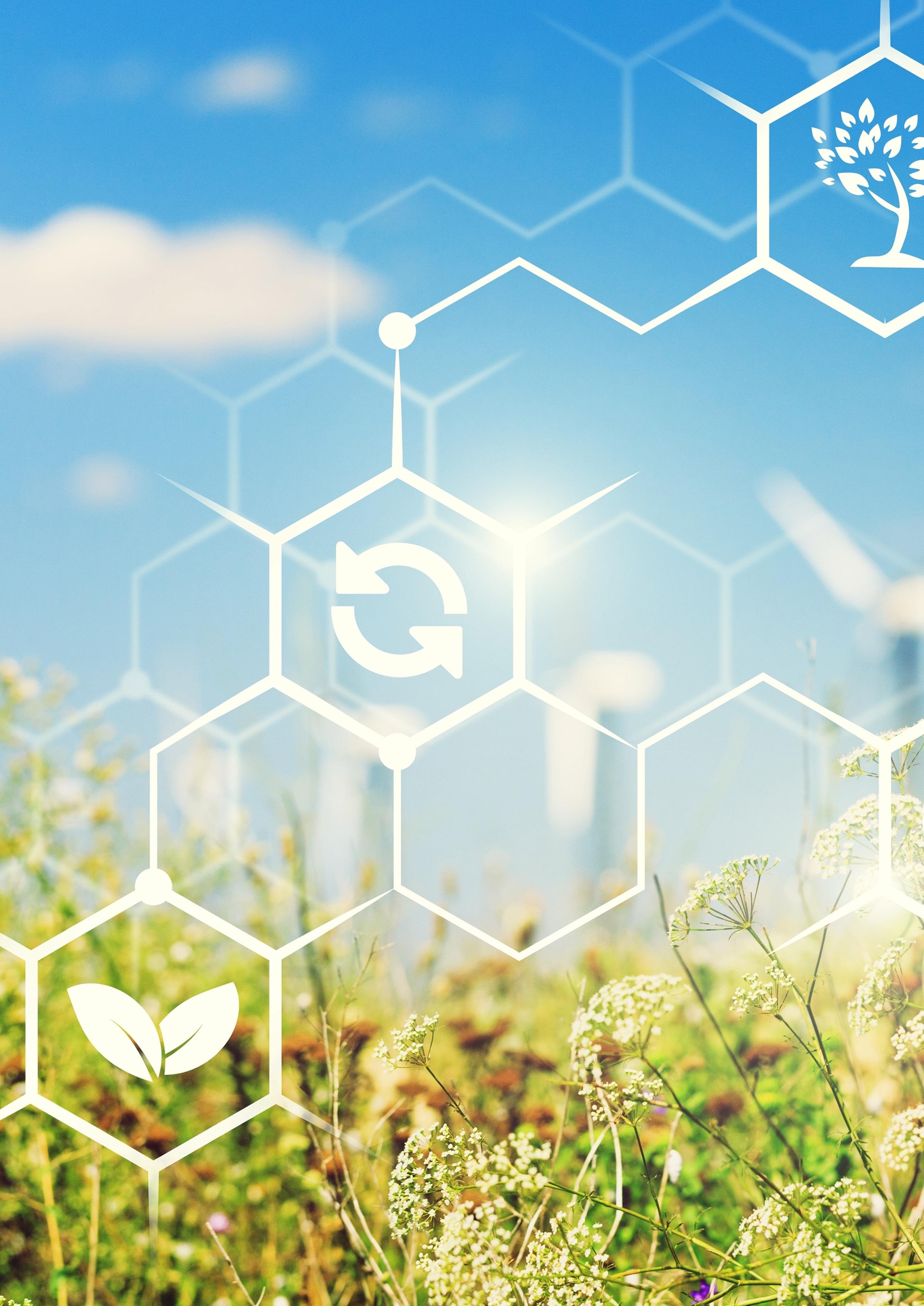
8 minute read
Embracing the simulation challenge
Bharat Naik and Phil Millette, Honeywell Process Solutions, discuss how simulation could drive value across the hydrogen market.
