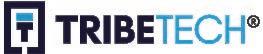
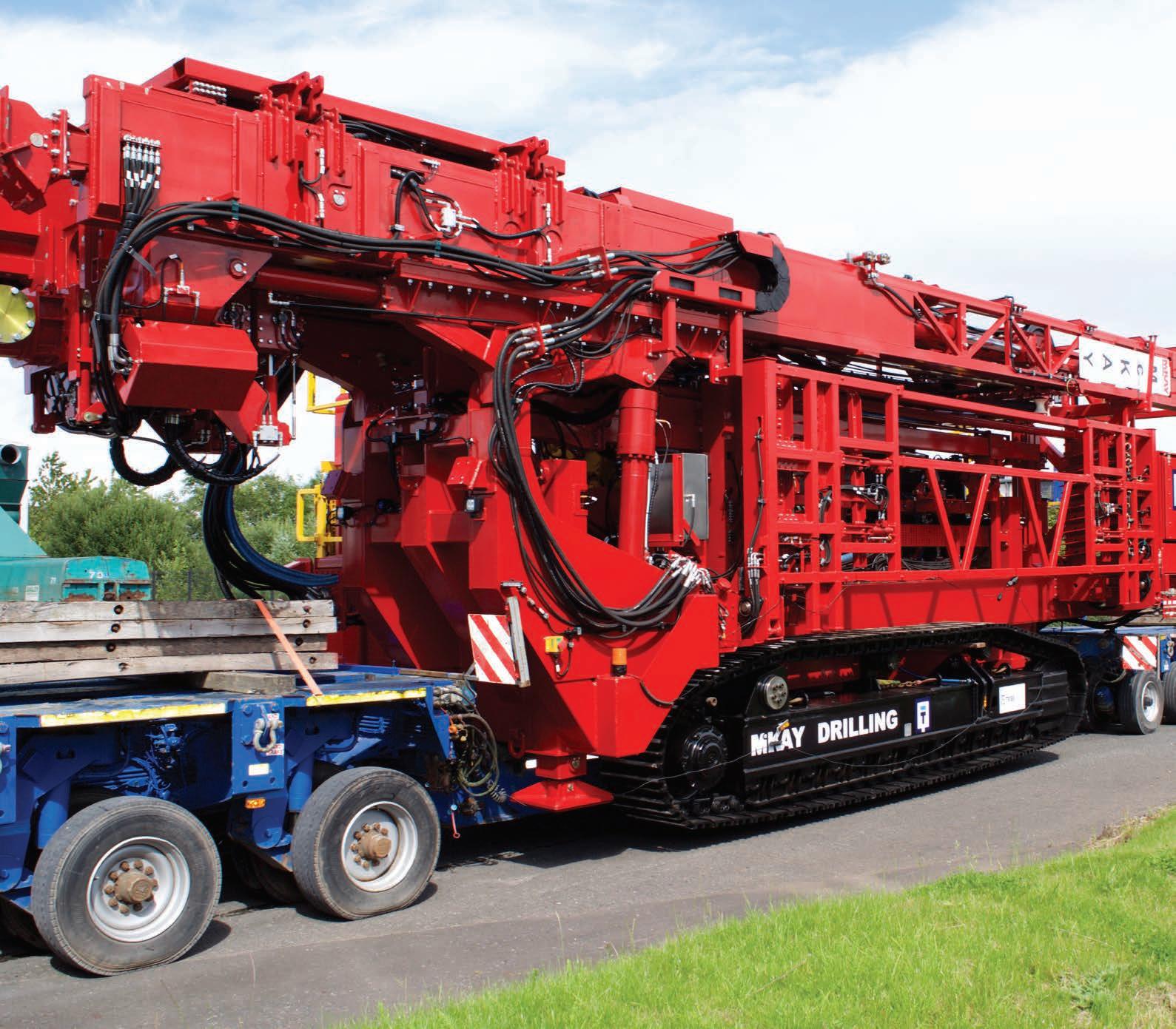
Leader in designing, developing and manufacturing driller-operated geospatial tools and instruments.
Extensive global network of service centres and operations-experienced support personnel. Simple to use technology, flexible solutions, responsiveness to operations.
Exclusive interview with Alex Deeds, Co-Founder &
Hy-Tech Drilling: Partner through and through by Julie Masse, Director of Communications & Marketing at Hy-Tech Drilling
STUDY
20 Controlling deviation to hit targets and make a difference in uranium discovery by Ryan Sunderland, Upper Management/ Shareholder at Bryson Drilling Ltd. /PRODUCT REVIEW
22 Seamless integration to any terrain with X-10 from TactEx by James Patterson, Co-Founder and Abbey Michelau, Business Development Coordinator at TactEx Industries
26 Tribe Technology Drilling System: Delivering quality solutions of the future, now by Derek Loughlin, CTO & Executive Director at Tribe Technology
/EXPLORATION & MINING GEOLOGY
31 Q&A from the experts: In conversation with Nick Oliver Lead Consultant & Director at HCOV Global
38 Fossils, gold and high school engagement: How palaeochannels are the perfect all-rounder by Leah Lynham, James Cook University
42 Transforming the Indian mining sector: Embracing technological innovation, sustainability, and gender diversity by Shreya Mukherjee, PhD Student at Georgia Institute of Technology
46 Geologists: A social anthropologist’s view by Kirsten Bell, Social anthropologist and author of the Silent but Deadly Substack /EXPLORATION DRILLING CATALOG
50 Drilling services
51 Drilling equipment & accessories
57 Survey equipment
57 Miscellaneous
Alex Deeds Co-Founder & CSO at NISS
Julie Masse Director of Communications & Marketing at Hy-Tech Drilling
Derek Loughlin CTO & Executive Director at Tribe Technology
Nick Oliver Lead Consultant & Director at HCOV Global
Mukherjee PhD Student at Georgia Institute of Technology
James Patterson, Co-Founder and Abbey Michelau, Business Development Coordinator at TactEx Industries
Leah Lynham James Cook University
CORING MAGAZINE
September 2024
Cover photo Tribe Technology Issue 28
ISSN 2367-847X
Not for resale. Subscribe: coringmagazine.com/subscribe
Contact Us
Coring Media Ltd.
57A Okolovrasten pat street, r.d. Manastirski Livadi, Triaditsa region, 1404 Sofia, Bulgaria
Phone +359 87 811 5710
Email editorial@coringmagazine.com Website coringmagazine.com
Publisher Coring Media
Executive Officer & Editor in Chief Martina Samarova
Editor Maksim M. Mayer
Section Editor – Exploration & Mining Geology
Dr Brett Davis
Digital Marketing Manager Elena Dorfman
Assistant Editor Nevena Lyubenova
Graphic Design Cog Graphics
Coring Magazine is an international quarterly title covering the exploration core drilling industry. Published in print and digital formats, Coring has a rapidly growing readership that includes diamond drilling contractors, drilling manufacturers and suppliers, service companies, mineral exploration companies and departments, geologists, and many others involved in exploration core drilling.
Launched in late 2015, Coring aims to provide a fresh perspective on the sector by sourcing authentic, informed and quality commentary direct from those working in the field.
With regular interviews, insightful company profiles, detailed product reviews, field-practice tips and illustrated case studies of the world’s most unique diamond drilling and mineral exploration projects, Coring provides a platform for learning about the industry’s exciting developments.
Alex M. Deeds began his journey in drilling as a teenager with Kettle Drilling, where his father was the CEO, more than 20 years ago. When Kettle Drilling was purchased by Timberline Drilling, Alex left the company to work in marine construction. While traveling home one day in 2009, he stopped by a mining convention and was offered a position in the National EWP startup. This job was a game-changer for Alex, as he learned from drilling veterans.
Afterward, Alex worked for several major players, including Vanguard Mining and American Drilling Corp., further honing his knowledge of the drilling industry and his leadership skills.
All of this came together when Alex became the Co-Founder of Nasco Industrial Services and Supply (NISS) alongside his close friend Lee Nusser (President & CEO). Nowadays, NISS provides Product Supply, Contract Mining & Construction, and Drilling Services across the US, and Alex is the company’s Chief Strategy Officer.
Grigor Topev: Let’s start with the usual, how did you get involved in the diamond drilling industry? Please share more about the early years of your career.
Alex Deeds: I started about 20 years ago when my father was the CEO of Kettle Drilling. Under his leadership, the company expanded rapidly, and he built a strong, capable team that drove its success. Joining during an exploration boom, and as a teenager from Hayden, Idaho, the opportunity to travel was exciting.
Kettle Drilling was operating up to 24 drills across the US and Mexico. Eventually, I left the company when Timberline Resources acquired it, and later, the drilling division was sold to its management team. Today, the company Timberline Drilling Inc. is much bigger, thriving, and well-respected in the US drilling industry.
Starting in the field for Kettle Drilling gave me a deep appreciation for the hard work involved, shaping my respect for the field crews.
GT: Please share about your further work experience and the companies that you have worked at.
AD: After my initial experience in core drilling, I transitioned to marine construction, including crane-operated vibratory hammer barge work. While traveling home, I stopped at the NW Mining Convention in Spokane, Washington, to reconnect with some old drilling friends, leading to an unexpected opportunity. I was offered a position with a new startup called National EWP. This was a pivotal moment in my career, as I was mentored by the owner and founder and his exceptional team of veterans in rotary and core drilling. Their guidance in executive leadership and field operations was invaluable to my development. That was all perfect timing as I was in the right place at the right time for that opportunity in my career.
Later, I joined forces with some friends at the time who also owned American Drilling Corp. to acquire a heli-supported drilling company. Unfortunately, we signed the deal just before a significant drop in metal prices, which caused fly core drilling work to dry up. We quickly adapted, shifting our focus to their underground drilling and contract mining divisions. Despite the challenges, we managed to launch a division in Canada and experienced notable growth even during the slower periods
in mining. These experiences taught me a great deal about resilience and the importance of strategic adaptation in the industry.
GT: Is there a project that turned out to be significant for you due to challenges or the lessons that it brought?
AD: One of our most significant projects was launching our drilling division during the COVID-19 pandemic. The demand was immense, with world-class producers, juniors, and small mines urgently seeking drilling. We responded quickly, scaling the division rapidly by acquiring new and used equipment, hiring at a fast pace, and taking on many projects.
However, in hindsight, this rapid expansion came at a cost. We grew too quickly without fully adhering to the KPI disciplines we pride ourselves on. This led to challenges and some setbacks that impacted our performance.
These experiences, though challenging, provided us with invaluable lessons. We’ve since taken decisive steps that revamped the division, assembling a top-tier team and upgrading and standardizing our equipment. Though we experienced setbacks, we learned to be more disciplined and let our core values and processes help guide our decisions. We are now stronger and better positioned for the future.
GT: What is happening in the US in terms of diamond drilling? Is the demand growing?
AD: Although metal prices are up, exploration budgets remain low. Additionally, we’re seeing a significant influx of international drilling contractors moving into the US market. This increased competition, along with skilled drillers preferring local construction jobs closer to home, makes the market more challenging despite the favorable metal prices.
However, we also have a lot of great companies turning in the US, and the arrival of new firms promotes healthy competition and drives quality. The thriving drilling contractors in the US today are run by outstanding teams, so staying competitive in this market requires companies to stay focused, driving safety, quality, and performance all while continually innovating.
GT: The topic about competition in the US drilling market is very interesting.
Would you elaborate a bit more on it, please? Are there any mergers?
AD: The US drilling market is highly competitive but marked by mutual respect among companies rather than rivalry. I haven’t seen many mergers in the US drilling market, but there’s been the usual labor competition ‘poaching’. There’s also been a noticeable amount of career movement from executives on down.
GT: Are there significant differences between the states where you operate? How do you accommodate for that?
AD: While we generally find that our clients maintain consistent operations across state lines, we do adapt to specific challenges as needed. For example, states like New Mexico and Arizona have stricter driller licensing requirements, which we accommodate accord-
‘The US drilling market is highly competitive but marked by mutual respect among companies rather than rivalry.’
that mines need to get bigger and deeper, and we embrace the challenge of balancing growth with responsible practices.
GT: Which US region seems particularly promising to you in terms of potential for discovery and projects?
AD: Nevada stands out as particularly promising due to its rich mineral deposits and favorable mining environment. Additionally, states like Arizona, Wyoming, and Idaho are gaining attention for their potential in critical minerals, making them key areas for future exploration and projects. NISS has established some great collaborations with some amazing clients in these areas that help driving our growth model in those regions.
GT: How did you decide to co-found your current company – NISS?
