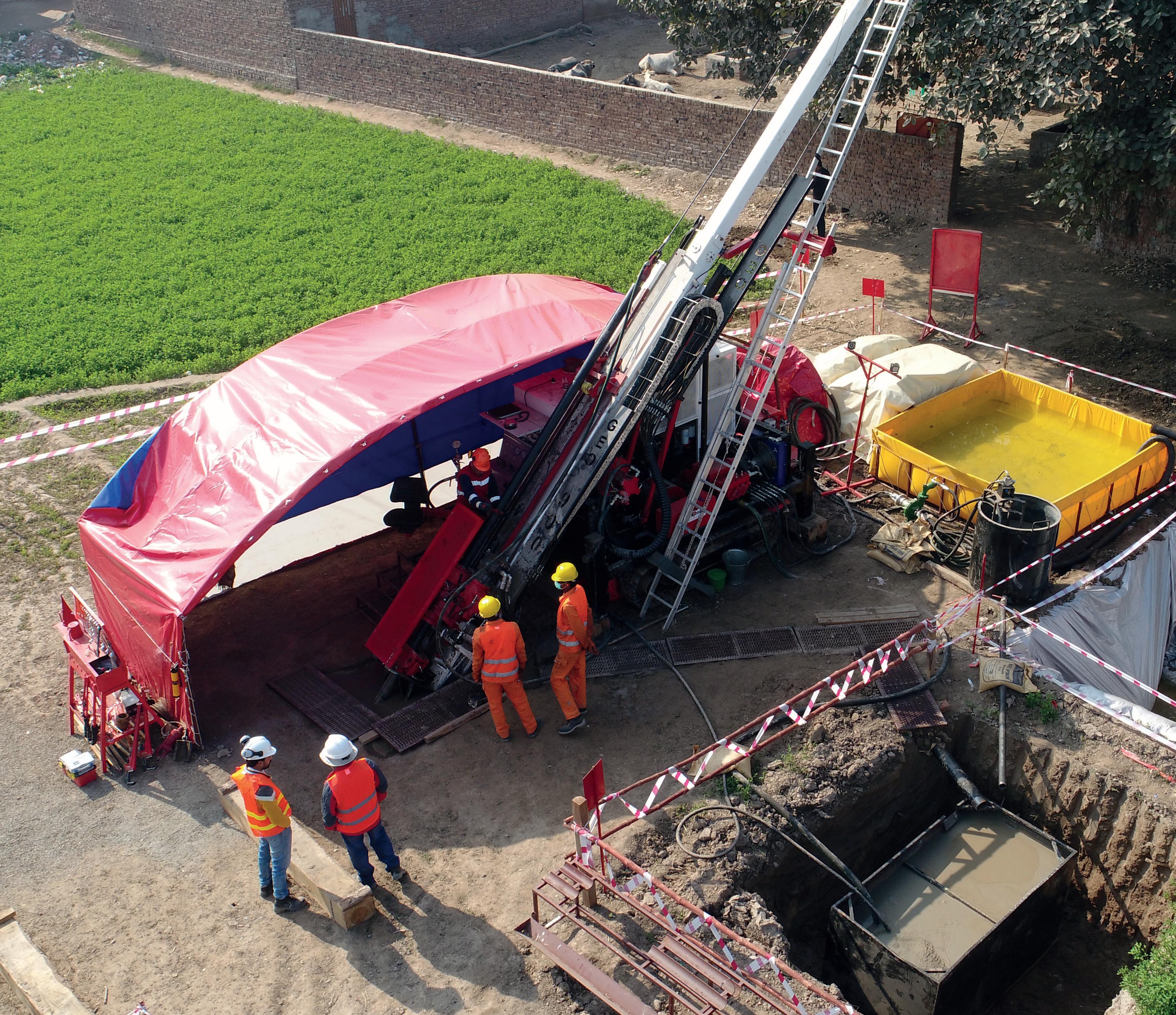
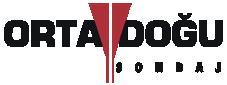
After extensive development and a thorough trial period, the DeviDrill RSS (Rotary Steerable System) is available as the latest directional drilling technology from Devico AS.
Building on the legendary DeviDrill, the non-coring DeviDrill RSS incorporates technology and solutions that secure superior directional drilling capability in all rock formations.
Contact us for further information and a non-committing feasibility study to see what the DeviDrill RSS can do for your exploration program.
6 Exclusive interview: Kelly Johnson - Senior VP - Operations North America and Africa at Major Drilling International, Inc. (Retired)
10 Ortadoğu Drilling: Turkey’s leading diamond drilling contractor by Ahmet Zeki Topdemir, Co-Founder, Mehmet Ruhi Akçıl, Co-Founder, and Sarp Ayken, Drilling Manager at Ortadoğu Drilling
22 Everything you wanted to know about pad building, but were afraid to ask by Brian Doubt, Owner at Skookum Exploration Services Inc.
/DRILLING STORIES
26 Another day on the rig by Mike Junkins, Core Drill Operator
28 A thousand reasons why DeviGyro has changed the game by Alex Butler, International Sales Manager at Devico AS
18 Arctic Drilling Company: Reaching targets through directional drilling in the Kevitsa mine area by Aleksi Autti, CEO at Arctic Drilling Company Oy Ltd
33 Q&A from the experts In conversation with Dr Sarah Jones, Structural Geologist at SJGeology Ltd
38 Economic potential of salt lakes by Roland Gotthard, Director at Playa One Pty Ltd
42 Silver is money by James M. Wise, Shareholder at Pan American Silver Corp., First Majestic Silver Corp. & Newmont Corporation
46 Becoming a female economic geologist in Turkey by Gülay Sezerer K. MScEng, CPG, EurGeol, UmrekCP, Economic Geologist & General Manager at GSK Geology Consulting
Coring Magazine is an international quarterly title covering the exploration core drilling industry. Published in print and digital formats, Coring has a rapidly growing readership that includes diamond drilling contractors, drilling manufacturers and suppliers, service companies, mineral exploration companies and departments, geologists, and many others involved in exploration core drilling.
Launched in late 2015, Coring aims to provide a fresh perspective on the sector by sourcing authentic, informed and quality commentary direct from those working in the field. With regular interviews, insightful company profiles, detailed product reviews, field-practice tips and illustrated case studies of the world’s most unique diamond drilling and mineral exploration projects, Coring provides a platform for learning about the industry’s exciting developments.
Senior VP - Operations North America and Africa at Major Drilling International, Inc. (Retired)
Kelly Johnson has 44 years of experience in the drilling industry, but that almost didn't happen. His life looked set for a career in banking before a summer job with Midwest Drilling (Midwest) made him change course.
Kelly remained with Midwest working in their warehouse for the next 20 years until Major Drilling purchased the company in 1998. Then everything changed.
Only several years later, Kelly was Major Drilling’s global inventory manager, traveling the world 260 days a year and teaching workers on five continents.
He returned home in 2007 as General Manager for Canada, then in 2010, he lead operations in countries in South America and Africa from Major Drilling’s headquarters in Moncton, New Brunswick. By 2017, he oversaw operations in North America and Africa as Senior VP.
Kelly retired in 2022 after showing the ropes to entire generations of drillers and managers.
Grigor Topev: Hi Kelly, thanks for accepting our invitation! It’s a pleasure to have you in our magazine. Let’s get started. It seemed you were set to go into a career of banking. Why and how did you decide to go into drilling instead? Please tell us the story.
Kelly Johnson: My whole family is bankers, and as such, I think there was an expectation I would probably go that route as well. I was lucky enough to graduate from high school at 16 years old, but my parents believed I was too young to go eight hours away to university, so I decided to work for a year and then go. Also, I needed to save money as my parents could not afford to send me. My dad’s friend said I might be able to get a job as a bull cook, which is a ‘kitchen helper’, in a drill camp with a company called Midwest Drilling so I went and applied. I started work the day after grad uation, but since there was no immediate position for a bull cook, they had me help around the yard and warehouse. After 14 months of working in the warehouse, I went to university in the fall. When I came home over the Christmas break, I went and saw all the people at Midwest, and I re alized that these people were hard-working, successful and happy and since I loved working with them, I decided to quit university and start a career in diamond drilling. I could see very clearly that with hard work and long hours, you could rise within the company.
GT: Continuing with the early years of your career, tell us more about Midwest Drilling.
KJ: Midwest was a family company originating out of Flin Flon, Manitoba where I lived at that time. We were mainly a western Canada drilling com pany with a majority of our drills running in Manitoba, Saskatchewan and the western part of Ontario. It was a very good company, and we were like a big family. Our branch was very busy, we ran more than 30 surface drills and 18 or so underground drills during the peak seasons.
GT: What were the challenges at the be ginning of your career? Could you tell us more about the first time you were on the field?
KJ: The challenges at the beginning of my career were many, but mainly there was a lot to learn and understand, as this is a specialized service industry. With almost all our surface work be ing remote, it became very clear that one little mistake in sending and setting up jobs could cost thousands of dollars in downtime. Not being that knowledgeable about mechani cal things, I had a lot to learn and I had to do it quickly. We set up a large base camp in the Wollaston Lake area of Saskatchewan, called Hidden Bay. It was a large workshop, man camp and warehouse, and I spent my first time in the field there in 1980, I believe, for about nine weeks. At that time, we had around 40 drills running in a 50-air mile region, mostly all drill ing B-size looking for uranium. Back then, our customers were all oil companies, like Gulf and Imperial Oil, as uranium was a new concept for creating energy.
GT: In general, what was drilling like back when you started?
KJ: Drilling was quite a bit different when I started. Wireline drilling was still very new, un til then all the rods had to be pulled out of the hole each time you drilled ahead 10 ft (3.05 m).
Drilling in our area was mainly B-size drilling and at that time we thought a 1000 ft or 300 m hole was a deep hole. We could generally put enough items on a 5-ton truck (≈ 4.5 tonnes) to go out and get started drilling a hole. Now it takes four-five semi-trailer loads for each drill. All the drills at that time were exact model JKS drills, so all components could be changed from one drill to another, and it took generally only a few bolts to do so. The drills all had tow ers with baskets, and the helpers would have to stay in the basket each time the rods were pulled for a bit change or end of the hole. At -35°F (-37°C) in Northern Saskatchewan, this was not a fun job at all.
GT: You were Senior Vice President and were overseeing Major Drilling’s operations in North America and in Africa. Where has the expansion taken full scale with satisfactory results?
KJ: Major Drilling is incorporated in around 20 countries, but we currently operate in 15 countries worldwide. Over the last decade, we have closed some unsuccessful branches and have put our focus on countries where we can grow to be number one or two. Our biggest branch is in Canada, followed close ly by the US, Australia, and Mexico. We are a
company continually looking for growth, but we also have a very high standard, so a lot of acquisitions no longer fit our current model of advanced, modern equipment.
GT: And talking about the not-so-success ful expansions, what would be the rea sons for the slow progress or its complete lack?
KJ: There are certain regions where we are not interested in working in because it is danger ous or risky from a political standpoint. We
distance of moves, distance to water and many other factors. All of these will help you bid accurately and avoid conflicts with your customers. Make sure that when items are not discussed, there is a clause in the contract that explains what happens if unforeseen things do occur.
