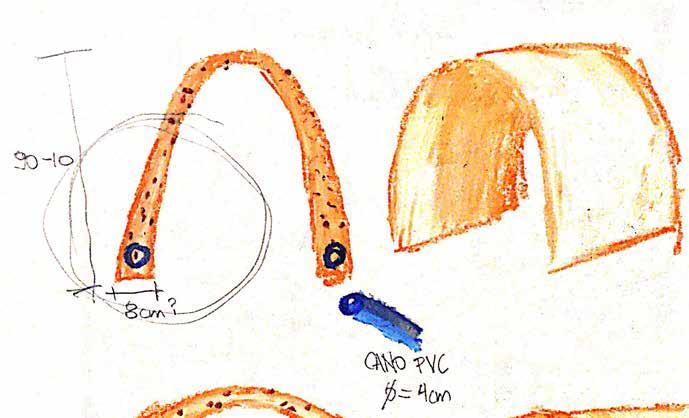
19 minute read
PROJETO
Entendidas quais poderiam ser as potencialidades atingidas pelas peças projetadas, a concepção partiu do princípio que os componentes deveriam ser os mais leves possíveis de acordo com a sua função. Ainda, as peças deveriam funcionar a partir de esforços de compressão, eliminando as telas e armações metálicas e simplificando suas manufaturas. Para isso, foi adotada a espessura mínima de 4cm para as peças em concreto reciclado, além de uma geometria que beneficie o desempenho estrutural desejado. Para os usos propostos as peças poderiam ser utilizadas como bancos, apoios, vasos, lixeiras e até bebedouros, mas principalmente possibilitando à população a sua utilização de formas não previstas pelo projetista.
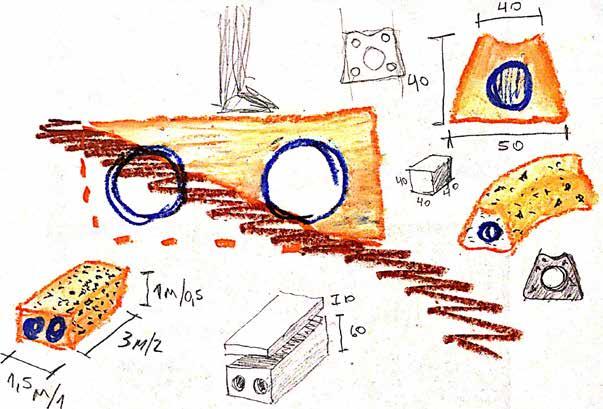
Advertisement
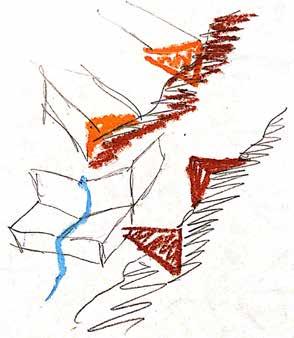
Imagem 52:
Croquis em giz pastel de intenções de peças e partidos de design.
78
Imagem 53 a 55:
Croquis dos três tipos de peça pensados, com dimensões e cálculo de pesos iniciais. 53
54
55
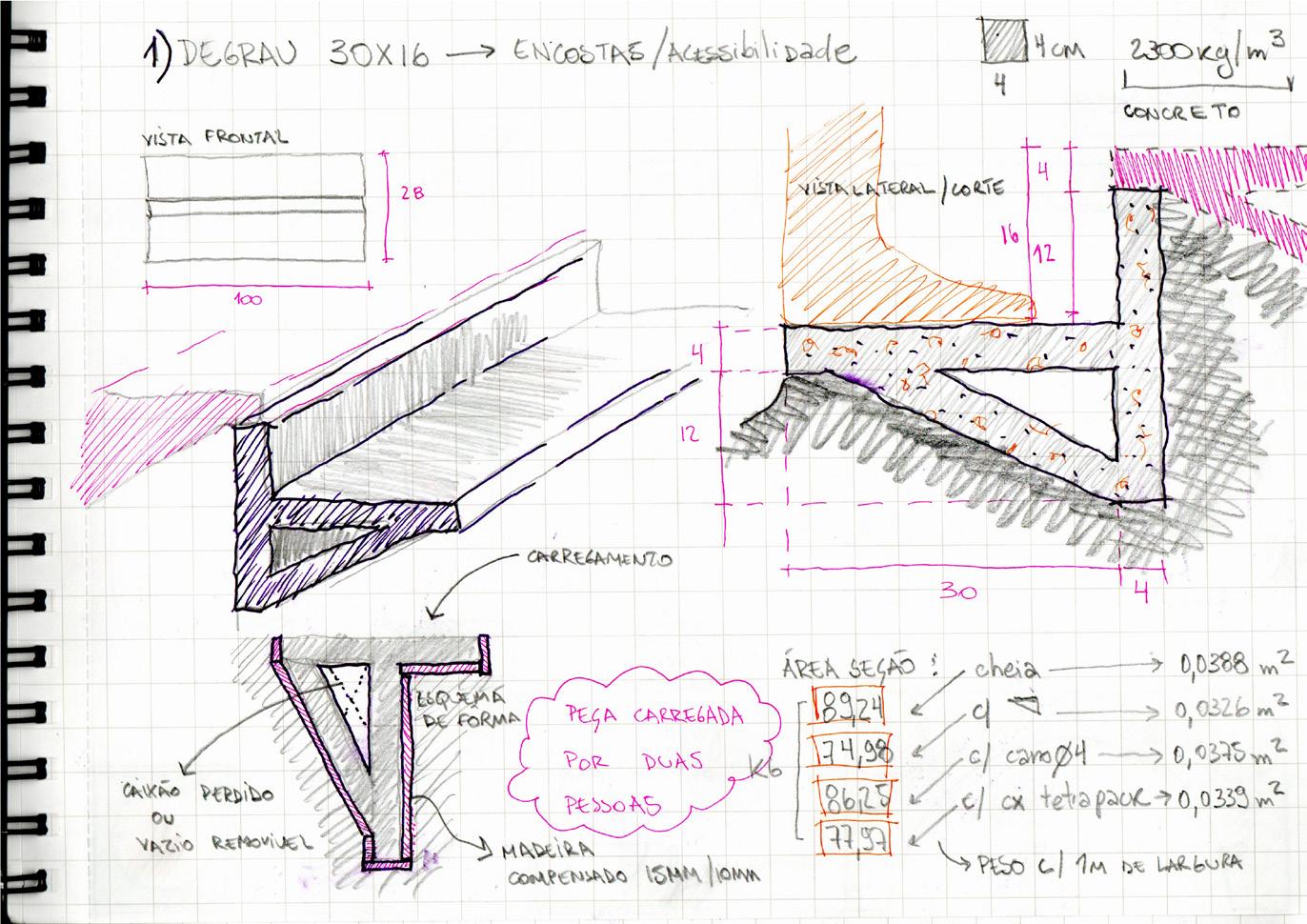
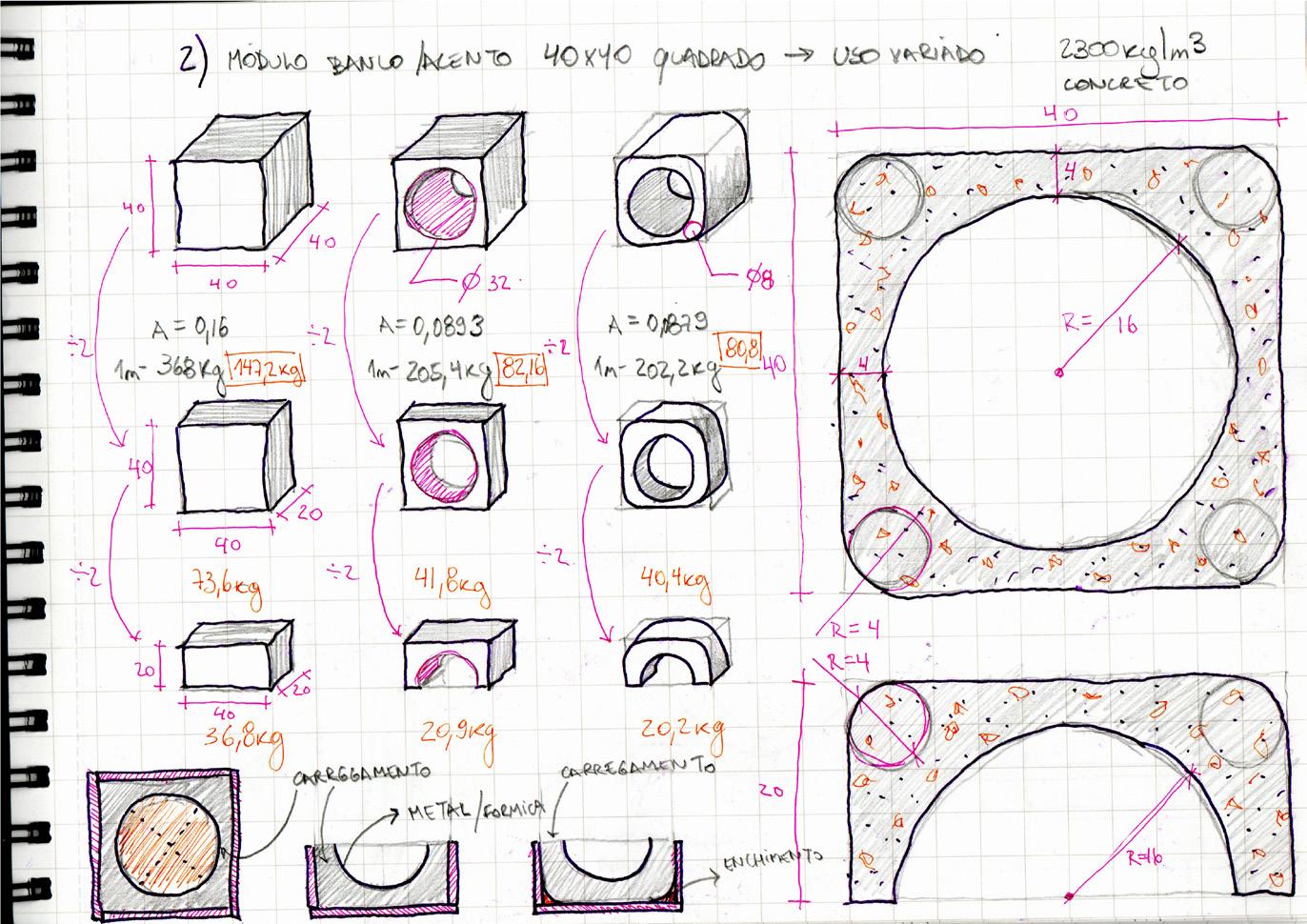
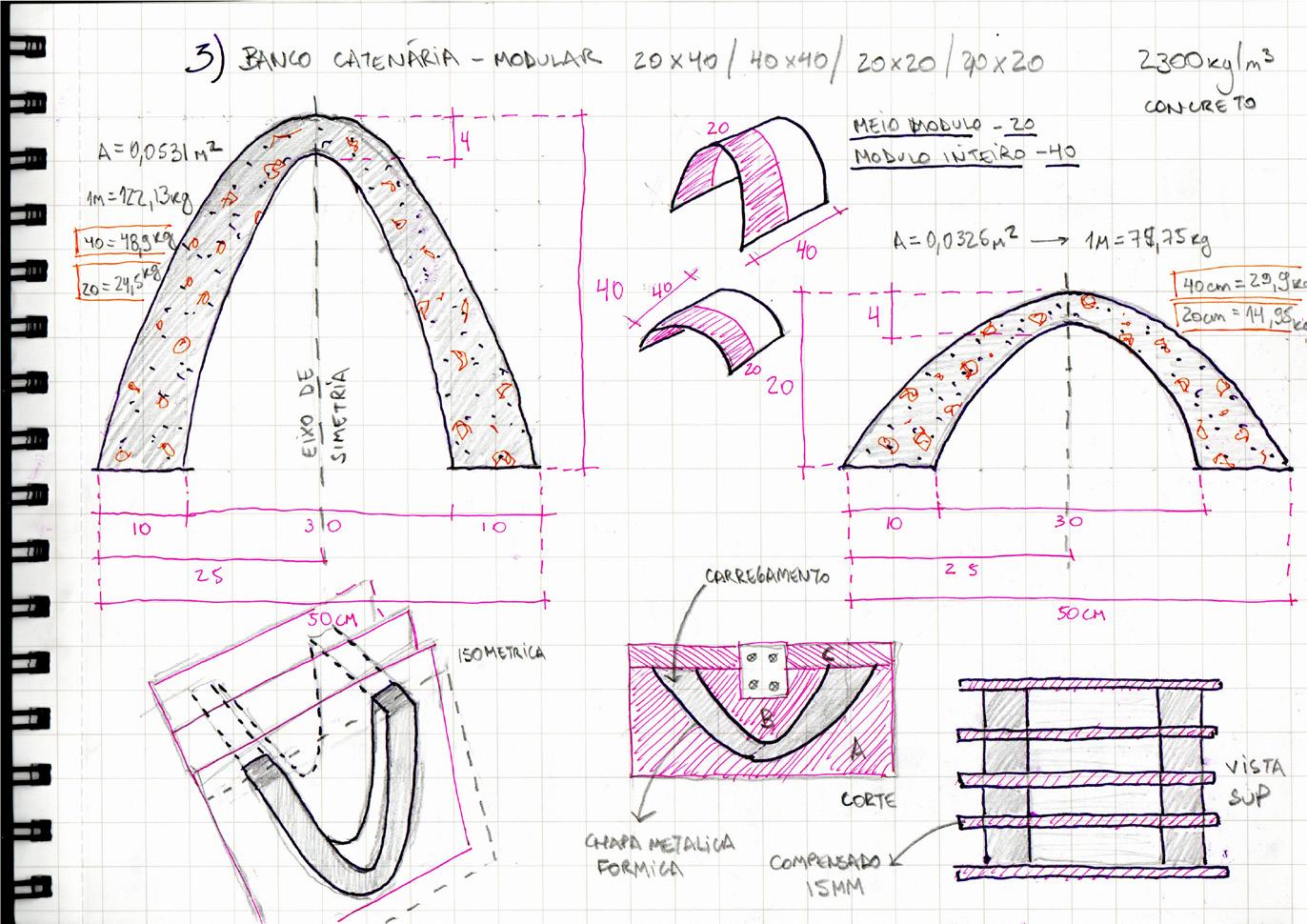
79
Tendo também como premissa a modularidade das peças, pensou-se em aproveitar das diferentes alturas de parábolas e geometrias simples facilmente modularizadas, como cubos e círculos. As dimensões pensadas foram as de 20cm e 40cm, para altura de apoios, e 1m para a largura de escadarias. Devido ao limite de tempo para o trabalho, decidiu-se pelo aprofundamento do projeto de três tipos de peças: um degrau e dois conjuntos de bancos.
