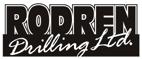
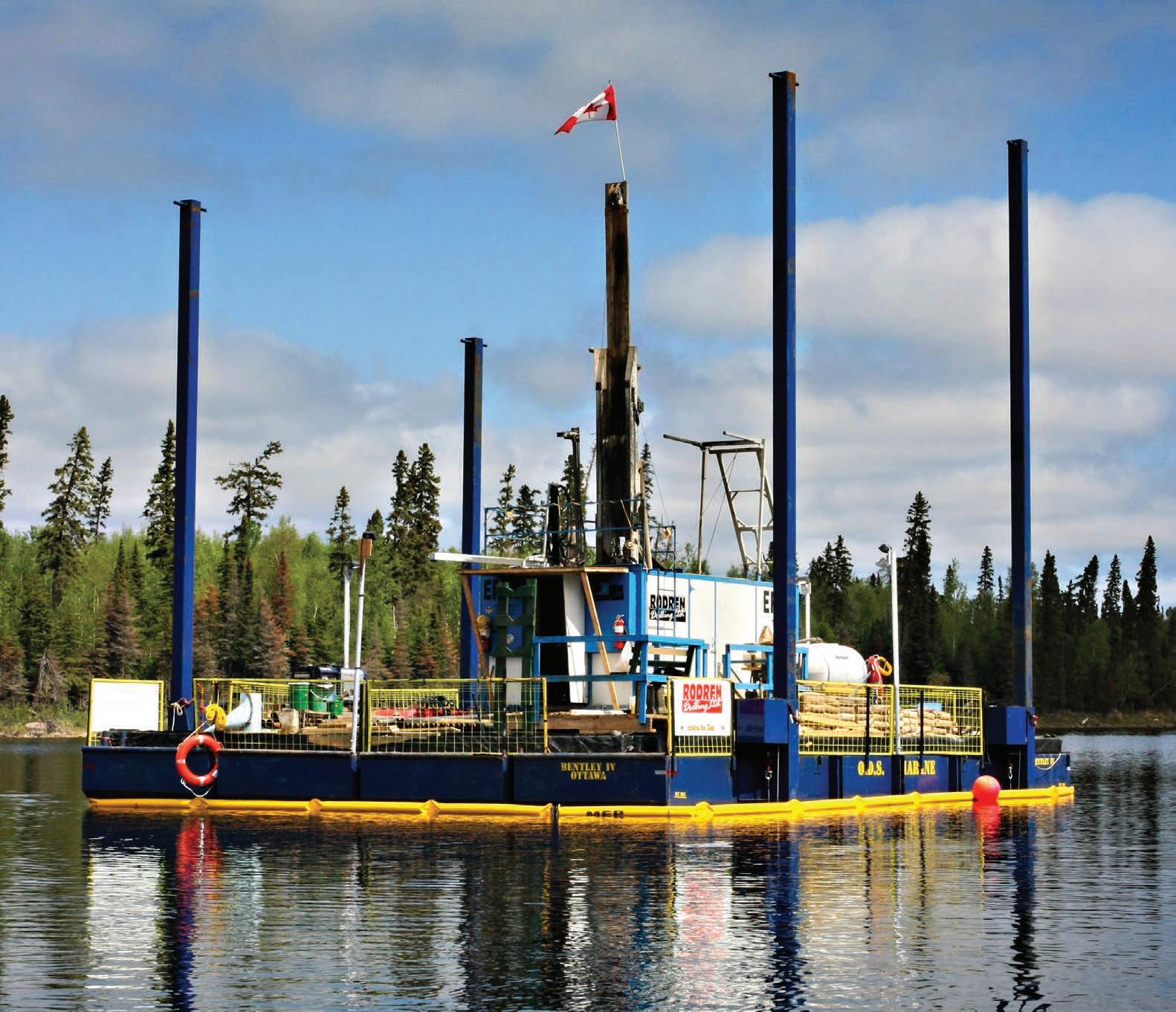
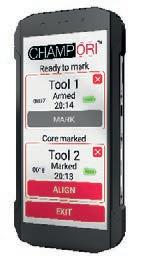

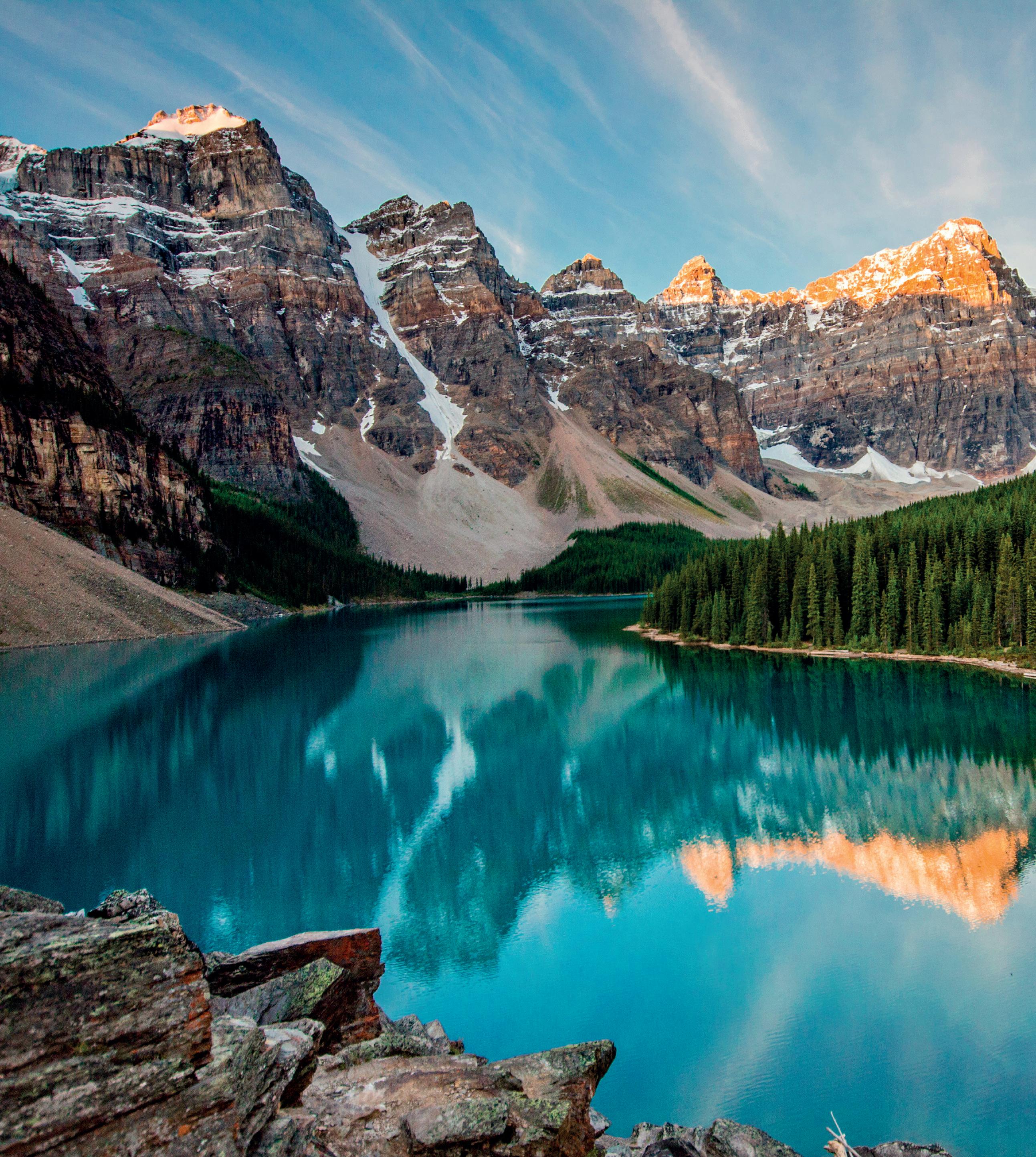
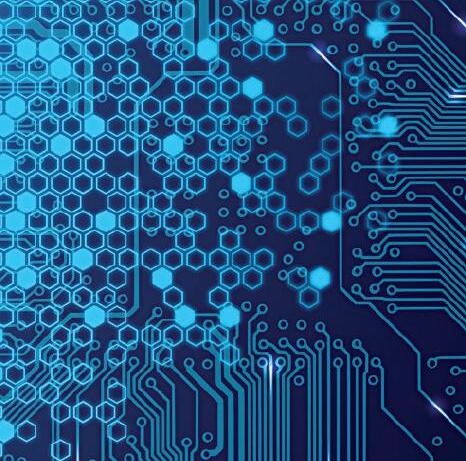
6 Exclusive interview: Harvey Tremblay, Chairman at Hy-Tech Drilling Ltd.
FOCUS
Rodren Drilling: Looking to the future by Kevin Norberg, President at Rodren Drilling Ltd.
20 Recon Drilling: Breaking records. Again. by Mark Scoles, General Manager LATAM at Recon Drilling SAC
22 HELM Diamond Drilling: Tackling the harsh northern terrain by Alan McPherson, Owner at HELM Diamond Drilling
26 How Fordia Powered by Epiroc and Major Drilling created a faster head assembly by Michelle White, Business Development and Key Account Manager at Fordia Powered by Epiroc
30 We welcome a new idea of the future by the Comacchio team
/EXPLORATION & MINING GEOLOGY
35 Q&A from the experts In conversation with Dr Richard Tosdal President at PicachoEx LLC
40 A few structural geology concepts for sediment-hosted Copper exploration
A case study from the Cashin Mine in the US by Dr Molly Turko, Structural Geology Expert & Dr Ali Jaffri, CEO at Applied Stratigraphix
46 Power to the people: How citizen development is driving a digital mining operations revolution by Udit Poddar, CEO and Vahishta Mistry, Content Lead at WorkOnGrid
50 What makes a geologist?
Thoughts on declining discovery rates, and other strange animals - a practising Ni-PGE-sulphide geologist’s (heretical) viewpoint by Richard A. Hornsey, Consulting Geologist, Ni-PGE Specialist at Richard Hornsey Consulting (Pty) Ltd
58 PDAC 2023: Back to the roots
Drilling services
Drilling equipment & accessories
Survey equipment
Miscellaneous
Harvey Tremblay Chairman at Hy-Tech Drilling Ltd.
Michelle White Business Development and Key Account Manager at Fordia Powered by Epiroc
Mark Scoles General Manager LATAM at Recon Drilling SAC
Alan McPherson Owner at HELM Diamond Drilling
Dr Richard Tosdal President at PicachoEx LLC
CORING MAGAZINE
February 2023
Cover photo
Rodren Drilling Issue 22
ISSN 2367-847X
Not for resale. Subscribe: www.coringmagazine.com/subscribe
Contact Us
Coring Media Ltd.
119B D. Petkov Str., Sofia 1309, Bulgaria
Phone +359 87 811 5710
Email editorial@coringmagazine.com
Website coringmagazine.com
Publisher
Coring Media
Editor in Chief
Grigor Topev
Executive Officer & Editor
Martina Samarova
Editor
Maksim M. Mayer
Section Editor –
Exploration & Mining Geology
Dr Brett Davis
Digital Marketing Manager
Elena Dorfman
Graphic Design
Cog Graphics
Coring Magazine is an international quarterly title covering the exploration core drilling industry. Published in print and digital formats, Coring has a rapidly growing readership that includes diamond drilling contractors, drilling manufacturers and suppliers, service companies, mineral exploration companies and departments, geologists, and many others involved in exploration core drilling.
Launched in late 2015, Coring aims to provide a fresh perspective on the sector by sourcing authentic, informed and quality commentary direct from those working in the field. With regular interviews, insightful company profiles, detailed product reviews, field-practice tips and illustrated case studies of the world’s most unique diamond drilling and mineral exploration projects, Coring provides a platform for learning about the industry’s exciting developments.
Open the box and GO. The GoGyro is fully integrated and designed specifically for simple, easy everyday use.
Configure your GoGyro as you need it for your surveys without unnecessary extra running gear. Simply add the needed fitting to run as:
• Core retriever
• Wireline
• Centralizers
Minimize downtime & Maximize efficiency. Simply GO Survey!
Chairman at Hy-Tech Drilling Ltd.
Harvey Tremblay started his career doing carpentry. He then climbed his way up from service work at drill sites, to exploration services, to working as both a driller and a foreman. He bought an off-theshelf JKS-300 drill rig from his old boss and launched Hy-Tech Drilling from his home in 1991. After a couple of small jobs, Harvey landed what turned out to be a nine-year contract. Over the next 30 years and countless completed projects, the company grew to a fleet of 75 drill rigs and 500 employees, operating throughout Canada, the US, Europe, and South America.
Nowadays, Harvey is the Chairman of Hy-Tech and in the past has served as Director of both the Canadian Diamond Drilling Association and the Association for Mineral Exploration in British Columbia.
Grigor Topev: Harvey, thank you for taking the time to answer our questions. Firstly, tell us your current business status and if there are any projects or initiatives you are working on. Harvey Tremblay: Hy-Tech Drilling has gone through an aggressive period of growth these last few years with projects across Canada, the US, South America and Europe. As we’ve grown, the company has effectively morphed into several companies – including a dedicated R&D arm to create new hardware and software for both surface and underground applications. It’s always been our goal to innovate and improve every aspect of what we do. Now we’re partnering with others who share the same vision, while looking at ways to open up and share many of these new technologies with the industry as a whole.
GT: You began your career in construction. Tell us the story of how you switched to drilling.
HT: I was doing carpentry work for a man named Henk van Alphen, who also happened to own an exploration services company. He asked me to help them build camps in some very remote areas, then one thing led to another. When you’re already out in the field, the jobs just keep coming because it’s too expensive to ship in somebody else. I was putting in the grid lines, setting up the power system, the water system, setting up radio antennas, taking soil samples, and staking new claims. At that time, I was also building drill pads by myself with a chainsaw – not a safe practice these days, but it was a huge learning experience.
Then Henk got his hands on a diamond drill, and everything changed. He’d hired a couple of drillers and I became one of the helpers. These guys wound up quitting as fast as they could be hired, so I was promoted very quickly until I became both the drilller/foreman and the
mechanic. I would work on the drill when the season was over, taking it apart, putting it back together, and learning a lot as I went. That’s how it all started.
When the industry went into a downturn, I made a deal with Henk to buy the drill. I only had enough money to pay for half, but another guy came on the scene to buy Henk’s dozer and after chatting for a bit, he offered to buy the other half with me. We went into business together for a few years, then I bought him out.
GT: So, I assume, this is the origin story of Hy-Tech Drilling, right? Where was your first project?
HT: Yes, indeed, the origin of Hy-Tech starts with my old partner Joe Nouch and the offthe-shelf JKS-300, which we’d bought fromHenk. We made a few modifications and ran the drill for two or three years on some small jobs, then Joe decided to get out of it and offered to have me buy him out.
Joe agreed to four payments over two years on a promissory note, so I had to work very hard in a short time. With a deal in place, I was able to get an operating line from the bank using the drill as collateral. It was ‘jump or walk away,’ and I decided to jump in with both feet.
The drill itself came with a small job that had already been booked with a company called Ore Quest, which gave us our start. Our next project was with Peter Holbeck from Homestake, and we were off to the races. These were pretty small jobs, but for one drill it was an ideal way to start. Having to do everything makes you into a very busy person – drilling all day, then going home at night to wrangle parts and supplies.
I had just paid off Joe and set out to build a better drill. At Homestake, a young Andrew Kaip was aware of my plans and called me with a project that required exactly the kind of drilling solution I had in mind. He asked me what I would need to tackle this job. I told him I’d need a CAD 50 000 advance, a contract in hand, and a month to get ready, which he agreed to. This allowed me to tackle a new design that would marry power with portability. Andrew’s project was proof of concept for our design, which then allowed us to land what turned out to be a nine-year job at Eskay – enabling us to build out much of the infrastructure that supports Hy-Tech to this day. When we built our shop, our largest competitor had just been sold and was in the process of shuttering theirs. We had a little corner of Northern BC to ourselves for a few years, along with a fly drill that could do
5000 ft (1524 m). The timing could not have been better.
