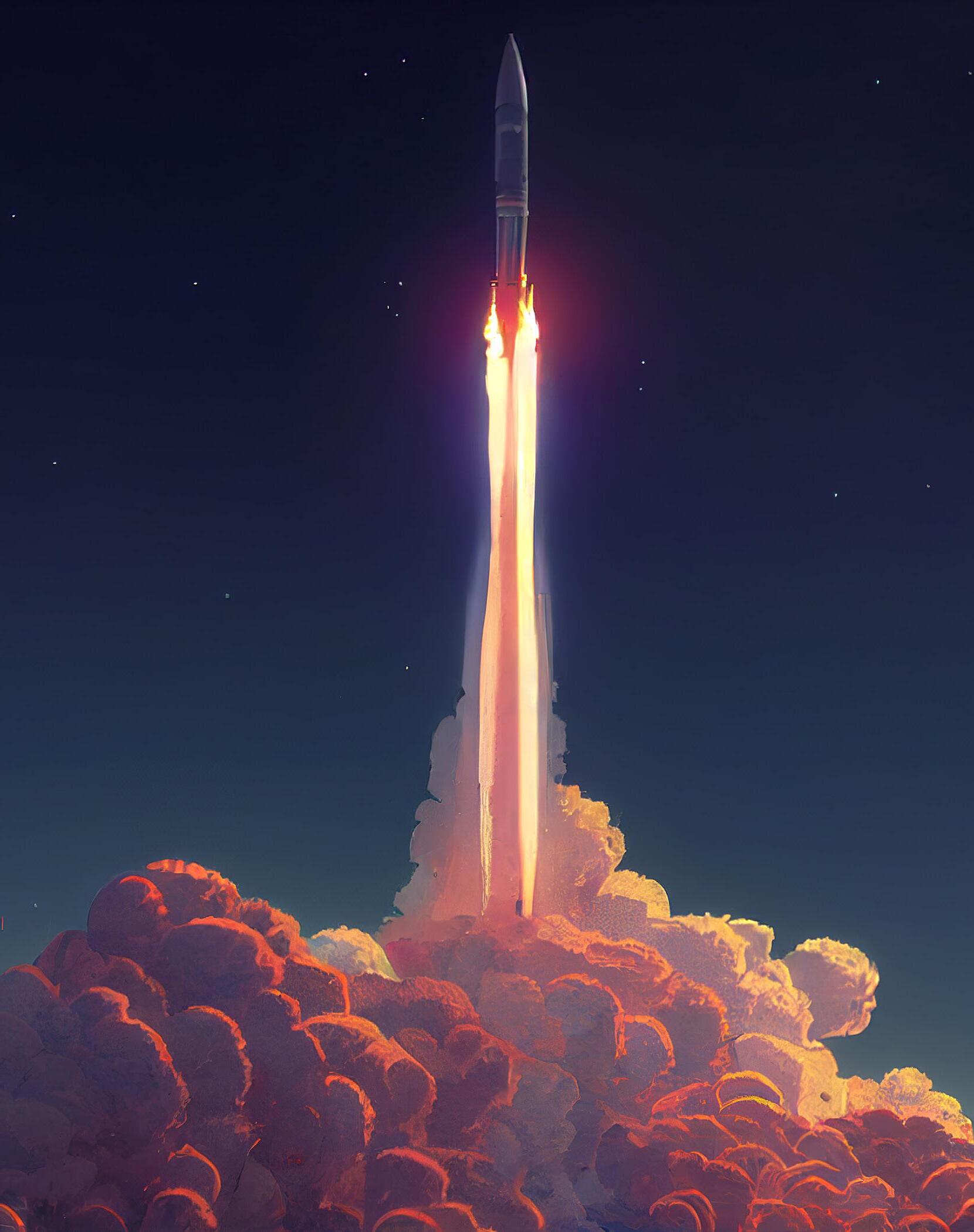
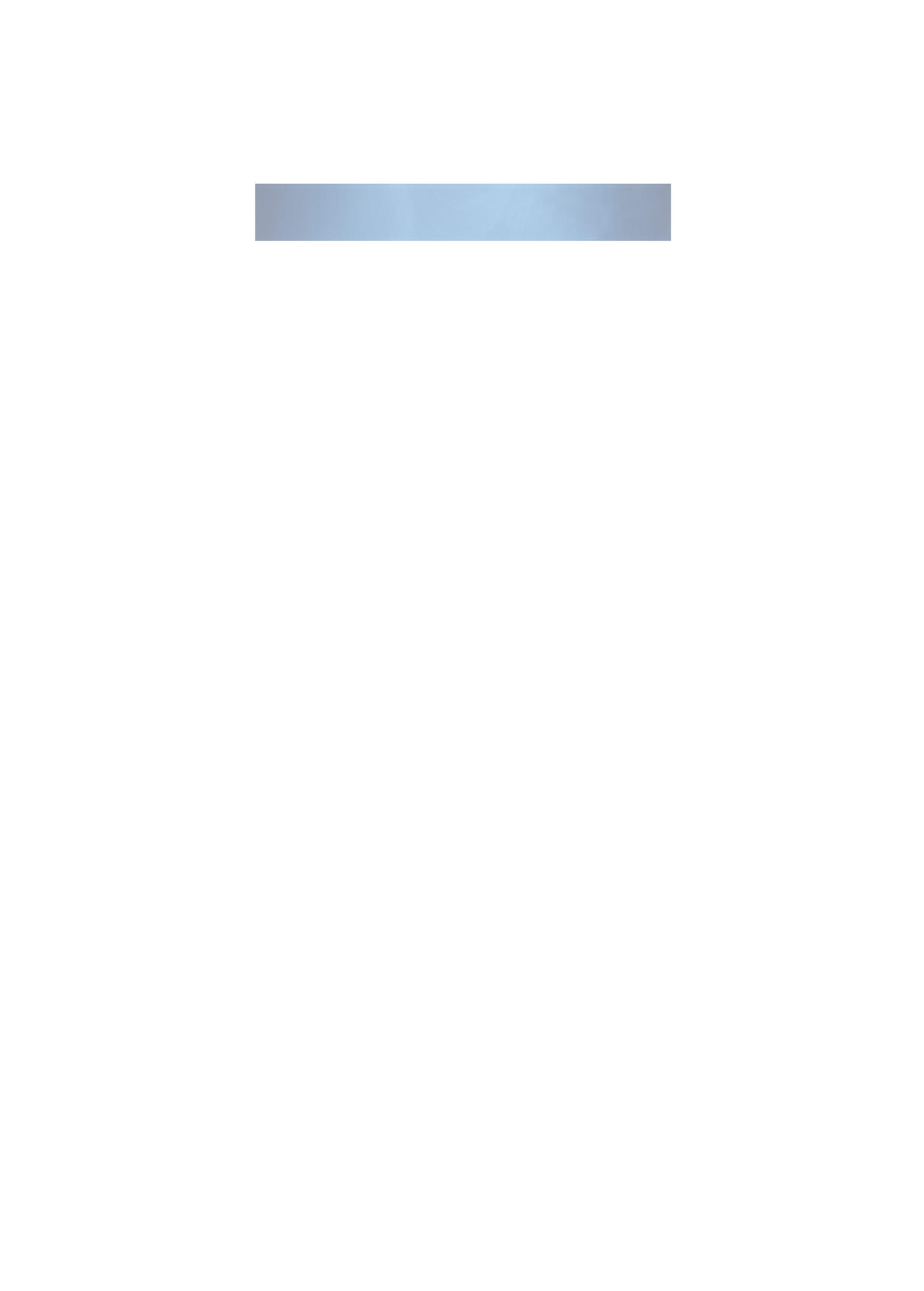
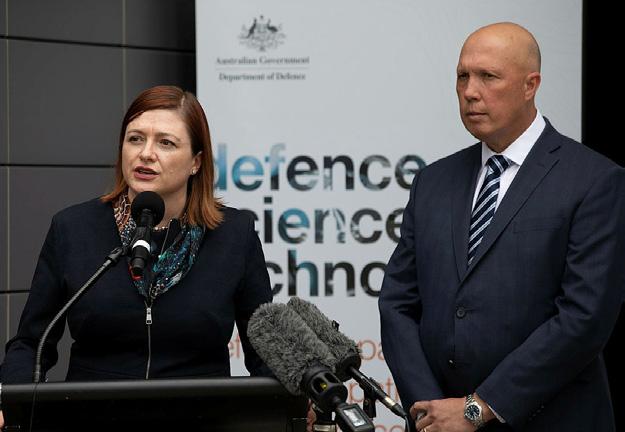
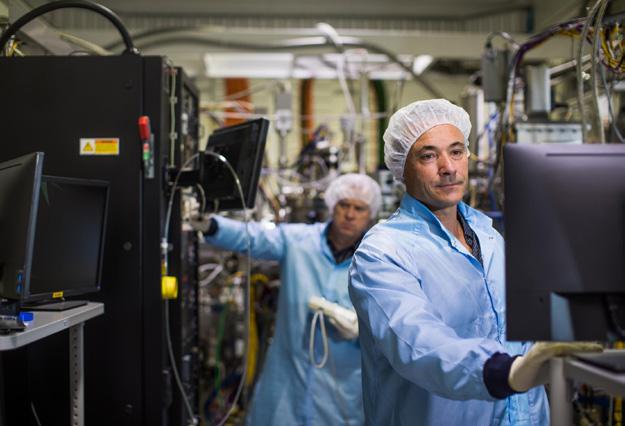
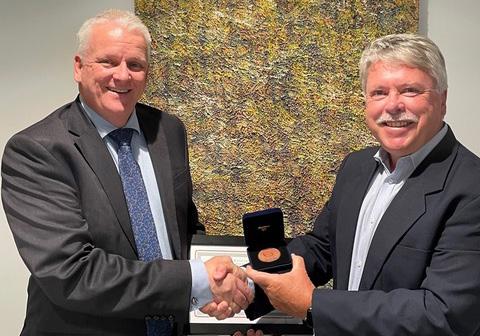
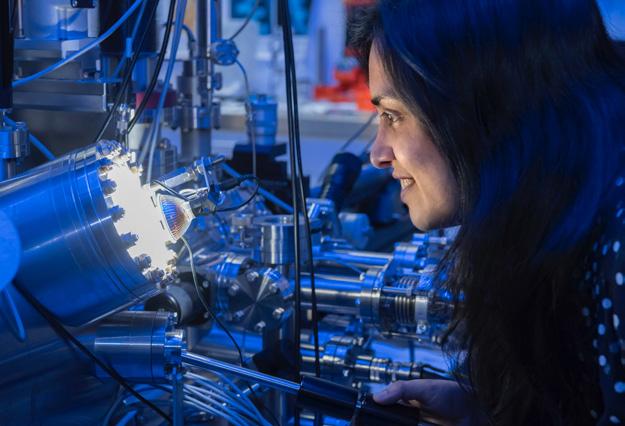
Welcome to the April 2023 edition of Materials Australia Magazine. For this month’s presidents message I thought it would be a great opportunity to look at the emerging topic of the use of artificial intelligence (AI) in materials science and engineering.
Artificial Intelligence (AI) is a rapidly growing field that has the potential to revolutionize many areas of research and development, including materials science and engineering. In recent years, there has been a significant increase in the use of AI in the physical sciences, with researchers utilizing AI techniques such as machine learning and neural networks to develop new materials and optimize their properties. The application of AI in materials science and engineering has opened up new avenues for research, development, and innovation, with the potential to improve existing materials
and create entirely new ones. The use of AI in materials science and engineering involves the application of machine learning algorithms and other AI techniques to large datasets of materials properties, structures, and behaviours. By using these AI algorithms, researchers can quickly analyse large datasets and identify patterns and correlations that would be difficult or impossible to detect using traditional methods. Data can be generated through a variety of sources, including experimental measurements, simulations, and theoretical calculations, and, as a result, optimization of materials and the methods through which to research them, becomes significantly more rapid. AI can also be used to improve the efficiency of manufacturing processes. For example, AI algorithms can be used to analyse the performance of different manufacturing processes and identify areas for optimization. This can lead to improvements in efficiency, reducing costs and improving the quality of the final product.
The use of AI in materials science and engineering has several benefits, including:
Accelerating Materials Discovery: The use of AI can help researchers to accelerate the discovery of new materials by predicting their properties, behaviours, and structures before they are synthesized or experimentally characterized. This can save time and resources and enable researchers to focus on the most promising candidates.
Optimizing Existing Materials: AI can also be used to optimize the properties of existing materials by predicting how they will behave under different conditions and identifying ways to improve their performance.
Reduced Experimental Costs: By using AI to generate predictive models, researchers can reduce the need for costly experimental measurements and simulations, as the models can be used to predict materials properties and behaviours accurately.
Enabling Multiscale Materials Design: AI can help researchers to design materials at different length scales, from atoms to bulk materials, and across different materials classes, from metals to polymers to ceramics.
Despite its potential benefits, the use of AI in materials science and engineering also presents several challenges, These include:
Data Quality: The accuracy and completeness of the datasets used to train AI models can have a significant impact on the predictive power of the models. Therefore, researchers must ensure that their datasets are high quality and representative of the materials they wish to study. As may be appreciated the risk of encountering data bias as the result of poor or minimal results may produce conclusions that may appear convincing, but are not necessarily correct.
Interpretability: The black-box nature of some AI models can make it challenging to interpret the predictions
they generate. This can be a significant difficulty for researchers who need to understand the underlying mechanisms driving materials properties and behaviours.
Computational Complexity: AI models can be computationally intensive and require large amounts of processing power and memory. This can limit the scalability of AI approaches and make them challenging to apply to large and complex materials systems.
Human Expertise: AI models require human expertise to design and interpret accurately. Therefore, researchers must have a deep understanding of both the AI techniques and the materials science and engineering principles they are applying them to.
The use of AI in materials science and engineering is still in its early stages, and there is significant potential for further development and innovation. Some of the key future prospects for AI in materials science and engineering include:
Incorporating Physics-Based Models: Combining AI techniques with physicsbased models can help researchers to generate more interpretable and accurate predictive models. These
MATERIALS AUSTRALIA CONFERENCE APICAM2023
21st - 23rd June 2023
The University of Sydney
hybrid models can also help to address some of the limitations of blackbox AI models, such as their lack of interpretability.
Multimodal Datasets: By combining data from different sources, such as experimental measurements and simulations, researchers can generate more comprehensive and representative datasets that can be used to train AI models more effectively.
Automated Experimentation: The use of AI can enable the development of automated experimentation platforms that can plan, execute and analyse experiments minimizing the need for manual intervention and eliminating the risk of human error. The goal of automated experimentation is to speed up the experimental process, reduce costs, and improve the accuracy and reproducibility of scientific research.
As AI continues to evolve and improve, it is likely that its use in materials science and engineering will only continue to grow. Researchers will need to work together to address the challenges and limitations of AI in this field, while also exploring new and innovative applications of this powerful technology. With continued
MATERIALS AUSTRALIA CONFERENCE LMT2023
9th -12th July 2023
RMIT University
Materials Australia National Office PO Box 19
Parkville Victoria 3052 Australia
T: +61 3 9326 7266
E: imea@materialsaustralia.com.au
W: www.materialsaustralia.com.au
NATIONAL PRESIDENT Roger Lumley
research and development, AI has the potential to transform materials science and engineering and unlock new possibilities for innovation and discovery.
I am sure many of you would already have guessed by now that the majority of this article (i.e. >95%) was generated by an artificial intelligence platform (ChatGPT). In this case I presented one or two questions to the AI and was able to generate multiple articles in under 15 seconds each, from which I chose the one I liked the best and completed final editing. The entire process of writing this presidents message took less than 20 minutes. This is an incredibly interesting topic that has implications to the way we teach, learn and prepare written information. There are many and varied ethical questions related to how scientists and engineers are using, or will use AI. As a professional community we need to begin the discussion about these kinds of topics, since they are going to enormously impact our careers and work lives over the next 10-20 years and beyond. What do you think?
Best Regards
Roger LumleyNational President Materials Australia
MATERIALS AUSTRALIA CONFERENCE MISE2023
29th - 31st October 2023
The University of Queensland
This magazine is the official journal of Materials Australia and is distributed to members and interested parties throughout Australia and internationally.
Materials Australia welcomes editorial contributions from interested parties, however it does not accept responsibility for the content of those contributions, and the views contained therein are not necessarily those of Materials Australia.
Materials Australia does not accept responsibility for any claims made by advertisers. All communication should be directed to Materials Australia.
Source: Jigneshkumar Dhimar, Branch Manager, LMATS Perth.
Jignesh Dhimar is a mechanical engineer with more than 15 years of experience working in NDT application industries. He has been actively involved in asset integrity inspection, refinery EPC projects, and pipeline corrosion mapping using conventional and advanced NDT techniques.
In NDT during manufacturing, requirements are often prescribed in specifications, codes and standards. With in-service NDT, the methods used depend on the component (e.g. structure, pipe, tube, pressure vessel, above ground storage tank), the material and the condition (e.g. surface condition, insulation, access, surface temperature). Jignesh emphasised the point that the choice of the right NDT method is crucial, and proceeded to outline recent advancements in NDT and to provide insights on their applicability in various industries.
