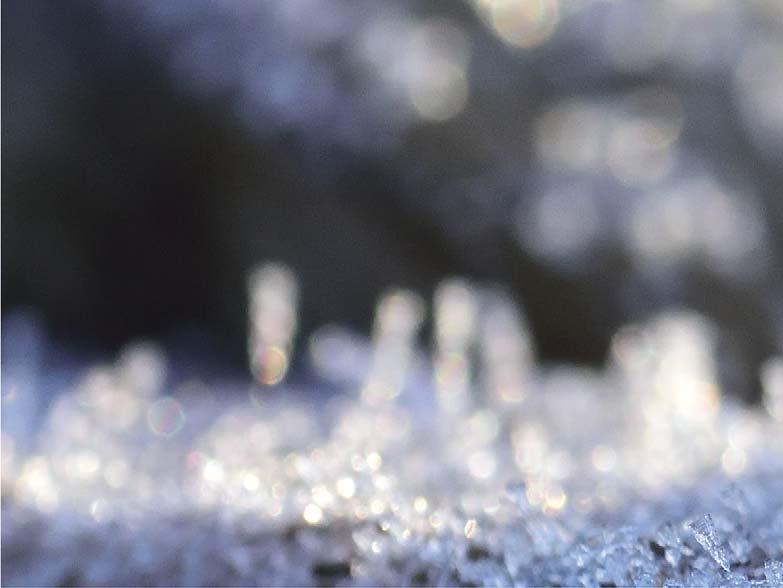
11 minute read
Strength In Uniformity


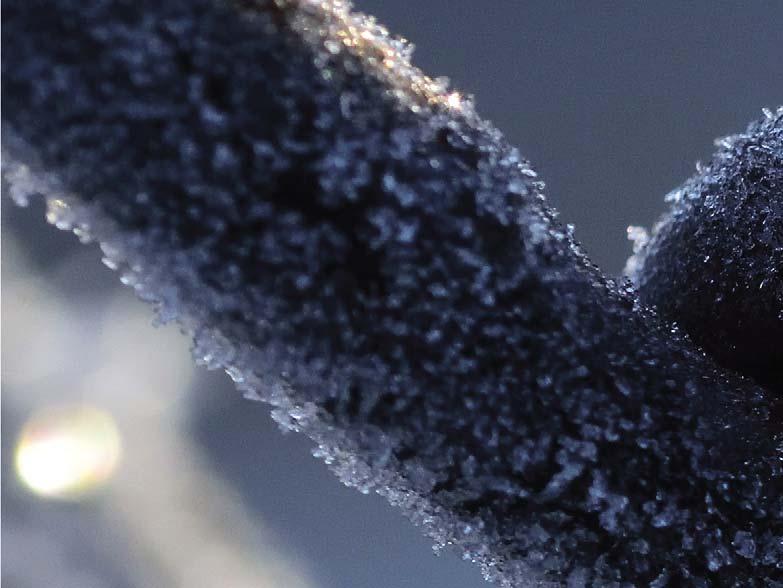
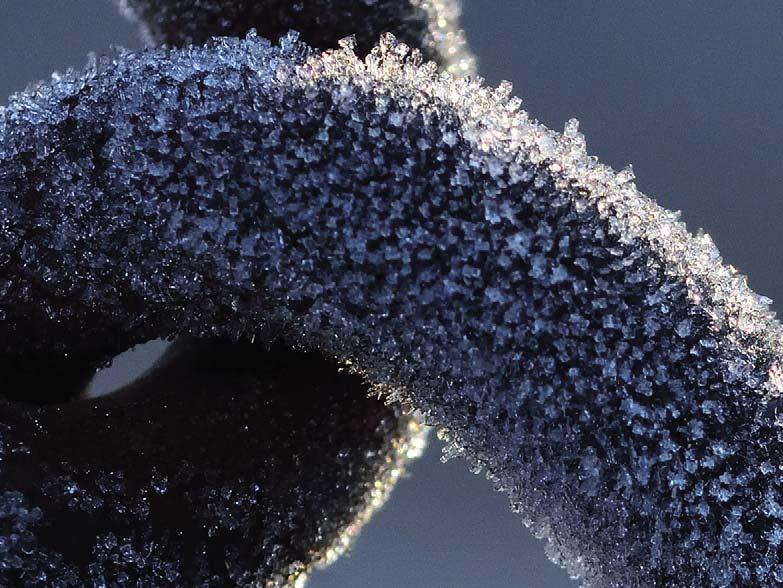

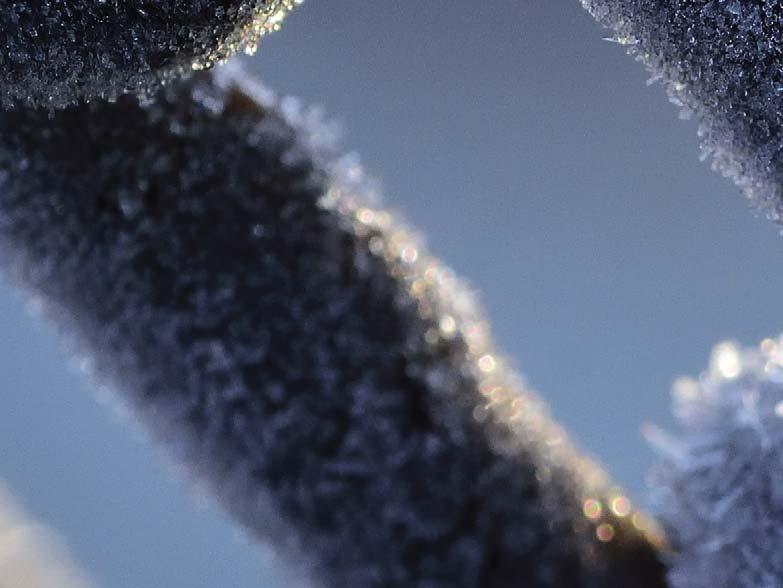
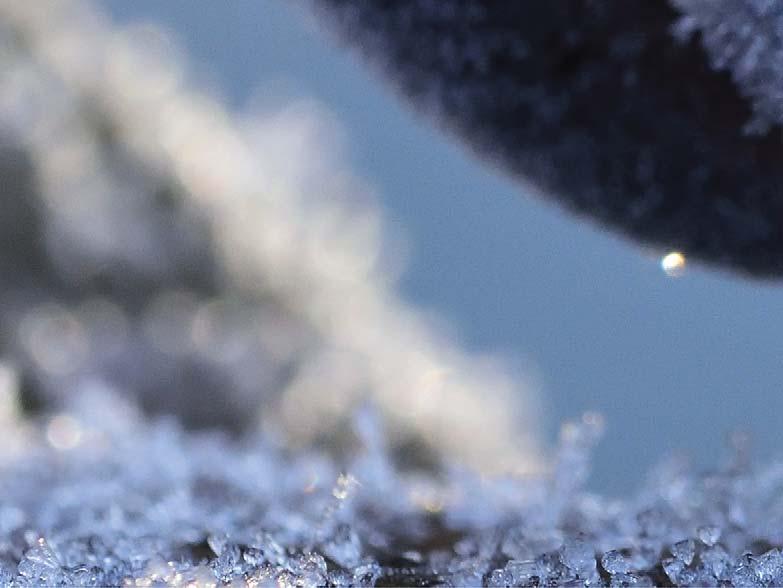
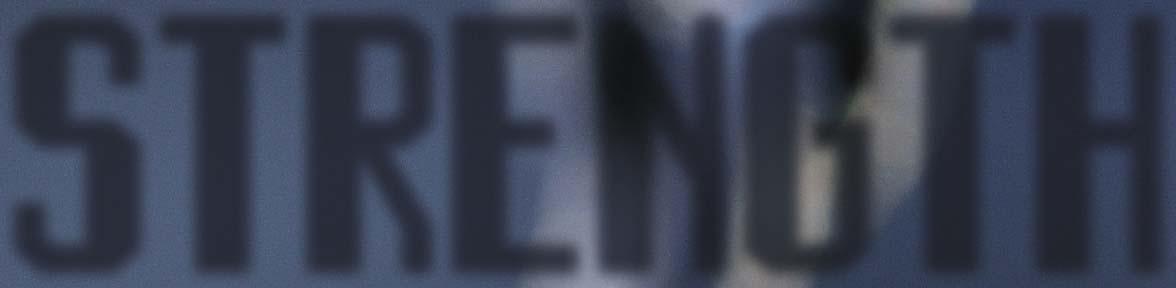
STRENGTH


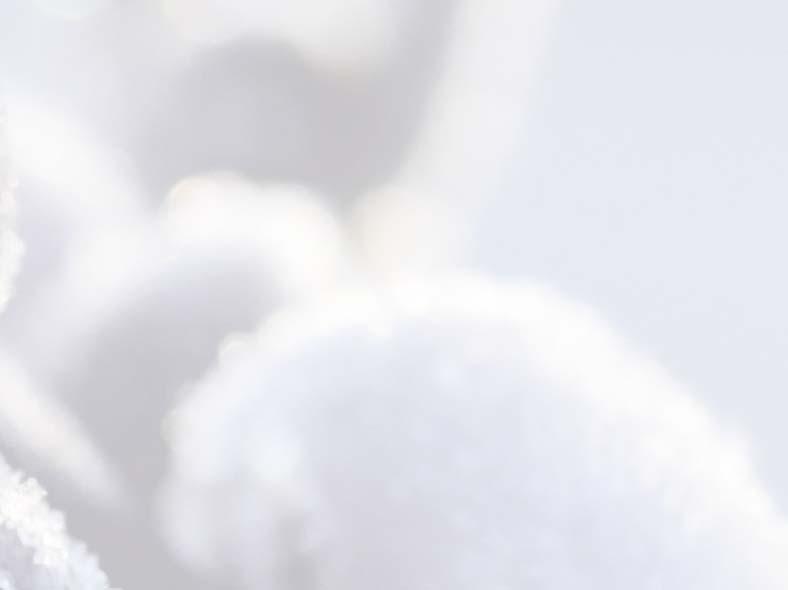
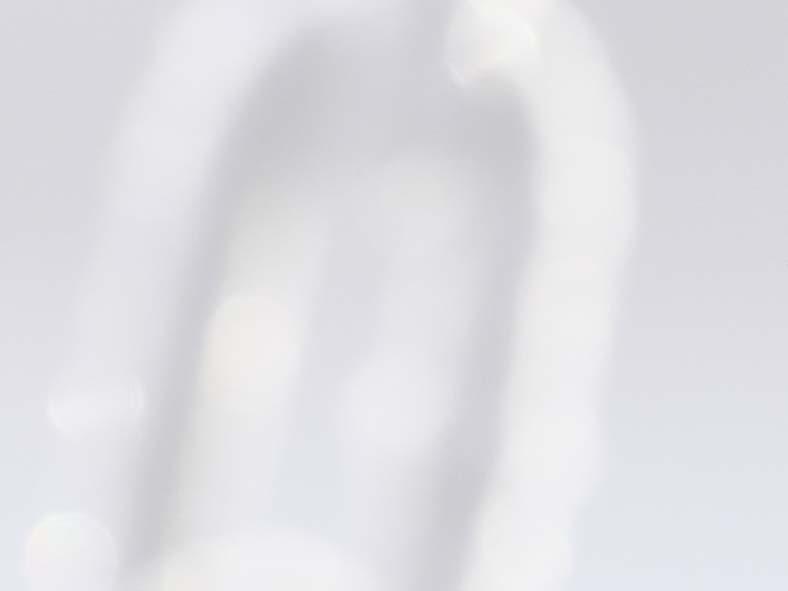

Christina M. Konecki, Arkema-ArrMaz, USA, examines the additives that can be deployed by producers to maintain uniform granule integrity across the fertilizer supply chain.
n the fertilizer industry, producers strive to make a high-quality
Ifertilizer product that maintains granule integrity from manufacturing to application on the farm. Unlike some commodity products, fertilizers are often transported and handled multiple times before arriving in the hands of the end user. There are many stops along the supply chain where fertilizer must continue to maintain its granule size and integrity. Some of the physical properties of fertilizer that are monitored and used to assess performance by the industry include granule size, density, porosity, moisture uptake, nutrient release profi le, dust, caking susceptibility and granule strength.
