

Integrated Core Orientation Has Arrived
No Extensions | No Maintenance | Just Drill
Integrates with standard head assemblies
No outer tube extensions or adapters
Communicate, mark core & drill next run without disassembly
Reduce orientation transfer error
Axis onSite™ data transfer with onSite™ Client Portal access or API enterprise integration



Table Contents
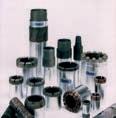

/DRILLING STORIES
28 A day in the life of a driller by Mike Junkins, Core Drill Operator /EXPLORATION & MINING
32 Tect Geological Consulting: An industry-leading specialist in Structural-Economic Geology by Dr Ian Basson and Dr Corné Koegelenberg, Principal Members and Michael McCall, Senior Geoscientist
38 Q&A from the experts: In conversation with Beau Nicholls, Director & Principal Consultant at Sahara Natural Resources
44 Exploration in the land of gold: A brief review of observations and techniques by Ahmed Atito, Exploration Geologist at Nubian Mining Company
46 The use of mineral exploration drilling to kickstart hydrogeology data collection for pre-feasibility mining studies and beyond by Kym L Morton, CEO and Consulting Hydrogeologist at KLM Consulting Services Pty Ltd
50 Six concepts to keep in mind when exploring structurally controlled mineralizations by Luca Smeraglia, PhD, Independent Structural Geology Consultant and Structural Geologist at the National Research Council of Italy
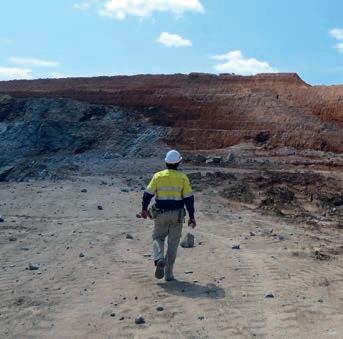
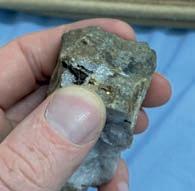
/INDUSTRY EVENT
54 PDAC 2022: The Super Bowl of the mineral exploration and mining world will be hybrid by PDAC’s Marketing Team /EXPLORATION DRILLING CATALOG
56 Drilling services
AZIWELL’S AZIDRILL® N-BTK consolidates the company’s position as a world leader of directional core drilling tools by Nils Ivar Iversen, Managing Director at AZIWELL AS, Norway
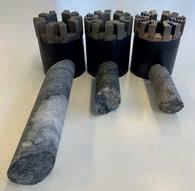

57 Drilling equipment & accessories
62 Survey equipment
62 Miscellaneous
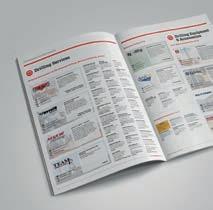
Authors in this issue
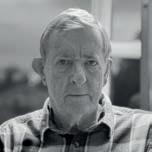

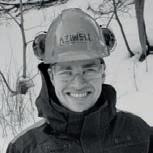
Tony Graham Partner at Diatool Diamond Products CO., LTD
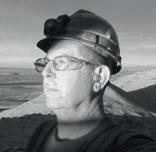
Mathieu Dionne President and CEO at Diafor


Mike Junkins Core Drill Operator
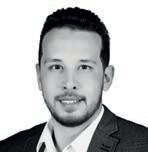

Dr Ian Basson, Dr Corné Koegelenberg
Principal Members and Michael McCall Senior Geoscientist at Tect Geological Consulting
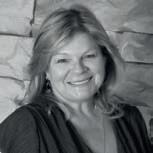
Nils Ivar Iversen Managing Director at AZIWELL AS, Norway
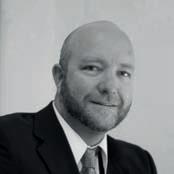

CORING MAGAZINE
April 2022
Cover photo Geosol
Issue 19
ISSN 2367-847X
Not for resale. Subscribe: www.coringmagazine.com/subscribe
Contact Us
Coring Media Ltd.
119B D. Petkov Str., Sofia 1309, Bulgaria
Phone +359 87 811 5710
Email editorial@coringmagazine.com
Website coringmagazine.com
Ahmed Atito Exploration Geologist at Nubian Mining Company
Kym L Morton CEO and Consulting Hydrogeologist at KLM Consulting Services Pty Ltd
Beau Nicholls Director & Principal Consultant at Sahara Natural Resources
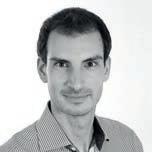
Publisher
Coring Media
Editor in Chief
Grigor Topev
Executive Officer & Editor
Martina Samarova
Editor
Maksim M. Mayer
Section Editor –
Exploration & Mining Geology
Dr Brett Davis
Digital Marketing Manager
Elena Dorfman
Graphic Design
Cog Graphics
Luca Smeraglia, PhD, Independent Structural Geology Consultant and Structural Geologist at the National Research Council of Italy
Coring Magazine is an international quarterly title covering the exploration core drilling industry. Published in print and digital formats, Coring has a rapidly growing readership that includes diamond drilling contractors, drilling manufacturers and suppliers, service companies, mineral exploration companies and departments, geologists, and many others involved in exploration core drilling.
Launched in late 2015, Coring aims to provide a fresh perspective on the sector by sourcing authentic, informed and quality commentary direct from those working in the field. With regular interviews, insightful company profiles, detailed product reviews, field-practice tips and illustrated case studies of the world’s most unique diamond drilling and mineral exploration projects, Coring provides a platform for learning about the industry’s exciting developments.
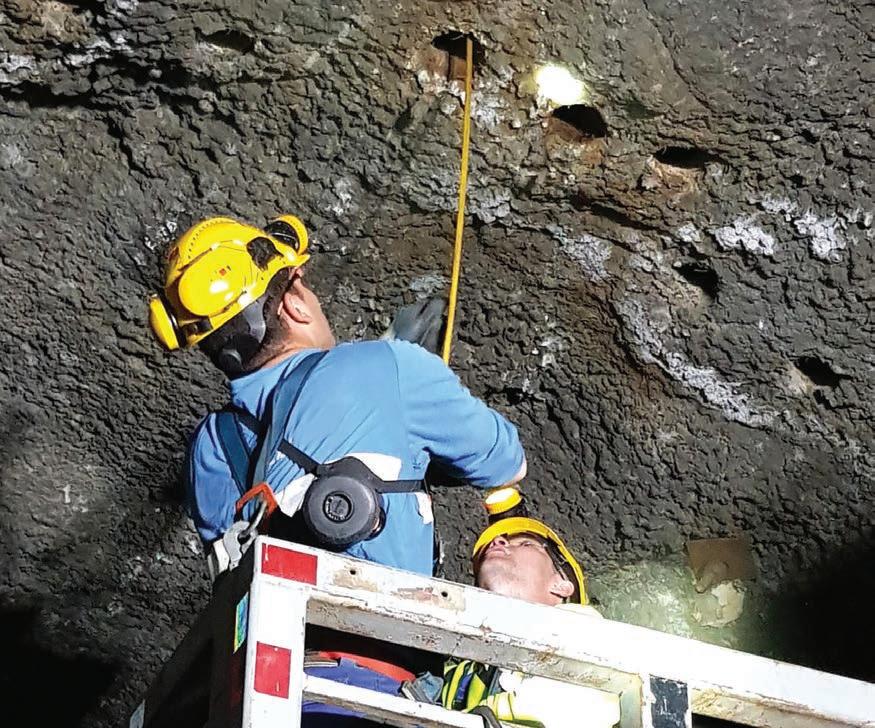

Tony Graham
questions
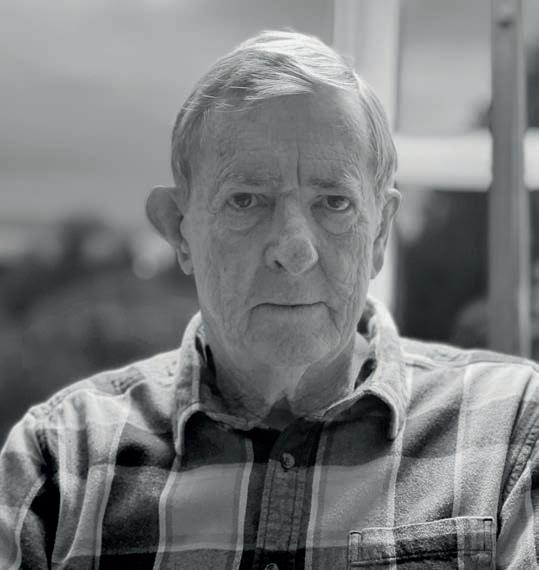
Anthony ‘Tony’ Graham is an expert in drill bits with over 60 years of industry experience. He was born in South Africa in 1940. He graduated the University of Natal with a BSc Hons in Geology. Tony then began working as a field geologist with Chartered Exploration (a division of Anglo American) in Lusaka, Northern Rhodesia (now Zambia), exploring for copper. Two years later, he moved back to South West Africa (now Namibia) to search for diamonds. Afterwards, he returned to Zambia to work for the Rhodesian Selection Trust (Rio Tinto) and later became an underground mine geologist at Mufulira Copper Mines.
In 1971, Tony began selling drilling products for Huddy Diamond Setting Company (Huddy Diamond) in Southern Rhodesia (now Zimbabwe). After six years of selling drill bits across Africa, Tony moved to Sudbury, Canada and later to Vancouver. There, in 1986, he became a shareholder in Hobic Bit Manufacturing Company, which over the next decade grew to become one of the industry leaders. Their success attracted the attention of Atlas Copco, and they bought the company in 2002.
Over the next few years, Tony worked in the stone industry and products related to it. It was in 2009 when he and several experienced colleagues formed Diatool Diamond Products. The company now has sales outlets and distributors in Asia, Australia, India, South and West Africa, Scandinavia, South America, Canada and the US.
Grigor Topev: My first question is about your education. You have a BSc Hons degree in Geology from the University in Natal, South Africa. How did you decide to study Geology and pursue a career in this sphere?
Tony Graham: Growing up, I had no early interest in Geology, I was more interested in auto mechanics. After finishing school, I didn’t want to go to university and was coerced into trying accounting as that was my Dad’s profession. However, after working in this field for a year, I found office work rather mundane and decided to attend university. I applied to enter General Science courses during my first year to keep my options open and studied Geology and Botany, Zoology and Geography. I found Geology very interesting, so I pursued this course as my major and after graduating carried on for another year, getting an Honours degree.
GT: You have worked in many countries. Which country left the strongest impression on you?
TG: I would say Nothern Rhodesia, which subsequently became Zambia, impressed me the most.
After graduating, I started as a field geologist working for Chartered Exploration, a division of Anglo American based in Lusaka. My job consisted of working in the bush searching for copper and other minerals for eight to nine months a year (from March to November).
Partner at Diatool Diamond Products CO., LTD
Exclusive interview with
Then I would go back to the head office during the rainy season and plot up all the information gathered from the field, making and updating maps. From the information gathered, we would decide on an area of interest that needed further investigative work the following year.
Life was pretty simple back then, as before going into the field every year, we had predetermined the area we were going to cover from aerial photographs and we knew where we would establish a centralized base camp. Then once we arrived and had the base camp set up, we would go on a foot safari for up to two weeks before returning. We would go out again after two or three days of rest to cover the adjoining areas and repeat this until the whole area was covered. We had up to 10 porters, who carried our very basic provisions including a lightweight canvas stretcher for sleeping and a tiny strip of tarpaulin in case it rained, plus a small combo rifle over shotgun for meat. We used aerial photographs to determine where we would collect soil, stream and rock samples and also plot where all these samples had been consolidated from. We would leave the samples to be picked up by the Unimog (four- to six-wheel drive Mercedes bush vehicle) or by a small Bell 47 bubble helicopter, depending on the terrain to be encountered.
I did this type of work for two years before deciding to move to South West Africa (now Namibia) to work for Marine Diamonds exploring for and mining diamonds off the Skeleton Coast for 15 months. It took me several days of being sick as a dog before I got my sea legs. The swells and waves were very big and often rough the weather was tough, but I really enjoyed this work and learned a lot. But after a year, it became very repetitive and being confined to a small vessel at sea for three to six weeks at a time was not my thing. So I applied for a field geologist position on the Copperbelt.
GT: And which company had the most positive influence on your development as a professional?
TG: I would say it was Rhodesian Selection Trust, a division of Rio Tinto, for which I worked after leaving Marine Diamonds. I was initially a field geologist based in Kalulushi, near Kitwe, Zambia, on the Copperbelt. I spent two years in the field looking mainly for copper and other minerals. Operations were not as basic as my first field experience with Chartered Exploration. The field camps were bigger and had small landing strips allowing the access of personnel, provisions, etc. We would
spend up to two months in the field, then back to the head office for a week or more to plot information, get assay results, etc., and it was back into camp again.
If anomalous readings were significant enough, pitting and or core drilling would take place. This was my first exposure to core drilling and it was baptism by fire, as on one project that I was in charge of, the drillers wanted to take the weekend off without permission from their head office. They asked me if I could cover for them and report progress. They showed me how to drill and I tried several times with supervision over the week before they took off.
‘Life was pretty simple back then, as before going into the field every year, we had predetermined the area we were going to cover from aerial photographs and we knew where we would establish a centralized base camp.’
On the first day of their absence, I did OK for a few hours, then stuck the rods and couldn’t get them out. I still reported to our head office the average footage they normally drilled for the two days they were absent. On their return, they had to work overtime with no pay to get things sorted and catch up. The drillers did appreciate the break but weren’t impressed by what I had done.
After two years in the field, I applied to work as an underground geologist at Mufulira Copper Mines, also owned by Rio Tinto, and was accepted. I spent the next four years there. There was a lot to learn, but I appreciated being in a town and enjoyed the work and variety of daily challenges. The mine had its own drilling department, which came under the geology department. After my first year, I was
one of the three geologists, who looked after procurements for the drilling department.
GT: So, this was your first exposure to drilling? It was mainly conventional at that time, right?
TG: Yes, that’s correct. There were twelve Canadian-made Boyles drills, all were screw feed air driven in an assortment of models, such as the BBU2, JVA and VEG. Drilling was conventional (non-wireline) in standard DCDMA sizes B, A and E. Hole depths varied from as little as 50 to over 300 m (164 to 984 ft) on the odd occasion.
I know that wireline actually came out in 1953 and was invented by Boart Longyear. But even when leaving Zambia in late 1970, all underground core drilling was still non-wireline.
GT: Continuing the topic of South Africa. I know that there were some deep holes drilled in the region, probably in the 1970s and the 1980s. Please elaborate on that.
TG: I have never worked in South Africa, but by hearsay, I believe that originally before wireline core drilling was introduced into South Africa, deep holes down to well over 2000 m (6562 ft) were using non-wireline standard rods like the BX and some of the holes even exceeded 3000 m (9843 ft).
These holes took up to six months or more to complete. The pre-starting site area would be cleared so the personnel could have their caravans as lodging and plant vegetables and other crops and even have chickens running around whilst the drilling was underway.
As mentioned, I myself didn’t work on these deep holes, which were mostly on the Witwatersrand goldfields around Johannesburg. In the early years, the big rigs were the Sullivan 50s that would go to more than 3000 m (9843 ft) plus using wireline on a regular basis.
I know that both Heath and Sherwood Drilling from Kirkland Lake (Canada) and Boart Longyear drilled some exceptionally deep holes there with modified wireline systems using aluminum rods with steel coupling wireline systems. Heath and Sherwood Drilling specifically were using their HNU system and their deepest hole reached 5422 m (17 792 ft), while Boart Longyear with their CUD96/CUD76 system reached a record depth of 5520 m (18 106 ft).
GT: Going back to when you were working underground with Rio Tinto at the Mufulira Copper Mines. Do you have any interesting memory from that time?
TG: I mentioned earlier that I was one of three geologists looking after the core drilling
at the mine and all drilling was standard (non-wireline). Most of the holes drilled were to a maximum depth of 300 m (984 ft) and some of the rock was very hard, so it was very slow drilling. This was because the bits used were set with natural diamond and you’d only get up to 30 m (98.4 ft) before you’d have to pull the rods.
It was an extremely laborious process to pull the rods, change the bit and then lower the rods back in and start the process again. We would do this probably every 40 or 50 m (131-164 ft).
Then in 1968, Atlas Copco approached us in the drilling department to give their subsidiary Craelius a contract to drill 10 000 m (33 0000 ft) using their small hydraulic drill. That was the Diamec 250 and their TT 46 mm non-wireline system and core bits. We agreed and we were surprised to see their production per shift double or triple what our normal production was.
At the time, I was thinking, ‘Wow, this is an eye-opener’, so I checked to see what their drill bits looked like and was surprised to see that they were not surface-set, but impregnated.
GT: Can you tell us more about the story of the first synthetic diamond drill bit?
TG: Well, up until then (1968) we used to buy all our diamond bits, which were natural surface-set bits, from Boart Longyear and also from a company called Huddy Diamond. Whereas the bits that Atlas Copco introduced were synthetic diamonds. They went three to five times further than the bits from natural diamond we were using.
After that, it didn’t take long for Huddy Diamond and Boart Longyear representatives to take some samples and carry out reverse engineering. Huddy Diamond was the first company to come back to us offering their own drill bits with synthetic diamonds to test.
GT: How did you choose to move from geology to become a drill bit salesman?
TG: After four years of working underground in Zambia, lots of things were getting more difficult to get, so I decided it was time to move to Salisbury, Southern Rhodesia in 1971 (now Harare, Zimbabwe), although I didn’t have a job to go to.
As I was settling in, most mineral companies shut down because of the political situation, and I couldn’t get a job as a geologist. So I approached Huddy Diamond, which was looking for a salesperson and decided to take the position.
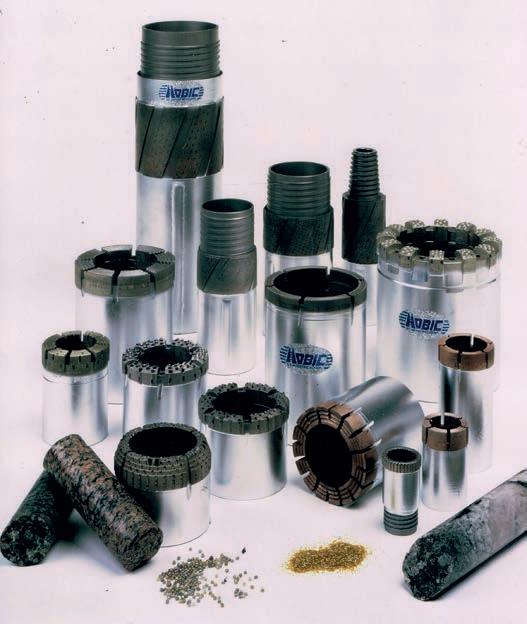
Selling drill bits for Huddy Diamond worked well for me, as I knew about the company and their products from my time working at Mufulira Copper Mines. I enjoyed getting out to various field operations and mine sites, meeting people and trying to get them to try Huddy Diamond’s range of products, such as rods, core barrels, casing, drill bits, etc. and learned a lot as well.
GT: How big was Huddy Diamond at the time?
TG: Huddy Diamond was a small company compared to Boart Longyear, but relative to other manufacturers of diamond drill bits, they were the second biggest in Southern Africa with two factories, one in Johannesburg (main operation) and the one in Salisbury (now Harare, Zimbabwe). Scale-wise combined both factories produced between 1000 to 2000 bits per month in early 1970. At this time surface-set bits were 95% of the market. Surface-set bits were labor intensive to manufacture - making and setting mold, sintering, then sending the bit to the field. That was just half of the work.
After drilling minimal meters depending on formations being drilled, the diamonds in the bit would get glazed or start penetrating

↑ Diamond products by Hobic Bit Manufacturing Company ↑ Diamond bits
slowly. So they would be pulled from the hole and returned to the manufacturer to be electrolytically removed. The used diamonds were sorted for stability of resetting and additional stones were added as needed, so they can be then sintered again.
So when impregnated bits started to work well, the number of surface-set bits decreased substantially.
GT: At some point, you moved to Canada. Looks like Huddy Diamond was expanding. Can you tell us more about that?
TG: Huddy Diamond, as mentioned earlier, was one of the first companies in Africa to manufacture a range of impregnated bits made with synthetic diamonds. However, there were impregnated bits made with natural blocky crushed diamond, which were mainly used if the rock was badly broken and/ or very abrasive, or for drilling steel in the hole. The impregnated bits with synthetic diamond were much better, so they took over this market as well.
As Huddy Diamond was looking for new markets, they believed it could be beneficial to look at the Canadian market and try to introduce their range of impregnated bits. So in 1976, they asked me to do a market survey which I agreed to. Before leaving, I contacted the Canadian Diamond Drilling Association in Toronto and inquired which were the bigger contractors in Canada.
Upon arriving in Toronto, I made a trip to the Rouyn Noranda area and met with Bradley Brothers and then over to Kirkland Lake to meet with Heath and Sherwood Drilling, then to Winnipeg for MidWest Drilling, and then to Vancouver to see DW Coates and Tonto Drilling. These were the five biggest contractors in Canada and I dropped off a few synthetic impregnated drill bits for them to try. They were all somewhat skeptical, telling me that they had tried impregnated bits before, but they were just okay to drill out broken formations. Regardless, I dropped off a few bits and asked them to get back to me after they’ve tried them. They all did and were pleasantly surprised. Each of the five asked to purchase a few more bits to try.
So in 1977, Huddy Diamond’s management asked me to move to Canada permanently and open a sales office. I did and set a shop in Sudbury. It wasn’t easy getting the mines and most contractors to try impregnated bits as they still had a bad opinion of early impregnated bits, made with natural blocky grit or crushed natural diamond. However, as Boart Longyear and another manufacturer from North bay were also introducing impregnat-
ed bits, things became easier in late 1978 and impregnated bits started to take over Canada.
GT: So, let’s see if I have the story correct. First, it was bits with surface-set diamonds, then came impregnated, but with natural diamonds, and finally impregnated with synthetic. Is that correct?
TG: Yes, surface-set diamonds were what everyone used in about 95% of core drilling. Occasionally, if there was steel down the hole, surface-set diamonds would get damaged straightaway. So they used a very blocky industrial natural diamond grit along or with a crushed natural diamond which was embedded in a matrix. It was more wear-resistant and it was used to drill through any broken or abrasive rock and steel in the hole. Basically, that was the early impregnated natural diamond bit.
I’d say that nobody used synthetic diamonds until the late 1960s, even though they were first made in 1954. In general, synthetic diamond was much tougher and finer, cheaper, and it penetrated faster.
Initially, you’d use at least three times the amount of natural diamond bits to get the same meters drilled using impregnated bits with synthetic diamonds. When they were first marketed, they were very expensive, but because they did three times the work. Since you had to send back the natural diamonds for a burn out then pay for setting and diamond charge, using an impregnated bit made with synthetic diamond was a no-brainer.
It didn’t take long for the impregnated bits made with synthetic diamonds to take over probably 95-98% of drilling. By the late 1970s or early 1980s, synthetic diamonds were dominant, although in some softer rock types like coal formations, natural surface-set diamonds were still used.
GT: Talking about a good-quality impregnated drill bit, is the secret in the matrix (the binding compound) or the diamonds themselves? Which one is more important?
TG: I would say it’s a combination of many factors. All are of equal importance.
The physical pressure applied before or during sintering, plus the furnacing type used, for example, hotpress induction temperature and so on is important, of course.
Naturally, the quality of the synthetic diamonds being used plus size coatings are of importance as well as the powders, etc. When it comes to synthetic diamonds, there are at least four big manufacturers, all of whom have excellent products.
GT: Can you tell us more about the use of silver in binding materials. Are the tendencies changing with the years?
TG: There are a variety of different metals normally used as a combination in binder materials. Yes, silver is still one of the important ingredients used.
In general, silver can be one the most important components used in some binders for drilling extremely hard fine-grained non-abrasive rock types since often, faster penetration with less pressure is achieved.
Like everything else, the price of silver has gone up from less than USD 5 per ounce in the early 1990s to USD 24 today, so it can be a big cost depending on the percentage used.
I should note that there are several other binder materials with no silver used commonly that work well, especially for medium to softer broken formations. Generalizing, most matrix types in the 1-6 range tend to have no silver in the binders, whilst most in the 7 and above range will have some silver.
GT: Let’s move on. You became a shareholder of Hobic Bit Manufacturing Company in 1986. Tell us more about that.
TG: I guess as I had worked for Huddy Diamond from 1971 and they asked me to come to Canada in 1977. Then I spent the next nine years selling drill bits for them.
So when John Huddy, who was the owner of Huddy Diamond, Rhodesia, whom I worked for, emigrated to the US, he started selling bits out of Denver. John heard that a company in Edmonton that made oil bits had gone into receivership. Since Huddy Diamond was also making oil bits in South Africa, mainly for Iran and a couple of other countries, John went to see the operation and made an offer. He purchased the company and invited me to become a minor partner, which I did. This was in 1986. We started manufacturing and selling oil bits, but the market was very competitive, and we were hardly making any money.
So after three years, we decided to start making core drilling bits as well. We had to make some money. We used the same name for our mining bits which was Hobic, an acronym for Huddy Oil Bit Industry Corporation. We moved to Vancouver in 1990.
Four years later, after we had completely stopped making oil bits, John Huddy decided to sell his share and I bought some of it. The company carried on manufacturing diamond bits and our market share increased considerably until we became one of the prominent manufacturers in Canada.
As a result of our success, in March 2000, a manager from Atlas Copco approached me
at our booth at PDAC and asked me, ‘Do you have time for a coffee?’. I said sure and they broached a question as to whether we may be interested in selling the company. I discussed this with my partners when I got back, and we were all happy to move on.
By September 2002, they had purchased the company. I worked for Atlas Copco for two years then got involved in the stone industry. We came to a gentlemen’s agreement with Atlas Copco to stay away from the bit manufacturing business for a while.
In early 2009, with a few associates, who have many years working for the major manufacturers, we formed a new core bit manufacturing company called Diatool Diamond Products.
GT: Do you think we will see any new developments in the next years in diamond drilling manufacturing? Do you think something will change dramatically?
TG: One would think that someone would come up with some sort of a new technology that would deliver a significant increase in penetration and footage drilled per bit, but I am not sure what it would be.
I remember that people were trying to develop a retractor bit, which could be replaced from down the hole. That didn’t quite take off and I don’t think that there has been any significant breakthrough in the last, I’d say, ten years.
Originally, impregnated bits when they first came in, were 3 mm. Then they went to 5 mm, and then to 6 mm. Then people went to 9 mm and stayed there for a long time and then it was 12 mm, and later 16 mm, and 20-24 mm and even some 30 mm bits. These incremental increases in impregnated depth have resulted in keeping bits down the hole longer.
Drills have been computerized and there are autonomous rod handling systems that have proved to be a great benefit in productivity
and safety. So a combination of these three has certainly benefited the industry, but as far as replacing a core bit, it’s hard to envisage what this will be!
GT: I think there is a lot of marketing involved in the growth of matrix depth. From my experience, those high matrixes are not suitable for all conditions. So, you are not saving money with them, rather you are spending more. Do you have a similar observation?
TG: Most manufacturers have found that there are only a limited amount of contractors with the expertise and the right ground conditions to fully utilize the 20 mm or deeper depth of impregnation.
Global usage, I would say, for 20 to 30 mm would be in the range of 5 to 10% of sales, 16 mm about 25%, 9-13 mm 50%, and the rest would be less than 9 mm. C
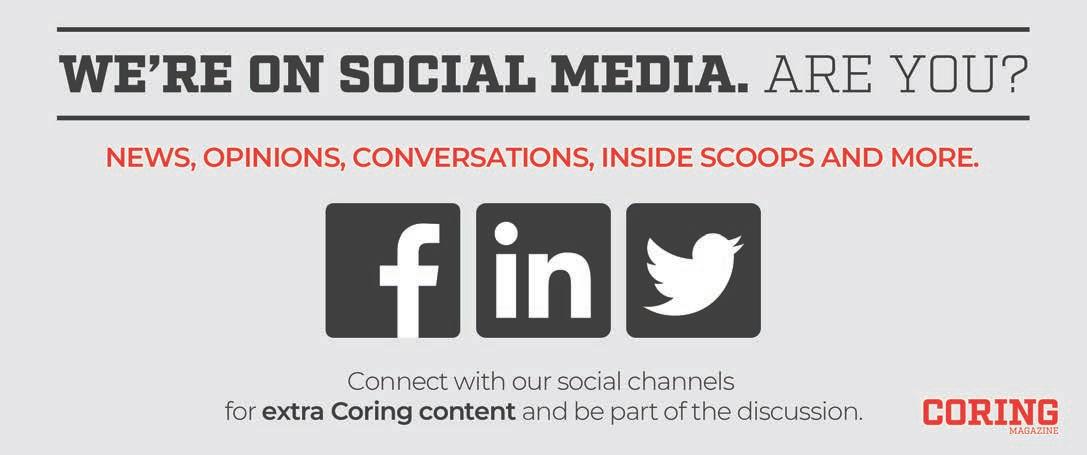
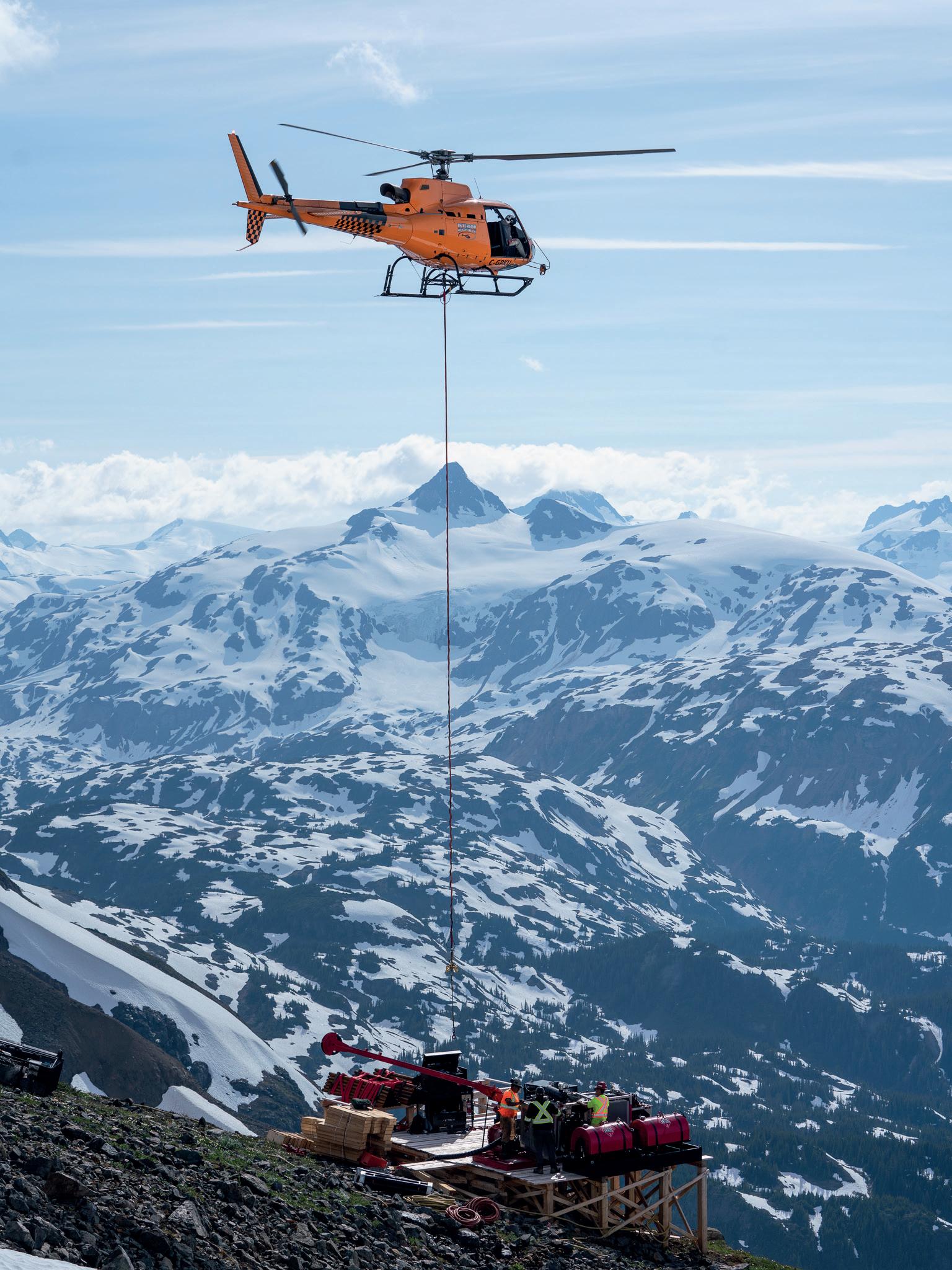
Helicopter Portable Diamond Drill
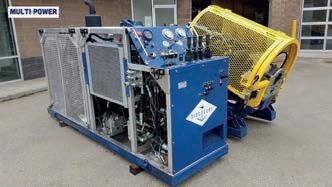
1400 Meter NWL Depth Capacity
Cummins Power Unit 160 or 260 HP
‘P’ Size Rotation Unit & Clamp
Safety Package: Full Guarding, Multiple E-Stops, Interlock Rod Guard & Power Lock-Out
Available in Heli-Portable, Skid Shack Mounted and Track Carrier
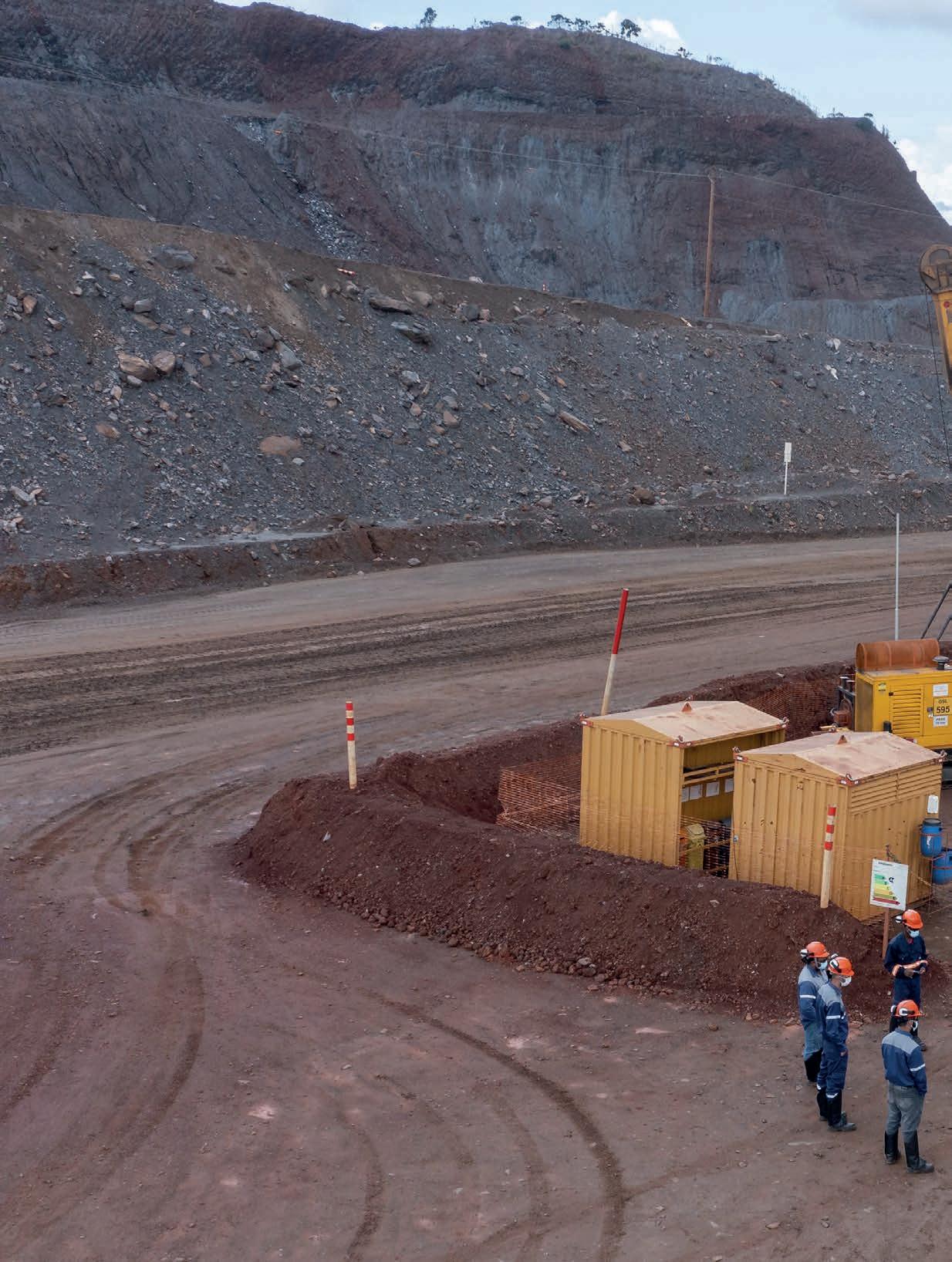
68 years of GEOSOL
With benchmark drilling services in Latin America, Geosol seeks excellence in mineral exploration in Brazil and overseas
by Geosol Team
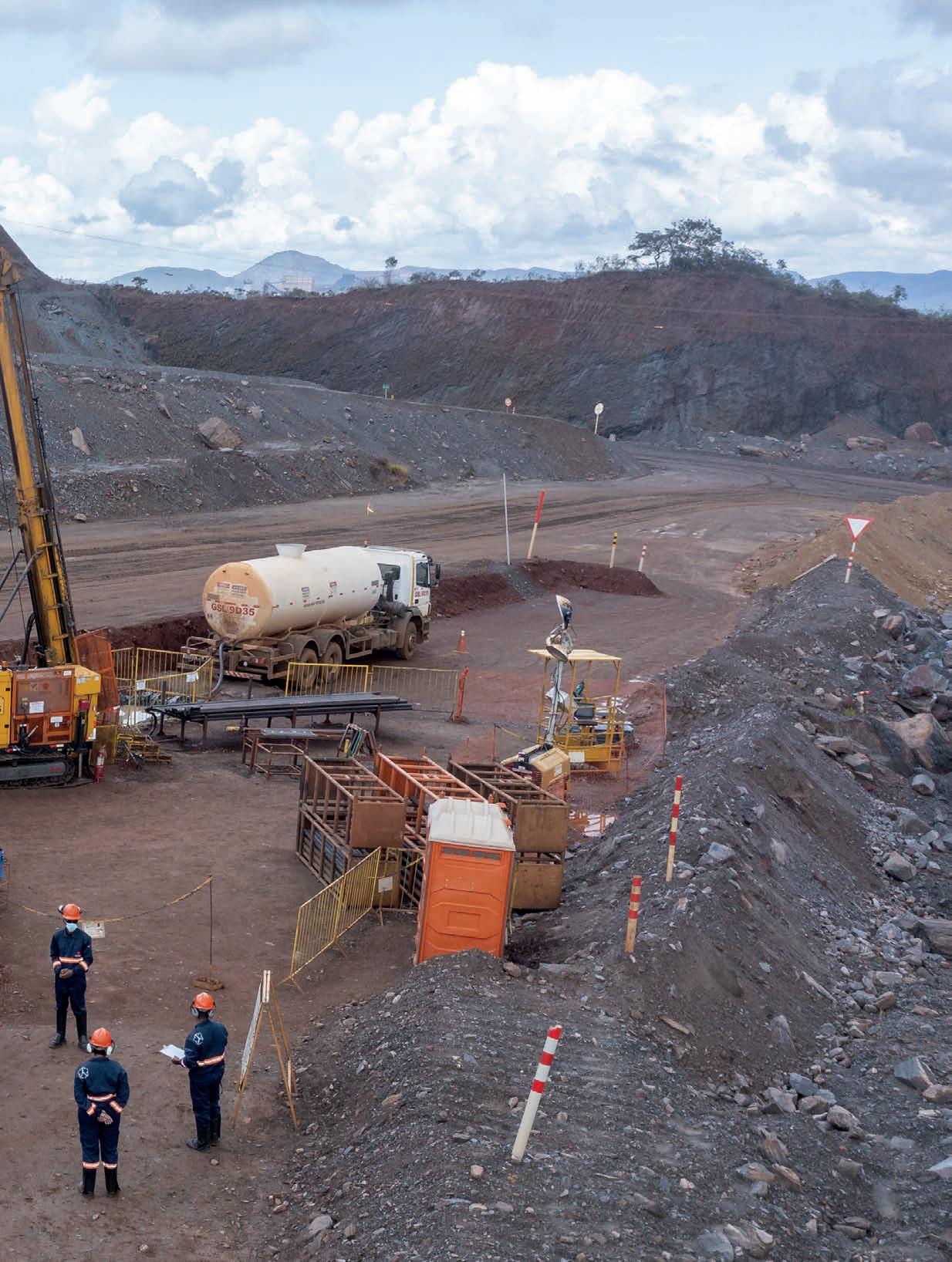
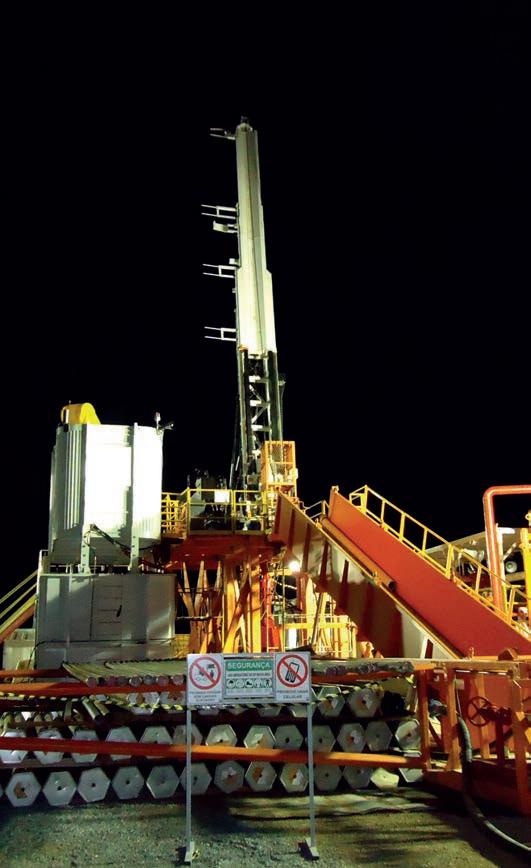
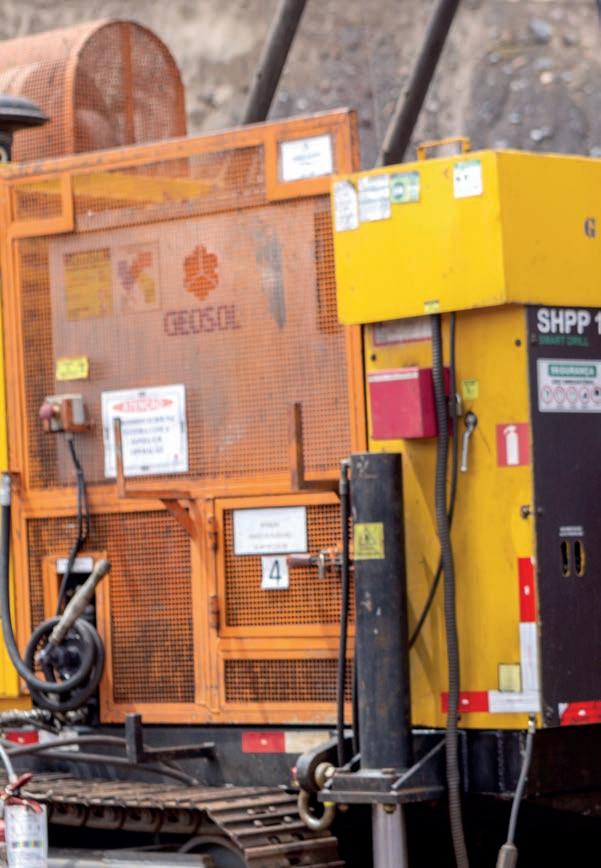
↑ Slim drilling for oil & gas
Rich history
In 1953, foreign capital was once again allowed in Brazil, and a new constitutional order of the national mineral sector would also make it the year GEOSOL was founded by Civil and Mining Engineer Victor Dequech in Criciúma, southern Brazil, a region rich in mineral coal. Initially, the company was named Geologia e Sondagens Ltda (Geology and Drillings Ltd.).
In the years following, the company began its expansion and worked in phosphorite research in the northeast regions of the country; in geotechnical drilling for the construction of the current federal capital, Brasília; in zinc research in Minas Gerais; and in shale reserves in southern Brazil.
In the early 1960s, with the national push towards the development of Brazilian mining, already under the name of GEOSOL - Geologia e Sondagens, the company signed several contracts with the National
↑ Tatiana: ‘I have just completed the first driller formation course for women, on Geosol’s Belo Horizonte training center.’
Department of Mineral Production (DNPM) and saw the ideal opportunity to expand its fleet. The company acquired new rigs and began excelling in projects involving both drilling and geology and geological interpretation of alkaline rocks and iron ore. These projects were very important for Brazil, as they led to the discovery of phosphate reserves, uranium deposits and immense niobium reserves. It also increased the knowledge of iron ore reserves in the Iron Quadrangle of Minas Gerais.
The work for the DNPM generated many samples that needed to be analyzed, which motivated GEOSOL to create the first laboratory in Brazil specialized in geochemical analysis, the Geolab.
The following decade was one of expansion in the field of drilling, prompting the company to purchase several imported rigs. In 1971, GEOSOL took a new important step, making the decision to transfer its headquarters to the city of Belo Horizonte, the mineral capital of Brazil. From then on, GEOSOL would practically become a ‘mineira’ company (from Minas Gerais), although operating throughout Brazil.
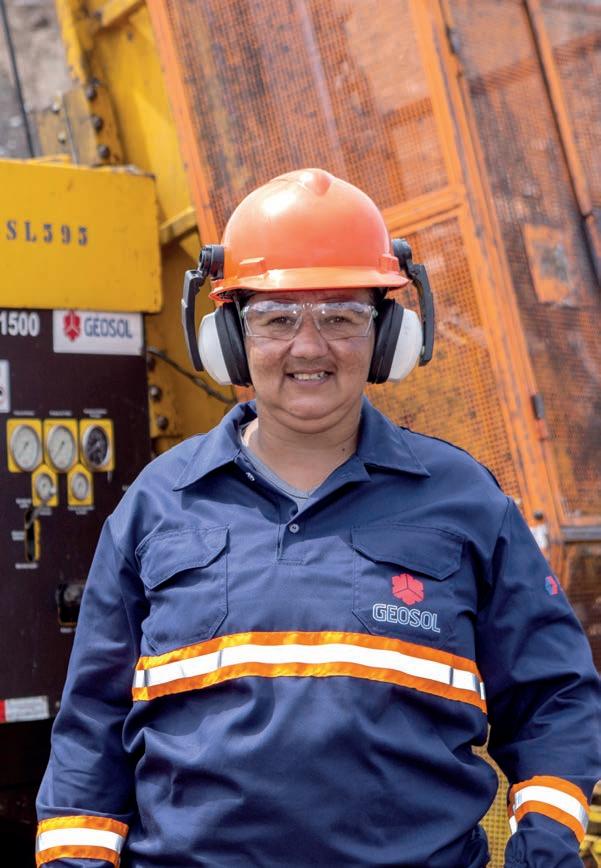

