping, and established the geological foundation of so many mineral districts. Their deep insights into structural and stratigraphic problems are extremely useful but are commonly overlooked.
BD: Has there been any single satisfying moment in your career that rates above all the others?
FR: Yup! It happened in a bar in Fort Frances in 1987 where Howard Poulsen, Rick Sibson and I were talking about vein systems at the end of a field day.
On a napkin, I sketched the array of steep reverse and flat-lying extensional veins at Sigma, pointing out the difficulty to explain the evidence of reverse slip along steeply dipping laminated veins during horizontal shortening. I also drew a Mohr diagram to show how the associated flat-lying extensional veins could form from pressurized fluids. Rick added a line representing reactivation of a pre-existing but misoriented fault, providing the missing link. This was the basis for the 1988 Sibson et al. fault-valve paper in Geology, which turned out to have a lot of impact. It was one of those ‘aha!’ moments.
BD: I’ll ask a question on the flipside of the previous one. Many of us have interfaced with less than savory individuals
or experienced toxic workplaces. Has there been any incident or incidents that really disappointed you?
FR: Of course, there have been unpleasant incidents over the years, and it’s not appropriate to expand on those here. But looking back, I am mostly disappointed with how poorly I handled some of the particularly difficult situations. With the maturity I gained since, I would deal with those quite differently and would achieve a better outcome.
BD: One of the things you are held in high regard for is your capacity for teambuilding. What makes a good geology team? And have you seen any truly dysfunctional ones?
‘I find recent graduates to be wellversed in genetic models, analytical techniques and relevant software, but at the expense of field skills.’
FR: There is no magic recipe, of course. From my experience, a successful team involves individuals who work for the greater good of the team or the company rather than for their own benefit. A range of skillsets within the team is critical: more than ever, exploration requires smart integration of multiple geoscience disciplines and technology (scanners, software, etc.) and no single geologist can master them all. A range of personalities is also important from steady deliverers to creative, free-spirited individuals. Leadership is also important in providing clarity and vision, and in instilling trust and respect among the team.
BD: I know you appreciate the value of good mentorship and have been a positive influence on many geologists, me included. What makes a good mentor?
FR: Mentorship, formal or informal, is very important to one’s career. I don’t consider myself a good mentor, but I gained experience at Barrick, with the Society of Economic Geologists (SEG), and in several other oneon-one situations.
In my view, part of the role is one of a sounding board and a guide, but not one to give specific answers. I first try to understand what or where guidance is needed: career choice, professional development, dealing with difficult colleagues or bosses, etc. Once this is clearer, I try to lay out a few possible options to consider, or actions to take, but I avoid providing a direct answer. The idea is to put options on the table, lay out their pros and cons and their ramifications, such that the mentee can decide on their own what’s the best course of action.
I also think of a good mentor as someone that is a good listener, open-minded, honest, not afraid to point out mistakes, and respectful of confidentiality. Easy to say but not always easy to do.
BD: As I alluded at the start of the interview, you are one of the rare breeds of geologists who work in industry but manage to maintain a publishing career. What inspires you to publish and how do you overcome the challenges, such as finding the time?
FR: I did indeed publish numerous papers or government reports over the years, but less so in the last 10 or so years. The main driver to publish was always to share results or ideas that I thought would be useful to the community and hopefully impactful. I only published a paper when I considered the work was of sufficient quality or significance to share.
It’s a real challenge to write papers or co-edit a volume like SEG’s Special Publication 23 on gold while working full-time. You need to be very well-organized and effective, but there is no magic: you need to put in the extra hours.
BD: One topic we commonly talk about but rarely put into print is of the health hazards of working in different countries and environments. Has your health ever been particularly challenged and, if so, what happened?
FR: Over the years, I ended up in remote places and under various conditions. But, touch wood, I never had significant health issues other than quickly passing stomach problems. I have always been careful with
water and food but, was it luck, or a robust immune system, or both? Who knows!
BD: If you had abundant financial funding, is there a fundamentally annoying geology question you’d like to solve or a topic you’d like to work on?
FR: In greenstone belts, we commonly invoke regional faults as a key control of the spatial distribution of gold deposits, although most deposit occur adjacent to these faults rather than within them. We don’t really know what these faults are, how they formed, and how they really influence the formation of deposits.
This is a topic that Howard Poulsen and I are slowly investigating in the field, by revisiting historical and new exposures of the infamous Larder Lake-Cadillac Break in Southern Abitibi. It doesn’t cost much and it’s fun.
BD: Now to some personal questions. Would I be correct in thinking that full
retirement won’t come easily to François Robert, and what does he do when he actually has some downtime?
FR: Full retirement? You are correct, not anytime soon, but certainly at a slowly reducing pace. I really enjoy my current part-time (50%) status and as long as I can contribute to our profession I will do so in some capacity. Besides geology, I enjoy time with family and friends, travel, and listening to a lot of music.
BD: Are you ever going to compile your memoirs? I imagine there is a treasure trove of stories there!
FR: I have been asked that question a few times. Lots of stories indeed, but I don’t have any plan to compile them. Who would be interested anyway? However, I have a well-organized collection of 35 mm slides and accompanying field notes from various gold deposits I’ve visited over the years. I am currently scanning them, and one thought is to
prepare a photographic atlas of host rocks, alteration and mineralization for a selection of deposits, supported by representative plan and section. Let’s see where this leads.
BD: Finally, any concluding comments or words of wisdom from an industry veteran
FR: I firmly believe that mineral exploration and mining are still very much based on quality field observation and mapping, interpreted maps and sections, integrating all relevant available datasets. Sounds simple but it’s not so easy and it takes time. Here is a quote from a very successful explorer: ‘There is no substitute for the geological map and section – absolutely none. There never was and there never will be. The basic geology still must come first – and if it is wrong everything that follows will probably be wrong,’ (S.R. Wallace, 1975, Mining Engineering, 27, p. 34-36). Thank you for the opportunity to share some of my views! C
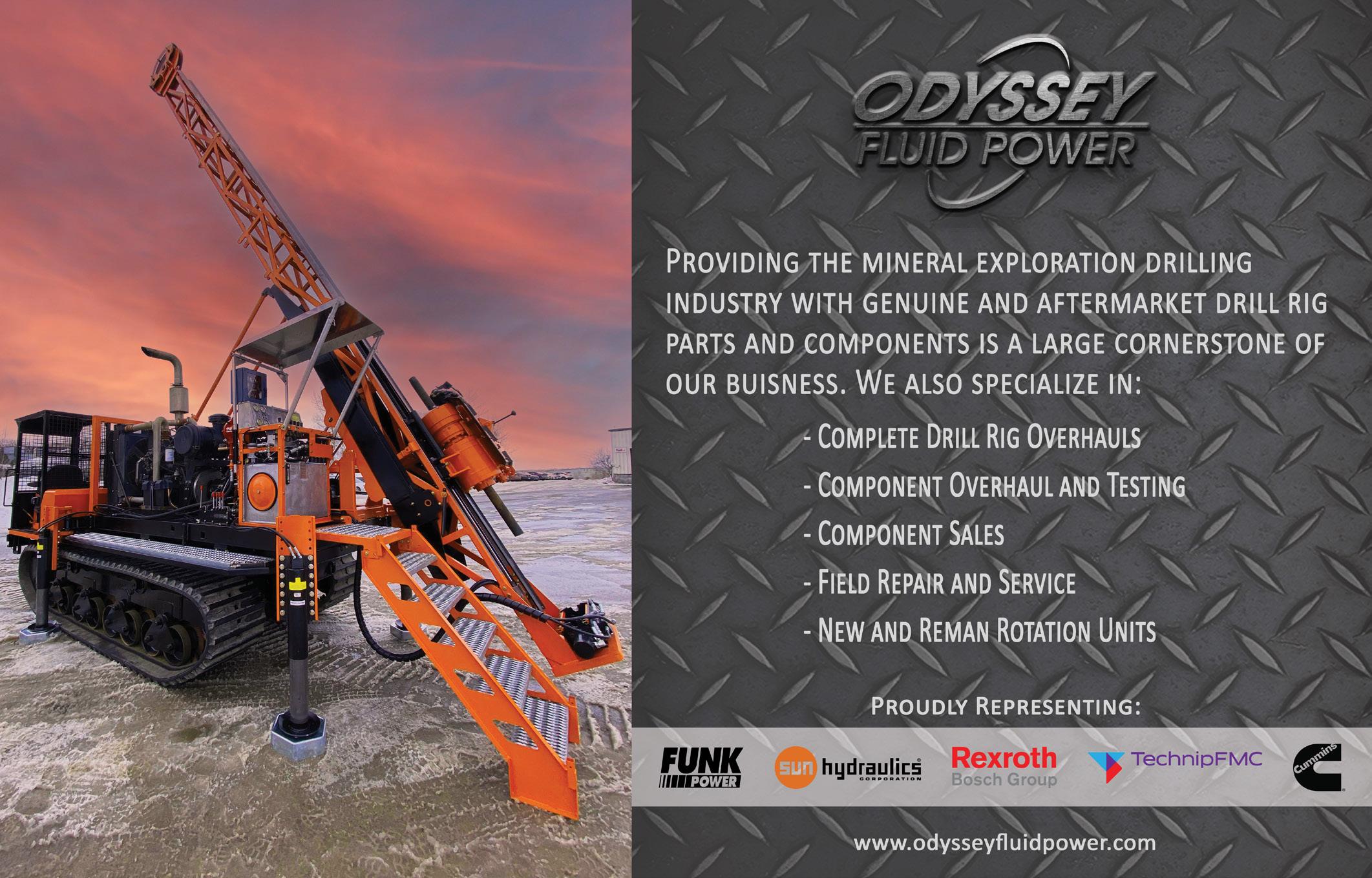
How to fail in mineral exploration but do it successfully
by Carl Brauhart, Principal Consultant at Camp Oven Exploration
In the depths of Greg Chappel’s international cricket form slump, he recorded four successive ‘ducks’ in an abysmal 1981-82 season where he was out before scoring seven times. He worked his way out of that terrible form slump by focusing on ‘process’ and doing his utmost to keep ‘results’ out of his mind. Greg Chappel was lucky. He enjoyed long periods of success with relatively few, relatively short, intervals of failure. The situation for exploration geologists is very much the reverse. Many of us suffer an entire career without being associated with a major discovery, or even anything of any economic value. Those working in genuine grassroots exploration are even more at risk of a whole career of failure.

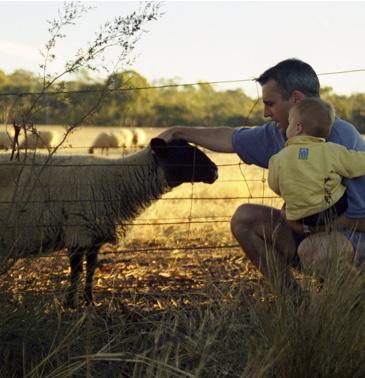
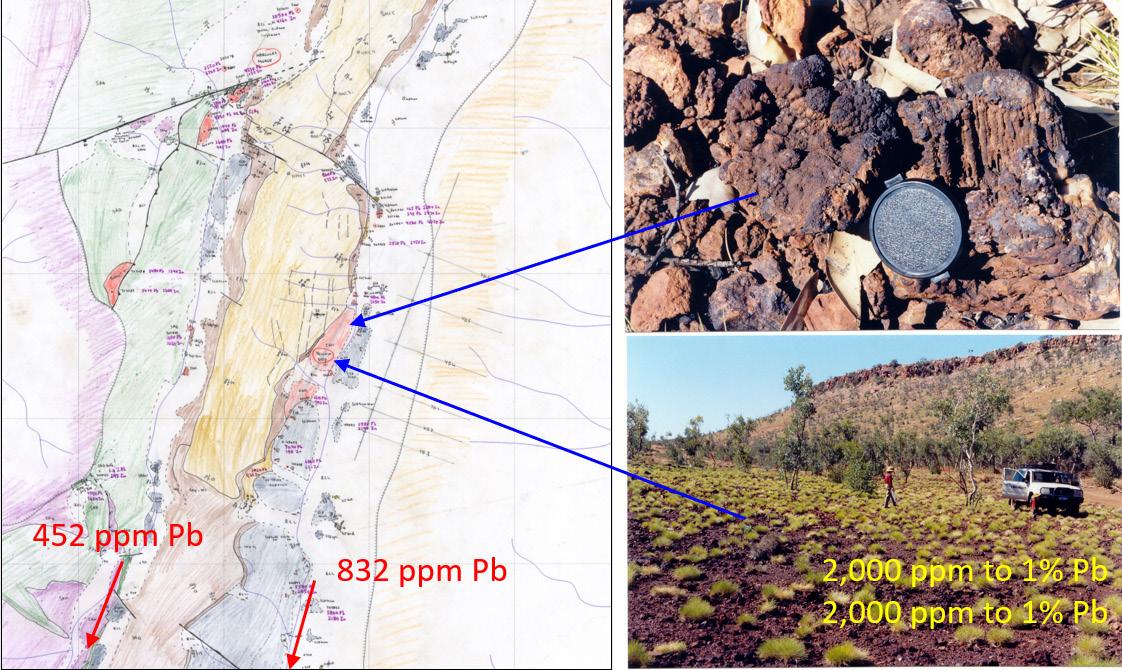
This article outlines four economic failures from my career in exploration geology but goes on to explain how, by focusing on process, each of them was conducted successfully. But first, what does exploration success look like? The magnitude of an exploration success can be gauged by the number of people trying to claim credit for the discovery. If the chief geologist, board of directors, geochemist, geophysicist, field crew and brokers are all clamoring for recognition, it’s a big one. We say that success has many fathers, whereas failure is an orphan, but what we need to remember is there has never been a single discoverer of any mineral deposit.
Ularring Rock – Southwest, WA 2000
In 2000, I was asked to follow up Au anomalies from the publicly available CSIRO laterite database over the southwest Yilgarn Block. I took my wife and first-born baby son on a three-day tour of the WA wheatbelt, taking 80 samples at, and around, those Au-pathfinder anomalies. After taking one of these samples at a CSIRO 16 ppb Au, 890 ppm Cu anomaly, we went further up the dirt road where I took a calcrete sample under a stand of gum trees, surveyed the landscape and said that there was nothing else to bother with here. My wife looked at a farm track that extended past the copse of trees and told me not to be lazy and have a look up there. Sure enough, there was a prominent laterite outcrop 50 m (164 ft) inside the fence which I duly sampled and
moved on. That sample returned 131 ppb Au, 32 ppm W, and 1.4 ppm Bi (only 16 ppm Cu though) and was duly followed up to reveal a substantial body of low-grade (subeconomic) Au-Cu-Bi-W mineralization. I was learning fast that any sensible husband listens to his wife, but the key takeaway was not to dismiss input from any member of the team. It is not possible to act on every suggestion, but take the time to carefully consider all data, and all suggested pathways to new data.
Dixon Range – Kimberley, WA 2002
A 2000 stream sampling program in the Kimberley northeast of Halls Creek, explored Paleoproterozoic strata that was considered prospective for Au, but it also strayed eastwards and included a few samples from the Neoproterozoic Wolfe Basin. Spectacular values of 832 and 452 ppm Pb in adjacent catchments of Wolfe Basin strata led to follow up rock chip sampling the next year and results of up to 1% Pb and 1% Zn in ironstone rocks with clear ex-pyrite textures. Systematic mapping and drilling followed in 2002.
Drilling at the best Pb-Zn targets in the now extended Neoproterozoic portion of the project were disappointing with a best result of 25 m (82 ft) at 530 ppm Pb, but similar intersections were returned on several sections. Critically, the down-dip samples looked very different to what was anticipated from the 400 by 50 m (1312 x 164 ft) Yellow Dog ironstone ‘gossan’. Rather than the anticipated massive sulphide, the weak mineralization comprised weakly weathered brown dolomite and minor ironstone chips.
↑ Map of the Dixon Range Project centered on the Yellow Dog prospect. Red arrows point to stream sediment samples described in the text.
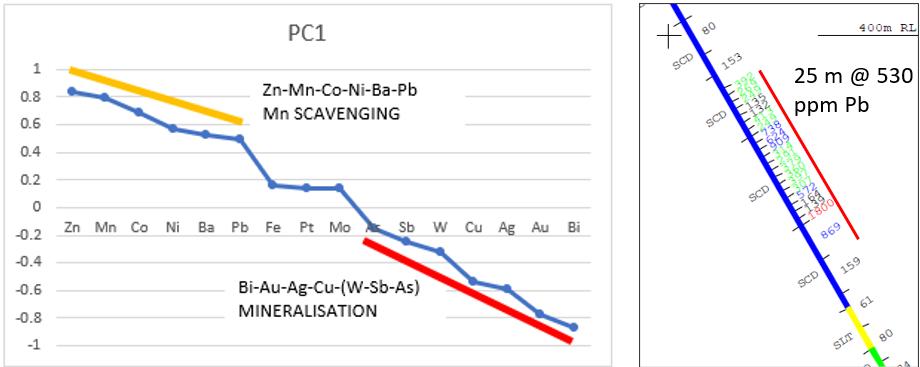
↑ Principal Component Analysis of Dixon Range Rock Chip data separating Mn scavenging with very minor Pb-Zn sulphide from minor Cu-Au-Bi mineralization in the Olympio Formation basement sequence (left image) and the best drill intersection at the Yellow Dog prospect (right image)
Weakly weathered rock at surface was still weathered more than 100 m (328 ft) below surface. An attempted water bore through the ‘gossan’ passed almost immediately into weathered dolomite with minor ironstone. Ouch.
The original exploration target to the west proved even more underwhelming. Repeat stream sediment sampling at every plus-10 ppb Au anomaly returned a result below the detection limit of 1 ppb Au.
There were many learnings from this project including:
• Carbonate rocks are treacherous. Although the terrain is rugged with relatively fresh rock, carbonate dissolves, rather than erodes away, thus it is perfectly possible to form a deflation lag. The field of rubbly ironstone outcrop is actually the residual lag from 20-30 m (66-98 ft) of very weak mineralization, not gossan after massive sulphide.
• Principal component analysis, and how to use it properly, would not be fully appreciated by me until about 2015. Returning to old data is critical to improve one’s competency. The very weak mineralization element association of Zn-Mn-Co-Ni-Ba-Pb in rock chip data is predominantly a Mn-scavenging signature, not that of a bona fide MVT. It was the same story for the initial stream data.
• Minus 2 mm (0.079 in) stream sediment sampling is very effective for pathfinder elements, but highly unreliable for Au. It seems obvious in 2024, but hard-won experience, coupled with the discipline of returning to one’s own data deepens one understanding of this lesson and delivers a more robust increase in competency. I now know, in detail, why I should turn to CSIRO’s recently developed Ultra Fine Fraction (UFF) technique in a similar scenario
Always apply new learnings to old data to increase your firsthand experience of that new learning.
Woodline Project – Eastern Goldfields, WA 2011
Sipa Resources held a large Au exploration project in the far southeastern Goldfields that, before my involvement, attracted Newmont as a
joint venture partner. They were encouraged by large auger calcrete and follow-up wide-spaced drilling Au anomalies that were supported by robust pathfinder element signatures, some examples of which are listed below. Sipa continued to invest at Woodline for years after Newmont departed, encouraged by the tantalizing scale of the anomalies coupled with their compelling geochemical signatures. However, many years of great effort, supported by high-quality data, did not lead to the definition of a resource. The main prospects included:
• Theofrastos Au-Cu-Bi-Mo-Te and Cu-Sn-Te-B both hosted by porphyritic intrusions;
• Heraclitus Au-W-B- (Ag-Pb-Tl-Mo) hosted by biotite gneiss;
• Ommaney Au-As-B-(Mo-W-Pb-Tl) hosted by mafic rocks;
• Cleanthes Au-Mo-Cu-Ag-W-Te-Bi-B-(Sn) hosted by granite-gneiss;
• Socrates Au-Bi-Te-Mo-W-(Sn-Tl) hosted by mafic rocks;
• Leucippus Au-B-W (only on one regional drill line) sericite-chlorite –tourmaline schist.
Regional-scale structural control was recognized and mapped, but the key lesson that came more clearly into view after later working more closely with structural geologists, is that the very likely key missing ingredient at Woodline is structural focus in the mineral system. There is a large orogenic gold system with plenty of ounces, but insufficient focus to generate economic mineralization. Better understanding of the distribution and zonation of metal signatures (unfocussed) and a greater investment in structural geology could have led to an earlier exit from the project and preserved more funds.
Monty Deposit – DeGrussa Project
Bryah Basin, WA
Monty was a small, but fabulously Cu-rich, VMS deposit discovered by Sandfire Resources, but my work on that project preceded their discovery. Sandfire engaged me as a consultant with CSA Global to review a data package over the ground that was then held by Talisman. The data contained anomalous Cu, but invariably with a truncated
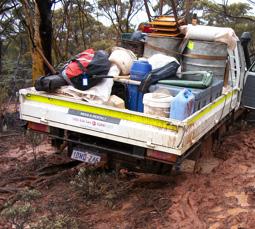
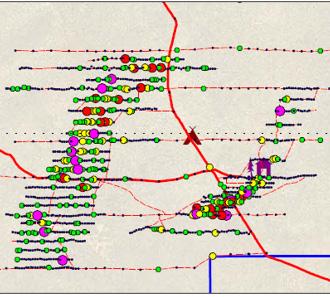
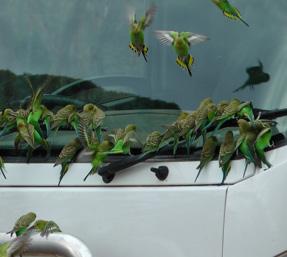
pathfinder element signature more akin to orogenic gold mineralization. Nowhere were there any samples with the diagnostic 10-15 pathfinder element signature that is all but diagnostic of VMS mineralization.
The best sample in the data was featured on the front cover of a Talisman annual report (see below) and returned high Au-Cu-Bi values, but insignificant Pb-Zn-Ag-Sn-As-Sb-Tl-Se-In-Cd abundances. Mineralization is quartz vein-hosted and almost certainly orogenic. After the joint venture was inked, Newexco, a geophysical consulting company, recommended that the same drill hole be reentered because available data suggested that there might be a nearby conductor. Better DHEM technology was required to be sure. Clearer definition of a conductor led to the discovery of the Monty deposit about 80 m (263 ft) from that quartz-chalcopyrite vein sample.
The lesson was certainly not that I should have paid more attention to orogenic Au-Cu mineralization and recommended VMS exploration nearby. The key lessons were:
• Exploring under cover is tough.
• Once, every so often, geophysics will find the prize and a disingenuous geochemist would do well not to come along afterwards and say that ‘Geochemistry could have found it too’.
• Integrate all the key disciplines. Know which rein to pull and when to pull it.
Conclusion
Greg Chappel finished his Test cricket career with over 7000 runs at a princely batting average of 53.86. That was his reward for applying his great talents intelligently. Focus on the process, and the results will look after themselves.
The term ‘continuous improvement’ always makes me cringe because it is almost invariably a platitude, but I hope that the failures described above show how an exploration geologist can always apply technical best practice to the level that their experience will allow. Continuing to review each one of your exploration failures in the light of new experiences is one way of turning failure into success.
The other way is exiting an unsuccessful exploration project as quickly as possible. Just as so many of us will find that our first love may not be our lifetime partner, explorers need to be able to leave unsuccessful relationships with exploration projects, sooner rather than later. As a consultant, one of the most valuable services that I now deliver is to act as prospect, or even project, killer. Millions of dollars could have been saved at Dixon Range and Woodline with the understanding that I have gained since working on those projects. Testing an unsuccessful project in a thorough, but rapid and cost-effective, manner is most definitely a successful failure in our industry. It allows one to arrive at that rare economically successful opportunity quicker, with more funds still in the bank. C
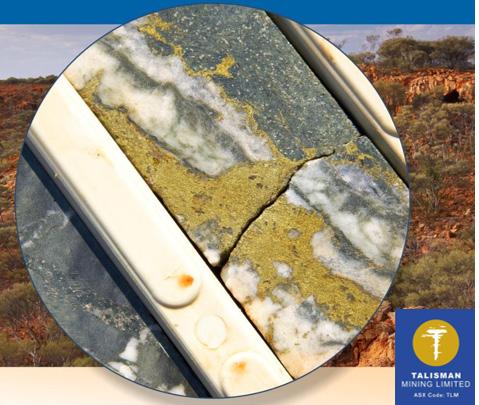
↑ A selection of images from the Woodline Project
↑ Quartz-chalcopyrite vein 80 m from the Monty VMS deposit
Preparation of diamond core for geotechnical logging
The dos and don’ts
by Lyndell Juggernaut, Engineering Geologist at MineGeoTech
Introduction
Geotechnical logging of diamond drill core is used to characterize the rock mass and the structural setting. The collected data is applied in geotechnical studies to design mine excavations (open pit slope angles and underground mine excavation sizes and required ground support schemes). Any feature that will influence excavation stability needs to be captured by logging. Geotechnical logging can occur on standard resource definition holes or specifically designed geotechnical investigation holes. The purpose of the hole often influences who will be doing the logging of the core. To ensure that the best possible outcome is achieved, diamond core drilled for geotechnical logging must be prepared to a much higher standard than regular exploration core.
A significant amount of geotechnical logging is done by contractors/ consultants. Low-quality core processing does result in the visiting geotechnical consultant or logger spending time bringing the core up to the required standard prior to logging. This could result in a lost opportunity to acquire accurate structural and rock mass data and in the worst cases, may require redrilling of the holes.
This article is intended to provide a basic guideline for the level of quality needed for reliable geotechnical data collection and will consider:
• Core orientation;
• Core loss;
• Meter markup;
• Geology markup;
• Feature allocation;
• Industry standards.