GT: On the topic of mentorship, what would be your advice for managers in the industry?
‘ Always be training your replacement so you have not only the strongest team you can but so you are ready for the next step in your career. Train and learn constantly, it is surprising how often your next promotion will come and catch you out of position to take it.’
KJ: Always be training your replacement so you have not only the strongest team you can but so you are ready for the next step in your career. Train and learn constantly, it is surprising how often your next promotion will come and catch you out of position to take it. Major Drilling believes very much in bringing people up from within, and for the last twelve years, we have been teaching an internal man agement and advancement course called Core College for our employees from all around the world. This is taught by Ben Graham, our VP of HR and Safety and me, along with a guest list of VPs, as well as the CEO, who would invite these employees to our head office in Monc ton, New Brunswick. We are a large public company, but we strive every day to act and treat our employees like we are still a family company.
GT: Any good piece of advice for junior drilling companies from an inventory point of view?
KJ: It is always harder for smaller junior com panies to carry all the inventory you can pos sibly need to be ready for any issue. One of the strengths of Major Drilling is that we car ry extensive amounts of inventory globally so are prepared for almost any problem and were better prepared than others when the recent shortage of inventory in specialized tooling happened after COVID-19.
also measure the risks of corruption, and we have a zero-tolerance policy for bribery.
GT: How to make a good drilling proposal? Any tips or advice?
KJ: The more information you have, the more accurately you can bid for the project, so your customer is happy, and you are profitable. Historical drill hole data is key. When drilling companies are given generic information, we often don’t trust it, so we usually assume it is a higher number than it is achievable. Always make sure you understand the true scope of the work, such as ground conditions, the
KJ: The main thing the industry lacks is females in all positions and sometimes a lack of diver sified workers. We are very lucky that work ing in so many countries as a global company, we can have local workers from within those countries. We have an ongoing goal to have a workforce that continues to reflect the makeup of the communities we operate in around the world, but this can be challenging. With such a shortage of workers, we need to seek out every avenue to entice workers to this industry.
GT: You have worked in many countries. Which one impressed you the most in terms of diamond drilling and why?
KJ: Every country has its own challenges and hurdles, so I am almost al ways impressed when I visit a drill in a particularly tough region. Wheth er it is the High Artic with permafrost drilling in Canada, the extreme heat of Arizona, the US, Australia or Africa, the ultra-high elevations of Chile and Argentina, or drilling in the middle of the Gobi Desert in Mon golia, to complete holes safely is a huge achievement. All branches have their unique issues ranging from holes that freeze immediately when the drill stops turning, to loss of water return, and huge fractures to con tend with. Our team is almost always able to find the best way to get to the bottom.
GT: Tell us a story or a couple of stories of interesting, memorable projects.
KJ: Being in this industry for 44 years, I can tell you many stories about projects not only throughout Canada but around the world. We had one project in Arizona, US, where we drilled for 18 years. We have areas where we have had branches for close to 80 years, so experience is our strong suit.
Ultimately though, our biggest strength is our people, and all stories within our company link to the character and characters of our company and the wild adventures they had along the way. We truly believe that we have the best workers in the drilling industry and we know that without them, we would be like every other company. It is our people that set us apart, and our culture that keeps these people at Major Drilling. We’ve had very few high-level people leave our company, and that is directly linked to the culture of caring that we have fostered.
GT: What do you think directional drilling lacks and what would you like to see improved?
KJ: Over time, there will be more of a move to technologies used in oil field drilling, and they are being used in a lot of locations already. Part of the issue is that this type of drilling is very expensive for the customer, and usually adds a lot of cost to the price per meter. The in-hole risk is also far greater, as bending holes too aggressively is one of the surest ways to lose a drill hole. Customers, drill hole technicians, and drillers need to work more closely together to plan holes to avoid the consequences of breaking off rods deep in the hole.
GT: Major Drilling is specialized in deep holes. How did that start?
KJ: We have always been a company that is proud of completing every hole no matter how challenging. We are proud to have drilled not only the deepest hole ever drilled in Canada, as well as many other very deep holes around the world. Over time, that willingness to push be yond the limits of our competitors has caused us to develop techniques to keep progressing forward, whether through directional drilling or any other means. Hole management and care are priority one on deep holes. Our people are very proud that they are able to complete deep holes that many others cannot.
KJ: We do not build drills, but we work close ly with all of our drill suppliers to develop and create the most modern drill and safety enhancements, as well as in-hole tool devel opment. We have a small team of innovation developers, who are constantly seeking out ways to drill and retrieve core faster, as well as manage water consumption, fuel consump tion and many other items in different stages of development.
GT: How do you assess the changes to drilling technology over the years?
KJ: The basic wireline system has changed very little since the original model of the 1970s. Ev eryone believes that their head assembly and in-hole tools are the best, but short of having more indication of landing on the bottom, or traveling faster, it has not changed that much. True technology is getting past the tough ground on deeper holes, using drilling fluids, and hole management and bits that last longer. The invention of rod handling and ultimately the move to hands-free rod and tube han dling is the biggest change and the one that opens this industry to more people as physical strength becomes less of an issue.
GT: What would be the next game-changing technology in your opinion?
KJ: The whole drilling and mining world wants people out of the most dangerous area;
that area where the rods are turning. Total hands-free rod and tube handling will be the next game-changing technology, but it comes with a very high cost and will t commitment from customers if they are se rious about wanting to take this to the next step. I believe it could almost double the cost per meter for drilling, but safety needs to be priority one.
GT: Is the drilling industry heading to wards a consolidation? We’ve certainly seen many high-profile mergers in the past few years…
KJ: The short answer is that there is very little barrier to entry in the diamond drilling busi ness. All you need to do is buy a drill rig and some tooling and you have a drilling company. It doesn’t mean they are safe or competent but it happens all the time. There will always be companies purchasing competitors, but con solidation to eliminate competition will never happen, as the smaller junior drilling compa nies will always have a place, especially for the overflow of work in an up cycle.
GT: Finally, how do you spend your time after retirement? What do you miss the most from work?
KJ: Honestly, we are just starting down the re tirement road this month, as I had a few out standing items to finish up, one being the Sep tember Core College course. My wife Pam and I both enjoy traveling and intend to do some and go back and visit some of the wonderful places we have been to for work where there was not enough time to enjoy the country. We have four daughters and 11 grandchildren, and we intend to see them a lot more often. I will be staying on with Major as a consultant working on mentoring and Core College over the next three years, but it will be very limit ed. I will miss the day-to-day conversations with all our people and just watching them all constantly growing. I feel like I am leaving be hind most of my best friends in the world, but I know them all well enough to be certain that we will stay in touch.
Visit: www.majordrilling.com
Major Drilling is one of the world’s largest drilling services companies primarily serving the mining industry, and maintains field operations and offices in Canada, the United States, Mexico, South America, Asia, Africa and Australia.
Ortadogu Drilling was established in 1995 with only two drill rigs and the sole purpose of drilling the deep mineral zones of the Anatolian Peninsula in Turkey, exploring the metallic minerals and coal beds of the country, and introducing them into the Turkish economy. Like all developing countries with a significant portion of GDP coming from underground resources, the political strategy in Turkey changed, and a new mining approach allowed for foreign capital investment into the mining industry. Therefore, despite the intention to continue with just a few drill rigs, seven years after the establishment of the company, its fleet exceeded ten rigs. This rapid growth was driven by the demand from investors and international mining companies for high-quality drilling services.
Ortadoğu Drilling needed a trusted partner, thus in 2010 the group company GEO Drill ing Machines Manufacturing Ltd. was es tablished. The new company’s main aim has been to meet the global demand and the most recent requirements of the drilling industry through the collective years of experience from Ortadoğu Drilling. GEO Drilling Ma chines Manufacturing Ltd. manufactures deep drill rigs with a capacity of 2500 m (8202 ft) of H-size under the brand name ‘GEO’, as well as drill pumps and wireline drilling equipment including drill bits and reaming shells inside an area of 15 000 m2. Thus, engineers are able to tailor solutions according to the requirements and the characteristics of the drilled forma tion and maximize the quality of the core sam ples and penetration rates.
With the GEO brand, the drill fleet grew more, and today Ortadoğu Drilling owns 35 drill rigs, making the company one of the few in the world, capable of manufacturing every thing required for drilling operations. Drill rigs and equipment are available for sale both for domestic and international markets.
In 2012, Ortadoğu Drilling decided to be come incorporated and strengthen its struc ture by establishing a board of directors. In this regard, the company included a num ber of CEOs, drilling and regional managers to its business structure. During 2012, Ortadoğu Drilling also decided to create a separate slim hole drilling division by establishing the Geo thermal, Oil & Gas Exploration Division.
Over the 27 years of its history, Ortadoğu Drilling has successfully completed hundreds,
closing in on one thousand, surface and under ground drilling projects. It is the biggest drill ing contractor in Turkey and one of the biggest in the Eurasian Region with an annual drilling capacity of 300 000 m (984 252 ft). The com pany also offers a full range of geotechnical and hydrogeological drilling services.
Ortadoğu Drilling is also the main drilling contractor for the big international and do mestic mining companies in Turkey. Some of the clients include: Eldorado Gold (Tüprag Metal in Turkey), Anagold, Centerra Gold (Öksüt Mining in Turkey), First Quantum Min erals, Teck, Koza Gold Co. (Koza Altın in Turk ish), Erdemir (a Turkish iron mining company), and ESAN (a Turkish metal mining company).
‘Over the 27 years of its history, Ortadogu Drilling has successfully completed hundreds, closing in on one thousand, surface and underground drilling projects. It is the biggest drilling contractor in Turkey and one of the biggest in the Eurasian Region with an annual drilling capacity of 300 000 m (984 252 ft).’
Ortadoğu Drilling is the first and only com pany conducting slim hole drilling with the purpose of exploring geothermal, natural gas and oil reservoirs in Turkey. With specially manufactured drill rigs that allow for the in stallation of blow-out preventers in separately designed well heads, Ortadoğu started drilling its first slim hole with the purpose of gradian exploration of geothermal reservoirs in 2010. The hole was completed at 1993 m (6538.71 ft) and became the first slim hole in Turkey. After the completion of the borehole, a temperature gradian (PTS) log was performed and some
hydrogeological tests were also carried out.
Following this successful project, the de mand for slim hole projects increased, and Ortadoğu started an exploration program for gradian drilling with the Italian company Enel Green Power. A total of ten deep holes were drilled in Turkey, and as a continuation, anoth er four were drilled in Italy. Apart from these, many other projects were completed success fully using the slim hole drilling technique; some even reached depths of over 2000 m (6562 ft). Additionally, for some of these proj ects, hole tests and wireline logging opera tions were also successfully executed.
The Geothermal, Oil & Gas Exploration di vision of Ortadoğu Drilling can also provide engineering services, such as mud logging, mud engineering, gas separation and mea
surements, all types of wireline logging, hole tests, etc.