↑ Brazilian iron ore core sample
‘By the early 1980s, GEOSOL was already a benchmark in diamond drilling and water well drilling, investing heavily to improve its technologies.’
Since the late 1960s, GEOSOL was conducting exploration and drilling work on the recently discovered high-grade deposit in the Carajás mineral reserve, which would later become the largest iron ore mine in the world.
In the late 1970s and the early 1980s, the drilling activities gained new impetus. GEOSOL made its first international foray, drilling in Paraguay and Uruguay. Several years later, the company began operating in Africa, in countries such as Zaire, Guinea, Liberia and Angola.
By the early 1980s, GEOSOL had already established itself as the standard in well drilling and borehole services and was investing heavily to improve its technical capabilities, mainly in terms of technology and equipment. In the period from 1988 to 1992, the company took another big step, moving to a new facility of 40 000 m2 (430 560 ft2), in the district of Olhos D’Água, Belo Horizonte (MG), where it is headquartered until now. Workshops, the lab, administrative buildings and a warehouse were all built there. This period, however, coincided with

a downturn in the Brazilian market, which led Geosol to run to artesian well drilling mainly in the Northeast region of the country, and to expand its range of services. In the 1990s, the company intensified its operation in Carajás, and decided to establish a branch in Parauapebas (PA), which to this day remains one of the most active fronts, thanks to a proud and motivated local team.
In 1998, motivated mainly by foreign investors, GEOSOL’s Geolab joined Canadian Lakefield Research, offering, in addition to analytical services for the mineral sector, analysis for the environmental control area as well. Later, with the acquisition of Lakefield by SGS, the lab company was renamed SGS Geosol and the scope of its activities became even more complete.
In April 2000, in another bold move, GEOSOL decided to acquire Geosedna Perfurações Especiais. The company was specializing in roto-percussion drilling in reverse circulation, as the process offered progression, expansion of drilling activities, drilling speed and reduced cost compared to diamond drilling.
Still in the early 2000s, the decision was made to embark on the process of certification by Total Quality ISO 9001, and 17025 (specific for labs). At this time, the company resumed its operations in Africa, serving large customers such as Arcelor Mittal, BHP Billiton, Rio Tinto and Vale. In 2013, maintaining the purpose of permanently seeking technological evolution, GEOSOL renewed its fleet of rigs with state-of-the-art hydraulic equipment, which offered higher technical quality for its ser-
vices and more productivity. At the same time, the company developed a qualification and training program for drillers, so that they could operate the new equipment safely and effectively.
Being visionary, the company invested in cutting-edge technology aiming at the development of fully Brazilian-made rigs to replace imported hydraulic drills. Due to the shortage of rig manufacturers in the country, GEOSOL decided to start its own manufacturing. Nowadays, the company produces automated rigs that can be operated remotely, which have been implemented with great success, placing itself at the forefront of the sector and becoming even more competitive.
The GEOSOL SDS - Smart Drill is a powerful rig with a 100% digital operation panel, which simplifies operations and keeps humans away from the rig. This digital panel is capable of generating, transmitting and keeping a record of all drilling parameters, and is controlled from a safe distance. It allows for a compact drilling rig, free of cables and hydraulic hoses that is quieter and very safe.
The SGS GEOSOL Lab has established itself as one of the leading geochemical laboratories in Brazil, with a multidisciplinary portfolio. Nowadays, in addition to geochemistry – which gave rise to the former Geolab – it operates in the analysis of water, soils and effluents (environmental services), mineralogy, outsourcing (installations and services at customer sites) and mineral processing.
In 2017, GEOSOL purchased the company REDE – Tecnologia em Sondagens - allowing the group to offer geological-geotechnical research,
↑ RC Drilling: Geosedna - Geosol’s subsidiary
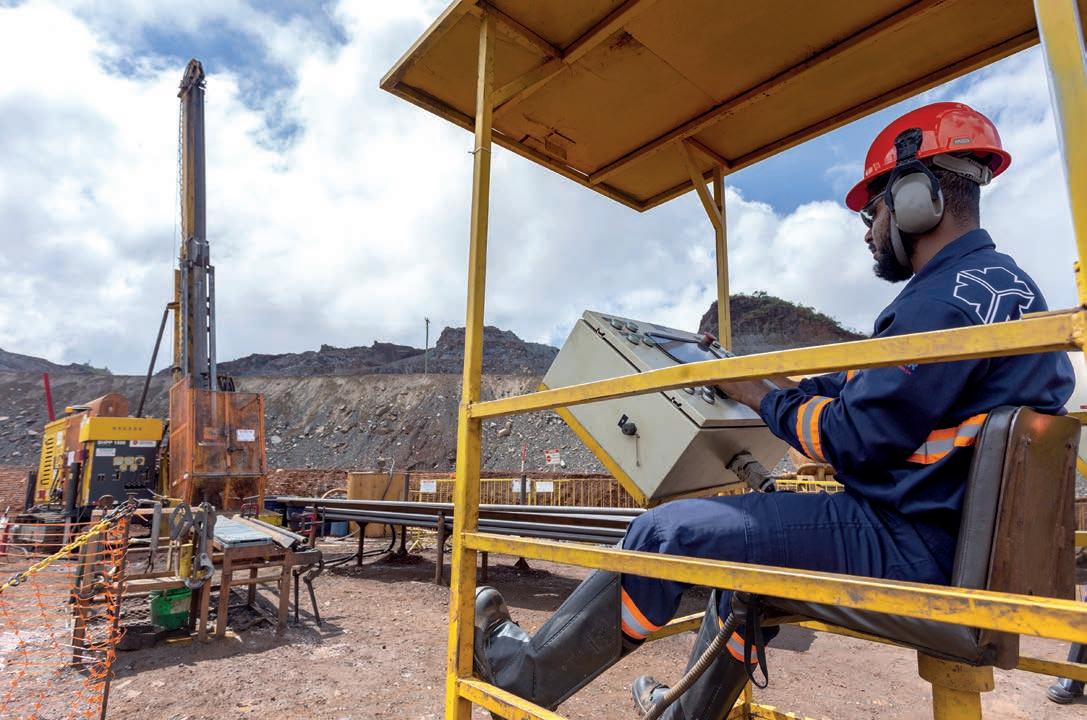
↑ Drilling operation with remote control
with a focus on special field tests, such as fracking tests and acoustic and optical logging for hole imaging.
In the same year, GEOSOL group was restructured, with the creation of the holding GEOPAR (Geosol Participações SA), which controls the companies GEOSOL, REDE, Geosedna, SLIM Drilling (Drilling for oil and gas), Localog (Real State Ventures), Geobit (Tools for Drilling and Borehole) and Inove (Machines and Equipment Lease).
Today, 68 years later, GEOSOL is the international standard in drilling services. It has over 13 million drilled meters (42 651 000 ft) and holds about 65% of the national drilling market for mineral research, and directly employs 2500 people.
Modern fleet
GEOSOL, throughout its history, has shown itself to be an efficient company and, therefore, customizes its equipment and develops specific processes to meet the real needs of the Mineral Sector. All this is performed in accordance to its Integrated Management System. With a modern fleet of rigs and complementary equipment, GEOSOL is capable of carrying out drilling campaigns in all geological conditions, even in remote areas, which are difficult to access. In all contracts, the emphasis is always on safety and quality sampling, with a high recovery rate and preserving the integrity of the samples obtained.
GEOSOL has exclusive software for drilling management, which pro-
vides drilling reports in real-time, indicating, among other information, the daily rate of production, consumption, maintenance plans, etc.
Safety culture and innovations
GEOSOL’s safety culture is disseminated throughout the operation, focusing on the maturity of its teams. This culture, linked to its main core value of respect for life, has reduced risks during operations, seeking a zero-accident rate, and is effectively retaining the company’s talent.
In order to be safe and act as an industry leader in a scenario where natural resources are increasingly scarce, GEOSOL pays attention to, and rigorously meets, the standards, legislation and environmental policies in force. Concerned with obtaining results responsibly, GEOSOL acts in the present, thinking about the future, offering innovative techniques for managing and optimizing resources and is always committed to sustainability.
If previously, the focus was on structuring and consolidating the company, today the biggest challenge is to keep GEOSOL holding on the path of growth, innovation and perpetuation in the face of the globalized market. Thus, reliability and credibility are also celebrated by everyone part of this production chain.
Today, investing in technology, training and development means to reflect Geosol’s actions in a simplified, digital, safe and quality operation.
GEOSOL MAIN SERVICES
• Diamond drilling;
• Reverse circulation drilling;
• Sampling for grade control;
• Slim drill holes with core samples for oil and gas exploration;
• Development and manufacture of high-tech drill rigs;
• Development and manufacture of down-hole drilling gear;
• Leasing of support mobile equipment;
• Geotechnical drilling with field assays;
• State-of-the-art laboratory services.
• Wireline exploration diamond drilling;
• Deep borehole diamond drills;
• Core sampling in large diameters for metallurgical tests;
• Man-portable drill rigs for remote areas or sites with environmental restrictions;
• Air core and hollow auger drillings with intact core samples for bauxite exploration;
• Heli-drilling; heliportable modular drill rigs;
• Underground drilling with electrical rigs.
Water wells
• Rotary drill rigs for water wells;
• DHT hammer drill rigs.
Geophysical profiles
• Surveys with gamma optical, acoustic, caliper probes for geophysical profiles.
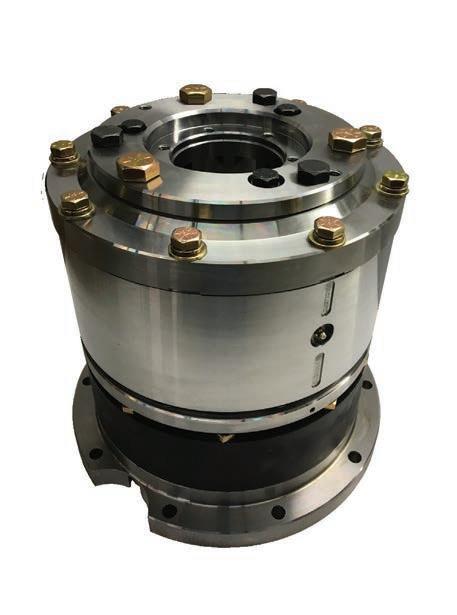
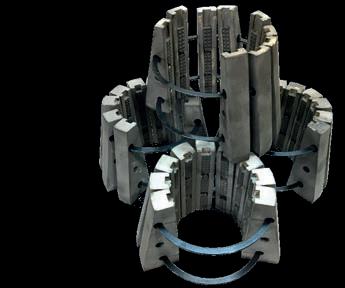
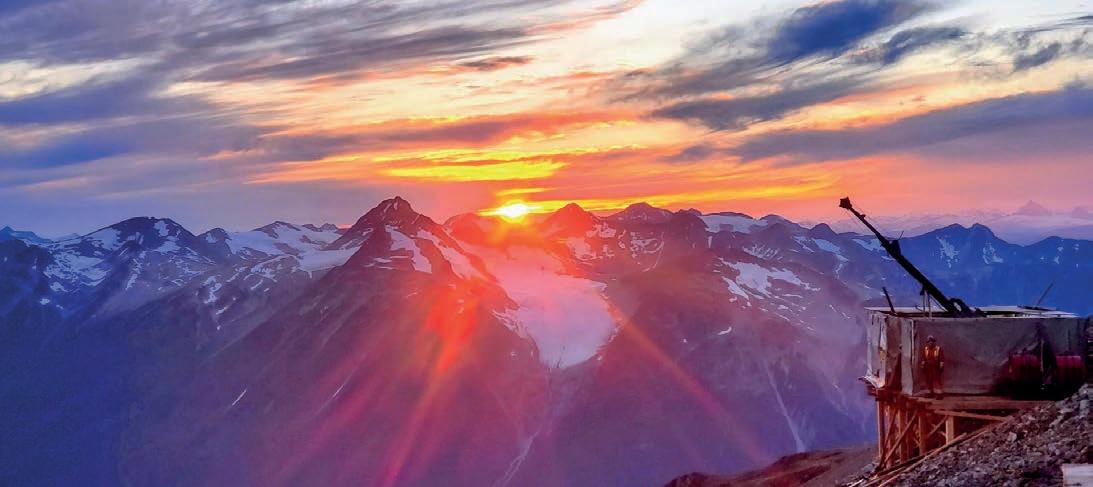
United. Inspired.




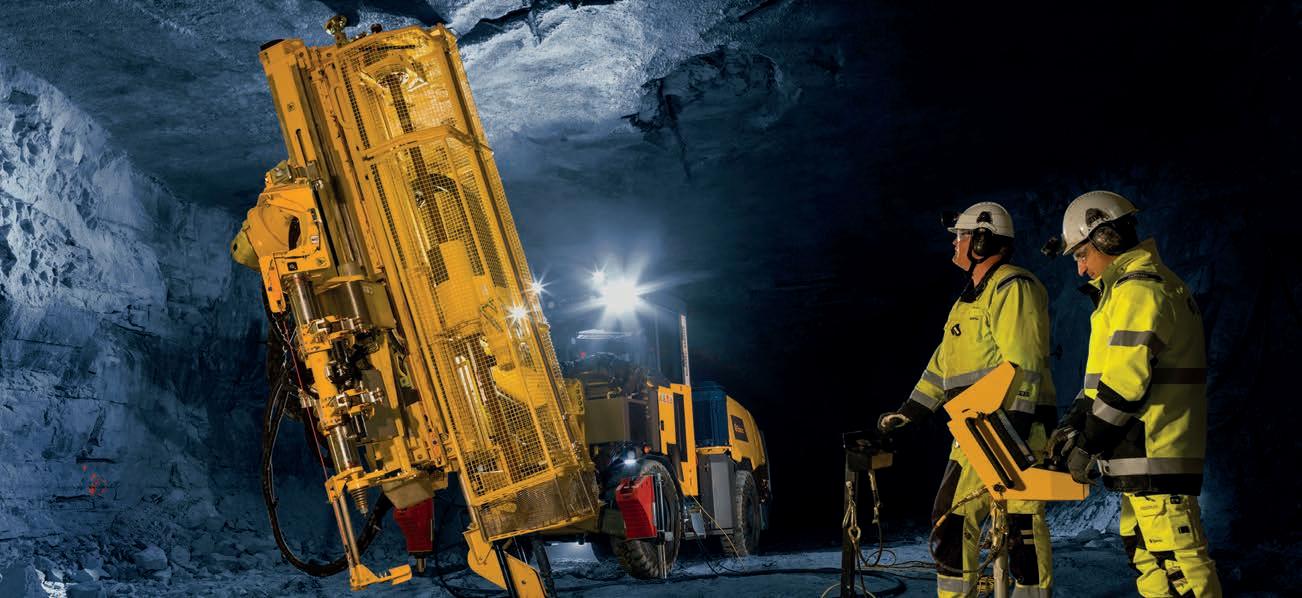
Depth and mobility
What do you get when you take one of the most respected underground core drilling rigs on the market and fuse it with a wellproven and mobile carrier? You get the Diamec Smart 6M.
Find out more at epiroc.com

