
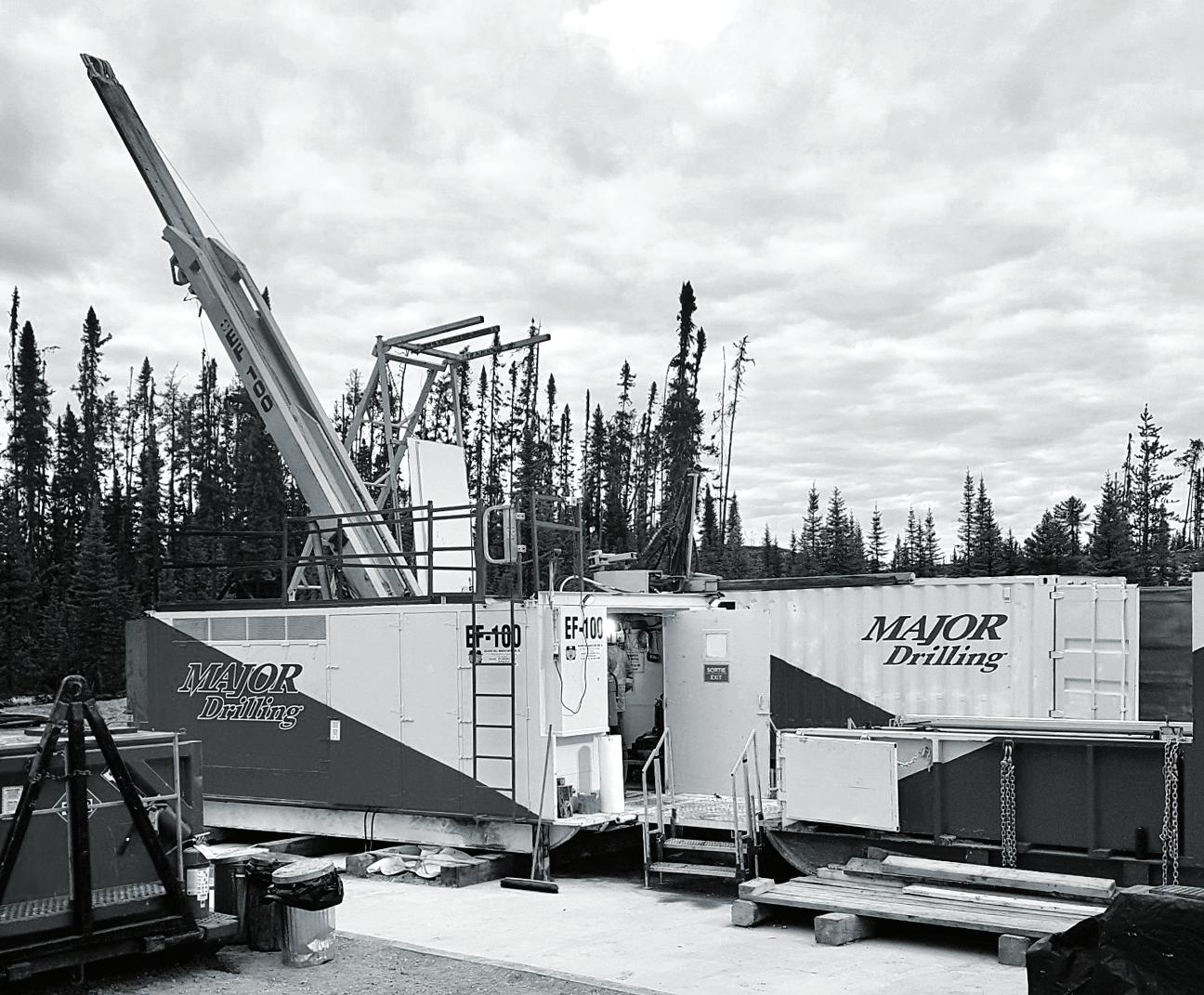
Align any Drill Rig with Confidence
Setup to Planned Alignment
Confirm Collared Azimuth with Survey Probe
Report & Audit Trail Push


Align any Drill Rig with Confidence
Setup to Planned Alignment
Confirm Collared Azimuth with Survey Probe
Report & Audit Trail Push
24 Diamond drilling in cold weather: What drillers need to know before braving the elements by Jeff Dagg, Head of Technical Support at Fordia Powered by Epiroc
30 Red Rock Drilling: The journey to carbon neutrality by Henry and Johnathan Taitt, Directors at Red Rock Drilling Pty Ltd
34 Comacchio launches a new range of drill rigs for a new era of safe exploration operations by Comacchio’s editorial team
38 Lantern’s new features are giving mining & exploration companies a serious upgrade to their drilling program by Andre Sonnichsen, CTO at Lantern
41 Q&A from the experts: Timothy Strong in conversation with Mark Saxon, CEO & President at Medallion Resources Ltd.
44 Working in the Arctic cold weather: Winter wonderland or frigid drudgery by Wren Bruce, Senior Project Geologist at Mercator Geological Services
48 The value of sample preparation when using portable XRF in mineral exploration by Richard Belcher, Consulting Geologist, RWB Exploration Ltd and James Cleverley, Global Products Manager-Geosciences, REFLEX Instruments Europe Ltd/IMDEX Ltd
52 Sail Pond project: Uncovering Canada’s next high grade silver district by Mathew Wilson, President & CEO at Sterling Metals Inc.
56 Challenge and Opportunity in the Mining Industry of Ecuador by Merlin Marr-Johnson, Executive Vice President at Salazar Resources Ltd
EVENT
60 PDAC 2021: The World’s Premier Virtual Mineral Exploration and Mining Convention /CATALOG
62 Diamond drilling services
Drilling equipment & accessories
Survey equipment
Dag Billger Owner & Business Manager at Inertial Sensing
Duncan McLeod Owner & Product Manager at Inertial Sensing
Kevin Slemko
Corporate Business Development Manager at Major Drilling Group International Incorporated
Cody Campbell Founder & President at CKC Ultralight
Matti Rautakoski
Business Manager at Oy Kati Ab Kalajoki
CORING MAGAZINE
March 2021
Cover photo
Major Drilling Issue 15
ISSN 2367-847X
Not for resale. Subscribe: www.coringmagazine.com/subscribe
Contact Us
Coring Media Ltd.
119B D. Petkov Str., Sofia 1309, Bulgaria
Phone +359 88 953 2653
Email editorial@coringmagazine.com
Website coringmagazine.com
Jeff Dagg Head of Technical Support, Fordia Powered by Epiroc
Henry Taitt Director at Red Rock Drilling Pty Ltd
Johnathan Taitt Director at Red Rock Drilling Pty Ltd
Mark Saxon CEO & President at Medallion Resources Ltd.
Wren Bruce Senior Project Geologist at Mercator Geological Services
Publisher Coring Media
Editor in Chief Grigor Topev
Executive Officer & Editor Martina Samarova
Editor
Maksim M. Mayer
Section Editor – Exploration & Mining Geology
Timothy Strong
Digital Marketing Manager
Elena Dorfman
Graphic Design
Cog Graphics
Printed by Dedrax Printing House
Richard Belcher
Consulting Geologist, RWB Exploration Ltd
James Cleverley Global Products Manager-Geosciences, REFLEX Instruments Europe Ltd/IMDEX Ltd
Mathew Wilson President & CEO at Sterling Metals Inc.
Merlin Marr-Johnson, Executive Vice President at Salazar Resources Ltd.
Coring Magazine is an international triannual title covering the exploration core drilling industry.
Published in print and digital formats, Coring has a rapidly growing readership that includes diamond drilling contractors, drilling manufacturers and suppliers, service companies, mineral exploration companies and departments, geologists, and many others involved in exploration core drilling.
Launched in late 2015, Coring aims to provide a fresh perspective on the sector by sourcing authentic, informed and quality commentary direct from those working in the field. With regular interviews, insightful company profiles, detailed product reviews, field-practice tips and illustrated case studies of the world’s most unique diamond drilling and mineral exploration projects, Coring provides a platform for learning about the industry’s exciting developments.
Together, Duncan McLeod and Dag Billger, specialists in inertial micro-sensor systems (MEMS), have more than 30 years of experience of developing commercial positioning and tracking systems.
Duncan and Dag have a strong focus on wellbore survey instruments. They work with a wide range of applications, which are relevant for the following fields: Mining, Oil and Gas, Geotechnical and Civil Engineering.
Duncan and Dag founded Inertial Sensing in 2010, and its goal is to create modern surveying technology that will give their customers a competitive edge.
How do magnetic survey tools work?
The simplest description of a magnetic electronic multi-shot survey (EMS) tool is that it is at heart an electronic compass that can be lowered into a borehole and stopped at a series of locations to measure where it is pointing with respect to magnetic north, to give the azimuth. It also contains inclinometers to measure how the tool is tilted away from the horizontal, to give the dip angle. The borehole path/coordinates are reconstructed from the measured angles of dip and azimuth in combination with the known depths of the stations, using a method such as minimum curvature interpolation.
EMS tools can also measure more information that is sometimes not presented, as it is not needed to reconstruct the borehole path. This includes the magnetic field strength and the magnetic dip/ inclination, which can be used as survey quality indicators.
The magnetic field strength, measured in nano-Tesla (nT), is simply how strong the magnetic field is. The strength of the Earth’s magnetic field typically ranges from 25 000 to 65 000 nT depending on the location. A quality EMS tool should be calibrated to read magnetic field strength in the range of zero to 100 000 nT.
The Earth’s magnetic field is a vector, which means that at any location it has a direction as well as a strength. The magnetic field usually points in a north direction, which is, of course, why compasses can be used for navigation. But the exact direction can vary significantly around the Earth because of the geology of local rocks and the
exact conditions in the Earth’s core, which ultimately generates the magnetic field. The strength and direction of the magnetic field also vary over time, with the geographical positions of the poles changing over the years.
The direction of the magnetic field can be broken down into two parts of interest. The first is the part that defines the compass heading, the direction of magnetic north. The second is the magnetic dip, which describes how the magnetic field is tilted up or down from horizontal. At the equator, the magnetic field is ideally horizontal and has a magnetic dip of 0°. At the magnetic North Pole, it is vertical and straight down, or -90°. At the magnetic South Pole, it is vertical and straight up, or +90°. In between these locations, it varies roughly according to latitude. Note that the Earth magnetic field does not vary exactly with latitude as there are large regional variations in different parts of the world.
Many EMS tools contain a full set of three perpendicular magnetometers to measure the complete magnetic field around the tool. They can then also measure the magnetic field strength, the magnetic dip and the azimuth. Apart from being interesting for investigating the geology of the local rocks, the magnetic field strength and the magnetic dip can also be used as quality indicators for survey results. This is because a magnetic disturbance in the borehole will most likely affect the magnetic field strength and the magnetic dip values, as well as the azimuth. Magnetic declination is one of the quantities of interest in magnetic surveys which are
not measured by the tool. The declination describes how the magnetic field at a location points away from the true geographic north. For a local field pointing to the east of the true north the declination value is positive. Since the Earth’s magnetic poles wander over time, the declination at a location also changes. It is therefore important to remain updated on these changes when surveying.
Various scientific bodies monitor the Earth’s magnetic field globally and locally for its strength, dip and declination. There is a variety of sources of information and online calculators are provided by various organizations, for instance by NOAA [1] and The British Geological Survey [2].
Solar activity can also influence the Earth’s magnetic field and cause disturbances that are large enough to affect the quality of a magnetic survey conducted during a solar storm. Solar activity is kept under scientific observation and it is possible to receive space weather alerts warning of conditions that might have a geomagnetic effect on Earth [3].
Is there a difference in the quality of sensors in magnetic survey tools that are available on the market?
EMS tools are a very mature technology and the quality of sensors and results from a reputable supplier should not be in question, nor should they differ significantly. Most manufacturers quote a general calibrated azimuth accuracy in the range of ±0.35 to ±0.5°.
However, that says nothing about other quality issues that may arise. The sensors used in a tool are only a part of a system that must come together to give good results. This includes the length of time that a good calibration holds for a tool, power consumption, ease-of-use, ruggedness, tendency to fail in certain situations and so on.
How can a surveyor assess the quality of magnetic survey tools, based on their results?
In general, it is difficult to use survey results to assess tool quality, unless you already have a good reference survey to compare with. But one can always compare two surveys of the same hole with the same tool to check for repeatability.
A tool manufacturer should be able to specify the accuracy of the tool, assuming it is in good condition and recently calibrated. One way to verify performance is to do tests in a magnetically undisturbed area. For instance, setting up an accurate reference
line using GPS, gyrocompass or similar and repeatedly measuring the line with the EMS tool. By rotating the tool around its long axis and taking measurements with different gravity highside positions one can also test for any ‘coning’ of the azimuth results which would indicate poor calibration or a bent tool. In addition to checking the azimuth results, the values of the local magnetic field and magnetic dip can be verified against the expected values.
Frequently, the reference value of the magnetic field strength (in nT) of a project is assumed to be the value taken from several undisturbed borehole survey stations. Is this good enough or is there a more precise and reliable way to find the magnetic reference value?
It is not ideal to use results from a survey in the hole, as we cannot be sure what is happening there. Often the best way to measure the local magnetic field strength is to use an EMS tool to take multiple measurements on the surface in an undisturbed area and average the results to get an estimate of the field strength. Of course, this depends on the tool being in good working order and properly calibrated. If this is not possible or practical to do, there are world magnetic models that are maintained by various scientific agencies, such as those from the aforementioned NOAA and the British Geological Survey. Magnetic data values within a survey can always be used to identify anomalies appearing locally over a short distance in the borehole. However, if there are disturbances of a more global nature affecting the whole body surrounding the borehole, this would affect the whole survey and then an independent exterior reference value is important.
What is considered as an acceptable fluctuation of the magnetic field strength that does not interfere with the azimuth reading?
Typically, in the borehole surveying industry, acceptable fluctuations are usually in the range ±1000 to ±1500 nT for the magnetic field strength and ±0.5° for the magnetic dip angle.
Is it possible to have azimuth and magnetic field strengths that appear stable and valid on all the records of the survey data but still differ from the actual ones? What could cause this to happen?
The azimuth calculated from the magnetic field components does not depend on the overall strength of the magnetic field, only its direction. If the magnetic field is disturbed so that its strength is very nearly correct, yet the direction is moved from what it should be, then the azimuth would be incorrect, but the field strength would not indicate the problem. In this case, the magnetic dip value can also be checked at each station, since this should be affected to some degree as well and indicate a possible error in the azimuth.
Contrary, for the same reason as mentioned above, in rare cases the value of the magnetic field can appear anomalous, but still its corresponding azimuth values may appear true (undisturbed).
It can be noted that while the azimuth does not depend on the strength of the magnetic field, the spread of repeated azimuth measurements at the same point is sensitive to the field strength. In a location with a weaker Earth magnetic field, the azimuth results will have a higher spread. For instance, see reference [4].
In vertical surveys, the tool is not pointing in any compass direction, but straight down. The magnetic field readings will be stable, but the azimuth results could also appear to be stable, depending on the setup of the system in the hole. But the azimuths themselves will be essentially meaningless.
‘The azimuth is determined by using the local gravity vector and the Earth magnetic field vector as reference directions.’
This also is true for near-vertical surveys, where the hole has a dip within about -87° to -90° of vertical. As the borehole dip comes close to vertical a lot of care must be taken in interpreting the azimuth results.
Another condition that should be kept in mind is that as the survey location moves closer to the Earth’s magnetic poles, the accuracy of the azimuth results decreases. This is the nature of the azimuth itself, as it is undefined at the poles. To visualize this, imagine standing at the North Pole… every direction from there is south and there is no single azimuth value! The same problem is encountered with north-finding gyroscope tools and is discussed in a previous article [5].
The azimuth is determined by using the local gravity vector and the Earth magnetic field vector as reference directions. The higher the magnetic dip angle is at a given location, the closer it will be to the local gravity vector. The closer these vectors are to each other, the more they represent the same information and gradually lose their significance as independent reference directions. The consequence is that a higher magnetic dip means lower azimuth accuracy, while a low magnetic dip angle means a higher degree of azimuth accuracy.
Finally, as with north-finding gyroscopes, magnetic survey tools are less accurate when surveying in an East/West direction and most accurate when surveying North/South. Thus, a stable magnetic field and azimuth result in an East/West direction is more likely to be in error than the same stable results taken from a hole pointing North/South. This is also discussed in the previous article mentioned in this section.
How can the magnetic dip be used to judge the quality of the survey data; can it improve data analysis and what is the added value from this additional parameter?
At any given point on the Earth, the magnetic dip should be reasonably well known and constant over a distance. So, if in a survey the magnetic dip varies too much outside a standard range (usually ±0.5°), we can be confident that there is magnetic interference in the ground and the survey results are probably unreliable.
In principle, all EMS tools containing a full set of three magnetometers should be able to give a value of the magnetic dip at every station, along with the azimuth and magnetic field strength, since the magnetic dip is just another number derived from the same calculations.
