
14 minute read
ACTUALIDAD INDUSTRIA AUXILIAR
Programa de mantenimiento programado
Seis de cada diez averías en las almazaras se podrían evitar con el servicio de mantenimiento programado de Pieralisi
Cuando una almazara se para en la campaña de aceituna por una avería, el contador que marca la pérdida de ingresos comienza a avanzar. Tener que parar uno o varios días de molturar puede suponer un auténtico agujero financiero para la fábrica que podría haberse evitado en el 60% de los casos sólo con previsión. Un informe de Pieralisi basado en la experiencia de más de medio siglo de esta multinacional líder en la producción de maquinaria de almazara determina que seis de cada diez averías de la maquinaria con la que se produce el aceite de oliva no se producirían si antes se hubiera una revisión general de la fábrica. Hace tres años que Pieralisi lanzó su programa de mantenimiento programado. Se trata de una campaña que incentiva a sus clientes a realizar las revisiones de almazaras y cooperativas con antelación para que, una vez en campaña, “no tengan que verle la cara a nuestros técnicos”. Lo afirma Antonio Carazo Lanagrán, responsable de Producto de Pieralisi para España y Portugal, quien asegura que el mantenimiento programado es ya un sistema arraigado en las principales zonas productoras de aceite de oliva de la Península Ibérica. De hecho, indica, ya son pocas las citas disponibles para las almazaras hasta que comience la campaña de recogida de aceituna 2022-2023. El mantenimiento programado incorpora un descuento económico del 20% al cliente, lo cual lo hace más atractivo a la hora de contratarlo. Se intentan evitar de este modo los cuellos de botella que sucedían de forma habitual en campañas anteriores cuando, tras el verano, la gran mayoría de las almazaras demandaba una puesta a punto de sus instalaciones.
LOS MEJORES EN REPARACIÓN Pero, ¿qué sucede con las fábricas que no han contratado un servicio de mantenimiento programado? Pieralisi también cuenta con una línea de servicio posventa destinada a ofrecer a sus clientes la atención más eficaz y rápida y evitar a toda costa que la almazara pierda tiempo debido a una avería. El servicio funciona los siete días de la semana hasta las diez de la noche y desde las siete de la mañana. Lo componen un equipo humano formado por treinta profesionales especializados repartidos estratégicamente por todo el territorio peninsular, unas importantes instalaciones -con una central en Mengíbar para atender a Andalucía, Castilla La Mancha, Extremadura y Portugal y una sucursal en Zaragoza destinada el resto de España- y una maquinaria de la mayor calidad para realizar estas reparaciones. Tal es la eficacia de este sistema, que, según indica Antonio Carazo, el 90% de las averías se logran solventar en una primera visita. No en vano, una vez que se da la voz de alarma por parte de la almazara, un coordinador se encarga de detectar con los afectados cuál es el problema con el fin de enviar el personal más adecuado y el material necesario a la fábrica.
REPARACIÓN Y SISTEMA DE CAMBIO DEL SINFÍN Una de las incidencias más comunes en las fábricas de aceite de oliva está relacionada con dos piezas fundamentales en la molturación de aceite de oliva: el sinfín y el reductor. Tras moler la aceituna y separar su aceite a través de la fuerza centrífuga del decanter, el sinfín es el encargado de conducir al exterior el orujo, o lo que es lo mismo, la pulpa, la piel y el hueso de la aceituna una vez desprovisto de su aceite y de su agua o alpechín. La avería del sinfín supone tener que parar toda la producción, algo que el sistema Pieralisi contrarresta con una atención rápida y un importante volumen de recambios, lo que conocen como su sistema de cambio. Esto le permite hacer la sustitución inmediata del sinfín a sus clientes una vez que se detecta un fallo. Se trata de no perder tiempo mientras se arregla el gran tornillo y se facilita que la almazara siga produciendo al mismo tiempo que su pieza original se repara en los talleres de Pieralisi.
FASES DE REPARACIÓN Esta calidad se da en cada una de las fases de las trece en total que suponen la revisión y reparación de un sinfín. Tras la recepción de la pieza, lo primero que se hace es desmontar y lavar de forma exhaustiva y con productos no agresivos. Lo segundo que se realiza es el corte de la hélice. En Pieralisi lo realizan de forma oblicua, lo que facilita una mejor soldadura después. La maquinaria para realizar este corte oblicuo normalmente no está disponible en otros talleres, por su complejidad y coste. Una vez hecho el corte, se puntea la pletina y se revisan las chapas del difusor y del scorner, un deflector longitudinal que impide la salida del aceite ya separado junto con el orujo. Después, se procede al soldado de la hélice y al torneado, con el que se eliminan los restos de soldadura. Otra de las fases cruciales es la recarga del rivetto con tungsteno, un metal que se aplica a través de robots. De este modo se garantiza un acabado homogéneo y deslizante, algo que no siempre sucede si se aplica este material a mano. Así, el sinfín podrá girar al mayor número de revoluciones por minuto sin sufrir, lo que también se logra con un buen calibrado y equilibrado, una de las fases finales del proceso de reparación del sinfín.
