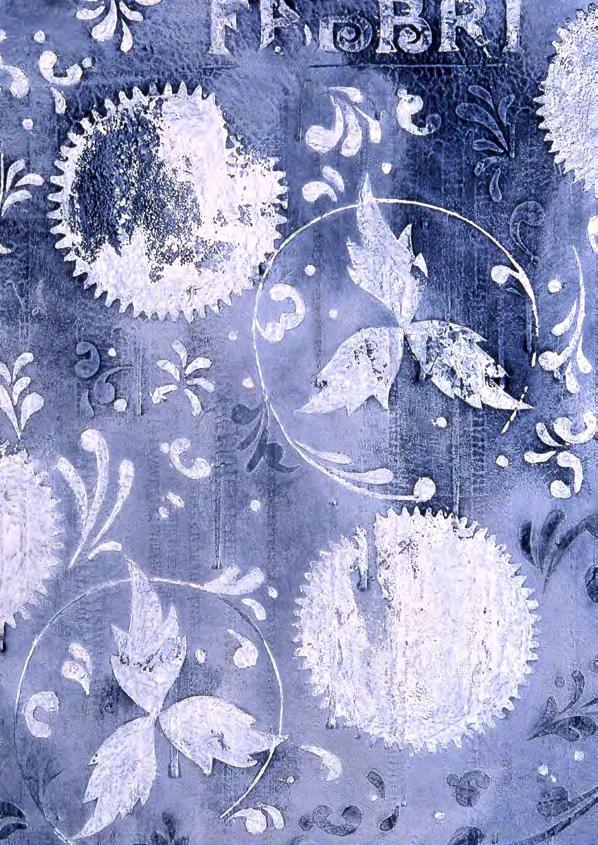
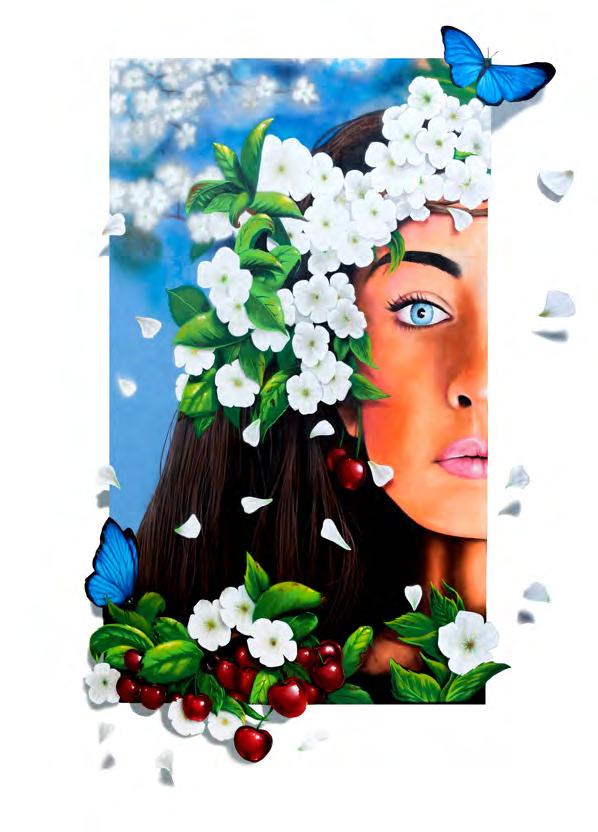
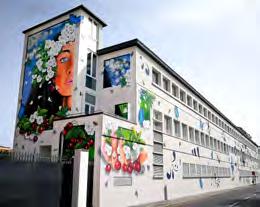
A work of art, an urban renewal project, an anti-smog installation.
The work is a true homage to the city of Bologna, which has been the company's home for more than 100 years. Fabbri 1905's idea of transforming the outer wall of its historic headquarters was born with the intention of decorating and adding beauty to the urban space. The protective finish not only preserves the work but also absorbs carbon dioxide.
The work’s creator is internationally-renowned artist Cheone.The Mural tells a poetic story: Mother Nature giving the gift of a bountiful harvest to the city, depicted with both realism and fantasy.
Today, after more than a century of development and evolution, we still strive to evoke the genuine, authentic flavours of yesteryear in all of our products.
The flavours of good Italian tradition.
Food safety, taste, and wellness have always been the pillars of our commitment. We believe that striving for excellence in our products and services means focusing on human beings first and foremost, and respecting each individual’s ethical and religious values.
For each individual and for the future of the planet, we strive to ensure that our designs, processes, methodologies and raw materials meet our goals of territorial balance, pollution prevention, environmental and landscape protection.
Because our ingredients for ice cream, pastry, mixology and coffees are part of the daily lives of our customers, at home and away from home, from breakfast to snack time and dessert.
Any time is a good time to share the flavour and joy of a recipe made with love, and to share a moment of happiness.
Michele Magli CEOOur story begins in 1905, when companies were small family businesses and recipes were handed down from generation to generation.
Building on a century of experience in the Italian culinary tradition, Fabbri 1905 S.p.A. (hereafter Fabbri 1905 or Fabbri), offers consumers and professionals products, premium ingredients and innovative solutions, with high added value, to bring their own personal creativity to life in the preparation of food and beverage specialities both in and out of the home. The great attention Fabbri 1905 pays to quality, both in its products and manufacturing processes, has made the company a sterling example of “Made in Italy” quality, both in Italy itself and abroad.
Fabbri 1905, an Italian market leader in food production, operates in four main markets:
1 2 artisanal gelato and pastry
3 4
FMCG food service (AFH)
semi-finished products for the food industry
The company has 150 employees and produces around 1,300 items, with 17 product lines and 23 packaging lines, distributed in over 100 countries worldwide
1,300 17 23 employees countries around the world
Distributed in over articles product lines packaging lines
150 100
In the retail channel, Fabbri 1905 operates through large-scale retail sales and digital sales, both through its own e-shop and through the best national and international marketplaces. The main products for consumers include, in addition to the original Amarena Fabbri and other specialities in syrup such as Strawberry and Ginger, Toppings, Syrups, Fruit in Liqueur, and, among the new products introduced in 2022, 3 spreadable creams and an exquisite praline, the Bombon Cuor di Amarena Fabbri;
For the “outside the home” market, aimed at beverage professionals in nighttime and daytime settings, cafes, and restaurants, Fabbri 1905 offers an extensive range of syrups and fruit pulps for modern mixology and for the creation of artisanal drinks and fruit slushes; additional service products such as cold creams, toppings and ingredients for smoothies and milk shakes are also available. The jewel in the company's crown is a signature line of liqueurs, “Premiata Distilleria G. Fabbri”, consisting of Fabbri Gin and Marendry Bitter, both made unique by the inimitable notes of Amarena Fabbri. Together with the Special “Cherries”, these “premium” liqueurs are born from Fabbri's longstanding tradition and extensive expertise in the liquor world.