GT: Please share with our readers the relative size of Hy-tech Drilling today.
HT: We have a fleet of 75 rigs, with no more than 50 turning at any given time. We currently sit at around 500 employees, drilling approximately 600 000 m (1 968 503 ft) on an average year. Hy-Tech Griffith is a recent partnership in South America, where we are operating another dozen rigs on some truly challenging terrain at very high altitudes.
come to life. This all comes back to our quality system to drive improvement. The other thing that stands out is our infrastructure. We pick an area to support, then we invest in it. If we had one drill in every country, it wouldn’t work out the same way. We focus on areas and support them fully.
From day one, innovation was a big part of our DNA. Designing and building our own rigs, shacks, support equipment – it’s again a driver for us to always be better and build better equipment, and we were effectively forced into it because other companies simply wouldn’t build drills the way we wanted them built. Going all the way back, our drill was designed around the specs of personnel-sized helicopters, versus ferrying in a medium sized one. This cut the bill from CAD 50 000 per move to CAD 1000, so it was a very big deal.
‘I think what people see more now is a reflection of the steps we took to manage quality. Adopting ISO 9001 helped us create a culture of constant improvement, where we’re always looking for new ways to add value and reduce any unknown variables.’
GT: What is your approach towards clients and partners and what do you think makes Hy-tech different from other companies? What were/are the key factors for success?
HT: What makes us different, I think, is that we’ve become quite proactive over the years. We have a talented group that used to pride themselves on their responsive firefighting abilities, and now we’ve become more focused on fire prevention. It’s not as ‘exciting,’ but we’ve always been very careful about maintaining quality and making sure that the things we say we’re going to do actually
GT: What is the most challenging drilling project your company has ever worked on?
HT: The one that really stretched us was called the ‘Sullivan Deeps.’ The Sullivan mine went for over 100 years, but when you looked at the ore body, it felt like only half of it had ever been realized. It was a common belief that half of it was still out there. The company we were working with was confident they had found it, but it also happened to be under the Kimberly Water Catchment Area.
There could be no roads to this site, and they needed us to drill 7000 ft (2134 m). We couldn’t guarantee 7000 ft, because at that point we’d only drilled 5500 ft (1676 m). We had to do a lot of modifications to the drill, but we ended up hitting the horizon of the ore body at 8856 ft (2699.3 m) in two holes, back-to-back. It was quite an unusual thing to tackle, where the best we could promise was to do our best.
Funny thing, we ended up trucking in this fly drill, because they got approvals to build a road at the last minute. So, the fly drill never saw any airtime, but it did the job anyway and showed what our little drill could do.
GT: Please share a particularly funny story from your drilling days.
HT: We had just bought the drill from Henk, we had our hands full with two little kids on a farm, we had a mortgage and all the bills that young couples have, and everything was on the line.
Late in that year, I was lucky enough to land a job to drill a project in the coastal mountains in some very challenging terrain.
I wanted to make sure the drill head was in good working order, but we didn’t have a shop to work in. So, I said to my wife, ‘I gotta bring this thing to the house.’ Much to her chagrin, I ended up doing all the work on our kitchen table!
Finally, we took it to work, and it did the job. It’s funny to think about servicing my first drill in our kitchen now, but I definitely wasn’t laughing back then. That’s what it looks like when you start a drilling company with no money. It forces you to be resourceful, because you must get the job done no matter what.
GT: Please share more about your mentors or the people that taught you drilling. What skills did you find useful?
HT: In the beginning, when Henk threw me in the deep end, I thought, ‘How am I going to keep up?’ No one was teaching me, so I figured I would do everything I could to teach myself. I ordered an old book from one of my suppliers called The Diamond Drill Handbook by James D. Cumming, and I studied it from cover to cover. It gave me a good understanding of how drilling had evolved over the years, a complete breakdown of all the tools, the case studies for different challenging projects, and the technical know-how to solve many different problems.
Out in the field, I had the pleasure of working with some old-time drillers – real rugged types who, in their day, would move drills around the bush with the hoisting cable of the drill. The frame of the drill was built like a toboggan, and they would winch themselves from tree to tree. The crazy lives these guys lived inspired me all on their own. It would take days to move from one spot to another, but they got it done. Once they got on a site, they’d make a tripod with three suitable trees and hang a pulley on it to pull rods. This was before hydraulics came into the picture. You had to use a wrench to tighten the jaws and they were all independent, so it was a challenge to keep them centered. This predated carbide inserts, so the steel jaws would get dull, and you’d have to tighten them like you would not believe.
Marcel Carrier was one of those guys who taught me a lot. He’d been all over, and just his stories while we were driving across Canada from North Bay and back – the questions I was asking and his can-do experiences from around the world – it all contributed to making me a better driller.
GT: By chance, I’ve visited a couple of HyTech drill sites. I was always impressed by how mobile, organized, and efficient
the working space was. How was that achieved?
HT: When we designed the drill, we made the footprint compact on purpose because we knew we’d be flying. What really shocked people was the fact that this small hydraulic fly drill could also reach 5000 ft (1524 m) in depth.
I think what people see more now is a reflection of the steps we took to manage quality. Adopting ISO 9001 helped us create a culture of constant improvement, where
GT: You have vast experience in the exploration drilling industry. How has it changed since you started?
HT: The beginning was a rough time. Hard hats weren’t even that common. Everyone smoked a lot, drank a lot, and it was rare to see ten fingers on any one person. It was not very disciplined at all. People just went in and did their best and worked very hard. Drilling depths in the thousands of feet versus hundreds of feet changed our industry immensely. Now, it’s bigger diameter and much deeper than it’s ever been. The equipment used to be all cable with a hoist, a basket, and winches. I called our business Hy-Tech Drilling because I wanted to go all hydraulic. I knew something had to change. I wanted to get out of the baskets and onto the deck. Our focus on hydraulics helped build our company.
‘ We’ve introduced some significant changes for drill performance , information tracking, water management, automation and most recently, new ideas around directional drilling for our customers. Faster, better, cheaper, safer - those are always good goals to have .’
we’re always looking for new ways to add value and reduce any unknown variables. Everything from the motor to the tools is standardized. Everything is brought to one standard, from the way we work to maintaining our drills. We figure out the best way, then we adopt it across the board. It’s saved us all a lot of time and trouble.
On every job, all the rigs are standardized. Europe sees these same rigs mounted on tracks, underground is an entirely different configuration, but it’s all the same components and quality standards at the end of the day.
GT: Is there a game-changer advancement or a new technology in diamond drilling that you wish existed nowadays?
HT: The advancement I wanted from DAY ONE was understanding what was going on at the bottom of the hole. When the bit was 8000 ft (2438 m) in the ground, and all you had was the sound of the exhaust and gear backlash to interpret, it was more art than science. Things have certainly improved, and we have more gauges that help us, but measurements are still from the surface. This is something that’s being actively worked on by a number of players, but I feel like we’re making real advances towards a solution. Truly, all our innovations center around better control and better information. We’ve introduced some significant changes for drill performance, information tracking, water management, automation and most recently, new ideas around directional drilling for our customers. Faster, better, cheaper, safer – those are always good goals to have.
GT: There is a well-known labor shortage within the industry, particularly in Canada. What do you think companies should do to solve it?
HT: I think it boils down to three things. The first would be automation to increase safety and reduce the physicality of the job, enabling a much larger workforce for us to tap into. The second would be to find ways to bring in more people from abroad. Lastly, I think the industry needs to do more to educate people around the life of a driller or driller’s helper. The job is kind of mysterious today, in that you have to hear about it
from another person who’s already working in it. We can do much more to increase the visibility of our industry, because let’s face it: you’ve really got to have a head in this business. Not everyone gets to be an astronaut. This is a job that’s heavily supported and requires the right kind of person to succeed.
GT: In your opinion what makes a good driller? What qualities should a driller possess in order to advance to foreman and even beyond?
HT: For us, the thing we look for is people that can get the job done, no matter what. It’s the ‘can do’ attitude we need, because there’s a million reasons why it can’t be done. Our people are our people because they can modify and change things up to keep it all moving forward. It’s an attitude.
You also have to be able to work with people. The wrong person in camp simply
won’t last. In the end, these people weed themselves out, because everyone has to depend on each other to be successful and safe. It’s all about the team. A healthy camp becomes a very close-knit group, with little tolerance for toxicity.
GT: What is your take on automated rod handlers? I have a feeling that Hy-Tech is not a huge fan of this technology…
HT: We have some rod handlers. We are huge fans of rod handlers. We just need to find a solution that’s practical. The early versions were as big as the drill itself, with too many moving parts.
I do wish we could eliminate the human element from rod handling because that’s where most of the safety and physicality issues happen. And we’re working to come up with a better solution for this – something the industry hasn’t explored enough yet.
If we could achieve this, we could open the industry to more diversity. We are putting in serious work to find a more elegant solution. The current solutions are just a bit too primitive. They cost a lot and take a lot of time. Long term, it’s our goal to create a solution that is cheaper, faster, better and above all, safer.
GT: Considering my background and involvement in directional drilling, I have to ask you: what does directional drilling lack and what would you like to see available?
HT: My view is that we need to find a better solution than the ones that are currently available. They are, for most clients, prohibitively expensive and time-consuming. It’s our goal to lower the cost and reduce
the time required for this type of work. Hitting the target every time would be nice to offer if the cost was reasonable.
GT: We are facing increased inflation (among many other difficulties). What are the changes you see in your business?
HT: Wages are far and away our largest cost, but the industry is still experiencing a shortage of workers. We’re always impacted by outside costs like steel because it affects so many of our own estimates. We need to think about these things when we’re bidding.
The cost to finance our growth is another consideration. On the one hand, we have an increase in work. On the other hand, the cost of borrowing is now much higher. The rising risk demands that we be more cautious about the companies we engage with. Do they rely on the market, or do they have their own source of revenue? Organic growth is great if it can be done without taking on significant long-term debt. It’s the small operators that rely on the junior market that are most vulnerable.
GT: Following up from the previous question, what is your advice for drilling company managers and leaders?
HT: Being financially conservative has certainly served us well over the years. The markets rarely go up at the same speed that they go
down – the rise is gradual, but the fall can be overnight. We’re in a big upcycle right now, but we all know it won’t stay that way. Being prepared for both success and failure puts you in a better spot.
GT: Harvey, a final question, looking into the next five to ten years… Do you think we will see an increase in diamond drilling activity?
HT: I would say it would be an increase in five, but the next ten are unknown. We may hit an apex before ten years. You can always bet on eventually hitting a saturation point. That would be my guess. I would expect things to ramp up to some level where we can keep up with demand. Today, it feels like there’s just not enough rigs to go around. But these things always get overbuilt, so there’s that. As always, there will be drillers that get checked out along the way. What I can say is there will always be room for big ideas and better solutions, regardless of where the market chooses to take us next. C
Trusted, proven, and precise. For generations, Boart Longyear has designed and manufactured some of the most advanced exploration products in the industry
Longyear diamond bits represent a long tradition of innovation and dedication to the drillers and geologists who rely on us every day. Find your local sales team online.
by Kevin Norberg, President at Rodren Drilling Ltd.
Rodren Drilling (Rodren) was founded by Rod Cyr on June 23, 1977, in Canada with one drill rig and one crew. The mission was to provide the best diamond drilling contractor service in North America.
Over the 45 years since, Rodren Drilling has continuously strived to upgrade their equipment, train their staff, work with a safety-first attitude, and grow responsibly in order to listen to, match and exceed the expectations of clients. The company built a fleet of 20 drills and 150 employees and countless successful projects throughout Canada and abroad.
The 45th anniversary of Rodren Drilling in 2022, was marked by a large event so that all suppliers, friends and industry people could celebrate at the Assiniboia Downs Racetrack in Winnipeg, Canada. Last year also marked another significant achievement: the completion of a 2610 m (8563 ft) deep hole.
With the company’s founder Rod Cyr retiring, Kevin Norberg was appointed president in order to create a vision for the next 45 years of business focusing on adding new services and strategic partners, new staff and reformed cultures, and expanding Rodren Drilling’s fleet with new drills, trucks, and support equipment and certainly new contracts.
With new leadership, growing team, vision, and culture, Rodren Drilling is ready to tackle anything the future has to offer!
Rodren Drilling is growing internally with both the addition of drill rigs as well as growth and diversity via strategic partnerships. The company has added many services to its menu via a very valuable partnership with Earth Drilling, based in Calgary, as well as Fasdrill Directional Services, a Calgary-based directional drilling firm. Rodren has supportive relationships with both companies allowing to offer nearly every drilling service available under its brand and it is currently negotiating other potential partnerships to expand its reach to better cover Canada’s Eastern regions.
Additionally, Rodren has strategic partners in all corners of the industry – fixed wing aircraft, bulk fuel, rotary aircraft, camps, logistics, land freight, drilling services, geotechnical drilling, directional drilling and supply chain management.
Rodren Drilling offers the following specialized services:
• Surface diamond drilling;
• Remote/arctic/permafrost/deep holes/deep overburden;
• Helicopter supported drilling;
• Ice-based drilling and construction;
• Underground drilling;
• Environmental and Geotechnical drilling;
• Barge drilling;
• Mud Motor Directional steering and drilling (GWD Drilling Technology).
Rodren Drilling enjoys a large number of clients and partners around the world and has provided the services needed with pristine quality. The new additions to the team at Rodren Drilling in 2022 bring a fresh outlook to a legendary and prosperous name in the diamond drilling industry.
The management team has diversified its client base and geographical footprint in the past twelve months and has added work in the US, based out of Nevada, Arizona and California. Rodren’s mission to work their home province of Manitoba has been successful. The company has mobilized their first underground rig and has increased their volume in the Canadian province to up to ten drills.
Rodren Drilling has completed various projects for its most valuable clients: Qulliq Energy Corp, Callinex, Hudbay, 1911 Gold, New Age Metals, International Lithium, CNRI, RESPEC, Q Gold, First Mining, Sinomine, Trillium Gold and many more to come in the future.
Rodren’s work in Baker Lake was completed for a client and involved a specific scope of work. The assignment was to mobilize an aircraft-portable diamond drill rig to Baker Lake from Winnipeg on short notice to drill a 600 m (1969 ft) permafrost borehole and install a specialized instrument to collect temperature data from the rock formation. The work was to be done in the summer originally, but due to permit delays, it was pushed to November.
This involved packing a complete drill package, trucking to Yellowknife and loading into a Lockheed L188 Electra aircraft and mobilize to Baker Lake in early November in absolutely terrible weather conditions. The crew was mobilized to move all of the gear to the pad where
they executed the plan. Drill the borehole, install the instrumentation and make it home before Christmas which they did as if it was easy.
The project was done within the timeline, the cost was completed within a few thousand of the budgetary estimates and the crew was able to pack up and make it home for Christmas.
Barge drilling enables drilling under a body of water by setting up a barge to support the rig on top of the water. The benefits of drilling on a barge are that it is more predictable than ice drilling, it is cost-effective, flexible and more time efficient, as the barge is simply moved to a new location without the hassle of preparing the site or using fly transport.
Rodren has always been known as the go-to contractor for specialized projects that involve barge and ice drilling for both exploration as well as geotechnical and specialized drilling assignments.
‘From pre-planning to demobilization, Rodren upheld a professional focus on safety, commitment to minimizing environmental impacts, while maximizing production of clean accurate core. 1911 Gold was extremely satisfied with Rodren's performance on our helicopter and land-based programs in 2022 and we look forward to new partnerships in the future,’
Devin Pickell, Chief Geologist, 1911 Gold Corporation.
↑ Rod Cyr and family on the 45th anniversary of Rodren Drilling
The company’s barge was mobilized to the drilling site, and a partner’s sonic drill was placed on to the platform. The drilling teams were able to achieve the clients’ goals while maintaining an ecofriendly and safe work environment.
