
6 minute read
Vibration Control In Prilling
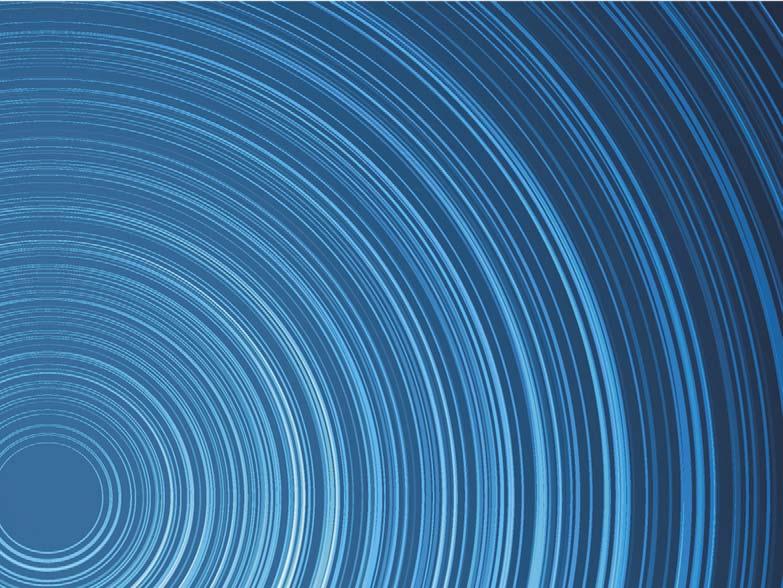
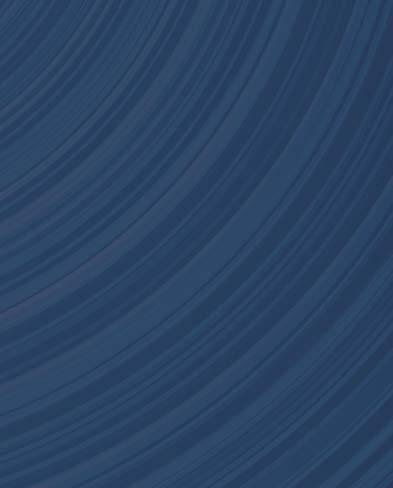
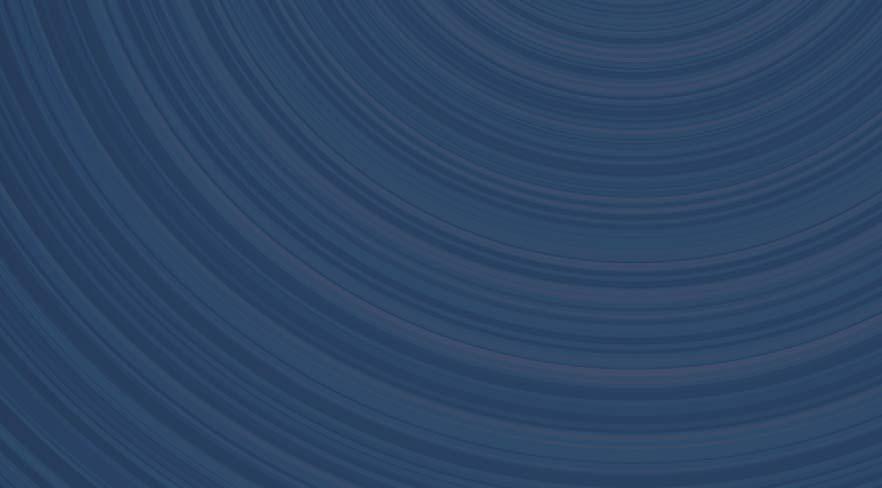
VIBRATION VIBRATION VIBRATION VIBRATION CONTROL CONTROL CONTROL CONTROL

IN PRILLING

Gabriele Marcon, Casale, Switzerland, charts the development of a new vibrating prilling bucket for urea producers.
