TMandTechnology PlantEngineering.com Machinery, softwareinstrumentationequipment,&solutionsALSOINTHISISSUE: • Extend switchgear life • Most cited OSHA violations • Sizing surge protection devices
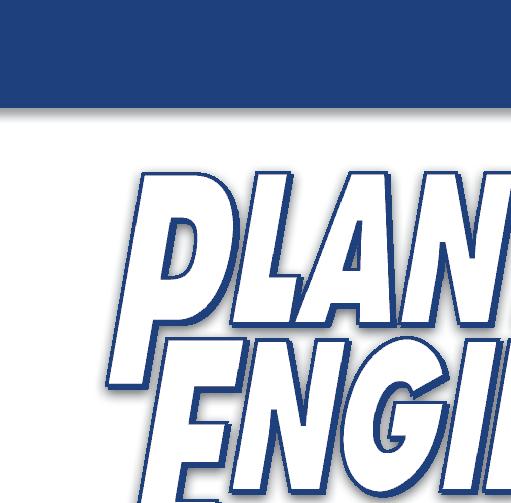
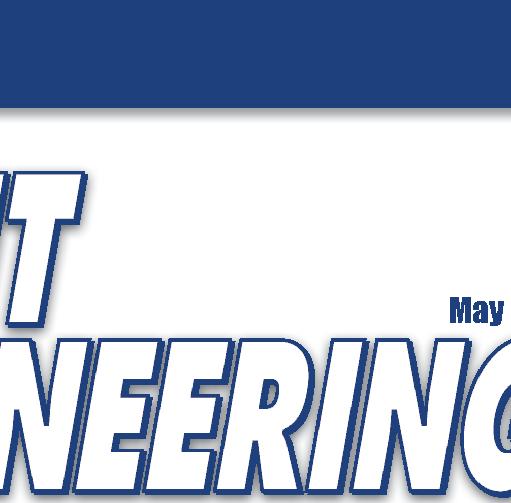



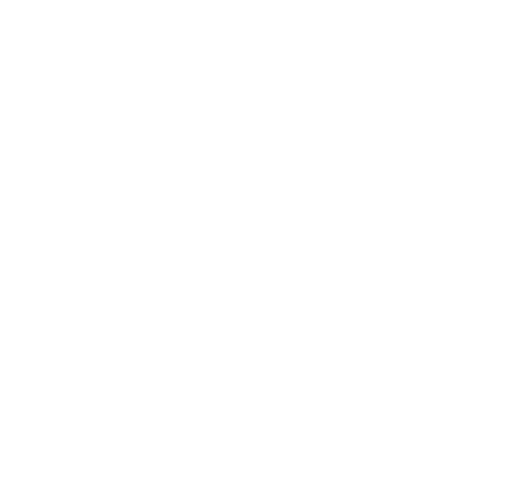
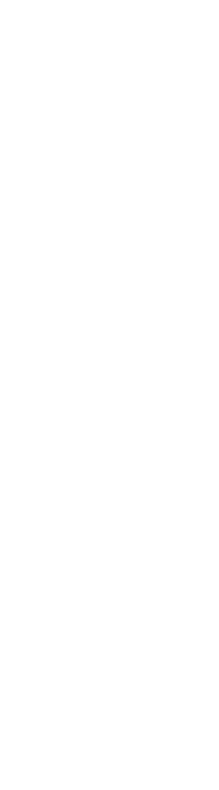
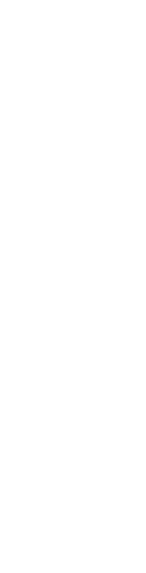
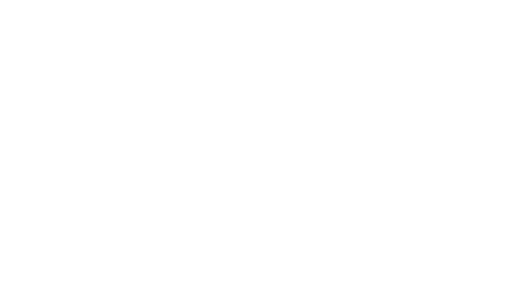
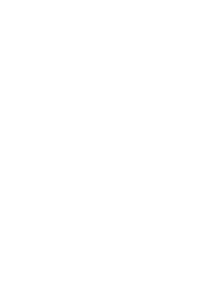

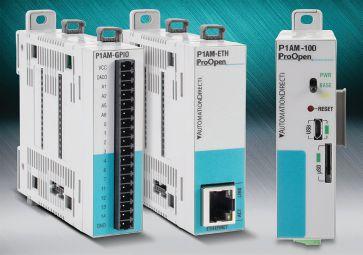
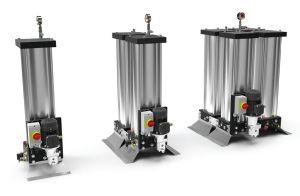
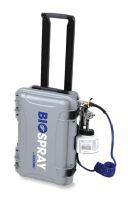
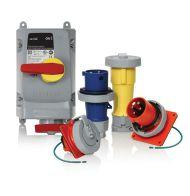
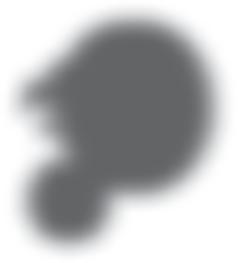
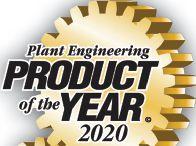
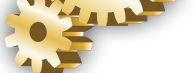
MAKER IN Productivi CPU LEFT-SIDE(LSX)EXPANSION RIGHT-SIDE(RSX)EXPANSION withOpen-Source(Arduino-Compatible)Industrial-GradeCPU$49AgilityIndustrial-Grade Toughness With the popularity of consumer-grade singleboard controllers and their growing use in industrial applications, our industry needed an open-source controller that would hold up in the most extreme conditions. The ProductivityOpen is that controller combining maker ingenuity with our Productivity controller family’s proven reliability. ProductivityBlocks is a graphical programming interface and add-on to the Arduino IDE. ProductivityBlocks helps you build your sketch program by dragging and dropping interlocking blocks; the associated C++ is generated for you saving you time and debugging headaches. Blocks Productivity • Industrial-grade discrete I/O modules • Industrial-grade analog/temperature I/O modules • Industrial-grade relay I/O modules • Industrial-grade specialty I/O modules • Industrial-grade power supplies • Industrial-grade shields • Generic & Arduino-brand shields including DIY modules
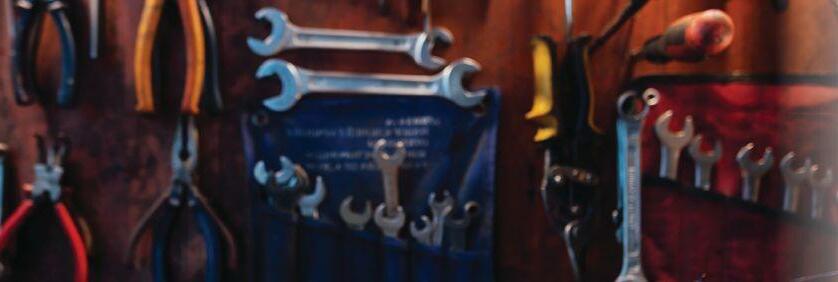
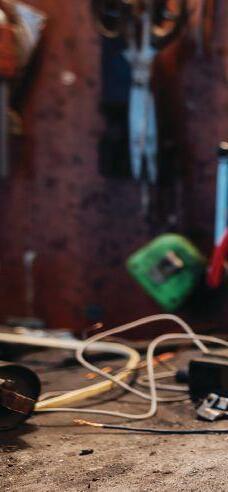
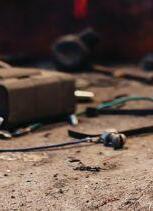
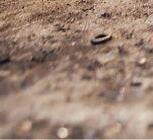
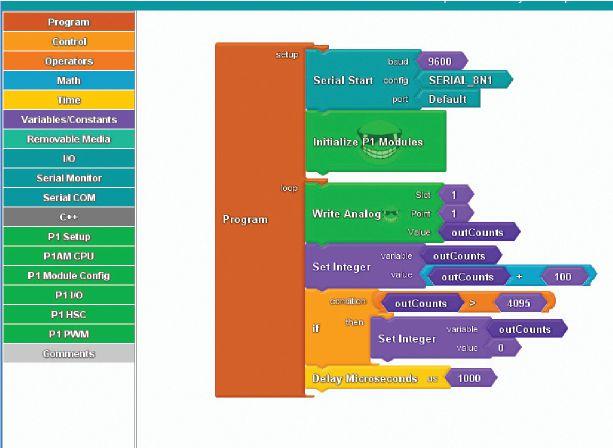
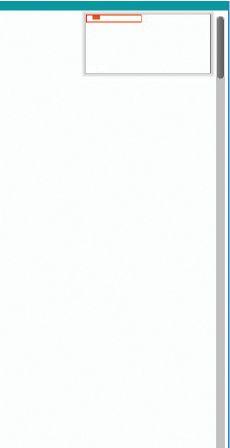

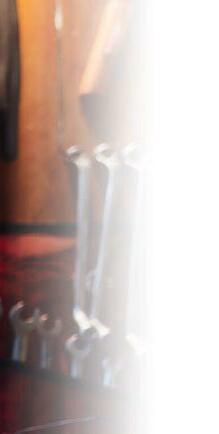
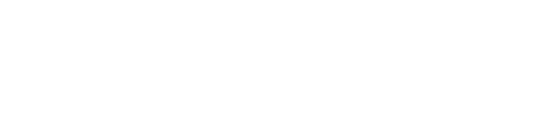
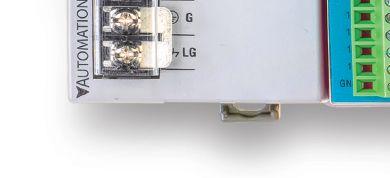
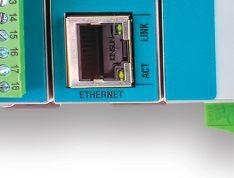
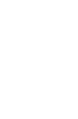
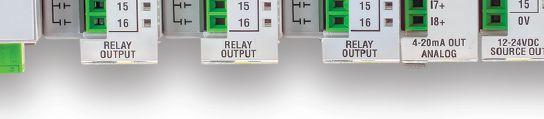
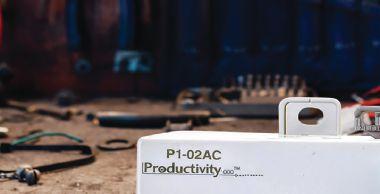
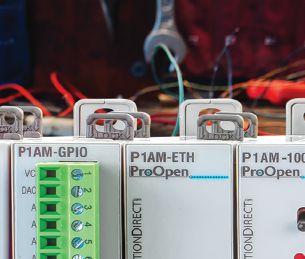
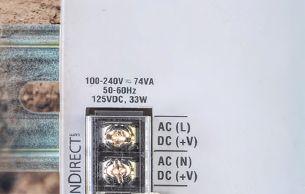
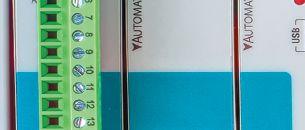
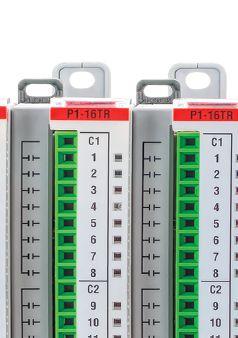
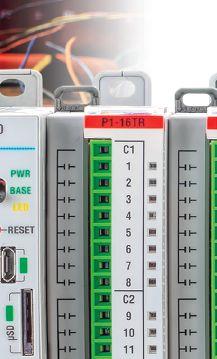
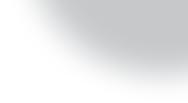
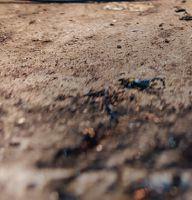
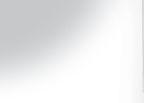
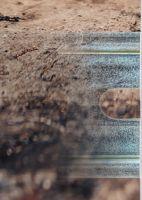
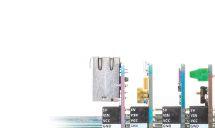
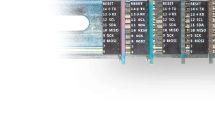
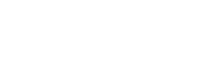
INDUSTRIAL OUT Overview Video: See what ProductivityOpen has to offer! go2adc.com/p1am-overview Openvity Research, price, buy www.automationdirect.com/P1AMat:
The P1AM-100 CPU is designed to reliably take open-source control into the industrial realm and we’ve also engineered a collection of industrial shields that can add needed functionality to the controller. Options including Ethernet can easily be added to the left side of the CPU along with readily-available 3rd party MKR shields. On the right side of the CPU, you can expand the system with low-cost Productivity1000 discrete, analog and specialty I/O modules. Up to 240 discrete I/O points are possible on the right-side. It’s your choice to select any configuration that meets your needs. #2 at www.plantengineering.com/information
programmingIDE.sketchinterlockingfor input
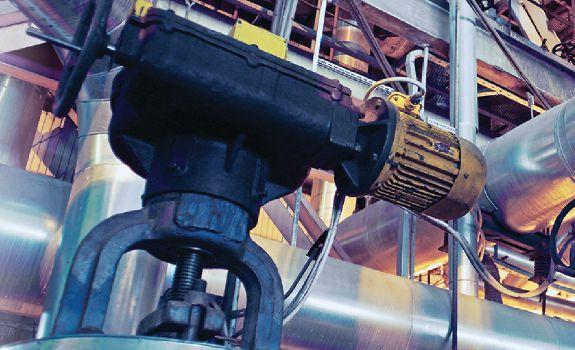
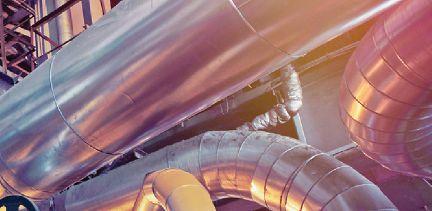
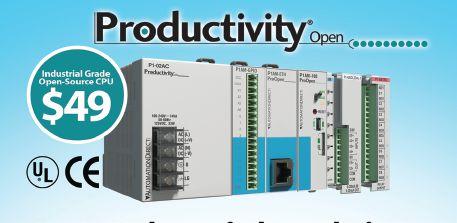

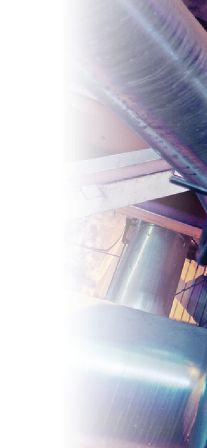
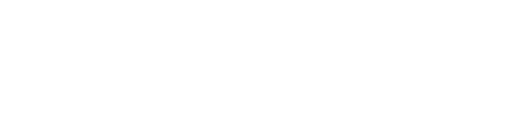

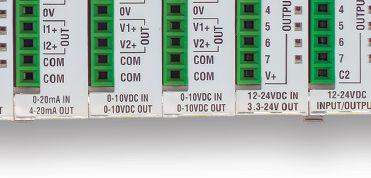
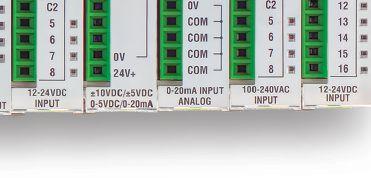
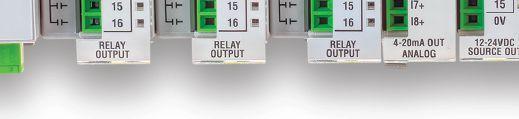
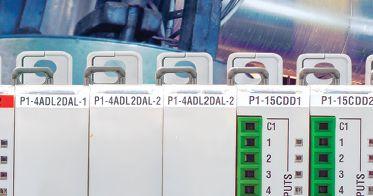
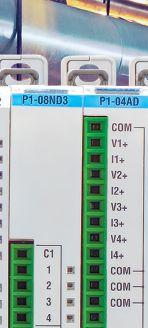
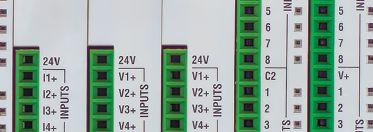
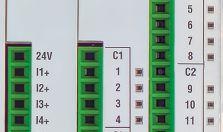
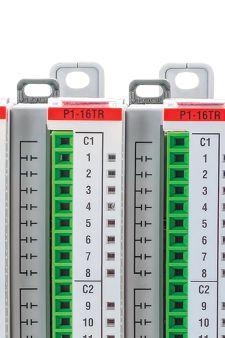

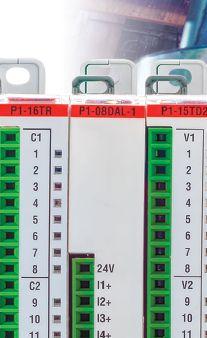
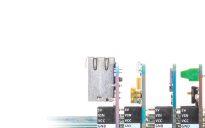

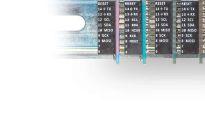
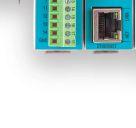
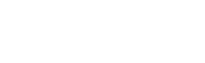
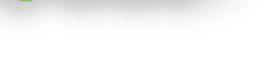
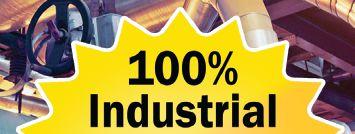
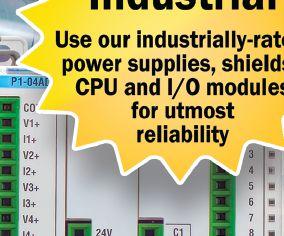
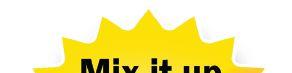
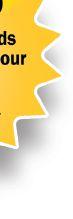
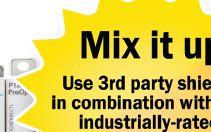
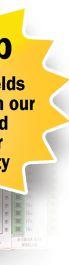
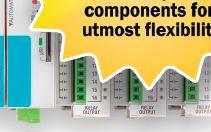
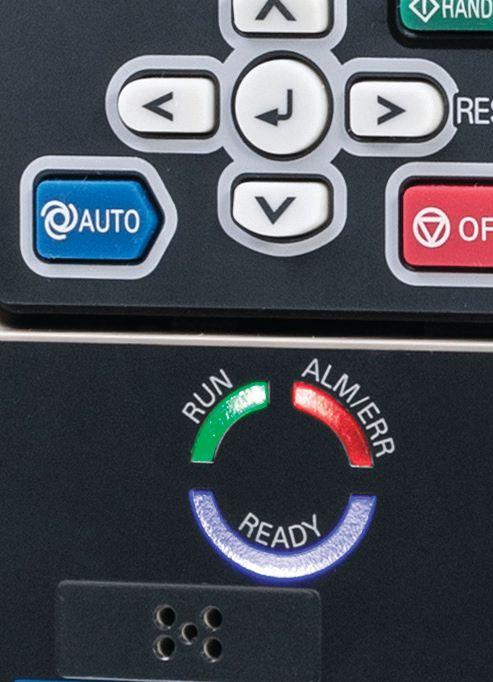
the #1 value in automation Order Today, Ships Fast! * See our Web site for details and restrictions. © Copyright 2020 AutomationDirect, Cumming, GA USA. All rights reserved. 1-800-633-0405 Product of the Year Grand Award Winner Industrial-grade open-source controller from AutomationDirect Productivity1000 industrial I/O 3rd partyMKRopen-sourceshields Grand Award 2020 The Productivity®Open UL/CE-certified open-source CPU mimics the Arduino® MKRZero microcontroller, seamlessly supporting both standard 3rd-party MKR shields and industrial PLC I/O. OpenProductivity And it’s only: $49! Turn the page for more on this popular controller input #1 at www.plantengineering.com/information
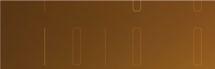
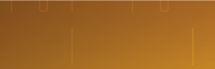
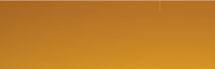

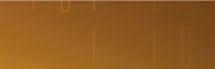
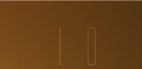
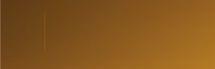
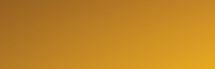
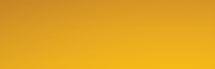
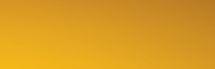
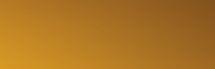

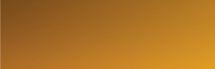
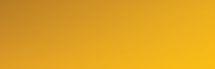
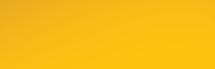
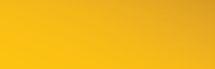
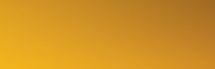
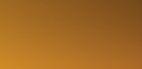
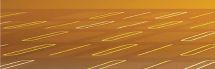
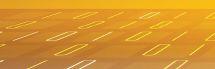

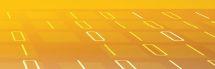
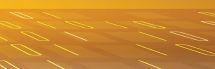
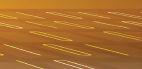
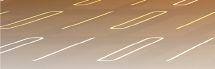
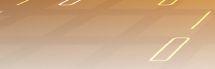

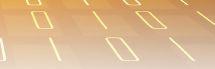
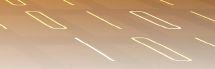
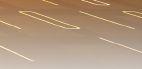
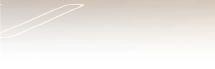
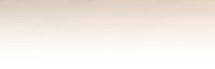

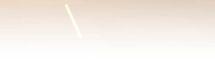
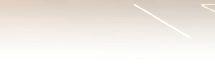
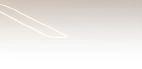
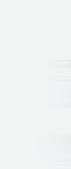
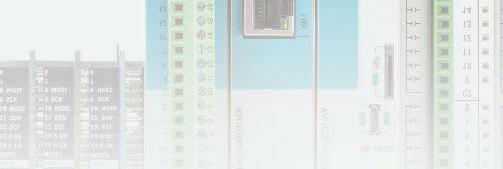
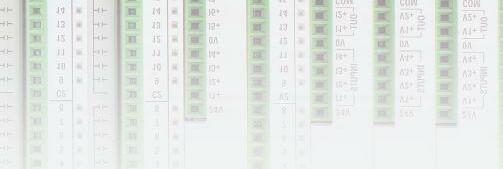
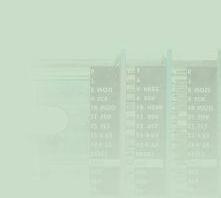
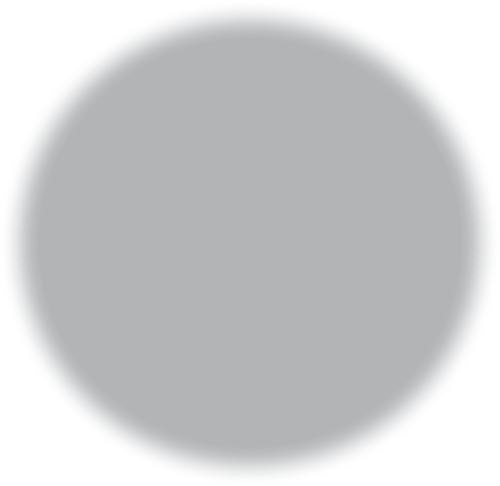

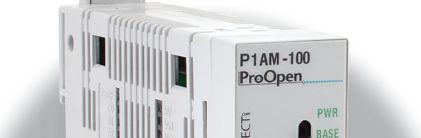

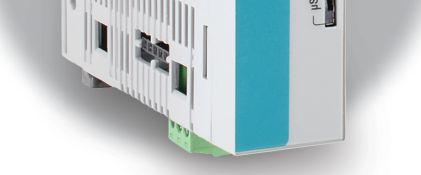
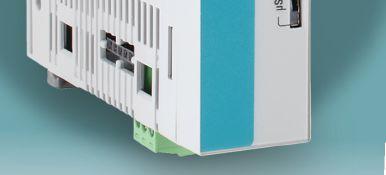
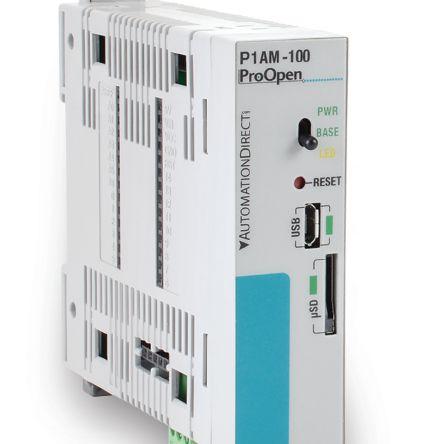
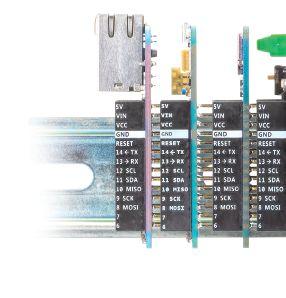

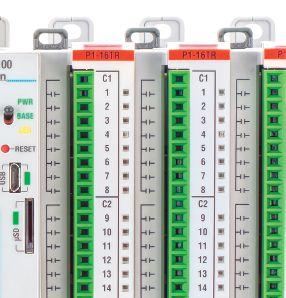
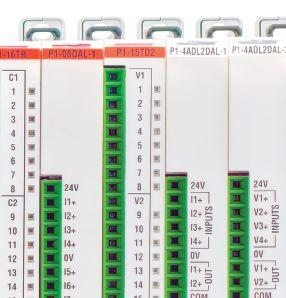
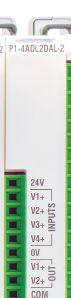
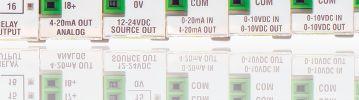
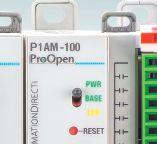








