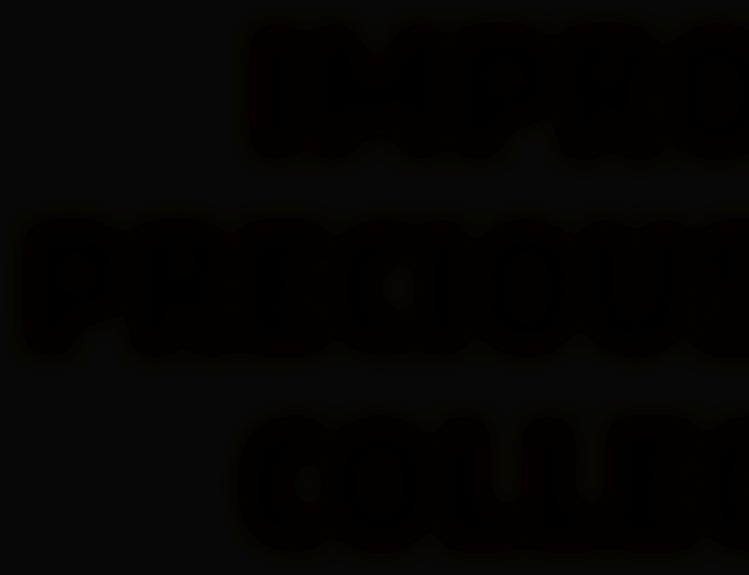
8 minute read
Improving Precious Metal Collection
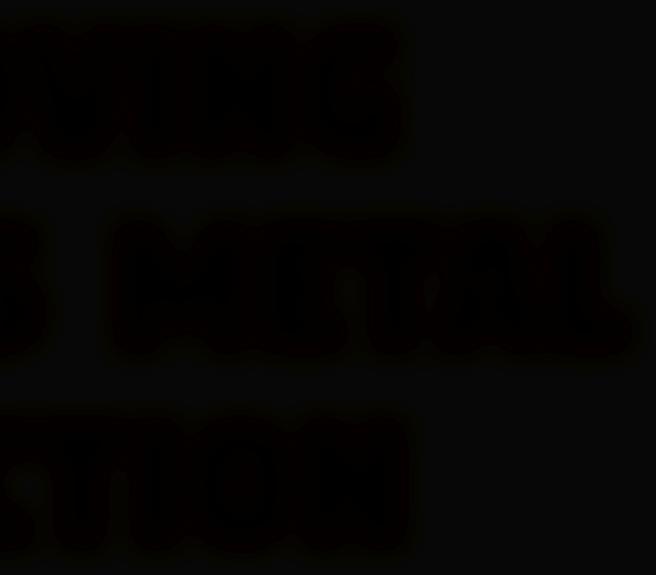
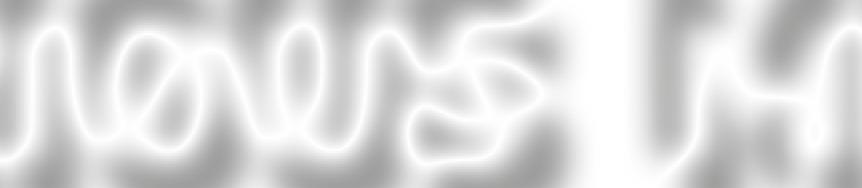
Chris Brown, K.A. Rasmussen, Norway, David Horbury, URSG, Europe, and Michael Schriner, URSG, USA, examine the available methods for precious metal recovery and recycling in nitric acid plants.