In 2022, Rodren was brought into a project with its one-of-a-kind EF 100 rig to provide a drilling service that ended up evolving into an important specialized project requiring drilling down to depths well beyond 2500 m (8202 ft) with specialized environmental protocols to meet and exceed permit requirements. The crews were up to the challenge and acted in accordance with the required protocols with ease.
Rodren Drilling has made a commitment to overhaul its entire fleet in 2022 which was done in-house with the exception of one drill that was completed by Perfect Performance based in Cooks
‘What separates Rodren from others is their dedicated team that goes above and beyond in every measurable category to make our exploration campaigns a success. They have the necessary experience, work ethic, equipment and relationships to overcome any challenge that is inherent with executing in varying work conditions typical in exploration,’
Max
Porterfield, President & CEO, Callinex Mines Inc.
‘Rodren has been great to work with so far. Both the knowledgeable drillers and up-to-date management systems have made our work together seamless,’
Aaryn Hutchins, Project Geologist, Tantalum Mining Corporation of Canada Ltd.
↑ Rodren’s EF-100 drill nicknamed ‘Pinky’, which aims to raise awareness for cancer care
Creek Manitoba. Currently, Rodren’s fleet consists of over 20 drill rigs, which can tackle a range of depths, techniques, and terrains:
• DDM EF-50
• DDM EF-50 Fly
• DDM EF-75
• DDM EF-100
• EF-75 Track Mount
• Duralite 1800N Skid/Heli-portable
• MPP Discovery 1
• MPP Discovery 1.5
• MPP Discovery 2
• Epiroc U6 Deep Hole
• Gus Pech Truck mount Sonic
• Boart Longyear LS 600 Full size Sonic
• Boart Longyear LS 250
• Foremost DR24 Dual Rotary
• TerraSonic TSI 150 Crawler Sonic
• BBS Classics
In drilling, every team can be a high-performance team, yet very few actually are. At Rodren Drilling, one of the goals is to build such high-performance teams on every project and for every hole.
A high-performance team can be defined as a group of people with specific roles and complementary talents and skills, aligned with and committed to a common purpose, who consistently show high levels of collaboration and innovation, that produce superior results. The high-performance team is regarded as tight knit, focused on their goal and nothing else. Team members are so devoted to their purpose that they will surmount any barrier to achieving the team’s goals.
Within the high-performance team, people are highly-skilled and are able to interchange their roles. Also, leadership within the team is not vested in a single individual. Instead, the leadership role is taken up by various team members, according to the need at that moment in time. High-performance teams have robust methods of resolving conflict efficiently so that conflict does not become a roadblock to achieving the team’s goals. There is a sense of clear focus and intense energy within a high-performance team. Collectively, the team has its own consciousness, indicating shared norms and values within the team. It feels a strong sense of accountability for achieving their goals. Members display high levels of mutual trust toward each other.
To make this theory of a high-performance drilling team a reality, Rodren believes that people are the most important asset to the company and invests heavily in both physical and mental health.
Continuous training for all staff is another important aspect. Alongside the training and courses, company members have a mentor/leader to guide them toward their goals, personal and career growth, and upskilling.
Drillers Edge drill rods by Di-Corp are earning a global reputation for reliable, long-lasting performance under some of the most challenging conditions.
What makes Drillers Edge drill rods different? Our choice of premium quality steel. Our approach to stress relieving heat treatments, precision machining, intense quality controls, and the unique, specialty finishing process we use to harden our R™ Thread for unmatched pull-back strength.
All these differences help Drillers Edge to produce premium coring rods that deliver:
• More even pin and box wear.
• Better deviated drilling performance.
• Superior drill string life.
Di-Corp is a registered trade name of Diversity Technologies Corp.
The company has a well-rounded team from various backgrounds, bringing their unique knowledge and experience to every project. Team members come not only from drilling and mining but also from the sectors of oil and gas, heavy equipment, construction, engineering, and industrial procurement and industry sales. The wide diversity, paired with the training and mentorship, has brought multiple novel solutions to problems to each of Rodren Drilling’s projects.
In order to have high-performance drilling teams operate to the best of their abilities, the company believes that there should also be an allstar support team. To this end, Rodren Drilling has established an excellent support team of certified industrial mechanics, procurement specialists, welders, and hydraulic techs that can develop custom-tailored solutions for every project and do in-house R&D when needed. Furthermore, there are fully-fledged departments to deal with operations management, accounting, payroll, and accounts receivable, so drilling teams can focus on drilling and be absolutely certain that everything else has been taken care of.
Culture is the number one driver to the Rodren Drillings approach to ensuring reduced risk of accident or environmental impact during projects. The company’s approach and slogan are tied to all of its Visible Felt Leadership training (visits by management to workplaces, create a platform for both management and employees to discuss daily
1.800.661.2792
info@di-corp.com
www.di-corp.com
safety challenges of the tasks at hand); we all judge ourselves on what we do when nobody is watching.
Rodren Drilling strives to have a transparent culture where all employees hold each other accountable regardless of position or title. The company stands by its values and sets boundaries where needed, so drillers do not take any unnecessary risks on behalf of clients and their own colleagues.
An equally important approach is when beginning a project – the entire company looks at all variables that teams may encounter in the process of obtaining and delivering the core samples to clients. They also look at the amount of equipment needed, the terrain.
Throughout Rodren Drilling’s history, safety and environmental responsibility have been paramount. The company takes great measures to ensure that crews are well-trained, equipped, and protected for every job they undertake. The Safety, Environment and Quality program ensures that all standards, be it clients’ or regulators’, are met and exceeded.
Rodren Drilling is CORTM Certificated with the Canadian Federation of Construction Safety Associations, which is recognized throughout the world.
The company has properly and thoroughly insured its equipment and practices a culture of safe drilling and proper resource documentation to ensure consistency. Their employees are insured and protected with well-documented health and safety practices, which include a full Environmental Impairment Liability policy, Bodily Injury, Property Damage, and Completed Operations.
Rodren holds weekly, monthly and large yearly meetings to continue to grow and change its viewpoint on the industry. Supervisors learn about the business aspect of diamond drilling and why the numbers are so important to continue a sustainable, profitable and respectful relationship with all industry partners. The saying in business holds true – ‘If you’re not profitable – your future is predictable.’
Rodren Drilling believes that it is essential to give back to the community. Especially, since much of the company’s operations are conducted in close proximity to indigenous ancestral lands. The company has provided travelling and registration support for the following local athletes, sports teams and events: Haylee Welwood, Team Manitoba 16U Girls 2023, North American Indigenous Games in Halifax NS, Basketball.
Rodren Drilling also attracted a lot of looks with Pinky – their pink drill EF-100 drill, which aims to make the drilling industry aware of Cancer Care. The slogan of the campaign is Drilling for a Cure Rodren Drilling is also a large supporter of the Manitoba Women in Mining chapter as well as the Manitoba Prospectors Development Association and the mineral sector of Manitoba in general. Recently,
the company sponsored and provided instructors for training for indigenous workers looking to join the industry at the Manitoba Mineral Convention, and is also a sponsor of all association events, including the famous Reconciliation Gala, which allows guests to support promoting and advocating indigenous rights.
The company also holds several junior venture partnerships with the communities they operate in.
The future looks bright for the drilling industry, Rodren’s staff, and partners as they move into a new age of exploration. Looking for critical and industrial metals, continuing to search for precious metals and adapting to new technologies and opportunities as they arise.
The company’s greatest motivation is to grow its workforce from within, cross-train its people and grow their skillsets, continue to add strategic partnerships and grow a specialized workforce that can look for opportunities, should they wish, within the healthy and transparent group of companies.
Rodren Drilling aims to continue to support the drilling sector and secure its future and people for at least another 45 years. C
“Devico shall be world leading within directional core drilling, borehole surveying and belonging software.”
EST. 1988, Viktor Tokle
by Mark Scoles, General Manager LATAM at Recon Drilling SAC
Recon Drilling (Recon) recently expanded into the Chilean market and landed at Atex Resources’ flagship Copper-Gold Valeriano project. The Project is located approximately 125 km (78 mi) to the southeast of the city of Vallenar, Atacama Region, Chile and 27 km (17 mi) northeast of Barrick’s Veladero Mine. The clients requested a total of 10 000 m (32 808 ft) of deep hole directional drilling and a company that could provide this service entirely inhouse. Within weeks of choosing Recon, they were already setting up in Chile and were contacting vendors to get the ball rolling!
This was to be the first directional drilling program implemented by a junior company in Chile and dependent on the success of the initial drilling, the program could be extended with another 10 000 m (32 808 ft).
The location of the Valeriano project could also prove a challenge for a less-than-prepared company. Elevations vary from 3800 to 4400 m (12 467-14 436 ft) above sea level, meaning that we had to choose the right drill and equipment for the job.
In preparation, two specially-prepared Sandvik DE740 track-mounted drills were selected. With capacities of 800 m (2625 ft) in P-size, 1200 m (3937 ft) H-size and 1800 m (5906 ft) N-size, a small footprint and
9 m (29.5 ft) pull they were the perfect choice for this project. Recon’s Maintenance Team for the LATAM region, which includes experts from Chile, familiar with the difficulties of working at high altitude (air is less dense), prepared the drills, which were required to be fully disassembled and upgraded for power and set up in Recon’s Lima workshop. The team has come through yet again as has been proved by the rigs’ performance!
Recon also invested into all new lightweight drill pipes from Boart Longyear with stronger joints, making them the perfect rod for this type of project, especially through the directional portion. Additionally, Recon chose Oriented core, gyro-surveying equipment and downhole motors, provided by IMDEX Chile.
Recon’s team at start up included Australian General Manager Mark Scoles, who conducted the hole planning in-house allowing for complete control of the operation and avoiding the common challenges, together with international directional drilling specialists with Chilean drill crews and supervisors. Since directional drilling is a relatively new technique in Chile, and the region, the company invested heavily to ensure local crews receive continuous training.
Drilling began in October 2022 and having designed the holes, Mark Scoles was on site
to drill and complete Recon’s first Navi cut (NX) in the southern half of South America. Everything went as planned. That first hole was completed at 2130 m (6988 ft) in N-size. A 1275 m (4183 ft) daughter hole was also completed.
With a continuous cut of 63 m (207 ft) –between 870 to 933 m (2854–3061 ft) – the final target was reached at a depth of 1650 m (5413 ft) within 5 m (16.4 ft) of radius. The team conducted a whopping 717 m (2352 ft) of free drilling after the cut without any corrections by using drilling barrel configuration and drilling techniques to keep the hole tracking.
This daughter hole commenced from a vertical hole at approximately 850 m (2788 ft) with a casing wedge used to deflect out of the parent hole followed up with
in action at Valeriano
a directional drilling run to line the hole up with the target.
With the success of the initial holes Recon is validating the value of using directional drilling for efficient deep exploration with holes over 2000 m (6560 ft) in length.
Drilling on the Valeriano project is still ongoing with two drill rigs and two more deep holes on the way.
Established in 2020, Recon Drilling provides diamond core drilling services to major,
intermediate and junior mining companies in Peru and in the LATAM region. With a modern fleet of drills adapted for high altitudes, the company specializes in deep directional drilling using DHM (Down Hole Motor) and wedging methods. Recon Drilling is a subsidiary of Geodrill Limited, best known for its extensive footprint throughout Africa and its enviable reputation of providing safe, professional specialized drilling services to major, mid-tier and small exploration companies. C For more information Visit: www.recondrilling.com
by Alan McPherson, Owner of HELM Diamond Drilling
HELM Diamond Drilling (HELM) is bringing highly skilled, new competition to one of Canada’s largest, and most competitive drilling sectors. This prospect would seem to be a difficult task for a new drilling company, but HELM is successfully doing exactly that.
Being a newcomer in a highly competitive drilling zone of Canada is no easy task. The number of competing companies in a single area generates some of the most challenging obstacles for a new diamond drilling company to face. The financial and production pressures that come with going up against bigger, more industry-established entities as a newcomer can be quite cumbersome for most, but the success that HELM has accomplished so far has greatly impacted the direction the company is going. HELM’s drive to accomplish some of the best results in this area came from a strategic forward-thinking mentality, a love for innovation, a keen focus on safety, and the proper investment into industry-leading equipment. These foundational pillars have led HELM to hold records in this area with the highest meterage recorded so far: 144 m (472 ft) in a single shift.
Among HELM’s active contracts is the exploration company Enduro Metals. Thanks to the relationship with the locals, the geological findings, and choosing the appropriate drilling company, this exploration team has one of the largest junior land positions in the famous Canadian region known as the ‘Golden Triangle’. It contains some of the most important gold deposits in the Canadian history. The name is derived from the abundance of gold, silver, and copper in the area and has played a major role in Canada’s mining industry for decades. This land position in the ‘Golden Triangle’ is located in northwestern British Columbia on the Tahltan First Nations territory. The property is known as ‘Newmont Lake’ and has at least four large mineralized systems: Burgundy, McLymont, Cuba, and Chachi.
To access the drilling location, HELM drill crews boarded a flight at a regional airport located in Terrace, British Columbia. A shuttle then transported the crew north on highway BC-37N for roughly six hours, passing three junctions before reaching a radio controlled dirt mining road. Once on this controlled road, the shuttle continued an additional hour into the valleys of the surrounding mountains to arrive at the designated camp location (Truffle). Once ready for shift, drill crews drive an additional kilometer and a half to a staging location before being airlifted by a helicopter to the drilling sites.
When drilling on top of the approximate 1900 m (6234 ft) above sea level zones, the task of dealing with a sufficient water supply becomes one of the more technical challenges posed. Due to the remote, elevated location, it is extremely difficult if not impossible at times to find a local water source that produces enough flow and pressure to
enable drilling at the depths required by the contract. This becomes even more challenging if drilling is continued past the 600 m (1969 ft) target depth. Drill crews have the laborious task of running high-pressurized hose lines across kilometers of undeveloped terrain which is largely traveled by foot.
Many challenges need to be faced when remote drilling, but there is one that cannot always be predicted; the weather. When working at such high elevations the weather sometimes does not coincide with the weather at the staging location where crew changes commence. With drill site locations being in such early stages of development, the focus of leaving minimal environmental impact is also of extreme importance and high priority. Due to this approach, there is often not enough space for the amenities the average person is familiar with when facing the changing meteorological conditions. When the weather fluctuates to either side of the spectrum, the drillers have to rely on strategically selected items previously delivered and assembled at the drilling sites. The weather can sometimes also affect crew changes if the pilot deems it to be unsafe for flying. Thankfully, HELM is always prepared for circumstances like these and takes the necessary precautions to be proactive as much as possible.
Before drilling can commence the team needs to fly in, via helicopter - at roughly 816 kg (1800 lb) a load - all the drilling equipment and water supply gear, along with all the safety equipment to accommodate for unforeseen circumstances. This safety equipment includes a survival shack, heating and sleeping gear, generators, and sustenance in case crews get stuck for long durations of time. This needs to be
↑ HELM’s crews are no strangers to drilling on the side of a mountain. Luckily, Multi-Power’s Discovery II makes the move as easy as possible.
methodically approached so the safety of the crews is the main priority while drilling takes a back seat until the conditions improve and are deemed safe. Once this is accomplished the drilling equipment is given the crews’ full attention, and loads are transported up piece by piece.
The choice of machinery was decided with safety, reliability, performance, elevation, and transportation in mind. In order to accomplish the required drill targets, the design choice of Multi-Power’s Discovery II drill was made. These drills have the capability and convenience of being transfigured for both ‘Skid’ and ‘Track’ mounted drilling, allowing for HELM to eliminate boundaries when considering a contract. The Discovery II has the power to drill up to 1285 m (4216 ft) with N-size bits and 875 m (2871 ft) using H-size with possibilities for expansion if needed.
Choosing this drill set up allows the entire drill rig to be broken into 10 pieces for fly transportation. These include the drill shack, stinger, drill head, control panel, engine, mud tank, rod rack, helper’s stand, toolbox, and frame. Having a system like this generates some of the most efficient drill moves attainable in this location with record timing, allowing the crew to safely continue drilling as soon as possible. With the mentality for constant improvement this will only get more efficient as HELM continues to grow.