The company provides pastry shops and gelato shops with all the necessary ingredients for excellent artisanal gelato prepared according to Italian tradition. Powder bases, anhydrous or sugar flavouring pastes, variegates, fillings, and toppings are just a selection of the many products offered by Fabbri.
Intended for the artisan pastry chef are products for the creation of cakes, parfaits, single-portions, baked classics and frozen desserts.
In addition to the sale of its products to consumers and to various professional categories, Fabbri 1905 is committed to training new talents: the Fabbri Master Class school, established in 1998, is today more than ever a training environment for novice professionals and for those who want to hone techniques and learn new trends. Training is offered, including on customer premises, in mixed drinks, coffee, gelato and pastry.
Fabbri 1905 collaborates with renowned Master Gelato Makers, Pastry Chefs and Mixologists such as Davide Malizia, Francesco Elmi, Bruno Vanzan, Gianni Cocco and Mattia Pastori, allowing the company to identify and interpret market trends in advance, developing products, recipes and new ideas to bring to the public, recognising the increasingly evolving needs of professionals and adapting its output accordingly.
Finally, there are a number of collaborations with other companies, both Italian and foreign, with whom Fabbri 1905 creates new products in comarketing, using in particular its most iconic product, Amarena Fabbri. These include Sammontana for the famous Sammontana Barattolino jar (single-portion or family size) with Amarena Fabbri, Industria Dolciaria Borsari for leavened pastries with Amarena Fabbri, Herbamelle with Fabbri Mint and with Amarena Fabbri, and the more recent sugared almonds with Amarena Fabbri produced in collaboration with Maxtris
1905
The young Gennaro Fabbri, then aged 45, opened a grocery store in Por tomaggiore (Ferrara) with a small distillery attached and transformed it into the “Premiata Distilleria G. Fabbri”. His first liqueurs were a great success, and the distillery was moved in 1914 to larger premises in Borgo Panigale (Bologna), still the company's headquarters today.
1915
Rachele Fabbri, Gennaro's wife, invented the legendary “Amarena Fabbri” cherries based on a peasant recipe called “marena con frutto”. Initially sold in demijohns, it also owes its success to its famous ceramic jar with white and blue decorations. The company’s founder came up with the idea and commissioned the design from the Faenza-based ceramist Gatti. Just a few years later, it could be found on bar counters all over Italy. Today, that unmistakable ceramic Amarena Fabbri jar is a symbol of good Italian taste all over the world.
1920s
Alongside the liqueurs, the production of syrups in addition to the Amarena began. Their success continued to grow. Gennaro's sons, Romeo and Aldo, actively participated in the company's development, assisting their father in devising a marketing policy that was revolutionary for its time. For example, Gennaro called his first liqueurs “Primo Maggio” (“May Day”) and “Amaro Carducci.” The first was a wink at socialist militants and sympathizers, and the second celebrates the Italian poet of national unity, who won the Nobel Prize in 1906. To expand distribution of his products, Gennaro sent his sons on a publicity tour of Italy in two legendary automobiles: the Isotta Fraschini, car of the divas, and the Itala, that car of the famous Paris-to-Beijing race of 1907. They immediately caught the nation’s attention and admiration.
1930s
Production continued to expand with cherries in liqueur, another product that quickly met with public favour, and fruit jams and preserves.
The company passed entirely into the hands of Gennaro's sons, Aldo and Romeo, and in that year changed its name to “Ditta G. Fabbri di Aldo e Romeo Fabbri”. The second generation brought new innovation with the launch of syrups that would later become known as “Inventabibite” (“Invent-a-drink”).
Gennaro bought the Bar Centrale in Bologna which, uniquely for the era, was kept open 24 hours a day: the Bar Centrale was Bologna's “well-to-do” salon located in the heart of the city centre, opposite the Sala Borsa, the centre of business and negotiations. The sons turned it into an elegant place where guests could enjoy, among many other specialities, homemade gelato, prepared by a famous gelato maker of the time with Fabbri’s first gelato-specific ingredients.
From post-war to recovery: Fabbri goes big. During the post-war years and economic recovery, the company was transformed into the jointstock company “G. Fabbri SpA”. In 1947 the initiative of the founder's grandsons, Fabio and Giorgio, led to a boost in production of liqueurs and traditional products such as Amarena Fabbri and Fruit Syrups.
Fabbri makes its debut in the gelato world. It was an idea destined to conquer the international market: Fabio and Giorgio industrialised the ingredients created for the homemade gelato at the Bar Centrale and created the “Cremolati”, i.e. pastes complete with creams or fruit which, with the addition of water or milk, become gelato once frozen and churned. Intended for the artisans who were then beginning to use the first electric gelato makers, these semi-finished products were a resounding success, opening up a new market: artisanal Italian gelato. The shops making Italian-style gelato could begin to spread around the world.
Vans equipped as laboratory schools travelled around Italy to teach gelato makers how to use Fabbri products to make excellent gelato. This was another innovation that boosted the brand’s visibility, at the same time as encouraging the growth of the profession of gelato-maker.
When the “Carosello” variety show made its television debut, the Fabbri brand entered the homes of millions of Italians. The famous “Salomone the chubby pirate” character remains a milestone in the history of television commercials. Also worth mentioning is the series “Un pittore alla settimana” (“A painter a week”) featuring then-unknown great painters the likes of Guttuso, Capogrossi, Gentilini, Cagli, and Salvatore, and the commercials with Buscaglione, Pisu, Adolfo Celi, and Tino Buazzelli.
In 1961 Romeo was made a Knight of Labour. The company was gradually taken over by the third Fabbri generation with brothers Giorgio, Fabio and cousin Stefano. Production was moved to the new plant in Anzola Emilia, where it continues to this day. The historic factory in Borgo Panigale was subsequently converted into offices. The Fabbri brand began to spread throughout Europe.
1980s 1990 1995 2005 2010
This was the decade devoted to establishing the brand in international markets, while the range of products designed for consumption outside the home continued to grow.
The fourth generation, represented by the founder's great-grandchildren, became active in the company: Andrea, Nicola, Paolo and Umberto.
Production further diversified, with products intended for the bar: Mixybar and Mixyfruit for mixed drinks, and flavouring products for coffee, chocolate, cappuccinos and tea.
The year of the Centenary: a celebratory "limited edition" ceramic jar, the Cento Anni Fabbri monograph, participation in the Venice Film Festival, the Fabbri Prize for Art, events, and much more marked a birthday shared with affection by Italians who see the brand as the emblem of “Made in Italy” confectionery around the world.
The first members of the fifth generation began to join the company.