AD: The decision to co-found NISS wasn’t something I actively pursued—it truly found me. From the very beginning, my partner Lee Nusser (President & CEO of NISS) has been both a close friend and a trusted colleague throughout most of my career. His experience and vision, along with the exceptional expertise of our other partners, were the key factors that attracted me to this venture.
ingly. However, the fundamental differences often come down to the unique challenges of each project’s terrain. Our processes are designed to be flexible, helping to reduce operational hurdles. In regions like Alaska, where challenges can be unique compared to Arizona or California, collaboration with clients and local communities is critical to ensuring smooth and efficient operations.
GT: What is the overall attitude from the local communities and governments towards drilling and mining in the states where you operate? Has it changed in the past years? If so, why?
AD: In recent years, there has been a noticeable shift toward prioritizing environmental responsibility and sustainability, which we fully support. This change is driven by increased public awareness and regulatory expectations, leading us to adapt and engage more closely with stakeholders. While these priorities are important, we also recognize
What really motivated us was the strong encouragement from some of the top world-class mining operators who practically pushed us to strike out on our own. We had long discussed how the mining industry didn’t operate like other industrial sectors, where combining contractor services with a supply division is the norm. Industries like Oil and Gas, Construction, and Energy have been led by companies that integrate multiple services, and we saw a unique opportunity to bring that model to mining. Our shared vision, supported by our clients, made NISS a reality.
GT: How big is NISS nowadays?
AD: NISS’s primary divisions include Product Supply, Contract Mining & Construction, and Drilling Services. Our Supply Division supports sites worldwide with a comprehensive range of products tailored to the mining industry, while our Contract Mining & Construction and Drilling Services divisions provide expert, integrated solutions for various mining needs.
The majority of our operations—roughly 75%—are in the US, with facilities strategically located in key mining jurisdictions like Montana, Idaho, Nevada, and Arizona. We also operate globally, with active projects in South America and Europe and we have plans for further expansion.
GT: What current projects is the company involved in?
AD: Currently, about 70% of our work is with the world’s leading gold and industrial metal producers, while the remaining 30% involves projects with emerging exploration and operating miners.
GT: Can you discuss a particularly challenging contract negotiation and how you secured a favorable outcome?
AD: NISS faced a challenging contract negotiation when a client requested us to complete an extensive drilling program involving more than eight drills. While we were very interested in performing the drilling ourselves, the rapid ramp-up posed significant risks. Instead of pushing for a drilling contract that risked not serving everyone well, we proposed a different approach: the mine could take the drilling inhouse, which we believed was in their best interest for this specific project.
NISS took on the role of sourcing the drills, tooling, and support equipment, and worked alongside their in-house team and third-party drillers to ensure a smooth operation. This approach allowed the mine to maintain control while benefiting from our drilling expertise and re sources, resulting in a win-win for all involved.
GT: Is there anything that NISS is planning to use as an advantage over the other American drilling companies?
AD: NISS’s Drilling Services Division operates with a ‘Special Forces’ mentality—a model that offers distinct advantages in today’s competitive drilling landscape. Unlike larger, publicly traded drilling contractors that often struggle with bureaucracy and slower decision-making processes, our leaner, highly skilled drilling team allows us to be exceptionally nimble and responsive to client needs.
GT: Do you see the advantages of gyros over magnetic survey instruments? In your opinion, does every project require a gyro?
AD: Gyros offer clear advantages over magnetic survey instruments, especially in environments where magnetic interference is an issue. They provide more accurate and reliable data, crucial for precise drilling. In my opinion, a gyro is often the best option. Unlike non-magnetic tools, which require exiting the rod string and pose a risk of being lost, a gyro stays within the rods, eliminating this risk.
GT: How do you stay updated with the latest technologies and advancements in diamond drilling, and how do you integrate them into your operations? For you, which is the best, most game-changing innovation to drilling?
AD: With NISS working in one way or another through product supply, underground construction, air quality, or drilling with the majority of the world’s top producers and mining contractors, we have the unique
Subsurface exploration requires careful evaluation of the underlying lithology. Accept no substitute; SONIC Drilling is the superior solution.
Terra Sonic Drill Rigs can generate near-in situ core samples of sand and rock with no premature refusal up to 10x faster than non-Sonic drilling methods. Have Questions? Let us know. www.terrasonicinternational.com/contact
firsthand from some truly amazing companies. This exposure allows us to stay ahead of the curve by regularly integrating the latest advancements into our operations.
For me, the most game-changing innovation has been the integration of AI-driven technologies. We’re seeing it firsthand transforming operations globally by optimizing decision-making, predicting maintenance needs, and enhancing overall efficiency.
GT: As a professional, how would you describe your management style?
AD: It’s a work in progress with attention to continuous improvement—definitely not perfect but aiming to get a little better each day. I try my best to empower the team while staying open to learning and growing myself. I want to guide with vision and humility. But this is easier said than done.
GT: What is your approach to training your teams?
AD: NISS’s approach to training involves engaging the entire team, from site foremen to senior leadership, in understanding our projects’ financial and operational status. We emphasize hands-on training, where everyone sees firsthand how every nut, bolt, and minute on the drill or onsite impacts the overall success. This transparency and involvement have led to remarkable growth in our team members as they gain a deep appreciation for how their efforts directly contribute to our goals.
GT: We’ve often heard stories of the clashes between drillers and geologists; I presume you don’t necessarily favor either side which puts you in a unique position amongst our interviewees. How can we reduce the friction between the two sides?
AD: I’m confident you could fact-check the math, but in my experience, 99.9% of the friction between drillers and geologists often stems from ego, particularly among less experienced or ‘green’ professionals. In contrast, seasoned and successful drillers and geologists usually share a deep respect for each other’s expertise. The key to reducing this friction lies in aligning both teams around shared goals.
At NISS, we strongly emphasize creating a culture where collaboration and mutual respect are paramount. By focusing on shared objectives and fostering open communication, we ensure that both drillers and geologists work together seamlessly. When everyone understands that they’re working toward the same end goal, it helps to minimize ego-driven conflicts and leads to more cohesive and successful projects.
GT: How do you foresee the future of diamond drilling evolving, and what steps are you taking to prepare for these changes?
AD: The future of diamond drilling is at a crossroads, driven by the need to reach deeper targets with minimal environmental impact, all the while the industry faces a shrinking skilled workforce and a smaller labor pool. This reality is shaping the strategies of leading companies in the industry, and NISS is no exception.
To stay ahead, NISS is deeply committed to innovation. Automation and data-driven solutions are vital to addressing tomorrow’s challenges. Our focus is on developing and integrating robotics for automated rod handling, which enhances safety and efficiency. We’re also prioritizing data collection and analysis advancements to support automated drilling processes. This not only optimizes operations but also provides real-time insights that are crucial for making informed decisions in the field.
Moreover, as the labor market tightens, we’re simplifying drill operations to reduce the training time for new drillers. This is critical in ensuring that we can onboard the next generation of professionals quickly and effectively. Fortunately, we’re finding that the latest wave of drillers is eager to adopt new technology and is motivated by opportunities for career growth—this aligns perfectly with our goals. In the next several years, NISS aims to lead the industry by continuing to push the boundaries of what’s possible in drilling. Our strategy is not just about keeping pace with change but driving it, ensuring that we remain at the forefront of the industry while maintaining our commitment to environmental stewardship and operational excellence.
GT: Thank you for taking the time to answer our questions! Lastly, let’s step outside the drilling world. What are your hobbies? What do you like to do to relax?
AD: Outside of the drilling world, my life is very much centered around my family. We raise livestock, and my kids proudly show them across the Western US. When not tending to the animals, we spend time outdoors—skiing, dirt biking, and enjoying Idaho. Our schedule is so active and fulfilling that we don't even have cable TV at home. It’s a lifestyle that keeps us connected to the land we love. C
Exploration & Geoscience
We believe efficient data collection and smart analytics are key in unlocking ore body insights, leading to better decisions.
With a stronger than ever offering and reinforced expert team, we can help you achieve this. From the initial hole in the ground, to the empowering data on your screen, we can accelerate exploration. United. Inspired.
An all-around review of the value of lasting partnerships in mineral exploration
by Julie Masse, Director of Communications & Marketing at Hy-Tech Drilling LTD.
Hy-Tech Drilling Ltd. is a name that’s been around since 1991. At the time, co-owners Harvey Tremblay and Joe Nouch modified an off-theshelf JKS-300 rig to turn it into a functional fly drill. Based out of Smithers, BC, Canada, the duo needed to think outside the box to get into the local mountainous terrain and deliver a much-needed product to the growing market.
Harvey Tremblay’s vision to harness hydraulic rigs inspired the name ‘Hy-Tech.’ This vision, further driven by Harvey and his wife Corry when they became sole owners in 1994, led to the continuous growth of the company’s fleet.
In 1995, Harvey’s innovative spirit led to the development of a new drill design, combining JKS-300 hydraulics with a much more capable JKS B-15 head. Completed just in time for a crucial opportunity with Homestake at the Bonsai project, this successful experiment paved the way to provide additional drills to the Eskay Creek project.
Over time, client requirements evolved, necessitating increased drilling depths from 1500 ft (457 m) N-size to between 5000 and 6000 ft (1524–1829 m). Demonstrating a collaborative approach, Hy-Tech Drilling frequently adapted their drill rigs, utilizing a slightly larger B-20 head married to some improved hydraulics, landed them on the TECH 5000 drill rig they rely on every day. Tremblay recalls, ‘I went into a hydraulics shop with a piece of cardboard, drew it all up and explained what I was looking for to the engineer. He got it right away – a simple and compact design, easy to troubleshoot and maintain. Without this platform, we would not have been able to scale up our business.’
This single project fostered a nine-year collaboration with Homestake and set the stage for Hy-Tech Drilling’s growth; a success that surely fed the idea that strong relationships can evolve into mutually beneficial partnerships.
Hy-Tech Drilling’s strongest team consensus is their profound desire to be considered a true partner, through and through. And not just by their clients but also their employees, the communities they operate in and even their supply chain.
Some of the strongest partnerships the team has built over time have been with clients. Their longstanding projects come from a variety of mining companies, some of the largest but also some of the most innovative mining groups. Following is a short selection of projects where Hy-Tech Drilling’s reliability and performance have reinforced their reputation as a trusted partner.
Hy-Tech Drilling started work at Denison Mines’ Wheeler River project in the Athabasca Basin region in Northern Saskatchewan, over fifteen years ago. Initial drilling took place in the early exploration days at the Wheeler high-grade uranium project. Drilling led to the discovery of two high grade deposits and has continued through to feasibility studies. Going through all these stages in close collaboration with the client, has fostered a trusting bond that has been beneficial for both parties.
In 2022, this long-lasting collaboration led Hy-Tech Drilling to form a partnership with North West Communities Management Company, a group of seven indigenous communities. A jointly owned drilling company called Rivers Drilling was then created, reinforcing the bonds between Hy-Tech Drilling and the local indigenous groups, in-line with their client’s priorities.
One of the strongest international partnerships that Hy-Tech Drilling has fostered is with the Lundin group of companies, which
Denison Mines is a part of. You’ll recognize Hy-Tech Drilling’s ways here, as their links to Lundin are rooted from relationships built with people met at Homestake Mining Company.
With over 17 years of collaboration, Hy-Tech Drilling has worked for them in multiple locations, namely in Canada, Portugal, Spain, Sweden, Ireland, Chile and Argentina. Working abroad with Lundin has led the team to work on some extremely complex projects, including deep directional holes, water recirculation and extremely high altitudes, such as the Filo del Sol project.
Tremblay explains: ‘When a partner asks you to go to the moon, you consider it differently than if a stranger asks! It’s only the weight of relationships that allows you to consider something like this, otherwise the risk would seem foolish!’
Located in the San Juan Province of Argentina, just a few kilometers from the Chilean border, Filo del Sol has literally taken Hy-Tech Drilling to new heights. Working relentlessly with their client to overcome technical challenges, the team has been able to set-up what might well be the highest shop on the planet. The shop is located at an altitude of 5000 m (16 404 ft) above sea level, and the highest drill sites around are at 5300 m (17 388 ft) – that is the altitude of the Mount Everest base camp. It’s hard work to deliver, and altitude is a real challenge!
‘There’s a sign in our shop at Filo that reads, “If you made it this far, you are a warrior. Stop, breathe and remember that your safety will always come first,”’ says Craig Spinney, Field Operations Manager. ‘Beyond the most challenging conditions we’ve ever faced, this is our commitment to each team member’s well-being. Nothing but our top priority.’
In Northern Saskatchewan, Hy-Tech Drilling currently works for Foran Mining, operating both skid and fly rigs within the Hanson Lake District. Their newly formed partnership with the Peter Ballantyne Cree Nation, has led to the creation of jointly owned drilling business, A2SKI Tek Drilling Ltd. This collaboration allows Hy-Tech Drilling to access a broader pool of local services within the Cree Nation traditional territory, ideal to support operations with tasks such as ice preparation and pad construction.
