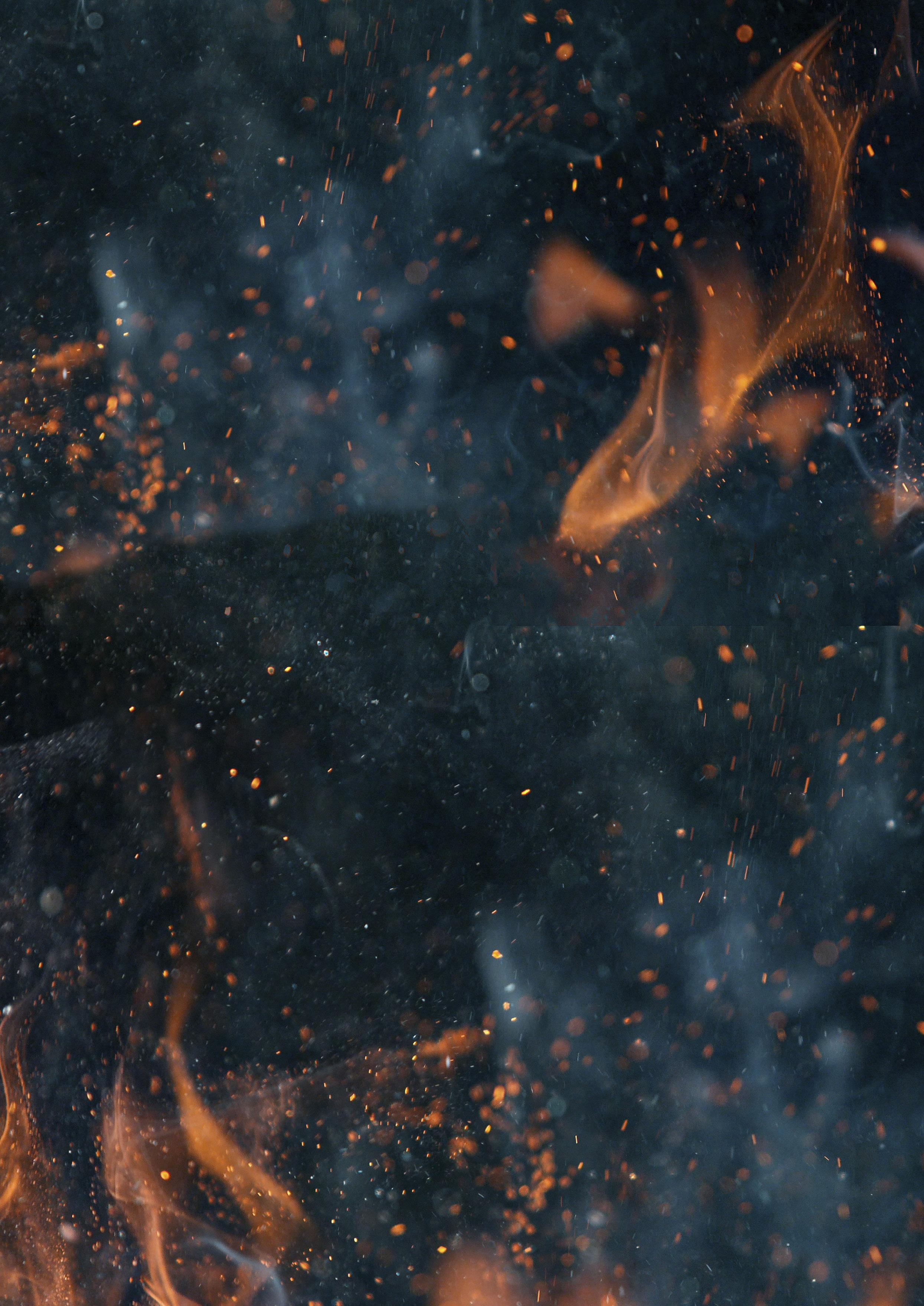
9 minute read
Creative combustion
Gilles Theis, Ali Gueniche, Christoph Strupp and Chuck Baukal, John Zink Hamworthy Combustion, A Koch Engineered Solutions Company, detail how radiant wall burner technology can combat the issues associated with introducing hydrogen fuels into combustion systems.
Hydrogen has the potential to be a very important fuel.1 Global demand for it is increasing rapidly,2 and interest in its use as a fuel continues to grow, mostly because it generates water when combusted, with little – if any – carbon dioxide (CO2), depending on how it is produced. Figure 1 shows that the more hydrogen that is present in a fuel, the less CO2 is produced.