One of the most comprehensive projects Or tadoğu Drilling has ever conducted was exe cuted with the purpose of iron ore exploration for the Government of Punjab, Pakistan. The project was composed of five work elements, namely diamond drilling, wireline logging, groundwater drilling and hole tests, geotech nical drilling, and surface geophysics. On this project, a total of 50 000 m (164 042 ft) of
drilling with an average hole depth of 1000 m (3281 ft) deep holes and related operations were completed successfully under the con sultancy of international companies.
One of the very early and perhaps the most important projects that Ortadoğu Drilling completed was a drilling project for the explo ration and development of trona for US Borax/ Rio Tinto in Ankara, Turkey. The project start ed in 1997 and lasted four years. A total of 40 exploration/development holes with an av erage depth of 1000 m (3281 ft) were drilled.
This project was so important for the com pany because of the challenges of coring the trona mineral. As trona can be easily melted by drilling fluids, various types of drilling mud were tested before a full core of trona could be retrieved. Twenty-five years ago, this project was a great learning experience in mud engi neering for Ortadoğu Drilling.
Besides wireline drilling, Ortadoğu Drilling carried out many other activities, such as con struction of deep observation wells, wireline geophysical logging, borehole cementation to prevent mixing of saline and fresh groundwa ter zones, and many hydrogeological borehole tests like deep packer tests. Today, the facility established for trona/soda production in the Ankara region is the biggest one in Turkey.
The eastern part of the Black Sea Region of Turkey is full of tea gardens, which are the mainstay for the local community. With to day’s owner, First Quantum Minerals, Cayeli Copper Enterprises is a very old, big under ground copper mine, located in the East ern Black Sea. Ortadoğu Drilling carried out many surface and underground exploration programs for copper in the region for over 15 years. Some surface exploration holes were deeper than 1500 m (4921 ft). Some of them
↑ Drilling crew onsite ↑ GEO Drilling Machines Manufacturing Ltd’s manufacturing facilitywere next to the residences and some were even inside the tea gardens.
This project was very environmentally sensi tive, Ortadoğu Drilling installed blow-out pre venters, which were used in slim hole drilling at the collar of each borehole inside the tea gardens. The exploration holes were drilled with slim hole technique – by cementing each size of casing to the preventer at the collar –to avoid pressurized groundwater discharge from the boreholes to the gardens. At the drill sites close to residents, each drill rig was completely covered by noise curtains to avoid disturbances to the community.
With the efforts of the drilling crew and thanks to all the necessary precautions tak en, these projects showed that it is possible to execute a drilling operation without any
disturbance to the environment and commu nity, even if the drill rigs work almost inside villages.
Ortadoğu Drilling believes that the drilling contractor plays an exceptional role in the exploration and development of projects; it is not about just drilling a hole in the ground.
Core recovery and quality, linearity and design of each borehole play a crucial role in the re serve calculation and the future of a project.
Each member of the company’s specialized crew is aware of the impact of drilling on the economy in mining planning.
Knowing this fact very well, Ortadoğu Drill ing can use a variety of drilling techniques en hanced by their own manufacturing division which makes unique diamond tools specific to the characteristics of the drilled rock to maximize core recovery. The company’s drill ing crews have vast experience in drilling in the most challenging geological formations of Turkey, which is a very tectonically active country. Ortadoğu Drilling is used to work ing in rough conditions. Even at over 3000 m (9843 ft) above sea level and under extremely cold temperatures, the crews can drill 24/7. For all extreme conditions, the crews can rely on special water heating systems and rig shacks.
Armed with their experience, gained through many years of drilling into highly-altered and
↑ Exploration with noise curtains at the Black Sea Regionfaulted zones, their drillers know how to core difficult and unconsolidated formations. Or tadoğu Drilling’s specialized drillers, super visors and drilling engineers are capable of drilling and surveying deep holes and execut ing all engineering applications to the highest international standards.
Ortadoğu Drilling is the only drilling contrac tor in Turkey whose entire crew is trained and certified by the U.S. Geology Survey gov ernment agency on safety procedures during drilling operations. Ortadoğu Drilling un derstands how important the requirements for accident- and incident-free operations of their clients are. To be able to meet these
requirements, their site safety teams, man aged by the company’s Health and Safety Department, are composed of experienced safety engineers, who monitor daily every single drill site and conduct periodical safety trainings for the crews.
Thanks to the hard work of the health and safety engineers together with the manufac turing team, the long-term project of ‘Handsfree Safe Operation on the Rig’ was finalized and all the necessary modifications were completed, so as of the beginning of 2022, all of the company’s drill rigs are equipped with a rod holder and rod spinner making ‘handsfree’ rod handling possible.
As a product of the company’s health and safety culture over the years, Ortadoğu Drill ing has an impressive safety record. In the last five years, they have recorded zero loss time injuries and no environmental incidents.
Ortadoğu Drilling’s priority is and will always be maintaining the mutual trust and cooper ation with its clients by providing high-quality drilling operations. Without providing good service and nourishing good relationships, in creasing the number of drilled meters would not be effective enough. Although the compa ny can increase the number of drill rigs easi ly, first they must be sure that the crews are skilled enough to operate these rigs.
On the other hand, the company is always open to expand into other countries and is ready for challenging projects. C
Visit: www.ortadogusondaj.com & www.geosondajmakine.com
Make the most of your drilling fluid. As the cost of drilling increases, the need to improve productivity is para mount. Additional costs caused by higher operational standards, environ mental restrictions and increased hole depths will continue.
As specialists in Drilling Optimisation, IMDEX’s vision is to ensure the execution of drilling programs to specification, on time, within budget, and safely.
IMDEX never stops exploring better ways to sustainibly find, define, and mine for the future of the industry.
Arctic Drilling Company Oy Ltd (ADC) has been the preferred drilling contractor of Boliden AB (Boliden), chosen to work on their projects both in Finland and Sweden since 2015. Over the past few years,
have brought along directional core drilling as an extra service for our customers. The introduction of this service has been made possible thanks to the cooperation of Aziwell AS (Aziwell) and their AZIDRILL N-B tool.
Boliden Kevitsa chose directional drilling to reach three targets in the Kevitsa mine area, in Northern Finland, which had a limited amount of appropriate drill sites. We were the first com pany to utilize directional core drilling there using Aziwell’s AZIDRILL. Boliden Kevitsa chose this method, as previously our teams have performed it successfully on other Boliden sites. We began planning for the project during the summer of 2021. Drilling started in October 2021 and ended with all targets reached before Christmas. Eventually, one of the three holes was drilled to over 1200 m (3937 ft), another one reached 1100 m (3608 ft), while the third hit 1000 m (3280 ft).
Through Aziwell’s method, the core is collected and oriented during the steering phase with the AZIDRILL that is B-size 36.4 mm (1.43 in) diameter. The curves are usually planned to turn 4-9 degrees every 30 m (98 ft). Steeper curves are possible, but increased stress and fatigue on the rods should be considered. With AZIDRILL, there are no limitations of depth or where to use the tool. The length of the directional core drilling phase is determined by branching depth and the distance between the mother hole and the target. All holes and targets are optimized independently to reach the best ratio between saved drilling meters and the duration of the directional core drilling.
In order to make directional drilling operations with Aziwell possible, back in 2018, ADC formed our first dedicated team of directional core drilling specialists, which were sent to Aziwell’s maiden project in Colombia to practice directional drilling. The main idea was to create a team that can handle conventional diamond core drilling but can also use the AZIDRILL tools for directional core drilling. Achieving this goal meant that external teams or contractors would no longer be needed when a client wants to use directional core drilling.
As a result, presently our team consists of seven drillers, who have been trained to operate the AZIDRILL tool independently on-site. The team is led by our directional core drilling super visor Kalle Säärelä, who has the most experience with this method within ADC.
The rest of the crew was formed by assistant drillers to help with the physical stress, as this is an omnipresent reality in surface diamond core drilling.
Aziwell has assisted us with our directional drilling projects since then and with the training of new candidates. In 2021 they helped us coordinate and complete the project in the Kevitsa mine area.
At ADC, we have always designed and built our own rigs from scratch, both underground and surface. We use a wide rubber track platform on all our surface rigs to enable independent mo bility with wireless remote control for difficult terrain. On the Kevitsa project, the drill site was in the middle of the mine site, so it was easy to access, and the terrain did not cause any issues. This is not usually the case in Nordic countries.
Our rigs have solid walls and are covered by a hood to keep the working space warm and dry during the Nordic winter, which can bring a lot of snow, temperatures of −35°C (−22°F), and other extreme weather conditions. All ADC surface drills have the capacity to drill down to 2000 m (6560 ft) depths with NQ2; we even have a rig that can go to 3500 m (11 483 ft). In Kevitsa, we chose a K2 rig with a 2000 m (6560 ft) depth capacity.
We always use a rubber track-based container unit for transporting and storing all the rods, tools, drilling fluids and other equipment during the moves between drill sites.
We started by drilling and steering the mother hole with AZIDRILL to its target. Directional core drilling was used between 600 m (1968.5 ft) and 686 m (2251 ft) after which we switched
back to conventional diamond core drilling and reached 945 m (3100 ft) depth. The first branch was done by wedging from 498 m (1634 ft) and after passing the wedge, steering towards the target began. We hit bro ken rock formation at around 542 m (1778 ft) depth, which also blocked the inner tube. As a normal procedure, we took the inner tube up and as a precaution, lifted the rods about 20 cm (≈ 8 in) from the bottom. Then we sent another inner tube down and once locked, we immediately dis covered that the water was not flowing through and the water pressure just kept rising, so we lifted the inner tube again to identify the issue. We tried to pull and rotate the rods, but they were stuck and were not moving at all. After several rescue attempts, we had to accept that we had lost that branch. We cut the rods above the core barrel and saved all the rods except the core barrel. We never found out what was the actual reason for the core barrel getting stuck, but we suspected that blasting two days earlier might have had some aftereffects, which caused hole collapsing in the broken rock formation. Fortunately, we had already steered the hole and could cut out from the branch bend at 524 m (1719 ft) and continue steering the hole towards the target as soon as a new branch was formed and cleaned with a proper reamer. Once the direc tional core drilling phase was completed at around 600 m (1968.5 ft) depth, we switched to normal diamond core drilling and drilled all the way to the target at 1218 m (3996 ft). The last target was cut from the branch at 561 m (1841.6 ft) and steered to 1118 m (3668 ft). The cutting method in directional core drilling is more recommended than using a wedge to form branches, as the wedge always adds one more variable to account for in drilling and may cause issues in terms of friction and losing rods in the hole.
The results in Kevitsa were satisfying for Boliden, thus they have de cided to use the same directional core drilling method again in Kevitsa starting in October 2022 with the ADC K2 rig and crew.
In conclusion, this is only one of the examples where ADC has used the AZIDRILL tool to help customers reach their targets. Additionally, Azi well has been working successfully globally on projects with the same tool that has been proven reliable to use, even when the hole needs to be steered at 2000 m (6560 ft) depth to hit the target.
ADC remains a diamond drilling company, but we aim to expand further our exploration capacity and possibilities through directional core drilling.
