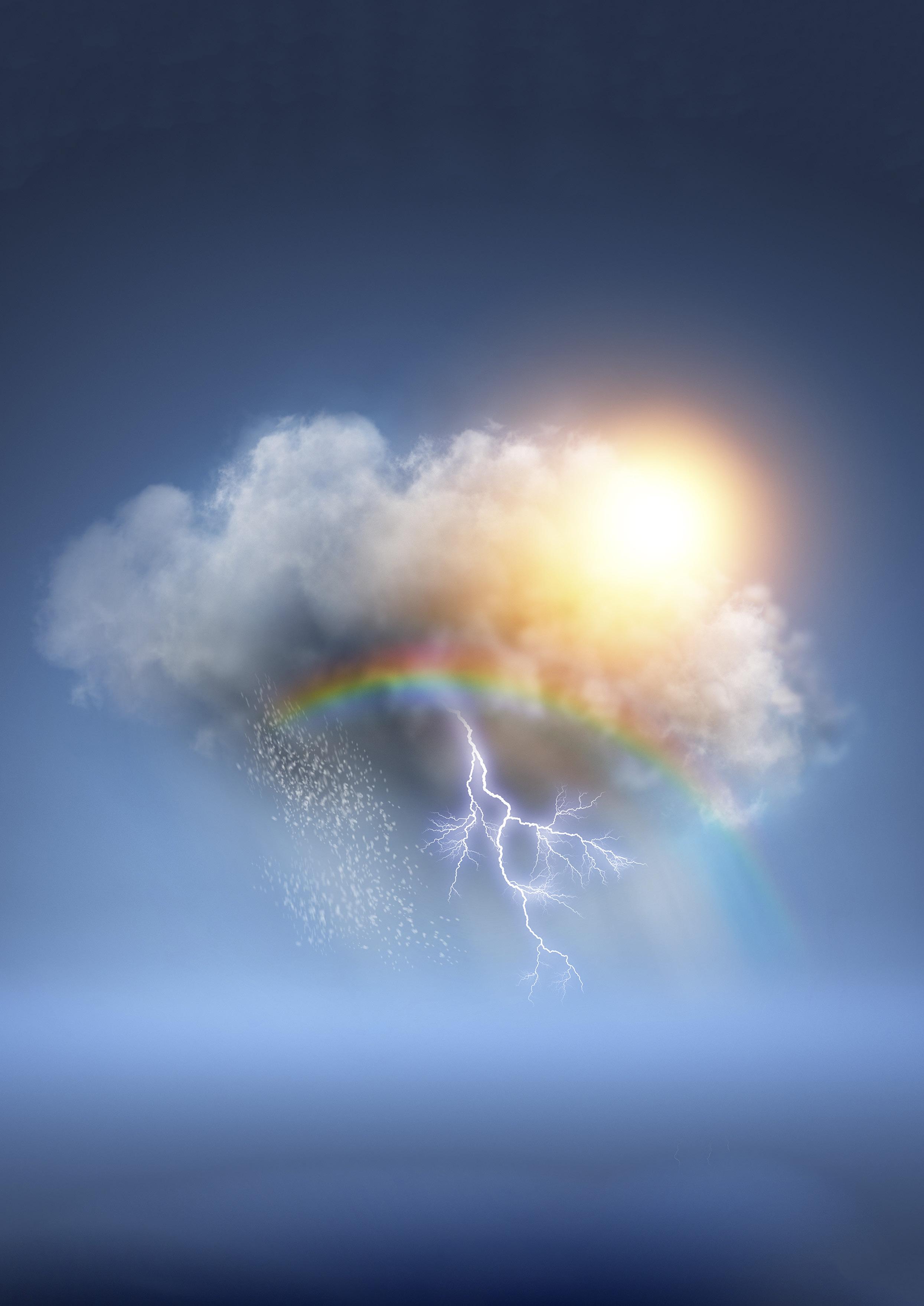
10 minute read
All-weather filtration
Eric M. Rud, Eaton, USA, explains why reliable lube oil filtration is an important consideration in the production of hydrogen at very low temperatures, and details a project that the company completed under sub-zero conditions.