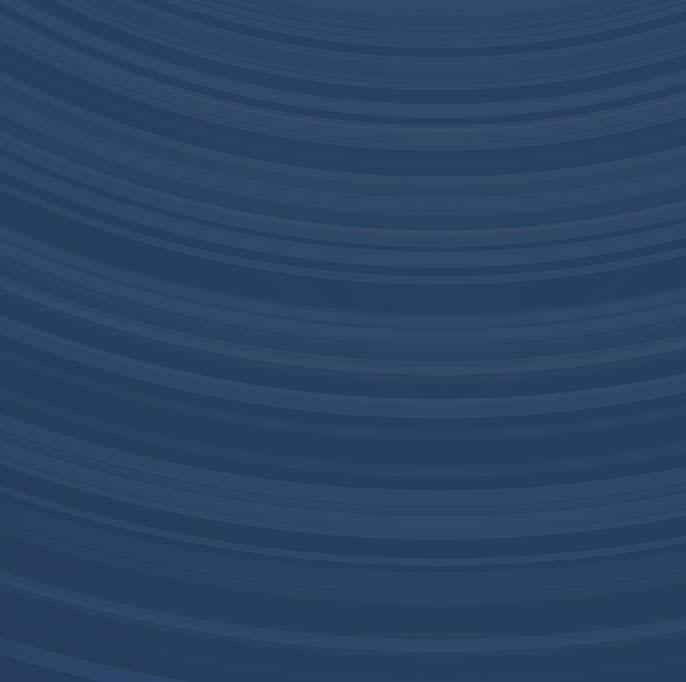
Coupling effi ciency with product quality is nowadays the main goal pursued by any urea producer, whilst at the same time fulfi lling increasingly stringent sustainability requirements. With that in mind, Casale has recently developed a solution aimed at improving product quality in the prilling fi nishing section, before dispatching the product to users. The R&D project, carried out with the support of Donald Snyder (founder of Tuttle Prilling Systems), focused on the development of a vibrating prilling bucket – the Vibrating Skin Bucket (VSB) – that is now available on the market.
From R&D programme to fi rst industrial application
The key features of the bucket (Figure 1) are: Suitable for prilling towers with a diameter of up to 28 m. Uniform prill size distribution. Low dust emissions. Low prill temperature. Able to function in a wide range of operating conditions.
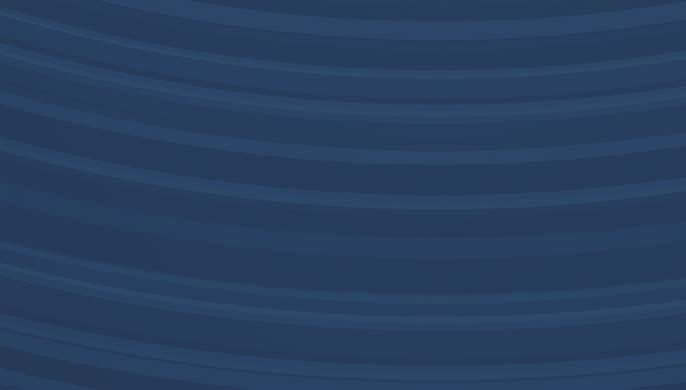
The R&D programme led, fi rstly, to the design of the bucket and then to the execution of experimental tests at pilot scale to validate the theoretical calculations.
The testing activities provided promising results, so the decision was taken to prove the technology at the industrial scale. The fi rst industrial application has now been successfully completed and the technology is available on the market for both small and large capacity urea plants.
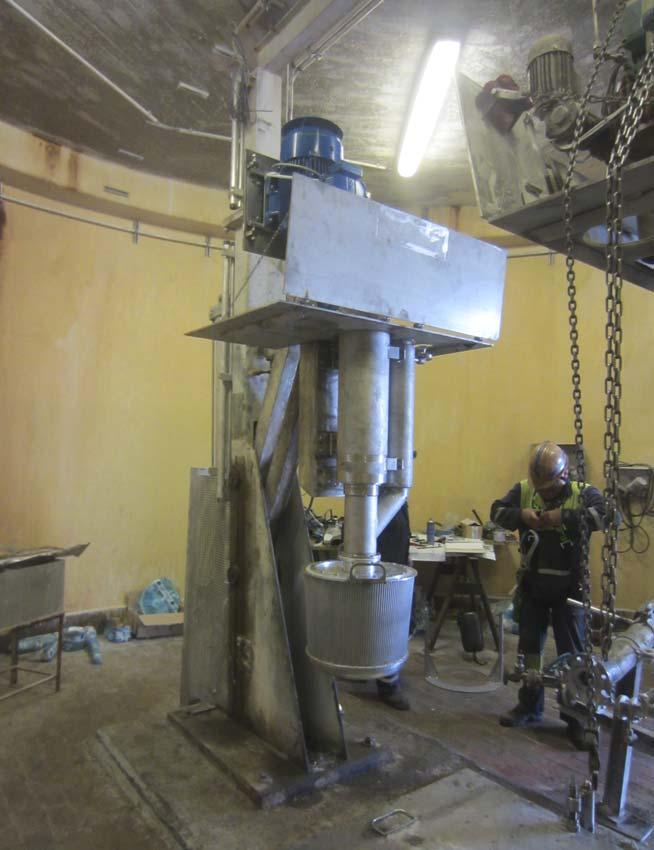
Figure 1. First industrial application of the VSB.