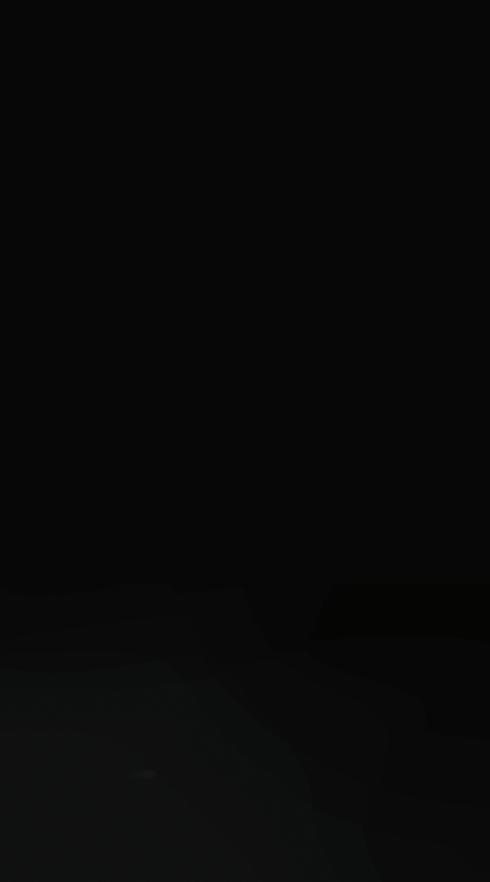
Precious metals, by their nature, are rare and there are a limited number of accessible areas around the world where they can be viably extracted. Precious metals are important for various reasons, including their array of special properties essential for many industrial processes, emissions reduction catalysts, bullion, investments and high-value jewellery. The properties of precious metals allow them to be used as inert, long lasting materials, often in harsh industrial environments as well as precision measuring instruments, sensors and high-tech catalysts.
