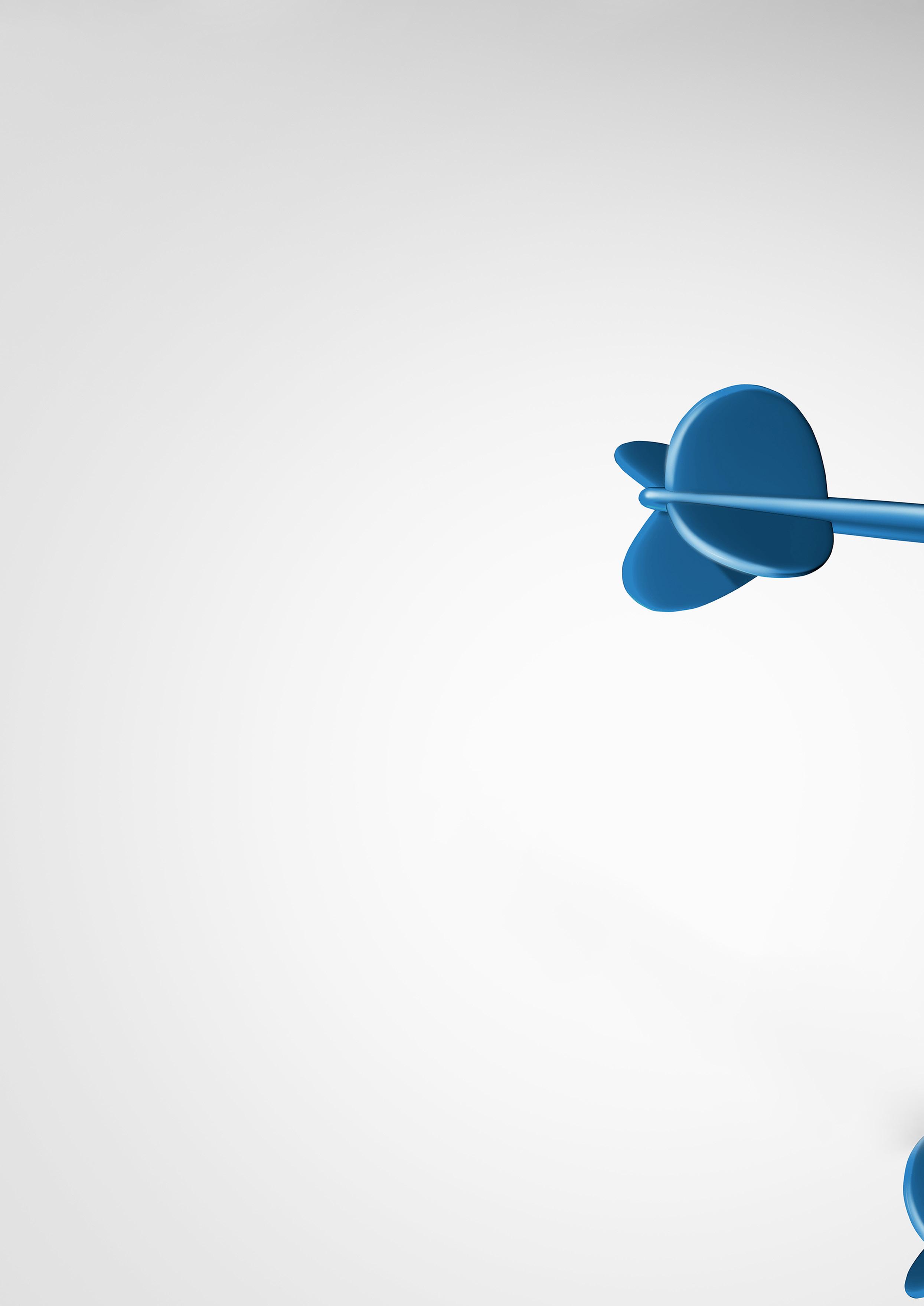
10 minute read
Perfecting pipelines
Ollie Burkinshaw, Neil Gallon and Jason Edwards,
ROSEN UK, address the challenge of integrity management of hydrogen pipelines.
Climate change is perhaps the biggest global challenge of the 21st century. If the world is to succeed in limiting global temperature increases to below 2˚C, all available solutions must be leveraged and accelerated.
