
7 minute read
Relying On Rugged Flame Detection
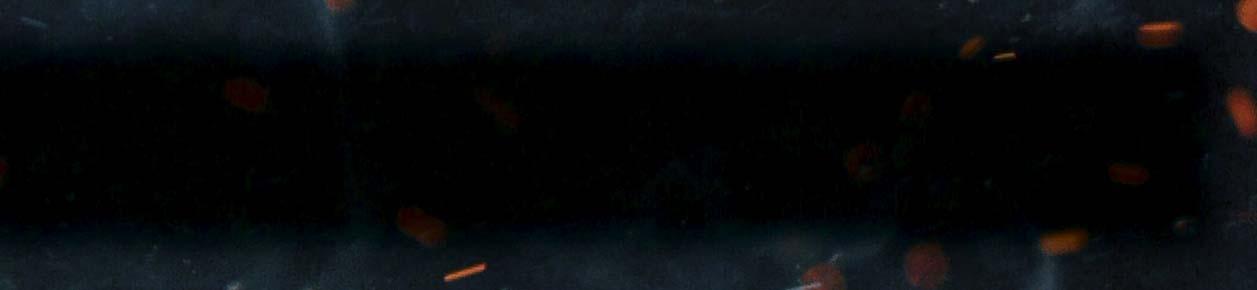
RELYING ON
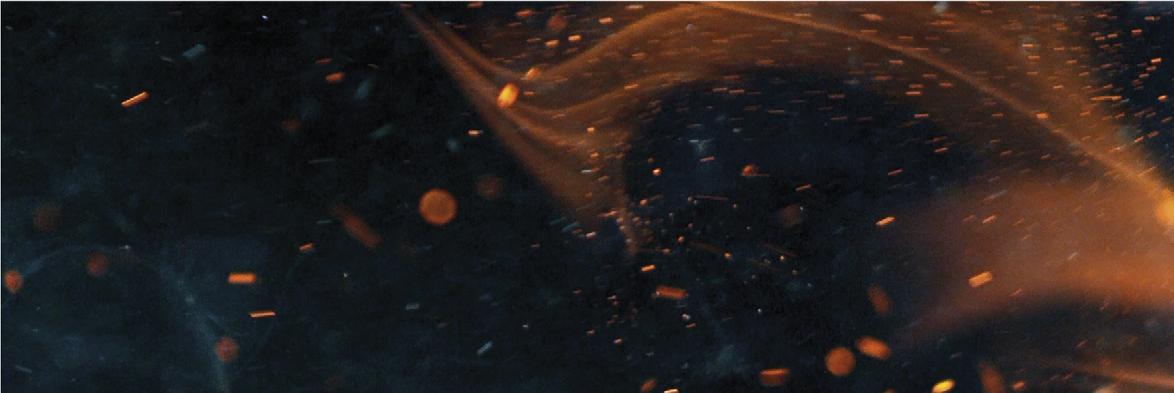

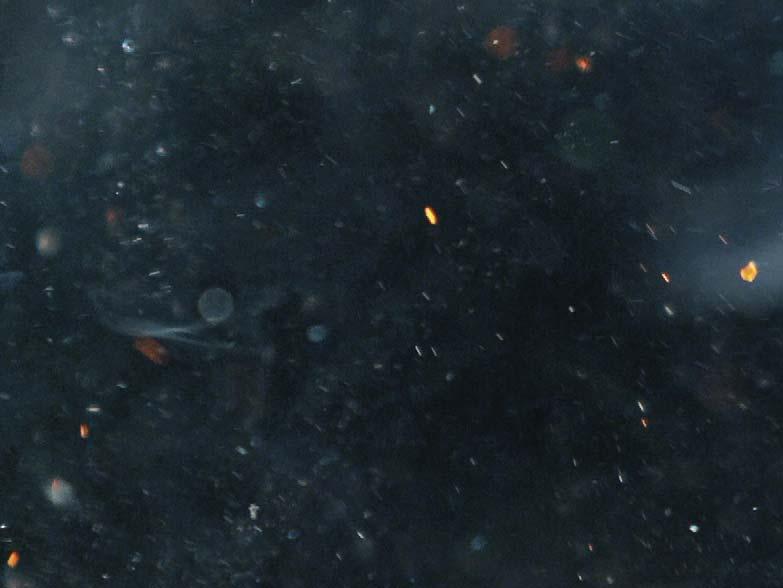

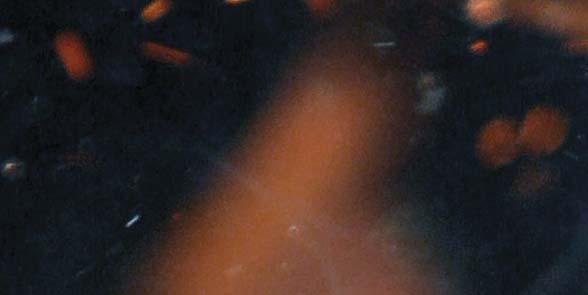

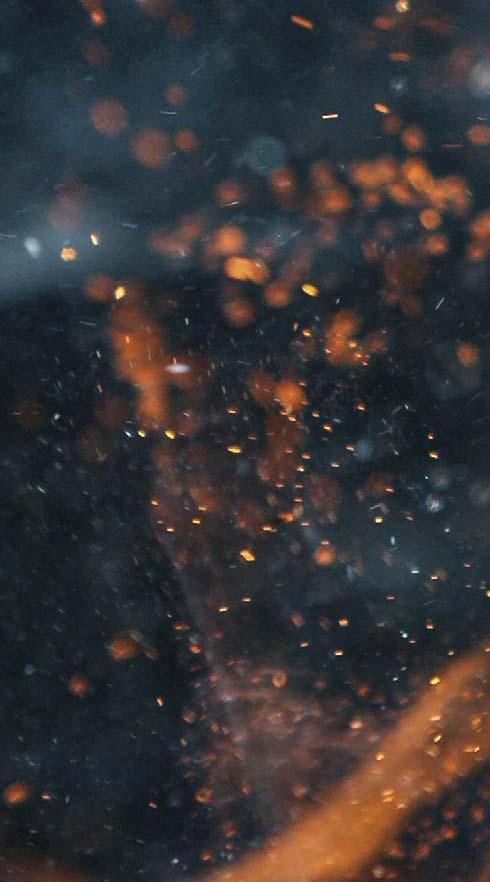


Mike Spalding, Reuter-Stokes, USA,
outlines the importance of flame detectors in the fertilizer industry.
Flame detectors, while comparatively small in size in the world of industrial equipment, play a large role behind the scenes in fertilizer production. These detectors are used to ensure that the steam methane reformers (SMRs) – a key piece of equipment in fertilizer and methanol production – have started up properly. The detectors sense that there is a lack of fl ame and transmit signals to the burner management system (BMS). The BMS responds to the lack of fl ame by shutting the fuel valves that feed the burners. An improper or failed start-up can result in an explosion, as the Yara Tertre plant in St. Ghislain, Belgium, learned in 2009.




