
9 minute read
Steel Goes Sustainable
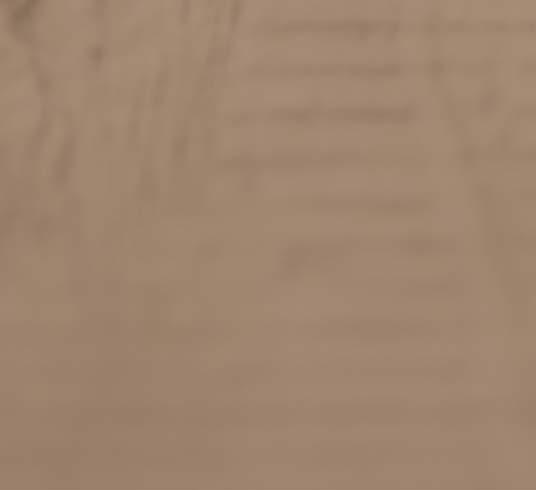
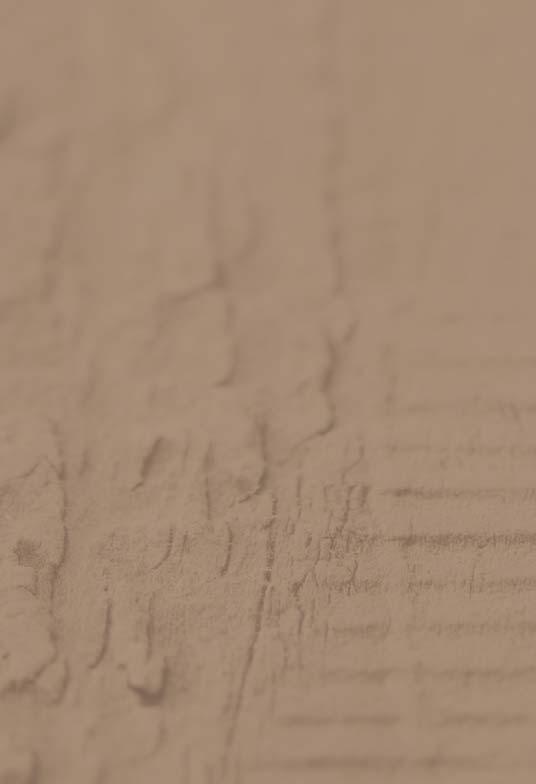


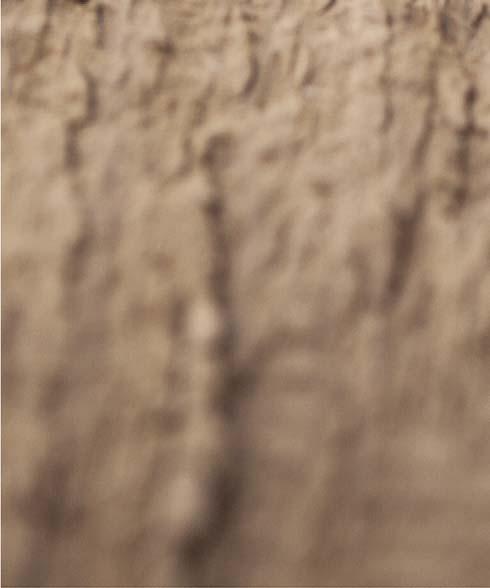
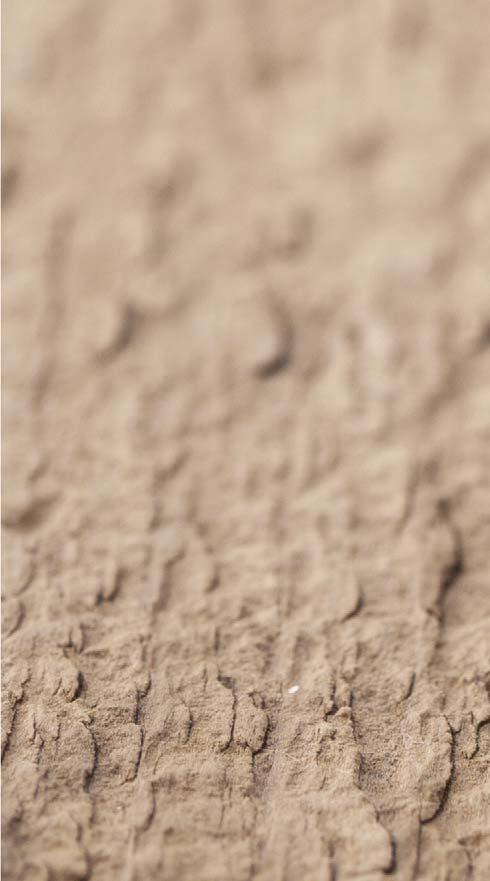

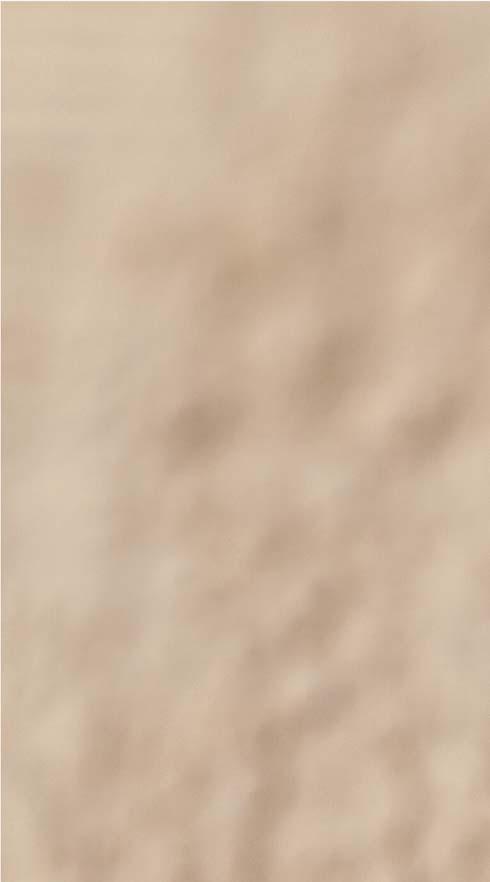
STEELGOES sustainable sustainable
Integration of circular systems and processes is one of the main directions for achieving industrial sustainability. As the world’s societies are accelerating their transition to a decarbonised future, circularity becomes even more important. The more materials fertilizer producers can recover, reuse and recycle, the more they can reduce their carbon footprint, while also helping other industries such as steel – which relies heavily on fossil fuels such as coal and natural gas – to contribute to the EU’s goals of climate neutrality by 2050 and meeting other climate commitments.
To address the challenge, Stamicarbon, the innovation and licence company of Maire Tecnimont Group, and Sandvik have created a buy-back programme for urea customers that allows recycling of precious alloys used in the manufacturing of urea equipment and piping. This is especially important for achieving a higher percentage of recycled raw material in the production of high-alloyed duplex steels that are able to withstand the challenging environments of the urea process, such as Safurex®.
Closing the loop
The direct buy-back programme was introduced in late 2019; Stamicarbon decommissions old equipment in plants and Sandvik then uses the recycled precious alloys in the production of new stainless steels. The programme represents a new type of collaboration between the industries, not only closing the loop in the lifecycle of Safurex material, but also lowering the need for virgin raw material in the production of equipment and piping for the urea industry. This is an important step, as reducing virgin material input leads to greater sustainability, less environmental impact and more effi cient use of resources.
