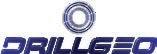
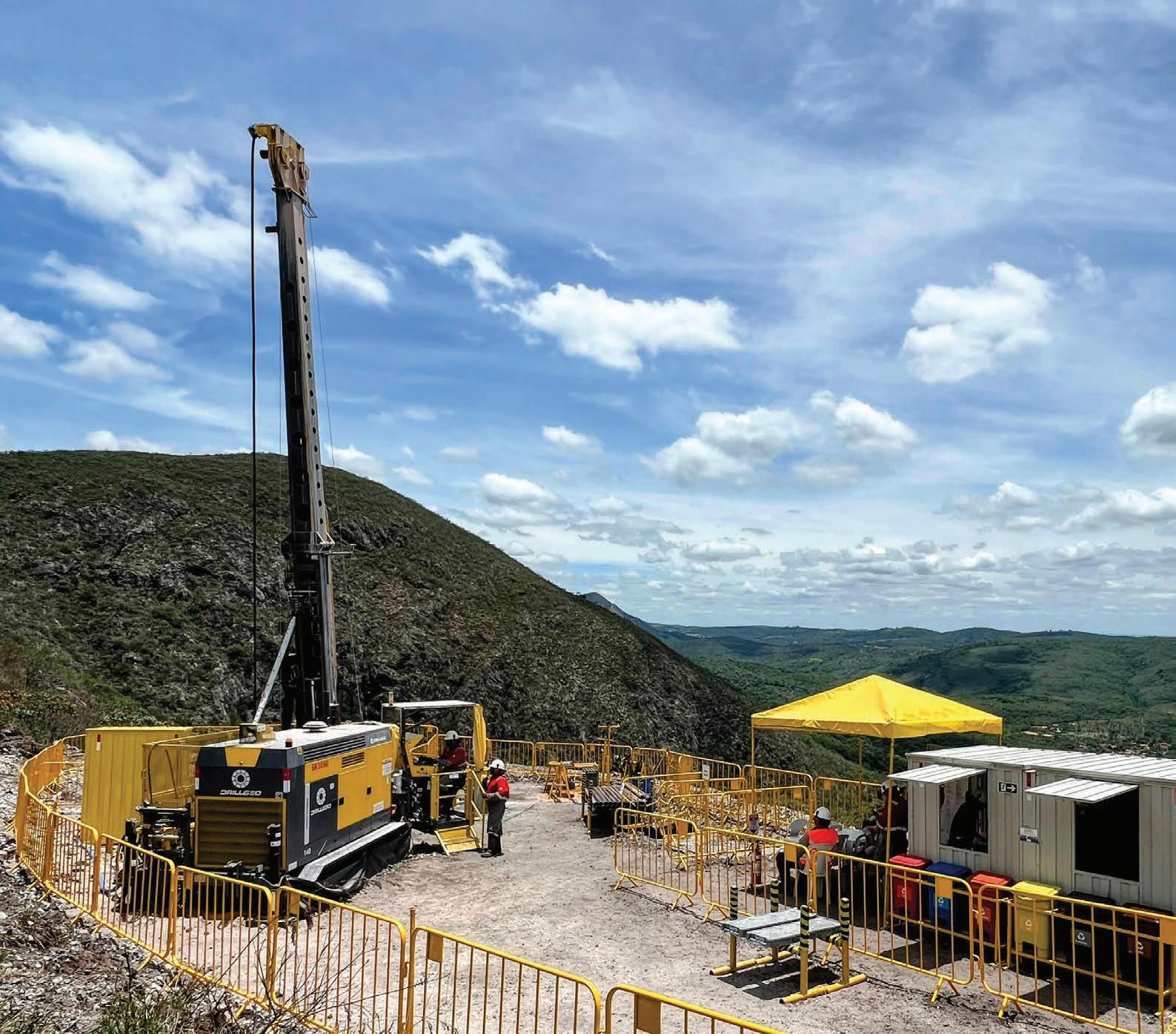

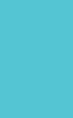

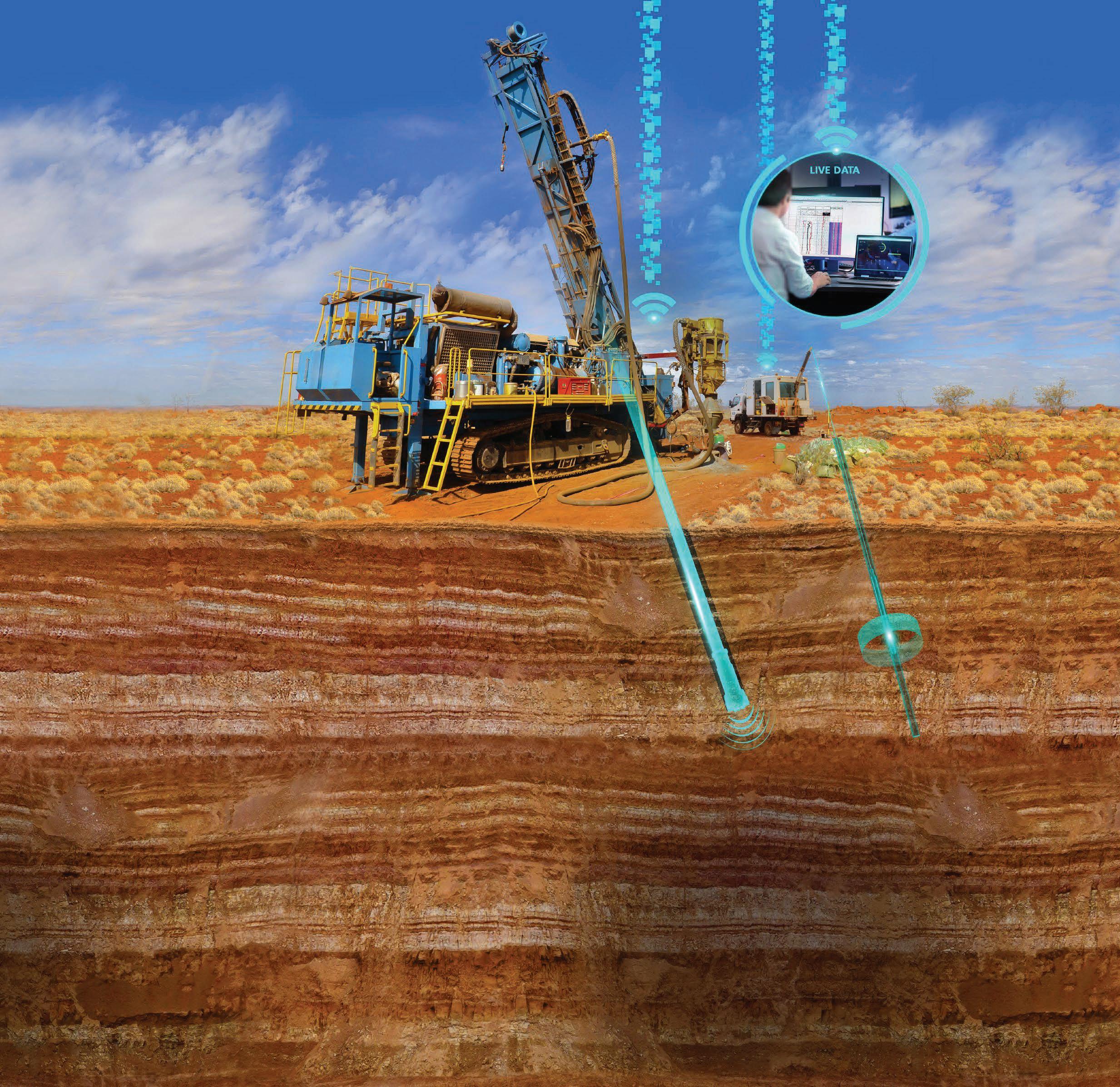

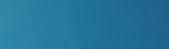
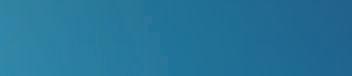

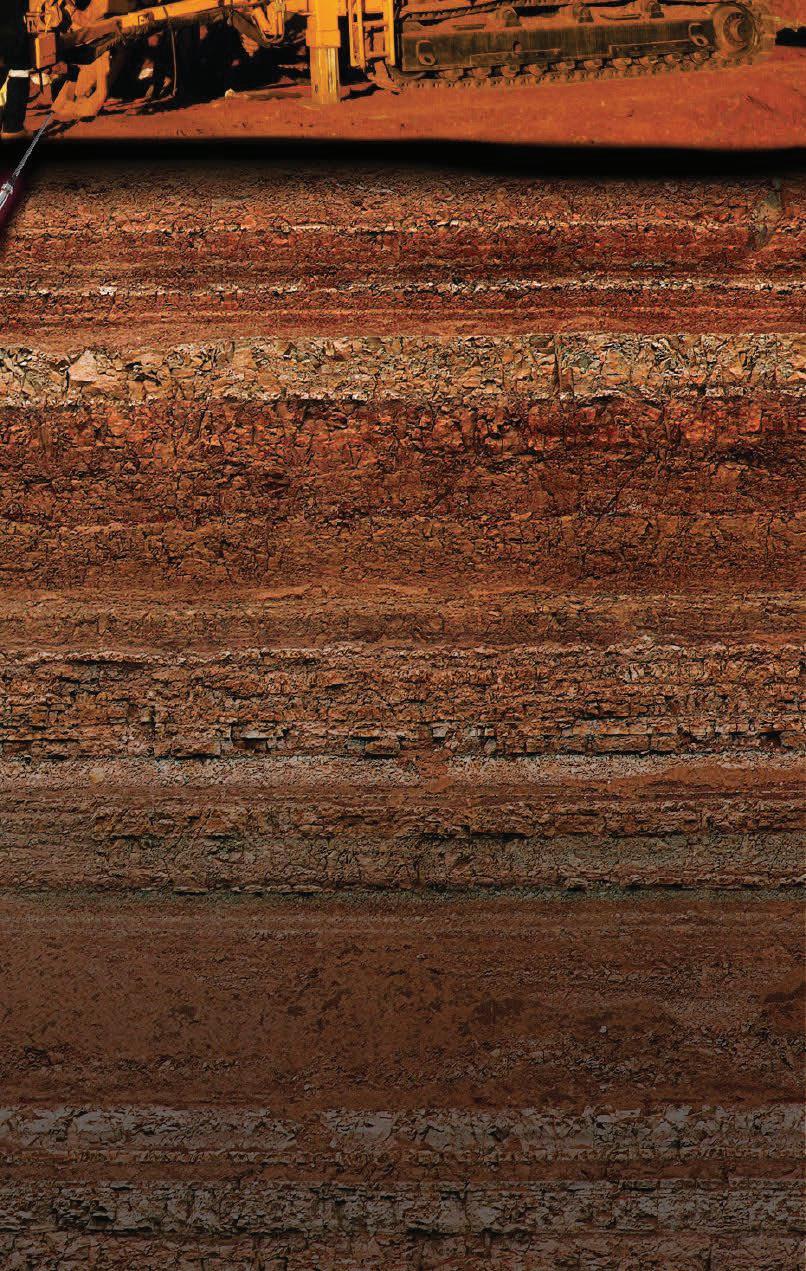
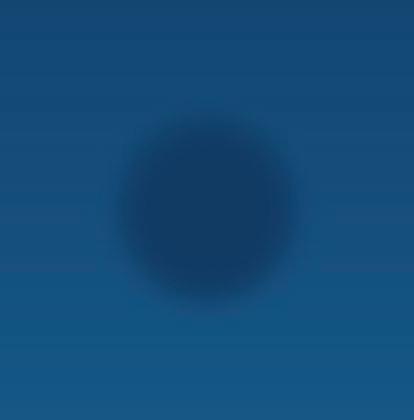

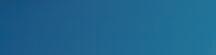

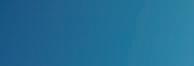






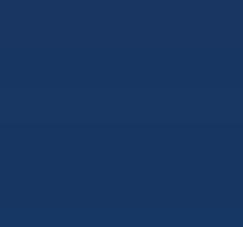


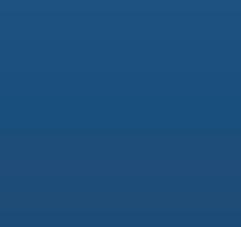
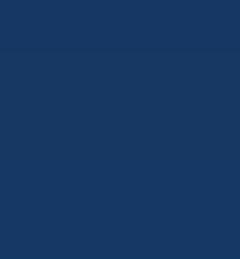
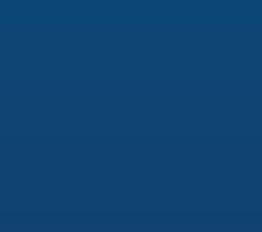

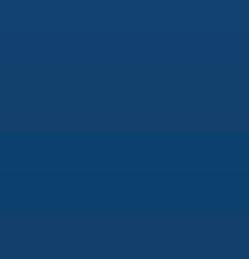
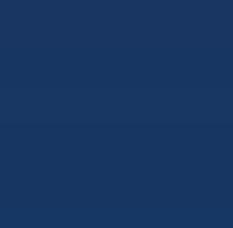

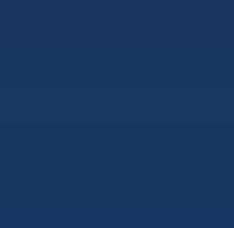

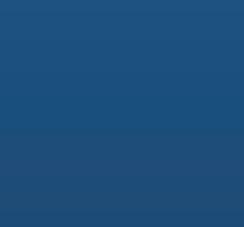

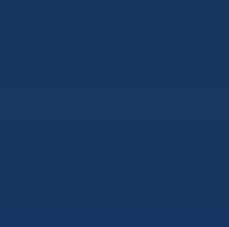
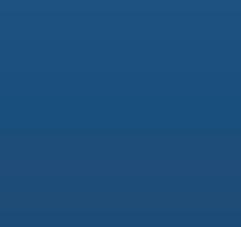




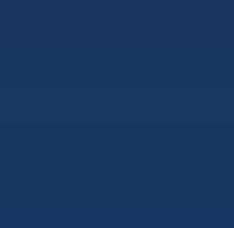

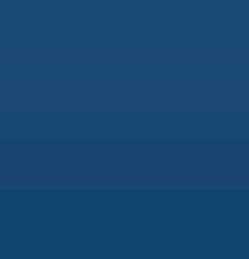


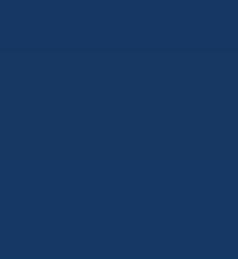
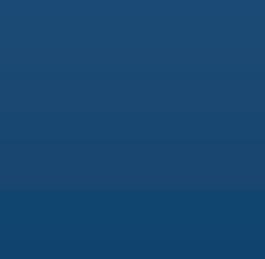
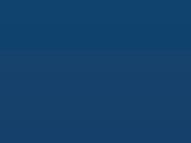
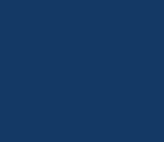
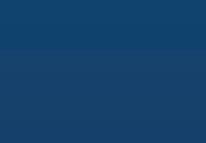
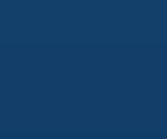
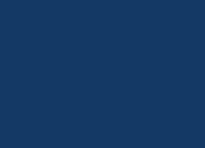
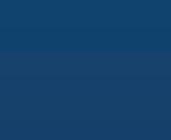
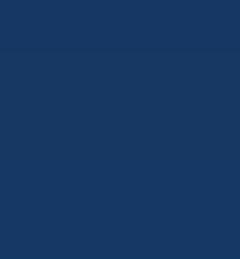
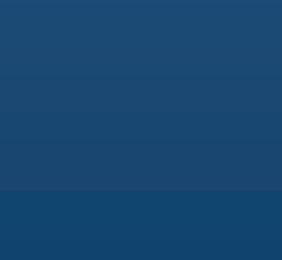
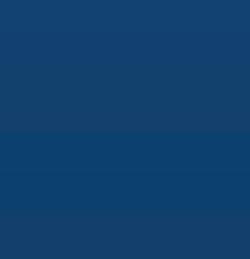
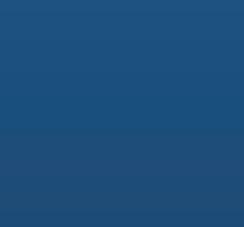
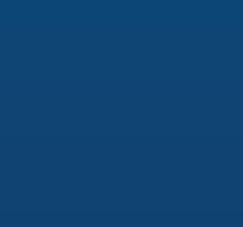
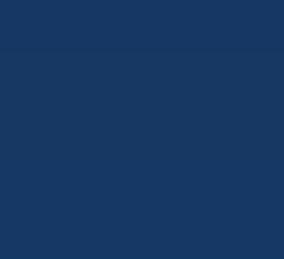

