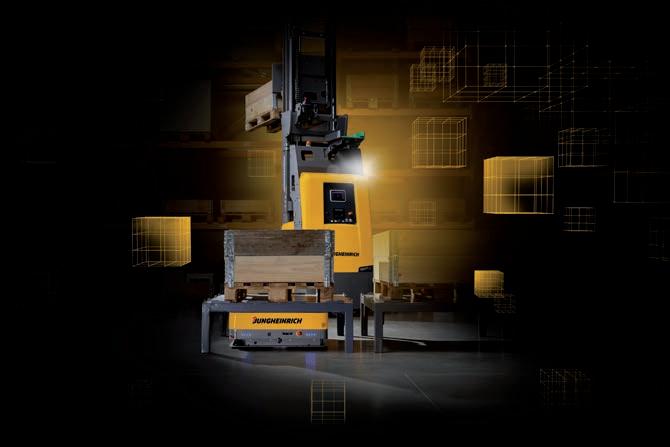
7 minute read
L’AMR, nouveau Graal de l’intralogistique ?
Présentée
PAR RENAUD CHASLE
Advertisement
L’emploi du mot explosion n’est pas usurpé pour évoquer la croissance du marché des robots mobiles logistiques depuis 3 ans. Le nombre d’acteurs a été multiplié par 4 sur la période, et le secteur de la logistique, après des tests et des projets pilotes, semble être désormais entré dans une phase d’adoption rapide. En 2019, le cabinet Wavestone identifiait près de 70 fournisseurs d’AMR dans le monde. « Aujourd’hui, on en dénombre 250, dont 55 % environ sont européens », indique son directeur Philippe Létard.
Ce chiffre comprend les startup comme les équipementiers historiques, qui ont pris le virage de la robotique pour ne pas se laisser distancer par la concurrence. Selon STIG Research, qui propose une analyse étendue au marché global de la robotique en intégrant les AGV et les logiciels (voir définitions en encadré page 26), on dénombrait dans le monde 10 éditeurs de logiciels de navigation pour robots en 2010, contre 30 en 2021 dans le monde. Le nombre de fabricants, vendeurs et fournisseurs de technologies de navigation ou d’intelligence artificielle d’AGV et d’AMR est passé de 176 en 2010 à 308 en 2021. Et les projections évoquent une croissance massive de la robotique.
D’après LogisticsIQ, le marché devrait atteindre plus de 18 Md$ d’ici 2027, avec un taux de croissance d’environ 24 % des AGV et 43 % des AMR. Au regard des prévisions, les AGV et les AMR vont collectivement atteindre une base installée de 2,4 millions d’unités en 2027. Les États-Unis, la
Chine et le Japon, l’Allemagne et le Royaume-Uni vont dominer le marché, avec une demande annuelle de plus de 200 000 robots mobiles d’ici 2027. Les fournisseurs français restent minoritaires en nombre ainsi qu’en capacité de production, notamment face aux acteurs chinois capables de produire jusqu’à 10 000 robots par an. En revanche, les acteurs tricolores se distinguent par des offres globales et des modèles de location longue et courte durée.
À l’assaut des entrepôts
L’adoption des robots mobiles est manifeste dans les entre- pôts, notamment pour les secteurs de l’e-commerce, du retail ou des produits pharmaceutiques. Elle concerne principalement les process de préparation des commandes, de gestion du stock ou de tri. « On voit aujourd’hui sur le marché une palanquée de systèmes AMR qui remplacent les systèmes fixes dans des zones fermées, par exemple de tri : des flottes de petits robots de tri remplacent les gros trieurs mécanisés avec convoyeur. Les fournisseurs de type Knapp ou Dematic proposent désormais ce genre de solutions. Les robots se déplacent en suivant des QR codes au sol. C’est beaucoup moins cher et cela apporte la flexibilité, la capacité d’en ajouter quand on veut, de déménager quand on veut, de commencer sur de petits projets puis d’élargir ensuite », indique Philippe Létard. Ce sont encore majoritairement les grands groupes, 3PL ou entrepôts industriels, qui déploient des AMR. Cet été, Geodis a ainsi annoncé le déploiement de 1 000 LocusBots de l’américain Locus Robotics sur ses sites au cours des deux prochaines années. Cette commande, l’une des plus importantes à ce jour, permet d’étoffer le parc en place de Locus, qui a déjà équipé 30 sites en Europe depuis trois ans. ID Logistics, depuis l’installation de l’AMR Astrid développé avec Wyca, dédié aux inventaires de stock et capable de traiter 5 000 palettes à l’heure contre 250 à 350 avec un drone, a créé le programme Roboost dans l’objectif de généraliser l’emploi de robots sur ses sites à l’échelle mondiale. « Les premières mises en place de robots ont démarré à Taïwan. Aujourd’hui, on en déploie en France, en Espagne,
AGV, AMR, de quoi parle-t-on ?