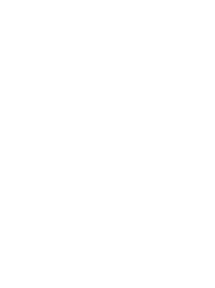
M E A S U R E M E N T | C O N T R O L | M O N I T O R I N G The ultimate tool for every test and measurement engineer. IOLITEr Standard IOLITE aluminium chassis is compatible and can be mounted in any 19-inch rack cabinet. This is perfect for the test-bed installations. The IOLITEr chassis height is 4U and can host up to 12 IOLITE I/O modules. IOLITE LX Embedded data acquisition system based on a low power Linux based ARM processor with open architecture being able to act like a standalone data logger, real-time system, and signal conditioning fronted, all at the same time. IOLITEs IOLITE DAQ system is also available in standalone rugged aluminium chassis compatible with SIRIUS data acquisition instruments. The IOLITEs chassis provides 8 slots for IOLITE input and output slices to be installed. www.dewesoft.com | sales.us@dewesoft.com | +1-855-339-3669 input #3 at www.plantengineering.com/information
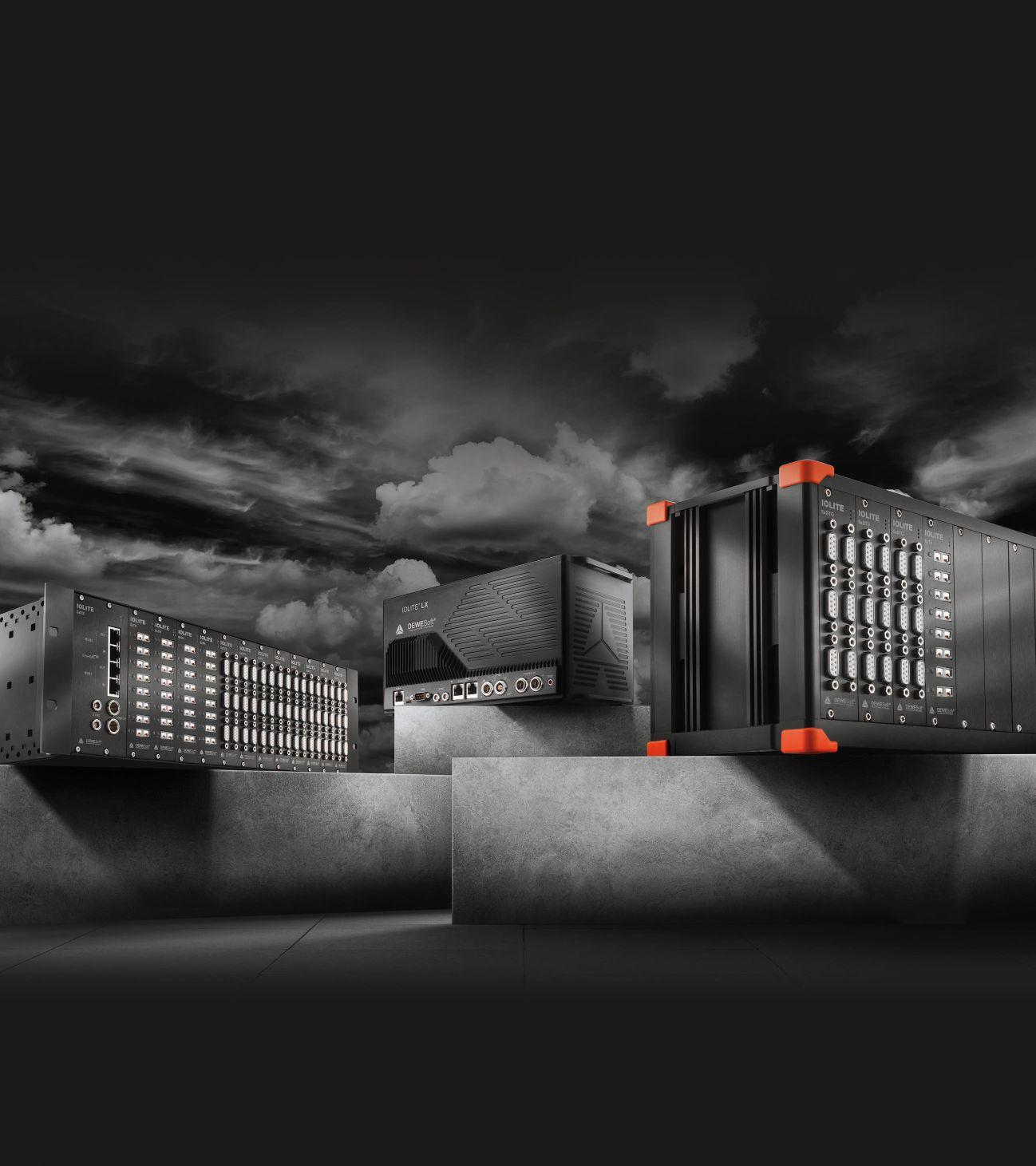
Tired of working nights and weekends on motion control projects? It’s time to contact an automation specialist at SEW-EURODRIVE to help solve your design challenges. Using the latest innovation, we provide complete package from start to finish including, project planning, design, software, components, commissioning, and worldwide support. Go home . . . we got this! seweurodrive.com / 864-439-7537 Overworked? input #4 at www.plantengineering.com/information
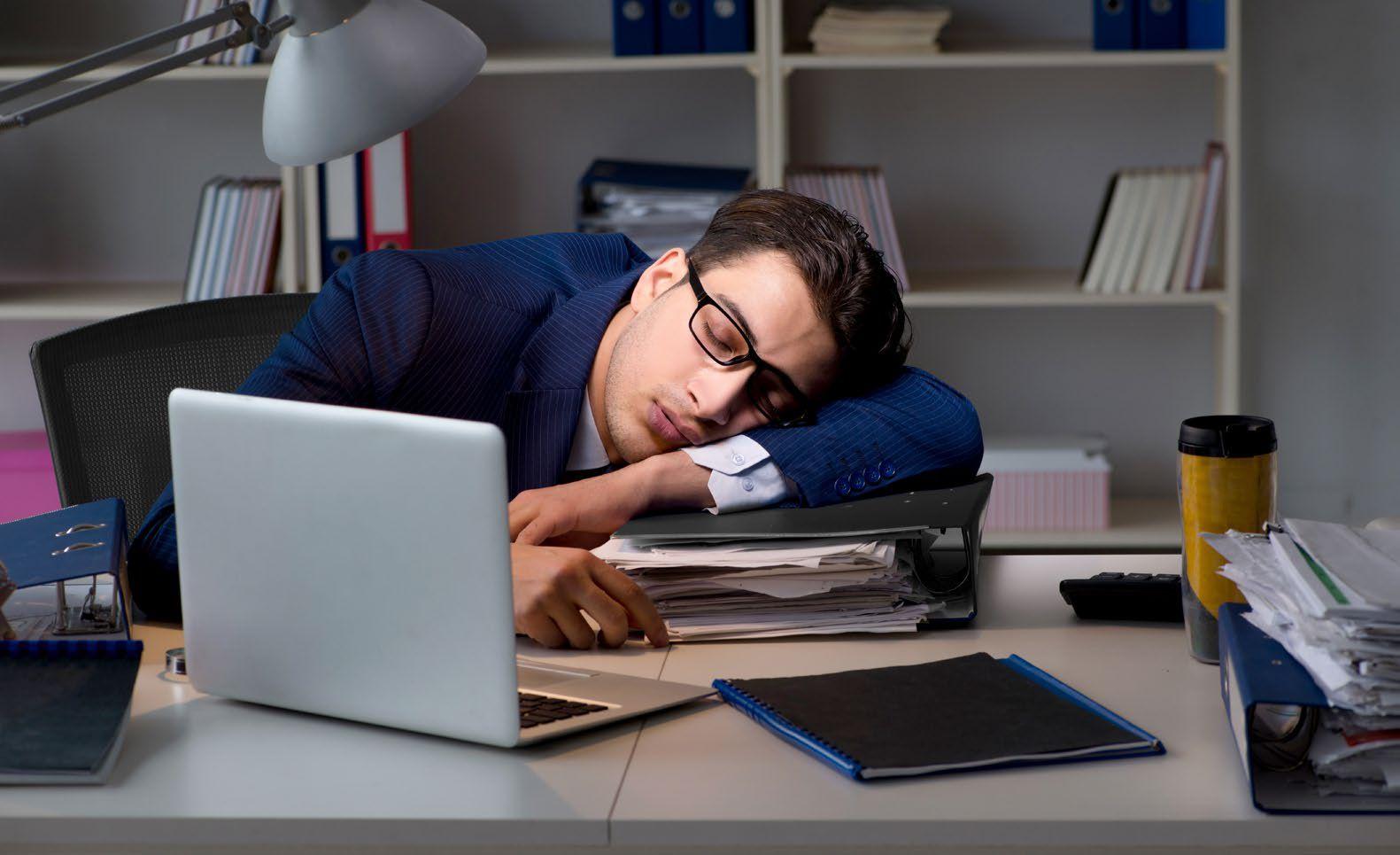

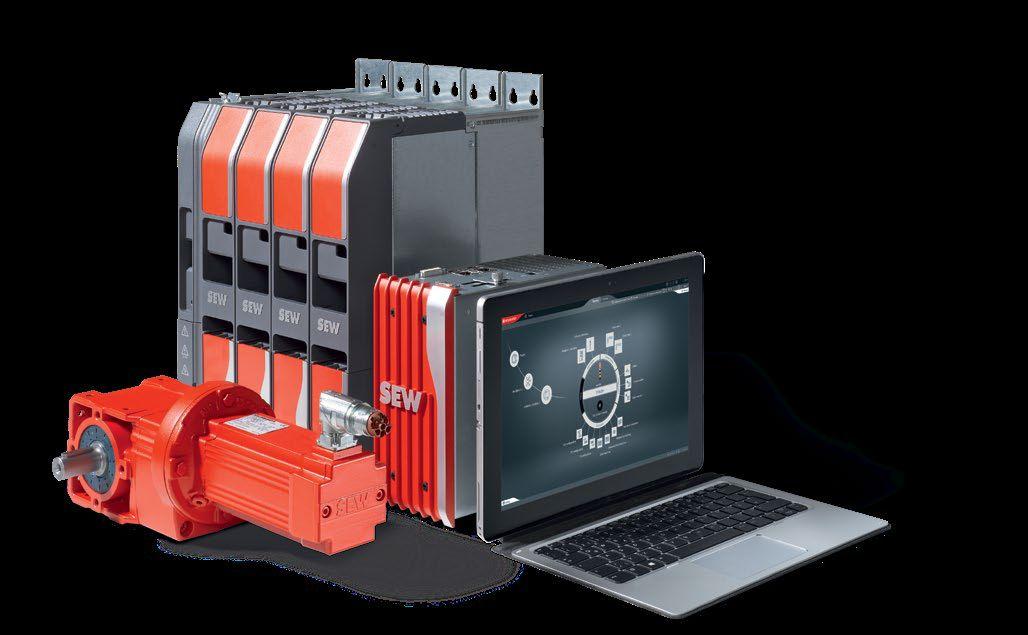
Printed in the USA. CFE
PLANT ENGINEERING (ISSN 0032-082X, Vol. 75, No. 4, GST #123397457) is published monthly except in January, July and November, by CFE Media, LLC, 3010 Highland Parkway, Suite #325, Downers Grove, IL 60515. Periodicals postage paid at Downers Grove, IL 60515 and additional mailing of ces. POSTMASTER: Send address changes to PLANT ENGINEERING, PO Box 348, Lincolnshire, IL 60069. Jim Langhenry, Group Publisher /Co-Founder; Steve Rourke CEO/COO/Co-Founder. PLANT ENGINEERING copyright 2021 by CFE Media, LLC. All rights reserved. PLANT ENGINEERING is a registered trademark of CFE Media, LLC used under license. Circulation records are maintained at CFE Media, LLC, 3010 Highland Parkway, Suite #325, Downers Grove, IL 60515. E-mail: pe@omeda.com. Publications Mail Agreement No. 40685520. Return undeliverable Canadian addresses to: PO Box PO Box 348, Lincolnshire, IL 60069. Email: pe@omeda.com. Rates for non-quali ed subscriptions, including all issues: USA, $165/yr; Canada/Mexico, $200/yr (includes 7% GST, GST#123397457); International air delivery $350/yr. Except for special issues where price changes are indicated, single copies are available for $30 US, $35 foreign. Please address all subscription mail to PLANT ENGINEERING, PO Box 348, Lincolnshire, IL 60069. Media,
7 | How to engage employees through plant optimization Plant optimization results in much more than increased productivity and KPIs 15 | Avoid over-specifying inverter-duty motors When combining a motor and inverter, the applications should reveal what type motor fits best 21 | How to build scalable data models with MQTT A key to bridging the OT/IT gap is enabling successful data modeling, which is how organizations define and organize their business processes 23 | How to use automation technology for remote operations Automation technology for remote operations and plant maintenance is becoming more prevalent MAY 2021 INSIGHTS SOLUTIONS
LLC does not assume and hereby disclaims any liability to any person for any loss or damage caused by errors or omissions in the material contained herein, regardless of whether such errors result from negligence, accident or any other cause whatsoever. www.plantengineering.com PLANT ENGINEERING May 2021 • 3 26 | How to ensure OT cybersecurity Despite advances, operational technology network security still lags information technology security 5 | U.S. manufacturing gains; supply chains falter 9 EDITOR’S INSIGHT COVER: Product of the Year. Product photos courtesy: Des-Case Corp., AutomationDirect, Eaton Corp. and Goodway Technologies. TMandTechnology 152129 | Why investing in electrical safety is more important now than ever An analysis of OSHA’s top 10 most cited violations for control of hazardous energy 9 | Innovative solutions address needs of today’s manufacturers Unconventional approaches suit readers’ choices PRODUCT OF THE YEAR 23
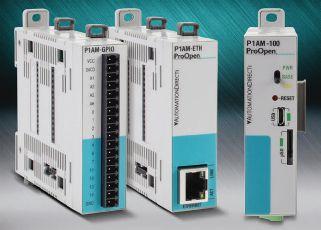
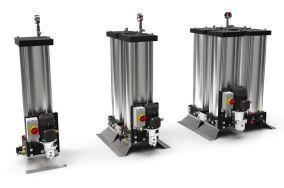
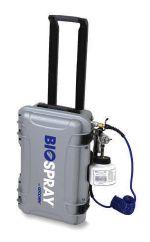
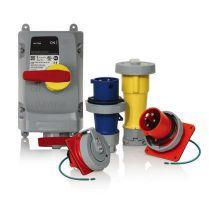
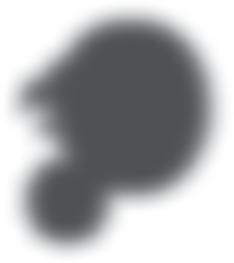

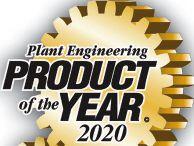
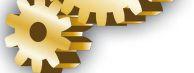

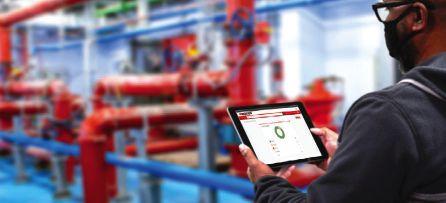


4 • May 2021 PLANT ENGINEERING www.plantengineering.com MAY 2021 SOLUTIONS INSIDE: OIL & GAS ENGINEERING SOLUTIONS 32 | Why commodity casters cause injuries Commodity casters are workplace injuries waiting to happen 33 | How to test for absence of voltage NFPA 70E and CSA Z462 harmonize absence of voltage requirements 36 | How to extend switchgear life and improve system reliability Improve system reliability of switchgear with relay upgrade projects 38 | The future of IoT: Collaborative solutions The future of the Internet of Things connectivity requires flexible solutions that address a wide variety of applications, use cases and device types 40 | Complex machine validations performed with multiphysics simulation Intelligent performance engineering provides improvements in simulation, design and connectivity for machine builders 43 | How to properly size surge protection devices To specify an SPD, understand the ratings associated with its application 45 | Best practices in mature engineering information management Nature engineering information management can save millions in operational costs 6 | Leveraging technology to reduce non-productive time Replacing seats and valves, a costly expense for oilfield operators 8 | Recent advances in fiber optic sensing systems Greater insight for O&G well completions and production operations 11 | Tapping into the data well How self-service analytics contribute to asset reliability and operational performance UPCOMING WEBCASTS MAY 11, 2021: Move the manufacturing enterprise to the cloud MAY 25, 2021: Power system harmonics: Mitigation practices and technologies MAY 27, 2021: Five key steps of an electrical safety program To view all upcoming webcasts for Plant Engineering WWW.PLANTENGINEERING.COM/WEBCASTSvisit 4336
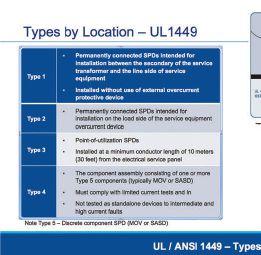
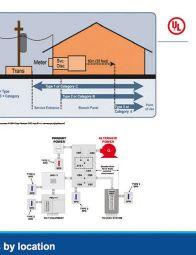
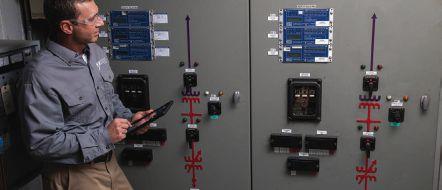

U.S. factory activity advanced in early April, though Reuters.ingdemandmaterialsstruggledmanufacturerstosourcerawasdomesticboomed,accord-toreportingfromDatafirmIHSMarkitsaiditsflashU.S.manufac-turingpurchasingmanag-ersindex(PMI)increasedto60.6inthefirsthalfofApril.Thiswasthehighest
DAVID SKELTON, Vice president and general manager Phoenix Contact Development and Manufacturing dskelton@phoenixcontact.com
* If the content meets criteria noted in guidelines, expect to see it first on our websites. Content for our enewsletters comes from content already available on our Websites. All content for print also will be online. All content that appears in our print magazines will appear as space permits, and we will indicate in print if more content from that article is available online.
CONTENT SPECIALISTS/EDITORIAL
EDITORIAL ADVISORY BOARD H. LANDIS “LANNY” FLOYD, IEEE Life Fellow H.Landis.Floyd@gmail.com
JOHN MALINOWSKI, Senior manager of industry affairs (retired), Baldor Electric Company
* Content should focus on helping engineers solve problems. Articles that are commercial in nature or that are critical of other products or organizations will be rejected. (Technology discussions and comparative tables may be accepted if non-promotional and if contributor corroborates information with sources cited.)
* Deadlines for feature articles intended for the print magazines are at least two months in advance of the publication date. Again, it is best to discuss all feature articles with the content manager prior to submission. Learn more at: www.plantengineering.com/contribute
MARK WATSON, Senior director, manufacturing technology, IHS Markit Mark.watson@ihsmarkit.com
JACK SMITH, Managing Editor JSmith@CFEMedia.com
AMANDA PELLICCIONE, Director of Research 860-432-4767, APelliccione@CFEMedia.com
INSIGHTS By Kevin Parker, Editor U.S. TMandTechnology
reading since the series started in May 2007. A reading above 50 indicates growth in manufacturing, which accounts for nearly 12% of the U.S. economy. The good news is tempered by concern in other areas, Reuters said. Strong demand is encountering supply constraints. The pandemic has disrupted labor and factories and their suppliers, causing shortages and rising prices. Supply shortages were causing backlogs of uncompleted work not seen in nearly a decade, continued the IHS Markit report. The raw material squeeze is most evident in the automotive industry, where a global semiconductor shortage has forced production cuts at motor vehicle assembly plants.
KATIE SPAIN NAREL, Art Director KSpain@CFEMedia.com
SUSIE BAK, Production Coordinator SBak@CFEMedia.com
SHON ISENHOUR, Partner, Eruditio LLC sisenhour@EruditioLLC.com
DR. SHI-WAN LIN, CEO and co-founder,Thingswise, LLC Industrial Internet Consortium (IIC) board member shiwanlin@thingswise.com
KEVIN PARKER, Editor KParker@CFEMedia.com
PlantEngineering.com 3010 Highland Parkway
BILLY RAY TAYLOR, Director of commercial and off-highway manufacturing The Goodyear Tire & Rubber Billytaylor@goodyear.com
Content For Engineers. That’s what CFE Media stands for, and what CFE Media is all about—engineers sharing with their peers. We welcome content submissions for all interested parties in engineering. We will use those materials online, on our Website, in print and in newsletters to keep engineers informed about the products, solutions, and industry trends.
The U.S. trade deficit in manufactured goods more than doubled in the most recent decade, McKinsey said. Analysts fear increased import dependence will leave some U.S. supply chains exposed to greater global risk, even as anecdotal and other evidence indicates widespread U.S. labor shortages as the economy recovers. PE U.S. manufacturing gains; supply chains falter Suite 325 Downers Grove, IL 60515 Ph. 630-571-4070, Fax 630-214-4504
www.plantengineering.com PLANT ENGINEERING May 2021 • 5
JOHN GLENSKI, President, Automation Plus jglenski@processplus.com
LARRY TURNER, President and CEO, Hannover Fairs USA lturner@hfusa.com
* www.plantengineering.com/contribute explains how to submit press releases, products, images and graphics, bylined feature articles, case studies, white papers, and other media.
The international scene At the same time, Bloomberg reported that Chinese manufacturers, especially those in upstream sectors, are benefiting from rising prices and profits, while the U.S. fiscal stimulus is giving a boost to exporters, allowing them to increase production.Incontrast, Europe’s economy shrank 0.6% in the first three months of the year as slow vaccine rollouts and extended lockdowns delayed recovery, Bloomberg reported. While the U.S. economy grew 1.6% during the first quarter, and 6.4% on an annualized basis, for Europe it was the second straight quarter of falling output, meaning the region fell back into recession. Europe’s unemployment rate increased to just more than 8% in March. The U.S. saw its jobless rate fall to 6% after spiking as high as nearly 15% during the worst of the pandemic, Bloomberg reported. The longer view Leaving the short-term statistical outlook aside, a McKinsey Global Institute “discussion paper” issued in midApril, “Building a more competitive U.S. manufacturing sector,” outlined 16 industries with strong growth prospects, including semiconductors, medical devices, communications equipment andThoseelectronics.withthe greatest potential to support jobs in a wide set of communities include autos and parts, metals, and machinery. These industries together employ 3.4 million workers and involve 75,000 suppliers. Pharmaceuticals, electronics, semiconductors, and medical devices support R&D spending, which underpins innovation. It starts with regaining lost ground, according to McKinsey. Although absolute output has grown, the past two decades have been marked by declines in the U.S. shares of global manufacturing gross domestic product (GDP) and gross sales. In real value-added terms, growth has slowed over the past three business cycles, from 4.9% in the 1990s to 1.4% in each of the last two decades. Moreover, much of recent growth was driven by design, services, and software rather than actual production.
CFE MEDIA CONTRIBUTOR GUIDELINES OVERVIEW

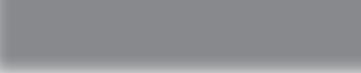
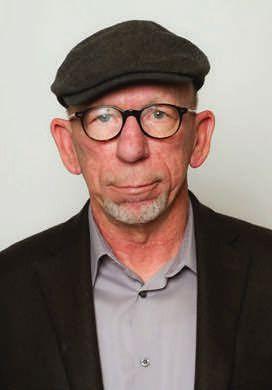
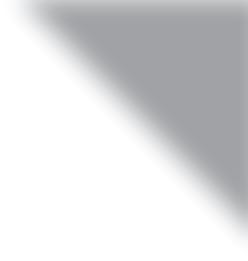
© 2021 Caterpillar. All Rights Reserved. CAT, CATERPILLAR, LET’S DO THE WORK, their respective logos, “Caterpillar Yellow”, the “Power Edge” and Cat “Modern Hex” trade dress as well as corporate and product identity used herein, are trademarks of Caterpillar and may not be used without permission. www.cat.com / www.caterpillar.com Your Northeast Cat® Dealers maintain the region’s largest fleet of high quality, low hour power rental solutions. They offer a rental product line specifically designed to meet the needs of commercial, industrial, institutional, and manufacturing facilities. Our line encompasses the most critical systems to your operations, including temperature control, compressed air, and of course, electric power products. We have the largest, most modern fleet of equipment in the Northeast, so you can be sure that you will have the right equipment to meet your needs wherever you jobsite is located. Learn more today by visiting POWERwww.necatdealers.com/standbyRENTAL FLEET WHERE THE NORTHEAST TURNS FOR RENTAL POWER » Power Generation » Temperature Control » Compressed Air » Ancillary Equipment » Cabling » Pigtails Cleveland Brothers Serving Pennsylvania and northern West Virginia www.clevelandbrothers.com 800-538-1020 SINCE 1948 Foley, Incorporated Serving New Jersey, eastern Pennsylvania, northern Delaware and Staten Island www.foleyinc.com 732-885-5555 SINCE 1957 H.O. Penn Machinery Serving Connecticut and southern New York www.hopenn.com 844-CAT-1923 Since 1923 SINCE 1923 Milton CAT Serving Massachusetts, Maine, New Hampshire, Vermont, Rhode Island, and Upstate New York www.miltoncat.com 866-385-8538 SINCE 1960 53 FOLEY,CONVH.O.PENNINC.CLEVELANDBROTHERSMILTONCAT MILTONCAT RENTAL SOLUTIONS » Cable Ramps » Load Bags » Fuel Tanks » Transformers » Decking Station input #5 at www.plantengineering.com/information
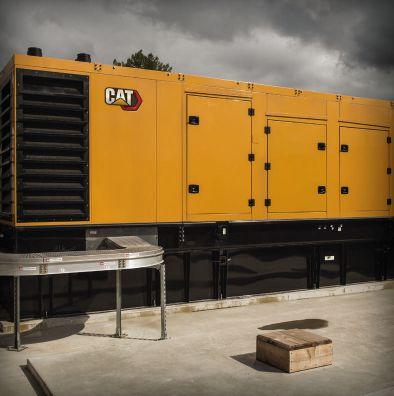
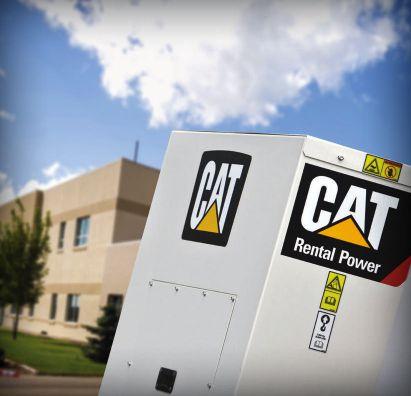
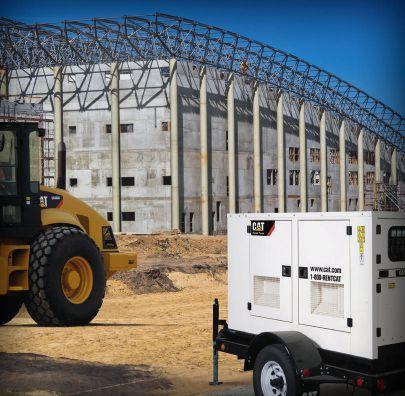
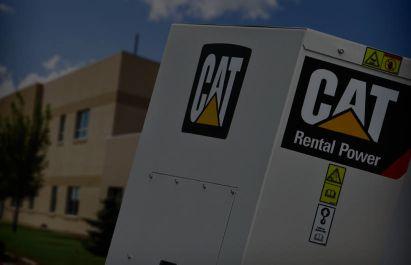
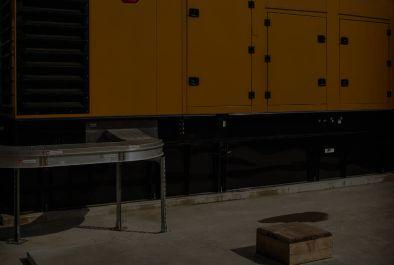

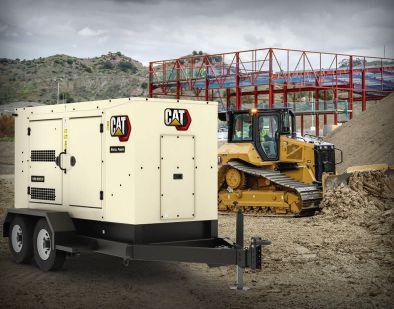

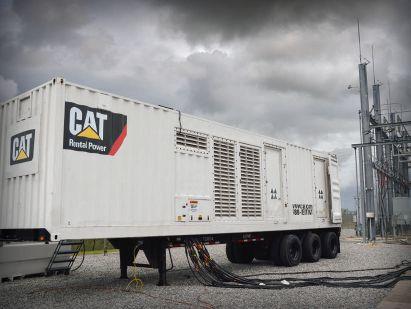
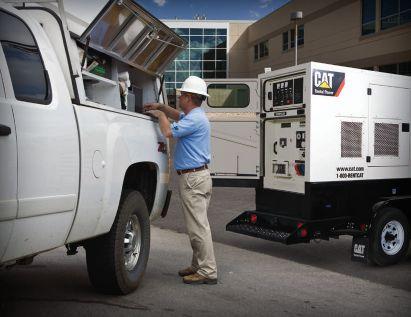
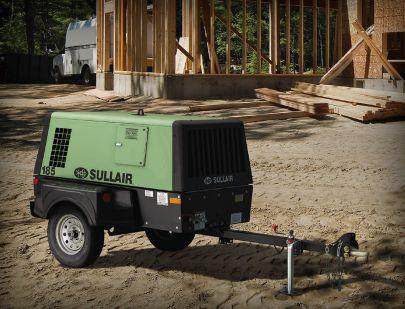
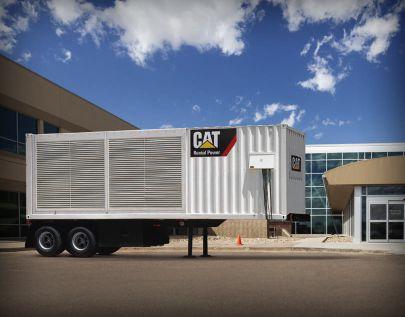

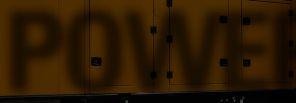
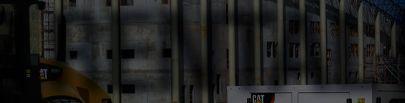
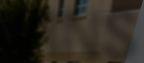
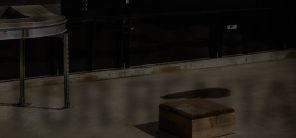
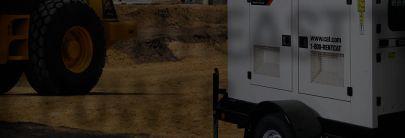
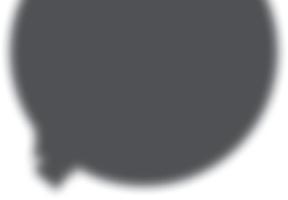



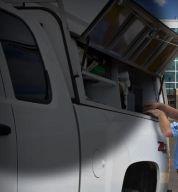
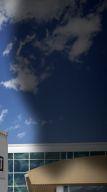
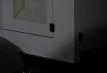
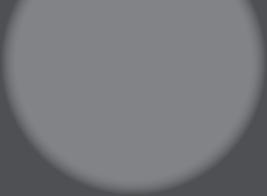

