
9 minute read
Tackling challenges head on
Marie-Laure Gelin, Howden, the Netherlands, explores the challenges associated with scaling up the use of hydrogen in support of the energy transition, and details a number of projects in which the company’s compression technologies have been used.
It is becoming increasingly clear that hydrogen will play an essential role in accelerating the global energy transition. Global hydrogen production is forecast to more than double by 2030, following international public and private sector commitments. As a cleaner and secure fuel source, hydrogen has the capacity to be a powerful enabler in the transition away from fossil fuels, as it can function as both a carrier and converter of energy. However, in order to harness its full potential to decarbonise energy systems, the challenge of securing sufficient supply must be overcome by developing global and local energy infrastructure – quickly, with commercially-viable technologies.
The development of renewable energy sources, and the switch to a low-carbon energy carrier, is aimed at decarbonising the energy system across the heavy industry and mobility sectors. Integrating hydrogen into the energy system will allow for the deployment of renewable energy in power-to-X and gas-to-power settings, depending on hydrogen storage and distribution demand.
The role of compression
Compression is a key aspect in hydrogen applications, to facilitate the efficient movement of hydrogen across the value chain, from production to consumption. The compressor is the heart of the system; if it fails, production comes to a halt. As a global provider of mission-critical air and gas handling products, Howden has provided hydrogen compression technologies to refineries, chemical plants, and industrial premises for over 100 years.
To meet the challenges of energy demand and the ongoing energy transition, there is a need for further investment in hydrogen infrastructure. Scaling up is required to support the wider adoption of hydrogen, which would lend itself to the efficient decarbonisation of industries. Given hydrogen’s molecular structure and behaviour (it is explosive, highly volatile, and capable of altering mechanical properties of metals), further challenges present themselves on a larger scale and in new applications. The development of new hydrogen value chains – producing more and cleaner hydrogen, to be stored and distributed on demand to reach end users – is changing compression solutions’ circumstances, leading to different operating environments and specifications that will require investment.
Hydrogen can provide cost-effective and clean energy. In order to reduce the overall cost per unit of hydrogen, economies of scale are necessary throughout production, distribution, and end use segments. The accommodation of larger flows will enable increased production, while greater pressures will allow for higher energy density. What positions hydrogen as an ideal energy carrier is the fact that it has a very high energy content per unit of weight (approximately 33 kWh/kg). However, it has low energy content per unit of volume at atmospheric conditions (90 g/m³), meaning that compression is mandatory in order to meet various industrial applications’ process conditions. Compression solutions are key to getting more energy out of the same volume.
Howden’s compression technology, based on reciprocating pistons and diaphragm compressors, enables

large volumes of hydrogen and associated high pressures to obtain the required energy values, while managing pressure differences through the transfer and storage of hydrogen to prevent pressure build-up and leakages, and delivering the highest gas purity when required. Developments in materials, lubricants, seal and valve design – together with computer-aided analysis and design – have resulted in proven marginal improvements in efficiency, reliability, and extended mean time between maintenance (MTBM).
For efficient and reliable operations, it is imperative that the correct compressor technology is selected, based upon the following: � Volumetric flow. � Increased pressure. � Static pressure range. � Temperature range. � Continuous or intermittent operation. � Flow and pressure regulation requirement.
When scaling up for hydrogen applications, flow and pressure regulation, as well as capacity control technology, are paramount. This is due to the fact that today’s process requirements often operate on shorter timescales, as customers are producing more on demand. Based on Howden’s proprietary calculation software, compressor module selection software packages, and knowledge of leading standards for certifications previously used in the petrochemical industry, a customised solution can safely address the known low volumetric density energy of hydrogen, while benefitting from its gravimetric density energy.
Howden designs and manufactures compression solutions as individually-engineered packages to meet the specific demands of unique applications and requirements.
The compression matter requires early engagement to integrate seamlessly into the hydrogen value chain that it serves. Howden’s consultation services ensure that equipment design, mitigation, and administrative systems supporting the required process meet the proposed compression solution, with minimum CAPEX and OPEX, and maximum safety, performance and availability. As the hydrogen value chains are building and gaining in maturity, Howden will systematically and consistently address every stage of the compressor’s life cycle – from concept design to future maintenance and monitoring considerations.
Reliability, safety and continuous performance are vital requirements for hydrogen compressors. However, it is equally important to understand how to operate equipment efficiently. Insight software, coupled with an increase in remote operation/control and reduced experience onsite, has introduced an opportunity to integrate machine learning and Internet of Things (IoT).