Companies looking toward net zero emissions are beginning to take actions to reduce their carbon footprint. Currently, there is a wealth of information that is being published by industry experts, which discusses the energy transition and technologies required to reach net zero. One of these technologies is the production of hydrogen from renewable energy sources, known as green hydrogen. As green technologies evolve and government policies develop, experts frequently mention the use of green hydrogen as a sustainable energy source, and it is seen by many companies as a key component of their net zero strategy.
Green hydrogen policies and initiatives can often be measured by the intended capacity of hydrogen production, initial plans, and envisioned growth. The growth expectations from the policies currently being announced in the medium-term (to 2030) and the longer-term (2040 and 2050) are significant. For example, the EU Hydrogen Policy, published in July 2020, plans for the installation of 6 GW of renewable hydrogen electrolysers by 2024, and 40 GW by 2030.1 This is a significant increase in capacity, given that at the start of 2021 only 1 GW was installed in the EU.2
Even though hydrogen is an energy carrier, it is neither a primary source of energy nor the first step in the value chain. Because green hydrogen is obtained through the electrolysis of water, the electricity required for electrolysis is the real front end of the value chain. This electricity can come from renewable sources such as wind or solar, or from hydroelectric or geothermal sources.
Since renewable power is the key starting point, Honeywell’s activity in battery energy storage, wind and solar facility SCADA, substation control, microgrid control, and virtual power plant control is also relevant to understanding and managing the performance of green hydrogen production. These areas can help when developing an approach to mitigating the intermittency of renewable energy, and ensuring reliable hydrogen production. The company’s activity also spans the rest of the hydrogen value chain, including process simulation, performance management, automation and management of efficient hydrogen production, storage, and integration.