Types of granular fertilizer
Granulation is a process that helps produce a high-quality granular product that has less dust and tighter particle size distribution in the fi nal fertilizer. Depending on the method of granulation used, the resulting product may be defi ned as one of the following:
Prills
Prills are formed via solidifi ed droplets of molten fertilizer solution. During this process the molten fertilizer is dropped from a height in a tower with upward air fl ow to facilitate the drying process.1 This method is common for urea, ammonium nitrate (Figure 1a) and some NPK grades, and produces smooth spherical particles.
Granules
Granular fertilizer is produced through the agglomeration of layers of liquid or slurry material to form a particle. Each layer solidifi es from crystallisation or drying, producing relatively spherical particles that are not as smooth as prills. A typical granular fertilizer is diammonium phosphate (DAP), as shown in Figure 1b.
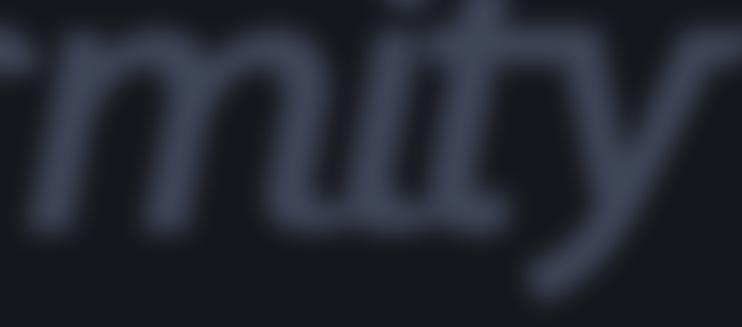



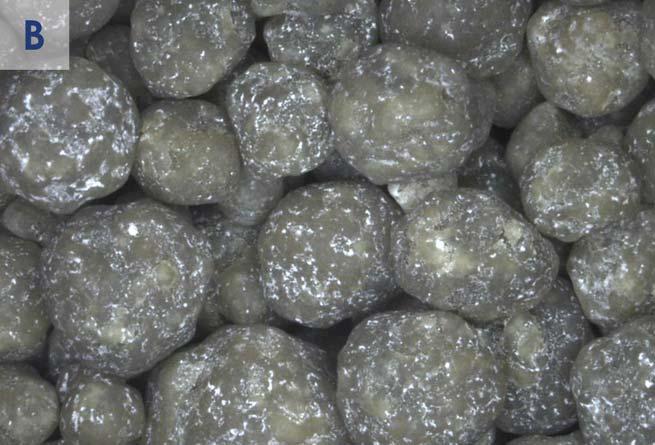

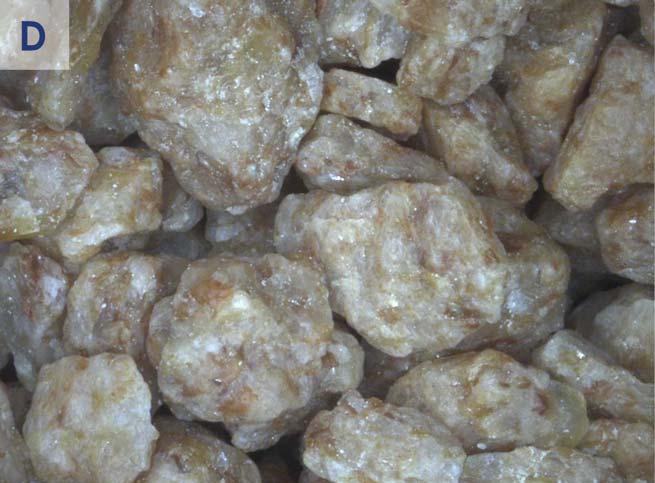
Figure 1. Arkema-ArrMaz laboratory microscope images at 25x of (a) prilled ammonium nitrate, (b) granulated DAP, (c) crystalline ammonium sulfate and (d) compacted MOP. Crystalline fertilizer is not spherical but resembles the shape of salt or sugar crystals that have sharp edges and fl at sides. The crystals are formed from a saturated solution where water is removed. Larger particles formed during this process are screened out and referred to as granules.1 Typical crystallised fertilizer is ammonium sulfate (Figure 1c) and some muriate of potash (MOP).