He set the scene by reminding the audience of the main types of conventional NDT:
• Radiography – mainly internal discontinuities, sensitive to volumetric discontinuities
• Ultrasonic – mainly internal defect, sensitive to planar discontinuities
• Eddy Current – surface discontinuities, only conductive material
• Dye Penetrant – open-to-surface discontinuities
• Magnetic Particle – surface and subsurface discontinuities, only magnetic material
Advances in electronics, computing, and information and telecommunications (IT) have led to the development of advanced forms radiography, ultrasonic testing (UT) and eddy current (EC) testing techniques:
• CRT – Computed Radiographic Testing
• PAUT – Phased Array Ultrasonic Testing
• TOFD – Time Of Flight Diffraction Ultrasonic Testing
• GWT – Guided Wave Testing
• ECA – Eddy Current Array testing
• PECT – Pulsed Eddy Current Testing
• LFEC – Low frequency Eddy Current Testing
Improvements in electronics allow more sensitive data capture, for example, replacing single-use radiographic film with a reusable cassette containing a scanned phosphor plate. Greater computational power has been instrumental in allowing more complex signal processing and data analysis. Improvements in IT apply across all testing methods, notably enabling traceable, paperless results to viewed by clients anywhere in the world.
The application of these improvements to UT has greatly expanded the scope of the method. In its original form, detection is limited to planar discontinuities directly under the combined source and detector. PAUT creates a steerable UT beam using interference between the ultrasound waves produced by an array of piezoelectric transducers. Steering the beam at angles either side of the through-thickness axis allows detection of non-planar defects and visualisation of data on a volumetric basis. This method has a high detection rate and is well suited to weld inspections, corrosion mapping, and monitoring and sizing defects for baseline data. TOFD, which can be used in conjunction with PAUT, detects discontinuities regardless of their orientation and is regarded the best NDT method for through wall sizing of defects. The tips of a crack that lies between a transmitter and a separate receiver (on the same surface) diffract waves that arrive at the receiver at different times, allowing the defect to be located both laterally and on the through-thickness axis.
A further extension of UT from throughthickness to axial defect detection is achieved with guided wave long-
range UT (GWUT). In this method, the ultrasonic wave travels axially, with defects located normal to the longitudinal axis being detected by the energy they reflect to the transmitter/ receiver. This allows their distance from the transmitter to be determined. This method is well suited to identifying relatively large defects, such as loss of wall thickness, in inaccessible locations, such as buried pipelines.
Eddy current testing has also advanced. Eddy Current Array (ECA) testing uses the same basic principles as simple eddy current testing. The difference is that electronics and signal processing area applied to allow a large number of exciting coils to be used simultaneously to cover a large area at once, and with greatly improved signal to noise ratio and reproducibility. This method can detect surface defects, far-surface corrosion and shallow subsurface defects. It can be implemented with flexible probes for complex shaped geometries.
Another of the improvements to eddy current testing made possible by improved signal processing is pulsed eddy current testing (PECT). In this method a step-function voltage is applied, producing a spread of
frequencies. Because the different frequencies penetrate to different depths, this allows simultaneous collection of information from a range of depths. This makes the method particularly useful for thickness measurement without removal of insulation (e.g. for corrosion under insulation), for measuring thickness of steel embedded under concrete or asphalt, and for detection corrosion of steel submerged in water.
Low frequency eddy testing (LFET) is applied to gather information deeper below the surface, though with relatively low resolution. Jignesh explained how LMATS applies this method for scanning for defects in boiler wall tubes.
Jignesh proceeded to describe factors affecting the selection of NDT methods, taking as an example inspection of heat exchanger tubes. He summarised the applicability of various methods in relation to tube material and tube form (e.g. with or without fins), and explained how the choice is further governed by the type of defect to be detected and the required sensitivity of detection. This was a comprehensive update, highlighting the range of techniques that are available locally.
Source: Dr Richard Macoun, Research Manager, Future Battery Industries CRC
Dr Richard Macoun studied physical and polymer chemistry (University of Sydney) before completing his PhD in nanotechnology and chemical engineering (UNSW). Richard also holds an MBA (UWA) and has worked in product and process innovation for over twenty years at CSIRO, BHP and BASF (Mining Solutions). He has had a long involvement in collaborative innovation efforts as Program Manager at AMIRA, and as Research Director at the Future Battery Industries CRC (FBICRC).
The FBICRC has been planned to have six-year life, “to live fast and die young”
with a mission to help develop a vibrant battery industry for Australia before the window of opportunity closes. Richard reminded the audience that while Australia possesses around half the world’s known reserves of battery materials, mining and chemical processing makes up only around 3 percent of the battery value chain.
While the centre is undertaking 15 projects across the value chain, Richard singled out one, the National Battery Testing Facility, for special mention. It is vital for providing certification for shipping lithium-ion batteries (LIBs) batteries. The point is that, unlike lead-
acid batteries, end-of-life LIBs present a significant hazard, which will soon be encountered in increasing volumes as electric vehicles (EVs) become eight to ten years old. The LIBs they contain will have to be processed somewhere, which will involve collection, storage, and transport, in addition to the processing.
The fundamental reason why LIBs are different is that they operate on flow of lithium ions between two electrodes (anode and cathode) neither of which is consumed in a chemical reaction (the way lead is consumed in a Pb-acid battery). Rather, the two electrodes
act as ‘sponges’ which can contain mobile lithium ions at differing energy states. Richard likened charging and discharging LIBs to ‘sopping up’ ions with the virtual sponge, and then ‘squeezing and wringing them out’. Extending the analogy, the basic problem is that the harder the sponges are squeezed and wrung out the greater the damage accumulated in each cycle. Unfortunately, internal failure of LBIs, particularly when being charged, can lead to runaway discharge with the potential for practically inextinguishable fires, which are now all too common.
The way LIBs work is not intuitively obvious. Indeed, the award of the 2019 Nobel chemistry Prize is an acknowledgment of their development as a triumph of materials science. The initial scientific breakthroughs, starting in the 1970s, were the discovery of materials that could accommodate lithium ions intercalated within layered crystal structures. Subsequently, the key to the development of LIBs into practical and widely used portable energy sources has been in finding electrode materials that allow higher capacity (for a given size and weight) and faster charging and discharging rates (power output), combined with adequately long life and affordable cost. The first LIBs had lives measures in hundreds of charge-discharge cycles, now they can withstand thousands, but the goal is for them to be able to withstands tens of thousands.
Currently, the most common anode material is graphite, typically ‘five nines’
purity, though graphene (single-layer graphite), lithium titanate and silicon are also options. Cathodes are mostly based on metal oxides, with several competing technologies in common use. Three of these five formulations contain cobalt, and the high cost of this element is driving the development of alternatives.
Richard outlined the production process for cathodes starting with manufacture of the cathode precursor material, which is the oxide structure that can hold the lithium ions. Lithium ions are subsequently introduced through combining the oxide with lithium carbonate and calcium, in powdered form. Details of the manufacturing processes are closely held trade secrets.
The third component of the cell is the separator and the fourth is the electrolyte, commonly lithium hexafluorophosphate. The flammability of electrolytes is a significant factor in LIB fires, which are made worse by the propensity of cells to explode and spread burning material for up to several metres, in all directions.
Richard briefly touched on manufacture of batteries, with a focus on the common small cylindrical-form cells that are the active components of most LIB packs. A rechargeable LED torch might typically have three such cells, while 18V power tool battery packs typically have five. However, battery packs for EVs contain 5000 or more of these small cells, connected electrically and structurally, together with cooling and power management modules.
The manufacture of the individual cells starts with preparing slurries of anode and cathode materials. These are used to form a three-layer sheet with a separator between the electrode layers, using processes like those in paper and film production. The spooled sheet is then rolled to form the cylindrical cells, a bit like forming a like a Swiss roll cake. The next step is to fill the cells with electrolyte and then apply a series of charge and discharge cycles to transport the lithium ions into the electrodes. Currently this final ‘formation’ process can take up to three weeks, resulting a considerable inventory of cells in production. The results of formation are not guaranteed, so cells are individually tested and graded before sale and subsequent assembly into battery packs.
Richard remarked that while EVs received the top-grade cells, the lower graded cells often end up in consumer products such as cheap scooters and power tools. It would appear no coincidence that such devices have been the cause of many house fires. Returning to his analogy, Richard’s advice was to treat an LIB like a sponge and not to wring it out too hard! He recommended keeping LIBs between 60 and 80 percent capacity, and not to leave them on-charge out of sight and out of mind.
The audience reception showed that Richard’s presentation maintained the established reputation of the Sir Frank Ledger Breakfast as a highlight of the WA Branch year.
alternative energy
palladium catalysts
glassy carbon
thin lm
screening chemicals
surface functionalized nanoparticles
zeolites
99.999% ruthenium spheres
diamond micropowder
janus particles
nickel foam
buckyballs
gold nanoparticles
III-IV semiconductors
organometallics
nanogels
metal carbenes ITO
bioactive compounds
nano ribbons
nanodispersions
3D graphene foam
osmium
MOFs
isotopes
ultralight aerospace alloys
Nd:YAG
cermet
epitaxial crystal growth
drug discovery
quantum dots
transparent ceramics
spintronics
mesoporous silica
sputtering targets
MBE
indicator dyes
macromolecules
silver nanoparticles
enantioselective catalysts
rhodium sponge
pharmacoanalysis
spectroscopy
anode excipients
superconductors
chalcogenides
rare earth metals
cryo-electron microscopy
CVD precursors
deposition slugs
laser crystals
calcium wires
platinum ink
tungsten carbide refractory metals
optical glass
graphene oxide
h-BN MOCVD
metamaterials
Fe3O4
uorescent microparticles
cisplatin
shift reagents
American Elements opens a world of possibilities so you can Now Invent!
ferro uid
dielectrics
Over 30,000 certi ed high purity laboratory chemicals, metals, & advanced materials and a state-of-the-art Research Center. Printable GHS-compliant Safety Data Sheets. Thousands of new products. And much more. All on a secure multi-language "Mobile Responsive” platform. www.americanelements.com
biosynthetics
dysprosium pellets
process synthesis
metallocenes
conjugated nanostructures
Source: Stuart Folkard
After graduating from the University of Queensland with a BSc in Metallurgy, Paul spent some time in materials consulting before joining Rio Tinto’s Wear Laboratory in Perth.
He thereafter joined Warman International where he provided specialist support to all of Alcoa WA operations (including field testing of leading-edge materials). During his four years at Austral Technologies in Perth, Paul led the introduction of high deposition PTA into the Australian market. Paul then joined Hardchrome Engineering in Melbourne where he was involved in providing leading edge surface engineering technologies (including laser cladding) to the mining and manufacturing industries.
Paul joined Gerard Daniels in 2005 and today is a Partner in the firm.
Paul has had a long-standing relationship with Materials
Australia:
During his time in Queensland, and Victoria he served on the local Branch Councils often leading the technical and training programs. Today, he is a current serving member on the WA Branch Council where is also a past Branch President. He is actively involved in organizing seminars and was instrumental in launching the Material Innovation in Surface Engineering series of seminars, which have been running since 2011. Over the last 10 or more years Paul has been the convenor of, and indeed seeing to the success of, this annual Sir Frank Ledger Breakfast (which is now mentioned in the Who’s Who Directory entry for Frank Ledger).
Paul is a director and member on the National Executive
Hitachi’s range of materials analyzers support the end-to-end metals production process from incoming inspection to final product assembly and finished goods testing to ensure product reliability, safety and regulatory compliance.
See the full range at: hhtas.net/read-the-metal Complete
Committee of Materials Australia where he is the Honorary Treasurer. In 2011/2012, the Institute went through a very difficult financial period and Paul was instrumental in developing fiscal strategies that saw MA pull through. We are in a much stronger financial position thanks to his contribution and we look forward to a bright future ahead.
The Distinguished Service Medal is presented to Paul Howard in recognition of the tireless support and enthusiasm given to Materials Australia.
21st - 23rd June 2023
The University of Sydney
The 3rd Asia-Pacific International Conference on Additive Manufacturing (APICAM) is the not-to-be-missed industrial application focused conference of 2023.
The 5th Asia-Pacific International Conference on Additive Manufacturing (APICAM) is the not-to-be-missed industry conference of 2023. APICAM was created to provide an opportunity for industry professionals and thinkers to come together, share knowledge and engage in the type of networking that is vital to the furthering of the additive manufacturing industry.
APICAM was created to provide an opportunity for industry professionals and academic researchers to come together, share knowledge and engage in the type of networking that is vital to the furthering of the additive manufacturing industry.
Some of the leading minds in the industry will give presentations on pressing issues and the ways in which innovations can navigate challenges. Important areas such as 3D printing and additive manufacturing in the automotive, biomedical, defence and aerospace industries will be covered by experts from each respective field.
Some of the leading minds in the field of additive manufacturing will give presentations on pressing issues and the ways in which innovations can navigate challenges. Important areas such as applications of additive manufacturing in the, biomedical, defence and aerospace industries will be covered by experts from each respective field.
The event is being curated by Materials Australia, the peak Australian materials technology body, which has drawn on its considerable pull in the industry to create a world-class event that is a must-attend for anyone involved in the additive materials industry.
The purpose of this conference is to provide a focused forum for the presentation of advanced research and improved understanding of various aspects of additive manufacturing.
Abstracts are able to be submitted in the following areas:
Additive Manufacturing of Metals
Additive Manufacturing of Polymers
Additive Manufacturing of Concretes
Advanced Characterisation Techniques and Feedstocks
Computational Modelling of Thermal Processes for Metallic Parts
The APICAM2023 organizing committee is seeking abstracts for either an oral or poster presentation.
The main features of APICAM 2023 will include presentations by experts as well as workshops that will help attendees sharpen their skills and then be able to pass on this knowledge to other industry professionals. The event has been designed to allow for ample networking time so that important knowledge-transfer can take place and partnerships can be created that will enrich the industry.
Enquiries:
Tanya Smith | Materials Australia
+61 3 9326 7266 | imea@materialsaustralia.com.au
Part Design for Additive Manufacturing
Failure Mechanisms and Analysis
Mechanical Properties of Additively Manufactured Materials
New Frontiers in Additive Manufacturing
Process Parameter and Defect Control
Process-Microstructure-Property Relationships
Enquiries:
www.apicam2023.com.au
Tanya Smith | Materials Australia
+61 3 9326 7266 | imea@materialsaustralia.com.au
Testing and Qualification in Additive Manufacturing
Source: Rachel White
The NSW branch committee has released its event list for 2023. We are in the process of planning these events and firm dates will appear on the Materials Australia website as we book dates. A list of these events is below. We will shortly be releasing our branch newsletter.
June – Careers event with Australian Ceramic Society. This is an online event with a panel of people working in different areas and roles in materials
science speaking about their careers and answering questions from attendees. The event is aimed at people undertaking studies and those in their early career to learn more about career paths.
August – our Metallurgy course will be running again this year. This course is well suited to people working in materials science who wish to refresh their skills or learn about metallurgy in more depth.
Lastek proudly introduced precision measurement instruments from the Helmut Fischer Group. Helmut Fischer is an innovative leader in supplying high-value products in industrial, process and laboratory measurement technology. Our products include instruments for measuring coating thickness, microhardness as well as material analysis and testing.
Handheld Instruments: Portable instruments for onsite measurements with interchangeable probes. Measure coating thickness on metals, electrical conductivity of metals, ferrite content in welded products, sealants on anodic coatings on aluminium, finding pores and defects on enamel, paint, rubber, bitumen and plastics.
September – Certified Materials Professionals (CMatP) Mini-Conference. Come along and hear from our newest CMatPs. This event will be online.
November – our popular Student Presentation Event will be run in-person and we will have a hybrid option if possible. Students present talks and posters on their research. Generous prizes are provided by our sponsors for this each year.
FUNDAMENTALS OF TITANIUM
CONTINUING EDUCATION WORKSHOP
The ITA is offering the Fundamentals of Titanium / Titanium the Ultimate Choice workshops in an in person format.
This comprehensive workshop will provide attendees with detailed information on the types, uses, and properties of common titanium alloys. Attendees will leave with an understanding of applied titanium metallurgy fundamentals.
Objectives & Content
Fundamentals of Titanium will prepare you to work effectively with job related functions that involve titanium. You will receive a complete overview of the titanium industry and a thorough grounding in its metallurgy, characteristics, properties and uses.
This workshop is brought to you by LMT2023 (Light Metals Technology 10-12 July 2023) www.lmt2023.com.au and sponsored by DMTC Ltd.
SESSION 1
• History
• Titanium from Ore to Metal
• Titanium Alloys and Heat Treatment
• Titanium Characteristics
• Corrosion
• Forming
SESSION 2
• Joining
• Finishing
• Properties & Design
• Comparisons with other Metals
• Applications
• Safety
• Recent Technology Advances
Donald E. Larsen
Donald E. Larsen is currently President of KineTic Engineering a consulting firm that provides expertise across the Titanium industry. Prior to this he spent over 30 years at Howmet Aerospace/Arconic retiring in 2018 as Vice President, R&D, General Manager Advanced Manufacturing for Arconic. In this role, he was responsible for leading R&D and production teams working on priority titanium technology projects, including 3D printing and advanced manufacturing activities. He also served as a liaison to the Arconic Technical Center (ATC) and Arconic’s Whitehall Technology Center. Don retired in Q3 of 2018 and temporarily took on the role of Interim Plant Manager Ti-Ingot Operation and Director of Special Projects.