The heart of HELM Diamond Drilling has a deeply rooted aboriginal connection, consisting of two owner/operators who are official indigenous members of Canada, making HELM 100% indigenous-owned.
Alan McPherson belongs to the Tahltan Nation located in the northern parts of British Columbia (and southern Yukon) while Devlin Luck is a member of the Binche First Nations group located in the Fort St. James area of central British Columbia. With over 30 years of combined drilling experience throughout Canada and connections to two highly economically active indigenous mining territories, HELM Diamond Drilling not only offers a leading approach in safety and innovative drilling, but also provides personal relations with each respective indigenous Band.
Incorporated on September 7th of 2020, specializing in mineral exploration, and beginning operations in December of the same year. HELM first spun rods at Gold Mountain Mining Corp’s ‘Elk Gold Project’, HELM has been building its name and expanding its capacity to numerous projects across BC. With the HELM headquarters situated on the Binche First Nations territory, the company respects the rich history of the indigenous peoples of Canada and actively seeks to follow aboriginal beliefs while safely integrating modern economic growth.
HELM Diamond Drilling looks forward to continuing its expansion and creative approaches to resolve any issues that may arise, no matter the complexity of the environment in which operations take place, while adhering to its number one concern; safety. This also includes actively seeking ways to properly train and introduce more indigenous members of all backgrounds into this industry with hopes to provide life changing careers and further build the capacity within aboriginal communities. C
For more information Visit: www.helmdiamonddrilling.ca
Helicopter Portable Diamond Drill
1400 Meter NWL Depth Capacity
Cummins Power Unit 160 or 260 HP
‘P’ Size Rotation Unit & Clamp
Safety Package: Full Guarding, Multiple E-Stops, Interlock Rod Guard & Power Lock-Out
Available in Heli-Portable, Skid Shack Mounted and Track Carrier
by Michelle White, Business Development and Key Account Manager
↑ The DiscovOre Prime is introduced to new sites in complete cases that ensure there is never a missing piece and that the first runs always go as smooth as possible
Early beginnings: safer, faster and better productivity with DiscovOre
Improving drilling performance has always been a priority on mineral exploration sites, so manufacturers have been focusing on ways to do that while still maintaining the safety of drillers. ↑ The DiscovOre Prime design is very similar to the regular DiscovOre, but those small changes make a huge impact on productivity (H-size shown above)
In 2016, Epiroc achieved that goal with the launch of the DiscovOre and Arrow 3S core barrel system, an innovation in drilling equipment that addressed both productivity and safety. After years of development, the Epiroc team, namely Patrick Salvador, applied their decades of in-depth diamond core drilling knowledge, along with extensive input from drillers in the field, to develop the most innovative coring system on the market in at least a quarter of a century. Some of the highlights include an automatic locking overshot that descends the back end faster, no roll pins and robust, leveraged latches that result in fewer stuck inner tubes and ultimately increase productivity. To this day, the DiscovOre has been vastly adopted across the globe.
‘When Ian Wilson, Innovation Manager at Major Drilling, was shown the DiscovOre, he was impressed,’ recalls Brent Kubish, Account Manager for Midwest Canada, at Fordia Powered by Epiroc. Yet, he felt that there was still more that could be done. Ian said, ‘Major Drilling is a leader in the industry for providing specialized drilling solutions. We have continual demand to meet expectations with the best solutions possible. That’s a big reason we were happy with this meaningful collaboration.’ Ian saw the potential for an even greater performance increase.
Working at one of the largest drilling contractors in the world, he knew that to sell this new concept in the field there would need to be a significant increase in speed.
As Innovation Manager, Ian and his team had been working on ways to improve drilling performance, always looking to be at the forefront of new solutions. The innovation team had recently developed a fast latch head assembly that focused on improving speed and he felt his team would be the perfect partner to collaborate with Fordia Powered by Epiroc to take the benefits of the DiscovOre even further. Both companies saw the synergy that was possible, and so a collaboration was born that resulted in the DiscovOre Prime, a premium, fast-descent head assembly.
The DiscovOre Prime was developed in partnership with drillers to be the safest and fastest core tube on the market. When the original DiscovOre was launched in 2018, it focused on mitigating the risk of injuries related to the roll pin and spearhead. It eliminated the failures associated with the spearhead design by using automatically locking lifting dogs and eliminating the roll pin altogether. What made the DiscovOre exciting was that these extra safety measures were automatic. With the DiscovOre and Arrow 3S, the built-in safety features are automatically engaged and did not require additional, manual steps. What’s more, the features did not add time to the coring cycle, so productivity was maintained.
Better speed was achieved with the Arrow 3S overshot which had a design that made it more efficient in terms of descent time. It was designed to be centralized in the drill string
for smoother, faster descent speeds. All in all, the DiscovOre system is still faster than any traditional head assembly, but with the work that Ian and his team had done, Ian thought that some of the team’s ideas for faster descent could be incorporated into this new product resulting in a significant performance increase.
Fordia has been manufacturing drilling equipment for mineral exploration since 1977 with a focus on exceeding customers’ expectations regarding both product quality and customer service. With offices across the globe, Fordia had been expanding successfully until 2019, when it was acquired by Epiroc, a global productivity partner for mining and infrastructure, creating Fordia Powered by Epiroc. The two companies combined their expertise to bring more to the world of mineral exploration.
Major Drilling International Inc. is one of the world's largest drilling and mine service companies primarily serving the mining industry. A global company with field operations and offices in Canada, the USA, Mexico, South America, Africa and Australasia, it provides a complete suite of drilling services for both surface and underground projects.
Major Drilling had been a customer of both Fordia and Epiroc and the collaboration on the DiscovOre Prime had started shortly before Epiroc acquired Fordia. Despite the timing, teams from all the parties worked together seamlessly to ensure the project would be a success.
The collaboration began in 2018 and within the year, the DiscovOre Prime was developed and ready to be tested. Both Fordia Powered by Epiroc and Major Drilling had set aggressive targets for speed and both are proud to say that the DiscovOre Prime exceeded those targets.
In addition to function, there was more focus on fluid dynamics in the design of the Prime. More emphasis on how the water runs through the assembly, providing more room for water flow, and the speed at which it moved through the equipment were a few
of the major differences between the DiscovOre and the new Prime version.
‘This thing will go as fast as you can feed it’
The feedback from drillers has been impressive and highlighted that as drillers become more experienced with the system, they are able to push it further, increasing speed while not reducing the proven reliability of the system. A faster head assembly means that a drilling company uses less water and fuel - and drills more meters.
‘This is not just another head assembly,’ explained Ian Wilson. ‘This is a system that was designed by drillers for drillers to help them get more core in the box. The result is a substantial increase in productivity - an experienced driller can double production at depth,’ he added. Results show that at a depth of 1000 m (3280 ft), up to 60+ m (197 ft) of core per shift is drilled as opposed to the usual 36-39 m (118-128 ft) of core. The Prime is also lighter, smaller, and easier to handle. The design also made sure that it’s easier to change latches and replace parts. As one driller said about the Arrow 3S overshot, ‘This thing will go as fast as you can feed it.’
Both Major Drilling and Fordia Powered by Epiroc are pleased with the results of their collaboration. Innovation has been a cornerstone of our operations. We are really pleased with how Major Drilling and our company have come together to develop solutions that benefit both customers and employees. These co-development opportunities help drillers outsmart drilling challenges which is one of our priorities.
The DiscovOre Prime is ideally suited for drilling companies that are focused on performance. Its higher price point is easily justified when you calculate the cost per meter drilled and payback can be as fast as a few shifts. Now the DiscovOre Prime and Arrow 3S overshot are available to all drilling companies worldwide. The system will be revealed to the drilling community at large at the upcoming PDAC, scheduled to take place on March 5-8, 2023, in Toronto. C
↑ A DiscovOre Prime head assembly being used by Major Drilling
↑ Drillers appreciate the DiscovOre Prime for its lightweight and impressive speed
What do you get when you take one of the most respected underground core drilling rigs on the market and fuse it with a wellproven and mobile carrier? You get the Diamec Smart 6M.
Find out more at epiroc.com United. Inspired.
by the Comacchio team
As the world faces a climate crisis, creating a sustainable future for mining is rapidly becoming a priority for the industry. As part of their strategy for sustainable mining, top miners across the global market including Anglo American, Rio Tinto and BHP have enacted change towards carbon neutrality across all operations and have committed to net zero in direct and indirect emissions by 2050 or sooner. To reach such ambitious targets, companies are reviewing the equipment they use, trying to offset the adverse effects of pollution and reduced energy efficiency connected to the use of diesel-powered machines.
On the path towards a cleaner and smarter future for mining, Comacchio is taking a major step by introducing the first battery-powered drill rig for mining exploration operations.
Building upon its extensive experience with the CX range, Comacchio introduced eGEO 405 – a fully-electric exploration drill rig using lithium-ion rechargeable batteries. The rig was first presented during the Bauma show in Munich in October 2022. It can be considered a milestone in the journey towards zero-emission drilling in exploration drilling programs around the world, explained Emanuele Comacchio, technical and sales manager at the company.
The ‘heart’ of the eGEO 405 drill is the battery pack, consisting of a modular battery system, delivering a total energy content of 52 kWh and reaching a nominal voltage of 350V. The battery system uses multiple subpacks in series, it is characterized by a high energy density, scalability and extensive safety features. The solution is said to be robust against harsh conditions and to score especially well in applications that require high peak power, fast charging and a large number of charging cycles. The estimated lifespan is 2000 cycles. The battery system has a compact size and is placed on the rear part of the machine in a separate and exchangeable box, designed to be easily handled using a forklift, telehandler or other ancillary lifting equipment. The battery system should allow a runtime of up to eight hours, depending on soil
conditions. To ensure continuous operations even under ‘extreme load’ conditions, the rig is supplied with two swappable ‘power boxes’. Switching out a depleted battery with a fully charged one requires just a few minutes. The depleted batteries can be recharged on site using the mains supply or taken to a charging point and recharged there. Recharging to 80% can take as little as 30 minutes, depending on the starting level and the power supply capacity of the grid.
‘We have updated the battery system to include an on-board charging device (OBC). It is compatible with the single-phase and three-phase input voltage and it is designed to manage the flow of current from the charging station to the battery regulating the input current according to customer’s needs. This will allow the drillers to recharge the batteries while continuing working in plug-in mode,’ continues Mr Comacchio.
The low-voltage DC (direct current) power provided by the battery pack is changed into conventional AC (alternating current) by power inverters located on the sides of the rig, protected from vibration and heat and easily accessible for repair and maintenance operations. The inverters allow precise control of the flow of power to any of the rig’s AC motor loads that provide motive power for the rotary head, pumps and winches equipping the eGEO 405.
Unlike most of the competition, Comacchio has chosen to electrify all main loads of the drill rig through the use of permanent magnet synchronous machine (PMSM) technology. The electric PMSM motors offer smaller dimensions, lighter weight and higher efficiency as compared to conventional technology such as induction machines. The use of several motors (rather than one) brings the power supply directly to the point where it is needed, thus eliminating the losses due to energy dissipation and ensuring maximum efficiency of the system as a whole.
‘The biggest challenge in electrifying a drilling rig is integrating the batteries into a piece of equipment designed to accommodate a thermal powertrain. We developed the battery system and the power management from the ground up, including designing and implementing a software solution to effectively and safely manage power and energy between the batteries, the inverters and the electric motors powering the main loads of the rig. The power supply of the machine is controlled by a vehicle control unit (VCU) using CANBUS technology, allowing all the components to communicate with each other and managing the current flow from the battery according to the actual operating needs. The operating parameters of the machine can be viewed on a display located on the control panel,’ elaborates Mr Comacchio.
The rig is equipped with a 6500 daN (14 600 lb) pull mast with 3500 mm (11.5 ft) stroke, featuring a hands-free clamping/breakout system with a clamping range of 45–325 mm (1.77 to 12.8 in). The high-performance rotary head can reach 850 daNm peak torque and a speed of 650 rpm. It can be operated in slow and fast gear, and the adjustment of torque and rpm according to the actual operating conditions can be carried out in an extremely precise manner. The machine on display at the Bauma industry event in Munich was equipped with a mud/water pump (with max flow rate 200 l/min and max pressure 45 bar), a 2000 kg (4500 lb) service winch, and a 600 kg (1320 lb) wireline winch. The eGEO 405 also features a rod rack holding up to twenty-eight 76 mm (3 in) rods with a max length of 3 m (9.84 ft) and can be thus transported with a total of 84 m (276 ft) of rods on board. The overall dimensions of the eGEO 405 are very similar to the diesel-engine equivalent, keeping the machine as compact as possible to facilitate transport. The transport weight ranges between 8500 and
↑ The Comacchio eGEO 405 features a modular battery system delivering a total energy content of 52 kWh and reaching a nominal voltage of 350V
9500 kg (18 750 and 20 950 lb), depending on accessories, including one battery pack.
cmyk - 100 / 69 / 0 / 0
cmyk - 75 / 64 / 60 / 78
Comacchio claims that the eGEO 405 is designed to perform as well if not better than the diesel-powered equivalent GEO 405. It can offer the same functionality and provide the maximum required power, regardless of drilling method, covering the full spectrum of applications connected with mineral exploration. Specifically, the eGEO 405 allows to carry out conventional and wireline coring using B-size, N-size, H-size and P-size rods at up to 350 m (1150 ft) depth. The machine can also be configured for RC drilling using DTH hammer, reaching 80–100 m (262-328 ft) depth. The multipurpose design of the rotary head allows to perform multiple drilling types with minor changes on the machine. This operational flexibility results in reduced unproductive time and lower total cost of ownership.
The safety features of the machine include protection against moving parts, such as interlocking guard meeting the European requirements of EN 16228. Furthermore, the eGEO 405 can be equipped with data logging system including ComNect, a remote monitoring software developed by Comacchio providing data that can be used for a variety of machine diagnostics and operational condition analyses.
The sustainability benefits are enormous and are expected to be a driving factor in the adoption of this kind of rigs. The use of eGEO 405 is to save up to 372 kg of CO₂, up to 0.62 g of particulate matter related emissions and is estimated to save up to 130 l of diesel over an eighthour workday. Ideally, if the batteries are charged from green energy sources, the drill generates complete zero emissions.
‘Thanks to the electric motor, the adjustment of torque and rpm according to the actual operating conditions can be carried out in an extremely precise manner.’
1. Higher energy efficiency. Diesel-run hydraulic drill rigs are estimated to lose 60% of energy due to the engine and another 30% due to the hydraulic system. Electric engines deliver 90% of energy at the output shaft and are therefore considered the most efficient option. Moreover, the use of electric motors eliminates energy losses and fuel consumption connected to idling times of both hydraulic pumps and diesel engines. With an electric drill rig, the current output from the battery is provided according to the actual load, accumulating operating hours only when truly in operation.
2. Low noise. Noise pollution is an underestimated threat to health and safety. eGEO O405 will help remove noise distraction, enhancing both productivity and safety on site.
3. Reduced maintenance required with electric drives compared to conventional combustion engines. Electric drill rigs have far fewer parts than their diesel alternatives. This means less breakdowns, longer service intervals and less maintenance. Over the course of their lives, the total cost of ownership for an electric drill rig is cut considerably in comparison to diesel-run variations. Additionally, the lifetime of an electric motor is much longer.
4. Optimal operational precision. High-performance motor control characterizing the electric PMSM motors equipping the rotary head and the main components of the rig provide accurate speed and torque control, offer smooth rotation over the entire speed range and have the advantage of sustaining full torque at zero speed, and fast acceleration and deceleration. This enables greater control of drilling parameters resulting in faster and better holes.