Compacted particles
Compacted fertilizer is formed from crushing down on a pressed sheet of material, resulting in irregular sized particles.1 Typical compacted fertilizer includes some MOP (Figure 1d).
Granulation processes
The most common granulation processes are rotating drum, fl uidised bed and high shear mixing.2,3
Rotating drum
A rotary drum mixer can be used with either dry feed or a slurry of fertilizer material. In the case of dry feed, water is sprayed onto the material to produce wet, granular material that is tumbled in a rotating drum, where a binder may be added. As the particles become tacky they agglomerate, resulting in larger granules.4
Fluidised bed
Fluidised bed granulation is a process whereby an air stream is used to suspend particles while spraying liquid onto the particles. Once the particles have reached the proper level of moisture, the agglomeration of particles begins to form granules.5,6
High shear mixing
High shear mixing is a process whereby a liquid binder is applied to dry material that is exposed to aggressive mixing, either from the top or bottom. Similar to other techniques, the tacky particles agglomerate as the material is mixed to form granules.7
Granulation aids
While optimising the fertilizer manufacturing process can improve some or all granule performance metrics, it is often necessary to use granulation aids or coating agents to further enhance and maintain granule integrity throughout the entire fertilizer supply chain.
Granulation aids, such as the additives (binders) in Arkema-ArrMaz’s Granulaid product line, are designed to promote rapid and uniform granulation formation, which is critical for effi cient, high-quality fertilizer production. They can improve the hardness and crush strength of granules, and can also provide the added benefi ts of dust and moisture reduction, enabling granules to maintain their shape and size throughout the fertilizer supply chain. Today, biodegradable options are also available to meet sustainability requirements.
During granulation, binders can be used to promote better agglomeration of the fertilizer substrate. Binders can be incorporated during both wet and dry granulation. Wet granulation incorporates water and the binding agent to alter the viscosity of the fertilizer slurry and promote coalescence of the substrate. In wet granulation there are three key stages of granule/pellet growth.6,8
This stage describes the start of the granulation process, where seed granules are used to initiate the process. In continuous granulation the undersized and crushed oversized granules are recycled in the process and used as seed granules.2 During this process, the fertilizer substrate is typically misted with water and/or a binder solution to create an environment that promotes fertilizer-liquid interactions. The resulting viscosity, surface tension and mixing method altogether impact binder distribution.9
Stage 2 – consolidation and growth
Once the granule begins to form, the process moves to stage 2 – consolidation and growth. The growth of the granule occurs with the addition of layers onto the seed or by coalescence (agglomeration of particles).10 The residence time in the mixing vessel also impacts the fi nal size and size distribution of the fertilizer. This stage encompasses the breakage of wet or dry granules through some form of impact.8
Classes of binders
During granulation, binders promote adhesion through spreading in the mobile phase, creating liquid bridges that strengthen during the drying or cooling process.11,12
There are several classes of binders that are typically used in the industry today, including starches, sugars, lignosulfonates and polymers. Granulaid binders were developed to help fertilizer producers improve the starting integrity of their product. They are custom-tailored to provide different levels of granule hardness – even following exposure to high humidity – and are customised to the inorganic salt combination present. But how can the performance of binders, such as those included in the Granulaid product line, be effectively measured?

Figure 2. SSP with 0.5 wt% binder.