In partnership with Microsoft, Howden has developed Howden Uptime with PTC – a digital platform that monitors rotating equipment performance and provides actionable insight with regards to operations. It can increase the life of assets by providing data to create a more predictive maintenance strategy and real-time communication options for customer support. Compressor performance is optimised using digital twin technology to avoid unplanned downtime, with expert advice close at hand.
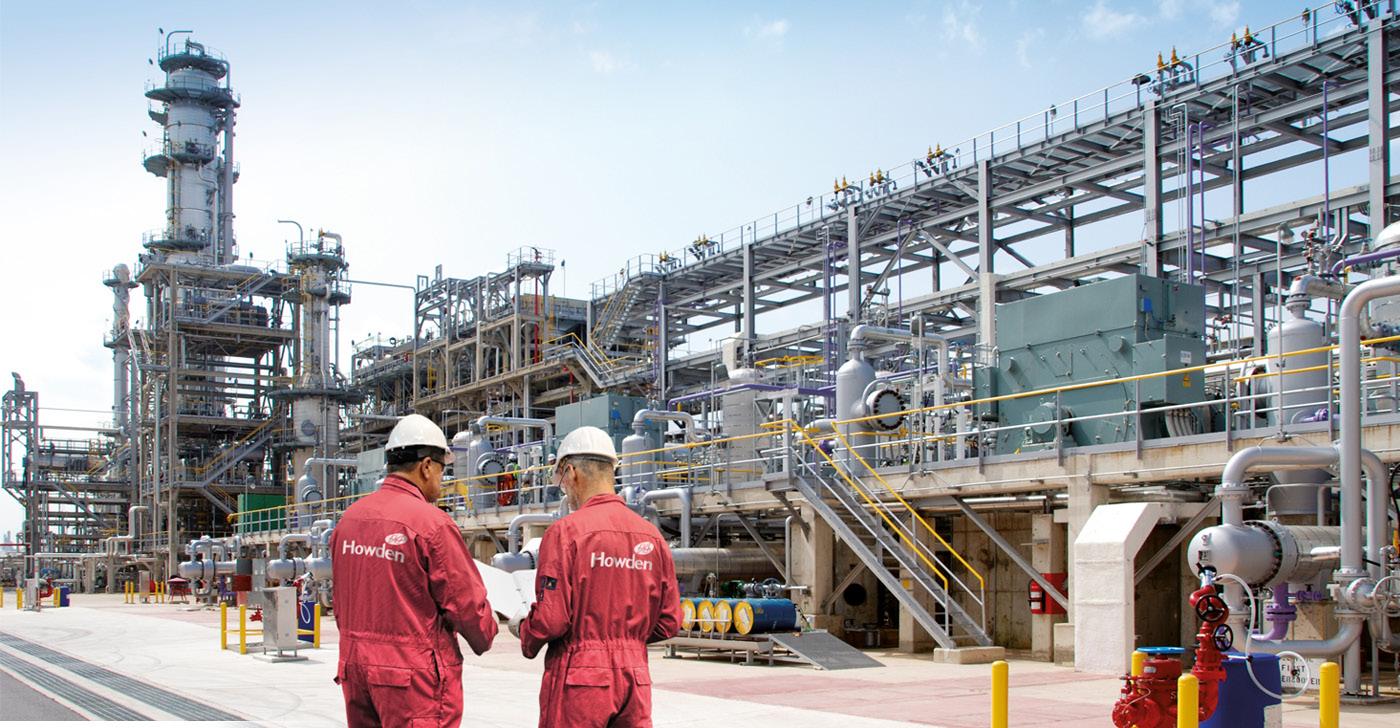
Figure 1. Howden’s reciprocating compressors in a refinery, providing support to a hydrogen process.
Figure 2. A containerised Howden diaphragm compressor for a renewable power-to-X application.