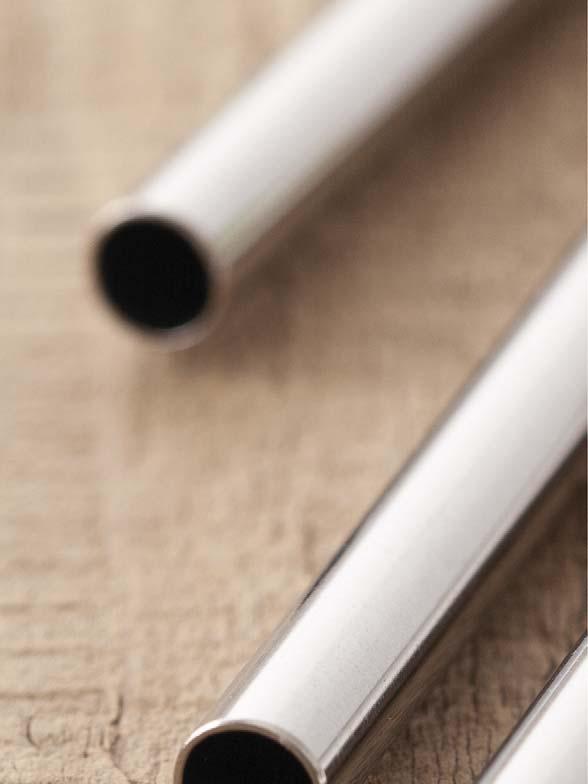


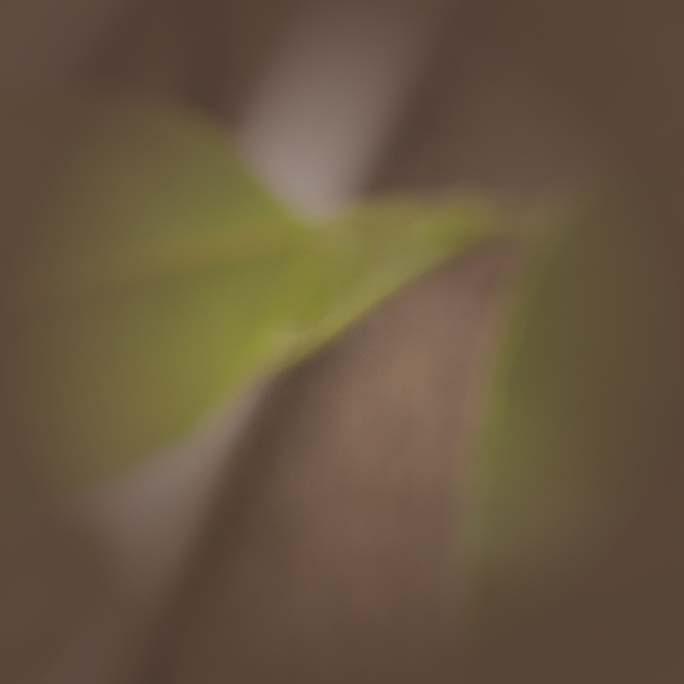
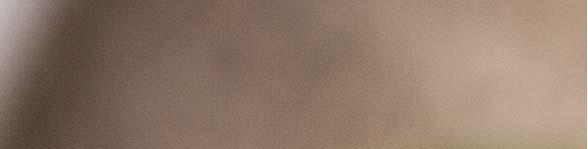

Anna Bashuk, Stamicarbon, the Netherlands, considers how the recycling of precious alloys at urea plants is helping the European fertilizer and steelmaking industries contribute together to the EU’s target of climate neutrality by 2050.