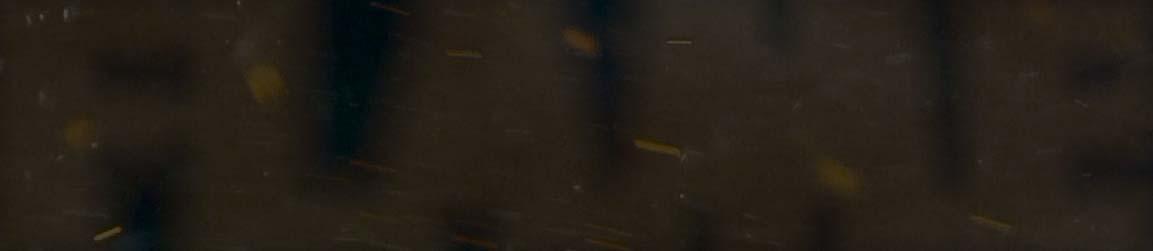


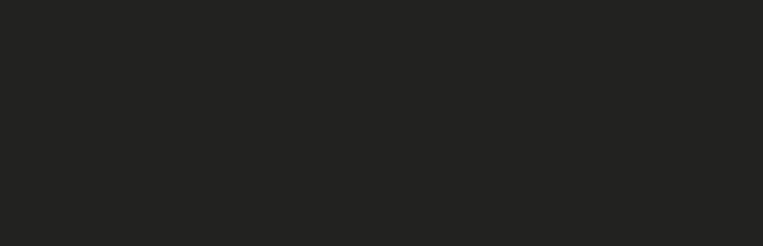
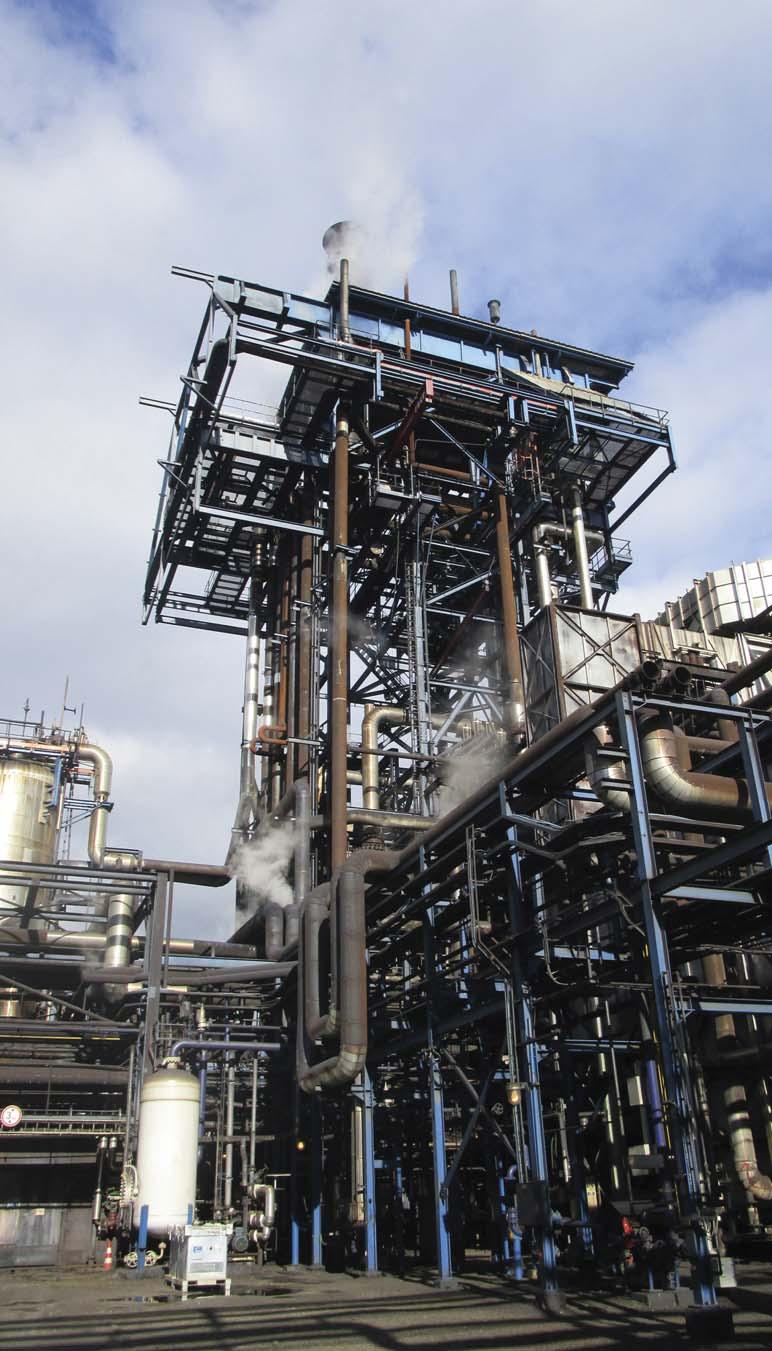
Older equipment and safety considerations
During the fertilizer production process, these SMRs produce a combination of hydrogen and carbon monoxide, known together as synthesis gas (or syngas), which is used in the industrial synthesis of ammonia and other chemicals.