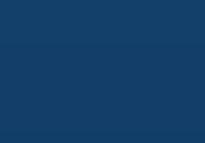
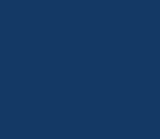
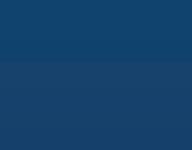
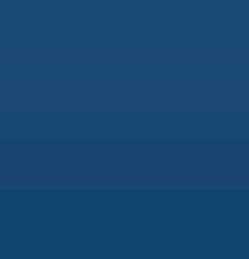
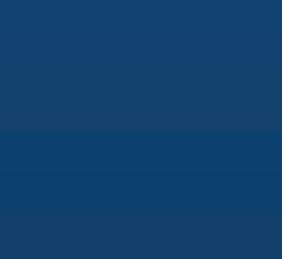

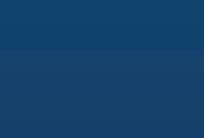
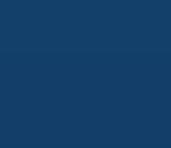
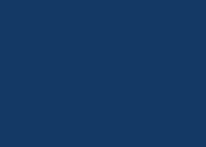

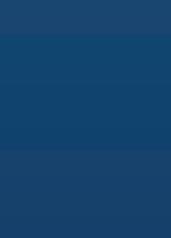

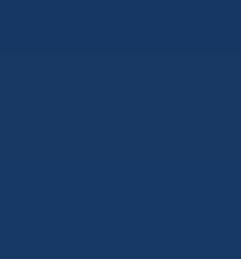
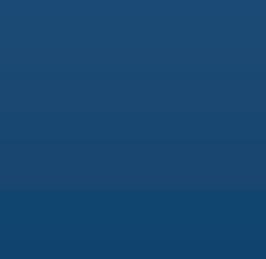

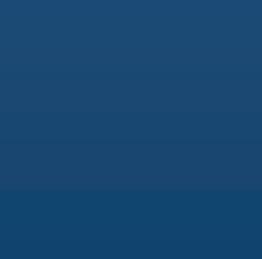
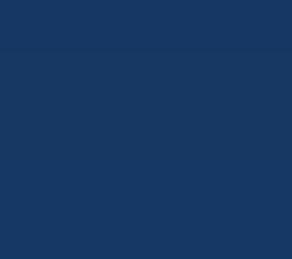
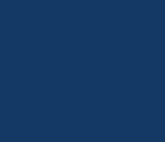