Core orientation
For geotechnical structural data collection, the geotechnical logger needs to take measurements on every single open natural break i.e. driller-induced breaks are excluded from the analysis. Hence drillers must be marking their breaks on the core that result from fitting the core into the tray or removal from the rods. Regular checks of the core recovery process at the rig by the supervising geologist/geotech is useful in this respect.
It is imperative that as much core as possible is connected to the driller’s orientation marks (a mark placed to indicate the bottom of the hole in cross section view), even if it is only one or two marks as the geotechnical logger will determine the reliability of the driller’s markup. Orientation lines should be drawn no-lock (section of core that cannot be joined) to no-lock, taking care to extend through orifails (driller was unable to place an orimark), poorly placed core loss blocks (see next page) and cave-in (debris that has fallen into the hole). Core loss and cave-in should be tested by attempting to lock solid ground across the interval.
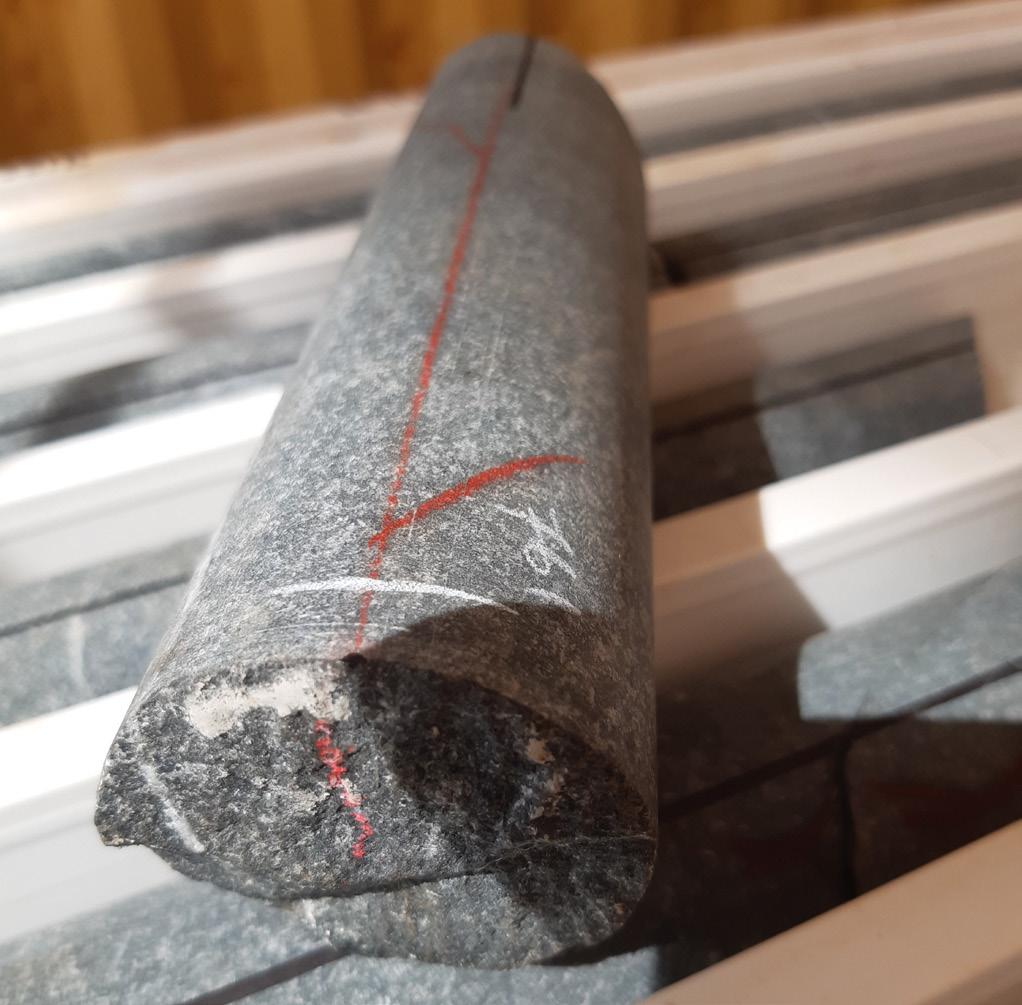
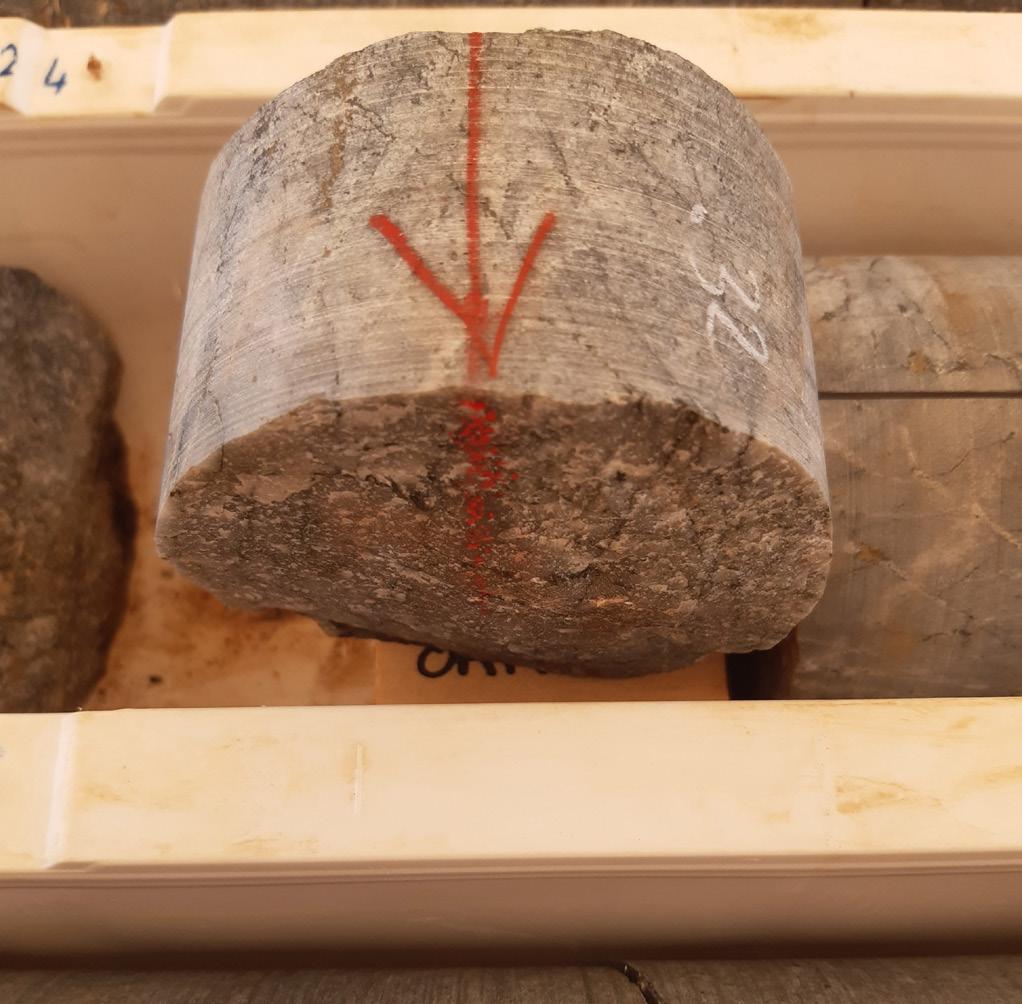
Typical errors identified when orientating core are:
• Not racking up enough runs to accurately assess the reliability of driller’s orientation marks. Ideally, at least two runs should be laid out drawing the oriline on the core surface. This requires longer core jigs to be used particularly for surface drilling.
• Relying on the orimark drawn on the surface (along hole length) of the core for accuracy. The orimark drawn on the core cross-section is often more accurate. Acceptable deviation for a driller’s mark from the drawn line is about 10-15 degrees. The best place to anchor the line and determine reliability is the point where the driller’s mark on the core face meets the mark on the core surface. Drawing the oriline over the top of the driller’s surface mark aids in the QA/QC (quality assurance and quality control) of the driller’s mark and eliminates the risk of error when the driller’s mark is crooked.
• Out of order core where the core has been dropped or put back into the core tray incorrectly. I have reoriented entire runs of core placed in the trays backwards!
• Running orilines through fragmented core. Drillers will often place loose fragments at the ends of the tray rows or the bottom of the run. If the oriline hits a no-lock do not give up straight away, cross-check against other no-locks and search for similar looking surfaces to the no-lock. Sometimes one of those little pieces at the end of the rows can make the lock happen. You do not need to match up every single piece of broken core to make a lock happen. For further information on drill core orientation best practice, see Brett Davis (2012).
Core loss
Always ensure that core loss has been located at the point where it occurred. The drilling teams have been typically trained to assign core loss to the bottom of the just completed run. This location is not
necessarily where the core loss occurred. Validate the core loss by attempting to match the core across the gap. If not here, reassign to the most likely location in the run. Some geologists like to disperse the core loss through several locations in the same run. When doing this, do not assign core loss to locations where clearly no core loss occurred. Sometimes core loss is caused by core being dropped in the rod, this core loss may be picked up by driller in the next run (core gain); take care to allow for core gain when calculating core loss location and meter marks. Always record core loss locations on the tray in the format start depth-length lost-end depth. Geotechnical rockmass logging is tolerant of multiple core loss reconciliation techniques; however, please only use one technique per hole and only one set of core loss markup at a time.
Meter marking
For geotechnical purposes, it is important to establish the actual location of major structures and the geotechnical domain boundaries. Meter marking is typically undertaken by the site technicians (particularly in fresh rock) prior to the commencement of geotechnical logging. The tape measures used are regularly observed to be in poor condition or have a non-zero start.
There are several places where meter marking can be cross-checked against an absolute borehole depth point. These are Start of Hole (SOH), End of Hole (EOH) and anywhere the driller did a rod count. These locations are calculated by the number of rods used x rod length, less height of first rod above ground (stick up) and are a good guide for determining whether the other driller’s blocks have been labeled correctly. Meter marking that has been done correctly nearly always comes back to one of these points. Always do meter marking after full core orientation has been completed. Ideally, meter marks should never deviate more than 10 to 20 cm (3.94 to 7.87 in) away (preferably less than 5 cm or 1.97 in out) from
↑ Example of a facemark not lining up (left) with the surface mark, alongside a correct mark
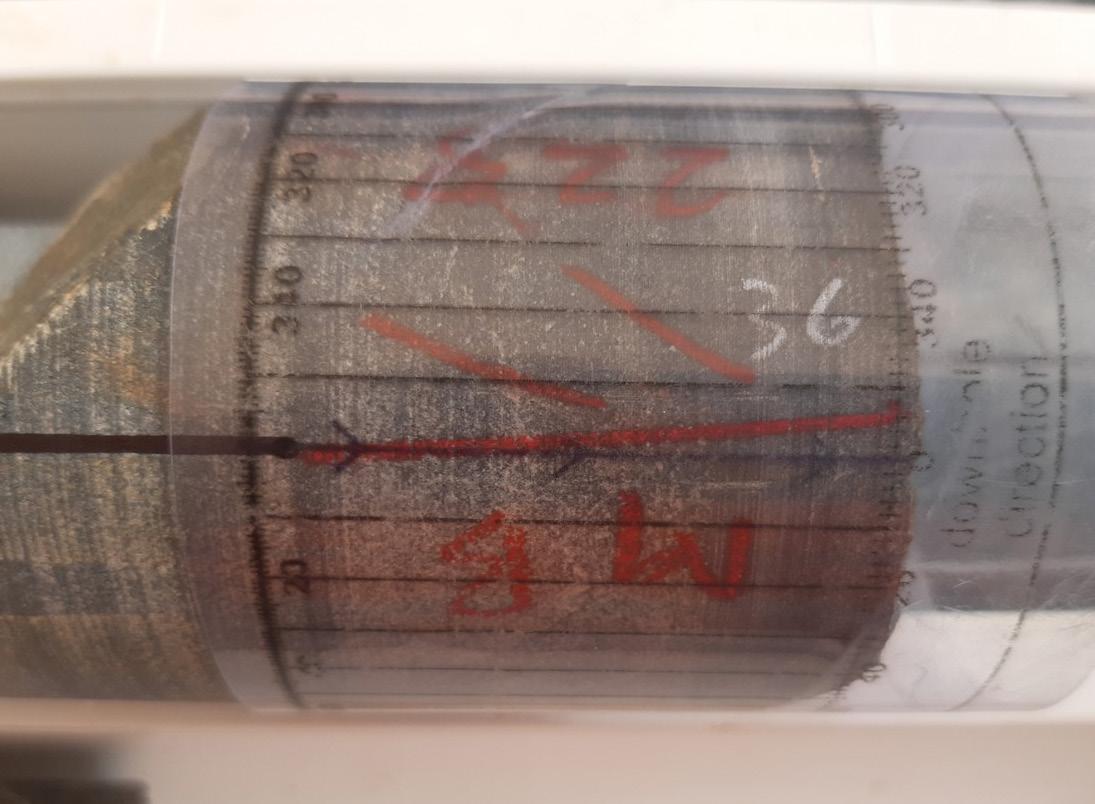
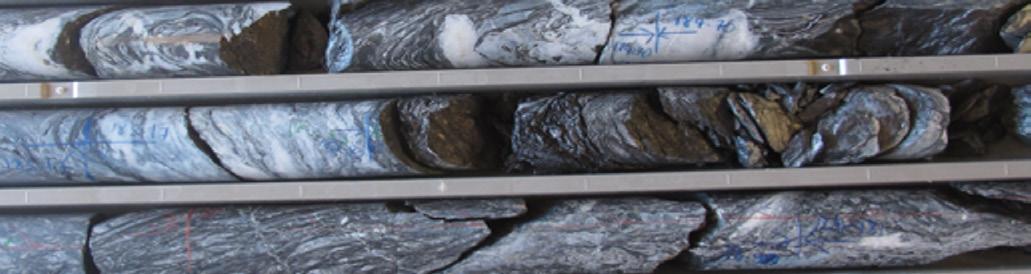
↑ Splitting up a fault zone: from top to bottom - ductile shearing, open fault, intense foliation
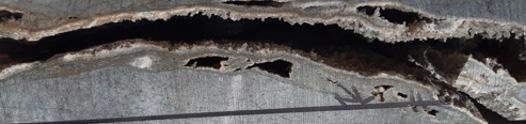
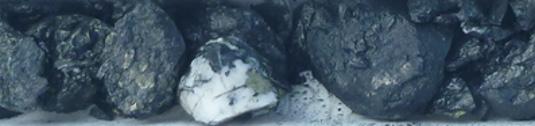
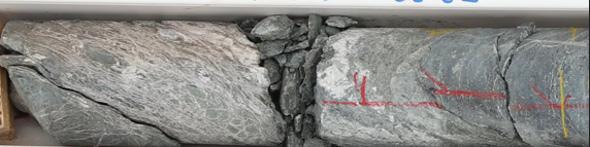
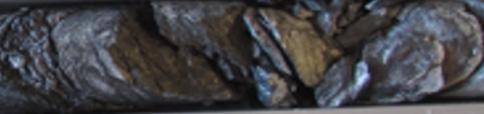
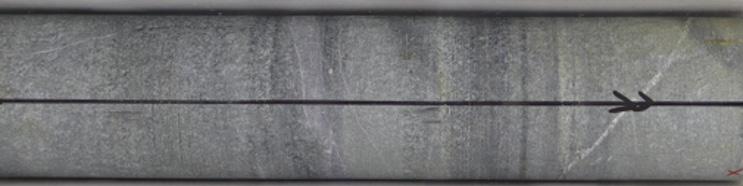
↑ Examples of geotechnically interesting structures versus massive rock
the value on the driller’s core blocks (some drillers do round to the nearest 10 cm/ 3.94 in). Drillers do make mistakes and sometimes the core blocks can be wrong. In most cases, these mistakes are detected and corrected going forward by the drillers.
When reviewing meter markings, cast an eye on the deviation keeping in mind that some technicians subconsciously add or remove 5-10 mm (0.19-0.39 in) of measurement per meter (creeping drift). When the difference between meter marks and core blocks is deviating too much, always go back and check for creeping drift first then continue to see if the blocks come back. Do not under any circumstance insert fake core loss or additional material into geotech core to correct for poor meter marking.
Geology markup
Geotechnical rockmass logging must lock into the major geological contacts. It is preferable that these are labeled directly onto the core with a simple geology code ‘+/-’ alteration. Geological logging of geotech core needs to be as simple as possible and consistent. Elaborate geological code systems that subdivide geology based on grain size, alteration, mineralization and/or texture are subject to misuse and are difficult to reconcile for modeling purposes. For example, if you give a geologist 20 possible codes for sandstone there is a very good chance there will be at least ten codes being used for a sandstone unit that has the same geotechnical properties. Keep the geology logging to significant changes in rock type and alteration. Keep the logging relevant to the target mineralization.
Recommended spacing for geology for an open stoping operation with similar geotechnical characteristics is firstly tens of meters when in gangue, for example, barren turbidites; secondly, at the meter scale when in outer alteration halo, for example, distal chlorite and or carbonate in a gold system; thirdly at the decimeter scale when in the inner alteration halo and or mineralization, e.g. areas of stringer and massive sulfides.
Do QA/QC of contacts. It is quite common for geologists to assign incorrect depths to contacts either via incorrect measurement from meter marks or ignoring the meter marks completely and measuring from the core blocks. If meter marks are determined to be incorrect during geological logging it is the responsibility of the logging geologist to ensure the marks are corrected.
Feature allocation
It seems to be quite common for geologists to lump fault zones into large geotechnically heterogeneous domains labeled as fault zones or shears but ignoring lithology. It is preferable to subdivide fault zones at the decimeter- to meter-scale via geotechnical characteristics using the dominant apparent host lithology. For example, a fault zone containing a healed dolerite breccia, a quartz vein, then a sheared black shale with a fault gauge, should be logged as separate domains. Logging the above as one unit would conceal the position of the shale contact and conceal the potentially problematic shale-hosted active fault beneath the quartz vein from numerical analysis.
Although geotechnical logging relies on the collection of every single open feature, structures measured for geological purposes can be useful. It is very important that any structure measured for geological purposes is clearly identified. It is a too common occurrence for a discontinuous healed micro-fault with a 1 cm (0.39 in) offset to be
↑ Example of a crooked drillers orimark
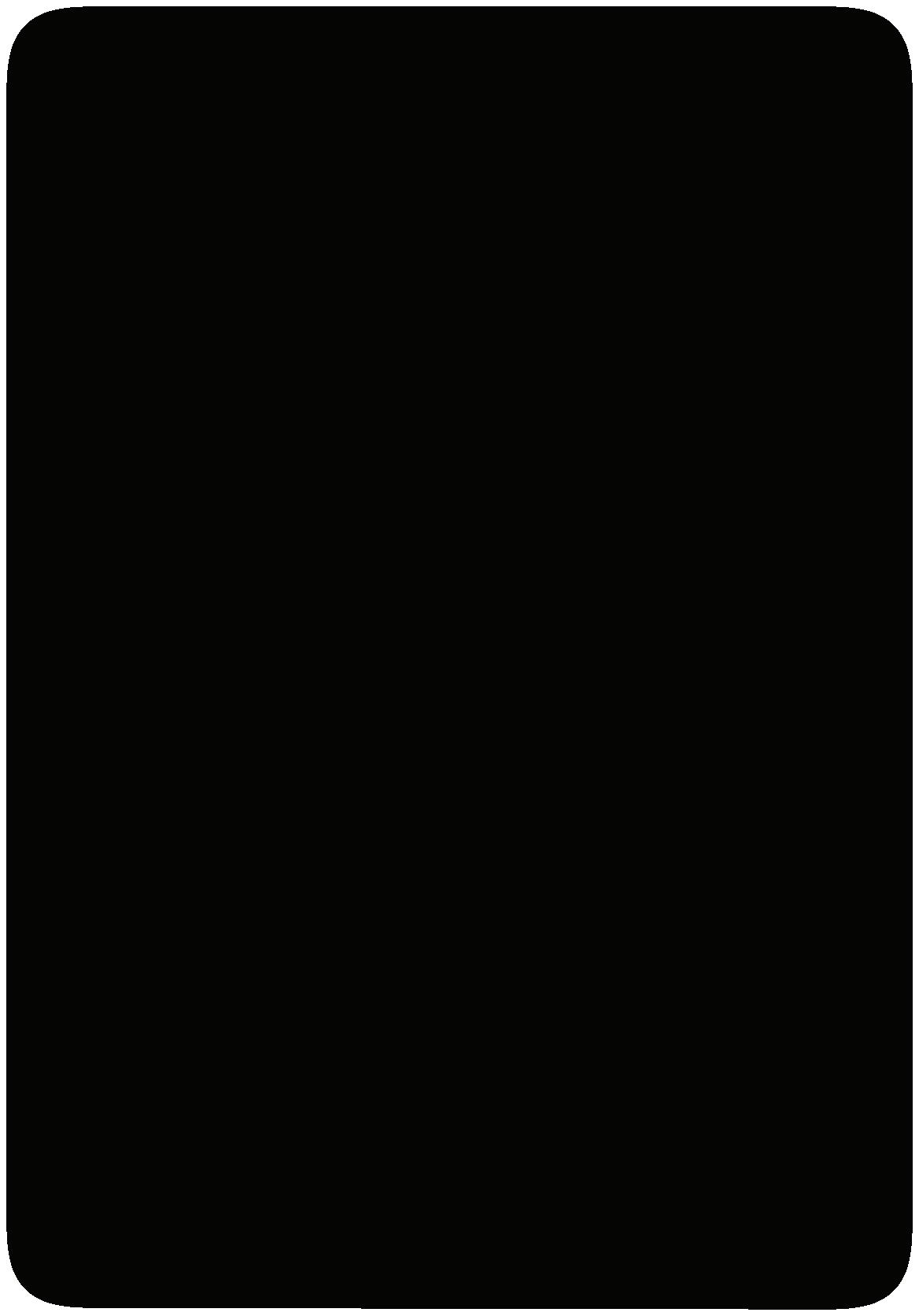

Example of basic geology markup
logged with the same moniker as an open major fault with several meters of offset. It is a good idea when selecting structures to ask the question ‘if I drilled a hole 10 m (32.8 ft) away could I find the exact same structure?’. Useful structural measurements for geotechnical purposes are open faults, shear planes, foliation, bedding and of course open joints (preferably all open joints observed should be measured).
It is important to ensure that the logger is using the correct sized orientation tool (of the many different forms available) and knows how to use it correctly.
Industry standards
Industry standards with regards processing core for geotechnical data collection have been slipping over the past five years. This slippage has occurred due to the combined effect of an influx of untrained staff, caused by the recent increased demand in the mining industry, and a legacy attitude towards the value of holding on to trained core shed staff from the employer dominated market of several years ago.
To resolve the slipping industry standards in geotechnical data collection there needs to be two parts:
1. A reset towards training and retention of competent staff.
2. An understanding what geotechnical data is collected for and that adopted collection standards need to comply with how they were intended to be collected and utilized.
Conclusions
This article has covered the common issues that can result in a slowing down and inaccuracies in geotechnical logging. Each section provides advice that will speed up the logging process for the geotech logger and ensure or improve quality data collection improving the reliability of the rock mass characterization and hence forecasting of rock mass response to excavation. The author does not expect potential clients to strictly adhere to the advice above, however implementation of these processes will pay back in the results achieved.
References
• Brett Davis, 2012. Drill core orientation – An Inconvenient Truth (Part 1 of 3).
Drill core orientation - An Inconvenient Truth (Part 1 of 3) (orefind.com)
• Brett Davis, 2012. Drill core orientation – An Inconvenient Truth (Part 2 of 3).
Drill core orientation - An Inconvenient Truth (Part 2 of 3) (orefind.com)
• Brett Davis, 2012. Drill core orientation – An Inconvenient Truth (Part 3 of 3).