Drilling for copper-zinc deposits on Foran’s properties, Hy-Tech Drilling deploys drastically different summer and winter strategies, to make the best out of terrain conditions, and the opportunities the cold weather brings.
‘We deliver a large ice-based drilling program for our client Foran during winter. We’ll drill at a given angle to get to the orebody, but when the ice melts and we move the drills back onto land, we still need to hit that same target,’ shares Jason Comeau, Field Operations Manager. ‘That’s an unusual bend, but we’re able to intersect with some efficient directional drilling executed by our skilled team.’
The success of this project, not unlike many others, lays on this strong network of partners coming together in the best way possible. Indigenous groups and skilled drillers alike, are essential partners enabling Hy-Tech Drilling to deliver on its promise at Foran.
Heading 700 km (435 mi) north of Winnipeg, we’re now taking you to Thompson, Manitoba, where Hy-Tech Drilling has some rigs turning for Vale Base Metals.
Drilling for nickel at this location, Vale emphasizes the values of its operations to support the global demand for the critical minerals required to drive the ongoing energy transition.
↑ The sun setting over a Hy-Tech drill at the Thompson project (Vale) in Manitoba, Canada, 2024. Photo credits: Ramone Jordan.
In alignment with the client’s priorities, Hy-Tech Drilling employs several strategies to reduce its impact on the environment – and the TECH 5000 is the perfect rig to deliver on this. Its small footprint but mighty capacity makes this machine a fantastic alternative for projects where clients are in need of equipment that is equally respectful of the environment and capable of reaching challenging targets.
Starting the new contract in 2024, Hy-Tech Drilling swiftly achieved unprecedented productivity levels, exceeding client expectations while maintaining strict safety standards.
What started as an initial surface project, contracted for 35 000 m (114 829 ft), is now blooming into a campaign that has expanded significantly, more than doubling the annual drilling meters. The collaboration between Vale and Hy-Tech Drilling certainly seems promising at this location.
True to its approach, Hy-Tech Drilling has consistently pursued strategic partnerships to expand its presence, namely in the South American market.
In 2022, Hy-Tech Drilling entered a joint venture with former competitor, Griffith Drilling. Today, Hy-Tech Griffith Drilling SpA successfully combines the unparalleled hole completion rates and proprietary
systems from Hy-Tech Drilling with the regional knowledge and experienced crews from Griffith in Chile, Argentina, and beyond.
Boyd Griffith, General Manager at Hy-Tech Griffith Drilling, comments: ‘It has been great seeing the relationship between our two Companies switch from a competitor mindset into a JV partnership – very quickly, we both saw the benefits of coming together into this market.’
Following this successful collaboration, Hy-Tech Drilling plans to replicate its strategic partnership model in other regions globally.
As earlier examples highlighted, engaging with local indigenous groups has been an important part of Hy-Tech Drilling’s approach.
When asked why, Jessica Mullen, Corporate Social Impact Coordinator and Harvey Tremblay’s daughter, has a strong voice: ‘Our community partnerships are motivated by a responsibility to do what we can. Together we try to find a way to benefit as big a group as possible. We’re all part of a community, and we have a role to play in its success.’
Joint ventures Tahltan Hy-Tech Drilling in British Columbia, Rivers Drilling in Saskatchewan and A2SKI Tek Drilling in Northeastern Saskatchewan, are three great examples of how the group has been able to act in this vision, and create a strong network of partners within the communities they operate in.
↑ Mountain view of a drill at the Brucejack project. Photo credits: Lyndon Werbiski.
Hy-Tech Drilling’s water management system also illustrates the advantages of cultivating robust industry relationships. While working at the Brucejack project, then owned by Pretium Resources, Hy-Tech Drilling was challenged to reduce water consumption in the drilling process. Teaming up with both client and innovation partners, HyTech Drilling was able to develop a system that addressed the client’s issue, by reducing freshwater consumption by up to 90% per day. Following this success, the owner of the project eventually changed to Newcrest, which in turn was acquired by Newmont. But three owners later, the team is still leveraging that collaborative spirit between client and contractor, as they are currently working on the next generation of rod handlers with robotic expert partners.
While collaboration does lead to innovation for Hy-Tech Drilling, it could also be said that innovation increases collaboration. A great example of this lays into Hy-Tech Drilling’s proprietary real-time database launched way ahead of its time. With more than two decades of data captured, the group states it has completed 516 projects with nearly 7 million meters drilled, showcasing a 99.7% completion
rate, and less than 1% downtime. These numbers would not have the same credibility if it wasn’t for this database.
The connected client-facing FieldView app translates into a wealth of knowledge for Hy-Tech Drilling’s clients. From drill bit consumption to every hour spent on the drill and live cost per meter, this is full transparency at its best. Clients can access thorough real time project monitoring, resulting in better and faster decision-making. Now that’s partnering with your client’s Exploration Manager!
A key factor in Hy-Tech Drilling’s success is its team of dedicated and skilled professionals. And in true partner style, they are in it for the long run! Hy-Tech Drilling has an average employee tenure of 4.3 years, with 1 out of 10 employees having at least a decade in seniority within the team.
The group prides itself on fostering a supportive and inclusive company culture. Hy-Tech Drilling offers comprehensive pre-drill site training, and an annual refresher. The team has access to internal development opportunities and mentoring from experienced professionals. The external training and professional development courses offered by Hy-Tech Drilling often lead to internal promotions and career advancement. As a result, the team expertise and dedication have been crucial in achieving the group’s high standards of quality and performance,
and they are proud that many of Hy-Tech Drilling’s Foremen started as Helpers.
Dwayne Ross, Vice President of Branch Operations, expresses his pride in the team: ‘I am incredibly proud of the expert team of people we have assembled over the years. We possess tremendous depth in knowledge, experience, innovative thinking, and pride. Despite facing challenging conditions, we continue to deliver on our commitments. We could not achieve this without our dedicated team.’
Hy-Tech Drilling has built a reputation of being a drilling partner, through and through. The team’s approach to building long-lasting relationships all around has been nothing less than fundamental to its
growth and success. Over time, they have become a notable partner in the core drilling field, and they are aware that this is also key to their future.
‘Mineral exploration is progressing into a new era - one that requires us to leverage the strong ties that have made our success, and to also foster new ones,’ says Brian Butterworth, President of Hy-Tech Drilling. ‘New technologies, new challenges and a new generation lay ahead of us. At Hy-Tech Drilling, we’re excited about the opportunities this brings!’
For such a global industry, yet niche market, collaborating with HyTech Drilling means tapping into the valuable extended network of a 360° partnership. Through these relationships with employees, communities, clients, and suppliers, Hy-Tech Drilling will be a strong partner in this important era of continued change and growth. The future certainly holds exciting times ahead for mineral exploration. C
Helicopter Portable Diamond Drill
1400 Meter NWL Depth Capacity
Cummins Power Unit 160 or 260 HP
‘P’ Size Rotation Unit & Clamp
Safety Package: Full Guarding, Multiple E-Stops, Interlock Rod Guard & Power Lock-Out
Available in Heli-Portable, Skid Shack Mounted and Track Carrier
by Ryan Sunderland, Upper Management/Shareholder at Bryson Drilling Ltd.
Bryson Drilling Ltd. is a diamond core drilling company with three generations of experience. Established in 2007, the company has grown significantly, now owning and operating eight Zinex A5 diamond drills, various specialized equipment, and fully operational camps. Bryson Drilling has provided surface and specialty drilling services across Canada, building strong bonds of trust through quality workmanship and efficiency, which has led to a loyal client base. Their expertise includes standard coring, deep overburden drilling, core orientation, and more. They continually strive to achieve the highest standards of health and safety while maximizing production and maintaining cost-effectiveness.
Since 2020, Bryson Drilling has been engaged in a critical uranium exploration project at the West McArthur Project. The project is operated by CanAlaska Uranium, in the Eastern Athabasca Basin of Saskatchewan, Canada, which is one of the most significant uranium-producing regions globally. The project area is located strategically, between 6 and 30 km (3.7–18.6 mi) west of the McArthur River mine, one of the world’s largest and highest-grade uranium mines. The ongoing exploration at West McArthur has been driven by successful drilling campaigns and the discovery of new uranium zones.
This partnership between CanAlaska Uranium and Bryson Drilling, now in its fourth year, has seen significant advancements, particularly following a promising discovery hole in 2022, which has extended the drilling campaign beyond initial expectations.
The ongoing skid shack drilling program at the West McArthur Project is focused on uranium deposits, requiring precision drilling to hit targets at depths between 700 and 1100 m (2297–3609 ft), with most holes reaching over 1000 m (3281 ft). Initially, the team faced significant challenges with deviation control. At such depths, it was crucial for hitting the small uranium targets which have radiuses of 3–5 m (9.8–16.4 ft) in most instances. In the early stages of the project, mechanical wedging was employed to address these concerns, but as the project progressed, Bryson Drilling transitioned to a more modern method involving directional motors. This shift required expert training and consultants for both Bryson’s workers and the client’s personnel, in order to adopt this advanced technology quickly, safely, and efficiently. Today, the team uses directional tooling, allowing for multiple branches on each mother hole, an approach that is highly cost-effective since it eliminates the need to redrill the top 500 to 700 m (1640–2297 ft) with each new hole. The focus remains on controlling deviation to ensure precision in hitting the small uranium targets at depth, a crucial factor in exploration.
In support of this drilling method, Bryson Drilling has deployed a Zinex A5 core rig housed in a Macon drilling shack, fully equipped with an AVD rod manipulator, leveling cylinders, and essential safety
features. This comprehensive setup not only ensures a safe working environment but also maximizes production efficiency. Rated for depths of up to 1200 m (3937 ft) in N-size, the Zinex A5 rig has the flexibility to push beyond these limits when necessary – with some stories of the A5 reaching 1500 m (4921 ft), providing the team with the capability to meet the demanding requirements of the West McArthur Project. Alongside the challenges posed by the drilling itself, the extreme conditions of the Saskatchewan landscape add further complexity. The team, consisting of 16 dedicated site workers, has spent over 120 days on-site this year alone, working in difficult terrain.
The rocky roads to the site, only accessible by utility terrain vehicles during the summer, test both equipment and endurance. When winter strikes, the team must contend with freezing temperatures, using indirect-fired glycol heaters and waterline heaters to maintain safety and operational efficiency. While the project is ongoing, Bryson Drilling has consistently met the client’s plans for core hole completion. The results from the West McArthur Project have made it an exciting and rewarding endeavor for Bryson Drilling. The company extends its gratitude to the CanAlaska team for the continued opportunity to contribute to this significant project. C
by James Patterson, Co-Founder and Abbey Michelau, Business Development Coordinator at TactEx Industries
TactEx’s X-10 diamond drill and its multi-terrain platforms stand out in the market due to their superior craftsmanship. At TactEx Industries, the assembly team includes technicians, designers, Red Seal mechanics, fabricators, and drillers who collaborate to manufacture all components in-house. Every aspect of TactEx’s drills and platforms, from design and material processing to machining, fabrication, welding, assembly, and shipping, is managed entirely in-house. Without the need to subcontract processes, TactEx can focus on quality parts and attention to detail. The TactEx team also has extensive industry experience, covering everything from fabrication to the execution of mineral exploration projects. The fabrication division consists of highly skilled craftsman welders, who are ticketed and trained on advanced
↑ The X-10 control panel provides all essential information to the driller, which allows smooth control for the drill while advancing towards the target depth or changing the bit
equipment with Canadian Welding Bureau (CWB) certifications. This level of quality control allows TactEx to meet clients’ unique timelines and develop not only a powerful and compact diamond drill but an entire modular system that enables clients to take on any drilling project.
TactEx’s X-10 diamond drill is quite different from any other on the market. It is specifically designed to seamlessly integrate from one multi-terrain platform to the next in under two hours. TactEx Industries has currently developed three platforms specifically designed to incorporate the X-10, meaning that clients can remove the X-10 diamond drill from their winter shack drilling project and utilize it for their heli-portable project in the summer. Clients have the choice between the 72 in (1.83 m) stroke feed frame or the 132 in (3.35 m) long stroke feed frame. The long stroke was introduced for customers drilling deeper and requiring a longer mast dump for track, shack, or truck mounting. This adaptability applies to the TactEx power pack as well. This unit is outfitted with an air-cooled hydraulics system, synchronized head and foot clamp, and advanced safety features. This versatility is further enhanced by the ability to use the same power pack across the SX-10, TX-10, and FX-10.