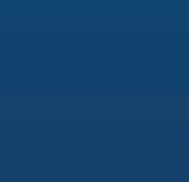
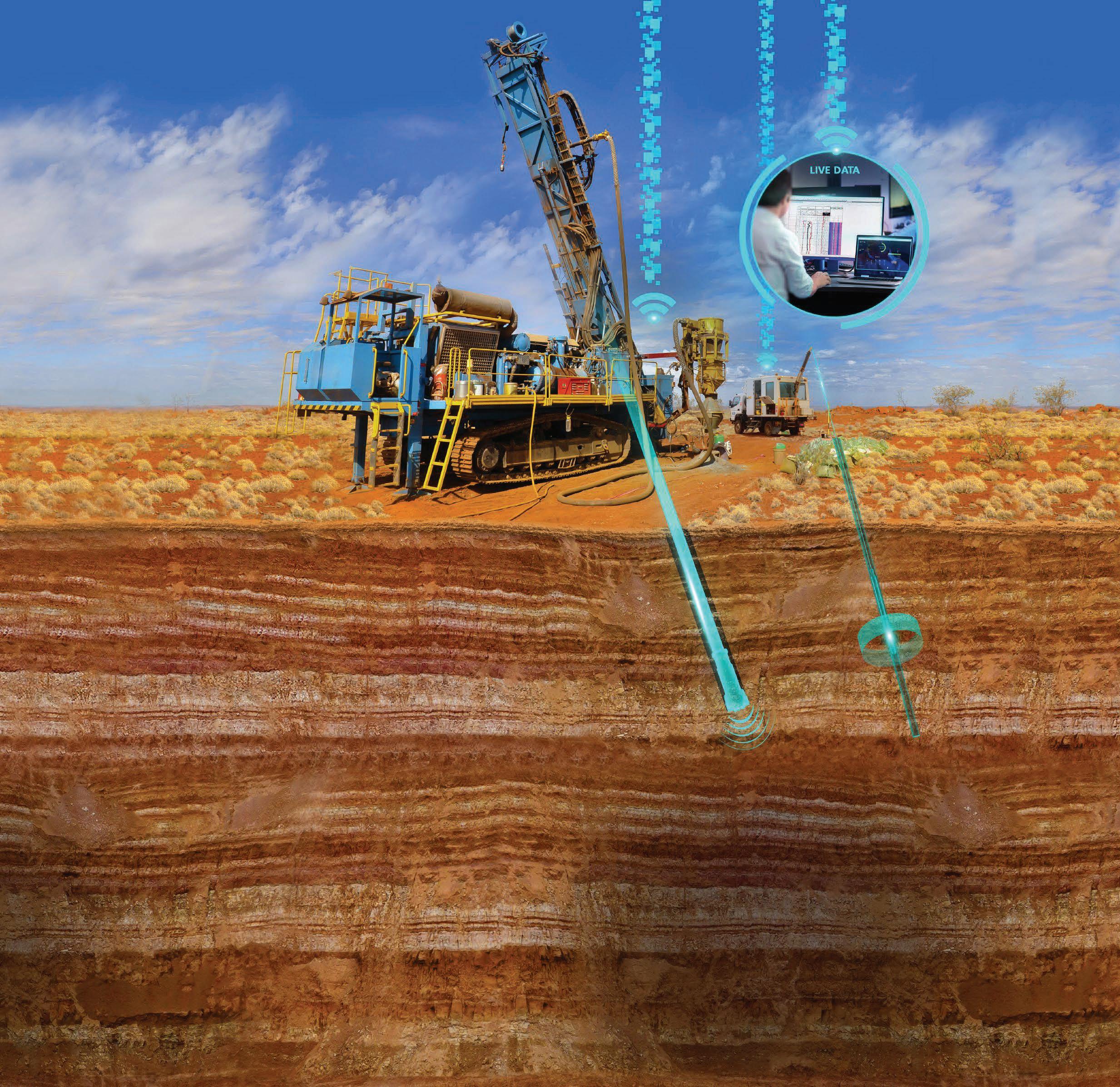
Exclusive interview with Pierre Alexandre, Founder & CEO at
Maximum quality, efficiency & sustainability for the Brazilian diamond drilling market by Francisco Sampaio, Director at DrillGeo
22 Unbeatable innovation in Blast Hole Quality Control: Precision Mining by Orlando Ramirez, CEO and Founder of Stockholm Precision Tools
26 Exploration in Remote Tanzania –A multi-faceted approach to tackling terrain & formation challenges by William Ward, Operations Manager – East Africa at Capital Limited /INDUSTRY EVENT
30 PDAC 2024: Creating connections since 1932 /EXPLORATION & MINING GEOLOGY
33 Q&A from the experts: In conversation with Dr Frank Bierlein Non-executive Director, Technical Advisor, Contract Geologist
40 Nearly 50 years of learning on the job, mostly with drillers by John Anderson, Formerly: Regional Exploration Manager at Aberfoyle Resources; General Manager Exploration Australia and Africa – MIM Exploration; Inaugural Managing Director – Investigator Resources
44 The Champion Project A tale of awe and ore by Dr Kris Butera, Managing Director at Plutonic Limited
18 CCT: Continuous Coring Tool BG Drilling launches its latest development to compete with Norwegian technology by Kiril Apostolov, General Manager at BG Drilling Solutions
52 Drill core scanning techniques: A review of the three main types by Rowena Duckworth, Founder & Petrographer at Mintex Petrological Solutions
Pierre Alexandre Founder & CEO at Orbit Garant Drilling
Francisco Sampaio Director at DrillGeo
Kiril Apostolov General Manager at BG Drilling Solutions
CORING MAGAZINE
February 2024
Cover photo
DrillGeo
Issue 26
ISSN 2367-847X
Not for resale. Subscribe: coringmagazine.com/subscribe
Orlando Ramirez CEO and Founder of Stockholm Precision Tools
William Ward
Operations Manager –East Africa at Capital Limited
Dr Frank Bierlein Non-executive Director, Technical Advisor, Contract Geologist
John Anderson Formerly: Regional Exploration Manager at Aberfoyle Resources; General Manager Exploration Australia and Africa –MIM Exploration
Dr Kris Butera, Managing Director at Plutonic Limited
Rowena Duckworth Founder & Petrographer at Mintex Petrological Solutions
Contact Us
Coring Media Ltd.
119B D. Petkov Str., Sofia 1309, Bulgaria
Phone +359 87 811 5710
Email editorial@coringmagazine.com Website coringmagazine.com
Publisher Coring Media
Founder Grigor Topev
Executive Officer & Editor in Chief Martina Samarova
Editor Maksim M. Mayer
Section Editor – Exploration & Mining Geology Dr Brett Davis
Digital Marketing Manager Elena Dorfman
Graphic Design Cog Graphics
Coring Magazine is an international quarterly title covering the exploration core drilling industry. Published in print and digital formats, Coring has a rapidly growing readership that includes diamond drilling contractors, drilling manufacturers and suppliers, service companies, mineral exploration companies and departments, geologists, and many others involved in exploration core drilling.
Launched in late 2015, Coring aims to provide a fresh perspective on the sector by sourcing authentic, informed and quality commentary direct from those working in the field.
With regular interviews, insightful company profiles, detailed product reviews, field-practice tips and illustrated case studies of the world’s most unique diamond drilling and mineral exploration projects, Coring provides a platform for learning about the industry’s exciting developments.
Open the box and GO. The GoGyro is fully integrated and designed specifically for simple, easy everyday use.
Configure your GoGyro as you need it for your surveys without unnecessary extra running gear. Simply add the needed fitting to run as:
• Core retriever
• Wireline
• Centralizers
Minimize downtime & Maximize efficiency. Simply GO Survey!
Fully integrated with SurveySafe for fast, convenient and secure online survey data management.
Founder & CEO at Orbit Garant Drilling
Pierre Alexandre began his career as a surface driller for various drilling companies, working from 1974 to 1983 across Canada.
Then, along with his brother, he became the Founder, President and CEO of Orbit Drilling (1986), a company specializing in surface and underground diamond drilling. Over the following decade the company expanded its fleet and operations to South America and Africa.
In January 2007, Pierre co-founded Orbit Garant Drilling, a merger between Garant and Orbit Drilling. Under his leadership the company has grown to become one of the most prominent Canadian operators in diamond drilling.
Pierre has more than 36 years of experience in the diamond drilling industry with expertise in operational planning and business relationship development.
Grigor Topev: Pierre, thank you for taking the time to answer our questions! Let’s start at the beginning. Please tell us about your early life and how and when you decided to get into drilling.
Pierre Alexandre: I began working in the town of Val-d’Or, in Northern Quebec, Canada. It is well-known as a mining hotspot. Then I followed in my brother’s footsteps, since he was already working for a drilling company called Modern Drilling.
GT: So, you stayed at Modern Drilling for seven years. Please tell us more about this period of your life.
PA: Modern Drilling had approximately 20 rigs. The company built unitized skid drill rigs. These drills were driven by hydraulic systems with 10-foot stroke engines and back then, this was very innovative. The drills moved faster than a regular drill.
There is one project I remember particularly well, when I was working at Modern Drilling, it was at the Doyon Mine, which was owned by Lac Minerals, Barrick Gold, Cambior and now Iamgold which was one of the biggest mining companies in Canada in those days.
After seven years at Modern Drilling, I decided to work for a smaller contractor, called Forage Benoit. It had 5-7 Boyles Bros 37 and Longyear 38 rigs. The difference between working at Modern Drilling and Forage Benoit, was that for Forage Benoit we worked with conventional rigs, while Modern Drilling used unitized skid drill rigs.
GT: In general, what was drilling like in Canada in the 70s and 80s? Which were the main contractors and manufacturers?
PA: Drilling and mining in the 70s and 80s in Canada were a lot different from today. Companies did not have the same technology that we have nowadays, there has been a tremendous evolution in this regard. The regulations were also a lot different, much looser, and have become more stringent since then.
The main contractors in Canada were Bradley Brothers, Boart Longyear, Morissette Drilling, and Midwest. JKS Boyles, Bradley, Atlas Copco and Boart Longyear were the manufacturers.
GT: You founded Orbit Drilling in 1986 with your brother, right? How did that happen; please tell us the story.
PA: Working with small drilling contractors made me realize that I had to make my own decisions on the terrain every day, so I decided that I would like to become an entrepreneur someday.
I began working at my brother’s company in 1983. He had a surface drilling company at the time, and then we had thoughts of adding underground drilling. So, in 1986, we decided to establish Orbit Drilling, which would specialize in both surface and underground drilling.
GT: The 90s was a decade of international expansion for your company. Which countries did you expand into at first? What were the challenges that you faced in South America and Africa and how did you overcome them?
PA: In 1992, we followed one of our main clients from Canada, who had begun a mining project in Guyana. Then we expanded in Suriname, French Guyana and Peru.
One of the biggest challenges was adapting to the different drilling conditions and training the local people. In those days there was less competition than there is today.
GT: What is the scale of your activities in South America and Africa at the moment?
drilling services. The synergy of our two enterprises led to us offering diverse services like underground, surface, and RC drilling and made our new company a dominant operator.
In 2008, we made an IPO on the TSX stock exchange, and the company became public. The IPO allowed for business expansion, access to capital and enhanced credibility. The challenges we were faced with were related to the time-consuming process of an IPO and ensured that the company met the strict regulatory rules and reported to the board of directors.
GT: Since the 90s, you’ve been manufacturing proprietary equipment. What advantages has this brought to your company?
PA: Manufacturing our own proprietary equipment gave us a greater chance of becoming more diversified in terms of the types of drilling we offer:
• Heli-portable drills gave us the opportunity to drill in the most isolated terrains.
• Rod Handlers were quite an innovation, since they reduce the risk of injury of our drilling crews. Our rod handlers are presently being sold at large to other mining contractors.
‘Presently, we have 208 rigs in operation and employ approximately 1300 workers. Our main areas of expertise are surface, underground, RC, directional, and geotechnical drilling services.’
PA: The scale of our activities currently in South America and Africa is approximately 25% of our sales. We have more than 30 drills deployed in those countries and most of our activities are presently in Chile.
GT: Orbit Garant Drilling was the result of an industry-changing merger in 2007. Tell us how it happened.
PA: From 2002 to 2007 we grew our business through acquisitions. Then, our company went through a major growth and then we consolidated two companies Orbit Drilling, specializing in surface and underground drilling and Garant Drilling - one of the major underground drilling companies in Québec and Ontario. The result of the merger was Orbit Garant Drilling, offering both surface and underground
• Computerized underground and surface drilling rigs reduce delays and our costs, while increasing our production rate. A computerized rig improves the physical factors of the job performance, and therefore makes the driller’s job safer and easier.
• We won some of our drilling contracts because of our capabilities of manufacturing and modifying some of our equipment to meet our clients’ exact needs.
GT: Let’s go to the present. Please tell our readers the size of Orbit Garant Drilling.
PA: Presently, we have 208 rigs in operation and employ approximately 1300 workers. Our main areas of expertise are surface, underground, RC, directional, and geotechnical drilling services.
In Fiscal year 2023 we drilled more than 1.6 million meters (5.2 mil. ft) and generated CAD 201 million in revenue. Approximately CAD 150 million were from Canadian operations and another CAD 50 million came from our international projects.
We work with important mining companies such as, Alamos Gold, Vale, Agnico Eagle, Eldorado Gold, Wesdome, AngloGold Ashanti, Endeavour, Anglo American, Freeport McMoran and Codelco.
In Fiscal Year 2023, we had drilling operations in:
• Canada
• Chile
• Burkina Faso
• Guinee
• Guyana
GT: Which specific project of Orbit Garant Drilling stands out to you?
PA: A couple of years ago, we carried out a very complex drilling campaign in Chile. We had to drill under a glacier in an underground mine. The environmental risks were very high. We had to manufacture four underground rigs with specific features to address these challenges. The drills were modified to be able to support the weight of the rods - more than 21 000 lb (9525 kg) excluding the weight of the waterfrom falling when drilling those upholes. We were drilling upholes at angles of +60° reaching more than 600 m (1969 ft) of length in H-size. Ultimately, we succeeded in this drilling campaign, and as of today, we are still working with the satisfied client.
GT: Orbit Garant has been operating in harsh conditions due to the extremes of the Canadian weather and geological environments. What methods and equipment do you apply to overcome the extreme cold and inaccessible terrains?
PA: Orbit Garant has adapted its equipment and experience to meet the harshest winter conditions and the perma-frost and inaccessible terrains.
Teamwork and the safety of our crews were our main concerns during the blizzards and whiteouts. So, we built survival shacks with food heating, and all the necessary items to survive in these extreme weather conditions.
We also adapted our recirculating systems, the methods for drilling in perma-frost, we worked on efficiently moving from one site to the other and adapting our drills so they can be mounted on skids, on tracks and become heli-portable.
GT: What are your day-to-day responsibilities as the CEO of one of the biggest companies in our industry? How is your work different from the old days of drilling?
PA: My day-to-day responsibilities are communicating, managing and executing with the management team. I am responsible for making strategic corporate decisions and being accountable to the board of directors.
This was a significant change from working on the drilling sites, and without the experience I have acquired in the past, I would have not been able to make the same informed decisions that I do today. As they all are crucial to the company’s success.
GT: This might be a hot topic… It seems that there is a bit of a rivalry/competition between English- and French-speaking Canadian drilling companies. It would be interesting for our international readers if you could tell us more about it.
PA: The competition is mostly in Quebec between French Canadians because this is the most competitive market in the country and maybe in the world. The market here is deeply segmented between many drilling contractors, so the competition is very fierce.
GT: There was and still is high inflation in the world. What are its main effects on the diamond drilling industry and how do you address them?
PA: Inflation is one of the biggest challenges in the diamond drilling industry presently. We are addressing the effects by conducting a thorough analysis of our cost structure and we’re actively trying to pinpoint areas where we can reduce the costs without compromising
on the quality of the work being done. We are always trying some new drilling products to increase our efficiency and reduce our costs. This is even more efficient because we work closely with our drilling suppliers to increase the quality of our services.
GT: What is your prognosis for the state of drilling in the next couple of years?
PA: Unfortunately, I do not have a crystal ball, so It’s hard to tell. There is a lot of uncertainty concerning the commodity markets in which we operate.
In recent years, we clearly saw a trend toward automation and equipment innovation and an increased environmental awareness across the mining industry. My assumption is that this trend will continue and probably it will only accelerate. Orbit Garant is well positioned for the future with its computerized drills, and more recently, with rod handling system.
Also, recent new mining discoveries tend to be in harsher environments with more extreme weather, in remote areas and on isolated
terrains. Because of that, we can expect to do more specialized drilling such as directional drilling, deeper holes, work in the middle of nowhere and brave the harsh elements. I expect this trend to continue in the next couple of years.
GT: What are three pieces of advice you would give to small drilling companies that are just launching?
PA: My piece of advice to the new launchers is that this is no different than any other business. You must know your clients, their needs, and you must have the passion for what you do. Perseverance and hard work are the key to success.
GT: Finally, what are your interests outside of the drilling industry?
PA: My family is the core of my existence, a treasure beyond measure and the foundation on which my life is built.
Some of my hobbies are fishing, hunting and traveling to explore new places, cultures and cuisines. This creates lasting memories. C
Rickard Lindström CEO at Xploration Products AB
LiPAD®-100 is the answer.
The well proven Boyles C6/C6C rigs are suitable for different project sites, confronting the most harsh conditions and environments. It offers superb versatility in the surface core drilling segment for 1 211 meter N-size borehole depths. Find out more at epiroc.com United. Inspired.
by Francisco Sampaio, Director at DrillGeo
Founded in 2000 in Brazil, DrillGeo is a company specializing in the full range of drilling services applied to geological research and geotechnical works.
Both founders of DrillGeo, Mr Gilberto Pedreira, current CEO, and Mr João Paulo Franco, current Vice President, had the dream of building a modern company, with an innovative mindset and integration to the technological advances, they aimed to meet the ever-increasing demands of their customers. Mr Pedreira has been involved in drilling ever since the 80s. He was convinced that he should start the business when he realized that the industry was going through a ‘perfect’ storm. There was a growing demand for services, while only few companies were specializing in core drilling, at the same time the Brazilian legislation was also bound to change. By then, he had drilled more than 1 000 000 m (3 280 840 ft) for companies, such as Doce Gel, Vale do Rio Doce, Icomi, Ferbasa, Mineração Caraíba, UniGeo, CBPM and Nuclebras.
DrillGeo’s trajectory and proven experience reflect the success of its founders.
Since 2000, DrillGeo has drilled a total of 1 500 000 m (4 921 260 ft) in the diameters 4 ½”, 5 ½”, B-size, N-size, H-size, P-size and ZW series, across mining projects and in the wild diversity of the Brazilian geological environments. It is worth highlighting the depths reached
- 800 m (2625 ft) in H-size for iron ore and 1583 m (5194 ft) in N-size, both ‘Q’ series, and 125 m (410 ft) in the ZW diameter (194 mm), which is used for metallurgical analyses.
In the last twenty years, DrillGeo has also undergone a revolution in its internal structure and drill rig fleet. Over the past 10 years, the company has invested heavily in modernizing its drill rigs, purchasing 100% hydraulic equipment from Epiroc, manufactured in Sweden and in China. It was certified by Bureau Verittas for Quality processes, through the ISO 9001 Standard, and doubled the size of its headquarters in the state of Bahia. Additional milestones for DrillGeo are:
• The opening of new branches in the states of Minas Gerais (in the city of Nova Lima) and in the state of Pará (in the city of Canaã dos Carajás), bringing the company closer to its customers and providing better service for the important mineral centers in Brazil. This also helped to attract and begin operation for BHP and Vale, the two largest mining players in the world.
• DrillGeo started offering RC drilling services.
• Investing in attracting and training the workforce to guarantee safe operations with DrillGeo’s modern equipment. To accomplish this, essential assumptions were established regarding the period of adjustment, assimilation, and the growth of technicians and operators. This brought forth excellent operational
procedure performance, cost reduction and improvement in customer satisfaction.
• In 2021, DrillGeo changed its company structure, becoming an S.A. (incorporated, in other words), allowing bigger capital injections, better control of contracts, and more transparency and adaptability to the ESG requirements of the market. In addition, the share capital also brought in new partners - Francisco Sampaio and Antonio Marcio, oil drilling engineers with more than 15 years of experience in various drilling methods, both working at DrillGeo since the beginning. Today, they are both directors.
DrillGeo has rigs capable of reaching depths of over 2500 m (8202 ft). The main services the company offers are:
• Core drilling;
• Reverse Circulation (RC);
• Drilling in large diameter (ZW) and underground;
• Guidance of testimonies;
• Directional drilling;
• Geophysical profiling;
• Geotechnical survey;
• Geological logging;
• Susceptibility test;
• Point load test (PLT);
• Provision of labor for geological activities;
• Geotechnical instrumentation.
The company is currently employing around 400 people directly, operating throughout the national territory. Among them are qualified professionals with more than 30 years of experience in drilling. The technical staff consists of drilling engineers, geologists, drill planners, safety specialists and mining/geology technicians.
DrillGeo has a total of 40 rigs for both surface and underground operations. Among these rigs are Christensen 140C, Boyles C5C, Boyles C6C, Boyles C8C, Explorac 100 and U6. The rigs have remote control functions with advanced systems and maintenance of rock cutting
power independent of the operator’s action, in addition to the low emission of noise and pollutants. To tackle all challenges, 100% of the equipment matches and exceeds Brazilian labor standards.
To maximize its RC operations, the company has recently acquired Epiroc’s Explorac 100 rigs for RC, capable of reaching depths of up to 250 m (820 ft). For diamond drilling operations, DrillGeo is expecting the arrival of six new CS140C rigs with Rod Handling System (RHS) from Sweden. The company also has several rigs for rotary drilling and roto-percussion drilling in RC.
It is not well-known in the Brazilian market, but DrillGeo has launched its own drilling control application. ‘Drillcore’ collects drilling information, daily production records, quality controls and safety data, eliminating the use of paper in the drilling environment and integrating operations in the Society 5.0 era. Any cell phone or tablet with minimal configurations supports the application, so that all its customers can have access to the complete information and with data imported into Power BI (data visualization software from Microsoft), facilitating the monitoring of the various KPIs of the work.