Drill core orientation - An Inconvenient Truth (Part 3 of 3) (orefind.com)
For more information Visit: minegeotech.com.au
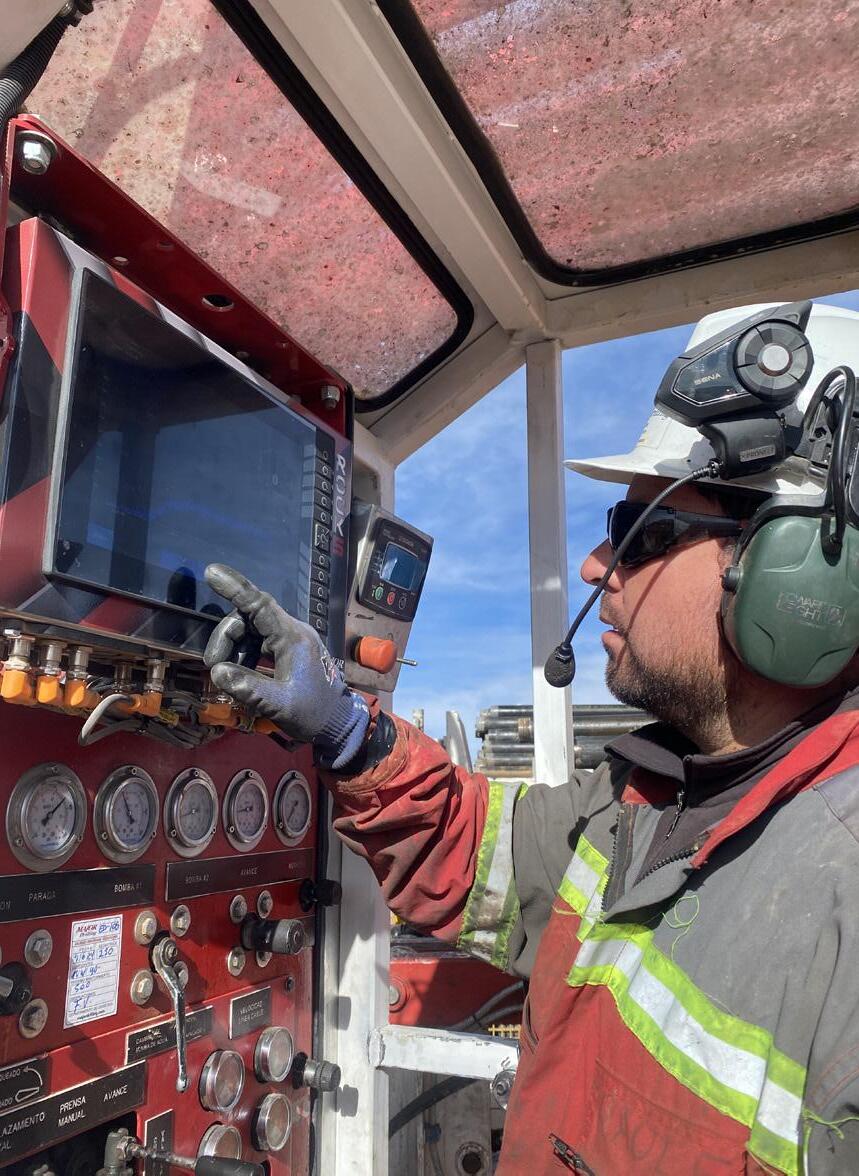
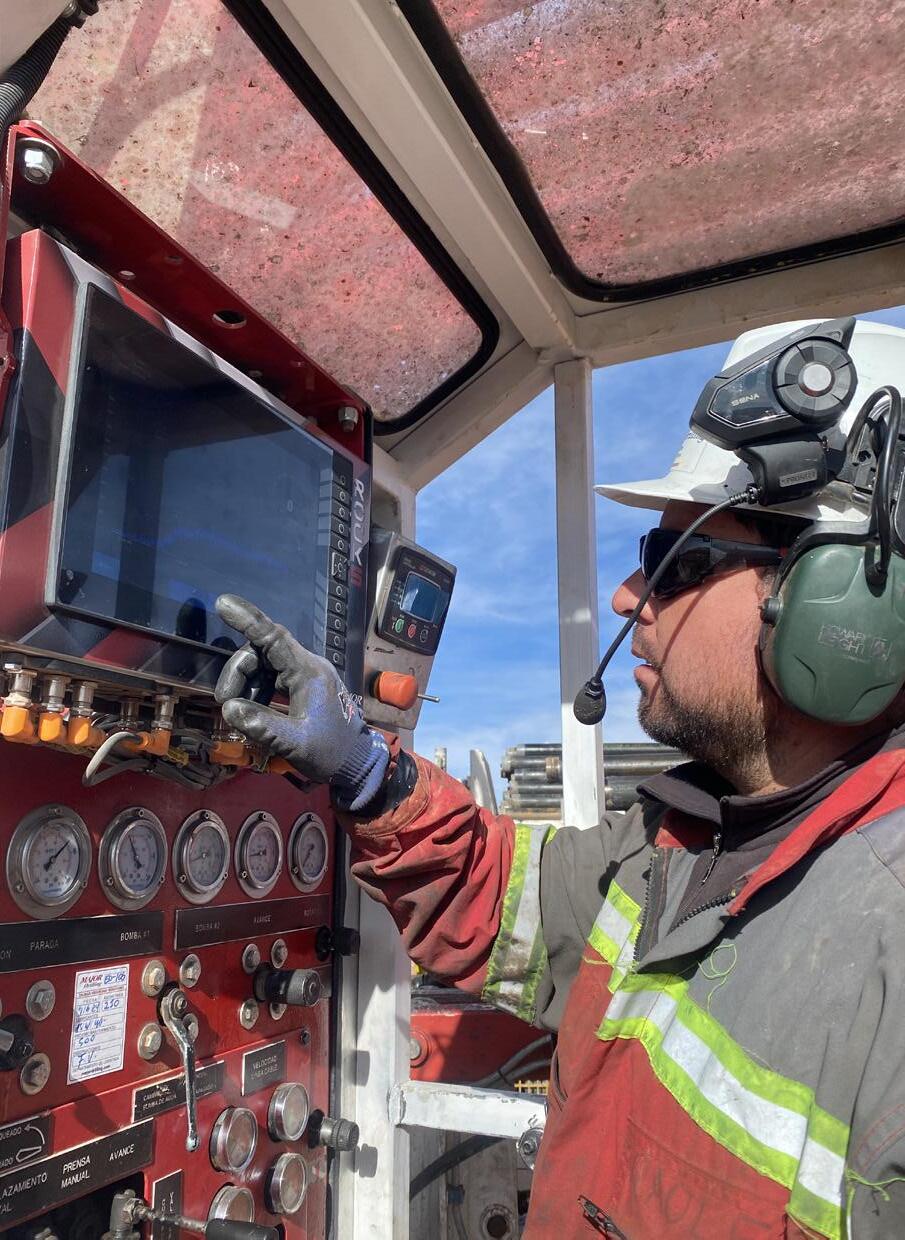
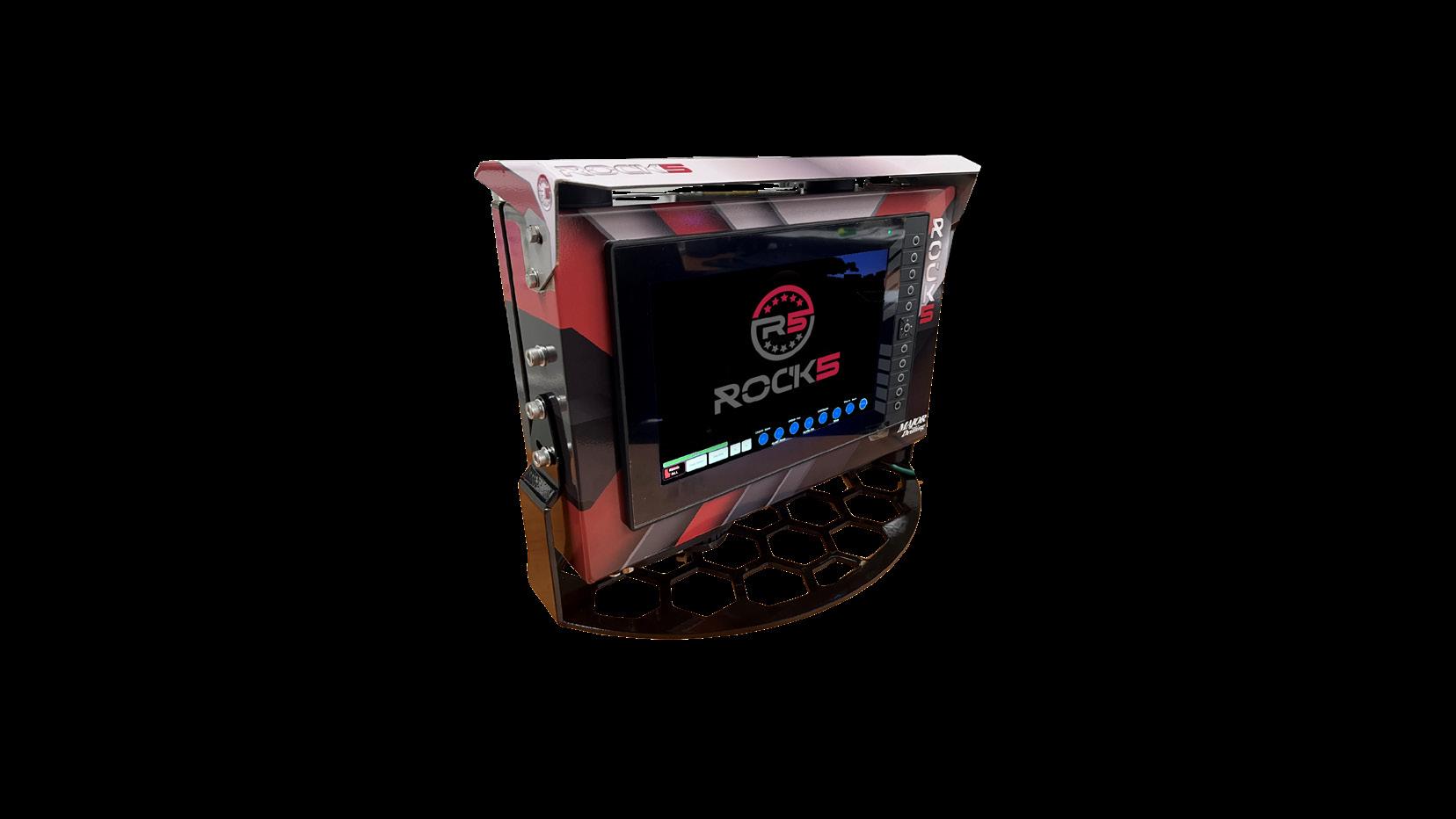
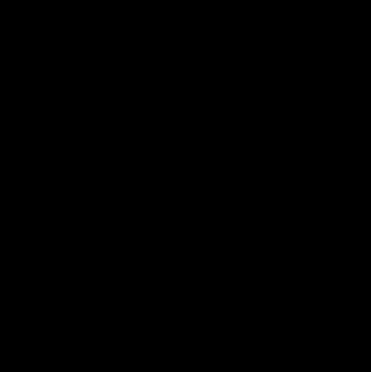
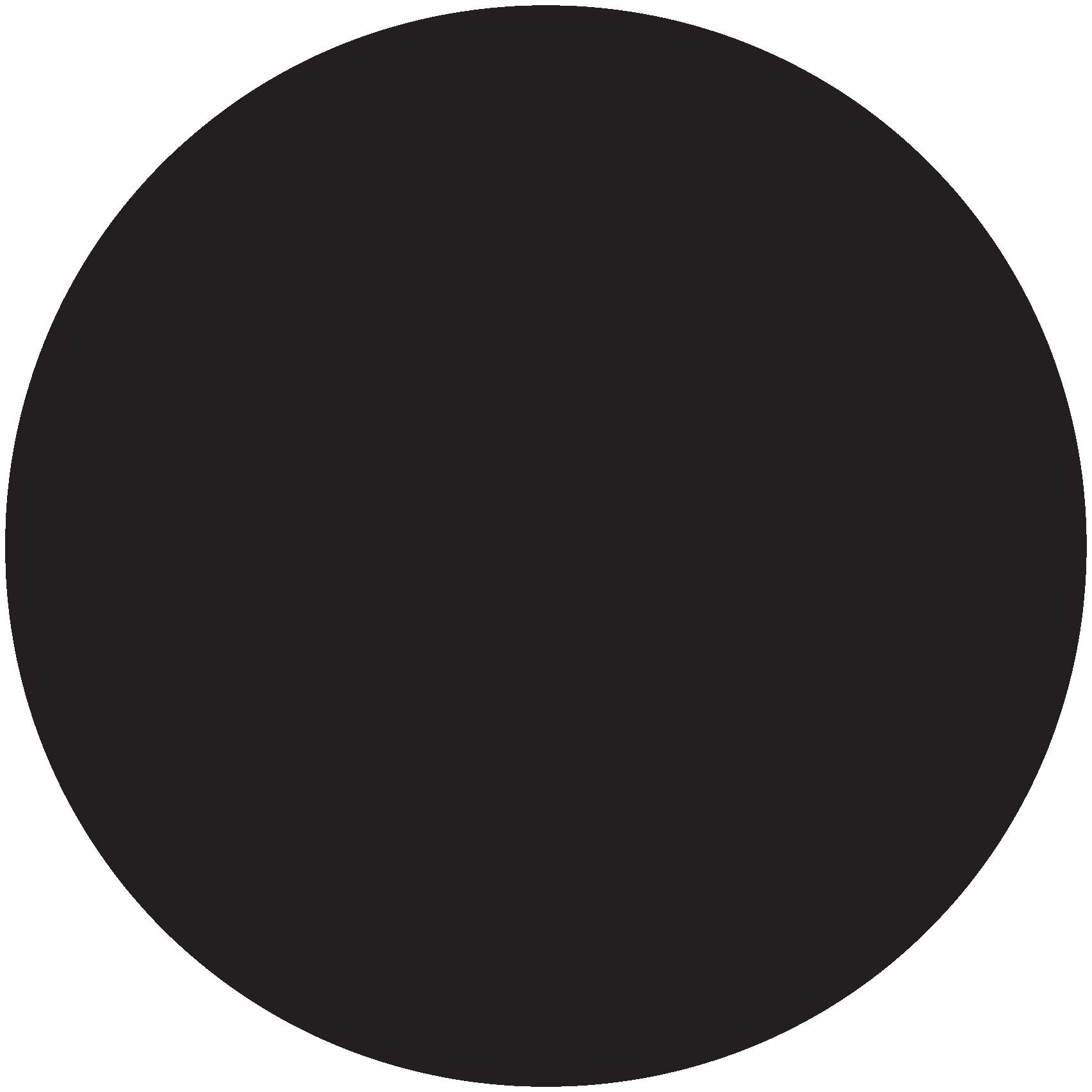
Drillside GeoSolutions by Major Drilling is a new innovation solutions suite of services that is revolutionizing the use of artificial intelligence and data technologies to deliver orebody knowledge like never before. We’re combining advanced drilling, borehole surveying and core logging at the drillside bringing greater downstream benefits for all.
Drilling data quality – more than just samples
by James Lally, Principal Consultant at Mining Associates
As part of my consulting work over the last 20-odd years, I have been using drill hole databases from companies spanning a range of project stages from early exploration through to resources and production. Almost without exception, these databases contain drill holes that can’t be used for resource estimation or geology modeling because of errors that could have been avoided if some basic validation had been carried out when the holes were completed. In these cases, the drill holes in question are almost worthless, with all the money, time and effort expended in drilling, logging, sampling and assaying wasted.
The advent of reporting codes, such as JORC and NI43-101, brought drill hole sampling and assaying quality control to the fore. While there are still improvements to be made in this area, the quality aspects I am concerned with relate to more fundamental data relating to drill holes from which the spatial location of samples and geological contacts is derived:
• Is the collar location correct?
• Is the hole path correct?
Collar locations
In these days of handheld GPS and its more accurate cousin Differential GPS (DGPS) one would imagine that collar location errors were a thing of the past. However, there are several types of mistakes that commonly arise in databases:
1. Incorrect drill hole ID assigned to a location. It is not uncommon for DGPS locations to be picked up by a surveyor after drilling is completed and they rely on the hole ID scribbled on a marker picket or PVC pipe. Errors arise especially where hole IDs contain a bewildering array of characters such as dashes and backslashes. On some occasions the collar is marked with a planned hole ID that is different to the final assigned ID (a practice that is almost guaranteed to cause confusion).
2. As with any data, transcription is the most common source of errors. Any process where coordinates are written or typed manually from one display medium to another is a potential error. Common examples of this include transposed northings and
eastings and ‘fat-fingered’ typing, where 2 is pressed instead of a 3, or missed digits.
3. Incorrectly recorded (or not recorded) datum and projection information for eastings and northings. Not usually a problem with the GPS reading itself but there needs to be a database field that specifies the coordinate system being used.
4. Collar locations (especially elevations) that don’t match terrain models and/or aerial photography. High-res. digital terrain models (DTM) are becoming increasingly more common with the advent of cheap airborne LiDAR and drone photogrammetry. When these data are acquired over a project, drill collar locations should be cross-checked against the DTM surface to ensure that any differences are within the accuracy limits of the DTM data. Checks apply not only to collar elevations but also to the relative locations with respect to tracks or other features that are visible on the terrain model. Any earthworks or pad construction that has been carried out after acquisition of the DTM data should be accounted for in this assessment.
5. Use of elevations from handheld GPS readings. While handheld GPS can provide adequate horizontal accuracy, the vertical accuracy is commonly three to five times worse. This difference is commonly overlooked and again highlights the need for checking collars against a local DTM and/or other more accurate elevation data.
Most horizontal location errors can be detected easily enough at the time of drilling by simply plotting collar positions on a map and checking against other holes and any DTM data to ensure that relative locations are correct. Creating a DTM solely from collar elevations is
a good way of highlighting spurious readings, especially when comparing collars that are close to one another. It is becoming harder to verify locations after drilling, especially in jurisdictions that require full rehabilitation of the pads and tracks after drilling is completed.
Hole paths
Downhole surveying technology has advanced in recent years with the advent of digital multi-shot magnetic and gyroscopic tools that should ensure greater survey accuracy and efficiency. However, as with collar positioning, I see avoidable errors in almost every database:
1. Excessive doglegs in downhole survey paths. This is probably the most common error and arises from not checking the survey data as soon as it has been collected. Validation consists of either examining the plotted hole path to look for unnatural deviations, calculating Dogleg Severity, or by comparing individual dip and azimuth figures in successive readings. A real example is shown in Figure 1. In most cases, the suspicious reading is easy to identify and can be deleted from the database. Some companies insist on retaining invalid survey readings in the master database and adding an identifier so that it isn’t exported but this can cause problems if a user isn’t aware of the system.
2. Large differences from collar to first survey. It is not uncommon to see the first instrument survey reading 10, 20 or 30 m (32.8 or 65.6 or 98.4 ft) downhole, with a collar dip and azimuth recorded at zero meters. This collar reading may or not have been confirmed by the geologist with a compass-clinometer when drilling commenced and is commonly quite different from the first survey. As with Point 1 above, a simple check of the numbers is all that is required: if the deviation is too high, delete the collar survey point and if a zero-depth reading is required, use the first downhole survey.
3. Use of inappropriate downhole survey tools. Several years ago, I worked on a project where mineralization occurred within an extensive low-grade magnetite alteration halo. The operators were saving money by using magnetic instead of gyroscopic survey tools, which for most holes worked if those surveys from the more magnetic intervals drilled were excluded. Two diamond holes drilled at a lower angle to the strike of mineralization were
more affected by magnetite and had to be removed from the resource estimate database due to their positional inaccuracy. Arguably the money saved by using magnetic tools was negated by losing the information from two drill holes.
4. North, north and north. A common source of confusion is the conversion of the azimuth measured by the survey tool into the azimuth of the grid that is being used to plot collar locations. For magnetic tools, the azimuth reading is relative to magnetic north, whereas for gyroscopic tools the azimuth is relative to geographic or true north. Both azimuths require corrections as described below:
• The conversion from magnetic to true north is determined by the magnetic declination at the project location. While most people understand how to find the correction factor it’s not uncommon for it to be applied using the wrong sign (i.e. subtracting instead of adding or vice versa). The extra catch is that declination changes over time, so the correction for historic drilling is not necessarily the same as today. For example, in Cuba where a colleague has recently been working, there has been a 2° change in magnetic declination over the last 20 years, which has a significant effect on historic holes.
• The correction from true north to grid north when using UTM grids seems to be less well-known than the magnetic declination correction. Due to the warping introduced by the UTM projection, grid north and true north are only aligned at or near the UTM zone central meridian. As the distance east or west from the meridian increases, the correction factor (grid convergence) also increases. Grid convergence also increases with latitude as the warping effect becomes more pronounced. Project data I recently worked on from northern Canada at a latitude of about 65° was near a UTM zone boundary and had a grid convergence of about 2°. This grid convergence correction needs to be applied to magnetic azimuths after they have been converted to true north.
5. The convention for drill hole dip should be clearly defined. Most drill hole plotting programs use the default convention of negative dips indicating ‘down’. I have been presented with examples of surveys where all readings except one were negative,

↑ Figure 1 - Plan view of hole path with suspicious survey reading (blue) indicated by dog-leg trace and path with reading removed (red). The table highlights an azimuth reading at 72 m (236 ft) that has a 10° difference from readings above and below (real data received). Probable transcription error, which should be 268.26°. Removing the suspicious survey shifts the end of this 240 m (787 ft) hole by about 2.5 m (8.2 ft). Plotting in Geoscience Analyst Pro software.
HOLE
which makes for some interesting plotting in 3D. It is of course possible to have upward-directed holes drilled from underground, so care should be taken not to simply select all dips in a database and set them to negative.
6. Holes not surveyed/partially surveyed. There are many valid reasons for not surveying a drill hole once it is completed but every attempt should be made to do so, especially for longer holes. Partial surveys occur when the hole collapses at some point near the bottom, or maybe when a survey tool has malfunctioned. Problems can then arise with determining the position of the end of the hole where the upper part has deviated because different software packages may treat this situation differently (an extreme example is shown in Figure 2). It is a fairly common practice to not survey ‘short’ RC holes on the premise that any deviation will be negligible. While this may be true, it would be preferable to have at least a start and end of hole survey for all but the shortest holes – less than 50 m (164 ft).
7. Other survey errors may be the result of defective or uncalibrated survey tools. Any survey tool should be periodically checked and calibrated in accordance with the manufacturer’s specifications. For gyroscopic tools there are two excellent articles in previous issues of Coring Magazine on calibration written by Dan Billger and Duncan McLeod of Inertial Sensing One AB.
Concluding remarks
It may seem like complaining about some of these errors is rather pedantic but there can be profound impacts on geology and resource models because of them. Effects of collar and downhole survey errors on models for example are exacerbated when drilling at lower angles to narrow targets, such as gold vein systems. They may result in incorrect correlation of individual veins in parallel systems and over- or under-estimation of volumes (and therefore resource tonnages) when used in modelling. Incorrectly located mineralization intercepts (from collar or downhole survey errors) may in extreme cases even create apparently ‘new’ targets that are followed up with further drilling. Downhole survey errors in cored holes impact any structural measurements made from orientated core and can generate spurious inflections or orientation sub-sets of structural elements such as foliation and veins.
It is always frustrating as a consultant to have to notify a company that their drill hole database requires re-validation because there are obvious errors in collar locations or downhole surveys. Having to exclude drill holes from modelling because of unresolvable location problems is extremely disappointing. The concern is always that the obvious mistakes are accompanied by smaller ones that are harder to
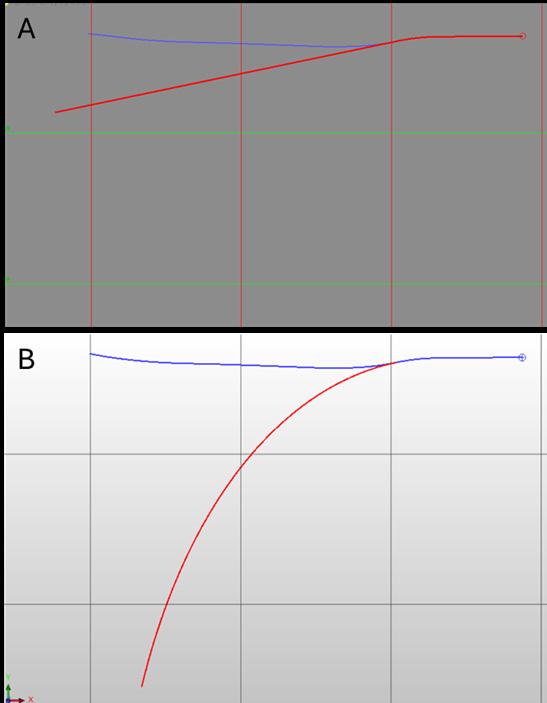
↑ Figure 2 - Different treatment of partially surveyed deviating hole paths by different software packages. Plan view of same hole as shown in Figure 1, with original data (blue) and assuming last survey was the suspicious reading at 72 m (236 ft) (red). A. Geoscience Analyst Pro plot (linear continuation from last survey), B. Geovia Surpac plot (continuation of curvature from last two surveys). Grid lines are 50 m (164 ft) spacing.
detect without more knowledge of the project. All the errors described above can be detected by some simple quality control procedures at the time of drilling: double-checking collar locations, comparing collars with high-res. DTMs and properly validating downhole surveys either by visual comparison of successive readings or by plotting in 3D. Finally, ensure that any corrections are written back into the master drill hole database, preferably with a comment or note specifying any changes that have been made and why.