Figure 2. 3D model of Vibropriller. Orange and purple denote the rotating and vibrating parts. Red denotes the static part – liquid melt distributor. The VSB rotates on the vertical axis, like a conventional prilling bucket. As a result of the design, the external conical wall of the bucket vibrates in a vertical direction, while the liquid contained inside the bucket is kept substantially free from vibrations. The vibrations are induced by an electronic actuator installed above the prilling bucket. Figure 2 shows the main components of the bucket.
The bucket’s operating mechanism is based on Rayleigh’s principle of controlled break-up of liquid jets, which guarantees the generation of liquid droplets with a predictable diameter.
As a result of its peculiar ridged shape and optimised hole size distribution, the ‘vibrating skin’ enhances the uniformity of the generated droplets and the degree of occupancy of the prilling tower cross area.
In comparison with a conventional rotating bucket, the VSB’s confi guration makes it possible to increase plant production as well as improve the uniformity (in terms of size and shape) of the urea prills. Moreover, a reduction in the fi ne particle content in the product and a decrease in the amount of dust emitted from the top of the prilling tower are obtained.
Table 1 shows the product size distribution achieved by the fi rst industrial application of the VSB compared to that obtained with a conventional bucket. In contrast to other vibropriller technologies currently available on the market, in the VSB the vibration is transferred only to the external wall of the bucket and not to the liquid inside. Therefore, a better control of liquid droplet generation can be achieved. Figure 3 depicts the general assembly of this technology.
The main components of the technology are: Vibrating bucket: the complete bucket (not including the urea melt distributor) rotates on its axis, driven by the electric motor. The electronic actuator, installed above the prilling bucket, transmits the vibration to the bottom cover and consequently to the conical perforated wall of the bucket.
The bucket is fed with urea melt through a pipe distributor. Shaft: the driver shaft has a hollow-tube design so that the electronic actuator can be installed inside of it. Electronic actuator: the electronic actuator, located inside the rotating shaft, allows transmission of the vibrations to the external skin of the bucket. A sinusoidal current of controlled frequency and voltage must be used for this purpose. The frequency of the vibration generated by the actuator is the same as that of the supplied current, while the amplitude is proportional to the voltage.

VSB control system
The rotation speed of the bucket is controlled by the inverter installed on the electric motor. The vibration, in terms of frequency and displacement, is controlled by means of a signal generator (powered at 220 Vac) that is able to regulate the frequency and Table 1. Prills size distribution the voltage of the signal supplied to the Standard rotating bucket VSB electronic actuator. This signal generator Load 100% 50 – 75% 75 – 100% 100 – 120% can be operated manually from a local panel or integrated in the distributed <1.25 mm 3% 1.8% 1.5% 1.6% control system (DCS). 1.25 – 1.5 mm 13% 6.4% 4% 3.9% Casale has developed a control 1.5 – 2 mm 54% 73.5% 73.2% 74% system for the VSB that can be easily integrated with the existing DCS and 2 – 4.5 mm 30.3% 18.3% 21.3% 20.5% supplied as an option.
This system allows the remote and automatic control of vibrations, in terms of frequency and amplitude, by measuring the urea melt fl ow rate fed to the bucket itself. Therefore, a simple function implemented in the DCS automatically adjusts both the frequency and the amplitude according to the plant load, without the need for any manual input. The rotating speed of the bucket is also automatically controlled from the DCS, in accordance with the urea melt feed fl ow.
Performance
The outputs of the VSB are: Product size distribution with uniformity index improved by 20%. The VSB can be specifically designed to meet the desired average prill diameter. Reduction of dust emissions by 25%. Steam saving due to reduction of the urea solution recycle from the scrubbing. Significant reduction in prill temperature. High quality of final product between 50 – 120% of urea plant load.