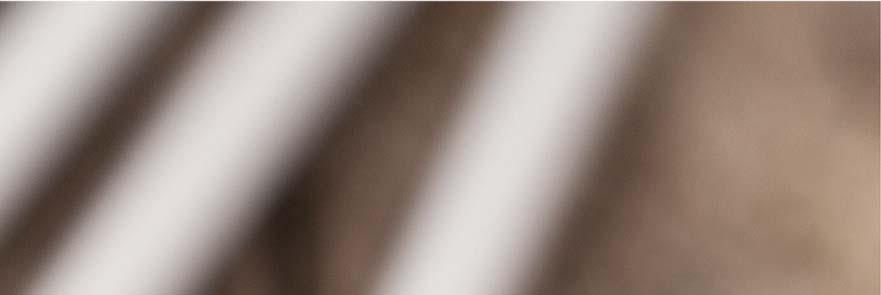
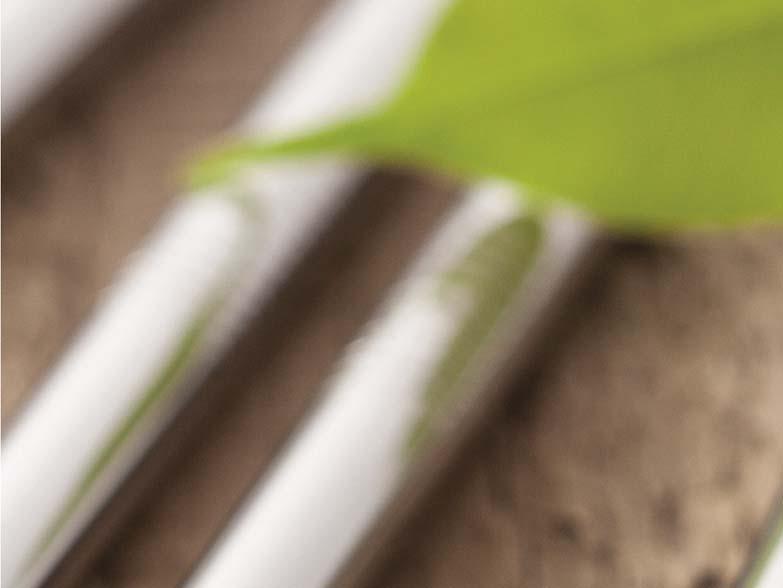
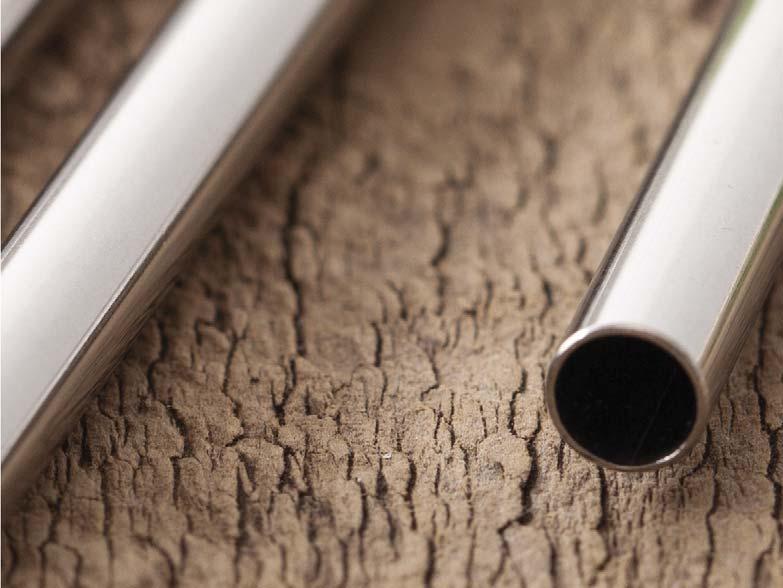
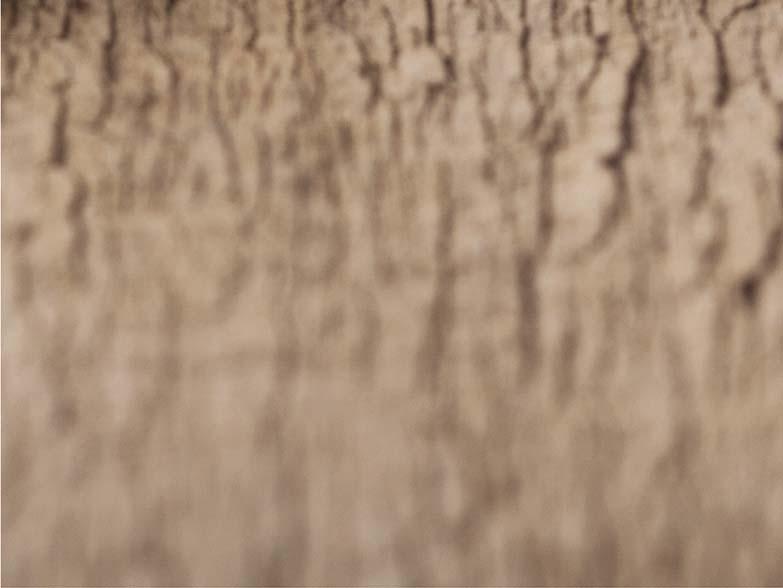
The programme is designed to make it easier for urea customers to dispose of old equipment and piping, which is otherwise a complicated and costly procedure. Instead of making their way to the scrapyard, precious alloys are collected and recycled in the manufacturing of steels that meet the demands of urea processes. To achieve the right material composition in a new melt, virgin alloys must be added. Naturally, the percentage of virgin raw material depends on the composition of the scrap, and lowering this percentage will contribute to building circularity and reducing the carbon footprint of both steel manufacturers and fertilizer producers. When the two companies considered the process of designing this ecosystem, or circular system, they looked at the best steel that they could obtain: steel that they already knew the composition of. Consequently, the next time the same steel is made, the right composition is almost ready from the start in that secondary raw material. An ecosystem, or a closed loop, is thus created – not very common in these types of industries.
The programme is an addition to their full lifecycle services, and started with the purchase of the Safurex high-pressure stripper heat exchanger tubes from a urea plant in the Netherlands in 2019 (Figures 1 and 2). The buy-back offer is now included in revamping packages for Stamicarbon’s customers when replacing old equipment in their fertilizer plants. Facilitating the shift towards a more sustainable fertilizer production is a key aim of Stamicarbon’s, and the programme has contributed signifi cantly to improving circularity in both the steel and fertilizer industries.