This gas is produced by using steam and methane or other hydrocarbons in the presence of a catalyst, at temperatures ranging between 950˚C and 1100˚C. In addition to being the feedstock, natural gas is also used as the heating fuel for the production material in the catalyst tubes.
Using high volumes of fl ammable materials makes steam methane reforming a high-risk process. Start-up is a critical event and poses the most risks for a fertilizer or methanol plant. If an SMR does not start properly, natural gas that has not been combusted can accumulate in the fi rebox and explosively ignite.
Outdated safety systems have been used for decades, with many plants incorrectly assuming they are suffi cient. Older systems, however, rely on human visual examination and checklists at start-up to bring the SMR up to the minimum operating temperature. When humans are involved, there are increased risks of unsafe conditions and even explosions.
The aftermath of an SMR explosion
Figure 1. Yara Tertre SMR.
Figure 2. Burner top view. Designed and built in the 1960s, Yara Tertre’s SMR unit featured nine rows of 20 Hamworthy burners per row. Like many of the SMRs from these early years, the start-up was not automated and relied on human intervention.
Over the years, this method worked. The Yara Tertre SMR consistently started up and ran smoothly. In 2009, however, an explosion rocked the plant, injuring two and destroying the SMR. Investigation revealed that erroneous accumulation of uncombusted gas in the fi rebox had caused the explosive combustion.
In the aftermath, Yara rebuilt the equipment and implemented an improved safety system, including the installation of fl ame sensors. Engineers installed 36 of these sensors on the fi rebox’s arch burners and connected them to the BMS to lessen the human element risk. The fl ame sensor outputs were used as inputs for the SMR start-up process to ensure safe operation.
Addressing fl ame detection challenges
After these important safety upgrades, the Yara Tertre plant went back online in 2011. When plant engineers tested SMR fl ame sensor positioning, they discovered that the sensors did not consistently detect fl ames due to the burner confi guration. The sensor-position location offered an indirect view of the fl ame, which delivers lower light intensity.