DrillGeo was initially established to meet the strong demand for copper and chromium ore drilling, conducting deep boreholes of over 1500 m (4921 ft) for mineral research for various clients. The company also engaged in lateritic nickel operations, utilizing triple tube (HQ3) systems to collect samples for mineral development and geotechnical assays. During this period, it developed effective drilling and recovery methods, significantly increasing its core sample recovery rate during campaigns. The company boasts substantial experience in drilling car-
bonate zones, renowned for their tendency to exhibit faults and caverns at considerable depths, successfully completing numerous holes for zinc exploration.
Subsequently, DrillGeo provided services for gold mines, where the primary challenges revolved around stringent borehole trajectory control and maximal recovery of deep mineralized zones. DrillGeo devised its proprietary method of passive trajectory control maintenance, employing wedges, followed by the subsequent implementation of directional equipment.
Over the years, the company has gained extensive expertise in iron ore drilling, focusing its operations in the states of Minas Gerais, Bahia, and Pará. In this context, DrillGeo developed its proprietary drilling method in the ZW diameter, with a focus on obtaining samples for geometallurgical testing of iron ore and lateritic nickel, presenting innovative solutions for its clients’ research plans.
Moreover, in its iron ore experience, DrillGeo has concurrently managed multiple projects for this valuable metal, utilizing approximately eleven drilling rigs in a single project, even conducting drilling in jaspilite and ‘serra azul’ rock formations within the Iron Quadrangle region. The company has also executed projects involving multiple rigs and consecutive boreholes exceeding 500 m (1640 ft) in H-size per hole. In 2015, DrillGeo had operations in the remote regions of Brazil in proximity to Bolivia drilling for phosphate.
Throughout its nearly two decades of history, DrillGeo has proven to be a resilient company with the ability to evolve and renew. It has been widely recognized for the quality of its services, attested by ongoing customer satisfaction surveys and deadlines consistently met, with a focus on workplace safety and environmental preservation.
DrillGeo is also affiliated with important industry associations, such as Ibram - the Brazilian Mining Institute, a national private non-profit
organization that represents companies and institutions operating in the mineral sectorand Adimb, the Agency for Development and Innovation of the Brazilian Mineral Sector, established in 1996 as a private non-profit entity with administrative, technical, and financial autonomy. It is an association of companies and institutions in the mineral sector, with the mission of promoting technical-scientific development and the training of human resources for the Brazilian mineral industry. DrillGeo recognizes the importance of organizing the mineral sector to address issues related to better representation, production, and socio-environmental interaction within the industry.
Currently, DrillGeo provides services to clients such as Vale, OZ (BHP), Nexa Resources, Ero Copper, Ferbasa, Bahia Mineração, Hor-
izonte Minerals, Valore Metals Corp, Mineração Caraíba S.A, among others.
DrillGeo prepares for the future. It has assisted and distance drilling activities in process and under development and has acquired rigs that have coupling of the rod handler system coming from the factory. One of the company’s main objectives is to continue the certification in the 45000 standard (Health and Safety Management), standing out in the sector and being increasingly involved in responding to the growing demands for safety, risk reduction and continuous improvement of working conditions that the market and society demand. Thinking about the quali-
For more information
fication of the company, its managers have the 18000 certification in mind, which will expand its activities and certify its entire management system for drilling activities, geological logging and sampling and technological control.
One of the reasons that led its managers to transform DrillGeo into an S.A is the change in the variable remuneration plan for employees. Aiming to increase engagement, strengthen the development and loyalty of employees, DrillGeo offers stock options for long-time employees, or those with important accomplishments, and for its customers.
DrillGeo is also attracting women into the industry by actively participating in the Women in Mining program and offering operator training. One of their main goals is to train 25 women by 2026. C
Visit: drillgeo.com.br or contact: contato@drillgeo.com.br and +55 (71) 9 9919-6565 .
Introducing CoreMatrix™, the new redesigned bit line-up from Di-Corp Drillers Edge.
The new CoreMatrix™ bits from Di-Corp are re-engineered for enhanced bit life and faster penetration rates across every ground condition.
With 21 matrices and a comprehensive matrix selection chart to guide you, it’s easier that ever to find the perfect CoreMatrix™ bit for your drilling conditions. Available with three waterway configurations and several specialty options for Abrasive conditions, Extended life, and Free-cutting matrices.
Drilling is tough. Get rugged to the core with the all-new CoreMatrix™ bits from Di-Corp. See them at
1.800.661.2792
info@di-corp.com www.di-corp.com
by Kiril Apostolov, MSc, General Manager at BG Drilling Solutions
heritage, tracing back to the seventies and eighties, includes Bulgar ian achievements such as the development and patenting of the first directional coring tool, core barrel’s roller latch system, bottom-hole shock absorber, and retrievable core bit. Drawing on this rich tradition and expertise, BG Drilling has carved out its niche, quickly gaining recognition as a trusted partner in the mineral exploration industry, with its dedication to field service excellence acknowledged by clients and competitors. Its mission has been clear from the start: to deliver tools that not only enhance field operations but do so in a cost-effective
core continuously while steering the hole. The core can be retrieved using an inner tube and overshot, just like with a regular wireline system. At the core of the CCT system lies the company’s CWT technology, with one of the main components being the acclaimed Roller Pad—a spring-operated mechanism that securely locks the stationary part of the tool, ensuring consistent directional control during drilling operations. By utilizing rollers to enhance grip, this innovative approach significantly reduces axial friction, markedly improving efficiency compared to other DCD systems.
The CCT is both effective and highly productive, averaging 15 to 20 m (49-66 ft) per shift. It is tailored for complex drilling plans, offering well-distributed deviations over long sections averaging 9° per 30 m (98 ft). An essential tool for projects with extensive and complex deviation requirements, it is capable of operating at depths of up to 3000 m (9843 ft). Versatile for both shallow and deep drilling, its applications range from precise hole navigation to branching, meeting the needs of core-critical projects in mineral exploration, geotechnical, and tunnelling sectors.
The CCT is currently offered in N-size, boasting an industry-leading compactness
In the competitive world of directional drilling, innovation isn’t just a buzzword; it’s the cornerstone of progress, efficiency, and the key to sustaining market position. BG Drilling Solutions (BG Drilling), a directional drilling supplier, has long stood alongside the pioneers of the industry. Known for its proprietary tool, the CWT, BG Drilling has consistently pushed the boundaries of technology and service. As the market evolves and competition intensifies, BG Drilling is determined to remain agile with its latest developments.
‘For years, we have been avoiding direct competition with the coring technology, guided by what some might call old-fashioned ethics. However, with the industry evolving through acquisitions and the arrival of new competitors, the landscape has shifted. We're now ready to showcase our full potential,’ shares Grigor Topev.
at 4.5 m (14.77 ft) long and weighing 45 kg (99.2 lb), facilitating safer and more efficient use in restricted areas. It delivers a 3 m (9.84 ft) core of 32 mm (1.26 in) diameter per core run.
A new design of the CCT, aimed at enabling B-size coring, is currently under development, with a target launch date in 2025. Additionally, BG Drilling Solutions is preparing CCT’s versions to accommodate the other two principal sizes of drilling holes, B and H, enhancing the tool’s versatility and application across various drilling scenarios.
BG Drilling emphasizes on mechanically driven tools for their ability to navigate challenges that other systems might face. Deep drilling operations are associated with significant hydraulic losses or may experience hydraulic instability which can impact the efficiency of hydraulic-dependent tools. Systems like steerable bottom-hole motors which demand significant volumes of drilling fluid, can face operational challenges, such as stalling or reduced penetration at greater depths. Additionally, these systems necessitate extra mud pumps and smaller-sized drill rods, adding further complexity and potential drawbacks to their operation. Similarly, the reliability of packer grip and toolface locking in existing DCD systems might be compromised, leading to directional errors. By contrast, mechanically driven systems like the CWT and CCT operate independently from these limitations, showcasing consistent performance, particularly at depths below 2000 m (6562 ft), where their reliability and efficiency become even more pronounced.
Alongside the exciting launch of the CCT, BG Drilling is thrilled to unveil another groundbreaking patent-pending development: the modified CWT, called CWT Dual Mode (CWT DM). This advancement sets a new industry benchmark by introducing the first-ever capability for down-the-hole dogleg severity adjustments, an achievement unmatched by any other in the field. This innovation streamlines tripping operations, significantly elevating the CWT’s operational efficiency.
With the provision of three types of directional tools on the market, BG Drilling has introduced a classification system to help clients choose the most suitable tools for their projects. This system categorizes directional drilling jobs into three categories based on the deviation required per intervention, enhancing understanding of each tool’s functionality, and streamlining the selection process for particular drilling demands. This strategy enables informed decision-making, ensuring that tool choices are perfectly aligned with the specific requirements of drilling projects until the resumption of standard diamond coring operations.
Short-Range Deviations: Typically involving deviations of up to 5°, short-range deviations are crucial for keeping drilling operations on track. The CWT, with its ability to make precise, minor corrections, is perfectly suited for navigation of straight holes, offering an efficient and cost-effective solution compared to more complex tools like DCD systems. Wedges and similar tools also fall under this category.
Mid-Range Deviations: These corrections, ranging from 5 to 15°, often involve realigning trajectories that have significantly deviated from the planned path or executing close-proximity targets in branching jobs. The CWT DM’s versatility and its ability to adjust DLS without tripping make it an invaluable asset, balancing precision with the need for minimal intervention.
Long-Range Deviations: For deviations exceeding 15°, the challenge intensifies, requiring tools capable of handling complex steering and longer correction paths. This category demands sophisticated engineering and operational finesse, areas where BG Drilling’s CCT, down hole motors, or other DCD systems shine, ensuring successful navigation of even the most demanding deviations.
It’s important to note that short-range deviation tools like the CWT perform well across the other two categories, but their effectiveness may decrease due to the increased number of short interventions and thus increased tripping. Conversely, more complex tools are versatile
across short and mid-range categories but come at a higher cost. The selection based on deviation categories does not apply when core retrieval is essential.
By offering a range of tools designed for specific deviation requirements, complemented by the exceptional on-site expertise of engineers with university degrees, BG Drilling secures a unique position in the drilling technology sector. As the company continues to innovate and refine its offerings, it is eagerly looking forward to presenting its latest achievements, including the CCT, at the upcoming PDAC in Toronto, Canada. Interested parties are invited to visit Booth 818 to explore the CCT and learn more about the company’s services. This event represents an excellent opportunity for BG Drilling to expand its impact, welcome new customers, and establish partnerships to bring its advanced solutions to new markets. C
‘Our focus has always been on R&D to supply the industry with state-of-the-art, cost-effective solutions. The mechanical tools are the pathway for major improvements in existing technology - they are rigid and reliable. Combined with other factors, they allow a substantial reduction of utilization expenses, nearly halving the service cost compared to the existing DCD systems.’ adds
Associate Prof. Shteryo Lyomov.
For more information Visit: bg-drilling.com
by Orlando Ramirez, CEO and Founder of Stockholm Precision Tools
Beyond the explosion, have you ever stopped to think about the impact of blasting on the mining production process?
Blast hole quality control is a common challenge for even the most experienced miners in the mining industry. It is not simply a matter of a blast deviating from its intended course; it takes on multiple dimensions that have far-reaching implications, including potential compromises to equipment and personnel safety, as well as long-term operational efficiency.
Blasting is an essential part of the mining industry, but it comes with inherent challenges that can hinder production operations. Accurate surveys of blast holes are critical to avoid costly secondary shots and ineffective rock fragmentation, which directly impacts the company’s bottom line. Meanwhile, the mining sector contends with stricter environmental regulations, where any inaccuracies in blasting operations can have severe serious legal and environmental consequences.
Nevertheless, the question remains: how can one ensure the accuracy and effectiveness of blasting activities? This is where blast hole surveying becomes essential.
The blast hole surveying process ensures that the execution is in line with the intended design. By pinpointing areas of excessive or insufficient blast energy, this technology optimizes operational efficiency and safeguards against problems such as inadequate fragmentation and potential safety hazards.
Stockholm Precision Tools (SPT) is transforming the concept of precision in this challenging field. GyroScout™ marks a new milestone in the evolution of directional survey tools.
A portable, solid-state Gyro, weighing only 2.4 kg (5.26 lb) and 37.4 inches (95 cm) in length, is designed for blast hole surveying in both underground and surface operations.
Utilizing GyroScout™ could lead to an average decrease of 18% in operational interruptions and a 13% reduction in outflows. This improvement is particularly noteworthy, considering that over 94% of clients who have integrated GyroScout™ have observed a marked enhancement in blasting operation efficiency.
Its implementation not only enhances safety and environmental sustainability compliance but also significantly boosts operational efficiency in mining operations.
SPT operates on a fundamental principle: deploying its developments and upgrades in real-world environments, both to showcase them to clients and to evaluate their efficacy under practical circumstances. In partnership with Rocha Blast Engineers, we’ve rigorously field-tested the latest GyroScout™ software upgrades, specifically designed for blasting applications. These tests, aimed at enhancing surveys, have
↑ The
app’ allows for non-stop survey of blast holes in a daisy chain sequence
‘Utilizing GyroScout™ could lead to an average decrease of 18% in operational interruptions and a 13% reduction in outflows.’
identified opportunities to improve performance, productivity, safety, and cost savings.
The successful integration of GyroScout™ and its handheld ‘SPT GyroScout™ app’ upgrades at the Riotinto mine blasting-site underscores a significant achievement. This pioneering mining site, an initiative, spearheaded by Atalaya Mining, a premier European copper producer, blends cutting-edge technological innovations with the rigorous safety and environmental sustainability principles inherent in modern mining practices. Integrating the software resulted in even more precise surveys, ensuring the exact layout of blast holes by verifying each data point collected during the surveys.
With the new GyroScout™ blast hole survey software ‘SPT GyroScout™ app’, it’s now possible to efficiently survey an entire blast hole run in record time. This innovative application enables surveying all the blast holes with one single setup instead of setting up one by one each time. This simple solution allows for seamless transition between blast holes without interrupting the survey process.
The highly intuitive system uses color coding to indicate to the user whether a blast hole has been previously surveyed, or if a repeat survey is required.
Included is a visualization software designed to make it easy to compare planned and surveyed blast holes. This graphical representation can display all partial blast hole data and simplifies individual analysis of each survey.
The latest GyroScout software enhancements provide customers with a reliable survey database to optimize blasting, reflecting the mining industry’s evolution toward data-driven decision-making. SPT stays true to this philosophy by providing innovative solutions that optimize mining production.
So how often is it recommended to survey blast holes? The answer is clear: blast holes should always be surveyed to ensure superior quality control, minimize risks and control costs.
You can rely on SPT GyroScout™ for high-accuracy data on your blasting operations. Our instrument ensures precision in quality control calculations for blast holes to keep excess dilution, overbreak and re-drilling at bay.
Build a solid and secure data foundation with SPT at your side. Optimize your processes and be ready to incorporate state-of-the-art technologies, including AI, machine learning, and optimize your mining production rate today. C
Designed for high speed blast hole survey without compromising precision.
Maximum portability
Unaffected by magnetism. Survey multiple blast holes in one go. Simple and easy.
High Precision Directional Survey Tools
A multi-faceted approach to tackling terrain & formation challenges
Capital Limited (Capital) was initially awarded an exploration drilling contract with Tembo Nickel Corporation Limited (Tembo), a subsidiary of Lifezone Metals Ltd. (NYSE:LZM), at the Kabanga Nickel Project, Tanzania in late 2021. The Project hosts one of the world’s largest and highest-grade nickel sulphide deposits.
by William Ward, Operations Manager – East Africa at Capital Limited
The Kabanga Nickel Project is situated in the northwest of Tanzania, close to the border with Burundi and within the highlands region of the country. It is approximately 800 km (497 mi) from Mwanza, the closest major center.
The Kabanga Nickel Project boasts significant nickel resources and exploration upside potential, with current estimates suggesting
over 87 million tonnes of high-grade nickel sulfide mineralization. Lifezone is progressing the site towards the completion of the Definitive Feasibility Study expected by the end of Q3 2024.
The Project is expected to be a direct-to-metal operation producing highgrade battery-grade nickel, copper and cobalt with local processing facilities. The refining operation will be constructed in the Kahama District, Shinyanga Region, and will use a Lifezone Metal’s Hydromet technology,
which is more cost-efficient than smelting and has a significantly lower environmental impact.
The site is located within the ultramafic rocks of the Tembo-Musongati Belt, the mineralization primarily consists of pentlandite, chalcopyrite, and pyrrhotite, with significant cobalt and copper by-products.
BHP has invested USD 100 million in the project which will be used to accelerate its development.
Capital’s exploration drilling activity at Kabanga through 2023 included more than 30 000 m (98 425 ft) of diamond core.
A number of diamond and deep hole diamond drill rigs were used at the project, with maximum N-size depth capacities of up to 1200 m (3937 ft) and B-size of 2200 m (7218 ft).
The Kabanga deposit presented both logistical, geological as well as site topography
challenges. Additionally, the project faced infrastructure challenges due to the location of the drill sites relative to the Kabanga Camp, with limited access to power, water, and transportation networks at the drill pads.
The closest airport is at Ngara, which is only capable of landing light aircraft. As a result, drilling inventory and consumables needed to be trucked in from Mwanza to ensure mechanical availability above 80% could be maintained.