‘While creating the eGEO 405 we have chosen the most proven electrification technology available on the market, in order to provide reliable operation in harsh operating conditions associated with exploration projects,’ concludes Mr Comacchio. ‘We are approaching companies that are willing to become early adopters of new technologies. Carbon reductions will become a more important differentiator as many mining companies publicly commit to ambitious net zero targets and want to score well on key Environment, Sustainability and Governance (ESG) performance indicators, which is increasingly important to investors. Such ambitions will likely accelerate in the next years and Comacchio is committed to exploring new solutions including not only purely battery-electric drives, but also hydrogen-powered motors. The eGEO 405 was designed with a view to future developments that include the use of fuel cells powered by hydrogen instead of drawing electricity from the battery. This is the first step of a long path towards a new idea of the future of mining exploration’.
Comacchio is a world-renowned designer and manufacturer of drill rigs for a vast range of applications. Born in 1986, Comacchio is a family-run company, operating from its headquarters in Riese Pio X (Italy). The company’s ability to assimilate ideas, insights and specific requirements coming from the market has allowed creating an innovative and differentiated range of products, offering a range of features, options and enhanced automation solutions designed for optimal safety, reliability and performance. C
↑ The multipurpose design of the rotary head equipping the eGEO 405 allows to perform multiple drilling types with minor changes on the machine
↑ The battery system powering the eGEO 405 is placed on the rear part of the machine in a separate box designed to be easily exchangeable using a forklift or telehandler
For more information Visit: www.comacchio.com/en/
Safety is the challenge, CX Line is the answer. Compact design, hands-free rod handling system for fully automated and remote controlled operations: the future of exploration drilling is already here. Are you ready to join in?
In this Issue:
Q&A from the experts
In conversation with Dr Richard Tosdal, President at PicachoEx LLC
A few structural geology concepts for sediment-hosted Copper exploration
A case study from the Cashin Mine in the US by Dr Molly Turko, Structural Geology Expert & Dr Ali Jaffri, CEO at Applied Stratigraphix
Power to the people:
How citizen development is driving a digital mining operations revolution by Udit Poddar, CEO and Vahishta Mistry, Content Lead at WorkOnGrid
What makes a geologist?
Thoughts on declining discovery rates, and other strange animals - a practising Ni-PGEsulphide geologist’s (heretical) viewpoint by Richard A. Hornsey, Consulting Geologist, Ni-PGE Specialist at Richard Hornsey Consulting (Pty) Ltd
Dr Richard Tosdal President at PicachoEx LLC
Richard M. Tosdal received a bachelor’s degree from the University of California at Santa Barbara (USCB) in 1974, an MSc from Queen’s University (1978) and a PhD from the USCB (1988). He has been a Research Scientist at the U.S. Geological Survey or USGS (1978-1999), and the Director of the internationally recognized Mineral Deposit Research Unit (MDRU) at the University of British Columbia (1999-2008). He serves on technical advisory boards to junior companies and consults the minerals industry on aspects regarding the metallogenic evolution of plate margins, the structural controls on ore deposition, and the evolution of porphyry Cu, sedimentary rock-hosted Au, and epithermal deposits.
Dr Brett Davis: You have worked with an enormous number of people over the years. Apart from me, who has inspired you in the field of geology?
Dr Richard Tosdal: I would rather think about this question not from inspiration, but in terms of who has helped or facilitated or opened doors for me over the years. Two people are important in this context.
I want to start with my first undergraduate advisor at UCSB, Robert Webb, who took a youngster who picked geology as a major without having the first clue what it entailed, and then transferred universities. The main thought in selecting the major was that I could surf my life away. Dr Webb showed me how I could graduate by the end of the normal four years and was always available to manipulate the accessory course requirements such that I graduated on time. Without him, I am not sure I would have discovered the desire and ability to make geologic maps as a profession.
Second is Gordon Haxel at the U.S. Geological Survey who hired me off the streets on contract and ran interference through the bureaucracy that eventually led to a full-time position, he also supported me through my PhD at the time.
These two perhaps unbeknownst to themselves were important at a critical time early in my career.
BD: You’ve worked for the United States Geological Survey, and you’ve run the Mineral Deposit Research Unit at the University of British Columbia. What were your most rewarding moments in these roles?
RT: Working for the Geological Survey provided me with the opportunity to be exposed to the full range of geosciences, thereby introducing
a young geoscientist to world-class scientists who readily shared knowledge. Although each of us at the USGS had an assigned project requiring a product mandated by the funding agency, each geoscientist was expected and given the opportunity to go beyond what was required and encouraged to publish the results in international journals. It was expected if one wished to advance in their career.
At the University of British Columbia, I ran the Mineral Deposit Research Unit (MDRU). This is a self-funded joint venture group between the mineral industry and the university. There was a funding mechanism for the administrative group, but all research projects undertaken to provide opportunities for graduate students and post-doctoral fellows required securing time-limited outside funding. This led to the development of some excellent applied projects found upon fundamental basic science principles that I suggest had a lasting impact on our exploration concepts. These are the rewarding scientific moments.
On a personal side, seeing graduate students move on to successful careers is somewhat akin to watching your children grow up. One cares about their success, but only wishes they would keep in touch. Yet, I suspect they were just as happy to not see ink on the thesis drafts, to finally finish, and move on as I was to quit reading their thesis.
BD: Given your success in the research space, including your publication record and the postgraduate geology students you supervised, what made you move into a consulting role in the industry?
RT: Running a research consultancy business is similar in minor respects to running a company, but in this case, the product is well-trained geoscientists. Maintaining a high level of productivity in a self-funded group is possible over the years, and I could
have continued. However, self-funded entities, such as MDRU, require reinvigoration on a regular basis as their direction and productivity directly reflect their staffing. Without staff turnover, research groups eventually fall into a rut of continually doing the same sort of projects. Only by changing senior staff can the internal excitement be sustained. So, it was my time to move on. Besides, it was my wife’s turn to dictate where we live as she is in the biotech industry, has more degrees than I do, and was essentially under-employed while living in Vancouver.
BD: I feel I’m giving you too many compliments. However, they are well-deserved, and I’ll state here that you are one of the rare breeds of people who genuinely understand structural geology in the context of intrusion-related mineral systems. Can you convey your perspective on the importance of understanding structural geology at all scales in terms of mineral systems?
RT: Too many geoscientists (including structural geologists) view structure as divorced from other aspects of geology, such as mineralogy, geochemistry, petrology, etc. This is simply not the case, as most would admit, I am confident. However, when you read structure reports or manuscripts, there is a tendency to ignore or minimize the interaction of structural fabrics with all the other aspects of geology that together make an orebody.
BD: Leading on from the previous question, what fundamental geological puzzles do you think remain unanswered in the mineral system space?
RT: Is anybody correct in their basic assumptions? But being a bit of a cynic, I think we have been playing in the mineral system space for hundreds of years. There is now a set of words to describe what we have been doing. Or is it just a portion of the mineral deposit community that has been thinking this way?
BD: Are you undertaking any active research at the moment?
RT: Each consulting or contract is essentially a research opportunity. I view long-term or repetitive involvement in projects, such as research programs, as involvement as the project moves forward, hopefully contributing positively. Most jobs do not result in any publications, apart from what we did collaboratively in Serbia. The publication of explored projects - whether they become economic or not - by those who actually did the work, is sorely lacking. Credit should go where credit is due, but as you know, the publication game is not always for the faint of heart, and one can become easily discouraged. Recently, I have been publishing the thesis results of many of my past graduate students, who do not seem to have the drive to do so. Their work was in part funded by the Canadian government, and their results should be available to the whole geoscience community and not be buried in a university library. But we are getting close to the end of that list. Maybe a couple more to go.
talents on a semi-regular basis. Long-term work currently has me in the western US, Canada, Colombia, and Turkey. I am sure this will change with time.
BD: What is the geological feature you find most interesting and enjoy working on?
RT: I am drawn to the bigger scale of a metallotect, a district, or a deposit. How do all the piec es fit together in a coherent or ‘least astonishing’ way? Fortunately, the time spent with the geological survey making maps at a huge range of scales has provided sufficient background
5-8,
to come up with an idea that an exploration program can then go and test. One hopes that you are not too far off, or as we say, be ‘the least incorrect’. One needs to be able to toss ideas out and away quickly in each case. Sometimes, it is hard to throw away a really neat model, but if it does not fit, then out it goes with the bathwater.
BD: How has technology impacted the way you work? Has it been useful or detrimental? I’ll hijack the interview for a second here and state that I think that many technologies are twoedged swords. Electronic logging devices are stopping people fully interrigating core. 3D visualization software such as Leapfrog has turned geologists into chair polishers and desk jockeys, instead of collecting and auditing data and understanding geological context. Is this your perception, or do you think I am being overly critical?
RT: Took the words from my mouth. Some of this derives from the needs or desires from corporate for information and data in ‘real-time’. However, it does provide opportunities for us ‘oldsters’ to quickly find the jewels or the holes in any particular model. Keep us busy.
BD: Much of the world is a geopolitical basket-case, has extreme security risks, or corruption at all levels. If we could toss these aspects aside, where are the holy grails for deposit discovery in terms of geological terranes that haven’t been touched by modern exploration and/or historical mining?
RT: Africa. I have not spent much time on the continent, but this is my impression from afar. For example, I suspect that if the Democratic Republic of Congo and Zambia could figure out the local issues, the Copper Belt could put many of the porphyry Cu deposits elsewhere in the world out of business.
BD: Do you think that geological societies, such as the Society of Economic Geology, have adapted with the times in terms of being useful entities for their members? Or are there basic things that such societies should be providing and/or promoting?
RT: Any society, company, government, and even individuals are generally slow to adapt to change, and usually lack the urge to do so. I am not much different, as I have yet to become proficient in GIS software as there is always somebody who can do it faster and better than me when on a job. Some of the resistance to change is due to stubbornness. One way has worked well, so why change?
Other impediments are the need to bring along the rest of the group to adapt to whatever change is required or just advocated. But most of the societies are trying their best within the framework of their structure. Change is always slow, and the impediments are generally people and their beliefs and associations.
BD: Being able to take complex concepts and ideas and convey them in simple terms that don’t leave out important details is a skill you have. Unfortunately, some people who interface with companies and the public are woeful communicators. Do you have any tips for people who want to be successful in getting their ideas across, especially verbally?
RT: Keep it simple and avoid all the jargon that makes one sound intelligent, but is only confusing the listener. Structural geology ranks up there as one of the worst for jargon.
BD: A skill we both share is proficiency in Spanish. Can you tell the readers how this has helped in your career?
RT: Although English (not the Australian version) has become the science language, being able to communicate in a different language opens doors for additional opportunities, new colleagues, and most importantly, friends. One does not need to be completely proficient in the second language, but you need to try and continue to communicate verbally. Learning to write in the language is another skill level that I have yet to achieve, and probably never will, unless I move to a Spanish-speaking country.
BD: You have worked in many countries. Which has been your favourite, and why?
RT: There is a certain nostalgia for Peru and Turkey. The former because of my first research project, and the latter since I had the opportunity to live there as a boy while my father was attached to NATO. Both are beautiful countries.
BD: If you had your time again, what would you do differently? That is, apart from moving to Queensland, Australia, which is the best place in the world.
RT: I will have to think a bit and essentially not answer the question. Perhaps the biggest challenge we (my wife and I) had was balancing two professional careers, and children, as a family. This is an on-going challenge not just for us, but for many in the exploration industry. There is always one member of the duo that gives more than the other. Finding the balance that allows both to progress equally in a professional career is tough, and many are not completely successful for a range of reasons. My wife and I were not completely successful in my opinion, which probably is my biggest regret. Nonetheless, we are still married after almost 40 years, so I must have done something well. These days, the buzzword is life-balance. Well, that, in my opinion, is a fancy term for taking control of your career and personal life and making decisions that are correct for personal and family reasons. This is not just having more time off from whatever job. Unfortunately, I get the impression that some, but certainly not all, view life-balance in those terms.
For myself, there are some decisions made that I think I might revisit now after I lived the result, but this is a useless exercise. So, I try to take the lessons from the past, look ahead, guess what is next, what opportunities might arise, but always maintain a balance and focus on how it will or might impact the family.
BD: You have suggested for a while that you are edging toward retirement. I find that hard to believe but, if so, what does the next chapter hold for Dick Tosdal?
RT: Who said I was retiring? But I will at some point as I am in my 70s. Getting up the hills takes a bit more work than it used to. This is truly distressing, I must admit. C
Tae Sung Co. is the leading manufacturer of exploration drilling equipment for Korea and the local region since 1980. We are specialized in the production of high quality impregnated diamond core bits, reaming shells, core barrels, casing, drill rods and more
We have been number one supplier in Korea for the last 35 years and preferred supplier to many other countries
Tae Sung produces diamond products of any size and any standard. Korea has a very long history in mining and
geology and our diamond products have been adjusted to meet the challenges of the Korean hard and extremely hard formations. Our impregnated diamond bits have proven track record and they drill with better penetration rates compare to other competitive products.
We promise to supply you with the best quality products and we will be glad to share with you our competitive pricing
Our clients are always welcome to visit us and our factory
Address: 31 Jangjeol-ro, Gwangmyeong-city, Gyeonggi-do, Republic of KOREA (14334)
Tel: +82-70-7687-0462
Fax: +82-(0)2-2683-6733 ghlee95@gmail.com www.taesungdia.com
by Dr Molly Turko, Structural Geology Expert & Dr Ali Jaffri, CEO at Applied Stratigraphix
Sedimentary rocks host approximately 25% of the world’s Copper. Sediment-hosted stratiform Copper deposits were a key target for exploration in the United States that peaked during the 1940-1970s. During these times, explorers were primarily focused on understanding concepts of geochemistry and hydrogeology while structural geology often took a back seat. Recent field work by Applied Stratigraphix on Copper-bearing Triassic-Jurassicaged strata of the Colorado Plateau, US, led to the conclusion that up to 80% of minerals are being deposited along fracture and fault networks. Concepts in structural geology and sedimentology have come a long way since the peak of exploration thanks to new technology, 3D seismic data as an example, and can be applied to future exploration of mineral deposits. Although these concepts might be simple to trained structural geologists, they will be vital to any sedimenthosted metal prospect and worthwhile to understand, even for a non-geologist.
These concepts include understanding the role of mechanical stratigraphy - the impact of fault geometries on fracture intensity and understanding how perturbed stress fields can impact fracture orientation and intensity. Before we get into the details of each of these concepts, let’s examine some of the observations from the field. We will focus on the Cashin Mine in southwest Colorado (Figure 1a). Cashin is a sediment-hosted copper and silver mine in the Paradox Basin that was discovered in 1896 with intermittent production from 18981946 with the last recorded production in 1976. The ore grade ranged from 7-12% copper and 8-134 oz (227-3800 g) of silver per ton, with one high grade shipment of native copper containing 89% copper. (https://www.mindat.org/loc-22531.html).
The copper at the Cashin Mine is hosted in the Jurassic age Wingate eolian succession that ranges between 290-300 ft (88-92 m) (MacIntyre, 2006). It’s capped by the Kayenta Formation which consists of fluvial sandstones and mudstones deposited in dryland ephemeral streams (Priddy and Clarke, 2021). Below the Wingate sits the Chinle Formation which consists of fluvial floodplain conglomerates, sandstones and mudstones (Hartley and Evenstar, 2017). The Kayenta and Chinle show some local bleaching, while the Wingate shows widespread bleaching of the sandstone. This bleaching occurred as buoyant hydrocarbons from deep in the basin moved along faults and into more permeable units which dissolved the iron oxides coatings from clasts within sandstone.
Prior to the Laramide Orogeny, the Paradox Basin was impacted by the Pennsylvanian Orogeny. During this time, contractional tectonics impacted the southwestern US while evaporites precipitated in the Paradox Basin. The salt moved subsequently with deformation of the basin and deposition of Pennsylvanian clastics resulting in linear salt anticlines (Figure 1a). The normal faulting observed at the Cashin Mine, occurred later during the Laramide Orogeny as some of these deeper salt anticlines collapsed. These faults then acted as great conduits for hydrocarbon migration followed by later migration of brines that provided the Chloride complexes needed to mobilize Copper. This later fluid flow event occurred during the Mid- to Late-Tertiary and could be related to a nearby igneous intrusion of the La Sal Mountains as well as the Colorado Plateau Uplift and increased hydrologic gradient. Copper carried by oxidizing, chloride complex-rich brines moved along faults and fractures till it encountered reductant in the form of bitumen, pyrite and organic-rich interdune microbialites.