TactEx has developed a system within diamond drill manufacturing that prioritizes modularity over modification. While other drill manufacturers offer multiple drill models to suit different project needs, TactEx provides one drill and three platforms. While the X-10 drill remains constant to maintain reliability in mineral exploration, the TactEx team continuously advances and evolves
its multi-terrain platforms to support the X-10 diamond drill. As mineral exploration projects change, the platforms adapt to meet new challenges, providing long-term value and versatility. Every surface drill is produced with the same base, creating efficiency in all areas of drilling. Every piece of this system has a part number and aligns with the overall X-10 proprietary system. If a client requires a part, they can easily identify it, and TactEx will always have it in stock due to its applicability to every drill the company manufactures. Additionally, with all hydraulic hoses having dedicated part numbers, customers can quickly have these replaced locally, eliminating downtime on drill sites. This structure aids efficient field support, safety, and overall eliminates unnecessary downtime. Furthermore, expanding a fleet is straightforward, as all drilling components are consistent, with no one-off drills. Although TactEx is committed to maintaining the design and functions of the X-10, customization and creativity are expressed through the three multi-terrain platforms. The TactEx team aims to constantly improve, which includes evolving the platforms to best suit clients’ needs.
The SX-10 is specifically designed to complement the X-10 drill. Built with input from industry experts as well as extensive experience from TactEx’s sister company, Macon Industries, which has built hundreds of diamond drilling enclosures, TactEx utilized the foundational design to create the ultimate
heavy-duty drill shack full of must-have features. The leveling cylinders with teeth provide stability. If minor adjustments are required, the dozer teeth keep the blade where it belongs. The hydraulic helper’s slide-out allows for a slim shack width while still providing enough room for the drill helper. This feature includes a core box table, tool racks, and a reinforced ring to help empty the core tube for additional safety and efficiency. The SX-10 also includes rod handling capabilities that can hold 1600 m (5249 ft) of stacked N-size within the shack, LED lighting for efficient round-the-clock operations, modern safety features such as fire extinguishers and emergency stop switches, and an integrated guard system that ensures compliance on any exploration site. TactEx has also implemented easy roof access with proper railings. The TactEx SX-10 is built for the X-10 so that when switching to a track drilling program or a heli-drilling operation, clients can easily
integrate the same drill using the same proprietary system for a variety of drilling contracts.
The TX-10 Platform highlights TactEx’s dedication to delivering versatile and efficient solutions. This track platform allows the drill to be self-propelled to the exploration target, utilizing the drill’s engine and hydraulics, reducing the need for skidding, or flying the drill into position, and with minimal support equipment needed. TactEx’s TX-10 track platform is fully equipped with features designed to enhance any drilling project, including integrated drill mounts and a drip tray that mitigates spills in environmentally sensitive areas and reduces the overall height of the drill on the platform. A removable undercarriage keeps spare parts interchange-
able between equipment. A remote control operates the hydraulic system hands-free, eliminating the extra size, weight, and cost of a ROPS system. The TX-10 also includes leveling cylinders, making any terrain easy to work on. Additional features such as extra valving and fuel tank are specific to this platform and stay with it, minimizing the need to transport multiple pieces of equipment to the drilling site. When the client’s track program is completed, they can remove the X-10 from the swing bolts on the TX-10 platform and utilize the base for their heli project if required.
TactEx Industries offers a heli-portable aluminum shack option in its FX-10 platform. The FX-10 is designed for quick moves, featuring certified lifting points and
↑ SX-10 fully loaded drill skid enclosure with all the bells and whistles, including interior and exterior LED lighting , mechanical rod handling, leveling jacks, and inter lock guard system. A pleasure to work in, in any season.
field-inspired aligning components. Similar to its sister platforms, the X-10 integrates into the FX-10 platform with ease, allowing clients to have the components they need for any drilling project, no matter the terrain. The heli-portable aluminum shack has access doors to service vital components, as well as an option for rod handling systems. The FX-10 modular base frame is designed for easy integration of the rod handling system, making deep holes on heli-portable jobs safer.
As Canada’s most innovative diamond drill manufacturer, TactEx delivers the most powerful and precise products to enhance any project. The team combines decades of field and design experience to create a
customizable drill that integrates into three multi-terrain platforms. Whether clients are looking for a new rig or specific parts, TactEx’s one-stop-shop helps them find the perfect fit, with some of the best service in the industry. All parts and equipment are built in-house, interchangeable, and offer advanced safety features. TactEx’s con tinuous advancement and evolution of its multi-terrain platforms ensure that as min eral exploration projects evolve, the sup porting infrastructure can adapt according ly, providing long-term value and flexibility. This approach, which prioritizes modularity over modification, ensures that the X-10 drill remains a reliable constant, even as the de mands of mineral exploration change. C
For more information
Visit: tactexindustries.com or contact: sales@tactexindustries.com
↑ One drill, three platforms
Delivering quality solutions of the future, now
by Derek Loughlin, CTO & Executive Director at Tribe Technology
The market for ‘Smart Mining’ equipment is anticipated to exceed USD 23 billion by 2028, fueling the demand and opportunities for automation in the industry. Inspired by this growth, Tribe Technology is dedicated to enhancing workplace safety and efficiency by providing solutions for RC drilling in grade control and exploration. Their innovations remove operators from one of the industry’s most dangerous manual tasks and significantly reduce environmental impact, land disturbance and fuel consumption.
Established in 2019 by Charlie King, Tribe Technology (Tribe Tech) is focused on developing its autonomous RC drill rigs and advanced sampling solutions that will revolutionize global mining & exploration operations and answer the market’s growing need for autonomy.
Based in Northern Ireland and Western Australia, Tribe Tech’s core activities involve the development, in-house manufacturing, and sale of autonomous RC drill rigs and sample systems, incorporating its core proprietary intellectual property, the Tribe Technology Drilling System (TTDS). The company’s RC drilling systems are designed to remove operators from the dangers involved in the traditional manually operated RC drill rigs, all the while significantly improving productivity, mechanical availability, and to provide deep hole capability. This technology will change the way drilling and mining companies operate, delivering quality solutions that positively impact operations and communities.
The first-generation TTDS GC 700 system was designed to create a highly efficient, reliable and safe product. In addition, the diverse group of hand-picked experienced Tribe Tech engineers from across the globe has designed TTDS with versatility in mind, having the ability to cater to customer needs dependent on the conditions and terrains in which it is operating in.
The first TTDS GC 700 track-mounted drill rig is a ground up new design incorporating numerous innovations and is the result of over 150 000 development hours. It shipped from the factory in Northern Ireland at the end of July 2024 to Western Australia where it will be combined with the sample system that is being built there. It was manufactured for and sold to McKay Drilling (a subsidiary of Major Drilling International), for deployment at a Tier I iron ore mining asset in Western Australia. TTDS GC 700 offers a drilling capacity up to 700 m (2297 ft) depth, remote control of operations, automated drill rod handling, automated collaring, rig set-up and packup, and a hands-free sampling system.
Tribe Tech continues work on their second complete RC drilling and sampling system which is being manufactured for Anglo American PLC, one of the world’s major mining companies with global operations. Additionally, existing customers of Tribe Tech have already expressed interest in purchasing further systems. While Tribe Tech’s initial market activities have been primarily focused in Western Australia, the company has started to receive inquiries globally, particularly from North and South America. Interest has primarily been from sector leaders among both Tier 1 mining companies and large drilling contractors.
The automating of the RC drilling process is a significant step change and one of the largest innovations in the industry. Tribe Tech provides the solution to the challenges the smart mining industry faces, balancing significant advancements in technology all whilst maintaining a competitive price to its customer base.
The company has also configured its autonomous RC sampling system so that it can be modularized and sold to customers for use in conjunction with other RC drill rig brands.
At its core, Tribe Tech is a company that has been founded on innovation. The company believes in a safer and more sustainable future for the mining industry, focused on delivering quality solutions to positively impact communities. It has focused on market-leading technology that will revolutionize drilling, while dramatically improving safety outcomes and streamlining operations.
Committed to Research and Development, Tribe Tech intends to strengthen its IP portfolio in order to expand its product range, including but not limited to, truck-mounted RC drill rigs.
The company is committed to building the technology of the future, boldly seeking to enhance safety and efficiency within this sector of the global industry. To that end, Tribe Tech has established strong working relationships with key global players. These companies understand the demand to develop and deploy autonomous equipment for safe and efficient use in the sector and trust in Tribe Tech to achieve this.
Furthermore, Tribe Tech is constantly looking for ways to develop its capabilities within the Smart Mining market using its drilling systems as a platform for orebody knowledge acquisition. More recently, the company has entered into joint development agreements with IMDEX and Veracio Australia Pty, (a subsidiary of Boart Longyear). Under the agreement with Veracio, both companies will jointly develop a new and novel system for blast hole chip sampling, incorporating Tribe Tech’s IP and Veracio’s proprietary technology. The agreement with IMDEX will see both companies leverage their respective IP to use the Tribe Tech RC drilling system as a platform for machine-operated orebody knowledge sensor deployment.
Tribe Technology stands at the forefront of innovation in the industry, driven by its vision to create a safer, more efficient and sustainable future. Through the development of its RC drill rigs, Tribe Tech aims to revolutionize mining operations worldwide, playing on their deep understanding of the challenges the industry faces and its commitment to delivering quality solutions of the future, now. C
Hard rock mining’s heavyweight - innovating, manufacturing and delivering end-to-end excellence in drilling and underground diamond coring. A partnership with us is an investment in safety and versatility improvements in diamond drilling like no other.
INDUSTRY-LEADING DIAMOND DRILL RIGS MATCHED BY A TEAM DETERMINED TO ALWAYS PERFORM BETTER THAN THE DAY BEFORE? THAT’S EXCELLENCE UNEARTHED. THAT’S SWICK.
DRILL INTO THE POSSIBILITIES.
In this Issue:
Q&A from the experts
In conversation with Nick Oliver
Lead Consultant & Director at HCOV Global
Fossils, gold and highschool engagement: How palaeochannels are the perfect all-rounder by Leah Lynham, James Cook University
Transforming the Indian mining sector: Embracing technological innovation, sustainability, and gender diversity by Shreya Mukherjee, PhD Student at Georgia Institute of Technology
Geologists: A social anthropologist’s view by Kirsten Bell, Social anthropologist and author of the Silent but Deadly Substack
Nick Oliver Lead Consultant & Director at HCOV Global
fieldwork was, and then the surprise of being fascinated by the petrographic microscope.
BD: What projects are you working on at the moment? And what is your level of involvement?
Nicholas (Nick) Oliver (BSc Hons UQ, PhD Monash) is a lead consultant and director within the Australian consortium HCOV Global, Adjunct Professor at James Cook University (JCU), and Honorary Professor at the Sustainable Minerals Institute at the University of Queensland. After positions with CSIRO, Carnegie Institute Geophysical Laboratory (Washington, DC), Monash and Curtin universities, he was Professor of Economic Geology at JCU from 1997 to 2010, and Director of the Economic Geology Research Unit (EGRU). For the last 14 years he has been a full-time consultant to the minerals sector, focussed on the fusion of structural, geochemical and geophysical data, and training. He has broad commodity experience from Au, Pb-Zn-Cu, REE, Fe and U in Precambrian poly-deformed metamorphic belts (Australia, Fennoscandia, Brazil, Guyana shield, West Africa and Canada) to porphyry, epithermal, skarn and other Phanerozoic systems in the Tethys, Middle East, Mongolia, SE Asia and the South American Cordillera. Brett Davis: Firstly, thanks for giving Coring the opportunity to interview you, Nick. I was really keen to pin you down for an interview, given your impressive international reputation in the mining and exploration industry. In combination with your research and teaching profile, it’s a pretty impressive resumé! I’ll start with my standard leadin question – what got you interested in a career in geology?
Nick Oliver: Thanks for the invite Brett, it’s an honor. My parents were often taking our family outdoors, driving, hiking and camping around my hometown of Brisbane, Australia. Then, I was lucky enough to take geology in Year 9 Science at high school, and then as a full course in the last two years. Since I was 15, I was fixated on geology. All it took (really) was a good teacher at school - Barry Whelan. Together with my childhood friends Charles (still a friend!) and Mel Wilkinson (both still active geologists), who took the same subjects at school, we wandered around northeastern NSW and southeastern QLD looking for gems, thunder-eggs, fossils, etc. It was quickly cemented by the very easy decision to do a geology major at University of Queensland, and realization of how much fun
NO: In-house training courses in preparation for FMG (Mount Isa) and B2Gold (online), and a public field structural geology training course in Finland. Several consultancies for repeat clients (juniors) in Chile. For one of these (Tesoro Gold El Zorro project) I’ve been involved right from the start, which has been pretty exciting as it looks like it will get into production in the years to come. I’m the external supervisor to a PhD student on that project too. There are a couple of jobs for new clients in Mongolia (online so far), Australia (greenfields), and an operating mine and related exploration in Finland. Probably, I will be back to the Middle East at the end of the year for in-house training and greenfields work. So yeah, semi-random global exploration and training with repeat and new clients.
BD: Coring started as a drilling magazine, and we like to keep to our roots. So, I’ll ask you a multi-faceted drilling-related question - do you do much work with oriented core? And do you work with other structure orientation methods pertaining to drilling?