It has become a common practice to do control gyro surveys in order to check survey data collected from magnetic tools. Often the check survey results in 2-to-3° difference in the azimuth values and the gyro data is accepted valid. Can there be cases when the error is not in the magnetic tool?
There are no perfect survey tools, nor is it possible to guarantee that a survey tool has always been used correctly. So, there stands a chance that a gyro can give a survey that
differs from an EMS tool, and for the EMS tool to be more correct.
If we assume the gyro is functioning properly then some sources of error that might be overlooked are:
1. For a north-finding gyro, incorrect latitude information was supplied to the tool.
2. For a reference gyro, the initial reference direction was incorrectly measured using GPS, a three-axis gyrocompass, optics or similar.
3. The gyro was over-rated (turned too quickly) at some point in the survey,
The Earth’s magnetic field has a strength or intensity that points at an angle (the magnetic dip or inclination) down into the Earth. The field also points towards local magnetic North. Local magnetic North in most cases is not the same as geographic North and the difference between the two is called the declination.
which typically adds a constant azimuth error.
4. The gyro was rotated excessively during the survey, allowing scale factor errors to build up and cause an azimuth error.
5. The magnetic declination was incorrectly applied when comparing magnetic and gyro survey data.
It should be noted that it is possible for both the gyro and the magnetic tool to be incorrect. This is particularly true for gyros that use FOG (fiber-optic gyro) technology, as these gyros are also magnetically sensitive through the Faraday Effect and can be disrupted by magnetic ore bodies or magnetized drill rods.
When comparing two surveys from any tool type it is very important to keep an open mind about where the differences may come from. There is no such thing as a survey tool that is immune to any human error or misuse!
[1] World Magnetic Model maintained by NOAA. https://www.ngdc.noaa.gov/ geomag/WMM/
[2] The British Geological Survey data services. http://geomag.bgs.ac.uk/ data_service/home.html
[3] Global Geomagnetic Activity with information on solar storm activity. http://www.geomag.bgs.ac.uk/data_ service/space_weather/Global_activity_ now.html
[4] ‘Accuracy prediction for directional MWD’, Williamson, SPE 56702, Society of Petroleum Engineers Annual Technical Conference and Exhibition, 1999.
[5] ‘Similarities between magnetic and north-finding survey tools’, McLeod & Billger, Coring Magazine, Issue 9, 2019.
by Kevin Slemko, Corporate Business Development Manager, Major Drilling Group International Incorporated
Right now, the mining industry is facing a problem. Declining exploration activity, and supply deficits expected within five years, have driven record pricing for commodities—especially gold and copper. Unfortunately, new deposits are harder to reach and are in greater demand than ever before. How can the industry overcome this problem?
Specialized drilling is the key. Using drills as ‘truth machines,’ Major Drilling unearths exploration potential for clients around the globe. The company is registered in over 20 countries on five continents. New and ongoing partnerships with senior and emerging exploration and mining companies keep drills turning.
Major Drilling is ready. With a fleet of more than 600 drills, many with automated features, and a workforce of over 3000, the company is well positioned to meet the demands of the next global mining upcycle.
While Major Drilling didn’t invent specialized drilling, the company’s focus on this specific area for more than
40 years truly sets it apart as the worldrenowned specialized drilling leader.
Specialized drilling means Major Drilling is highly experienced at drilling with distinct equipment and techniques in difficult to access areas. Services, including deep hole, directional and heli-supported drilling for projects that go deep underground, are situated in remote locations or reach high altitudes. Each drilling project adheres to top safety standards, with some requiring even more complex safety measures— an area where Major Drilling excels.
‘We deliver on the toughest sites by leveraging our knowledge, extensive experience, focus on safety and commitment to meeting the local needs of every customer,’ said Denis Larocque, Major Drilling President and CEO. ‘With the best people on the ground and a modern, diversified drilling fleet, we partner with our customers and local communities for outstanding results.’
Major Drilling sprouted in 1980 around the Brunswick Mine in Bathurst, New Brunswick, then rapidly grew across Canada, achieving international reach by the early 1990s. Success came by following a winning formula: acquire quality equipment, retain top talent and effectively respond to market cycles to maintain a strong balance sheet. In 1995, the company began public trading on the Toronto Stock Exchange as ticker symbol MDI.
Today, Major Drilling’s senior management team is a robust amalgamation of former drillers, operations managers, financial experts and innovative corporate leaders. Together, the top 40 members of this management team have over 1000 years of combined experience in the drilling business. Universal values of quality, safety and results guide every project. Significant acquisitions in the past decade include Norex Drilling in 2019, Taurus Drilling in 2014 and Bradley Group in 2011. Through Norex, Major Drilling
expanded both surface and underground drilling operations in the profilic region of Northeastern Ontario, Canada. With Taurus, underground percussive drilling became a new focus in Canada and the United States. Bradley Group assets expanded Major Drilling’s geographic footprint in Northern Quebec, Northern Ontario, the Philippines, Mexico and Suriname.
Specialized drilling is in demand. Expansion into Suriname continues to yield results for a senior mining partner enlarging surface gold mine operations through blast hole drilling with a recently purchased D65. Major Drilling works on a variety of exploration, infill and blast hole drilling projects at the site. More than 80 team members drill blast holes and perform other specialized drilling including horizontal drilling, dewatering wells and various small geotechnical programs.
The strategic purchase of equipment is a tactic Major Drilling can employ because it is
cash positive and effectively positioned for a surge in mining activity.
In Indonesia an esteemed client continues to call on Major Drilling’s specialized drilling expertise in the earthquake-prone ‘Ring of Fire,’ the Pacific zone where tectonic plates collide. For more than 20 years, drilling services at the mammoth gold mine require innovations including recent hydrofracking and block cave monitoring—the process of inducing fractures to assist with ore movement, reducing the intensity of seismic activity and monitoring controlled cave-ins.
Drilling teams meet the challenges of this large-scale, challenging drilling environment by working productively and safely alongside the client. Records in 2020 totaled over three million lost time injuryfree hours at four different project sites. When a client in Mongolia needed to expand its massive copper project, it turned to Major Drilling. The drilling teams completed a 2000 m (6561.68 ft) PQ3 diameter hole—an extremely deep hole for P-size—which required both experience and expertise. They met the challenge to
The Major Drilling team stands with its UDR5000 drill used in Mongolia at one of the world’s largest copper-gold mines. They celebrate the extremely deep 2000-meter PQ3 drilling record completed on October 22, 2020.
reach the record-setting depth and the requirement to approach at a 65-degree dip.
For 104 days, the project yielded an average 10 m (32 ft) per shift while intersecting eight faults. The hole is an incredible achievement for Major Drilling. What’s more, the client can now pursue additional deep hole drilling and expansion at the project.
In 2020, Major Drilling broke records not only in Asia, but also in Canada, where deep diamond drilling brought about a new record at a world-class gold deposit in Quebec.
The drillers knew it would be a historic achievement from the beginning, so they assembled an experienced team from within the Major Drilling ranks. That experience paid off when the team, confronting challenging geology, used 11 wedges to meet the target.
Fortunately, the drillers understood these obstacles. Their knowledge and the power of the EF-100 drill ultimately prevailed. They made it to the historic 3467 m (11 374.67 ft) length N-size and broke Major Drilling’s standing Canadian diamond drill record on January 26, 2020.
‘Discovery One is a great success and achievement,’ Osisko Mining President and Chief Executive Officer, John Burzynski, said. ‘We are very proud of our Osisko team and Major Drilling for their tremendous work completing this hole.’
Major Drilling places value in its people. The company employs the expertise of crew,
staff and management already established in the business and provides them with the best equipment. This results in a company that adapts to changes, has personnel who persevere through downcycles and upcycles, and has a great measure of reassuring continuity for partners.
‘Our partners benefit from the extensive drilling knowledge of our drillers and senior managers, the majority of whom have hands-on field experience and understand specialized drilling from every angle,’ Mr Larocque said. ‘We outperform our competitors through this expertise.’
The fleet is modern, with innovative additions like rod handling capability and recent refurbishments. Customers appreciate the responsiveness and flexibility to relocate equipment for mining and drilling operations around the world.
Revenues in fiscal 2020 were CAD 409 million. With a leadership team willing to adapt and adjust to market conditions, revenue across
The Major Drilling Canada team celebrates its 3467-meter-deep diamond drilling record on January 26, 2020
the past four years shows continued growth, despite COVID-19 setbacks. Major Drilling effectively weathered initial and ongoing impacts of the pandemic by reacting quickly and effectively to protect employees from, and to slow down, the spread of the virus.
Fortunately, Major Drilling was well positioned financially to endure setbacks and stay on track with clients as they restarted projects with new health and safety measures in place. Safety is a prevailing hallmark of the company’s value system.
So, what does safety look like at Major Drilling? After clocking in, grabbing a safety booklet or logging into a safety program, team members begin each shift with safety at
The center of onsite safety programs is the TAKE 5 risk assessment. Critical risks are managed through a set list of critical controls. When employees encounter
Major Drilling innovations include client-oriented data portals
a critical risk during their shift, they must stop and complete the corresponding critical control checklist. Each team member knows and regularly reviews the 10 Lifesaving Rules to ensure personal and team safety is top of mind.
Major Drilling invests in continued training and programs because clients depend on this first-rate approach to safety. Each project’s safety records include tallies of lost time injury-free hours from contractors, and Major Drilling is proud to have millions of injury-free hours logged with customers.
Human Resources and Safety Vice President, Ben Graham, heads Major Drilling’s safety programs. He works to excel world-class safety programs that adapt and improve as the mining industry evolves.
‘Safety is a core value in our operations,’ he said. ‘Knowing how to avoid risk means our expertly trained teams are ready to do each job well and safely.’
It’s also gratifying to be recognized by the industry. In 2020, Major Drilling received the Safe Day Everyday Gold Award for the third year in a row from the Association for Mineral Exploration (AME) and the Prospectors & Developers Association
of Canada (PDAC). The company also marked lost time injury-free milestones at projects in Indonesia and Brazil.
When it comes to innovation, more really is more. Major Drilling is adding more analytics, more automation and more safety innovations than ever before.
That’s why, since 2015, the company has dedicated an innovation team to developing products that are changing the way data productivity and safety work. These include:
• The Trailblazer Analytics system, computerized analytics dashboard system. It can be retrofitted to surface and underground coring drills to capture drilling parameters.
• A client-oriented web portal intended to provide clients with daily project visibility, information and progression.
• A new hands-free horizontal stacking rod handler, the Major Drilling SafeGrip. This innovation is the next generation manipulator for surface coring rigs.
• Five new drills for Canada and US projects showing commitment to ‘smart’ systems that provide more automation for worker safety and mobility for clients. This results in less downtime and more value over the life of a project.
With these innovations, Major Drilling is moving into the future as the innovation team continues to build platforms that bring value and transparency to clients and support crews.
Being extremely well positioned for the expected multi-year drilling upcycle didn’t happen by chance. Neither is it by chance that Major Drilling is the contractor of choice for a customer base led 80% by senior mining companies.
‘Our clients at all echelons in the industry come to us for our strengths—namely our experience, strong balance sheet, diversified revenue sources, innovation and equipment purchases,’ Mr Larocque said.
With these drivers, Major Drilling is confidently forging ahead into its fifth decade of operations.
The company will always invest in its greatest asset—its workforce. Continued investment in people includes the development of local drillers. After spending years in the company, many of them grow to become managers.
Responsible, forward-looking management also comes through the development of a robust environmental, social and governance policy and accompanying initiatives. No longer seen as simply a risk management issue, Major Drilling is enhancing environmental, social and governance (ESG) value and sustainability as it operates globally in areas such as diversity, reducing greenhouse gas emissions and community partnership.
For instance, partnerships with nearly a dozen First Nations and Inuit communities provide meaningful opportunities for indigenous communities in their traditional territories in Canada. This is possible through community involvement, employment and support for local suppliers. It is a mindset that starts at the top with Mr Larocque.
‘It’s a duty for all of us in the industry to be more aware of environmental,
social and governance issues and be responsible corporate citizens,’ he said.
As the mining industry meets the demands of the coming decade and potential exploration upcycle, Major Drilling remains its reliable drilling partner. Commodities will be discovered in ways that only specialized drilling services can supply. With its experience, strong cash position and preparations for the next drilling upturn, Major Drilling has solutions. It will continue to strategically approach the industry’s needs with the right equipment and innovations for data, mobility and safety.
For today’s operations and tomorrow’s drilling demands, Major Drilling stands ready and is proud to continue to be the world leader in specialized drilling. C
For more information
Visit: www.majordrilling.com
by Cody Campbell, Founder & President at CKC Ultralight
The Ultralight Fabric Drill Shacks being developed by CKC Ultralight were first conceptualized in 2012 by the team at Ridgeline Diamond Drilling. Ridgeline was a small, familyowned and operated contractor that focused on completing remote, heli-portable diamond drill projects that required crews to be comfortable working in weather conditions ranging from
extreme sun and heat to low temperatures and blowing snow at high altitudes. They were heading into a couple of early season projects in Northwest British Columbia (BC), Canada, followed by a late-season drilling program in the Yukon mountains, planned to take place at an altitude of 8000 ft (2438 m).
From their experience in the preceding seasons, management knew that the Yukon project posed a number of challenges for their existing setup of equipment and support gear. First, the mobilization involved the use of a Twin Otter airplane in combination with a Hughes 500 helicopter. This required everything to be both compact and lightweight, in order to fit in the plane but also to minimize the cost to the client by reducing the number of trips from the staging area into the project airstrip.
The second challenge was the timing of the program and the expectation that it would run late into the fall when the days were getting shorter and the weather was turning colder. The longer night shifts combined with mist, wind and fog at the drill’s elevation meant that the probability of the crew having to spend time at the drill beyond the 7 a.m. crew-change was very high. These reasons led the team at Ridgeline to come up with a shack solution that would allow the crew to conduct their work warm and dry but also protect them from the elements and provide a safe shelter in the event the helicopter was unable to conduct crew change at the allotted time.
Traditionally, if drill crews had fly shacks as part of their equipment repertoire, they were made of plywood walls formed around a steel tubing frame. These walls were pinned together by the crew and braced and bolted. Most contractors will agree that while these shacks do shelter the crew from the weather, they can be time-consuming to assemble, and almost impossible for a crew of two to put together in a strong wind or inclement weather. In the case of the Yukon project for Ridgeline, they were not an option due to their weight. It was at this point that the team began seeking an alternative solution.
Anybody who has worked outdoors can attest that many tasks are less frustrating if you are able to remain dry. Once the drill engine begins to run and the temperature rises, crews find that in addition to being dry, the shacks are also very warm places to work in, as the windproof walls cause the warm air to circulate within them. For the crew at Ridgeline, working at 8000 ft (2438 m) above sea level in the Yukon in late September, being warm and dry was not only a luxury to appreciate but it contributed to safer operations.
There were multiple days when the helicopter was unable to conduct crew change due to fog and rain and without the drill shack, the crew would have battled with fatigue along with the elements, risking hypothermia, frostbite or exposure concerns. For this project, the client was limited in the amount of lumber they were able to mobilize to the project; therefore, they were unable to provide a ‘safety shack’ at or near the drill. This problem was solved when the Ridgeline drill crew was equipped with an emergency kit at the drill containing sleeping bags, cots, non-perishable foods and a small cookstove. Thus the fabric shack was utilized as a perfectly acceptable survival shack as it provided a warm, dry, windproof shelter for the men on the mountain.
‘For the crew at Ridgeline, working at 8000 ft (2438 m) above sea level in the Yukon in late September, being warm and dry was not only a luxury to appreciate but it contributed to safer operations.’
In the search for alternatives to the plywood shack, the president of the company, Doug Campbell leaned on his 38 years of experience and designed an aluminum frame measuring 16 ft by 16 ft (4.88 m by 4.88 m) (in order to fit on lumber pads) and weighed very little in comparison to the alternatives. From there, the team sourced a PVC fabric that was both waterproof, windproof, and flame resistant while also being lightweight. Once the type of fabric was settled upon, design began so that it could be sewn to fit over and around the frame. After some stitching and design tweaks, the shack was completed and ready for its first season of mineral exploration.
The entire shack weighed 420 lb (190.5 kg) and could be mobilized in the Twin Otter in one single trip. The simple, straightforward design meant that it could be broken down for moves in 10-15 minutes and re-assembled in that same amount of time. This design is flown from site to site the same way one moves a lift of drill rods with chokers and endless straps. Pilots have commented that it is the easiest shack they’ve ever had to move. There is no requirement for the pilot to weave the drill mast or engine in and around a shack already assembled on the pad, nor is there any reason for them to strain the helicopter to move a plywood walled unit weighing near the lifting capability of the machine. That fabric shack began to show its advantages right away in that first season of its use.
When fully assembled, with two roof panels enclosing the drill, the CKC Ultralight Fly shack provides the crew with a dry place to work.