The drill locations were positioned on steep, sloping hills, with limited established roads in, requiring track-mounted rigs to navigate the terrain. With multiple small targets to hit, traversing between hole locations was arduous.
To optimize the cost efficiency of directional drilling operations at Kabanga, Capital strategically adjusted barrel configurations during the drill program, including core barrels with varying sizes and types of bits and reamers, utilized to optimize drilling efficiency and accuracy. Barrel configurations were chosen based on the site’s rock type, ground conditions, and desired intersection angles.
Core barrel orientation within the drill string was also adjusted to control borehole trajectory and target specific intersections accurately. This precision targeting
minimized the need for the use of costly navigation motors.
Core orientation tools, such as gyroscopic surveys and electronic orientation devices, provided real-time data on core barrel orientation.
In addition to barrel configuration adjustments, Capital took proactive measures to enhance diamond drill bit performance in the hard and abrasive quartz-rich ground conditions.
Capital worked closely with bit designers that traveled to the site to tailor the drill bits to the specific geological conditions encountered at Kabanga. They studied the geological characteristics of the quartz zones encountered and analyzed drilling data to customize their drill bit designs to ensure performance was optimized for the site conditions. These preferences incorporated features, such as specialized diamond configurations, cutter layouts, and compounds tailored to maximize bit life and drilling efficiency.
In what can be typical of quartz formations, fractured zones during drilling created some water loss issues. To ensure fluid recovery
and hole stability, Capital organized regular site visits by their mud engineers to advise on the best lost circulation materials to use in the conditions to maintain hole formation and stability.
Capital employed directional drilling techniques to ensure it hit the required targets, working closely with Well Force International, its rig site technology and software subsidiary company and the client.
Survey data obtained with Well Force’s North Seeking gyros was uploaded to their proprietary borehole management software, HiTT. In close collaboration with the client, progress to the target was tracked and downhole directional changes were managed through the use of core barrel configuration changes and as required, wedges.
The use of top drive rigs facilitated a safer, easier installation of wedges when required, given the clear configuration of the drill mast when lowering wedges.
By using directional drilling in the challenging terrain, Capital was able to drill up to six targets off the original drill hole. This eliminated the need to prepare and move rigs to new drill sites for each target across the difficult conditions while delivering financial savings.
It is noteworthy that all of the drilling crew operating at Tembo are Tanzanian employees. Their competency in managing the challenging terrain, remote location and at times difficult drilling conditions while delivering on the client’s drill program objectives reflects Capital’s training and development investment in their local teams, as well as the crew’s own dedication and resilience in executing drilling operations efficiently and safely.
Capital’s focus on ensuring it not only delivers drilling programs accurately but also efficiently and cost-effectively, is reflected in the number of approaches taken to achieve
the goals of this drilling program. Despite the challenging formation, holes remained stable and retained integrity to depth through the combination of techniques, from adjusting barrel configurations and drilling muds to customizing diamond drill bit preferences. In addition, the crews worked closely with the client’s on-site geological team to further reduce costs, resulting in significant cost-saving outcomes for the project.
The aim of any exploration drill program is to generate information on the ore body. Through its use of directional drilling techniques combined with the state-of-the-art accuracy of Well Force’s downhole gyros and HiTT software, precise drilling trajectories were achieved; every hole was in line and delivered every target intersection to aid in maximizing resource recovery. Additionally, it was achieved with zero redrills across the program.
Capital Limited is a leading mining services company providing full-service mining, drilling, maintenance and geochemical analysis solutions to customers within the minerals industry. The Company’s services extend across the mining value chain providing customers with a fully integrated mining services solution including exploration, delineation and production drilling; load and haul services; maintenance; and geochemical analysis. Our reputation is built on an unwavering commitment to safety, delivering professional mining solutions and working closely with our customers to deliver operational efficiencies.
The Group’s corporate headquarters are in the United Kingdom, and it has established operations in Côte d’Ivoire, Canada, the Democratic Republic of Congo, Egypt, Gabon, Ghana, Guinea, Kenya, Mali, Mauritania, Nigeria, Pakistan, Saudi Arabia, Tanzania and the US. C
Helicopter Portable Diamond Drill
1400 Meter NWL Depth Capacity
Cummins Power Unit 160 or 260 HP
‘P’ Size Rotation Unit & Clamp
Safety Package: Full Guarding, Multiple E-Stops, Interlock Rod Guard & Power Lock-Out
Available in Heli-Portable, Skid Shack Mounted and Track Carrier
PDAC 2024, The World’s Premier Mineral Exploration and Mining Convention, will take place March 3-6, 2024 in Toronto, Canada. The award winning PDAC Convention is widely considered the ‘Super Bowl’ of the mineral exploration and mining community and is the leading event for people, companies and organizations connected to mineral exploration.
The convention brings together up to 30 000 attendees from over 130+ countries for educational programming, networking events, business opportunities and fun.
Since it began in 1932, the convention has grown in size, stature and influence. Today, it is the event of choice for the world’s mineral industry hosting more than 1100 exhibitors and 700 speakers.
Spread over both the North and South Buildings of the Metro Toronto Convention Centre (MTCC), PDAC 2024 will showcase another full slate of exhibitors from across the globe.
Attendees will be able to visit 600 exhibitors showcasing the world’s leading technologies, products and services, and meet government representatives from across the globe.
This includes the Northern Ontario Mining Showcase (NOMS) – the largest pavilion at PDAC featuring over 110 exhibitors and interactive displays showcasing innovative products and services to help plan, build, maintain, and rehabilitate projects around the world!
The Core Shack will provide a unique venue for companies to display their core samples. Attendees can get up close to new or ongoing projects that are generating exciting drill results. The latest discoveries from all corners of the Earth will be featured along with maps, charts and technical information.
Visitors will be welcome to discuss investment potential with 450 junior mining companies, mid-sized producers, major mining companies, financial institutions and prospectors to discover new business opportunities.
The Prospectors Tent is the door to the heart of the industry. Self-employed prospectors will be there to discuss their maps, samples and claim results.
The SMC brings together geoscience students and industry professionals to highlight innovative student research on projects essential for the successful evolution of the modern mining industry. Students (BSc, MSc, PhD) working on projects linked to mineral deposits including mapping, mineralogy, geochemistry, geophysics, environmental and hydrogeology will have the opportunity to share their research with an audience of academics and industry professionals.
An initiative aimed at showcasing work of talented artists from across Canada, increasing the presence of Indigenous vendors on the show floor. C
For more information Visit: www.pdac.ca/convention
MARCH 3 - 6
Metro Toronto Convention Centre Toronto, Canada
NETWORK
Connect with delegates from 130+ countries
DISCOVER
Experience 1,100 exhibitors showcasing the best of the industry
LEARN
Expand your knowledge with hundreds of hours of programming led by international experts
INVEST
Engage with institutional, private and retail investors, plus senior executives
Q&A from the experts
In conversation with Dr Frank Bierlein
Non-executive Director, Technical Advisor, Contract Geologist
Nearly 50 years of learning on the job, mostly with drillers by John Anderson, Formerly: Regional Exploration Manager at Aberfoyle Resources; General Manager Exploration Australia and Africa – MIM Exploration; Inaugural Managing Director – Investigator Resources
The Champion Project
A tale of owe and ore by Dr Kris Butera, Managing Director at Plutonic Limited
Drill core scanning techniques: A review of the three main types by Rowena Duckworth, Founder & Petrographer at Mintex Petrological Solutions
Dr Frank Bierlein Non-executive Director, Technical Advisor, Contract Geologist
Brett Davis: Firstly, thanks for giving Coring the opportunity to interview you, Frank. I was really keen to pin you down for an interview, given your impressive international profile in the industry. I’ll start with my standard leadin – what got you interested in a career in geology?
Frank Bierlein: Right back at you, Brett – it’s an honor to be interviewed by Coring Magazine, and by someone with your stellar reputation and track record, to boot!
I ended up becoming a geologist via a somewhat circuitous route. That is, in high school I had aspirations to become a medical doctor, to the point where I labored through seven years of attempting to learn ancient Greek and Latin – which, at the time, was a requirement to enroll in medicine at any German University. Another prerequisite was the completion of a six-month hospital-based practical studies stint. This I undertook in a private hospital in Courbevoie, just across the Seine from Paris, France. My experiences there put me off entirely, as far as the pursuit of a career in medicine.
Working as a landscaper and tennis coach in Mallorca were merely stop gap solutions until I figured out the answer to the question
Frank Bierlein has about 35 years of experience as a geologist, including his three years as a field geologist for the Swedish Geological Survey prior and in parallel to completing his MSc degree at the University of Heidelberg (1989-1991). During that time, he almost drowned on a couple of occasions, broke through the surface of bottomless moors, and got chased by a brown bear once. After he obtained his PhD from the University of Melbourne in 1995, he spent the next 12 years in academia working on mineral resources related projects across six continents as a post-doctoral (senior) fellow at various universities in Ballarat, Curtin-UWA and Monash, Melbourne.
After that, Frank made the switch to the industry, first as an independent consultant, then as Manager of Generative Geology for Afmeco Australia, the AREVA Group, and Qatar Mining. He also joined and held the position of Chair of the advisory board of a Luxemburgbased private equity fund. He held each of these positions for about three years. This was followed by a 3.5-year-long stint with QMSD in Sudan, until COVID-19 put an end to his adventures in the MENA region (something a coup and a popular uprising, respectively, failed to do in the preceding two years). Having escaped Sudan on a 28-year-old B737 held together by duct tape, he got stuck in Europe for seven months during the second half of 2020. So, he started working as an advisor and quasi-analyst for an institutional investment fund with significant exposure to several ASX and TSXlisted mineral resources companies. Through this work, he joined the board of several junior explorers as a non-executive director while continuing to work as a technical consultant and advisor.
He is also a longstanding member of the SGA and the SEG, as well as a Fellow of the AIG, a former regional VP of Australasia for the SGA, and a vocal supporter of various public outreach programs.
of ‘where to from here?’, so I went travelling across North America in search of an epiphany. Which happened as I was standing one day on the southern edge of the mighty Grand Canyon, completely blown away by its grandeur and geological significance. Subsequent hikes through the Death Valley and Yosemite National Park and spending some time exploring the gold-rich Californian Foothills and Lassen Volcanic Park only served to strengthen my conviction that my professional future was in Geology.
I credit the amazing Professor Lluis Fontboté for instilling me with the passion for ‘big holes in the ground’. That is, his teaching style and vast knowledge as conveyed in the lecture theatre and practicals, as well as a couple of extraordinary field trips to operating mines in the south of France and northern Spain, and getting exposure to real-life explorers and miners while attending ‘Gold ‘88’ in Toulouse, made me fall irrevocably in love with mining and exploration. Not least because of their fundamental importance to
every facet of our society. I mean, if it can’t be grown, it has to be mined, right?!
BD: What projects are you working on at the moment? And what is your level of involvement?
FB: Geez, that’s a bit of a tough one. I am the Group Geologist of an as-yet unlisted Canadian entity that is exploring for PCDs and VMS deposits in the Arabian Nubian Shield. As such, I am providing input to, and review exploration strategies and targeting exercises with the team. I am also a technical advisor for ASX-listed Firetail Resources and, together with another consultant, manage an exploration program for them that focuses on the development of a laterite-hosted Ni project in Central Queensland. I am a Technical (non-executive) Director of Variscan Mines (ASX: VAR) and Impact Minerals (ASX: IPT), with the former providing a fantastic opportunity for some hands-on involvement aimed at advancing an exciting Zn project in Cantabria (as you would know!). Impact is largely a project incubator with some excit-
ing early-stage projects in WA and in NSW, while also trying to develop a world-class high-purity alumina project in the Forrestania region of WA.
I very much enjoy working with, and learning from, the dynamic and highly motivated team at IPT led by Dr Mike Jones. Then there is my involvement at the board and technical committee levels with Blackstone Minerals (ASX: BSX), an energetic junior company that is driving the ‘green’ Ni transformation via its project in Vietnam and several strategic NiS assets in Canada. And as mentioned previously, I provide technical advice and input on a case-by-case basis to a DAX-listed investment fund. While largely desktop-based, this work also involves the odd site visit and onground technical due diligence work, which I thoroughly enjoy. The opportunity to get my hands and knees dirty in the context of going underground or spending time inside an open pit, examining core or even just walking over fascinating outcrop always gets my juices flowing!
BD: Your early education was in Germany, followed by doctoral studies in Australia. Are there any fundamental differences in how geology is taught and perceived in the two systems? And how did you choose Australia as a ‘final’ destination for study?
FB: That’s an excellent question – let’s start with the second part. Following on from what I mentioned above about having irrevocably fallen in love with big holes in the ground, I wanted to study and work in a country that had a strong, active and diverse mining culture. Something that simply did not exist anywhere in Europe at the time, despite its 1000+ year history of mining. Australia, Canada and South Africa were the obvious choices and I was fortunate enough to receive PhD scholarship offers from universities in all three of these countries. However, part of my reasoning also considered the dreary, long and cold winters in Europe that I wanted to escape from. So that ruled out most of Canada! South Africa at the time was still undergoing some political upheaval, so I settled on Australia. You only have to read Geoffrey Blainey’s brilliant and captivating book ‘The Rush That Never Ended’ to get an appreciation of the role of mining and exploration in Australia’s economic development since the 1830s.
A major difference between the way Geology is taught in Australia and Germany concerns the depth and breadth of undergraduate courses at all levels. It took me a while to realize and appreciate the rationale behind this disparity. In Germany the focus of what is essentially a five-year course is on academic knowledge and a broad understanding of all facets of geology. While here in Australia the emphasis of a three-year B.Sc. course is to provide a student with a sound basis that can be expanded upon while working in the industry or across government and survey organizations, with the option of further study via an Honors and/ or Master’s degree. There are advantages and disadvantages to both approaches, with one of the biggest drawbacks being the age at which a geologist tends to graduate with the equivalent of a Master’s degree (the socalled ‘Diplom’) from a university in Germany. The Powers That Be have recognized this and for some time now, so many universities in Germany have adopted the British system of providing a somewhat watered-down three-year-long Bachelor's degree in Geology. I’d say as far as perception, there is not a great deal of comprehension of what a ‘Geologist’ actually does in Germany, unless it en-
tails hydrogeology, environmental services or academia. By contrast, the vast majority of geologists in Australia are connected with or employed by the mineral resources and oil and gas industry, and as such, enjoy a much higher profile of directly contributing to the country’s wealth and development. Unless they blow up caves or behave badly in airport lounges.
BD: Your geology-related career has spanned academia, consultancy, and corporate arenas. Very few people can boast the impressive research profile you have. Correct me if I’m wrong, but you have approximately 150 individual or collaborative peer-reviewed papers in international journals and you are still publishing. What is the secret behind your drive and publishing success?
FB: Well, you could argue that my chosen career path perhaps made me somewhat of a jack of all trades, but (unlike you) master of none! When I look at many of my peers and their incredibly impressive and diverse careers in the industry, I feel like I have gained nowhere near as much experience as those highly respected heavyweights. On the other hand, I’d like to think that having had the opportunity to formulate, plan and undertake applied research with direct relevance to the mining and exploration industry, and study aspects of mineral deposit formation at all levels, as well as elucidate the intricate links that exist between metallogeny, tectonics, fertility and endowment through space and time, has provided me with a bit of an advantage when it comes to generative exploration, project development and asset evaluation. I have always been driven by a quest to find, or assist with finding, answers to ‘big’ questions, such as ‘Why a given deposit is where it is?’, ‘What determines, at a fundamental scale, the size and endowment of a given deposit, mineral camp or belt?’, and ‘Where can we find analogous deposits?’. Managing multi-million-dollar research grants that involved a slew of co-workers from industry and government organizations also helped to hone my project management and communication skills. As far as publishing (and ignoring for the moment the immense pressure on academics to publish the findings of their research, or literally ‘perish’ if they fail to do so), I firmly believe that one has almost an obligation to share relevant output from original (and often, at least in part, taxpayer-funded) research. Basically, if relevant (let’s call it ‘pre-competitive’) work does not get published in due course,
it is almost like it never existed, right? The timely dissemination of new ideas and infor mation is key to the advancement of our sci entific knowledge, but, importantly, also for the purpose of these findings to be applied in exploration targeting, improve our under standing of mineral deposits, and how to find and exploit them more cost-effectively.
BD: Many people have careers that start off in academia and then transition to in dustry-related roles. A lot of people I see in the industry positions are doing this toward the end of their careers. What sponsored you to move into the industry arena, well before (I hope) the end of a successful research life?
FB: In all honesty, it was a bit of a combina tion of things. While I thoroughly enjoyed working on fascinating projects across six continents in my passionate pursuit of scien tific knowledge and sharing this new-found insight with students and fellow researchers, the time away from my young family took a toll on all of us. I was never, and still am not driven by financial reward, but financial considerations nevertheless played a role, courtesy of my less-than-stellar academic income, and my super-human wife having to work full-time to make ends meet while also doing most of the heavy lifting at home. The absence of that elusive permanent position in academia, while trying to generate fund ing for, undertake and publish the results of my research, supervise and teach students (which I thoroughly enjoyed), develop curric ulums, take on a raft of administrative duties, etc., also meant that I eventually lost some of that youthful idealism of what being an academic was supposed to mean. The aca demic community in Australia is relatively small and can be cutthroat as it competes for a limited pot of research and industry funding. I also felt that I was missing out on ‘real-world’ experiences such as being part of an industry-led team whose primary ob jective is to discover an orebody, rather than just hypothesizing about it.