In the past, using hydrogen as a fuel was only economical in certain applications. Reducing
CO2 emissions and concerns about fossil fuel depletion are two major recent drivers for considering fuels that contain a high percentage of hydrogen for more applications.³
The importance of hydrogen fuel depends on the way in which it is generated.⁴ Today, large-scale hydrogen production is carried out by steam methane reforming (SMR). SMR furnaces generate CO2 emissions. If those emissions are captured, this is referred to as blue hydrogen. Oil and gas producers are particularly well positioned to produce blue hydrogen, as natural gas is relatively low cost and because those producers have the infrastructure to produce hydrogen.5 If the CO2 is not captured, this then becomes
grey hydrogen. Hydrogen made with renewable energy, such as wind or solar energy powering an electrolysis process, is referred to as green hydrogen.
While there is increased interest in using hydrogen as a fuel, high levels of hydrogen have been used in certain applications, such as boilers and fired heaters, for many years. For example, the off gas from ethylene crackers using ethane as the feedstock is 70 – 85% hydrogen, which is used as fuel for the cracking furnaces.
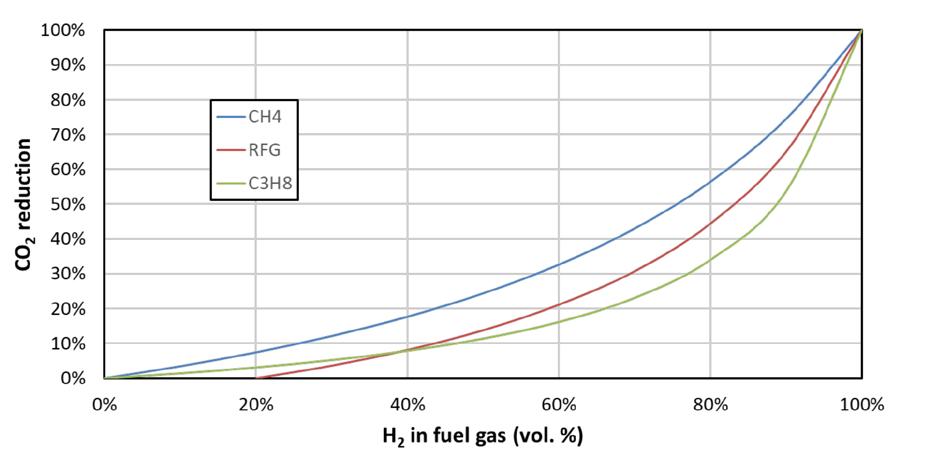
Figure 1. CO2 reduction with hydrogen added to various fuels (refinery fuel gas [RFG] = 20% hydrogen, 55% methane [CH4], 10% ethane, 10% propane, 5% butane). This assumes that no CO2 is produced whilst making the hydrogen.
Figure 2. Combustion air is required, and wet flue gases are produced, for blends of hydrogen in CH4 (15% excess air assumed).
Table 1. Properties of some common fuels
Property Hydrogen Methane Propane
Molecular weight 2 16 44 LHV (MJ/Nm³) 10.8 35.8 91.2 LHV (MJ/kg) 119.8 50 46.3
Adiabatic flame temperature* (˚C) 2048 1878 1904
Maximum flame speed (cm/sec.) 325 44.8 46.4
Flammability limit (vol% air) 4 – 74.2 5 – 15 2.1 – 9.5