ADC’s history goes back to 2004. Since then the company has quick ly grown to the largest diamond core drilling company in Scandinavia. ADC offers diamond core drilling, BOT drilling and RC drilling services. The company has long roots in R&D, which has also led to drill rig man ufacturing and sales on the global market. ADC is certified for ISO9001, ISO14001 and ISO45001 to ensure high-quality and environmentally friendly operations, and employees’ safety during drilling. C
Visit: www.adcltd.fi/en/
In today’s exploration industry, heli-portable drills are becoming more common. Governments and stakeholders are looking for ways to cause less disturbance, as we explore for deposits. Drill pads have become an essential part of the exploration process, not only in mountainous terrain but also in remote areas where less impact is preferred. As a pad builder, I’ve seen the growth firsthand, and I’m happy to witness this trend, not only for obvious self-serving reasons but for their smaller environmental footprint.
During my 35 years in mineral exploration, I’ve seen the industry change dramatically because of increased safety, environmen tal standards, and stakeholder involvement, and I am happy to be a part of such a responsible industry. This brings us back to drill pads. Once you realize you’re going to require them, planning becomes essential for a smooth program. Choosing a pad-building company is as important as choosing a drilling company, a helicopter company, or the project geologist you require for your program. The wrong company may not have the capability to build the pads you need. Safety is paramount in this situation, as well as planning in advance, months in advance.
The further in advance you plan your program, the better it is. Once you’ve chosen your drill contractor and pad builder, getting them to communicate is essential. Pad builders need to know the specifica tions of the drill, plus how the drillers prefer their pads, and whether they have any special requests. Once they’ve done this, you can get your lumber list from the pad builder and order your wood. Ordering months head is always best. If you wait too long, you may end up with lower quality or wet timber, which can weigh twice as much as seasoned dry wood. This makes the wood harder to work with, and less can be trans ported by helicopters in a sling load, obviously raising expenses.
Getting the wood delivered to your site slightly before or simultane ously with the arrival of the pad builders is preferable. They will need to complete a couple of pads before the drillers come. There’s nothing pad builders hate more than causing drillers to wait while they’re finishing off a pad. Depending upon the depth of a hole, the number of holes per pad, and the ease of drilling, you’ll need to figure out how much further ahead the pad builders need to be in order to stay ahead of the drillers.
Once the drillers arrive, they’ll want to see the pads to ensure that they meet their standards, as well as to be certain that the pads have all the features they need. Depending on the safety protocols of the drilling company and the jurisdiction, the pads will need to be inspected by the drillers, the senior geology staff on site, and the builder, to ensure that everyone’s standards are met. This is usually when the drillers make their special requests, if any. If you have a good pad builder, they’ve
↑ A series of drill pads on a steep mountain inclinealready anticipated the drillers’ requests, and are very happy to accom modate the drillers’ additions.
Consider how much force is exerted by a drill during its operation on your drill pad. The pressure is immense, meaning that lives and equip ment are at stake. Like it or not, it’s dangerous work, therefore, a lot de pends upon the integrity of the drill pad. This is an area in your program that can be problem-free with the right pad builders, or a total disaster if you’ve hired the wrong crew. I recommend seeking pad builders with experience and a proven track record. Ensure you are dealing with a company that carries adequate liability insurance, WorkSafe coverage, and the personnel with the needed skills. The more complex or steep your terrain, the more experience you’ll need from your pad builders. There are several good companies out there that offer everything re quired, however, this is not an area that you can skimp on, especially if you have challenging terrain.
Pad building is a service that can be overlooked if you don’t consider the risks of having a sub-par builder. It usually takes a few seasons for a helper to gain the experience needed to become a skilled pad builder. Some builders have no experience in rocks or talus, while others may have never built a pad on a glacier. Additionally, some might cut corners to finish quickly, while others may use the wrong materials, causing un seen weaknesses that won’t be apparent until the pad fails. These are all risk factors when considering which pad builders to use.
In the end, planning ahead and doing some due diligence in your se lection process will ensure a smooth field season. Pad builders should arrive on site with all the tools and supplies they need to complete the work. Adequate PPE and safety standards are also important. Attitude is paramount, as the job of the builders is to help you complete your project in a safe and efficient manner. Listening to their advice may just save you thousands of dollars, so all in all, pad builders are a key partner in the success of a heli-portable drill program. C
United.
What
Find
I woke up at 4:11 P.M. on this frigid after noon in February. The location was West Forks, Maine, US. I was getting ready for a 12-hour night shift on Alder Pond. Yes, we had the rig set up on the ice to hit a specific tar get. This job was an exploratory contract. We were looking for copper-bearing sulfide. We had to cross shifts at the drill. The extreme ly cold temperatures would freeze the water line very quickly if anything went amiss. The pump could quit, the line could come apart, or the suction line could freeze. There were too many variables to leave entirely to chance. Without question, the water supply system had to be monitored closely.
Imet my helper, Jacque, in the dining room. We said our hellos and both yawned simultaneously. Reg was the cook’s name. He got our meals and made-up sack lunches for us to take to the rig. He also made up the rooms and cleaned the place by himself. We were the only guests at this time of the year. The town was literally dead in the winter months. In the summer, the town came alive with white water rafting enthusiasts. The Kennebec River flowed on the opposite side of the street from where the hotel was located.
Reg brought our meals and said he would go and make sandwiches for the shift. We thanked him and began eating the Goulash with a really nice corn bread. There was also a green salad. I never seemed to lose any weight on these jobs.
We finished up our meal and grabbed our sack lunch. I made sure my thermos was filled with hot coffee. Jacque preferred Mountain Dew for some reason. Caffeine comes in many forms. We had our cold weather gear in the rear seat of the crew cab pickup. We made a quick stop at the only convenience store in town for a couple of candy bars – some quick energy for that 3:00 A.M. time when things got a bit yawny. It was about 16 miles (25.75 km) of logging road to get to the drill site.
Preparing to set up on the frozen pond, we had placed 12 cedar logs on the ice and packed snow between them. We’ve wet down the snow and let it freeze in overnight. Then the drill was skidded out across the fro zen pond and up onto the Cedar/ice raft. We used a Timberjack skidder to move the rig and rod sloop. There was nearly 2 ft (91 cm) of good ice on the pond. The insurance demanded no less than 18 inches (45.7 cm) of ice before they would cover the rig in this type of setup. Casing had been run down 42 ft (12.8 m) before we even had to turn a rod. The hole was at +90 degrees, so no slings had been necessary. The slings were used under the ice to stabilize casing that was being run in at an angle like -45 degrees or higher. This process involved ‘walking planks’ under the ice and it was a royal pain in the butt. Hopefully, only a small number of holes would be angle holes on this project.
For more information Get in touch with Mike on LinkedIn
We drove the truck out across the ice-covered pond to the rig and not ed the smoke rising from the wood stove in the corner of the shack. The day shift helper would yard a couple of Beech or Birch trees out to the rig during his shift. The night shift helper would saw the trees into stove length and split what needed to be split. We used a propane torch and a coil stove at the pump shack to heat the water as it was sent to the drill. We had about 700 ft (213.4 m) of water line buried under the snow from the pump to the rig. We could not pump water from the pond because it was so full of silt that it kept plugging the suction screen. Instead, we were pumping from a casing onshore from a previous drill hole. The cas ing had an artesian flow, so the water was already 48 degrees Fahrenheit (8.9°C) or warmer coming out of the casing. This was an old drill hole that had been done during the previous summer.
Normally, we cement up these artesian holes when completed. In this case, we knew we were going to need a water source for the winter drill ing, so we cleared it with Chris, the head geologist, to leave it open for now.
We walked to the rig and entered the shack. Don was the driller, and he was sitting on a polymer bucket by the stove filling out his report. Brad was his helper and he was wiping down the pipe wrenches and other tools as an end of shift courtesy. Don told me that everything was drill ing well. Good stick rock. The hole was only 340 ft (103.6 m) deep with a proposed TD of 1000 to 1200 ft (304–365 m). TD stood for ‘technically done’. When a hole was completed we said it was TD’d. We had cased off with N tools and were drilling 10 ft (3 m) B-sized core. That was nice be cause it was light and fast to work with. As long as the formation stayed competent, we should have a highball night. In this type of drilling, we only used polymer as a mud additive. Our mud tank was inside the shack
and had a hydraulic Bean Pump along with a hydraulic mud mixer. Both were very efficient for these cold weather projects.
There was room inside the shack for Jacque to dump the tubes. Barring a rod trip, we should be able to stay warm by the glowing wood stove. We kept tinfoil at the rig so we could toast our sandwiches at lunch time.
Brad told Jacque that he should fuel the supply pump by 10:00 or so and he might also have to change out the propane tank. The propane tank was a 100 lb (45.36 kg) tank that usually lasted about 36 hours. If the propane ran out, we had about 30 minutes to get it back on before the water in the line started slushing up.
The night was uneventful. We knocked out a 280 ft (85.3 m) shift. That should keep Chris busy logging core all day. He had a semi-trailer parked up on shore with a propane heater, where he logged the core samples. He used our Muskeg truck to transport the core to the trailer. He had an assistant, who cut some of the mineralized core to be bagged and sent in for assay.
Jacque had checked on the pump and propane a final time at around 4:00 A.M. All was good and the pump was full of fuel. We added wood to the stove, and I began making out my report. It felt nice to drill without any drama during the shift. Don and Brad arrived right on time. It seemed like they had just left moments ago. I told Don everything was purring along. He was impressed with our productive shift. I let him know that he had a tube down and a 10 ft (3 m) stick up. Two ft (0.6 m) off bottom and ready to turn and burn.
Reg had eggs, bacon and some French toast when we got back to the hotel. I would watch TV, read some of the newspaper and hit the hay. Another day, another dollar. C
In December 2019, Devico released its first downhole gyro system. Less than three years later, an astonishing 1000 DeviGyro units have been produced, far exceeding Devico´s expectations, and clearly documenting how the industry was ready for a new and innovative gyro system.
In this article, Alex Butler from Devico, gives us a direct insight into the top five reasons why so many companies are choosing DeviGyro.
Firstly, DeviGyro is an advanced, miniature rate gyro survey instru ment designed for recording precise downhole navigational data, as quickly as possible for a large variety of mining and civil drilling applications.
Incorporating state-of-the-art gyroscope technology and propri etary navigational algorithms, the DeviGyro precisely detects and quantifies any movement the instrument is subjected to as it tra verses the drill hole. Providing highly accurate, repeatable data at any angle and location on the planet.
The physical DeviGyro system is best described as ultra-versa tile. With the complete instrument being so small and capable, we have been able to develop a leading range of interchangeable, pur pose-built running gear configurations. Each configuration suits specific drilling applications for length, weight, material, centraliz er type and range. This modular type of offering has resulted in the DeviGyro being widely accepted as the preferred solution world wide for many leading companies in the mining and civil space.
It is also worth mentioning that we do not only supply the Devi Gyro for standard borehole surveying requirements, but it is also integrated with Devico’s Directional Core Drilling (DCD) barrel, DeviDrill, and in the new non-coring directional drilling barrel, DeviDrill RSS.
For Devico, survey tool running gear assemblies are much more than just pressure-proof instrument containers. Over the past de cade, we have developed several leading running gear technologies that have proven to both enhance survey accuracy and survey tool reliability.
