SEPTEMBER 2022www.im-mining.com HIGHBAUMAREMOTENETWORKSSHAFTAUTOMATIONSINKINGMINESPREVIEWPROFILE:Sandvik, UFR
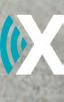
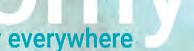
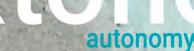
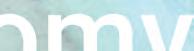


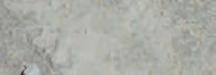

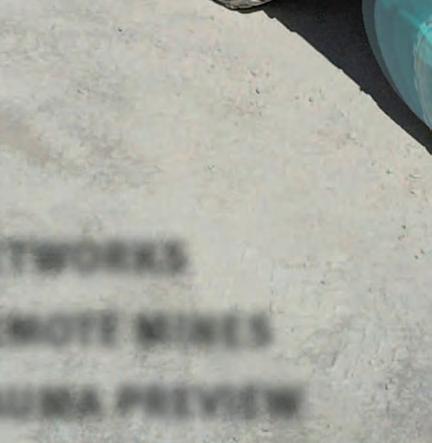
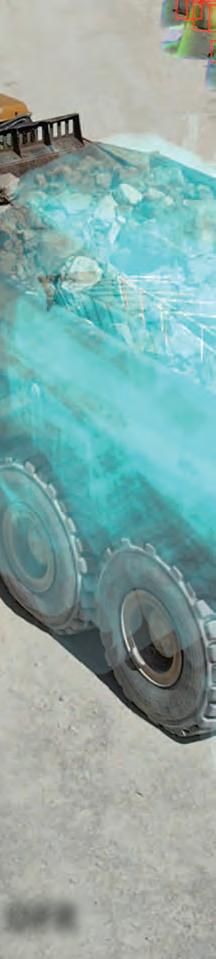
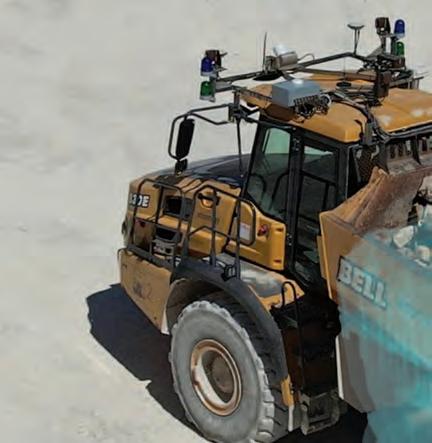
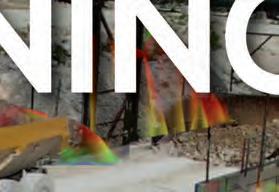
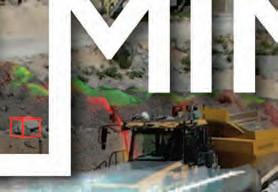


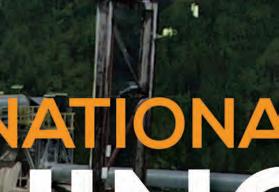

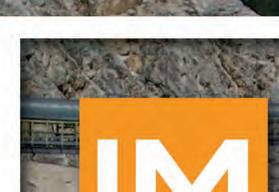
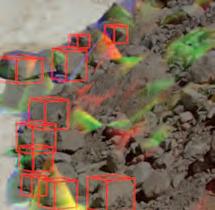
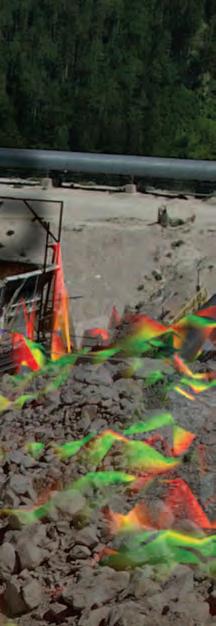


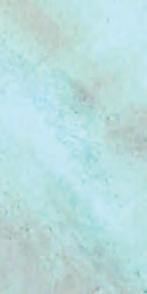
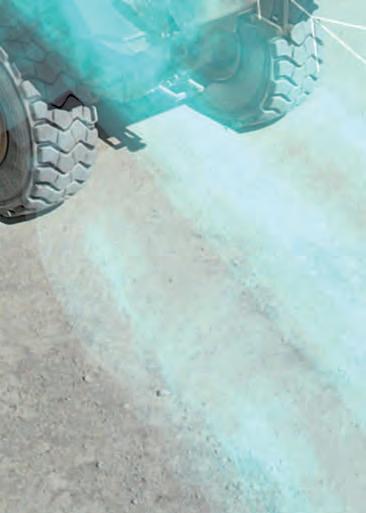
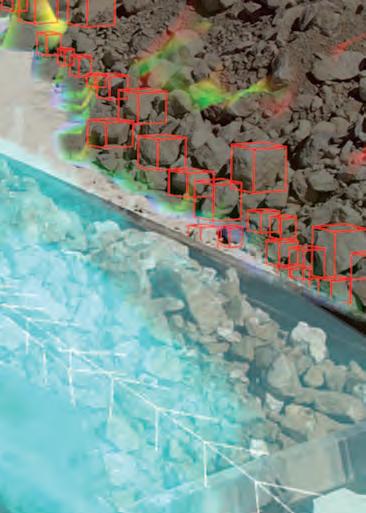
“CONEXPO-CON/AGG SHOWS US THE FUTURE OF OUR INDUSTRY, WITH INNOVATION, EQUIPMENT AND IDEAS YOU CAN’T FIND ANYWHERE ELSE.” — GRANITEROCK, AROMAS,TAKINGCA CONSTRUCTION TO THE NEXT LEVEL. MARCH 14-18 / 2023 / LAS VEGAS / NEVADA 250,000 sqm of Exhibits 130,000 Attendees 1,800 Exhibitors 150 Education Sessions REGISTER at conexpoconagg.com Save 20% with promo code SHOW20
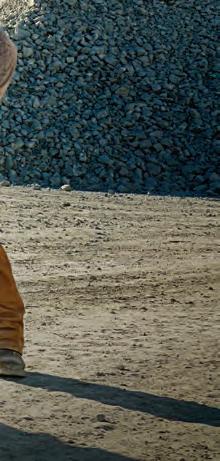

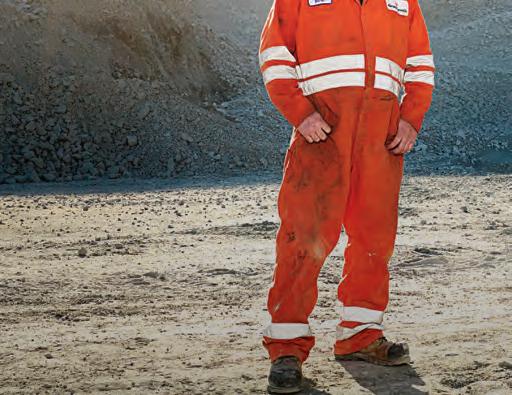


56 SURFACE AUTOMATION

Speed and safety are not typically good bedfellows, hence the reason why shaft sinking has historically been considered a dangerous mine development arena. New technology and thinking are changing that, as Dan Gleeson explains
Taking place in a new season and with new focus areas, Bauma 2022 will set the scene for the next three years of construction and mining equipment developments. Dan Gleeson looks at what we can expect to see
MINING NETWORKS


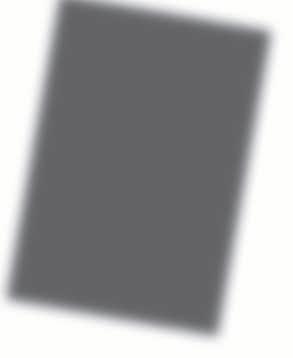
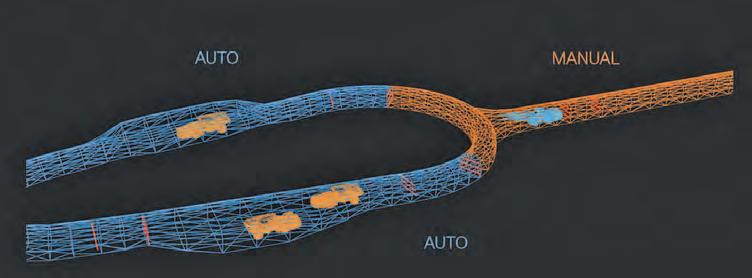
90 REMOTE MINES
75 HIGH PROFILE UFR









81 SHAFT SINKING

The increasingly autonomous mine is posing more challenges to comms networks – Paul Moore spoke to two of the market leaders in 4G LTE/5G solutions as well as the leading supplier of industrial wireless mesh in mining
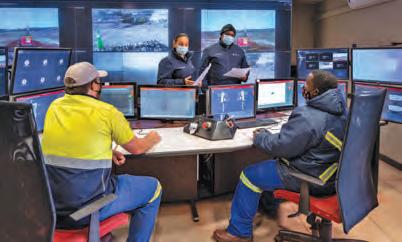
76 UNDERGROUND AUTOMATION

14 BAUMA PREVIEW
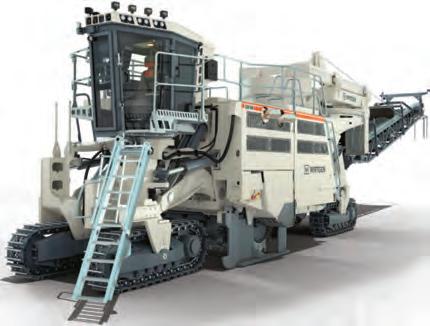
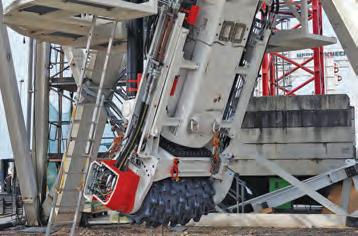














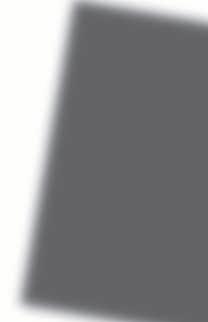
This month’s cover shows the xtonomy Autonomous Haulage System (AHS) that enables autonomy everywhere. After unloading one truck has freely planned its route towards an assigned loading position. A queued truck awaits clearing of its path and dumping permission by indurad’s iCrusher solution. The xtonomy AHS is adaptive for different mine sizes and ever-changing conditions, enabling autonomy for highly dynamic smaller and medium to complex large sites. Its robust radar-first onboard mapping and ML object detection continuously perceives the environment. Its AI motion planners handle interaction of multiple trucks on free paths in unstructured environments. www.xtonomy.ai
g m PTEMBER 2022 INKINGTION REMOTEORKWNETRKSMINES HIGHBAUMAPROP SandviOFILE:PREVIEW ik, UFR 7 6 9 0 1 7 5 5 6 4 6 8 1









COVER: xtonomy
Paul Moore reviews the electric, automated and super-sized borer minerbased Sandvik mining systems that will be used at BHP’s advancing Jansen potash operation

46
In this extensive look at fleet automation in open pit mines, Paul Moore looks at how fleet autonomy is diversifying in scope into smaller trucks & ancillary vehicles but with an eye on keeping it economically viable
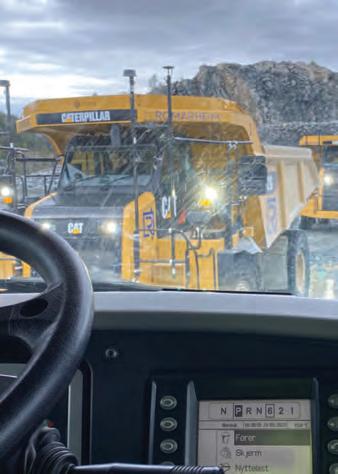
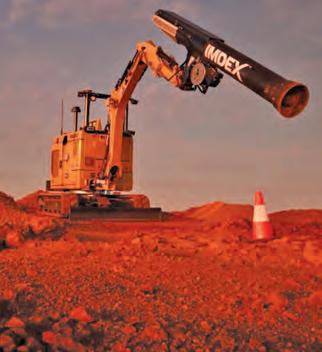
CONTENTS SEPTEMBER 2022 SEPTEMBER 2022 | International Mining 1 AROUND THE WORLD 3 The Leader 6 World Prospects 96 Forthcoming Events IBC Tailings
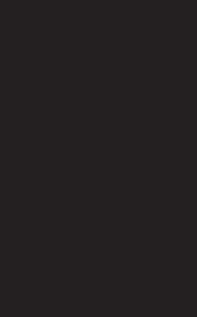
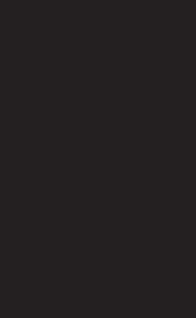
44 HIGH PROFILE Sandvik
Paul Moore takes a detailed look at why autonomy of trucks has lagged LHDs underground and where the major players are in terms of offering and development
‘Remote’ no longer means ‘disconnected’ when it comes to operating mines today, Dan Gleeson reports
Universal Field Robots Managing Director, Jeff Sterling, outlines how the greater use of robotic technology can at the time make operations safer and more efficient

LIGHTS CAMERA Contact: Phil@im-mining.com for pricing and availability Ask us about our booth video interviews at the show Showcase what’s new at bauma Previous videos have featured:
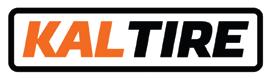
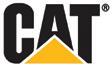
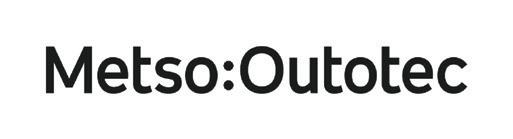

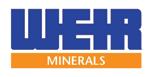


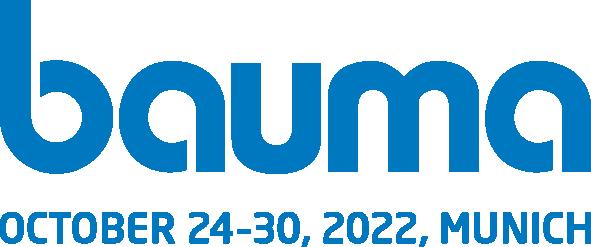
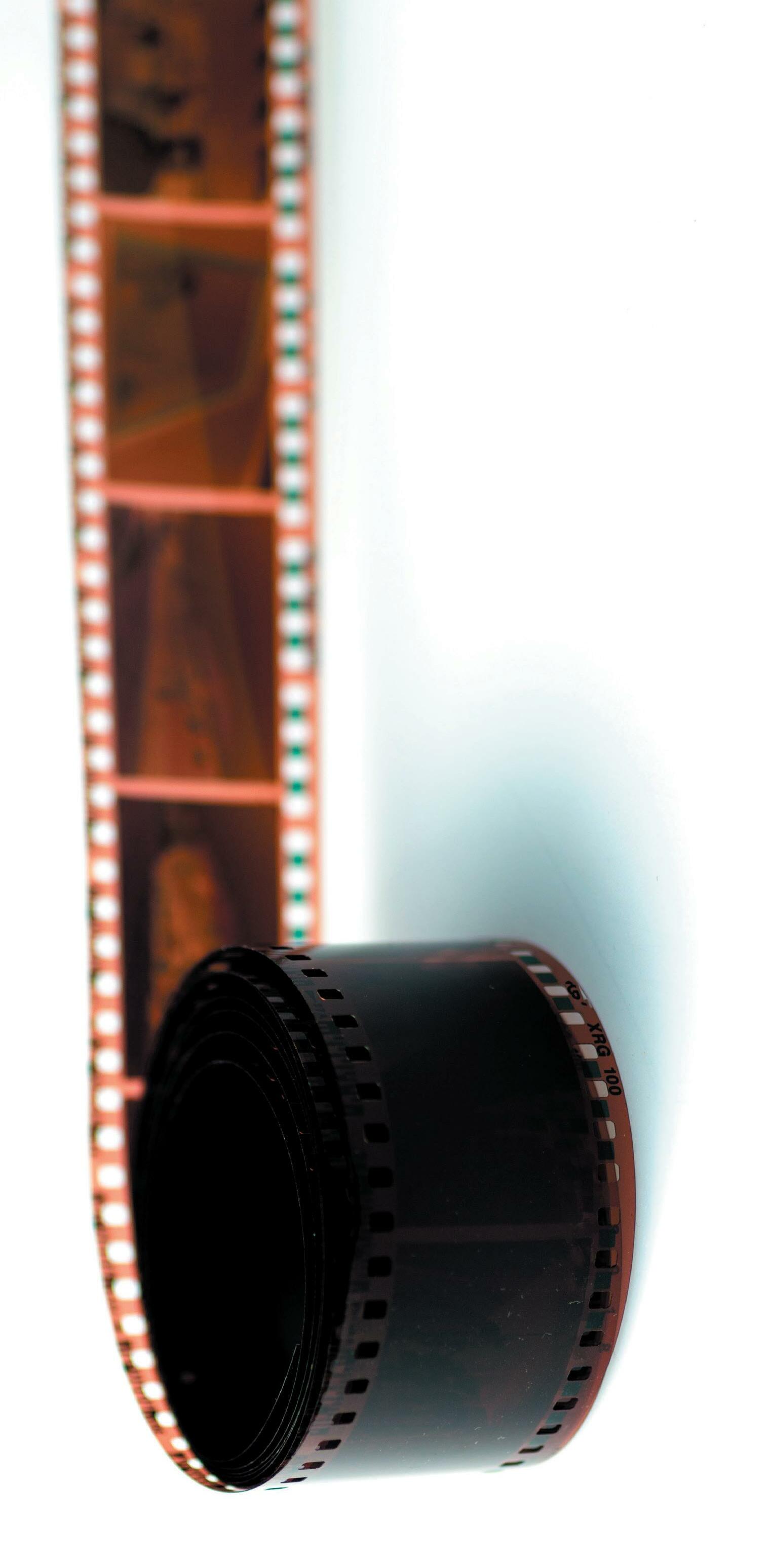

“The machine-learning algorithms we use –neural networks and time-series algorithms –ensure we consistently optimise the operation of our solutions,” Govindan told IM. “These tools make sure we always use the right performance metrics and don’t lose efficiency in the face of variability.”Thealgorithms cannot change the hardware built into the water treatment plant, but it can, for instance, change the speed of the pumps or blowers. “We call it balancing, which is all part of our IP portfolio,” Govindan said.
Email: UKEmail:Emmawww.im-mining.comEmail:Trevorcirculation@im-mining.comJanejo@im-mining.comJoannanicolas@im-mining.comNicolaEmail:Lynne+44Email:PhilAdvertisingdaniel@im-mining.comSales:Playlephil@im-mining.com(0)1442870829PublishingAssistantLanelynne@im-mining.comAccountsManagerShuklaMarketingAssistantEnglishBA(Hons)CirculationAssistantAlterDesignandProductionSheldonsheldonmann@gmail.comWebsite:AnnualSubscriptionEnquiriesSmithemma@im-mining.comAnnualSubscriptionandEurope£160, €230
Printed by The Manson Group, St Albans, UK
“Not only this, but we also have complete oversight of these parameters from remote locations, meaning you can monitor the systems from remote operating centres and not remain on site after installation.”
IM uses, as preference, SI units throughout, so, for example, all tonnes are metric unless otherwise stated.
One significant nickel miner in Australia with a brine stream is using this solution to recover large amounts of concentrate it can feed through to its captive processing plant to produce an end-use
SEPTEMBER 2022 | International Mining 3 THE LEADER VOLUME 17 • NUMBER 9
With mines getting more remote and hiring local employees getting even harder with the well-documented skills shortages, Gradiant feels its solutions will continue to win miners over.
POSTMASTER: send address changes to International Mining, 17B South Middlesex Avenue, Monroe NJ 08831
Liquid to solid
When considered together with the energy savings (75%), freshwater savings (25%) and environmental benefits, Gradiant continues to see high interest from miners around the world to adopt its solutions, it says.
For mining companies looking to employ water treatment tools at their operations, this results in Gradiant’s technology being able to concentrate metals to a higher degree than any
All dollars are US unless otherwise stated
other solution on the market, according to Govindan.“Wecan concentrate an aqueous solution to the point where you can produce a solid material that miners can then process,” he Consideringsaid. desalination applications represent a significant portion of the company’s work to this point – through its CFRO process –the mining sector has already provided some wins.The CFRO process enables remote inland desalination and water reuse that was not previously possible due to a lack of viable brine management solutions, according to Gradiant, concentrating brines to saturation for disposal or crystallisation while producing a purified product water stream for beneficial reuse.
Daniel Gleeson Editor daniel@im-mining

“Gradiant’sproduct.technologies enable clients to recover more than 50% of the nickel and cobalt from leached brine – this stream would have otherwise been wasted without our solutions,” Gradiant said. “Overall, this was a client benefit of about 20% increase in nickel and cobalt production across the entire operation.”
Rest of the world US$270
This includes the RO Infinity™ (ROI™) platform of membrane-based solutions for complex water and wastewater challenges, which combine Gradiant’s patented counterflow reverse osmosis (CFRO) technology with reverse osmosis and low-pressure membrane processes. ROI solutions enable customers around the world to achieve sustainability goals to reduce their water and carbon footprint, the company says.This platform is complemented with AI-backed SmartOps™, an integrated digital platform for asset performance management to optimise and predict plant operations using historical and real-time process data, resulting in performance and cost Prakashefficiencies.Govindan, Co-Founder and COO of the company, says most water solutions on the market are built for consistent liquid/solid feeds and work effectively when the input is in accordance with these specifications. When the feed changes, they often become ineffective, needing to be updated or changed out, which costs money and impacts the various processes on either side of the water treatment section.
International Mining (ISSN No: 1747-146X) is published monthly by Team Publishing Ltd, GBR and is distributed in the USA by Asendia USA, 17B South Middlesex Avenue, Monroe NJ 08831 and additional mailing offices. Periodicals postage paid at New Brunswick NJ.
Editorial Director
© Team Publishing Ltd 2022 ISSN 1747 -146X
Mining companies have historically been wary of suppliers that serve a variety of industries, believing their needs rarely cross over with the requirements of other industries. Gradiant believes it is different in that its solutions incorporate not only the hardware and software to fine-tune water technologies, but also the artificial intelligence (AI) to ensure the tools being used are effective regardless of the inputs.
Paul Moore BSc (Hons), MSc
That is before even factoring in the other complementary benefits that come with using SmartOps.“Allourproducts benefit from in-built sensors that not only allow us to update the operating parameters based on the detected materials, but also carry out scheduled maintenance on the hardware using these algorithms,” Govindan said. “This allows us to carry out 30-40% less service intervals than many conventional suppliers as we only take the solution out of operation based on what the data is telling us.
Email: paul@im-mining.com
That is a big remit, hence the reason why it caters to at least nine industries on a global basis in mission-critical water operations, with over 70% of its clients being Fortune 100 companies in the world’s essential industries.
There are plenty of mining applications one can see Boston, Massachusetts-based Gradiant’s end-to-end water technology solutions serving. A spinout of the Massachusetts Institute of Technology, the company calls itself the “experts” of industrial water, water reuse, minimum liquid discharge (MLD) and zero liquid discharge (ZLD), and resource recovery of metals and minerals.
DanielEditor Gleeson BA (Hons)
We ke kekepb adidvanccing Hih youy litPd ur busisituViV tdS sinessus@bauma2022 t s HighFlexibleEfficienqnt Supply qualityoorld-ClaCProduleWChainassManufacuctsandSycturingystems The world relies on mining to drive human progr rely on us to drive progress underground. By re help keep their mines open and the world advanress. And mining companies inforcing their operations, we ncing. We reinforce progress.

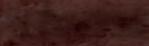




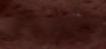
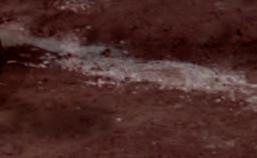



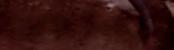

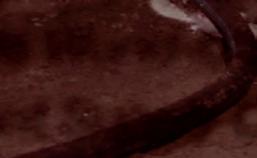
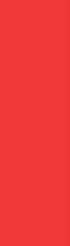
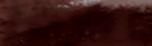
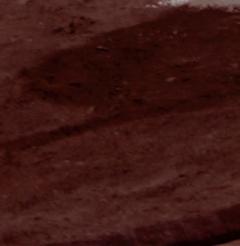



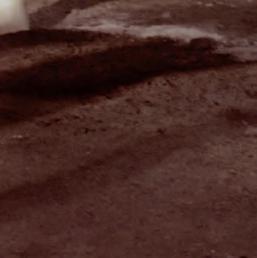
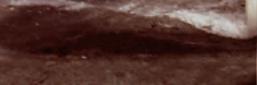
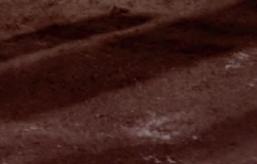
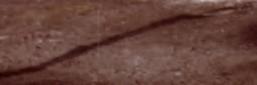
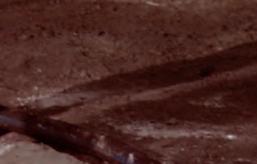

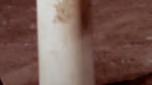
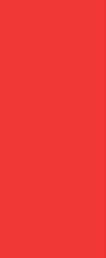

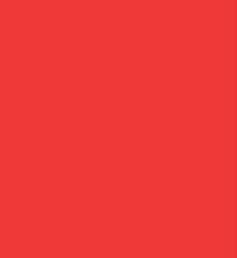

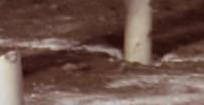
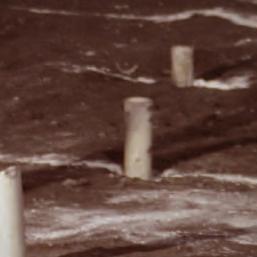
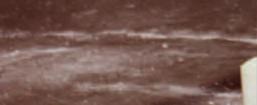
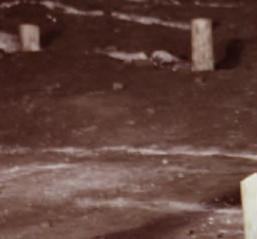
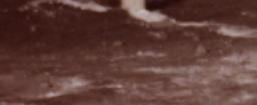
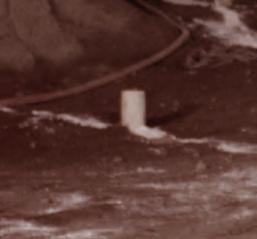



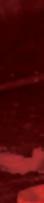
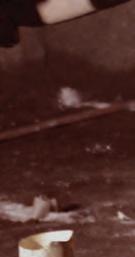
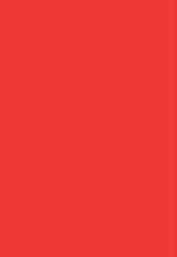

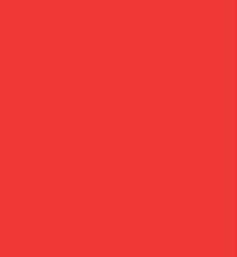


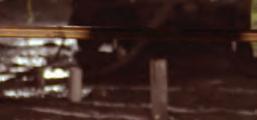
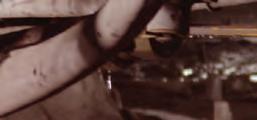
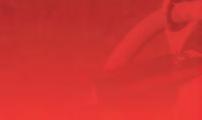
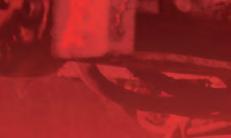

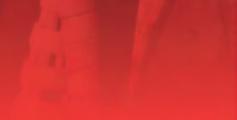
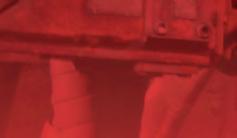

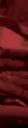
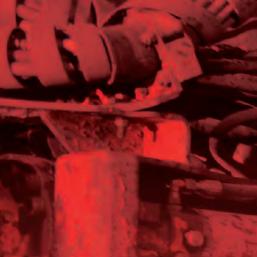
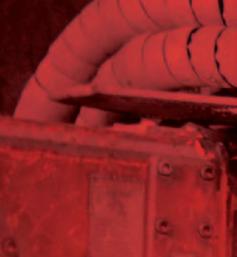
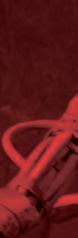
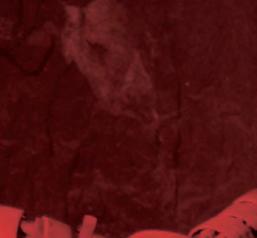

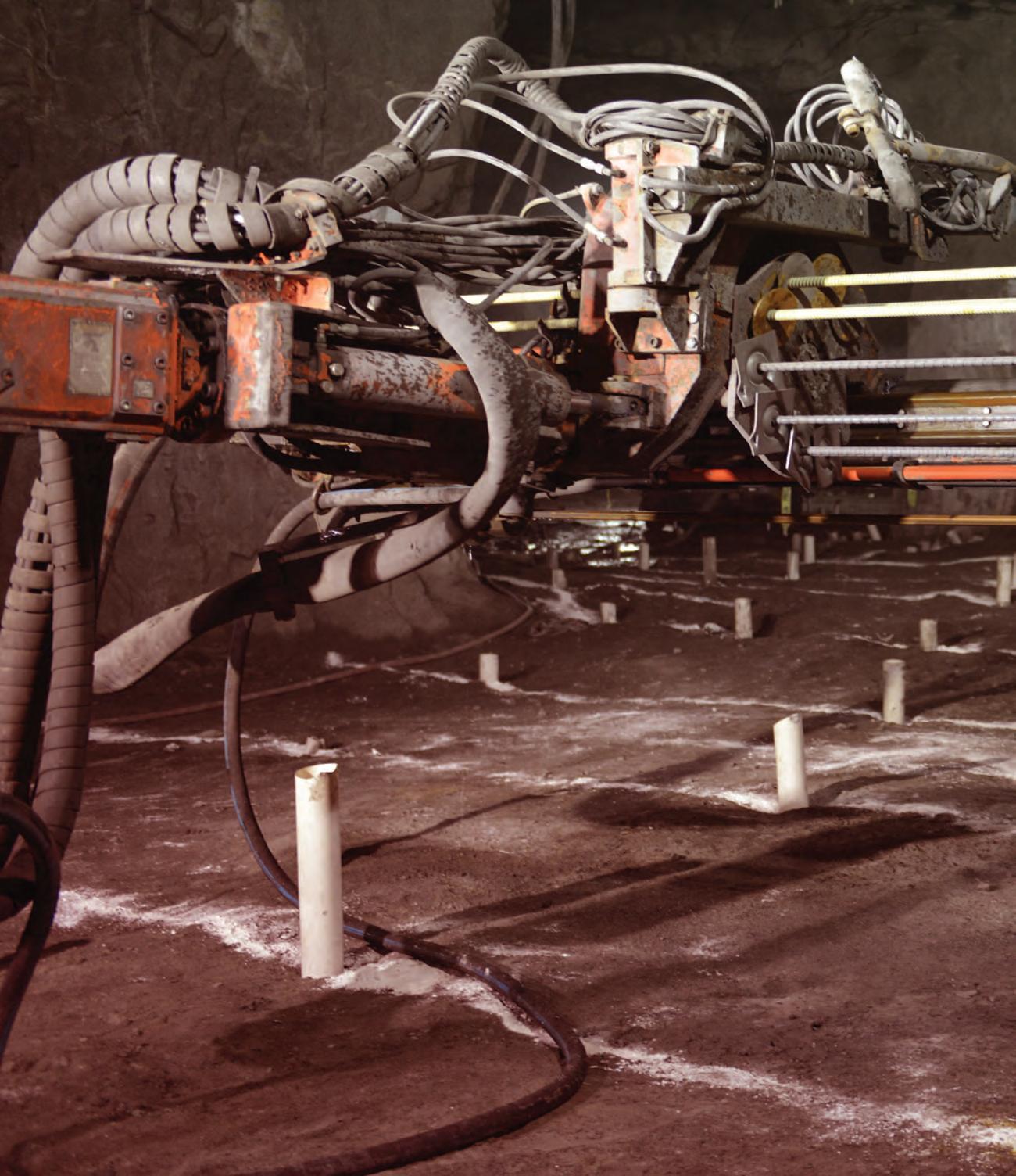
Dii hlT DrivinRespPassisionateponsiblePeopSusechnoloengTplestainabilityogy dsiunderground.com
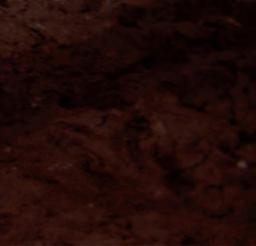
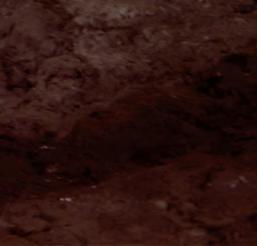



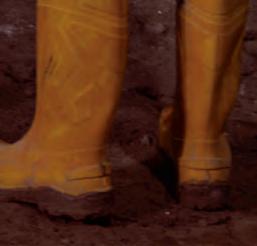

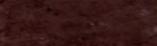


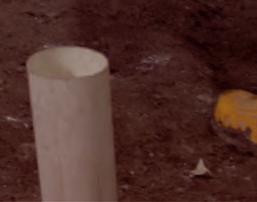

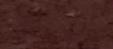
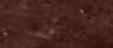
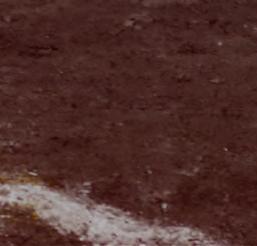
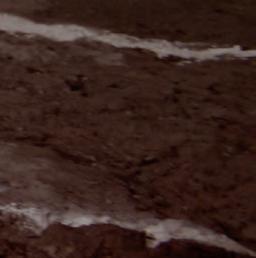
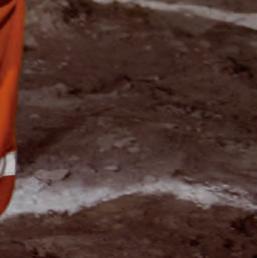
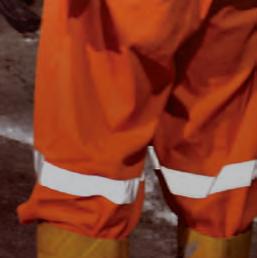

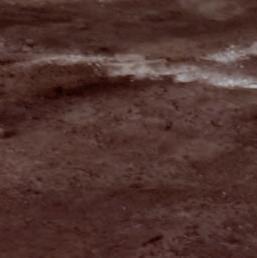
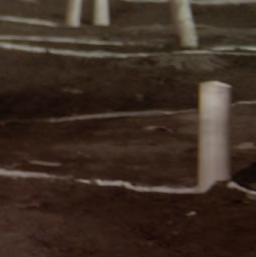
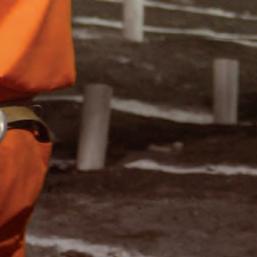

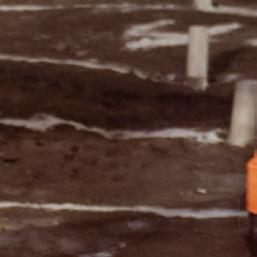
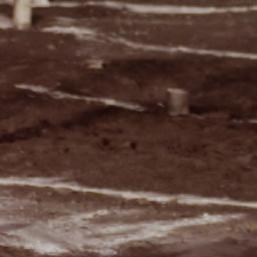

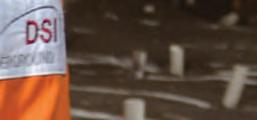
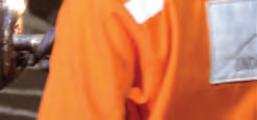
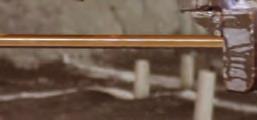

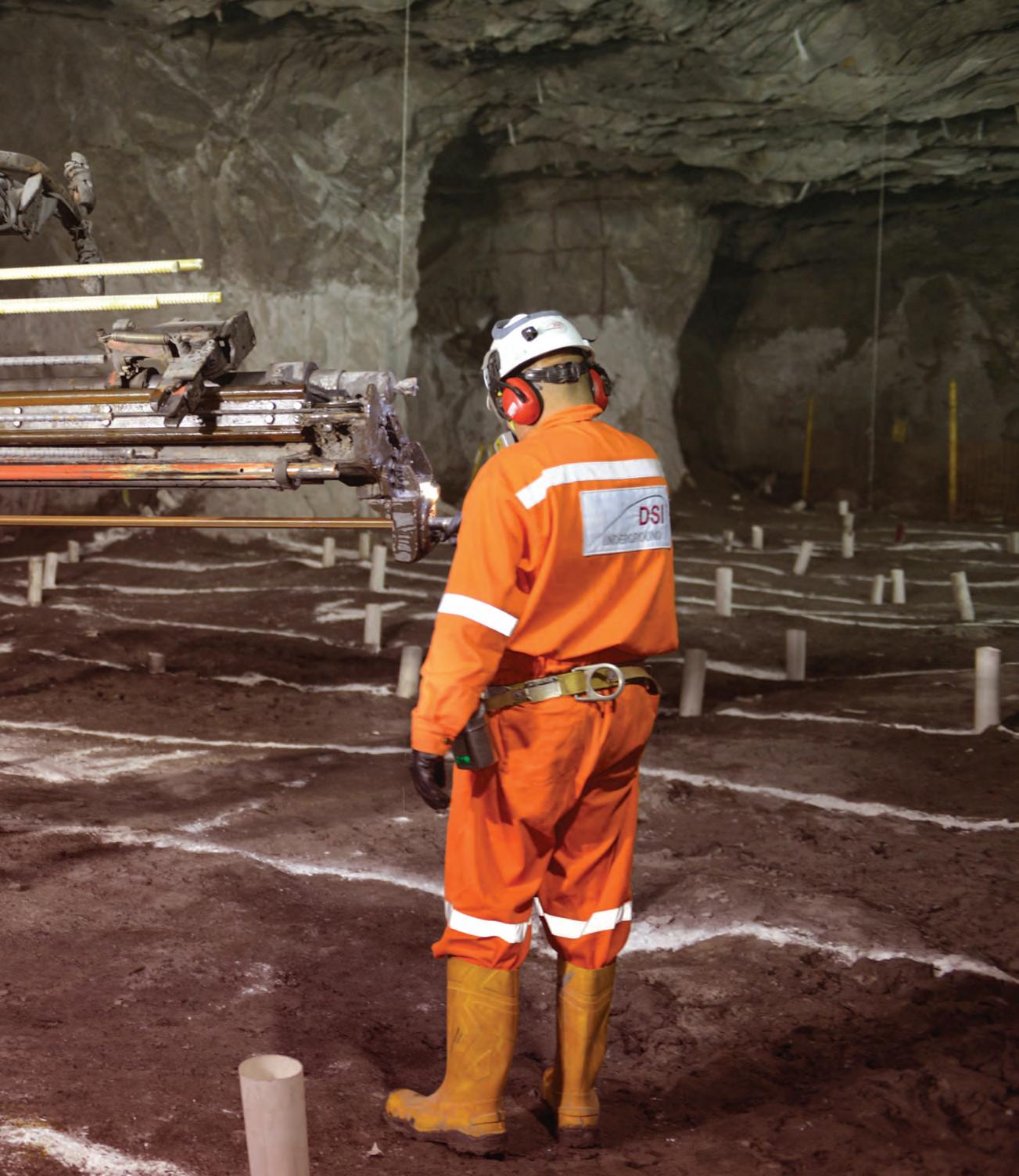
new Sandvik loaders are also expected to bring major cost savings across their entire lifecycles, according to Woods. They are likely to require fewer replacement parts than their predecessors, and servicing is also more efficient and simpler.
With this technological innovation, the trucks will see reduced CO2 emissions by between 20 and 25% and PM emissions by more than 30%, maintaining their current performance, and it will also mean economic savings for the mining operation. There is already international dual fuel mining truck experience – mines in Mexico, Turkey, Russia, Australia, USA, Canada, among others – that have showed the same results.
“This piloting is key in the process of changing to cleaner energies. The hydrogen route is not yet available, so we will incorporate
Chilean
Chile and is a concrete action that demonstrates the commitment of both ENGIE Chile and CMP to decarbonisation. In addition, it is in line with our purpose of acting to accelerate a carbon-neutral economy with mature technological solutions available today, economically competitive, and that leverage the fulfillment of the goals proposed by Chile regarding climate change in its Level Determined Contribution. National (NDC) to 2030,” explained Andrés Peragallo, Gas Product Manager of ENGIE Chile.
these six Sandvik loaders into service over the next two years,” Max Woods, Asset Manager for Byrnecut, said. “Not only will the use of electric vehicles significantly improve the working environment underground, but it will also help our customers to work toward their emissions reduction goals – something that is increasingly important in the mining sector.”
Byrnecut to use Sandvik 18 t BEVs at OZ Minerals ops
“The first Sandvik battery-electric loaders only began arriving in the country about a year ago, and the interest has been extremely strong,” he says. “We’re very pleased that Byrnecut and Oz Minerals see the benefits of this technology and is demonstrating it to the rest of the industry. We have always had an excellent working relationship with Byrnecut and look forward to cooperating with them throughout the roll-out and beyond.” sandvikwww.byrnecut.com; https://www.rocktechnology.

iron ore miner Compania Minera del Pacífico (CMP) together with ENGIE Chile have signed an alliance that they say represents a major step in the decarbonisation of mining: the first pilot of haul trucks in Chile powered by natural gas in the form of LNG. The project contemplates the modification of two trucks, over a period of six months, from a diesel combustion system to a dual fuel system, which will be mostly operated with natural gas. The truck type was not given but an accompanying image showed a Caterpillar 793F which is the main truck type used at the operation.
Under a deal with Sandvik Mining and Rock Solutions, Byrnecut will take delivery of the LHDs in 2023 and 2024 for use at the Prominent Hill copper, gold and silver mine, south-west of Coober Pedy, and the Carrapateena copper and gold mine, north of Port Augusta. Byrnecut has been engaged by OZ Minerals to provide underground mining services at the mines and currently has a fleet of Sandvik LH621i loaders equipped with autonomous solutions operating on both sites.“We’re excited tobeleading the way with battery-electric vehicles in Australia by putting
The pilot project – which will be carried out at CMP’s Los Colorados mine located in the Atacama region – is in a first stage of development and implementation that includes the importation of the necessary equipment, the conversion of the trucks to dual fuel, the implementation of the LNG refuelling station on site and, finally, the formalisation of this initiative before the Superintendency of Electricity and Fuels (SEC). With an eye on the expected results, this technological innovation could not only be applied to the entire fleet of CMP mining extraction trucks and other support equipment, but also to other medium and large mining sites in Chile. www.cmp.cl; https://engie-energia.cl
LNG and while we reduce our impact, we will learn to operate with gaseous fuels. We believe that we are on the right path, taking concrete steps towards decarbonisation,” said Claudia Monreal, Deputy Manager of CMP Development. To arrive at the plan, CMP worked for a year researching different motor conversion solutions. Finally, a laboratory test was carried out on a mining truck engine that allowed validation of the expected results in terms of performance, which marked the initial catalyst to be able to offer this type of solution to mining.
Battery machines produce no underground exhaust emissions and significantly less heat than traditional diesel engines, supporting the mines to reach sustainability targets, through reduced CO2 emissions.AndrewDawson, Business Line Manager for Load & Haul at Sandvik, praised Byrnecut for helping to pioneer the use of BEVs in Australia.
WORLD PROSPECTS 6 International Mining | SEPTEMBER 2022
Woods says the purchase of the electric loaders is part of Byrnecut’s commitment to explore and embrace new technologies that make its operations safer, more efficient and more sustainable.“Eliminating emissions from loaders from the underground environment helps us create a better workplace, as does AutoMine technology that enables operators to work from comfortable remote control rooms,” he said. Another major benefit to Byrnecut is predecessors,”ownershipdeliveringmanualprovidebothvariousSandvikloaders could provide,performancethe anticipated increasedthenewSandviksays.Thecompanyworkedcloselywithpriortopurchasetomodelapplicationscenarios,includingmanualandautomatedoperation.“We’reexpectingtheloaderstogreaterthroughput inbothandautomatedmodes whileasimilartotalcostofpertonnedeliveredtotheirWoodssays.The
“This project marks a milestone for mining in
CMP to trial dual fuel
Leading Australia-based contract miner Byrnecut is embracing the many benefits of battery-electric vehicles (BEVs) by purchasing six powered loaders with AutoMineSandvik battery-® foruse at OZ Minerals’operations inSouth Australia.
Sandvik 18-t battery loaders are the most compact on the market, according to the OEM. The powerful electric motors, innovative electric driveline and the smaller tyres on the rear compared with the front, result in a small machine size, high payload with good visibility and unmatched speeds.
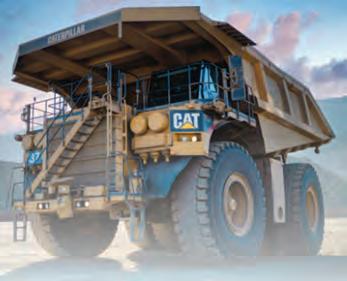
UPLIFT YOUR ORE GRADE
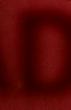
With demand for raw materials increasing and ore grades declining, it’s more important than ever to optimise process plant efficiency.
Download the bulk ore sorting brochure at:
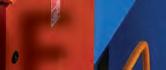




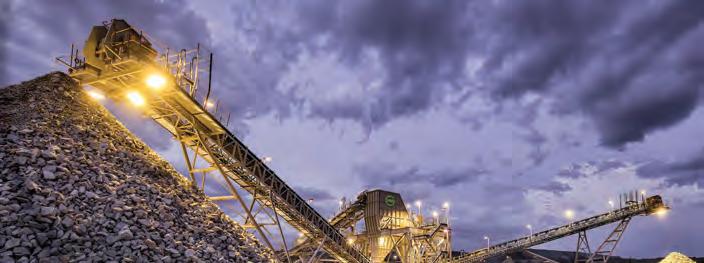
Whether you have an underground or open pit operation, our network of technical experts can help develop a tailor-made in-pit sorting solution to boost productivity and deliver a leaner, greener mine.
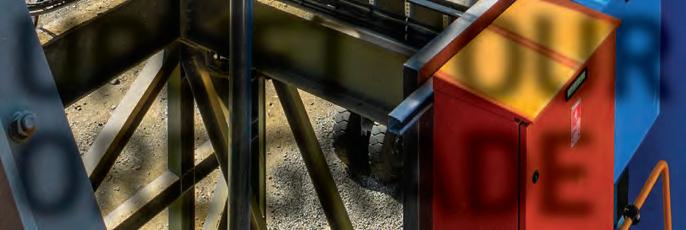
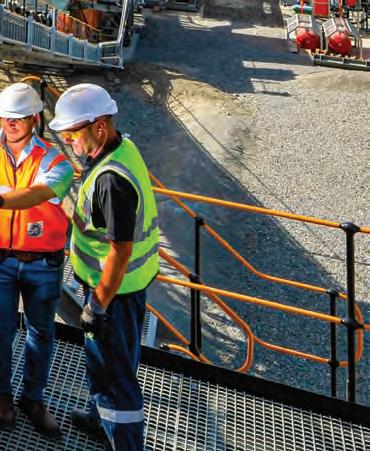
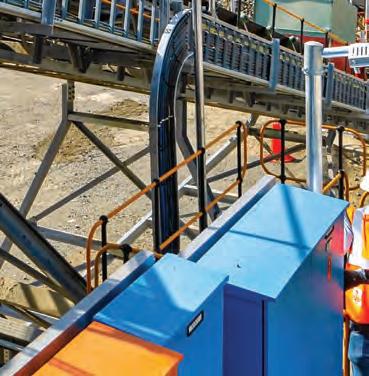
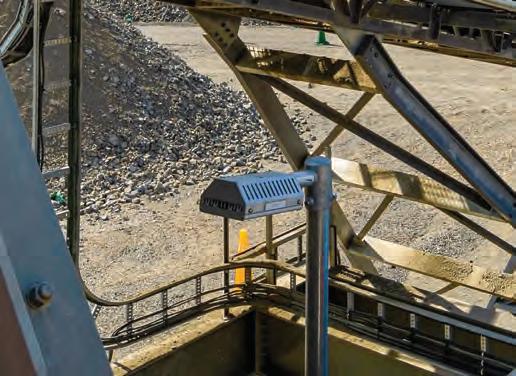
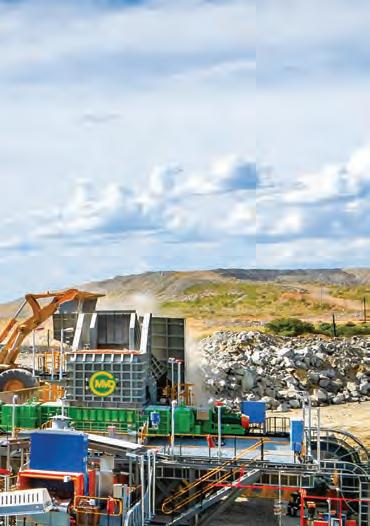
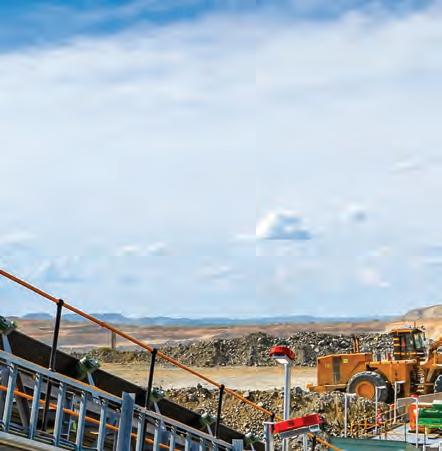
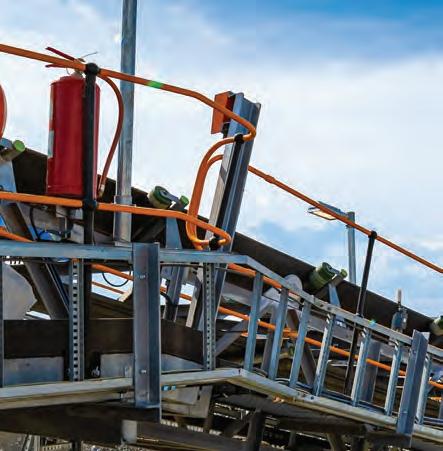
In-pit analysis and separation of ore and waste
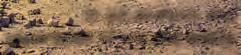

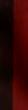


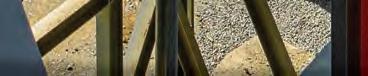
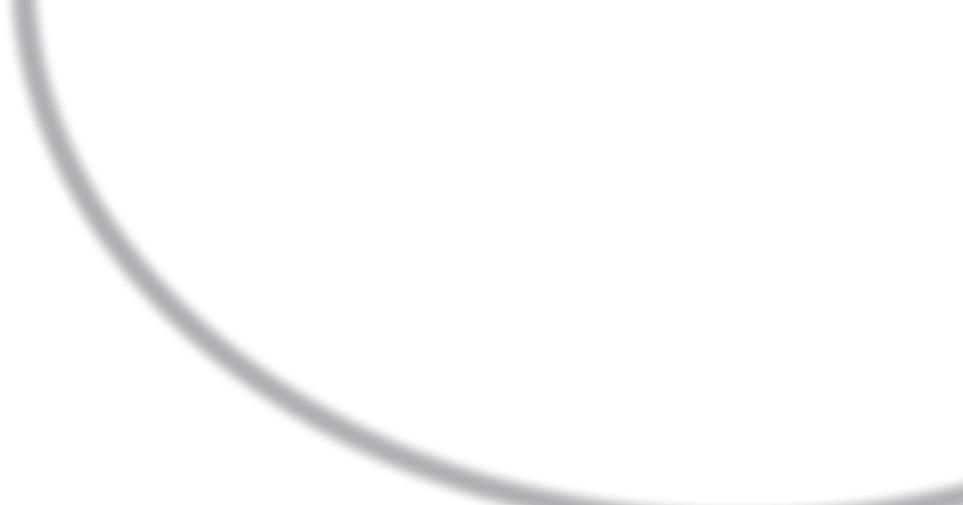

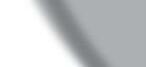


Our proven mobile sizing and ore diverting solutions, alongside new ore sensor technologies, can make this happen –separating ore from waste in the pit whilst uplifting ore grades through fines recovery. Introducing an automated ore sorting solution into your existing system ensures only the pay material is hauled to the process plant – meaning your mine can improve production whilst reducing energy usage and water consumption.
WWW.MMDSIZERS.COM/BOS

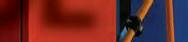

WATCH VIDEO
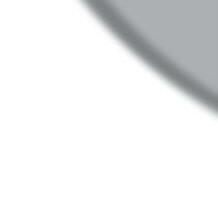
“Komatsu’s autonomous technology helps drive job creation, with a focus on safety, diversity, upskilling and an innovative flexible work force that meets the needs of people and communities with business goals,” says Sean Taylor, CEO & Managing Director, Komatsu Australia. “Not only does Komatsu’s autonomous haulage technology have a proven record in safety, productivity and lower haulage costs, but we pride ourselves on our ground-breaking contributions to autonomous technology solutions in the industry.”
early June 2022, the first four of a fleet of 41 290 t Komatsu 930E haul trucks began autonomous operations at BHP’s South Flank iron ore mine in the Pilbara region of Western Australia – with the trucks controlled from a purpose-built control facility at the site. The transition to autonomous haulage is expected to be completed at South Flank by September 2023.
BHP has stated the introduction of autonomous haulage at South Flank is expected to deliver farreaching safety, production and equipment utilisation and reliability benefits, and offers new
“Our extensive experience in delivering complex mining and petrochemical projects of scale and our proven ability to operate a global execution model continue to position us as the ideal technical partner. We’re delighted to build on our strong relationship with Enter Engineering and look forward to working closely to achieve the full value of the investment in these worldclass projects.”
WORLD PROSPECTS 8 International Mining | SEPTEMBER 2022
industries while also meeting the world’s surging demand for special petrochemical products and energy transition materials.
Wood,
the global consulting and engineering company, has secured two new contracts from Enter Engineering with a combined value of over $200 million, to deliver major capital investment projects in Uzbekistan.Thefirstwill see Wood’s Projects business deliver the full engineering scope, including front-end engineering design (FEED) and detailed design for a world-class mineral processing plant. The MOF-3 copper-concentration complex, in the city of Almalyk, will also require Wood’s technical assistance during the procurement, construction, commissioning and start-up stages to deliver the world’s largest copper concentrator, WoodBacksays.inJune, Metso Outotec announced it had signed a contract to deliver key process technology to the MOF-3 copper-gold-
Automation. According to Povah, Komatsu is on track to have over 430 autonomous trucks operating in Australia by the end of 2022, in mines across Western Australia and Queensland.
skills and opportunities for BHP’s mining and maintenance teams.
https://mining.komatsu/; www.bhp.com
In
Another IPCC order for TAKRAF in India with SCCL
In
The main elements of the semi-mobile crushing plants are ramps (truck-bridge) to facilitate the unloading of Run-of-Mine (ROM) material with 100 t dumpers feeding the crushing plant hopper, a feed hopper, apron feeder and spillage conveyor, TAKRAF primary sizer, discharge conveyor equipped with magnetic separator, metal detector and discharge chute.
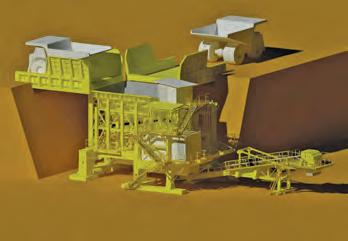
Selvakumar Devendran, TAKRAF India: Manager – Sales, had this to say recently when questioned regarding the order: “We are delighted to have attracted a premier Indian government entity as a client and to be able to supply them with a complete solutions package. All colleagues and all stakeholders involved in
Since July 2020, a fleet of Komatsu 930E autonomous-ready haul trucks, configured as conventionally driven trucks, has been moving iron ore and materials. In January 2022, BHP approved moving the US$3.6 billion mine to autonomous haulage, to be phased in across five Autonomous Operation Zones (AOZs), from June 2022.
Wood engineering world’s largest copper concentrator in Uzbekistan

“All 41 of the 930E’s on site are now in the process of being upgraded to fully autonomous operation, at the rate of four a month,” said Garry Povah, Komatsu’s General Manager Mining
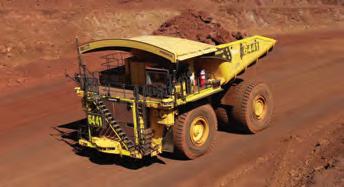
https://www.takraf.com; https://scclmines.com
At peak, the MOF-3 and MTO projects will each require the support of over 400 colleagues from across Wood offices, including Chennai, Johannesburg, Madrid, Milan, Santiago, Singapore and Woking, in addition to Wood’s newly established office in Tashkent, Uzbekistan. https://www.woodplc.com; https://www.agmk.uz
First Komatsu trucks operating autonomously at BHP South Flank
a first contract to be received from the government-owned entity M/s. Singareni Collieries Company Limited (SCCL) for its Ramagundam mine located in Telangana, TAKRAF India is again showing its in-pit crushing and conveying (IPCC) credentials in India by supplying two semi-mobile relocatable crushing plants with TAKRAF primary sizers. The turnkey order is expected to be completed in 2023, with the crushing plants adding to and enhancing the capacity of the plant’s current arrangement of four semi-mobile crushing plants with crusher. The primary sizers produce a product size of -200 mm from a maximum feed size of 1,000 x 800 x 800 mm at a capacity of 1,000 t/h.
South Flank is located 156 km north-west of Newman and 9 km south of BHP’s Mining Area C facility in the Pilbara region of Western Australia. It is Australia’s largest new iron ore mine in more than 50 years. When it merges with the neighbouring Mining Area C operation, it will form the largest operating iron ore hub in the world, producing 145 Mt of iron ore each year.
winning this important award must be commended on their dedication and hard work in providing the client with a solution that satisfies their needs. This project serves to only entrench and bolster TAKRAF’s premier crushing plant and comminution solutions in India.”
molybdenum concentrator complex, owned by Almalyk Mining and Metallurgical Company. Wood will also provide detailed engineering and procurement assistance services to build a new methanol-to-olefin-based gas-chemical complex, located in the Bukhara region. Giuseppe Zuccaro, President of Process & Chemicals at Wood, said: “These projects mark a significant and strategic investment in Uzbekistan as the country accelerates its economic diversification plan, satisfying the needs of its domestic
ME ComminutionElecmetal Solutions Innovative Solutions - Proven Performance www.me-elecmetal.com ME Elecmetal o ers more than mill liners — we o er innovation, support, custom designs and valuable tools to develop a total comminution solution speci c to your needs. We are on the ground with our customers — setting common goals and providing timely responses based on e ective collaboration. Drawing on over 100 years of experience and advanced technologies, we will help you optimize processes, extend the lifespan of wear parts, reduce operational risks and increase pro tability. Innovative Mill Lining Solutions for SAG, AG, Ball, Tower & Rod Mills • Steel • Rubber • Composite Premium Quality Forged Steel Grinding Media for SAG, Ball & Rod Mills • ME Super SAG®: 4.0” to 6.25” • ME Ultra Grind®: 1.5” to 4.0” • ME Ultra Grind®II: 2.0“ to 4.0” • ME Performa®: 7/8” to 1.5” Wear Components for Primary, Secondary & Tertiary Crushers • Gyratory Crushers • Jaw Crushers • Cone Crushers Solutions to positively impact priority KPIs


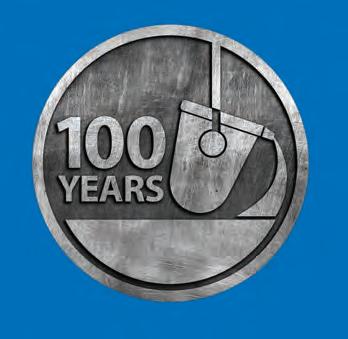
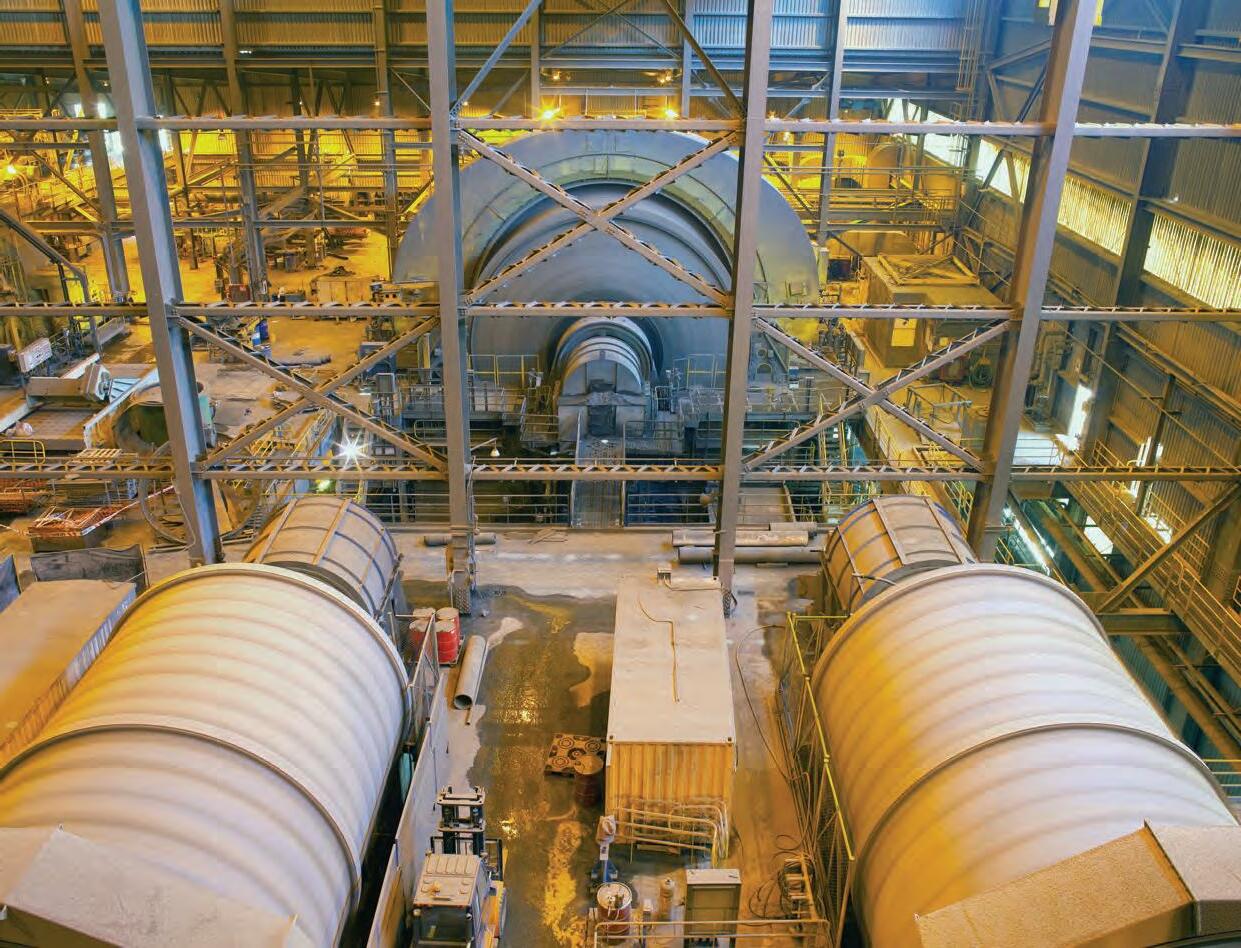
This will be ERG’s first proprietary wind farm project, and forms part of the Group’s ambitious ESG Strategy and decarbonisation programme. In total, by 2030, ERG plans to reduce its emissions to air by 56%, emissions to water by 30% and water consumption by 33% through its Environmental and Energy Strategy.
https://www.cummins.com/
Further impact of the transaction, including updated financial guidance for 2022, will be communicated no later than in connection with the release of FLSmidth’s financial results for the first nine months of 2022 on 8 November 2022. www.flsmidth.com
Inc. has celebrated in August the grand opening of its new microgrid lab, the Power Integration Center (PIC) at its Power Systems facility in Fridley, Minnesota. The PIC is a state of the art facility that allows for the configuration, integration and testing of power system technologies including diesel and natural gas generator sets, PV solar panels, battery storage systems, fuel cells, transfer switches, switchgear and system level controls.
and build power systems to meet sustainability goals for a greener future,” said Gary Johansen, VP – Power Systems Engineering and Project Sponsor.
Eurasian Resources Group (ERG), the leading diversified natural resources producer, has announced that it plans to invest nearly US$230 million in building a major wind power plant in Kazakhstan, the Group’s country of origin.
With changing government regulations, increasing cost of operation, inclement weather conditions, and the instability of power grids, customers, including in the mining industry, are driving the needs for more reliable and efficient microgrid solutions. The PIC allows the ability to experiment with multiple potential power system solutions directly along with Cummins engineers.
great success, and one that we will look to replicate at ERG’s other facilities. We hope that the construction of this wind farm serves as an example for other large enterprises in Kazakhstan, and takes the country closer to the ambitious goal of becoming a carbon-neutral state.”
The powerful IEC S-class turbines to be used at the wind power plant can generate electricity in a range of weather conditions and with wind speeds from 3-25 m per second. This will ensure that the necessary power output can be generated, despite the extreme continental climate of Western Kazakhstan.
The wind turbine park will extend over 150 hectares near the town of Khromtau in Kazakhstan and will be constructed using the latest engineering and technology. Around 300 jobs will be created during the construction phase, and the facility will provide 30 permanent jobs once it is commissioned.
WORLD PROSPECTS 10 International Mining | SEPTEMBER 2022
TK Mining is a leading full-line supplier of solutions for mining systems, material handling, mineral processing and services. The combination of FLSmidth and TK Mining will create a leading global mining technology and
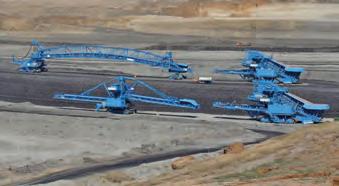
on August 11 announced that all conditions and requirements for the acquisition of thyssenkrupp’s Mining business (TK Mining) have been met. In accordance with the sale and purchase agreement, final closing of the transaction will take place on the last business day of the month. Accordingly, the transaction was to close on 31 August 2022. All regulatory clearances have been obtained without imposition of any competition related remedies.
To be commissioned in 2024, the new renewable energy facility will have a capacity of up to 155 MW, making it the most powerful plant in the Aktobe region, and is expected to reduce CO2 emissions by around 520,000 t annually.
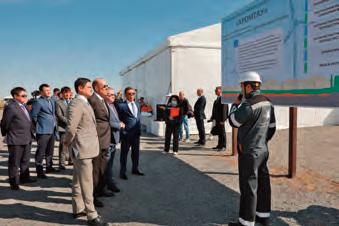
Cummins opens Power Integration Center
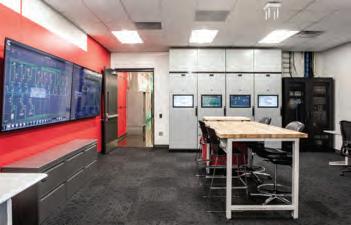
ERG to power Kazchrome Donskoy mine from new wind farm
ERG’s Chairman of the Board of Directors Dr Alexander Machkevitch, members of the Board of Directors Patokh Chodiev and Shukhrat Ibragimov, and the local head of government (Akim) of the Aktobe region Ondasyn Orazalin have attended a capsule-laying ceremony at the construction site of the wind power plant.
“The PIC is the realisation of a significant investment in engineering technology and innovation that will impact how companies use
FLSmidth
milestone in the history of FLSmidth. We are very excited to soon welcome our ~2,000 new colleagues and TK Mining’s customers to FLSmidth. The completion of the acquisition contributes to FLSmidth’s strategic growth ambitions within Mining. Our combined company will offer customers a stronger, complementary value proposition, while creating significant aftermarket opportunities, driving value creation through compelling synergies and further strengthening our sustainability and digitalisation agenda.”
Dr Alexander Machkevitch said: “President of the Republic of Kazakhstan Mr Kassym-Jomart Tokayev recently announced that Kazakhstan intends to achieve carbon neutrality by 2060, and ERG is in full support of this initiative. This new plant is an important step and I believe that Donskoy GOK’s transition to wind power will be a
service provider with operations from pit-to-plant with a strong focus on productivity and sustainability. The new company has particular market strength in comminution including primary gyratories and HPGRs as well as in-pit crushing & conveying (IPCC).
FLSmidth Group CEO Mikko Keto commented: “Today’s announcement marks a significant
The wind power generated will be used to supply ERG’s Kazchrome Donskoy GOK plant, the largest industrial enterprise in the Aktobe region, and cover the plant’s growing energy needs as it increases its production capacity in the coming years. In addition, the wind farm will supply
Cummins
This allows for timesaving, cost-saving and the ability to optimise a unique power system for their project. “With this center, we’ll be able to enhance our offerings throughout the product lifecycle,” said Satish Jayaram, IDEA Program Office Leader and Project Sponsor.
energy to neighbouring industrial facilities and the Aktobe region more widely, thereby reducing Kazakhstan’s usage of coal.
FLSmidth completes TK Mining acquisition
https://www.eurasianresources.lu
MINERAL TECHNOLOGIES. Innovative WIRTGEN surface miners, robust KLEEMANN impact crushers and screens plus customized services make the WIRTGEN GROUP a reliable partner for all mining applications. Take advantage of innovative solutions from the technology leader. www.wirtgen-group.com www.wirtgen-group.com/mineral Powerful!CLOSETOOURCUSTOMERSAJOHNDEERECOMPANY Booth FS.1011
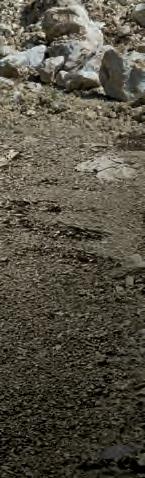
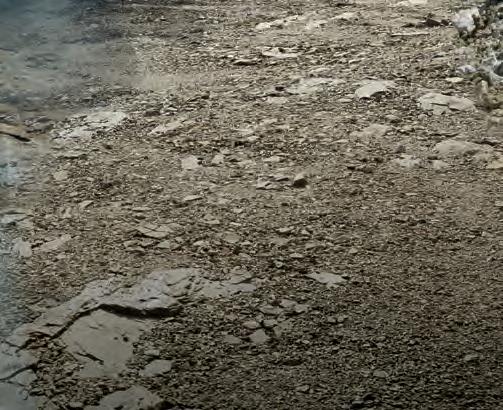
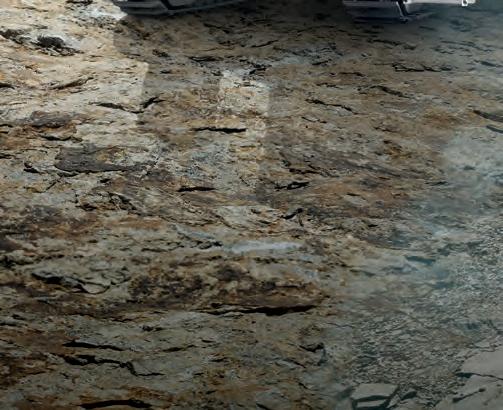

World-class shaft-sinking experience and customised solutions
Extensive practical knowledge in all areas of underground excavation and construction, and the experience to deliver on projects and meet milestones, enable Redpath to achieve its goal of being the ‘go to’ contractor of the global mining industry.
Recognised as a global leader in shaft sinking, Redpath has dedicated teams around the globe, who design and build shafts and mine infrastructure, as well as provide a full suite of shaft-related services. These include audits, rehabilitation, and infrastructure improvements.
The Redpath raiseboring manufacturing team has continually innovated to deliver the latest technology and customised designs for more than 40 years. This has resulted in the evergrowing Redbore family of raise drills, featuring the Redbore 30X, 40, 50, 50X, 60UR, 65, 70, 80, 90 and 100 models. The latter is also known as ‘Queen Louise’, the world’s largest proven capacity raise drill. With unique power output and compact design, Redpath’s raise drills can handle a full range of diameters of raises and depths. Redpath meets the demands for conventional, box-holing (up reaming), down reaming and autonomous reaming.
Full service mining and innovation solutions since 1962
Global mining expertise driving innovation in challenging conditions
Six decades of experience have positioned Redpath as a leader in the global mining sector. The company draws upon expertise from across the world and many disciplines, including inhouse engineering and technical services teams. Our rich source of global expertise and experience represents real value for our clients in an increasingly competitive market. Our ability to quickly mobilise our people and transport materials wherever our clients need us, helps make Redpath a trusted industry delivery
Mine development applying modern underground fleet and innovative solutions

With one of the most modern and comprehensive contractor fleets in the industry, Redpath provides a full range of underground
Record-breaking raisebore contracting and manufacturing with extensive fleet
12 International Mining | SEPTEMBER 2022
The company’s Australian operations recently landed the largest single raiseboring contract in the Redpath Group’s 60-year history. The contract scope involves three Redbore rigs; Redbore 100, Redbore 90EX and Redbore 90, contracted for eight holes, totalling 5.3 km. All three rigs are designed and manufactured in North Bay, Canada
is a multinational, full-service underground mining contractor.
Established in 1962, the company provides expertise and services to a comprehensive list of international clients. Redpath has built a reputation for meeting deadlines and delivering practical, innovative solutions. Skilled personnel, committed to safety and quality, and superior technical and operational know-how, are key to Redpath’s success.
innovative, state-of-the-art solutions to conquer tough challenges in diverse environments. From sinking shafts in the Gobi Desert of Mongolia, to developing tunnels high in the mountains of Indonesia, from the frozen Arctic, at extreme - 5,000 m above sea levelaltitudes, to the heat of sub-Saharan Africa, Redpath is ready to meet the challenge.
Timelystations.front-end engineering and design models, as well as selection and sourcing of hoisting facilities, allow us to fast-track any shaft project. This seamless project-planning phase has continually proven to yield high quality products that exceed our clients’ expectations. Whether the job calls for conventional drill and blast, mechanised sinking or fully automated shaft-boring methods, our integrated engineering and shaft teams get it done.
Groundbreaking milestones in 2021 include the longest raisebore hole in the Northern Hemisphere and all of the Americas at a length of 3,312 ft (1,010 m). The hole at Macassa Mine
development and construction services. We excavate hundreds of kilometres globally every year. Lateral development, ramps/declines and mass excavation are prime elements of our mine development services.
Redpath
ADVERTISEMENT FEATURE
We have a broad range of experience in using split-feed jumbos in lateral development projects around the world. We have also partnered with some of our clients to work towards reduced emissions and operator exposure by employing zero-emission, batteryoperated equipment. These methodologies provide not only environmental benefits, but also improve safety, productivity and versatility.
Redpathpartner.uses
Every shaft-sinking project presents challenges, and no two projects are alike.
Mining Contractors and Engineers
Noteworthy shaft-sinking projects include the
INTERNATIONAL MINING PROFILES
The Redpath Deilmann team from Germany has attracted a lot of attention on its highly successful Nezhinsky Potash Shafts project in Belarus, where it has set a new benchmark in mechanised shaft sinking on two potash freeze shafts
Mining companies and tunnelling contractors demand new ideas and customised solutions and that is what Redpath delivers.
Known for our ability to offer solutions for varying and difficult ground conditions, our expertise in performing high-quality mining in extreme climate situations is unique in the industry.
The list of Redpath’s services includes mine development, shaft sinking, mass excavation, production mining, raiseboring, mechanical excavation, engineering, technical and specialty services.Redpath also designs and manufactures the Redbore family of raise drills, including the world’s largest proven capacity raise drill, the Redbore 100. The company has a record of safe, low-cost, on-time project delivery, while providing a level of service that exceeds industry standards.
Nezhinsky Mine in Belarus, involving two freeze shafts and approximately 9,000 m of horizontal excavations. Another notable project is Oyu Tolgoi, Mongolia, Shaft 2, a 10 m diameter x 1,400 m-deep concrete-lined shaft, which includes the excavation and construction of five shaft
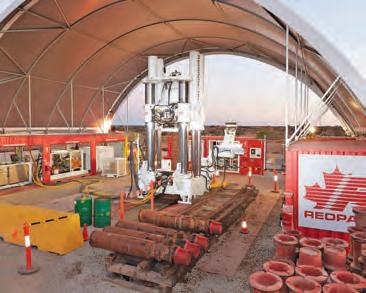
Underground construction, demolition and rehabilitation
In-house engineering and technical services for enhanced project control and integration
Trusted global partner
With 60 years of service, over 6,000 employees and offices in Canada, the US, Indonesia, Mongolia, Germany, South Africa, Zambia and Australia, Redpath continues to attract clients and employees to its doors, all over the world.
ADVERTISEMENT FEATURE
Redpath provides leadership development training, utilises robust safety management systems, the latest technology and professional trainers to ensure that our employees have the necessary skills, tools and equipment to work in a safe and productive manner.
Reinforcing a culture of Safety –First, Last and Always.
At Redpath, the health and safety of our employees and stakeholders are of the utmost importance. We passionately believe that all injuries are preventable and that the work we undertake can and will be completed safely, with no harm to people, the environment or the communities in which we work.
Contract mining from concept to turnkey infrastructure
Redpath has expansive regulatory knowledge, regional expertise and experience in completing culturally and environmentally sensitive projects, ensuring the impact on the surrounding area and local wildlife is minimal. Our thorough understanding of procurement and logistics, gives us an advantage when mobilising equipment and supplies around the world.
Working together from design through to installation and commissioning, Redpath’s globally-mobile and experienced technical experts provide innovative and reliable designs with the ability to offer a total mine package. The company’s integrated scheduling systems enable efficient decision making, project control and value management. Examples of services include 3D comprehensive rendering, site management, supervision, design, managing and construction of crushers, complete hoisting facilities, shaft services, material handling systems, conveyance systems, shaft conveyances and custom sinking set-ups.
We continually strive to achieve the highest standards in health and safety – zero harm. Through the development of a safety culture, built on a common understanding of safety principles and a commitment by all employees, we will meet our goal of ‘Safety – First, Last and Always’.
ESG commitment based on timehonoured corporate values
With a focus on driving efficiency and achieving bottom-line objectives for our clients, we provide a complete scope of services.
Clients all over the world commission Redpath to perform production-mining services, involving engineering and design to complete turnkey operations. Services include construction engineering, planning development, production drilling, blasting, ore haulage, crushing and conveyance to surface for processing. Redpath can assist with any scope of the project, from beginning to completion.
With skilled personnel committed to safety and quality, plus unequalled technical and operational know-how, Redpath has built a reputation for meeting deadlines and delivering practical, innovative solutions more information, please visit www.redpathmining.com

including ventilation, ore and/or waste passes, production slot raises and narrow vein mining. Redpath’s mechanised raise mining innovations include a battery-operated climber, providing flexibility, speed and economy.
Redpath applies its expertise and experience to the development of tunnels for civil infrastructure projects. Conventional drill and blast, and continuous mining methods using road headers or TBMs, may be used for underground civil infrastructure projects. Access tunnels, sewer tunnels and dewatering tunnels are a few types that have been completed for end uses such as hydro-electric, roadway, water transfer, public transit and mine exploration projects.
Mechanised raise mining offering flexibility, speed and economy
in Canada was accomplished in two stages with two machines drilling concurrently; a Redbore 70 underground and a Redbore 90EX on surface. The feat took place merely three months after Redpath broke another record at Niobec Mine in Québec, Canada. The raise at Niobec Mine was completed with the Redbore 90EX raisedrill and became the largest ever completed in the Americas and the Northern Hemisphere, and the third biggest globally, at 875 m by 6.3 m diameter. The Redbore series of raisebore machines used for these milestones were designed and manufactured in-house by Redpath in North Bay, Canada.
Foremost amongst the ‘Guiding Principles’ is this simple principle: “We are honest, fair and responsible.” This approach, coupled with the equally important declaration, “We work by our principles of safety first, last and always”, establishes the firm foundation, which Redpath continues to build our organisation on. It defines how we deal with our clients, employees, business partners and other stakeholders in the projects we undertake and in the countries in which we work.
SEPTEMBER 2022 | International Mining 13
Redpath has a longstanding commitment to the incorporation of environmental, social and governance (ESG) criteria into our organisation. It is based on Redpath’s ‘Philosophy’ and ‘Guidelines for Success’ penned by Redpath’s founder, Jim Redpath, in 1962. The commitment is a fundamental part of all our dealings with clients, business partners, subcontractors, suppliers, employees and the communities in which we live and do business.
Redpath is also a market leader in providing advanced mechanical excavation solutions to mine owners across Australia and the globe.
Experienced management, quality supervision and a highly capable workforce ensure that all project demands are met,
Redpath provides a world of experience in fullrange mine construction and installation for all project sizes and complexities. Skilled in new infrastructure development, we are also recognised for dewatering, rehabilitating, upgrading and re-commissioning mines that are re-entering production. We build underground shop facilities and refuge stations, ore handling and conveyance systems consisting of chutes, grizzlies, conveyors, ore transfers, ore and waste bins, crushers and loading pockets. Mechanical and electrical installations include internal hoists, substations and ventilation systems. The excavation of large caverns primarily for housing complex crusher systems is also a Redpath specialty.
Having amassed the industry’s largest mechanised raise mining equipment fleet, Redpath’s innovative approaches, patented designs and concepts have been providing safe drill and blast raise-mining services and solutions since 1975.
Speciality services for construction/mechanicalcivilexcavation
For
October’s fest
Taking place on October 24-30, the organisers, Messe München, are expecting around 3,000 international exhibitors to attend, spread over 614,000 sq.m of space at the ICV.
Bauma
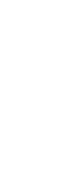
display at the show, featuring what Liebherr says will be “an impressive demonstration of the Trolley Assist System”.
Bauma 2022 organisers, Messe München, are expecting around 3,000 international exhibitors to attend, spread over 614,000 sq.m of space at the ICV (credit: Messe München GmbH)
Liebherr’s new generation 8
2022 is set to, once again, set a benchmark for all construction fairs across the globe.
Construction remains the main target market, yet there is plenty to get excited about from a mining perspective, as IM reveals.
The hydraulic excavator to be displayed at Bauma 2022 has already entered the testing phase, with the company planning the start of serial production in early 2024.
Taking place in a new season and with new focus areas, Bauma 2022 will set the scene for the next three years of construction and mining equipment developments. Dan Gleeson looks at what we can expect to see
As the second machine within the Liebherr mining portfolio to receive the “Generation 8” label after the R 9600 excavator, which was launched in 2021, this new model comes equipped with the latest Liebherr technology products, the company says.
Among its booths at Bauma 2022, Liebherr is set to unveil a brand-new mid-size-class hydraulic mining excavator with the exhibition of a preseries model.
BAUMA PREVIEW 14 International Mining | SEPTEMBER 2022
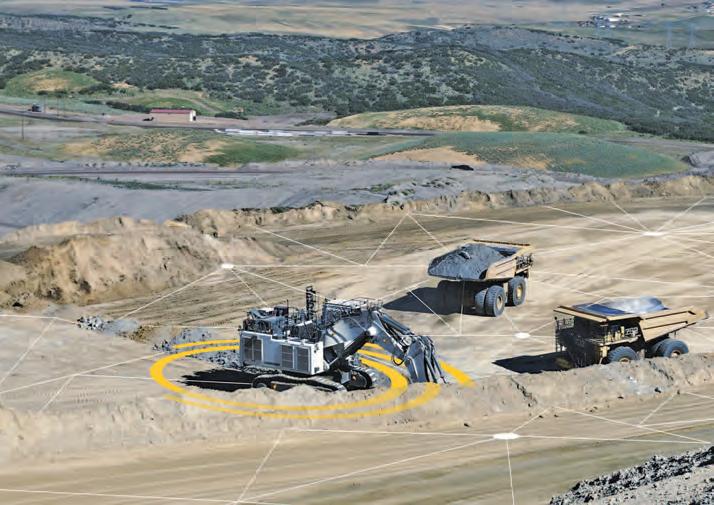