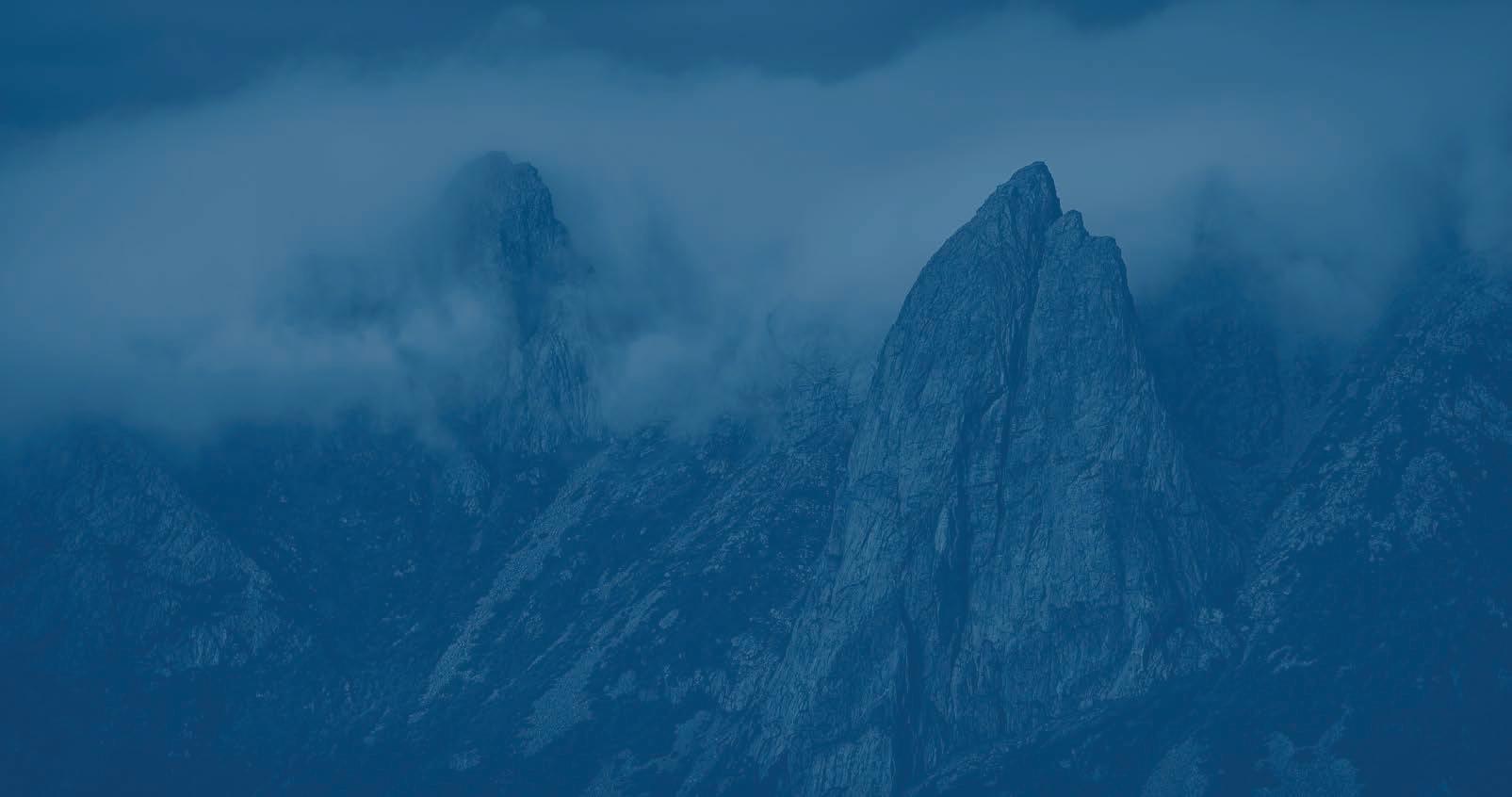
Leaders
in
directional
core drilling, borehole surveying solutions and belonging software
What does quality mean to us at Devico?
Well, our policy says it all: ”Devico will provide a competitive advantage to its customers through on/time delivery of innovative, high quality products and services, driven by a culture of systematic, continuous improvement in competency and organization.”
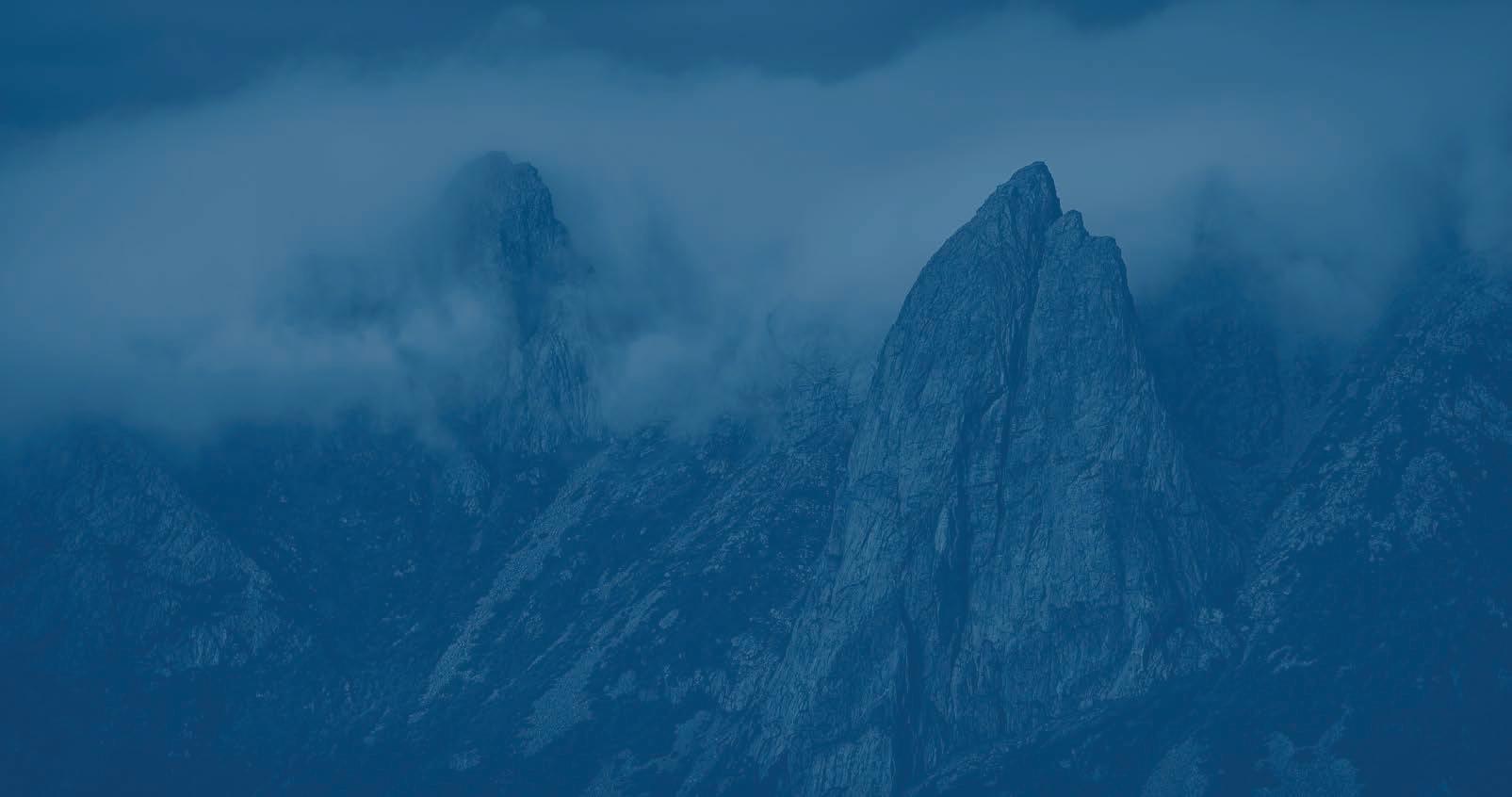
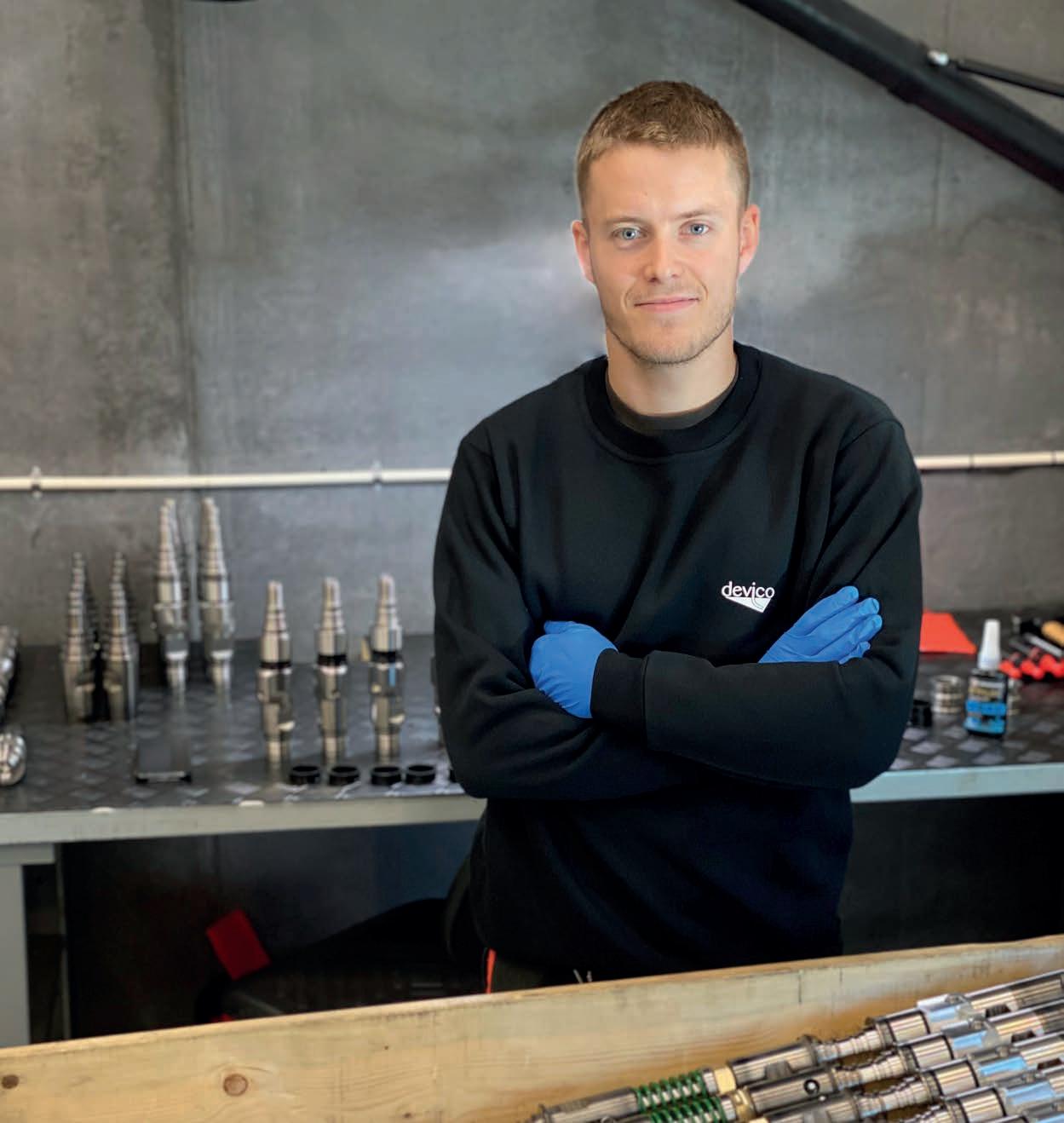
State of the art products, made in Norway
• Directional Core Drilling
• Downhole Navigation
• Core Orientation
• Rig Alignment
• QA/QC Data Management
Save time, meters and money
Drilling through hostile grounds
by Mathieu Dionne, President and CEO at Diafor
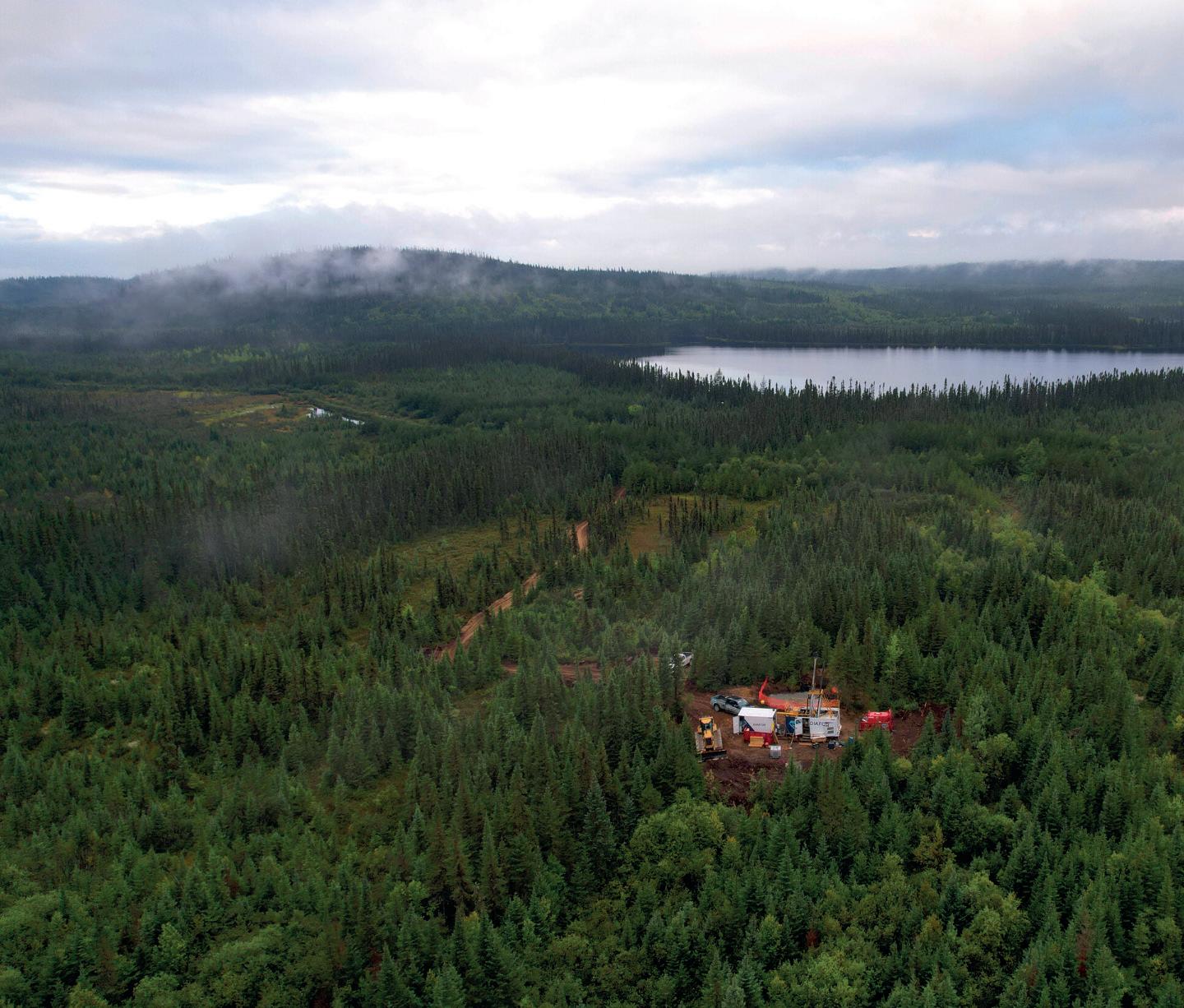
Diafor Inc. (Diafor) is a diamond drilling company specializing in surface operations and based on the world-class Cadillac Break in the Abitibi region in Quebec, Canada. The company is new, but it is very well organized, has experienced employees and is building a great reputation.
In the summer of 2021, Diafor was drilling for Laurentia Exploration and Canada Silver Cobalt Works Inc. (CCW) (TSX-V:CCW) on the Graal property. The drill rig was installed for a 2500 m (8200 ft) N-size deep hole, pioneering the depth for this area of Northern Quebec, looking for battery metals. Past shallow exploration in the region had shown very favorable ground for drilling, but this deep hole had surprises in store.
Responding positively and successfully to great technical challenges like the ones encountered at Graal is one of many occasions for learning, forging a positive attitude in problem-solving and developing innovative solutions. They benefit Diafor employees, the client, and the drilling sector in general.
The equipment
Diafor’s fleet consists of AVD Drill Rigs’ VD5000 diamond drill rigs. They were well-suited for the job as the main components, shared with the VD8000 model, are known to be frequently used for holes as deep as 3000 m (9843 ft) on parallel-walled N-size rods and were also tested on holes deeper than 3400 m (11 155 ft) on V-wall and W-wall rods.
The hole
Within the first few hundred meters of the hole, the team already recognized some geological (or rock-related) particularities that needed to be addressed in order to optimize the drilling process.
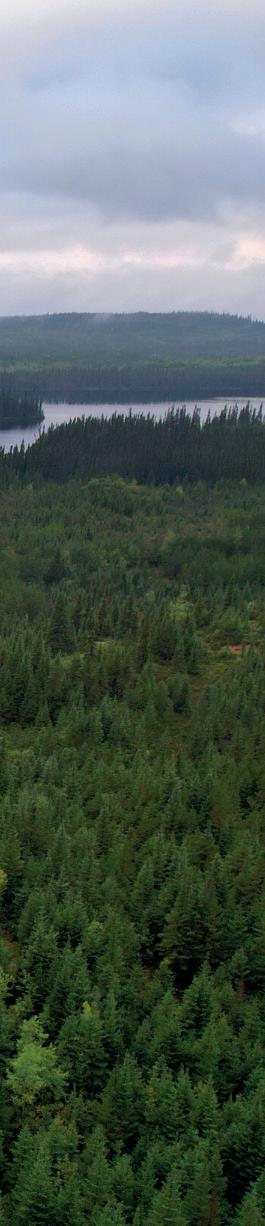
‘Responding positively and successfully to great technical challenges like the ones encountered at Graal is one of many occasions for learning, forging a positive attitude in problemsolving and developing innovative solutions.’
Magnetic rock formations
The magnetism of the surrounding rock made the whole rod string and all the steel-made downhole equipment magnetized, slowing down the whole drilling process, especially during the descent of the overshot, and of the inner tube. In general, this problem is especially important for deep holes, since, with the depth, those two steps of the drilling process become more and more time-consuming. In order to resolve it, the team replaced some of the critical components on the downhole equipment with brass-made components, which were not influenced by the magnetism and thus increased the speed of descending.
Abrasive, magnetic and heavy drilling cuttings
The rock was not only magnetic, but it also had a high weight-per-volume, very abrasive part, so the bit life couldn’t get above the 70 to 100 m (200-300 ft) mark. Imagine how difficult it is to flush heavy, magnetic and abrasive cuttings away from the bit, then up the annular space along the drill rods and the wall of the borehole in a deep hole. The team couldn’t get a brass rod string, for obvious economical and physical reasons, so they had to resort to using drilling additives to improve performance; proper lubrication on the diamond tool surfaces, and all along the core barrel and rod string. They also had to reduce the annular velocity (water consumption) needed to lift those heavy and sticky cuttings out of the hole by increasing fluid viscosity. The main goals were to increase diamond tools’ life and protect the core barrel and rod string from excessive wear. The solution came from the Imdex Val d’Or office with their AMC products line. They agreed to make a site visit and propose the ideal recipe of additives. The result was about 10 to 15% extension of tools’ life and the overall improvement to drilling performance of about 2-4%.
The fault
The team realized that troubles weren’t over yet. The core barrel got stuck at the depth of 1297 m (4255 ft). The drillers couldn’t expect the rock that seemed stable by looking at the fresh core, to suddenly collapse. They had to cut the rods right above the core barrel, set a bypass wedge 50 m (164.04 ft) above the start of the danger zone in solid rock, and prepare for a take-two.
Knowing that ground conditions were getting more difficult, the team attempted take-two with a single (3 m or 10 ft) round (non-hex) core barrel and a heavier mix of drilling additives with an improved recipe in order to avoid swelling, and to tie the formations so they don’t collapse on the core barrel. The team progressed by raising the bit up to the safe depth before retrieving the inner tube every single time. They also needed to re-drill what had collapsed below to reach the bottom back every time. At the depth of 1327 m (4354 ft), things got even more complicated when the team hit voids filled with a kind of heavy metallic sand. It felt like when the bit touched that sand, it was rushing and sticking on the diamond tools and squeezing between the core barrel and the wall of the borehole. This sand created a tremendous amount of torque and a dangerous situation where the rods could snap and jam the equipment again.
That’s where the team decided to consolidate the borehole from 1297 m (4255 ft) to 1327 m (4354 ft) by using cementation. The drillers had to rely on a permanent consolidation method - not just additives - because they couldn’t take the chance of a later hole collapse, which would bury approximately 1 km (≈ 0.62 mi) of rod string. And they also needed to prepare for moving the wedges through this pass later in the hole.
The team used a mix of ‘cement fondue’ and developed a new technique allowing to precisely pump the mix at the right place, with almost no dilution with water, and through the bit. Picture using 1.3 km (≈ 0.80 mi) of rod string as a
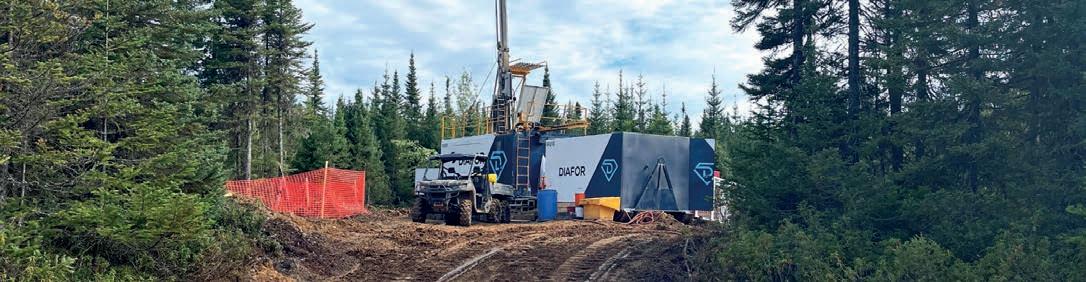
↓ Diafor’s drill site
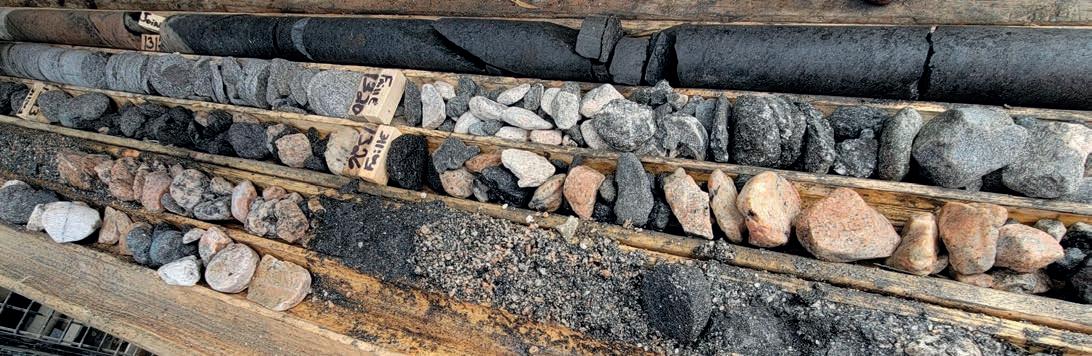
gigantic syringe. The operation was successful, except that the team noticed that the cement was taking twice the usual amount of time to cure. This was probably caused by the chemistry of the surrounding ground, so they had to fine-tune the ‘cement fondue’ recipe to correct the issue.
Once the drillers got past the cement - only 0.5 m (1.64 ft) - things started to get very difficult once again. There was more of that metallic sand causing problems. The team had to progress as far as they could, just to the point where drilling would become risky, then stop and consolidate the hole through cementation again.
The drillers were able to progress like this by cementing every 1 to 2 m (3.28 to 6.56 ft). The cement recipe was perfect because not only it was consolidating the borehole and penetrating the loose formations surrounding it, but it also seemed to have infiltrated in the formation around and below, as evidenced by the core retrieved in the inner tube while drilling past the cement.
The cement mix and the technique used were on point, but there was one major inconvenience when done repeatedly - the curing time. The drillers began looking into accelerating the process without sacrificing reliability and borehole stability. This was where the team at Imdex came into play again with AMC. They recommended using the AMC Bos Tool in order to make Bos Fix product injections in-between cementations to accelerate the pace. The Bos Fix product has the same ad-
vantage of being pumped through the bit, but more importantly, it sets almost instantly. The Bos Fix injections accelerated the pace of getting through the voids and sands and the final cementation at the depth of 1332 m (4370 ft) brought a more permanent consolidation of the borehole.
Conclusions
Passing voids filled with sand is never easy, but this borehole was completely different. Containing metallic sand with coarse granulometry as the surrounding ground formations, core barrels and rod strings were magnetized. This made it a great technical challenge, and a great technical success. Everybody was involved, we were able to transport the equipment needed quickly on-site with the help of Laurentia Exploration, and they also supported and trusted us every step of the way towards this feat.
About IMDEX:
At IMDEX our core value is ‘Together We Thrive’, and that’s delivered through our product-leading brands, AMC and REFLEX, which provide a unique, integrated suite of technology and intelligence solutions from exploration to extraction. We partner with our valued customers and know our end-to-end solutions improves productivity, reduce costs and gain access to relevant, reliable information for critical decision making, anywhere and at any time. C
For more information
Visit: www.diafor.ca

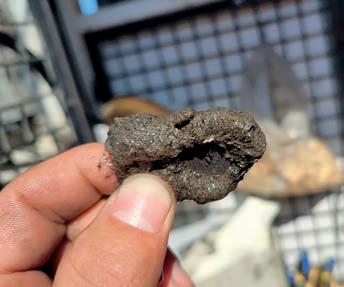
↑ Metallic sand and steel chips from the core barrel and rod string being worn out by the abrasiveness. Caught in the water return with a magnet.
↑ Sand formations consolidated by Diafor’s cement mix
↑ A part of the voids zones, which contained gravel and metallic sand
Together We Thrive

Reflex
Is renowned for its real-time subsurface intelligence solutions for the global minerals industry. REFLEX technologies include downhole instrumentation, data management and analytical software for geological modelling. These market-leading technologies - recognised for their ease of use and accuracy - are complemented by unrivalled expertise in geoscientific data analysis and interpretation
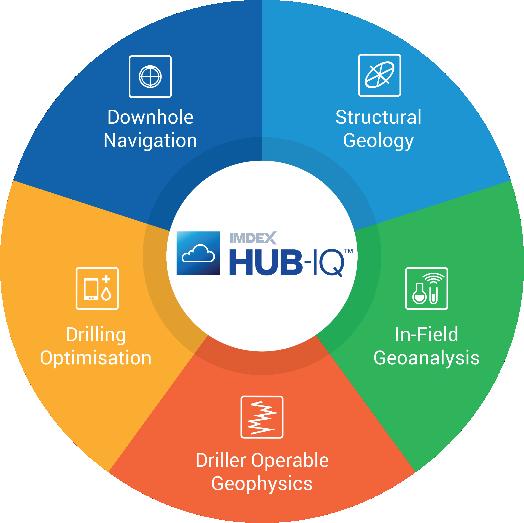
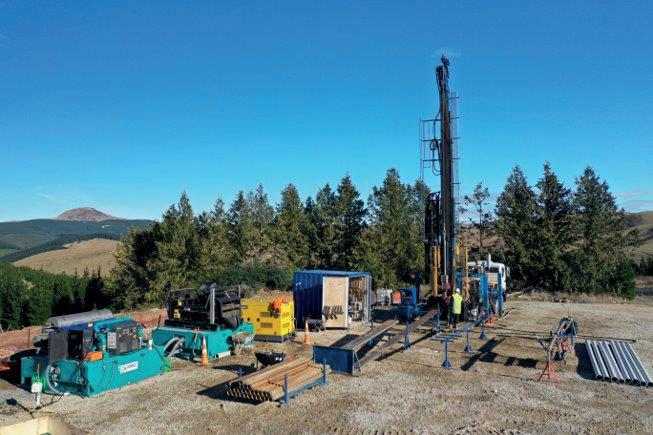
AMC
Redefines the way drilling fluids, equipment, technologies and software are used to optimise drilling programs. It is renowned for maximising productivity while enhancing safety and sustainability. AMC has a strong presence within the global minerals, horizontal directional drilling, waterwell and civil construction sectors
For more information contact your local IMDEX representative or visit our website at
AZIWELL’S AZIDRILL® N-BTK
consolidates the company’s position as a world leader of directional core drilling tools
by Nils Ivar Iversen, Managing Director at AZIWELL AS, Norway
AZIWELL is pleased to introduce the AZIDRILL N-BTK Directional Core Barrel (DCB). This innovative new design allows for the collection of a core sample closer to the industry standards in conventional diamond drilling and brings directional core drilling to exciting new heights.
AZIWELL is a Norwegian engineering company that develops, commercializes, and operates tools for directional core drilling and borehole surveying. The main tool in their arsenal to date has been the Azidrill N-B wireline operated directional core barrel which was commercialized in the summer of 2018. It quickly became a hit at exploration projects worldwide, setting a new standard for directional drilling due to its efficiencies in downhole steering and control of deviated, and multi-branch boreholes.
AZIDRILL® N-BTK
AZIWELL is proud to present a new standard of directional core drilling equipment with the release of their improved drill – The AZIDRILL N-BTK. The AZIDRILL N-BTK collects BTK-size (40.7 mm or 1.60 in) core samples, an increase of 25% in core volume relative to the previous AZIDRILL N-B, B-size (36.4 mm or 1.43 in) core samples, and 67% larger core volume relative to competing technology! The increased core size pushes the boundaries of what is possible
to collect with an N-size steerable core drill. These improvements include:
• Collecting oriented BTK-size core samples, offering an increased sample for geological information.
• Measured tool face orientation and borehole inclination during each run with no extra time spent.
• Increased drill bit penetration over previous steerable core drills due to less cutting surface at the bit.
• Less tendency to polish drill bit.
• Less tendency to core block.
• Fewer cuttings produced in the borehole.
• Better core recovery and more competent core.
• The physical length of DCD is similar to standard core barrels offering easy handling and use when entering drill into the drill head. No need to dismantle the drill as the AZIDRILL is only 0.3 m (0.98 ft) longer than standard core barrels.
• Enables the operator to freely adjust the flow rate or even cut it down to near zero for sharpening the bit, without affecting
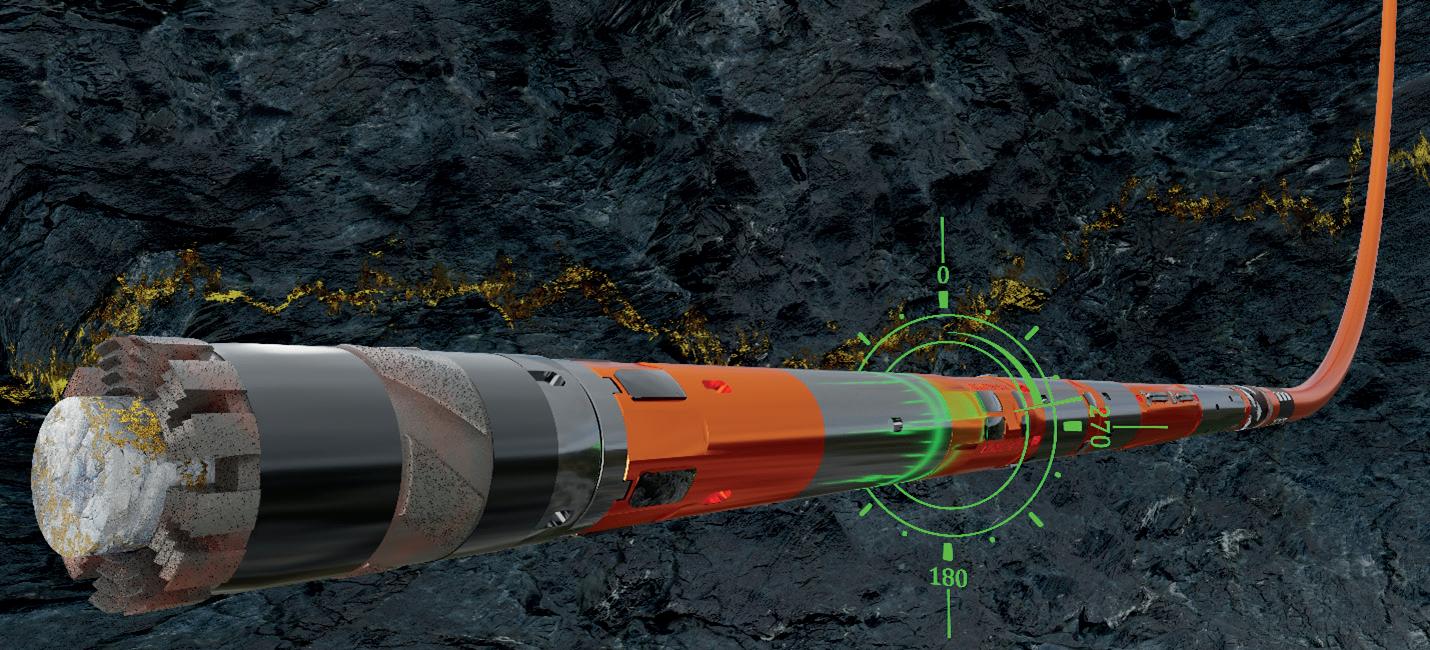
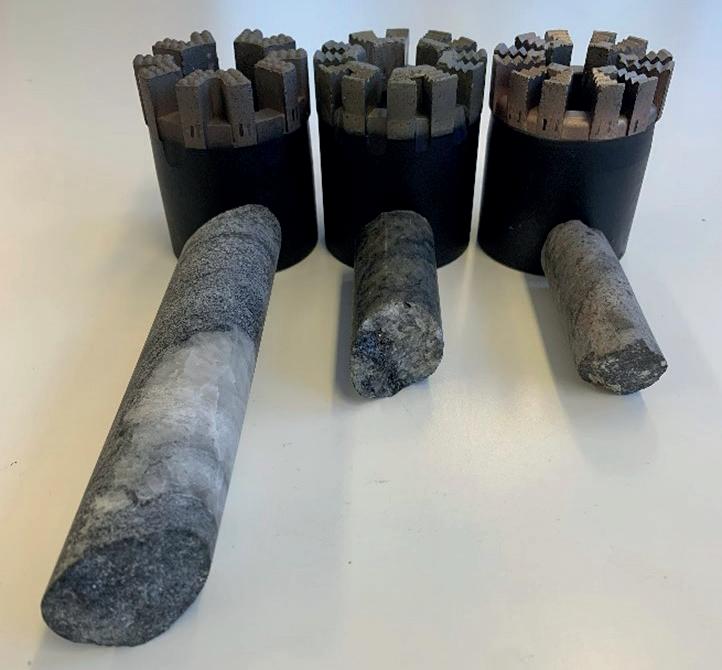
↑ SIZE MATTERS! BTK-size core compared to B-size and A-size core
packer functionality or directionally controlled tool face.
Additionally, the AZIDRILL N-BTK’s newly-designed improvements help to extend the lifetime of critical wear parts increasing the overall robustness of the tool. As a result, the AZIDRILL N-BTK increases the production rate on the rig. This has been a key measure for all Aziwell’s R&D activities. This achievement represents another step in our goal of becoming the world’s leading company in directional core drilling technology.
Increased core size
AZIWELL believes the core size of this tool will benefit geological recovery during directional procedures when compared to other N-size DCDs and conventional N-size drills, as the difference between BTK-size core and
N-size core (47.6 mm or 1.87 in) is only 37% by volume.
AZIWELL engineering team
The AZIWELL engineering team has more than 25 years of experience within R&D and field services related to directional core drilling. All AZIWELL design engineers have taken part in extensive fieldwork as part of their employment. Practical knowledge related to the operation of the tools has proved to be a key factor in successfully bringing the best innovations from the office to the field.
Field testing
The main objective set forth by AZIWELL is to complete downhole operations without bringing the drill to surface for servicing.