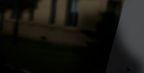

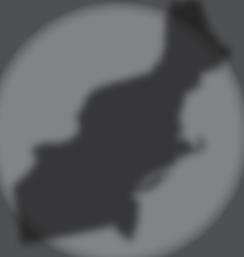

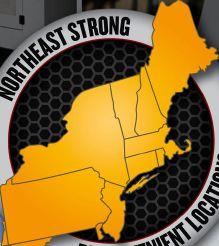

www.plantengineering.com PLANT ENGINEERING May 2021 • 7 PLANT OPTIMIZATION Figure 1: CompanyTireGoodyearCourtesy:(KPIs)indicatorsperformanceplant’simproveflooronandknowledgetotheassociatesgivesoptimizationPlantcapabilityapplyskillstheshopandtheirkeydaily.The&Rubber
Boosts employee engagement and recognition
These are reviewed by our PO leaders for potential certification as a new best practice. This system has fostered a company-wide practice of knowledge sharing. We see a lot of enthusiasm among associates who are eager to share their successes and look to other plants for ideas. For example, our associates have told us that the PO process and methodologies engage the team, which helps sustain the results.
Reinforces a winning culture It is exciting to see how passionate our plant associates are about PO. In many instances, they have transformed the culture of their teams to make PO the “way we work.” PO has established a process to recognize and share great work at the monthly and global PO meetings, and quarterly town halls. Most of these meetings are about the plant associates. During these meetings, managers are invited to share what plant associates deserve recognition for their contribution. One common topic across the board: Behind hard metrics on improvements in safety, quality, delivery and cost is the passion, involvement and engagement of associates. When the common theme of recognition is beyond cost and savings, it reinforces and strengthens the site’s culture.
We have a formal process in place for associates to share key learning results across plants. This process empowers associates to propose best practices in our system.
Initially, the primary goal of PO was to increase our plants’ capabilities in a pragmatic way; and we’ve been successful. Since launch, we’ve reduced overall safety incidents, improved year-to-date operational effectiveness (OE) yield above 90% and closed our global gap in plant maturity levels by 31%. In addition, we’ve seen improved machine reliability, reduced waste and lowered our cost per tire. But then, we saw something even more compelling and encouraging: the lasting effects PO had on our people. In plants where PO has been deployed, is advancing and is sustained, our plant associates feel empowered to identify issues and opportunities, solve problems and drive improvements. It has also built a culture of trust, strengthened our culture of safety and health and created common understanding and mindset toward zero losses. If PO is done right, the following described ways it can benefit teams within an organization.
G oodyear launched plant optimization (PO) to standardize processes in its 33 manufacturing facilities across the globe; it is the company’s operating system. At Goodyear, PO is not a program, project, methodology or set of tools, but an integrated set of practices, indicators, enablers, mindsets and behaviors to relentlessly improve quality and efficiency to safely deliver sustainable value.
Develop an ongoing growth mindset
Goodyear’s PO operating system continuously develops associates’ problem-solving and decision-making skills. We accomplish this through the PO Academy, which includes ongoing learning experiences and workshops on various technical and soft skills to close capability gaps. In addition, our Global Manufacturing Leadership Program provides training and mentoring to develop the next generation of plant leaders. It is essential to instill a culture of continuous improvement in any organization. Giving employees the power to be responsible for the reliability of their equipment creates a sense of ownership. To date, more than 925 associates have completed the formal two-week PO Academy, including field projects, to apply their learning. The number of associates who completed PO Academy eLearning courses rose to more than 20,400 in 2020, increasing from 13,484 in 2019 and 10,783 in 2018. Due to the COVID-19 pandemic in 2020, we piloted a virtual training methodology and program Plant optimization results in much more than increased productivity and KPIs Ricardo Estok
How to engage employees through plant optimization
INSIGHTS By
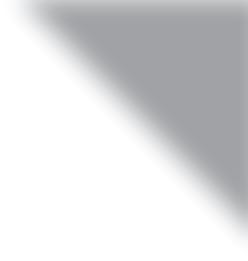
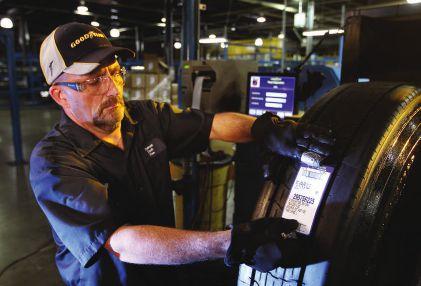
PLANT OPTIMIZATION
Capabilities. We ensure associates are clear on the why, what and how of PO as well as their roles and value add.
to keep building capabilities in the “new normal” environment. It does not stop there. We also ask our plant leadership about skills needed for the next two to three years so we can start developing training now to make ourselves future proof. Makes associates’ jobs more practical For associates, PO makes their jobs more practical and even easier in some cases. It gives them the capability to apply knowledge and skills on the shop floor and improve their plant’s key performance indicators (KPIs) day in and day out (see Figure 1). An example is our Daily-Weekly-Monthly management system, which is a standard way to manage plants’ ongoing planning activities, standardizing, reviewing and taking action that supports a dashboard of cascading KPIs and targets. Since PO is embedded into this system, associates have a clear understanding of expectations, follow-ups and where to focus efforts. PO is part of the “way they work” and not an isolated workstream or improvement project. PO does not become, “one more thing I need to do.”
To ensure that your operation is performing at optimal levels with the lowest possible total cost of ownership, IoT-connected wireless monitoring technology can help to save both money and time. However, not all equipment necessarily needs to be monitored, and not all monitoring systems are financially viable.
Daniel.Phillips@regalbeloit.com Regalbeloit.com/Perceptiv
pe202105_wpcrHlf_regalBel.indd 1 4/22/2021 4:31:26 PM input #6 at www.plantengineering.com/information
A Practical Use Guide To Wireless Technologies
This white paper explores the factors to consider when exploring whether your maintenance team and your equipment could benefit from wireless monitoring technology. For example, how much time is needed to prepare spare parts and labor when a machine fails? How much does lost production time cost? What resources are available to analyze the data generated from monitoring devices? For equipment that has a high cost for lost production, is located in remote locations, or is not stationary, the benefits of wireless systems are explored. The strengths and weaknesses of both wireless and wired systems are also briefly explored.
Register to download the paper at: https://bit.ly/2QIhqFA
While operationalizing and optimization does impact the hard skills, it is the PO mindset and behaviors that end up emerging stronger. We tested a formula of four variables to see what kind of outcome they produced: Capabilities + clarity + recognition + walking the talk = (how would you solve this equation?).
•
INSIGHTS
Daniel Phillips | Technical Director, PTS Monitoring and Diagnostics
Clarity. We equip associates with information and skills they can apply to their jobs daily. Recognition. We put recognition systems in place for when associates go above and beyond and when a red flag is raised to identify an obstacle. Walking the Talk. Plant leadership — at all levels — is visible and publicly models PO values and behaviors. What we found: Capabilities + clarity + recognition + walking the talk = A path to increased empowerment for problem solving and performance improvement. Together, we are building a work environment that is producing the right products for customers as well as focusing on producing people, culture and teams committed to operational excellence. PE Ricardo Estok is the director of plant optimization transformation at The Goodyear Tire & Rubber Company. to in the “new normal” envi-
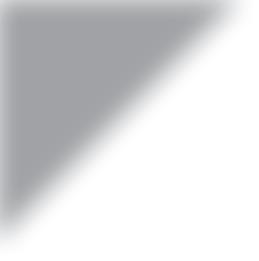
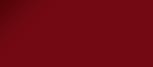
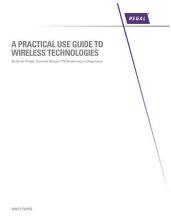
In total, the awards program identified three winners across each of 12 categories for a total of 36 gold, silver and bronze award winners, besides the grand prize. Unfortunately, this year as well as last, winners of the Plant Engineering Product of the Year awards would likely have attended the CFE Media & Technology Engineering Awards in Manufacturing event traditionally held in April in Chicago. The event brings together representatives from a wide range of companies focused on furnishing the manufacturing industries with innovative products, services and solutions. CFE Media sister publication Control Engineering has a similar awards program, and the Plant Engineering Plant of the Year award is also presented at the event. Postponed because of Coronavirus restrictions, CFE Media is hoping to begin scheduling live events againPleasesoon.refer to the chart following to see all the 37 award winners in all 12 product categories.
“FACTS Engineering has worked with us on many successful product lines. Their knowledgeable staff and dedication to quality always produces reliable products. Working together with FACTS to produce the ProductivityOpen controller and ensure it lives up to its promise of reliability was well worth the effort and we’re pleased that Plant Engineering’s readers are happy with the outcome,” Dehner concluded. Asset management rules
The ArduinoplatformProductivityOpenfromAutomationDirectprovidesallthefeaturesofastandardplustheaddedpowerandreliabilityofanindustrialcontroller.
Innovative solutions address needs of today’s U.S. manufacturers
CPUino-compatibleP1AM-100sorconditions.extremethattrolleropen-sourcetionDirectAutoma-saysancon-isneededholdsupinindustrialTheproces-circuitoftheArdu-mimicstheArduinoMKRZero microcontroller. It is compatible with most available Arduino MKR format shields and industrially hardened ProductivityOpen shields and can utilize most Arduino sketch programs found on open-source websites.
Using the Arduino integrated development environment, the P1AM-100 is programmed using C++ code; the ProductivityBlocks graphical programming interface uses a more visual approach that simplifies coding and reduces syntax errors.
www.plantengineering.com PLANT ENGINEERING May 2020 • 9
Unconventional approaches suit readers’ choices SOLUTIONS 2020 PRODUCT OF YEAR AWARD WINNERS
By Kevin Parker A utomationDirect.com, the first industrial controls company to successfully use a direct sales catalog for PLC products, and now an online superstore, received the grand prize in the 2020 Plant Engineering Product of the Year awards competition for its ProductivityOpen platform. That Plant Engineering readers chose an Arduinocompatible open-source hardware and software platform from a company that can deliver that winning product (or almost any industrial control product) direct to your doorstep says something about the last year’s stresses and strains, as well as perhaps indicating the way forward as the U.S. economy surges. “We believe this way of doing business is especially attractive to the younger generations just entering the industrial workforce,” said Bill Dehner, technical marketing manager, AutomationDirect. “As an online supplier our mission is to provide a better shopping experience with 24/7/365 product ordering and fast delivery. Our product engineers stay in tune with industry trends. An industrialized open-source controller was a rising need we felt we could definitely meet.”
The ProductivityOpen platform provides all the features of a standard Arduino plus the added power and reliability of an industrial controller. With the growing popularity of single-board controllers and the risks of implementing them in industrial applications,
Produced in conjunction with FACTS Engineering, the ProductivityOpen platform combines the ingenuity and the proven reliability of the AutomationDirect Productivity controller family.
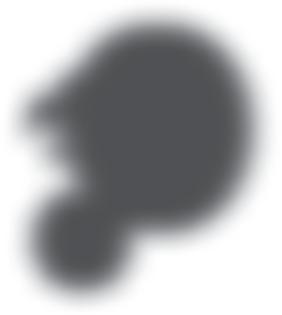
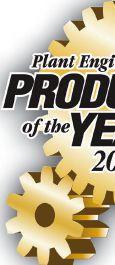
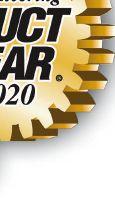
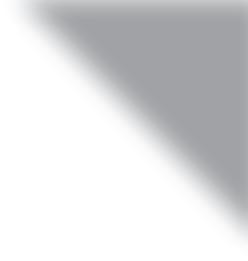
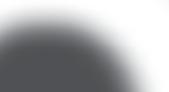

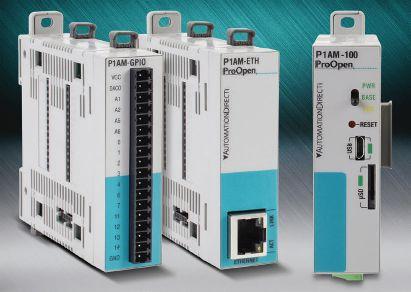
PRODUCT OF YEAR AWARD WINNERS2020 YEAR AWARD
While smart instruments provide diagnostics to indicate problems with electronics or subcomponents, this is often done by way of the automation system. “This type of solution presents problems. Networks can be unduly burdened with data transmissions, historians can become bloated, and there can be time lags between data collection and recognition by the IIoT software,” said Ryan Williams, product manager for solutions & services, Endress + Hauser America. A better solution, Williams suggested, is to deliver all of the edge data to IIoT software via the cloud, thus bypassing the automation system completely. By connecting instruments to an Ethernet-based network, the data can be captured by an edge device to transmit it to IIoT software in the cloud. Software and hardware are needed to extract data from the plant’s Ethernet network or devices and transmit it to that cloud-based software.
The gold award in the analytics & design category went to PTC ThingWorx Kepware server industrial connectivity software. Industry 4.0’s benefits make it a critical pursuit for manufacturers who want to remain competitive. But for many companies, the prospect of connecting to their myriad of factory assets — particularly trusted older equipment — is simply too daunting. Industrial connectivity helps manufacturers break widely implemented operational technology systems like MES, SCADA, PLCs and CNCs out of niche-protocol silos. Doing so means manufacturers get more out of valuable machine data, making it actionable, preventing maintenance and downtime, and ensuring equipment compliance. PTC Kepware is probably best known for its comprehensive library of device drivers. However, besides drivers, other tools are relevant based on the type of connectivity involved. One example would be a bespoke proprietary format. In fact, Kepware’s latest universal device driver includes scripting capability to allow connection to a wide range of ancillary devices. This approach to connectivity culminates in ThingWorx Kepware Server.
• Improved Scatterplot in Workbench: conditional filtering and more display options help users find relationships among signals more quickly
The SIMOTICS Advantage Series medium voltage, totally enclosed fan-cooled motors combine flexibility and performance to meet or exceed basic application requirements.
ThingWorx Kepware Server leverages OPC — the automation industry’s standard for interoperability — and ITcentric communication protocols, such as SNMP, ODBC, and web services, to act as a single source for industrial data.
10 • May 2020 PLANT ENGINEERING www.plantengineering.com SOLUTIONS
Additional R22 features include:
In this introduction, we’ve been able to highlight only a few of the award winners. All of them, however, are worthy of your attention. To examine them in detail, feel free to visit the CFE Media Products for Engineers Database. In future, our editors predict that the provision of managed services by automation suppliers will become an increasingly powerful force in the manufacturing industries. PE Efficient, reduced frame motors meet requirements for pump and compressor applications
For the important category of asset management, readers’ awarded the gold to Endress + Hauser America’s solution for the IIoT ecosystem, called Netilion. Instrument makers have software that uses that data from the edge to diagnose problems and schedule maintenance.
With three new frame sizes, this motor series is configured with all necessary standard features and pre-engineered modifications to power general industrial applications such as large compressors, blowers, coolers, mixers, conveyors, extruders and pumps, among many others. Not only do these motors have up to 33% more power as a result of innovative cooling technology, but they are also up to 38% Theseutilization.plantmeansLessinothercomparedsmallertoframesthemarket.spacebetterlayoutmotors
ThingWorx Kepware Server provides a single source for industrial automation data to all of an enterprise’s applications. Users connect, manage, monitor, and control diverse automation devices and software applications through one intuitive user interface.
Netilion Connect includes the edge devices, cloud platform and
needtheyprovidingtion,”appropriateandprocessincludestechnologyis(API)programmableapplicationinterfacestodothat.“TheNetilionecosystembasedonanopen-sourceplatformthatanalyticssoftware,healthdiagnosticsthemeanstoaccessdocumenta-saidWilliams,thustechnicianswhatwillhaveincreasingforinthefuture.
Seek and you shall find Another winner in the analytics category was Seeq Corp. for the R22 release of its advanced analytics software for process manufacturing. New R22 features support enterprise data governance initiatives and priorities to support Seeq expansion in large organizations. For example, Seeq Integrated Security honors OSIsoft PI security restrictions for PI data access and enables administrators to set signal-level permissions on data in historians and other time-series data stores. Users therefore only have access to the data they need, facilitating data access compliance.
• NOAA Weather Service Connector: data from the National Weather Service API can be easily integrated into Seeq analytics
are NEMA Premium Efficient as well as optimized for motor efficiency and reduced electrical power consumption. A gold medal winner in the energy management category, Eaton’s Smart EBMX enclosure combines an explosion-proof clamping enclosure design for hazardous environments with IoT-enabled circuit breakers and intelligent motor management relays.
Avoid paralysisanalysis
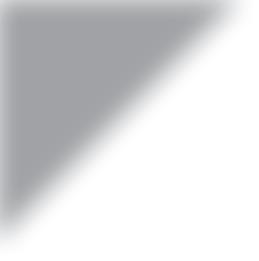
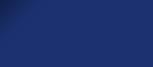


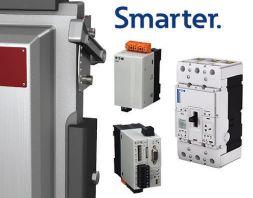
Siborg Systems Inc. 24 Combermere Crescent, Waterloo, Ontario, Canada N2L 5B1 Phone: 1-519-888-9906 Fax: 1-519-725-9522 www.Siborg.com www.LCR-Reader.comBudget LCR MeterBudget LCR Meter Systems Inc. Automatic L, C, R & ESR measurements1oz.weight Automatic range selection Manual mode selection One button navigation Bright OLED One-Handeddisplayuse Ideal for all components Basic Accuracy 0.5% Test Frequency: 100 Hz, 1, 10 kHz Test Signal Level: 0.5 +/- 5% Vrms LCR/ESR Oscilloscope SignalFrequencyGenerator AC/DC CurrentAC/DC Voltage LCR-Reader-MPA®All-in-OneMultimeter Optional Bluetooth model for data logging and quick Pass/Fail assessmentcomponent 2020 Winner L-C-R, AC/DC Voltage/Current ESR, LED/Diode/Continuity Test Frequency,OscilloscopePeriod, Duty Cycle Signal Generator Super Cap Testing up to 1 F Basic Accuracy 0.1% Test Frequency: 100 Hz to 100 kHz Test Signal Level: 0.1, 0.5, 1.0 Vrms Made in Canada Fabriqué au Canada input #7 at www.plantengineering.com/information
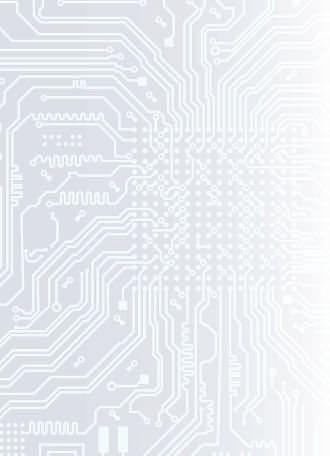
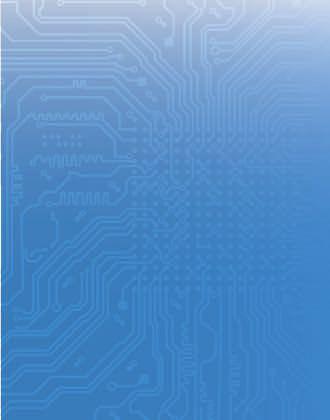
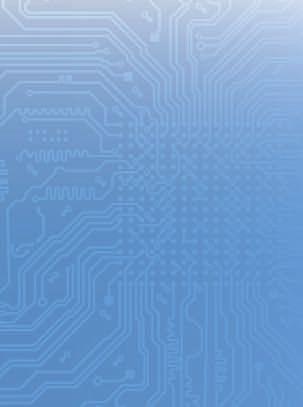
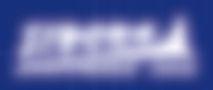
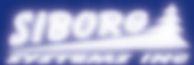
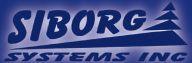

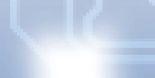

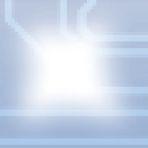



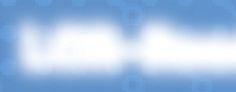
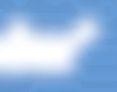



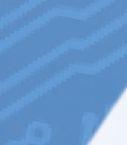
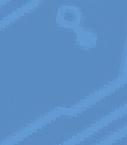
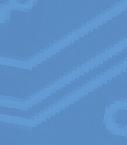
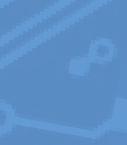
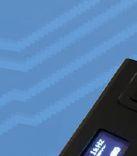
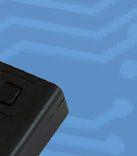

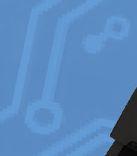
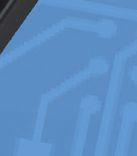
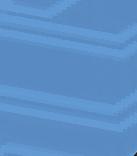

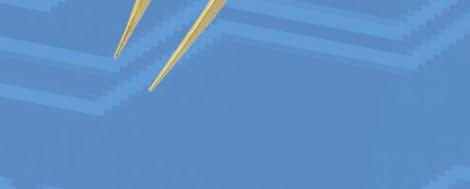
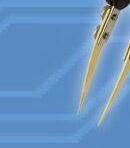

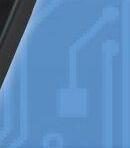
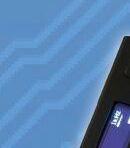
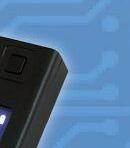
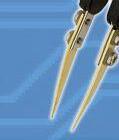
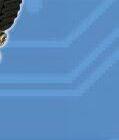
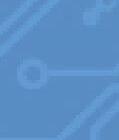
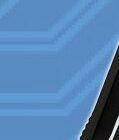
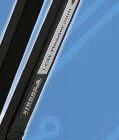
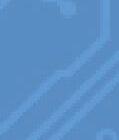
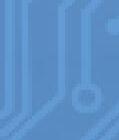
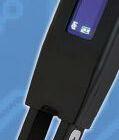
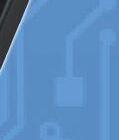
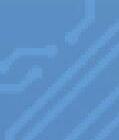
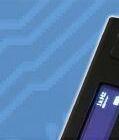
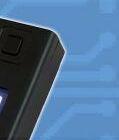
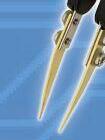
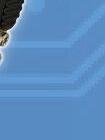
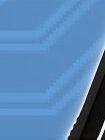
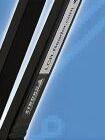
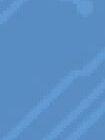
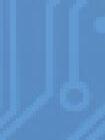
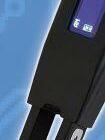
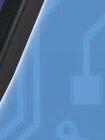
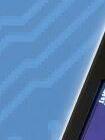
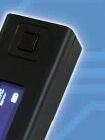
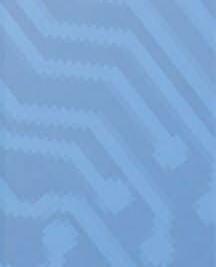
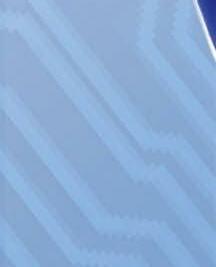
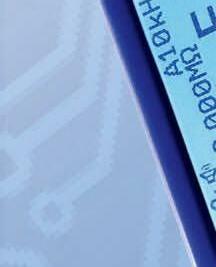

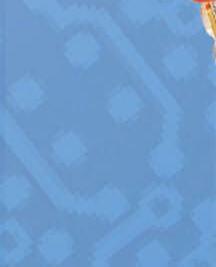
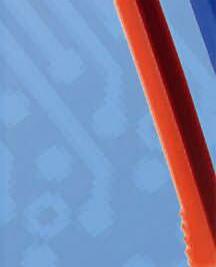
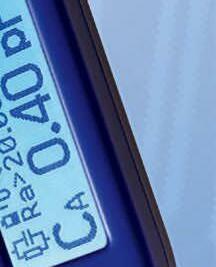
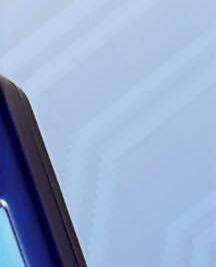

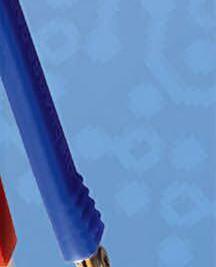

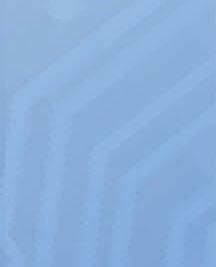
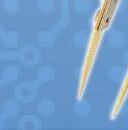
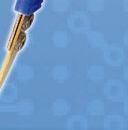
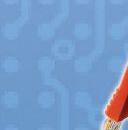


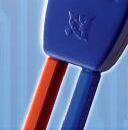
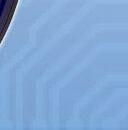

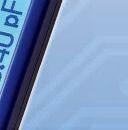
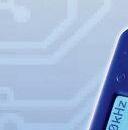
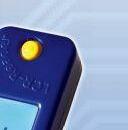
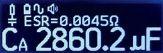
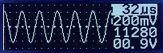
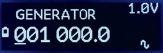
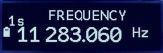
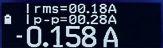
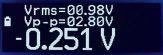
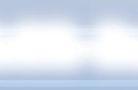
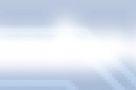
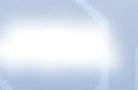






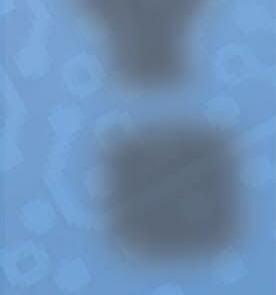
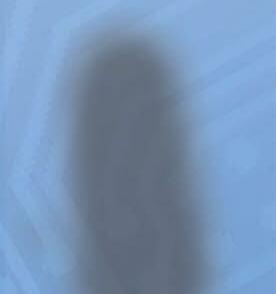
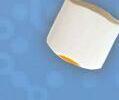
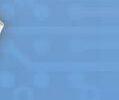
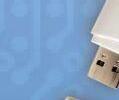
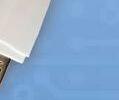
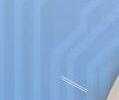
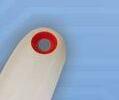
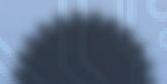
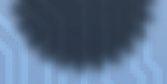


12 • May 2020 PLANT ENGINEERING www.plantengineering.com SOLUTIONS PRODUCT OF YEAR AWARD WINNERS2020 YEAR AWARD Category Award Product Manufacturer GRAND ProductivityOpen Arduino-compatible controller AutomationDirect Asset Management Gold Netilion IIoT solution platform Endress+Hauser Silver AMS Asset Monitor Emerson Automation Bronze ControlGate control system gateway Grace Technologies Automation & Controls Gold ctrlX Automation controls platform Bosch Rexroth Silver VTScada V12 integrated HMI, SCADA platform Trihedral Bronze OSA Remote +Flow industrial control system Bedrock Automation Compressed Air Gold NxHE two-stage rotary screw air compressor FS-Curtis Silver QOFT rotary tooth compressor Quincy Compressor Bronze Mobilair M500-2 portable compressor Kaeser Compressors Electric MotorsDrives& Gold Simiotics Advantage motor Siemens Industry Silver ctrlX Drive compact modular drive system Bosch Rexroth Bronze Mangoldt 5-in-1 Type ACL line/load reactor Allied Industrial Marketing Energy Management Gold Smart EBMX enclosure Eaton Corp. Silver EMpro energy monitoring device Phoenix Contact Bronze EnergyPQA.com cloud-based energy management system Electro Industries/GaugeTech Environmental Health Gold BioSpray-5 ultra-portable surface sanitation system Goodway Technologies Silver SilverStreak 2020 hands-free sanitizer dispenser PowerSafe Automation Bronze GMM21004 social distancing floor sign New Pig Fluid Handling Gold EF6010SS no-drip external mix atomizing nozzle Exair Silver Blackmer MAGNES sliding vane magnetic drive pump PSG Bronze FLT753 oil and sediment catch basin filtration insert system New Pig Maintenance Software Gold PredictPulse remote monitoring application Eaton Silver Enabled Services control system health and performance software Honeywell Process Solutions Bronze MVP Plant V2.8 computerized maintenance management system CMMS Data Group Maintenance Tools Equipment& Gold Varnish Removal System Des-Case Corp. Silver 6103 EasySwitch wet-dry vacuum Exair Bronze LCR-Reader-MPA all-in-one digital multimeter Siborg Systems Material HandlingSystems Gold 303SS air conveyor Exair Silver Automatic production assistant (APAS) Bosch Rexroth Bronze NR/NDR-DC/EC narrow aisle reach truck Yale Materials Handling Corp. Plant AnalyticsDesign& Gold ThingWorx Kepware Server industrial connectivity software PTC Kepware Silver EcoStruxure Power Advisor analytics software Schneider Electric Bronze Seeq R22 advanced analytics for process manufacturing Seeq Corp. Safety Gold LEV IEC 60309 pin and sleeve device Leviton Manufacturing Co. Safety Crouse-Hinds Champ CPMV LED wallpack Eaton Corp. Bronze Impact-A-Track LED for door tracks TKO Doors
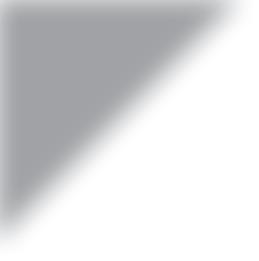
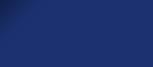

EDUCATION for ENGINEERS www.plantengineering.com/webcasts | www.plantengineering.com/research | www.plantengineering.com/ebooks | cfeedu.cfemedia.com www.plantengineering.com PLANT ENGINEERING May 2021 • 13 One(1) certifiedprofessional development hour(PDH) available for all attendees. Course runs until Aug. 12 2022 One(1) certifiedprofessional development hour(PDH) available for all attendees. RESEARCH: OT, IT collaboration helps IIoT Course runs until Dec. 31 2021 Sponsored by SPRING EDITION Sponsored by Sponsored by SPRING EDITION SPRING EDITION ROBOTICS MANAGEMENTENTERPRISEASSET by
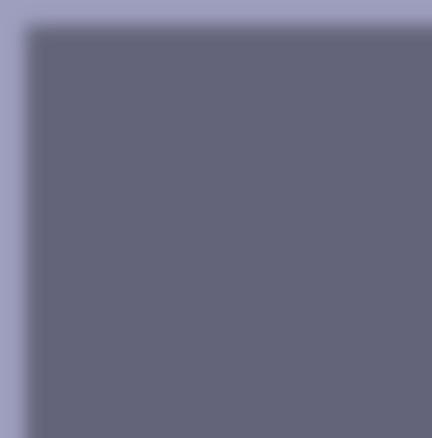



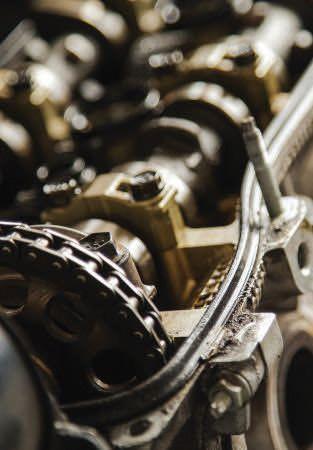

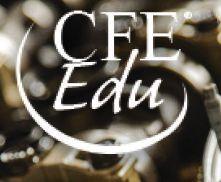
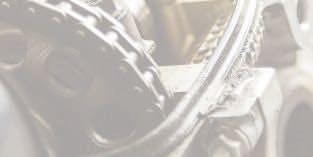
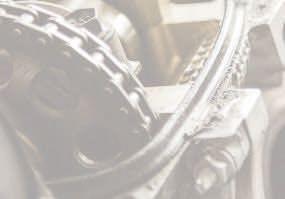
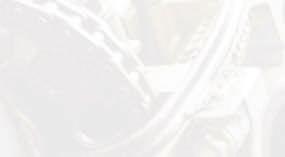
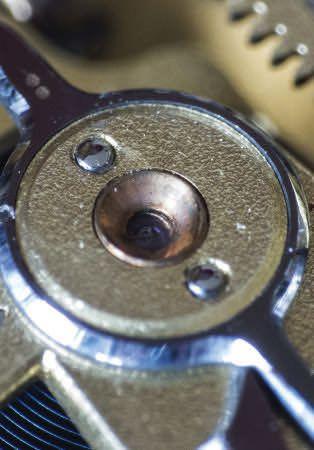
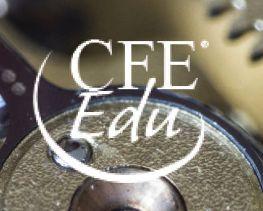
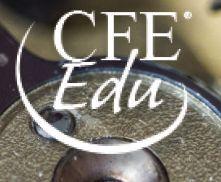
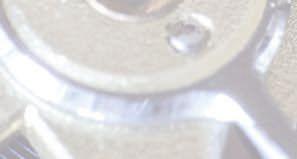
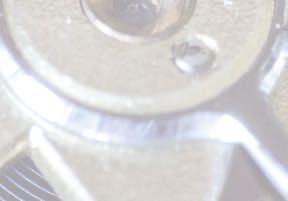
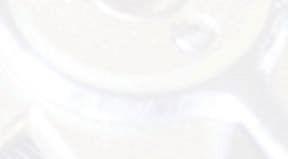

