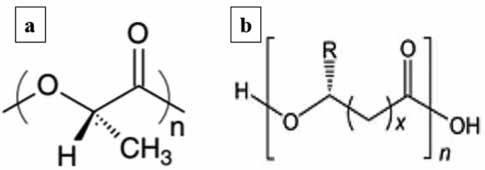
14 minute read
Progress in bioplastics: PLA and PHA
Samantha P Bunke a , Dr. Susan Fullerton a , Dr. Eric Beckman a a DAMP Nanoionics and Electronics Laboratory, Department of Chemical Engineering, University of Pittsburgh, PA, USA
Samantha Bunke is a Chemical Engineering graduate from the University of Pittsburgh. During her time at Pitt, she conducted research in the Nanoionics and Eletronics Lab under Dr. Susan Fullerton for the past year, and she has also completed a co-op program with EQT Corporation. She will be working for Lubrizol as their Physical Properties Intern until she attends graduate school next fall at Stanford University.
Samantha Bunke
Susan Fullerton
Susan Fullerton is an Assistant Professor and Bicentennial Board of Visitors Faculty Fellow in the Department of Chemical and Petroleum Engineering at the University of Pittsburgh. She earned her Ph.D. in Chemical Engineering at Penn State in 2009. Prior to joining Pitt, she was a Research Assistant Professor in the Department of Electrical Engineering at the University of Notre Dame from 2009 - 2015. Fullerton’s work has been recognized by an NSF CAREER award, a Marion Milligan Mason award for women in the chemical sciences from AAAS, a Ralph E. Powe Jr. Faculty Award from ORAU, and the 2018 James Pommersheim Award for Excellence in Teaching in Chemical Engineering at Pitt.
Eric Beckman
Eric Beckman received his Ph.D. in polymer science and engineering from the University of Massachusetts-Amherst in 1988. After postdoctoral research at Battelle’s Pacific Northwest Laboratory in 1987-88, Dr. Beckman assumed his faculty position at the University of Pittsburgh (1989). Dr. Beckman was promoted to associate professor in 1994, and full professor in 1997. Dr. Beckman received a Young Investigator Award from the National Science Foundation in 1992, and the Presidential Green Chemistry Award in 2002. Dr. Beckman’s research group examines the use of molecular design to solve problems in green engineering and in the design of materials for use in tissue engineering. In 2003, with support from the Heinz Endowments, the Bevier estate, and John Mascaro, Dr. Beckman created the Mascaro Center for Sustainable Innovation, a school of engineering institute that examines the design of more sustainable products and infrastructure. Dr. Beckman’s group has published over 200 papers and he has received over 40 patents.
Significance Statement
The findings in this article provide background on the plastic accumulation dilemma and insight on the current state of bioplastics. Bioplastics, such as PLA and PHA, have been proposed as a solution to this problem, and this paper assesses their pros and cons.
Category: Review paper Keywords: Bioplastics, biodegradation, PLA, PHA
Abstract
Plastic has become a paradox and encumbrance in the modern age as a one-use product that is designed to last forever. The contradictory nature of plastic is why the material is now accumulating in landfills as well as the natural environment and is causing major issues in today’s society. Recycling is not a solution to this crisis since it is typically more expensive than manufacturing virgin plastics, and it only makes up 9% of the life cycle of all currently produced plastic [1]. However, a possible solution has presented itself in nature: bioplastics. Bioplastics are defined as plastics made from any biological material [2]. Their attractiveness lies in their potential to biodegrade in nature and to reduce greenhouse gas emissions in the production stage. However, research has determined that this is not always the case. This paper reviews the manufacturing process and degradation methods of two widely used bioplastics, polylactic acid (PLA) and polyhydroxyalkanoate (PHA). Considering the pros and cons of each biopolymer, the future of bioplastics may lie in expanding past these two materials to other biopolymers, possibly combining two or more into composites possessing the positive attributes of each, rather than looking at these bioplastics on an individual basis.
1. Introduction
Roughly 6,300 metric tons of plastic waste have been produced since 2015 alone [1]. 9% of this amount was recycled, 12% was incinerated, and 79% found its way into landfills or the environment [2]. Following this trend, the amount of plastic waste that will accumulate in landfills or the environment is projected to reach 12,000 metric tons by 2050 [3]. The most frequently used plastics are derived from petrochemicals and are not biodegradable [3]. The only methods of permanent disposal include combustion and pyrolysis, which also release highly toxic pollutants [3]. While most organic materials undergo biodegradation where bacteria break the material down into smaller, useful compounds, the only “decomposition” experienced by petrochemical-based plastics is the fracture into microplastic beads [3].
