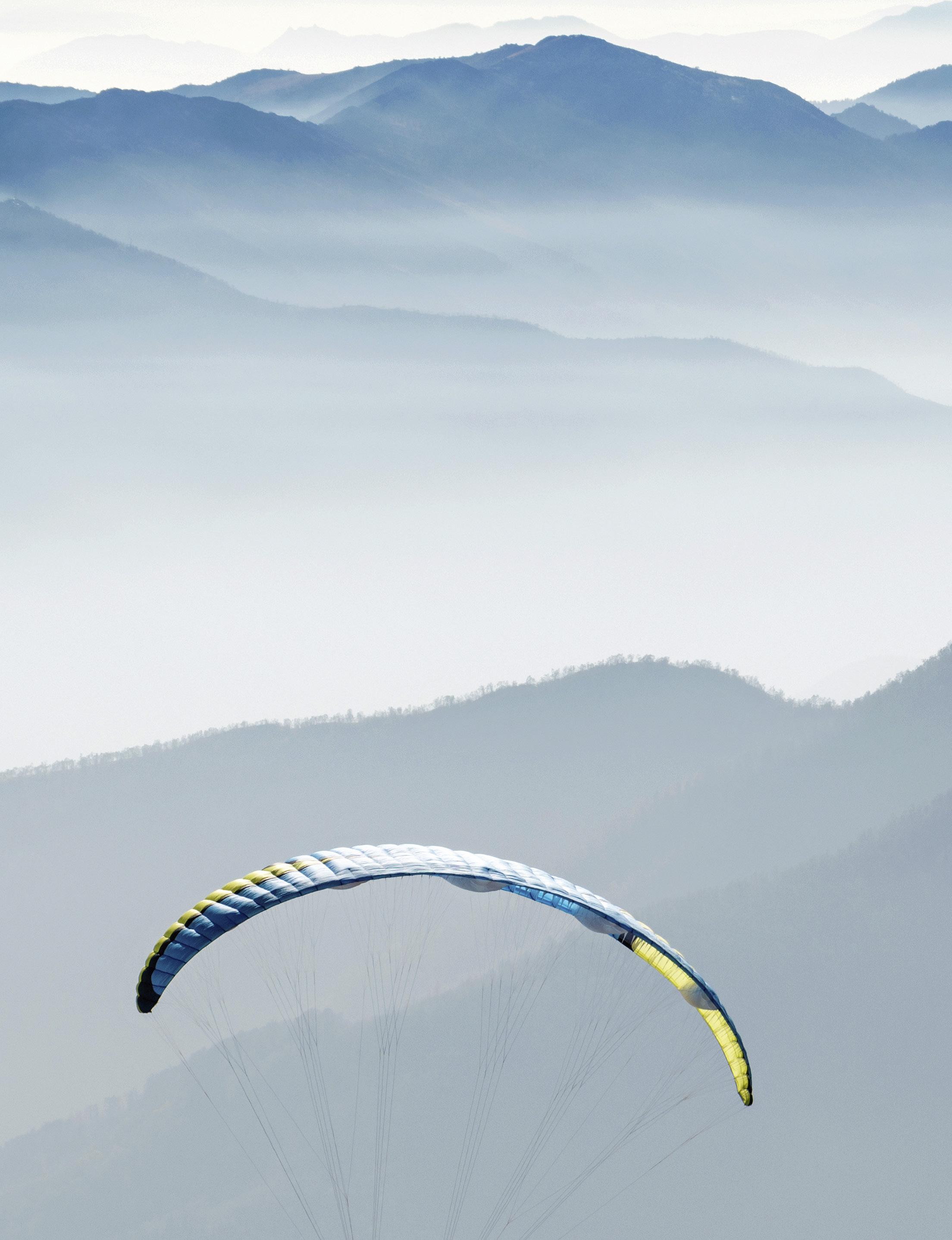
8 minute read
Reaching new heights
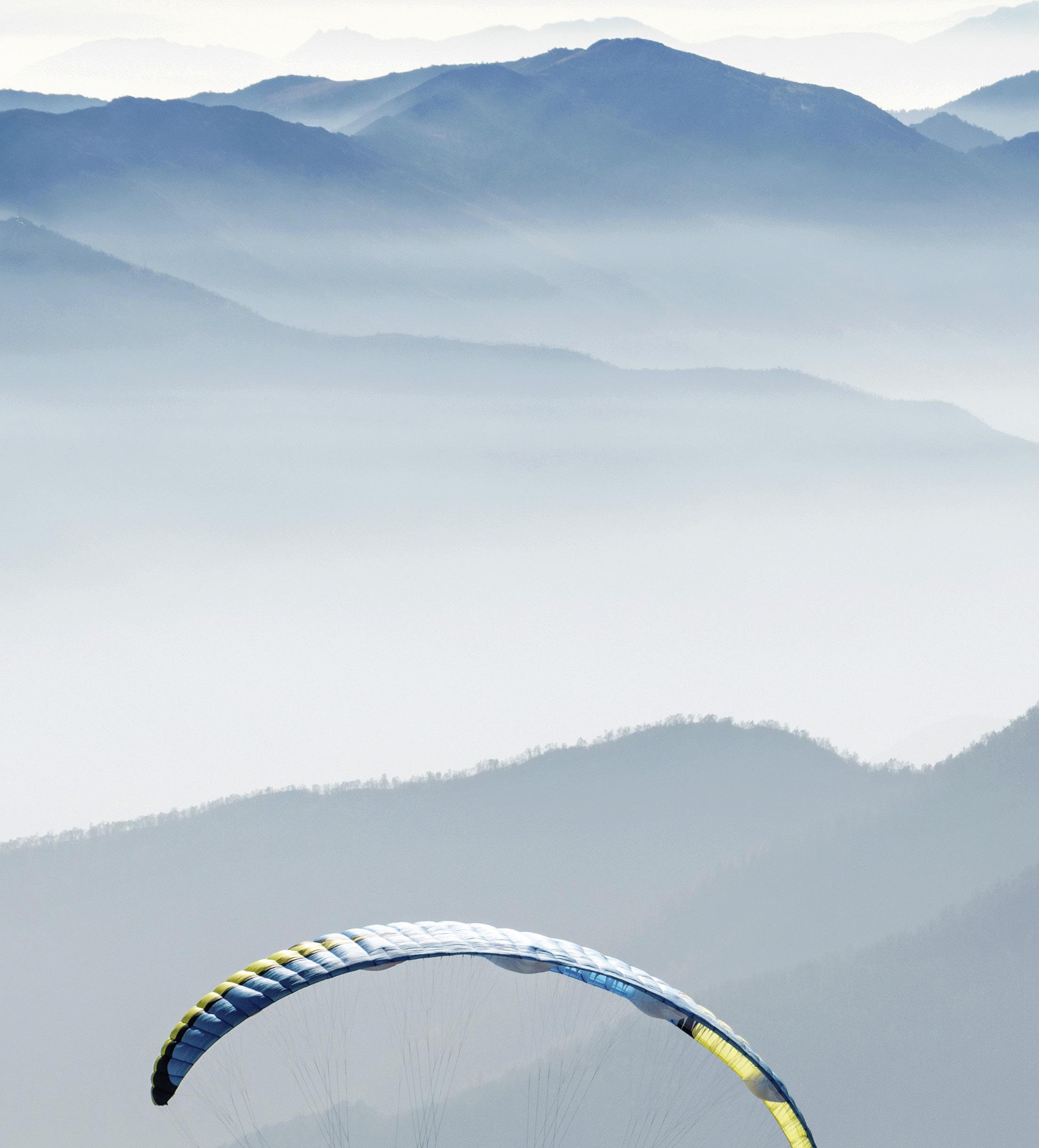
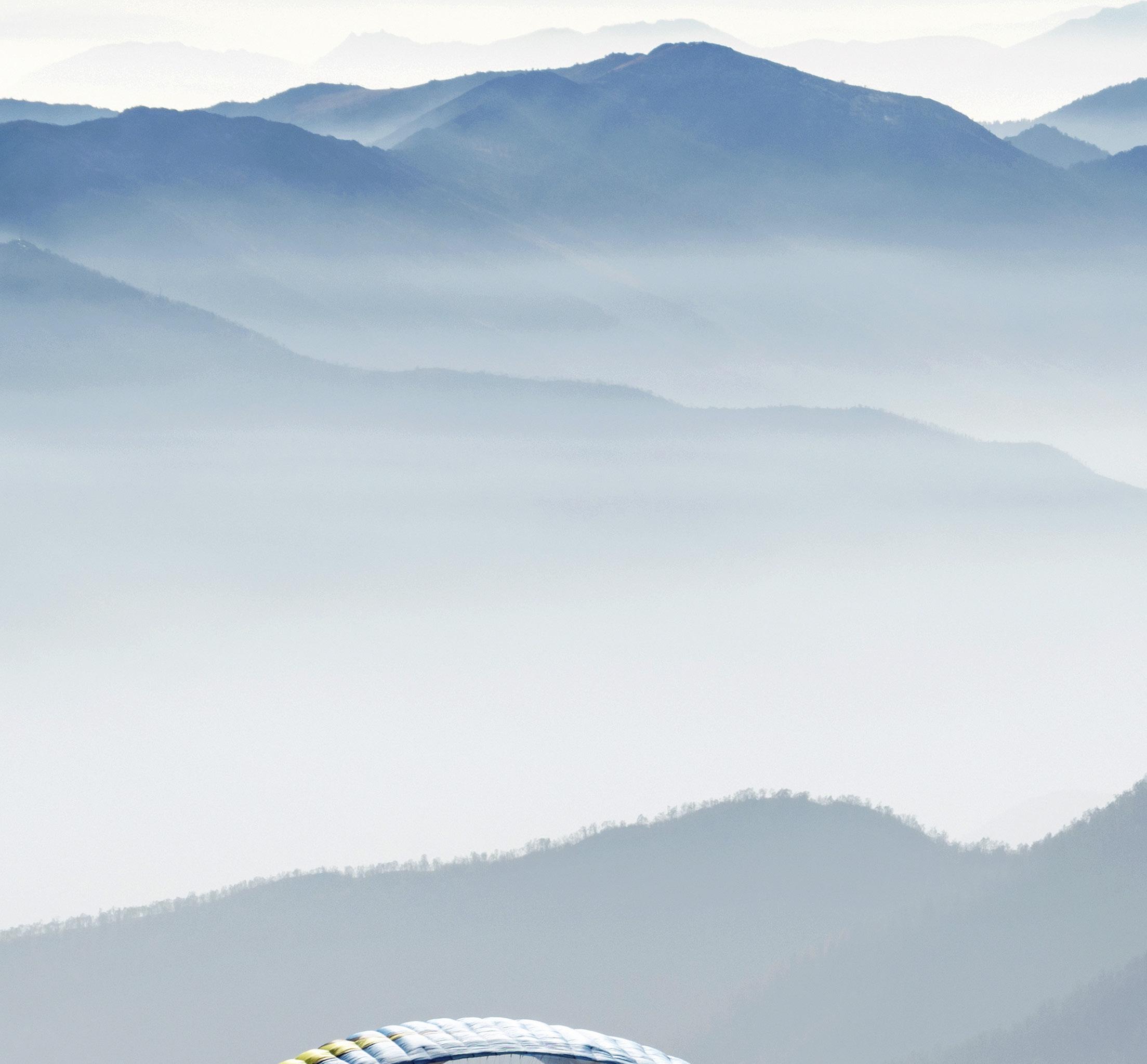
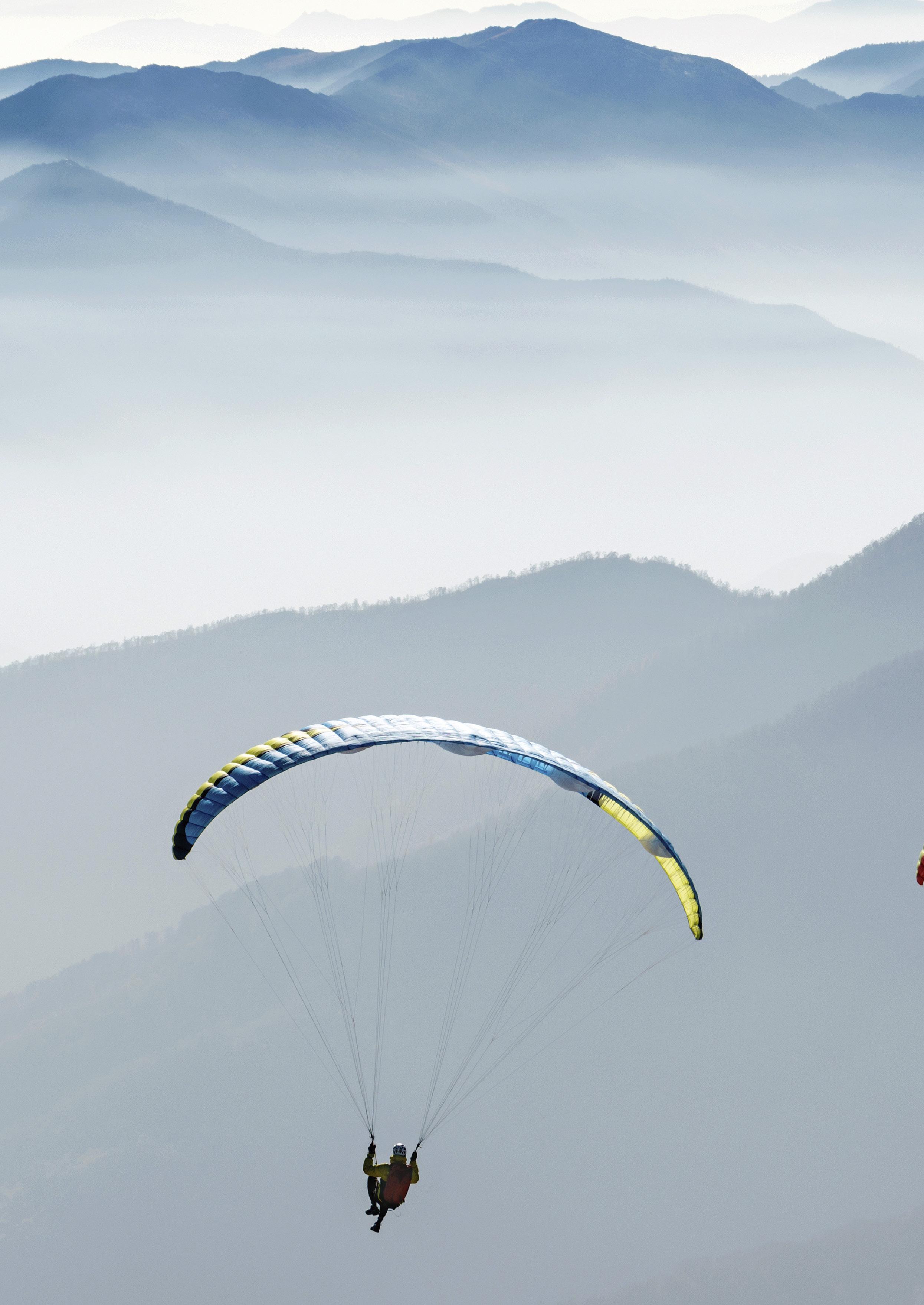
Joost Meeuwissen, Calderys, the Netherlands, describes how pre-cast, pre-fired catalyst support domes are setting new standards when it comes to long-lasting durability.
Any industrial process involving high temperatures requires refractories in order to operate. Heat is not, however, the only issue that these materials face. In most chemical processes, refractories will be exposed to a range of other stresses, including mechanical (abrasion), thermal (wide swings in temperature), and chemical stress.
With any industrial operation, the first step in refractory selection is to identify the operating conditions that will determine the origin of the refractory wear. These will differ depending on the industry process in question: in some conditions, certain types of wear