* Based on 10% excess air; air temperature: 20˚C
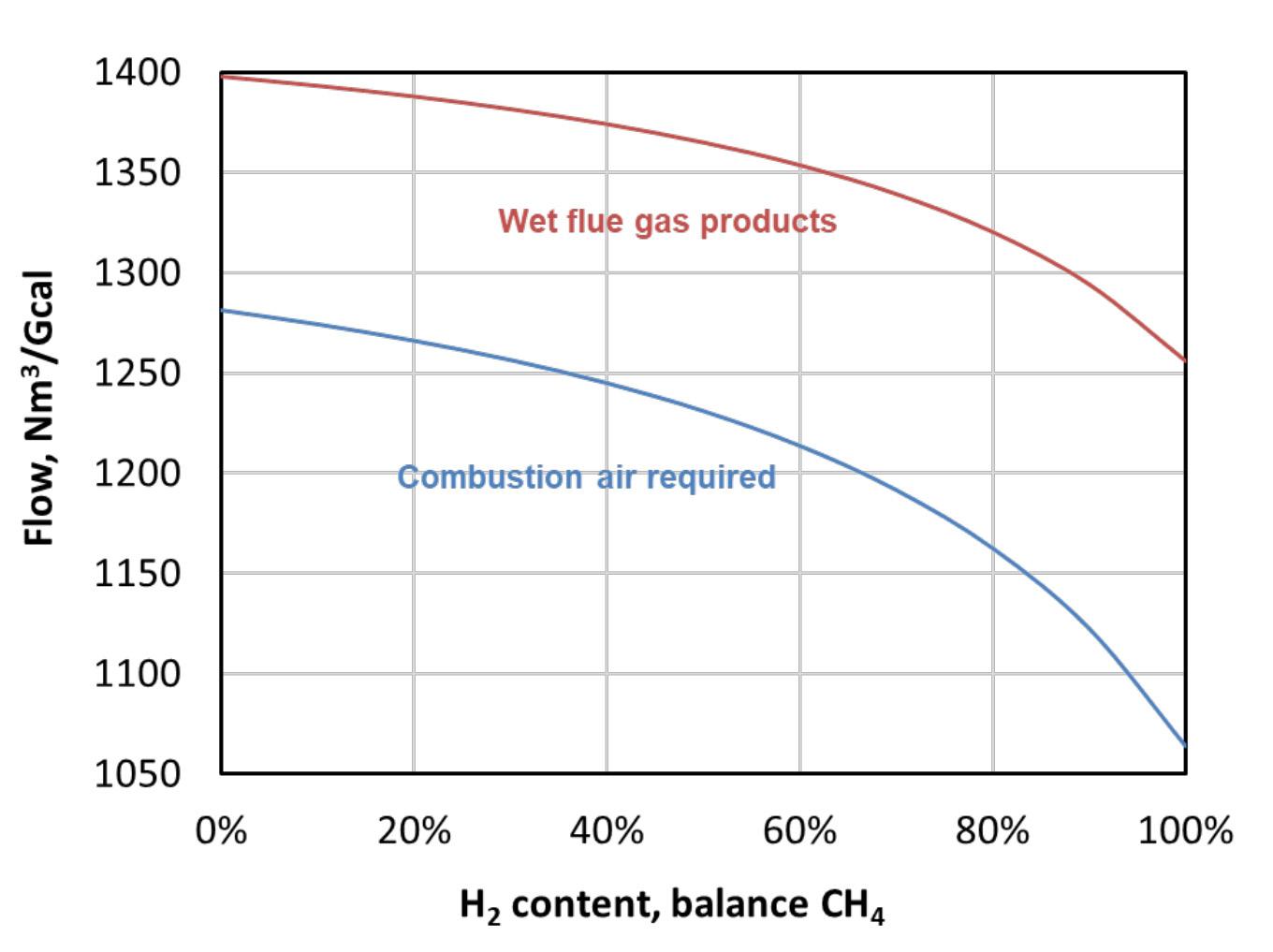
Hydrogen combustion
There are important challenges to consider for new applications using a high volume of hydrogen in fuel. These fuels may impact the combustion system, which means that it may not be a simple transition from existing hydrocarbon fuels to hydrogen fuels.
Hydrogen is an element whose natural state at atmospheric temperature and pressure is gaseous. In that state, it has low density and can easily leak from piping systems. Additionally, this fuel gas has many unique properties compared to common hydrocarbon fuels (see Table 1). It has a very high heating value on a mass basis, but a very low heating value on a volume basis because of its low density. Hydrogen’s low volumetric heating value results in much higher volumetric flow rates for a given heat input when compared to other common fuels. Higher volumetric flows result in higher fuel gas pressure.
Hydrogen also has a higher flame speed and ignition temperature compared to many common fuels. It has very low minimum ignition energy, so it is easily ignited with a spark. In addition to this, it has a relatively high adiabatic flame temperature and wide flammability limits compared to other fuels. It also requires considerably less combustion air per unit firing rate, and generates fewer combustion products (see Figure 2).
Potential advantages
An important potential advantage of using pure hydrogen as a fuel is that the combustion products do not contain CO2. However, if hydrogen is generated by conventional SMR, then CO2 is a byproduct of the production process. If hydrogen can be produced using renewable energy, it is possible to minimise or even eliminate CO2 generation, depending on the process. Another benefit is the absence of carbon in the fuel, which means that no soot (smoke), carbon monoxide (CO), or unburned hydrocarbons are emitted to the atmosphere.