The iconic Amarena Fabbri turns 100: an all-female edition of the Fabbri Prize for Art celebrates and honours its creator, Rachele Fabbri. The Storie di Amarena (Amarena Stories) collect people's thoughts and words about the Amarena.
In the Special Register of Italian Historical Trademarks (established by decree of 10 January 2020 by the Ministry of Economic Development) there are as many as four “Historical Trademarks of National Interest” recognised to Fabbri 1905, an almost unique case. It is exceptional evidence of the company’s deep connection with the history of the country, its customs, society and its manufacturing industry. Historical trademarks are the “Fabbri” corporate brand, the “Amarena Fabbri” product brand, the Faenza ceramic vase with blue designs on a white field identified as the company's hallmark, the unmistakable packaging of Fabbri's syrup bottles, and the “Inventabibite”.
Gelato and pastry, FMCG, beverages and coffee: a family holding that distributes in more than 100 countries, led by the fourth Fabbri generation, Nicola, Paolo and Umberto, now joined by the fifth generation of the family represented by Carlotta, Stefania, Federico, Pietro Fabbri, Michele Magli, Giovanni Quattrocchi and Fabio Macrì. Following in Gennaro's footsteps, the ethos and philosophy of the first generation still resonates through the company and family history today.
At Fabbri, projects, processes, and methodologies take into account the development of scientific research and extensive experience in environmental matters, in order to respect the territorial balance, prevent pollution, and protect the environment and landscape.
The greatness of a company, however, lies not only in the quality of its products and processes, but also and above all in the people who work there. Fabbri 1905 seeks to embody this quality and the extraordinary passion with which its workers pursue this mission, through the constant innovation of its products and the technologies used.
Since 2022, Fabbri has decided to undertake a formalized path to integrate and systematize sustainability in its operations, drawing up the first Sustainability Report based on the most solid and widespread European reporting standards, the Global Reporting Initiative Standards (GRI Standards). The drafting of this document involved the entire front line of the company, which followed a training and awareness-raising course on sustainability issues, and contributed to the creation of the Report.
For a company that has always enhanced the value of the earth’s products, the relationship with the environment is a natural thing.
[GRI 3-1] [GRI 3-2]
Fabbri 1905, aware of today's global sustainability challenges, has decided to work towards integrating sustainability into its business model. This document is Fabbri 1905's first Sustainability Report, and its function is not only to prepare the company for future reporting obligations, but also represents an opportunity to better understand and measure its environmental and social impact. This Sustainability Report is a valuable tool through which Fabbri can and will innovate and communicate its work, responding to complex issues and to the needs of its stakeholders.
In this context, the UN's Agenda 2030 provides a fundamentally important framework for companies wishing to actively contribute to the pursuit of sustainable development goals. In fact, the Agenda is an action plan to promote sustainable development worldwide by setting 17 Sustainable Development Goals (SDGs), which cover a wide range of environmental, economic and social issues and represent a framework for building a systematic and strategic approach to sustainability.
With this in mind, Fabbri has identified the following 8 Goals that the company intends to contribute to:
Ensuring a healthy life and promoting well-being at all ages for all people
Ensuring high-quality, inclusive and equitable education and promote lifelong learning opportunities for all.
Achieving gender equality and emancipating all women and girls
Ensuring everyone access to cheap, reliable, sustainable and modern energy systems
Promoting lasting inclusive and sustainable economic growth, full and productive employment and dignified work for all
Promoting the implementation of the UN Ten-Year Programme for a sustainable consumption and production model
Fabbri's sustainability strategy also considers SDGs 9 "Innovation and Infrastructure" and 13 "Climate Action" as facilitating of and broadly relevant to all future activities.
Building a resilient infrastructure, and promoting innovation and fair, responsible and sustainable industrialisation
Promote actions, at all levels, to combat climate change
The materiality analysis consists of identifying certain sustainability issues that are particularly relevant to the company, defined as “material issues”, on which a relevance analysis is conducted in order to prioritise the themes both from the company's point of view (internal relevance) and from the stakeholders' point of view (external relevance), in order to position them in a matrix defined as the “Materiality Matrix”. This process is carried out to identify the strategic sustainability guidelines on which the company can focus in the medium term.
As part of the preparation of its first Sustainability Report, Fabbri 1905 approached materiality analysis for the first time. During the course of the year, Fabbri's key leaders identified some material issues useful for building the sustainability strategy:
Managing business activities in a sustainable manner, considering environmental and social sustainability factors in the various activities of governing bodies, ensuring transparency in communications, and structuring its governance in such a way as to systematise sustainability in normal business operations. Defining a clear corporate identity and a method of institutional communications directed to all stakeholders, paying particular attention to the accuracy and truthfulness of information.
Conducting business and business relations in a responsible, transparent, credible and consistent manner. Adopting organisational models to enforce anti-corruption, anti-money laundering, and anti-trust regulations.
Innovating both in terms of products and potential business activities through research and development, in order to implement best practices in terms of production, also considering possible solutions to reduce the environmental impact of activities while maintaining product quality standards.
Using socio-environmental criteria to evaluate the supply chain in relation to the social and environmental impacts of procurement activities, including in relation to the policies applied to suppliers to ensure workers' human rights and the right to health and safety. Safeguarding the supply chain by evaluating climate change actions towards core suppliers.
Safeguarding the health and safety of employees and contractors, promoting correct behaviour within company premises and ensuring people’s well-being.
• Human capital and skills development
Planning and implement professional and skills development paths for employees, in order to ensure the professional and personal growth of human resources.
Diversity, inclusion and human rights
Creating an inclusive work environment that fosters equal opportunities in the workforce and values diversity, including through programmes and activities promoted by the company itself. Extending good practices on diversity and inclusion as far as possible to the entire value chain.
• Impact on communities
Considering the impact that the business activity may have on the communities in which it operates, acting to maximise positive impacts and reduce negative impacts.
Consumer health and safety
Promoting initiatives and activities aimed at ensuring consumer health and safety through high-quality products.
• Direct environmental impact of corporate production and management
Assessing the environmental impacts directly related to production and managing them responsibly, while at the same time overseeing office activities with the aim of limiting waste and rubbish.
• Circular economy
Evaluating processes/methods of revalorisation of waste from the Production Phase, and other waste from other office activities or packaging circularity.
As anticipated, the materiality analysis would require conducting a study of material issues also involving stakeholders external to the company. As this is the first year of reporting for Fabbri 1905, it was decided to limit ourselves, for the time being, to an analysis of the issues by the company's managers alone, who in dedicated workshops took on the roles of some identified stakeholder categories (customers, consumers, employees, suppliers, sales networks, associations, bodies and institutions, and the media and community), in order to build an initial materiality matrix:
Fabbri 1905 plans to strengthen the methodology for defining the materiality matrix, thus including a more detailed mapping of stakeholders as well as their direct involvement, in future reporting.
