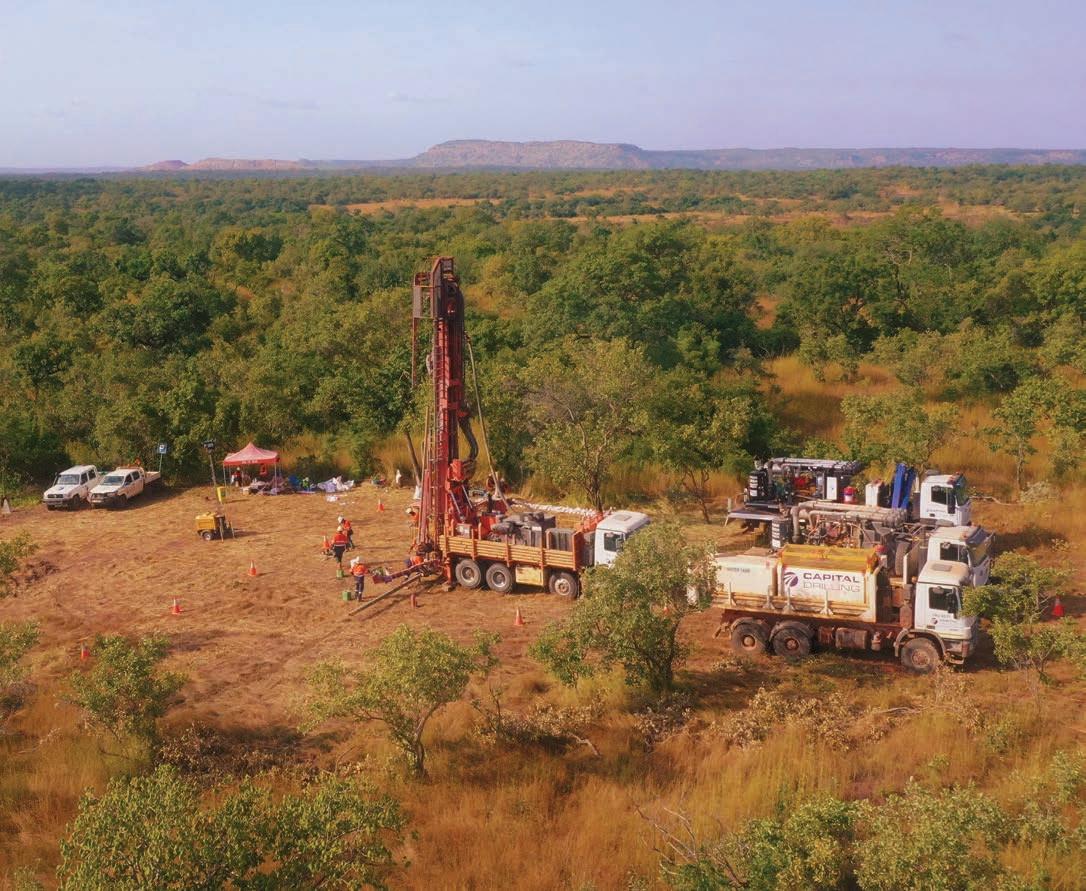
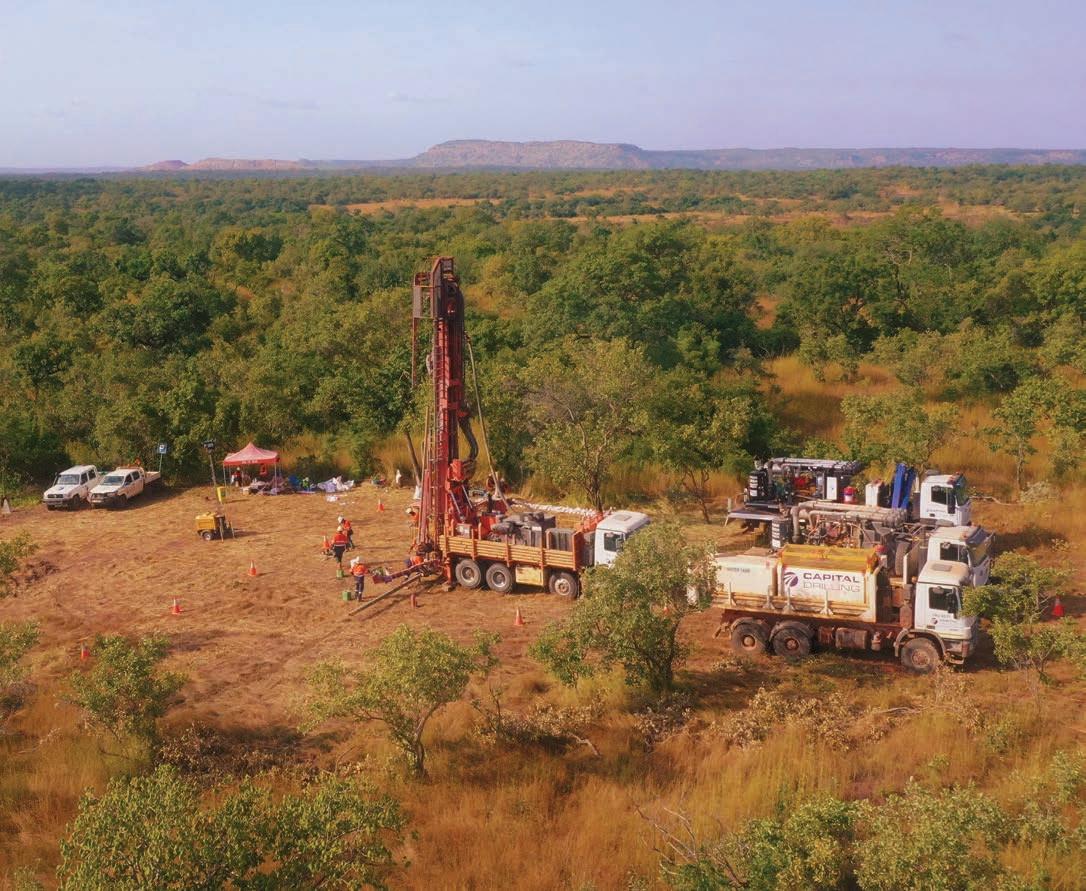
DAILY DRILL REPORTS
Get rid of paper plods and spreadsheets with Axis onSiteDDR, an easy-to-use mobile app which digitally captures and reports your drilling activities and safety data from site to the office.
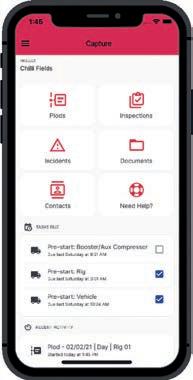
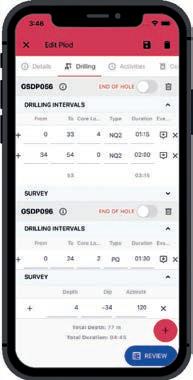
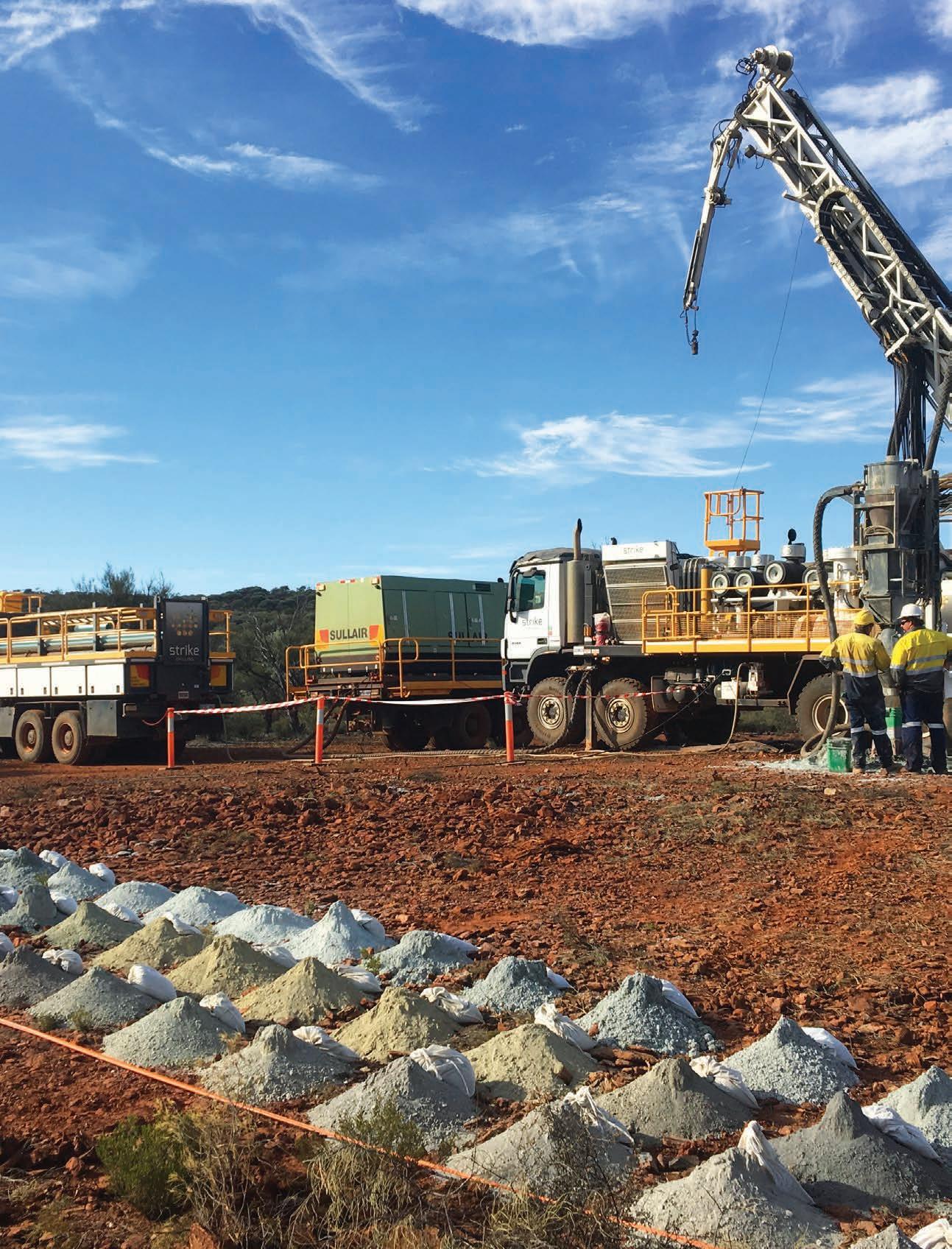
Automate your workflow
Get real-time visibility
Approve & edit plods on-the-fly
Fast track client approval
Integrate your accounting system
Implement efficiencies daily
Table Contents
Exclusive interview: Grigor Topev, Editor in Chief at Coring Magazine in conversation with Sylvain Brisson, Owner at Drillco Mining & Exploration

FOCUS 10 Capital Drilling: Africa’s largest diversified driller by Brian Rudd, Executive Director at Capital Drilling Limited

16 Bryson Drilling’s ‘Ace’ team: Defeating extreme weather and harsh terrain to complete a challenging multi-client project by Ryan Sunderland, Shareholder and Supervisor at Bryson Drilling Ltd.
18 Taking an innovative approach to solve old problems by Jeremy Lauzon, President at Hydracore Drills Ltd.
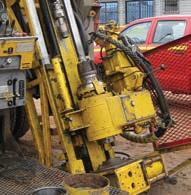
22 The new way of survey by Christian Martin Spannagel, Sales & Marketing Manager at LITEF /COMPANY ACHIEVEMENT
26 Swick Mining Services reach 12 742 000 meters drilled milestone - the equivalent of drilling through the Earth by Robert Burnett, Business Development at Swick Mining Services Ltd /STRATEGIC ALLIANCE
28 MBI Global & VersaDrill grow their strategic alliance into a merger by Daniel Misiano, President at MBI Global /ARTIFICIAL INTELLIGENCE
32 Designing resource drilling as an investment decision and not a cost by Andrew Dasys, President at Objectivity.ca /DRILLING AUTOMATION
38 McKay Drilling and Tribe Tech: The autonomous alliance slated to change the industry /EXPLORATION & MINING GEOLOGY
41 Q&A from the experts: Timothy Strong, Section Editor at Coring Magazine in conversation with Dr Alan Wilson, Director and Chief Geologist at GeoAqua Consultants Limited
46 Welcome to the jungle: Exploration on the frontline of one of West Africa’s forgotten gems: Liberia by Rowan Thorne, Project Geologist at Origin Exploration Ltd.
50 Metamorphic Mexico: The Sierra Madre Occidental by Jane Lockwood, Spotlight Mining
54 The Ewoyaa Lithium Project by Iwan Williams, Exploration Manager Ghana, Lennard Kolff, COO & Abdul-Razak Shaibu Ballah, Senior Geologist Ghana at IronRidge Resources Ltd.
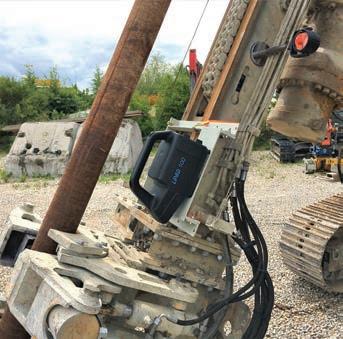
/EXPLORATION DRILLING CATALOG
58 Diamond drilling services
59 Drilling equipment & accessories
65 Survey equipment
66 Miscellaneous
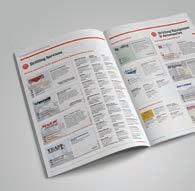
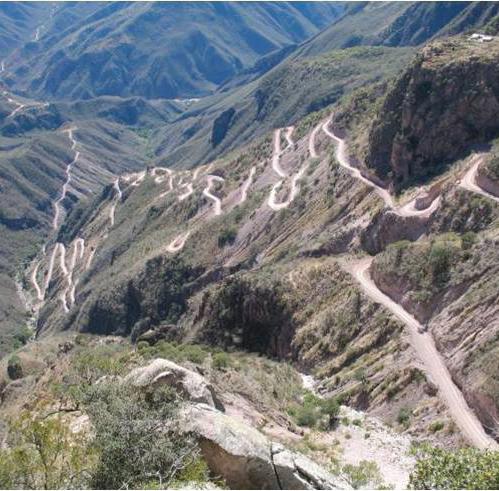
Authors in this issue
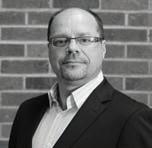
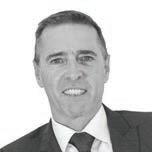

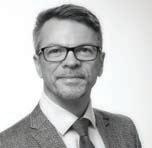
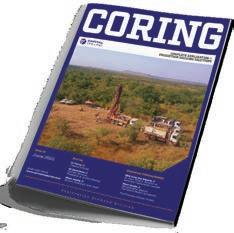
Sylvain Brisson Owner at Drillco Mining & Exploration
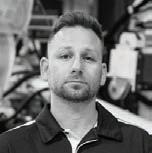
Brian Rudd Executive Director at Capital Drilling Limited
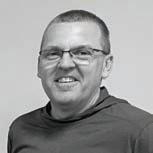
Jeremy Lauzon President at Hydracore Drills Ltd.
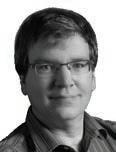
Christian Martin
Spannagel Sales & Marketing Manager at LITEF
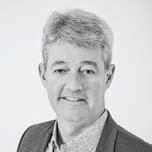
CORING MAGAZINE
June 2021
Cover photo
Capital Drilling
Issue 16
ISSN 2367-847X
Not for resale. Subscribe: www.coringmagazine.com/subscribe
Contact Us
Coring Media Ltd.
119B D. Petkov Str., Sofia 1309, Bulgaria
Phone +359 88 953 2653
Email editorial@coringmagazine.com
Website coringmagazine.com
Robert Burnett Business Development at Swick Mining Services Ltd
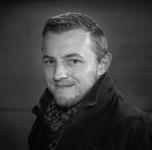
Daniel Misiano President at MBI Global

Andrew Dasys President at Objectivity.ca
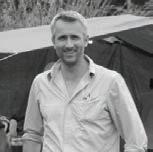
Dr Alan Wilson Director and Chief Geologist at GeoAqua Consultants Limited
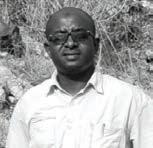
Rowan Thorne Project Geologist at Origin Exploration Ltd.
Iwan Williams Exploration Manager Ghana at IronRidge Resources Ltd.
Lennard Kolff COO at IronRidge Resources Ltd. Abdul-Razak
Shaibu Ballah Senior Geologist Ghana at IronRidge Resources Ltd.
Publisher
Coring Media
Editor in Chief
Grigor Topev
Executive Officer & Editor
Martina Samarova
Editor
Maksim M. Mayer
Section Editor – Exploration & Mining Geology
Timothy Strong
Digital Marketing Manager
Elena Dorfman
Graphic Design
Cog Graphics
Printed by
Dedrax Printing House
Coring Magazine is an international triannual title covering the exploration core drilling industry.
Published in print and digital formats, Coring has a rapidly growing readership that includes diamond drilling contractors, drilling manufacturers and suppliers, service companies, mineral exploration companies and departments, geologists, and many others involved in exploration core drilling.
Launched in late 2015, Coring aims to provide a fresh perspective on the sector by sourcing authentic, informed and quality commentary direct from those working in the field. With regular interviews, insightful company profiles, detailed product reviews, field-practice tips and illustrated case studies of the world’s most unique diamond drilling and mineral exploration projects, Coring provides a platform for learning about the industry’s exciting developments.
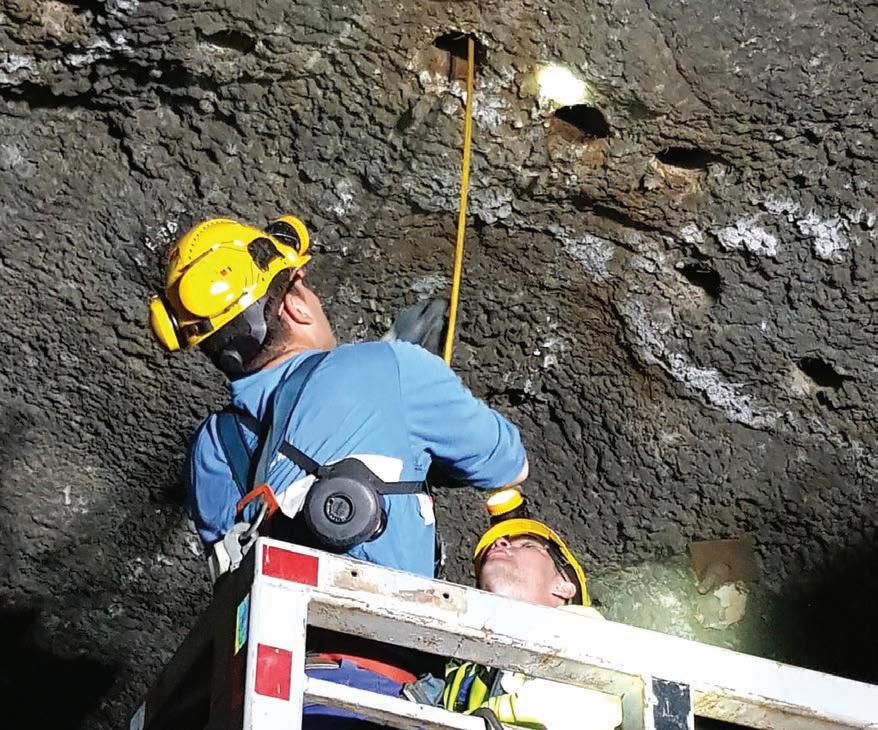
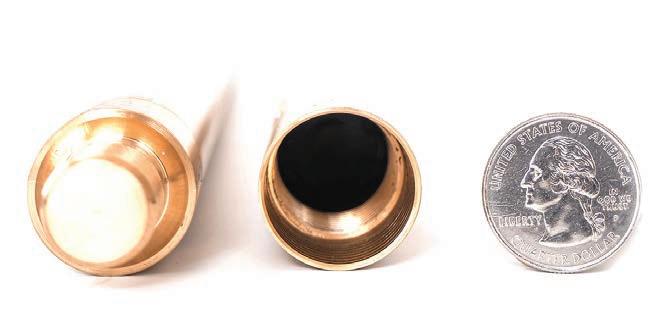
Sylvain Brisson
questions
Sylvain Brisson was born and raised in a small community in Quebec, Canada. After college, he spent five years as a welder fitter, before being offered a job working on the ‘drills’ in 1988.
Initially, he wanted to return to university, but quickly he got hooked and never looked back. He started at the bottom as a drill helper, then he was promoted to a driller and later to a supervisor, before taking on his first specialized drilling job at Cameco's McArthur River. Successful results lead to a challenging two-year tunneling project in Switzerland.
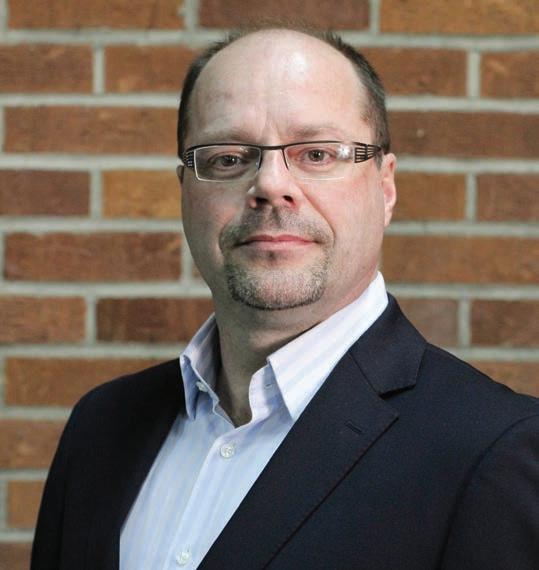
Grigor Topev: How did you start out in drilling?
Back in Canada, Sylvain was promoted to a field supervisor then to an underground operations manager, focusing on special projects. In 2007, he joined HyTech Drilling in Smithers, British Columbia. A few years later, Sylvain joined a team to start a brandnew drilling services company in Central Canada. After four years of growth it was time for Sylvain to begin making a difference to the entire industry.
In 2013, he became president of Drillco Mining and Exploration, an innovative drilling equipment manufacturer. Their first project was a mini raise bore and then they had the crazy idea of creating a modular system based on clean-tech and advanced technology that could operate in surface, underground and heliportable configuration. Today, after eight years and many sacrifices, Sylvain’s company is finally taking off.
Sylvain Brisson: I grew up near some of the major mining camps in Canada knowing and seeing many friends and people I know working on rigs and making careers in the industry. In the spring of 1988, I was offered a job as an underground drill helper, decided to give this a try for a year or two, save some money and go back to University to become a metallurgist. After a few months on the job I was hooked and never looked back.
GT: You have been working in the drilling industry for more than 30 years. Please share a positive or a negative field experience that you will never forget.
SB: By far, my best experience was managing a contract in Switzerland on the Lötschberg Tunnel. This was the turning point in my career, seeing the level of required expertise, precision, accuracy, efficiency and how differently Europeans were operating. This experience really made me see things from a new perspective and to this day, it was by far the largest influence in my career - it took my blinders off, really opened my mind and allowed me to look at things in a different way/ outside the box. Likely, it would have never happened had I not worked in both Cigar Lake and McArthur River where I was trained and gained valuable experience on specialized drilling by some of the best in the industry.
Owner at Drillco Mining & Exploration
GT: You worked as an Underground Operations Manager at Boart Longyear for almost 20 years. What is the most important drilling-related lesson that you have learned during this time?
SB: I started with N.Morissette Drilling, which later became the underground division for Boart Longyear. N.Morissette and Boart Longyear were the very best, which allowed me to work with top professionals from the industry and on some of the most challenging projects. I had to earn my way up, starting at the very bottom. However, I was blessed and fortunate enough to have some of the managers believe in me and my potential, groom me by putting me through just about every position, and allow me to learn and become well rounded in every aspect of the job. Without this, who knows where I’d be? It also allowed me to move my career ahead to where I am today.
GT: What was it like to be a part of Boart Longyear during their ‘golden’ years? Share your thoughts on the company now and then?
SB: It’s hard to beat the awesome feeling of knowing that you are working and learning from the very best. For the longest time, I did not see myself anywhere else, thought I’d be retiring with them. But new opportunities came up to advance my career, so I moved on. It looks like Boart Longyear is climbing their way back, but it’s going to be tough with the shortage of good quality industry people. I think we can all learn from Boart Longyear, for becoming the industry leader they were.
GT: Tell us more about the specifics of underground drilling. Which are the most important factors that make underground drilling operations successful?
SB: Underground is vastly different in so many ways from surface drilling. There are countless challenges because you have to constantly adjust to your environment. To give you an example, for many years, the industry has been trying to make a good rod handler. While some are good quality, they are still crude, bulky and limited to what you can do with them.
Equipment design remains one of the biggest challenges and there is still lots of room for improvement.
GT: What piece of drilling equipment, surface or down-the-hole, has impressed you with its design, functions or features?
SB: Directional drilling is a science in itself, especially on deep hole drilling. Tooling-wise, I still think Boart Longyear is the industry leader on innovation and make real advancement.
GT: Could you share a serious drilling problem which you overcame?
SB: Working on the project in Switzerland was challenging drilling but doing it in a very tight time frame required changes in procedures, processes and equipment modifications - extremely challenging work but very rewarding. We had to drill ahead of the miners. We had less than five days to move two rigs (one rig for core samples and one destructive) with all BOP’s (blow-out preventers) from surface, drill a 21 m (68.9 ft) standpipe and 2 x 250 m (820.21 ft) H-size holes, for core samples, geo-physics, water permeability tests, pressure grout with both holes using a full
‘Drilling is a science and we are continually learning new things every day and, in my opinion, this is what makes our career so interesting.’
BOP stack and move out. Certainly, this was one of the greatest accomplishments I have done in my career.
GT: Could you share some tips and tricks that can help boost drilling production?
SB: While working with Boart Longyear, I used to test and work alongside their engineering department on tooling development. I remember making charts while drilling and seeing where time was spent during a shift and realized that we were only spending maybe at best 30–40% of the time actually drilling, with the remainder spent pumping, handling tubes and rods.
Drill bits have drastically improved, but tooling and different methods still have room for improvement. We still need to maximize drill-
ing time and reduce handling time as much as possible.
GT: What are the most common mistakes that drilling contractors can make when choosing a drill rig?
SB: Purchasing equipment that is too small for the job to be done. Typically, equipment starts losing efficiency at around 60–70% of the drill rating, and selecting a piece of equipment that is rated only for the holes to be drilled results in productivity loss on the last 30 to 40% of the hole.
GT: What is your message to nowadays mineral exploration drillers?
SB: Not everybody will like this answer, but pay attention to your basics, and have the drive to learn more than just being an operator. Drilling is a science and we are continually learning new things every day and, in my opinion, this is what makes our career so interesting.
With over 30 years in the business, for me, every day is still a new adventure and I know I will learn something new. My desire to learn is what drives me and what took me where I am today.
GT: Being frank, are there aspects of today’s drilling business that you consider wrong or even immoral?
SB: The world has changed a lot since I got into this business. There is a strong industry-led movement to explore and operate in an environmentally responsible and productive manner. When operators and companies are irresponsible, I think this is wrong.
GT: When talking about drilling contractors, what quality would help a company stand out above the others?
SB: Be progressive, be a leader and stay ahead of the pack! Use industry leading equipment, hire and train professionals. Make your employees feel that they belong and make a difference. A healthy culture within your company is key and the ability to quickly adapt will help with your success. Maintain a vision for the future.
GT: In 2013 you founded Drillco Mining. Tell us more about your transition from drilling contracting to manufacturing?
SB: Going from always working on operations for somebody else or having someone lead you to making the final decisions was a huge leap of faith. Going into manufacturing and everything that comes along with it was like going back to school. While I really enjoy the
business part, system design and operations are still my favourite things to do.
GT: What is the most significant factor that differentiates the Drillco drills from all the others?
SB: I think it’s the ‘think outside the box’ principle that differentiates Drillco from the other manufacturers. We are innovative and create cost effective solutions for the drilling industry.
GT: Do you consider manufacturing other drilling products besides drill rigs?
SB: With the drilling industry booming, I really haven’t had a chance to think of anything else. Knowing how I work, once the routine settles in, I am confident something will pop up for sure.
GT: Proper drill rod count has always been an issue, which is critical when performing special operations like fishing, wedging, cementing, steering, etc. Any solutions from the manufacturers that would eliminate the manmade mistakes?
SB: Artificial Intelligence (AI) is the future. Using AI, logic, algorithms and computer software and programming will improve most areas of drilling.
GT: Talking about R&D, what does it take to implement new equipment on the market? What sort of testing is involved and how should it be done?
SB: If you can afford it, test it yourself. Unless you partner with a very large and progressive contractor with deep pockets and a goal to help develop new equipment. Most contractors need to drill to make money, pay their bills and don’t have the time and patience to work on developing equipment. This makes R&D testing very difficult to complete with contractors in the field. We now have our own equipment out in the field being tested and this makes a huge difference. We released our first drill with full data logging and telematics and will be starting to work on AI and automated drilling sometime this year. The Drillco equipment was always
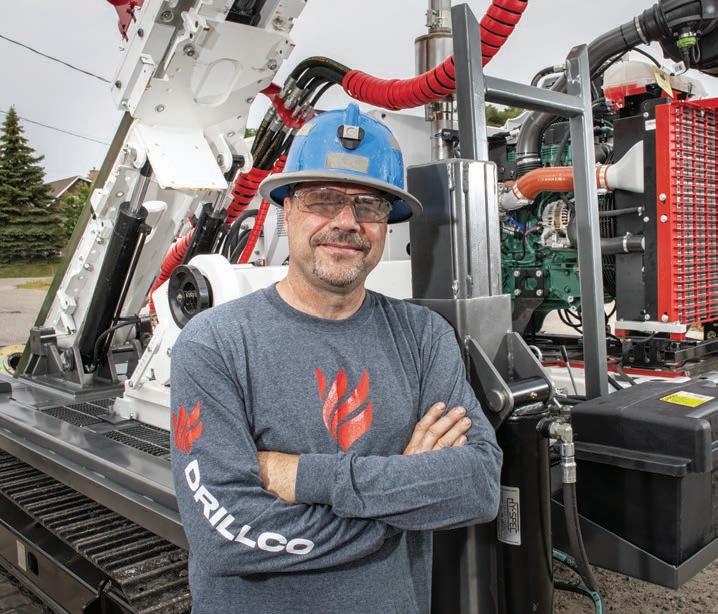
Sylvain
Brisson in front of a Drillco rig
built and designed with that in mind and we are ready to move forward... very exciting times!
GT: What tips and tricks can you give drilling contractors in order to minimize drill rig stand by?
SB: Following proper equipment maintenance programs is a huge factor. Training and mentoring drill operators is essential, so a strong culture of safe productive drilling is achieved.
GT: What is the situation with intelectual property for drill rigs? Which drill rig components are likely to be patented? How can manufacturers protect themselves from copycats?
SB: In my opinion, this is a huge issue in the industry. When you start applying for patents and protection, you realize that it’s not that easy to protect what you have and that can be quite onerous. You need to determine what key components are worth protecting and focus on what makes your equipment different.
GT: What are the technical innovations that the industry needs moving forward? Will automation and AI become the standard for drilling rigs?
SB: With the severe labor shortage, limited capacity to train (with the industry either being crazy busy or too slow to generate revenues) I believe Telematics, AI and Automation are the future of the industry.
We just released our improved data logging with telematics for testing and have already started working on AI components. I hope to be one of the industry leaders in this space. C
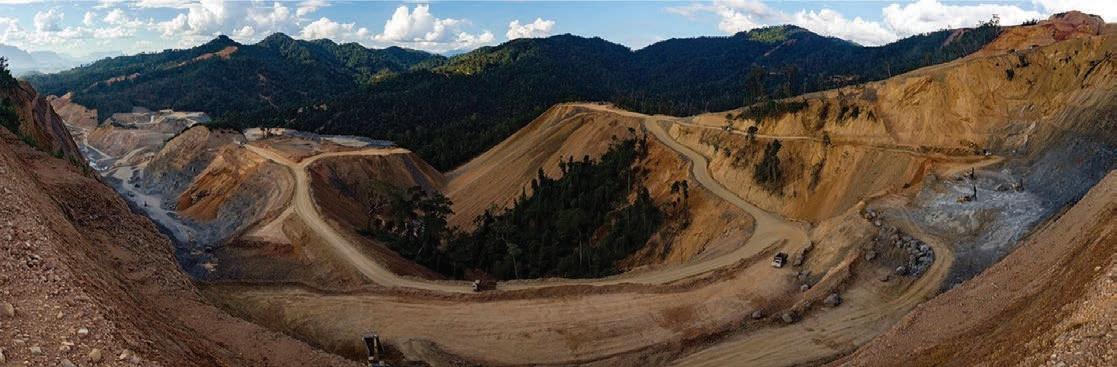
Tae Sung Co. is the leading manufacturer of exploration drilling equipment for Korea and the local region since 1980. We are specialized in the production of high quality impregnated diamond core bits, reaming shells, core barrels, casing, drill rods and more.
We have been number one supplier in Korea for the last 35 years and preferred supplier to many other countries
Tae Sung produces diamond products of any size and any standard. Korea has a very long history in mining and
geology and our diamond products have been adjusted to meet the challenges of the Korean hard and extremely hard formations. Our impregnated diamond bits have proven track record and they drill with better penetration rates compare to other competitive products
We promise to supply you with the best quality products and we will be glad to share with you our competitive pricing
Our clients are always welcome to visit us and our factory.
Address: 31 Jangjeol-ro, Gwangmyeong-city, Gyeonggi-do, Republic of KOREA (14334)
Tel: +82-70-7687-0462
Fax: +82-(0)2-2683-6733 ghlee95@gmail.com www.taesungdia.com