Despite the drawbacks, the demand for plastic continues to increase. Bioplastics have been introduced as replacement materials since they can possess similar properties to conventional plastics while offering other benefits, such as biodegradability and/or reduction in the carbon footprint [2]. The current global production rate for bioplastics is only at 912 thousand metric tons, but is predicted to rise to 1.3 million metric tons by 2023 [2]. This paper will review two major bioplastics currently being utilized, polylactic acid (PLA) and polyhydroxyalkanoate (PHA), and their environmental impact.
2. Production 2.1 PLA
PLA is an aliphatic polyester produced from the fermentation of renewable biomass, such as corn and sugarcane [4]. This fermentation process produces lactic acid which can then be converted into PLA using one of two processes: direct condensation of the lactic acid or ring-opening polymerization of the cyclic lactide dimer [5]. Due to the difficulties of removing the water by-product that would drive the equilibrium reaction forward, the condensation reaction approach limits the molecular weight of the final polymer [5]. The current method used in industry combines both production routes. Lactic acid is made from the fermentation of dextrose from corn and then undergoes a continuous condensation reaction to achieve a PLA prepolymer at low molecular weights [5]. Next, the prepolymer is introduced to a catalyst to cause a highly selective intramolecular cyclization reaction and purified in a vacuum distillation column [5]. This lactide stereoisomer mixture is then polymerized into high molecular weight PLA using a catalyzed ringopening reaction [5]. The monomer of PLA is shown in figure 1a. 2.2 PHA
PHA is a natural polyester synthesized by bacteria to act as an energy reserve under nutrient stress [6]. This polymer can be extracted from the bacteria, processed, and then used as a plastic material in a range of applications. Currently, largescale production of PHA uses expensive sources of organic materials, making the polymer an unattractive substitute for cheap, conventional plastics [7]. Although these organic materials are often renewable resources, such as starch, cellulose, triacylglycerols, and sucrose, alternative substrates are being researched to lower the cost of production [8]. Waste streams, such as agriculture feedstock, industrial by-products, or food waste, are currently being tested as carbon sources for small-scale PHA production systems [7]. This method follows a circular-economy approach by reclaiming waste products rather than immediately disposing of them, which is considered a more environmentally-friendly practice. However, large-scale execution would require improvements in industrial equipment and technology for using waste streams, posing an additional obstacle [7].
3. Properties and Use 3.1 PLA
PLA possesses similar physical properties to polypropylene (PP), polyethylene (PE), and polystyrene (PS), which is why it is currently being used to make a variety of plastic products such as cups, films, food containers, packaging, and more [4]. It has also been utilized in the medical industry as screws, pins, rods, sutures, and other medical devices that are required to biodegrade within the body [4]. PLA is a thermoplastic, meaning it becomes flexible and moldable at elevated temperatures and can be treated using the majority of polymer processing equipment already in existence [5]. It can be injection molded, thermally crystallized, or stress crystallized, making it simple to work with [5]. However, the cost of producing this bioplastic is roughly $4.40/kg, which remains greater than petroleum-based plastics and limits PLA’s success in the commodity sector [5].
3.2 PHA
Over 100 different monomers have been discovered as building blocks for storage PHA, allowing this biopolymer to be produced with a variety of properties [8]. A generalized form of the PHA monomer is shown in figure 1b. Although the size and composition of the polymer depends on the bacteria used to produce it, PHA chains typically have a molecular mass high enough to portray similar mechanical properties to most synthetic plastics, such as polypropylene [9]. PHA is also highly crystalline, isotactic, piezoelectric, optically active, insoluble in water, and is a thermoplastic [8]. These valuable properties allow PHA to be used in a wide range of applications, including packing, commodity items, and medical devices [8]. The price of production is highly dependent on the carbon source used, but it currently ranges between $4/kg and $16/kg [8]. This is why waste streams are a desirable option for carbon substrates since they can considerably lower manufacturing costs [8].
Figure 1: The monomer structures of a) PLAand b) PHA [5,10].