Honeywell has made its own public commitment toward achieving carbon neutrality at its facilities and within operations by 2035.³ This commitment also includes the responsibility of sustainable innovation and helping customers reduce their own emissions. As the company’s net zero commitment extends to digital transformation sustainability solutions for clients, it is using software and expertise available today to support the sustainability goals of plant operations, while focusing on future innovations aligned with its culture of continuous improvement.
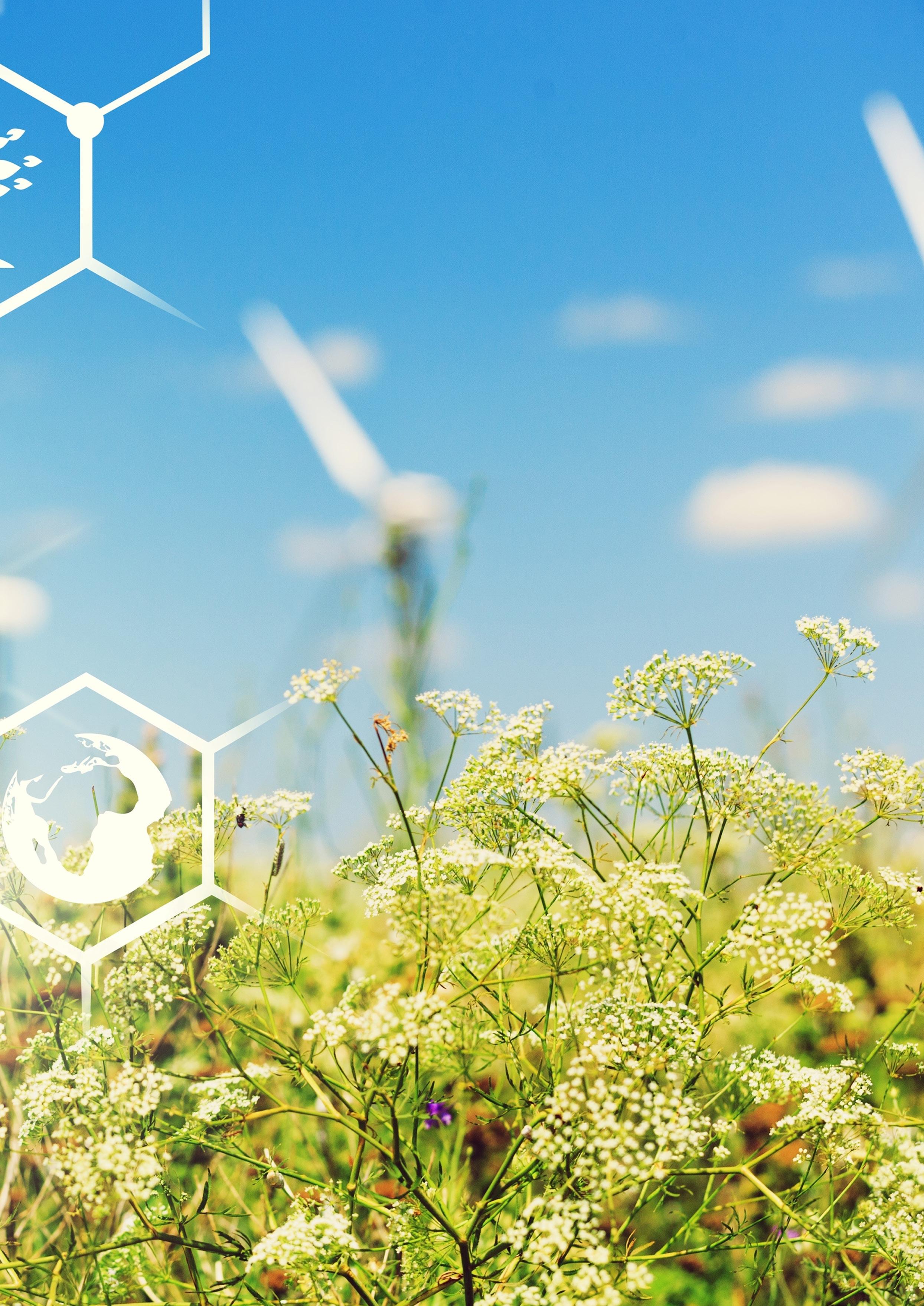
The simulation challenge and scope
Modelling a green hydrogen plant requires the representation of a wide scope of process equipment, including the electrolyser stack, water treatment and disposal facilities, electrolytes, and standard equipment such as gas/liquid separators, compressors, pumps, tanks, heat exchangers, and dryers.
The overall plant layout can include power supply transformers and rectifiers, utility supply (water, or potassium hydroxide [KOH] or steam, as relevant), drying, purification of hydrogen, hydrogen compression, and local pressured storage. It can also include water or KOH circulation, and purification of generated oxygen.
This does not include further upstream processing that is considered for some projects, including water desalination, nor any downstream ammonia or methanol units that are themselves considerable investments.
Multiple electrolyser stacks are typically required to achieve the desired capacity, hence the requirement to combine multiple electrolysers into a single performant simulation model. Furthermore, the unique physical characteristics of hydrogen require specific and accurate thermodynamic models to support the effective design and modelling of green hydrogen production.
The modelling scope can address the complexity of: � Reliably producing hydrogen at expected production rates and of sufficient quality, with overarching safety requirements. � Storing hydrogen and maintaining quality and safety. � Transporting hydrogen efficiently, reliably and safely.
The intermittency of many renewable power sources poses a primary challenge to efficient hydrogen production. In some projects, intermittency will be mitigated by the project scope itself, such as additional battery storage, green energy contracts to the grid, or designing the facility to handle extreme energy fluctuations. To meet these challenges, accurate simulation of hydrogen electrolysis and power variability mitigation strategies will be a critical component in project planning, design, and operational performance management of green hydrogen production.