Capital Drilling Africa’s largest diversified driller
by Brian Rudd, Executive Director at Capital Drilling Limited
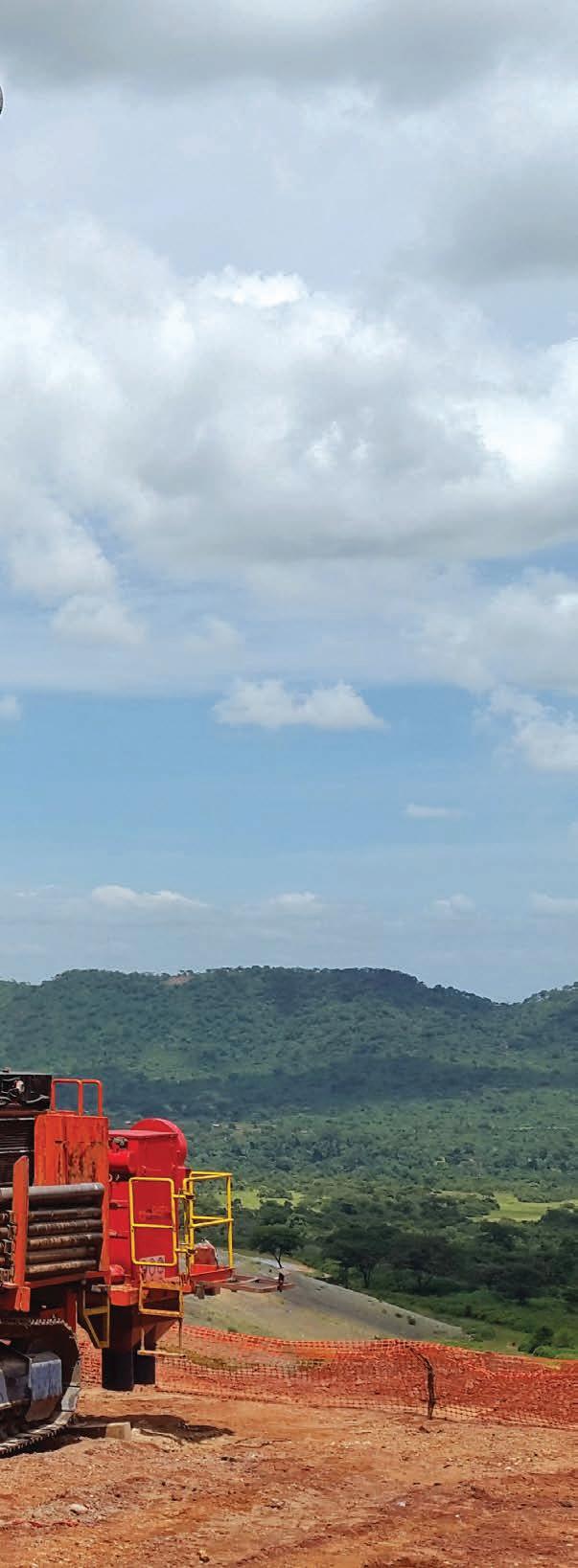
Exploration and mining companies need skilled drilling contractors who operate professionally and deliver quality sample results, as it is these samples that ultimately guide key decisions, often with significant financial implications.
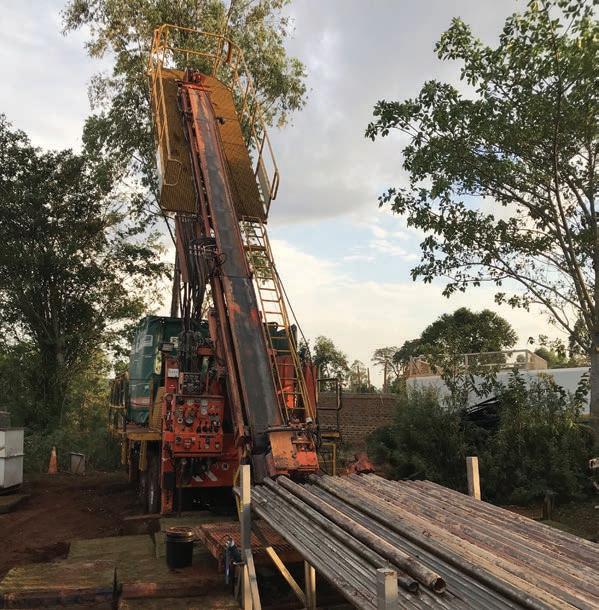
Since its inception in Tanzania in 2005, Capital Drilling (Capital) has built a reputation for delivering professional and safe drilling services and high-quality results. Consequently, their evolution from an exploration driller to one providing a complete range of drilling services was driven by their customers.
Capital’s proven high standards in executing their drilling contracts saw customers requesting production drilling services in addition to their initial exploration drilling services. This led to the introduction of blast hole, grade control, dewatering, pre-splits and underground drilling services to form a full-service drilling offer.
While most drilling companies can drill holes, Capital believes that contractors should deliver customers a good quality core or AC/RC sample, as ultimately that is what the client is buying. This is what they train their crews to deliver, while drilling meters is important, delivering quality samples for customers is the priority.
Capital has developed relationships with some of the largest mining companies in the world, including the likes of AngloGold Ashanti, Barrick Gold and Centamin. As a result of their high-quality service delivery, they have now provided drilling services to Centamin’s Sukari Gold Mine in Egypt since 2005 and AngloGold Ashanti’s Geita Gold Mine since 2006.
Diamond drill rig in Tanzania
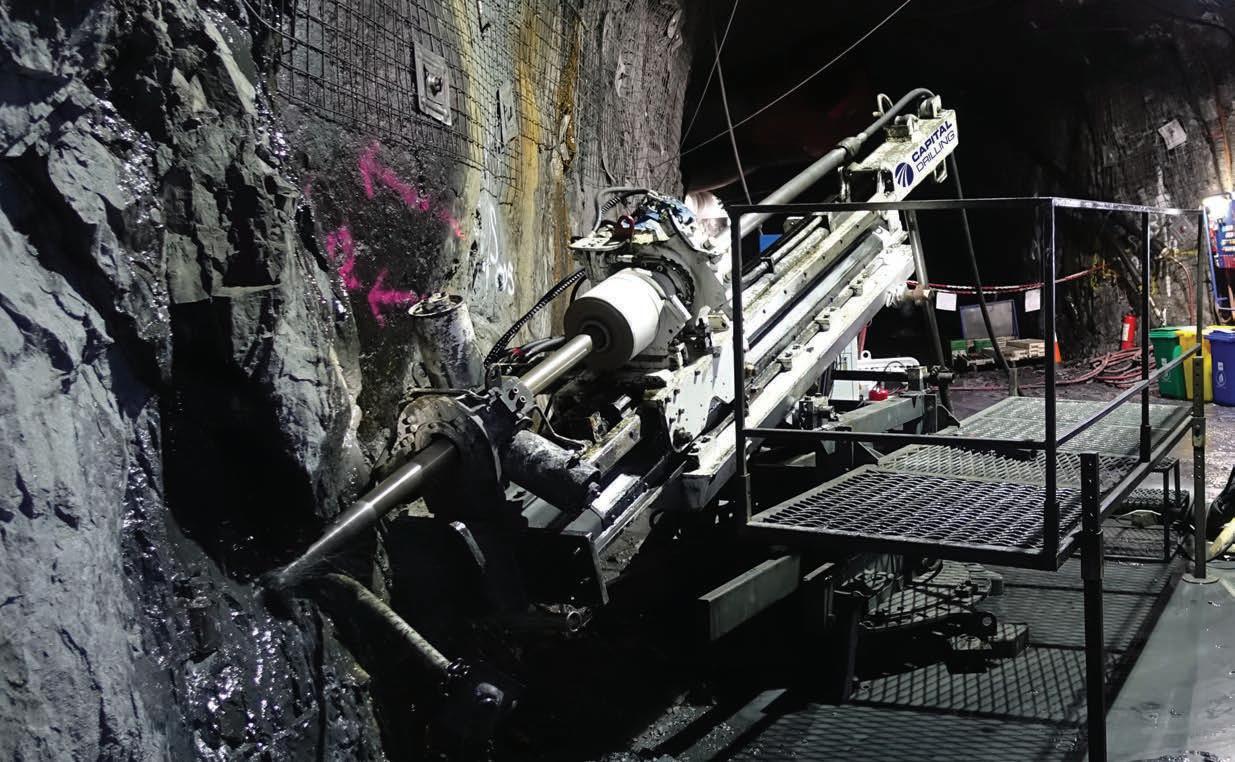
Underground drilling
The company’s evolution in recent years has continued, and Capital has grown its service offering further diversifying into complementary ancillary services. It now provides geochemical analysis services via its laboratory business, MSALABS, mine-site maintenance services via its fledgling maintenance business, MSM, and most recently, load and haul services via its Capital Mining division.
Capital’s well-established drilling operations now benefit from the ability to offer their clients an extended, fully integrated mining services solution. Their clients profit from a partner with extensive working knowledge across their project, translating to operational and management efficiencies.
Focus on Africa
Capital focus on the African markets. While they have experience drilling around the world in South America, Asia-Pacific and Europe, since 2017 they have concentrated on the African continent where the company initially commenced operations. Capital’s traditional markets are in East and North Africa, with well-established operations in Tanzania and Egypt in particular. From early 2018, they have undergone a strategic expansion into the high-growth West African region.
The West African expansion is driven by the much higher activity levels in the area than their traditional operational countries. Additionally, projects in West Africa enjoy significant equity market support, with S&P Global Market Intelligence figures indicating USD 4.9 billion has been raised for projects in the region since 2009, while it featured as the third top region for 2020 gold exploration budgets. Much of this investment focusses on gold exploration across the Birimian Greenstone Belt – a world-class formation in West Africa.
Nearly half of Capital’s drill fleet has now been relocated to this region across Burkina Faso, Cameroon, Cote d’Ivoire, Guinea, Mali and Mauritania. Additionally, major operational and support hubs have been established in Bamako, Mali and Abidjan, Côte d’Ivoire. This enables the company to provide a high level of service to clients in the region, and with inventory stores at each location, operations keep running smoothly. This investment is paying off, with the company’s rig utilization nearing 70% in the first quarter of 2021 and a growing portfolio of new clients and contracts.
With Capital’s shift into West Africa, its revenue generation is now split almost evenly between its three major operating areas, with the balance from the rest of the world and other operations, including its subsidiaries MSALABS and MSM.
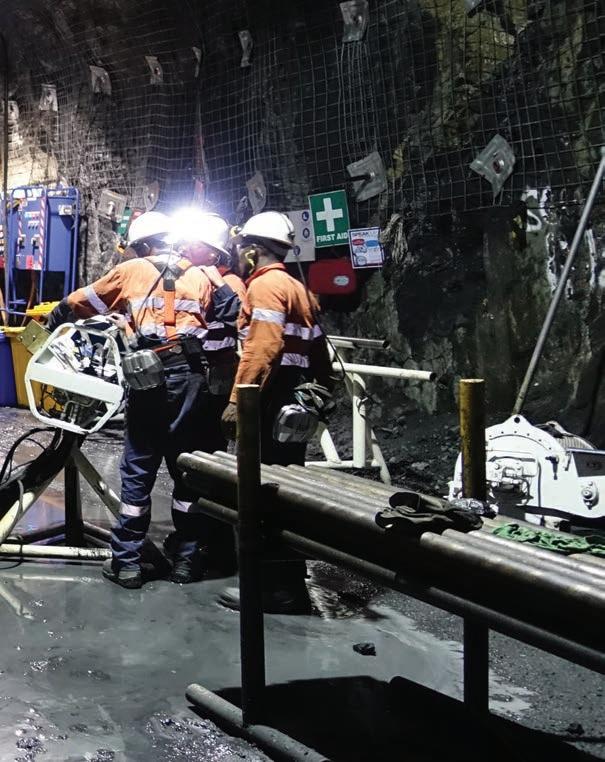
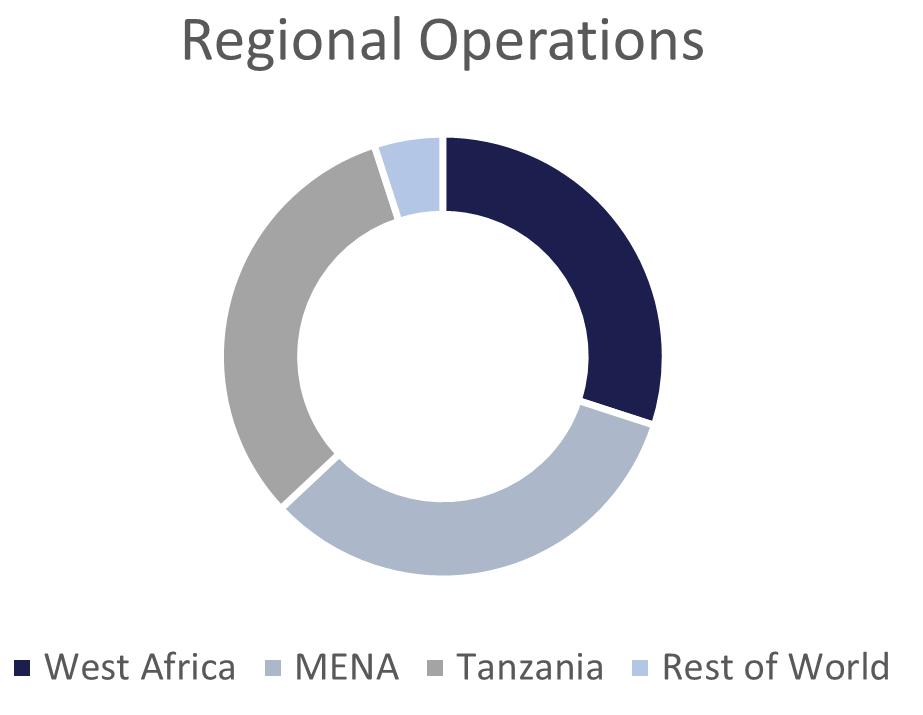
‘Capital’s crews take a broader view of the drill program – it is not just about getting the meters, it’s the quality of the core, it’s looking at other issues a client may be facing around their drill programs and coming up with solutions that work.’
Formula for success
Capital Drilling was established with the philosophy of providing firstworld quality service levels to the emerging markets, through their equipment, safety standards and providing training and career opportunities for their staff, particularly national employees.
This commitment has set the company apart from many of its competitors by ensuring its services are delivered by a safe and reliable fleet, by a competent, well-trained workforce and importantly, by crews with an uncompromising focus on operating safely.
A key part of this approach has also been working closely with clients to ensure projects are well executed and to consistently and proactively look for opportunities to initiate improvements. This pragmatic approach, one that focusses on finding solutions, whether they are operational, safety or other, and delivering more than just drilling meters for their customers, has been instrumental in the company’s success since its inception and remains a core part of its culture today.
Capital’s crews take a broader view of the drill program – it is not just about getting the meters, it’s the quality of the core, it’s looking at other issues a client may be facing around their drill programs and coming up with solutions that work. This might mean drilling the program with fewer rigs, reducing costs or introducing equipment to recycle drilling fluids
Capital Drilling’s regional operations split
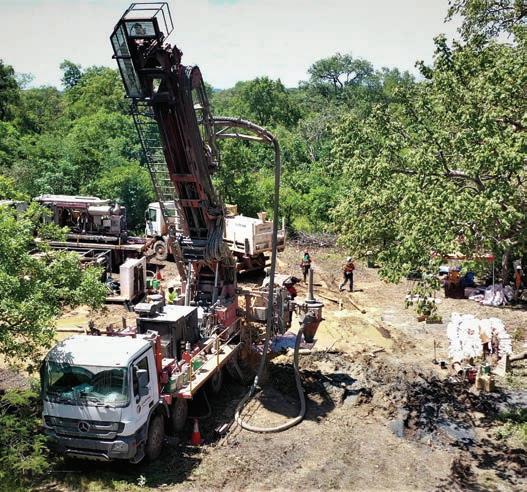
to save water and reduce environmental impact. Every project has its own unique challenges, and the Capital team will proactively look at how they can add value, how they can make it better and safer. Given that the company operates across multiple countries and cultures, it takes time to understand the local people and adapt its operations accordingly, another key factor to success. An example of this is changing shifts during Ramadan to night shifts to accommodate those who are fasting. As a result, Capital enjoys a long-term, stable workforce at its major projects, benefitting clients by maintaining consistently professional service delivery.

Providing career opportunities
The key to ensuring Capital can deliver quality services to their clients is the capability of their team. The company invests significantly in training and professional development programs to provide their employees with the skills and competency levels required. This involves both practical, site-based training together with theoretical assessments.
The company’s portfolio of long-term contracts provides the opportunity to develop ongoing career opportunities for its national employees. Capital emphasizes the development of its national teams and builds training schools at long-term contract sites to upskill workers in order to replace the expat roles. In Egypt for example, with all the training and hard work that has gone into their operations at the Sukari Gold Mine since 2005, Capital now has 95% Egyptian crews for drilling operations, and that is out of 301 people with 14 drill rigs and a world-class maintenance workshop.
As a result of the training and opportunities provided by the company, many of its national employees are now working in expatriate roles at its operations across the continent and hold experience and qualifications that enables them to work around the world.
Corporate responsibilities
Capital recognizes the impact its operations can have on the local communities, which is far broader than providing careers for local people. The company actively engages with these communities to build sustainable value in the region, by providing a range of support to local residents, sporting organizations and charities.
Capital client, Tim Livesay from Oriole Resources says, ‘In my experience of using the Capital teams over the last 20 years or so I can honestly say they have some of the best and most positively impactful social programs for their staff and the communities in which they operate.’
Safety above all
The company has a proud history of achieving outstanding safety records, which demonstrates the strength of its safety culture. Its 2020 Total Recordable Injury Frequency Rate (TRIFR) was just 0.77, substantially below its peers, while many of its key operational sites achieved multi-year Loss Time Injury-free milestones.
The company’s uncompromising commitment to the occupational health and safety of its employees and others means it expects visible safety leadership from all levels of the business. Senior management and the Executive team will regularly conduct Safety Risk Leadership Walks at operational sites to work directly with employees. They clearly communicate and identify potential hazards and provide support to eradicate behaviors or conditions that have the potential to cause harm. This also ensures management have a clear understanding of the risks faced by employees.
Capital also understands the importance its clients place on safe operations – free of incidents, hazards and near misses. The company strives to diligently exceed the most stringent safety requirements, and deliver safe, productive drilling solutions that contribute positively to the project’s safety performance.
In addition, significant focus is placed on monitoring and continuous improvement of its safety processes to address leading indicators, trends, behaviors and conditions influencing Class 1 Risks. Capital works continuously with its employees to ensure they understand the controls to mitigate any risk and are empowered to act if they identify an unsafe condition or behavior in their workplace.
Exploration drilling in Mali
Blast hole drilling in Tanzania
Extensive, reliable rig fleet and capabilities
Capital has the largest rig fleet in Africa, with 98 rigs as of the end of March 2021 and a robust rig acquisition plan for the remainder of the year. Its fleet is one of the most reliable with a proactive asset management program that also includes regular rig upgrades and complete rebuilds. The fleet maintains rig availabilities above 85% as a result, ensuring clients programs aren’t interrupted by unplanned rig downtimes.
Capital’s rig fleet includes: diamond core, air core, deep hole, multi-purpose, grade control, RC, blast hole, and underground rigs. This broad fleet capacity ensures the company can provide the complete range of drilling services from greenfield exploration through to production.
Capital’s crews are trained to understand what clients need at the different stages of a project. Our exploration crews mobilize quickly and consistently deliver what exploration projects need - accurate drilling, quality samples and drilling programs executed on time.
The company’s crews operating on mine sites have the technical skills and competence needed and understand their contribution to keeping the mine plan on schedule. Blast hole crews are trained to deliver the optimal distribution of blast energy to improve down-stream productivity, while the grade control teams focus on accuracy and recovery, getting the holes in the right place every time to provide accurate data on the ore body.
Technology driven safety, productivity and data collection
New technologies are now a vital part of the drilling industry to drive improved safety, productivity and data collection. Capital incorporates the latest industry-leading technologies into its drilling operations, ensuring clients receive the safest, most efficient service.
Drill rigs incorporate safety features that ensure employees are kept away from sources of energy and moving parts where possible, including hands-free rod handlers and remote Drill Control Modules for blast hole rigs. Rigs are also fitted with cameras that provide a real-time view of the site for safety and security monitoring.
The latest data collection software is also used on Capital’s drill sites. From the latest gyro technologies to cloud-based data platforms transmitting daily plod information, the company ensures it can provide the most accurate data, direct from site daily. C

Bryson Drilling’s ‘Ace’ team: Defeating extreme weather and harsh terrain to complete a challenging multi-client project
This winter season Bryson Drilling (Bryson) was awarded a multi-client project for Terralogic Exploration Inc. on behalf of SKRR Exploration/ Taiga Gold Corp. on the remote Irving/ Leland property in Saskatchewan, Canada, located about 60 km (37 mi) away from the nearest access point. The Irving/Leland Project is a large land package covering more than 23 500 hectares strategically located within 10 to 20 km (6–12 mi) of SSR Mining’s very successful Seabee Gold Mine operation, the largest orogenic gold deposit in Saskatchewan.
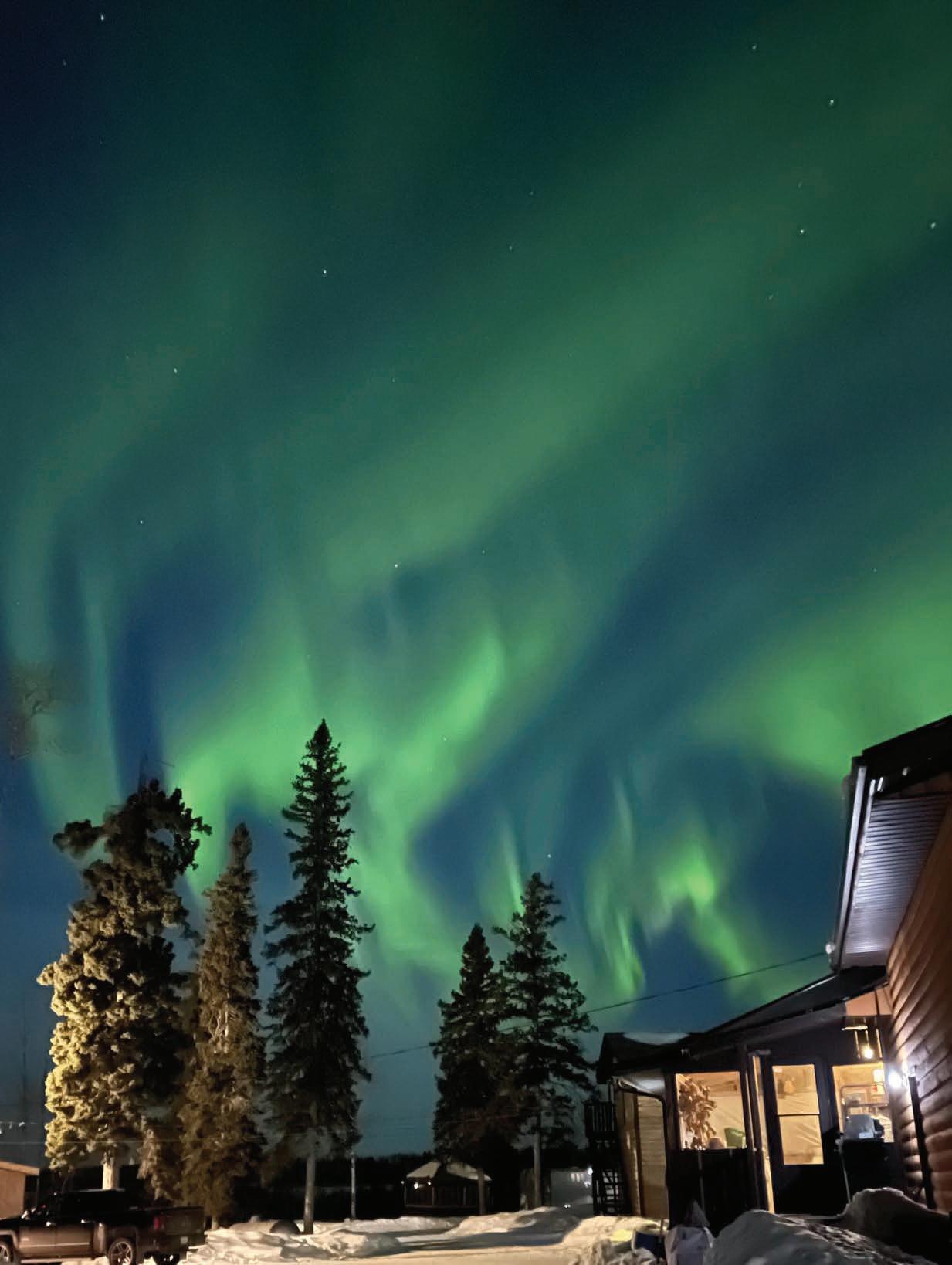
by Ryan Sunderland, Shareholder and Supervisor at Bryson Drilling Ltd.
Irving/Leland is located approximately 100 km (62 mi) North of La Ronge at a heading of 58° Northeast. The location required significant preparation and planning to ensure a successful project completion. Even though the majority of Bryson’s exploration is in the Uranium industry, in this particular project gold was the main commodity we were looking for, with several other base metals including copper and zinc.
We sent our ‘Ace’ team of eight people to the site - three drillers, three helpers, one foreman and an eight man - a local indigenous worker, who was hired to work on the project. They were successful due to their wealth of experience and commitment to seeing the project through despite the extremely challenging conditions.
The team had to endure several weeks of extreme temperatures well below freezing. Due to the harsh and challenging environment, the operation required heli- and plane-portable equipment mobilization. The extreme temperatures of -50°C (-58°F) made helicopter and plane runs even more difficult. Therefore, equipment and gear preparation was a key aspect. We used a specially customized modular drill for fly-in areas with packages that weighed less than 1250 lb (567 kg) so it could be moved by the Bell 206 helicopter easily, and yet was powerful enough to drill up to 600 m (1969 ft) of N-size. We also designed our own fully custom modular shacks that were easy to transport with the Bell 206 helicopter and very quick to assemble and take down in order to move with a Single Otter plane.
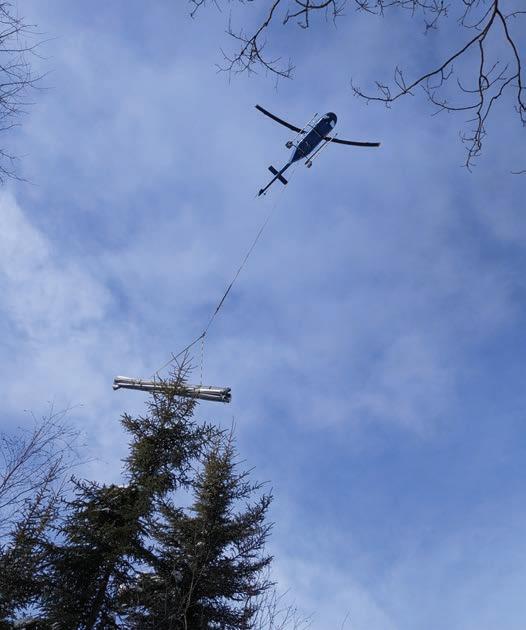
Heli-portable equipment mobilization
Working for prolonged periods in such conditions can be perilous and may lead to accidents or even injuries. That’s why we had to adapt our drilling scheduling to three shifts of eight hours, rather than the regular two by twelve to allow our men to rest and stay safe in the cold. The on-site survival shack that we prepared, was equipped with emergency supplies. There were 700 000 BTU of heat to keep the equipment and work area at safe working temperatures, as limited hours of daylight could affect crew changes and resupplying. The water lines also needed heaters and snow packs for insulation.
Due to the remote nature of the project, we performed crew changes by plane and availed ourselves of local accommodations. The limited access to supply chains was also a concern, therefore, local communities and accommodations were utilized as much as possible. Thus we developed relationships with them and helped engage their business and employment. Prior to working on the project, Terralogic Exploration had also undergone extensive consultations with local communities and indigenous bands to ensure any concerns relating to their traditional lands and potential impact were addressed.
Bryson continues to encourage local engagement to create sustainable future on all lands, while creating potential for future employment in remote areas and recognizing land use rights.
Despite all difficulties, our team completed a total of 34 holes over 66 operating days accumulating 4605 m (15 108 ft) between three properties with one drill in the period from January to April 2021. Because of our careful preparation and the innovations, the jobs were completed on schedule with zero loss time or environmental impact incidents. Our team’s commitment to safety and quality work was key in meeting these results.

Bryson’s drill site
Following this success, our team moved some 130 km (81 mi) away from Leland/Irving to Fathom Minerals Rottenstone property utilizing only two helicopters (B3 & Bell 206) and one Twin Otter ski plane.
About the company
Bryson Drilling was created by three generations of hard-working mineral exploration drillers who passed on the learned knowledge that only experience, time and passion teach. After working in North and South America, Europe, Ecuador, Chile, etc., Bryson officially opened its doors for business to provide surface and specialty drilling services across Canada in 2007. With over 100 years of combined experience, Bryson remains a locally family-owned and operated business based out of Archerwill, Saskatchewan.
Bryson’s headquarters are located on Treaty 6 land. The traditional hunting, travelling and gathering land of the Blackfoot, Cree, Saulteaux, Dene, Dakota and Lakota Sioux Nations and the Homeland of the Metis Nation. Bryson Drilling acknowledges Canada’s colonial history.
Bryson began operations in the Athabasca Basin of the Northern Canadian Shield and has subsequently successfully completed large-scale projects in numerous locations nationwide for some of the industry’s largest companies. Bryson is proud of our earned reputation. Our clients often become repeat clients due to our impressive work ethic, quality control, stewardship of the land and commitment to the environment. C
Taking an innovative approach to solve old problems
by Jeremy Lauzon, President at Hydracore Drills Ltd.
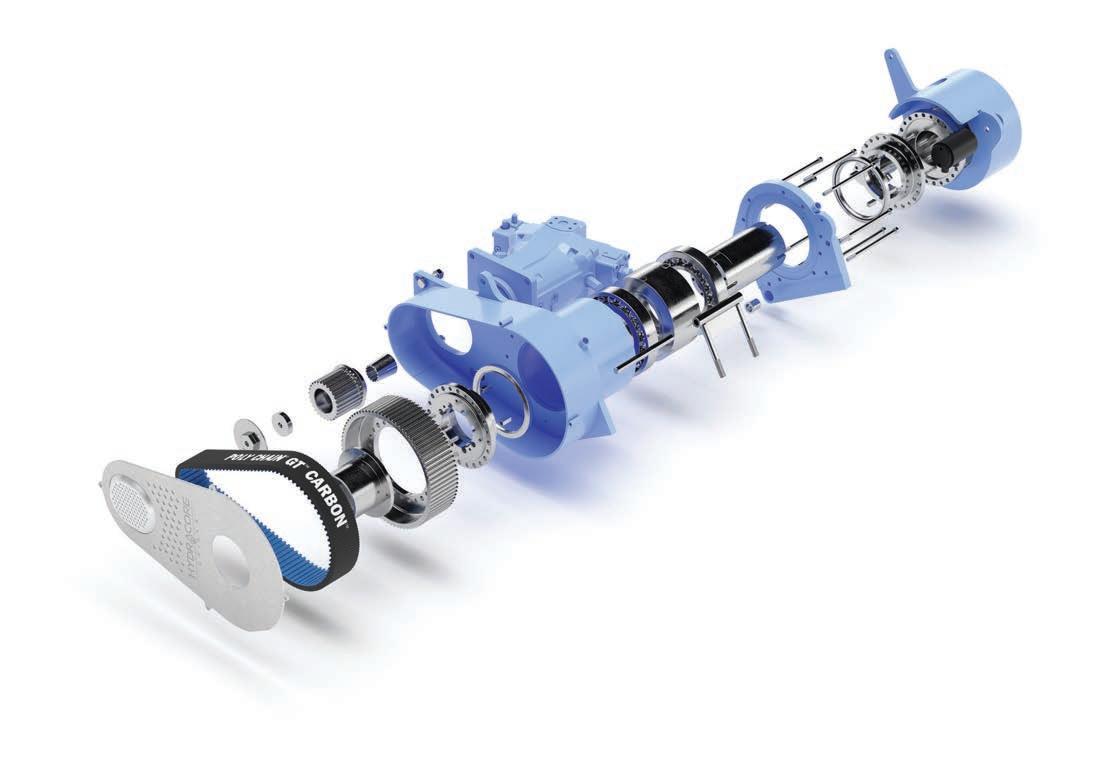
Typical exploration drill heads have not advanced in design over what Boyles, Longyear and others supplied in the 1970s. Why buy a new drill that has a drill head based on technology that is 50 years old? Drillers are used to the problems with these drill heads, and they try to work with what they have. Even if there was a drill with a better head the expense of replacing the entire drill might be a deterrent. This is why Hydracore came up with a cost-effective solution that allows you to upgrade your current drill. We call it the ‘Hydracore Drill Head Replacement Program’.
The Head Replacement Program all started with a call from a client that owned an EF-50. They liked the machine, but the drill head was a constant source of problems. One program alone cost over USD 28 000 in drill head parts for a single rig. Mark, the mechanic in charge of repairs, had previously worked on Hydracore HC2000 drills. It was his idea to convert the drill head to a Hydracore. The changeover went seamlessly and the increase in reliability was incredible. Word quickly spread through the industry and we have now made many successful conversions with most coming back for a second or third.
Mark knew that eliminating problems saves money. Using Hydracore’s 50 years of experience and long-term policy of simpler designs with less parts we have developed ‘H’ and ‘P’ drill heads that eliminate the common problems associated with other heads. These designs have been refined over a 15-year period; hundreds are currently in use. Make the move, I doubt you will miss broken gears, tearing apart your chuck and constantly fighting to chase down the next oil leak.
What is the impact of these problems on your bottom line? When your client sees your drill down for repairs on a regular basis will they call you back next year? Do your drillers want to miss out on their meterage bonus due to broken equipment? Maybe this causes your best employees to look for work elsewhere? A lot of the costs are impossible to quantify, but the direct costs and missed revenue associated with the downtime can be estimated.
We spoke with several clients running drills manufactured by other leading suppliers in Canada. In many cases it was found that the drill head was the ‘Achilles Heel’ of their drill. We discussed the repairs made, and the time and cost required to complete these. It was found in several cases that spare drill heads were supplied on every job due to the frequency of failure. This gave us the confidence that the market was ready for a change.
Hydracore drill heads have less than half the parts of a conventional drill head.
The problems and the costs associated with them
Let us examine each problem individually, in terms of the costs associated and the solution achieved. For this comparison we will use the revenue per 10-hour shift at USD 3250–5000 and repair work as USD 120/hr. In cases where the repair can be completed by a driller during their shift no extra cost is added for repair labour.
Hydracore ‘P’ Drill Head exploded view

The gearbox
The common gearbox found on most core drill heads is a Funk 23000 Series. These are rated by the manufacturer for a maximum input of 100 hp (75kW), 200 lb-ft (271Nm) and no-load speed of 3000 rpm. Drill manufacturers have been greatly exceeding these ratings which results in frequent gear failures. The broken gear teeth from this catastrophic failure often enter the drill head housing. The gearbox will need to be repaired or replaced and the drill head completely disassembled for inspection, repair and cleaning before drilling can re-commence.
The solution
Hydracore has solved this problem by using a large Bent Axis Variable Displacement hydraulic motor that has sufficient range of adjustment in speed and torque to eliminate the need for a gearbox. The Hydraulic motors last for five to ten years and are easily replaced in the field in one to two hours.
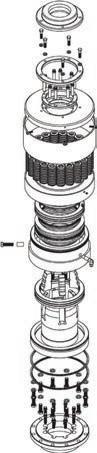
Oil leaks from the drill head housing
Gearboxes and head housings on common industry designs hold a combination of gears, chains and bearings. All of these items require lubrication, and typically an oil-filled head is used to satisfy this need. The oil-filled head introduces unavoidable leaks that are unsightly and potentially damaging to the environment. If a client requires an inspection of your equipment, oil leaks from the head are generally on their checklist.
Hydracore Industry Standard
Atlas Copco CS14 with release cylinder bearing and cylinder failure
Comparison
(left)
Standard Chuck (right)
The solution
Hydracore Drill Heads are 100% leak proof! We have a bit of an unfair advantage here as our heads do not have any oil in them. Our design incorporates a carbon belt drive system, rated at 500 HP, the system gives us two benefits: one, it does not require any lubrication and second, with no metal-on-metal wear it is virtually maintenance free.
Chuck release bearing and release cylinder failure
The industry standard Drill Head Design uses a central release cylinder and typically two release bearings. Due to the diameter and speed of the main spindle, the designers were left with only brush seals to prevent the dirt and water from entering the release bearings and release cylinder. Brush seals are exactly as they sound and if you tried to use a brush to sweep up muddy water, you can imagine what passes through them. The bearings and piston seals fail in short order once the contamination passes the seals. If you are lucky just the piston seals and bearings need to be replaced but often the piston and expensive main shaft become scored and need to be replaced as well. Access to these components is a large job and requires a complete disassembly of the chuck.
Overheating
In a chuck type drill head, large diameter bearings are required to accommodate the drill rods to pass through the center of the main spindle. With large bearings comes a great deal of friction and therefore power you could use for drilling is wasted producing heat. The chains, gears and large bearings create a need for an oil lubrication and heat removal system. The lubrication system typically incorporates a lube pump, filter and in some cases a radiator. This type of system adds another unnecessary complexity that can and will eventually fail. Unless caught immediately, failure of the lubrication system requires a complete rebuild of the drill head which is a costly affair.
Our solution
Hydracore’s unique drill head design does not require release bearings. The release cylinders used are externally mounted and designed to require a single piston seal. The design of these cylinders also allows for a standard wiper seal to protect the cylinder from contamination. If a leak does occur, the cylinders are mounted to the outside of the chuck and can be replaced in minutes.
The solution
Through a careful design process, we have optimized our bearings to handle both the high speeds and high loads without creating excess heat, there are only two bearings in the entire head. The reduction in heat and lack of gears and chains means we have eliminated the need for oil, lubrication pumps, filters and radiators. A couple of shots of grease daily is all that is required to have a cool running head.
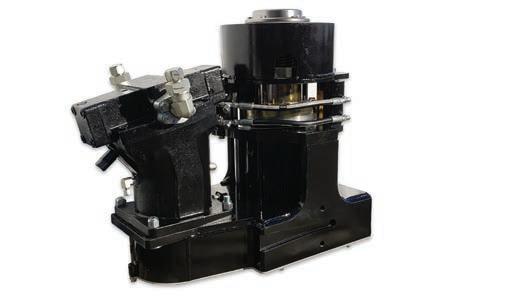