NO: Yes, quite a lot, though probably not as much as you. You’ve seen a few posts of mine on LinkedIn that have mirrored yours regarding core orientation. It is alarming to see the broad range of behaviors with respect to core orientation techniques and structural measurements from core, from completely ridiculous to absolutely perfect – even within one company!
The horror stories relate in part to my expectation that a big, high-flying company is likely to send me good structural data for desktop review, then finding I’ve wasted a few days playing with bad data (that I can’t charge for), followed by having to review the whole database, trying to fix it up as best I can, and then seeing what the problem was, or is, when examining the drill core. This was hypercharged by Covid when companies
were asking me to do desktop reviews, before, or without visiting the site. There are two main issues: firstly technical, it seems there is misuse of any device put in front of geologists, even your favorite and trusty rocket launcher in the cases where the ori line is incorrect, e.g. wrong side of the core or off by 20+ degrees, etc., etc.
My favorite tool is IMDEX’s IQLogger, and I thought it was foolproof. You have to work really hard to stuff this one up. But one company at least has found a way. First of all (add sarcastic tone), use the IMDEX Hub (that provides all the collar/survey data in the cloud) but do it so that people will think that everything is going to be OK (false sense of security). Secondly, instead of recording dip/direction directly, only use the calculated alpha/beta, so that it matches your old database. That way, you can send it to your clunky old corporate spreadsheet that calculates dip/direction and allows someone in the company to pretend that they are in charge of all company-wide structural data. This person might provide you with the ‘answers’ a few months later, by which time the
core has been well and truly packed away never to be seen again. Oh – and you should make sure that you don’t check the software for whether it is recording the ori line on the bottom or top of the core. So, this process meant that about two years’ worth of structural measurements was entered into the database incorrectly, so therefore no one would ever trust that structural data again. Have they changed their procedure? Probably not. I could name and shame this company but they probably wouldn’t care.
And another very major company had done similar at one of its operations and yet were producing perfect structural data at another. An easy solution to the uncertainty associated with whether the method is working is to hold up the drill core in the orientation it should have been in the ground (using whatever imaginary ‘north’ you like), and check to see if the orientation of the structure of interest ‘makes sense’. You could even record these guessed dip/direction data in a datasheet, to see if any subsequent verification matches approximately. If you are using a rocket launcher then this happens by default,
but if you are not, it is a crucial check – which should be repeated as often as possible. The other issue of course is education. People don’t know what to do, what to measure, or why. This is the responsibility of the geologist in charge but often gets left to hapless consultants like you or me. This goes back to the root cause which is increasingly poorer geology training at university but also the perception that senior and chief geologists must immerse themselves in administration and schedules and assume that the less experienced geologists are well-enough trained that they can sort it out themselves. Or else the seniors are afraid because they don’t want to admit they don’t know how to do it (which a 10-second internet search would solve – so it’s just laziness). The tendency is to measure and record everything without adequate structural classification, particularly intensity and thickness of the structure of interest. Minor structures are often assigned the same weight as major ones, so the result is cluttering on drill string displays and in 3D, so the data is then regarded as ‘useless’.
The bottom line to all of this is education; there are too many examples now of poor (actually wrong) datasets and ultimately it leads to poor decisions on drill targets, etc. I’ve seen one small company go belly up, partly as a consequence of generating a structural model for their system that couldn’t be verified by drilling because the model was built from incorrectly recorded structural data in the first place.
BD: Your geology-related career has spanned academia and consultancy. Very few people can boast the impressive research profile you have, especially the number of individually authored or collaborative peer-reviewed papers in international journals. And you’re still publishing! What is the secret behind your drive and publishing success?
NO: Well, the drive now is just a residual habit, and I’m nowhere near as productive now as when I was an academic. As an academic, it was core business as well as the main outcome of the whole scientific endeavor, so there seemed to be a natural driver in the system – the old ‘publish or perish’ syndrome. I consider myself lucky to have been in a golden age of university-based R&D in Australia (1980-90s in particular), which helped and also surrounded by teams of equally enthusiastic mentors, peers and students who could make these publications flow. With a few co-authors, it was simply great fun to work with them (notably Rick Valenta, Paul Bons and June Hill), and the topics were ‘hot’, so it was pretty easy to bolt together the papers. Sometimes, even with great coauthors, the topic was so hard that it took a lot of effort (e.g. some big papers with Bruce Hobbs and Alison Ord). Sometimes the geology itself would drive the demand for the paper to be written, notably much of my early work on the role of structural heterogeneities controlling fluid flow and consequent isotopic and geochemical patterns.
BD: Many people have careers that start off in academia and then transition to industry-related roles. A lot of people I see in the industry positions are doing this toward the end of their careers. What sponsored you to move into the industry arena, well before (I hope) the end of a successful research life?
NO: I thought I was a born academic. I enjoyed teaching and research, had success at grant writing, great mentors and colleagues, etc. My main regret now – not that it’s strong, is that I didn’t leave the university
sector about 5 years earlier. I was 50 when I quit. Our earth sciences department had been decimated by a merger in 2005-6 with a large and fairly ineffectual geography school. JCU had always been one of the high performers in the Australian geology scene –particularly in the 1980–2000 period when you and I overlapped there for a while.
In 2002 alone, we produced more papers, graduates, grant money and industry links than any other group in Australia including Monash, UTas CODES and UWA CET. So this was a brutal merger, we went from 13 fully centrally funded academics, eighth or ten postdocs, 60 PhD students and a strong cohort of technical and administrative staff, to three staff, one postdoc, almost no technicians and a half-dozen PhD students, in the space of around five years. Almost 100% academic staff turnover in eighth years. I was the second last rat to leave the sinking ship –Tom Blenkinsop lasted another three years. And this ongoing trend of poor university governance and lack of care by (both sides of) government concerning the relationship between Australia’s wealth and what drives it, has led to the dramatic decrease in functional geology groups around the country. This is at a time when Australia is the 3rd richest country per adult in the world, largely as a consequence of mineral commodity exports. We are all aware of this problem, and personally I’m part of that problem – academics leaving the sector when the sector is in poor shape. OK, that’s the negative stuff. What I didn’t expect when I moved fully into industry is a) how much fun I would have and how many great new friends I would make, b) how much I would learn – as much as in the best days of my doctoral study, and c) how much the difficulty and challenge to produce rapid results via short consultancies would suit me so well, relative to the typical, academic research program of one to seven years duration. It’s been a blast, and I’ve used my previous academic career to full benefit, including being employed by many previous students!
BD: Apart from me, who have been some of the positive influences in your career?
NO: Ha-ha, well, we didn’t overlap for long at JCU, Brett, but your smile was always a positive influence.
It’s a long list, starting with my parents and family – a good school, a great learning environment, and endless encouragement. And I won’t list below all of the graduate students I’ve had – they all had an influence (and they would know how).
Directly regarding my career, first and foremost my longest-term mentor was Rod Holcombe, winner of the Hobbs medal for structural geology about 7 years ago. I’ve known Rod since I was 18 and he was 33 - at this time he showed me a refolded fold in gneisses around Einasleigh in north Queensland on an informal geology trip. I couldn’t believe such folds could exist. By 2nd year he had our entire class doing hand-drawn but geometrically constrained 3D projections of refolded folds from data and field observations we had to process ourselves. And now I guess I’m one of a dying breed of geologists who can see, interpret, and enjoy refolded fold patterns. It used to be such a thing back then! And I love stereographic projections. Rod was also the main stepping stone to my industry career, as he had done the same thing, jumping from academia, about 5 years beforehand. And he was kind enough to get me involved with his consultancy consortium, which I’m now more-or-less in charge of (HCOV Global). Brilliant structural geology teacher, an understated world ‘great’, and a very good friend.
The late and great Vic Wall, my main PhD advisor, taught me everything about the toughest parts of petrology and hydrothermal geochemistry. He was a real taskmaster, very critical, and I responded well to this (unlike some of his other students…). I ended up with his job at Monash when he also jumped to industry, and it was a great pleasure to work with him again as a consultant on a major project in Colombia.
Gordon Lister (Monash, ANU) and Tim Bell (JCU) gave me great jobs at the right time! Bruce Hobbs and Alison Ord (CSIRO, UWA) introduced me to the world of geomechanical modelling and numerical geoscience, but I’ve never really been able to keep up with them as my maths is weak, but it’s always been a real eye-opener. John McLellan (JCU, GMEX) was one of the beneficiaries of this geomechanical legacy and we’ve worked on many R&D and consultancy projects together over the years, with John using the modelling software as his main commercial consulting tool. Doug Rumble of the Geophysical Laboratory in Washington, DC greatly improved my understanding of stable isotopes during my late-80s postdoc (and how much I didn’t want to work in an analytical lab). Several colleagues from Monash (1984-1993) I’ve kept in touch with or worked with for many years, and are very much part of who/ what I am as a geologist – most notably Rick Valenta, Andy Wilde, Paul Bons, Dave Cooke, June Hill. Greg Dipple was my first postdoc and he taught me more than I taught him
(I’m pretty sure) as he was a whizz with reactive transfer, which has really helped with my understanding of mineral systems. We’ve remained lifelong friends. My partner of 18 years, Haidi has put up with my gallivanting lifestyle (certainly better than former partners, eh-hem), and we plan to continue traveling globally while we can, especially now we’ve found a good dog+cat+house minder. Dogs have certainly been a positive influence on my career too, for all the obvious reasons any dog (and cat!) lover would know. Some of the readers will remember Otto the wonder-dog, who found his way into many hearts over his years as field camp morale-booster and geo-travel companion in the 1990s.
BD: Given the current multi-commodity mineral boom, are you doing a lot of work outside of the commodities and deposit styles you have traditionally worked on?
NO: Yeah, I had a very distinct and quite strong shift from mostly Precambrian R&D metamorphic-structural-economic work as an academic (Fe, IOCG, orogenic Au, some U), into the wonderful world of Mesozoic to recent porphyry-epithermal systems since then, while keeping up a portfolio of global Precambrian work. This has been an amazing learning experience for me, a highlight being standing at a height 5100 m (16 732 ft) near the border of Chile and Argentina during a month-long high-altitude stint for GoldCorp in the Maricunga porphyry belt (thanks Pablo Morelli!). I’ve also had a long-term project looking at hydrothermal REEs in NW Australia (thanks Robin Wilson and Kurt Warburton). All in all, this has sent me to quite a few parts of the world…
BD: I have to ask – political instability/ insecurity aside, what part of the world do you think is highly prospective for finding new world-class orebodies?
NO: Saudi Arabia is an obvious one seeing they’ve only been open for new minerals business for a relatively short time. Tim Coughlin (Royal Road Minerals) sent me there recently. Other than that, it seems likely there are probably giant gold deposits still lurking in the Guyana shield, and it’s also not clear that exploration under till in northern Fennoscandia and Arctic Canada (and Russia) has finished providing decent gold discoveries.
BD: Is there a particular mineralization style or deposit type that interests you, and why?
NO: I greatly enjoy the diversity of deposits I work on. It gives insights into all the others. I love really messed up ones, irrespective of commodity. And anything where mineralization is hosted in breccias. Well, also veins, which cover a lot! I love ones where there is widespread disagreement about ore genesis. And ones that are sitting in the middle of rocky deserts. Or thick jungle.
BD: Leading on from the previous question - everyone has a handful of deposits that have left a mark on them, be it because of the amazing geology, the hideous conditions, the people they worked with, etc. Which deposits do you hold dear, and which ones really were difficult to work on?
NO: Obuasi (Ghana) is the biggest deposit I’ve worked on (72 Moz Au+) and probably the most difficult. Sunrise Dam (Western Australia) I have a very soft spot for, because my work there with Mike Nugus, June Hill and James Cleverley straddled my transition from academia to industry, and we were really able to get our teeth stuck into it. Cerro Casale in the Maricunga of Chile was great because of the people and the scenery; that was an amazing crowd, sad to see the deposit ‘on-hold’ at present. The Wolverine REE deposit in NW Australia for similar reasons, great people, great country, and particularly odd geology. I worked on the discovery holes from Ernest Henry IOCG deposit (Queensland) and still haven’t fully worked it out, it remains a lifelong obsession. This is a great deposit, and its genesis has taunted me for 30+ years.
BD: Nick Oliver has operated all over the world. Do you have any travel horror stories or cultural mishaps that you can share?
NO: Fingers crossed, hardly anything. Worst was being on the sidelines in Russia (Chukotka) while Rod Holcombe went through a logistical and bureaucratic nightmare following an accidentally washed passport and visa. Missed a couple of planes through stupidity and talking too much, that’s about it. The only other mishap was one client from Mongolia who never paid me for a big job –30 days’ worth – but I heard recently that he subsequently spent several years in jail for fraud, which made me feel a bit better, and his company did let me see rather a lot of that country so I think of that lost income as an unusual tourist experience.