Fast forward to 2020 and the Ridgeline Drilling crew decided to move on from the drill contracting space and sold their drill and support equipment. After multiple inquiries as to where the fly shack went, and whether it was available for sale, Cody Campbell, a member of Ridgeline Drilling’s management team, decided to branch out and fill that demand for Ultralight Fly Shacks and CKC Ultralight was formed to do just that.
The first customer of CKC Ultralight was Driftwood Diamond Drilling, a very successful contractor in Canada with operations across the country and in Peru. Their first fly shack was dispatched to a project in Golden Triangle, BC, for Scottie Resources. Most people in the industry have heard of the Golden Triangle and for those who don’t have first-hand experience, know that weather there can change in an instant. Most of the drilling is conducted high in the mountains on steep slopes. Coupled with strong winds, rain and snow, operations can get complicated by extreme weather conditions at any time throughout the year.
At first, the Driftwood crew had doubts about the durability of the fabric shack - after all, this is an industry where most things are built from heavy-duty steel and bolted together. The utility of the CKC shack was soon realized shortly after a drill move early in the program. The weather had been inclement for a couple of days and both fly drills were ready to move to their new pads as soon as there was a break in the weather. When that break came in the afternoon, the crews scrambled ‘all hands on deck’ and along with the Yellowhead Helicopters pilot Jeff Patmore, both drills were moved to their new pads just before crew change and nightfall. It should be mentioned that throughout the move and over the course of the following night shift the weather was not friendly to the crews with strong wind, freezing temperatures and rain. One of the drills was outfitted with the traditional plywood walled shack while the other was traveling with the CKC Ultralight Fabric Shack. At crew change the following morning, the night shift teams reported to the foreman. One crew said that they were unable to set
up the plywood shack in the wind and this severely hampered their production through the night, being wet and cold. The other drill crew came into the crew room and stated: ‘I love that shack, not only were we dry, but setting up in the dark wasn’t a problem since it was so bright in there with the white walls’. That same crew, after setting up their drill following the move, had installed their anchor, run their casing and cored to 60 m (197 ft) depth. This kind of production may not have been possible without a shelter that allowed them to work unimpeded by the weather and the elements.
From that first shack sold to Driftwood Drilling, CKC Ultralight has now sold multiple units to contractors operating in the Golden Triangle and Yukon. Most of the shacks are intended to be utilized in the summer drilling season; however, recently there has been a push by multiple provincial permitting agencies to reduce and minimize disturbance levels of drilling programs. This shift in government paradigm has led to a number of drill programs that would typically take place as road access skid jobs, to be designed as heli-supported fly jobs. This has seen CKC Ultralight deliver shacks into Northern Saskatchewan, Canada for work in February, where temperatures are expected to average around -30°C (-22°F). Modifications to the shacks for this winter work include a fully enclosed roof, along with passthrough flaps in the walls to allow for frost fighter hoses to provide auxiliary heat to the drill crew.
One of these shacks has been delivered for Bryson Drilling, an extremely experienced and well-known contractor, for a winter fly job on a Gold exploration program in Northern Saskatchewan. After the first few holes, all reports from the project are good. Not only is the drilling going really well but Derek Sunderland, a partner and field supervisor for Bryson says ‘according to the boys [the shack] is absolutely wonderful. Using one frost fighter at -40°C (-40°F) and they are all warm inside it’
With the CKC Ultralight Shacks being utilized all across Western Canada and in all seasons and types of weather, there really are no limitations as to where these fabric units can be utilized. If there is a program that would benefit from providing a roof over the heads of the crew, or a wall providing shelter from the elements, these CKC Ultralight Shacks can be customized to suit each contractor’s needs. The lightweight nature and minimal setup and takedown would work well in international programs where man-portable drills are being utilized; just as they would prove particularly useful in places like Mexico, or Nevada, where crews need a roof over their head to provide shade and minimize the risk of exposure to the sun. A drill program in the jungle where there are periods of rain each day, could benefit from having a roof and shelter around the rig.
CKC Ultralight Drill Shacks start as a basic design and feature construction elements such as double-stitched seams utilizing UV and
chemical resistant thread, extremely strong industrial hook and loop (Velcro) and 12 oz (407 g/m2) PVC fabric. Each unit can be modified and customized according to the specifications of the drill it is surrounding, along with how the contractor lays out and sets up their equipment on the fly pad during heli-portable projects. There is truly little that can’t be customized on the CKC Ultralight Shacks. Doors and openings can be moved and placed according to the desires of the drill crew, wall heights and the overall size of the shack can be modified for drills that require a larger shelter, or perhaps a smaller, more compact unit.
The advantages of having a complete shack surrounding on fly projects are numerous. The simplicity and ease of set up allows for crews to assemble them safely and efficiently. In turn, they spend more time setting an anchor, running casing and collaring the drill hole. While working, the crew remains warm and dry and after all, a happy crew is a more productive crew, typically spending more time at the controls drilling rather than taking breaks to warm up and get comfortable. The shacks also serve as safe, warm shelters in the event the crew needs to take a break and rest, an essential part of a fatigue management plan. Additionally, the white walls provide a bright reflective surface for the night shift crews.
‘I love that shack, not only were we dry, but setting up in the dark wasn’t a problem since it was so bright in there with the white walls.’
In between holes, during teardown of the drill, if left up until the move, the shack provides shelter from the elements. It also prevents water and other environmental contaminants from getting into the hydraulic lines of the drill. The lightweight nature means that helicopter pilots never have to struggle to get it moved to the next pad. Also, when servicing the drill with a helicopter, the shack makes for a cleaner, tidier drill site as the little things that inevitably blow around under the rotor-wash (i.e.: loose burlap, gloves, core box lids, empty buckets, etc.) remain contained within the walls of the drill shack rather than blowing down the mountain slope or across the drill site.
CKC Ultralight has provided fabric fly shacks to contractors in BC, Yukon and Saskatchewan. The best testament to the quality and durability of the CKC Ultralight Shacks is having experienced, reputable contractors, such as Driftwood Drilling and Bryson Drilling, acquire multiple units to surround their equipment and protect their crews for the upcoming 2021 summer drilling season. C
by Matti Rautakoski, Business Manager at
You need both equipment and know-how, to survive and even flourish in a cold environment. If you miss either, you are going to jeopardize the success of the entire project. You must understand the perils of the combination of snow, ice and darkness, the risks it produces and how to tackle them.
While we were drilling in Northern Finland and Sweden, it was not so rare to have more than -40°C (-40°F) and on rare occasions even -50°C (-58°F). In such temperatures, it is essential to remember not to shut down any vehicles or machines, if you want to use them. If you shut them, it may be difficult to start them again until the weather gets warmer.
Once we had a tricky situation where only the drill rig and one single snowmobile were left running, all other machines were completely frozen in the -43°C cold (-45.4°F).
As usual, we would have driven the snowmobile from the rig to the parking area, which was on a lake shore, and then taken a car to our accommodation. In that instance, when we reached the cars, we found them frozen; we were stranded. We thought to give the cars a boost and warm them up with a generator. We started the generator inside the rig, as it was warm there, put it on the snowmobile sledge and set off on the eight km (5 mi) where our cars stood. It was so cold that even though the generator was running at the beginning, it stopped after a couple of kilometers. We drove the generator back to the rig and tried again and again, only to have the same issue. In the end, we had to weather the whole way to the accommodations on the snowmobile. We had a similar case with a geologist working for our client. He was also traveling to our rig by a snowmobile. His snowmobile fizzled out halfway and he had to walk several kilometers to the rig. When he finally appeared, he looked like a snowman, his beard all white and covered from head to toe in ice and frost. Our driller gave him a mug of hot coffee and the geologist was overjoyed by relief, as walking in the Arctic cold is one of the most unpleasant and dangerous experiences. His ill-fated snowmobile remained frozen until the weather got warm enough to start it again.
As we have four seasons during the year, it also means that we need to be aware when they change. For instance, we have to measure ice thickness both in early winter and in early spring to know when we can enter an area or assess whether it is time to leave while we still can.
Equipment is another story. Due to the location of our projects, light is often of great importance. During the winter, it is dark for most of the day, so it is essential to have good general lights inside the rig and outside and equip each person with good headlamps. We want to give our employees the best possible working conditions. This means that our rigs must be fully covered, allowing us to warm up the interior of the drill rig, and give pleasant inside working temperatures for the drillers.
One of the highest safety risks in winter conditions is slipping on icy terrain, which may result in serious injuries.
We are using technical solutions to keep the rig floor free of ice.
Water is essential in core drilling, and we need to use it, which may cause problems in cold weather. Keeping the water pump running without even a minute break is important. Sometimes the waterlines happen to freeze and getting them to work again is not an easy task. In such cases, you must have some spare line to put into use and even then you will lose valuable time. The water line could be buried in snow to prevent freezing, as snow will isolate the line from cold air. However, if that is not possible, there are some heater solutions that can also help. Sometimes if it is very cold and you have been working inside the rig, there might be humidity due to the handling of water. Clothing and safety gear are particularly important then, as when you go outside, your clothes may freeze instantly. Since there is a range of personal clothing and safety gear to choose from, one should pay attention to how they work in a cold climate.
Cold and snow are much more than just an issue to be solved: they make it
After the darkest time of the year, there is plenty of daylight in March and April and also a lot of snow
possible to go for exploration in places not accessible otherwise. Such is the case with our contract with AA Sakatti Mining.
Kati Oy hold a drilling contract with AA Sakatti Mining, a Finnish company owned by Anglo American Plc. This has been a long-standing project, running for over ten years now with some idle years in between due to permitting. It is the great cooperation between us and Anglo American that has helped our company grow. Every year, we have been able to use the innovations and ideas from this project on others, benefitting exploration drilling on all of our drill sites.
The AA Sakatti deposit has multiple minerals: copper, nickel, cobalt and PGEmetals. It is located in Northern Finland, about 150 km (93 mi) north of the Arctic Circle, meaning it is not possible to enter unless there is sufficient snow cover on the ground. In a usual drilling season (December-April) we drill about 25 000 m (82 000 ft) with six rigs with different sizes. The biggest can drill up to 2200 m (7218 ft) with N-size. Hole depths vary from several
hundred meters up to over 1000 m (3281 ft). Hole sizes are N-size and H-size. About 50 people are involved in the project. The extreme cold is only one of the challenges we face. The area has some significant characteristics, which must also be taken into account. It is a protected nature conservation, so it is of utmost importance that we don’t leave any traces, spills or other marks. This has forced us to carefully identify all the risks, process them and come up with good preventive solutions.
The ground on each of the drill sites, where the rig can stay up to one or two months, is protected with sufficient snow cover and tarpaulins. We are using biodegradable hydraulic oils, which have different properties than the standard ones and that is the negative side, as they require more frequent changing and more care when working in the cold. Another matter which we have to take care of is drill cuttings. No cuttings are let to flow to the ground, everything has to be collected and transported out of the area. This is possible with our closed system equipment
– solids removal unit (SRU), which we have designed and built by ourselves. The idea for designing something like this was born on this very project in 2010. Today the closed system is working excellently in arctic conditions and also helps us use drill additives efficiently.
We can only enter the area when there is snow on the ground. Often we are forced to keep waiting eagerly at the start of the season for sufficient coverage. To solve that, we came up with an innovative approach, which buys us more drilling time over the period, allowed in the drilling permits. We have started to make artificial snow to get the routes and drill pads ready. This gives us several weeks more time to drill and speeds up the development of the whole exploration project. It has been a challenge for us to learn how to make snow efficiently and we are grateful to our client for their input and ideas.
Our rigs make a comfortable space to work even in harsh winter weather, as they have full cover, heating, good lighting and work
Drilling on top of a mountain in Norway
ergonomics. Thanks to the improvements in the newest ones, used in this project, we have reduced the amount of hydraulic oils by 50% and we take numerous measures to minimize the risk of leaks. The drill rigs are mounted on tracked vehicles, such as the Morooka carrier. They are designed to be as environmentally friendly as possible and leave fairly small traces to the ground.
We have developed a method for hole plugging in this project, which is an important factor in terms of controlling waters in the area, both on the surface and underground. We also do packer testing to create an understanding of the hydrogeological structure of the area. The testing provides valuable information for underground mine planning.
We have a dedicated measurements team and really helpful partners. The team does hole deviation surveying with real northseeking gyro (Gyromaster) from Stockholm Precision Tools. Our partner companies Geovisor and Palsatech are also involved, doing other fieldwork for the project.
Additionally, we are doing directional core drilling with Devico AS from Norway. This helps us achieve more drill meters at the locations which really are of interest, and also helps our drills hit the exact targets.
In 2021, drilling is moving as scheduled. With the help of artificial snow, possibly all of the projected meters shall be drilled during this drill season. We just completed a H-size hole with 950 m (3117 ft) depth. On that hole, we were able to go through a fault zone which has been of great interest geologically. This is the deepest H-size hole we have ever done and drilling was completed in 21 days. C
Kati Oy is a Finnish private-owned drilling company. It was founded in 1980 as the first private exploration core drilling company in Finland. Kati Oy operates mainly in the Nordic countries. Rig fleet size is 16, revenue generated in 2019 was EUR 20 million. Clients are both junior exploration companies and mining companies like Anglo American, Rio Tinto, Boliden and LKAB. The Kati Oy way of working emphasizes smooth cooperation with clients, creating solutions to their needs, being a pioneer in eco-friendly drilling and a great place to work for the employees.
Learn more: www.oykatiab.com/en/
by Jeff Dagg, Head of Technical Support at Fordia Powered by Epiroc
Drillers often work in extreme weather conditions, from severe heat during summer months, to brutal cold in the winter. When winter hits, diamond drilling can become problematic because the cold brings difficulties to the drill site, from health and safety considerations to equipment problems. A little prevention and foresight can protect drilling crews and save time.
Working in an environment of about 22°C (73°F), with 45% humidity is comfortable for the majority of people. If physical labor is involved, workers can easily tolerate and prefer lower temperatures. However, there is more involved than simply measuring the temperature. Other factors will affect how the body perceives the cold, and the biggest culprits are humidity and wind chill.
Cold weather combined with high levels of humidity makes you feel colder because water conducts heat away from the body faster than dry air leaving. If humidity levels are very high, the moisture in the air can saturate clothing, leaving a cold environment feel even colder. Wind chill measures the rate of heat loss caused by exposure to wind. The body will feel colder as the wind increases.
The human body will always try to maintain a normal internal temperature when faced with extreme cold. It will first try to constrict blood
Safety first while drilling in cold environments – choose tools and gear wisely
vessels and limit blood flow to the extremities and the skin’s surface so that less body heat from the blood is lost through the skin.
The body’s other defense against the cold is shivering, which generates heat by increasing the body’s metabolism.
Beyond discomfort and inconvenience, cold temperatures can pose serious threats to drillers’ health. Frostbite and hypothermia are the most common ailments. Frostbite occurs when your skin or muscle tissue freeze from exposure. The early signs include tingling, stinging or an aching feeling in the exposed area that is then followed by numbness. Frostbite is treated by covering affected areas with dry, soft, clean cloth bandages. Avoid massaging the area as it can worsen the damage to the tissue.
Hypothermia is a more serious and potentially fatal condition that requires immediate medical attention. The body temperature falls and presents symptoms such as shivering, the inability to perform complex motor functions, mild confusion and lethargy. If the temperature falls drastically, loss of consciousness and heart failure can occur.
The symptoms of ailments related to the cold can be easy to miss. Drillers should know how to identify the conditions and treat them effectively. A prevention and treatment program should be in place.
The drill site should have procedures for working on ice. Drillers should be aware of changing weather conditions as these will have an impact on the ice. Additionally, the drill rig, as well as the grab on mast floor, should always be free of ice.
A tented tower, showing that every effort counts in trying to preserve heat for the crew
The drill shack has limited space but must accommodate the driller and the drill station and also offer enough room for the helper to empty tubes, maintain equipment and perform other tasks. Although it is a small space, it can be hard to heat because while you can try to keep it enclosed, it is almost impossible to keep all the cold air out. The helper’s job includes bringing in core boxes, rods or other equipment, moving full core boxes outside, checking the supply pump and more. To do that, he is opening the door repeatedly, allowing cold air to enter.
To make matters worse, there are holes in the shack. There is a large hole in the roof where the mast from the drill rig pokes through. The mast can be covered with a tent-like structure, or the hole may be blocked off with plywood or hinged doors, however, neither of these will work if you are using a rod handling system. There is also another hole in the shack floor that allows passage of the drill rods and casing. This hole
allows cold air to enter from below the drill rig and is appropriately referred to as the ‘pneumonia hole’.
Sometimes the radiator fan on the diesel engine can be used to change the temperature inside the drill shack. In winter it can be turned so that it draws hot air into the drill shack. In the summer months, it can be turned the other way to exhaust the hot air out of the drill shack. Ideally, supplemental heat must be added in cold weather, usually the kind of heater used in construction.
Cold weather is not just related to geographical location. Drillers may have to deal with cold weather combined with a high altitude. Drilling that is performed at altitudes that are higher than 15 000 ft (4572 m) is considered high altitude and drillers will encounter adverse conditions
that can affect their health and safety. Additionally, these conditions will affect how drilling equipment performs. At altitudes greater than 10 000 ft (3048 m), getting enough oxygen becomes a challenge not just for drillers, but for the engine and hydraulics as well. Safety issues for drillers include lack of oxygen and altitude sickness.