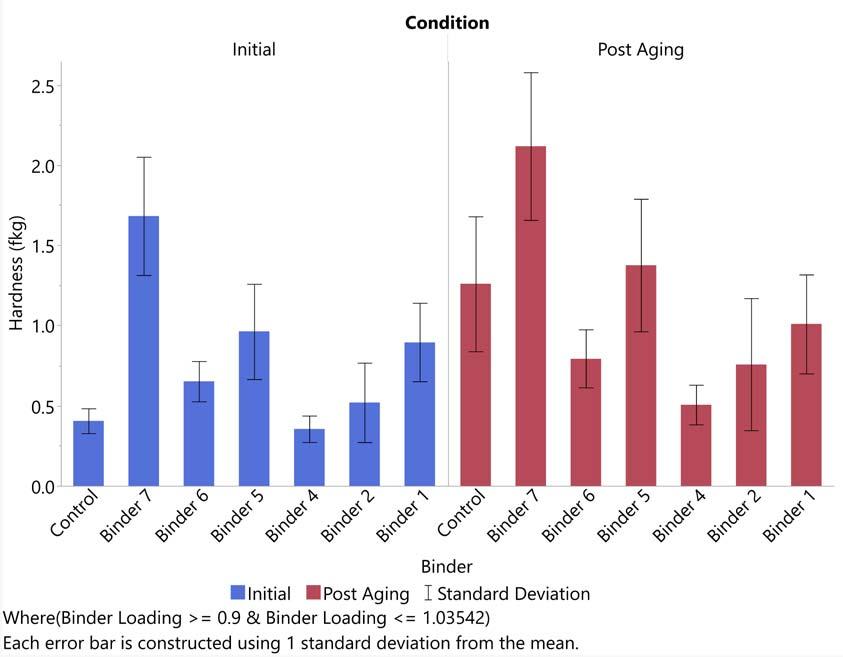
Figure 3. SSP/TSP/Calcite 0.9 wt% loading.
Measuring performance
One way to evaluate the effi cacy of the granulation process is to measure granule hardness. If the granule is strong enough to resist breakage during transportation and handling, there will be less dust and hence reduced losses of the fi nished product. To evaluate the effectiveness of Granulaid binders, Arkema-ArrMaz evaluated three fertilizer types – SSP, an SSP/TSP/Calcite Blend and a urea-based NPK – made with experimental binders. Pellets were produced by combining fertilizer powder with water and the binder agent, and then extruding into 4 mm thick pellets. Once the pellets were dry, an initial hardness value was collected (Figures 2 – 5).
To evaluate the performance of the binder further, the pellets were exposed to 30˚C and 65% relative humidity (RH) for 3 hours and then allowed to dry; the results are represented in Figures 2 – 5 as ‘Post Aging’. The control group for all fertilizers was water. Overall, binders 1 – 7 were evaluated and the effi cacy was dependent on the substrate to be bound. Granule hardness is presented as the average force required to break 30 granules, measured as kg of force. It should also be stated that the laboratory method typically produces a higher break strength than what is experienced in the fi eld, although performance trends have been proven to scale up into plants.
SSP was evaluated with a dry binder content of 0.5 wt% (Figure 2). On initial pellet hardness, binders 5 and 6 showed improvement over water. After ageing, binders 1, 4, 5 and 6 all yielded pellets with increased granule hardness. Binder 6 showed an initial hardness improvement of 20% and, after ageing, continued to improve pellet strength by 115% compared to the control.
When looking at the SSP/TSP/Calcite blend, binder 6 was not effective at improving pellet strength post-ageing (Figure 3). However, binders 5 and 7 improved initial and post-ageing strength at both 0.9 and 1.8 wt% binder loading (Figures 3 and 4). While the improved strength is good at 0.9 wt%, the strength improvement of the blend signifi cantly
increased when binder loading was increased. The initial strength was greater than 700% and post-ageing strength was greater than 100% with the binder content of 1.8 wt%. This fertilizer blend illustrates that while one binder may work well on an individual component, when substrates are blended into one pellet/granule a different binding agent could prove more effective. In addition, binder loading can have a signifi cant impact on granule strength. When considering a binder that is already in use or when evaluating new binders, binder type and loading will be critical in determining the true effi cacy of the product.
The last fertilizer type evaluated was a urea-based NPK (25-00-16-0.67), which had a binder loading of 2.25 wt% (Figure 5). The NPK trended the same as SSP, where binders 5 and 6 were very effective granule-strengthening agents. Both binders improved the pellet strength by over 600% compared to the control, regardless of condition.