will be more relevant than others. Refractory properties should therefore be optimised to the specific process environment in order to maximise refractory life at the lowest cost.
Within the growing hydrogen economies, specialised equipment such as autothermal reforming (ATR) and other reformers will be in demand for flexible and more efficient hydrogen, and for producing blue hydrogen and green ammonia with a lower carbon footprint.
When considering refractories for hydrogen production units, chemical corrosion is the main concern. Although process temperature is high, it is constant, reducing the risk of thermal shock caused by large fluctuations in the thermal profile. Meanwhile, processing units only contain gas; there are no solids or liquids. As a result, abrasion is minimal and does not represent a major concern.
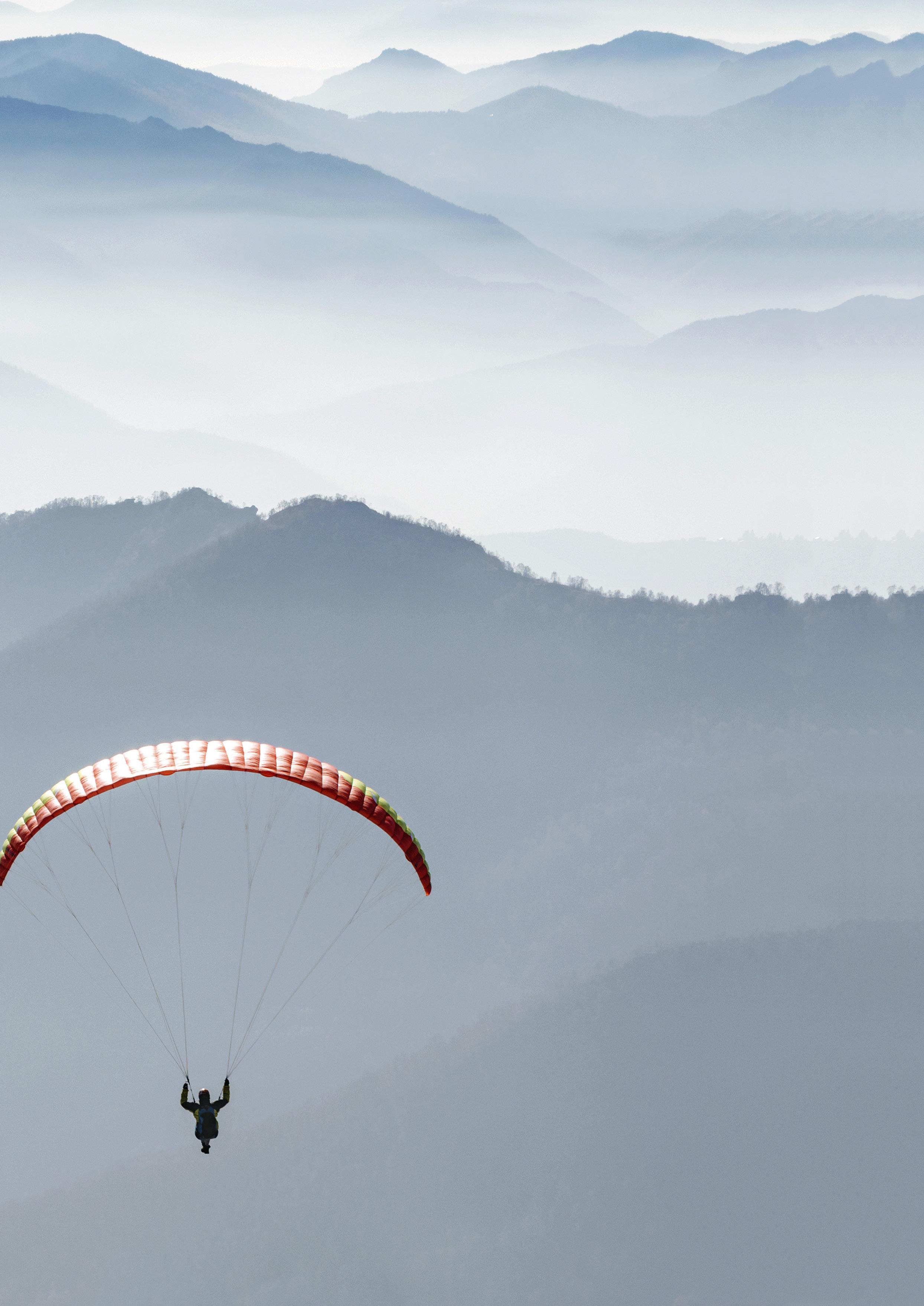
Catalyst support domes are installed in various chemical production processes (such as ammonia and syngas) that contain secondary reformers.