↑ Nils and his BTK-size core sample
Recent requests have indicated that geologists can benefit from longer steered sections in boreholes, with some requiring holes to be brought from vertical to horizontal. During the testing programs carried out in 2021 and 2022, AZIWELL successfully finalized 100 m sections (approx. 328 ft) of directional core drilling to target without noticeable signs of wear.
Availability
The AZIDRILL N-BTK will be commercially available from January 2023. The AZIDRILL N-B is available today!
Where we are
AZIWELL’s main office is located in Trondheim, Norway with satellite offices established in Canada and Chile. C
For more information Visit: www.aziwell.com. You can also visit us at PDAC 2022 (Booth #539) in Toronto, Canada, or Euro Mine Expo in Skellefteå, Sweden, in June 2022
A day in the life of a driller
by Mike Junkins, Core Drill Operator
Stepping outside the motel’s squeaky door I breathed in the twenty-degree Fahrenheit air (- 6.7⁰C) and became fully awake. My Matterhorn boots made a crunching sound in the three inches (7.6 cm) of fresh snow. I made my way across the parking lot to the Dodge crew cab. The windshield was crusted with frost from the cold night. I wondered how did the night shift fare with that funky heater?
Igot in and held the preheater for a moment before starting the rumbling diesel. I headed to the motel office to grab a coffee before rousting my helper and water truck driver. Anna was behind the front desk half asleep after nearly ten hours on the job. ‘Coffee is hot and fresh,’ she said automatically as I entered the lobby.
‘You know me all too well, Anna,’ I replied. Living in motels for months at a time we all became familiar with the staff. They did their best to make us comfortable during these lengthy stints away from home. I filled my cup and told Anna to get some sleep on my way out the door.
‘Be careful you guys,’ she said as I closed the door.
A couple of pulls on the scalding, bitter liquid and I began to feel human. We would stop at ‘Scary Larry’s’ café for some breakfast to go. The food was quick, hot and remarkably greasy. Just the way we enjoyed it.
I knocked on 207 and 208. Both men were up and grumbling that they would be out in a minute. We had worked together for most of this winter. The water truck driver, Artie, was the new hand. He had gotten out of prison for a bar brawl about two months previously. He had done a six-month stint after breaking the bouncer’s jaw during the encounter. This was one of the few places where these folks could find decent-paying work even with a record. He was a nice guy and a good hand. When the water tanks were full, he would come in and help Frank, my helper, with the core boxes and dumping tubes. He also gave us a hand when it came time to trip pipe.
‘A couple of pulls on the scalding, bitter liquid and I began to feel human.’
The old Dodge was defrosting nicely. These diesels take a few minutes to start throwing any good heat. My phone rang. That’s never good. My cross shift, Charlie, asked me to stop by the parts van on the way in. We apparently needed a new swivel hose as the one we had on was leaking. We had some hoses pre-made in the trailer for situations like this. Swivel hoses took a beating. The hole was 1800 ft deep (549 m) when I left
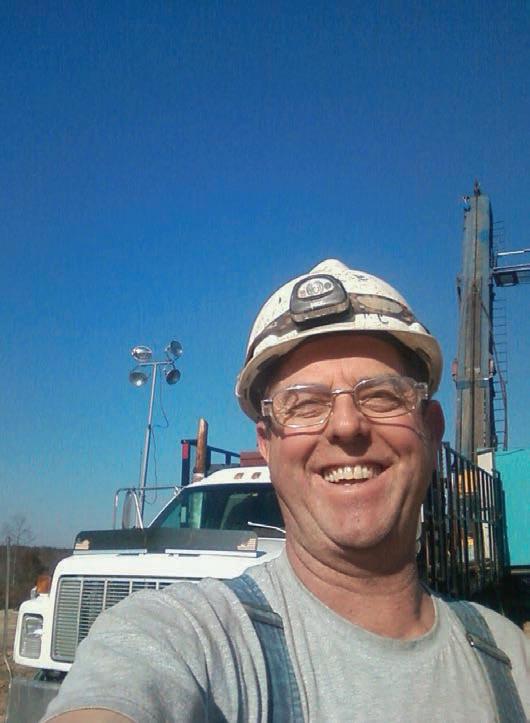
↑ Haile Gold Mine near Kershaw, South Carolina
last night. If Charlie squeezed out a hundred more that old drill was probably working hard. We were still running H-size tools. The geologist was expecting a fault zone and he wanted us to cross that formation before reducing to N-size. I hoped we hit the fault zone soon.
Artie and Frank came out of their rooms at the same time. They climbed into the truck without speaking. They would get their coffee at ‘Scary Larry’s’, and would become more animated afterwards. I climbed into the driver’s seat, and we set off. The roads were not ideal after last night’s snow.
I pulled into ‘Scary Larry’s’ café and parked near the front entrance. I told Frank to get me a breakfast sandwich and another coffee. I stayed in the vehicle to call Roque at the office in Montrose to let him know we would need a replacement swivel hose when he came to the site later in the day.
The drive to the rig site was about eighteen miles (29 km) or forty minutes since the last two miles (3.2 km) were on a winding dirt road. I caught myself humming along to Mellencamp’s ‘Jack and Diane’ as it played on the radio. Artie and Frank were catching a few extra winks on the drive. We pulled up to the rig and I breathed, ‘Black leg guys’. They both knew this meant the rods were standing in the tower and they were either coming out or going back in. We would find out soon. I met Charlie in the doghouse filling out his report for last night’s shift.
‘Matt looked at the core and told me that it looked like the fault zone he had been expecting. From the other holes drilled here previously, we knew the fault to be between forty and sixty feet (12.2 and 18.3 m) across. I knew that meant some blocky runs that would slow us down, but once we were on the other side, it should be ‘scream stone’, otherwise known as bonus rock or gravy.’
He explained that the bit was pressuring, and penetration rate was deathly slow. He was about halfway out of the hole at this point. We had a new Hobic 7AA bit on the shelf. Charlie also motioned to the last box of core on the rack. It was broken and gravelly, indicating that we were likely in that fault that Matt, the geologist, was looking for. That was a welcome sight.
The night shift told Frank and Artie what they needed to know about fuel, mud supplies, etc. I filled out the header on my daily shift report and we got ready to rip and trip. Get these bitches back on bottom, so we could make some hole.
Once we had changed the bit and tripped back in to about twenty feet (6 m) off bottom, I set the rods slowly rotating in the hole. I was pumping to wash before reaming slowly back to bottom so as not to plug the bit with anything that might have settled in the hole during the trip. Charlie had drilled about seven feet (2.1 m) into the fault zone. I saw lights coming and I knew it was likely Matt coming to check on our progress.
Matt looked at the core and told me that it looked like the fault zone he had been expecting. From the other holes drilled here previously, we knew the fault to be between forty and sixty feet (12.2 and 18.3 m) across. I knew that meant some blocky runs that would slow us down, but once we were on the other side, it should be ‘scream stone’, otherwise known as bonus rock or gravy. Matt indicated that once we had fifty feet (15.2 m) of good sulfide rock, we could reduce the hole to N-size. It took about twenty minutes to clean out the hole to bottom. The water tanks were full, so I sent Artie to the mud laydown to get bentonite, polymer, tube lube and some clay inhibitor.
As he was leaving, I chided Matt about spending the day in the core trailer with Victoria. Vicky was known as a teck. She was doing her master’s degree in geology. Working with Matt on this project was a sort of work-study program for her. She also got college credits for her experi-
ence, as well as a taste of real-life geology. She was pretty as well as knowledgeable. Kidding Matt, who was single, was just a part of our daily banter.
We lost circulation at about twenty-two feet (6.7 m) into the fault. This was not unusual or unexpected, but it would hinder our progress somewhat. We mixed up two nice mud bombs with cottonseed hulls and cedar fiber and pumped them down. I had the bit about six inches (15.2 cm) off bottom and we waited for the water pressure to spike indicating that the void/fracture was being sealed off. It took nearly two hours to get the fluid returning so that we could proceed. Fingers crossed that we did not have more circulation issues before getting into the Sulfide formation on the backside of the fault zone.
We managed to get about twenty feet (6.1 m) of good stick rock on the other side of the zone by the end of our shift. The fault ended up being forty-three feet (13.1 m) wide. Charlie was in for a tough shift tonight. I told him that an-
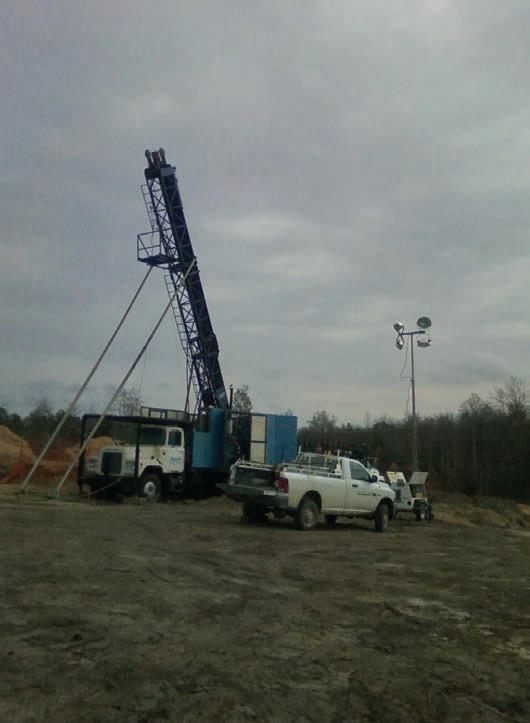
↑
Connors 40 HH Drill Rig on site
‘They were used to dad being away, but they knew I was working for them. I wanted them to have more opportunities than I had been afforded.’
other thirty feet (9.1 m) of sulfide and he could bring the N-size trailer in and reduce the hole. Get as much done as possible and we could finish up in before the morning. Another long but rewarding day was in the books.
Charlie’s truck lights were a welcome sight. Twelve hours was a grueling shift. We worked seven days a week every week; rain or shine. Forty days on-site and then ten days at home.
Back at the motel, I saw Anna just heading in the door to the office to begin her own long night shift. She was going to college for business management, so she was able to study while she covered the desk duties. I told Artie
and Frank not to play too hard, as tomorrow would likely be a busy day.
I called Maria, my wife. She put the kids on, Matty was four and Abby was six. They were used to dad being away, but they knew I was working for them. I wanted them to have more opportunities than I had been afforded. They told me about their day, and I kissed them goodnight through the phone. Nine more days and I could fly home for a welcome break. Now, a hot shower, a cold beer and a microwaved can of Chunky Soup. After that, I would fall asleep with the TV on and dream of home. C
For more information
Get in touch with Mike on LinkedIn
DIATOOL is a young and dynamic company, founded in 2010. The company manufactures impregnated and set core bits, casing shoes, reaming shells, and geotechnical drilling bits. DIATOOL products are sold in North and South America, Australia, Asia, Africa, and Europe.
DIATOOL Diamond Products are manufactured in a modern well-equipped plant, using the latest Canadian and Australian manufacturing technology. The personnel at DIATOOL have experience in the mining and mineral exploration and core drilling industry going
back to the 1970s. Their experience in designing, engineering, and manufacturing, has placed DIATOOL at the forefront of diamond drill bit technology. Using sophisticated, proprietary furnacing techniques, and experts in powder metallurgy, DIATOOL is able to manufacture a broad range of matrices to achieve the best possible bonds for everyday drilling demands.
Specializing in prompt technical problem solving, we pride ourselves in our ability to respond to customer demands, with the supply of high-
401-6333 West Blvd., Vancouver, BC V6M 0C1 Canada аnthonygraham6@gmail.com
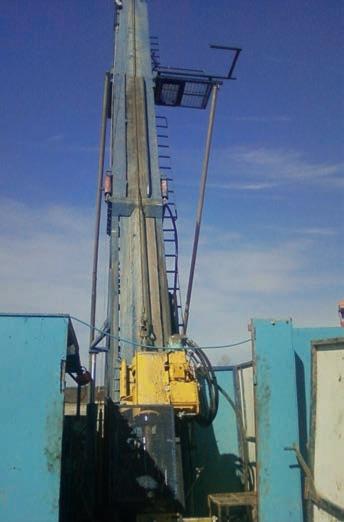
↑ 40 HH drilled 4208 ft (1283 m) hole with H tools in Crescent Valley, Nevada
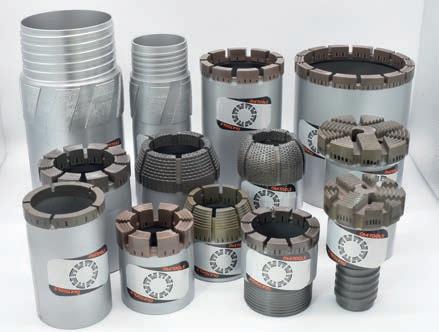
quality products at competitive prices.
The founding partners have in excess of eighty years of combined Canadian and Australian expertise in the areas of matrix metallurgy, technical design, manufacturing processes, and quality control systems.
apang@lickhang.com.hk
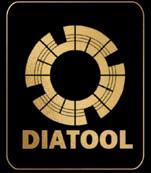
On the cover:
Tect Geological Consulting Exploration Mining Geology
In this Issue:
Tect Geological Consulting: An industry-leading specialist in Structural-Economic Geology by Dr Ian Basson and Dr Corné Koegelenberg, Principal Members and Michael McCall, Senior Geoscientist
In conversation with Beau Nicholls, Director & Principal Consultant at Sahara Natural Resources
Exploration in the land of gold: A brief review of observations and techniques by Ahmed Atito, Exploration Geologist at Nubian Mining Company
The use of mineral exploration drilling to kickstart hydrogeology data collection for pre-feasibility mining studies and beyond by Kym L Morton, CEO and Consulting Hydrogeologist at KLM Consulting Services Pty Ltd
Six concepts to keep in mind when exploring structurally controlled mineralizations by Luca Smeraglia, PhD, Independent Structural Geology Consultant and Structural Geologist at the National Research Council of Italy
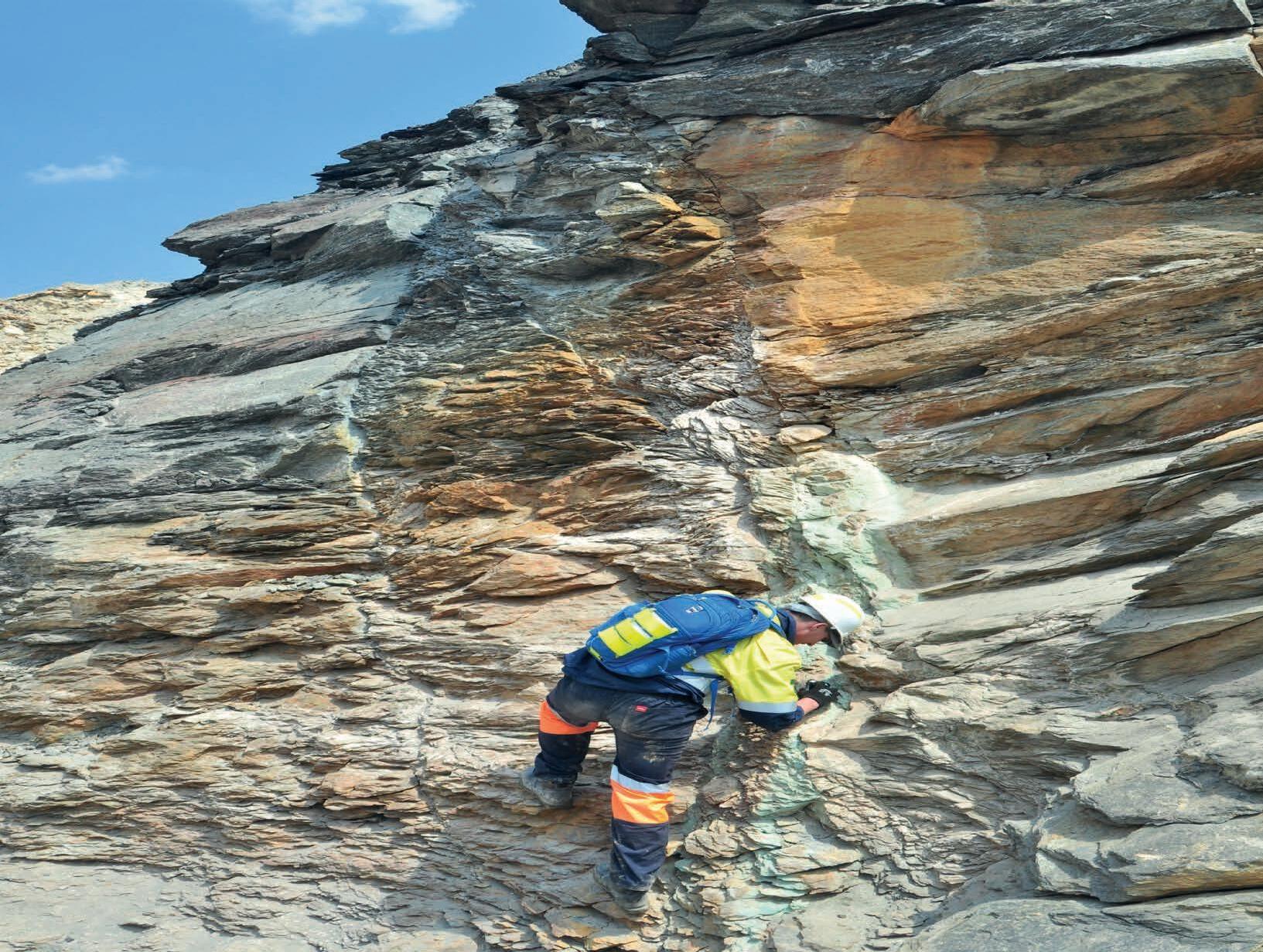
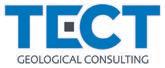
Tect Geological Consulting An industry-leading specialist in Structural-Economic Geology
by Dr Ian Basson and Dr Corné Koegelenberg, Principal Members and Michael McCall, Senior Geoscientist
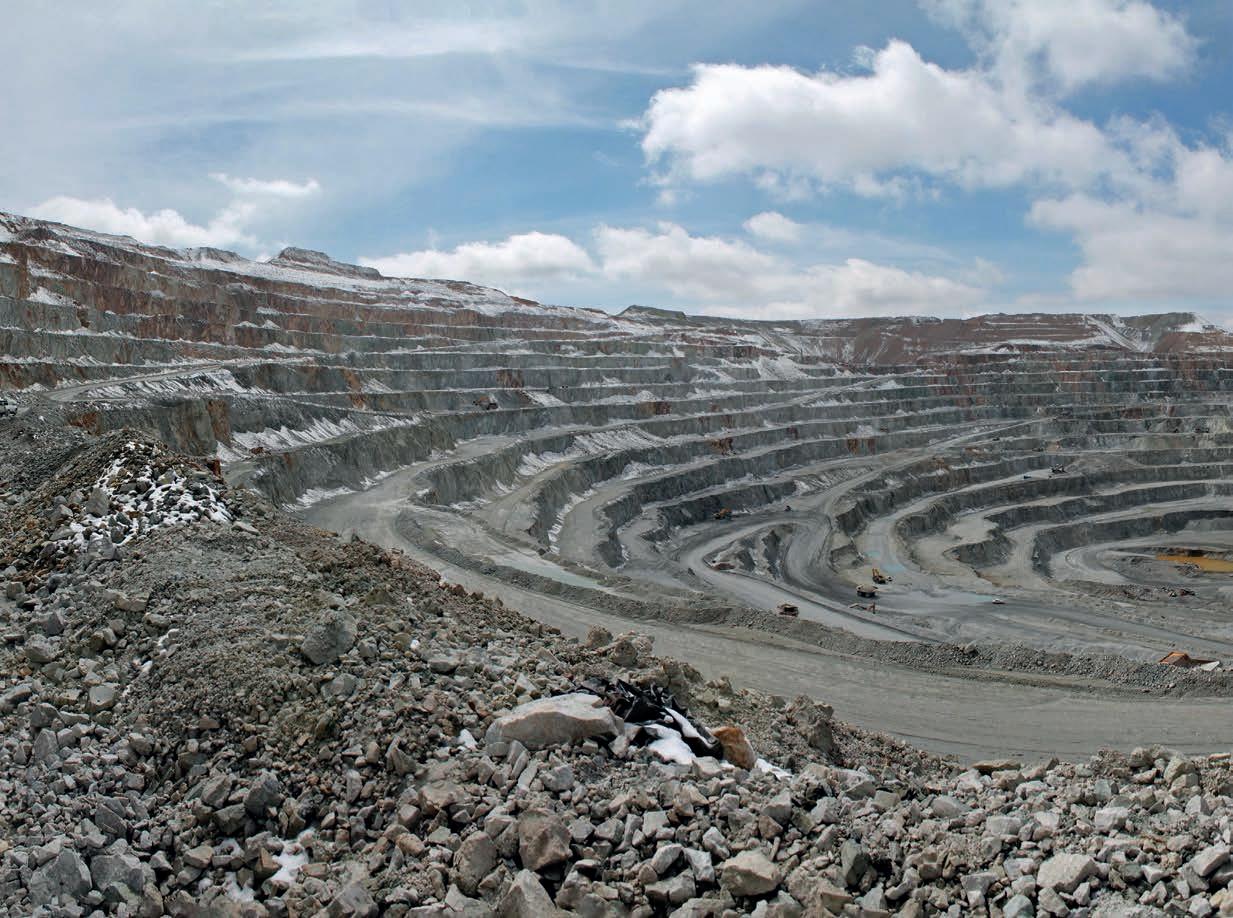
Tect Geological Consulting (Tect) is an industry-leading specialist in StructuralEconomic Geology with well-established experience across the world, and a particular focus on Africa and the Middle East. Over the last 22 years, Tect has addressed over 180 projects in the mining, exploration and investment industries, building longstanding, value-driven partnerships focussed on comprehensive and sustainable structural data collection, analysis and interpretation. The outcomes of these projects are robust, fully-constrained, fit-for-purpose, 3D geological models that are used in various Geotechnical, Mineral Resource Management (MRM), Mine Planning and Geohydrological applications. Such models are paramount to de-risking and optimizing projects.
Company history and development
Over two decades ago, Tect undertook detailed structural mapping and 3D geomodeling at Rössing Uranium Mine in Namibia and De Beers’ Venetia Mine in South Africa. Since then, Tect’s philosophy of careful, high-resolution mapping, structural interpretation, data custodianship and advanced, best-practice 3D geomodeling has resulted in over 100 fully-constrained 3D models of major structures, country rock and orebody geometries, alteration zones, fracture domains and bedding/ foliation domains. Although the core of our business is in Africa and the Middle East, Tect’s Associate Consultants and Associate Researchers
have consulted on mining projects in Bosnia, Brazil, Canada, Ecuador, Finland, India, Kazakhstan, Malaysia, Portugal, Spain, Sweden, Vietnam and Australia. Recently, two experienced Structural Geologists were added to the list of Tect’s Associates: Dr Brett Davis and Prof. Alex Kisters. Howard Baker, who is a Mineral Resources Specialist, and Damian Smith, a PGE specialist, joined Tect’s Associate group a few years ago. Tect’s high-quality 3D models have been developed for most of the super-pits and large underground operations in southern Africa, including Venetia, Jwaneng, Orapa, Voorspoed, Cullinan, Letlhakane, Damtshaa, Sishen, Kolomela, Thabazimbi, Mogalakwena, Northam, Lonmin,
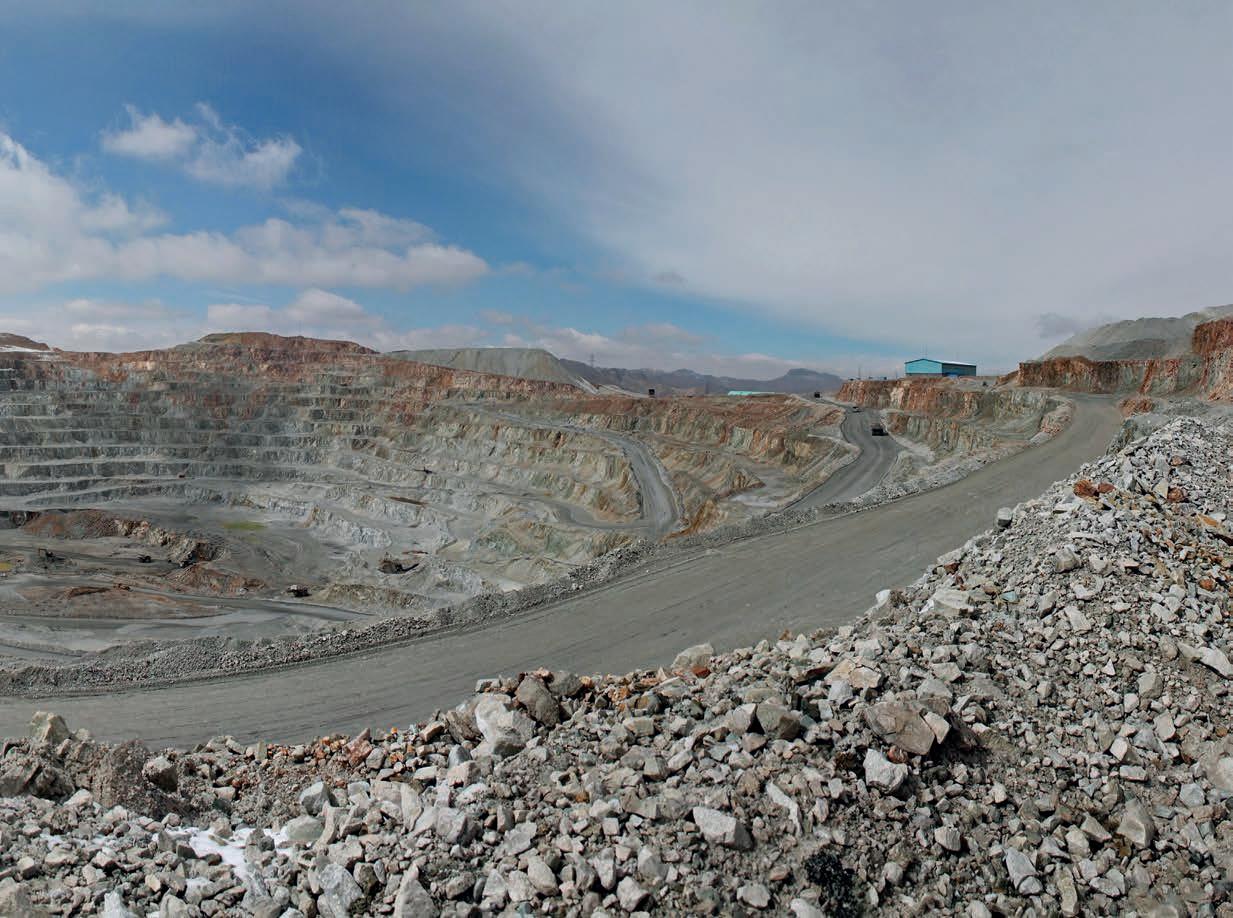
Amandelbult, Booysendal, Waterberg/PTM, Rössing, Chimiwungo, KOV, Mutanda, Kansanshi, Lubambe, Frontier, Palabora and, in the Middle East, Miduk and Gol-e-Gohar. Tect has also resolved the geometries of underground precious metal mines and exploration projects, including recent, very successful projects such as Bisie, Wassa, Blanket, Mopani, Bibiani, Shanta, Osino and Xtra-Gold. More information on these and other projects may be found at www.tectgeological.com.
Back to basics
High-quality mapping data underpins any structural and lithological interpretation. Tect undertakes direct surface and underground mapping, accompanied by the characterization of structural and lithological features, using the latest mobile GIS platforms and differential GPS systems. These datasets are combined with quality-controlled mapping data from the Client, high-density photogrammetry and LIDAR surveys and colorized or false-colorized point cloud surveys, to delineate structures and lithological contacts. Additional data sets comprise downhole data, such as OTV/ATV and the data from oriented core logging. With a focus on resolving the structural evolution of the volume of interest, attention is paid to all features: lithology, alteration, mineralization and fabrics, in addition to more regional geophysical and remote sensing datasets. Structural features are characterized according to their surface geometry, fill, aperture and other parameters as required by Geologists,
Geotechnical Engineers and Geohydrologists for their downstream analysis, modeling and forward-planning.
Each Project Leader takes custody of the entire value chain, from mapping and data-mining, through background research and structural interpretation, to workshops, reporting and handover. This is one of the ways that Tect distinguishes itself from most of the larger geological consulting firms. Customized, project-specific Standard Operating Procedures that describe these workflows form part of the deliverables, with a view to handing over data and model upkeep to the Client’s technical team.
Tertiary analysis: Post-processing for geotechnical design
The integration and representation of relevant, scaled geoscientific data is translated into dynamic 3D implicit models, primarily aimed at bridging the gaps between Geology, Geohydrology, Geotechnical Engineering, Resource Estimation, Mine Planning and Exploration Departments. Tect uses a combination of Leapfrog Geo and Micromine, with solutionand data-specific modeling methodologies. Assessing and quantifying the interaction of geological features represented in fully-constrained, implicit 3D geological models (bedding, foliation, contacts, faults and fracture/joint domains) with a mine design or Whittle Shell, is essential for forward Geotechnical design and planning. This process is often, however, understated or oversimplified and companies resort to radial,
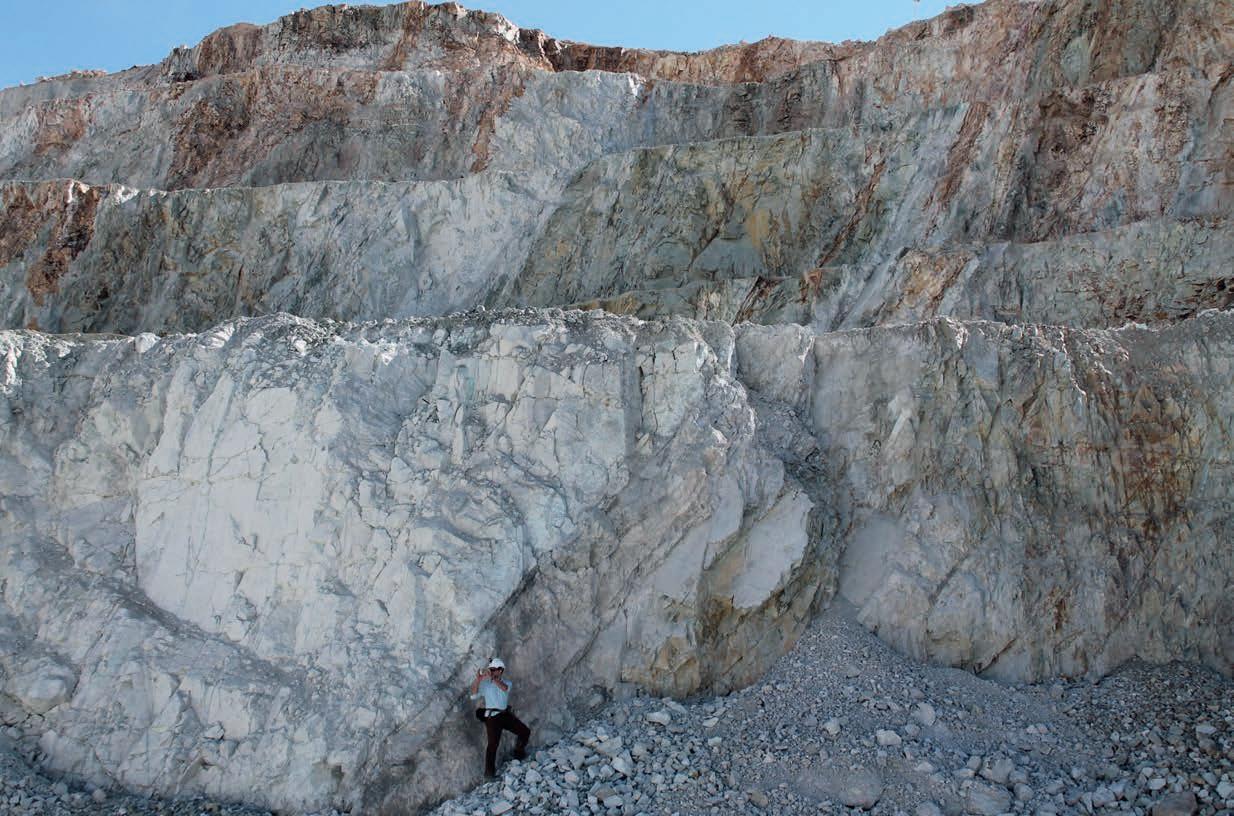
section-based analysis which suffers from numerous limitations. Tect utilizes mainstream software packages, and customized, proprietary scripts in MATLAB and Python 3 to extract and quantify the way in which these features interact with the pit or design surfaces, thereby allowing apparent dip and conditional shear-failure to be calculated as spatially-continuous parameters. The results of these analyses, which Tect pioneered and implemented for Venetia Mine in 2015, allow for the definition of 3D structural-geotechnical domains that are translatable into Geotechnical block models. This methodology has now been adopted at Jwaneng, Kolomela, Mogalakwena, KOV and Chimiwungo, providing the Mining and Geotechnical teams with a robust tool for the prediction of areas that might react adversely to mining or which need closer monitoring.
Another development that Tect has been closely involved in is 3D modeling for the prediction and quantification of palaeosinkholes. Using a workflow that is very similar to Weights-of-Evidence or Model-Driven approaches in the exploration industry, Tect has successfully predicted the position, size and depths of karstic palaeosinkholes within mining volumes using 3D spatial queries.
What about exploration?
Structural geology and the understanding of kinematics as applied to fluid movement and mineralization is one of Tect’s fortes. In collaboration with partners, New Resolution Geophysics, Xpotential and Remote Exploration Services, quantitative modeling and inversion, across a range of Geophysical methods has been undertaken, subject to the
availability, quality and coverage of data. This created fully-integrated, shared-earth models, incorporating all data sets in 3D and thereby providing a more rigorous targeting process. Over 80 Geophysical interpretation projects, of varying complexity, have been undertaken to date. Basic products include an interpretation of ductile and brittle structures, and geophysical domaining. First-pass proxy geological maps, generated from these geophysical domain maps, are generated by ground-truthing and integration with other geological data. This enables units to be targeted, often with the inclusion of soil Geochemistry, to test one or a series of mineralization models. More advanced targeting studies, involving Weights-of-Evidence and Model-Driven approaches have been applied to IOCGs, IOAs, Birimian-style and orogenic/lode Gold, Copper-Cobalt, Iron-Manganese, Carbonate-replacement and Mississippi Valley-Type Lead-Zinc projects in Africa and the Middle East.
Peer-review
There are not many groups of Structural-Economic Geologists that publish their work in peer-reviewed international journals. Tect has a strong focus on putting our work out there, in the form of topical, data-driven articles that are co-authored by our Client’s Geologists and Geotechnical Engineers. To date, Tect Geoscientists and Associates have published in excess of 120 papers on structural and economic geology, which are viewable and available on request by contacting us via our website. The formulation of papers, as a team, has a beneficial spin-off: Tect’s standard and quality of reporting are recognized as being industry-leading.
↑ Corné mapping major structures at Miduk Mine, a major porphyry copper deposit, Urumieh-Dokhtar Magmatic Arc, Iran
Additional services
As part of our services, Tect provides Due Diligence and Structural Audits, Exploration Geoscience Management and Regional Data Compilations. In collaboration with Ken Lomberg of Pivot Mining and Howard Baker, we have worked on numerous CP/QP reports, developing accurate 3D models that are fed into this process. The recent successes of Shanta Gold, Blanket Mine, Goldenstar/Wassa, Alphamin/Bisie and Chesser Resources speak for themselves. During the evolution of Tect, we have also branched off into UAV surveys via a new company, Geoflight (see www.geoflight.co.za). Lastly, by way of establishing the regional context of the projects we have worked on, we have compiled an African-wide, interrogable, spatial database of geological features, derived from open-source data. This is hosted and showcased at www.geopoint.co.za
Training
While consulting, we get an idea of what Clients want in terms of training. To this end, we have developed three courses, which we routinely provide to Clients, to the Geological Society of South Africa’s Directorate of Professional Programs (DPP) and to Universities in South Africa. The first of these is 3D Geomodeling, which is a 16-module course. In order to confidently use 3D models for downstream processes, such as mine design, Mineral Resource Estimation and Geohydrology, an understanding of the parameters used in their construction is essential. The course describes model inputs, validation, verification and common pitfalls. It explains the recent shift from explicit, section-based, geomet-
rical modeling to attribute modeling, to rules-based, implicit modeling, such as that employed by Leapfrog. Such insight is particularly useful for Geoscientists that represent companies that are looking to change their geomodeling software.
The request for a refresher course on Structural Geology from industry professionals frequently arises. Although Structural Geology is an often-intimidating university course, it’s a discipline that is routinely required in mapping, data gathering and interpretation of prospects and deposits. It is therefore worth keeping up with the topic and with new developments. The course consists of 12 modules, covering tectonics, fabric, strain, stability, Mohr diagrams, cataclasis, rheology, application to ore fluids, application to petroleum systems, mylonites, ductile shear zones, shear criteria, kinematic indicators and SPO/CPO/LPO fabrics. The course is particularly useful to Geoscientists that require a refresher on the subject, who are interested in topics that were not covered in undergraduate courses or for those that are interested in the application of Structural Geology to mineralization and 3D modeling.
Tect has, in collaboration with Seequent/Bentley, the distributors of Leapfrog, developed a Leapfrog Masterclass. This is a 3-day course comprising 11 modules focused on resolving structurally-complex geology in Leapfrog. This uses comprehensive real-world datasets in a variety of structurally-complex geological environments. The interactive course covers Leapfrog’s advanced 3D modeling tools. Focus is placed on structural geology and multiple data types to derive realistic geometries. Practical exercises provide users with a hands-on introduction to advanced modeling techniques, guided by best-practice principles and strategies employed by experienced Structural-Economic Geologists. For more information, please see www.tectgeological.com
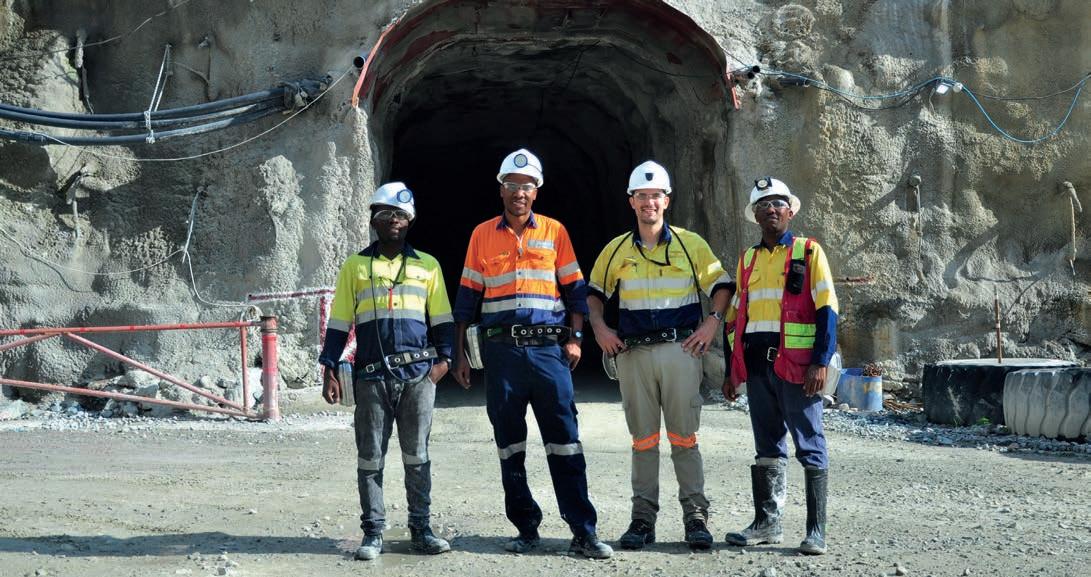
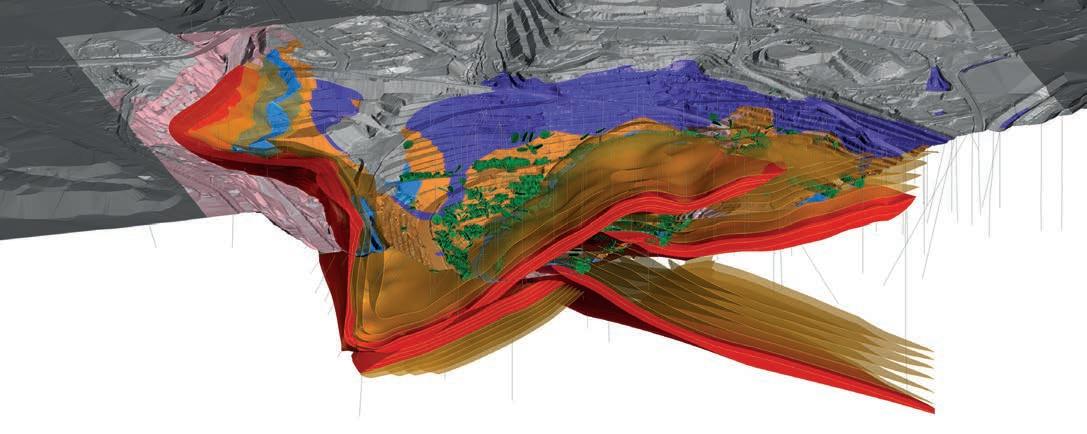
↑ Form interpolants of bedding and major contacts in large-scale, Cu-Co-bearing olistoliths, Lufilian Arc, DRC
The Tect team and partners
Geoscientists: Dr Corné Koegelenberg, Dr Ian Basson, Ben Stoch, Michael McCall, Jonathan Gloyn-Jones, Heike Fourie, Luke Carlton and Caitlin Jones.
Associates: Dr Brett Davis, Prof. Alex Kisters, Dr Pieter Creus, Dr Jodie Miller, Howard Baker and Damian Smith.
Partners – Itasca, Seequent, Micromine, New Resolution Geophysics, Xpotential, Remote Exploration Services, Pivot Mining Consultants, Incaic Exploration SPA
2022 and beyond
The trend is for newly-discovered prospects and deposits to be deeper and more structurally complex. Getting the geometries of these prospects and deposits correct is becoming increasingly crucial. If the geometry of the orebody that is fed into the Mineral Resource Modeling process is incorrect, then the estimation is necessarily incorrect. Similarly, if the geometry of the ore body, country rocks, major structures and rock fabrics is not accurate or sufficiently representative, undesirable and unexpected events will occur during mining. Tect, along with its Associates and industry-leading partners, will continue our tradition of carefully constructing the best 3D geomodels for the mining and exploration industry. C