Hydrogen is fundamental to a global sustainable economy, as it is an environmentally-friendly, mobile energy source that can be stored, and is carbon neutral when used in manufacturing.
When utilised as a fuel, its only combustion product is water.
Beyond vehicles, many energy-intensive industries such as steelmaking can benefit from a combustion process that is free of carbon-containing pollutants.
Hydrogen also plays an important role in fertilizer production for farming. In the Haber-Bosch process, hydrogen and nitrogen form ammonia, which is the basis for a number of different fertilizers. Increasingly, hydrogen production is carried out at large-scale across the world to support the growing demand for fuel cells, transportation fuels, and a ready supply of gas that is critical to petroleum refining, food processing, metal treatment, and other industrial processes.
In the production of hydrogen, all system components must perform at maximum capacity, especially under extreme weather conditions. Hydrogen is produced worldwide, including in regions where exceptionally cold winters are a challenge for the industry. One of these cold regions is also home to some of the largest fertilizer manufacturers in the world, and has seen numerous production facilities being built in recent years, including one in an area where the winter season tends to be harsh and long.
The compressors at this new hydrogen plant were used at temperatures ranging from as low as -58˚F (-50˚C). This presented challenges for the filtration of the lube oil in the machinery, which is subject to a high degree of wear and tear. A team of Eaton filtration experts accepted the challenge of helping to place the plant into initial service on time.

Figure 1. Increasingly low temperatures can present challenges for the filtration of lube oil in machinery.
Figure 2. The duplex configuration of the ASME-certified stainless steel pressure filter can be used for continuous operation. If a filter element is subject to maintenance, or the element must be replaced, the operator can redirect the flow through the filter from one side to the other.
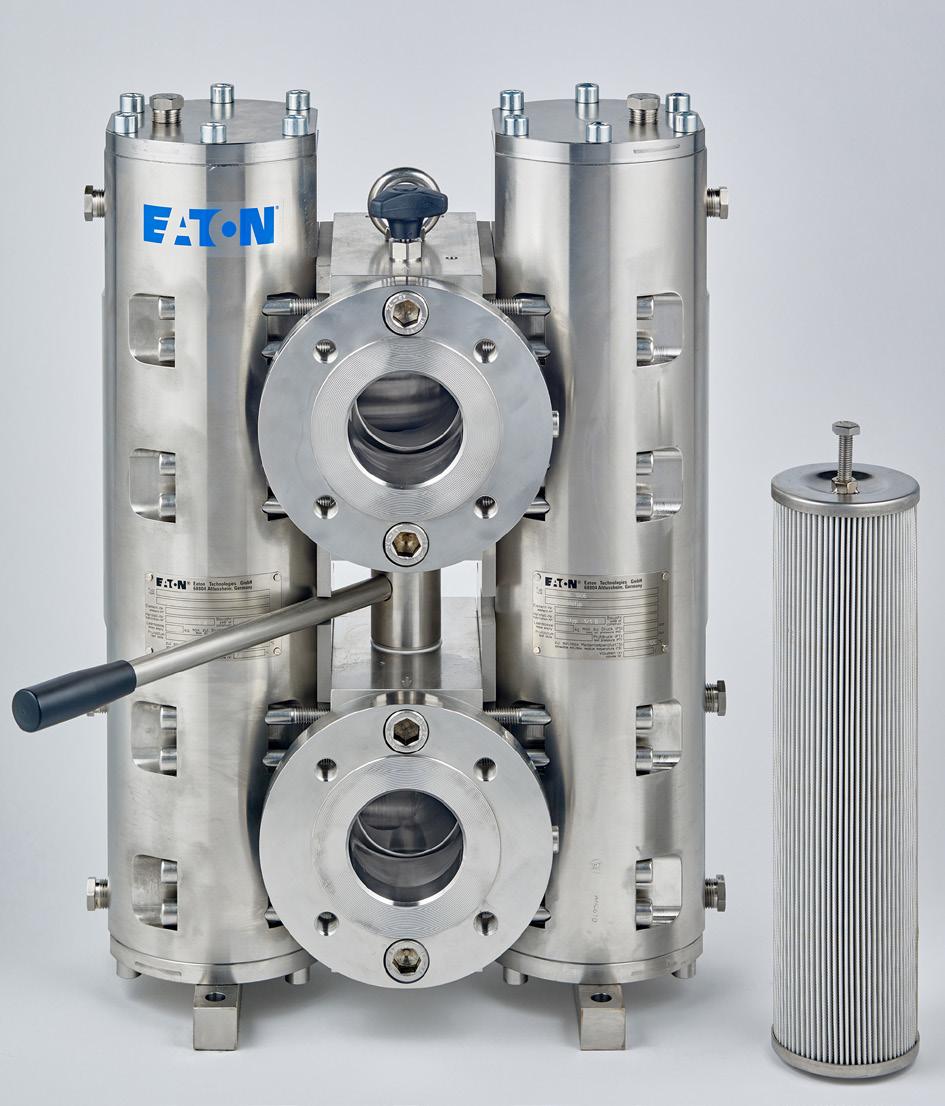
Case study
Recently, an Eaton distributor engaged this new plant in discussions centred around reliable filtering of lube oil at sub-zero ambient temperatures. Understanding the steep challenges ahead, this distributor was seeking a solution that would help the fertilizer manufacturer to achieve its goals.
The challenge