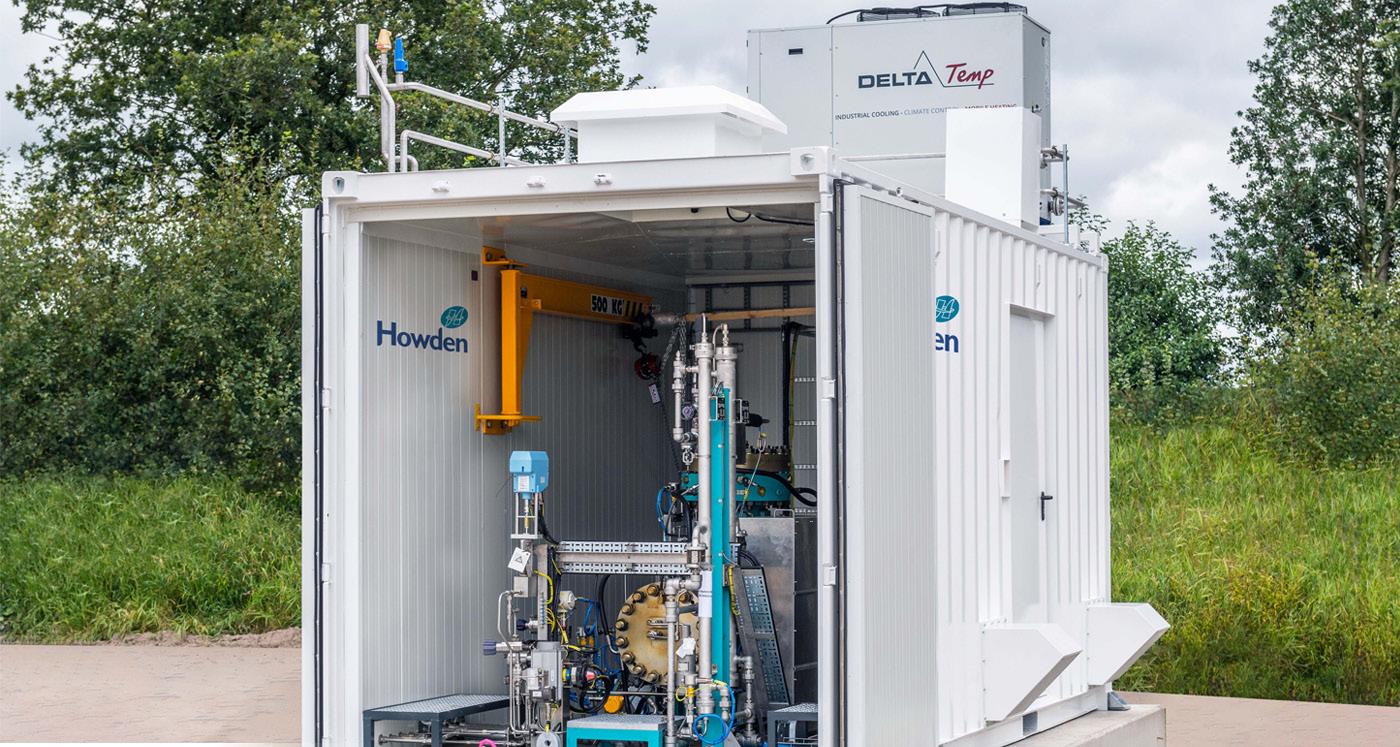

Figure 3. The Howden team working on a compressor.
Case studies
Chile
An e-fuel project in Chile uses the green hydrogen produced from wind farms, as well as carbon captured directly from the air, to produce e-methanol. Howden supplied technology, equipment and advisory services to the project to deliver approximately 900 000 l/yr of e-methanol in 2022, with future full-scale production units forecast to be ready by 2026. These will have the capacity to deliver 550 million l/yr of e-fuels.