4. Environmental Impact 4.1 PLA
PLA dominates 43.1% of the global market share for bioplastics [11]. This large share is due to the attractive properties that PLA possesses and its potential as a sustainable alternative to petroleum-based polymers. A 2018 life cycle impact assessment conducted on the carbon footprint of certain bioplastics versus conventional plastics found that PLA has a 23% lower global warming potential (GWP) than low-density polyethylene (LDPE), based on a cradle-to-grave analysis [11]. This analysis was also based on the assumption that both ended their life-cycles in a landfill, rather than PLA’s intended “grave:” an industrial composting facility [11]. One of PLA’s main manufacturers, Cargill Dow, conducted its own assessment of the polymer’s environmental impact based on a cradle-to-pellet analysis. The comparison of PLA’s CO2 production versus petrochemical-based plastics can be found in figure 2.
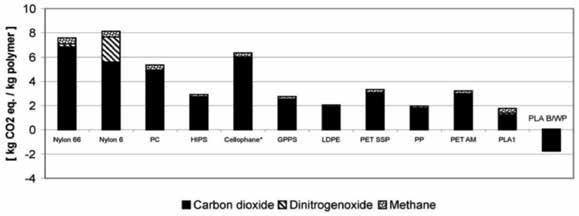
What is supposedly the most attractive quality of PLA, and is the lead motivation behind pushing this material as a “green” alternative, is its biodegradability. Its degradation occurs in two steps. First, the PLA polymer chains must be broken up into lactic acid and smaller oligomers by hydrolysis under high heat (~58ºC) and moisture (50% relative humidity) [12, 13]. Once this occurs, microorganisms can feed on the compounds to produce water, carbon dioxide, and humus [15]. PLA cannot be broken down in residential composting piles or the natural environment since it requires extreme conditions, but the polymer should sufficiently degrade in industrial composting facilities within two months [14]. In spite of this fact, out of the 50,000 tons of PLA waste that was produced in 2013, only 10% was recovered through composting [16]. What seems to be the main obstacle preventing composting from being the primary disposal method of PLA is that many industrial composting facilities will not accept it [13]. PLA is often indistinguishable from conventional plastics making it difficult to separate the bioplastic from the rest, which can lead to contaminating compost piles with non-compostable materials [13].
4.2 PHA
A study completed in 2012 found that on average, PHA production emits 2 kg of CO 2 less than petroleum-based plastics and reduces fossil fuel usage by 30 MJ per l kg of material manufactured [8]. Unlike PLA, PHA can biodegrade in almost any environment, not just industrial composting facilities [8]. This means that PHA can be composted in homes and will break down in the environment. What is more unique is PHA’s ability to degrade in aquatic environments, even with a maximum temperature of 6°C [8]. The time it takes to completely biodegrade depends on environmental factors, such as temperature, moisture content, microbial activity, and pH [8]. Biodegradation speed also depends on the properties of the polymer itself, such as crystallinity, composition, molecular weight, and surface area exposure [8]. In an industrial composting facility, biodegradation lasts about seven weeks [8]. In aerobic conditions, biodegradation of PHA produces carbon dioxide and water, while anaerobic conditions result in carbon dioxide and methane [8].
Figure 2: CO2 production of petrochemical polymers versus PLA. PC=polycarbonate; HIPS=high impact polystyrene; GPPS=general purpose polystyrene; LDPE=low density polyethylene; PET SSP=polyethylene terephtbalate, solid state polymerization (bottle grade); PP=polypropylene; PET AM=polyethylene terephthalate, amorphous (fibers and film grade); PLAl=polylactide (first generation); PLAB/WP (polylactide, biomass/wind power scenario) (15).
5. Conclusion and Outlook
Plastics acquired their popularity because of the durability, low costs, and convenience they offer to businesses and consumers. They laid the foundation for the linear-economy we live in today, in which production, consumption, and disposal follow a straight path right into landfills and the environment. This has now revealed itself as a major problem as these seemingly indestructible materials have been accumulating since they were first introduced and are now posing an environmental threat.
Bioplastics offer an opportunity to maintain the convenience that consumers have grown accustomed to, without building upon the already existing issue. They are often manufactured using renewable sources, lowering greenhouse gas emissions during the production stage, and are biodegradable, preventing them from accumulating in the environment. PLA and PHA have shown a lot of promise as the future of the plastics industry, as one is already being mass-produced and the other is being researched extensively. However, each bioplastic comes with its own obstacles. PLA is highly durable and possesses the properties necessary to make it a prime replacement for conventional plastics, but these properties come at a cost; it cannot biodegrade on its own in the environment because it requires more extreme conditions. This obstacle can be overcome with the implementation of industrial composting facilities, but these facilities are still very limited and many of them will not even accept PLA because of the difficulty of separating it from non-compostable plastics. With the high likelihood of this bioplastic accumulating in landfills, critics have labelled PLA as corporate “green washing,” meaning it is a ploy to trick businesses and consumers into believing they are actually making a difference when in reality, they are still contributing to the plastic crisis.