To ensure that hydrogen production would be safe and reliable even at the local temperatures, all components of the fertilizer plant were designed for such conditions. Notably, the facility’s compressors needed to meet a special challenge: the plant had to manage the staged compression of hydrogen and other gases in production, at pressures of as high as 5075 psi (350 bar). Uncompromising reliability is vital under these conditions, as the entire production chain would quickly come to a halt if a compressor were to fail. When the facility was planned, a decision was made to use a manufacturer with experience in building large-scale piston compressors, using engines delivering up to 1000 kW, as is required to produce hydrogen.
However, these higher requirements not only affect the machine as a whole, but also affect each individual component and all consumables. The lube oil is especially important. It must perform as intended, thereby mitigating the risk of compressor failure as much as possible. As in other critical industries, hydrogen producers rely on both high-quality oils and filters to effectively remove dirt particles.
The solution
After careful evaluation, the Eaton team recommended a stainless steel duplex configuration filter solution for the fertilizer plant. Offering excellent filtration capacity and high intrinsic stability, this ASME-designed filter could be used in continuous operation in the plant, in compliance with the API STD 614 standard (lubrication, shaft-sealing, and oil-control systems and auxiliaries), thus providing durable protection for hydrogen production system components.
The selected filter works as a pressure changeover solution in numerous compressors, turbines, and large pumps that all function similarly. The medium enters the filter housing and is filtered by the filter element in one of two filter compartments. A pressure gauge displays the status of the filter element inside the active filter compartment. If the element is especially dirty, or even blocked, the centre-mounted changeover ball valve permits the redirection of the flow to the second filter compartment. The contaminated filter element can then be flushed or replaced without interrupting the filtration process.
Making the filter suitable for use at frigid temperatures, however, was no simple task. Eaton’s engineers checked the filter, component by component, testing and
modifying it to meet the plant designer’s requirements. A decision was made to use size 633 (29 in. [738 mm] long x 7.9 in. [200 mm] wide x 25.7 in. [652 mm] high) as the basis to reliably filter the required flow volume, as well as two NL filter elements made of glass fibre, with a 10 �m filter unit.