Massive benefits + no risk = easy decision
It is easy to lose sight of the total cost overruns when faced with these problems one at a time. Adding the costs to the lost revenue and organizing them into a logical manner displays how quickly these problems add up to a considerable sum.
Hydracore is confident in the reliability and cost savings of these heads. Three-month demonstration units are available to qualifying candidates for field testing. Adapting your drill to work well with another head is not an easy task. We have done the heavy lifting, so you don’t have to.
To date, all clients that have completed and tested the Hydracore head conversion have experienced immense success motivating them to convert more of their units:
‘The Hydracore head has been excellent for our drilling operations. It’s able to run HW casing through the head which is a big plus. The EF-50 drill has great features, except for the head. Running hydraulic oil through it has been a nightmare, we’ve had to rebuild it countless times. Now with the Hydracore head there’s no more worries. Two grease nipples are all there is for lubrication, the cylinder for the actuator is awesome, and easy to replace. Also, the support we’ve received from Hydracore has been amazing.’ Moe
Debler – Drilling Manager
Have we opened your mind to the importance of the right drill head? I hope so, as the benefits for your business, your employees and the environment really make this an easy decision. C
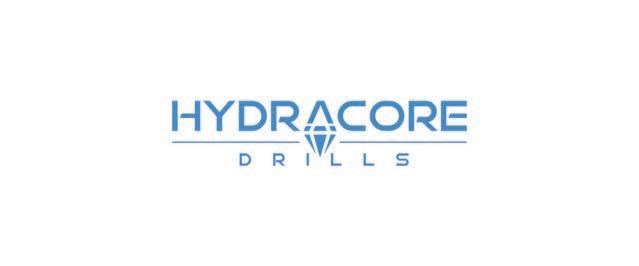
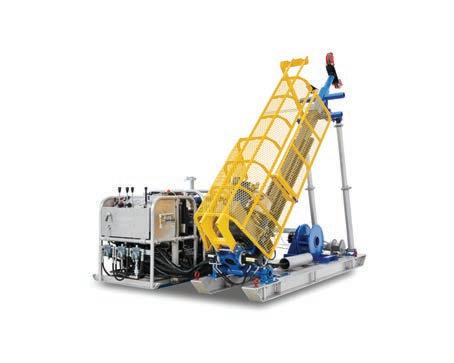
The new way of survey
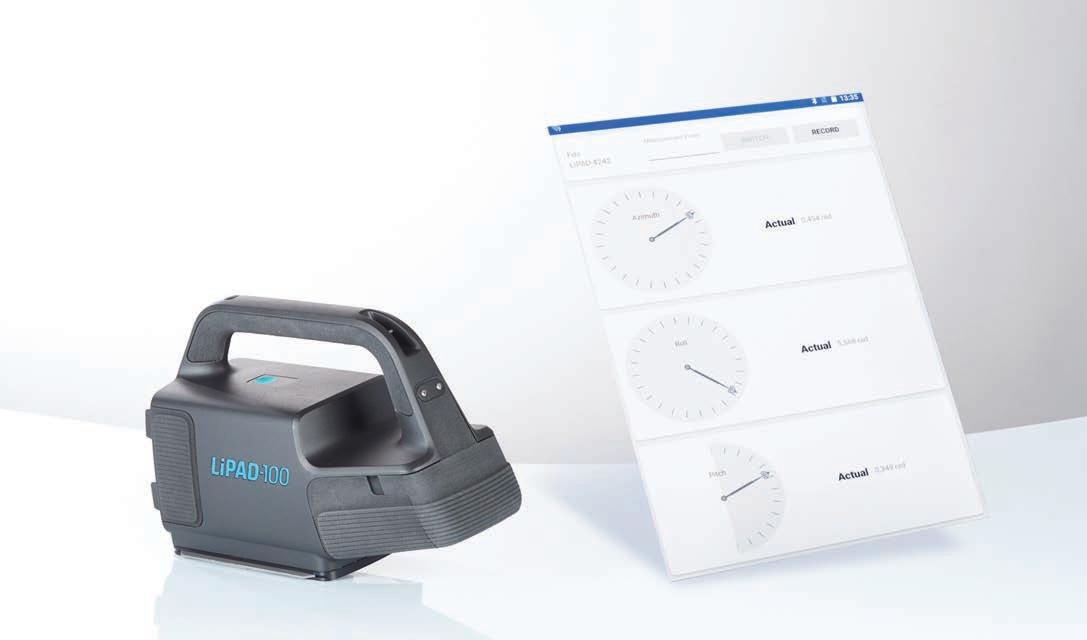
by Christian Martin Spannagel, Sales & Marketing Manager at LITEF
Has it always been your dream to hold a device in your hands that shows your exact orientation? Regardless of where you are and when? Unless you happen to be at either of the arctic poles, we can make your dream a reality. Outstanding tasks often drive technology development. At LITEF, we understand this very well. With almost 60 years of experience in the development and manufacturing of safety-critical inertial measurement systems, we are a proud pioneer, introducing new technologies, such as fiber-optic or MEMS-based inertial systems in avionic, marine and defense.
Mining operators and civil construction engineers have long been looking for an easy-to-use surveying instrument. A reliable device, ready to operate anytime, anywhere without additional setups or equipment, simple to operate – yet safe and reliable. Especially in underground operations, it is important that the instruments work independent of environmental influences, such as magnetic disturbance, temperature variations, shock and vibrations.
Now imagine a compact, hand-held device that meets all these requirements. A device that can be used for surveying, monitoring, alignment, adjustment and much more. We took up the challenge and converted one of our safety-proofed inertial measurement systems into a battery-powered North finder gyrocompass. The result: LITEF Portable Alignment Device, LiPAD®-100.
Drive for reliable independence
LiPAD®-100 is designed as a hand-held stand-alone system weighing less than five kilograms (11 lb). Roll, pitch and north heading directions
are provided in real-time. It is designed for one-man operation in small or complex environments. No special skills, additional alignment equipment or survey setup are required. Alignment, built-in test, performance control - everything is done internally.
In your hand, you hold the newest generation of navigational-grade fiber-optic gyroscopes and MEMS accelerometers. Combined, this advanced inertial system allows you continuous measurements - wireless and in real time - in environments where standard equipment is too bulky or GPS-dependent.
The LiPAD®-100 offers Bluetooth® connectivity to communicate with your hand-held device. An Android-based software app (free download in Google Play online store) enables the operator to control the device and view the measurement data in real time. All data can be stored and shared along with the operator reference, project name, date/time, and - if available - GPS information of your current position.
The base plate can be used for repeatable reference measurements as well as for attaching customized fixture mounts. The compact design en-
ables the operator easy handling, even in confined spaces. Two replaceable and rechargeable batteries ensure that you never run out of power. A battery charging device, a storage/transport case and a technical manual are provided with the system.
Uniqueness meets ease-of-use
LiPAD®-100 saves a lot of time on your measurement task. Measurements that normally take hours, are completed in just a few minutes. No wasting time until a surveyor has been contacted and is available on site. Thus, LiPAD®-100 drastically reduces downtimes during surveying tasks. The available personnel (e.g. drill rig operators) can carry out the survey independently, including measurement data storage and reports for evidence.
The success to-date confirms our approach: not long after commencing series production, LiPAD®-100 is now in use worldwide. We have received consistently positive feedback from mines in North America and Sweden, and from construction projects in Austria, Slovakia, Germany and Bhutan on the efficiency of this multi-talent. Moreover, new

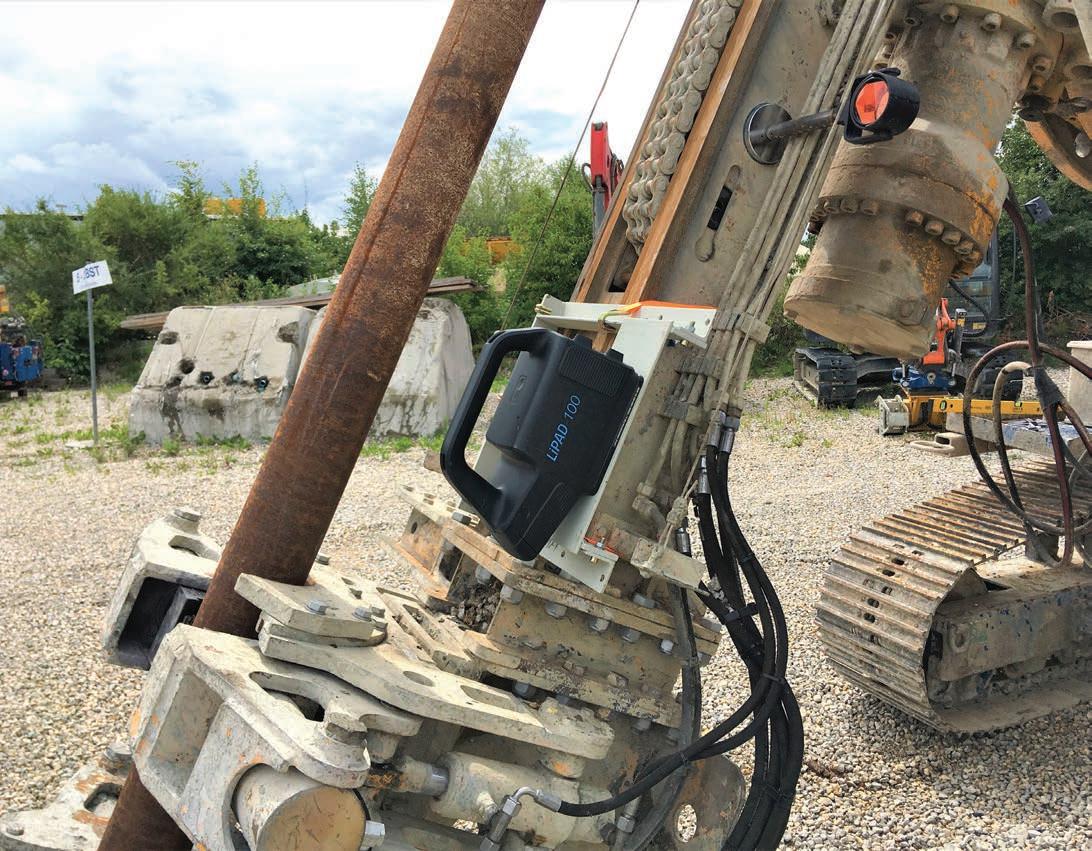
World map by Joel Wisneski, the Noun Project
Drill rig setup by Claus Kühne from LITEF
applications are constantly being added, about which even we are amazed to learn.
To illustrate what is possible with this measuring device, we have three examples of how it has been applied below:
Example 1: Perform approximately 300 injection drills in the cramped basement of a historical building in Vienna
A new subway line is to be built in Vienna’s city center. The tunnel will pass under a historic building of the University of Vienna, at a corner of the building and a depth of 26 m (85.30 ft). At this point, the building is to be secured by an additional concrete foundation. To construct the foundation, a renowned Austrian specialist civil engineering company was commissioned to drill over 300 boreholes, each 12 m (39.37 ft) long, from the basement of the building. The concrete was pressed through these boreholes into the ground at high pressure, each creating a cylinder with a length of approximately 10 m (32.81 ft) and a diameter of approximately 1.5 m (4.92 ft). The boreholes were drilled down vertically into the ground or at defined azimuth and pitch angles, so that each cylinder could also be created below the existing foundation walls. With LiPAD®-100, the drilling machines could be aligned quickly and with the required accuracy. Due to the limited space in the basement, the compactness of the device was key to continuous operation. This flexibility reduced the construction time from 21 to 15 days. The equipment and personnel were available for the next job six days earlier.
Example 2: Tunnel stabilization at hydroelectric power plant in Bhutan
Due to a collapse in an underground cavern at the Punatsangchhu-2 power plant on the Puna Tsang Chhu river, 18 000 m (59 055 ft) of soil injection and 19 000 m (62 335 ft) of anchors for back-anchoring were needed to stabilize the subsoil. Time was of the essence, so up to five drilling machines had to operate simultaneously, which also led to extremely tight conditions inside the tunnel. The handy LiPAD®-100 could easily be moved between the drill rigs to adjust the drilling direction. Measurements are always made individually without being affected by previous measurement error accumulation. The gyrocompass does not require a direct line-of-sight and the recorded data maintains overview of the large amount of the individually drilled holes.
Example 3: Borehole trajectory measurement at a landfill site
At a landfill site, drainage pipes are laid in the foundation of the landfill. In this particular case, one such pipe was defective and needed to be rehabilitated. For this purpose, a vertical shaft had to be sunk at the position of the damaged area. In order to determine the exact position, the course of the drainage pipe had to be determined from an existing shaft. The distance of the damaged area from the existing shaft along the pipeline was known from a previously performed video survey31.4 m (103.02 ft) along the pipeline. The course of the drainage line was determined with a small-sized MEMS memory rate gyro system from Inertial Sensing (isGyro). This tubular probe was pushed in manually with a rod and then pulled out again with a cable. Initial measurements of the heading, pitch and roll of the isGyro were taken during entry and exit with the LiPAD®-100.
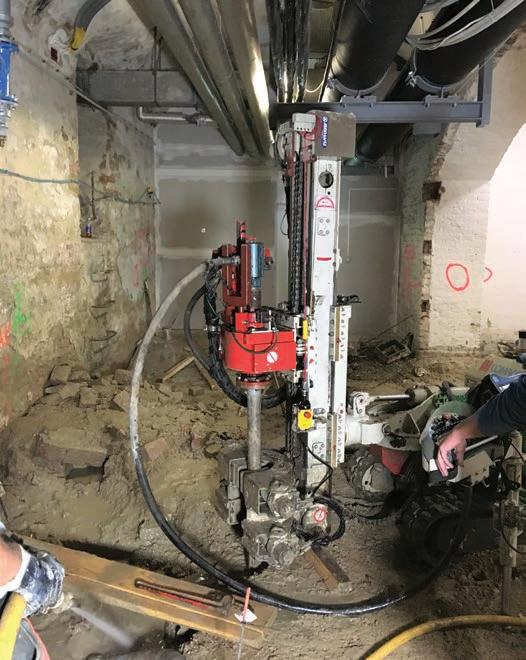
The isGyro used measures relative position changes throughout the survey process. The determination of the initial direction with respect to geographic north was carried out with the portable LiPAD®-100 fiber-optic gyrocompass. The combination of these two gyro tools resulted in an accurate trajectory over the complete length of 31.4 m (103.02 ft). Particularly in mining, small probes are often used for surveying and exploration. In combination with the LiPAD®-100, not only the trajectory but also holes’ absolute orientation may be determined.
Summary
LiPAD®-100 is a compact, easy-to-use gyrocompass that provides accurate north direction, roll and pitch angle in real time to your Android device. Its flexibility is suitable for alignment, surveying and monitoring applications, regardless of environmental conditions. Any operator can conveniently use the measurement device in the field, without necessitating time-consuming survey equipment setups. Especially for drilling work in mining, the battery-powered system works independent of magnetic influences, shock/vibration effects, temperature variation or harsh settings, like dust and mud – a solid companion for all circumstances. C
For more information
Visit the new LITEF website: www.litef.com
Basement drill setup by Claus Kühne from LITEF
Explore Advance and
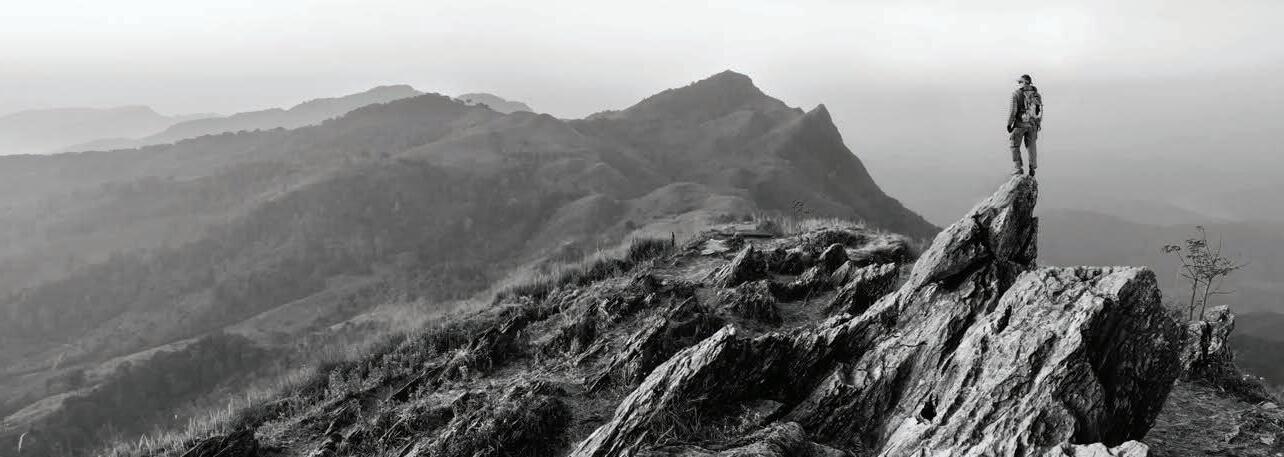
For over 35 years, Multi-Power
Products have been engineering and manufacturing an extraordinary line of exploration drilling equipment from our facility in Kelowna, Canada. Specializing in compact and portable solutions, our products include surface and under-ground diamond core drills, reverse circulation drills and support equipment.
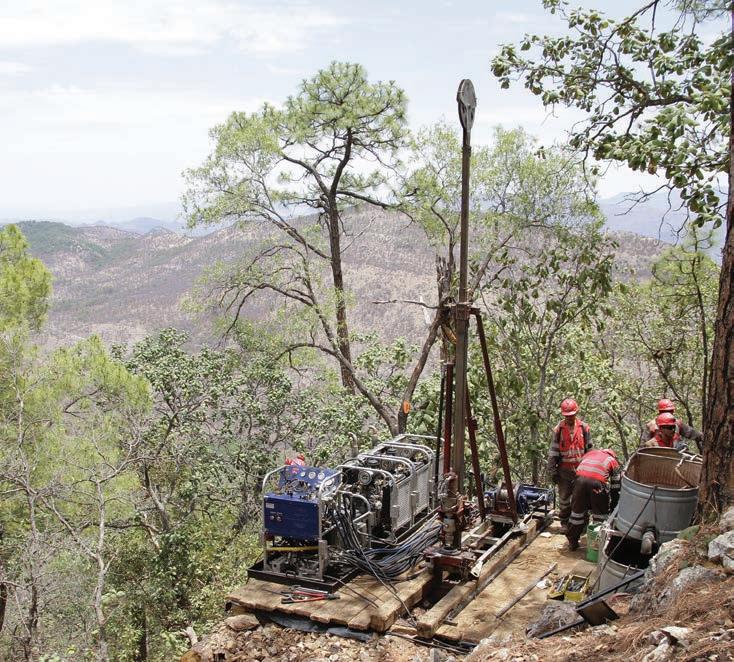
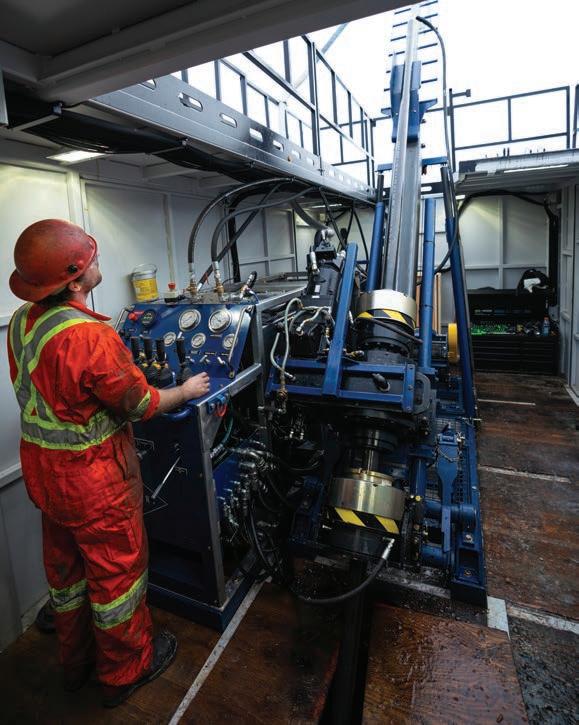
WE DESIGN AND BUILD:
• Helicopter and Man Portable Drilling Equipment
• Diamond Core and Reverse Circulation Drill Rigs
• Paramount Centrifuge – Fluid Recycling Systems
• Tracked Drill and Support Carriers
• Drill Rig Components – Level Wind Winches, Water Pumps, Rotation Units, Clamps and Parts Get the
Swick Mining Services reach 12 742 000 meters drilled milestone –the equivalent of drilling through the Earth
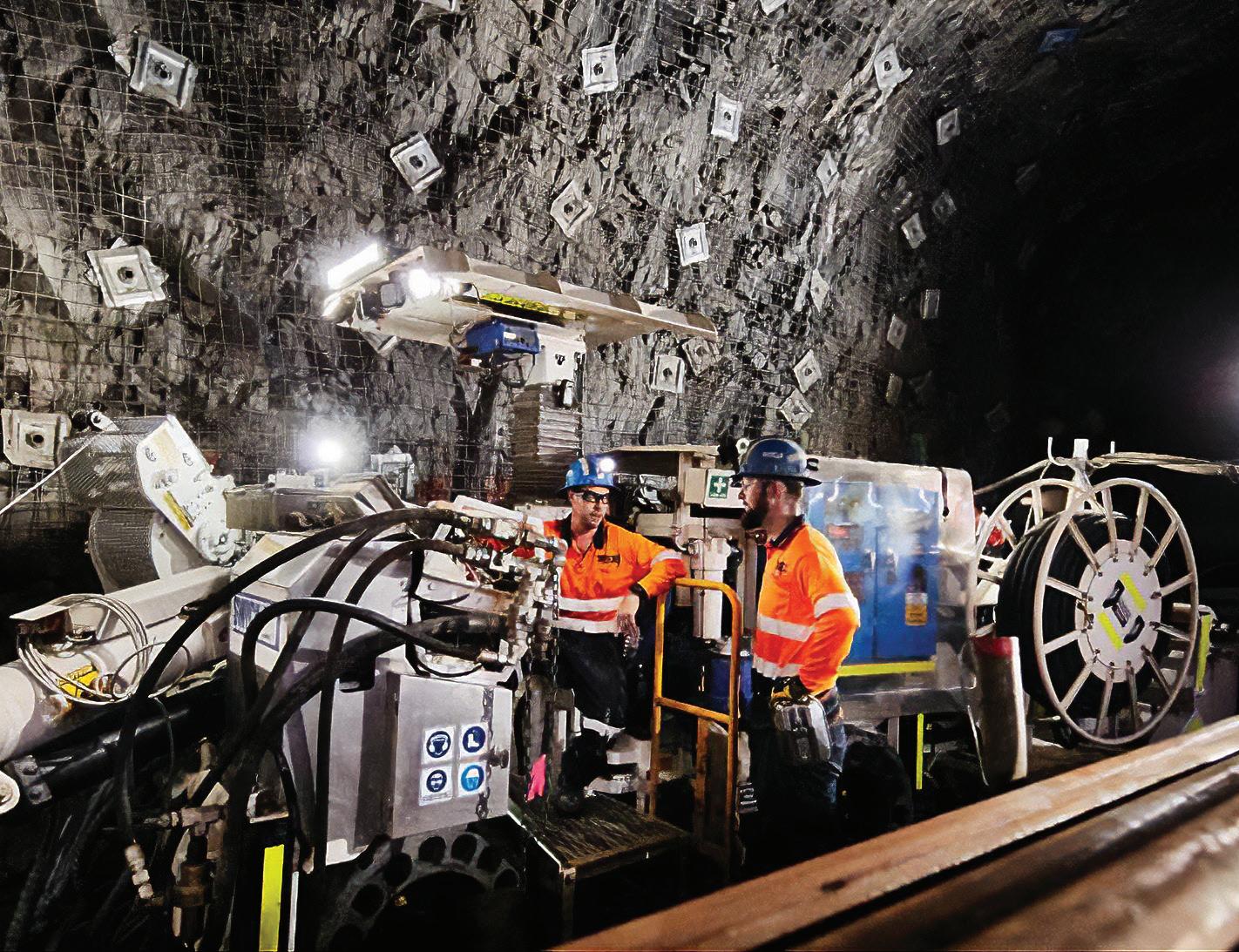
by Robert Burnett, Business Development – Swick Mining Services Ltd
Swick has reached the incredible milestone of ‘drilling through the Earth’ – a total of 12 742 000 m (41 804 462 ft) of core drilled as of March 2021.
To put that into perspective:
• The total weight of that core would equate to around 100 000 tonnes (all handled by hand)
• To fly over that amount of core at cruising speed in an A380 jet would take over 14 hours
• Swick has consumed over 100 000 drill bits to meet that goal
• To achieve that milestone around 6375 rig months have been drilled or 531 rig years (24 hours a day, 365 days a year)
• With two men per shift that is 9.33 million manhours of hard work by the specialist underground crews (a huge effort and a lot of wages)
Reaching the distance of 12 742 000 m (41 804 462 ft) has also come with many challenges: intensive underground grade control drilling, underground exploration drilling, navigational drilling, geotechnical and geophysical engineering/service/paste hole drilling, water control drilling, and gas control drilling.
Swick’s History
Since initially commencing as a longhole underground production contractor in 1997, the company has supplied drilling services to some of the most well-known and respected global mining companies across Australia, Europe and North America.
In early 2004, Kent Swick, Founder and Managing Director saw an opportunity to grow and expand his business by entering the underground diamond drilling market. Being a mechanical engineer who was used to working with a large mobile mining fleet, it was surprising for him to see that the underground core drills were skid-based and very tedious and time consuming to move around the mine. As a result, Swick was able to quickly generate a competitive advantage by placing underground diamond drill rig components on a mobile single boom development jumbo and the Swick mobile diamond drill was born. Swick’s first underground diamond coring client was Reliance Nickel at the Beta Hunt mine in Kambalda, Western Australia and has since worked with 52 individual clients. Swick’s current workforce is now in excess of 600 employees with a fleet of 77 underground drill rigs globally.
Kent Swick’s personal objective was to make a difference to the underground mining sector and Swick will continue with its objectives to improve the safety and productivity of the under-
ground diamond drilling industry. Swick achieves this by supplying a high level of professionalism, reliable performance, strong client relationships and invests heavily in the training and development of its staff.
Swick has a strong engineering acumen in the business and has constructed its own drill rigs since 2004 and invests heavily in research and development of drilling equipment and systems. Providing safe, reliable and efficient drilling helps our clients execute their mine plans with less unknowns, producing a longer sustainable mine life.
The key part of any business is its people, and Swick aims to ensure our crews feel supported and part of our global family. Swick’s retention of staff in 2021 has seen over 100 employees inducted into the 10 Year Club, which helps to maintain Swick’s core values. Swick’s reputation for creating the best drillers within the industry through its intensive training packages has strengthened the entire market and are highly sought after by our competitors.
Swick understands that innovation is the key to our continued success as market leaders in the Drilling industry. Innovation hasn’t been reserved for just our equipment. Our award-winning Induction Facility has improved staff retention and set the foundation for strong safety and reporting culture. Innovation in our equipment design will ensure continued success in safety and further reduce risk and injuries to our staff.
Our partnerships with clients have resulted in the successful delivery of numerous major R&D initiatives that have greatly influenced the global underground diamond drilling industry. We continue to develop new innovative solutions to mitigate safety hazards, maximize productivity and reduce crew fatigue. Swick, with all its innovations and advancements, has increased productivity by 17% since 2016. In a work environment that only gets deeper and more complex each year, that’s a solid achievement.
A great example of the constantly evolving improvements through rig design has seen Swick recently complete an outstanding shift drilling 200 m (656.17 ft) for the first time in its

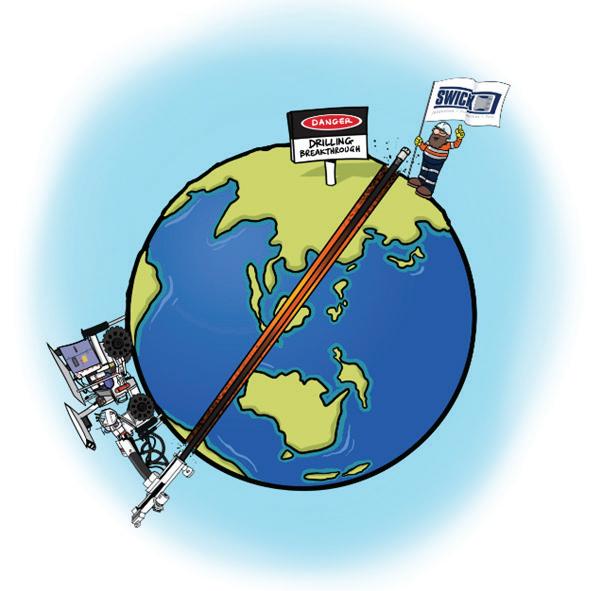
unique history. There are many elements to achieving this amazing effort, forward planning, time management and clear communication with Driller and Offsider optimizing the Swick’s Gen II innovation.
Swick’s new dedicated deep drilling division, DeepEX, can drill diamond drill holes to over 2000 m (6561.68 ft) from a standard underground drill site. The goal of DeepEX is to meet the needs of Swick’s customers as mines get deeper and drilling exploration holes from surface become less applicable due to depth, angle of attack, permitting or access.
Operating an underground DeepEX drill rig is done at a significantly lower cost than surface rigs so shallower holes at a much lower cost per meter are expected to attract customers and allow optionality for miners when considering targeting extensions to their mines.
More information can be found at: www.swickmining.com C
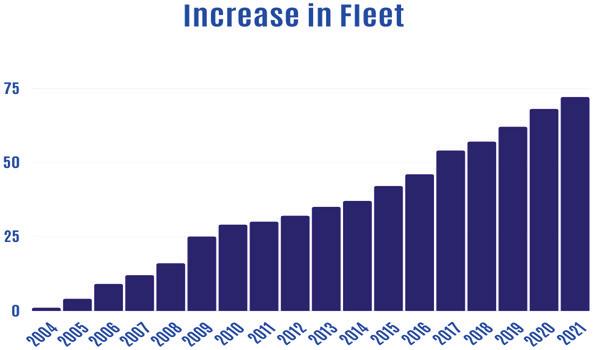
The graphs represent the climb in meters to meet the milestone
the journey
MBI Global & VersaDrill grow their strategic alliance into a merger
by Daniel Misiano,
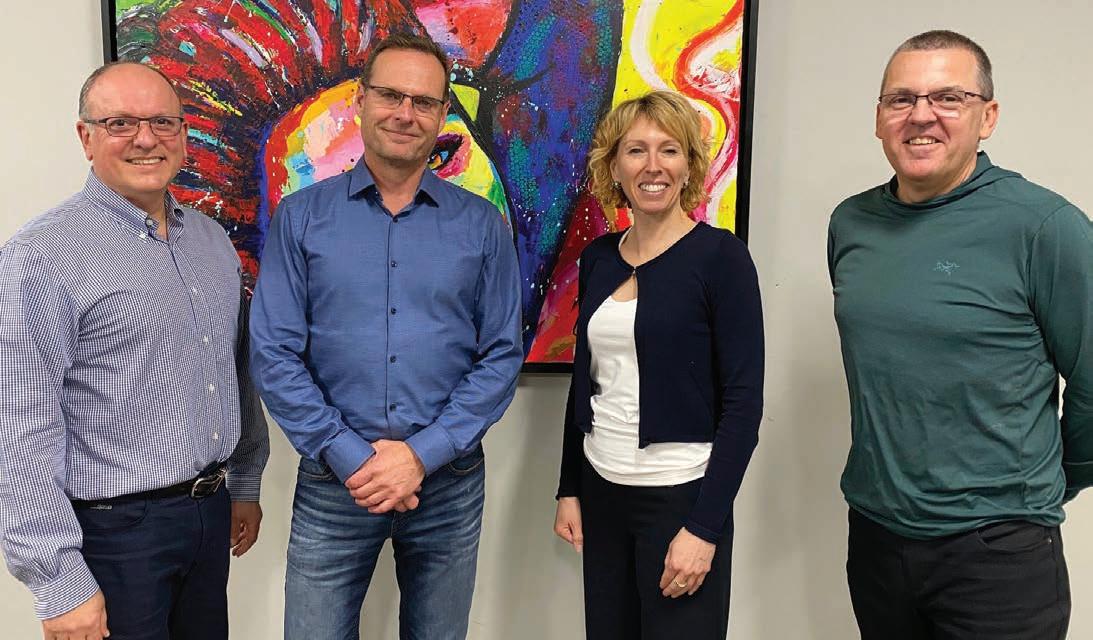
After seven years of a strategic alliance, we are proud to announce that MBI Global and VersaDrill Canada merged in early May, 2021. The new entity, under MBI Global, will benefit the market with a complete offering of capital equipment (VersaDrill) and consumables (MBI Global) for the mineral exploration segment as well as capital equipment (soon to be supported by consumables) for the geotechnical drilling segment under the Gtech product line. The industry can expect to have service and support in over 15 distribution points and across more than 30 countries globally. We plan to offer the market new innovations over the next few years with a focus on safety, increased productivity, automation and improved efficiency.
President at MBI Global
The new MBI Global management team (left to right): Pietro de Ciccio – COO, Mario Rouillier – Chairman of the board, Claudine Bellehumeur – CFO, Daniel Misiano – President

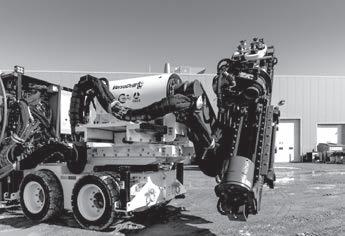
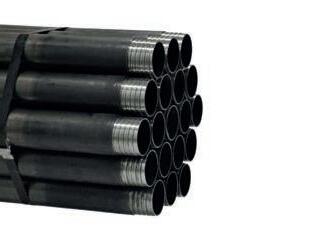
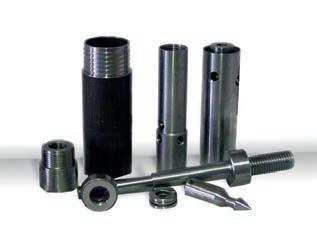