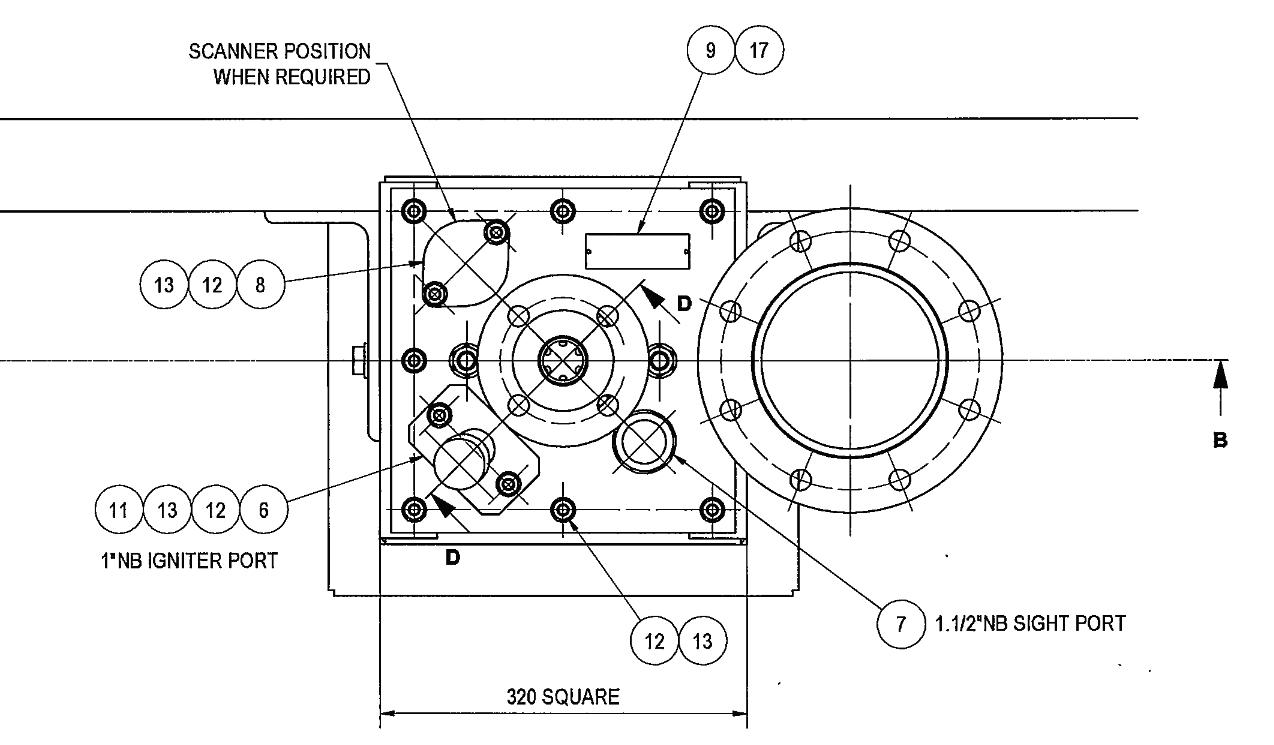
Engineers reinstalled the sensors in the igniter port, which offers a direct view of the fl ame. However, during start-up the detectors needed to be removed from the burner to allow an igniter to be inserted in the port. Sensors were then reinstalled after ignition.
The specifi ed fl ame sensors were not up to this task. The top-fi red design of the Yara Tertre SMR houses the arch burners and sensors in a penthouse above the fi rebox. This location posed temperature issues with the sensors.
Ambient temperatures on the burner fronts could easily exceed 150˚C, a level that is well beyond the temperature capability of most modern fl ame detectors. The sensors installed during the post-explosion rebuild had a maximum operating temperature of 93˚C. The high temperatures in the penthouse caused these sensors to fail.
The technology was not robust enough to handle the harsh environment in Yara Tertre’s SMR application. As a result, the detectors were bypassed and ignored during start-up. Engineers realised they needed to fi nd a more rugged and reliable sensor.
Technology built for harsh environments
Beyond needing a fl ame detector that could deliver reliable performance in the SMR penthouse, the company knew it also wanted one that was sensitive enough to detect fl ames with an indirect view. After reviewing the many options on the market, the Reuter-Stokes Flame Tracker Dry 325 (FTD 325), a sensitive UV sensor built for harsh environments, was selected.
A single-piece assembly that is hermetically sealed from end to end, the sensor features a hot end that attaches to the burner sight tube, a 30 ft mineral-insulated cable and a cool end that is used for amplifi cation and signal conditioning. The hot end has a maximum operating temperature of 325˚C, which reaches well beyond the ambient temperature near the SMR penthouse’s burner fronts.
Yara chose to test one of the FTD 325 sensors on the SMR before committing to a complete installation. Engineers took initial temperature measurements on four burners over a 24-hour period and tracked infrared temperature

Figure 3. FTD 325 hot end connected to the sensor position of the burner.