Don joined Howmet Aerospace in 1988 and served in a number of roles focused on the research, development and production of titanium products. He has also held operational and sales and marketing roles with the company. Don has a master’s degree in metallurgical engineering from The Ohio State University, and is the holder of 11 U.S. patents. He has published more than 30 technical articles in the field of titanium.
$450+GST MA MEMBER
$500+GST NON MEMBER
$250+GST STUDENT
NOW
Enquiries: Tanya Smith Materials Australia +61 3 9326 7266
imea@materialsaustralia.com.au
Orthopaedics project, and that led to Hannah being employed by SEAM as a postdoc for the industrial companies of D&T Hydraulics and Engineering, Titomic, and King’s Flair.
While all the projects are rooted in materials engineering, each project has its own specialty. The D&T Hydraulics and Engineering project uses laser cladding to repair and refurbish worn and damaged mechanical parts, the Titomic project is developing machine learning models for optimisation of their cold spray additive manufacturing process, and the King’s Flair project is developing bioactive coatings. Hannah works mainly in project management, and collaborates with fellow ECRs and colleagues like Dr Samuel Pinches (another SEAM postdoc) to lead the D&T and Titomic projects. There are currently 6 active PhD candidates working industriously with SEAM ‘s industry partners to solve critical materials science problems. The feedback from the industry partners has been energising, with the universitybased R&D solutions being applied to commercial real world products. The work done by Hannah and the team at SEAM keeps young Australian researchers at the frontier of national and international STEM innovation.
Hannah King is a Postdoctoral Fellow with the Australian Research Council (ARC) Industrial Transformation Training Centre on Surface Engineering for Advanced Materials (SEAM) at Swinburne.
Hannah is an analytical chemist by training, with a PhD in chemistry (2020) from James Cook University in Queensland. Like many young researchers, Hannah was faced with a plethora of unknowns and opportunities once her PhD was completed; Was it best to continue blue sky research? Was it time to move from academia to industry and face real world technical problems? Was research and development (R&D) a viable career option in Australia? Then, lightning struck -literally. Hannah was offered an R&D postdoctoral position working with a wholly Australian
owned company called Lightning Protection International (LPI) on the next generation of lightning strike protection devices (i.e. lighting rods). Funded through the Innovative Manufacturing CRC (IMCRC), Hannah begun a postdoc career with the SEAM ARC training centre.
This was the best of all worlds; creative R&D work grounded in a real world problem. Hannah was able to apply her existing chemistry knowledge of materials characterisation to the project, but had to learn quickly the industrial-scale engineering systems which would be used to manufacture the lighting rod prototypes. The LPI project completed in 2022, but Hannah had her foot-in-the-door for real world R&D at SEAM: The LPI project led to another SEAM affiliated Allegra
Hannah appreciates that as a woman in science and engineering, she is given a greater opportunity to promote her work and have her story told. She understands that there is a unique power in being seen as a woman at the forefront of innovation by both young girls who inspire to a career in STEM, and fellow material scientist/engineers who understand the importance of closing the gender gap. The ARC and SEAM are thanked for providing equal opportunities to women of merit, such as Hannah, and are praised for their strong vision for diversity and inclusion.
For more information about SEAM, please visit www.arcseam.com.au/ or email seam@swinburne.edu.au.
10 TH INTERNATIONAL LIGHT METALS TECHNOLOGY CONFERENCE
9-12 JULY 2023 RMIT UNIVERSITY, MELBOURNE, AUSTRALIA
The Light Metals Technology (LMT) Conference is a biennial event that focuses on recent advances in science and technologies associated with the development and manufacture of aluminium, magnesium and titanium alloys and their translation into commercial products. The conference presents an opportunity for academic researchers, students and industry to discuss cutting edge developments and to facilitate new collaborations.
You are invited to submit abstracts on topics within the themes of Net Shape Manufacturing, Solid State Transformations and Mechanical Performance, and Translation to Applications. For example, but not limited to:
Opportunities for sponsorships and exhibitions are available, see below for contact details.
▶ Alloy development
▶ Solidification and casting
▶ Thermomechanical processing and forming
▶ Machining and subtractive processes
▶ Mechanical behaviour of light metal alloys
▶ Corrosion and surface modification
▶ Advanced characterisation techniques
▶ Joining
▶ Applications in bio-medical, automotive, aerospace, and energy industries
▶ Simulation and modelling
▶ Integrated computational materials engineering
The following members of Materials Australia have been certified by the Certification Panel of Materials Australia as Certified Materials Professionals.
They can now use the post nominal ‘CMatP‘ after their name. These individuals have demonstrated the required level of qualification and experience to obtain this status. They are also required to regularly maintain their professional standing through ongoing education and commitment to the materials community.
We now have nearly 200 Certified Materials Professionals, who are being called upon to lead activities within Materials Australia. These activities include heading special interest group networks, representation on Standards Australia Committees, and representing Materials Australia at international conferences and society meetings.
A/Prof Alexey Glushenkov ACT
Dr Syed Islam ACT
Prof Yun Liu ACT
Dr Karthika Prasad ACT
Dr Takuya Tsuzuki ACT
Dr Olga Zinovieva ACT
Prof Klaus-Dieter Liss CHINA
Mr Debdutta Mallik MALAYSIA
Prof Valerie Linton NEW ZEALAND
Prof. Jamie Quinton NEW ZEALAND
Dr Rumana Akhter
Anna Paradowska
Elena Pereloma
Miss Ana Celine Del Rosario VIC
Dr Yvonne Durandet VIC
Dr Mark Easton VIC
Dr Rajiv Edavan VIC
Dr Peter Ford VIC
Mr Bruce Ham VIC
Ms Edith Hamilton VIC
Dr Shu Huang VIC
Mr Long Huynh VIC
Mr. Daniel Lim VIC
Dr Amita Iyer VIC
Mr Robert Le Hunt VIC
Dr Michael Lo VIC
Dr Thomas Ludwig VIC
Dr Roger Lumley VIC
Mr Michael Mansfield VIC
Dr Gary Martin VIC
Dr Siao Ming (Andrew) Ang VIC
Dr Eustathios Petinakis VIC
Dr Leon Prentice VIC
Dr Dong Qiu VIC
Mr John Rea VIC
Miss Reyhaneh Sahraeian VIC
Dr Christine Scala VIC
Mr Khan Sharp VIC
Dr Vadim Shterner VIC
Dr Antonella Sola VIC
Mr Mark Stephens VIC
Dr Graham Sussex VIC
Dr Kishore Venkatesan VIC
Mr Pranay Wadyalkar VIC
Dr Wei Xu VIC
Dr Ramdayal Yadav VIC
Dr Jayantha Epaarachchi
Dr Jeff Gates
Mr Payam Ghafoori
David Harrison
Dr Damon Kent
Miss Mozhgan Kermajani
Mr Jeezreel Malacad
Dr Jason Nairn
Mr Sadiq Nawaz
Mr Bhavin Panchal
Mr Bob Samuels
Dr Mathias Aakyiir
Mr Ashley Bell
Ms Ingrid Brundin
Mr Neville Cornish
A/Prof Colin Hall
Mr Nikolas Hildebrand
Mr Mikael Johansson SA
Mr Rahim Kurji SA
Mr Andrew Sales SA
Dr Thomas Schläfer SA
Dr Christiane Schulz SA
Prof Nikki Stanford
Prof Youhong Tang
Mr Kok Toong Leong SINGAPORE
Mr Madhusudhanan Jambunathan UK
Mr Devadoss Suresh Kumar UAE
Dr Shahabuddin Ahmmad VIC
Dr Ossama Badr VIC
Dr Qi Chao VIC
Dr Ivan Cole VIC
Dr John Cookson VIC
Dr Sam Yang VIC
Dr. Matthew Young VIC
Mr. Mohsen Sabbagh Alvani WA
Mr Graeme Brown WA
Mr Graham Carlisle WA
Mr John Carroll WA
Mr Sridharan Chandran WA
Mr Conrad Classen WA
Mr Chris Cobain WA
Ms Jessica Down WA
Mr Adam Dunning WA
Mr Jeff Dunning WA
Dr Olubayode Ero-Phillips WA
Mr Stuart Folkard WA
Mr Toby Garrod WA
Prof Vladimir Golovanevskiy WA
Mr Chris Grant WA
Mr Paul Howard WA
Dr Paul Huggett WA
Mr Ivo Kalcic WA
Mr Ehsan Karaji WA
Mr Biju Kurian Pottayil WA
Mr Mathieu Lancien WA
Mr Michael Lison-Pick WA
Dr Evelyn Ng WA
Mr Deny Nugraha WA
Mrs Mary Louise Petrick WA
Mr Johann Petrick WA
Mr Stephen Rennie WA
Dr Mobin Salasi WA
Mr James Travers WA
Source: Materials Australia
Accreditation as a Certified Materials Professional (CMatP) gives you recognition, not only amongst your peers, but within the materials engineering industry at large. You will be recognised as a materials scientist who maintains professional integrity, keeps up to date with developments in technology, and strives for continued personal development.
The CMatP, like a Certified Practicing Accountant or CPA, is promoted globally as the recognised standard for professionals working in the field of materials science.
There are now well over one hundred CMatPs who lead activities within Materials Australia. These activities include heading special interest group networks, representation on Standards Australia Committees, and representing Materials Australia at international conferences and society meetings.
Benefits of Becoming a CMatP
• A Certificate of Membership, often presented by the State Chapter, together with a unique Materials Australia badge.
• Access to exclusive CMatP resources and website content.
• The opportunity to attend CMatP only
networking meetings.
• Promotion through Materials Australia magazine, website, social media and other public channels.
• A Certified Materials Professional can use the post nominal CMatP.
• Materials Australia will actively promote the CMatP status to the community and employers and internationally, through our partner organisations.
• A CMatP may be requested to represent Materials Australia throughout Australia and overseas, with Government, media and other important activities.
• A CMatP may be offered an opportunity as a mentor for student members.
• Networking directly with other CMatPs who have recognised levels of qualifications and experience.
• The opportunity to assume leadership roles in Special Interest Networks, to assist in the facilitation of new knowledge amongst peers and members.
What is a Certified Materials Professional?
A Certified Materials Professional is a person to whom Materials Australia has issued a certificate declaring they have attained all required professional
standards. They are recognised as demonstrating excellence, and possessing special knowledge in the practice of materials science and engineering, through their profession or workplace. A CMatP is prepared to share their knowledge and skills in the interest of others, and promote excellence and innovation in all their professional endeavours.
The criteria for recognition as a CMatP are structured around the applicant demonstrating substantial and sustained practice in a field of materials science and engineering. The criteria are measured by qualifications, years of employment and relevant experience, as evidenced by the applicant’s CV or submitted documentation.
Certification will be retained as long as there is evidence of continuing professional development and adherence to the Code of Ethics and Professional behaviour.
Contact Materials Australia today: on +61 3 9326 7266 or imea@materialsaustralia.com.au or visit our website: www.materialsaustralia.com.au
Regardless of whether you are working with lithium-ion (Li-ion) batteries, alkaline batteries, lead-acid batteries, fuel cells, MOFs, or any other energy storage device; there are critical component properties that must be characterised for performance and safety considerations. A high energy density, high power density and long cycle life has driven the adoption of Li-ion batteries toward renewable solutions in applications like automotive, grid energy storage and consumer electronics With demand expected to continue to grow, developing domestic battery supply chains, including battery manufacturing capacity is becoming increasingly important.
Micromeritics technologies offer analytical solutions for every step in the Li-ion battery manufacturing process, from precursor consistency to the electrode slurry preparation, coating, drying, and calendaring, and final cell electrolyte filling. Understanding the porosity of the electrodes and separators is important to guarantee the right ion accessibility and safety performance while BET surface area helps to optimise battery capacity and charging. Here we discuss pore structure and surface area determination using two proven techniques, namely mercury intrusion porosimetry and gas physisorption.
The AutoPore V uses mercury porosimetry with intuitive software to characterise Li-ion battery separators and electrodes. This uniquely valuable technique delivers a wide pore measurement range plus speed and accuracy critical to battery safety, energy density, and longer cycle life.
Separators are an important component that mechanically separates the anode and cathode while allowing maximum ionic conductivity of the Li-ion containing electrolyte. Its design and performance directly affect the capacity, cycle life, and safety performance of the battery. The separator must have sufficient porosity to hold liquid electrolyte, but excessive porosity hinders the ability of the pores to close which shuts down an overheated battery. The pore size must be smaller than the particle size of the electrode components, be uniformly distributed, while also having
a tortuous structure. This ensures a uniform current distribution helping to suppress the growth of lithium dendrites on the anode – a neural-like network of metallic growth that can form during charging that can short circuit the battery and cause the battery to catch fire.
The porosity of a separator or diaphragm is commonly measured directly by the mercury intrusion method, and the porosity result is generally about 40%-60%. Separators are thin films, less than 100 μm thick and to improve the statistical reliability of the measurement, a test sample consists of several pieces, sized to fit within the sample holder, or penetrometer. However during the test, mercury will be intruded into gaps at low pressure between these
sample test pieces and appear to indicate the filling of very large pores that are not characteristic of the material. As the pressure is increased, smaller and smaller sized pores are filled. The Autopore method identifies and eliminates the contribution of the interstitial filling to the porosity analysis of the separator thereby correcting the apparent pore volume distribution, which can be a critical property for the safety and reliability of li-ion batteries. Figures 2a and 2b show the cumulative intrusion and log differential intrusion as a function of applied pressure and pore diameter, respectively, for the separator. This example shows the wide dynamic range of pore volume measurement available, with most at sizes larger than 10,000 nm, due to the filling of interstitial space.
Electrode microstructure resulting from the manufacturing process has a direct influence on energy density, power, lifetime, and reliability of the lithium-ion cell, therefore understanding surface topology is critical. Increasing the surface area of the electrode will facilitate the ion exchange, however it does have limitations due to the degradation interaction of the electrolyte at the surface and resultant capacity loss along with thermal stability. While nanoparticles hold much promise to increase surface area without capacity loss, lower surface area materials are better suited for improved cycling performance of the cell resulting in longer battery life.
Micromeritics offers several physisorption systems like the 3Flex, for the development of cathode and anode materials that impact power and energy density as well as thermal/ chemical stability and enhance battery life and charge cycling.
DFT surface energy reveals surface topology and the level of interactions with an adsorptive gas present on the sample surface. The method uses an experimental isotherm based on the library of model isotherms of non-porous surfaces with different surface energies. The incremental surface area is plotted against the adsorptive potential energy which relates to the isosteric heat of adsorption. The colder the temperature the fewer interactions between the surface and the adsorptive gas and visa-versa. Adsorption
potentials ranging 50-60K represent basal planes; below 50K are prismatic surfaces; above 60K are defects, and those near 20K and 100K represent nitrogen condensation and presence of micropores, respectively, so they are unrelated to the surface energy of the material. The DFT surface energy distribution in Figure 3 shows graphene had stronger interactions with nitrogen than the graphite anode sample and graphene oxide exhibited the strongest interactions with the most surface area and defects.
Contact us for more information today!
ATA Scientific Pty Ltd
+61 2 9541 3500
enquiries@atascientific.com.au www.atascientific.com.au
Reference:
1. Micromeritics.com/lithium-ion/. CHARACTERIZING LI-ION BATTERY SEPARATORS. [online] Available at: https://www.micromeritics.com/ wp-content/uploads/12.08.21-AutoPore-APP-Note.pdf [Accessed 27 March 2023].
2. Micromeritics.com/lithium-ion/. CHARACTERIZING ADVANCED BATTERY ANODES WITH GAS ADSORPTION BET SURFACE AREA AND DFT SURFACE ENERGY. [online] Available at: https://www. micromeritics.com/Repository/Files/AppNote-202-Anode.pdf [Accessed 27 March 2023].
Monash University researchers recently demonstrated a counterintuitive way to protect atomically-thin electronics by adding vibrations.
Researchers squeezed a thin droplet of liquid gallium, and then painted graphene devices with a protective coating of glass, gallium-oxide. This oxide was remarkably thin and covered centimetre-wide scales, which made it potentially applicable for industrial large-scale fabrication.
“The oxide not only enhances and protects our devices when we first transfer it, but also later, during subsequent processing and fabrication,” said co-author Semonti Bhattacharyya.
The protective gallium-oxide delivered surprising results, as it reduced the electrical resistance in graphene, which is caused by thermal vibrations due to heat in the surrounding materials.
Lead author Matthew Gebert said gallium-oxide encapsulation is a mechanical transfer technique, which makes it different from other deposition methods. “That’s surprising because in effect we are actually adding extra vibrations, to reduce total vibrations.”
The study was the first time such a strategy to reduce the resistance due to thermal vibrations has been demonstrated in a graphene device.
The Monash team from the ARC Centre of Excellence in Future Low-Energy Electronics Technologies (FLEET) used a novel liquid-metal printing technique to create galliumoxide (Ga2O3) glass. The glass film that formed on the surface of droplets of liquid gallium metal is more than 5,000 times thinner than a human hair.
However, it can be reliably ‘printed’ from the surface of the liquid metal to form uniform continuous layers over centimetre-sized areas.
The liquid-metal method offers two advantages to protect
devices. Firstly, the layer-printing prevents growth damage, while the transferred layer is a good barrier for further processing.