One example is the Brilliant Blue Technology (BBT) activation and patented Bluetooth wireless antenna system, enabling quick set up, data transfer and wireless download without cables or having to open the instrument.
Another example is our patented low-friction wheel-based helix centralizer systems that combat residual bias and greatly improve accuracy.
In addition, we have advanced vibration damping in several steps, both in axial and radial directions to maximize robustness.
The best example of what we mean by ‘purpose-built running gear’ is the DeviGyro Overshot Xpress (The OX), our overshot sur vey solution for diamond core drilling, proven to increase drilling productivity compared to conventional overshot survey systems.
Overshot surveying is a highly beneficial survey method for dia mond core drilling, enabling surveys to be conducted while retriev ing core tubes, effectively integrating surveying into the drilling process, and maximizing available drilling time per shift.
Manual handling and operator safety, however, are key factors that also must be considered.
Unlike other overshot survey tools on the market with typical lengths of several meters, the OX is purpose-built for this applica tion. It is not a survey tool that is just adapted to be used in over shot surveying mode, it’s built just for it.
With a short 1.2 m (3.94 ft) length and 7.4 kg (16.3 lb) weight,
‘... the success of the DeviGyro is mainly down to these points: the right tool for the job, built to last, advanced functionality, high quality and easy to use from start to finish.’
the OX is the ideal overshot surveying solution for both surface and underground diamond core drilling applications, and especially beneficial for surveying underground and in other confined space environments. Not only maximizing the beneficial productivity gains that come with overshot surveying but safer operation and minimal impact on the operator as well.
All DeviGyro components are designed, built, and tested in-house at our headquarters in Norway. All stages of this work are per formed by qualified mechanical and electrical engineers with many years of experience and over 90% of all materials used are sourced locally. This is how we ensure quality control.
Throughout the development process of the DeviGyro, a key el ement was to make a small, lightweight and nimble system that could be used in multiple applications. Not only does this give a system that is easier and safer to handle for the operator, but a key reason was also that a small and lightweight electronics and battery solution significantly contributes to robustness, because the size and weight of an instrument clearly correlate with shock resistance.
Additionally, the advanced damping technology we have devel oped for the various running gear configurations offers superior protection for the DeviGyro sensor compared to conventional, fully integrated survey tools.
As a result of these careful design considerations, the failure rate for the DeviGyro is extremely low (and significantly lower than our competitors’ products according to our clients). Even with so many units produced, only a handful of gyros have had to come back for repair. There have even been occurrences where, due to an incident during surveying, the running gear has come back severely dam aged, but the DeviGyro instrument has been unharmed, and ready to be placed in a new running gear after an onsite calibration check. Even in the toughest of drilling environments, such as drill and blast, reverse circulation, or the high-impact method of overshot surveying, DeviGyro excels as an easy to handle and extremely ro bust survey tool, setting a new standard for what our customers can expect and saving time and money for everyone involved.
To enable continuous improvement and efficient delivery of all new functionality, our engineers developed the Android DeviGyro app with key parts of the intelligence of the system not in the instru ments themselves, but in the subsequent processing of the data. The logic behind this is that it is much easier to update an app to add new features than it is to remotely update instruments that are deployed all around the world.
This system allows our customers to simply do the latest app update and obtain added functionality through OTA (Over-The-Air) programming. Hence a customer who has bought one of the first DeviGyro kits in 2019 has access to the same functionalities as a customer who buys their tool next week. And at no extra cost. Effec tively ensuring all DeviGyro customers take part in advancements.
One of the greatest updates so far is undoubtedly the introduction
of ADE (Automatic Depth Estimation), which was released in mid2022. ADE is a new function within DeviGyro that enables contin uous borehole surveying without the use of a wireline counter. The depth is instead estimated from the instruments’ onboard sensors and new proprietary algorithms. This feature is free for all DeviGyro customers through a simple app update.
Having developed borehole survey solutions for over 30 years, we know that ease-of-use is often more important to operators than most other survey tool features. For the DeviGyro we have put a lot of effort into developing a survey system which is guided via intuitive steps in the operating application, so that it does not take an expert to learn the application and get an optimal survey result.
Simplicity is always at the forefront to minimize the room for con fusion and guesswork. As a consequence of this, the feedback we often get from customers all around the world is that the DeviGyro is the easiest instrument to use on the market.
This point is well documented by the fact that the large majority of DeviGyro customers have been successfully onboarded with the product via a one-two-hour, remote, online training session only.
When it comes to pre-survey set up time, all DeviGyro kits are designed for easy assembly and quick activation. Resulting in an extremely efficient survey process and time savings.
Finally, the onsite processing, transfer, and management of bore hole survey data are more streamlined and user-friendly than ever with the combination of DeviGyro and DeviCloud.
In a nutshell, DeviCloud, our uncomplicated cloud-based plat form, enhances the data transparency and quality of DeviGyro surveys.
Not only does it provide fast processing, instant QA/QC data analysis, comprehensive plotting and inspection parameters, along with advanced reporting functionalities, but all while supporting secure two-way communication between site and office. Making it
possible to share and sync data directly to and from the handheld device at the drill site, with ease.
We see that this not only improves efficiency but provides stron ger insight and ownership for everyone in the chain, from the drill site to the head office. In a way, this system is making survey data more democratic and transparent.
We see the success of the DeviGyro is mainly down to these points: the right tool for the job, built to last, advanced functionality, high quality and easy to use from start to finish. But we also recognize that without our people, our global network of employees and dis tributors having the experience, capability, and trust within the global market, the DeviGyro would not be as successful as it is. And for that, we are eternally grateful.
Well, despite proving that the DeviGyro is a leading solution for the large majority of drilling applications, we recognize that a north-seeking gyro could be preferred in some cases. And hence are currently launching the DeviStar north-seeking gyro. This new product, which is now being released gradually into selected mar kets, will complement our already strong portfolio of borehole surveying solutions. C
To learn more about any of the products or systems mentioned, please contact us directly, or simply visit devico.no, and sign up to DeviNews and follow us on LinkedIn.
After 23 years of living and working in Australia, I moved back to New Zealand in late 2019 to start my own consultancy business (SJGeology Ltd). I now reside in Cromwell, Central Otago and luckily can do the work from home without the need to travel constantly.
I started my working career as an exploration geologist at the Darlot Gold Mine in Western Australia, and after two and a half years, I moved to Hobart to start a PhD at CODES on a massive sulphide deposit in the middle of Vancouver Island, BC, Canada. After I completed the PhD, I moved back to Australia to Kalgoorlie and worked there for four and half years as a regional mapper in the Eastern Goldfields. This was followed by a stint as a consulting structural geologist for RSG Ltd., then about ten years of working as a structural geologist for mining companies, such as Consolidated Minerals Ltd., St Barbara Ltd., and Gold Fields Ltd.
My interest in geology started early, as I was always collecting rocks wherever we went. However, I didn’t start studying geology at university until my mid-20s. When I left school, I started a computer programing course at a polytechnic institution, but after a month, I decided it wasn’t for me and left. To offset the bad news to my mum, I found a job on the way home at Farmers (a department store) in their cosmetic department. I stayed there for a year, then completed a three-year apprenticeship in Typography. Once I started studying geology, I’d found my niche and never looked back.
Dr Brett Davis: Firstly, thanks for giving Coring the opportunity to interview you, Sarah. Very few people have a career like yours, where you’ve worked across the spheres of academia, government surveys, mining, and exploration, plus gained enormous respect in the geological community while you’ve been doing it. Can you tell us what interested you in a career in geology?
Dr Sarah Jones: I’ve always had a rock collection. Our summers were spent on the Coromandel Peninsula, New Zealand, and my twin sister and I would explore the beaches and creeks bringing home buckets of quartz crystals. So, when I started university in my mid-20s, I thought I’d give geology a go, even though I didn’t have much of a science background.
BD: You did your PhD in Canada. Can you provide a snapshot of what that involved and if that influenced your career path going forward?
SJ: My PhD was on a volcanic-hosted massive sulphide deposit at Myra Falls on Vancouver Island, Canada. The mine, which is over 100 years old, is in a beautiful part of the Strathcona National Park. The study was based on data from underground mapping, core logging and field map ping. The PhD made it possible to pursue a technical path for the rest of my career that started with regional mapping with GSWA, then in the industry as a structural geologist.
BD: One of the things that I admire about you is the regularity with which you publish in peer-reviewed international geology journals. Many people in academia haven’t got a publishing
record as you have. What motivates you and what are the more onerous aspects of publishing while working in industry?
SJ: Working in the industry has provided excellent access to the deposits and the people who work closely with them (resource, mine and explo ration geologists). This has given me a different perspective on docu menting the geology. I feel that when you have a good story, it should be published to build our collective knowledge. As I prepare my company’s technical reports, I try to write them in a way that can be later turned into a published paper. The aim of the papers is to highlight the practical aspects that can be of use in exploration or deposit geology later. The onerous aspect is of course the time spent during the weekends turning the reports into paper manuscripts and the ongoing revision of manuscripts. It’s worth it though when you finally get one published. I’m also grateful that I’ve worked with management and companies that have allowed me to publish.
BD: Typically, geologists enter the minerals industry in junior roles and work their way to retirement by culminating in man agement roles or joining a company board and sitting back and collecting director’s fees. You don’t seem to have aspired to follow that route. Would I be right in assuming you still prefer to do geology?
SJ: I’ve always been driven by my love of geology, and I know I’d be no good at managing people, so it was a natural choice to stick with the technical roles. That’s why I left the industry to do a PhD which certainly helped me stay with the technical geology roles.
BD: You made major contributions to the geological understanding of Western Australia during your time with the Geological Survey of Western Australia. What were the important things you took from that job when you transitioned into the mining and exploration industry?
SJ: I think the main thing working as a regional mapper for GSWA was the importance of understanding the regional scale. When you are map ping on a 1:100 000 map sheet of ≈ 40 x 50 km (≈ 24.85 x 31.07 mi) you can’t get bogged down with the detail in an individual outcrop. You have to keep moving, and if you don’t understand a particular outcrop, by the time you’ve seen five more, a pattern starts to emerge. These ideas were helpful when I started consulting as a structural geologist because they taught me to just keep making observations and wait for the pattern to emerge, rather than trying to apply a pre-conceived model.
BD: I’ve heard it said that some of your bosses have called you completely unmanageable. How do you respond to that, given that I was one of those awesome bosses?
SJ: Haha – I’m not unmanageable, just give me interesting work that I want to do and there’s no problem.
BD: There are far too many reports of the unsavory experiences women have experienced in our industry. Given you have straddled major sectors of the industry, have you experienced any truly negative ones?
SJ: I have come across some bad behavior during my working career. In one instance, I was at sea south of New Zealand in the Puyseger Trench, collecting samples from a deep-sea dredge on a fishing research vessel and the guy that ran the day shift refused to work with a woman. I just got around it by working with the night shift crew. When I come across bad behavior, I tend to avoid those people and shift my focus to the pos itive ones, which are the vast majority.
BD: There are very few women globally who compile industry-based technical geology reports to the standard you do (I know – I’ve read quite a few of them). What is your perception of the standing of women in the industry in technical roles like yours? Are they respected and rewarded adequately?