Summary
Fertilizer producers are being challenged to manufacture high-quality fertilizer products that maintain granule integrity across the fertilizer supply chain. Granulation aids, such as binders, are often needed to enhance and maintain granule integrity from production to fi eld application. There are multiple factors that must be considered when selecting a binder for the granulation process, including: Type of fertilizer substrate. Loading level. Binder type. Manufacturing capabilities.
It is important to work closely with a granulation aid formulator, such as Arkema-ArrMaz, to receive specifi c product recommendations, screen all available product options to identify the best performing binder for a given substrate and benefi t from technical support to further optimise the granulation process in the manufacturing facility.
References
1. United Nations Industrial Development Organization (UNIDO) and
International Fertilizer Development Center (IFDC), Fertilizer Manual (1998).
2. RAMACHANDRAN, R., POON, J. M-H., SANDERS, C.F.W.,
GLASER, T., IMMANUEL, C.D., DOYLE, F.J., LITSTER,
J.D., STEPANEK, F., WANG, F-Y., and CAMERON, I.T.,
‘Experimental studies on distributions of granule size, binder content and porosity in batch drum granulation:
Inferences on process modeling requirements and process sensitivities’, Powder Technology, Vol. 188,
No. 2 (December 2008), pp. 89 – 101. 3. RODRIGUES, R.F., LEITE, S.R., SANTOS, D.A., and
BARROZO, M.A.S., ‘Drum granulation of single super phosphate fertilizer: Effect of process variables and optimization’, Powder Technology, Vol. 321 (November 2017), pp. 251 – 258. 4. FEECO International, ‘FEECO Granulation Drums’ https://feeco.com/granulation-drums/ (Accessed 8 June 2021). 5. Spraying Systems Co., ‘Fluid Bed Processing’ https:// www.spray.com/-/media/dam/industrial/usa/salesmaterial/catalog/c12b_pharm_fluid-bed-processing. pdf (Accessed 8 June 2021). 6. BURGGRAEVE, A., MONTEYNE, T., VERVAET, C.,
REMON, J.P., and DE BEER, T., ‘Process analytical tools for monitoring, understanding, and control of pharmaceutical fluidized bed granulation: A review’, European Journal of Pharmaceutics and
Biopharmaceutics, Vol. 83 (January 2013), pp. 2 – 15. 7. Glatt GmbH, ‘High shear granulation’, https://www. glatt.com/en/processes/granulation/high-sheargranulation/ (Accessed 8 June 2021). 8. IVESON, S.M., LITSTER, J.D., HAPGOOD, K., and ENNIS,
B.J., ‘Nucleation, growth and breakage phenomena in agitated wet granulation process: a review’, Powder
Technology, Vol. 117, No. 1 – 2 (June 2001), pp. 3 – 39. 9. XUE, B.C., LIU, T., HUANG, H., and LIU, E.B., ‘The effect of the intimate structure of the solid binder on material viscosity during drum granulation’, Powder
Technology, Vol. 253 (February 2014), pp. 584 – 589. 10. ADETAYO, A.A., LITSTER, J.D., and DESAI, M., ‘The effect of process parameters on drum granulation of fertilizers with borad size distributions’,
Chemical Engineering Science, Vol. 48, No. 23 (1993), pp. 3951 – 3961. 11. TARDOS, G.I., IRFAN KHAN, M., and MORT, P.R.,
‘Critical parameters and limiting conditions in binder granulation of fine powders’, Powder Technology,
Vol. 94, No. 3 (December 1997), pp. 245 – 258. 12. SIMONS, S.J.R., ROSSETTI, D., PAGLIAI, P., WARD, R., and FITZPATRICK, S., ‘The relationship between surface properties and binder performance in granulation’,
Chemical Engineering Science, Vol. 60, No. 14 (July 2005), pp. 4055 – 4060.

Figure 4. SSP/TSP/Calcite 1.8 wt% loading.

Figure 5. Urea-based NPK 2.25 wt% loading.