This truck bridges the gap between the T 284 (363-t payload) and the upgraded T 264 (240-t
payload) and was launched last year with the Liebherr Trolley Assist System available as an option.Thetrolley assist system uses an overhead pantograph to connect the electric-drive system to a mine site’s electrical network, powered by the customer’s energy source of choice. It offers
Liebherr’s new mid-size class hydraulic mining excavator launching at Bauma 2022 comes equipped with the latest Liebherr technology products like the Liebherr Mining Assistance System
The T 274, a 305-t mining truck, will also be on
THEAUTOBITROCKTECHNOLOGY.SANDVIKDRILL MUST GO ON The key to productive mining operations is to always keep your machines busy. Autobit has an extended first grinding interval, lasting up to three hours. It enables your automated rig to drill during shift changes. The result is several hours of extra productivity every day. Ready to minimize your downtime? Read more at www.rocktechnology.sandvik/autobit
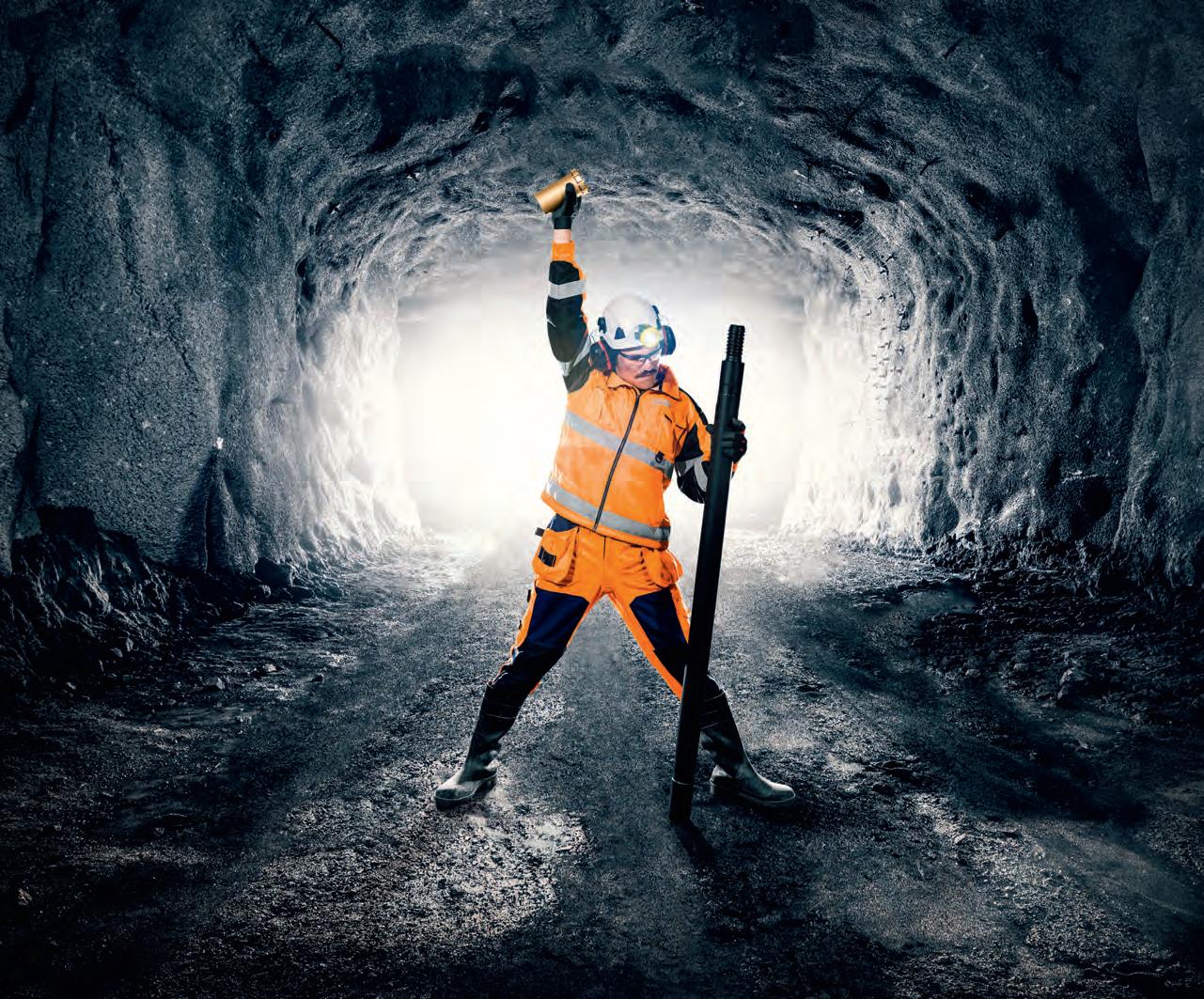
Electric-drive and smart solutions
Across its plus-7,000 sq.m of Bauma space, Komatsu is set to present attendees with a record number of machines – 42 – that are new or well-recognised products and services that, it says, improve total job site efficiency and create real customer value.

already has 56 trucks fitted with the system operating out in the field across three mine
BAUMA PREVIEW
The phased supply of haul trucks as part of this agreement is anticipated to commence following a two-year joint development period. This is intended to enable the development and integration of Fortescue’s proprietary-owned battery electric and fuel cell electric power system into Liebherr’s proprietary-owned base truck.
Komatsu Germany Mining started to build the first electric-drive hydraulic mining excavator in
Back in June, the two companies signed an agreement for the development and supply of mining haul trucks integrating zero emission power system technologies being developed by Fortescue Future Industries and Williams Advanced Engineering.
Machinery operating in the hostile conditions of mining, quarrying and construction requires an engine that
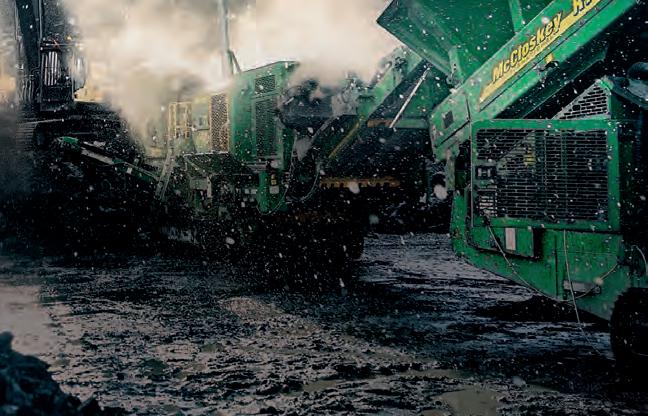
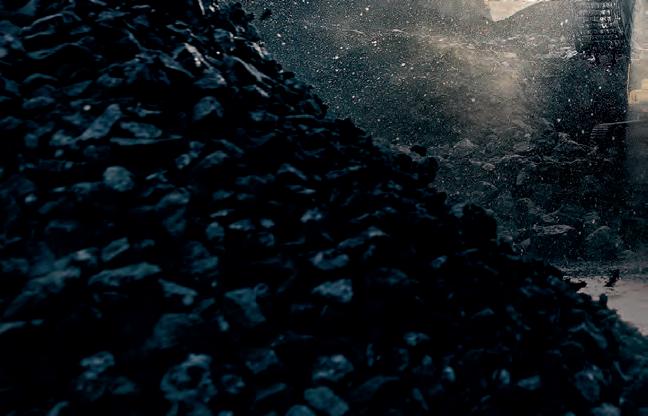
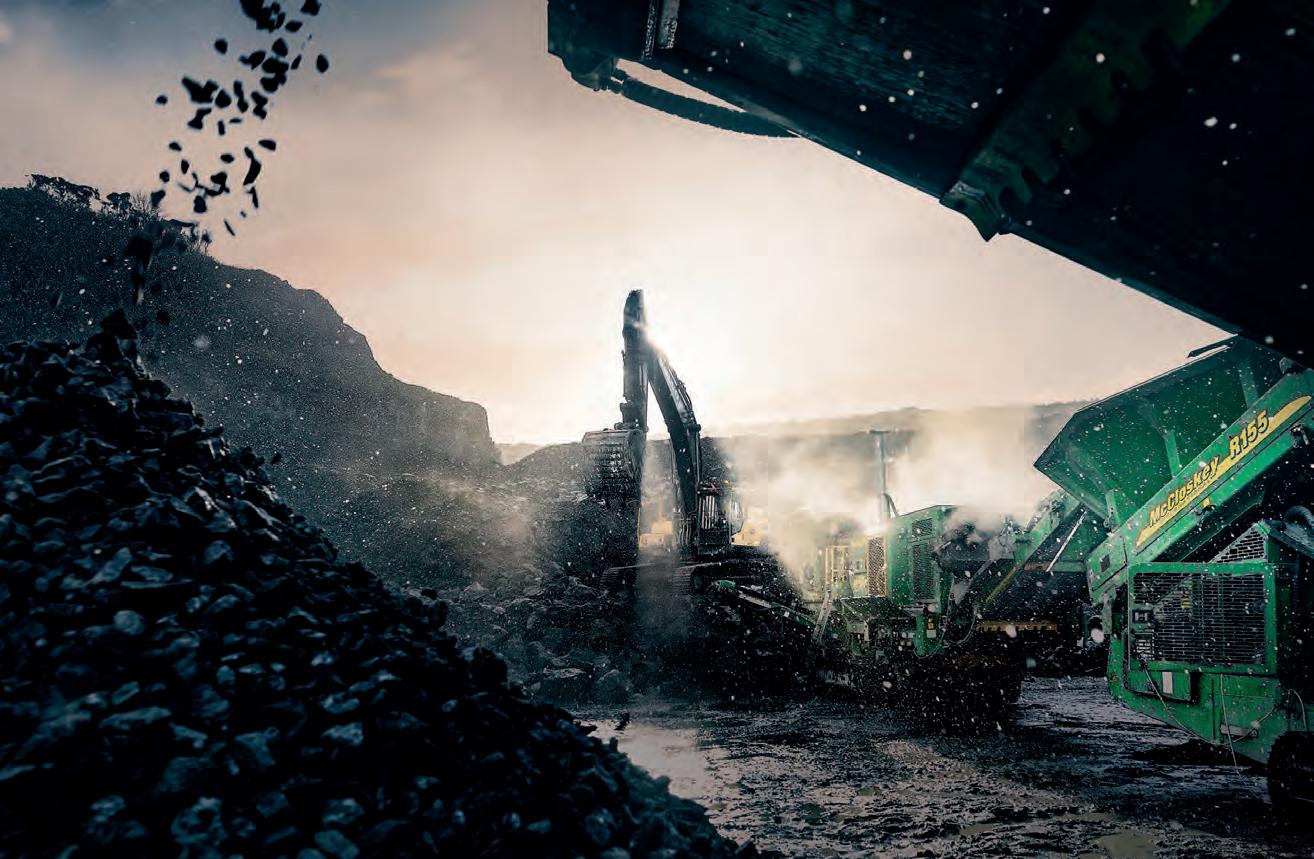
The standout on the Komatsu stand at Bauma 2022 will be the PC4000-11 electric drive excavator, which, with its 22 cu.m shovel capacity, is a match for 150-240 ton (136-218 t) trucks
Thesites.company’s recently launched Technology Product portfolio will also be showcased in Munich, with the Truck Loading Assistant, Performance Monitoring and Application Severity analytic products among the list of solutions on show. Liebherr Power Efficiency and the Bucket Filling Assistant, the latter of which offers the first step towards excavator automation, will also beMiningpresented.company attendees will also gain some insights into the OEM’s hydrogen strategy, with Liebherr Components’ first hydrogen engine, the H964, being highlighted at the event.
Torque of the town
increased truck fleet productivity and the potential for a reduction in fleet size while retaining the same productivity compared with the use of standard trucks, according to the company.Thepotential for a significant reduction of diesel fuel consumption and a smaller carbon footprint by decreasing the truck fleet’s CO2 emissions confirms the Trolley Assist System as an effective first step on the road to zero emission mine sites of the future, according to Liebherr.Liebherr
The standout among these will be the PC400011 electric drive excavator, which, with its 22 cu.m shovel capacity, is a match for 150-240 ton (136218 t) trucks. It is also representative of the
Liebherr will also discuss its recently announced tie-up with Fortescue Metals Group, which has a hydrogen element to it.
company’s knowledge and experience in developing, manufacturing and maintaining electric driven hydraulic excavators.
BAUMA PREVIEW
Equipped with the KOMTRAX Plus system, KomVision and Argus PLM, the PC4000-11 is digitally connected, benefits from constant monitoring, is equipped with safe operating mechanisms and offers efficient loading operations, the company says.
Digitalisation is another essential element for improved productivity and, at Bauma 2022, Smart Construction/Earthbrain will show a new way of working, with unique solutions to support and improve customers’ businesses, Komatsu says.Smart Construction is a solution for implementing highly productive, clean and safe work sites by connecting various site-based
Twice as fast as drillconventional&blast ROBBINS ROBBINSTBM.COMMDM5000 The world’s first successful rectangular tunnel boring machine The Robbins MDM5000 is designed with mines in mind, capable of boring long drifts and access tunnels at 10-12 m/day in hard rock.
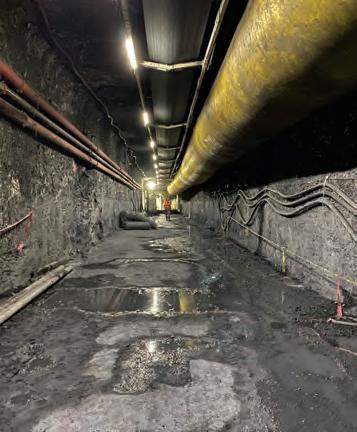

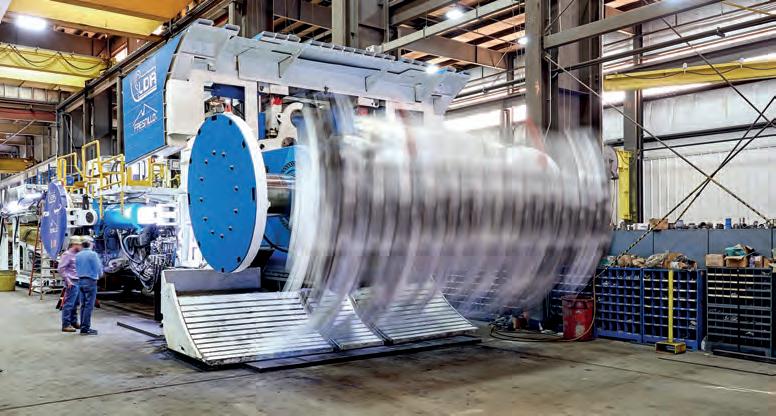
New ADT entrant Hyundai Construction Equipment (HCE) is set to display 23 machines in Munich, with some of the display 23 machines in Munich, with some of the key highlights being a new articulated dump truck (ADT) and a hydrogen concept vehicle.
The company’s stand is 30% larger than in previous years, representing the ongoing growth journey it is on.
The entry of HCE into the ADT market involves the launch of two models, using proven, innovative design and technology to deliver high productivity and superior mobility on site, the
The Komtrax Next Generation and Komtrax Data Analytics booths, meanwhile, will explain how Komatsu’s wireless monitoring system can simplify decision making for all those who work to deploy equipment effectively or to improve fuel efficiency, to maximise productivity or to plan periodic maintenance.
the early 1980s. Now, almost 40 years later, Komatsu has delivered more than 250 of them worldwide.“Withover 7 million operating hours, Komatsu is one of the most experienced and most successful companies developing, manufacturing and maintaining this type of machine,” it says. “The unique advantage of the electrically driven hydraulic excavator lies in the reduced operating costs, made possible by the elimination of diesel costs and the fact that they are not obliged to comply with any emission regulations.”
In addition, SANY will introduce the first models of a new ground-up range of telehandlers developed especially for Europe – the STH1440 and STH1840 – and the recent extension of its wheel loader range with the 4-t-payload SW305K. The company also has plans to present a new drill at the show that has mining applications.BackinMarch,
SANY may be viewed by many in the Western mining sector as a China-only manufacturer, but the European arm of the company, SANY Europe, will be showcasing its international offering in October.TheEuropean and Chinese arms of the group recently collaborated on the first 200-t excavator in China, the SY2000. The 200-t version is just the start, with plans in the pipeline to bring 400t, 600-t and 800-t versions to Europe, IM understands.Aminiexcavator, the SY19E, powered by an alternative, environmentally friendly drive concept, will also be displayed, highlighting a
Other machines set to feature on the Komatsu stands include the 92.2-t-payload HD785-8 rigid frame off-highway haul truck and the 20.7-t capacity WA800-8 wheel loader.
SANY became the first Chinese company to list on Switzerland's stock exchange via global depositary receipts as it looked to diversify geographically. The construction of a new plant able to build 10,000 excavators a year in Germany, plus an R&D centre in the country, are also aiding this pursuit.
information via ICT. EARTHBRAIN, a new company setup by Komatsu, NTT DOCOMO, Sony Semiconductor Solutions and Nomura Research Institute, incorporates digital twins at sites based on its visualisation devices and applications for real-time remote monitoring, analysing and optimising of terrain, equipment, operators, materials, safety and environmental factors.
potential electrification platform for larger-sized machines on SANY’s books.
SANY brings more products to Europe
Visit us at Bauma 2022 at Booth 203 in Hall B2 or discover more online at FLSmidth.eco

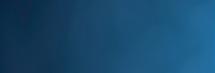
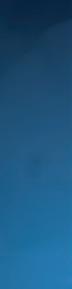
What is the MissionZero Mine and what productivity and sustainabilty benefits can it really deliver? To answer this, we re-examined the entire mining flowsheet with an emphasis on areas with the most potential, such as a low-impact grinding circuit, flotation, ecobeneficiation and water management.
How can the MissionZeroMine deliver sustainable productivity?
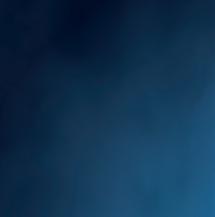
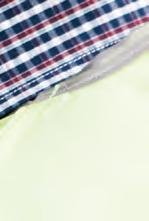
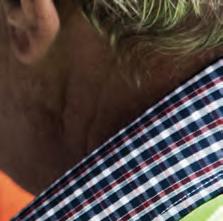
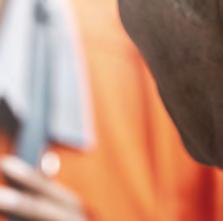
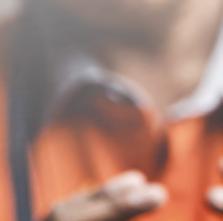
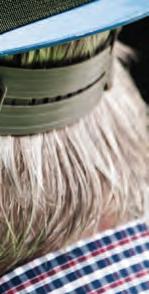
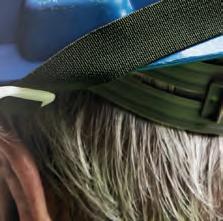

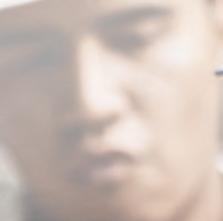

At Bauma 2022, we will be taking customers through current and future technologies and solutions that can move us towards greener and moreefficient mining processes.
Our aim is to enable miners to produce more but with optimised resource use, lower costs and a smaller footprint – what we call sustainable productivity. MissionZero, our sustainability ambition, supports this goal across the flowsheet.
At the upper end, the Bell B60E 4x4 – with a 55-t payload and 35 cu.m dump body capacity –is, Bell says, a benchmark for all-weather operations on undulating ground in open-pit mines or large quarries. At the bottom of the range, the Bell B30E 4x4 (28 t, 18.5 cu.m) is a compact and highly economical solution for sand and gravel pits, material handling or underground operations.
Both machines offer a compelling advantage to customers with specific requirements, it says.
Driver-related assistance systems on board these ADTs include, for example, Hill Assist as well as loading and tipping routines that ensure productivity and safety in equal measure. All electronic assistance and status displays are based on real-time measurement data from the networked vehicle sensors (on-board scales, tilt and roll sensors, etc). Much of this information is also available for computer analysis and tracking using Bell’s satellite-based machine monitoring system Fleetm@tic®.
Bell first demonstrated that cost-effective remote control is achievable with the right building blocks when it successfully operated a B45E with a video game controller. Since early 2020, the company has been working with indurad and voestalpine on a lime quarry site in the Alps where the industrial radar specialist has fitted its iTruck autonomous haulage system (AHS) on Bell B30E ADTs with excellent results, the company says.
HCE says the Hyundai HA30A and HA45A ADTs provide an ideal excavating partner for a wide range of crawler excavators and wheeled loading shovels and are designed primarily for major earthmoving and muck shifting projects, highways construction and mine and quarry operations.TheHW155H concept wheeled excavator, powered by a hydrogen fuel cell, meanwhile, features a 14-t payload that can offer eight hours of operation with a 20-minute refuelling time, according to the company. It is based on proven hydrogen commercial vehicle technology, HCE says, with the only emission from the machine being water.
Bell Equipment’s focus is on the execution of instructions from those third-party suppliers.
As an ADT specialist, Bell Equipment is using the Munich backdrop to showcase its newest generation of the two-axle Bell B45E 4x4 ADT and a vehicle that comes with a width of less than 3 m (the B30E ADT).
Bell Equipment’s Manager: Electrical and Software, Eben Lemmer, says: “We were first to develop our own telematics solution, Fleetm@tic, and to introduce onboard weighing, which is standard on our ADTs. When we introduced an inclinometer to improve our on-board weighing accuracy, we saw an opportunity to improve the safety of our trucks with our Hill Start and Tip Safe features that prevent rollback on slopes and rollovers due to tipping at unsafe angles. Similarly, by adding further layers on top of the existing PDS ISO standards, we have created an autonomous-ready platform that uses an open communication protocol principle to integrate easily with third-party suppliers.”
BAUMA PREVIEW
The digital advances for ADTs do not end there, with achieving an autonomous-ready platform a natural progression for Bell after it successfully integrated its ADTs with pedestrian detection systems (PDS) and collision avoidance systems (CAS), as standard, in 2019.
Lemmer explains: “In the work environment, the guidance software processes all the sensory input, plots a path and sends instructions to the Bell drive-by-wire interface, which electronically controls the acceleration, braking and steering of the truck. Our communication simulator provides the ability to collaborate with service providers by allowing them to test communication and response in the desktop environment prior to going live in-field. This makes it easier to develop and test new software for controlling the Bell ADT.”
The HA30A has a 16.8 cu.m heaped body
capacity that rises to 17.8 cu.m with the fitting of a tailgate. The larger HA45A offers a 24.4 cu.m heaped capacity, rising to 26 cu.m with a tailgate.
The HA30A and HA45A are equipped with a full hydraulic retarder, combined with an electronic engine brake as standard. This supports the oilcooled wet disc brakes to achieve an extended service lifetime of up to 15,000 hours. A hydraulically-activated mechanical parking brake, meanwhile, holds the machine when stationary.
The trucks have a compact chassis design to aid manoeuvrability, with a sloping rear frame and a front-mounted differential integrated into the ZF transmission, allowing for a shorter front frame
Hyundai has employed powerful EU Stage Vcompliant Scania diesel engines for both trucks.
The trucks are supplied with a gradient meter, with flip-over protection and a Body Over Centre of Gravity function, to assist drivers when tipping and operating on rough terrain. The sloping rear chassis section evenly spreads the load between the front and rear axles.
The two ADTs are the first joint product development between Hyundai Construction Equipment Europe (HCEE) and Hyundai Doosan Infracore (HDI), following the purchase of the Doosan business last year by Hyundai Heavy Industries Group.
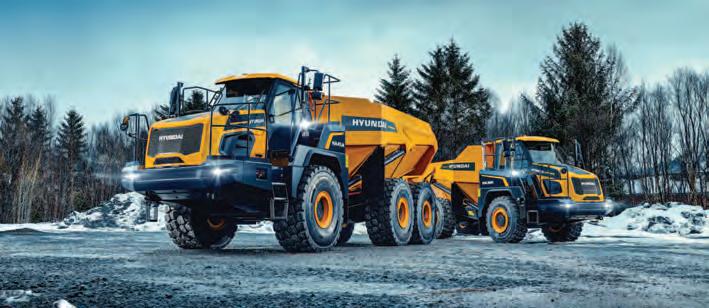
Aimed at the 30-t and 45-t sectors, the HA30A and HA45A are built around a full-time six-wheel drive concept, with front and rear limited slip differentials and a longitudinal differential that can be manually locked, for maximum drive and traction on difficult terrain.
This,section.thecompany says, results in the smallest turning radius in the sector, alongside outstandingSelf-levellingstability.hydro-gas suspension on the front axle further supports a comfortable ride, delivering maximum traction in tough ground conditions. The mounting of the turning ring in front of the chassis articulation point also provides increased stability and traction.
As a supplement to its range of seven “traditional” 6x6 ADTs, with payloads from 18 t to 45.4 t, Bell Equipment has, in the past six years, become the only articulated hauler manufacturer to offer a parallel range of two-axle ADTs, it says.
SEPTEMBER 2022 | International Mining 19
Hyundai Construction Equipment’s HA30A and HA45A ADTs are the first joint product developments between Hyundai Construction Equipment Europe and Hyundai Doosan Infracore, following the purchase of the Doosan business last year by Hyundai Heavy Industries Group
In the right applications, these machines outperform conventional rigid dump trucks that need good haul roads and three-axle ADTs designed for extreme off-road mobility to operative effectively, Bell claims.
ADT automation
A collaboration with US-based safety and automation technology developer, Pronto AI, followed, with Pronto officially launched its product at MINExpo 2021 in Las Vegas in September. In the next few months, a fully-
company says.
Epiroc will also, for the first time, bring the New Concept Mining team from South Africa to Bauma to present a skid pump resin mixing and injection system.
projects, the company claims.
highlighting more of its telematics capabilities as more clients look to automate certain functions –capabilities that can be fitted in Amsterdam as part of the Customised Solutions platform.
For this reason, 3D excavator guidance is typically only called upon for large scale projects,infrastructureaccording to the fasterallowingcompanies,morebenefitsexpandingwilliDigcompany.3DConnectdisruptallthis,theof3Dtoevenfinishtimeson
Excavator guidance advances
HCME Solution Linkage Manager, Ryo Kurihara, says: “By taking advantage of a factoryfitted Leica Geosystems solution, operators can start work immediately after machine delivery. Also, owners have peace of mind that the machine control system has been installed and tested to Hitachi standards, and it will be fully supported by their local Hitachi dealer in conjunction with the local Leica Geosystems specialists.“Wearepleased to offer this new turnkey option to customers, which will not only save them time, but also make their Hitachi excavators even more efficient, productive and versatile. By delivering customised solutions such as this we aim to become their first-choice solutions provider.”Thecompany will also display a Hitachi ZX8907 large excavator at the event. This machine, which has a backhoe bucket ISO heaped capacity of 3.5-5 cu.m, offers up to 20% reduced fuel consumption compared with previous models. This is on top of the enhanced efficiency that comes through using the HIOS V hydraulic system.HCME will also be presenting a 5.5-t electric excavator im Munich. In addition to this, it will be
2D successfully presented this guidance system concept to the market, iDig 3D Connect makes the process even easier to follow.
fledged test site will also be open to the public near Orlando, Florida, where three autonomously-operated Bell B45Es and a Bell B50E will be working on an established sand mine using this platform.
France-based iDig is readying a new tool in its own attempts to improve excavator guidance at construction, mining and infrastructure sites, with iDig 3D Connect set to launch in Munich, in October.Withthe iDig system operators can manage distances, depths and desired slopes through a combination of advanced technologies that use no cables, are powered by radio communication and come with simplified installation and solar charging.WhileiDig
A bit more life
Epiroc has frequently been viewed as a pioneer in the world of hard materials for drilling, and the introduction of Powerbit X rock drilling tools with diamond-protected buttons furthers thisThereputation.technology, called PCD (polycrystalline diamond), allows drill bits to work for longer – 10 times longer than existing bits on the market, Epiroc says – providing longer service life, fewer bit changes and less risk exposure for operators.
BAUMA PREVIEW 20 International Mining | SEPTEMBER 2022
New Hitachi platform
The 2-mm diamond layer can help improve workplace safety, reduce downtime and minimise CO₂ emissions, the company says.
For users new to 3D guidance, the main advantage is that the software works with a GNSS-generated site map, enabling precision digging relative to the area and making the process even quicker, simpler and ecofriendly than with 2D, which is already in use on large mining-sized excavators in Australia, IM understands.Morefeatures will be revealed at the 3D Connect launch in Munich, including another
The two-component system is delivered by a pump unit and is injected through a nozzle. The mixed resin begins to gel immediately, setting into a strong solid mass with excellent
“In most cases an autonomous operation will also need the end customer to set up their site to work differently; there may be special traffic control measures, berms or even different roads needed,” Lemmer says. “At this point in time, Bell has an autonomous-ready solution available for customers that are interested in doing proof of concept work in their application.”
Epiroc’s mining focus in Munich will be two-fold, highlighting the development of new drilling technologies and a two-component system for improved ground support.
Resemin is planning to bring its MUKI LHBP-2R to Bauma, a long hole production rig for sublevel stoping in narrow-vein mining. Boasting compact 1.05-m-wide-by-2-m-high dimensions, the drill rig is able to work in sections as small as 1.8 m wide, by 3 m high. In addition, this versatile rig can drill very close to the ribs, reducing dilution due to its two-unit rotations. It is capable of drilling 64-mm diameter holes up to 15 m – upwards and downwards. All these features make the MUKI LHBP-2R the most competitive rig on the market for narrow-vein mining, according to Resemin
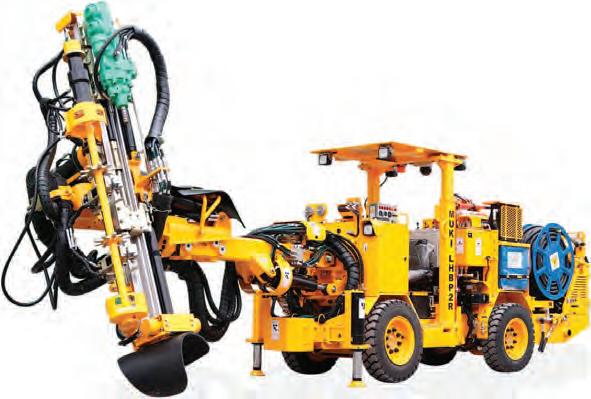
To demonstrate its expanding range of connected machinery at Bauma, Hitachi Construction Machinery (Europe) NV (HCME) is showcasing a Zaxis-7 medium excavator with a 3D machine control solution from Leica Geosystems. This has been fitted in HCME’s factory in Amsterdam as part of the new Hitachi Customised Solutions platform.Adding Leica Geosystems machine control technology to the ZX210LC-7 increases efficiency on the job site while lowering running costs, the company says. It also enables work to be completed on time, on specification and to budget, safely and sustainably. From simple slope grading to blind and submerged cuts, the machine control solution provides operators with an easy-to-use system to rapidly excavate to the reference design. This ensures more uptime and operator satisfaction, according to HCME.
“True to iDig’s signature less-is-more concept, the 3D Connect has just one GPS/GNSS that’s easily removable for use as a rover,” the company said. “This feature marks a major breakthrough in excavator guidance because it enables contractors to easily stake out points and map a site just like surveyors.”
Traditionally, only companies with an in-house surveyor would stand to benefit from 3D guidance because most equipment is sold with one or more permanently installed GNSS receptors. This requires either an expensive, independent GNSS, or working with a surveyor to stake out the points that determine the boundaries of a site.
aspect that is unique to the industry, according to iDig CEO, Albert Gamal.
The company, which acquired New Concept Mining in 2019, explains: “Rock bolting can sometimes be the bottleneck within the drill and blast cycle, leading to difficulties to predict work task scheduling. A recent development is the use of two-component pumpable resin for the anchoring of rock bolts and cable bolts.”
where we belong – at the world’s leading exhibition for the construction industry. We’ll proudly present some world premières and, in true Liebherr style at Bauma – the future. www.liebherr-bauma.com 24 – 30 October 2022 Messe München – exhibition center Exhibition booth in the outdoor area: booth 809–810 and 812–813 Components: hall A4, booth 326 • Mixing technology: hall C1, booth 425 Attachments: hall B5, booth 439 THINK BIG! Training at Liebherr: ICM Foyer, hall B0, booth 105
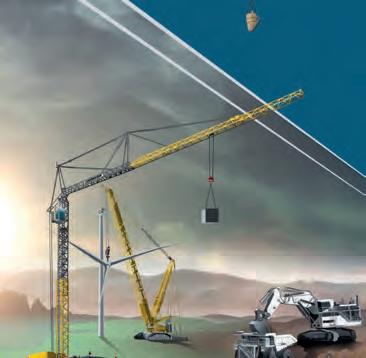
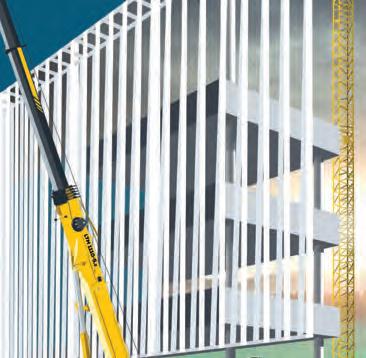
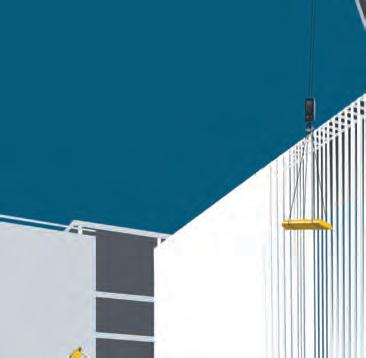

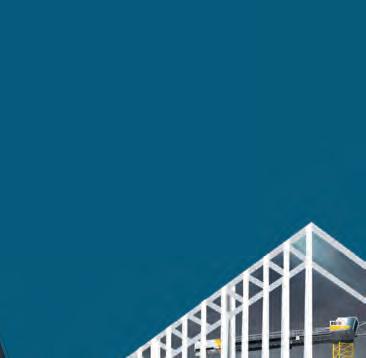

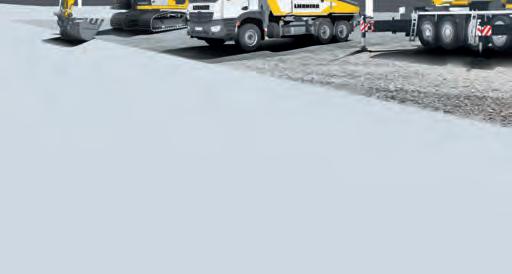
Back
On your site


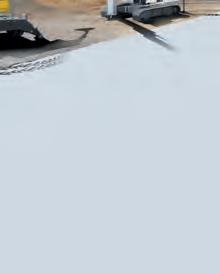
spring-mounted fully suspended front axle, according to the company.
“Thisstraight.means the user can dig a more accurate trench much faster,” Epiroc says. “It basically works like a bucket, which makes it easier to use, friendlier for the carrier and a lot less energy and time consuming.
The PAUS dump truck PMKM 8030, meanwhile, is designed for narrow-vein operations, with a compact yet powerful configuration.Thecombination of the improved design and characteristics with the latest electronics and a preliminary setup for smart equipment will provide a future-oriented solution in terms of operator comfort and safety, but also efficiency, productivity and operating cost for haulage in narrow-vein mines.
With a payload of 16,000 kg, the machine is fitted as standard with a 8 cu.m dump box and can be further customised for transport of bulk materials with higher or lower densities.
“A seemingly simple solution with extraordinary effectiveness, the V Cutter enables energy savings of up to 40%.”
PAUS delivers the UNI 50-5 BM-TM with an engine power of up to 173 kW with Deutz or Mercedes Benz engines. The machine can also be fitted with Stage V compliant engines.
The pumpable resin can be pumped into the borehole through an injection pipe prior to insertion of the cable or bolt, with the setting time adjusted to achieve a longer open time, enabling installation of a cable or solid bolt into a pre-filled borehole.
The PScale series allows operators to adjust and check hammer parameters directly at the face instead of adjustments on the surface, while the operator’s cabin outperforms international ROPS/FOPS requirements. Other risks can be further alleviated by using additional configurations, such as plug-and-play for the remote control, 3P safety belts, a brake test button, hill start assistance and a pressurised cabin.For working heights up to 10 m, Paus additionally offers the PScale 10-T.
The larger UNI 50-5 carrier, which highlights the new chassis of the UNI series, comes with a payload of up to 17 t, increased ground clearance, a more powerful driveline and a
many more. Further to that, PAUS is offering a variety of customised configurations and options to meet the individual requirements of the different underground operations and conditions. The carrier can also be equipped with different types of changeable systems for carrying cassette- mounted superstructures.
After already showcasing its battery-electric vehicle and corresponding electric driveline concept at Bauma 2019, PAUS is intending to bring even more new developments to the 2022 edition later this year.
PAUS’ forward-looking approach
At Bauma, Epiroc will introduce the latest addition to the V Cutter range – a smaller model suitable for carriers of 15-28 t.
PAUS’ PScale series allows operators to adjust and check hammer parameters directly at the face instead of adjustments on the surface
“In underground operations rock falls could potentially lead to fatalities, injuries and damage to underground personnel and infrastructure,” the company said. “To ensure a higher safety working environment, any loose rock needs to be removed before the follow-up processes can be started.”Thehighest performance possible is ensured thanks to the use of a high power output engine, 20° tiltable cabin, individual parameter adjustment of the hydraulic hammer, and operation and diagnostic display, which help provide higher reliability and quality of the scaling process.
The PAUS concrete mixer UNI 50 BM-TM offers a transport solution with a higher payload as well as safe and comfortable driving characteristics, even on rough terrain, PAUS says.
In addition, compared with a chain cutter, the user saves more than 40% on picks and up to 50% on maintenance time; the investment is up to 25% lower than for a chain cutter and the lower weight makes it possible to use a smaller carrier, Epiroc says.
The machine is also available with smart
column bond independent of the size of the hole.
BAUMA PREVIEW 22 International Mining | SEPTEMBER 2022
“The pumpable resin is available in different reaction times and requires a 1:1 volumetric ratio between the resin and catalyst,” Epiroc says. “Deviations from the ratio result in a reduction in cured resin strength.”
In April, Epiroc launched its V-shaped drum cutter, heralding it as a brand-new way to work with rock, concrete wall and surface profiling, trenching, soft-rock excavation, frozen soil excavation and demolition. A patent-pending solution, it has been tested in all these applications.Mountingthe drums in a V-shape enables a cut with a flat base where no material is left untouched between the drums, according to Epiroc. Where a regular drum cutter would move from side to side to create an even trench – an approach that causes extra wear on the carrier arm – the V Cutter can reach the same result by going
The machines to be showcased in October include the PAUS Scaler PScale 8-T, the PAUS concrete mixer UNI 50-5 BM-TM and the PAUS dump truck PMKM 8030.
The well-established sister machine, PMKM 8010, is designed with less width at increased length and height, but the new PMKM 8030 comes with a broader, shorter and narrower design at a reduced loading height and with improved driving characteristics thanks to the lowered centre of gravity, larger tyres and new axles with integrated oscillation, PAUS says.
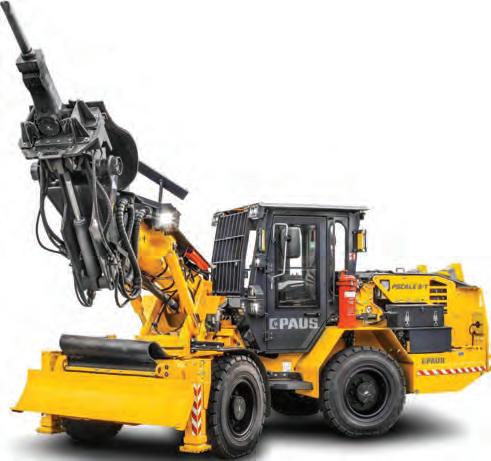
Bauma’s mining-focused attendees might also be interested in an update to an Epiroc product aimed at the trenching and quarrying markets.
In addition to the brand-new designs and productgeneraltechnologiesfeaturedmachines,characteristicsindividualofthedisplayedallofthemwillbewiththelatestaspartofPAUS’andforward-lookingdevelopments.Safety,performance,sensitivity and high durability are the design principles and values PAUS used for the development of its new PAUS Scaler PScale 8-T generation in order to provide what it says is a “unique scaling experience”.
With an available volume of up to 7.5 cu.m, the
Once mixed, the set resin is unaffected by water, while the product is non-foaming and can even adhere to damp surfaces.
Epiroc developed this resin mixing and injection system for its Boltec rock bolting rigs, ensuring a quality resin mix for every installation. The closed loop system controls the flow rate of each component separately, ensuring the ratio is maintained and the volume of resin injected is monitored. The skid pump system is a replica of the Boltec resin injection system, allowing off-rig pumping and installation of pumpable resin rock reinforcement systems.
MINING / CONSTRUCTION / DREDGING Visit us at bauma 2022, hall A6 booth 437 STAMPS MAIN VERSION MTG sinceCorp1999MTG since 1957 mtgcorp.comDiscovermoreon Tough digging made easier and smarter with the new generation of GET. Detection of GET detachments in less than 3 seconds, with zero false alarms. All technical information at your fingertips. QR-CODE GET DETECTION


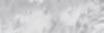

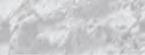
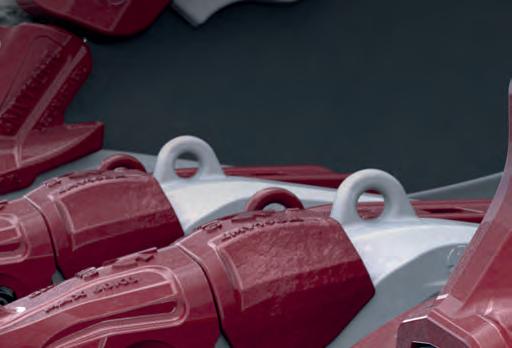
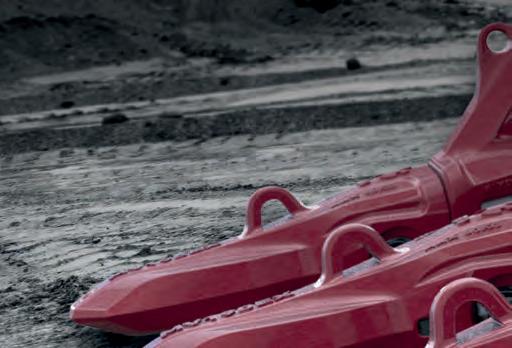
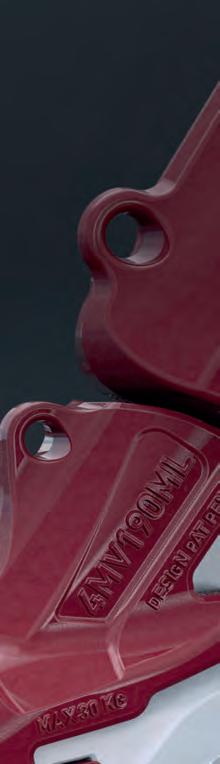
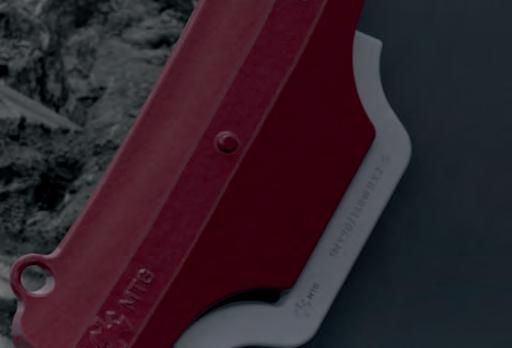
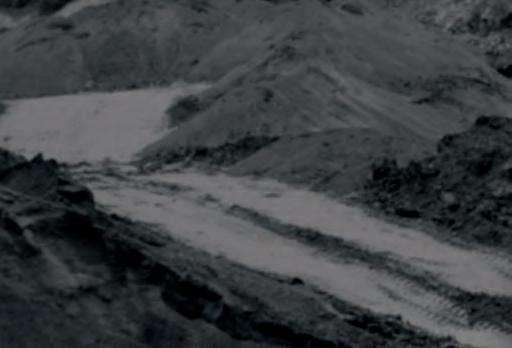


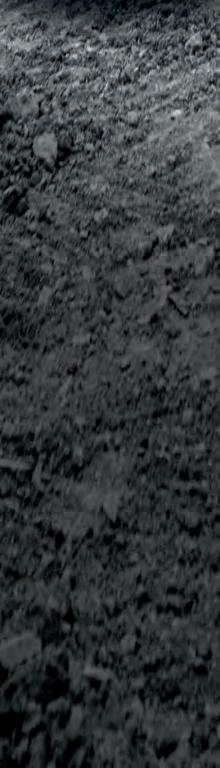
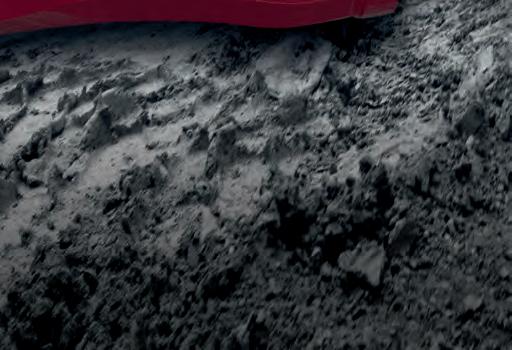
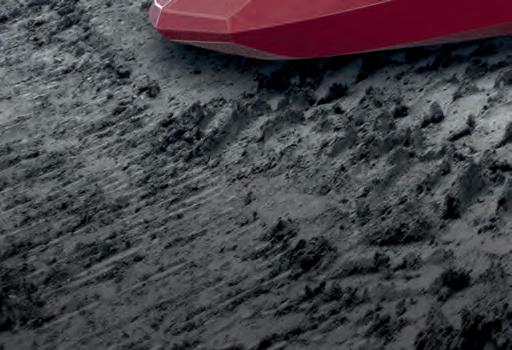
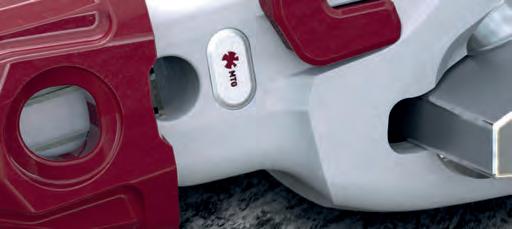
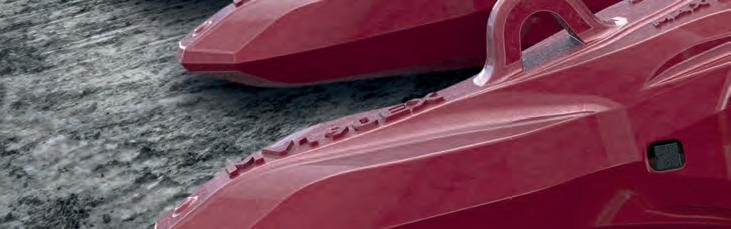
Showcasing its plans to provide future sustainable power solutions to meet the industry’s net-zero ambitions, the company’s display will provide an overview of how its current portfolio of ultra-efficient D5 to D16 diesel engines – and EU Stage V-compliant models, in particular – has resulted in technological advances and market share gains that support its transformation journey.
PAUS concluded: “The multifaceted portfolio, the variety of options and the customised features available along with our machines will provide the basis for almost every task – it doesn’t matter how individual the solution needs to be.”
systems like a bird’s eye view camera, tyre pressure control and load weighing, all of which can be wireless monitored and displayed via PAUS
SBTi-backed initiatives
PAUS says it is already working on new solutions like a special mine rescue vehicle –currently being developed in cooperation with Dräger and a major European supplier for firefighting equipment. In addition to that, the “Scale Sense” project of the Germany-based RWTH Aachen University – for the detection of loose rock to use with PAUS scalers – is close to reaching the next development stage for extended field testing.
BAUMA PREVIEW 24 International Mining | SEPTEMBER 2022
The company will show its off-road product portfolio, commitment to customer lifecycle value and future vision for industrial equipment, which includes the electrification strategy for e-
TheCONNECT.PMKM8030 comes with a rotating driver’s seat for long distances of driving backward at high speeds (bidirectional) and a spacious and comfortable cab.
powertrains; an electric equipment demonstrator; Yanmar/ELEO modular, highdensity battery system; and extended five-year warranty for its TN Series engines.
Yanmar is also launching a new five-year warranty (or 5,000 hours) offer, further enhancing sustainability and extended ownership of the current line-up of clean diesel solutions during the transformation to carbonneutral power solutions, it says. This extended warranty is free of charge and valid for TN Series engines sold in Europe and operating on European territory.
Another company looking to make a statement in Munich is leading manufacturer and supplier of undercarriage parts, Berco
Through this presentation, Yanmar says it will establish itself as the all-in-one systems integrator for smart electrified power solutions tailored to the application-specific needs of individual OEMs. In its capacity as a systems integrator, it will implement system engineering, design and manufacturing of e-powertrains, while also providing control development, system evaluation, procurement, manufacturing and qualityYanmarassurance.willshow an electrified demonstration vehicle that shows the practical application of the company’s system integrator technologies. Powered by an electric drive and 48 V batteries with fast charging capability, the electric excavator is a quiet, zero-emission machine designed to meet the most demanding emissions restrictions, it says.
The company has chosen the event to reveal the transformation it is undergoing, which will see Berco become a true global service provider that reaches far beyond the delivery of components for the undercarriage, it says.
“With that as a base, we can optimise the design and adapt the complete electric driveline system for a specific vehicle, considering the exact application, usage, climate and environment it will operate in.”
Proximity to both original equipment and aftermarket customers is at the heart of this new strategy, with data management gathered through Berco’s latest digital applications, such as the Bopis Life cloud-based platform, playing a key role. This, ultimately, will further strengthen Berco’s technical expertise when creating tailored solutions for each customer around the world.
take a system-supplier approach which means that we can create a flexible, bespoke electric driveline solution for a specific vehicle and application. We are very experienced in a variety of different segments, so, by using that knowledge and combining it with the Volvo Group’s proven electromobility experience, we can build the best modular platform for our customer’s applications.
“In the short-term, the focus is still very much on internal combustion engines, and we will continue our development work in this area to stay competitive,” Blomgren concluded. “Our engines are already able to run on hydrotreated vegetable oil and biodiesel, and, to further support our transformation journey to zeroemission solutions, we are also looking into powering them with compressed natural gas, biogas and hydrogen, as well as the use of hybridisation – all of which are likely transitioning solutions for those markets that cannot yet support fully-electric solutions.”
Volvo Penta’s commitment to supporting the current and future needs of mining and construction customers will be in sharp focus when it returns to Bauma in October.
The machine also includes the PAUS standard safety package for underground mining machines, eg SAHR brakes, a ROPS/FOPS cabin, enhanced LED lighting, etc.
The latest major innovation supporting Volvo Penta’s Science Based Targets initiative (SBTi)backed plans to reach net-zero value chain emissions by 2040 will take pride of place on its booth.The electric driveline, which recently entered production in Rosenbauer’s RT and RTX fire trucks, was originally unveiled in 2019 as a proof of concept in a modified terminal tractor, highlighting the versatility and configurability of Volvo Penta’s electric solutions. This platform could possibly be scaled up for mining-class mobileMorganequipment.Blomgren, Director Strategy & Business Development for Volvo Penta, said: “We
As one of Volvo Penta’s most popular engines for mining and construction applications, the new D16 received the 2021 Engine of the Year award. This was largely in recognition of its increased output (585 kW), which was achieved at the same time as an up to 10% reduction in fuel consumption. By incorporating water-cooled charged air, its dual-stage turbo engine delivers high performance right across the operational range, enabling maximum torque to be produced at both low and high engine speeds. A D16 unit will be taking pride of place on the Volvo Penta stand in Munich.
Berco to spin off Aftermarket division
It also comes with a choice of different Cummins and Caterpillar diesel engines complying with varying regulations and offering power of up to 190 kW.
Used in a wide range of machinery from crushers and screens to underground mining trucks, Volvo Penta Stage V-compliant diesel engines and gensets have been fully optimised to meet customer needs in terms of productivity, uptime and total cost of operations, the company says. Passive regeneration of the aftertreatment system has been maximised, for example, eliminating unplanned stops during operation, while fuel consumption has been reduced by up to 5% over the Stage IV-compliant models.
All-in-one systems integrator
Yanmar, a provider of power solutions and industrial machinery, plans to introduce its electrification strategy for off-road vehicles and equipment at Bauma 2022.
An important milestone for realising the urgent environmental challenges that must be overcome is Yanmar’s acquisition of battery-technology company ELEO, a developer and manufacturer of high-performance modular battery systems. This acquisition will further Yanmar’s electrified powertrain capabilities with versatile, customised solutions for off-road applications, it says. ELEO is building a new battery production plant, increasing its annual battery production capacity tenfold to 500 MWh – the equivalent of approximately 10,000 battery packs.
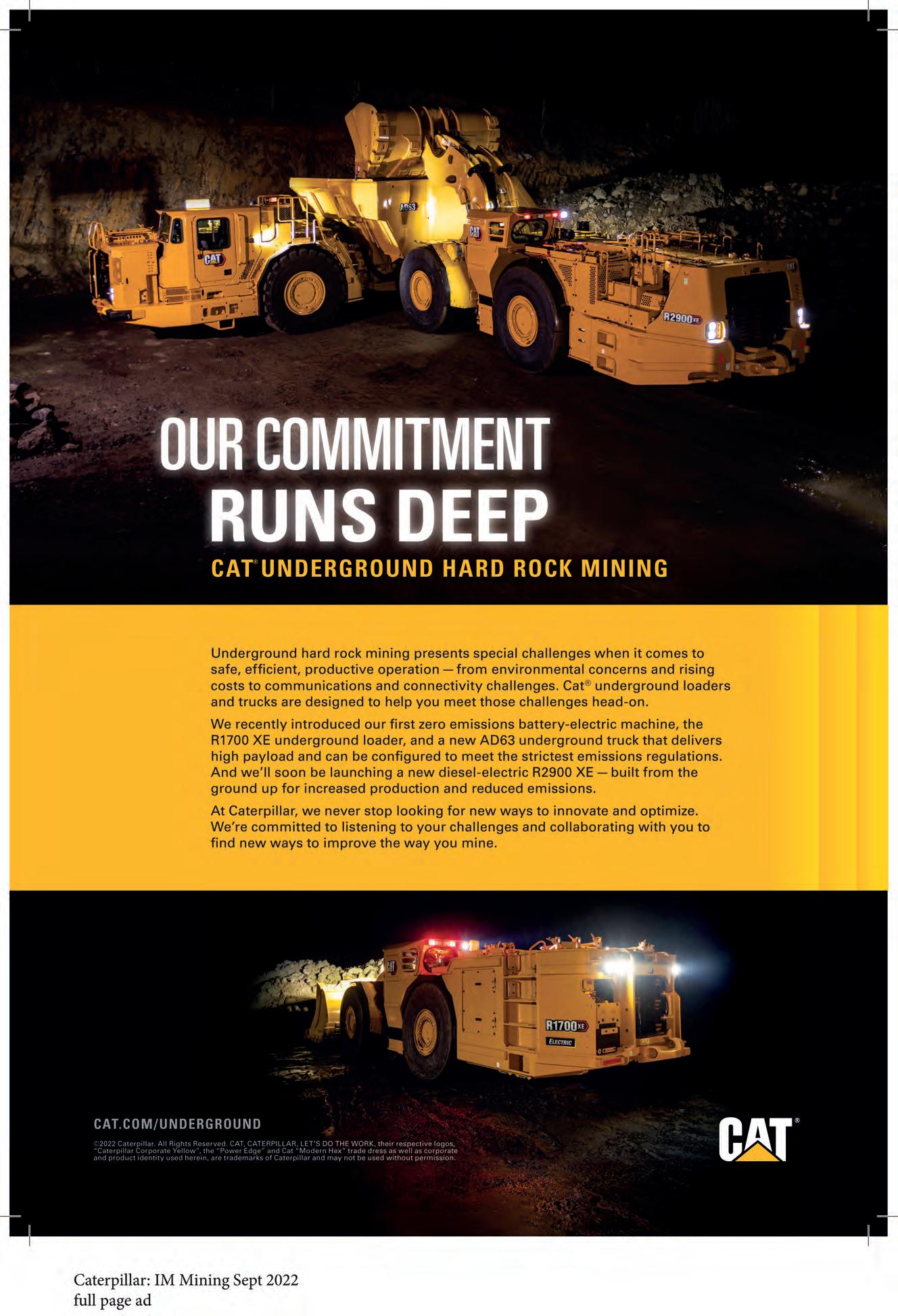
developments backed up by a proactive and flexible Aftermarket organisation.
As part of this new approach, the Aftermarket business will be placed at the centre of the company’s development.
VEEMET, which will be visualised on the stand with a 3D printed model, also features an optimised locking option for quick and easy assembly and disassembly; reinforced pins; and a slim tooth design for enhanced penetration and increased machine efficiency, MTG says.
Among the mining-related launches due to be presented at the world’s biggest trade fair is VEEMET, a versatile system for excavators and loaders of between 20 t and 250 t equipped with plate lip buckets, and its ground engaging tool (GET) detection system called GET DETECTION.
This has resulted in the creation of a spin-off solely dedicated to the Aftermarket, with all operations bundled together. The focus of this business entity will be a customer-specific service based on a new supply chain concept. This dedicated team is headed by Diego Buffoni and located in Bologna, Italy.
“In collaboration with our customers, our goal is to develop the best solution for each of their specific requirements and applications in any environment, wherever in the world,” Piero Bruno, CEO of Berco, said.
Back in November during the opening of Berco’s new R&D facility in Copparo, Italy, Buffoni said there was potential to address a market worth some €23 billion ($23.5 billion) in the future with key production additions and
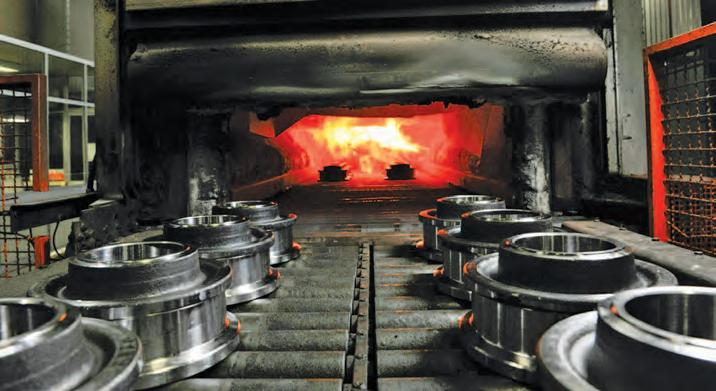
The US, first, will receive additional focus, with Berco strengthening its level of support on the ground. This approach will soon be replicated in other important markets like Asia.
in terms of GET detection systems, MTG says it
ESCO buckets at Bauma Weir ESCO’s offering of mining buckets, developed to meet demanding needs and the toughest applications, will feature all over its Bauma stand.
MTG’s digital first MTG, a Barcelona-based specialist in the design and manufacture of high-quality wear solutions for earth moving machinery, is planning to present some major new innovations in October.
Berco says it plans to become a true global service provider that reaches far beyond the delivery of components for the undercarriage
is the first major player in the industry that has developed its own in-house platform with GET DETECTION.Thelaunch follows successful field tests in Europe and Australia where the system – made up of magnetic field sensors and actuators integrated into the corresponding GET components, antennas, ECUs and an operator tablet – was able to show its ability to improve operational safety and avoid unplanned downtime, MTG said.
Berco’s transformation is designed to satisfy market demand for increasingly customised solutions, and, to this end, it is looking to increase its technical presence in geographical areas closest to its customers.
BAUMA PREVIEW 26 International Mining | SEPTEMBER 2022
The system, which is embedded in the nose of the GET adapter instead of the teeth, can detect a detachment in less than three seconds, allowing direct action and a fast return to production, the company says.
This offering includes a range of custom options to meet specific mine site requirements with full wear protection for severe abrasion and impact conditions. All tooth-style buckets come standard with ESCO’s Nemisys® tooth system for improved performance.
One of the company’s new dragline buckets set to be displayed is the ESCO ProFill® Delta dragline bucket, built using proprietary cast alloy construction.WhileallProFill buckets are built to deliver superior productivity and maximum durability under the toughest digging conditions, the new ProFill Delta bucket provides increased productivity and cost savings with the added benefit of reduced rigging complexity.
GET DETECTION is the first in a series of in-house developed digital solutions from MTG

“The core impact of this transformation process, however, is the incorporation of 4.0 digitalisation standards,” Berco said. “With over 100 years of expertise in both development and engineering, Berco is now benefitting even more due to its approach to data management.”
As the successor to the STARMET system, VEEMET has been optimised for increased performance and user-friendliness, according to MTG. It offers improved stability due to its Vshaped fitting, which provides more resistance against torsional loads.
The batteries on the sensors last for 5,000 hours, which means they can be directly aligned with maintenance intervals.
The first series of in-house developed digital solutions, GET DETECTION will be displayed on MTG’s stand for visitors to learn live how it works.While still early days, the company’s next digital solution could be focused on the area of automation, IM understands.
The wide range of self-sharpening teeth and plate lip adapter designs are suitable for any construction, quarrying and mining application, according to the company, providing a better digging performance.
Data generated in the field by Berco’s latest patented ‘Smart Undercarriage’ system or Bopis Life application are evaluated and processed through the company’s R&D department, with this data archive being the source for future systems solutions for both Original Equipment and Aftermarket, it says.
Find out more about Hardox® 500 Tuf at www.hardox.com.
Hardox® 500 Tuf is also tough enough to perform as a structural steel, allowing for a stronger and lighter mining body that can take high impact loads with less supporting structures.

Visit us in Hall A6, stand 439
Hardox® 500 Tuf is the latest grade of Hardox® wear plate. It combines the hardness of Hardox® 500 with the toughness of Hardox® 450. The high wear resistance of Hardox® 500 Tuf makes it possible to increase the load capacity by using a thinner plate and still have the same outstanding service life. Or stay with the same thickness and increase service life by 30% or more, depending on the abrasive material.
hardox.com LIGHTER MINING TRUCK EMPTYLESSSERVICEEXTENDEDCAPACITYHIGHERBODYLOADLIFEFUELONRUNS Explore the world of Hardox® wear plate
“During replacement of parts on one bucket, a crew is exposed to hundreds of touchpoints which are eliminated with the ToolTek system,” the company explains. “Advantages of the ToolTek system include enhanced worker safety, fewer workers to replace GET components, all required parts and tools on one truck and safer disposal of worn parts.”
The company also plans to showcase a range of wear material options that include Infinity® chrome white iron button and blocks, ESCO AR 400 and 500 plate, Infinity chromium carbide overlay plate, Kwik-Lok® II cast steel wear runners, as well as cast corner wear shoes and cast Nemisys and Toplok® wing shrouds.
IM reported earlier in the year that the launch of ToolTek in Australia had resulted in two orders from mine sites.
The ToolTek system includes a boom crane mounted tool head that is remotely operated, well out of harm’s way during replacement of worn components. New parts are pre-staged on racks conveniently positioned on the flatbed truck outfitted with the hydraulic crane. The system can remotely engage and disengage the GET locking mechanisms during a changeout,

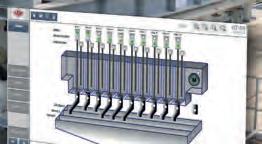
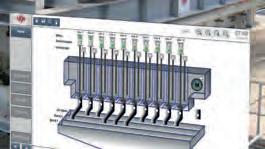
making the process truly touchless and safe for mining maintenance personnel, Weir ESCO says.
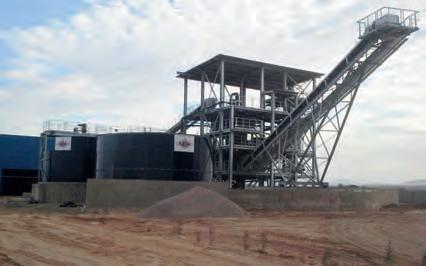
Meanwhile, eliminating the lower spreader bar and associated components reduces rigging weight by up to 15%, according to the company.
As a global leader with a history of innovative engineering and, like Weir ESCO, part of the Weir Group, Weir Minerals has an array of technologies to choose from for its Bauma presentation, with its booth set to feature several

BAUMA PREVIEW
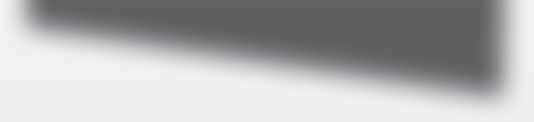
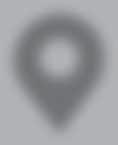
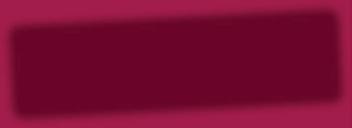
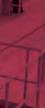
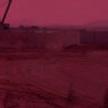
Weir ESCO’s lip and GET systems are complemented by the ESCO ToolTek™ System for safer installation and replacement of Nemisys points and adapters.

Adhesives, IoT and washing
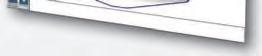
Technical Laboratory & Trials EquipmentEngineering& Process Units Plant OURSpareRealizationParts&ServiceCAPABILITIES YOUR PARTNER FOR CUSTOMIZED SOLUTIONS IN SAND BENEFICIATION, CD&E WASTES VALORIZING, FINE SAND RECOVERY AND PROCESS WATER RECYCLING Dienhof 26 92242 GermanyHirschau www.akwauv.comB2.524 NEW RELEASE! AKOREL SOFTWARE INNOVATION #WetTreatmentAtItsBest B VISIT US AND LEARN MORE! LINATEX LOCTITE - LINA 88 is a mining-industry-first, solvent-free adhesive range for rubber lining applications with zero volatile organic compounds
Alongside the ProFill Delta will be the ESCO Production Master® dipper lips – single-piece castings poured in premium alloys for toughness and weldability; a range of mining-class hoe buckets, designed using advanced finite element analysis tools; performance-driven face shovel fronts and backboards for 120-800-ton-class (109-726-t-class) machines; and a variety of wheel loader buckets.
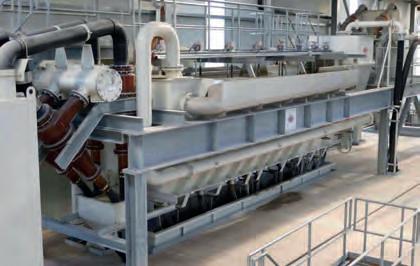
showcased the first steel ever made using hydrogen instead of coking coal.
A cutoff of that steel plate will be on display at
REDUCE DILUTION

One of these is LINATEX® LOCTITE® - LINA 88™, a mining-industry-first, solvent-free adhesive range for rubber lining applications with zero volatile organic compounds, delivering multiple environmental and safety benefits, as well as best-in-class bond strength, the company says.The company will also use the event to showcase its Synertrex® Intelligence Ecosystem, which continuously monitors and assesses equipment condition and performance. This information is then converted into actionable insights and recommendations, providing operators with unrivalled real-time decision support, according to Weir Minerals.
In 2016, SSAB, LKAB (Europe’s largest iron ore producer) and Vattenfall (one of Europe’s largest energy companies) joined forces to create HYBRIT. Using HYBRIT technology, SSAB aims to replace coking coal, traditionally needed for orebased steelmaking, with fossil-free electricity and hydrogen. It aims to be the first steel company in the world to bring fossil-free steel to theVolvomarket.Construction Equipment, part of the Volvo Group, recently became the first manufacturer to deliver a construction machine to a customer built using SSAB fossilfreeThesteel.Volvo machine, an A30G articulated hauler, was handed over from Volvo CE to NCC earlier this year. The milestone came just nine months after Volvo unveiled the world’s first vehicle concept using fossil-free steel as part of testing the implementation in an ordinary production setup, and ten months after SSAB
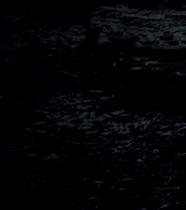
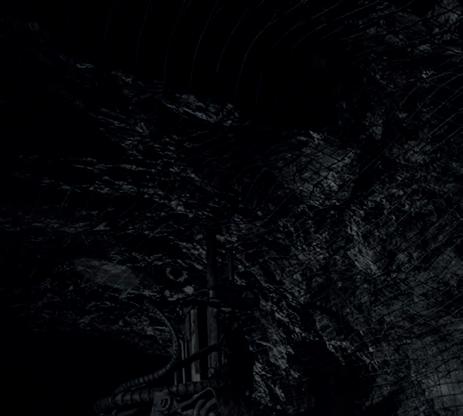
The T-Class, Haver & Boecker Niagara says, retains the technical benefits the original concentric technology is known for while improving screening uptime and performance with new features. It provides producers with a cost-effective,maintenance-friendlysolutiontoprocessawiderangeofmaterialswithinindustries
A cutoff of the very first steel plate produced with hydrogen-reduced sponge iron at SSAB in Oxelösund, Sweden, will be on display at Bauma
BAUMA PREVIEW
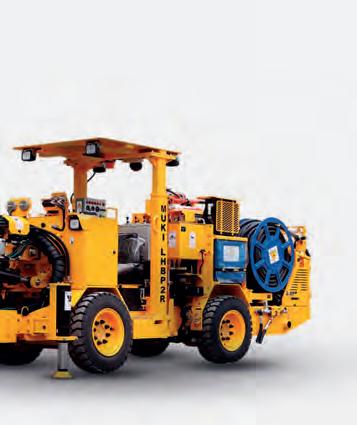
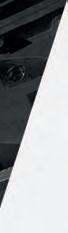
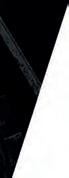

The very first steel plate was produced with hydrogen-reduced sponge iron at SSAB in Oxelösund, Sweden, on August 18, 2021, and delivered to Volvo Group.
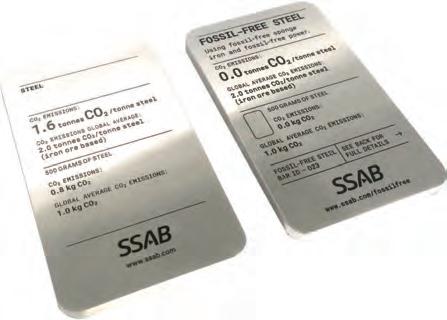
For miners is key to reduce dilution by drilling very close to the ribs. The MUKI LHBP 2R does it and has been doing so since its launching to the market in 2017. That´s why it is the preferred long hole drill rig for Narrow Vein Mining.
SSAB will be showcasing its fossil-free steel for people to touch in Munich for the first time.
A new screen class Haver & Boecker Niagara’s next-generation Niagara T-Class vibrating screen will be one of the highlights on the company’s Bauma stand.
of its market-leading products and solutions.
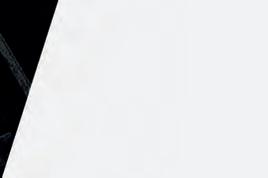
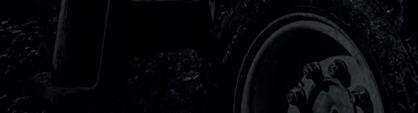
There will also be a sand wash plant solution on display. Designed to remove excess fines or coarse material, this solution provides exceptional washing results while delivering a clean, low moisture product for conveying or stockpiling, the company says.
Fossil-free steel
SSAB’s Hardox® 500 Tuf wear-resistant steel and Strenx® high-strength structural steel will also be on display at the event as the company highlights its current commercial offering for multiple industries.
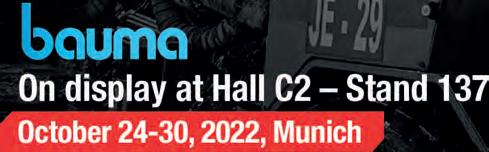
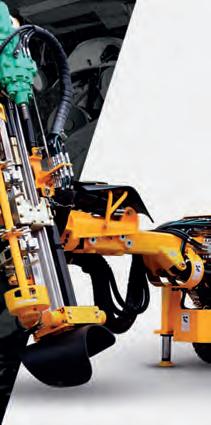
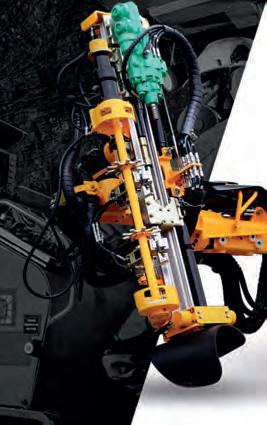
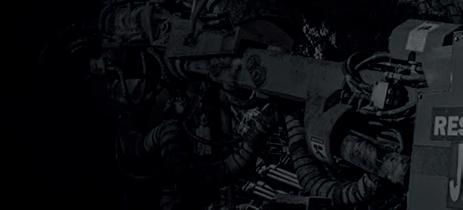
the show, with its sustainability experts explaining the unique HYBRIT technology and how fossil-free steel can be used as a platform for creating end-customer products that largely eliminate greenhouse gas emissions.
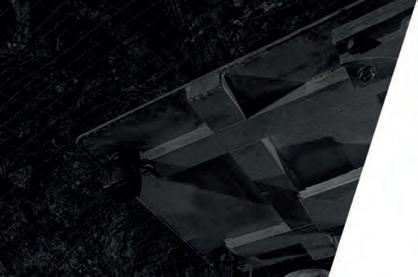
n Maximum user-friendliness;
BAUMA PREVIEW 30 International Mining | SEPTEMBER 2022
Even at high throughputs from 40-500 t/h (depending on the size), the AKOREL classifier consistently produces high-quality building sands with the same product quality, independent of the sand feedstock.
In addition to the target of providing the customer with a robust, reliable and low-wear installation, much attention has been devoted in recent years to intelligent use of modern control technologies for data acquisition and processing. The objective of this has been to make classification more flexible and cost efficient, and, thus, contribute more decisively to the conservation of resources.
These software capabilities have gained significant market acceptance over the years, according to the company.
Thisintervention.updatedsoftware can be retrofitted on existing AKOREL classifiers, ensuring customers can leverage these benefits for many more years, the company says.
Enerpac, a leader in high pressure hydraulic tool, controlled force products, portable machining, on-site services and solutions for precise positioning of heavy loads, plans to use the upcoming fair to showcase not only its construction-focused offering, but solutions for handling and maintaining mining equipment.
The new design allows producers to upgrade their vibrating screen with Haver & Boecker Niagara’s new Drop Guard system, further minimising maintenance. The liners provide 100% cross beam protection, both reducing wear and extending the life of the vibrating screen, according to the company. The system drops over the cross beam with no adhesive or tools required, making installation quick and easy, it says.