Pumps specialist
for fertilizer industry
Rheinhütte Pumpen is a specialist in the field of pumping fluids such as nitric acids, ammonium nitrate, sulphuric acid and phosphates for many decades. Optimal customer and engineering solutions are provided in a large selection of more than 30 metal, plastic and ceramic materials combined with special shaft seals.
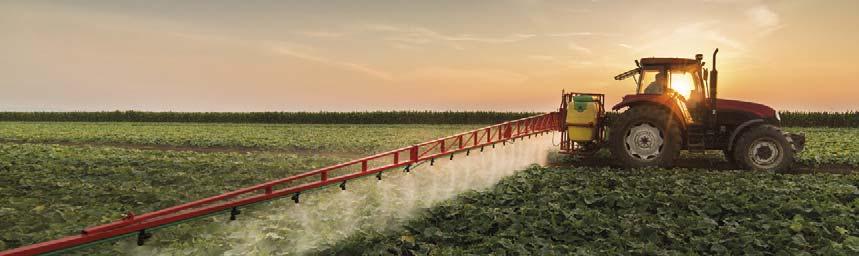
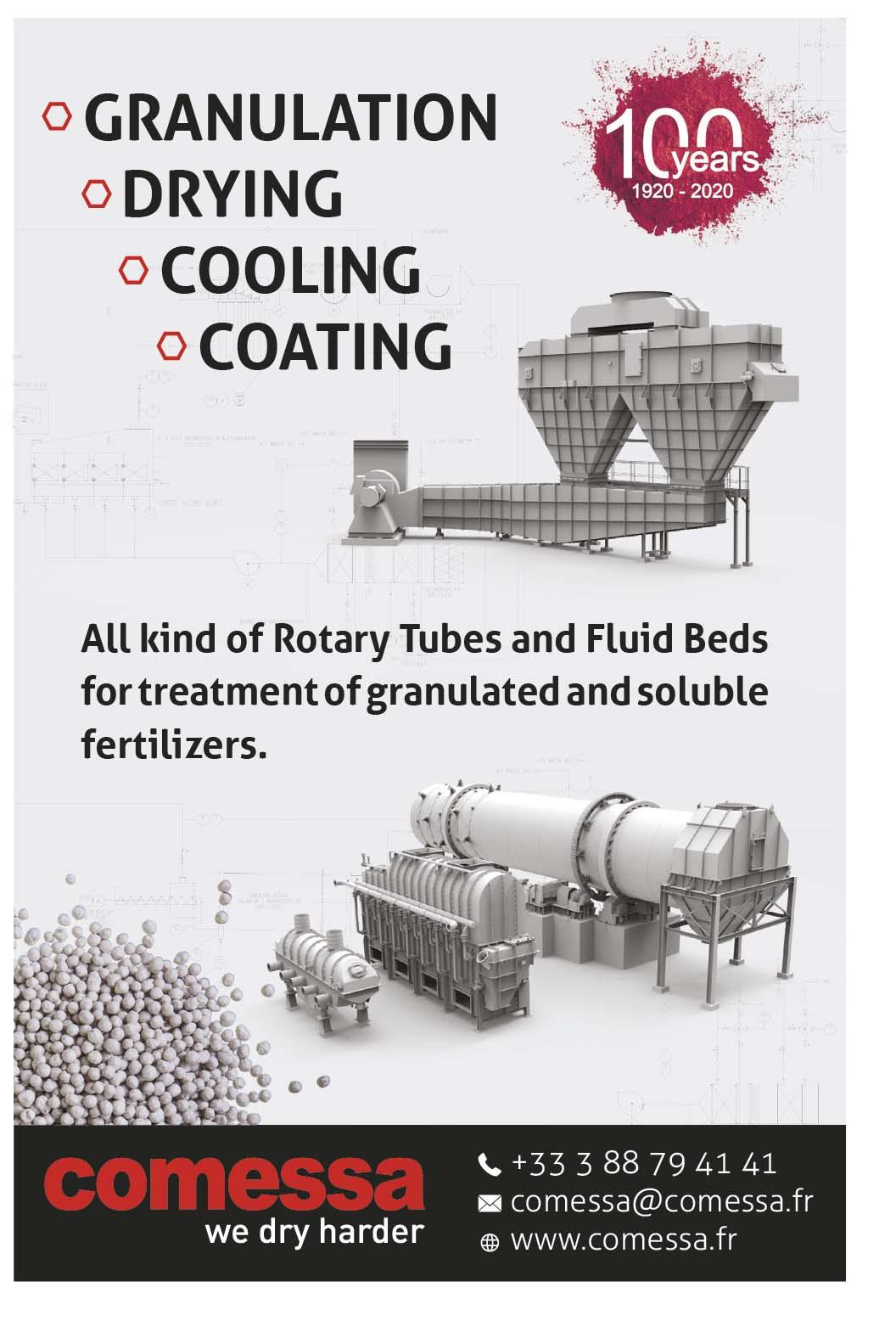
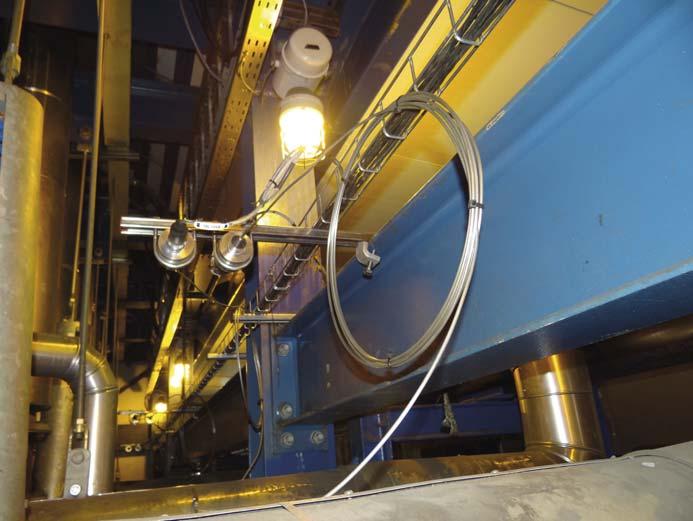
Figure 4. FTD 325 cool ends with excess MI cable in a loop.
measurements on these burners near the scanner position on the burner front. Measured temperatures ranged from 108˚C to 159˚C.
The plant’s team then installed the sensor on one of the burners in the sensor position. The sensor performed fl ame supervision using an indirect view for 6 months with ‘very satisfactory’ performance and zero reliability issues. Yara realised the system’s temperature capability was the missing link to installing a successful detection solution in the penthouse. Based on this successful, 6-month test with a single FTD 325 sensor, Yara installed 17 additional fl ame detectors on arch burners. The team placed two sensors on each of the nine burner rows and easily connected the sensors’ hot ends to the burners’ scanner positions. They are not installed in the igniter ports and do not interfere with the ignition process. The output from the cool ends was connected to the BMS.
Yara performs several permissive checks during use, including a fi rebox purge, before any start. The sensors are used during the light-on sequence to confi rm one row of burners is lit before lighting the next row. This occurs for each of the rows.
Since the initial installation in 2018, there have been at least 10 starts, and the sensors were used in each start. The sensors have performed well in the penthouse’s harsh environment with zero failures, and now play an important role in making this SMR safe in Yara Tertre’s harsh environment.
Conclusion
With start-ups in fertilizer and methanol plants posing clear hazards due to human error or poor sensing conditions, it is important to ensure that fl ame detectors are designed for extreme environments and have high sensitivity for low-light environments.
High maximum operating temperatures are key for top-fi red reformers. Modern sensing technology has eliminated the human element in fl ame detection and restores confi dence in high-risk applications at fertilizer and methanol processing plants.
Global Publication Stay informed
Keep up to date with us to hear the latest World Fertilizer news