The conditions experienced by these domes are severe: environments comprising significant percentages of carbon monoxide (CO), carbon dioxide (CO2), hydrogen (H2), water (H2O), and nitrogen (N2), at maximum temperatures of about 1300°C and high pressures of approximately 35 bar, are common. In such conditions, the performance of the refractory lining is critical. Aluminous refractories, which are low in both silica and iron oxide, are typically recommended. These are usually as pre-fabricated, sintered bricks, from which the dome is constructed.
The major consideration when selecting the support dome is the compressive stress that is placed on it by the weight of the catalyst bed. Combined with the high-pressure conditions inside the secondary reformer, and high process requirements of the plant, the dome would be liable to crack over time. However, novel solutions that extend refractory lifetime and reduce turnaround time for replacement offer key benefits. The first pre-cast, pre-fired (PCPF) catalyst support dome has been demonstrating these benefits over the past six years of operation.
Improved quality and delivery time of a PCPF catalyst support dome
Figure 1. A 3D computer model of the PCPF support dome.
Figure 2. Calde Cast LT 93/1 PCPF secondary reformer dome. Assembled dome for mock-up in the ready shape production facility (left). The actual onsite assembly of the dome in progress is inside the secondary reformer (right).
This first dome was supplied to a US chemicals manufacturer by Calderys in 2015 as a significant part of the refractory construction. The faster fabrication time of the PCPF dome compared to traditional refractory brick construction meant that it could be delivered just before installation, without causing any delays to the project.
In fact, that same year, another PCPF catalyst support dome was ordered from Calderys based on quick delivery, as there was no spare dome available, and the original brick supplier was not able to produce and supply the spare dome within the delivery time required to hit the onsite installation date. This meant that Calderys had to produce the monolithic and prepare moulds, as well as pre-cast, pre-fire and pack the dome blocks in its workshop for shipment.
Finding the desired strength to avoid hairline cracks
Occupying the space between a full monolithic solution and bricks are ready shapes, which are made from monolithic refractory materials, shaped and thermally treated at the refractory manufacturing unit, before being dispatched to the job site. Their primary advantage is the time needed for their production, which is typically about 50% shorter than that needed for bricks. Lead times can be reduced by a further 50% by employing the latest 3D printing technology to create precise moulds.
Apart from this, there is a greater freedom in the choice of moulds, mould materials, and mould shapes.