BD: Is there anything that you miss from your academic career? For example, I
miss the opportunity to undertake dedicated microstructural study of deposits, something that I feel is fundamentally lacking in many deposit studies.
NO: I miss teaching first years, trying to get that spark of interest going by raving on about chemosynthesis around black smokers and how that relates to the origin of life, the carbon cycle from death to diamonds, and getting them to build volcanoes using peanut butter and strawberry jam on a hot summer’s day to get across the concept of magma viscosity and its connection to plate tectonics. Several other aspects of academia I’ve been able to continue within industry – supervising grad students, running short courses and masters training, and the odd bit of microscope and microprobe work.
BD: We hear all about the advances and benefits of technologies such as 3D modelling, geochemical analysis, AI, and utilization of drones. Have you noted any negative impacts to effective exploration and mining as a result of these e.g. less people out kicking rocks?
NO: Well, it’s a leading question and one that’s been troubling many people. Dick Sillitoe suggests that there is a causative, inverse relationship between eyes on rocks and mineral discoveries. As I get older, I tend to drift towards that idea as well, but I’ve spent too much time learning and understanding through computational geology to really believe it. And in case young readers here think this is just an old-person’s state of mind, Bruce Hobbs today, in his 80s, is one of the true modern pioneers of computational geoscience, having grown up with fieldbased structural geology at his core. Yet, trying to reverse the decline in fundamental observation skills in the field and core yards is a major part of my consulting/training business, but it gets frustrating at times. Firstly, there’s no question that geochemistry is fundamental to exploration, and one piece of geochemical software ioGAS is so powerful that it’s been driving a wave of new approaches to geoscientific understanding. I’ve used it directly in a discovery (shame it was in Colombia just before the current political leadership froze the Mining Act). Leapfrog has almost the same impact, but geometry alone doesn’t reveal as much as the quite amazing way ioGAS helps you learn and understand at the same time, at least if you have some geochemistry background. I’ve used, benefited from and transferred the results from geometric and geomechanical 3D modelling over the years. I haven’t
directly used drones, but I’ve played with some drone products – not quite ‘there’ yet it seems.
The lure of AI, like previous computational advances before it, potentially takes young geos too quickly through a learning path to the hunt for instant answers, so I’m mostly worried about this in an educational sense –how does it relate to the scientific method?
ioGAS takes you on a learning path; no doubt this would be the same for computational/data experts currently using AI, but I’m worried about all the obvious abuses of its widespread accessibility to everyone. I haven’t used ChatGPT yet, as I really enjoy both reading and writing for myself. Probably I’ve been using AI without knowing it, which is also a bit scary. And my stepdaughter, doing an Engineering degree, recently told me that >50% of her class had been picked up for AIbased plagiarism in an assignment, by an academic who specializes in the field. Hard to tell where this will go. Look what the internet has done – great but dangerous, simultaneously benefitting, growing and damaging society – I think AI will follow that path.
BD: Leading on from the previous question, where do you see the most exciting
technological developments being made in mineral exploration and mining going forward? Do you think that there are any mineral exploration strategies or technologies that are under-employed, but could make a big difference to an exploration campaign if people used them more?
NO: I suspect the biggest opportunity lies in the better use of teams of people, in a social science sense, without that process being dictated by administrators. There are few people working at this interface, many scientists regard it as ‘soft’. The technical successes I’ve been a part of have largely involved the best teams, rather than the best technology.
Technologically, I think the most important things will be the tools that re-connect people to the rocks. Some recent examples are hand-held spectral tools, portable XRF, and the IQLogger I’ve already mentioned. I think some of these have a way to go, in the difficult area of technology versus education and training so that this machine/human interface doesn’t produce more data with less precision and accuracy (see comments above). Picking decent drill targets at depths
deeper than our current comfort zones remains very high priority, and this requires better fusion of surface and shallow structural geology (mostly) with better and better geophysical tools and methodologies. I think geophysics remains inadequately utilized –but it’s mostly not a technical issue - we need stronger inter-personal geology-geophysics links within active exploration teams. There’s often a disconnect with outsourced geophysical contractors not being a core part of exploration teams. I think there are cutting-edge developments in understanding complex and chaotic systems (e.g. research by Ord and Hobbs) that need to be supported to get them to the point where their potential value can be pragmatically assessed – but this requires stronger investment from universities and other research organizations, as well as belief from industry that it might be game-changing. It’s wait-and-see at the moment.
Mining complex orebodies is a very multi-disciplinary area and geoscience research is not well connected to production issues very well. For example, the imbalance between JORC reporting requirements, resource definition modelling and the reality of structurally complex ores is not working very
well it seems (but I’m out of my depth on this topic). I think there is a slight over-obsession with micro-chemical analysis in the research sector, partly technologically driven, to the detriment of fundamental experimental science (particularly metal behaviors in fluids). But neither micro-geoscience nor experimental geoscience speak well to the scale of genuine exploration problems unless the teams are prepared to fully integrate that work across multiple scales.
BD: This is a double-pronged question. Firstly, what is your opinion of the geological skillsets, experience, and knowledge of geologists today? Do you perceive a looming skills gap, due to the retirement of many academic and industry veterans, combined with the closure of many earth science institutions?
NO: Young geos today are way more skilled at 3D computational work and data than we were when young. I think they are worse at clearly recognizing the scale of geological problems because the pace of data generation and gathering doesn’t allow much time to think about what the best approach would actually be. But that’s experience speaking. The skills gap isn’t looming, it’s here. It’s glaring in structural geology, which is sad given the legacy of the great structural geologists of the last 50 years, a few of whom are still alive (including a few I’ve mentioned). A lot of the blame is on an uncaring attitude of politicians on both sides of the fence (at least in Australia), but it is reversible – noting an increase in geology enrolments in several countries elsewhere. Maybe the search for ‘critical metals’ will improve matters.
BD: Has there been any single satisfying moment in your career that rates above all the others?
NO: That’s a tough one. Not really, there have been too many golden moments. I’ve been lucky. Perhaps getting a job at Monash despite being a trouble-making grad student there? Standing on top of the Andes? Running a field trip for 75 geos through my doctoral field area in north-west Queensland? Mapping solo on several occasions in 100% exposure?
BD: I’ll ask a question on the flipside to the previous one. Many of us have inter-
faced with less than savory individuals or experienced toxic workplaces. Has there been any incident or incidents that really disappointed you?
NO: Almost none when I’ve been a consultant. Maybe the one I mentioned before with the completely screwed-up structural drill-core procedures. But I’ve seen so many happy geos and mostly happy work environments that it’s difficult for me to think of seriously disappointing situations. Again, lucky. But there were a few incidents in the last few years I was at JCU that I’ve tried to forget, I was just swamped with work (see the next question) and couldn’t stop a few people from messing up good projects and spreading bad vibes through the team, and the impact of the merger with geography was pretty devastating.
BD: We both know how hard it’s been to try to coordinate time together on a project, due to client and personal commitments. Given the many professional hats that you wear, what is Nick Oliver’s secret to time management, or doesn’t he have one and simply ‘wings it’?
NO: This is hilarious. I’m a shocking example of time management. If I did this better, I would have made more commitment to professional organizations, but I was fairly burnt out after JCU and decided I’d given enough. Maybe I’ll get back to that as I attempt to slow down (after I’m 70?, 80?). My office is a mess. My computer structure is a mess. I rely on a good bookkeeper, accountant and travel agent to keep afloat these days. I don’t like much about organized structures, except that they help me constrain what would otherwise be a chaotic lifestyle. Yeah, so ‘winging it’ probably applies.
BD: Taking the answer to the previous question into account, what does Nick Oliver do in his ‘downtime’? Does he have any favorite hobbies or passions he pursues? Please make this an interesting answer or I will take editorial privilege and make stuff up!
NO: It’s changed over my life, as you’d expect, so here’s a rough chronological order. Military modelling (not dressing up like a soldier, the plastic kits), playing squash, drinking
too much with friends, motorcycling, dogs, heavy rock music from the 70s (e.g. Iggy and the Stooges), leatherwork, making verandahs, visiting art galleries (especially modern art or crazy sculpture). Well, I think you can see a pattern there. It’s called ‘attempting to slow down’. Others might call it ‘growing up’ but I don’t know much about that.
BD: If you had abundant financial funding, is there a fundamentally annoying geology question you’d like to solve or a topic you’d like to work on?
1. The origin of cement-supported hydrothermal breccias (Ernest Henry whom I referred to), there’s something we are really missing, and it gets back to the decline in people working on phase separation in geological fluids.
2. It would need a huge effort and is probably not worth it, so let’s call it a dream: inserting a full hydrothermal speciation dataset into ioGAS, plus capacity to recognize and map chaotic behavior, to kick the geoscience world back into geochemical-geomechanical prediction space that finds mineralization (needs about five lifetimes and a few more Cooperative Research Centers) – but this is too hard.
3. I try and do anyway, to provide the data and logical reasoning to consider that reworking of older metal accumulations is part of the normal budget of many or most mineral systems. This won’t win Nobel Prizes but over-polarization of ore deposit models doesn’t necessarily drive the science forward, either. This is probably the Old Nick speaking, not the Young Nick.
BD: Finally, any concluding comments or words of wisdom from an industry leader?
NO: What’s the phrase? ‘If you enjoy your work, you won’t work a day in your life’. So, I’ve worked maybe two or three years in my mid-40s and I’m 64. And yeah, go look at some more rocks, it’s good for you. C
For more information
Reach out to Nick via LinkedIn
24T PULLBACK | 22T MAIN WINCH | HANDS FREE ROD HANDLING ON BOARD AIR/MUD | DATA LOGGING | TIER 1 SAFETY
by Leah Lynham, James Cook University
Palaeochannels: Most geologists working in the Eastern Goldfields will have explored them and most prospectors will have found gold in them. Many old timers would have followed deep leads leading to riches that turned out to be palaeochannels (such as Kanowna). But is gold all they’re good for? Absolutely not.
As a palaeochannel researcher, I am often dismayed at how little exploration geologists know about the rich and diverse palaeoenvironmental history contained within palaeochannels of the Eastern Goldfields. Drowned forests, marine transgressions (yes, more than one), macro and microfossils and a rich rainforest palynoflora are all present, spanning just 30 million years of geological time. Imagine, a rainforest where red dirt dominates the Kalgoorlie landscape today.
How did a girl from London used to 24/7 conveniences pack up her bags to move to an outback mining town to call home to research the microfossils of an ancient drainage that once coursed underneath the streets and houses? David Attenborough. And a very nonlinear path. I credit David with my career. When I was a child I watched his documentary, ‘Lost Worlds Vanished Lives’ which inspired me to become a palaeontologist. I used to use my Lego to build my own prehistoric worlds. In my teen years, in a low socioeconomic area, I buried the dream. Palaeontology was a career for other people, not girls that needed to work full time as soon as they left school. But, with some sheer determination (and chronic sleep deprivation) I managed to get to college where I did study geology. But that was a complete accident. I thought gemstones were pretty, so ended up in a geology A-Level. I quickly fell in love with the subject realising that I could actually make a career of this. I went on to read geology at the University of Plymouth where I had several amazing lecturers who encouraged my love of palaeontology and palaeoenvironment. Even the structural geologists knew it was a lost cause trying to get me over to their side
when I used graptolites in a structural exam as evidence for closure of the Iapetus Ocean and suture development. I developed a passion for marine micropalaeontology and benthic foraminifera in my second year and went on to specialize in biostratigraphy for oil and gas exploration, tailoring my MGeol year to all things palaeoenvironment. I was lucky enough to work with Fugro Robertson on North Sea Oil and Gas samples.
Then I moved to Australia, and there is not much opportunity for a benthic foraminifera biostratigrapher out here, so I packed my dream away, and went into exploration. For a few years I worked on a range of commodities including Au, Fe and Li but my passion for palaeontology never left. Coming off maternity leave, my husband’s then boss asked me if I wanted to see some fossils they had pulled out of an open pit, and truth be told I thought he had been in the sun too long. Fossils in a gold mine on the Yilgarn? But there they were, a block of marine bivalves (Figure 1). This got me excited and after a lot of emails back and forth between the mining company, myself and JCU, a PhD research project was formed. I found myself in a niche little world I’ve continued to carve for myself, a regolith geologist straddling both industry and academia, using the palaeoenvironment to assist palaeochannel exploration activities.
Enough about me, what geological riches has my research found? Logging over a hundred drill holes, both diamond and RC, newly discovered outcrops and pit wall exposures, it’s clear that the stratigraphy is not as simple as the current model shows. We do not have the basic
layered package of gravel, clay, lignite, spicules. Every environment interfingers with another spatially across the Lefroy Drainage, making for a very confused looking attempt at a 3D model, but this does give us further insights into palaeocurrent directions and the timing and separation of the Lefroy and Cowan drainage systems.