Fabbri is aware that an effective governance model is crucial for success and the achievement of long-term goals. For this reason, the company is committed to maintaining an effective and sustainable governance model, with the aim of ensuring that decisions on various aspects of the company are made responsibly and transparently.
Total
members
4 4 3 1
In order to improve the company's knowledge in the field of sustainability, the members of the Board of Directors and the company's front line took part in a training course for a total of 24 hours between 2022 and the beginning of 2023, which led, among other things, to the definition of the materiality matrix and the KPIs for the reporting of this document.
In addition, it should be noted that all board members are informed of the organisation's anti-corruption policies and procedures.
For Fabbri, the health and safety of its consumers and customers is among its main objectives. For this reason, the company is not only committed to strict compliance with the regulations on labelling and marketing communications, but also certifies its products to make them accessible to those of particular religious and dietary needs: Fabbri currently offers more than 500 Kosher products and more than 300 Halal products. During 2022, there were no instances of non-compliance concerning marketing communications.
The company's commitment to quality production is also embodied in its focus on its careful choice of ingredients and strict quality controls. Fabbri has the most accredited international certifications to ensure that products are manufactured according to well-defined quality standards and in compliance with clear and verifiable requirements. The main certifications include:
- UNI EN ISO 14001 CERTIFICATION
- ISO 9001 CERTIFICATION
- BRC FOOD CERTIFICATION
- IFS FOOD CERTIFICATION
Finally, Fabbri also protects customers by paying special attention to regulations on labelling and customer information. In 2022, there were no incidents of non-compliance concerning impacts on the health and safety of products and services. Fabbri 1905 complies with all legal requirements concerning information and labelling of products and services, from procurement, to the content of substances that may cause environmental impact, to disposal, and the only non-compliances from this point of view concern internal company self-regulation codes.
The recorded cases of non-compliance were handled and resolved through a specific company procedure on managing company traceability. Finally, no cases of non-compliance were registered concerning marketing communications.
In order to clearly and transparently define the values and principles guiding the Company, as well as the criteria of conduct regulating its activities, since 2021 Fabbri 1905 has followed the Organisation and Management Model pursuant to Italian Legislative Decree 231/01 and the related Code of Ethics, compliance with which is required of all those who in any capacity contribute to the exercise of the company's activities. All employees have in fact undergone training to learn the model, and in contracts with third parties parties this model is stated among the rules governing the contract to ensure their awareness and acceptance of the rules stated.
According to the provisions of the Model, it is prohibited to engage in, collaborate in or induce conduct which, taken individually or collectively, directly or indirectly constitutes the offences of bribery between private individuals and incitement to bribery between private individuals defined respectively in Article 2635, paragraph 3 and 2635-bis, paragraph 1 of the Italian Civil Code and referred to in Article 25-ter of Italian Legislative Decree 231/2001.
In particular, in managing relations with interlocutors of private companies or entities, it is forbidden to:
offering, promising or making undue gifts of money or undue recognition of other benefits;
2 4
distributing free gifts and presents in excess of normal business or courtesy practices. Permitted gifts are always characterised by small value;
making unjustified entertainment expenses for purposes other than the mere promotion of the corporate image or for purposes not in accordance with specific corporate procedures;
These prohibitions also extend to third parties (e.g. agents or distributors) acting in the interests of the Company.
From a financial point of view, all inflows and outflows, both those pertaining to ordinary transactions (receipts and payments) and those referring to financial requirements (liquidity, short, medium and long-term financing, risk hedging, etc.) or extraordinary transactions (e.g. liquidations, investments or asset disposals), must be legitimate and performed in compliance with the regulations, traced, reconstructible ex post, adequately motivated, authorised and responding to company needs.)
1 3 4/ FABBRI'S GOVERNANCE
The Model therefore requires the company to behave correctly, transparently and cooperatively, in compliance with the law and internal company procedures, in all its activities, and to behave in compliance with the rules established on free competition and fair competition with other companies.
In the event of doubts as to the proper implementation of the ethical-behavioural principles during the performance of operational activities, the person concerned is obliged to consult his or her Manager (in the case of Company employees) and internal contact person (in the case of third parties) and formally submit a request for an opinion to the Supervisory Board.
TOTAL NUMBER AND PERCENTAGE OF EMPLOYEES TO WHOM ANTI-CORRUPTION POLICIES AND PROCEDURES HAVE BEEN COMMUNICATED
150
TOTAL NUMBER AND PERCENTAGE OF BUSINESS PARTNERS TO WHOM ANTI-CORRUPTION POLICIES AND PROCEDURES HAVE BEEN COMMUNICATED
EMPLOYEES BUSINESS PARTNERS
1,825 100%
2 %
No incidents of corruption were recorded during 2022.
With respect to tax governance, this is done internally through the preparation of declarations to be submitted. These declarations are verified both by the Group CFO and the Board of Statutory Auditors, as well as Auditors and finally by the Board of Directors. The approach to fiscal risks, including how risks are identified, managed and monitored, is described in the Management Document referred to in Italian Legislative Decree 231/01. With regard to compliance with the governance and risk management model, the Whistleblowing procedure is active within the 231 Model, which allows any transgressions to be reported anonymously via a specific email from the Supervisory Board outside the company organisation. Every six months, the Supervisory Board verifies compliance with Legislative Decree 231/01. Finally, any tax defence, following any sanction reports, will be carried out by external consultants (tax and tax experts) together with the Group CFO.
Francesco Casolari
Bolo Amarena 3000
Technique: Etching 94x117cm, 2022
Managing the environmental and social impacts of procurement plays a crucial role when it comes to the sustainability of production processes and economic activities.
The supply chain is the set of activities from producer to final consumer, and includes the production, processing, distribution and sale of goods and services. Managing the environmental and social impacts of the supply chain requires a set of tools and methodologies to identify, assess and mitigate sustainability risks and opportunities.
PROCUREMENT BUDGET USED FOR LOCAL SUPPLIERS
PROCUREMENT BUDGET USED FOR NON-LOCAL SUPPLIERS
Most of Fabbri 1905’s suppliers are based in Italy There are currently no assessments of new or existing suppliers from an environmental or social point of view. Notwithstanding this, Fabbri implements controls and audits on its suppliers to verify the integrity of the supplier, to be understood as compliance with applicable regulations. % %
Source: Direct material supplier turnover 2022 (source Purchase Analysis)
Innovation is a fundamental part of Fabbri 1905, a company that has been offering top-quality products for over 100 years with the aim of creating a link between tradition, innovation and quality, responding to the increasingly evolving needs of professionals and consumers.