Gallium-oxide encapsulation not only offers protection, but can also enhances performance because of its High-K dielectric qualities.
it is fundamentally different to alternative deposition methods, such as atomic layer deposition, evaporation, sputtering and vapor deposition, which have undesirable attributes such as high temperature requirements. Because gallium metal is liquid close to room temperature (30 0 C), this process has a lot of advantages for industrial adoption.
The vibrations of materials due to heat, which cause electrical resistance in materials, are called phonons. These vibrations cause the atoms in a solid to oscillate, and flowing electrons bounce off these oscillations and change their direction, which leads to electrical resistance.
The thermal vibrations of the carbon atoms in graphene itself cause remarkably little resistance, which is one reason why graphene is such a useful material for electronics.
However, the thin nature of graphene means that thermal vibrations in surrounding materials can have a large effect on electrons in graphene, and these are the predominant cause of electrical resistance in graphene at room temperature.
“You can think of this scenario as a fence. The fence (the 2D graphene) is affected by the actions of neighbours on both sides (the insulating materials on either side of graphene). One neighbour might have a clean environment on their side of the fence (a good insulator, with few phonons) but the other neighbour might have an overgrown garden that damages the fence,” Gebert said.
An automated, three-station, BET surface area and porosity analyser that delivers excellent repeatability and speed of analysis . Krypton option, allows measurements in the very low surface area range, as low as 0.001 m2/g.
MICROMERITICS TRISTAR II
MALVERN MASTERSIZER 3000
Market-leading laser diffraction particle size analyser (10nm to 3.5mm) to consistently deliver the accurate and reliable data for both wet and dry sample analysis. Intuitive software with built-in expertise informs critical decision-making throughout R&D and manufacturing processes.
Fully integrated desktop Scanning Electron Microscope (SEM) provides an easy-to-use interface with full-screen images in <40sec from sample loading. Ideal for large samples up to 100mm x 100mm. Live element ID using integrated X-Ray (EDS) detector.
PHENOM XL DESKTOP SEM
MICROMERITICS ACCUPYC
Non-destructive gas displacement pycnometry system provides high-speed, high-precision measurements of true density of powders, solids, and slurries. Monitoring true density of the electrode material ensures stability of the slurry coating and drying process. DENSITY
Universal powder tester for measuring the rheological properties of powders, pastes and semi-solids. Determine a powder’s Specific Energy, an indicator of inter-particular friction to reduce agglomerates in the electrode slurry.
Laser Metal Deposition (LMD), also known as laser cladding, is an innovative additive manufacturing (AM) technique that injects metal powder into a laser beam to create a new, strongly-bonded layer on top of a substrate. This technology has gained significant attention recently as a cost-effective and time-efficient repair method that can sometimes enhance material properties in the repaired area.
However, LMD can result in residual stresses and intricate microstructures that may negatively affect the performance of repairs. To tackle these challenges, the Australian Nuclear Science and Technology Organisation (ANSTO) has partnered with leading institutions, including the Royal Melbourne Institute of Technology (RMIT), Swinburne University of Technology (Swinburne), Defence Science and Technology Group (DSTG), and Rosebank Engineering, under
the auspices of the Defence Materials Technology Centre (DMTC), to develop advanced numerical models that capture the development of residual stresses and microstructure during the LMD process. These high-fidelity multi-physics numerical models can significantly enhance the optimisation of the LMD process and thus ensure the fatigue life of repaired components.
ANSTO's previous research on stainless steel and nickel alloys showed that thermo-mechanical models could predict welding-induced residual stresses accurately. However, modelling residual stress development in lowalloyed steels requires accounting for metallurgical and transformationinduced plasticity strains and heat treatment (tempering) of the material during the deposition process. To address these challenges, ANSTO has developed a high-fidelity thermometallurgical-mechanical numerical model for predicting the microstructure and residual stresses associated with a multi-pass (14-pass), single-layer LMD repair.
ANSTO’s numerical model, developed using the SYSWELD finite element package, takes into account the kinetics of solidstate phase transformations (SSPTs) and tempering (heat treatment) that occur during the
low-alloyed steel powder deposition on a matching low-alloyed steel substrate. The validity of the developed numerical methodology was assessed by comparing numerical predictions with experimental measurements. Microstructure predictions were indirectly validated through hardness measurements (Figure 1), while residual stress predictions were directly validated using X-ray measurements (Figure 2).
The comparison between hardness predictions and experimental measurements depicted in Figure 1 shows a good agreement, confirming the numerical model's accuracy in capturing the resulting microstructure consisting of bainite, martensite, and their tempered equivalents. The model correctly predicts the initial formation of martensite in the fusion zone (FZ) and its softening in the earlier LMD passes (P1 – P4) due to tempering from heating during subsequent material deposition. Later passes (P5 – P12) show higher hardness, suggesting a limited amount of tempered martensite, while in the absence of further deposition, the final two passes (P13, P14) remain in the as-formed (untempered) martensite condition.
When it comes to the prediction of residual stresses, the numerical model reveals a relationship between residual stresses and the formed microstructure. Regions with higher hardness containing more significant amounts of untempered martensite experience compressive residual stresses (P5 – P14), while softer regions with higher amounts of tempered martensite are under tensile residual stresses (P1 – P4). Similarly, the heataffected zone (HAZ) containing large
Figure 1: The developed model predicts the formation of complex microstructure containing martensite, bainite, and their tempered equivalents. The accuracy of the microstructure predictions is performed indirectly through hardness measurements. The excellent agreement between the predicted and measured hardness values validates the applied methodology, confirming the model's accuracy in predicting the resulting microstructure in an LMD repair.
amounts of soft tempered bainite is under tensile residual stresses. The modelling results demonstrate that martensite formation is associated with the development of compressive residual stresses, which is a result of the volumetric expansion of the crystal lattice upon cooling during the austenite-to-martensite (AtM) SSPT. The AtM SSPT counteracts the formation of tensile stresses, which is a common residual stress inducing mechanism in materials without AtM SSPTs. The model also shows that subsequent tempering of the formed martensite leads to the relief of compressive residual stresses, leaving tempered martensite regions under tensile residual stresses. The presence of residual stresses in components can significantly impact their life under operating conditions, as these stresses may either enhance or diminish the component's overall resistance to crack nucleation and propagation. Tensile residual stresses at the surface of the deposited layer can initiate crack nucleation and accelerate its propagation, potentially undermining the performance of LMD repair in realworld operating conditions. The current fatigue crack growth analysis indicates that cracks originating in regions of high tensile stresses of earlier passes (P1 – P4) grow considerably faster and deeper than those that form in regions of compressive stresses (P12 – P14). However, it is important to note that although the compressive residual stresses are often preferred, the presence of untempered martensite in the material can result in brittle characteristics that may not be desirable for all applications. It is, therefore, crucial to consider the benefits and drawbacks when optimising the LMD process for specific repair applications.
The high-fidelity, multi-physics numerical model of the LMD process developed by ANSTO can effectively capture the evolution of microstructure and residual stresses during the material deposition process. Hence, validated numerical simulations have the potential to revolutionise the LMD process by providing a faster method of testing a wide range of processing parameters with the aim of obtaining an optimal microstructure and residual stress distribution within a repaired component. As a result, the numerical simulations can reduce costs, shorten turnaround times,
and improve material properties in repaired regions, making LMD repairs an increasingly attractive option for industries seeking cost-effective and reliable repair technologies.
With the ongoing advancements in numerical modelling and additive manufacturing technologies, the future of LMD repairs is poised to become even more promising and transformative for the manufacturing and repair sectors. As research and development efforts continue to push the boundaries of LMD technology, industry stakeholders can expect further improvements in the efficiency, reliability, and performance of LMD repairs. By harnessing the power of high-fidelity numerical simulations, the collaborative efforts of ANSTO and its partners are paving the way for a new era of advanced repair solutions that cater to the diverse needs of various industries.
As LMD technology becomes more prevalent, industries worldwide will continue to benefit from the advancements driven by ANSTO and its collaborating partners. The high-fidelity numerical simulations developed through this collaboration have the potential to leave a lasting impact on the way repairs are conducted, leading to more efficient and reliable solutions for a broad array of applications. By continuing to refine and enhance the high-fidelity, multiphysics simulations, researchers and
engineers will unlock new possibilities for the LMD process, ultimately resulting in a more sustainable and innovative manufacturing landscape for years to come.
In summary, the collaborative research undertaken by ANSTO, RMIT, Swinburne, DSTG, and Rosebank Engineering has yielded valuable insights into the complex interplay of factors that influence LMD repair performance. This work has shown that by leveraging high-fidelity multi-physics numerical simulations, researchers and engineers can better understand these factors and develop more efficient and reliable repair techniques tailored to specific applications, ultimately benefiting a wide range of industries, from aerospace and automotive to energy and infrastructure.
Source: Sally Wood
Engineers in Melbourne recently used sound waves to boost production of green hydrogen by 14 times, through electrolysis to split water.
The team believe their invention offers a promising way to tap into a plentiful supply of cheap hydrogen fuel for transportation and other sectors, which could radically reduce carbon emissions and help fight climate change.
By using high-frequency vibrations to divide and conquer individual water molecules during electrolysis, the team managed to split the water molecules to release 14 times more hydrogen.
Electrolysis involves electricity running through water with two electrodes to split water molecules into oxygen and hydrogen gases, which appear as bubbles.
This process produces green hydrogen, which represents just a small fraction of hydrogen production globally due to the high energy required. Most hydrogen is produced from splitting natural gas, known as blue hydrogen, which emits greenhouse gases into the atmosphere.
Associate Professor Amgad Rezk
from RMIT University said the team’s innovation tackles big challenges for green hydrogen production.
“One of the main challenges of electrolysis is the high cost of electrode materials used, such as platinum or iridium.”
“With sound waves making it much easier to extract hydrogen from water, it eliminates the need to use corrosive electrolytes and expensive electrodes such as platinum or iridium. As water is not a corrosive electrolyte, we can use much cheaper electrode materials such as silver,” Rezk said.
The ability to use low-cost electrode materials and avoid the use of highly corrosive electrolytes are gamechangers for lowering the costs of producing green hydrogen.
The team recently secured an Australian provisional patent application to protect the new technology.
First author Yemima Ehrnst said the sound waves also prevented the buildup of hydrogen and oxygen bubbles on the electrodes, which greatly improved its conductivity and stability.
“Electrode materials used in electrolysis suffer from hydrogen and oxygen gas build-up, forming a gas
layer that minimises the electrodes’ activity and significantly reduces its performance,” said Ehrnst, who is also a PhD researcher at RMIT’s School of Engineering.
As part of their experiments, the team measured the amount of hydrogen produced through electrolysis with and without sound waves from the electrical output.
“The electrical output of the electrolysis with sound waves was about 14 times greater than electrolysis without them, for a given input voltage. This was equivalent to the amount of hydrogen produced,” Ehrnst said.
The Potential Applications of The Team’s Work
Distinguished Professor Leslie Yeo, who was one of the lead senior researchers, said the team’s breakthrough opened the door to using the acoustic platform for other applications.
“Our ability to suppress bubble buildup on the electrodes and rapidly remove them through high-frequency vibrations represents a major advance for electrode conductivity and stability,” said Yeo.
“With our method, we can potentially improve the conversion efficiency leading to a net-positive energy saving of 27 per cent.”
While the innovation is promising, the team hopes to overcome challenges with integrating the sound-wave innovation through existing electrolysers to scale up the work.
The fifth International Materials Innovations in Surface Engineering (MISE) conference will be convened in Brisbane, Australia. The conference will be located at the state-of-the-art St Lucia Campus of the University of Queensland: twenty minutes from the centre of Brisbane.
MISE2023 features eminent academic and industrial plenary, keynote and invited speakers who encompass the engineering modification of a material’s surface to improve its performance.
The conference will cover topics such as:
> Coatings and Thin Films for Extreme Industrial Environments
> Surface Modification for Industrial Applications
> Surface Modification for Biomedical Applications
> Modelling and Simulation related to Surface Engineering
> Vacuum Deposition Coatings and Technologies: PVD and CVD
> Thermal Spray Coatings and Technologies
> Weld Overlays and Technologies
> Laser Processing and Technologies
> Characterisation of Surfaces, Coatings and Films
> New Horizons in Coatings and Thin Films
> Educational and Training of Early Career Researchers in Surface Engineering
> Case Histories for Surface Engineering, including Failure Analysis
> Corrosion, Bio-corrosion and Coatings for Corrosion Protection
> Wear of Materials
> Surface modification for Wear and Corrosion Resistance
Abstracts
Abstracts open 1 December 2022 and can be submitted online through the MISE website - www.mise2023.com.au
• Guidelines and an abstract template can be downloaded
Sponsorship and Sponsorship and Industry Displays
A number of limited sponsorship packages will be available. There will also be opportunities for sponsors to reserve space to exhibit their products and technologies. Please see the MISE2023 website for details.
Why should you participate in MISE?
Enquiries
Tanya Smith
Materials Australia
+61 3 9326 7266
imea@materialsaustralia.com.au
• Networking opportunities to kick-off and maintain your research profile
• Interacting with leading, global industrialists to promote future activities
Contribute to your Continuing Professional Development (CPD) portfolio
Learn of the emerging manufacturing technologies that are on the near-term horizon
• A post-conference intense workshop
Source: Sally Wood
When thinking of renewable energy sources, it is often solar or wind that spring to mind first. But what about ocean energy?
The ocean covers more than 70 per cent of the earth’s surface, which provides enormous potential for renewable and clean energy. Institute for Frontier Materials (IFM) researchers hope to unlock this potential.
In a paper published in the Journal of the American Chemical Society, IFM researchers have demonstrated how new advanced two-dimensional (2D) nanomaterial membrane technology can improve blue energy harvesting processes. Blue energy harvesting is a renewable energy that uses the salt content difference between river water and seawater to generate electricity.
“Ocean energy is made up of five forms—tidal, water waves, ocean currents, temperature gradients and salinity gradient energy, offering a potential alternative, limitless energy resource,” said Associate Professor Weiwei Lei, who is leading the sustainable energy generation project at IFM.
“Therefore, harvesting ocean energy through artificial devices has attracted tremendous interest. Salinity gradient energy, also called “osmotic energy” or “blue energy”, provides significant promise for the development of renewable energy.”
Associate Professor Lei and his team members introduced a strategy to optimise the nanochannels within the 2D nanomaterial membranes, which harvest more energy through higher volumes of water.
Researchers constructed nanochannels from graphene oxide nanosheets. The sheets were chemically exfoliated, which altered loose reactive nanosheet fragments called oxidative fragments, which then became charged in alkaline conditions. The negatively charged channels attracted positive ions in sea water. The osmotic pressure can then ‘push’ the ions through the channels
to create a net current that can be harvested.
“However, the energy harvesting efficiency of these membranes is still too low to meet the demands of practical applications due to their high internal resistance and low selectivity of ions.”
“New advanced 2D nanomaterial membranes with novel and robust properties will solve this problem, which is in high demand now,” Associate Professor Lei said.
Through this approach, the membrane overcame the trade-off between permeability and selectivity.
Together, it ensured Associate Professor Lei’s membrane received a boost in energy generation compared to graphene oxide membranes that have not been treated to include negatively charged nanosheet fragments.
“This means we can harvest more energy through high volumes of water. This boosted energy generation is due to the enlarged nanochannels together
with the enhanced local charge density of the detached oxidative fragments,” he said.
The new strategy provides an alternative and facile approach for many applications that can exploit the ionic charges.
While the research is still limited to laboratory-sized equipment, researchers are planning to purchase a large facility to fabricate large membranes and other devices for large-scale applications.
“In the real-world we think that membranes could be installed in river mouths or at exit points for wastewater from industry,” Associate Professor Lei said.
“We are now looking for industry partners who are interesting in the development of new membrane technology for renewable energy generation.”
This work was supported by the Australian Research Council Discovery Program and the Australian Research Council Future Fellowship.
A serendipitous discovery has the potential to revolutionise embryo models and targeted drug therapies.
Materials scientists at UNSW Sydney recently showed that human pluripotent stem cells in a lab can initiate a process resembling the gastrulation phase. This involved cells differentiating into new cell types much earlier than what typically occurs in mother nature.
For an embryo developing in the womb, gastrulation occurs at day 14. But in a lab at UNSW’s Kensington campus, Associate Professor Kris Kilian oversaw an experiment where a gastrulation-like event was triggered within two days of culturing human stem cells in a unique biomaterial.
“Gastrulation is the key step that leads to the human body plan.”
“It is the start of the process where a simple sheet of cells transforms to make up all the tissues of the body—nerves, cardiovascular and blood tissue and structural tissue like muscle and bone,” said Kilian.
“So it’s really exciting that we were able to see this happening in vitro.”
The achievement was recently reported in the journal Advanced Science, and offers new treatments in medicine including cell therapy, targeted drug development and CRISPR gene-editing technologies.
Gastrulation is the key event in an embryo’s development when a mass of undifferentiated cells begin the first steps of a long journey in the womb towards formation of a human being.
This is one of the reasons that work on embryos left over from IVF is forbidden beyond 14 days, when gastrulation occurs.
Associate Professor Kilian said that up until now, it has been difficult to study this process in humans.
“Controlling gastrulation using materials alone will provide an
entirely new way for studying human development.”
“We currently can’t do this because embryo research beyond 14 days is often viewed as unethical, and it’s currently impossible in vivo because you’d need to observe an embryo in a pregnant human mother,” said Kilian. While there are animal models to study, and other researchers have induced gastrulation-like events in the lab using chemicals, this is the first time culture conditions alone have initiated gastrulation outside of a human body.