En la planta de Vendinha, en Évora
Centrifugación Alemana construye la almazara más grande del mundo para la familia De Prado

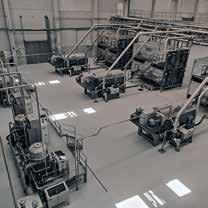
Centrifugación Alemana, en su apuesta por la tecnología en el marco de la eficiencia en el consumo y la máxima calidad en la producción, asumió el gran reto que le proponía la familia De Prado: construir la almazara más grande del mundo -o una de las más grandes en base al volumen de toneladas de aceitunas a procesar diariamente para la extracción de aceite. Con más de 20.000 ha. de olivares superintensivos para procesar en un tiempo récord de 45- 50 días, el ambicioso proyecto de la familia De Prado en Portugal pretende transformar los frutos en su momento ideal de maduración para obtener un aceite de la más alta calidad, preservando así la múltiples beneficios del preciado oro líquido, realizándose este proceso en menos de seis horas desde su recolección. En la planta de Vendinha, en Évora, se combinan varios principios fundamentales de la industria agroalimentaria, apoyándose en la tecnología de la empresa Centrifugación Alemana –proveedor de líneas de extracción de alta capacidad y pérdidas de grasa imbatibles– para llevar a cabo el proceso de extracción del aceite. Una fase, la fase de extracción, donde es fundamental que cada uno de los elementos instalados cumpla con el nivel de exigencia requerido. La instalación de los equipos prevista por los técnicos de ambas empresas - con la coordinación de Engenharia Iradu - se completó en tiempo récord: los movimientos de tierra para las obras civiles comenzaron en abril de 2021 y solo siete meses después, el 11 de noviembre de 2021. En 2021, todas las líneas de producción ya estaban en funcionamiento y funcionando de manera óptima. En total, se instalaron cinco líneas de procesamiento, cada una compuesta por una batería de molinos con asistencia electrónica para optimizar el consumo de energía con respecto a la producción sin reducir la capacidad requerida. El transporte se realiza mediante bombas con la ayuda de válvulas automáticas, que son determinantes en las exigencias del proceso desde la recepción de la aceituna hasta la molturación. Una variante muy influyente en la calidad del producto es la instalación de un Sistema frigorífico para realizar una primera extracción en frío -aún con las altas temperaturas de la fruta en aceite al inicio de la campaña- mediante el aislamiento térmico de las termomezcladoras, evitando la condensación no deseada y preservando el producto de temperaturas inadecuadas para una calidad superior. Para la separación de la pulpa se instalaron decantadores con una capacidad de 500 t./día para igualar los tiempos de trabajo y ajustar perfectamente los tiempos de dilaceración y micelarización en el proceso. Finalmente, para una eficaz supresión de pequeñas partículas sólidas en suspensión mezcladas con el aceite, que producirían mal sabor en la cata organoléptica de los aceites frescos, se instaló una batería de centrífugas de aspiración centrípeta que también relaciona el proceso tanto en volumen de aceite y eficiencia, limpiando el producto a niveles casi absolutos. Todo este sistema está perfectamente interconectado a través de un software que permite controlar cualquier variable deseada, tanto a nivel de post-proceso como de inicio, integrando el sistema de molienda y extracción con el resto del proceso (laboratorio, calidad, trazabilidad, logística y gestión) por un sistema MES (Manufacturing Execution System). El nivel de programación, uno de los más complejos instalados en un molino, garantiza la versatilidad necesaria para permitir la eficiencia y excelencia requeridas.