The main fault at the Cashin Mine is oriented northeast-southwest and drops down to the northwest. A second fault also oriented approximately northeast-southwest drops down to the southeast creating a graben-like structure and linking with the Cashin Fault (Figure 1b). Fractures were studied in two field areas, one along a cross-sectional view of the Cashin Fault (Area 1) and one along strike of the fault (Area 2) looking at internal deformation of the fault zone. Fault offset is estimated to be around 66 ft (20 m) at the Cashin site. An intense zone of fracturing, about 20 ft (6 m) wide, is present at Area 1. Fracturing and faulting continue away from the main fault zone but with less intensity. Where fault and fracture planes are exposed, mineralization is apparent and hard to miss with Malachite and Azurite hues against the bleached sandstones (Figure 2a). It is obvious that much of the mineralization prefers the fracture/fault planes, however in a few areas the Malachite does precipitate into more permeable units (grainflow facies) (Figure 2b). Observations in Area 1 showed the mineralization was preferential to the fracture networks related to the immediate faulting and the damage zones away from the faults.
Area 2 exposes along-strike deformation of the Cashin Fault where much of the mining efforts commenced. What is left are exposed fault planes that have been mined out and some remaining brecciated fault blocks. Figure 3a shows an exposed hanging wall that was dug out leaving behind remnants of oxidized copper and iron minerals along with slickenlines indicating normal slip. Figure 3b shows a block of fault breccia speckled with azurite and malachite. Notice that in both of these figures, the mineralization is restricted to the fault and fracture planes whereas the matrix rock shows significantly less mineralization. As we continued to explore and observe the rocks surrounding the Cashin Mine, it became very apparent that identifying the faulted and fractured areas would have been incredibly significant to the success and development of this mine. This led us to think about several key structural geology concepts that could aid in future exploration and development projects focused on sediment-hosted metals including mechanical stratigraphy, fault geometries, and perturbed stress fields.
After observing such a strong structural control on deposits at Cashin, it is worthwhile to review a few structural geology concepts that may aid future exploration and development. These include mechanical stratigraphy, fault geometries, and perturbed stress fields. Mechanical stratigraphy represents the mechanical properties of the rock, the thickness of the mechanical layers, and the frictional properties at the boundaries (Ferrill et al, 2014). The terms brittle verse ductile are common language when referring to mechanical stratigraphy and can be impacted by mineralogy, depositional texture, porosity, and competence. It is also important to note that the term brittle should be regarded as a behavior and not an inherent rock property. In other words, it refers to how much the rock will deform before failing or breaking. Both internal and external factors can impact the brittleness of a rock. As an example, external factors, such as higher pore pressure, higher stress differential, and/ or a higher strain rate, can all increase brittle behavior. However, an increase in confining pressure and/or high temperature can result in more ductile behavior. One of the biggest internal factors impacting brittle behavior is the mineralogy of a rock. Generally speaking, a rock consisting of quartzite or chert would be considered very brittle, followed by dolomite, sandstone, limestone, then mudstone. However, the internal structure can also impact brittle behavior such as the grain size, grain sorting, cement type, porosity, and any pre-existing weaknesses or heterogeneity. Figure 4 illustrates some of these concepts. By understanding the mechanical
↑ Figures 5a, 5b & 5c
stratigraphy of a rock column, a geologist can start to predict where they might find a greater degree of fracturing, whether the fractures are related to faulting or simply background fracturing. In regards to bed thickness, studies have show that there is a relationship between mechanical bed thickness and fracture spacing. The thinner the bed, the closer the fractures will be spaced.
Detailed structure maps are vital to mineral exploration and one of the key factors to consider is the geometry of fault planes. Whether through field mapping, or subsurface data, mapping the fault planes can aid in finding areas of enhanced fracturing. Figure 5 illustrates how fault planes with an outer arc (outside bend) can create a zone of higher tensional strain whereas an inner
arc (inside bend) can create a zone of higher compressional strain. Rocks tend to be weaker under tension (low confining stress) so the expectation would be a higher degree of fracturing in the tensional areas. Regions of extension and contraction can also develop along strike-slip faults as they step or bend along strike. A good rule of thumb is that a left-lateral fault with a left step or bend will result in extension, or a right-lateral fault with a right step or bend will result in extension. So, when the step or bend is in the same offset as the fault, right-lateral with a right step, the result is extension. If the step or bend has the opposite sense of offset the result is contraction. For example, a left-lateral strike-slip fault with a right step will result in a region of contraction, as will a right-lateral strike-slip fault with a left-step. These relationships are illustrated in Figure 6a and occur at all
scales from the thin-section to large scale tectonics.
Relay ramps along normal faults are also regions where enhanced fracturing can be expected. As normal (or reverse) faults begin to initiate and grow laterally, they will interact with each other and eventually link up. Figure 6b illustrates this process for a normal fault. The region between the two faults is what is called the relay ramp and tends to become more highly fractured than the surrounding rock. Figure 6c illustrates how the mechanical stratigraphy can impact the geometry of the fault plane. The fault planes are shallower in more ductile units, and steeper in more brittle units resulting open ‘conduits’ adjacent to those brittle units as the fault begins to move. Those open conduits may become filled with minerals over a period of time making them an ideal spot to target. Although simplified, these rules of thumb on fault geometries can help with
↑ Figures 6a, 6b & 6c
identifying areas of enhanced fracturing, which may very well be conduits for mineral rich fluids.
Perturbed stress fields occur when stresses deviate from regional expectations, usually due to some discontinuity such as a fault. Figure 7a shows a left-lateral strike-slip in map view. The regional orientation of the maximum horizontal stress is oriented north-south and represented by the vectors. Notice that as the vectors approach the fault they deviate from the regional north-south orientation. The fault also contains four quadrants, two extensional and two contractional. In the tensional quadrants, the vectors rotate to become perpendicular to the fault plane whereas in the contractional quadrant they become parallel. These regions where the vectors have become rotated represent the perturbed stress field. Figure 7b shows an image from Google Earth where fracture trends are becoming rotated around the Moab fault zone in Utah.
The orientation at which fractures form is dependent on the stress field at which they formed. Based on Andersonian Faulting Theory (Anderson, 1951), the general relationship between fractures/faulting and stress is shown in Figure 8. Mode I fractures, opening mode, tend to form parallel to ơ1 and ơ2 (maximum and intermediate principle stresses) and open in the direction of ơ3 (minimum principle stress). Mode II fractures (shearing mode) form close to +/-30 degrees to ơ1, parallel to ơ2, and perpendicular to ơ3. These relationships give some degree of predictability to fracture trends and orientations if the stress field is understood, whether that’s a regional stress field or a local perturbed stress field. If these fractures then become conduits for mineralized fluids, having a good understanding of the fracture orientations then becomes vital for exploration and development of a prospect.
These simple yet vital structural geology concepts may very well aid in predicting areas of enhanced fracturing. Just as we saw at the Cashin Mine, fractures were the primary conduits for hydrothermal
fluids that carried the metals. Understanding the spatial relationships of a fault/fracture system backed by essential field work will lead to better exploration and development projects, particularly for sediment-hosted stratiform copper deposits. While geochemistry and hydrogeology led the way in historical production, structural geology may very well be king in future developments. C
References
The dynamics of faulting - E. M. Anderson, 1951
Control of mechanical stratigraphy on bed-restricted jointing and normal faulting: Eagle Ford Formation, south-central Texas - Ferrill et al., 2014 Fluvial architecture in actively deforming salt basins: Chinle Formation, Paradox Basin, Utah – Hartley and Evenstar, 2017
Fault-controlled hydrocarbon-related bleaching and sediment-hosted copper mineralization of the Jurassic Wingate Sandstone at the Cashin Mine, Montrose County – Colorado MacIntyre, 2006
Spatial variation in the sedimentary architecture of a dryland fluvial system - Priddy and Clarke, 2021
by Udit Poddar, CEO and Vahishta Mistry, Content Lead at WorkOnGrid
There is much evidence to suggest that we are living through a fourth Industrial Revolution. If the first Industrial Revolution was heralded by the use of water and steam power in the 18th and 19th century, then widespread electrification of industrial processes, and the rise of automation can be said to be the second and third revolutions. Each period of change brought with it huge gains in productivity and efficiency. We stand now on the brink of what experts are calling Industry 4.0: an industrial revolution brought about by the use of cyber-physical systems.
The advent of Industry 4.0 has the potential to be no less than an enlightenment era of our times. However, the misconception that digital transformation offers a better value for money for digital industries than for more traditional industries such as mining, energy, manufacturing, logistics, etc. still plagues the overall concept. Nokia Bell Labs estimates that around 70% of all industries reliant on digital workflows (what we would call white collar, or ‘office’ industries) have invested heavily in pervasive 5G networks combined with solutions such as augmented intelligence, edge cloud, private networks and as-a-service business models, thus embracing the principles of Industry 4.0. Comparatively, only 30% of industries whose workflows and outputs are rooted in the physical world (such as mining, manufacturing, etc.) have made similar investments. However, physically-rooted industries account for over 70% of most countries’ GDP contributions. There can be only one conclusion from these statistics, we need to completely change our attitude towards digital transformation in physical industries, like mining, in order to capitalize on growth potential. In particular, when you consider that the need for clean energy and materials will drive up the demand for rare earth minerals by 500% by 2050, according to the World Bank, the need for mining and mineral exploration companies to begin the process of digitalization becomes imperative.
According to McKinsey, historical data from mining and exploration companies indicates a decline in the productivity index. Faults and failures in an industry that involves massive capital, workers, assets, and legal constraints will only lead to significant losses. Thus, mining must evolve to become more financially sustainable and environmentally progressive. In order to accomplish this, we need to innovate and transform in order to:
• Track primary productivity drivers in real-time, namely production, employment, capital expenditure, and operating expenditure;
• Digitalize the entire value chain end-to-end from exploration to product commercialization, and subject every stage to continual improvement;
• Minimize operating costs and unplanned downtime by utilizing invaluable insights from data.
By switching from traditional data gathering systems to a digital system, decision makers will be able to acquire a holistic view of the daily operations and take informed steps ahead of time, leading to highly efficient production.
Despite digitalization’s exciting potential, mining and mineral exploration businesses face certain obstacles that prevent them from realizing it. The underlying cause is that the industry is still in a very rudimentary stage of digital development. This further exposes the digital literacy gap in mining's workforce, which constitutes the majority of its labor-intensive operations. Thus, migrating to software handling complex operations would disrupt the value chain, further complicating productivity. As a result, a comprehensive analysis of your business’s digital transformation plan, especially the long-term adoption and implementation, is critical before investing in new technology.
Most businesses opt for traditional canned software as a cost-effective readymade solution, but over time, as they scale, they start running into problems like:
• Lack of mobile access;
• Rarely used bloated features;
• Lack of desired integrations;
• Lack of requirement specificity in the software resulting in frequent support needs;
• Long reiteration cycles due to operational changes.
In response, many businesses invest significant budgets in custom software that takes nearly a year to set up and implement. Due to the nature of custom software, there is often an increase in unforeseen complications, as a lot can change within a year. The project can even land in development hell, where time and capital are both wasted on iterations. Moreover, you have to involve the vendor for every update, making an already expensive process even more costly. As we can evidently notice, businesses are essentially bound by developers and heavily reliant on them for scaling operations.
The aforementioned shortcomings have inspired continuous advancements in the way software is developed, distributed, and used, leading to the rise of no-code/low-code platforms for software development. These platforms have democratized the process of creating software applications, taking the power of creating applications from engineers and coders and putting it into the hands of a new breed of programer: the citizen developer.
Today, across all industries, citizen development has emerged as a beacon of hope to make technology more accessible than ever before. It bridges the disparity between digital and physical industries, and empowers non-IT-trained employees with a platform for functional applications on the go. They can now create enterprise-grade apps that meet all their needs without relying on anyone else. In other words, people working in the industry wouldn’t have to dedicate time and resources to learning how traditional canned software works, adapting it to their business processes, and so forth.
Citizen development, or the idea of enabling non-technical staff to create technical solutions without the use of bespoke programming, is not new. We see this process playing out in various fields of business and computing. One such example comes from the world of marketing emails. About ten years ago, sending out a marketing email to a large mailing list would have involved serious programming investment: one would have to write (from scratch) the CSS and HTML code that would render the email correctly in recipients’ inboxes. Today, programs and services like Mailchimp, Sendinblue and a host of other email service providers allow marketers with absolutely no programming knowledge to create, design, and send fully-featured marketing messages via email to vast lists of recipients, all with just a few clicks and no code.
Similarly, automatically-generated mobile applications can today be quickly and easily created by non-programers using drag-and-drop interfaces, on a variety of platforms. The key benefit here is that the task of creating the application moves from a professional programer (who is an expert at coding, but not the subject matter of the application being developed) to someone who better understands how the application will be used and so is in a better position to create a more intuitive and useful application.
The low-code/no-code platforms that facilitate citizen development also effectively eliminate the need for businesses to rely on IT teams for maintenance and customization. Reduced reliance on skilled software engineers drops the cost of development and data management by as much as 80% while improving efficiencies by up to 65%. We have discovered that consuming infrastructure, applications, and services via a centralized citizen dev platform enables mining businesses to be far more flexible, as these services can be tailored, and then adapted
to the businesses’ needs as they evolve. It gives greater control to people over the running of the mines and also helps in making quick decisions.
In one example of a Western Australian mineral exploration company, our research showed that they possessed the expertise to run largescale surveys, assess indicators and variables of soil and rock samples, tectonic evidence, and even archaeological data to determine optimum drilling sites. However, this knowledge and expertise needed to be captured, quantified, and eventually mapped out using modeling tools. Hence, they were looking for the right technology to save the time spent on data cleaning and standardization, and integrate their data entry platform and modeling database.
Their choice of a no-code platform enabled them to:
• Optimize their frontline operations to a much higher degree of customization;
• Create an end-to-end automated exploration logging platform that integrates with a consolidated database of all their exploration operations;
• Visualize their data on a custom dashboard for real-time progress tracking, drill location planning and workflow setups;
• Freely build more applications for their project monitoring needs.
The geologist teams alone saved over 60% of their time as a result. With citizen development, they were able to create and integrate apps and workflows within hours rather than weeks or months.
Today, mining companies are estimated to be operating at 70% efficiency, with approximately 40% costs spent on maintenance. These figures translate to huge potential for increased productivity and profitability. Businesses that have transformed digitally have managed to exploit this potential, and witness a 10-15% increase in profits. If there is one key takeaway, it’s that by adding in the power of no-code to a robust digitalization plan, that percentage stands to increase even further, bringing the mining and mineral exploration industry even closer to the ideal Industry 4.0 standard. C For more information Visit: www.workongrid.com
•
•
•
by Richard A. Hornsey, Consulting Geologist, Ni-PGE Specialist at Richard Hornsey Consulting (Pty) Ltd
I was asked to write a contribution to Coring Magazine by Brett Davis, whom I met on a few occasions during the period at which I was employed by MMG Ltd as Global Ni Project Generation Team Leader.
Brett was undertaking consulting work on an ‘as-needs’ basis and came to Brazil to undertake a structural review of our Limoeiro Ni-sulphide project. In addition to being a very competent, personable expert in his field, Brett is one of the few consultants that adopts a ‘bigger picture’ approach and listens to the team without ramming his ideas and concepts down their throats. In addition to the above quality, we have similar musical tastes, therefore without question, Brett is a super fellow. This impression has not been blunted by asking me to put pen to paper and write something for this magazine, which, I assume, is read by a very diverse group of people of various technical disciples. I am a self-employed consulting geologist with 32 years of experience in most aspects and sectors of
the business, therefore will put forward, on a pretty forthright basis, a few ideas, concepts, and opinions on the exploration industry. I trust no-one will be offended, but I am a child of the 1960s, so I am of the generation, who at an early age, learned to climb trees, light fires, cycle to school at the age of seven, and play in the street after dark, and take advice with a pinch of salt, as well as treat ladies, other folk, my betters, and elders with due respect!