O degrau foi desenhado a partir da geometria necessária para que a peça não deslize ao ser implantada em um arrimo improvisado, alcançando o peso de 80kg por peça. Para os bancos, pensou-se em peças mais leves que permitam a ampla apropriação de sua geometria. Balizando pelas dimensões de 20x40cm ou 40x40cm, o resultado foi de peças em formas de cubo, paralelepípedo e catenária (abóbada).
Assim que foram decididas as formas das peças, os esforços moveram-se para o campo prático, para a preparação das matrizes e matéria prima. Para os moldes das peças em concreto foram construídas na Fábrica da Escola da Cidade (FAEH) seis fôrmas, duas para cada peça levada a diante para a prototipagem. O principal desafio para o desenvolvimento dos moldes era encontrar um material resistente o bastante para aguentar a fundição mais de uma vez, porém maleável o suficiente para alcançar as curvas desejadas. Para isso, foram utilizados pedaços de laminado melamínico de 2mm1, que poderia ser facilmente incorporado nas fôrmas de madeira. Para as partes planas do molde, chapas de compensado foram cortadas e encapadas com laminado plástico autoadesivo2, nas faces internas da matriz. Para a fixação das peças dos moldes entre si foram utilizados parafusos e barras roscadas com porcas borboletas, de acordo com o encaixe e desforma pensada. Ainda, para os acabamentos arredondados nas quinas das peças cúbicas e em forma de paralelepípedo, utilizou-se de perfis de PVC para acabamento de tetos e paredes.