Lack of oxygen will also affect your drilling equipment and machinery. A diesel engine will not run properly when oxygen is depleted as the air will be too thin. The engine will be starved for air and you will see a loss of power with a fluctuating torque output. The loss in horsepower can be as much as 3% for every thousand feet above sea level.
Diesel powers your equipment, so as you lose power, you will lose pumping force and water circulation could become a problem. Rotation and feed pressure can also be affected. Make sure to flush the pump. If possible, get a high-altitude kit for your engine and pressurize your hydraulic reservoirs to ensure proper functioning. Mountainous conditions also mean that the rock or ground will be in poor condition so drilling fluid additives will probably be needed.
In certain situations, drilling will occur in arctic-like conditions where the temperatures are much lower than what the crews have experienced in the past. Once you are below 15 ft (4.57 m) depth, the ground temperature is always 12°C (53.6 °F), unless you are in permafrost where it will be colder. When drilling in permafrost, special considerations need to be taken to prevent water freezing.
Once water gets to the drill, the challenge is to keep it from freezing on its way down the rods and back up the hole. In areas of permafrost, this can be a serious challenge. Some drillers add salt to the drill water. The presence of salt in water reduces its freezing point. The more salt in the water, the lower the freezing point will be.
Some drilling sites can be directly on the ice of a frozen lake or on another body of water. Companies must develop a Best Practices Plan to ensure the safety of workers and equipment. The ice must be thick enough to withstand the weight of all the equipment that will be positioned on it. This calculation must account for permanent equipment, such as the drill rig, drill rods, consumables the drillers themselves, the core and any other gear that may be required.
When drilling on ice, environmental regulations must also be respected. Drill sites must be cleaned so no oil or drill cuttings can be left behind. Managing used drill water can be complicated so a water treatment system is recommended. For example, a water treatment system like EDDY treats drill water in order to separate the cuttings. Once most of the water is removed, the cuttings can be handled and disposed of more easily and the water reused. Most cutting removal systems must be housed in a warm area to prevent freezing.
One thing that is certainly not impacted by cold weather, is the heat down at the bottom of the hole. Make sure that you are cooling your diamond core bit sufficiently at all times. The core bit doesn’t care how low the temperature goes on the surface, if a continuous flow is not maintained, the diamond tools will suffer immediately. Operations may have to stop if water freezes and causes equipment to become stuck in the hole. Keeping everything warm is a full-time job, so make sure you plan ahead!
‘One thing that is certainly not impacted by cold weather, is the heat down at the bottom of the hole. Make sure that you are cooling your diamond core bit sufficiently at all times.’
It’s important to note that drilling additives do not offer the same results when saltwater is used. If saltwater is used instead of freshwater, two or three times the usual amount of polymer may have to be used to obtain the same results. Another option is a product such as Slo-Freeze, an environmentally safe fluid that extends the freezing time of water and does not contain alcohol or glycol.
Calcium chloride can also be added to water. It generates heat as it dissolves, and this forms an ice-melting brine. Calcium chloride is relatively harmless to plants and soil and as a de-icing agent, it is much more effective at lower temperatures than salt.
A potential safety issue is that calcium chloride can irritate the skin, so drillers must be sure to have their protective personal equipment (PPE) with them when using calcium chloride.
Core drilling demands a constant source of water. Winter brings the challenge of frozen water lines, broken pumps, ice buildup from leaky lines and components and a host of other issues. The key to preventing freezing is to keep the water moving. Water will not freeze if a constant flow is maintained. However, long distances will require a coil heater to warm the water enough to keep it from freezing as it travels from your water source to the drill rig. Many drillers will use snow as a way to insulate the water from the cold air, but this can’t be done if there is no snow. The temperatures can dip into the freezing zones even in the absence of snow.
For best results when pumping from a lake, river or reservoir, set up a steel shack on skids at the water source. This mobile shack should contain the pump, a diesel engine (with a heavy-duty alternator to generate a little more power to accommodate lights and power the oil burner), a battery and the coil heater.
Drillers can choose between two types of heaters. The first is a diesel-fired coil heater that is fitted with an oil burner exactly like the furnace in a house. This is often the best choice as diesel is already needed for most of the equipment on-site, including the drill, pump and mobile equipment.
The second option is a propane burner equipped with a thermo-coupler that will turn the gas off if the flame is blown out, which is a must for safety. Keep in mind that propane can be problematic in cold conditions, as it contracts when it’s cold. In extreme cold, the volume of propane inside the propane tank will shrink, creating a loss of pressure.
To counteract this, drillers will hook up a series of 100 lb (45.36 kg) tanks, allowing more of the available propane in each of the tanks to be used.
Coil heaters have an inlet and an outlet, and water is pumped through the coil on the inside of the heater. A flame from an oil or propane burner is forced through the center of the coil, heating the water as it flows through. The pump will draw the water from a nearby lake, river, reservoir or beaver pond, push it through the coil heater and from there, through the water hose, to the drill rig. It is important to use a driller hose for this purpose as lay-flat hoses are not suitable for longer distances. This process ensures that the water stays above the freezing point for the trip to the drill. However, in extreme cold, the suction line remains vulnerable. One trick is to tape the hot water line from the exhaust port of the coil heater to the suction line of the pump, all the way back to the source (usually a hole in the ice). The two lines can be insulated so that the heat from the hot water line will keep the suction line from freezing.
If the water is travelling a great distance and the temperature is too low, there is a chance it may freeze. In this case, another coil heater could be installed along the way. It can also be wise to have a thermometer in the water tub in the drill, so the water temperature can be monitored, and action taken before a complete freeze-up occurs.
A water heater can heat the water from the reservoir to the pump and the borehole. Suppliers offer various water heaters, either oil or propane fired. Fordia’s standard version comes with an Easy Flow Coil system that eliminates high pump pressures and ensures maximum heat exchange for excellent efficiency and easy draining. Make sure the unit you select has a heavy-duty base and roll cage. This will help make the unit portable, easy to handle and will provide added protection.
Diamond drilling happens outdoors, and cold weather can be difficult as drillers have to deal with bulky clothing, numb fingers, shivering and hard to breathe icy air. A good safety program, the right equipment and advance planning can help ensure that your drilling operation is successful and that everyone remains safe and warm. C
What do you get when you take one of the most respected underground core drilling rigs on the market and fuse it with a wellproven and mobile carrier? You get the Diamec Smart 6M.
Find out more at epiroc.com United. Inspired.
Helping drillers improve their performance. Even when socially distanced. Reach out easily at www.fordia.com/support.
by Henry and Johnathan Taitt, Directors at Red Rock Drilling Pty Ltd
Creating a lasting legacy takes courage and commitment but when it comes to negating climate change, the process is not as challenging to execute as you may think.
The example of Red Rock Drilling is a case in point when it comes to the mining industry.
Based in the West Australian outback town of Kalgoorlie, Red Rock Drilling is a small operation, focusing on reverse circulation (RC) drilling. Originally formed six years ago, the operation has transitioned since 2017 when Henry Taitt took full ownership and was then joined in partnership by his twin brother, Johnathan, in 2018.
Having grown up on a cropping and grazing farm at Fingal, in Northern Tasmania, they
Bracing for the storm, Goldfields region, WA
have always had a keen awareness of their surroundings and impact on the environment – farming for the future was somewhat of a mantra.
While their home-town was renowned for coal mining activities dating back to the 1800s, it would be the goldfields of Kalgoorlie where they would venture in their early 20s to seek their fortunes.
With two decades of hard work under their high-vis vests, the 38-year-olds are now forging their future by showing professional
leadership to enhance climate change action in the mining industry. They’re leading the way to a carbon neutral future and if they can do it, they believe it is incumbent on others within the industry to follow suit.
Red Rock’s journey to become the first business of its kind in Australia to achieve Carbon Neutral Certification under the Federal Government-backed Climate Active Group, started in 2019. The pair had been discussing how they could best give back to the community that supported their business activities.
While they initially investigated traditional financial donations to different charities and organizations around the Kalgoorlie area, it was decided that achieving Climate Active Group accreditation for Red Rock Drilling would actually do so much more locally and globally in the long-term. And so, for six months, Red Rock embarked on the process to understand its output.
To become carbon neutral, the business had to determine the greenhouse gas emissions generated by its activities, such as fuel, electricity use and travel.
Red Rock has a drill rig working across the country providing services to clients who are predominantly exploring for gold and proving up gold deposits. It may not sound like a significant operation in the scheme of a mining industry that is worth more than AUD 200 billion to the Australian economy, but the twins were actually genuinely shocked by the results they received.
The process of RC drilling consists of an outer drill rod with an inner tube and the hollow inner tubes allow the drill cuttings to be transported back to the surface in a continuous, steady flow using high pressure air. This process results in the use of between 800-1200 L (211–317 gallons) of diesel a day. It was deemed that this was the biggest factor to pollution and Red Rock’s level of CO2 emissions was around 480 tonnes (960 000 lb) per annum.
With the assistance of Brisbane-based carbon accounting consultants Conversio, who verified the business’s MYOB data to ensure accuracy and Susan Ridding of Sustainable Business Consultants based out of Adelaide they developed a plan to start reducing and offsetting emissions with investment in new technology.
Any remaining emissions would need to be cancelled out by the purchase of carbon offset units, which are generated from activities that prevent, reduce or remove greenhouse gas emissions from being released into the atmosphere.
It may sound complex, and the pair admits they were concerned about being buried in jargon and bureaucracy, but they promise the Climate Active Group process was not difficult.
They immediately knew there was room for efficiency improvements on a day-today basis in their business and quickly discovered that some of the changes were easy and cost effective to implement.
Red Rock changed to a biodegradable hammer oil, which lubricates the drill hammer during the drilling process and will start using a new carbon-neutral oil called Castrol Vecton, which is the first certified carbon neutral lubricant range on the market. The business is set to install 20 solar panels which will deliver a 34% reduction in energy bills. Red Rock’s long-term goal is to be completely off grid with the implementation of a solar battery pack initiative in the near future.
Solar water heating will be installed, and office lights have been replaced with LED alternatives.
‘Perhaps the biggest choice the business made during the process was contributing to the Chakala Wind Power Project in Maharashtra, India, as an offset measure.’
Personal use vehicles have been changed over to more fuel-efficient options and all Red Rock employees now engage in the simple act of offsetting flights, with all major airlines offering good carbon offset initiatives.
Red Rock has also improved recycling protocols and made more environmentally conscious choices when buying printing materials.
Perhaps the biggest choice the business made during the process was contributing to the Chakala Wind Power Project in Maharashtra, India, as an offset measure.
The Taitts knew their investment in the Indian wind energy project would not only go towards a sustainable energy supply for a country crippled by population and pollution challenges but also provide a number of jobs to the poverty-stricken region.
Red Rock is paying to offset 530 tonnes (1 060 000 lb) at around AUD 4 per tonne, with an expectation this cost will increase into the future as the price of offsets rises.
When you combine the impact of the above outlined local and international strategies, it was enough for Red Rock to officially gain Carbon Neutral Certification on June 5, 2020.
The reaction has been significant, with Red Rock since receiving a number of enquiries from other mining businesses keen to learn about the process and follow suit.
Red Rock’s promoting the fact that its trailblazing initiative will eventually help its bottom line, not only with cost savings via smarter technology and energy efficiencies, but by an increased number of clients who want to engage with carbon neutral suppliers.
The pair believes it makes sense for businesses to surround themselves with those at the forefront of innovation and carbon neutrality falls into that category. Especially when it comes to the mining industry. Not only is it a feelgood gesture, it’s also a means of obtaining more positive attention via social and traditional media outlets.
Henry and Johnathan are now actively imploring other bigger businesses to flex their financial muscle and do what is right for the environment and future generations. They believe it is imperative to improve the reputation of the mining industry.
The repercussions if mining businesses don’t take collective small steps to affect climate change are scary. C
Safety is the challenge, CX Line is the answer. Compact design, hands-free rod handling system for fully automated and remote controlled operations: it’s the new range of exploration drilling rigs. Are you ready for the new era?
Established in 1986 in Italy, Comacchio is one of the world’s leading manufacturers of hydraulic drilling rigs. Initially focused on the production of small and medium diameter drilling rigs for geotechnical site investigation and foundation construction, the familyowned company has expanded their range throughout the years to embrace the most diversified drilling applications, meeting the needs of customers across the entire spectrum of work, including foundations, geotechnics, water well, geothermal and mineral exploration.
‘From the very beginning, Comacchio stood out for the ability to meet market needs and to assimilate ideas, insights and different practices and turn them into finished products that met individual needs that vary from country to country and client to client,’ explains Emanuele Comacchio, Territory Sales Manager at the company.
Based on this philosophy, Comacchio works closely with clients to identify ways to constantly enhance and improve the equipment design and adapt it to individual conditions and working methodologies. The result is a combination of innovation and pragmatism that distinguishes every Comacchio drill rig, and the constant evolution and extension of the range, counting over 80 models and a vast array of configurations. With the launch of the new CX line (Comacchio eXploration line) Comacchio aims to further extend their presence in the mining exploration industry.
‘We have long-term experience in serving customers in this industry,’ says Emanuele Comacchio, ‘but with the launch of our CX line we want to move our solutions to the next level, thanks to several innovations which we believe will set new standards in terms of safety and efficiency of exploration operations, just like we’ve done in the past in other fields.’
The CX line comprises six crawler- and four truck-mounted units, weighing from 9 to 22 tonnes (19 850 to 48 500 lb) and providing up to
30 tonnes (66 150 lb) pull up force. All drill rigs are multipurpose units, capable of both reverse circulation (RC) drilling and diamond coring. The flexible design, based on the use of highly efficient hydraulics, is supported by a comprehensive range of rotary equipment and the vast choice of accessories, meeting specific application needs, soil features and operating conditions. Most important, all CX line rigs are designed to incorporate advanced safety features complying with the strict safety regulations adopted in the industry.
‘The mining industry places great emphasis on operator safety. International mining groups have developed stringent corporate health and
Comacchio CX 1515, a 15-tonnes-pull drill rig (33 100 lb) configured for remote operation diamond drilling, equipped with hands-free rod handling system
safety requirements. The design and construction of exploration drill rigs must therefore consider all relevant aspects, from exposure to respirable dust and noise protection up to the use of technologies that automate unsafe and potentially hazardous job activities. One of the objectives Comacchio has set itself for this new product line was eliminating manual handling of the drilling equipment. We can count on twenty years’ experience in developing a wide range of manual, automatic and semi-automatic rod handling systems. For the concept of the CX line, we have taken all this knowledge and expertise to develop what we think is currently the most advanced package of rod-handling solutions available on the market, meeting the specific needs of the exploration drilling industry,’ elaborates Mr Comacchio.
Depending on the application, the new CX line rigs feature three different types of pipe handling systems.
A true breakthrough in drilling automation is brought by the CX 2520, a unique grade control rig featuring a super-efficient fully automated feed system and a rod handling system that holds up to 192 m (640 ft) of RC pipes. The rod loader is a patented carousel-type solution that can hold up to sixty-four 3 m (10 ft) long rods. Installed on the side of the rig, the carousel works as a sort of conveyor belt that automatically slides the rods in the required pick-up position. An arm picks up the rod from the carousel and aligns it with the mast and the rotary head, while the next rod is moved in the same pick-up position. This system makes the CX 2520 the most advanced RC grade control rig currently available on the market, incorporating, along with the rod carousel, an air conditioned operator cabin, dust control and prevention system, a frame for
on-board installation of the cyclone, video cameras for monitoring, and telemetry system for performance control and data collection. With the high-capacity carousel and auto-feed making quick work of any project, on-site drilling can be accomplished by a single driller in around half the normal time, without the need for assisting operational personnel. This new generation grade-control rig is easy to load on one truck with the required drill pipe length and offers fast set-up and movement between boreholes.
Rigs that are used for diamond core drilling are equipped with a manipulator arm mounted on the rig base carrier that lifts the rods out of the side rack using two clamps and places them in the right alignment. Unlike other manipulator systems that are conceived as free-standing ancillary equipment and require the use of large rod racks or tables, taking up a lot of space in front of the rig, the new Comacchio rod handling system features a very compact design that allows for its complete integration in the machine body. This has the advantage of speeding up and simplifying transport and set-up operations and offers the benefit of reducing the overall footprint of the equipment inside the mine. ‘Our onboard rod handling system leaves the operator plenty of workspace in front of the rig and it minimizes surface disturbance. In fact, we are able to offer diamond coring rigs that can be easily transported in one load including 270 m (900 ft) drill pipe, with minimum mobilization costs and environmental damage,’ claims Mr Comacchio. This rod handling system is suitable for all size of drill pipes (B-size to P-size). It is designed to ensure accurate thread alignment and to be robust, efficient and low maintenance, focusing on operator comfort and user-friendliness. Like all CX line handling systems, it can be remotely controlled using radio control. ‘Thanks to the total automation of the rod handling processes and the use of Comacchio proprietary radio control system, the operators can easily and effectively operate the rig from a safe distance, or even from an air-conditioned control cabin next to the machines. Our radio control system controls all machine functions, including tramming, set-up, drilling and rod handling. The remote-control interface has also been adapted to be application-specific and user-friendly.’