In 2022, several research and development projects were undertaken, both in the product and process areas, which were necessary due to changing market conditions. Fabbri brought new products to market in all three of its Business Units:
In the retail sector, two new product lines were launched in 2022: Fabbri's first line of spreadable creams, which uses the advantage of the already iconic Fabbri jar to bring a very high quality product to the market, and Cuor di Amarena bombons, with the idea of offering a 'ready to eat' product.
In the professional field, in addition to Fabbri Gin with pure Amarena cherry distillate, a new range of “plus” syrups was introduced, representing a real innovation in the field of mixology.
As a result of careful and continuous research, Fabbri has also brought important innovations to the world of gelato and pastry making.
From a plant engineering point of view, in 2022 the company invested in technology, in order to ensure the continuous improvement of product quality and the working environment, perfecting the existing “ultra clean” solutions implemented in recent years, particularly for syrups at risk of fermentation, and insulating a large part of the plant in order to minimise energy consumption and its impact.
With regard to innovation in the process, the Company continued the development of lean manufacturing, holistically redesigning the digital ecosystem in order to offer users an experience that combines web, e-commerce and social marketing. Advancing towards greater digitisation within the company, Fabbri also presented a continuous digital training path for its employees and, in line with the technological development path undertaken, migrated its management system to Dynamics FO365. Lastly, Fabbri has strengthened its Training Schools in order to grow internal technical, management and commercial skills through a pull of specific courses, many of which are in an e-learning format.
Total € invested in research and development in 2022
Total trade marks registered in 2022
1,350,724 290
Renewed brands
New brands
31 9
Consumer health and safety is a key priority for all companies that, like Fabbri, operate in the food sector. All stages of the supply chain must be handled with great care and rigour to ensure maximum food safety for consumers.
At the heart of Fabbri's consumer safety is compliance with food safety and quality standards, such as those established by the Hazard Analysis and Critical Control Point (HACCP) System and local and international regulations. Fabbri also regularly carries out tests and checks on product quality, safety of equipment used, and storage conditions Fabbri currently carries out an assessment of health and safety impacts for three of its product categories, on which it has found no instances of non-compliance with regulations and/or self-regulatory codes concerning the health and safety impacts of the products.
As shown by the Materiality Matrix, Fabbri considers the health and safety of its consumers to be a top priority, and guarantees it throughout the entire production chain through various activities that start from punctual verification of compliance with mandatory regulations to maintenance of food safety standards such as BRC and IFS. Even at the design level, Fabbri protects its consumers by offering a wide range of products that meet different dietary requirements, including 40 Vegan products, over 600 gluten-free products, and over 400 lactose-free products.
[GRI 416-1] [GRI 416-2] [GRI 418-1]
The verification processes involve the entire supply chain, starting with suppliers on whom document verifications and audits are carried out at their plants. From this point of view, Fabbri is also committed to the careful selection of suppliers, by searching for products with a certified supply chain (e.g. IGP Piedmont Hazelnut).
During acceptance, the materials raw are checked both from an organoleptic point of view, in order to ensure a high quality standard, and through a plan of chemical and microbiological analytical controls for compliance with mandatory food safety regulations. Technical specifications are also drawn up at the acceptance stage to guarantee high quality levels.
During the production process, control points ensure a reduction of the risk posed by foreign bodies through the use of x ray, metal detector, and IR sorter, as well as through in-process chemical analyses that guide production to compliance with binding parameters.
In addition, in the design phase the trend towards “clean label” products, i.e. those with few, healthy ingredients, is gaining strength. The company's policy has therefore long been directed towards a substantial decrease in the use of artificial ingredients, such as colourings and flavourings. The review of the design process, referred to as the "Phase&Gate", finally provided the R&D staff with the necessary information to be able to develop new references that meet consumer demands.
Finally, Fabbri protects customers and consumers not only from a food point of view, but also by paying special attention to personal data protection: in 2022, there were no proven reports of leaks, theft or loss of customer data.
1 2 3
documentary verification and audits at their premises
organoleptic testing and chemical and microbiological analysis
use of x ray, metal detector, IR sorter, and inprocess chemical analysis
reduction in use of artificial ingredients
develop new references that meet consumer demands
customer and consumer protection
The protection of health and safety is considered a priority and is fundamental to the planning and performance of every working activity at Fabbri 1905. For over 10 years Fabbri, in line with the commitments set out in the Code of Ethics, has formulated the “Personnel” policy, with the aim of contributing to the creation of a positive, safe, and inclusive working environment, based on the respect and involvement of its people, to whom it offers a quality experience and a path of growth and continuous development. As at 31 December 2022 Fabbri 1905's workforce numbers 150 employees, stable compared to the pre-covid period, of whom more than 41% are women. As job stability is a Fabbri prerogative, over 93% of employees have permanent contracts
To guarantee the safety of workers in the pandemic period and at the same time ensure the continuation of activities, Fabbri has strengthened the digital transformation process, managing to leverage remote working as a great opportunity, involving more than 53% of people during the years 2020 and 2021. For all workers during the Covid period, the company chose, in agreement with the RSU, to adhere to the Regional testing plans, first with antigenic analyses, then with swab campaigns, by adhering to the company vaccination programme also offered to employees' family members, and also by offering employees without a Green Pass reimbursement for mandatory swabs. These measures were in addition to the normal practice of offering flu shots and doctor’s visits in addition to the normal health observation for workers who request them. Lastly, during the pandemic period, while complying with legal provisions and safety protocols concerning access to catering services, the company agreed on a catering service with individual lunches to be consumed by each person in separate locations.
Starting in June 2021, as a concrete tool to facilitate work-life balance, remote working became official on Fridays, with the possibility of requests for different personal arrangements, in order to facilitate the matching of supply and demand for flexibility by the company and the people. In this sense, the main initiatives for satisfying the needs of employees for flexible work, defined through union and collective agreements (see Supplementary Company Contract and CCNL), are:
1
2
3
4
5
part-time contract;
flexibility in working hours;
care leave other than parental leave;
paid leave for study, medical examinations, therapeutic treatment, trade union meetings, deaths of family members;
initiatives to support parenting and caregivers through paid and unpaid leave, time bank, company benefits.
Over the years, a system of opportunities has also been developed, comprising:
Insurance coverage against occupational and non-occupational accidents in addition to compulsory coverage for certain categories of workers;
For middle managers and some whitecollar employees, there is additional supplementary health care guaranteeing reimbursement of expenses incurred for health and hospital services at public and private facilities;
Supplementary pension funds for employees, largely funded through company contributions.
With regards to benefits defined at the company level, these are granted to all employees. The bonuses included in the 2nd level bargaining are also granted, when the target is reached, to agency workers provided they have not terminated their employment prematurely. Life insurance (VITA of the national collective bargaining agreement), on the other hand, is only provided for permanent employees, while health insurance (FASA of the national collective bargaining agreement) is intended for all permanent or fixed-term employees with an initial contract of more than 9 months, full-time or part-time.