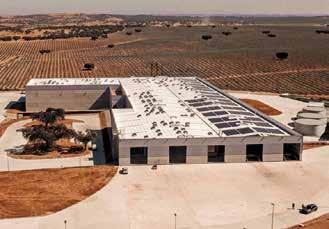
Networking e intercambio de experiencias
Con una participación de más de 300 profesionales oleícolas de toda España y Portugal, el XVI Encuentro de Maestros y Responsables de Almazara de GEA, se celebró en el Auditorio Guadalquivir del Centro de Convenciones de Ifeja (Jaén), unió la formación de primer nivel con el networking y el intercambio de experiencias entre los maestros y responsables de almazara. Los temas principales que se abordaron en esta edición fueron la digitalización y automatización de almazaras, la gestión del alpeorujo y la apuesta por la sostenibilidad de las plantas de producción de aceite de oliva. Esta edición del Encuentro de Maestros y Responsables de Almazara de GEA fue inaugurada por el presidente de la Diputación Provincial de Jaén, Francisco Reyes; el delegado del Gobierno de la Junta de Andalucía en Jaén, Jesús Estrella; la segunda teniente de alcalde del Ayuntamiento de Jaén, África Colomo, y el presidente de GEA Iberia, Álvaro Martínez. Tras la inauguración oficial, se desarrolló una ponencia técnica en la que se comparó las dos y tres fases y su aplicación al decánter, a cargo de David González, responsable de Servicio Técnico del Centro de Excelencia para Aceite de Oliva de GEA, y Pedro Joaquín Collado, coordinador de Servicio Técnico del CEAO de GEA. A continuación, fue el turno de la mesa redonda “Hacia la Almazara 5.0: Biodiversidad y Sostenibilidad”, en la que intervinieron Raúl Verano, responsable de aplicaciones especiales del Grupo Agroisa; Rafael López Uceda, director del Área de Ingeniería de Iada Ingenieros; Virgilio Gámez, gerente de Aceites Guadalentín; Joaquín Morillo, director de Operaciones de Grupo Oleícola Jaén, y Javier Martínez, gerente de Bioento Farm, con el consultor Juan Vilar como moderador. También se expuso el caso de éxito de GEA y Oleícola Jaén, centrado en el proyecto de nueva almazara de la firma baezana con una firme apuesta por la eficiencia, sostenibilidad, digitalización y automatización. Participaron Remigio Morillo, director de Calidad y Compras de Grupo Oleícola Jaén; Antonio López, responsable de Automatización y Digitalización del Centro de Excelencia para Aceite de Oliva de GEA y Francisco Javier Reche, director comercial de zona de GEA, con Natalia Sánchez, responsable de Marketing de GEA Iberia, como moderadora. La ponencia final fue ofrecida por la nadadora Gemma Mengual, titulada “Una vida dedicada al agua”, donde explicó a los asistentes el proceso de aprendizaje que ha experimentado desde sus inicios en un deporte tan exigente como la natación sincronizada y la importancia de soñar para llegar a ser algo importante.
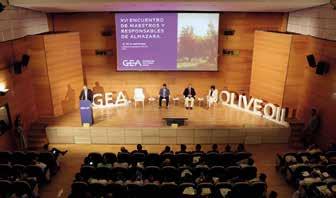
Software de Tupl Agro
Nuevo servicio de alertas personalizadas de Medifer
La empresa alicantina de fabricación y distribución de fertilizantes en el mediterráneo, Medifer, apuesta este año por la digitalización del campo. El objetivo: promover una agricultura más eficiente y sostenible e incrementar la rentabilidad de las explotaciones de sus agricultores. Para ello, pone a disposición de su red de distribuidores Agro Advisor, un servicio diseñado por la empresa malagueña Tupl Agro que permite enviar a los agricultores alertas y recomendaciones útiles, personalizadas y concretas en el momento preciso a través de WhatsApp. El software de Tupl Agro – que en esta primera fase está dirigido a agricultores de olivar, cereal y cítricos- analiza la finca del agricultor 24/7, 365 días al año y facilita alertas sobre poda, posibles plagas, densidad de cultivo, humedad, condiciones meteorológicas adversas, etc. También envía recomendaciones agronómicas puntuales y periódicas, entre las que destacamos los mapas de riesgo, mapas agronómicos, mapas de humedad, recordatorios de analíticas de suelo o foliares, alertas de abonado, etc. Además, mantiene a los agricultores informados de las últimas novedades de su sector. Antonio Manuel Adrián, responsable de la empresa malagueña, asegura que ya podemos hablar de Agricultura 5.0: “La principal barrera que observamos es la necesidad de interpretar y comunicar la información relevante al agricultor de una manera eficaz y sencilla, y es justamente la que salva definitivamente Agro Advisor a través de la implementación de su servicio de WhatsApp”. Por su parte, Carlos Cerezo, Director General de Medifer, afirma: “Después de dos años trabajando en este proyecto, es un placer poderlo ver en marcha. Agro Advisor es una apuesta por la transformación digital y es una alianza con la que ganamos todos. Los agricultores, porque reciben la información que necesitan para hacer sus negocios más rentables, eficientes y sostenibles; los distribuidores, porque obtienen una herramienta con la que cuidan y dan valor agregado a sus clientes; y nosotros, porque avanzamos en nuestro compromiso por la innovación, las nuevas tecnologías y la sostenibilidad”.