The T-Class, Haver & Boecker Niagara says, retains the technical benefits the original concentric technology is known for while improving screening uptime and performance with new features
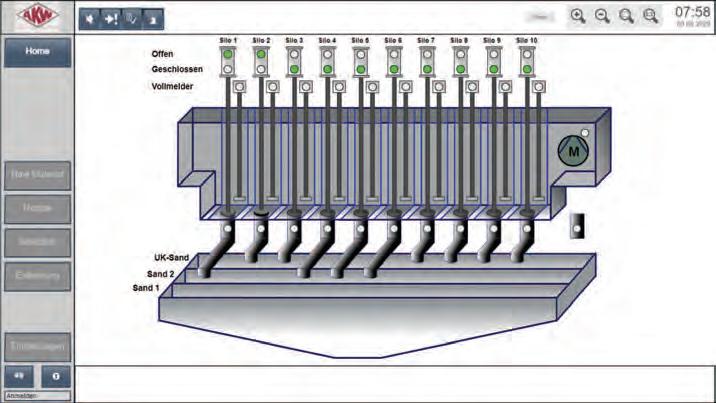
n An automatic recipe adjustment to raw material fluctuations, without operator
By decomposing the sand feedstock into six to 16 individual fractions, and re-blending them afterwards with the use of a user programmable control unit, the AKOREL can generate one or two quality sands with the desired grain size range.
To offer customers even more convenience, AKW has made the software even easier to use through an optimisation process that factors in the need to accommodate throughput, operational, grain size fluctuation and product quality requirements from customers. This will mean customers, in the future, can benefit from:
Innovation in control software
AKW has looked to make its AKOREL control software even easier to use through an optimisation process that factors in the need to accommodate throughput, operational, grain size fluctuation and product quality requirements from customers
n State-of-the-art technology including the newest features; and
The centrepiece of the Enerpac stand will be the new SBL600 telescopic hydraulic gantry, along with the company’s entry-level gantry system for handling mining equipment – the ML40 Mini Lift Gantry. The new E-mover batterypowered load skate will also be demonstrated
the middle of the machine – where it’s needed most. Each update was engineered with ease of maintenance in mind, to keep downtime low while providing cost efficiency.
The T-Class can be manufactured for sidetensioned or bottom deck end-tensioned screen media. Each new side-tensioned machine comes with Haver & Boecker Niagara’s signature TyRail™ quick-tensioning system, which cuts screen change-out times in half, the company claims.Duncan High, the Product Manager behind Haver & Boecker Niagara’s new T-Class design, said: “The new, more robust T-Class was designed specifically to offer more strength in
This focus has seen the company offer two different levels of control systems to its clients: the ‘Basic Standard-Control Option’ suitable for
n A simplified, clear arranged software display and interface;
the production of simple and constant quality sand output, and the ‘Premium-Control Option’ for when the production requires flexibility in the handling of various input and outputs.
Enerpac to do the heavy lifting
Additionally, Haver & Boecker Niagara redesigned the flat deck frames of the new TClass vibrating screen for simplified maintenance. The pin and anchor deck frame is adaptable to virtually any pin-style modular screen media. It features polyurethane anchors that are easy to replace and prevent premature wear on the deck frame. Additionally, the open design of the modular deck prevents material build-up on the bar rails. The cap and slide deck frame, meanwhile, is adaptable to virtually any groove-style modular screen media and features full rail protection.
now primarily lockbolted rather than welded to provide optimum strength, reliability and safety. Lockbolts have proven to be more effective in ensuring the machine’s structural integrity than welding in the demanding, load-bearing, high-vibration operation of a vibrating screen, the company says. The robustness of the machine also permits cross beams to be positioned and lockbolted every 1.2 m instead of every 0.6 m, allowing for better clearance and easier maintenance.
The company has been supplying the AKOREL freefall classifier technology for many years, offering a wet classification solution that corrects the sieve curve of raw sand ranging from 0-2 mm or 0-4 mm, in line with customer requirements.
AKW Equipment + Process Design’s AKOREL control software will be one of the major talking points on its Bauma stand.
NEEMISSYS® AND M MOTION miningESCO with a Dig Superior ® METRIC g buckets equipped with th AdvantagePerformanceital CS® othe Nemisys to ownership and for maximum m prosystem are AI tenow with a powerful, loweachine productivity as the market leadergqppven chnology option r total cost of for durability and OCOJ 2022C T 24-30, SIN U B bitifESCO HALBOO137THOLA6UUMAA Oiibkt thNit thtcadatandom solutions to wor the power of Mo mbination of ESCOk for you. tion Metrics O mining bucketss, the Nemisys toooth system .esco.wwww weir Copyright ©20 eir Gre022 ESCO Group LLC, The W All rights reserved.roup PLC
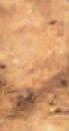

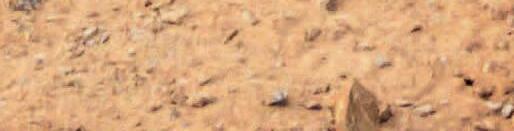


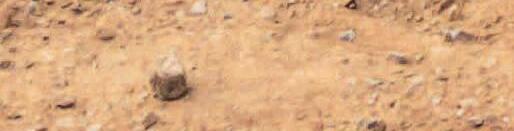



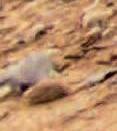
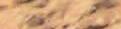
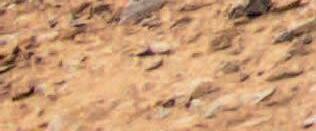




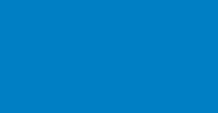


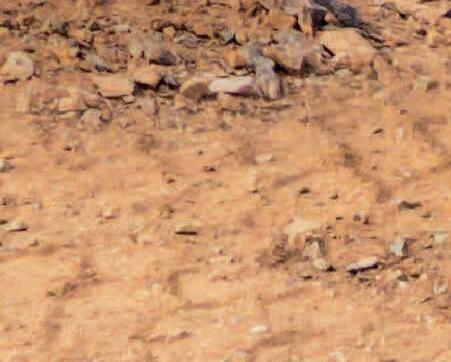




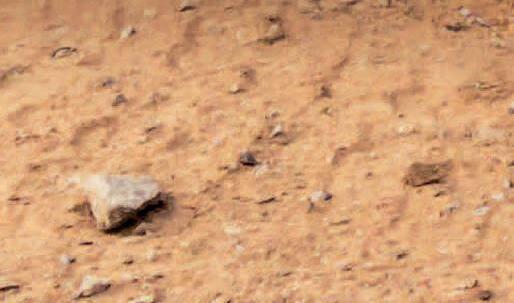



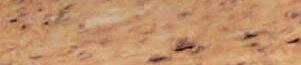




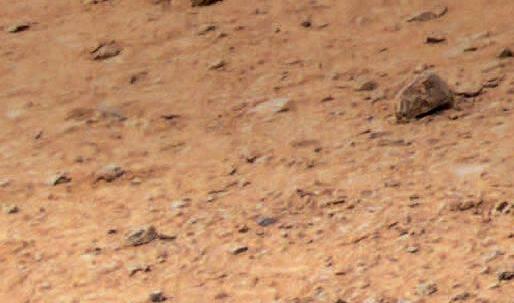

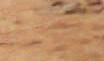
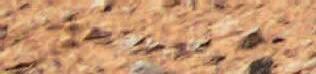
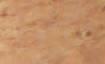
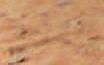
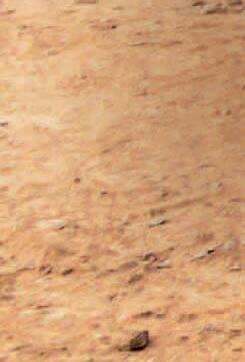
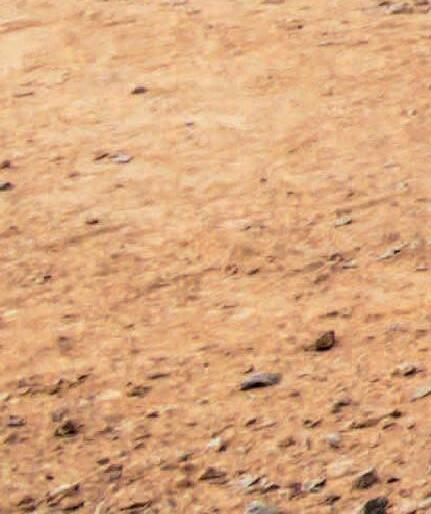

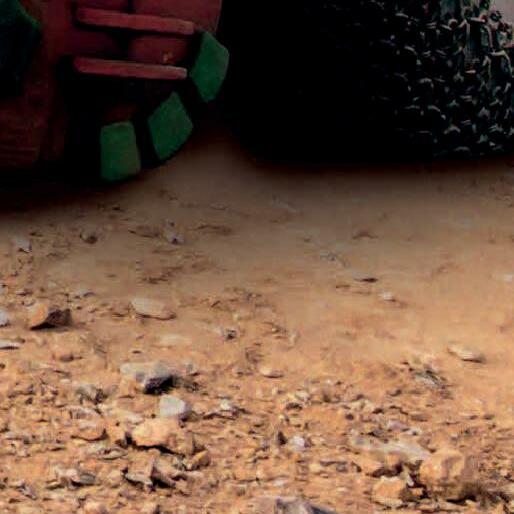

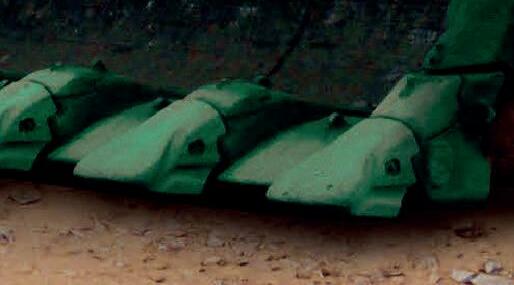












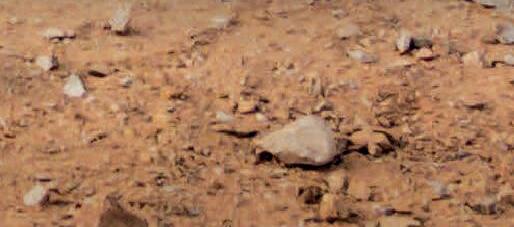

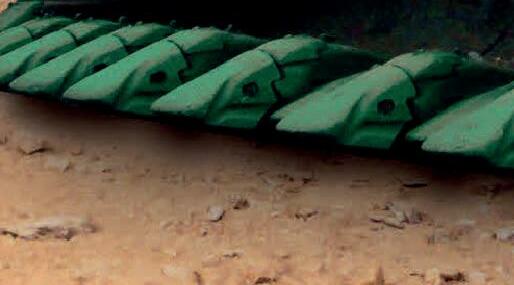













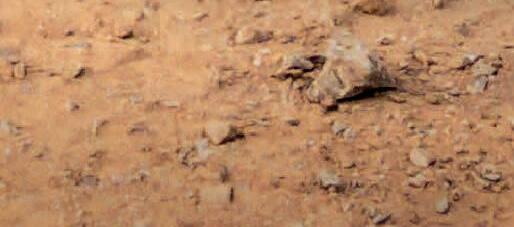
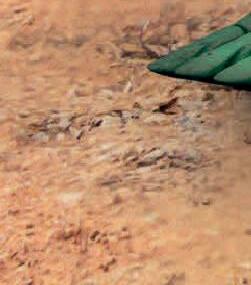












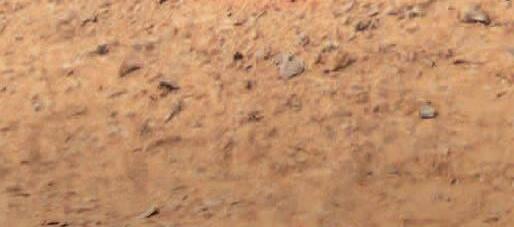

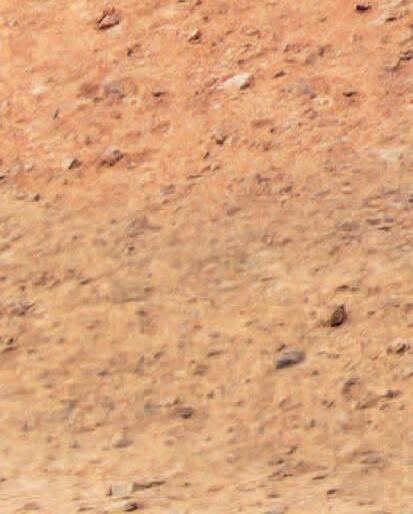
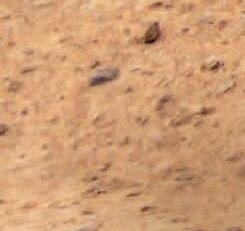

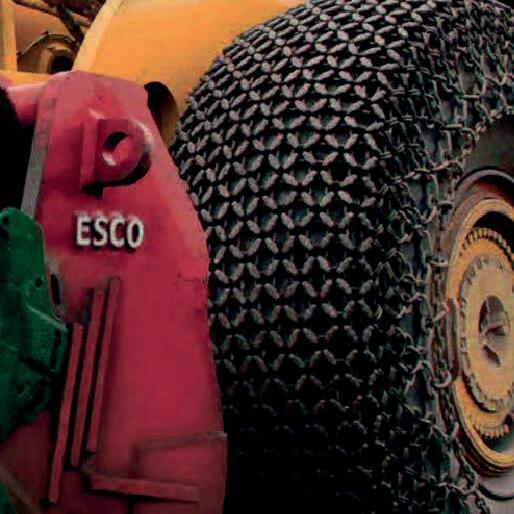
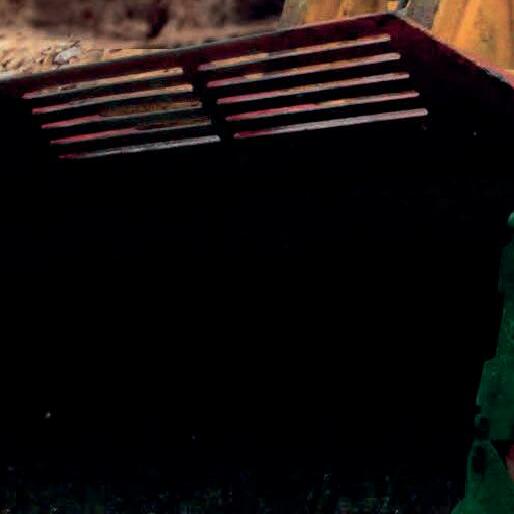
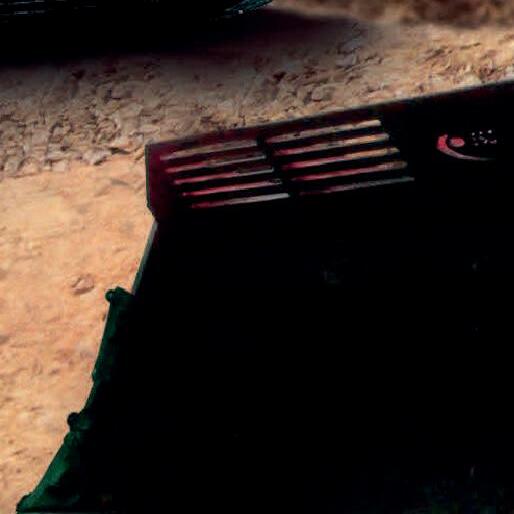
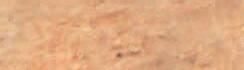

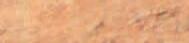
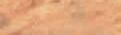
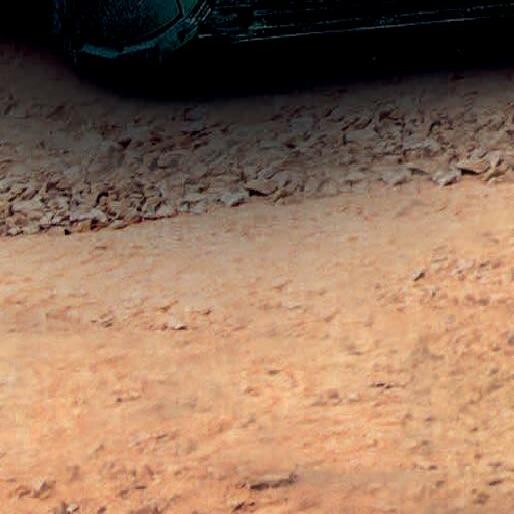


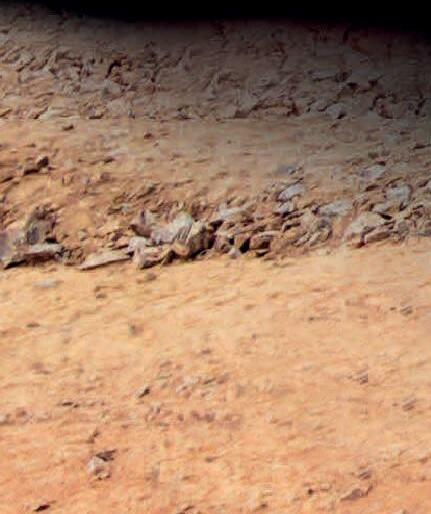

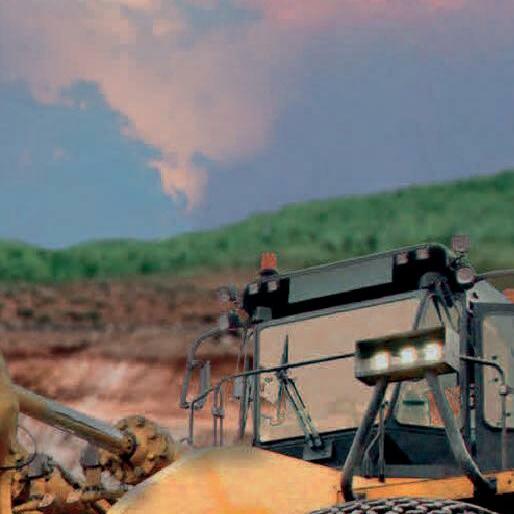
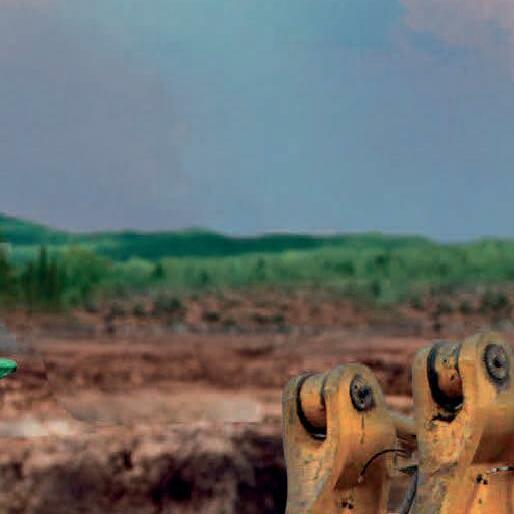
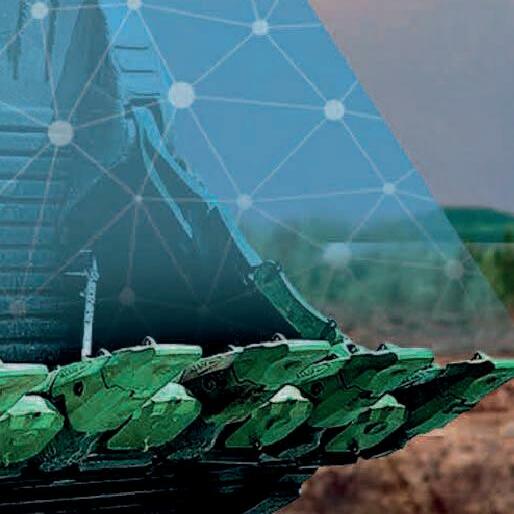
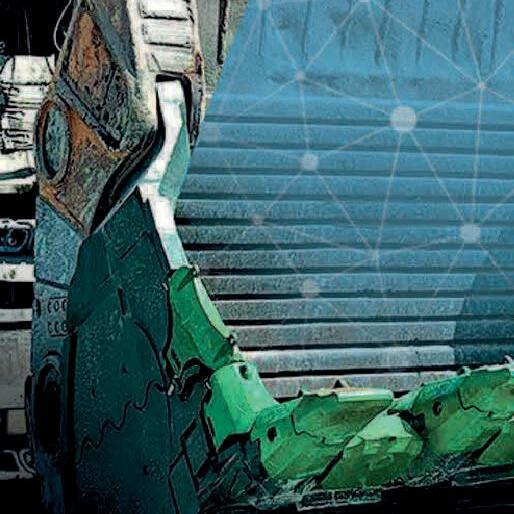
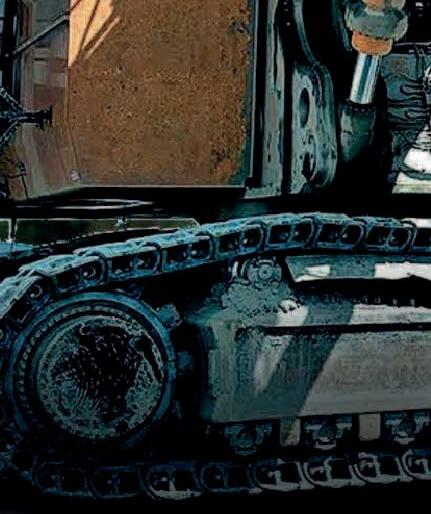


















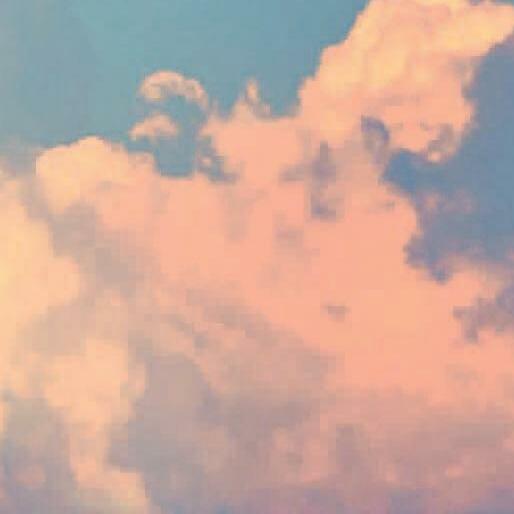



































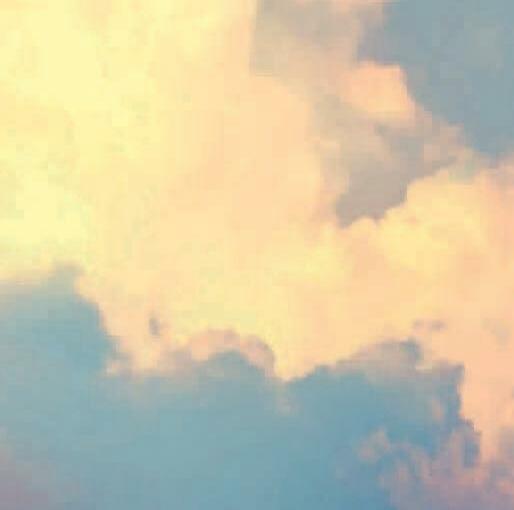



















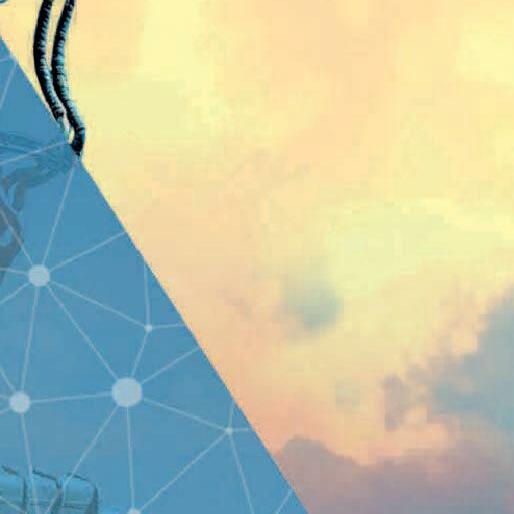
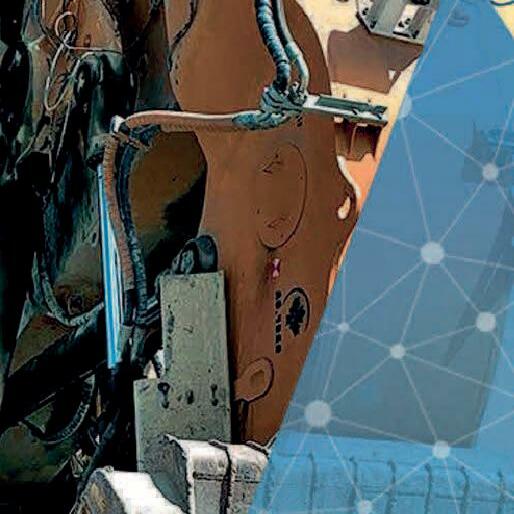




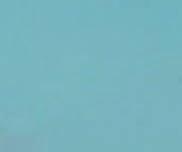
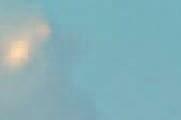
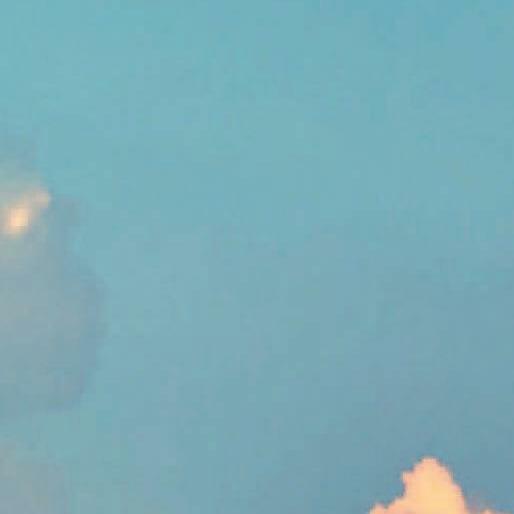
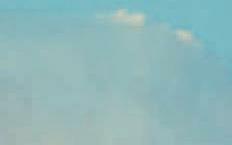
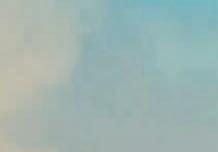

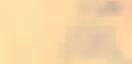


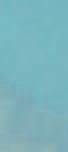
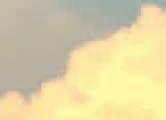
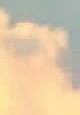
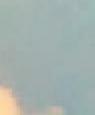

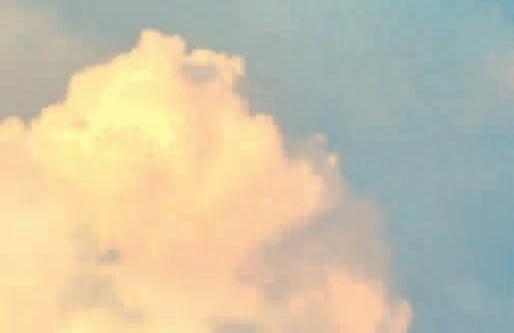

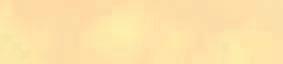
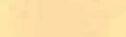
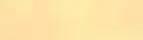
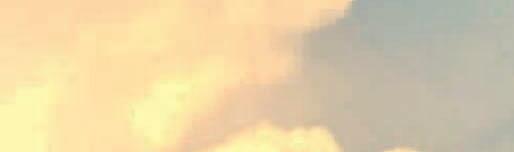
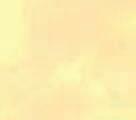

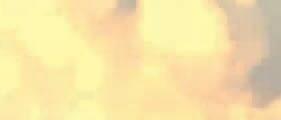

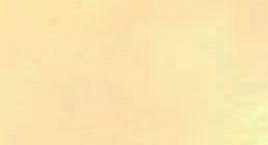

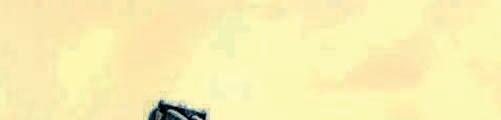
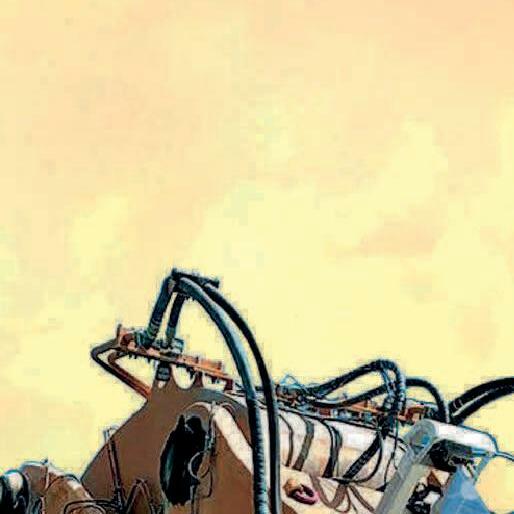

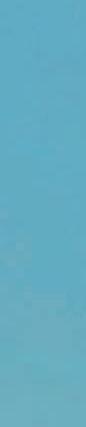
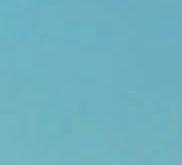

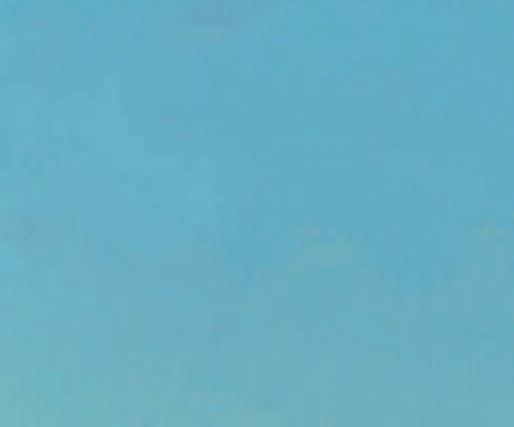

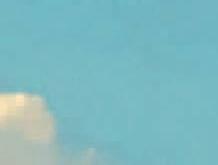


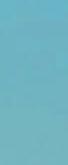
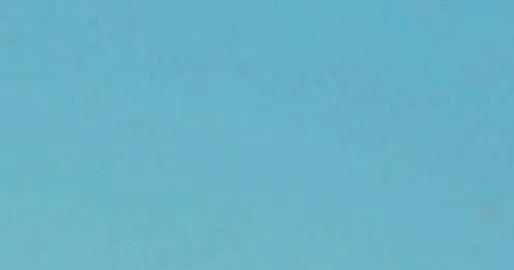
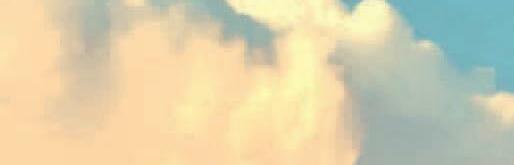
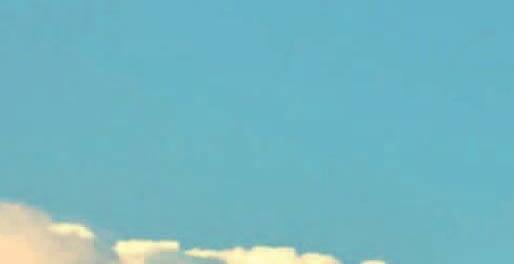
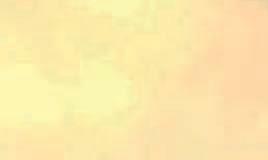
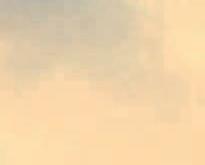
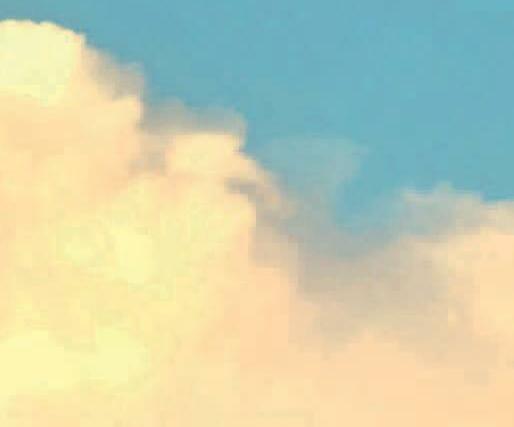

Riser Lifting Jack is a self-locking jack that performs automatic locking during lifting, lowering and holding. Available with 54-ton, 90ton, 136-ton and 181-ton capacities with either pneumatic or electric pumps, the Power Riser Lifter is supplied with 3.5 m pendant cord for airdriven units with pneumatic valves and 6 m pendant cord for electric-driven units, keeping operators away from the load. It is a readilyportable unit with 102 mm ground clearance for transport over rough terrain. A three-position handle, meanwhile, provides easy tilt back and transport, the company says.
Heavier lifts
Enerpac strand jacks pack tremendous lifting capacity into a small footprint, acting like a linear winch.This sees steel cables or strands guided through a hydraulic cylinder; above and below the cylinder are anchor systems with wedges that grip the cables or strands. By stroking the
together with the SCJ-Series 50T Cube Jacks-Ups. It will also feature the Enerpac Power Riser for safe and mobile load lifting of mining vehicles. In addition to the hydraulic gantries and cube
Capacities of the JS-Series Jack-Up range from the JS-125’s 125 ton (500-ton lift with four towers) capacity to the JS-750, 750 ton (3,000ton lift with four towers) capacity, with each solution offering lifting heights from 6 m to 20 m, respectively.Theseflexible solutions can be moved in and out of sites and – importantly – are classified as intrinsically safe, meaning they can be used in the Australian market.

SBL600 Hydraulic Gantry
BAUMA PREVIEW 32 International Mining | SEPTEMBER 2022
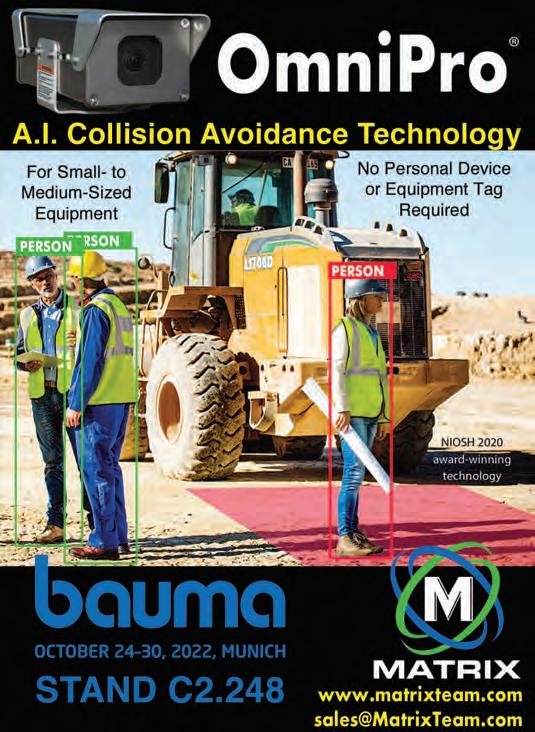
Accurate synchronised heavy lifting is the hallmark of Enerpac heavy lifting systems, which, the company says, is exemplified by the SCJ-Series Cube Jacks and Enerpac’s larger JS-Series Jack-Up.
Capacities of Enerpac’s JS-Series Jack-Up range from the JS-125’s 125 ton capacity to the JS750,s 750 ton capacity, with each solution offering lifting heights from 6 m to 20 m, respectively
The SBL600 Super Boom Lift hydraulic gantry is a three-stage telescopic hydraulic cylinder with rectangular boom for increased capacity and first stage lifting capacity of 674 tons (611 t) and 416 tons at the third stage. The SBL600 fits in nicely between the SBL500 and SBL900 gantries, offering a lifting height of 10.6 m, compared with 8.6 m and 11.3 m, respectively.
Enerpac Power Riser
jacks, the booth will feature a JS-250 Jack-Up, and multi-point lifting EVO system used to maintain mining shovels.
The Enerpac Cube Jack has set the standard for ease-of-use and productivity for compact, portable lifting solutions, according to the company. It uses a base lifting frame and selfaligning, lightweight steel cribbing blocks –together with automatic incremental locking – to provide high-capacity and stabilised lifting. It is a safer, controlled, more efficient and environmentally friendly alternative to climbing jacks with tropical hardwood cribbing, Enerpac says.Enerpac
Lifting Jack
Synchronised lifting
Jeremy roadtwoallows9,100self-weightInpermittingwithoutstandardforfoldabletheanotherofTechnology,EnerpacCommercialStubbs,Director,HeavyLiftingsaid:“Easetransportationiskeybenefitofnewgantry.Aboomallowsshippingonflatbedtrucksspecialandrouting.addition,withthelessthankg,theSBL600fortransportoflegsonasingletrucktrailer.”
The Enerpac Power
JS-Series Jack-Up Systems, meanwhile, are transforming the way many heavy-lift projects are executed, Enerpac says.
The Jack-Up is a synchronised lifting and lowering system with self-contained hydraulics in each unit for uncluttered work areas. Loads are lifted in increments as steel boxes, called “barrels”, and are stacked together to form lifting towers to mechanically hold the load. The JS-250 Jack-Up system uses computer controls for seamless synchronous control, raising and lowering all towers at the same time.
synchronous lifting system recently came to the rescue of WesTrac in Western Australia, providing an efficient, portable and safe solution to lift its 200 t Cat® 994K wheel loader.
“Whethersays.itbe hydraulic control, automation, connectivity or electrification – software plays a central role in the highly dynamic off-highway market,” the company says. “In order to achieve
Innovation out of tradition - It pays to talk to a specialist!
An Enerpac EVO multipoint synchronised lifting system is used to simultaneously control up to 12 cylinders, creating an accurate and synchronised lift. Operated using a PLC, hydraulic cylinders connected to an EVO Synchronous Lifting Pump enable each lifting point to be monitored and controlled by a single operator. The EVO pump maintains accurate positional control within 1 mm between lagging and leading cylinders and includes built-in warning and stop alarms for optimum safety, the company
BAUMA PREVIEW info@takraf.com www.takraf.com For more information about our bulk material handling solutions, please click on the qr-code. 3,500 t/h TAKRAF stacker for iron ore in Australia

Bosch Rexroth’s myBODAS on trial Bosch Rexroth says it is opening its mobile electronics software, BODAS, to all manufacturers and partners as part of a move to accelerate the launch of new machines and functions by OEMs.
Enerpac’ssays.EVO
The company plans to offer manufacturers of off-highway machines free access to the entire standard portfolio of BODAS software for controlling mobile machines, with Bosch Rexroth set to highlight this at the upcoming event in Munich.Viathe digital myBODAS platform, OEMs can download validated software packages for a range of applications, free of charge, to test and adapt them to suit their own requirements.
series production. The modules are developed in accordance with current standards and already meet functional safety requirements, the company
Proven modules within the platform minimise the time, investment risks and costs involved, with the service only billed via a payment model based on credits if the software is used during
cylinder in and out while the grips are engaged in the anchors, a lifting or lowering movement is achieved. The motion of the cylinders is driven by hydraulic power packs, with the Enerpac SCC software program synchronising the motion of the strand jacks and adjusting the motion to the loads per lifting point.
TAKRAF is recognized as a leading global technology brand when it comes to handling high capacity run-of-mine and bulk material handling. Stackers form only a part of our portfolio and we supply the complete range of machines for the heaping of circular or longitudinal piles, as well as for the homogenizing and blending of bulk material.
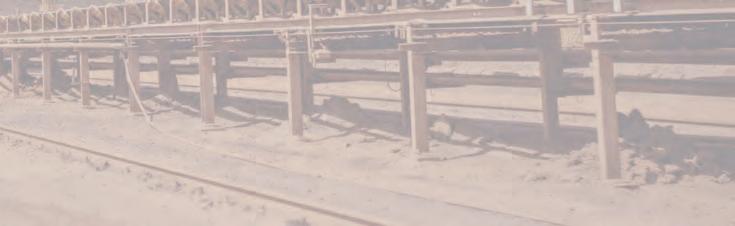
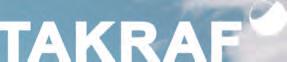
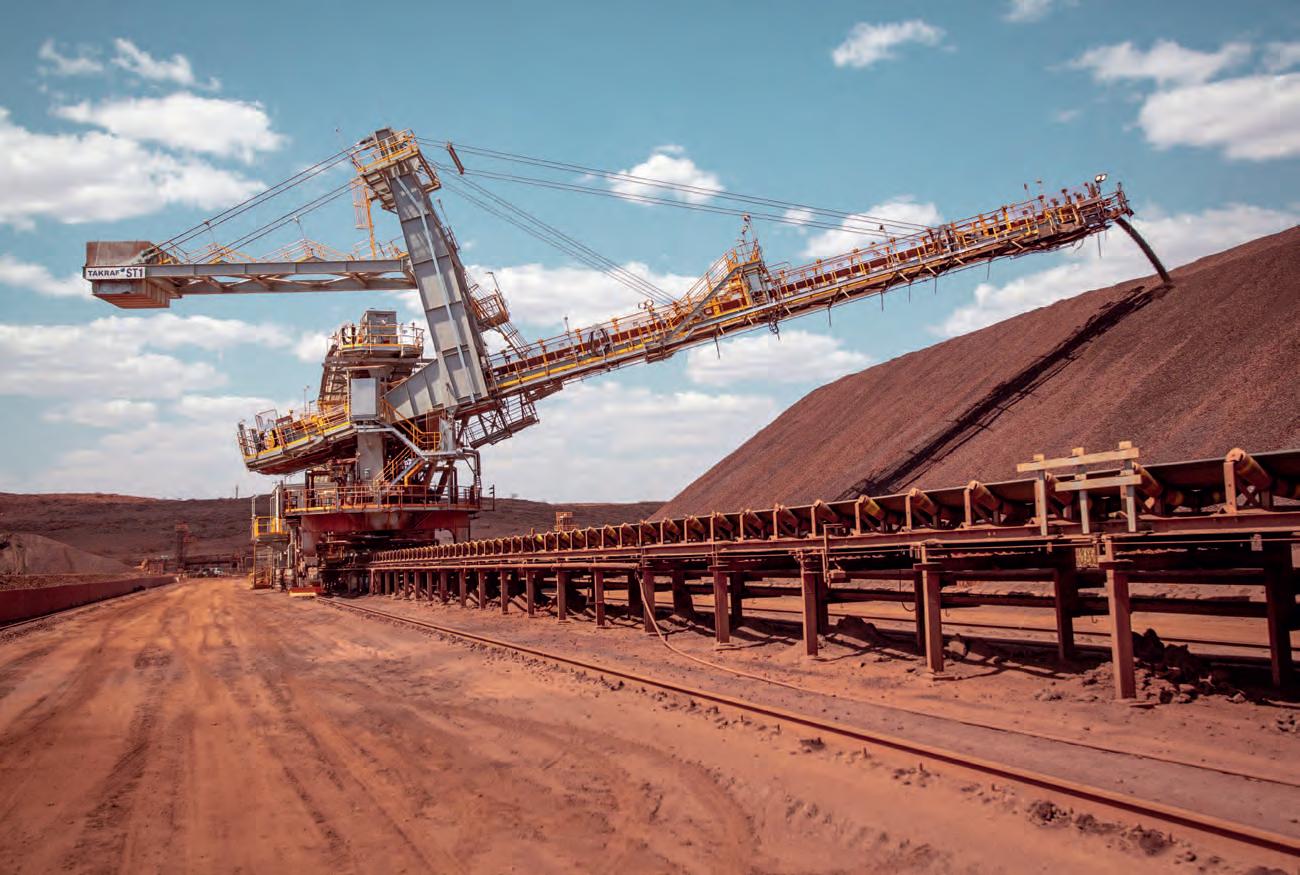
Bosch Rexroth will present an integrated portfolio for needs-based automation of offhighway machines, such as excavators, wheel loaders and telehandlers, at Bauma 2022 with the assistance functions covering, among other elements, virtual walls and emergency braking assistants for greater work safety

With perfectly uniform illumination at automotive level, the series provides much better visibility in the work area, improving safety and efficiency on sites, the company claims.
“In Ultra-Wide mode, we still achieve a light intensity of one lux at a distance of 90 m, and that’s absolutely unique,” Chris Kosmala, who is responsible for lighting system development at Continental, said. Overall, this increases the brightness in the corners and sides or at the end of the illuminated area away from the spotlights.
The work lights in the NightViu series feature an efficient reflector lens design with six powerful LEDs and four cover lenses. Offering approximately 100 lumens per watt, these LED lights have an enhanced light efficiency level when compared with other LEDs for construction and mining machinery – protecting sensitive vehicle electronics and preventing short circuits caused by excessive power consumption.
Just one of the Continental launches slated for Munich is its NightViu lighting series, developed specifically for applications in the construction and mining sectors.
This entire automation portfolio will be based on the BODAS platform for hardware, software and telematics.
ABB’s team will discuss how everything fits together in the all-electric mine, powered, managed, monitored and protected through automation and digitalisation.
BAUMA PREVIEW 34 International Mining | SEPTEMBER 2022

ABB partnership model on show
The mining experts at ABB, made up of specialists across digital, automation, electrification, grinding, motors, drives, conveying, material handling, automotive wiring harness protection and traction, have a hand in most of the exhibition’s themes. They will discuss the importance of mining in ensuring a ready supply of the materials needed for the energy transition, including metals and minerals for modern technologies such as wind turbines, smartphones, electric vehicles and medical devices.ABB’s latest solutions use products and
The open ecosystem of BODAS is being expanded constantly with standardised, extensively-documented modules. myBODAS, thus, offers an updated toolkit for various control tasks involving mobile machines, the company explains.Related to this, the company will present an integrated portfolio for needs-based automation of off-highway machines, such as excavators, wheel loaders and telehandlers, at Bauma 2022
methodologies as part of a wider integrated system and the company has taken decisive industry actions to partner directly with customers, original equipment manufacturers (OEMs) and technology innovators, enabling mining leaders to move towards their zero emissions targets more quickly while ensuring efficient, reliable and profitable operations, it says. This has been facilitated by working together and making a world of difference in every area where ABB is well placed to influence. This includes digital, electrification, motion, charging, energy storage and component protection systems for both onboard batteryelectric vehicles and around the mine site.
And, as a hardware platform for higher automation levels, Bosch Rexroth will announce a microprocessor-based, ROS2-compatible robotic control unit.
Lighting up the site
For object recognition and terrain mapping, Bosch Rexroth is working with Bosch to develop a ROS2-compatible perception stack. On this basis, Bosch Rexroth plans to offer complete function packages in the future – from sensor integration and object recognition to machine intervention.Thenewcontrol platform is currently being developed, with prototypes for pilot projects available from the middle of 2023.
success with their mobile machines, OEMs must reduce the development time in a cost-effective manner while reducing functional and financial risks.“This way, the OEMs’ software developers can concentrate on selected customer values and speed up the launch of new functions and machines. They can also scale their own offering more quickly with software modules validated for Rexroth hardware.”
At Bauma 2022, ABB will take visitors on a journey to the reality of tomorrow, presenting not only its industry-specific portfolio, but showcasing its approach and methodologies.
ABB will showcase its digital portfolio, including ABB Ability™ MineOptimize solutions and the ABB Ability eMine™ suite of electrification and digital systems designed to accelerate the decarbonisation of the mining sector.In2022, the ABB Ability eMine portfolio has continued to emerge as one of the industry’s foremost electrification strategies, with a successful project commissioning for the eMine Trolley System at Copper Mountain’s operation in Canada and ongoing testing of pilot eMine™ FastCharge. The latter, part of the eMine Charging Systems family, is set to become the worlds’ fastest and only fully automated charging system for mining trucks, offering up to 600 kW of power, ABBMeanwhile,says. the company has designed and manufactured Harnessflex® Specialist Conduit Systems. These include flexible conduit systems and connector interfaces, protecting critical electrical and electronic wiring assemblies on automotive machinery from mechanical abrasion, liquid ingress, dust and salts.
The unique modular housing concept has a minimum level of component complexity and offers users the flexibility to cover a wide range of lighting requirements, according to Continental. It also boasts highly increased lighting efficiency when compared with systems previously available on the market.
The assistance functions cover advanced sensor systems and intuitive operating devices, including driver assistance for more efficient working and virtual walls and emergency braking assistants for greater work safety.
Luminous flux options range from 1,500-3,500 lumens, with the light beams covering a wide variety of lighting scenarios for the work area around the vehicle; from close-range to far-field illumination. These beams have different lighting patterns, ranging from highly focused spotlight illumination to floodlighting, and from a wide to extremely wide illumination field.
Continental has also designed a unique housing concept that, it says, enables the three
The work lights in the Continental NightViu series feature an efficient reflector lens design with six powerful LEDs and four cover lenses
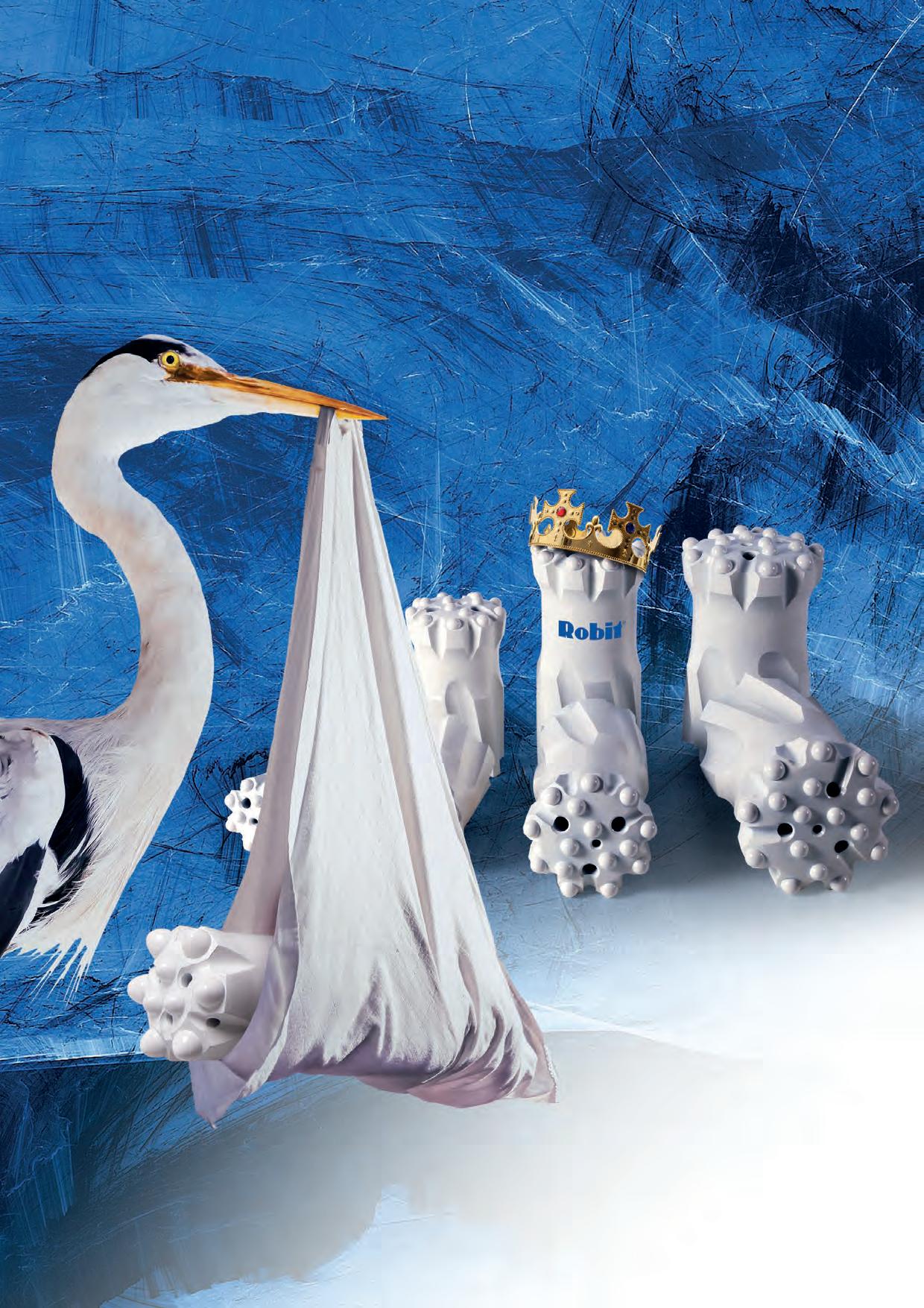
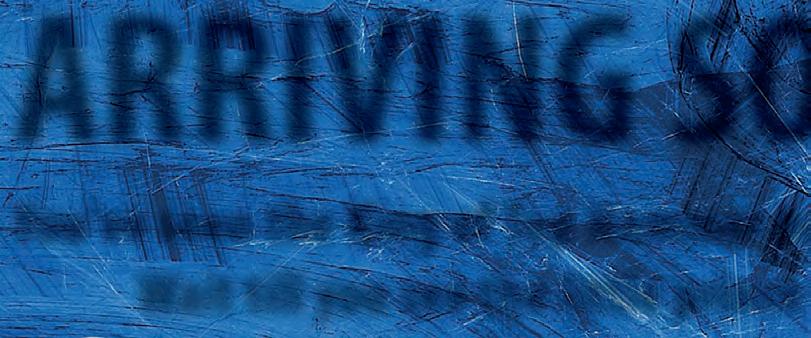
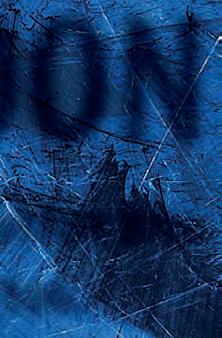

BEUMER Group explained hybridisationthe of the two: “The troughed belt conveyors allow high mass flows even in case of heavy and robust materials. Their open design makes them suitable for coarse materials and very large volumes.“Thepipe conveyors, on the contrary, present other advantages.specificThe idlers form the belt to a closed tube protecting the material transported against materialemissionsenvironmentinfluencesexternalandthefromsuchasloss,dust or odours. Partition plates with hexagonal cuts and idlers in a tubearrangementstaggeredkeeptheshapeclosed.The
The aluminum housings are designed for hard off-highway use and are protected against water and dust in compliance with the IP6K8 standard. The lights also withstand temperatures between40°C and +90°C and pass vibration tests of up to 12 g RMS – verified through tests in Continental’s certified quality laboratory.
The lights’ flexible installation system for standard or heavy-duty mounting also enables retrofitting in many different positions on vehicles, the company says.

With many ports shifting focus away from coal to handle different materials, the P-U Shape conveyor’s increased capacity and higher lump size flexibility could be of benefit in brownfield applications, he added.
The T-U-Shape conveyor is a U-shape conveyor designed like a normal troughed belt conveyor with a 30% reduction in width, allowing the ability to take on tighter curves, Prevedello says. This looks to have many applications in tunnelling.TheP-U-Shape conveyor, as the name would infer, is derived from the pipe conveyor, but offers 70% higher capacity within the same width and 50% higher lump size allowance, Prevedello says, explaining that it could allow BEUMER Group to consider the use of pipe conveyors in space-constrained environments.
Wirtgen’s ‘all-rounder’
New installations will obviously be targeted as part of this new product launch, but Prevedello says there are both greenfield and brownfield application possibilities.
“In this way, the complexity of the NightViu series is kept in check, but we can still meet every conceivable requirement of our customers,” Kosmala said.
The FAM Group, headquartered in Magdeburg, Germany, is a manufacturer of conveyor systems and a leading supplier of full-range bulk handling and processing equipment for applications such as in-pit crushing and conveying. It plans, designs and manufactures turnkey plants and systems for mining, extracting, loading and storing minerals, raw materials and goods.
BAUMA PREVIEW 36 International Mining | SEPTEMBER 2022

BEUMER Group, an international leader in the



BEUMER Group bulks up
pipe conveyors allow the implementation of more narrow curve radii and larger angles of inclination than open troughed belt conveyors.”
There has plenty of change at BEUMER Group of late, with Rudolf Hausladen installed as the new CEO, succeeding Dr Christoph Beumer, the FAM Group joining the company and the launch of new conveyor technology.
With the new 280 SM(i) surface miner, Wirtgen says it has developed another efficient and practice-oriented solution for the extraction of primary resources, with innovative technologies that enable high machine utilisation rates and maximum productivity.

wimmer.info | mini-badger.at For tunnel cross sections from 6.2 m² Entrance height 2.3m, Operating weight 12t High breakout and tear TunnelingRadio-controlledforceExcavator
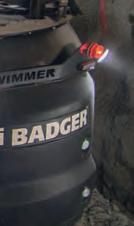
With requirements changing – the quantities of bulk materials growing, conveyor routing becoming increasingly complex and environmental considerations rising – BEUMER Group found the need to develop the U-Shape conveyor.Within the family are two products that offer higher curve flexibility, higher capacity, bigger lump size allowance, no spillage and reduced power consumption, according to Prevedello.
manufacture of intralogistics systems for conveying, loading, palletising, packaging, sorting and distribution, has held a stable position in the bulk materials technology market for decades, and, with the acquisition of FAM, it has significantly strengthened its market position in the minerals and mining sectors.
different luminous flux options and four different light patterns to be freely combined without needing more than one housing design.

BEUMER Group has also recently responded to the changing demands of dry bulk customers with two new products that leverage its existing expertise in pipe and troughed belt conveying technology.Speaking at a recent virtual media event, Andrea Prevedello, CEO of BEUMER Group Austria, announced the new additions under the U-Shape conveyor family.
The 280 SM(i), which will be on show in Munich, is designed for the reliable and selective extraction of primary resources by direct loading, sidecasting or cut-to-ground. Raw materials are extracted and crushed in-situ in the purest quality in a single operation – without drilling and blasting, and with minimal environmental impact.The280 SM(i) is driven by four steerable and height-adjustable crawler units. This makes the machine highly manoeuvrable, able to quickly turn at the end of a cut, according to the company. The LEVEL PRO ACTIVE automatic levelling system maintains the specified cutting
Leveraging the advantages of pipe conveyors and troughed overland belt conveyors, U-Shape conveyors enable environmentally friendly and efficient operation in port terminals, BEUMER Group says, allowing the implementation of more narrow curve radii than a troughed belt conveyor with higher mass flows than a pipe conveyor, all with dust-free transport.
The T-U-Shape conveyor has more ‘new’ installation opportunities in tunnelling applications, he said, with the tight turning radii benefits allowing for small installations in tunnels.
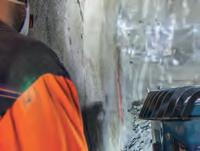
The modular approach also allows different light cones to be combined, reducing the number of lights required but still ensuring a highly uniform illumination and the avoidance of shadows, according to Continental.
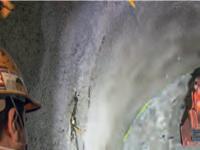
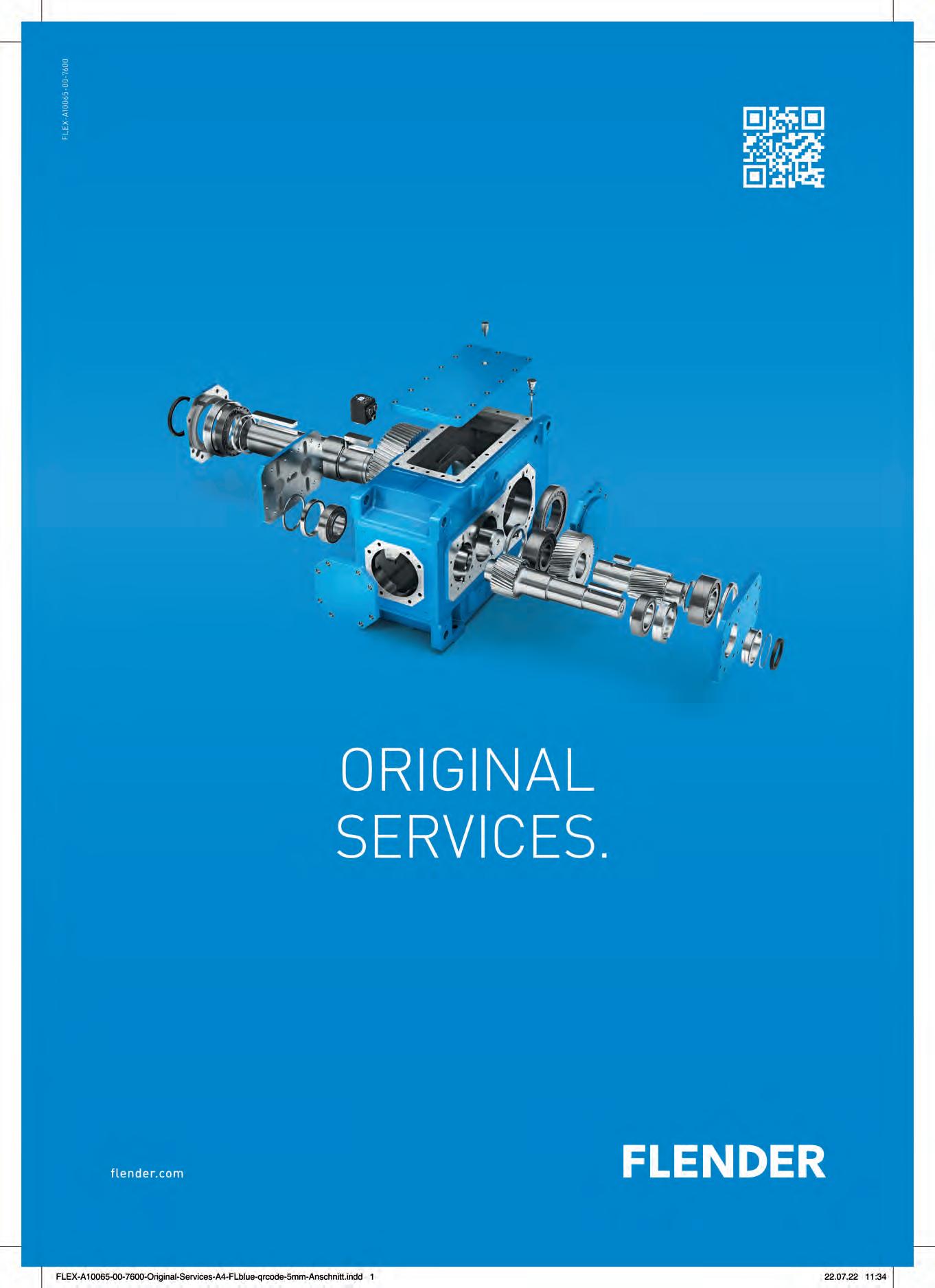
Entirely new standards are set by the dustsealed and air-conditioned, positive-pressure cabin on the new surface miner with fresh air filtration. This, the company says, prevents the ingress of dust into the operator’s workplace.
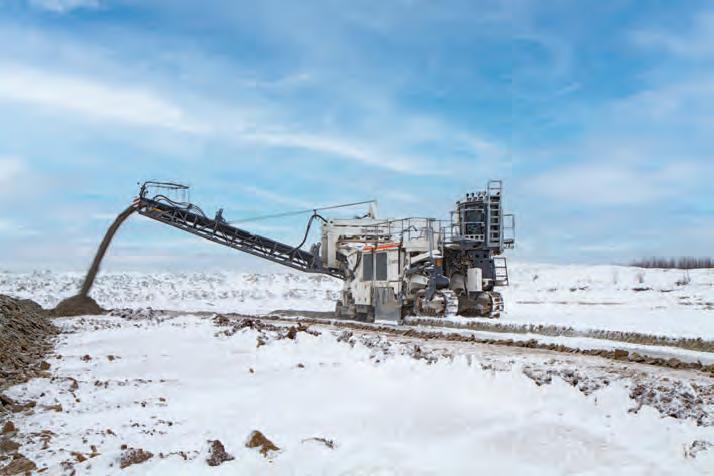
depth with consistently high precision and without further aids.
reduces the risk of fatigue, assists the operator in achieving high productivity rates and improves the overall efficiency of the process, the company says.Thanks to the reduction of carbon emissions by low specific fuel consumption, an efficient water management system and effective solutions for the minimisation of dust pollution, the 280 SM(i) shows that ecological and economic considerations are compatible and closely interconnected, Wirtgen concluded.
In terms of hardware, the company will also be talking up the introduction of new line-operated DRU.. series asynchronous motors in the IE4 energy efficiency class in Munich.
Mounted on the front left chassis column, the operator’s cabin has all-round glazing and is decoupled from the machine body to offer 90° rotation in both directions. Up to six cameras can also be installed to provide even better all-round vision, while various automated functions further contribute to operator comfort. This potentially
Moving to drive mode
Still along the lines of sustainability, the Bruchsal-based drive specialist recently introduced GearFluid, a premium lubricant for
Among the benefits that come with this update to the X.e series of helical and bevel-helical gear units are a higher thermal limit rating, a longer bearing service life, and higher nominal and application torques
After launching Generation X.e in 2019, SEWEURODRIVE says it is once again setting new technology standards.
The helical and bevel-helical gear units of the X.e series cover a torque range from 6.8 to 475 kNm across 23 graduated sizes.
BAUMA PREVIEW 38 International Mining | SEPTEMBER 2022
The 280 SM(i) is an “all-rounder” for all rock hardnesses and applications, Wirtgen says. The 2,750 mm cutting drum unit, with a cutting depth of up to 650 mm, is precisely adaptable to each specific application and achieves outstanding cutting performance with minimal pick wear, it added.Wear-resistant toolholder systems ensure optimal pick utilisation and minimal downtime.
While the soft-rock cutting drum unit is designed for high material flows in soft rocks, the hard-rock cutting drum unit ensures maximum durability and long life in hard-rock applications, according to Wirtgen.
Digital data models and the latest calculation methods have laid the foundations for a further improvement in the performance of its Generation X.e series. Among the benefits that come with this update are a higher thermal limit
These same gear units, to be displayed at Bauma, are part of the company’s “Industrial gear units to go” program for shorter delivery times, aiming to supply SEW-EURODRIVE industrial gear units to customers even faster.This sees standard drives from the X.e – up to 175 kNm – and P series – up to 360 kNm – leave the plant just five working days after receiving an order. Gear units that require design adaptations – such as special output shafts or preparation for use at low temperatures – are ready for shipping within 15 working days.
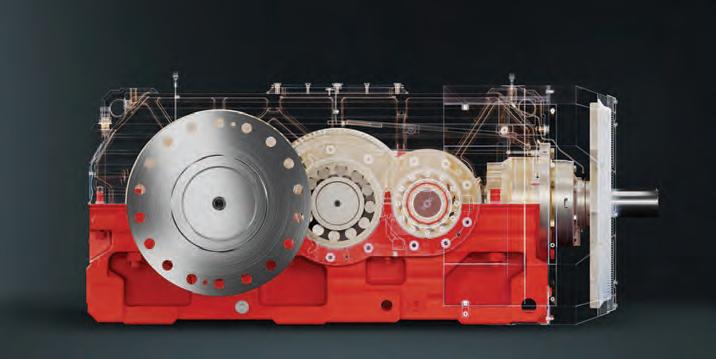
The 280 SM(i) is an “all-rounder” for all rock hardnesses and applications, Wirtgen says
The hydraulically, height-adjustable rear discharge conveyor with a movable counterweight can be slewed to the right and left by 90° and enables the loading of mining trucks with payloads of up to 100 t. Whats’ more, the operator can continuously vary the speed of the belt independent of the engine speed to reduce belt wear dependent on the material volume and the size of the mined material.
rating, a longer bearing service life, and higher nominal and application torques. Moreover, larger application angles are permissible with the maximum overhung load.
The launch takes place ahead of the July 1, 2023 deadline stipulated in the third stage of the European ecodesign regulations for motors, (EU) 2019/1781 and (EU) 2021/341.
The new IE4 AC motors with 4-pole design will be available in a power range of 0.75 kW to 200 kW and can be combined either directly with SEW gear units, or as standalone motors in all footmounted and/or flange-mounted designs.
One potential result of this optimisation is a smaller gear unit size. Besides reducing the oil volume, energy consumption and total cost of ownership, this also means the units are lighter and take up less space in the plant. Particularly in the case of drives that are subject to high loads, mechanical safety – and, thus, the potential for preventing damage – is also further improved. What’s more, a lower oil-bath temperature and a higher bearing service life mean reduced unplanned maintenance.
SERVICE,SAFETY,ANDINNOVATIONJENNMARdesignsandmanufactures a wide range of dependable ground control products, from bolts and beams to channels and trusses, resin, rebar, and more. We’re proud to make products that make the mining, tunneling, civil, and construction industries safer and more e Becausecient.


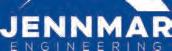


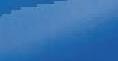
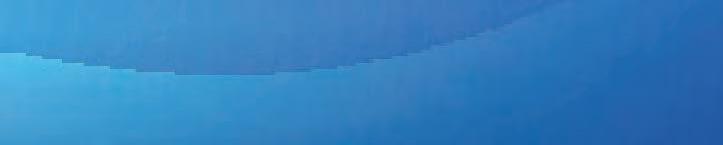
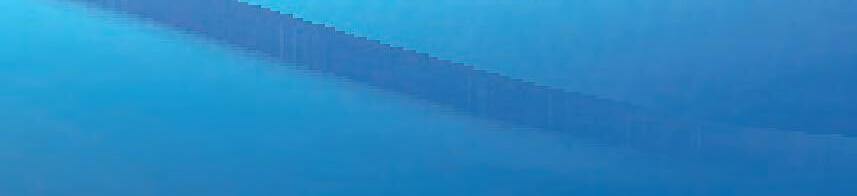

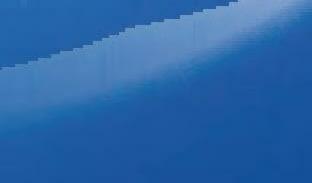
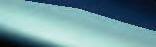

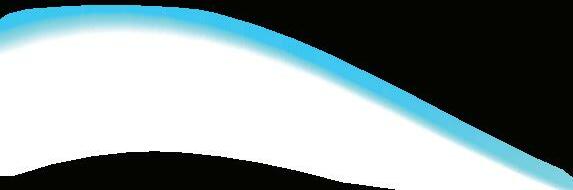
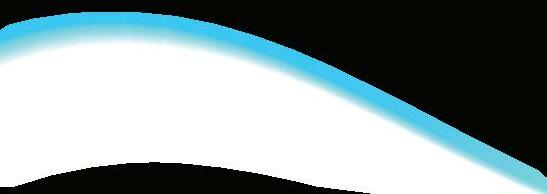

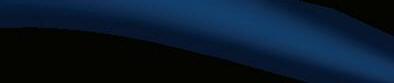


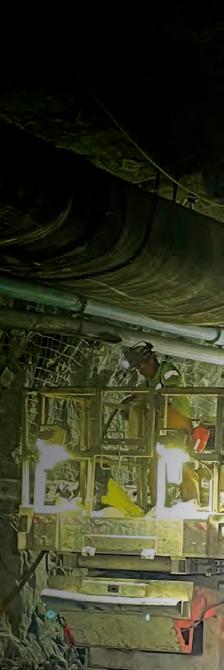
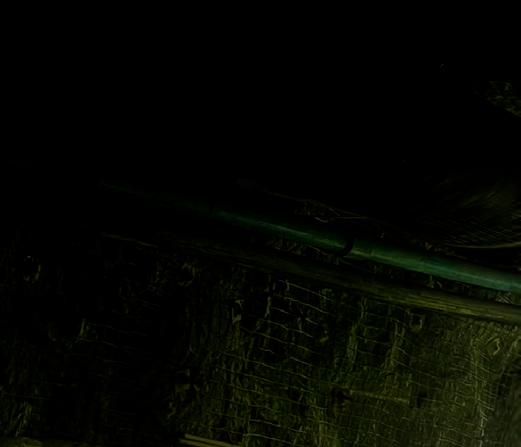
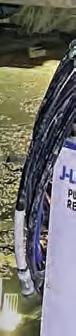
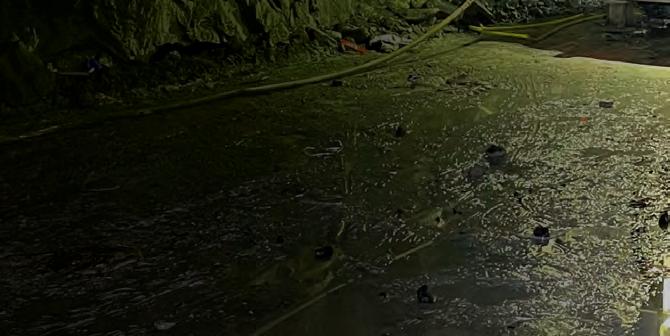
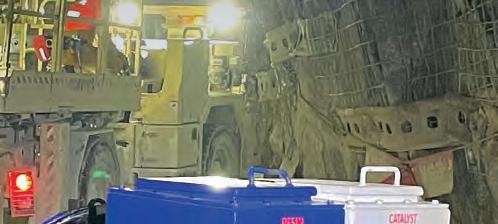

We feel it is essential to develop a close working relationship with every customer so we can understand their unique challenges and ensure superior customer service. Our commitment to the customer is guided by three words: SAFETY, SERVICE, and INNOVATION. It’s these words that form the foundation of our business. It’s who we are.
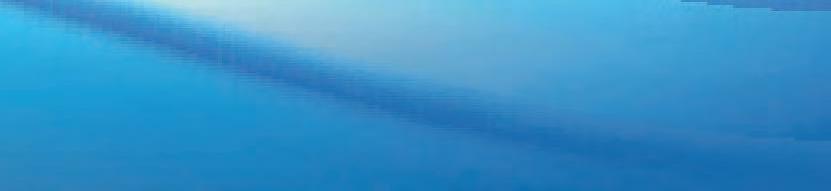
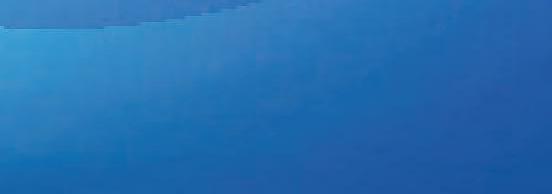


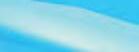





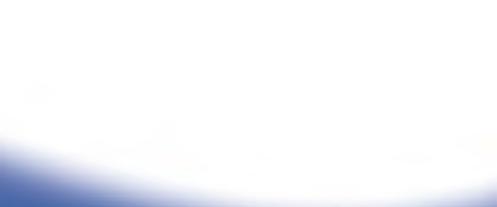
we understand the ever-changing and demanding conditions above and below ground we have built the richest portfolio of diverse and complementary brands. JENNMAR sets the bar in every industry we serve and as we continue to grow, our focus will always be on the customer.

J-LOK P polyester based resin is designed to deliver stronger and more reliable bolt encapsulation. With a variable set time that starts as fast as ten seconds, it’s a rapid and e cient solution. JENNMAR is the only company in the world that uses Polyester Resin. For more information on J-LOK P and our portfolio of diverse and complementary brands email us at info@jennmar.com or visit us at www.jennmar.com
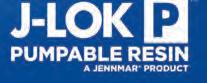
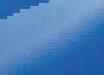

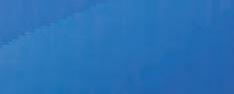


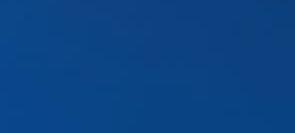
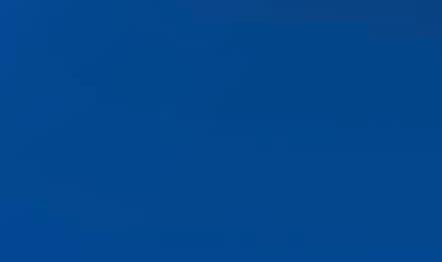



DEMANDCONDITIONSDEMANDINGJENNMAR GLOBAL HEADQUARTERS PITTSBURGH, PA USA • (412)-963-9071

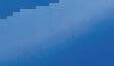
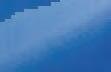
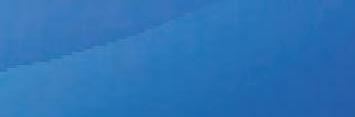
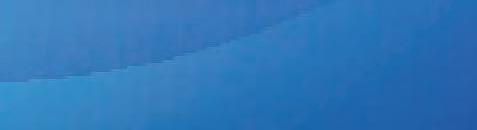
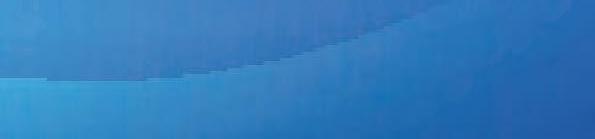
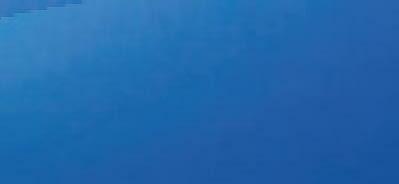

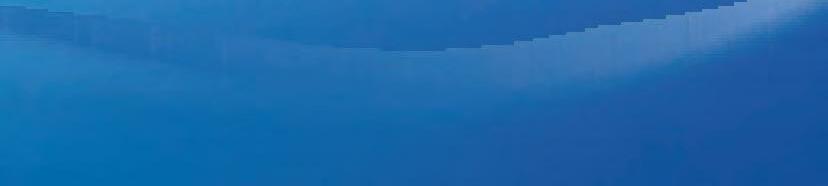

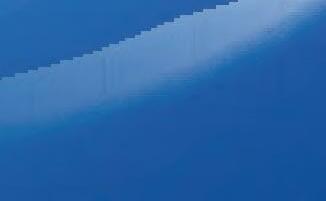
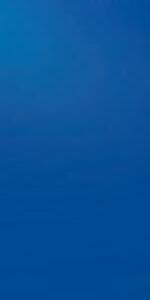




Mine development options
GearFluid Poly 220 E1 is the first CO2-reduced gear unit lubricant on the market made from sustainable biomass, with CO2 emissions at the end of the lifecycle of GearFluid Poly being 84% lower than conventional polyglycol oils, according to SEW-EURODRIVE. Consequently, this new premium lubricant helps customers reduce their overall corporate carbon footprint.
size. Tsurumi states a pumping capacity of 2,200 litres/min.Completing the safety trifecta will be Tsurumi’s Connect system for monitoring of pumps and other machines, including those from third parties. Via a small box on the unit, the operator can determine the location, read out performance data and set alarm and error scenarios. The aim is to raise safety and efficiency to a new level, with the first systems already in use on the market.Themanufacturer will also use the show to provide information on many other pump models, including the LSC2.75S residue dewatering pump, and the KTZ and KRS pump series.
gear units made from sustainable biomass.
For the first time, the exhibitor is coming to the show with a workbench where visitors can demonstrate their skills. The task is to service a pump, especially in the sensitive areas of hydraulics and electrics, reinforcing the need to carry out regular maintenance to avoid pump failures.Safety is also the focus of the new product presentation, which the Japan-based company has saved as a further treat.
BAUMA PREVIEW 40 International Mining | SEPTEMBER 2022
For the
To this point, Austria-based Wimmer has set its
The introduction of the Yellow Fox is where the company could potentially find further mining applications.Basedoffa Liebherr 914 Compact Litronic superstructure with a Liebherr 920 Compact Litronic undercarriage, the Yellow Fox can be used for working heights of 4.2-7 m. As with the Badger family, the excavator boom is custommade by Wimmer, offering high breakout and tear force alongside a boom that can be swivelled by 45°. All heads can also be switched out, changing from, say, a roadheader attachment to a drill, depending on the application.
Tsurumi, a dewatering pump leader, intends to lift the veil on its new safety pumps at Bauma 2022, offering visitors the chance to learn how to service a pump properly.
While offering maximum wear protection for the gearing and the rolling bearings, the premium lubricant’s low friction coefficients increase gear unit efficiency and, compared with conventional biodegradable oils, GearFluid extends the interval between lubricant changes by up to 300%.
Pump servicing workshop
sights on the tunnelling industry, with its flagship Blue Badger tunnel boring machine (TBM) being used around for tunnel cross-sections from 3.5 m in height.Sincethe release of the original Blue Badger in 2018, the company has supplied around 20 machines to projects across the globe. One of these was for a gemstone mine owned by Suacuai Mineracao LTDA in Brazil where the machine was previously boring through rock that had a uniaxial compressive strength of 60-120 MPa.The company has expanded this range with the miniBadger – for driving tunnels with a crosssectional area of 6.2 sq.m or more where the working height is 2.7 m – and the eBadger – a TBM driven by an electric motor that delivers up to 50 kW of power on battery for tramming and positioning and is connected to the mains infrastructure while tunnelling.
The company will debut the KRDX, a model in its new series of safety pumps that are approved according to IECEx and ATEX standards.
The Yellow Fox is powered by a 90 kW US Tier 4 Final-compliant engine.
The three-phase submersible heavy-duty pumps are designed for slurry drainage/pumping and have motor outputs from 3.7 kW to 7.5 kW. They are equipped with an agitator and an outlet of up to 100 mm to pass solids up to 33 mm in
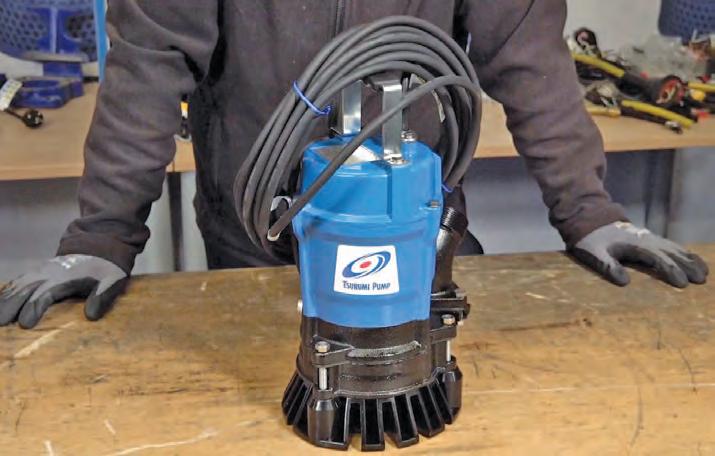
Wimmer’s Blue Badger progressing through rock at a gemstone mine owned by Suacuai Mineracao LTDA in Brazil first time, Tsurumi is coming to Bauma with a workbench where visitors can demonstrate their skills
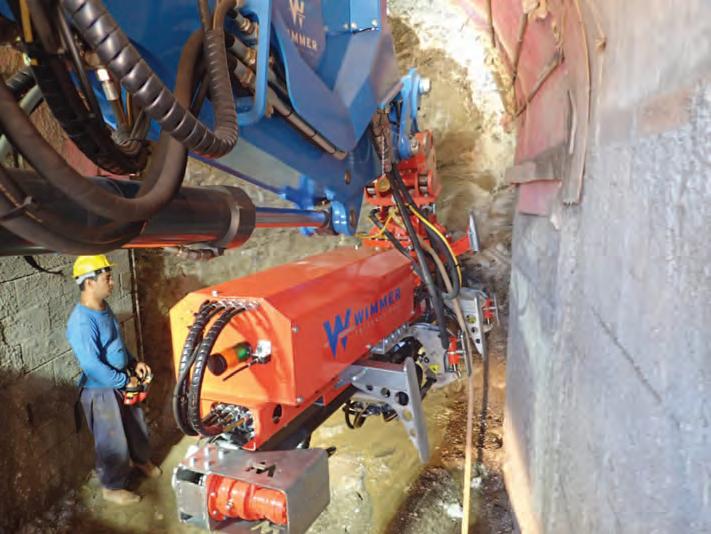
YOUR PARTS ARE IN STOCK AT L&M We’re celebrating our 60th Anniversary thanks to the confidence our customers have shown around the world in over 100 countries. Supplying Transmission, Torque Converter, Differential, and Planetary Axle parts from all the top OEM’s. L&M Powertrain; the worlds heavy equipment parts & component supplier that always has your part in stock! LMPOWERTRAINPARTS.COM Celebrating 60 Years of Service Worldwide L&M POWERTRAIN PARTS LIMITED 201 Snidercroft Road, Concord, Ontario, Canada L4K 2J9 Telephone: 905-669-2292 Fax: 905-669-6319 Toll-Free in North America: 1-800-387-3765 Email: parts@landmparts.com Off-Highway Systems
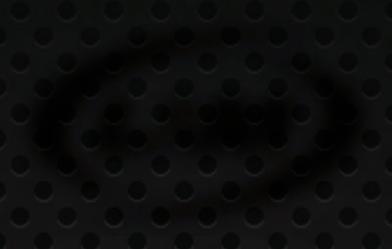


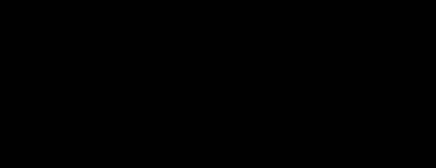
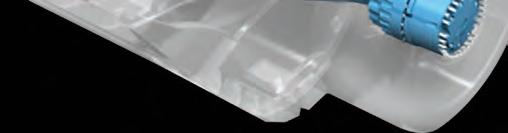
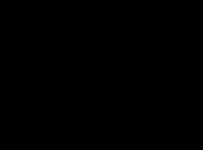
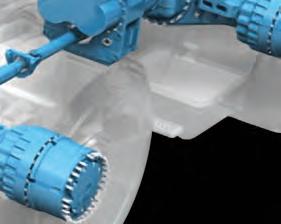

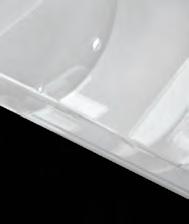
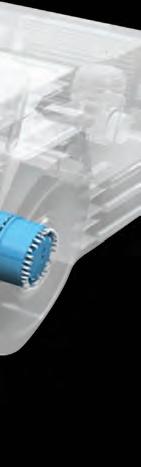
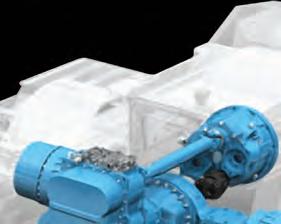
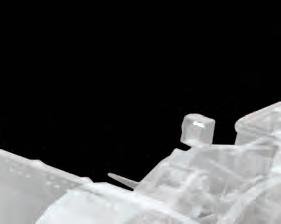
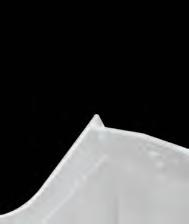
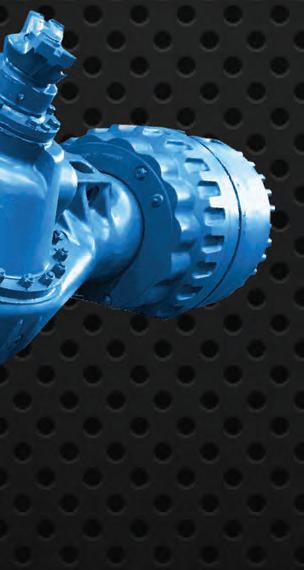



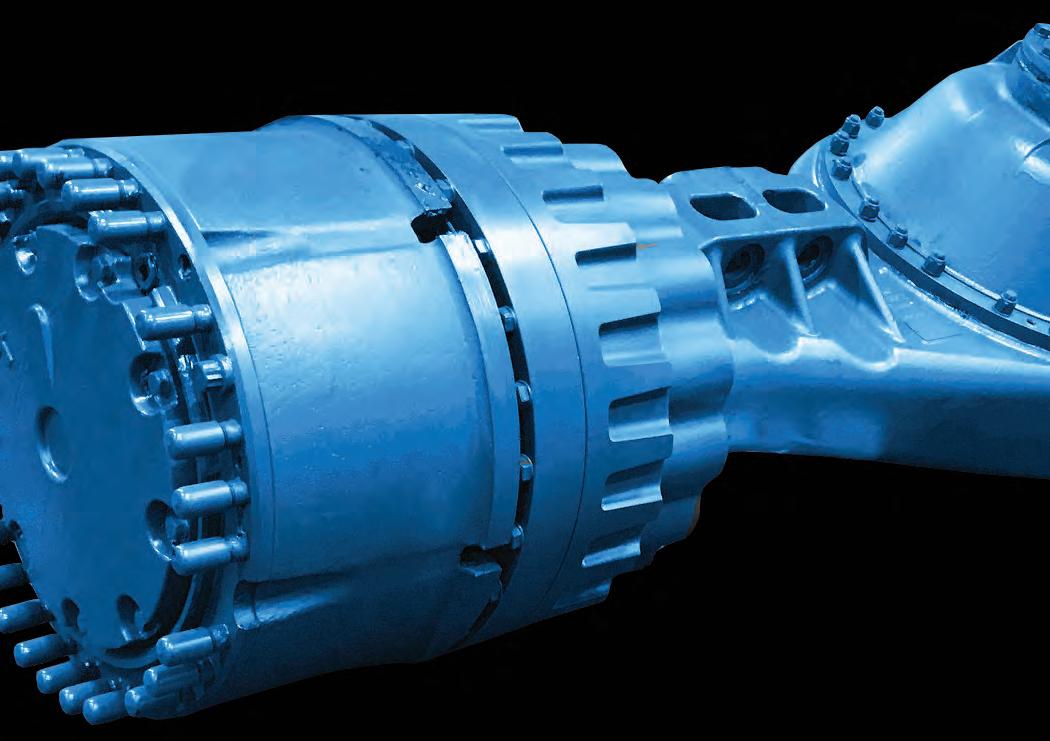
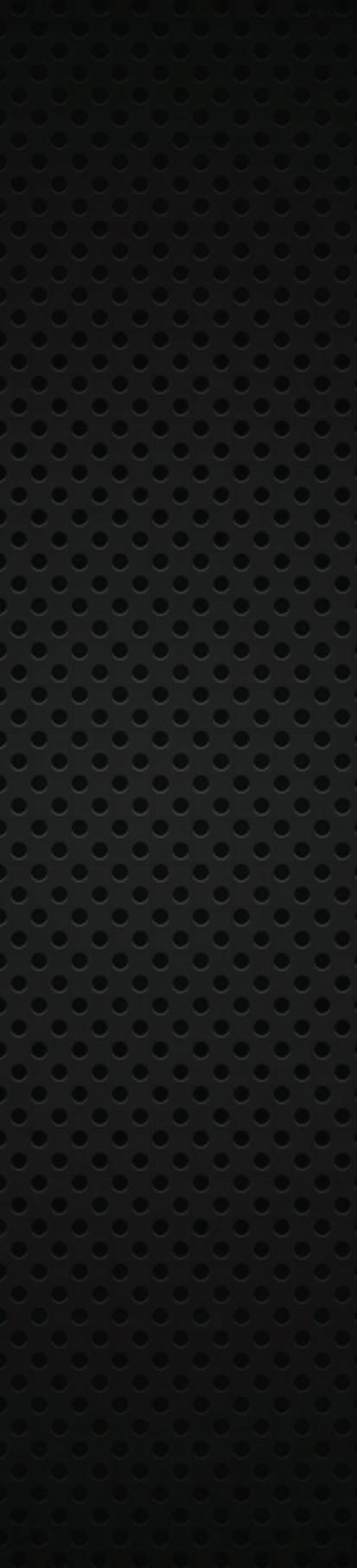
Designed in cooperation with Duplomatic MS, the new MS range includes central bypass, sixway, open-centre directional control valves for mobile applications. The range is designed for high performance with a wide range of configurations and options to meet customer needs.Key features include compact and modular construction, with a single pump able to supply one to 12 services that cover pressures up to 350 bar.The
IM BAUMA
It launched the TTC 2300, the first member of its complete and scalable TTC 2000 series designed to meet the needs of automated and smart off-highway vehicles and mobile machines, earlier this year.
MatrixThroughsaid.its Visual A.I. object recognition technology, OmniPro has been taught to identify and report on a library of “objects”, including people, vehicles, equipment, stop signs and pedestrian signs. The user can select which objects will be included, whether to integrate with the machine or operate as alert-only, and whether the alert will be visual, audible or tactile. Additionally, depending on the operation’s needs, OmniPro’s wireless solution can trigger a stop sign, pedestrian light, voice alert or crossing arm. All incidents are recorded and can be reviewed to provide insights for additional safety training as needed.OmniPro’s cost-effective and customisable solution can be adapted to match any operating environment through its programmable field-ofview zone grid configuration tool, which enables it to meet the safety requirements of different operations, Matrix claims. Rear-facing cameras can be used alone and, in multiple-camera systems, OmniPro will auto-switch to only monitor the vehicle’s direction of travel. Each system operates independently and is easy to install, the company added.
One company talking up the use of autonomous operations at construction and mining sites at Bauma 2022 will be TTControl
TTControl, for its part, is helping facilitate this automation collaboration through the provision of a new generation of electronic control units for vehicle manufacturers.
It recently helped initiate an Autonomous Operation Cluster (AOC) formed of Ammann, PALFINGER, Prinoth, Rosenbauer and TTControl, looking at collaborating on application-oriented solutions within this field.
AI-backed collision avoidance Matrix Design Group, an ISO 9001:2015 certified manufacturer that designs, develops and markets safety and productivity technology for use in mining and industrial applications, will feature the OmniPro Visual A.I. collision avoidance system for small-to-medium sized vehicles at its Bauma booth.
OmniPro is an application of the Matrix technology that received the 2020 NIOSH Mine Safety and Health Technology Innovations Award PREVIEW
A joint-venture company of TTTech Group and
At Bauma, Hydreco Hydraulics plans to present its new range of directional control valves, the MS series, and the new multifunctional ergonomic handle, the MHC.
HYDAC International, TTControl offers control systems and operator interfaces for mobile machinery and off-highway vehicles.
The multinational companies will jointly develop key technologies for autonomous operation elements for series production of mobile machinery functions and off-highway vehicles, with the aim being to accelerate the development of advanced assistance functions through collaboration.
This year, the partners are focused on defining a technological solution and developing a proof of concept and initial prototypes. Further application implementation based on specific use cases will continue in 2023.
42 International Mining | SEPTEMBER 2022
Bauma 2022 offers a meeting place for Hydreco customers to find out about this new offfering, and will also provide the company with a chance to update the market on Daikin Industries’ plans for the wider Duplomatic Group, following its acquisition of the entity earlier this year.
New products and direction for Hydreco

new MHC handle, meanwhile, has been designed to host a wide number of controls in a compact space. This sees the new electroproportional roller, as well as the full range of switches and devices, available on Hydreco handles.Hydreco currently sells around 70% of its products direct to OEMs, with many of its CAN BUS-based joysticks used on underground mining machines. The company is also looking to provide a direct offering to the market through other channels.
TTControl’s Autonomous Operation Cluster
This innovative application of visual artificial intelligence (Visual A.I.) and machine learning enables line-of travel and blind-spot pedestrian and vehicle alerting for mobile equipment, such as dozers and wheel loaders. Consisting of up-tothree 120° field-of-view cameras, the OmniPro system works without personal wearable devices or tags, and not only “sees” and identifies people and hazards, but also photographs and reports zoneOmniProbreaches.isan application of the Matrix technology that received the 2020 NIOSH Mine Safety and Health Technology Innovations Award,
It will also use the event to display the most recent developments of the external gear pumps made in its new production site in Parma, Italy.
Up to increaseproductivity40% OperationSafer Up to payloadaverage98%target LEARN PatentFullywww.mmdsizers.com/surge-loaderMORE:MobileSurgeLoaderPending;UKPatentApplicationNo1709467.3
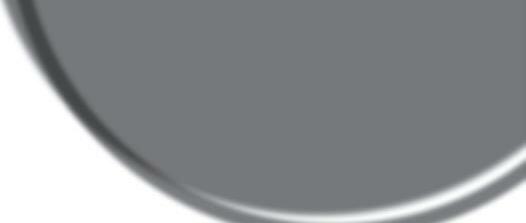
Wherever you are, we have the local resources to boost your productivity, maintain your equipment and give you the edge.
MINE LOADSMARTERQUICKER
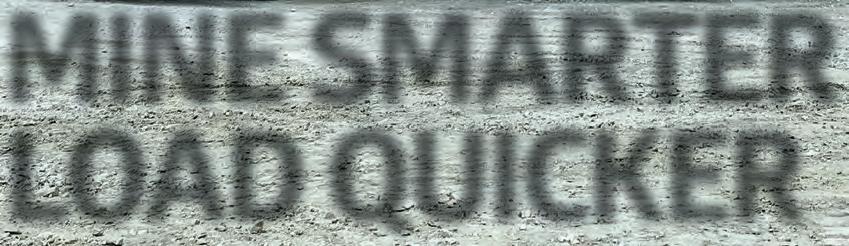


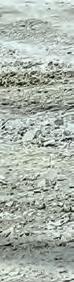


The Surge Loader™ will transform open pit mining –harnessing the full capabilities of the shovel to deliver continuous mining using your existing truck fleet.