RC drilling rigs are equipped with a more ‘conventional’ type of rod handling system based on the use of a loading arm that picks the rod from a rod table in front of the rig and aligns it with the rotary head and the mast. The pipe handling arm is a heavy-duty proven solution to handle double wall RC drill pipes of 4 in (101 mm) to 4.5 in (114 mm) diameter, up to 6 m (20 ft) length. It can also handle common diamond coring rods in a range of diameters from 45 to 220 mm (1.75 to 8.75 in) (B- to P-size). The pipe loading arm was specially designed and configured so that it can prevent the fall of any pipes due to thread breakage.
The innovation brought by the Comacchio CX line is also in the software and data analysis technology powering the rigs. ‘With the launch of the CX line we have introduced a unique fleet control system that was tailored to the needs of exploration drilling. Our ComNect™ system gives clients a complete overview of the equipment status and operations in real time, 24/7, from anywhere in the world, from a PC, phone or tablet,’ says Mr Comacchio. ComNect™ collects and communicates vital equipment data to the client via a web portal. If no Internet connection is available, the data is stored in the device memory and can be exported on a USB-key. All the information can be viewed on a touch-screen display installed on the rig, which makes data access much more user-friendly. Thanks to the use of state-of-the art sensor technology, ComNect™ gives clients a full overview of the efficiency and performance of their machines. At the same time, the ComNect™ system ensures accurate drilling parameters recording, thus allowing to monitor the progress of the
drilling project. ‘The ComNect™ software focuses on the acquisition of data that is critical for exploration applications,’ explains Mr Comacchio, ‘ensuring a more complete and accurate dataset and meeting reporting requirements set by the mine’.
The economic advantages that are plain to see: ComNect™ highlights peak performance levels and warns of problems. If calculated and interpreted correctly, this data can significantly maximize production and reduce downtime and repair costs. The availability of data gathering and the use of analysis tools helps predict when problems will likely appear. With the use of these modern artificial intelligence tools, clients can create a truly proactive and more cost-effective maintenance schedule, custom-made for each machine.
‘The proactive approach is not just limited to maintenance and preventing downtime. One of the most critical and costly aspects in exploration drilling is the drilling tools wear. Our ComNect™ system offers valuable insights into the use and life of the drilling equipment. Tests have shown that thanks to our software and data analytics, the bit life can be considerably extended. Fixing minor issues before they become worrisome keeps the equipment working in prime condition. And this just the beginning. We are confident that the insights yielded through this advanced telemetry system will be the basis for further research and development activities that are already underway and that will allow us to further optimize equipment operation and drilling processes,’ continues Emanuele Comacchio.
The development of these new generation drill rigs allowed Comacchio to sign a contract with the mining services group Rosond for the supply of a total of 32 machines that will be used for greenfield and brownfield exploration work and grade-control drilling in the Northern Cape, South Africa. The drilling contract is one of the largest on the continent. The mining giant, who has awarded this contract, described it as part of a broader initiative to ‘modernize its geoscience operations, and extend the life-of-mine of two major iron ore mines in the Northern Cape, as well as to elevate safety standards, and improve productivity’. The first units that were introduced in the Northern Cape within this project have been in operation for five years. The tests conducted have proved that the rigs were able to perform core drilling up to 800-meters deep (2630 ft) using P-size rods, achieving the drilling outcome in 40% less time, due to both the higher efficiency of the rigs and reduced downtime. ‘Drawing from the latest technological developments across various disciplines, we have achieved the combined effect of a rig that gets the job done effectively and efficiently and offers the operator and those around the rig enhanced safety,’ concludes Mr Comacchio. ‘We are confident that with the new CX line we will be able to make a substantial contribution to consolidating the safety performance of our clients specializing in exploration drilling’.
With the new CX line of exploration drilling rigs, Comacchio is well positioned to meet the increased demand for safety and automation in the mining exploration industry. C
For more information
Visit: www.comacchio.com/en/
Tae Sung Co. is the leading manufacturer of exploration drilling equipment for Korea and the local region since 1980. We are specialized in the production of high quality impregnated diamond core bits, reaming shells, core barrels, casing, drill rods and more. We have been number one supplier in Korea for the last 35 years and preferred supplier to many other countries
Tae Sung produces diamond products of any size and any standard. Korea has a very long history in mining and
geology and our diamond products have been adjusted to meet the challenges of the Korean hard and extremely hard formations. Our impregnated diamond bits have proven track record and they drill with better penetration rates compare to other competitive products
We promise to supply you with the best quality products and we will be glad to share with you our competitive pricing. Our clients are always welcome to visit us and our factory.
Address: 31 Jangjeol-ro, Gwangmyeong-city, Gyeonggi-do, Republic of KOREA (14334)
Tel: +82-70-7687-0462
Fax: +82-(0)2-2683-6733 ghlee95@gmail.com www.taesungdia.com
by Andre Sonnichsen, CTO at Lantern
Enterprise Resource Planning (ERP) tools are simply too costly to develop and maintain, requiring a substantial investment to continuously update the system and customize features to suit the evolving needs of individual projects. For all but the largest mining companies, these tools are out of reach.
With this in mind, we set out to build Lantern as a powerful, affordable, easy-to-use platform that revolutionizes how drilling companies manage projects and share progress with their clients. An evolving solution, allowing both drillers and their clients to monitor, review, approve, and optimize virtually every aspect of their drilling programs in real time, across multiple contracts.
Developed in collaboration with drillers, mining and exploration companies in the field, Lantern is a lightweight, cloud-based tool for drilling programs of all sizes; streamlining everything from timesheet entry and invoicing, to site audits and safety docs, to tracking meters and costs per shift. Fast, intuitive, and error-free.
As the platform has grown, we’ve added new features including enhanced dashboard customization and an offline app for remote timesheet entry at the drill site, with or without an active data connection. Now, with our latest round of improvements, we’re giving mining and exploration companies the power to test drive and implement Lantern for free – whether they’re starting a new project, managing multiple contracts at once, or looking for a better way to track their progress mid-season.
invoices. Even at this level, the platform’s ability to monitor costs, track performance, and unearth new insights will surprise you.
Want to run a few scenarios? There’s an option to generate contracts across a number of applications including underground, surface and fly, all with realistic sample data for timesheets, materials, services and tests based on real-world results. Just set up a few parameters including the number of drills and length of project, and Lantern will populate the rest for you.
‘Once ready, Lantern makes it easy for mining and exploration companies to set up their own
contracts
and invite
their drillers
to the platform, in much the same way that drillers can invite clients as well.’
After a quick sign-up on the Lantern website, you’re free to put the platform through its paces. For mining and exploration companies with limited access to their drill data (or little desire to enter it), Lantern can reverse-engineer a visualization of your results from just a handful of
Once ready, Lantern makes it easy for mining and exploration companies to set up their own contracts and invite their drillers to the platform, in much the same way that drillers can invite clients as well. This gives both sides the ability to bring Lantern online at any stage of the project, quickly and easily. There’s also a multi-contract view to allow you to compare any contracts between drillers or clients, group multiple drillers and contracts as part of a whole project, or track the performance and costs of all projects across the entirety of your organization. In the meantime, we’ve also doubled the amount of data exploration widgets to track anything you could possibly want.
Ready to see what Lantern can do for you? Get started for free at DrillWithLantern.com. C
Q&A from the experts: In conversation with Mark Saxon, CEO & President at Medallion Resources Ltd.
Working in the Arctic cold weather: Winter wonderland or frigid drudgery by Wren Bruce, Senior Project Geologist at Mercator Geological Services
The value of sample preparation when using portable XRF in mineral exploration by Richard Belcher,Consulting Geologist at RWB Exploration Ltd and James Cleverley, Global Products Manager-Geosciences at REFLEX Instruments Europe Ltd/IMDEX Ltd
Sail Pond project: Uncovering Canada’s next high grade silver district by Mathew Wilson, President & CEO at Sterling Metals Inc.
Challenge and Opportunity in the Mining Industry of Ecuador by Merlin Marr-Johnson, Executive Vice President at Salazar Resources Ltd.
Mark Saxon CEO & President at Medallion Resources Ltd.
Mark Saxon is an Australian geologist, who graduated from the University of Melbourne, Australia in 1991 with a BSc (Hons) degree. After his graduation, Mark spent nine years (from 1992 until 2001) working at Pasminco Ltd, formerly the world’s largest producer of zinc. Afterward, he became the CEO of Tasman Metals Ltd, a Scandinavian Rare Earth Element (REE) explorer. More recently, Mark has held roles with Mawson Gold, also in Scandinavia, and until last year was the CEO & President of Leading-Edge Metals Corp, an EU-based graphite miner and REE explorer. In 2020, Mark became the CEO & President of Medallion Resources Ltd (Medallion), a company which is focused on the production of high-value REEs from monazite feedstocks.
Timothy Strong: What were your biggest influences when you first started out in geology?
Mark Saxon: I was very fortunate to be selected straight from university into the Graduate Recruitment Program for one of the Australian majors (Pasminco), who were a strong mining house with an active exploration group. This program gave me a rapid industry overview and introduced me to a diverse group of geoscientists who quickly taught me how much I didn’t know. I was also lucky to be paired early on with a great field assistant, who kept me pointing in the right direction. Graduate Recruitment Programs for geoscientists were an important part of the industry at the time, and it would be great to see more emphasis placed on similar mentoring today.
TS: Which country has left the strongest impression on you and why?
MS: That would definitely be Peru. Pasminco completed a corporate takeover of a company with a significant operation in Peru, and a few of us were sent from Australia to the office in Lima. At first, it was well outside of my comfort zone
as my prior roles had been in Australia, but it quickly became home.
The Peruvian experience became the foundation of my career and provided a deep personal and professional network that survives today.
TS: What has been the proudest moment of your career to date?
MS: I’ve been involved with a couple of major discoveries that come to mind. The Ayawilca ZnAg project being developed by Tinka Resources in Peru is one that myself and my business partner Michael Hudson generated as a pure greenfield target. The discovery path there has been great to watch, as it has become one of the world’s most significant undeveloped Zn deposits.
Next to that would be the Norra Kärr REE project in Sweden, which we discovered as Tasman Metals Ltd in 2009 by following up some unusual looking rocks in the archive of the Swedish Geological Survey. We drilled the first holes into the project and took it through to a very positive pre-feasibility study. Norra Kärr is the most important REE resource for Europe and can be a producer for many decades.
TS: You have a considerable amount of Scandinavian experience, what are some of the challenges for mineral exploration in a cold/arctic environment?
MS: The Nordic conditions are cold and challenging, and the safety of staff and contractors is paramount in such an environment. The biggest surprise in coming from Australia, however, was how quickly the seasons change up near the Arctic Circle. The opportunity for planned sampling or mapping can be lost for six months with an early snowfall so work needs to be well planned to match the seasons.
TS: What is the most important rule (or set of rules) that geologists have to follow in order to overcome these challenges and secure a successful operation when working in extremely cold environments?
MS: Employing local people is the only real path to success and safety when working in a challenging environment. The issues that seemed rare and unique to our ex-pats were just daily life for our Swedish team: knowing what gear to have with you at what time, and that there are days when it is just
smartest to stay home. The forestry industry works almost year-round, and with the right preparation, the exploration industry can as well.
Good planning is essential, particularly when drilling is involved. Most drilling occurs in the winter when frozen ground makes access easier, but you have to know where your drill sites are and building drill snow roads is a time-consuming process. The right team and funding need to be in place at the right time to achieve this.
TS: Scandinavia, whilst being a relatively safe jurisdiction in terms of exploration risk, can be an expensive place to operate, how do you mitigate these higher costs?
MS: The perception that the Nordic region and Sweden, in particular, are expensive is something we have dealt with many times. There are certainly some areas where costs are high, but this is mitigated by the great infrastructure and the high skills of local people. It is very easy to employ the right person for the right job, and the high education standard means that even graduates are immediately work-ready.
The infrastructure of the Nordic region is an amazing benefit to exploration that keeps costs under control. The national and forest road networks mean that driving almost everywhere is possible, and drilling is done, even in the Arctic, without helicopter support. There is a network of local villages, so exploration camps aren’t needed, and mobile phones work across the entire region, removing the need for more expensive options.
Efficiency and predictability in decisionmaking by permitting authorities is a key factor for attractive mining jurisdictions. Sweden has struggled in this regard in the past five years, with many projects trapped by slow decisions.
TS: You have worked a lot with REEs, not a common commodity choice for a geologist. Can you briefly explain their importance and how did you get into the field?
MS: I was working in Sweden in early 2009 when the first round of interest in REEs began to build. We began to take a look at project ideas, and quickly learned that Sweden is ‘the home of REEs’, as most had been discovered and named there. Through some research, first-mover advantage and good fortune, we managed to discover one of the largest known heavy REE deposits.
REEs are a small but very important part of the mining industry. Their importance is in part due to the supply-demand imbalance where Chinese suppliers hold control over key parts of the supply chain. But most critically, REEs make an important contribution to technology for low carbon-emitting energy generation, storage and use, thus their demand is growing rapidly.
TS: Rare Earth Elements are a hot topic at the present time, especially with Investors in the US. Could you let us know what the current ‘state of the market is’?
MS: The REE market is hot at present, along with most battery and EV metals. The recent RTO by MP Materials is a strong sign of market health and stocks are almost all trading near their medium-term highs.
The physical market for REEs is complex, as we are talking about 17 elements, each with unique properties and customers. However, in terms of value, the market is being driven by demand for the metals that are used in REE permanent magnets. This is neodymium, praseodymium and to a lesser degree dysprosium and terbium, all of which have seen more than a 50% rise in price over the last 12 months.
The REE industry remains strongly influenced by Chinese production and Chinese investment into external projects.
TS: Where is the REE market heading?
MS: The price development for most REEs looks positive over the coming five to ten years, as no major mining project has been developed or is in the pipeline, and demand is growing strongly. We need to be mindful, however, that these are industrial minerals, so the price that customers are willing to pay is capped at a point where substitution can occur. A huge price spike will not help our industry develop over the longer term.
The capital and technical risk hurdle for mine development in REEs are still very high. This is pushing the industry to consider by-product minerals and recycling, as output can grow progressively in line with demand.
TS: There has been a focus on carbonatite hosts of REEs, these have proven to be hard to extract and process, what is the solution?
MS: Hard rock REE project development is challenging, and the last major investment was in Mt Weld, Western Australia by Lynas Corp, around 10 years ago. This project became a great success but took a long time to get there and required patience and support from the Japanese partners. The mining industry outside of China does not have much experience in commissioning REE projects.
Carbonatite and alkaline intrusions are mineralogically complex, each requiring unique processing solutions to be perfected on an industrial scale. For carbonatites, the REE grade can be high (>3%) but the distribution of the REEs may not be appropriate for the magnet metals Nd Pr. Alkaline intrusions will have lower grades (>0.5%) but are more skewed to the higher value-heavy REEs and often have attractive by-product metals.
Lots of test work by experienced groups, which can support both the chemistry and the engineering, is the only answer. More broadly, utilizing waste and by-product materials that can be rich in REEs is gaining more support.
TS: Tell us more about Medallion Resources and what makes it different?
MS: I am presently CEO of Medallion Resources (TSX.V:MDL), a Canadian-listed company working on technologies to extract REEs from mineral sand monazite, and separate these REEs into high-value products ready for the magnet industry.
This is a unique business model, different from most of our peers in the REE industry, but one built on observing what has worked for decades for Chinese REE producers. We are not limited by one project that may sit in a remote or challenging location but can build our processing facility in an optimal location near mineral sand suppliers or REE customers.
As we utilize a by-product mineral that is presently passing to waste streams, the Medallion Monazite Process does not require additional mining. Our research focus has been to optimize the extraction of REEs, alongside the reuse of acid and re-capture of heat to deliver a very efficient process. By pairing this with an efficient REE separation technology, we believe we can be a very low-cost and sustainable REE supplier.
TS: What was the driving force for Medallion to focus on REE extraction from mineral sands?
MS: Mineral sand monazite is an abundant high-grade Nd Pr feedstock. It is relatively low cost, as it is produced as a by-product from the mining of zircon and titanium minerals. By utilizing a by-product, we do not require any additional mining, which is great for the economics of our process. It is also very positive from a life cycle assessment point of view, as we are minimizing the carbon footprint of REE production.
Any mineral sand monazite that is traded today ends up in China for processing. Medallion saw the opportunity to develop a new and highly-efficient technology, then divert some of this monazite to provide REEs to ex-China customers.
TS: What is the importance of mineral sands in future REE production?
MS: Medallion Resources has been a lone voice outside of China and India describing the attractive nature of a mineral sand monazitebased business. In the last six months, we have seen a number of companies also seeking opportunities in the sector, so I feel the importance of this feedstock will soon be recognized.