The collaboration between MBI Global and VersaDrill began in 2014. Our vision was to create a complete exploration core drilling solution for the industry. Since the industry was still in a depressed mode, we continued to push forward with the intention to adapt to the market reality and its needs. Slowly but surely, we initiated a project to propose drill components (heads) that could be adapted to existing drill fleets of other manufacturers and it succeeded.
‘Our company believes that any gains relevant to production stem from better understanding of the user realities, challenges, and reciprocal feedback.’
VersaDrill also opted to realign its strategic mission to innovative safety-oriented products for the exploration segment as well as new product lines, intended for geotechnical drilling. As the market demand grew, so did the successful collaboration between our companies. Today both help benefit the industry and our merged companies through collaborative projects aimed to improve mineral exploration and geotechnical drilling.
Going forward, one of the main goals of the united company will be to further expand our geographical footprint to support our growing customer base and offer them a sense of improved proximity. Whilst the industry continues to evolve, customer support and interaction are still the most valued criteria asked and appreciated by clients and distributors alike.
The new company will offer new products, the majority of which will stem from the VersaDrill product line where safety, productivity and efficiency are put at the forefront. The services segment will be better adapted with improved support and access to products, product documentation and technical support.
Our company believes that any gains relevant to production stem from a better understanding of the user realities, challenges, and reciprocal feedback. As such, several developments already announced - and soon to be - will continue to be driven from these baselines. Customer and end user interaction have been key elements in the process of innovation in both exploration and geotechnical segments and will continue to be a cornerstone of our values for better and improved adapted products. As the industry segments that we service are on the upside, we aim to take note of some of the key challenges, such as growing lack of qualified labour, quicker than expected promotion of operational staff, thus increased need for automation and training support, need for added safety features to address the new inexperienced work force which is constantly asked to produce more. Our industry is at a very interesting chapter and we aim to take full advantage and the leadership role. C
For more information
www.mbiglobal.ca www.versadrillcanada.com www.gtechdrill.com
Expect more announcements and new products from MBI Global and VersaDrill in the next Coring issues.
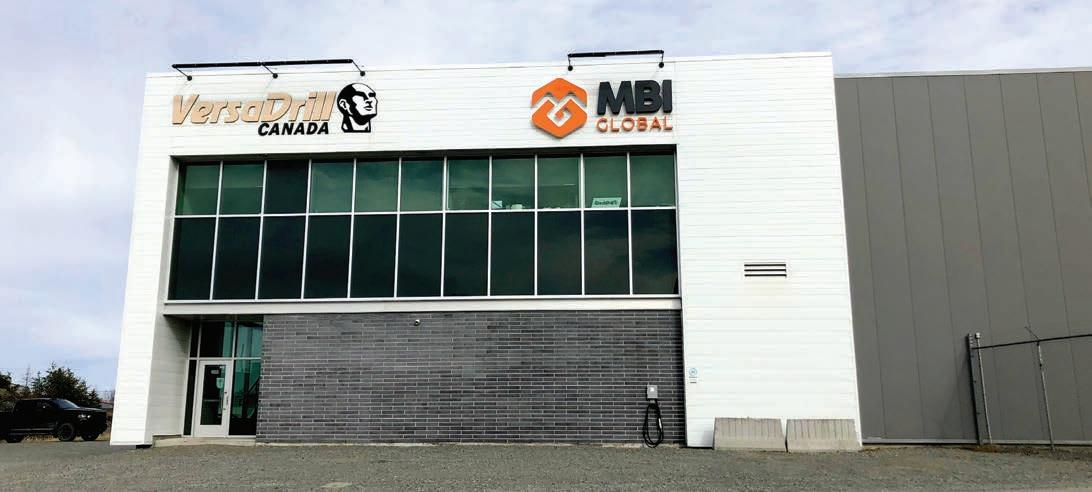
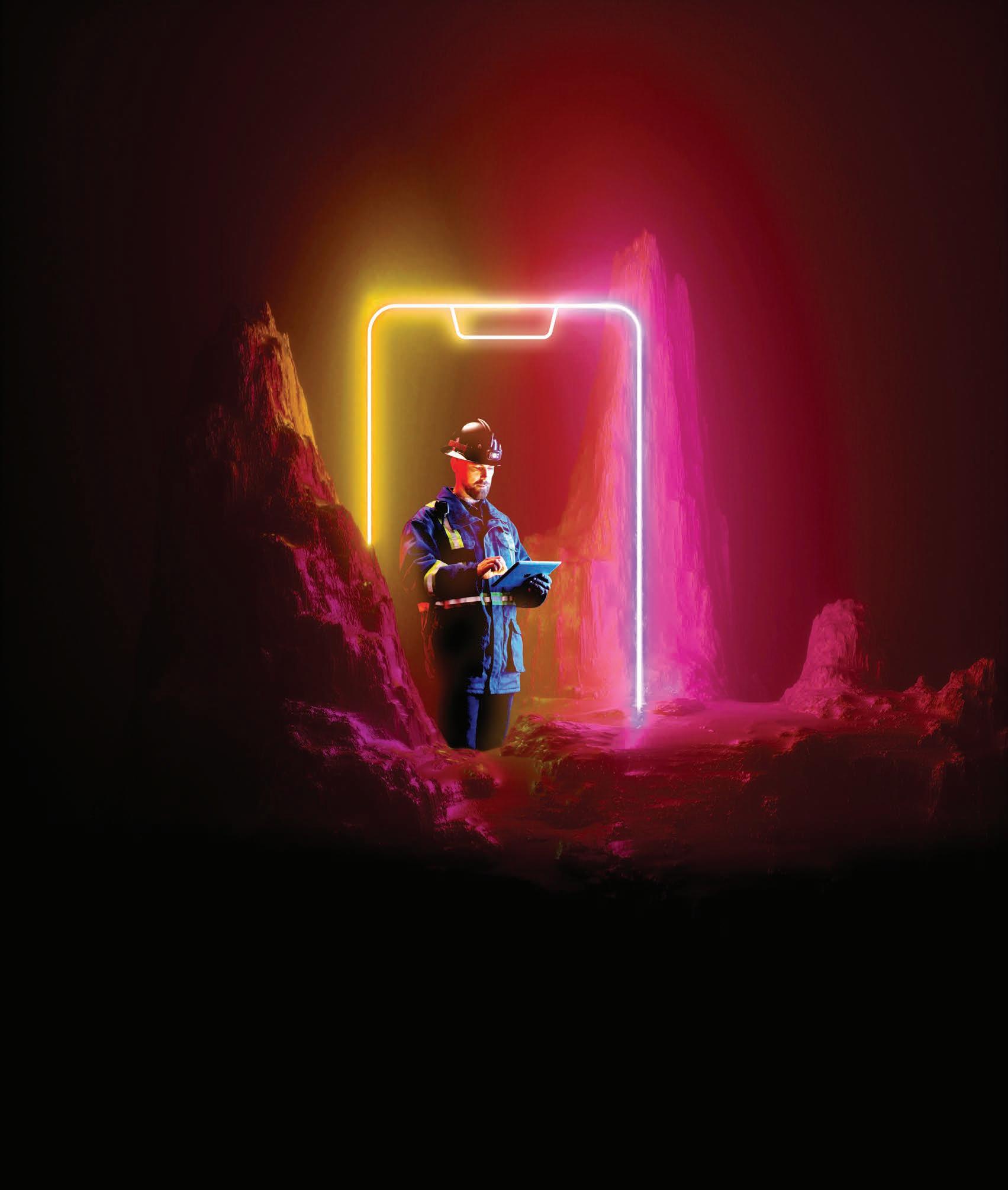

Designing resource drilling as an investment decision and not a cost
by Andrew Dasys, President at Objectivity.ca
If you could, would you take the opportunity to de-risk a mineral property faster:
• without changing the qualified person’s sampling requirements,
• without affecting existing drilling accuracy,
• without adding new constraints to the production department,
• without needing any new capital investment, and
• while decreasing in field risks at the rigs.
Not only does it sound like a no-brainer it is also an objective that mining has to be able to reach. Bringing mineral resources into production quicker is critical to improve how the investment world sees the mineral industry. In 2019, a study by MineEx Consulting1 summarized that between 2005 to 2017 the cost of finding and bringing a Tier-1 property into production increased 3.8 times, while the meters drilled increased 2.8 times. Even more interesting is that the value of metal found between 2008–2018 is less than the cost required to find it giving the industry a ‘bang per buck’ of 0.55.
Objectivity.ca is trying to help solve part of this problem by focusing on increasing the efficiency of drilling and de-risking a late-stage mineral property. What we have found across a range of projects is that Artificial Intelligence (AI) software and changing practices can make a bigger improvement than faster drills.
Since being selected as a semi-finalist in the Integra/Goldcorp’s Disrupt mining challenge, Objectivity’s resource optimization system (DRX), which stands for ‘Drilling, Reporting, and Targeting, where X marks the spot’, has been used globally to improve drilling efficiency on a wide range of resource drilling projects. DRX is an Artificial Intelligence tool which ad-
1 www.minexconsulting.com
dresses industry needs and maximizes the use of limited capital and human resources to improve project execution.
When compared to existing drill layouts, DRX’s AI algorithms increased resource conversion efficiency by more than 20% in 95% of the cases. These projects included underground drilling, surface drilling, combinations of the two, with and without actively deviated drilling. Improved efficiencies were obtained regardless of the drill plan and deposit type.
The efficiency improvement, calculated as the number of meters required to upgrade a cubic meter of resource from inferred to indicated to measured, can either:
• decrease drilling time,
• reassign budgeted meters to discovery or step-out drilling, and/or,
• increase the tonnes/Oz of metal being de-risked for a given amount of drilling.
Having the capability of quickly generating complete drill programs meeting all site constraints, provides the project teams with improved confidence in their drilling designs and in the program’s expected deliverables. This significantly reduces the risk of delineating or upgrading any project.
You already own ‘clean’ data
Unlike many machine-learning based exploration targeting systems, DRX does not rely on finding multi-dimensional relationships within historically collected geoscience data. Instead, DRX focuses on maximizing the value of the drilling investment based on information available in most technical reports. This means that all projects that have an initial resource have ‘clean’ data that can be immediately used to improve the next phase of resource development - data quality and quantity are far less of an issue.
‘The
El Peñón post drilling analysis
indicated a
15–40% reduction in drilled meters
required
to convert
inferred
to indicated resources between the manual drill planning and Objectivity’s DRX optimized drill plans, demonstrating the significant cost savings potential of the tool/ process. DRX was one of the AI technologies deployed at El Peñón’, said H. Marsden, Yamana Gold Senior VP of Exploration
The technical report also provides a clear description of the QP/CP-required estimation and classification requirements. Combined with the site’s geometry and volumetric information, the objectives to optimize the detailed drilling plans moving from inferred through measured resources also exist.
Adapting to changes
DRX provides project teams with options and the confidence that they are drilling the best possible plans given the information that they currently have. Varying the objectives allows the teams to explore the value/cost of maximizing sampling for specific geoscience information: e.g., metallurgy, structure confirmation, continuity etc.
Unlike most drill hole planning tools, DRX does not require drill holes to be individually planned and drawn. This frees up geology staff time to focus on more complex tasks, such as interpretation.
Unlike many resource optimization methods, DRX does not change the search parameters to decrease drilling costs. Instead, DRX uses a unique targeting model that combines both quantified data and qualified interpre-
tation. In conjunction with field constraints, DRX can produce specific drill plans to meet the immediate planning needs and update in near-real time as new information is produced by the drills (location) and by project geologists (assay, interpretation).
It’s about integration
Planning produces efficiency. Production generates value. DRX is designed for IOT connectivity, allowing data channels, when available, to feed directly into the targeting algorithm. Times are changing, drills are producing more data, assaying time is decreasing and becoming more accurate, and this increases the amount of data that a geologist has to process. By allowing geologists to focus on strategy, DRX’s IOT-ready design deals with the detailed data streams to optimize drilling campaigns.
It’s about money
DRX uses AI and optimization algorithms empowering project teams to make informed decisions on how drilling budgets can be maximized to increase resource conversion while
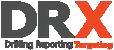
Constraints
also improving orebody knowledge (geochemistry, geotechnical, geology structures). Because DRX produces a variety of plans across a range of budgets, it uniquely provides an investment curve (see Figure 1). Project teams can make informed, objective decisions as each point on the investment curve corresponds to a full drill plan.
DRX provides sensitivity analysis for drilling programs. And since the investment curve is non-linear, the more you drill, the less incremental value you are generating. You can al-
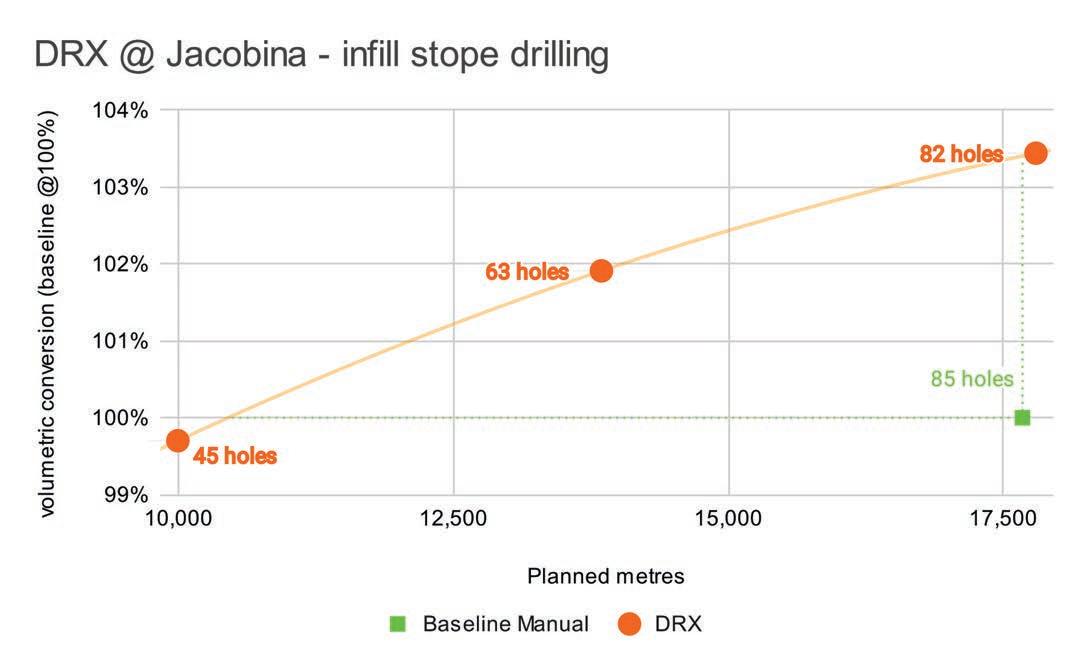
Figure 1 - DRX investment curve at Jacobina project
Geology
DELIVERING INNOVATION WORLDWIDE SINCE 1988
Having successfully completed over 500,000 directional meters since 1988, and delivering game changing innovations for over 30 years, we are the standard in directional core drilling and leading suppliers of borehole surveying instrumentation and belonging software.
// Directional Core Drilling Services
// Downhole Navigation
// Core Orientation
// Rig Alignment
// QA/QC Data Management Software
If the goal of exploration is to find, why not find everything possible?
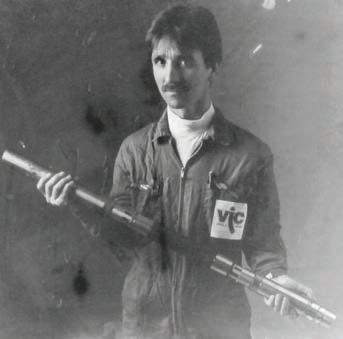
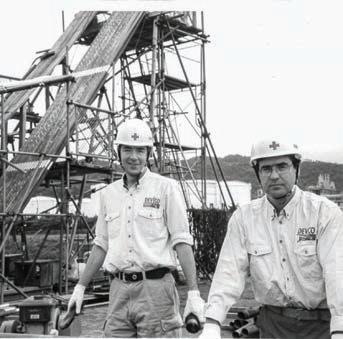
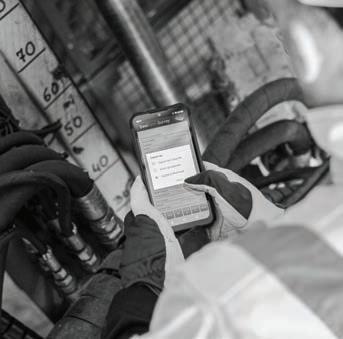
1988
• DeviDrill, the world’s first directional core barrel invented. Devico AS is founded
• DeviSoft directional drill planning software launched 1992
1995
• DeviTool invented for toolface orientation of DeviDrill, first onboard electronic survey tool during drilling
• DeviTool launched as standalone Electronic Multishot (EMS) survey instrument 2000
2002
• DeviDrill wireline was introduced. PeeWee 30 mm EMS tool with integrated running gear was launched
• DeviFlex non-magnetic survey tool with robust strain gauge technology launched 2003
2006
• DeviCore core orientation system launched
• DeviShot EMS and DeviCore BBT with bluetooth wireless communication launched
2017
2013
• DeviFlex RAPID, first driller operated, continuous survey tool launched, with at-rig QA/QC software
• DeviAligner north seeking rig alignment system launched, setting a new industry standard for accuracy and settling time
2019
2018
• DeviGyro, continuous high speed miniature survey instrument with modular design for a large variety of applications ranging from 30 to 400mm
• DeviGyro Overshot Xpress released, continuous overshot surveying with minimal survey time/impact to drilling process
2021
2020
• DeviCloud is launched, the complete survey data management system for mining and civil applications/for drillers, geologists and engineers
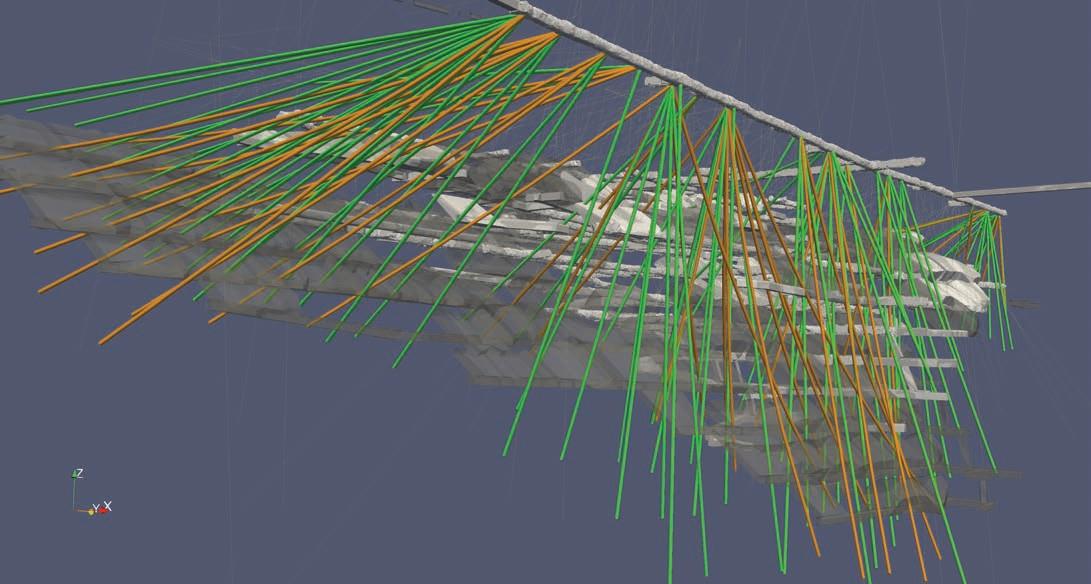
locate drilling capacity to maximize resource/ reserve drilling to meet production requirements if you have multiple zones available.
Underground projectYamana Gold’s Jacobina mine
Figure 2 shows the drill hole locations for a baseline plan (green) and one of the DRX generated plans (orange). The drill plan is designed for a highly constrained stope and in-fill drilling program at Yamana Gold’s Jacobina mine. In this case the drill program is being designed to de-risk stopes a final step before moving to production. The working environment is highly constrained by the fact that drill rigs setup is dependent on production timing. Additionally, safety offsets from the existing and planned drifts/crosscuts greatly limit the location where holes can be ‘threaded’ to hit the deposit.
Having been given the mine’s detailed sampling criteria for the planned stopes, DRX generated a number of plans meeting the availability and geometric constraints. Each of the DRX plans also reported on how each of the required KPIs was being met.
Although drill plans are three dimensional, DRX results are initially presented as a 2D
investment curve. Because each point on the curve corresponds to calculations made on an AI-generated drill program that meets all project specific constraints the team can quickly decide how many meters should be invested in each drilling program.
Figure 1 shows the DRX investment curve where the 17.5 km (10.9 mi) 85-hole baseline plan is shown in green. Plans that plot to the upper left produce higher volumetric conversion for less drilling. Each point on the curve corresponds to a complete drill hole program incorporating natural deviation, meeting all constraints and adapting to new data. The project team can decide what is of higher priority given their current constraints: decreasing drilling meters, and time, for the same conversion or increasing the volume being de-risked.
The DRX curve also shows how increasing the percentage of a volume that is de-risk, properly drilled off to meet a sampling requirement, demands a non-linear amount of drilling. Getting the last 5% of the volume derisked will always require many more meters than de-risking the first 5%.
With a number of plans and their associated KPIs, mine staff can objectively access the plans and decide whether continuing to drill is adding significant value. If you consider that all mines have more volumes to explore and derisk than drilling capacity, ensuring that each
volume is drilled efficiently allows drill capacity to be re-allocated elsewhere in the mine. This increases the opportunity to grow the resource (step out drilling) or drill new exploration holes.
Many of the emerging geoscience-based Machine Learning AI tools focus on exploration and discovery, they will help you decide where to drill. DRX will tell you when to stop drilling. Ultimately, DRX is a business decision support tool that integrates drill hole layouts to maximize the value of each meter drilled.
Open pit project –Royal Nickel Corporation’s (RNC) Dumont project
Royal Nickel Corporation applied DRX to their Dumont open pit project, located 25 km (15.5 mi) northwest of Amos, Quebec, Canada, to evaluate our technology. The Dumont project posed many challenges, such as minimum drill hole spacing, limited surface drill setup locations due to waterway exclusions, limited dip angles, potential structural exclusion zones etc. This meant expensive drilling setups, so RNC needed significant improvements to conversion efficiency of a volume of ground from the indicated to the measured category, while meeting all project constraints.
Figure 2 - Jacobina 85 hole baseline plan (green) and DRX 45 hole plan
RNC was interested in DRX’s capability of producing multiple drilling plans based on varying budgets. Creating multiple valid options enabled the company to select the appropriate plan that best aligns with its strategic goals and budgets.
When compared to the manual layout, the DRX-3 solution decreased the total number of drill holes from 64 (in manual) to 54, by finding locations where two or more drill holes could be drilled from the same drill setup. Not only that, but it also produced a 48% increase in conversion rate (2975 m3/m in manual versus 4394 with DRX-3). Such an increase in resource conversion efficiency saved money, but more importantly, it saved time.
In conclusion, maximizing the value of each meter drilled increases the value of each limited drilling season or may decrease the time required to bring a resource to market. Notwithstanding the optimizing capability, DRX provides real choice flexing rapidly changing economic, operational, geologic, and even social/political conditions.
Increasing operating time while decreasing operator risk
Another outcome from optimizing a resource drilling operation, such as the Dumont project, is that the algorithm can often decrease the
number of drill pads/stations required to complete a program.
In Figure 3 we compare a DRX generated program to a baseline ‘optimized’ program. The decrease in drill pads does not affect conversion efficiency, in fact the DRX program increases de-risked metal, while also decreasing total meters drilled. The decrease in meters drilled proportionately decreases the time required to complete the program.
The most interesting point in this program is that the DRX plan almost halves the number of setups required. This has several positive outcomes.
The overall environmental footprint and ground disturbance is reduced. Fewer pads mean fewer access roads. If existing pads can be used, then there is no additional ground disturbance and a potential reduction in permitting requirements.
Operator risk and exposure is reduced by eliminating the need to mobilize and demobilize the drill rigs.
And finally, because there are fewer drill rig moves the rig spends a larger proportion of its time drilling producing valuable data. C
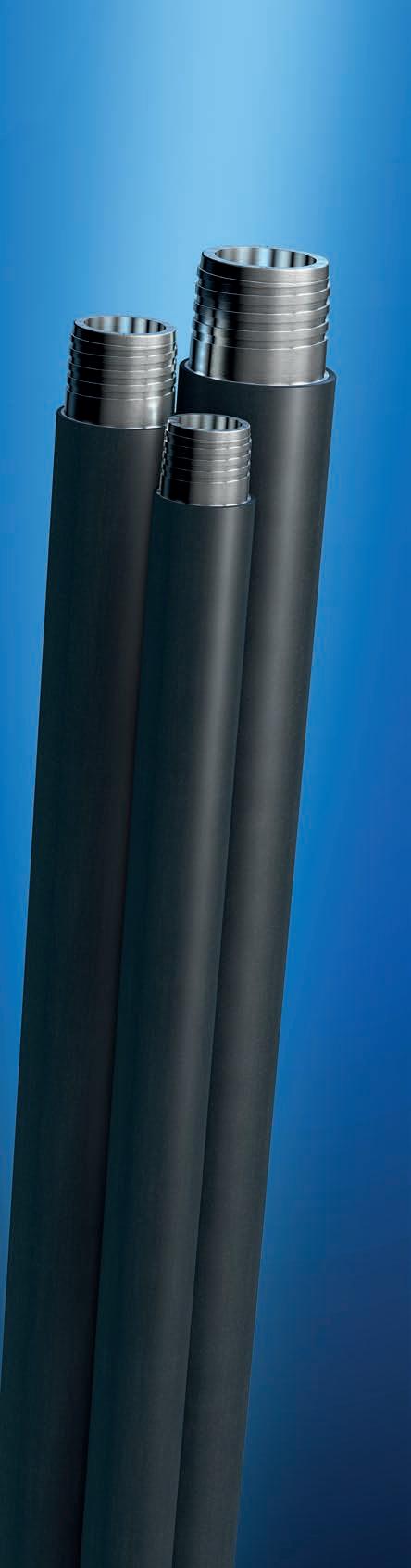
McKay Drilling and Tribe Tech: The autonomous alliance slated to change the industry
The World Economic Forum in 2017 predicted that automation and digitalization could save more than 1000 lives and avoid more than 44 000 injuries over the next decade.
With workforce safety being a key issue within the mining industry for decades, the move to autonomous has long been seen as the next step to bring greater safety to mine sites. There has been only one obstacle – the impossibility of removing the human factor from on-site drilling operations. Until Tribe Tech (Tribe) came along.
Tribe Tech is the first Original Equipment Manufacturer (OEM), in the world to successfully develop a completely unmanned Reverse Circulation (RC) drill rig. Their rigs not only remove workforce risk but increase drilling time by 100%. Now, McKay Drilling (McKay) has partnered with them to purchase their world-first autonomous RC drill rig.
An alliance with the potential to change drilling
Tribe Tech was founded in 2019 to create a safer, more efficient work environment in the mining industry. Backed by a combined 257 years of experience, the company was originally established in Australia to service its multinational clients. Since then, Tribe have increased its staff to become the largest dedicated RC drill engineering team in the business, and have developed a reputation for automating the toughest tasks in the industry. In the process, Tribe has grown globally with offices and world-class manufacturing facilities in Belfast, Northern Ireland. They offer contractors a roadmap for improved safety and technology, putting them at the top of the list for contracts with Tier 1 mining companies.
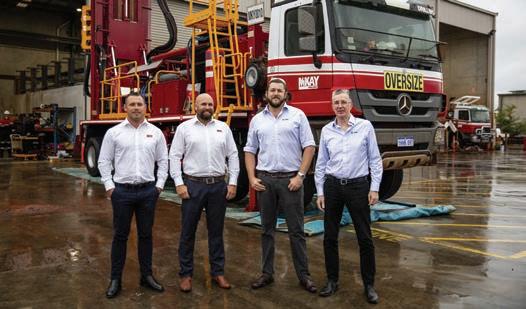
‘Tribe Tech was born from a real desire to improve safety and efficiency in the mining industry,’ says Managing Director Charlie King, who boasts more than 15 years of hands-on experience in the mineral industry. ‘We saw the opportunity to reduce workforce risk and operational costs, while increasing productivity and efficiency,’ he continues.
At first Aaron Earl, General Manager of McKay Drilling thought Tribe Tech’s, as well as many other similar projects, too far fetched. Until he saw their solution for removing all the people from RC rigs. ‘The uptake from our blue-chip clients has been phenomenal, we have just been awarded our largest contract to date on the back of this technology and our team’s technical expertise,’ says Earl.
A partnership built on synergy
Established in 1990, McKay Drilling has provided a high-end drilling service to the exploration and mining industries for over three decades. Operating throughout Australia and internationally, McKay set the standard for drilling as the provider of choice for the mining industries Tier 1 companies.
Charlie King is no stranger to McKay Drilling, working on tools there at the beginning of his career a decade ago. King’s knowledge and lasting connections with the company led to a phone call with McKay’s Drilling Operation Manager Chad McKay about Tribe’s latest development, starting the idea for the partnership.
‘It’s great to be working with the McKay team again after all these years, it’s great to have the support and technical input from the leaders in RC drilling,’ says King. ‘The synergies were fantastic. They had been working on their own automation programs and have unparalleled technical expertise.’
Looking forward
Off the back of the alliance, Tribe Tech has received growing interest in its product offering and its ability to tackle other automation challenges in different drilling methodologies and beyond. McKay, on the other hand, have not only received their biggest contract ever but have also announced that they have sold to industry leader Major Drilling for up to USD 62 million. The deal is expected to close in June 2021. Afterwards, McKay will retain its brand and leadership.
With the sale, the alliance between McKay and Tribe Tech is in prime position to develop and deliver the innovative solutions to solve many of the industry’s biggest challenges now and well into the future.
‘It’s a really exciting journey we are on and the opportunity to increase efficiency and safety at the same time is an exciting space to be in,’ concludes King. C
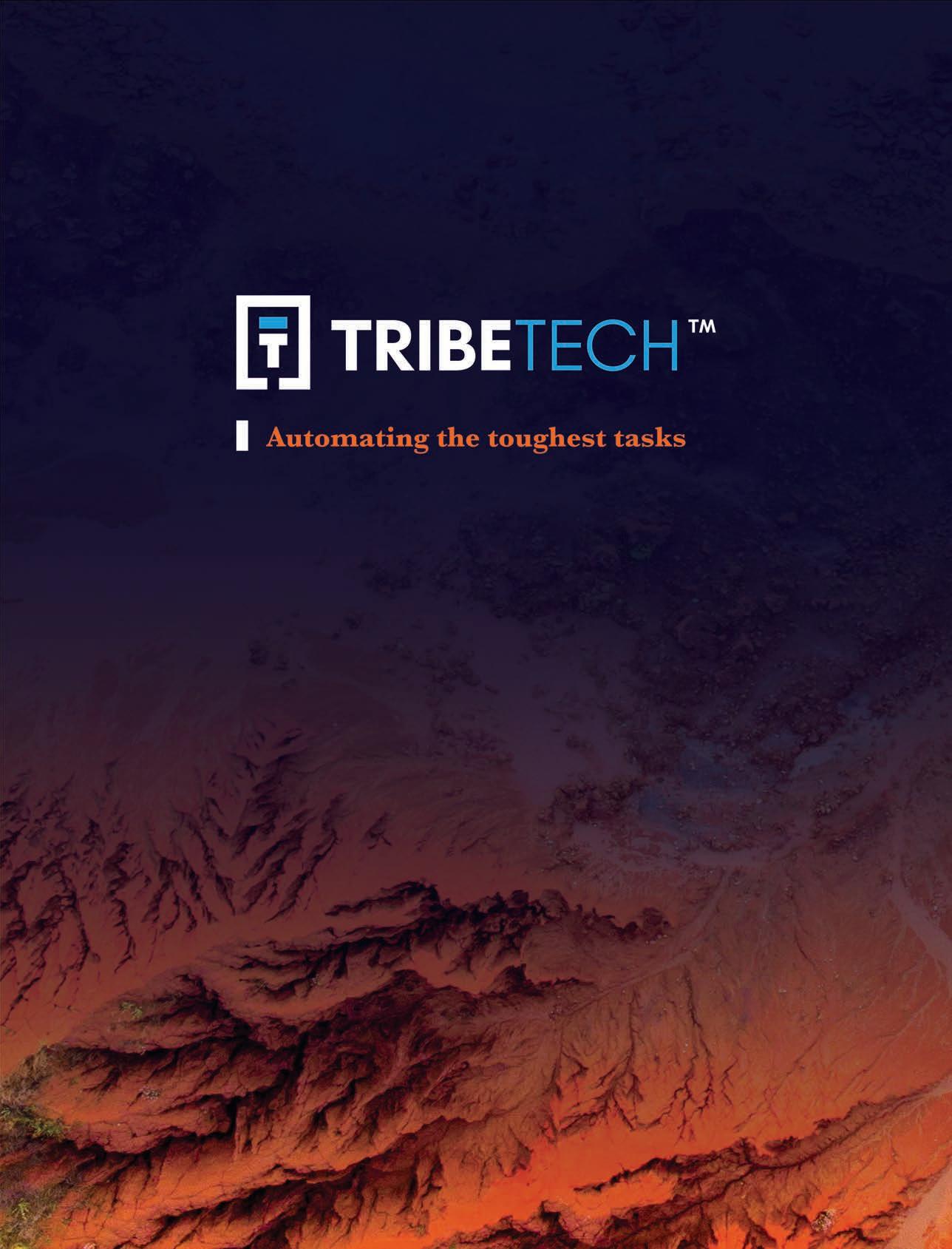
Members of the McKay Drilling and Tribe Tech teams standing in front of the McKay Rig 10
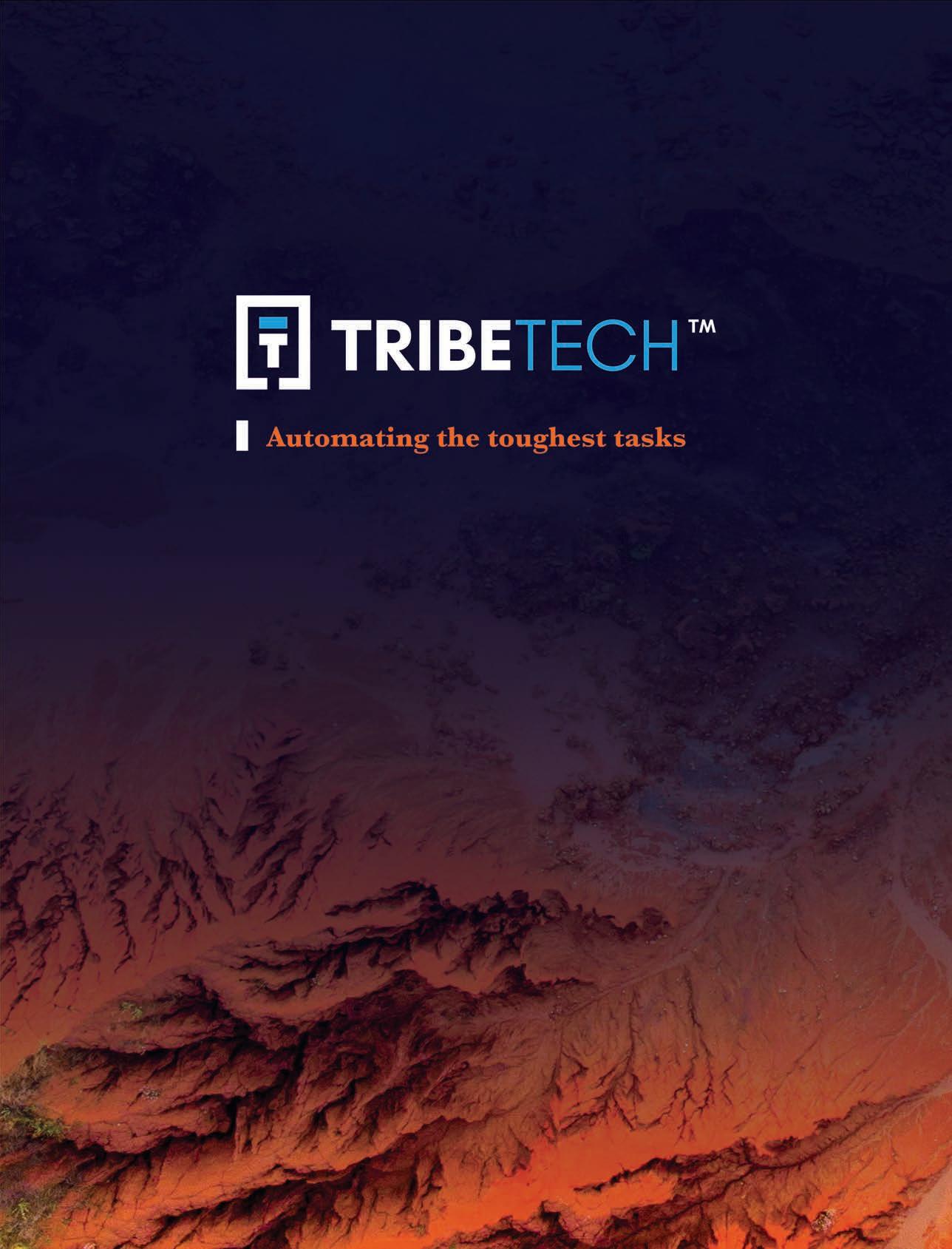
Exploration Mining Geology
In this issue:

Q&A from the experts: In conversation with Dr Alan Wilson, Director and Chief Geologist at GeoAqua Consultants Limited
Welcome to the jungle: Exploration on the frontline of one of West Africa’s forgotten gems: Liberia by Rowan Thorne, Project Geologist at Origin Exploration Ltd.
Metamorphic Mexico: The Sierra Madre Occidental by Jane Lockwood, Spotlight Mining
The Ewoyaa Lithium Project by Iwan Williams, Exploration Manager Ghana, Lennard Kolff, COO & Abdul-Razak Shaibu Ballah, Senior Geologist Ghana at IronRidge Resources Ltd.
FROM THE EXPERTS
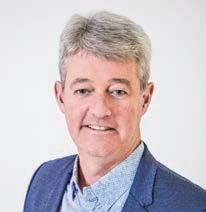
Dr Alan Wilson Director and Chief
Geologist at GeoAqua Consultants Limited
Timothy Strong: How did you decide to pursue a career in mineral exploration? Was it something that you had planned?
Alan Wilson: I had an interest in the outdoors from an early age, mainly due to family hiking trips in the Scottish Highlands. It was a holiday to Italy, and a trip to the top of Vesuvius that sparked my interest in geology, which I followed up with my Geology degree at Edinburgh University. During those studies, I became interested in ore deposits, so that, combined with a love of travel and the outdoors, is how I ended up pursuing a career in mineral exploration.
TS: Which country has left the strongest impression on you and why?
AW: Without a doubt, Bolivia. Working and living there in the mid-1990s was fascinating on many levels. Not only was the geology varied, prospective and challenging, but the culture, history and geography of the country were captivating. Being able to travel the length and breadth of the country both for work and pleasure allowed me to appreciate its diverse nature, from Andean volcanos and salt flats in the west to the Amazonian jungles of the east. The people were (generally!) welcoming and the cultural history of the
In conversation with Dr Alan Wilson
Dr Alan Wilson graduated from Edinburgh University (UK) with a Bachelor’s degree in Geological and Earth Sciences, immediately followed by a Master’s in Exploration and Mining Geology from the University of Leicester (UK) in 1991. Ten years later, he built upon that with a Doctoral degree in Economic Geology at the University of Tasmania (Australia), graduating in 2003. Between his Master’s and Doctorate, Alan worked mainly for Rio Tinto and BHP Billiton, based in Ecuador, Bolivia and Peru. Post PhD, Alan has held increasingly senior positions in companies such as Anglo American as Copper Commodity Leader, and with Antofagasta as International Exploration Manager.
Alan is an experienced economic geologist having worked on grassroots to brownfields exploration projects in over 30 countries on five continents. Since leaving Antofagasta in 2019, Alan has resided in Anguilla, British West Indies where he and his wife run a private consultancy, GeoAqua Consultants, which provides expert technical and strategic consulting services to the mineral exploration and integrated water management sectors.
country, including the pre-Columbian archeological sites of Tiwanaku and Samaipata, the silver mines of Cerro Rico de Potosí, the Casa Nacional de la Moneda (National Mint) in Potosí and the Jesuit missions of Chiquitos are all sights that people need to see.
TS: What has been the most satisfying moment of your career to date?
AW: There have been lots of highlights in my career so far, and hopefully more to come, but I think the most satisfying period has been since venturing out as an independent consultant. Being able to apply my experience to help clients understand the geology of their exploration targets and making recommendations that transform into ore grade drill intersections is very pleasing. I also enjoy the
training and mentoring aspect of my consulting role, being able to help younger geologists develop the skills needed to be successful explorers and well-rounded applied economic geologists.
TS: You have worked for some of the biggest mining and exploration houses in the world, how did that shape your career?
AW: My experience working with the major mining companies early in my career was positive and provided a strong foundation on which to develop the skills needed to be successful. Lots of useful field time, practical mentoring by more experienced colleagues, and the opportunity to visit mines regionally were all essential components to my early career development. So too was
the opportunity to attend technical conferences locally and regionally, which not only provided further exposure to technical ideas but also enabled me to develop a network of international contacts in the exploration community, many of which I have remained in touch with over the years.
Finally, being exposed to early-stage exploration in countries such as Ecuador and Bolivia, especially in the early 90s when modern exploration by Western exploration companies was less common than today, demanded that I learn Spanish fluently and quickly, and also sensitized me to the concerns and needs of indigenous communities when strangers come on to their lands seeking untapped mineral wealth.
TS: From your point of view, what is (are) the most important factor(s) that make a good exploration geologist?
AW: It is a bit of a cliché, but to be a good exploration geologist, you need to see lots of rocks and ore deposits, and be mentored in how to interpret, in a practical and applied sense, what the rocks are trying to tell you in the context of ore deposit models. Today, rock observation is complemented by an array of additional data layers and tools (e.g. multi-element geochemistry, applied lithogeochemistry, spectral and hyperspectral data, deep penetrating geophysics and associated inversions, mineral chemistry, etc.) that are all potentially useful in the discovery process, but without a solid understanding of
the geological framework of an exploration target, these additional datasets can confuse, rather than assist, interpretations. Additionally, a successful exploration geologist will question exploration models if the target under evaluation does not easily fit into a well-recognized deposit style, as models are only there to guide exploration and need to be constantly challenged and tested against new geological information generated during exploration programs.
TS: What is the most interesting deposit you have ever worked at?
AW: Of the ones I can talk about publicly, it would have to be the Cadia Au-Cu alkalic porphyry district in NSW, Australia. This was the subject of my PhD research, and notwithstanding the fact that I concluded this study almost 20 years ago, I have recently been researching what the upper parts of these systems may look like, so as to apply new models to exploration projects for alkalic porphyry deposits in the appropriate belts of rocks. These porphyry deposits differ from their more abundant calc-alkaline counterparts in that they do not develop the visually distinctive lithocaps that provide a footprint to guide exploration. Instead, alteration appears quite distinct, and understanding what the footprint of the upper and distal portions of alkalic porphyry deposits looks like is a real exploration opportunity. Remember, Cadia is host to 50 Moz of gold and 10 million tonnes of copper, so these deposits are
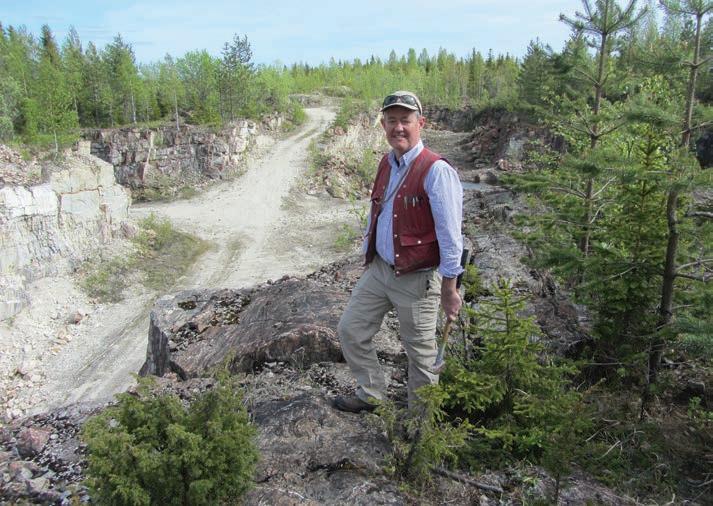
valid exploration targets that have likely been overlooked in many parts of the world.
TS: How is the current COVID-19 pandemic affecting the mining industry, in particular the consulting side of the business?
AW: Border closures, quarantine restrictions and the general disruption to both domestic and international travel have seriously impacted all business, not just the mining and exploration industry. For those that rely on travel to carry out their normal business, such as geological consultants, the pandemic has accelerated the adoption of new technology to allow seamless access to data, thus enabling some tasks to be completed from home. Whilst it is essentially impossible to log drill core using high quality digital photos, access to such data, when used with spectral and geochemical data does allow for a good degree of remote interpretation. Companies have also adapted to the concept that, whilst not ideal, having consultants work remotely does still deliver value. So, for me personally, I have remained essentially fully booked since the start of the pandemic, though I am looking forward to a return to the field when conditions allow.
TS: Do you think there will be an increase in residential roles when the COVID-19 pandemic clears?
AW: No, I don’t think so, as very few mining companies are set up to run operations with a fully residential work force that includes workers’ families. So, for most operations, drive-in, drive-out (or FIFO) will remain the norm in my opinion, though both companies and employees will need to remain flexible as we ride out the remainder of the pandemic.
TS: You have been fortunate to work all over the world, with bases including Australia and Canada. How do these two places differ in their views on mineral exploration?
AW: Both Australia and Canada have a long history of mining and mineral exploration, with state and federal governments that are broadly supportive of a robust mineral resources sector. With regards to facilitating mineral exploration, I would say that Australia is more forward-looking than Canada, with all states and territories providing key pre-competitive datasets, such as geological maps, detailed geochemical and geophysical data, mineral occurrence information, etc. Most importantly, however, state-run core libraries that store hundreds of thousands to millions of meters of drill core from past exploration drilling make core available not only for examination, but also for further non-de-
Dr Alan Wilson in the field
structive study. As an example, the core reference library of South Australia holds over 7.5 million meters (24 606 299 ft) of drill core and associated metadata, with samples dating back over 130 years of prospecting and exploration history. What an amazing resource to kick-start new exploration programs!
TS: You have worked at the Telfer deposit, Paterson Province, WA in collaboration with the Telfer mine geology team in order to develop a holistic exploration model for district and regional exploration for similar gold-copper systems. Please share more about the deposit and the exploration model.
AW: The Telfer sediment-hosted gold-copper deposit has had a number of geological models since its discovery in the 1970s, as all complex orebodies should. The bedding-parallel nature of outcropping mineralization led early explorers to propose a syngenetic to early diagenetic model for ore deposition, though later explorers and researchers proposed a genetic relationship to magmatic rocks. Our recently published descriptive paper on Telfer is the culmination of over 40 years of exploration and research on the deposit and concludes that gold-copper mineralization is located in a distal position to as-yet-unidentified felsic causative intrusion. Evidence to support this interpretation includes a strong affinity with the element tungsten that is commonly associated with intrusion-related gold deposits, as well as geophysical data, fluid inclusion and isotopic studies and most importantly, the local presence of fingers of mineralized felsic intrusive rock in deep drilling in the West Dome sector of the deposit. All of these datasets can be used to construct an exploration model for the broader Paterson Province, although recent discoveries elsewhere in the province, whilst being broadly similar in that they are gold-copper deposits hosted in sedimentary rocks, have sufficient differences to Telfer to indicate that the exploration model for ‘Telfer-type’ deposits remains a work in progress.
TS: Antofagasta is a well-known name to those within the industry but not so renowned on the outside, why do you think that is?
AW: I would argue that the names of many large mining companies are not well-known outside of our industry, not just Antofagasta. Our industry has a history of keeping a low profile, unfortunately only appearing in the public eye when there is an event of environmental or cultural destruction. Whilst publicity for avoidable incidents such as these is absolutely warranted, I think it is incumbent
on our industry to stand up for itself and educate the general public about the critical role the mining industry plays in the creation of a modern and sustainable society. This role will only become more important as the world moves towards a ‘green economy’. It is also incumbent on our industry to show the public that mining can and does take place using 21st century technology, with innovation and sustainability at the core of everything it does.
TS: Tell us about Heliostar Metals, a company to which you recently joined the Board.
AW: Heliostar is a junior precious metals exploration company with exploration-stage projects in South-eastern Alaska, US and Sonora, Mexico.
Its flagship asset is the Unga project, a large, intermediate sulphidation epithermal vein system with associated porphyry copper-gold mineralization, located on Unga and Popof Islands, in the Aleutians, Alaska. Due to my technical and commercial background, I was asked to join the Board by Heliostar’s President and CEO, Charles Funk, with whom I had worked previously in a number of joint venture agreements on copper projects in British Columbia. I think the assets are high quality, and Charles has the right leadership skills and drive to make the company a success, so hopefully, I can be an integral part of this success story as work advances.
TS: What changes have you observed over the past 20 years in the way in which drilling contractors work?
AW: The biggest change that I have seen is that most contractors now view themselves as partners in a drill program, rather than just contractors. Typically, there is strong collaboration on safety and technical innovation, to improve drilling performance whilst reducing safety risks and environmental impact of drilling activities. Many drill companies now have their own innovation departments and collaborate in research projects aimed to deliver products that provide near real-time measurement of downhole structure, assay data, geophysical information, etc. So, the relationship with a drill contractor today is much more than just drilling holes; it is about collaboration to deliver maximum value from the core or chips produced, in the quickest time possible and with no safety or environmental impact.
TS: You have drilled at high altitude; does this pose any challenges?
AW: Absolutely. When drilling projects in Bolivia, typically at altitudes of greater than 4500 m (14 763 ft), I quickly learned from
the drillers and the drill rig manufacturers that rig performance diminishes by about 1% for every 100 m (328 ft) elevation. So, at 4500 m, rig performance is compromised by about 45%. This has a significant impact on how the drillers operate their machinery and they have to work hard to find a balance between optimal rig performance under difficult conditions and maximum rig production. It has been a few years since I have drilled at those altitudes however, so there may have been some engineering advances that have overcome some of the challenges my drillers faced in the mid-90s.
TS: What makes a drill campaign successful?
AW: Assuming you have all permits in place and the required approvals from the local community, the most critical part of a drill campaign is contractor selection. Not only does the contractor need to have the right equipment for the job, even more critical is the provision of suitably experienced drillers. Assuming that both equipment and drillers are up to the task, the other key contributing factor to a successful drill program is support for the drillers from their operational base. Breakdowns are inevitable, and so as to minimize lost time, efficient and practical support from the driller’s operational base is essential in order to provide spare parts or engineering assistance as quickly as possible. Whilst it is true that the cost of breakdowns is generally borne by the drilling company, all drill programs have the standing cost of having exploration staff in the field, camp running costs, etc., so getting a rig back up and running again in the shortest period of time is in everyone’s interest.
TS: You have a lot of copper experience, copper is having a hot time now, where do you see the price going from here?
AW: I am not a market analyst so am not qualified to make any informed prediction as to what future copper prices may be. However, when you look at the global shift to a low carbon green economy that reduces our reliance on fossil fuels, the future for copper can only be viewed as positive. Whilst substitution provides a natural cap on the price of any commodity, the physical properties of copper make it extremely hard to completely replace in the process of electricity generation and transmission.
Decisions being made by governments and companies around the world today, whether to adopt wind or solar as a low carbon alternative for power generation or to transition to electric vehicles, will only add to the demand for copper, with
the natural consequence of higher prices until supply exceeds demand. Additionally, the natural antibacterial and antiviral properties of copper, long known to geologists and also to past civilizations, provide an additional growth market in healthcare, public transport, and areas of high human transit, particularly in light of the on-going global pandemic.
TS: With the lack of large deposits being found, what is next for copper exploration?
AW: Two things come to mind. First is that sustained increase in the price of copper will render previously uneconomic deposits profitable, thus allowing for their development in a responsible and sustainable way. Secondly, I am firmly of the opinion that a large proportion of future mines, not only for copper but for all commodities, will be largescale underground operations, for social and environmental reasons. This trend has been recognized by exploration and mining companies that have shifted their exploration focus to targets at greater depth, using improved exploration models and geophysical data. Deposits such as the Resolution porphyry system in Arizona, US and the Oak Dam IOCG
discovery in South Australia, both of which lie at more than one kilometer below the surface, will be the mines of tomorrow.
TS: What does the future hold for Mineral Exploration in general?
AW: There is a bit of a dichotomy facing the mineral exploration industry and the industrializing world. Increasing urbanization of countries such as China and India, with the associated growth of a wealthy middle class, leads naturally to increased demand for a whole range of natural resources. However, with wealth and urbanization often comes the opinion that mining is a ‘dirty’ industry that should take place ‘somewhere else’. So, the dichotomy is that developed countries are the largest consumers of natural resources, but are often reluctant to develop valuable and potentially highly profitable resources that lie within their own territorial borders to assuage the concerns of their materialistic voter base. The only long-term solution to this issue is if countries accept their individual responsibility to sustainably, and with as small an impact as possible, develop profitable resources within their borders.
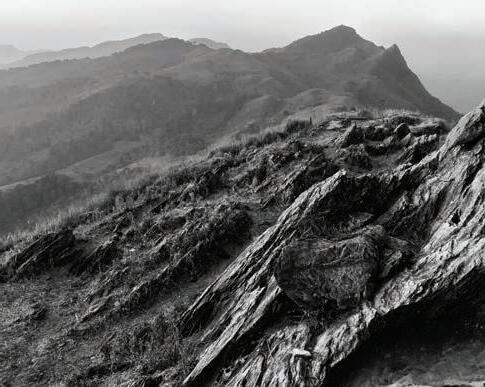
As for mineral exploration companies, selecting a jurisdiction in which to invest hard won exploration dollars is no easy task. Highly developed nations such as countries in Europe and North America may offer a safe, corruption-free operating environment, but the risk of development being stymied by communities and NGOs in the event of discovery is high. However, going to a prospective exploration frontier in a less-well explored corner of the world, such as the Sahel or Myanmar, may reduce discovery risk but comes not only with significant operational risk but also risk of security of tenure, exposure to corruption, etc. Equally, there is no guarantee that discoveries in high-risk jurisdictions can transform into mines, highlighting the importance of solid ESG programs from the commencement of exploration.
Having said all of this, the future for mineral exploration has to be bright; as the old bumper sticker says: ‘If it can’t be grown, it has to be mined!’. C

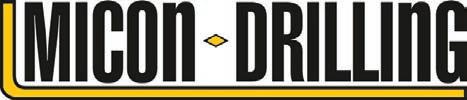
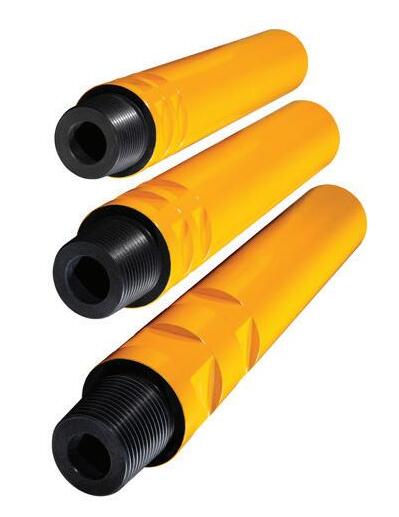

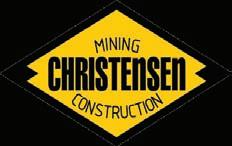
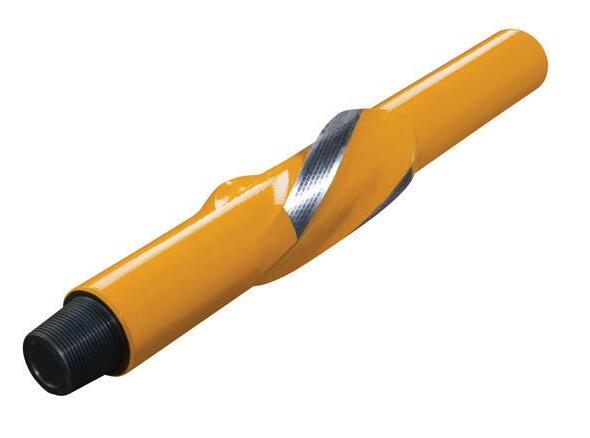
BHA Equipment







Core barrels
Stabilizers
Reamers
Crossovers
Drill collars

Diamond bits
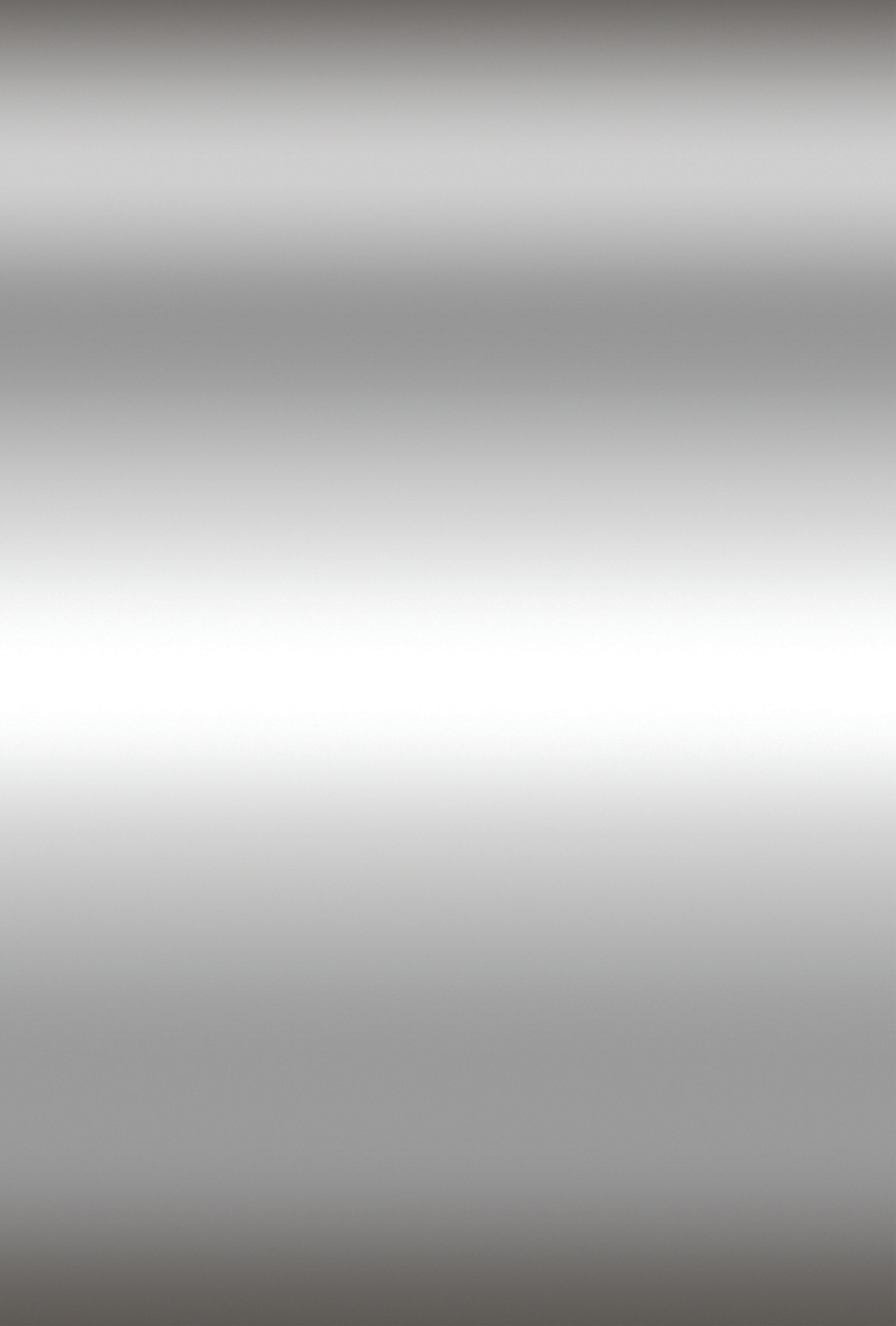
Raise bore tools







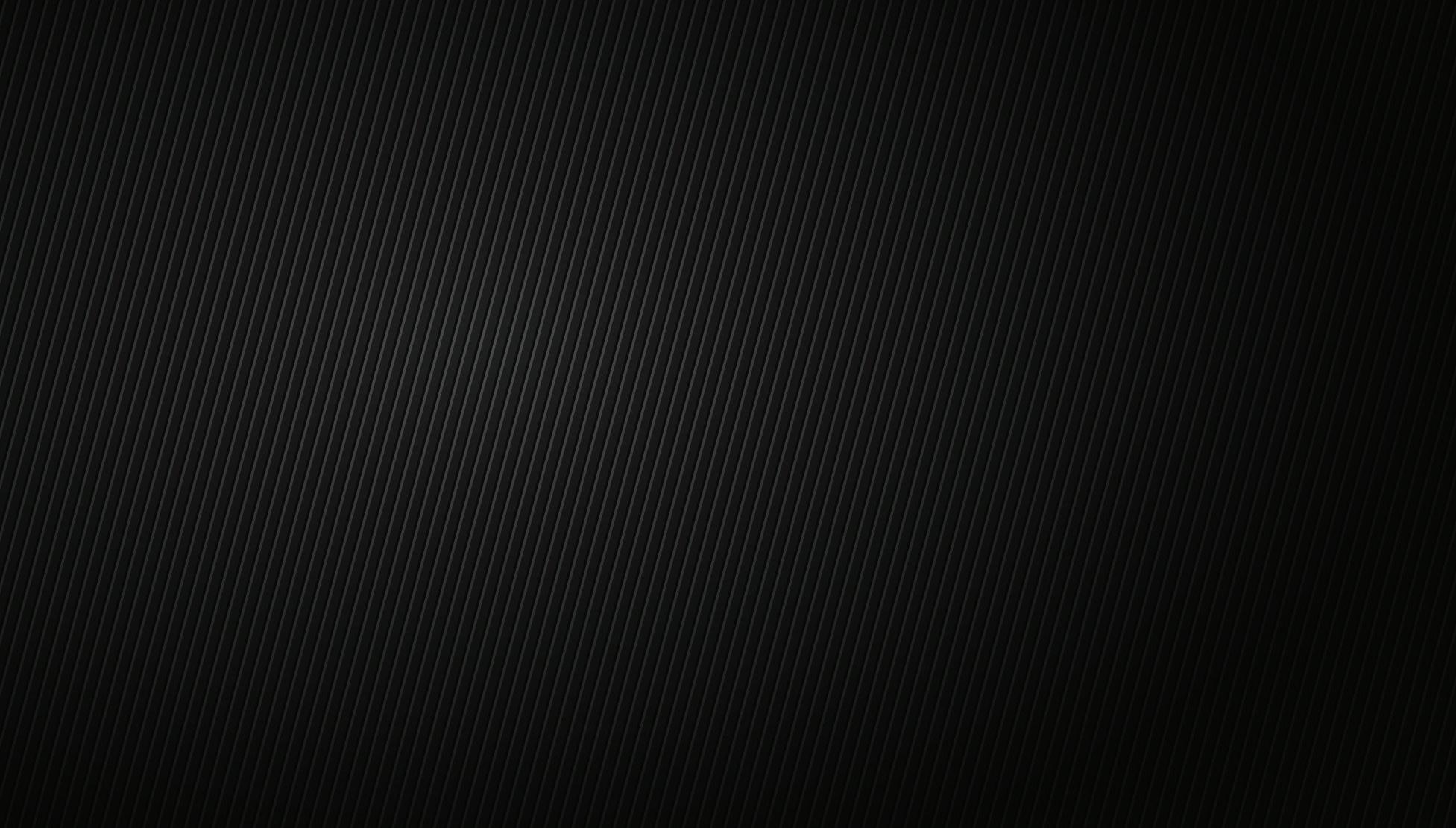
Additional services
Coring service
Directional drilling
Borehole survey
Rental stock
Engineering
Workshop Maintenance