Listados todos os materiais utilizados para a confecção dos moldes para as peças, vale-se comentar de que os elementos mais utilizados são fruto do reuso de materiais deixados na FAEH como o compensado e o laminado melamínico, sendo um fator para a confecção das peças a facilidade para se encontrar materiais para construir seus moldes.
Já para a matéria prima, desde a conclusão do primeiro processo prático – em agosto de 2019 – foi possível armazenar para essa segunda empreitada uma serie de RCDs coletados de forma espontânea, em caçambas no bairro da Barra Funda,
1. Material que se tornou popular a partir do produto da marca Fórmica. 2. Material que se tornou popular a partir do produzido pela marca Contact.
80
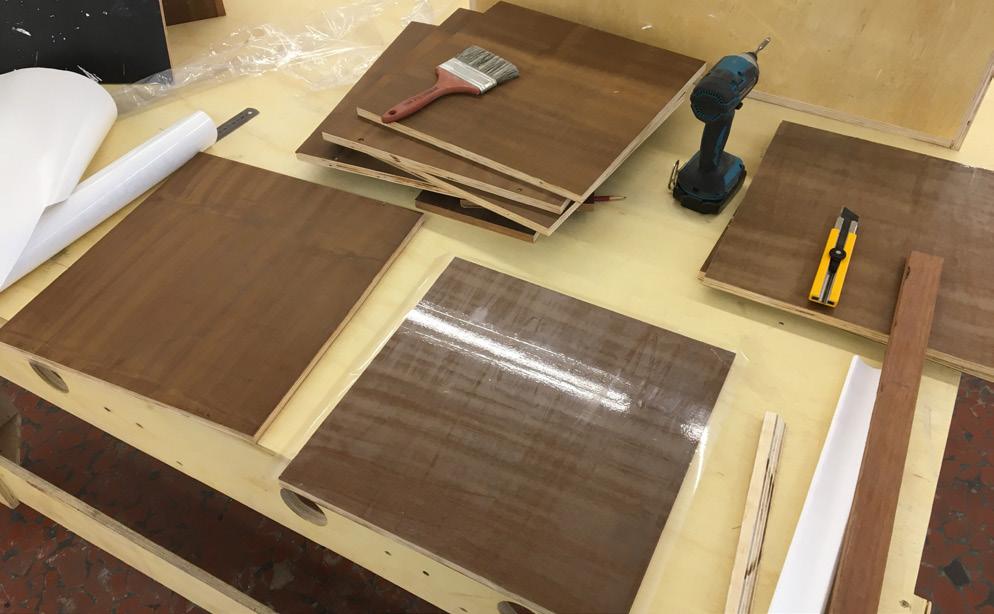
56
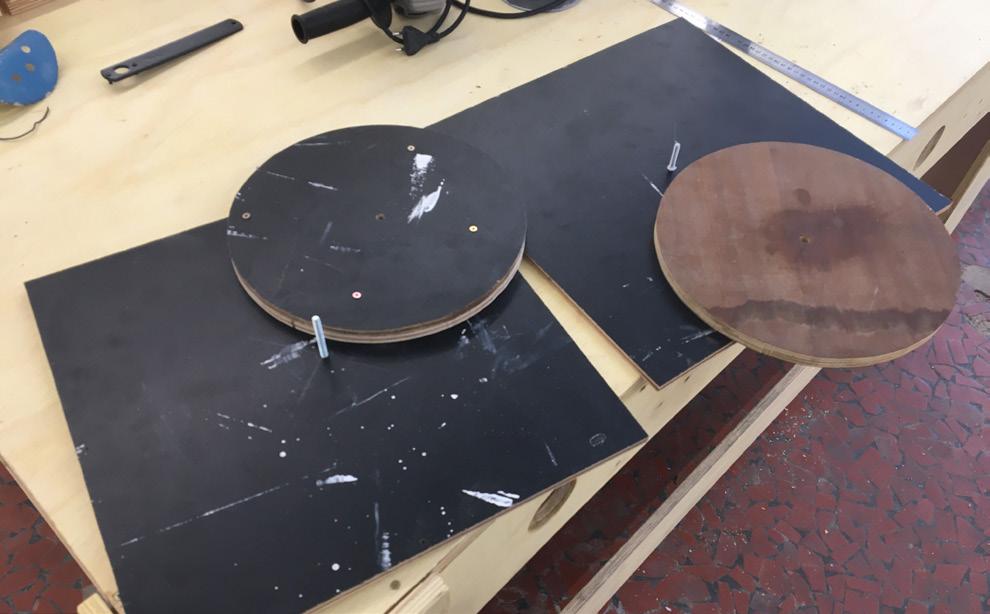
58 57
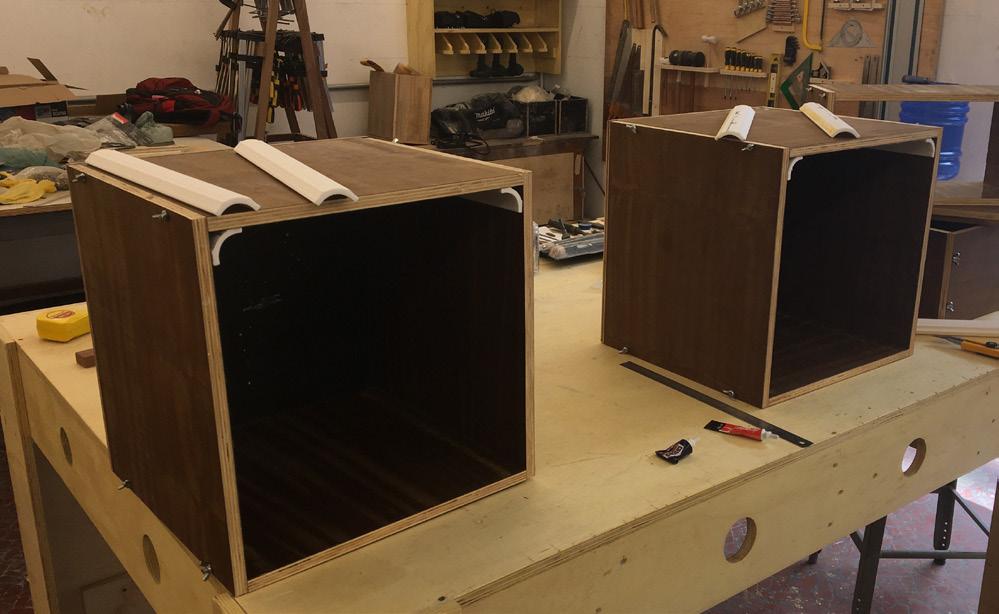
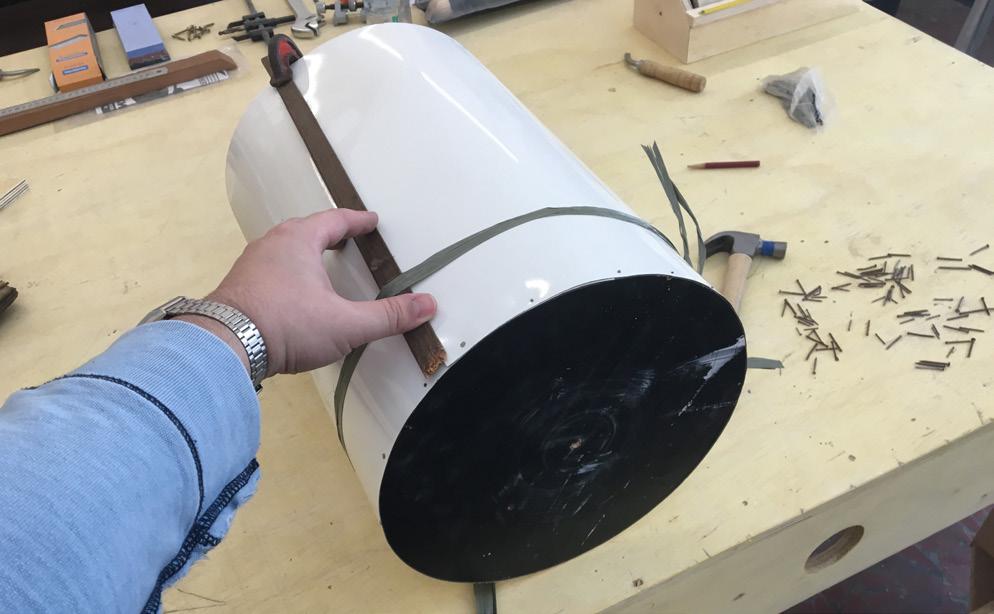
59
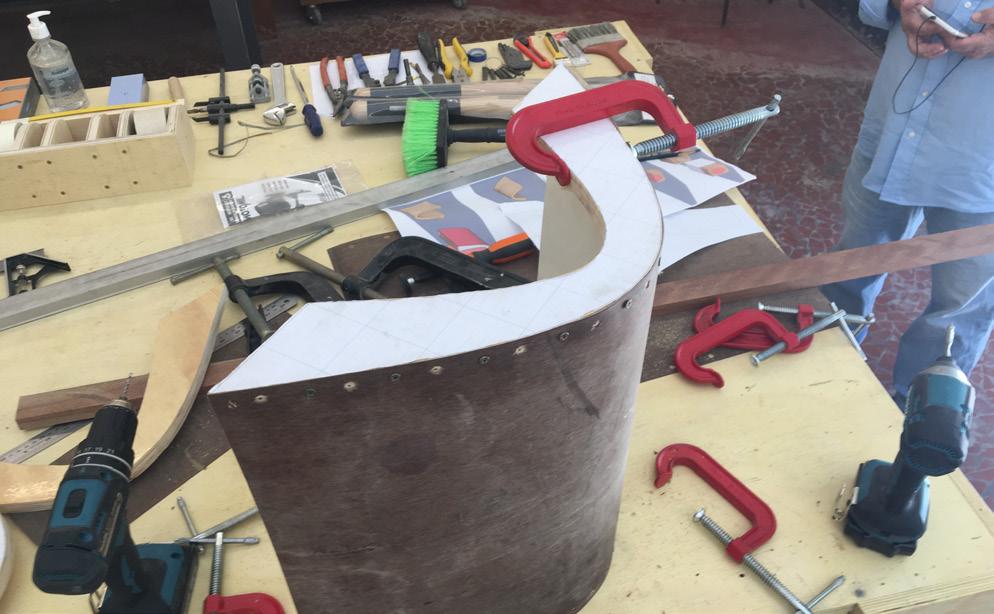
60 61
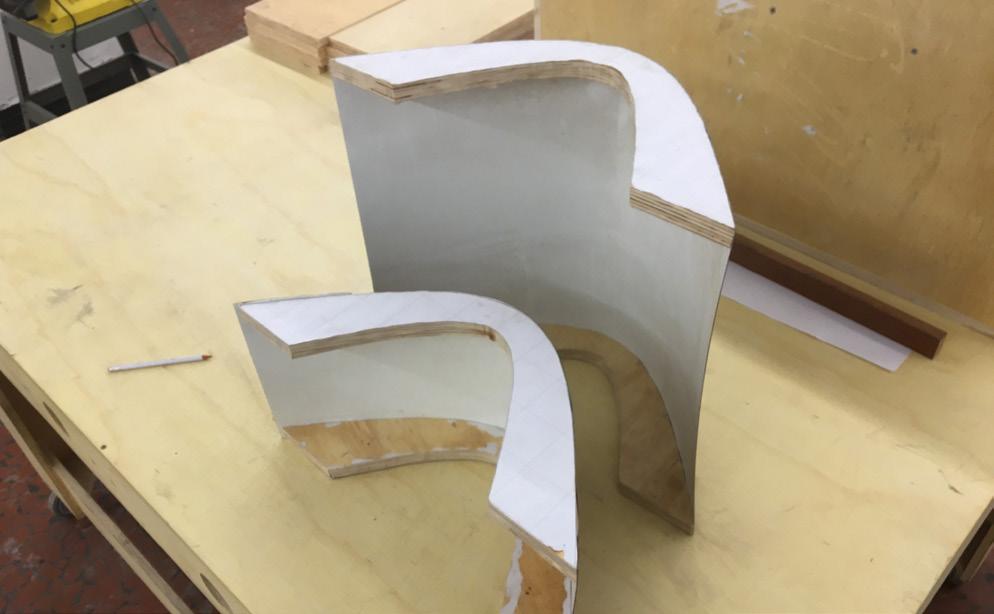
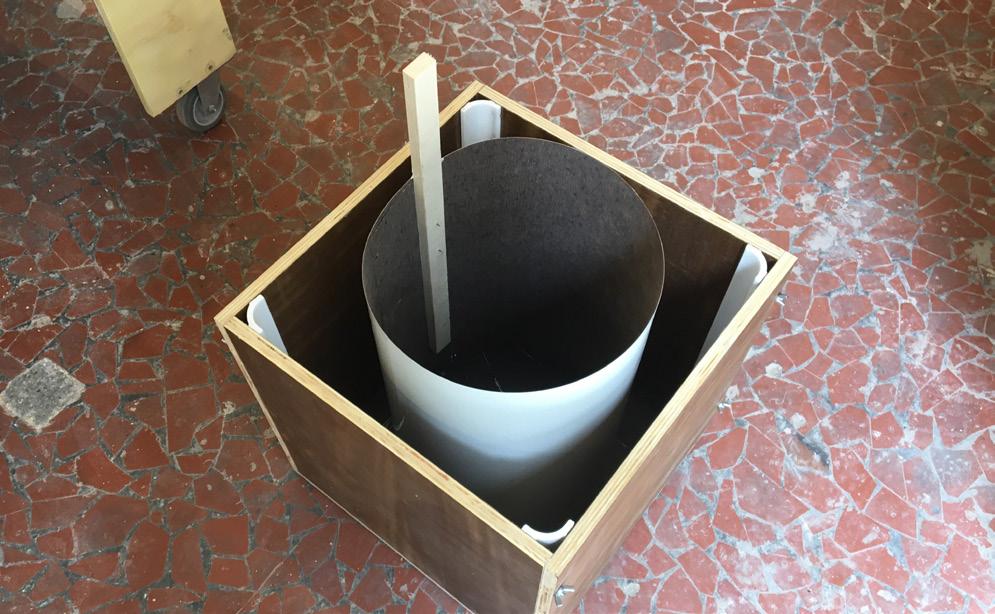
62 63
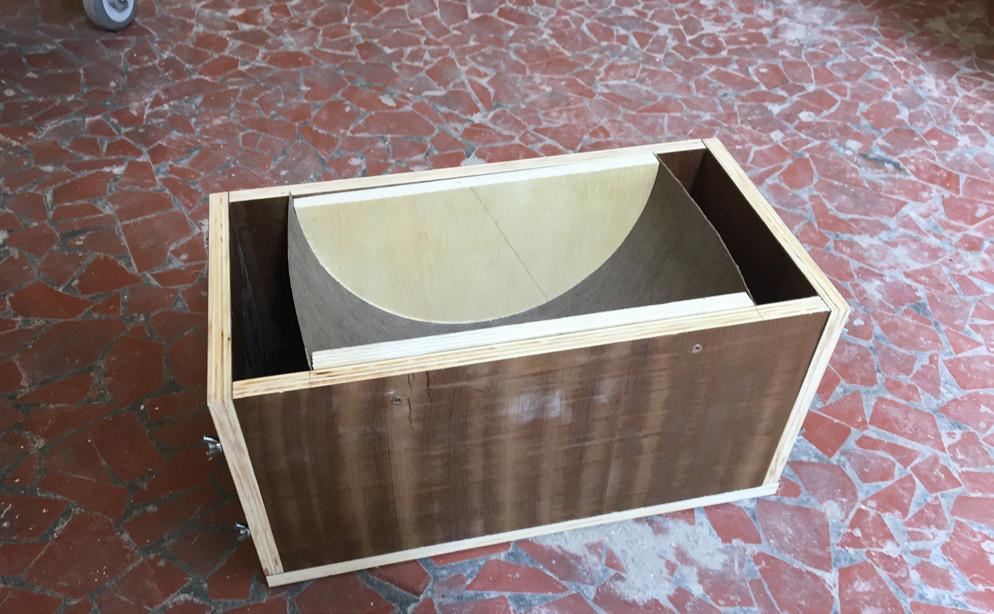
Imagem 56 a 63:
Processo de construção dos moldes em marcenaria com laminado melamínico. Aplicação do lamina plástico autoadesivo (56); Instalação dos perfis PVC para acabamento (57); Confecção do cilindro vazio para a fôrma cúbica (58 e 59); Confecção das fôrmas em formato de abóbada (60 e 61) e fôrma cúbica (62) e de quarto de cubo (63) finalizadas.