TS: You recently became involved as a technical advisor with a UK junior gold explorer, Origin Exploration Ltd. Do you see Africa as an important source of metals in the next ten years?
MS: The discovery potential of Africa is diverse but excellent, including the metals and materials that will become important in the energy transition. Large deposits of lithium, graphite, copper and cobalt have been discovered and are being developed. African-sourced materials should become a cornerstone of the EV and battery industries in coming years.
However, supporting the EV and battery industries is not easy. High purity materials are required, which can be both chemical- and energy-intensive to manufacture. Supply security, sustainable and ethical production and the ability to deliver over the long term will all be important if Africa or other emerging regions seek to fulfill the needs of the EV market.
TS: Do you think investor sentiment towards exploration in Africa will change and become more positive?
MS: Without a doubt. The discovery potential is exceptionally strong, across a wide range of metals and deposit styles. The challenge is for companies and countries to demonstrate that projects can be developed in a timely manner while meeting and exceeding the sustainability and ESG expectations of investors in the UK, Australia or Canada.
TS: Which is the most commonly used method for REE drilling?
MS: As REE deposits tend to be mineralogically complex, diamond drilling is used over other forms of drilling to get the clearest view on the deposit.
TS: From your point of view will REE exploration drilled meters per annum increase globally?
MS: We are very likely to see substantial growth, in line with the demand for discovery and development of all battery and EV metals and minerals.
TS: Can you share your most interesting experience with an exploration diamond drilling contractor?
MS: I’m fortunate to say most of my drilling experiences have been positive ones. We did have an interesting one when a small group of anti-mining protestors arrived on a drilling site and locked themselves to the rig.
The drillers shut the rig down, secured the site and went and had a long lunch. After a number of hours, the protestors called the police to see when they would be evicted. As there had been no complaints lodged by the drillers, the police didn’t know or care about the protestors, so they were left to unlock themselves and wander away.
TS: Name an industry development or technology that turned out to be a total game-changer.
MS: For me, it would be accurate and affordable GPS. The start of my career involved sticking pins through aerial photographs to try and work out where samples came from or where drill holes should go. In remote locations, it was a real challenge to get a surveyor on site, so to be able to be accurate quickly was a huge leap forward.
TS: If you could go back to the very beginning of your career and give yourself a single piece of industry-related advice what would that be?
MS: To recognize and accept the cyclical nature of the exploration and mining business. I’ve seen many share prices go up when they should go down and down when they should go up, based on the theory of the ‘tide lifting all boats’ (the concept that an improved economy will benefit all participants). It is important to respect where you are in the commodity cycle, know that it will turn and keep on trying to do good work on the best projects you have available.
TS: What is in the future for mineral exploration?
MS: I think our industry is one that we can be very proud of, with a bright future. The energy transition has shined a spotlight on how important exploration and mining are. The need for ethically produced lithium, REE, graphite and copper for batteries and EVs is launching a new exploration and mining super-cycle that may last for decades. While there are many opportunities for improvements in our industry, I believe it is deeply committed to a path of continual improvement and greater sustainability. C
by Wren Bruce, Senior Project Geologist at Mercator Geological Services
The sound of a trilling mobile phone interrupted my sleep and I scrambled for it, reaching out of my warm covers. I answered it with eyes squinted trying to read the time displayed against a brightly lit backdrop: 2 a.m. Outside was pitch black and I could hear the wind brushing snow against the window. On the other end of the line, I heard the drone of an idling diamond drill rig and a voice shouting over it, ‘We’re done!’ The night shift driller was a man of few words, but I knew he meant I needed to be onsite to officially shut down the current drill hole so the drillers can begin preparing for their drill move to another site, a process done countless times before. Welcome to 24-hour project geologist duties.
Do you know how much preparation is involved in changing out of pajamas into winter gear to go shut down a drill rig? Start with the base layer: thermal top, thermal bottom, and wool socks. Add a neck gaiter, a long-sleeved shirt, cozy sweater and wool vest. Top everything with ski pants and parka, don’t forget a hat and of course, stop by the kitchen for pocket snacks. Stuff your headlamp and extra batteries into your pack where the emergency winter kit lives permanently, consisting of assorted possible life-saving goodies like extra socks and clothes, dry food and a small first aid kit. Since driving in safety toes can be obnoxiously un-
wieldy, the snow boots worn to leave camp accommodations are only used to drive the truck to the driller laydown area located a kilometer or two from the actual drill site. Once inside the toasty driller dry shack, switch footwear and lace up winter safety toe boots as the snowmobile warms up outside. There are lights on the shack, but outside of their cast the moon is shining brightly. Finally, pull on a balaclava, slip on a winter helmet before brushing off the snow from the snowmobile seat and begin motoring along the beaten path towards the drill site perched atop a ridge.
Working as a field geologist has allowed me to participate in winter drill programs all over Canada, exploring for uranium in Saskatchewan; in Quebec, and the Northwest Territories, for diamonds; and even to Finland for gold. Obviously, winter is usually associated with being cold and dark, but the three most common words used to describe winter drill program life amongst my colleagues are challenging, unique and surreal. To my delight, a close friend used the phrase ‘working in a gigantic freezer’ to characterize their take and it’s hard to argue with something so entertainingly accurate. Winter conditions are a whole different ball of wax compared to summer ones logistically speaking. Not to mention Arctic conditions - with average temperatures of -20°C (-4°F) and below - are a special subcategory within the aforementioned wax ball. Either way, you’re battling against daylight hours for flying, temperature constraints and safety precautions constantly throughout the day. For me, I feel the further north one travels, the more layers of complexity are added to the lifestyle of working a job in what can be one of the harshest areas of the planet, especially during the winter field season.
There are a few memories that stick out when I reflect over the last 10 years and the spectrum ranges from events that seem like exercises in finding out just how many expletives I could shout out loud in aggravation at an unobliging inanimate object to placid days where everything
proceeds swimmingly accompanied by the rewarding feeling of productivity and conclusion at the end of my shift.
As with anything, winter drilling programs have their highs and lows. Lows include one maddening night when I assisted a drill helper encircle ropes around his body into a makeshift harness to attach half the downhole survey equipment to his back in preparation to trudge up a steep incline that was not suited for driving a snowmobile. He trotted behind me as I dragged up the other half of the equipment. When we finally reached the top, panting with exertion, where I spent the next two hours fighting with frozen o-rings and syncing issues between the uncooperative downhole tool and a field laptop. Or when my snowmobile headlight had gone out, likely due to the fact the prime of the snow machine’s life was probably the same year Macintosh computers were developed, and I resorted to using my feeble mobile phone flashlight app to light the way. The result was traveling at a snail’s pace, awkwardly holding the phone aloft in one hand while holding down the throttle in the other, finally arriving in camp with cramped icy fingers malformed into mishappen claws.
But for every situation that I’ll refer to as a character-building experience, there is an equal number of astonishing and indelible moments. Yes, it can be cold and dark most of the time, but watching the sun rise at 11 a.m. in the Lapland Arctic can be heavenly, looking at a sky
swathed in pinks and gold behind a shimmering landscape of snow laden trees. It can be so very silent, a shocking juxtaposition against the familiar yet constant hum of a drill rig that is just over the last peak. I’ve remembered fondly when it was 3 a.m. in the Northwest Territories and the night sky was lit up in splashes of greens, purples and whites as the aurora borealis danced overhead, truly the breathtaking experience people describe in poetry, songs and stories. It is in those occasions of serenity and untroubled repose that I fully appreciate my fortuity to experience working in a snowy remote corner of the world.
Sometimes there are battles against planning helicopter flying hours that are so finite that drill moves become logistically unforgiving if the timing isn’t perfect or bad weather that will delay the next shift change resulting in grumpy overworked coworkers. Not all the days are figuratively (and literally) sunny, but I’ve learned that there is strength in being adaptive and resilient while working in wintry conditions. If you are offered the opportunity to work in a snowy remote place, take it. Bottom line, while working in the winter can result in unpredictable series of events and a lot of energy spent preparing against frostbite, the memories and work experience are going to be unforgettable. C
Wren Bruce is a MSc graduate of University of British Columbia and is currently a Senior Project Geologist with Mercator Geological Services, Ltd based in Dartmouth, Nova Scotia that provides services globally. Her ten years of experience in the exploration field has brought valuable expertise to the consulting team that comprises multi-disciplinary backgrounds in mineral exploration management, regulatory compliance and mineral resource services. Her experience ranges from field mapping/ sampling to core logging and drill management, to data compilation and 3D modeling. She hopes to continue working as a field operative. Wren is dedicated to being a mentor for the next generation of field geologists as well as a support for women in the sciences.
Learn more: www.mercatorgeo.com
A diamond rig drill shack glows amongst a snowy landscape at night in Lapland, Finland
Core barrels
Stabilizers
Reamers
Crossovers
Drill collars
Diamond bits
Raise bore tools
Additional services
Coring service
Directional drilling
Borehole survey
Rental stock
Engineering
Workshop Maintenance
by Richard Belcher, Consulting Geologist at RWB Exploration Ltd and James Cleverley, Global Products Manager-Geosciences at REFLEX Instruments Europe Ltd/IMDEX Ltd
Portable X-Ray Fluorescent (pXRF) instruments have been utilized in mineral exploration for almost 20 years and are a common sight in field camps and mine sites the world over. Approaches to their use generally fall into two groups: as a qualitative tool to produce relative values for internal review and decision making, or as part of a workflow to generate quantitative data, for internal review and external reporting. Many explorers switch between these two end member cases depending on the requirements of the program and the nature of the decisions needed. Portable XRF technology offers users a rapid way to generate a chemical analysis that covers most of the critical elements of interest. The quick turnaround time for results means that there is potential to bring forward critical milestone decisions but also add dynamism to the project, allowing decisions to be made when they are the most valuable. The advances in pXRF technology mean that with modern instruments data quality is no longer related to the hardware but instead relates to the operation, data and workflow management and the quality of the sample.
Accuracy (how closely the analyzed value represents the true value) and the precision (repeatability of analysis) are the two key factors that are commonly discussed during reviews of the use of pXRF. The former is now significantly improved through technological and software advancements in the instruments. This has widened the spectrum of elements that can be analyzed, reduced Limit of Detection (LOD) and resolved element peak overlap and spurious values. In addition, instrument calibration and internal Quality Assurance-Quality Control (QA-QC) procedures have also helped address accuracy.
Precision, however, is primarily a function of the material presented to be analyzed, which for pXRF analyzers is a function of the samples grain size, moisture content, density, smoothness and/or airgap and homogeneity. The process of sample preparation and its presentation for analysis is often overlooked. It does not matter how comprehensive and rigorous the QA-QC procedure and the instrument calibrations are, this will not address precisions issues. The misunderstanding of these factors and how they contribute to the perception of poor-quality data by pXRF analysis lead to user frustration and the erosion of the value the technology can add to exploration programs. It is the inconsistency and noise in the data (related to precision) that is a far greater barrier to the routine adoption in mineral exploration now than lower ppm detection limits or speed of analysis.
Sample analysis using the Olympus VANTA pXRF and REFLEX XRF CONNECT software allowing connection to IMDEXHUB-IQ and ioGAS for further real-time analysis of the data
pare and return needs to be taken into consideration. Again, this is a trade-off between the extra time, effort and cost and the improvement in the results.
For companies looking for qualitative or semi-quantitative results, then a workflow that includes some basic sample preparation or multiple sample analysis is common. Simple hand crushing to create a more representative sub-sample and/or multiple analyses of the sample and then using an average value, are examples of the attempt to mitigate these problems. These are common approaches in sieved soil and stream sediment samples, but variations of this approach can also be done on drill chips samples and the fines produced from sample cutting. However, issues around sample heterogeneity and presenting an ideal sample (fine-grained, dry, dense) still need to be addressed.
For companies looking for more representative and quantitative values, then the above approach needs refinement. The way to address this is to incorporate sample preparation and produce homogeneous, fine-grained, dense samples to present to the pXRF analyzer. In-house crushing and grinding of the samples using a hammer followed by a pestle-and-mortar partly addresses some issues, but not all. This approach comes down to a trade-off between the extra time and effort it takes to prepare the samples (and thus ultimately the cost) to the improvement in the results obtained. The use of a sample preparation facility is ideal, but logistically inconvenient if none is available nearby, and again the cost and time required to send samples, the facility to pre-
Commonly, the method used is a function of the aim of the program and tailoring the procedure to fit the perceived deliverables needed. However, a data-driven exploration strategy that generates quality reliable data at all stages of the project lifecycle should be part of all exploration strategies. For example, collecting quality pXRF data supports lithogeochemistry (geological models, rocks types/sources, alternation and trends), element associations (both for use as pathfinders and geometallurgy) or could identify an association/feature not considered and thus change the perception of the project. This approach increases the understanding of the project and adds value by allowing more informed decisions to be made and the potential to bring key decision points earlier in the project lifecycle.
A new approach now available is the use of portable sample preparation equipment, which allows the quick preparation of samples on-site, and thus produces high quality, repeatable and auditable assay results with a pXRF to support the above data-driven strategy. REFLEX Instruments, one of the leading IMDEX brands, produce equipment that is specially designed for preparing the best possible samples to present for pXRF analysis. The equipment is portable, and is in three parts: a crusher for rock chips, <2 cm3 (<0.12 in3) producing <2 mm (<0.079 in) sample, a mill for pulverizing (produces 90% passing 100 microns), followed by a puck press for producing a dense sample which can then be analyzed with a pXRF (or another sensor). All the equipment comes in its own, ruggedized storage box. The equipment can be set up very quickly, anywhere with a power source, e.g., in a field camp running off
a generator, back at an office or storage facility. QA-QC and instrument calibration is managed through REFLEX XRF CONNECT which connects directly to the Olympus VANTA pXRF. This data can then be uploaded to IMDEXHUB-IQ for on-line storage and remote data access/monitoring to allow, for example, the supervising geologist to review the data as it is produced when not on-site, and the data to be added into the company’s database as soon as it is validated and approved.
This process of hardware and software provides not only robust and reliable quantitative data, but it is also quick, cheap and available onsite wherever required. This data can be made available securely, anywhere, in a very short turn-around to aid decision-making and make programs more dynamic. The benefits of this in exploration are obvious, where programs are not rigid but adjust to new data as it becomes available, and real-time decision making is possible.
A commercial trial of the complete set-up was recently undertaken in the UK on rock chip and soil samples, which were taken as part of an early-stage exploration project. Rock chips were broken into smaller, manageable pieces with a lump hammer before going through the sample preparation procedure (crushed, milled and a press puck produced). Soil samples were initially dried and then sieved to remove larger stones and organic material and then milled and pressed. In this trial, a team of two undertook the sample preparation and analysis, completing approximately 50 samples per day, although optimization of the process is possible. This set-up produced a much larger robust dataset than what would have been produced following some of the approaches above, including geochemical data to support rock type classification and potential alteration styles, as well as trace element associations. Not only does this support the data-driven approach, but the data was available only a few days after the samples were taken allowing key decisions to be made during the program. C
The entire sample preparation and analysis equipment ready for transport
For more information
Regarding In-Field Geoanalysis Technology, contact James at james.cleverley@imdexlimited.com or www.reflexnow.com.
For technical support to exploration programs, contact Richard at richard@rwbexploration.com or www.rwbexploration.com
IT HAS NEVER BEEN EASIER TO CONTROL A LARGE NUMBER OF BOREHOLES.
The innovative one man hand-held system works independent of environmental distraction and provides unsurpassed accuracy. You‘re looking for a fast, economical and reliable solution? LiPAD®-100 is the answer.
Levent 2002 RX-4 is designed by taking into consideration comfortable controls and ease of use to enable more e ective drilling. This rig also has a hold back feature, which enables much longer bit life.
The mast and feed features are powerful and stable and present minimum vibrations directly into boreholes, making lifting and holding easier. The rod guide with a telescopic mast allows easier transportation.
The telescopic mast makes the drill easy to transport while the dump feature allows mounting on platforms of various sizes.
The rotation unit has four speeds (funk), which enable the required torque and rpm speed levels necessary for coring. It can drill e ectively from 45° to 90° angles, make and break rods (by using the control panel), and it also incorporates safeguards.
The rod holder opens hydraulically and closes using gas pressure. In the event of a loss of hydraulic pressure, the drill string is immediately blocked by the rod holder stopping the drop of the drill string into the hole.
The wireline hoist is mounted on the chassis and has an adjustable level wind angle. It does not need to be moved when changing drilling angle.There is an automatic winding system to prevent the rope from making straight or mixed winding.
The Cummins engine is acclaimed for its prolonged durability, high e ciency and low fuel consumption even in the most challenging drilling operations.
The engine conforms to Tier III/ Stage 3A.
A Stage V diesel engine is available far US and European markets
Levent 2002 RX-4® surface coring rig
• A fully hydraulic surface coring rig;
• Designed for exploration drilling;
• With three types of carriers: trailer-, skid- and crawler-mounted.