Design considerations
While firing on pure hydrogen, a more conventional fuel such as natural gas may be used at start-up before switching to a high level of/pure hydrogen. This typically occurs when hydrogen is produced by SMR, for example. Burners that are designed to fire on hydrogen are initially started up with natural gas, until the SMR process is established and hydrogen is being produced. This means that burners may need to be capable of firing on both natural gas and fuels containing a high level of hydrogen. As the combustion characteristics between hydrogen and other fuels can be significantly different, this could complicate burner design concept and operation.
Potential challenges for premixed process burners
The actual impact on retrofitting existing burners is very dependent on the burner design. Traditional premix burner designs, as shown in Figure 3, use a venturi system and fuel gas pressure to aspirate combustion air into the furnace.
There are many potential challenges when using fuels with a high level of hydrogen in a premix burner: � Hydrogen has a considerably higher flame speed, which makes it much more susceptible to flashback in a premix burner. Flashback describes the phenomena when undesired internal combustion takes place inside the burner, leading to fast destruction (see Figure 4). This means that existing premix technology, if not specifically designed for higher volumes of hydrogen, may not operate safely on a new high hydrogen concentration. � Higher adiabatic flame temperature will have an influence on thermal NOx produced by the burner.
Evaluation on a case-by-case basis would be required to understand whether permit levels can still be met or exceeded with a fuel change. � Increasing the fuel gas pressure within the burner when increasing the hydrogen content – as shown in Figure 4 – will generate a higher noise level. � The aspiration of air by premixed burners is dependent on the fuel gas pressure. Figure 5 shows the fuel gas pressure on a constant fuel orifice for different fuels.
For the same fired capacity of the burner, there are considerable differences in fuel pressure. As such, air aspiration can be impacted.
To overcome these limitations, John Zink Hamworthy has developed the patent pending/patended WALFIRETM technology for process heaters (see Figure 6). Mainly targeted for use in high temperature applications such as ethylene cracking furnaces or reformers, the technology works as a diffusion style burner. The main distinguishing characteristic for a diffusion burner is that air and fuel gas are not premixed prior to combustion, but rather at the location where combustion is supposed to take place. With such a design, flashback cannot take place, and no limitation of hydrogen concentration in the fuel gas applies.
To sustain and complete combustion, the adequate amount of combustion air needs to be supplied from the burner inside the firebox. As opposed to the premix burner, where the fuel gas pressure and fuel gas composition are the dominating factors when it comes to air aspiration (refer to Figure 5), WALFIRE technology uses the furnace’s negative pressure to aspirate and measure air. The burner’s operation becomes independent from fuel gas pressure and composition, which Figure 3. JZHC PMS premix burner series.
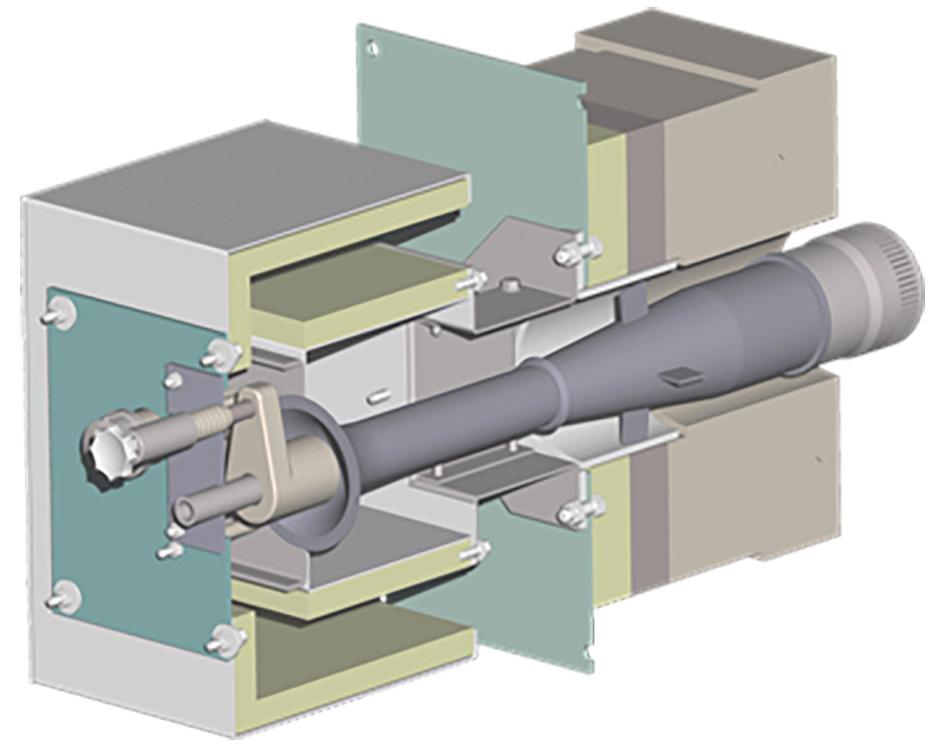
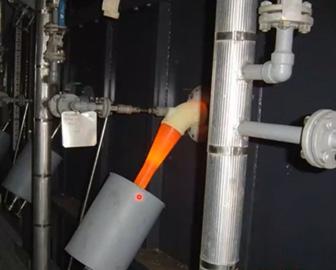
Figure 4. Glowing venturi of a premix burner. Figure 5. Fuel gas pressure for same heat duty on different fuel compositions using constant gas orifice.