With regard to employee safety, Fabbri 1905's policy on this matter sets out the key principles to be observed in terms of Workers' Health and Safety, and aims to ensure, among other things, compliance with applicable health and safety legislation in force, as well as non-statutory but voluntarily signed requirements, a commitment to continuous improvement of its performance and the creation of a “safety culture” around the people who work at and on behalf of Fabbri. Among the levers identified for the pursuit of these principles are constant monitoring of risks, the assessment of environmental aspects and hazard factors when designing new activities, processes, products and facilities, training and empowerment of personnel, raising awareness of suppliers and employees and researching the best available technologies for prevention and protection. Fabbri has a safety management system in place that ensures the assessment of workplace risks through a systematic process of analysis of activities and tasks (weekly EHS audits). The staff of the EHS office (employees and external consultants) have specific skills both in terms of many years of experience in the field and in terms of training qualifications (RSPP qualifications with regular and comprehensive training updates).
Employees are trained in occupational health and safety on the basis of the State-Regions Agreement, and education and training is provided on specific topics such as: use of PPE, handling hazardous substances, fire emergency plan, and training and education for new employees. In addition, staff may report any hazardous situations to the Workers' Safety Representative or directly to the EHS function. There is also a box for anonymous reports, as well as the possibility to communicate via e-mail directly to ODV. No cases of occupational diseases have been recorded in 2022.
Accidents at work* Total hours worked
6 272,800
* excluding deaths and serious injuries, which also amounted to 0 in 2022.
The occupational accident rate is 0.08% for an IF index of 21.9 calculated as the ratio of the total number of accidents to the total number of hours worked, using a multiplication factor of 1,000,000.
Finally, Fabbri 1905 guarantees all workers the right to freely express their thoughts, to join associations and to carry out trade union activities. The Italian national collective bargaining agreements (Food Industry and Industrial Executives) apply to all workers. The exercise of trade union activities can count on meeting spaces and workers can use dedicated leave in accordance with the applicable regulations and the applicable employment contract. All workers can refer, regarding issues of interest to them, to the Unitary Trade Union Representatives (RSU) which are periodically renewed through elections.
Percentage of employees covered by collective agreements
100%
At Fabbri, people are our greatest asset. Training is not only a tool to enrich people's employment opportunities, but also a lever to support organisational integration and change management That is why the company invests in the development and consolidation of the professional and managerial competence system through:
• dedicated training and development programmes, including on-the-job training; forms of job rotation;
• company placement paths with internship projects agreed upon with universities, aimed at stabilising the resource;
• a Sales Academy for in-house sales staff and company partners;
• continuous digital training for employees, and Training Schools to improve internal technical, management and commercial skills through a pull of specific courses; identification of key figures among the company's resources for the development and implementation of computer programmes who will then be the references for their colleagues.
These activities are based on a constant partnership with various internal functions to foster the design and continuous improvement of training courses, increasing their effectiveness in accordance with the needs of the individual and the Company's objectives.
*The difference in indices between men and women is linked to the high number of male employees in the blue-collar bracket, the category for which the largest number of training hours is reserved.
In keeping with the Code of Ethics, Fabbri 1905 respects the dignity of each individual and offers equal opportunities in all aspects of the employment relationship, such as recruitment, training, remuneration, promotions, and avoiding any form of discrimination that may arise from differences in gender, age, health, nationality, political or religious opinions.
In regards to the adoption of measures to promote equal treatment and opportunities between genders in the entire company organisation, initiatives to foster inclusion have been implemented for years. Among the activities carried out by Fabbri to integrate the principle of equal treatment into the processes governing all stages of professional life and human resource development, the following practices, defined by specific internal operating rules, are worth mentioning:
• transparent and non-discriminatory management of recruitment and the overall selection process (anonymous graphical analysis); training made equally accessible to all staff.
Because gender diversity is a priority for Fabbri, we seek to provide talented women with opportunities to maximise their potential with the aim of engaging women in middle management and supporting them in exploring more managerial careers.
Finally, Fabbri supports generational change, including the technological changes that will be necessary to cope with the introduction and development of ever new information systems, by hiring new resources.
No. 88
Total employees
150
Total permanent employees
142
Total temporary employees
8
59% MEN
No. 84
59% MEN
No. 4
50% MEN
No. 1
Total part-time employees
2
GRI 2-8: NON-EMPLOYEE WORKERS
No. 62
41% WOMEN
No. 58
41% WOMEN
No. 4
Total number of nonemployees whose tasks are controlled by the organisation
50% MEN
No. 1
50% WOMEN
8
The figures shown refer to employees in force as of 31.12.2022 and were taken from the employee management report. Non-employees are represented by production workers.
GRI 401-1: NEW RECRUITMENTS AND TURNOVER
Total number and percentages of new hires during the reporting period: of whom men of whom women of whom under 30 of whom 30-50 of whom over 50
GRI 401-1: EMPLOYEES WHO LEFT THE ORGANIZATION
Total number and percentage of employees who left the organisation during the reporting period: of which men of whom women of whom under 30 of whom 30-50 of which over 50
GRI 405-1: DIVERSITY IN GOVERNING BODIES AND EMPLOYEES
Total governing body members of whom men of whom women of whom under 30 of whom 30-50 of whom over 50
Total employees
EXECUTIVES of whom men of whom women of whom under 30 of whom 30-50 of whom over 50
MIDDLE MANAGEMENT of whom men of whom women of whom under 30 of whom 30-50 of whom over 50
WHITE COLLAR WORKERS of whom men of whom women of whom under 30 of whom 30-50 of whom over 50
BLUE COLLAR WORKERS of whom men of whom women of whom under 30 of whom 30-50 of whom over 50
For Fabbri, one of the keys to the company's success is its ability to keep its ties to the local area intact and alive, focusing on its people and their quality of life. For this reason, Fabbri 1905 is committed on many social fronts, from the inclusion of the disadvantaged in the workforce to the support of scientific research, without forgetting the importance of the labour inclusion of women, all of which can be traced back to a common theme: valuing human beings and their talents.
Women have always been a fundamental part of Fabbri, ever since Rachele Fabbri, wife of founder Gennaro, created the company's iconic product, Amarena Fabbri. The focus on the female component thus goes back to the very beginning and has been realised over the years through two projects supporting entrepreneurship and employment:
• Lady Amarena, since 2015 the only international competition reserved for female bartenders from every corner of the planet1; The professional course in artisanal ice cream making reserved for incarcerated mothers as part of Soroptimist International's “Si sostiene” project2
Fabbri supports research not only financially, but also through an active commitment to inventing new formulas and languages to raise awareness and involve the younger audience.