BD: Apart from me, who have been some of the positive influences in your career?
FB: You know darn well that you are one of my true heroes - for real! The indefatigable Professor David Groves certainly has had a strong and lasting influence on my way of thinking about mineral deposits, and the linkages between metallogeny, endowment and tectonics. I have already mentioned Professor Lluis Fontboté, with Professor Reinhard Greiling being largely responsible
Major Drilling is one of the world’s largest drilling services companies primarily serving the mining industry. We maintain field operations and offices in Canada, the United States, Mexico, South America, Asia, Africa and Australia.
Visit our team at PDAC 2024 March 3-6 | Booth 330
for my interest in structural geology. Others that I have had the immense pleasure of working with were mentors to me whom I learned heaps from, include David Gray and David Foster (what is it about all of these ‘influencers’ being named ‘David’?!), Paul Ashley, Gilbert Stein, Markus Elsaesser, Holly Stein, Dennis Arne, Leon Bagas, Andy Wilde, Peter Cawood, and Doug Kirwin.
BD: Given the current multi-commodity mineral boom, are you doing a lot of work outside of the commodities and deposit styles you have traditionally worked on?
FB: As a matter of fact, I am. I would consider orogenic and Carlin-style gold, every kind of uranium style of mineralization, VMS copper, nickel sulfide and sedimentary-hosted base metal deposits as those that I have ‘traditionally’ worked on for most of the last 30-odd years. In contrast, until relatively recently I knew nothing – and I mean absolutely nothing! – about lithium deposits. Though I would venture a guess that this applies to the majority of geologists who are now kneedeep in lithium brines and/or are considered veritable experts on all things LCT pegmatites. Through the work for FTL and the investment fund, I have gained new-found knowledge and appreciation of lithium, though I still wouldn’t consider myself a true Li ‘expert’. Likewise, the recognition of what is possibly the world’s lowest cost HPA project at Lake Hope, WA, by IPT has allowed me to delve into another previously unknown to me commodity.
Assisting that Germany-based fund with building up a strong equity position in just about every advanced silica sand project in Australia has led to my gaining a pretty good understanding of why the world is running out of high-purity sand. In fact, the exposure to, and liaising with some sixty ASX-listed mineral resources companies, meant that I had to get my head around a bunch of ‘new’ commodities and deposit styles, including carbonatite-hosted REEs, layered intrusion-hosted PGM, and lateritic Ni.
BD: You are a technical advisor to several projects and a non-executive director on some. Is it easy to translate technical geology into pragmatic, understandable points for people who make decisions at corporate levels but don’t have technical geology backgrounds?
FB: Define ‘easy’! Regardless, I actually relish what sometimes can be quite a challenge, but I’d like to think that my passion for teach-
ing has helped me with the concept you are referring to, as has the enjoyment of public speaking (to be sure, this wasn’t always the case).
I remember putting together a series of seminars for my Qatari bosses at Qatar Mining, whereby I literally had to start with ‘What is a rock?’, and then take them all the way through to how different types of mineral deposits form and why we as a ‘mining’ company would want to explore for them. By contrast, at least in my experience, I think most, if not all non-technical executives of ASX-listed exploration companies do have a quite sound knowledge of geological concepts. Which I deeply respect. I mean, if the situation were reversed, I’d flunk out of CFO or mining engineering tests quite rapidly, I think.
BD: I have to ask – political instability/ insecurity aside, what part of the world do you think is highly prospective for finding new world-class orebodies?
‘I love every style of mineralization equally, and am fascinated by the ‘where’, ‘how’ and ‘why’ of their formation.’
FB: Hands down, the Arabian Nubian Shield (ANS), especially the Red Sea Hills of northeastern Sudan. Back in 2016, I literally stumbled across and mapped out a hitherto unknown VMS occurrence while undertaking regional reconnaissance work to constrain the depositional environment of what turned out to be a highly fertile backarc setting (where VMS deposits typically form). As Exploration Manager for QMSD, I subsequently had the opportunity to test and drill out this occurrence, which still has significant upside potential. This came after the team I was a part of discovered the first confirmed porphyry Cu-Au deposit (Jebel Ohier; around 600 Mt at 0.33% Cu) in the ANS a few years earlier. And there are
numerous as yet untested porphyry copper, orogenic gold and VMS occurrences that are waiting to be tested and drilled out across almost 1 million km2 (386 102 mi2) of what is essentially a Neoproterozoic analogue of the present day Southwest Pacific – arguably the most prolific, metallogenically fertile and highly endowed geological region in the world.
BD: Is there a particular mineralization style or deposit type that interests you, and why?
FB: Not really. I love every style of mineralization equally, and am fascinated by the ‘where’, ‘how’ and ‘why’ of their formation. That said, I guess, I always had a soft spot for orogenic gold deposits. The combination of structural complexity, their epigenetic nature, global distribution, huge size variations and of course, the ‘shiny’ nature of the commodity itself, makes for an absolutely fascinating blend, wouldn’t you agree?!
BD: Leading on from the previous question, everyone has a handful of deposits that have left a mark on them, be it because of the amazing geology, the hideous conditions, the people they worked with, etc. Which deposits do you hold dear, and which ones really were difficult to work on?
FB: I have been very fortunate to visit, and work on a large range of deposits across six continents and collaborate with amazing people while I was at it. Yet, in terms of favorites, I’d say that the Kumtor deposit in Kyrgyzstan would have to be right up there. The scenery surrounding this world-class orogenic gold deposit is simply stunning, with a fast-moving glacier more or less adjoining the huge open pit mine, which sits at around 4000 m (13 123 ft) above sea level in a remote part of the Tien Shan Mountains, south of Lake Issyk Kul. The Jebel Ohier deposit is close to my heart for obvious reasons, and working on a bunch of orogenic gold deposits across the Altiplano of Argentina was pretty cool, too. From an exploration viewpoint (we were testing the potential of the Thule Basin for unconformity-type uranium deposits), it doesn’t get much better than northwest Greenland, I think.
Working approximately 1.6 km (1 mi) underground at Mt Isa (3000 North Cu orebody) had its challenges (the steel meshing kept moving, you could barely touch the rock face and chalcopyrite would literally burn your fingers) and I almost died from carbon dioxide poisoning a couple of times while
working underground in small and poorly ventilated gold deposits in central Victoria, Nova Scotia and New Zealand. Dealing with artisanal miners at Nyakafuru in Tanzania was scary, especially once they had set fire to the tires of our vehicles, and I faced the wrong end of a double-barreled shotgun several times in California, where many of the historical gold mines sit on privately owned land. But almost nothing tops trying to advance and develop any kind of project in Queensland, when it comes to ‘difficult to work on’ projects!
BD: Frank Bierlein has operated all over the world. Do you have any travel horror stories or cultural mishaps that you can share?
FB: Does this include countless lost bags, endless flight delays, flying with dodgy carriers, and trip cancellations? Or accidentally eating dog entrails in Shandong because I thought it was a pasta dish and my local minder hadn’t paid attention to what I ordered? Oh, and how about when I first arrived in Australia and mistook Vegemite for Nutella? The atrocious taste of that thickly coated slice of toast still lingers. I have since
come to appreciate vegemite very much, though, thank you!
While working at the Orcopampa Mine at an altitude of around 4500 m (14 764 ft) in Peru, I somehow - well, I actually have a pretty good idea of how it happened - managed to contract Giardia (a parasite causing diarrheal disease giardiasis), which nearly killed me. I was also held up at gunpoint by three thugs in Lima during the same trip, so in spite of the spectacular scenery and some amazing people, Peru has unfortunately left me with some rather unhappy memories. Though, as my wife keeps reminding me, the silver lining is that I actually survived and lived to tell the tale(s)!
I escaped a kidnapping attempt in Jujuy Province, Argentina, and as I alluded to earlier, I was caught up in the popular uprising (2018) and military coup (2019) that toppled the long-reigning dictator of Sudan, Omar Bashir. I spent several anxious weeks on both of these occasions locked up in my apartment, while tanks were rolling past my front door and protestors were chased down the street and mowed down with machine gun fire. A British expat acquaintance of mine was shot in the head and killed by a
stray bullet during the city-wide protests in Khartoum. Those experiences kind of make getting chased by hungry bears and territorial taipans look almost innocuous. Especially when you consider what humans are tragically capable of doing to their fellow humans.
BD: Is there anything that you miss from your academic career? For example, I miss the opportunity to undertake a dedicated microstructural study of deposits, something that I feel is fundamentally lacking in many deposit studies.
FB: I totally agree! When you work on a fascinating project in the capacity of a consultant, you commonly identify knowledge gaps and propose how to fill them to the effect of increasing the owner’s chance of exploration success, or to increase the deposit’s resources, etc. But once you hand over your report, that’s it and it is then entirely up to the project owner to pursue, or ignore, your bright ideas. I am a big fan of age dating, for example, and would love to see much more geochronological data being generated for the purpose of understanding a given deposit’s relative and absolute timing in the context of the host terrain’s evolution.
DIATOOL is a young and dynamic company, founded in 2010. The company manufactures impregnated and set core bits, casing shoes, reaming shells, and geotechnical drilling bits. DIATOOL products are sold in North and South America, Australia, Asia, Africa, and Europe.
DIATOOL Diamond Products are manufactured in a modern well-equipped plant, using the latest Canadian and Australian manufacturing technology.
The personnel at DIATOOL have experience in the mining and mineral exploration and core drilling industry going
Australia 12 Bonney Street
Meningie SA. 5246
South Australia herman@internode.on.net
back to the 1970s. Their experience in designing, engineering, and manufacturing, has placed DIATOOL at the forefront of diamond drill bit technology.
Using sophisticated, proprietary furnacing techniques, and experts in powder metallurgy, DIATOOL is able to manufacture a broad range of matrices to achieve the best possible bonds for everyday drilling demands.
Specializing in prompt technical problem solving, we pride ourselves in our ability to respond to customer demands, with the supply of high-
Canada 401-6333 West Blvd., Vancouver, BC
V6M 0C1 Canada аnthonygraham6@gmail.com
quality products at competitive prices.
The founding partners have in excess of eighty years of combined Canadian and Australian expertise in the areas of matrix metallurgy, technical design, manufacturing processes, and quality control systems.
This is something many companies don’t assign a lot of practical value to, though. Likewise, the systematic use of alteration vectors via multi-element analysis, rather than just analyzing for the target commodities, is commonly underappreciated. Granted, there is a cost involved, but the potentially huge benefit of (selective) multi-element analysis typically far outweighs this.
BD: We hear all about the advances and benefits of technologies, such as 3D modelling, geochemical analysis, AI, and the utilization of drones. Have you noted any negative impacts to effective exploration and mining because of these e.g. less people out kicking rocks?
FB: That’s a bit of a leading question, isn’t it? We might be dismissed as a pair of grumpy old farts who reminisce about the good old days, but I fully agree with you that there is most certainly a steady decline in the number of people who are actually out there and getting their hands and knees dirty in the field. Geological mapping is almost becoming a lost art. Don’t get me wrong, I think that our industry has benefitted enormously from recent, and not so recent advances in technology. The use of cost-effective drone-
based remote-sensing tools, innovative 3D modelling, applications such as Leapfrog and ioGas, GIS-based mineral prospectivity analysis (which I am a huge fan of from the viewpoint of providing a cost-effective decision-making tool), portable XRF and hyperspectral equipment, coiled tube drilling techniques, etc., are all absolutely brilliant developments. But for all the enormous investment in these technological advancements, and their application, has our success rate gone up accordingly? I think not.
Geology departments are being shut down at an alarming rate, the cost of running field trips has become unsustainable (not to mention the public liability specter) and an entire generation of experienced hands-on university lecturers is retiring without being replaced. At the same time, many graduates prefer city-based positions and shy away from ‘roughing it’ during weeks-long stints in the field. So it is little wonder that field-based exploration has a problem on its hands. Until we are in a position, perhaps, when we can send out remote-controlled or independently operating androids to do the ‘dirty’ work for us…
BD: This is a multi-faceted question. Firstly, what is your opinion of the geological skillsets, experience, and knowledge of geologists today, especially those who are newly graduated? Do you perceive a looming skills gap, due to the retirement of many academic and industry veterans, combined with the closure of many earth science institutions?
FB: You only have to look at recent editions of the very informative and telling AIG surveys about age distribution, experience and skills gap in geology. I know, and work with several young geos that are driven by discovery and learning, who want to be out there and are keen as mustard to discover an orebody. So it’s not all doom and gloom. To be sure, some of these are either foreign nationals who have come to Australia in search of opportunities, much like myself some 30-odd years ago, and with the same motivation. Others work in the country of their birth (and/or university training), but are just as passionate and driven. Longer-term, it remains to be seen how our industry will cope with the steady decline of new graduates, while more and more experienced geologists ride off into the sunset.
BD: Has there been any single satisfying moment in your career that rates above all the others?
FB: For my kids to tell me that they understood, and were proud of what I was doing! They think exploration and mining are relevant, and concur with me that we need to continue to dig big holes in the ground. As long as these are managed in a responsible way, that is (I won’t use the word ‘sustainable’, because by their sheer nature, mines are anything but!).
Besides this unassailable peak, being involved in the discovery of ore deposits, playing a critical role in a USD 33 million JV, co-directing a >50% increase in value of a private equity fund within 12 months, receiving recognition for demonstrating that orogenic gold deposits in central Victoria formed up to 70 million years prior to the emplacement of spatially (but clearly not genetically) related granitoid intrusions (these were long believed to be the source of the gold and the hydrothermal fluids, which had implications for the prevailing exploration targeting model), being responsible for a 25% increase in mineral resources via the application of mineral prospectivity models, contributing to over 1700 days of zero LTIs, mentoring young geos of vastly different cultural backgrounds, and working with amazing people in incredible places are all some of the reasons for why I love what I do.
BD: I’ll ask a question on the flipside to the previous one. Many of us have interfaced with less-than-savory individuals or experienced toxic workplaces. Has there been any incident or incidents that really disappointed you?
FB: I think it is virtually impossible that, during a 30+ year career, one does not encounter at least a few situations or workplace arrangements that were, shall we say, sub-optimal. That goes for both academia and industry. Indeed, I have had my share of superiors and co-workers who I felt were less than competent (and I acknowledge that I have a low tolerance for professional incompetence), lacked relevant management or technical skills, especially when in a position of power and influence, and undermined my own passion and drive to bring a project or a program to its successful completion at every turn. Of course, it always takes at least
two and it won’t do to simply blame the ‘antagonist’ for everything that has gone wrong without trying one’s best to make things work and put strategies in place aimed at dealing with such unsatisfactory conditions. Ultimately, and if one comes to the realization that nothing seems to be able to resolve a toxic work environment, however, it might be a matter of pulling the ripcord. Life is too short to put up with toxicity that can literally kill you in the long run.
BD: Given the many professional hats that you wear, what is Frank Bierlein’s secret to time management?
FB: Who says I am any good at it?! In general, I tend to prioritize tasks based on their importance and time sensitivity. I dislike leaving tasks half-completed so I aim at finishing and dispatching them. I take a flexible approach to work hours and don’t mind putting in the extra time if and as required, especially given the distribution of projects and affiliates I interact with across literally 24 time zones. Though I am not a big fan of having to get up (or stay awake) for 2 a.m. Zoom calls with Toronto or London…
BD: If you had abundant financial funding, is there a fundamentally annoying geology question you’d like to solve or a topic you’d like to work on?
FB: AMIRA ran the extremely successful West African Exploration Initiative (‘WAXI’) from 2007 to 2015. This undertaking involved geological survey organizations from something like ten countries, a large group of industry partners and several research organizations in Africa, Europe and Australia. I would love to see something analogous getting off the ground in Eastern Africa, with a focus on the ANS and/or the Victorian Greenstone Belt and its surrounds.
WAXI made an enormous contribution to our understanding of the make-up and evolution of the Archean and Proterozoic building blocks in West Africa, and had a tangible influence on the discovery of a raft of mineral deposits. The ANS remains poorly constrained, yet undoubtedly has the potential to host numerous as yet undiscovered world-class mineral deposits of Au, base metals, Li, PGM, REE, etc.
BD: You were an editor for Mineralium Deposita, the official journal of the So-
ciety for Geology Applied to Mineral Deposits (SGA). Do you think that geological societies, such as the SGA and the Society of Economic Geology (SEG), have adapted with the times in terms of being useful entities for their members? Or are there basic things that such societies should be providing and/or promoting?
FB: I was also on the editorial board of Ore Geology Reviews and the Australian Journal of Earth Sciences for several years, but who’s counting?! By and large, I think the relatively steady membership numbers of professional societies, such as the SGA and SEG, demonstrate that these societies have adapted quite well and continue to provide a fantastic source of support, education, and professional development. The trick, as always, is to remain relevant and continue to attract ‘new blood’. SEG does this best, in part because of the North American model of sourcing donations from across the membership base, and funneling these resources largely towards the support of graduate geologists, sponsorship of student chapters, conferences, outreach and field trips. The economy of scale is also important, which is why there have been several proposals to merge the SEG with SGA, and likewise the GSA with AIG and/or the AusIMM. But just like major political parties, what might make financial sense runs the risk of becoming too broad in its objectives and stated raison d'etre (from French literally ‘reason for being’). After all, the global geological community represents a relatively small group of likeminded professionals when compared to, for example, engineers or medical practitioners.