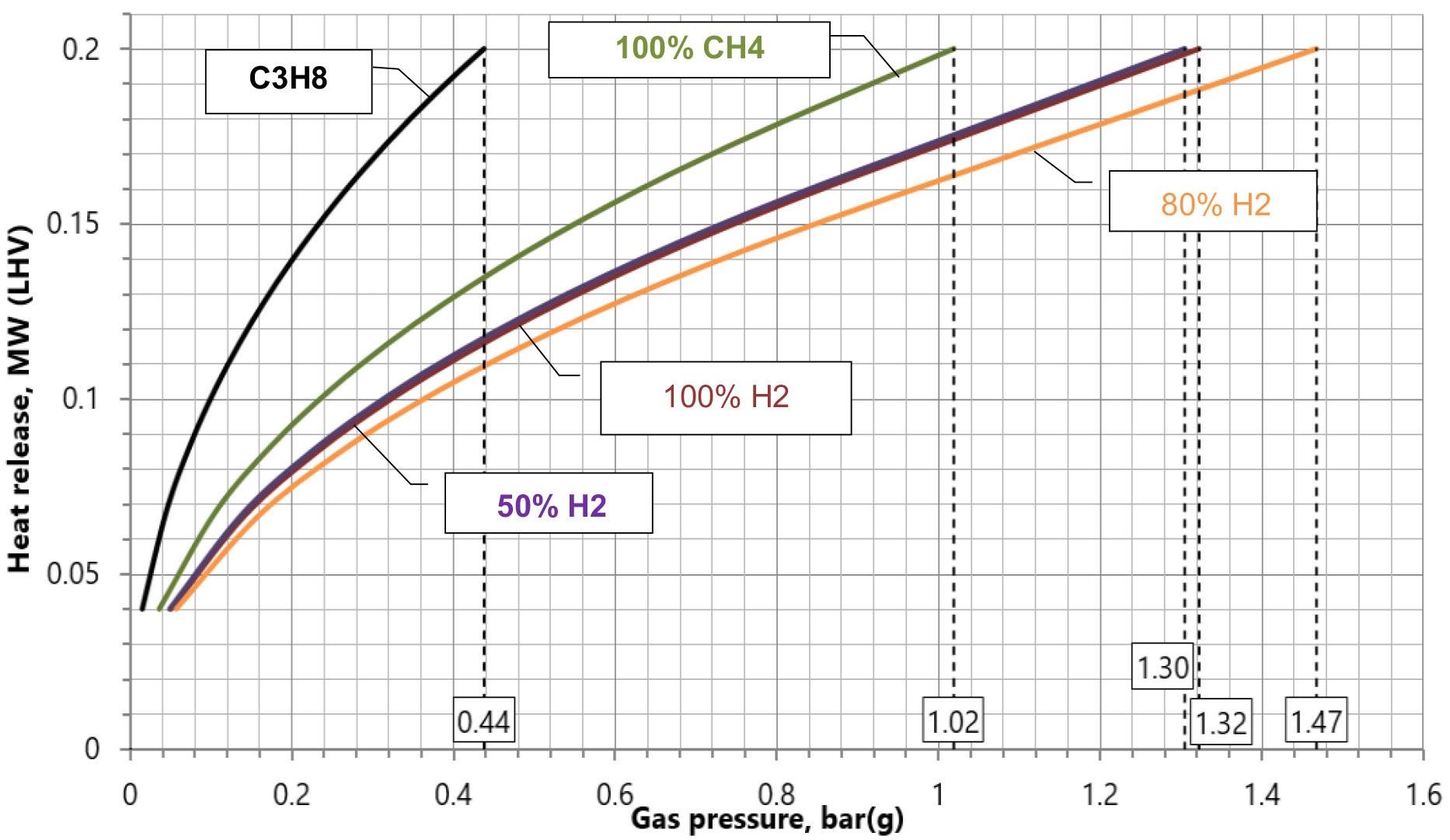
makes fuel quality adjustments easier during operation, as there is no longer a need to re-adjust air registers on the burner.