81
centro de São Paulo. Um diferencial destas coletas é que nelas foram recolhidos materiais de mesma composição, uma vez que foi possível triar, na própria caçamba, os elementos coletados para a experimentação. Assim sendo, a coleta de matéria prima para a experimentação contava com aproximadamente 60kg de entulho cerâmico3, de concreto4 e de gesso5 cada.
Em adição ao RCD já coletado e triado, foram recolhidos mais nove sacos de entulho (80x50cm) sem triagem, de uma caçamba próxima a área de experimentação – Centro de São Paulo – que continha entulho de tijolos comuns, vazados cerâmicos e pedaços de pisos e azulejos cerâmicos, que de acordo com a idade da construção de que o entulho saia deveriam ser da década de 60. Todo o RCD foi coletado e armazenado na FAEH, para então ser triado, moído e peneirado.
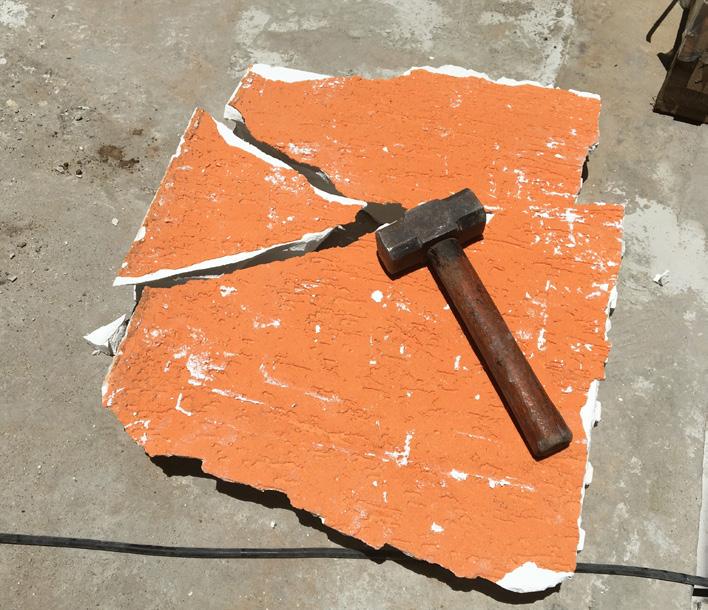
64 65
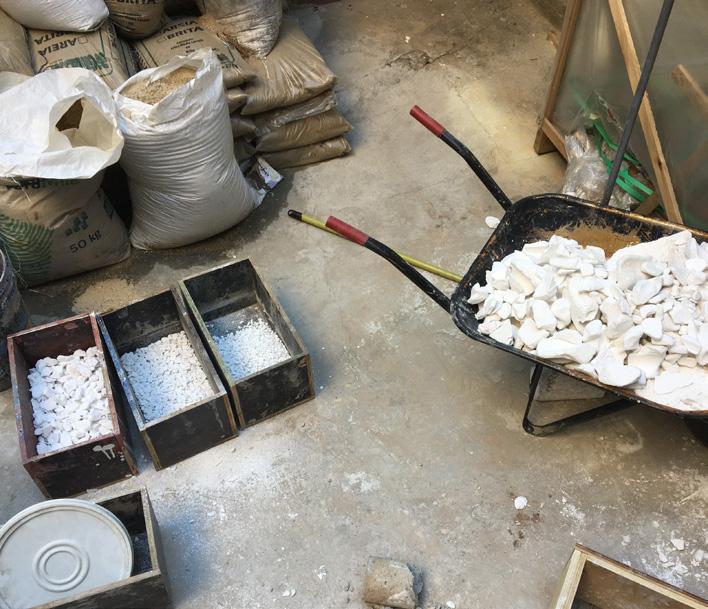
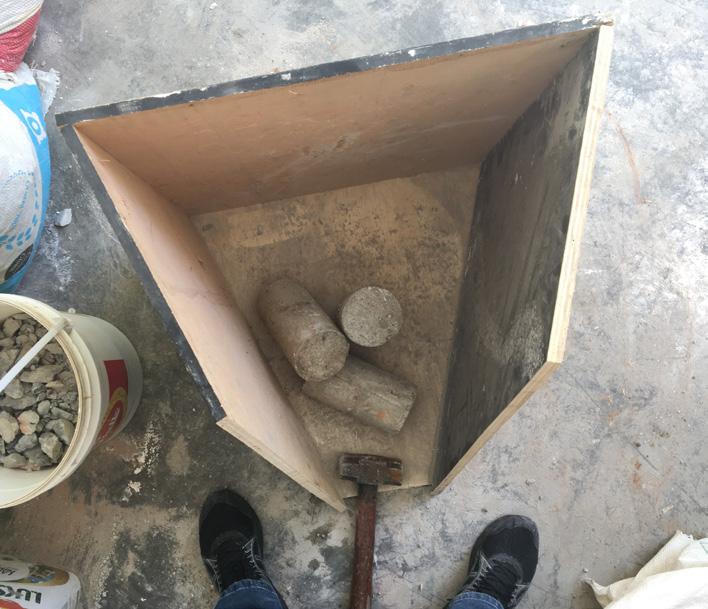
66 67
3. Material proveniente da troca de fachada de azulejos de um edifício, e restos derevestimentos de pequenas obras próprias. 4. Corpos de prova em concreto anteriormente utilizados como gola de um canteiro nas proximidades da FAEH. 5. Pedaços de Drywall descartados pela Escola Nossa Senhora das Graças - Gracinha.
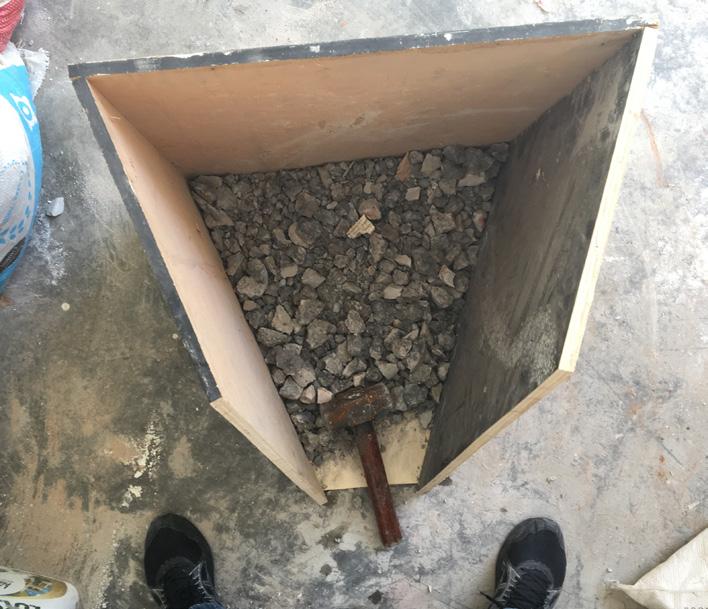
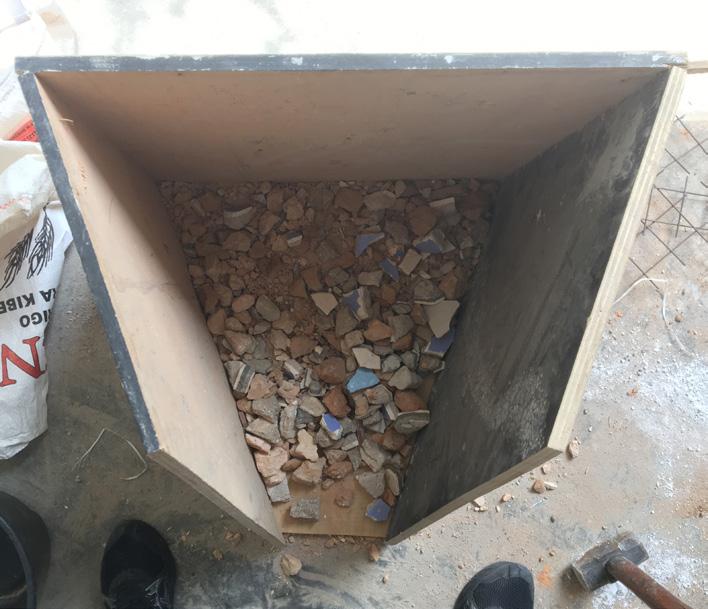
68 69
Imagem 64 a 69:
Processo de triagem e trituração dos entulhos de gesso (64 e 65), concreto (66 e 67) e de RCD sem separação (68 e 69).