Sweden
At a fossil-free steel plant in Svartöberget, Sweden, Howden provided a storage compression solution. This initiative led
Introducing the Palladian Energy Podcast
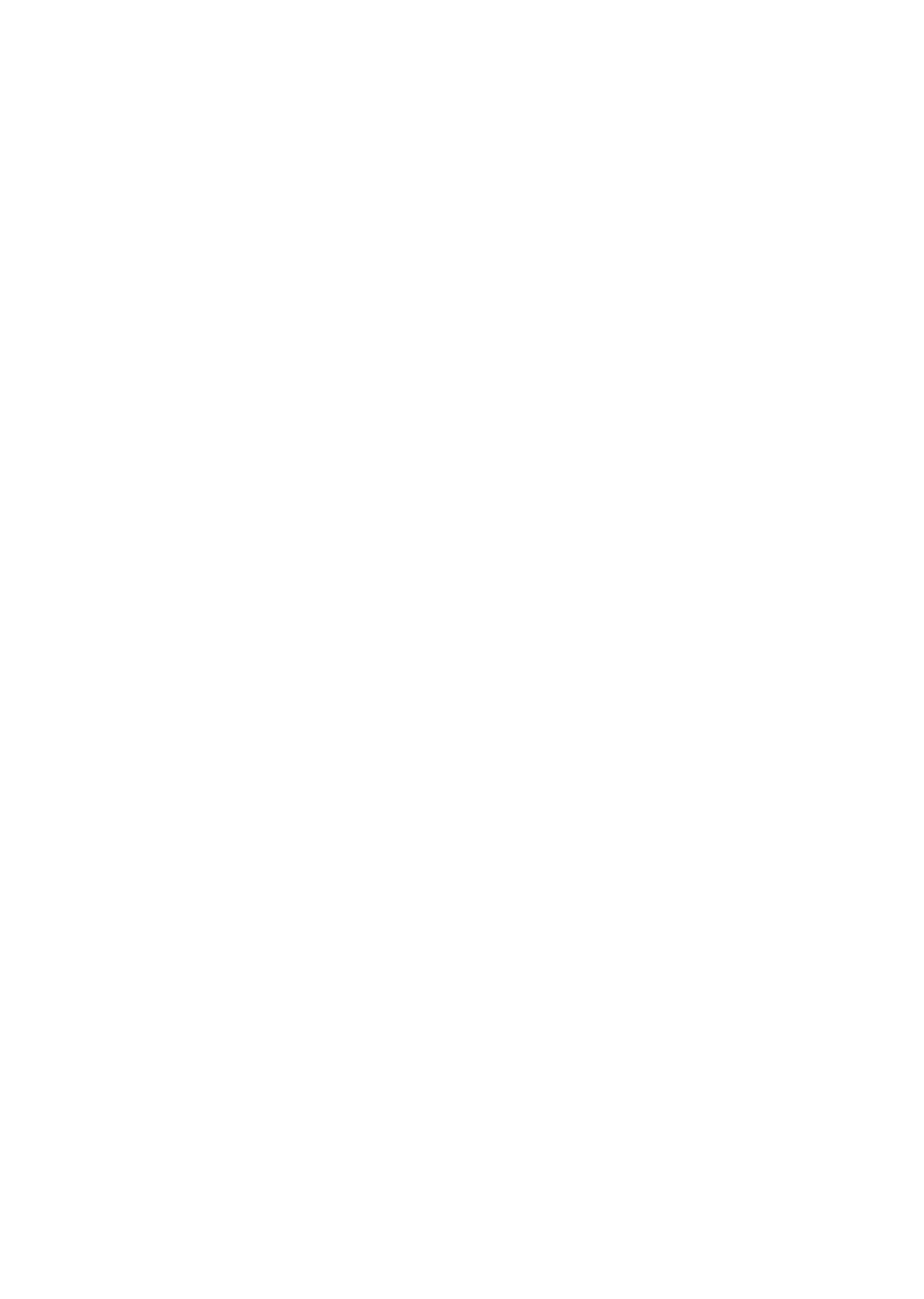