Case study: a petrochemical plant in the US
A customer in the US was experiencing high maintenance intervals and frequent flashback on their installation of ultra-low NOx (ULN) radiant wall burners in an ethylene cracking furnace. The design limitation on the radiant wall burners limited the overall amount of hydrogen in the fuel system, as the flashback conditions would worsen, and higher operator awareness and maintenance would be required.
The ethylene cracker has a mixed firing concept, e.g. the firing equipment is a combination of ultra-low NOx, diffusion-type floor burners, and ULN premix radiant wall burners. As the floor burners do not limit the hydrogen concentration in the fuel mix, the customer decided to replace the wall burners with WALFIRE burners. The burners were designed in such a way that no modifications to the existing steelwork of the furnace, nor the fuel connection, were required (see Figure 7).
After successful installation, the furnace was started up together with John Zink Hamworthy Combustion service engineers onsite. Figure 8 (left) shows the WALFIRE radiant wall burners during light off. The heating curve of the furnace was followed, and consequently more burners were brought into service as the heater temperature increased.
Figure 8 (right) shows all of the wall burners in operation with the furnace at design load. During design operation of the furnace, flue gas was sampled in different locations inside the radiant firebox, as well as after the convection section of the heater. Analysis of this data showed that the ULN emissions performance of the fired equipment was identical to the historical data of the furnace.
After two years of successful operation of the unit, the customer decided to proceed with installation of additional heaters.
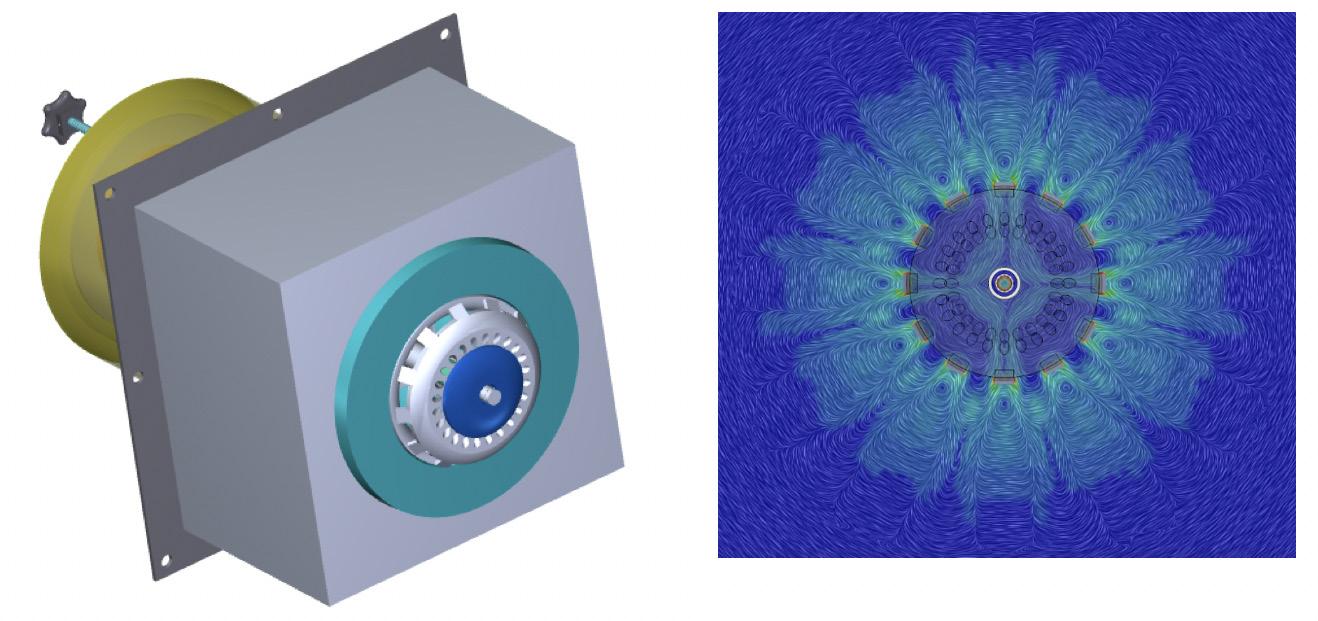
Figure 6. 3D WALFIRE burner (left) and WALFIRE CFD velocity profile (right).