Due to the specific challenges of the environment, these modifications were necessary to ensure that all components of the duplex filter solution were suitable for extended use in sub-zero temperatures.
The gaskets of the filter presented a greater challenge. In addition to chemical stress placed upon elastomers by the lubrication medium, the seals are subject to vibration and mechanical stresses, as well as low ambient temperatures.
While a wide variety of materials are suitable for this type of gasket, only a few are fundamentally compatible with sub-zero conditions. As a result, finding the right combination of temperature and chemical durability was difficult, especially as the fertilizer producer insisted upon a safety buffer being designed into its facility. Ensuring that the selected filter would withstand temperatures of as low as -58˚F was paramount.
The Eaton team drew on the company’s years of partnership with leading gasket manufacturers to solve the problem. While the frigid temperatures proved challenging even for these experienced suppliers, discussions soon uncovered a low-temperature gasket material that would stand up to the harsh conditions of the job.
Eaton provided a non-functioning filter prototype to the compressor manufacturer that was built to exact dimensional details. This allowed the manufacturer to install the compressor in the facility during the summer months by using the prototype, and to finish welding all of the pipelines while Eaton’s engineers were completing design adaptations to the functional filter. This helped to significantly reduce the time needed to build the facility.
The result
Less than two months passed between the engineering request and the plant starting initial operations. The fertilizer producer received an effective filtration solution in a short time that not only met its specifications and all necessary ASME requirements, but also used components that can reliably withstand sub-zero temperatures. The hydrogen plant, with its complex production process, now benefits from continuous, uninterrupted filtration using an inline-mounted duplex filter that allows for simple and quick maintenance and is designed for long service life. The construction of the plant was significantly accelerated by providing a prototype filter during the building phase, as work was able to continue while the production filter completed laboratory testing and validation.
Trial operation soon demonstrated that the compressors were capable of operating at an optimum level of lubrication. The filtration of the lube oil using the adapted filter works as smoothly as planned, and the plant has remained in routine operation while supplying hydrogen – a basic element for fertilizers that contribute to global food supplies – on a daily basis.
Global Hydrogen Review Online
The home for the latest hydrogen news, analysis and events

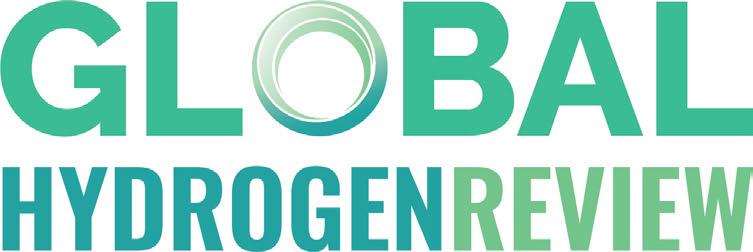
Wood to engineer Total Eren’s large-scale green hydrogen project
Wood will provide conceptual engineering for Total Eren’s H2 Magallanes Project, a large-scale green hydrogen production facility to be located in the commune of San Gregorio, in the Magallanes region, Southern Chile.
Wood’s scope covers the development of a complete off-grid integrated energy complex to produce ammonia from green hydrogen – avoiding up to 5 million tpy of CO2. The engineering package will include up to 10 GW of installed wind capacity, coupled with up to 8 GW of electrolysis capacity, a desalination plant, an ammonia plant, power transmission and back-up, and port facilities to transport the green ammonia to national and international markets.
Wood’s studies will provide ground for Total Eren and the UMAG to deliver precise environmental impact assessments and risk analysis surrounding the H2 Magallanes Project, in accordance with the high environmental and social standards defined by the Chilean authorities.
Gasunie and Vopak have entered into a cooperation agreement. The aim is to jointly develop future terminal infrastructure projects that will facilitate the necessary imports of hydrogen into Northwest Europe via Dutch and German ports. Both parties have been working together on the Gate LNG terminal in the Port of Rotterdam, the Netherlands, which came into operation in 2011.