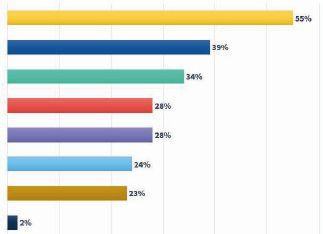
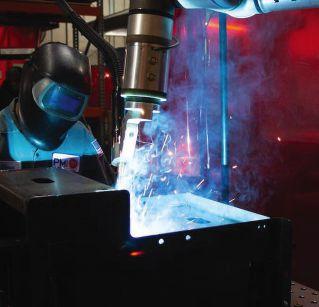
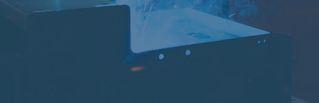
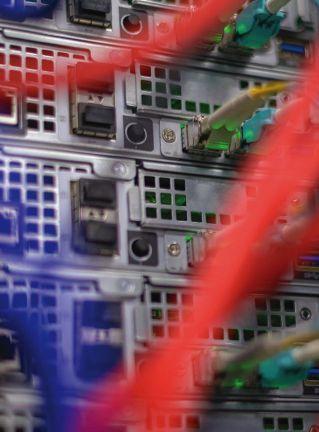
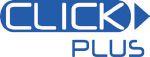
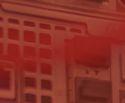
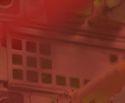
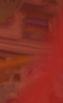
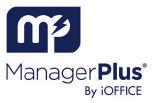
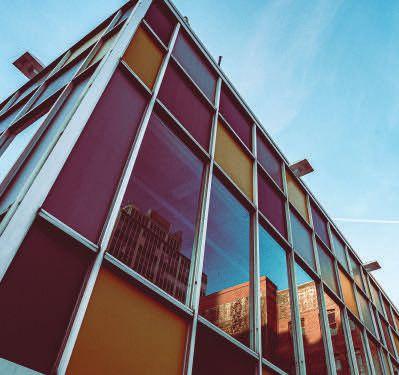

Newark, NJ 07105 / Toledo, OH 43605 / 800-733-4755 To learn more visit us at: www.lubriplate.com INCLUDED AT NO ADDITIONAL CHARGE ES P Lubriplate’s Complimentary Extra Services Package COLOR CODED LUBE CHARTS & MACHINERY TAGS PLANT SURVEYS / TECH SUPPORT / TRAINING LUBRICATION SOFTWARE / FOLLOW-UP OIL ANALYSIS Perma automatic lubricators provide clean, safe, reliable and consistent machinery lubrication every day around the clock. They are fully programmable and deliver the right amount of lubricant consistently, day after day, week after week. A wide range of types and sizes are available to meet your exact needs. All come ready to install pre-filled, available with a wide variety of Lubriplate Quality Greases and Oils. They save time, lower maintenance costs and improve workplace safety. Permas Are Cost Effective Permas Prevent Breakdowns & Downtime Permas Are Fully Programmable Permas Improve Workplace Safety Contact Lubriplate’s Perma Specialist Conner Cusack to learn more Call 800-733-4755 or email: ccusack@lubriplate.com AROUND THE CLOCK BEARING PROTECTION PERMA AUTOMATIC LUBRICATORS PRE-FILLED WITH LUBRIPLATE QUALITY GREASES & OILS. input #8 at www.plantengineering.com/information
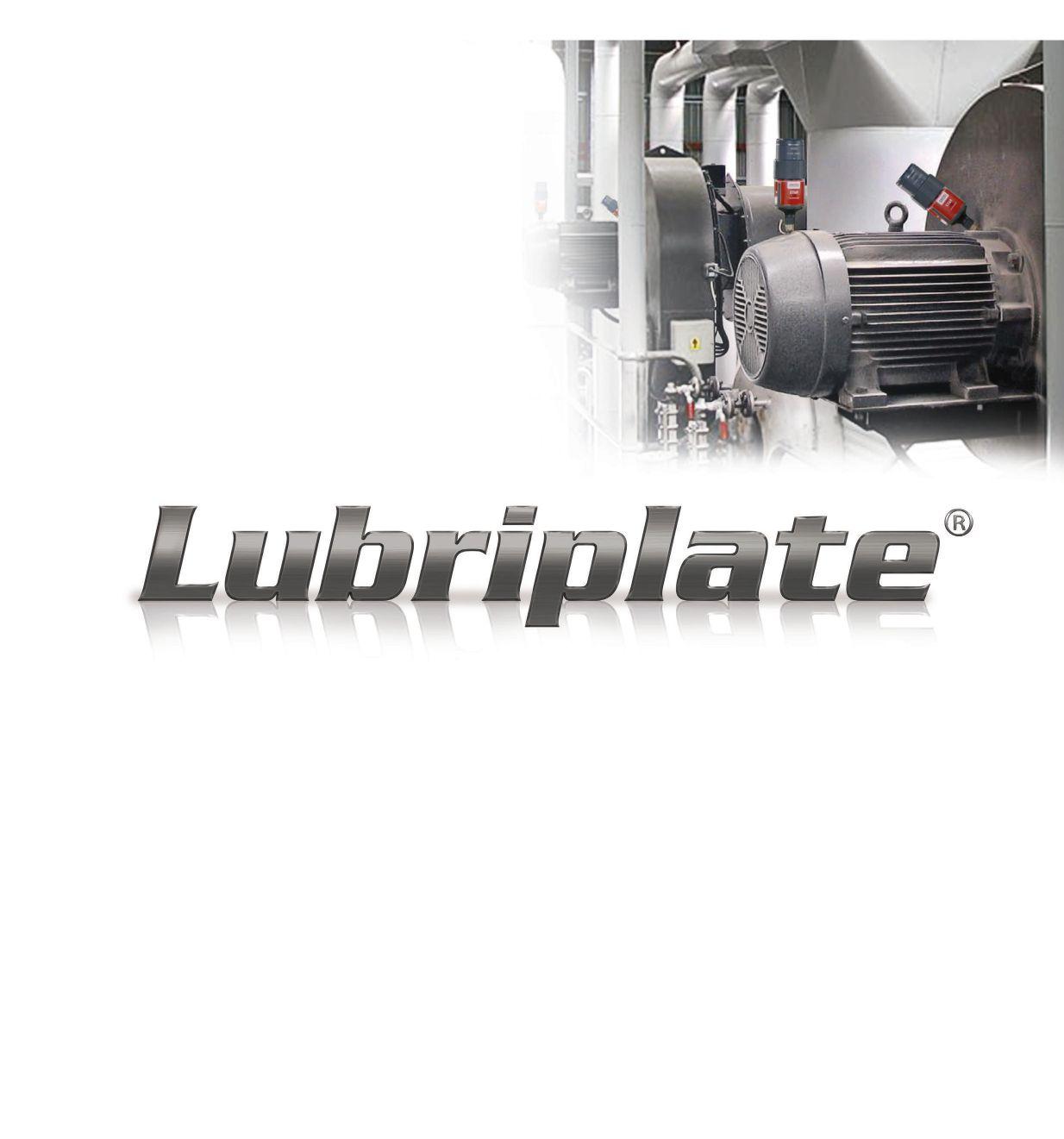
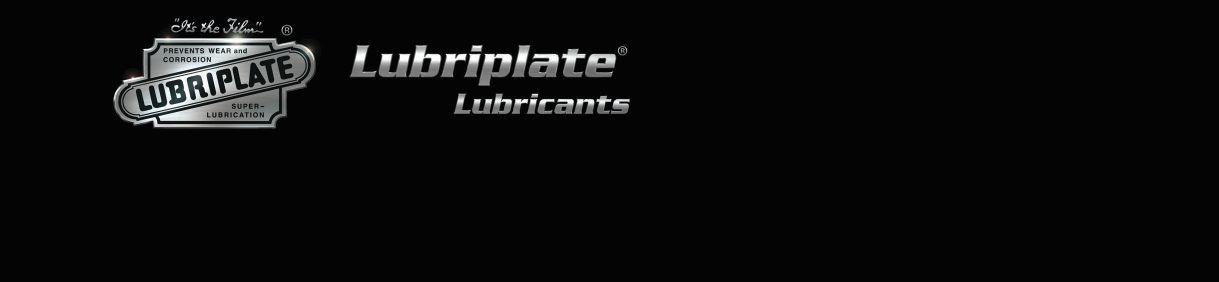
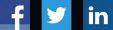

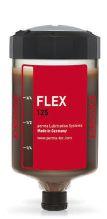
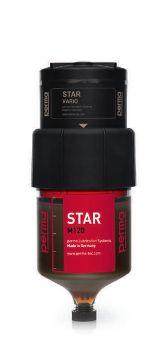
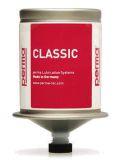
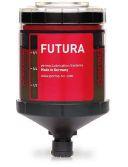
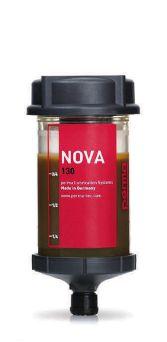
By John Malinowski
S ince this article was first published some years ago, confusion about specifying ac motors used with adjustable speed drives (ASD) has persisted. Today, ASDs are used to regulate the flow of air and water from motordriven fans and pumps. In doing so, old style dampers and flow valves are eliminated, and the motor’s adjustable speed regulates the flow. More importantly, adjusting the motor’s speed saves energy when using these variable torque loads. Also, ac motors and drives can be used to replace old dc motor technology used on constant torque loads such as conveyors and extruders. To maximize the life of motors used with ASDs, it is important to understand the motor features needed for operation with a drive, so designs that are more robust and expensive than required are not specified. Why ASD are used An ac ASD changes the input voltage and frequency to the motor, which changes the motor’s speed. There are several types and loads, each with specific load characteristics that affect the motor. The most common type is a variable torque load, where the horsepower required varies by the cube of the speed change. This is called the affinity law. On a centrifugal pump load (assuming pump efficiency remains constant), Table 1 provides the required horsepower at various speeds, volumes and pressures. Since most equipment is sized for worst-case conditions, it rarely runs at full capacity. On a variable torque load such as a pump, the normal running condition may be at 60% of full speed, which requires only 22% of the motor’s horsepower. The reduced wattage drops the operating cost significantly. A 100 hp motor operating continuously could cost $27,139 annually operating at full speed. At 60% speed, the operating cost would be reduced to $5,970, a $21,169 annual savings.
A second type of load has constant-torque characteristics. The torque requirement remains constant and does not change as speed is adjusted. Such applications are conveyors, extruders, mixers and positive-displacement pumps. There is a lower energy requirement as speed is adjusted on a constant-torque installation. Using a drive on a constant-torque application may save energy through increased productivity and be measured through benchmarking the number of widgets produced per kWh. Selecting a motor General-purpose integral horsepower NEMA Premium efficiency motors from most manufacturers can be used for all variable-torque and many constant-torque applications. These 3-phase lowvoltage ac squirrel-cage induction motors (less than 600 V) are built with an inverter-ready or invertercapable insulation system. They are mostly NEMA Design A or B motors that can be started across the line or used with a bypass should the inverter fail. Enclosures for general-purpose motors are usually totally enclosed non-vented (TENV) or totally enclosed fan-cooled (TEFC) with a cooling fan on the motor shaft. Open drip-proof (ODP) motors have an open enclosure and circulate air through the motor for cooling. These motor enclosures work well on variable-torque loads because as the speed decreases, the amount of power the load requires also decreases — as does the amount of cooling the fan can supply. When we talk about the speed range for a motor with a variable-torque load, it is called variable-torque speed range (VTSR) and is usually quite General-purposewide.NEMA Premium efficiency TEFC motors also can be used for constanttorque loads, but their speed range may be limited. For example, a constant-torque speed range (CTSR) is expressed as 10:1, or the motor can operate from base speed to 1/10 of base speed (180 to 1,800 RPM). Generally, lower-horsepower general-purpose motors can operate over a wider Avoid inverter-dutyover-specifyingmotors
When combining a motor and inverter, the application should reveal what type of motor ts best; follow these guidelines to avoid more than is necessary
SOLUTIONS www.plantengineering.com PLANT ENGINEERING May 2021 • 15 MOTORS AND DRIVES
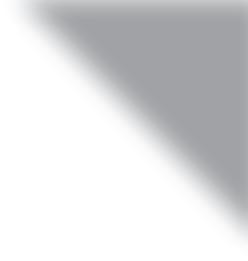
The style of an inverter-duty motor described above may look like a standard smooth steel band, cast iron or aluminum-finned NEMA or IEC motor, but another type exists that has a frame made of the exposed motor lamination. The motor is longer, has lower rotor inertia for fast response and is built in a smaller-diameter frame. These motors typically have higher power densities than the typical cast iron frame NEMA designs. Because of their power density and nonstandard foot mounting dimensions, these exposedlamination motors may not be a drop-in replacement for a conventional NEMA or IEC general-purpose motor.Ultimately, the application will dictate the motor used based on a variabletorque load (pump or fan) or a constant-torque load (conveyor or extruder). If it is a variable-torque load, general-purpose NEMA-premium efficiency TEFC or ODP motors should be adequate for the application. If it is a constant-torque load, the speed range and amount of torque needed at low speed will dictate the motor. On many CTSR applications, a general-purpose TEFC motor may be adequate if it provides 4:1 to 10:1 speed range. On applications requiring rated torque at very low speeds (down to zero speed), use of an inverter-duty or vector-duty motor may be required. NEMA is currently in the process of revising the definition for motors operated on ASDs in NEMA MG 1 Part 30 and 31. The IEC is also working on this and is a bit further along with definitions in IEC 60034-25 with the following:
• A converter-capable motor is an electrical machine designed for direct online start and is suitable for operation on a converter [inverter or ASD] without special filtering and meets impulse voltage insulation class (IVIC) of C/B or qualified in accordance with IEC 60034-1842 (IVIC) 5/4. o Such motors include, but are not limited to IEC design N, NE, H or HE, or NEMA design A, B or C, which may be subject to energy efficiency regulation in the EU, North America or other locations.
SOLUTIONS MOTORS AND DRIVES 16 • May 2021 PLANT ENGINEERING www.plantengineering.com
Figure 1: General purpose NEMA premium efficient motor. Courtesy: ABB Motors and Mechanical Inc.
Small fractional-horsepower ac motors may be limited as to the operating voltage from an inverter. It is not uncommon for these motors to be limited to 230 Vac input from inverter power because it is difficult to machine insert phase paper in these motors. Consequently, they do not hold up well to high-voltage overshoots common in the output waveform of most drives. Only applications requiring a motor to produce constant torque over a wide speed range require a true inverter-duty motor as defined in NEMA MG 1, Part 31. Inverter duty motors do not have a NEMA Design Code and may not be designed to start across the line. In addition to TENV and TEFC enclosures, inverter-duty motors may also have a separately powered constant velocity fan to ensure cooling at low speeds and are totally enclosed blower-cooled (TEBC). These motors usually have a 1,000:1 CTSR and with a flux vector drive can provide full torque at zero speed.
speed range (20:1) because of their lower temperature rise. Larger motors (100 hp and up) may be limited to 4:1 or 2:1 CTSR due to the effectiveness of the TEFC cooling, which is reduced when operated at low speeds.
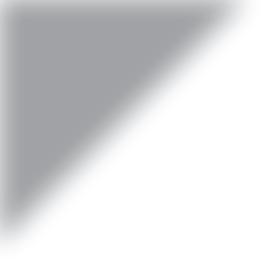
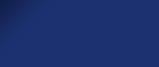
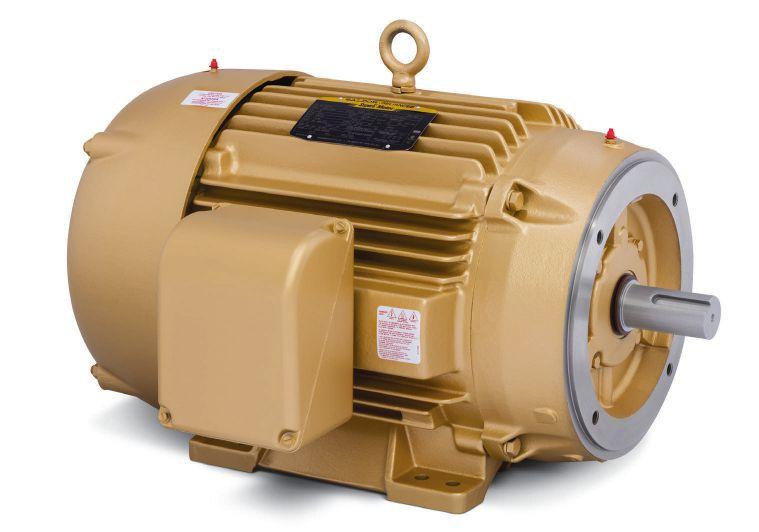
insights
you
insights. Time
Spreadsheets weren’t designed for time series data analytics. Seeq is. © 2021 Seeq Corporation. All Rights Reserved. OptimizationAsset SituationalAwareness Investigation Troubleshooting& OperationalExcellence Learn more www.seeq.comat With Seeq®, difficult and time-consuming work in spreadsheets is a thing of the past. Seeq’s multiple applications enable you to rapidly investigate and share insights from data stored in multiple enterprise data historians, such as OSIsoft PI, Honeywell PHD, and GE Proficy, as well as contextual data sources such as SQL Server, Oracle, and MySQL.
your
you’ve
challenges. input #9 at www.plantengineering.com/information
Seeq’s support for time series data and its challenges – connecting, displaying, interpolating, cleansing, and contextualization – relieves of hours and days of fruitlessly searching for in process manufacturing data. Seeq helps you get more value from the data that already been collecting, and gives organizations data transparency and the ability to execute on those series data analysis poses unique

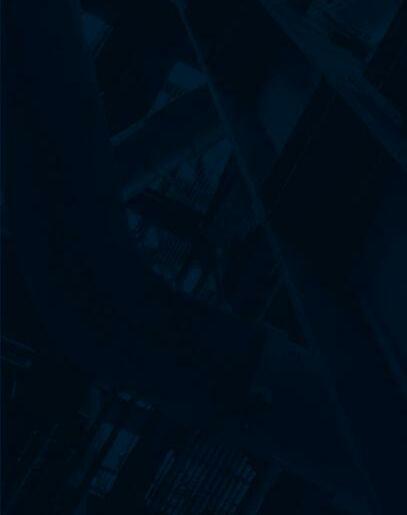
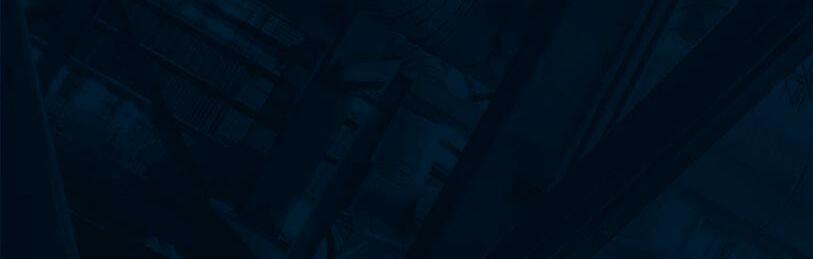
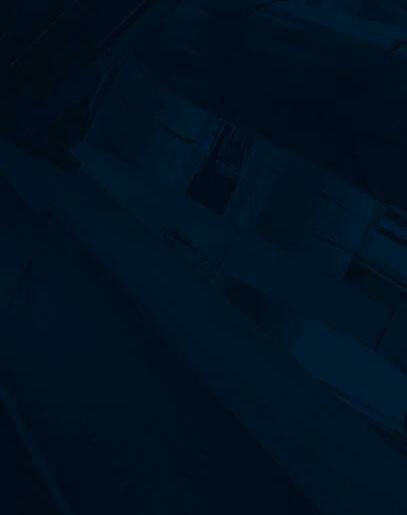
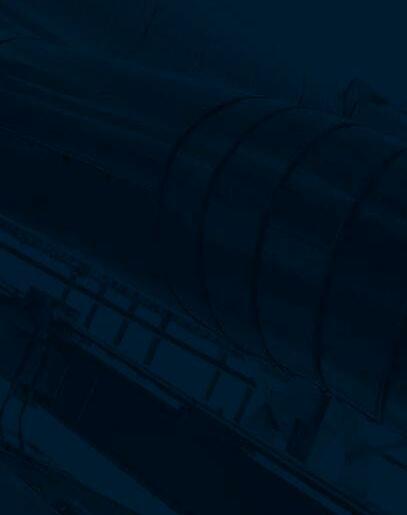
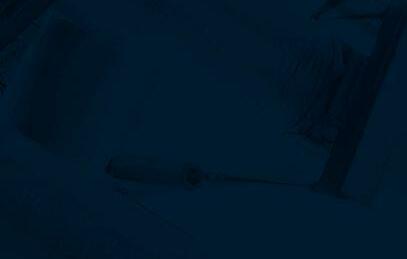
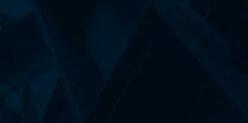











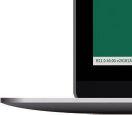
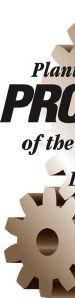
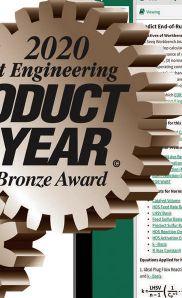
Understanding motor insulation systems
There are two philosophically different approaches to dealing with this sort of stress. One keeps the stresses below a level that causes any damage, while the alternative is to design winding systems to slow down the rate of accumulated damage. NEMA MG 1 states that low-voltage inverter-fed motors should be designed to withstand spikes of 3.1 times the rated voltage. Manufacturers should test to ensure they can meet or exceed these levels. Materials are available that degrade much more slowly in the presence of PD activity. Micabased materials are a common example of what has been used historically in medium-voltage systems. Because PD activity is initiated when there is a high dielectric gradient in the presence of a gas such as air, the common approach to PD avoidance is to reduce dielectric stress gradients and to eliminate air from any regions that may still have a high dielectric gradient.
manufacturers have long recognized that low-voltage (less than 600 Vac) 3-phase ac squirrel-cage induction motors fed by PWM inverters experience higher dielectric stresses than equivalent line-fed motors. The fast-switching transistors used in modern pulse-width modulated (PWM) inverters have helped produce more sinusoidal currents as well as more efficient and compact inverters. The fast transitions (turn on and turn off) of the transistors helped to enable these improvements but also create higher stresses in the motor insulation. These higher stresses are seen phase to phase, phase to ground and turn to turn. The failure mechanism associated with these higher stresses is primarily related to partial discharge (PD) activity. While PD is normally associated with medium-voltage (e.g., 4 kV) motors, in inverter-fed motors, it can be created on lowvoltage systems as well. This PD (also known as corona inception) damage is a cumulative process, much like fatigue failures on a mechanical component. This is a type of localized emission resulting from transient gaseous ionization in an insulation system when the voltage stress exceeds a critical value. The corona inception voltage can be tested on a motor with modern equipment. Some manufacturers perform a type test, while others test each motor that has an inverter-ready or inverter-duty insulation system. Such a production test will also identify damaged wire (insulation pin holes or scrapes) that may fail prematurely in operation.
SOLUTIONS MOTORS AND DRIVES 18 • May 2021 PLANT ENGINEERING www.plantengineering.com
The motor’s insulation system is what makes a motor capable of operating with an inverter power supply. Older motors may experience failure with inverter use. Newer motors that have modern insulation systems designed for inverter compatibility are required. These insulation systems may be configured in many Motorways.
For low-voltage inverter-fed motors, the manufacturers of magnet wire have produced PDresistant products. In cases where PD cannot be avoided, these wires can provide longer life. When the motor can be designed to avoid PD activity altogether, such magnet wire provides no incremental benefit.
Motors have been built using PD-resistant wire using the term inverter-spike-resistant wire. After continuous improvements in insulation systems and manufacturing processes, including thousands of partial discharge inception voltage (PDIV) measurements, many motors are now being manufactured as “PD-free.” This allows the attainment of full insulation system life without the use of spike-resistant wire. Such an insulation system has proven to be as robust, or even more so, than the use of specialty magnet wire. Most inverter-capable and inverter duty motors use the same insulation system for low voltage motors (less than 600 V).
o Such motors have no IEC design or NEMA design letter and are exempt from energy efficiency regulation in the EU, North America and other locations. Which motor should be specified? For variable torque and many constant torque applications, general-purpose motors with NEMA Premium efficiency can be specified. On applications with constant torque use at low speed or constant horsepower operation above base speed, an inverter duty motor should be considered. Check the speed and torque capabilities of the motor with the application’s requirements and contact the motor manufacturer for any questions.
www.plantengineering.com PLANT ENGINEERING May 2021 • 19
General-purpose motors are required by law to have minimum efficiencies in the U.S., Canada, EU and other locations. In the U.S. and Canada, most general-purpose motors in the 1 to 500 hp range are required to have a nominal premium efficiency no lower than NEMA MG 1-2011, Table 12-12. Appendix A to Subpart B of 10 CFR 431 issued by the U.S. Dept. of Energy states: “Motors with features or characteristics that do not meet the statutory definition of ‘electric motor’ are not covered, and therefore are not required to meet EPCA requirements. Examples include motors without feet and without provisions for feet, and variable-speed motors operated on a variable-frequency power supply. Similarly, multi-speed motors and variable-speed motors, such as inverter-duty motors, are not covered equipment, based on their intrinsic design for use at variable speeds. However, NEMA design A or B motors that are single speed, meet all other criteria under the definitions in EPCA for covered equipment and can be used with an inverter in variable-speed applications as an additional feature, are covered equipment under EPCA. In other words, being suitable for use on an inverter by itself does not exempt a motor from EPCA requirements.”
What this means is that marking a NEMA design A or B general-purpose motor as inverter-duty does not exempt it from U.S. Department of Energy (DOE) coverage. This DOE rule is like Canadian law. Only true special-purpose inverterduty motors as discussed in NEMA MG 1-2016 Part 31 are exempt in the U.S. and Canada. In the EU, inverter-duty motors are exempt from their regulations as well. Such motors cannot be used as general-purpose motors operating from a standard sine wave line and easily line started. The windings are optimized for use with an inverter power supply. How ac drives work AC adjustable-speed drives came into the market in the 1970s as high-capacity power transistors became readily available. These drives are also known as inverters, variable-frequency drives (VFDs) or ASDs. The drive takes ac power, uses rectifiers to Figure 2: TEBC inverter duty motor with a separately powered blower for 1000:1 constant torque speed range. Courtesy: ABB Motors and Mechanical Inc.
• A converter-duty motor is an electrical machine designed solely for operation fed by a converter [inverter or ASD] with a temperature rise within the specified insulation temperature class or thermal class.
o The intent of the converter-capable motor is to run within the thermal class of the insulation system. But as the harmonic content of the converter [inverter or ASD] output voltage varies between different drive topologies, coordination with the manufacturer may be required by the end user.
Which energy efficiency regulations apply?
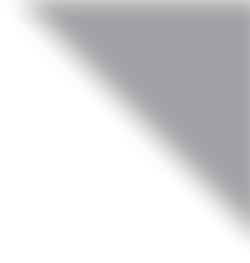