Electricity and gas will continue to fulfil complementary roles in the future integrated energy system. Electrification of all industrial and residential energy demand is not feasible, and certain industries cannot be readily electrified. In terms of low-carbon energy supply, hydrogen is a logical means to address these issues, as it is easy to transport and store using a significant proportion of repurposed infrastructure. In the medium-term, it appears inevitable that blue hydrogen – whereby hydrogen is extracted from natural gas, and the carbon dioxide (CO2) is stored to prevent emissions (carbon capture and storage [CCS]) – will play a large role. Longer-term, green hydrogen predominantly generated via electrolysis using renewable energy sources is an effective solution for the storage and transportation of intermittent and excess power, providing flexibility and resilience in our energy supply.
Regardless of the colour of the hydrogen, pipelines will be required to transport it. This has been recognised globally with initiatives such as the European Hydrogen Backbone, a growing group of now 29 European gas infrastructure companies targeting a hydrogen transmission network of 39 700 km by 2040, with further growth expected after 2040.1 The capital cost of repurposing existing pipelines is expected to be between 10 – 25% of the cost of building new pipelines. For hydrogen pipeline infrastructure (either with 100% hydrogen or a blend of hydrogen and natural gas) to be economically feasible, a significant proportion of the existing global pipeline infrastructure (of which there are several million kilometres) must be leveraged to form the future hydrogen pipeline infrastructure. The European Hydrogen Backbone currently projects that approximately 70% of future hydrogen pipelines will be repurposed existing pipelines.
The challenge
While the concept of hydrogen pipelines is not new or inherently impossible – there are already thousands of kilometres of hydrogen pipelines in service – the introduction of hydrogen into existing natural gas transmission and distribution networks creates unique challenges. The challenges associated with converting existing pipelines can be summarised in two simple questions for pipeline operators: � Can my existing pipeline be safely converted to hydrogen service? � How can the integrity of a hydrogen pipeline be managed?
Apart from the general integrity challenges and threats to any pipeline, the integrity challenges and damage mechanisms specific to hydrogen transport can be split into two main areas. Hydrogen can cause cracking directly (hydrogen-induced cracking), though this is generally not likely from gaseous hydrogen exposure alone and would require high concentrations of hydrogen typically resulting from sour service conditions or cathodic over-protection. More relevant for gaseous hydrogen service, however, is the more insidious influence of hydrogen negatively affecting the material properties of steel line pipe. The most important mechanical properties of steel line pipe are strength (yield strength and ultimate tensile strength), ductility, fracture toughness, and resistance to fatigue cracking. The effect of hydrogen on these properties are summarised in Table 1.