↑ Palaeosinkhole mapping and prediction, using implicit 3D models and Weights-of-Evidence, in a karstic terrane, South Africa

and major structural
For more information Visit:www.tectgeological.com
↑ Apparent dip map
traces at Jwaneng Mine, Botswana
Mineral Exploration Drill Rigs and Equipment

Rigs from 30,000lb up to 95,000lb Pullback World Class Safety as a Standard Proven Performance and Reliability
An Independent Diamond Rod Handling System that is compatible with Multiple Machines and Eliminates Hazardous Hands-on-Steel Operations associated with Diamond Drilling
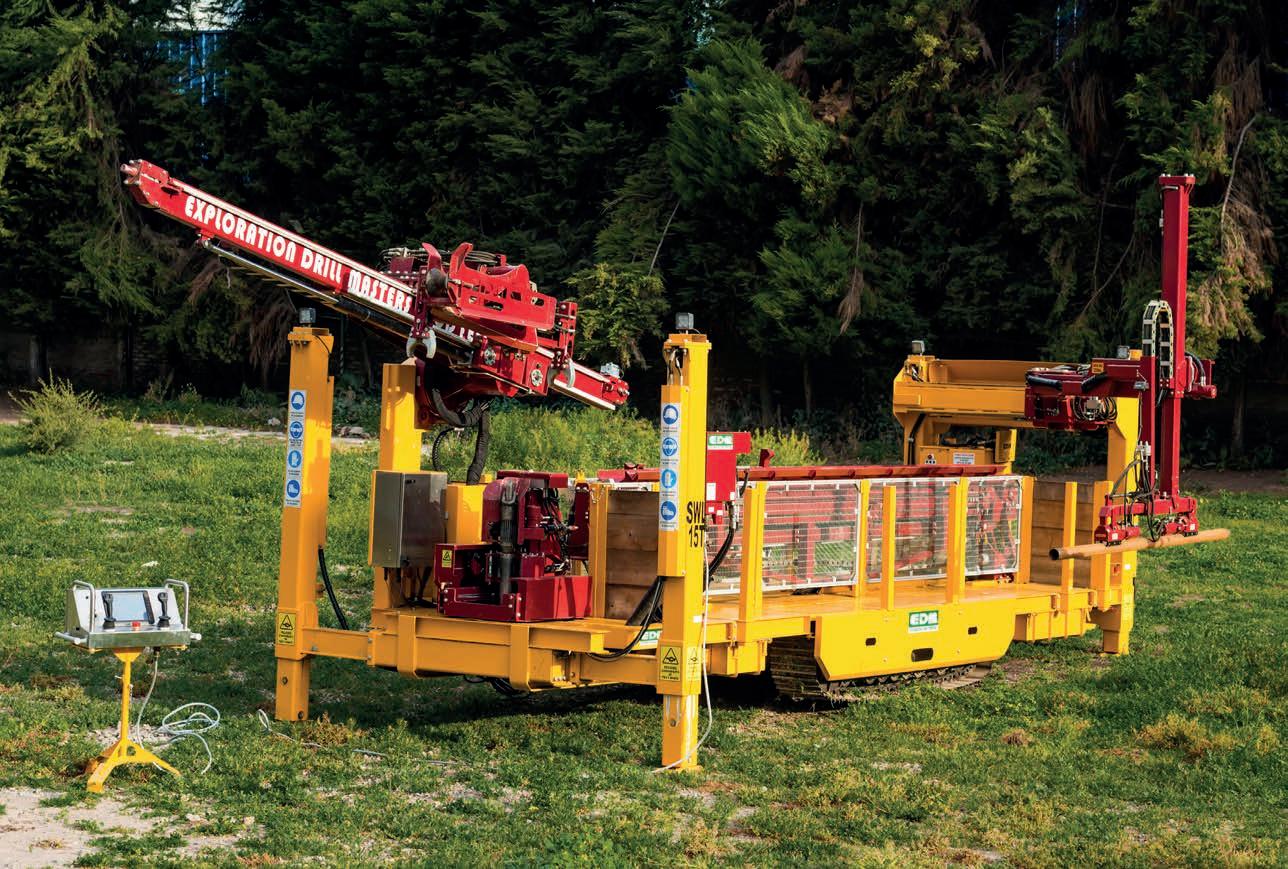
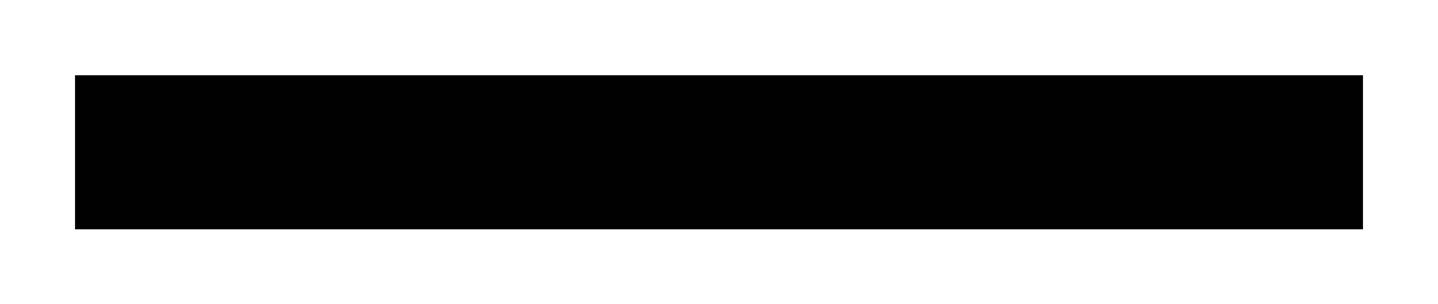
In conversation with Beau Nicholls
FROM THE EXPERTS
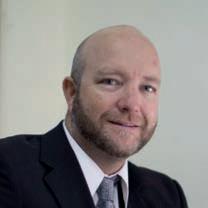
Beau Nicholls Director & Principal Consultant at Sahara Natural Resources
Dr Brett Davis: Firstly, thanks for giving Coring the opportunity to interview you. You’ve had a long and diverse career in the mining and exploration industry. Can you tell us where the story began?
Beau Nicholls: My interest in mining started back when I was about seven years old and I visited my uncle and grandfather, who were working on a small-scale gold mine in Dunnsville, Western Australia. Dunnsville (now a ghost town) was about 50 km (31 mi) away from Coolgardie and was discovered in 1894. The town thrived for more than 30 years before the prospectors moved on and the gold ran out. As a 7-year-old, almost 100 years later, I had a great time, running around the bush, entering old mines and digging up old bottles from the old, abandoned town, and searching for gold. It made an impression that is with me till today.
Ten years later, as a farm boy with an older brother, who had started on the family farm, I decided to study geology and attended WASM in Kalgoorlie.
Beau is a geologist with over 28 years of experience. Beau started from a remote farm in the Wheatbelt of Western Australia and completed a Geology degree at Western Australian School of Mines (WASM) in Kalgoorlie in 1994. He then spent over five years at the Telfer gold mine, before starting an expatriate career working in over 20 countries across Australia, Africa, Eastern Europe, and North and South America.
He is a founder of West Africa-focused exploration contracting group, Sahara Natural Resources (Sahara) which has pioneered the hugely successful technique of Auger Geochemistry into Africa and sits on a number of boards in Australia and South America.
BD: You’ve worked in a lot of countries and on a lot of continents. Are there any skills or mindsets that have helped you in your roles in these places?
BN: Being from a relatively remote farming community, we had no TV and no mains electricity as I was growing up. I had learned to drive a tractor, fix a tire and kill a sheep before going to boarding school from age 11. Leaving home at such an early age, I became independent with a practical set of skills for living. They come essential when you go overseas for work.
BD: I’ll ask you a few drilling-related questions first because you’ve managed lots of drilling programs utilizing many different techniques. Which technique(s) do you enjoy the most and why?
BN: I enjoy all methods of drilling for their specific benefits and use throughout the exploration and mining cycle, but the most exciting drilling method I find is Auger geochemistry. The discovery of a grass roots project is far
more interesting than repetitive RC Grade Control (I did the first-ever RC Grade Control program in Telfer Gold Mine in 1996) or deep directional diamond drilling. I introduced Auger Geochemistry into West Africa in 2006 and we have since drilled over 4 million m (13 123 360 ft) there. It is the most effective technique for new discoveries through cover. The most interesting ‘drilling’ technique I have ever been involved in was in Rosia Montana, Romania. Our initial drilling program that defined the first 8 million oz (out of more than 18 million oz) was by hand and chisel, channel sampling over 200 km (124.3 mi) of Roman and communist underground workings. There is great professional satisfaction in being part of a new discovery.
BD: Have there been any particularly challenging drilling programs, and what did you do to overcome these?
BN: Every drilling program has its challenges, and I could talk for days about some of them. Ninety percent of the time they are not drilling
technical challenges, the three that come to mind are:
• Telfer Open Pit (1996) - Manage the change from Blast hole sampling to a new technique ‘RC Grade Control’ which included ‘barcode sampling’. ‘WHAT!’, no numbers on bags?
• Underground drilling in Rosia Montana, Romania (2000) - We had to excavate the drill cuddy with dynamite (Yes, it was dynamite), hand shovels and wheelbarrows, move the rigs by manpower, and when one old lady would not let us drill in her back yard, I designed an up hole and drilled it for 120 m (393.7 ft) stopping just 10 m (32.8 ft) below her kitchen!
• Bongou, Burkina Faso (2019) - With the deteriorating situation with terrorists in Burkina Faso, we were drilling on-site when the first improvised explosive device (IED) went off 5 km (3.1 mi) from camp. We at Sahara Natural Resources had already completed a comprehensive site security review and after the client declined to pay for our additional security costs, we demobilized from the site to ensure the safety of our personnel. Tragically, two months later 19 people were killed and many wounded in a violent attack on the mine workers’ bus.
BD: Core orientation is a fundamental aspect of exploration and drilling. Which method do you prefer and why? Do you have any horror stories with regard to core orientation?
BN: While I was with RSG Global in West Africa, we used to undertake training in the exciting new core orientation techniques in the industry and would enlist specialist structural geologists like you, Brett, and Dr Julian Stephens. There was the spear, which was simply a spear, then the Ezy Mark, which was far more sophisticated with pencils and nails, and then came the Reflex ACT tool which used NASA technology that told you which was down. The Reflex ACT orientation tool during its time was far better, as it was not as susceptible to operator error.
The best unit on the market currently I think is the ‘Champ Ori Tool’ by Axis Mining Technology, mainly because it doesn’t require extra tooling for the driller. The Champ screws in the backend and takes no additional time or tooling for diamond drilling. If you want a core orientation done accurately then it needs to be a simple process.
I’ve seen my fair share of horror stories that happened when trying to join core from a spear.
BD: I’ve known you for a long time and have enjoyed watching the evolution and success of Sahara Natural Resources. Can you tell us where has that begun and what path has the company taken?
BN: Sahara began with RSG Global in 2005 in West Africa. RSG was a great exploration and mining consulting company that started with geology legends Rick Yeates and Julian Barnes in Kalgoorlie in the 1990s. They opened an office in Ghana towards the end of the decade. I became the Regional Manager, West Africa in 2005 and spent some great years there with an amazing team of West African professionals. Our team was directly responsible for the development of many deposits, of which Sabodala Gold Mine (first gold mine in Senegal), the Inata and Batie Gold deposits in Burkina Faso, Nyinahin and Kibi Bauxite in Ghana, Kourroussa Gold in Guinea, and Tonkolili Iron ore in Sierra Leone during my first three years in West Africa.
RSG Global was then purchased by Coffey International, and I moved to Brazil as Geology Manager. Unfortunately, once the twoyear handcuffs came off the RSG managers, most of them moved on. I did the same at the time and we formed a team to start Sahara with a great friend and geological colleague of mine from Ghana/Burkina, Mohammed Munkailah. Sahara evolved from where RSG Global had left off. We focused on the region of West Africa and Coffey Mining ceased to exist a few years later, so Sahara ended up purchasing Coffey’s remaining assets in West Africa and rehired the original A-team from RSG.
BD: You were based in West Africa for a long time. Increasingly, we are seeing unrest in the form of coups and fundamentalist violence. Given your increasing global presence, how have you dealt with the nuances of the various countries in terms of security?
BN: The death of Libya’s Muammar Gaddafi in 2011 unleashed instability to the north of West Africa, and the terrorism we see today is a result of this. Much like killing Saddam Hussein unleashed it on the rest of the world.
We have had to become a sophisticated explorer, and have formed strategic partnerships with specialist security group MS Risk, which has served us well till today.
Coups are a part of life in Africa, sometimes they are good, and sometimes they are bad. The way Sahara has dealt with Sovereign risk in West Africa is by spread. We operate in six countries across West Africa at any one time,
and we allow for one of them to have some ‘troubles’.
BD: Which countries have you enjoyed working in the most?
BN: Of the 20 odd I have worked in, all of them have their good and bad moments and all have great people and lifelong friends. Currently, I am enjoying working back in Australia and not getting on airplanes.
BD: I’ve worked in a lot of countries but my language skills besides English are rudimentary. Do you have a method for learning new languages and avoiding cultural faux pas, given you are dealing with people from drillers through to community groups and management?
BN: The best method to learn a new language is immersion. I spent one year in Romania at Rosia Montana and had lessons twice a week. After twelve months of working with a number of expats and translators, my Romanian was rubbish.
The next year I went to Zlatna Gold Project, a small ‘remote’ village in the Transylvanian mountains, and I was the only one who spoke English in the entire village. I quickly learned to ask for toilet paper and was speaking more in the first month at Zlatna, than the prior 12 months at Rosia Montana, where I had the help of fellow expats and translators.
BD: Given the current multi-commodity mineral boom, how is Sahara Natural Resources managing labor requirements? I imagine it is hard to both find and retain quality staff?
BN: Sahara in West Africa are big trainers and recruiters of young geologists. In any given year, we would employ and train over 50 young geologists on how to log and sample on a rig. We have also been fortunate to retain some of our original employees and although we cannot meet the big player salaries that often destroy a labor market, we offer diversity and a variety of experiences. Keep in mind that the geologist that sees the most rocks is far more valuable than the one that gets paid the most money.
We have managed well during the COVID-19 pandemic, despite enormous challenges, but even across West Africa, we have had to ensure we recruited local.
BD: Does Sahara Natural Resources provide training and/or professional development for its employees?
BN: Sahara is a training ground for young geologists in West Africa. This work is typically on-
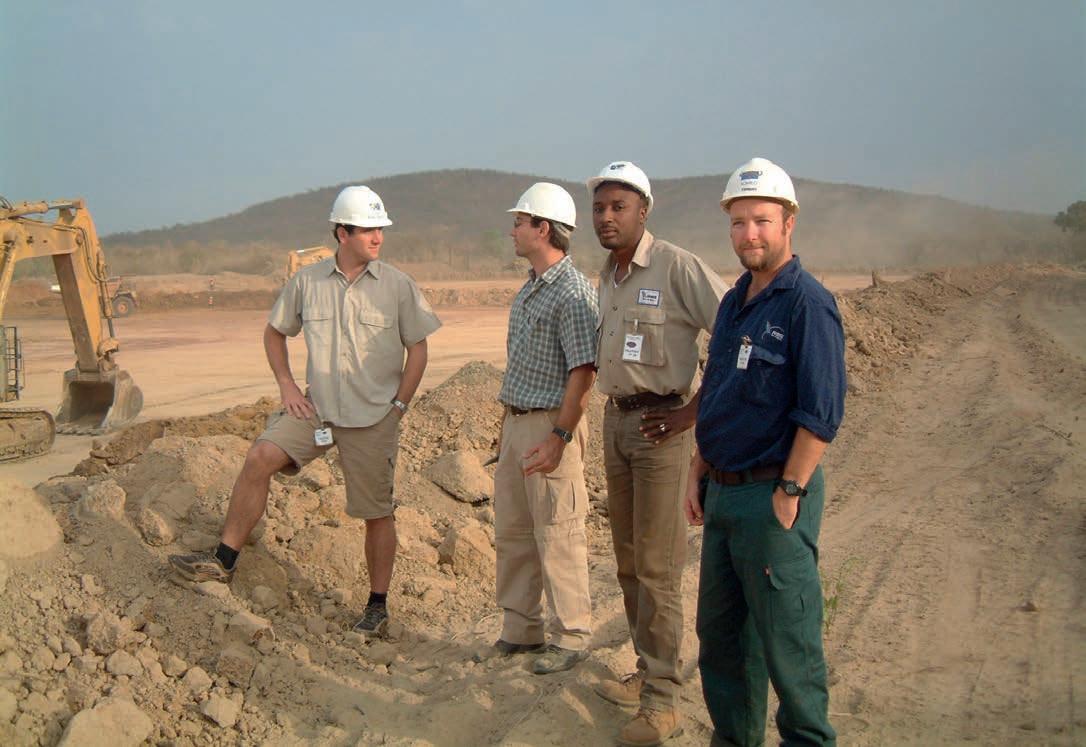
the-job training, but we attempted to provide a three-year graduate program where possible. We provided external training for clients and undertook hundreds of Mapinfo/Discover sessions across West Africa. One of the bestknown training courses we have established is the Structural Geology Course undertaken at Busua Beach Resort in Ghana. This has been running every few years since 2005.
BD: One topic we commonly talk about but rarely put into print are the health hazards of working in different countries and environments. Has your health ever been particularly challenged and, if so, what happened?
BN: Touch wood, I have never had a serious health issue when working and living overseas, aside from the odd stitches here and there.
One of my first health issues as an expat was in Rosia Montana, Romania, where I ended up with Scabies from sleeping in a bed that was
previously owned by a dog. After two months of severe scratching and no sleep, I finally drove four hours to Cluj-Napoca in snow and ice to a doctor that knew what it was in one second and fixed me with some cream there and then.
The other common high risk is Malaria. I have had Malaria three times while working in West Africa. If left untreated, it will likely kill you. I could stay in Accra for 12 months without issue, but as soon as I was in the field away from air-conditioning - and sleeping in a tent - within 10 days, the terrible Malaria would hit. It is an odd symptom, but when my eye sockets would begin to hurt when I looked sideways, this was my sign I needed to spend the next three days in bed with Malaria. Over the next ten years, I never travelled anywhere without a packet of Coartem tablets in my bag (extremely effective in killing the parasite that is Malaria).
BD: As a widely travelled geologist, what part of the world do you think is highly
prospective for finding new world-class orebodies?
BN: I personally do not think we have scratched the surface yet. The world is covered in recent transported material called ‘Cover’. It can be 30 cm (≈ 12 in) of soil, or it can be 300 m (984 ft) of sediments, but if the deposit has cover, there is a fair chance, you will miss it if you only sample the cover material. I have five regions that I have worked in that I rate highly:
Nubian Shield - One of the most unexplored regions of Earth is the Nubian Shield, which encompasses Sudan, Egypt, Saudi Arabia and a few other countries. There are challenges in these regions, but once systematic exploration is undertaken, then the orebodies will reveal themselves
West Africa – It will continue to define world-class orebodies. In 2005, there was ‘no gold in granites’ until Ahafo came along. There was one gold project in Burkina Faso in 2005, now there are over 15 gold mines in
↑ Standing on edge Loulo ‘starter Pit’ in 2005 (10Moz)
the country. Cote d’Ivoire was a cocoa farming country in 2008, and Guinea is starting to reveal itself with some big deposits to come. Sahara has been a key part of unlocking this wealth.
South America – Brazilians still use a diamond rig to explore for gold. You need many drill holes to find gold. But once they start using RC and Auger Geochemistry and pattern drilling, Brazilian states like Para and Tocantins will get better and better
Australia – We thought we were well-explored, then Chalice found one the biggest Ni-Cu-PGE deposits in the world, a mere 60 km (37 mi) from Perth, the home to mining around the world. Now the rush is on again.
And finally, my favorite is the Sahara Desert – Sand cover starting from Mauritania - Tasiast outcrops - across Africa to Saudi Arabia.
BD: Is there a particular mineralization style or deposit type that interests you, and why?
BN: As an open pit and underground mine geologist with five years of experience, the Telfer copper/gold mine in Western Australia was the first deposit I mined in close detail, blast by blast, cut by cut, bench by bench. Fascinated with the domes and the reefs that go to all depths we drilled (at that time was I30 discovery 1 km down)
formed them, and how big and rich it is. All deposits have some form of structural control and pumping station behind them.
BD: Where do you see the most exciting technological developments being made in mineral exploration going forward?
BN: The black art of geophysics will always present new and exciting technology, and when we start to drill deeper, it will become our first port of call. It is important for a geologist to stay close to geophysics developments.
I see the most exciting developments in geologists applying unmanned vehicles both
in-situ uncontaminated sample below cover. It is the cheapest, fastest and most effective first pass exploration tool on the market. Companies are often baffled into trialing alternate ‘Ultrafine’ and ‘MMI’ magical techniques that can see through cover. But no one can explain how they see through cover. Ten geologists will give ten different theories. So, companies then have to spend excessive amounts of money using aircore drilling to define false soil anomalies.
Ninety-five percent of West Africa has on average 5 m (16.4 ft) of laterite cover. It can be Residual, Erosional or Depositional (RED), but 95% of geologists (including myself) cannot tell the difference, so the KISS principle (‘Keep it simple stupid’) is best to adopt in the early stage.
‘The black art of geophysics will always present new and exciting technology, and when we start to drill deeper, it will become our first port of call. It is important for a geologist to stay close to geophysics developments. I see the most exciting developments in geologists applying unmanned vehicles both aerial and ground to a geology day to day tools, with real-time assays just like it is happening with drill rigs today.’
Rosia Montana epithermal gold in Romania with over 18 million oz - with Rosia Poieni porphyry copper deposit being 2 km (1.24 mi) away - was a beautiful deposit I got to explore from over 200 km (124.3 mi) of underground working.
Araxa Carbonatite in Brazil, full of Niobium, REEs and down deeper it is a phosphate mine, is a fascinating and extremely valuable deposit.
Arara Tin and coltan project in Brazil which I was able to take from discovery to Preliminary Economic Assessment (PEA). It is boring to look at and you could walk over it for years without even stopping, but it is a 3 km (1.86 mi) wide massive granite greisen mineralization, a box of treasures with all sorts of elements forming by heat and pressure.
I prefer not to class a mineral deposit by age/style/type, as there are far cleverer geologists to do this. I tend to think of them as what structures control the fluids that have
aerial and ground to a geology day to day tools, with real-time assays just like it is happening with drill rigs today.
I hope that one day we will develop hundreds of solar-powered batteries attached to drill rigs on tracks, which will pattern drill across the remote Sahara Desert, taking the geochemical samples and providing a first pass 53 element analysis in real-time to a geologist in Australia. Maybe we will also see a UAV quad that can drill to 1 m (3.3 ft) and can fly over remote unexplored regions, once again controlled from a central exploration headquarter.
BD: Do you think that there are any mineral exploration strategies or technologies that are under-employed, but could make a big difference to an exploration campaign if people used them more?
BN: Yes, Auger Geochemistry is completely underutilized across the world. The simplest and most effective geochemistry tool that gives an
BD: We hear all about the advances and benefits of technologies such as 3D modeling, geochemical analysis, and utilization of drones. Have you noted any negative impacts to effective exploration and mining as a result of these e.g. less people out kicking rocks?
BN: Yes, the virtual geologist is always an issue. As a geologist, you need a good mix of field and office. Do the generative work on the computer, but then go out and kick the rocks to prove your GIS info. It is impossible to tell which way it dips from a GIS.
BD: What is your opinion of the geological skillsets, experience, and knowledge of geologists today, especially those who are newly graduated?
BN: Young geologists I meet today are far more tech-savvy than geologists 25 years ago. For one, they can actually afford a computer at a young age, and smartphones are also becoming a daily geology tool.
If a young geologist can combine their tech skill with the rocks in the field and measuring structures, dip and azimuth, then they can become very good.
BD: Given your increasing management roles, are there any qualities that you think have helped you thrive in the industry?
BN: The more you see, the more you know. As a contractor and then a consultant, it is important to continue to learn. The concept of
continuing professional development (CPD) is one of the key programs of the Australian Institute of Geoscientists (AIG).
One thing I know is that the more I learn, the more I realize how little I know about our complex Earth. As a doctor, you can learn the nervous system and veins that pump the blood around. They are normally in the same place, but as a geologist, you will never completely know the veins that feed a deposit.
BD: Many of us have interfaced with less than savory individuals or experienced toxic workplaces. Has there been any incident or incidents that really disappointed you?
BN: Many, far too many to mention, and normally comes down to individuals. It is unfortunate that we are often forced to deal with high self-worth individuals that have been successful by pure luck in the form
of a timely investment. There is normally a certain amount of luck in a discovery, but why some absolute idiots are blessed with this luck is hard to understand and it is even harder to work for them, as they end up trying to run a company with absolutely no skills.
BD: I have to ask the obvious question – how has COVID-19 impacted you, your work and your business interests?
BN: Apart from the hardships and pain, for West Africa, Sahara have seen an improvement to our business that may not be apparent to most. Rather than a mining company sending a ‘consultant’ to West Africa to undertake a professional program, such as geotechnical logging of core, or an independent Geologist report, they have used us at Sahara and have come to understand that there is exceptional talent in our region. Sahara stopped using expats in West Africa five years ago.
West Africa has exceptional talent and I believe companies need to start putting more time into developing their national workforce rather than sending expats with less skills to do consulting work.
BD: Finally, any concluding comments or words of wisdom from an industry veteran?
BN: Always treat your young employees with respect and always help and support them to grow professionally, as one day they may well be your boss. C
more information Visit: www.saharanr.com
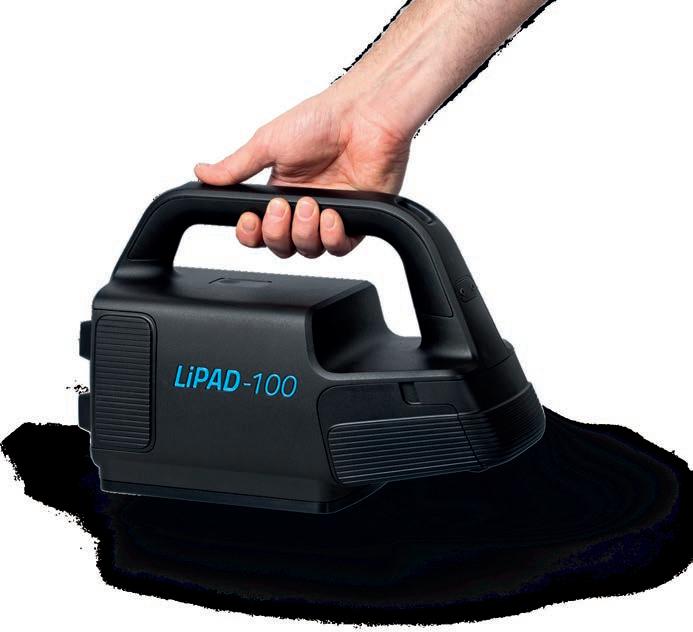
IT HAS NEVER BEEN EASIER TO CONTROL A LARGE NUMBER OF BOREHOLES