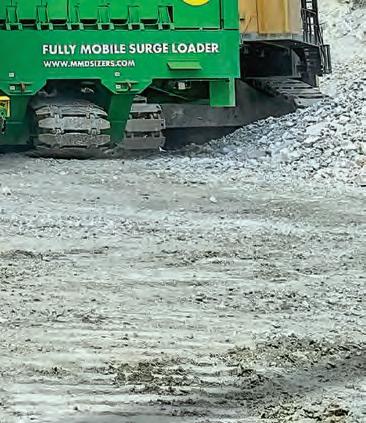
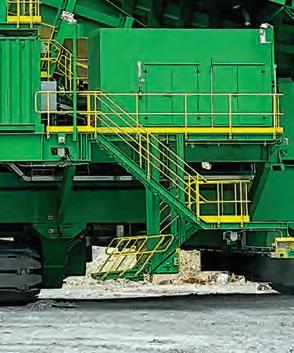
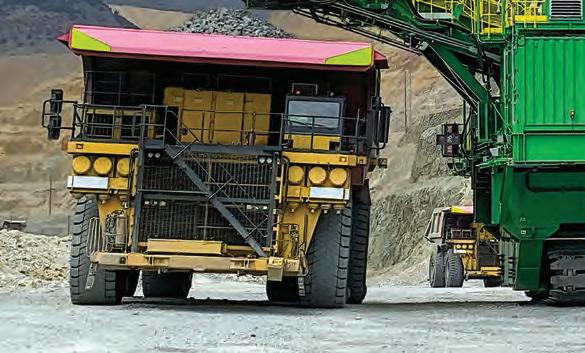
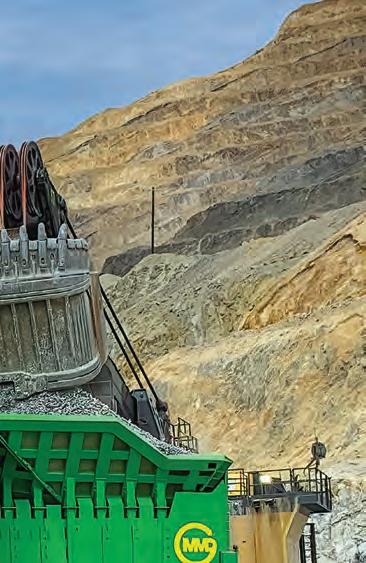

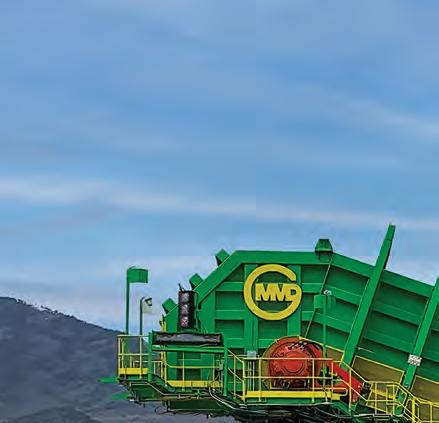
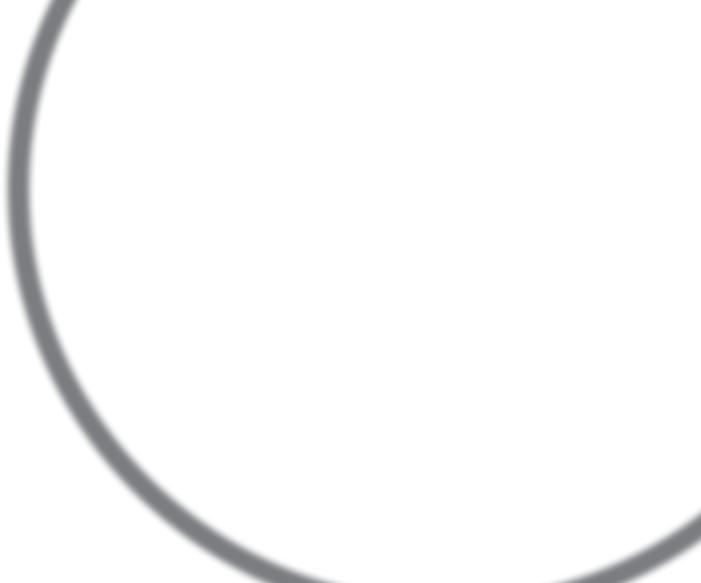
By stockpiling material and delivering a regulated flow on demand, the Surge Loader boosts productivity, reduces truck demand and eliminates trucks reversing in the loading area. So you benefit from a safer mine with improved truck and shovel efficiency – driving down your cost per tonne, slashing your operating expenses and taking your bottom line to the next level.

shaft area for hoisting at the service shaft. Production mining is supported by a fleet of continuous miners, battery haulers, LHDs, maintenance vehicles, and personnel carriers. So BHP is bringing together the new ultra large borer miner design with an advanced conveyor system as well as BEV rubber tyred equipment.
44 International Mining | SEPTEMBER 2022 HIGH PROFILE
On the technology side, at the recent Bank of America Smartmine conference in June 2022, BHP Chief Technical Officer, Laura Tyler said: “Jansen will be the most advanced and sustainable potash mine ever built. As a new operation, we do not have to retrofit technology and we can install at design. It will be difficult, if not impossible, for existing potash miners to retrofit and recreate the operational advantages that we are seeking to capture over the next couple of years. For example, during design we wanted to provide a proven alternative to the conventional active borer technology, so we partnered with Sandvik to look at the options…we will introduce a high degree of automation, integrated design and eventually a remote operation centre like we see at WAIO, BMA and Escondida to drive the borers of the future. We will be connected to it from surface, potentially even from Saskatoon.” Jansenisexpected to emit ~50% less CO2e per tonne of product versus the “average performer” in Saskatchewan potash mines. Underground mining and support fleet will be more than 80% electric, but BHP will pursue 100% electrification as well as aiming at all carbon neutral electricity through commercial partnerships. It will also look to implement technologies like carbon capture and storage to mitigate natural gas
Paul Moore reviews the electric, automated and supersized borer miner-based Sandvik mining systems that will be used at BHP’s advancing Jansen potash operation
Mining will be some 900 m underground, excavating the top of the Prairie Evaporite Formation. The actual mining height will be variable between 3.7 m and 4.4 m, with an average cutting height of 3.8 m.
In Stage 1, the mine is expected to produce approximately 4.35 Mt/y of potash. Jansen Stage 2 would then add around an additional 4 Mt/y. Across all four stages at Jansen, BHP has a long term roadmap to between 16 and 17 Mt of annual production. For now, global events have brought first planned production from Stage 1 forward – the company is now looking at late 2026 first production instead of 2027.
emissions in the processing plant.
Potash
The MF460 will cut a width of 6 m per cut (and as stated a height of up to 4.4 m). One cut and a return cut will be up to 1.8 km in length, leaving a room of 12 m wide. The full face mining machine has a cutting head that can vary in height and will have ground penetrating radar, to minimise dilution while managing ground conditions. The MF460 machine integrated with the EBS has been in development by Sandvik and BHP for more than a decade to de-risk this new approach, including a full-scale underground trial in a salt mine in Heilbronn, Germany that has been running for several years. In addition to the borer miner led mining system, Sandvik is also supplying a fleet of battery electric LHDs which will be integral to the support of Jansen’s underground operations. BHP has ordered 10 underground battery electric loaders along with one electric tethered loader.
mining is booming, a combination of fertiliser demand globally in conjunction with world events affecting supply from Russia and Belarus. And, as with other types of mining, a major focus for operators, existing and new, is reducing GHG emissions, while at the same time increasing efficiencies. BHP from the outset wanted to make its new Jansen potash mine in Saskatchewan as automated and as emissions free as possible. A low water footprint and low emissions were embedded in the mine design and mining method from the beginning.
IM
Tyler added: “Stage 1 will have just four mining systems,capable of producing the equivalent of 10 to 14 typical systems, able to monitor the ground ahead and adjust its mining height to match the orebody. This is a sustainable advantage, with around 60% less fleet creating around a 10% operating cost saving as well as fewer active mine faces, so therefore increasing stability, and a smaller environmental footprint. Jansen, we believe, will set a new benchmark for equipment and decision automation in the potash industry. We will have three times the number of process sensors and 10 times the number of machine health monitoring sensors compared to the next largest producer in Saskatchewan.”
Jansen’s super-sized borers
The ultra large borer miner – the cable-powered Sandvik MF460 – will be teamed with a Sandvik PO140 EBS. This integrated system is notable for being much larger than other mining machines in the Saskatchewan Potash basin. Four of these systems, developed in close cooperation with Sandvik, will each be capable of about 2.7 Mt for a total potential production capacity of 10.8 Mt/y. The MF460 led system means less workers, so a lower labour cost per tonne, but also a lower overall equipment cost per tonne of potash produced which it believes will give an operating cost advantage over other Saskatchewan potash majors like Nutrien and Mosaic.
The Sandvik MF460 has been developed in close co-operation with BHP
This, married together with the latest processing technology, means BHP expects to achieve an industry-leading recovery rate of around 92%, and Jansen Stage 1 will have approximately 50% less carbon emissions per tonne than the average in the basin and approximately 60% less fresh water consumed on the same basis. The high recovery rates will be enabled by separate fine and coarse flotation with on-stream analysis and crystallisation which recovers fine potash from waste streams.
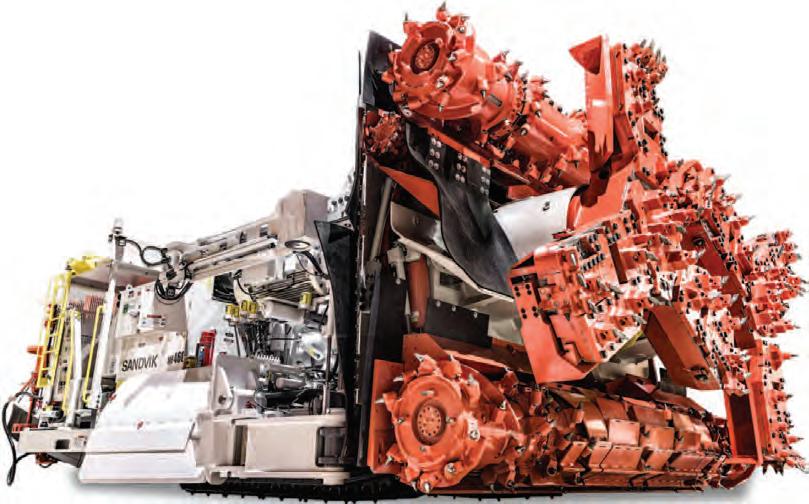
Operator safety: Elphinstone WR810 Water Cannon (Tier 4) with relay station and wireless remote
Elphinstone
The Haulmax® 3900 series truck is purposebuilt for extended distance, off-highway, surface mining applications and is available in many configurations, including dump truck, service truck water cart or tow tractor for a 160-t capacity lowboy trailer. Designed to operate on cycles of approximately 50 km, the narrow width of the 3900 allows it to work on roads 15-m wide. Increased tyre and brake capacity, plus a load management system, enable the truck to travel at higher speeds over longer distances.
At the heart of both platforms are proven Cat® powertrains featuring Caterpillar's proprietary ACERT technology and control module. The WR810 features the C7.1 ACERT Tier 3 engine arrangement rated at 168 kW (225 hp) as the standard option for less stringent emission regulations. The C7.1 ACERT Tier 4 Final engine arrangement is optional, also adhering to EU Stage V exhaust emission standards. The engine arrangement offers a dual horsepower configuration set at 151 kW (202 hp) for a higher performance rating. A reduced ventilation rating at 129 kW (173 hp) is possible through a simple software change performed by a Caterpillar dealer. The WR820 features the C11 ACERT Tier 3 engine rated at 242 kW (325 hp).
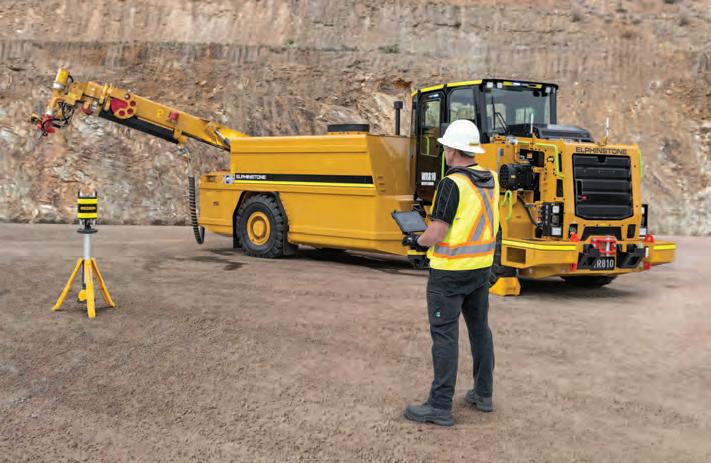
ADVERTISEMENT FEATURE
The Elphinstone W35® Water Tank module, designed to fit Caterpillar 740C, 745C and 745 articulated truck chassis, is utilised for dust suppression in the construction and mining industry. The tank has a capacity of 35,000 litres with five fully adjustable and individually controlled spray heads, a water cannon and many otherElphinstone,features.
The chassis design and component commonality of both platforms is shared across many applications, providing the highest level of reliability, durability and superior parts availability worldwide through the Caterpillar dealer network.
ELPHINSTONE PT Y LTD
Elphinstone works in agreement with the Caterpillar dealer network, providing greater reach and support to its global customers. Highly trained field support technicians provide an unprecedented level of technical support for both the customer and dealer. Dealer feedback and the ‘Voice of Customer’ (VOC) are reviewed to ensure all products are accepted and meet the requirements of the global market.

based in Tasmania, Australia, continues to support and rely upon the specialised design, engineering and manufacturing knowledge of its skilled local workforce. This highly capable and advanced manufacturing supply chain has steadily evolved over its 45-plus-year association with the global mining industry. The company continues to develop a high volume of new products, delivering over 240 machines worldwide to locations in Argentina, Australasia, Brazil, Canada, Chile, Democratic Republic of the Congo, Guyana, India, Jamaica, Mali, Mexico, Mongolia, New Zealand, Peru, Russia, Saudi Arabia, South Africa, Suriname, USA and more.
Phone: 61+ 3 6442 7777
SEPTEMBER 2022 | International Mining 45
Pty Ltd is an authorised Caterpillar Original Equipment Manufacturer (OEM) and a leading manufacturer of quality products for the global underground and surface mining industries. The product range features specialised underground support vehicles and surface mining solutions, including extended distance off-highway haulage trucks and water tanks to suit Caterpillar articulated trucks.
ELPHINSTONE UNDERGROUND AND SURFACE MINING SOLUTIONS
2 Ormsby Street, Burnie, Tasmania, Australia 7320
Elphinstone® range of underground support vehicles includes agitators, delivery trucks, service trucks, water cannons, water tanks, motor graders and other specialised support equipment. There are two base platforms, the 20-t WR820 series and the 10-t WR810 series.
Elphinstone’s dedicated sales, marketing and product support personnel travel the world helping Caterpillar dealers support their customers by conducting site visits, facilitating meetings, training sessions and providing specialised technical product support. All products come with a 12-month Elphinstone factory-backed, unlimited-hour warranty. The Total Cost of Ownership is key to any machine evaluation, with each machine designed and manufactured to be safe, reliable, productive,
Elphinstone underground support vehicles: WR820 20-t base platform, WR810 10-t base platform and M&K series graders
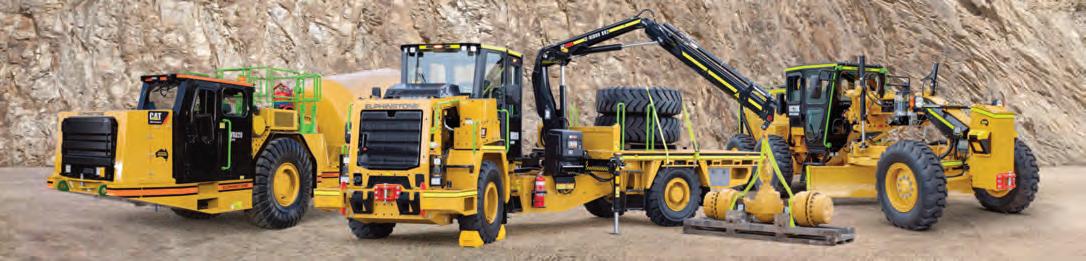
ergonomic and easy to service, maintain and rebuild.The
As an authorised Caterpillar OEM, all Elphinstone products, technical assistance and access to spare parts are available through the global Cat dealer network, supported by the Elphinstone Product Support team.
INTERNATIONAL MINING PROFILES
Email: sales@elphinstone.com
Operational accuracy is increased too for productivity gains. “Hang time reduction is one example of this. The accuracy enabled by
Finally, mining operators need to take a holistic approach when adopting Industry 4.0 capabilities. For example, in the case of autonomous haulage, you need to provide the interoperability between the mining trucks, often built with legacy WiFi connectivity in mind, into the wireless network. “This means working hand in hand with all ecosystem partners to rigorously validate solutions before they are deployed. By partnering with companies experienced in delivering end-to-end communications solutions for mines, they can implement new use cases faster.”Swedish miner Boliden is one company already experiencing the benefits of private wireless at its Kevitsa open pit mine in Sodankylä, northern Finland. A Nokia 4.9G/LTE private wireless network provides seamless indoor and outdoor connectivity across its facilities at Kevitsa, supporting tele remote vehicles and drilling, which the company plans to transition to autonomous drilling. The network also supports remote environmental measurements and quality control activities, for example, triggering alerts to a driver if they are about to dump materials in the wrong location. By monitoring equipment remotely, the company has also been able to implement preventative maintenance capabilities. Nokia has also been highly successful of late in introducing private LTE networks in Latin American copper mines to facilitate autonomous haulage fleet trials & pilots ahead of full automation implementation – recent examples include at Antofagasta Minerals’ Centinela mine plus at Codelco’s Radomiro Tomic and Minister Hales divisions.
He adds that mining companies should first implement the Industry 4.0 capabilities that will have the biggest impact on their specific operational, safety and sustainability goals.
“Talking to operations teams will help make that decision. Start with capabilities such as predictive maintenance which uses data collection of operational technology (OT) from sensors, combined with machine learning and artificial intelligence (AI) to reduce downtime and costs, and to extend equipment life.”
The increasingly autonomous mine is posing more challenges to comms networks – Paul Moore spoke to two of the market leaders in 4G LTE/5G solutions as well as the leading supplier of industrial wireless mesh in mining
Autonomous Komatsu 980E being loaded at the Minera Centinela Esperanza Sur pit
Jaime Laguna, Head of Nokia’s Digital Industries for Vertical Oil & Gas and Mining

For this reason, many mining companies are turning to 4G/LTE and 5G private wireless networks based on the 3rd Generation Partnership Project (3GPP) cellular standards. “With the capacity to support thousands of connections at the lowest latency, private wireless enables a constant heartbeat link with connected machines offering the reliability, predictability and performance that WiFi just can’t deliver.”
46International Mining | SEPTEMBER 2022
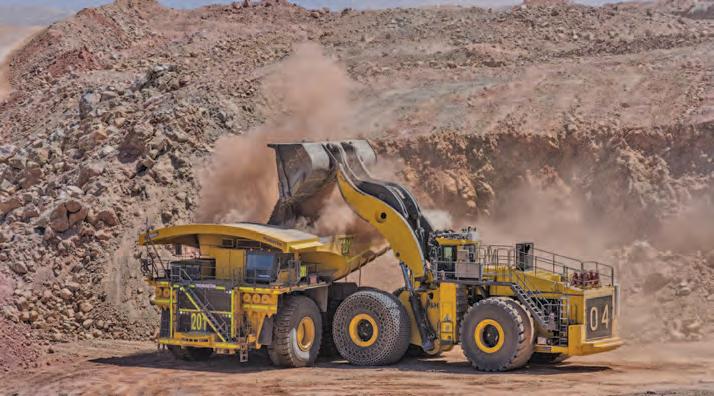
it comes to connectivity, mining has a very distinct set of challenges. Jaime Laguna, Head of Nokia’s Digital Industries for Vertical Oil & Gas and Mining told IM: “These challenges are driving the need for mining digitalisation – or Mining 4.0 – to enable compelling use cases such as data-driven operations, predictive asset maintenance and autonomous drilling and haulage, among others. With the ability to send only machines into hazardous areas, workers are better protected, while productivity gains and costs savings are enabled by more predictable behaviour. But if autonomous equipment isn’t backed by reliable communications networks, issues can occur as they can disconnect from the network, halting productivity or even causing collisions.”
autonomous operations means that a truck and shovel can be aligned perfectly the first time, reducing the time a shovel must hang idle waiting for a person to maneuver the truck into the correct position. Over time this delivers huge productivity boosts.”
Critical comms
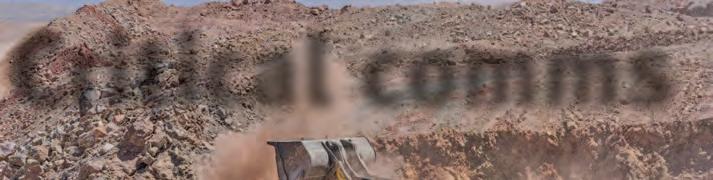
By converging operations onto a single private wireless solution, network maintenance activities can be reduced too.”
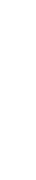
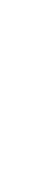
By deploying a private wireless network, mining operators can consolidate operations. Traditionally, in addition to WiFi, mines use twoway radio systems, like Terrestrial Trunked Radio (TETRA) and Project 25 (P25), for mission-critical voice communications as well as other proprietary overlay networks. Laguna adds: “Using private wireless, they can leverage the Internet of Things (IoT) connectivity of low-power sensors, support the demands of mission-critical operations and allow teams to communicate via mission-critical push-to-talk (PTT) and push-tovideo (PTV) as well as video, while also supporting broadband data and video streaming.
The mining industry is getting well advanced with the rollout of connectivity for automation of large haulage trucks. That really took off in surface mines four or five years ago with 4G LTE and this technology still dominates in terms of live deployments and it is now well established globally in all the major mining hubs including Latin America and Africa. As discussed with Ericsson’s Jeff Travers, Customer Success LeadDedicated Networks, what has changed is that there is now a big interest in taking the automation to the next level, and this is a dialogue firstly with the major equipment manufacturers. “Mines are an ecosystem and the mine needs to put a number of things together to
Automation is another use case that will deliver significant gains from the outset. Because of the predictability of movement, reduced acceleration and braking activity, and the constant monitoring of vehicle data, such as tyre pressure, a well-maintained self-driving haulage fleet will contribute to sustainability goals and costs by reducing fuel consumption.
When
MINING NETWORKS
Mine connectivity moving up a level
What do leading mines and Rajant’s network have in common? That’s why Rajant Kinetic Mesh® is deployed in more than 270 of the largest open-pit and underground mines in over 75 countries today. Our network powers 24/7 productivity in these ever-changing environments with no fiber or cell towers Autonomouslyneeded.self-optimizes to needed coverage shifts in real-time, providing mission-critical connectivity Works peer-to-peer to maintain hundreds of connections simultaneously for ‘never break’ mobility The only private network enabling machine-to-machine communications required for autonomy Mobility and autonomy with unmatched uptime. Request a free demo at rajant.com/im-mining Industrial Wireless Networks Unleashed. IF IT’S MOVING, IT’S RAJANT.

All of this means that you get to a point where connectivity is no longer just good to have, it is fundamental to the operation because we are moving from connecting just the haul trucks to connecting the whole mine operations. “You are getting into more advanced levels of automation, including the ability to use remote control to take over when needed, and remotely managed operations in general. Much of this has been sped up by economic and practical factors after the pandemic. Mines want the ability to be able to take control of equipment if there are any connectivity outages, significant labour issues, or other unforeseen events like pandemic related restrictions. It is already happening in other industries – in the logistics industry for example, some warehouses are moving towards remote control forklifts, where operators in one central control office will control forklifts at multiple warehouse locations. The same applies to mining, where Integrated Remote Operations Centres manage autonomy and remote control where applicable across more than one site.”
Travers added that automation does not mean there are no workers onsite, it just puts them in different places and with different roles. You have the mentioned remote operations centre autonomous controllers and remote control operators; but you also still have core maintenance teams on site who need to be able to interact with the autonomous equipment. Several studies are underway into how onsite workers will effectively and safely carry out their roles alongside diverse connected equipment
For more than 20 years, the Zijin Mining Group has regarded scientific and technological innovation as its primary driving force, becoming it says one of the few multinational mining companies in the world to be equipped with autonomous system technology and engineering management capabilities, with a well-established scientific research system and practice platform,” Fan Zhiyu, MD and CEO of Nkwe Platinum Ltd, said. “In May 2021, at the mine launch, we stated that we would build the Zijin Garatau Platinum Mine into a project with advanced technology, solid safety, and environmental protection practices. The adoption of this 5G smart mining solution will certainly enable the Zijin Mining Group to deliver on that promise, and to establish the mine’s technology-led global competitiveness.”
At the same time, workers will require new tools to augment their capabilities, to be effective in a digital environment and alongside new technologies in the field. Stepping up to the next level of automation for a mine and worker augmentation is also a big investment and business case to make – “one of the things we help them to do is de-risk that decision by engaging with the ecosystem including the OEMs so that when the time comes the miner knows that its equipment suppliers are both ready and capable. It is a key requirement that if a mine adopts a certain technology like 5G, that the main equipment suppliers can support it. And we work with the OEMs to ensure that as they build 5G into their machine, that it will perform to the specifications needed – that it can handle the uplink and latency and resilience. This also means we work with the device vendors who put gateways and modules into the equipment – we test them within Ericsson first in cooperation with the equipment OEMs.”
Another development in 360 degree mine connectivity is more intensive deployment of sensors. The whole sustainability argument is looking at how do ensure mines have less of a carbon impact – and to know about your Scope 1 emissions in detail and in real time for example, you need data about the mine environment and how your equipment is operating. “To ensure energy efficiency and sustainability you will only activate autonomous equipment when it is needed, and underground bring ventilation online when it is needed. Greater autonomy also means preventative maintenance becomes much more important.”
bring advanced automation into play, including the connectivity layer which needs to be supported by the ecosystem and the haulage and drilling equipment suppliers themselves have a role to play. These companies are looking at a different sort of automation – namely smaller and more widely deployed autonomous and remotely-controlled vehicles, including for the underground fleet as well. The mines are turning to the equipment providers saying we want more automation and remote control beyond the large haul trucks – what can you do for us? The OEMs need to be a couple of years ahead of the cycle, so they are building capabilities into their equipment now which they can then put into the market in the coming years.”
Nkwe Platinum Limited and South Africa Zijin Platinum (Pty) Ltd (wholly owned subsidiaries of multinational mining company, the Zijin Mining Group), have joined hands with African telecommunications giant MTN and global ICT provider Huawei, and signed a collaboration agreement to build what they say is the southern Africa region’s first 5G-enabled smart metal mine.
Zijin joins hands with MTN and Huawei
In terms of use cases, Travers referred to NEXGEN SIMS as a good example of what is NETWORKS
48 International Mining | SEPTEMBER 2022
MTN and Huawei are to provide 5G-based ICT solutions for the smart mining requirements including, not only high-speed 5G broadband access, but also smart mining solutions like vehicle remote control, IoT, and enterprise digital transformation. “Once complete, the mine will mark a significant step forward in the digital transformation of the local mining industry. It will effectively demonstrate how a number of emerging technologies can be combined with 5G to improve functions across the mine.”
Jeff Travers, Ericsson Customer Success LeadDedicated Networks
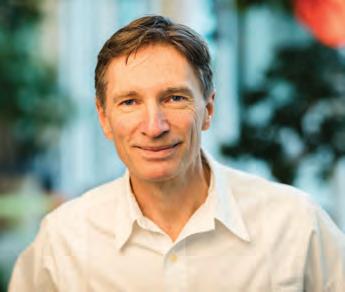
MINING
In terms of network capability and performance, Ericsson of course would emphasise that LTE and 5G are hugely powerful. “But there is another point to be made in terms of ecosystem support – you want to know that you current product and device gateway fit together, but there will be add ons – more products. What the whole smartphone world proved was that if you standardise certain technology and interfaces, which was done in the telecomms world with 3GPP, you open up things for very fast product development across many companies. So you quickly build a rich ecosystem to draw upon which gives you choice but also brings down the cost and the price. As mines becomes more autonomous ecosystem support will become an important factor.”
and be empowered in largely automated mines. So do technologies like WiFi and wireless mesh still have a role to play in the autonomous mine? “There is always a place for those technologies, it just depends what you want to do with them. But I would say that often they are not economic for wide area coverage and heavy capacities. Also for those who want a certain level of latency consistency and reliability they may not be enough. For remote control for example, you want a 75 millisecond round trip –say for remotely operating torque tools for remote maintenance, WiFi will not offer the required consistency as there will be latency spikes, then the remote operator will experience drops and freezes when the tool does not respond smoothly and instantly. Overall, mines will still use WiFi for the right use cases. But for the functionality they want to bring in now, they are looking to go straight to 5G.”
TELEMETRYVIDEOWI-FIRFIDVOICE We get you through the last mile quicker. Race to the Face. “THE FIRST GIGABIT NETWORK PROVIDING BOTH DATA AND POWER USING COAXIAL CABLE.” maestrodigitalmine.com Plexus PowerNet™ Plexus PowerNet™ delivers a high speed, low latency digital communication network that provides PoE+ power to Wireless Access Points, cameras and any IP based device. The system eliminates the need for costly outside fiber optic contractors and can be installed and maintained by any internal tradesperson.
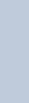



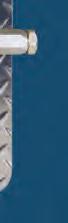
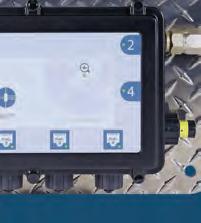
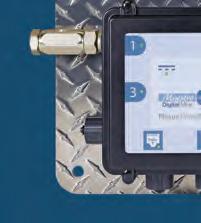



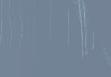





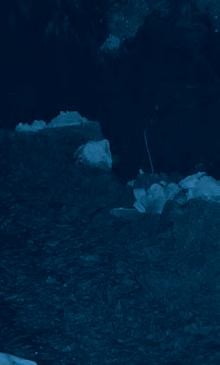
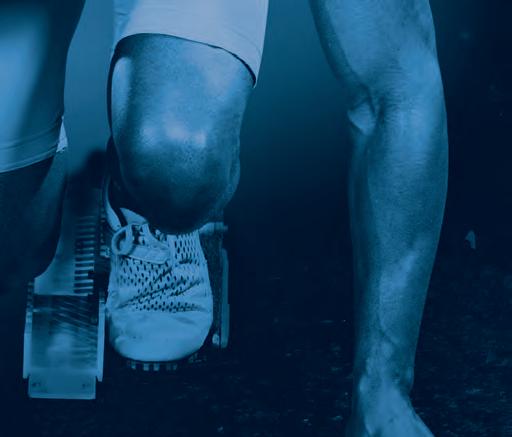
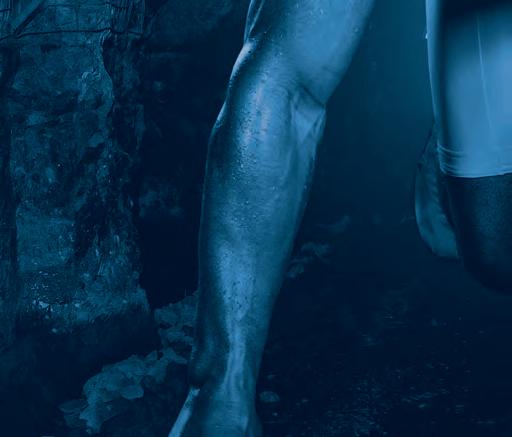

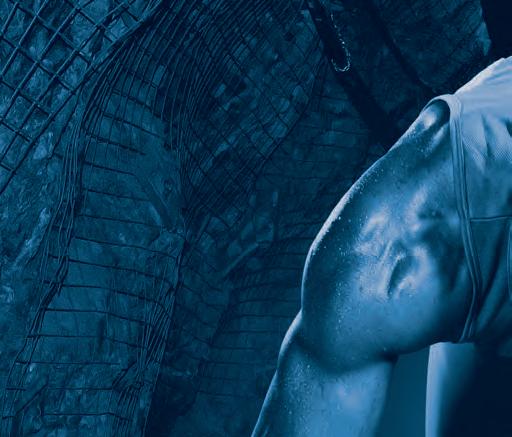

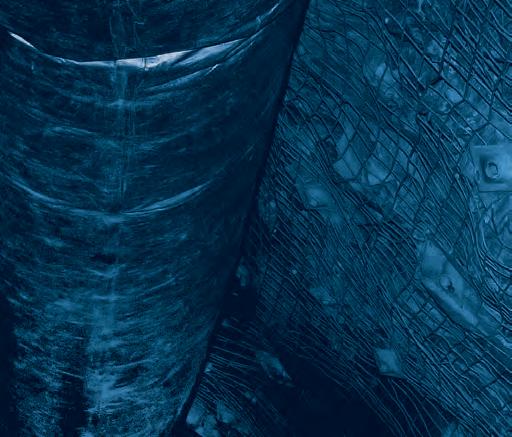

Intelligent Communications Solution for Mining can help the industry realise the benefits of digitalisation. It provides a highly transportable end-to-end broadband solution including terminals, network, data centre and command and dispatch centre. It is capable of supporting sophisticated automation, data analytics, and all the voice, video, data and M2M/IoT applications used in the mining industry.”
“Hytera's communications solution supports a rich ecosystem of real-time intelligence, which enables teams to work more efficiently, productively and“Thesafely.”Hytera
“To enable collaboration and digital applications at our mining and processing sites, we require widespread, high-speed connectivity,” said Chuck Holley, Global Manager of IT Network Infrastructure, Albemarle. “A private LTE/5G network is a great way we can do this costeffectively, and NTT was our first choice to pilot a design, prove the technology and show the value. With a private LTE/5G network, we’re able to continue to seek out innovative solutions to some of our most pressing challenges.”“We’reincredibly proud to be partnering and consulting with Albemarle on this innovative pilot,” said Parm Sandhu, Vice President, Enterprise 5G Products and Services, NTT. “A private LTE/5G network will continue to transform business outcomes in mission-critical environments for Albemarle, and this is just the start of their journey. We look forward
MINING NETWORKS 50 International Mining | SEPTEMBER 2022
NTTdevices.worked closely with the manufacturer to determine the best use of connectivity dependent on the location or use case, always enabling the best possible coverage. Following the pilot in Kings Mountain, Albemarle plans to roll out the network to additional sites.

Hytera's solutions have been successfully applied in the mining industry where they have helped customers solve their communication problems. For example, JSC AK Altynalmas has deployed a Hytera Hytalk (PoC) LTE platform and terminals in Kazakhstan, while the Letpadaung Copper Mine in Myanmar is using an integrated Hytera DMR and LTE solution.Hytera's Intelligent Communications Solution for Mining it says provides instant voice, video and data communications to deliver team members the information they need to know to carry out their work.
The various technologies can all be managed using one unified command and visualised dispatch centre and a remote control centre, which receive and distribute real-time information from and to the field operations. The network infrastructure also supports intelligent data analytics and artificial intelligence applications.
to working closely with the manufacturer as it continues to digitally transform its business for the future.”
NTT has deployed a pilot private LTE/5G and WiFi network at Albemarle’s hard rock lithium mine in Kings Mountain, North Carolina
Operatingpowders.mining and manufacturing facilities across three continents, Albemarle needed a network that would allow its global engineers to connect with technicians for remote site surveys and assists. Previously, it was difficult for global engineers to visit Albemarle’s site due to COVID-19 travel restrictions, which significantly impacted the process of decision making and timing. The use of private LTE/5G will enable Albemarle to enhance its hybrid working process and reduce the amount of global travel needed to operate.
The fully 3GPP-compliant 4G/5G solution provides a complete wireless broadband network including radio access network (RAN), backhaul, LTE core, device and network management. Multiple services can be run simultaneously over the high throughput and resilient 4/5G network, including: Mission Critical Push-to-X (Voice/Data/Video); real-time video streaming; telemetry/SCADA; and M2M/IoT sensor monitoring. Low latency transmission rates (< 100ms) enable precise control of remote automated operations.
Utilising NTT’s global expertise in connectivity, Albemarle can now use integrated technologies to ensure that surveys, assists and maintenance activities can be conducted remotely. Albemarle is also looking at additional use cases to leverage wireless networking at their manufacturing sites. A private network provides the organisation with enhanced security, high technology performance, and coverage to enable IoT
Other players in mining private LTE
While the market for 4G LTE and 5G in the mining industry is led by Nokia, Ericsson and Huawei – there are other players out there which have had successes in mining – two examples being NTT and Hytera NTT Ltd, a world-leading global technology services provider, announced in May 2022 it is working with Albemarle Corp, the speciality chemicals company with leading positions in lithium, bromine, and refining catalysts, to deploy a pilot private LTE/5G and WiFi network at Albemarle’s hard rock lithium mine in Kings Mountain, North Carolina. The 800 acre site sits on one of the richest spodumene ore deposits in the world. In addition, this site produces battery-grade lithium hydroxide, lithium bromide, lithium chloride, USP-grade lithium carbonate, high purity lithium carbonate, battery grade lithium metal products and lithium alloy
Ready anything 4.0@nokiaindustries Ready anything 4.0@nokiaindustries Our mission-critical networks are ready for digitalizing your mining operations. One reliable and predictable network for open pit and underground mines. nokia.ly/mining nokia.ly/mining The connected digital mine will improve safety, sustainability, productivity and efficiency. Private wireless networks are the key to making your mining automation work.
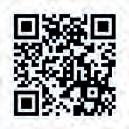
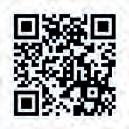


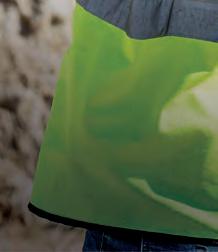
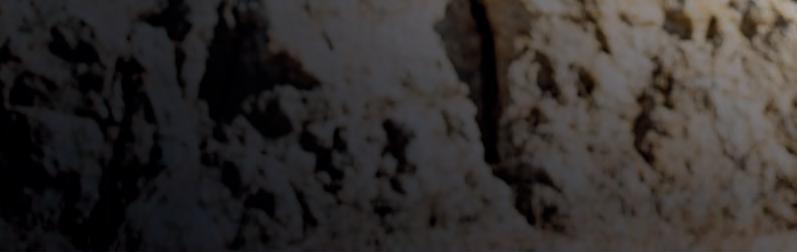
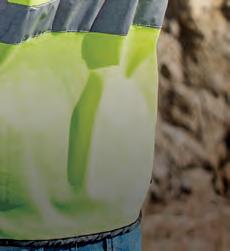
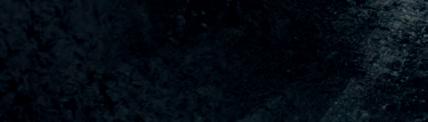
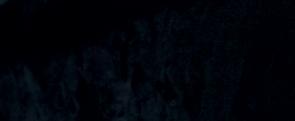
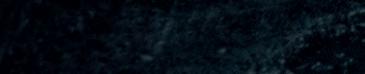
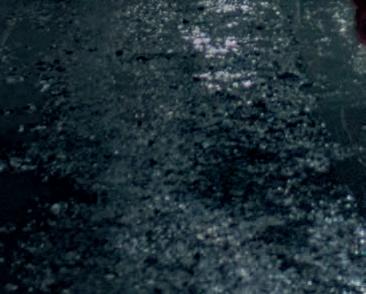
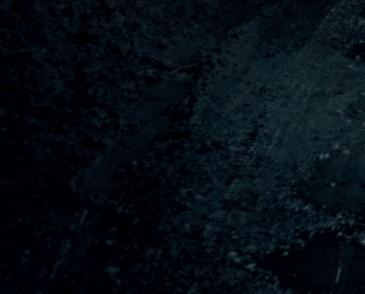

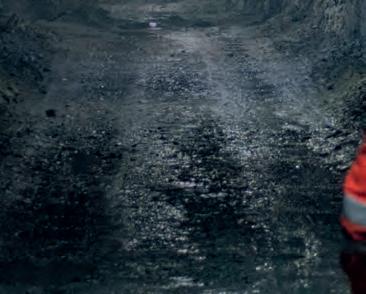
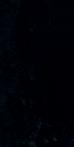
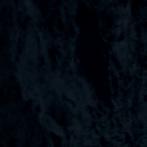
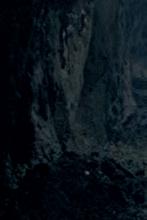
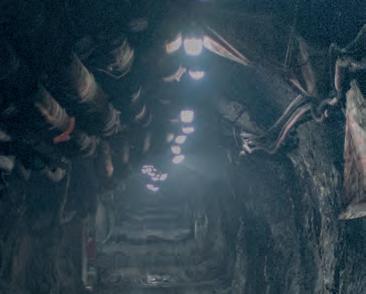
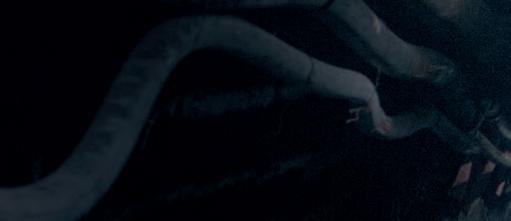

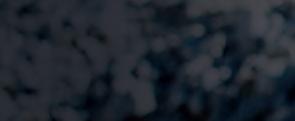
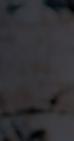
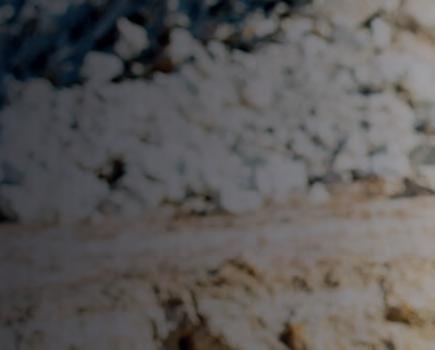

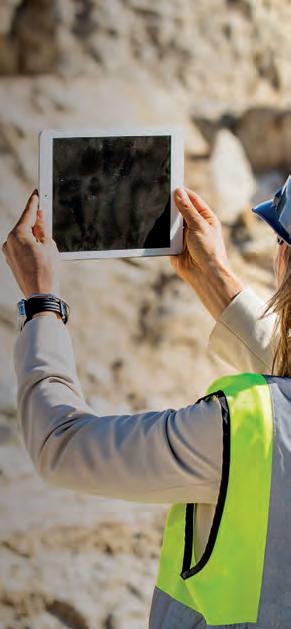
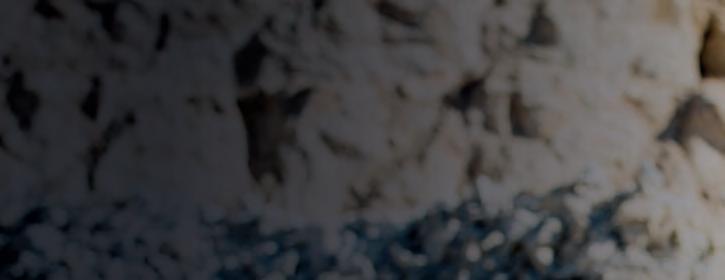
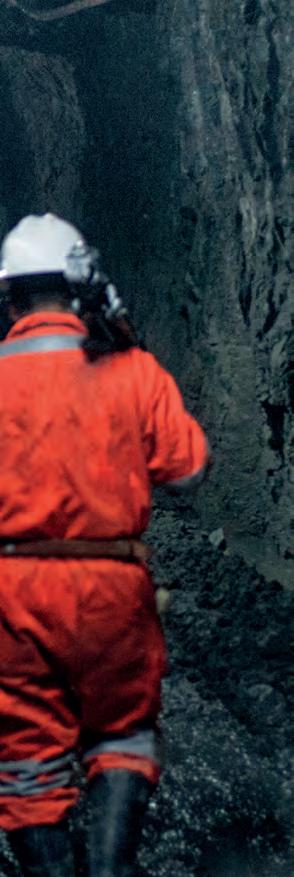
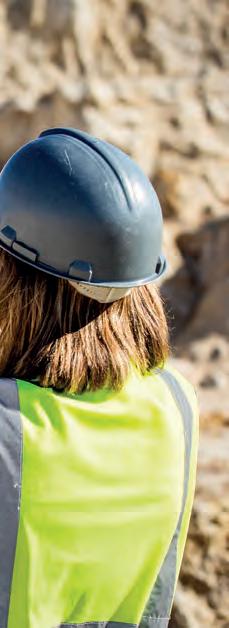
“Improving the operational safety and productivity of mining operations is the byproduct of Rajant Kinetic Mesh. It is the only industrial wireless network enabling machine-to-machine (M2M) connectivity and mobility in markets like open-pit and underground mining,” shares Geoff Smith, EVP of Sales and Marketing for Rajant.
being done. “At that R&D project we are working with total visibility. It has brought together OEMs like Epiroc and connectivity companies like Ericsson with major miners like Agnico Eagle, K+S, OZ Minerals, KGHM and Boliden. We are responsible for the connectivity part; specifically what connectivity is needed for next generation autonomous (and electric) equipment functionality. One focus area is intensive use of autonomous loaders and trucks to be able to work through post blasting downtime. Then you have the use of drones and sensors for monitoring for gas as well as visual observations. Another work program is focused on rock stress testing in a mixed human and autonomous environment.” The load and haul program is well advanced now, with technology vendors and OEMs looking to deploy the new capabilities into machines for commercial availability. The drones program is also advanced while the rock stress testing element is at an earlier stage.
As another discussion point, how does Ericsson operate effectively in country where mines are located? “It is important that new technology gets introduced consistently and commonly as there are multiple mine locations and diverse players. A lot of the dialogue we have had up to now with mines now is about ‘the pilot mine’ but now they are saying this is not enough, they want to talk about rollout in several of their mines across different countries. They want to know that they can be sure that the connectivity environment they have for the pilot mine will still apply for their mines in a different continent. They want to know from us that the tech applied will be the same and perform the same. This is another important discussion with the OEMs – making sure that the tech standard which the OEM expects and requires of the mine when it sells its latest autonomous equipment, is handshake with us and therefore will work in whatever countries it is required to.”
Rajant is already co-deployed on Komatsu mining equipment in more than 100 mines globally and is now ready to support Komatsu’s autonomous solutions. “Achieving Rajant certification with Komatsu reflects the work of many individuals and addresses a key request from our mutual customers to continue utilising both companies’ advanced solutions,” shares Sagar Chandra, Vice President of Sales –Americas.
Rajant gets key OEM autonomous validations for Kinetic Mesh
instrumental in allowing our joint customers to scale their autonomous solutions. This includes not only Epiroc drills but opens the door for all connected equipment at the mine site.”
Private LTE is by no means the only option for mines wanting to go autonomous. Rajant
Finally, there is an important role telecomms partners. “Increasingly the major mining houses turn to the major telecom operators they trust, and work with them to design and architect a network blueprint for their mines, with our 5G technology at its heart. They then hand over network deployment and operations to the local in-country telecomms operator with the required spectrum, which may or may not be a subsidiary of the global telecomms company that designs the blueprint. We are often the middle trusted party in that dialogue. It works smoothly as the system has been designed centrally but with the local requirements factored in.”
IM
“Unlike other wireless networks that are dependent on fixed infrastructure, Rajant mobile BreadCrumbs can communicate with each other allowing machines to interconnect which adds additional layers of connectivity and redundancy while Rajant networking software InstaMesh® is self-optimising to overcome the constant environmental changes, data loads, interference, and on-the-move requirements of modern mines.”
Rajant and Epiroc have announced successful validation of Kinetic Mesh® wireless networks for both semi-autonomous and autonomous drilling
Rajant and Komatsu, developer and supplier of heavy equipment and services for the construction, mining, forklift, industrial, and forestry markets, have achieved Rajant certification for Komatsu’s FrontRunner® Autonomous Haulage Solution (AHS). Validation for FrontRunner AHS was completed in just six months.“Reliable communications networks that offer continuous mobile connectivity are crucial to successful autonomous haulage operations,” said David Haukeness, Komatsu’s Product Manager for autonomous systems. “Rajant’s low-latency Kinetic Mesh and support for LTE and WiFi make their network a key part of our efforts to help our customers achieve their autonomous goals.”Komatsu’s FrontRunner AHS uses a wealth of onboard technology and requires continuous, reliable wireless communication with the central office. Rajant Kinetic Mesh machine-to-machine (M2M) InstaMesh technology provides autonomous solutions like Komatsu’s FrontRunner AHS with higher reliability and network resiliency with low latency, which is critical to maintaining ‘always-on’ connectivity for autonomous machines.
Adds Brian Doffing, Epiroc’s VP of Integration: “Rajant’s unique technology offering has been
Corporation, the pioneer of Kinetic Mesh® wireless networks, has recently announced key validations for its connectivity solutions with two of the leading OEMs in autonomous mining –Epiroc and Komatsu. Rajant and Epiroc, the major equipment supplier & productivity/sustainability partner to the mining and infrastructure industries, have announced successful validation for both semi-autonomous and autonomous drilling. As part of the validation, deployment best practices guidelines were created to support the deployment of Epiroc drills with Rajant BreadCrumbs®Epirochasa permanent deployment at their test facility in South Africa to demonstrate semiautonomous and autonomous drills using Rajant BreadCrumbs. Rajant is deployed on dozens of semi-autonomous and autonomous Epiroc drills globally, some of which include semiautonomous drills at Anglo American’s Sishen (iron ore), Mogalakwena (platinum) and Los Bronces (copper) mines plus autonomous drills at Exxaro’s Grootegeluk coal mine.
MINING NETWORKS 52 International Mining | SEPTEMBER 2022

Learn from more than 450 mining leaders and resource experts with six concurrent conferences covering the entire mining value chain. Gain strategic insights from c-suite executives on minimising disruptions and building resilience, progressing ESG, accelerating mining’s energy transition and the future workforce. Whilst technical talks will delve into exploration, discovery and project developments, minerals processing, digital technology, and mining innovation.
Across three days, there are thousands of opportunities to network, brainstorm, and knowledge share, providing the perfect platform to obtain invaluable new business contacts, connect with the industry’s leading figureheads and explore new ideas.
Meet over 7,500 decision makers, mining leaders, policy makers, investors, innovators, and educators from more than 100 countries. As the largest gathering of mining professionals in Australia, IMARC provides unmatched networking opportunities, serving as the meeting ground for the mining industry.
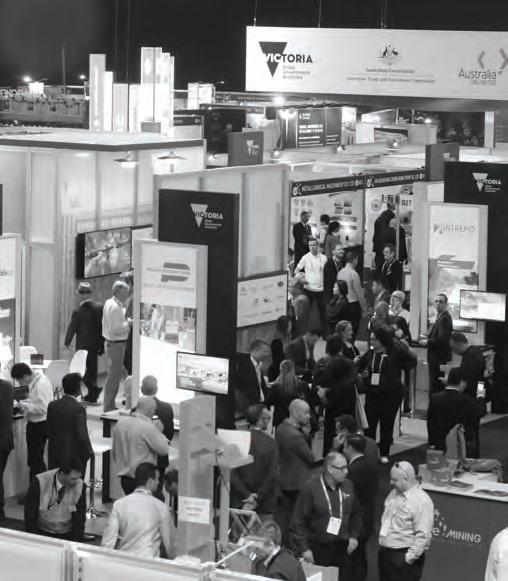
WHERE GLOBAL MINING LEADERS CONNECT WITH TECHNOLOGY, FINANCE AND THE FUTURE
VISIT IMARCGLOBAL.COM TO REGISTER FOR AUSTRALIA'S MOST INFLUENTIAL MINING EVENT AND RECEIVE 10% OFF WITH THE DISCOUNT CODE IMINING10

As Australia's largest and most influential mining event, IMARC creates a global conversation, mobilises the industry for collaboration and attracts some of the greatest leaders in the mining, investment, and technology industries for three days of learning, deal-making and unparalleled networking.
The International Mining and Resources Conference (IMARC) is where global mining leaders connect with technology, finance, and the future.
2 - 4 NOVEMBER 2022 | ICC SYDNEY
Discover inspiration and new ideas, find practical solutions, and see demonstrations of the latest products and innovations from startups through to some of the biggest names in the mining industry with more than 470 exhibitors throughout the 17,000m2 expo floor all under the one roof.
All of this means that 2023 is arguably the most significant year in the history of mine haulage, as the electrification transition progresses at pace and becomes a reality. Likewise, mine energy infrastructure is having to evolve to support this
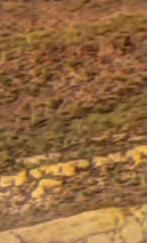
Michael Bobotis Engineering Coordinator, Open Pit Mining Hatch
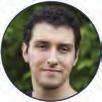
Max Luedtke Global Head of Mining ABB
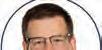
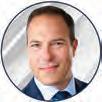
MAY 23-25
Mine conference since 2019, therefore, is a vitally important gathering to bring key stakeholders together – OEMs, mining companies, contractors, consultants, component suppliers and think-tanks.
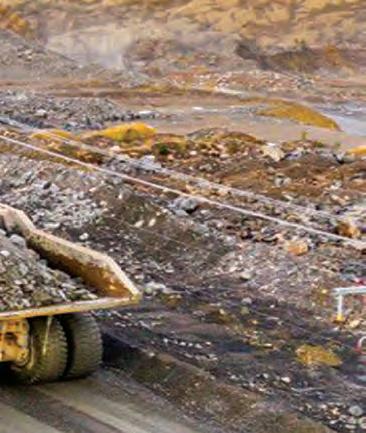
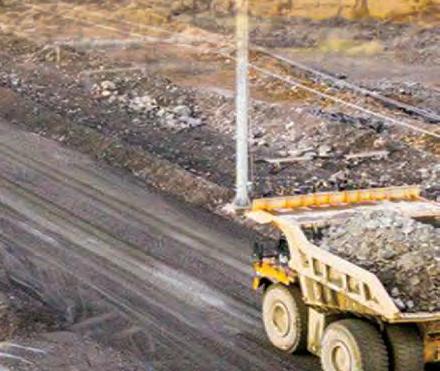
Marie-France Laurin Director of Business Development, Generation AV Stantec President Sandvik Mining and Rock Solutions
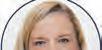
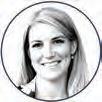
We are now at a crossroads with surface and underground mining fleets, as the industry works to meet interim reduced emissions and final net zero targets. A big part of that is moving away from diesel to reduced or zero emission alternatives, whether that be battery, hydrogen, e-fuels or hybrid combinations.
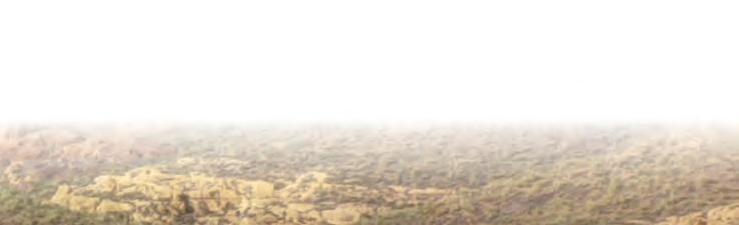
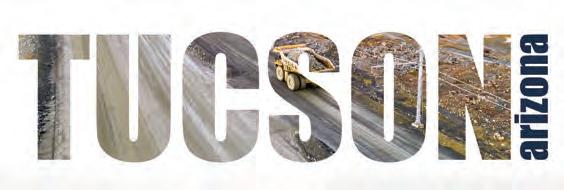
Jess Kindler President, Parts and Services Epiroc
The Westin La Paloma Resort & Spa
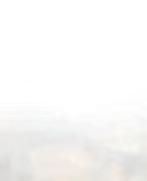
Barry Flannery Founder and CEO Xerotech
This,transformation.thethirdElectric
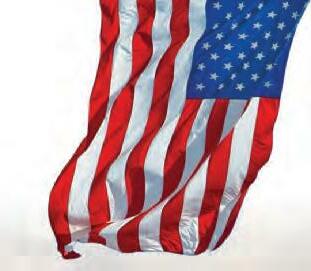
The world’s only global mine electrification event

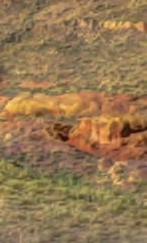

Denise Johnson Group President - Resource Industries Caterpillar Inc

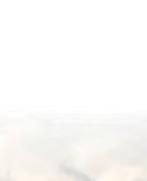
Trolley assist and in-pit crushing & conveying, until relatively recently seen as inflexible or costly options, are now ramping up fast due to favourable economics, while ventures like the Charge On Innovation Challenge and the Electric Mine Consortium are using collaboration to overcome issues like charging strategy and infrastructure.
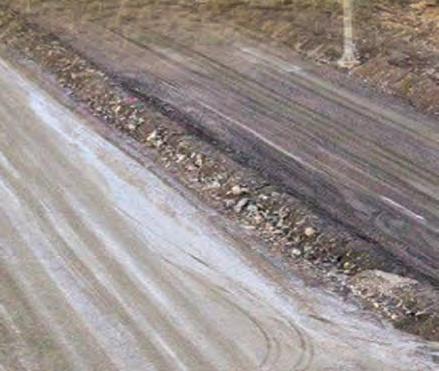
Bappa Banerjee Vice President Mining Equipment Wabtec
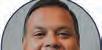
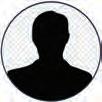
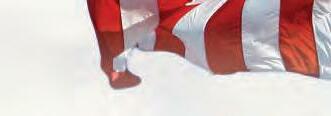
Headline presenters for The Electric Mine 2023 include:
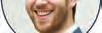
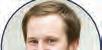
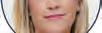
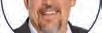


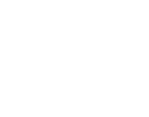
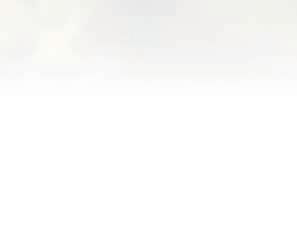
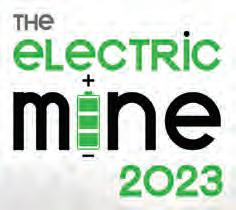

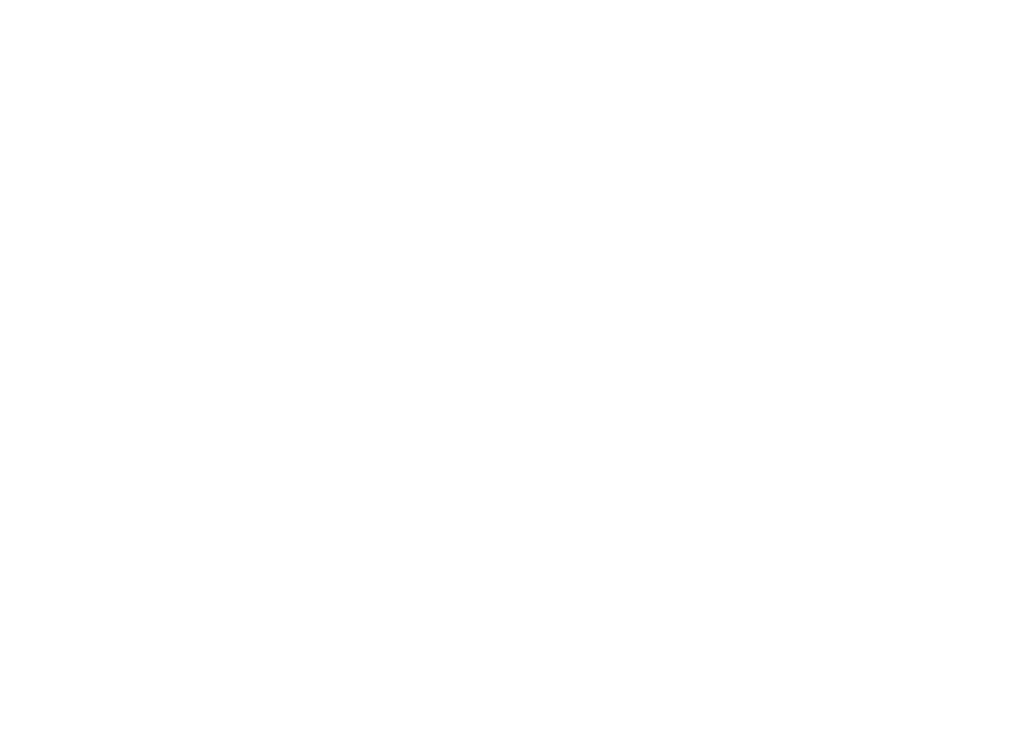




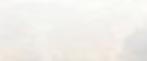
IPCC & Electric Mine come together!

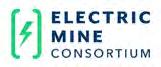
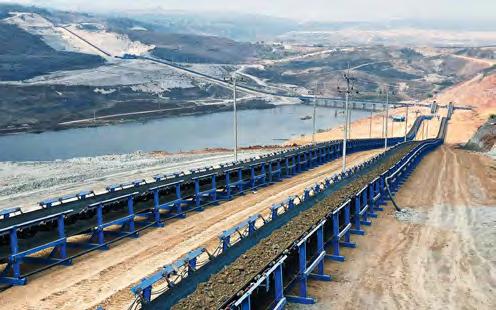

@theelectricmine www.theelectricmine.com#TheElectricMine
SUPPORTER PLATINUM SPONSORS GOLDGREENSPONSORSSPONSORSSHOWCASE SPONSORS
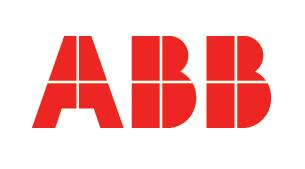


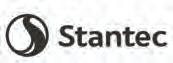
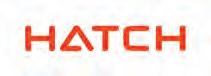
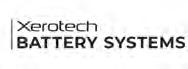
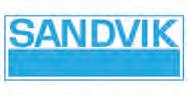
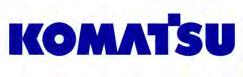


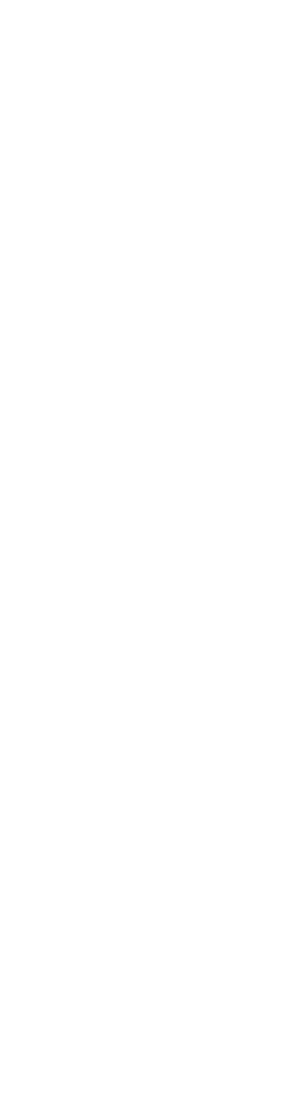


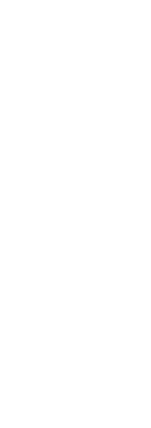
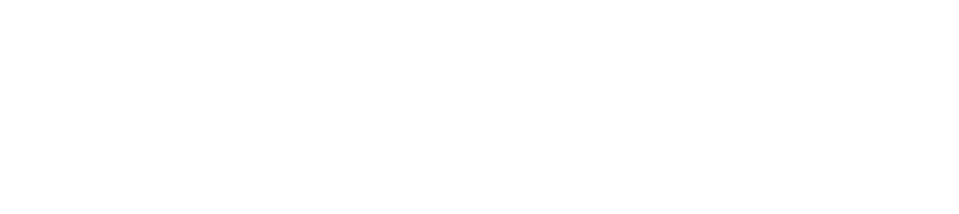
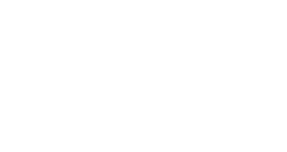
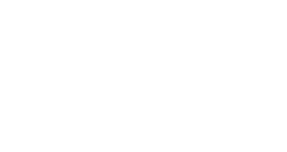
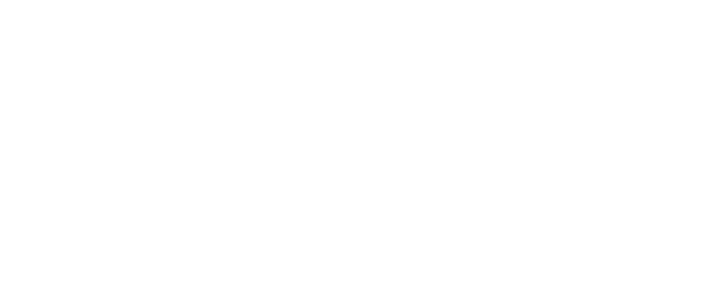
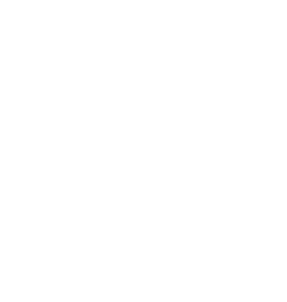
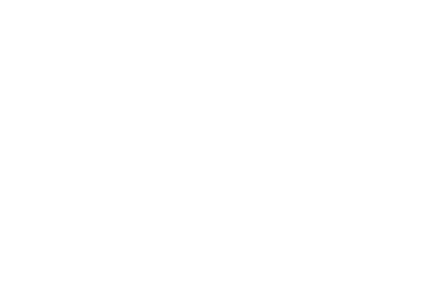


Our longest established conference, running since 2011, is In-Pit Crushing & Conveying (IPCC) – venues having included Brazil, Germany, Chile, South Africa, Indonesia and most recently, Mexico. In 2023, we took the decision to bring it into our larger Electric Mine event in Tucson as a dedicated full day, standalone gathering.The main reason for this is that IPCC represents such as crucial part of helping miners reach 2030 interim and 20 0 final decarbonisation targets – both through truckless mines as well as using elements of IPCC to allow for reduced truck fleets and shorter hauls. Conveying and stacking equipment also play a vital role in helping mines manage waste and tailings without large haulage fleets.
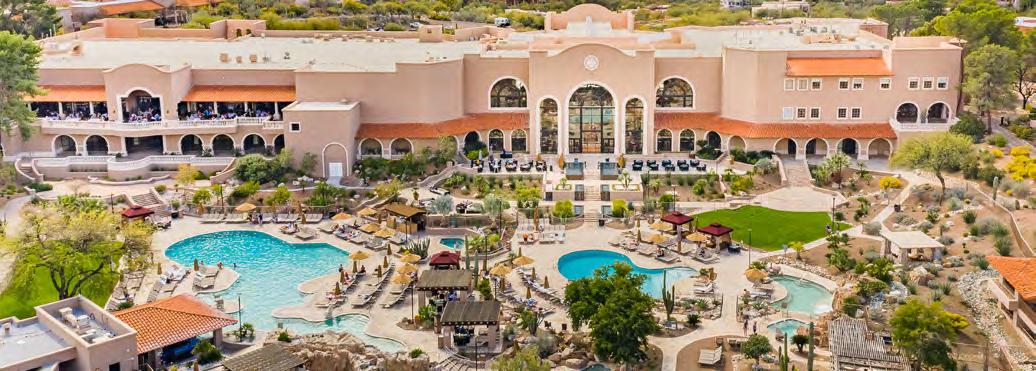
The market is also changing from level 4 automation to level 5 – where no controller interaction is needed at all and where the trucks
Then the elephant in the room is how to marry autonomy with the transition away from diesel. Again this is being worked on – mainly by the big OEMs currently as they know they have to get there to make the zero emissions solutions work in the first place, accounting for battery charge management. Even autonomous trucking under trolley is something not yet achieved in the market.Sothe mining truck market is becoming more
AHS for the masses
In this extensive look at fleet automation in open pit mines, Paul Moore reviews how fleet autonomy is diversifying in scope into smaller trucks & ancillary vehicles but with an eye on keeping it economically viable
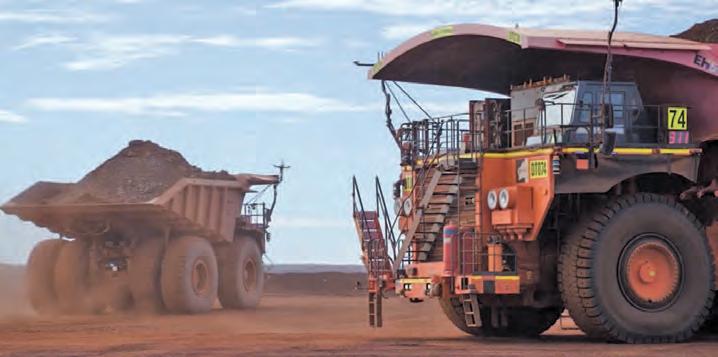
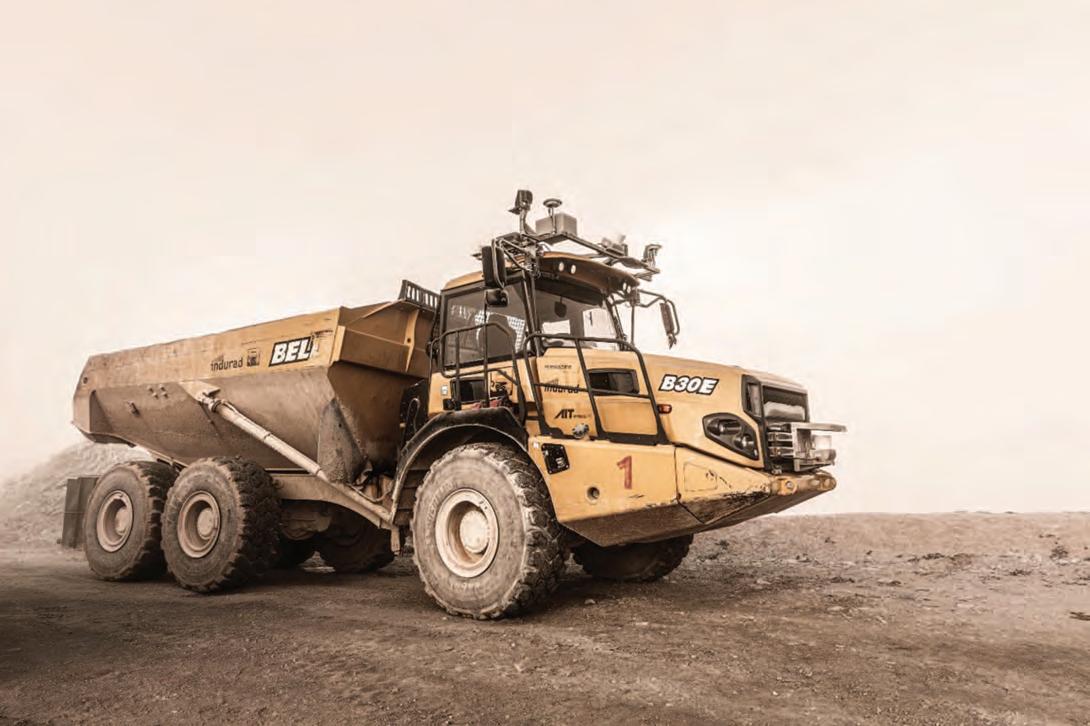
Bell B30E fitted with xtonomy AHS kit
These systems are by nature expensive, and increasingly require the latest network infrastructure such as 4G LTE to function efficiently, depend on controller input in certain situations, plus with the exception of the Roy Hill project still lock the user into a particular fleet management system – Cat AHS still requires the use of MineStar and Komatsu requires use of Modular. But they are very well proven and the benefits have been enormous both from a safety and efficiency point of view. And it isn’t just about a few first mover operations today – Caterpillar told IM it now has 540 autonomous mining trucks operating (this is an increase of 40% from 2020). This is across 23 sites and with 13 separate customers. Komatsu’s numbers are similar.
make AI-based decisions, such as how to react to an unknown obstacle themselves. This is happening in two ways – Cat and Komatsu are already making updates to their systems to allow machines to react on the fly, while the new players are aiming to embed these capabilities from the outset.
Autonomous Cat 793 and Hitachi EH5000 trucks at Roy Hill mine running on ASI Mining system
in surface mining is changing and it is changing fast. Up until now, and still today, the market more or less 100% consists of automation of large primary rigid haul truck fleets, working with either Caterpillar or Komatsu and their Command for Hauling or FrontRunner systems respectively, with a couple of exceptions – Hitachi Construction Machinery (HCM) having its system running at one site in Australia, and ASI Mining close to handing over its solution that it has supplied to Roy Hill via an overall mine contract with Epiroc.
Autonomy
But there is also a second market for autonomy – mines want the benefits of autonomy for mixed fleets, for ancillary machines and for smaller machines. There are several reasons. Some big miners are looking at using larger fleets of smaller trucks to reduce maintenance and other costs, including for longer hauls and
ASI’s technology is also aimed at a more open solution, an example being it forming part of Liebherr’s open autonomy offer, which includes interoperable autonomy products for mixed fleet applications. Hexagon technology, including its autonomous mission management system, will also be used in the mine automation options offered by Liebherr to customers.
56 International Mining | SEPTEMBER 2022
not restricting trucks to the pit itself; while smaller miners and quarry operators want a more flexible and open solution. Of course the big OEMs are working on this, and some details are given later, but a raft of new autonomy players are working on it too – companies like Wenco with Oxbotica, ABD Solutions, Steer, SafeAI, Pronto, xtonomy and Auto-mate.
TOPROCKTECHNOLOGY.SANDVIK/TH-XLHAMMER XL: EXPAND THE LIMIT OPEN UP A WORLD OF POSSIBILITIES Our latest innovation in top hammer drilling is proof that a seemingly marginal difference can make a significant change. With the Top Hammer XL drilling system, you can now drill 140 to 178 mm (51/2" – 7") blast holes, more fuel-efficient and cost-effective than before. The components of the systems – Pantera™ DP1600i drill rig, RD1840C rock drill, and LT90 rock tools – are all designed to work seamlessly together for optimum drilling performance and, at the same time, a radical reduction of your CO2-emissions. Want to know more about the benefits? Contact your local Sandvik sales office or visit www.rocktechnology.sandvik/th-xl to discover more and try our Top Hammer XL calculator.
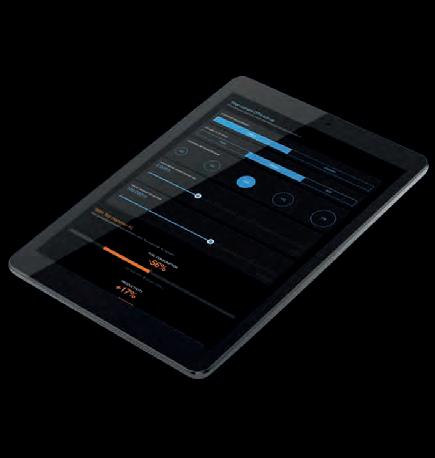

Butetc.Pyne
open and customised in terms of power source, but also in terms of autonomy. The big miners will likely stick with the established OEM AHS systems for new mines and new fleet replacements. But for existing fleets, mixed fleets, ancillary machines, new projects involving smaller class trucks, they are likely to also consider other options – both the OEMs and the newButplayers.toomuch diversity across different operations even within the same company is also likely to create inefficiencies – these new technologies have to introduced only where it makes economic and operational sense to do so. The reality is that there remains a lot of uncertainty as to how the mining industry will look by 2030 and that applies to autonomy, power source, battery strategy (charging or swapping) if using battery, the right size of truck…the list goes on. For some mines there is no doubt that a better option may be to go truckless with IPCC if it is economic. For others the solution may be different set-ups at different operations.
Based on what Wenco has done already and commitments that customers have already made, Pyne said he is confident that there will be major mines running larger fleets of smaller class autonomous trucks, certainly by 2030 and maybe even earlier – but probably not before 2026. While NDAs mean details cannot be released, Wenco and Oxbotica have an autonomy pilot running at a major mine in North America, currently on a 220 t unit and going through multiphase testing but with a view longer term of using it on smaller class electric machines. Pyne said the value proposition was the ability to retrofit and get the benefits of autonomy from existing fleets, but also to be able to keep control of your mine and allow you to buy whatever truck you want. “It also provides the customer with a lot more data than they are
58 International Mining | SEPTEMBER 2022
Wenco International Mining Systems, owned by HCM, is one company that is confident of the new value proposition level 5 open autonomy brings to mining’s new level playing field. President and CEO Andrew Pyne told IM: “We committed ourselves to drive meaningful change to the autonomy paradigm back in 2017 because our Wencomine FMS customers wanted to start their autonomous journey but didn’t want to be forced in to using another FMS. We decided to go down the open autonomy route in a way that was right for the industry and would allow us to compete on our merits. We set out to be an innovator and disruptor, and some major miners that had little interaction with us have already told us they see us as a next generation autonomy provider. While it might seem altruistic, we believe we will be rewarded in time by focussing on new value creation for the customer. What started as a concept has moved on to some intensive engineering collaborations, but this is new technology so the projects will take time to mature.”Itsactive projects also include the ASI/Epirocled project at Roy Hill, as Wencomine is the inplace FMS, which has provided invaluable experience as part of the world’s most advanced mixed fleet and OEM agnostic AHS project to date.Ithas
A new level playing field
also been closely involved in testing and trials relating to the option of using larger fleets of smaller trucks in West Australian Iron Ore mines. Pyne told IM: “The value proposition is that for the next generation of their iron ore mines, the big players need to either build more
AUTONOMOUS SURFACE MINING
cycle – increasingly the digging part will remain manual as that’s where the operator feel really exists, but the swing and load elements will be automated.”Intermsof the number of trucks increasing to many hundreds of smaller class machines, Pyne also believes that the use of mobile surge loading – in the form of the patented MMD Fully Mobile Surge Loader – will become more important, to decouple the excavator from the smaller trucks. This will of course allow mine operators to keep their existing large excavator fleet, while avoiding excessive queueing and represent more of a continuous loading process. What about the fleet management layer? “This is a big part of it – replacing 60 trucks with say 300 is a very different mine to manage and control. We need to re-architect our system so we can horizontally scale up in hardware terms – the cost per unit per truck has to come down for example. And when they become battery powered instead of diesel, how do we build that into the dispatching algorithms to account for battery charging or swapping?”
Wenco continues to work closely with Oxbotica, with whom it signed a partnership agreement to work on open autonomy solutions for mining back in 2020

overland conveyors, extend railheads with added crushing infrastructure, or long haul the ore from the mines. And for the latter option, switching to a fleet of smaller trucks that are capable of electrification and have a level 5 autonomy system on them could represent very significant costBacksavings.”toopen autonomy and Wenco continues to work closely with Oxbotica, with whom it signed a partnership agreement to work on open autonomy solutions for mining back in 2020. Pyne told IM: “We perceive, based on quite a lot of research, that they still have the most technically capable autonomous-vehicle software, but also the right group of experienced people, to deliver something that is truly transformational.” He also referred to the fact that these emerging autonomy systems designed for smaller trucks and ancillary machines, retrofittable to any brand, as well as incorporating more AI, will still have to get regulatory approval when used outside of established AHS hubs like WA. Then there is the fact they will have to handle climate extremes including dust, fog, snow, temperature highs and lows
is also well aware that Wenco is just one of a group of next generation autonomy solution providers but argues that the capabilities of new options are being somewhat overstated. “I think despite what you read from companies in this space, we are all still a couple of years away from saying – ‘yes we can operationalise a large fleet with this technology.’ Why is this? First off while it is relatively easy to automate one truck and trial it, this is leagues behind orchestrating an autonomous fleet. Plus there are more specific aspects. Look at the excavator operator that currently calls in and kicks out the large autonomous rigid trucks –that role is already very challenging for them and it isn’t widely known but in some mines they are using two operators on one shift as it is too much for one operator to handle the AHS panel and their other tasks. The big OEMs are already being asked to semi-automate parts of the loading
Change starts withCO 2 reduction