BD: Finally, any concluding comments or words of wisdom?
FB: I am not sure I would consider myself an ‘industry leader’. I feel privileged and very fortunate to have had a diverse and always exciting career, and continue to thoroughly enjoy working with, and learning from amazing people (yes, that includes you, Brett) while visiting some truly awesome places that make you appreciate just how cool Geology is, and what a magnificent planet we live on. Thanks heaps for the opportunity to express my passion and explain to your readership why I love what I do. C
Often the drill is the ‘Truth Machine’ in mineral exploration
by John Anderson, Formerly: Regional Exploration Manager at Aberfoyle Resources; General Manager Exploration
Australia
and Africa – MIM Exploration; Inaugural Managing Director – Investigator Resources
I was 19 when I first engaged with drillers on a vacation job near Cobar, Australia. I was hired to stand in for the sole geologist running two diamond rigs and a RAB rig along a stretch between Canbelego and Nymagee. Unfortunately, the drillers were away during the one-day handover, so I had to introduce myself.
The first words I heard from a diamond driller were ‘I don’t like Jimmy’, or something to that effect. On asking who Jimmy was, I was advised he was our field assistant in similarly unrepeatable words. I then tried my luck with the RAB driller. He immediately pounced on me complaining about the line clearing. Things were going fantastic. Back in Cobar, I found the preferred earth mover was unavailable due to a family tragedy. I realized university was only a steppingstone to a real-life education.
It was the summer of 1974. Darwin had Cyclone Tracy while Cobar had the fires. Probably related to climate change before we were made aware of it. The diamond drillers dropped their rods and headed off for two weeks fighting the fires with the Army along the Wilcannia Road.
I stayed in Canbelego with the RAB rig, although managing to spend 12 hours on the back of a Toyota hosing down a local lightning strike. Finishing Honors, I ended up at Broken Hill as an underground sampler, barring down backs and collecting core trays. Becoming a dab hand at knapping half core samples with a hammer, I was to become a probationary junior mine geologist after a six-month trial. Cominco offered me a job as a straight up junior exploration geologist for AUD 500 a year less than my sampler wage. So off I went in 1976 to drill for nickel near Kalgoorlie. I was the lone geologist reporting to the Adelaide base. There were about a dozen exploration geos remaining in Kalgoorlie after the nickel boom and they took me under their wings.
Boart Longyear were the diamond drillers and Northbridge did the percussion drilling. Ken Phillips offered to trial a new drill technology called Reverse Circulation. After struggling for a day, I said it would never work. Not the first or last time I ate humble pie as I learned that patience and persistence are virtues. One thing I particularly remember with the core drilling was using HF to etch test tubes to measure hole inclinations with tables to compensate for the meniscus. We also used single-shot downhole orientation cameras.
Once that drill program was over, I was able to enjoy the Kalgoorlie community more with touch rugby on Saturdays before I went out Sunday camping and mapping 30 mi (48.3 km) north of Kalgoorlie over another six-day working week. Things got busy again later in 1976. Mapping laterites north of Leonora and staying in the White House Hotel, one evening I was watching ABBA’s Mamma Mia being played over and over on the first video machine I had seen. A driller walked in and knowing I was a geologist, pulled out a pocketful of chalcopyrite asking what I thought. I may have been the first geologist to see Teutonic Bore mineralization. I neglected to mention this to my Adelaide boss until two days later, then all hell broke loose. I suddenly had a resident boss in Kalgoorlie, and I was on pegging and gossan search duties competing with crews from many companies. Kalgoorlie came alive again.
That story continued with my early arrival at the Palace Hotel one Friday afternoon to find Anaconda geologist Ilmars (Bill) Gemuts lounging alone at the back bar with the grin of a Cheshire Cat. Not forthcoming about his grin, we were being gradually joined by the regulars such as George Compton. Suddenly Peter Allchurch of Seltrust burst in abusing Bill. It turned out Bill had hired a helicopter that day and hopped along the Teutonic line of gossans sampling his rightful 12 lb (4.5 kg) or so of rock per Mineral Claim. With Peter in hot vehicular pursuit eventually catching up with Bill in Kalgoorlie. Dare I say it, those were the days.
I subsequently got a better roster and joined Wally Unger and Keith Biggs in their squash team and met my future wife in the back bar of the Palace Hotel. We attended the last annual rocket firing of the WA School of Mines students. A rocket backfire ignited all the propellent supply and burnt about five people. The eternal image is all the nurses in the crowd including my partner leaping over picnicking people to treat the injured and evacuate them to Kalgoorlie Hospital.
I missed the gold boom in Kalgoorlie, being transferred in late 1978 to NSW to explore for tin around the Ardlethan mine. Drilling early-stage targets with an Investigator Mark 3, I remember the driller ordering a new differential from Dubbo. This duly turned up in the back of his wife’s Jaguar. In that campaign we only found tungsten that went down the gurgler along with tin in the early eighties. But wait, that’s now a Critical Mineral!
In 1980, I had an interlude restarting exploration at the Drake silver gold prospects in northern NSW with Northbridge again doing the drilling. Being wary of bias through sample loss, we decided to make an annular steel tray to capture all material spilling out around the
collar. The contraption was ordered from an engineering firm in Lismore. It was delivered with the driver asking if we had a crane to load it off the truck. The measurement in feet had become meters (to clarify, this is nearly 3.281 times longer). And we thought the Y2K changeover was a problem!
I really got amongst the core in 1984 with a study of the Zeehan tin prospect in Tasmania. Most of the core was burnt by the 1981 bushfires, however enough survived for the study. The burnt core trays had collapsed into archeological layers for which the sequence of hole numbers and tray depths were separately recorded, but the core and blocks were largely white oxidized mush. In 1988, I resumed my relationship with Boart Longyear on the Menninnie Dam and Angas lead zinc discoveries in South Australia. Angas was particularly interesting with drilling in a limestone quarry on the edge of a historic town. Having local John Nitschke as
the percussion driller greatly assisted our engagement with the Strathalbyn community. Aberfoyle also had a strong relationship with Budd Drilling initially exploring for mineral sands in the Murray Basin with Investigator Mk4s then moving to diamond core rigs on the Eyre Peninsula.
Joining MIM in 1994, I was exposed to precision drilling of 2 km (1.2 mi) long holes under George Fisher and for remnants of the small high-grade Tick Hill deposit. My most serious work accident was a Ravenswood driller dropping the head drive onto his boot with the steel cap severing a toe. Being Site Senior Executive for all MIM’s EPMs, I flew up to Townville to join the investigation with the local Mines Inspector. The replacement driller proudly showed us the cage he had just welded around the mast. He and I got a rollicking for interference with the scene of an accident. We were still learning.
For more information
Get in touch with John Anderson on LinkedIn
Persisting with four companies in the northern Eyre Peninsula, Investigator Resources eventually made the Paris silver discovery. The quality of modern drilling in difficult conditions was exemplified there by Titeline and Bullion. Safety is now paramount and technologies like directional drilling and mud doctoring are routine these days. The South Australia Chamber of Mines and Energy requested ideas to put to the State government. I submitted a proposal to use the Brukunga mine site in the Adelaide Hills as a national drill testing and training site preferably with Boart Longyear’s involvement. A year later, the Deep Exploration Technologies CRC commenced with that objective. Great minds think alike.
Now the industry is aspiring to rapid coiled drilling, bit-face recording and labat-rig assaying. We have come a long way since acid etching and hammer knapping. Happy drilling! C
Dive into a new era of efficiency and safety with Comacchio CX line rigs. Our multipurpose rigs redefine the industry standards, providing you with the flexibility to excel in diamond drilling and reverse circulation drilling applications, and boosting your safety performance by minimizing manual handling.
CX line: one rig, multiple possibilities.
by Dr Kris Butera, Managing Director at Plutonic Limited
I sit perched in the northeastern corner of the Simpson Desert in the Australian Northern Territory, overlooking a landscape carved by extreme elements.
The fiery hell of scorched desert winds has carved out a terrain that is as unforgiving as it is beautiful. Sand dunes, like waves frozen in time, partially obscure a likely continental margin, hinting at mysteries hidden beneath. A place some have come, and few have lasted.
These desert dunes have captured minds – and sometimes lives – in the quest for the hidden treasures beneath the surface. This story is etched into the grains of the Simpson Desert, a narrative woven with missed opportunities, flies, and gold. We leap into the realm of folklore and venture into the unknown with the Champion Project.
For years this land was untouched with its secrets buried deep. Many explorers have been drawn by the lure of untold riches only to leave empty-handed. Perhaps they couldn’t see what is hidden in plain sight. Had they had Ploutōn (Pluto), the ancient god of the hidden underground treasures on their side, perhaps those who walked this dusty patch of earth before me would’ve understood the secrets that lie beneath the rocks.
Plutonic Limited, the current explorers of the Champion Project, are guided by Pluto’s hand thanks to our remarkable team enabling us to see what’s deep below. Maybe it’s fate or mere coincidence that the company shares a name with the deity. Whatever the reason, we have been able to see what others missed.
Working on the Champion Project is an adventure unlike any other. Every day is a journey into the heart of the earth. Every rock kicked is a reminder of the geological puzzle that begs to be solved. The landscape is a testament to ancient geological forces - a flat expanse interrupted by massive outcropping epithermal veins and lithocaps. Silicic alteration zones stretch as far as the eye can see, a testament to the volatile history of this ancient land. The geology is complex; breccias within brecciated breccias tell a story of a protracted storm of pulsating fluids, gases, explosions, and metals.
The Champion Project is a geological maelstrom, frozen in time, waiting for its secrets to be unravelled. Around the campfire at night, the air fills with the musings of tired but excited explorers. ‘What the hell is going on here?’, is a common refrain, a mix of bewilderment and awe at the complexity of the geological formations we come across during the day.
The Champion Project is more than just a geological puzzle. It’s a journey into the past, a connection to the ancient stories and myths that have been passed down through generations. The land speaks of a time when the earth was younger, when the forces of nature were unbridled and untamed.
As I delve deeper into the project, I carry the lessons of those who’ve come before me. The wanderers and explorers who have braved this harsh landscape in search of fortune, the indigenous people who have lived in harmony with the land for thousands of years, and even to Pluto himself. Every rock, every grain of sand, every vein tells a story. As we piece together these stories, it becomes clearer that the Champion Project is more than just a quest for mineral wealth. We chase the pursuit of the unknown.
One of the most famous fables of the area is the story of Lasseter’s Reef.
Heading south toward our Asgard Dome prospect through thick bulldust-laden tracks of one of the cattle stations the project rests on, we suddenly come to a junction in the spinifex covered desert country.
‘Lasseters’ the very old crumply tin sign reads as it points to the southeast.
We were aware of Bill DeCarli’s decades-long quest to demonstrate that Lasseter’s Reef occurred somewhere in the area. We’d met with him and studied his story, his evidence and his conviction. We didn’t doubt it but weren’t firm believers either. Yet, meander along the track a little further, and you’ll begin to see huge quartz veins poking up along the horizon. Lots of them. And when I say large, I mean quartz veins many kilometers long and many tens of meters wide in some cases.
Perhaps like the folklore, many of these reefs were partially (and I suspect many fully), obscured by the deep orange sands that Lasseter described. So, does Lasseter’s Reef exist? It doesn’t matter to us. Because there are hundreds of large reefs out there, and it’s a much bigger story than a simple reef with some visible gold. But we’ve honored the fabled history surrounding the reef by naming it Lasseter’s View; a soaring behemoth of a quartz vein, the top of which has spectacular view of veins in all directions for miles and miles.
When the heat of the day ebbs, the air stills and the star-lit black night sky illuminates the camp you’re reminded you might be in one of the most remote and desolate places in the country. A sudden wind whips up the sand, a startled mob of cattle or the baying of dingos in the distance are frequent visitors after dark. It keeps us on our toes and gives us something to talk about around the morning campfire as we are gearing up for the day.
For us, the Champion Project is a reminder of why the Plutonic team is passionate about discovery.
The project delivers more than just sensational geology and picturesque landscapes. It reminds us of the adventure, the romance, the trials and tribulations of remote mineral exploration. And as we lament these escapades and memories, we become aware of what secrets the ground holds.
What was once an area thought of as hosting perhaps a few orogenic quartz veins or a deeply buried iron oxide copper-gold deposit, appears to be a new district scale epithermal and porphyry belt.
The Champion Project, I hope, will be Plutonic’s legacy, a story that will be passed down to future generations of explorers. It is a reminder that the world is full of hidden treasures, waiting to be discovered by those who dare to think differently and to look beyond what can be seen on the surface.
After a few sun- and wind-burnt field seasons; often seeing us chased out by violent storms which rapidly emerge from bright blue skies - we now know there’s a near endless arena of low sulphidation epithermal veins, porphyry geochemical and alteration footprints, advanced argillic alteration forming topography to guide us to the interesting systems, breccia fields, geyserites, silica caps, lithocaps, skarns. Perhaps they are connected to the major mineralizing events of the Tasmanides to the east.
A rodeo of metals, an incursion of flies, plus a team of misfits, eccentrics, autists and with a vision of something big. A romance of science, spirit and the quest for glory – the Thrill of Discovery. I’m sure this all sounds all romantic and endearing, but there’s still the hardcore science and layers of strategy at the core of the unveiling of the potential hidden riches.
Our primary approach has been raw boots on the ground – a massive feat given the approximate 5000 km2 (1931 mi2) for us to explore. We’ve only covered a small portion so far and have already amassed many targets. We’ve combined good old-fashioned geology with advanced algorithm-driven structure detection, novel 3D magnetic inversion modelling, structural and alteration mapping and analysis, detailed rock chip sampling and subsequent innovative modelling of that data to generate porphyry and epithermal footprints.
Ahead of the curve, straight to
Directional Core Drilling with precision, efficiency and reduced environmental impact.
• Reach multiple targets from the same borehole at optimal angles of intersection
• Correct for natural borehole deviation
• Overcome environmental challenges to reach otherwise inaccessible areas
• No requirement for additional water pumps, drill strings or survey instruments
↑ Figure 5 - (a) Porphyry and (b) Epithermal Gold favourability maps covering the Apotheosis and Icarus prospect and surrounding areas (the field of view is the same in both images). Prospectivity models were constructed by combining several different ‘layers’ of HyMap data, with each model input being carefully selected to represent a critical component of the mineral system. The resulting maps are a useful first-pass indicator of relative prospectivity and a powerful targeting tool.
The net outcome of the previously mentioned work is a multitude of multi-kilometer scale targets across the project. Some of these prospects have weird names, like ‘McLovin’, ‘I’m Not a Vampire’, ‘Apotheosis’ and ‘Asgard Dome’. We think the names add character to the targets, but don’t be fooled – the science is what underpins their prospectivity.
McLovin is a 6 by 2 km (3.73 by 1.24 mi) corridor of large epithermal veins. The surface expressions of which are dominated by quartz replacement blade textures – signs that the low sulphidation epithermal gold-silver target, if it exists, is fully preserved below the surface. With outcrops up to 15 m (49.2 ft) wide, it’s a good sign that should the system be well mineralized at depth, it would likely have a strong economic scale to it. Coupled with up to 0.3% bismuth, scatterings of elevated gold, silver and tellurium, the geochemical and geological framework gives an enhanced opportunity for a major gold discovery at depth.
The next phase in the discovery process is to screen and map out the prospect with induced polarization (IP) to map out potential large feeder zones at depth, and the key ‘boiling zone’ for which the economic metals are expected to be deposited.
I’m Not a Vampire has recently expanded to the now Greater I’m Not a Vampire prospect as we have seen a major upscale in the size of the system. It’s grown from a 1.5 km (0.93 mi) colossal vein sticking up through the sand dunes hosting beautiful hydrothermal breccias
and gold-silver and adularia-bearing colloform quartz bands, to now a field of mineralized vein systems, ancient fossil geysers and potentially even sniffs of a porphyry spanning over 15 by 5 km (9.3 by 3.1 mi) with the edges yet to be defined.
At Apotheosis we find a strongly advanced argillic alteration in hyperspectral data (pyrophyllite-dickite-kaolinite) and residual quartz indicative of being above a porphyry, where the target itself is a high sulphidation epithermal gold-copper-silver system.
Geochemically, even the very limited number or rock chip samples have generated a large porphyry system at depth, with the prospect sitting over the very large Icarus porphyry target defined by interpreted phyllic and propylitic alteration in hand samples and hyperspectral data.
Asgard Dome is a large-scale anticlinal dome - 28 by 18 km (17 by 11 mi) hosting the most abundant and massive veins I’ve ever seen in my life.
From the previously mentioned Lasseter’s View reef to a plethora of other giant epithermal veins, the opportunities at the Champion Project are endless. The presence of specular hematite and phyllic alteration in some areas indicates that there is a potential porphyry overprint. So having the opportunity to discover both large epithermal and porphyry deposits presents another amazing opportunity to generate real value.
The many additional targets provide just as much excitement, if not more, across the project – there’s simply too much to mention. But none of that, the targets or prospective geology, is useful without having a strategy suited to the project. While many might go out and
start drilling any of the large colloform-crustiform metal bearing low sulphidation veins to get some numbers on the board, we’ve opted for an approach consistent with the fundamental mechanics of mineral exploration success.
Mineral discovery is simply a game of chance, and the more times you roll the dice the better the chances of making a big discovery, which is what we’re after. We didn’t come to this pocket of the desert for the ordinary. We’re only interested in giant and supergiant deposits.
Of course, anything smaller that we cross paths with. But to maximize our chances of finding a true Tier-1 system - or ideally a new mineral belt full of them - we seek to fully understand the scale of the mineralizing system first. To do that, we need to map out and generate a plethora of world-class targets, and then to drill them all to bring home a simple message – there are still plenty of globally significant deposits yet to discover.
Mineral exploration can be a sustained endeavor of value accretion beyond putting the first deposit discovered into production. Too often
the first find for a company is rushed into production before really knowing where you should and shouldn’t put the tailings dam. Many tailings facilities and infrastructure have been built over economic orebodies that should have been found before development.