Exploration on the frontline of one of West Africa’s forgotten gems: Liberia
by Rowan Thorne, Project Geologist at Origin Exploration Ltd.
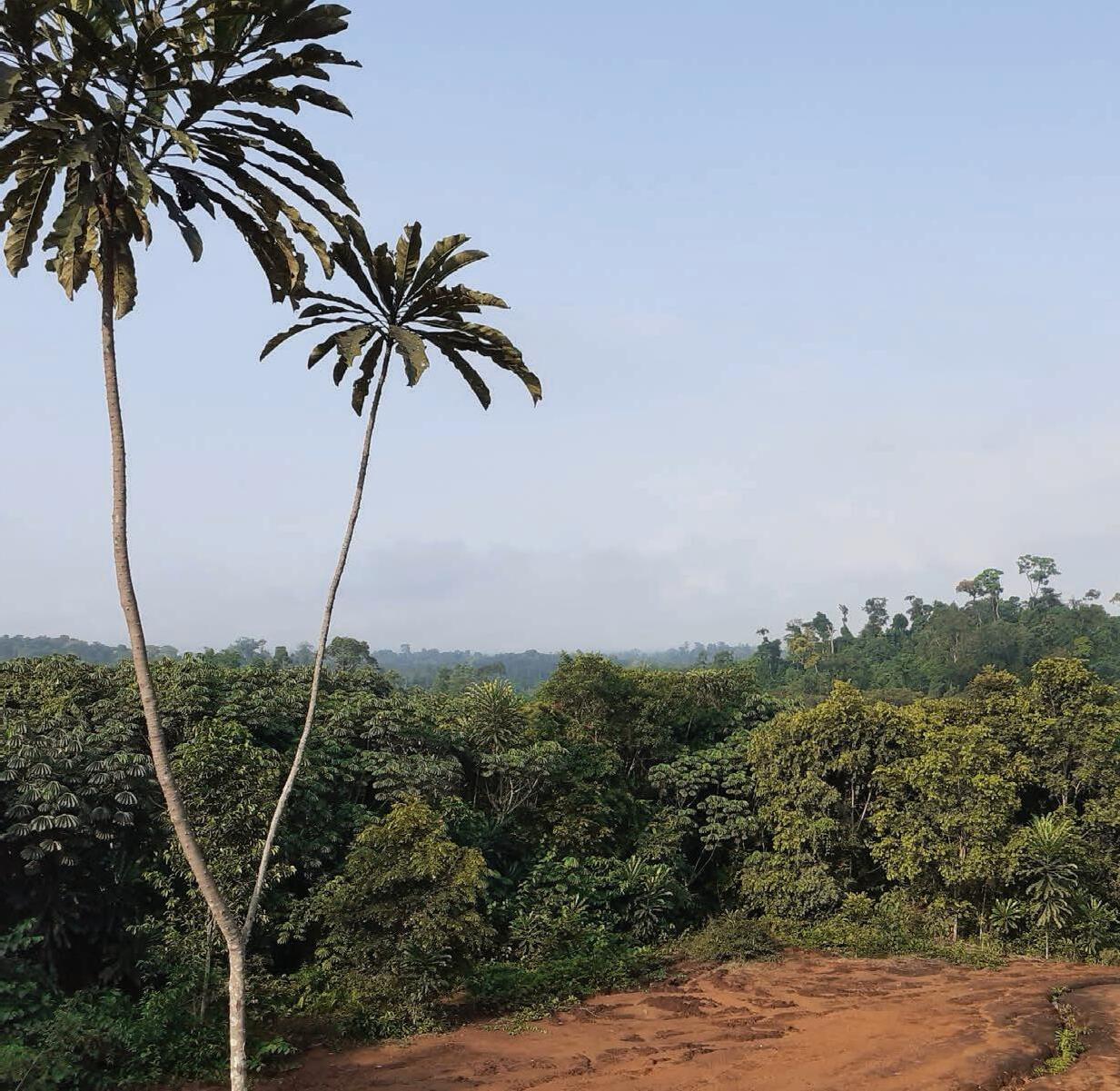
‘Boss, which line am I on today?...’, ‘Do we have any spare batteries?’, ‘Are there any biscuits left to take to the bush?’ are some of the questions that hit you every morning whilst trying to get the field crews ready for the daily jaunt into the wild.
No amount of planning and preparation the night before can prepare you for the variety and minutiae of questions and challenges that await you in the morning before heading out to explore one of the most challenging environments one could encounter as a geologist. However, this is what we signed up to when we chose to go into this profession, the unknown, the unpredictable and the persistent optimism that today could be ‘the day’ you find the mineralized outcrop that could turn out to be the next big discovery; this is what it means to be an exploration geologist.
After getting all the field crews mobilized, organized and confident in their day’s objectives, it’s time to grab the Thurya satellite phone and wander up to the highest point in the immediate proximity to the camp and undertake the usual 8:00 check-in to the office back in Monrovia.
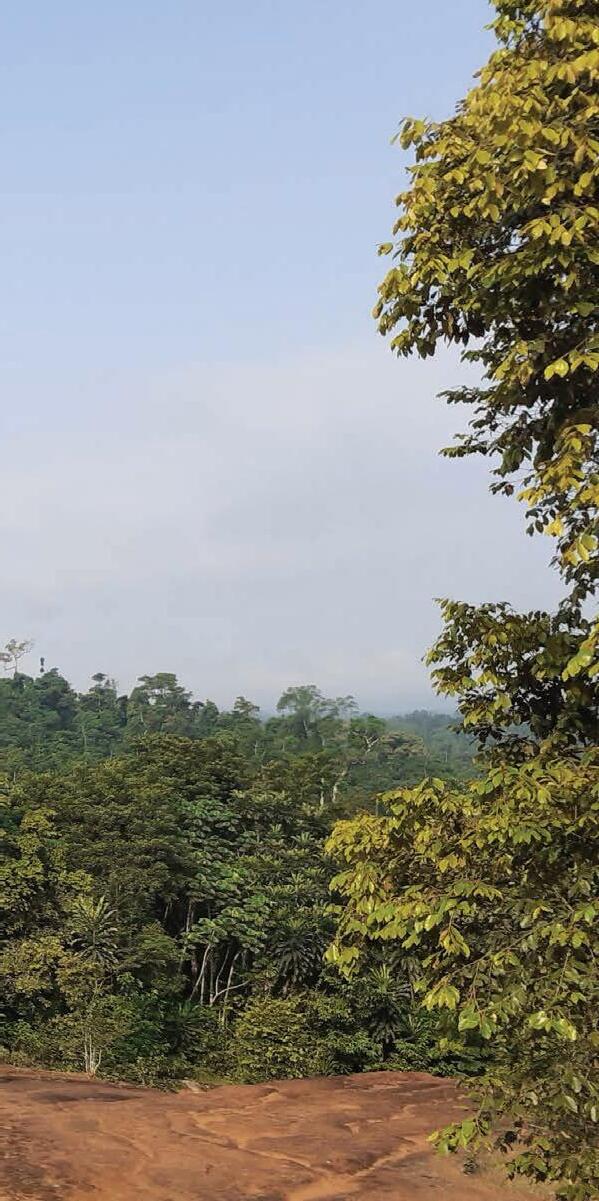
The ‘sat phone’, a device that resembles some form of early mobile phone from the 90s, is typically the only lifeline and form of communication connecting anyone working in the bush to the outside world, and this is certainly the case in the Liberian jungle. Once the morning chores are completed, it’s time to mobilize myself, checking that all the geological essentials (compass/clinometer, hand lens, hammer, safety glasses, notebook, etc.) are packed into my rucksack and numerous pockets, making sure to leave plenty of space to carry the voluminous liters of water required to survive the unforgiving heat and humidity of the Liberian bush, which easily reaches 30°C (86°F) on a daily basis. From this point, my challenges turn from logistical to geological, if I and my crew of a field assistant and local guide are lucky, our route into the wild could be a straightforward trek along a bush track between many
of the numerous villages in the region until we have to cut through the vegetation to reach the topographic high that correlates closely with a magnetic anomaly, identified in the historical aerial geophysical survey. From this point, anticipation and concentration override the feelings of discomfort from the searing heat and conversations surrounding the culture and history of Liberia between myself and my crew, turn to statements of geological observations; the change in color of the saprolite or the occurrence of a 2 m (6.56 ft) diameter felsic boulder. After cutting our way through dense bush for what feels like 5 km (3.1 mi) but is actually only 1.5 km (0.93 mi), such is the physical effect the jungle has on you, the relief begins to steepen, the vegetation starts to thin and the statements of geological observation become more frequent. We approach the top of the hill, the occurrence of mafic dark grey/black boulders at our feet now becoming more common than not, my field guide tapping each one he walks past with the end of his cutlass to draw my attention.
Eventually, we finally reach the crest of the hill where, after finally relinquishing on its stubbornness, the Liberian jungle reveals that ever-elusive outcrop. We scramble over the outcrop, dropping our rucksacks knowing that we will be camped here for a while; as outcrop in these geological environments is sparse due to the fact that these 2.3 Ga old rocks have undergone millennia of tropical weathering, leaving limited outcrop to be discovered. I pull out my hammer and put on my
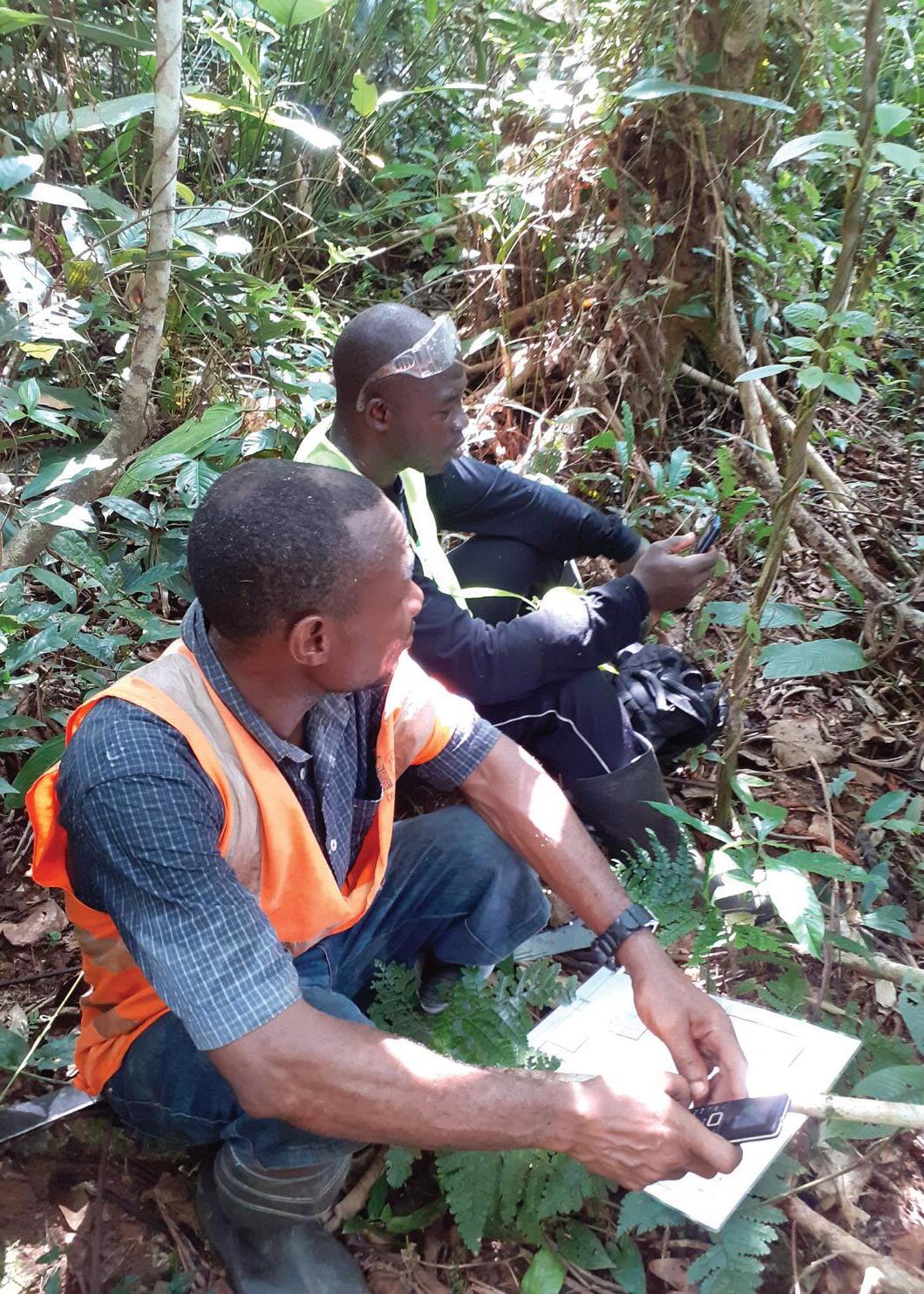
Field Assistant John Benson and Local Guide Samson
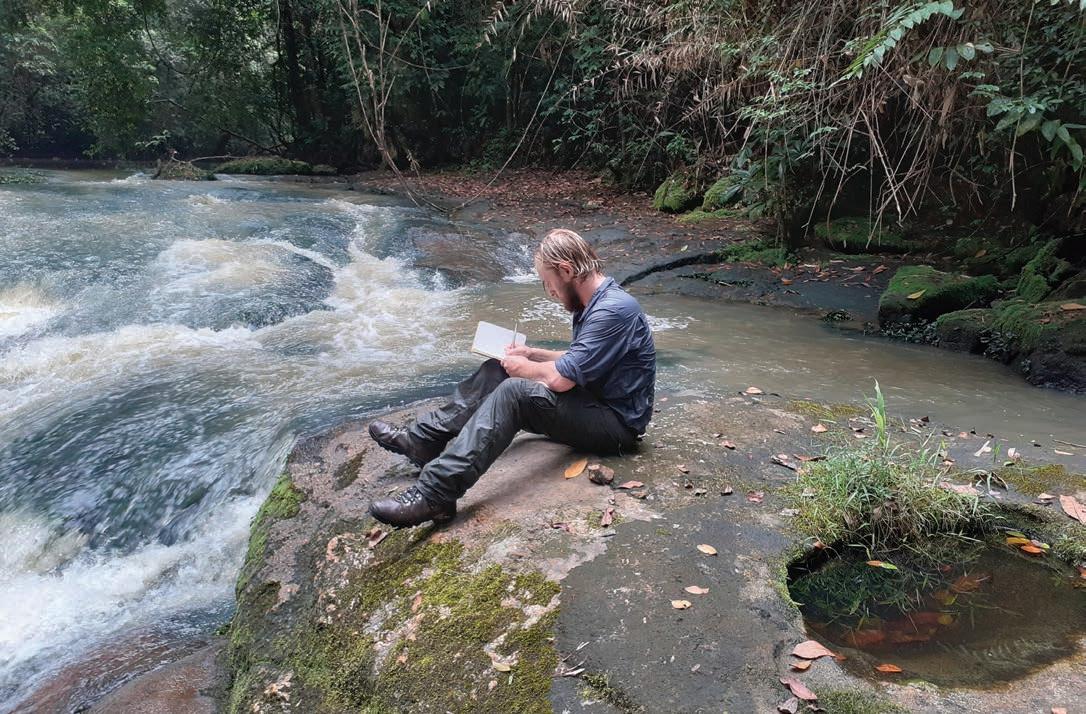
safety glasses and proceed to remove chips off the outcrop to be inspected with my hand lens and observations recorded in my notebook, with my field assistant already pulling sample bags out of his rucksack and proceeding to write sample numbers knowing, like me, that this could be ‘the one’ that we are looking for and could be the first indication of a potential discovery.
Nothing quite prepares you for working in such a challenging environment like that of West Africa. Having been lucky enough to work in many different countries throughout the world on numerous different projects from monitoring diamond drilling projects in -20°C (-4°F) in Finnish Lapland to undertaking soil sampling and mapping programs 2500 m (8 022 ft) above sea level in the Lesser Caucasus Mountains of Armenia, Liberia certainly poses new challenges both logistically and geologically. However, these challenges are exactly what every exploration geologist lives for, being the first to chip away at an outcrop that nobody has mapped before, applying new and novel forms of geochemical and geophysical exploration to generate datasets that greatly enhance the geological knowledge of a region and finding that first bit of mineralization that could lead to a new discovery.
Liberia, as referred to in the title of this article, is certainly one of the forgotten gems of West Africa, often dwarfed by more familiar and de-
veloped countries in the region, such as Côte d’Ivoire and Ghana among others. Liberia has already given Africa its first female president and was the first independent nation on the continent, but it still has much more to offer. Geologically, it is still very underexplored and provides geology comparable to some of the most prospective regions in the world, coupled with a highly educated and trained workforce that can effectively support any exploration program, this was all certainly evident throughout my experience in the country.
It is well documented that these regions are logistically and personally difficult, but Liberia is a country that is able and prepared to meet these challenges and reward anybody who is willing and has the vision to work there. Furthermore, working in Liberia not only provides a great professional experience, but its natural beauty, the friendliness and hospitality of the people and its unique culture have left a lifelong impression on me. And one day soon I hope it will get the attention it deserves and provide one of the future’s next great geological discoveries. C
Rowan Thorne making notes of an outcrop
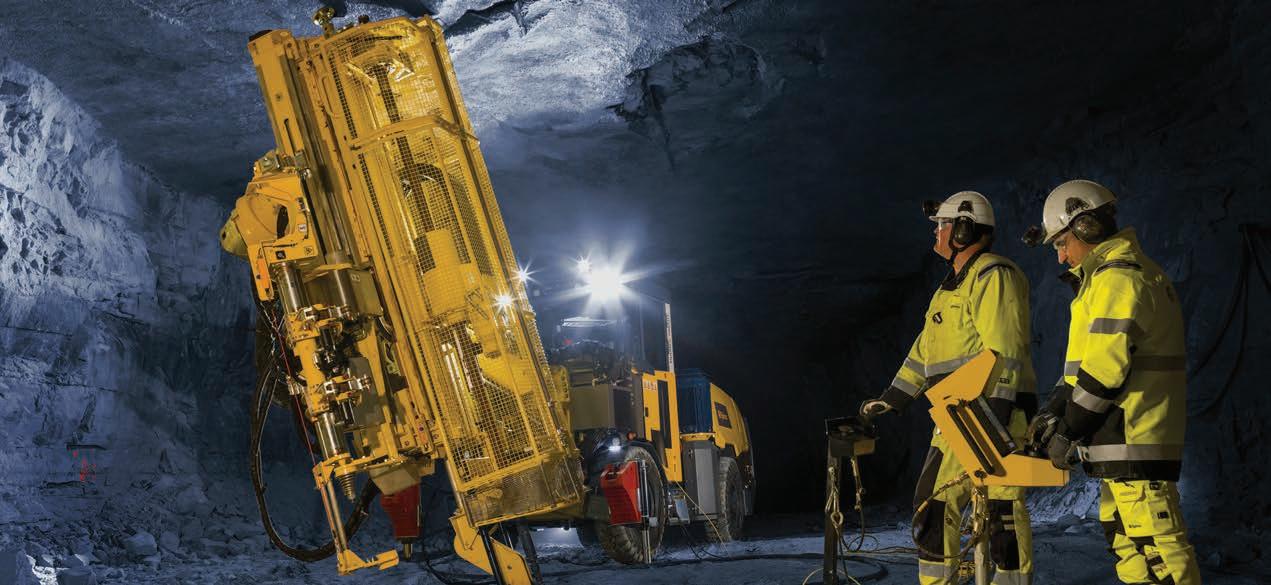
Depth and mobility
What do you get when you take one of the most respected underground core drilling rigs on the market and fuse it with a wellproven and mobile carrier? You get the Diamec Smart 6M.
Find out more at epiroc.com
United. Inspired. Helping drillers improve their performance. Even when socially distanced. Reach out easily at www.fordia.com/support.
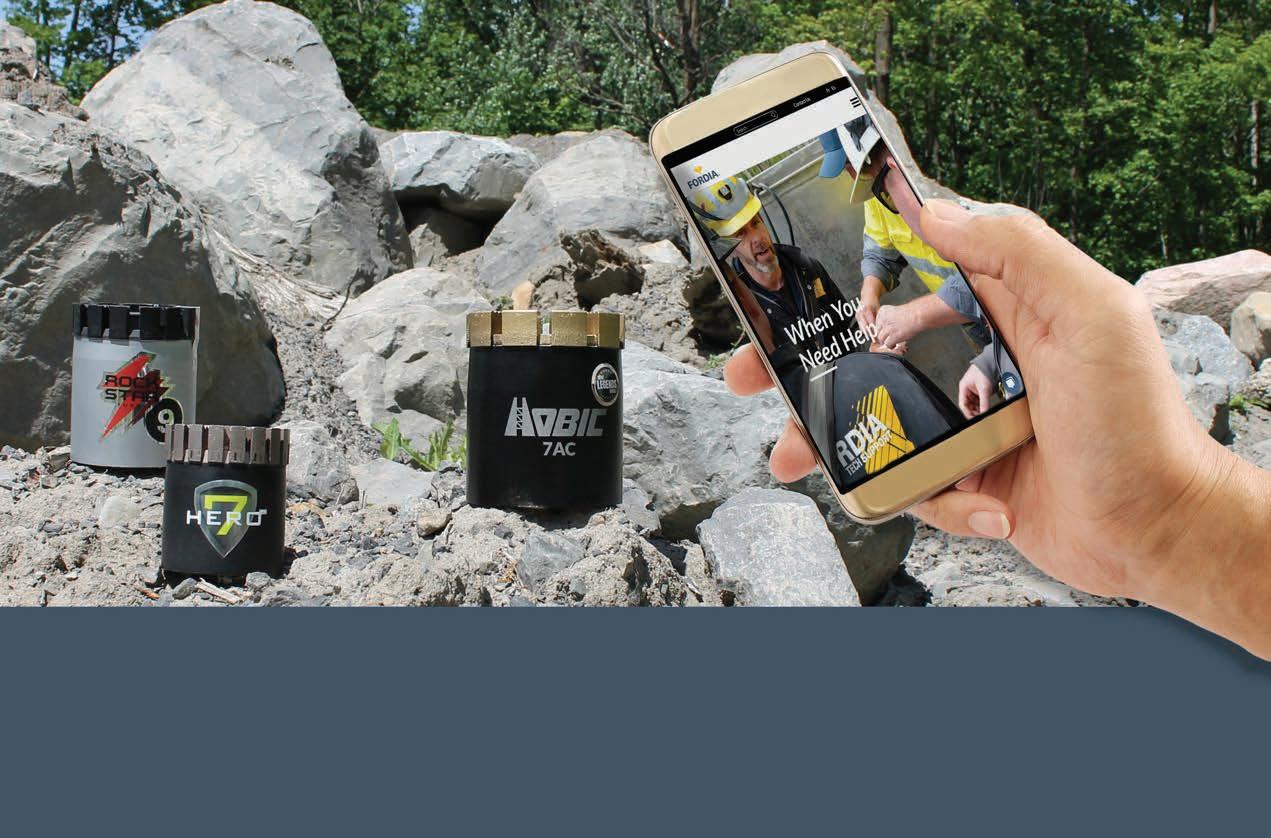
Metamorphic Mexico: The Sierra Madre Occidental
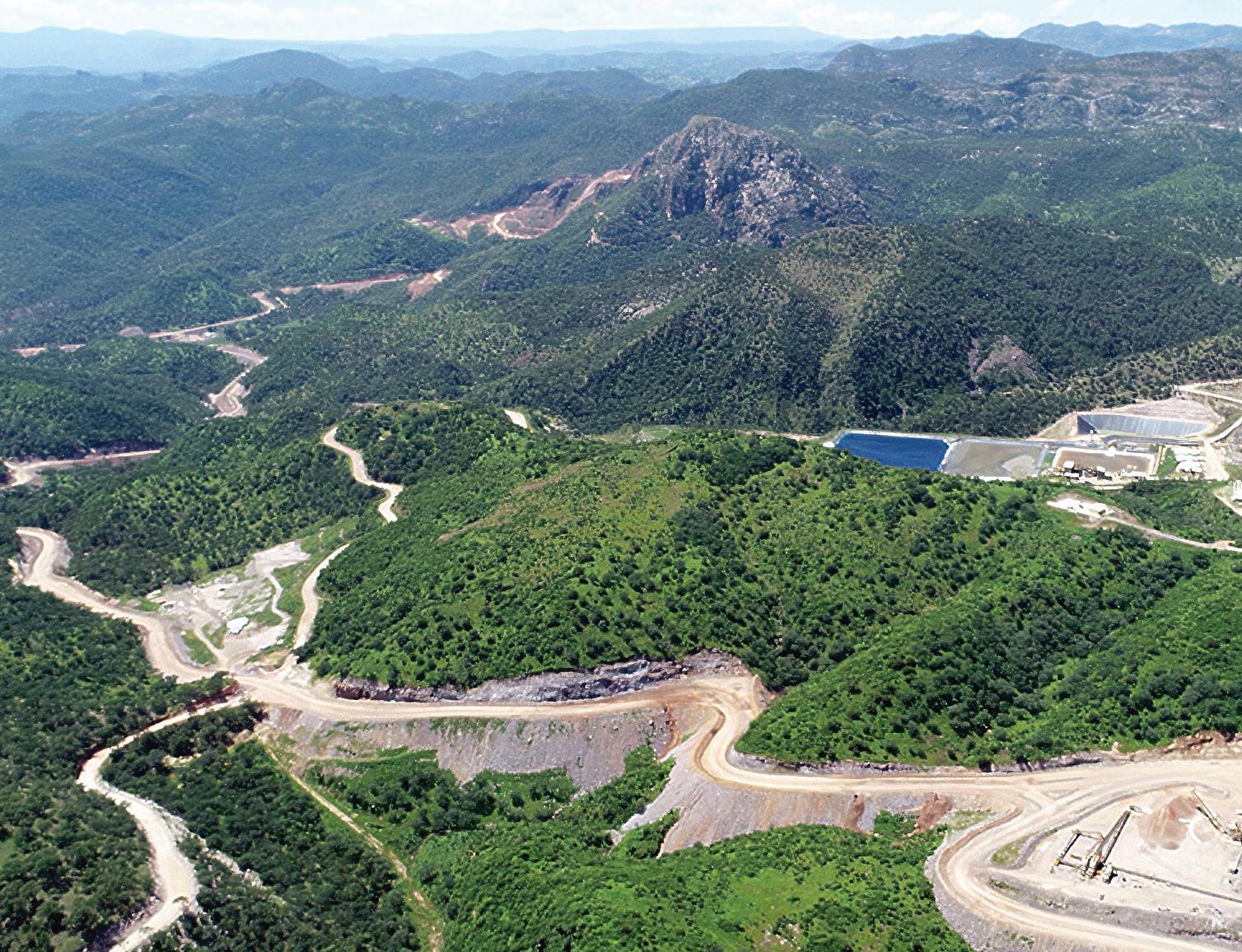
by Jane Lockwood, Spotlight Mining
Abundant gold and silver in the Sierra Madre Occidental have driven colossal enterprise over the last two centuries, with Mexico standing in 2017 as the world’s largest silver producer (200 Moz/year) and eighth largest in gold (125 t/ year), chiefly sourced from this mountain range. This is in the face of significant difficulties in obtaining geological and other data, especially until the turn of the 21st century, thanks in large part to the presence of the Sinaloa and Los Zetas drug cartels in the region causing high levels of risk for greenfield exploration. Nonetheless, the lure of precious metals has been strong enough to establish both large and small mining operations in the region, with the mountains hosting several world-class Au-Ag deposits.
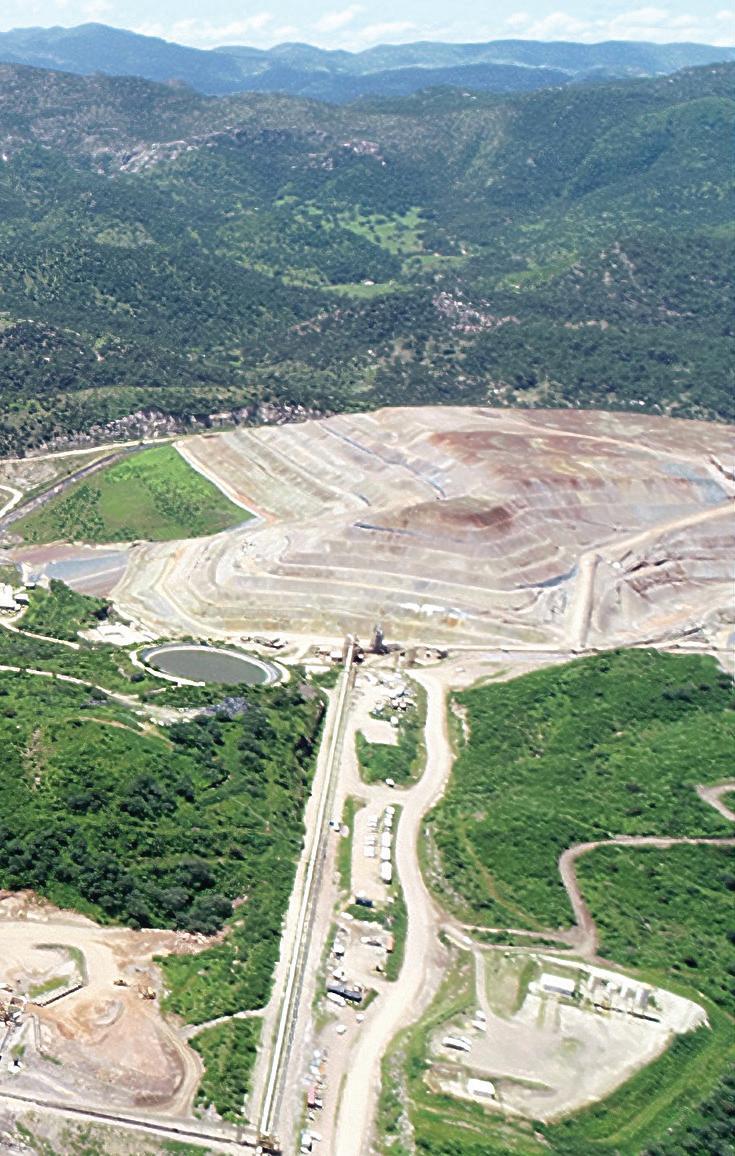
The Sierra Madre Occidental range overlies a complex basement, and the major formations of economic interest are in the two Cenozoic volcanic sequences. The first of these is dated to the Cretaceous and associated with the Laramide Orogeny. This Lower Volcanic Supergroup (LVS) is at least 2000 m (6652 ft) thick, and it contains the majority of the gold and silver mineralization in the area, with abundant sulfides in most outcrops. The LVS consists of lava flows, ranging from basaltic andesites hosting many of the gold-silver veins, to silicic species, interlayered with ignimbrites and tuffs, pointing strongly to an island arc origin.
It is mildly to moderately brittly deformed and forms a close association with a series of batholiths thought to be a continuation of the Sierra Nevada and Peninsula Ranges batholiths in the US. The LVS is unconformably overlain by the heavily ignimbritic Upper Volcanic Supergroup, which forms the spectacular high plateau of the Sierra Madre Occidental. Many mines from the early and mid-20th century exploited deposits in the LVS, but over the last decades more and more have been identified in the upper volcanics as well.
The classification of the Sierra Madre Occidental Au-Ag deposits has undergone something of a reshuffling over the last decade. While many deposits in the area, including those in the important San Dimas district,
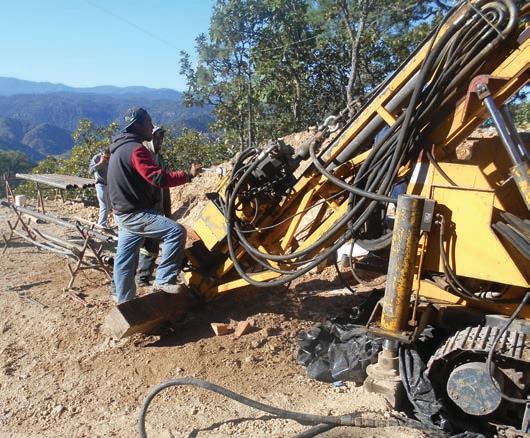
were originally thought to have been emplaced by a single magmatic pulse associated with batholith formation around 10 million years ago, new data suggests a much more complex history, with three metallogenetic events. The first of these is the Late Cretaceous gold-copper porphyry event associated with the subduction of the vanished Laramide slab beneath the continent, which is the source of the generally uneconomic copper deposits in the area. Next came the Ag-dominant deposits at around 40–41 million years ago, likely associated with the Piaxtla batholith, since the silver is concentrated in East – West oriented tension structures in its proximity. The Au-dominant event came last, with gold clustered in North - West striking systems associated with Oligocene bathloliths. The Ag and Au events also display highly distinct mineralization and textures in host veins, with trace element studies revealing different metal sources, or at least mineralization conditions, for the two events. In this conception, an originally deep, intermediate-sulphidation silver province was uplifted and overprinted by a shallower, classically epithermal gold deposition event. Nevertheless, the structures infiltrated by the two temporally distinct fluids are generally the same, leaving most veins with a mix of Au and Ag enrichment.
It was evident to early European visitors to the Sierra Madre Occidental that the region could be a major source of gold and silver. For example, the area around Alamos Gold’s Mulatos mine (TSX:AGI, NYSE:AGI) in the eastern part of the state of Sonora was reported on by Jesuit priests in 1635, and throughout colonial history, including during the Mexican revolution, mining continued in the area. Today, major and mid-tier miners scramble for claims in the region. Notable producers include Newmont’s (NYSE:NEM, TSX:NGT) giant Peñasquito mine, which the company gained during its acquisition of Goldcorp, and which is the largest gold and second largest silver producer in Mexico, running two open pits and with mine life expected to run at least another ten years. Another major player is Agnico Eagle (NYSE:AEM, TSX:AEM) with La India, which has reserves of 490 000 Oz of gold and 1.2 million Oz of silver, and several exploration targets on site. Mining operations in the
Mammoth Resources Drilling
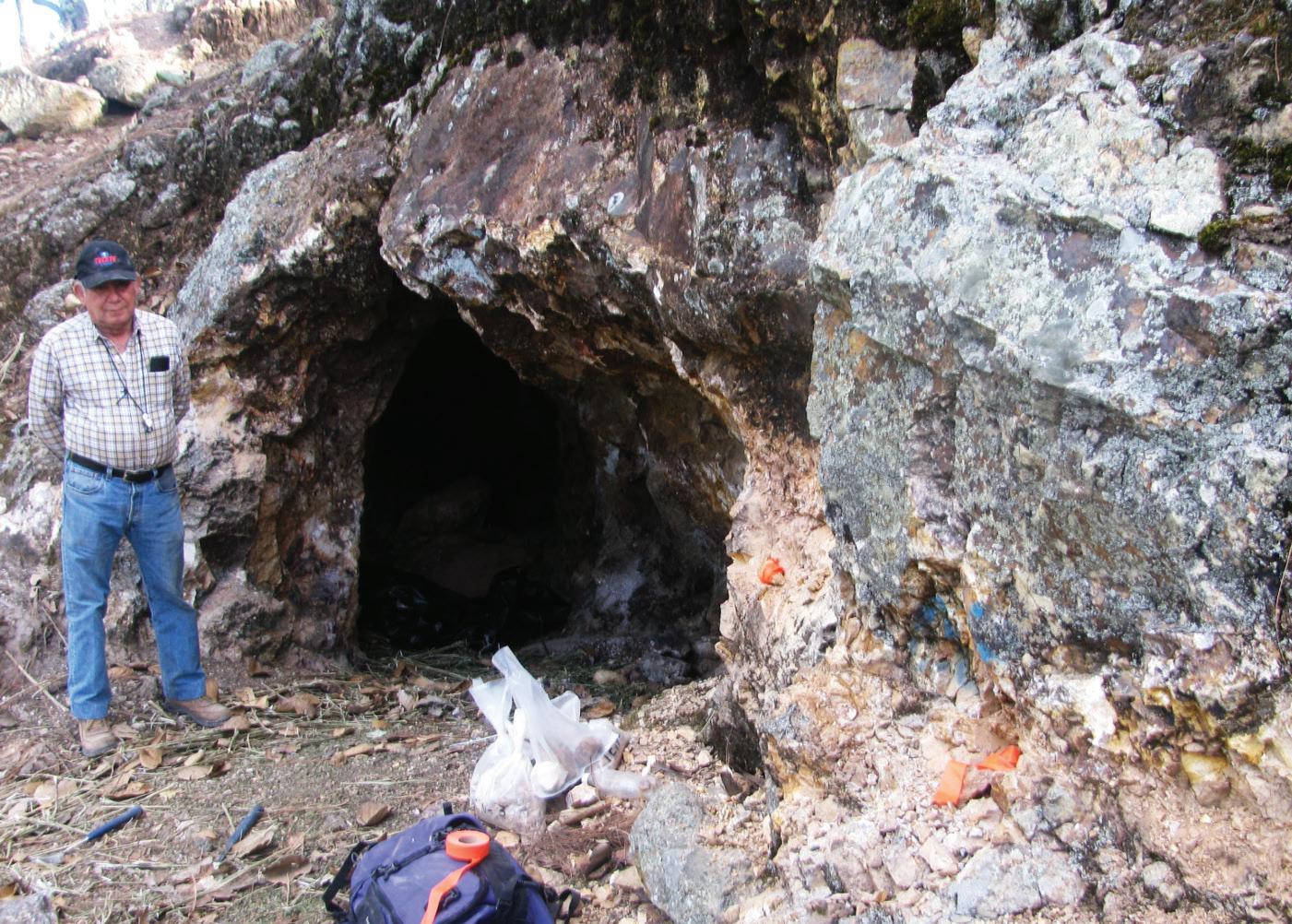

area commonly use the heap leach method to extract precious metals, and mines tend to have large output but relatively short lifespans – for example, La India is expected to operate for another four years, having started commercial production in 2014.
The Sierra Madre Occidental is not exclusively the domain of big mining business, however. Juniors such as Mammoth Resources (TSX:MTH) have understood the potential in the area, and Mammoth has a 100% owned Au-Ag prospect, Tenoriba, which includes a 6 km (3.72 mi) mineralization trend. Centerra Gold (TSX:CG) previously drilled the property, and the exploration data is extensive, with mapping conducted and over 3000 surface samples collected. Drilling was performed over 26 holes totaling around 5000 m (16 404 ft) along the mineralized trend, with intersections of potentially economic zones along much of it. One such instance was a 58.2 m (191 ft) section grading 0.81 g/t of gold equivalent at a 65:1 gold to silver ratio. The company is currently undertaking IP/Mag geophysical surveying at the site to fill in gaps along the trend, and new 3D models are under development, which already show attractive features. In addition, old geophysical data is being reprocessed with a technique more sensitive to the fine-grained mineralization style specific to Tenoriba. Field data is still being collected, with current goals including the establishment of volcanic flow vectors
to direct further exploration, and characterization of the breccias that host so much of the mineralization in the region. Further soil sampling is also expected to considerably expand the sampling grid.
Despite the long history of gold and silver mining in the Sierra Madre Occidental, there is certainly scope for exciting new discoveries throughout this spectacularly rich region. With the big and mid-tier miners focusing much of their exploration on brownfields near proven resources, it may be up to smaller players, such as Mammoth, to bring truly novel deposits to light. C
Sierra Madre