“Our method could lead to a new approach to mimic human embryogenesis outside of a person,” said Kilian.
As with most great discoveries in science, serendipity played a role.
In fact, the research team were not actively looking to bring on gastrulation when they dropped some stem cells onto the hydrogel substrate.
Lead author Dr Pallavi Srivastava was surprised by what she observed.
“Initially I was trying to get stem cells to attach to our hydrogels and planned to differentiate them in the conventional way.”
“The difference between cells cultured on glass and those on our gels was very striking. I remember thinking, ‘wow, something is going on here. I need to investigate.’ This led to a big shift in my project, and ultimately this exciting discovery,” said Srivastava.
The researchers believe they can continue exploring the benefits of their discovery by understanding how materials can guide embryogenesis and beyond.
In order increase IVF success rates and reduce stress on embryos, Fertilis, the Australian medtech startup, has developed and patented a unique environment for the critical life phase between fertilisation and implantation of the embryo. This was done by more closely mimicking the human body than other products currently on the market. The first-of-its-kind 3D-printed micro-device incorporates features 0.05 mm in diameter, allowing embryologists to precisely monitor and control the culturing process of the fertilised egg, eliminating the need for IVF-practitioners to move cells between petri-dishes, a process that is fraught with risk.
It is exactly those minuscule features –channels with a diameter smaller than a human hair – that proved challenging in the production of the device – especially with material and printers from other manufacturers. UpNano GmbH (Austria) achieved this by choosing specific base resins for a new material - UpFlow, a photopolymerising material – by keeping the viscosity of the material low until a final UV-exposure hardens the material and makes it ready to use. Additional advantages of the material include a high optical transparency –
making it ideally suited for microscopic inspections of the incubated embryos –and a very low autofluorescence.
Fertilis uses the brand new UpFlow resin, which was specifically developed for microfluidics, together with UpNano’s NanoOne 2PP 3Dprinter delivered last year to the Australian National Fabrication Facility (ANFF) at the University of South Australia. The NanoOne is an ultra-high-res 3D
printer that can print features down to 0.2µm and structures all the way up to 40x40x40mm. The 3D printer not only improves the quality of the 3D-printed micro-device for incubating embryos, but also the speed of production could be decreased from a full fortnight to only 4h by using a new feature called adaptive resolution. This enables the user to specify a combination of highquality areas and structural parts with less critical requirements.
The new procedure allows for a 30 –40% reduction of implantation cycles as commonly required to get pregnant, thus saving patients’ emotional and financial pain.
UpNano 3D printers and inks are distributed in Australia by AXT PTY LTD who offer a range of 3D printing and bioprinting solutions and related products.
This year marks the 50th since Rigaku pioneered the benchtop XRD. At the time, the concept was revolutionary with the system being significantly smaller and more affordable than anything before it. As such, it made XRD so much more accessible, bringing it out of highend research and into smaller labs and industry and is now referenced in more than 43,000 papers and patents.
Rigaku have continued to innovate to ensure they maintained a leadership position and the MiniFlex has registered several firsts:
• 1995 - First benchtop XRD to run on a Windows PC
• 2005 - First to benefit from a fast 1D detector
• 2010 - First to be powered by a powerful 600W X-ray generator
• 2017 - First to be compatible with a 2D detector
The MiniFlex is amongst Rigaku’s best selling product lines around the world. With its ability to generate publication quality data, it has helped XRD become more widely utilised with the ability to determine such things as:
• Crystalline phase identification (phase ID) and quantification
• Percent (%) crystallinity
• Crystallite size and strain
• Lattice parameter refinement
• Rietveld refinement
• Molecular structure
In Australia, the MiniFlex has become
an important teaching instrument helping groom students for life in both research and industry. Meanwhile, there are also numerous installations in industry where they are used in testing and QC labs, with options such as automatic sample changers, high temperature stages and various sample stages that can be added that make it suitable for a range of applications such as materials and chemical identification, development of battery materials, geology and mineralogy, pharmaceuticals as well as education and research.
Source: Sally Wood
The University of Adelaide stands tall as one of the world’s leading organisations for education and innovation. Founded in 1874, the University became the first in Australia to grant science degrees. In addition, it offered degrees in arts, law, medicine and music before the 1900s. Today, it is a member of The Group of Eight, which includes Australia’s top research-intensive universities.
It consistently features as a high ranking institution, with many international bodies placing the University in the top one per cent worldwide. Over 100 countries are represented in the student population, who total 7,868 of the 21,142 overall students.
The University also has an impressive list of alumni, including five Nobel Laureates; Australia’s first Indigenous Rhodes Scholars recipient; and Australia’s first female Prime Minister – Julia Gillard.
Quantum Materials is an exciting field at the boundary of condensed matter and quantum physics, material sciences, and a variety of engineering disciplines around optoelectronics and photonics. Researchers in quantum materials harness quantum mechanics to develop new or improved states of material leading to innovative devices and systems, with the goal of furthering our understanding of nature and creating new or improved technologies.
The University of Adelaide is delivering revolutionary technologies for next-generation communications, navigation, computing, cybersecurity and biomedicine. Quantum materials research at the University of Adelaide is focused on:
• Accelerated Material Discovery, including semiconductors, superconductors and aterials, nanoparticle doped optical glasses
• Ultrawide bandgap UV Photonics – Emitters, Detectors, and Modulators
• Ultrawide bandgap power electronics – Power Amplifiers, Transistors, Power Diodes
• Integrated quantum photonics, single photon sources, nanoscale solid-state spin qubit, modulators and detectors
• High-power, high-temperature, mechanical wear resistant, and ultra lightweight devices and sensors
• Integrated technologies for biological processes, food sciences, and agriculture
Advanced materials research and design is taking a step forward at two facilities at the University of Adelaide.
“The University of Adelaide’s Advanced Materials Facility and Silanna’s QuFab facility are set to push the boundaries of
advanced materials research, design and fabrication,” said the University of Adelaide’s Acting Vice-Chancellor Professor John Williams.
“By having industry and businesses such as Silanna on our campuses we are changing the very culture and nature of our campuses. Silanna’s expertise links into many different cutting-edge areas across the University including advanced materials research and teaching in our new facility.”
Advanced materials are made by modifying existing materials or creating new ones so that they have superior performance. They can be structural and functional, inorganic, organic or a hybrid of these, and can be soft or hard depending on their characteristics. These materials will make homes, vehicles and gadgets more energy efficient and environmentally friendly.
QuFab and the Advanced Materials Facility are both located on North Terrace campus in the University’s Faculty of Engineering, Computer and Mathematical Sciences.
“Today’s undergraduates and postgraduates will undertake their studies in the Advanced Materials Facility at the same time as having the unparalleled opportunity to tap into the minds of the experts working at QuFab,” said the University of Adelaide’s Professor David Lewis who is the Head of the School of Chemical Engineering and Advanced Materials.
“Our students will have access to a diverse range of facilities in which they will discover the world of advanced materials through engineering research, educational teaching and training activities, with a strong focus on new materials for energy, catalysis and semi-conductors.”
“These labs are where the future minds of the advanced materials industry will be trained.
“In the same way that the brightest minds will be attracted to study here, some of the world’s top research talent in this area is also being attracted to work here.”
Silanna Chief Scientist Dr Petar Atanackovic is focusing on designing and making prototypes of the next generation of semi-conductors at QuFab.
“At QuFab here in Adelaide, we are designing and manufacturing atomically engineered crystalline
semiconductors using applied quantum mechanics and proprietary atomic layer deposition technologies. These new compositions of matter are then fabricated into electronic and optoelectronic devices for applications including power conversion and extreme ultraviolet light detectors and emitters – we are unlocking new technology areas of fundamental physics, chemistry, electronics and photonics,” Dr Atanackovic said.
“Silanna’s UV-C light emitting diode (LED) technology is already commercialised and the work here at QuFAB is building the next generation of improved materials and technology. To achieve these goals we need talented and highly skilled people and it is one of the main reasons we have embedded ourselves into the University of Adelaide.”
Dr Atanackovic studied at the University of Adelaide and pursued a career in Silicon Valley before returning to Adelaide.
“I wanted to try and create some of the unique opportunities given to me while at Stanford University and Silicon Valley and bring them here to Adelaide. A whole ecosystem is beginning to appear, not only with large infrastructure investment like QuFAB, but also having the support of the University in building an environment for knowledge creation in this new area of quantum engineering,” he said.
In 2018 global semiconductor sales were worth $490 billion in total of which the diode, laser and LED segment of the market was worth $38 billion.
“The QuFab facility and the Advanced Materials facility, located here at the University of Adelaide, demonstrate how South Australia is investing in the future,” said Trade and Investment Minister Stephen Patterson.
“Innovation, global connectivity, hi-tech research and design into this cutting-edge technology, will have a snowball effect. South Australia’s hi-tech sector is gaining a worldwide reputation and partnerships like this enable our state to have the rare ability to rapidly scale to meet the skilled workforce needs of global technology companies.”
“The investment in research, design and education here and now, will have far reaching and long-term benefits for our economy and society.”
Silanna’s UV-C light emitting diode (LED) technology is already commercialised and the work here at QuFAB is building the next generation of improved materials and technology.
Credit: University of Adelaide.
There are several research facilities and institutes at the University of Adelaide focused on solving the next generation of advanced materials problems. Just some of these are outlined below.
The ARC Research Hub for Graphene Enabled Industry Transformation is a collaborative research team across six Australian universities—including the University of South Australia—and five industry partners who are committed to developing a sustainable graphenebased industry in Australia.
Graphene is an exceptional two-dimensional material with superior conductivity, flexibility and strength. It can be used to enhance existing products as well as producing entirely new products. Researchers in the Hub are developing graphene-based technologies and products for application in many sectors including mining, oil, gas and energy, biomedical, transport, construction, environmental, defence and space industries, with a view to developing an advanced materials manufacturing industry in Australia.
The Braggs Building is home to IPAS researchers and students from a broad range of scientific disciplines.
Credit: University of Adelaide.
The Institute for Photonics and Advanced Sensing (IPAS) fosters excellence in research in materials science, chemistry, biology and physics and develops disruptive new tools for measurement.
Many of the challenges we face as a society can only be solved by pursuing a transdisciplinary approach to science. IPAS has been created to bring together experimental physicists, chemists, material scientists, biologists, experimentally driven theoretical scientists and medical researchers to create new sensing and measurement technologies. IPAS is built on a strong ongoing partnership with DSTG and their support of numerous research projects and positions.
Gold may hold the key to unlocking an elusive but highly desirable reaction pathway. In fact, a new Australian-led study recently found gold atoms could be key to unlocking organic reactions.
Organic molecules are the building blocks for materials used every day—from clothes and coffee cups to the screen displays of mobile phones. Controlling reactions of these organic molecules is the key to designing materials with functional properties. However, reactions targeting carbon-hydrogen (C-H) bonds have long been of scientific interest given that almost all organic molecules contain these bonds.
FLEET researchers at Monash University recently found individual gold atoms may provide a low energy route for reactions, which can target specific C-H bonds.
“We used atomic-scale experimental techniques – scanning tunnelling microscopy and atomic force microscopy—to image and characterise the samples,” said lead author Benjamin Lowe, who is a FLEET PhD student at Monash. “These techniques revealed unusual covalent bonds between the carbon atoms of the DCA molecules and the gold atoms.”
The research team used state-of-the-art nanomaterial synthesis and scanning probe microscopy techniques to work on the synthesis of novel materials, which could be used in ultra-low energy electronic devices.
Researchers believe the broad interest in reactions of organic molecules could lead to a promising reaction. It could hold the answer for many applications like polymer fabrication and modification of pharmaceutical products. The study was led by the School of Physics and Astronomy at Monash University, with co-authors from the Institute of Physics, and Palacký University in the Czech Republic.
Organic (DCA) molecules combine with gold atoms (Au) on a silver surface, (Ag)
Scanning tunnelling microscopy (a) and non-contact atomic force microscopy (b) at Monash University of bonded DCA molecules and Au atoms allow direct observation of the chemical structure with covalent C-Au bonds. Scale bars: 0.5 nm.
Gold atoms provide a low-energy reaction route, allowing breaking of C-H bonds at room temperature, and formation of covalently bonded DCAAu-DCA structures. Grey: C, white: H, blue: N, black: Ag (surface), yellow: Au.
Scientists at RMIT University believe their latest research could advance the potential of nanomedicine to cure conditions that are currently incurable. This research could be a gamechanger for dementia and motor neurone disease. The work explores how nanoparticles would interact with cells in humans and provides fundamental knowledge to help improve nanomedicine and develop the next generation of personalised biomedical technologies.
Dr Aaron Elbourne is one of the lead researchers on the project, who said nanoparticle technologies could ultimately improve drug delivery, cancer treatments, disease diagnostics and antimicrobials.
“Nanoparticles have been investigated as advanced nanomedicines, but they often miss the mark or fail to deliver their treatment to a specific location within the body. The main challenge is to control how nanoparticles engage with cells to accurately deliver the medicine. This has been poorly understood until now, but our latest work offers a clearer picture of what is happening at that nano level.”
The latest study, in collaboration with the University of Durham, was published in the ACS Nano journal.
One of the main barriers to finding a cure for diseases such as dementia and motor neurone disease is the current inability to deliver treatments that can cross the blood-brain barrier.
Dr Andrew Christofferson, who was another researcher on the project, said the work was unique.
"What makes this work unique is that we combine experiments and modelling to show a level of detail not seen before, and this will serve as a platform for future studies of nanoparticles and biological materials."
A new low-cost battery, which holds four times the energy capacity of lithium-ion batteries and is far cheaper to produce, could significantly reduce the cost of transitioning to a decarbonised economy.
Dr Shenlong Zhao from the University of Sydney developed the battery using sodium-sulphur, which is a type of molten salt that can be processed from sea water.
Researchers used a simple pyrolysis process and carbonbased electrodes to improve the reactivity of sulphur and the reversibility of reactions between sulphur and sodium. The battery then shook off its formerly sluggish reputation, and exhibited super-high capacity and ultra-long life at room temperature.
It is also a more energy dense and less toxic alternative to lithium-ion batteries, which, while used extensively in electronic devices and for energy storage, are expensive to manufacture and recycle.
According to the Clean Energy Council, 32.5 per cent of Australia’s electricity came from clean energy sources and the industry is accelerating in 2021.
“Our sodium battery has the potential to dramatically reduce costs while providing four times as much storage capacity. This is a significant breakthrough for renewable energy development which, although reduces costs in the long term, has had several financial barriers to entry,” said Dr Zhao.
The lab-scale batteries have been successfully fabricated and tested in the University of Sydney’s chemical engineering facility.
The researchers hope to improve and commercialise the fabricated Ah-level pouch cells.
“We hope that by providing a technology that reduces costs we can sooner reach a clean energy horizon,” Dr Zhao said.
To keep pace with these solar capacity forecasts, annual global production of silicon and its purified form - polysilicon - will have to materially increase.
Australia can become a global superpower in solar PV energy generation and export, but it must develop its own fully integrated domestic solar supply chains, according to a landmark new report.
The Australian Silicon Action Plan sets out the actions needed to participate in a fully-fledged supply chain for silicon and solar cells. The report was commissioned by Australia’s national science agency CSIRO, and found that while Australia has immense potential, its reliance on overseas supply chains holds us back.
“Australia already has the highest per capita deployment of rooftop solar in the world, and there are several megaprojects in the solar development pipeline,” said CSIRO Senior Principal Research Scientist Dr Chris Vernon. “But one of the greatest risks to Australia’s solar ambitions and energy future is our reliance on overseas supply chains for solar cell technology.”
The Australian Silicon Action Plan sets out recommendations and actions to take across three horizons:
1. actions that can commence immediately to develop an integrated silicon and solar cell supply chain
2. actions focused on expanding Australia’s supply chain activity
3. actions that will lead to an integrated, low-carbon and circular solar cell supply chain in Australia.
“Australia has enormous potential when it comes to supplying solar power for its own and also the region’s energy needs, but our current reliance on concentrated silicon and solar cell supply chains poses risks to Australia’s energy independence,” Dr Vernon said.
The battery has a longer life span compared to previous sodium-sulphur batteries. Pixabay.Scientists recently developed a positive electrode material that does not diminish after repeated charging cycles, for the manufacture of durable solid-state batteries.
Electric cars are widely regarded as the best bet to replace conventional cars with a more environment-friendly alternative. However, electric cars and other electric vehicles will most likely run on lithium-ion batteries, which do not deliver the necessary performance and durability at a reasonable price.
A team of scientists led by Professor Naoaki Yabuuchi of Yokohama National University in Japan, recently investigated a new type of positive electrode material with unprecedented stability in solid-state batteries.
When ball-milled down to an appropriate particle size in the order of nanometers, this material offers high capacity thanks to its large quantity of lithium ions, which can be reversibly inserted and extracted during the charge and discharge process.
The researchers analysed the origin of this property and concluded that it is the result of a fine balance between two independent phenomena that occur when lithium ions are inserted or extracted from the crystal.
“We anticipate that a truly dimensionally invariable material – one that retains its volume upon electrochemical cycling— could be developed by further optimising the chemical composition of the electrolyte,” Professor Yabuuchi said.