FACTORY DIRECT ERGONOMIC WORKBENCHES Price your requirement then place your order online. Use our secure shopping portal to calculate your quantity discount and place your order today! Factory Direct Your order ships in 5 days or less. Quantity Discounts Available Built in the USA workbenchmarket.com (800) 739-9067 Other models including height adjustable, pack benches, lab benches and cantilever designs are available. Our most popular model. SOLUTIONS MOTORS AND DRIVES 20 • May 2021 PLANT ENGINEERING change it from ac to dc, stores the dc in a capacitor bank (like a battery) and chops the dc into a simulated sine waveform for each of the three phases. A basic inverter uses voltage and frequency changes to adjust the speed of the motor. The voltage and frequency ratios (V/Hz) can be adjusted to provide different characteristics from the motor, such as a specific starting torque, or provide operation above the motor’s base speed. V/Hz-based drives work well with variable-torque loads such as pumps and fans. Some advanced drives carefully control the current to the motor with vector control or direct torque control and can operate the motor over a wider speed range while providing full-rated torque for constant-torque applications such as conveyors andSinceextruders.amotor becomes a generator when spun at speeds above its synchronous speed, an overhauling load on a hoist or conveyor can cause the motor to generate excess energy that is pushed into the drive. This energy must be discharged through a braking resistor, or the drive protects itself with an over-voltage trip. Some drives are designed with an active front end, which is another set of transistors to rectify the input power that can also be used to synthesize a sine wave back to the input line as line regeneration.Asfasterswitching transistors were developed, voltage overshoots began to cause insulation failures on motors. Some spikes from 460 V inverters can reach 2,400 V. These high voltages can break down the motor’s insulation system (see “Understanding
TABLE 1: Affinity law: Horsepower for centrifugal pump load at various speeds, volumes and pressures Speed Volume Pressure/head Horsepowerrequired 100% 100% 100% 100% 90% 90% 81% 73% 80% 80% 64% 51% 70% 70% 49% 34% 60% 60% 36% 22% 50% 50% 25% 13% 40% 40% 16% 6% 30% 30% 9% 3% motor insulation systems”). Additionally, the harmonics on a pulse-width modulation (PWM) waveform can lower the motor’s efficiency when compared to operation of a sine wave. Additional heating occurs in the motor, which may also lower the amount of torque provided at low speed. For most applications, a generalpurpose NEMA-premium motor is adequate for use with an inverter. These motors should work well with most centrifugal pump and fan loads with variable-torque characteristics. For constant torque loads with wide speed ranges, general-purpose motors may work, but check with the motor manufacturer to determine if that motor can be operated over the specific speed range. For extreme constant-torque speed ranges, true inverter-duty motors should be specified. Such inverter-duty motors may have special windings that do not allow operation without an inverter, or they may have separately powered auxiliary cooling fans. PE John Malinowski is an industrial motor consultant and an IEEE Fellow. input #10 at www.plantengineering.com/information
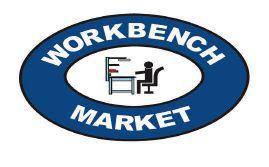
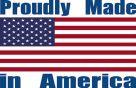
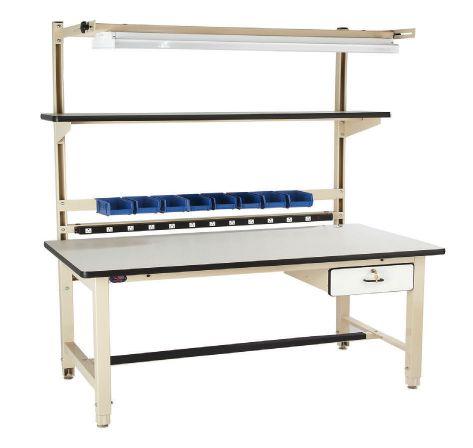
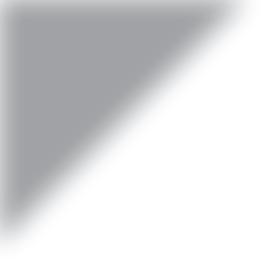
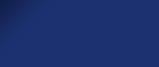
A
SOLUTIONS www.plantengineering.com PLANT ENGINEERING May 2021 • 21 DIGITAL TRANSFORMATION
Figure
A key to bridging the OT/IT gap is enabling successful data modeling. Data modeling is how organizations define and organize their business processes to unlock the value of their data. Unless they put the data into a unified format into the Cloud (the model) they cannot do anything useful with the data. As many like to say, “garbage in will be garbage out.” Data models allow everyone in the organization to understand and use the data more effectively with a single source of truth no garbage. Successful data modeling can lead to business improvements ranging from reduced cycle time to fewer errors to improved collaboration. However, there is a challenge in the IoT solutions market today: How to connect OT data to IT systems for data modeling and data integration. Companies have done it, but it requires a great deal of custom work, code and a spider web of technologies. So many customers try to collect their data and get it to the Cloud, but they end up with a huge number of process variables in a data lake somewhere in the Cloud. They haven’t really solved the data model problem; they have just moved it down the road. System integrators often oversimplify the process, telling customers they will come in and write some code, but then the most common problem is that the solution will not scale. No matter how much code they write, without a data model, it is not scalable. Message queuing telemetry transport (MQTT), an openstandard, publish/subscribe network protocol, combined with the Sparkplug Eclipse specification, provides a much simpler answer. An OT-centric data model MQTT Sparkplug has been touted as an excellent IoT protocol because it is a lightweight,
S ome companies undergoing digital transformation expect a straight, simple line from operational technology (OT) data to enterprise applications (see Figure 1). They hope to collect the data, add some information technology (IT)/Cloud tooling and achieve a simple internet of things (IoT) solution. In reality, OT data comes from myriad sources with various data types requiring complex IT/Cloud tooling to make sense of it all. OT data needs vary greatly from IT data needs, and companies need a way to satisfy both sides to successfully embrace IoT and digital transformation. OT data consists of proprietary protocols and multiple data formats, varies across market segments and includes no contextual information. The data is designed for operations and is retrieved with poll/ response methodology, then is directly coupled to applications over isolated networks. IT requires data for data objects and modeling, in standard data formats, with contextual information and it must be secure and easy to integrate. The data should be decoupled to the enterprise and is best retrieved with publish/subscribe methodology.
butlooksDigitaltransformationsimple,OTdataisverycomplex.Courtesy:CirrusLink
How to build scalable data models with MQTT Sparkplug key to bridging the OT/IT gap is enabling successful data modeling, which is how de ne and organize their business processes
organizations
By Arlen Nipper 1:
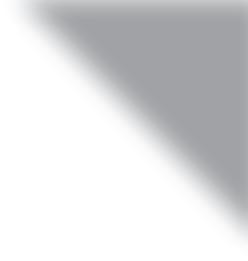
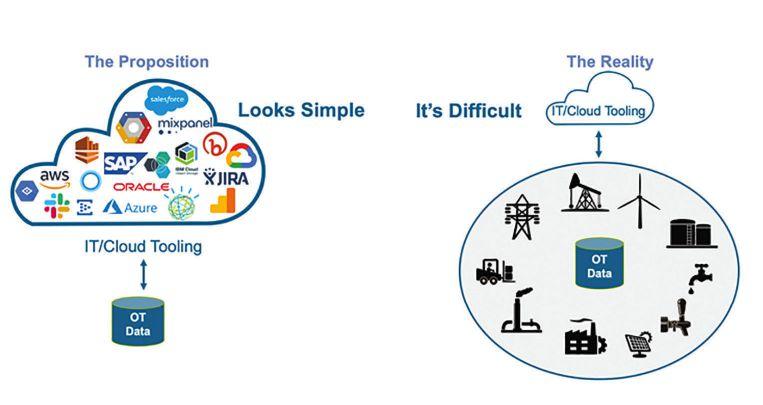
SOLUTIONS DIGITAL TRANSFORMATION 22 • May 2021 PLANT ENGINEERING www.plantengineering.com
publish/subscribe network protocol that is simple, efficient, secure and open with no vendor lock-in. MQTT is a message-oriented middleware, so the client connects to the broker and then publishes information. The data is decoupled, so one edge device can publish a metric and 100 applications (or more) can subscribe. The benefits are well documented. However, the purpose here is to focus on one benefit of the Sparkplug B specification — that it defines an OT-centric data model/asset. Sparkplug is a new specification within the Eclipse Tahu project that defines how to use MQTT in a mission-critical, real-time environment. Sparkplug defines a standard MQTT topic namespace, payload and session state management for industrial applications while meeting the requirements of real-time supervisory control and data acquisition (SCADA) implementations. The Sparkplug B specification provides the data model needed to define a tag value for use with OT, while also providing data to IT, making it 100% self-discoverable and easy to consume. MQTT Sparkplug establishes a single source of truth for models, assets and tags at the edge, enabling OT data from various data sources and protocols and defining it for IT (see Figure 2). When customers are designing an IoT system, when they start their design, it is ideal for the data model to be as far to the edge as possible. Ideally, the data model should be in the device to establish that reliable, single source of truth.
Windfarm example CirrusLink built a sample use case for the MQTT Sparkplug data modeling capabilities at a windfarm. We connected a wind turbine, added attributes and process variables with MQTT Sparkplug, then created the model in AWS SiteWise. The benefit of this solution is companies can start where the expertise is, at the edge, at the wind turbine and then create the model to be consumed by any third party or Cloud application. MQTT Sparkplug provides the technology to create a model that says, “This is a wind turbine, at this location, with these process variables: windspeed, RPM and direction.” Then MQTT Sparkplug provides a model all the way from the edge to the Cloud for a single source of truth. Now, any IoT platform, solution or application can be either a consumer or a provider of data models. There is no other technology besides MQTT Sparkplug that allows companies to build a generic data model, then an asset and then populate the asset. Without coding? Unheard of. OPC UA data models compete on some level but you can’t create those yourself. Plus, the true beauty of the solutions is this proper model/ asset/tag definition enabled by MQTT Sparkplug allows the solution to be replicated at scale. The unique capabilities built into MQTT Sparkplug to define the data model and asset is proving to be an important differentiator in the IoT marketplace. PE Arlen Nipper brings more than 42 years of experience in the SCADA industry to Cirrus Link as president and CTO.
Tags are the only piece of this puzzle typically addressed by IoT platforms and solutions, but MQTT Sparkplug goes beyond tags to create a single source of truth for models and assets as well. Without custom code, scripts, Python, Java or anything else complex and homegrown rarely scales or works long term. When OT data is collected and then the model/asset/ tags are converted to MQTT Sparkplug, the data can be sent to Cloud and enterprise applications for the autocreation of data models without any programming or coding required. OT data is converted to IT data, then put in a standard interface for Big Data, which leads to scalable data insights and business improvements.
Figure 2: Using dataconnectSparkplugMQTTtoOTasasinglesourceoftruth.Courtesy:CirrusLink
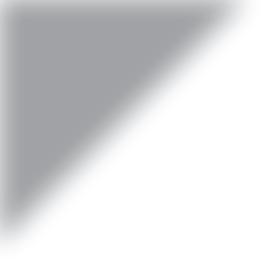
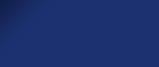
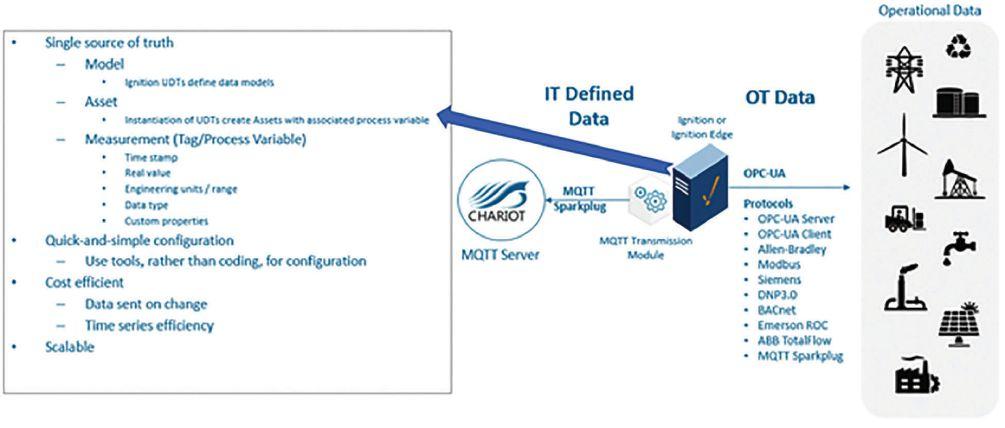
Leveraging big data
SOLUTIONS www.plantengineering.com PLANT ENGINEERING May 2021 • 23 REMOTE OPERATIONS
A s factories, distribution centers and other industrial environments become more automated, business leaders must be sure to invest in the proper technologies to maximize productivity and efficiency. Running an operation remotely could mean managing a production line from the other side of the plant or from the other side of the world, and the networking tools needed for each case are different. Cloud technology and 5G cellular networks show a lot of promise for remote work, but they have their challenges as well. Cybersecurity is the chief concern of many technology professionals in the industrial world, and many companies draw a line in the sand when it comes to connectivity and remote control. That line generally separates process automation control from the public internet via firewalls and other security measures. Many industrial technology players address those challenges by using Industrial Internet of Things (IIoT) solutions for equipment and process monitoring exclusively and leaving controls out of the conversation. That method is producing a hybrid approach that could dominate the industry for years to come in which insights are discovered in the cloud from Big Data streaming out of the plant and actions are taken separately by personnel onsite after suggested changes are approved. The future of remote operations will be defined by the advances of today’s industrial equipment manufacturers as more data collection hardware and software are built into machinery. The proliferation of “smart” or “connected” devices in the industrial world will continue to enable more opportunity for remote operations as cybersecurity innovations solidify the efficacy of that future reality.
There are many reasons why remote operations have become the goal of industrial leaders, though they are predominantly centered on leveraging the decisionmaking power of Big Data and streamlining the headcount and expertise of human resources. Consider these two topics a little further. At this point in the fourth industrial revolution timeline, we have only begun to scratch the surface of the benefits promised by Big Data analytics. The potential is endless for optimizing decisions on the factory floor — from machine reliability, to product quality, to inventory control and process efficiency. The truth is that human beings cannot compete with advanced analytics software when it comes to evaluating trends and correlations within data from multiple sources. We are even less capable of manually collecting applicable data from the floor in the first place. Sensors, cameras, scales and other data collection devices continually monitor their respective applications, which results in exponentially more data than technicians can chart during a walk-around evaluation. As industrial leaders continue to rank data collection and analysis among their top priorities, productivity and efficiency gains will be discovered around every corner. Imagine every decision from the factory floor having a clear reason backed by data instead of managing by tradition (see Figure 1). “That’s the way we’ve always done it” will no longer be a valid justification, and businesses will thrive because of it. Managing headcount has always been a priority for managers from a budgetary perspective, but now it may be more important than ever for a different reason: a shrinking pool of skilled labor. The shortage of mechanics, electricians, machinists, equipment operators, engineers and other technical human resources is putting a squeeze on leaders’ ability to staff their facilities appropriately, especially at multiple sites. Existing skilled labor positions are being vacated at increasing rates due to the Baby Boomer generation moving into retirement and the trend among younger generations to change employers more frequently than prior norms. Capturing the knowledge of those experienced employees and quantifying their knowledge into algorithms for data-driven decisions is a key component of this newTheredispensation.aremany scenarios that could qualify as a remote operation. Imagine a generic example in which How to use automation technology for remote operations Automation technology for remote operation and plant maintenance is becoming more prevalent
By Justin Lesley, Timothy Albers and Pranesh Rao
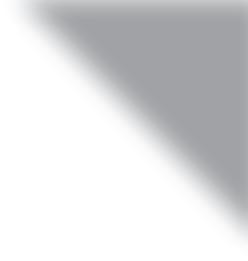
There are two characteristics in common with each technology: collecting and analyzing massive amounts of data, and the connectivity to stream data to remote locations in real time. Cloud computing is a popular solution for the analysis and storage requirements of using Big Data. Though cloud use is commonplace in many industries, business leaders remain wary of security threats. These concerns are exponentially greater when a cloud or internet-based data source can affect a physical operation. While cybersecurity is at the top of the list of concerns for leaders, it isn’t the only challenge standing in the way of true remote operations. Network latency and reliability are also factors to consider in any case where a real-time input is needed for process controls. Does your internet service work flawlessly 100% of the time? Most of us have experienced service interruptions, and many leaders are not ready to depend on continuous cloudbased inputs to control their facilities.
a corporate team is managing multiple production sites in different geographic locations. Consider three technology domains that will enable remote operation in our example and contribute to its proliferation in the real world: digital twins, predictive maintenance and augmented reality. Digital twins A “digital twin” of a production process is a graphical model of the line populated with metrics and key performance indicators (KPIs) from the actual process in real (or near-real) time. The digital twin may be created in 3D modeling software by modeling raw materials, conveyor belts, processing equipment, assembly robots, quality checkpoints, packaging stations and so on. Once a visual model exists, dynamic performance metrics are inserted within the appropriate portions of the digital production line. These KPIs may be variables such as times, weights, pressures, temperatures, vibration levels, speeds, part counts and reason codes for quality defects. In addition to the information generated by sensors on the line, live video feeds may also supplement the digital twin for further enhancement of management capabilities. Digital twins may also be used for comparing “design” performance against actual performance. Any variation between the two outside a certain allowed band can be used as an early indicator of potential flaws in the line or equipment. It can also be used to fine-tune the process to get maximum efficiency or throughput. Predictive maintenance “Predictive maintenance” (PdM) is a modern practice enabled by continual monitoring of machine health and performance via sensors and analytics software. The goal of collecting and analyzing machine health data (like temperature, vibration, energy use, etc.) is to be more effective with maintenance efforts. Rather than depending on traditional time-based maintenance procedures that may not be appropriate for a given application, PdM solutions allow leaders to focus their resources on assets that have the greatest risk of failure based on performance data. With PdM tools, leaders can schedule their maintenance efforts to be executed before the asset degrades to a critical failure state. The measurement, planning and evaluation of the maintenance can occur remotely, with only the actual maintenance having to occur onsite.
Augmented reality “Augmented reality” (AR) is an interactive technology that can be leveraged in multiple remote applications. If you’re not familiar with AR, think of a live, hands-free video conference in which the video feed interfaces with the real world around you. An AR solution may include a helmet-like wearable component that creates visual projections in the user’s immediate field of view while not obscuring their vision. One popular AR application is for a technical expert working remotely to guide a novice technician through a procedure on the factory floor. The guide, in this case, can see and hear everything in the field user’s environment and coach the novice through a procedure while populating the field of view with instructional graphics. In other AR applications, procedures can be recorded in a step-by-step fashion to create a digital instruction manual so users can educate themselves in real time while performing procedures. AR technology is actively being used in industry, particularly for service and repair.
SOLUTIONS REMOTE OPERATIONS 24 • May 2021 PLANT ENGINEERING www.plantengineering.com
A method used to alleviate some of the cybersecurity and network concerns is a hybrid cloud and edge architecture. In this approach, most of the continuous
Figure bytheImagine1:everydecisionfromfactoryfloorhavingaclearreasonbackedbydatainsteadofmanagingtradition.Courtesy:NidecandMotion.
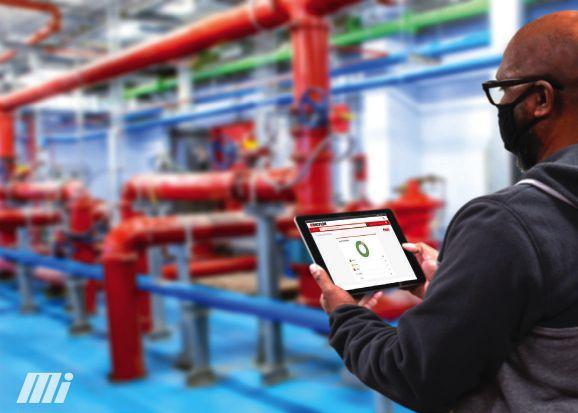
Timothy Albers is the director of product management for Nidec Motor Corporation’s Commercial and Industrial Motor Division/US Motors. His current responsibilities include product management, product planning and new product development for the Commercial and Industrial motors. Albers has held various positions in marketing for Nidec Motor Corporation and Emerson Motor Company over the last twenty-two years, including product-line manager for NEMA motors. He is a senior member of IEEE and serves on many Hydraulic Institute technical committees. He also spent 12 years in active and reserve duty as a U.S. Navy officer, and was a qualified operating engineering officer.
Pranesh Rao is director of new products, electronics and software for Nidec Motor Corp. He is responsible for the development of Nidec’s integrated motor drives and IIoT platforms. He has product development and entrepreneurial experience in the utility, industrial and renewable energy businesses.
So is the way you use information.
CFE Media delivers a world of knowledge to you. Personally. Engineering is personal. www.csemag.com www.controleng.com www.oilandgas.com www.plantengineering.com 2021_CFE_General_HalfHorizontal.indd 1 5/6/2021 1:32:43 PM operation and analysis is carried out locally on servers or industrial computers (edge devices). The edge machines communicate to the cloud periodically and/ or use predefined rules. The cloud platform receives these selected inputs, performs analysis and adjusts the algorithms that are sent down to the edge computers. This approach is like running antivirus software on a PC. The virus “definition files” are updated periodically, for example once a day, but the antivirus software runs continuously on the PC using the last available definition files even if there is no internet connection. Automation technology for remote operation and plant maintenance is becoming more prevalent. While there are legitimate technical and practical concerns that have not yet allowed complete remote operation, the technology is evolving rapidly, and businesses are finding creative ways to realize some of the benefits afforded by remote operation. PE Justin Lesley is the Industry 4.0 innovation manager at Motion. He directs IIoT strategy and partnerships related to the MRO industry. His career centers on operational efficiency supported by his Lean manufacturing and Six Sigma certifications combined with his engineering credentials. Lesley guides manufacturers along their digital transformation journey by helping them use connected predictive maintenance solutions.

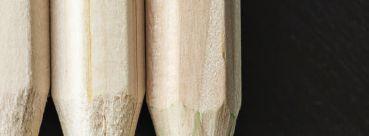
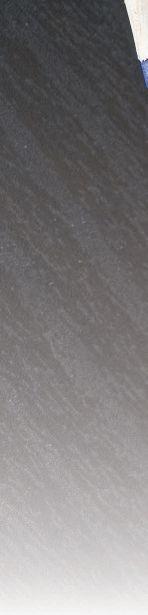
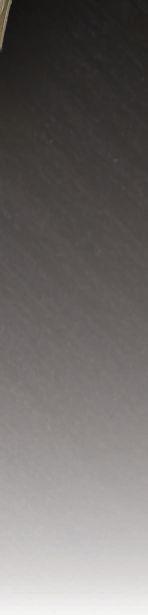



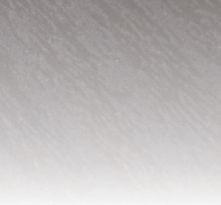


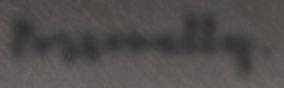
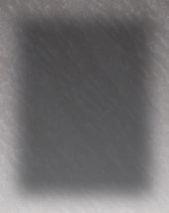
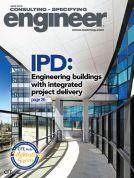
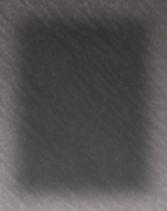
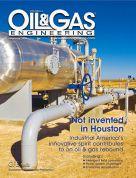
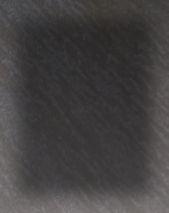
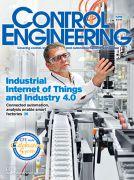
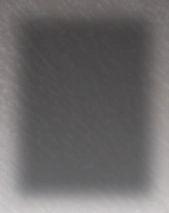
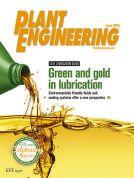
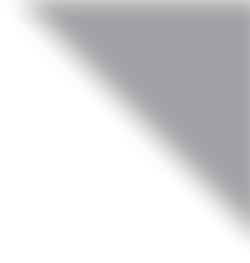
Although IT networks are usually safeguarded with sophisticated cybersecurity countermeasures, OT networks still include many legacy devices and often have less protection. This is because the systems are complex, and it is quite difficult to effectively implement cybersecurity measures. In addition, these networks often have long lifecycles, where legacy devices are not regularly updated with cybersecurity features. OT protocols are not usually encrypted and often lack authentication mechanisms. Also, hackers are becoming more familiar with OT protocols, networks and devices, enabling them to target programmable logic controllers (PLCs), human-machine interfaces (HMIs) and supervisory control and data acquisition (SCADA) systems more easily.
Cybersecurity gap between IT and OT
Why OT networks lag behind. Industrial OT networks prioritize availability and focus on controlling processes that cannot tolerate downtime. Unlike IT assets, OT networks are made up of PLCs, HMIs, meters and other pieces of equipment that are difficult to upgrade or patch. These devices can be in harsh and difficult to reach environments, and are often subject to extreme temperatures, vibrations and shocks. Different demands in different domains Industrial applications have requirements that differ depending on the sector, as well as varying levels of cybersecurity maturity. Although industries in the public sector are generally better protected than private manufacturing businesses, most OT networks still lag behind their IT counterparts in terms of cybersecurity. In general, IT departments administer the cybersecurity policies for OT networks, but those policies are merely at the IT level, which means they do not take into consideration the characteristics and requirements of OT networks. In addition, many also continue to lack segmentation between their IT and OT networks. Regardless of the industry, many OT networks lack sufficient security controls and are not managed by OT operators. Factory automation Manufacturers typically have lower levels of cybersecurity maturity and are primarily revenue driven and
How to ensure OT cybersecurity advances, operational technology network cybersecurity still lags information technology cybersecurity
With more people working remotely due to the COVID-19 pandemic, companies need to enable more remote connections to their business and production networks. Although these remote connections do enable employees to work from the safety of their homes, they also unfortunately open the gate to new cyberthreats.
SOLUTIONS 26 • May 2021 PLANT ENGINEERING www.plantengineering.com CYBERSECURITY Figure Although1:connecting OT networks to the itpossibilities,enablesInternetnewalsointroducesnewthreats.Courtesy:Moxa
New opportunities bring new threats As new IT technologies and Internet connectivity become available to OT networks, many different opportunities are opened for greater productivity and efficiency. Although connecting OT networks to the Internet enables new possibilities, it also introduces new threats (see Figure 1).
S ecuring operational technology (OT) networks and increasing network durability are key to enhancing operational resilience, as OT network protection still lags information technology (IT) cybersecurity. This article explains the reasons behind the lag, how this gap manifests across different industries and outlines four steps OT operators can take to better protect OT networks from cyberattacks and enhance operational resilience.
Despite
By Jesse Ku
The reason for the discrepancy between the maturity of IT and OT cybersecurity is closely related to different business priorities that often conflict with each other (see Figure 2). Why IT networks are better protected. Enterprise IT networks prioritize confidentiality and focus on data integrity. IT assets include computers and servers located in climate-controlled office environments, and are easy to upgrade, patch or replace regularly.
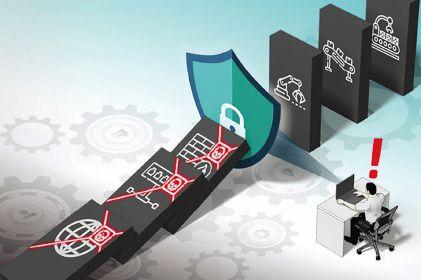
• Vertical segmentation involves adding an industrial demilitarized zone (IDMZ) between the IT Figure 2: The reason for conflictprioritiescloselybetweendiscrepancythethematurityofITandOTcybersecurityisrelatedtodifferentbusinessthatoftenwitheachother.Courtesy:Moxa
Cybersecurity for power grid applications is mostly driven by government policy. However, dedicated OT networks for power automation have low visibility of network assets, limited protection and are in the process of transformation from remote terminal unit (RTU) to Ethernet technologies. These applications are primarily concerned with passing government audits and meeting international standards (IEC 61850, IEC 62351, IEC 62443 and ISO 27001), preventing misconfigurations from operators, and preventing disruptions to power distribution. Water treatment Similarly, water treatment applications are comprised of dedicated OT networks that have low asset visibility. The abundance of legacy devices as well as a lack of access control and network segmentation indicate a need for strengthening cybersecurity beyond government audits and deploying firewalls and intrusion prevention systems (IPS).
For example, OT operators can start to determine who can and cannot access the network by leveraging access control lists (ACL) or other authentication mechanisms. Also, there are simple mechanisms OT operators can set up to define which PLC can be connected to the network by port access control or sticky MAC. In other words, everything on the trusted list is allowed to go through the network, and anything not specified on the trusted list is blocked. Managing the OT network (instead of relying on the IT department) also allows OT operators to respond more quickly to downtime and troubleshoot issues more rapidly.
Intelligent transportation systems Cybersecurity in intelligent transportation systems (ITS) is also primarily government driven. ITS applications are characterized by distributed networks with various devices and systems at each traffic intersection. Although each device often uses a different network, security is centralized at the IT level. Although ITS applications follow prescribed government guidelines and are pretty good at establishing cybersecurity policies and deploying firewalls, they are still concerned about cyberattacks on traffic signals and sensors, as well as the possibility that someone could break into an equipment cabinet relatively easily and gain direct access to the network that way. Four steps to resilience Considering how different IT and OT networks are, how can we bridge the gap between these two domains and secure OT networks from cyberattacks? To enhance operational resilience, OT networks must ensure their cybersecurity measures are as mature as those used in IT networks. The following four steps describe how users can secure OT networks and increase resilience.
1. Manage OT networks. Users cannot protect the assets they do not know they have. That’s why the first step to enhancing operation resilience requires OT operators to monitor everything on their networks in a similar way to how IT network administrators often have complete visibility. Is everything that should be on the OT network actually there? Is there anything on the network that should not be there?
Power utilities
TABLE 1: Different types of factories and their concerns Factory types Traditional factories Transforming factories Modernized factories Status • Full of systemslegacy • Lack of architecturenetwork • Lack of resourcesawarenesssecurityand • Mixture of new and legacy systems • Complex environmentsnetwork • Wider attack surface • Have awarenesssecuritybut it might not be a priority • High automation and cybersecurity maturity • Assignedcybersecurityresources • Integration with SOC • Holistic cybersecurity Concern Cybersecurity is not a priority and they do not have protectionsufficient Managing both legacy and new networks at the same time Preventing operational disruptions deployedcybersecuritywithmeasures
2. Segment OT networks. Unlike IT networks that can be segmented by dividing the network into different departments with their own set of permissions, OT networks are essentially one giant intranet where everything is connected. This makes OT networks more difficult to segment, but not impossible. There are two ways users can segment an OT network:
www.plantengineering.com PLANT ENGINEERING May 2021 • 27 focused on maintaining availability and uptime rather than on security. Even though the level of security awareness varies depending on whether the manufacturer is traditional, transforming or modernized, IT and OT roles and responsibilities continue to be vaguely defined in factory automation (see Table 1).
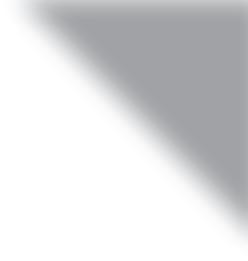
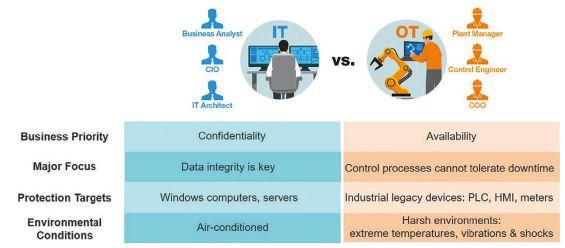
Final thoughts Besides managing and segmenting OT networks, OT operators also need to ensure their systems are properly patched and remote connections are secure. These steps not only help reduce the gap between OT and IT departments, but also protect industrial control systems, which are increasingly being connected to the Internet, from cyberattacks. PE Jesse Ku is a cybersecurity technical consultant at Moxa USA.
SOLUTIONS
• Horizontal or lateral segmentation involves creating and separating cells, zones and sites on the OT network. A cell is essentially a tiny place where all equipment is stored, such as a cabinet. Several cells can form a zone, and multiple zones can form a site.
3. Patch vulnerabilities. Since equipment and devices running on OT networks cannot be upgraded or replaced as frequently as endpoints on IT networks, OT networks still have many legacy devices that may even be running on operating systems as old as Windows 95. Many legacy OT devices remain unpatched and are relatively easy for hackers to exploit. If no patch is available from the original equipment vendor, consider putting a virtual patch on a device that goes in front of legacy devices.
Segmenting OT networks using either method, or both, allows operators to prevent cyberthreats from spreading to other parts of the network.
4. Secure remote connections. Protecting the data transmitted from the plant or remote site back to the monitoring and control center is absolutely crucial. Ensure each remote connection to the OT network is authenticated and encrypted. “Authentication” verifies the identity of the user requesting access, whereas “encryption” ensures the data transmitted is securely encoded and cannot be easily deciphered by prying eyes.
CYBERSECURITY network and OT network. Although this separation should be mandatory, many companies still have not segmented their OT networks from their IT networks.
PRODUCTM ART Input #106 at plantengineering.hotims.com OIL MIST & SMOKE IN YOUR SHOP? www.mistcollectors.com Tel: 1-800-645-4174 Input #108 at plantengineering.hotims.com www.mrshims.com Belt/Sheave Laser Alignment System your answer to better alignment for rotating machinery Mr. Shims New Green laser delivers these important benefits: ● Reduces Vibration ● Eliminates downtime and productions ● At an affordable price ● Visible indoors and Outdoors ● Brightness great for long distances 1-800-72-SHIMS (1-800-727-4467)Go online to view all Plant Engineering eBooks! www.plantengineering.com/ebooks Sponsor an eBook today! Input #107 at plantengineering.hotims.com Need Work Benches ? workbenchmarket.com In Stock-Factory Direct 28 • May 2021 PLANT ENGINEERING www.plantengineering.com
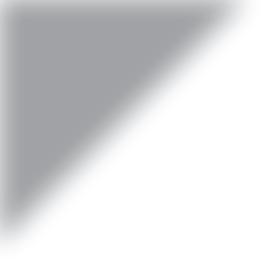
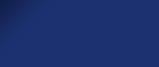