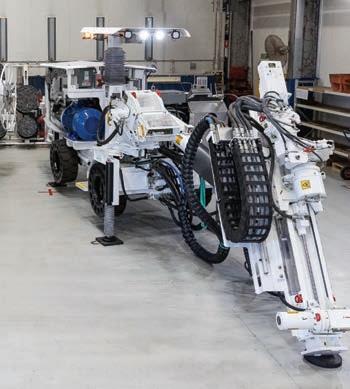
The Ewoyaa Lithium Project
by Iwan Williams, Exploration Manager Ghana, Lennard Kolff, COO & Abdul-Razak Shaibu Ballah, Senior Geologist Ghana at IronRidge Resources Ltd.
Coinciding with increased interest in lithium and its application in the stored energy space, IronRidge Resources Ltd. (AIM:IRR) commenced a top-down desktop review of the Birimian terrain of West Africa, following the discovery of the Goulamina deposit in Mali. The margins of the Cape Coast batholith were considered prospective for pegmatites, further enhanced by their proximity to operational infrastructure and pro-mining jurisdiction.
Literature review highlighted that pegmatites were first recorded in the area by the Geological Survey in 1916, but it was not until the period 1963 to 1965 that the current site of the Ewoyaa discovery was recognized in mapping, trenching and bulk sampling. A further literature review provided more encouragement through the Master’s thesis by S. Amoako Mensah on the spodumene pegmatite occurrences of Saltpond.
The Ewoyaa Lithium Project (Ewoyaa) was (re)discovered by IronRidge with fieldwork commencing in January 2016. In May 2017 historical trenching over Ewoyaa was located and a discovery drill hole was announced in August 2018 – 128 m (420 ft) at 1.21% Li₂O from 3 m (9.84 ft). This lead to a JORC-compliant maiden mineral resource estimate of 14.5 Mt at 1.31% Li₂O in the inferred and indicated category, including 4.5 Mt at 1.39% Li₂O in the indicated category announced in January 2020. Thick vegetation, deep tropical weathering, localized alluvium cover, rare outcrop and the extreme mobility of lithium in this environment make exploration very challenging.
Through joint venture and application, the Company has achieved a combined lithium portfolio covering 684 km2 (264 mi2) collectively called the Cape Coast Lithium Portfolio. Exploration auger and RC drilling is currently ongoing, testing new targets in order to grow the resource base.
Regional geology
Western Ghana is characterized by a thick sequence of steeply dipping metasediments, alternating with metavolcanic units of the Proterozoic age (2.2–2.3 Ga). These Birimian Supergroup sequences extend for approximately 200 km (124 mi) along strike in a number of sub-parallel north-easterly trending volcano-plutonic belts and volcano-sedimentary basins. The rocks of the
volcano-plutonic belts and the volcano-sedimentary basins appear to represent partly contemporaneous lateral facies equivalents, as most of the sediments appear to be derived from the adjacent volcanic belts. The Ewoyaa project sits close to the western margin of the Kibi-Winneba Volcanic Belt within the Cape Coast Basin.
The Eburnean (2.1 Ga) tectono-thermal orogenic event is responsible for the folding and metamorphism of Birimian Supergroup rocks and, at the same time, the development of high-strain zones along the Birimian belt/basin boundaries. The Birimian basins were preferentially intruded by extensive, late and syn-kinematic granitoids of the Eburnean Plutonic Suite (2116–2088 Ma) including the regionally extensive Cape Coast
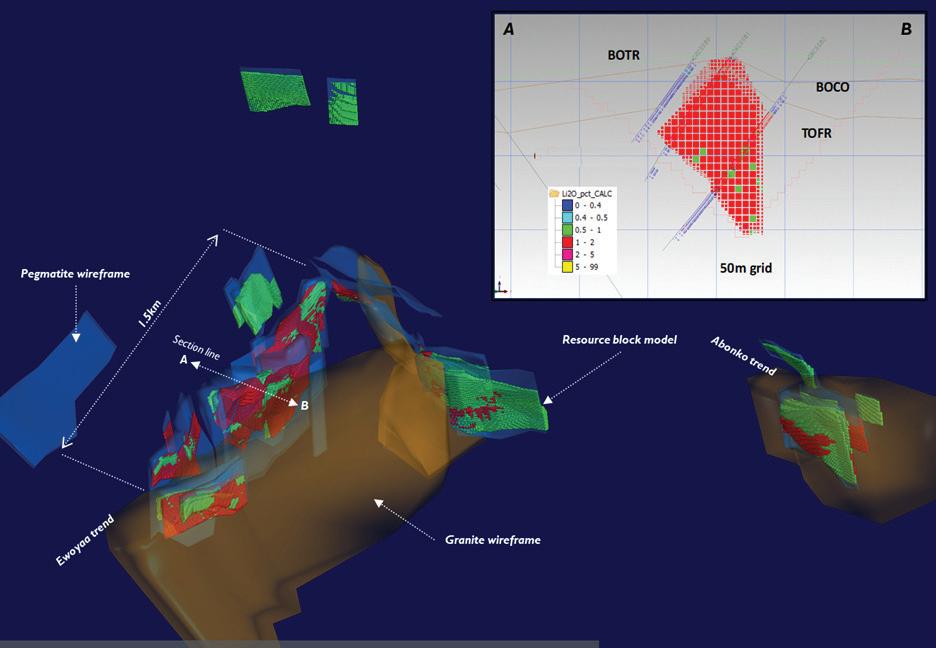
3D wireframe geology and mineralization block model view looking north-east of the Ewoyaa deposit with cross-section block model insert
undifferentiated biotite granitoid pluton, the dominant geological feature of this region. The last manifestation of the Eburnean plutonism may be the pegmatite intrusions which are spatially associated with a portion of the pluton’s margin and have been dated to 2072 Ma but could be the result of metasediment anatexis.
Exploration
Exploration is challenging, where outcropping pegmatite is rare in the region, due to deep tropical weathering with well-developed lateritic soil profiles and localized alluvium cover, combined with ubiquitous impenetrable dense secondary growth vegetation, thus nearly all ground exploration work requires line cutting.
All the granted tenement areas have been flown with high-resolution heliborne magnetic and radiometrics, and soil sampled on a 100 x 100 m grid (328 x 328 ft), and the resultant geophysical and geochemical data interpreted to develop exploration targets. The soil samples have all been prepped and analyzed in-house using bench-mounted PRESS, pXRF and pLIBS providing rapid results and significant cost savings. Man-portable, yet strong, powered auger rigs are used for follow-up prospecting work along hand cut traverse lines, drilling down 5–10 m (16–33 ft) through the laterite, duricrust, stone lines and saprolite to identifiable lithology. Infill auger traverses are used to delineate pegmatite targets at surface, ready for initial RC drilling on broad spaced drill fences.
‘The soil samples have all been prepped and analyzed in-house using bench mounted PRESS, pXRF and pLIBS which provides rapid results and significant cost savings.’
odiorite or other granitoid where locally developed. Two dominant mineralized pegmatite trends have been observed at the Ewoyaa; the North-Northeast-South-Southwest en-echelon pegmatite array of the ‘Ewoyaa trend’ and the Northwest-Southeast to East-West orientated pegmatite dykes of the ‘Abonko trend’. The Ewoyaa trend pegmatites are subvertical or dip steeply to the east, while the Abonko trend pegmatites range from subvertical to dipping 45o North-East. Individual pegmatites range in thickness from less than 1 to 60 m (3 to 197 ft) and have variable strike length from 150 to 600 m (492 to 1969 ft) but with en-echelon pegmatite dyke arrays collectively extending over 1500 m (4921 ft) of strike open in many directions.
The mineralogy of the spodumene bearing pegmatites is very consistent throughout the Ewoyaa project, with predominantly albite (+/-microcline)-quartz-muscovite with accessory apatite and rare beryl and local secondary Fe-Mn-Li bearing phosphates. Mineralized pegmatite has been classified by grainsize in drill core into geo-domains, with coarse grained (>20 mm (>0.79 in)) P1 being dominant to the finer grained (<20 mm (<0.79 in)) P2. P1 type spodumene crystals in lengths of up to 80 cm (31.5 in) and 20 cm (7.87 in) in diameter have been observed at the Abonko quarry outcrops.
Mineral resource estimate
The pegmatites of the Ewoyaa project predominantly intrude a host rock of biotite/mafic schist, however, the host rock can also be gran-
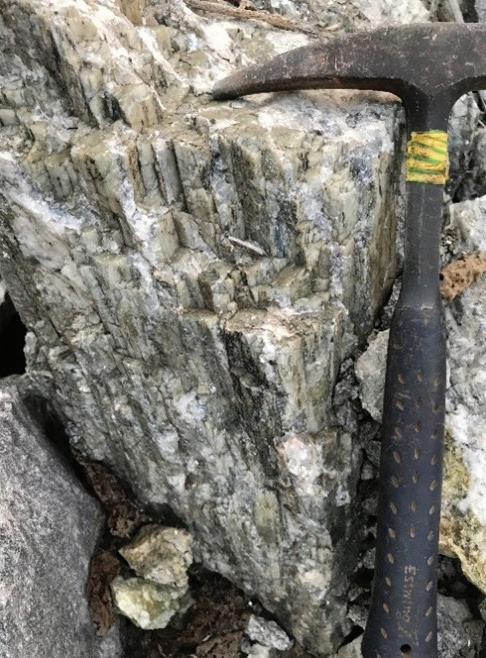
The 2019 indicated and inferred JORC (2012) compliant resource of 14.5 Mt at 1.31% Li₂O, with 4.5 Mt at 1.39% Li₂O in the indicated category
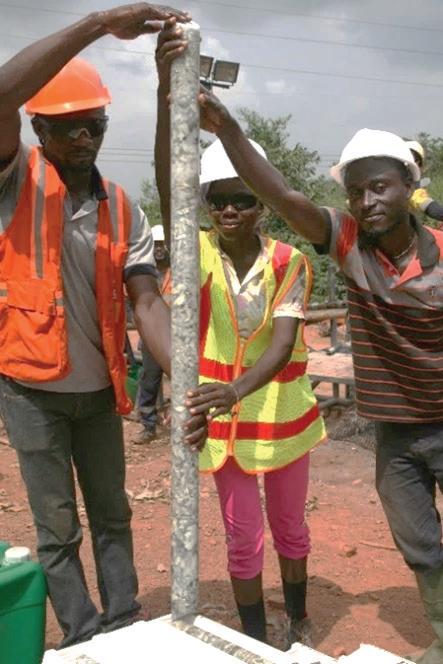
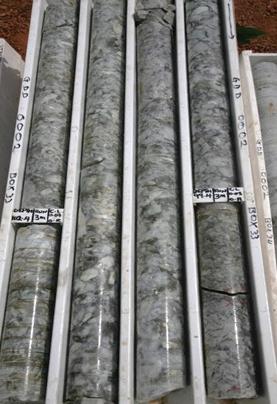
On the left – Coarse grained P1 type pegmatite at the Abonko quarry; Center and right - Field geological team holding drill core of coarse-grained pegmatite from the Ewoyaa deposit
(0.5% Li₂O cut-off) at the Ewoyaa, are the product of 198 RC drill holes totaling 25 574 m (83 904 ft) and eleven diamond holes for 1394.3 m (4574.48 ft) and extends over an area of 2.6 by 2.4 km (1.62 by 1.49 mi).
Recent auger and RC drilling has expanded the current footprint of the spodumene mineralized pegmatite swarm to 3.6 by 2.4 km (2.24 by 1.49 mi), a footprint that continues to grow as our exploration team evaluates untested exploration targets within the combined 684 km2 (264 mi2) tenement holding with RC drilling still ongoing at the time of writing.
Scoping study
The Project fundamentals support a robust Scoping study with conventional open cut mining from surface with low stripping ratios and close proximity to logistics and infrastructure – only 1 km (0.62 mi) away from the highway and 110 km (68 mi) by road from the deep-sea port of Takoradi, ensuring low operating costs. Good geological continuity and excellent metallurgy result in simple processing via coarse 6.3 mm (2.48 in) crush and conventional gravity flowsheet producing a premium 6% spodumene concentrate with significant value-add potential from feldspar credits providing for low capital costs.
The Scoping study supports a business case for 2.0 million tonnes per annum production operation over an eight-year life of mine. Mean-
ing production of an average of 295 000 tonnes per annum of 6% Li₂O spodumene concentrate with total revenues exceeding USD 1.55 billion, at a capital cost of USD 68 million with <1 year payback.
The Ewoyaa project has a post-tax net-present value (NPV8) of USD 345 million, internal rate of return of USD 125%, and operating costs of USD 247 per tonne of 6% lithium spodumene concentrate. Thus, the project has an average EBITDA of USD 105 million per annum with a significant potential to extend life of mine.
The Company demonstrates sound ESG initiatives with a strong national Ghanaian team, employment and training within the communities where we operate, environmental rehabilitation programs and hydro-electric, solar and logistic advantages providing for a potential low carbon footprint.
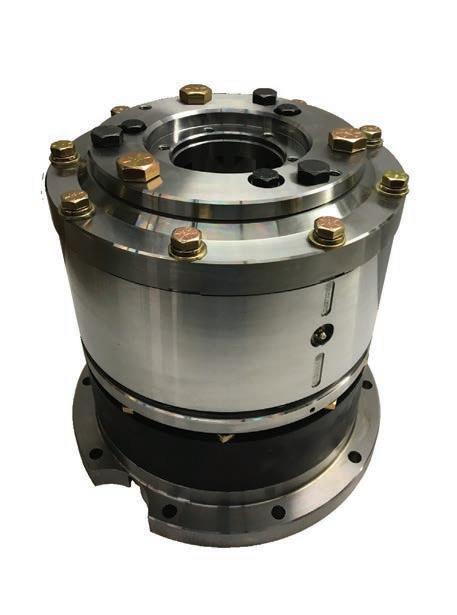
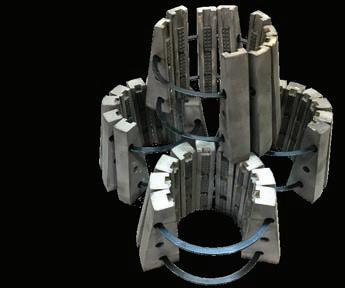
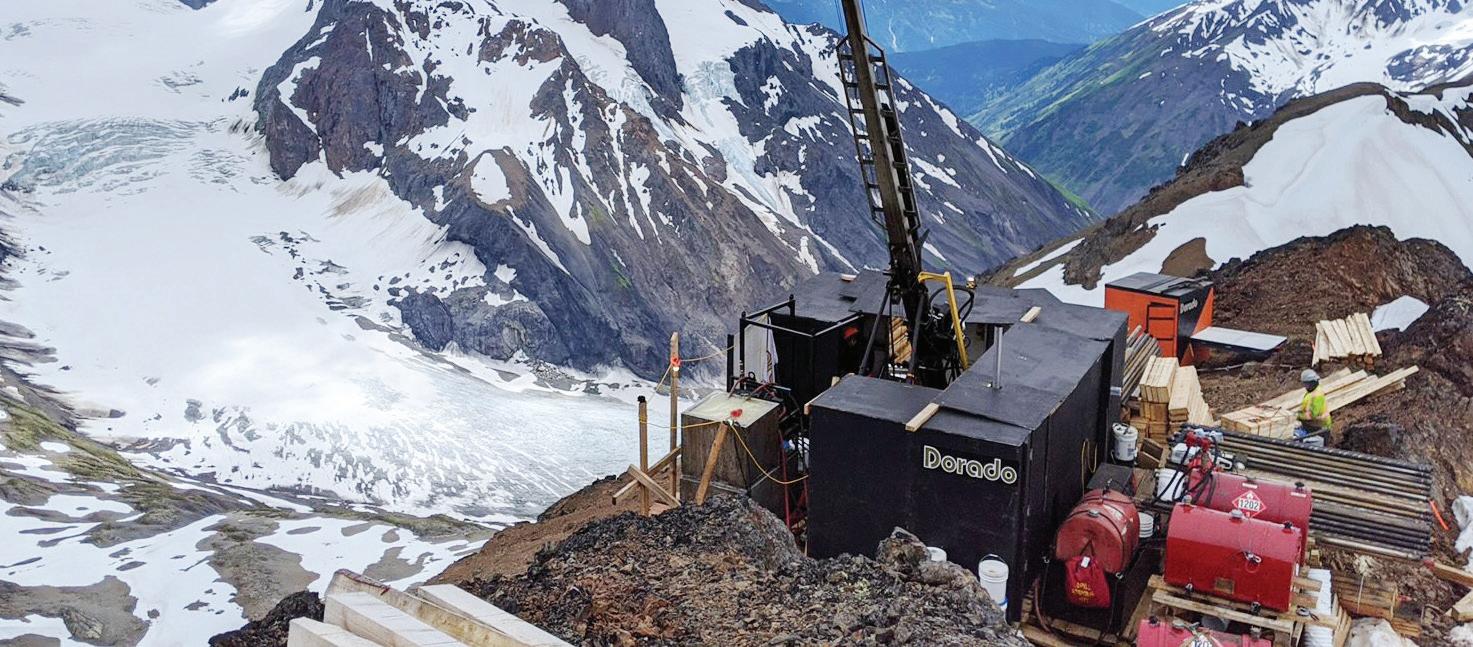
Explore the difference with RX-4 : keep doing the best, proudly
Levent 2002 RX-4 is designed by taking into consideration comfortable controls and ease of use to enable more e ective drilling. This rig also has a hold back feature, which enables much longer bit life.
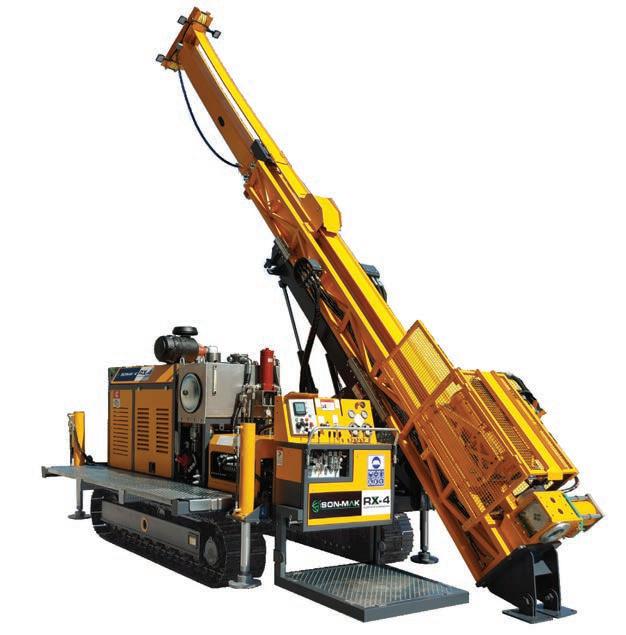
The mast and feed features are powerful and stable and present minimum vibrations directly into boreholes, making lifting and holding easier. The rod guide with a telescopic mast allows easier transportation.
Telescopic mast
The telescopic mast makes the drill easy to transport while the dump feature allows mounting on platforms of various sizes.
Rotation unit
The rotation unit has four speeds (funk), which enable the required torque and rpm speed levels necessary for coring. It can drill e ectively from 45° to 90° angles, make and break rods (by using the control panel), and it also incorporates safeguards.
r Rod holde
The rod holder opens hydraulically and closes using gas pressure. In the event of a loss of hydraulic pressure, the drill string is immediately blocked by the rod holder stopping the drop of the drill string into the hole.
Wireline hoist
The wireline hoist is mounted on the chassis and has an adjustable level wind angle. It does not need to be moved when changing drilling angle.There is an automatic winding system to prevent the rope from making straight or mixed winding.
Power unit
The Cummins engine is acclaimed for its prolonged durability, high e ciency and low fuel consumption even in the most challenging drilling operations.
The engine conforms to Tier III/ Stage 3A.
A Stage V diesel engine is available far US and European markets
Levent 2002 RX-4® surface coring rig
Advantages
• A fully hydraulic surface coring rig;
• Designed for exploration drilling;
• With three types of carriers: trailer-, skid- and crawler-mounted.
• A remote control feature that enables the driller to operate from a safe distance
What makes Levent 2002 RX-4 unique is the awless combination of veri ed concept and durable components. The rig adopts the most advanced technology for diamond core drills and the latest developments, in order to carry out e ective drilling.
The rotation speed, power and rotation unit aperture of Levent 2002 RX-4 are made to present optimal performance in 60-122.6 mm (2.36 - 4.83 in) (B-P) diameter wireline or conventional drilling. As far the spindle bore, its diameters is 127 mm (5 in).
Levent 2002 RX-4 has all the necessary features and safeguards to protect the driller from the hot and moving parts.
Self-contained control panel
The rig has a self-contained control panel, a mast dump, hydraulic jacks, and a telescopic mast, which allow an easy setup. Its ergonomics and safety bring a serious advantage; both for the driller and for the environment.
Drilling depth guidelines
The bellow drill depth capacities only serve as guidelines and refer to vertical down drilling. SON-MAK cannot guarantee that these results can be achieved in all drilling conditions
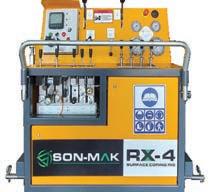
Kayapa I Organize San. Bölgesi, Kayapa Sanayi Bulvarı, BURSA, TÜRKIYE
Drilling Services
Drilling Contractors (A-Z): Diamond Drilling, Reverse Circulation, AirCore
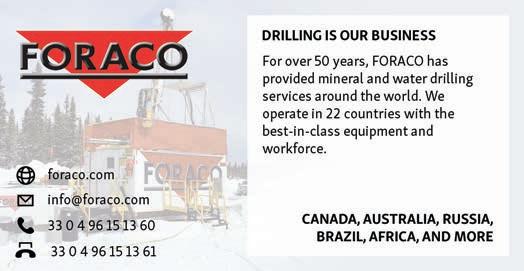
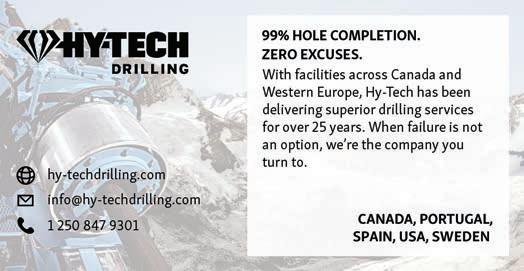
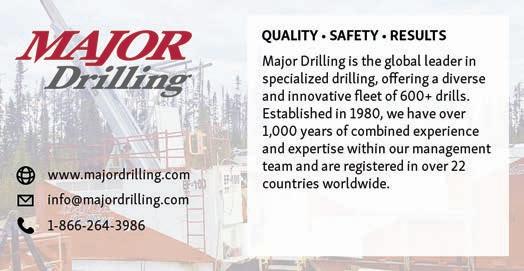
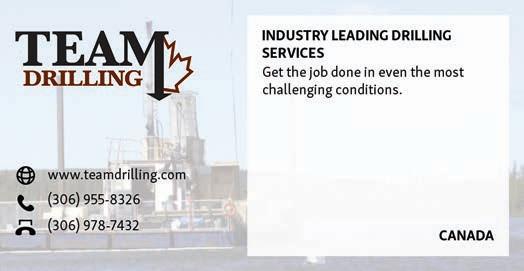
AARDVARK DRILLING
Phone 1-877-726-9340 info@aardvarkdrillinginc.com www.aardvarkdrillinginc.com Canada, United States, England
AGGRESSIVE DRILLING
Phone (306) 975-1523 adrill@sasktel.net www.aggressivedrilling.com Canada
AUSDRILL
Phone +61 8 6159 4407 info@ausdrill.com.au www.ausdrill.com.au
Australia
BUNDOK DRILLING
Phone (+63 46) 460 5310 info@bundokdrilling.com www.bundokdrilling.com Philippines
CABO
Phone (604)527-4201 info@cabo.ca www.cabo.ca Canada
CARTWRIGHT DRILLING
INC.
Phone 709 896 4446 www.cartwrightdrilling.ca Canada, Greenland, Madagascar, Malawi
CONTINENTAL DRILLING
Phone +502 2382-5070 info@continentaldrilling.com www.continentaldrilling.com Guatemala, El Salvador, Honduras, Nicaragua, Costa Rica, Panama
DDH1 DRILLING
Phone +61 08 9435 1700 admin@ddh1.com.au www.ddh1.com.au
Australia
DEPCO DRILLING
Phone (07) 4928 1133 info@depco.com.au www.depco.com.au Australia
DORADO DRILLING
Phone (+1) 250-351-9440 admin@doradodrilling.com www.doradodrilling.com Canada
DRILLCON AB
Phone +46 587 82820 Fax +46 587 311895 drillcon@drillcon.se www.drillcon.se Scandinavia, Portugal, Spain
EXPLOMIN PERFORACIONES
Phone +51 (1) 295-7070 contacto@explomin.com www.explomin.com/en/ Peru
FALCON DRILLING
Phone 001 250 564 7786 www.falcon-drilling.com Canada, United States, Mexico, Burkina Faso, Mongolia
FIRST DRILLING
Phone 1 (970) 249 3501 info.usa@firstdrilling.com www.firstdrilling.com United States, Australia
GEODRILL LTD
Phone +44 1624 676 585 contact@geodrill-dh.com www.geodrill-gh.com
Ghana
GEOSOL
Phone +55 (31) 2108-8000 geosol@geosol.com.br www.geosol.com.br Brazil
GEOTEC
Phone (511) 326 – 5494 geotec@geotec.com.pe www.geotec.com.pe Peru
GLOBAL DRILLING & EXPLORATION GROUP
Phone +65 6543 9375 www.globaldrill.com Singapore, Indonesia, Papua New Guinea, Asia, Australia Pacific, Europe, Middle East, Africa
GÜNZEL DRILLING CC
Phone + 264 81 322 89 28 info@guenzeldrilling.com www.guenzeldrilling.com Namibia
HARDROCK DIAMOND DRILLING jordan@hardrockdrilling.ca www.hardrockdrilling.ca Canada
LOGAN DRILLING
Phone 902-639-2311 logan@logandrillinggroup. com logandrillinggroup.com Canada, United States, Colombia
KATI OY
Phone 0207430660 info@oykatiab.com www.oykatiab.com Finland
MITCHELL SERVICES LIMITED
Phone +61 7 3722 7222 info@mitchellservices.com.au www.mitchellservices.com.au Australia
NPLH DRILLING
Phone 705-268-7956 Fax 705-268-5174 ablaquiere@nplhdrilling.ca www.nplhdrilling.ca Canada
ORBIT GARANT DRILLING
Phone 819 824-2707 Fax 819 824-2195 info@orbitgarant.com www.orbitgarant.com
Canada, United States, West Africa, South America
PEAK DRILLING
Phone 250-897-0930 Fax 250-897-0960 info@peakdrilling.com www.peakdrilling.com Canada
RUEN DRILLING
Phone (208) 266-1151 Fax (208) 266-1379 office@ruendrilling.com www.ruendrilling.com United States, Peru
SUMMIT DRILLING
Phone 800-242-6648 Fax 732-356-1009 info@summitdrilling.com www.summitdrilling.com United States
TIMBERLINE DRILLING INC
Phone 208.665.7211 info@timberline-drilling.com www.timberline-drilling.com
United States
TITELINE DRILLING
Phone +61 3 5338 3800 Fax +61 3 5337 6100 info@titelineinternational. com.au
titelineinternational.com.au Australia, Ecuador, Indonesia, Mongolia, Myanmar
Directional Drilling (A-Z)
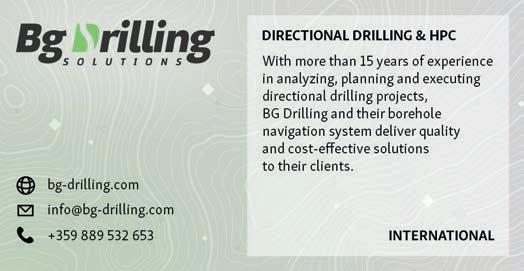
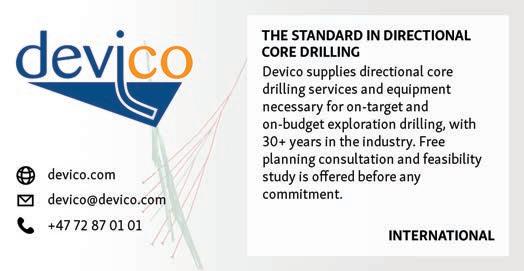
I3 DIRECTIONAL
DRILLING SOLUTIONS
Phone 1-705-495-6363
roque@i3dds.com www.i3dds.com Canada
REI DRILLING
Phone +1 801 270-2140
Fax +1 801 281-2880 www.reidrilling.com United States
TECH DIRECTIONAL
Phone (705) 524-6222 info@techdirectional.com techdirectional.com Canada
TRUST SOLUÇÕES
GEOLÓGICAS
Phone +55 (62) 3575 3720 contato@trustsg.com.br www.trustsg.com.br Brazil
Drilling Equipment & Accessories
Drill Rigs & Accessories (A-Z)
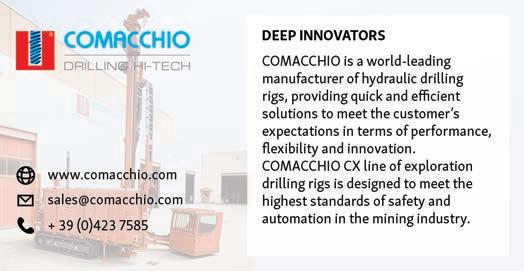
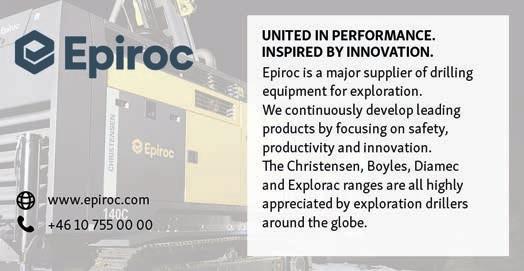

Surveying & Geophysics (A-Z)
CORE TECH
Phone (511) 255-5701
ventas@coretech.com.pe www.coretech.com.pe Peru
DIGITAL SURVEYING
Phone +27 18 788 6349
sales@digitalsurveying.co.za www.digitalsurveying. com.za Africa
DOWNHOLE SURVEYS
Phone +61 (0) 8 9361 4745 sales@downhole.com.au www.downhole.com.au Australia
GYRODATA SERVICES
CANADA
Phone +1 705 494 0075 don.black@gyrodata.com www.gyrodata.com Canada
INTERNATIONAL
DRILLING SERVICES
Phone +1 480-824-7100
IDSinfo@IDSdrill.com www.idsdrill.com United States, Canada
TRUST SOLUÇÕES
GEOLÓGICAS
Phone +55 62 992720023 contato@trustsg.com.br Brazil
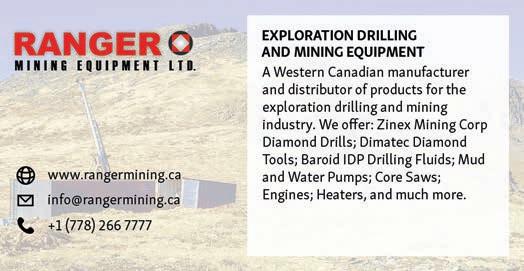
Rigs & Accessories (A-Z)
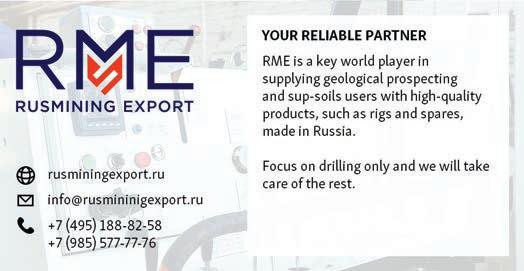
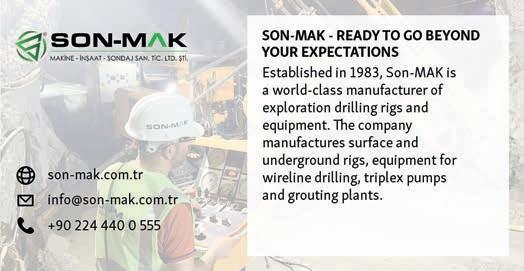

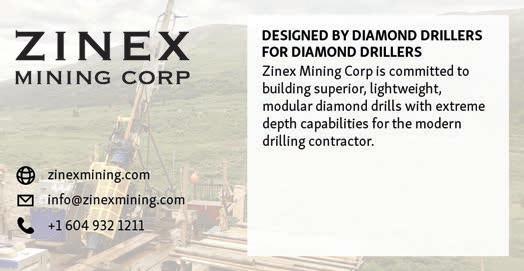
ACKER DRILL
Rigs & Accessories (A-Z)
Phone 570-586-2061 Fax 570-586-2659 sales@ackerdrill.com www.ackerdrill.com
ATELIER VAL-D’OR
Phone (819) 824-3676 Fax (819) 824-2891 info@avddrills.com www.avddrills.com
AUSTEX
Phone 08 9450 9400 Fax 08 9478 2316 enquiries@austexeng.com.au www.austexeng.com.au
BARKOM
Phone 90-312 385 60 50 Fax 90-312 385 35 75 info@barkomas.com www.barkomas.com
DANDO DRILLING INTERNATIONAL LTD Phone 01903731312 www.dando.co.uk
DELTA MAKINA
Phone +90 312 386 15 41-42 Fax +90 312 386 15 43 delta@deltamakina.com www.deltamakina.com
DISCOVERY DRILL MANUFACTURER
Phone 1-506-542-9708 Fax 1-506-542-9709 info@discoverydrills.com www.discoverydrills.com
DURALITE DIAMOND DRILLS
Phone 709 263-7221 Fax 709 263-7231 duralitedrills@nf.sympatico.ca duralitediamonddrills.com
FORSUN ULTRA-HARD MATERIAL INDUSTRY
Phone +86-731 84254020 Fax +86-731 84252208 info@forsuntools.com www.forsun-tools.com
GEO DRILLING MACHINERY MANUFACTURING
Phone +90-312-354-8576 Fax +90-312-385-6215 www.geosondajmakine.com
HYDRACORE DRILLS
Phone +1 604-940-4937 Fax +1 604-940-4919 info@hydracore.com www.hydracore.com
Drill Rig Parts (A-Z)
MASSENZA DRILLING RIGS
Phone +39 0521 825284 info@massenzarigs.it www.massenzarigs.com
MAXIDRILL INC
Phone +1 450-763-0212 Fax +1 514-221-2356 info@maxidrill.com www.maxidrill.com
ODYSSEY FLUID POWER Phone 705 707 1780 info@odysseyfluidpower.com www.odysseyfluidpower.com
PRD RIGS Phone +91 90470 87755 marketing@prdrigs.com www.prdrigs.com
SINOCOREDRILL
Phone 86-510-82723272 Fax 86-510-82752846 sales@sinocoredrill.com www.sinocoredrill.com
USINAGEM MARCOTTE Phone 1-819-824-3977 www.umvd.ca
VERSADRILL Phone 1-819-874-4404 www.versadrillcanada.com
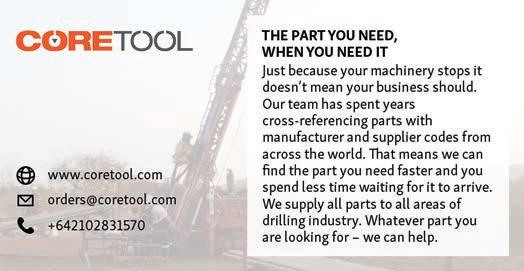
PROLENC
Phone (250) 563-8899 Fax (250) 563-6704 khodgins@prolenc.com www.prolenc.com
Drill
Drill
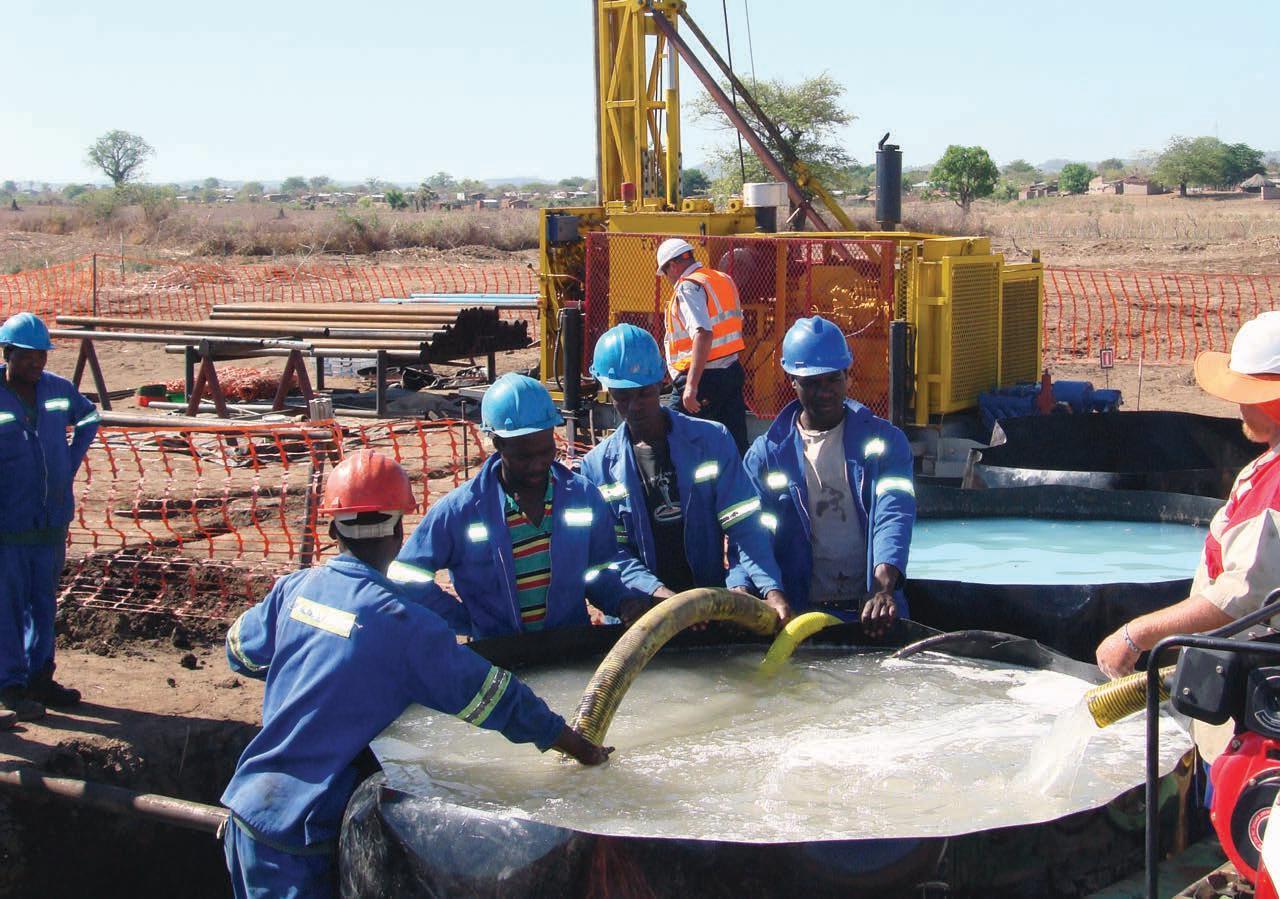
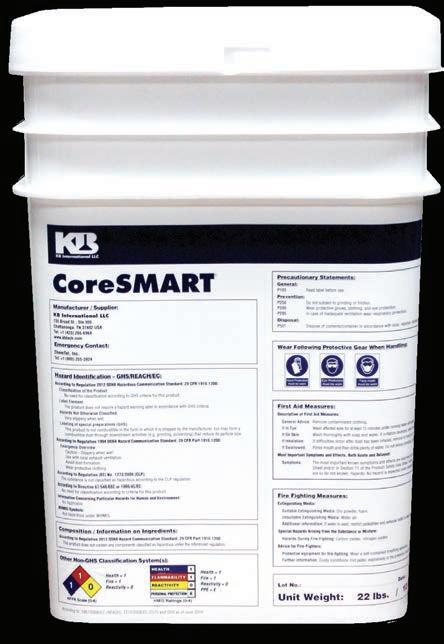
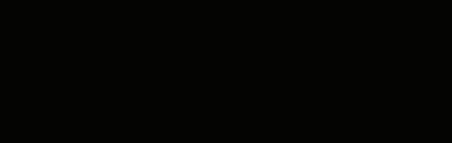
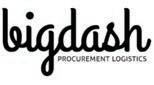
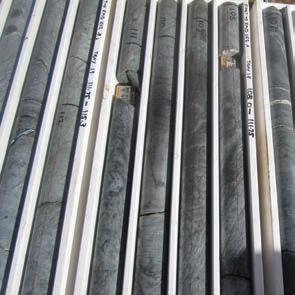
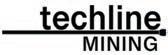
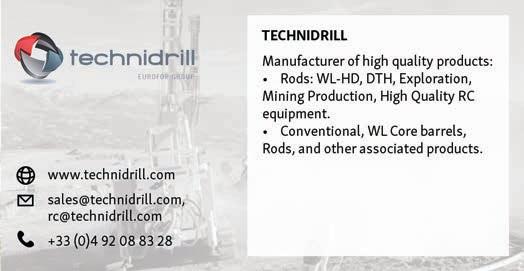
BOART LONGYEAR
Phone 1-801-972-6430
Fax 1-801-977-3374 www.boartlongyear.com
FORDIA POWERED BY EPIROC
Phone 514-336-9211 Fax 514-745-4125 info@fordia.com www.fordia.com
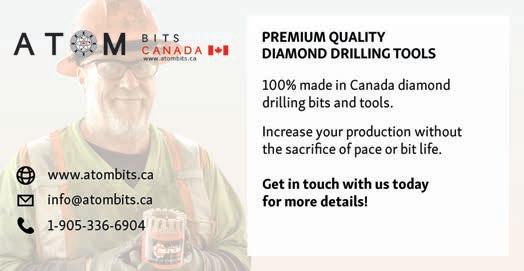
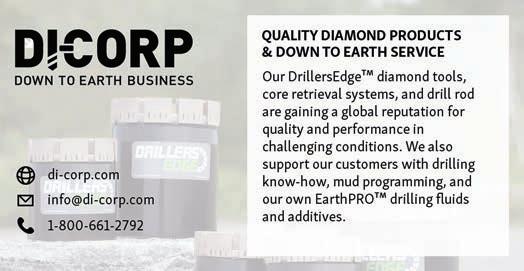