Over recent years, supply and demand dynamics have highlighted the sensitivity of precious metals, reflected most noticeably in their market pricing. The importance of recycling as a prerequisite for securing raw materials has always been a strong part of working with precious metals, and events in recent years have reiterated the importance now and for the future from around the world.
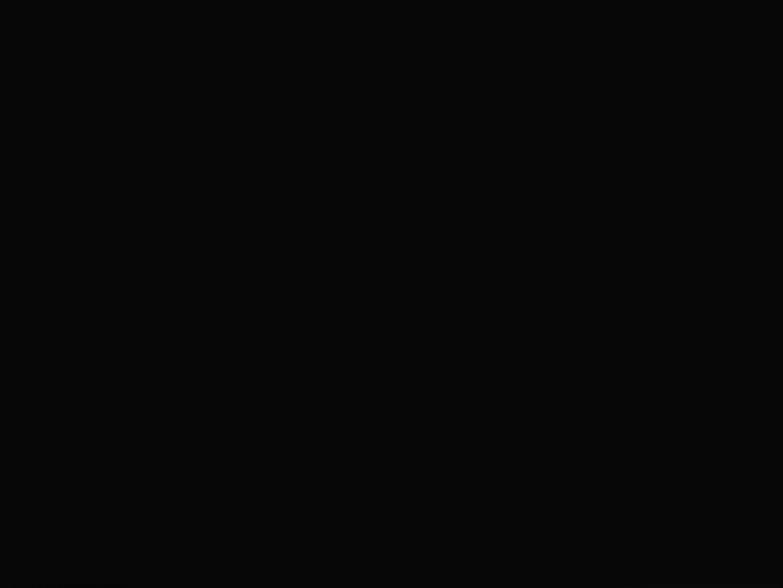
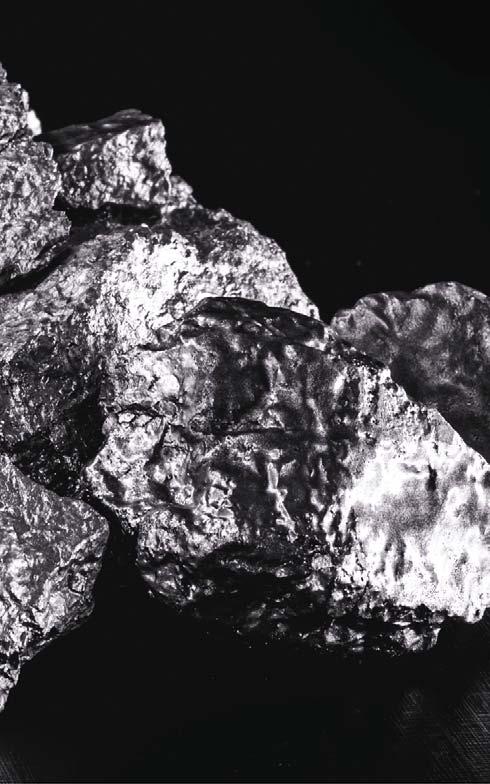
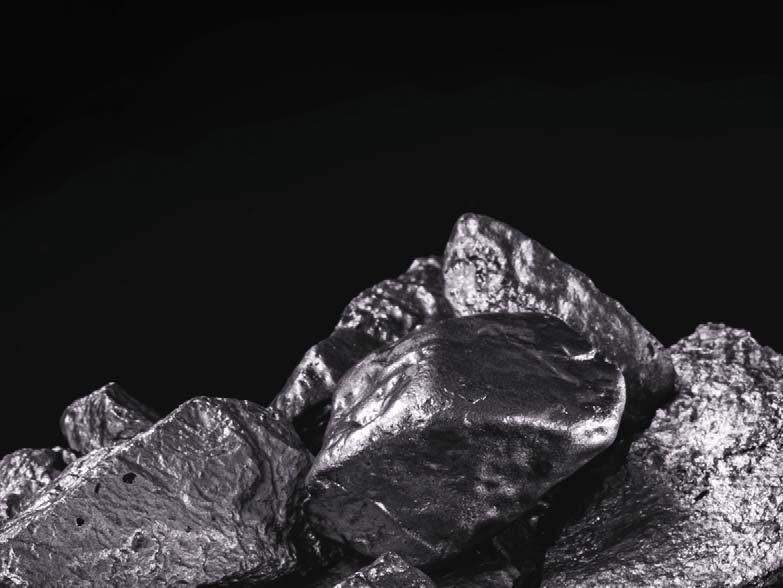
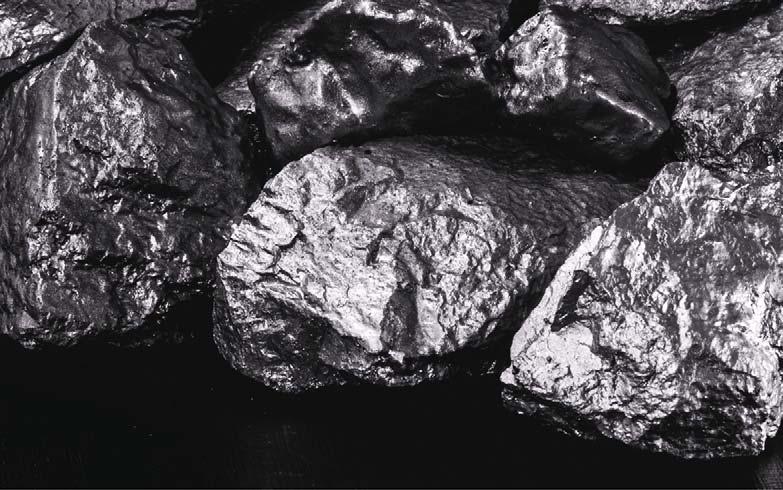
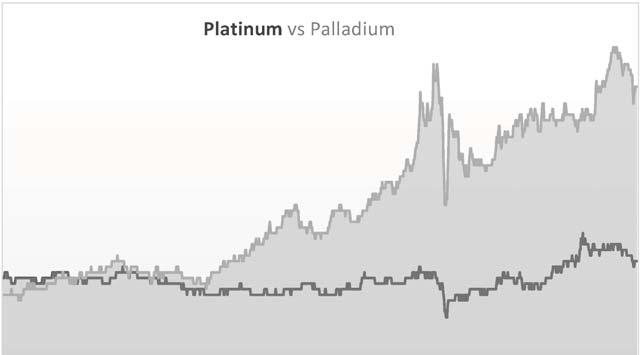
Figure 1. Chart highlighting the recent divergence of platinum versus palladium market prices.