The development of long-life and high-performance solidstate batteries could be the answer to some of the problems faced by electric vehicles
“In the future, for instance, it may be possible to fully charge an electric vehicle in as little as five minutes,” Professor Yabuuchi said.
ANSTO’s own meteorite hunter—planetary and instrument scientist Dr Helen Brand—recently took part in an expedition that found the largest meteorite strewn field in Australia since the famous Murchison meteorite event in 1969.
The team worked in collaboration with Monash University and Curtin University’s Space Science and Technology Centre, and the support of the Bureau of Meteorology.
“It is quite exciting to be involved in this find, which took place in September. In the future, as part of the research plan, we will look at this meteorite on several of the synchrotron instruments to unlock the secrets of its journey through space as well as its history on the surface of our own planet.” said Dr Brand.
“As a meteorite, it is quite dark which reflects that it is fresh, fell to earth not that long ago,” she explained.
Freshly fallen meteorites have a distinctive black fusion crust formed when the object enters the atmosphere at extremely high temperatures.
However, the scientists were able to define a search area on the ground in an area north of Port Augusta. Over a period of several days 44 meteorites were recovered, totalling a little over 4kg in mass. The team estimated it weighed six tonnes when it entered the atmosphere in 2013.
“It is not a rare type of meteorite, but the quantity of meteorites could be substantial. After a very short search, we located about four kilograms but there could several more out there,” said Dr Brand.
Monash University researchers recently found how substrates affect strong electronic interactions in twodimensional metal-organic frameworks. Materials with strong electronic interactions can have applications in energy-efficient electronics. When these materials are placed on a substrate, their electronic properties are changed by charge transfer, strain, and hybridisation.
The study found that electric fields and applied strain could be used to ‘switch’ interacting phases such as magnetism on and off, allowing potential applications in future energyefficient electronics.These effects have uses in magnetic memory, spintronics, and quantum computing, and makes them appealing for emerging technologies.
“We observed this effect when the material was grown on silver, but not when it was grown on copper, despite them being very similar,” said Bernard Field, who is a co-author of the study.
“So that begged the question: why did the material behave so differently on different substrates?”
The researchers simulated the metal-organic framework, which allowed the team to quickly and easily explore a wider range of systems with fine control over the important parameters. The study also showed that applied strain could turn magnetism on and off. This could be achieved using piezoelectric materials. It is also an important consideration for flexible electronics.
“The team is continuing to investigate strong interactions in 2D metal-organic frameworks, which provide a rich platform to explore novel quantum physics applied for energy-efficient electronic devices,” said Professor Nikhil Medhekar, who is a corresponding author on the study.
Substrates can change the magnetic properties of 2D MOFs via three key variables: charge transfer (which can be controlled by electric fields), strain, or hybridisation.
A 2D metal-organic framework (MOF) on a substrate. Strong electronic interactions in the MOF allow local magnetic moments (arrows) to form in the molecules.
Researchers at RMIT University have found an innovative way to rapidly remove hazardous microplastics from water using magnets.
Lead researcher Professor Nicky Eshtiaghi said existing methods could take days to remove microplastics from water, while their cheap and sustainable invention achieves better results in just one hour.
The team have developed adsorbents, in the form of a powder, that remove microplastics 1,000 times smaller than those currently detectable by existing wastewater treatment plants.
The researchers have successfully tested the adsorbents in the lab, and they plan to engage with industry to further develop the innovation to remove microplastics from waterways.
“The nano-pillar structure we’ve engineered to remove this pollution, which is impossible to see but very harmful to the environment, is recycled from waste and can be used multiple times,” said Professor Eshtiaghi from the School of Engineering.
“This is a big win for the environment and the circular economy.”
Developing a cost-effective way to overcome the challenges posed by microplastics remains a critical task for researchers.
“Our powder additive can remove microplastics that are 1,000 times smaller than those that are currently detectable by existing wastewater treatment plants.”
“We are looking for industrial collaborators to take our invention to the next steps, where we will be looking at its application in wastewater treatment plants.” Professor Eshtiaghi said.
The research team worked with various water utilities across Australia, including Melbourne Water and Water Corporation in Perth on a recent Australian Research Council Linkage project to optimise sludge pumping systems.
Professor Ali Abbas has become Australia’s first Chief Circular Engineer, after taking a new role at Circular Australia to accelerate the nation’s transition to a circular economy.
Professor Abbas, who is from the School of Chemical and Biomolecular Engineering at the University of Sydney, said he was honoured to be appointed into the role.
“I’m delighted to be joining Circular Australia as the first Chief Circular Engineer to support the critical work of removing barriers to an Australian circular economy by 2030.”
“The circular economy is a systems framework based on three principles—the elimination or ‘design out’ of waste and pollution, the circulation of products and materials at their highest value, and the regeneration of nature,” he said.
The Chief Executive at Circular Australia, Lisa McLean said the transition to a net zero circular economy is one of the biggest challenges of this generation.
“With science and innovation leading, Australia can deliver new industries and hundreds and thousands of jobs— positioning itself as a global circular economy powerhouse.”
“Circular Australia is excited to be working with Professor Abbas who is bringing fresh ideas and new approaches to traditional engineering practices and driving innovative design thinking for the new circular economy,” she said.
Decoupling economic activity from the consumption of finite resources, and designing waste out of the system is based on three principles: designing out waste and pollution; keeping products and materials in use; and regenerating natural systems. The value of the Australia circular economy is around $1.9 trillion.
Scientists in New Zealand and Australia, who are working at the level of atoms recently created something unexpected: tiny metallic snowflakes.
Nanoscale structures (a nanometre is one billionth of a metre) can aid electronic manufacturing, make materials stronger yet lighter, or aid environmental clean-ups by binding to toxins.
To create metallic nanocrystals, scientists have been experimenting with gallium; a soft, silvery metal, which is used in semiconductors and, unusually, liquifies at just above room temperature.
The Australian team worked in the lab with nickel, copper, zinc, tin, platinum, bismuth, silver and aluminium. Metals were dissolved in gallium at high temperatures. Once cooled, the metallic crystals emerged while the gallium remained liquid.
Meanwhile, the New Zealand team carried out simulations of molecular dynamics to explain why differently shaped crystals emerge from different metals.
“What we are learning is that the structure of the liquid gallium is very important,” said Professor Nicola Gaston, who is from the University of Auckland.
“That’s novel because we usually think of liquids as lacking structure or being only randomly structured,” she explained. Interactions between the atomistic structures of the different metals and the liquid gallium cause differently shaped crystals to emerge, the scientists showed. The crystals included cubes, rods, hexagonal plates and the zinc snowflake shapes.
Professor Gaston believes the research has opened a new, unexplored pathway for metallic nanostructures. “There’s also something very cool in creating a metallic snowflake!”
This metallic snowflake is about 100 microns across, roughly the thickness of a human hair.
Super-thin chips made from lithium niobate are set to overtake silicon chips in light-based technologies, according to world-leading scientists in the field, with potential applications ranging from remote ripening-fruit detection on Earth to navigation on the Moon.
They say the artificial crystal offers the platform of choice for these technologies due to its superior performance and recent advances in manufacturing capabilities.
RMIT University’s Distinguished Professor Arnan Mitchell and University of Adelaide’s Dr Andy Boes led this team of global experts to review lithium niobate’s capabilities and potential applications in the journal Science.
The international team, including scientists from Peking University in China and Harvard University in the United States, is working with industry to make navigation systems that are planned to help rovers drive on the Moon later this decade.
More than $4.8 million will be allocated to 10 research projects aiming to innovate and expand the University of Newcastle’s knowledge of the universe.
The researchers will tackle some key challenges, including managing the recovery of coral reefs from bleaching events, and improving the prediction of extreme space weather events, which pose an increasing threat to our technologically-dependent society.
In one project, $364,430 will be allocated for research for a new single-layer diamond, which is a new frontier of material research.
Preparation is still in infancy with many structures predicted possible even though they have not been made experimentally. The project will address a research gap towards synthesising new diamante-like nanostructures and developing an in-depth understanding of the chemically induced phase transformation.
Preliminary data points to both feasibility and impact for discovering new materials and technologies, which will bring foreseeable scholarly, economic, and social benefits.
In another project, $268,080 has been allocated to analyse Australian clays as raw materials of slow-release phosphate fertiliser.
It will then develop activated clays using Australian raw clay minerals to formulate effective slow-release phosphate fertilisers. The project will be led by Professor Ravi Naidu; Dr Bhabananda Biswas; and Dr Tom Cresswell.
Discovery Projects is the scheme for fundamental research and the largest scheme, which provides funding of between $30,000 and $500,000 each year for up to five consecutive years.
The 2022 ARC Discovery Projects scheme forms part of the University of Newcastle’s commitment to learning about the environment, and how to protect it.
As it is impossible to use global positioning system (GPS) technology on the Moon, navigation systems in lunar rovers will need to use an alternative system, which is where the team’s innovation comes in.
By detecting tiny changes in laser light, the lithiumniobate chip can be used to measure movement without needing external signals, according to Mitchell.
“This is not science fiction – this artificial crystal is being used to develop a range of exciting applications. And competition to harness the potential of this versatile technology is heating up,” said Mitchell, Director of the Integrated Photonics and Applications Centre.
Hypersonic flight has well and truly taken off. But what exactly makes hypersonic technology so special?
When an airborne vehicle travels at hypersonic speed, it is moving at more than five times the speed of sound, otherwise known as Mach 5. For context, a trans-atlantic plane typically flies below Mach 1, while an F35 Joint Strike Fighter flies at Mach 1.6.
As such, hypersonic technology could be the key to the future of international air travel, where flights from Sydney to London could be undertaken in under three hours.
Australian researchers are at the forefront of this technology.
Practitioners from the University of Queensland have already developed new materials for use through the Hypersonic International Flight Research Experimentation (HiFiRE) program.
The initiative—one of the largest collaborative research programs between Australia and the United States—developed the 5B experimental rocket. The rocket has hit targeted speeds of Mach 7.5 (9,200kmph) and reached a height of 278km from Earth.
Professor Michael Smart said the flight placed the Australian aerospace industry on the international stage. "We’re excited by the contributions this and future HIFiRE flights will make to the advancement of hypersonic flight technology.”
HiFiRE 5B is one of 10 experimental flights as part of the international collaboration, which investigates the physical phenomenon of flying faster than five times the speed of sound.
The partnership places the US Air Force Research Laboratory, Boeing and HiFiRE in the same room, alongside world-
class Australian researchers, to deliver sustainable solutions.
“The knowledge gained from these experiments will be applied to develop future flight vehicles and testing of advanced air-breathing hypersonic propulsion engines, known as scramjets,” Professor Smart said.
What is Hypersonic Technology?
Australia punches above its weight when it comes to developing hypersonic technology.
In the 1960s, Ray Stalker increased the maximum velocity limits on the ground-based testing of hypersonic flow by developing the free-pistondriven hypersonic shock tunnel at the Australian National University in Canberra.
Mr Stalker and his colleagues made significant inroads in their understanding of hypersonic flows with real gas (finite-rate chemistry) effects. These results have proven to be critical to the design and operation of re-entry vehicles such as NASA’s Space Shuttle.
At the same time, Australia was pioneering free-piston hypersonic shock tunnels, and used the research from those tunnels to power the next generation of flight.
By the 1980s, the scramjet engine was introduced as a combustion of fuel in a stream of air, which offered a highly efficient forward motion. The first demonstration of an in-flight pure supersonic combustion scramjet flight was tested at Woomera in 2002.
These achievements are the benefits of government-funded research, which is then suited to the needs of end-users in the global hypersonic market.
However, like all research endeavours,
materials are the key to unlocking a hypersonic future.
New materials are constantly needed to deal with a range of environmental conditions and threats. From the coatings that repel water on a cargo ship, to the post-heat treatment on commercial jetliners; the benefits of materials science is far and wide.
As such, researchers work with end-users to develop, validate, and test a variety of structural designs, components and materials that are able to withstand the extremities of hypersonic flight.
In an ever-changing security and defence landscape, hypersonic technology is the key to skimming the stratosphere to hunt down long-range missiles and targets.
As such, the Federal Government is pouring additional funding into developing hypersonic technology to protect Australia’s national interest. In 2022, a $14 million purpose-built hypersonic research and collaboration facility was unveiled in Brisbane. The Eagle Farm establishment is tipped to supercharge Australia’s defence research. The purpose-built facility seeks to advance the nation’s understanding and use of hypersonic technology through flight test vehicles.
Defence Chief Scientist Professor Tanya Monro said the new precinct would demonstrate that Australia has the maturity to be able to contribute and create real deterrence.
“The technology developed here says the government will give Australia the ability to strike back should anything similar ever be used against us.”
“We have great confidence in our ability to make vehicles that really do withstand those intense and extreme conditions,” Monro said.
More than 60 staff will work at the facility, which will support collaboration between Defence, industry, universities and international partners to advance the development of hypersonic technology.
The research and development efforts will focus on high-speed and hypersonic flight research, and technologies. Researchers from the Department of Defence will work together to develop and characterise sovereign hypersonic technologies. They will also generate ‘true’ hypersonic flight conditions at a large scale in a classified laboratory. This builds on the HIFiRE project, which was formed to investigate hypersonic flight technology, the fundamental science and technology required, and its potential for next generation development.
It has received funding from the
Queensland Government National and International Research Alliances Program.
In September 2021, Australia, the United Kingdom, and United States announced a defence and security pact, which became known as the AUKUS alliance.
It supports trilateral ties across the Indo-Pacific region in an increasingly challenging geopolitical environment. The deal was centred around a fresh class of nuclear-propelled submarines, which would be stationed in Australia.
After the deal was announced, the AUKUS leaders expanded the agreement to include hypersonic technology in Australia.
Prime Minister Anthony Albanese said the AUKUS alliance is crucial for maintaining an international order, which includes a peaceful resolution of disputes free from coercion.
“We have also made significant strides in our trilateral cooperation on advanced capability initiatives: hypersonics and counter-hypersonics, electronic warfare capabilities, cyber, artificial intelligence and autonomy, quantum technologies, and additional undersea capabilities,” he said.
At the time, Minister for Defence Peter Dutton said industry, universities and international partners will collaborate to advance Australia’s understanding and use of hypersonic technology through flight test vehicles.
“It’s a complex technological challenge to build vehicles capable of flying at five times the speed of sound, that skim the stratosphere, to target any location on the planet.”
“The technology that is developed here will help us to better defend against the malign use of this technology and give us the ability to strike any potential adversaries from a distance and deter aggression against Australia’s national interests,” he said.
The Federal Government has also announced a $3.5 billion fund to bolster Australia’s missile program. It includes plans to upgrade Australian missile manufacturing through the Eagle Farm facility in Brisbane.
Dr Malcolm Davis is a Senior analyst at the Australian Strategic Policy Institute, who said the challenge will be to deploy the capability at a high technological readiness level.
“We spend a lot of time doing science in the lab but then we don’t turn that science into actual capability whereas the Russians and Chinese seem to move more swiftly to deploy hypersonic weapons.”
Australia has had a long history of working with the United States on various defence projects. For instance, the two nations signed a collaborative agreement to develop and test hypersonic cruise missile prototypes under the Southern Cross Integrated Flight Research Experiment.
This program is based on more than 15 years of collaboration between Australia and the United States on science and technology research into hypersonic scramjets, rocket motors, sensors, and advanced manufacturing materials.
The new weapon will be a Mach 5-class precision strike missile that is propulsion-launched and powered by an air-breathing scramjet engine, which will be capable of being carried by tactical fighter aircraft such as the F/A-18F Super Hornet, EA-18G Growler and F-35A Lightning II.
Similarly, the HIFiRE program achieved some significant milestones, such as the design, assembly and pre-flight testing
of the hypersonic vehicles and the design of complex avionics and flight systems.
This made it one of the most advanced hypersonic programs in the world.
But there is still more work to do. In fact, Australia is working with the United States and other partners on blending hypersonic technology into space.
The Brisbane-based aerospace engineering start-up, Hypersonix Launch Systems recently announced it was looking to launch a zero CO2 emissions hypersonic spaceplane capable of deploying small satellites into low Earth orbit.
The start-up signed a Master Research Agreement with the University of Sydney to research and manufacture the components of the zero emissions spaceplane.
Hypersonix hopes to build and operate a small satellite launch system in Australia for international customers.
“This is really important; if Australia can develop that sort of capability then that would be world-leading,” Mr Davis at the Australian Strategic Policy Institute said.
“The potential use of this hypersonics research park shouldn’t just be for defence applications in terms of missiles, it should also be applied to space access because that’s an area where we could potentially leap-frog ahead of other countries.”
There are over 100 small launch vehicle companies in development around the world. However, unlike Hypersonix, few use green hydrogen as a fuel, and none use scramjet technology for small satellite launches.
Hypersonix is seeking to create the world’s leading sustainable hypersonic technology, which disrupts the way humans fly to space and around the world.
This will reduce the technological risks and time to market, which secures a lower cost structure for end-users.
Quickstep is a carbon fibre composites manufacturer who is working with the Department of Defence to identify, analyse and test high temperature materials.
The end-user driven research— powered by the Defence, Science and Technology Group (DSTG)—is the first step towards the development of future hypersonic aerostructures.
Hypersonic aerostructures are components of an aircraft's airframe that are capable of withstanding extreme conditions experienced during hypersonic flight.