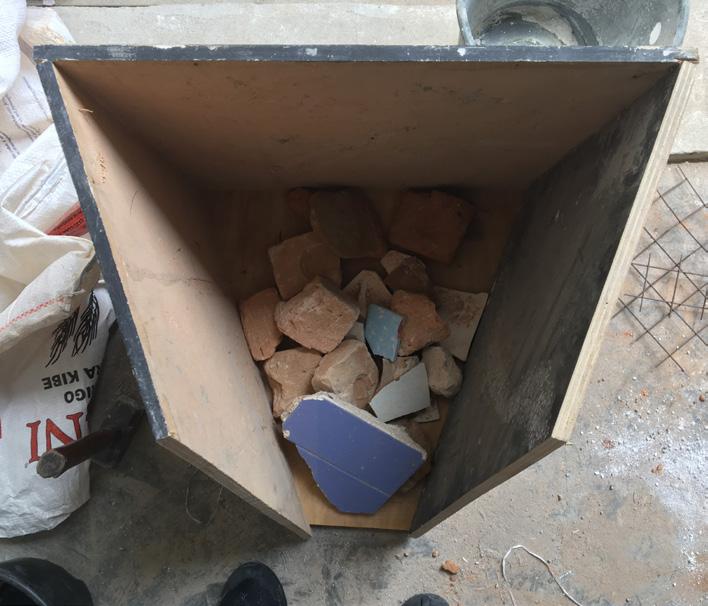
82
Imagem 70:
RCDs coletados, triados e peneirados prontos para a próxima etapa de prototipagem.
A triagem do RCD resumiu-se em retirar dos sacos coletados materiais que não seriam moídos e testados na pesquisa, ao passo que se despejava parte do conteúdo do saco para a moagem. Dentre os materiais encontrados, os mais recorrentes eram bitucas de cigarro, tampas de garrafas PET e restos de canos PVC. O material triado era então moído manualmente com o auxilio de uma marreta em pequenas porções, e então peneirado.
Para este segundo processo prático da pesquisa, a peneira projetada em 2019 foi redesenhada para o fortalecimento da sua estrutura e criação de um coletor de poeira em sua base. O Anexo V (p.143) é uma coletânea de registros do projeto, apresentando desenhos técnicos e fotos da nova peneira. Não obstante, é válido lembrar que a triagem inicial dos materiais foi respeitada até após a peneira, resultando em cinco granulometrias diversas de RCD
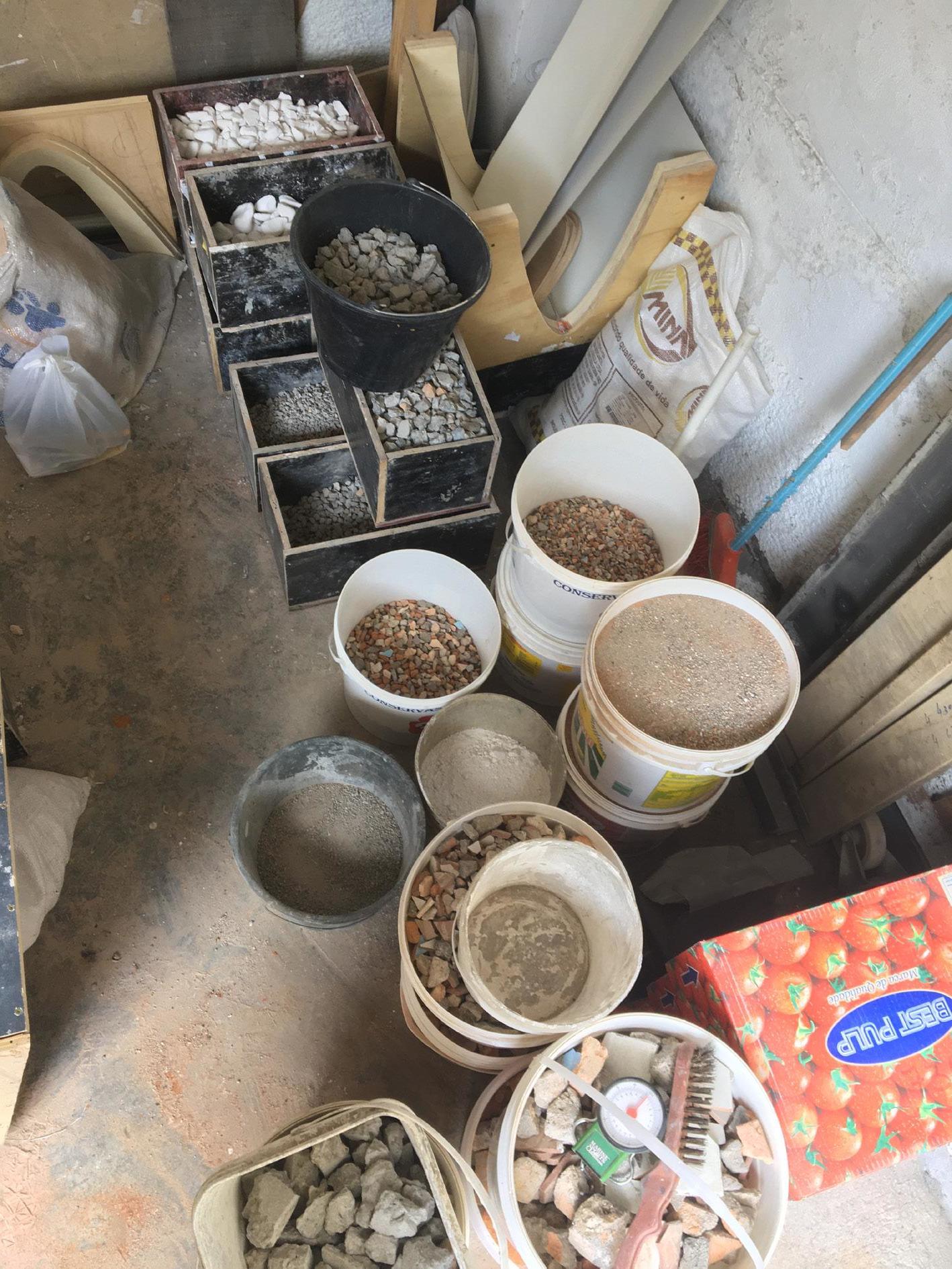
83
cerâmico, concreto, gesso e entulho não triado. Após moagem e peneiramento do RCD foi possível clarificar que a grande maioria da granulometria (>25mm) era composta de fragmentos grandes demais para o uso nas peças projetadas – com grossura máxima de 5cm em algumas partes – e, portanto, foram descartados para a experimentação, sendo moídos e peneirados novamente.
O processo de construção dos moldes e triagem da matéria prima fez com que o cronograma e a extensão do trabalho fossem revistos. Até então era planejado o desenvolvimento de duas linhas de bancos e uma peça para ser usada como degrau. Entretanto, considerando a quantidade de trabalho para triar o RCD e transportar a peca fundida, o degrau não foi levado adiante na prototipagem. Além disso, a falta de sentido em produzir um degrau apenas para o trabalho sem ter onde instalá-lo posteriormente, desmotivou ainda mais a concepção da peça. Ainda na mesma etapa, uma das variações do banco tipo abóbada (de 40cm de altura) não foi pra frente pois os laminados melamínicos disponíveis na Fábrica não abaulavam o suficiente para criar a parábola desejada, rachando e dificultando o manusear do material.
Assim, após a etapa de construção dos moldes, o trabalho contava com quatro tipos de fôrmas – e consequentemente de peças – desenhados e construídos. Os quatro componentes a serem fundidos eram variantes de duas famílias de bancos desenhados, tanto cúbicos quanto em formato de abóbada. Ao final deste trabalho estão em anexo as fichas de construção dos bancos cubo (VI - p.145), quarto de cubo (VII - p.147) e abóbada (VIII - p.149).
Na primeira fundição – que ocorreu no dia 04/12/20, sexta feira – utilizou-se cimento comum de CP II6 e os agregados peneirados dos sacos de entulho sem triagem de material, uma vez que era o tipo RCD mais abrangente na amostra para a prototipagem. O traço escolhido foi o mesmo para concreto no processo da pesquisa experimental, uma parte de cimento para duas de areia e três de agregado (1:2:3). Para as partes de areia, decidiu-se por substituir metade pelo RCD reciclado de gramatura <5mm. Já para as partes de agregado, empregou-se em partes iguais o entulho reciclado de gramatura <25mm e >15mm (tipo B7) e o de tamanho <10mm e >5mm (tipo D).
As peças curaram dentro das fôrmas até dia 09/12/20, quando foram desenformadas. O laminado melamínico, por ser o material mais frágil a ser manejado nas fôrmas acabou por ser o primeiro a se deteriorar no processo de fundição e desforma, tendo rachado ou desprendido em todas as fôrmas em que foi
6. O Cimento CP-II (NBR 11.578) é assim conhecido porque tem a adição de outros materiais na sua mistura, que conferem a este cimento um menor calor de hidratação, ou seja, ele libera menos calor quando entra em contato com a água e também apresenta melhor resistência ao ataque dos sulfatos contidos no solo. 7. Na página 58 deste trabalho há o diagrama de explicação da correlação entre nomenclatura de grão e sua granulometria.
84
empregado. Na fôrma do banco cúbico 40x40x40cm o cilindro vazio central teve de ser destruído para se desprender do corpo de concreto, o que já era esperado uma vez que o cilindro não tinha forma perfeita. Já nas fôrmas dos bancos em formato abobadado fora necessário afixar nas extremidades do laminado melamínico pontaletes de madeira para que o material não embarrigue nas seguintes fundições. Por fim, notou-se que o perfil PVC para acabamento das bordas não tinha sido instalado dentro das fôrmas do banco quarto de cubo, o que gerou uma peça com os vertices bem demarcados, ao invés de curvos.