Series 1: Digitalisation in the oil and gas sector
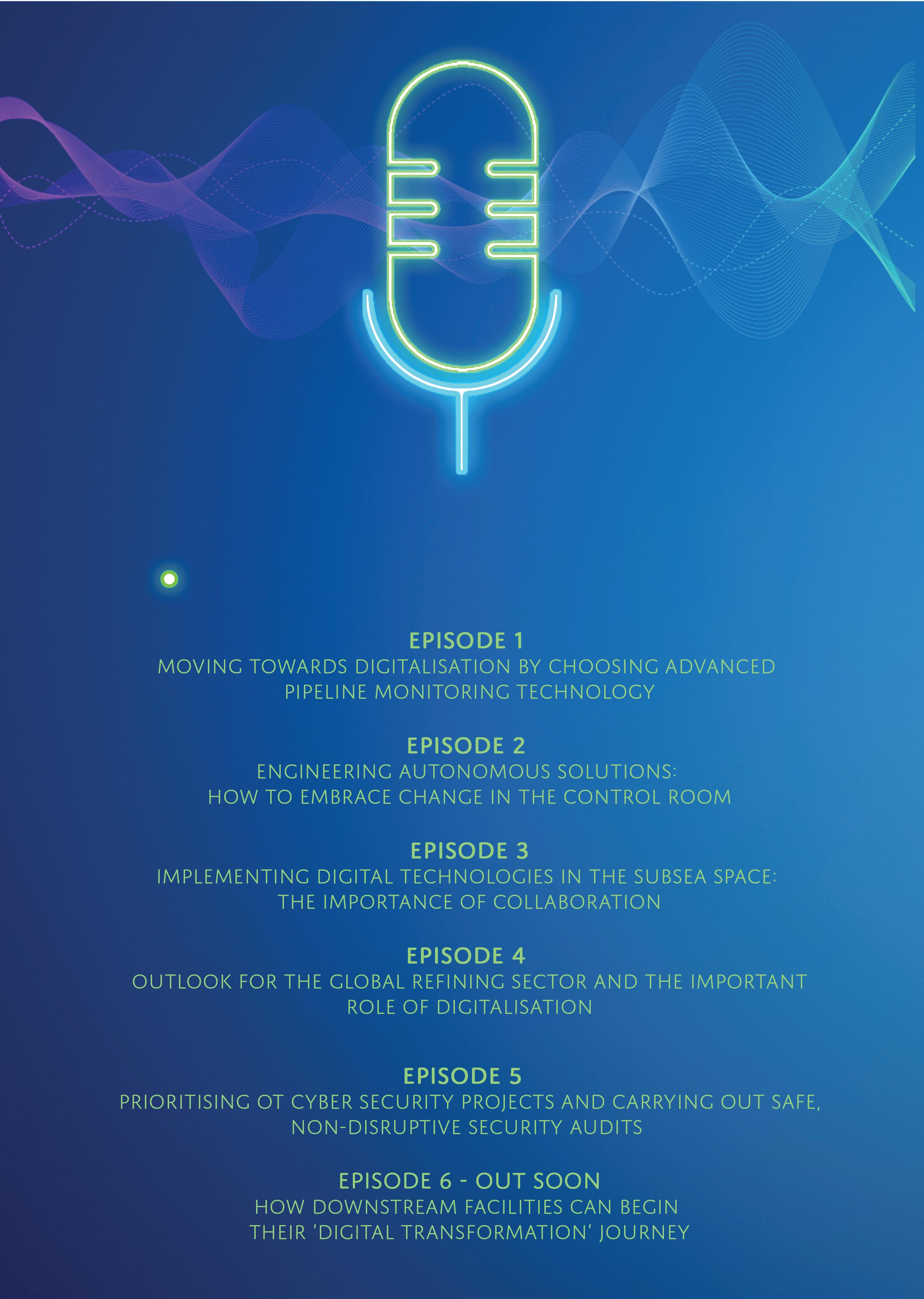
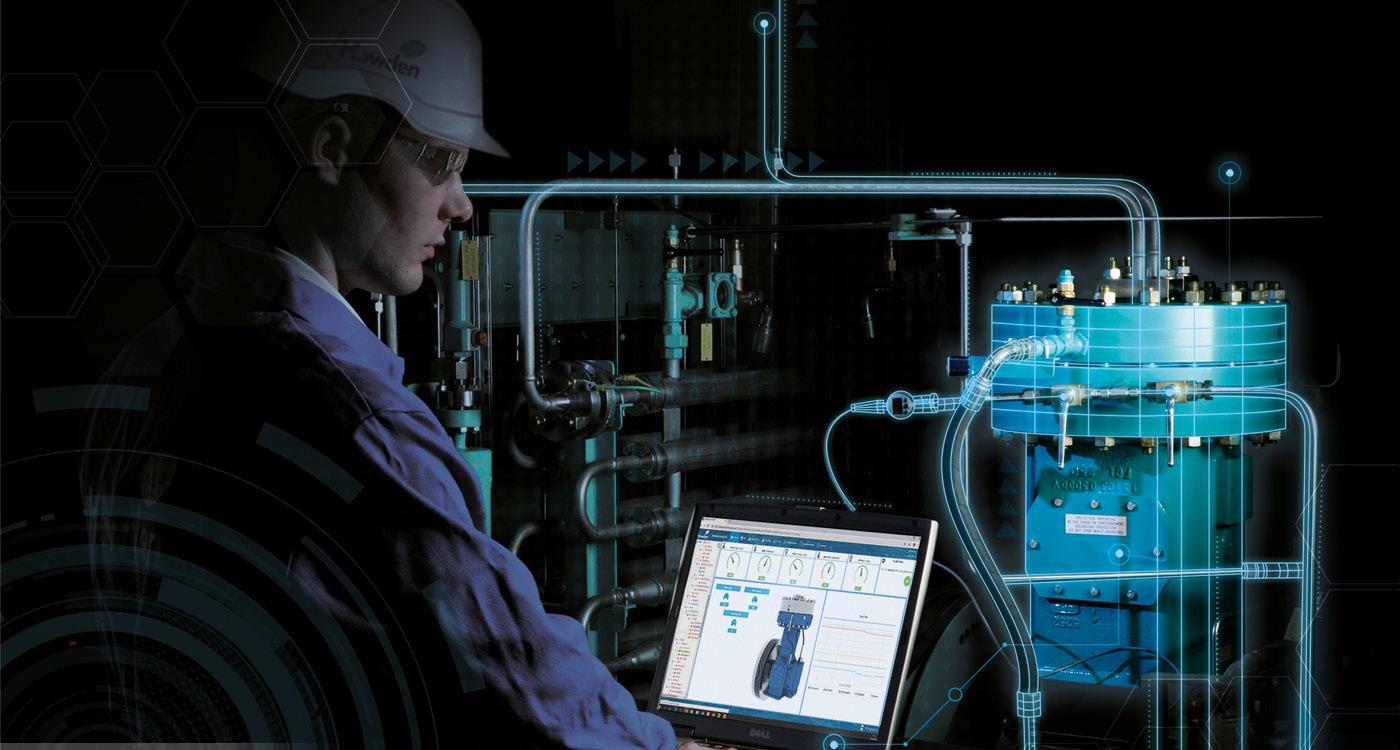
Figure 4. Howden Uptime – the data-driven advantage and digital twin.
Figure 5. Howden’s Thomassen Compression