Figure 2. Chart indicating the recent rhodium market price volatility.

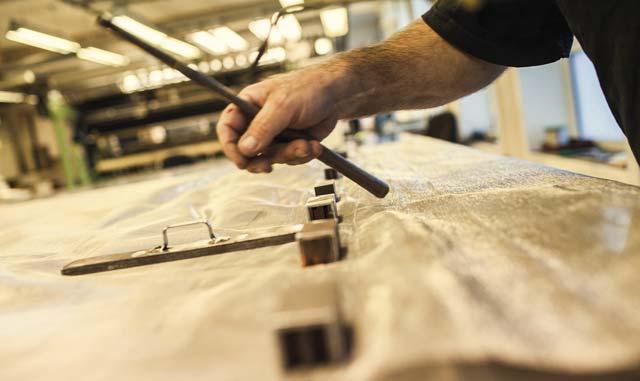
Figure 3. A precious metal catalyst gauze.
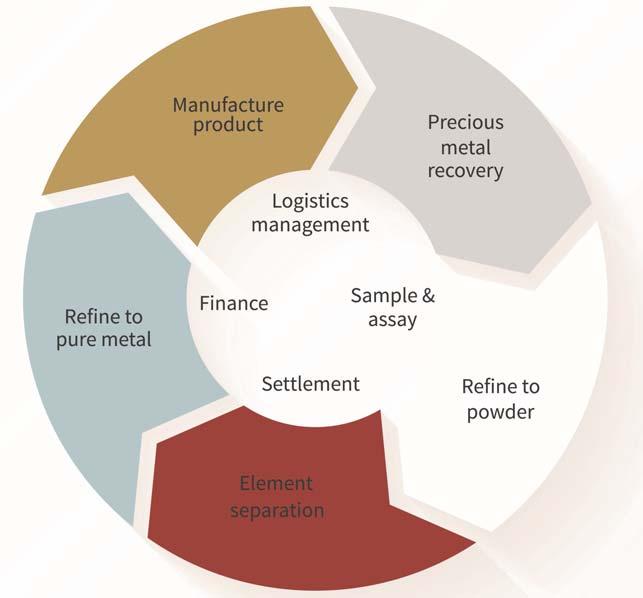
Figure 4. Precious metal recycling. The recycling journey for precious metals after they have been mined encompasses all the key aspects of good recycling practices. The use of precious metals catalysts in the production of nitrogen-based fertilizers via nitric acid production (Ostwald process) is a prime example of where full-circle recycling can be applied to precious metals, reducing the quantity of new metals required from mines around the world.
Precious metal gauzes are high-efficiency catalysts used to ensure the efficient running of the industrial plants in which they are installed, enabling companies to minimise the use of ammonia, a valuable ingredient in the production of nitrogen-based fertilizers. During the production process, precious metals volatilise (evaporate) from the gauzes and can be deposited through the heat-train and equipment in the plant.
There are a number of approaches to recovering the deposited precious metals, and innovations have enabled safer, sustainable and more environmentally-friendly processes to be used.
Once materials have been collected from the plants, they need to be transported to a precious metals refinery, fulfilling any appropriate legislation where the next stages of recycling begin. In order to refine, separate and purify the precious metals from the recovered materials, a number of technology steps are needed. Once the processes are complete, elemental precious metals can be used to create the pure metal alloys needed to manufacture new gauzes and start the cycle again.