Conclusion
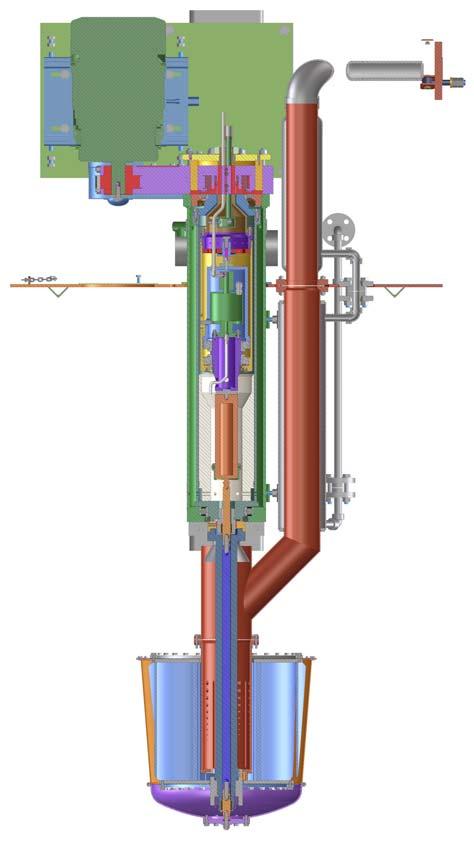
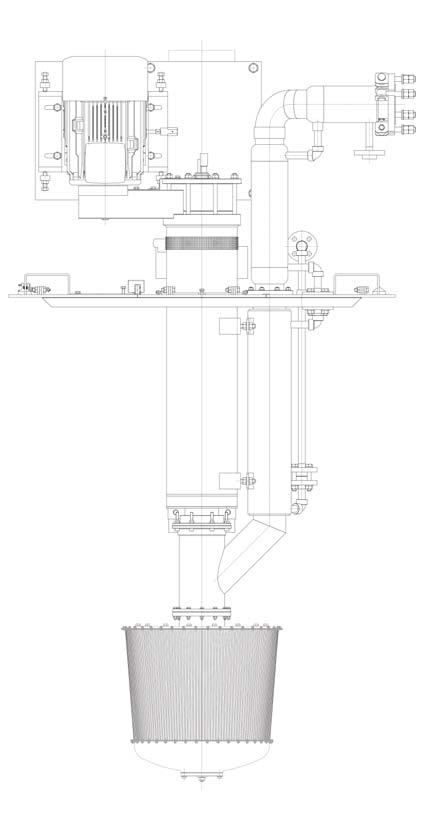
Figure 3. VSB general assembly: mechanical drawing (left) and 3D model (right).
New solutions in urea technology, with the aim of further strengthening plant effi ciency and providing the end user with a high standard of product, are being proposed and successfully tested and operated at the industrial scale.
The Doyle and EMT Alliance
Can provide you with all the Blending, Bagging and Transport equipment you need.

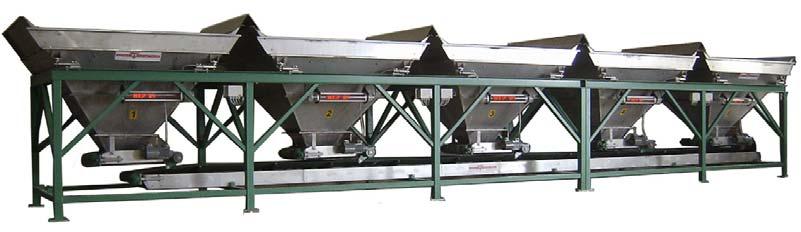
Weighcont Blender
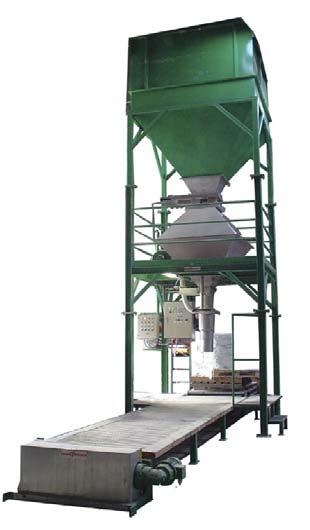
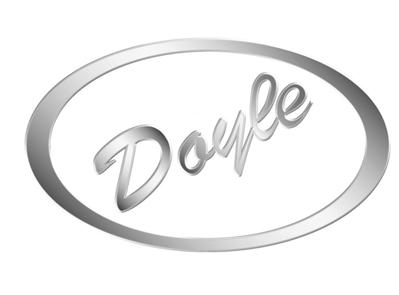
* Capacity of 20 to 200 ton per hour. * Unlimited number of hoppers. * Computer controlled. * Custom built. Fertilizer Inhibitor Treating Unit
* Portable. * Stainless steel. * Computer controlled. * High Capacity 120 m³ per hour.
EMT
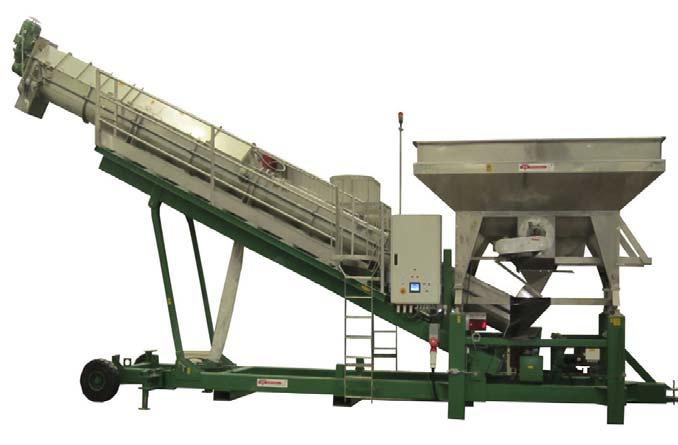