Dr James Lally is a Principal Associate Consultant with Mining Associates Pty Ltd, a Brisbane-based geological, resource and mining consultancy group. C
For more information Get in touch with James Lally on LinkedIn
EEXCELLENCE ARTH-SHATTERING
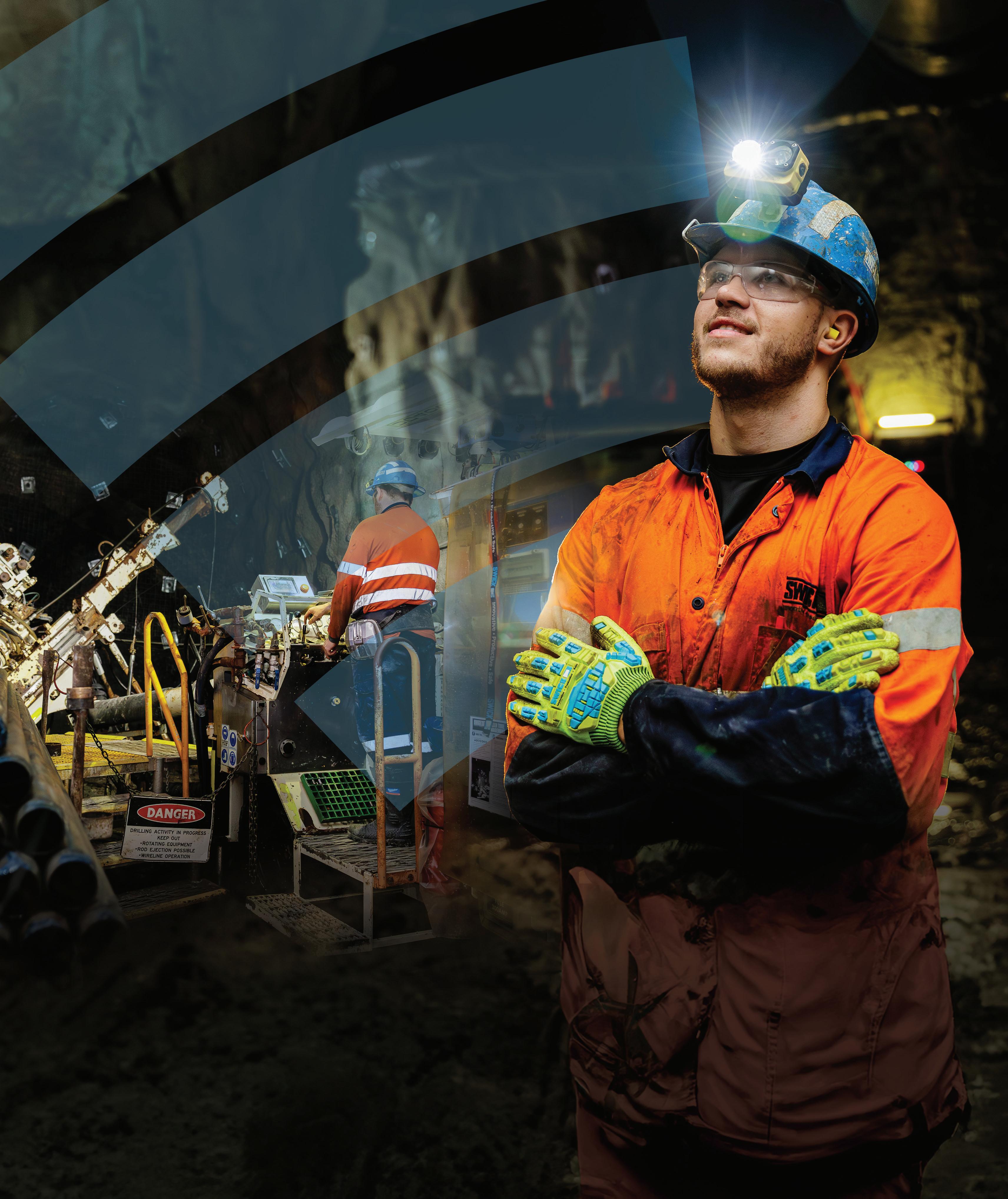
WE ARE SWICK ENGINEERING.
Hard rock mining’s heavyweight - innovating, manufacturing and delivering end-to-end excellence in drilling and underground diamond coring. A partnership with us is an investment in safety and versatility improvements in diamond drilling like no other.
INDUSTRY-LEADING DIAMOND DRILL RIGS MATCHED BY A TEAM DETERMINED TO ALWAYS PERFORM BETTER THAN THE DAY BEFORE? THAT’S EXCELLENCE UNEARTHED. THAT’S SWICK.
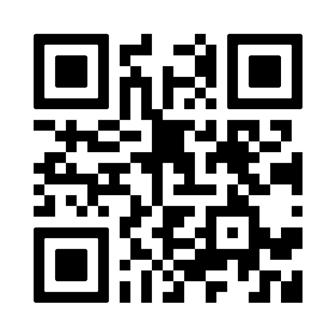
DRILL INTO THE POSSIBILITIES.
Drilling Services
Drilling Contractors (A-Z): Diamond Drilling, Reverse Circulation, AirCore
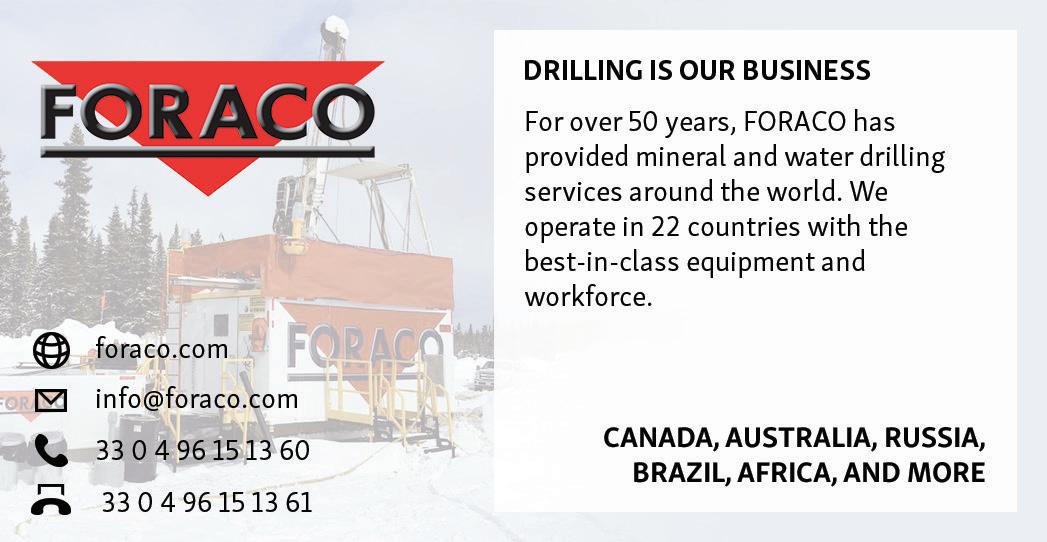
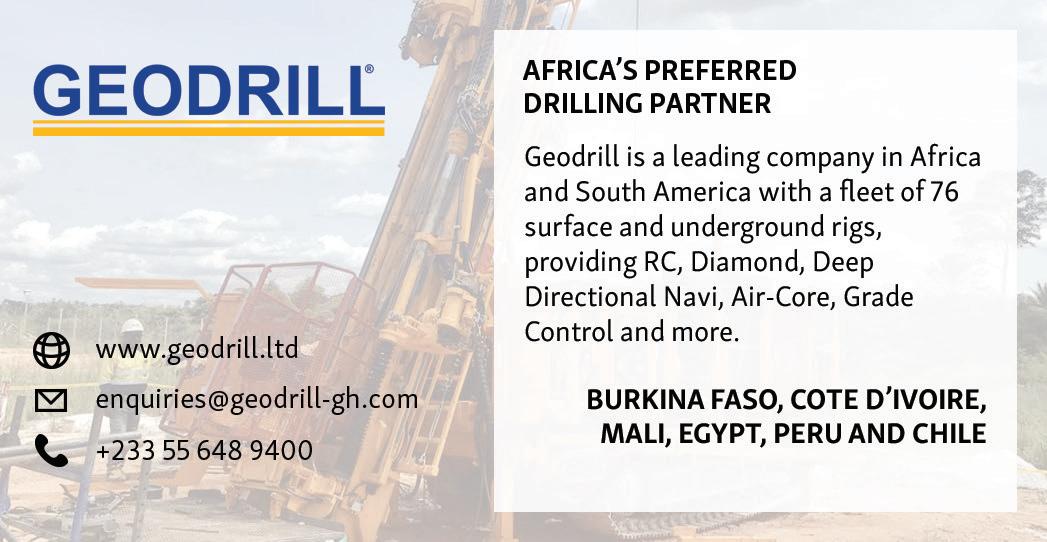
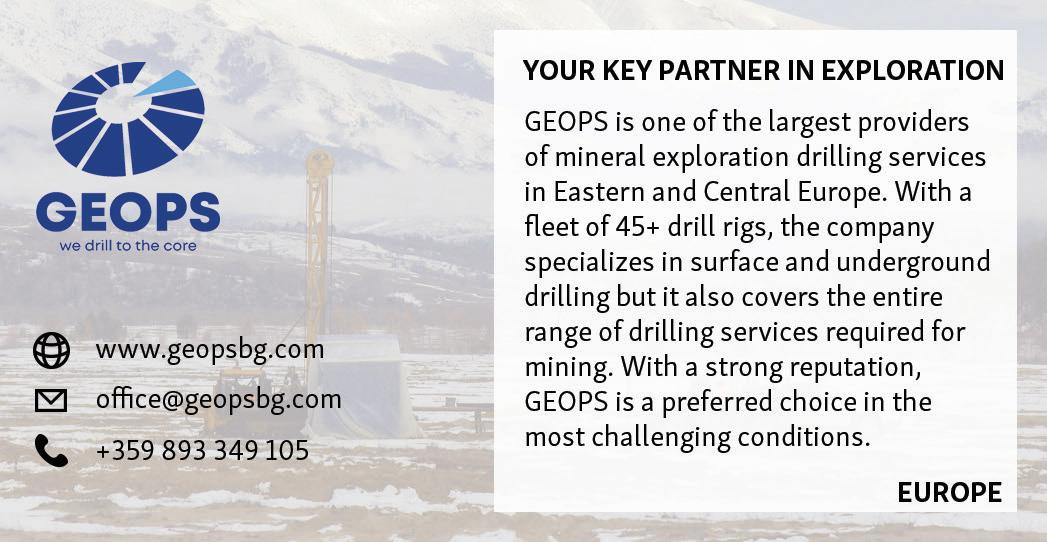
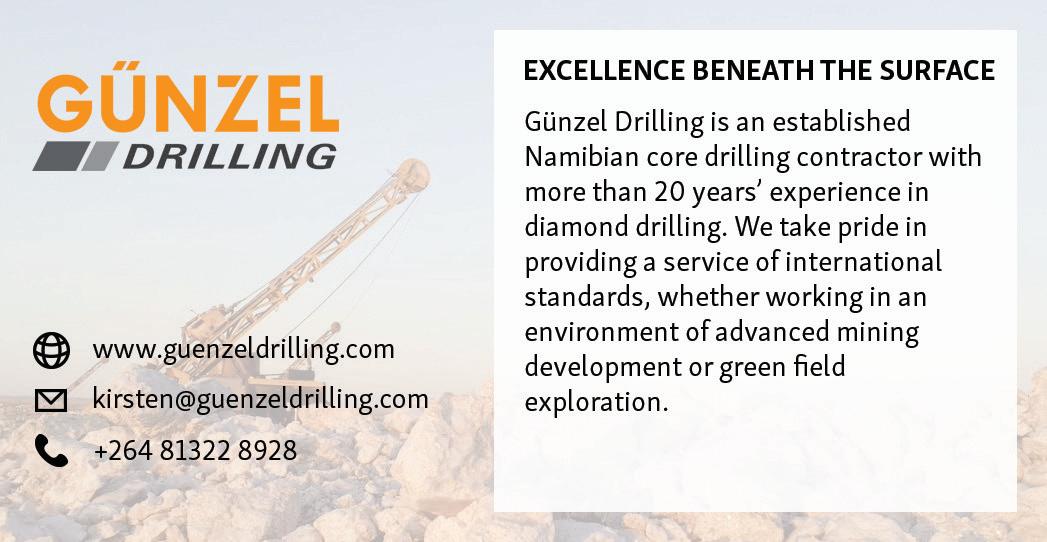

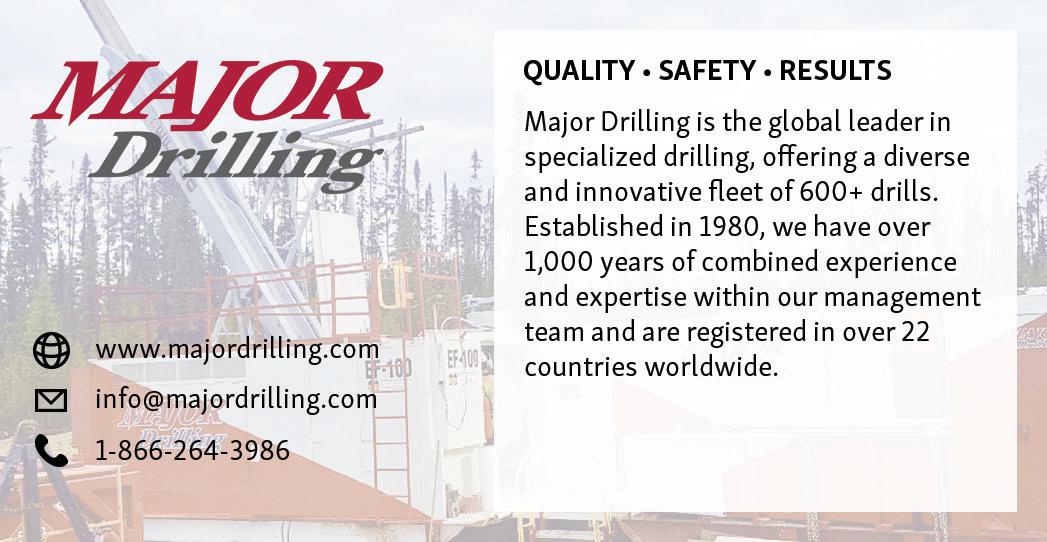
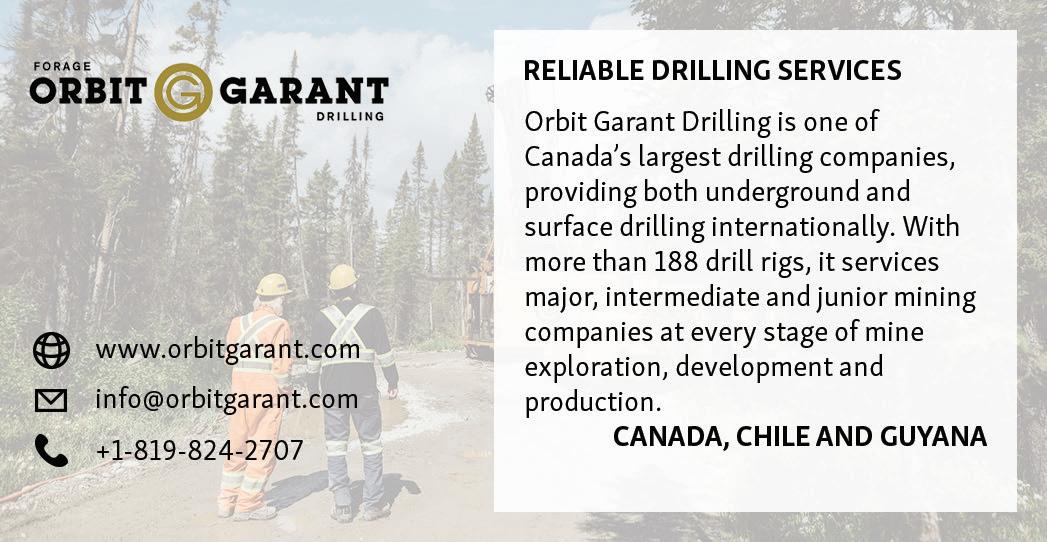
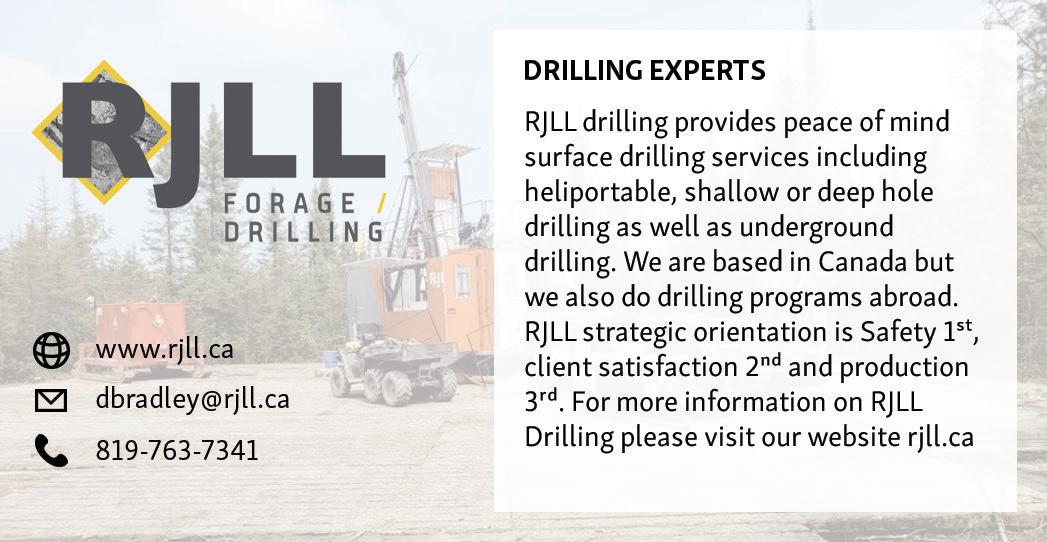
Drilling Contractors (A-Z): Cont.
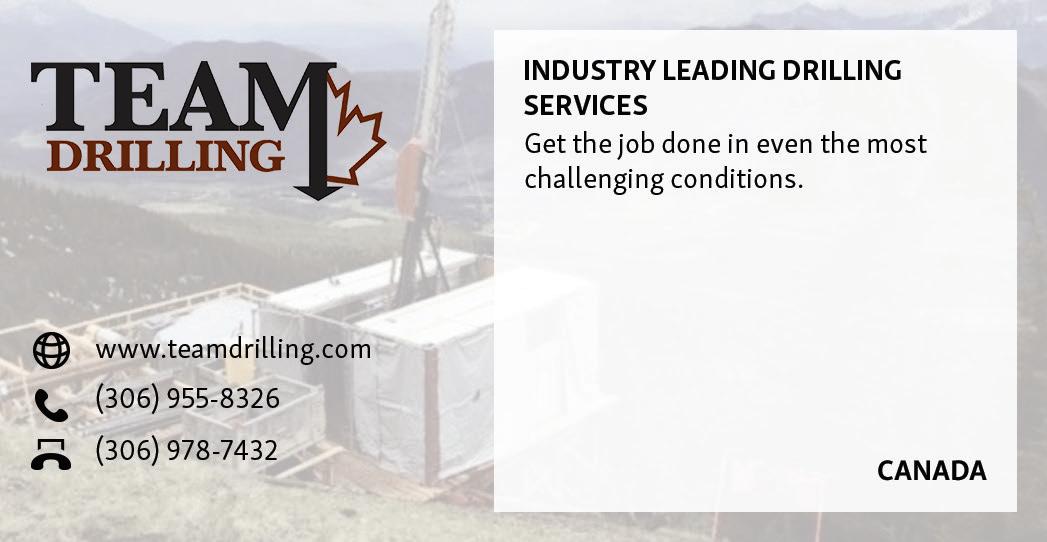
BRYSON DRILLING
Phone 306-323-2202 Fax 306-323-2203 info@brysondrilling.ca www.brysondrilling.ca Canada
CAPITAL DRILLING
Phone +230 464 3250 info@capdrill.com www.capdrill.com East, North and West Africa
DDH1 DRILLING Phone +61 08 9435 1700 admin@ddh1.com.au www.ddh1.com.au Australia
DIAFOR Phone (819) 860-3957 info@diafor.ca www.diafor.ca Canada
KATI OY Phone 0207430660 info@oykatiab.com www.oykatiab.com Finland
MITCHELL SERVICES Phone +61 7 3722 7222 Fax +61 7 3722 7256 info@mitchellservices.com.au www.mitchellservices.com.au Australia
Directional Drilling (A-Z)
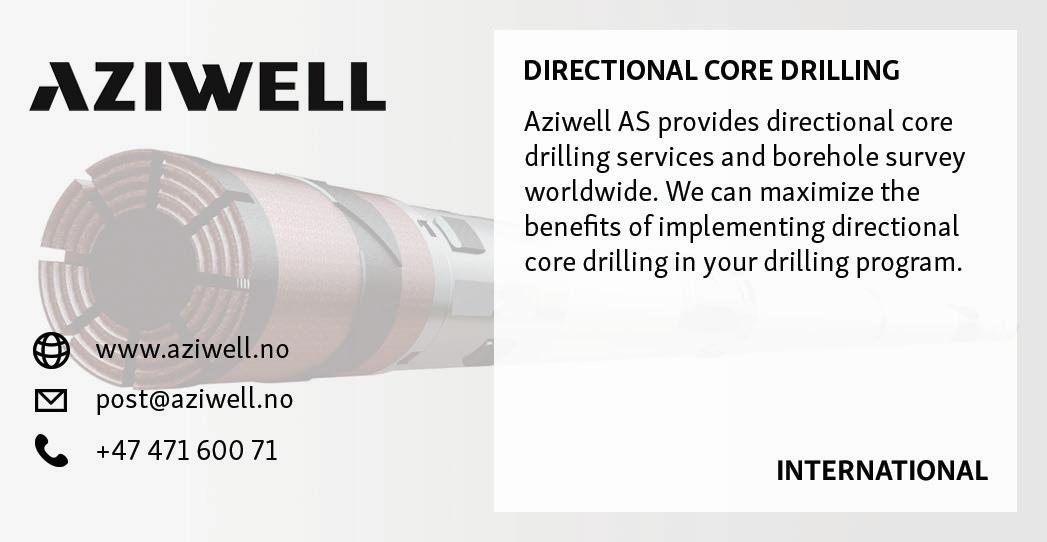
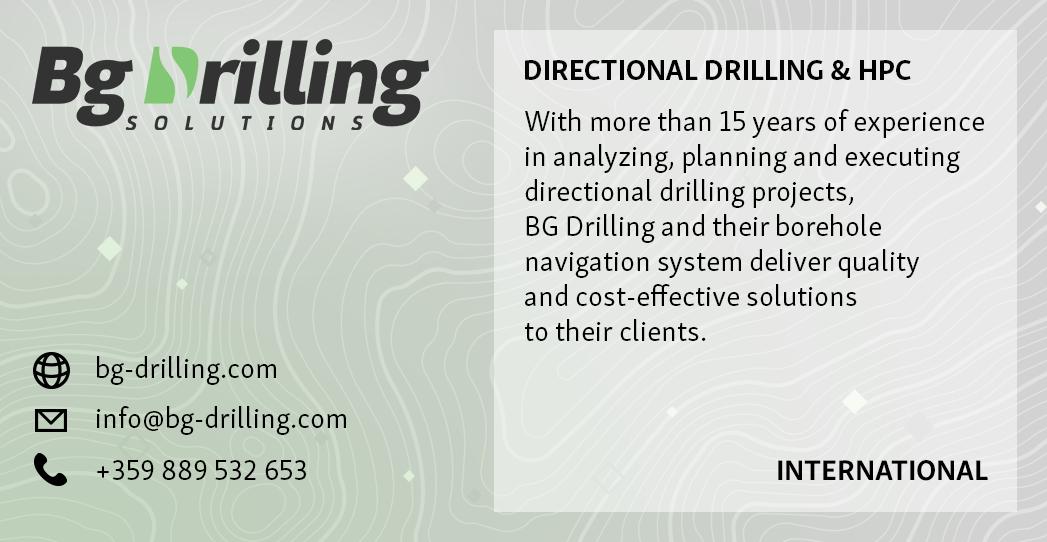
Drilling Equipment & Accessories
Drill Rigs & Accessories (A-Z)
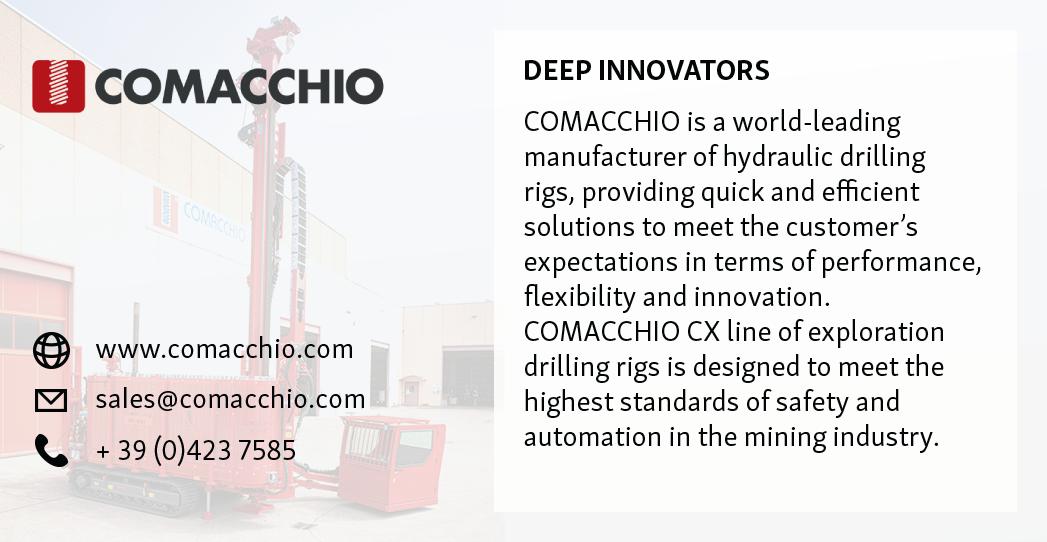
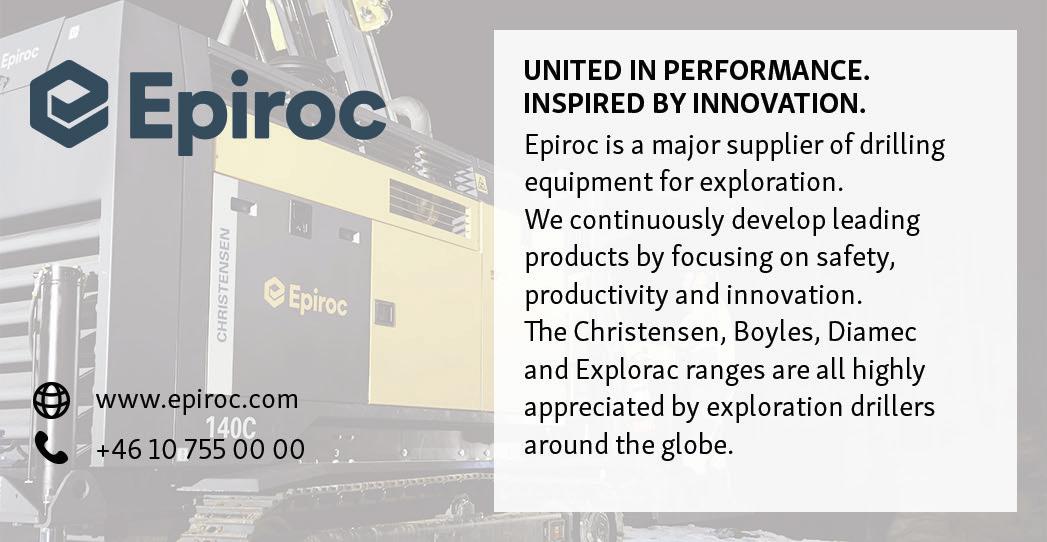
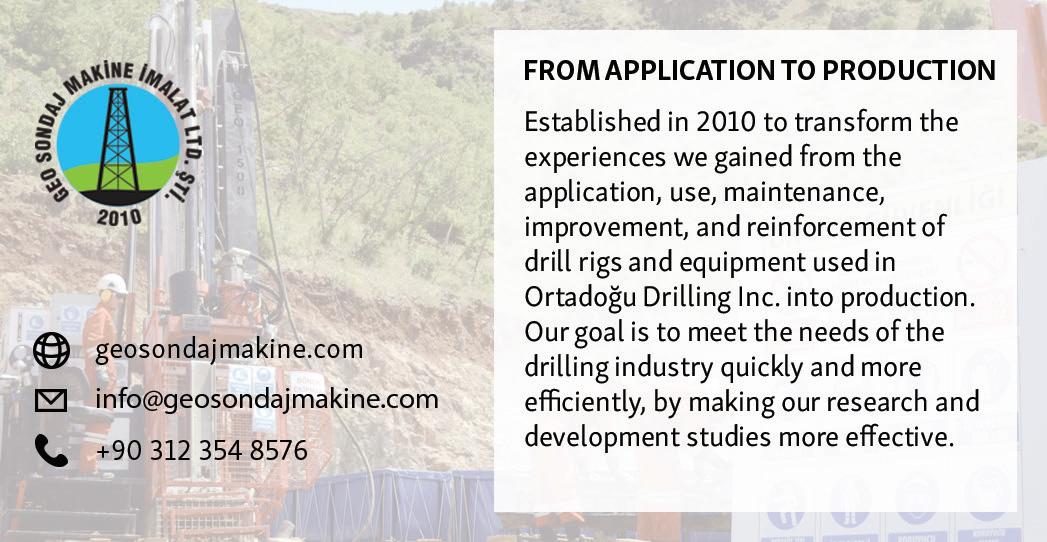
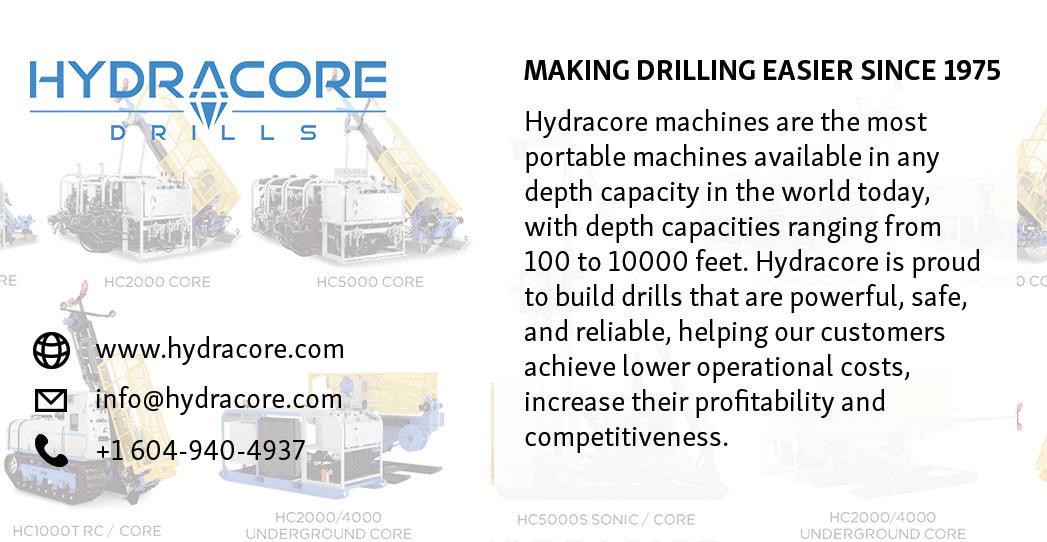
Drill Rigs & Accessories Cont.