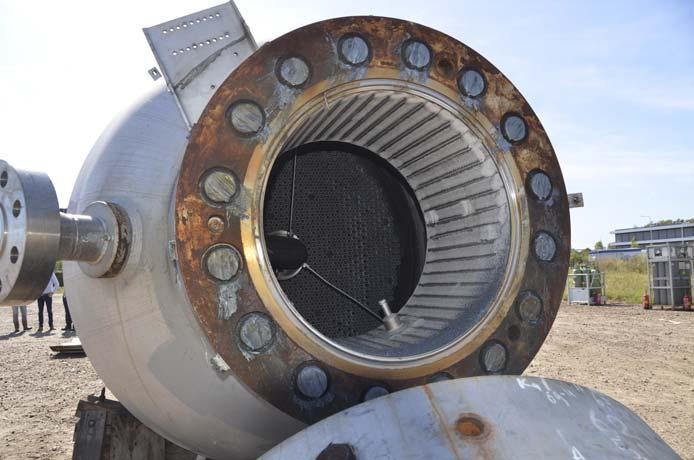
Sustainable materials for urea plants
Figure 1. Decommissioning of a Safurex high-pressure stripper. Urea industry processes are demanding in terms of temperature and pressure, which means that the equipment used has to be manufactured from strong, light and corrosion-resistant materials. Stamicarbon partnered with Sandvik in the 1990s on the development of Safurex, a duplex stainless steel designed to withstand the adverse conditions of the high-pressure synthesis section of the urea plant and the high corrosiveness of ammonium carbamate. Keeping in mind that different pieces of equipment in the high-pressure synthesis section require dedicated material applications to ensure optimal performance, three grades were developed: Safurex INFINITY∞ is the standard super duplex stainless steel used in the high-pressure synthesis section of urea plants, because of its mechanical properties and corrosion resistance. Safurex DEGREE° is a super duplex stainless steel fabricated via the Hot Isostatic Pressing (HIP) method, which enables the enhancement of the material’s mechanical properties at low temperatures (-35˚C). It is used in liquid dividers in the high-pressure stripper to eliminate the risk of cross-cut end attack, as well as the housing of the radar level measurement equipment to eliminate cross-cut end attack in combination with condensation corrosion. Safurex STAR* (Figure 3) is specifically designed for application in demanding equipment, such as heat exchanger tubes in the high-pressure stripper for all stripping processes. It helps to reduce the passive corrosion rate below detectable limits, extend the lifetime of the stripper, lower the need for maintenance and reduce the frequency of eddy current inspections.