Évoquons le jargon de la robotique car tout se mélange ! On parle tantôt d’AGV (automated guided vehicle, véhicules autoguidés), d’AMR (autonomous mobile robot, robot mobile autonome) ou PAAMR (picking assistant AMR), d’ASRS (automated storage and retrieval system, système de stockage automatisé).
Pour simplifier l’identification de ces technologies d’automatisation, on peut considérer que les AGV sont des chariots de manutention dotés de systèmes de navigation autonome, sans conducteur. Leur usage concerne souvent le transport de charges lourdes pour les opérations de palettisation, de mise en stock ou de traction de conteneurs. Les AGV sont limités à un parcours prédéfini, matérialisé par des systèmes de guidage laser au sol ou de rail.
Les AMR sont plutôt utilisés dans les phases de préparation des commandes goodsto-person. Il s’agit d’une base technologique sur roues, capable de soulever des étagères ou de transporter des colis à l’unité vers les postes de picking. Sur ces bases robotisées viennent s’ajouter des modules, par exemple des plateaux, des miniconvoyeurs, des contenants de bacs ou des bras robotisés qui assurent le prélèvement des produits. Ils ont des capacités de charge de plus en plus importantes, mais restent encore majoritairement utilisés pour de petits colis ou produits. Les AMR sont des bases mobiles autonomes qui évoluent dans des périmètres ouverts. Enfin, les ASRS s’inspirent des systèmes de convoyage mécanisés et de goulottes vers des puits, mais ce sont des robots qui vont chercher les produits le long d’immenses systèmes de stockage et les déposent dans des goulottes menant à un poste de préparation ou de tri. Ces robots évoluent au sein d’une grille ou d’une cage, sans intervention humaine. Ce sont par exemple les machines d’Exotec ou d’AutoStore. Néanmoins, toutes ces technologies fusionnent, ou du moins se rapprochent. Par exemple, les AGV commencent à embarquer les mêmes technologies de navigation que les AMR, les algorithmes de Slam (simultaneous localization and mapping algorithm). À l’inverse, de nouveaux AMR arrivent avec la capacité de porter de lourdes charges, ce qui était auparavant l’apanage des AGV. Quant aux petits robots utilisés pour les systèmes ASRS, ils sont sur un plan technologique très similaires aux AMR, mais embarquent moins d’intelligence de reconnaissance de l’environnement puisqu’ils n’évoluent pas au milieu des salariés.
aux Pays-Bas, en Pologne et au Brésil », indique Benoît Boiron, responsable innovation d’ID Logistics.
En Pologne, FM Logistic a déployé en début d’année un AMR MiR500 pour le transport de palettes dans le centre de distribution de son client Ikea. Mobile Industrial Robots (MiR) progresse également sur le marché français. Selon Fernando Fandiño Oliver, directeur des ventes Europe, la France, où MiR est actif depuis plus de six ans avec une présence commerciale et technique sur tout le territoire et des clients tels que Lenze, DHL ou Forvia, représente l’un des trois premiers marchés du fabricant en Europe, avec une croissance à deux chiffres chaque année. À l’échelle mondiale, les ventes de MiR ont progressé de 42 % le distributeur de livres MDS a déployé 55 robots Scallog et 255 étagères mobiles pour alimenter 8 stations de préparation dans son centre de distribution de Dourdan. L’enseigne Decathlon utilise des AMR Geek+ dans ses centres de distribution en France, en Italie et en Pologne. D’autres, comme C-Log, ont choisi de concevoir leurs propres robots (voir interview page 33). Un peu partout, les installations d’AMR se multiplient à mesure que l’offre s’étoffe avec un nombre croissant des fournisseurs.