For now, Champion is like a playground. It’s full of fun, adventure, imagination formed around the things we see and full of opportunity. The literal blood, sweat and tears of the team has yielded, perhaps, a once in a generation new mineral belt ready for multiple discoveries.
I am proud of them.
The Champion Project, I hope, will be Plutonic’s legacy. A story that will pass down to future generations of explorers. A reminder that the world is full of hidden treasures, waiting to be discovered by those who dare to think differently and to look beyond what can be seen the surface.
The Champion Project is a gateway to a world of adventure, awe, and ore, a world whose secrets are being eroded away like the glacial till that my camp stool rests. As I look up to the darkening firmament, I see a thousand twinkling stars smiling down on us and feel a warmth that not even the frosty desert wind can dull.
As I write these final words while gazing into the flickering flames of the mulga-fuelled campfire, I know that this is still just the beginning of something bigger and bolder than what we thought possible. C
by Rowena Duckworth, Founder & Petrographer at Mintex Petrological Solutions
FerroMagnesian Minerals
Amphibole
Biotite
Chlorite
Epidote
Clay Minerals
Mg-Smectite
Nontronite
Kaolinite
Al-Smectite
White Mica Minerals
Hydrous Micas (Smectite-Illite)
Intermediate Micas (Illite)
Anhydrous Micas (Sericite)
Other Minerals
Non-phyllosilicates (Quartz-Feldspar)
↑ Figure 1 - Hyperspectral imaging of drill core (Michaux and O’Connor (2019), referencing AMIRA 2009 & GeoTek https://www.geotek.co.uk/sensors/hyperspectral/)
Exploration drilling plays a fundamental role in identifying and evaluating potential mineral deposits. It follows that analysis of drill core samples from exploration projects provides valuable insights into the geological composition and potential economic viability of mineral resources. This article delves into the various scanning techniques commonly used in the study of drill core samples, namely, hyperspectral imaging, X-ray scanning and laser-induced breakdown spectroscopy (LIBS). These techniques all deliver comprehensive mineralogical data that help with mineral identification, lithological characterization, elemental composition determination, alteration mapping, and ultimately, make or break decision-making processes in mineral exploration.
Paul Ashley neatly summarized the benefits of petrographic analysis on drill core sample in Issue 23 of Coring (May, 2023; p. 46). Petrographic analysis involves the detailed microscopic examination of thin sections of rock samples, and provides essential information about the rock's mineralogy, texture, and structure. In an ideal world, thin section petrographic studies should always be conducted prior to, or complementary with, other geochemical analysis.
Hyperspectral imaging captures the reflectance or emission spectra of rock at numerous narrow and contiguous spectral bands. It enables the identification and mapping of minerals and alteration minerals based on their unique spectral signatures.
Imaging can be conducted on half core samples using core scanning machines or handheld field portable spectrometers. The spectra provide information about the mineral composition, chemical bonds, and structural features of the minerals present in the drill core.
Hyperspectral core scanning instruments consist of a spectrometer, a hyperspectral camera, and a motorized stage to move the drill core sample. The spectrometer measures the intensity of reflected or emitted light at different wavelengths. The hyperspectral camera captures the spatial information and generates high-resolution images of the drill core.
Most hyperspectral core scanners cover a broad spectral range, typically spanning from the visible to the near-infrared (VNIR) or shortwave infrared (SWIR) regions. The spectral resolution can range from a few nanometers to tens of nanometers, allowing fine discrimination of spectral features.
Drill core is placed on the stage, and the hyperspectral scanner moves along the length of the core, capturing data at regular intervals. Hyperspectral data can be processed using various techniques, such as spectral unmixing, classification algorithms, and mineral libraries. Spectral unmixing helps identify and quantify the abundance of different mineral components within the core. Classification algorithms classify the spectra into different lithological or mineralogical classes
↑ Figure 2 - Example of down hole chemical plots generated from the Minalyze core scanner. Source: https://minalyze.com/portfolio/geochemical-core-logging.
↑ Figure 3 - Example of output from ELEMISSION LIBS core scanner. Source: Critcon Conference abstract volume 2023-University of Adelaide-Duckworth et al. LIBS automated techniques for the mineralogical and elemental characterization of critical mineral deposits.
based on their spectral properties. Mineral libraries compare the acquired spectra with known reference spectra to identify specific minerals present in the core (Figure 1).
Hyperspectral core scanning is especially good for the various mica and clay phases. For example, different types of mica minerals, such as muscovite, biotite, and phlogopite, have distinct spectral features related to their chemical composition and crystal structure. Similarly, clay minerals – including kaolinite, illite, smectite, and chlorite – also exhibit specific spectral signatures due to their mineral structure and composition. This technique is particularly effective in mapping alteration patterns and zoning within the drill core as hydrous alteration minerals often exhibit distinct spectral signatures.
The main limitations of hyperspectral core scanning are in detecting minerals that lack unique spectral features or occur in low abundances. The technique is sensitive to surface conditions and requires careful handling of the drill core to avoid contamination or alteration. Data analysis can be computationally intensive and requires expertise in spectral analysis and mineralogy. Chemistry of the cores is not obtained.
XRF core scanning operates on the principle of X-ray fluorescence spectroscopy. The technique involves irradiating the drill core sam-
ple with high-energy X-rays, which causes the atoms in the sample to emit characteristic fluorescent X-rays. These emitted X-rays are then measured, and their intensity is analyzed to identify the elements present and quantify their concentrations.
XRF scanning can be conducted on half core samples using core scanning machines or handheld devices (pXRF). It provides valuable information about major, minor, and trace elements present in the sample, aiding in mineral identification and characterization, which help with identifying mineral zoning, alteration patterns, and lithological changes, facilitating geological interpretations (Figure 2).
The drill core samples are typically cut into half and positioned within the scanning machine. The samples may be placed on a moving conveyor belt or mounted on a rotating stage for analysis. The XRF core scanning machine emits high-energy X-rays which penetrate the outer layers of the sample, interacting with the atoms in the material. The emitted fluorescent X-rays are then detected by a solid-state detector, such as a semiconductor or scintillation detector, within the scanning machine. The detector captures the energy and intensity of the X-rays. The XRF core scanning machine processes the detected X-ray signals and generates elemental data for each point or interval along the drill core. This data is often presented in the form of elemental concentration profiles or elemental maps, providing insights into the distribution of elements within the sample.
It is important to remember that XRF scanning is influenced by the matrix effect, which refers to interactions between the elements in
the sample and the surrounding matrix. The presence of certain elements or minerals can affect the accuracy and precision of the measurements, leading to potential errors in quantification. XRF scanning therefore requires calibration and standardization to ensure accurate and reliable results. Calibrating the instrument for different elements and matrices can be time-consuming and requires expertise. Changes in sample composition or matrix may necessitate recalibration, adding to the complexity. Also, as this is an X-ray technique, relevant permits need to be obtained to comply with radiation safety regulations.
XRF core scanning generates large volumes of elemental data along the entire drill core. When combined with other geological data, such as hyperspectral imaging or geophysical surveys, it enhances the comprehensive understanding of subsurface geology, enabling more informed decision-making in exploration and mining projects.
LIBS is an elemental analysis technique that utilizes a high-energy laser pulse to vaporize and excite a small portion of the sample’s surface. The resulting plasma emits light, which is collected and analyzed to determine the elemental composition of the sample. The LIBS core scanner collects the emitted
light using a spectrometer, which disperses the light into its different wavelengths. The spectrometer may employ various methods to separate the wavelengths. The dispersed light is captured by a detector which measures the intensity of the light at different wavelengths. This data is referred to as the LIBS spectrum.
The LIBS spectrum is then analyzed to identify and quantify the elements present in the drill core sample. Each element emits characteristic wavelengths, enabling their identification based on the wavelengths detected in the spectrum. The LIBS core scanner processes the spectral data and generates elemental concentration information for each point or interval along the drill core. This data can be presented as elemental profiles or maps, providing insights into the elemental distribution within the sample. Mineral maps can also be generated allowing for a complete mineralogical and textural picture of the drill core (Figure 3).
Laser scanning analyses multiple elements simultaneously. The multi-elemental analysis capability of LIBS scanning allows a first pass look of the drill core before any assay samples are chosen, which can streamline the exploration process and cost. Whole core as well as half core can be analyzed due to the wide focusing range of the laser, allowing analysis prior to core cutting if necessary.
One of the key advantages of LIBS scanning is its ability to analyze the light elements, including lithium, which XRF cannot see, making it a perfect tool for lithium exploration. LIBS scanning is also a minimally destructive
testing method, as only a thin 30-micron layer is ablated form the sample, allowing sample preservation for other analytical methods. LIBS core scanning provides real-time elemental analysis on-site with no sample preparation required. This allows exploration teams to obtain immediate results, facilitating faster decision-making and minimizing operational delays.
LIBS provides rapid and simultaneous analysis of multiple elements from hydrogen to uranium, making it suitable for real-time, on-site measurements. In mineral exploration, LIBS analysis of drill core samples can quickly provide elemental data, aiding in mineral identification, mapping alteration zones, and assessing potential mineralization. LIBS offers advantages such as portability, non-destructiveness, and the ability to analyze samples without extensive sample preparation.
Petrographic, whole rock geochemical, hyperspectral, XRF and LIBS analysis of drill core samples are powerful mineralogical and geochemical tools in exploration projects. These techniques offer complementary information on mineralogy, lithology, elemental composition, alteration patterns, and potential mineralization.
Hyperspectral, XRF, and LIBS core scanning techniques offer distinct advantages and capabilities. All provide rapid and non-destructive analysis of drill core samples, enabling
SCANNING TECHNIQUE PROS
HYPERSPECTRAL
Detailed mineralogical and textural information
Identifies various mineral phases and compositions
Can detect subtle mineral variations and alterations
Useful for geological mapping and structural analysis
XRF Elemental analysis
Quantifies major, minor, and trace elements
Non-destructive technique
Suitable for environmental assessments and soil analysis
LIBS Rapid qualitative and quantitative elemental analysis
Identifies light elements and rare earth elements
No sample prep require- can analyze whole core
Provides element and mineral maps
Can provide semi-quantitative and quantitative chemistry
CONS
Relatively slower data acquisition compared to XRF/LIBS
Limited ability to quantify elemental concentrations
Requires careful calibration and standardization
Sensitive to lighting and environmental conditions
Requires specialized software to interpret results
Limited penetration depth, analyzing only surface layers; Slow scanning time
Matrix effects can affect accuracy and quantification
Limited capability for mineralogical characterization
Requires calibration and standardization
Requires specialized software to interpret results
Limited penetration depth, analyzing only surface layers
Sample heterogeneity may impact accuracy
A 30-micron layer of the sample is ablated
Requires specialized software to interpret results
Calibration may be required for different sample matrices for quantitative chemistry
further investigations or additional analysis to be conducted on the same sample if needed. Table 1 summarizes their pros and cons.
Hyperspectral scanning employs infrared spectroscopy to identify and quantify minerals and geological constituents and provides detailed mineralogical and textural information, allowing for comprehensive analysis of mineral composition and geological features.
XRF scanning used X-rays to offer rapid elemental analysis, enabling quick assessment of major, minor, and trace elements in the sample, aiding in mineral identification and characterization. However, like traditional XRF, the technique struggles with the lighter elements in the periodic table.
LIBS scanning uses lasers to generate plasma, enabling rapid identification of elements and minerals in the sample. It is an excellent tool for rapid and visual characterization of whole core rock texture and chemistries. Scanning a whole core tray at high resolution can be done in an hour or so, and element maps are automatically generated. Mineral libraries and maps can be created on a project-by-project basis to add further understanding to the element deportment and textural observations seen in the high-resolution scan photos. Reliable detection of mineral containing the light elements, such as hydrogen, oxygen, lithium and sodium, as well as the heavier elements, such as base metals and REE elements, makes LIBS an excellent first pass scanning methods for all deposit styles. A main selling point is the ability to distinguish lithium and other light element that are not
detectable by traditional XRF-based scanning technologies, and the LIBS system is also a more rapid scanning system. The laser-based system also means less permitting than X-ray based scanning systems in many states/countries.
Overall, each technique adds another layer of information to the exploration toolkit and like all tools, selecting the right one for the job at hand is important. By utilizing these scanning methodologies, geologists and mineral exploration companies can make informed decisions and optimize exploration strategies, reduce costs and increase the chances of discovering economically viable mineral deposits. C
• Ashley, P., 2023. Power of the microscope: petrographic analysis and mineralogy in the exploration and mining industry. Coring Magazine, 23, 46-49.
• Duckworth, R. and Narbey, M., 2023. LIBS automated techniques for the mineralogical and elemental characterisation of critical mineral deposits. Critcon 2023 - Discovery, characterisation and processing of critical minerals. Abstract Volume, 22-26 May 2023, The University of Adelaide. Page 28.
• Michaux, S., and O’Connor, L., 2019. How to set up and develop a geometallurgical program. GTK Open File Work Report 72/2019. Geological Survey of Finland, Economic Minerals Unit, Espoo. 245 pages.
• Minalyze website: https://minalyze.com/portfolio/geochemical-core-logging.
For more information Visit: mintexpetrologicalsolutions.com
Drilling Contractors (A-Z): Diamond Drilling, Reverse Circulation, AirCore
BRYSON DRILLING
Phone 306-323-2202 Fax 306-323-2203 info@brysondrilling.ca www.brysondrilling.ca Canada
CAPITAL DRILLING Phone +230 464 3250 info@capdrill.com www.capdrill.com East, North and West Africa
DDH1 DRILLING
Phone +61 08 9435 1700 admin@ddh1.com.au www.ddh1.com.au
Australia
DIAFOR Phone (819) 860-3957 info@diafor.ca www.diafor.ca Canada
info@oykatiab.com www.oykatiab.com
Finland
Australia
ATELIER VAL-D’OR
Phone (819) 824-3676
Fax (819) 824-2891
info@avddrills.com www.avddrills.com
BARKOM
Phone 90-312 385 60 50
Fax 90-312 385 35 75 info@barkomas.com www.barkomas.com
DISCOVERY DRILL MANUFACTURER
Phone 1-506-542-9708
Fax 1-506-542-9709 info@discoverydrills.com www.discoverydrills.com
www.terrasonicinternational.com
sales@terrasonicinternational.com
+1 740.374.6608
+1 740.374.3618
WE ARE YOUR SONIC DRILLING PARTNER
Terra Sonic International knows what it takes for you to succeed. We are committed to making the world’s most productive and reliable SONIC Drill Rigs and SONIC Tooling while providing the best service and support in the industry. Experience the Terra Sonic Difference today.
DELIVER A SEISMIC SHIFT FOR MINING OPERATIONS.
The Swick GenII Mobile Diamond Drill Rig optimises resource extraction, reduces costly site moves and unearths mine asset value with proven 97% mechanical availability in the field.
PROLENC
Phone (250) 563-8899
Fax (250) 563-6704 khodgins@prolenc.com www.prolenc.com
BOART LONGYEAR
Phone 1-801-972-6430
Fax 1-801-977-3374 www.boartlongyear.com
FORDIA POWERED BY EPIROC Phone 514-336-9211 Fax 514-745-4125 info@fordia.com www.fordia.com
NORTH BAY MACHINING CENTRE
Phone (705) 472-9416 Fax (705) 472-2927 luc@nbmc.ca www.nbmc.ca
PROLENC Phone (250) 563-8899 Fax (250) 563-6704 khodgins@prolenc.com www.prolenc.com
Diamond Products (A-Z)
www.boartlongyear.com marketing@boartlongyear.com
www.diatoolglobal.com anthonygraham6@gmail.com
DIATOOL is a young and dynamic company, founded in 2010. The company manufactures impregnated and set core bits, casing shoes, reaming shells, and geotechnical drilling bits. DIATOOL products are sold in North and South America, Australia, Asia, Africa, and Europe. DIATOOL Diamond Products are manufactured in a modern well-equipped plant, using the latest manufacturing technology.
DIAMANTINA CHRISTENSEN
Phone +562 2620 7808 christensen@christensen.cl diamantinachristensen.com
DIASET
Phone 1-800-663-5004 bits@diaset.com www.diaset.com
BOART LONGYEAR
Phone 1-801-972-6430
Fax 1-801-977-3374 www.boartlongyear.com
HOLE PRODUCTS
Phone 909-939-2581
Fax 909-891-0434 www.holeproducts.com
Drill Rods & Casings (A-Z)
BARKOM
Phone 90-312 385 60 50 Fax 90-312 385 35 75 info@barkomas.com www.barkomas.com
CORE TECH
Phone +51 983 856 666 info@coretech.com.pe www.coretech.com.pe
SINOCOREDRILL
Phone 86-510-82723272 Fax 86-510-82752846 sales@sinocoredrill.com www.sinocoredrill.com
FORDIA POWERED BY EPIROC
Phone 514-336-9211 Fax 514-745-4125 info@fordia.com www.fordia.com
WE ARE YOUR SONIC DRILLING PARTNER
Terra Sonic International knows what it takes for you to succeed. We are committed to making the world’s most productive and reliable SONIC Drill Rigs and SONIC Tooling while providing the best service and support in the industry. Experience the Terra Sonic Difference today. www.terrasonicinternational.com sales@terrasonicinternational.com
+1 740.374.6608
+1 740.374.3618
FORDIA POWERED BY EPIROC
Phone 514-336-9211 Fax 514-745-4125 info@fordia.com www.fordia.com
REFLEX
Phone 1-705-235-2169 Fax 1-705-235-2165 reflex@imdexlimited.com www.reflexnow.com
SONDA PARTS
Phone 55 – (31) 3391 3810 Fax 55 – (31) 3391 3810 comercial@sondaparts.com.br www.sondaparts.com.br/
sptab.com sales@sptab.com +34 952 17 99 18
ADVANCED DOWNHOLE SURVEY TOOLS FOR EXPLORATION AND BLASTING
SPT is your global partner for downhole survey technology. We manufacture advanced solutions for high precision downhole and blasthole survey data. Our commitment to quality and accuracy has made us an industry leader. Request a free demonstration today.
Drilling Fluids (A-Z)
AMC Phone 1-705-235-2169 www.amcmud.com
DI-CORP Phone +1 (705) 4727700 info@di-corp.com www.di-corp.com
Surveying & Geophysics (A-Z)
CORE TECH
Phone +51 983 856 666 info@coretech.com.pe www.coretech.com.pe Peru
DIGITAL SURVEYING Phone +27 18 788 6349 sales@digitalsurveying.co.za www.digitalsurveying. com.za Africa
Mudex Phone +61 (8) 9390 4620 info@mudex.com.au www.mudex.com.au
TRUST SOLUÇÕES
GEOLÓGICAS
Phone +55 62 992720023 contato@trustsg.com.br Brazil
Trays (A-Z)
CORE TECH
Phone +51 983 856 666 info@coretech.com.pe www.coretech.com.pe
DYNAMICS G-EX
Phone +61 7 54826649 sales@dynamicsgex. com.au www.dynamicsgex.com.au
Core Orientation (A-Z)
COREFINDER Phone +55 62 992720023 contato@corefinder.com.br www.corefinder.com.br
DEVICO AS Phone +47 72870101 devico@devico.com www.devico.com
PROSPECTORS
Phone +61 (02) 9839 3500 Fax +61 (02) 8824 5250 sales@prospectors.com.au
For more information regarding our catalog options and rates, get in touch at: editorial@coringmagazine.com
Environmentally safe drilling fluid systems and lubricants for diamond drilling, horizontal directional drilling, rotary and percussive drilling.
Downhole lubricants
Specialty polymers
Foams
Tool lubricants
Blast hole stabilizers
Thread compounds
All of our proprietary, vegetable oil-based products improve penetration rates and reduce drilling costs.
Drilling MADE EASIER