Em linhas gerais, a primeira fundição se mostrou um sucesso, visto que nenhuma das peças foi concretada de forma descuidada e nem romperam durante o desenformo. Todavia, é válido comentar a presença de bolhas de ar na superfície das peças, o que seria facilmente resolvido com a utilização de uma mesa vibratória durante a fundição. Por outro lado, a confecção das fôrmas cobertas por laminado plástico autoadesivo deu às peças um acabamento brilhante em suas superfícies, que não era necessário, uma vez que a etapa seguinte é a de lixamento das faces das peças.

71 72
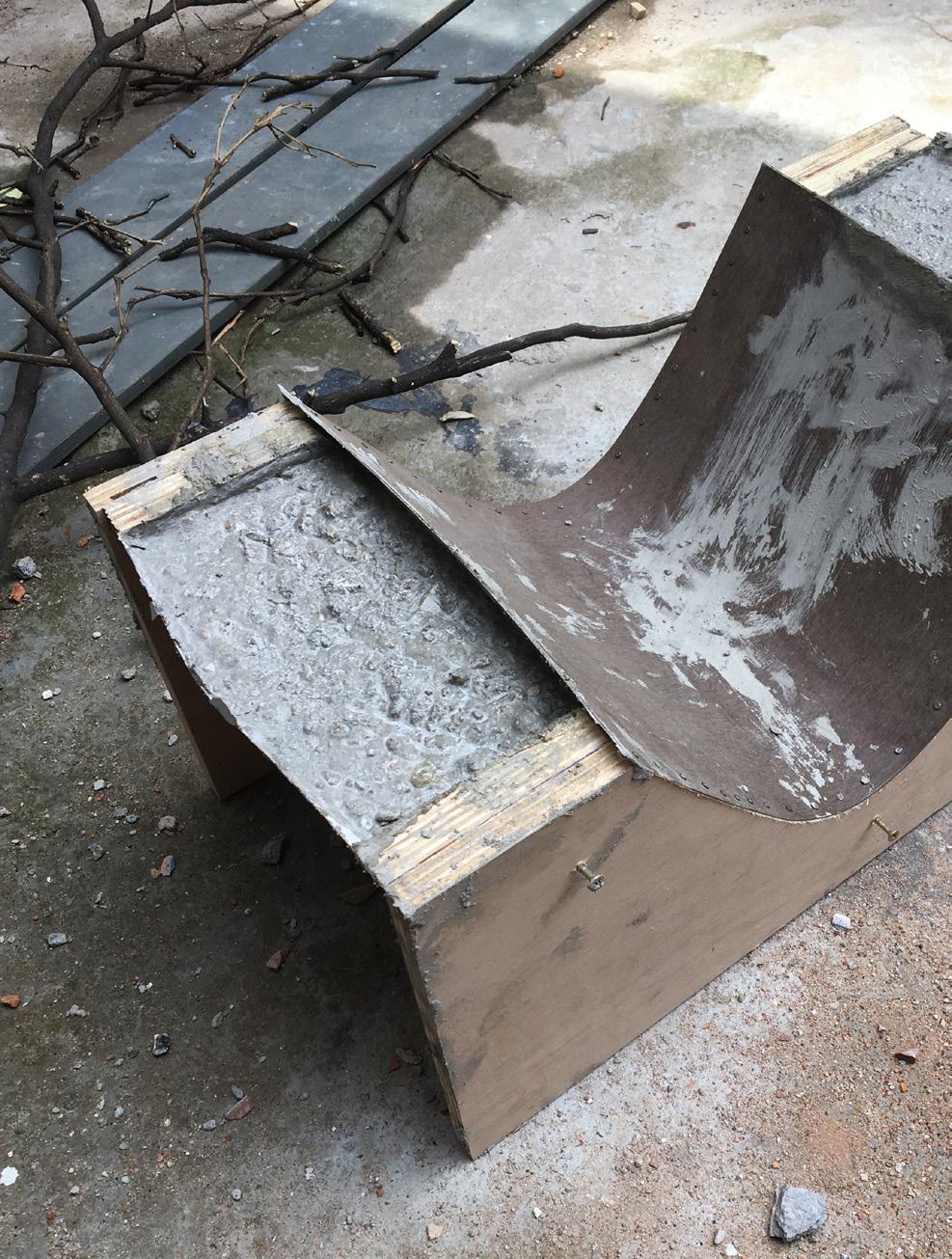
Imagem 71 e 72:
Dificuldades na utilização do laminado melamínico. Desvencilhamento da fôrma durante a desconcretagem (71) e embarrigamento do material após a fundição (72).
85

73
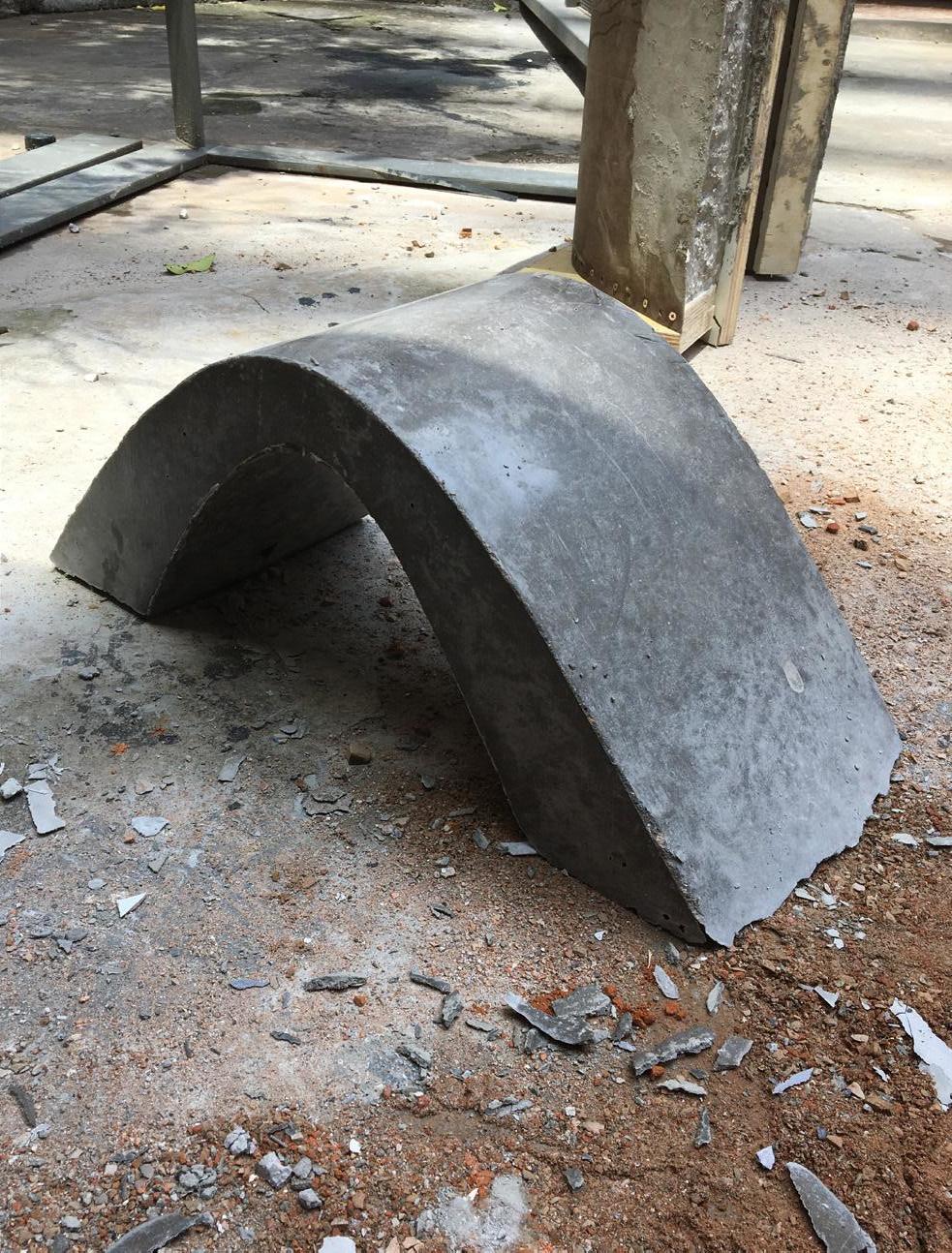
75 74
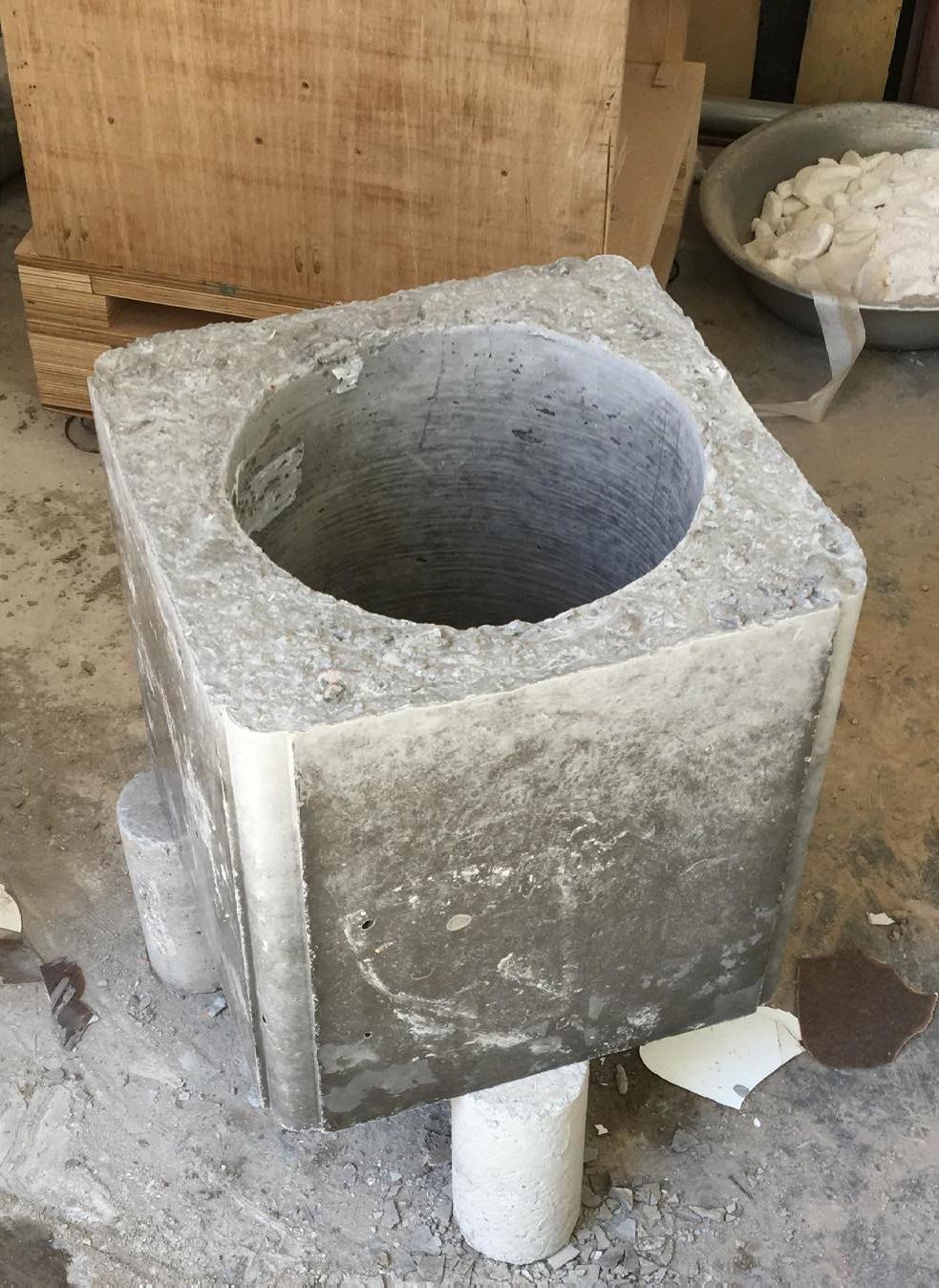
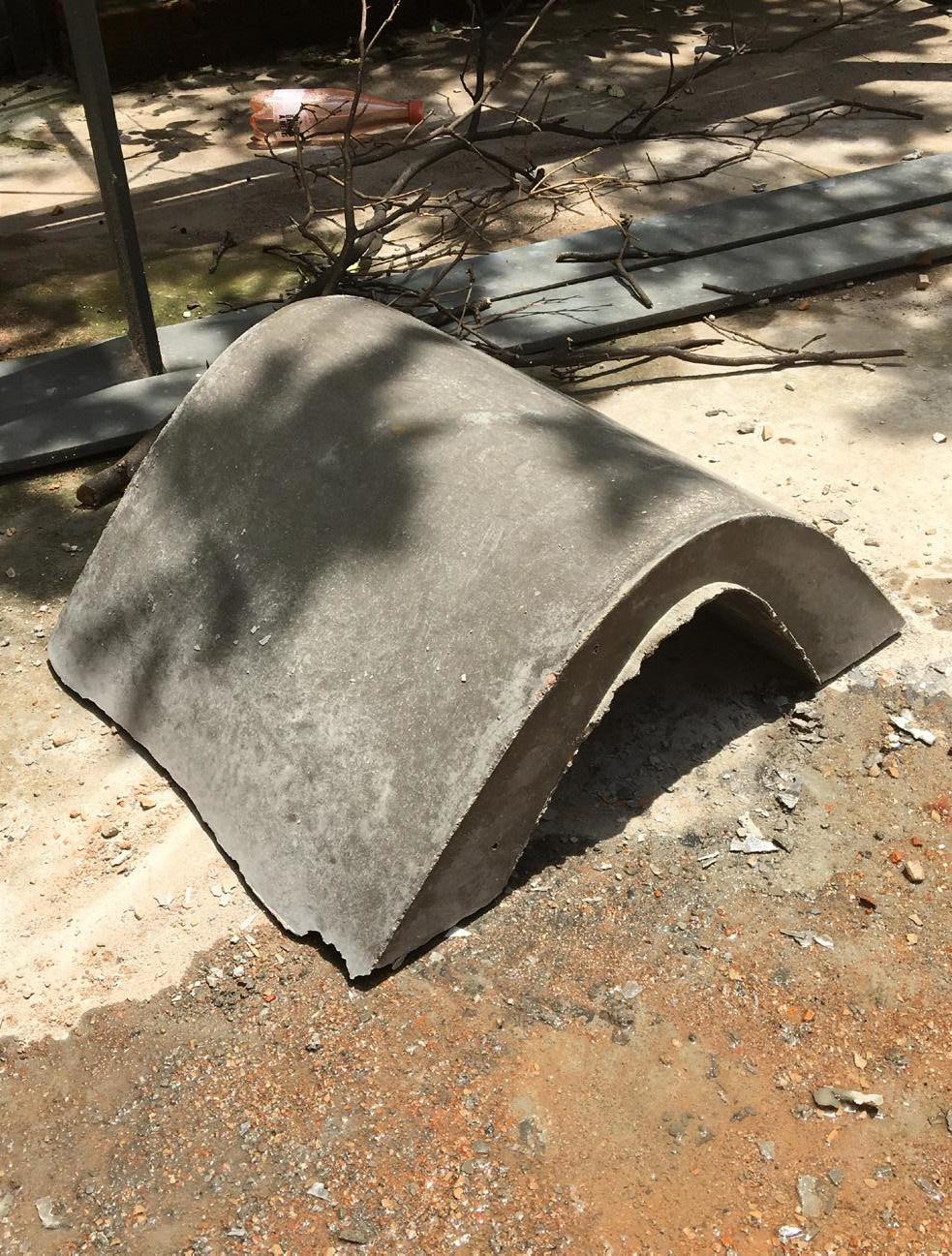
76
Imagem 73 e 76:
Primeira leva de peças desformadas. Quarto de cubo com vértices bem demarcados (73); cubo (74) e abóbadas de 20cm (75) e 40cm (76).
86
Para lixar as peças foi utilizado um disco de desbaste metálico para concreto, que foi fixado a uma lixadeira de disco, e então utilizado manualmente sobre as peças. O manejo do maquinário é de difícil aprendizado uma vez que a tendência é desbastar mais e mais a peça ser lixada continuamente. Um dos desafios encontrados foi o de lixar o suficiente para mostrar o acabamento dos azulejos coloridos em meio a mistura da peça, porém sem lixá-los demais para que o esmalte colorido saia. O acabamento final da peça foi o de um tipo de granilite, só que este feito com materiais reciclados e baixo recurso.