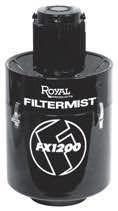
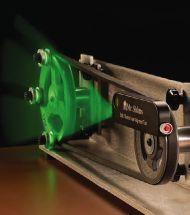

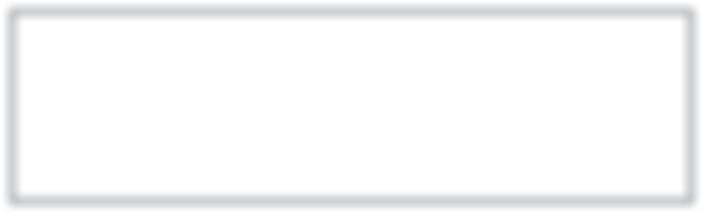


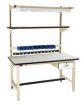
An analysis of OSHA’s top 10 most cited violations for control of hazardous energy
By Nick Schiltz
Applicable to electrical safety
I n March 2021, the official OSHA top 10 violations for 2020 were published after an understandable delay not unlike what we had grown accustomed to amid the COVID-19 pandemic. This year’s top 10 saw the Standard (1910.147) for The Control of Hazardous Energy (Lockout/Tagout) drop to the No. 6 spot with 2,065 total violations — 541 less than the previous year. Each year, safety conscious employers depend on the OSHA’s top 10 most cited violations data to better inform them on the riskiest scenarios in their safety programs. The total violations are typically released at the end of the fiscal year in September.Veteransafety consultants urge employers to keep an eye out for the annual OSHA top 10 report. This list is one of the best starting points on the path toward fostering a robust safety culture. In an interview with Safety+Health magazine, one safety consultant advises, “Minimally, an employer should have the responsibility of asking, ‘Do any of these top 10 affect me?’ Because this is the easiest place if our friends from OSHA should come to visit,” said JoAnn Dankert, senior safety consultant from the National Safety Council (NSC). With our electrical safety background, Grace Technologies look at this list to analyze the most cited violations for the Control of Hazardous Energy standard CFR 1910.147, and provide solutions on how to avoid the most common mistakes in electrical safety. The most important item to note is that the training and communication regulation CFR 1910.147(c)(7) is frequently at the top of OSHA’s most cited violations for Control of Hazardous Energy. As the pandemic wreaked havoc on industry revenues in 2020, experts were concerned with how organizations would respond with their training programs. “When revenue goes down, organizations tend to sometimes pull back on training,” said Dankert, “and I would encourage people not to pull back on your safety training. With some things, we’re struggling within organizations because maybe we’ve done classroom training, but now because of physical distancing and so forth, we don’t want to put too many people in an area. That might mean we’ve got to have more classroom training sessions.”
This is true as it relates to electrical safety and the control of hazardous energy. When training in your electrical safety program, start by looking at the recurring top 10 most cited OSHA violations related to the control of hazardous energy. This standard covers the servicing and maintenance of machines and equipment in which the unexpected energization or startup of the machines or equipment, or release of stored energy, could harm personnel. One of the consistently most cited violations under control of hazardous energy is the communication and training regulation CFR 1910.147(c)(7). As Dankert pointed out, the CDC guidelines for operation have changed the way we can perform training. In addition, loss of revenue is a primary factor for maintaining the integrity of your electrical safety program. The most important investment an employer can make is in their employee's health and safety. This should be the last area cut from the budget, not one of the first. Failure to perform proper mechanical or electrical lockout/tagout (LO/TO) can lead to electrocution, electrical shock, arc flash and other hazards. In addition to huge penalties, these hazards often result in lost time wages, compensation claims, permanent disability and fatalities. Employers cited under this standard failed to establish an energy control procedure, either partially or altogether, while others were cited for failing to provide adequate employee training, failing to conduct periodic evaluations of procedures and failing to use LO/TO devices or equipment.
At the National Safety Council 2019 Congress & Expo, Patrick Kapust, deputy director of OSHA’s Directorate of Enforcement Programs reported: “These are SAFETY Why investing in electrical safety is important now more than ever
SOLUTIONS www.plantengineering.com PLANT ENGINEERING May 2021 • 29 ELECTRICAL
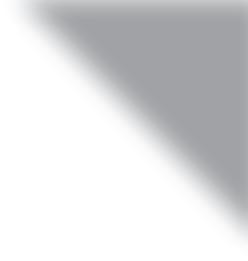
Furthermore, human error plays a vital role in failing to comply with standards. Despite thorough training, documentation and experience, there will always exist that risky margin of a person just simply making a mistake, no matter how many times they have performed the task at hand. For example, qualified maintenance personnel performing mechanical LO/TO are tasked with isolating electrical energy. As part of the verification of deenergized condition, OSHA requires a person to operate the equipment controls, also known as a try/test, to ensure the equipment cannot be restarted. There are several significant risks associated with solely relying on the try/test. These risks often include isolating the wrong controls, accidental restart of the equipment, getting caught in the equipment or contact with a live source of energy at the machine level.
Safety conscious and forward-thinking companies understood these risks early on and started to require electricians to perform absence of voltage testing for mechanical LO/TO. With the advent of NFPA 70E: Standard for Electrical Safety in the Workplace and research on arc flash, employers began to realize through job hazard analysis that this task, while reducing the hazards of the energized condition of the equipment, greatly increased the exposure to electricity in performing the test itself. Additionally, the involvement of an electrician in a simple mechanical LO/TO further hampered productivity.
common violations that we’re finding — they’ve been in place for a lot of years. The answers are out there, and employers shouldn’t feel like these are very complex issues. If you don’t know the answers, we encourage you to contact OSHA,” Kapust said. “I would like to remind people, as difficult as it is to comply, that’s the minimum we must do to protect employees. OSHA doesn’t have a standard for every possible hazard we might have in our facility or on our jobsite,” Dankert said. “So, as difficult as it is to be compliant, we also need to understand the inherent hazards in our processes that OSHA doesn’t cover and seek those best practices to continue to protect ourStrivingemployees.”forthe minimum requirements of compliance does not lead to achieving minimum risk or maximum productivity levels available today.
SOLUTIONS ELECTRICAL SAFETY 30 • May 2021 PLANT ENGINEERING www.plantengineering.com
A safety-by-design solution was found for this scenario in an externally mounted LED voltage presence indicator. This provides an alternative means to verify the voltage presence inside an electrical panel while safely unexposed from the outside in addition to the OSHA required try/test. Without a voltage indicator, a mechanic performing mechanical LO/TO would be required to work in tandem with an electrician using a voltmeter to physically verify voltage inside an electrical panel (see Figure 1). In this case, the electrician is exposed to voltage. With the combination of the try/test and through-door LED voltage presence indicators, the mechanic can solely verify when the panel is in an energized condition without any voltage exposure. Who needs training? When it comes to OSHA and LO/TO, the code recognizes two categories of people that need training: authorized and affected employees. Under the training mandated to companies by OSHA, “Each authorized employee shall receive training in the recognition of Figure 1: An electrician using a voltmeter physically verifying voltage at an electrical panel. Courtesy: Grace Technologies
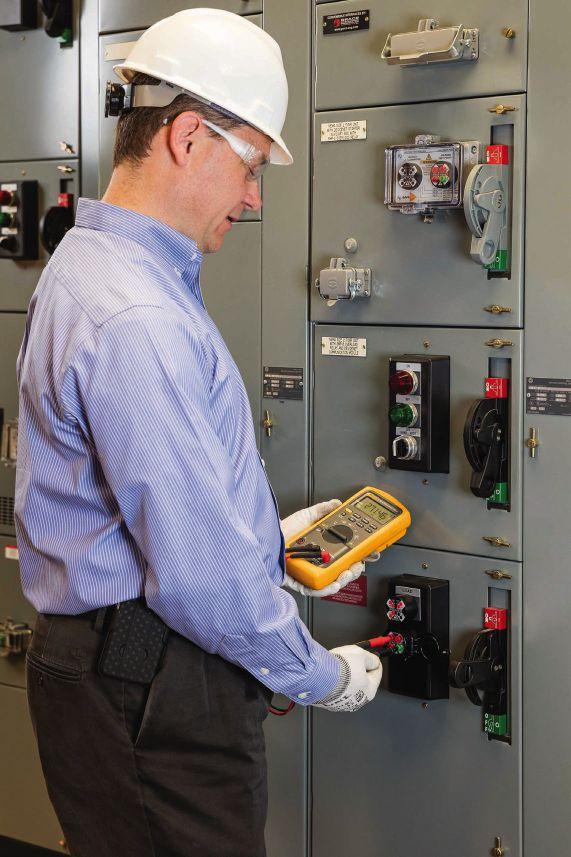
MEDIA SHOWCASE F OR E NGINEERS Input #103 at plantengineering.hotims.com Input #104 at plantengineering.hotims.com Input #105 at plantengineering.hotims.com SuperiorSignal.com/PE Find Compressed Air Leaks Fast! • Also any Gas, Refrigerant or Vacuum • Rugged Design for Harsh Environments • Sealed to Resist Water, Oil, Dust, Chemicals • Professional’s Choice for Air Leak Surveys AccuTrak® VPX-WR The Ultimate Air & Gas Leak Detector
A robust electrical safety program goes beyond legislation and minimum compliance. A highly productive and efficient environment is a culture where employees are safe, secure and cared for. According to the U.S. Department of Labor, a safe and healthy workplace not only protects workers from injury and illness, but it can also lower injury/illness costs, reduce absenteeism and turnover, increase productivity and quality and raise overall employee morale. In other words, fostering a safety culture is not just a good practice, it is good for business. PE Nick Schiltz is a copywriter for Grace Technologies located in Davenport, Iowa. The company specializes in electrical safety products and predictive maintenance solutions. During his five years at Grace, Schiltz has published more than 250 blog posts ranging in topics from electrical safety best practices to the future impact of the industrial Internet of Things (IIoT) in the industrial space.
applicable hazardous energy sources, the type and magnitude of the energy available in the workplace and the methods and means necessary for energy isolation and control. Each affected employee shall be instructed in the purpose and use of the energy control procedure.”
To summarize, “authorized employees” are those who are applying the locks and “affected employees” are those in the area during a lockout. The latter can range anywhere from operators to third-party contractors. If they are within the vicinity of the procedure, they are Whileaffected.OSHArequires all authorized and affected employees receive periodic training, the implemented training program at any organization can be customized to meet precise needs. However, as previously stated, companies training their employees to meet the minimum compliance standards does not result in achieving maximum safety and productivity. Even before the pandemic, employers were consistently failing to comply with minimum performance requirements and it is becoming more apparent that we’re far past the time for them to adopt safety-bydesign solutions. Companies must start looking at safety as an investment. OSHA’s Regulatory Analysis has proven that for every $1 invested in health and safety, employers can expect a return of $4 to $6.
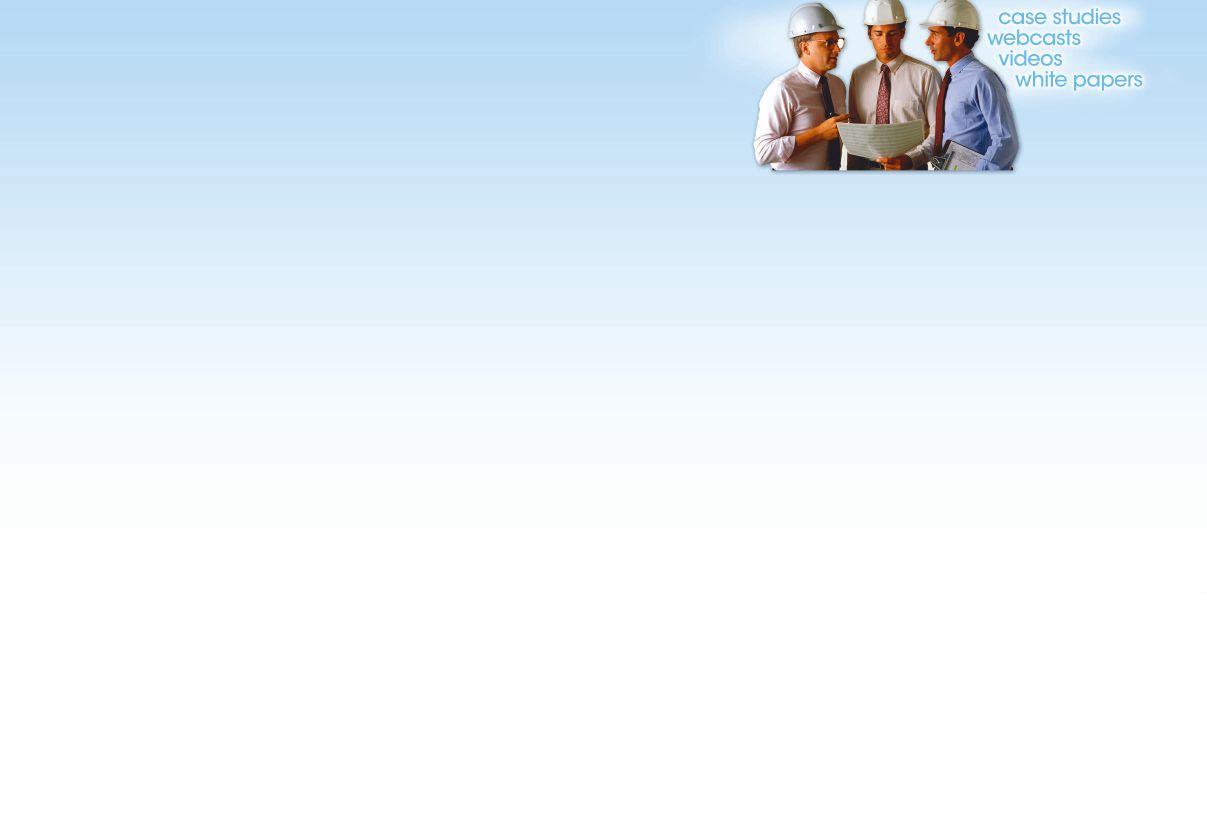
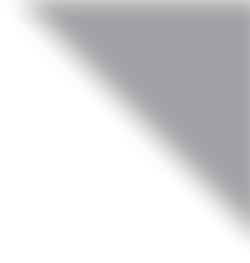
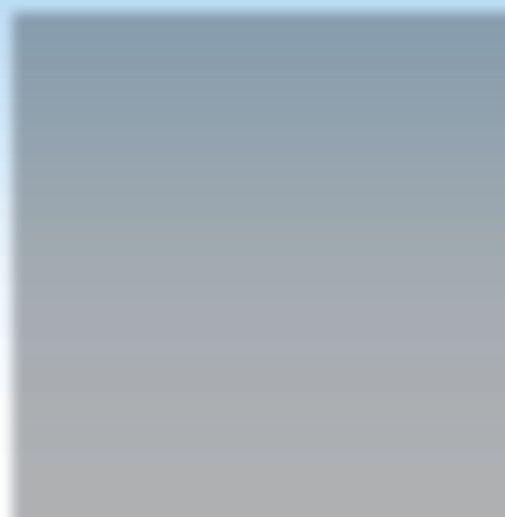
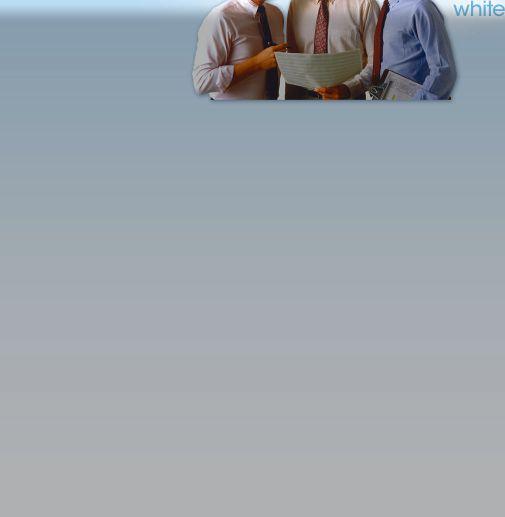
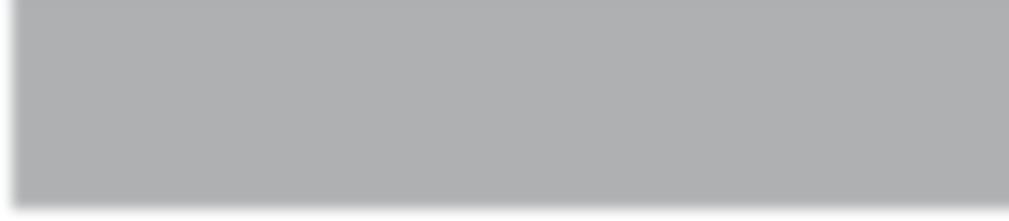


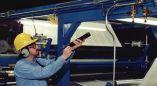
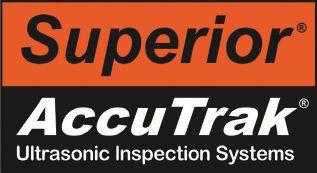

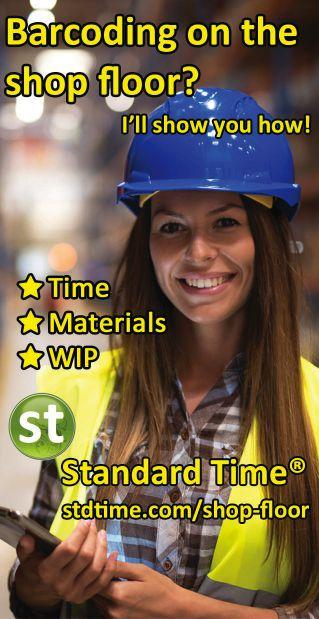
SOLUTIONS 32 • May 2021 PLANT ENGINEERING www.plantengineering.com MATERIAL HANDLING
Why commodity casters cause injuries
Commodity casters are workplace injuries waiting to happen By Eric Hassen
Cart manufacturers are continually looking for ways to reduce costs, and that may mean skimping on the casters. They may specify a lower cost caster that uses inferior materials and not customized to the application. No frills. Bare bones. The carts may have ideal material-handling functionality but contribute to workplace injuries. Casters 101 Commodity casters typically feature a kingpin design, the number one failure point on a swivel caster. Typically, commodity casters do not have the correct bearing for the application. The wheel tread is likely an inexpensive and ineffective material option like phenolic or a type of hard plastic (see FigureCombining1). poor quality construction with incorrect bearings increases the friction forces during manual operation, making the wheels more difficult to rotate. Commodity casters also tend to have a standard swivel lead, the distance from the center of the top plate to that of the axle. As a result, commodity casters cannot get into the trailing position when trying to pivot. By design, short swivel lead casters are more difficult to turn, which can result in expensive push/pull injuries. The caster fights itself when trying to maneuver into the trailing position. A standard swivel lead has a short distance roughly straight up and down from the center point of the kingpin to the center point of the axle. Applicationspecific casters can come with an extended swivel lead. This added distance enables reduced push-pull forces, improved maneuverability and decreased noise and chatter.Commodity casters typically have an open raceway design. Their two sets of ball bearings — one on top and one on the bottom — are open to the elements. Dust from the plant environment gets inside the raceway and binds up the grease. If not greased on a regular basis, the bearings or swivel raceways will create costly caster issues. If an operator tries to push a cart and the wheel doesn’t move, the risk of ergonomic-related injuries increases dramatically. Think differently about casters When many purchasing agents choose carts and casters, they are likely looking for the lowest initial cost, thinking, “a caster is a caster.” When maintenance and injury-related costs are calculated, the total cost of ownership becomes the issue. Plant management examining what causes continuous issues with carts and contributes to workforce ergonomic issues should keep these considerations in mind. Advances in replacement casters provide plant engineering and operations a choice for improving workplace safety while increasing productivity and giving material handling carts an extended useful life. PE Eric Hassen is director of business development for Caster Connection, a manufacturer and distributor of high-performance casters, wheels and other material handling products based in Columbus, Ohio.
Figure 1: Poor quality commodity casters combined with insufficient maintenance practices can lead to chipped wheels that fall apart and pick up debris, leading to potential pushpull injuries for workers.
F ailed kingpins and faulty tread materials are among the leading causes of caster failures on material handling equipment and of safety incidents within manufacturing and distributionOverloadedcenters.carts or carts specified with casters with high rolling resistance can cause physical overexertion, the number one cause of workplace injuries. Why are casters such a hidden danger in the workplace?
Courtesy: Caster Connection
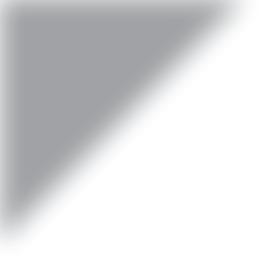

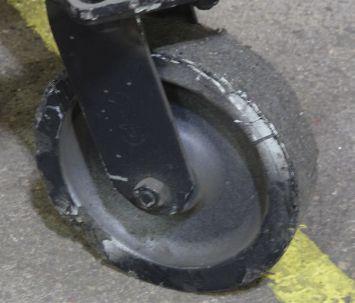
SOLUTIONS www.plantengineering.com PLANT ENGINEERING May 2021 • 33 ELECTRICAL SAFETY
In 2018, an exception was introduced in NFPA 70E that described how permanently mounted absence of voltage testers also meet the requirement without the need for additional verification with a handheld, or portable tester. The 2018 edition of CSA Z462, however, added complementary language as an informational note, not an exception. The 2021 harmonization updates the CSA language from an informational note to an exception.
The 2018 informational note in CSA Z462 did not have the same power as an exception, meaning that facilities following that standard could How to test for absence of voltage
BugarisFigure
1: Electrical enclosures protected by VeriSafe remain locked until absence of voltage is verified. Courtesy: Panduit Corp.
NFPA 70E and CSA Z462 harmonize absence of voltage testing requirements
What’s the difference? Exception 1 to NFPA 70E-2021 120.5 (7) describes how a permanently mounted absence of voltage tester meets the requirement by itself, without further use of a handheld tester. That empowers facilities to forego the complexity and added exposure to electrical hazards of a handheld testing procedure, and design in permanently mounted testers as an engineered control for reducing risk.
By Rachel
A work condition is not considered safe just by turning a system off. According to updated NFPA and CSA standards, a work condition is not even considered safe once lockout devices are put in place. The 2021 editions of NFPA 70E: Standard for Electrical Safety in the Workplace and CSA Z462-18: Workplace electrical safety updated critical language that describes the process of establishing and verifying an electrically safe work condition to now include the crucial step of testing for the absence of voltage. The updated, harmonized standards now agree on important requirements for permanently mounted absence of voltage testers, providing manufacturers and businesses operating across North America with unified guidance on design solutions that helps reduce risk during the testing process. A closer look clearly demonstrates how these harmonized exceptions on absence of voltage testing present an opportunity to ensure consistent and efficient electrical safety in the workplace. From information to exception For both standards, an “exception” is a fully approved method, an alternate for meeting a requirement; as opposed to the more common meaning of an allowance for a rare circumstance, as if it’s something to be avoided. Before 2018, testing for absence of voltage required an adequately rated test instrument, with no distinction made between portable testers and permanently mounted testers. That meant somebody had to physically check for the absence of voltage, a procedure that typically involved a qualified person with personal protective equipment (PPE) opening an electrical enclosure to test with a handheld tester.
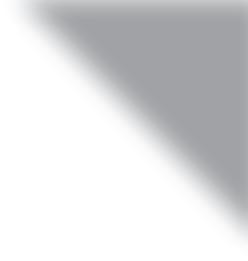
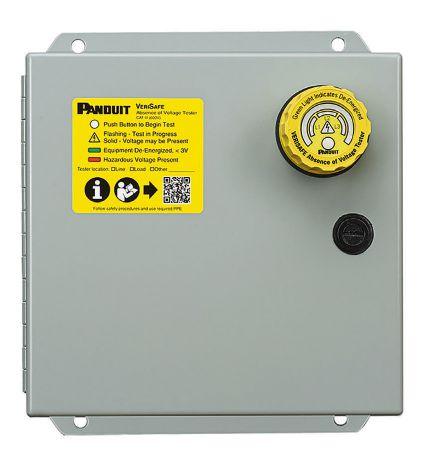
While such supplementation obviously added a layer of safety, it deprived facilities of the ability to build safety procedures to fully take advantage of a permanently mounted tester.
Now that CSA Z462-2021 has added Exception 2 to 4.2.5(g), permanently mounted absence of voltage testers are an approved alternative to the handheld test instrument.
only supplement verification with a permanently mounted absence of voltage tester, not replace it.
To satisfy the requirements of the process for verifying an electrically safe work condition, an absence of voltage tester must test the conductors and circuit points at the point of work, must test for both ac and dc voltage, phase-to-phase and phase-to-ground, must be verified as operating satisfactorily before and after testing and must be listed and labeled for the purpose of verifying the absence of voltage. The informational note is important because the requirements given in NFPA 70E and CSA Z462 do not include any technical specifications, ratings or design standards that would indicate a device’s acceptability under the exception.
NFPA 70E and CSA Z462 also harmonize in two other important ways. First, they list requirements an adequately rated permanently mounted absence of voltage tester must meet. The second is they include an informational note to help interpret whether such a device meets the requirements in the exception by referring to UL 1436, or Underwriters Laboratories’ Standard for Outlet Circuit Testers and Similar Indicating Devices.
Together with the requirement the tester be listed and labeled for the purpose of absence of voltage testing, the reference to UL 1436 clarifies what testers qualify as adequately rated and permitted to be used for the purpose. In addition, UL 1436 provides requirements for other features necessary for reliably determining the absence of voltage with a permanently mounted tester. This includes features such as an installation test, active indicators and functional safety requirements, among others.
It’s important to note that if a facility plans to use permanently mounted absence of voltage testers to improve their safety procedures, the tester chosen must meet the requirements of being listed and labeled for the purpose. NFPA 70E and CSA Z462 harmonize on this language, and it’s crucial to point out there are other permanently mounted products that may measure voltage, or in the case of voltage test portals, facilitate voltage measurement, but do not meet the requirements described in the exception. Devices that aren’t absence of voltage testers The requirements help clarify which devices may have useful functions, but don’t actually verify an electrically safe work condition. For instance, panel meters and voltage indicators should alert a person to the presence of voltage, but neither is sufficient for verifying absence of voltage. Wary (and experienced) engineers are already ahead of the game here. A test designed to indicate something is present isn’t the same as a test designed to tell us something is absent.
Even more agreement
SOLUTIONS ELECTRICAL SAFETY 34 • May 2021 PLANT ENGINEERING www.plantengineering.com
In the case of a panel meter, absence of voltage is not guaranteed because of several failure points, including how the sensors are connected to the source. In addition, the panel meter fails crucial Figure 2: The visual display makes it easy for anyone to determine voltage levels in electrical units protected by VeriSafe.
Courtesy: Panduit Corp.
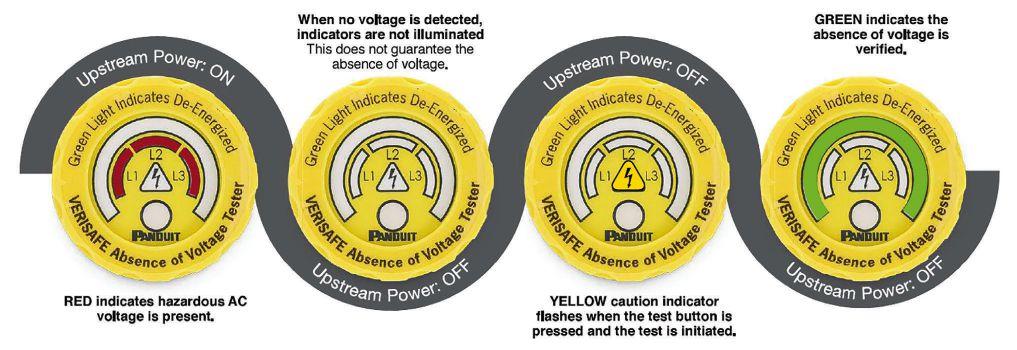
The 2021 editions of NFPA 70E and CSA Z462 help manufacturing and commercial facilities looking to improve electrical safety procedures by providing clear and harmonized standards for using permanently mounted absence of voltage testers as part of the process for establishing an electrically safe work condition (see Figure 3). As more facilities look to implement safety procedures less susceptible to human error, engineered solutions like AVTs help facilities reduce risk. For more information on using AVTs for a more efficient, engineered approach to safety, reach out to your electrical infrastructure solution partner. PE Rachel Bugaris is a business development manager at Panduit Corp., where her work focuses on electrical safety solutions for the workplace. She has a background in R&D, designing products ranging from absence of voltage testers to arc resistant equipment, has multiple patents and has written several technical papers on electrical safety topics. Bugaris has a Bachelor of Science in mechanical engineering from the University of Notre Dame. She is a member of IEEE and SWE.
A test portal seems like it would help verify the absence of voltage before a panel has to be opened. However, where they seem to help is where they hurt — when testing through the portals, a person can’t confirm the probes are in proper contact. A false negative is therefore possible, and exactly what we’re trying to guard Similarly,against.testportal leads bring voltage to the door and are often fused, which for other safety purposes is ideal, but in the case of verifying absence of voltage, a negative test could be the result of those fuses acting as designed, verifying that the safety equipment of the test portal has operated correctly, instead of verifying that the source is de-energized. Actual absence of voltage testers
What about voltage test portals?
An absence of voltage tester (AVT) is specifically designed to prove absence of voltage, without requiring a qualified person to open equipment doors and potentially expose themselves to electrical hazards (see Figure 1). AVTs allow a person to push a button that starts a test sequence that meets all the requirements for verifying the absence of voltage. The AVT automatically self-tests with a known voltage source and checks for direct contact with the circuit at time of testing (see Figure 2). It then tests for absence of ac and dc voltage — phase-to-ground and phase-to-phase. The push-to-test capability of AVTs allows a facility to build in efficiency, and unlike manual testing, is performed without exposure to electrical hazards. Ensuring the efficient process is also safe is the purpose of UL 1436, which is beyond the scope of this article to fully describe, but it includes a number of fail-safes and extensive reliability functions.
requirements for the exception: It does not have a self-test function and (most likely) only measures phase-to-ground, not phase-tophase. Voltage indicators suffer similarly: They don’t self-test, don’t test phase-to-phase and don’t test the conductors and circuit parts at the point of work. Not only aren’t voltage indicators listed and labeled for the purpose of verifying absence of voltage, OSHA has stated its position that voltage indicators cannot be used to verify de-energization of equipment.
Figure 3: Ease of installation and maintenance make VeriSafe a low-cost, high-value safety enhancement. Courtesy: Panduit Corp.
www.plantengineering.com PLANT ENGINEERING May 2021 • 35
Looking ahead
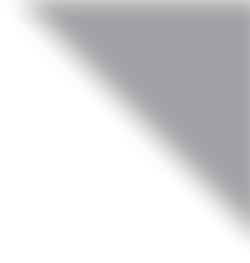
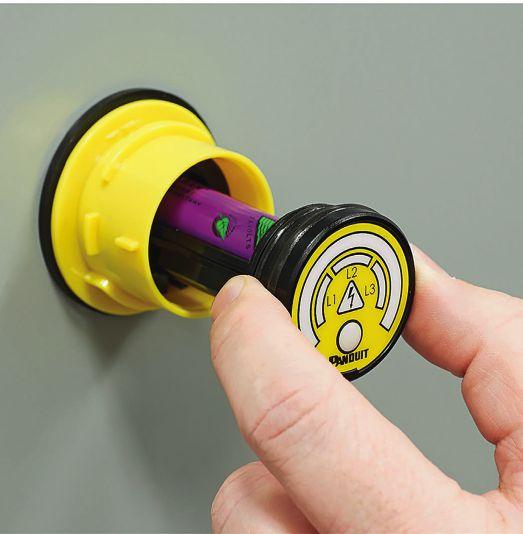
How to extend switchgear life and improve system reliability system reliability of switchgear with protective relay upgrade projects
By Jeff Brittain and Andrew Kaster
A semiconductor manufacturing facility was experiencing challenges with its switchgear control system. The facility had two medium-voltage utility feeds. The original switchgear, which dated back to the 1970s, contained an auto throwover (ATO) control scheme to operate the main-tie/main breaker and maintain power to the switchgear if one of the utility sources is lost. The vintage ATO was comprised of control relays, voltage relays, timers, resistors, capacitors and a significant amount of wiring. The parts for this vintage system are now obsolete and no longer supported by the manufacturer, thus a repair to the system would be difficult and slow, resulting in an extended and possibly unplanned outage (see Figure 1). The High Voltage Maintenance (HVM) team performed an engineering evaluation to assess the system and make recommendations for a path forward. The protection relays were an original electromechanical overcurrent relay style, and even though they had been properly maintained throughout the years, HVM developed a solution that would use the relays in conjunction with a logic processor to act as the new ATO control system. This design took advantage of the communications, individual relay element functions and configurable internal logic within the relays to work in tandem with a separate logic controller to function as the ATO. The new relays also took over the circuit protection role. The project was performed as a turnkey solution. As a manufacturing facility with production at full
SOLUTIONS 36 • May 2021 PLANT ENGINEERING www.plantengineering.com ELECTRICAL SYSTEM RELIABILITY Figure 1: Before and after Maintenancerelayprotectiontheupgrade.Courtesy:HighVoltage
These projects provide microprocessor relays that have many advantages for the overall power system. Even in situations where the protection relays have been maintained and are fully functional, the benefits of upgrading to modern relays can justify the expense. Once the decision to upgrade has been made, performing this as a turnkey project offers many benefits. A workflow of a turnkey relay upgrade can be broken into several distinct phases: Engineering, procurement, bench testing, installation, field testing and startup. Consider the following use case while keeping in mind these phases are applicable to any protection scheme upgrade.
Protective relay upgrade projects
During the smartphone revolution, electrical protection and control system technology also advanced considerably. With the advent of microprocessor-based protection relays, the modern relay can do much more than protect a circuit. They now can perform communications on multiple protocols, system monitoring, alarms and self-alarms, arc flash mitigation, controls, time delay and remote breaker operations, event reporting, increased safety and more. As facility electrical systems age, the demand for production is not slowing down. Plant facilities and maintenance personnel are asked to maintain a wellfunctioning electrical system and minimize system outages. While complete replacement of original electrical distribution switchboards and switchgear is a possibility, the cost and outage time required do not align well with facility budgets and production demands. An alternative to a complete replacement is extending the life of the existing switchgear and increasing system reliability by performing a protective relay upgrade project.
N ot long ago, a telephone had a specific purpose: making phone calls. In the early 2000s, cell phone manufacturers took advantage of new technologies to enable users to not only make phone calls from anywhere, but also take photos, play games, identify the species of trees in the backyard, get a weather forecast and so on. The possibilities of applications for modern smartphones extend as far as the imagination can go.
Improve
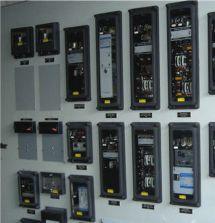
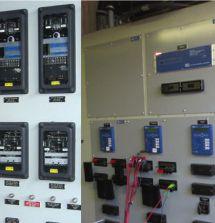
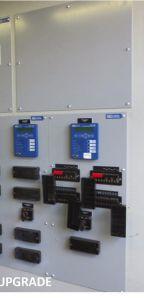