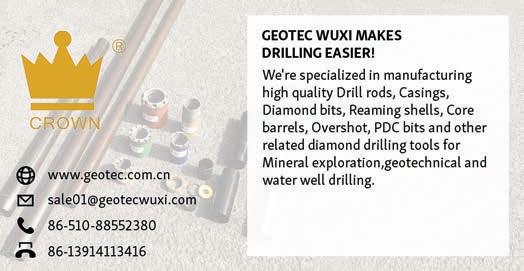
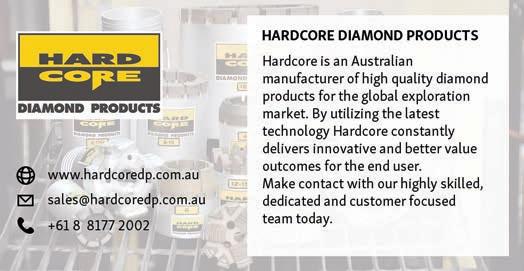
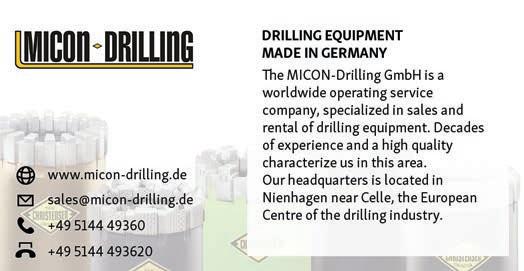
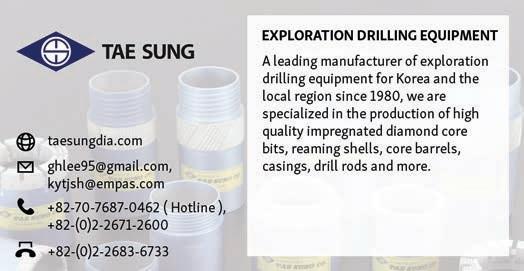
RC Equipment (A-Z)
Diamond Products (A-Z)
Diamond Products (A-Z)
Diamond Products (A-Z)

ASAHI DIAMOND
Phone + 61-2-9997-7033 Fax +61-2-9997-8313 sales@asahi-diamond. com.au www.asahi-diamond.com.au
CHRISTENSEN RODER
Phone (11) 5069-5900 roder@roder.com.br www.roder.com.br
DIAMANTINA
CHRISTENSEN
Phone +562 2620 7808 christensen@christensen.cl diamantinachristensen.com
DIASET
Phone 1-800-663-5004 Fax 604-940-9534 bits@diaset.com www.diaset.com
DIMATEC
Phone 1-866-538-5732 Fax 1-204-832-4268 info@dimatec.com www.dimatec.com
DRILLING HQ
Phone 1 (208) 690-3111 Info@DrillingHQ.com www.drillinghq.com
FORSUN ULTRA-HARD MATERIAL INDUSTRY
Phone 86-731 84254020 Fax 86-731 84252208 info@forsuntools.com www.forsun-tools.com
HARGRAND DRILLING TOOLS
Phone 86-010-58412500 +8618610425267 Fax 86-010-58412501 eric@hargrand.com www.hargrand.com
HOLE PRODUCTS
Phone (888) 465-1569 Fax (320) 631-0064 www.holeproducts.com
HUD MINING SUPPLIES
Phone 27 (0) 11-974-1500 info@hud.co.za www.hud.co.za
JUFERMA
Phone 34-91 498 93 07 Fax 34-91 498 93 06 diamondjuferma@juferma. com www.juferma.com
LEVANTO DIAMOND SOLUTIONS
Phone 358-9-511-470 Fax 358-9-5114-7470 info@levanto.fi www.levanto.fi
SAFARI DIAMOND DRILL BITS
Phone 604-275-2487
Fax 604-275-2487
info@safaridiamonddrillbits. com safaridiamonddrillbits.com
SINOCOREDRILL
Phone 86-510-82723272 Fax 86-510-82752846 sales@sinocoredrill.com www.sinocoredrill.com
Specialized Machine Works (A-Z)
NORTH BAY MACHINING CENTRE
Phone (705) 472-9416
Fax (705) 472-2927
luc@nbmc.ca www.nbmc.ca
Core Barrels (A-Z)
PROLENC
Phone (250) 563-8899 Fax (250) 563-6704 khodgins@prolenc.com www.prolenc.com
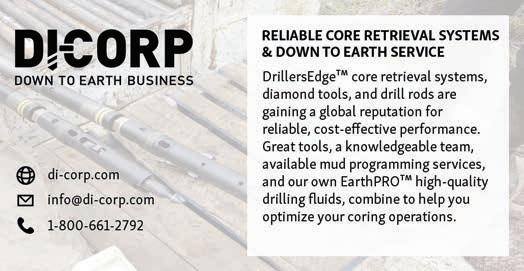
Core Barrels (A-Z)

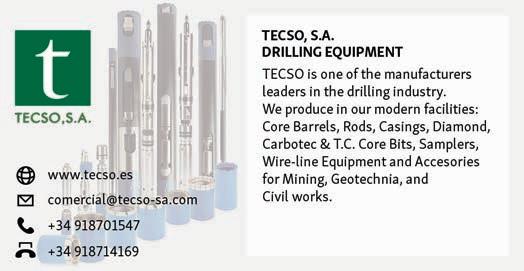
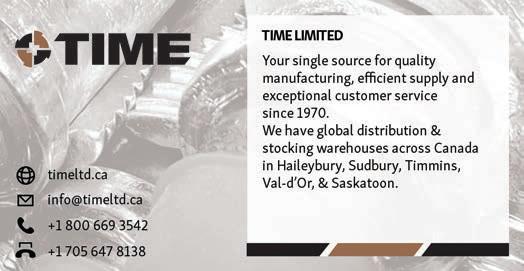
BOART LONGYEAR
Phone 1-801-972-6430 Fax 1-801-977-3374 www.boartlongyear.com
DIAMANTINA CHRISTENSEN
Phone 56(9) 7707 9371 christensen@christensen.cl diamantinachristensen.com
DRILLING HQ
Phone 1 (208) 690-3111 info@DrillingHQ.com www.drillinghq.com
FORSUN ULTRA-HARD
MATERIAL INDUSTRY
Phone 86-731 84254020 Fax 86-731 84252208 info@forsuntools.com www.forsun-tools.com
HARGRAND DRILLING
TOOLS
Phone 86-010-61599828 Fax 86-010-61599828 whp@baoqizt.com www.hargrand.com
HOLE PRODUCTS
Phone 909-939-2581 Fax 909-891-0434 www.holeproducts.com
ICEMS
Phone (16) 3367-3126 Fax (16) 3361-5073 icems@icems.com.br www.icems.com.br
K. MAIKAI
Phone 81-3-3490-8433 Fax 81-3-3490-8622 www.kmaikai.co.jp/eng
MBI GLOBAL
Phone + 1 819 762-9645 dmisiano@mbiglobal.ca www.mbiglobal.ca
SINOCOREDRILL
Phone 86-510-82723272 Fax 86-510-82752846 sales@sinocoredrill.com www.sinocoredrill.com
TERRA TEAM OY
Phone 358-9-849-4030 info@terra-team.fi www.terra-team.fi/en
Drill Rods & Casings
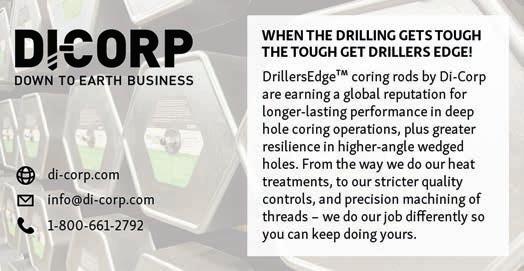
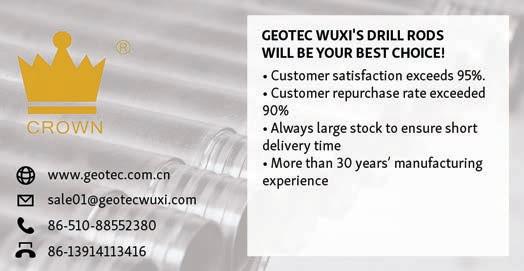
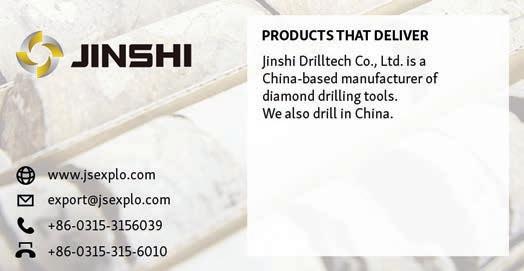
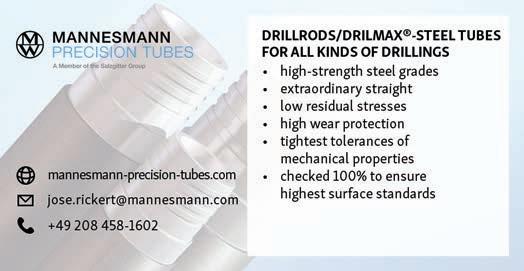
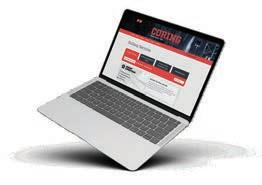
Drill Rods & Casings
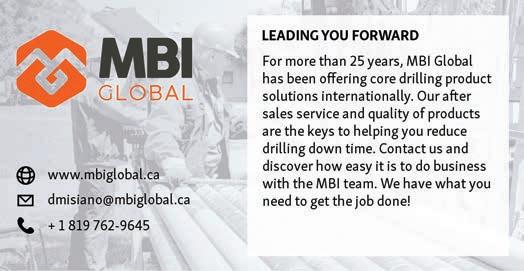

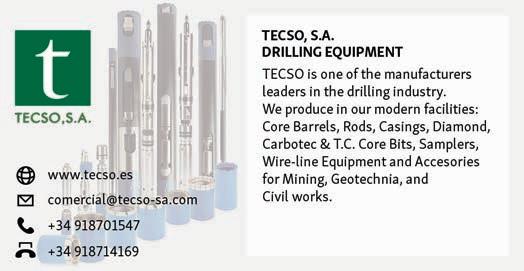
BARKOM
Phone 90-312 385 60 50 Fax 90-312 385 35 75 info@barkomas.com www.barkomas.com
BOART LONGYEAR
Phone 1-801-972-6430 Fax 1-801-977-3374 www.boartlongyear.com
CORE TECH Phone (511) 255-5701 ventas@coretech.com.pe www.coretech.com.pe
DIAMANTINA CHRISTENSEN
Phone 56(9) 7707 9371 christensen@christensen.cl www.diamantinachristensen. com
FORDIA POWERED BY EPIROC
Phone 514-336-9211 Fax 514-745-4125 info@fordia.com www.fordia.com
GEO DRILLING MACHINERY MANUFACTURING Phone
www.geosondajmakine.com
info@son-mak.com.tr www.son-mak.com
Wedges (A-Z)
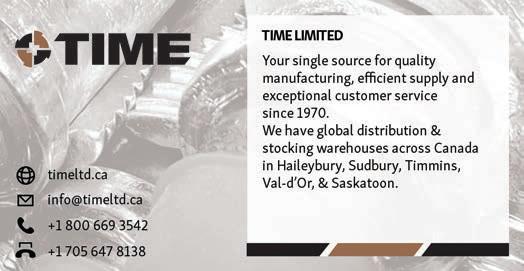
FORDIA POWERED BY EPIROC
Phone 514-336-9211 Fax 514-745-4125 info@fordia.com www.fordia.com
REFLEX
Phone 1-705-235-2169 Fax 1-705-235-2165 reflex@imdexlimited.com www.reflexnow.com
SONDA PARTS
Phone 55 – (31) 3391 3810 Fax 55 – (31) 3391 3810 comercial@sondaparts.com.br www.sondaparts.com.br/
TERRA TEAM OY
Phone 358-9-849-4030 info@terra-team.fi www.terra-team.fi/en/
Water Treatment System (A-Z)
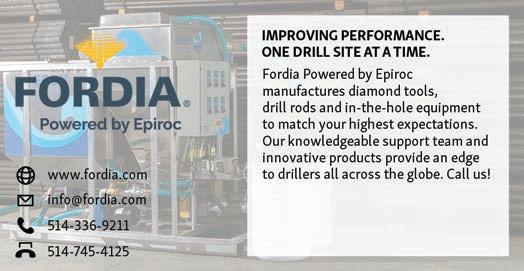
Survey Equipment
Survey Tools (A-Z)
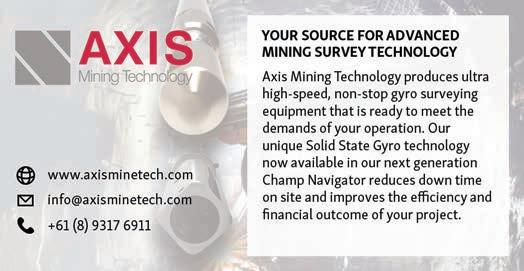
Survey Tools (A-Z)
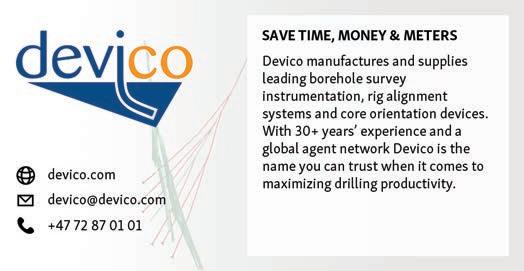
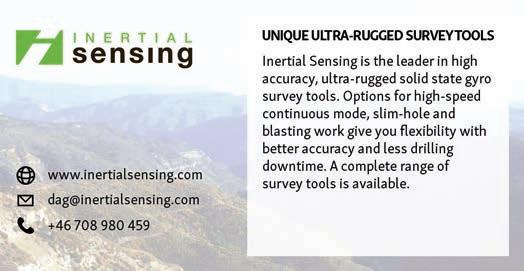
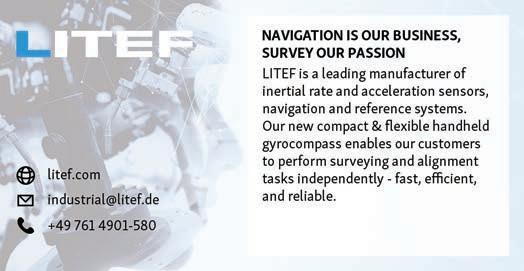
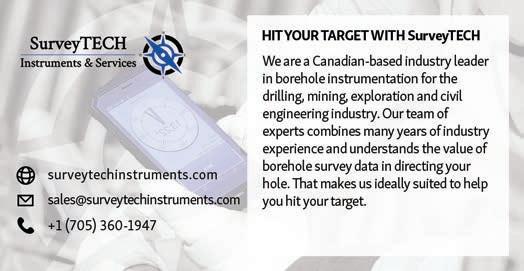
AZIWELL
Phone + 47 471 600 71 post@aziwell.no www.aziwell.no
BOART LONGYEAR
Phone 1-801-972-6430 Fax 1-801-977-3374 www.boartlongyear.com
ICEEFIELD TOOLS
Phone +1 (867) 633-4264 Fax +1 (867) 633-4217 support@icefieldtools.com www.icefieldtools.com
Survey Tools
REFLEX INSTRUMENTS
Phone 61 8 9445 4020
Fax 61 8 9445 4040 reflex@imdexlimited.com www.reflexnow.com
Core Orientation (A-Z)
BOART LONGYEAR
Phone 1-801-972-6430
Fax 1-801-977-3374 www.boartlongyear.com
COREFINDER
Phone +55 62 992720023 contato@corefinder.com.br www.corefinder.com.br
STOCKHOLM PRECISION TOOLS
Phone 46-8-590-733-10
Fax 46-8-590-731-55
info@stockholmprecisiontools.com stockholmprecisiontools.com
DEVICO AS Phone +47 72870101 devico@devico.com www.devico.com
REFLEX INSTRUMENTS
Phone 61 8 9445 4020
Fax 61 8 9445 4040 reflex@imdexlimited.com www.reflexnow.com
Core Trays (A-Z)
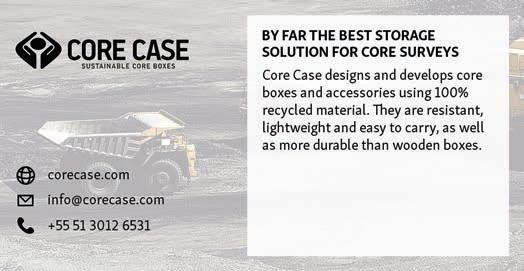
DYNAMICS G-EX
Phone +61 7 54826649
sales@dynamicsgex.com.au www.dynamicsgex.com.au
Miscellaneous
Drilling Fluids (A-Z)

CEBO HOLLAND B. V. (BAROID)
Phone +31 255 546 262 info@cebo.com www.cebo.com
CORE TECH
Phone (511) 255-5701 ventas@coretech.com.pe www.coretech.com.pe
DI-CORP
Phone +1 (705) 721-3300 info@di-corp.com www.di-corp.com
JC PORTAL DRILLING SUPPLIES
Phone (33) 3810 6099 (33) 1561 6618 ventas@jcpds.com.mx www.jcpds.com.mx
MUDEX
Phone +61 (8) 9390 4620 info@mudex.com.au www.mudex.com.au
TIGER FLUIDS
Phone +61 (0) 417 60 11 00 info@tigerfluids.com www.tigerfluids.com
PROSPECTORS
Phone +61 (02) 9839 3500
Fax +61 (02) 8824 5250 sales@prospectors.com.au
Catalog rates
Combined listing
700€ per year (3 issues)
Featured listing published both in our print and web catalog.
Featured listing
200€ per issue
450€ per three issues
A large, advert-sized listing featuring your choice of image as a background, your logo and strapline, 240 character spaces and your company contact details.
Highlighted listing
120€ per issue
260€ per three issues
Similar to the basic insert in size, yet with a color background, for improved visibility and exposure.
Basic listing
80€ per issue
150€ per three issues
A text-only listing including your company name and contact details (phone, fax, email and website).
For more info, get in touch at: editorial@coringmagazine.com
Packers (A-Z)
HOLE PRODUCTS
Phone +1 909 939 2581 Fax +1 909 891 0434 holeproducts.com
SON-MAK
Phone +90 224 482 44 40
Fax +90 224 482 44 39 info@son-mak-com.tr www.son-mak-com.tr
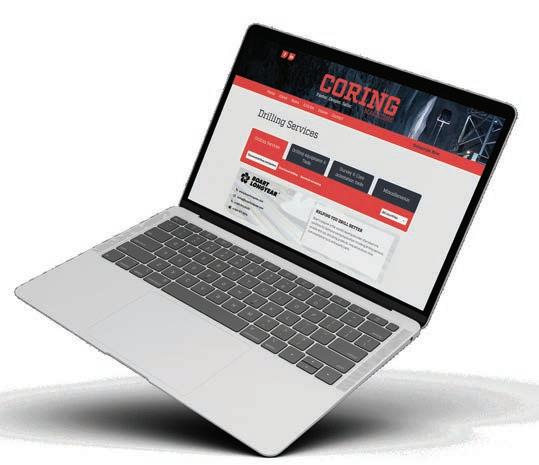
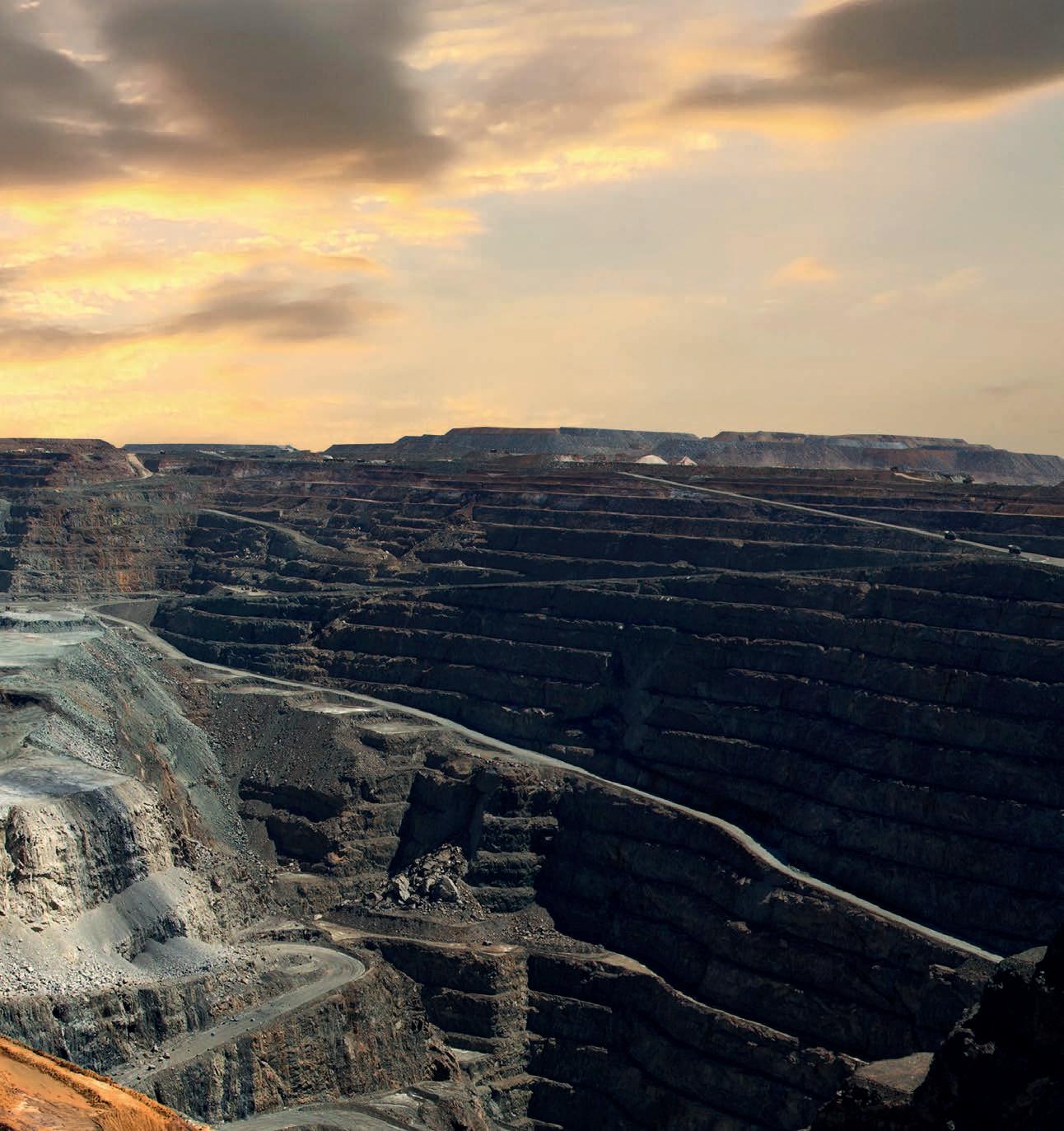
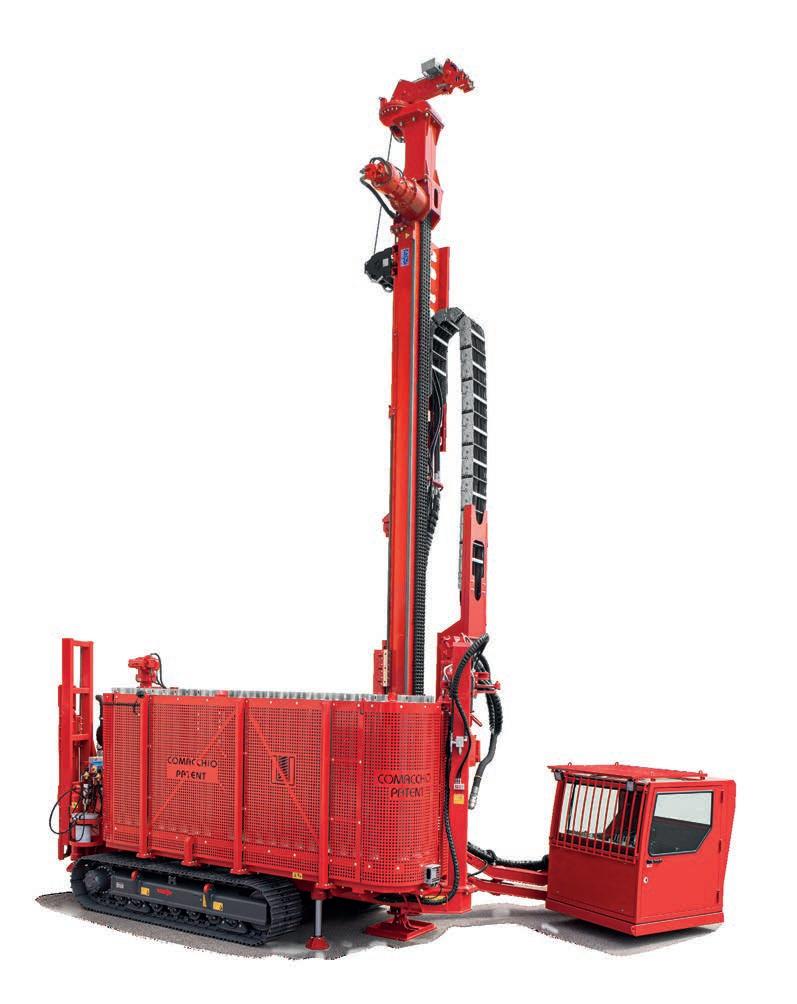
Safety is the challenge, CX Line is the answer. Compact design, hands-free rod handling system for fully automated and remote controlled operations: it’s the new range of exploration drilling rigs. Are you ready for the new era?
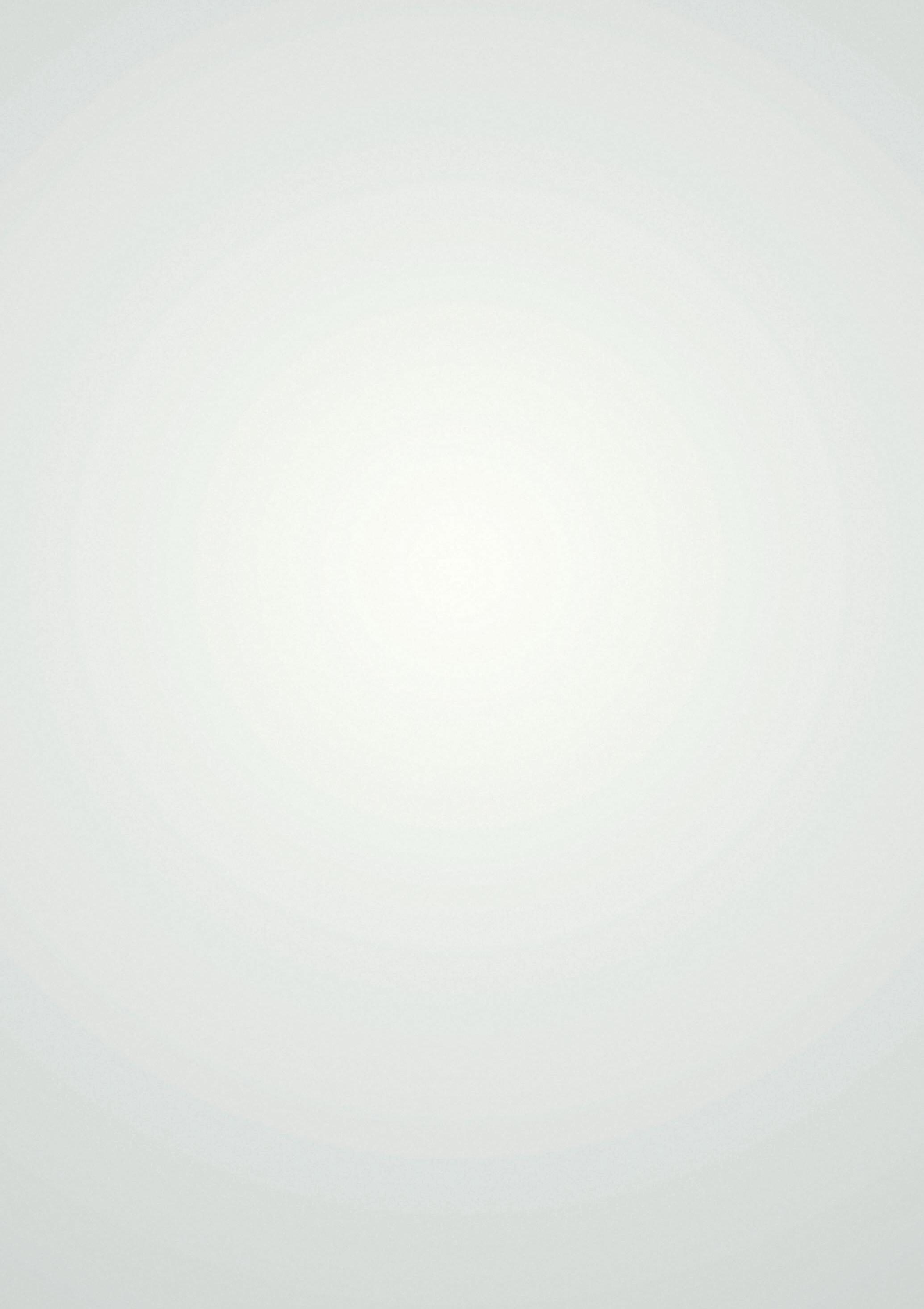
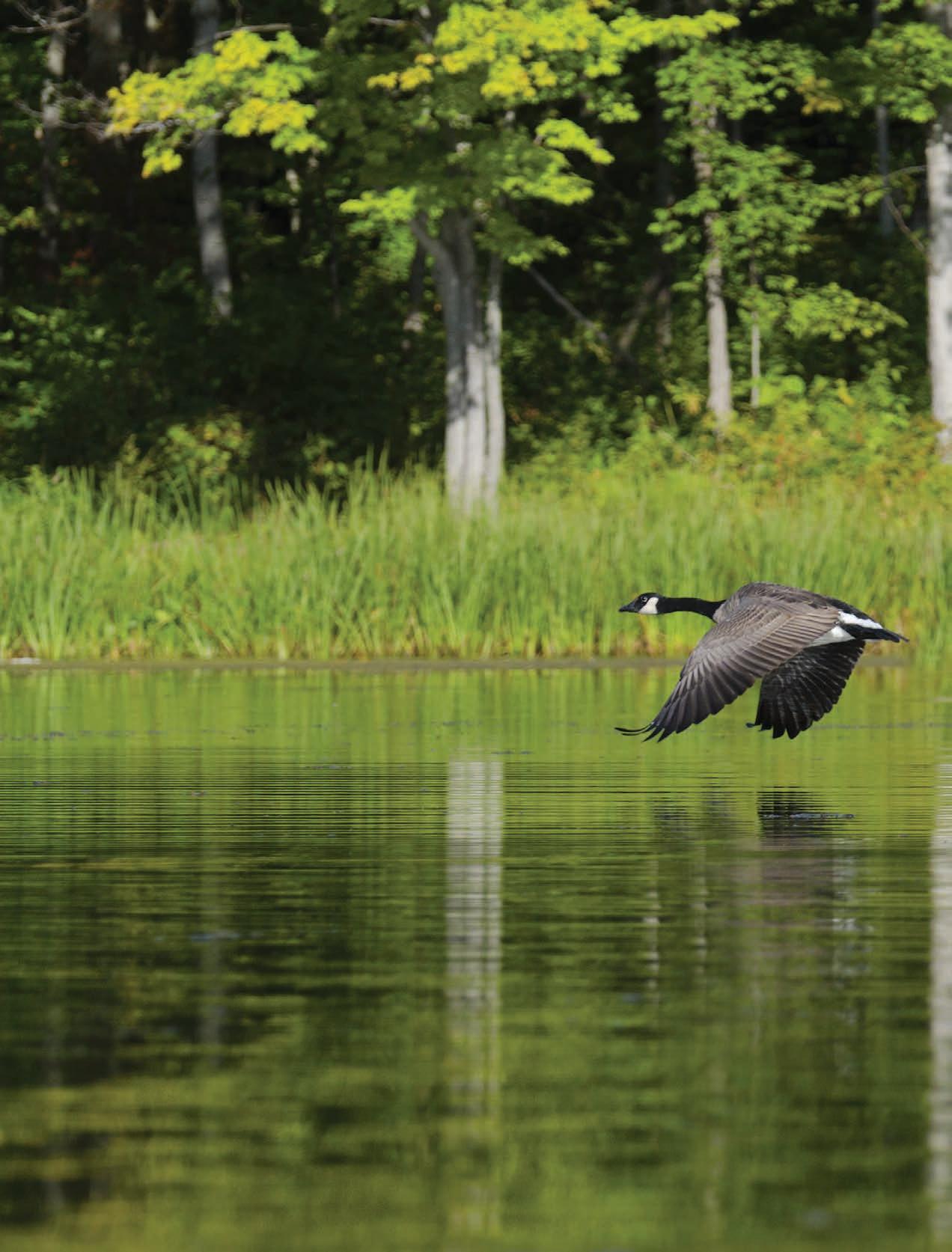
TORQUELESS
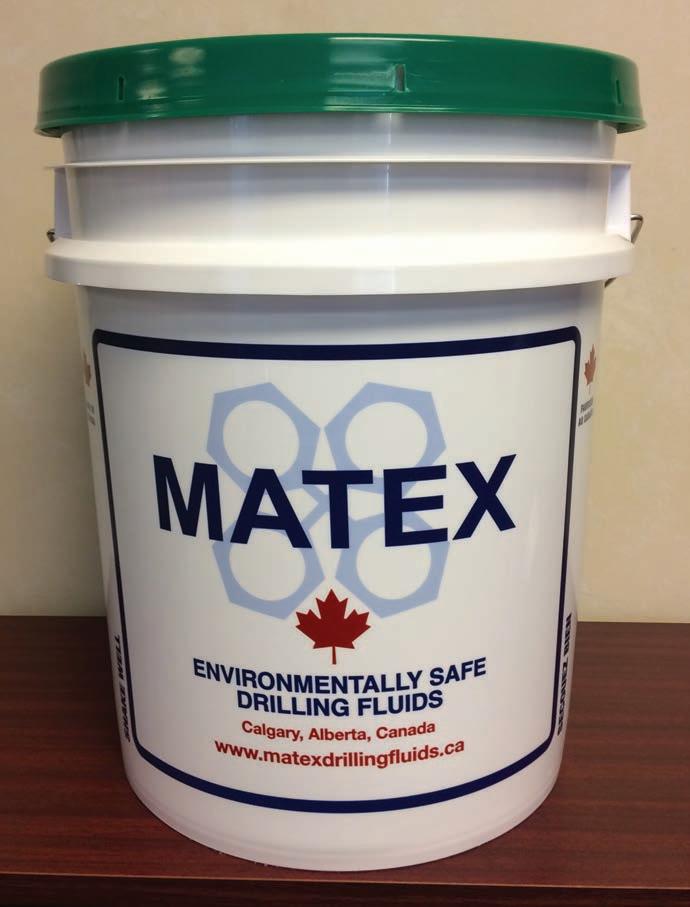
• Enhances both bit-life and penetration rates during drilling operations.
• Extremely effective for lubricating down hole motors and eliminating magnetization of drill rods.
• Protects drill rod wear when using wedges in diamond drilling.
• Increases tool joint life by reducing torque in the hole.
• Inhibits swelling of clay-like materials such as saprolites, talcs and kimberlites.
• Enhances the effectiveness of powdered mud systems.
• Non-sheening when accidentally introduced into a water course.