If you share our ambition to lower carbon emissions, ourCOReduction Program is good news. Let’s work together, set goals and keep you on target. Read more at volvoce.com/changestartshere 2
Volvo Construction Equipment
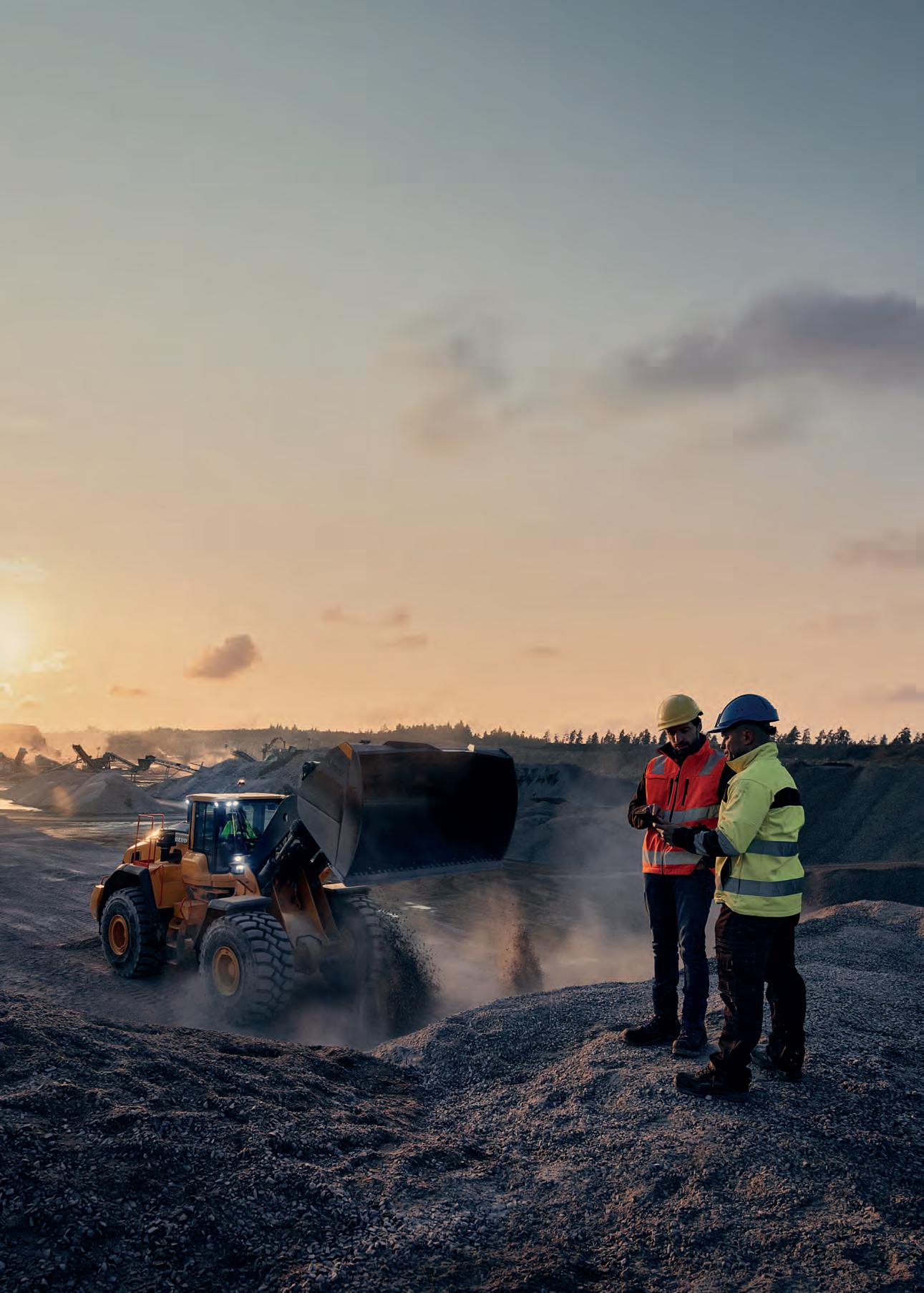
the market to bring more effective, efficient and scalable autonomy to heavy industry. The company even launched the world’s first comprehensive, safety-certifiable operating system purpose-built for autonomous heavy equipment in 2021, lowering the technologicaland resource-related barriers to entry for autonomy in heavy industry across the board. Another critical differentiator is SafeAI’s retrofit approach. Some startups in autonomous construction and mining try to boil the ocean, building custom autonomous equipment from the ground up. This approach is costly, inefficient and inherently not scalable. Instead, SafeAI’s retrofit model enables companies to optimise existing fleets, including mixed fleets, instead of limiting them to purchasing new, manufacturer-built autonomous vehicles. By upgrading existing equipment, we’re able to move quickly and scale rapidly, simultaneously ramping up individual projects while advancing autonomy in the industry at large. Our autonomous solutions are also easy to deploy making it attractive to customers with small construction fleets as well as large mining fleets.
Continued on p62
SafeAI is one of the leading new players in autonomous mining, and recently hired mining truck stalwart Sudhanshu Singh, as Senior Vice President (SVP) of Global Operations. Backed by decades of experience in heavy industry, Singh will oversee SafeAI’s best-in-class operations and customer success team to support the scaling and growth of SafeAI’s business and customers. Prior to joining SafeAI, he was part of Caterpillar mining team, most recently as General Manager of the Mining Center of Excellence in Caterpillar Resource Industries and prior to that for nine years as Global Product Manager for Caterpillar Large Mining Trucks. Paul Moore caught up with him to talk SafeAI’s innovation and potential
Q Can you outline what SafeAI as a company does, and your role within that?
A SafeAI delivers the latest in interoperable autonomous technology to industries like mining and construction, making heavy industry safer, smarter and more productive. The company retrofits heavy equipment, like haulage trucks, with autonomous hardware and AI powered software to enable safe, 24/7 operations. With its retrofit model, SafeAI empowers companies to upgrade existing equipment, regardless of manufacturer or vehicle type, instead of limiting companies to purchasing new, manufacturer-built autonomous vehicles, which is costly and typically more difficult to scale. SafeAI’s unique OEM- and vehicle-agnostic tech allows industry players to convert their existing fleets into self-driving assets. As Senior Vice President of Global Operations, I oversee SafeAI’s operations and customer success team to support the scaling and growth of SafeAI’s business and customers. I am responsible for leading the successful endto-end deployment of SafeAI technology for its customers worldwide, as well as supporting teams to identify and pursue new opportunities for growth as demand for autonomous heavy equipment continues to grow.
instrumental role in the company’s sales and marketing efforts to introduce these new vehicles to the market. With deep experience in the heavy machinery industry, I have seen firsthand that there is an urgent need for OEMagnostic and easy to implement autonomous solutions. Many construction and mining companies want to deploy autonomy because of safety, productivity, sustainability, cost and overall value chain efficiency benefits, but with already existing and often mixed fleets this can be a really daunting and costly task. I was drawn to SafeAI because it addresses this need head on and meets the customer requirement for existing fleets, as well as new fleets of machines by offering retrofit kits that make autonomy possible when it otherwise wouldn't be.
Sudhanshu Singh, the new Senior VP – Global Operations at SafeAI
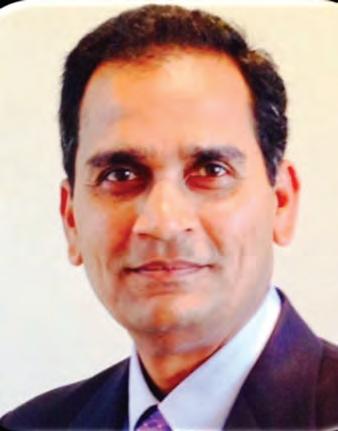
Q From a geographical standpoint, what are the largest markets for deployments for SafeAI? How do you predict these markets will change in the future?
Q You have vast experience with mining, quarry and construction equipment at companies like Terex, Bucyrus and Caterpillar. What influence did your background have on your decision to join SafeAI?
A I’ve been in the industry for over 30 years, dating back to my time at Terex Corporation. Prior to joining SafeAI, I was a member of the Caterpillar mining team where I led the global large mining truck business for several years and launched a number of new electric drive, Tier 4 and autonomous trucks. I also played an
A We’re currently focused on a few major markets for heavy industry including Australia, Japan and India. Australia has one of the biggest mining markets in the world. SafeAI has a partnership with MACA, one of the world’s leading diversified contracting groups, and recently announced plans to retrofit 100 of MACA’s vehicles, which will be one of the world’s largest autonomous fleets. In Japan, the construction market is the largest in the world and we have a partnership with Obayashi Corporation, a Japanese-based global leader in construction, where we have successfully retrofitted a Caterpillar 725 for use at a construction site. Most recently, we announced plans to scale our work with Obayashi, in partnership with Siemens. SafeAI and Siemens will retrofit a couple of hundred of Obayashi’s vehicles to be both autonomous and zeroemission – combining two of the biggest trends in heavy industry. Additionally, the Indian construction market and mining market is growing at a fast pace. SafeAI is working closely with customers to bring autonomous construction to India. Both the demand and interest in autonomous vehicles continues to grow across the globe. We can expect to see
Q There is clearly a market demand for the development of automation for smaller mines, smaller trucks, and ancillary machines that a number of companies including the large truck OEMs are now working on - what does SafeAI's offering bring to the table that is game
AUTONOMOUS SURFACE MINING
60 International Mining | SEPTEMBER 2022
One of the things that sets SafeAI apart is its advanced, AI-powered autonomous technology. The company’s engineering team is made up of industry experts across all facets of autonomy –from mining to passenger vehicles. This team has been laser focused on building sophisticated AI algorithms to power the industry’s safest, smartest autonomous ecosystem from day one. From the latest multimodal sensors (LiDAR, radar, camera) to detect surroundings, to perception-based localisation with GNSS, to emerging AI technologies like deep neural networks, SafeAI leverages the most advanced technologies on
Empowering mining
Achanging?
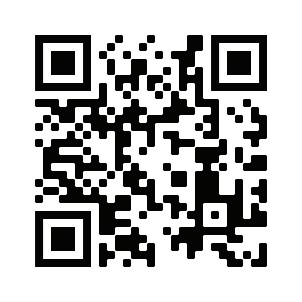
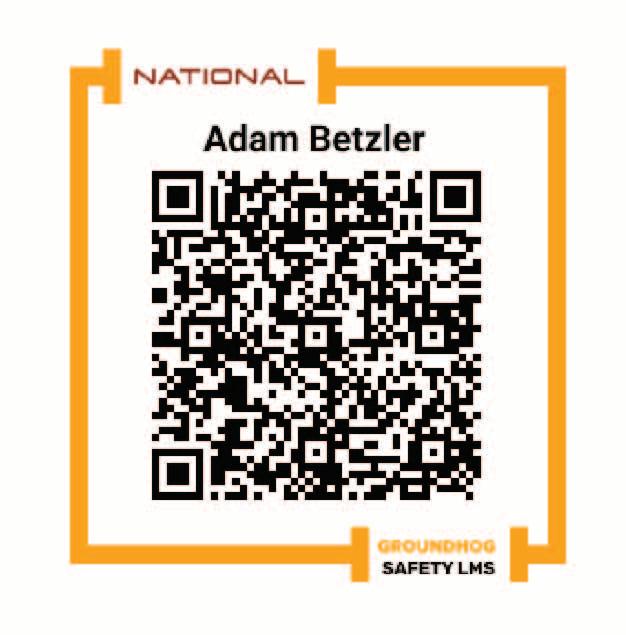
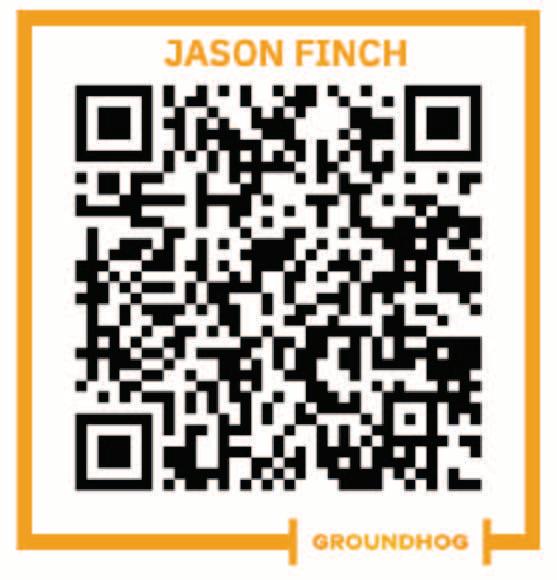

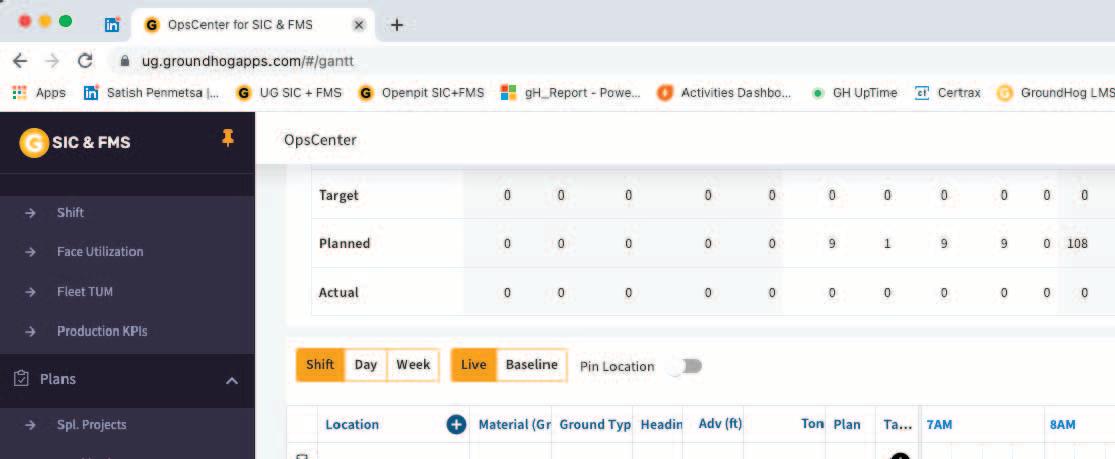


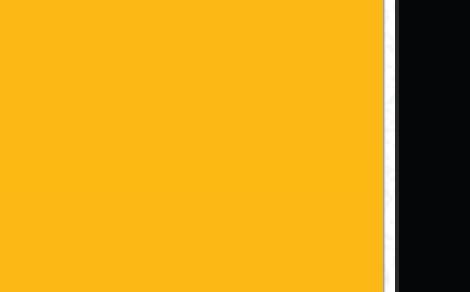

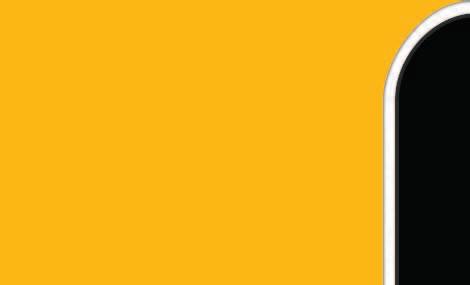
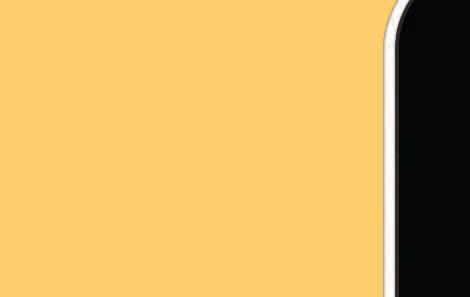
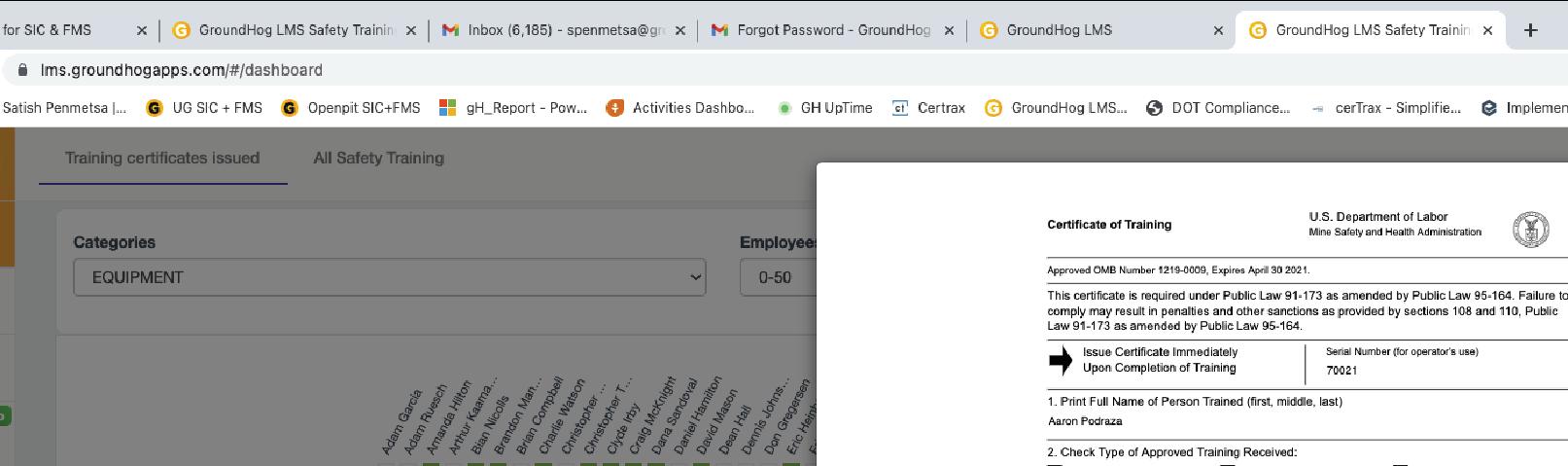
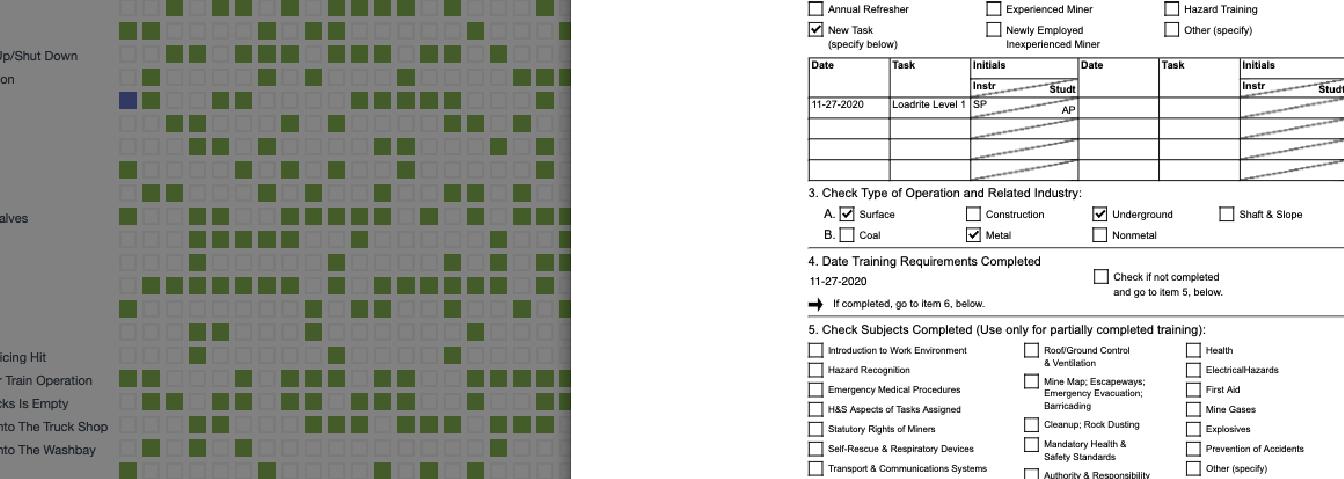
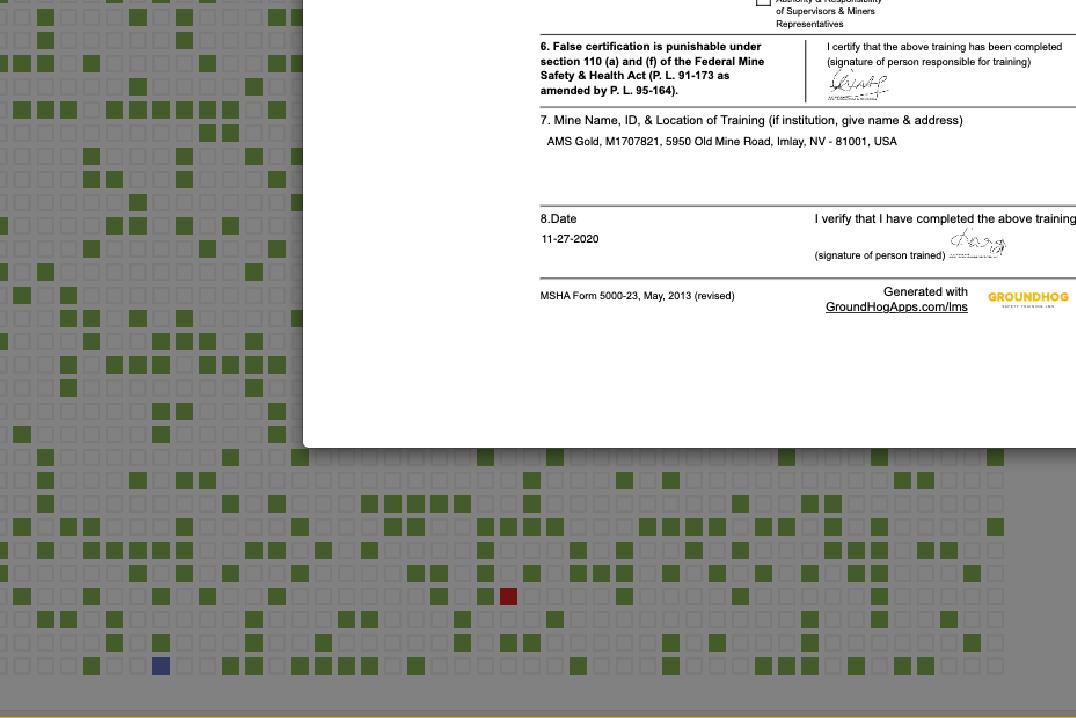
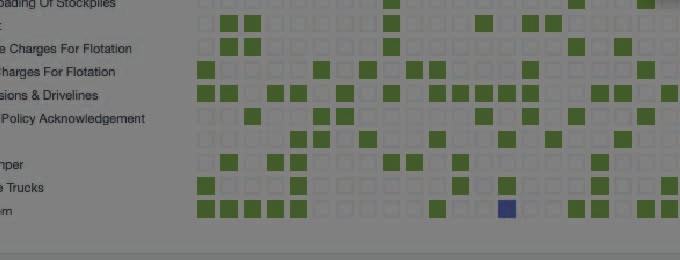
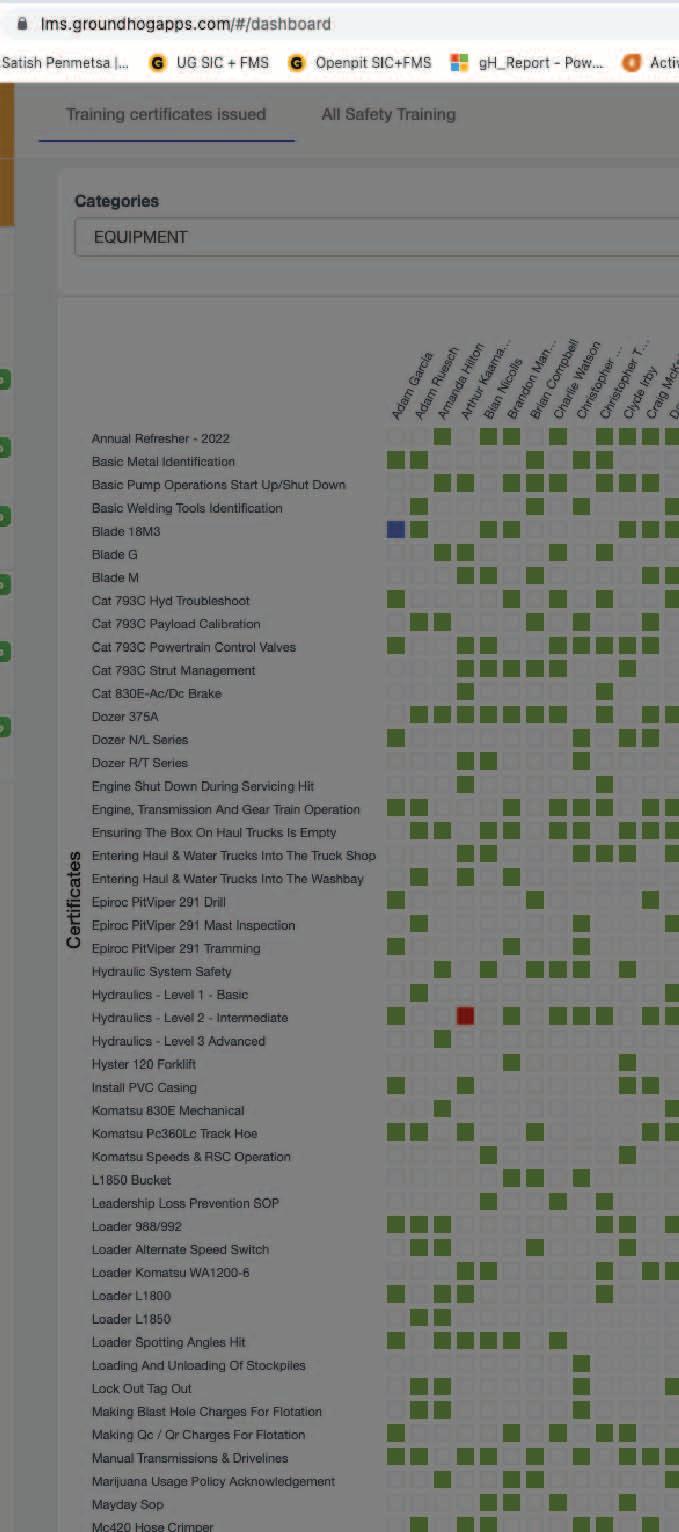
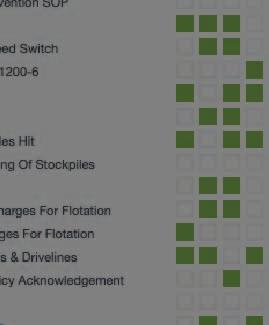
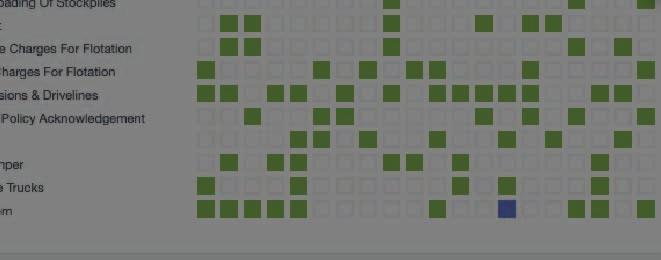
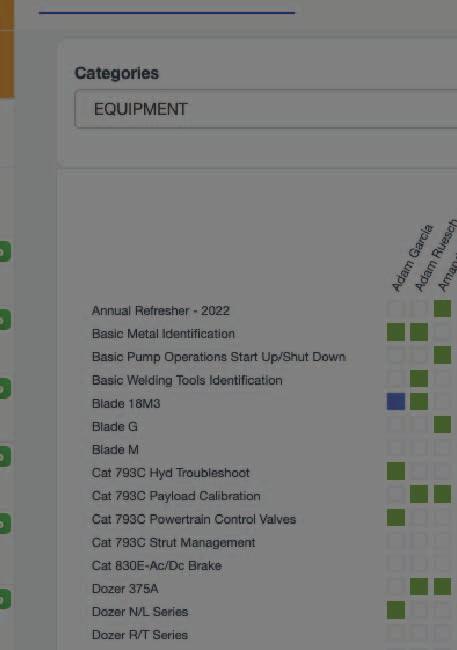
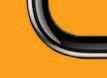


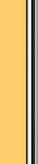










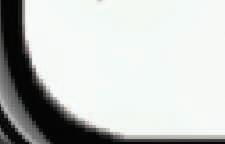

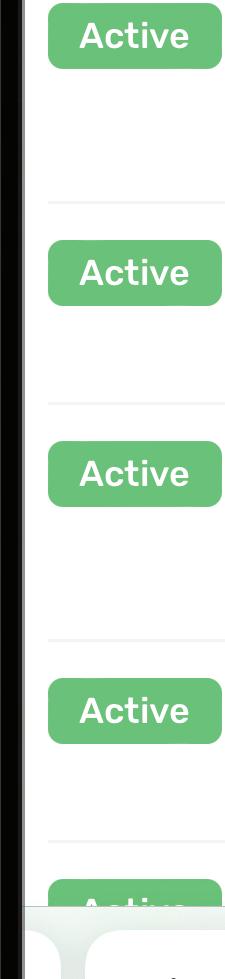


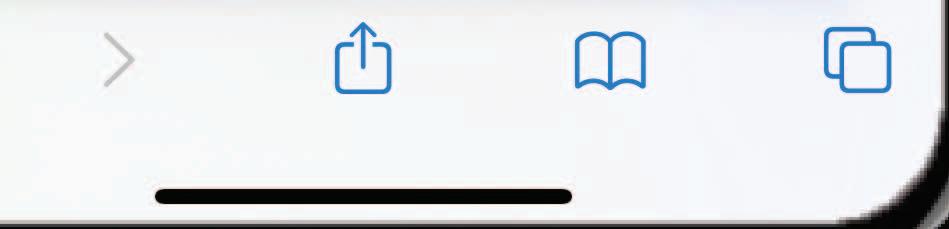

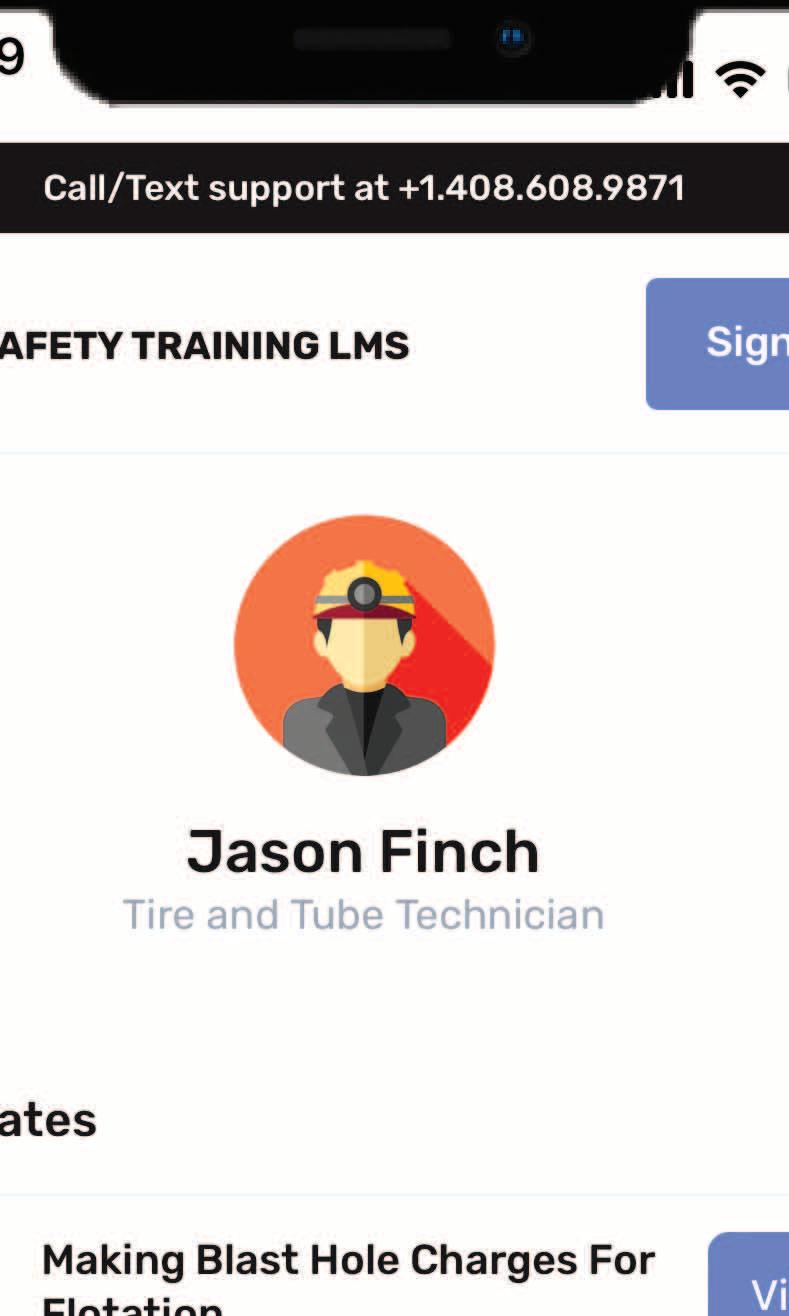
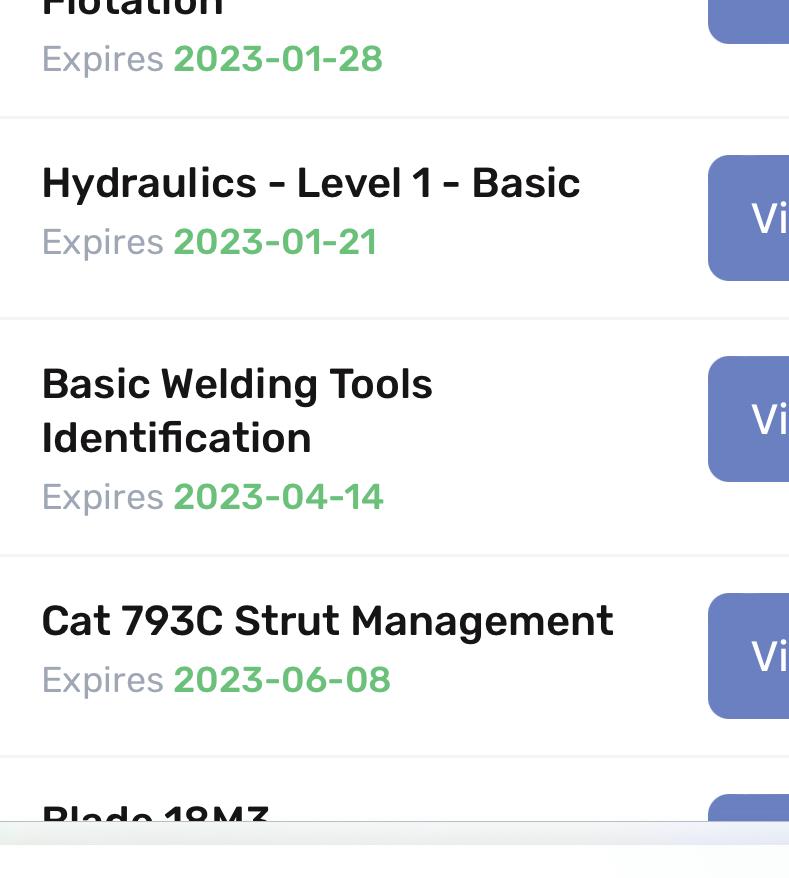
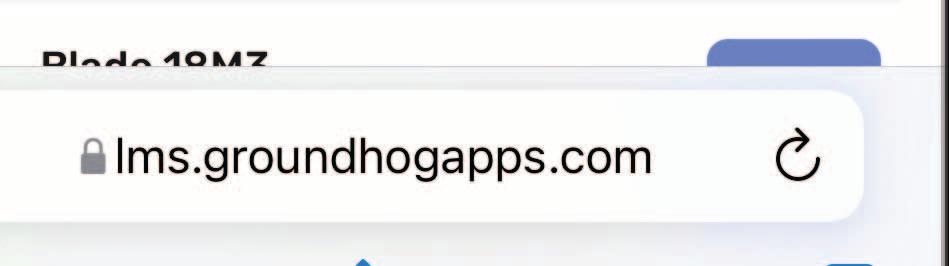
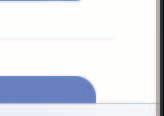

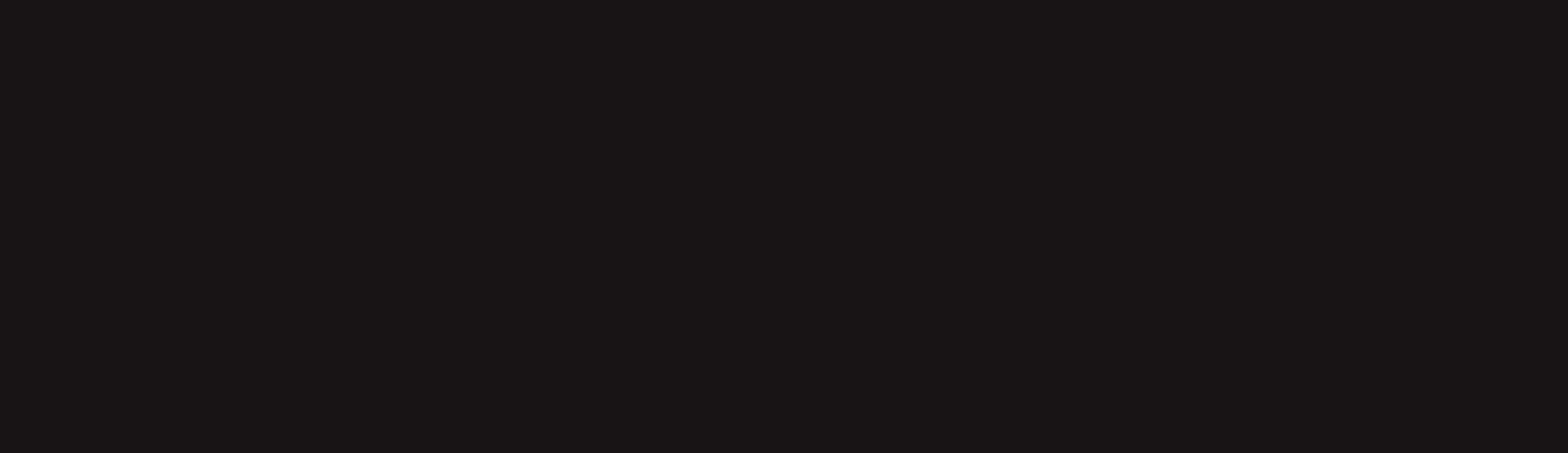
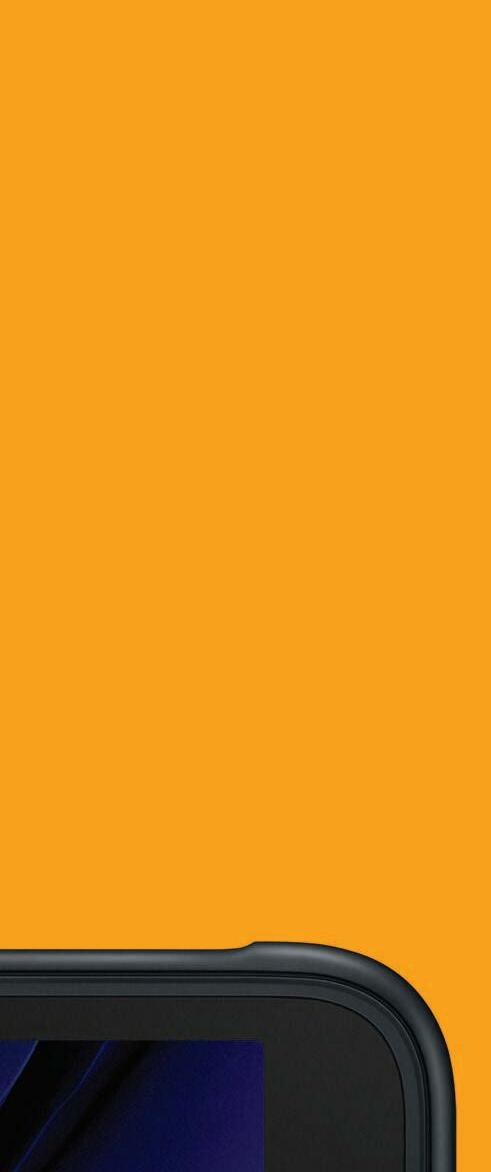
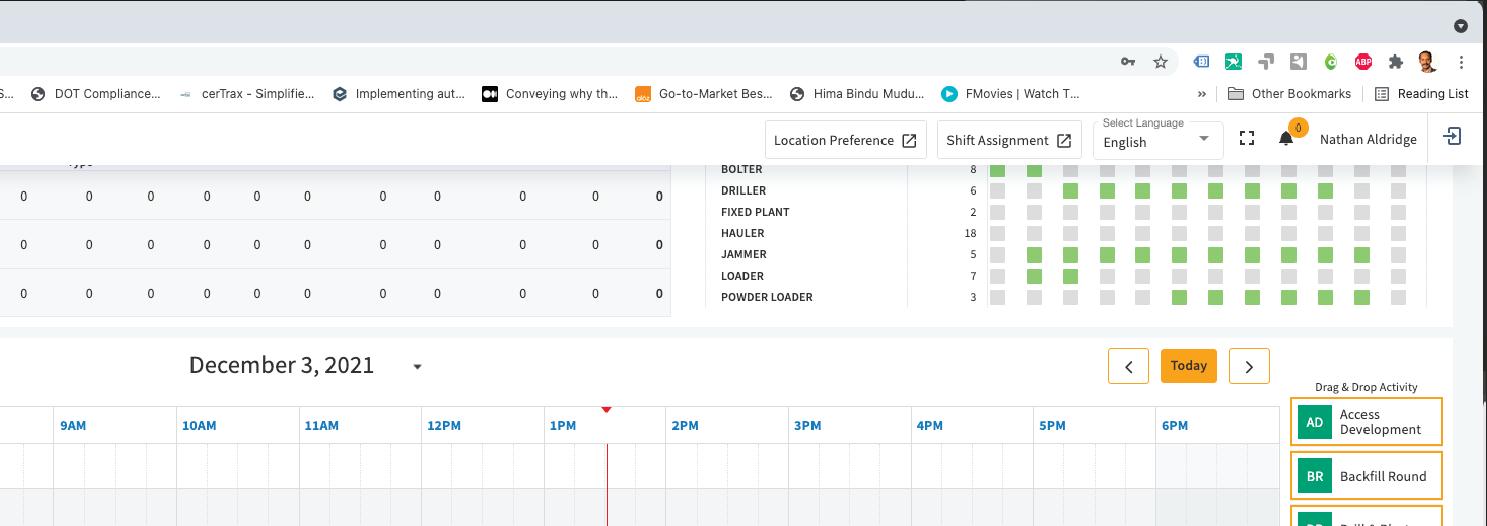
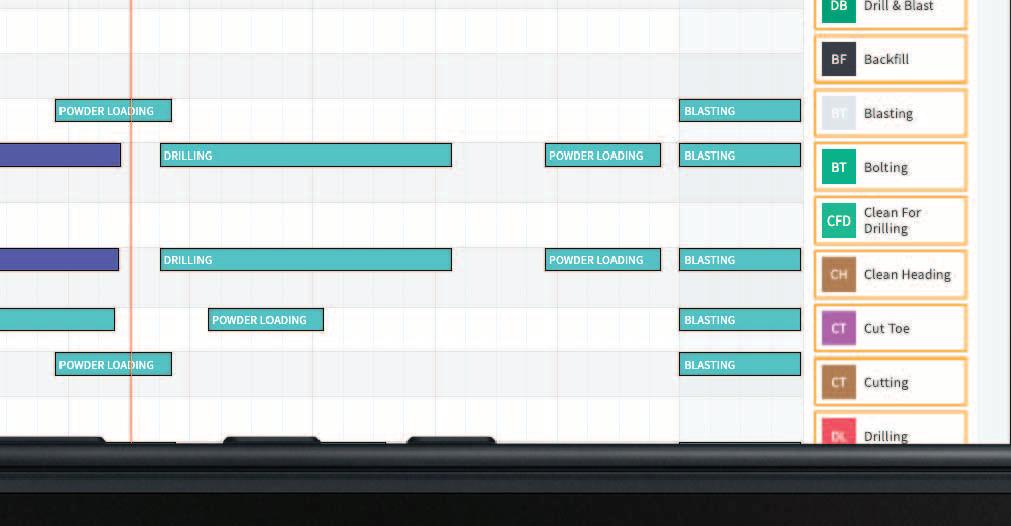
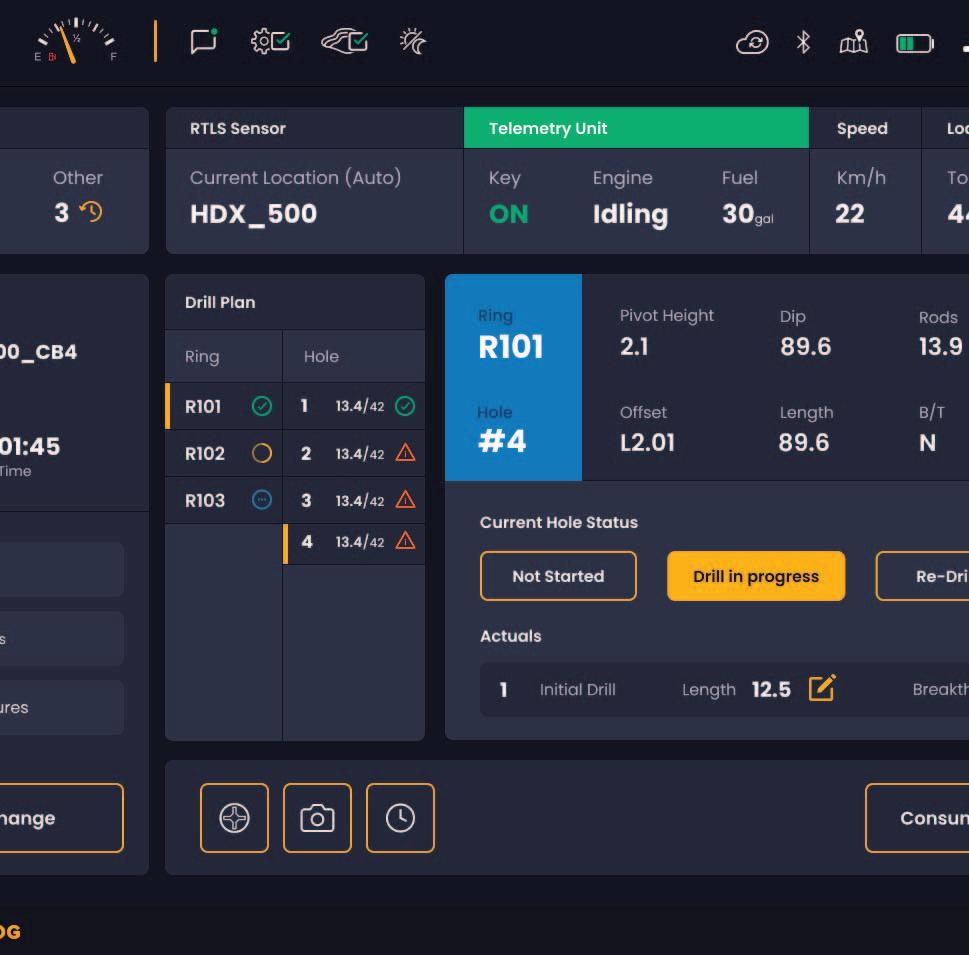
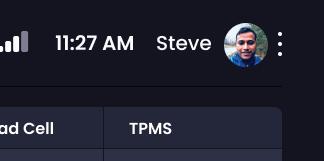


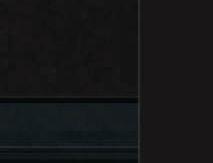

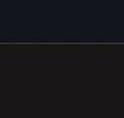


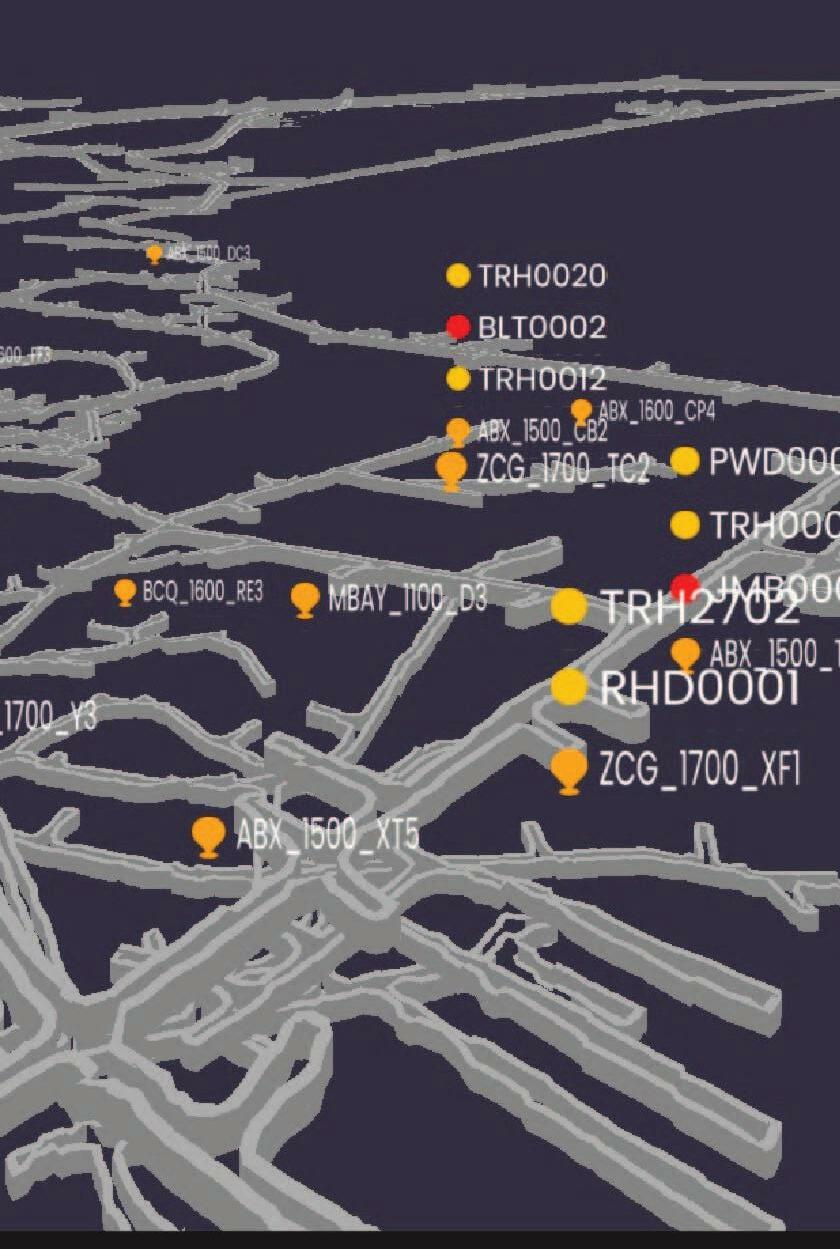
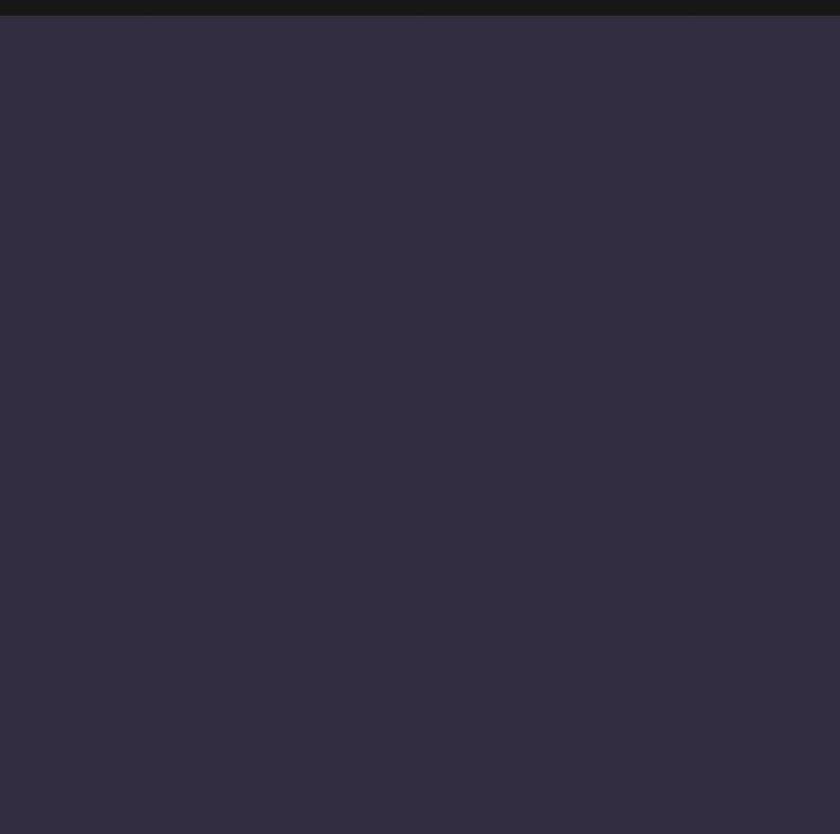
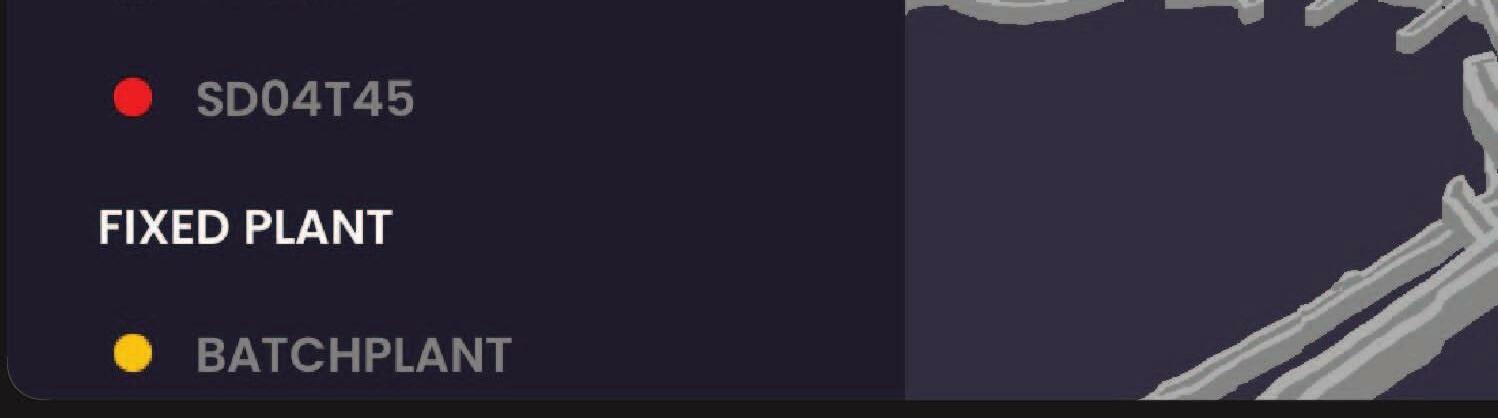
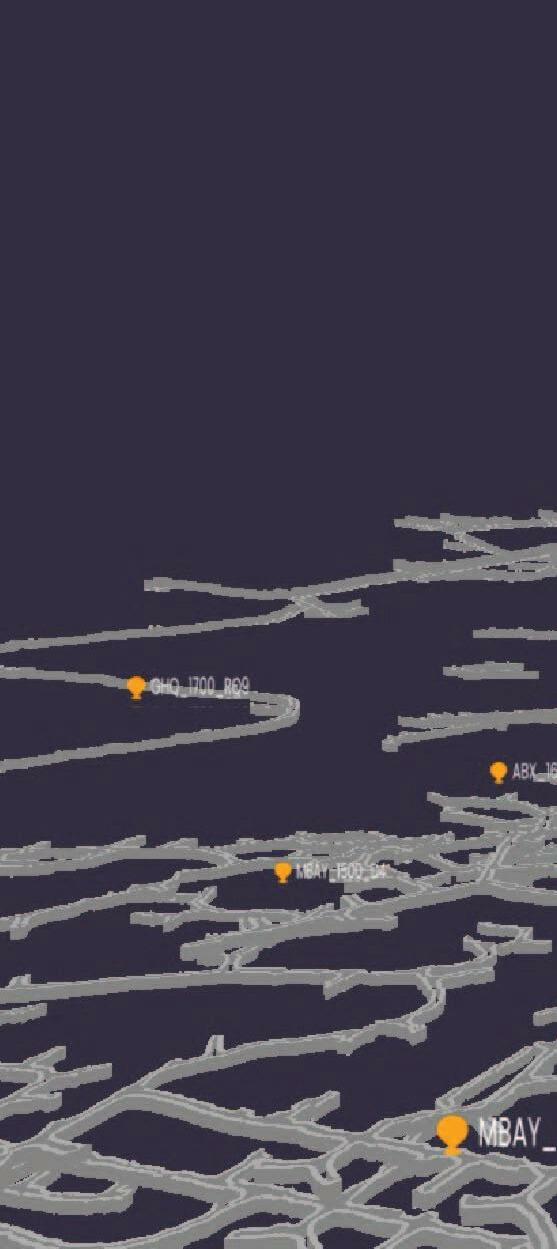
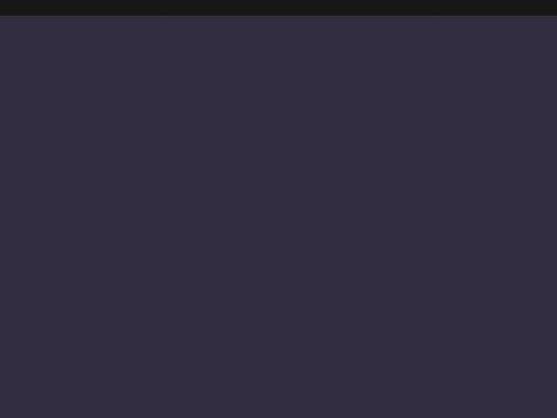
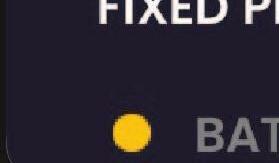

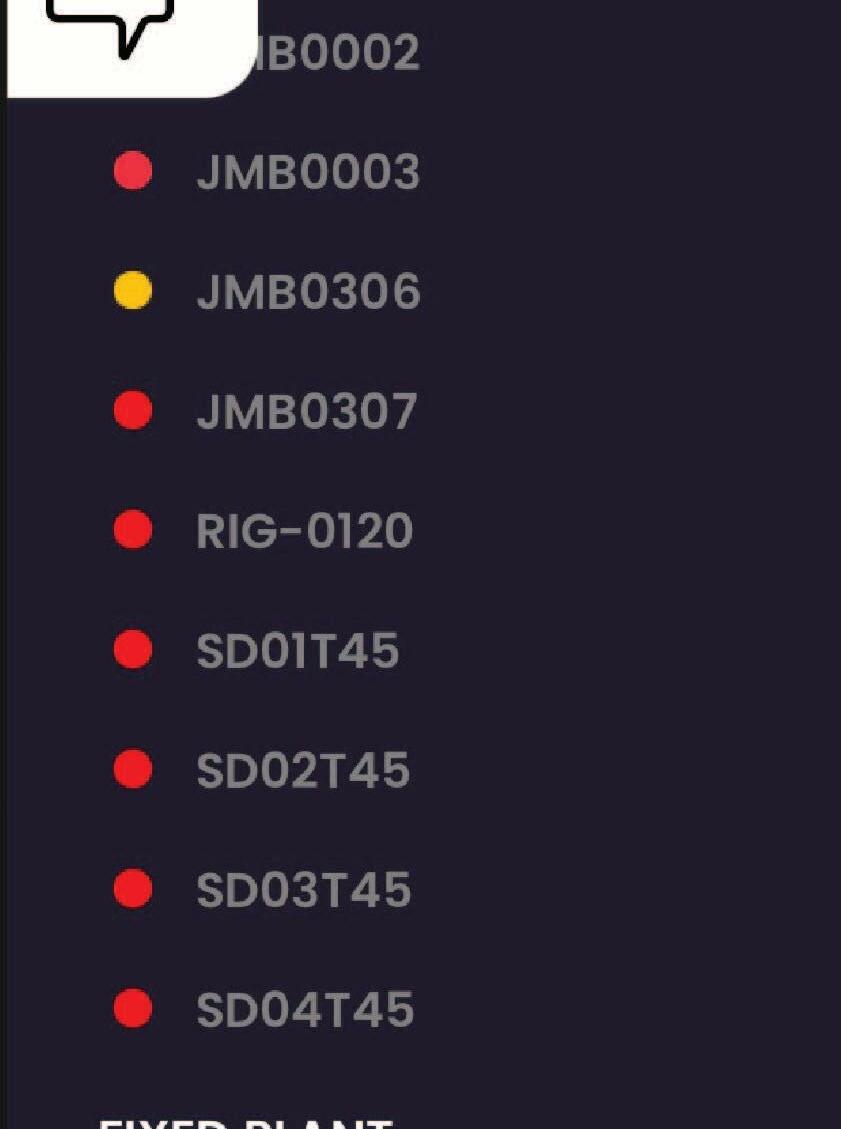
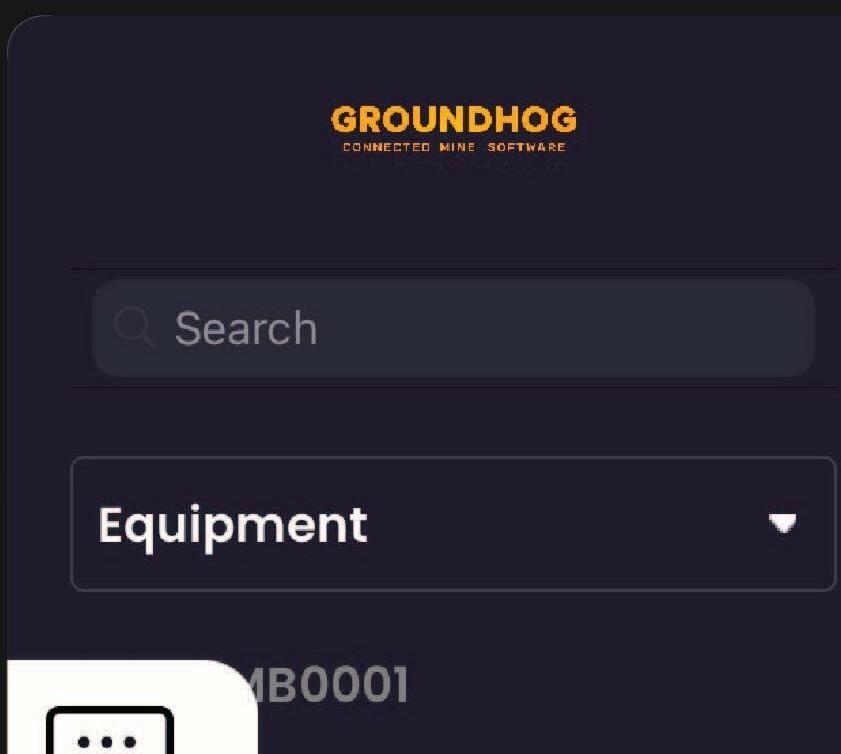
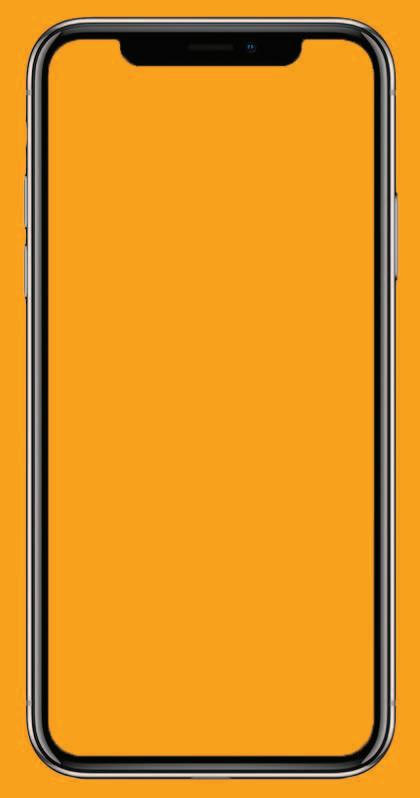
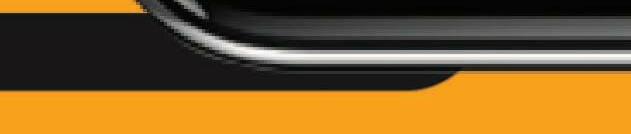
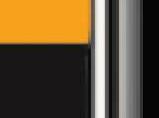
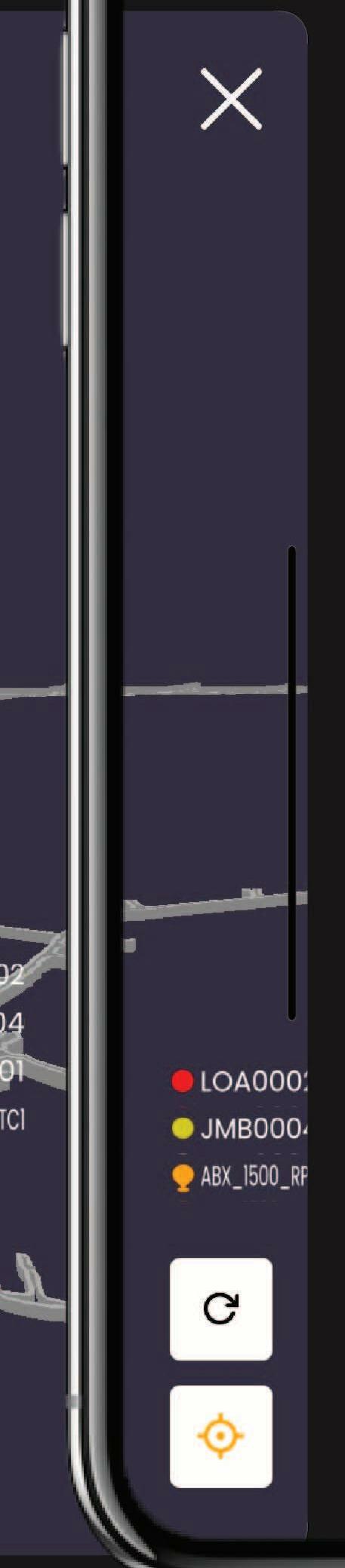
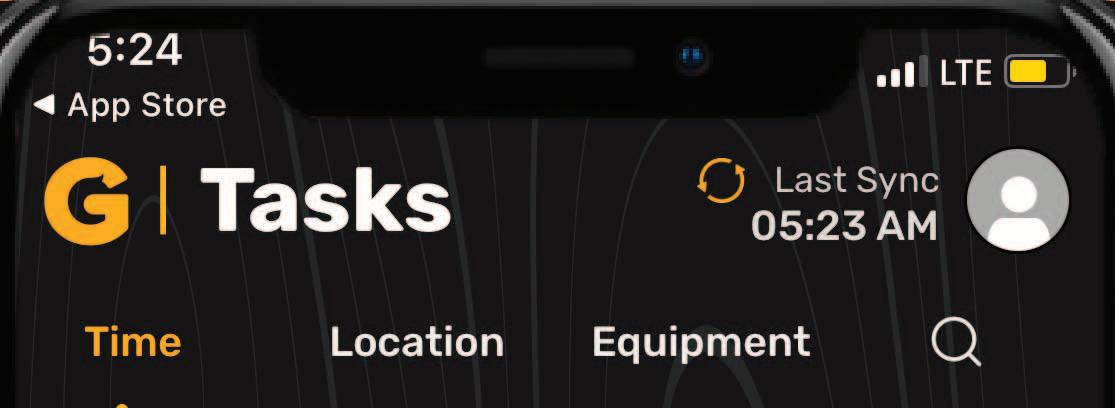

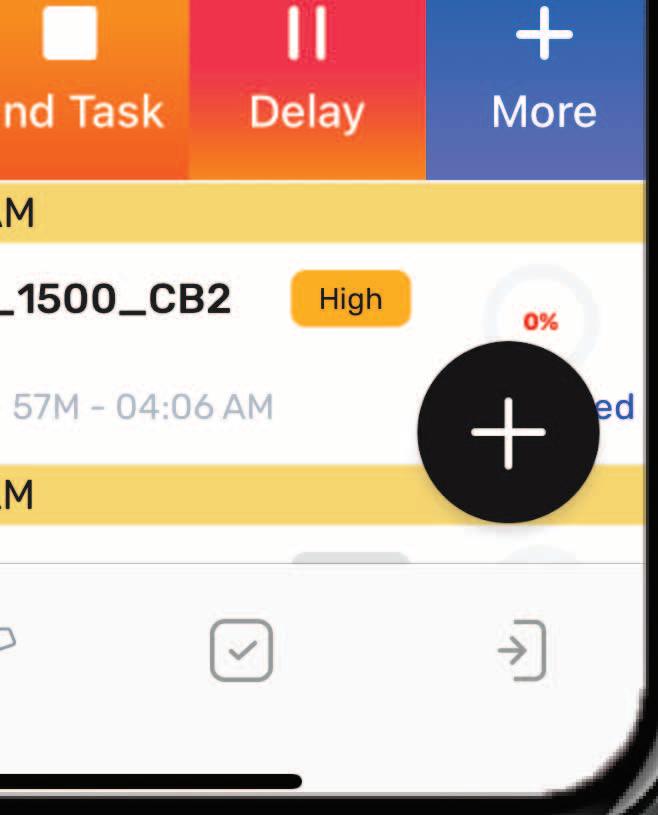
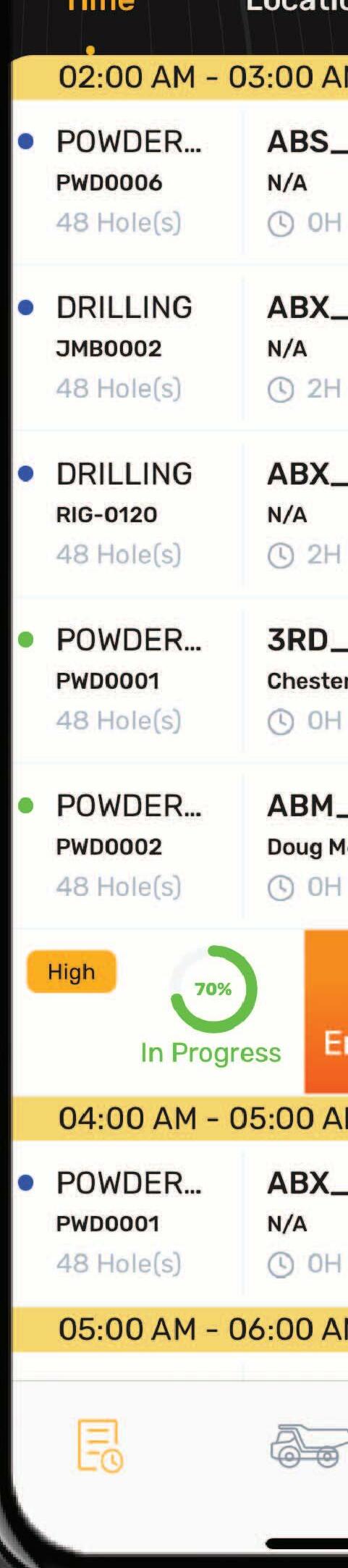


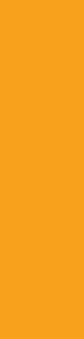
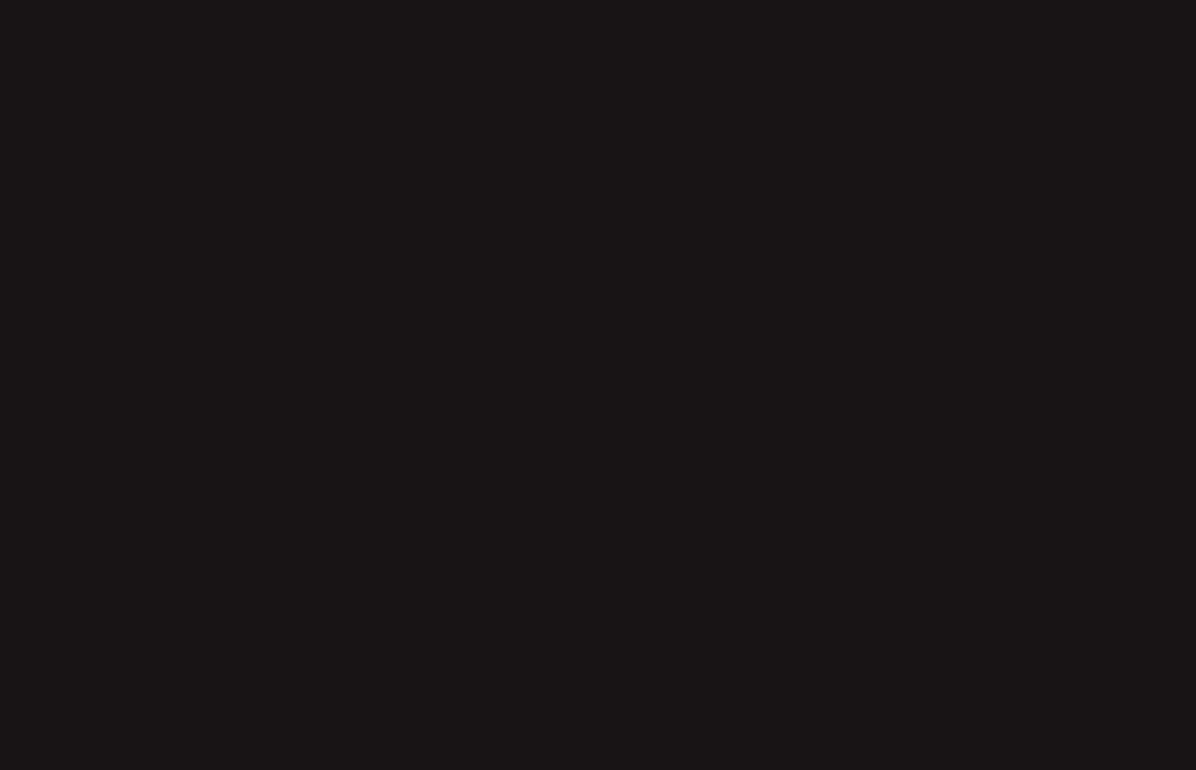
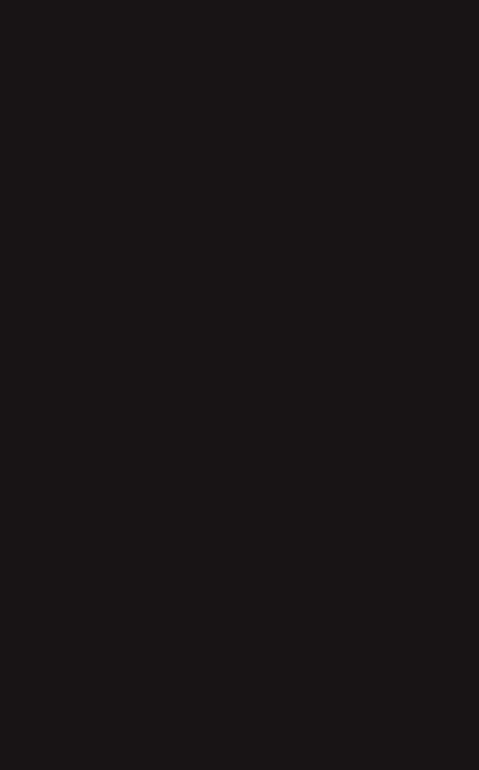

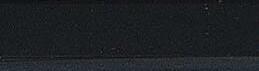
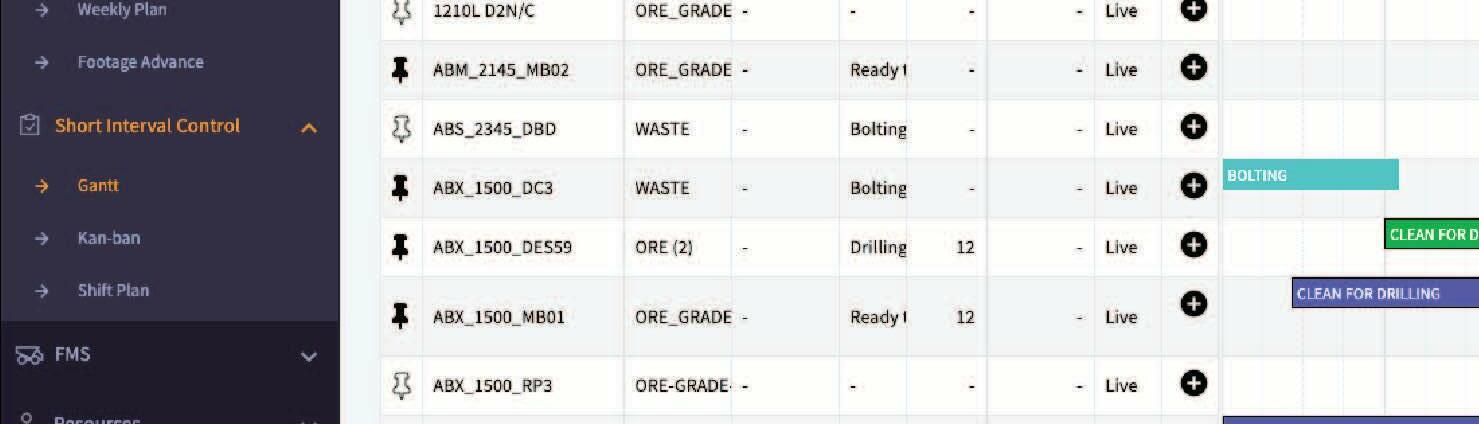
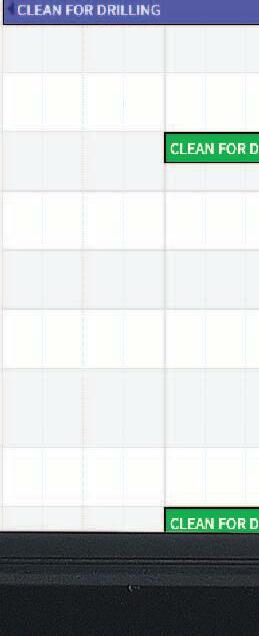
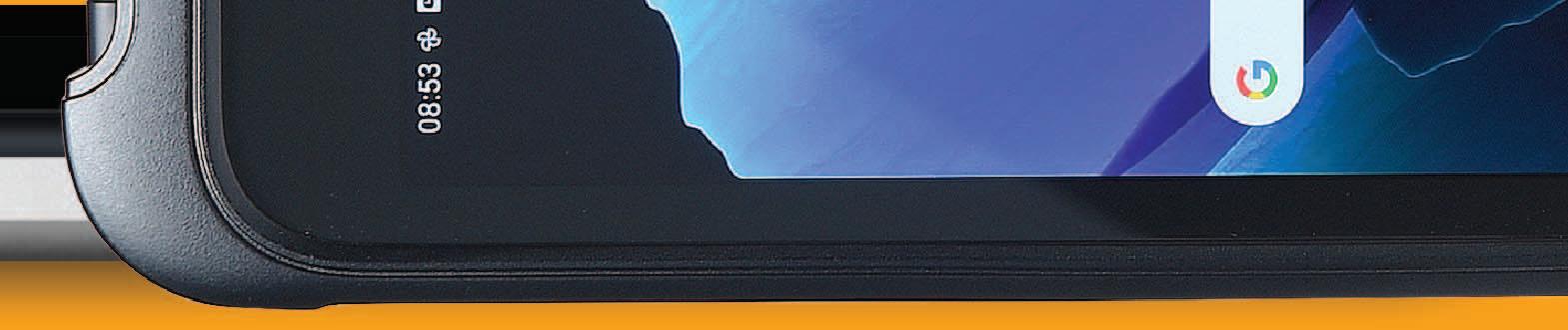
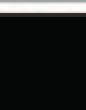



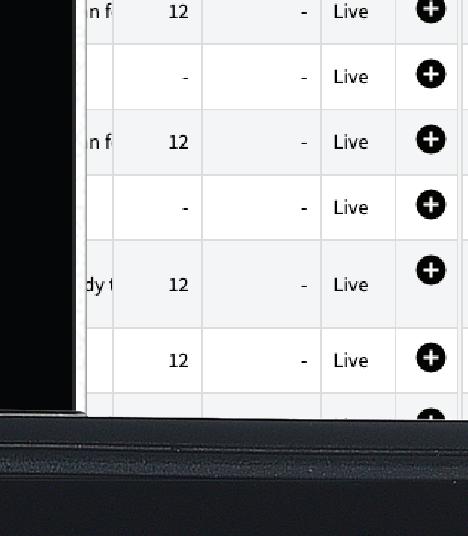


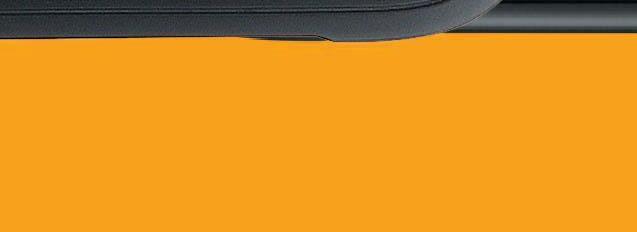
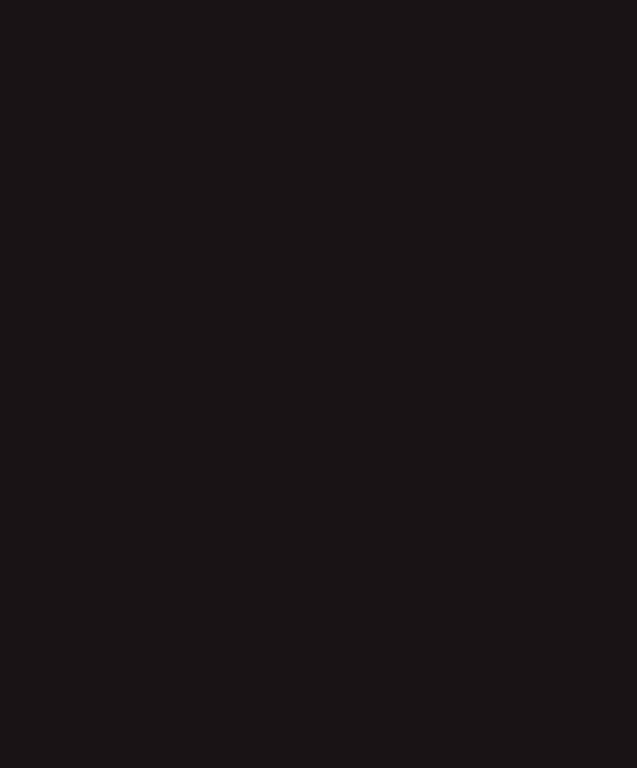

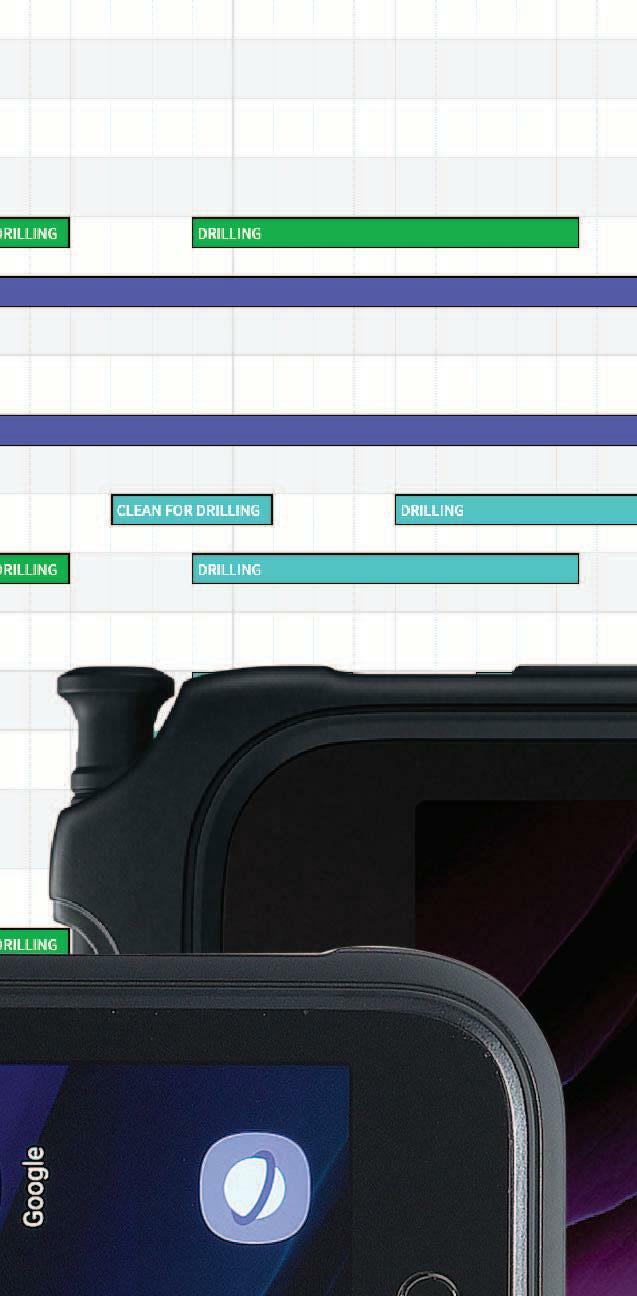


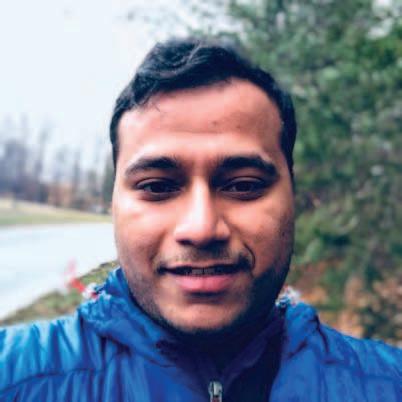
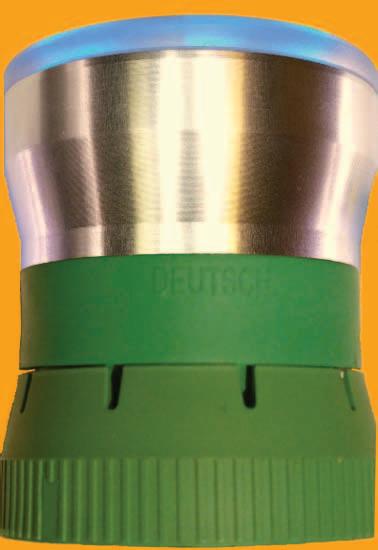
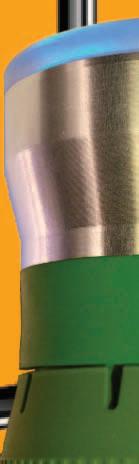