With more than 25 years in the industry, Brittain has amassed great knowledge of power system electrical testing, maintenance and engineering.
Final thoughts
Andrew Kaster, EE, PE, NETA IV, is manager of systems integration at Electrical Reliability Services (ERS).
www.plantengineering.com PLANT ENGINEERING May 2021 • 37 capacity, operations required a maximum outage time of 36 hours. To accommodate this requirement, the phases of the project were designed with this outage requirement in mind. Engineering. The engineering phase typically consists of data collection, field observations, measurements, review of existing drawings and an analysis of the existing system functionality. Once the data collection is complete, the engineering work can begin. Since the system was not a complete replacement and much of the existing wiring was to remain, the original drawings were revised according to the new system design. The original drawings were only available in hard copy, so they first had to be recreated in AutoCAD. Once there was a working set of AutoCAD drawings, HVM created three sets: one each for demolition, construction and installation. The installation team used the demolition set to remove devices, components and a circuit that was not needed in the new design. The installation drawings showed each applicable item color-coded with the required action. For example, devices or wires to be removed were highlighted in green, wires to be relocated in purple and items to remain did not have any highlight. Being able to also deliver a final set of construction drawings to the client ensures proper documentation of the completed installation and a record should future modifications be needed. Procurement and bench testing. After the engineering was complete, procurement and bench testing were implemented for the more advanced electrical components of the project. This phase incorporated protective relays, panel/door prefabrication and any ancillary components such as relay test switches, wiring and the like, required to make the system fully functional. Once the prefabrication panel/door modifications were complete, panel/door mounted equipment along with any interconnect to and from the devices were installed. Relay settings (provided by the engineering phase of the project) were then downloaded and the relays were bench tested on the programmed setting. Having all this work completed offsite saved valuable time during the outage at the client’s facility. Field Installation, functional testing and startup. Once delivered to the site, the field wiring and components required for field installation are completed according to the installation drawings. All wires are marked at the terminal strips. Any field-installed component testing was then completed along with point-to-point wire checks. A functional test plan was developed, and the complete system was tested against the plan to ensure proper operation (see Figure 2). The last phase of the project required the lead test technician to be onsite during startup to verify phasing, download advanced relay waveforms, set event parameters, and so on, and everything is documented on the final project report.
Protective relay upgrade projects with advanced style relays provide many ways to improve system operation, reliability and safety. These relays provide enhanced protection and control features that bring old infrastructure into the 21st Century and extend power system equipment lifecycle. Partnering with a company that can provide a complete turnkey solution also provides the added advantages of consistent engineering throughout the project, prefabrication with offsite testing, quality installation and thorough testing to ensure a fully functional and well documented project. Proper project phasing enables the project to be completed during a limited onsite outage and offers improved facility reliability and uptime, which saves the client valuable budget dollars. PE Jeff Brittain is Midwest region sales manager at High Voltage Maintenance (HVM). Since joining HVM, Brittain’s focus has been on improving generation, transmission and distribution system reliability, uptime and safety for critical power customers. Throughout his career, he has worked in various operations and sales roles while promoting a reliability-centered maintenance approach that meets the customer’s needs and budget.
Kaster has more than 15 years of experience in design, testing and commissioning generation, transmission and distribution systems from 208 V through 500 kV.
Figure 2: thethefunctionalAtestplanwasdeveloped,andcompletesystemwastestedagainstplantoensureproperoperation.Courtesy:HighVoltageMaintenance
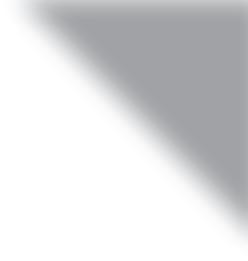
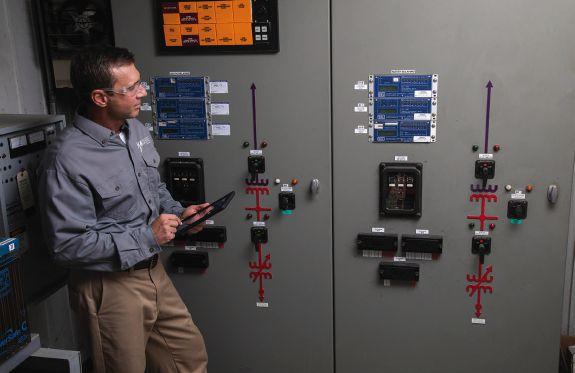
The connectivity landscape A McKinsey report predicts approximately $700 to $900 billion will go into initial installations of 5G, covering about 25% of the world’s population over the next decade. For manufacturing, 5G will open up completely new possibilities for the industry to retrieve information and trigger actions independent of the real location of machines. This improves flexibility in production, machine availability and overall equipment effectiveness (OEE). But 5G isn’t the only option and there is a range of alternative technologies that offer flexible, cost-effective power and low bandwidth options for IoT deployments in manufacturing facilities (see Figure 1). These technologies can be used in tandem with 5G or singularly as the use case calls for it. One of those technologies is LoRa, a device-to-cloud platform built for applications requiring long range, low power (see Figure 2). LoRa devices provide the communication layer for the LoRaWAN open protocol, a low power, wide area networking (LPWAN) protocol. Due to the long range, low power and long battery life of LoRa-based devices, sensors in manufacturing plants can relay critical data to a LoRaWAN network where it can be analyzed, and businesses operations can be optimized. Gateways leveraging the LoRaWAN protocol also enable geolocation capabilities to track and monitor assets and their locations to improve logistics, prevent theft and enhance factory operational efficiency.
Leveraging established networks By 2026, ABI Research estimates that LoRa will be the leading non-cellular LPWA network technology, accounting for more than half of all non-cellular LPWA connections. Additionally, the firm estimates that total non-cellular LPWA connections will reach 1.3 billion,
SOLUTIONS 38 • May 2021 PLANT ENGINEERING www.plantengineering.com CONNECTIVITY
The future of IoT: Collaborative solutions
A s the demand for connectivity continues to grow, so does the reliance on the Internet of Things (IoT). In the manufacturing industry, IoT devices can enable smarter factories, but with so many different options available, an emerging challenge is the lack of interoperability between connectivity platforms. While the goal of leveraging IoT solutions is to make life easier for the end user, and in this case factory workers, having multiple solution offerings inherently makes things more difficult. Factory plants are full of “connected things” including machines, conveyor belts and robotics, but if IoT devices and solutions do not work together, busy factory floors can quickly become hard to navigate and nearly impossible to troubleshoot. For example, if the line goes down, it becomes challenging to pinpoint where the errorWebegan.must ask the question: “How can technology evolve to promote working together?” The future of IoT connectivity requires flexible solutions that address a wide variety of IoT applications, use cases and device types. The massive IoT connectivity landscape is fragmented, with no single solution thetionscases.ityageubiquitousofferingcover-andthecapabil-toaddressalluseIoTapplica-benefitfrombroadrangeof available connectivity technologies chosen based on various factors, including network technology characteristics, commercial environment, business model and implementation environment. Today, leading technologies such as LoRa/LoRaWAN, NB-IoT, Zigbee, Wi-Fi, Bluetooth (BLE) and 5G dominate the industry.
The future of Internet of Things (IoT) connectivity requires exible solutions that address a wide variety of IoT applications, use cases and device types
By Marc Pegulu
Figure 1: A range of alternative technologies offer flexible, cost-effective power and low bandwidth options for IoT deployments in manufacturing facilities.
Courtesy: Semtech
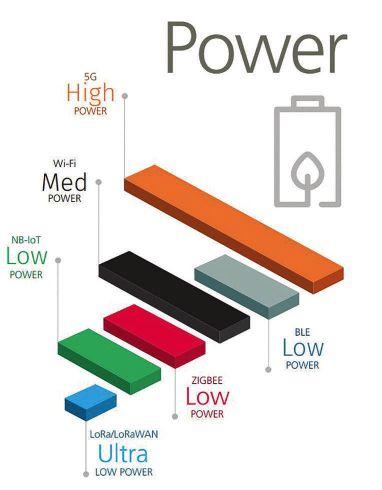
Working together Manufacturing plants will benefit from simple solutions that work together to provide a seamless connection between the many devices in indoor and outdoor environments. As more IoT devices enter manufacturing plants, 5G networks will complement existing solutions like LoRa, Wi-Fi and BLE as a way to access network technology and to backhaul data from gateways in remote areas to the cloud or head-end systems. With hybrid networks, manufacturing plants can better deploy IoT-connected sensors and introduce always-on monitoring functions into production. PE Marc Pegulu is vice president of IoT Strategy and Products at Semtech. Figure 2: LoRa is a platformdevice-to-cloudbuiltforapplicationsrequiringlongrangeandlowpower.Courtesy:Semtech
MOVE SECURELY INTO THE CLOUD FIELD TO CLOUD CONNECTION • IIoT-ready with Sparkplug, native MQTT and TLS encryption • Built-in VPN and Firewall for increased network security • Run Docker Containers in parallel with PLC logic • Interface with existing controls via onboard fieldbus gateways SECURITYBUILT-IN www.wago.us/IIoT IIoT_CE_Half Page.indd 1 4/15/21 2:57 PM input #11 at www.plantengineering.com/information and cellular LPWA connections, including NB-IoT, LTE-M and 5G, will reach 1.5 billion connections, including the large 2G customer base migrating toward NB-IoT and LTE-M. Devices leveraging LoRa are simple to deploy because they easily plug into existing infrastructure. Additionally, the LoRaWAN protocol has a communication range that can reach up to six miles or more, so no matter how big the facility is the device will be in range. Manufacturing facilities are typically large, have complex designs as well as leverage dense building materials. All these factors make it challenging for communication signals to get through, including 5G, but LoRa’s low power qualities and ability to penetrate such materials make it ideal. Another driving factor for LoRa-enabled deployments is the cost-effectiveness of its network architecture without needing a licensed spectrum, which is well suited for manufacturing cases.
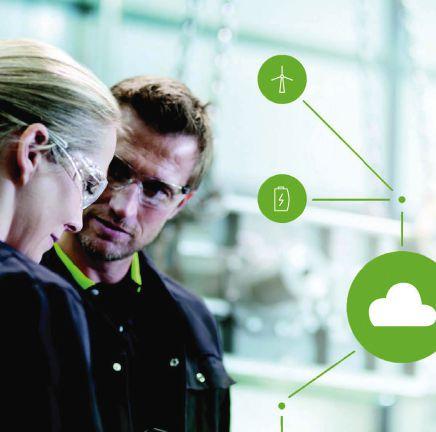
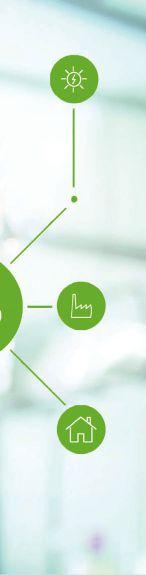
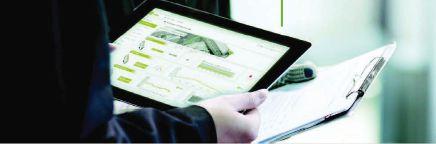
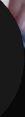



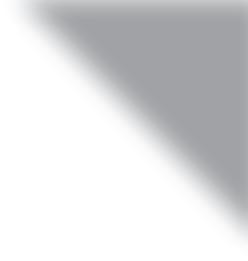
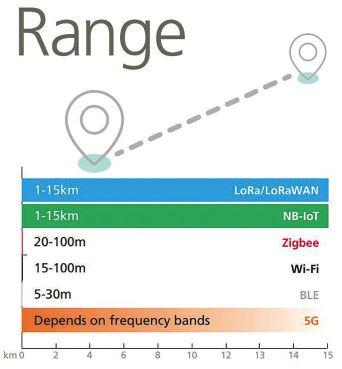
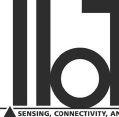

Complex withvalidationsmachineperformedmultiphysicssimulation
F actory and plant management worldwide see how digital transformation can help innovate in response to changing demand, global competition and an altered technology landscape. The demand is for more intelligent, flexible, configurable and automated industrial machinery equipment. Industrial machinery suppliers will need best practices to keep pace with their machines’ growingAcomplexity.connecteddigital thread can automate information sharing among design teams, analysts, production test teams and service engineers. This process allows teams to evaluate the capabilities and limitations of product variations efficiently. An intelligent performance engineering solution focuses on improvements in simulation, design and connectivity for machine builders. This happens by applying multiphysics simulation, which balances multi-attribute engineering to deliver a broad range of physics and other disciplines under one umbrella. Complex product requirements When new materials and methods are applied to manufacturing, it increases product complexity. But the benefits can be significant: Products are now lighter, smaller and more easily customizable to meet consumer demands. Multiphysics simulations enable machine builders to explore the physical interactions complex products encounter, virtually. It tracks interactive data of product performance, safety and longevity. It measures the interactions of fluid force performance, thermal effects, structural integrity and electromagnetic radiation. Isolating these forces individually to examine them can deliver inaccurate predictions of product behavior. It is optimum to consider all loads simultaneously during real usage simulation. This challenge is a global concern, as digital transformation addresses changing customer demands and adopting new technologies. Simulation tools critical A critical aspect of designing new industrial equipment, or modifying existing designs, lies in validating performance before the machine reaches the customer. It costs less to fix problems when designing rather than in product development. Adopting digital simulation and analysis tools allows original equipment manufacturers (OEMs) to understand how design choices affect a component, device or Manufacturers can use multiphysics simulation in a collaborative environment, integrating designers, analysts and live data to create better analysis practices and improve machine performance.
SOLUTIONS 40 • May 2021 PLANT ENGINEERING www.plantengineering.com THE AGE OF ANALYTICS
Courtesy: Siemens
Intelligent performance engineering provides improvements in simulation, design and connectivity for machine builders By Rahul Garg
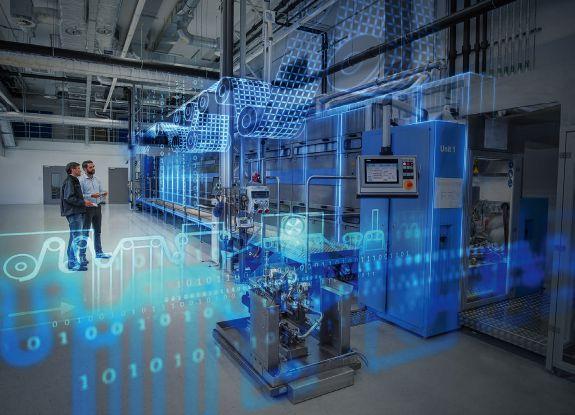
www.plantengineering.com PLANT ENGINEERING May 2021 • 41 machine's performance and failures. Traditionally, there are manual handoffs between the design and simulation processes. Design level simulation is used to secure a baseline assessment of a project to determine whether it is complete or needs advanced simulation.Equipment manufacturers are now delivering machines with faster cycle rates and compressed delivery schedules, so teams are motivated to perform advanced simulation upfront. In addition, power errors and increasing interdependence between multiple forces is a more accurate prediction of machine behavior, thus not limited to one area. This dynamic is often the effect of heat generation while the machine is operating and subsequent vibrations that result from heat displacement.
A world leader in textile manufacturing machines, the Picanol Group, with world headquarters in Belgium, produces weaving machines for the fabrics industry. The company develops complex machines that address diverse needs and fabrics, including cotton, silk, jute bags, fiberglass material draperies, upholsteries and car seats. The fluctuating needs of end customers in this market require these machines to be compliant with their performance and speed requests. It is essential to maintain the entire weaving machine’s structural integrity, while minimizing vibration and thermal concentrations. For example, a roller that imposes a pattern, fabric or paper may be subject to thermal contact and rotational forces. If, during validation, contact stress is considered but thermal load is ignored, disaster may follow. A multiphysics simulation approach analyzes issues individually and feeds the results back as input for future simulation. By examining thousands of possible solutions with minimum modification to the physical geometry, the best answer will satisfy the thermal needs of the fabric behavior’s life and vibration simultaneously. Fabric behaves differently under changing vibrations and thermal conditions. It is essential to manage the mechanics by considering extreme kinetic forces and high-speed movement during fabric delivery. Multiphysics simulation provides the ability to determine the optimum methods to address these challenges, including speed, thermal and vibration needs, using innovative tools and capabilities.
helpedsimulationMotionsolutionsPicanoltrimdownradialbearingforcesthroughfurtherweightreductionofmovingandoscillatingparts.Courtesy:Siemens
Multiphysics simulation case studies Connected data fosters collaboration between multiple teams and disciplines. Intelligent performance engineering leverages multiphysics simulation technology to achieve this relationship. Thus, simulation and multi-domain collaboration provide concurrent performance. A case study represents the multiphysics experience, addressing product complexity, performance, environmental conditions and other related factors to meet customer demands and maintain product and machine integrity.
A key part of intelligent performance engineering and multiphysics simulation is the ability to reduce the need for testing and physical prototyping, improving the overall speed for delivering a final design. As higher fidelity modeling integrates into the design organization, it improves collaboration between experts, permitting each to view their domain cohesively. Therefore, a machine simulation is not merely under one environment but is working across all the environments worth consideration. Hence, multiphysics unites the relevant experts attending to end-customer needs and helps them address any unexpected discoveries. These collaborations extend beyond the actual manufacturing environment, where multiphysics simulation helps OEMs and their broader supplier network connect data and act smarter. Subsequently, as a comprehensive digital twin is built, there is an analysis that proceeds from small components to encompass the entire machine, evaluating explicit characteristics. These components must work within the context and implementation of a specific machine. Therefore, collaboration is critical when working across multiple organizations, integrating the designers, analysts and live data to enable OEMs to adopt better analysis practices. Consequently, machine performance improves while ensuring safety, reliability and cost-effectiveness.
Picanol enhanced its weaving productivity by more than 15%, significantly reducing noise and vibration while discovering new techniques for creating machine driver mechanisms. Also, the company saw the fatigue life of repair parts increase, eliminating the need to build prototypes that would have been necessary without multiphysics simulation technologies.
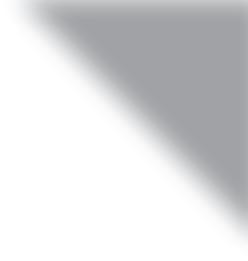
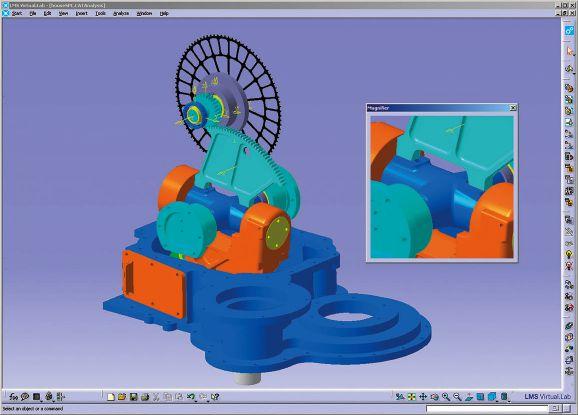
Siemens Digital Industries Software drives the transformation that enables a digital enterprise where engineering, manufacturing and electronics design meet within the Siemens Xcelerator portfolio. Xcelerator is a comprehensive, integrated portfolio of software and services that constitutes an application development platform, which accelerates the transformation to the digital enterprise. It unlocks a powerful industrial network effect — an essential requirement to leverage complexity as a competitive advantage, no matter the industry or company, to transition seamlessly to create tomorrow’s complex, efficient machines. PE Rahul Garg is the vice president for industrial machinery & SMB program, Siemens Digital Industries Software. He is responsible for defining and delivering key strategic initiatives and solutions and global business development. He and his team are responsible for identifying key initiatives and developing solutions for the industry while working closely with industry leading customers and providing thought leadership on new and emerging issues faced by the machinery industry. Garg’s experience and insight are derived from a 25-year career delivering software-based solutions for product engineering and manufacturing innovation for the global manufacturing industry. Picanol, a leading machineweavingmanufacturer,usedsimulationtoidentifydurabilityhotspotsforthoselocationsfacingstressvariationsthatmetorexceededmaterial-specificendurancelimits.Courtesy:Siemens
SOLUTIONS THE AGE OF ANALYTICS 42 • May 2021 PLANT ENGINEERING www.plantengineering.com
This example spotlights the interdependencies and benefits when simulation occurs effectively. It can be an intimidating mission to design, validate and manage modern manufacturing and assembly operations without considering the relationship between structural vibration and thermal. Both simulation and testing are essential to providing a holistic approach. Simulation and testing
The combination of simulation and testing provides a significant competitive advantage that is most effective in validating a design. You perform the simulation for testing, and the results provide a helpful indication of the appropriate physical sensor placements. After possessing the physical sensor measurements, you apply this data to the digital twin to validate it, correlating the results from reality to a numerical model. There are several measurable attributes associated with the performance of a machine, including acceleration or noise force. However, other parts can’t be accessed by sensors, like a working part’s temperature. Therefore, the virtual sensor results are obtained from the simulation model and combined with actual measurement results to synchronize any physical measurements with the running simulation. In this instance, it is measured from the digital twin, providing output from a specific point in the model, representing the evolution of a certain characteristic over time. This function is synchronized with the physical measurement to precisely understand the temperature’s value at a particular point while varying the acceleration. This holistic approach of simulation and testing provides a competitive advantage for machine builders through a comprehensive top-class suite of validation. Industry demand
The machinery industry requires sophisticated machines suitable for new materials and for manufacturing complex products, pushing builders to introduce innovative technologies, including intelligent performance engineering expertise to validate and perform analysis practices in the field.Intelligent performance engineering and multiphysics simulations allow the customer to explore the real-world physical interactions complex products encounter. This process impacts product performance, safety, longevity, fluid forces, thermal effects, structural integrity and electromagnetic radiation performance. When isolating these forces and examining them separately, the result is not always an accurate prediction of product behavior. Subsequently, it is vital to consider all loads simultaneously during the real usage simulation, which IPE Multiphysicsprovides.simulation reduces the need for testing and physical prototyping, improving delivery speed. It allows collaborating with experts to address the end-customer needs and what that means in terms of the product. Industrial machinery is a highly competitive field able to introduce dynamic innovations, using software and digital tools, that exceed customer expectations.
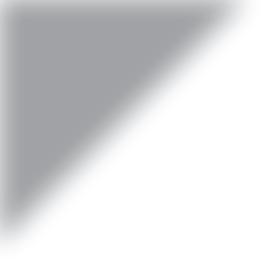
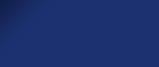
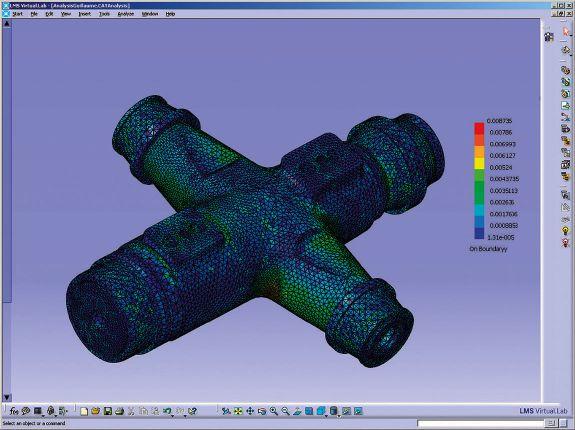
IEEESurgeCascading1:SuppressionStandard1100.Courtesy:SolaHD
Figure 2: Once it has been determined where the SPD units are to be installed, help in determining the surge rating (level of protection) can be found by referencing the panels' ampere rating.
The UL1449 standard was developed to take the ambiguity out of the marketplace and ensure proper protection with a level playing field. However, it has undergone many changes over the years and any SPDs (or filters) installed in your facility or equipment prior to 2009 should be examined for compliance.
SOLUTIONS www.plantengineering.com PLANT ENGINEERING May 2021 • 43 ELECTRICAL SAFETY
Cascaded surge protection provides additional suppression from large transients that step their way through from the service entrance by further reducing the let-through voltages. Also suppressed are more frequently generated internal transients.
By Mark Dziedzic
Courtesy: SolaHD
Performance values and ratings associated with an SPD include maximum continuous operating voltage (MCOV), voltage protection rating (VPR), nominal discharge current (In) and short circuit current rating (SCCR). The most misunderstood rating is the surge current rating, typically quantified in kilo-amperes (kA).
A tendency exists to assume the larger the panel, the larger the kA device rating needed for protection. Another misconception is if 200 kA is good, then 400 kA must be two times better. This is not always the case. Based on experience in the electrical industry, Emerson has generated some guidance on how to apply surge current ratings.
W hen an electrical surge occurs, voltage greatly exceeding accepted peak voltage levels could pass through building circuits to electrical equipment. Without proper protection, this equipment is susceptible to damage or failure. A surge protective device (SPD) can negate these Specifyingspikes.theSPD requires identifying and understanding the ratings associated with its application.
How to properly size surge protective devices
Guidance on SPDs Little published data or even recommendations exist on the correct level of surge current (kA) rating for different locations. The Institute of Electrical and Electronics Engineers (IEEE) provides input on what surge ratings are but does not publish recommendations. Unfortunately, no proven equation or calculator is available that allows inputting system requirements and receiving a solution. Any information a manufacturer provides, via calculators or other means, is merely a recommendation.
Let-through voltage is the voltage appearing on the equipment side (load side) of an SPD when an impulse voltage/current of a defined wave-shape and amplitude is applied to the line side of an SPD. It can be used to compare different SPD’s abilities to lower the surge voltage to the equipment requiring protection.
To optimize suppression throughout a system, SPDs should be installed at all levels of the electrical distribution system. This is known in the electrical industry as cascading or layering. IEEE refers to it as “protection in depth.”
Figure
To specify an SPD, understand the ratings associated with its application
Cascading protection
IEEE Standard 1100 recommends cascading levels of protection from the service entrance to distribution
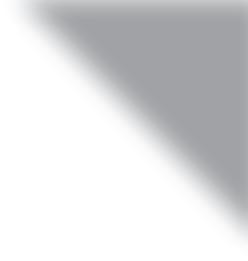
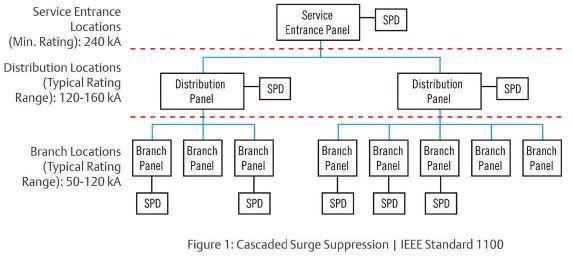
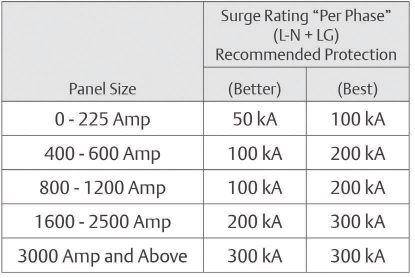
• For direct lightning strikes, SPDs alone are not a replacement for comprehensive lightning protection.
Figure 3: UL/ ANSI 1449 types
and branch panels, and even protection for individual critical loads. The closer to the service entrance, the more robust the device rating should be. This protection in-depth strategy protects the facility and critical loads.
Choosing the appropriate surge rating for an SPD comes down to two things: 1) the location of the SPD within the electrical distribution and 2) the facility’s geographic location.
In recommending a kA per phase rating, a general rule of thumb — “the 3-2-1 rule of thumb” applies: The service entrance should be 300 kA, distribution panels 200 kA and finally branch panels can be 100 kA per phase.
Larger, more destructive surge currents are mostly found at the facility service entrance. On rare occasions, if, for example, the exposure level is “extreme” as in states like Florida, it might be wise to increase surge current ratings. In these cases, the SPD will be exposed to larger surge events more frequently. With the correct surge current rating for your application, the SPD can be exposed to a higher number of surge events before needing replacement.
Final thoughts The purpose of a surge protective device is to shunt and suppress transient voltages being introduced into an electrical distribution system from either an external or internal source. Selecting the proper surge currentrated SPD throughout the electrical distribution system provides the best performance life for equipment. When selecting SPDs, keep these key points in mind:
Emerson recommends the above surge current ratings based on SPD location within the electrical distribution using the general “3, 2, 1 rule of thumb” mentioned earlier.
Types of SPD locations
• Service panel: 300 kA/phase
• Providing proper surge suppression to a facility and its equipment requires more than a single SPD located at the service entrance. We recommend cascaded SPDs with a proper surge current rating for each location. This provides superior suppression for a service panel or critical load.
location.byCourtesy:SolaHD
Recommendations
• Branch panels: 100 kA/phase.
SOLUTIONS ELECTRICAL SAFETY 44 • May 2021 PLANT ENGINEERING www.plantengineering.com
• Type 1 is intended for permanent application at the service entrance. It can even be before the main disconnect. A UL1449 Type 1 device can be installed on the primary of buildings or the first disconnect.
• Type 3 is for specific devices, referred to as “point of utilization” in the standard.
Panel size does not play a major role in the selection of a kA rating. What is much more important is the location of the panel within the facility. UL1449 defines the location types within a facility as:
• Type 5, which is the basic component, such as a metal oxide varistor (MOV), silicon avalanche diode or gas discharge tube. These clearly can’t be directly installed into a facility.
• Type 2 is intended for installation on the load side of the main entrance panel.
• Type 4 would be a component device intended to be part of a larger assembly and is not approved for standalone use without additional safety evaluation. Be careful if you are offered a Type 4 device to be installed into a control panel. The panel builder would be responsible to submit for third-party safety approval, otherwise it wouldn’t be covered in a catastrophic failure.
• Oversizing an SPD for its application cannot hurt a system, but under-sizing the SPD can result in premature SPD failure.
Following these guidelines for sizing and placing SPDs throughout an electrical distribution system takes the guess work out of it and maximizes surge suppression at every point. Remember, bigger isn’t always better. Size appropriately for the load and protect critical panels and loads to ensure a maximum return on investment. PE Mark Dziedzic is senior product marketing manager, SolaHD power quality products, Appleton Group. SolaHD is part of the automation controls group at Emerson.
Experience with SPD products shows that a device carrying a surge current rating between 240 and 250 kA for a service panel or critical load provides many years of service in “high to medium” exposure locations over time.
• Distribution panel: 200 kA/phase
Location kA:
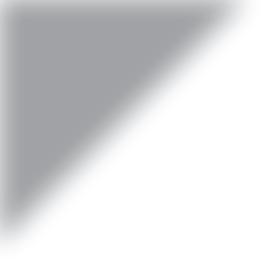
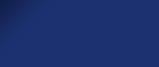
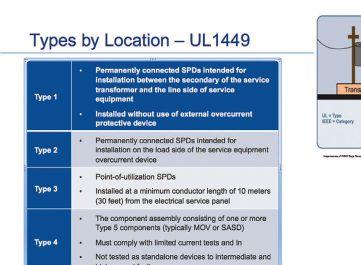
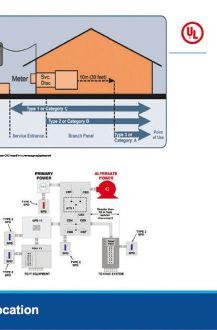