• A remote control feature that enables the driller to operate from a safe distance
What makes Levent 2002 RX-4 unique is the awless combination of veri ed concept and durable components. The rig adopts the most advanced technology for diamond core drills and the latest developments, in order to carry out e ective drilling.
The rotation speed, power and rotation unit aperture of Levent 2002 RX-4 are made to present optimal performance in 60-122.6 mm (2.36 - 4.83 in) (B-P) diameter wireline or conventional drilling. As far the spindle bore, its diameters is 127 mm (5 in).
Levent 2002 RX-4 has all the necessary features and safeguards to protect the driller from the hot and moving parts.
The rig has a self-contained control panel, a mast dump, hydraulic jacks, and a telescopic mast, which allow an easy setup. Its ergonomics and safety bring a serious advantage; both for the driller and for the environment.
The bellow drill depth capacities only serve as guidelines and refer to vertical down drilling. SON-MAK cannot guarantee that these results can be achieved in all drilling conditions
by Mathew Wilson, President & CEO at Sterling Metals Inc.
Canadian high-grade silver districts bear a rich history. In the early 1900s, the discovery of the Cobalt Camp in Ontario initially provided over 10% of the world’s silver and has contributed over 450 Moz since its discovery. In Yukon, Canada, Keno Hill is still one of the world’s richest silver districts producing 200 Moz of silver from just 5.3 MT since its discovery in 1913. Now, over 100 years later, and without a globally significant silver discovery since, there is smoke emerging from the eastern corner of Canada in the form of an early stage, high grade, district-scale potential silver project.
The Sail Pond project in Northwest Newfoundland was discovered in 2016 and while it is without a drill hole, the preliminary data demonstrates the potential for a districtscale discovery due to a large geophysical and geochemical footprint. Preliminary work has identified a 9 km-long (5.6 mi) combined strike of two zones via a large soil grid, geological mapping and trenching, and several geophysical programs. Grab samples from trenching have yielded world-class
grades up to 4500 g/t Ag and 15% copper while grab samples from an outcrop of similar veining, nearly 12 km (7.5 mi) away, have yielded grades up to 300 g/t Ag. The asset is held in a small junior exploration company listed on the TSX Venture exchange with an experienced team familiar with recent large discoveries in Canada and in Newfoundland. The project will be drilled for the first time this spring and perhaps the eastern side of Canada can join the west and the central in
providing a globally significant high-grade silver district to the world.
In December 2016 local school principal Tony Kearney discovered rock samples from an outcrop yielding up to 464 g/t silver, 2.48% Cu, and 4.53% Zn and 2.48% Pb. After staking 30 claims, he sold the project to Altius Resources, a leader
in Newfoundland exploration, which then went on to stake an additional 600 claims to amass a land package of over 15 000 hectares (37 065 acres).
Over the next two years, Altius defined two primary zones of combined 2 km (1.24 mi) and 7 km (4.35 mi) in strike via soil sampling, trenching and via grab samples that yielded grades over 2000 g/t Ag and 8% Cu. In 2018, after refining the land package to 13 500 hectares (32 124 acres), the project was optioned by the now dominant Newfoundland gold explorer Newfound Gold that spent the next two years commissioning an IP survey, gravity and magnetics. In February 2020, with the emergence of Newfound Gold’s terrific Queensway gold project, Newfound Gold returned the earlystage Sail Pond project to Altius minerals. In October 2020, Sterling Metals entered
into an agreement to earn 100% for USD 1.5 million in spending over 3 years and issued 19.9% of its stock to Altius.
Since then, Sterling has undertaken an additional Geochemistry and Geophysics program to fill in a few holes of the last three years. These programs have yielded grades up to 4500 g/t Ag, 15% Copper and 15% Pb+Zn from grab samples within trenches and grab samples of over 300 g/t Ag from an outcrop over 12 km (7.46 mi) away from this high-grade sample.
Both the North and South Zones are distinguished by thick, massive sequences of pervasively altered (i.e. silica ± calcite ± sericite) dolostone (or dolomitized limestone) of the St. George Group (possibly Catoche and/or Aguathuna formations)
Geological map of Newfoundland
which seems to be the primary rheological (± chemical) trap rock for fluids in this region. Commonly, these dolostones are folded and bounded by shear zones or thrust faults, and often deform brittlely. Conjugate quartz veins are the predominant host for the Ag-Cu-Pb-Zn-Sb (± Au) mineralization and are found almost entirely within sequences or blocks of massive dolostone. Quartz veins can constitute upwards of 30-40 volume percent of the exposed rock, with individual quartz veins generally less than 10 cm (4.94 in) in thickness but can reach up to 2 m (6.56 ft) in some locations. Mineralization has been observed in both sets of quartz veins. Similar styles of mineralization are present throughout the property, albeit hosted in narrower units of dolostone with widths of 0.5-5 m (1.64–16.4 ft) and there has been little work conducted thus far to evaluate these areas.
Sulphide mineralization within the two zones is comprised mostly of chalcocite, tetrahedrite, tennantite, sphalerite, boulangerite, galena and locally trace to minor amounts of pyrite, bornite, covellite, mimetite, sulfosalts, fluorite and apatite. Silver is almost exclusively associated with the tetrahedrite. Mineralization is generally within, or spatially associated with quartz veins; as open-space infilling (clots), disseminations and as vein-parallel massive bands or veinlets. Mineralization also occurs within the matrix of dolostone breccias, possibly as a solution breccia matrix replacement similar to MississippiValley-type sulfide mineralization.
Vein-hosted silver-lead-zinc deposits hosted within metasedimentary sequences have several key criteria. These include:
1. Vein networks consisting of structurally controlled quartz +/carbonate vein swarms hosting variable amounts of sphalerite and galena with various Sb-Ag-(As)bearing sulfosalts (e.g., tetrahedritetennantite, pyrargerite, argentite);
2. They are typically hosted in greenschist facies metamorphic sequences dominated by shales, sandstones, and/ or carbonates and calc-silicate rocks;
3. Alteration associated with mineralization is not laterally extensive and is often proximal to the veins (within meters), consisting predominantly of clay (phyllic) alteration (e.g., sericite-chlorite) owing to the typical low-temperature nature of the ore-forming fluids;
4. Mineralization is often proximal to regional-scale structures, but not necessarily hosted directly within the main structures (i.e., on subsidiary faults). The faults can be thrusts, transtensional or extensional faults. In some cases, they can be hosted within the cleavages of folds (e.g., Coeur d’Alene; Leach et al., 1988 );
5. The metals for the mineralization are interpreted to have been sourced from basement rocks; sulfur is interpreted to be at the site of deposition and derived from local country rocks; and the fluids are interpreted to be a combination of metamorphic-hydrothermal fluids, meteoric fluids, and potentially basinal brines that range from dilute to saline;
6. Mineralization forms as a result of mixing of fluids and/or fluid boiling within structurally favorable domains and/or reactive host rocks (i.e., orogenic vein systems) in conjunction with interaction with a proximal sulfur-rich country rock;
7. Exploration targeting can be undertaken using a combination of geological and structural mapping; geophysical methods and induced polarization due to the low sulfide content and lack of connectivity of sulfide lenses of the mineralization; and surficial geochemical methods. While it is still early, the quartz-(carbonate)like nature of mineralization, and the Ag-Sb-rich nature of the primary Zn-Pb mineralization could suggest this is similar to the structurally hosted Zn-Pb-Ag-(Sb) veins found in metasedimentary belts around the world such as Coeur d’Alene in Idaho or Keno Hill in Yukon.
The company is funded for a strong initial >5 000 m (16 404 ft) drill program this spring targeting both known areas of mineralization identified from surface work as well as strong and robust geophysical and geochemical anomalies which point to mineralization at depth. The kilometric size and scope of the system, as identified through systematic soil sampling and geophysical tools, potentially point to a very large body of mineralization. Comparable silver districts, including the Keno Hill district of the Yukon – 23 300 hectares (53 576 acres) – are comparable in size to Sterling’s 13 500 hectares (32 124 acres) land package. Led by a team and advisory board that have been part of some of the top discoveries in Canada over the last 10 years and a host of preliminary work and target generation done to date, investors can now look forward to an exciting inaugural drill campaign. While early, it is clear that there is a robust high-grade silver target in northwest Newfoundland. C
“During the course of the Alpala drilling program the use of the Devico drilling technique delivered a saving of 23,997.6m of drilling, or approximately $12M USD.”
Benn Whistler SolGold PLC
by Merlin
If you want to make a major new mineral discovery, Ecuador is one of the best places in the world to explore. The Andes are central to world copper supply, with 25% of annual production coming from northern Chile and a further 15% from Peru. Magma fertility studies show that Ecuador has the same geological and metallogenic potential as its southern neighbors. Potential has been matched by a track record of spectacular discoveries as the country has gradually opened up to systematic exploration. It is one of the few countries in the world where large, good grade ore bodies are still being found at the surface, and the current roster of companies investing in Ecuadorian exploration includes global leaders such as BHP, Fortescue Metals, First Quantum and Anglo American.
Disclaimer
This article contains the personal beliefs and opinions of its author, and not the ones of Coring Magazine. Coring remains neutral, assuming no responsibility for the author’ s overall and political points of view thus can not be held liable for any of the information presented by him in the text.
And yet the country’s mining sector is still at an early stage of development, with only two operating mines that were both commissioned in 2019. Chinese-owned Mirador became the first large-scale copper mine, aiming to produce 94 000 tonnes of copper cathode per annum. TSX-listed Lundin Gold’s Fruta del Norte became the first large-scale gold mine, aiming to produce 340 000 ounces of gold per annum. There are many companies ready to invest but they are struggling to get their money into the ground. Exploration dollars are backing up, poised to test theories of early-stage targets, to delineate recent discoveries or to advance resources through technical and financial evaluation in the approach to production.
From 2015 onwards when Ecuador opened up to the idea of a responsible, well-regulated mining industry, employment was set to boom, dollars were set to flow and the mining sector was set to become a mainstay of the economy. By 2018, foreign companies had committed to invest a billion dollars into exploration, resource definition and technical studies within four years; quite apart from the capital investment associated with construction and commissioning.
The rationale for a modern mining industry in Ecuador was simple then and remains compelling today. Ecuador runs a US-dollar denominated monetary system and therefore cannot print its own currency. This leaves debt, foreign direct investment (FDI) and export earnings as the only ways to increase money supply. With the debt options (via the IMF and China) largely exhausted already, Ecuador needs dollars from FDI and exports, and mining fits the bill perfectly. Mining is the only Ecuadorian industry that offers growth potential as agriculture, tourism and the oil industry are ex-growth with structural problems, and the mining industry is keen to invest heavily and generate future earnings.
The socialist government of Rafael Correa (2007-2017) learned about the potential for mining to fund the country while in power and it acted swiftly. It pivoted from being staunchly anti-mining, with punitive taxation, and at one stage a total ban on mining, to making the mining code fiscally competitive with peers and placing mining as the cornerstone of economic growth plans. In 2015, Ecuador was proudly declared open to the mining sector.
Under the leadership of Lenin Moreno (2017-2021), however, few mining permits have been issued, no new concessions applications have been allowed and companies have struggled to elicit scout drilling and water permits to enable ongoing work. Not only that but a vocal anti-mining cohort has gained support.
The highest profile anti-mining indigenous leader, Yaku Perez, has been behind a number of referenda aimed at protecting the Amazon rainforest from mining and deforestation. On the National Assembly elections his Pachakutik Party achieved 27 seats, almost five times more than previously.
Perez’s progressive environmental agenda has proven to be a compelling platform, as the illegal mining sector in Ecuador is vast, unsafe, polluting and destructive and does not generate FDI or tax revenue to the economy. COVID-19 has shrunk the country’s GDP by 9%, resulting in double unemployment and reduced government spending, particularly in the Amazon basin. With even less oversight from the government, illegal mining has skyrocketed, increasing the pressure on the Indigenous nations of Ecuador. Under these factors, Perez’s staunch anti-mining position appears difficult to enforce.
In the first round of the Presidential Elections held in early February, the ‘Correa’ candidate Andres Arauz emerged as the front-runner with 33% of the vote. The support for Arauz is rooted in the experiences of life under the Correa administration from 2007 onwards. The early Correa years were a time of high commodity prices, significant investment in national infrastructure and a rejection of the ‘IMF-led capitalist ways’. Correa effected a major wealth-redistri-
bution in Ecuador and earned the loathing of the powerful elite and the initial approval of the broader population. He, and by extension Arauz, are still popular even after his corruption trial (and conviction) last year highlighted unaccountability and authoritarian tendencies, including suppression of the press. Arauz, being a convert to the potential of the sector, is likely to champion a responsible mining industry from day one in office.
Opposing Arauz in the run-off on April 11, 2021 is Guillermo Lasso. He gained the second place with 19.74% of the vote, narrowly beating Perez (19.39%). Lasso, representing the old elite, is an ex-banker with a support base in the populated coastal region and the backing of the business community. He is expected to work closely with the IMF on tackling debt and his campaign is focused on creating jobs by increasing investment into oil and mining extraction.
Not only did Lasso come second by a large margin but Yaku Perez and the Pachakutik party have stated they will not support either presidential candidate, which will only serve to widen the gap. Lasso’s chances of defeating such a popular socialist, in the face of Andres Arauz, are slim, given that over 75% of the votes cast in Round One of the elections were left-leaning. The final outcome will be decided in six weeks.
What is certain is that Ecuador is in a difficult position. The petroleum industry is in crisis and there are claims that national oil company Petroecuador needs to buy 7.5 million barrels of crude oil during 2022 if it is to meet its contractual supply obligations. But all is not gloom and doom - the two operating mines in Ecuador are
proving to be a great success. Ecuador exported USD 810 million of copper and gold from January to November 2020, contributing 4.4% to total exports.
Putting the ideologies of the candidates aside, by far the most important subject is the state of the economy. Once the identity of the new President is declared then the real business of establishing how to fund the country will begin. To external observers, the case for growth through mineral resource development seems glaringly obvious, and the expectation is that sense will eventually prevail. C
Salazar Resources is an Ecuadorian exploration company with a proven track record of discovery. The company aims to make the country’s next commercial copper-gold discovery. It is currently advancing three grassroots exploration projects in Ecuador which provide multiple value catalysts.
Core to all of its activities is the team’s commitment to ensuring that it has a positive impact on Ecuadorian communities and the
The mineral exploration and mining industry will come together – virtually –on March 8-11, 2021, for the Prospectors & Developers Association of Canada’s (PDAC) 2021 Convention. This year marks the 89th year for the iconic event.
As the COVID-19 pandemic continues to affect travel and major gatherings, PDAC recognizes that staying connected is more important than ever before for members, exhibitors, sponsors, attendees and numerous partners. PDAC Convention has always been unmatched in its ability to connect participants to the international mining and exploration community and keep them informed of the latest industry news and trends through extensive programming.
‘The PDAC Convention is the world’s premier mineral exploration and mining industry convention. We are excited to provide the high-quality programming attendees have come to expect by offering a fully virtual experience to participants for the first time,’ says Felix Lee, PDAC President. ‘We are encouraged by the prospect of reaching an even greater number of international attendees who may not be able to attend our event in person.’
Attendees will engage in 100+ hours of high calibre content across a diverse
spectrum of highly-acclaimed programs including Capital Markets Program, Indigenous Program, Short Courses, Sustainability Program, Technical Program, Keynote Program and new International Stage (formerly known as Presentation & Reception Rooms) highlighting experts on commodities, mineral outlook postCOVID-19, as well as technological advances. Continued education will be accessible even beyond convention though the new presentation content uploaded postconvention and available for three months.
The International Mines Ministers’ Summit (IMMS)—a unique event bringing together Mines Ministers from around the world—is returning for the sixth consecutive year. Co-hosted with the World Economic Forum, the IMMS provides a communal setting for sharing insights and taking part in discussions that are aimed at enhancing the positive impacts the industry can provide to communities and regions globally.
As the largest marketplace of its kind, PDAC 2021 will have the online exhibit hall featuring customized booths with downloadable content, company brochures, investor materials, videos and much more. Attendees will be able to book meetings with exhibitor representatives via video or text chat.
As the world’s number one mining and investment show, PDAC 2021 will offer personalized access to targeted contacts, while helping to strengthen ties with new and existing partners. After answering a series of questions, the matchmaking
algorithm will suggest a list of other likeminded attendees, sessions that align with your interests and exhibitors matching your selected criteria. In addition, every attendee will be able to browse the attendee directory by name, company, country and other criteria based on your goals. Meaningful connections can be made from anywhere on the platform in real time though text or video chats.
Enjoy the social side of PDAC 2021 with musical acts, exclusive tours, interactive events and more! A variety of engaging entertainment will be showcased throughout the four days of convention. Earn rewards and win prizes just by participating! Visit select exhibitors, view sessions, learn about new products and more - there are a number of engaging ways to collect points and win. NEW for 2021: All pass holders will have access to the Awards Gala (previously a ticketed event) and connect with the Award recipients via live chat. Stay tuned for event details as they are announced.