Optimising collection methods for precious metals
Nitric acid plants operate with different ammonia oxidation pressures, temperatures and nitrogen loading, depending on the type, size and production rate of the plant. All of these variables affect the quantity of precious metals evaporating from the gauzes during plant operation, and optimising the recovery of these metals is therefore specific to the plant’s operating conditions. Platinum can be recovered using palladium gauzes below the catalyst as part of the platinum group metals system, with the advantage that captured platinum can be recycled regularly and the quantity of platinum progressing downstream into the heat-train of the plant is therefore reduced. In plants where getters are less frequently used, other technologies exist which – for high-pressure/high-loading plants – may include the use of hot-gas filters to collect precious metals lost from the catalyst gauzes during operation and also provide a method of regularly recovering precious metals.
Some precious metals are known to continue further downstream and recoveries can be achieved using in-line liquid filter systems. However, over time precious metals can also build up in storage tanks or other vessels in the plant. Recovery and recycling of precious metals from storage tanks requires careful planning to ensure the environment of the tank is carefully controlled to allow tasks to be executed safely using appropriate methods and safety equipment.
There are a variety of designs of storage tank and, over time, some tanks can accumulate good quantities of precious metals which can be a valuable source for recycling.
Plant cleaning operations – what, why and how often
Traditionally, plant cleaning operations focused primarily on precious metals recovery from the heat-train equipment and were planned relatively infrequently. However, with the focus of recycling and sustainability at the forefront of business culture, it is important to consider the other effects of plant cleaning and how the results are achieved.
By cleaning the plant, precious metals are recovered from the pipes and exposed surfaces of heat exchangers, which can allow the plant to increase its thermal efficiency.
Thermal efficiency is important because not only does it help capture energy; in certain circumstances it may prolong the life of equipment or potentially reduce the quantity or frequency of tube failures in exchangers due to operational temperatures. This is an area which would need careful analysis, and should include a review of heat generation and thermal efficiency of heat exchangers that considers design capacities and production outputs to ensure the heat exchangers are operating effectively. An interesting area for discussion is whether plants should be cleaned for either recovery of precious metals or for thermal efficiency, or for both.
Further to onsite plant cleaning and precious metals recovery operations, end of life heat-train equipment can yield significant quantities of precious metals by destructive recovery processes, beneficial for recycling. In addition, steels are also recycled, yielding value to clients as well as maximising the recycling of materials. A key component of a nitric acid plant is the absorber, which dissolves the nitrogen dioxide (NO2) gas with water to produce nitric acid of various strengths, depending on the plant and downstream requirements. It is possible to recover precious metals from the absorber, although quantities and accessibility are plant-dependent, and it would be recommended to review this as part of a plant overhaul where other precious metals recovery activities are taking place.
Maintaining the good condition of absorption columns can achieve a number of positive results, which include improved production volumes but also reduced emissions. Aside from the engineering aspects of maintaining the absorber, benefits can be achieved by taking actions to ensure good water flow is achieved; significant improvements are possible, especially in warmer conditions.
In addition to the cost of precious metals and the available benefits of recycling, as we look to a future where the cost of energy and emissions may increase, the topic of maximising energy efficiency is likely to be a strong consideration along with available


Helping them grow!
Fertilizing Expertise. Technologies and Equipment to meet your needs.
GEA provides process solutions for a sustainable and cost-eff ective fertilizer production.
Our solid know-how supports you every step of the process with profi cient unit operations:
• evaporation and crystallization • centrifugal separation • drying (rotary and fl uid bed dryer) • solid cooling (contact fl uidizer and cooler) • rotary granulation and coating • dedusting (bag fi lter and wet scrubbing)
With customer-tailored service and in-house testing facilities at your disposal, your performance and productivity are our priority here at GEA.