Two clear catchments are seen in the basal Au producing gravel, one the standard quartz gravel well known throughout the Goldfields, but a second smaller source catchment consisting of immature polymictic conglomerate also exists and may indicate more than one provenance of basal placer deposit. Muds associated with the polymictic layer have been dated in collaboration with MGPalaeo (a Perth based geological and stratigraphical consultancy specialising in palynology) and give us the same N. asperus zone, as the quartz gravel so we know they were deposited at the same time.
Thanks to my Industry Partner Gold Fields and their St Ives Mine Site I’ve been able to join their geologists in visiting open pit sections of palaeochannel and through this discovered a drowned forest type environment in the Werrilup Formation, something previously seen in the Cowan Drainage system, but not reported on from the Lefroy. It’s incredible to look up at a pit wall and see clear columns of lignitic material, flooded by fine grained clays, giving a wonderful insight into what it would have been like in Kambalda ~35Ma. We would have been standing in a vast anastomosing river valley, in a temperate rainforest, with lazy water ways. There has not been any evidence of terrestrial fauna but I hold out hope that it will be found.
Along with these new discoveries come insights of onshore material, for the first time a clastic shallow marine interval, equivalent to the Pallinup Formation has been described. This is an earlier unit, representing the Tuketja Transgression, and the change from swampy clays and lignite deposited in an anastomosing river environment, to a widespread shallow sea, reaching far in-land, in what we have deemed the ‘on-shore’ Eucla Basin. This is the unit that sparked my research. When viewed underneath a microscope it is surprisingly full
of microfossils. It turns out these microfossils (Figure 2) have never been described from the Yilgarn before, and I am identifying them ready to share them with the world. The deposition of this clastic material was followed by deposition of the well-known marine Princess Royal Spongelite member of the Pallinup Formation. But sponge body fossils were not known from the Lefroy drainage system, as it was previously believed to be a marginal marine, high energy environment. New field locations from this research have discovered a shallow water sponge reef (Figure 3), covering a couple of hundred meters across and around 3 m (9.8 ft) high, much further inland than previous shorelines have been placed. Many of the species are believed to be novel to science, and a collaboration with palaeontologists in Poland will bring this information to life.
Field work in previously under explored areas of the lower reaches of the Lefroy Drainage System have revealed extensive new outcrops of sponge body bearing spiculitic sediments, extensively bioturbated spiculitic sands, and even a few outcrops of fluvio-glacial material. This may help define exactly when these large-scale drainages traversing the Yilgarn were incised. I have even found a coccolithophore (a calcareous nannofossil and type of phytoplankton) accidentally when analysing legacy material under the SEM (Figure 4), and I am almost 100% confident it’s the first coccolithophore ever seen from the Yilgarn. I do not doubt that continued exploration of the buried drainages of the Yilgarn will discover more treasures just waiting to be described.
The knowledge gained throughout my PhD research isn’t just an insight into the Eocene environment of Western Australia. Nor just a potential useful vector for gold exploration by using palaeoenvironmental knowledge to hopefully predict where the next big placer gold
deposit will be found. My favorite use is getting children excited about earth sciences.
My main passion lies with educating tomorrow’s earth scientists. I bring tangible evidence of changing landscapes from where they live into the classroom. I have worked with many schools across Western Australia, creating incursions and excursions for students from Kindergarten to Year 12. Fossils are highly engaging and capture the attention of all students and foster interest in the changing world they live in. Show students a 35-million-year-old marine gastropod shell and ask them what they think it is. They all say ‘seashell’, and then you tell them it was found just 15 km (9.3 mi) away in the very open pit many of their parents work, in the middle of a red dirt desert and you have captured their attention and imagination.
‘Really, Miss? A seashell? But there’s no ocean here.’
‘There isn’t,’ I’ll reply, ‘but there used to be.’
Then begins my spiel about diverse and changing landscapes and natural history (Figure 5). I paint a picture of how Kambalda and Kalgoorlie were once covered in a shallow ocean filled with marine life. How where we stand today was at one stage a rainforest and of course how geology really should be considered a career. After all, the students live here every day exposed to the outdoor classroom; this exposure and accidental knowledge will be a major advantage should they pursue a career in earth science. I often take school groups to Mount Hunt, a location many geologists in the area are familiar with as it contains evidence of a much older sea floor in the form of 2.6 Ga Paringa Basalt pillow lavas. This site expands their concept of where we live and understanding of geological time. They are surrounded by tangible evidence for deep geological time and the repeating cycle of land and oceans on the planet. This is also a good time to whip out the toothpaste experiment for pillow lava formation.
My approach to educating the next generation is not without difficulty. Many mining companies simply do not appreciate the rich geological heritage of the 30-100 m (98-328 ft) of stratigraphy overlying basal palaeochannel gold. It is the overburden to be stripped away and dumped. However, as I have discovered that overlying stratigraphy is filled with novel fossils and knowledge and has become the perfect vehicle for getting the next generation involved in Earth Sciences. I have made it my one-woman mission to spread the good word of the middle-late Eocene palaeoenvironment of the Eastern Goldfields, but also to stress how it can be useful in determining potential loca-
tions for palaeochannel deposits. As my parting words, I am going to implore mining companies to save their RC chips, to save some diamond core of channels, photograph it like you would your hard rock, both wet and dry, and extra images of interesting features, and teach your geologists how to log it properly. We have lost so much knowledge due to poor logging and disinterest in the geological knowledge for knowledge’s sake. The mine I’m working with for my research has been exploiting palaeochannel gold for over 30 years, but the presence of microfossils had not been documented until I looked at some of the Neptune open pit marginal marine sediments under my microscope. How much information have we lost over the years?
And with that my final words. We need fresh minds if Australia wants to continue to be a resource powerhouse, and to find fresh minds, Earth Science communication is all of our responsibility. Save a sample, talk to a child, share a post, sponsor a book for a local library. Keep our field thriving for decades to come. C
For more information Contact Leah at leah.lynham@my.jcu.edu.au
The Comacchio EGEO 405 is the first fully electric geotechnical and mineral exploration drilling rig. Powered exclusively by electric batteries, the EGEO 405 eliminates the environmental drawbacks of traditional diesel engines, offering unmatched energy efficiency, operational precision, and sustainability. Join the leaders in sustainable drilling and discover the versatile drilling capabilities of the EGEO 405. Comacchio - Pioneering the Path to Zero-Emission Drilling.
Embracing technological innovation, sustainability, and gender diversity
The Indian mining sector stands on the cusp of a technological renaissance, where the integration of cutting-edge innovations is reshaping traditional methodologies and driving the industry towards unprecedented efficiency and sustainability. In this comprehensive exploration, we delve into the scientific intricacies of this transformative journey, examining the evolution of autonomous technology, its impact on safety, productivity, and sustainability, and the strategic imperatives poised to propel India's mining sector into a new era of excellence.
by Shreya Mukherjee, PhD Student at Georgia Institute of Technology
At the heart of this technological metamorphosis lies the adoption of drone-based surveying and advanced geological modelling techniques. Drones equipped with state-of-the-art payloads, including magnetic scanners and LiDAR systems, have revolutionized ore body mapping and hyperspectral imaging, offering unparalleled precision and detail. This scientific precision not only expedites exploration endeavors but also ensures proactive environmental monitoring in mines, thus aligning with India’s escalating focus on environmental stewardship.
In parallel, the industry’s commitment to sustainability has ushered in a new era of technological synergy, epitomized by the deployment of biofuels and electric vehicles (EVs) in mining operations. The transition towards EV dumpers and surface miners heralds a significant reduction in carbon emissions, underscoring a concerted effort towards ecological preservation. Furthermore, the adoption of surface miners and rippers, equipped with environmentally friendly alternatives to conventional blasting, underscores a holistic approach to sustainable mining practices.
Against the backdrop of India’s ambitious energy transition goals and the imperative of achieving Net-Zero emissions by 2070, regulatory reforms have assumed a pivotal role in fostering the exploration and mining of critical minerals. The enactment of the Mines and Minerals (Development and Regulation) Amendment Bill, 2023, signifies a strategic pivot towards the exploration and extraction of critical minerals, thus addressing the burgeoning demand for essential resources in a rapidly evolving industrial landscape.
However, the sector grapples with a myriad of challenges, ranging from regulatory hurdles to inadequate mineral exploration and burgeoning import dependency. Regulatory frameworks mandating limited mining lease areas and the scourge of double taxation impede seamless operational scalability, while the dearth of comprehensive mineral exploration perpetuates India’s import dependency for crucial minerals and metals.
To unleash the full potential of India’s mining landscape, a multifaceted approach is imperative. Incentivizing domestic exploration, fostering private sector participation in critical mineral mining, and
↑ Setting up drone before take off
establishing an independent regulatory authority are strategic imperatives. By embracing automation and fostering a conducive regulatory environment, India can unlock the full potential of its mining sector, paving the way for a future characterized by enhanced efficiency, sustainability, and technological prowess.
The adoption of autonomous technology emerges as a linchpin in augmenting the efficiency and safety paradigm within Indian mining operations. Autonomous mining operations, underpinned by a synergy of operational and information technologies, offer a transformative blueprint for enhanced productivity and reduced operational costs. The delineation of mining operations into dependent, semi-independent, and independent autonomy levels underscores a progressive trajectory towards fully autonomous mining operations.
Global deployment trends underscore a burgeoning adoption of autonomous haulage system (AHS) trucks in both open-pit and underground mining operations, with exponential growth observed over the past two decades. Furthermore, the deployment of automated drills in open-pit mines has witnessed a commendable surge,
propelled by technological advancements and the imperative of enhanced productivity.
The future trajectory of Indian mining hinges on a confluence of factors, ranging from regulatory reforms and technological advancements to strategic collaborations and a steadfast commitment to sustainability. Embracing automation and fostering a conducive regulatory environment are pivotal in unleashing the full potential of India’s mining sector, thus paving the way for a future characterized by enhanced efficiency, sustainability, and technological prowess.
Amidst the sweeping transformations in the Indian mining sector propelled by technological advancements and regulatory reforms, there exists a lingering challenge that demands urgent attention – the persistent underrepresentation of women. Despite concerted efforts to promote inclusivity, gender disparities continue to hinder women’s entry and progression in mining-related occupations. While recent amendments to the Mines Act of 1952 have expanded opportunities for women to work in both underground and opencast mines during specified hours, they still occupy a disproportionately small fraction of the mining workforce, predominantly relegated to lower-paying roles.
Several formidable barriers impede women’s full participation and advancement in the mining sector. Cultural norms and societal expectations often dictate traditional gender roles, discouraging women from pursuing careers in mining or assuming leadership positions within the industry. Safety concerns, particularly in physically demanding and hazardous mining environments, further deter women from entering the sector. Limited access to education and training opportunities, especially in remote mining regions, exacerbates the gender gap in skills and qualifications. Moreover, the challenge of maintaining a work-life balance, particularly for women with caregiving responsibilities, presents another significant hurdle to their professional advancement in the mining sector.
Despite these challenges, there exist promising avenues to advance gender diversity in the Indian mining sector. Technological advancements, particularly in automation and digitalization, hold the potential to create new job opportunities for women while alleviating some of the physical demands associated with mining work. Furthermore, the industry’s shift towards sustainable mining practices presents a unique opportunity to promote gender inclusivity and empower
women in decision-making roles. Women are inherently positioned to advocate for environmentally responsible mining practices and prioritize community well-being, thus contributing to the sector’s longterm sustainability and social impact.
Women have a crucial role to play in driving the transition to sustainable mining practices in India. Research suggests that women are more likely to advocate for environmentally responsible mining practices, given their inherent inclination towards community well-being and environmental stewardship. By actively involving women in planning and implementing mining projects, India can achieve more sustainable outcomes that benefit both the industry and local communities. Women’s perspectives and contributions are invaluable in shaping a more inclusive and environmentally conscious approach to mining, ensuring the sector's long-term viability and social license to operate.
In conclusion, the Indian mining sector is undergoing a profound transformation fueled by technological innovation, regulatory reforms, and a growing emphasis on sustainability. However, amidst these advancements, the issue of gender diversity remains a crucial dimension that requires urgent attention. Despite the challenges, there are significant opportunities to advance gender inclusivity in the industry, with women playing a pivotal role in driving sustainable practices and fostering innovation. By addressing barriers, promoting education and training, and leveraging technological advancements, the Indian mining sector can unlock its full potential and pave the way for a more prosperous, inclusive, and sustainable future. C
by Kirsten Bell, Social anthropologist and author of the Silent but Deadly Substack
I come from a family of geologists. My father, sister and brother are trained geologists, as is my husband, my brother-in-law and my brother’s partner. Moreover, I was constantly surrounded by geologists growing up. Because my father is a retired academic geologist, we had a long parade of his PhD students staying with us throughout my childhood.