The cooperation agreement includes import projects for hydrogen through green ammonia, liquid organic hydrogen carriers, and liquid hydrogen technologies.
Vopak and Gasunie will focus on developing import infrastructure related to storage that enables further distribution of hydrogen to end users (e.g. by means of pipeline, vessels, road and rail) and contributes to the security of supply in Northwest Europe.
In April 2022, Gasunie, Vopak and HES International announced that they have joined forces to develop an import terminal for a hydrogen carrier in the port of Rotterdam, named ACE Terminal. Green Hydrogen Systems has signed a supply agreement with Logan Energy to deliver electrolysis equipment for a project in Scotland.
The order includes the supply of two GHS HyProvide® A90 electrolysers with a combined capacity of 0.9 MW. The electrolysers will be deployed in a 40 ft container as a complete green hydrogen plant used in the ARBIKIE Distillery in Scotland. Green Hydrogen Systems will be responsible for delivering the electrolyser units, and will assist the project with onsite maintenance and remote monitoring and support, as part of a three-year service agreement.
The project will comprise a 1 MW wind turbine on the distillery’s farmland, which will export the electricity generated to Green Hydrogen Systems’ electrolysis plant. When fully operational during 4Q22, the electrolysers will have the capacity to provide up to 389 kg/d of green hydrogen.
Gasunie and Vopak develop future open access hydrogen import terminal infrastructure Green Hydrogen Systems receives electrolyser order from Logan Energy
Alberta government to invest in the region’s hydrogen sector
The Alberta government will invest US$50 million to create a Clean Hydrogen Centre of Excellence, which will drive innovation in the production, deployment and use of hydrogen across the economy. The centre is a pillar in Alberta’s Hydrogen Roadmap, which lays out the path to growing the provincial hydrogen economy and accessing global markets.
Alberta is already the largest hydrogen producer in Canada. Hydrogen is expected to be a US$2.5 – 11 trillion industry worldwide by 2050 and Alberta is ready to emerge as a leader in that global market.
The centre of excellence will support research, development and demonstration that will help companies and entrepreneurs that are building hydrogen technologies. It will bring together industry, researchers and small businesses from across the province to take technology that is in the early stages of development and prepare it for the move into the global marketplace.
Peak oil may be three years away, reports McKinsey & Co.
The energy transition continues to gain steam, with oil demand projected to peak in this decade, perhaps as soon as 2025, according to new research by McKinsey & Co.
This year’s ‘Global Energy Perspective’ launched when global energy markets were facing an unprecedented array of uncertainties, including the conflict in Ukraine. Nonetheless, the long-term transition to low-carbon energy systems continues to see strong momentum and, in several respects, acceleration. Key findings of this year’s report include: the global energy mix is projected to shift towards low-carbon solutions, with a particularly strong role for power, hydrogen and synfuels; renewables are projected to grow 3x by 2050; hydrogen demand is expected to grow 4 – 6x by 2050, driven primarily by road transport, maritime, and aviation; and hydrogen and hydrogen-derived synfuels are expected to account for 10% of global energy consumption by 2050.
For the latest hydrogen news, click here and follow us on social media
@Hydrogen_Review @HydrogenReview Global Hydrogen Review
www.globalhydrogenreview.com
Page Number Advertiser
41 Atlas Copco Gas & Process 35 Burckhardt Compression 55 Calderys OFC & 31 Chart Industries 21 Elliott Group 07 Honeywell Process Solutions 17 Koch Engineered Solutions 61 Matrix Service Company 45 NEO Monitors 09 NEUMAN & ESSER 47, 65 & 71 Palladian Publications 18 Quadax Valves Inc. 02 ROSEN Group IFC Shell Catalysts & Technologies 23 Valmet 29 ValvTechnologies 15 Zwick Armaturen GmbH