SJ: I think by the time you’ve gotten into a technical role you’ve done a lot of work to get there. So, in my experience, I don’t feel that I get treat ed or remunerated any differently to men in technical roles.
BD: Which geological environments do you most enjoy working in? And which deposit have you found most interesting?
SJ: I like to work in structurally complex areas (with at least three de formation events) as I really like to peel back the different deformation events and look for the early basin history. Because of this, I enjoy work ing in the Eastern Goldfields of Western Australia. The Agnew and Le onora areas have been particularly fascinating, as the gold deposits in these camps show such a wide range of structural settings from early D1 extensional to D3 compressional settings.
BD: Given the current focus on energy metals, have you noticed a change in the focus of your work?
SJ: Not really, as I mostly work for gold companies. I worked in manga nese before the big shift in focus to energy minerals.
BD: I have to ask – what sort of geological feature most fasci nates you and that you never get tired of seeing?
SJ: I think it’s growth faults. I like to look through deformation events to understand the earliest phase of basin development and growth faults, active at the time of basin formation are fascinating. I’ve been lucky to work in a few places where they’ve been well exposed. Probably the best place for these structures was at the Woodie Woodie manganese mine in Western Australia. These structures don’t disappear with subsequent
Safety is the challenge, CX Line is the answer. Compact design, hands-free rod handling system for fully automated and remote controlled operations: the future of exploration drilling is already here. Are you ready to join in?
deformation, instead they remain important conduits for mineralizing fluids. This is particularly obvious in the open pits at Woodie Woodie, with high-grade fault-hosted manganese in the early normal faults. We also see this in the gold camps, with high-grade shoots associated with early basin-controlling structures, e.g., the Waroonga and Redeemer de posits, Agnew Camp, WA.
BD: Do you do much work with oriented core? If so, can you comment on your orientation audit process and your preferred data collection techniques?
SJ: I constantly work with oriented core, nowadays mostly from core photos as I’m based in New Zealand. I think the most important thing when working with oriented core is to have a good understanding of the geological system (e.g., bedding, foliation orientations) so that you can spot bad orientations versus interesting structural anomalies. I’m also using ‘core-profiler’ software from Datamine on the historic oriented core photos. This allows me to add a lot more structural information to the projects and to verify existing structural readings.
BD: You’ve traveled and worked widely. What is your opinion of the geological skillsets, experience, and knowledge of geologists today, especially those who are newly graduated?
SJ: I really think that it has always come down to the individual geolo gist. There are always going to be young graduates that don’t really have the passion for geology. Then you come across the ones that just love
geology and are so enthusiastic and keen to learn. These are the ones that build an excellent geological skillset.
BD: Apart from meeting me, what do you consider the most satis fying moment in your professional career so far?
SJ: Apart from meeting you Brett – I think getting the regional D1 study for the Eastern Goldfields published two years ago. This work comprised a study that began when I was at GSWA, then involved many years of underground mapping and fieldwork at various mine sites in the East ern Goldfields. A bonus for this study was the collaboration with you and Kevin Cassidy.
BD: We are seeing increasing implementation of new technology into mining and exploration geology. For example, drone surveys, core scanning and software such as Leapfrog. Are there technolo gies that you find particularly important for exploration? And do you think the use of these technologies is making better or worse field geologists?
SJ: I think the immediate information provided by core scanning to en hance drillcore logging is particularly important to understanding alter ation systems. In brownfields exploration, many deposits are in areas with relatively dense historic drilling. If this historic drill core can also be scanned, this can greatly add to the understanding of the entire system. I find that historic drill core is typically ignored and is a huge, underuti lized resource.
BD: Do you think that there are any mineral exploration strate gies or technologies that are under-employed, but could make a big difference to an exploration campaign if people used them more?
SJ: I think that relogging and scanning historic drill core can add signifi cantly to a brownfields exploration campaign for relatively little cost. Even just the relogging to look for patterns in alteration, lithology, and structure that may not have been recognized previously.
BD: If you had abundant financial funding, is there a fundamen tally annoying geology question you’d like to solve or a topic you’d like to work on?
SJ: I think I’d like to continue with the D1 study, but look at a comparison with the Abitibi Belt. Of course, I’d need abundant financial funding for the fieldwork in Canada!
BD: What have you learned from field practice and your job expe rience that is not taught at university?
SJ: My first job as an exploration geologist at Darlot Gold Mine was a bit like doing an apprenticeship. I’d already done one of those as a typogra pher in the mid-1980s before I went to university. It was very enjoyable, and I learned the practical aspects of being an industry geologist. This is invaluable and I would not expect to learn that side of the job at univer
sity. It’s the place for gaining theoretical knowledge and I wouldn’t want to see that change.
BD: Here’s the familiar question that hopefully won’t be asked as much in future interviews – how has COVID-19 impacted life for you personally and professionally?
SJ: Yes, like everyone COVID-19 has impacted me personally and pro fessionally. When the pandemic started, I was pretty anxious, as I’d just moved to New Zealand to start my new consultancy business and all of my work was on the other side of the Tasman. Luckily, my work mostly comprises structural analysis of ore deposits using existing drill core and mapping. So, I could continue to do this from my base in New Zealand. Technology has improved and I can log in via VPN to the drives in Perth allowing me to access all the data I require. As far as personal impact, living in a small town meant less exposure to COVID-19 and we didn’t have the prolonged lockdowns imposed on cities like Wellington and Auckland.
BD: Finally, any concluding comments or words of wisdom from an industry veteran?
SJ: Follow what you love doing and the work will appear. If you real ly love geology, I recommend following the technical route, as you will have a satisfying career that never gets boring. C
The innovative one man hand-held system works independent of environmental distraction and pro vides unsurpassed accuracy. You‘re looking for a fast, economical and reliable solution?
LiPAD®-100 is the answer.
GYRO COMPASSING SYSTEM IT HAS NEVER BEEN EASIER TO CONTROL A LARGE NUMBER OF BOREHOLES
For geological units that amount to little more than muddy ponds, salt lakes are perhaps some of the most economically important geomorphological features on the planet. This is because of the presence in the Andean Cordillera, of brines containing lithium within some salt lake systems. Some ten million tonnes of lithium reserves are available in the salt lakes of Chile and Argentina, representing about USD 0.75 trillion in lithium carbonate equivalent at today’s prices. This is about 400 million ounces of gold equivalent. Ten years ago, however, the same lakes were worth 1/8th as much, or less.
With the economic importance of salt lakes demonstrated, it’s time to pay a bit more attention to these geological formations that, for a lot of geologists and explorers, are something you drill through to get to the ore, or drive right around on the way to drill for ore. Salt lakes clearly deserve far more of our attention, in Australia and worldwide, if we are to meet sustainable and circular economic models in the future. This article will serve as a brief introduction to their geology and economic potential.
Salt lakes are evaporitic systems formed in endorheic basins – water sheds which have no exit – also known as saline sumps. Salt lakes can be several meters across, to vast areas such as Salar de Uyuni at over 10 000 km2 (3861 mi2). Whilst sodium chloride salt is a ubiquitous com ponent, salt lakes are highly variable in mineralogy, with almost no two lakes identical.
Salt lakes themselves can also vary meter by meter in mineralogy, chemistry and in terms of water chemistry. It is not unknown for super acidic pH 1.5 water to exist several meters away from pH 11 groundwater.
Water that falls into the drainage basin, or enters via groundwater discharge, leaves only via evaporation, and when evaporation rates out weigh rainfall, this will result in salt lakes of some form or another.
Water interaction with the rocks of the drainage basin controls groundwater chemistry. As bedrock is weathered to clay, alkalis (sodi um, calcium, potassium) and other soluble elements (magnesium, chlo rine, sulphur) are carried into the sump via subsurface flow through the soil and aquifers.
cyanobacteria
Dilute groundwater is concentrated by evaporation, forming min erals. The chemistry of the brine solution determines a series of min erals which precipitate, with the first usually being calcite. Thereafter, Mg+Ca:SO4 ratios determine if magnesium minerals or gypsum precip itate next, and this determines the evolution into alkaline, sulphate or calcium brine end-members.
The evolution of brine mineralogy is somewhat regular and predict able, with diagnostic mineral assemblages precipitated in the drainage basin allowing brine chemistry to be deduced from the salt and sedi ments. These brine trajectories also control the potential of a ground water tract to contain economic mineralization.
Economic components of salt lake systems occur in three parts: the aquifers wherein salts are carried dissolved in brines; salt encrustations and efflorescences at the surface; and the solid residuum within the sedimentary succession, including salts, muds, clays and minerals with in and around the lake beds.
Brines within salt lake systems contain one of the most important el emental concentrations on the planet – lithium in brines hosted within salt lake aquifers. However, other important elements are extracted from brines, such as sulphate of potash (K2SO4), muriate of potash (KCl), sodium carbonate and sulphates, borates, and table salt.
Important by-products of brine production, in certain areas, include bromine and iodine. The world production of bromine is dominated by the Dead Sea, in Israel. Metal is obtained from brines, either as magne sium produced from bitterns, and sodium and chlorine which is obtained by electrolysis of sodium salt.
Brine extraction involves pumping the aqui fer brine into evaporation ponds, where the sun is used to evaporate the brine to satura tion with salt (normally NaCl) which is then re moved, and the resulting brine concentrated to precipitate the next salt such as potassium sulphate, with the residual bitterns enriched in magnesium. The same process is used to concentrate lithium brines.
Salt encrustations, usually dominated by simple table salt (NaCl) are mined from the surface of natural and artificial salt lake sys tems. Artificial salt lakes, such as the Dampier, Shark Bay and the proposed Mardie salt oper ation, evaporate ocean water to produce the salt, however in some areas salt is mined from natural accumulations within salt lakes.
The solid residuum of saline groundwater systems and salt lakes can contain significant mineralization in the clays, fringing aprons of carbonates, and even in dunes of salt blown off the surface of the lakes.
Western and South Australia’s world-class endowment of high-quality gypsum mineral ization is produced by ablation of salt efflo
rescences (gypsum crusts and crystals) formed on lake surfaces during hot summer months, with prevailing winds pushing the fine gypsum crystals into complex kopi dune systems. These accumulate on the down-wind margins of the salt pans, and can constitute hundreds of thousands of tonnes of 99% purity gypsum.
Within the fringing aprons of carbonate minerals that occur in the upstream and upper watersheds of salt lakes, calcrete and dolocrete may form significant cementation within sediments. Magnesite can form within the salt lake uplands as the groundwater chemistry evolves, and can even form evaporite crusts in certain alkaline lakes.
Calcretes can host mineralization, such as uranium and vanadium. Here the groundwater evolution of the aquifer from oxidized to reduced conditions occurs in concert with deposition of calcium carbonate; ura nium and/or vanadium in the palaeochannel is then deposited within the pore space. Australia’s vast, ancient regolith systems dominated by uranium-rich granite, which feed into palaeochannels and eventually salt lakes, contain world class uranium deposits.