Process simulation as an engine to drive value across an asset’s life cycle
Process simulators, such as Honeywell’s UniSim® Design Suite, are applicable across the entire life cycle of a green hydrogen project, including feasibility studies, option analysis, engineering design, detailed engineering, operator training, operations, and optimisation. UniSim Design’s process simulation is central to analysing the various options that will determine the economic and operable feasibility of a selected design. The early conceptual phase of a green hydrogen project will include sorting through numerous options with the following key process variables: � Electrolyser technology: alkaline, proton exchange membrane (PEM), or solid oxide. � Variability of electrical supply. � Electrolyser water quality. � Discharge water quality. � Main electrolyser stack parameters. � Battery limit conditions of product streams.
Near-term innovations in process simulation are focused on the accurate replication of the electrolyser stack design in order to accommodate evolving electrolyser technology. The electrolyser stack will contain proprietary technology and knowledge about the internal details that will not be available outside the development company. Therefore, the electrolyser stack model, within a process simulator, must be broad and generic to accommodate a variety of designs. Much like a catalytic reactor in a refinery, the final design of the electrolyser will be supplied by the technology vendor. The process simulation will represent the overall performance of this stack, and the balance of the plant.
Choosing the best design
The design of a new green hydrogen facility carries with it unique challenges, due to factors such as power supply intermittency, the various levels of electrolyser technology maturity, hydrogen storage requirements, and the disconnect between hydrogen demand and electricity supply. Hence, the decision on an optimal size and design of the plant will require the evaluation of tens, if not hundreds, of cases. The goal will be to minimise CAPEX and levelised hydrogen production costs while utilising available plot space and consistently meeting expected hydrogen demand.
The true CAPEX investment required of a green hydrogen project extends far beyond the electrolyser stack. Additional major blocks must be considered to estimate the investment required and to make decisions about plant design. These blocks include electrical supply stations, water purification units, electrolyte supply and discharge, cooling systems, wastewater treatment, hydrogen and oxygen distribution network, and ancillary systems including safety systems and storage tanks.
Aside from CAPEX considerations, other key aspects of designing a green hydrogen plant include ensuring that the design software has the requisite capabilities to precisely replicate the produced hydrogen and produced oxygen networks through a wide range of pressures and temperatures.
Additionally, modelling the electrolyser to accurately predict performance and hydrogen production can be very complex. Assuming most viable technologies today are alkaline and PEM electrolysers, the following are key variables to model: � Current density: affects hydrogen produced per active area.
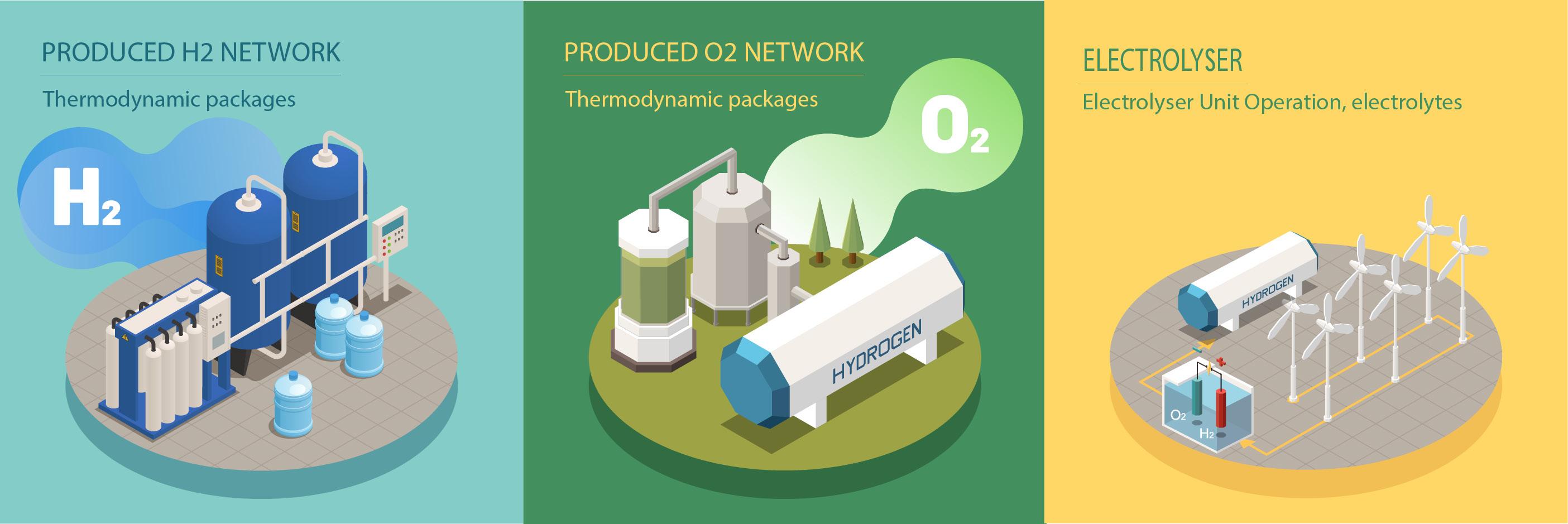
Figure 1. Produced H2 network, produced O2 network, and electrolyser.