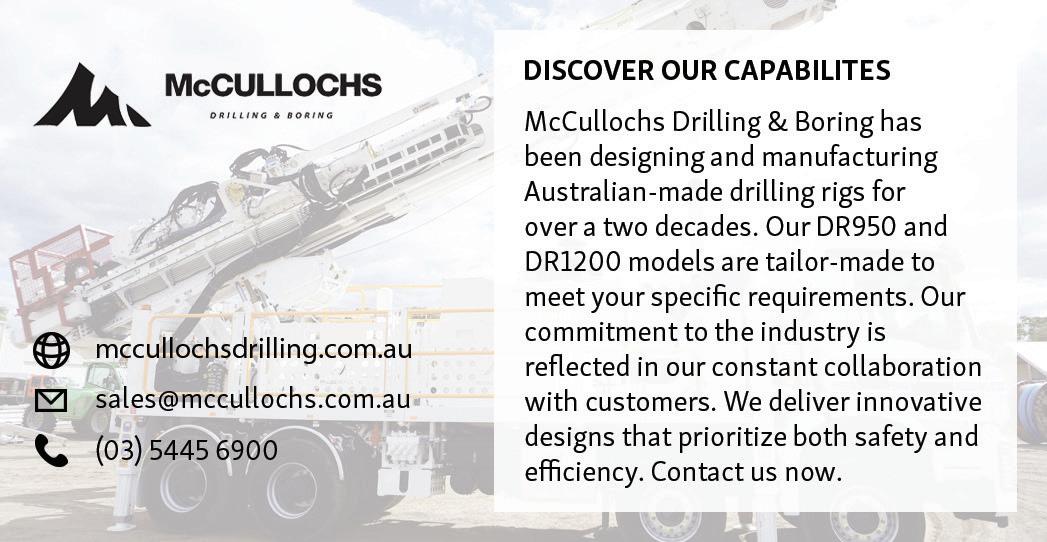
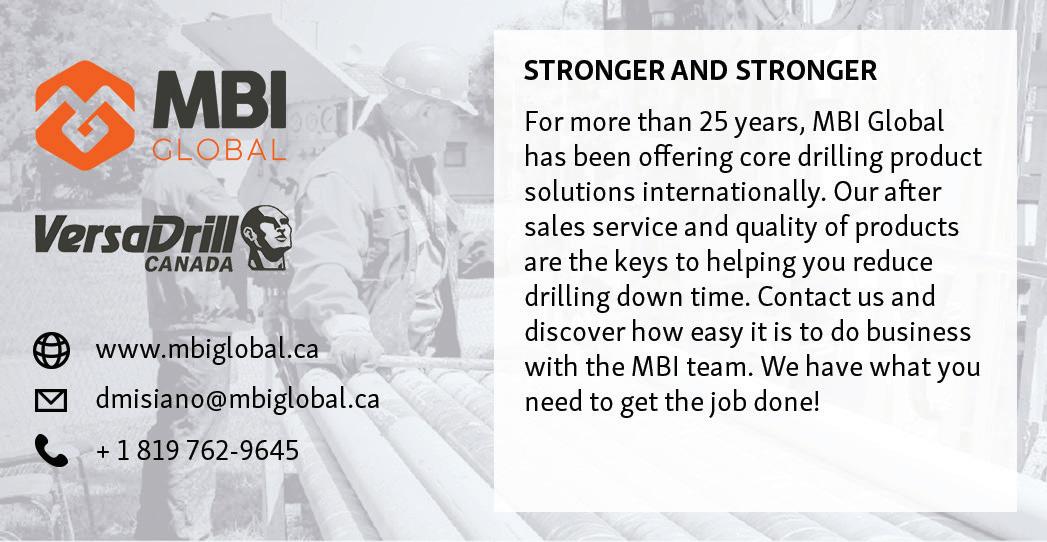

ATELIER VAL-D’OR
Phone (819) 824-3676
Fax (819) 824-2891
info@avddrills.com www.avddrills.com
BARKOM Phone 90-312 385 60 50 Fax 90-312 385 35 75 info@barkomas.com www.barkomas.com DISCOVERY DRILL MANUFACTURER Phone 1-506-542-9708 Fax 1-506-542-9709
info@discoverydrills.com www.discoverydrills.com
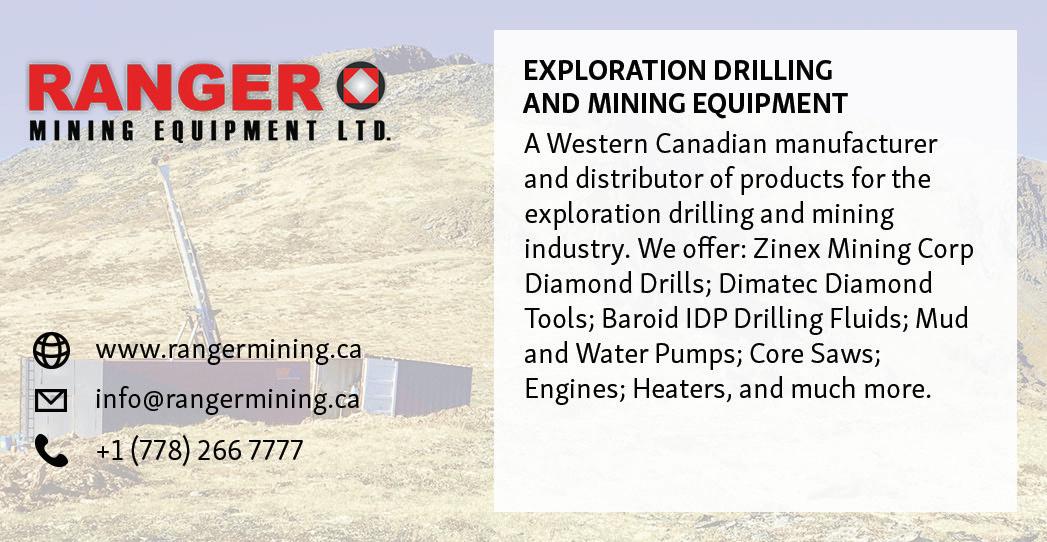
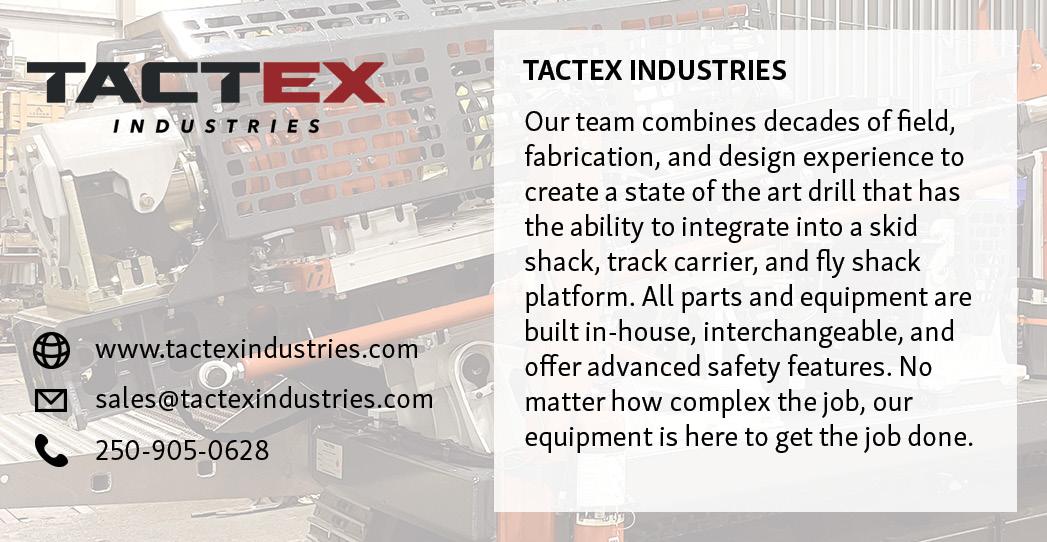
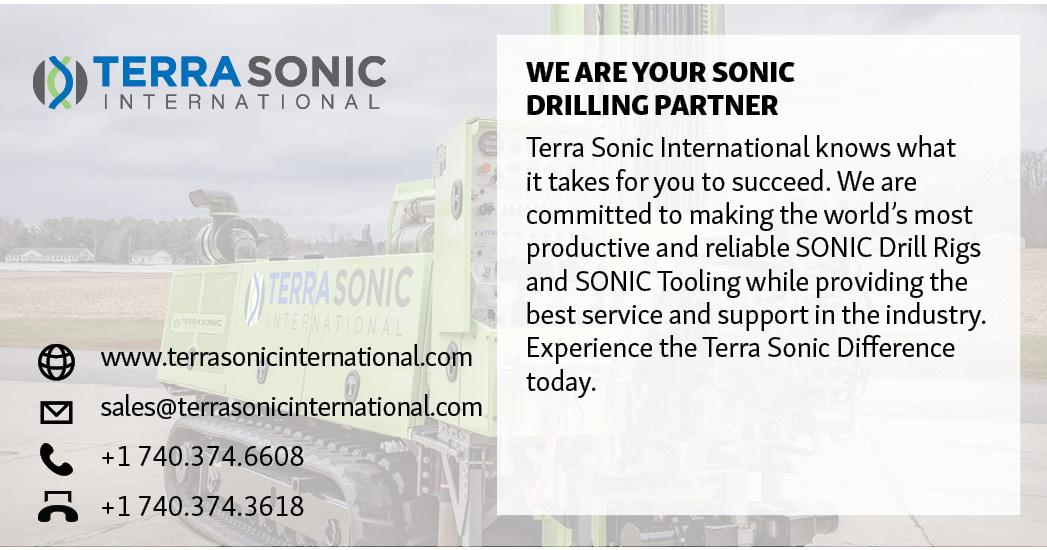
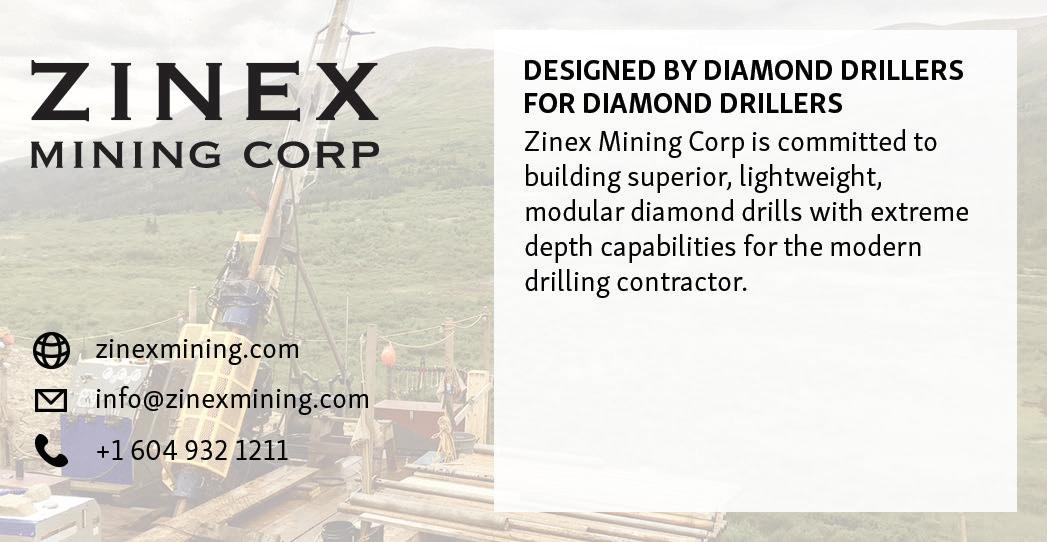
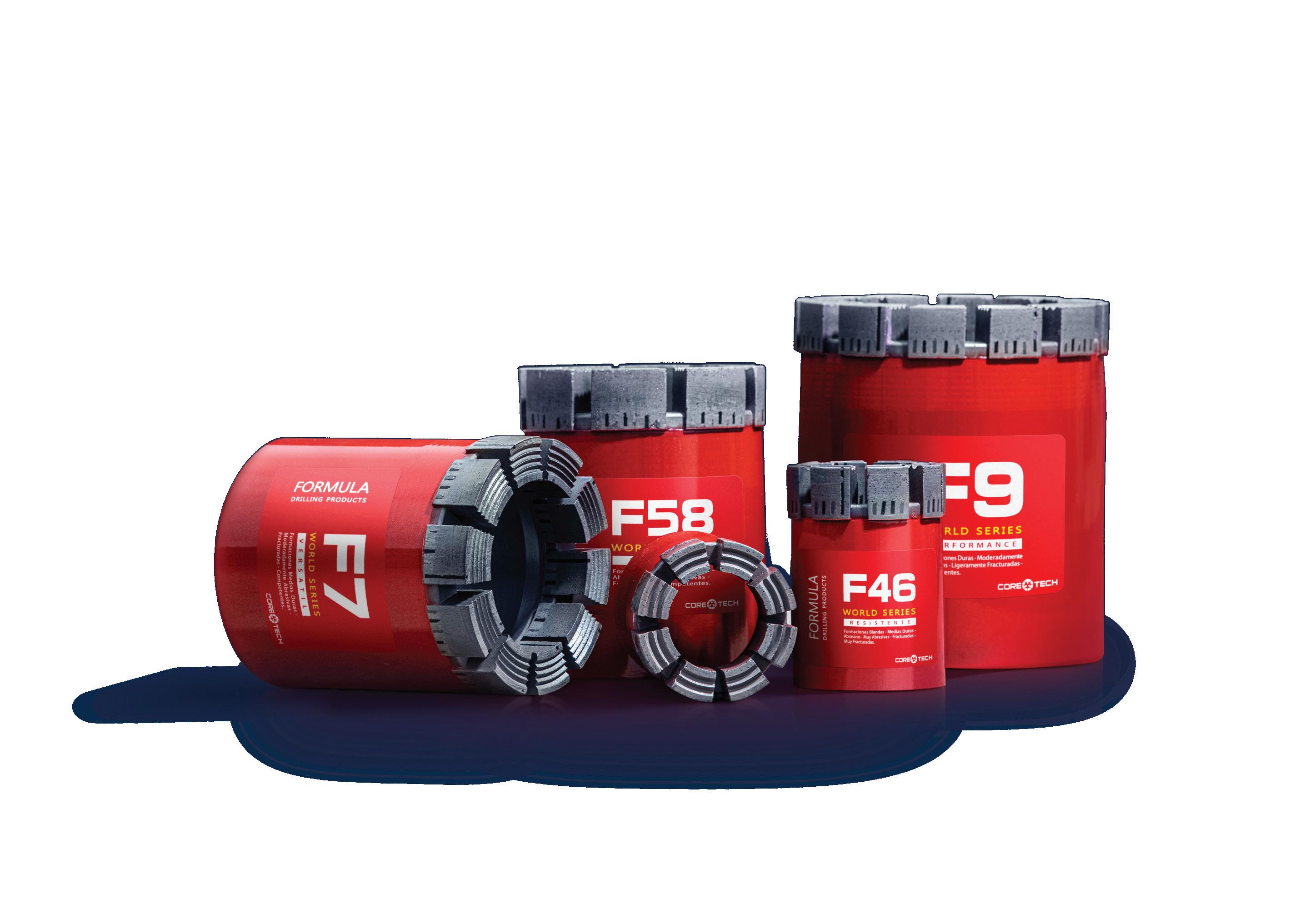
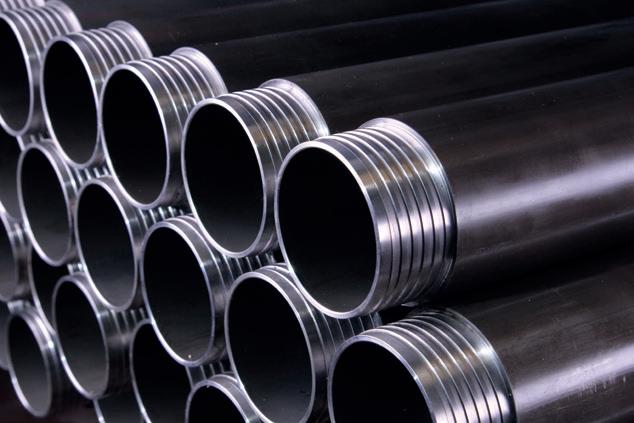
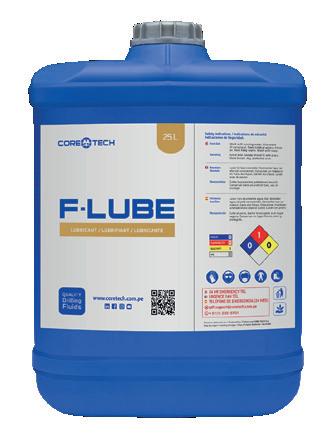
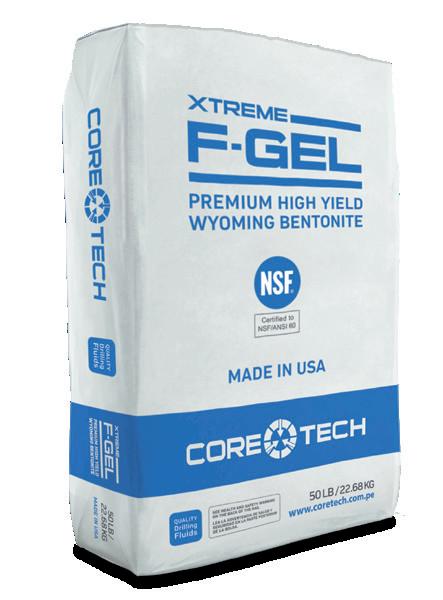
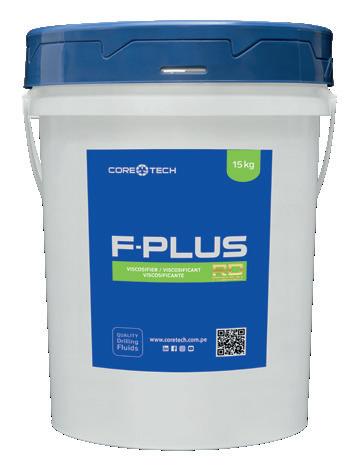


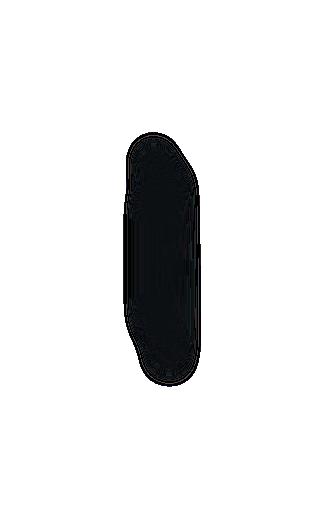
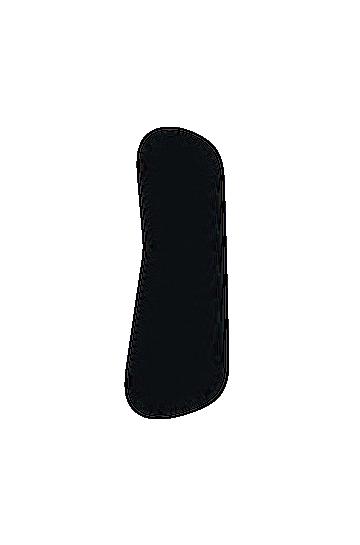
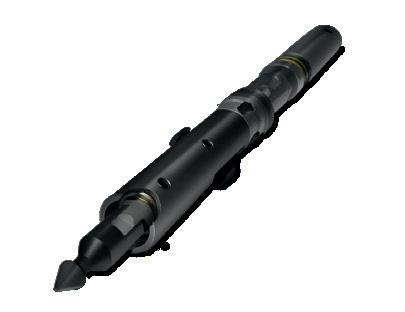
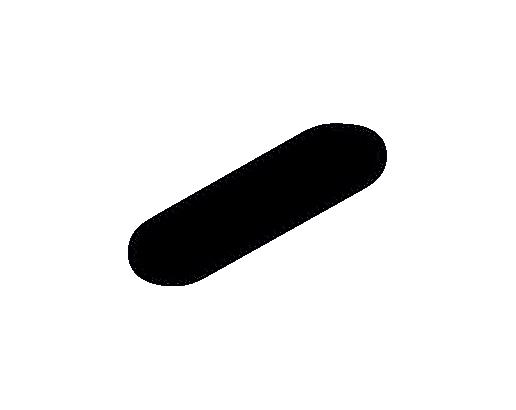
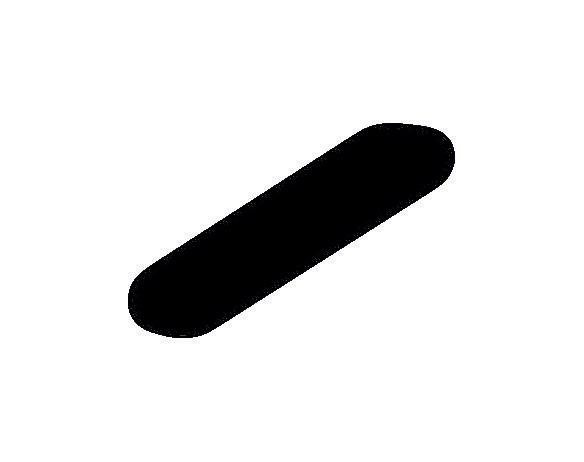
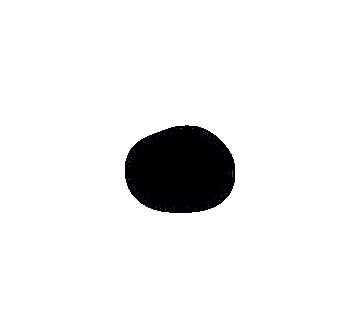
Drill Rig Parts (A-Z)
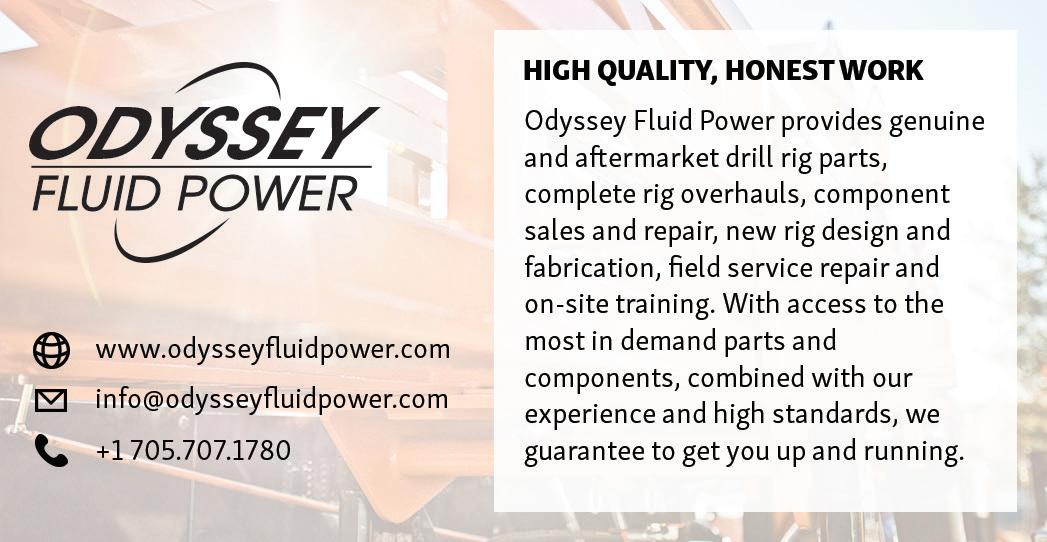
PROLENC
Phone (250) 563-8899
Fax (250) 563-6704 khodgins@prolenc.com www.prolenc.com
RC
Equipment (A-Z)
BOART LONGYEAR
Phone 1-801-972-6430
Fax 1-801-977-3374 www.boartlongyear.com
Specialized Machine Works (A-Z)
NORTH BAY MACHINING CENTRE
Phone (705) 472-9416
Fax (705) 472-2927 luc@nbmc.ca www.nbmc.ca
PROLENC
Phone (250) 563-8899 Fax (250) 563-6704 khodgins@prolenc.com www.prolenc.com
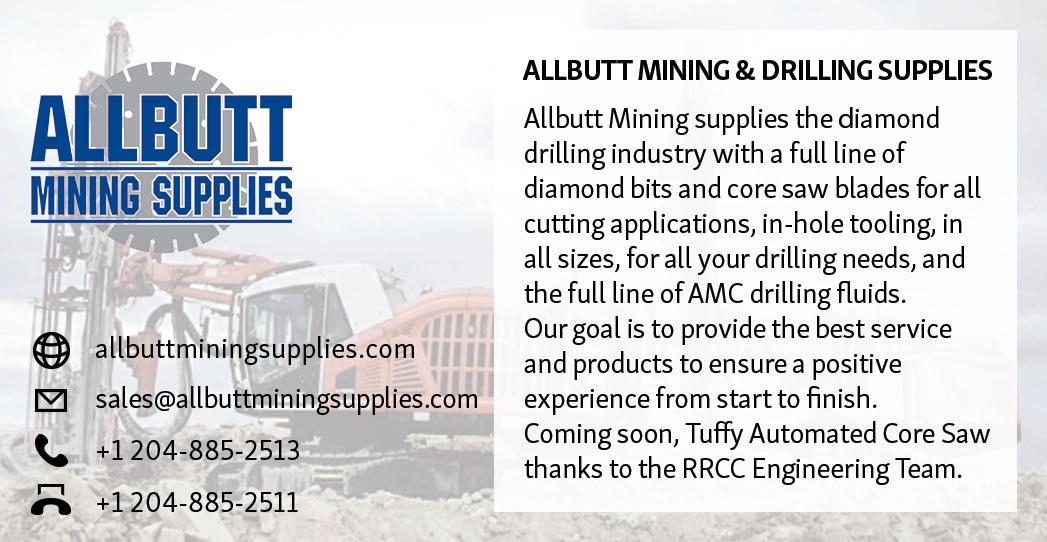
DIAMANTINA CHRISTENSEN
Phone +562 2620 7808 christensen@christensen.cl diamantinachristensen.com
DIASET Phone 1-800-663-5004 bits@diaset.com www.diaset.com
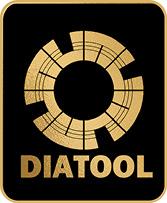
www.diatoolglobal.com anthonygraham6@gmail.com
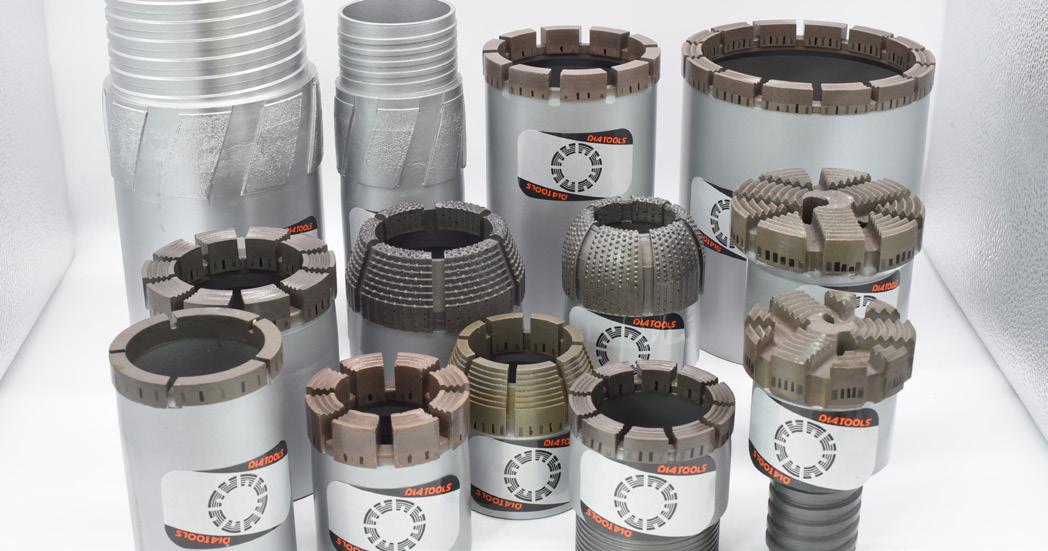
QUALITY AND EXPERTISE
DIATOOL is a young and dynamic company, founded in 2010. The company manufactures impregnated and set core bits, casing shoes, reaming shells, and geotechnical drilling bits. DIATOOL products are sold in North and South America, Australia, Asia, Africa, and Europe. DIATOOL Diamond Products are manufactured in a modern well-equipped plant, using the latest manufacturing technology.