Despite the intensity of my exposure to the field, I have made a heroic effort to learn as little as humanly possible about geology. To my father’s intense dismay and my mother’s deep relief, I became a social anthropologist instead. Basically, my brain has been trained to go into ‘la-la’ mode as soon as rocks or mining stocks come up in dinner conversation. Still, I have picked up enough of the lingo over the years that I could probably pass as a geo – to a non-geologist, at least. For example, I don’t know what a porphyroblast inclusion trail is, but I know they are the key to orogenesis.
In what follows, drawing on my professional skills as a social anthropologist and my personal observations of geologists in their natural habitat for the past 50-odd years, I aim to articulate the (ahem) core traits of The Geologist as a distinct social breed.
The first thing that strikes me is how well defined the contours of the geologist are in popular culture. Unlike most scientists, who are treated in TV and films as an undifferentiated, lab coat-wearing mass, geologists are portrayed as quite distinct. This difference was the source of a running gag in the TV show The Big Bang Theory, where they were the regular target of derision. Geologists, Sheldon (a theoretical physicist) frequently proclaimed, weren’t ‘real’ scientists – going so far as to assert that ‘Geology is the Kardashians of science’.
This is, in part, because geology is an interpretive science where what is observed in nature can’t be straightforwardly replicated
in a lab. However, it probably doesn’t help that a high proportion of geological terms seem like they were coined by a 14-year-old boy. To wit, conversations between geologists typically sound like they’re discussing the aftermath of a sexual encounter – you’ll hear references to everything from cleavages, shafts, thrusts, cross-bedding, dry holes and orogenic belts to my personal favorite: dickite. (Seriously, who names a mineral ‘dickite’?).
Geologists are also presented as far more athletic and outgoing than your usual scientist – there is nary a lab coat to be found in the numerous films featuring them. Instead, the dress that geologists tend to be uniformly associated with is field gear – khakis, many-pocketed shirts or vests, boots, sports watches, etc. This look is exemplified by Brad Pitt’s fake geologist in the film Ocean’s Thirteen, although female geologists are often presented in much the same way – e.g., Rhonda in the 90s cult classic Tremors. Also common to Hollywood depictions of geologists is a down-to-earth, straighttalking demeanor. Interestingly, despite the fact that most geologists work in an increasingly vilified and misunderstood industry (mining), geologists themselves are generally shown in a favorable light as honest, honorable types. In an analysis of representations of geologists on the silver screen, Erik Sturkell and his colleagues conclude that geology is generally portrayed as ‘an upstanding profession, albeit one with an appallingly high death rate’. (An inviolable rule of disaster
films seems to be that unless the geologist is the main character, or their love interest, they’re going to die.)
The stereotype of the unflappable, downto-earth geologist is probably best captured in the South African humorist James Clarke’s article about a failed Survivor-type series featuring geologists. The show never made it to air because the cast failed to generate the required level of dramatic tension, preferring to mostly work alone or in pairs, and the production budget was quickly overrun as a result of the costs of transporting their rock samples and keeping them supplied with beer. (Beer is a key part of the geologist’s professional identity, as Wired footage from an American Geophysical Union conference attests.)
Of course, these are stereotypes. I know plenty of geologists whose preferred choice of beverage is not beer, along with, admittedly, a very large proportion for whom it is. But there is probably a grain of truth to the stereotypes insofar as they provide a cultural model to emulate (albeit one that’s been called out for being hyper-masculine). Geologists unquestionably do tend to perform their identity through their choice of clothing. As I’ve previously noted in an analysis of LinkedIn profiles, geologists on the platform often eschew formal attire in favor of hard hats, high-vis gear and khakis – unless, that is, they’ve moved into corporate roles.
I also find it interesting that of all the tools of the geologist’s trade, the one almost universally used to symbolize the profession is
↑ Selection of logos of geological societies
↗ Geological field excursion to Harpers Ferry, West Virginia, 1897 (public domain, via Wikimedia Commons)
not a hand lens, compass, or indeed, rocks themselves, but the geopick (a.k.a. the rock hammer). While crossed geopicks might look like a symbol of fraternity to your average geologist, to virtually everyone else they look like an instrument of death, making them a far more aggressive logo than the beakers and atoms that tend to feature on the crests of chemistry and physics societies. For example, change the background of the above photo from the mountains of West Virginia to the streets of New York City and you could be looking at a scene from the movie Gangs of New York
A frequent topic of discussion on Nick Tate’s Geology Upskill channel, one gets the impression that the geopick is more than just a tool. Indeed, for most geologists I know, a geopick is multifunctional object, useful not just in obtaining rock samples but handy as a burglar deterrent, a substitute hammer and a virtually universal means of determining scale, not just in rock formations but whatever else you would like to measure, whether it be babies or cats. And, of course, there is a long history of geologists throwing geopicks for fun.
Still, although they might be rarely used to symbolize the discipline, for most geologists, the love of rocks runs deep. Indeed, geologists tend to love rocks in a way that’s deeply annoying to non-geologists – such as their
tendency to stop in the middle of a highway to admire the cross bedding revealed by a road cutting. And trying to pick a stone countertop with a geologist? Save yourself some grief and go for engineered stone is my advice. You will be looking for a durable and attractive countertop for your kitchen or bathroom. They will be looking for one with visible garnets, or foliated gneiss, or fossilized ammonites, or whatever hastens the beat of their geologist’s heart.
And, for the love of god, do not get a geologist started on the topic of art – unless, that is, you want to hear someone wax lyrical about the beauty of thin sections viewed under a polarizing microscope, which every geologist I’ve ever met insists would make a fortune if someone decided to photograph them and sell them as art. (Newsflash, geologists: Etsy has been selling thin section art for years, and I doubt there are any millionaires amongst the sellers, so you have got to move on from the whole thin-section thing.)
Given that this article is being published in Coring Magazine, I have one final observation to make about geologists. If asked, most geologists will probably tell you that their natural adversary is drillers. As Erik C. Ronald observes, ‘Many geologists view drillers as most people view their home dishwasher: useful when working, messy when broken, but don’t try to get a meaningful conversa-
tion out of them’. Conversely, drillers view geologists as ‘overpaid, know-it-all, foureyed oddball(s) who get their kicks licking rocks all day’.
However, I’m not convinced this is true - certainly in terms of the relationship be tween female geologists and drillers, most of whom, to quote one unnamed source, ‘have either dated a driller, or gone to a strip joint with one’. Based on my observations, the geologist’s greatest enemy is actually the mining engineer. Better at maths and less fond of the outdoors, mining engineers are typically paid better and are more likely to be groomed for management positions than geos. As the saying goes, ‘geologists create the dream; mining engineers kill it’. In sum, love them or hate them, geologists have managed a feat that few other scientists have accomplished, which is to carve out a distinct public identity. Whether their repu tation as the most grounded and down-toearth of the sciences is deserved or bespeaks a serious failure of imagination, one thing’s for sure: geologists, as Bill Bryson observes, are never at a loss for paperweights.
Drilling Contractors (A-Z): Diamond Drilling, Reverse Circulation, AirCore
BRYSON DRILLING
Phone 306-323-2202 Fax 306-323-2203 info@brysondrilling.ca www.brysondrilling.ca Canada
CAPITAL DRILLING Phone +230 464 3250 info@capdrill.com www.capdrill.com East, North and West Africa
DDH1 DRILLING
Phone +61 08 9435 1700 admin@ddh1.com.au www.ddh1.com.au
Australia
DIAFOR Phone (819) 860-3957 info@diafor.ca www.diafor.ca Canada
info@oykatiab.com www.oykatiab.com
Finland
Australia
ATELIER VAL-D’OR
Phone (819) 824-3676
Fax (819) 824-2891
info@avddrills.com www.avddrills.com
BARKOM
Phone 90-312 385 60 50
Fax 90-312 385 35 75 info@barkomas.com www.barkomas.com
DISCOVERY DRILL
MANUFACTURER
Phone 1-506-542-9708
Fax 1-506-542-9709
info@discoverydrills.com www.discoverydrills.com
PROLENC
Phone (250) 563-8899
Fax (250) 563-6704
khodgins@prolenc.com www.prolenc.com
RC Equipment (A-Z)
BOART LONGYEAR
Phone 1-801-972-6430
Fax 1-801-977-3374 www.boartlongyear.com
FORDIA POWERED BY EPIROC
Phone 514-336-9211 Fax 514-745-4125 info@fordia.com www.fordia.com
NORTH BAY MACHINING CENTRE
Phone (705) 472-9416
Fax (705) 472-2927
luc@nbmc.ca www.nbmc.ca
PROLENC
Phone (250) 563-8899
Fax (250) 563-6704
khodgins@prolenc.com www.prolenc.com
www.diatoolglobal.com anthonygraham6@gmail.com
QUALITY AND EXPERTISE
DIATOOL is a young and dynamic company, founded in 2010. The company manufactures impregnated and set core bits, casing shoes, reaming shells, and geotechnical drilling bits.
DIATOOL products are sold in North and South America, Australia, Asia, Africa, and Europe. DIATOOL Diamond Products are manufactured in a modern well-equipped plant, using the latest manufacturing technology.
DIAMANTINA CHRISTENSEN
Phone +562 2620 7808 christensen@christensen.cl diamantinachristensen.com
DIASET Phone 1-800-663-5004 bits@diaset.com www.diaset.com
DIAMOND PRODUCTS Phone 852 2871 9028 diatool@163.com www.diatool@global.com
www.holeproducts.com
BOART LONGYEAR
Phone 1-801-972-6430
Fax 1-801-977-3374 www.boartlongyear.com
HOLE PRODUCTS
Phone 909-939-2581
Fax 909-891-0434 www.holeproducts.com
SINOCOREDRILL
Phone 86-510-82723272
Fax 86-510-82752846
sales@sinocoredrill.com www.sinocoredrill.com
BARKOM
Phone 90-312 385 60 50
Fax 90-312 385 35 75 info@barkomas.com www.barkomas.com
CORE TECH
Phone +51 983 856 666 info@coretech.com.pe www.coretech.com.pe
FORDIA POWERED BY EPIROC
Phone 514-336-9211
Fax 514-745-4125 info@fordia.com www.fordia.com
Cont.
FORDIA POWERED BY EPIROC
Phone 514-336-9211
Fax 514-745-4125 info@fordia.com www.fordia.com
Water Treatment Systems (A-Z) Survey Tools Cont.
REFLEX
Phone 1-705-235-2169
Fax 1-705-235-2165 reflex@imdexlimited.com www.reflexnow.com
SONDA PARTS
Phone 55 – (31) 3391 3810 Fax 55 – (31) 3391 3810 comercial@sondaparts.com.br www.sondaparts.com.br/
Survey Tools (A-Z)
sptab.com sales@sptab.com +34 952 17 99 18
ADVANCED DOWNHOLE SURVEY TOOLS FOR EXPLORATION AND BLASTING
SPT is your global partner for downhole survey technology. We manufacture advanced solutions for high precision downhole and blasthole survey data. Our commitment to quality and accuracy has made us an industry leader. Request a free demonstration today.
MUDEX
Phone +61 (8) 9390 4620 info@mudex.com.au www.mudex.com.au
www.di-corp.com
Drilling Fluids Cont.
CORE TECH
Phone +51 983 856 666 info@coretech.com.pe www.coretech.com.pe
DYNAMICS G-EX
Phone +61 7 54826649 sales@dynamicsgex. com.au www.dynamicsgex.com.au
PROSPECTORS
Phone +61 (02) 9839
3500 Fax +61 (02) 8824 5250 sales@prospectors.com.au
Core Orientation (A-Z)
COREFINDER
Phone +55 62 992720023
contato@corefinder.com.br www.corefinder.com.br
DEVICO AS Phone +47 72870101 devico@devico.com www.devico.com
Cloud Solutions (A-Z)
Surveying & Geophysics (A-Z)
CORE TECH
Phone +51 983 856 666 info@coretech.com.pe www.coretech.com.pe Peru
DIGITAL SURVEYING
Phone +27 18 788 6349
sales@digitalsurveying.co.za www.digitalsurveying.com.za Africa
TRUST SOLUÇÕES
GEOLÓGICAS
Phone +55 62 992720023 contato@trustsg.com.br Brazil
An environmentally safe DSPA (Dry Suspended Polyacrylamide) used for removal of cuttings, borehole wall conditioning, and in hole torque reduction:
A superior product for borehole stabilization and encapsulation of solids. Imparts excellent viscosity yield.
E ective in drilling conditions where borehole temperatures exceed 150° F.
Enhances both bit-life and penetration rates during drilling operations.
Inhibits swelling of clay like materials such as saprolites, talcs & kimberlites which in turn eliminates bit balling.