Clays within salt lake systems may also be important targets for eco nomic mineralization. Groundwater compositions within salt lake sys tems can reach extremes unknown elsewhere in nature, such as extreme acidity or alkalinity, and extreme salinity. These are highly unusual fluid conditions which can result in alteration to unusual mineralogy. Two prime examples of the influence of extreme fluid compositions in saline environments are the mineral polymorphs halloysite, and palygorskite. Halloysite, a tubular form of kaolin, forms in acidic groundwater condi tions, and deposits are known underneath acidic salt lakes in South Aus tralia. Palygorskite, a tubular morphology of attapulgite-type clay, forms in highly Mg, Ca and Cl enriched saline lake and palaeochannel systems.
↑ Brine evolution pathways and mineral assemblages of evaporites (creative commons Australia 3.0 License, via Geoscience Australia)
Salt lakes contain 75% of the world’s lithium endowment and will re main an important source of the metal for decades to come. Exploration for lithium in brines worldwide is relatively mature but commissioning and proofing of evaporation processes is technically complex, and much work remains to exploit known but uneconomic brines that have not yet been proven up.
Brine abstraction and evaporation is a small but growing source of potassium sulphate in Australia and globally. Massive resources of potassium sulphate are reported from the Danakhil Depression in Ethi opia with more than 200 years of resources identified.
The exploitation of magnesium from brines in saline systems looks set to have a renaissance after the 2021 magnesium metal supply crunch. Magnesium brines in the USA, Canada and elsewhere are capable of producing magnesium chemical precursor salts as feedstocks for mag nesium metal with lower carbon footprints than the current carbon-in tensive Chinese smelting. Significant potential also exists for magne sium by-products in the Danakil Depression, with millions of tonnes of MgCl identified.
The economic potential of the solid residuum of salt lakes is poorly understood and woefully underappreciated. The chemical evolution of brines, saline groundwaters, and both alkaline and acidic chemistries, provides opportunities for concentration of many valuable elements, from transuranic elements, chalcophile elements, to those sensitive to eH and pH changes. Analogues of other clay-hosted deposits of lithium, magnesium, potassium and other critical elements are all potentially extractable from salts, clays, and carbonate aprons around salt lakes. Thorough understanding of the co-evolution of brine chemistry and mineralogy of sediments shows potential for identifying critical miner als – an example being halloysite and palygorskite.
Salt lakes are relatively sterile environments due to the harsh chemical environment, with extreme salinity, acidity and alkalinity possible – of ten wildly varied even within the same lake-bed. They are also, relatively speaking, quite durable environments capable of literally swallowing up almost any disturbance humanity wishes to inflict upon them – including whole bulldozers at times. On this basis, they can be prime locations for extracting minerals with lower ecological costs than other landforms.
Salt lakes and evaporite deposits within them are also quite young and replenish relatively quickly. The age of residuum in Australian salt lakes is from less than 2000 to 12 000 years, postdating the last glacial maxi mum. Evaporitic deposits have formed quickly and will replenish quickly if left to do so.
However, salt lakes are sensitive environments particularly regarding flux of water. One needs only look to the Great Salt Lake of Utah, where excessive use of surface and groundwater threatens to dry out the salt lake entirely, which may precipitate an almost unimaginable disaster. This threatens the survival of brine shrimp and migratory bird popula tions that rely upon them. Dusts from the lake bed carry heavy metals, and if they blow into the urban areas, catastrophic damage could be in flicted. Examples of salt lakes gone bad include the Salton Sea, in Califor nia, which is now a horrific alkaline wasteland due to over-extraction of water for agriculture.
Lakes are also not completely sterile. Extremophile bacteria thrive, and one only needs to visit Lake Hillier in Western Australia, to understand that salt lakes can be extraordinarily striking places to visit. Balancing
↑ ASTER scene of salt lakes near Meeline, Western Australia, with ferrous magnesite (red) and iron oxide (blue) showing carbonate apron and alteration of sediments in the catchment
tourism, environmental preservation and mineral extraction is always delicate. However, there are over 11 000 lakes in Western Australia alone, so there are plenty to choose from.
It is clear that one should visit salt lakes, and take what one needs, but they are environments which should be managed carefully, because they are such extreme environments, and such extreme concentrations of chemicals, salts and metals. Sustainable mineral extraction in these en vironments requires care and cannot occur without careful understand ing of hydrogeology, hydrology, and competing water uses.
Salt lakes are clearly extraordinary reservoirs of economic potential that, unlike other ore bodies, one can quite literally stumble across and walk upon billions of dollars of minerals – and you may not realise it. Salt lakes contain the key to a low-carbon future, both in terms of their endowment in lithium, but also in lower-carbon magnesium, uranium and are important sources of halides, borates and potassium.
Responsibly handled, mining on salt lakes can contribute materials for our modern society and future needs. We have only just scratched the surface of these fantastic formations in Western Australia and elsewhere. C
• Mernagh, T.P (editor). A Review of Australian Salt Lakes and Assess ment of their Potential for Strategic Resources GEOSCIENCE AUSTRA LIA RECORD 2013/39
• Warren J.K. Evaporites through time: Tectonic, climatic and eustatic controls in marine and nonmarine deposits. Earth-Science Reviews 98 (2010) 217–268
Get in touch with the author on LinkedIn
Silver is money. It has been for thousands of years. The white metal was first widely, or most famously, distributed in the Roman coin called the Denarii. Subsequently, the Spanish empire had for centuries a currency based on the silver peso, while the British had the sterling pound. For 76% of the US history, the country had silver coins being minted and circulated until the government of President Lyndon B. Johnson halted its use in 1964.
Disclosure: The author holds shares in Pan American Silver Corp., First Majestic, and Newmont, amongst other non-silver mining companies; company name mentions are not investment recommendations.
Today silver is held for investment purposes, but is also broadly used in jewelry, electroplating, photography to a diminishing extent, and industrial applications including use in solar panels. Considered a precious metal, silver is about eight times more abundant in the Earth than gold, but still remains an important primary ore in mining and has a role as credit in zinc, lead, and copper mines. And as in all post-Industrial Revolution expansion of mechanization and economy of scales, the amount of silver being produced has steadily been increasing. This is despite the extreme price swings that are prone to exaggerated lows and short speculative highs.
The silver price over the last several centuries was remark ably stable as many currencies were referenced to it along with gold. After the removal of the US dollar from the gold standard in 1971, known as the Nixon Shock, the price of silver climbed according to inflation but also had marked peaks pertain ing to market speculation. The major peak in 1981 came from the well-known attempt by the Hunt brothers to corner the market. The metal price went through a long depression in the 1990s, such that in the year 2000 it was at USD 6 per ounce and many of the historic silver camps in Peru were closed. The post-Global Financial Crisis of 2008 saw an all-commodity ‘Supercycle’ that peaked in 2011 with silver price spiking up to USD 49.80 per ounce and averaged at USD 35.16 for the year. The average price retreated to USD 15.66, which in 2015 had many of the Peruvian mines working near a breakeven basis. The current price hovering around USD 20 per ounce is not much higher, inflation-adjusted, from the low price in 2015. The to tal world silver production throughout history comes to 58.2 billion ounces, which at USD 20 per ounce equals USD 1.16 trillion.
Silver comes from many geological deposit types, including low-sulfidation epithermal veins where it occurs with gold, often mixed in electrum. Silver is a significant credit recovered from por phyry copper concentrates, such as at the open pits of Cerro Verde (Peru), Chuquicamata (Chile), Escondida (Chile), Butte (US), Bingham Canyon (US), and Antamina (Peru). The metal is found in carbonate replacement deposits, which are abundant in Peru and Mexico, skarn systems and from sediment-hosted base-metal deposits such as those in Poland. In the near-surface weathering environment the silver minerals breakdown and reconstitute easily, such that silver also forms a native metal, which provided some of the early met
al used across ancient societies. The Freiberg mines of Germany are particularly noted for their fine occurrences of horn silver, the natural, almost fibrous and twisty branches of silver. The main sil ver-bearing minerals, or silver sulfo-salts, are acanthite, argentite, argentiferous galena, cerargyrite, proustite, polybasite, tennantite, and tetrahedrite.
In 2021, the top-producing silver countries were Mexico, China, Peru, Australia, and Poland. Global production totaled to 822.6 mil lion ounces. Both Mexico and Peru, over the last 400 years, typical ly have been the leading world producers of silver. The companies with the greatest production in this last year were Fresnillo, KGHM, Glencore, Newmont, and Codelco. The companies that are mainly silver producers, each with more than 10 million ounces of annu al production, are Pan American Silver Corp., First Majestic Silver Corp., Silver Crest Metals, and Hecla Mining. The five largest silver deposits in the world are Potosi district or Cerro Rico of Bolivia with over 2 billion ounces mined (other recent estimates suggest it had over 3 billion ounces produced), Coeur d’Alene district of Idaho with a production of 1.2 billion ounces, Penasquitos deposit in Mexico with ~1.27 billion contained ounces, Rudna and Polkowice-Seinawa Kupferschiefer deposits in Poland each bearing 1 billion ounces of silver as credit to the primary copper mineralization. Deposit sizes can be classified as those having greater than 1 billion ounces of sil ver being supergiants, between 1 billion and 500 million as giants, at less than 500 but more than 250 million as mid-tiers, and those below 250 million ounces as lower-tier or small districts. The world has over 500 silver mines, many of which fall into the smaller side of endowment.
Exploration continues for silver, although it receives less media attention than gold, copper, and lithium these last few years. The Silver Sands discovery in Bolivia, held by New Pacific, has about 155.9 million ounces in its measured and indicated resource that is at a pre-feasibility stage. Other idle resources pending development and permitting is the massive Navidad 632.4 million ounce deposit (2022 M&I resource) in southern Argentina, controlled by Pan Amer ican Silver Corp, Pascua-Lama project in Chile holds some 675 mil lion ounces of Ag in addition to the gold resource, and the Udokan porphyry occurrence in Russia with about 1 billion ounces of silver.
Some examples of exceptional 2021 drill intercepts of silver are worth considering because the number of ounces required are greater than those reported for gold projects or mines:
• Brixton Metals Corp’s Langis project in Canada drill hole LM20-133 intercepted 2 m @ 188 oz/tonne.
• Radius Gold Inc.’s Marcicela project in Mexico had in drill hole RSM103 3 m @ 92.5 oz/tonne.
• Silvercorp Metals Inc.’s La Yesca had in the exploration drill hole ZK081 3.3 m @ 53 oz/tonne.
• Vizsla Silver Corp.’s Panuco project in Mexico hit in hole CS20-11 2.52 m @ 51 oz/tonne.
• Eloro Resources Inc.’s Bolivian project of Iska intercepted 8.11 m @ 32.9 oz/tonne in drill hole 11_C53_4.13.2021.
In general, for underground vein mining, equivalent silver values require a minimum of 5 oz/tonne to be economic. This may be higher depending on country taxes, dewatering requirements, ground sta bility and mining method, or if the CapEx on a new operations needs to pay for a mill and equipment.