� Power density: the required electricity and power supply/rectifier size. � Gas crossover: helps determine limitations to maintain safety and achievable faradaic efficiency. � Operating temperature: increasing temperature improves kinetics and thermodynamics and decreases overpotentials, but decreases stability and may increase crossover. � Heat management: the reaction is endothermic, but overpotentials generate excess heat. � Pressure: elevated hydrogen pressure at stack reduces downstream compression stages, but increases crossover. � Feed water purity/composition: impurities lead to stability issues and recycling leads to product impurities. � Internal flow dynamics and temperature gradients: affect local performance.
Additional near-term modelling developments will mirror electrolyser innovations, with capabilities to support alkaline and PEM technologies, including solid oxide electrolysers.
UniSim Design’s integrated case scenario manager further supports the green hydrogen evolution via right and fast analysis of various design scenarios by simultaneous execution of several cases with minimal user intervention. Results of various cases can be easily integrated with cost-estimating software Cleopatra Plus for developing techno-economic analysis and selection packages.
In addition to helping determine an optimal process design, UniSim Design can also be applied throughout the life cycle of a green hydrogen project, including: � Feasibility studies. � Basic engineering design. � EPC phase. � Operator training utilising UniSim Dynamics via Honeywell’s
Workforce Competency. � Opportunity analysis via what-if scenarios. � Operational performance tracking and optimisation via
UniSim Live.
Green hydrogen and the path to net zero
In summary, the emerging field of green hydrogen faces many challenges to consider and overcome, such as product supply infrastructure, cost optimisation, operations under varying inputs, technological feasibility/operability, reliability, and safety. The end goal is to build a safe and reliable facility while maximising the use of plot space and minimising the levelised cost of hydrogen. Solving these challenges and optimising process variables through modelling is the first step toward sustainable hydrogen production. Across the entire value chain and life cycle of green hydrogen projects, process simulation will be a key tool that helps enable the success of these projects, and contribute to a net zero future.