The major advantage of PHA is that it can biodegrade in a vast range of environmental conditions so it will not accumulate in landfills or in nature. It has many attractive properties which means it can replace conventional plastics in a variety of applications. However, due to the carbon sources and extraction methods being used to produce it, PHA is much more expensive then petroleumbased plastics and is currently not a viable option. Technological advancements need to be made in order to recover waste streams and use them as carbon sources for PHA production, not only lowering the costs of this bioplastic, but also developing a circulareconomy model.
Despite these complications, biopolymers still have the potential to aid in the plastic struggle. PLA and PHA are on the correct track of becoming smarter, more environmentallysensible materials, but they have yet to reach the point of actually replacing conventional plastics. A possible solution to one of PLA’s obstacles is to require PLA products to be labelled to make them distinguishable from non-compostable plastics. To overcome PLA’s inability to biodegrade quickly and easily in industrial composting facilities, PLA could be blended with another biopolymer, such as PHA, polyalginate, lipids, starch, etc., to enhance its biodegradability, while maintaining PLA’s strength and durability. These additional biopolymers are currently being trialed, and perhaps they will possess the correct properties needed to replace conventional plastics—even without blending—and succeed in reforming the “throwaway” society.
6. Acknowledgements
Funding was provided by Swanson School of Engineering, the Office of the Provost, and the Ellen MacArthur Foundation.
7. References
[1] “The Veolia Institute Review: Facts Reports.” Veolia Institute, 2019. [2] “Bioplastics—Facts and Figures.” European Bioplastics, 2017.
[3] R. Geyer, J. R. Jambeck, K. L. Law, “Production, use, and fate of all plastics ever made.” Sci. Adv. 3, e1700782 (2017). [4] Rogers, Tony. “Everything You Need to Know about Polylactic Acid (PLA).” Creative Mechanisms, 7 Oct. 2015, https:// www.creativemechanisms.com/blog/learn-about-polylactic-acidpla-prototypes.
[5] Henton, D. et al. “Polylactic Acid Technology.” Natural Fibers, Biopolymers, and Biocomposites, 11 Feb. 2005. [6] “Everything You Need to Know about PHA.” Creative Mechanisms, 22 Jan. 2017, https://www.creativemechanisms. com/blog/everything-you-need-to-know-about-phapolyhydroxyalkanoates
[7] Rodriguez-Pereza, S. et al. “Challenges of Scaling-up PHA Production from Waste Streams. A Review.” Journal of Environmental Management, Academic Press, 6 Oct. 2017. [8] Reddy, C.S.K. et al. “Polyhydroxyalkanoates: an overview.” Biosource Technology, 2003. [9] Raza, Z. et al. “Polyhydroxyalkanoates: Characteristics, production, recent developments and applications.” International Biodeterioration & Biodegradation, 2018. [10] Li, Z. et al. “Polyhydroxyalkanoates: opening doors for a sustainable future.” NPG Asia Materials, 2016. [11] Choi, B. et al. “Carbon Footprint of Packaging Films Made from LDPE, PLA, and PLA/PBAT Blends in South Korea.” Sustainability, 2018. [12] Henton, D. et al. “Polylactic Acid Technology.” Natural Fibers, Biopolymers, and Biocomposites, 11 Feb. 2005. [13] Castro-Aguirre, E. et al. “Poly(lactic acid)—Mass production, processing, industrial applications, and end of life.” Advanced Drug Delivery Reviews, 2016. [14] “The Sustainability of NatureWorksTM Polylactide Polymers and IngeoTM Polylactide Fibersa: An Update of the Future.” Macromolecular Bioscience, 2003. [15] Vink, E. et al. “Applications of life cycle assessment to NatureWorksTM polylactide (PLA) production.” Polymer Degradation and Stability, 2002. [16] EPA, “Advancing Sustainable Materials Management: Facts and Figures.” 2013. Access date Oct 5th 2019.