Systems, developed and built in the Netherlands.
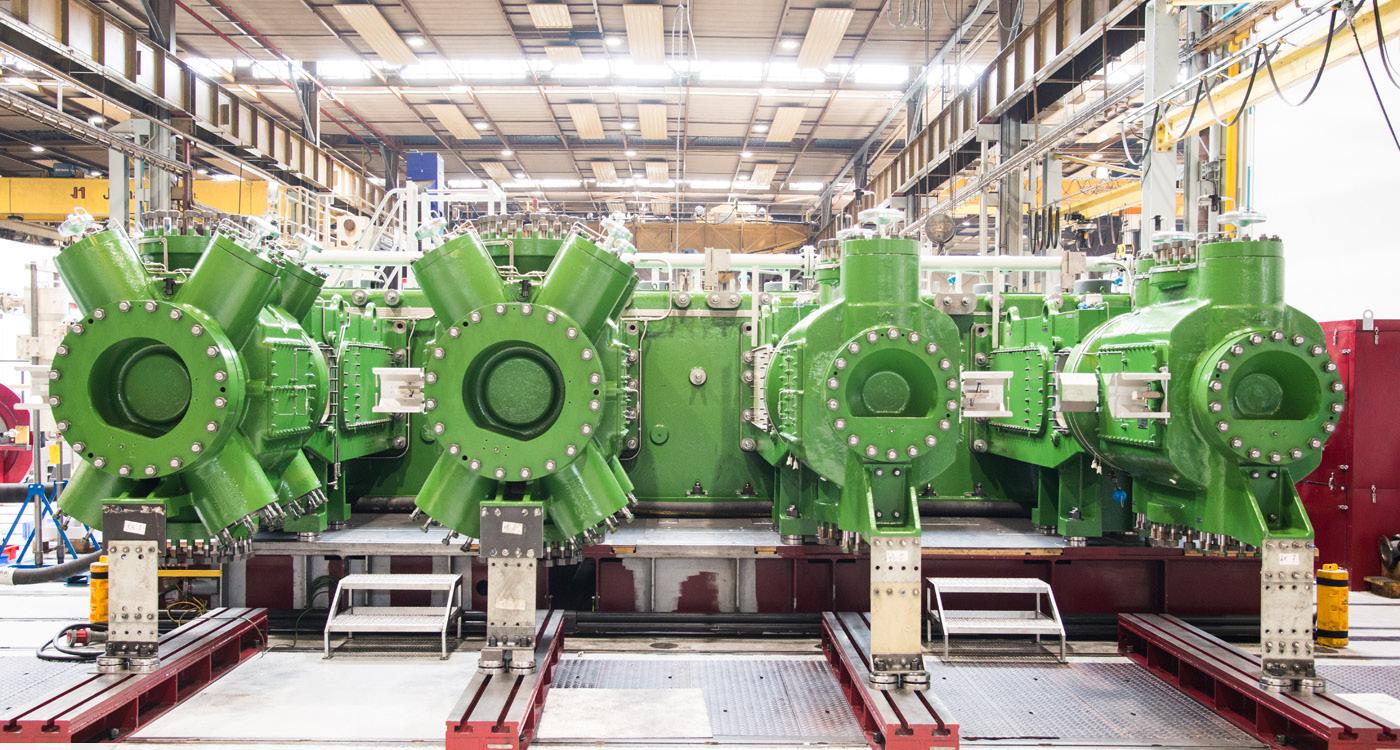
to the development of a fossil-free value chain for the iron and steel industry, in order to address renewable hydrogen storage.