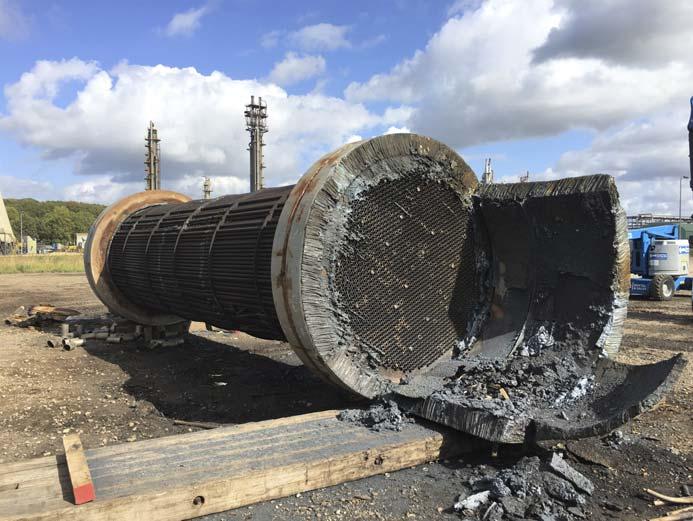
As of now, Stamicarbon has built over 400 pieces of equipment with Safurex and has used it as a standard material for all high-pressure equipment and piping in urea plants designed by the company since 2003. During this time, active corrosion or rupture of Safurex heat exchanger tubes has never been observed. Apart from its durability and corrosion resistance – which are both crucial for ensuring safe and effi cient plant operations – the manufacturing of Safurex is also more sustainable than that of other steels used in urea
Figure 2. Dismantling a Safurex high-pressure stripper.
Figure 3. Safurex STAR heat exchanger tubes.
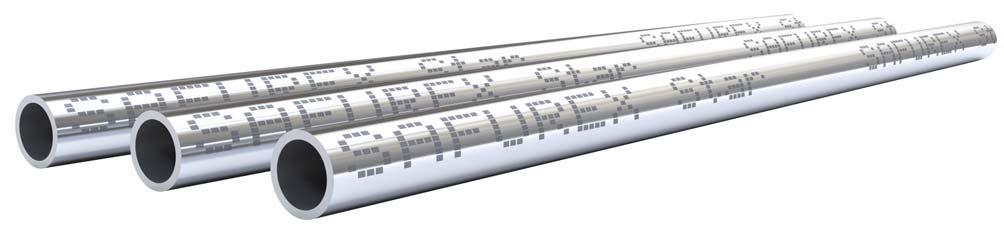
plants, due to a more environmentally friendly heating process and a high percentage of recycled materials used in the melt. In 2020, Sandvik Materials Technology produced 16 heats of Safurex with an average scrap content of 74.6% (72.2 – 79.4%). In 2021, seven heats with an average scrap content of 73.9% (72 – 77%) have been manufactured so far.