Myself, I am a Yorkshire lad, born and bred. I was fortunate to grow up during a period of intense social change, to see the first lunar landing at the age of nine months, and receive the type of outdoors upbringing that is almost unheard of nowadays. At the age of seven or eight, I used to visit my grandmother, who sadly became terminally ill from when I was about nine or ten years old, in a small East Yorkshire village and, encouraged to look after myself, I would disappear after breakfast and reappear at sundown after a full day’s solo hunting for adventure, searching for fossils, Roman mosaic stones, and anything of interest. Without knowing it, this trained me in several aspects –
I became physically fit, developing stamina that has lasted to this day, and a keen sense of observation, able to spot an old coin or fossil right under other people’s noses – critical skills for an economic geologist. I was fortunate to attend good schools – and although not the most diligent of pupils, managed to achieve entry to the University of Newcastle-upon-Tyne to read Geology. This was not my first choice; since the age of 16, I had worked in my school holidays for a stone mason and spent a gap year working in Huddersfield and Sheffield. I could have quite happily done my apprenticeship and continued. I was however, politely mentored by one of my older colleagues that since I was educated, and had gained an entry, I would be taking the place of someone less fortunate should I not use it, sage advice for which I am now very grateful. Throughout my University years, I worked for the largest cable contracting company in the UK, installing cables at various power stations, industrial plants, banks, and other interesting places. This job does not require intelligence, but does require stamina, the ability to work very long hours, and teamwork. I was working with people of all backgrounds in a pretty tough environment, where if you did not perform, either the pay-packet was distributed amongst the rest of the team, or the van did not pick you up ever again. This also taught me some critical skills – how to get a job done, teamwork, the importance of respecting all your colleagues regardless of background, and being straight-talking, not soft-soaping bad news – a person needs to clearly know if there is an issue rather than talking in circles.
I graduated in 1990, the only honor received was being awarded ‘Most Astute Observer’ during our final year’s field excursion. This was during an unprecedented period when there were no jobs in the oil or hard-rock sector, globally. Together with two other students, I had been recruited by JCI, a former South African powerhouse, to work at the new H J Joel Mine in the Free State sector of the Witwatersrand Goldfield. Two weeks before leaving, I was retrenched… Fortunately, I had my permanent residence permit and certificate of fitness to work on the mines, so was recruited by Anglovaal to work at the Sun Project, a deep Wits drilling program in the Free State, north of the Loraine Gold Mine. At that time, this was the largest and deepest drilling program that had ever been undertaken, we had over 40 rigs over an area of almost 1000 km2 (362 mi2), to depths in excess of 4500 m (14 764 ft). My deepest intersection was at 4033 m (13 232 ft) at hole SLP2.
From the technical drilling perspective, there were some interesting aspects. The rigs used were predominantly Sullivan 50s, but we also, prior to my involvement, used an oil drill rig at the adjacent Oribi sector of the project. The drilling was conventional, so at depth, we got 6 m (20 ft) of core per 24 hours. The rigs were static for periods of up to five years, often with the same driller and team, all living on the job. Multiple short and long deflections were drilled, some had over 20 directional wedges to achieve offsets of 1-200 m (3.28-656 ft) from the mother holes. We also had a world-class standard procedure for reef intersection collection, whereby the core was handled by one person, including capture from the core barrel, logging, crushing and milling samples, and delivery to the lab. This was way ahead of any codes, National Instruments etc.
I also saw my first disruptive changes during this period. Each geologist was responsible for three rigs, and we used to happily log our 18 m (59 ft) per day, plot sections, etc. All was peachy, until a Canadian company called Universal HS Drilling arrived with aluminum rods.
In addition to throwing great parties, they also used wireline drilling to depths previously unachievable, suddenly, we were receiving 50–60 m (164-197 ft) of core per rig per shift! This period impressed the importance of production on the entire team, following standard procedures, naming conventions, and data import. Core logging is a fundamentally important geology skill that needs to be done rapidly, comprehensively, and to an appropriate level of technical detail. I lose patience with geologists who agonize over every entry, taking weeks to log a single hole, or worse, leave it to an unsupervised or mentored junior colleague to do the logging, then wonder why the product is not up to scratch. In the Klerksdorp exploration office, we had several geologists of all experience levels leading to a high quality product. My team was mentored by Dries Ferreira, an experienced Chief Geologist, who played a huge role in my career development. We were fortunate to work alongside a very competent structural geologist, Steve Jolley, who was kicking his heels around a bit for work, so spent time on the project. He was able to identify structures, cleavage direction changes, and other interesting features that enabled understanding the complex structure of the project. Core logging is not merely about capturing intervals, there is a whole world of rock relationship information, very rarely recognized, understood, captured or utilized that can inform fundamentally critical exploration decisions. This includes the primary relationships between lithologies, relative timing, fractionated or non-fractionated stratigraphy in intrusions, mineralization relationships to the surrounding rocks, vein morphologies, compositions, ad infinitum.
Following Anglovaal, I spent three years at Lonrho’s Western Platinum Mine (now Sibanye-Stillwater-owned). This was also a critical formative period, as at Lonrhro, unlike JCI (now Amplats) and Impala Platinum, we had very few geologists, and we were utilized on a mine-wide basis, not confined to a single reef on a single section or shaft. I was fortunate to have the entire mine to play with, particularly after my underground mentor David Mooney moved to Eastern Platinum Mine. For three years, I did not use a PC, I was underground just about every day, and together with my small team of geological observers, mapped over 15 km (9.3 mi) of raise and haulage development a month, plotting it onto paper G-Sheets. I also completed my Rock Mechanics Elementary ticket, as this allowed me to visit other mines, which was not possible for a geologist in those days. This period provided an intimate detailed knowledge of the entire Bushveld Complex, as when I left Lonhro, I had visited every Platinum Mine apart from Atok and Messina.
From the drilling aspect, the Bushveld Complex is a strange animal. While current practice is to drill on a relatively tight spacing, mainly to comply with the Mineral Resource Codes, it was a bit different when I was at Lonhro. Although the property was drilled at very wide spacing, during my period, we used to drill only sparingly. In the Bushveld Complex, particularly for the UG2, it is not critical to drill at shortrange to establish the PGE grade, as it is remarkably consistent. We primarily drilled to resolve geological problems. On one memorable occasion, we drilled an underground hole to establish the elevation of the UG2, at approximately 150 m (492 ft) below the mined out Merensky Reef. The AX-size hole burnt in at about 140 m (459 ft), so after much deliberation, it was decided to set a wedge, the thinnest one I have ever seen! For some long-forgotten reason, we decided to set
and drill the wedge through the blast, which was okay because the hole was in the intake airway of the mine. Not to be missed, I joined the driller Johann Meyer for the surreal experience, the Kempe rig spinning as fast as possible, whining like a banshee, and all around us the booms of the underlying UG2 stopes being blasted. Needless to say, the mission was successfully accomplished.
Throughout my subsequent career, I have endeavored to see as many projects as possible, not only in my core field of Ni and PGE, but also other sectors as this provides comparative insights, or operational methods that may be transferable. I am very fortunate to have worked in regional new business teams, focused on both PGE and Ni-sulphide, as these are simply two endmembers of a geological continuum. It is an old saying that the best geologists have seen the most rocks – while this is true, just seeing the rocks is not sufficient, it is more critical to see them, understand what is being looked at, contextualize, relate to analogs elsewhere and identify similarities of process. I also think it is very important to ‘leave a bit behind’ in that I have always tried to engage with the teams, and discuss the projectour core review - ask for opinions, and discuss the features observed. I have always found this is appreciated and welcomed, and, particularly during my final years at MMG, when it was blatantly obvious that
the company would be exiting the Ni sector, viewed it as a potential means of securing consulting work afterwards. It pays to advertise, and no-one would subsequently employ a visitor who does not display any empathy or wisdom.
Observation and deduction are critical requirements for economic geology. Surprisingly, this appears to be a very rare skill indeed throughout the profession. During my early career, I was told by Jan Mostert, Chief Consulting Geologist at Anglovaal, that a competent geologist should be able to work out exactly what a company is working on within a couple of minutes, should they visit a competing exploration office. This is because often, plans are laid on tables, put up on office walls, and memos are left on desks – another critical skill is to be able to read upside down! We were therefore always encouraged to keep a tidy workspace, and never let anyone into our offices unnecessarily. The same applies to ASX information releases. It is amazing how much critical technical detail is unwittingly released in public documents. This particularly applies to core or drill chip photographs.
A case in point, in 2012 or thereabouts, Sirius, following the Nova discovery, released an image of polished drill chips. At that time, like all other Ni-focused geologists, we were keeping a pretty tight watching brief, and in the absence of information, the detailed setting of Nova within the Fraser Range was not known. The deposit was being described by Sirius as a hitherto unidentified style of mineralization. MMG had recently undertaken a review of the Ntaka project (Tanzania), with which I was familiar from Lonmin days, and although the intrusion was described as intensely deformed, it became apparent that this was not the case. The intrusion is predominantly post major deformation, with primary mineralogy. The Nova drill chips had identical mineralogy to Ntaka, therefore it was indicated that this could be a similar setting, and the intrusion therefore had to be late orogenic, which ran counter to all other interpretations. I was even asked why I was the only geologist in Australia who believed this to be the case! Subsequent work by the CSIRO team and IGO has confirmed the late-orogenic setting, indicating the critical importance of such observations from very limited data.
Interestingly, I recently worked for a geologist who has developed the same skillset, but for another commodity. From outcrop photographs, he is often able to work out mineralogy, deduce mineral percentages, and then make an educated guess on recoverability. I clearly need to up my game a bit!!!
Throughout my career, I have been fortunate to work with a very diverse range of men and women of many different backgrounds, cultures, and creeds. The almost overwhelming common trait is that all of these people are predominantly open-minded, intellectually inquisitive, ‘can-do’ characters. In South Africa, in the early 1990s, I was among the first to work underground alongside female geologists, who were previously excluded from working there. I have worked together with, mentored, and watched the career development of numerous people who were previously denied the opportunity to fulfil their ambitions. I have worked in South America and all over Africa with indigenous geologists who have all the skillsets necessary to be world-class and have personal work ethics, respect, and a willingness to learn that would put many in the developed world to shame.
So what qualities are required to become a leading geoscientist? In my opinion, there are several, all of which become important when the chips are down.
Firstly, physical fitness, stamina, and self-determination – and before I am accused of being sexist, in my experience, it is often the females of the team who have these qualities! These become essential on the long traverses in the tropical heat, when often that last outcrop is the important one. The best geologists do not give up and keep on going to see the most rocks!
Secondly, an ability to make observations, not only seeing what is there, but more importantly, what is not there, and identifying anomalies of potential significance. This ‘left-field’ deductive capability based upon an imperfect dataset sets a great field geologist apart from the average. It also is the single most important reason why the current trend towards using AI for exploration purposes will not replace a capable human for the foreseeable future. This is also what makes leaps of deductive faith based upon only partially fitting analogs, or unexplained observations from elsewhere that are stored in the subconscious mind. I have found over the years, that people who grow up in a rural environment have much greater observation skills than those from urban areas. Furthermore, African geologists generally have the best observation skills and memory of specific locations of any persons with whom I have worked.
Third, the ability to operate within a team, be flexible about leadership roles, but be respectful towards people when they have a point to make that could be worth listening to. Being sufficiently comfortable within a team to make a potentially game-changing comment or suggestion, and equally being able to provide an answer that is honest and not demeaning. If communication is stifled, nobody wins. It is quite amazing how rarely such team principles are applied, particularly within the larger corporations, which in my experience are characterized by a cut-throat competitive culture where sharing is tacitly discouraged.
Fourth, keeping your tools sharp! In my case, although I have undertaken many management roles over the years, I have always tried my utmost to be a geologist first, and everything else second. Managers are ten a penny, whereas competent geologists are a very scarce breed. This means taking an active role in project work, undertaking tasks that other members of the teams may not be capable of, while providing mentorship to spread and grow skills.
Designers and manufacturers of inflatable packers and associated equipment
Learning new skills from team members, who often have experience that is new. All of this contributes to a technical growth culture. Finally, a thirst for knowledge is absolutely critical. This means personal growth, undertaking higher degrees, particularly if they can be fit into a work-related topic. Attending management training courses to develop project management skills and theory, field excursions, and focused conferences and seminars. Using the various digital platforms available to download and listen to technical presentations. Reading, and critically appraising academic papers, bearing in mind that not all that is written is cast in stone!
A common industry theme relates to the declining discovery rates over the last 30 or so years of exploration, despite significant exploration spending increases. These presentations, particularly those by Richard Schodde, provide excellent insight into the expenditures and locations of global exploration. From the grass-roots perspective, after spending 30 years in the sharp end of the business, I would propose that there are some issues that perhaps have not been raised. Investment in skills development and mentoring: despite what some companies may claim, serious investment in developing the personnel and experiential skillsets required to advance what is a highly technical, research and development-based business have been fundamentally ignored for almost 30 years. This period of time is sufficient to realize that the predicted outcome of this is a global shortage of skilled geologists to replace those that have retired. At the time, the catchphrase was that it would be ‘possible to source world-class skills from the market’, therefore skill development was not viewed as a return on investment. The global retrenchment that accompanied the ‘just-in-time’ revolution arguably directly led to the junior explorer success during the 1990s to 2000s, as a pool of highly technically skilled professionals saw their various projects and regions canned. Many were successfully resurrected following independent capital raising. These human resources simply no longer exist, and the concurrent almost total lack of sustained exploration by major companies, which realistically are the only ones with the longevity and budgets to provide longer-term career pathing, has compromised the ability to replace them. Major explorer inadequate budgets, short-termism, and over-reliance on junior explorers: currently, major exploration companies undertake less exploration in almost direct proportion to increasing expenditure. It is interesting to compare major explorers’ annual budgets to the funding provided by successful explorers, such as Ivanhoe. The Ivanplats project indicates sustained investment immediately adjacent to Amplats most successful mine has achieved a discovery that was not achieved by other companies with decades of exploration pedigree in the Bushveld Complex. Exploration and mineral discovery is one of the most technically challenging sectors of any business.
It is comparable, if not more technically difficult to the pharmaceutical sector, yet the difference in R&D budgets is staggering. Most current exploration budgets barely cover overhead costs, leading to management criticism of the lack of discovery and subsequent team disbanding. Yet the teams are hamstrung from day one. This leads to a related issue, short-termism, and perceptions of failure. This afflicts most major and mid-tier companies with very few exceptions (IGO being a notable one). A company will decide to become an explorer or rebuild a capability. Invariably, promises are made, to huge fanfare and expectation, but it is not realized that successful exploration is a 10–20 year business investment. This is particularly true if, as is often the case, the company decides to ‘bust open new terrains’. It takes five years simply to recruit a team, enter a country, form partnerships, and acquire or generate the basic datasets. During this period, incremental knowledge is gained that needs to be understood, benchmarked, interpreted, and adequately warehoused. Generally, such knowledge only becomes useful once a technical breakthrough is achieved, or hard data is acquired that enables a more robust interpretation of, for example, a geophysical dataset. If there has not been continuity of personnel, or adequate document management, or all the documents have been shipped to Singapore (notably), this breakthrough may never be realized. Therefore, the whole exploration ship sinks, companies become disillusioned, and the exploration effort is disbanded. One simply has to review the recent history of most major explorers, as all are guilty of this recklessly stupid short-term destructive cyclicity. A further comparison may be drawn to the pharmaceuticals sector, which has not seen a similar strategy implemented as the relationship between R&D and revenue is more closely understood. During the recent COVID-19 period, had a similar industry-wide retrenchment of capabilities occurred, it would have taken years, rather than months, to re-engineer and develop the vaccines that broke the virus.