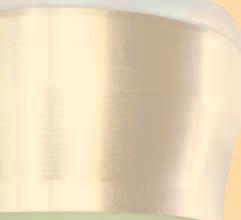
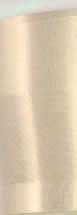
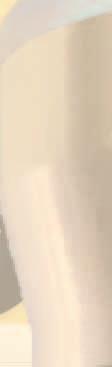
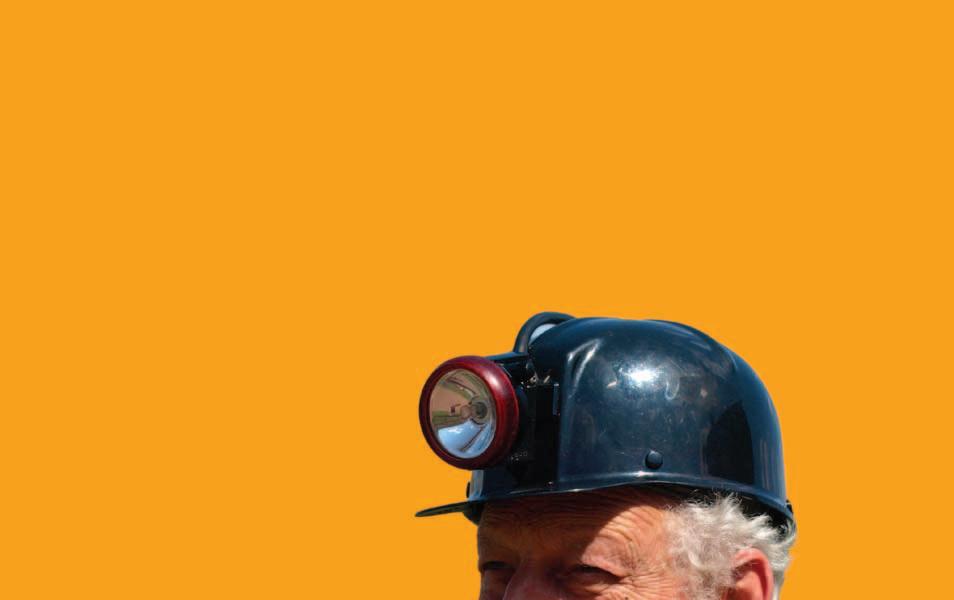
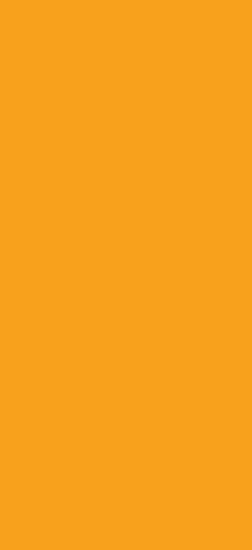


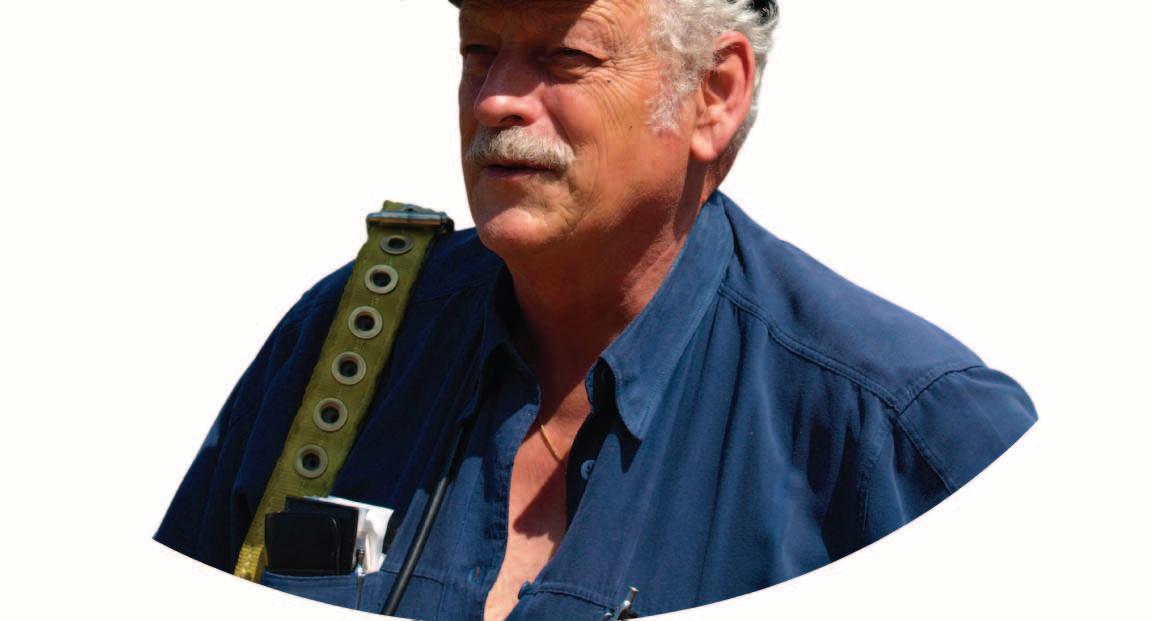
A SafeAI’s Autonomous Solution is powered by a suite of sensor component hardware (LiDAR, radar, cameras), along with a best in industry onboard compute platform that’s powered by our AI driven autonomous software. This technology allows equipment like haul trucks and bulldozers to safely and independently navigate a project site, complete important functions like load-haul-dump cycles and communicate with other autonomous and nonautonomous vehicles on the worksite. Additionally, our technology is able to detect and decipher between objects, dust particles, and unknown terrain notifying vehicles to stop, work around, or continue forward without human interference. With this technology, heavy industry can experience tremendous benefits immediately – including increased site safety and thousands of additional hours of productivity annually. Projects utilising SafeAI’s industry-leading hardware and software will ultimately be completed 20% faster and at 25% less cost.
Q What are your predictions for the future of autonomy, specifically in heavy industry?
Q Autonomy is just as much about the complexities of whole fleet management as it is retrofitting single units - what work do you still have to do to achieve whole fleet
Autonomy for mobile mining fleets is anything but a fixed or set system – it is constantly evolving with technology upgrades and functionality additions. Caterpillar Inc. through its Site 17 facility at its Tucson Proving Ground
Continued
from p60
A Adoption for autonomous heavy equipment is at an inflection point. Companies have seen the tremendous benefits this technology can bring, and they want to capitalise on that. We’ve seen good traction in the last couple years, but we’re about to see autonomy really take off in construction and mining. In terms of industry players, I expect that we’ll start to see some consolidation in the next couple of years. Those with the best technology and, as importantly, the ability to adapt and scale that technology to meet any customer’s needs, are most likely to come out on top.
Cat on leading automation’s evolution
Q Can you give some examples of how AI can improve on existing technology such as how trucks respond to obstacles and unexpected situations more efficiently?
currently getting off the OEM autonomy systems. Plus the nature of the sensor and localisation technology means you don’t actually have to fit every vehicle on the mine with the autonomy system – today with level 4 OEM systems, the system doesn’t just involve the big mining trucks themselves - every single machine in the pit has to be fitted with all sorts of sensors, antennae and software, at great cost. A big mine might have over 200 light vehicles alone.” Then there is the remaining controller intervention needed when a truck stops due to an obstacle that it doesn’t recognise. It usually requires someone from a dedicated pit team to go and check it out and give the OK for the truck to restart. With the Wenco system all this would be handled by the truck’s onboard AI. It responds more like a human brain – the truck can sense where it is, understand its localisation compared to everything around it, and then make a decision to proceed or not, and which path to take around the obstacle. Plus you won’t have a tether of GPS either so are able to operate in GPS-denied environments. “The truck is only using a combination of radar, LiDAR and cameras with an AI layer over the top. It will choose the right combination of sensors based on the conditions and what you are trying to do. This ability to not rely on GPS also means you have a much larger addressable market.”
Moving on to another topic, what about Wenco’s being owned by Hitachi Construction Machinery? HCM of course has its own AHS running at Whitehaven Coal’s Maules Creek in which Wenco has been closely involved. HCM has also recently introduced the ConSite® Mine remote machine analytics solution on which it has worked with Wenco. Pyne suggested that the two companies are now working much more closely and strategically beyond Wenco just supplying the autonomy layer to HCM’s solutions and becoming more of a close partner in customer projects. Whilst the HCM AHS is a level 4 AHS system (like the other OEM systems) and still largely designed to operate with Hitachi equipment it is available now for customers to adopt. As the Wenco level 5 open autonomy solution becomes commercially available over the next few years, it gives HCM an option for its customers for small and ancillary vehicles, nonHitachi rigid truck fleets and longer haul trucks. Overall, Pyne stated that it is fair to say that on autonomous mining strategy, HCM and Wenco are converging more than ever before.
Aautomation?
We are testing an exciting suite of products with our creative and innovative fleet management team. In addition, we are working closely with customers to further enhance this solution to not only address machines in the autonomous fleet, but also help customers with the entire ecosystem onsite site. We will be announcing more details in the near future so stay tuned.
SafeAI and MACA recently announced a partnership to retrofit autonomy to a mixed fleet of 100 mining trucks across numerous site locations
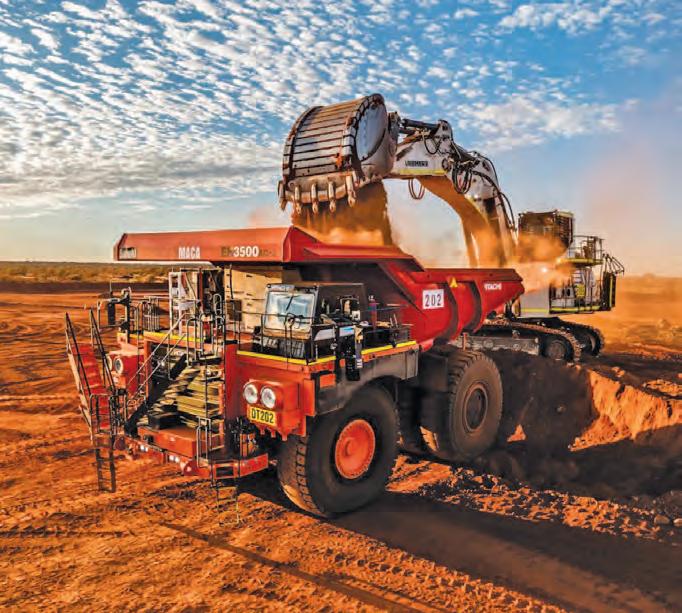
62 International Mining | SEPTEMBER 2022
these markets scale as well as new markets emerge while looking to rapidly accelerate their entry into autonomous heavy equipment as a result of seeing the massive impact the technology has had.
AUTONOMOUS SURFACE MINING
business in, the mining industr y.
komatsu.c /aautonomous
If an endless stream of driverless trucks moving across the mine site is what comes to mind, you might want to think again.
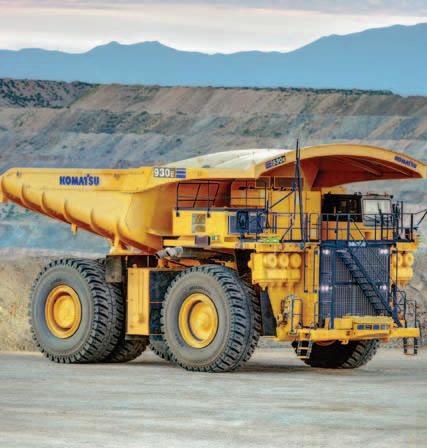
worldwideucks onomousunner aut 00+ diltkior
When you autonomouspicturmine,whatdoy
haul FrontRutr cture an us youmine,see? 5
With a tech-forward workforce and next-level equipment and solutions, we can work together to move mining toward a more innovative and sustainable future.
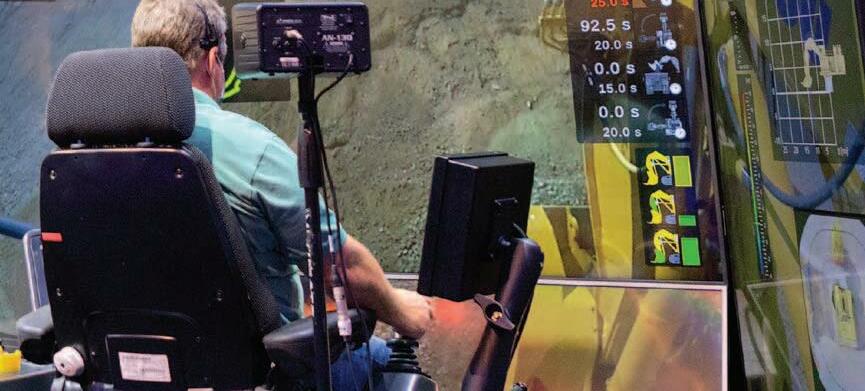

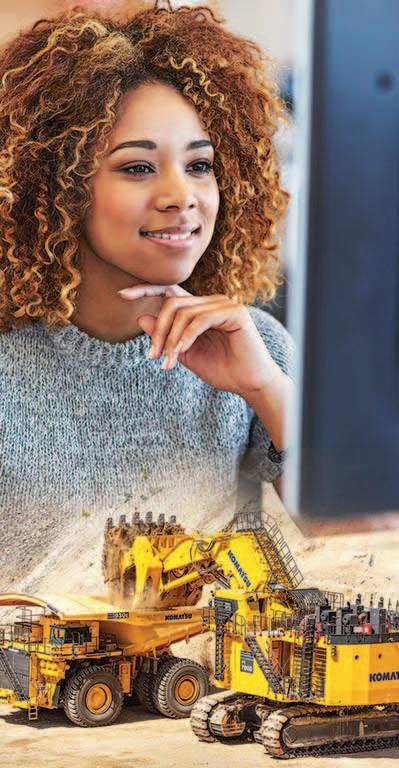
Through advances in the FrontRunner Autonomous Haulage system and the teleoperation surface mining excavat r,, our customers are moving toward more productive operations, while upskilling personnel to transition from the cab to the control room. Komatsu’s autonomous and thlitilllidsemi-autonomous
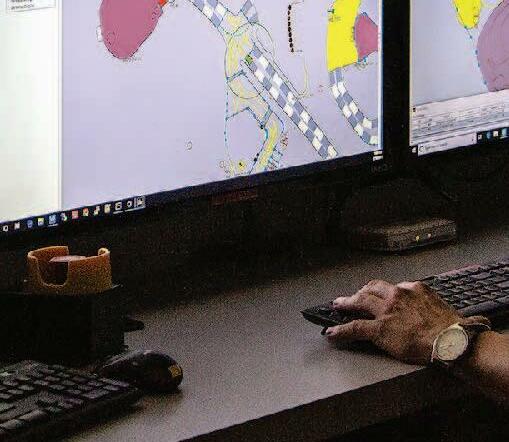
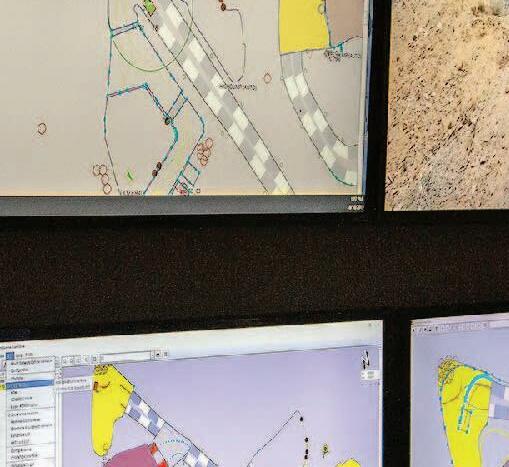
Scan to om/ y technology is continually evolving and
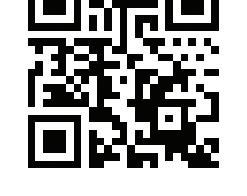
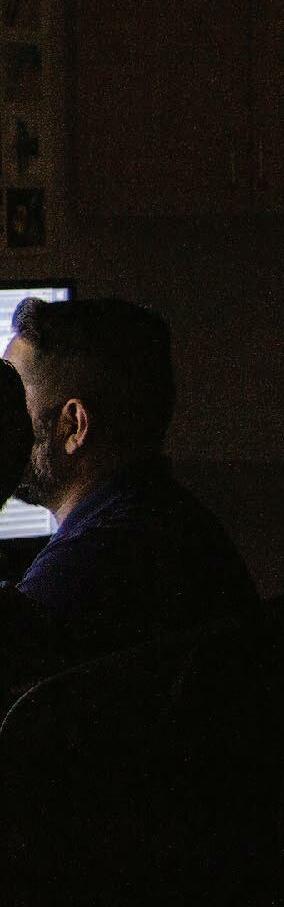
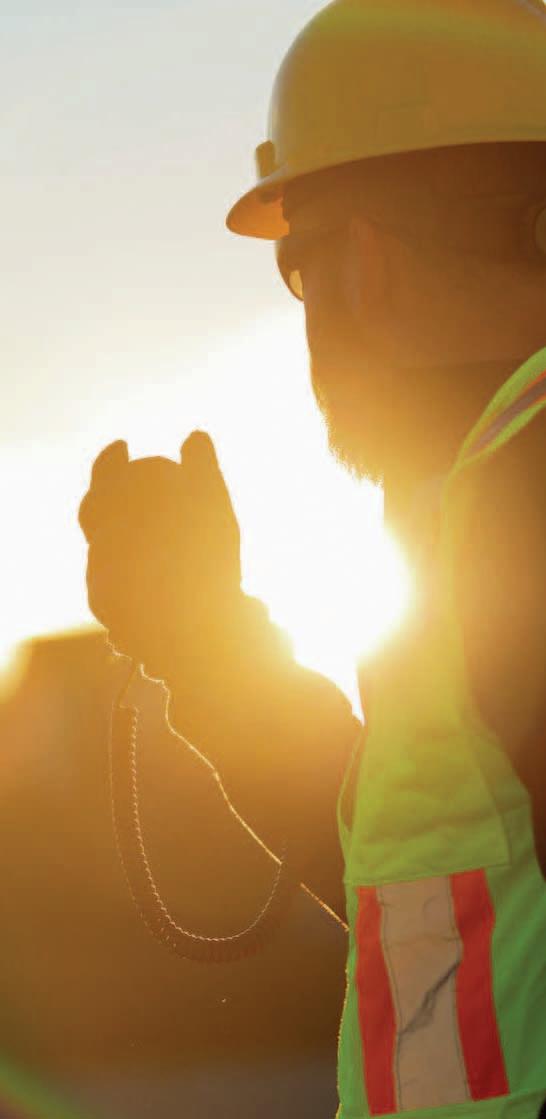
learn more
© 2022 Komatsu Ltd. or one of its subsidiaries. All rights reserved.

On the machineandhavetheonautonomousknowofahigh-precisionhavearetrucks.autonomousanddozers,waterincludingoverautonomoussites,Commandlargestforhaulingthereareover70trucksand300othervehicleslightvehicles,trucks,graders,wheelloadersevenothernon-rigidAllthosevehiclesonMineStarandaradiotransmitter,GPSanddisplay.Theoperatorsthosevehiclesmustwherethetrucksare–anautonomoussite,autonomoustruckstherightofwaythemannedoperatorscan
Caterpillar acquired select assets and hired employees from Marble Robot, Inc., a San Francisco, California based robot and autonomy technology solutions company. The acquisition was part of the company’s automation and autonomy strategy to meet the needs of smaller mines as well as the construction and quarrying, plus industrial and waste industries. The first machine to be equipped with the new autonomy system is a Cat 299D3 Compact Track Loader (CTL), based on a first customer in solar power. The CTL delivers solar panels into position. At a typical solar farm during the construction phase, there are solar modules and other components that need delivering across a large area.
Caterpillar takes the customer site design files and develops available routes for autonomy, which are then integrated with a tablet which is in wireless communication with the CTL. Using remote control, the operator can pick up a pallet then tell the CTL where it wants it delivered on the map, switching to autonomous mode in which the CTL can deliver and return with no interaction and no further network input needed as it has all the necessary information onboard. With this technology, one operator can manage up to four CTLs at the solar farm site.
What about other new Command for hauling functionalities that are being developed? Vance states: “We are working to add more automation to the process to make the trucks smarter. Today we are in the final testing stages of technology that is camera based – the camera allows the operations team to see what the obstacle is so if it is something like a contractor vehicle that happens to not be MineStar connected and shouldn’t be in that area, then they can intervene. The technical challenge is merging the camera image with the LiDAR image, but we have done this.”
On a recent visit to the TPG, IM had a unique insight into the depth of R&D that goes into Command for hauling. It included discussions with Michael Vance, Engineering Manager; Jag Samaraweera, Command for hauling Commercial; and Joe Forcash, Electronic Engineering Manager, Autonomy & Automation.
AUTONOMOUS SURFACE MINING
electrification we believe the combination of autonomy, connectivity, and electrification, when knit together, provides customers the safest and Autonomous Caterpillar 794 AC trucks at Anglo American's Quellaveco copper minemost productive sites.”
Vance talked about the industry desire for a ‘lighter weight’ autonomy solution for some mine sites. “At one end of the spectrum, you have Command for hauling that is tech heavy, with high-end sensors like LiDAR. At the other end you have smaller sites which require a less tech heavy solution to get similar functionality on sites with less infrastructure, for example, relying more on cameras and being able to bring in the latest technology from automotive. The two will converge somewhat and the solution will really depend on the individual customer site – based on the need and the application. Command for hauling didn’t get where it is by accident – the big mines need the extra functionality and capability that it has – but other mines may not.”
But the market for application of autonomy onto quarry class and smaller mining class machines is also a space where Caterpillar also has big plans and Forcash gave some insight into thisInproject.June2020,
What about its evolution up into larger wheel loaders, articulated dump trucks and other nonmining-class equipment? “Right now we are supporting customers at two ends of the spectrum – we have light construction, exemplified by the CTL, and
Command for MEI Conferences www.min-eng.com/conferences/ PROCESS MINERALOGY ‘22 November 2-4, 2022 | Sitges, Spain Sponsored by: Zeiss, Bruker, Promet101, Capstone Copper, Tescan, Minerals Engineering & International Mining COMMINUTION ‘23 April 17-20, 2023 | Cape Town, South Africa Sponsored by: King’s Ceramics & Chemicals, Russell Mineral Equipment, Keramos, Starkey & Associates, Grinding Solutions, Glencore Technology, ME Elecmetal, Derrick Corp., ZEISS, Hudbay Minerals, Magotteaux, Metso Outotec, Sino Grinding International, Dakot, Maelgwyn Mineral Services, Bradken, Capstone Copper, Eracles -Ceramiche Tecniche, Minerals Engineering, International Mining, Minerals Association BIOMINING ‘23 June 5-6, 2023 | Falmouth, UK Sponsored by: International Mining & Minerals Engineering SUSTAINABLE MINERALS ‘23 June 7-9, 2023 | Falmouth, UK Sponsored by: International Mining & Minerals Engineering
Forcash stated: “It’s a nice introduction to a smaller machine – and is applicable to ancillary machines in mining but right now is focussed on a semi-autonomous, remote control solution for a solar farm site which is very isolated, where you have no network access. Over time we intend to integrate the technology into MineStar so you would have the ability to control it via a Command station. It is similar to what we have today with our semi-autonomous tractor system for our crawler dozers plus Command suite solutions for small wheel loaders and excavators that are already being used in port material handling.”
typically puts out on average two software updates for its Command for hauling system every year – ensuring that its mining customers have access to the best that autonomy can offer.
64 International Mining | SEPTEMBER 2022

see where they are. Blue lanes denote active autonomous truck routes where those trucks own that lane. Green is just a lane that exists in the mine model, and yellow means the autonomous truck has been assigned there but doesn’t yet have permission. These colour codings are very useful at intersections so manned vehicle operators know if they can go or wait for the autonomous truck to go past.
One of the areas Samaraweera talked about the importance of autonomy in Caterpillar’s journey towards zero emissions mining trucks –with the first battery trucks planned for rollout at multiple customer sites before 2030. “Command will play a key role in managing battery trucks. With diesel trucks, MineStar can assign the truck to the fuel bay, ‘once you’re at 20% fuel level you need to go to the fuel bay.’ With battery trucks you will need to know the battery level, and at a set point send the truck to charge or adjust its route to charge its battery so it always has enough power to complete its haul cycle. Autonomy is a crucial part of the journey of getting to battery electric – in many ways the best route will be to start with a good foundation of running autonomy as is, then the transition to battery will be a lot easier. It will also make the change management a lot smoother. As many operations migrate toward autonomy and fleet
Pioneering
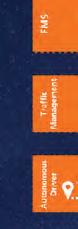
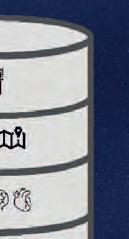


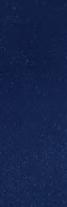
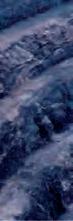
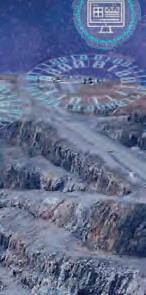

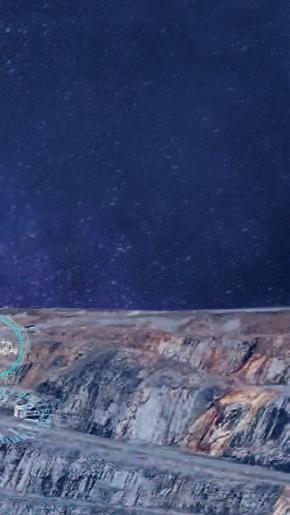
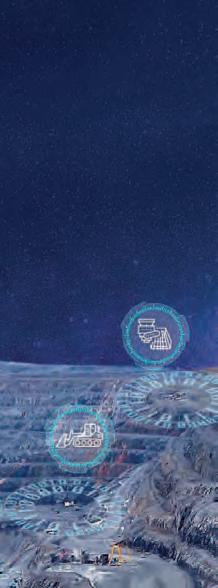
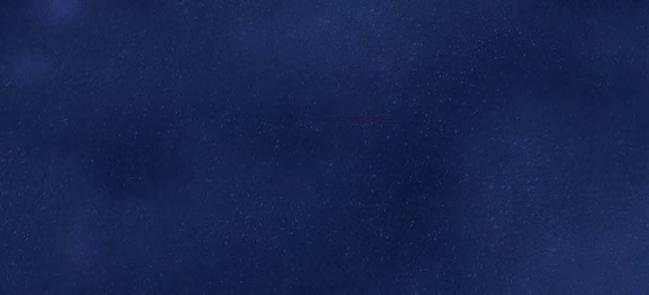
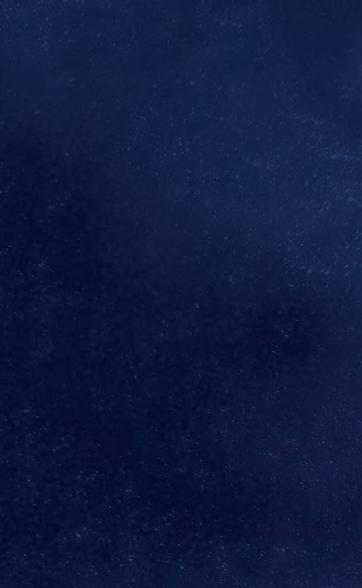


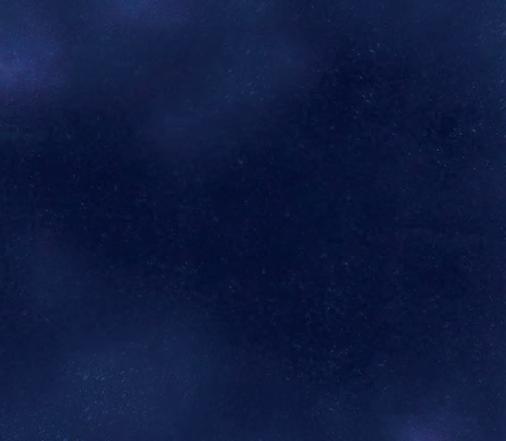
Open Autonomy for the Mining Industry “We will champion the enabling of new entrants to autonomy. Customers should have the choice to use whatever vendor they desire while leveraging their existing infrastructure.” — Hideshi Fukumoto, CTO of Hitachi Construction Machine CIM 2019 Conference, Montreal, Canada – April 25, 2019 CLOSED STACK AUTONOMY OPEN AUTONOMY Wenco’s vision for Open Autonomy empowers mines to... • Operate using mixed fleets • Maintainexisting technologies • Avoidvendor lock-in • Leverage best-of-breed solutions • Eliminate autonomy-only zones • Choose the solutions they use for their business Learn more at www.wencomine.com
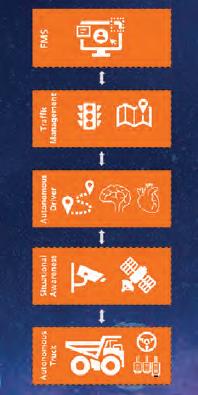
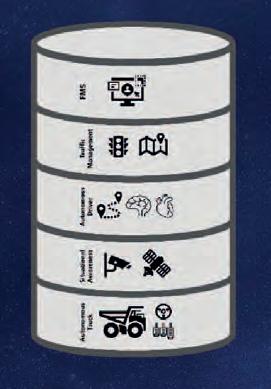
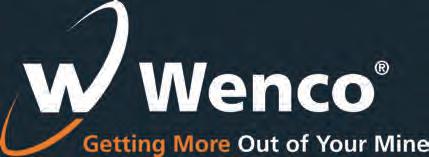
The global miner stated: “Across the mining industry, there’s been a long-held view that ‘bigger is better’. Enormous haul trucks provide economies of scale, allowing operations to move more material more quickly by leveraging the large trucks’ power and carrying capacity. But we’re challenging our thinking on size and why size matters. Larger haul trucks, while already automated, consume more energy than current electric-vehicle power sources can generate. By exploring truck size, we want to assess how big and small trucks can both be a part of the solution to reduce our emissions in the Pilbara and find fitfor-purpose solutions in mining.”
66 International Mining | SEPTEMBER 2022
involve the 40 t class Scania XT 8x4 model, with the XT trucks specifically aimed at tough construction and mining applications. The trials have also offered an opportunity to use a more open autonomy approach, where the AHS rollout does not restrict the operator to a particular truck OEM or fleet management system; and on this Rio Tinto has been working closely with Wenco International Mining Systems.
an operator would. We see extended parts lifecycle with AHS mostly in chassis parts – in the front and rear suspensions spindle hub and brake, and park brake.” He says Komatsu mining truck customers are typically changing out these parts depending on the application anywhere from 10,000 to 16,000 hours. With autonomy it is seeing up to a 40% extended parts life on these components.Butofcourse there are always other aspects to consider – because the truck doesn’t have an operator to provide ‘operator feel’ feedback and just runs – visual inspections like walkarounds become much more important, which are typically done during the fuelling. Though this also means the truck doesn’t have to be brought in for issues like the windscreen wipers not working or the windows not rolling down – these can be addressed in scheduled maintenance instead of immediately.
Is bigger always better?
There were some interesting comments from Rio Tinto recently in an article focussing on its transition to renewable transport in the Pilbara, specifically with regard to what is the right size haul truck for its operations – and that bigger is not always better for some applications, plus offering more electrifcation wins at an earlier stage.
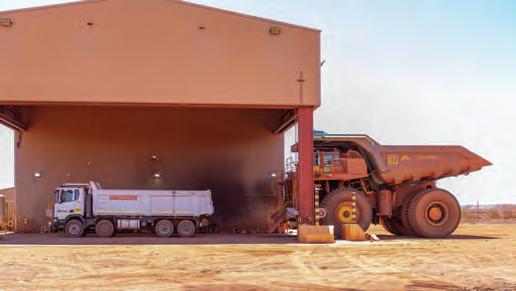
While big productivity gains combined with safety are the most obvious upsides to autonomous haulage, there are others – and one less obvious one is the extended component lifecycle that automating equipment brings with it. IM spoke at length to Tony Wickenheiser, Komatsu Mining Product Manager, Autonomous Systems about this phenomenon. He commented: “Operating the equipment within the design parameters is critical to optimising production but also for longer life of parts. When you automate the equipment, the machine is operating within the design parameters, which brings extended tyre, cylinders, motor components, and various equipment assembly parts. This automated practice also reduces waste with fluids and other consumables for the parts. All of these seemingly ancillary benefits add up to become big cost savings and big opportunities for decreasing waste for mining companies.”
AHS and longer lasting parts
AUTONOMOUS SURFACE MINING
So how is maintenance handled differently for AHS? “Overall it is similar. But there is an electrical component that changes on our trucks which is part of our IP that is devoted to autonomous troubleshooting and is monitored by our technicians. The rest of the truck is dealt with as normal, including the use of distributors or the mine’s own maintenance crews for truck repairs and the use of the onboard KOMTRAX system for both proactive and preventative maintenance. Some mining customers are also adding further sensors of their own to provide even more diagnostics in specific areas such as
Wickenheiser said that Komatsu did an initial deep dive into this subject going back a couple of years – based on the biggest bank of data that it had which was out of the Pilbara. “And it really correlates with what has been seen on tyre life and AHS. You see an increase in tyre life because you see an increase in change management when it comes to autonomous operation – such as better road maintenance and traffic management. Autonomous trucks drive in a manner that doesn’t push the limits of the truck –things like maybe not taking a corner as fast as
At its Channar iron ore mine in the East Pilbara, Rio Tinto is now working with Scania to trial smaller automated trucks that could more readily be electrified to reduce its carbon emissions, and could improve its zero emissions speed to market. The project builds on experience gained with autonomous Scania trucks dating back to 2018 at Rio Tinto’s Dampier Salt operation. Both projects
Hauling for large miners. Our engineers are working toward leveraging our capabilities at both ends to provide a scalable solution across multiple customer applications,” Forcash continued. “The more repetitive the machine movements the more ready it will be for autonomy. This lighter weight approach to autonomy with the CTL allows Cat to bring autonomy to operations with a different cost structure – quarries and construction sites don’t operate with the same cost approach to big mines. Mines generally have all the network infrastructure already in place, so that every machine on the site can be connected relatively easily. The CTL can run fully autonomous without any network so is a lot easier for a quarry application from a long-term point of view. And where it makes sense, we will also drive the best elements of this technology into mining.”
These trucks could also reduce emissions and costs while improving mining practices across site infrastructure and operations. “Smaller trucks can operate on narrower roads, allowing us to cut steeper pit walls and reduce vegetation disturbance. This reduces the amount of earth we need to move to access the ore, which means the smaller trucks don’t just produce lower or no emissions –they also help reduce our overall energy usage while we’re constructing and operating our sites.”Ofcourse payload is king and Rio Tinto is also exploring options to further reduce emissions of larger trucks through its partnerships with Komatsu and Caterpillar. “Working with Komatsu, we will pilot a fleet of their future 220 t+ zero emissions autonomous haul trucks in the Pilbara. We’re also working with Caterpillar to advance development of their future 220 t+ zero-emission autonomous haul truck, which we’re exploring the possibility of deploying at our Gudai-Darri smart mine.”
He adds: “The solution is a combination of three things. First, what we have learned and developed for autonomous mining, including components and some of the software. Second is our Command remote control technology. And third, what we acquired with Marble. Those three pieces have really come together. It has been designed not as a one off but as a technology we can integrate and grow into the Cat product line. Automotive progress has also helped drive down cost in terms of hardware to help us be able to bring these Command solutions to smaller equipment – it would not have been possible even five years ago.”
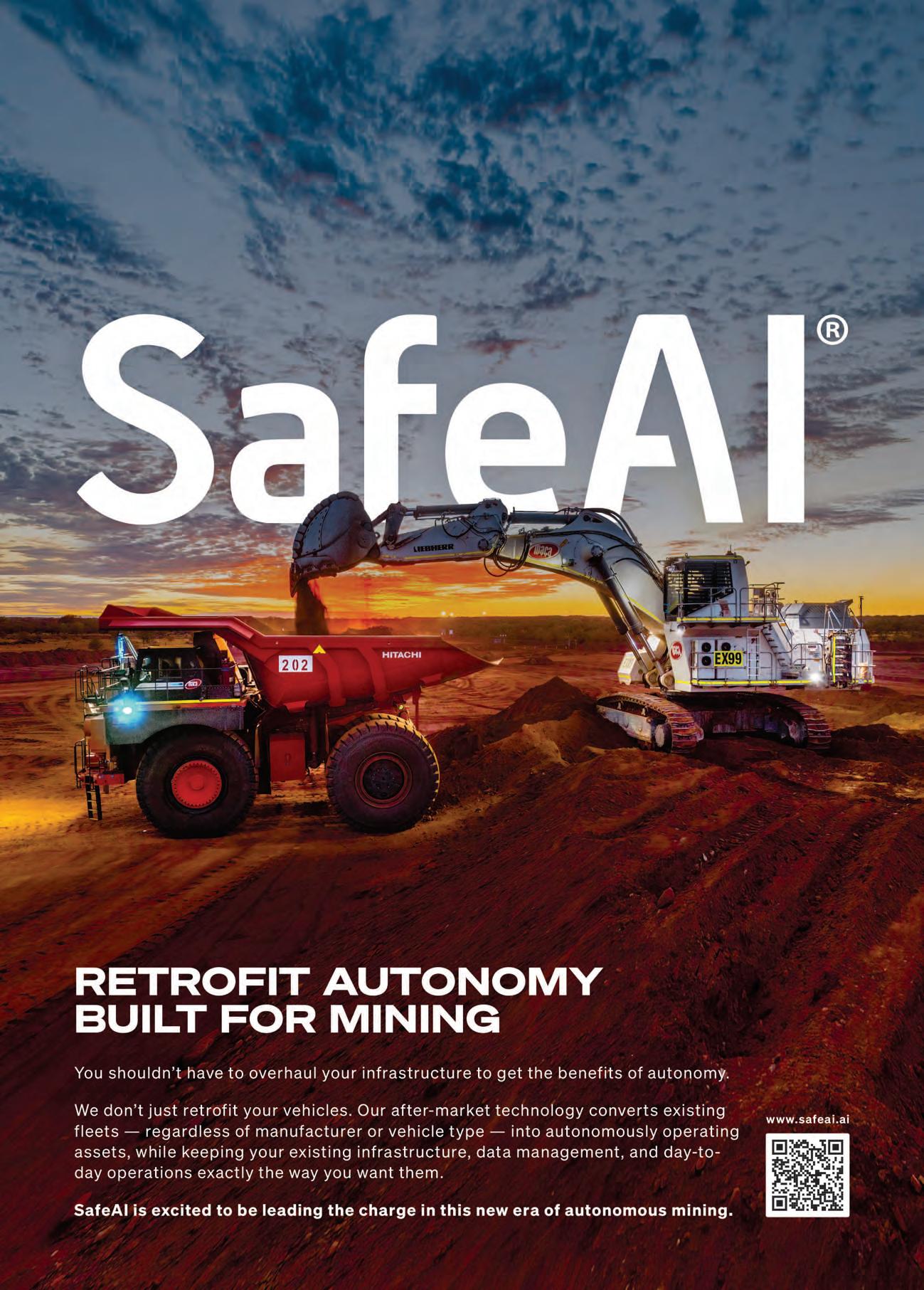
The advantage of route path planning Auto-mate – another one of the leading “new autonomy” innovators says putting a brain on the mining truck gives you a Route Path Planning (RPP) advantage. “While that certainly sounds impressive – here is what it means for you; if you’re a CEO of a mining company, it means a faster return on your investment with minimised risk of downtime, if you’re an operations manager, it means meeting your targets more efficiently, as an operator, it means confidence and ease of use, and as an HR manager it means a simple transition for the team to autonomy.”
The company continues: “You take your time
For Auto-mate, the recently held Diggers & Dealers Conference in Kalgoorlie in Western Australia included a range of conversations on autonomy – including the RPP advantage.
With no operator, which is normally the first line of defence, maintenance scheduling becomes very important, such as for the mentioned visual inspections for leaks and any other abnormalities. In addition, the KOMTRAX data also becomes critical in understanding any faults before they become serious. But using data analytics in the right way also means components in some cases can be run longer but still safely. “Taking rear suspensions as an example, if the scheduled replace and repair point is 18,000 hours, but there are no leaks and they’re holding pressure, then you can go well beyond that. And the AHS customers are doing that – pushing those component lives out. Less scheduled maintenance also means lower labour costs.” Komatsu has a dedicated analytics team that is actively quantifying and collating all of this lifecycle data from its growing number of AHS sites and fleets, to produce a meaningful cloud-based database “to help the customer quantify performance, productivity and truck health.”
When you look at engine life, this is based on volumes of fuel consumed. There are fuel savings as it is running more continuously so overall you are moving more tonnes per litre with a higher utilisation but from a fuel consumption point of view the AHS versus operator truck is about
Rely on
“You’re a haul truck controller, yes that’s right, not the driver, and you’re very excited to be part of the new automation team – you’ve been allocated the position of planning and monitoring the routes for the autonomous trucks at a particular mining operation and you’re looking forward to watching as the automated vehicles do what they should. The mine site has just completed a transition to automation for three of its Cat 775 trucks, and as a supporter of this transition, you’re looking forward to reporting on the success of the move to automation to your operations manager and CEO.”
On the wider autonomous market, Wickenheiser also confirmed that Komatsu is actively looking at bringing autonomy to its smaller truck classes as well as developing autonomy to manage its new power agnostic truck platform. “Smaller gold and coal mines, plus quarries and industrial minerals operations are all looking to the advantages of autonomy but they have both smaller trucks and smaller fleets – we just have to find a way to make the AHS proposition economic for these operators, and of course competitive and profitable for us. But it’s a challenge, especially in emerging markets where many mines use smaller trucks but have a totally different cost structure.”
worth pointing out the economic benefit from extended parts and overall truck life with AHS is somewhat balanced by the fact that maintaining roads at the highest quality, also being wider (in some cases to allow for multiple tracks to avoid rut development) and with wider turns and wider load and dump areas to enable AHS comes with significant associated higher cost. Also, autonomy comes with its own additional expenses beyond just road maintenance – such as network upgrades and the fact every AHS truck has other vehicles supporting it – equipped with what Komatsu calls EMV kits – these include light vehicles for pit patrollers, graders, dozers and shovel operators.
AUTONOMOUS SURFACE MINING
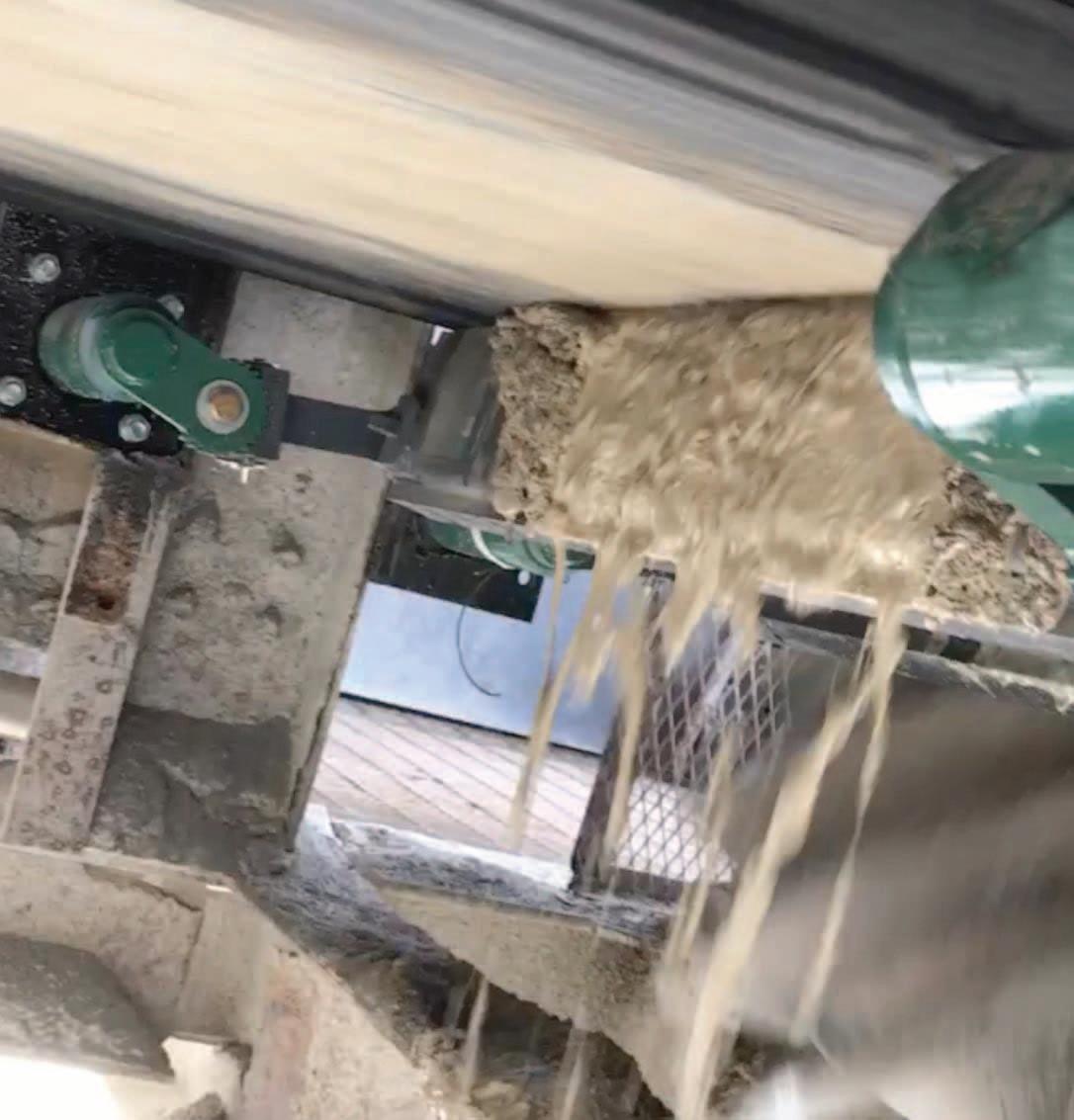
neutral.Itisalso
turbos to monitor temperatures. In many ways AHS is paving the way for the most advanced remote health monitoring yet achieved in mining.”
AUTONOMOUS SURFACE MINING

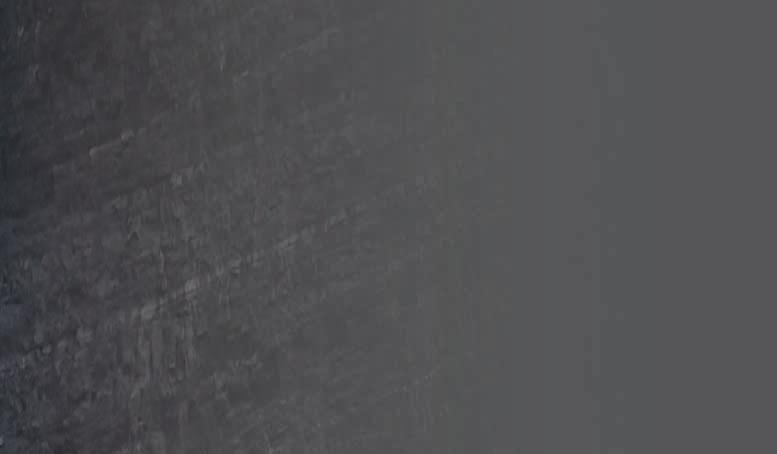
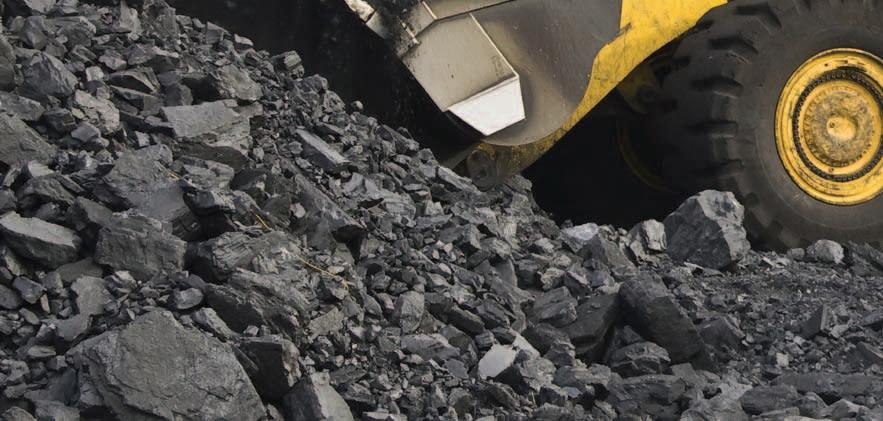

Today, this takes a little time to resolve, as a person is required to visually inspect the environment and to determine the safest way to resolve the issue and enable the truck to proceed on its autonomous path. “Finally, you’re informed that the obstacle was a medium sized rock from a
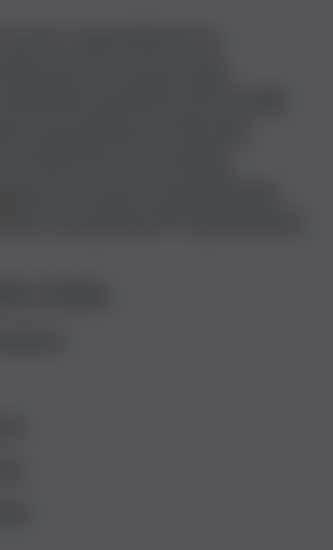
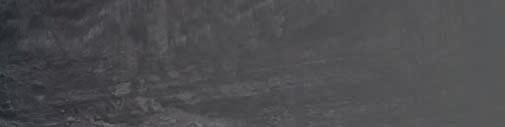
considers 100+ factors constantly to determine the optimum path for assets to travel, avoiding obstacles, navigating terrain and complying with all mission parameters.”
The company was founded in 2011 as a R&D subsidiary of indurad GmbH - the industrial radar company. The full xtonomy spin-off from indurad has recently been launched with the longstanding experience of its robotics team. “The objective of this new venture is to bring our unique and proven autonomy ecosystem to market as a stand-alone company that has envisioned to provide autonomy everywhere. We have extensive experience in mobile machine automation based on radar perception, applied in underground and surface mining as well as industrial applications. We work in a consultative and solution-oriented manner in close
What’s your TPH and cost/t? Get Accurate Payload Measurement with Loadrite Scales. To improve your mining operations, visit goloadrite.com Use Loadrite in your operations to help reduce costs per ton, increase report your mine operations. Get the most from your mine by accurately measuring payload on your equipment and ensuring that every load is optimized. SOLUTIONS FOR: Wheel loaders HaulConveyorsExcavatorsLHDstrucks
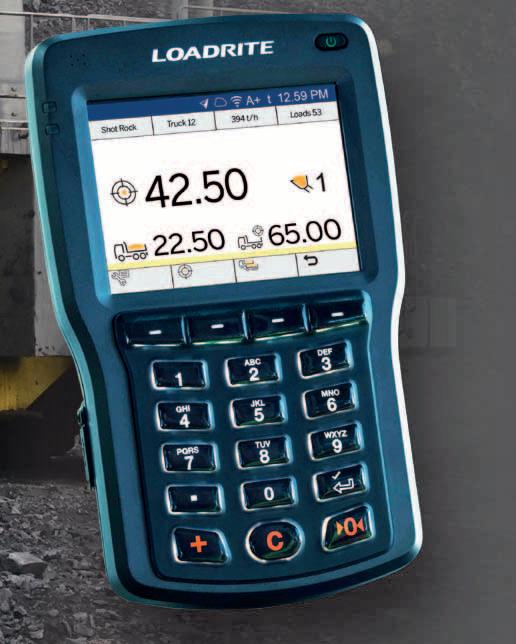
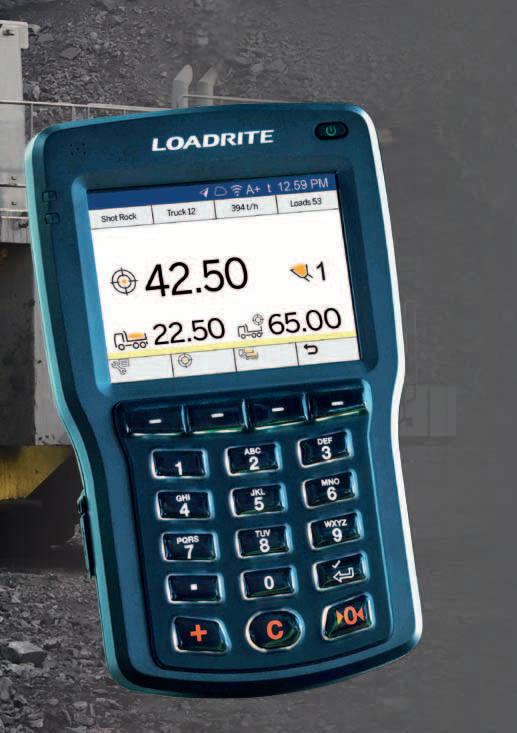
You can see a digital rendering of the operation, and you can see the autonomous truck making its way along a mine road as planned. But then the truck stops, and as a result, all autonomous vehicles that need the lane it was using will need to wait and there are strict mine safety regulations in place for anyone approaching the stopped truck. The sensors on the truck have detected an unexpected obstacle.

Your bubble of excitement is fast deflating… considering the downtime of not only the truck, but the other assets held up behind it, as well as the negative tone from the inspection team, this is not going to be the planned, very impressive, kick off report to the operations manager, let alone the CEO.
on planning the route, taking care in ensuring the waypoints are accurate. It takes a little longer than anticipated as the route includes some inclines and declines which need to be considered in determining the waypoints as you will need to specify the Z axis (height) as the site scan file came back corrupted this morning. The significance of this plan is not lost on you – the CEO is keen to report back to the board on the savings and efficiencies gained, illustrating the value for money invested in automation, to the board. Finally, when the automated trucks are on their way, you can sit back and enjoy the comfort and convenience of the operations centre located a way away from the hot and dusty environment in which the truck is operating, autonomously.”
previous spill event and it has now been cleared from the lane. Frustratingly the inspection reports that there was more than enough space for the truck to pass it to the side and safely continue on its route and it was a pity there wasn’t someone in the cab to make the decision and continue on. However, it is now on its way.”
Auto-mate describes itself as a unique mining automation provider that offers asset level automation which determines optimum pathing and executes missions. “Auto-mate’s RPP

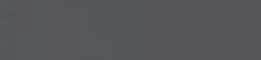
So what does RPP do and why is it a key element? “With RPP the waypoints are there merely to show the planned route, however, this planned route includes a corridor within which the vehicle will find the optimal path. The width of the corridor, the area within which the vehicle can choose its optimal path, is adjustable too, allowing maximum flexibility for the vehicle. Should an obstacle be detected, the onboard intelligence of the autonomous solution will assess if it is safe to pass within the autonomous corridor, and if so, it will continue on its planned route with no stopping or downtime.”
xtonomy and the rise of radar xtonomy’s mantra is to provide “autonomy everywhere.” It says its AHS offering for trucks finds application in mining environments, autonomously hauling material and interacting with semi-automated shovels, loaders and crushers, while utilising a robust radar-based perception systems for GNSS-denied and rough environments. Within its automation ecosystem it also provides starting points towards full autonomy, like operator assistance, teleoperation and collision avoidance systems.
cooperation with our customers.”
trucks still have to maintain or exceed current production levels. The trucks have already been running at more consistent speeds with less queuing at the loader. Going to the next level without operators in the trucks will also allow them to run for more hours, upping productivity further – crucially it will allow the quarry to switch to two shifts. There will only be two haulage fleet workers – the loader operator and a second controller working from a control room on the site – this is already running for tests ahead of the fully autonomous switch. They will not have to stay in the room all the time, as the site has a camera-based system for recognition and push-warning in case of arrival of vehicle and personnel in to the autonomous operating zone; so they will be able to also carry out other tasks such as managing road and vehicle maintenance as well as traffic management.
vehicles in tunneling or utility vehicles. Based on +15 years of experience in R&D robotic domains, xtonomy has developed and utilises a unique belief-aware reasoning-AI for a highly dynamic, adaptive and smart mission planning. The AI mimics the way a person would flexibly reason about his tasks, while being fully comprehensible andHedeterministic.”adds:“Ourverifiable risk-aware
A lot of innovation in autonomous haulage is happening around the world - another great example being Steer AS in Norway – and IM recently spoke to CEO Geir Ståle Kleppe. He commented: “Where our technology is working now, the initiative was taken by the customer, haulage contractor, Romarheim AS at a 2 Mt/y quarry owned by DC Eikefet Aggregates AS. Romarheim fulfils a weekly tonnage total of rock into the crusher. They wanted to make the operation as efficient and safe as possible and had seen Steer’s track record in machinery remote control; plus approached us at a time when we were already well into building our autonomous capability.”
The contract with Romarheim allowed Steer to build on this experience in mining, and to start trials in conjunction with further development towards a higher degree of automation. Kleppe adds: “The truck operators have to date stayed in the truck cabs as part of what has been a semi-autonomous solution, providing continuous feedback and with the ability to switch from autonomous back to manual as needed. As an ODS has been refined this has also added an extra layer of safety.” However, an operator has only had to intervene once in the several years the trucks have now been running due to a software bug that was quickly resolved.
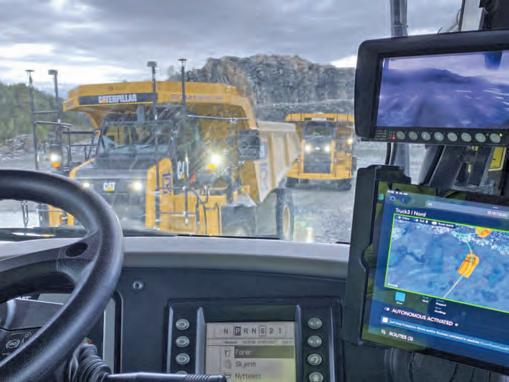
CEO Christian Riedel: “The modular architecture enables automation of all mobile machines in off-highway applications including their work functions. Besides haulage trucks or loaders in surface, underground or hybrid applications, the system enables automation of a great variety of machines, such as multi-service
Steer AS’s background dates back to a 2009 contract its construction company majority owner Gjermundshaug Group took on with the Norwegian military to clear an artillery range using remote control with a safety distance of 1 km. At that time there was not a lot of technology available to do this with good signal and low latency. Remote control excavators were filling remote control haul trucks which were remotely driven out of the site and along mountain roads out of the restricted area. As the area was highly controlled there were not the same requirements as in a mine for object detection systems. Steer AS was then spun off as a standalone company in 2018.
The mounting on the machines is currently done by Steer based on the interfaces of the particular models but long term Kleppe believes this may be subcontracted to distributors and dealers of the equipment OEMs. Even today it only takes a week. Further down the road, onsite service and maintenance may be taken care of by the mine’s own technical personnel or by service dealers from the OEM. Software and online support will be taken care of by Steer.
AUTONOMOUS SURFACE MINING
Steering automation for small mines
be progressively upgraded to meet new operational requirements.
Steer has had visits to the quarry from major cement companies operating limestone mines as well as one of the leading global industrial minerals groups. Another focus is to widen the application of the AHS to other brands beyond Caterpillar – and the company has already had talks with Norwegian Komatsu dealer Hesselberg Maskin and is looking for a potential mining or contractor customer with Komatsu machines.
The next step is having the trucks fully autonomous and this is imminent, possibly in September 2022, as Steer’s ODS is now close to being fully operational – it comprises LiDAR sensors with Steer’s own software allowing system decision making. The main ODS challenge has been the climate, as the quarry in the Bergen area sees rainy conditions throughout the year. Of course as this is a live mine, the all autonomous
xtonomy says its modular technology platform enables differing levels of automation, from proximity detection and collision avoidance to full-fleet mixed autonomy. The technology platform leads to increased operator safety, machine availability and performance while reducing costs for clients. The systems are retrofittable to any vehicle and the solution can
70 International Mining | SEPTEMBER 2022
So how is the Romarheim operation currently controlled? Similarly to the large AHS mines, the system is managed by the loader operator, in this case a Volvo 950 excavator, which has a control panel enabling the setting of the loading point, defined by the excavator bucket position. A wheel loader is also equipped with the system, and has been used until it was recently replaced by the excavator. The loader operator calls in the next truck in line to the defined point, loads the truck and then kick it out. Today, there are three Caterpillar 772G trucks running in the main quarry with the technology installed on a further two, which are going to another nearby quarry. Steer has enjoyed good working relations with the Norwegian Cat dealer Pon Power AS on digital interfacing – this allows any machine warning message to be transmitted to the loader operator. Each vehicle also has its own iPad for autnomous settings and control. The loader operator is having both an iPad and a button control panel.
Kleppe concluded on the future: “We are not restricting ourselves to the Norwegian market – we are looking to expand as soon as we have our autonomous haulage system fully proven. Our system has a lot of versatility and potential in smaller mines as it is simple and scalable –comprised of components that are readily available – but is run and importantly has been proven in a real mine using our own proprietary software.” As an example the quarry that will run two autonomous trucks only needs a 4G cell network and GNSS access to operate.
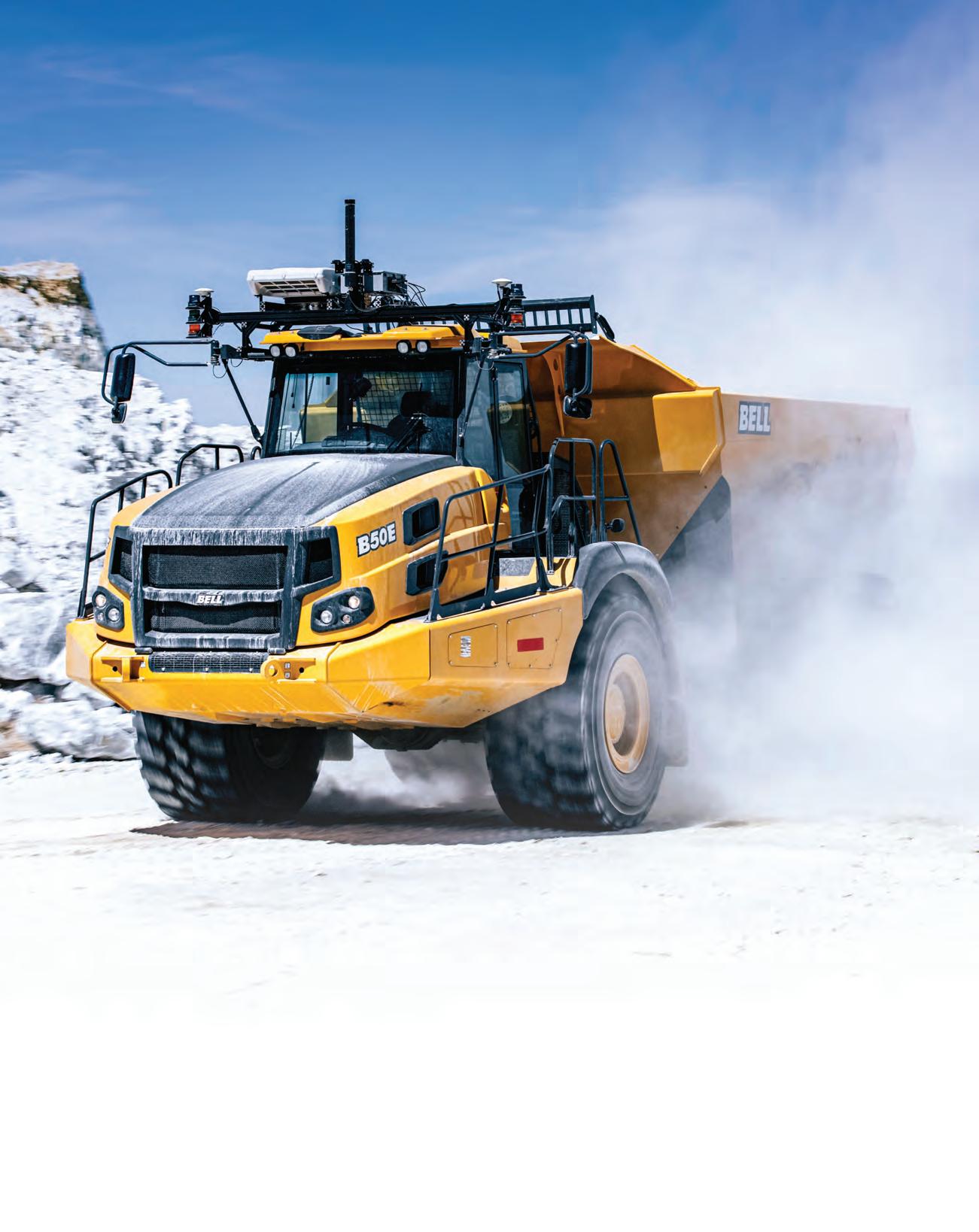
Furthermore, the autonomous haulage trucks continuously adapt its loading position to the current shovel position.”
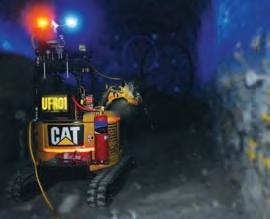
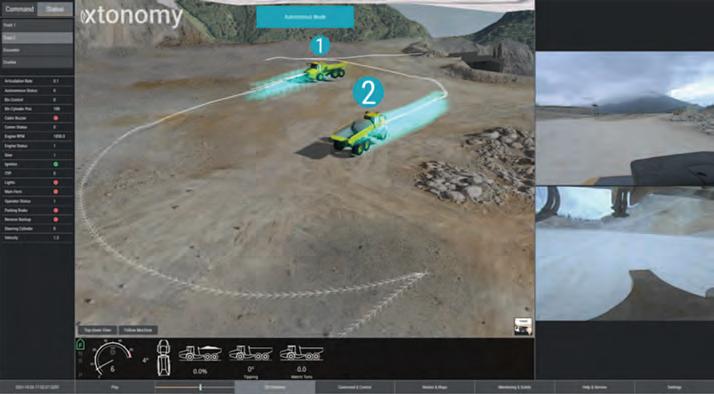
There are several major benefits to automating vehicles in the mining industry; it reduces risk to personnel in dangerous environments, increases efficiencies, reduces emissions, and maximises the life and versatility of legacy vehicle platforms and
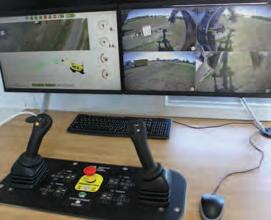
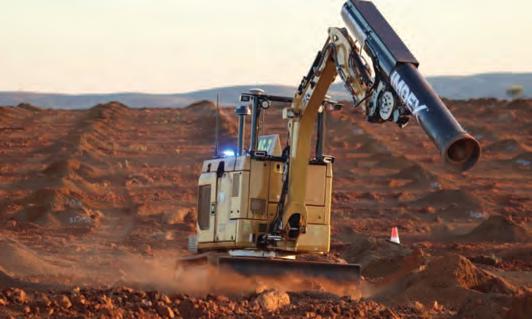
autonomous decision-making AI enables a high recovery capability from failure modes leading to highest OEE and is capable of adaptively planning even very complex tasks, allowing autonomous operation in partially unknown and changing environments/situations. This advanced networked belief-aware fleet traffic optimisation maximises productivity of the autonomous fleet operation in a holistic context such as loading and unloading equipment or manual participants. In practice this means that the system automatically resolves bottlenecks in the material flow process from face to crusher.
AUTONOMOUS SURFACE MINING 72 International Mining | SEPTEMBER 2022
area, routes, etc are constantly changing. By using robust radar onboard mapping and object detection it continuously perceives the environment. Its motion planners freely plan the best routes and dynamically react to changes. Furthermore, it handles the interaction of multiple trucks in such unstructured environments. This is only possible through leveraging Machine Learning (ML) and AI for a very high degree of autonomy at highest system levels."
Ininfrastructure.aminingenvironment where tasks are often repetitive, all the vehicles involved can be synchronised. Task planning software can ensure that all the vehicles take the most efficient route, reducing fuel consumption and the time to complete the operation. Vehicles that have the ability to detect obstructions can communicate them to the fleet management system to prevent others from encountering the same issue. Once the obstruction has been flagged the vehicle management system can generate an alternative verifiable risk-aware autonomous decision-making AI in action
xtonomy’s
xtonomy says it is implementing the latest machine learning techniques for the development of highest detection and classification capabilities in its radar and vision perception modules. This means that even smallest objects, such as rocks in highly complex and unstructured environments may be detected and consequently avoided by the autonomous vehicle. Furthermore, this enables highly reliable radar mappingdriveabilityofentire mines but also critical work areas such as the truck spotting or crusher entry zone. “Consequently, tyre damage may be also minimised for manual vehicles and berms may be monitored for safety loadingenvironments,unstructuredalsopre-mappedonlymediumdynamicbutworksconditions,andfordesigned"Thecompliance.”Riedelconcluded:xtonomyAHSistobeadaptivedifferentminesizesever-changingmineandthusnotonlyinlarge,alsoforhighlysmallerandsites.Ithasnotproventoworkonpaths,butinverywherezones,drivable
ABD Solutions launches Indigo Drive

Described as a complete solution to add autonomy to existing vehicles; “Indigo Drive is an ecosystem of technology that provides existing vehicles with autonomy, quickly and costeffectively,” says Matthew Price, Managing Director of ABD Solutions. “The mining industry is continually looking to extend the lifecycle of its existing fleets and automation is a critical part of this. Not only does vehicle automation have clear safety benefits, it also allows for significant cost savings.”Indigo Drive offers all hardware and software required to provide a complete, integrated, automation solution, available from a single supplier.Retrofitting existing vehicles with autonomy requires a flexible solution that can be tailored to a specific vehicle, environment and operational scenario. A core modular, certified and secure software eco-system is used to build the various elements required for automation; including vehicle management, vehicle control actuation, communication, sense and detect, health and diagnostics and third-party integration.
This modular approach enables Indigo Drive to integrate with core and third-party technologies to ensure that specific requirements are met. The result is almost any vehicle can be retrofitted with autonomy and then fully integrated into any end user’s existing operational/fleet management system.
Accelerate your automation collaborate for success universalfieldrobots.com.au +61 7 3666 0006 hello@universalfieldrobots.com.au
Ognen Stojanovski, COO & Co-Founder, who before Pronto helped launch Otto and Uber Freight, both of which focused on developing technology for the trucking industry, told IM: “We didn’t start off looking to build a mining or even an off-road autonomy system. Much of our leadership team has been closely involved with on-road autonomous vehicles for some time –almost 20 years in fact – making a lot of breakthroughs with new technologies. We started out with some advanced driver assist solutions for on-road trucks and we had a customer with a commercial trucking fleet but which also had some material haulage contracts in mines and wanted to use the same tech in what was a much more controlled environment and not only that, use it to its fully autonomous capability. The more we learned about mining, the better fit we saw it having with our technology.”
Today Pronto has already deployed not just for R&D and trials – vehicles equipped with its system are hauling ore in daily production and it believes
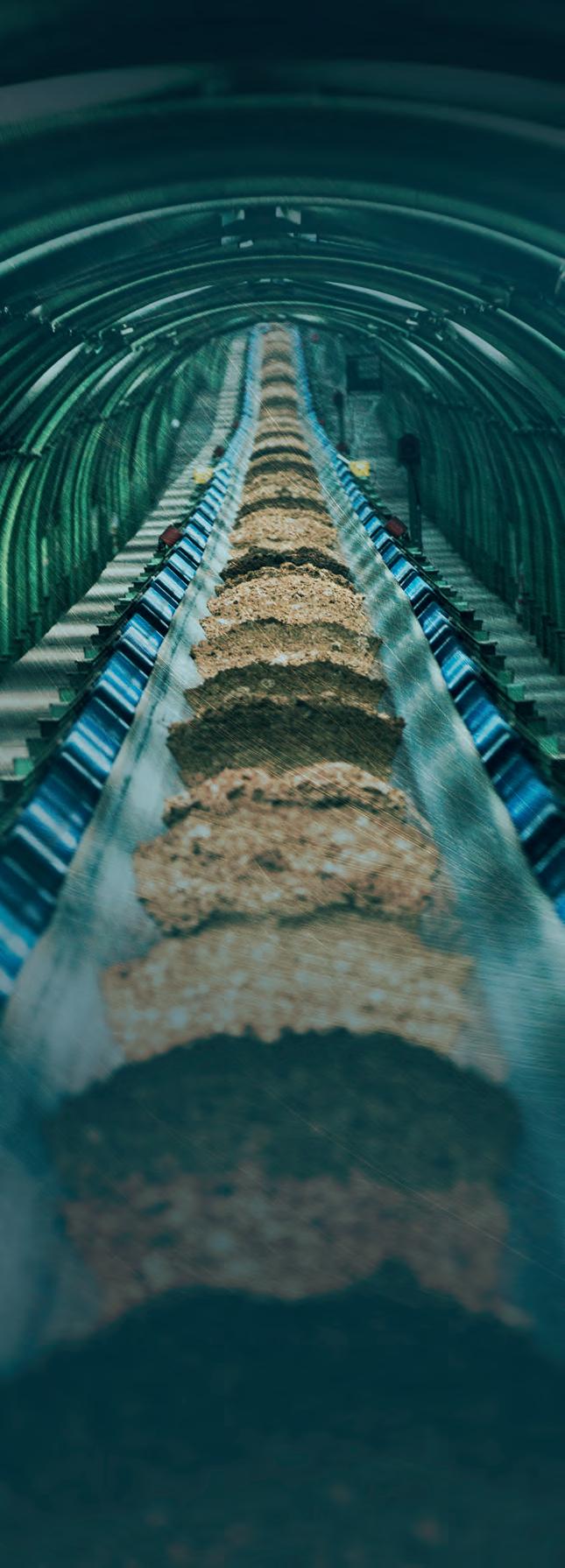
Knowing what you don’t know
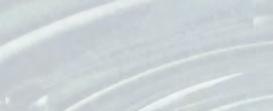
route or a human can remote into the vehicle to immediately assess the situation.Oneof the welcome side effects of autonomy is the digitisation of information from the vehicle. It creates new data streams that are invaluable to fleet operators. The vehicle’s speed, location, fuel level, diagnostic status, distance to target etc. can all be relayed via the vehicle management toolset. Data analytics can process this information to assist with operational decisions, fleet maintenance scheduling and procurement and routeABDplanning.Solutions is a member of the AB Dynamics Group and says it will benefit from its knowledge of developing and supplying thousands of driving robots to the world’s leading vehicle manufacturers, proving grounds and regulatory authorities. The Group has decades of experience in vehicle autonomy and simulation.
Stojanovski said the Pronto team initially assumed from what they had seen the large OEMs doing that autonomous mining was already solved, “but we quickly realised it was hardware heavy and essentially restricted to ultraclass truck primary haulage and that our software and AI heavy approach could offer a much more general autonomy for mining, able to handle a much greater range of mining environments with a lot fewer sensors, much lower costs and much less operational restrictions. We seriously started looking at mining in late 2019 and by October 2020 we were already running loads unmanned in quarries.”
Visit bauma,us!Munich, Germany October 24– 30, 2022 Hall B2, Stand 413 beumer.com SOME THINK THAT DIFFERENT.WETRUCKING.REQUIRESTRANSPORTMATERIALSRAWTHINK
“AB Dynamics has been automating vehicles in one way or another for development and test purposes for decades,” continues Price. “Now, through ABD Solutions and the development of Indigo Drive, the mining industry can take advantage of this expertise to automate their existing fleets today.”
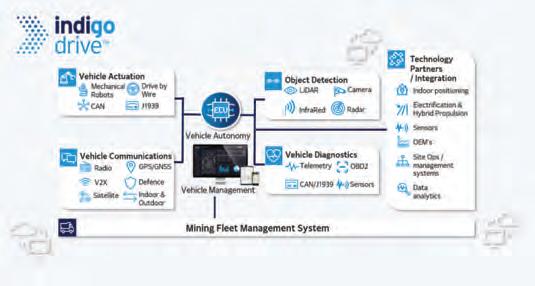
One of the newest entrants to the mining autonomous haulage space is Pronto, which many in the industry first encountered at MINExpo 2021 Having cut its teeth in state of the art on-road autonomous driving, the San Francisco-based company has approached mining AHS from a new point of view with its A2B solution.

Pronto tech equipped autonomous ADT during loading
that it is camera vision based with no radar or LiDAR. Cat Culkin, Pronto CTO: “The benefits of camera-based systems are many in mining. First off, they are relatively speaking much lower in cost as we use automotive grade cameras; plus they are very robust in dusty and high vibration environments. There aren’t moving parts that can get damaged by dust or water ingress. Our software allows us to upgrade our digital imagery capabilities on the fly, unlike existing AHS requiring the latest sensors which often need to be upgraded by replacement. Neural networks processing data from cameras are also very good at classification of things in the vehicle’s path such as correctly identifying whether it is debris or a tyre or a person. But they are also good at knowing what they don’t know. They see the world more like a person does – seeing where the berms are, assessing the driveable area on a muddy, wet and changeable road. In foggy or snowy conditions, the cameras perform slightly better than the human eye and at night can just use the headlights to light up the road as a manually driven vehicle would. Our main front-facing camera behind the windscreen will maintain its clear view by coordinating with wipers just as in mannedRedundancyequipment.”isprovided by V2V on other vehicles. The software analyses the imagery in real time and can decide the safe speed to drive given the conditions while still maximising efficiency. “If something comes into the driveable space like an animal which then clears the space, the truck will retard or slow down but won’t need to stop. And again, almost eliminating false positives that other sensors are affected by is a big advantage. So our system is really good at stopping for things that need to be stopped for and for ignoring those that don’t.”
AUTONOMOUS SURFACE MINING 74 International Mining | SEPTEMBER 2022
it was the first in the US to do so. It also believes it was the first to be in regular mine production using autonomous vehicles in the smaller equipment classes. While he wouldn’t give specifics, he said that it involves multiple sites; still mainly today quarry environments with auto ADTs but also on smaller rigid trucks. IM has also previously published information on its growing partnership with South Africa-headquartered global ADT major Bell Equipment while Pronto says it also has a lot of new projects in the works.Stojanovski adds on the potential: “You are looking at a whole other part of the market. Many of our customers don’t even have a fleet management system – quarries and small mines with five or six, or in some cases only two trucks. You can manage our system with just a phone app and sufficient connectivity through existing public LTE – which we can also upgrade in-house if needed as we have our own private LTE company.”Fromthe mining perspective, Advisory Specialist Owain Morton commented: “From my career in mining, we had mixed fleets which was one major issue, but also quickly realised how deep the investment had to go with the big truck OEM AHS providers into hardware to support the AHS plus a very long term commitment to that one supplier which at the time we just weren’t ready to do and we weren’t the only major miner taking that position. We were focused on mine production and our metals revenue stream. Not only that but these autonomous systems were adding to already huge data lakes which were causing their own headaches. Pronto gives a simpler solution.”
What does the on-road experience bring to mining? Morton says: “On-road has much faster traffic, meaning AI decision making has to be faster, you are closer to a larger number of vehicles and they are less predictable, plus required stopping distances are shorter. You have more delineated lanes, crossroads, roundabouts, signs to be followed. Even from a collision avoidance and object detection perspective, we feel our solution is more flexible, creates less false positives and doesn’t interrupt production. In fact, the stack needed for our collision avoidance alone can effectively drive the truck autonomously. There has been resistance in mining to using technology developed for onroad with the argument that it is too different –but truck operators in mines when they finish their shift are getting in their private cars that have more advanced systems and many times more AI than the mining vehicles have that they just drove, so why not have some of that in the mine vehicles where it is applicable?”
Plus, despite the current Pronto operations being mainly US-based, the company has global ambitions. So far the focus has been on North America, but Pronto is in discussions about other projects in Europe and South America, with updates to be given in due course. Ognen said that the first deployment outside the US is set to start operation in September 2022.
He believes that for the tier 2 large scale mines but also for all the other small mines out there that Pronto hits the target from an outside in perspective. “For all the operators you can take out of smaller than ultraclass trucks – it
could be possible to redeploy and re-certify in many other areas in mining where there are huge skills shortages. Plus, there are many regions where there are already shortages of truck operators – especially in contracting companies. Many tier 2 miners don’t have the required fleet management system in place or the depth of relationship with the big OEMs to move complex AHS deals forward.”