Specifically, the company supplied a high-pressure diaphragm compression package to integrate the storage cycle of hydrogen production. This included installation and commissioning of a packaged, three-stage diaphragm compressor. The reliability, efficiency and safety delivered by this solution meets large-scale hydrogen storage requirements, relative to the storage conditions and the evaluation of the amount of time during which the compression pressure remains at the desired level. The facility consists of 100 m³ of hydrogen storage, built in an enclosed rock cavern approximately 30 m below ground. This offers a cost-effective solution to storing large amounts of energy in the form of hydrogen, at the required pressure. HYBRIT supports the EU’s Hydrogen Strategy and its ambition to install at least 6 GW of renewable hydrogen electrolysers across the EU by 2024, and at least 40 GW by 2030.
This project has the potential to reduce Sweden’s total carbon dioxide (CO2) emissions by at least 10%. The steel industry currently accounts for approximately 7% of the world’s global carbon emissions, and so the creation of a zero-emission steel may help to reduce emissions from iron and steel production worldwide in the long-term.
China
Howden supplied three hydrogen diaphragm compressor packages for use at Hypower’s Daxing hydrogen refuelling station in Beijing, China. The project has the capacity to produce 4.8 tpd of hydrogen, and refuel up to 600 hydrogen fuel cell vehicles, including large vehicles such as trucks and buses. The Daxing hydrogen refuelling station is part of the 200 000 m2 Beijing International Hydrogen Energy Demonstration Zone.
France
As the move from large, centralised operations, to smaller-scale, decentralised applications has emerged, regional infrastructure is being developed in tandem – such as in Etrez, France, and in Wunsiedel, Germany – so that hydrogen production and supply can be closer, based on the possibility of local renewable energy generation to feed local industries and transport, as needed. The commercial viability of projects is at stake, and as hydrogen remains delicate to transport, the development of ecosystems (where possible) appears to be a good alternative. Here, there is demand for specific compression solutions.
As an illustration, the green hydrogen infrastructure in Etrez is a project that aims to demonstrate the feasibility of underground hydrogen storage to support the development of the hydrogen economy in Europe and ultimately lower the economy’s carbon usage. Located north-west of Bourg-en-Bresse, the critical demonstration facility intends to assess the role of underground storage in the hydrogen value chain. It will also assess industrial-scale green hydrogen production and storage in salt caverns and the technical and economic reproducibility of the process to other sites throughout Europe.
As part of the development, Howden will supply a containerised, high-pressure diaphragm compressor, as well as a tube trailer filling station. The reliability, efficiency and safety delivered by Howden’s compression solution aligns with the large-scale hydrogen storage and distribution system requirements, and will also meet injection, extraction and storage conditions.
The facility is one of France’s leading natural gas storage sites in salt caverns in terms of capacity. It will rely on local renewable energy (photovoltaic [PV], hydraulic) to produce 400 kg/d of green hydrogen – the equivalent of the consumption of 16 hydrogen buses. This is fully in line with the objective of lowering the economy’s carbon intensity. It also addresses the integration of underground storage into the hydrogen value chain.
Conclusion
Hydrogen can do so much, across many applications, and is currently emerging as an undeniable key player in our energy mix. Similarly, national ESG commitments favour an industry shift towards an environmentally and economically sustainable energy source such as hydrogen. As individuals become aware of the environmental impact of economic activity on their surroundings, hydrogen has the opportunity to take on a major role in leading the fight against climate change. Fundamental understandings in the field of climate change, combined with Howden’s compression solutions with digital twin and augmented reality (Vuforia) technologies, will contribute to the emergence of a new energy production and distribution model supported by policies and investments.