‘We are committed to providing a firstclass experience to participants—wherever they are in the world,’ says Lee. C
Head to: www.pdac.ca/convention for more #PDAC2021 information and the latest programming details.
The Convention will take place within a virtual venue called a platform, comparable to a physical venue. Event components that attendees would traditionally experience in-person will be presented virtually. A virtual convention offers attendees more benefits than ever before!
MARCH 8 - 11
JOIN FROM ANYWHERE IN THE WORLD
REGISTER AT pdac.ca/convention #PDAC2021
Access to a broader global audience and even more valuable business connections with thought leaders, investors and industry colleagues worldwide.
Facilitated matchmaking based on all participants’ interests in order to deliver the most focused networking experience.
Discover solutions that help push your business forward, book meetings with leading companies and chat with exhibit staff.
Attend various interactive presentations with breakout sessions, group discussions and be among your peers, just like being in the room together.
Accessed from all mobile and desktop devices, all you need is an internet connection. Attend virtual networking lounges, educational sessions and entertainment all from the comfort of your home or office.
AARDVARK DRILLING
Phone 1-877-726-9340
info@aardvarkdrillinginc.com www.aardvarkdrillinginc.com Canada, United States, England
AGGRESSIVE DRILLING
Phone (306) 975-1523 adrill@sasktel.net www.aggressivedrilling.com Canada
AUSDRILL
Phone +61 8 6159 4407 info@ausdrill.com.au www.ausdrill.com.au Australia
BUNDOK DRILLING
Phone (+63 46) 460 5310 info@bundokdrilling.com www.bundokdrilling.com Philippines
CABO
Phone (604)527-4201 info@cabo.ca www.cabo.ca Canada
CARTWRIGHT DRILLING INC.
Phone 709 896 4446 www.cartwrightdrilling.ca Canada, Greenland, Madagascar, Malawi
CONTINENTAL DRILLING
Phone +502 2382-5070 info@continentaldrilling.com www.continentaldrilling.com Guatemala, El Salvador, Honduras, Nicaragua, Costa Rica, Panama
DDH1 DRILLING
Phone +61 08 9435 1700 admin@ddh1.com.au www.ddh1.com.au Australia
DEPCO DRILLING
Phone (07) 4928 1133 info@depco.com.au www.depco.com.au Australia
DORADO DRILLING
Phone (+1) 250-351-9440 admin@doradodrilling.com www.doradodrilling.com Canada
DRILLCON AB
Phone +46 587 82820 Fax +46 587 311895 drillcon@drillcon.se www.drillcon.se Scandinavia, Portugal, Spain
EXPLOMIN PERFORACIONES
Phone +51 (1) 295-7070 contacto@explomin.com www.explomin.com/en/ Peru
FALCON DRILLING
Phone 001 250 564 7786 www.falcon-drilling.com Canada, United States, Mexico, Burkina Faso, Mongolia
FIRST DRILLING
Phone 1 (970) 249 3501 info.usa@firstdrilling.com www.firstdrilling.com United States, Australia
GEODRILL LTD
Phone +44 1624 676 585 contact@geodrill-dh.com www.geodrill-gh.com Ghana
GEOSOL
Phone +55 (31) 2108-8000
geosol@geosol.com.br www.geosol.com.br Brazil
GEOTEC
Phone (511) 326 – 5494 geotec@geotec.com.pe www.geotec.com.pe Peru
GLOBAL DRILLING & EXPLORATION GROUP
Phone +65 6543 9375 www.globaldrill.com Singapore, Indonesia, Papua New Guinea, Asia, Australia Pacific, Europe, Middle East, Africa
GRID DRILLING
Phone 07 4157 8080 admin@griddrilling.com www.griddrilling.com Australia
HARDROCK DIAMOND DRILLING jordan@hardrockdrilling.ca www.hardrockdrilling.ca Canada
LOGAN DRILLING
Phone 902-639-2311 logan@logandrillinggroup. com logandrillinggroup.com Canada, United States, Colombia
KATI OY
Phone 0207430660 info@oykatiab.com www.oykatiab.com Finland
MITCHELL DRILLING
Phone +61 7 3722 7222 info@mitchellservices. com.au www.mitchellservices. com.au Australia
NPLH DRILLING
Phone 705-268-7956 Fax 705-268-5174 ablaquiere@nplhdrilling.ca www.nplhdrilling.ca Canada
ORBIT GARANT DRILLING
Phone 819 824-2707 Fax 819 824-2195 info@orbitgarant.com www.orbitgarant.com Canada, United States, West Africa, South America
PEAK DRILLING
Phone 250-897-0930 Fax 250-897-0960 info@peakdrilling.com www.peakdrilling.com Canada
ROCK DRILL GROUP
Phone (01) 518 7100 info@rockdrillgroup.com rockdrillgroup.com Peru
RUEN DRILLING Phone (208) 266-1151 Fax (208) 266-1379 office@ruendrilling.com www.ruendrilling.com United States, Peru
SUMMIT DRILLING
Phone 800-242-6648 Fax 732-356-1009 info@summitdrilling.com www.summitdrilling.com United States
TIMBERLINE DRILLING INC
Phone 208.665.7211 info@timberline-drilling.com www.timberline-drilling.com United States
TITELINE DRILLING
Phone +61 3 5338 3800
Fax +61 3 5337 6100 info@titelineinternational. com.au
titelineinternational.com.au Australia, Ecuador, Indonesia, Mongolia, Myanmar
Directional Drilling (A-Z)
Surveying & Geophysics (A-Z)
CORE TECH
Phone (511) 255-5701 ventas@coretech.com.pe www.coretech.com.pe Peru
DIGITAL SURVEYING
Phone +27 18 788 6349 sales@digitalsurveying.co.za www.digitalsurveying.com.za Africa
DOWNHOLE SURVEYS
Phone +61 (0) 8 9361 4745 sales@downhole.com.au www.downhole.com.au Australia
I3 DIRECTIONAL DRILLING SOLUTIONS
Phone 1-705-495-6363 roque@i3dds.com www.i3dds.com Canada
REI DRILLING
Phone +1 801 270-2140 Fax +1 801 281-2880 www.reidrilling.com United States
GYRODATA SERVICES CANADA
Phone +1 705 494 0075 don.black@gyrodata.com www.gyrodata.com Canada
TECH DIRECTIONAL
Phone (705) 524-6222 info@techdirectional.com techdirectional.com Canada
TRUST SOLUÇÕES GEOLÓGICAS
Phone +55 (62) 3575 3720 contato@trustsg.com.br www.trustsg.com.br Brazil
INTERNATIONAL DRILLING SERVICES
Phone +1 480-824-7100 IDSinfo@IDSdrill.com www.idsdrill.com United States, Canada
Drill Rigs & Accessories (A-Z)
TRUST SOLUÇÕES
GEOLÓGICAS
Phone +55 62 992720023 contato@trustsg.com.br Brazil
ACKER DRILL
Phone 570-586-2061
Fax 570-586-2659 sales@ackerdrill.com www.ackerdrill.com
ATELIER VAL-D’OR
Phone (819) 824-3676
Fax (819) 824-2891 info@avddrills.com www.avddrills.com
AUSTEX
Phone 08 9450 9400 Fax 08 9478 2316 enquiries@austexeng.com.au www.austexeng.com.au
BARKOM
Phone 90-312 385 60 50 Fax 90-312 385 35 75 info@barkomas.com www.barkomas.com
DANDO DRILLING
INTERNATIONAL LTD Phone 01903731312 www.dando.co.uk
DELTA MAKINA
Phone +90 312 386 15 41-42 Fax +90 312 386 15 43 delta@deltamakina.com www.deltamakina.com
DISCOVERY DRILL MANUFACTURER
Phone 1-506-542-9708 Fax 1-506-542-9709 info@discoverydrills.com www.discoverydrills.com
DURALITE DIAMOND DRILLS
Phone 709 263-7221 Fax 709 263-7231 duralitedrills@nf.sympatico. ca duralitediamonddrills.com
EVERDIGM
Phone 82-2-801-0800 Fax 82-2-801-0799 info@everdigm.com www.everdigm.com
FORSUN ULTRA-HARD MATERIAL INDUSTRY
Phone +86-731 84254020 Fax +86-731 84252208 info@forsuntools.com www.forsun-tools.com
GEO DRILLING MACHINERY MANUFACTURING
Phone +90-312-354-8576 Fax +90-312-385-6215 www.geosondajmakine.com
HYDRACORE DRILLS
Phone +1 604-940-4937 Fax +1 604-940-4919 info@hydracore.com www.hydracore.com
MASSENZA DRILLING
RIGS
Phone +39 0521 825284 info@massenzarigs.it www.massenzarigs.com
MAXIDRILL INC
Phone +1 450-763-0212 Fax +1 514-221-2356 info@maxidrill.com www.maxidrill.com
ODYSSEY FLUID POWER
Phone 705 707 1780 info@odysseyfluidpower. com www.odysseyfluidpower. com
PRD RIGS Phone +91 90470 87755 marketing@prdrigs.com www.prdrigs.com
SINOCOREDRILL
Phone 86-510-82723272 Fax 86-510-82752846 sales@sinocoredrill.com www.sinocoredrill.com
USINAGEM MARCOTTE
Phone 1-819-824-3977 www.umvd.ca
VERSA DRILL
Phone 1-819-874-4404 www.versadrillcanada.com
Drill Rig Parts (A-Z)
RC Equipment (A-Z)
Diamond Products (A-Z)
PROLENC
Phone (250) 563-8899 Fax (250) 563-6704 khodgins@prolenc.com www.prolenc.com
BOART LONGYEAR
Phone 1-801-972-6430 Fax 1-801-977-3374 www.boartlongyear.com
FORDIA POWERED BY EPIROC
Phone 514-336-9211 Fax 514-745-4125 info@fordia.com www.fordia.com
ASAHI DIAMOND
Phone + 61-2-9997-7033 Fax +61-2-9997-8313 sales@asahi-diamond.com.au www.asahi-diamond.com.au
CHRISTENSEN RODER
Phone (11) 5069-5900 roder@roder.com.br www.roder.com.br
DIAMANTINA CHRISTENSEN Phone +562 2620 7808 christensen@christensen.cl diamantinachristensen.com
NORTH BAY MACHINING CENTRE
Phone (705) 472-9416 Fax (705) 472-2927 luc@nbmc.ca www.nbmc.ca
DIASET
Phone 1-800-663-5004 Fax 604-940-9534 bits@diaset.com www.diaset.com
DIMATEC
Phone 1-866-538-5732 Fax 1-204-832-4268 info@dimatec.com www.dimatec.com
DRILLING HQ
Phone 1 (208) 690-3111 Info@DrillingHQ.com www.drillinghq.com
FORSUN ULTRA-HARD MATERIAL INDUSTRY Phone 86-731 84254020 Fax 86-731 84252208 info@forsuntools.com www.forsun-tools.com
HARGRAND DRILLING TOOLS
Phone 86-010-58412500 +8618610425267 Fax 86-010-58412501 eric@hargrand.com www.hargrand.com
HOLE PRODUCTS
Phone (888) 465-1569 Fax (320) 631-0064 www.holeproducts.com
HUD MINING SUPPLIES
Phone 27 (0) 11-974-1500 info@hud.co.za www.hud.co.za
JUFERMA
Phone 34-91 498 93 07 Fax 34-91 498 93 06 diamondjuferma@juferma.com www.juferma.com
LEVANTO DIAMOND SOLUTIONS
Phone 358-9-511-470 Fax 358-9-5114-7470 info@levanto.fi www.levanto.fi
SAFARI DIAMOND DRILL BITS
Phone 604-275-2487 Fax 604-275-2487 info@safaridiamonddrillbits. com safaridiamonddrillbits.com
SINOCOREDRILL
Phone
86-510-82723272 Fax 86-510-82752846 sales@sinocoredrill.com www.sinocoredrill.com
PROLENC
Phone (250) 563-8899 Fax (250) 563-6704 khodgins@prolenc.com www.prolenc.com
BOART LONGYEAR
Phone 1-801-972-6430
Fax 1-801-977-3374 www.boartlongyear.com
DIAMANTINA CHRISTENSEN
Phone 56(9) 7707 9371
christensen@christensen.cl diamantinachristensen.com
DRILLING HQ
Phone 1 (208) 690-3111 info@DrillingHQ.com www.drillinghq.com
FORSUN ULTRA-HARD MATERIAL INDUSTRY
Phone 86-731 84254020 Fax 86-731 84252208 info@forsuntools.com www.forsun-tools.com
HARGRAND DRILLING TOOLS
Phone 86-010-61599828 Fax 86-010-61599828 whp@baoqizt.com www.hargrand.com
HOLE PRODUCTS
Phone 909-939-2581 Fax 909-891-0434 www.holeproducts.com
ICEMS
Phone (16) 3367-3126 Fax (16) 3361-5073 icems@icems.com.br www.icems.com.br
K. MAIKAI
Phone 81-3-3490-8433 Fax 81-3-3490-8622 www.kmaikai.co.jp/eng
MBI GLOBAL
Phone + 1 819 762-9645 dmisiano@mbiglobal.ca www.mbiglobal.ca
SINOCOREDRILL
Phone 86-510-82723272 Fax 86-510-82752846 sales@sinocoredrill.com www.sinocoredrill.com
TERRA TEAM OY
Phone 358-9-849-4030 info@terra-team.fi www.terra-team.fi/en
Water Treatment System (A-Z)
BARKOM
Phone 90-312 385 60 50 Fax 90-312 385 35 75 info@barkomas.com www.barkomas.com
BOART LONGYEAR
Phone 1-801-972-6430 Fax 1-801-977-3374 www.boartlongyear.com
CORE TECH
Phone (511) 255-5701 ventas@coretech.com.pe www.coretech.com.pe
DIAMANTINA CHRISTENSEN
Phone 56(9) 7707 9371 christensen@christensen.cl www.diamantinachristensen.com
FORDIA POWERED BY EPIROC
Phone 514-336-9211 Fax 514-745-4125 info@fordia.com www.fordia.com
FORDIA POWERED BY EPIROC
Phone 514-336-9211 Fax 514-745-4125 info@fordia.com www.fordia.com
REFLEX
Phone 1-705-235-2169 Fax 1-705-235-2165 reflex@imdexlimited.com www.reflexnow.com
www.geosondajmakine.com
44 40 - 41 Fax +90 224 482 44 39 info@son-mak.com.tr www.son-mak.com
SONDA PARTS
Phone 55 – (31) 3391 3810 Fax 55 – (31) 3391 3810 comercial@sondaparts.com.br www.sondaparts.com.br/
TERRA TEAM OY
Phone 358-9-849-4030 info@terra-team.fi www.terra-team.fi/en/
BOART LONGYEAR
Phone 1-801-972-6430
Fax 1-801-977-3374 www.boartlongyear.com
COREFINDER
Phone +55 62 992720023 contato@corefinder.com.br www.corefinder.com.br
AZIWELL
Phone + 47 471 600 71 post@aziwell.no www.aziwell.no
BOART LONGYEAR
Phone 1-801-972-6430 Fax 1-801-977-3374 www.boartlongyear.com
ICEEFIELD TOOLS
Phone +1 (867) 633-4264 Fax +1 (867) 633-4217 support@icefieldtools.com www.icefieldtools.com
REFLEX INSTRUMENTS
Phone 61 8 9445 4020 Fax 61 8 9445 4040 reflex@imdexlimited.com www.reflexnow.com
STOCKHOLM PRECISION
TOOLS
Phone 46-8-590-733-10 Fax 46-8-590-731-55 info@stockholmprecisiontools. com stockholmprecisiontools.com
DEVICO AS Phone +47 72870101 devico@devico.com www.devico.com
REFLEX INSTRUMENTS
Phone 61 8 9445 4020 Fax 61 8 9445 4040 reflex@imdexlimited.com www.reflexnow.com
CEBO HOLLAND B. V. (BAROID)
Phone +31 255 546 262 info@cebo.com www.cebo.com
CORE TECH
Phone (511) 255-5701 ventas@coretech.com.pe www.coretech.com.pe
HOLE PRODUCTS
Phone +1 909 939 2581 Fax +1 909 891 0434 holeproducts.com
SON-MAK
Phone +90 224 482 44 40 Fax +90 224 482 44 39 info@son-mak-com.tr www.son-mak-com.tr
DI-CORP
Phone +1 (705) 721-3300 info@di-corp.com www.di-corp.com
JC PORTAL DRILLING SUPPLIES
Phone (33) 3810 6099 (33) 1561 6618 ventas@jcpds.com.mx www.jcpds.com.mx
DYNAMICS G-EX
Phone +61 7 54826649
sales@dynamicsgex.com.au www.dynamicsgex.com.au
MUDEX
Phone +61 (8) 9390 4620 info@mudex.com.au www.mudex.com.au
TIGER FLUIDS
Phone +61 (0) 417 60 11 00 info@tigerfluids.com www.tigerfluids.com
PROSPECTORS
Phone +61 (02) 9839 3500 Fax +61 (02) 8824 5250 sales@prospectors.com.au