The innovative one man hand-held system works independent of environmental distraction and provides unsurpassed accuracy. You‘re looking for a fast, economical and reliable solution? LiPAD®-100 is the answer.
GYRO COMPASSING SYSTEM
SWICK GEN II UNDERGROUND MOBILE DRILL RIG
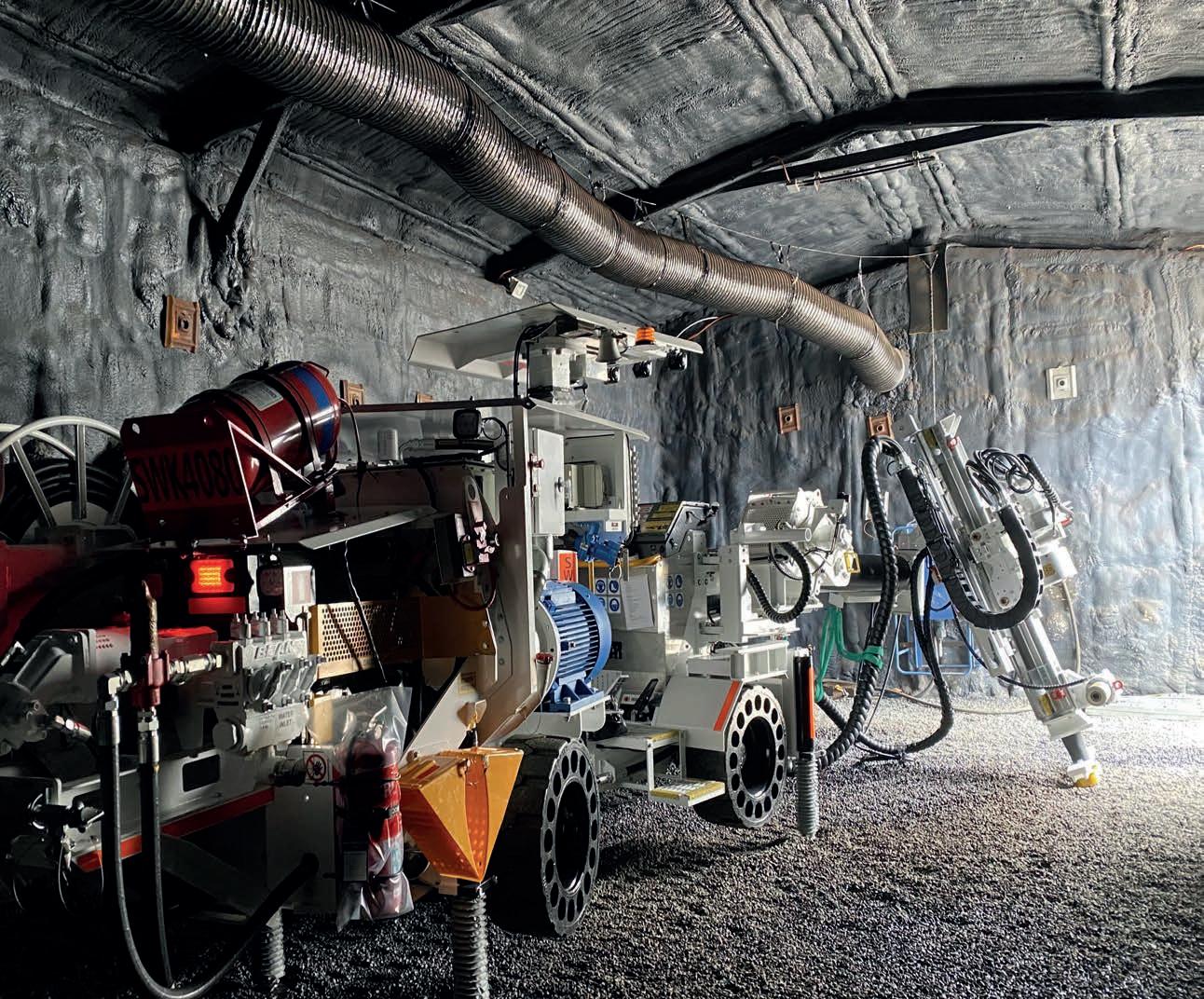
Key
•
•
•
•
•
•
Exploration in the land of gold
A brief review of observations and techniques
by Ahmed Atito, Exploration Geologist at Nubian Mining Company
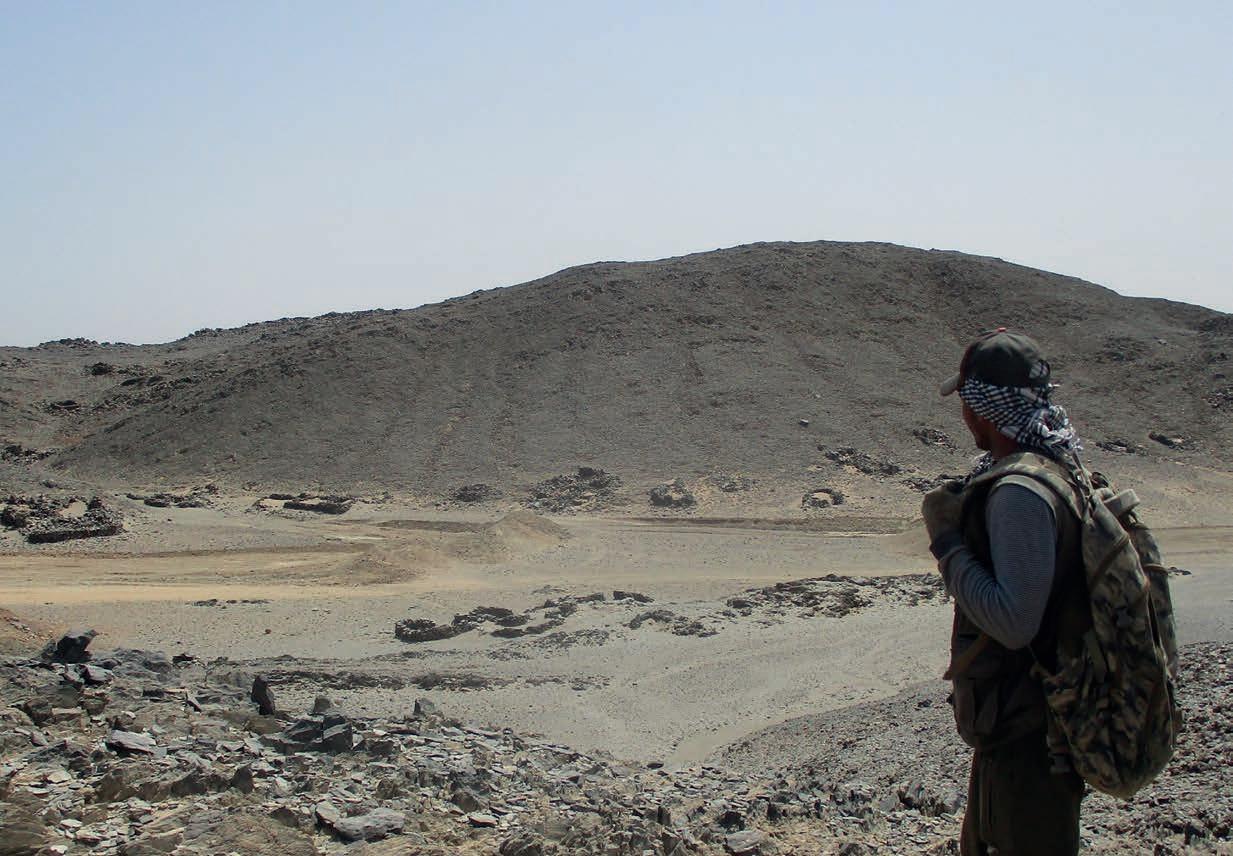
When someone asks, what is your job? You can say, ‘I’m a geologist’, but in my case, when you’re working in Egypt, you can answer, ‘I’m not just a geologist. I’m a time traveler’.
It is not easy to work in such an environment, to be honest. It is always boiling hot with temperatures easily reaching 50°C (122°F) in the summer. This is the case in Wadi Allaqi, one of the farthest places in Southern Egypt, with a granted license over a 600 km2 (231.66 mi2) concession for gold exploration. There is no network, and the nearest city is a 4-hour drive from the camp.
Prospecting for mineral deposits is a big adventure and the heat is up when you can take a journey back in time from the place that you are exploring. During one adventure, I saw prehistoric carvings of The Nubian Ibex on the wall of a small cave while collecting samples from the area. It is amazing to see a place that was inhabited by humans maybe thousands of years ago.
I also remember my first day on the project when I saw the remains of a big ancient town of Roadstone huts, and I was surprised by how many there were and how people could live there, in the very tough conditions of the desert. But, the answer was that these remote communities were searching for gold!
Ancient Egyptians began mining for gold in Predynastic times (c. 6000-3150 BCE) using different methods like open pits and underground excavation. They managed to build powerful kingdoms for centuries because of the unequaled riches of the Egyptian gold deposits. But this is not the end!
During field reconnaissance activities, we found many artisanal works by local miners who had come to the desert and walked the track taken
by the miners of old, while they were looking for gold. The quest for gold has become widespread in Egypt over the last decade. You can say it is a gold rush era and miners are targeting mineralized quartz veins not exceeding 15 cm (5.91 in) in thickness most of the time.
The artisans test the gold potential of the veins by taking small pieces of quartz. After that, they begin to crush it into very fine powder before panning it in a small plate until they can see gold. They start exploiting the quartz veins using electrical breaker hammers to make pits and trenches along the strike of the veins. These miners can dig deep pits that could reach 20 m (49.21 ft) with simple tools.
As an exploration geologist, my mission is to find ore deposits and to do that, I always rely on tools like GPS, compass, hand lens, hammer, notebook, safety goggles and sample bags. They are the main tools in the field. Sometimes I take 5 m (16.4 ft) and 30 m (98.43 ft) tapes to take survey of potentially prospect areas, just in case I find something interesting or if I want to take channel samples.
Regardless of the tools I mentioned above, I find that the most powerful tool utilized during fieldwork is the tablet. I believe that using the latest exploration techniques and novel technologies is the way to create and accomplish a successful exploration program. I use the tablet to import a wide variety of data that will help to manage my project rapidly, efficiently and accurately. In order to commence my reconnaissance exploration, I insert many types of data like satellite images, locations and descriptions of each sample and assay results, which is everything
I need. When I’m taking a sample, I can always refer to previous samples from the same area. I also use the tablet in field mapping to draw different features and record descriptions in the field in addition to taking photos which I can link with the location that they were tak en from. The data can be easily transferred to my laptop and I can manage it as I want.
My Wadi Allaqi project went through many phases since 2020, from collecting every bit of available data about the project area, in cluding research and old maps, target gen eration, geochemical sampling with QA/QC, reconnaissance and detailed mapping, data analysis and RC drilling.
When it comes to drilling, the detailed maps of every target area that contains valuable in formation, such as different rock units, min eralized zones and structural geological data like strike, dip and extension of every feature, such as veins and dykes, should be ready be fore the drilling start.
We had to drill perpendicular to the dip of the targeted quartz veins with alteration zones, so the team made a cross-section for every planned borehole before the com mencement of drilling. This was done to in fer the expected thickness of mineralization and the positions of the hanging-wall rocks
and foot-wall rocks to be intersected by ev
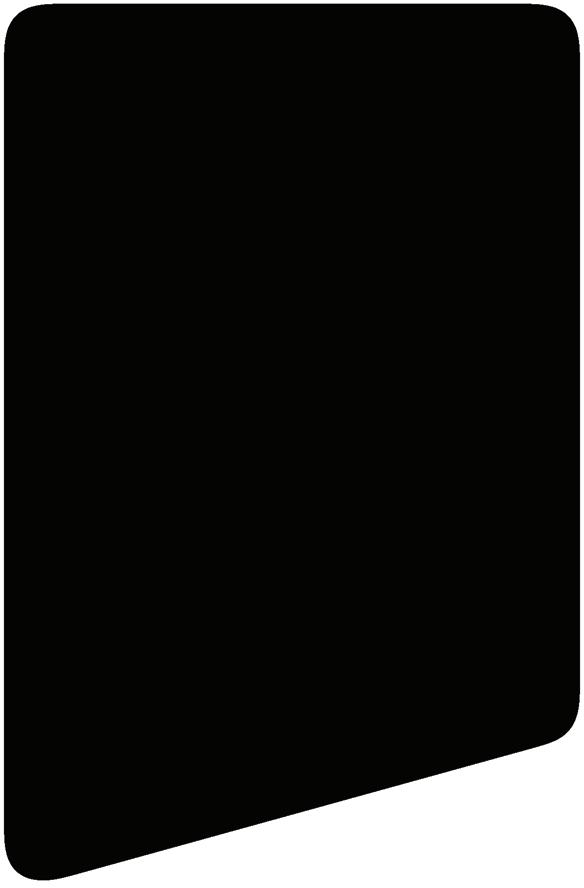


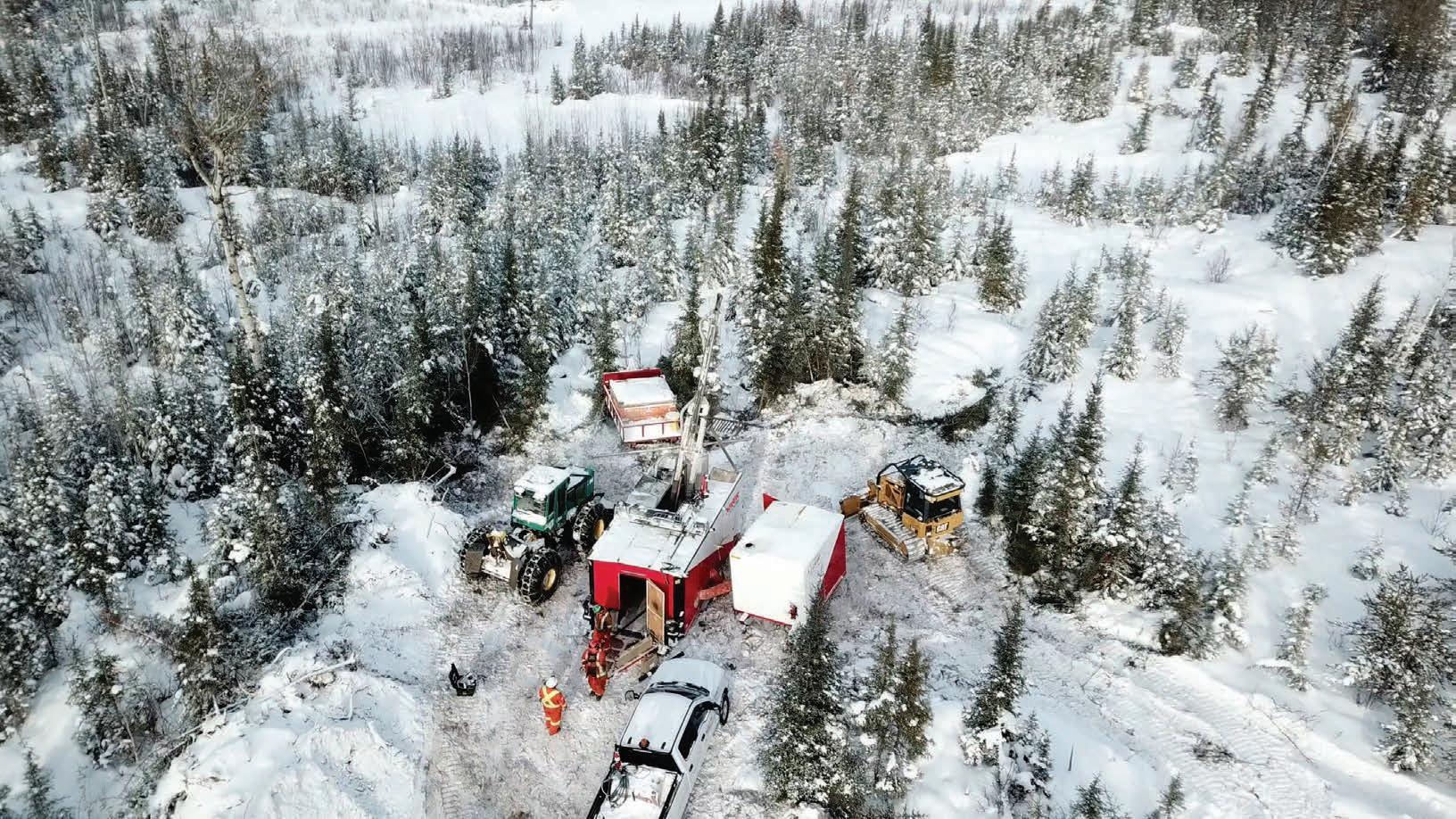
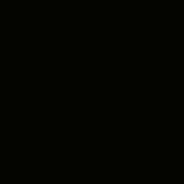
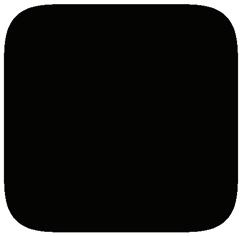
Major Drilling is one of the world’s largest drilling services companies primarily serving the mining industry, and maintains field operations and offices in Canada, the United States, Mexico, South America, Asia, Africa and Australia. info@majordrilling.com
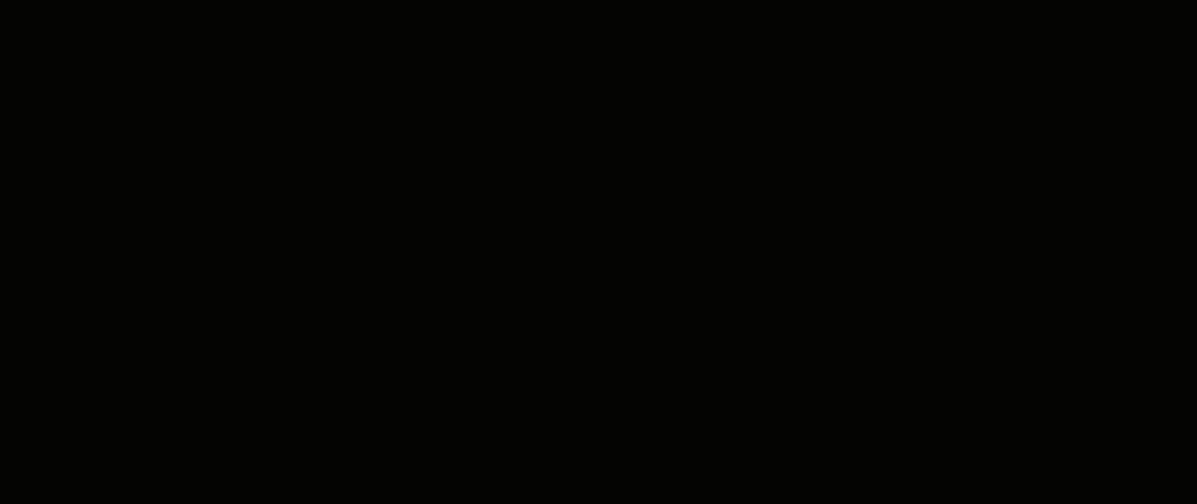
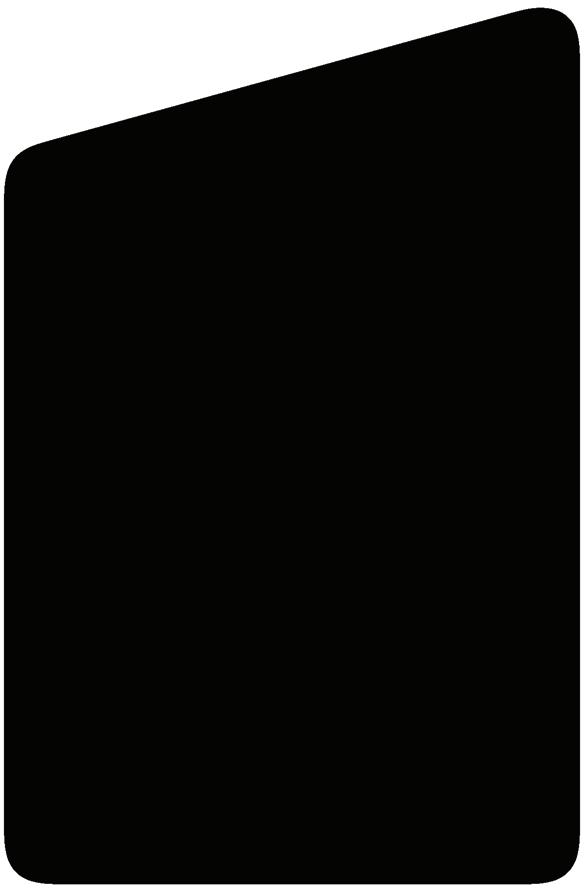
↑ Visible gold recovered from a 15 cm (≈ 6 in) vein in the artisanal pit
The use of mineral exploration drilling
to kickstart hydrogeology data collection for pre-feasibility mining studies and beyond
by Kym L Morton, CEO and Consulting Hydrogeologist at KLM Consulting Services Pty Ltd
Valuable groundwater information becomes available as soon as drilling starts, particularly during early mineral exploration campaigns. Often groundwater information is not collected because its value does not become evident until the exploration sites become under scrutiny for mine development. Drilling and logging of exploration coreholes most often only emphasize the characterization of an orebody, even neglecting to properly log the overburden (future waste-stripping). But capturing basic groundwater information when logging exploration coreholes will significantly reduce the future cost of initial hydrogeological studies and can be valuable at all feasibility and operational stages.
All holes drilled encounter water ranging from damp to undrillable. Drillers record a lot of data on water strikes, water levels and drilling fluid loss circulation records which give important information on zone(s) of high permeability. Useful information that can be collected by the site geologist include depth to water intersections, drilling fluid circulation losses, basic water chemistry and rest water levels. Each drill hole may be used to determine the depth of the water table whether aquifers are confined or not. Thus, some holes can be equipped for use as long-term water level monitoring, water chemistry information and a long-term record of water level movement prior to mining or preserved for use at a later stage. Such holes can reduce the cost of the design of water supply, dewatering and environmental studies.
Often a planned mine area has a very high density of drill holes used for exploration, but if these holes have not been used to measure water levels, additional new holes will have to be drilled at pre-feasibility stage creating additional cost. Figure 1 shows an example of drill hole density for a project in plan.
Best practice is to seal drill holes so that they cannot become conduits for flow into mine workings, but where possible the drill holes must be sealed using cemented-in vibrating wire
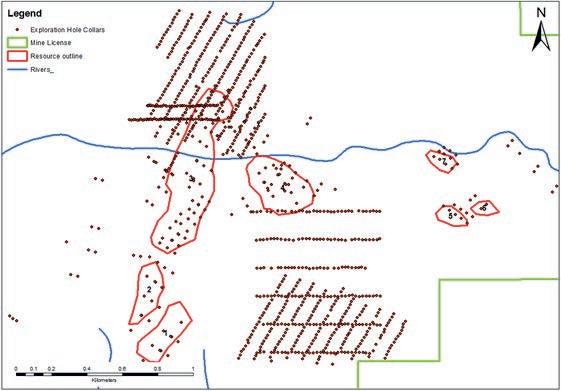
↑ Figure 1 - Typical exploration drilling density in plan and isometric
piezometers (VWP) to provide a 3D monitoring network of the groundwater prior to and during mining. This valuable information can be used in dewatering design, water supply, water balance reporting, environmental impact studies, closure design and post closure planning.
Drilling stage
It is very important to log the depth of weathering as this can be a significant aquifer or water susceptible zone when the mine is designed. Geotechnical engineers are also interested in the depth and types of weathering, which can be recorded on the standard drilling and geological logs.

During core drilling, the driller monitors a minimum of three gauges on a drill rig: water pressure, feed pressure and torque pressure. They are integrated onto the control panel. When the water table is encountered the driller notices that water pressure will start to increase. Also, when lowering the overshot to lift the core tube, there will be slack in the line - also the sign of a water table in front of the core bit. The website drilling.fordia.com/ essential-guide-to-drilling-parameters describes all the parameters monitored by a driller and their use in recording the water encountered in the formation.
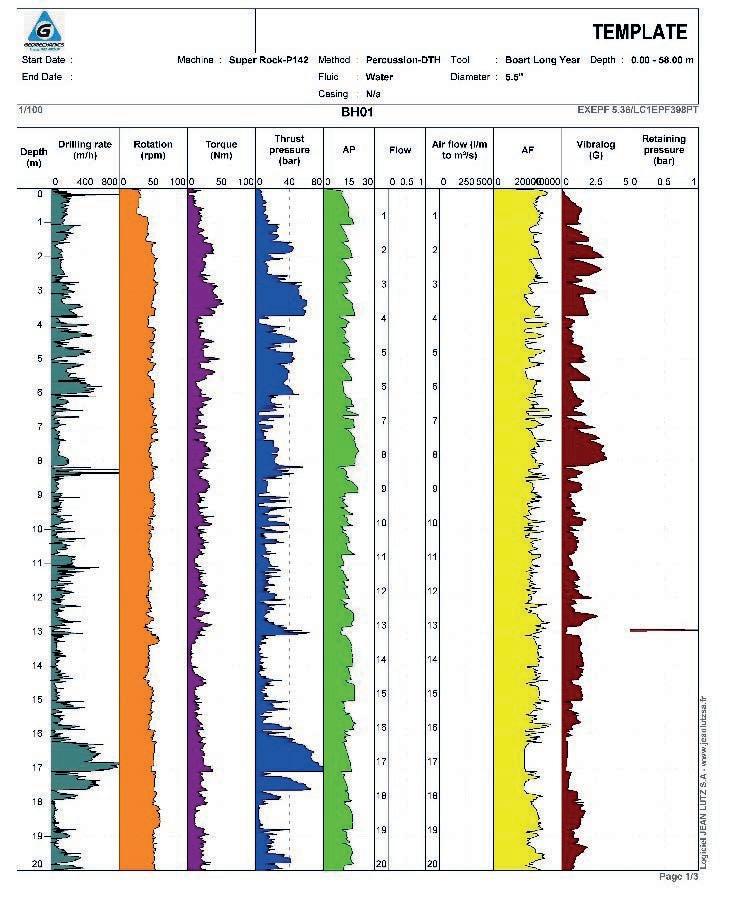
During drilling by any method, the depth of the first water strike should be recorded by the driller on daily drill logs and the drill sheets. Most drill sheets are primarily focused on details for invoicing the client, however it can be specified in the drilling contract that all water strikes, water losses and water levels must also be recorded and shared with the site geologist. Water levels should be reported in meters above mean sea level.
Water strikes and the subsequent measurement of water levels can indicate the presence of confined aquifers. When encountered in
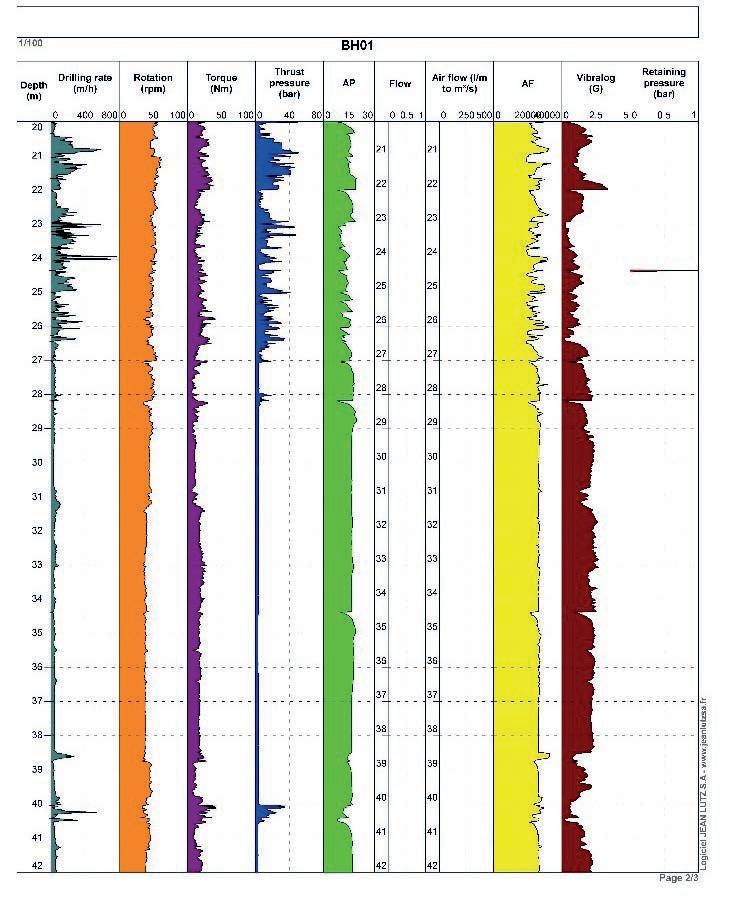
↑ Figure 2 - Water level intersection of an unconfined aquifer and of a confined aquifer
↑ Figure 3 - Example of automated drilling log (Geomechanics)
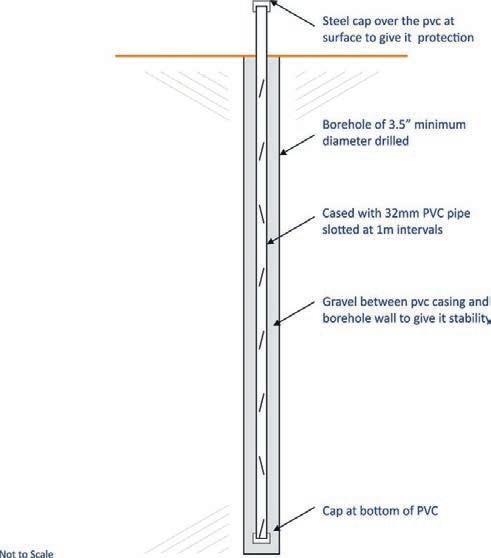
↑ Figure 4 - Simple open hole piezometer construction to create a monitoring borehole
confined aquifers, the resultant water level is the phreatic or pressure surface for the area, thus the measurements may enable understanding of the groundwater regime and possible impact on the proposed mine.
Figure 2 shows water level intersection of an unconfined aquifer and of a confined aquifer.
Air percussion and rotary drilling can be used to measure the yield of a water strike in liters per second (l/sec) or meters cubed per hour (m3/hr). Core drilling does not enable the measurement of yield, however, if a permeable zone (possibly an aquifer or water bearing fracture) is intercepted, the driller will note circulation losses and need to top up the corehole with water and drilling fluids. The more water and fluid used indicates greater permeability and provides information on the groundwater potential for pumping yields. Heinz, in his book Diamond drilling handbook (1989) describes all the types of formations that can be noted from circulation losses including:
• Sands and gravels
• Cavernous or vugular limestone and dolomite
• Naturally fractured/fissured rocks
• Induced fractures in solid rocks
A recommended daily drill log is available on the Coring Magazine website (use the QR code to access it).
During core drilling, the level of drilling fluid in the core hole represents the hydraulic pressure being maintained by the driller to keep the hole open, the bit lubricated and to optimize the efficiency of the drilling. If the drilling is stopped for any reason (e.g., a drillers’ break weekend or at the end of the hole), the fluid level will equilibrate to the actual rest groundwater level. Hole depth, water level and date/ time should be recorded. As the drill hole deepens, different aquifers with different groundwater pressures may be encountered. The level of fluid in the corehole should therefore be measured after any cessation of drilling over 24 hours. It is possible that artesian conditions, where
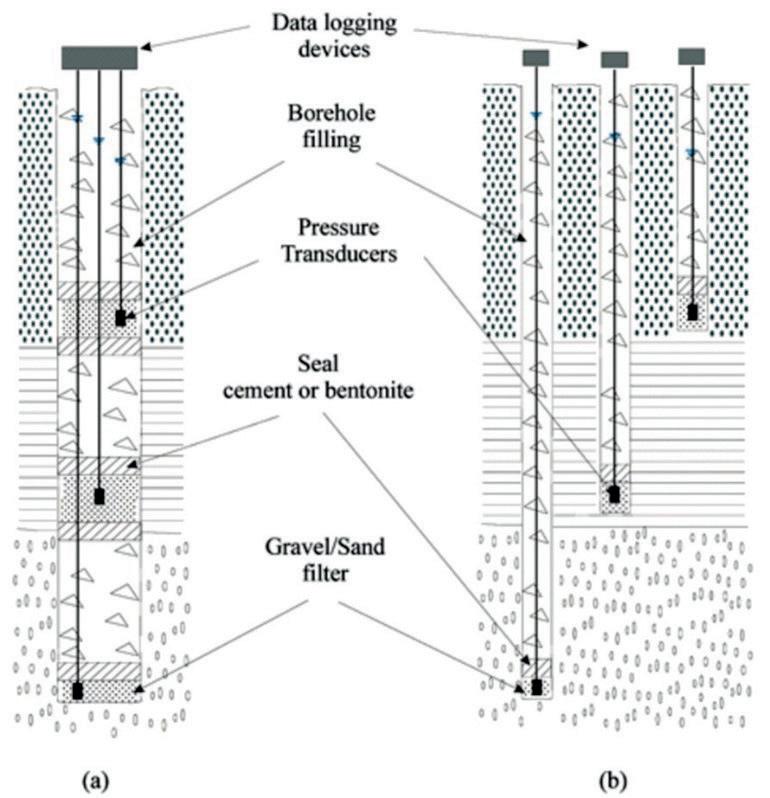
↑ Figure 5 - Multistage open hole piezometers in one or multiple boreholes
the fluid flows out of the corehole, may be encountered and these too should be noted.
During drilling, the pH and the electrical conductivity of the water encountered may change indicating interception of different aquifers. Some drilling companies, such as Geomechanics (Pty) Ltd (‘Geomechanics’), offer automated logs of drilling information. Figure 3 is an example of a log created by Geomechanics.
When plotted with the geological log the information can highlight more permeable zones.
Down the hole geophysics
On drill hole completion, exploration coreholes are often surveyed using down-the-hole (DTH) geophysical probes to record information on the ore body. The DTH logging probes can also provide information on the aquifers encountered in the corehole (Bouw and Morton, 1987). At the very least, the probes will record when water is entered and thus provide a record of the water level in the corehole on a specific date. Gamma-gamma and resistivity probes reveal porosity and permeability. Temperature and electrical conductivity probes indicate zones of water flow or different aquifers. Groundwater geophysical logging can be piggybacked on the mineral exploration DTH logging for very little additional cost.
Drill hole closure
Following drilling, the hole is often contaminated with mud, grease, and oil. This needs to be cleaned out to unclog the side walls and enable the hole to be used for monitoring either as a temporary (it will collapse if not kept open) open hole or as a permanent water level monitoring hole. A hole can be kept open using plastic conduit or more robust casing.
The conduit/casing requires slotting, a cap at the bottom and protection at surface. Figure 4 shows a recommended design:
When water strikes or multiple aquifers have been encountered during drilling then multi-stage open piezometers can be installed. Figure 5 shows a multi open hole piezometer constructed in one hole or using several holes.
If open pit mine or underground mine dewatering is anticipated, then sealed vibrating wire piezometers (VWP) are recommended as these measure groundwater pressure for known depths. A network of VWPs will give the distribution of pressure and plot flowlines in 3D providing valuable information for the interception of mine water and accurate dewatering design. Figure 6 shows the construction of a VWP type point piezometer and data logger sealed into the backfilled core hole using a tremie pipe.
Post exploration
Once exploration is complete, or at least its first phase, the project is evaluated at either pre-feasibility (PF) or feasibility levels to obtain funding for either further exploration to improve confidence or to design and open the mine. The initial monitoring network adds confidence to the studies needed for environmental permitting, water supply and mine dewatering designs. For very little expenditure, the monthly plotting of groundwater level fluctuations significantly increases the understanding of the groundwater regime and provide essential data for use in modeling and calibration of the water flow for the planned mine.
As more disciplines become involved drill holes can provide multiple uses. An example of a drilling sign-off log is available on the Coring Magazine website (QR code). The sign-off log is to ensure a new drillhole supports Geology, Geotechnical studies, Mine planning, Engineering and Environmental stakeholders. The form was developed at the De Beers Group for use prior to the drilling of all holes. The document shows the layout and length of the planned hole, its construction and planned use. The design is signed off by all before the hole is drilled.
As the mine project advances and new exploration holes are added, the monitoring network can be expanded, and data collection frequency can be increased. The more hydrological seasons that are covered by monitoring water levels improves confidence in numerical modeling, the initial water control, water supply and dewatering designs.
Data management
It is important that the groundwater information is filed in a dedicated database for use later in the project development. AcQuire® and QuickLog® are two of the geological logging programs that can store water level and water strike information. Other water data packages include water chemistry information.
The data needs to be easily accessible and attached to the dates measured for use in conceptual and numerical modeling.
Conclusions
Exploration drilling programs can be used, at very little extra cost, to collect information on groundwater. Drill holes can be used to create an initial water level monitoring network. The longer the monitoring record, the greater the confidence in the hydrological studies required for permission to mine.
Groundwater data can be obtained at all stages of drilling and provides valuable information for project water supply, mine dewatering design, water balance reporting, mine water management and environmental impact studies. C

↑ Figure 6 - Vibrating wire piezometer in a corehole backfilled with cement
Acknowledgements
• The assistance of Geomechanics Drilling, Grant Rijsmus (the Geogroup) is gratefully acknowledged.
• Dr Steve Westhead of AIMC and Dr Matthew Field of Mining Plus are thanked for their comments.
References
• Bouw, P C and MORTON K L, (1987). ‘The importance of geophysical logging of boreholes’. Borehole water Journal Vol 6. South Africa
• Heinz W F 1989 Diamond drilling handbook Johannesburg, South Africa ISBN 0-620-13785-1
For more information
Get in touch with the author at: kmorton@klmcs.co.za
Scan the QR Code to access the supplementary materials:

Six concepts to keep in mind when exploring structurally controlled mineralizations
by Luca Smeraglia, PhD, Independent Structural Geology Consultant and Structural Geologist at the
National Research Council of Italy
As a structural geologist born and raised in Italy, most consulting and research projects associated to structural geology are supplied by the oil and gas industry. With only a few economic geology courses taught in Italian universities and one active mineral exploration project in northern Italy, for a young geologist the mining industry recalls ancient mineral workings during the Roman Empire, the golden era of mines in Sardinia during the 70s and 80s, and the exotic far lands of Africa, Australia and Canada.
Therefore, as expected, I started my career working on projects focused on understanding structural controls exhibited by fault zones during hydrocarbon migration. However, I soon realized that the traces of paleofluid flow within faults, and broadly speaking within the Earth’s crust, are mineral veins. While wandering for structural mapping projects across multiple countries, veins associated with different geological structures immediately captured my interest. In the summer of 2019, a conversation with a structural geology consultant working in the mining industry opened my eyes. I understood that all the previous experience gained in mapping structurally controlled veins and geological structures can be converted and applied to mineral exploration with just a little reskilling.
Structural geology can be perceived as a dark science by some mineral explorers, especially those working dominantly with quantitative geochemical data. A structural sketch can be seen as a fancy paint on a dirty field book in a world of coding and data science. However, most mineral deposits are structurally controlled. A few basic concepts in structural geology can be simply learned by anyone after a small amount of training, and used in order to better focus on exploration, drilling, and resource exploitation. Here, I would like to share with you, using several field examples from different projects around the world, six concepts to keep in mind when exploring structurally controlled mineralization.
Be respectful of old structures
While working on a project in Germany, a single-layered calcite vein up to 10 m thick (32.81 ft) and 30 m high (98.43 ft) suddenly appeared within a limestone open pit. As you can see from Fig. 1a-b, the vein is oriented parallel to a well-developed joint set. Fluid pressure reopened pre-existing joints and precipitated a vein parallel to the main joint set. Keep in mind that old structures can be easily re-activated and mineralization precipitated. Therefore, when looking into a new geological terrane, always start to understand the orientation of old structures. They can be re-opened during evolving geological time if tectonic stresses are optimally oriented with respect to them.
Dilation, dilation, and dilation
Faults are not straight railways across an empty desert. They bend, curve, arrest, and interact with each other in order to find their way home, losing displacement at their tips. If two undulose surfaces move apart, a new space is created, and fluid can find a good conduit for movement. Dilation commonly occurs along the undulose trace of strike slip faults. However, prospective dilational sites can occur also along the dip of normal faults, such as shown in Fig. 1c from the Ionian
fold-and-thrust belt in Greece. Always look at fault bends to see if dilation occurred.
Competence matters
Stiff rocks can be fractured, and minerals can precipitate within fractures. Soft rocks can behave as a plastic material and muffle tectonic stresses as a pillow. In Central Oman, shale layers are alternated with stiff limestone beds within Triassic rocks (Fig. 1d). Limestones are veined, shales are not. This principle can be applied also within ancient volcano-sedimentary rocks within greenstone belts. They seem like hard rock, but, because volcanic-intrusive rocks are stiffer compared with the nearby schists, the former can be easily fractured and veined. Always look at the stiffness contrasts among your local stratigraphy. The millefeuille cake effect is served.
Linkage occurs not only on LinkedIn
Faults want to interact, but interaction is not always easy, like among humans. Therefore, within dilational sites (see point 2) veins and fractures can be easily created. Oman is a wonderful place, where you can go looking for small-scale linkage structures between strike-slip faults. Keep in mind that concepts I refer to as RR and LL rules, can be applied from regional- to outcrop-scale. When a set of right-stepping (R) and en-echelon #1 #2 #3 #4
AZIDRILL® N-BTK: New Direc�onal Core Barrel!
• Biggest direc�onal core in the world
• N-size drill / BTK-size core
• Easy to operate
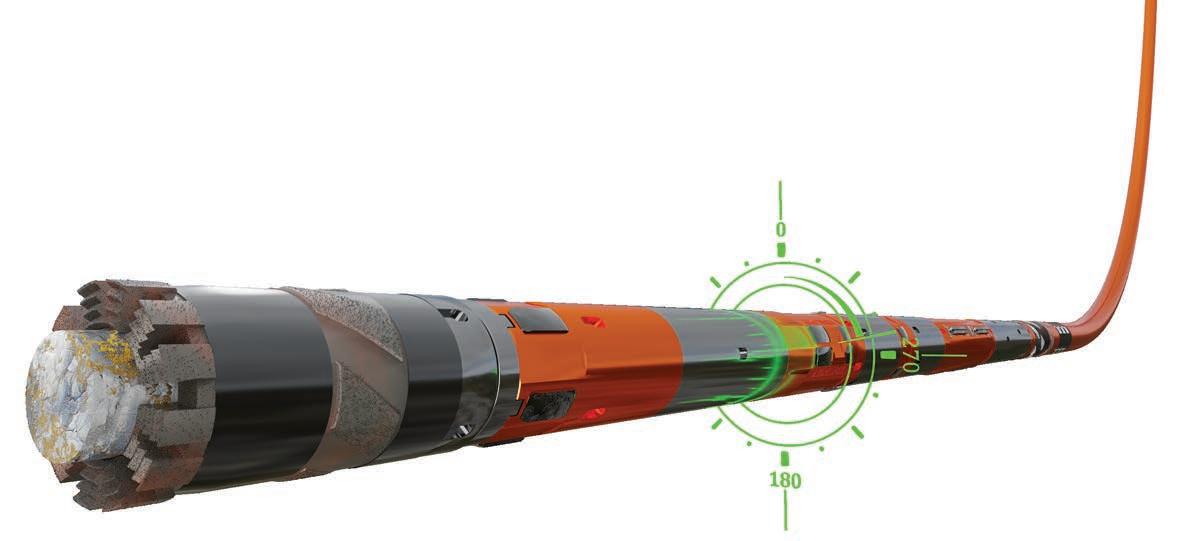
AZIDRILL® N-BTK
The new AZIDRILL N-BTK is a revolu�on in direc�onal core drilling, providing a core sample closer to the industry standars in conven�onal diamond drilling.
The AZIDRILL N-BTK comprise a range of innova�ons that makes direc�onal core drilling highly beneficial for a broad range of projects, by saving �me and money!
Advantages of the AZIDRILL N-BTK:
• More geological informa�on than prior DCB’s
• Increased drill-bit penetra�on due to less cu�ng surface
• Be�er core recovery and more competent core
• Similar penetra�on rate as conven�onal diamond drilling
• Easy to handle, only 30cm longer than a standard core barrel
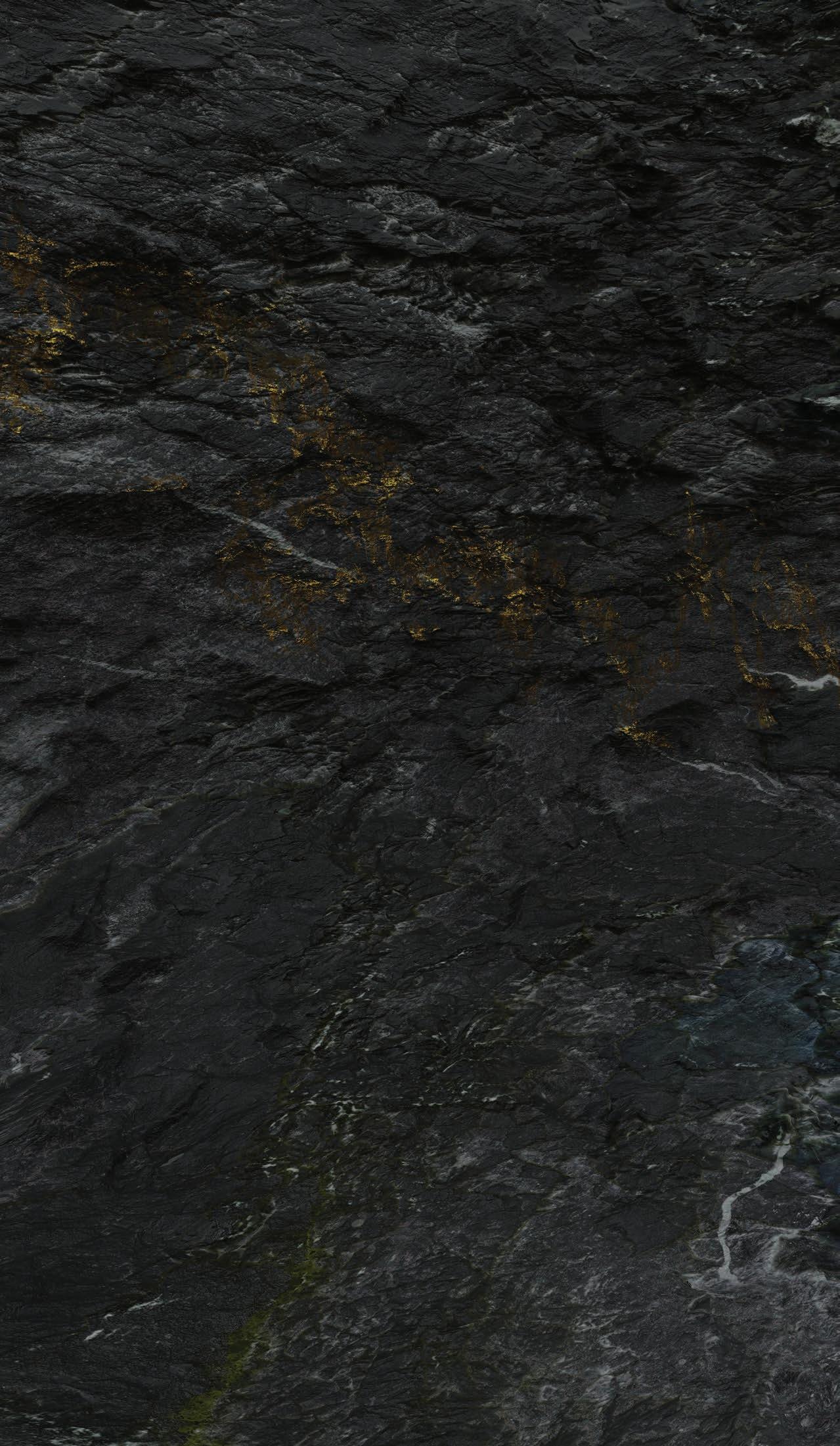
Advantages of Direc�onal Core Drilling:
• Fast and easy downhole steering and mul�-branch boreholes
• Hits any target with high accuracy and smooth curvature
• Faster penetra�on and no restric�on in rock hardness.
• No special pumps, rods or rigs needed on site
right-lateral (R) strike-slip faults occur, dilation is created within the fault overlap zone (Fig. 2a). The same applies when a set of left-stepping (L) and en-echelon left-lateral (L) strike-slip faults occur (Fig. 2b). If you see in map view right-stepping and right-lateral strike slip faults (RR) and/or left-stepping and left-lateral (LL) strike-slip faults, have a look in the area of fault overlap, because you could find some interesting veins and/or dilation sites with breccias.
Do not undervalue the small structures
We all want that thick and long high-grade vein. Unfortunately, main faults do not always carry thick mineralization. Luckily, main faults are always associated with a cohort of minor and sometimes undervalued structures, such as en-echelon veins oriented at a low angle with respect to a principal thrust from Omani Mountains (Fig. 2c). When drilling across the main shear zone, it is possible to miss the minor mineralized structures that are subparallel to the drill holes. Always have a look around the major structures to find the small ones with different orientations.
Bending and stretching
Saddle reefs within fold hinges are widely known for hosting ore shoots along the fold axis. However, it is always worth to emphasize this concept. This is also valid for synclines as shown in Fig. 2, where the hinge of an open syncline from the Ionian fold-and-thrust belt of Greece is intensely fractured and mineralized by calcite. While anticline hinges are the perfect example of saddle reef structures, do not undervalue gentle syncline hinges and try to test them.
All the previous examples are certainly an incomplete list of structurally-controlled mineralization. However, these simple concepts can be easily learned by everyone, tested in the field, and also while reviewing drill cores, using new eyes and perspective. Structural geology trains you to think in three and even in four dimensions if you are keen to collect data, especially if you resolve the cross-cutting relationships between different vein generations. But this might be the topic for another piece. Times are now exciting for structural geologists wishing to pursue a career into mineral exploration and who want to keep working as field geologists. C
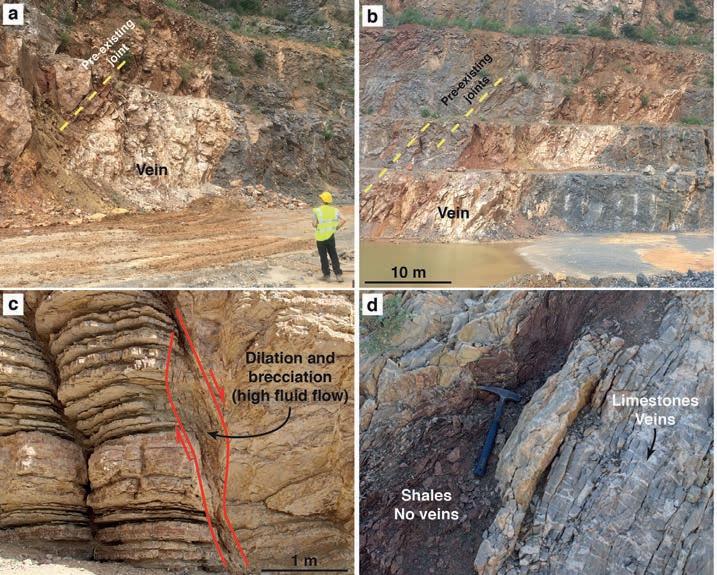

Figure 2 - (a) Dilational jog between two right stepping faults with apparent strike-slip dextral movement
(b) Dilational jog between two left stepping faults with apparent strike-slip sinistral movement (Oman). (c) Minor en-echelon veins oriented at low angle with respect to a principal thrust (Oman). (d) Hinge of an open syncline intensely fractured and mineralized by calcite (Greece).
↑ Figure 1 - (a,b) Thick calcite vein oriented parallel to the main fracture set (Germany). (c) Dilational site along the dip of a normal fault (Greece). (d) Veins in competent limestones (Oman).
↑
(Oman).
Safety is the challenge, CX Line is the answer. Compact design, hands-free rod handling system for fully automated and remote controlled operations: the future of exploration drilling is already here. Are you ready to join in?
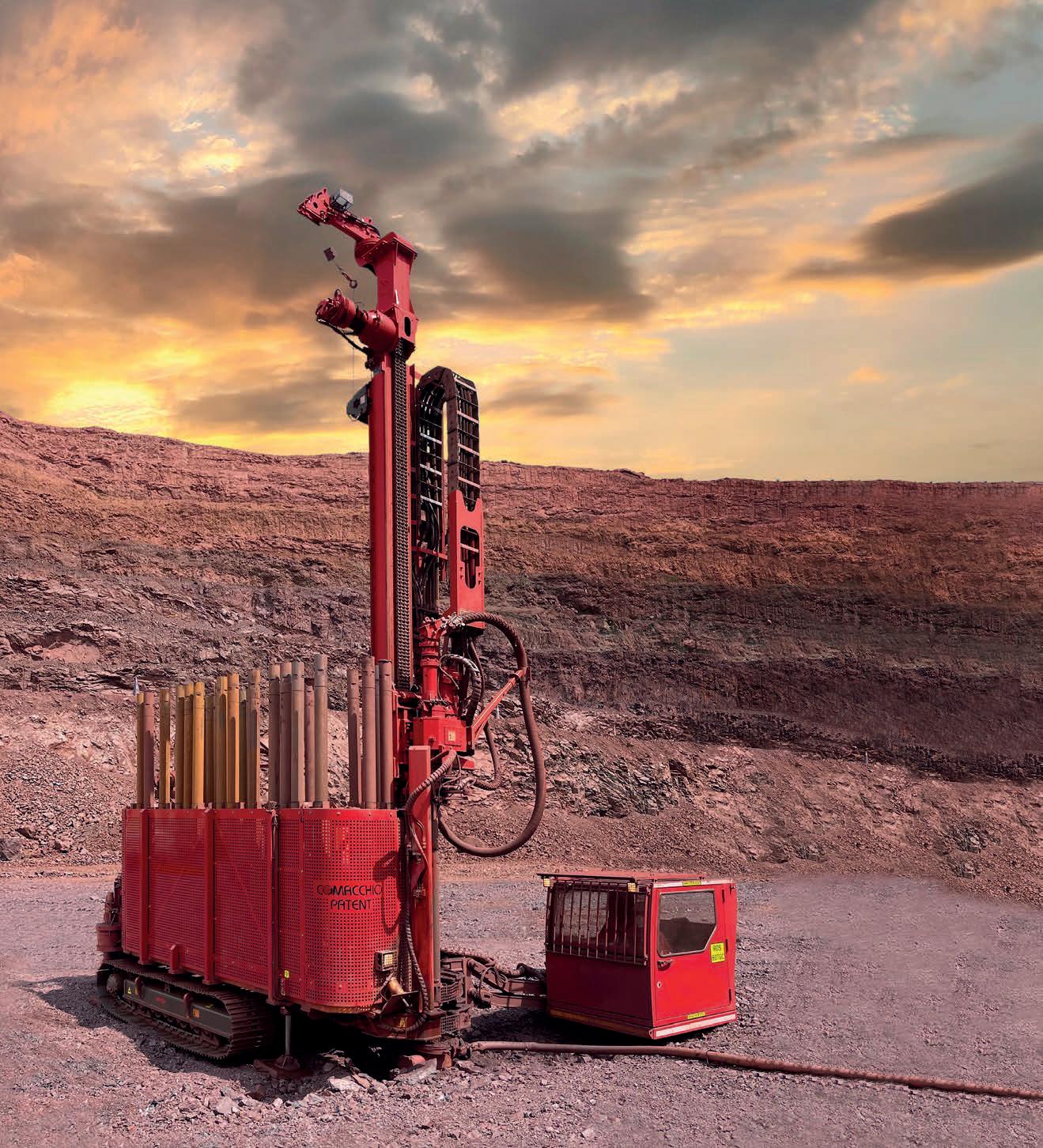
Live the experience on: comacchio.com
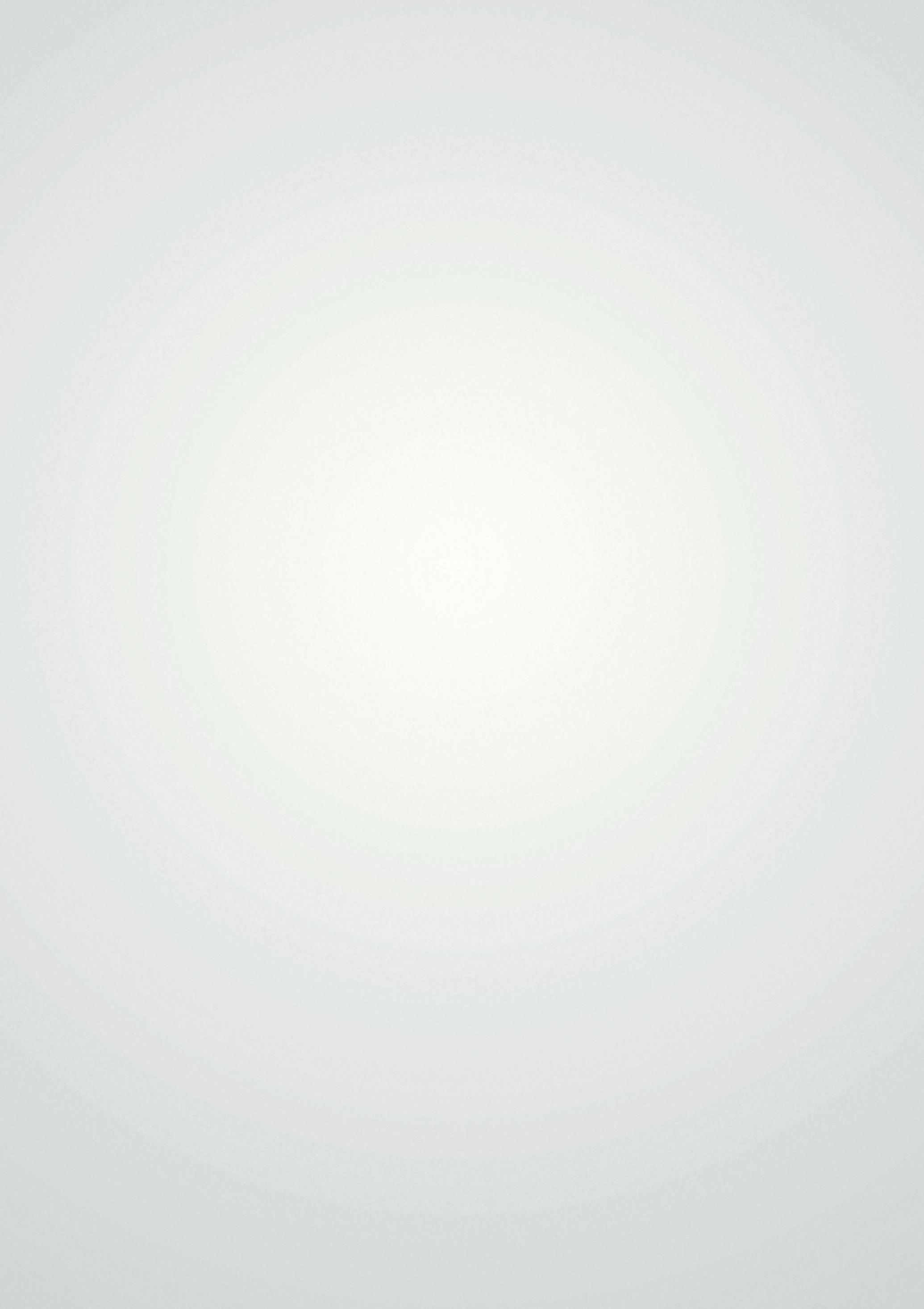
PDAC 2022
The Super Bowl of the mineral exploration and mining world will be hybrid
by PDAC’s Marketing Team
The annual PDAC 2022 Convention— the world’s premier mineral exploration and mining event—will be held in person and online for the first time in its 90-year history. It will take place from June 13-15 in person and June 28-29 online. The PDAC Convention in downtown Toronto is widely considered the ‘Super Bowl’ of the mineral exploration and mining community. The PDAC Convention is unmatched in its ability to connect participants to the international mining and exploration community, and keep them informed of the latest trends and technologies shaping the sector through extensive programming. Over the past decade alone, this must-attend event has brought together upwards of 30 000 attendees from over 130+ countries annually to network, conduct business, and learn.
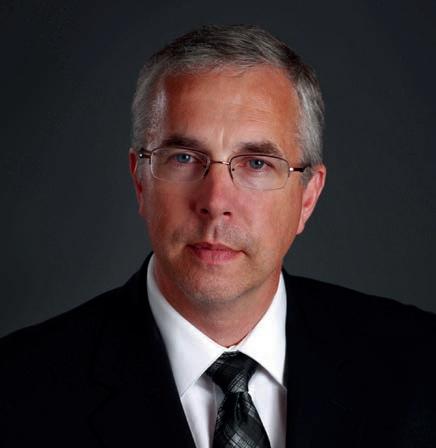
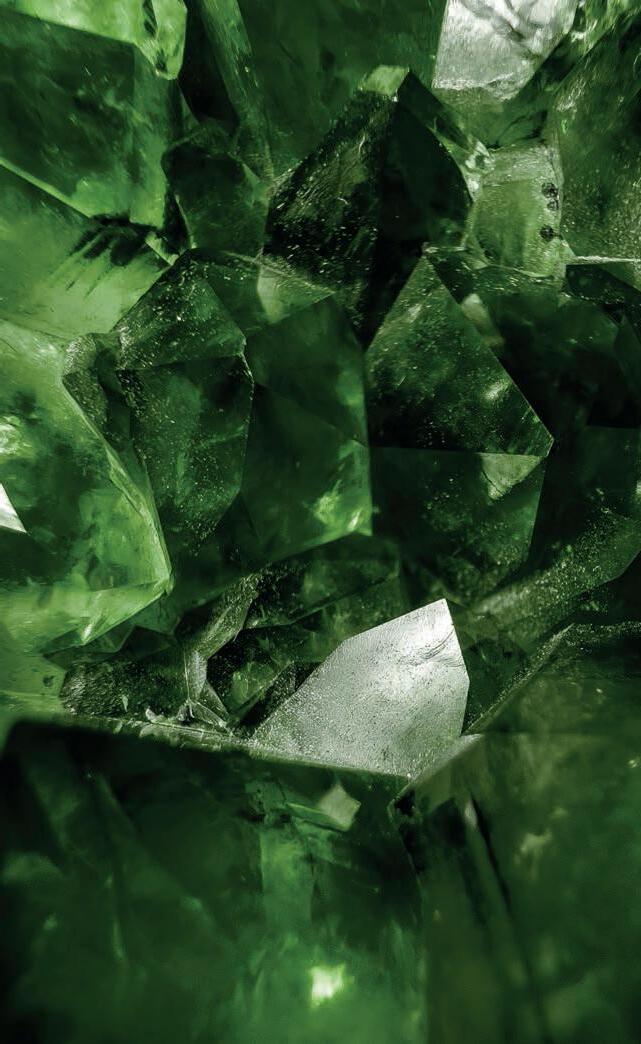
Welcome message from PDAC President Alex Christopher
While our passion for mineral exploration and mining has not changed, some things in the world most certainly have—including the dates and appearance of the PDAC Convention.
The dedicated team at PDAC has flexed its muscles yet again. By listening to feedback from stakeholders and embracing innovation, the PDAC 2022 Convention will be offered in person in Toronto and online. This is the first time that a hybrid event is being offered at PDAC. I am proud to be President of the Association during this time of unprecedented global challenge and am excited to deliver a successful event to mark this important milestone anniversary.
Over the past year, the international spotlight continued to shine on our sector. The role of mining in the transition to a low carbon future remains dominant. Canada is uniquely positioned in this conversation as a leader in exploration and mining practices, as well its ability to deliver many of the minerals and metals required to make the shift.
The COVID-19 pandemic showcased once more the importance of precious metals as gold prices soared to record heights. It also demonstrated the significant social and economic impacts that exploration and mining can have on communities around the world, where we have seen the industry provide much needed support where it may otherwise not exist.
Essential Programming and Short Courses at PDAC 2022 reflect these and other trends taking shape throughout the sector. The expanded Keynote Program provides a platform for experts to present on commodities, the mineral outlook, innovation and new discoveries. The in-person convention also marks the return of exciting networking opportunities that have kept attendees returning to Toronto for decades.
For those joining in person, health, safety and wellness remain our top priority and we will continue following Canadian and local government directives. We understand that these requirements may evolve and will ensure attendees are kept informed of new developments.
No matter how you connect, in person or online, the PDAC 2022 Convention is where the world’s mineral industry meets. I look forward to welcoming you there (in a much warmer month).
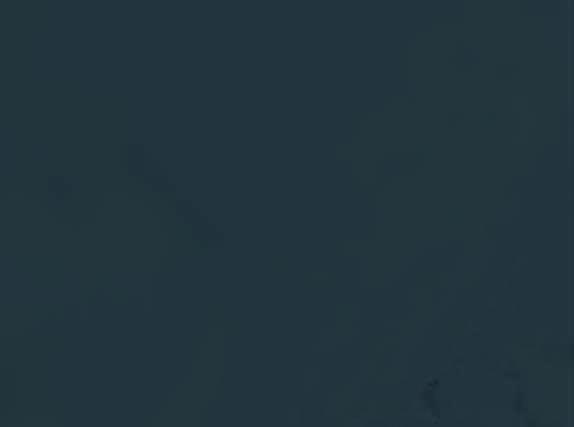
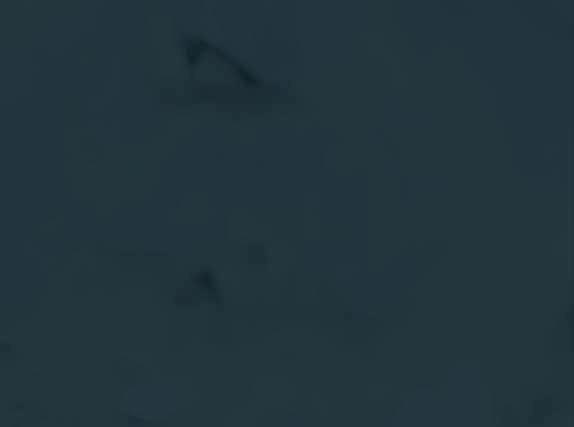
REGISTER AT pdac.ca/convention #PDAC2022
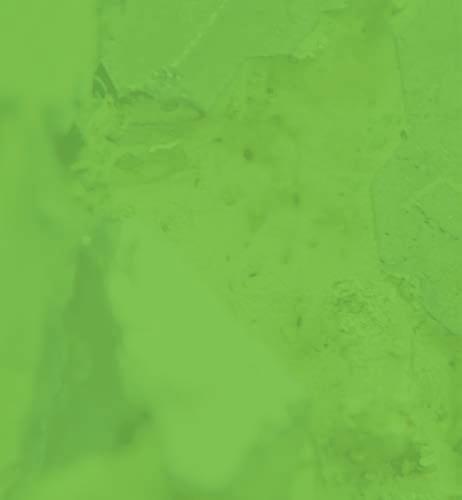
JUNE 13-15 IN PERSON TORONTO, CANADA
JUNE 28-29 ONLINE ANYWHERE
Access top-quality programming
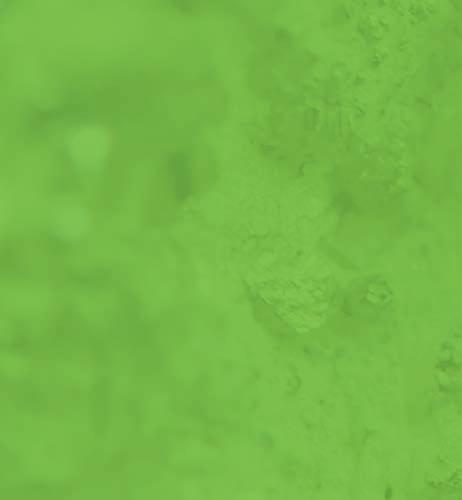
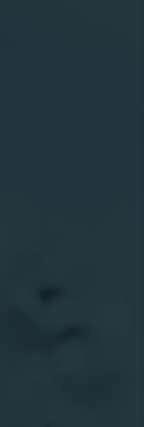
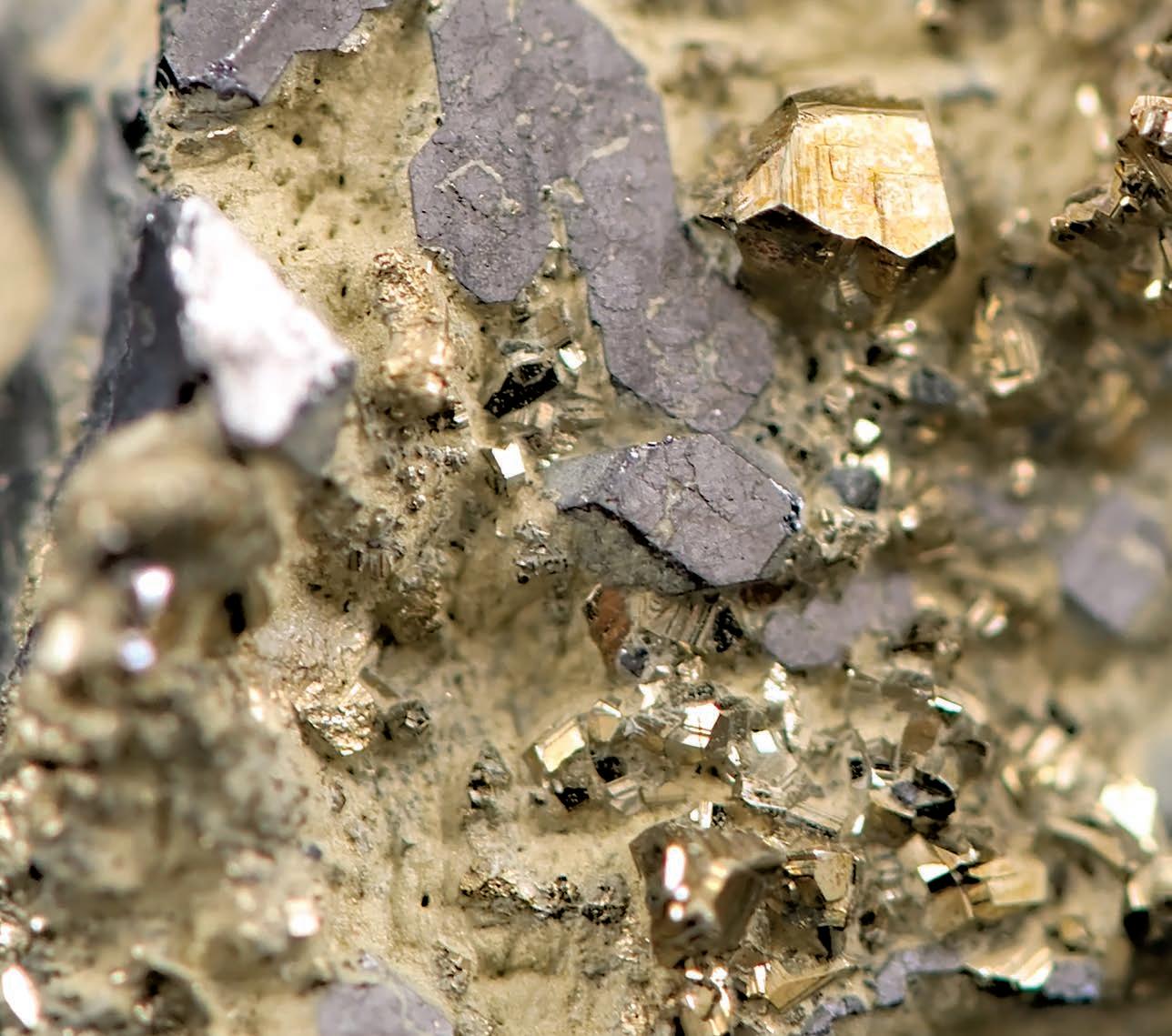
Reconnect with a diverse community of exhibitors
Gain insight from industry experts Valuable networking opportunities
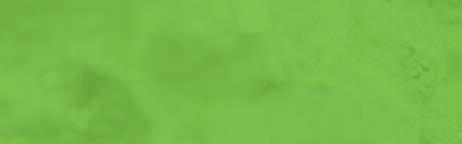
Drilling Services
Drilling Contractors (A-Z): Diamond Drilling, Reverse Circulation, AirCore
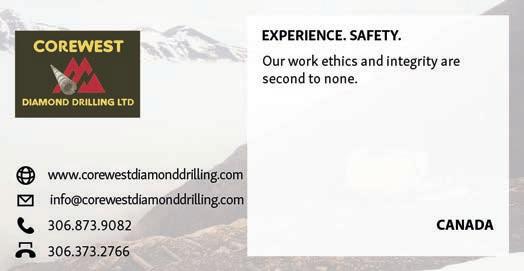
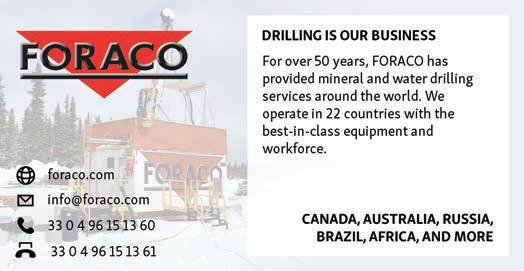
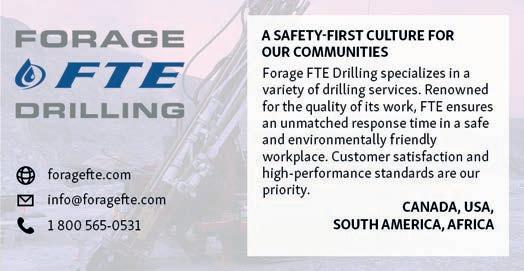
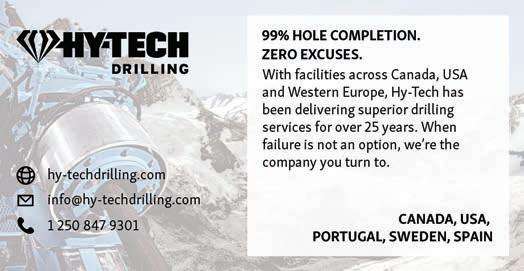
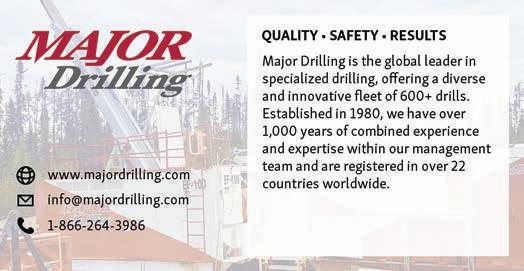
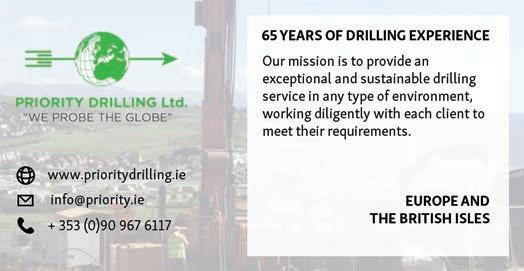