Through the use of equipment made of Safurex, it is possible to achieve a 7% reduction in energy consumption for the tube system’s lifetime, or 265 000 t of carbon dioxide (CO2), compared to standard tube materials in urea plants. However, Safurex requires the presence of special alloys such as nickel, chromium and molybdenum in the right composition, which makes it challenging to fi nd enough scrap as feed. Although the percentage of secondary raw material that goes into production is approximately the same as for other duplex steels at Sandvik, more virgin chromium needs to be added due to stricter requirements concerning the purity of the fi nal product. This highlights the importance of the buy-back programme and the need for more collaboration between the fertilizer and steel industries, in order to recover and recycle precious materials.
Sustainable steelmaking
Steel products have a long lifecycle and can be recycled indefi nitely without losing their mechanical properties, so they can be designed for reuse or remanufacture. Sandvik’s use of steel has a recycled component of, on average, 82%, which – while aiming to continuously increase the use of secondary raw material – represents a high sustainability number for the steel industry as a whole; typically the amount of recycled steel in new products averages 37%.1
Sandvik selects secondary raw materials with a chemical composition as close as possible to the fi nal product, and adds raw materials to achieve the desired composition. All materials rejected during production go back into the feed. For high alloy steels, the recycled component could be lower than the average 82%. For low alloy steels, scrap can represent as much as 95 – 97% of the fi nal product.
Once secondary raw material (purchased recycled steel and internal recycled materials rejected in production) is collected, it is charged into an electric arc furnace (EAF) in its metallic form and melted using electricity (Figure 4). Then, its chemistry is checked and virgin metals and alloys are added to reach the required material composition. Unlike the traditional blast furnace-basic oxygen furnace (BF-BOF) steelmaking process – which occupies more than 70% of industrial steel manufacturing2 – EAF is a more carbon-effi cient and thus more future-proof method. As part of the move forward towards a carbon-free society, this process combined with 100% steel scrap feed could lead to a 70% reduction in energy consumption and a 74% reduction in CO2 emissions from the steel industry.3

Figure 4. EAF at Sandvik Materials Technology’s Sandviken site.
Why this matters
Traditionally, neither steelmaking nor the fertilizer industry have been considered sustainable, and both sectors need to reduce their CO2 emissions signifi cantly to make their processes more future-proof. To help accelerate the change, Stamicarbon is also participating in an EU-funded project called ‘INITIATE’ (Innovative industrial transformation of the steel and chemical industries of Europe), a novel symbiotic and circular process that transforms residual steel gases into feedstock for urea production. Carbon-rich off-gases from steel mills will be captured using modular carbon capture utilisation and storage (CCUS) technology, which integrates the fl exible conditioning of steel gases with ammonia synthesis.
The global sustainability shift means that the steel industry will need to embrace sustainable practices where possible in the future, and building more circularity through reuse and recycling of materials is an important step on this journey. Moving forward towards a carbon-free society, the shift away from conventional industrial steelmaking processes and increased use of recycled materials can help reduce CO2 and NOX emissions by the industry, while also positively affecting water and energy use indicators. As international commitments and legislation on climate drive the need for the industry to catch up, these factors will play a critical role in addressing the sustainability challenge and moving closer to achieving the EU target of net zero emissions by 2050.
References
1. World Steel Association, ‘Steel Recycling’, https://www.worldsteel. org/steel-by-topic/sustainability/materiality-assessment/recycling. html 2. International Energy Agency, ‘Global crude steel production by process route and scenario, 2019-2050’, https://www.iea.org/dataand-statistics/charts/global-crude-steel-production-by-processroute-and-scenario-2019-2050 3. MADEDDU, S., UECKERDT, F., PEHL, M., PETERSEIM, J., LORD, M.,
KUMAR, K.A., KRÜGER, C., and LUDERER, G., ‘The CO2 reduction potential for the European industry via direct electrification of heat supply (power-to-heat)’, Environmental Research Letters, Vol. 15,
No. 12, https://doi.org/10.1088/1748-9326/abbd02