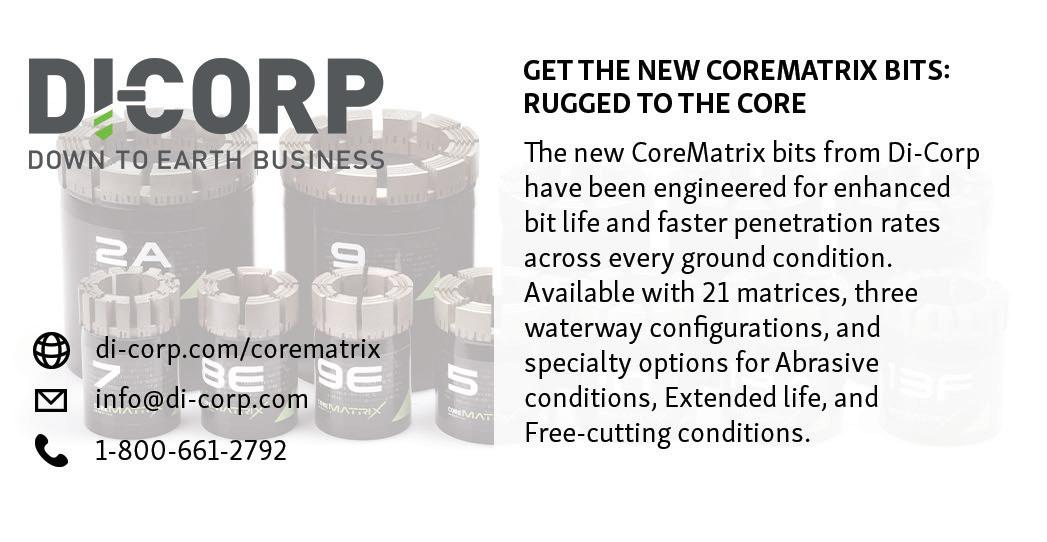
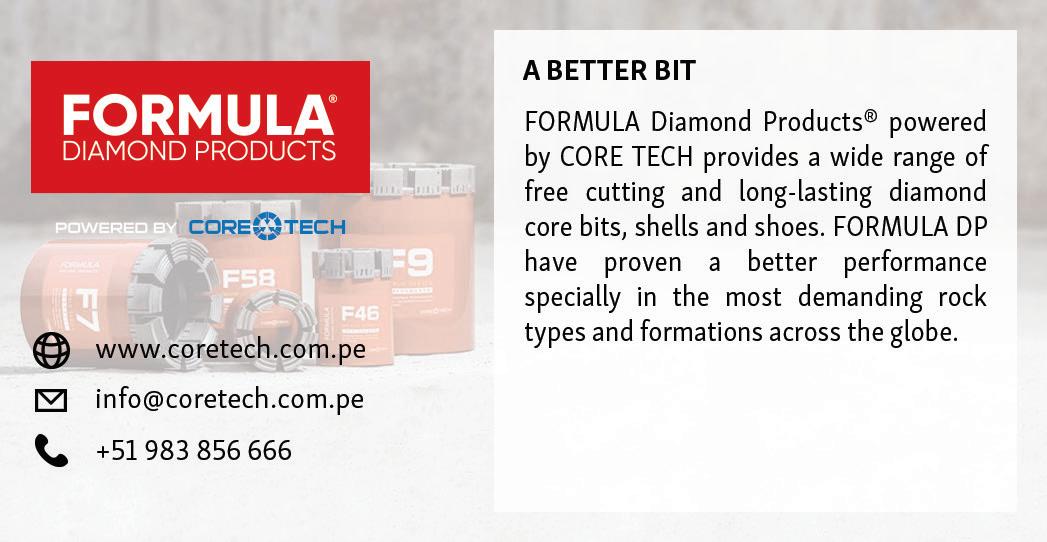
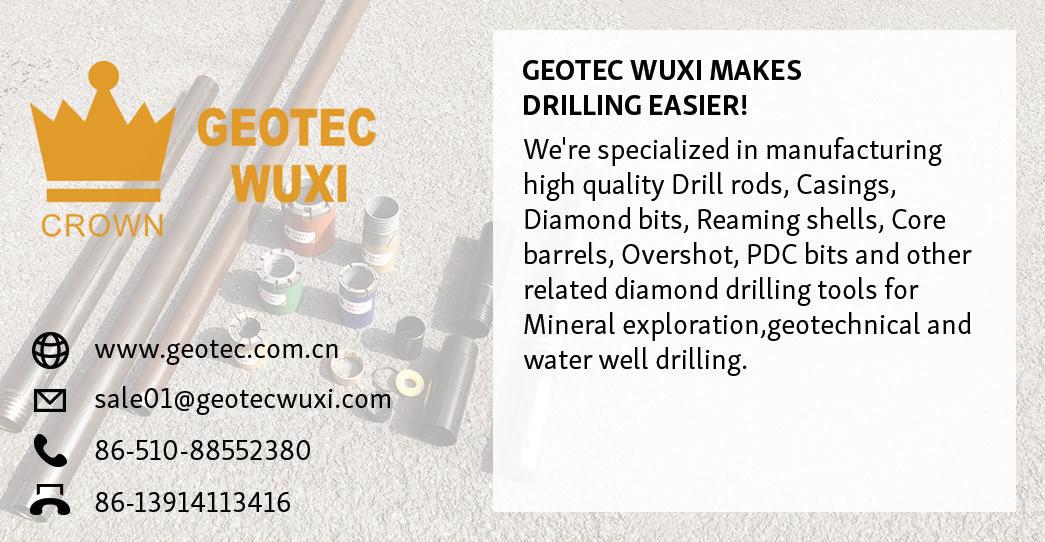
DIATOOL DIAMOND PRODUCTS Phone 852 2871 9028 diatool@163.com www.diatool@global.com
HOLE PRODUCTS
Phone (888) 465-1569 Fax (320) 631-0064 www.holeproducts.com
Diamond Products (A-Z)
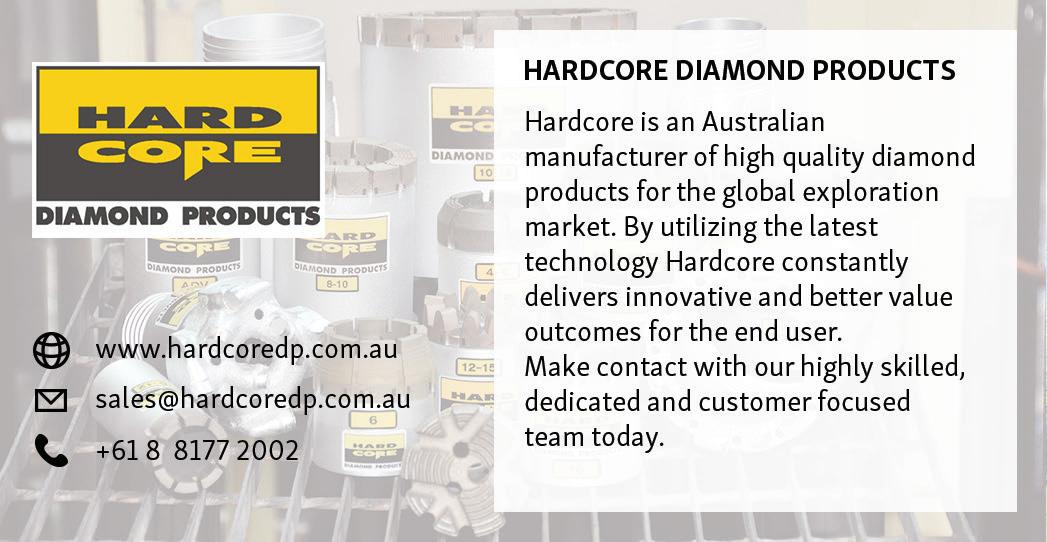
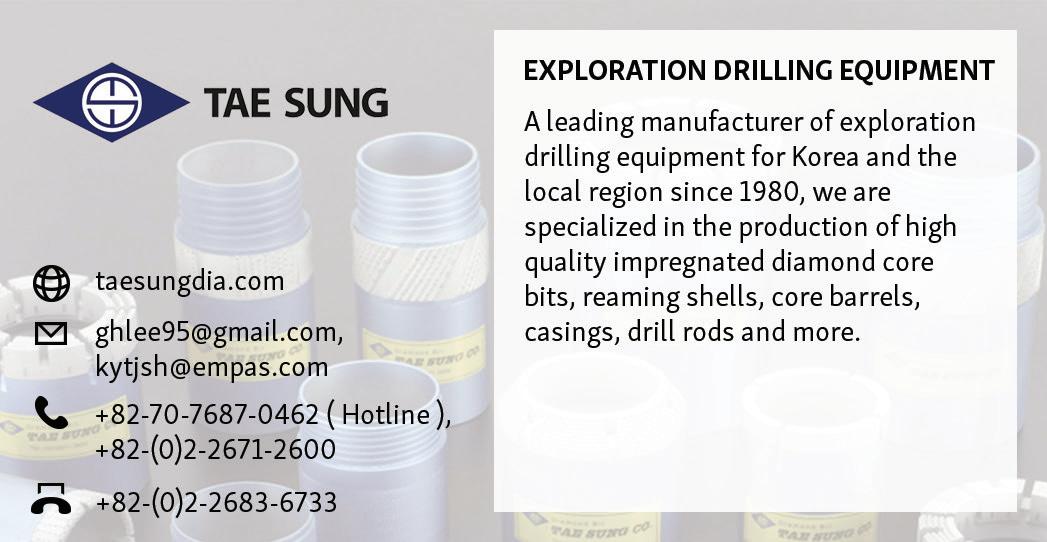

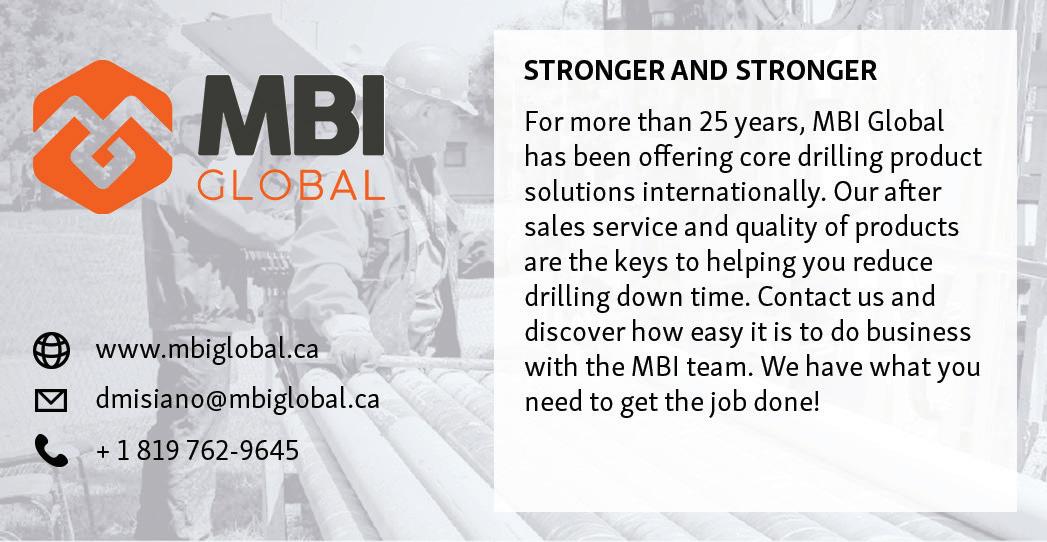
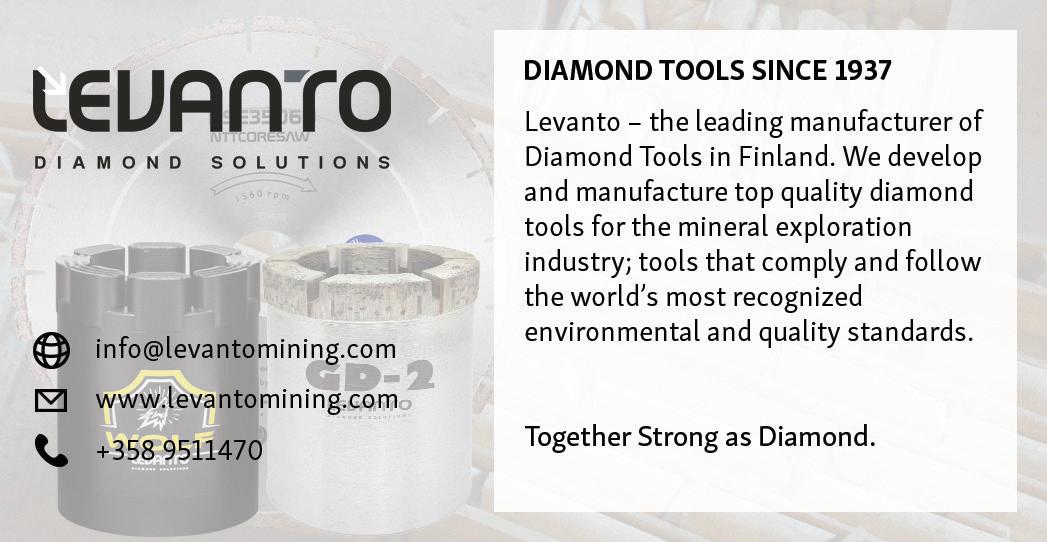
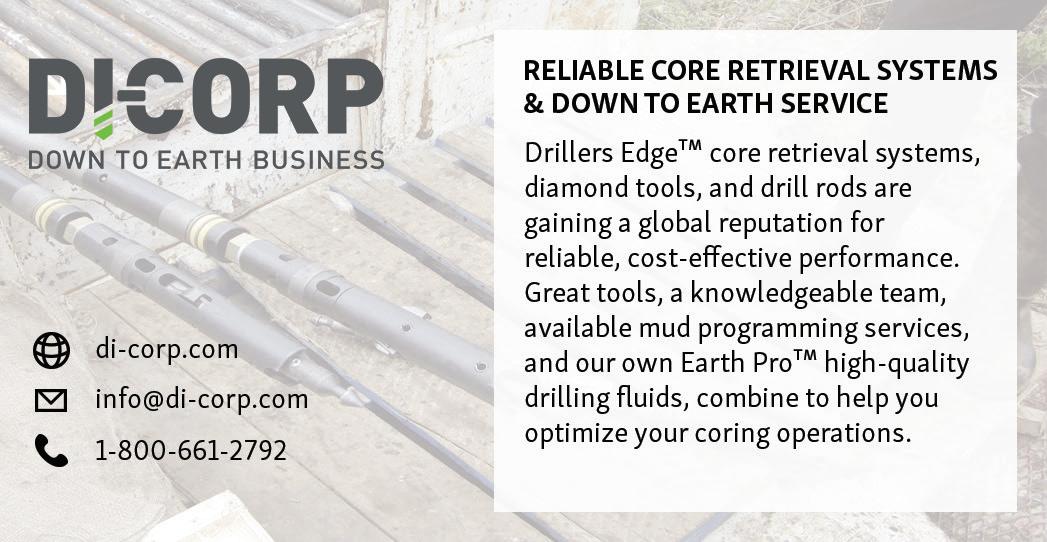
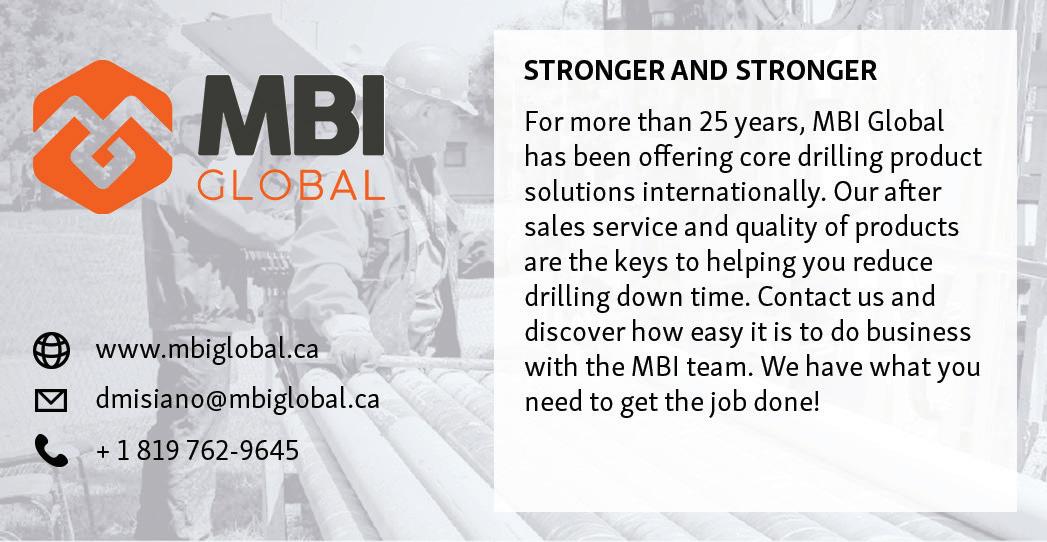
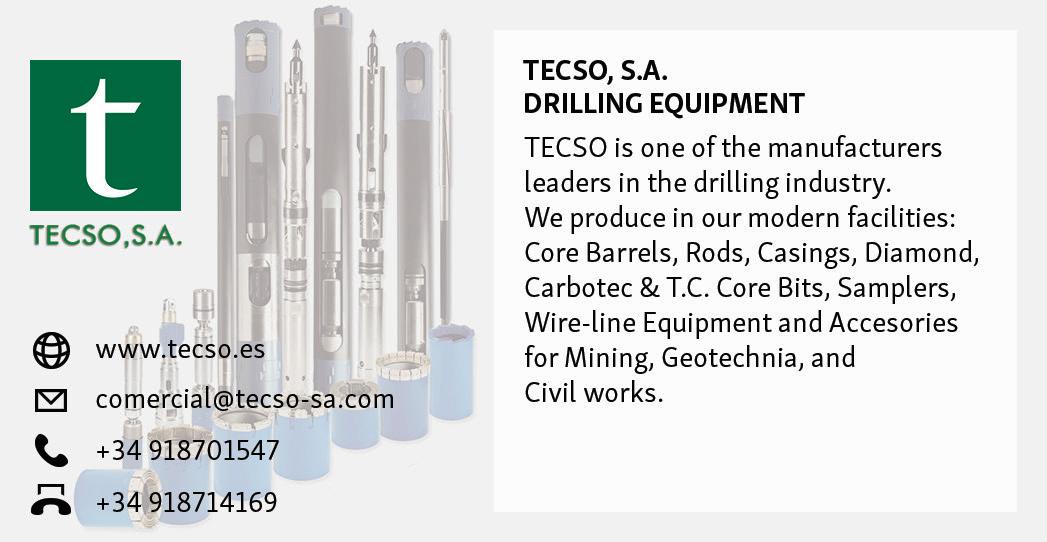
Core Barrels (A-Z)
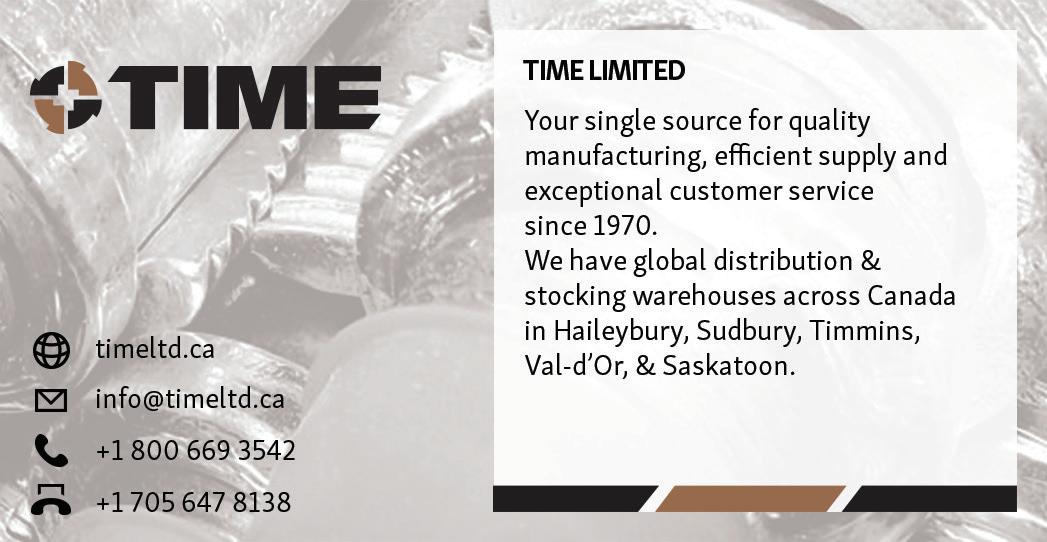
BOART LONGYEAR
Phone 1-801-972-6430
Fax 1-801-977-3374
www.boartlongyear.com
HOLE PRODUCTS
Phone 909-939-2581
Fax 909-891-0434 www.holeproducts.com
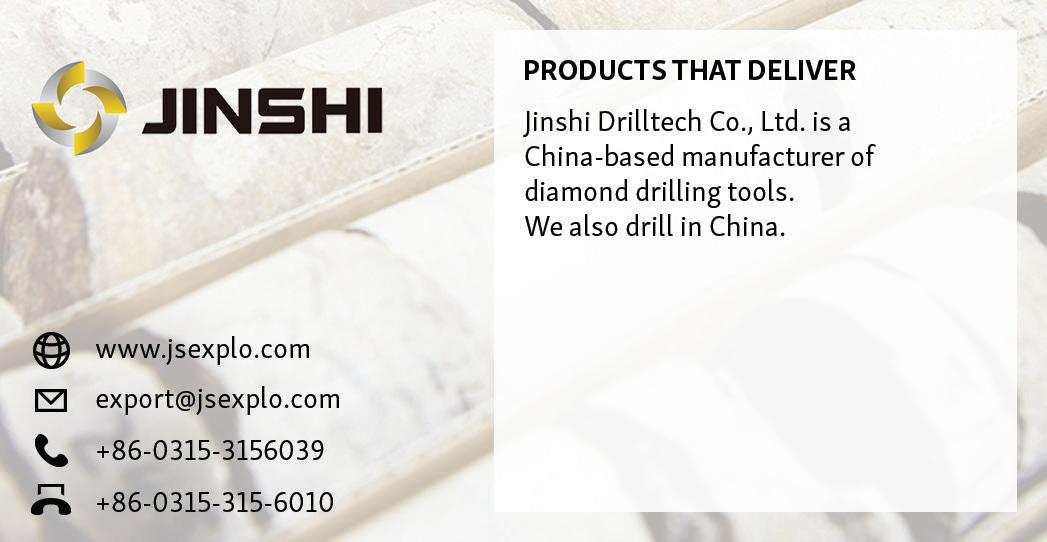
SINOCOREDRILL
Phone 86-510-82723272
Fax 86-510-82752846
sales@sinocoredrill.com www.sinocoredrill.com
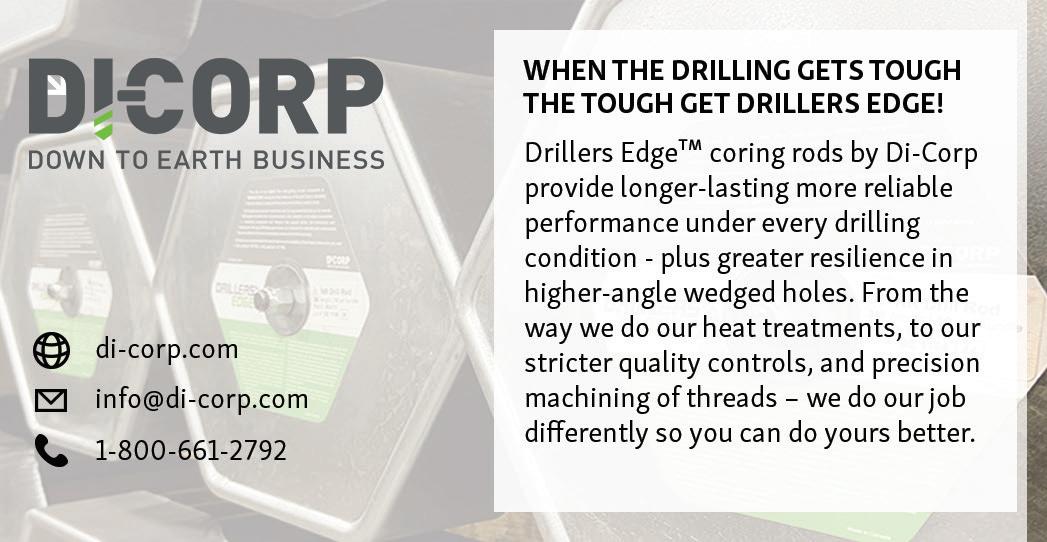
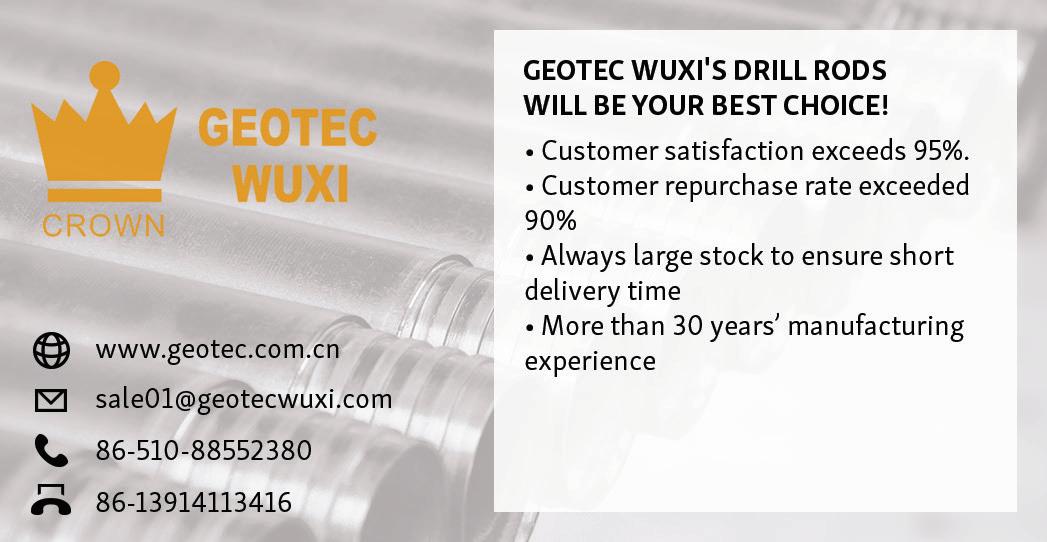
BARKOM
Phone 90-312 385 60 50
Fax 90-312 385 35 75 info@barkomas.com www.barkomas.com
CORE TECH
Phone +51 983 856 666 info@coretech.com.pe www.coretech.com.pe
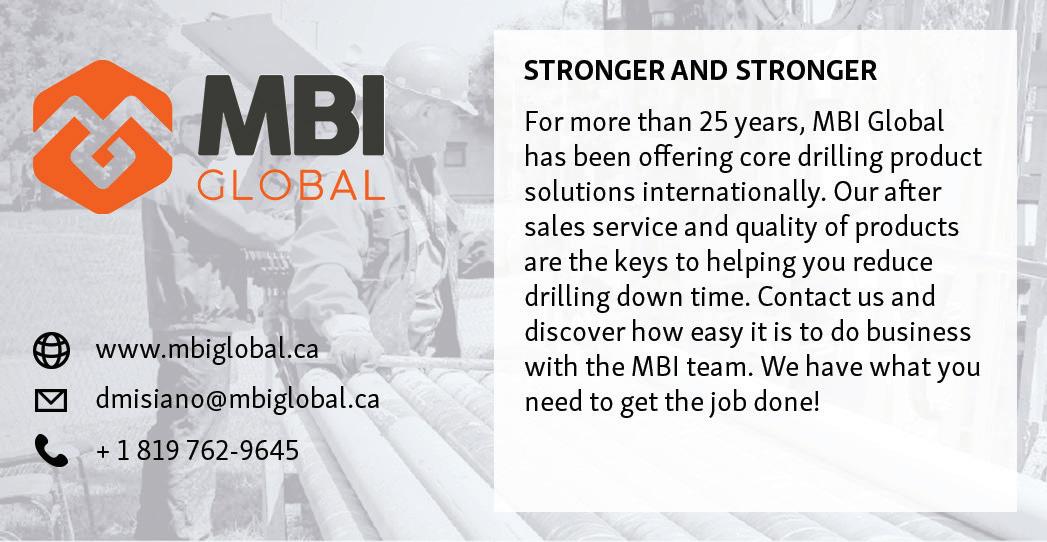
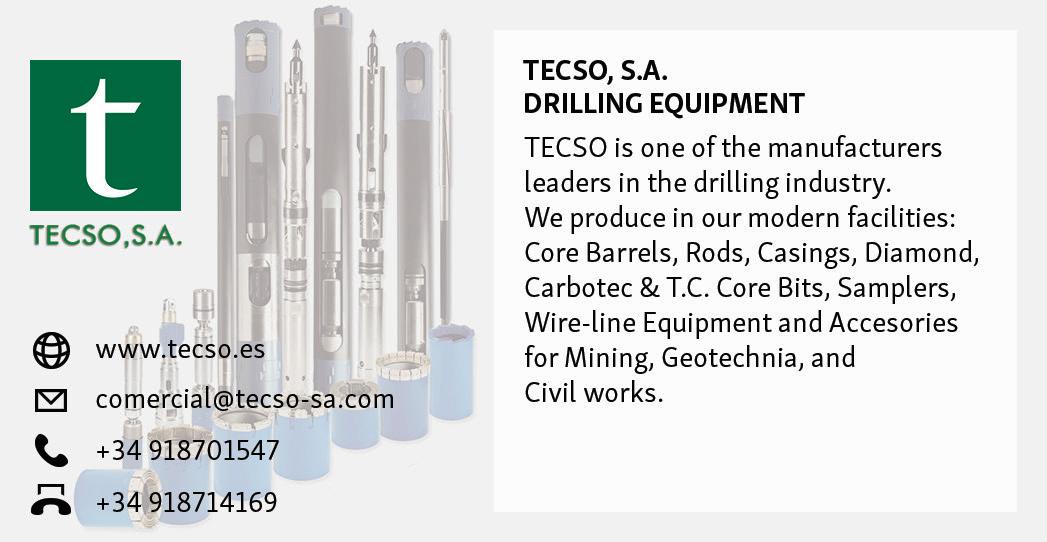