Conclusion
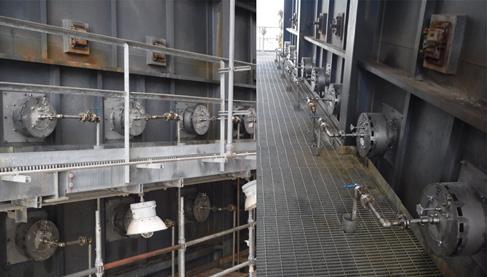
Using fuels with a large volume of hydrogen has the potential to dramatically reduce or eliminate CO2 emissions compared to conventional hydrocarbon fuels, depending on how the hydrogen is produced. Hydrogen has many unique characteristics, such as a higher flame speed and adiabatic flame temperature, compared to conventional fuels. However, there are many challenges and design issues that need to be considered when using these fuels.
New burner concepts, as detailed in this article, have proven to safely widen the operating window of radiant wall burners, while eliminating the risk of flashback and increased maintenance requirements.
Figure 7. WALFIRE furnace installation.
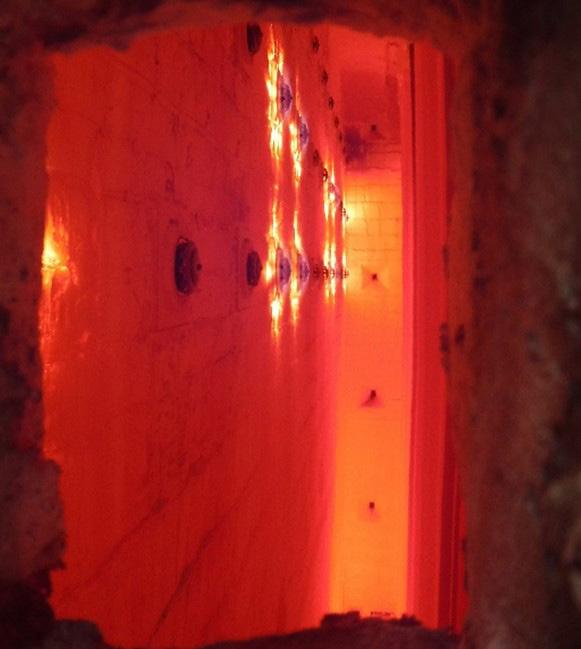
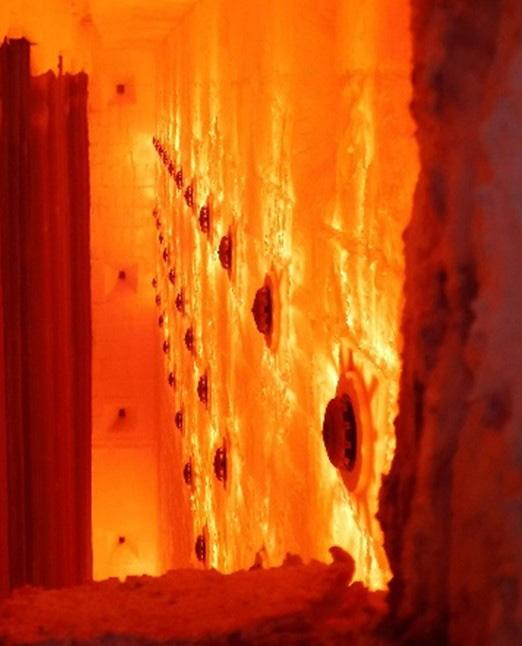
Figure 8. Furnace start-up (left) and design operation (right).