Imagem 77:
Peça quarto de cubo desbastada até a aparição dos grãos de RCD reciclado. Em evidência um antigo azulejo, agora parte da massa.
87
Na segunda fundição – que ocorreu no dia 16/12/20, quartafeira – utilizou-se o mesmo cimento CP II, só que desta vez os agregados peneirados eram de fontes variadas. O traço escolhido foi o mesmo para concreto 1:2:3, e igualmente uma das partes de areia foi substituída pelo RCD reciclado misto, de gramatura <5mm (tipo E). Para inovar, nas partes de agregado empregou-se uma parte do RCD cerâmico triado de tamanho <25mm e >15mm (tipo B); uma parte e meia de RCD de concreto triado – também tipo B – e meia parte do mesmo RCD de concreto, porém de tamanho <15mm e >10mm (tipo C).
Após a fundição das peças, os moldes foram agitados manualmente para o desprendimento de bolhas de ar em sua superfície, em busca de um acabamento mais uniforme para os componentes. Ainda, antes de serem deixados em repouso, as fôrmas foram cobertas com uma camada de água para auxiliar na cura do concreto, que tem sua resistência aumentada quando curado submerso. Entretanto, esta ação está ligada a rápida degradação que as fôrmas tiveram após esta segunda leva de peças, apresentando diversos pontos de apodrecimento e fungos, além de faces inteiras de compensado se desgrudando do laminado plástico autoadesivo.
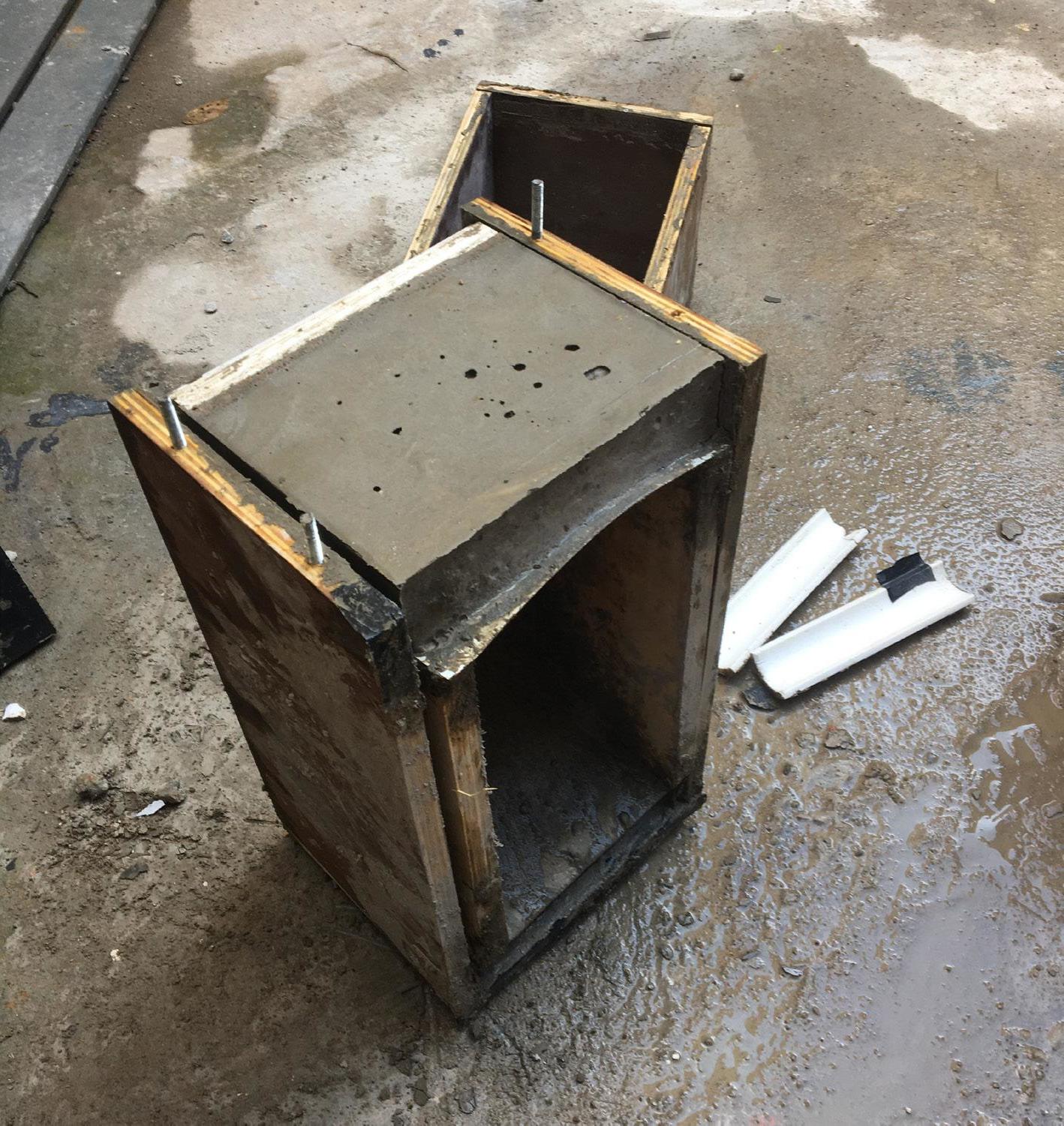
Imagem 78:
Bolhas de ar na superfície da segunda fundição da peça quarto de cubo.