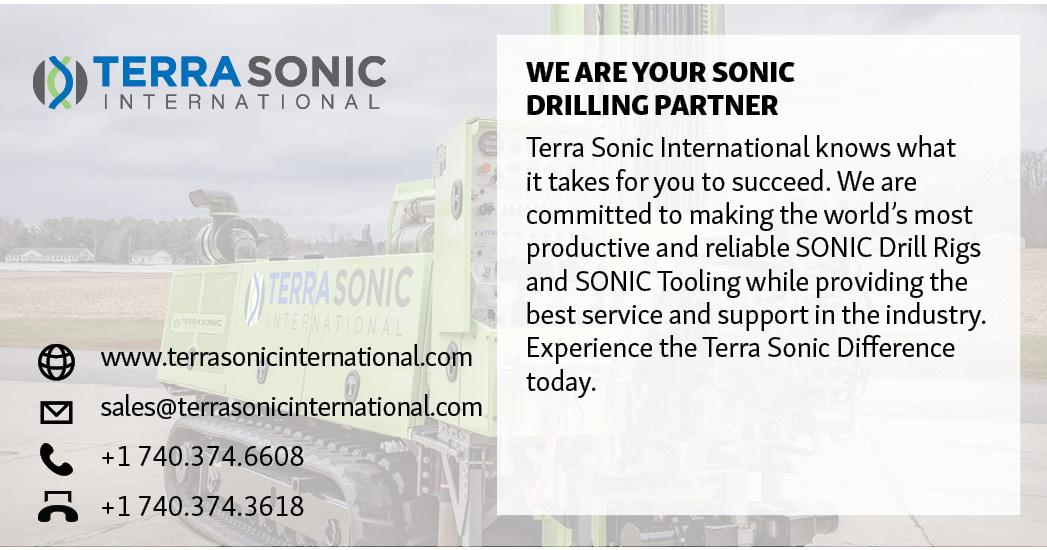
Drill Rods & Casings Cont.
Drill Rods & Casings (A-Z) Core Barrels Cont.
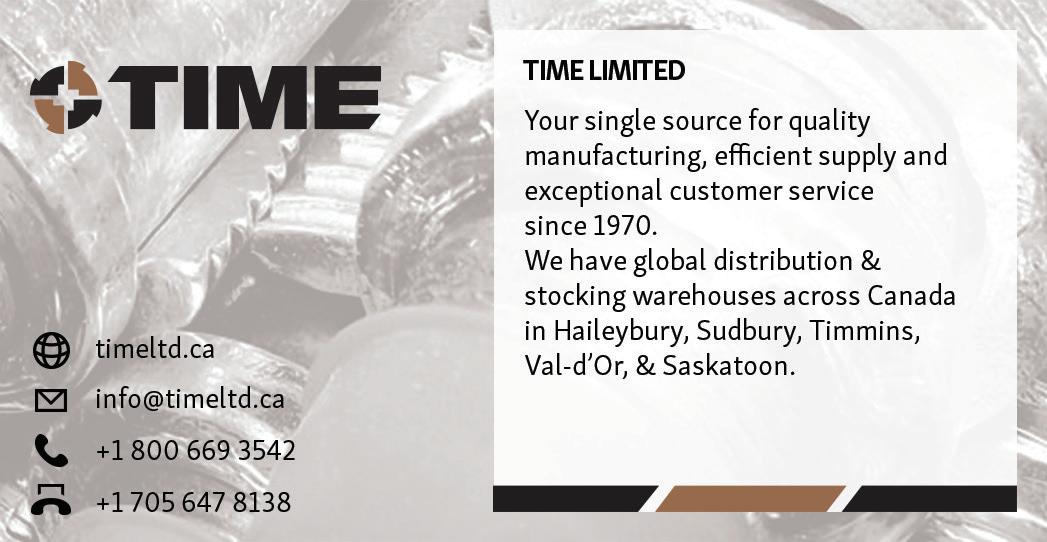
REFLEX
Phone 1-705-235-2169 Fax 1-705-235-2165 reflex@imdexlimited.com www.reflexnow.com
SONDA PARTS
Phone 55 – (31) 3391 3810 Fax 55 – (31) 3391 3810 comercial@sondaparts.com.br www.sondaparts.com.br/
Survey Equipment
Survey Tools (A-Z)
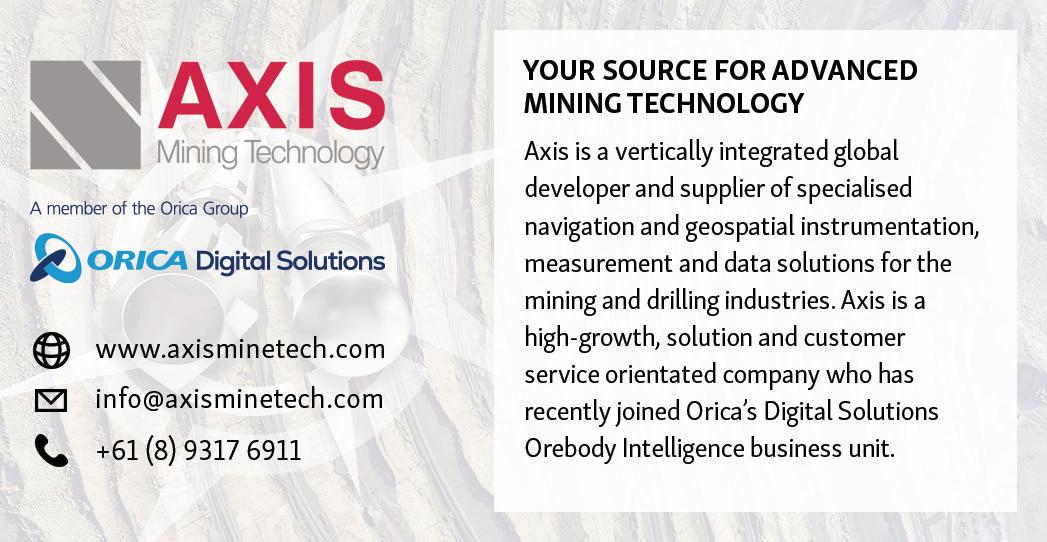
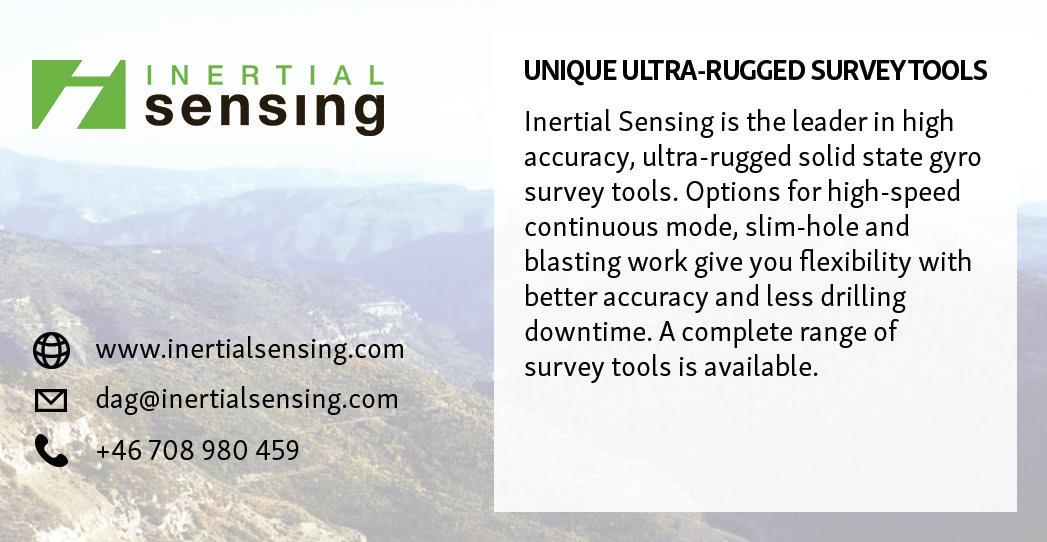
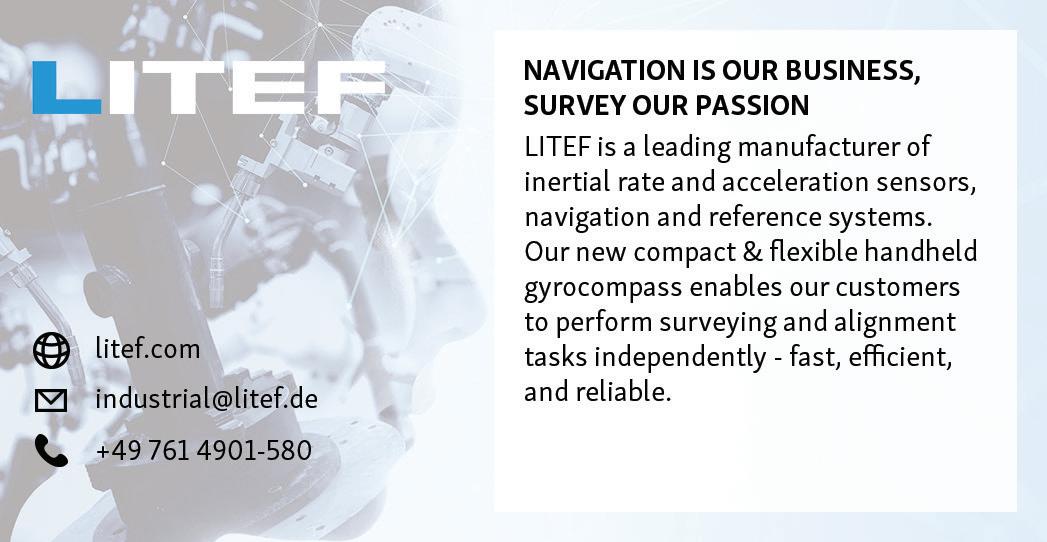
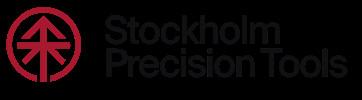
sptab.com sales@sptab.com +34 952 17 99 18 Survey Tools Cont.
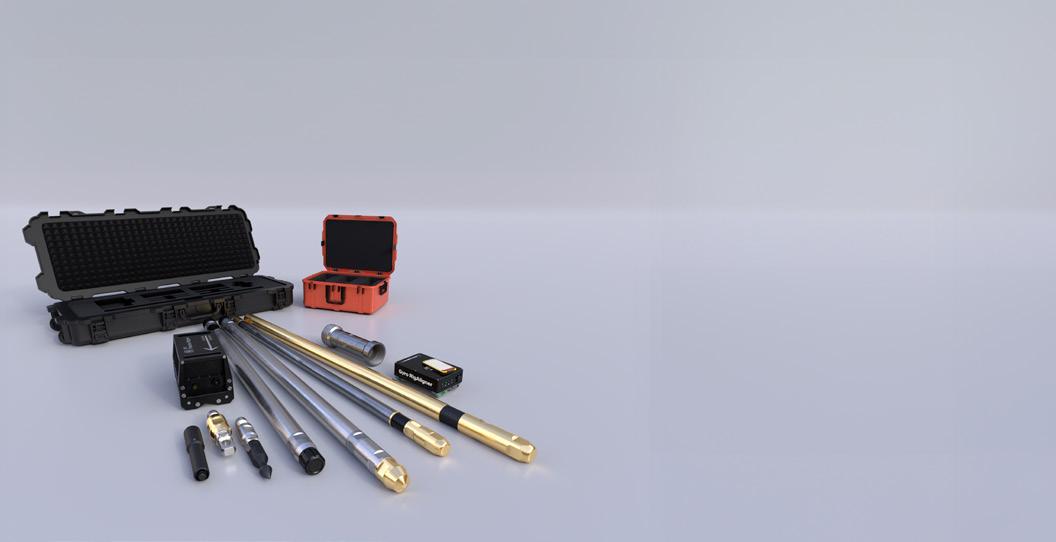
ADVANCED DOWNHOLE SURVEY TOOLS FOR EXPLORATION AND BLASTING
SPT is your global partner for downhole survey technology. We manufacture advanced solutions for high precision downhole and blasthole survey data. Our commitment to quality and accuracy has made us an industry leader. Request a free demonstration today.
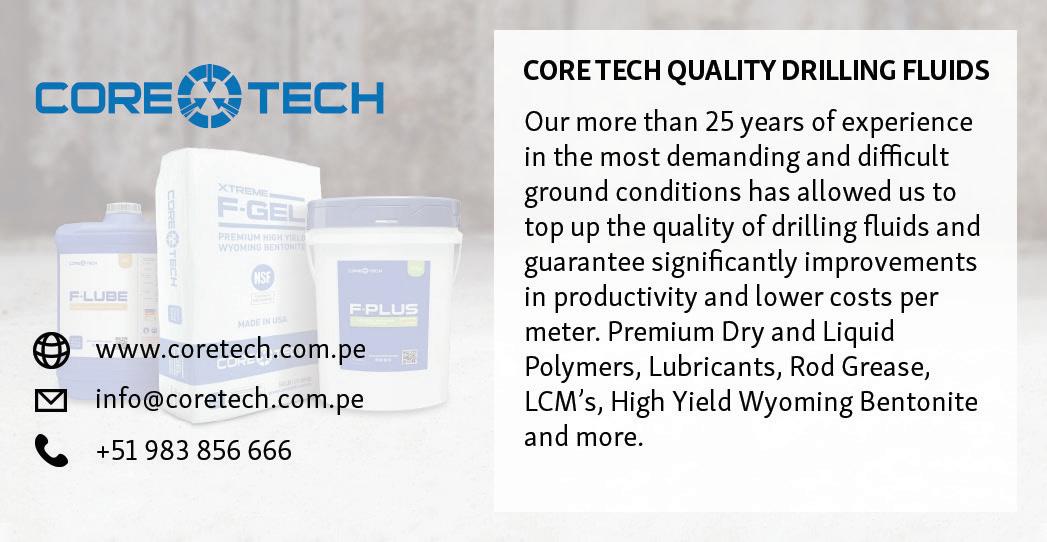
AMC Phone 1-705-235-2169 www.amcmud.com DI-CORP
Phone +1 (705) 4727700 info@di-corp.com www.di-corp.com MUDEX
Phone +61 (8) 9390 4620 info@mudex.com.au www.mudex.com.au
Drilling Fluids (A-Z)
Wedges (A-Z)
Drilling Fluids Cont.