Pallet Jaén incorpora su primer megatrailer en sus nuevas instalaciones
Palletways Iberia crece en el sur de la península ibérica
Palletways Iberia, la red de distribución exprés de mercancía paletizada, perteneciente a Imperial Logistics (Imperial), ha ampliado sus servicios en Jaén, gracias al miembro de la Red Ibérica de Palletways, Pallet Jaén. La plataforma, que está obteniendo unos excelentes resultados en las instalaciones de Bailén, incorpora su primer megatrailer para responder a la gran demanda de la zona andaluza. El miembro Pallet Jaén crece a buen ritmo. Desde la apertura de su nueva nave en Bailén, en noviembre de 2021, la plataforma ha ido agregando mejoras operativas que le han permitido captar nuevos clientes y sumar más volumen. Por eso, recientemente ha incorporado a su flota su primer vehículo de alta capacidad que facilitará el movimiento de mercancía paletizada hacia el Hub Central. Pallet Jaén ha puesto en marcha este megatrailer debido al aumento del volumen de las rutas nacionales. Con el fin de ofrecer una mejor cobertura, realizará la ruta Jaén-Alcalá de Henares. Esta nueva incorporación, supondrá un gran beneficio tanto para la delegación, al mejorar los costes y los tránsitos, como para el Hub Central, al atenderlo de forma más eficiente. “El positivo resultado del traslado de las instalaciones a Bailén, estamos empezando a valorarlo ahora, y continuaremos observando este crecimiento en el futuro, ya que la mayor capacidad de rutas que supone estar ubicados en Bailén nos acerca a clientes con perfiles de volúmenes mucho más altos, a los cuales no podríamos haber dado el servicio desde Jaén”, explica el gerente de Pallet Jaén,
Jesús Mulero.
Por su parte, la nave destaca por su amplitud, lo que le permitirá en un futuro acoger más vehículos de alta capacidad. Estos camiones, que se caracterizan por reducir las emisiones de CO2, son parte del compromiso tanto de Palletways como de sus miembros por adherir medidas sostenibles. De hecho, hace tres años en Pallet Jaén se sustituyeron las carretillas elevadoras de gasoil por las de gas licuado de petróleo (GLP), más respetuoso con el medio ambiente.
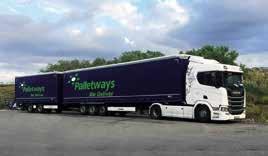
Cuenta con la certificación Frustration Free Packaging (FFP) de Amazon
Nueva solución de packaging sostenible antirrotura para el envío de líquidos por e-commerce
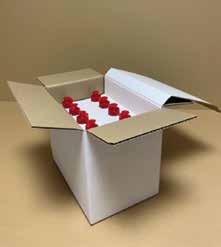
El flujo logístico del canal online es muy diferente al canal de distribución tradicional. El paquete puede manipularse hasta 20 veces más durante los envíos por e-commerce, por lo que el diseño de embalajes que faciliten su manipulación en las distintas fases de la cadena logística y protejan el producto para que llegue a su destino en perfectas condiciones constituye un reto en sí mismo para el sector del packaging. Para dar respuesta a esta realidad, Hinojosa ha creado y patentado un nuevo sistema de packaging diseñado para solucionar las incidencias que se producen actualmente en el transporte de botellas de contenido líquido enviadas por e-commerce. Se trata de un embalaje pionero en el sector, completamente sostenible, monomaterial y 100% reciclable. La solución está especialmente pensada para productos de limpieza como detergentes o lavavajillas, que por sus características pueden ser difíciles de transportar sin que se produzcan roturas, deslizamientos o derrame del contenido y para las que, actualmente, se usan principalmente envoltorios de plástico desechable como embalaje. Aún así, puede adaptarse para el transporte de cualquier tipo de botella contenedora de líquido con tapón.
UNA SOLUCIÓN BASADA EN DOS PIEZAS El nuevo packaging, adaptable a cualquier tipo de botella y tapón, se basa en dos piezas que constan de una caja exterior (tipo B1 o americana) con un separador obtenido a partir de las aletas inferiores y un insert aparte especialmente diseñado para inmovilizar las botellas y proteger los tapones. Además, para eliminar cualquier riesgo de daño del producto durante el transporte y garantizar que llega en perfectas condiciones, el embalaje cuenta con dos espacios o compartimentos donde las botellas se agrupan y se sujetan en la parte superior a otra segunda pieza con orificios troquelados que, a su vez, genera una cámara de protección de los tapones y las botellas.