BRYSON DRILLING
Phone 306-323-2202 Fax 306-323-2203 info@brysondrilling.ca www.brysondrilling.ca Canada
DDH1 DRILLING
Phone +61 08 9435 1700 admin@ddh1.com.au www.ddh1.com.au Australia
DIAFOR Phone (819) 860-3957 info@diafor.ca www.diafor.ca Canada
GÜNZEL DRILLING CC
Phone + 264 81 322 89 28 info@guenzeldrilling.com www.guenzeldrilling.com Namibia
KATI OY Phone 0207430660 info@oykatiab.com www.oykatiab.com Finland
MITCHELL SERVICES
Phone
Fax +61 7 3722 7256 info@mitchellservices.com.au www.mitchellservices.com.au Australia
Directional Drilling (A-Z)
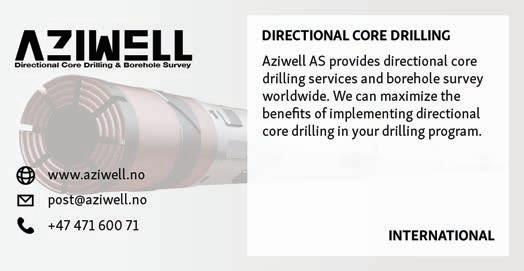
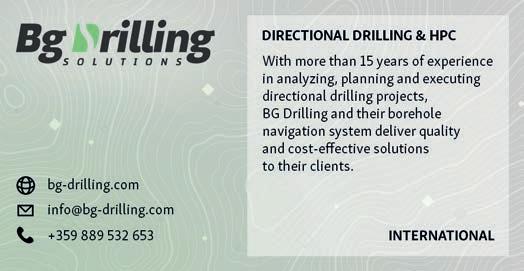
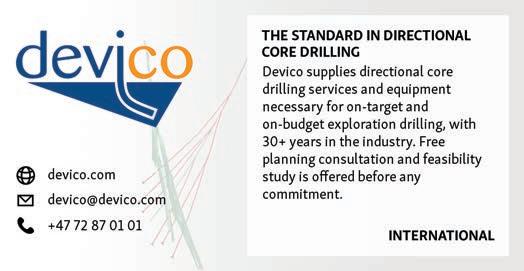
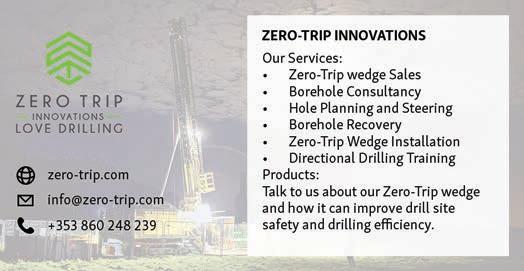
Surveying & Geophysics (A-Z)
CORE TECH
Phone (511) 255-5701
ventas@coretech.com.pe
www.coretech.com.pe
Peru
DIGITAL SURVEYING
Phone +27 18 788 6349
sales@digitalsurveying.co.za www.digitalsurveying.com.za
Africa
TRUST SOLUÇÕES
GEOLÓGICAS
Phone +55 62 992720023
contato@trustsg.com.br
Brazil
Drilling Equipment & Accessories
Drill Rigs & Accessories (A-Z)
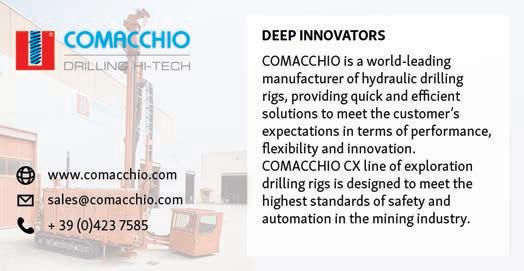
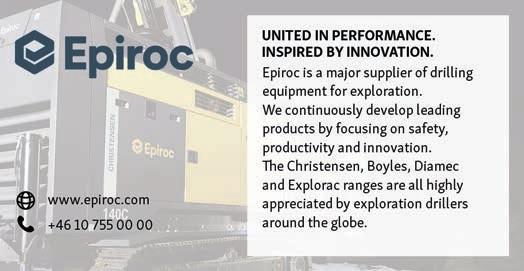

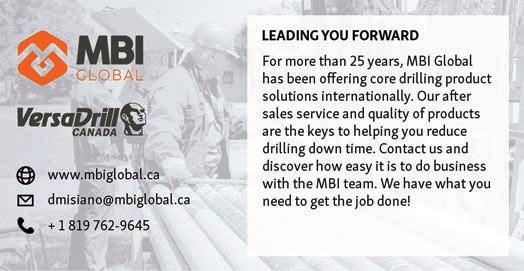
Drill Rigs & Accessories (A-Z)
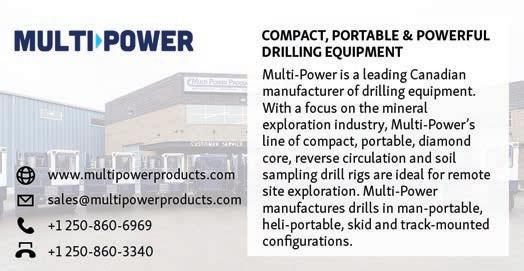
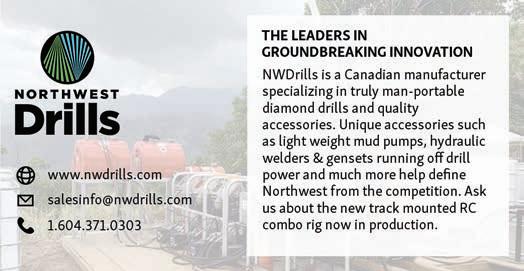
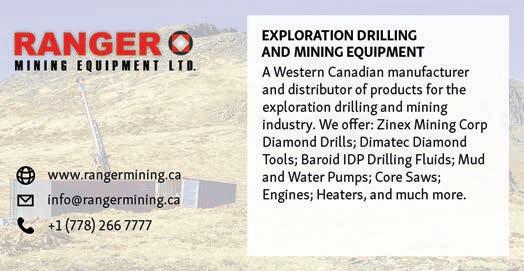
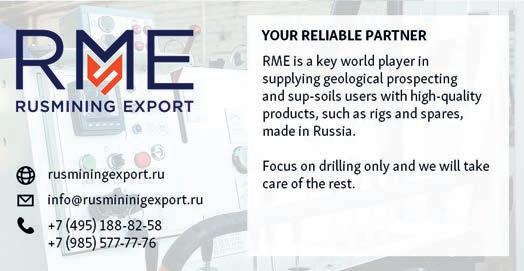
ATELIER VAL-D’OR
Phone (819) 824-3676
Fax (819) 824-2891
info@avddrills.com www.avddrills.com
BARKOM
Phone 90-312 385 60 50 Fax 90-312 385 35 75 info@barkomas.com www.barkomas.com
Drill Rigs & Accessories (A-Z)

Drill Rig Parts (A-Z)
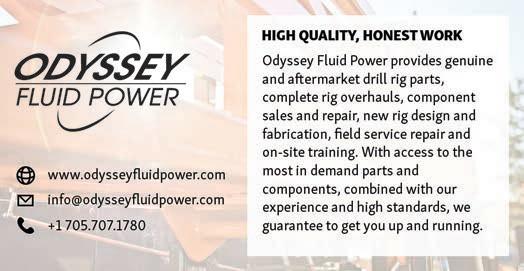
PROLENC
Phone (250) 563-8899 Fax (250) 563-6704 khodgins@prolenc.com www.prolenc.com
RC Equipment (A-Z)
BOART LONGYEAR
Phone 1-801-972-6430 Fax 1-801-977-3374 www.boartlongyear.com
FORDIA POWERED BY EPIROC
Phone 514-336-9211 Fax 514-745-4125 info@fordia.com www.fordia.com
Specialized Machine Works (A-Z)
NORTH BAY MACHINING CENTRE
Phone (705) 472-9416 Fax (705) 472-2927 luc@nbmc.ca www.nbmc.ca
DISCOVERY DRILL
MANUFACTURER
Phone 1-506-542-9708 Fax 1-506-542-9709 info@discoverydrills.com www.discoverydrills.com
Core Orientation (A-Z)
COREFINDER
Phone +55 62 992720023
contato@corefinder.com.br www.corefinder.com.br
PROLENC
Phone (250) 563-8899 Fax (250) 563-6704 khodgins@prolenc.com www.prolenc.com
DEVICO AS Phone +47 72870101 devico@devico.com www.devico.com
REFLEX INSTRUMENTS
Phone 61 8 9445 4020 Fax 61 8 9445 4040 reflex@imdexlimited.com www.reflexnow.com
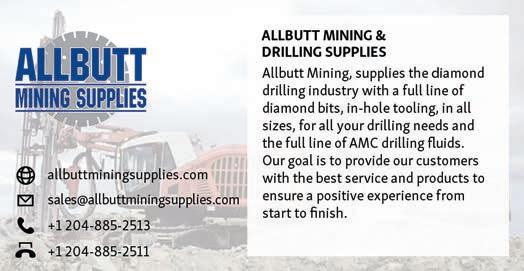
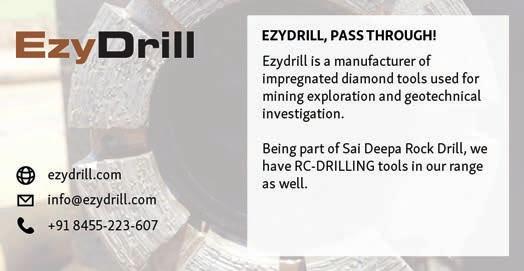
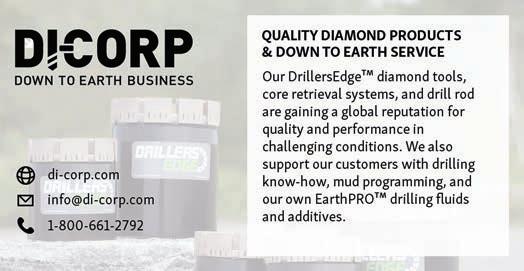
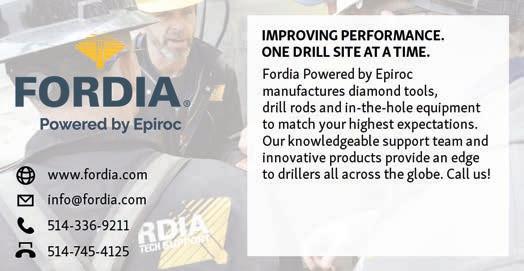

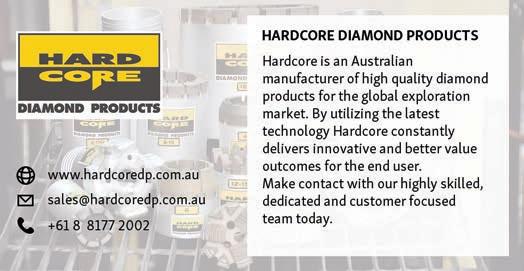
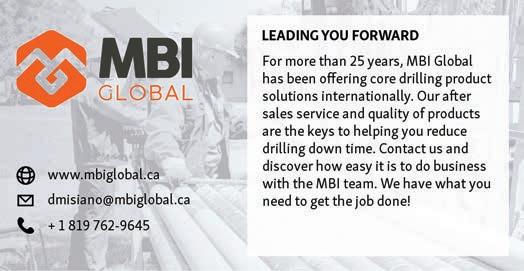
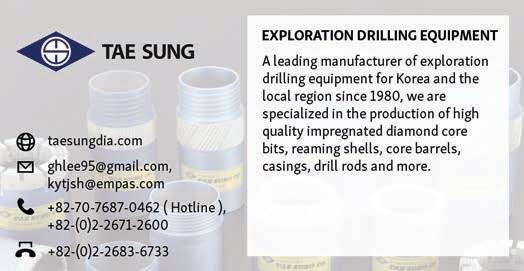
Diamond Products (A-Z)
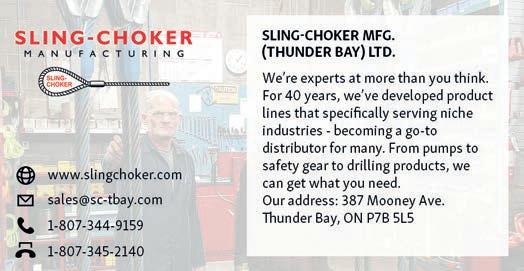
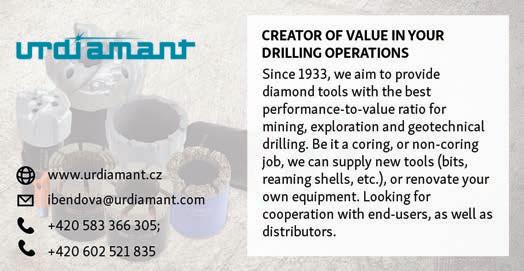
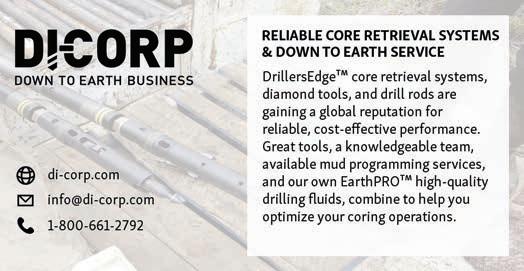
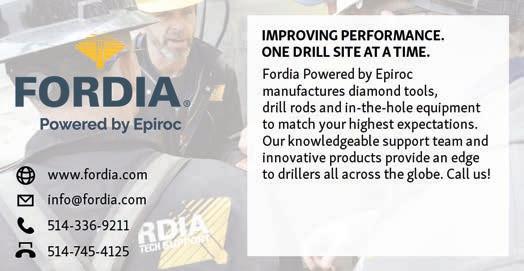
BOART LONGYEAR
Phone 1-801-972-6430
Fax 1-801-977-3374
www.boartlongyear.com
DRILLING HQ
Phone 1 (208) 690-3111
info@DrillingHQ.com www.drillinghq.com
Core Barrels (A-Z)
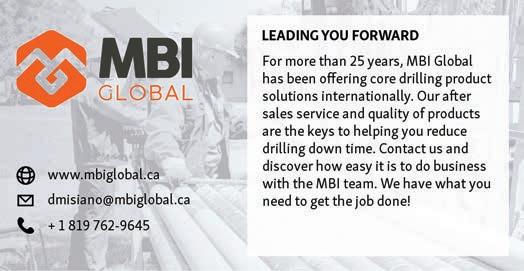


HOLE PRODUCTS
Phone 909-939-2581
Fax 909-891-0434 www.holeproducts.com
HARGRAND DRILLING
TOOLS
Phone 86-010-61599828
Fax 86-010-61599828
whp@baoqizt.com www.hargrand.com
SINOCOREDRILL
Phone 86-510-82723272
Fax 86-510-82752846
sales@sinocoredrill.com www.sinocoredrill.com
Drill Rods & Casings
TERRA TEAM OY
Phone 358-9-849-4030
info@terra-team.fi www.terra-team.fi/en
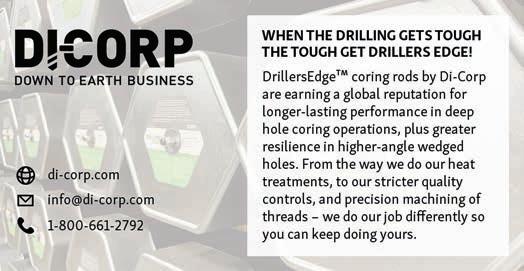
Core Barrels (A-Z)
Drill Rods & Casings
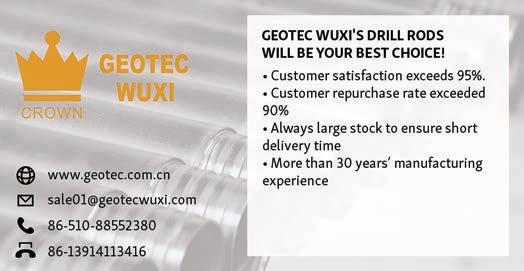

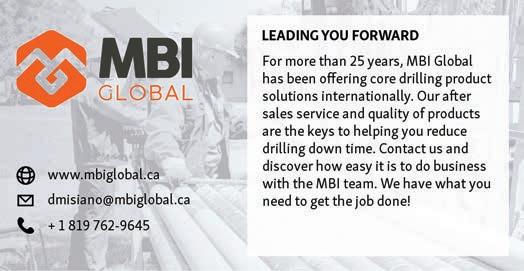

BARKOM
Phone 90-312 385 60 50 Fax 90-312 385 35 75 info@barkomas.com www.barkomas.com
CORE TECH Phone (511) 255-5701 ventas@coretech.com.pe www.coretech.com.pe
Wedges (A-Z)

FORDIA POWERED BY EPIROC Phone 514-336-9211 Fax 514-745-4125 info@fordia.com www.fordia.com
REFLEX Phone 1-705-235-2169 Fax 1-705-235-2165 reflex@imdexlimited.com www.reflexnow.com
Water Treatment System (A-Z)
SONDA PARTS
Phone 55 – (31) 3391 3810 Fax 55 – (31) 3391 3810 comercial@sondaparts.com.br www.sondaparts.com.br/
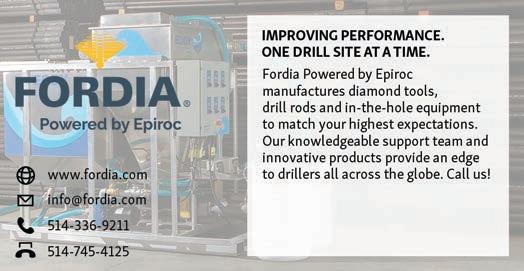
FORDIA POWERED BY EPIROC Phone 514-336-9211 Fax 514-745-4125 info@fordia.com www.fordia.com

Survey Tools (A-Z)
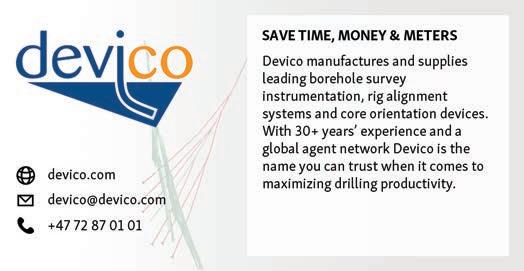
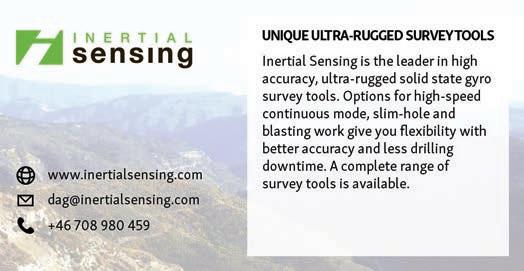
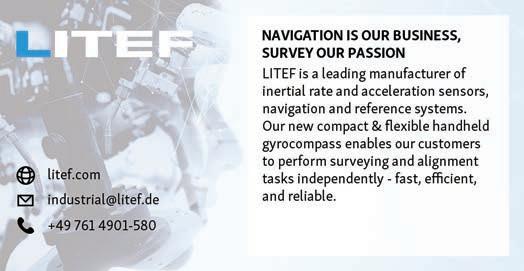
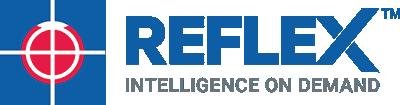
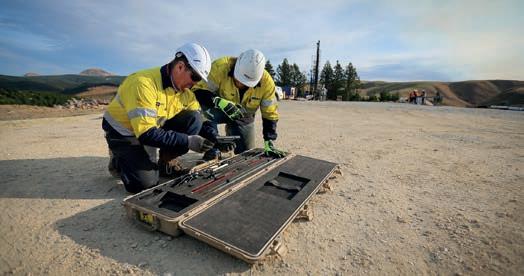
www.reflexnow.com reflex@imdexlimited.com 1-705-235-2169
REFLEX - A LEADING IMDEX BRAND
REFLEX forms part of Imdex Limited, a leading Mining-Tech company. Our unique end-to-end solutions for the mining value chain integrate IMDEX’s leading AMC and REFLEX brands. Market leading REFLEX technologies enable drilling contractors and resource companies to drill faster and smarter, obtain accurate subsurface data and receive real-time information for critical decision making.
Survey Tools (A-Z)


Miscellaneous
Fluids (A-Z)
AMC Phone 1-705-235-2169 www.amcmud.com
DI-CORP Phone +1 (705) 472-7700 info@di-corp.com www.di-corp.com
MUDEX Phone +61 (8) 9390 4620 info@mudex.com.au www.mudex.com.au
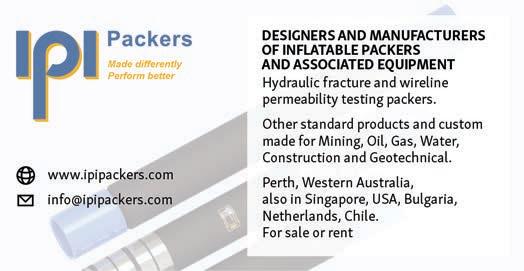
CORE CASE Phone +55 51 3012 6531 info@corecase.com corecase.com
DYNAMICS G-EX Phone +61 7 54826649 sales@dynamicsgex.com.au www.dynamicsgex.com.au
Drilling
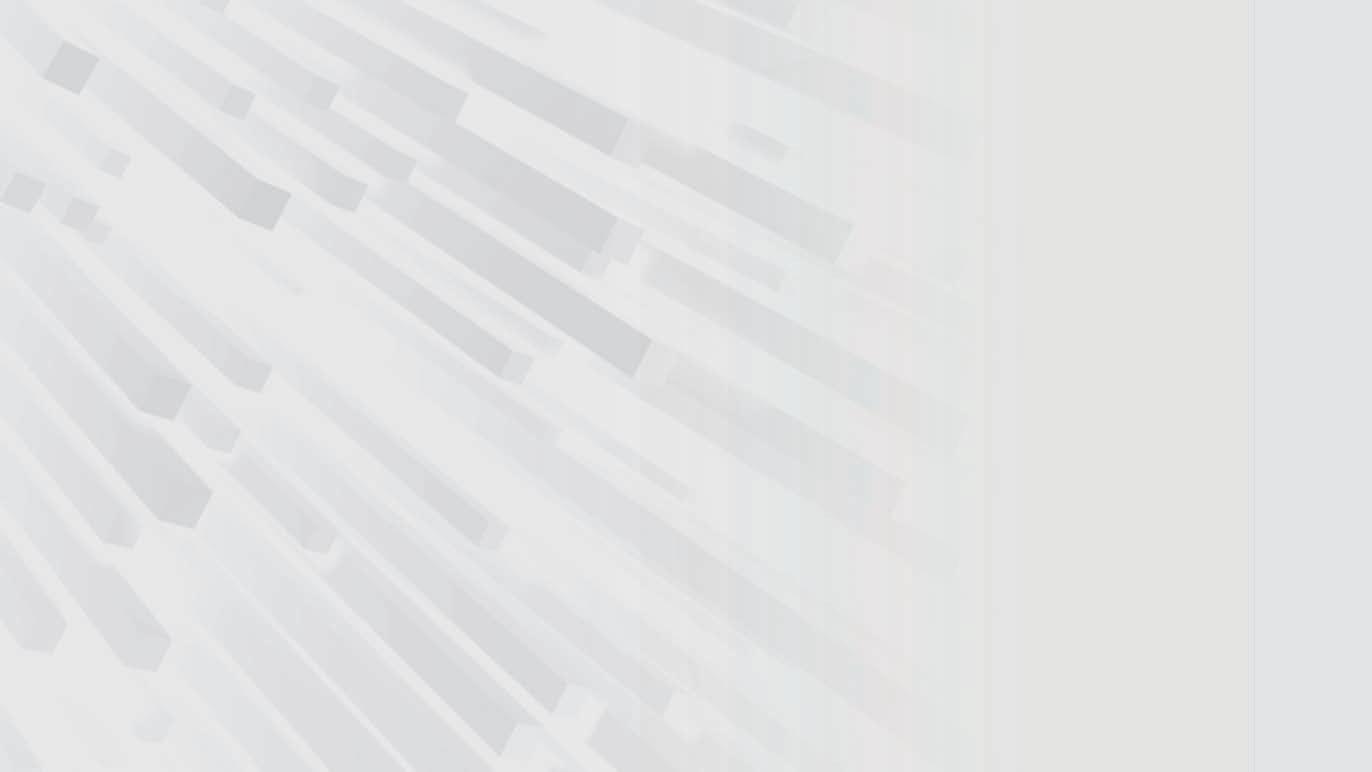
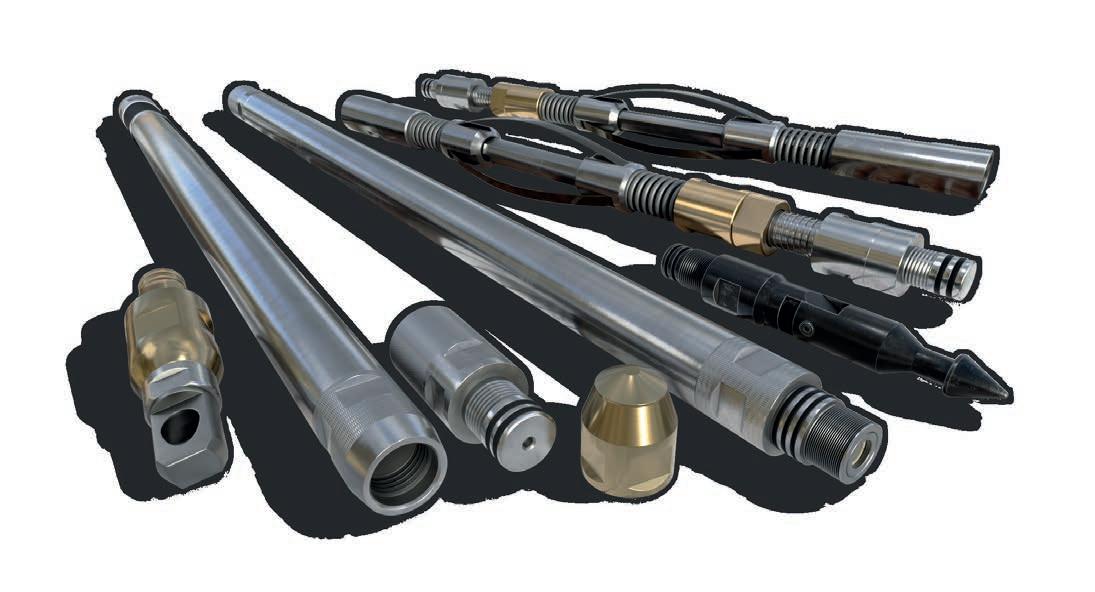
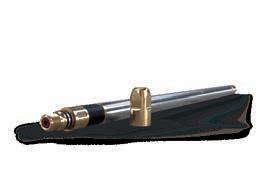

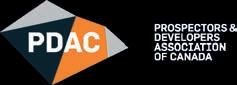
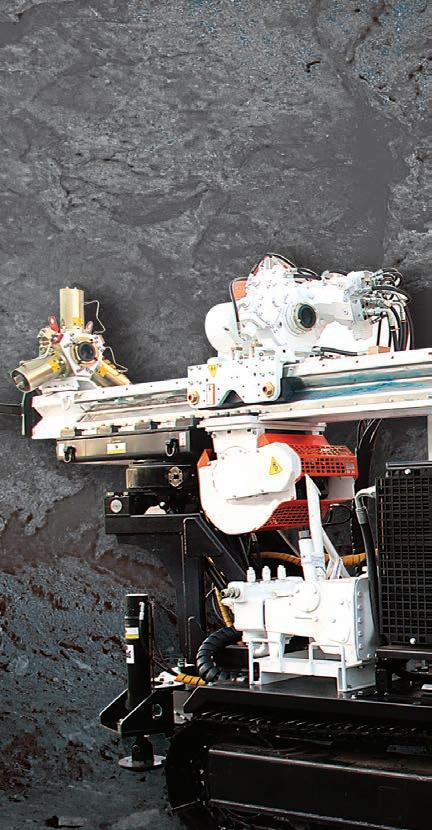
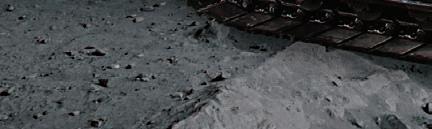
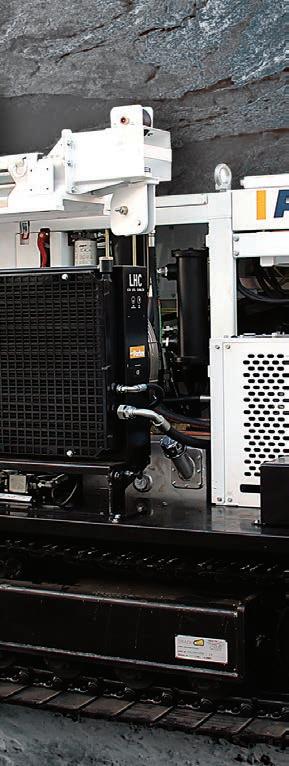
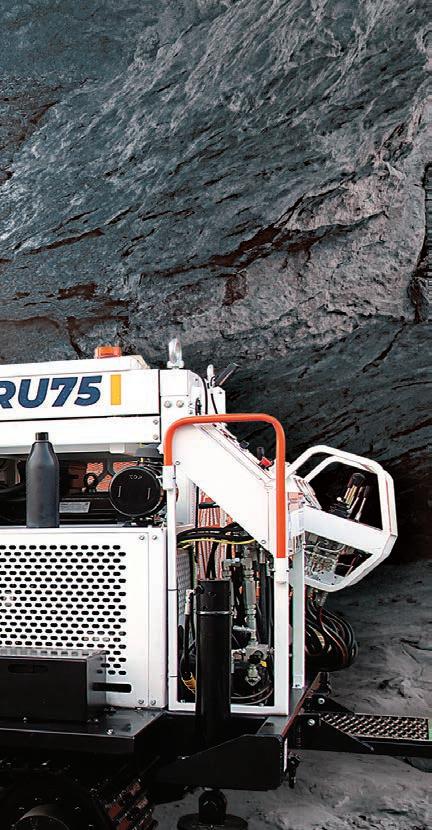
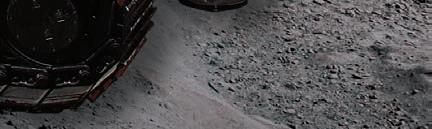
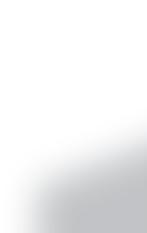
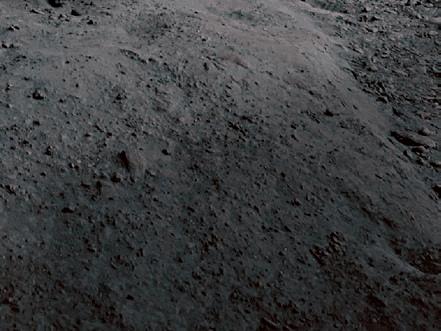
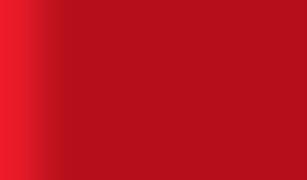
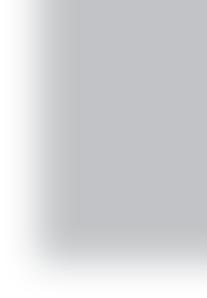