Since 2015, Fabbri has supported AIL (the nonprofit Italian Association against Leukaemia-Lymphoma and Myeloma)3, the year in which Cockt-AIL, the first travelling benefit competition for bartenders, was launched.
The company has also contributed financially to the success of “The Bitter Taste of Leukaemia”, an Italian research project that has opened up an important new avenue in the treatment of a disease that predominantly affects young people. In addition, Fabbri 1905 supports AIL's Christmas and Easter campaigns with Amarena Panettoni and Colombe, a donation that turns every euro collected into more than 3 euros of Social Value, and that places the company among AIL Bologna's Major Donors.
Finally, Fabbri has always been close to Fondazione ANT Italia Onlus4, the largest non-profit organisation in Italy providing free specialist home assistance to cancer patients.
Fabbri has had deep roots in the Bologna area since its foundation. In 2022, the street artist Cheone created a mural on the walls of Fabbri 1905's historic headquarters in Borgo Panigale, a tribute to the district that has safeguarded the company's soul for over one hundred years. In order to provide a service to the city community, the company has undertaken to cover the surface of the work with an innovative, Italian high-tech product: Airlite Hystoriqa. In addition to protecting the mural, this compound is able to purify the air of pollutants such as nitrogen oxides (NOx).
Fabbri supports communities not only in Italy, but also abroad. In particular, Fabbri supported the opening of Cremedoce De Fronteira, a gelato shop and training centre in Ressano Garcia, a small town in Mozambique on the border with South Africa. Inaugurated on 26 April 2019, the centre was created as a charity project to promote entrepreneurship and is supported by: Rotary Club Bologna - Valle dell'Idice, Rotary Foundation, District 2072 Emilia-Romagna and San Marino Republic and D.4905 Argentina Buenos Aires of Rotary International, Bruto and Poerio Carpigiani Foundation, A.G.A.P.E. ONLUS, Fabbri 1905 and the master pastry chef Gino Fabbri, trainer of the World Pastry Champions, IS still in charge of training and assisting the gelateria staff.
Fabbri 1905 actively supports art as it enriches the artists who create it, the viewers who savour it and the patrons who believe in the value of people and creativity. Fabbri supports young artists with the FABBRI ART PRIZE
Finally, Fabbri is a member of several associations, including:
Consorzio Italia del Gusto
• Associazione italiana dell’industria di Marca (Centromarca)
Unione italiana Food Ex AIIPA
Stazione sperimentale per l’industria delle conserve alimentari (S.S.I.C.A.)
IBC Associazione Industrie beni di consumo (Ex INDICOD)
• Comitato Leonardo Club delle Mignonettes
In general, food production has a significant impact on the environment as it requires major consumption of resources such as energy and water. The impacts on the environment generated by Fabbri 1905's activities are mainly due to the use of fuel and electricity necessary to carry out production activities, as well as transportation and distribution along the value chain. This consumption is also linked to the generation of climate-changing gas emissions. To save energy, Fabbri 1905 has implemented a renovation project aimed at reducing heat dispersion, and adopted energy-efficient lighting. Fabbri 1905 Spa has been purifying waste water from production departments for over 40 years, with the utmost respect for the environment. One of the first companies in the sector to purify wastewater independently, Fabbri has made large investments over the years without burdening the community coffers. At the Anzola dell'Emilia plant, a two-stage (aerobic and anaerobic) industrial wastewater treatment plant is installed, which treats and purifies all wastewater from production departments. The water purified in this way is then fed into the municipal sewage system, well below the regulatory limits imposed by law, and is subject not only to periodic checks and inspections by the competent authority, but also to accurate self-inspections on a weekly basis, which Fabbri 1905 has instructed to ensure that the purification process is carried out perfectly, even through external laboratories.
To limit the spread of unpleasant odours due to the water purification process, Fabbri 1905 installed a deodorising system consisting of a filter bed made of plant material.
Fabbri 1905's activities produce other direct impacts on the environment, related in particular to the use of water resources and the production of waste. Specifically, operations carried out within the production sites require the withdrawal of water resources from owned wells, purified with a biological filter, and generate discharges of water that require purification treatments to be returned to public networks. Water used for cooling purposes, on the other hand, is recovered. Fabbri 1905's wastewater does not contain any hazardous, toxic, harmful or carcinogenic substances, and total suspended solids are 90% below the limit defined by law.
The waste generated, if not reused or recycled within the production phase, is sent for recycling or external disposal (refer to the chapter “Circular Economy”
[GRI 302-1]
for more information).
In order to prevent and mitigate the environmental impacts generated by production activities, the Company operates as follows:
• meets the requirements of environmental law; assesses, monitors and tends to minimise, where possible, the environmental impact of processes and products; manages activities through an efficient use of energy, water and materials pursuing the reduction of environmental impact, waste and garbage production.
In particular, the Company actively engages in:
• reducing the impact of packaging by encouraging the introduction of more sustainable packaging material, pursuing the reduction of material consumption;
• improving energy efficiency and water savings:
energy and water use in the plants are closely monitored and the company has adopted an energy efficiency plan by applying insulation to the plants to eliminate dispersion and thus reduce energy consumption;
• improving production processes so as to save water and reduce waste production;
promoting proper waste management through efficient recycling and disposal policies;
using an Environmental Management System and maintaining UNI EN ISO 14001Certification;
• carrying out plant-engineering interventions aimed at energy saving and the production of energy from renewable sources.
GRI 302-1: ENERGY CONSUMPTION
Total energy consumption of which natural gas for heating of which purchased electricity of which vehicle fleet consumption (petrol) of which vehicle fleet consumption (diesel)
GRI 305-1: DIRECT GHG EMISSIONS (SCOPE 1)
Direct GHG emissions (Scope 1)in gross tonnes of CO2 equivalents
Gas
Company vehicle fleets - Petrol
Company vehicle fleets - Diesel
GRI 305-2: INDIRECT GHG EMISSIONS FROM ENERGY CONSUMPTION (SCOPE 2)
indirect GHG emissions from energy consumption (Scope 2) gross location-based in tonnes of CO2 equivalent
GRI 303-3: WATER WITHDRAWAL
Total water withdrawal
From surface water
From groundwater
From seawater
From protected water
From third-party water resources
Fabbri believes that thecircular economy is of great importance to ensure the long-term environmental, social and economic sustainability of the company Given this conviction, a number of initiatives have been launched over time in order to reuse discarded production waste, reduce waste of resources, and generally reduce consumption through practices capable of increasing the circularity of the company and its products.
Normally, in addition to the waste generated by ordinary company management, Fabbri generates waste, organic and otherwise, related to the production of products, including packaging.