Flexibilité et ROI rapide
Philippe Mezerette, responsable business development de Locus Robotics explique le succès des AMR par la montée en cadence des entrepôts : « Depuis 2018, on voit une croissance exponentielle, motivée par le manque de disponibilité de main-d’œuvre et l’enjeu d’atteindre les objectifs de productivité et de services. C’est l’effet Amazon, qui associe une poussée des volumes par l’e-commerce à une plus grande rapidité d’exécution des commandes ». Selon lui, les AMR apportent aux entrepôts la flexibilité ou l’évolutivité, grâce à une solution qui permet d’accroître l’activité par ajout de robot à la volée au fil du temps. La solution, rapide à implanter, s’adapte aux périodes de pics d’activité. « L’AMR permet aussi de gommer les temps masqués et d’optimiser les déplacements des personnes et les distances parcourues. Un préparateur peut aujourd’hui parcourir 15 km par jour. Avec un robot Locus, on limite entre 3 et 4 km le déplacement d’un opérateur. Cela peut représenter jusqu’à 60 % de la masse salariale de l’entreprise pour la préparation des commandes », précise-t-il. Autre avantage des AMR par rapport à des systèmes mécanisés ou même aux AGV qui nécessitent une infrastructure de guidage au sol, leur mise en œuvre est rapide. « Il faut 3 à 6 mois de mise en œuvre contre 18 mois pour une solution mécanisée. Cela permet de s’engager sur des contrats de 3 ans plutôt que de 7 ans, mais aussi de moins perdre en cas de baisse des flux à moyen terme », explique Philippe Létard. Avec des délais rapides d’implantation et plus de flexibilité pour l’entrepôt, le ROI des AMR est assez court. « À but équivalent et ergonomie équivalente, on est sur le même tarif qu’une solution mécanisée. En revanche, grâce à la flexibilité qu’offre la location dans le dimensionne- ment initial de la solution puis son extension en cas de pics d’activité, les logisticiens peuvent gagner de l’argent en minimisant l’investissement. Les robots coûtent entre 20 000 et 50 000 €. Les gros faiseurs sont encore hésitants, peut-être qu’en adressant le marché avec plus de force et de plus gros volumes, les prix baisseront », complète-t-il. À la rapidité d’installation s’ajoutent aussi des temps de formation des personnels divisés par 3, selon Locus Robotics, par rapport à une solution de préparation de commandes manuelle à l’aide de terminaux mobiles radiofréquence. En permettant de réduire la pénibilité dans l’entrepôt, de concentrer les collaborateurs sur des tâches à plus forte valeur ajoutée et de monter en compétence pour devenir pilote de flotte robots, les logisticiens estiment aussi que la robotique peut devenir un argument de recrutement et de motivation auprès des jeunes générations. n
En Europe, les robots mobiles doivent respecter les standards fixés par la norme NF EN 1525 (sécurité des chariots de manutention – chariots sans conducteur et leurs systèmes). Depuis février 2020, une nouvelle norme ISO 3691-4 :2020 détermine le cadre sécuritaire des robots logistiques autonomes qui s’applique aux fabricants, intégrateurs et utilisateurs. Leurs fabricants doivent respecter cette réglementation afin d’être en conformité avec l’article L.4311-3 du Code civil, qui interdit la commercialisation d’un robot mobile autonome ne répondant pas aux règles de conception qui lui sont applicables. Cela implique une analyse amont des risques, afin d’identifier les phénomènes dangereux à partir des caractéristiques, performances et modes opératoires de la machine pour adapter leur conception. Les fabricants doivent ainsi fournir une notice d’instructions, et dans certains cas compléter par une formation adaptée, contenant notamment toutes les informations pour mettre en place, utiliser, régler, entretenir et dépanner le système robotisé en cas de besoin. Notons par ailleurs que l’association allemande de l’industrie automobile (VDA) et l’association de manutention et d’intralogistique VDMA travaillent à l’élaboration de la norme VDA 5050, afin de rendre interopérables des robots mobiles de différents modèles et marques.
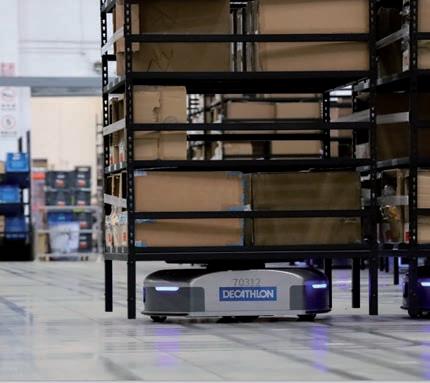