88

Imagem 79:
Peça abóbada de 20cm rompida, junto a mistura em partes iguais de cola branca e cimento.
O desenformo da segunda leva de peças ocorreu dois dias após a sua fundição, na sexta feira dia 18/12/2020 com algumas surpresas, para além da degradação das fôrmas. A primeira é de que a peça abóbada de largura de 20cm foi desformada quebrada, não sabendo se o rompimento da peça ocorreu durante o manejo da fôrma ou durante sua desforma. Para recompor o banco foi utilizada uma mistura em partes iguais de cimento CP II e cola branca atóxica (de base PVC), utilizando a massa gerada como rejunte entre as duas metades da peça, o que foi extremamente bem-sucedido. Ainda, ao manejar as peças recém desenformadas teve-se a surpresa de que pouco adiantou a agitação dos moldes no dia da fundição, uma vez que todas as peças ainda apresentavam marcas de bolhas de ar em suas superfícies.
Assim, para terceira – e última – leva de peças a ser feita, as fôrmas precisaram passar por reparos para que não fosse perdida a qualidade do acabamento dos componentes criados,
89
o que aconteceu no dia 22/12/2020, terça feira, o mesmo dia em que ocorreu a terceira fundição. Para este processo, o mesmo cimento CP II foi utilizado, e mais uma vez as fontes dos agregados utilizados foram variadas. Desta vez, os RCD triados em maior volume já tinham sido utilizados nos processos anteriores, sendo pensada para esta ultima fundição a confecção de três misturas de mesmo traço (1:2:3) porém com conteúdos diferentes. Cada tipo de mistura foi pensada para um tipo de peça, sendo as sobras de concreto despejadas em fôrmas retangulares 20x40cm.
Para as duas fôrmas da peça quarto de cubo, o traço 1:2:3 foi repensado da seguinte maneira: as partes de areia foram subsistidas por partes iguais de RCD reciclado misto e de concreto de gramatura <5mm (tipo E), enquanto as partes de agregado foram substituídas por duas partes de RCD reciclado misto, de tamanho <15mm e >10mm (tipo C) e uma parte da mesma gramatura (tipo C) de RCD reciclado porém só de gesso. Contudo, é válido registrar aqui que a fundição dessas peças com esta mistura foi de maior dificuldade, uma vez que a mistura parecia seca demais e com volume de agregado maior que o normal.
Para a fôrma da abóbada e largura de 40cm, o mesmo traço (1:2:3) teve suas partes de areia substituída em partes iguais de RCD reciclado misto e de concreto, de gramatura <5mm (tipo E). Já suas partes de agregado foram substituídas por duas partes de RCD reciclado de concreto, de tamanho <10mm e >5mm (tipo D) e uma parte de RCD reciclado misto, de gramatura <15mm e >10mm (tipo C). Para a peça abóboda de 20cm de largura, o traço 1:2:3 teve somente seus agregados substituídos por RCD reciclado: meia porção – uma parte e meia – de entulho triado misto, de gramatura <15mm e >10mm (tipo C) e a outra parte e meia de mesma quantidade de gesso, na gramatura tipo C e tipo D em partes iguais.
Ainda no mesmo dia foram lixadas as peças geradas pela segunda fundição, salientando a dificuldade em se manter um nível ou um padrão de superfície simplesmente com a desbastadora de concreto. Para o alcance de superfícies mais niveladas e lisas foram compradas lixas de disco de gramatura no24, que serão utilizadas nas peças geradas pela segunda e terceira fundição. Já as peças desbastadas da primeira fundição foram impermeabilizadas com um verniz incolor acrílico semi-brilho, que fora aplicado com trinchas de 4 e 3 polegadas em quatro demãos uniformes de verniz. O verniz acabou sendo empregado no a acabamento das peças para oferece-las maior resistência às intempéries do clima e do uso, além de oferecer um acabamento de concreto pouco brilhante que ressalta os grânulos de RCD reciclado na mistura.
90
argamassa 3
1,5 parte de B misto 1,5 parte de D misto 1 parte de E misto 1fundição cimento 1 parte de areia 1fundição1,5 parte de B misto 1,5 parte de D misto 1fundição2fundição 1:2:3 1,5 parte de B misto1 parte de E misto1,5 parte de B misto1 parte de B cerâmico 1,5 parte de D misto1 parte de areia 1,5 parte de D misto1,5 parte de B concreto 1 parte de E mistocimento 1 parte de E misto0,5 parte de C concreto cimento 1 parte de areia 2fundição 1:2:3 1 parte de B cerâmico fundição 1:2:3 3 1 parte de B cerâmico 1,5 parte de B concreto 0,5 parte de C concreto cimento 1 parte de areia 2fundição 1:2:3 1 parte de B cerâmico cimento 21 parte de E misto 1 parte de areia fundição 1:2:3 1:2:3 1,5 parte de B concreto 0,5 parte de C concreto 1 parte de E misto 1 parte de areia 1,5 parte de B concreto 0,5 parte de C concreto2 parte de D concreto 1 parte de C cerâmico
1: : 2:3
1,5 parte de C misto 2 partes de C misto cimento 1 parte de E misto 1 parte de areia 3fundição 1:2:3 1:2:3 1:2:3 :cimento 3fundição 1:2:3 2 parte de D concreto 1 parte de C cerâmico 1,5 parte de C misto 1,5 parte de C+D gesso 1:2:3 1:2:3 2 partes de C misto 1 parte de C gesso cimento 1 parte de E misto 1 parte de areia 3fundição 1:2:3 1:2:3 1:2:3 : : cimento 2 partes de E misto cimento areia : 1,5 parte de C+D gesso cimento 1 parte de E misto 1 parte de E concreto 1 parte de C gesso : : :
2 parte de D concreto2 partes de E misto2 parte de D concreto 1 parte de C cerâmicocimento1 parte de C cerâmico 1,5 parte de C mistoareia1,5 parte de C misto 1,5 parte de C+D gessocimento1,5 parte de C+D gesso 2 partes de C misto1 parte de E misto2 partes de C misto 1 parte de C gesso1 parte de E concreto1 parte de C gesso
2 partes de E misto2 partes de E misto cimento: cimento areiaareia cimento:cimento 1 parte de E mistocimento 1 parte de E misto 1 parte de E concreto1 parte de E concreto cimentocimento
argamassa 3 argamassa 3 argamassa 3
Imagem 80:
Diagrama de composição das misturas.
91
A terceira e última leva de peças foi desformada na segunda feira, dia 28/12/2020, último dia para a atuação prática deste trabalho. Esta desforma final também guardou algumas surpresas, para além da presença de bolhas de ar na superfície. Mais uma vez, a peça abóbada de largura de 20cm foi desformada despedaçada, porém desta vez mostrou-se claro que o problema foi na fundição (a mistura não tinha ocupado a fôrma por completo). Por outro lado, uma surpresa positiva foi de que a mistura que no dia da fundição parecia desequilibrada – das peças quarto de cubo – não teve problemas na sua cura.
Uma outra hipótese para a fragilidade maior da peça foi o emprego de gesso como agregado, material que acaba por enfraquecer a mistura por ter sua resistência inferior ao do concreto (de 5 à 14Mpa). Ainda, se o gesso é empregado como agregado em uma taxa maior que o de 5% do volume da mistura o material acaba por retardar a pega do concreto. No mais, a tonalidade do concreto das misturas em que foi empregado gesso era muito mais escura do que as em que o material não foi utilizado, indicando uma maior retenção de água pelas misturas mais escurecidas.

Imagem 81:
Peça abóbada de 20cm rompida durante a sua desforma.
92
Imagem 82:
Peça abóbada de 40cm parcialmente lixada para a comparação entre os acabamentos antes e após o uso do disco de desbaste.
Por ainda estarem úmidas e recém desformadas, o lixamento das peças requereu menos esforço físico, como que parecendo ser de um material mais macio que os antes trabalhados. Contudo, a facilidade em lixar as peças dificultou o controle do nível do disco de desbaste, culminando em peças com o acabamento mais profundo e irregular em relação as levas anteriores. Para aplanar as faces já desbastadas foi utilizado o disco de lixa de gramatura nº24, que funcionou muito bem para os fins desejados.
Após o desbaste das peças, ambas as levas – a segunda e a terceira – foram impermeabilizadas com o verniz acrílico. Em teoria, o correto seria esperar as peças curarem por 28 dias para então serem envernizadas, o que não pode ser seguido de acordo com o cronograma apertado no fim do trabalho. Ainda, a terceira leva foi coberta de verniz ainda úmida da fundição, fato que pode acarretar em problemas de impermeabilização da peça que só serão descobertos no futuro. Assim, com todas as peças envernizadas, foi possível fazer uma seção de fotos dos produtos na própria FAEH, que será apresentada após as conclusões deste segundo processo prático de experimentação.