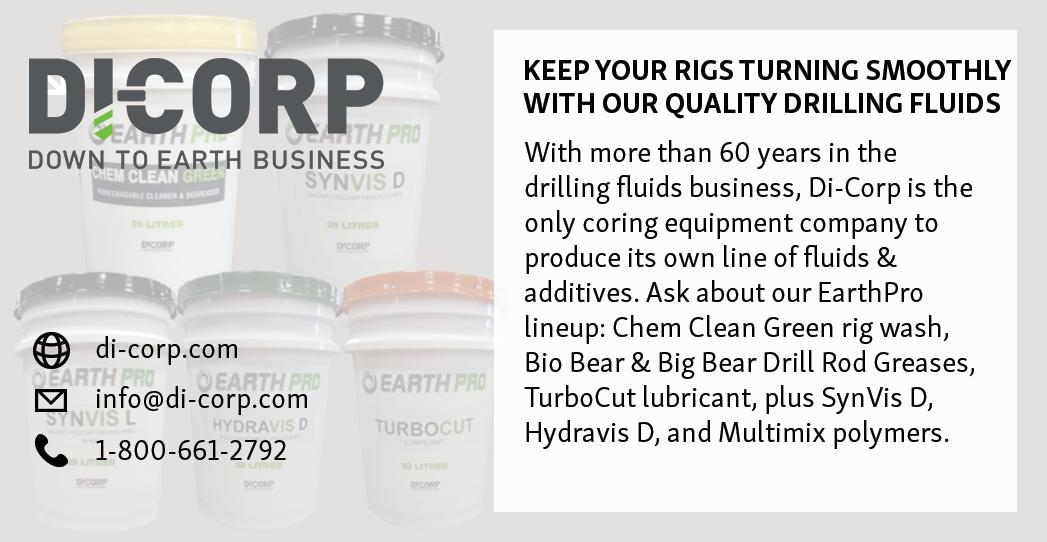
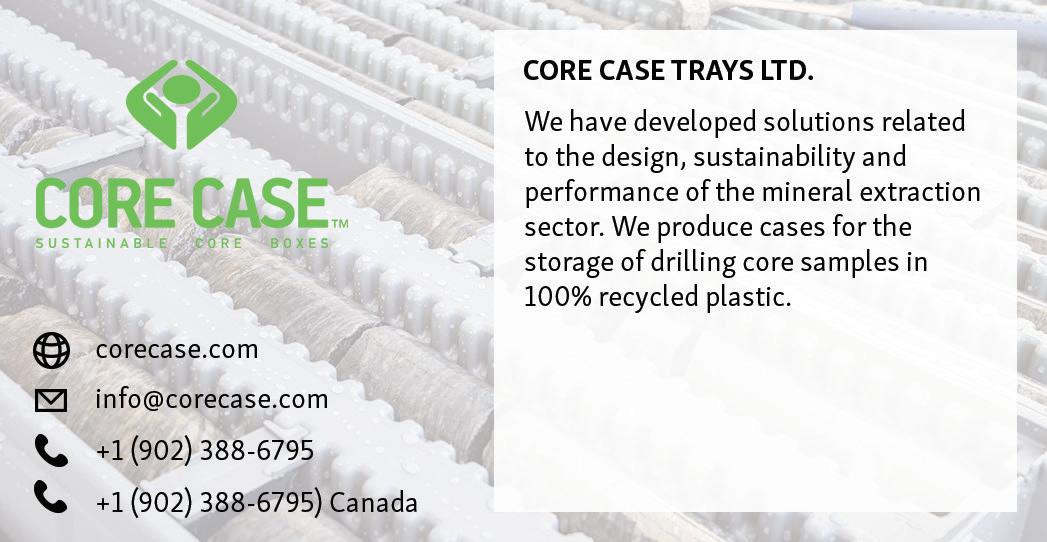
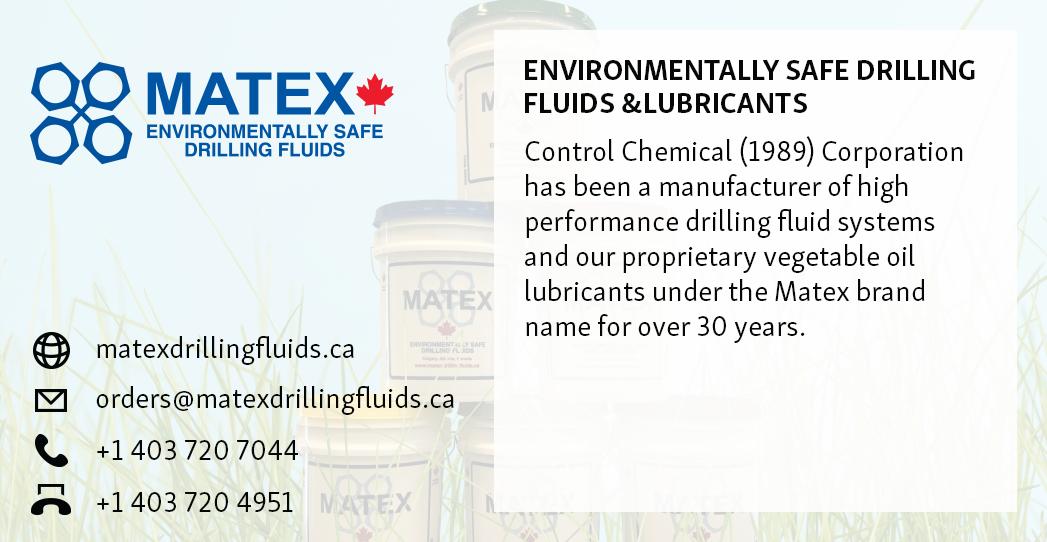
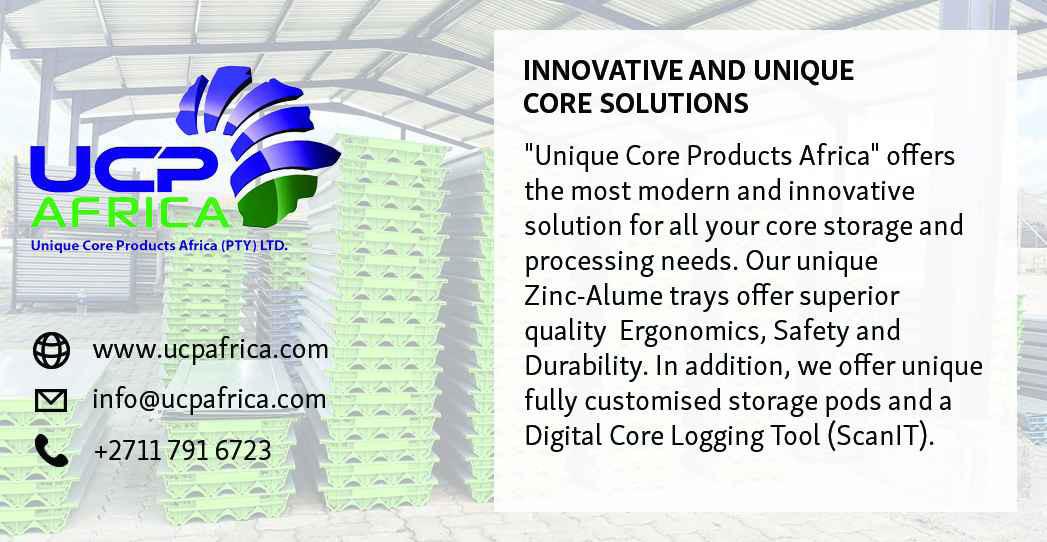
CORE TECH Phone +51 983 856 666 info@coretech.com.pe www.coretech.com.pe
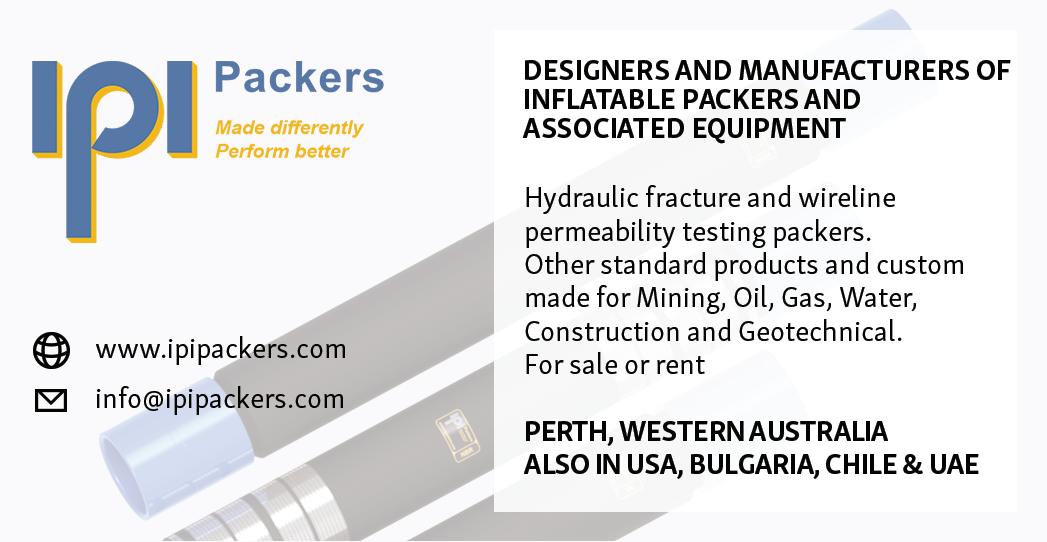
Orientation (A-Z)
COREFINDER
Phone +55 62 992720023 contato@corefinder.com.br www.corefinder.com.br
DYNAMICS G-EX
Phone +61 7 54826649 sales@dynamicsgex. com.au www.dynamicsgex.com.au
PROSPECTORS
Phone +61 (02) 9839 3500 Fax +61 (02) 8824 5250 sales@prospectors.com.au
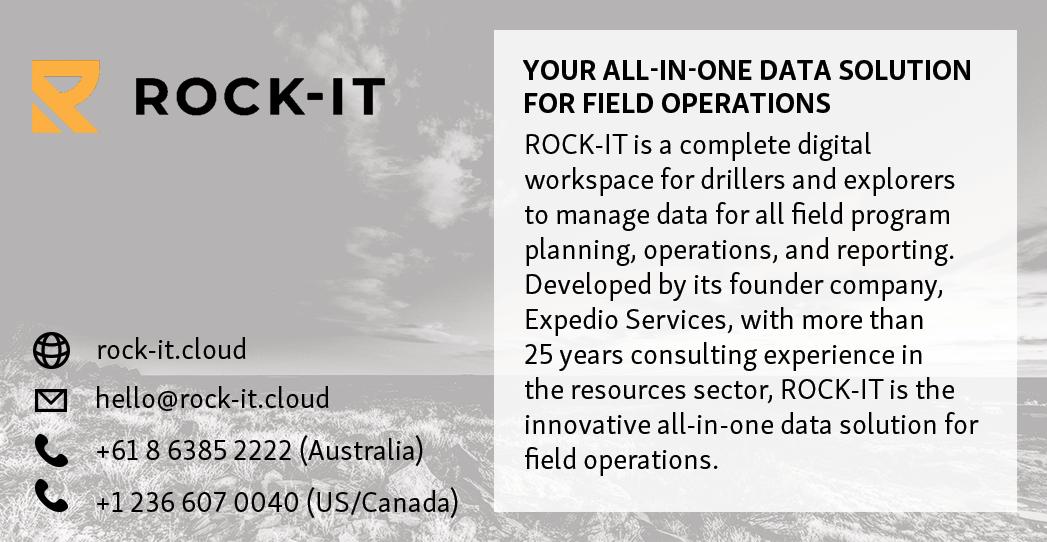
DEVICO AS Phone +47 72870101 devico@devico.com www.devico.com
Surveying & Geophysics (A-Z)
CORE TECH Phone +51 983 856 666 info@coretech.com.pe www.coretech.com.pe Peru
DIGITAL SURVEYING Phone +27 18 788 6349 sales@digitalsurveying.co.za www.digitalsurveying.com.za Africa
TRUST SOLUÇÕES GEOLÓGICAS
Phone +55 62 992720023 contato@trustsg.com.br Brazil
Packers (A-Z)
Core Trays (A-Z)
Cloud Solutions (A-Z)
Core
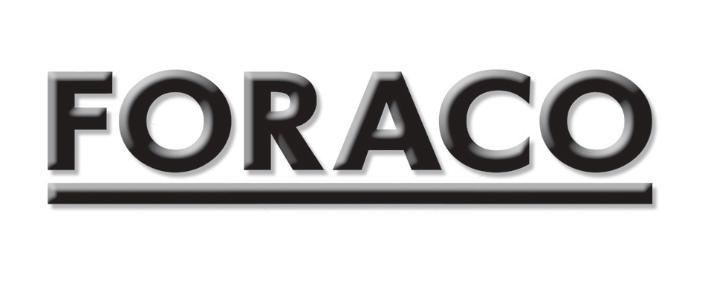
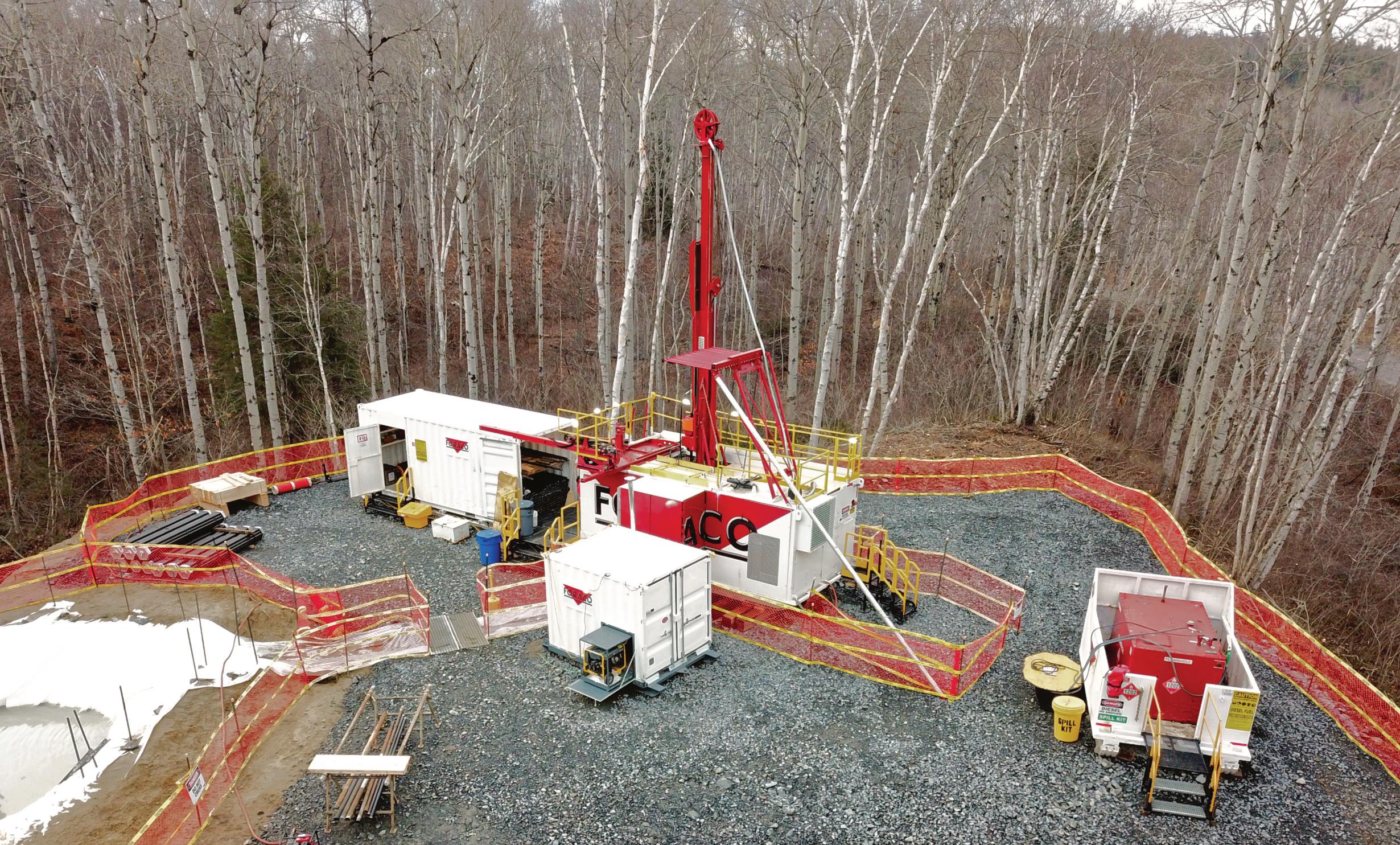
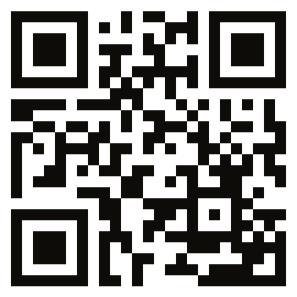
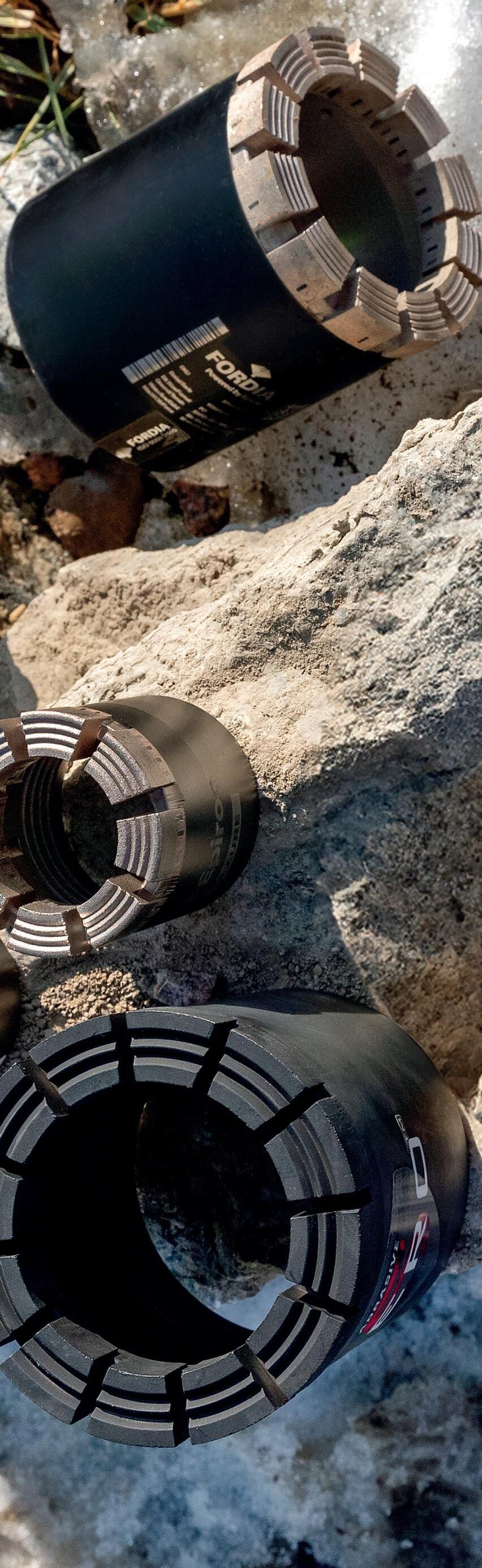
Unlock ore body insights
United. Inspired.
Exploration & Geoscience
We believe efficient data collection and smart analytics are key in unlocking ore body insights, leading to better decisions.
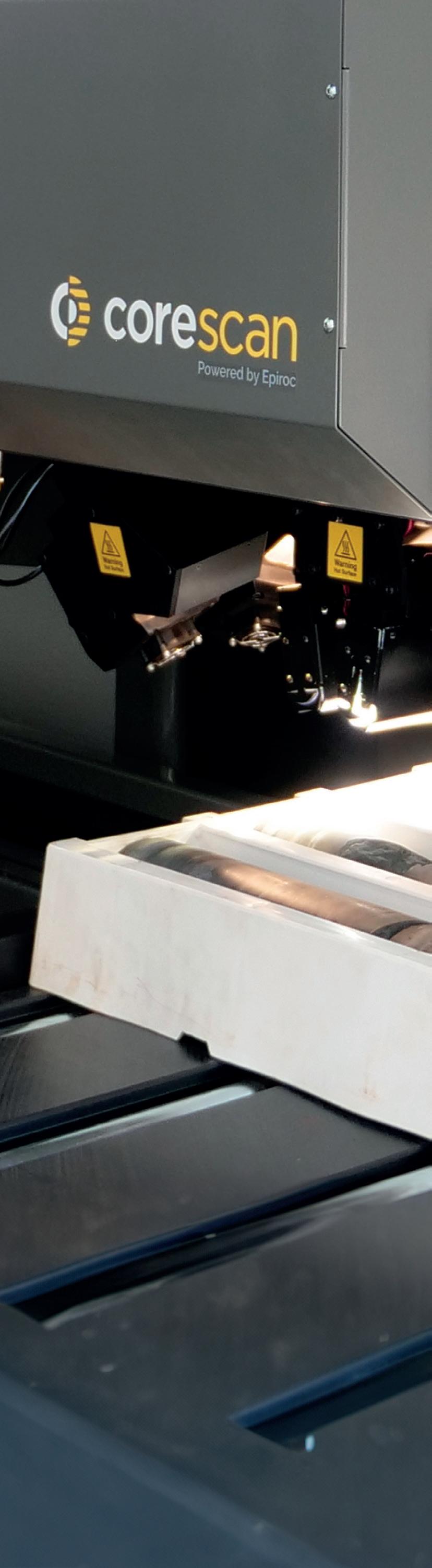
With a stronger than ever offering and reinforced expert team, we can help you achieve this. From the initial hole in the ground, to the empowering data on your screen, we can accelerate exploration.
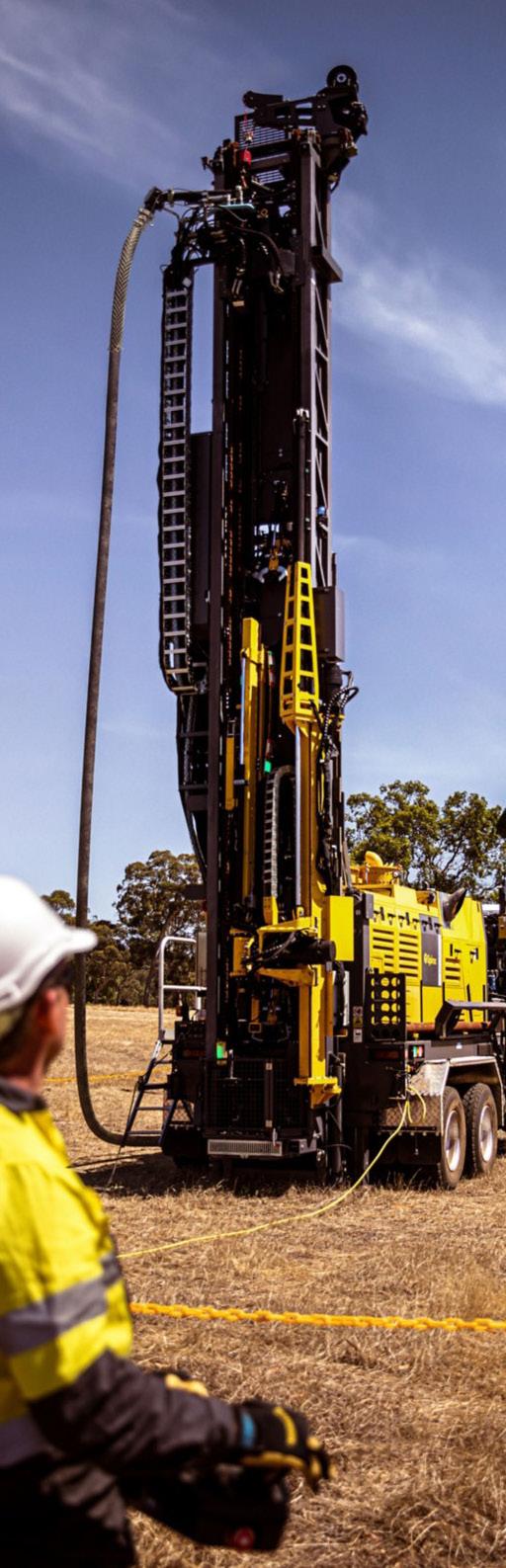
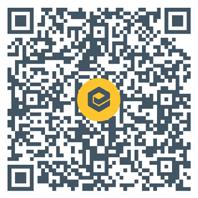