The company will obtain commercialisation rights to any newly developed intellectual property, with the ownership retained beneficially for Australia’s sovereign defence capability by DMTC Ltd.
The project will also involve highly technical experts from the University of NSW who specialise in the field of hypersonic technology.
Hypersonics are not a new phenomenon but countries are currently in an arms race to develop the next generation of missiles that cannot be intercepted or detected.
The project, dubbed ‘Hype-X’, will initially focus on the applicability of existing high-temperature materials
for the manufacture of hypersonic aerostructures.
It will then move to develop novel materials and manufacturing processes to fill capability gaps.
Mark Burgess is the Chief Executive Officer and Managing Director at Quickstep, who said the company is well-positioned to deliver this research feat.
“Quickstep is well known for its advanced composite aircraft structures and has a long history of developing and commercialising advanced composites processes and technologies in new applications.”
"Innovation is at the core of Quickstep, and the Hype-X partnership positions the company in the development of sovereign hypersonic aerostructures and will further diversify and grow our business over the long term,” he explained.
As geopolitical tensions continue to evolve, countries are working to develop manoeuvrable hypersonic vehicles and missiles.
There are two theorised ways to achieve this. First, a hypersonic cruise missile that could see a rocket blast to Mach 5 before using an air-breathing engine, or scramjet, to maintain its momentum.
The second, known as a glide vehicle, could involve a rocket blasting into the sky before releasing a separate hypersonic missile, which has built up enough velocity to travel under its own speed.
This two-step system can cruise along in the upper atmosphere with enough space to maintain lift but without too much to create drag.
Current examples of such technology include the Avangard (Russia), the Conventional Prompt Strike system (United States), and the Dongfeng-17 (China).
DMTC Chief Executive Dr Mark Hodge praised the exceptional leadership in applying science and technology to safeguard Australia and its national interests.
“I’m delighted that DMTC’s relationship with DSTG continues to grow and to have this opportunity to collaborate with Quickstep, an Australian company with a deep history of developing aerospace composites, and with UNSW.”
"We are bringing expertise from across the nation’s leading aerospace R&D organisations to the fore in the development of hypersonic materials, which has far-reaching and important defence and national security applications,” he said.
The University of Queensland has had hypersonic flight in its sights for over a decade.
Researchers, scientists, students and industry professionals work together to develop new technologies for the next generation of Australia’s defence sector. For example, Queensland is the home of development for a hybrid rocket, which has launched small satellites into low-Earth orbits.
Dr Ingo Jahn worked with the Gold Coast-based Gilmour Space on propellant feed systems and cycles for launch vehicles in space.
He said having researchers and industry work closely together was invaluable for Australia’s space industry.
“Rather than buying products from overseas, the rockets and components will be manufactured in Australia, and this is an essential step towards developing a space launch vehicle industry in Queensland with many expected flow-down benefits to our
manufacturing industries.”
The University of Queensland team have focussed on developing and validating the fuel feed system, which must meet the stringent control and performance requirements of the launch system, while also remaining as light as possible.
“Fuel delivery systems for rockets are one of the most complex engineering challenges,” Dr Jahn said.
“They are located at the intersection of multiple systems; to stay light they have to be incredibly power dense, they must operate across wide temperature and pressure ranges and they are safety critical.”
“Finding effective and safe engineering solutions to meet all these requirements, while remaining light weight is the challenge we have to overcome,” he explained.
Meanwhile, Gilmour Space is at the forefront of development for nextgeneration hybrid rocket technologies
that are safer and more cost-effective than traditional chemical-propulsion rockets.
Chief Operating Officer and company co-founder James Gilmour said the pandemic sparked a busy period for the group as it developed and tested the various rocket systems in the orbital launch vehicle.
“We’re grateful to UQ and the government for supporting our efforts to grow a space launch industry here in Queensland,” Mr Gilmour said. Similarly, Dr Jahn said the partnership is an excellent opportunity, which combines know-how and fundamental research.
“Seeing your research adopted into a product is the dream of every researcher and engineer—what could be better than seeing your research fly to the stars?”
The University of Queensland has been at the forefront of hypersonic development since 2012, when the iconic SCRAMSPACE project passed its critical design review.
SCRAMSPACE is a free-flying hypersonic scramjet, which has the capacity to reach 8600km/h.
It became the first and largest project funded by the Australian Space Research Program.
“A scramjet is an airbreathing engine for hypersonic craft that travel at many times the speed of sound, for high speed transport in Earth’s atmosphere or along trajectories to space, said Professor Russell Boyce.
"They improve the efficiency and reliability and reduce the cost of inserting satellites into orbit,” he added.
The program was supported by a $14 million international consortium of partners in five countries, and led by The University of Queensland’s Centre for Hypersonics.
Research for this project was conducted at the University of Queensland’s T4 shock tunnel, as well as the very large shock tunnels at the German Aerospace Centre in Göttingen, Germany and at the Japanese Aerospace Exploration Agency near Sendai, Japan.
“It gives us a voice in the international space arena, to be able to participate in discussions on space regulations and activity that will affect us,” Professor Boyce said.
The research team used a hypersonic wind tunnel and a X3 expansion tunnel to perform ground tests.
Materials testing took place in a plasma hypersonic wind tunnel at the Italian Aerospace Research Centre in Italy.
“We are dependent on space, yet far from self-sufficient, and the fragile space environment is congested and cluttered with debris. For both reasons, we are vulnerable.”
“We need to be able to provide leadership in the councils which regulate the space environment and space activities, in order to minimise our current vulnerabilities in space,” Professor Boyce said.
Researchers continue testing new materials to withstand the extreme heat experienced by hypersonic vehicles in flight to ensure they can fly for substantially longer.
For example, research teams have tested scramjets at Woomera in South Australia, where scramjet engines made of conventional materials have been tested.
When scramjets and other hypersonic materials are tested, researchers are looking at whether they encounter any problems with extreme heat including melting, and if they can be re-used.
In high-speed aircraft, air friction can cause extreme heating of the leading edge, where temperatures on the surface of an object travelling at Mach 5 can reach 1,000 °C.
These higher temperatures cannot be sustained by most materials.
Extreme heating of the leading edge was the cause of the Space Shuttle Columbia accident during re-entry
in 2003. The accident was preceded by damage to protective tiles on the leading edge which occurred during take-off.
However, researchers are working to design materials that can ablate at high temperature.
Professor John Drennan is the Director of the University of Queensland’s Centre for Microscopy and Microanalysis. He is also a pioneer in ceramic composite materials, who is looking at several concepts to enable hypersonic vehicles to handle extreme heat for prolonged periods.
“The technologies we are developing will have application anywhere where performance is needed from materials in high temperature environments for long periods,” he said.
“Some potential uses for the new materials might include in power plants and for exhaust nozzles of jet engines.”
Professor Drennan said the technologies developed would benefit Australian industry by providing further capabilities in materials science.
“Australian industries will be able to build components of aircraft, rather than having to import these materials from the U.S. and Europe,” he said. Another challenging problem area is inside the scramjet engine, which must handle a corrosive mix of hot oxygen and combustion products, as well as high thermal, mechanical and acoustic loadings.
Scramjet-based launch systems promise safe, reliable and economical access to space for launches of communications satellites.
Although scramjet technology has been known since the 1950s, it has proved a hard nut for international scientists to crack.
Australia’s first professor of space engineering, Emeritus Professor Ray Stalker began studying scramjets in 1982.
His research was pivotal to the University of Queensland’s Centre for Hypersonics, which remains one of the world’s largest space engineering university groups.
The aerospace industry has been at the forefront of modern-day innovation. From humble beginnings, aerospace technology now boasts space rockets that can re-land safely back on earth [1], advanced fighter jets, and hypersonic vehicles capable of breaching the sound barrier 5 times over (and even greater). Hypersonic technology currently covers advanced high-speed systems that will offer significant technological advancement in both military and commercial use if certain engineering obstacles currently limiting the technology are overcome.
Speeds such as Mach 5 and Mach 10 may be easy to say; but understanding the sheer magnitude of such speeds can be hard to conceptualise. Designing structural components for hypersonic flight poses additional design hurdles to subsonic flight, due to the variance in major flight principles. The physical nature of the airflow over the flight vehicle changes as the Mach number increases. At
great speeds, the shock layer (the flow layer that forms between the shock and the vehicles body) becomes very thin, hot, and dense. The challenge faced here is at the stagnation point that forms at the leading edges of the body, which can experience temperatures exceeding 2250 °C at Mach 10. Few materials can survive such conditions while maintaining structural integrity, which is a design criterion that is crucial to maintain the aerodynamics and flight control of the vehicle.
In addition to a temperature that will melt most materials, hypersonic flight within the atmosphere exposes these edges to an oxygen rich environment resulting in elevated rates of oxidation. Oxidation is accelerated due to the high temperatures since the oxygen molecules are chemically excited to the point of dissociation [2], thus becoming very reactive. The build-up of oxide scales often leads to both deteriorated strength and resistance to thermal loads, which when occurring at high speeds leads
to the surface oxide that is formed ablating and chipping, leaving an uneven surface that is further exposed to reaction with the oxygen [3]. The outer structure of high-speed vehicles, the part that will be directly exposed to such extreme conditions, is referred to as the thermal protection system (TPS). The material selection process for TPS’s is vital in mitigating the effects of oxidation. The hypersonic environment provides consistently high temperatures and pressure conditions, where only a few material compositions can resist oxidation while maintaining structural integrity [4]. The current solution is to coat the structures with non-reactive, oxidation resistant materials.
Ultra-high temperature ceramics (UHTC) are known for their good high-temperature properties and oxidation resistance, and thus popular candidates for this application. Research undertaken through RMIT University aims to integrate such materials into the outer surface of a
multi-material structure capable of being manufactured through laser powder bed fusion (LPBF).
The oxidation resistance of most UHTC's is effective, however a certain solid solution between two of the leading ceramics stands alone. A study [5] observed the oxidation of tantalum carbide (TaC), hafnium carbide (HfC), and TaC-HfC solid solutions under the extreme temperatures and oxygenrich environments produced by a plasma torch to be exceptional. While the pure samples of TaC and HfC showed high resistance to oxidation, having an oxide layer thickness of 305 and 190 μm respectively after 300 seconds of plasma exposure, it was found that combining the materials to form a 50:50 TaC:HfC solid solution resulted in a much reduced oxide layer of only 28 μm after 300 seconds [5]. When HfC oxidises due to the penetration of its grain boundaries the HfO2 formed is porous and is easily ablated (Figure 1). However, with the addition of TaC, Ta2O 5 forms a molten layer. When combined with the
porous HfO2 , the liquid Ta2O 5 reforms a solid oxide layer that experiences cracking, which is alleviated through crack healing due to the liquid phase reforming (Figure 2), preventing oxygen from further penetrating the scale.
So why aren’t UHTC’s, especially TaC:HfC in use for such applications?
Well, despite its clear advantages, a structure made entirely of a UHTC would prove more similar to the ceramic tiling of a spacecraft rather than an atmospheric aerospace leading edge. As such, internal base structures are being explored to be manufactured in-situ with the UHTC surfaces. The materials being explored are refractory metals, which refer to a group of metals sharing multiple key properties, including extremely high melting temperatures (>2000 °C), high density, and high hardness. The leading candidate for this application being none other than tantalum (Ta).
Both UHTC and refractory metals have properties that make them
ideal candidates to be integrated into hypersonic leading-edge applications. However, on the other hand, both have significant drawbacks that need to be addressed. UHTC’s are limited by their processing ability, in particular their high melting temperatures, extreme hardness, and varying viscosity, all of which add complexity during additive manufacture (AM). For example, the thermal stresses induced in the UHTC during manufacture through melting and re-solidification can often lead to a failed print due to cracking. Conversely, refractory metals have proven manufacturability via AM. However, refractory metals have poor oxidation resistance at high temperatures, thus the necessity to incorporate a UHTC material to coat the structure.
Cermet materials that combine UHTC’s and metal’s show promise for hypersonic applications. Multimaterial structures can often be utilised to combine the preferred properties and characteristics from a range of materials, while alleviating
the negative effects of single materials. Implementing such compositions into muti-material sandwich structures offers a potential high temperature, oxidation resistant structure that can minimise both oxidation and thermal stress gradients, as well as alleviate such drawbacks as a high mass, through the implementation of additively manufactured lattice structures. Currently laser powder bed fusion (LPBF), a common AM technique, holds the potential to produce such structures, especially when coupled with a high-temperature build platform such as the Aconity3D system recently installed at the RMIT Centre for Additive Manufacturing. Suitable manufacturing capabilities and an understanding of the impact of relevant process parameters will be required, but if such a technique is found feasible, not only will multiple gaps within the AM of ultra-high temperature materials be addressed, but alternative designs will also be readily available for both hypersonic and other extreme high temperature applications.
The use of LPBF to fabricate UHTC’s such as HfC and TaC does not seem to have been attempted before and no studies have been reported in this area so far. However, that’s not to say that the technique is not viable. Both TaC and HfC have been extensively tested at high temperature as either bulk materials or as specific compositions, however the manufacturing technique always employed has been spark plasma sintering [6]. A laser melting study investigating materials with the highest melting temperature explored various compositions of TaC-HfC, and showed the viability of
melting such compositions using a similar laser power to those found on LPBF machines [7]. Further, a proposed method to produce TaC:HfC compositions (while alleviating the chance of increased thermal stresses induced on the part) is to additively manufacture Ta metal powder with added HfC powder, and through the melting process, allow the carbonrich HfC to carburise the Ta to form a TaC-HfC composition solid material. This reaction has been reported to be feasible during the manufacture of HfC powder combined with both a Ta fibre net and also a Ta foil [8]. This concept will be explored throughout the project and developed if initial feasibility testing indicates the viability of such a technique.
The future of using AM techniques to produce hypersonic components is unknown, exciting, and may be inevitable. LPBF offers a unique opportunity to produce cermet materials with exceptional properties that can be applied in hypersonic applications, and still allow the manufacture of detailed and complex structures, unlike current methods. The LPBF technique is novel in this context, nevertheless, time will tell if it proves feasible. But if it is, an entirely new technique of producing ultrahigh temperature, oxidation resistant, complex structures will be opened for exploration.
About the authors: Michael Ives, PhD candidate, Ma Qian, Distinguished Professor, Simon Barter, Professor, and Raj Das, Professor, are all with the Centre for Additive Manufacturing, School of Engineering of RMIT University.
References:
[1] E. Howell. "Watch a SpaceX rocket ace landing on a drone ship in stunning new video." https://www.space.com/spacexfalcon-9-rocket-landing-video-gps-iii-sv05 (accessed 6 Oct, 2022).
[2] S. D. Kasen, "Thermal management at hypersonic leading edges," University of Virginia, 2013.
[3] Y. Bai, P. Wang, B. Zhang, H. Du, and L. Cheng, "Comprehensive oxidation mechanisms of heterogeneous laminated HfB2–SiC/Ti ceramics under oxyacetylene conditions," Journal of the European Ceramic Society, vol. 42, no. 7, pp. 31073117, 2022/07/01/ 2022, doi: https://doi. org/10.1016/j.jeurceramsoc.2022.02.030.
[4] M. Opeka, I. Talmy, and J. Zaykoski, "Oxidation-based materials selection for 2000°C + hypersonic aerosurfaces: Theoretical considerations and historical experience," Journal of Materials Science, vol. 39, 10/01 2004, doi: 10.1023/B:JMSC.0000041686.21788.77.
[5] C. Zhang, B. Boesl, and A. Agarwal, "Oxidation resistance of tantalum carbidehafnium carbide solid solutions under the extreme conditions of a plasma jet," Ceramics International, vol. 43, no. 17, pp. 14798-14806, 2017/12/01/ 2017, doi: https:// doi.org/10.1016/j.ceramint.2017.07.227.
[6] C. Zhang, A. Gupta, S. Seal, B. Boesl, and A. Agarwal, "Solid solution synthesis of tantalum carbide-hafnium carbide by spark plasma sintering," Journal of the American Ceramic Society, vol. 100, no. 5, pp. 18531862, 2017, doi: https://doi.org/10.1111/ jace.14778.
[7] O. Cedillos-Barraza et al., "Investigating the highest melting temperature materials: A laser melting study of the TaC-HfC system," Scientific Reports, vol. 6, no. 1, p. 37962, 2016/12/01 2016, doi: 10.1038/srep37962.
[8] P. Xiao, S. Wang, Y. Yu, B. Fang, and H. Li, "Improved toughness of HfC with tantalum fibre net and tantalum foil," Ceramics International, vol. 47, no. 13, pp. 1926019266, 2021/07/01/ 2021, doi: https://doi. org/10.1016/j.ceramint.2021.03.218.
Fatigue and corrosion damage to structural components can be a major threat to the safety and airworthiness of civil and military aircraft.
ANSTO researchers have used nuclear techniques to evaluate a technology to repair corrosion and fatigue damage on the structural components of aircraft.
The researchers have worked with scientists and engineers from the Aerospace Division of Defence Science and Technology Group (DST Group).
Dr Wyman Zhuang, who led the research, said the team’s experiments confirmed deep surface rolling improved fatigue performance.
“Residual stresses that are found in materials and components are one of the most important factors impacting the fatigue performance of aircraft structural repairs,” he said.
The DST Group tested fatigue performance of the specimens made up of aircraft structural materials with various repair and post-repair enhancement conditions, and examined the fatigue cracking in the specimens after the fatigue testing.