IM
Current AHS trucks mainly follow a set route or factor in slight deviations to that route each time to avoid rut generation. Pronto’s system can do this but also has dynamic path planning, not only for wear levelling but also to allow for the excavator having just moved along the face, for example. The loader operator still brings the trucks in and sends them out but the truck itself is best able to determine an optimum path to the loader in the first place. This also applies to following the best path to a dumping area whether that be a waste dump, stockpile or crushing station. “Manned vehicles entering our autonomous vehicle zones just need a small transponder. The loader still manages trucks coming in and out but just has to hold up the bucket which will tell the system the spotting point automatically.” Pronto says it aims to deliver full autonomy to any truck, in any mine, anywhere, and is deployable today; simplifying autonomy for the industry.
But how does the Pronto tech actually work? The big difference to anything else out there, and this also relates to the on-road experience, is
While robots are delivering efficiency, they are also paving the way for safer operations via zero entry mining. One example is voids in hazardous mining areas that can have tragic consequences. Natural and historical mining voids can cause a collapse of ground with no warning. Robots can drive over ground of unknown competency, map voids, reduce delays and improve productivity, while eliminating operator risk. UFR’s development roadmap features safe robotic solutions commencing with all blasting activities.
In collaboration with multiple mining clients and METS Ignited, UFR is developing a new robotic application for zero entry work on underground production blastholes. The robots first capabilities are cleaning and surveying –some of the remaining dirty, dangerous, and diabolical underground mining tasks. This requires work at heights in a basket to push a hose ~30 m up a blast hole, resulting in rock and water showers along with damaging high-
The new robot drives to a ring and uses perception to find/align the specially designed attachment that pushes a hose into the blastholes. Training has been completed at our test mine in Brisbane and trials have commenced on minesites in Queensland and Western Australia. The development team has found some blastholes can require 3-4 cleaning cycles, but as it’s an automated process, the robot doesn’t work up a sweat. Operators are happier being far from the showering gravel and noise and can make coffee while checking on the robots via the remote-control station. Our collaboration partners recognise the importance of eliminating hazardous activity with significant health and safety improvements.
To simplify setting up remote control at a safe distance, UFR has also released a containerised remote-control station that can be quickly deployed with mesh radio. The containerised RCS is insulated and air conditioned with a desk incorporating two operating locations for a variety of scenarios with ample room for a coffee machine.Newuser interface enhancements continue, some via operating partner suggestions. New work applications are demonstrating LIDAR perception value with its detailed and accurate capture of surroundings. Complex tasks are assisted with camera views, LiDAR images and cartoon reimaginations from gamified angles. One South African mining partner has requested the user interface show drone captured changes in the mine environment to enhance operators’ situational awareness.
HIGH PROFILE
More robots for better mining
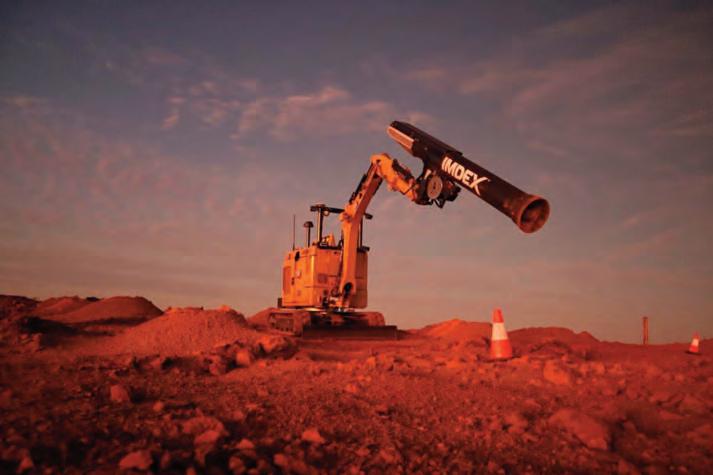
allows us to reimagine the future, adjust some computer code or settings and squeeze even higher levels of performance from our robot team. Shaving a few seconds off an action mightn’t sound like much but repeated 200 times a day 24/7 it quickly results in higher levels of performance and profitability. The repeatability of robotics can’t be beaten for tasks like working on thousands of blastholes that appear almost identical from the surface.
Universal Field Robots Managing Director, Jeff Sterling, outlines how the greater use of robotic technology can at the time make operations safer and more efficient
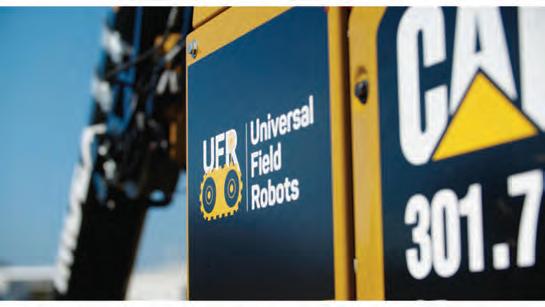
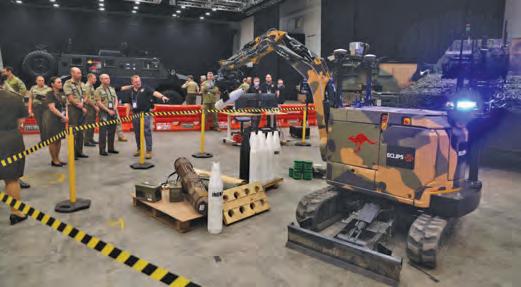

Robot capabilities built for one application can also quickly be adapted to benefit others. This platform approach also works across sectors with cross pollination of ideas accelerating capability roll out. Enhanced movement control and better AI vision developed for a defence project can be shared to boost performance of other applications.It’searlydays and what we can do now is almost certainly a fraction of what is possible. Robotics that allows people to avoid hazards is available and is the only way for operators to truly be safe. What are we waiting for? IM
a mantra of more robots for safer mining, Universal Field Robots (UFR) sees a future involving swarms of small robots inhabiting the space between bigger mining equipment and activities. The pandemic is still impacting mining, with skills shortages and many critical tasks delaying production. UFR is working towards having the largest robot fleet on the planet and has enrolled robots to manufacture these robots. Robot manufacturing provides high quality and speed, with lower cost a valuable byproduct.Incollaboration
With


with IMDEX Limited, UFR is building BLAST DOG™ robots in increasing numbers, with a presence on multiple mine sites across the globe. BLAST DOG™ is an autonomous system to optimise blasting based on highresolution three-dimensional material models built from the sensor data the robots collect from blastholes. UFR is advancing the BLAST DOG™ automation application and each new release brings improvements in operating performance and new Supportingcapabilities.swarms of robotic machines around the world is a new challenge, which is supported by technology. Working robots record what they see and feel and UFR has built infrastructure to capture these moments. Robot memories can be teleported to the cloud allowing robotics engineers to replay an event to find the cause of a performance decline or operations glitch. This
pressure air noise.
SEPTEMBER 2022 | International Mining 75
Robotic hauls underground
UNDERGROUND AUTOMATION 76 International Mining | SEPTEMBER 2022
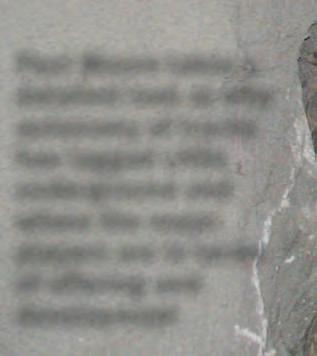

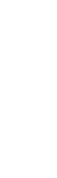
Sandvik AutoMine equipped truck at Williams gold mine in Hemlo, where an autonomous truck loop ran for 16 years
Epiroc says Minetruck Automation provides a full autonomous cycle with automated dump function and programmed routes. One operator can control a mixed fleet of automated trucks and loaders
Paul Moore takes a detailed look at why autonomy of trucks has lagged developmentofplayerswhereundergroundLHDsandthemajorareintermsofferingand
So far in the underground mining equipment market – two of the market leaders, Sandvik Mining & Rock Solutions and Epiroc, have released or partly released autonomous truck solutions into the market. Sandvik AutoMine®-enabled truck loops have actually operated underground for many years –notably at the Finsch diamond mine in South Africa, as well as at the Williams gold mine in Canada.Epiroc made a pre-release of its Minetruck Automation solution, which is part of its 6th Sense offering, in 2021, and is now refining its offering at Garpenberg. Caterpillar has not yet publicly released formal information but is working on its first autonomous truck offering which will be applied on the AD45.
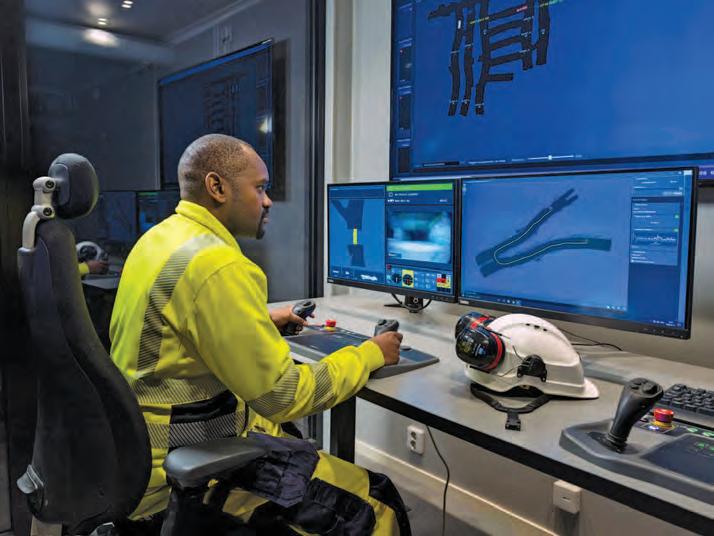
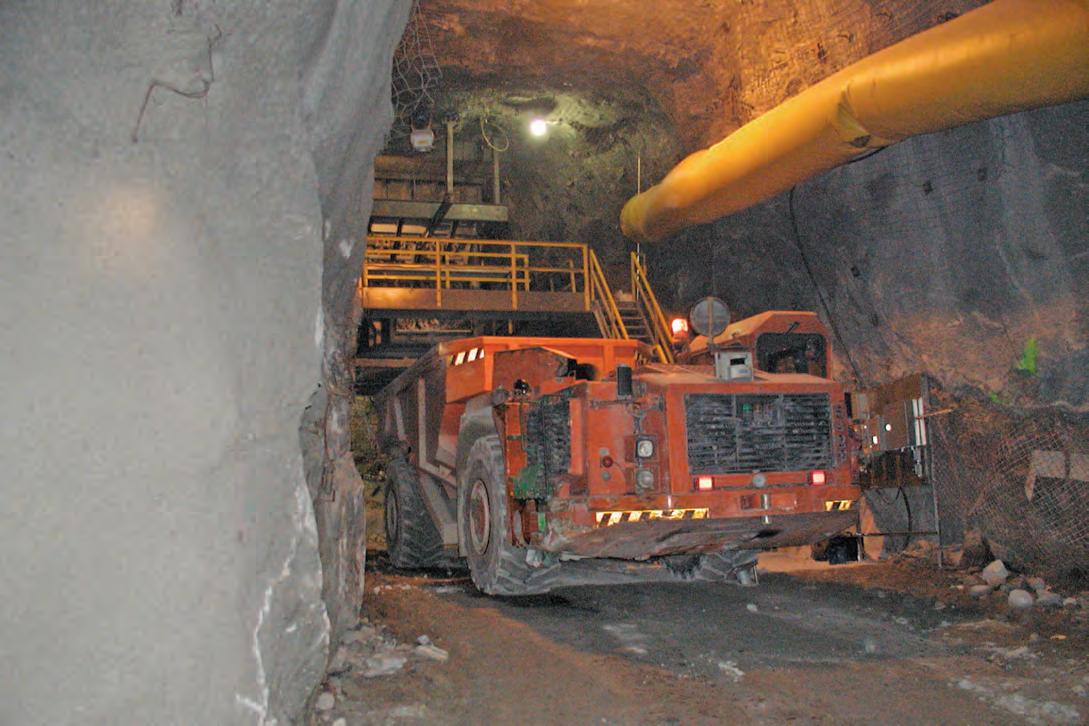
speeds than loaders and over a longer, often much longer, tramming distance. Secondly, the truck itself has to be loaded by something – that may be a chute, but it also may be a loader so then you have another machine to deal with, whether it is also automated or not. Third, in
First off, we spoke to Vladimir Sysoev, Epiroc’s Global Portfolio Manager 6th Sense about the company’s evolving offering. He had this to say: “From the broader perspective, in Epiroc we use our Rig Control System (RCS) that is common across all our automated and autonomous machines. The question is how far can you take the solution with trucks that is already globally proven on loaders? The major difference when automating underground trucks, and this is true for all the major OEMs, not just us, is that currently it is still necessary to seal off the autonomous working area of the mine, usually with laser gates. In the case of loaders this is not as much of an issue – normally the tramming distance for an autonomous loader is not more
than 200 m, so the segregated area is relatively small. While it still creates constraints with mine planning, if you just have loaders going from the stopes, or drawpoints in the case of a block cave, the need for interaction with manually operated vehicles is limited.”
He adds: “When it comes to trucks, there are some significant differences – first of all, generally you will be running the trucks at higher
one level, running from chute to ore pass.”



At Boliden’s Garpenberg operation, Epiroc has an autonomous truck operating on one level –this project represents the beginning of the industrialisation of the company’s auto solution for Minetrucks – applying all the technology that has been developed to date in real mine
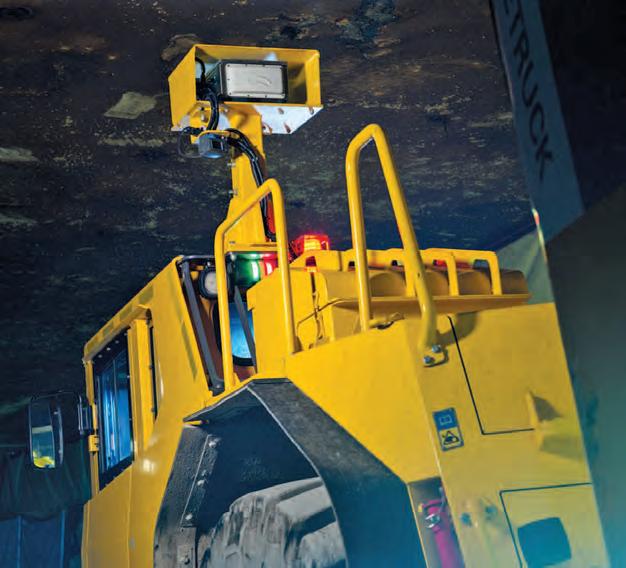
involved a MT42 truck loaded with a ST18 loader, the release in Q4 2022 will cover automation across the full Epiroc truck range. Epiroc has also already started to take orders from some of its major customers for the solution. But as each mine has specific truck automation requirements, each project is effectively a slightly different customised offering with some new engineering
UNDERGROUND AUTOMATION


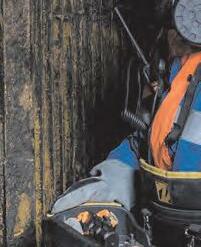
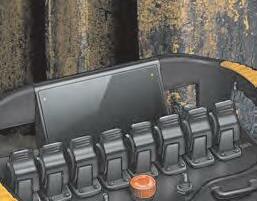



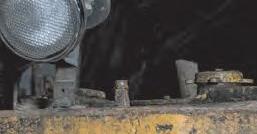
many underground truck use cases, they will haul ore via a decline all the way to surface –usually involving a fleet of trucks so they will pass each other, requiring traffic management. They will also generally share the decline with other vehicles coming in and out of the mine – utility machines, shotcrete trucks, ANFO transporters, light vehicles etc. So from an autonomy point of view, each one of these points brings its own set of challenges. And it narrows the type of truck operations where autonomy can today be applied – it is no coincidence that up until today most dedicatedapplicationsundergroundautonomoustruckinghavebeentruckloopson






conditions. The mine production is not reliant on this truck yet; as it remains in testing phase, but it has been contributing extra tonnes to the operation. Sysoev commented: “A big
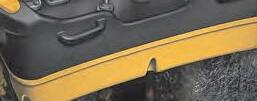
Epiroc has begun its Minetruck Automation commercial journey with an MT42 at Boliden Garpenberg
achievement is the fact that the truck is loaded with a teleremote loader on the same level and in the same area. It represents quite a significant productivity step as one operator can manage both machines – the operator tells the returning autonomous truck where to spot stop and then switches to the loader from the same teleremote operator station to load the truck and releases the truck to autonomously tram and dump – effectively a semiautonomous cycle. Overall, the Garpenberg project will lead to the imminent formal release of AutomationMinetruckbyEpiroc.”WhileGarpenberghas
W H E N S IZE RE TALLYYMA TER i n ch 3 N E 4. 8 UMA 2 SMEET U 220 ATT A d! The Sinclude ompatibleand c emost e pOurne ey clop function is independentt ystS sange of BUe with a wide r foorcoullablomizustycasks. Ft e f e+ets the SIL3, PLd and mertifie feeedaphicd graileor detems. F al f , m oyx hompleolling cntr e rin gfentimetr, e s wide, o ff 2 , BOOHALL A at3 stC g eary on the lelrouancback y Te and industrial machinerybil ast num bfooravy of space f GERMA19TH3 y istfeor displol3” c4. . Safetobust8 is rQ TW7aTEhe Supr e theo handlols tontrer of c NY Seellallocesationssorafothewebsitef WWW.MOC. SAFEMARTSS
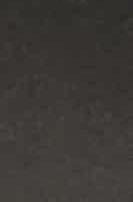
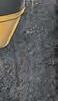




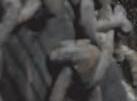


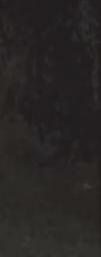


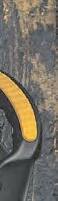

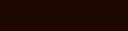



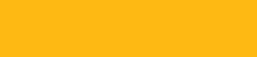


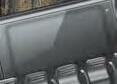



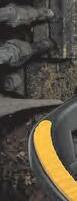




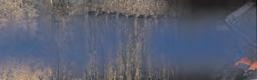


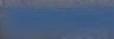
Sandvik autonomous trucksseamless to surface
Lastly the question of mixed fleets, interoperability and autonomous trucking. “We tell our customers we have two main goals – one is the fully autonomous load and haul cycle underground, but the other is to have a mixed fleet solution, which means mixed in the sense of being able to manage an autonomous fleet of different OEM brands of loader and truck, but also a mixed fleet in terms of autonomous machines, non-autonomous or semi-autonomous machines, and personnel. All of course without compromising on safety. We have made some progress – the project at Newcrest’s Cadia East in Australia, where we achieved a semi-autonomous integrated production level, is a great example, where automation capability has been adopted not only on primary load and haul fleet but on support equipment as well. For now it includes our loaders and MacLean utility vehicles, having a common safety and traffic management system.”
benefiting from Sandvik’s intelligent AutoMine unmanned mining trucks. Most recently, it has been the first to enable autonomous underground trucks to operate on the surface, plus says it is the first to add seamless truck movements through mines with the Access Control System (ACS). And it says it is also the first to combine fleet automation and mining process optimisation and analytics solutions as one integrated and seamless production system.
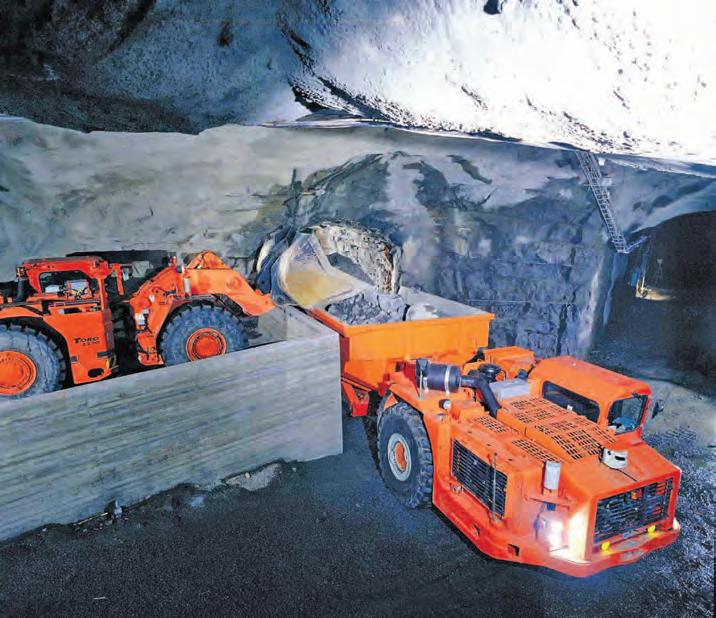
What about truck autonomy and battery and/or trolley? “We have started with diesel trucks because they have by far the largest installed base and the technology is much more mature. However, of course as the industry transitions to zero emissions it is in our long term roadmap to have both battery and trolley or battery-trolley autonomous machines. To automate a battery Minetruck is not that complex in the sense in that you are just swapping the power source, a bigger effort is to include the battery swapping or fast charging as parts of the autonomous cycle. Trolley applications are connected to similar challenges and we are focusing on proving the concept firstly with diesel hybrid machines before adding the autonomous functions. The fact that not even the trolley assisted haulers used in surface mining have been automated tells you that this is not easily achieved but we will get there for sure.”
There are three different platforms. AutoMine Fleet is a highly advanced automation system for a fleet of Sandvik underground loaders and trucks sharing the same automated production area. It provides automatic mission control and automatic traffic management for the equipment fleet, while system operators remotely supervise theAutoMineprocess. Multi-Lite is an automation system which enables each system operator to remotely control and simultaneously supervise multiple automated Sandvik underground loaders and trucks. With AutoMine Multi-Lite each piece of equipment completes automated missions in its
Loading an autonomous AutoMine equipped Sandvik truck with a manual Sandvik LHD on a slightly raised level at Finsch mine
78 International Mining | SEPTEMBER 2022
AutoMine connects seamlessly to OptiMine, which automatically commands trucks to execute production missions, dynamically adjusting trucks based on production requirements and traffic flow. OptiMine Scheduler enables efficient production planning while OptiMine Task Management gives real-time information to improve operational productivity and profitability.
and adaptation. Regarding the sensors used on the Minetrucks, the aim is to preserve commonality with the loaders – both currently use a SICK LiDAR for example, however, Epiroc added it is open to using other LiDARs to suit specific truck use cases.
UNDERGROUND AUTOMATION
safety barrier only stops machines that are an immediate hazard in the closest zone. The fleet in other zones keeps on running.
With AutoMine, operators can also supervise and control multiple trucks from a surface control room anywhere within the operation. “Mines can either get trucks that are AutoMine ready or retrofit your current fleet. Trucks powered by AutoMine can run at times when manual trucks need to wait for blast clearance, adding between four and eight production hours per day.”
For years, mining operations have already been
On battery swapping, initially any autonomous battery trucks will still see battery swapping done by an operator, whether they are in the battery swap bay itself or via teleremote. An automated process removing the need for manual input is in early phases of development by Epiroc – Sysoev says they are applying a stepwise approach to the development and that customer priorities will influence when there will be a finalised product.
The company adds: “Now including new functions such as OptiMine® connectivity, upgraded Access Control System for greater flexibility, and the ability to extend the truck fleet’s autonomous production cycles from underground to surface tipping; they are safer, more efficient with a lower cost per tonne. AutoMine for Trucks reduces operating costs by up to 50% and increases production by up to 30%.”Autonomous trucks with Sandvik technology can now work both underground and on the surface. The system uses a seamless automatic handover between the underground and surface positioning system where trucks keep moving without stopping at the portal. After dumping, they immediately continue with the next production cycle to get another load from underground.Thethirdgeneration ACS is a generic safety solution that can be applied to different mining methods and areas. It enables the movement of machines between zones without hardware changes or complex configurations. Zones can be merged into larger automation areas or split separately to allow manual operations. Tripping a
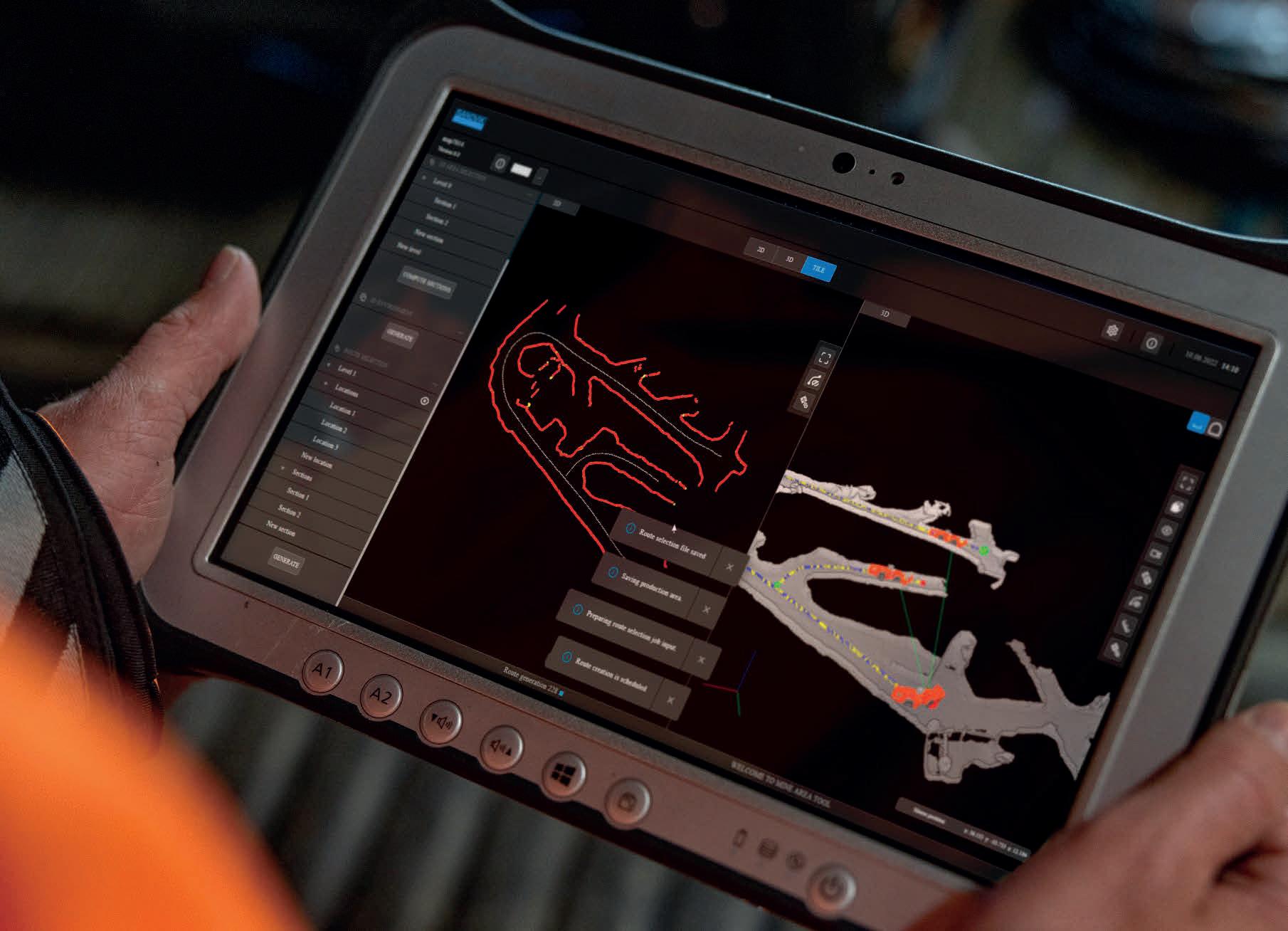
“AutoMine Mapping Solution’s innovative technology reduces the time and cost involved in manual mapping and enables a safer, more efficient autonomous underground operating environment.” It can be used on all types of underground equipment including trucks, eliminating the need for dedicated equipment and resource to map the area.
As part of its strategic alliance with gold mining major Newmont announced in November 2021, Caterpillar will by 2026 develop its first battery electric zero-emissions underground truck to be deployed at the Tanami operation in Australia's Northern Territory, almost 540 km from Alice Springs. The deployment includes a fleet of up to 10 battery-electric underground haul trucks, supported by Caterpillar’s advanced electrification and infrastructure system. This includes first-ofa-kind battery electric haulage technology for underground mining in 2024, the introduction of battery autonomous technology in 2025, with full deployment in 2026. In surface mining, the Newmont alliance covers introduction of an automated haulage fleet of up to 16 vehicles at CC&V planned through 2023, with a transition to haulage fleet electrification and implementation of Caterpillar’s advanced electrification and infrastructure system with delivery of a test fleet in 2026. Actions include validating first-of-a-kind battery electric haulage technology in the years prior to full production of autonomous electric haulage equipment. Together, Newmont and Caterpillar plan to validate equipment, infrastructure, technologies and processes to transform both surface and underground mining, focusing on safety, automation, decarbonisation, optimisation, data and asset management across Newmont’s global operations. Leveraging Newmont’s scale and operational capabilities, the alliance sets the stage for the rapid development and deployment of the technologies, ultimately improving miningefficiencyproductivitysafety,andenergyacrosstheindustry.


























































AutoMinedata.Mapping







solution provides a powerful way to take advantage of the full machine performance through automation and offers substantial
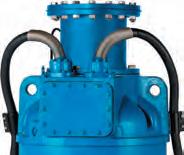
Recently, Sandvik has introduced its AutoMine Mapping Solution, an innovative new product designed to maximise productivity and improve safety of autonomous vehicle navigation in underground mining operations by utilising mapped
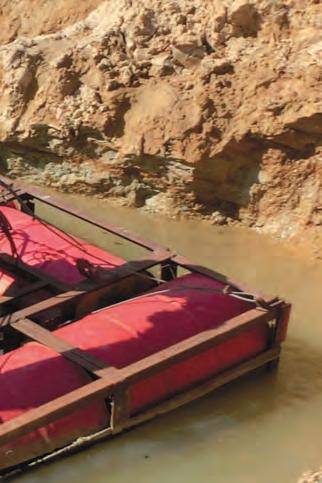
benefits of increased productivity, safety and cost-efficiency in mining operations.
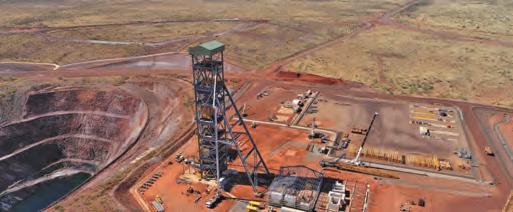
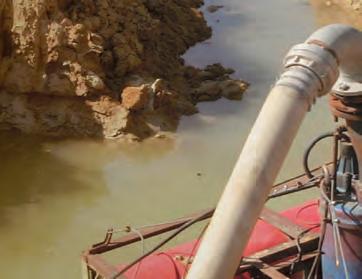
UNDERGROUND AUTOMATION


Solution enables a vehicle to safely record an underground 3D environment and convert 3D maps to 2D. Faster configuration, and the possibility to continue to operate other equipment within the area while it is being mapped, increases productivity and efficiency.
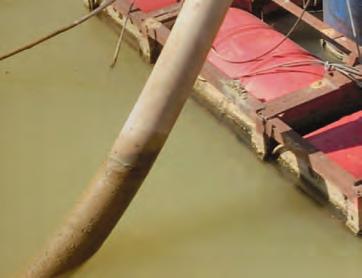
dedicated production area. In addition, AutoMine Multi-Lite 2 includes intelligent teleoperation with operator-assisting automatic steering. The
Newmont Tanami to phase in battery autonomous Cat trucks

AutoMine Lite is an automation system for a single Sandvik loader or truck, including both optimised route-based automation and intelligent teleoperation with operator-assisting automatic steering. “The solution provides an easy way to start exploring the full potential of Sandvik equipment automation and achieve benefits of increased productivity, safety and cost-efficiency in mining operations.”
IM



















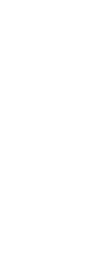
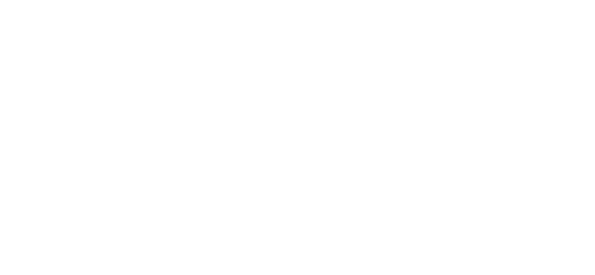
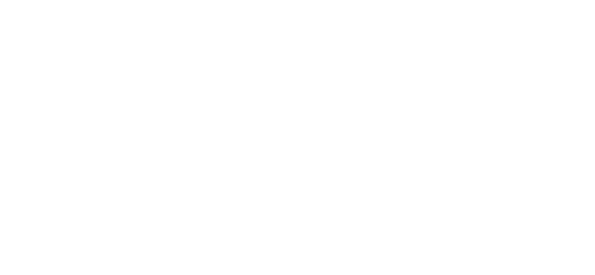


If future shaft sinking work also becomes electrified – ie uses more cutting/boring technology – one can expect the sustainability tradeoff between the two vertical development methods to fall further into the court of shaft sinking.
In the case of OZ Minerals, this was more than just a statement, with the company applying a carbon price that factored in such emissions reduction potential in the study.
Other potash projects in Kazakhstan and Brazil are on this list, while the company has had conversations with a silver miner in the Americas where the mechanised sinking technology could have an application.
“This contributes to the lower ventilation requirements, and significantly lower diesel usage,” it says.
“All the discussions are at various stages,” Jochen Greinacher, Managing Director of Redpath Deilmann, told IM. “One future deployment may even be in Germany for one of the nuclear storage sites looking at developing a new shaft.”
Shaft collar construction works are now complete for the 1,329-m-deep, 7.5-m diameter concrete-lined Wira shaft at Prominent Hill
Earlier this year, when evaluating a third, even larger expansion of its Island underground gold mine in Ontario, Canada, it said the shaftsupported plan was expected to reduce greenhouse gas emissions by 35% over the life of mine with the shaft connected to clean, lowcarbon intensity grid power. This would also see Island’s already “industry-low” GHG emissions per ounce fall by 31%, Alamos said.
From concept to reality
Sustainable sinking
While Redpath Deilmann is busy with the Shaft Boring Roadheader (SBR) sinking work at Woodsmith (see Woodsmith SBRs re-start cutting process box), it is also fielding enquiries from across the globe to use the Herrenknechtowned technology.
By transitioning from a ramp-supported operation to a shaft-equipped one, the company can skip ore to surface and truck it to the mill circuit. This means even with a 100% boost in throughput to 2,400 t/d, the operation can remove the required need for 13 42-t-payload haul trucks out of what would be an 18-strong fleet in a ramp-supported operational scenario.
Speed and safety are not typically good bedfellows, hence the reason why shaft sinking has historically been considered a dangerous mine development arena. New technology and thinking are changing that, as Dan Gleeson explains
In a sustainability-conscious environment, other miners are also highlighting the benefits of choosing shafts over ramps, with OZ Minerals stating in its Wira Shaft Mine Expansion study that its Prominent Hill operation’s Scope 1 emissions were expected to reduce by circa20,000 t of carbon dioxide with the introduction of shaft haulage over diesel-powered trucking.
SHAFT SINKING SEPTEMBER 2022 | International Mining 81
The drive for decarbonised mining operations may lead more mine operators to go down the shaft sinking route if Alamos Gold’s example is anything to go by.
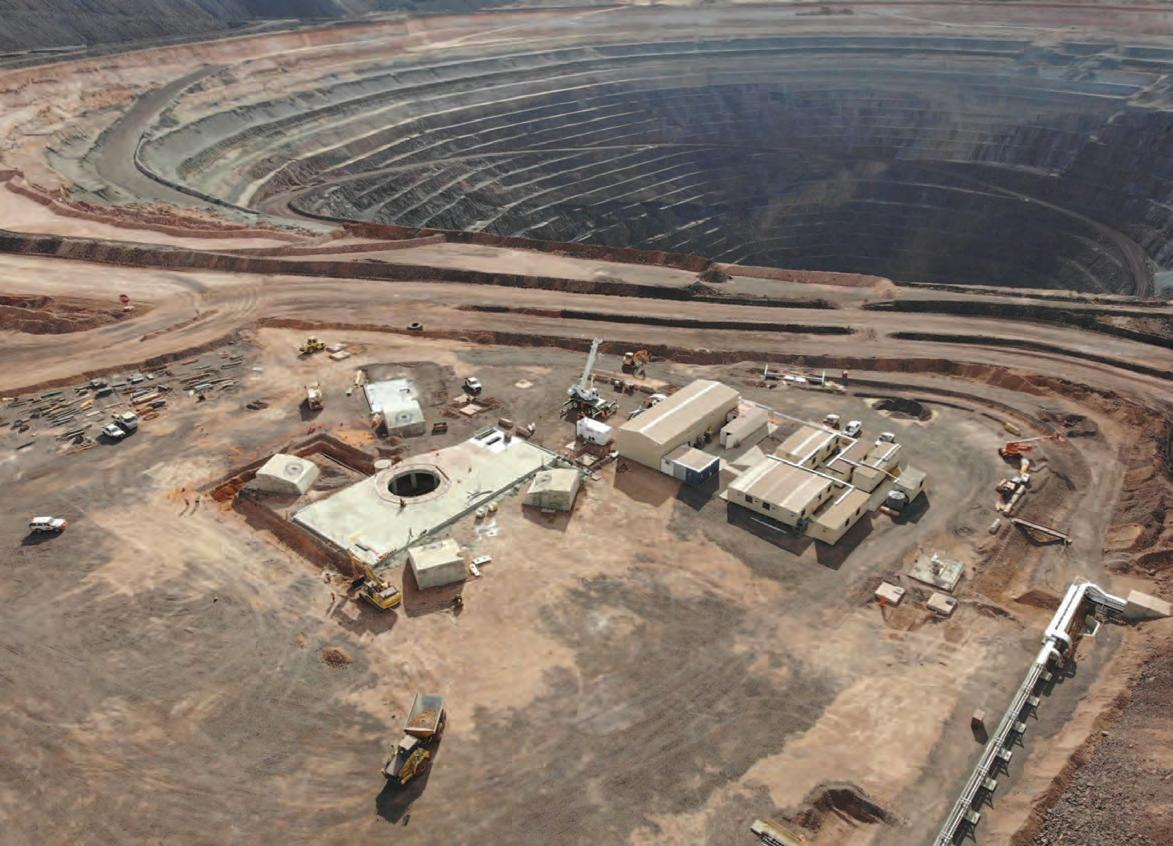
The Shaft Boring Cutterhead (SBC) technology being progressed by the two companies has been
As mentioned in this same report last year, the company, in tandem with Herrenknecht, is working on bringing mechanised technology to more than just the soft-to-medium rock (100 MPa and below) shaft sinking market.
Redpath already has a prototype machine equipped with a 0.75 cu.m bucket (1 cu.m possible) and a drilling device with twin feed for blasting of a round length of 5 m. In its facility, the shaft excavator bucket is currently being putting through its paces.
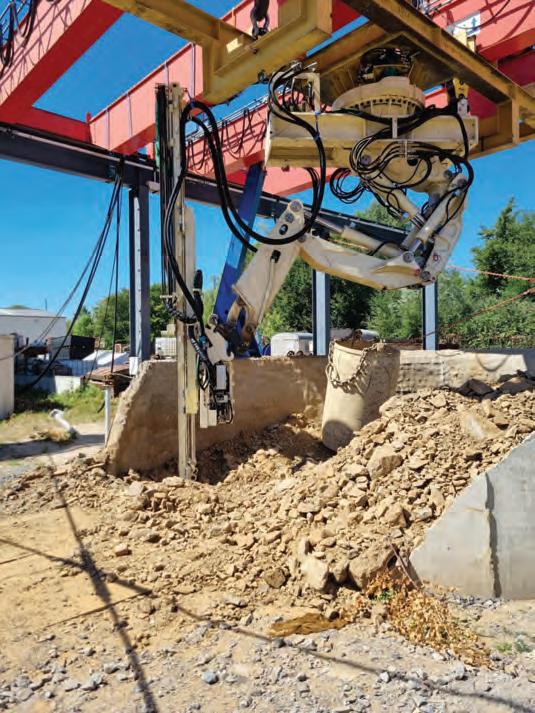

working range of 6.95 m,
It will do this using this hardware, sensors, the Redpath Shaft Control System, 3D cameras and a stable wireless network, which will allow operators on surface to oversee the process going on within the shaft.
By early next year, the testing could be finished, with the RD S100 ready for a commercial deployment, according to Greinacher.
The combination of the two sinking methods speaks to both the expertise of the shaft sinking contractor, Cementation Canada, as well as the unusual nature of the project; being an extension of the Craig mine that already goes down to circa-1,730 m Cementationdepth.Canada commenced the full-face blind sinking in October 2021 and, according to Eric Kohtakangas, Senior Executive Vice President, the crews reached the first of three shaft stations around the 2,490-m-depth level in July.This is already the deepest shaft station in the Sudbury Basin – which has its fair share of deep underground mines – with a further two stations to be established on its way to reaching the final 2,630-m-depth.Anotherfirst on the project is the further development of Cementation Canada’s digital shaft sinking initiative and the inclusion of short interval control (SIC) technology.
Cementation gains more control
developed for medium-to-hard-rock applications up to 250 MPa. It is suitable for similar diameter and depth parameters as the SBR – 7-10 m and up to 2,000 m, respectively – and offers increased shaft sinking speed and continuous muck removal from the shaft bottom.
A prototype Hydraulic Shaft Mucker RD S100 equipped with a 0.75 cu.m bucket (left) and drill jumbo (right) is being put through its paces at Redpath Deilmann’s facility in Dortmund, Germany
82 International Mining | SEPTEMBER 2022
SHAFT SINKING
Having started off as a 3-m-diameter raisebore pilot and slash at the 1,200-m level, it has since transitioned to a blind sink method for the lower half of what will be an approximate 7.2-mdiameter, 1,435-m-deep internal shaft (winze).
Offeringconsuming.amaximum
The Onaping Depth project in Sudbury, Ontario, is being closely watched by many in the industry due to its planned use of an all-electric production and support equipment fleet, but it also represents a rarity in the shaft sinking sector.
bucket digging force of 110 kN, a digging depth (below the telescopic boom) of 8.7 m and increased flexibility in terms of boom swing and movement, the RD S100 is expected to go some way to automating what has been to now a very manual process, allowing multiple tasks, such as mucking and concrete applications, to be conducted concurrently.
Greinacher provided details of this solution back in May at the CIM Convention and Expo in Vancouver, Canada, outlining the new-generation Hydraulic Shaft Mucker RD S100, a semiautonomous system to enable concurrent mucking and liner installation during shaft sinking.Thesystem is designed for the attachment of a shovel, double drill feed, cutting drum or other tools for mucking, drilling, ripping, cutting and cleaning to take place on a tele-remote basis. All these attachments are connected to the galloway within the shaft via a telescopic boom that also reduces the need to continuously lower the galloway during mucking – a process that can be time
IM understands the company has already lined up a future project to use the RD S100 on.
The 3-m-diameter cutterhead that facilitates the cutting of this rock has now moved from conceptual design to prototype, with testing of this and the accompanying pneumatic mucking system taking place at Herrenknecht’s Schwanau facility in Germany.
Still in Germany, but at Redpath Deilmann’s facility in Dortmund, more innovative work for shaft sinking is taking place.
“The SIC program gives you access to critical real-time information as the shaft sinking process moves on,” Kohtakangas told IM. “It allows us to make data-driven decisions on the bench rather than wait for end-of-shift reports.”Thisensures all stakeholders are aware of shaft sinking progress in real time, providing visibility that has positive ramifications for short-term planning and reconciliation with the original sinking plan.
The raiseboring of a 459-m-deep shaft at the Solvay Chemicals #5 shaft in Green River, Wyoming, involved the use of a reaming head that could be diminished in diameter rather than manufacturing different diameters of outside wings
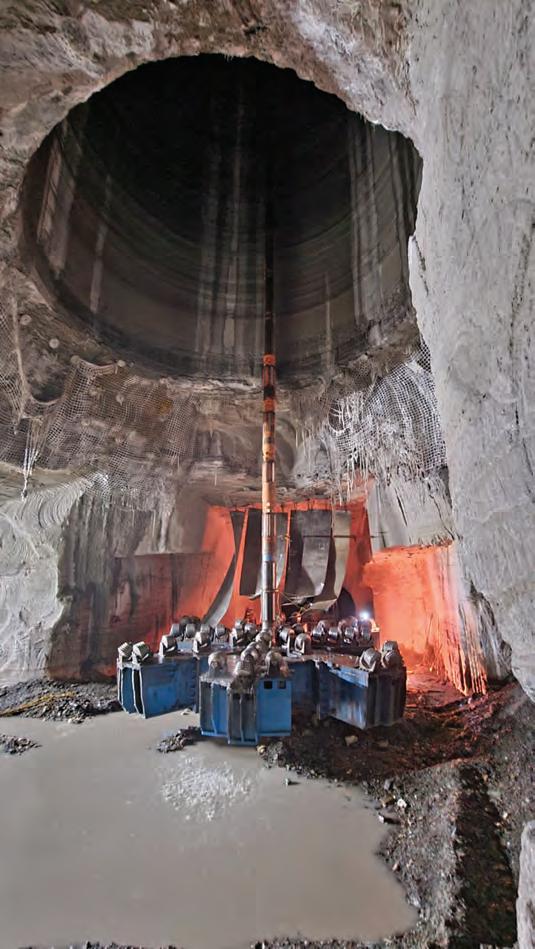
SEPTEMBER 2022 | International Mining 83
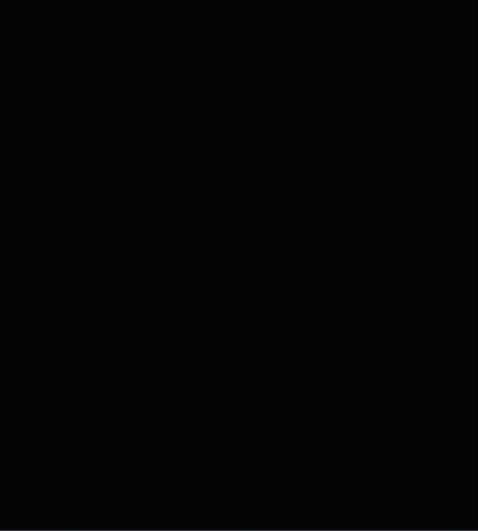
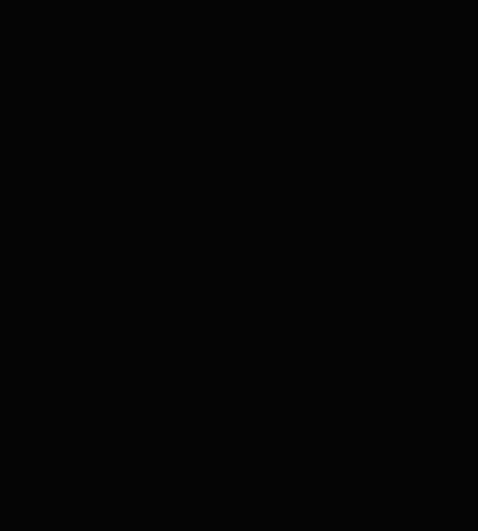
“The app allows us at any time to monitor actual progress against planned tasks and make any necessary adjustments to the work plans,” Kohtakangas added.
The success of the SIC app trial and performance improvement system
Coming up to a year ago, Cementation Canada started working with GroundHog on a SIC project, adapting the solution the digital-focused company had for production and lateral development environments into a fit-for-purpose shaft sinking platform.
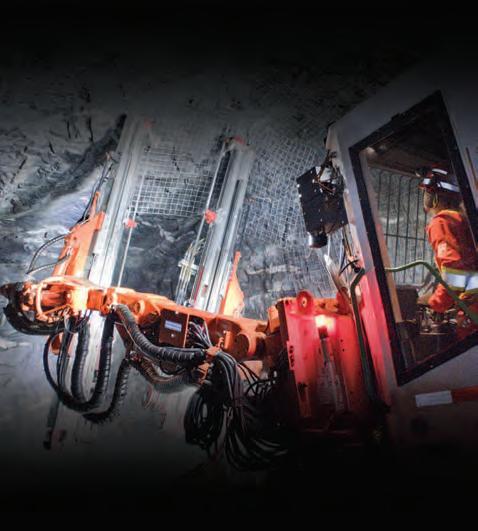
When combined with a “performance improvement system”, this data can support daily shift reporting and help facilitate feedback sessions on variances against plan to drive improvement actions, he explained.
SHAFT SINKING

SHAFT SINKING 84 International Mining | SEPTEMBER 2022
Additionally, it has navigation cylinders that always monitor the direction of the
Recently, DMC steered a BBM1500 to complete its first bore hole at the Codelcoowned El Teniente mine in Chile, where a 46 m excavation was completed.
excavation, minimising deviations and allowing excavation of rock at angles up to 60° inclination. This machine can reach a performance of over 1.5 m/h in good quality rock and does not require a concrete slab for installation, according to DMC.
benefit from the advances the mining-centric digitalisation, electrification, interoperability and automation solutions company is making across various group companies.
that comes into the company’s shaft sinking remit.With Insig Technologies, the Australia-based underground mining technology company, now fully embedded into the Murray & Roberts Group, Kohtakangas is expecting Cementation Canada to

For the excavation of vertical and inclined slot holes in underground mines, Herrenknecht developed the Boxhole Boring Machine (BBM) in 2011. It drills faster, safer and more economically than previous methods and equipment, it claims.
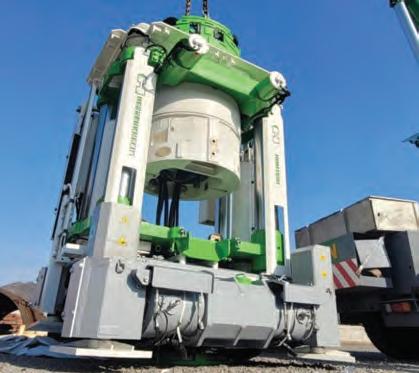
The BBM-1500 MI-052 performs raise excavations with diameters of 1.5 m and lengths up to 70 m, DMC says
This is unlikely to be the only digital initiative
“Insig have been working on many applications across the Murray & Roberts mining
means Cementation Canada is likely to offer it on any shaft sinking work it bids on going forward.
DMC Mining Services expanded its vertical development fleet recently by adding a fifth piece of equipment to its offering for clients in Chile.
“If the project has a fibre network to act as the communication backbone, we will be recommending it,” Kohtakangas said.
This version of the BBM-1500 equipment incorporates the latest elements of innovation and technology available in the market to deliver a service with the highest standards of safety, quality and efficiency to customers, DMC says.
The BBM-1500 MI-052, with its new design, offers multiple improvements based on the recent experiences obtained in the operation of its four Boxhole machines already available in Chile since 2019, DMC explained.TheBBM-1500 MI-052 performs raise excavations with diameters of 1.5 m and lengths up to 70 m.
Shaft sinking | Raise boring | Mine development | Contract mining | Mine construction | Engineering Our world revolves around you. Client-centric mining solutions with industry-leading safety.
Boxhole technology uses feed tubes of a similar diameter to the excavation, which sees the rock of the raise walls confined both during the feed and the removal of the tubes and reaming head. In addition, this excavation method can incorporate downward mechanised lining without exposing personnel, which, in turn, protects and provides a longer life span to the excavation.DMC’sboxhole equipment, which is unique in Chile, has developed 16 “chimneys” and one shaft with full mechanised shielding, while demonstrating the highest standards in safety, quality and performance, the company says.
7.6-m diameter for the next 87 m of shaft and 7.5-m diameter for the final 163 m of shaft to surface.“Idon’t think this has ever been done before,” Kohtakangas said. “You can ream up at a certain diameter, drop down and change the reamer head and carry on the raiseboring, but that takes time. We didn’t have to do that; all we had to do was take off the outside section when needed to bring it back to the required diameter.”
With a modest number of greenfield projects coming through the pipeline, Kohtakangas had a parting technological thought that, he believes, could change the dynamics in favour of developing more shaft-supported mines in the future.“Ihave challenged our group to look at how we incorporate battery-electric technology into shaft sinking,” he said. “If you look into these sinking plants, they all require lots of power, which, typically, in a greenfield project where shafts are involved, is not going to be available until some type of high voltage transmission
Followingkg. completion of 21 m of deep collar excavation and lining, and a 0.4-m diameter pilot hole drilled using Cementation’s Strata 950 Raise Drill and Micon’s rotary vertical drilling system (RVDS), the team settled on three diameter options. This saw the first leg of the shaft reamed to 7.9-m diameter for 179 m of shaft, followed by
n It was completed without incident; and
Due to the need for the concrete liner thickness to increase as the depth of the Solvay Chemicals #5 shaft increased, the initial concept was to complete a pilot slash raise with a raisebore drill and then slash from the top down to achieve the differing diameters.
platform that include asset maintenance, operational effectiveness and autonomous operations,” he said. “Insig has the capability and technology to build the required digital mining models for real-time enterprise reporting and business forecasting that comes from transparent, aggregated and timely information from our project sites. This means better connectivity for equipment intelligence, personnel and plant through underground instrumentation.“Aswemoveforward, the information capture will be endless and it will allow us to utilise this information across all aspects of our business, from tendering to execution to controls and reporting.”Whenitcomes to hardware, Cementation Canada has also been continuously evolving, with its renowned large-diameter raiseboring team continuing to innovate.
n It was one of the largest raises ever pulled in the Americas;

The raiseboring teams at the Solvay Chemicals #5 shaft have now handed off to the shaft crews to complete the lining, but the company continues to be busy across the Americas on several projects.
At BHP’s Jansen project in Saskatchewan, it is carrying out the post-liner excavation, steel and
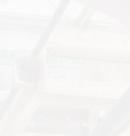
Cementation instead proposed a full face raisebored shaft solution with variable diameters for each section, collaborating with Sandvik on a reaming head able to provide a flexible solution to carry out the task.
The final design of this reaming head allowed for five diameter options, going from a maximum of 8.1 m, down to 7.5 m, in increments of 168 mm. This used a reamer that consisted of 12 individual sections, 46 cutters and weighed 61,689
n It involved the use of a reaming head that could be diminished in diameter rather than manufacturing different diameters of outside
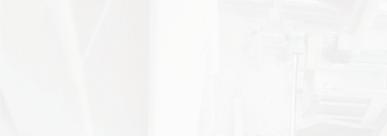
equipping for the two shafts already sunk at the potash project. The company is also carrying out some shaft guide realignment work for Hecla Mining at its Lucky Friday mine in Idaho.
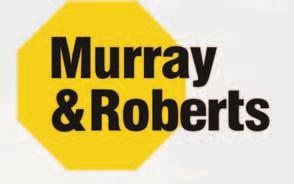
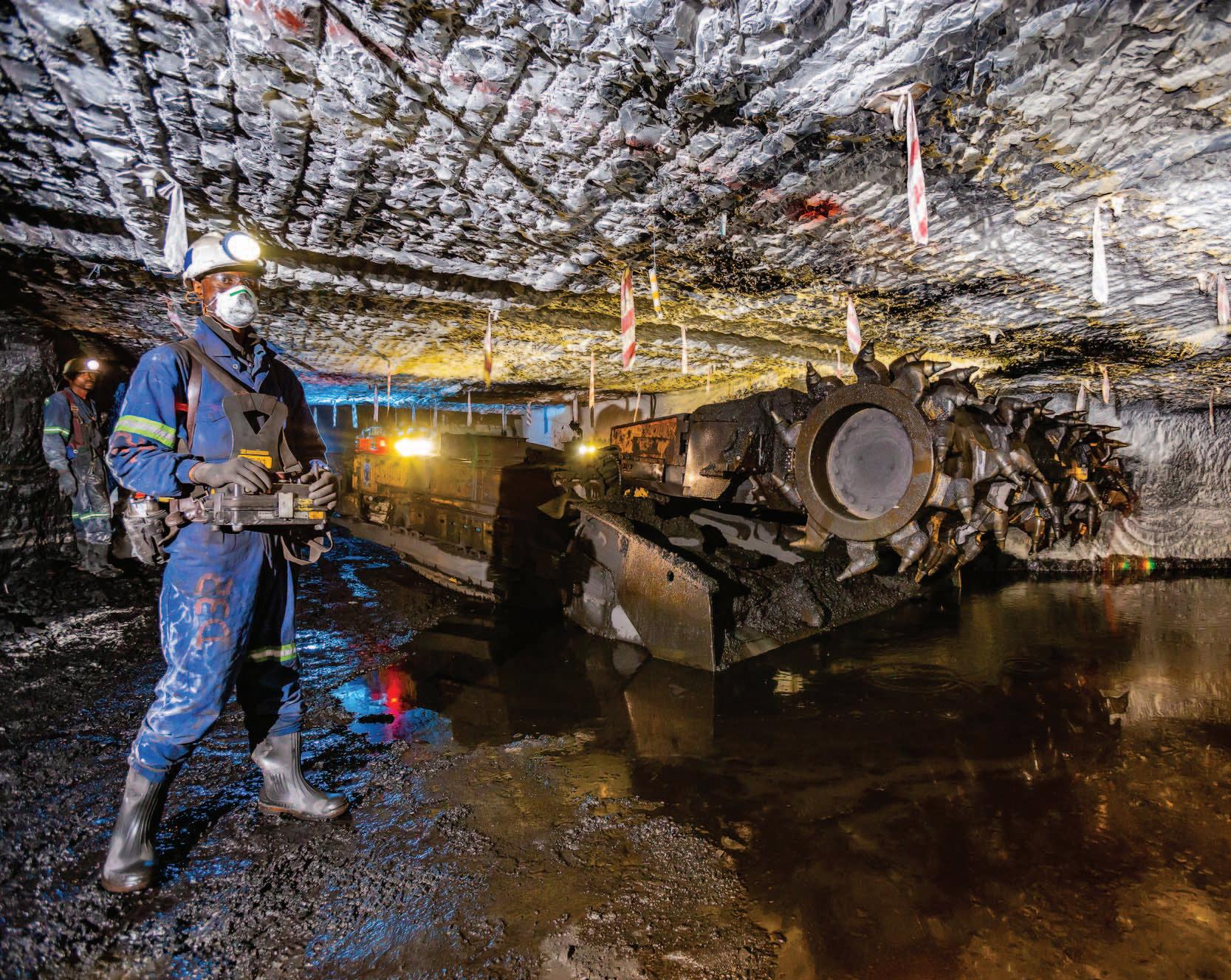
This project, Cementation Canada says, was significant for several reasons:
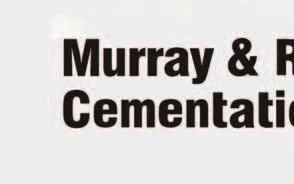
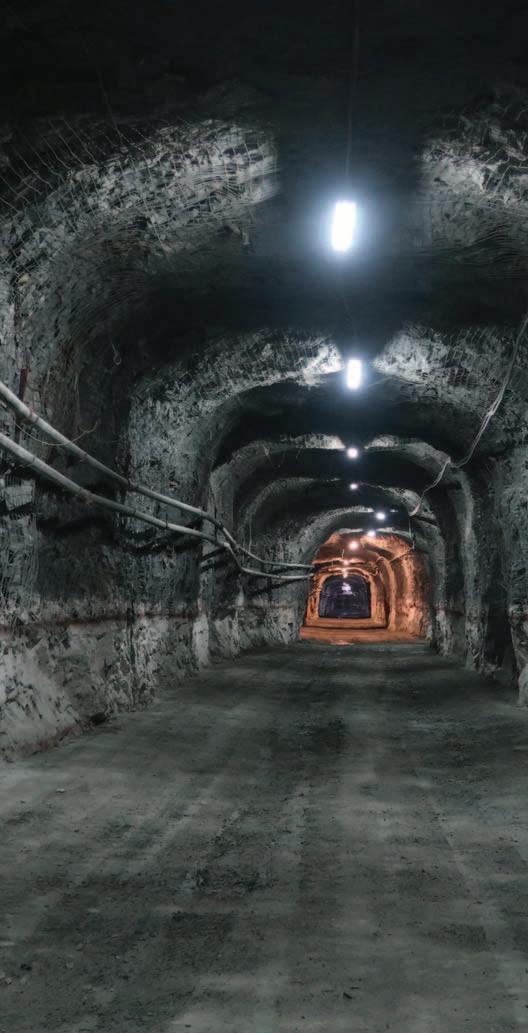
Itwings.isthe latter element that has the potential to change the way raiseboring projects are carried out in the future.
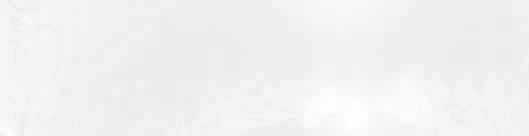
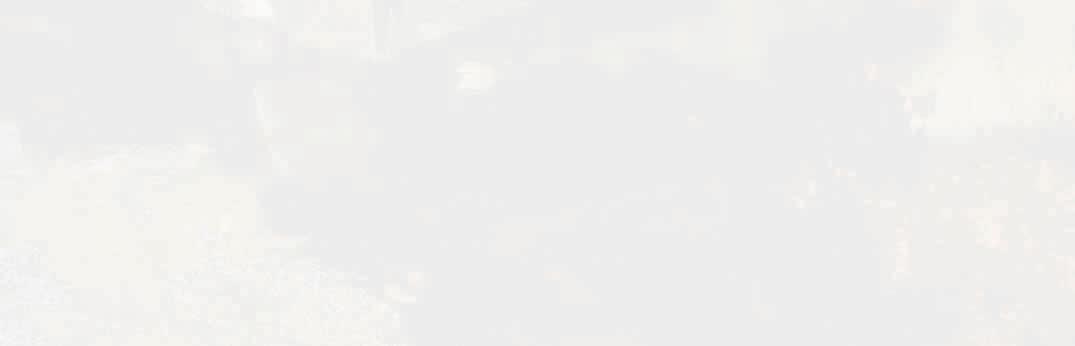
SEPTEMBER 2022 | International Mining 85 MRAdvert2020_ApprovedIMA5.indd12020/09/0315:23:21
SHAFT SINKING
A snapshot of this was seen on the Solvay Chemicals #5 shaft in Green River, Wyoming, USA, where the company, with the help of Sandvik and Micon, recently completed a full faced raisebored shaft down to 459-m depth.
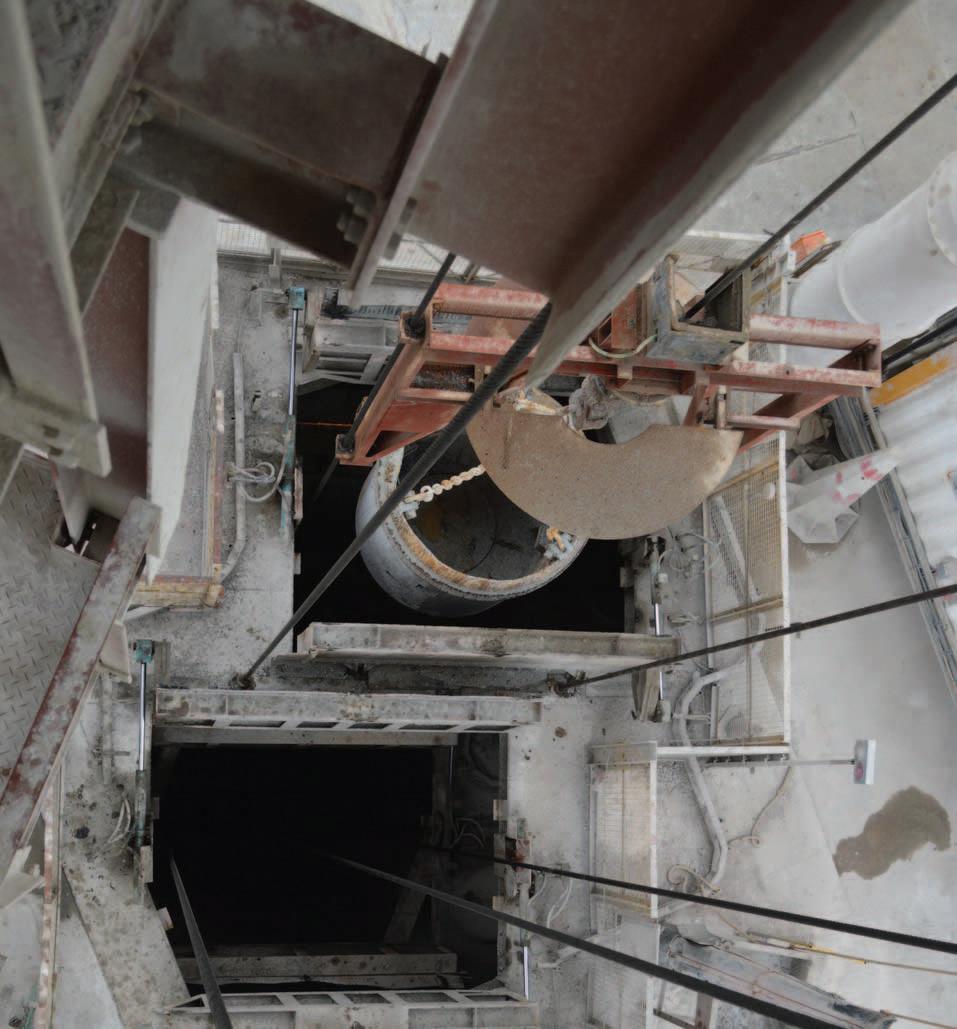
“If we can come up with a way to use battery technology for sinking, utilising these big battery cells that are coming to market, I think we can bring some of these greenfield projects online earlier for our clients, compressing the timelines associated with mining – which are now often 1015 years from exploration to production – and providing investors with a much quicker payback.”
Tel.: +49 231 2891 395/396
lines are brought in to connect to site.
Master Drilling Group is also looking to accelerate project paybacks with its vertical development technology.
OZ Minerals confirmed Byrnecut Group had been awarded the contract back in 2021, saying
Earlier this year, Director Koos Jordaan highlighted a potential first deployment of the company’s Shaft Boring System (SBS) at Royal Bafokeng Platinum’s Styldrift mine in South Africa.This machine was initially billed as a blind shaft boring system able to sink 4.5-m diameter shafts in hard rock down to 1,500 m depth. It was developed as a 45-m long, 450-t machine able to progress through rocks with uniaxial compressive strengths of 200-400 MPa and carry out cutting, mucking and shaft reinforcement concurrently.Lastyear,Jordaan said it planned on bringing a “smaller scope system” to the table as part of its introduction to the industry. He said at this time

Wira win for Byrnecut
For more than 130 years we have safely and successfully sunk more than 500 shafts with a depth of over 230,000 m.
first SBS being built is a 4.1-m-diameter scope machine with a capability of sinking shafts up to 1,500 m depth, according to Jordaan, who explained that the “smaller shaft scope” was part of a plan to lower the machine’s implementation cost.
“But we are already engaged with opportunities regarding a larger scope of service,” he clarified. “The cost benefit of this method drastically increases as the scope increases versus conventional sinking.”
the contractor had extensive experience of shaft sinking in the Asia-Pacific region. The two companies know each other well given Byrnecut is the underground mining contractor at OZ Minerals’ Prominent Hill and Carrapateena mines.Back in August 2021, the OZ Minerals Board approved construction of a hoisting shaft at Prominent Hill, paving the way for a mine life extension and throughput expansion.
We provide our customers with a complete range of services from design and engineering to construction, maintenance, reconstruction and rehabilitation. Contact us with your shaft-related inquiries.
One of the more coveted shaft sinking projects in Australia in recent years comes from OZ Minerals and its Wira shaft, part of the Prominent Hill copper-gold operation in South Australia.
that the company had signed a letter of intent with a prospective South Africa-based project that could see a machine start sinking activities in the first half of 2022.
Coming with a pre-production capital expenditure of A$600 million ($420 million), the Wira Shaft expansion project will see Prominent Hill’s underground production rate increase to 6 Mt/y from 2025. At this point, the average annual copper and gold production is expected to be circa-54,000 t and circa-108,000 oz, respectively, some 23% higher than expected in the current trucking operation.
ANY MINERAL. ANY GEOLOGY. ANYWHERE.
The shaft mine expansion also enables generational province potential with further mine life extensions possible as 67 Mt of resource remains outside the shaft expansion mine plan, OZ Minerals says. Further, an exploration program has also identified that mineralisation remains
In the most recent update, he said the letter of intent was with Styldrift.
LEADERS MECHANIZEDIN (SBR) SHAFT SINKING Shaft station level 700 m, Slavkaliy mine Nezhinsky, Belarus www.redpathdeilmann.com
SHAFT SINKING
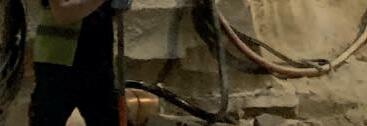
The shaft design comprises a 1,329-m-deep, concrete-lined shaft with a diameter of 7.5 m. Construction of the shaft will be via conventional strip and line method, with the sinking period approximately two years, OZ Minerals said.
REDPATH DEILMANN GmbH
We are a member of The Redpath Group, operating on all five continents and belonging to the world market leaders in the field of mine contracting and construction.
SBS for Styldrift?
Haustenbecke 1, 44319 Dortmund, Germany
“We are now building the SBS and working towards hopefully converting the letter of intent from RB Platinum to a contract award; we already engaged with them in investigation and readiness work should approval be granted,” he said.The
timeline was confirmed as having shaft sinking completed by mid-2025, ahead of the underground ore and waste handling system being completed and shaft hoisting fully commissioned in 2026.
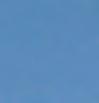
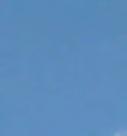
A conventional blind sink methodology will be used providing improved schedule reliability with minimal impact on existing operations, according to Alamos. The underground ore and waste handling and loading pocket will be a
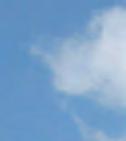

A 5-m diameter concrete lined shaft will be constructed with a steel head frame, with the shaft housing two 12-t skips in dedicated compartments for ore and waste movement, and a double-deck service cage for the transport of personnel and materials.
Redpath Mining, a Canada-based subsidiary of the Redpath Group, is set to carry out shaft sinking work on Alamos Gold’s Island gold mine in Ontario,HavingCanada.beenupgraded from a 2,000 t/d operation to a 2,400 t/d operation with the release of the results of a Phase 3+ Expansion Study earlier this year, the Island
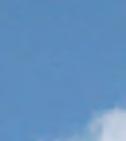
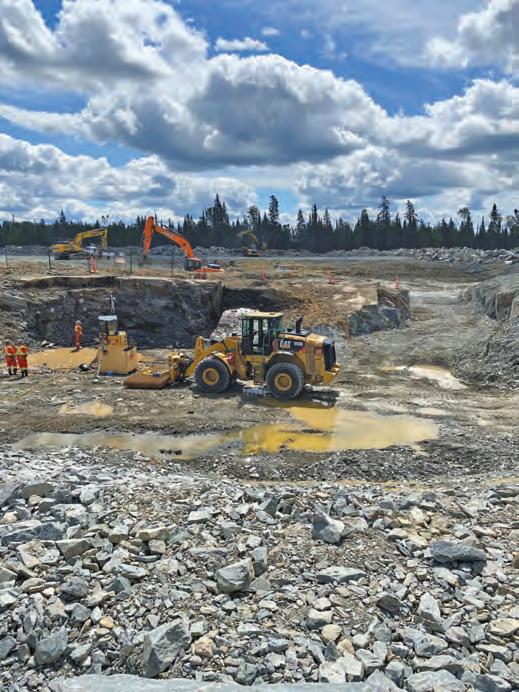
The shaft will be sunk to an initial depth of 1,373 m, but the hoisting plant is designed for an ultimate depth of 2,000 m providing flexibility to accommodate future exploration success. At the initial depth of 1,373 m, the shaft has a capacity of 4,500 t/d, more than sufficient to accommodate the peak mining rates of 3,600 t/d (ore and waste).
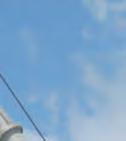
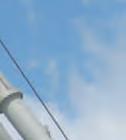
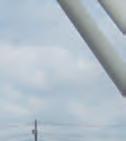
Redpath to sink at Island Gold
beyond the current resource boundary, potentially accessible via theInshaft.themost recent June quarter results update, OZ Minerals said all shaft pre-sink equipment for the Wira shaft mine expansion was on site with pre-sink works planned to commence shortly upon completion of additional temporary structural support for these activities. Delivery of the main sink stage and winders is planned for the December quarter of 2022, with installation and commissioning activity in the March quarter of 2023, representing a slight delay due to supply chain constraints.
P +1HONE(705) MINEHOIST.COM495-8587 We offer a single-source supply of all mine hoisting plant services to North American and International mining industries. We maintain a huge inventory of mine hoists, and more than 80 stage winches – up to 130,000 pounds – that are available for rent. Mine Hoists International brings together our knowledge and retains outside experts with world-wide experience. This combination of expertise allows us to offer you exceptional services. YOUR ELEVATINGJOB A DIVISION OF
As of August, shaft pre-sink work had commenced at Alamos’ Island Gold III expansion project
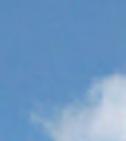
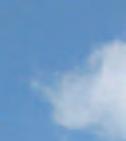
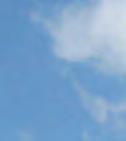


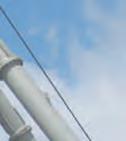

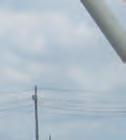
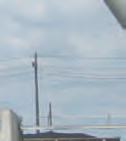

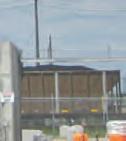
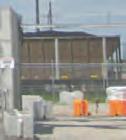

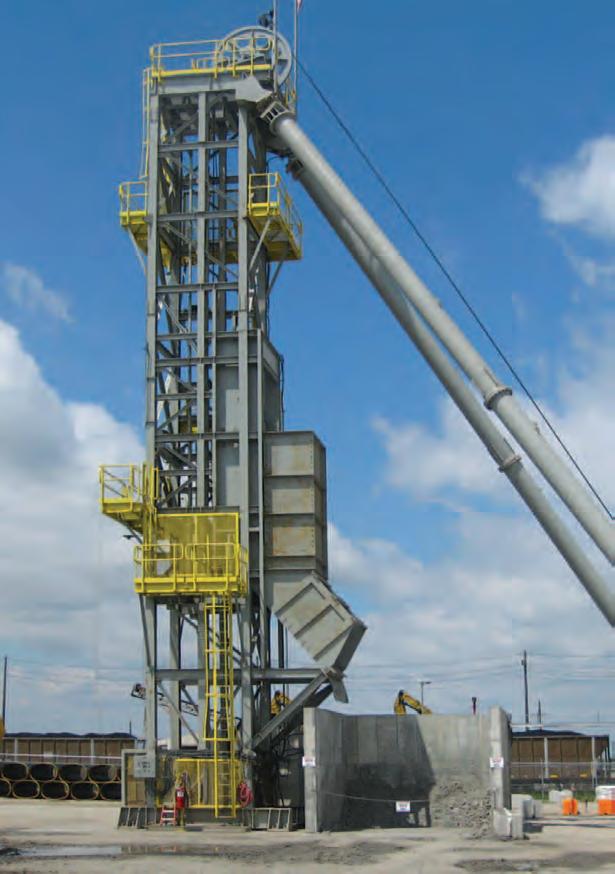
SHAFT SINKING

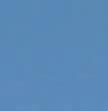
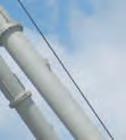
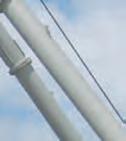
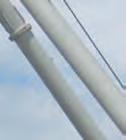
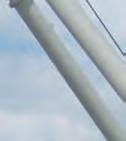
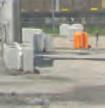

THE
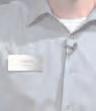
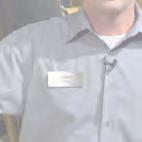
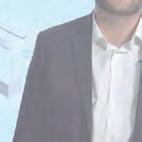
Insight Series VIDEO INTERVIEWS IM Conducted in numerous global locations by Editor Dan Gleeson and Editorial Director Paul Moore, these interviews are unique collaborations by IM and the world’s leading mining technology suppliers, getting the lowdown from the key people involved in development and design
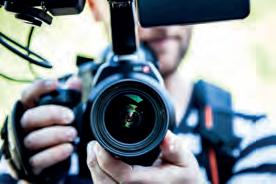

MINEXPO 2021 International Mining brings you insights from key FLSmidth personnel at MINExpo 2021 in Las Vegas Weblink: minexpo-2021/https://im-mining.com/interviews/flsmidthSUSTAINABLE SLURRY PUMP SOLUTIONS An interview with Jonathan Samuel, GIW Industries President & CEO, on site at MINExpo 2021 Weblink: https://im-mining.com/interviews/ sustainable-slurry-pump-solutions/ KOMATSU
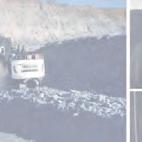
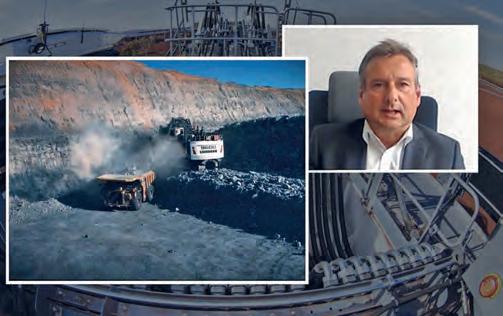
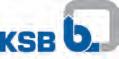
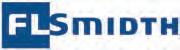
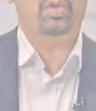

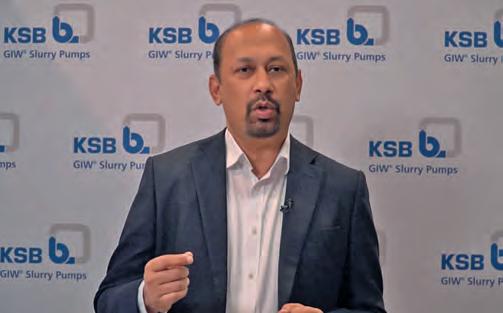
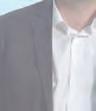
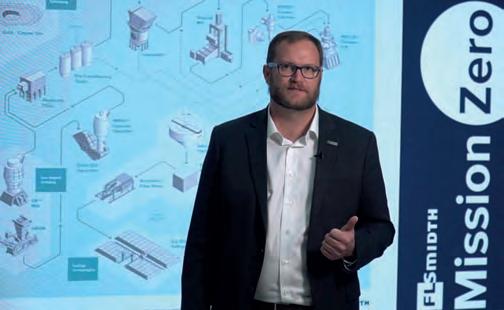
NEXT GENERATION – LIEBHERR’S R 9600 An interview with LiebherrMining’s Michel Runser, Head of Product Management Excavator; Otmar Wehrle, Sales Director; and George Barturen, Senior Product Manager Excavator Weblink: https://im-mining.com/interviews/nextgeneration-liebherrs-r-9600/
MINEXPO 2021 International Mining brings you insights from key Komatsu personnel at MINExpo 2021 in Las Vegas Weblink: minexpo-2021/https://im-mining.com/interviews/komatsu-
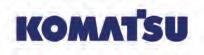
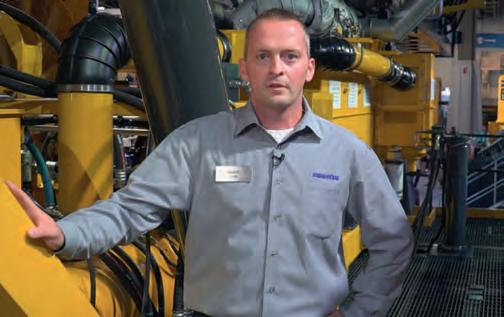
FLSMIDTH AT AT
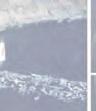
Insight Series VIDEO INTERVIEWS IM THE P&H 77XR – COMBINING DRILL POWER WITH FLEXIBILITY An interview with Sergio Li, ProductManager–RotaryDrills,KomatsuMiningWeblink:https://im-mining.com/interviews/ph-77xr-combining-drill-power-flexibility/ FORWARD THINKING –THE MISSIONZERO MINE An interview with Wayne Douglas, VP, Head of Mining R&D and Innovation, FLSmidth Weblink: thinking-the-missionzero-mine/https://im-mining.com/interviews/forwardPOWERING A SUSTAINABLE MINING FUTURE An interview with Sean Lynas, DirectorMiningOEM Business, Cummins, and Robert Schaefer, Director Growth & Innovation, Cummins Weblink: sustainable-mining-future/https://im-mining.com/interviews/powering-ANEWDIMENSIONTOMINERALANALYSISAninterviewwithEddyHill,–NaturalResourcesandMetals,ZEISSMicroscopyWeblink:https://im-mining.com/interviews/a-new-dimension-to-mineral-analysis/ PUMPING UP MINERAL PROCESSING AnFLOWSHEETSinterviewwithDiwakar Aduri, ProductManager, up-mineral-processing-flowsheets/GlobalMillDischarge&DredgePumps,MetsoOutotec&TiagoOliveira,VP,PumpsServices,MetsoOutotecWeblink:https://im-mining.com/interviews/pumping-IfyouareinterestedinworkingwithusonanIMInsightSeriesvideointerviewpleasecontactEditorialDirectorPaulMooreatpaul@im-mining.comorEditorDanGleesonatdaniel@im-mining.comforratesandmoreinformation
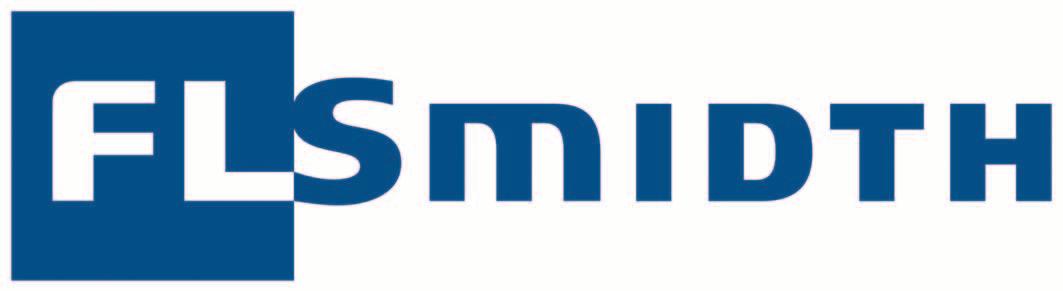
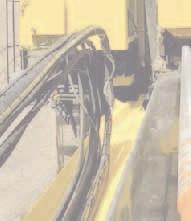
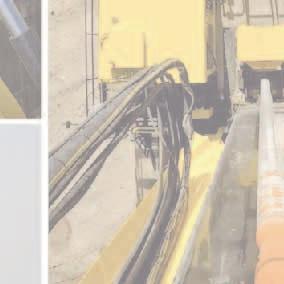
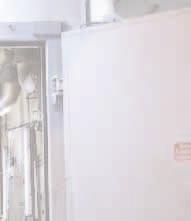
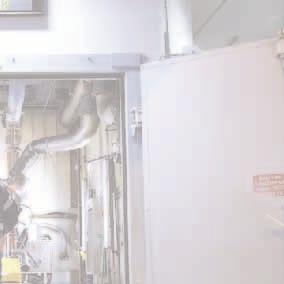