References
1. ‘EU hydrogen policy: Hydrogen as an energy carrier for a climate-neutral economy’, European Parliamentary Research Service, (April 2021), https://www.europarl.europa.eu/RegData/etudes/BRIE/2021/689332/
EPRS_BRI(2021)689332_EN.pdf 2. ‘The European hydrogen strategy’, Watson Farley & Williams, (3 February 2021), https://www.wfw.com/articles/the-europeanhydrogen-strategy/ 3. ‘Honeywell Commits To Carbon Neutrality In Its Operations And
Facilities By 2035’, Honeywell, (8 April 2021), https://www.honeywell. com/us/en/press/2021/04/honeywell-commits-to-carbon-neutrality-inits-operations-and-facilities-by-2035
Powering the energy transition
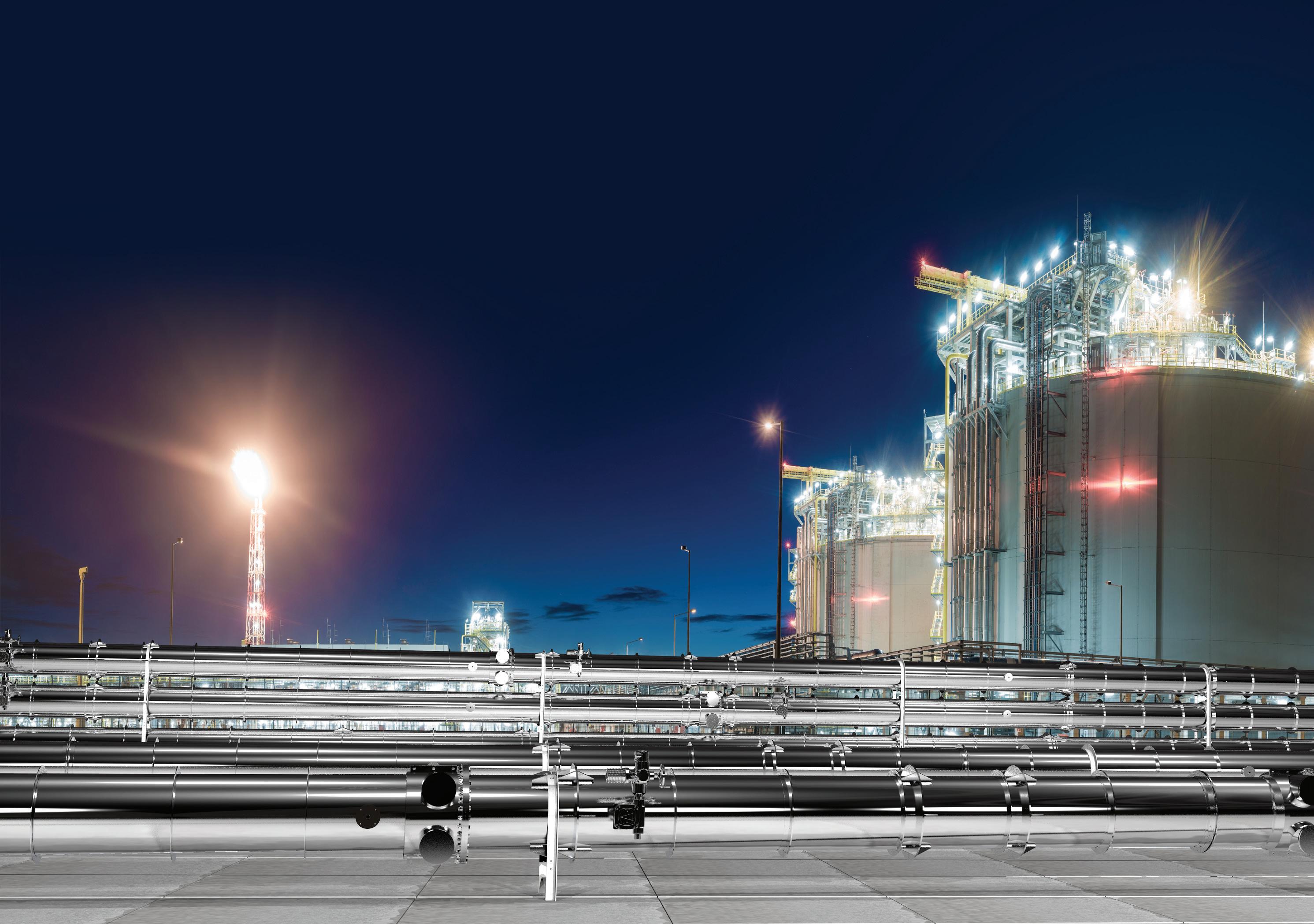
Atlas Copco Gas and Process is well prepared to support our customer’s business and process requirements – especially through H2 Production, Usage & Transportation. Building on decades of experience in hydrogen-dominant processes, Atlas Copco Gas and Process centrifugal turbocompressors and turboexpanders enable many critical processes in hydrogen, new energy and beyond.