This destructive process also occurred at MMG, formed with a mandate to grow through acquisition and exploration, during the ten years following its formation during 2009. At one point MMG was the only large company actively exploring for Ni-sulphide, and was provided opportunities to purchase Eagle, Kabanga, Noront, and Tamarack, which, apart from Nova, were the best pre-development projects globally. Noront could have been purchased outright during 2016 for a little more than a single year’s exploration budget, approximately CAD 90 million. The recent Wyloo Minerals purchase valued the company at over CAD 620 million. Had the strategy been implemented, MMG would have currently held all the largest, highest grade Ni-sulphide projects globally, and been at the forefront of the current green resource sector. Although hindsight is always 20/20, the greater importance of foresight, and staying power are more often totally lacking in corporate strategic thinking.
An often-mentioned solution is to ‘let the juniors make a discovery and then purchase’. However, this is in itself a flawed strategy for the reasons outlined hereafter, especially, as pointed out by Schodde and others, exploration becomes deeper and more conceptual in nature. The exploration cost and risk exclude almost all junior explorers from this sector of the business. Junior explorers are much more effective in less-developed countries that are relatively under-explored, and within which surface discoveries are more likely to be made. When examining the global exploration and discovery maps, it is clear that the Anglophone countries feature very prominently. This directly reflects the quantity of exploration that has taken place – easier funding based upon language and legal familiarity equals more exploration, which leads to more discoveries being made. This situation will change, as the cost and technical difficulty of doing business will force juniors to enter the frontier countries.
A common failing of many exploration teams is over-reliance on academic, rather than economically-focused literature. This is partly a result of industry confidentiality, although that has significantly changed, and partly the demobilization of internal company centers of excellence that undertake more economically-focused research and orebody genetic modelling. This has led to an almost total reliance on the academic literature.
Throughout my career, I have tried to work with, provide opportunities to, and learn from the subject experts in the various academic fields related to my area of expertise with mixed success. I have found that the main issues are that firstly, academic specialists are extremely focused to the extent where they often ignore or are not aware of associated specialties. A case in point relates to mafic and ultramafic intrusions, a field currently dominated by experts with a petrological or geochemical background. However, emplacement of an igneous intrusion is a physical process that occurs at any location from mantle to crust and is subject to various geological controls that may be fundamental to ore genesis. These physical processes result in mappable features, both within the intrusions and the country rock, and therefore their recognition is of direct importance to an economic geologist. However, very few of the technical papers that are used by most exploration teams to define exploration strategy consider these processes, or processes invoked are totally contradictory to all physical observations such that they are unworkable. As pointed out by Brett in a previous edition, the ‘genetic diagrams’ presented in various
technical papers show intrusions that do not exist in reality, and do not feature the real-life mappable features that may lead to discovery. Therefore, the current generation of explorers are pursuing models that are fatally flawed in almost every aspect. The only solution to this problem is to build and mentor commodity-focused teams, led by an industry-experienced technical specialist who has visited, worked on, studied, and understood as many real-life projects as possible in the global sense. Furthermore, such teams should not be ring-fenced to a single commodity, as is often the case, which limits opportunities to share ideas and technologies.
The junior exploration sector is often viewed as the panacea to all industry woes. ‘They will get out there and do what the majors cannot do themselves! They will innovate and find new solutions! They are more cost-effective! They will train the next generation!’ All these phrases are bandied about, but it has to be asked whether any of this is actually true. As previously indicated, a junior explorer has to work extremely hard to raise a relatively small amount of capital. Due to the nature of the business, this capital is generally only advanced to companies that have a direct line into drilling, and definition of mineral resources. A conceptual project is simply non-fundable. The timeframes required to be committed to for drilling are often too short to undertake an exploration program that will optimally evaluate a wide range of possibilities and drilling a scientific conceptual target hole for non-discovery purposes is akin to walking into a bar in Manchester with a Leeds United football shirt on! Together with the current social-media-led reporting hysteria for news flow every time the driller breaks wind (apologies readers), this is totally counter-productive to success. Given the above, it is remarkable for anyone to expect that training forms any part of a junior explorers’ agenda. There is simply no room, and no budget for training, particularly in an environment where mainly contractors are employed. The contractor is often placed in the unenviable situation of getting three years of experience 20 times over before retirement, not conducive to skills and experience development, and few are lucky enough to break out of this mould.
Of course, exploration is in many ways akin to blowing your cash on a game of two’s-up, and we all accept it, but to put our hopes on the junior sector is mind-blowingly optimistic. It will not solve any of the current Tier 1 discovery problems faced by the exploration industry.
Many companies, of all sizes, tend to adopt exploration ranking strategies, based upon critical parameters of the target discovery. These often relate to deposits that do not exist. Alternatively, they can place constraints on exploration despite all the evidence saying, ‘here I am!’ My current favorite stories in this regard are the Kamoa (Congo) and Sakatti (Finland) discoveries, both of which were made despite subject experts from a major company saying they were not possible! The Ni-sulphide potential of the Fraser Range was also written off by an industry expert. These examples form a fundamental reason why AI exploration will not provide a solution as none of these discoveries fit the ‘model’, and programming is done by humans who believe in
● Near in-situ continuous core samples.
● Highly accurate mineral resource value determination.
● Geotechnical and environmental program drilling.
● Install straight pre-collars through difficult overburden for diamond coring.
● Can easily be converted to drill diamond coring tails on short holes.
generic models and checklists. From my personal perspective, I often hear exploration for Ni-sulphide premised upon intrusion into sulphur-bearing sediments to induce saturation and deposition. However, this often flies in the face of sulphur isotope information, and also with respect to the genetic model – sulphide liquid needs to efficiently mix to sequestrate metal, which is at odds with local saturation. Mantle-derived magma interacts with crust at every stage through the crust, therefore contamination and sulphur saturation are ubiquitous. These non-informed constraints provide a barrier to discovery until someone who has not read the checklist arrives and simply follows their nose!
The exploration industry is a dynamic, extremely technically challenging, and difficult business sector that is trying to understand and predict extremely complex processes that have occurred in the Earth’s crust. Unfortunately, or fortunately for some, the very nature of the challenge means that it is also possible for a farmer in
the Outback, or a herdsman in Tanzania to stumble upon a worldclass discovery just by being observant and in the right place at the right time. While these discoveries may occur, there is no chance for them to provide a sustainable supply of metal to resource the growing and changing world. The exploration sector is also at a position at which there is a clear shortage of ability to meet the anticipated demand. This has been exacerbated by 30 years of minimal investment in capability and expertise building, along with obscene levels of financial revenue extraction to shareholders and bonuses. I argue that we are approaching an experiential tipping point, and that there needs to be a major rethink among the industry leaders. The major and larger mid-tier companies are the only potential solution to the crisis. Discovery-focused technical teams need to focus on economic geology as a separate, though aligned sector to academia, which is not equipped to fulfil the required role. Finally, mentorship and skills transfer should be prioritized before these skills and experience retire from the industry. C
Get in touch with the author on LinkedIn
The annual Prospectors & Developers Association of Canada’s (PDAC) 2023 Convention will take place from March 5-8. The event will be in-person in the Metro Toronto Convention Center, Canada. The convention attracts up to 30 000 attendees from over 130 countries for its educational programming, networking events, outstanding business opportunities, and fun. That is why PDAC is regarded as the ‘Super Bowl’ of mineral exploration and mining and the leading event for people, companies, and organizations conected to it.
PDAC 2023 will feature over 1100 exhibitors from across the globe showcasing leading technologies, products, and services spread over the North and South Buildings of the convention center. The Core Shack is a unique venue for companies to display their core samples. Attendees can explore new or ongoing projects that are generating exciting drill results.
The Convention will host keynotes and presentations from industry leaders and experts, providing visitors with knowledge and new concepts. Some of the highlights include Exploration Insights, showcasing technical, policy, and academic presentations, the Captial Markets Program, and a corporate presentation forum for investors.
The convention will also host in-person industry events and ample opportunities for networking for the first time in several years.
Among many other social activities, guests may have drinks, snacks, and conversation with potential business contacts while enjoying PDAC’s favorite The Network with Duelling Pianos by A.B. Live Custom Entertainment.
‘PDAC 2023 will be another industry-leading showcase spread over almost 600 000 square feet of both the North and South Building of Toronto’s Metro Toronto Convention Centre,’ promises Alex Christopher, president of PDAC.
Since it began in 1932, the PDAC Convention has grown in size, stature, and influence. Today, it is the event of choice for the global mineral industry hosting more than 1100 exhibitors and 2500 investors. The deadline for early registrations is February 10, 2023. C
Expand your network with attendees from 120+ countries
1,100+ exhibitors showcasing the best in the industry
Hundreds of hours of programming presented by industry experts
Engage with private, retail and institutional investors and senior executives
5 - 8
1. A type of hole surveying tool
4. A deep narrow shaft drilled in the ground to reach an exploration target
6. The cutting part of the drill bit
9. An additive that assists in the cutting removal
10. A main part of a core drill
11. A hole data that represents the position of the hole along its axis
12. The borehole drilled first in multi-lateral drilling
13. The beginning of a hole
14. Where a drill is placed, and drilling takes place
15. A container where core samples are kept
2. The outer part of the core barrel outer’s body
3. Hard hat
5. Another main part from the core barrel
7. A force that tends to cause rotation
8. Unwanted departure from an established course or accepted standard
11. A device that is installed in the drill hole to bypass a piece of equipment left in the hole or to side-track a new branch
BRYSON DRILLING
Phone 306-323-2202 Fax 306-323-2203 info@brysondrilling.ca www.brysondrilling.ca Canada
DDH1 DRILLING
Phone +61 08 9435 1700 admin@ddh1.com.au www.ddh1.com.au Australia
DIAFOR
Phone (819) 860-3957 info@diafor.ca www.diafor.ca Canada
GÜNZEL DRILLING CC
Phone + 264 81 322 89 28 info@guenzeldrilling.com www.guenzeldrilling.com Namibia
KATI OY
Phone 0207430660
info@oykatiab.com www.oykatiab.com Finland
MITCHELL SERVICES
Phone +61 7 3722 7222 Fax +61 7 3722 7256 info@mitchellservices.com.au www.mitchellservices.com.au Australia
Surveying & Geophysics (A-Z) Drill Rigs & Accessories Cont.
CORE TECH
Phone +51 983 856 666
info@coretech.com.pe www.coretech.com.pe Peru
DIGITAL SURVEYING
Phone +27 18 788 6349
sales@digitalsurveying.co.za www.digitalsurveying.com.za Africa
GEOLÓGICAS
Phone +55 62 992720023 contato@trustsg.com.br Brazil
Drill Rigs & Accessories (A-Z)
Fax (819) 824-2891 info@avddrills.com www.avddrills.com
www.barkomas.com
Phone 1-506-542-9708 Fax 1-506-542-9709 info@discoverydrills.com www.discoverydrills.com
Drill Rigs & Accessories Cont.
www.terrasonicinternational.com sales@terrasonicinternational.com
+1 740.374.6608
+1 740.374.3618
WE
Terra Sonic International knows what it takes for you to succeed. We are committed to making the world’s most productive and reliable SONIC Drill Rigs and SONIC Tooling while providing the best service and support in the industry. Experience the Terra Sonic Difference today.
PROLENC
Phone (250) 563-8899
Fax (250) 563-6704
khodgins@prolenc.com www.prolenc.com
BOART LONGYEAR
Phone 1-801-972-6430
Fax 1-801-977-3374 www.boartlongyear.com
FORDIA POWERED BY EPIROC
Phone 514-336-9211
Fax 514-745-4125 info@fordia.com www.fordia.com
NORTH BAY MACHINING CENTRE
Phone (705) 472-9416
Fax (705) 472-2927
luc@nbmc.ca www.nbmc.ca
PROLENC
Phone (250) 563-8899
Fax (250) 563-6704
khodgins@prolenc.com www.prolenc.com
www.boartlongyear.com marketing@boartlongyear.com
www.diatoolglobal.com anthonygraham6@gmail.com
QUALITY AND EXPERTISE
DIATOOL is a young and dynamic company, founded in 2010. The company manufactures impregnated and set core bits, casing shoes, reaming shells, and geotechnical drilling bits. DIATOOL products are sold in North and South America, Australia, Asia, Africa, and Europe. DIATOOL Diamond Products are manufactured in a modern well-equipped plant, using the latest manufacturing technology.
BOART LONGYEAR
Phone 1-801-972-6430 Fax 1-801-977-3374 www.boartlongyear.com
DRILLING HQ
Phone 1 (208) 690-3111 info@DrillingHQ.com www.drillinghq.com
HOLE PRODUCTS
Phone 909-939-2581 Fax 909-891-0434 www.holeproducts.com
SINOCOREDRILL
Phone 86-510-82723272 Fax 86-510-82752846
sales@sinocoredrill.com www.sinocoredrill.com
Drill Rods & Casings Cont.
WE ARE YOUR SONIC DRILLING PARTNER
Terra Sonic International knows what it takes for you to succeed. We are committed to making the world’s most productive and reliable SONIC Drill Rigs and SONIC Tooling while providing the best service and support in the industry. Experience the Terra Sonic Difference today. www.terrasonicinternational.com sales@terrasonicinternational.com +1 740.374.6608 +1 740.374.3618
BARKOM
Phone 90-312 385 60 50 Fax 90-312 385 35 75 info@barkomas.com www.barkomas.com
CORE TECH Phone +51 983 856 666 info@coretech.com.pe www.coretech.com.pe
FORDIA POWERED BY EPIROC Phone 514-336-9211 Fax 514-745-4125 info@fordia.com www.fordia.com
REFLEX Phone 1-705-235-2169 Fax 1-705-235-2165 reflex@imdexlimited.com www.reflexnow.com
SONDA PARTS Phone 55 – (31) 3391 3810 Fax 55 – (31) 3391 3810 comercial@sondaparts.com.br www.sondaparts.com.br/
COREFINDER Phone +55 62 992720023 contato@corefinder.com.br www.corefinder.com.br
DEVICO AS Phone +47 72870101 devico@devico.com www.devico.com
REFLEX INSTRUMENTS Phone 61 8 9445 4020 Fax 61 8 9445 4040 reflex@imdexlimited.com www.reflexnow.com
FORDIA POWERED BY EPIROC Phone 514-336-9211 Fax 514-745-4125 info@fordia.com www.fordia.com
www.reflexnow.com reflex@imdexlimited.com 1-705-235-2169
REFLEX - A LEADING IMDEX BRAND REFLEX forms part of Imdex Limited, a leading Mining-Tech company. Our unique end-to-end solutions for the mining value chain integrate IMDEX’s leading AMC and REFLEX brands. Market leading REFLEX technologies enable drilling contractors and resource companies to drill faster and smarter, obtain accurate subsurface data and receive real-time information for critical decision making.
AMC
Phone 1-705-235-2169 www.amcmud.com
DI-CORP
Phone +1 (705) 472-7700 info@di-corp.com www.di-corp.com
Mudex
Phone +61 (8) 9390 4620 info@mudex.com.au www.mudex.com.au
CORE TECH
Phone +51 983 856 666 info@coretech.com.pe www.coretech.com.pe
DYNAMICS G-EX
Phone +61 7 54826649 sales@dynamicsgex. com.au www.dynamicsgex.com.au
PROSPECTORS
Phone +61 (02) 9839
3500
Fax +61 (02) 8824 5250 sales@prospectors.com.au
Basic listing
110 USD per issue 330 USD per four issues
A text-only listing including your company name and contact details (phone, fax, email and website).
Featured listing
275 USD per issue 830 USD per four issues
A business card-sized listing featuring your choice of image as a background, your logo and strapline, 240 character spaces and your company contact details.
Combined listing
1250 USD per year (four issues)
A featured listing published both in our print and web catalog.
For more info, get in touch at: editorial@coringmagazine.com
Make the most of your drilling fluid.
As the cost of drilling increases, the need to improve productivity is paramount. Additional costs caused by higher operational standards, environmental restrictions and increased hole depths will continue.
As specialists in Drilling Optimisation, IMDEX’s vision is to ensure the execution of drilling programs to specification, on time, within budget, and safely.
IMDEX never stops exploring better ways to sustainibly find, define, and mine for the future of the industry.