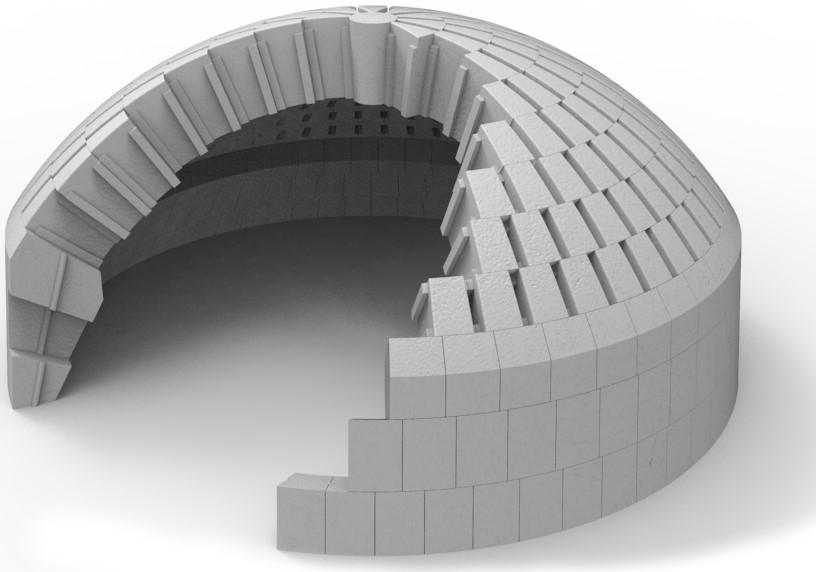
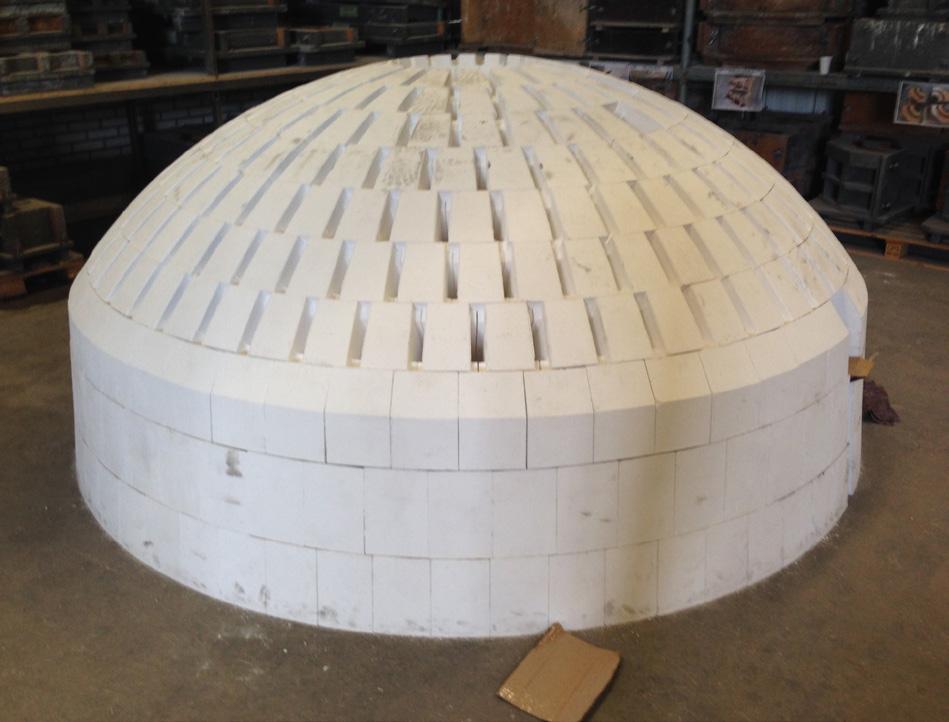
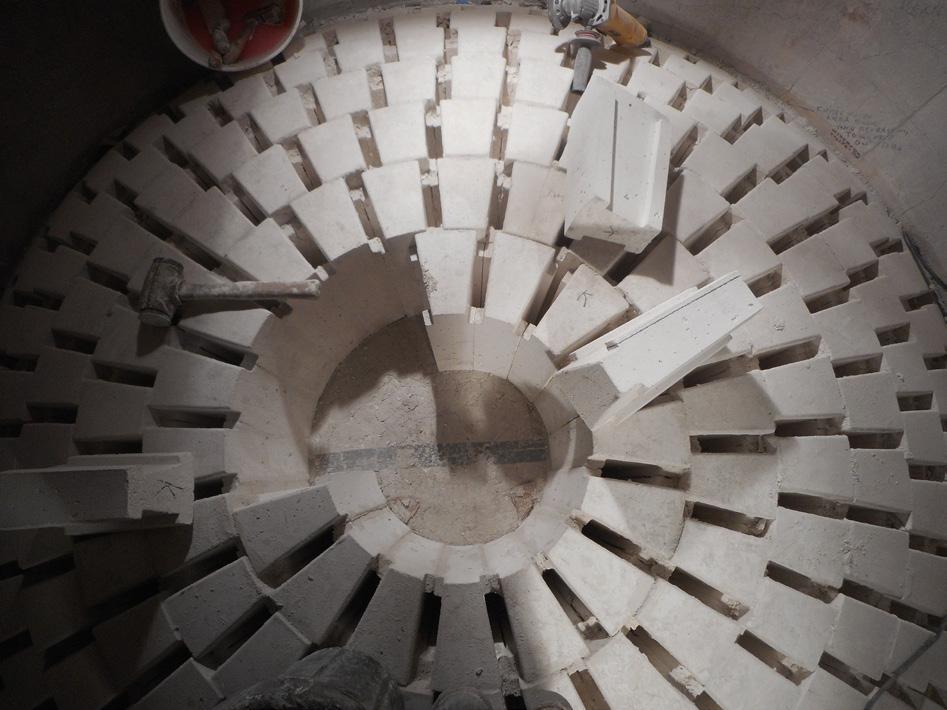
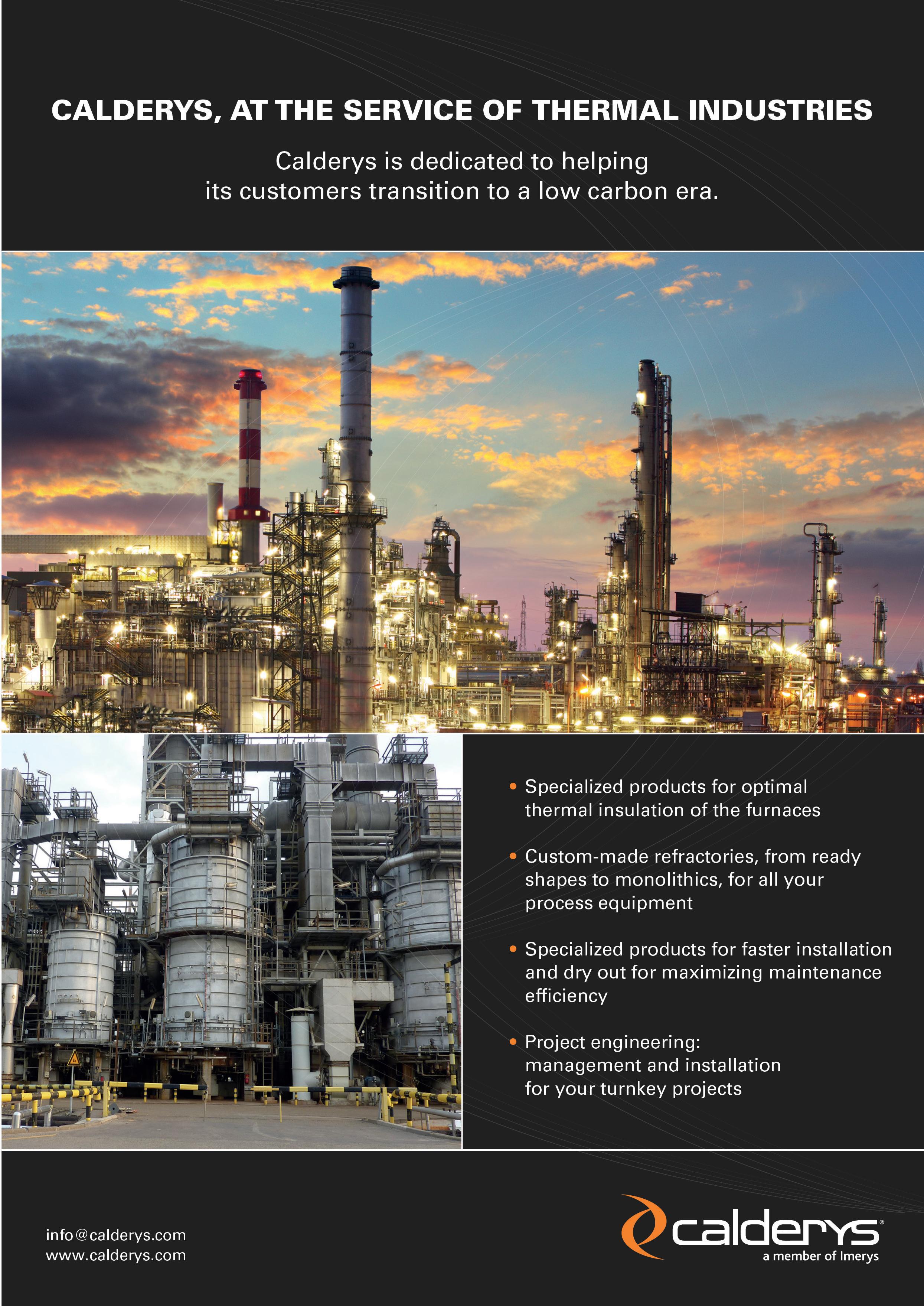

1008.5 Max
1004.5 1000.6 996.62 992.67 988.71 984.76 980.8 976.85
972.89 Min

2.8692e6 Max
2.194e6 1.5188e6 8.4358e5 1.6838e5 -5.0683e5 -1.182e6 -1.8572e6 -2.5324e6
-3.2076e6 Min
Figure 3. Thermal field on the upper part of the dome (left); tensile stress in the centre of the dome (right).