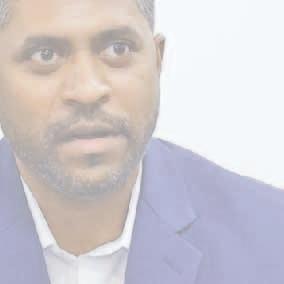


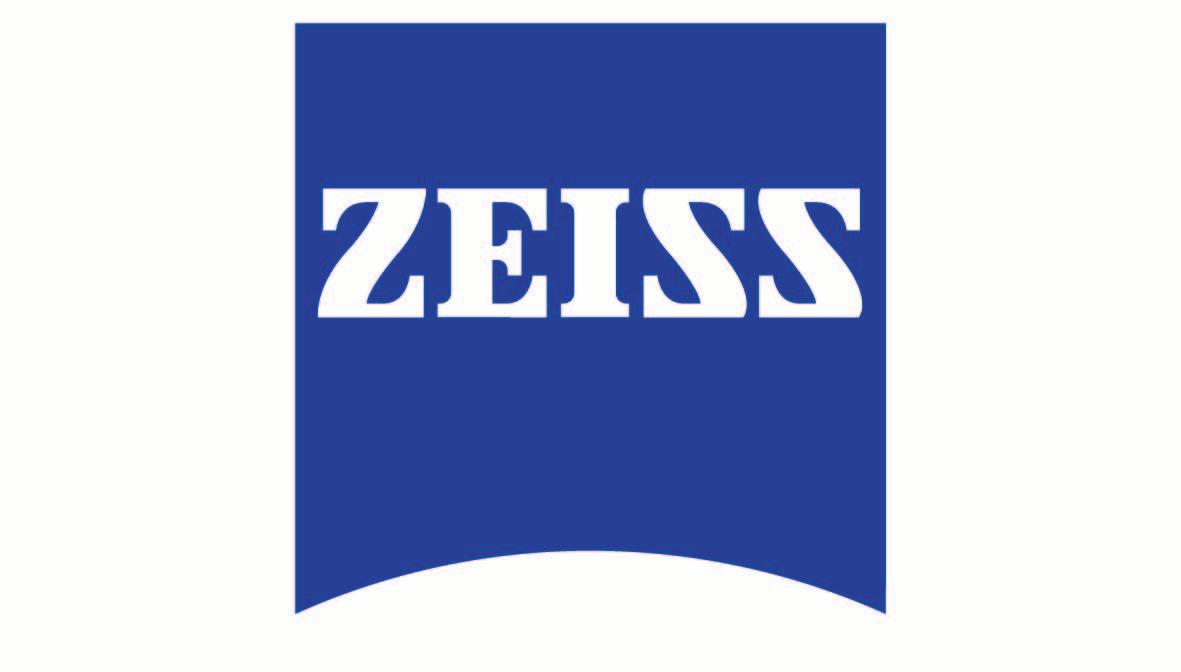
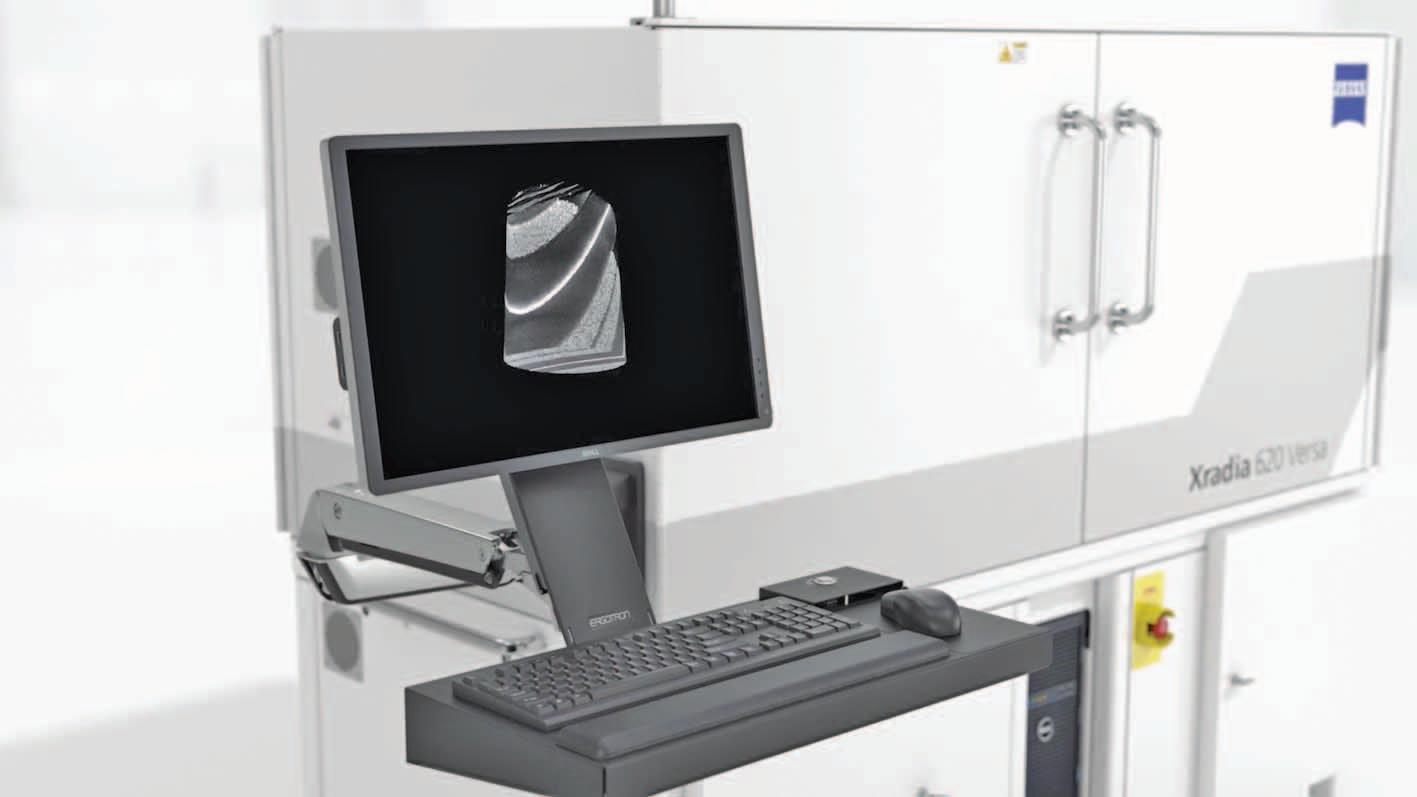
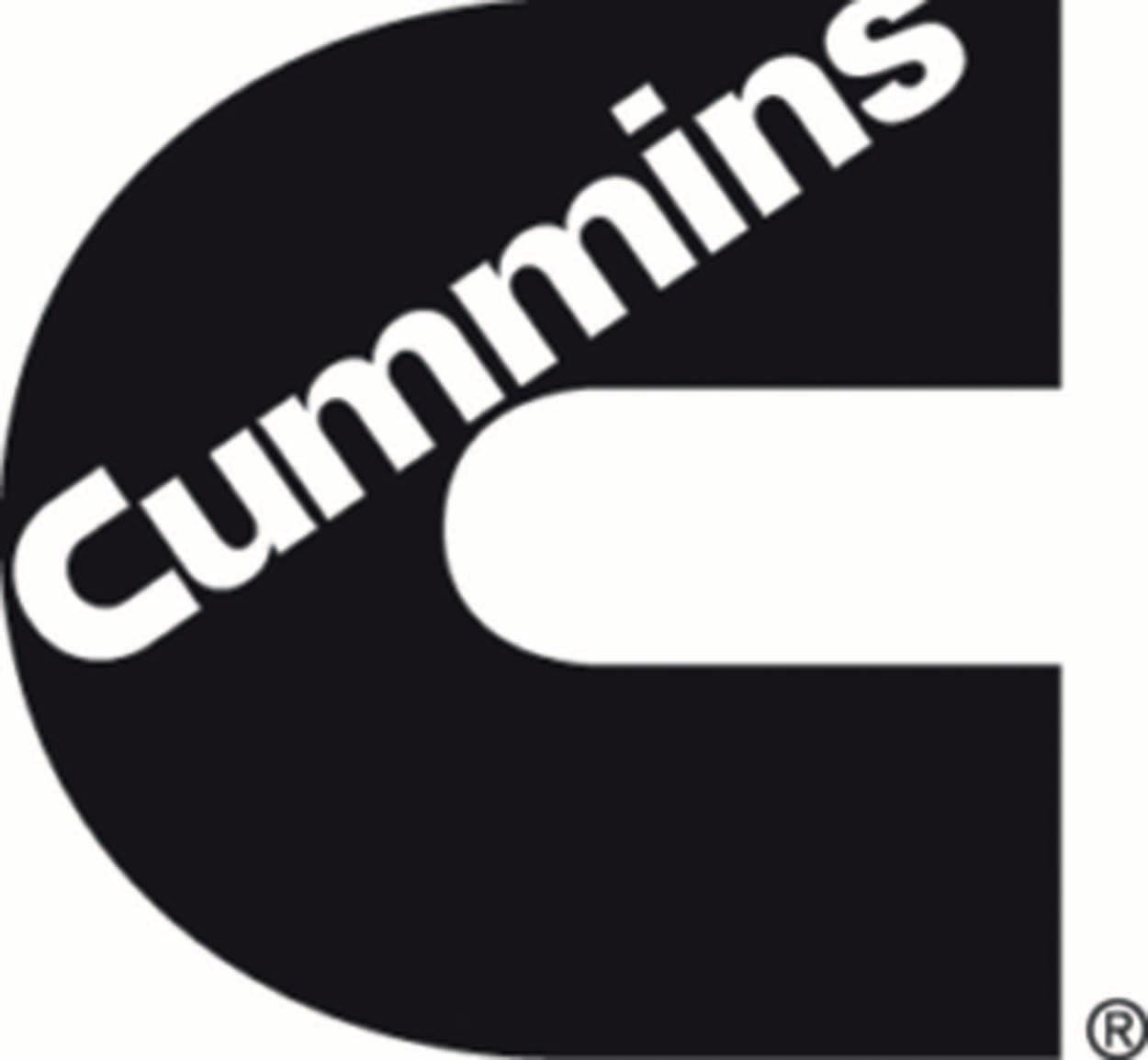
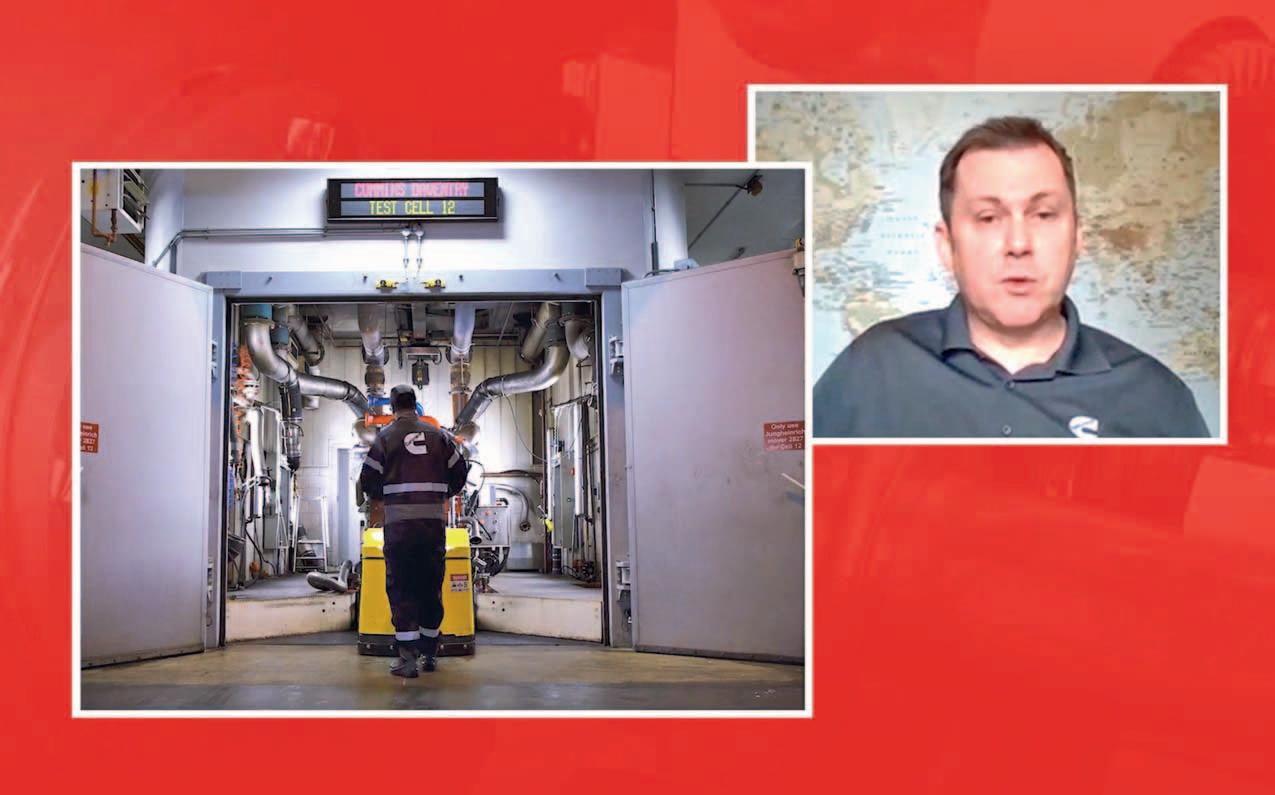
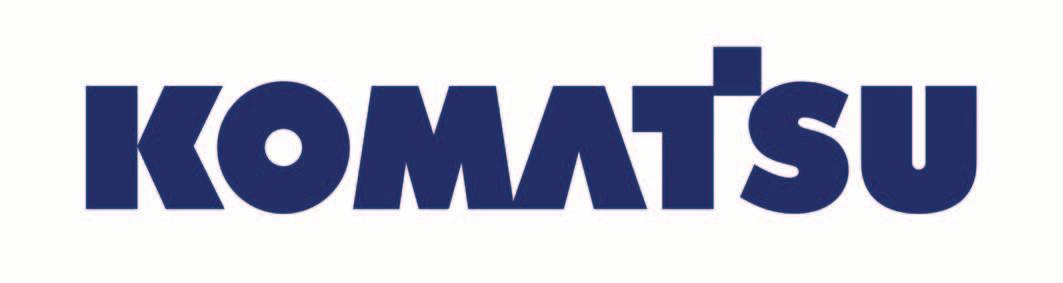
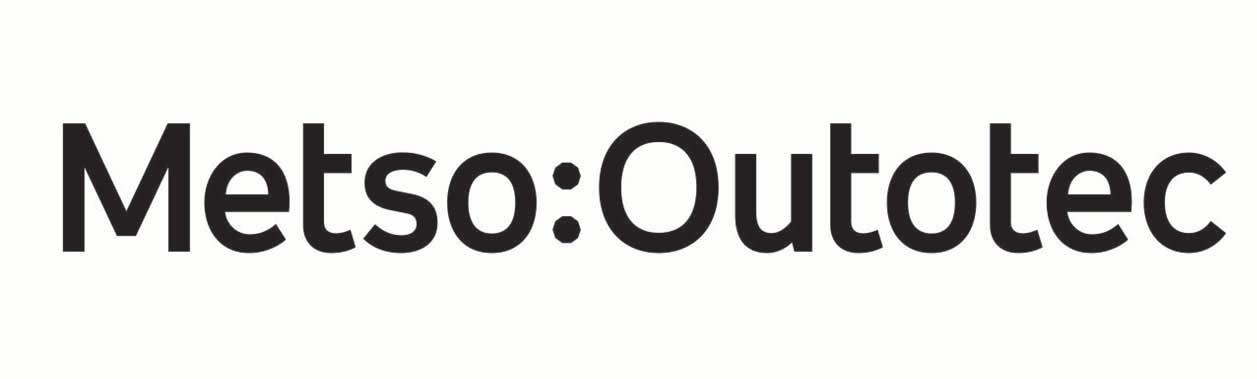

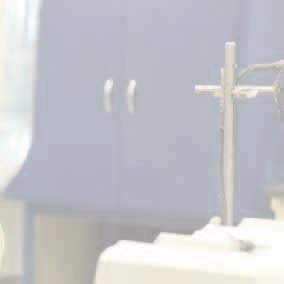
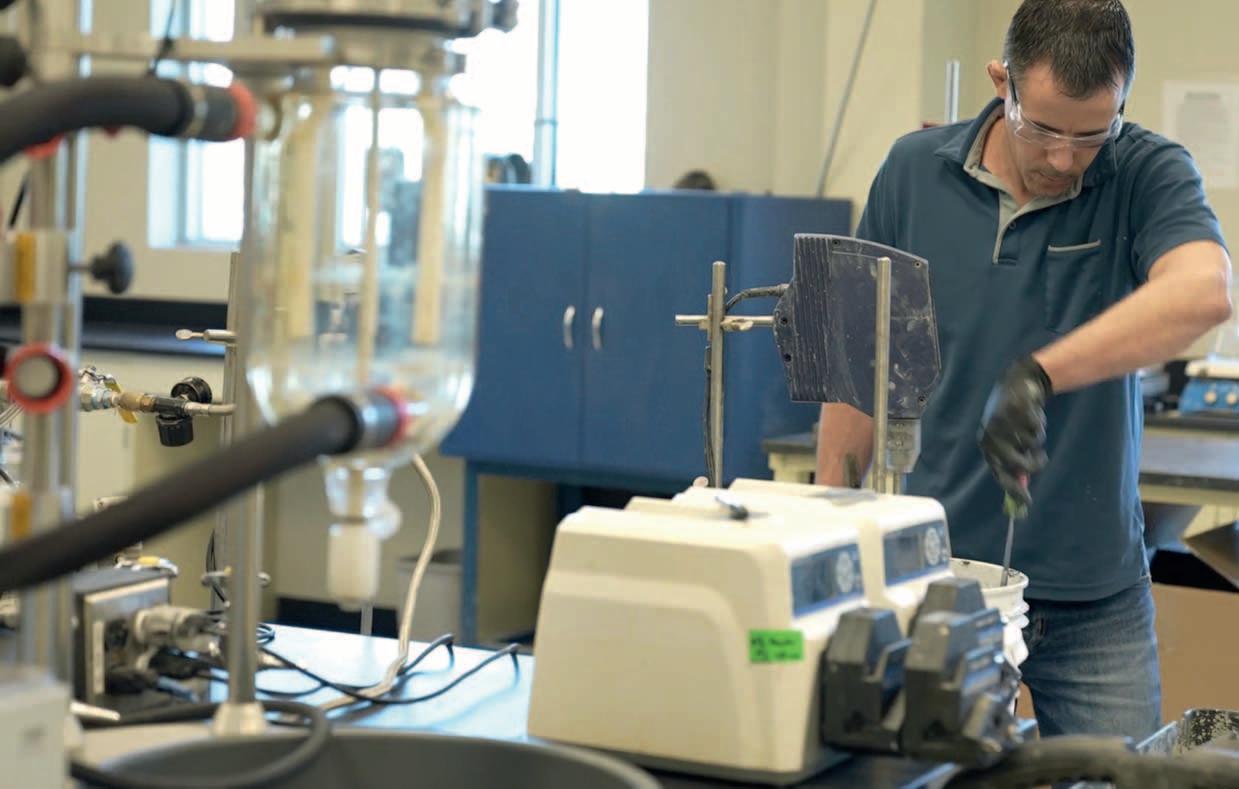
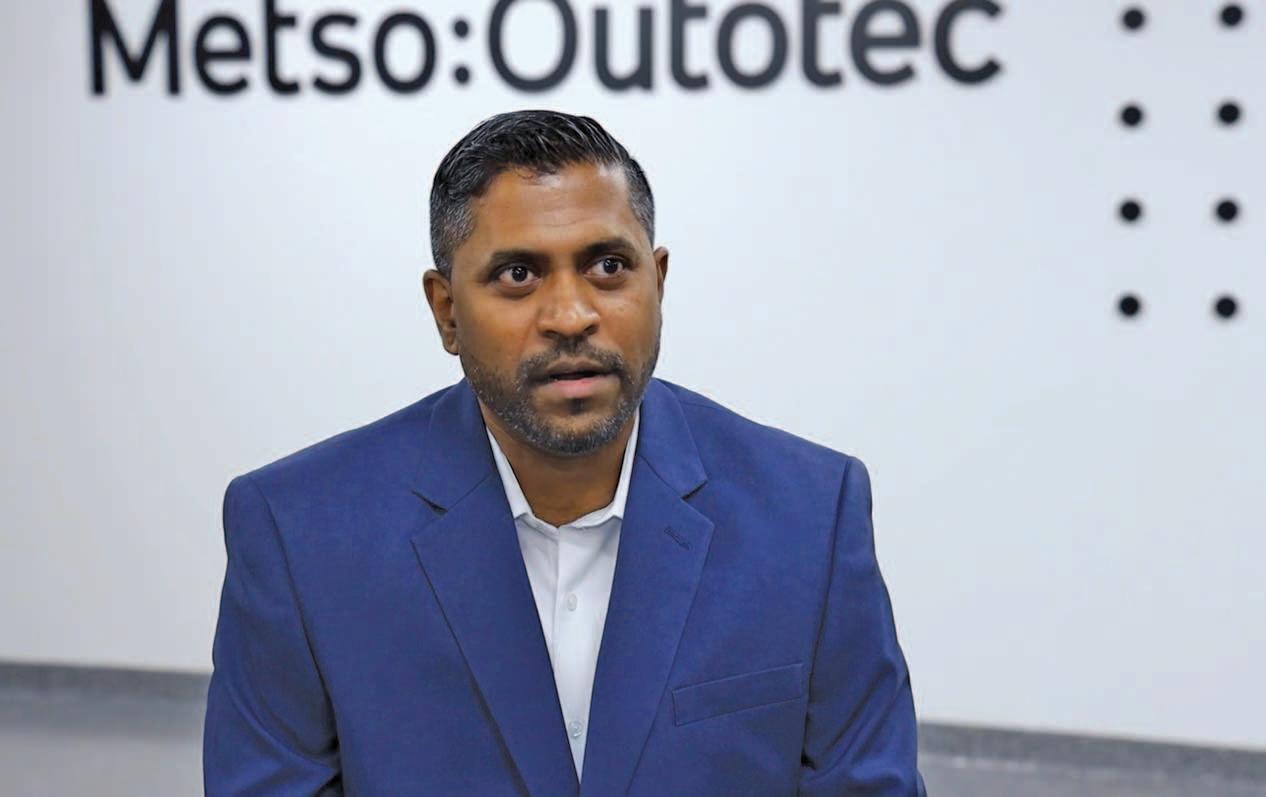
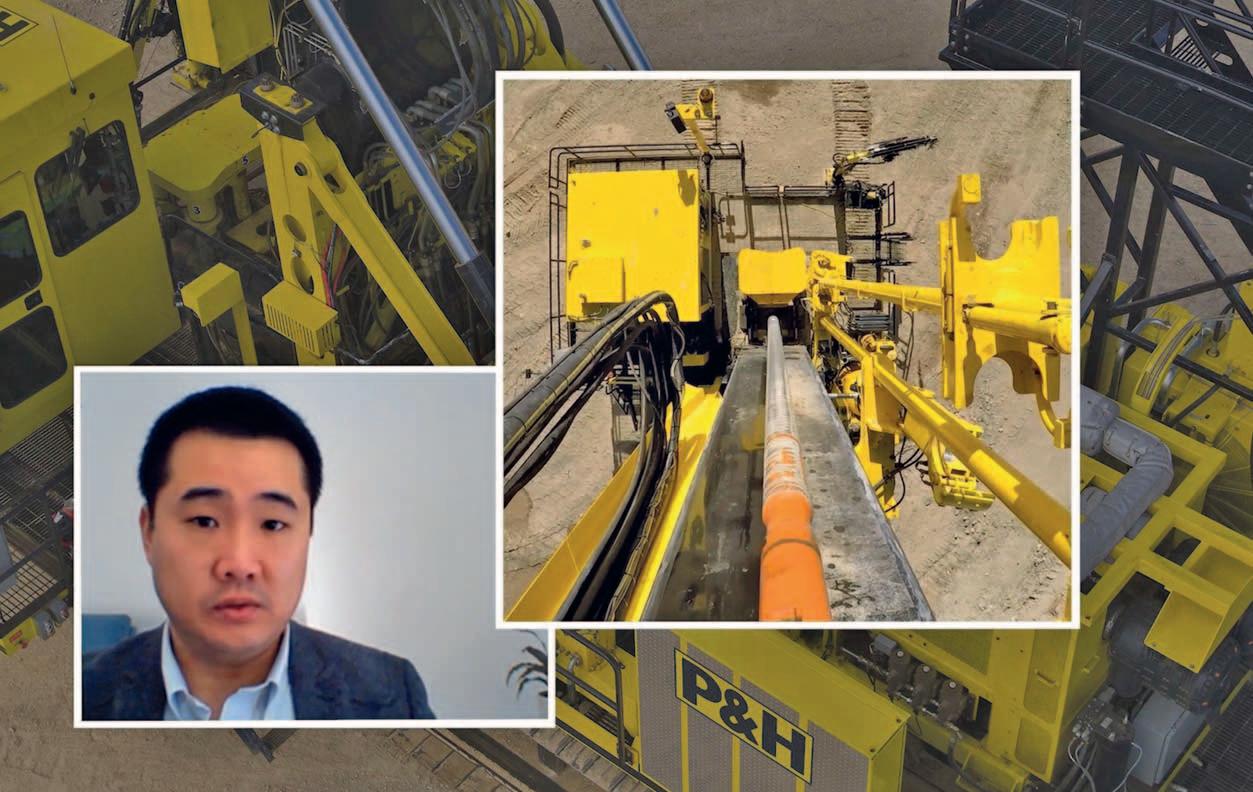
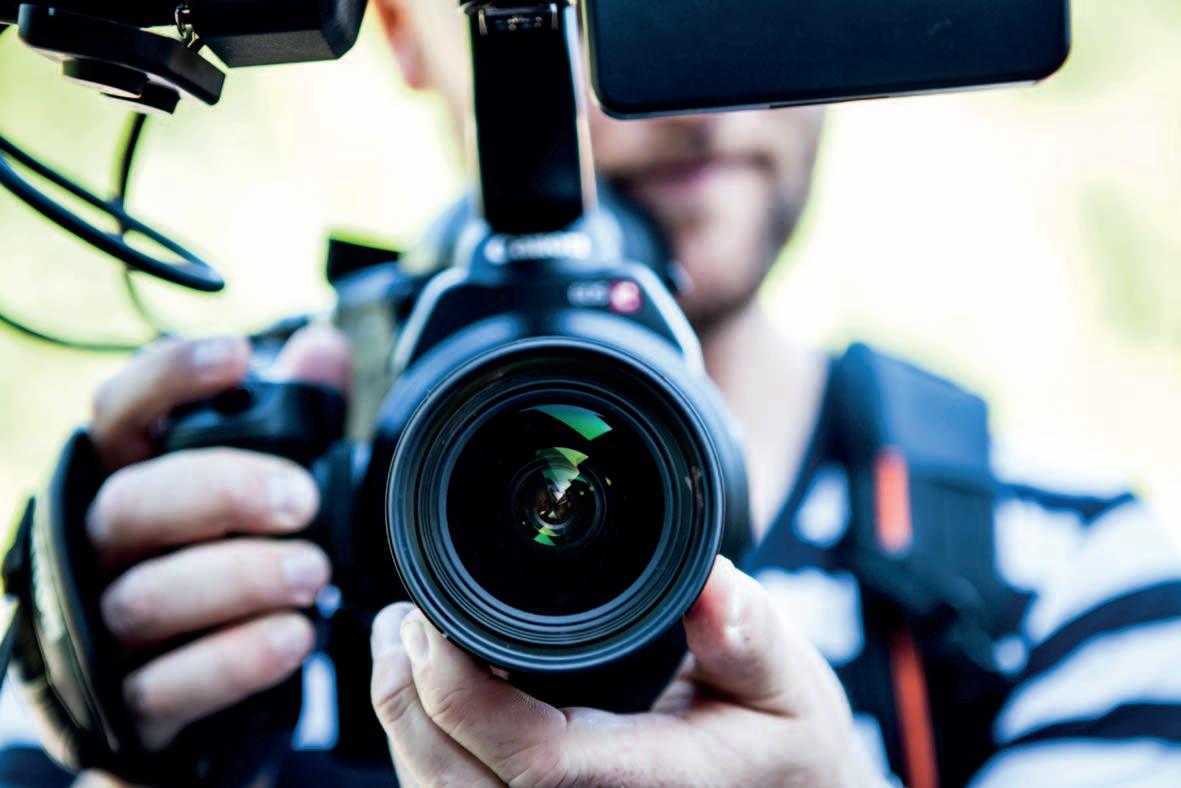
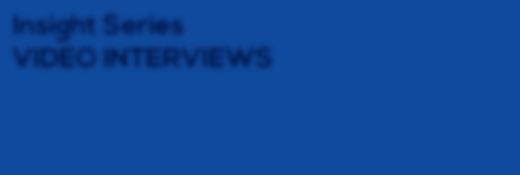
Originally guided by Sirius Minerals, the 10 Mt/y project was acquired by Anglo American in 2020, a transaction that came with a fresh look at the whole project execution phase.
The SBR was chosen for Woodsmith by Sirius over the conventional drill and blasting method due to its advantages in improving safety and schedule. This methodology, Sirius said, would allow the company to satisfy several operational objectives, moving away from the use of explosives and providing a safer, more predictable work method.
Various shaft sinking rates have been mooted in the past at Woodsmith, and Anglo American says it is currently working to develop the optimal solution for the facility based on technical standards.
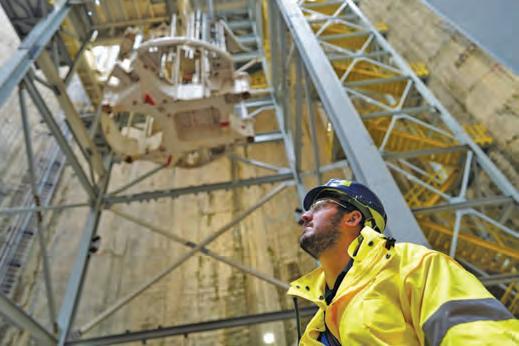
Work on the service shaft commenced in 2021 with former Anglo
The sinking at Woodsmith represents a different challenge to the two previous SBR projects conducted to this point.
IM: “Shaft sinking and concurrent concrete lining is scheduled to take 18 months, which includes development of three shaft stations and a loading pocket. The steady-state sinking rate,
installation including all supporting infrastructure is expected to be C$229 million ($177Johnmillion).Fitzgerald, VP, Projects, at Alamos, told
SHAFT SINKING 88 International Mining | SEPTEMBER 2022
Herrenknecht, with its experience in mechanised tunnelling, developed the SBR for the mechanised sinking of blind shafts in soft-to-medium rock. Based on the proven technology of the Herrenknecht Vertical Shaft Sinking Machine, the SBR offers improved safety performance compared with conventional shaft sinking methods while also achieving higher advance rates, according to the company.
The SBR is a 60-m tall, suspended shaft sinking machine, with 12 work decks and two service platforms. A telescopic, boom-mounted cutting head is used to precisely excavate rock via a partial-face cutting method. The cutting head works in a cycle, starting each cut from shaft centre to shaft wall, repeating until a layer of material is removed. Excavation proceeds in 1-m increments, followed by SBR lowering sequences.
Instead of a linear process, the SBR allows work to be completed concurrently as the shaft is sunk, as well as minimising damage to exposed host rock, and further improving safety while minimising downtime. Work decks above the cutting head allow workers to install shaft lining and tubbing as excavation continues, while a pneumatic mucking system removes waste rock.
The SBRs are being supported by four triple sheaved winches from SMS SIEMAG and conveyors from Herrenknecht-owned H + E Logistik GmbH, among other support equipment.
American Chief Executive, Mark Cutifani, confirming in July of that year that the “first cut” with the SBR had taken place in the shaft.
One of the most-watched shaft sinking projects in the sector right now is located in the UK, with the Woodsmith project in north Yorkshire having been on the radar for a number of reasons.
This progress was made while the company was still completing a detailed technical review on Woodsmith to ensure the technical and commercial integrity of the full scope of its design. This review has a particular focus on the sinking of the two main shafts, the development of the underground mining area, and the changes required to accommodate both increased production capacity and the more efficient and scalable mining method of using only continuous miners, Anglo American said.
the MTS level to consider at Woodsmith, with plans to carry out lateral development work around the 360-m-level to join up the production shaft and the MTS level, where polyhalite ore will be transported along a 37-km tunnel to Wilton near the port. This means vertical cutting and loading may be halted while the MTS level connection is established.Allthesefactors, along with the performance of previous SBR work, will be incorporated into the engineering work Anglo American is carrying out at Woodsmith, but, in terms of the SBR, cutting at the service shaft has now recommenced, with plans to start sinking in the production shaft by the end of the year.
The change in ownership and re-assessment of plans drawn up by Sirius – a much smaller company guided by different investor pressures and operating procedures – led to Anglo American relieving the lead shaft sinking contractor of its duties.
After debuting at the Jansen potash project in Saskatchewan, Canada, where it excavated two 8-11 m diameter blind shafts down to circa-1,000m-depth, SBR 2.0 – the second generation of the technology – was put to the test in Belarus at the Slavkaliy-owned Nezhinsky potash project. It ended up breaking shaft sinking records under the guidance of contractor Redpath Deilmann on a project to sink two 8-m diameter shafts (one to 750-m depth and one to 697-m depth).
For starters, there is no ground freezing expected to take place at Woodsmith – unlike what happened in Canada and Belarus. This process, while time consuming and only used to freeze unstable water-bearing strata around the shaft, can create more rock uniformity to aide consistent cutting
Woodsmith SBRs re-start cutting process
Thererates.isalso
Redpath Deilmann and Anglo American have now re-started cutting operations using Herrenknecht’s SBR at Woodsmith
The third generation of technology – which builds on the first two deployments with, among other things, the addition of two retractable robotic probes to test and grout the ground ahead for safer excavation and an additional control cabin on surface for more remote operation – is due to sink production and service shafts at Woodsmith. The Sirius plan had these shafts pegged as being 6.75 m in diameter and going down to depths of 1,594 m (production) and 1,565 m (service).
First off, it is a project that has changed hands recently.
Another reason for watching the project is the planned use of SBR technology from Herrenknecht.
Since the first cut was made in July 2021, however, Anglo American and Redpath Deilmann – which is now leading the sinking project as shaft sinking contractor – have been reviewing the existing plans for sinking with the SBRs, carrying out minor hardware changes on the machines and ensuring all staff have the appropriate training to facilitate the completion of the shaft sinking process. Redpath is also involved in the drill-andblast-based sinking for the materials transport system (MTS) shaft, which, under the Sirius plan, was due to reach a depth of around 350 m.
conventional configuration like that of Alamos’ Young-Davidson. Once skipped to surface, ore will be trucked to the expanded mill circuit. The total construction capital for the shaft
UMS has been contracted to engineer and design the shaft sinking of 750-m-deep production (8.5-m-diameter) and ventilation shafts (6-m-diameter) at the mine.
UMS has since been appointed to undertake the engineering and procurement for a new 1,500-m-deep shaft at the mine in Brazil.
While the prefeasibility study on the Island III expansion assumed one bucket for hoisting rock from the shaft face, Redpath’s plan is for two buckets, which will reduce the mucking time, with the double-drum production hoist utilised for this purpose, according to Fitzgerald, adding that the service hoist will be used to install shaft utilities, allowing for more concurrent work.
SEPTEMBER 2022 | International Mining 89
A globally reliable partner, providing a customized approach delivering value through all project stages. Mine Development & Construction • Shaft Sinking • Raise Boring Contract Mining • Mining Material Handling Solutions Crushing & Conveying Systems • Mobile Stacking Systems Feasibility & Design Engineering • Project & Construction Management Cementation Americas IM
funds for the project, we were going full steam ahead with procuring long-lead items,” he said.
“Even though this happened during the COVID pandemic, it didn’t delay the project and we are about to go into full sink on both shafts.”
As of August, shaft pre-sink work had commenced, with a plan to kick off actual shaft sinking in the September quarter of 2023.
Lucara Diamond Corp, the majority owner of Karowe, confirmed in its June quarter results that the shaft sinking phase had now commenced.
“Two slick lines will be used for concrete delivery, located on opposite sides of the shaft, allowing concrete liner placement from two locations concurrently,” he said. “Redpath will be using shaft jumbos (for drilling) slung from the headframe, rather than nested on the galloway structure, which has provided space for the second bucket and allows ready maintenance of the jumbos in the headframe.”
It said pre-sink activities for both the production and ventilation shafts were completed, including placement and erection of headgear for the production shaft. It added that the production shaft stage winder was installed and roped-up, while commencing of the main sinking for the production shaft was expected to take place later in the year.
SHAFT SINKING
Over the last five years, the United Mining Services (UMS) Group says it has evolved its operations to combine the capabilities of the UMS METS and UMS Shaft Sinkers businesses, and facilitate a seamless project transition for clients from concept to prefeasibility, feasibility and into execution.
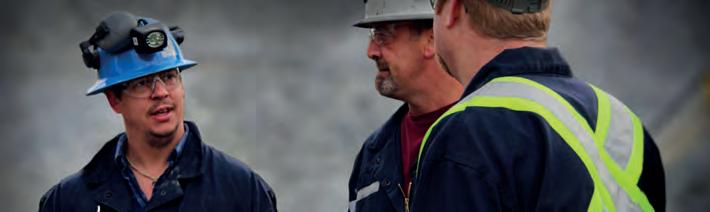
The sinking project is part of the Karowe UGP,
He added: “While not new to the industry, we have seen significant benefits from having Redpath work with our engineering consulting group and steel supplier/fabricator for headframe design to provide the required functionality for both sinking/equipping and production phases.”
Redpath will be using its instrumentation and control technology to ensure maximum safety and productivity on the project, which will allow up to four conveyances to work concurrently in the shaft, according to Fitzgerald.
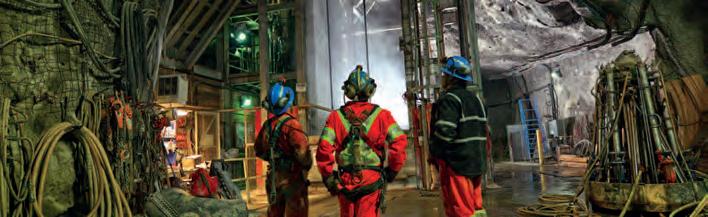
The client approached UMS with a feasibility study to convert the open-pit mine to underground to extend the mine life to at least 2040.“We did the trade-offs first, followed by the detailed design, and, while the client was raising

which is expected to extend the mine life to at leastMacnab2040.says a copper project in Brazil is currently going through a similar process.
“The client approached us with a concept for transitioning the mine from open cast to underground that proved to be unsuitable,” he said. “We came up with a solution within 10 weeks, developed that to the next phase, and were able to cut off about a year of the cycle of getting the project off the ground simply because we had inhouse designs, costing and schedules that we could draw on from our UMS METS business, saving the client time and money in the feasibility phase.”
The Karowe Underground Mine Expansion Project in Botswana is a prime example of a client benefitting from UMS’ front-end capability, according to Murray Macnab, UMS Group Executive Technical Director.
excluding shaft stations and loading pocket, is planned to be 3.2 m/d, with the initial sink to 200-m depth at 70% of this rate. Following sinking and lining, shaft equipping is scheduled to take two months which includes shaft stations and the loading pocket.”
Front-end engineering capability
location of your average mine site is no closer to city centres today than it was decades ago; in fact, it is probably further away.This reality has meant the technology required to connect these operations to HQ, regional operational hubs or increasingly Remote Operating Centres (ROCs) has had to come to them.
‘Remote’ no longer means ‘disconnected’ when it comes to operating mines today, Dan Gleeson reports
The L-band powered IDP communication service is billed as offering low latency, consistent data transmission, as well as worldwide coverage. It also offers 99.9% network availability over the I-4 global satellite network, according to Inmarsat.
The
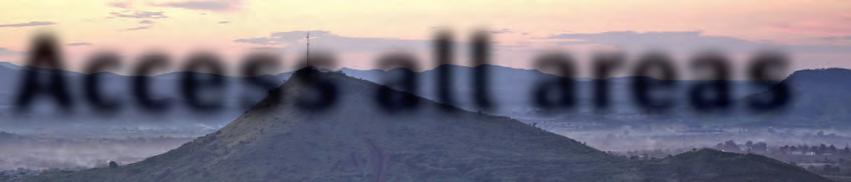
Severalcamps.solutions
IM takes its annual look at the supply side of the market that is ensuring any mine site –regardless of location – stays connected.
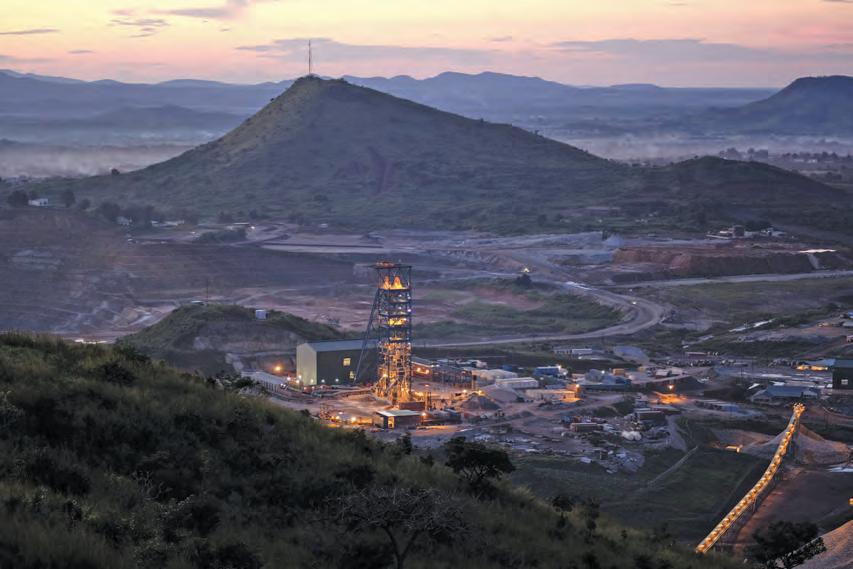
At remote operations, satellite-based communication systems are increasingly being called upon to fill the voids that terrestrial connectivity would normally take at established mining
REMOTE MINE SERVICES
It did this through providing access to its Skywave IDP-780 solution, powered by its L-band connectivity service, to enable a mission-critical telemetry solution for tracking assets.
The solution at Kamoa-Kakula allows the control centre to visualise the vehicles and includes several geofences that were set up to enforce policies introduced by Ivanhoe Mines to improve driver and public safety and security.
“This provides a consistent and reliable communications network between control centre and vehicles, delivering real-time updates to Ivanhoe Mines on vehicle status and location, enabling the company to act to secure the safety and security of their staff and assets, if necessary,” Inmarsat said.
SES and AXESS Networks say they are accelerating the digital transition of the mining industry with a collaboration focused on SES’s secondgeneration medium earth orbit system, O3b mPOWER
Inmarsat, a leader in global mobile satellite communications, has been proving this point regularly through many mining-focused deployments.AttheKamoa-Kakula copper project in the Democratic Republic of the Congo, for instance, it helped Ivanhoe Mines, the operator and 39.6% owner of Kamoa-Kakula, understand where vehicles are and how quickly they are moving, to ensure safety and security at the mine site.
The satellite backbone
90 International Mining | SEPTEMBER 2022

Bos concluded: “We have seen a notable decrease in issues for our drivers out on the roads, and the speed of resolution of these


At the Kamoa-Kakula copper project in the Democratic Republic of the Congo, Inmarsat helped Ivanhoe Mines understand where vehicles are and how quickly they are moving, to ensure safety and security at the mine site
exceeds 80 km/h over a period of time or over 30 km/h in certain zones, the office is notified and can contact the driver to instruct them to slow down.“We can also monitor location with pinpoint accuracy, so that if a vehicle hasn’t moved in some time, we can contact the driver to establish whether they’ve had an accident or a breakdown.”Inmarsatsays its satellite connectivity has been critical to the success of Ivanhoe’s Kamoa-Kakula driver safety project. The fleet management solution required consistent connectivity across the entire field of operations, large areas of which are not covered by cellular networks. It, therefore, provided a dual satellite-cellular tracking device and fleet management solution, using GSM connectivity where available and then switching to Inmarsat’s satellite connectivity when required.
Access all areas
have come to the market in recent years looking to showcase the capabilities of satellite-based systems, going some way to defying the perception that they only provide a temporary fix for mines being developed or in the initial phases of production ahead of more ‘permanent’ communications infrastructure.
Matthieu Bos, Vice-President, Corporate Development at Ivanhoe Mines, explained some of the measures introduced by the company: “We wanted to reduce the speed at which our drivers travel on the roads, to reduce the damage done to vehicles if they hit potholes or other obstructions and the risk of an accident. Inmarsat’s solution enables us to track the speed of every vehicle every minute, and, if this speed
Visit us on www.sika.com/mining For more than a century, Sika is pioneering underground construction and has been involved with the most challenging tunneling and mining projects ever built. We will continue forging ahead to bring modern day mining a step ahead. Backfill - Shotcrete - Concrete - Grout - Injections Sika® Aliva® Equipment - Asset Maintenance - Infrastructure Repair SINCEUNDERGROUND1910
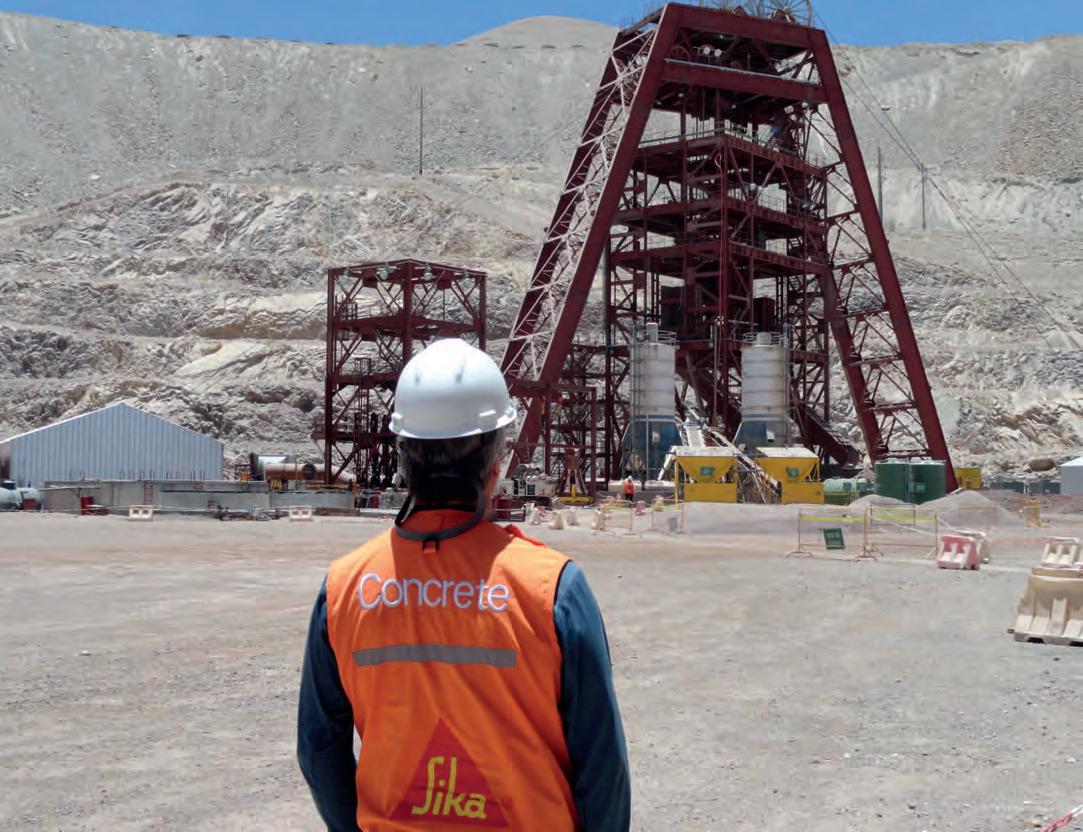
To drive efficient, sustainable and remote operations at Salares Norte, the operation, majority owned by Gold Fields, is now installing ABB’s enterprise-grade digital platform, ABB Ability Genix Industrial Analytics and AI Suite.
“Starting with data capture and integrating cross-functional data, ABB Ability Genix connects operational, business and engineering systems,” ABB says. “It then collects, contextualises and converts data through advanced analytics into meaningful information to unlock productivity improvements by driving smart business decisions.”
The mine is expected to produce 3.7 Moz of gold over an initial mine life of 11 years after it starts up, with the ore mining operation employing drilling and blasting, and loading and hauling. It has an installed production capacity of 2 Mt/y.
Max Combes, Project Director of Gold Fields, said: “Salares Norte deploys a high level of digital industrial software and technology. This is critical to this project due to its remote location – the nearest town being Diego de Almagro, 180 km away, the altitude of the project and adverse weather conditions which make site access and fieldwork challenging. It demanded a solution for the remote monitoring centre in Santiago that could integrate and contextualise information from many systems, including some common to Chile, as well as perform data analytics.
92 International Mining | SEPTEMBER 2022
issues has also improved immensely. We now have complete confidence that we will be instantly aware of any issue with a driver or vehicle and can respond immediately to provide assistance. Additionally, we have improved relations with people from our local communities by reducing disruption as our vehicles pass through their villages.”
ABB has been involved in the project for several years, having already deployed its ABB Ability™ MineOptimize solution to supply an integrated power and automation system comprising six electrical rooms and a suite of process and power controls, all under the ABB Ability System 800xA distributed control system (DCS).
n A development program for IoT solution providers, system integrators, machinery manufacturers and OEMs looking to scale, who will be able to take advantage of Inmarsat’s ELERA satellite network and footprint;
Being located 1,300 km from Santiago, 180 km from the nearest town (Diego de Almagro) and among the highest peaks of the Andes Mountain range with elevations of between 4,200 m and 4,900 m, Salares Norte is undoubtedly considered a ‘remote’ project.
The mine operator will monitor the gold-silver mine in the Andes Mountains from a remote monitoring centre in Santiago, Chile
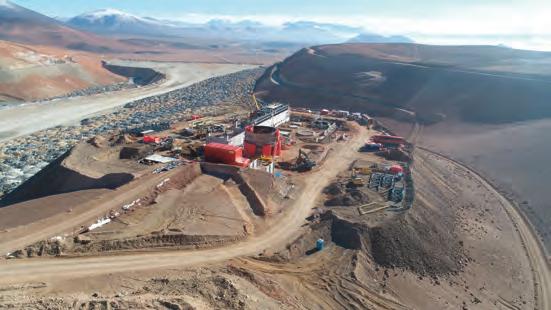
Iván Villegas, Hub Product Marketing Manager Automation – South America, ABB, added: “ABB will deliver a comprehensive integrated electrification, automation and digitalisation solution at Salares Norte. ABB Ability Genix, set to be fully commissioned in record time, will help Gold Fields to use their data from operations better, by combining it with engineering and information technology data for multi-dimensional decision making.”
ABB’s scope also includes Dynamic Process Simulator, which reviews plant control logics, reducing commissioning times and allowing Gold Fields to train operators to acquire the skills required to achieve highquality operations.
ABB Ability Genix will help visualise and analyse all information required to support Gold Fields reporting and drive its environmental commitments, helping the company achieve its vision of becoming the global leader in sustainable gold mining, according to the company.
REMOTE MINE SERVICES
Called Inmarsat ELEVATE, the program’s three key pillars are:
n A partner ecosystem to enable organisations to access each other’s knowledge and collaborate with other organisations within the satellite IoT sector; and
n An online marketplace to promote IoT solutions that work seamlessly anywhere in the world – no matter how remote – to ensure every business can benefit.
The recent launch of a new partner program to support businesses throughout the IoT ecosystem is aimed at doing exactly this.
In the next five years, the goal of Inmarsat ELEVATE is to help partners achieve double digit growth, as well as establish Inmarsat ELEVATE as the leading IoT marketplace for solutions that work anywhere in the world, Inmarsat says.
Hiber will continue using its own proprietary
Remote connections
These include the Power and Process Control Library and Camera Connect (the ABB video system embedded in the control platform for optimised process monitoring), while ABB Ability Knowledge Manager is also used to manage information production through the Plant Information Management System, alongside ABB Ability Asset Vista Condition Monitoring.
One such IoT development partner is Hiber and its Hiberband low-cost, low-power network for IoT Inmarsatproducts.andHiber recently signed an agreement that will see Inmarsat provide the satellite connectivity backbone on which Hiber will continue to build Hiberband. This pairs the ELERA network with Hiber’s IoT-as-a-service ecosystem to, Inmarsat says, provide easy-touse, low power and cost-effective IoT solutions and services to transport, logistics, agriculture, mining and other industries worldwide.
At the same time as providing solutions such as this, Inmarsat is looking to leverage its Lband, Ka-band and S-band spectrum portfolio for integration into IoT platforms to help mining companies further their digitalisation and automation ambitions.
This Genix suite is in a remote monitoring centre for the mine in Santiago, 1,300 km away from Salares Norte, which is able to support Gold Fields personnel with data insights that will help them increase industrial productivity and operational excellence, while reducing costs, ABBRemotesays. connectivity will help reduce the number of people needed at the actual mine location, thus improving safety, it added.
ABB Ability Genix combines the power of industrial analytics and artificial intelligence to integrate 25 engineering, operational and information technology systems across different functional areas, including the mine, processing, geology and exploration, asset management, finance, legal and human resources.
Mike Carter, President at Inmarsat Enterprise, said Inmarsat’s ELERA satellite network provides an “essential backbone” to IoT innovation that enables its development partners to scale and grow their operations backed by its reliability and “seamless global connectivity”.
“ABB is already a proven digital partner and ABB Ability Genix will further unlock the power of data at this project.”
protocols that allow for ultra-low power and low-data consumption levels to connect to Inmarsat’s ELERA network and power its IoT solutions. Additionally, the partnership will enable Hiber to support a range of new industrial IoT applications and provide its customers with reliable, affordable connectivity even in areas without dependable cellular or Wi-Fi network availability, Inmarsat says.
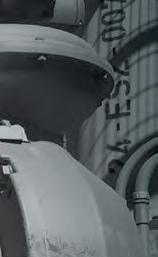
Roel Jansen, Hiber CEO, said: “This strategic partnership with Inmarsat creates the most powerful global network for IoT available and helps Hiber to focus on rural, remote and industrial IoT solutions, which is where the real life-changing innovation will happen.”
SES’s Onshore Energy & Mining mPOWERED service will provide the highest throughput available from a satellite system and deliver dedicated and carrier-grade networks to AXESS’ customers reliably regardless of their remote locations, according to the companies. O3b mPOWER, meanwhile, can deliver up to multiple gigabits per second per site, enabling AXESS’ customers to accelerate the digitalisation of their operations and sites globally, providing access to new applications and efficiency, as well as improving staff safety and welfare.
Telstra Purple, which brings together Telstra Enterprise’s business
attioasive applplicabr ultlt,fficWe know dif Valveageo LeakZeroven e Soluti base in the industry? eivicry ser egest slure larWhy do we have th r inionsnns.™alledstd TINGHOERAOPOVER 500 MILOURSLION t: +1 832-652-24/7 e:Suppor+1713-860-0400honP om.c SERVICE.VALV.COM USEVERE SLIN TING HO3607URRY

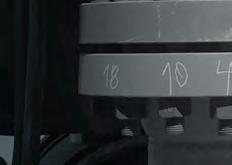
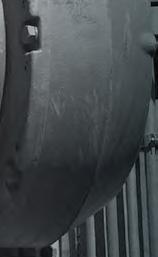
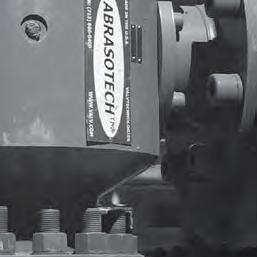
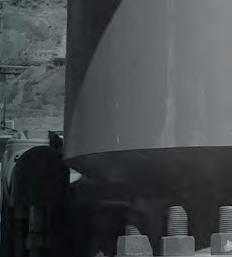
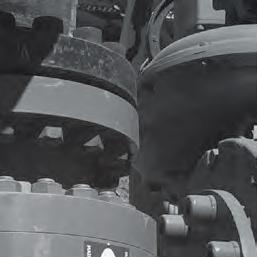
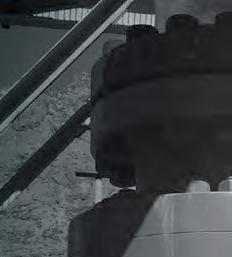
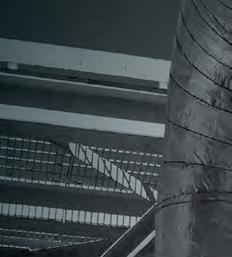
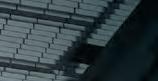

Similarly, SES and AXESS Networks say they are accelerating the digital transition of the mining industry with a collaboration focused on SES’s second-generation medium earth orbit (MEO) system, O3b mPOWER.
This is before factoring in other potential problems like challenging terrain or, in the case of landlocked countries, the need for cable systems to travel from landing stations in major coastal cities through multiple countries and telephone company networks before reaching the mine.
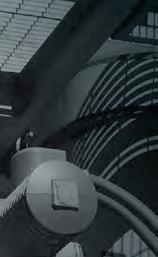
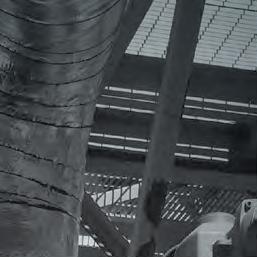
“SES’s O3b and its second-generation O3b mPOWER constellations help overcome the limitations of terrestrial infrastructure, while delivering carrier-grade, fibre-like, low latency satellite connectivity service to any location needed, point to point, straight into the mine, from a O3b mPOWER gateway located in one of the major cloud service provider’s data centres,” Gatty Saunt says.
Facilitating change
Simon Gatty Saunt, Vice President of Networks Sales for Europe at SES, says traditional, wire-based infrastructure is not always a practical solution at mine sites, with remote operations often devoid of the fibre-optic cables or other pre-existing traditional infrastructure required to deliver strong connectivity.“Thismeans that an operator would have to lay dozens of miles of cables to benefit from these solutions,” he told IM
This latter benefit ensures real-time information can be relayed to the cloud-based infrastructure effectively and efficiently, empowering, for example, “artificial intelligence or remote operation of some complex systems”, he said.
REMOTE MINE SERVICES

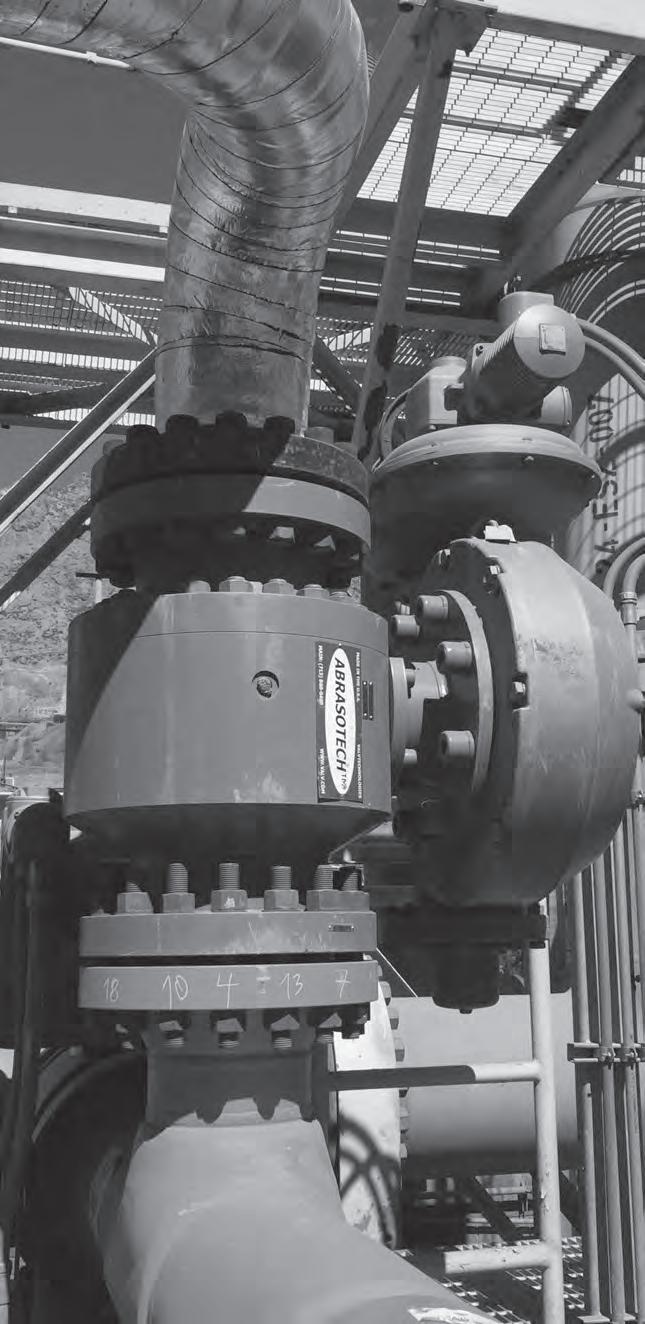

Network, entertainment access

Aqura Technologies has increasingly become known for establishing industrial-grade wireless and fixed networks in remote and underground mining operations in Australia, a status that was highlighted when Telstra Purple acquired the company earlier this year.
Such issues can often reduce the network uptime significantly, adding latency as there is a greater likelihood of points of failure enroute.
He concluded: “With the carrier-grade O3b mPOWER connectivity, using any necessary application at the remote site becomes possible.”
SES’s second-generation MEO connectivity service also brings the cloud closer to end customers and can enable edge computing to support the use of 5G and IoT in the mining industry, according to the company.
Under a recently signed multi-year, multi-million-dollar agreement mining sector users can now benefit from the cutting-edge low-latency Onshore Energy & Mining mPOWERED connectivity service, they say.

The new standalone broadband network will support PPA’s extensive marine digital platforms, enhance worker mobility and provide seafarers with independent high-speed connectivity when visiting the Port of Port Hedland, it said. Port Hedland is a major export facility for Pilbarabased iron ore producers.
The project has kicked off with the network planned to be live by the end of 2022.
REMOTE MINE SERVICES 94 International Mining | SEPTEMBER 2022
This CAN platform also allows Aqura to set up in-room entertainment networks for remote mine sites in Australia.
Aqura Chief Operations Officer, Alan Seery, said: “Our installation of Private 4G at the Port of Port Hedland will leverage the expanded capabilities of Private 4G that will assist the PPA in driving safety, productivity and efficiency initiatives.“Thecommunications network, upgradeable to 5G as technology advances, also offers more control and flexibility to support Industry 4.0 use cases and other technologies such as IoT.”
The private network will also enable PPA staff to access their corporate and operational systems reliably and securely from anywhere
Private 4G requires the delivery of several prioritised services for a range of different enduse cases. The network leverages the embedded Quality of Service capability and high throughput of 4G and is dimensioned to ensure the extensive marine sensors network that PPA uses has reliable and robust connectivity for the safe passage of vessels through challenging waterways in the area, according to Aqura.
The application Sandvik has developed is a central database that opens the door to all the company’s collective knowledge about almost
VR- and app-backed field support
This capability has been proven of late through contracts with the likes of Roy Hill and the Port Hedland-based operation of Pilbara Ports Authority (PPA).
Under the terms of the new agreement, Aqura worked closely with DXC Technology as the facilities manager for the respective villages.
Using a new app and virtual reality training and digital inspections, Sandvik field service engineers are solving the most complex problems, no matter where in the world, according to the OEM.
technology services capabilities and several recently acquired companies, said the acquisition enabled it to offer professional and managed services capabilities in exactly this field.
COVID-19 restrictions prevented travel, and a desire to minimise the carbon footprint of field technicians means that if problems can be solved remotely, or at least fixed first time, they should be.
Aqura Technologies CEO, Travis Young, said at the time that the extended reach of the Roy Hill Private LTE network would “accelerate” the realisation of benefits from its Autonomous Haulage Systems and digital transformation initiatives.ThePPA contract, meanwhile, will see Aqura design and deliver an advanced Private 4G network for the Port Hedland-based operation.
“Some engineers worry that they will be judged negatively if they don’t know how to solve a problem with a machine, but that couldn’t be further from the truth,” August said. “It’s more about coaching and helping than judging; like having a really clever friend on site with you to help.“At the end of the day, it’s about empowering service technicians with digital tools so that we
across their port operations, which enhances productivity and improves access to digital safety systems and procedures, it added.
The A$1.4 million ($970,203) agreement with DXC Technology for a global Tier 1 miner meant Aqura was managing accommodation content access and entertainment networks across some 31,000 accommodation rooms.
The scope of the engagement saw Aqura’s inhouse specialists provide remote and field-based support to ensure the efficient operation and upgrades of the end client’s Video Entertainment System, network distribution and Wi-Fi networks.
In the future, there is no reason why a simple smart phone could not carry out the same task, cutting costs and widening the availability of the technology, Sandvik says.
Last year, the company was awarded a threeyear Managed Services Agreement along these lines to support accommodation village entertainment networks across 17,000 additional rooms in the Pilbara.
To ensure the wellbeing and welfare of seafarers is enhanced while being restricted to their vessels at berth or at anchor, Aqura will leverage its Complete Access Network (CAN) platform to deliver a secure, user-friendly service.
“Whatever has happened, chances are someone in our Sandvik service team around the globe has seen it before and knows a fix,” August said of using the app. “You can use it to search issues, open fault tickets, look at product schematic PDFs, submit photos, watch tutorial videos; even talk to an expert team back at base. Sometimes it’s good to just have a chat with someone and talk through problems together.”
anything that can go wrong with a machine, according to Steve August, Global Field Support Manager with Sandvik’s Parts & Services Division. It is complemented with virtual reality goggles used in the field by mining technicians.

In addition, the Managed Services Agreement will see Aqura provide large-scale Managed Wi-Fi, Distribution networks (Fibre-optic and DOCSIS), MATV (free to air TV) and Network management platforms, which integrate to provide a seamless and positive user experience, it said.
The former contract, which builds on Aqura’s first phase delivery of Roy Hill’s new Private 4G LTE network in May 2021, will see Aqura support Roy Hill in the design, installation and commissioning of an expansion of an advanced Private 4G LTE network at its Pilbara iron ore mining operations in Western Australia.
Aqura Technologies’ Travis Young says the extended reach of the Roy Hill Private LTE network would “accelerate” the realisation of benefits from its Autonomous Haulage Systems and digital transformation initiatives
It also solidifies Aqura’s track record of delivering “leading-edge, high performance Private LTE networks underpinning the digital transformation programs of large-scale operational activities in highly remote locations”, the company said.
Although initially being rolled out to Parts & Service field technicians, longer term, this type of technology could be offered to customers as well, according to Sandvik. The app uses a stateof-the-art headset with a built-in screen that shows the wearer tutorials/product guides, a microphone and earpiece to talk to product experts and cameras to show the experts back at base exactly what the technician is seeing.
Qantas Group CEO, Alan Joyce, said acquiring the remaining shares in Alliance meant QantasLink could better compete in the highly competitive charter segment, particularly given the shared fleet type of Fokker aircraft.
A pilot roll-out of the technology has seen 400 Sandvik technicians carry out trials. By the end of 2022, the app will be mainstream and a standard part of the service delivery, the company says.
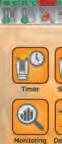
Qantas Group CEO, Alan Joyce, said acquiring the remaining shares in Alliance meant QantasLink could better compete in the highly competitive charter segment, particularly given the shared fleet type of Fokker aircraft
can get customer machines up and running perfectly again – that’s the only driver of this technology.”
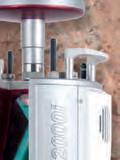

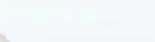
FIFO consolidation
REMOTEIM MINE SERVICES



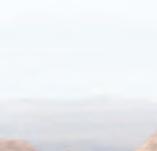

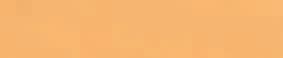

RIEGLLFORMINNINGSERARSVG NER
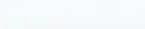


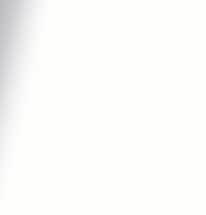




YSIS AND PROCESSING

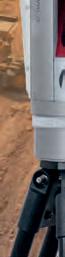
5 mm tten in Python programming language or remote operation and data transfer G/4G cquisitionLTE scheduling ue quiredsetting–webserver on scanner ata and result publication ys and optimal per ppsyinthefieldyinthefield PPS FOR YREAL TIME ANAL • ranges up to 2500 m • customized apps writ • cloudconnectivityfo RIEGL VZ-i Series for highest accuracy RIEGL MINING AP cloud connectivity fo via LAN, Wi-Fi, and 3G • flexible scan data ac • flexible threshold valu • no extra software req for browser-based da RIEGL Mining Ap for highest efficiency Monitoring A data compa to the referen Design Com data visualizationcompao Slope Angle calculation a and the area PERPAAITEWWHH T App rison and visualization of differe nce data set pare App rison to a given 3D design mod of undercut and overcut App and visualization of local slope a as above the critical slope angle E P encesdel,anglese RiCustomer Applicatione SLinV-RIEG Austria | USSAA | Japan | China | www ExploreLiDthe full portfolio o RIEGL DAAR sensors and sy w..riegl.com L V s s Managementk intoCappabilitieIntegrationand a onitoriint Mermmanenr PfooScanners f r WIDERIEGL WORLD E | Australia | Canada | f proven ystems r s i sk g:United Kingdom
The introduction of smart tools and technologies may help reduce the need for increasing levels of personnel on mine sites but, in Australia at least, flyin, fly-out (FIFO) requirements continue to remain strong.

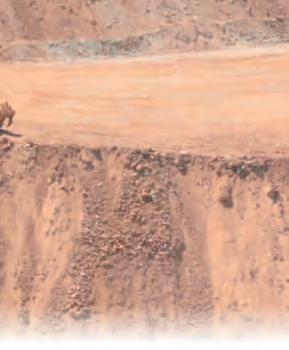
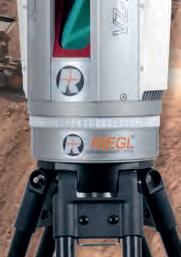
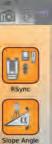
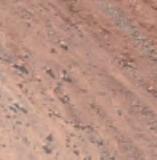
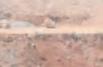
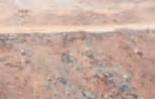
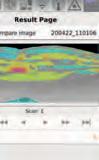

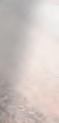
Qantas recently acquired Australia-based operator, Alliance Aviation Services Ltd, in a consolidation play that, Qantas says, will enable it to better serve the growing resources sector with FIFO options.
He added: “The resources sector continues to grow and any new tender for airline services will be very competitive. It makes a lot of sense for us to combine with Alliance to improve the services we can offer, which is a positive for both airlines as well as the travelling public.”
S SiZ- SERIES SC CAT R V VZZ-iSeriiesScannerssRIEGLV Z r r foorppg AMinin s f


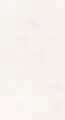
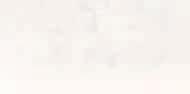

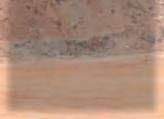
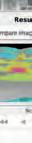



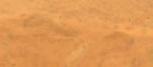








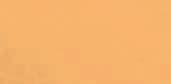

The agreement saw Alliance become a wholly-owned part of the Qantas Group and followed a February 2019 deal that saw the national carrier acquire 20% of the airline at the same time as flagging its interest in taking up 100% of the company.
“Alliance’s fleet of Fokker aircraft are perfect for efficiently serving resources customers in Western Australia and Queensland,” he said. “They also have a big inventory of spare parts that would significantly extend the practical life of a combined fleet of around almost 70 Fokkers.
m, accuracy
formance
Alliance has a fleet of 70 jet aircraft that seat up to 100 people each, making it well suited to charter operations. Between these charter services and a small number of passenger routes that overlap with large mine sites, Alliance accounts for around 2% of the total domestic market, according to
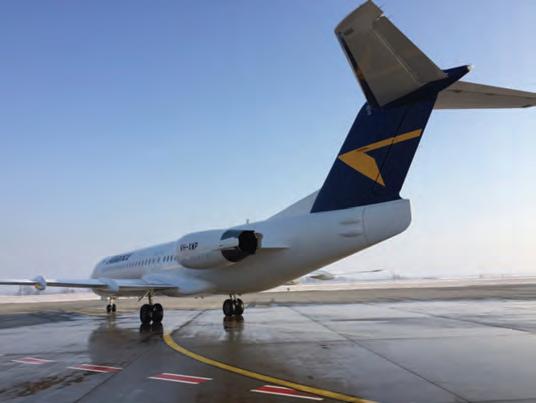
Just some of the mine sites that Alliance Aviation serves include BHP’s iron ore and Nickel West operations in Western Australia, St Barbara’s Leonora mine in Western Australia and Incitec Pivot’s Phosphate Hill operation in Queensland.
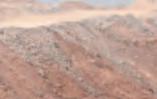
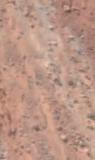

Qantas.Qantas is Alliance’s biggest single customer, with a long-term agreement that sees Alliance operate up to 18 newly acquired E190 jets for QantasLink. This arrangement has helped open new direct routes and increase frequency across regional Australia, Qantas says.
AANN


“Keeping these aircraft operating reliably for longer than either carrier could achieve by themselves will help keep costs down, which is ultimately good news for charter customers. There are also benefits from bringing together our operations planning and training facilities.”
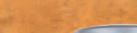
Murray & Roberts Cementation 85 www.cementation.murrob.com
Pronto 71 www.pronto.ai
RIEGL 95 www.riegl.com
Mine Hoists International – a division of Mining Equipment 87 www.minehoist.com
Nokia 51 www.nokia.ly/mining
Robit 35 www.robitgroup.com SafeAI 67 www.safeai.ai
Sika Group 91 www.sika.com/mining SSAB 27 www.hardox.com
Fax: +39 02 orcsanfilippo@rancatinet.it70300074arancati@rancatinet.it
Resemin 29 www.resemin.com
Europe (exc. Italy) & CIS, South Africa, US East & West Coast & Canada, Australia & New Zealand
96 International Mining | SEPTEMBER 2022 IMADVERTISER INDEX




The Electric Mine 2023 Conference 54-55 www.theelectricmine.com
Advertising
Elphinstone Pty Ltd 45 www.elphinstone.com
India Deven Singh Block 10/502 Heritage Estate, Dodaballapur Road Yelahanka, Bangalore - 560064
September 2022
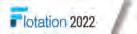
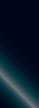

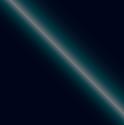
Volvo CE 59 www.volvoce.com/changestartshere Volvo Penta 16 www.volvopenta.com
Tel: +1 (630) lapham@jpmediainc.com865-2806
Caterpillar Underground 25 www.cat.com/underground Cementation Americas 89 www.cementation.com CONEXPO-CON/AGG 2023 IFC www.conexpoconagg.com
DSI Underground 4-5 www.dsiunderground.com
Robbins 17 www.robbinstbm.com
Japan Akiyoshi Ojima
MEI Conferences 64 www.min-eng.com/conferences
Sandvik Mining & Construction 15, 57, 79 www.rocktechnology.sandvikwww.rocktechnology.sandvik/th-xlwww.rocktechnology.sandvik/autobit
Tel: +55-11-3895 josephyoung@terra.com.br8590
DMC Mining Services 84 www.dmcmining.com
or lynne@im-mining.com ADVERTISING SALES REPRESENTATIVESFORTHCOMINGEVENTS is a media sponsor for these forthcoming events in 2022 5-9 September 2022: Electra Mining, Johannesburg, South www.encuentrometalurgia.com/flotation-2022Flotation9-11https://mei.eventsair.com/process-mineralogy-22Spain.Process2-4https://imarcglobal.comIMARC2-4https://bauma.de/enbauma24-30https://expo-katowice.comPoland.International6-9www.electramining.co.zaAfrica.September2022:TradeFairKatowice,October2022:2022,Munich,Germany.November2022:2022,Sydney,Australia.November2022:Mineralogy'22,Sitges,November2022:22,Lima,Peru.




Tele Radio 77 www.tele-radio.com
China Huang Shusheng(黄术升) huang_shusheng@hotmail.com+86-13501022196
Maestro Digital Mine 49 www.maestrodigitalmine.com
Brazil Joseph MinériosYoung&Minerales Magazine
Komatsu 63 www.komatsu.com/autonomous L&M Powertrain Parts 41 www.lmpowertrainparts.com Liebherr International 21 www.liebherr-bauma.com
FLSmidth 18 www.flsmidth.eco
Andrea Rancati
Tel: +44 (0)1442 870 phil@im-mining.com829

Phil Playle
Fax: 81(0) 45 319 ojima@media-jac.co.jp4743
Flender 37 www.flender.com
Richwood 68 www.richwood.com
ME Elecmetal 9 www.me-elecmetal.com
2: Coal Log India 2022, Kolkata, India. www.coallogindia.com
Redpath 12-13, 83 www.redpathmining.com
TAKRAF 33 www.takraf.com
Groundhog 61 www.groundhogapps.com/im22
MTG 23 www.mtgcorp.com
UK,
J.P. Media Inc
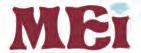
Tel: +39 02 70300088
South America Editec S.A.
Kevin Lapham,
ABD Solutions OBC www.abdsolutions.com
Tsurumi Pump 80 www.tsurumi-global.comwww.youtube.com/user/amenics
Cent & Mt
US Mid-West,
Tel: 81 (0)45 319 4742
Wimmer International 36 www.wimmer.infowww.mini-badger.at Wirtgen 11 www.wirtgen-group.comwww.wirtgen-group.com/mineral Xtonomy FC www.xtonomy.ai
Tel: +44 (0)1442 870 829 emma@im-mining.com
Weir ESCO 31 www.esco.weir Wenco 65 www.wencomine.com
5-9: Electra Mining Africa, Johannesburg, South Africa. www.electramining.co.za 6-9: Katowice Mining Expo, Katowice, Poland. https://expo-katowice.com 12-15: Exposibram, Belo Horizonte, Brazil. https://ibram.org.br
Rajant 47 www.rajant.com/im-mining
Jennmar 39 www.jennmar.com
Redpath Deilmann 86 www.redpathdeilmann.com
AKW 28 www.akwauv.com
IMARC 2022 53 www.imarcglobal.com

Italy Claudio Sanfilippo or
Tel: +56 2 2757 editec@editec.cl4200
Beumer Group 73 www.beumer.com
Classified
Tel: +91 74064 devksingh2005@gmail.com64314
Loadrite 69 www.goloadrite.com
Emma Smith or Lynne Lane
MMD 7, 43 www.mmdsizers.com/surge-loaderwww.mmdsizers.com/bos
Universal Field Robots 72 www.universalfieldrobots.com.au ValvTechnologies 93 www.valv.com
Rancati Advertising
Japan Advertising Communications, Inc
Matrix Design Group 32 www.matrixteam.com
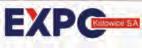
September 2022
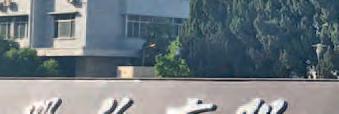
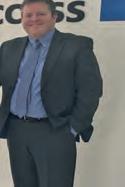


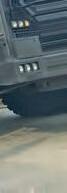








In 2019, Editorial Director Paul Moore went on a threeweek trip to China from Shenyang in the North to Liuzhou in the South to gain exclusive insight into how the country’s mining equipment & technology suppliers have established themselves at home and abroad. He visited six companies, interviewing management, touring facilities and getting up close and personal with machines and solutions. He also engaged with two other majors at industry events. Seven of the companies have already been featured in IM articles, with one to come!
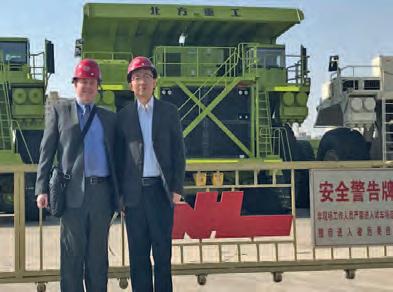
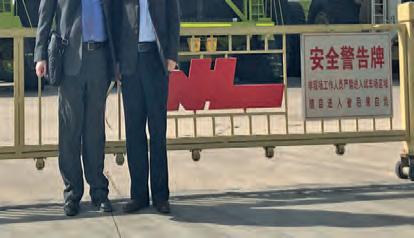
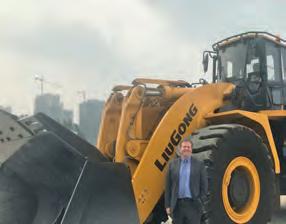
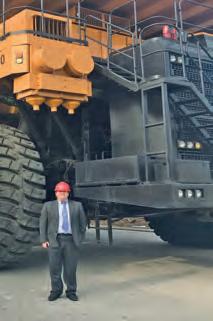


14-15: Lithium Battery and Energy Metals Conference 2022, Perth, Australia. 14-17:events/lithiumwww.ausimm.com/conferences-andMining Indonesia, Jakarta, Indonesia. 15-17:www.mining-indonesia.com SDIMI (Sustainable Development in the Minerals Industry) 2022, Windhoek, Namibia. www.saimm.co.za/ 18-20:10th-international-conferenceevents/upcoming-events/sdimi-2022-saimmCoaltrans Asia, Bali, Indonesia. 18-21:www.coaltrans.com Maintenance, Engineering & Reliability/ Mine Operators MEMO 2022, Sudbury, Canada. http://memo2022.cim.org/home
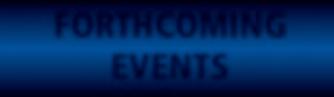
FORTHCOMING EVENTS TAILINGS FEBRUARY 2018 www.im-mining.com ANALYSIS & SORTING MINING BATTERYSOFTWAREUNDERGROUNDMINERALEXPLORATIONBATTERYUNDERGROUNDMINERALEXPLORATION YUMARRandHIGHTECHNOLOGYCONVEYINGPROFILE:FAMUR IM FEB18NEW_proof 08/08/2018 12:37 SEPTEMBER 2018 www.im-mining.com WEAR MECHANISEDPARTS COAL SHAFT EuroChemOPERATIONMANAGEMENTREMOTESINKINGFACILITIESFOCUS:Usolskiy IM GET To subscribe to INTERNATIONAL MINING please go to www.im-mining.com and complete the subscription form which can be found after clicking ‘Get IM Free’ in the menu bar IM FREE IM has been building its presence on key social media channels LinkedIn and Twitter, with over 90,000 followers combined on these platforms. Featuring exclusives and monthly magazine articles, this is one of a number of ways we ensure your company gets its marketing messages out to a global audience. To get more eyes on your company’s advertising, contact Phil Playle (phil@im-mining.com) More channels more exposure
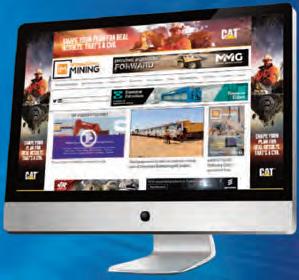

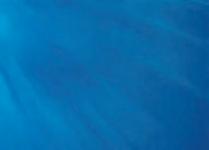
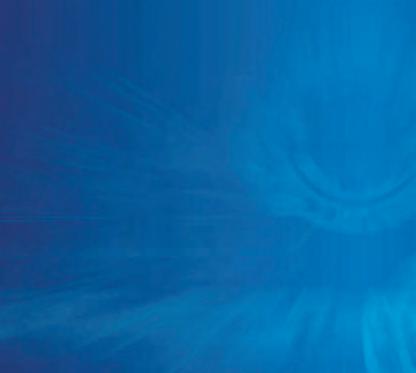
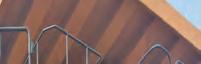










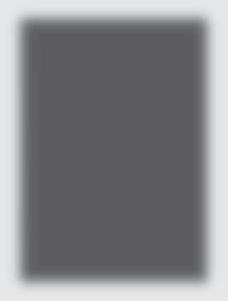












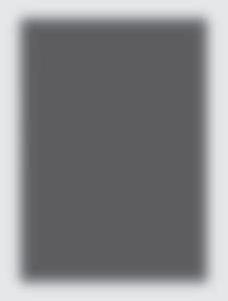


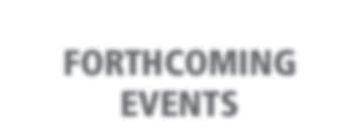
His visitsXCMGincluded: JCHX MiningLiuGongManagement Inner Mongolia North Hauler Taiyuan Heavy Industry CITICXEMCHIC Sany Heavy Industry


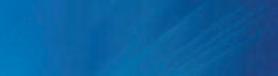
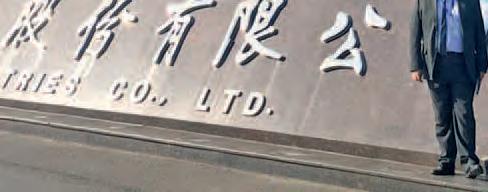
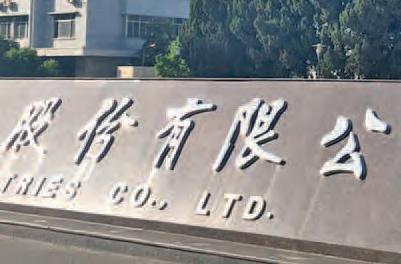
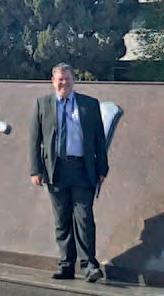
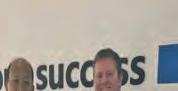
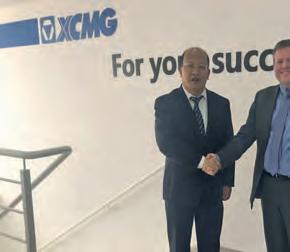









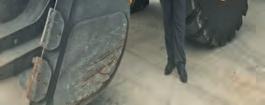




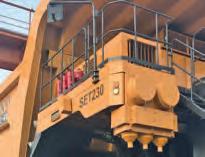
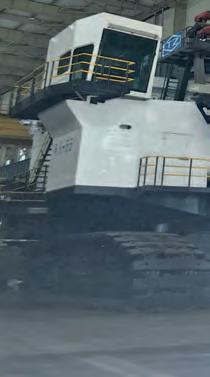












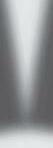




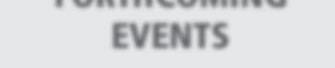
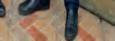
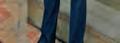
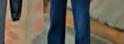
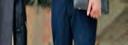
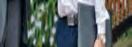
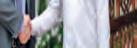


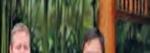


Our mission is to bring autonomy to any fleet, even in the harshest environments. Your existing fleet, but driverless. As part of the AB Dynamics Group, with decades of experience in vehicle autonomy and delivering solutions to the world’s leading vehicle manufacturers, we’ve learnt from the best. abdsolutions.com Enhanced Safety Retrofit Autonomy Task Automation Reduced Emissions Increased Productivity Optimised Costs
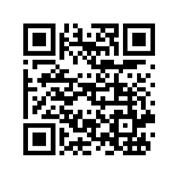

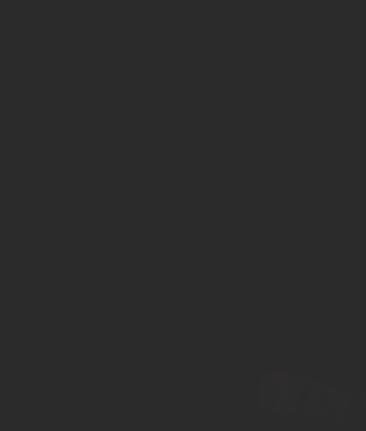

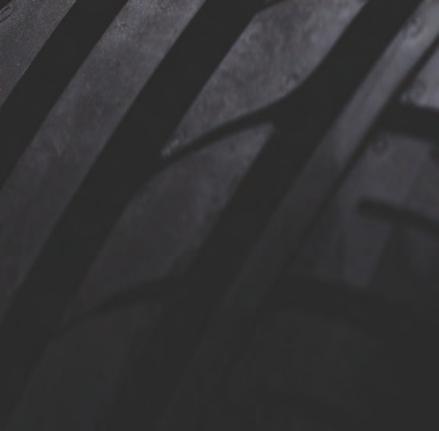
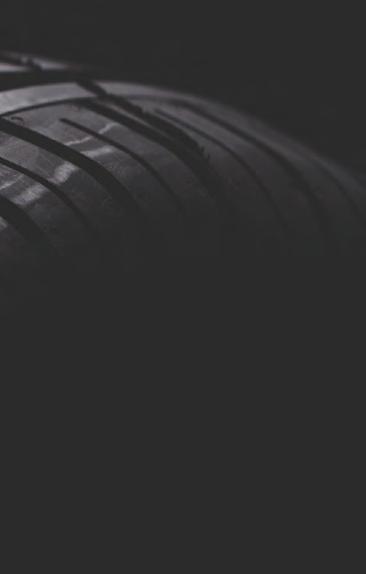
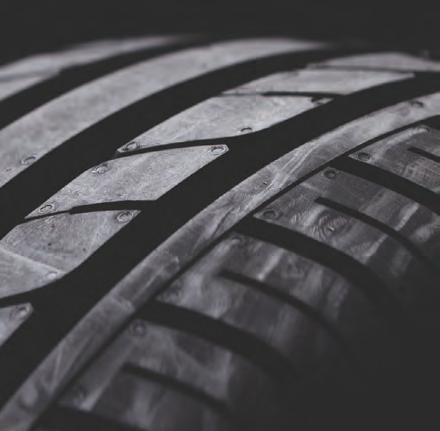
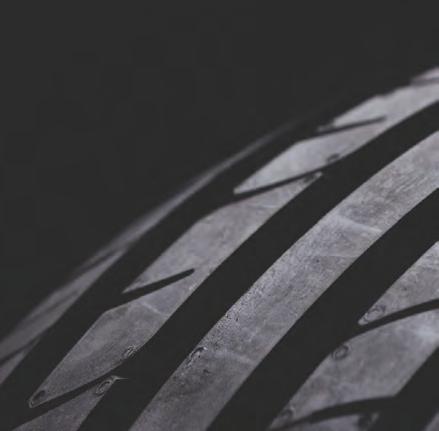