Figure 1: The Capability Maturity Model stages. Courtesy: M. C. Paulk, B. Curtis, M. B. Chrissis and C. V Weber
Maturity assessments are borne from the belief that if processes are well defined and executed, the result of that process is also of the desired quality. This concept originates from the software development world in the late 1980s. Software projects were of an extremely high cost and rarely delivered the desired results. The software Engineering Institute, with support from Mitre Corp, developed the first Capability Maturity Model, to measure the quality of the software development process.
The Capability Maturity Model (CMM) describes a series of increasing capabilities that can be measured (see Figure 1). Translate this to the engineering information management world and take the example of assigning new equipment numbers for a project executed in the facility. For example, a process at the initial level would describe that the organization is not even aware of the need for a process (see Figure 1). The result of this is that equipment numbers are assigned at free will by either an engineering, procurement and construction (EPC) contractor or the engineer that might be working on the project. As a result, there is a duplication of numbers, no consistency and no alignment between the different systems that use this information. The result of this is it becomes difficult to find information or establish if the information is accurate. People do not trust the information and often do a field check to make sure what they have is accurate. Consider the opposite scenario, a process description at the optimizing level would, for example, describe a software solution controls the assignment of equipment numbers, there is a procedure that describes this, and the system is aligned with industry standards and there is a yearly review on the quality of the information (see Figure 2). Best practices in mature engineering managementinformation
W With the year 2020 behind us, many companies have adjusted to different operational models. Remote working is a prime example of how companies have changed. From a survey conducted by PWC, 22% indicated remote work was not an option. Work methods were not digitized causing remote work to not be possible for their role. This realization among companies has led to a further acceleration of digital projects. To reap the full benefits of these projects, automating end-to-end processes is key. This is where questions arise concerning focus, organizational and culture changes, technology systems and more. To help establish a roadmap for improvement, maturity assessments can be a great management tool. What are maturity assessments?
SOLUTIONS www.plantengineering.com PLANT ENGINEERING May 2021 • 45 MANAGEMENT
Mature engineering information management can save millions in operational costs
By Edwin Elmendorp
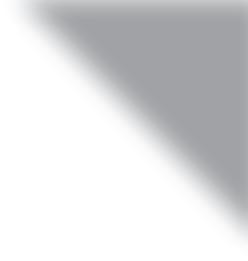
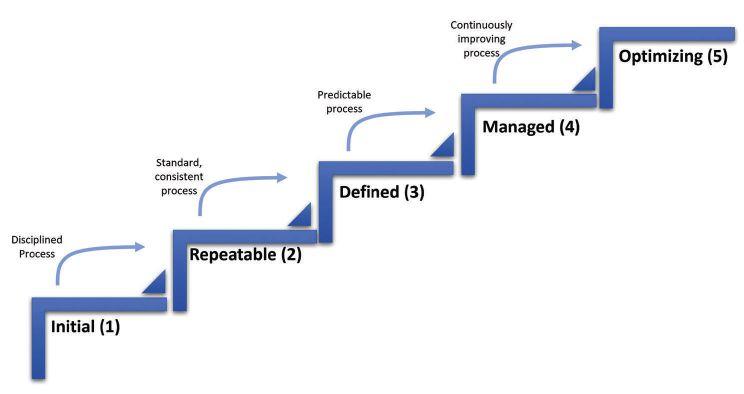
SOLUTIONS MANAGEMENT 46 • May 2021 PLANT ENGINEERING www.plantengineering.com
As a result, information is accurate, unique, consistent, concise and clear. Based on open application programming interfaces (APIs), the information is also made available for other systems and removes the need for duplication or issues with manually entering the equipment tag into other systems. How equipment tags are managed is only one example. Professional maturity models can have hundreds of these types of indicators across many different areas.
When we look at the cost savings aspect, direct and indirect factors will emerge. One of the challenges with this topic is most of the savings come from indirect sources such as productivity gains. The research performed on this topic — specifically toward engineering information management — is limited. To help quantify the savings, consider these aspects based research and experiences.
• Perceived reliability — 60%: from a study conducted in 2016, among nine petroleum production facilities and 133 interviews, 60% of the group described that communication and access to information, combined with the efficiency of the tools available, have a large influence — in a negative way — on the perceived reliability of the equipment.
• Trust — 50% or worse: from a limited poll during a live event, among process manufacturing companies, 50% of the attendees rated the trust level of their information at 50% or worse. Meaning that at a minimum a field check is required, and multiple systems would need to be verified, before committing changes to critical information.
Figure 2: Sample engineering information management (EIM) maturity assessment outcome. Courtesy: Kinsmen Group
Figure 2 shows a condensed and completed maturity model for a sample company. This model has seven different areas to build a holistic picture concerning engineering information management. In Figure 2, note the column “organization” has the lowest score, whereas the columns “process” and “system” score highest. Engineering information management professionals often hear that “our system is not working,” but in the sample case from Figure 2, the problem is at least also an organizational issue. Perhaps people are not properly trained or there is insufficient documentation and when individuals leave the company, managing information quickly turns into chaos. Based on the results from an assessment, an organization can start to think about the areas upon which it wants to improve. Models like the one above, provide guidance and steppingstones to raise the level of maturity. How improved engineering information can save cost
The case for engineering information is no different. One should not just think about the systems, but also how these systems are managed, how the processes are defined, how people are trained in these systems, how the company assigns budgets, how the initiative is supported, how strategies are set up and much more.
The input gathered for such an assessment is across various stakeholders in the organization. For each indicator, every stakeholder selects a rating (initial, repeatable, etc.) for how the company is performing. This then builds thousands of data points that can reveal underlying barriers that can resolve structural information management issues.
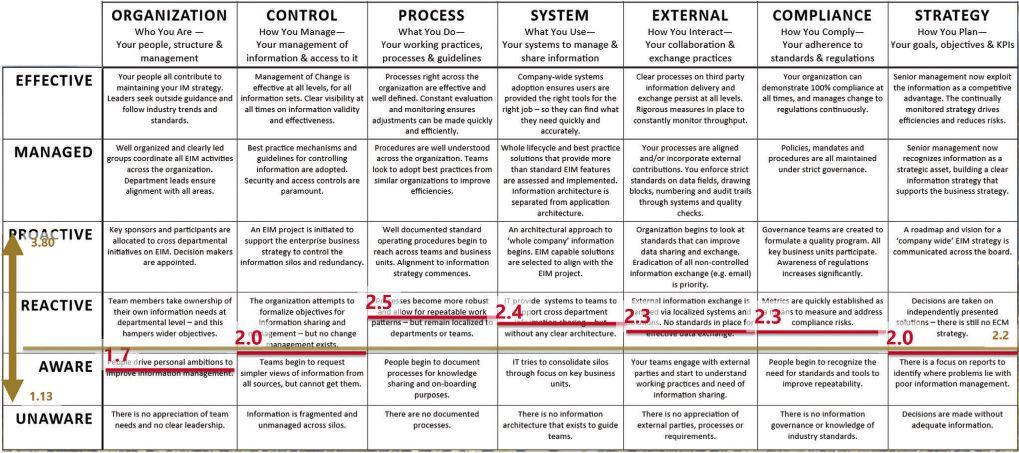
• Safety/incidents — 86%: When an incident (or near miss) happens, 86% of the attendees believed that poor, missing and/or not timely information had a large contributing factor to the event. This was a question asked during a live event among process manufacturing companies.
• Cost — 10% of the operating budget: From a recent study in 2019, it was concluded that up to 10% of an annual operating budget could be lost because of poor engineering information. Many variables are used and depending on the specific situation, these numbers will vary considerably. However, the range of potential cost is significant for any asset that provides a solid start for a business case.
• Cost — $15.8 billion per year: From a well-known report produced by the National Institute of Standards and Technologies (NIST), it was estimated that the inadequate interoperability of information is costing the capital facility industry a staggering amount yearly. Although this study was performed in 2004, reviewing some of the more recent research shown above, the presented number still seems relevant. Based on the above findings, finding a business case should be straightforward. The reality is challenging. Due to the nature of mostly soft savings, organizations tend to focus more on investments that have a direct operationalPerformingimpact.anassessment can help in this sense. A well thought out assessment will provide a holistic picture of how an organization performs. Secondly, these assessments can inspire the organization. There can be many topics that were not previously thought of but could be valuable topics for improving the organization. Translating results to actual goals With the outcome of an assessment, the next step is to determine where to go next. An assessment will provide insights into how the organization performs today. The goal should be to raise the level on the maturity scale and implement improvements step by step, across all the different areas. If for example, the organization acquires a new software solution to manage engineering records, this system must be embedded in the corporate framework. If there are not appropriate resources for continued training, the solution will quickly end up in the digital landfill.
While a maturity assessment will validate and provide direction, it is key to identify practical goals that can be resolved within a foreseeable timeframe and build success. Organizations currently use the phrase “business agility,” meaning there is a desire to address problems quickly as the business evolves in an ever-changing landscape. The purpose of an assessment is it will provide a roadmap to which identified improvements can be executed, contributing to the goals of the company. One methodology is to discuss the different areas of the assessment and rate low scoring areas on a priority scale, considering the company goals, budgets, resources available and so on. Based on the selected areas (e.g., deliverables management) the organization then uses the SMART goals to define the improvement
• Cost — 1.5% of annual revenue: From research performed by ARC Advisory group, it was concluded that the cost of poor asset information can be up to 1.5% of annual revenue for an organization. Throughout the study, these numbers have been validated against other known studies to contrast, compare and validate the outcome of the study.
Theproject.SMART criteria is defined as follows:
• Measurable: This describes how the success of the goal can be measured.
• Assignable: This describes who in the organization (internally or externally) will be responsible for this goal.
• Specific: This describes what the project will accomplish with a specific goal.
• Realistic: This describes why this goal is realistic.
The SMART goals, combined with the outcome of the assessment, provides management with the instruments to measure the status, but also any future progression. The defined goals provide a method to execute specific projects that will raise the level of maturity on the topic of data quality.
• Time-related (time-bound): This describes the timeframe for when the goal is to be completed.
PE Edwin Elmendorp is the information architect at Kinsmen Group, a team of engineering information management specialists with a passion for applying innovation to prominent oil, gas, pharmaceutical and utility companies. Elmendorp lives in Houston and has nearly 20 years of consulting experience for engineering information management. After graduating as an electrical instrumentation engineer, he added a computer science degree and recently graduated cum laude with a master’s in business process management and IT. Aside from a solid academic background, Elmendorp has worked with many owner-operators to digitally transform how companies manage their information assets spanning many different software solutions.
www.plantengineering.com PLANT ENGINEERING May 2021 • 47
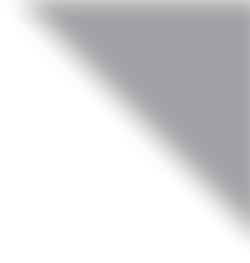
48 • May 2021 PLANT ENGINEERING www.plantengineering.com CONTACTS Advertiser Contacts for plant engineers Request more information about products and advertisers in this issue by using the http://plantengineering.hotims.com link and reader service number located near each. If you’re reading the digital edition, the link will be live. When you contact a company directly, please let them know you read about them in Plant Engineering. PlantEngineering.com 3010 Highland Parkway, Suite 325 Downers Grove, IL 60515 Ph. 630-571-4070, Fax 630-214-4504 CONTENT SPECIALISTS/EDITORIAL KEVIN PARKER, Editor KParker@CFEMedia.com JACK SMITH, Managing Editor JSmith@CFEMedia.com KATIE SPAIN NAREL, Art Director KSpain@CFEMedia.com AMANDA PELLICCIONE, Director of Research 860-432-4767, APelliccione@CFEMedia.com CHRIS VAVRA, Production Editor CVavra@CFEMedia.com SUSIE BAK, Production Coordinator SBak@CFEMedia.com PUBLICATION SERVICES JIM LANGHENRY, Co-Founder & Publisher JLanghenry@CFEMedia.com STEVE ROURKE, Co-Founder SRourke@CFEMedia.com KATIE SPAIN NAREL, Art Director KSpain@CFEMedia.com PAUL BROUCH, Director of Operations PBrouch@CFEMedia.com COURTNEY MURPHY, Marketing and Events Manager CMurphy@CFEMedia.com MCKENZIE BURNS, Marketing and Events Manager MBurns@CFEMedia.com MICHAEL ROTZ, Print Production Manager 717-766-0211, Fax: 717-506-7238 mike.rotz@frycomm.com MARIA BARTELL, Account Director, Infogroup Targeting Solutions 847-378-2275, maria.bartell@infogroup.com RICK ELLIS, Audience Management Director 303-246-1250, REllis@CFEMedia.com LETTERS TO THE EDITOR Please e-mail your opinions to KParker@CFEMedia.com INFORMATION For a Media Kit or Editorial Calendar, e-mail Susie Bak at SBak@CFEMedia.com CUSTOMER SERVICE OR SUBSCRIPTION INQUIRIES (800) 217-7972 e-mail Plant Engineering at PE@omeda.com REPRINTS For custom reprints or electronic usage, contact: Shelby Pelton, Wright’s Media 281-419-5725 x138, cfemedia@wrightsmedia.com PUBLICATION SALES Robert Levinger, Midwest RLevinger@CFETechnology.com 3010 Highland Parkway #325 Tel. 516-209-8587 Downers Grove, IL 60139 Karen Cira, Southeast KCira@CFEMedia.com 879 Autumn Rain Ln. Tel. 704-523-5466 Charlotte, NC 28209 Fax 630-214-4504 Diane Houghton, AL, FL DHoughton@CFEMedia.com 38 Charles River Drive, Tel. 508-298-9021 Franklin, MA 02038 Fax 630-214-4504 Richard A. Groth Jr., NJ/ E. PA RGroth@CFEMedia.com 12 Pine St. Tel. 774-277-7266 Franklin, MA 02038 Fax 508-590-0432 Stuart Smith, International stuart.smith@globalmediasales.co.uk SSM Global Media Ltd. Tel. +44 208 464 5577 Fax +44 208 464 5588 Reader Advertiser Page Service # Web site ABB Motors & Mechanical C-4 13 www.new.abb.com AutomationDirect C-2, IFG, OFG 1, 2 www.automationdirect.com Caterpillar - Northeast 6 5 www.necatdealers.com/standby CFE Media LLC 25 www.cfemedia.com DEWESoft 1 3 www.dewesoft.com Lubriplate Lubricants Co 14 8 www.lubriplate.com REGAL 8 6 https://www.bit.ly/2QIhqFA SeeQ 17 9 www.seeq.com SEW-EURODRIVE, Inc. 2 4 www.seweurodrive.com Siborg Systems Inc 11 7 www.siborg.com WAGO Corp 39 11 www.wago.us Workbenchmarket 20 10 www.workbenchmarket.com Yaskawa America, Inc C-3 12 www.yaskawa.com TMandTechnology GET ON THE BEAT Keep your finger on the pulse of top industry news WWW.INDUSTRIALCYBERSECURITYPULSE.COM
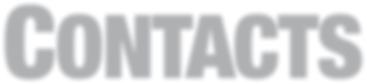
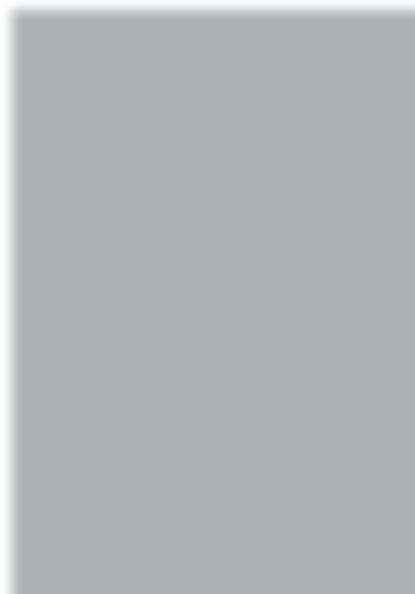
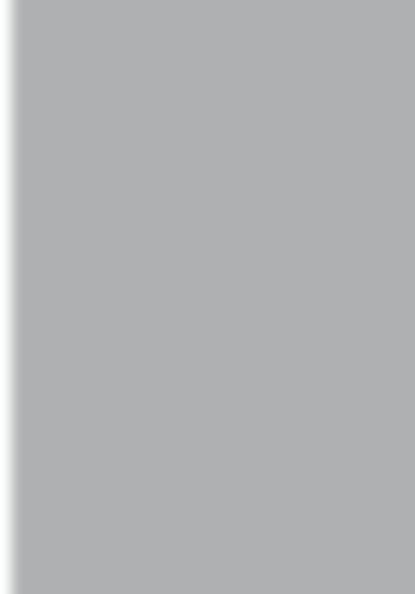
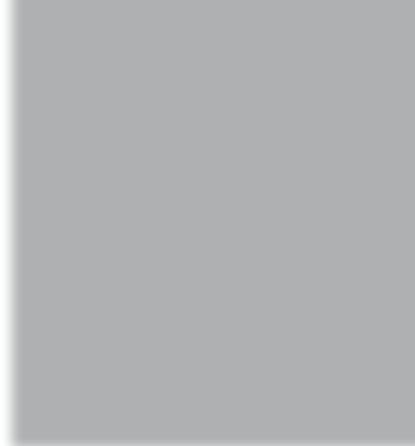
SAFE & SOUND Your time is valuable. The new, easy-to-use GA800 AC Drive from Yaskawa gives you the power to make all of your operations better. • Rest easy with legendary Yaskawa quality and embedded functional safety. • Experience ultimate ease-of-use with DriveWizard® Mobile and optional Bluetooth® connectivity. • Enjoy incredible torque production and network connectivity. LYour days are complicated enough. Let us help simplify them. To learn more, visit or call Yaskawa today at 800-YASKAWA. Yaskawa America, Inc. 1-800-YASKAWA For more info: https://www.yaskawa.com/ga800-drive | yaskawa.com input #12 at www.plantengineering.com/information
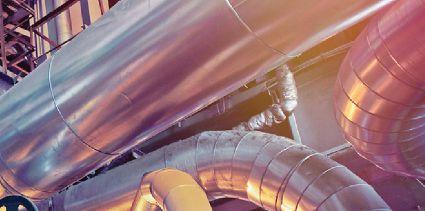
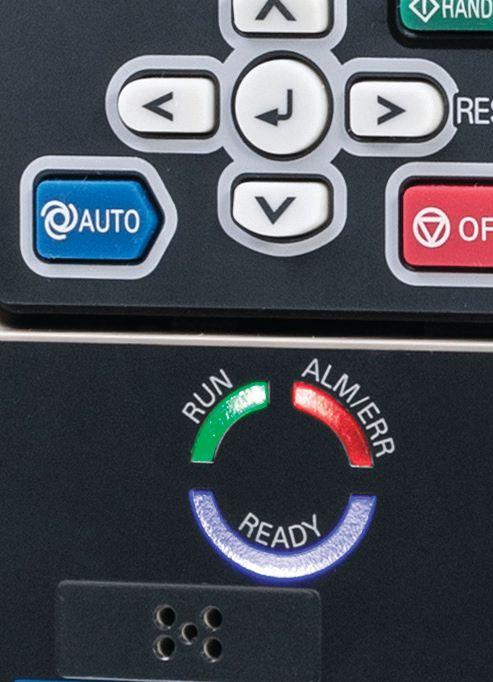



productivityImprovesstopsunplannedEliminates
input #13 at www.plantengineering.com/information
The ABB AbilityTM Smart Sensor for mechanical products is an easy-to-use, wireless sensor which monitors the health of mounted bearings and gear reducers. The sensor provides warnings when health status declines, reducing the risk of unplanned downtime. In addition, connectivity and trend data allow maintenance to be planned proactively instead of reactively, and remote monitoring capabilities keep employees away from areas that are difficult or dangerous to access. Operate safely. Reduce downtime. Improve reliability. new.abb.com
Condition— monitoring For mechanical components
safetyemployeeIncreases
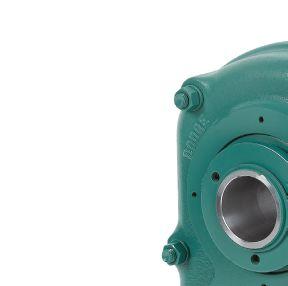
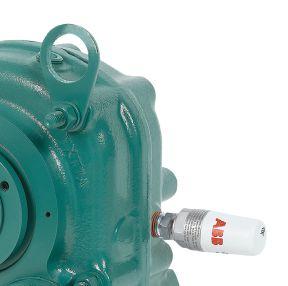
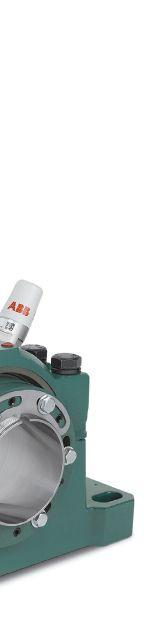
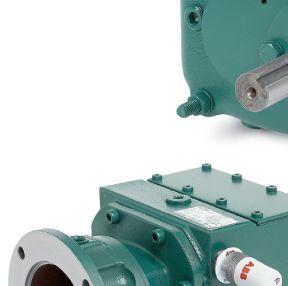
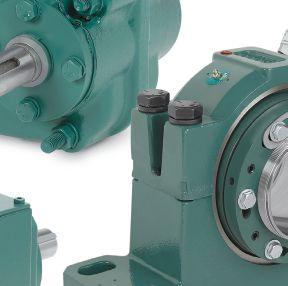
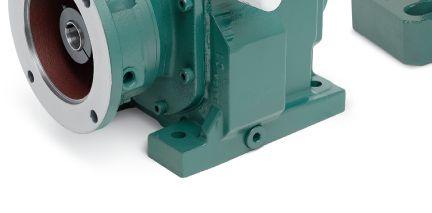
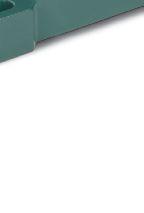
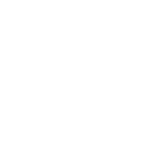
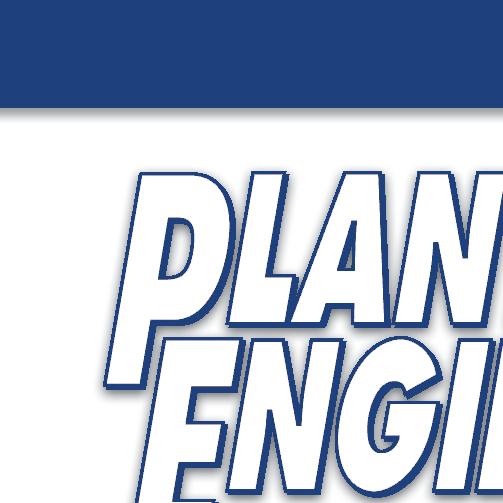