Compressive strength was therefore a key factor: traditional sintered bricks could only offer the minimum required in the specifications (80 MPa). In contrast, the monolithics provide strengths of up to 100 MPa. This high compressive strength comes from the fact that it is vibrated in the mould during the production process, compacting from multiple directions. Bricks, on the other hand, can only be compressed from one press direction.
The properties of the material used for ready shapes, CALDE® CAST LT 93/1, are equivalent to the white, tabular, alumina-based bricks recommended for use in reformers, and this solution is one of Calderys’ spinel-containing raw materials, comprising 92.5% aluminium oxide (Al2O3) and 5.7% magnesium oxide (MgO). This higher-than-standard MgO content is integrated within the crystal lattice of the spinel, improving the strength of the material; there is no ‘free’ MgO or periclase, even at very high temperatures (> 1800°C).
This product is low in both iron oxide and silica, demonstrates high hot and cold strength and, above all, has very high creep resistance in compliance with the specification of the product recommended by the licensors for the secondary reformer dome. As a result, the Calderys team could be sure that the dome would remain stable, despite its large size of about 2.5 m dia. x 1.5 m height.
During the detailed design stage, Calderys took a close look at the mechanical strength and heat inside the PCPF ready blocks to determine in advance whether there was any risk of hairline cracks or other damage. The company’s Science & Technology Department was able to support this by using the numerical simulations tool. Different studies were realised to better understand the conditions and optimise the geometry.
After defining the initial thermal conditions (1400°C on the upper part of the catalyst bed, and 1000°C below the dome), it was possible to precisely define the thermal field appearing on the dome.
After defining the initial mechanical conditions (weight of the catalyst bed on the upper face of the dome), the company was able to get a clear idea of the mechanical stress inside the dome.
Even working with simplified conditions, the numerical simulations tool helped to optimise the design of the dome, and clearly show that the level of stress appearing in the dome due to gravity and weight of the catalyst bed is always lower than maximum tensile stress (20 MPa) and compressive stress (90 MPa) permitted by the CALDE Cast LT 93/1.
The turnaround on a brick dome is normally two to three years after start-up. After this, the catalysts are usually washed or replaced, along with the dome. Calderys intended to deliver the monolithic dome on the basis of a five-year lifetime. However, the dome is still in place after more than five years in operation and through a number of maintenance stops.
Additional domes
Based on the performance of the original domes, Calderys teams have been able to supply a like-for-like spare dome to the same customer.
With a maintenance stop coming up early in 2022, it was thought prudent to have a spare dome on standby to ensure process continuity, should it be necessary to replace the dome. It would also be standard to consider upgrading the design of the dome at this point. However, the performance of the dome has surpassed expectations, and the customer decided that it was not necessary to make any changes.
Since the original installation, Calderys has supplied a second and even a third, heavier dome to other customers. The challenge is always with the specification of the licensor, which tends to require a 99% Al2O3 material. Calderys has always looked beyond specifications with a view to delivering performance and results that exceed operations expectations. Chemical composition is an important feature of Calderys’ products, but the company continues to look at other parameters that might deliver greater value to customers.
A complete refractory portfolio
Calderys envisions a bright future for PCPF domes. Despite this, it also recognises that there will always be customers for brick domes, and so will continue to offer domes as pressed bricks and as PCPF monolithics shapes. PCPF solutions are also applicable for other applications where bricks are being used as the refractory lining. This results in a much quicker installation, as PCPF solutions can be fabricated at a much larger size than bricks, limited solely by the ability of the workshop and job site to handle such materials. By increasing the size of the refractory blocks, there is less work required onsite for the construction of the lining, ultimately saving time, equipment, and manpower.