In conclusion, silver is a valuable commodity that contributes to the economics across numerous deposit types. The metal price tends to move, although not perfectly mirroring, the price of gold, and when it does, the percent change can be a couple multiples of the gold price movement. While Reddit fans and hack cell-phone investors have been hyping silver stacking or hoarding, hoping for a social media movement for a market squeeze, the long-term out look regarding silver is reliable given its thousands of years of use and finite character for supply as compared to the inflatable fiat currencies of today. We have numerous undeveloped large silver re sources being held up for various social-political reasons and at the same time, relatively few new large deposits are being discovered. The upside on silver investing remains as a safe-haven for monetary collapse, and is suggested as being more exchangeable under said crisis than its golden big brother. C
If I am going to express the relationship between me and the earth sciences as an aphorism, I would call it a butterfly effect. When I was a child, a man brought a chalcopyrite-galena-pyrite-bornite to my father’s shop. I was immediately astonished by this sample, comprising part of a mineralized handspecimen assemblage, which would later become the cornerstone of my curiosity. Afterwards, I was of course going to study it during my time at university.
At university, one of my mentors said that you must do your best wherever you are. I took this advice because I was raised to be a perfectionist by my family. All my life I’ve tried to do the best thing any way, so I kept following this advice and applied it early in my career, even before I turned 30.
During my high school and university years, Turkey was in a political conflict, which af fected everything, for example, the economy, education, etc. Because of these conditions, geological engineering was a required subject for me. However, as I started studying it, earth sciences attracted me. Before going to univer sity, I had never been to a village or a town, I’ve always lived in the center of the city. So, on my first field trip at uni, I slipped and fell into a river. I learned my first real lesson that day: no matter how successful you are in your studies, real achievements won’t come until you put your knowledge into practice in the field.
For me, the first step towards those real achievements was learning how to walk prop erly on tough terrain and not be afraid of flies. During my geology internship and over the years since, I learned how to read nature, how to get to know people and myself, and earth sciences even taught me how to understand the philosophy of science - every chemical reaction that occurs in humans is similar to earth’s geochemical events.
In the end, after I graduated from a presti gious public university with an honors degree, I started working in different places and on a variety of projects. I began my career at a gov ernment institution called The General Direc
torate of Mineral Research and Exploration, or MTA (analogous to USGS in the US), which takes cognizance of the mentor-apprentice relationships. MTA is the only state geolog ical research institution in Turkey that was sending junior geologists to a general geolog ical mapping camp and was giving projects according to their specialization. I’ve always felt lucky during my years there as I found my mentors and completed a master’s degree in geological engineering. I would like to express
my gratitude to the managers there, as they provided gender equality in the workplace. If you were willing to see something, they would send you to the field to gain some experience. I started working on metallic mineral depos its geochemistry projects in accordance with my master’s degree. In particular, I gave sup port to projects involving precious and base metals, nickel, iron, etc. I carried out field stud ies and laboratory studies, such as mineralo gy-petrography, alteration petrography, fluid
Gülay exploring for ruby gemstones in Tanzania
inclusion studies, and ore microscopy. Over the 20 years in MTA, my life was spent in the mountains in the summer and on the micro scope in winter. For the development of me tallic projects, I worked both in the field doing mapping, drilling tracking, logging, etc., and in the laboratory with rock petrography, alter ation petrography, ore microscopy, and fluid inclusion studies.
During my time at MTA, some of the projects I’ve worked on were the Kayseri-Pınarbaşı Iron Project in Turkey, the Southern Anatolia Geochemical Exploration Project (base metal, precious metal) across the cities Diyarbakır, Elazığ, Adıyaman, Malatya, and the gold-silver project across Kırşehir, Kaman-Savcılıebeyit, and Terziali. I loved all my projects as if they were my children. However, my heart was always set on the ones involving base metals and gold. The experience I gained from work ing with my mentors, was the most valuable asset from my years with MTA.
After leaving MTA, I moved to Tanzania and started a consulting company called GSK Ge ology Consulting (Gskgeo). As soon as I got there, I immediately plunged into the depths of Africa with my geologist hammer in my hand and the love of science in my heart. I observed the rocks of granulite and eclogite facies and Banded Iron Formations (BIFs),
whilst working in the field. I was walking on the oldest continental craton and it was an incredible feeling for me. As a female econom ic geologist, the most important person that brought me here was Mustafa Kemal Atatürk, the founder of my country, who also gave women equal rights. Then and there, my heart filled with gratitude and my eyes with tears. After working at MTA for 20 years, I started supporting a private consulting firm in Tan zania and worked on different projects across many regions of the country, focusing on base metals, gold, and gemstones. Tanzania has dif ferent geology, commodities, and terrain from Turkey, for example, granulite and epidote fa cies rock units, and BIFs.
As an idealistic economic geologist, I have been trying to support projects both in my country and abroad for more than 30 years with Gskgeo. I especially can’t get enough of the pleasure of exploring new greenfields for gold. Some of my new findings in Turkey are the Sivas-Bakırtepe Gold Mineralization, Kırşehir-Boztepe Çimeli Gold Mineralization, Sivas-Yıldızeli Yavu Gold Mineralization, Kay seri-Pınarbaşı, Dikilitaş Gold Mineralization, Sivas, Hafik- Aktaş Gold- Silver Mineralization. In this adventure, as a female geologist, I know that I have to keep fighting as much as I can. If you love your job, everything is easier. C
↑
BRYSON DRILLING Phone 306-323-2202 Fax 306-323-2203 info@brysondrilling.ca www.brysondrilling.ca Canada
DDH1 DRILLING Phone +61 08 9435 1700 admin@ddh1.com.au www.ddh1.com.au Australia
DIAFOR Phone (819) 860-3957 info@diafor.ca www.diafor.ca Canada
Phone + 264 81 322 89 28 info@guenzeldrilling.com www.guenzeldrilling.com Namibia
KATI OY Phone 0207430660 info@oykatiab.com www.oykatiab.com Finland
MITCHELL SERVICES Phone +61 7 3722 7222 Fax +61 7 3722 7256 info@mitchellservices.com.au www.mitchellservices.com.au Australia
CORE TECH Phone (511) 255-5701 ventas@coretech.com.pe www.coretech.com.pe Peru
Phone +27 18 788 6349 sales@digitalsurveying.co.za www.digitalsurveying.com.za Africa
GEOLÓGICAS Phone +55 62 992720023 contato@trustsg.com.br Brazil
Terra Sonic International knows what it takes for you to succeed. We are committed to making the world’s most productive and reliable SONIC Drill Rigs and SONIC Tooling while providing the best service and support in the industry. Experience the Terra Sonic Difference today. www.terrasonicinternational.com sales@terrasonicinternational.com +1 740.374.6608 +1 740.374.3618
Phone (819) 824-3676 Fax (819) 824-2891 info@avddrills.com www.avddrills.com
Phone 90-312 385 60 50 Fax 90-312 385 35 75 info@barkomas.com www.barkomas.com
Phone 1-506-542-9708 Fax 1-506-542-9709 info@discoverydrills.com www.discoverydrills.com
www.diatoolglobal.com anthonygraham6@gmail.com
DIATOOL is a young and dynamic company, founded in 2010. The company manufactures impregnated and set core bits, casing shoes, reaming shells, and geotechnical drilling bits. DIATOOL products are sold in North and South America, Australia, Asia, Africa, and Europe. DIATOOL Diamond Products are manufactured in a modern well-equipped plant, using the latest manufacturing technology.
PROLENC
Phone (250) 563-8899
Fax (250) 563-6704 khodgins@prolenc.com www.prolenc.com
BOART LONGYEAR
Phone 1-801-972-6430
Fax 1-801-977-3374 www.boartlongyear.com
Phone 514-336-9211 Fax 514-745-4125 info@fordia.com www.fordia.com
NORTH BAY MACHINING CENTRE
Phone (705) 472-9416
Fax (705) 472-2927 luc@nbmc.ca www.nbmc.ca
PROLENC Phone (250) 563-8899 Fax (250) 563-6704 khodgins@prolenc.com www.prolenc.com
DIAMANTINA CHRISTENSEN
Phone +562 2620 7808 christensen@christensen.cl diamantinachristensen.com
DIASET
Phone 1-800-663-5004 bits@diaset.com www.diaset.com
DIATOOL DIAMOND PRODUCTS
Phone 852 2871 9028 diatool@163.com www.diatool@global.com
HOLE PRODUCTS
Phone (888) 465-1569 Fax (320) 631-0064 www.holeproducts.com
Get in touch at: editorial@coringmagazine.com for more information
Phone 1-801-972-6430 Fax 1-801-977-3374 www.boartlongyear.com
Phone 1 (208) 690-3111 info@DrillingHQ.com www.drillinghq.com
HOLE PRODUCTS Phone 909-939-2581 Fax 909-891-0434 www.holeproducts.com
Phone 86-510-82723272 Fax 86-510-82752846 sales@sinocoredrill.com www.sinocoredrill.com
BARKOM Phone 90-312 385 60 50 Fax 90-312 385 35 75 info@barkomas.com www.barkomas.com
CORE TECH Phone (511) 255-5701 ventas@coretech.com.pe www.coretech.com.pe
Phone 514-336-9211 Fax 514-745-4125 info@fordia.com www.fordia.com
Terra Sonic International knows what it takes for you to succeed. We are committed to making the world’s most productive and reliable SONIC Drill Rigs and SONIC Tooling while providing the best service and support in the industry. Experience the Terra Sonic Difference today. www.terrasonicinternational.com sales@terrasonicinternational.com +1 740.374.6608 +1 740.374.3618
Phone 514-336-9211 Fax 514-745-4125 info@fordia.com www.fordia.com
REFLEX Phone 1-705-235-2169 Fax 1-705-235-2165 reflex@imdexlimited.com www.reflexnow.com
Phone +55 62 992720023 contato@corefinder.com.br www.corefinder.com.br
DEVICO AS Phone +47 72870101 devico@devico.com www.devico.com
Phone 55 – (31) 3391 3810 Fax 55 – (31) 3391 3810 comercial@sondaparts.com.br www.sondaparts.com.br/
Phone 61 8 9445 4020 Fax 61 8 9445 4040 reflex@imdexlimited.com www.reflexnow.com
www.reflexnow.com reflex@imdexlimited.com 1-705-235-2169
REFLEX forms part of Imdex Limited, a leading Mining-Tech company. Our unique end-to-end solutions for the mining value chain integrate IMDEX’s leading AMC and REFLEX brands. Market leading REFLEX technologies enable drilling contractors and resource companies to drill faster and smarter, obtain accurate subsurface data and receive real-time information for critical decision making.
AMC Phone 1-705-235-2169 www.amcmud.com
DI-CORP Phone +1 (705) 472-7700 info@di-corp.com www.di-corp.com
MUDEX Phone +61 (8) 9390 4620 info@mudex.com.au www.mudex.com.au
CORE CASE Phone +55 51 3012 6531 info@corecase.com corecase.com
DYNAMICS G-EX Phone +61 7 54826649 sales@dynamicsgex.com.au www.dynamicsgex.com.au
PROSPECTORS Phone +61 (02) 9839 3500 Fax +61 (02) 8824 5250 sales@prospectors.com.au
For over 25 years, we’ve manufactured and perfected our proprietary Matex vegetable oil-based lubricants. Our product lineup includes downhole lubricants, specialty polymers, foams, tool lubricants, blast hole stabilizers, and thread compounds.