In line with the current market trend, Fabbri 1905 is paying special attention to packaging, which is essential to protect and preserve food products during transport, distribution and storage, but which can generate significant amounts of waste. Recently, glass syrup bottles have been replaced by PET bottles, which represent a fully recoverable packaging that can be disposed of in plastic waste collection together with the cap and label. Currently, other initiatives are being considered for the revalorisation of PET waste, by carrying out, with the support of the Technical Department and the Purchasing Department, trials of purchasing bottles made from recycled material. For some types of plastic packaging further sub-sorting is carried out to enhance recovery. For example, for CER 0150102 plastic packaging, which covers all types of plastic packaging (HDPE, PELD, PET, etc.), HDPE cisterns/drums are kept subdivided and sent to direct recovery operations, thus avoiding subsequent sorting that often generates more waste and residues.
Packaging waste made of paper, cardboard, wood, glass and metal is used to make new packaging or other objects.
In order to avoid food waste, Fabbri 1905 donates products, which, although edible, are no longer marketable, to various associations dedicated to the recovery of foodstuffs: in 2022, goods worth around €40,000 were recovered. In addition, Fabbri supplies part of the edible production waste to a third company for compost production. Finally, solutions are being studied for the reuse of waste materials as by-products for energy production by external entities.
In general, the waste generated that cannot be reused is managed and sent to recovery processes by authorised external operators.
Total energy consumption of which paper and cardboard of which toner of which tin plate of which glass of which plastic (secondary packaging) of which plastic (secondary packaging)
Other*
*”Other” includes ceramics, multicomposites and displays
Total waste generated
paper packaging
plastic packaging
Sources: loading and unloading registers, FIR, MUD; Ecos management software.
This document represents the company's first Sustainability Report, drawn up with the aim and desire to make its stakeholders aware of the commitment Fabbri has made to increasingly transparent communication about the company's operations, its sustainability strategy, and its positive and negative economic, social and environmental impacts.
The Report has been prepared following the guidelines and principles of the GRI Sustainability Reporting Standards, as updated in 2021 and effective from 1 January 2023, adopting the “with reference to” approach.
The Sustainability Report covers the period from 1 January 2022 to 31 December 2022, and the reporting boundary of the data and information contained therein relates to the administrative plant in Bologna and the production plant in Anzola dell'Emilia, which together represent “Fabbri 1905”.
At the end of the document, the GRI Content Index is shown, which displays a schematic view of the GRI indicators selected to cover the material issues identified in the materiality analysis (please refer to the chapter "Sustainability at Fabbri" for more information).
Since this document was drawn up on a voluntary basis, it is emphasised that no third-party assurance analysis was carried out.
2-8 Non-employee workers
2-9 Governance Structure and Composition
2-14 Role of the Highest Governance Body in Sustainability Reporting
2-17 Collective knowledge of the highest governing body
2-22 Statement of Sustainable Development Strategy
2-27 Compliance with Laws and Regulations
2-28 Membership of associations
2-30 Collective Agreements
GRI 3: Material Issues (2021)
3-1 Process for Determining Material Issues
3-2 List of material issues
MATERIAL ISSUE: EFFECTIVENESS OF THE GOVERNANCE MODEL AND COMMUNICATION
GRI 3: Material Issues (2021)
GRI 205: Anticorruption (2016 version)
3-3 Management of Material Issues
205-3 Established incidents of corruption and actions taken
205-2 Communication and training on anti-corruption policies and procedures
GRI 207: Taxes (2019 version)
207-1 Approach to Taxation
207-2 Fiscal Governance, Control and Risk Management
207-3 Stakeholder Engagement and Addressing Tax Concerns
MATERIAL ISSUE: SUSTAINABLE PROCUREMENT MANAGEMENT
GRI 3: Material Issues (2021)
GRI 204: Procurement practices (version 2016)
3-3 Management of Material Issues
204-1: Proportion of spending on local suppliers
MATERIAL ISSUE: CONSUMER HEALTH AND SAFETY
GRI 3: Material Issues (2021)
GRI 416: Customer health and safety (version 2016)
3-3 Management of Material Issues
416-1 Assessment of health and safety impacts by product and service categories
416-2 Incidents of non-compliance concerning impacts on the health and safety of products and services
GRI 418: Customer privacy (2016 version)
418-1 Proven complaints regarding breaches of customer privacy and loss of customer data
MATERIAL ISSUE: EMPLOYEE PROTECTION AND WELL-BEING
GRI 3: Material Issues (2021)
GRI 401: Employment (2016 version)
GRI 403: Health and Safety at Work (version 2018)
3-3 Management of Material Issues
401-2 Benefits provided for full-time employees, but not for part-time or temporary employees
403-1 Occupational health and safety management system
403-2 Hazard identification, risk assessment and accident investigation
403-5 Occupational health and safety training for workers
403-9 Accidents at work
403-10 Occupational Diseases
MATERIAL ISSUE: HUMAN CAPITAL AND SKILLS DEVELOPMENT
GRI 3: Material Issues (2021)
GRI 404: Training and Education (Version 2016)
3-3 Management of Material Issues
404-1 Average hours of training per employee per year
MATERIAL ISSUE: DIVERSITY, INCLUSION AND HUMAN RIGHTS
GRI 3: Material Issues (2021)
GRI 401: Employment (2016 version)
3-3 Management of Material Issues
401-1 New recruitments and turnover
GRI 405: Diversity and Equal Opportunities (Version 2016)
GRI 406: Non-discrimination (Version 2016)
405-1 Diversity in governing bodies and employees
406-1 Incidents of discrimination and corrective measures taken
MATERIAL ISSUE: IMPACT ON COMMUNITIES
GRI 3: Material Issues (2021)
GRI 201: Economic performance (Version 2016)
3-3 Management of Material Issues
201-1 Economic value directly generated and distributed
MATERIAL ISSUE: DIRECT ENVIRONMENTAL IMPACT OF CORPORATE PRODUCTION AND MANAGEMENT
GRI 3: Material Issues (2021)
GRI 302: Energy (Version 2016)
GRI 303: Water and waste water (Version 2018)
3-3 Management of Material Issues
302-1 Energy consumption within the organisation
303-2 Management of Impacts Related to Water Discharge
303-3 Water withdrawal
GRI 305: Emissions (Version 2016)
305-1 Direct greenhouse gas emissions (Scope1)
305-2 Indirect greenhouse gas emissions (Scope2)
MATERIAL ISSUE: CIRCULAR ECONOMY
GRI 3: Material Issues (2021)
GRI 301: Materials (Version 2016)
GRI 306: Water and waste water (Version 2016)
3-3 Management of Material Issues
301-1 Materials used by weight or volume
306-1 Waste generation and significant waste-related impacts
306-2 Management of significant wasterelated impacts
306-3 Waste generated
fabbri1905.com amarenafabbri.com cocktailfabbri.it premiofabbri.it