The figures in Table 1, which are supported by literature and industry testing, show a wide range of hydrogen-related effects on the different material properties, with varying degrees of severity. Although this wide range is partially accounted for by the different test protocols, hydrogen concentrations, and temperatures used in the studies, it is also largely a function of the very significant variation in how different materials respond to the presence of hydrogen. Line pipe in existing pipeline infrastructure can be up to 100 years old, with the majority in the US and Europe having been installed between 30 – 50 years ago.
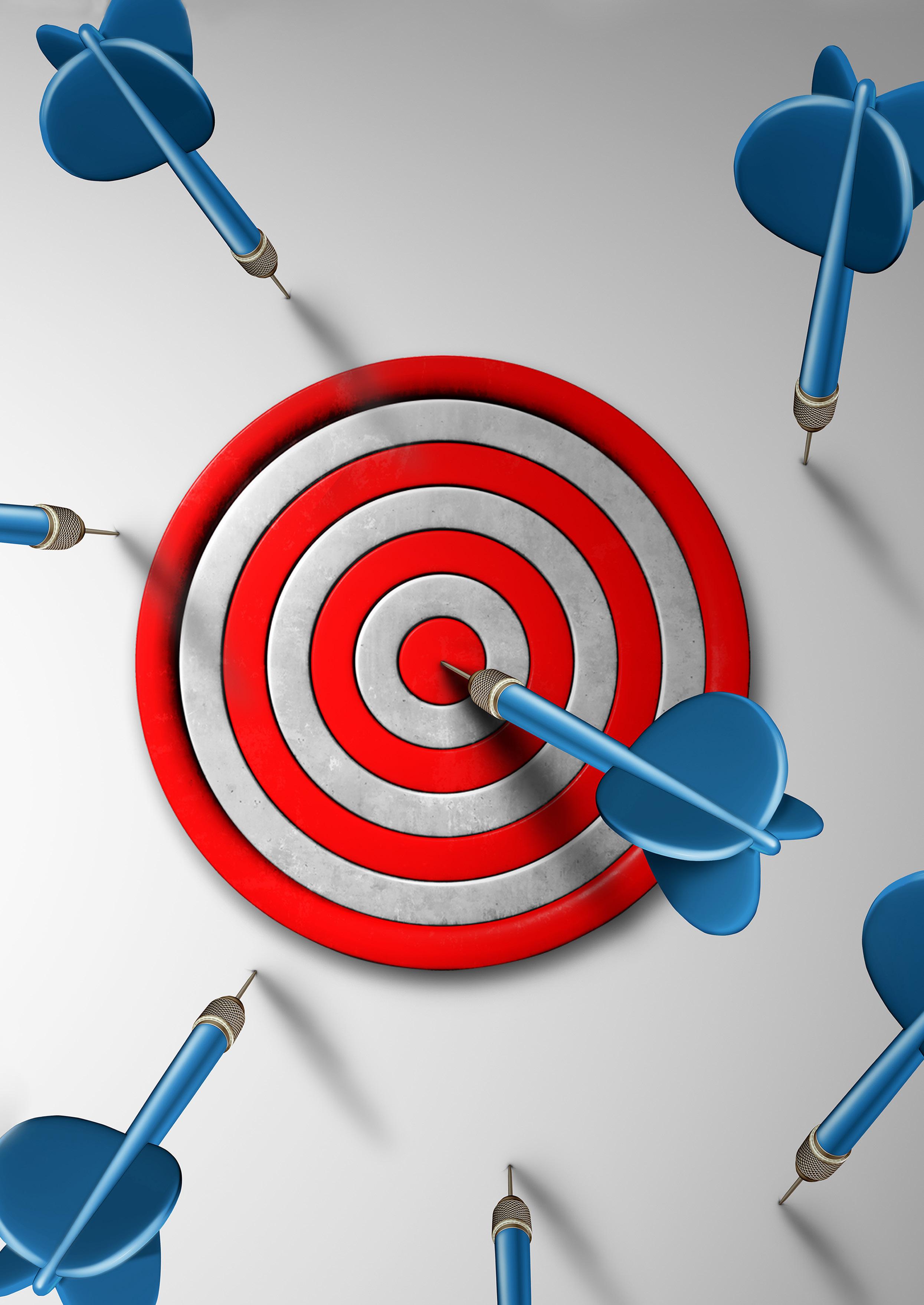
During this time, metallurgy, manufacturing and welding processes have changed and evolved dramatically. Existing pipelines therefore encompass a whole spectrum of different pipe grades, microstructures, chemical compositions and welding techniques, and these different materials are found to respond very differently when exposed to hydrogen.
The vast majority of existing hydrogen pipelines have been specifically designed, built or operated to hydrogen-specific codes and standards, which tend to be significantly more restrictive than their natural gas equivalents. Operating pressures and pipeline design are generally specified to ensure lower hoop stresses as a percentage of specified minimum yield strength (SMYS). Another key aspect of codes for purpose-built hydrogen pipelines is in the selection and specification of materials: grades are more tightly specified (in terms of allowable chemical composition and mechanical properties). In an attempt to limit susceptibility to hydrogen embrittlement effects, grades are also generally restricted to X52 (corresponding to an SMYS of 52 ksi [360 MPa]) or below. Additionally, qualification testing is conducted to ensure sufficient toughness to guarantee adequate flaw tolerance. For existing pipelines, grades of up to X80 (corresponding to an SMYS of 80 ksi [550 MPa]) are common.
Material considerations
When considering converting an existing pipeline to hydrogen service, it must be recognised that the materials present – in particular, older line pipe materials – may have not been specified or manufactured with any minimum toughness requirements at all, and toughness may be very low in the parent and weld materials. Introducing hydrogen to a pipeline for which there is uncertainty around the properties of the materials present leads to unquantified risks. Flaws that may have been stable for a long time when transporting natural gas may become critical when hydrogen is introduced, and without robust knowledge of the pipeline materials, the results could be highly unpredictable.
Understanding the different materials within a pipeline (both parent and weld), and their behaviour in hydrogen environments, is therefore incredibly important. Although some operators may have records of the original pipeline material, many do not, and a complete understanding of the pipeline history in terms of modifications, repairs and replacements might not be obtainable. Over time, confidence in historical records can easily be eroded as operating companies are bought and sold, key staff changes, processes evolve, and paper records are lost. This can result in significant uncertainty regarding how many different material types exist within the pipeline, as well as their locations.