Get in touch today at gea.com/contact
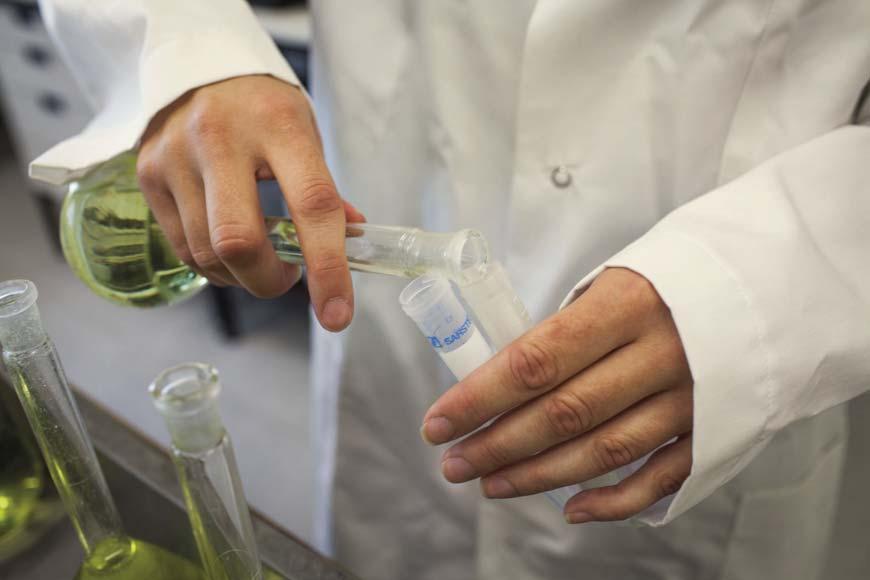
Figure 5. Precious metal laboratory analysis.
methods to sustainably achieve the desired results, whilst minimising risks to the plant, personnel, equipment and the environment.
Precious metal management – best practice strategies
In order to maximise the recycling and recovery of precious metals for all of the methods described, best practice metals management strategies should be employed at all times.
Best practice strategies for precious metal management apply in a wide range of scenarios, for example: Handling and packaging during the removal of gauzes and hot-gas filters. End-of-life equipment, during removal from plant, transport, dismantling and processing. Handling and refining operations, including batch separation and traceability at the precious metals refinery. To ensure metals are assayed accurately and maximum recovery is achieved, materials should be evaluated prior to the refining process and treated with great care and attention.
The results achieved by planning, developing and integrating best practice strategies can make a valuable difference to the recovery of precious metals, increasing the proportion of recycled metals used in manufacturing and working towards achieving the long-term sustainability goals of the industry.
PROCESS CONTROL IN REAL TIME
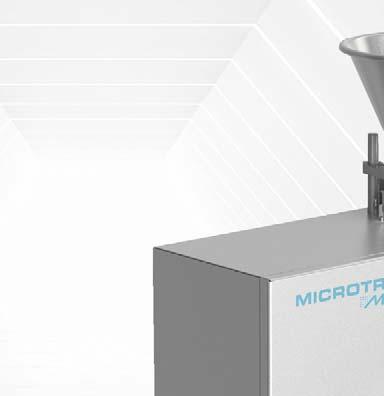
Meet us at SFPT Forum 20 - 23 Sept.
CAMSIZER® Online stands for fast and reproducible in-process particle characterization based on Dynamic Image Analysis.
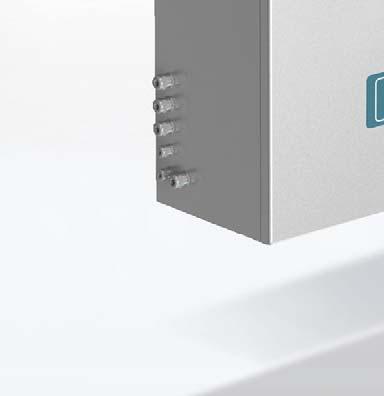
Your benefits:
I Online system for process integration with 3rd party sample feed systems I Measuring range: 22 μm - 35 mm I Self-cleaning
WATCH VIDEO OF ONLINE ANALYSIS OF FERTILIZERS WITH CAMSIZER ONLINE!