References
1. BAUKAL, C., JOHNSON, B.,
HAAG, M., THEIS, G., and WHELAN, M.,
‘Hydrogen: potential superfuel?’,
Decarbonisation Technology, (November 2021), pp. 33 – 35. 2. ‘Hydrogen’, International Energy
Agency, https://www.iea.org/fuelsand-technologies/hydrogen 3. NIKOLAIDIS, P., and POULLIKKAS, A.,
‘A comparative overview of hydrogen production processes’, Renewable and
Sustainable Energy Reviews, (2017), pp. 597 – 611. 4. DINCER, I., ‘Green methods for hydrogen production’, International
Journal of Hydrogen Energy, (2012), pp. 1954 – 1971. 5. ROBINSON, J., ‘US oil, gas producers advantaged in blue hydrogen adoption: S&P Global Ratings’,
S&P Global Platts, (23 April 2021), https://www.spglobal.com/platts/en/ market-insights/latest-news/electricpower/042321-us-oil-gas-producersadvantaged-in-blue-hydrogenadoption-sampp-global-ratings
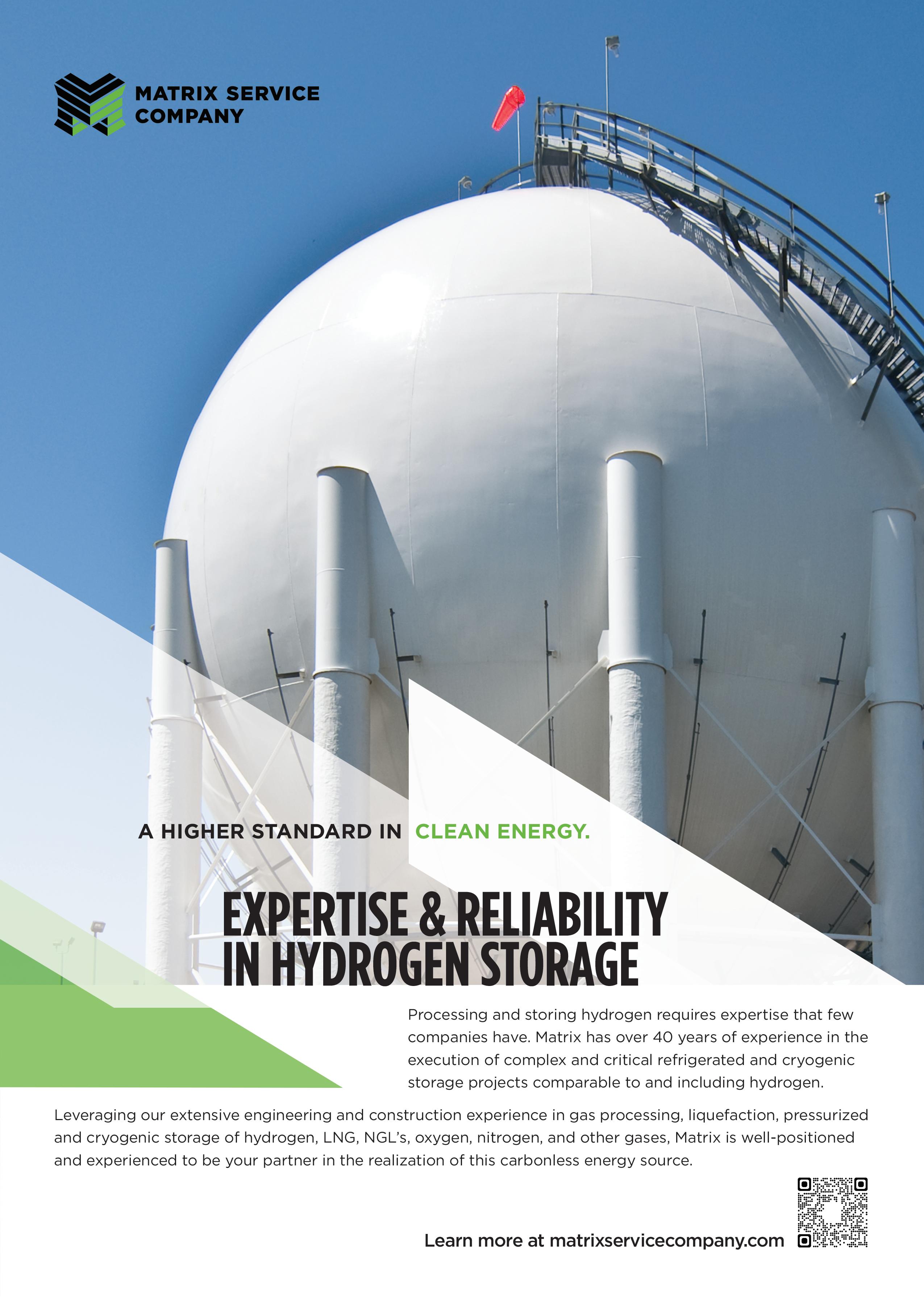