Table 1. The effects of hydrogen on the mechanical properties of pipelines
Property Effect of hydrogen compared to natural gas Typical approximate range of effect from testing in literature
Strength Minimal effect < 5%
Ductility Significant decrease 20 – 80%
Fracture toughness Significant decrease 35 – 70%
Fatigue-crack growth rate Significant increase Up to 10x
The solution
To support pipeline operators in this process, ROSEN has developed a holistic Hydrogen Pipeline Integrity Framework (see Figure 1) based on an integrated asset management approach, recognising that every pipeline is unique and will have its own specific set of circumstances. This framework provides a structured but flexible roadmap for the safe and efficient conversion of existing pipelines to hydrogen, and for the reliable integrity management of hydrogen pipelines.
This integrity approach is founded on research of issues such as material susceptibility to hydrogen embrittlement and accelerated fatigue cracking, as well as both well-established and novel or emerging diagnostic technologies targeted at detecting and quantifying the associated threats.
The first stage of the integrity framework consists of understanding the potential threats. This aspect is fundamental. In essence, the potential threats can be divided into three main categories. The first is threats that exist regardless of the medium being transported, such as external corrosion or third-party
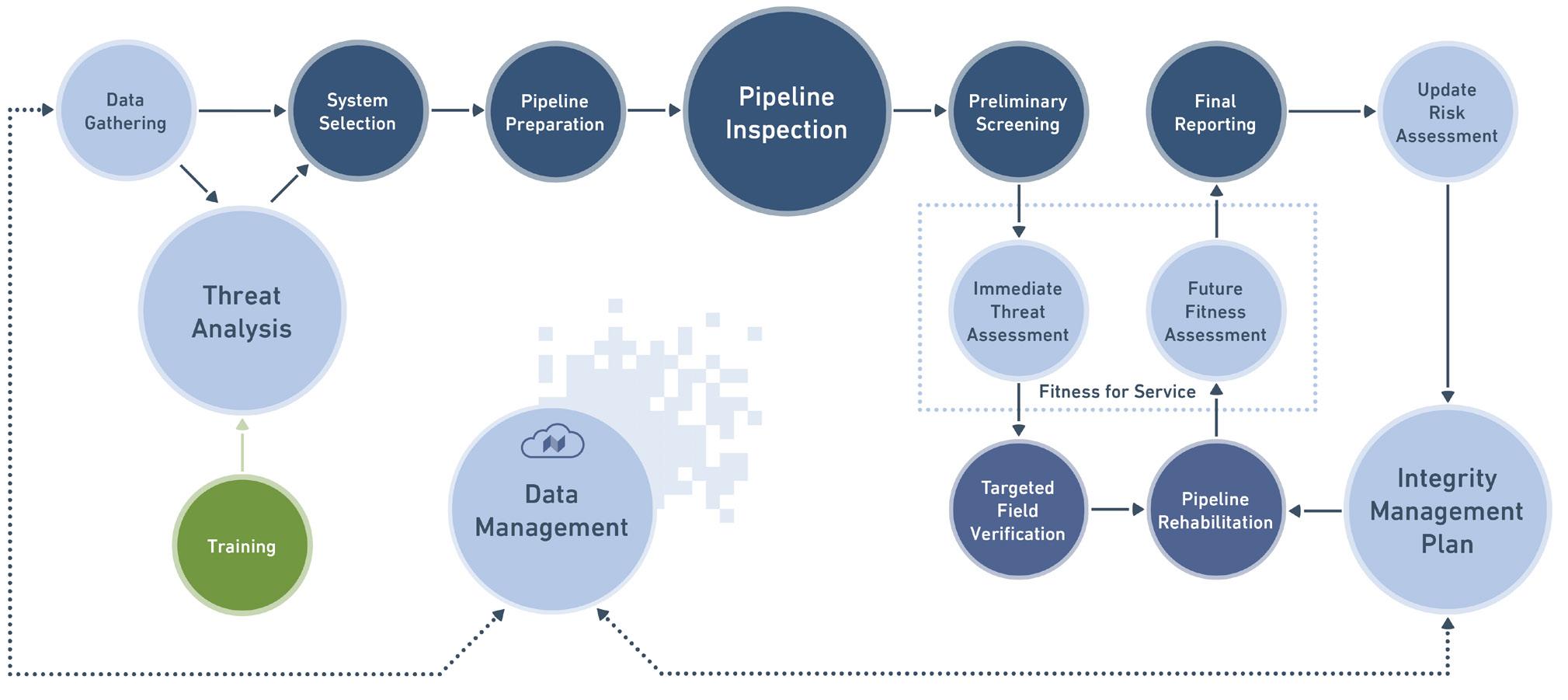
mechanical damage. The second is direct threats caused by hydrogen, such as cracking. The final threat is hydrogen-induced changes to pipeline material properties such as embrittlement and increased fatigue susceptibility. These threats should then be assessed against existing knowledge about the pipeline, current condition, operating and failure history, known presence or susceptibility to certain threats or feature types, environmental conditions, material properties, seam types, and welding procedures used during construction. An essential outcome of this assessment is the identification of any knowledge gaps that must be filled to enable accurate risk assessment and ongoing integrity management in the context of hydrogen service.