This last step was conducted by using scanning electron microscopy.
“Structural integrity requirements for aircraft parts are of the highest level. The repaired components need to demonstrated that the restored component shall have a structural strength condition, equivalent or better than its original configuration, Dr Zhuang said.
ANSTO has a research agreement with the DST Group to collaborate on a number of projects, including a government radiological and nuclear spectrum database to help counter threats to Australia’s national security.
ANSTO provides access to a range of complementary techniques for multi-disciplinary materials to make technological advances to reduce detection of Australian Defence Force platforms and improve ballistic and
shock protection.
Traditional materials characterisation methods can be enhanced by techniques that are available using ANSTO’s neutron beam instruments at the OPAL reactor, synchrotron X-ray and infrared beamlines at the Australian Synchrotron, advanced microscopy, imaging and computer modelling.
“We have had considerable success on a range of projects collaborating with the defence industry, DST and university partners,” said Di Pietro, who was pivotal to lifting these projects off the ground as the Head of Innovation and Integration at ANSTO.
“This partnership reflects a coinvestment in research and development activities that strengthen Australia’s defence priorities on ambitious but attainable projects,” he said.
In addition, ANSTO’s materials science research supports aerospace and space endeavours in Australia and internationally.
Building on experience gained in materials for advanced nuclear systems, ANSTO’s activities in this area are focussed on development, performance and in-service degradation of:
• nickel-based superalloys
• reinforced carbon-Carbon (C/C) composites
• ultra-high temperature ceramics (UHTC).
These materials are required to withstand a combination of challenging in-service environmental conditions such as high temperature, corrosion/oxidation, high-energy particle radiation and photon gamma irradiation.
ANSTO’s work has delivered innovative solutions for the production of high performance materials and systems for use in both supersonic rocket and hypersonic scram jet propulsions systems.
ANSTO has collaborated on the development of advanced sensors and hypersonic materials to support Australia’s defence and national security objectives.
From fixing jets to testing rockets, discovering planets to looking for aliens, the University of Southern Queensland is at the forefront of space and defence research.
RThe Institute for Advanced Engineering and Space Sciences is Australia’s hub for cutting-edge technologies, industry solutions and knowledge.
The facility boasts space and defence research specialising in hypersonic propulsion systems, rocket fuel development, astrophysics, and advanced materials.
The Institute is broken down into three research streams:
1. Hypersonic testing: researchers use the only long duration hypersonic wind tunnel in Australia to test in free-flight hypersonic aerodynamics.
2. Rocketry: the only solid propellant manufacturing facility within Australia is used for hypersonic research.
3. Diagnostics: researchers study high speed and high enthalpy flows.
Researchers understand the value of working with industry stakeholders. Therefore, the Institute partners with global companies like NASA; the US Air Force; Boeing; and John Deere.
Together, researchers work with end-users on commercial pathways to deliver impact in an ever-changing
renowned for its hypersonic research, with its rocket laboratory, static rocket testing facility and long duration hypersonic wind tunnel.
“The work we’ve done to date, and continue to do, has put us on the map globally.”
“That’s really important for developing the profile of the university, attracting new students and helping develop the new generation of researchers,” he said.
The Institute’s Centre for Future Materials—one of Australia’s largest dedicated composite materials manufacturing and testing facilities—provides novel design, manufacture, and testing for industry.
Researchers are using next-generation composites in aircraft repairs and developing faster cycle time in composite aerostructure manufacturing for clients like the Defence Science and Technology Group, and Boeing Aerostructures Australia.
Hypersonic innovation requires research that moves at high speeds. As such, the University of Southern Queensland recently received an Australian Research Council grant for over $1 million. The project will investigate remote diagnostics for space-access flight testing.
Professor David Buttsworth will lead the newly funded project to develop ways to maximise science outcomes from test flights.
“Aerospace flight testing is essential for assessing the reliability of space-access technologies including re-useable rockets and hypersonic air-breathing systems,” Buttsworth said. “These tests give us vital optical data in video and scientific formats, and we’re looking at ways to gain even more insight from these flights.”
The team will design a suite of new instruments suiting various platforms (airborne, ground-based and high-altitude drones) for observing high-speed flight tests conducted
during research into launch-to-space and return-from-space technologies.
The project will also seek to fine-tune computational simulations of the flight tests and develop ways to deduce the aerodynamic and thermal conditions experienced during high-speed flight.
Buttsworth said by advancing essential optical diagnostic tools and techniques, his team aimed to establish an enduring capability for space-access flight testing in Australia.
“This work has the potential to accelerate the research and development pathways for Australian enterprises and will designate our country as a prime destination for international aerospace businesses.”
In addition, the University of Southern Queensland will work with Hypersonix Launch Systems, LSM Advanced Composites Romar Engineering on the DART CMP Airframe—a reusable hypersonic platform.
The project is funded by a $2.95 million Cooperative Research Centre grant from the Federal Government.
Together, they will develop an unmanned aerial vehicle that can travel at hypersonic speeds of up to Mach 12, which is twelve times the speed of sound.
It is powered by the SPARTAN hydrogen fuelled scramjet engine, which takes oxygen from the atmosphere, and reduces weight by 60 per cent compared to rockets.
The project will deliver a new sovereign manufacturing capability for high temperature ceramic matrix composites.
Hypersonix Managing Director David Waterhouse said DART CMP is the composite version of the DART AE due for launch this year.
“AE stands for Additive Engineering and is the fully 3D printed version out of high temperature alloys that are already available in Australia,” Waterhouse said.
“The type of high temperature composites we require for DART CMP are currently not available here, therefore there is an urgent need to develop these materials in Australia.”
“We are thankful that the government acknowledged this gap and responded with accepting our application. We can’t wait to have these materials ready in mid 2025,” Waterhouse explained.
Hypersonix is developing several hypersonic vehicles that fly at speeds between Mach 5 and Mach 12 with zero CO2 emissions, use water vapor, and have applications in both satellite launch and high-speed aviation.
The University of Southern Queensland boasts Australia’s only hypersonic wind tunnel, which is capable of testing up to Mach 8.
Lachlan Noller is a PhD student who is focussed on things that move fast. As such, he has his sights on upgrading the University’s current hypersonic wind tunnel.
He said the facility should test the starting function of
hypersonic inlets utilised on Scramjets—a form of airbreathing propulsion that gives the capability of moving five times the speed of sound.
“The new component will allow us to produce a larger airflow area which can generate a Mach 7 flow—which corresponds to a speed of approximately 8750kph,” Noller said.
“The main part, which requires the bulk of the research and development, is the hypersonic nozzle which is used to accelerate stagnate, pre-compressed air up to the desired speeds.”
Noller was recently awarded a Queensland Defence Science Alliance Higher Degree to turn this dream into a reality.
“To design the new nozzle, I’m using computations of fluid dynamic simulations to determine the required nozzle geometry coupled with analytical methods developed here at the University.”
“Using this design methodology will provide us with evidence that the designed nozzle will indeed generate the desired flow conditions,” he said.
The University of Southern Queensland’s Hypersonic Group has rallied behind Noller.
“Had the team not had the reputation it has, which was built up over many years, I feel like my chances of receiving the grant would have been significantly lower. Hypersonics research is a massively re-emerging field at the moment worldwide,” Noller said.
Ultra-efficient 3D printed catalysts could be the solution to overheating in hypersonic aircraft.
RMIT University researchers have pioneered a revolutionary solution to thermal management across countless industries.
The highly versatile catalysts are costeffective to make and simple to scale.
The team’s lab demonstrations show the 3D printed catalysts could be used to power hypersonic flight while simultaneously cooling the system.
Dr Selvakannan Periasamy is the lead researcher on the project, who said the work tackled one of the biggest challenges in the development of hypersonic aircraft.
“Our lab tests show the 3D printed catalysts we’ve developed have great promise for fuelling the future of hypersonic flight.
“Powerful and efficient, they offer an exciting potential solution for thermal management in aviation—and beyond.
“With further development, we hope this new generation of ultra-efficient 3D printed catalysts could be used to transform any industrial process where overheating is an ever-present challenge,” Dr Periasamy said.
Controlling the incredible heat that builds up when planes fly at more than five times the speed of sound has been a key challenge for researchers and industry personnel alike.
Only a few experimental planes have reached hypersonic speed, which is defined as above Mach 5—over 6,100km an hour or 1.7km per second. In theory, a hypersonic aircraft could travel from London to Sydney in four hours. However, many challenges remain in the development of hypersonic air travel, such as the extreme heat levels.
First author and PhD researcher Roxanne Hubesch said using fuel as a coolant was one of the most promising experimental approaches to the overheating problem.
“Fuels that can absorb heat while powering an aircraft are a key focus for scientists, but this idea relies on heatconsuming chemical reactions that need highly efficient catalysts.”
“Additionally, the heat exchangers where the fuel comes in contact with the catalysts must be as small as possible, because of the tight volume and weight constraints in hypersonic aircraft,” Hubesch said.
To make the new catalysts, the team 3D printed tiny heat exchangers made of metal alloys and coated them with synthetic minerals known as zeolites.
When the 3D printed structures heat up, some of the metal moves into the zeolite framework. This process is crucial to the unprecedented efficiency of the new catalysts.
“Our 3D printed catalysts are like
miniature chemical reactors and what makes them so incredibly effective is that mix of metal and synthetic minerals,” Hubesch said.
“It’s an exciting new direction for catalysis, but we need more research to fully understand this process and identify the best combination of metal alloys for the greatest impact,” she added.
The next step for the research team includes optimising the 3D printed catalysts by studying them with X-ray synchrotron techniques and other indepth analysis methods.
The researchers also hope to extend the potential applications of this work into air pollution control for vehicles and miniature devices to improve indoor air quality.
UNSW Canberra Space hosts a premiere team of engineers and scientists who continue to shape Australia’s direction and capability in the space sector.
Researchers know that what happens in space is vital for life on Earth. From GPS navigation to crucial emergency services and support, investment in space is an important area.
UNSW’s facilities allow researchers and industry stakeholders to design, develop and operate satellite missions from start to finish.
Researchers work on developing and testing new materials to find stateof-the-art solutions for hypersonic technology.
Associate Professor Sean O’Byrne said there is no real magic number for how fast a vehicle travels.
“On the ground sound travels at about 340 metres per second. If you go faster than that, then it's supersonic. And if you go more than about five times faster, it's called hypersonic.”
“Our hypersonic shock tunnel can make a flow that's like flying at 40 kilometres altitude at 10 times the speed of sound, or it can make a flow that looks like a vehicle entering into a planetary atmosphere like Mars, but only for a millisecond, only for a thousand for the second,” he said.
The UNSW Canberra T-ADFA Free-Piston Shock Tunnel facility is an Australiandeveloped experimental device.
The device can generate up to 12 times the speed of sound, and test temperatures similar to the re-entry of Earth.
The facility has become worldclass because of the wide range of experimental measurements available.
“The technology that we're developing will certainly inform the design of the next generation of hypersonic propulsion systems and planetary entry systems.”
“The work that we do tells people how these devices should work and helps them to make more efficient
engines that will operate over a wider range of flow conditions than we can,” Associate Professor O’Byrne said.
The UNSW Defence Research Institute links global academic and industry partnerships to create next-generation security solutions.
The Institute works with the Department of Defence locally and internationally to bring the best research to life and enhance security.
Researchers and practitioners work on a variety of new materials to bolster Australia defence sector.
For example, testing structural designs, and validating components and materials to operate in the extremes of hypersonic flight is a crucial focus.
High temperature materials are exposed to the thermal-structural conditions representative of hypersonic flight, which ensures optimisation of vehicle designs and an overall reduction in the requirement for expensive flight testing.
UNSW Canberra has a competitive
advantage through its unique inhouse expertise in the design and testing of aerostructures, which can withstand the extreme conditions experienced by a vehicle during hypersonic flight.
Associate Professor Sean O’Byrne said the Institute opens a world of opportunities for UNSW Canberra researchers and partners.
“It's possible that in the future we might be able to do mining on places like Mars.”
“It's a very long view, but having access to those kinds of resources will be very important, potentially, into the future,” he said.
These short courses provide you with an engaging learning experience. Courses may include flash animations, video of instructors teaching the course in a classroom, video segments from ASM’s DVD series relevant to the learning material, and PDFs of instructor Power Points used in the instructor led training. All online courses require internet access for reading and viewing course content. Both HTML pages and PDF files for each lesson are downloadable and printable for easy offline access. www.materialsaustralia.com.au/training/online-training
Steel is the most common and the most important structural material. In order to properly select and apply this basic engineering material, it is necessary to have a fundamental understanding of the structure of steel and how it can be modified to suit its application. The course is designed as a basic introduction to the fundamentals of steel heat treatment and metallurgical processing. Read More
Have you ever been handed a failure investigation and have not been quite sure of all the steps required to complete the investigation? Or perhaps you had to review a failure investigation and wondered if all the aspects had been properly covered? Or perhaps you read a failure investigation and wondered what to do next? Here is a chance to learn the steps to organise a failure investigation Read More
This course provides students with a fundamental understanding of the design process necessary to make robust medical devices. Fracture, fatigue, stress analysis, and corrosion design validation approaches are examined, and real-world medical device design validations are reviewed. Further, since failures often provide us with important information about any design, mechanical and materials failure analysis techniques are covered. Several medical device failure analysis case studies are provided Read More
This course provides essential knowledge to those who do not have a technical background in metallurgical engineering, but have a need to understand more about the technical aspects of steel manufacturing, properties and applications.
Read More
Profit from failure analysis techniques, understand general failure analysis procedures, learn fundamental sources of failures. This course is designed to bridge the gap between theory and practice of failure analysis.
Read More
This course is designed as an extension of the Introduction to Heat Treatment course. It discusses advanced concepts in thermal and thermo-chemical surface treatments, such as case hardening, as well as the principles of thermal engineering (furnace design) Read More
Composites are a specialty material, used at increasing levels throughout our engineered environment, from high-performance aircraft and ground vehicles, to relatively low-tech applications in our daily lives. This course, designed for technical and non-technical professionals alike, provides an overarching introduction to composite materials. The course content is organised in a manner that guides the student from design to raw materials to manufacturing, assembly, quality assurance, testing, use, and life-cycle support Read More
An ideal first course for anyone who needs a working understanding of metals and their applications. It has been designed for those with no previous training in metallurgy, such as technical, laboratory, and sales personnel; engineers from other disciplines; management and administrative staff; and non-technical support staff, such as purchasing and receiving agents who order and inspect incoming material.
Read More
Taking a fundamentals approach, this course is presented as an introduction to the world of induction heat treating. The course will cover the role of induction heating in producing reliable products, as well as the considerable savings in energy, labor, space, and time. You will gain in-depth knowledge on topics such as selecting equipment, designs of multiple systems, current application, and sources and solutions of induction heat treating problems Read More
Titanium occupies an important position in the family of metals because of its light weight and corrosion resistance. Its unique combination of physical, chemical and mechanical properties, make titanium alloys attractive for aerospace and industrial applications. Read More
Bruker Nano Surfaces provides industry-leading surface analysus instruments for research and production. Bruker’s AFMs are enabling scientists around the world to make discoveries and advance their understanding of material and biological systems. Their tribometers and mechanical tests deliver practical data used to help improve development of materials and tribolocial systems.
Industry-leading quantitative nanomechanical and nanotribological test instruments are specifically designed to enable new frontiers in nanoscale materials characterisation, materials development, and process monitoring.
Whatever your surface measurement and surface analysis needs, materials or scale of investigation, Bruker has a specialised high-performance solution for you.
Tribology
Universal tribology platforms
Fast and cost-effective in-lab rapid screening of new friction materials
Nanoindentation
In-situ TEM/SEM nanomechanical instruments
Stand alone nanomechanical test systems
Wide range of environmental measurement options
Optical Profiling Next generation ContourX platforms
Improved optical resolution
Unmatched precision and repeatability
High-resolution AFM Microscopes
New NanoScope 6 platforms, improved speed and data capability
High resolution for all applications, all environments
www.materialsaustralia.com.au
Materials Australia members are involved in all aspects of materials science, technology and engineering. Members include manufacturing technical officers, professional engineers, academics, research scientists, technical staff and students. Our members are experts in polymers, nano and biomaterials, ceramics, metals, composites and all of their engineering applications.
There are two types of Materials Australia membership available: Individual and Corporate.
Individual members can join Materials Australia as a Student Member, Graduate Member, Standard Member, Retired Member or a Certified Materials Professional (CMatP).
Corporate members can opt for a Standard, Premium, or Premium Plus membership package.
• Accreditation as a Certified Materials Professional (CMatP) if eligible.
• Discounts on all Materials Australia conferences and training courses, including the CAMS and APICAM Conferences.
• Digital subscription to Materials Australia Magazine, our quarterly publication that is jam-packed with industry, product, technical and research news.
• Discounts on advertising in Materials Australia Magazine.
• Conferences, training courses, workshops and regular branch meetings, designed to facilitate continued professional development.
• Outstanding networking opportunities through regular branch meetings, conferences and training courses.
• Regular branch newsletters full of information on local activities.
• Discounts on advertising in Materials Australia Magazine.
• Editorial support for articles in Materials Australia Magazine.
• Digital subscription to Materials Australia Magazine.
• Free employment listings on the Materials Australia website.
• Free company listing on the Materials Australia website.
• Free company listing in the Materials Australia Magazine.