
5 minute read
Q&A with
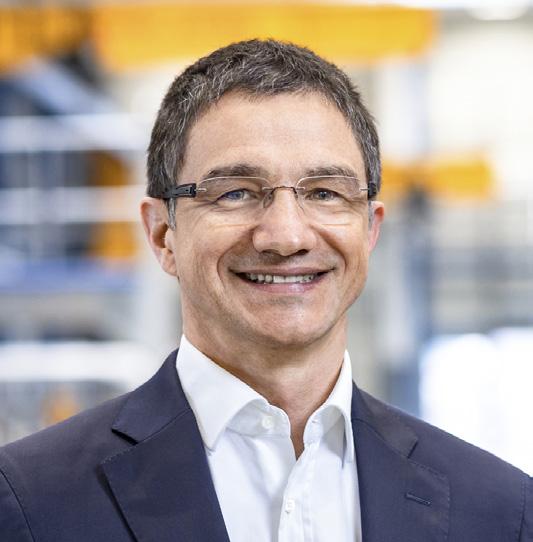
Fabrice Billard, CEO, Burckhardt Compression
Following a Master of Science at the Ecole Centrale in Paris, France, and a year in the Netherlands, Fabrice Billard started his career in 1994 with the Hay Group and the Boston Consulting Group (1999 – 2004). He then went on to join Sulzer, where he held various positions in Switzerland and Singapore at Sulzer Pumps Services, at Sulzer Chemtech as Head of the Mass Transfer Technology Business Unit, and as Chief Strategy Officer of the company. Fabrice joined Burckhardt Compression as President of the Systems Division in 2016, and has been CEO of the company since 1 April 2022.
Hydrogen offers huge potential for car and truck mobility nowadays. What prospects does it provide specifically, and what are the main persisting challenges and technological obstacles?
While hydrogen is indeed used in the industry, energy and transport sectors, mobility is the main application at present. Hydrogen-powered cars and dedicated gas stations have been available for several years now. While the technical feasibility of vehicles is irrefutably clear, we’re now faced with new challenges, including: � Cutting the cost per kg of hydrogen at the pump by a factor of approximately three, so that hydrogen as a product is as competitive as diesel or gasoline. � Increasing the reliability and durability of all gas station components, including the dispenser and compressor. � Changing the scale to make gas stations capable of delivering several tons of hydrogen daily in order to fuel a growing number of cars, not to mention the trucks that have only more recently become available on the market and offer a promising alternative to electric battery-powered trucks.
More specifically, the change in scale requires technological developments in the field of compressors: the challenge involves developing compressors with flow rates that are 10 times higher than current solutions, for pressures ranging from 500 to 900 bar. This is a huge task as the sensitivity of the vehicles’ fuel cells means the hydrogen must not be polluted with compressor lubricants. Two stand-out technological opportunities are currently being combined to remove this obstacle: � Using industrial piston compressors to enable this scaling up at a competitive cost and with greater reliability � Developing high-pressure, lubricant-free sealing systems by combining existing technologies and new materials.
How is Burckhardt Compression positioning itself in this context? What solutions are you providing to the various stakeholders to address these challenges?
We’ve been compressing hydrogen at several hundred bars in industrial applications for 50 years and in (lubricant-free) mobility applications for over 20 years. We’ve got all the technological building blocks and a range of products to support hydrogen development for mobility, as well as for industry, green ammonia production or energy. We are producing, assembling and testing our compressors on all the major hydrogen markets: Europe, China, the US and South Korea.
Beyond the compressors field, we’re leveraging our skills to design complete systems that take our customers’ constraints and parameters into account, allowing us to optimise overall project costs.
Compression is an important link in the hydrogen production chain. At what level can you intervene in this context?
There are many applications that require compression solutions upstream of gas stations. The hydrogen may come from a hydrogen production and liquefaction plant. High-capacity compressors are needed to liquefy this hydrogen. Hydrogen stored in liquid form generates evaporation gas that has to be recompressed constantly. While hydrogen is indeed produced by renewables and electrolysers, it also needs to be compressed for transport in pipelines or trucks. If hydrogen is to be transported over long
distances, it can also be compressed so it can be combined with nitrogen to make ammonia and transported by ship – an operation that also requires hydrogen compression on an industrial level.
To sum up, hydrogen is very versatile and needs to be compressed in most applications. And, at our level, we’re intervening in all these applications by leveraging our expertise and our specific products.
You’re also interested in producing green ammonia, which can be used as a fuel for ships. Could you tell us more about this prospect?
While this is still an emerging application, it’s one that has huge potential for development. Ammonia is an alternative to liquid hydrogen for long-distance transport. What makes ammonia advantageous is the fact that it has a much higher energy density than liquid hydrogen and can be transported in liquid form at less extreme temperatures. But it is a toxic product, so mature and controlled processes like those used in transporting LNG are vital.
In its production and use chain, green ammonia is produced from hydrogen from renewable energy sources, which is compressed to combine with nitrogen to form ammonia. Once liquid, ammonia generates evaporation gases that usually need to be recompressed. This ammonia can then be used in this state in ship engines that are under development, or it can be separated back into hydrogen and nitrogen following transport.
This will enable green hydrogen production in countries and regions with high renewable energy generating capacity, such as Australia, the Middle East or South America, and then transportation to consumption centres in Europe, the US, China, South Korea or Japan. Several avenues are being explored at present. But there will certainly still be a considerable need for industrial compressors.
What are your hydrogen goals? What main projects are you currently working on?
The fight against climate change has caused things to speed up on the market over the last 18 months. But there are many unanswered questions even today, such as: in what form will the hydrogen be transported (gas, liquid, ammonia, etc)?
Meanwhile, several parameters have to be taken into account, such as the cost, the availability of renewable energies, the existence of the transport infrastructure, the speed of cost cutting for each technology, etc. Some scenarios are more favourable than others for compressor manufacturers in this regard. We’re considering all cases and would like to provide our customers with the full range of compression solutions required for the development of the hydrogen industry.
With this in mind, we’re working on three main projects. In the field of ‘lubricant-free’ technology for higher and higher pressures and volumes, we’re developing a piston compressor that can supply a heavy-duty hydrogen station (for trucks). The first model has been launched with 550 bar of discharge pressure. This will be followed by a model for 900 bar.
We’re also working to increase the capacity of our lubricant-free compressors for hydrogen production and liquefaction plants.
Finally, as we’ve got decades of experience in evaporative gas treatment on vessels transporting LPG and LNG, we’re assessing technologies and products for liquid hydrogen and ammonia vessels.
At the same time, we’re still developing our plants and global supply chain to optimise the cost of these solutions and to help ensure that the hydrogen industry is an economic success. Our goal is to contribute to the sustainable development of the energy sector.

Figure 1. Burckhardt Compression solutions for hydrogen mobility and energy.