Data gaps can be filled using a combination of existing in-line inspection (ILI) tools, direct assessment, in-situ non-destructive testing, and destructive testing from coupons or cut outs. Of particular relevance for ILI services in the conversion process of existing natural gas pipelines to hydrogen are metal loss, deformation (such as dents and buckles), cracks and crack-like features, and material property determination.
ILI services for the detection of metal loss and deformation are well-established and mature services, though advances are still being made to improve their detection and sizing capabilities. Crack-detection technologies are well-established for liquids lines. More recently, however, electromagnetic acoustic transducer (EMAT) technology has been developed to allow for crack detection in gas lines without the need for a liquid couplant. The evolution of EMAT technology capability is therefore of prime importance for crack detection and thus for the facilitation of integrity management programmes for hydrogen service.
The identification of different pipe materials that are present, as well as their properties, has historically not been possible, aside for spot checks at above-ground locations or a small number of excavations. However, recent technologies have transformed the industry’s capability to identify and measure material properties in a way that is financially and operationally viable.
ROSEN’s material property inspection tools include a unique ILI service, RoMat PGS, that can reliably identify the different pipe materials present within a pipeline down to each individual pipe spool, and group them into ‘populations’ with shared material properties and attributes. This service is also able to report the strength, and therefore grade, of each pipe, enabling operators to directly identify grades, which are an essential factor in calculating maximum allowable operating pressure (MAOP) and derating factors specified in hydrogen pipeline design codes such as ASME B31.12. Another service in the RoMat family, RoMat DMG, is able to reliably detect and size hard spots, which may act as locations for stress concentrations, severe hydrogen embrittlement, and crack initiation. With ROSEN’s modular inspection technologies, hard spot, pipe grade, metal loss and deformation data sets can be captured in a single inspection, maximising efficiency for operators.
It is also important to note that synergistic benefits can be gained from running multiple inspection technologies, since the information can be overlaid (integrated) and analysed in combination to assist with improvements in probability of identification, feature classification, segmentation, and risk assessment. Depending on the existing knowledge and the current conditions of the pipeline, it may be essential to run a combination of diagnostic tools as a baseline inspection before and after conversion to hydrogen service – firstly, to ensure safe operation, and secondly, to facilitate efficient comparison of pipeline condition and feature sizing following the introduction of hydrogen.
Apart from the effects on line pipe that have been outlined above, hydrogen can also affect the performance and integrity of ILI tools. ROSEN has already made and used ILI tools that can operate in up to 100% hydrogen at 100 bar at ambient temperature, using specific designs for sealing, special materials for discs and cups, and hydrogen-proofed electronic components, alloys, and magnets. These tools have been proven in service, and successful inspections of hydrogen pipelines have already been performed.

Figure 2. While ROSEN’s PGS ILI tool measures the pipe grade strength of each pipe joint, the RoMat DMG identifies hard spots in the pipe steel.
Figure 3. ROSEN’s RoCD EMAT service detects cracking or crack-like features in gas pipelines and can be ideally applied to integrity management programmes for hydrogen pipelines.

Conclusion
Once the appropriate pipeline inspection runs have been identified and successfully performed, the gathered information can be analysed and assessed. These integrity assessments will support strategies for validation and remediation, and provide data for input into fitness-for-service and remaining life assessments. Finally, these results must be reflected in an updated risk assessment that serves as input for robust future integrity management plans and processes. A holistic and structured approach using ILI as the foundation is essential to supporting accurate risk assessments and paving the way for an economic and safe conversion and operation of existing assets to hydrogen service.
Reference
1. ‘European Hydrogen Backbone’, Gas for Climate, https://gasforclimate2050.eu/ehb/